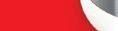
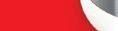
AND DRINK FOOD AND DRINK NETWORK



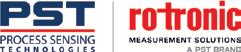

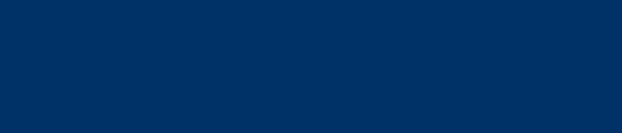
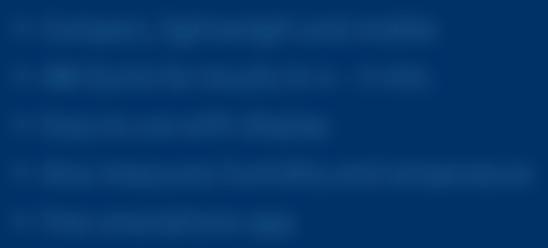
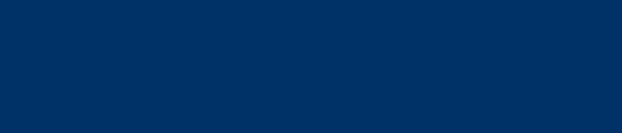
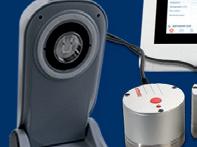

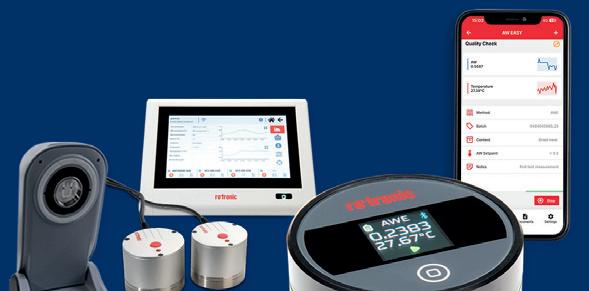
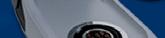
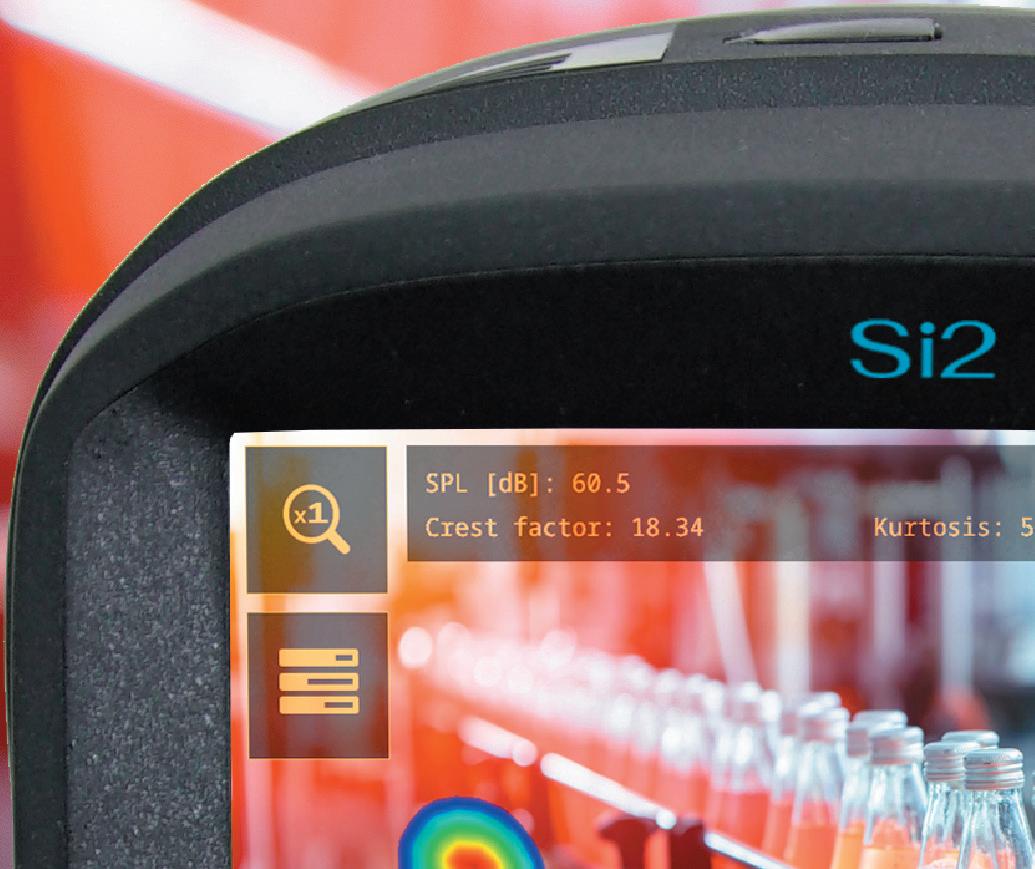
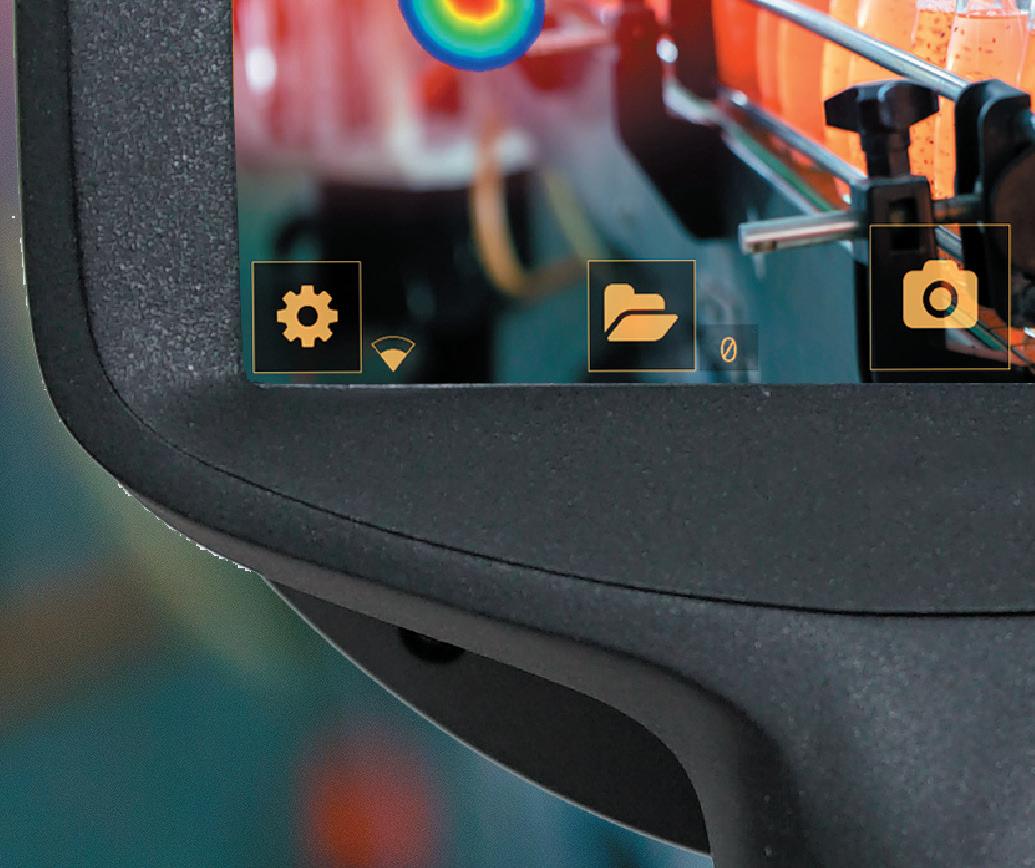
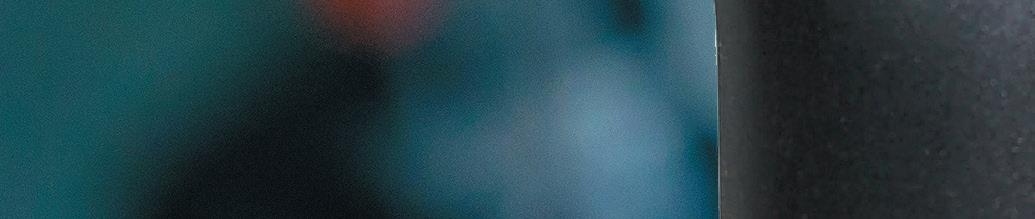


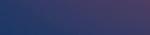
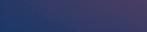
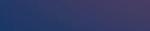


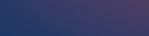
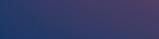
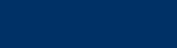
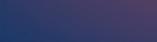
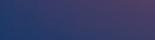
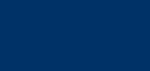
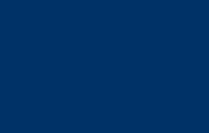
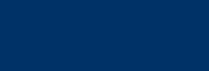
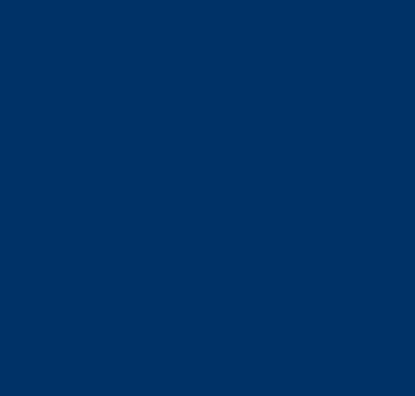
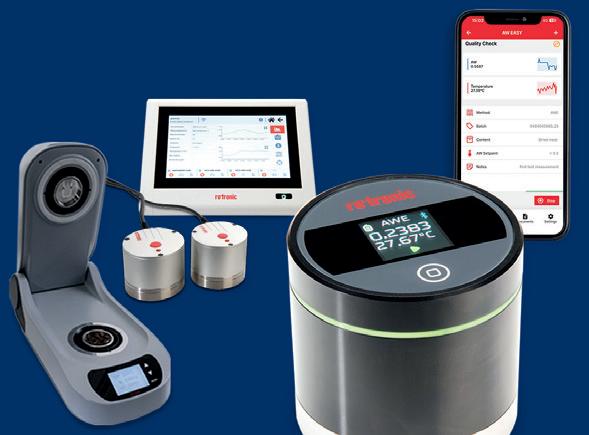

THE FLIR SI2 REVEALS HIDDEN LEAKS AND MECHANICAL FAULTS FOR OPTIMIZED OPERATIONS
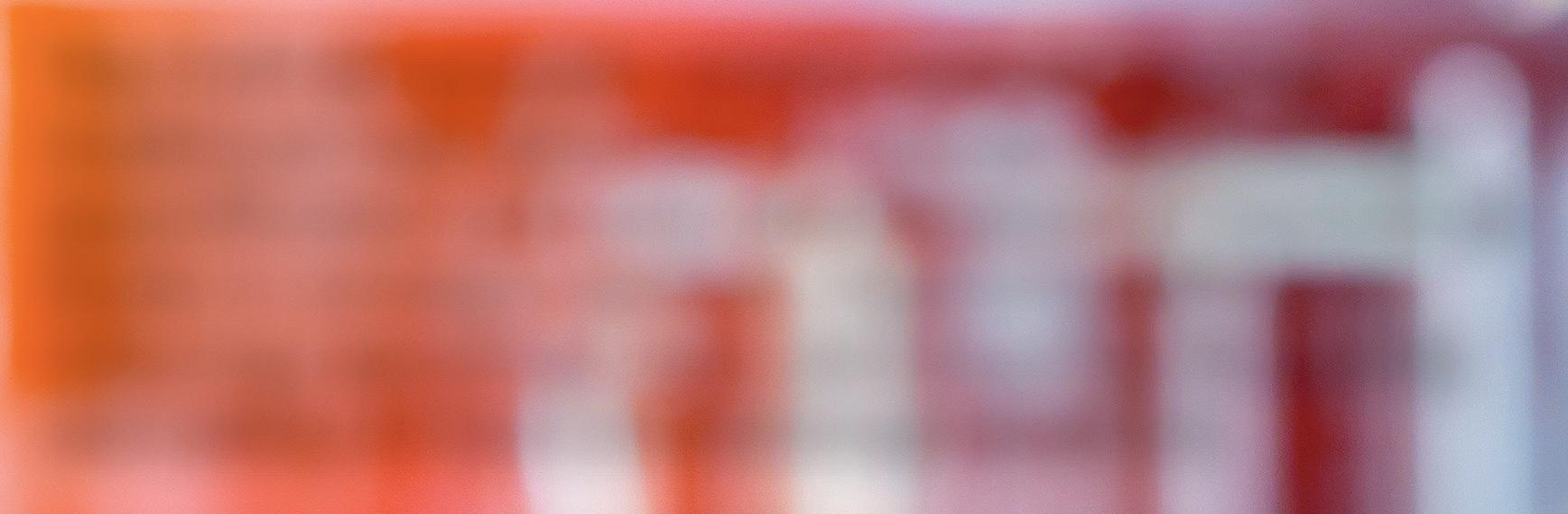
The FLIR Si2 acoustic camera extends beyond traditional leak detection to include industrial gas quantification and early identification of mechanical faults in conveyor systems, improving e ciency, reducing operating costs, and ensuring the quality and safety of food and beverage products.
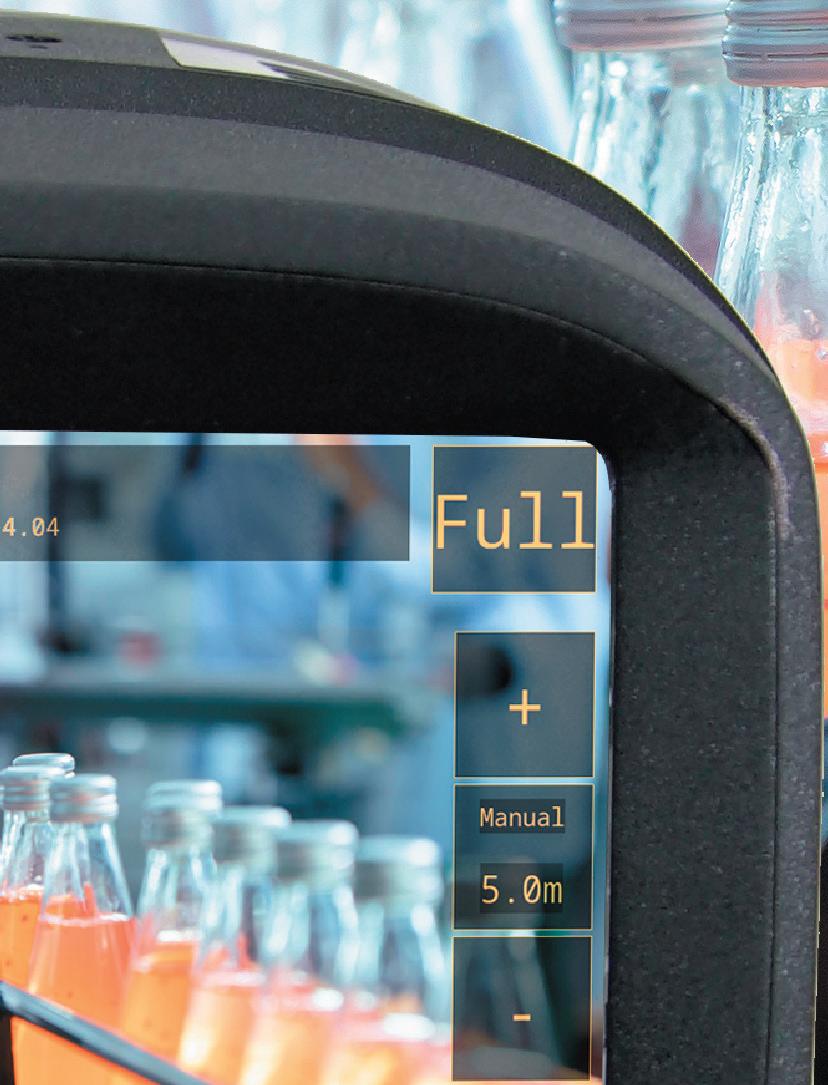
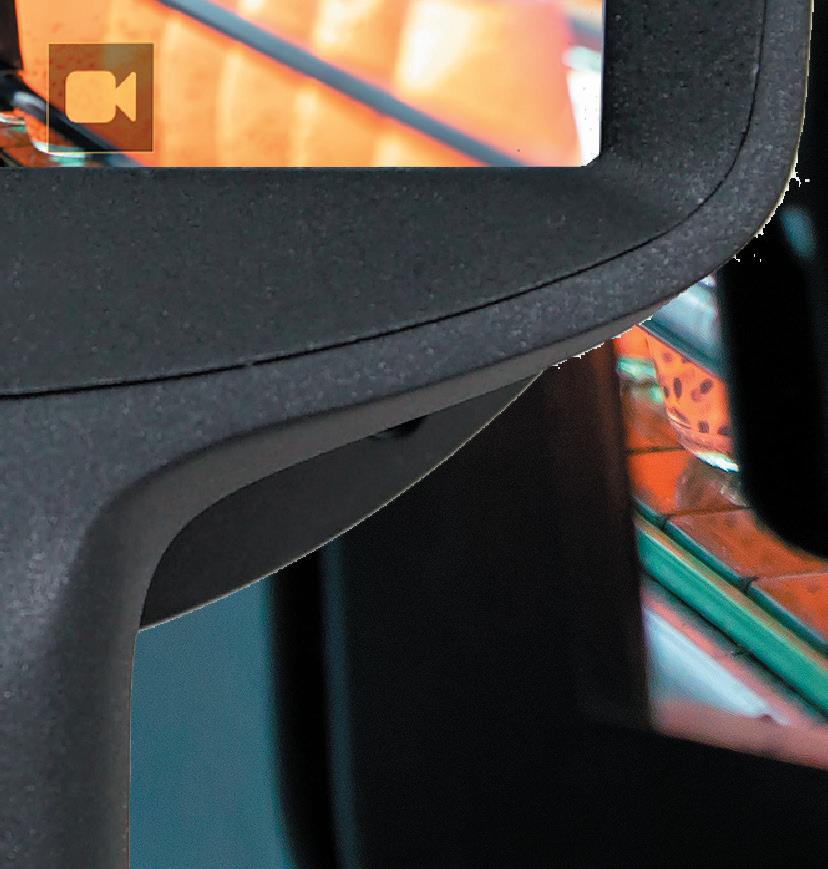
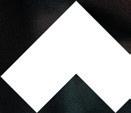
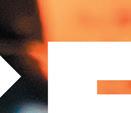
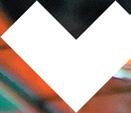
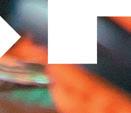
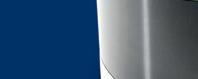
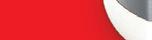

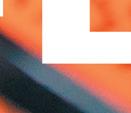
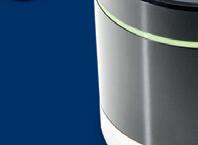
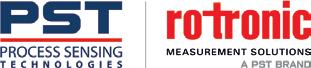
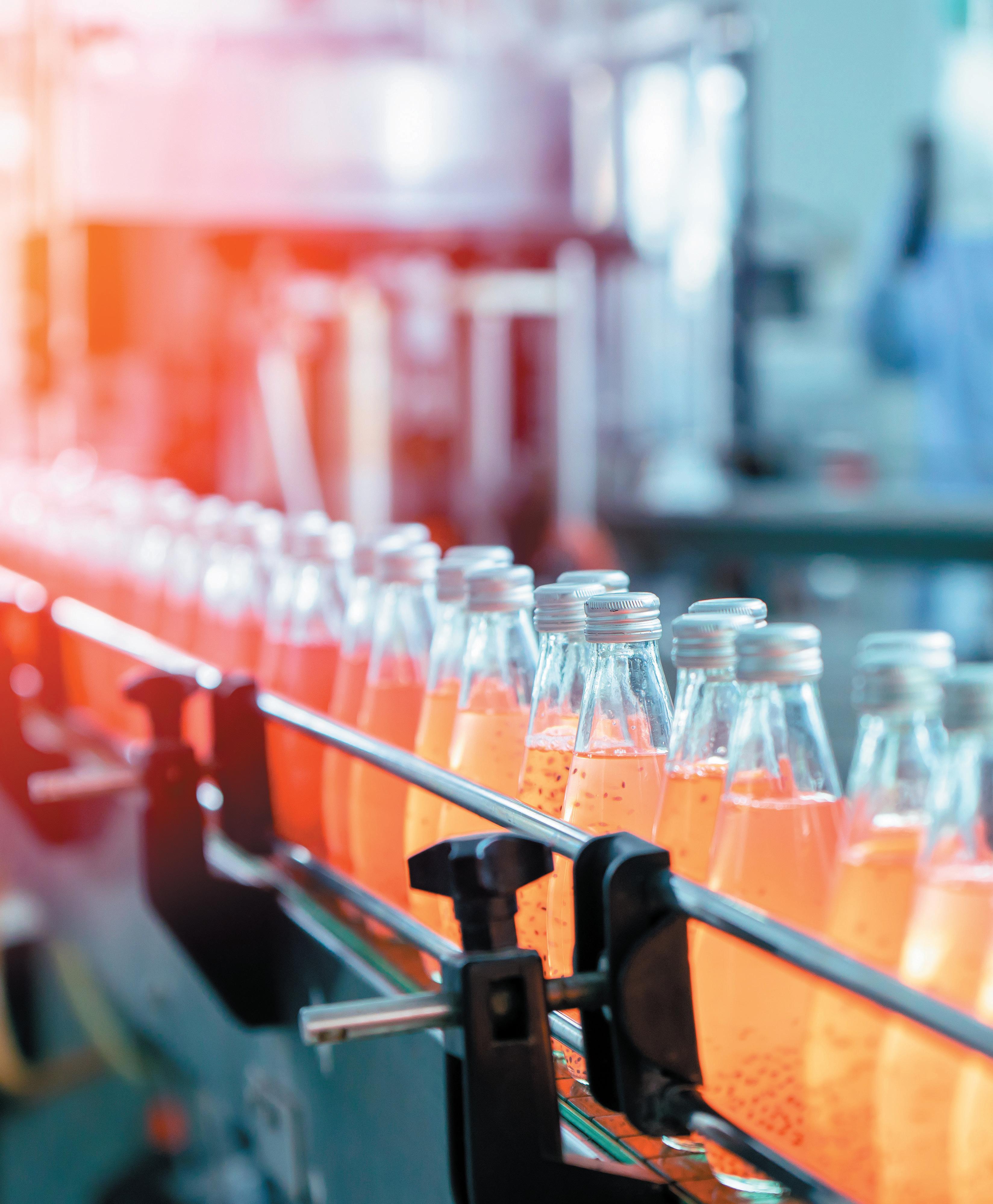
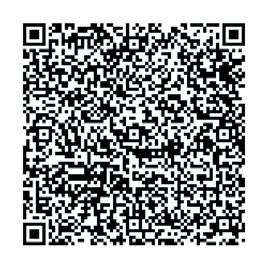
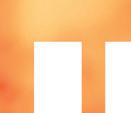
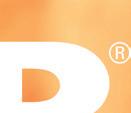
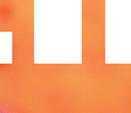
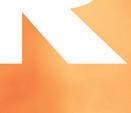
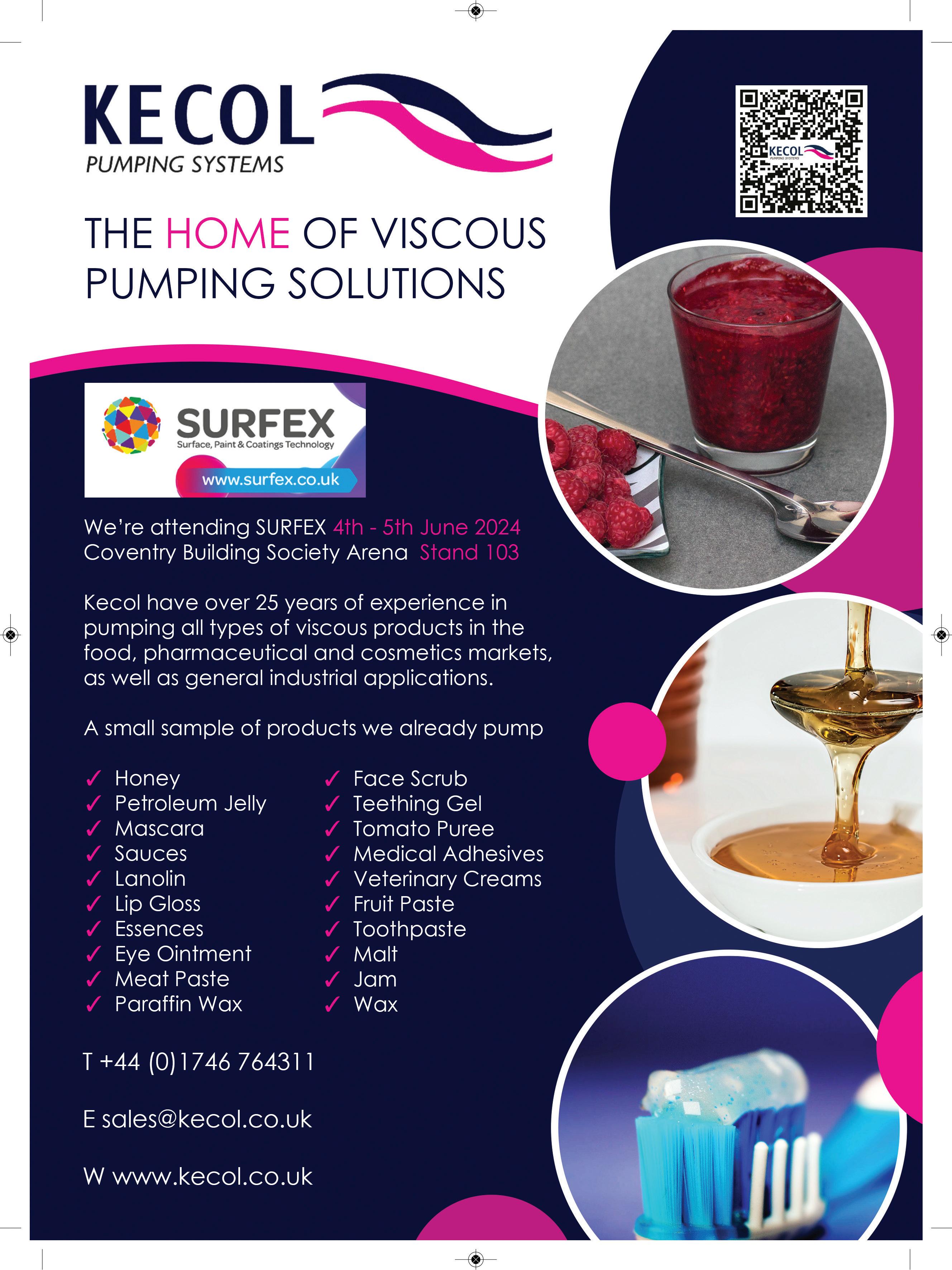
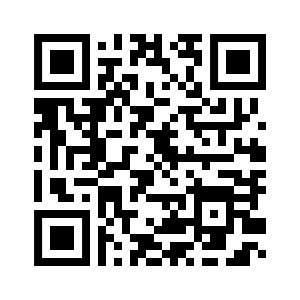
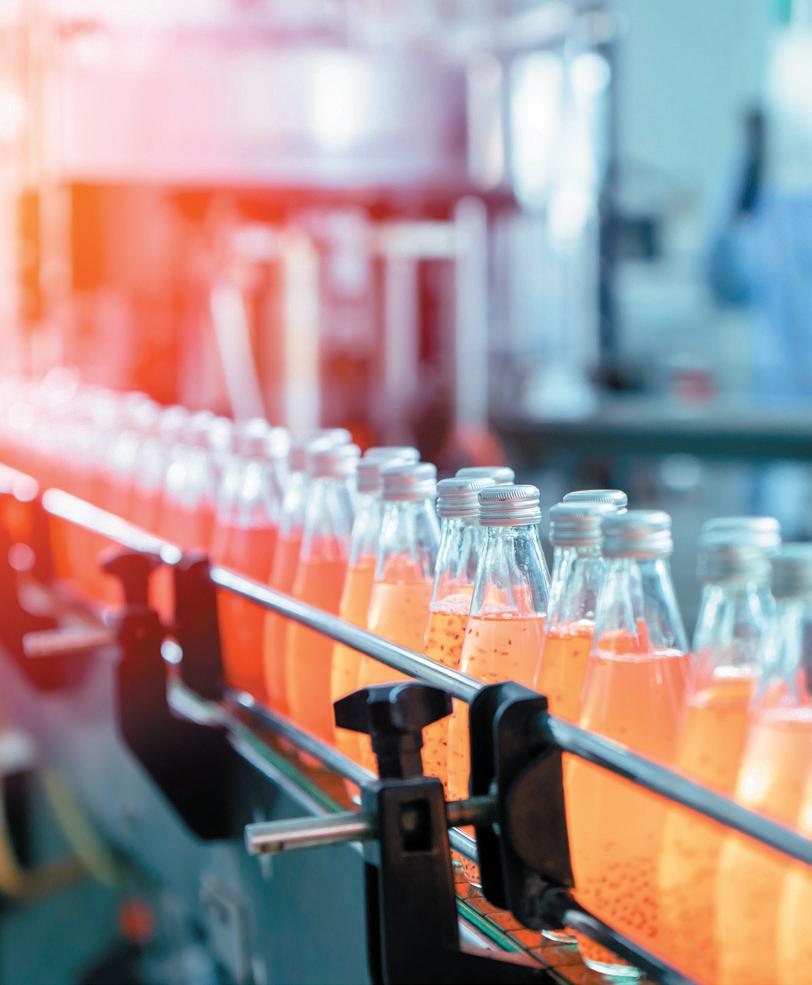

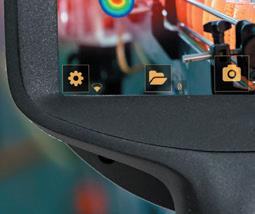
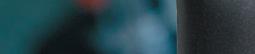
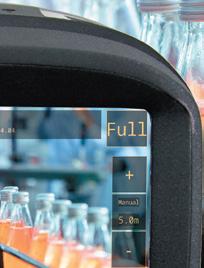
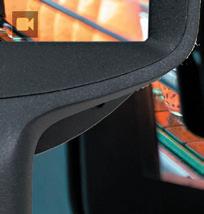











Automate UK
Automation Uk Multimodal
MVC
Conker Communications
Harford control
Nineteen group
PPMA
EDITORIAL: 02 NEWS NETWORK
Rosemullion Distillery Ltd
ADVERTISEMENT SALES:
KIMBERLEY READ (Advertisement Sales Manager) GINA MADDISON
AMANDA WALMSLEY EVELYN WOOLSTON
STUART TURNBULL - Studio Manager RACHEL RILEY - Designer
WALTONS PUBLICATIONS LTD
46 HENEAGE ROAD, GRIMSBY N.E. LINCOLNSHIRE DN32 9ES
Kimberley Read at: kimberley@ foodanddrinknetwork-uk.co.uk or Gina Maddison at: gina@foodanddrinknetwork-uk.co.uk
foodanddrinknetwork.co.uk


@fdnetworkuk
Smart Manufacturing & Engineering Week Innovation and MRO take centre stage at SM&E Week ‘24
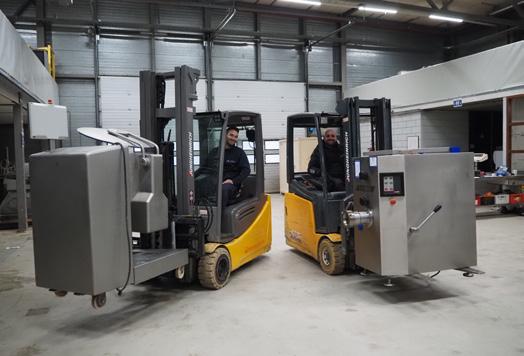
12 issues - £84.00 (inc. postage) A guide to the exhibitions and events
in the Food and Beverage Industry: In Conversation with Industrial Auctions 09. Automation UK Automation UK unveils an impressive keynote speaker 11. Multimodal 2024 The Future of Logistics Unfolds
Machine Vision Conference The 8th Machine Vision Conference opens in 2 months’ time
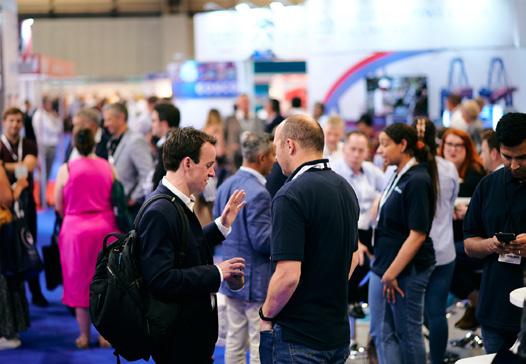
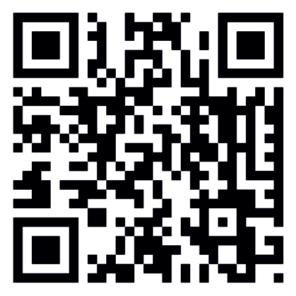
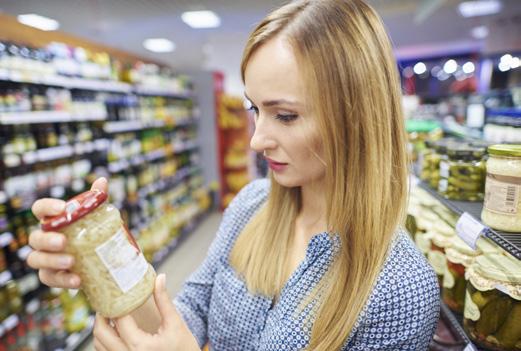
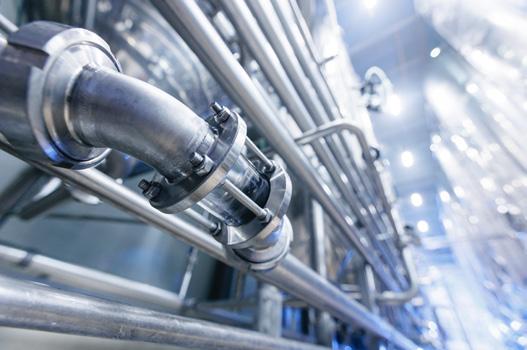
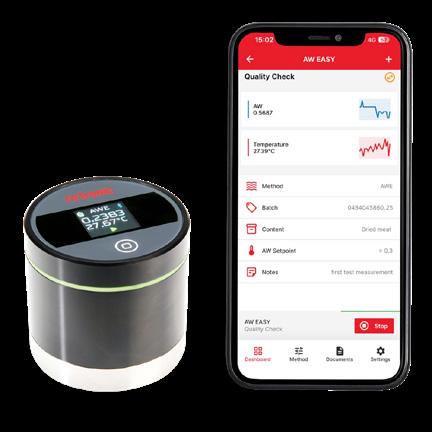

