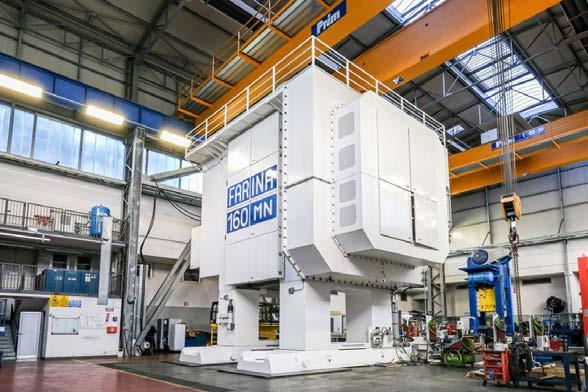
10 minute read
Indrukwekkende smeedpers
Dankzij de constructie met een kruksleufoverbrenging (Scotch yoke) is de 16.000 ton smeedpers met een totale hoogte van 14 meter duidelijk kleiner dan gebruikelijke machines.
Persenbouwer Schuler en haar Italiaanse dochterbedrijf Farina hebben aan een internationale groep van zestig smeedpers-experts de grootste mechanische smeedpers ter wereld gepresenteerd. Een video uitzending vanuit de productielocatie in Suello bij Milaan toonde de indrukwekkende eigenschappen van de pers met 16.000 ton vermogen en een slag van 600 mm live in actie.
De pers is inmiddels opgebouwd bij thyssenkrupp Gerlach, dat er voorassen voor vrachtauto’s en krukassen mee gaat produceren; 360.000 componenten per jaar.
Hoge excentrische belastingen
“Farina noch Schuler zou alleen in staat zijn geweest een machine in zo korte tijd op te stellen”, benadrukte verkoopdirecteur Klaus BerglarBartsch van Schuler. “We hebben al onze engineering capaciteit bij elkaar gebracht om dat de realiseren.” Dankzij de constructie met een kruk-sleufoverbrenging (Scotch yoke) is de pers met een totale hoogte van 14 meter duidelijk kleiner dan gebruikelijke machines. Dit maakt ook hoge excentrische belastingen, een hoge slagfrequentie en een buitengewone hoge nauwkeurigheid mogelijk. Aan de buitenzijde ziet de machine van het type GLF eruit als een conventionele pers, inclusief vliegwiel, koppeling en tandkrans. In haar hart werkt evenwel de Scotch yoke direct in de stamper, wat de grond voor de compacte bouwwijze is. De massieve pers met een totaal gewicht van rond 1850 ton bestaat verder uit een gietstalen tafel en gelaste staanders. “We hebben de order in april 2019 gekregen”, aldus Farina-direteur Marco Gritti. “In december 2019 werd het ontwerp gemaakt en begonnen we bestellingen bij onze toeleveranciers te plaatsen.” De belangrijkste delen kwamen binnen in het voorjaar van 2020, dus aan het begin van de coronapandemie. Desondanks begon Farina in september met de montage en slaagde erin die in januari te voltooien. “Het was een harde tijd”, herinnert Gritti zich. Medio april arriveerden alle delen inbouwklaar bij thyssenkrupp in Duitsland. Al met al werd het project in slechts 26 maanden afgerond.
Nauwkeurigheid
Bij de live demonstratie liep de machine op halve kracht met 16 slagen per minuut. Het online publiek kon zien dat het vliegwiel precies in het midden van het kopstuk is geïnstalleerd. “Daardoor kan de pers bij het smeedproces nauwkeuriger werken”, verklaarde Gritti. “De nauwkeurigheid van de delen is daardoor hoger dan bij een traditionele pers.” Dankzij de Scotch yoke constructie is de perskracht van 16.000 ton, die door een aandrijving van 800 kW wordt gegenereerd, ook 500 mm naar rechts en links beschikbaar.
20.000 Ton?
“De overname van ons bedrijf door Schuler in 2018 heeft het Farina mogelijk gemaakt te groeien en nieuwe markten in andere delen van de wereld te ontsluiten”, maakte Gritti duidelijk. “Dit project is een direct gevolg daarvan.” Volgens de Farina-directeur zou de volgende stap de bouw van een mechanische smeedpers met een capaciteit van 20.000 ton kunnen zijn.
Wilvo robotiseert zwaar én complex zetwerk

Joris Meesters (links) van Bystronic Benelux overhandigt de traditionele Zwitserse koebel aan COO Dennis Geerings van Wilvo voor de investering in de buigcel.
Het robotiseren van een kantproces biedt meerdere voordelen maar levert slechts zelden een verkorting van de cyclustijd op. Bystronic heeft bij Wilvo echter een buigcel geleverd, waarmee de cyclustijd van een zwaar en lastig te hanteren buigdeel bijna is gehalveerd. De ontwikkeling van deze cel was geen sinecure. “Dit soort projecten slaagt alleen als de leverancier en de klant bereid zijn om er samen echt hun tanden in te zetten.”
