9 minute read
Perfi l da empresa: Kapoor Glass India
Next Article
Negócio familiar com melhoria no seu ADN
Fabricante de frascos, produtor de ampolas... e criador de equipamento de vidro. Perante a perspetiva de adquirir tecnologia europeia de produção de vidro dispendiosa, a Kapoor Glass optou por uma abordagem única: personalizar a própria maquinaria. Greg Morris falou com Udit e Dhruv Kapoor sobre o sucesso da empresa.
Ofabricante de vidro farmacêutico Kapoor Glass recebeu recentemente o prémio CK Somany de Inovação e Tecnologia pela All India Glass Manufacturers Association (AIGMF) pelo seu trabalho no avanço da indústria.
Os juízes da AIGMF elogiaram a empresa pelo desenvolvimento de uma variedade de equipamentos personalizados de fabrico de vidro que lhe permitiu competir com grandes empresas europeias no setor do vidro farmacêutico, onde os padrões de qualidade são incrivelmente rigorosos.
Os juízes felicitaram o Diretor da Kapoor Glass, Udit Kapoor, pelo desenvolvimento da empresa de um «sistema de câmara hot-end interno, em conjunto com software operacional, para obter um controlo online da automação sobre os principais parâmetros de produção para terminar com a produção de qualidade de frascos de vidro com padrões internacionais.»
Entre os sistemas que Kapoor desenvolveu encontra-se uma unidade de inspeção de câmara hot-end para ampolas, um sistema de inspeção cold-end para frascos de vidro, bem como um sistema de inspeção estética para frascos.
O prémio foi o culminar de uma estratégia adotada pela empresa em 2010 para se focar no mercado farmacêutico europeu. Significou a produção de vidro de elevada qualidade para cumprir os padrões exigentes dos clientes europeus, mas, frequentemente, a preços inferiores - ou «da China».
Uma Honra
Kapoor afirmou que era um privilégio ser reconhecido pela AIGMF.
Referiu: «Foi uma grande honra receber esse tipo de reconhecimento, estávamos a trabalhar muito no nosso quintal e, em seguida, obter esse reconhecimento à escala global foi uma prova para a nossa equipa, colaboradores, administração, parceiros e fornecedores. Todos se juntaram e significou muito para nós receber esse reconhecimento.
«Enviámos a candidatura à AIGMF sem esperar realmente ganhar. Quando nos contactaram a dizer que tínhamos ganho, ficámos bastante surpreendidos. Os juízes disseram que éramos a empresa mais interessante. Quando viram a nossa candidatura, muitos dos principais intervenientes da indústria indiana perceberam que estavam a importar este equipamento sem perceberem que estava a ser fabricado no seu próprio quintal.»
O sistema da câmara hot-end, chamado Dimension+, foi desenvolvido em resultado do aumento das velocidades das linhas de enchimento de ampolas e dos requisitos resultantes de precisão
dimensional, normas de qualidade da inspeção, e assim, fiabilidade dos seus produtos.
O sistema foi totalmente desenvolvido a nível interno, incluindo o desenvolvimento de software e todos os componentes mecânicos.
O sistema tem resultados comprovados a velocidades de funcionamento de até 100 ampolas/ minuto, com rejeições inferiores a 1 % e um desvio padrão de menos de 0,05 mm no diâmetro do tubo/ de vedação da ampola e tolerâncias dimensionais mais estreitas para diâmetros de constrição e do reservatório.
Isto origina uma abertura melhorada das ampolas por parte de organizações médicas com pressões consistentes e uma produção inferior de partículas de vidro.
Estratégia
Kapoor referiu que a empresa mudou de estratégia há aproximadamente uma década, quando decidiu focar-se no mercado farmacêutico europeu.
Kapoor trabalhou com fabricantes europeus de tecnologia de vidro, como OCMI de Itália, Modern Mecanique de França e Ambeg da Alemanha, para comprar equipamento de moldagem.
Em seguida, comprou hardware, como câmaras e robôs de grandes fornecedores de todo o mundo. Por fim, a sua equipa de engenheiros internos personalizou o equipamento para cumprir os requisitos específicos da empresa.
No início, foi uma curva de aprendizagem íngreme para a empresa.
Udit, na fotografia em baixo, à esquerda, afirmou: «Começámos devagar, mas aprendemos muito rapidamente! Fomos ao Japão, fomos às principais empresas destes setores e aprendemos todos os detalhes complexos sobre os processos.