&
Markem-Imaje Revolutionising Brand Marketing: Unleashing the power of QR codes
National Flexible Crafting Exceptional Coffee
Penn Packaging Produce recyclable spouted pouches economically
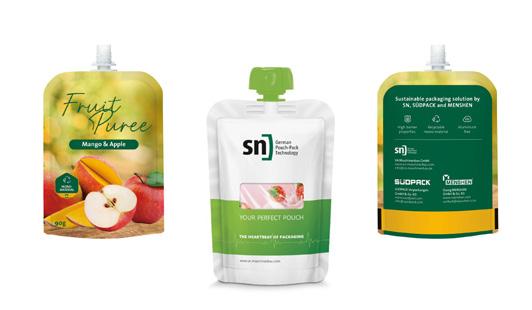
Zarecki Expands Production with Integrated Conveyor System from Key Technology
Processing over 6,000 metric tons of fresh fruit every year, Zarecki brings together locally grown produce and modern technology to provide food manufacturers with top quality ingredients for their breakfast cereals, snack bars, confectionaries and more. In 2022, while expanding production with a new line that sweetens and dehydrates different types of berries, Zarecki turned to Key Technology and selected an integrated vibratory conveyor system with five Impulse™ shakers.
Designed for processing and packaging lines that require precise metering and low maintenance drives, Key’s Impulse shakers are ideal for product mixing, ingredient feeding, scale feeding and more because they start and stop quickly, which helps maximize product quality, throughput and line efficiency. Impulse is equipped with dedicated solid-state controls that enable conveying pan amplitudes to range from zero to 100 percent for superior
Dehydrated fruit processor Zarecki has made a name for themselves across Europe since launching in 2017. production versatility. Running at speeds of up to two metric tons of fruit per hour, Zarecki’s new line sweetens cherries, currants and blueberries with infusion tumblers, which discharge the syrupy product into a flume system. From there, product is run through a series of three Impulse conveyors with specialized screens that de-syrup and de-juice the fruit. Next, an Impulse transfer conveyor directs the product 90-degrees around a corner and feeds an Impulse spreading conveyor featuring custom-designed lanes, which perfectly spread the infused fruit for presentation to the dryer’s infeed system.
Top of the Tree
Rosemullion Distillery’s iconic dry gin is voted the best in England (World Drinks Awards 2024). Outperforming big brands for 6 years, 61 awards and counting
Helford based, family run Artisan distillery, Rosemullion, are delighted to announce that they have again come out on top, winning the England title at the World Drinks Awards 2024 for their iconic Dry Gin. This prestigious accolade now brings their award tally to 61, making Rosemullion one of the most awarded distilleries in the country. This winning cycle, which began in 2019, is all the more remarkable for this small but dedicated distillery as it has consistently outperformed bigger or more long established brands in doing so well for so long.
The World Drinks Awards are highly respected by both consumers and traders alike and are crucial in recognizing, rewarding and promoting the world’s best spirits to all markets. The selection process is rigorous and includes blind tasting by a carefully chosen panel of International experts. Rosemullion’s winning Dry Gin is based on a traditional recipe made by the Bradbury family and their team – it ‘presents’ as a clean tasting, big-hearted drink which is based on a bold blend of juniper, citrus fruits and botanicals.
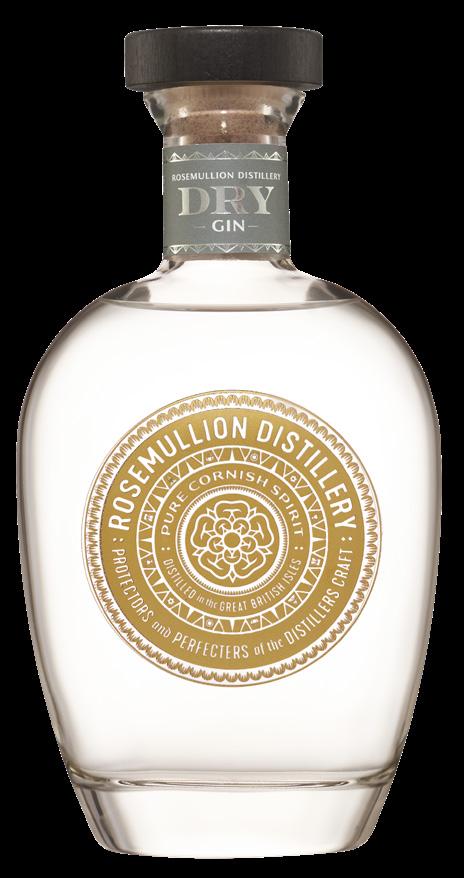
Rosemullion’s continuing success story owes a lot to the background of its founders Liz and Andy Bradbury – both are chemists with years of past experience in product development and improvement processes such as Kaizen, 6-sigma and TQM. Speaking today, Andy explains why, in his opinion, Rosemullion spirits have been so successful - “utilizing our experience, we make classic spirits, not sugar flavoured, additive laden spirits, so our Gins purely taste of gin, not ‘fruit shoots’. Similarly, we want our rums to taste of rum and not be hidden by sugars and vanilla etc. To achieve good gin, rum and whisky the foundation is in the fermentation, which provides a firm footing
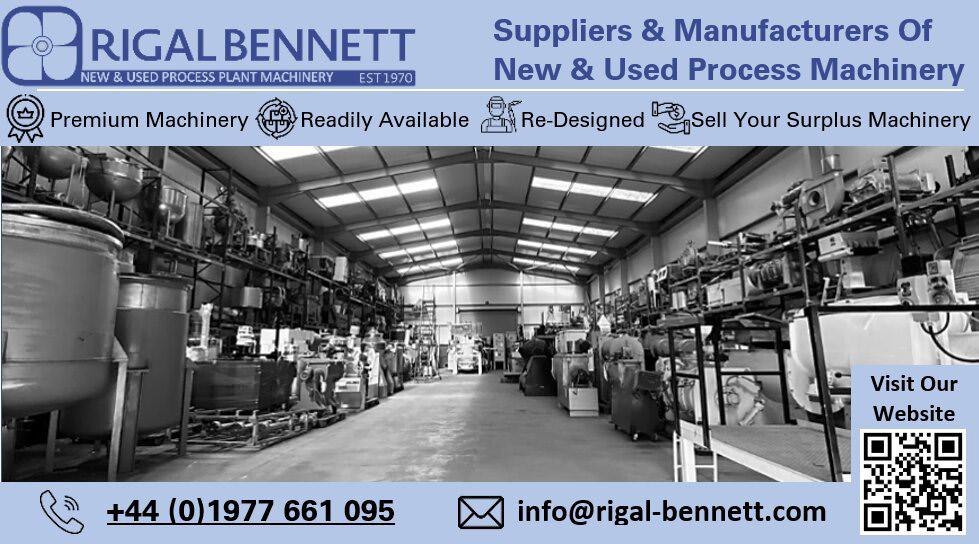
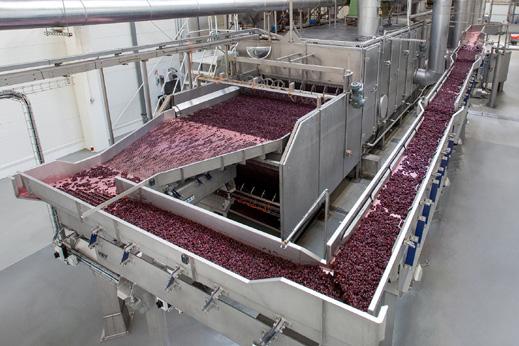
Key Technology, Inc. | For more information, visit www.key.net. Duravant | For more information, visit www.duravant.com.
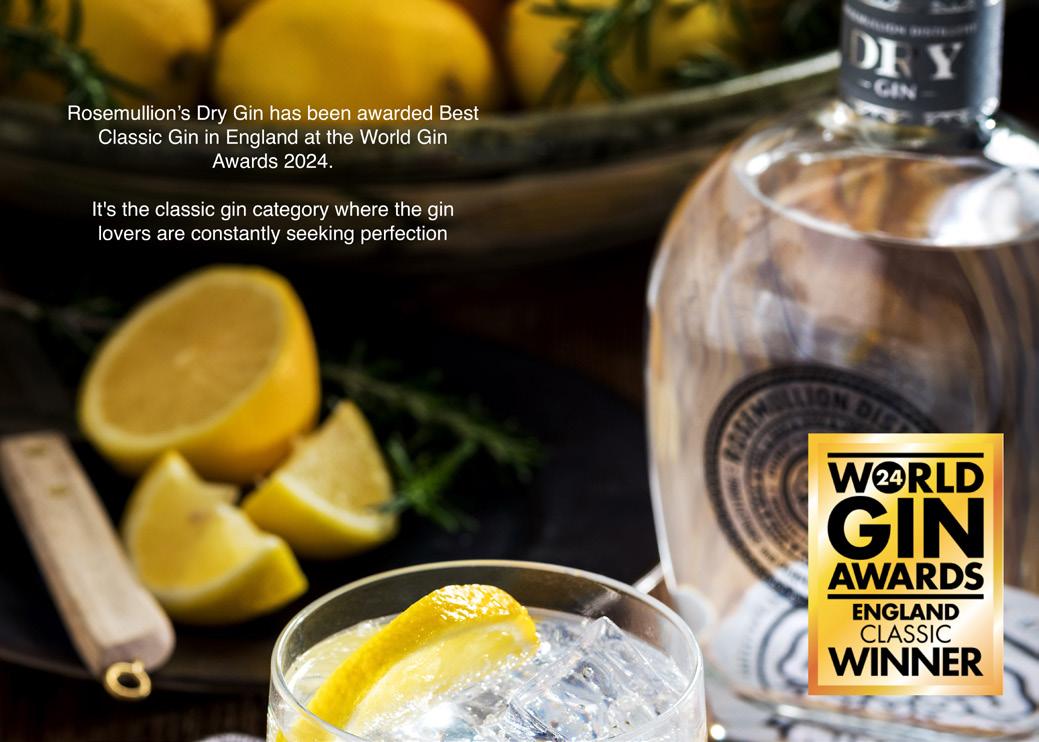
for creating great spirits. We also draw upon our unique surroundings to underscore our provenance – Helford rainwater is used in the fermentation and distillation process, complemented by local Cornish ingredients plus seasonal fruit from our own orchard and vines. We only produce small batches to ensure optimum quality control. We aim always to be the protectors and perfecters of the distillery craft, constantly looking to improve even category winners”.
In addition to the previous factors, Rosemullion also strives to maintain ethical, responsible and sustainable practices. Rosemullion are registered with Cornwall Council’s ‘Made in Cornwall’ scheme – hence they are audited in terms of what they say they do, covering the fermentation, distilling and aging processes carried out on their site. In terms of minimizing their environmental impact they have a rainwater catchment system and minimize their water consumption by recycling their cooling water for use in the fermenters. They also minimize the use of plastic from suppliers and all their own plastic and cardboard waste is sent to recyclers. Finally they pay more for their distribution boxes so they can reuse them.
For more information visit: www.rosemulliondistillery.com
If you would like to see your Newsworthy articles, regarding the Food & Drink Industry, published in the next issue of ‘Food & Drink Network UK’ email:
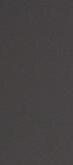
Fearne & Rosie widens UK distribution & secures first international listing
Asda confirmed as latest supermarket launch Spinneys secured as first international listing CLF & CN Foods secured as new wholesale partners.
This April, British Jam brand Fearne & Rosie, celebrates securing wider UK distribution for its range of reduced sugar jams. ASDA, which is the brand’s newest national supermarket win, will take two SKUs; Strawberry and Strawberry Super Berry from 6th April, rolling out across 407 stores (RRP: £3.20/310g jar).
This month also marks the brand’s first foray onto the international supermarket scene, with Spinneys in Dubai confirmed to take all five flavours. The brand will also be widening its availability to independents, having confirmed a duo of wholesale wins with CLF and CN FOODS who will list the full range. Pitched as perfect for spreading, stirring, baking and dolloping, the Fearne & Rosie range prides itself in being packed with 70% more fruit and 40% less sugar than standard Jams. Made using 100% natural ingredients and absolutely no concentrates, the Great Taste Award-winning spreads are
Cablevey Conveyors launches revolutionary mobile system for automated food conveyor cleaning
Leading materials handling company, Cablevey Conveyors, operating as part of Automated Handling Solutions (AHS), has announced the launch of Cleanvey - a groundbreaking development in the automation of Clean-in-Place (CIP) processes for tubular drag conveyors. The solution is set to redefine standards in food safety and production efficiency within the food processing industry.
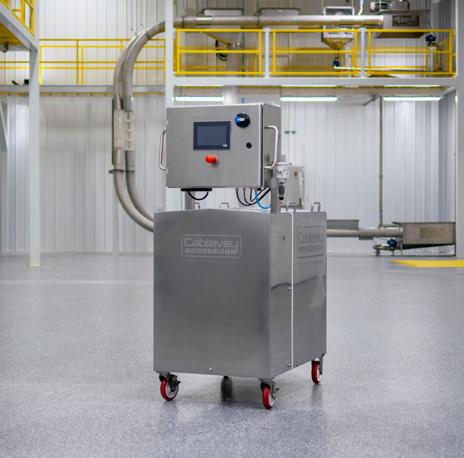
Cleanvey is engineered to automate the CIP process, allowing for efficient, thorough cleaning of tubular drag conveyors, crucial in maintaining sanitary compliance and ensuring the safety of food products. Designed with integrated water line hookups and pre-programmed cleaning options, this mobile unit simplifies the cleaning process, enabling a technician to initiate a comprehensive cleaning cycle with just the press of a button. Tailored to meet the industry’s demand for a more streamlined, less labourintensive cleaning process, Cleanvey significantly reduces the time and effort traditionally required for conveyor cleaning, offering a customisable, user-friendly approach that enhances productivity and minimises downtime. In addition to its cleaning capabilities, the solution offers advanced features such as optional sprayballs for targeted cleaning of residues and a sanitary blower that drastically reduces drying times, both further accelerating the readiness of conveyors for subsequent use.
Customer demonstrations will be available at the new AMP/AHS facility in Darwen, Blackburn-Lancs, from early Summer 2024.
For further details on how Cablevey’s Cleanvey solution can transform your food processing operations, please visit https:// cablevey.com/cleanvey/
Love
Corn
turns
deliciously crafted with whole fruits delivering taste and health in unison.
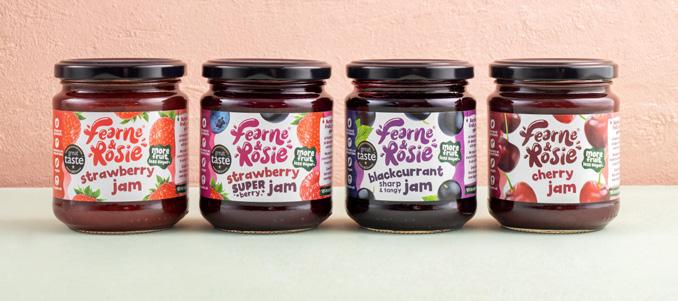
Fearne & Rosie was launched to market by teacher turned entrepreneur Rachel Kettlewell in November 2019 with the aim of providing the nation with delicious, fun and healthier food choices. Already the fastest growing Jam in UK grocery (+300% growth YOY) with a revenue forecast of £2 million for the current financial year, the new listings will further accelerate its mission to become the go-to jam brand for contemporary adults and families.
Visit the website to find out more or follow the journey on instagram: @fearne_and_rosie
Fountain Food Machinery providing factory clearance services as they celebrate a decade in business
With over 10 years experience, Fountain Food Machinery Ltd, based in Norfolk have become renowned as one of the leading UK buyers and sellers of quality used food processing and packaging machinery.
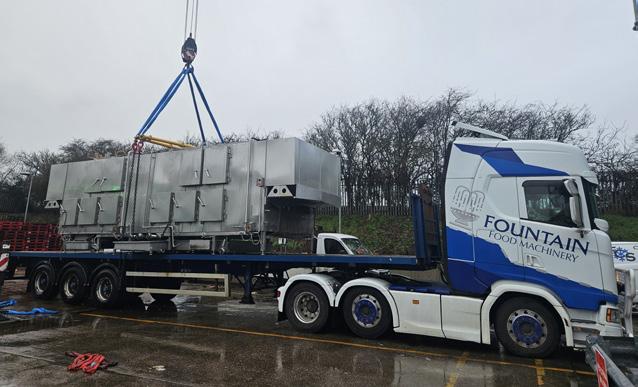
With business growth, comes the ability to diversify, which has led to Fountain Food Machinery now able to offer factory clearance services nationwide. Their highly qualified team have previous large scale and small scale experience, not only of clearing closed down factories, but also reinstating machinery in factory relocations. Using their own fleet of Lorries and lifting equipment, the team are fully insured, with banksman and Safe Contractor accreditation, ensuring that no job is too big or small. Fountain Food Machinery offers a bespoke service which can also involve purchasing your entire business premises, including all the machinery within.
Director, Rober Lunn says: “Thanks to our fantastic team, we are able to cater to our customer needs, working around their business, this can include nights and weekends.
We offer FREE viewings and quotations, and can give competitive pricing to purchase all machinery as one lot. We will often quote from images, or attend at a convenient time in person, achieving completion of sales with ease, efficiency and confidence.”
To find out more about what Fountain Food Machinery has to offer, head over to their website www. fountainfoodmachinery.co.uk
up the volume with the launch of their new flavour...
Sour Cream & Bouncin’ chives
UK’s fastest growing snack brand adds a brand NEW flavour to its range of Delicious Crunchy Corn.
In response to exceptional customer demand, LOVE CORN is launching a bold new flavour to its ever-growing range of Delicious Crunchy Corn. Their new flavour, Sour Cream & Chive has the perfect crunch and is set to make taste buds dance with this moreish flavour and simple ingredients. Sour Cream & Chive, which comes in various sizes, might just be their best tasting flavour yet. Now with seven flavours in the range they’ve got a flavour for everyone. Their delicious Sour Cream & Chive offers another simple, great tasting choice to those looking for a healthy snack alternative with 50% less fat than a packet of crisps, as well as being high fibre, low sugar, gluten free and vegan.
LOVE CORN, the UK’s fastest growing snack brand* is perfect for those looking for an on-the-go snack – whether in a lunch box, on a road trip or
something to crunch on in-between meals.
The new launch is also spot-on for serving at home, with a beverage and is a flavoursome crunchy topper to a salad, soup or even on a cheeseboard. Perfect for all snacking occasions!
LOVE CORN Sour Cream & Chive, 115g retails from £2.20 and is available in Sainsbury’s, Ocado and Amazon. p.s. find love in the simple things!
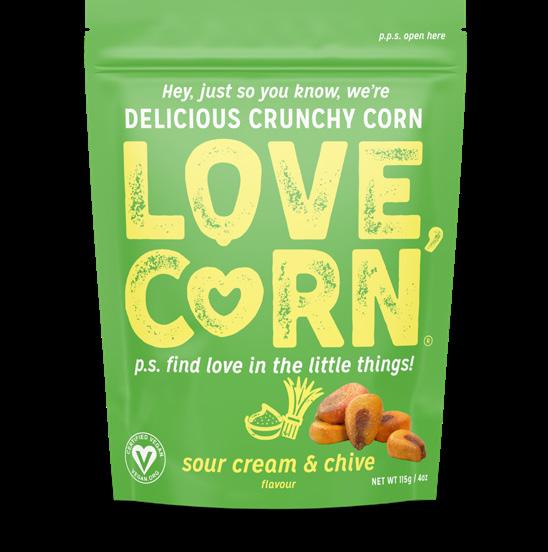
For more information on the LOVE CORN range of Delicious Crunchy Corn snacks, visit: lovecorn.co.uk
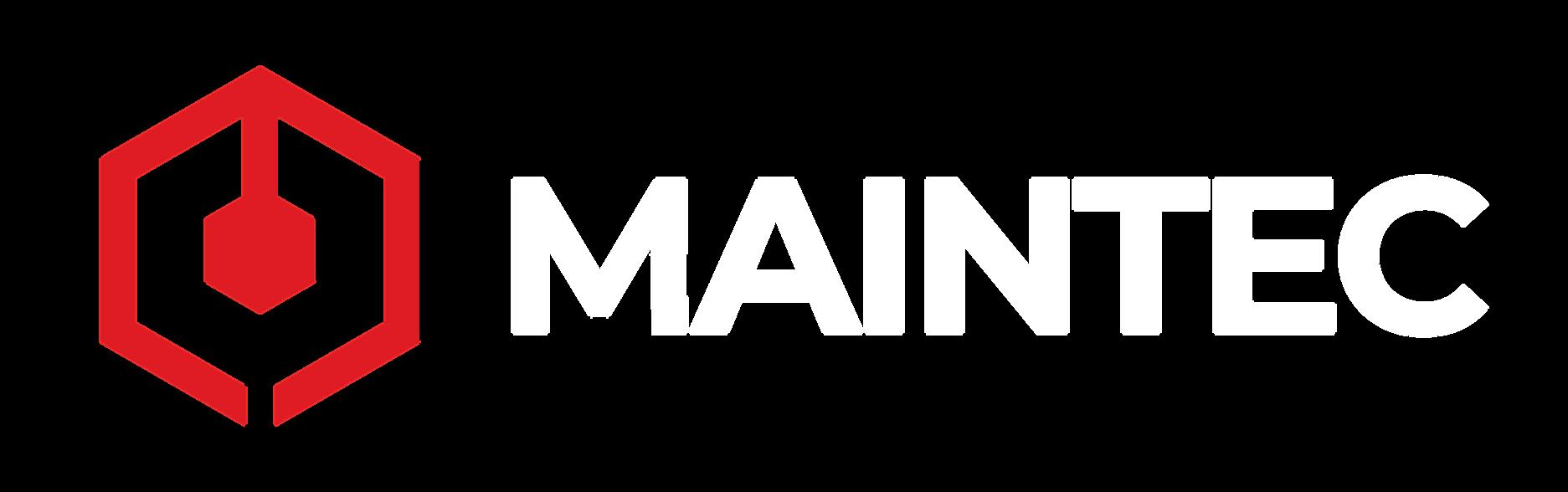

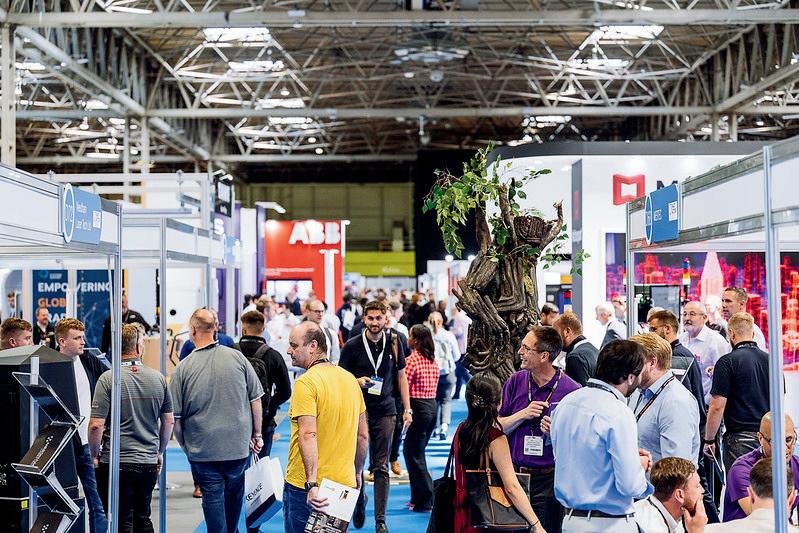
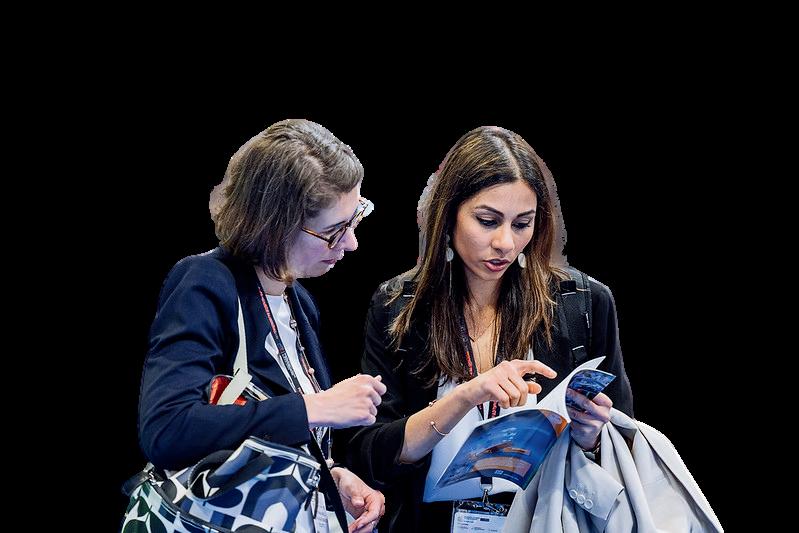
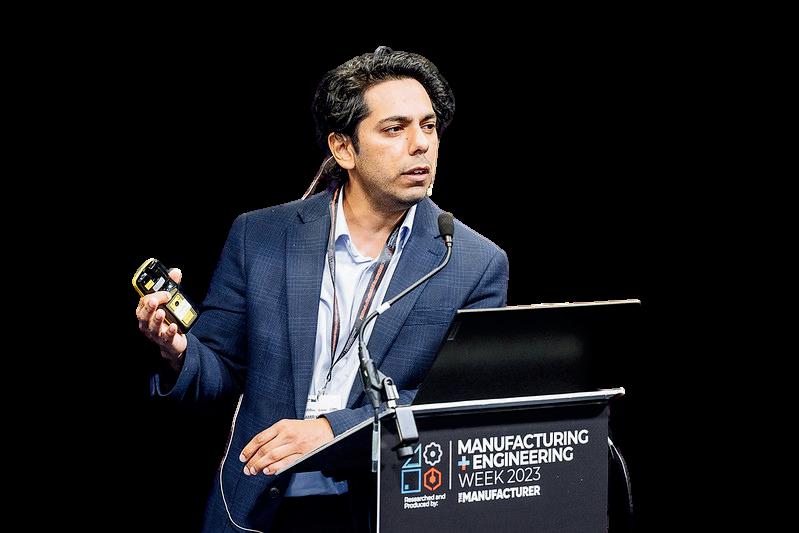
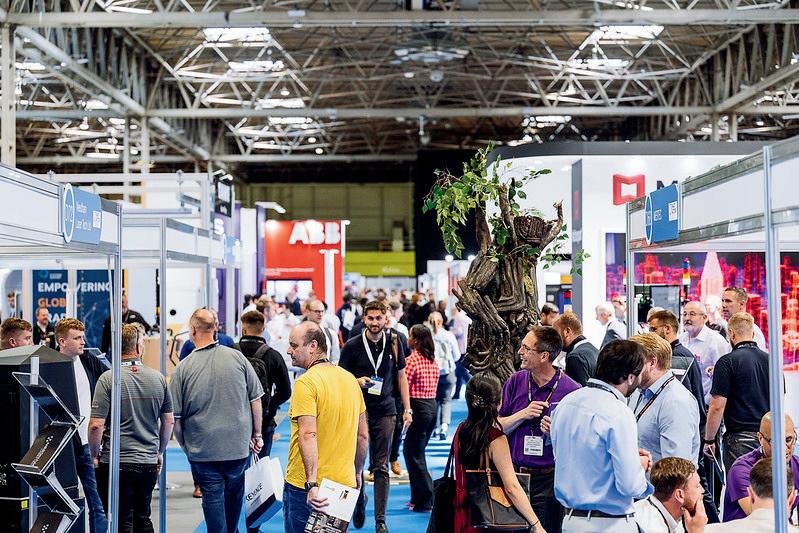
Innovation and MRO take centre stage at SM&E Week ‘24
The live events for Smart Manufacturing & Engineering Week 2024 take place at the NEC, Birmingham on the 5th and 6th June. In this article we dig a little deeper into what visitors can expect at the event amid the myriad of activities taking place.
Across its two halls, six exhibitions, two summits and eight education theatres Smart Manufacturing & Engineering Week addresses the key issues that concern manufacturing and engineering businesses currently. The main themes that the wide-ranging event covers are innovation, MRO, the supply chain, sustainability, digital transformation and people and skills.
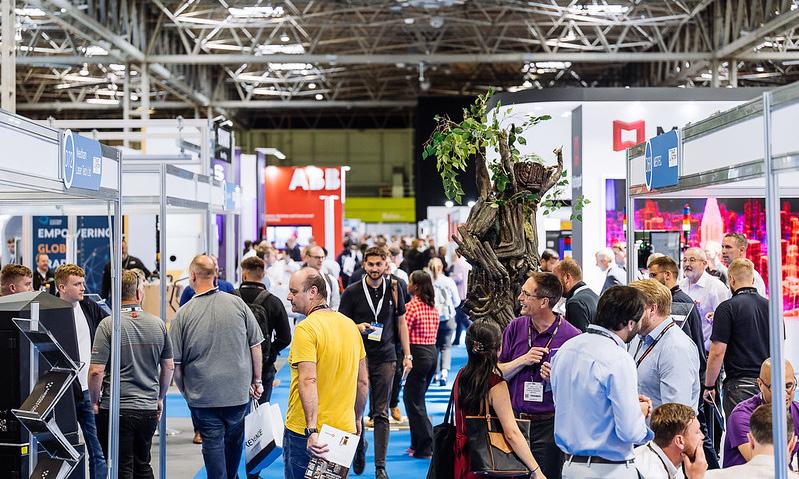
EXPLORING MAINTEC: A CLOSER LOOK AT HALL 4
Central to SM&E Week are the exhibitions, of which there are three taking place in Hall 4. Of great importance to readers is the newly invigorated Maintec, the UK’s longest standing exhibition dedicated to the maintenance, reliability and asset management industry.
Maintec has its own education theatre and the ability for visitors to access the major maintenance, repair and operations product and service suppliers as well as all the other content taking place makes the event more relevant for visitors and has brought it to life.
To ensure that visitors access the information they want there will also be a ‘Maintenance Safety Trail’ which visitors can follow to ensure they see the right businesses and technologies dedicated to ensuring maintenance is
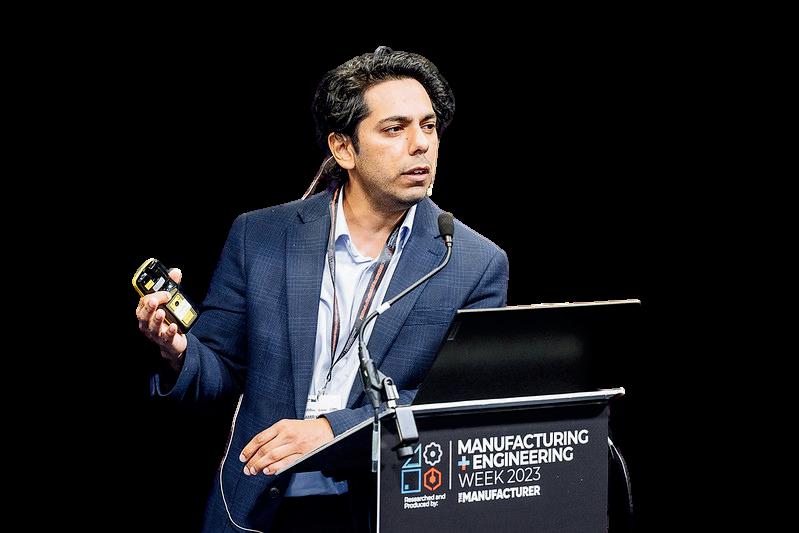
Hall 4 is not just about showcasing the latest developments in the world of maintenance; it also hosts several co-located exhibitions like Smart Factory Expo, which features a worldclass showcase of advanced manufacturing solutions from
both startups and established companies. The Design & Engineering Expo is also in Hall 4, focusing on optimising design processes and engineering solutions to drive cost efficiency and innovation in manufacturing.
KEYNOTE SPEAKERS
One of the main attractions of the SM&E Week is the variety of keynote presentations. Speakers from the food and beverage industry include Mircea Oprisan, Senior Director Data & Analytics Delivery at Mars, who will present a case study entitled Value Unlocks Leveraging Decision Intelligence in Supply Chain within the Industrial Data & AI Theatre on 6th June. Elsewhere, Dale Crow, Electricity & Automation Leader at Nestle, will talk about Leveraging Technology to Maximise Functionality and Performance in the Fluid Power Solutions theatre.
BRING THE NOISE...AND THE SMOOTHIE
One of the most popular ‘festival style’ attractions of SM&E Week returns in 2024, namely the Guitar Legends Competition. Entrants get the opportunity to play and record a piece of music entries are then judged by a professional musician. For the more energetic visitors there is the chance to power the production of their own smoothie via a bike challenge.
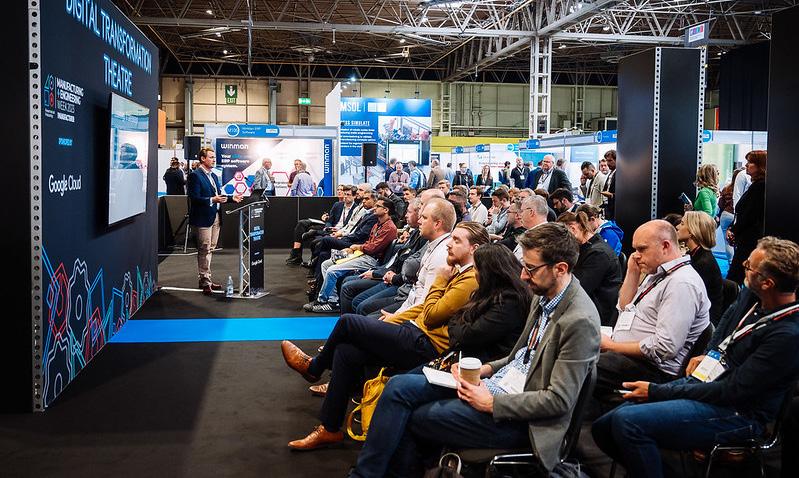
With so much going on during Smart Manufacturing & Engineering Week attendees can tailor their experience to their own areas of interest.
To build a personal “visitor trail” register in advance at: https://www.mandeweek.co.uk/
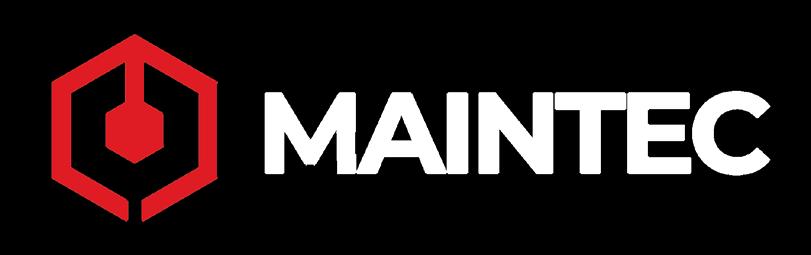
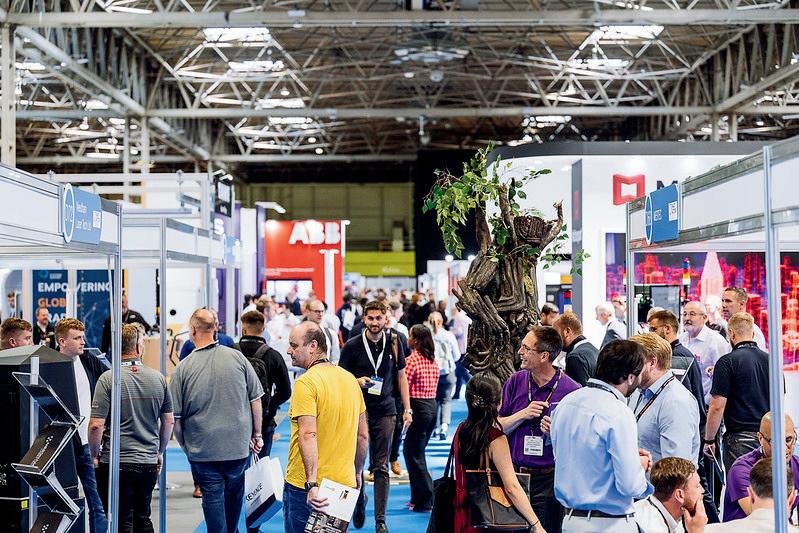