Wilvo in Bergeijk is in de afgelopen vijf jaar verdrievoudigd in omzet. Begonnen als specialist in het bewerken van dun plaatstaal en licht constructiewerk, is het bedrijf uitgegroeid tot een sterke toeleveringspartner voor klanten in binnen- en buitenland (vooral Duitsland), die in staat is om zowel eenvoudige als complexe projecten in een korte tijd te realiseren. CEO Rob Lemmens ziet goede mogelijkheden om de komende vijf jaar nogmaals te verdubbelen in omzet. “Die kansen liggen er zeker. We worden momenteel overvraagd door bestaande klanten en dat is structureel aan het worden. Klanten komen nu naar ons omdat er schaarste is in het aanbod én wij profiteren van mond-tot-mond reclame in met name Duitsland. We moeten daarom opschalen.”
Focus qua producten en klanten
Lemmens voorziet dat Wilvo verder kan groeien door steeds nadrukkelijker te focussen. Enerzijds qua producten: de Brabantse toeleveringspartner gaat steeds meer voor de complexe producten, die zowel worden geproduceerd als samengesteld tot modules/producten. Anderzijds qua type klanten. Lemmens: “Wij verschuiven naar de steeds
Wilvo is een sterke toeleveringspartner voor klanten in binnen- en buitenland, die in staat is om zowel eenvoudige als complexe projecten in een korte tijd te realiseren.

veeleisender klant. Naar OEM’ers die zelf geen voorraad willen hebben in hun fabriek, maar wel 100 procent willen kunnen vertrouwen op de leverbetrouwbaarheid van hun toeleverancier. Die zeker willen weten dat wat ze ’s avonds of zelfs in het weekend bestellen, de volgende dag om 12.00 uur op de stoep staat.” Het is lang niet iedere toeleverancier gegeven om dat te kunnen realiseren. Procesmatig moet hiervoor alles goed worden georganiseerd en juist daar steekt Wilvo veel energie in. Zo hebben bijvoorbeeld tweehonderd medewerkers (Wilvo telt in totaal 280 fte’s) allemaal hun eigen tablet. Hierin vinden ze alle info die ze nodig hebben. De tablets zijn gekoppeld aan de aan de Isah ERP-software en aan een planningstool die Wilvo zelf heeft ontwikkeld. Zo kunnen medewerkers bijvoorbeeld via hun tablet snipperuren aanvragen. Zodra deze worden gehonoreerd, worden ze direct in de capaciteitsplanning verwerkt. Ook kunnen ze direct communiceren met de engineers en de kwaliteitsdienst.
Automatisering in machinepark
Daarbij beschikt Wilvo over een omvangrijk machinepark. Hierin wordt steeds meer geautomatiseerd, met flexibiliteit als een belangrijk uitgangspunt. “Sterker nog: we kopen geen enkele machine meer die niet flexibel is”, zegt COO Dennis Geerings. “Korte insteltijden zijn voor ons key.” In de productieruimte in Bergeijk staan onder andere meer dan twintig kantbanken. Daaronder zijn twee gerobotiseerde buigcellen voor kleinere producten, waardoor Wilvo reeds de nodige ervaring heeft met geautomatiseerd zetten. Maar bij het volgende automatiseringsproject op de kantafdeling ging het bepaald niet om kleine producten. Voor een grote Duitse klant in de textielbranche buigt Wilvo al jaren zware onderdelen met een gewicht van 70 kilo en een lengte van 2,85 meter. Deze moeten worden voorzien van drie buigingen. Dat gebeurde door twee medewerkers, die de plaatdelen handmatig inlegden en met behulp van een buighulp zetten. “Dat was niet langer houdbaar want we buigen deze onderdelen in grote series, het hele jaar door. Als je er op één dag tien doet, dan voel je dat echt wel in je armen en je rug”, aldus Rob Lemmens.
Flexibele oplossing
Wilvo ging dus op zoek naar een oplossing om dit proces te automatiseren. Een flexibele oplossing wel te verstaan. Dennis Geerings: “We wilden een buigcel niet alleen voor dit product. Want als je gaat automatiseren, probeer je altijd wat meer producten te verzamelen. In dit geval niet alleen dat zware product van die Duitse klant, maar ook enkele complexe producten, waaraan bijvoorbeeld geplet moeten worden met een dichtdrukgereedschap.” Hierover ging Wilvo in gesprek met meerdere machineleveranciers. De meesten kwamen tot een opstelling van een robotarm met twee kantbanken om ook de complexe producten in één geautomatiseerd proces te kunnen zetten. “Maar twee kantbanken was niet wat we
Snijcapaciteit fors uitgebreid
Inmiddels heeft Wilvo ook de volgende investering alweer gedaan. De snijcapaciteit is uitgebreid met een Bystronic ByStar Fiber met 10 kW vermogen.