«A nossa política era comprar apenas o melhor hardware porque resolvia 90 % dos problemas. Temos uma boa equipa de eletrónica e acreditamos que alguns dos melhores engenheiros de software do mundo se encontram na Índia atualmente. Comprávamos o equipamento e, depois, os engenheiros de software escreveriam um programa para fazer tudo funcionar e, em seguida, integrávamo-lo.
«Temos de dar aos clientes o que eles querem e os nossos clientes querem o melhor. O software tem de ser flexível porque não há dois clientes que queiram o mesmo. Todo o equipamento que construímos, criamos e implementamos tem de se adaptar, especialmente quando temos clientes globais com padrões diferentes.»
Dhruv acrescentou: «A qualidade exigida pelos clientes muda todos os dias, à medida que o mundo
«Estamos muito honrados com a direção que o nosso produto está a tomar, é farmacêutico, estamos num negócio salva-vidas, por isso, o nosso principal objetivo é não dececionar
os nossos clientes, independentemente do que acontecer»
Continuação>>
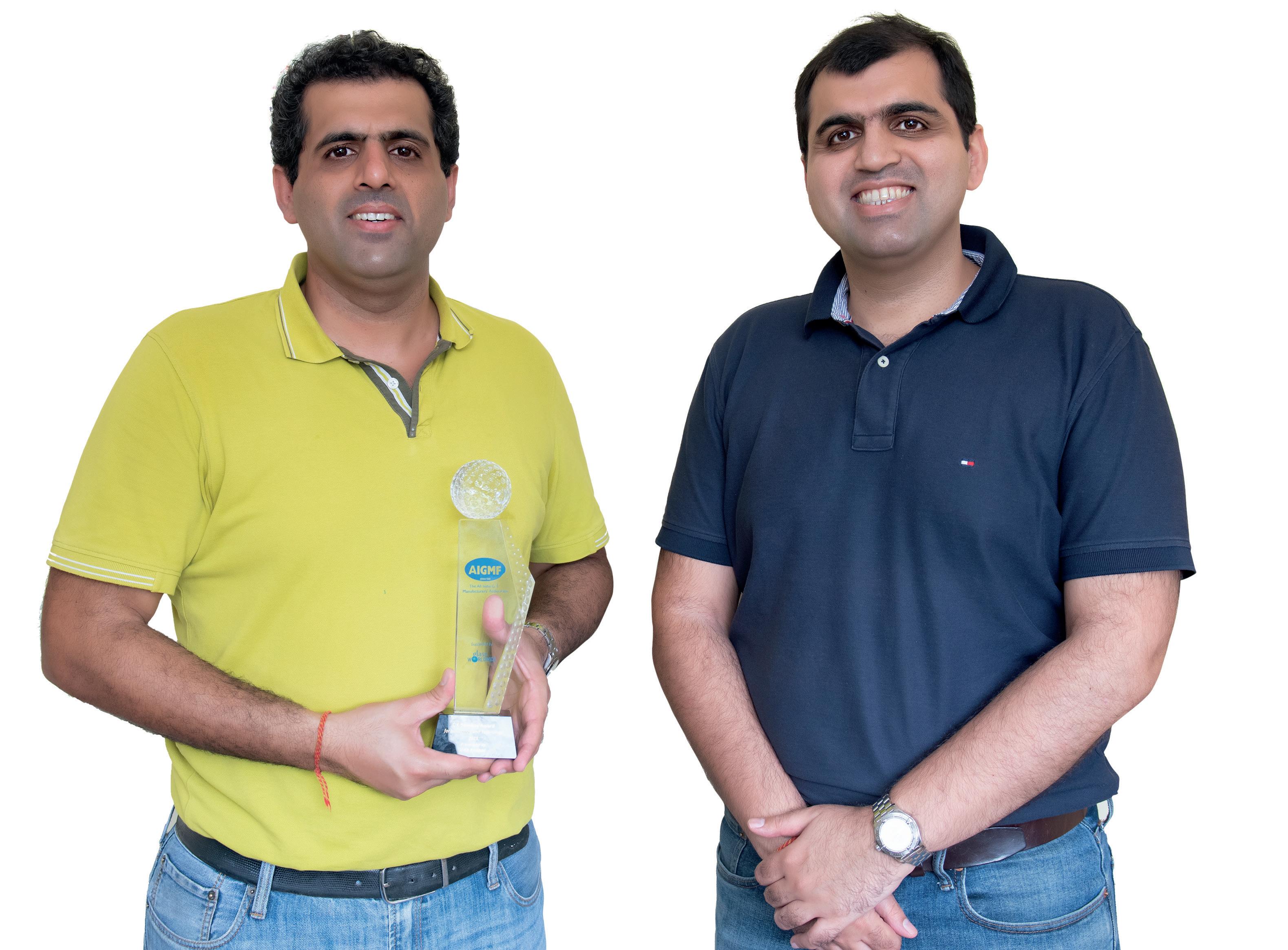
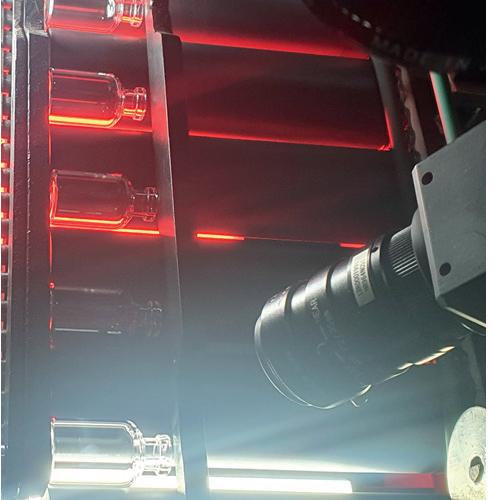

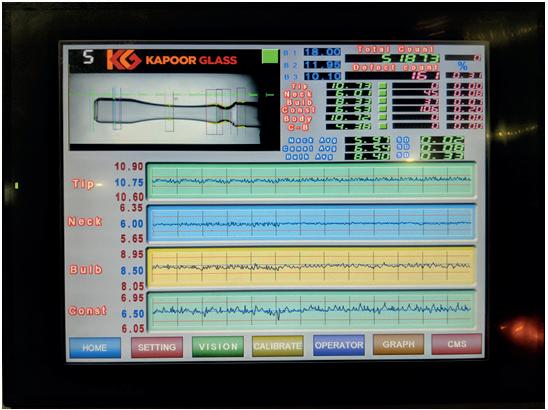