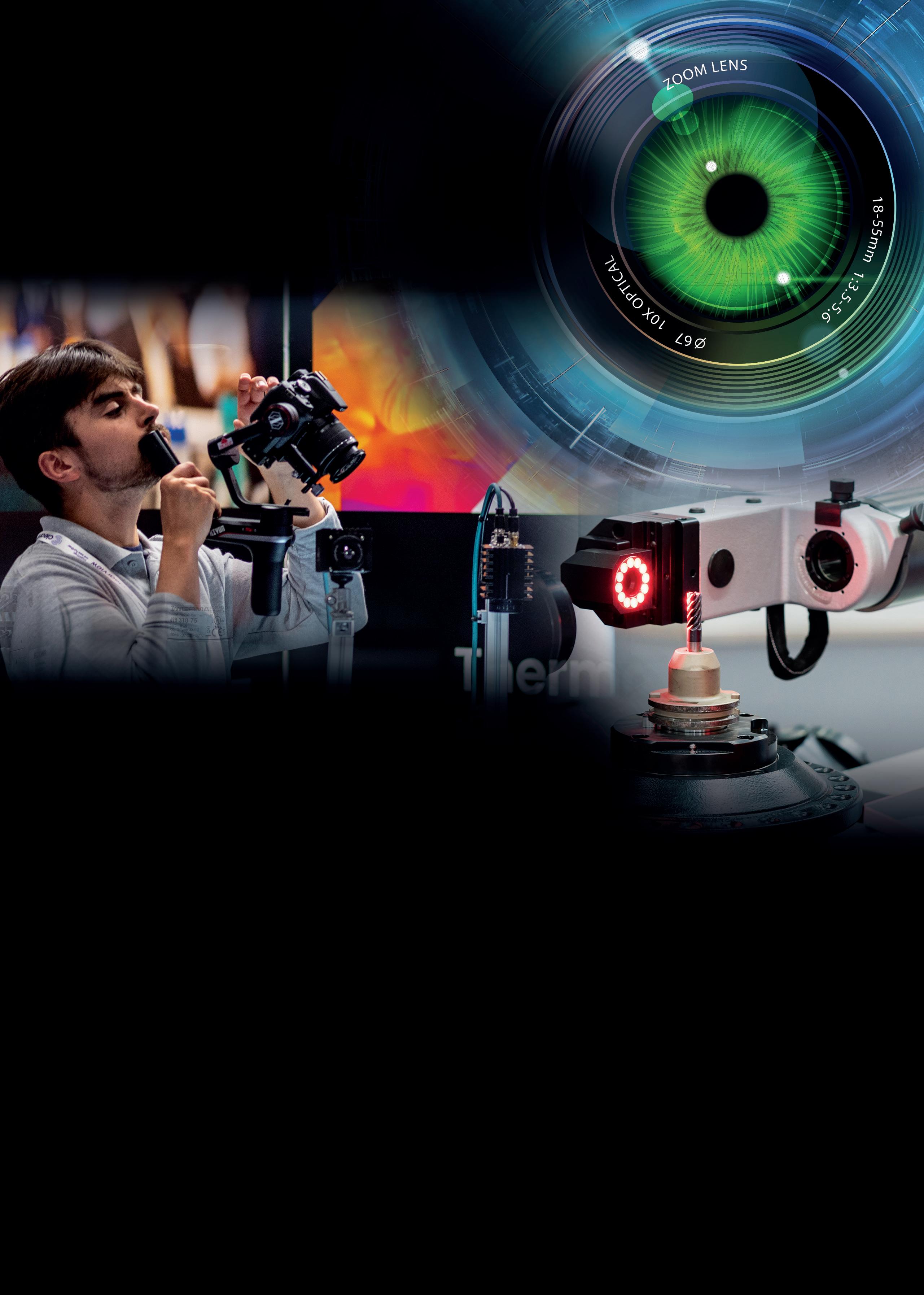
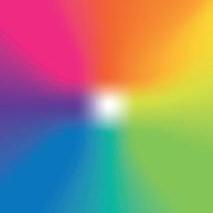

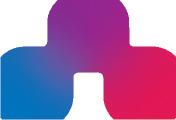
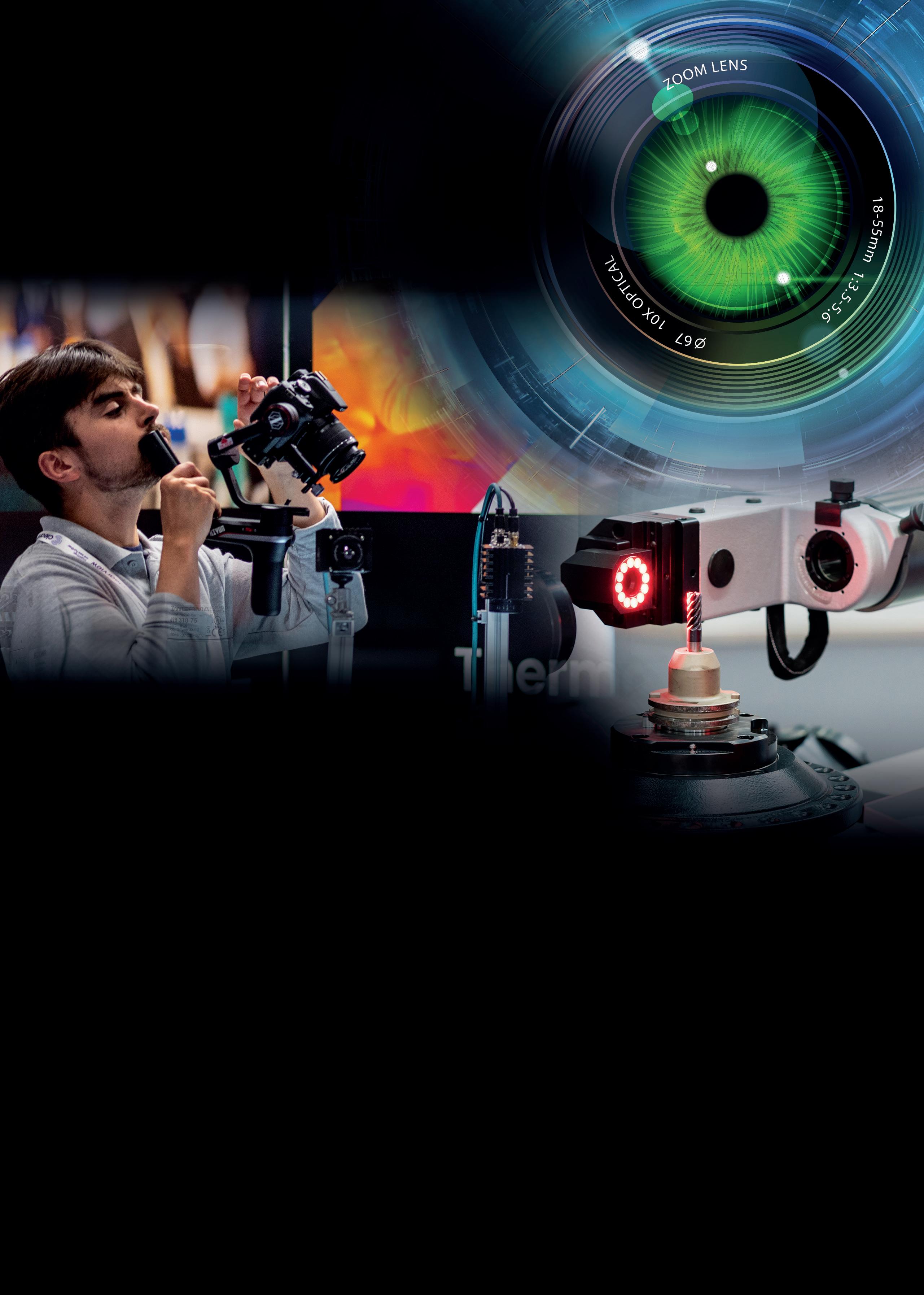

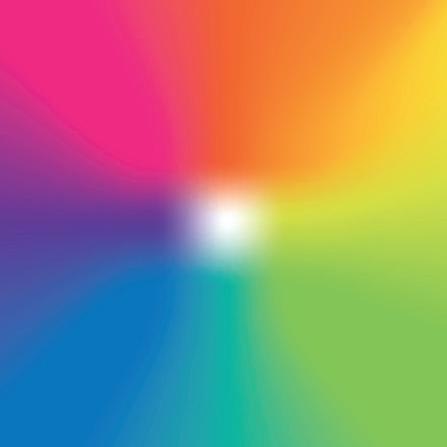
The 8th Machine Vision Conference opens in 2 months’ time
The annual Machine Vision Conference is renowned worldwide as the principal event that captures the very best in machine vision technology, from the latest cutting-edge industrial vision to innovative imaging technologies. This year’s MVC will be held between 18-19 June at the Coventry Building Society Arena where the MVC visitors will also have the unique opportunity to visit the co-located Automation UK which showcases the latest automation and robotics all under one roof.
Machine vision solutions have already been applied to many industries, from food, beverage and pharmaceutical to healthcare, automotive, traffic and transport. Implementing these solutions has been recognised as offering significant benefits to various businesses by enhancing process efficiency, which often results in improved financial performance.
The versatility and adaptability of machine vision technology can be used for automated inspection, object recognition and defect detection, which will in return minimise errors and reduce wastage. Through incorporating these solutions, businesses can streamline their operations, improve quality control and boost productivity. It is proven that in fast-growing industries, businesses who embrace and take advantage of these innovative machine vision solutions will benefit from improving their overall performance and competitiveness.
The MVC’s reputation to provide an impressive and comprehensive machine vision event attracts a diverse range of visitors, including those from big global brands. These companies are keen to discover the latest innovative solutions to enhance their businesses. The 2023 visitors included: Airbus, BMW, DeBeers, Jaguar Land Rover, McVities Cake Company, Mercedes AMG F1, Mitsubishi Electric, Morrisons, Nestle UK, Nissan, Ocado, Panasonic, Rolls-Royce, Siemens, Sony,
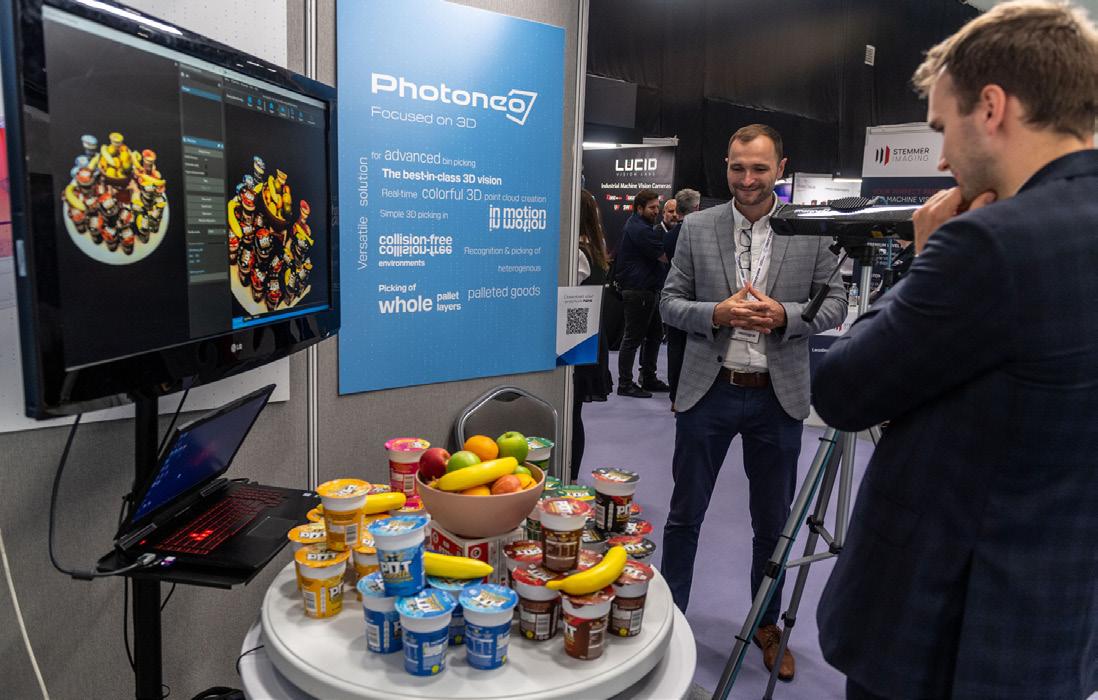
Tata Technologies, Tesco, The Co-Op, Unilever, Vodafone, and Warbutons.
The event organisers, UK Industrial Vision Association (UKIVA), which is part of Automate UK alongside British Automation and Robot Association (BARA), is anticipating over a thousand visitors during the two-day event. MVC will host more than 50 wellknown brands exhibiting their state-of-the-art products, services and solutions and over 40 technical presentations from leading industry experts. MVC is a ‘must attend’ event for visitors to expand their knowledge on machine vision.
Andrew Mark Peacock, Director at Peacock Technology Ltd visited the 2023 MVC and described it as: “A unique opportunity to meet suppliers and industry experts covering the full machine vison stack.”
There are many other compelling reasons to visit MVC which provides a perfect combination for existing vision users and engineers as well as educating those new to the world of machine vision. Visitors can explore the content packed event with plenty of opportunities to meet and connect with industry peers, talk to exhibitors who can directly help their businesses, see live demos, hear from industry experts about new machine vision technology, and captivating product launches.
Scott McKenna, Deputy Chief Operating Officer at Automate UK said:
“Last year’s Machine Vision Conference was a huge success. Co-located with the brand new Automation UK exhibition, and capitalising on the synergies that exists within these sectors, visitor numbers were at an all-time high. We very much look forward to growing the event this year, with even more informative content and innovative technology on display.”
Irrespective of visitors’ level of expertise in machine vision, the event will have something for everyone. Anyone planning to attend MVC in June can register for a free pass by visiting: https://www.machinevisionconference.co.uk/
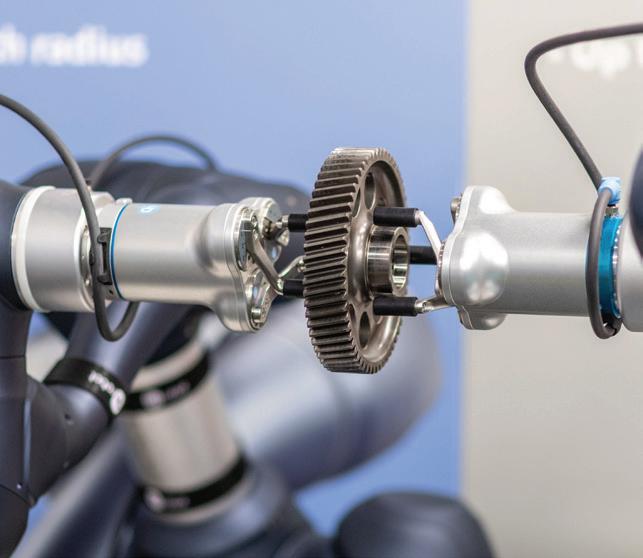