Bystronic en Wilvo hebben een lange relatie op het gebied van lasersnijden. Een CO2-laser van Zwitserse makelij staat al jaren in de productieruimte in Bergeijk te snijden. “Dag en nacht, onvermoeibaar”, zegt Rob Lemmens tevreden. Met de nieuwe aanwinst is de productiecapaciteit significant uitgebreid. De productiviteit van de 10kW ByStar Fiber in het stikstof snijden is circa vier keer groter in vergelijking met de bestaande CO2 lasersnijmachine.

Een monteur van Bystronic is bezig met het operationeel maken van de nieuwste aanwinst van Wilvo op snijgebied, een 10 kW ByStar Fiber.



Ook dit complexe product, waaraan onder andere geplet moeten worden met een dichtdrukgereedschap, buigt Wilvo in de gerobotiseerde buigcel van Bystronic.
wilden”, aldus Geerings. “Want dan staat er altijd één kantbank stil. Bovendien neemt zo’n opstelling veel ruimte in.”
Betrouwbaar proces
Bystronic gaf aan dat het wel mogelijk moest zijn om ook de complexe producten te zetten met één robotarm en één kantbank. En dat is uiteindelijk ook gelukt. Bystronic heeft een buigcel geleverd waarin een robot met een payload van 240 kilo op een track van 12 meter en een kantbank Xpert Pro met een vermogen van 250 ton en een werklengte van 4300 mm de belangrijkste onderdelen zijn. De robot pakt de plaatdelen op, buigt deze in de kantbank en wisselt ook de gereedschappen. De kantbank kan zich zelf instellen en is voorzien van een dynamische bombering die zichzelf kan corrigeren en een LAMS hoekmeetsysteem. Het is een combinatie die resulteert in een betrouwbaar proces. “Dat is voor ons essentieel”, zegt Lemmens. “Vanwege onze werkwijze, maar ook omdat we in deze cel enorme tonnages materiaal buigen. Als iets niet goed gaat, moet je wel heel veel materiaal weggooien.”
Intensieve samenwerking
Het heeft wel wat voeten in de aarde gehad voordat de cel in deze configuratie kon worden geïnstalleerd. Hans van de Meerakker, sales manager van Bystronic Benelux: “We kregen een aantal producten van Wilvo. Niet alleen dat zware buigdeel, maar ook een aantal andere complexe producten. Daar hebben we een analyse op losgelaten, waarbij de technische afdeling van Bystronic heeft geadviseerd. Zo kwam bijvoorbeeld het voorstel tot stand om twee verschillende ondermatrijzen te combineren in één matrijs. Dat maakte het mogelijk om in de cel met één kantbank uit te kunnen. Ook aan de producthandling is veel aandacht besteed. Hoe pak je een product op voor verschillende zettingen? We hebben er echt een project van gemaakt en daar veel in geïnvesteerd. Wilvo heeft hetzelfde gedaan. En dat moest in dit geval ook. Want dit zijn trajecten die alleen kunnen slagen als ook de klant bereid is zijn tanden er in te zetten.” Zo ziet Dennis Geerings het ook. “De ontwikkeling van deze cel is typerend voor Wilvo. Wij onderkennen de moeilijkheden, pakken die op en slaan met betrouwbare leverancier de weg in naar een oplossing. Ook wij zijn echt een tijd met deze cel aan het stoeien geweest. Een productieleider en een afstudeerder hebben er hard aan gewerkt. Zo hebben we deze cel echt samen werkend gekregen.”
Kortere cyclustijd
Het buigen van het zware product voor de textielbranche gebeurt nu automatisch in de buigcel. Dit heeft Wilvo een kortere cyclustijd opgeleverd, wat zeker niet vanzelfsprekend is bij het robotiseren van een kantproces. Waar voorheen twee medewerkers 9 minuten zoet waren met het zware buigdeel, doet de buigcel er nu 5 minuten over. Daarnaast zijn de medewerkers natuurlijk verlost van zwaar werk. Met het buigen van dit onderdeel is de cel een aantal dagen in de week gevuld. De rest van de week wordt gebruikt om ook met andere producten aan het werk te gaan. Een tweede product is inmiddels ook voor elkaar en een derde product wordt nu geprogrammeerd. Als ook dat is gelukt, gaat er zo veel werk door de cel, dat deze helemaal is gevuld. “Misschien moeten we dan al wel naar een tweede cel”, zeggen Lemmens en Geerings.
Zowel Bystronic als Wilvo ondervindt voordelen van de intensieve samenwerking. Bystronic kan de kennis die is ontwikkeld vertalen naar nieuwe projecten bij andere klanten. Wilvo kan de nieuwe kennis op het gebied van productieautomatisering ook elders in het bedrijf gaan benutten. De stagiair die betrokken was bij de ontwikkeling van de cel, is daarom nu in dienst getreden op de nieuwe afdeling productieautomatisering.
www.wilvo.nl www.bystronic.nl