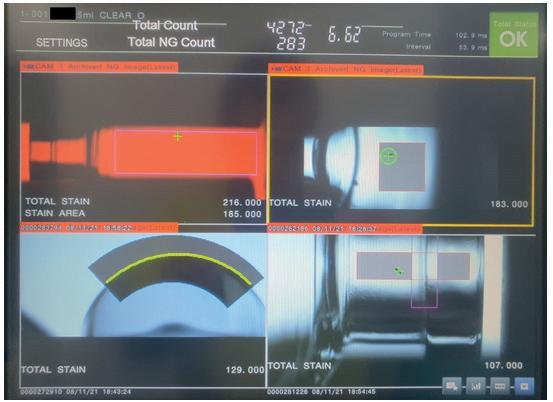
caminha na direção de zero defeitos.»
«Isso significa que temos de inovar continuamente, tentamos sempre melhorar. Perguntamo-nos continuamente como estamos melhor hoje em comparação com onde estávamos ontem. É esse o nosso lema. Existe uma mentalidade de melhoria contínua que é, essencialmente, como obtemos zero defeitos?»
Inovação
Um caso de inovação foi a recente implementação de sistemas de inspeção estética para frascos de vidro, destacados pelos juízes da AIGMF.
Um sistema personalizado dos fornecedores europeus não teria justificado o custo. Em vez disso, o grupo criou uma esteira de transporte que incluía um robô de seis eixos que conseguia identificar e localizar cada frasco na esteira, pegas especiais não poliméricas, uma lente telecêntrica para evitar erros de paralaxe, quatro câmaras de alta velocidade que podem captar, pelo menos, 25 imagens por frasco e iluminação especial para observar o maior contraste entre a marca a detetar de forma fiável.
O sistema que agora é o modelo para uma sucessão de esteiras de transporte será adotado em todas as suas instalações no futuro.