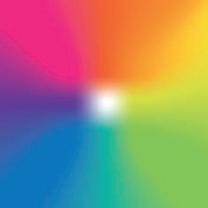
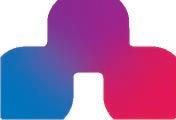
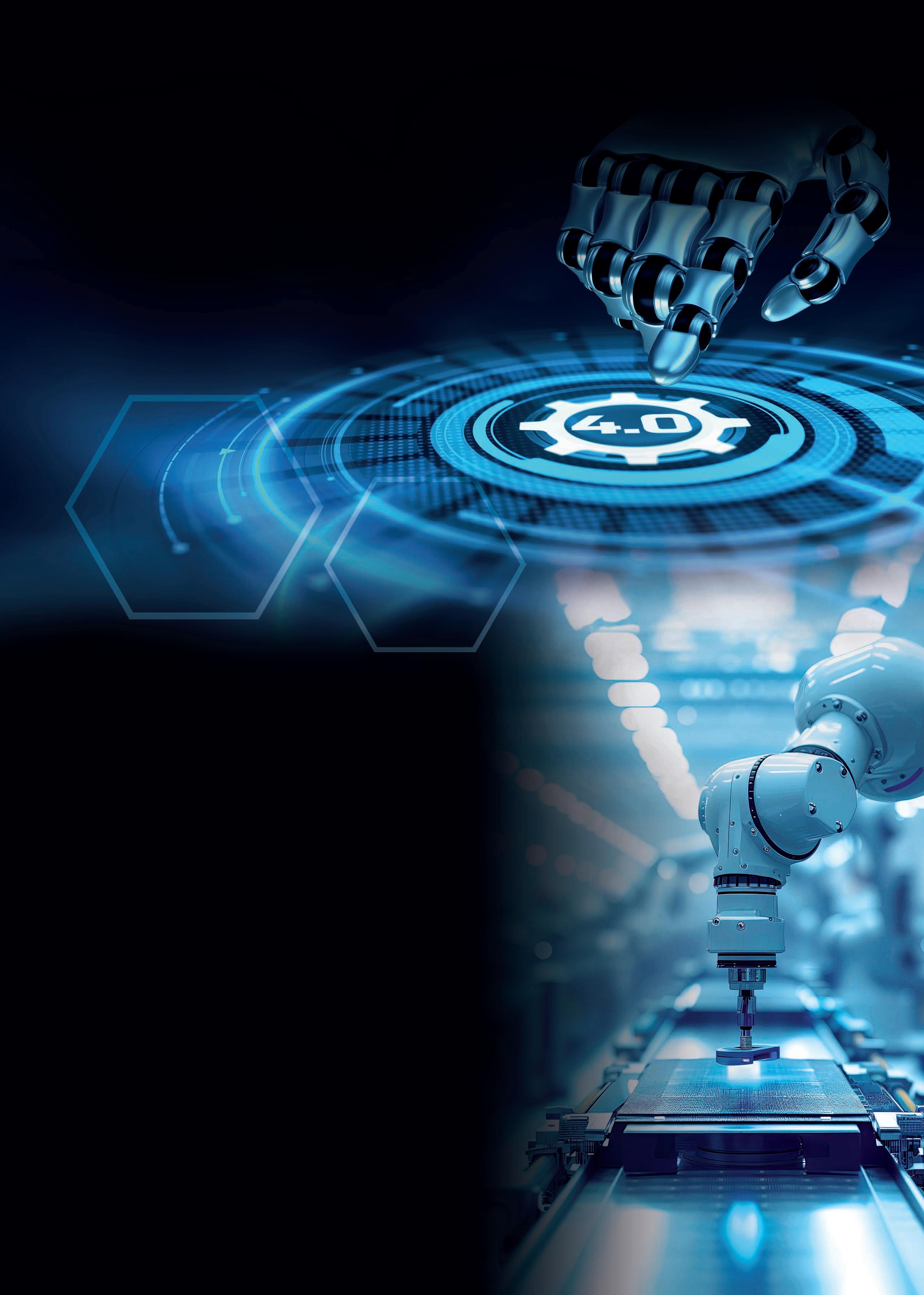
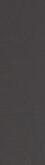
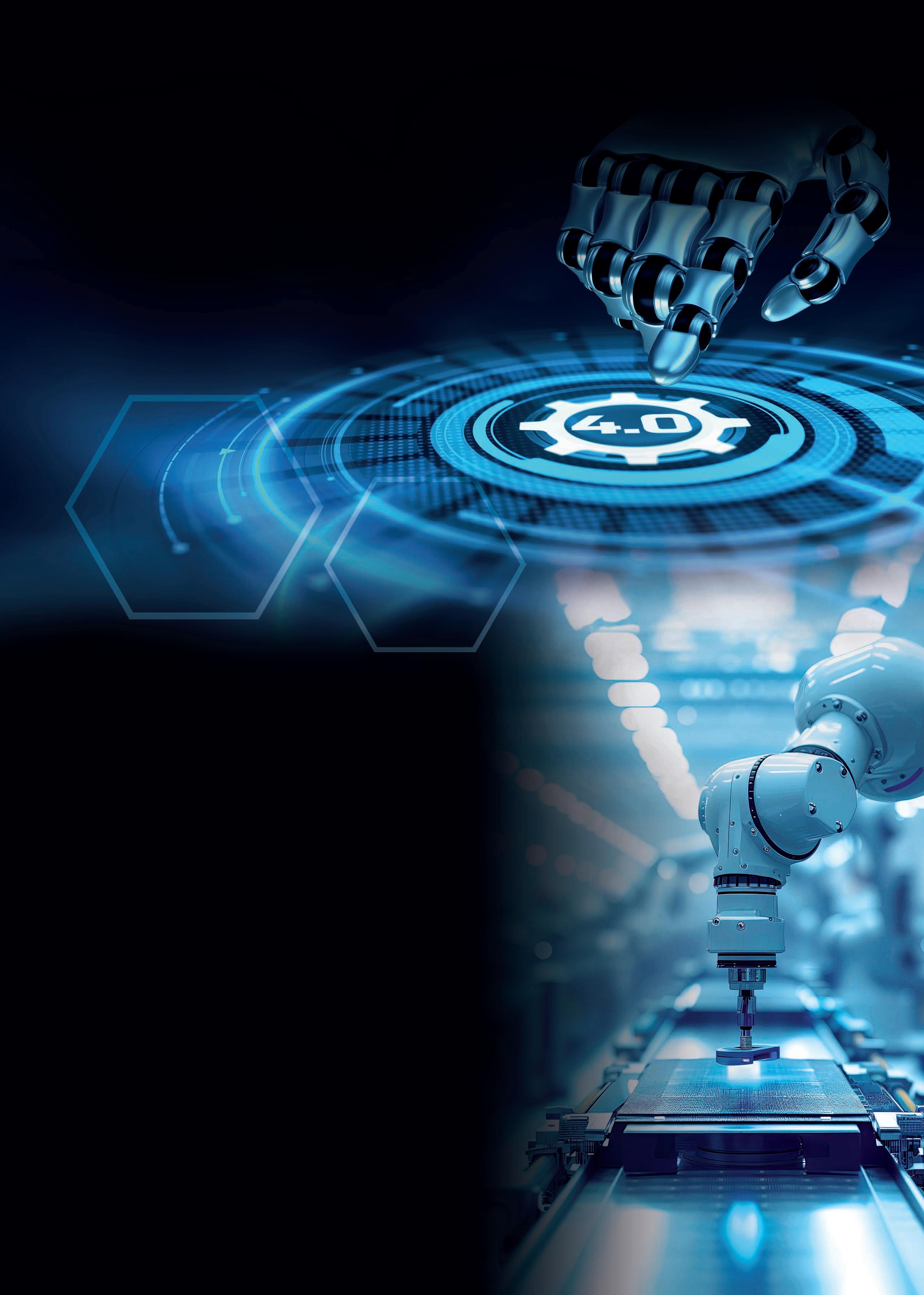
Automation UK unveils an impressive keynote speaker
In less than 2 months time the two-day Automation UK opens its doors at the Coventry Building Society Arena in Coventry. The show, on 18-19 June, provides a fantastic platform for visitors to explore a wide range of the most up to date cutting-edge automation and robotics technologies and solutions. The content led seminar programme will be packed with thought-provoking presentations from leading industry experts which will provide visitors with a wealth of knowledge and inspiration for use in their businesses. There will also be an abundance of networking opportunities with over a thousand peers and experts which are expected to attend in June.
British Automation & Robot Association (BARA), organisers of Automation UK, are excited to reveal a leading industry expert as a keynote speaker.
Vanessa Loiola, the founder of Valoy Automation will talk about ‘Enhancing Robotic Cell Performance with Strategic Programming Solutions’ which explores those manufacturing companies that face the challenge of inefficient processes caused by outdated programming methods. Vanessa highlights the importance of modern solutions that can optimise robot functionality, reduce downtime, and increase productivity. She shares exciting benefits that implementation of strategic programming techniques can deliver to manufacturers. These can revolutionise their operations, achieving peak efficiency and competitiveness in today’s ever-evolving market.
BARA will soon be sharing more information about further inspiring speakers and sessions that will be part of the Automation UK seminar programme.
The two-day show, including the seminar programme, will act as a catalyst to motivate and encourage visitors to take the necessary steps to invest in these technologies and solutions. As well as this investment being important for the growth of the UK economy there are a number of other significant benefits to businesses, such as increased productivity delivered by automation and robotics performing repetitive and manual tasks. In addition, they can create a safer working environment and help solve labour and skills shortages. These benefits can ultimately deliver improvements in the financial performance of a business who commit to invest in automation and robotics.
“The real highlights have been seeing some of the newer technology, both in automation robotics side of the business and the vision side of the business, really giving that flexibility to the customers.”
Steve Banton, Global ProgramManager – Social Selling & Inside Sales, ABB Robotics
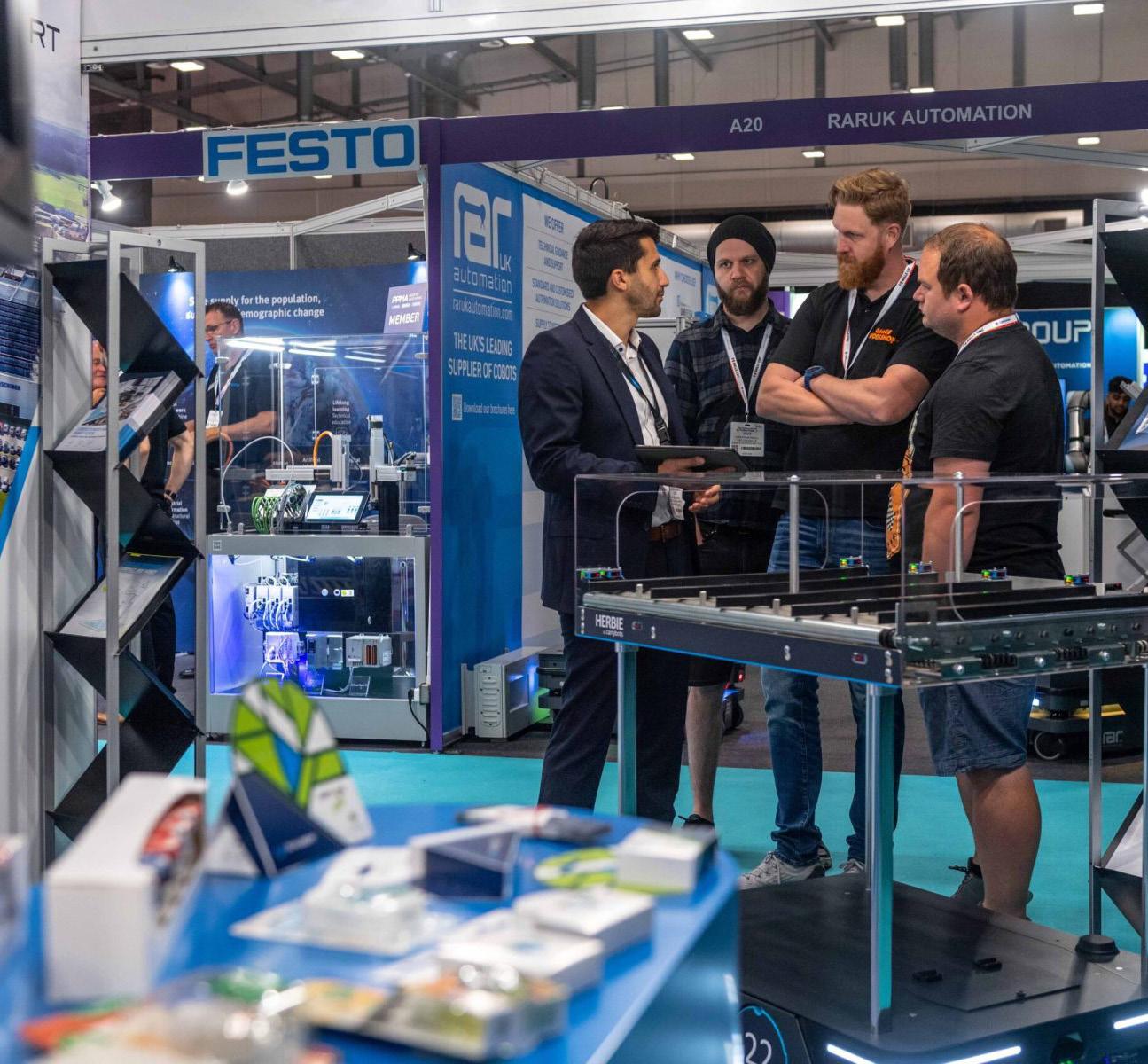
This comprehensive show will provide plenty to explore and experience. The show will be buzzing with around 50 well-known brands showcasing their latest innovative products and services, including robots, robotics systems, systems integration, automation control parts and systems, and sensor and machine safety. Visitors will be captivated by the live demonstrations and fascinating new product launches. These exhibitors will be keen to engage and interact with visitors about understanding their requirements and the benefits of adopting a particular solution as well as sharing their technical expertise.
Some of the founding exhibitors include ABB, Fanuc UK, Festo, Piab, KUKA Robotics UK, Schubert UK, and RARUK Automation.
The Automaton UK event will also provide plenty of exciting networking opportunities with leading industry experts, exhibitors and peers which provides a platform to develop sustainable and mutually beneficial business relationships.
One of the visitors to the Automation UK 2023, Shreyansh Agrawal, Founder at Kairos Diagnostics said:
“Coming to this event will help you grow your business, network and automate your way to the future.”
For more information, please visit: https://www.automation-uk.co.uk/
Multimodal 2024 celebrates 17 years of bringing together shippers and cargo owners with exhibitors and sponsors who can offer products and services to help them make their supply chains more efficient and more cost effective. Visitors attend to meet new suppliers, compare new routes and modes, source new products and ideas to improve their efficiency and to network with the industry.
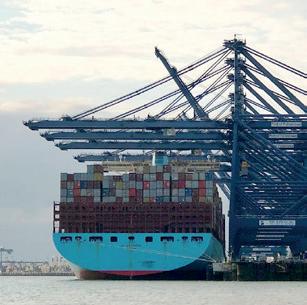
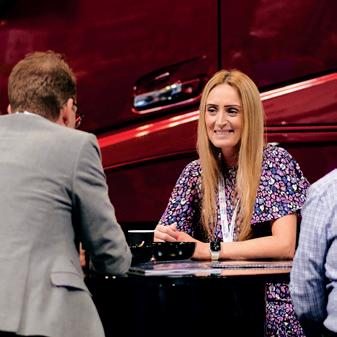
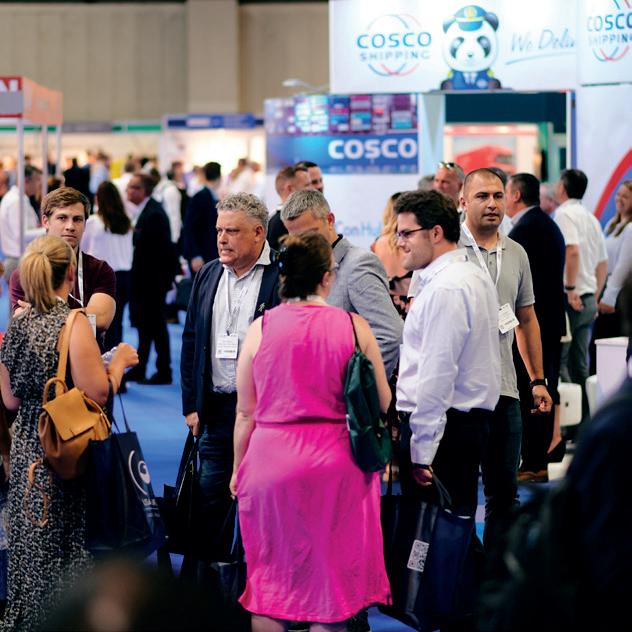
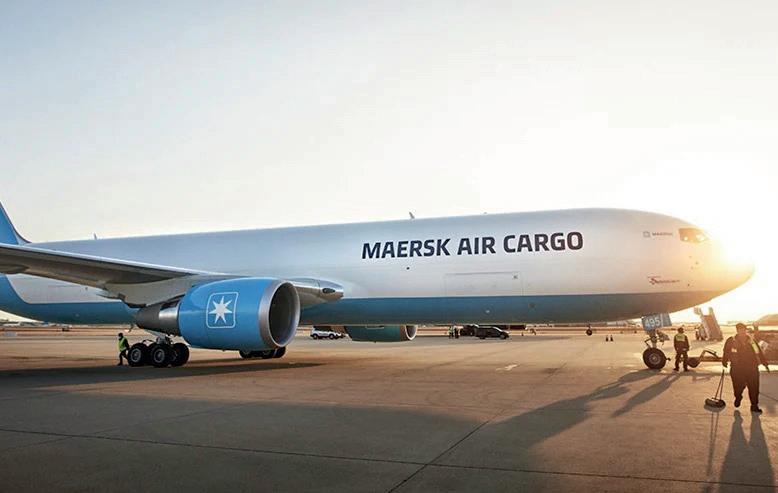
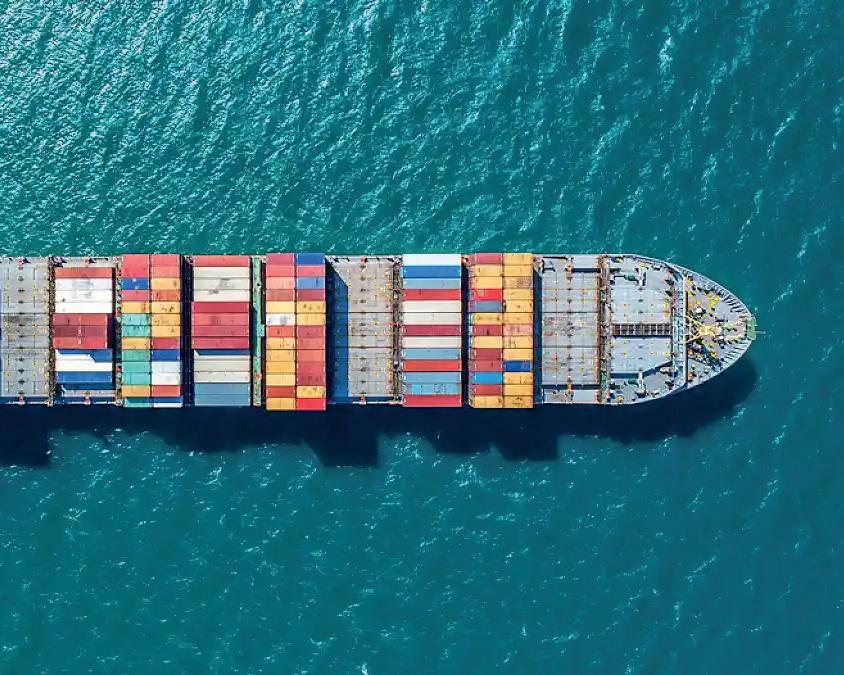
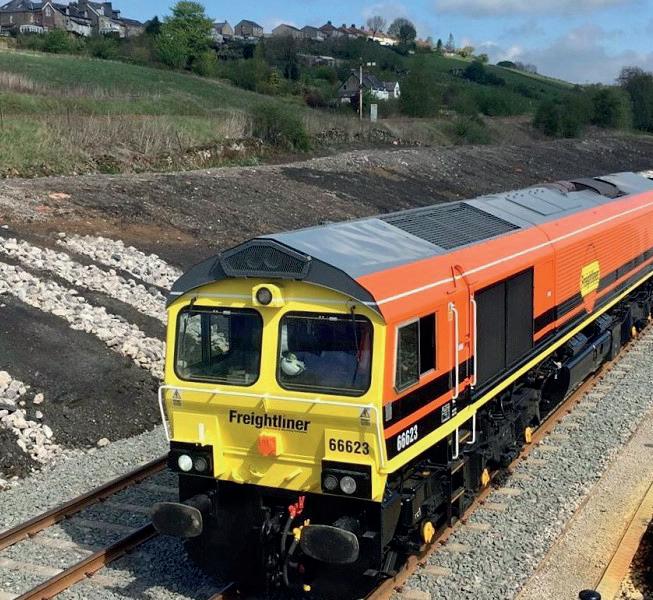
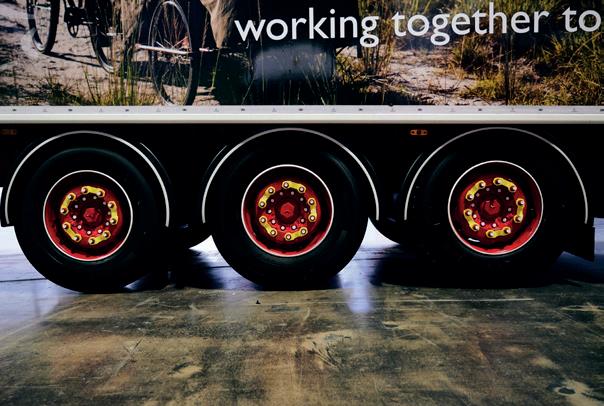
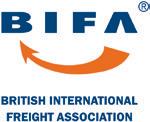
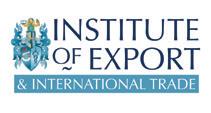
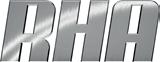
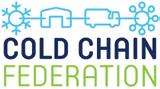
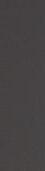
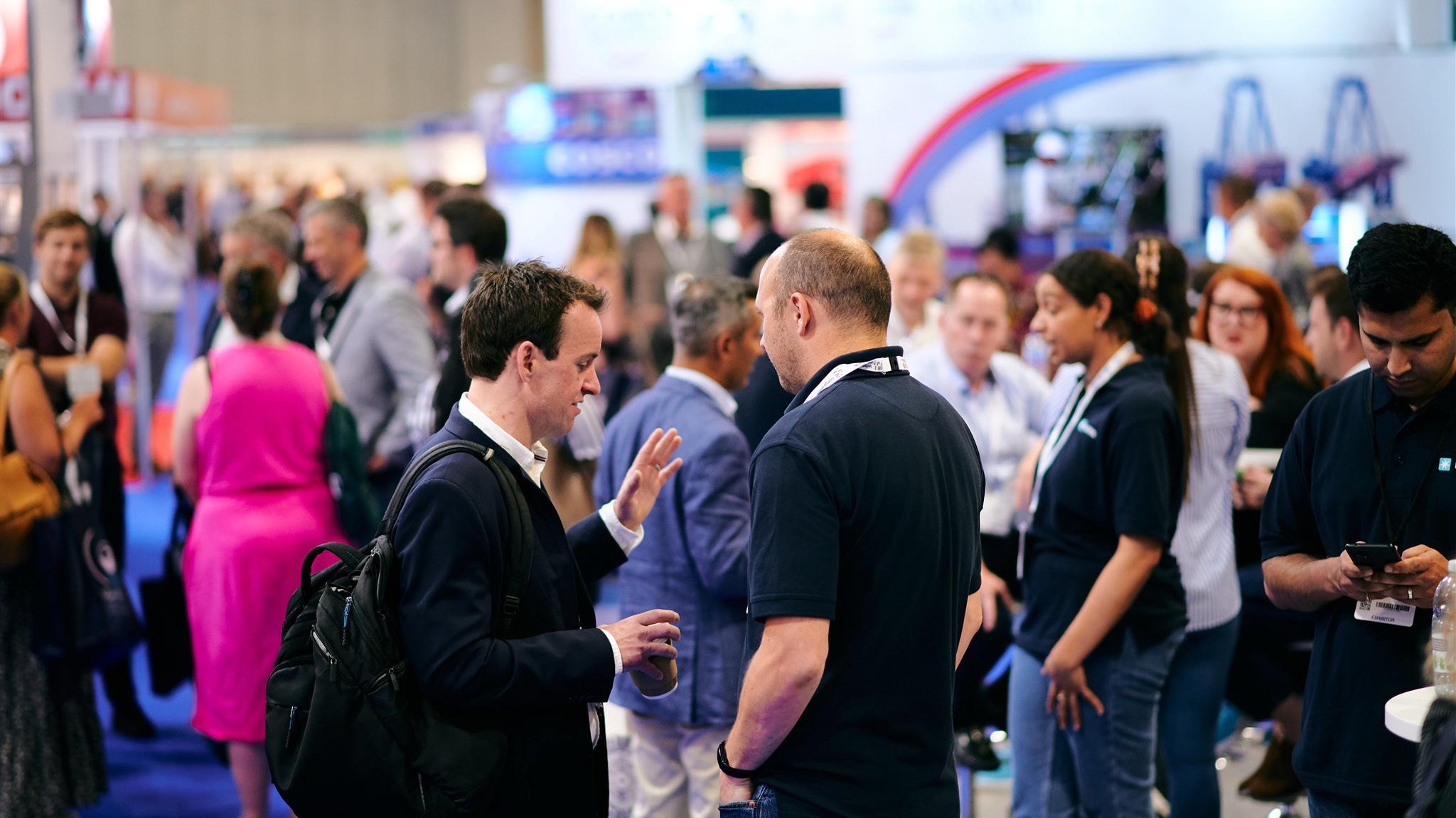
THE FUTURE OF LOGISTICS UNFOLDS
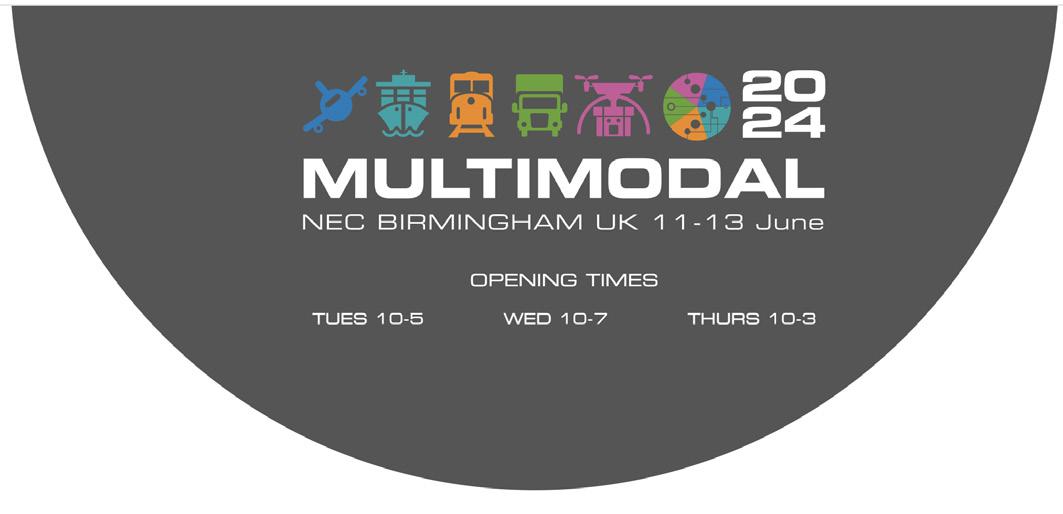
Bigger and better than ever, Multimodal 2024 is already smashing records with over 230 exhibitors already signed up, including industry giants such as Amazon, CEVA Logistics, DP World, Hapag-Lloyd, Kuehne+Nagel, Maersk, Maritime Transport, Malcolm Logistics and Samskip Services. With expectations to exceed 300 exhibitors, this year’s event will offer unparalleled networking and business opportunities for the 12,000+ visitors over the three days of the show.
Multimodal is the one-stop shop for shippers and cargo owners to discover ways to move their goods more sustainably, efficiently and more cost effectively. The three-day show between 11-13 June 2024 at the Birmingham NEC, offers unique opportunities to make valuable face-to-face contact with new prospects and existing companies.
It’s free to visit Multimodal 2024, registering in advance is recommended, to save time on arrival, at www.multimodal.org. uk All the conference sessions are free to attend too and with 4 theatres there is something of interest to everyone.
You’ll be in great company as already registered are representatives from Sainsbury’s, Aldi, Whitworths, Nestle UK&I, Diageo, Lovering Foods, Rowan International, Bunzl Catering, Glanbia Nutrition, Crops UK, Kingsland Drinks, AB World Foods and Poundland to name just a few.
Multimodal works in partnership with the leading trade associations ensuring all aspects of the industry are served, also ensuring that relevant topics are covered in the free to attend conference sessions. Partner associations include Logistics UK, the Cold Chain Federation, the Rail Freight Group, The Chartered Institute of Transport and Logistics, the British International Freight Association, Institute of Export and International Trade, the United Kingdom Warehousing Association, and the Road Haulage Association.
A special highlight of the three days is the Multimodal Awards, which recognise outstanding industry-leading supply chain businesses and individuals. With seats for the awards always selling out, and just 50 places currently remaining, attendees are now being urged to secure their seats for the 11 June evening ceremony as soon as possible.
The 2024 Awards include some new judged Awards to continue the development and evolution of the event. The evening will be hosted by Kevin Keegan, an incredible host who brings enormous professionalism and fantastic humour. Places at the Awards can be booked at www.multimodal.org.uk/awards
The networking event you won’t want to miss! Be there for the Multimodal Mixer on 12 June. It’s a fun relaxed drinks reception open to all visitors and exhibitors, hosted by DP World on their stand in the Hall from 5pm, giving everyone a chance to mingle in a relaxed and fun atmosphere.
To find out more about attending, entering the awards, exhibiting, or sponsoring, visit www.multimodal.org.uk, or contact Robert Jervis, Director on +44 (0) 20 7384 7760 or robert.jervis@clarionevents.com
Why are Food Products with Mislabelled Allergens Still on the Shelf?
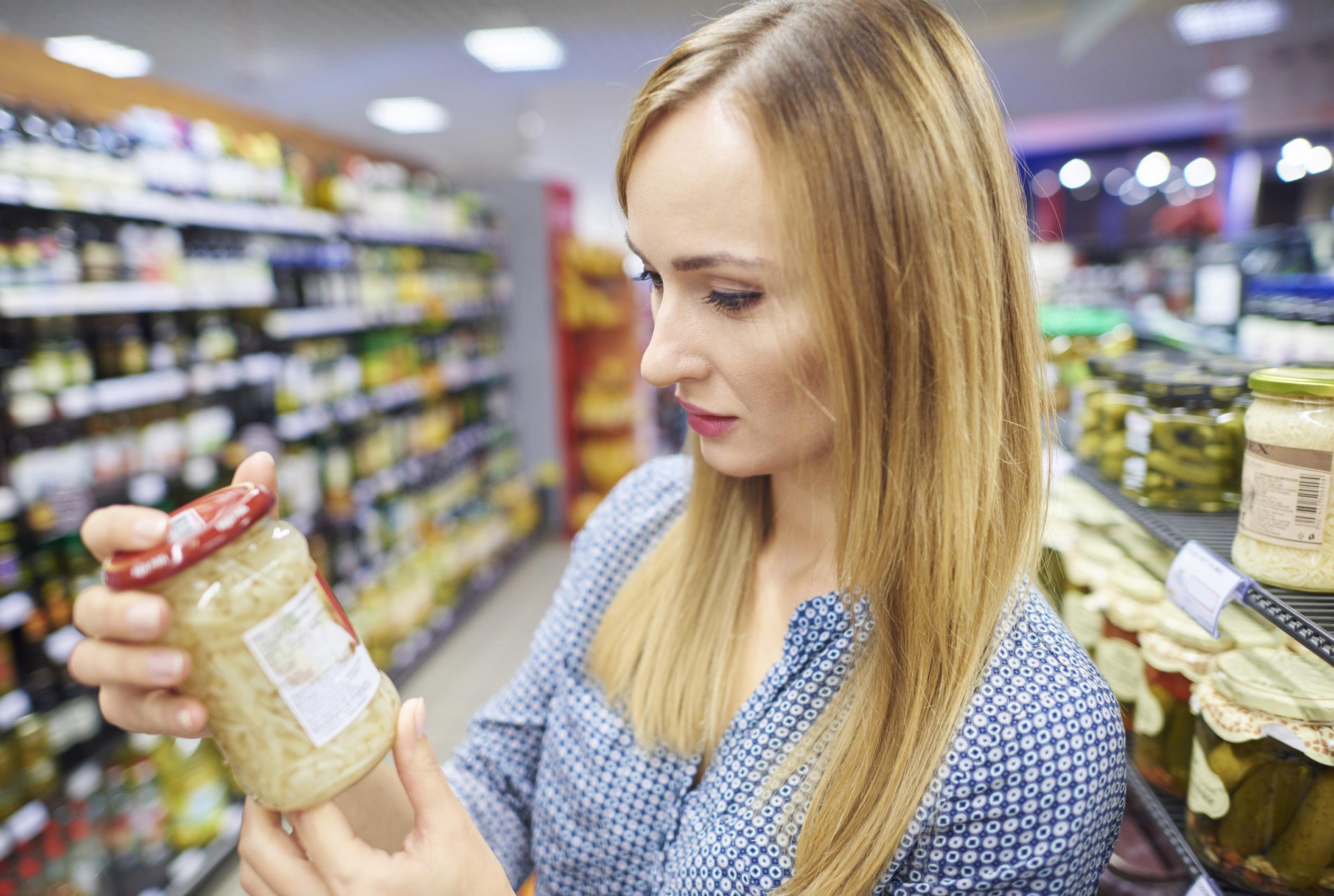
Food
recalls due to allergen mislabelling are still very common in the UK.
An article By Roy Green, Harford Control Ltd. May2024
Food Standard Agency data shows that 314 allergy alerts were issued in the reporting period for 2022/23. The consequence of food recalls not only leads to tragic loss of life, but also causes serious damage to the brand’s financial health.
Pret a Manger set aside £10m to cover legal costs after Natasha Ednan-Laperouse died from consuming mislabelled baguettes in 2016 and Celia Marsh suffered from a fatal reaction to a ‘vegan’ wrap in 2017.
Around two million people in the UK are thought to live with food allergies. It’s the manufacturers’ responsibility to ensure correct allergen labelling. During the production process, checks need to be made vigilantly and diligently throughout the supply chain, in order to ensure that all goods are clearly marked, especially where allergen content is involved.
What Allergen Information Needs to Be on the Label?
Where a food product contains allergens, the allergen information must be listed and highlighted using a different font, style, background colour, or by emboldening the
text. Manufacturers should also list them in the ingredients list.
There are 14 allergens in the group including celery, cereals, crustaceans, eggs, fish, lupin, milk, mollusc, mustard, peanuts, sesame seeds, soya, sulphur dioxide and tree nuts (Food Standard Agency).
The UK has implemented Natasha’s Law and Regulation (EU) 1169/2011 to prevent further fatal issues occurring from food allergy mislabelling and to ensure that all food and drink manufacturers follow the allergen labelling instructions.
However, there are still many incorrectly labelled allergen products on the shelves. Unilever recalled Viennetta Vanilla because milk and soy were not displayed in English on the label. Origin Kitchen recalled all Spread & Stir and Bessert products because peanut were not mentioned on the label.
Why do Mislabelled Food Products Still Exist in Retail?
Whilst efforts are made to ensure allergens are properly labelled, there may be instances where food and drink manufacturers are not fully aware of the allergen labelling guidance or overlook potential allergens in their products.
“Around two million people in the UK are thought to live with food allergies. It’s the manufacturers’ responsibility to ensure correct allergen labelling. During the production process, checks need to be made vigilantly and diligently throughout the supply chain.
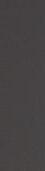
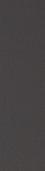
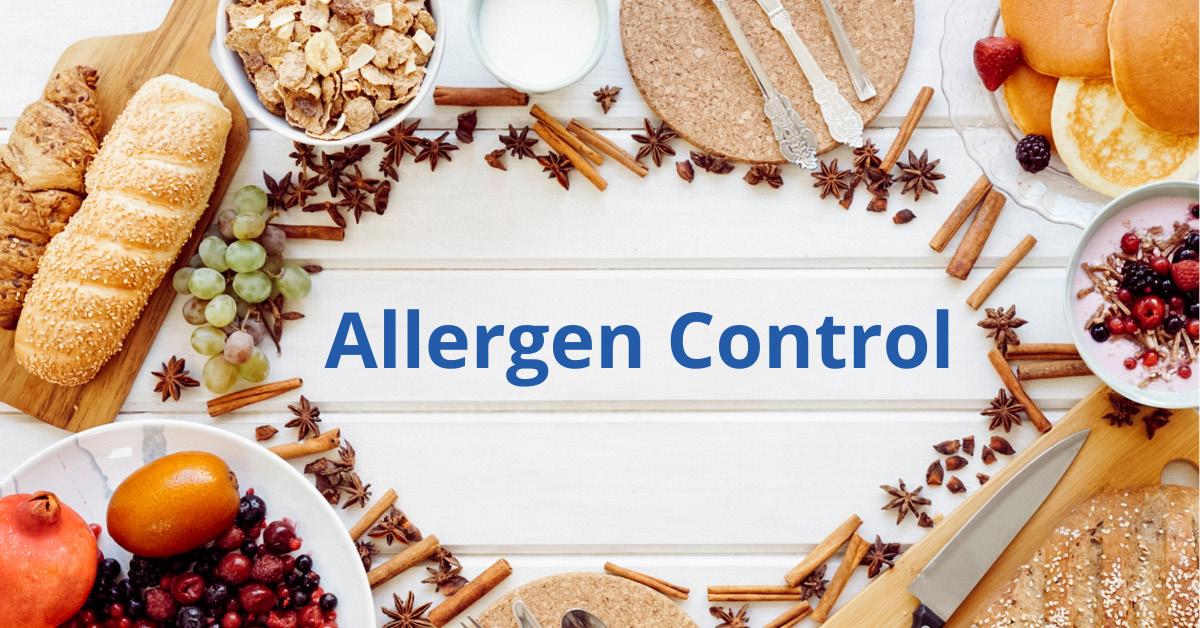
Besides, some manufacturers are aware of the regulations, but don’t want to invest further in ensuring correct allergen labelling. Faced with the dilemma of rising input prices, such as raw materials, energy prices, and increased labour rates, and with little or no opportunity to pass on these rising costs to their supermarket customers, some manufacturers may choose to ‘hope for the best’, rather than solve the root cause of mislabelling. Hope is not a strategy.
Other manufacturers have integrated solutions to ensure correct labelling, but these solutions are not always effective. One example of this is that a few factories have set up print rooms to ensure accurate labelling.
“Harford Autocoding Solutions help manufacturers ensure 100% verification of packaging accuracy, to avoid inaccurate label information and unnecessary wastage. The solutions can be integrated into production lines to send real-time actionable data directly to those who need it.
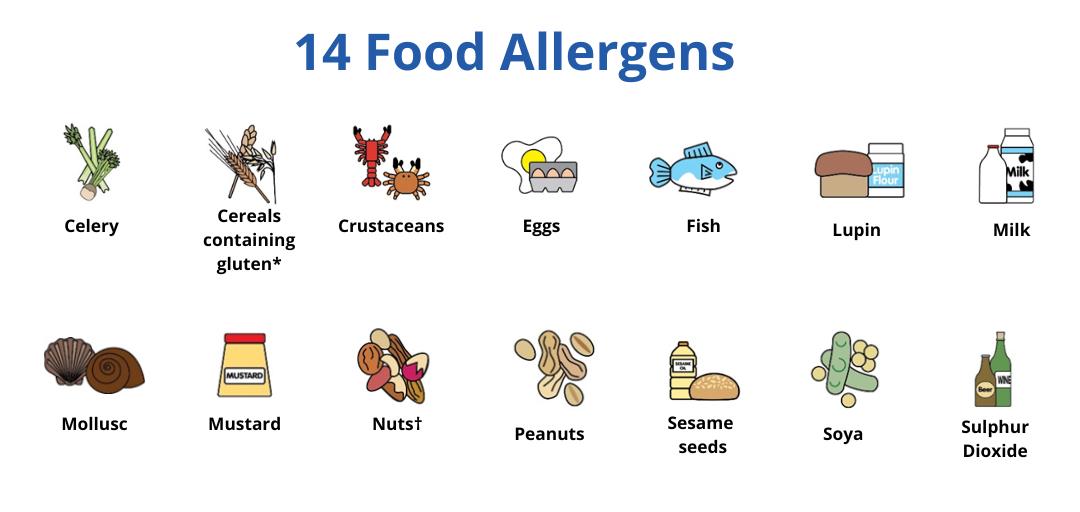
”On one hand, whilst a print room in a factory can certainly produce labels with accurate information, it cannot be solely responsible for ensuring that products are accurately labelled (that the right label goes on the right product), as workers may overlook allergens or ingredients. On the other hand, the print room may not have access to all the necessary information. If a supplier fails to provide accurate information about the ingredients in a particular product, the labels produced by the print room may not be accurate.
How to Ensure Accurate Allergen Control?
From raw materials to finished products, it’s the manufacturers’ responsibility to ensure allergen control and provide clear and safe products to retailers and consumers. Allergen control must include but is not restricted to:
• Supplier verification: Verify that suppliers provide accurate information about allergens present in their ingredients and adhere to appropriate safety standards.
• Allergen testing: Implement regular testing of both ingredients and finished
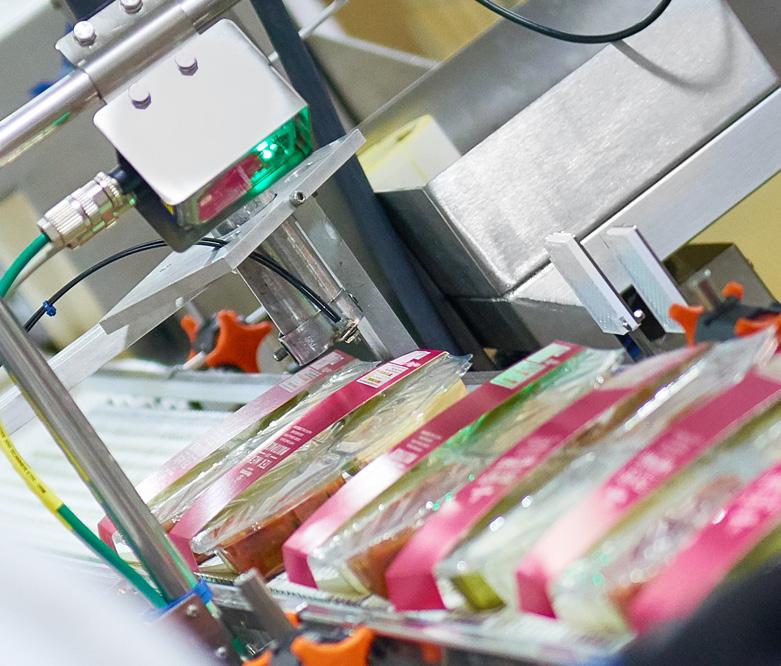
products to verify the absence of allergens and detect any contamination. This can include laboratory testing as well as on-site testing methods such as allergen swabbing.
• Accurate labelling: Review and improve their labelling and inspection procedures regarding allergen declarations to ensure clear and accurate labelling of all known allergen ingredients. Instead of having a label print room, it would be safer and more efficient to install integrated coding and labelling systems within the production lines. This can help ensure that the correct label is attached to the right product.
Harford Autocoding: 100% Verification of Packaging Accuracy
Harford Autocoding Solutions help manufacturers ensure 100% verification of packaging accuracy, to avoid inaccurate label information and unnecessary wastage. The solutions can be integrated into production lines to send real-time actionable data directly to those who need it. At the start of each production run, the system will ensure that label printers are set up accurately and in-line barcode scanners are configured to check that the correct packaging materials and labels are used – on each individual product, case or pallet. In some instances, on-line integrated cameras may also be required to ensure that the pre-printed packaging displays the correctly highlighted allergens.
Though this is a huge, essential step towards ensuring compliance, it must also be said that no automated system can ever guarantee total compliance, and full training and operator engagement are also essential to provide world class due diligence.
Harford have enormous experience in helping food and drink manufacturers ensure greater accuracy of labelling for control of allergens, date coding, quality and much more – thus giving manufacturers greater confidence in the labelling of their packages and products.
If you are ready to eliminate risk and improve labelling accuracy using Harford Autocoding, please reach out to us at info@harfordcontrol.com or give us a call on +44 (0)1225 764461.
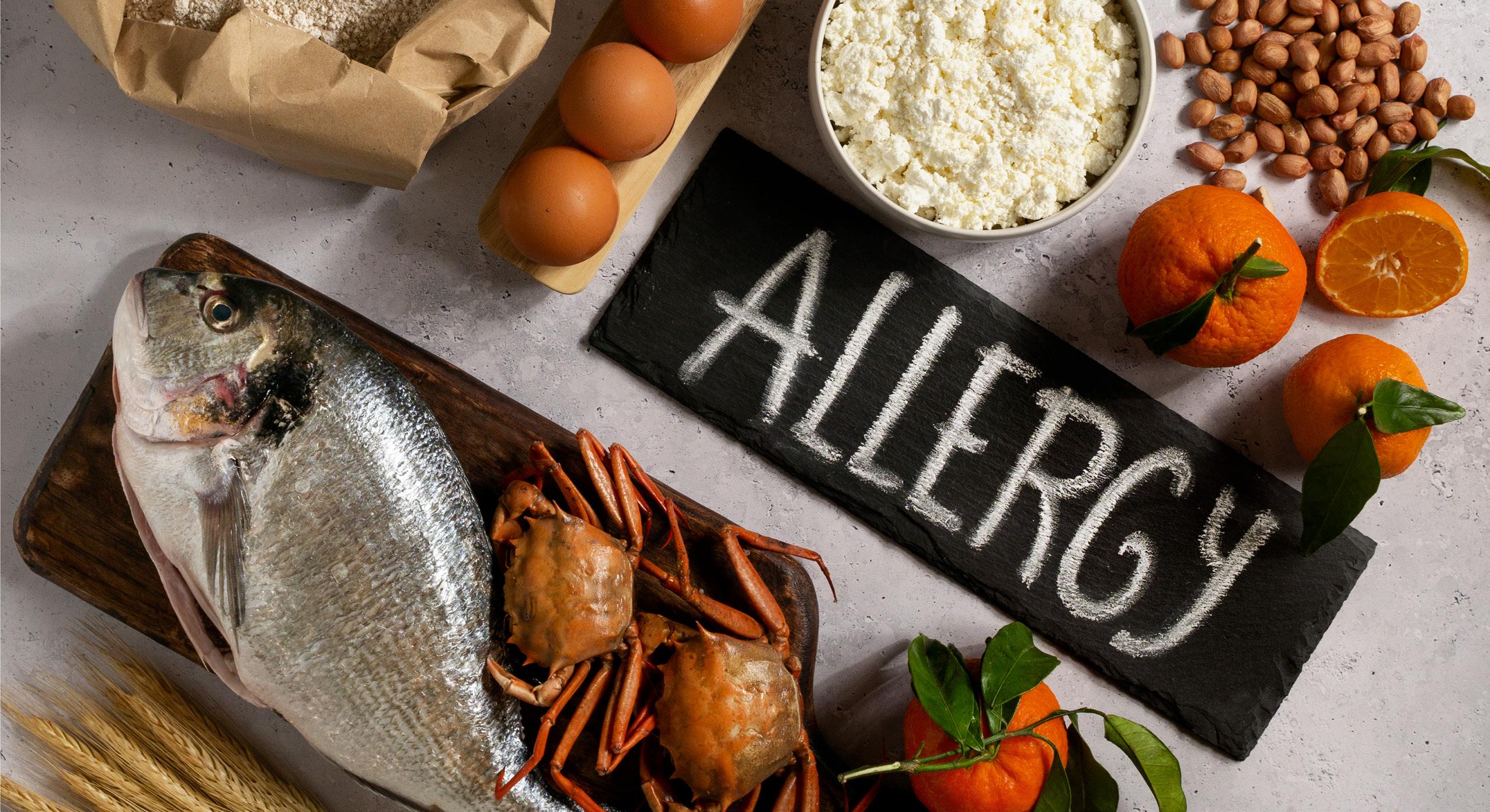
Send real-time actionable information directly to those who need it. Allergen Control
Ensure allergen information on each package and outer case is accurately labelled.
Efficiently automate coding processes with streamlined batch control capabilities.

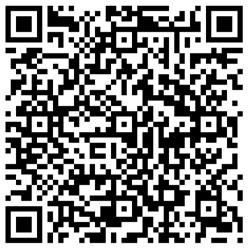
Automatically initiate certain actions based on predefined triggers.
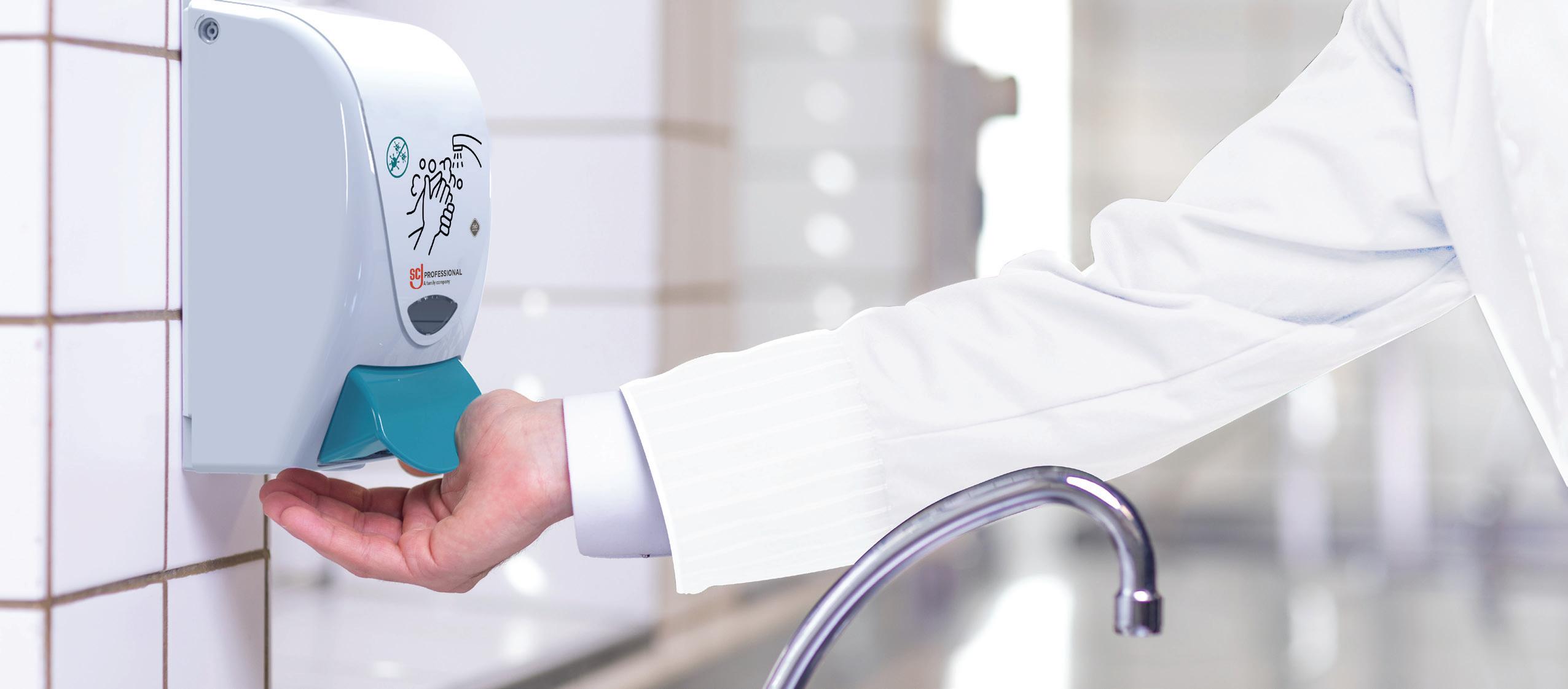
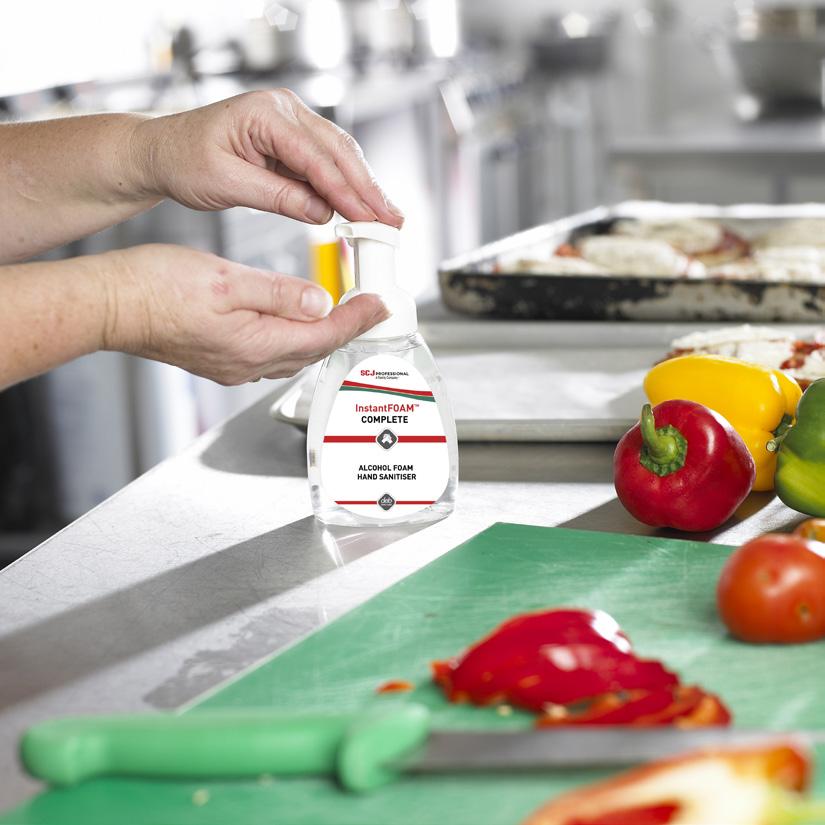
HOW HAND HYGIENE BEST PRACTICE CAN HELP TO IMPROVE FOOD SAFETY WHILST PROTECTING EMPLOYEES
Every year in Europe, more than 23 million people fall ill from eating contaminated food, resulting in 5000 deaths1 A high standard of cleanliness – including hand hygiene – that is strictly enforced is key to reducing the risk of cross-contamination in every step of the chain, from production to plate.
Foodborne pathogens of concern
It is important to be familiar with pathogens that may cause harm if proper hand hygiene protocol is not followed. The following can be identified amongst the main causes of concern for the food industry2:
• Campylobacter3 - transmitted by cross-contamination and ingestion of undercooked contaminated food.
• Listeria monocytogenes3 - transmitted to humans through food.
• Salmonella enterica3 – transmitted to humans via raw / undercooked food including meat and eggs.
• Escherichia Coli (E.coli)3 – known to cause serious food-borne illnesses (FBD).
Reduce the risk of cross-contamination and recalls
To encourage hand hygiene best practice, proper infrastructure must be in place. This should include protective creams, biocidal hand wash, sanitisers and moisturising creams developed specifically for the food industry; these help to promote good skin health before, during and after working hours. Hygienically sealed cartridges can also reduce the spread of micro-organisms by preventing the ingress of air into the cartridge during use.
The importance of best practice
For successful hand hygiene compliance – particularly in the food industry – it is key to follow best practice to help promote good skin health and hand hygiene. This best practice should include educating on the range of products, as well as why and when to use them.
Why use protection creams?
Using protection creams can make skin quicker and easier to clean with milder hand cleaners. Not only do they help the skin to retain natural lipids and moisture in whilst working, protection
creams help improve comfort when wearing gloves, help improve grip when using hand-held equipment, and protect skin against exposure to workplace substances and environmental conditions (i.e. ultraviolet (UV) rays or exposure to water-based or oily contaminants).
Why use appropriate hand cleaners?
Proper hand cleaning using the appropriate product helps remove germs and prevents physical contaminants from becoming ingrained in the skin. Using hand cleaners that are too light for what is required can lead to over-scrubbing and not fully clean skin, whilst hand cleaners that are too heavy can in turn be too harsh on the skin.
Why use hand sanitisers?
Sanitisers can provide broad-spectrum antimicrobial activity against many common germs, and should be used when hands are physically clean but need to be hygienically clean. They can be used without water at the point of use and help keep the skin in good condition, even after frequent use.
Why use restore creams?
Restore creams support the skin’s natural barrier, make the skin feel smooth and supple and help to maintain its condition, keeping it strong and healthy whilst avoiding dryness.
SC Johnson Professional’s free best practice resources can help you to promote good hand hygiene in your workplace. Head to https://www.scjp.com/en-gb to find out more.
1 The burden of foodborne diseases in the WHO European region, World Health Organization 2017.
2 Food Standards Agency https://www.food.gov.uk/safety-hygiene/campylobacter#howcampylobacter-is-spread
3 Ministry of Agriculture and Fisheries General, Financial Secretariat, social and logistic affairs department Oct. 2008
Introducing Industrial Auctions Food Machinery Auctions
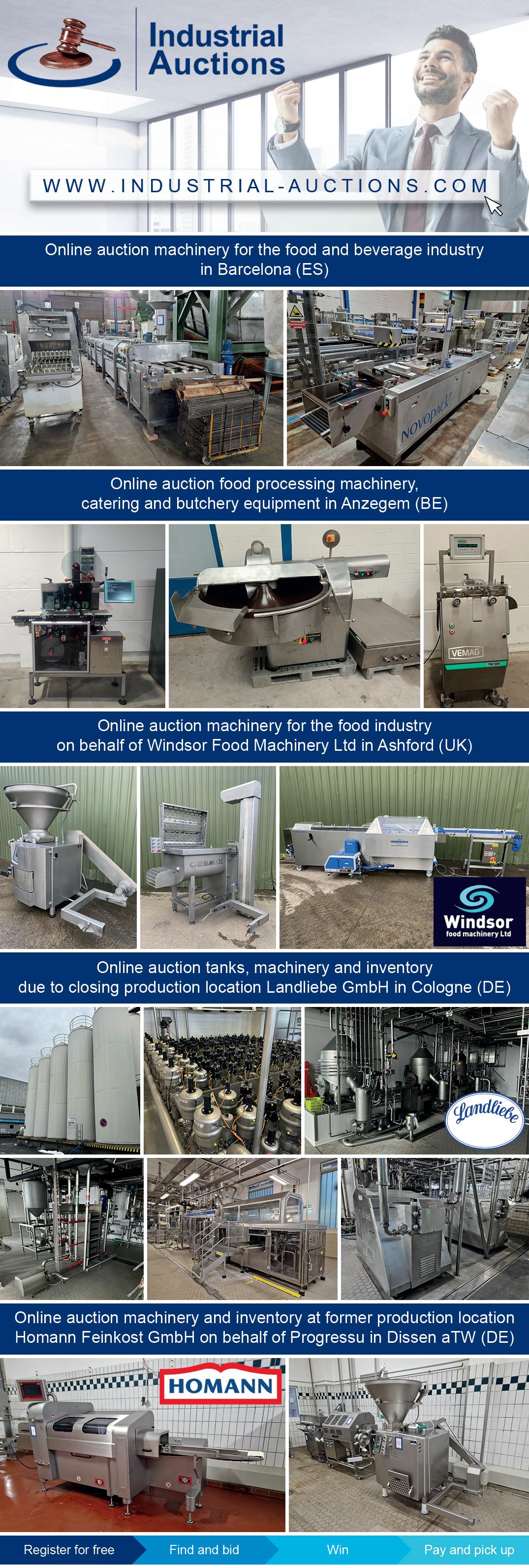
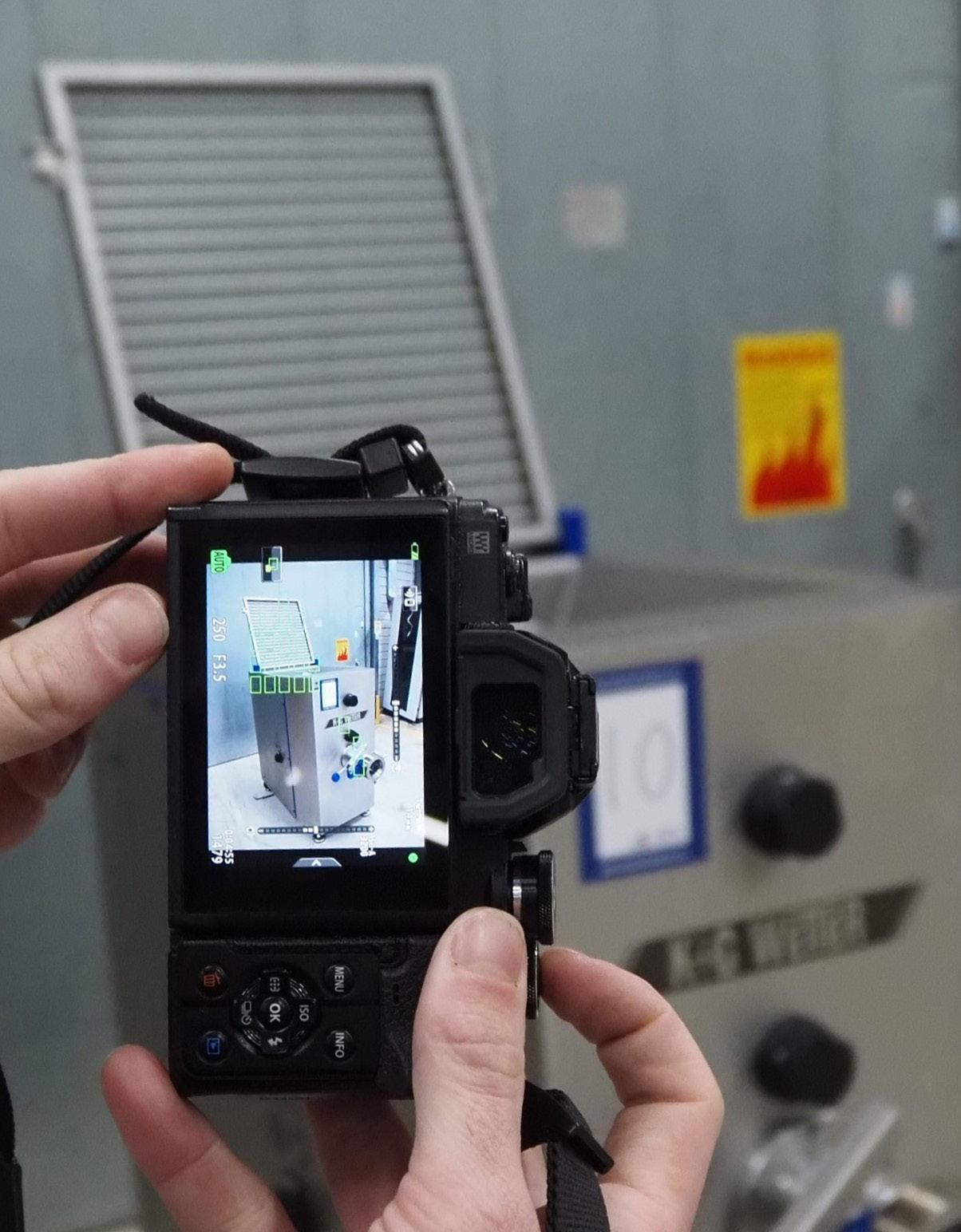
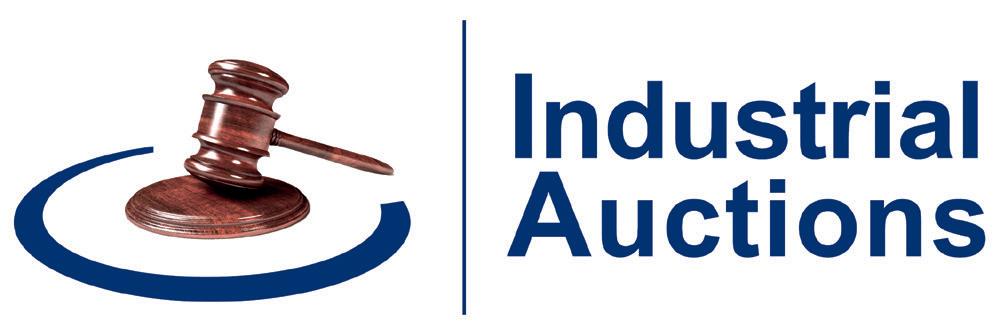
In the ever-changing world of the food and beverage industry, trends are constantly changing, shifting priorities and introducing new technologies. But how can manufacturers within this industry respond to these trends quickly and effectively?
Establishing a valuable long-term relationship with buyers and contractors are the starting points of our core values: specialized, sustainable, transparent, and service-oriented.
We are talking to Lina van Loon, marketing employee at Industrial Auctions. Industrial Auctions is the auction platform specialized in the online auctioning of used food and beverage machinery. We will discuss the main trends and explore how this company can assist producers in this rapidly changing market full of new developments.
FURTHER
AUTOMATION
While automation is now indispensable in the food and beverage industry, it remains a continuous trend that is constantly evolving. More and more factories are relying on advanced machines and robots to perform tasks that were previously done manually. This not only improves efficiency and productivity but also combats waste and ensures product quality. Additionally, it contributes to a safer working environment, enhancing the sector’s image. This is becoming increasingly important given the current challenges in terms of labor force, where producers must compete to attract and retain qualified personnel. Industrial Auctions addresses this by offering high-quality, used machinery that producers can use to further automate their production processes.
CHANGING NEEDS
A noticeable shift in consumer needs is emerging within the food and beverage industry. “We see a growing demand for plant-based options, sustainable packaging and an increase in convenience products, but also an
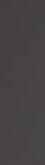
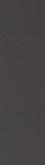
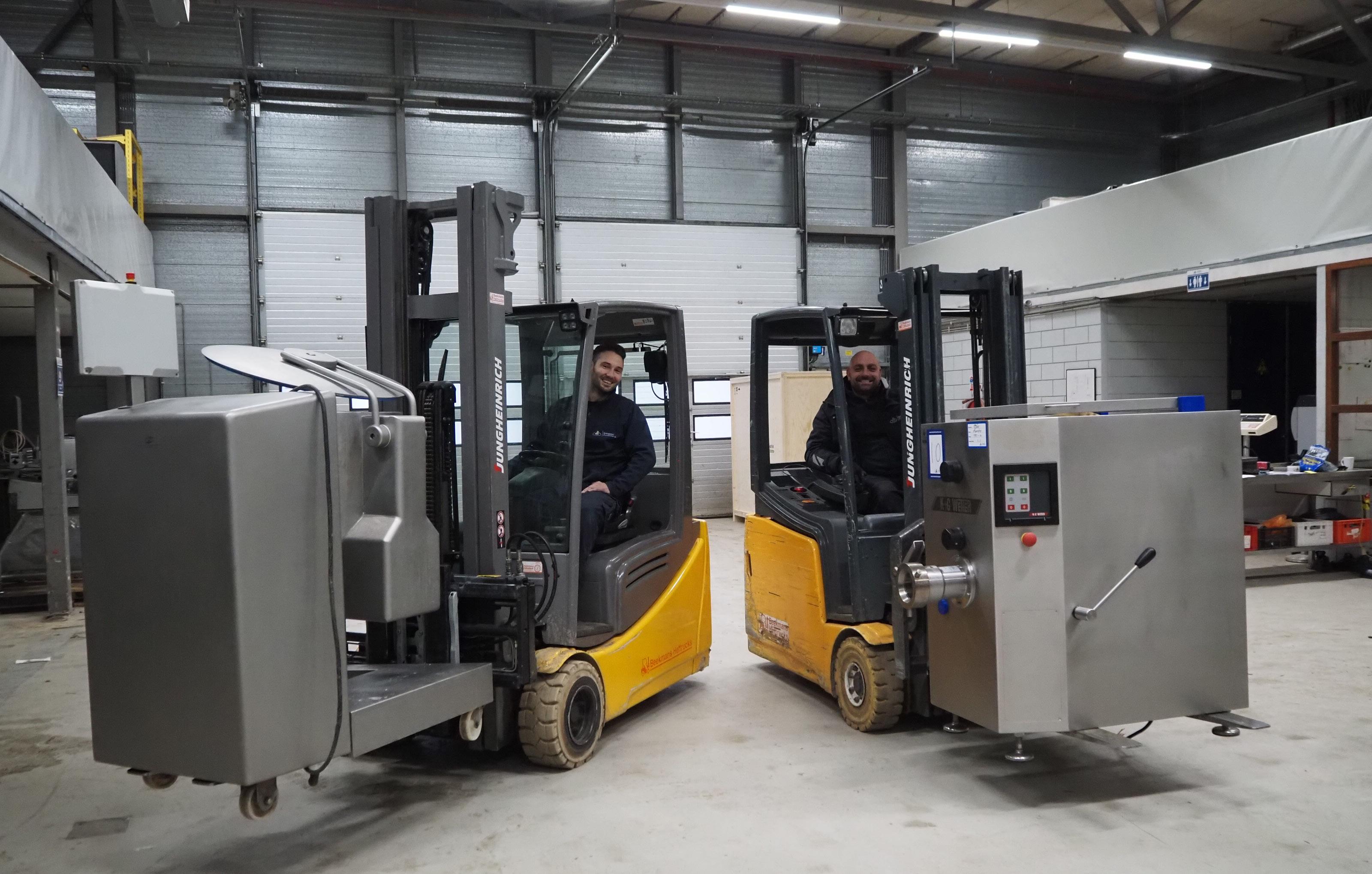
TRENDS IN THE FOOD AND BEVERAGE INDUSTRY: IN CONVERSATION WITH INDUSTRIAL AUCTIONS
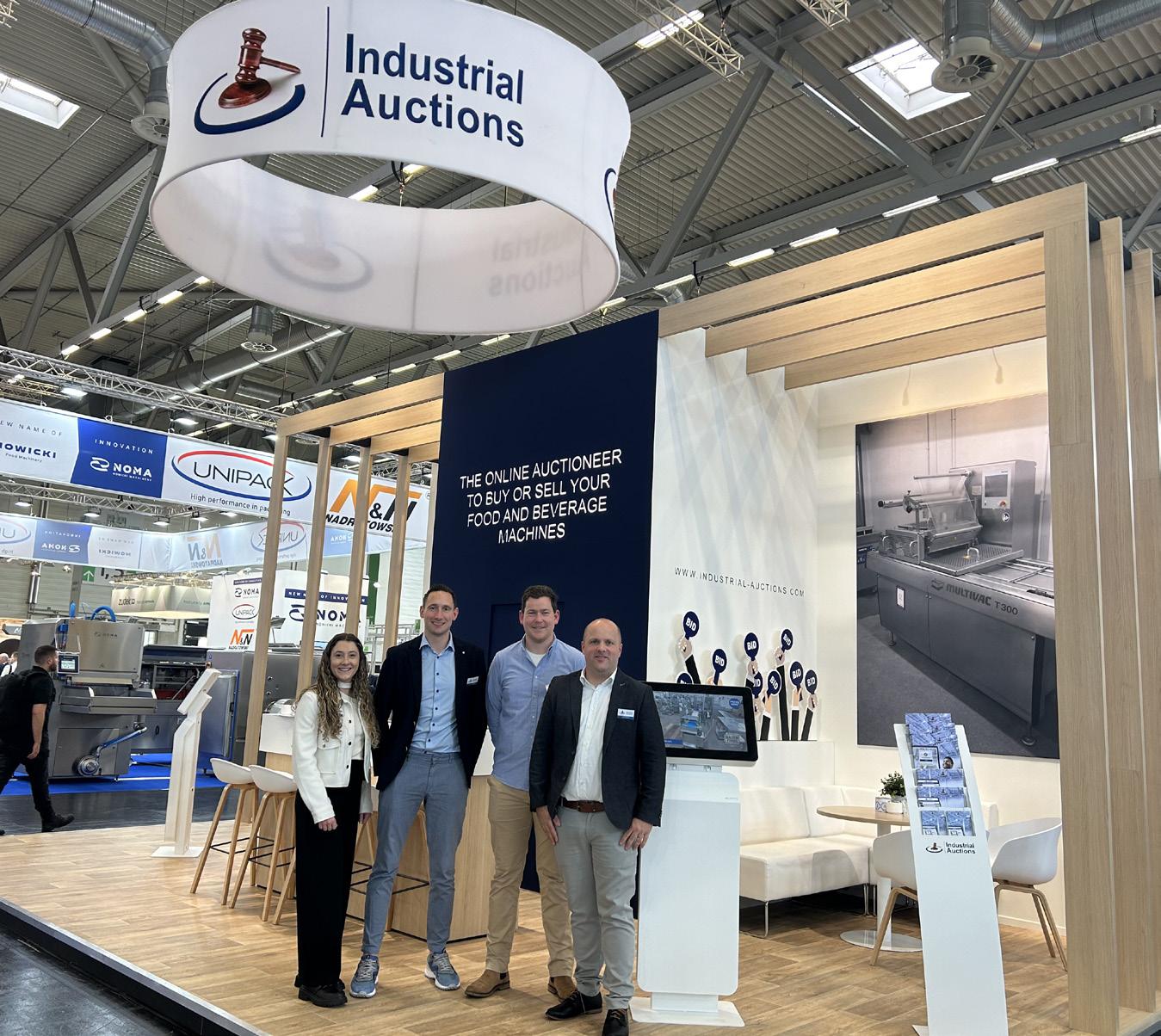
increasing awareness on both our health, animal welfare and the impact of food production on the environment.” In response, manufacturers are focusing on reducing their carbon footprint by, among other things, adopting more sustainable packaging and minimizing food waste. However, Van Loon also contends that deploying new machinery isn’t always necessary. “For example, a plantbased burger can be produced with the same forming machine as a burger made of meat, and existing packaging machines can also accommodate more environmentally friendly alternatives.”
RISING COSTS
Everything is getting more expensive, so too for producers in the food and beverage industry. “To remain profitable, cost increases need to be offset, and secondhand machines offer an affordable solution. They are significantly cheaper than buying new ones, allowing producers to maintain profit margins even with rising inflation. By purchasing used machines, manufacturers contribute to a circular economy and reduce the need for new raw materials.” States Lina.
All in all, an industry that is constantly subject to various trends, which presents challenges. Despite these challenges, Industrial Auctions maintains a positive outlook, emphasising how the company can assist producers in addressing these challenges. Trends are closely monitored and emphasized. Competitors in production are already taking action, so being left behind is not an option.
How to ensure your process is free of metal contamination
Employing Eriez powerful magnetic separators for ferrous contaminants and metal detectors for both ferrous and non-ferrous metals ensures your product is free of dangerous tramp metals. Regardless of your process and material, Eriez offers a solution for gravity, conveyed, pneumatic or liquid line flows.
Below are several factors to consider when choosing a magnetic separator for your food application.
Temperature: Permanent magnetic materials lose strength when exposed to elevated temperatures. Some losses are reversible, so that when the temperature is returned to normal, the magnetic strength returns. Depending on the specific material, permanent magnets heated beyond certain temperatures may also suffer irreversible loss—a reduction in strength that cannot be recovered by cooling. When specifying a magnet application, it is important to note the ambient as well as any clean-in-place (CIP) temperatures to ensure a proper magnet design suitable for long-term separation performance.
Flow characteristics: Many products exhibit different flow characteristics when damp or moist. Are there large chunks that may plug an opening or gap in the separator? Will the product flow freely through the selected magnetic separator? For example, brown sugar with any significant moisture content will not flow between the tubes in a grate magnet assembly, although they may be positioned only 1 inch apart.
Process issues: How will the material be presented to the separator? Is the material metered or do you need to handle surge flow? Can the system be stopped for cleaning or is a selfcleaning magnet required? Is access available for cleaning? Is there ferrous material in the area that may create a hazard for magnet handling? How much contamination is to be removed? And finally, what level of product purity is required?
ERIEZ_BEstDefence_HalfPgAd_F&DN_4_24.qxp_Layout 1 3/22/24 5:13 PM Page 1
Flow rate: Magnetic separators perform best when the contamination is presented to the surface of the separator. It is best to select a magnetic separator configuration that provides for a thin “burden depth” or thickness of the material layer over or under the magnet to ensure the magnet will havethe best opportunity to capture the ferrous contamination.
Understanding these considerations will help select the appropriate equipment to ensure your process is free of metal contamination.
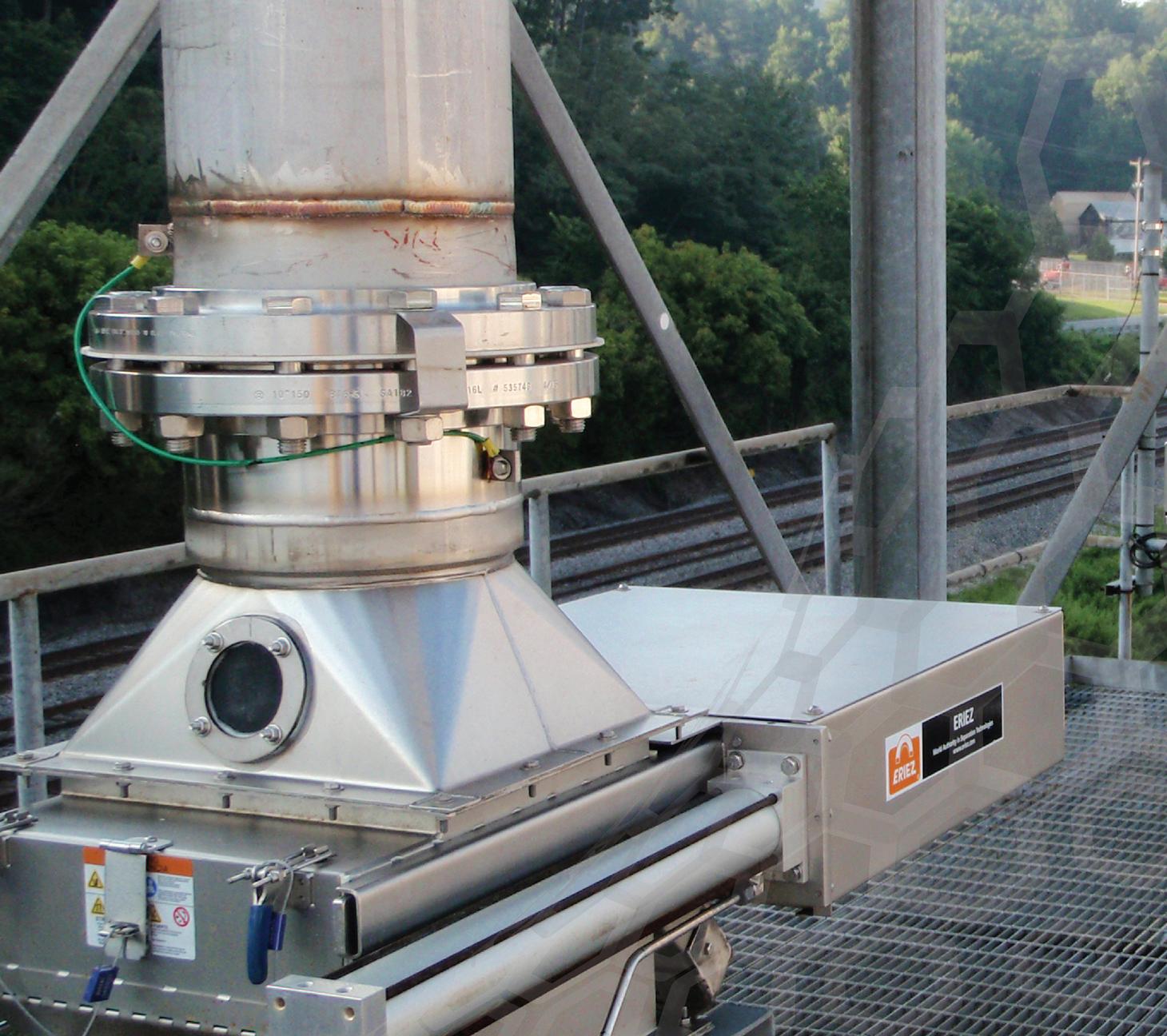
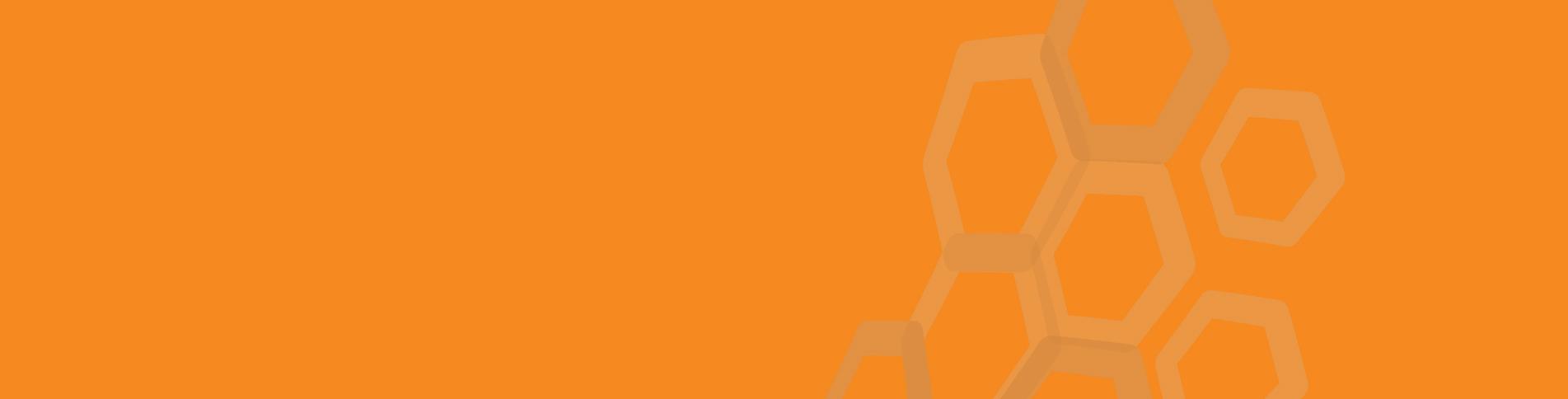
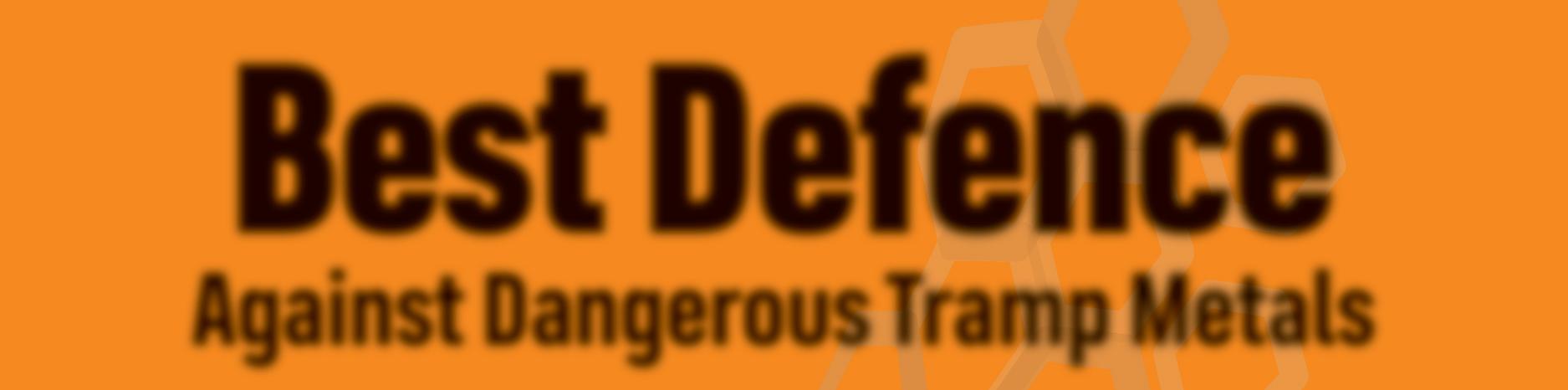
Eriez offers a wide range of magnetic separators to get metal out
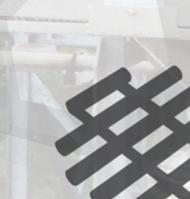
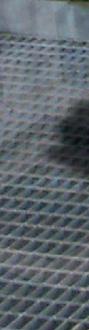
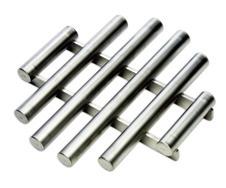
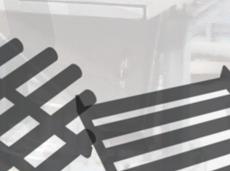
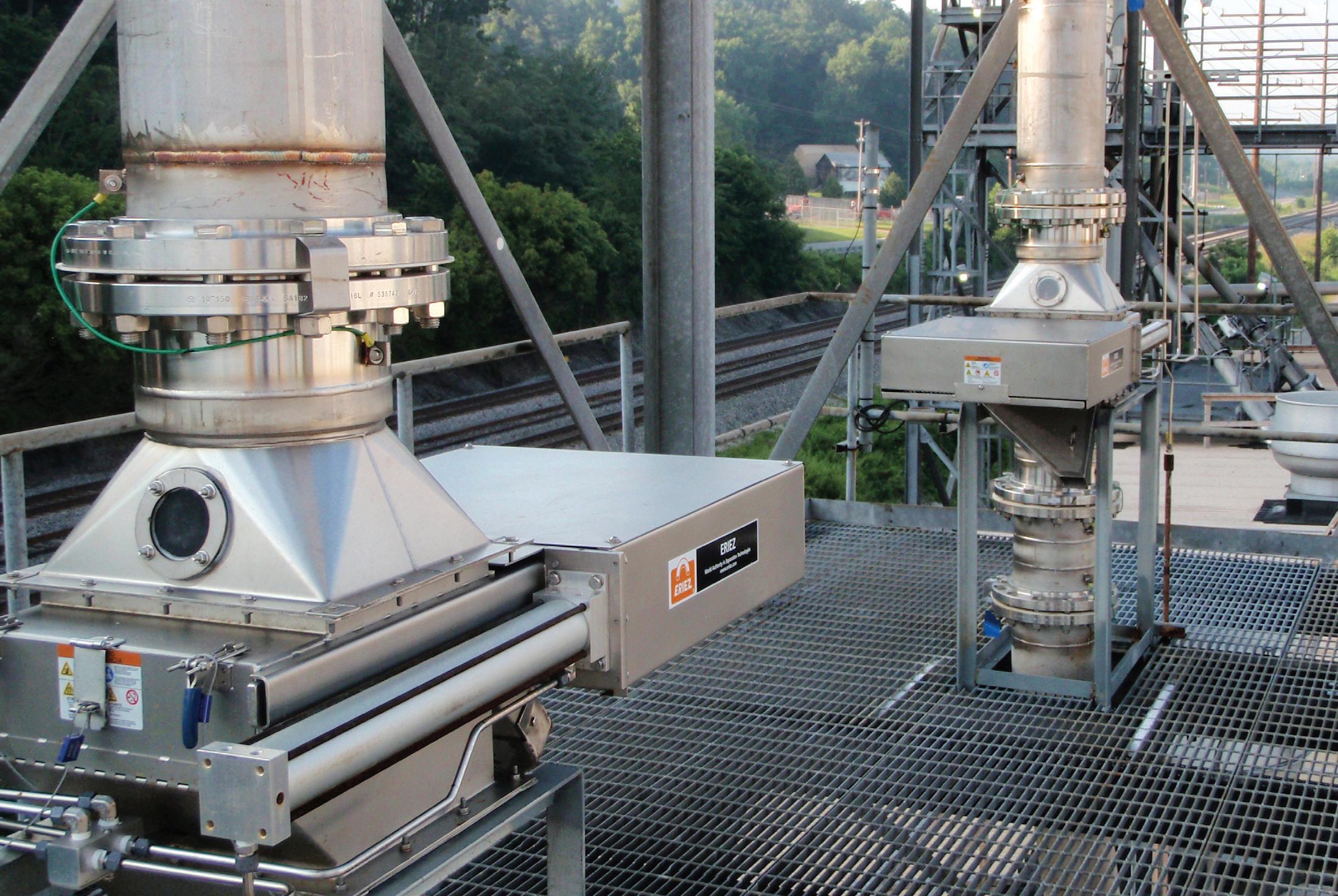
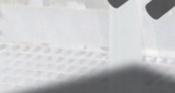
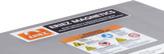
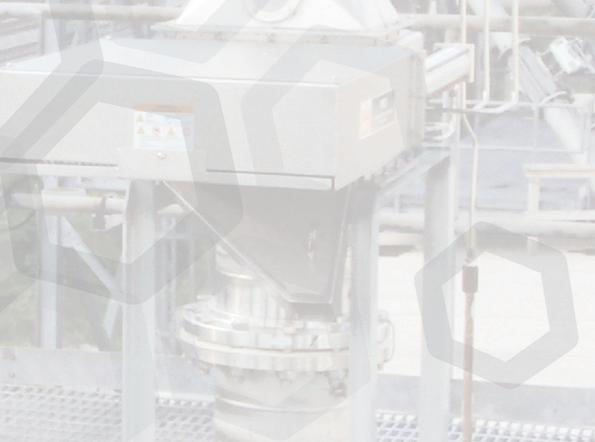