História
Udit é a terceira geração da família Kapoor a trabalhar na empresa. Aluno na Universidade de Southampton, no Reino Unido, concluiu uma licenciatura em Engenharia Elétrica e entrou para a empresa há 17 anos. A empresa foi formada em 1962 por Dharmender Kapoor e é totalmente detida pela família desde então. O pai, Sanjeev Kapoor, foi a segunda geração da família a trabalhar no negócio e, atualmente, é Diretor Executivo.
Após se focar originalmente no mercado nacional indiano, atualmente serve 32 países, sendo a Europa Ocidental a sua maior região. Anteriormente, era um fornecedor nacional, mas, após a expansão de gigantes empresariais externos no mercado indiano, aliada à importação de frascos e ampolas da China, mudou de tática.
O irmão de Udit, Dhruv, entrou para a empresa em 2016, depois de concluir uma licenciatura em Engenharia Elétrica na Universidade de Cranfield, no Reino Unido. Atualmente, é Diretor Comercial.
Expansão
O grupo irá expandir-se para novas instalações localizadas do outro lado da estrada do seu hub de produção de Bombaim no fim do ano. A mudança para a Unidade 3 irá aumentar a capacidade de produção da empresa para 2 milhões de peças por dia. O hub irá concentrar-se na produção de cartuchos para os setores da insulina e dentário em especial e criará até 75 novos empregos.
Um aspeto importante das instalações de produção de vidro será o seu foco na automação e equipamento de produção relacionado com a Indústria 4.0. As instalações terão espaço para expansão para um setor de frascos Prontos a Utilizar (RTU) e a empresa já tem planos para uma linha piloto relacionada com isto.
Dhru afirmou: «As novas instalações são onde estamos mesmo a tentar construir algo único, onde tudo está online e focado na Indústria 4.0.»
A empresa planeia expandir o seu impacto novamente para a Índia. Apesar de 90 % da sua produção ser atualmente exportada, planeia vender mais para o mercado nacional. Está a explorar novas instalações de produção no norte e sul da Índia para diminuir os prazos de entrega aos clientes.
O mercado dos cuidados de saúde da Índia começou a fazer a transição para padrões mais altos mesmo antes da pandemia, mas acelerou após os confinamentos.
«Há cerca de 15 anos, a empresa mudou de rumo e focou-se no ocidente. Houve uma mudança no mercado nacional e queremos estar envolvidos novamente. Os clientes indianos pretendem produtos de melhor qualidade nos cuidados de saúde e no estilo de vida. Atualmente, sem perturbar o nosso negócio de exportação, pretendemos aumentar o nosso impacto na Índia,» afirmou Dhruv.
«Estamos muito honrados com a direção que o nosso produto está a tomar, é farmacêutico, estamos num negócio salva-vidas, por isso, o nosso principal objetivo é não dececionar os nossos clientes, independentemente do que acontecer.» �
Kapoor Glass Índia, Nova Bombaim, Índia https://www.kapoorglass.com
Reciclagem: O processo da recuperação económica e utilização de TODOS os detritos de vidro
Steve Whettingsteel* discute alguns dos desafios da criação de vidro verdadeiramente sustentável e destaca uma série de soluções de refinamento.
Contrariamente à crença popular, é uma impossibilidade técnica que todo o vidro usado ou reciclado seja considerado uma matéria-prima pronta para o forno.
Todavia, infelizmente, o público, a indústria e os legisladores foram levados a acreditar, de forma errónea, que «garrafa para garrafa» é a única verdadeira forma de reciclagem de vidro.
Apesar de isto ser o ideal numa economia circula utópica, na realidade, a nível global, são produzidos mais de 50 milhões de toneladas de vidro anualmente e menos de 40 % são utilizados para a produção de vidro novo.
Por isso, não considerar quaisquer outros mercados finais para os resíduos de vidro processado resulta numa grande percentagem em aterros como cobertura diária ou utilizada como substituto de baixo valor acrescentado.