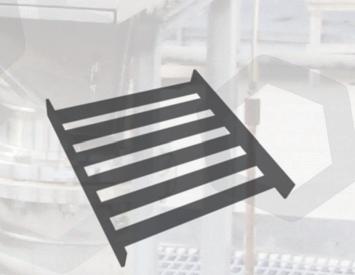
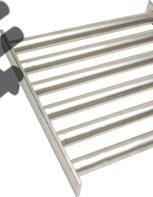
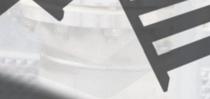
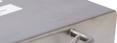
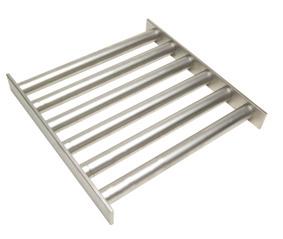
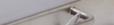
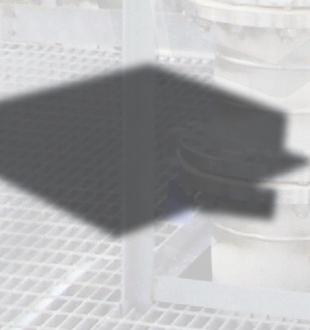
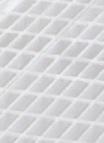
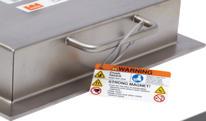
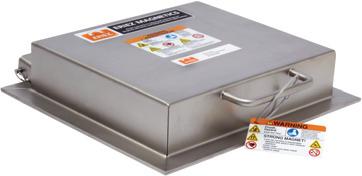
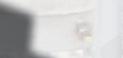
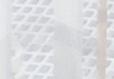
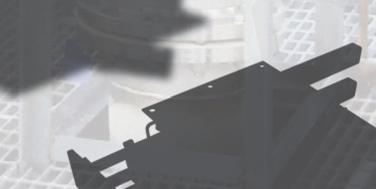

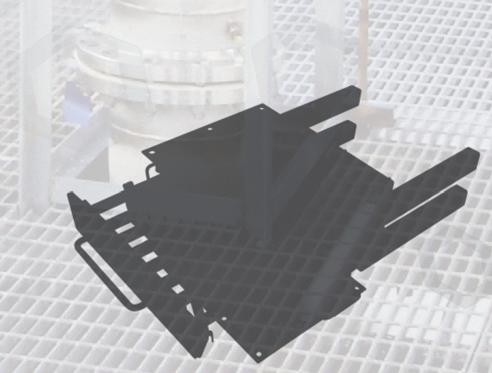
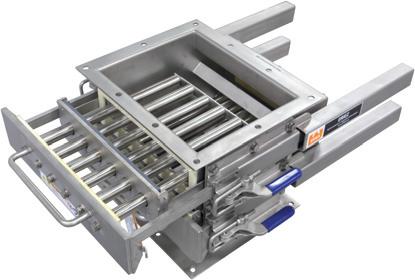

Valve & Process Solutions
How hygienic valves are optimising process performance in the UK food and beverage industry
Valve & Process Solutions launches Pentair Südmo into their product portfolio, being appointed as the UK’s only authorised Channel Partner for Pentair Südmo Spares & Components. This partnership reflects Valve & Process Solution’s commitment to excellence and marks a significant milestone in delivering market-leading hygienic solutions to the food and beverage industry in the UK.
Südmo’s hygienic valve range is engineered with the highest standards of quality and reliability, addressing the unique challenges faced by food and beverage manufacturers. From dairy processing to brewing, these valves are designed to meet stringent hygiene requirements while maximising operational efficiency. Let’s explore the significance of optimised process performance and the role hygienic valves play in shaping the future of food and beverage production in the UK.
Compliance and Quality Assurance
The UK food and beverage industry is subject to strict regulations and standards to ensure the safety and quality of products. Optimised processes not only help companies meet these regulatory requirements but also exceed them, demonstrating a commitment to excellence and consumer welfare. Hygienic valves play a pivotal role in ensuring the safety of processes in the food and beverage industry through optimum cleanability and excellent surface quality. Their specialised design means there are no sumps or domes where media could hide, minimising the risk of bacteria growth and residue build up. By preventing contamination and maintaining product quality, hygienic valves safeguard the integrity of the final product, thereby offering peace of mind stringent hygiene standards are met.
Adaptability in a Changing Landscape
From shifting consumer preferences to new regulatory standards, the food and beverage industry is constantly evolving. Optimised processes enable companies to adapt quickly to changes in the market, seize new opportunities, and stay ahead of the curve. The consumption of food and beverage products is growing rapidly, and as a result, producers need flexible and sustainable processes. This is where innovative valve technology comes into play to meet these challenges with versatile hygienic and aseptic integrated solutions that accommodates changing requirements.
Sustainability and Responsibility
As global concerns about sustainability and environmental impact continue to grow, optimising processes becomes increasingly important. By minimising waste, conserving resources, and reducing energy consumption, companies can demonstrate their commitment to responsible production practices and appeal to environmentally conscious consumers. By using high-quality materials and with longevity in mind, hygienic valves reduce environmental impact while providing total solutions that meet strict regulations and international standards.
Building a Sustainable Future for the UK Food & Beverage Industry
Whether it’s enhanced operational efficiency, safety and quality compliance, fast-changing market requirements, or peace of mind knowing you’re investing in top-quality components, the use of specially designed hygienic valves helps support customers with their safety and sustainability needs.
For more information or to enquire about our range of valves and flow control equipment, please contact sales@vandpsolutions.com or visit www.vandpsolutions.com. We look forward to supporting you and keeping industry flowing!
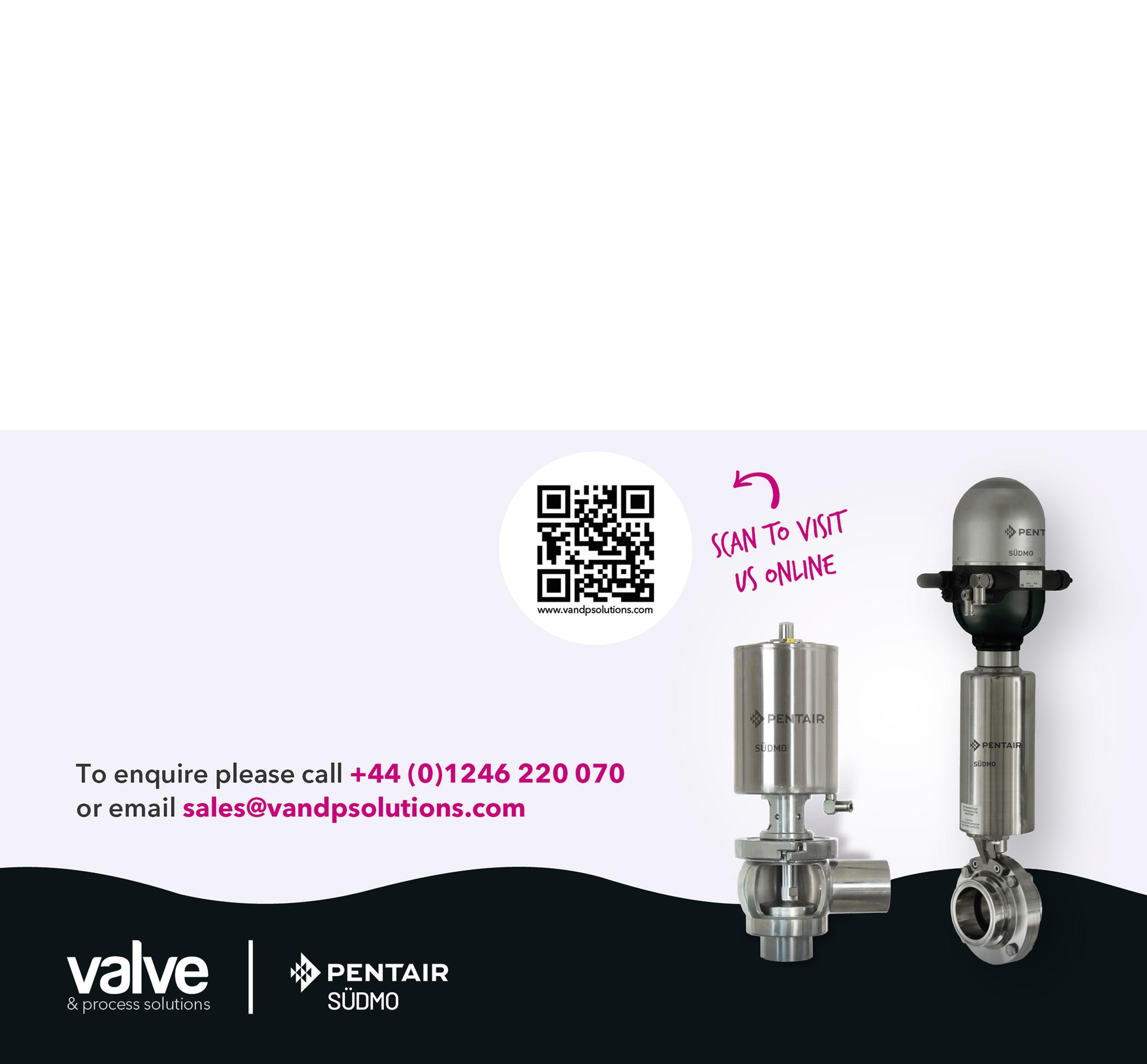
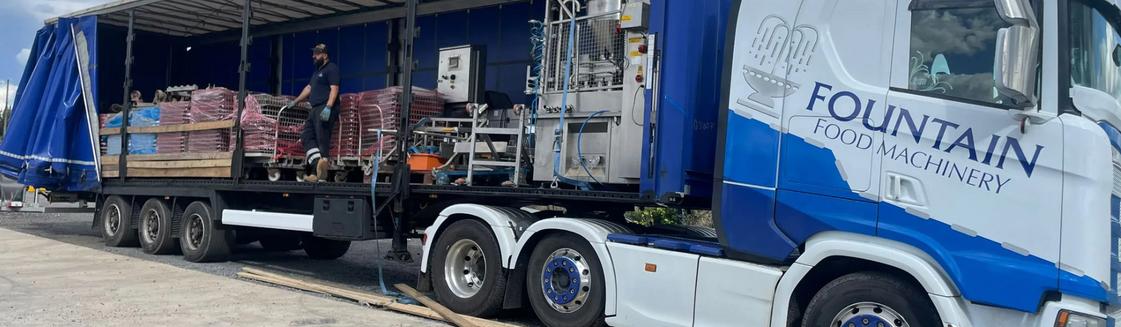
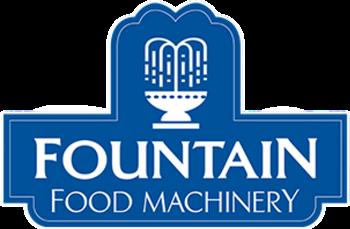
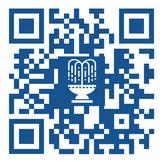
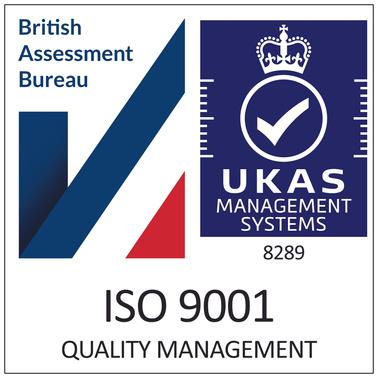
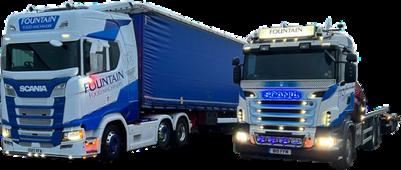
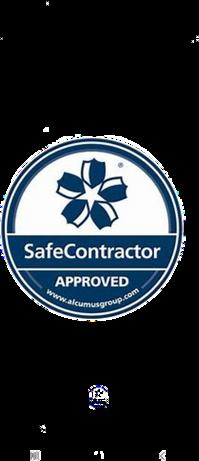
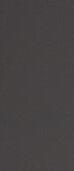
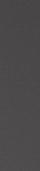
Innovations in Food Processing: A Focus on Pipework Systems
The food processing industry is undergoing a transformative phase, with a heightened emphasis on new product development and innovation.
As the global demand for food products continues to rise, the food processing equipment market is poised for steady growth, driven by factors such as an increasing population and the integration of automation.
Bakery and Confectionery Leading the Way
In the evolving landscape of food processing, the bakery and confectionery products segment is projected to take center stage. Additionally, the demand for hygienic meat products is expected to drive sales in the food processing equipment market, particularly
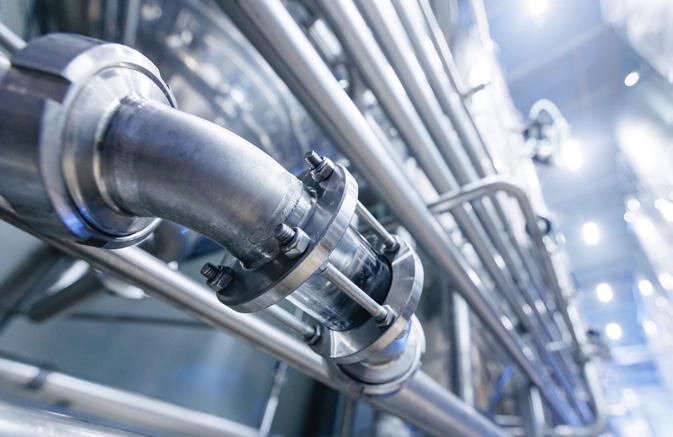
in meat and poultry applications. This shift underscores a growing consumer preference for safe and high-quality food products.
Pipework Systems: A Cornerstone of Food Safety
A significant portion of investment in the food and drink sector has been directed towards innovative solutions that enhance production and processing facilities. One such critical aspect is the development and implementation of modular pipework systems. For food manufacturers, operating a safe and reliable processing plant is paramount. Hygiene and safety considerations are crucial, and this is where high-quality hygienic pipework systems come into play. These systems, known as food grade lines, are designed to be easy to sanitize, cost-effective, and simple to install.
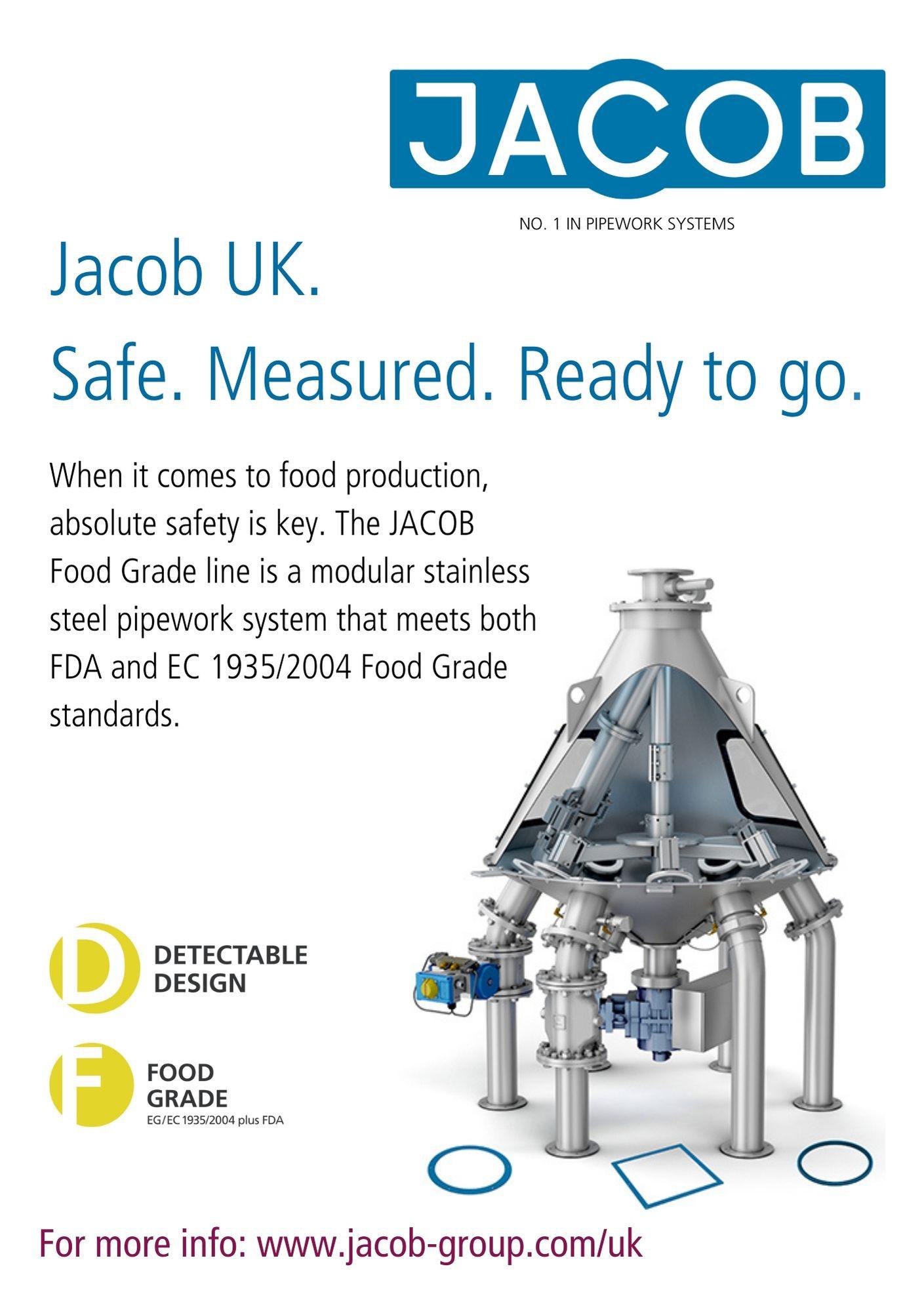
Meeting Stringent Standards
In the food and drink industry, the highest standards of safety and cleanliness must be met. Food grade lines are engineered to fulfill these strict demands, ensuring that all components in contact with food meet rigorous criteria. The modular stainless-steel pipework system, known as the food grade line, comprises over 3,000 products meticulously tested and optimized for the food industry.
Materials and Compliance
Pipework systems in the food and drink sector use carefully selected materials, with components in direct contact with products made exclusively of stainless steels featuring a minimum grade of V2A/1.4301. These materials adhere to European regulations EC 1935/2004 and FDA standards in the United States. The components are highly resistant to mechanical loads, high temperatures, chemicals, and solvents, ensuring durability and reliability.
Collaborative Approach for Customisation
Experts in pipework systems collaborate closely with clients in the food and drink industry, tailoring solutions to meet specific requirements. These systems have been developed to not only meet but exceed the strict hygiene and safety standards mandated by the food and drink processing sector.
Process Sensing Technology
Innovative Bluetooth water activity meter from Rotronic sets new standards
Rotronic, part of Process Sensing Technology (PST) and the specialised manufacturer of humidity and temperature instrumentation, has launched a combined Bluetooth Water Activity meter with smartphone and tablet app.
Called the AwEasy, the new stand-alone instrument is advanced, lightweight and compact, and is designed to produce extremely accurate reading simply and quickly – up to ten times faster than traditional devices. This makes it ideal for use by laboratory analysts, quality control teams and production staff who need to take spotwater activity measurements in the food, pharmaceutical, cosmetics and chemical industries.
The new AwEasy is the most recent addition to Rotronic’s existing range of water activity analysers, meters and probes. The company believes that it is the first of its type to offer both Bluetooth connectivity with the ability to use a smartphone or tablet app, to store and analyze data and then automatically output reports as pdf documents, for use in quality control and traceability regimes.
The AwEasy features a robust stainless steel and aluminum housing, measuring just 65mm tall and 68mm in diameter, with a topmounted color LCD display, indicator ring and single control button. The instrument also incorporates Rotronic’s latest humidity and temperature sensing technologies. These are capable of providing levels of accuracy to within plus or minus 0.008aw, which is far better than competing devices in the same price range, while ensuring exceptional repeatability and stability.
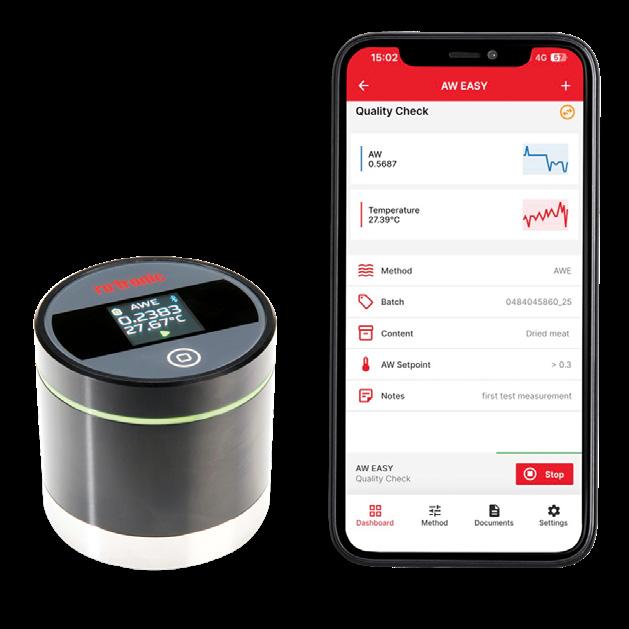
Set-up and operation is carried out via the iOS or Android compatible app, with measurement simply requiring a test name and batch number. Analysis is automatic and can be displayed in detail, as raw data or on a choice of charts, with reports being exportable as pdf or csv files.
The AwEasy has also been designed to minimize the time required for water activity measurements. These normally take up to 50 minutes, but with the AwEasy in Quick Function mode this time can be significantly reduced to around 5 minutes. Combined with the in-depth analysis reports, this enables the new AwEasy to offer considerable improvements in productivity, quality control and traceability.
In areas such as factory environments, where connectivity may be an issue, or where the use of Smartphones is prohibited, the new AwEasy can be used on its own. Control of each analysis can be carried out directly from the front panel, with data being displayed on the LCD control panel and then automatically uploaded once the smartphone is back within range.
As part of the PST group, Rotronic is able to provide a comprehensive range of technical and sales support services, including training, sensor calibration and repairs.
Rotronic AwEasy – Standalone Bluetooth Water Activity Monitor


Compact, lightweight and mobile
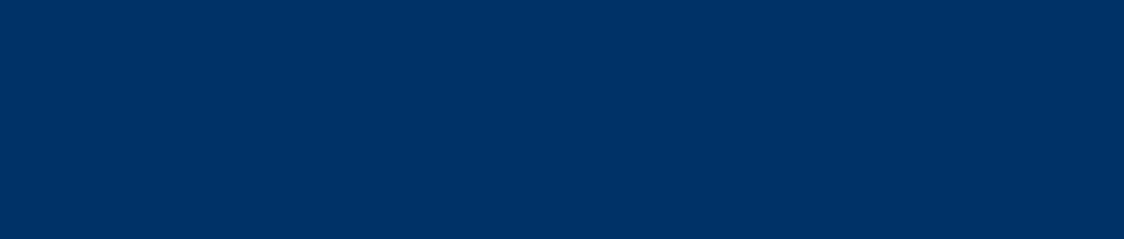
• AW Quick for results in 4 – 5 min.

• Easy to use with display



• Also measures humidity and temperature
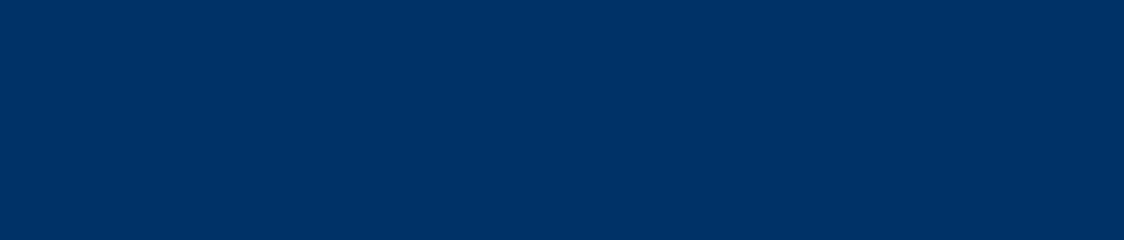


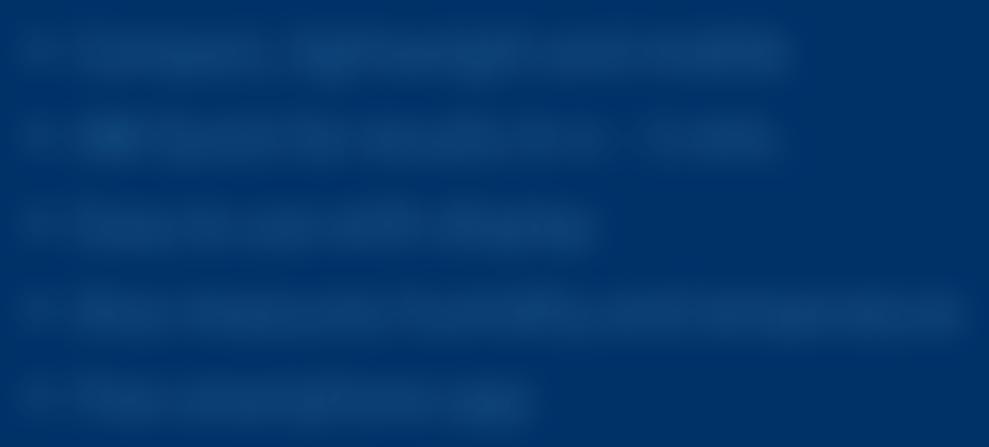
•

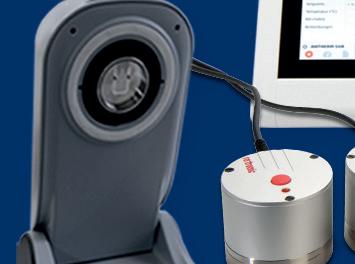

• Free smartphone app









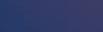
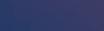
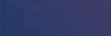
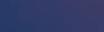





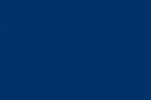

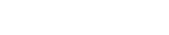
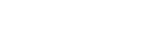
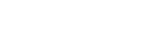
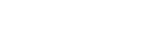
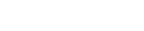
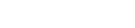
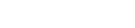
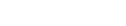
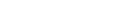

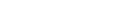





Auto-report nction

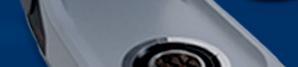
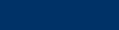


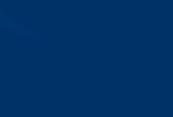
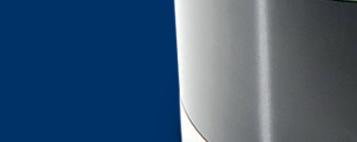

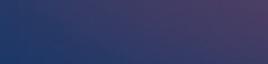
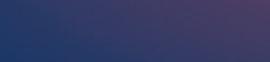
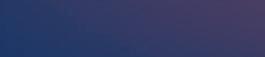


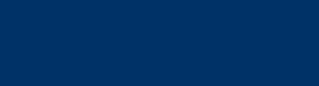

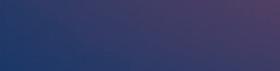
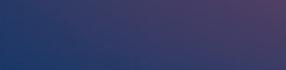
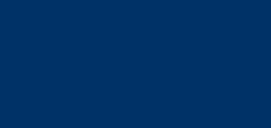
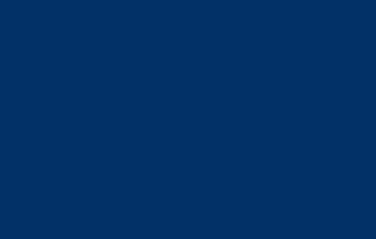




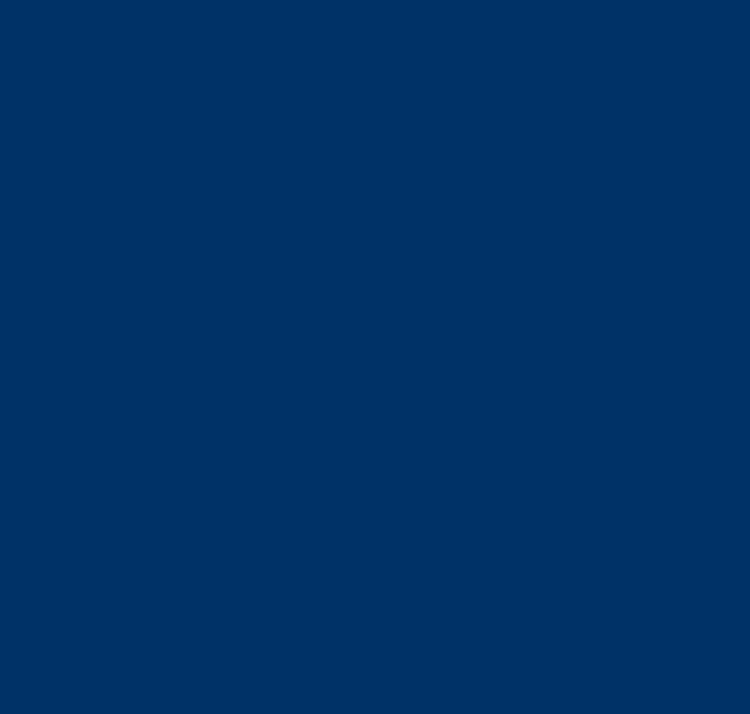
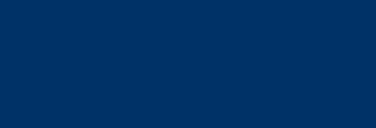
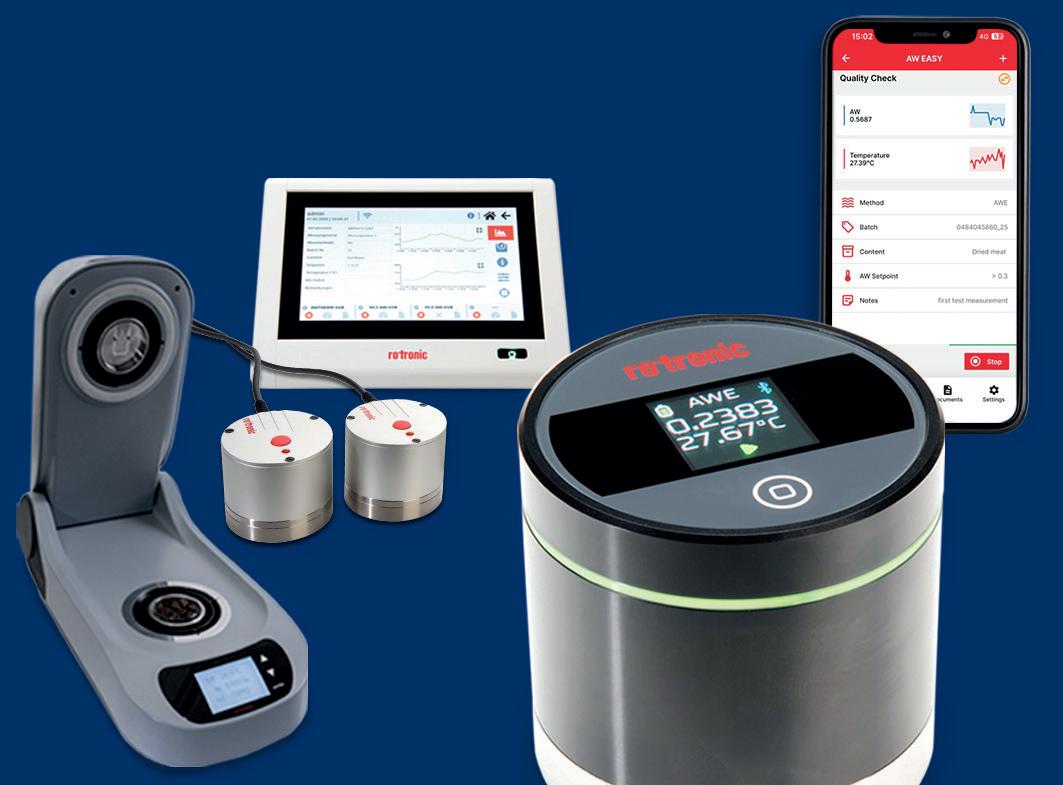

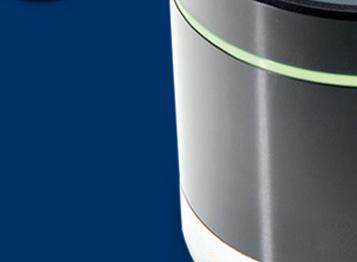
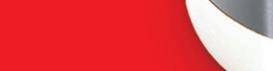
The new AwEasy complements our range of water activity measurement devices perfectly. Measurement probes, penetration probes, laboratory benchtop and handheld devices can be combined flexibly according to your requirements. Bene t from the highest accuracy, e ciency, and easy calibration to optimize processes and ensure product quality. ProcessSensing.com
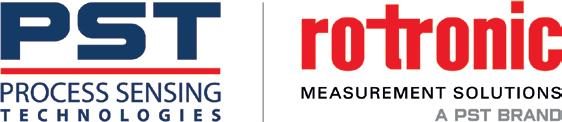
The FLIR Si2 acoustic imager delivers a comprehensive solution that extends beyond conventional leak detection to uncover industrial gas leaks and mechanical faults for optimized operations.
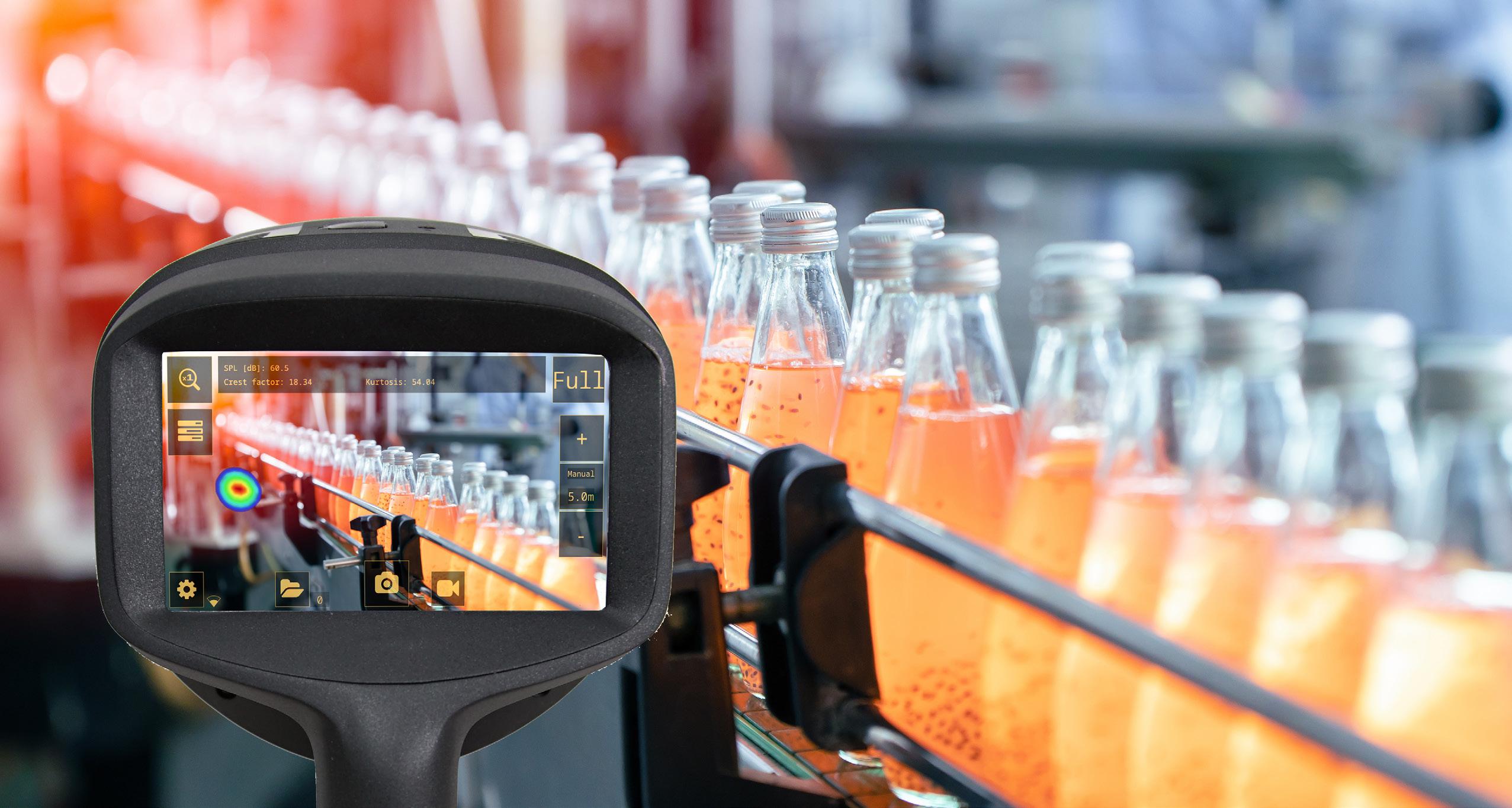
Redefining Predictive Maintenance:
The FLIR Si2 Acoustic Imager Provides Advanced Leak and Mechanical Fault Detection for a New Era of Safety and Efficiency
Compressed air and industrial gases are widely used in the food and beverage industry for various purposes, including production chains, packaging, and cleaning. Most production phases also involve the use of conveyor systems, which are critical for the process but prone to wear and tear and inaudible to the human ear. If left undetected and unaddressed, leaks and mechanical faults can lead to severe problems. As 24/7 operations are not uncommon in the industry, additional costs caused by issues like reduced performance and equipment malfunction can quickly accumulate into significant amounts.
Introducing The FLIR Si2 – The Next-Generation Acoustic Solution That Does It All
To avoid problems like impaired product quality, increased operating costs, and consumer safety risks, a regular predictive maintenance inspection routine is needed to ensure that pneumatic equipment and conveyor systems are functioning correctly and free from leaks and mechanical faults. The FLIR Si2 acoustic camera helps identify even very small leaks and faults promptly, improving efficiency, reducing operating costs, and ensuring product quality and safety. The Si2 also allows for accurate leak detection from a long distance in noisy environments typical for the industry, without the need to halt operations. To further facilitate decision-making, the AI-driven automated leak size and cost estimates deliver immediate support for proactive measures.
Pressurized Gas Leak Detection for Substantial Savings
Delivering a complete solution for the food and beverage industry’s needs, the Si2 acoustic camera extends beyond compressed air leak detection to also identify industrial gas leaks and mechanical faults in conveyor systems. Pressurized industrial gases are used in various
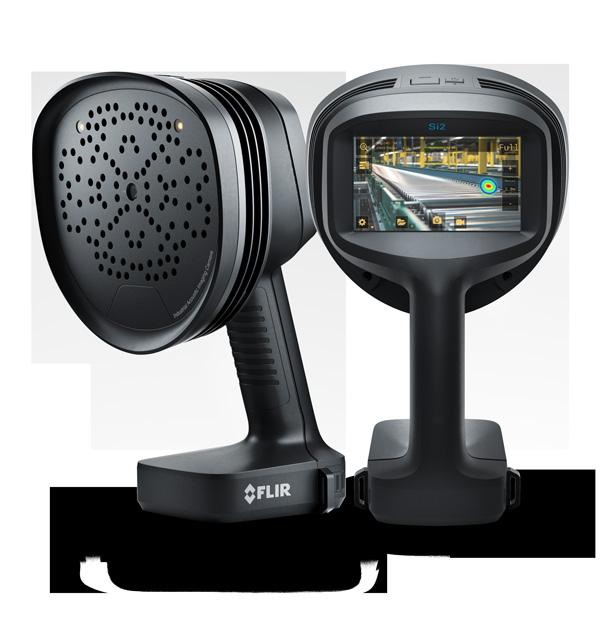
stages of food and beverage manufacturing. Carbon dioxide (CO2) is used for beverage carbonation and modified atmosphere packaging (MAP), whereas oxygen (O2) is used for MAP and fermentation. Argon (Ar) is also used for MAP and beverage dispensing systems, and helium (He) is used for leak testing and beverage dispensing systems. As these specialty gases are a costly commodity, leaks not only cause negative impacts on performance, equipment, and product quality, but also lead to significant additional costs.
Uncovering Critical Faults Keeps Conveyor Systems Rolling
Conveyor systems are essential for transporting raw materials, ingredients, and finished products throughout the production process, and mechanical faults can cause equipment downtime, decreased productivity, and increased maintenance costs. By allowing for effortless detection of mechanical faults in conveyor systems and their components, the Si2 enables predictive maintenance and prevents unplanned stoppages in production.
The FLIR Si2-Series consists of three acoustic imagers for different applications: the Si2-LD for leak and industrial gas detection and mechanical fault issues, the Si2-PD for partial discharge detection and the Si2-Pro including all modes of operation.
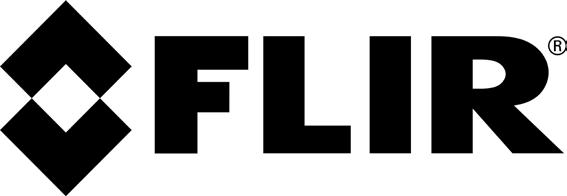
Learn more at https://www.flir.com/instruments/conditionmonitoring-solutions/choose-flir-si-series/
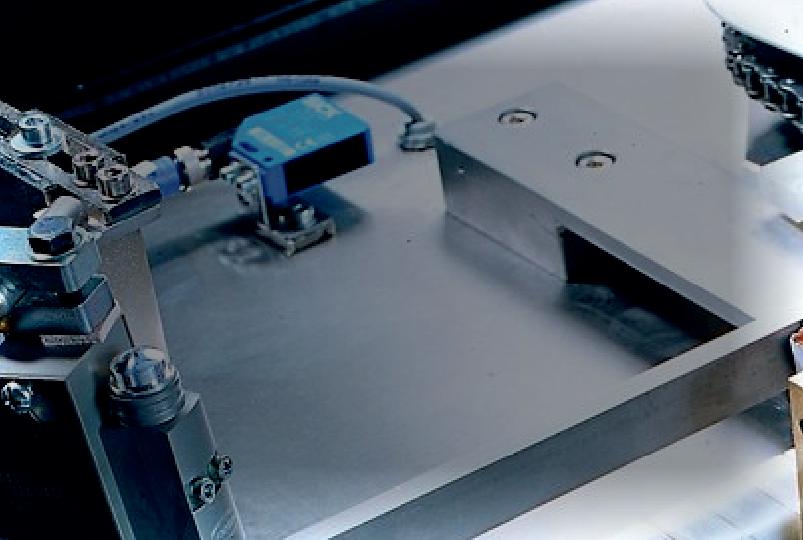
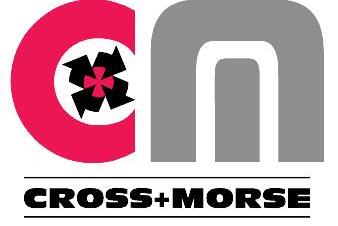

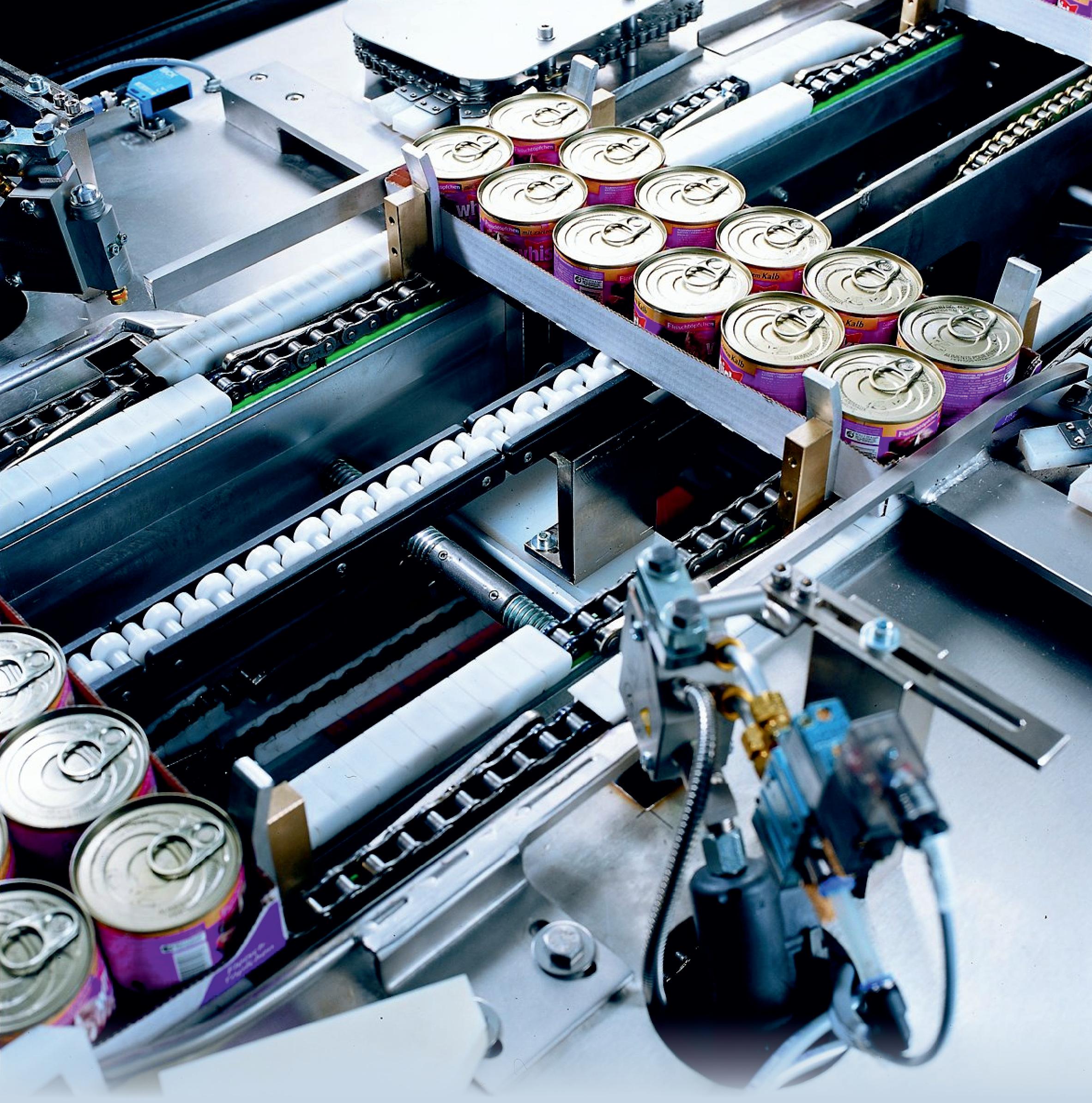
At Cross+Morse we aim to fulfil all industry demands, from the simplest to the highest level of precision required. Our objective is to offer a complete solution - not just products - to your power transmission challenges.
Cross+Morse are known in the industry as pioneers in quality standards, which is why we take our quality control processes very seriously. Quality assurance is central to our organisation with controls encompassing all aspects of design, manufacture, logistics and customer service. We are ISO 9001:2015 accredited and have been for over 30 years.
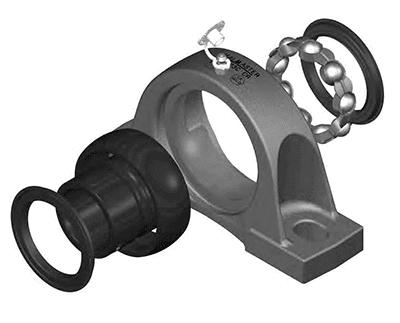
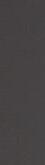
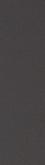
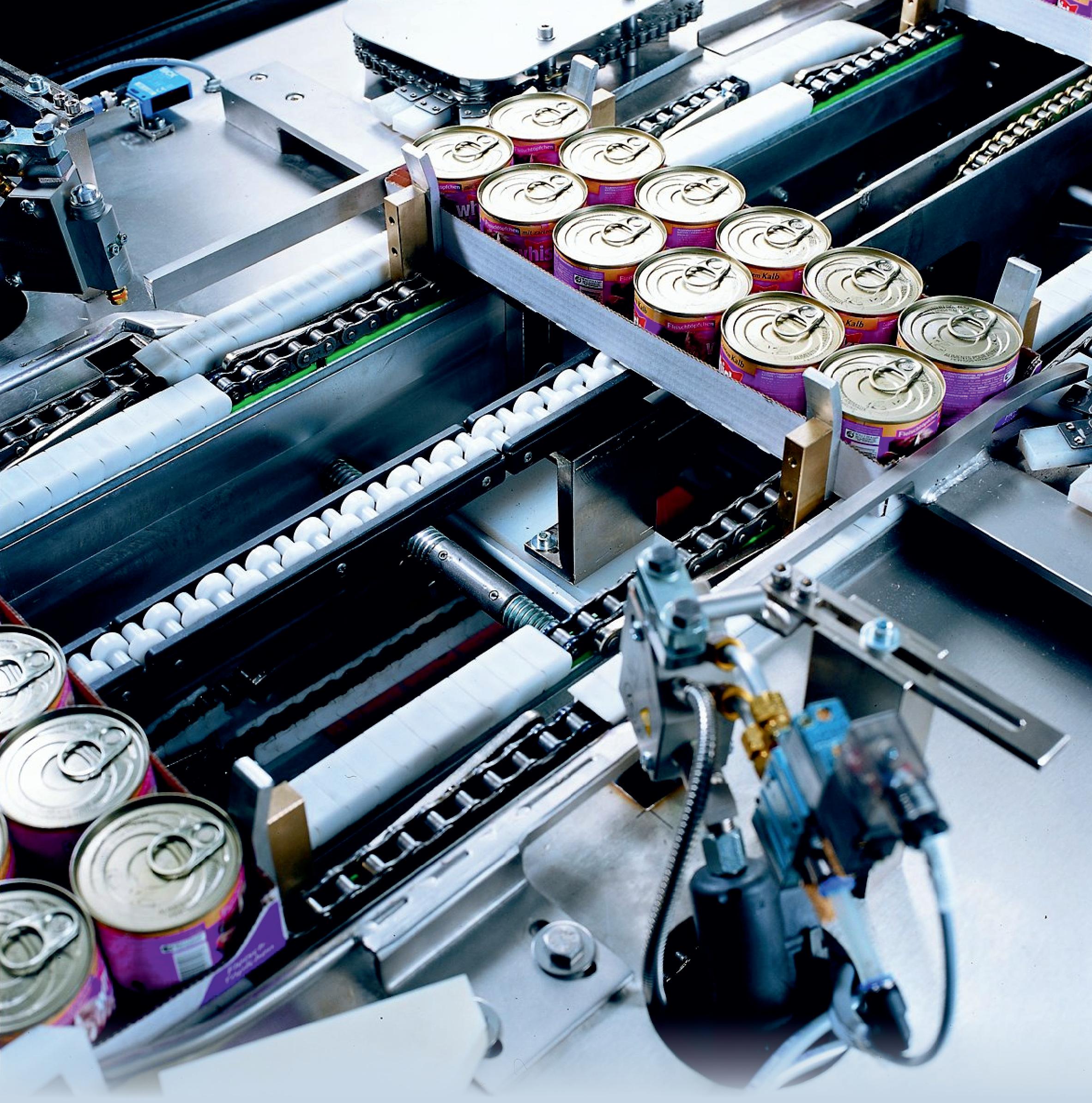
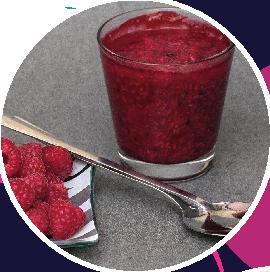
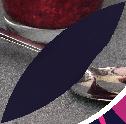
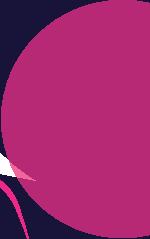
Power Transmission Solutions
freewheels, roller ramp clutches, combined sprag and bearing units and many more.
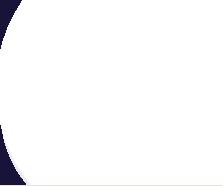

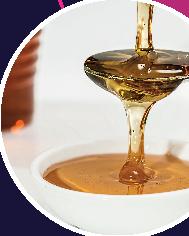
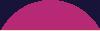
At Cross+Morse we have continuously invested in top of the range measuring equipment: Co-ordinate Measuring Machine (CMM), digital tri-bore gauges and micrometers which are constantly calibrated to comply with ISO standards. Our stringent inspection process guarantees that when manufacturing each operation is thoroughly inspected by either a highly trained shop-floor staff supervisor or an inspector, ensuring that manufacturing is only allowed to continue when each phase has been approved. Our hardening treatment is checked using either our Rockwell or Vickers hardness testing machines.
We review our quality procedures continuously to provide up-to-date mechanisms for ensuring conformity to the quality system; different audits are carried out on all activities in the company throughout each year.
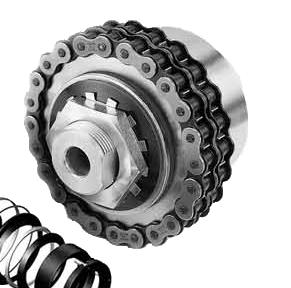
Cross+Morse is the largest authorised distributor and stockist for American transmission products manufactured by RegalRexnord (formerly EPT) in the United Kingdom. The range includes Sealmaster®, Browning®, Jaure®, Kop-Flex®, McGill® and Morse®.
Inverted tooth chain: including the standard SC type from 3/16” to 2” pitch and HV type from 3/8” to 2” pitch; as well as conveyor chains up to 12” width in centre or outside guide construction. We manufacture standard and special sprockets in-house for a complete drive solution.
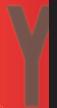
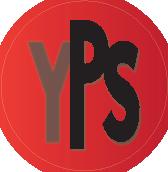
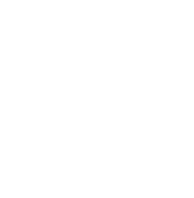
We pride ourselves in offering a complete range of overload protection devices ranging from the simplest to the most accurate and precise overload clutch: Sheargard range of overload clutches, wedge pin type, available as a chain coupling and the option of low inertia rubber elastic couplings for higher speed drives. The Crossgard range, ball detent type, comes in 3 versions and also available with roller chain and low inertia rubber coupling option. The Safegard CS series, ball/roller detent type, comes in 2 two basic types (standard or mini) and also available as shaft couplings. Series CZ and CN zero backlash Safegard clutches for responsive overload protection, available in both basic and shaft coupling types.
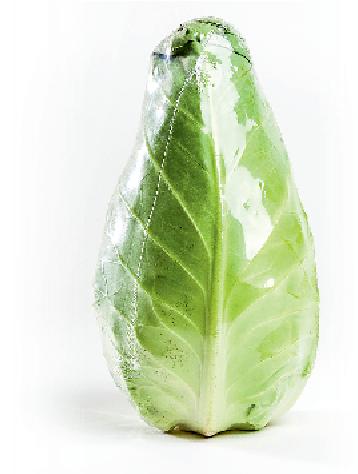
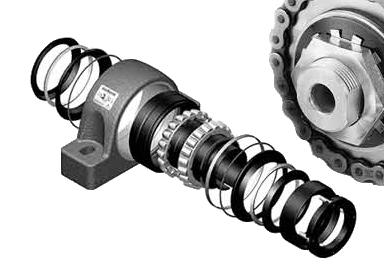
We offer a wide stock range of flexible shaft couplings to accommodate different types of misalignment: Jaw couplings, elastomeric couplings, roller and Delrin® chain couplings, gear couplings GFA & GFAS, polymer gear couplings, Morflex elastomeric disc couplings and Crossflex disc couplings.
Our Crossbore® rework service includes reboring, keywaying and setscrewing of standard sprockets, pulleys and gears in a dedicated production area with specialised CNC machines for a rapid response. Induction hardening of teeth is also offered in-house.
For further information contact:
Shaft clamping elements for precision transmission of torque with no backlash: a complete range from stock.
Our range of Freewheel clutches for overrunning, indexing and backstopping applications; including sprag clutches, industrial ratchet
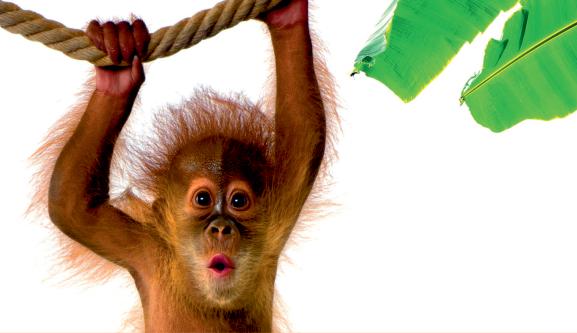
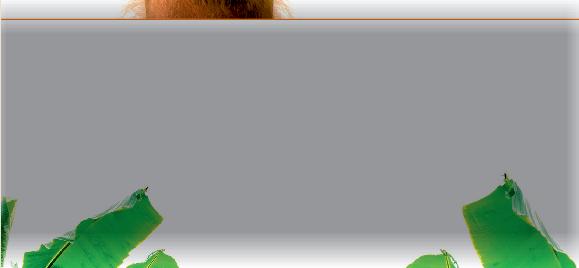
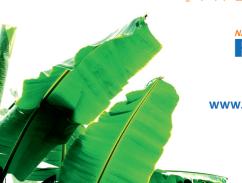
Telephone: +44 (0) 121 360 0155 Email: sales@crossmorse.com or visit www.crossmorse.com
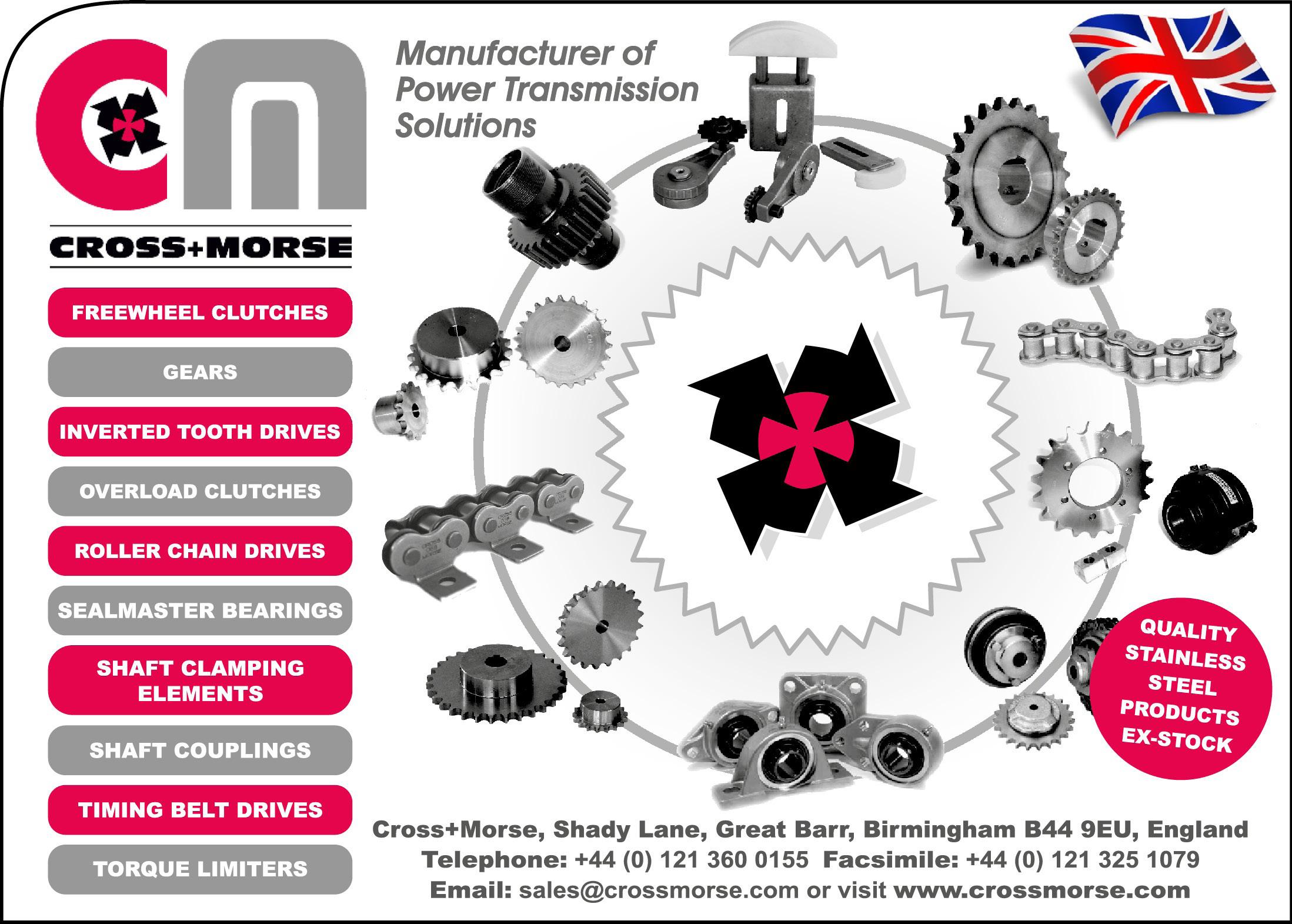
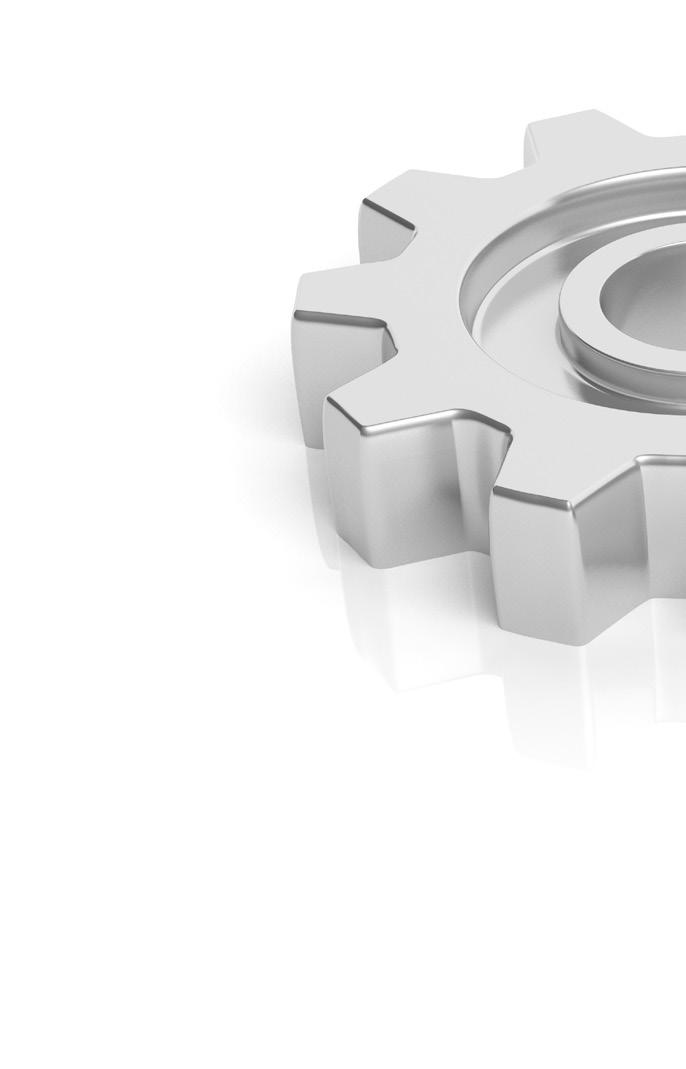
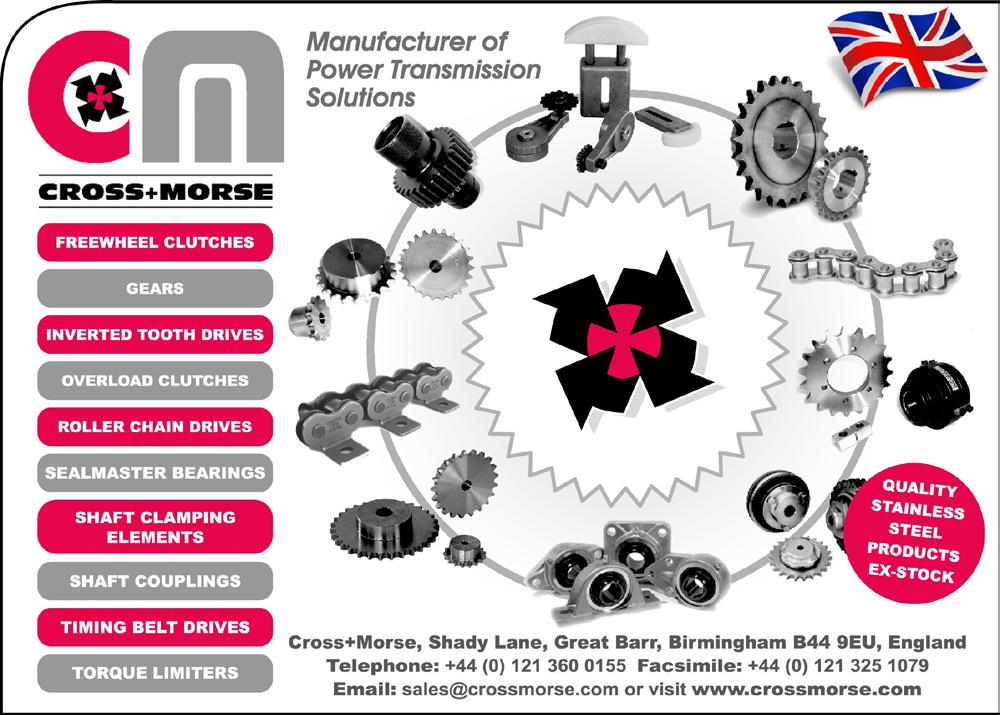
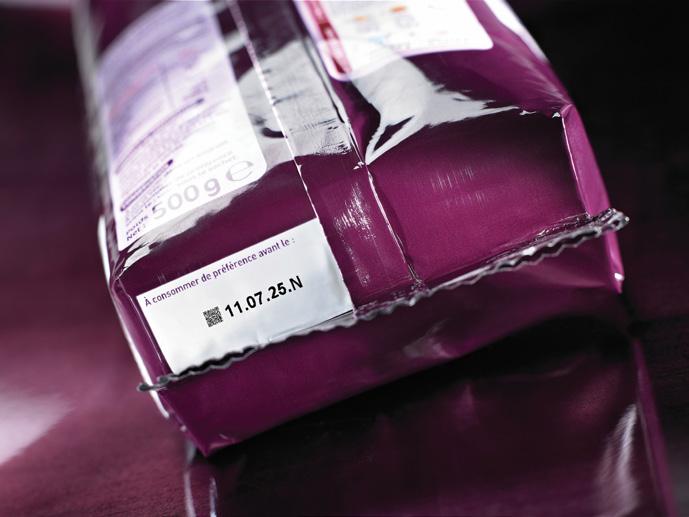
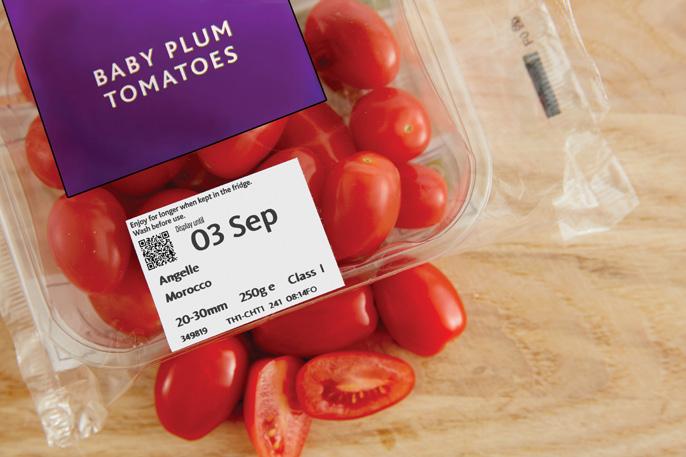
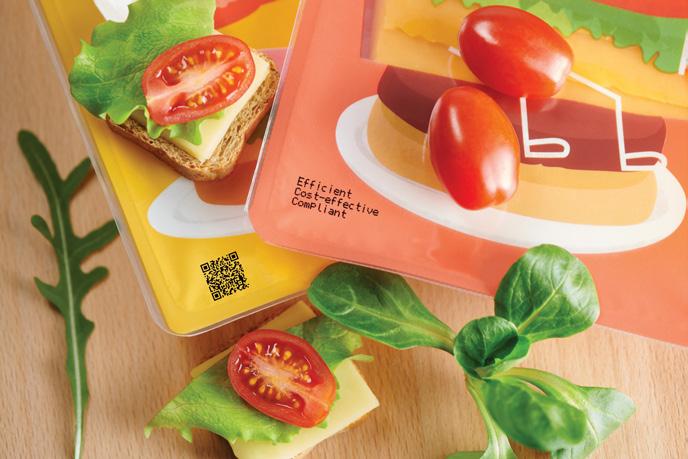
Revolutionising Brand Marketing: Unleashing the power of QR codes
Despite the ever-growing inclusion of QR codes on products, companies often miss out on marketing opportunities that could transform their brand from a one-off experience to a long-term customer favourite.
With a lot of alternative brand choices out there, leveraging a strategic marketing approach to ensure enduring brand loyalty is more important than ever. While a Quick Response or QR code is a powerful way for producers to digitalise, personalise and energise their entire brand story, the inclusion of QR codes on a product require a considered and informed strategy to be effective.
Beyond payment to customer engagement
There is still a perception among some businesses that the QR code is simply another mechanism for providing static brand and company information or customer payments. Yet a product code executed effectively can go far beyond this, being a way to share content that is exactly in tune with where that individual is in their buying or decision-making journey. This has the power to quickly accelerate customer engagement and boost brand marketing. A key advantage of the QR code is its capacity to personalise the content a customer sees, based around their particular tastes and priorities.
Advancing marketing potential
As we have previously mentioned, the QR code is the perfect vehicle to communicate information on traceability and sustainability, as well as the history and back story of a brand. But these benefits go even further. For almost any Fast-Moving Consumer Goods (FMCG) brand, QR codes have the potential to enhance and enrich customer experience. The forms of marketing that QR codes can deliver are wide-ranging and can meet the needs and interests of nearly every demographic of the product user. This could include discounts and loyalty programs to enhance customer retention, competitions that relate directly to a product or a venue or even trying to cross-sell by alerting loyal customers to other products they might also enjoy. QR codes can even empower brands to leverage the power of gamification to boost engagement even further through options such as collecting points towards free or reduced-price products, and prizes when customers attend a certain venue. At the heart of all of this is personalisation, through which a well-executed QR code delivers content that exactly matches the profile and personality of the customer, especially those with associated online accounts, whether that’s the ability to compare their favorite brand to a friend’s or being able to view the ethical impact of their purchase and contribution to a brand’s community or charity support programs. As with many types of tech innovations, the QR code is not a magic wand. To achieve its potential, it must be planned and executed in a way that provides the customer with content that they find attractive, interesting or entertaining. The focus should be on what the consumer can experience when they scan the code. Because scanning a code may be the only opportunity a brand has to connect with the individual, the content needs to be dynamic and non-static to cater to their interests and priorities.
Connecting at the right moment
Connecting with the customer is everything to brand loyalty, yet many businesses miss their moment. Buying a product of a particular brand instead of another other brand can be either an emotionally driven purchase or just down to a lower price tag. This means that brands need to create value and a connection with their customers, especially those who may switch to another product over a small price difference. A precisely planned and implemented QR code has
the power to present content customised to individual consumers based on their preferences and their stage in the buying journey. With a carefully crafted approach, a QR code has the power to boost any brand marketing and customer loyalty with the right message, in the right place, at the right time.
Leverage the power of packaging
Every business understands the impact of packaging on marketing success. More than half of consumers are more likely to buy a product if they have connected with the packaging. A QR code placed strategically and in keeping with a producer’s overall brand can transform a product into an additional point-of-sale outside of the retail space. In this way, an effective QR code can reduce the risk of missing out on sales because it provides a new and valuable direct-to-consumer sales channel that drives tap-to-purchase, exclusive product launches and other targeted initiatives.
Accelerating brand loyalty
More than ever, brands need to be able to show that they are unique, ethically driven and in tune with what their customers care about. A strategically executed and dynamic QR code such as those delivered by our Blue Bite brand can achieve this and much more. The rewards are high but without the right approach, so are the risks. To maximise QR codes and reap the many potential benefits, brands should aim to work with a trusted partner with proven experience in connecting brands dynamically and thus more powerfully with their users. By doing so, they are more likely to achieve long-term customer loyalty. Through sharing a relevant and compelling marketing story, the QR code can help brands ensure that their product is the one that consumers choose.
A world of brand marketing possibilities
Our Blue Bite brand has been one of the pioneers in the smart products space for more than 15 years. We work with both big and small companies across a multitude of sectors, such as footwear and wine. By replacing traditional static online pages with dynamic content generated by using advanced logic and artificial intelligence, we can create unique digital experiences that reflect our customers products, engage their users and boost brand satisfaction. With the Smart Products platform, unlike a TV or online ad, brands can communicate digitally with consumers where and when they want, turning static labels into interactive experiences with a simple scan. Blue Bite’s Experience Studio allows brands to personalize the content customers receive to further grow the connection between consumer and brand. Why not concentrate on other pressing matters while you let Blue Bite do the heavy lifting to grow your brand loyalty hassle-free?
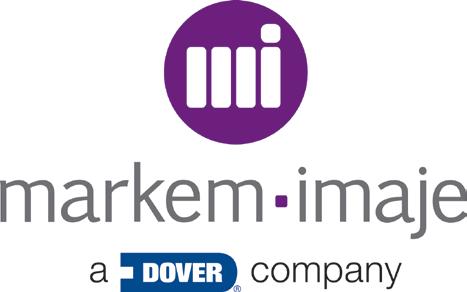
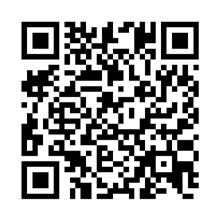