Quando possível, os resíduos de vidro refundidos devem ser sempre o principal mercado para o vidro reciclado, mas as limitações da capacidade do forno em muitos países, o baixo custo do vidro
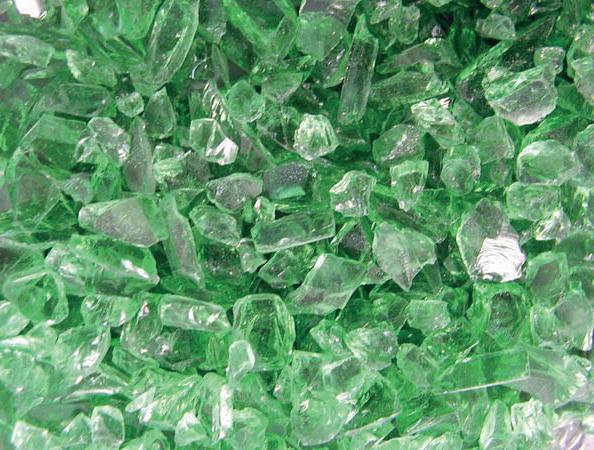
� Imagem 1. Resíduos de vidro de qualidade refundidos separados de cor verde. importado, a disparidade de cores, a qualidade, a contaminação, a localização e a economia provaram ao longo de décadas ser o principal desafio na criação de sustentabilidade.
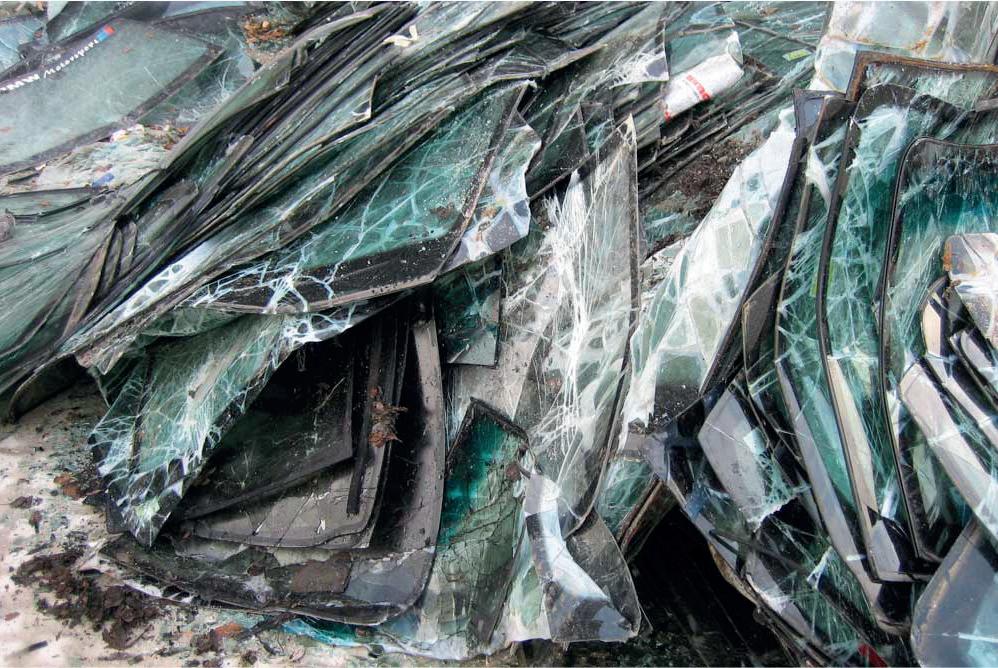
O Mito da Garrafa para Garrafa
Outro desafio é o custo de CO2 de cadeia longa da colocação do vidro num forno, o alegado benefício de CO2 de usar resíduos de vidro não tem em conta a sua recuperação, reciclagem, transporte ou eliminação do vidro que é não é adequado para refundição num aterro (imagem 1).
Ter um valor demonstrável claro de CO2 para resíduos de vidro ou outros produtos de vidro ao longo de qualquer parte da sua recuperação, processamento e reutilização deve fazer parte de qualquer estratégia responsável e utilizar o vidro de uma forma em que o verdadeiro custo de CO2 de cada produto ou mercado determina a sua utilização.
Contrariamente à crença popular, os mercados alternativos eficientes e eficazes para o vidro desadequado para refundição podem desempenhar um papel substancial na redução geral de CO2 da indústria de reciclagem de vidro.
Muitos governos e autoridades aderem cegamente à política de «a única verdadeira reciclagem de vidro é a produção de vidro novo», sem equacionar a capacidade total dos fornos numa distância económica nem a questão dos requisitos de resíduos de vidro coloridos que esses fornos têm.
Isto costuma levar ao colapso de um programa de reciclagem de vidro ou indicar um custo desproporcionalmente alto, acabando por ter de se admitir a