Crafting Exceptional Coffee
200 Degrees Coffee are passionate about one thing: crafting exceptional coffee experiences that delight the senses and elevate the everyday. Founded in Nottingham, UK, in 2012, their journey began with a simple mission – to roast and serve the finest coffee beans with unwavering dedication to quality, sustainability, and authenticity.
What sets 200 Degrees Coffee apart is their commitment to excellence at every step of the coffee journey. From sourcing the finest beans from around the world, to carefully roasting them at 200° Centigrade in small batches to unlock their full flavour potential, they take pride in every aspect of their craft. Their skilled baristas (a.k.a proud coffee geeks) then expertly brew each cup of coffee to perfection, ensuring that every sip of the full bodies, smooth taste, is a moment to savour. With the taste and product perfected, their packaging had a lot to live up to.
Not just the external covering of your product, packaging is the true essence of your brand, the first customer touchpoint, and the protective barrier to keep its contents and consumers safe. After speaking with our team here at National Flexible, we worked together to produce a printed gusseted bag for the retail packs which they supply to their baristas. The 12PET/12MET/60PE film has two colours and a matt varnish, giving the packaging clear, shelf appeal presence.
200 Degrees Coffee needed their packaging to keep their product as safe and fresh as possible so together, we produced a pre-made valve, providing a clever system for expelling gasses and keeping the coffee super fresh. So not only does the coffee taste perfect, but the packaging also looks perfect too!
Whether you’re a seasoned coffee connoisseur or just beginning your coffee journey, we urge you to try their delicious coffee –where every cup tells a story, and every moment is an opportunity to savour the extraordinary.
If you would like assistance in finding the right packaging for your product, our team can help. From protection and safety to attractiveness and usability, there are so many different factors to consider when looking for your perfect packaging, it can be difficult to know where to start. That’s why our team are on hand to guide and support you through your packaging needs.
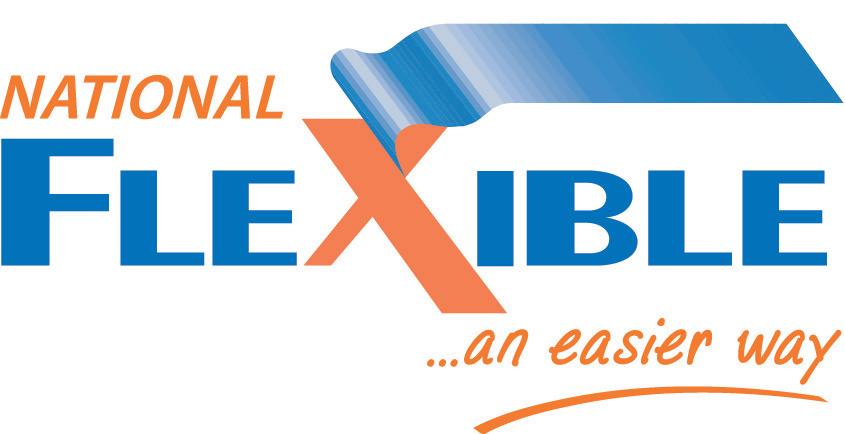

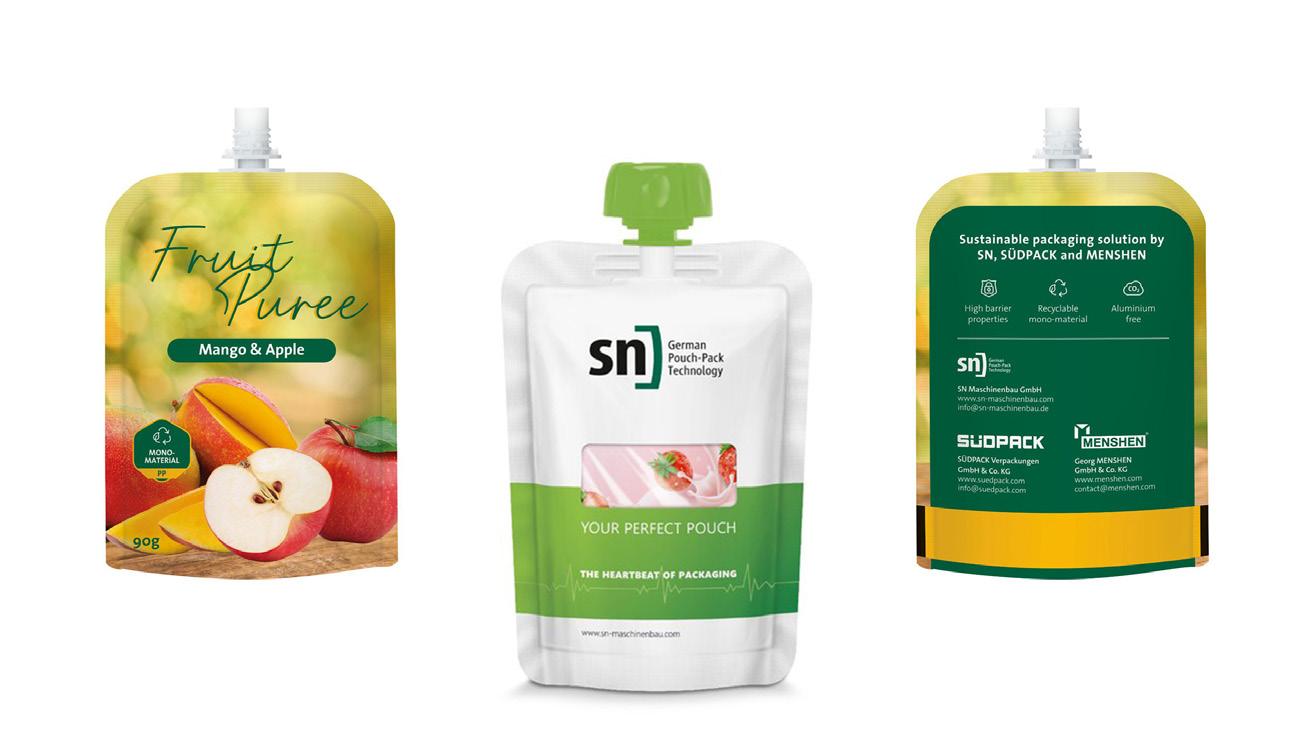
Penn Packaging Packaging & Labelling
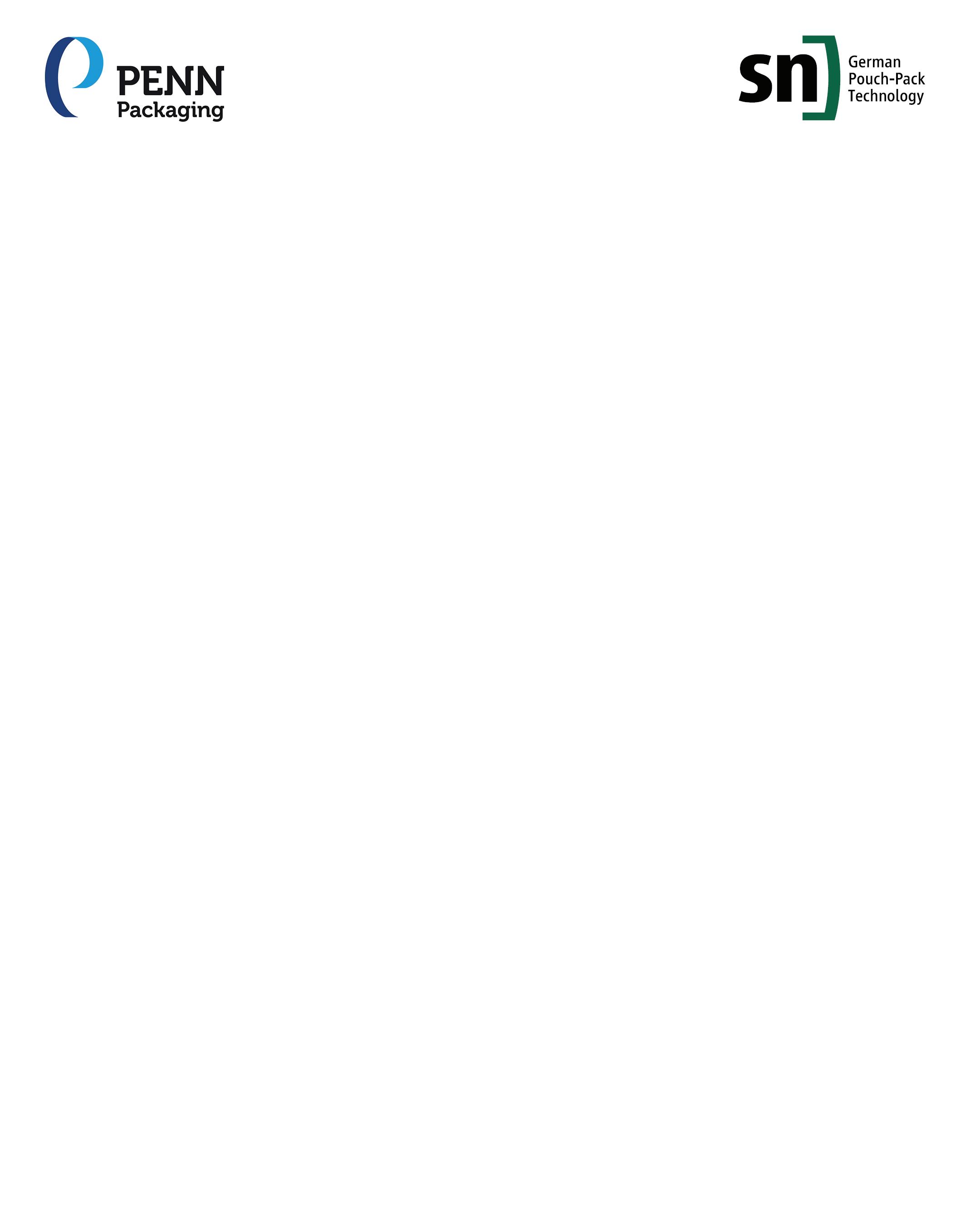
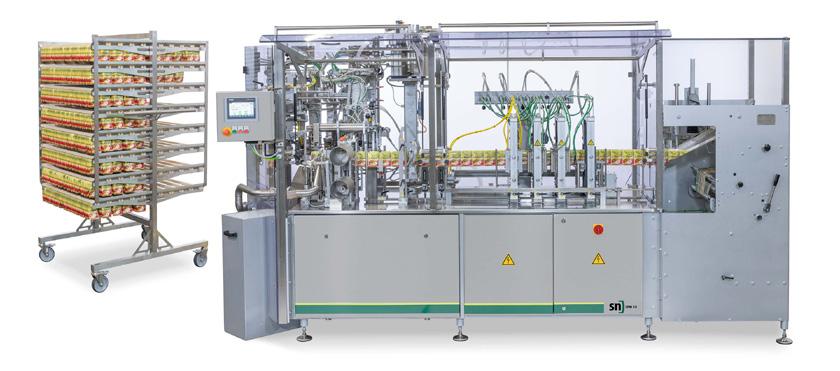
In a new packaging development partnership, SN Maschinenbau and Südpack have developed an overall concept for the in-house production of stand-up pouches with spouts, which is designed for the packaging of paste and liquid products. The concept is aimed at food manufacturers and bottlers who previously use premade spout bags and will be presented at Anuga FoodTec 2024.
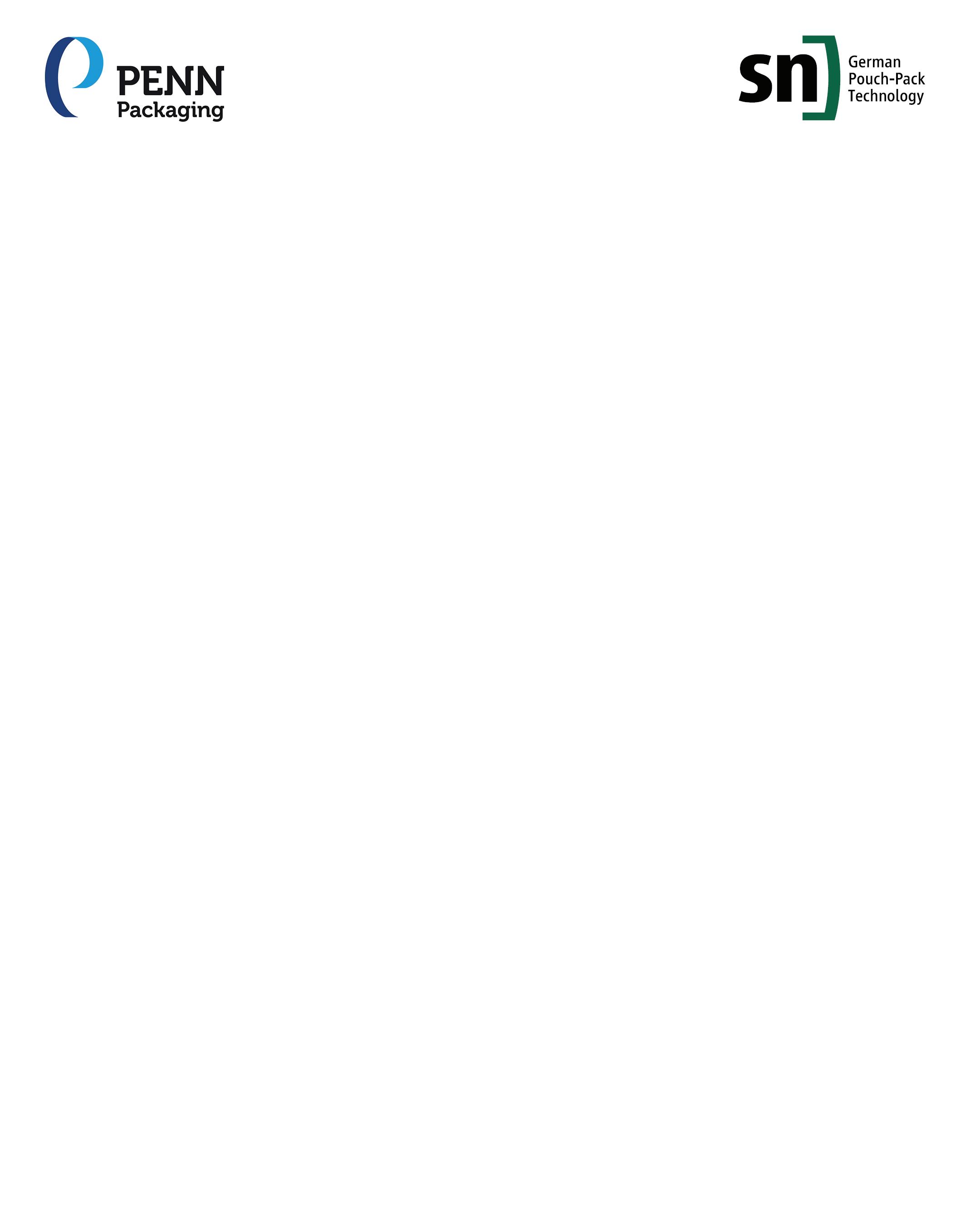
makes handling much easier and allows staff to process a larger number of pouches more efficiently, for example because there is no need for timeconsuming separation of the rails. The low-maintenance machine works highly efficiently and, thanks to its compact design, can also be used in production environments with limited available floorspace. This means it can be set up flexibly either directly on the filling machine
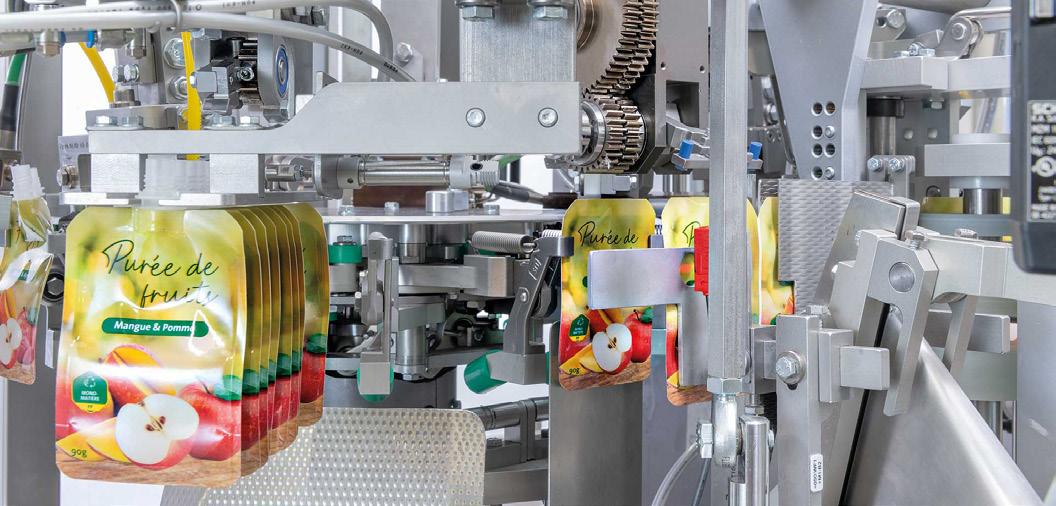
Ecofill AutoclavesRevolutionising Sustainability in the Food & Drink Industry
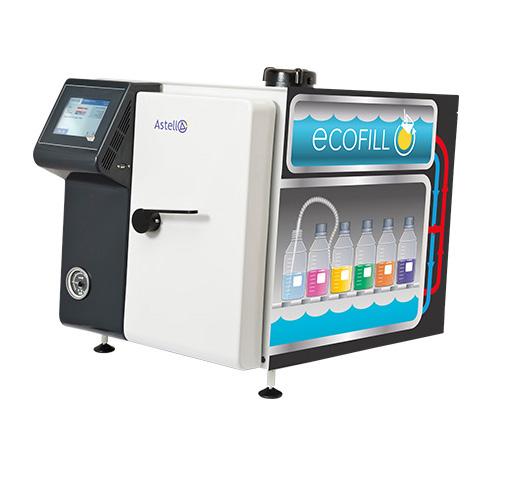
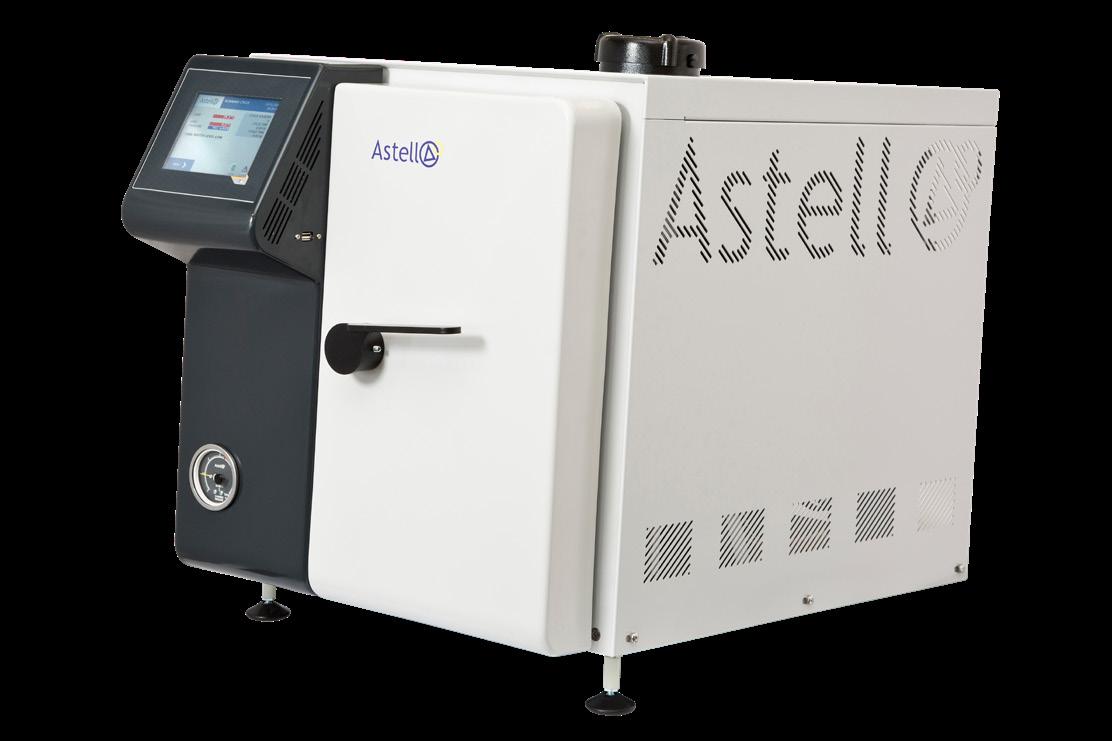
The food and drink industry, a critical component of the global economy, is increasingly focusing on sustainable practices to reduce environmental impact and operational costs.
A breakthrough in this endeavor is the integration of Ecofill technology with benchtop autoclaves, exemplified by the AMB benchtop autoclave with Ecofill. This innovation marks a significant step towards eco-friendly and cost-effective sterilisation processes in the industry.
THE ECOFILL ADVANTAGE
At the heart of this technological leap is the Ecofill system, a cutting-edge solution designed to capture and reuse water and heat energy. Traditional autoclaves require significant amounts of water and energy for sterilisation processes, often leading to high operational costs and environmental strain. The Ecofill system
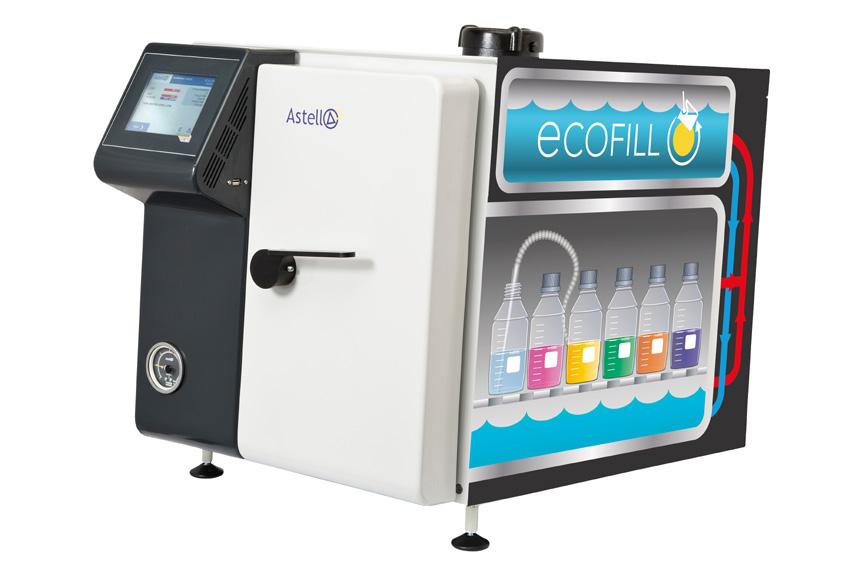
addresses these challenges by enabling the autoclave to recycle water and heat, drastically reducing waste and energy consumption.
ENHANCED EFFICIENCY WITH AMB BENCHTOP AUTOCLAVE
The AMB benchtop autoclave, when combined with the Ecofill system, becomes a powerhouse of efficiency and sustainability. This autoclave is engineered to require less frequent refilling, thanks to the Ecofill’s water recycling capabilities. This not only saves water but also reduces the labour and downtime associated with refilling the unit.
Moreover, the Ecofill technology’s heat recovery feature plays a crucial role in reducing electricity consumption. By capturing and reusing the heat generated during sterilsation cycles, the AMB benchtop autoclave with Ecofill requires less electrical energy to maintain operating temperatures. This translates to lower energy bills and a reduced carbon footprint, aligning with the industry’s growing commitment to environmental stewardship.
ECONOMIC AND ENVIRONMENTAL IMPACT
The economic benefits of using the AMB benchtop autoclave with Ecofill in the food and drink industry cannot be overstated. Reduced operational costs are a direct consequence of lower water and electricity usage. Businesses can expect a noticeable decrease in utility bills, contributing to improved profitability in an increasingly competitive market.
From an environmental perspective, the reduced consumption of water and electricity signifies a substantial decrease in the industry’s ecological footprint. By embracing this technology, businesses in the food and drink sector can actively contribute to global efforts in combating climate change and promoting sustainable resource usage.
FUTURE OUTLOOK
The integration of Ecofill technology with autoclaves like the AMB benchtop model is more than just an innovation in sterilisation - it’s a testament to the food and drink industry’s potential to lead in sustainability. As businesses continue to seek environmentally friendly and cost-effective solutions, technologies like Ecofill will play a pivotal role in shaping a more sustainable future.
In conclusion, the adoption of the AMB benchtop autoclave with Ecofill represents a significant stride in the food and drink industry’s journey towards sustainability. By capturing and reusing water and heat energy, this technology not only enhances operational efficiency but also exemplifies the industry’s commitment to environmental responsibility and economic viability. As this technology gains wider adoption, it sets a precedent for other industries to follow, marking a new era of eco-conscious industrial practices.
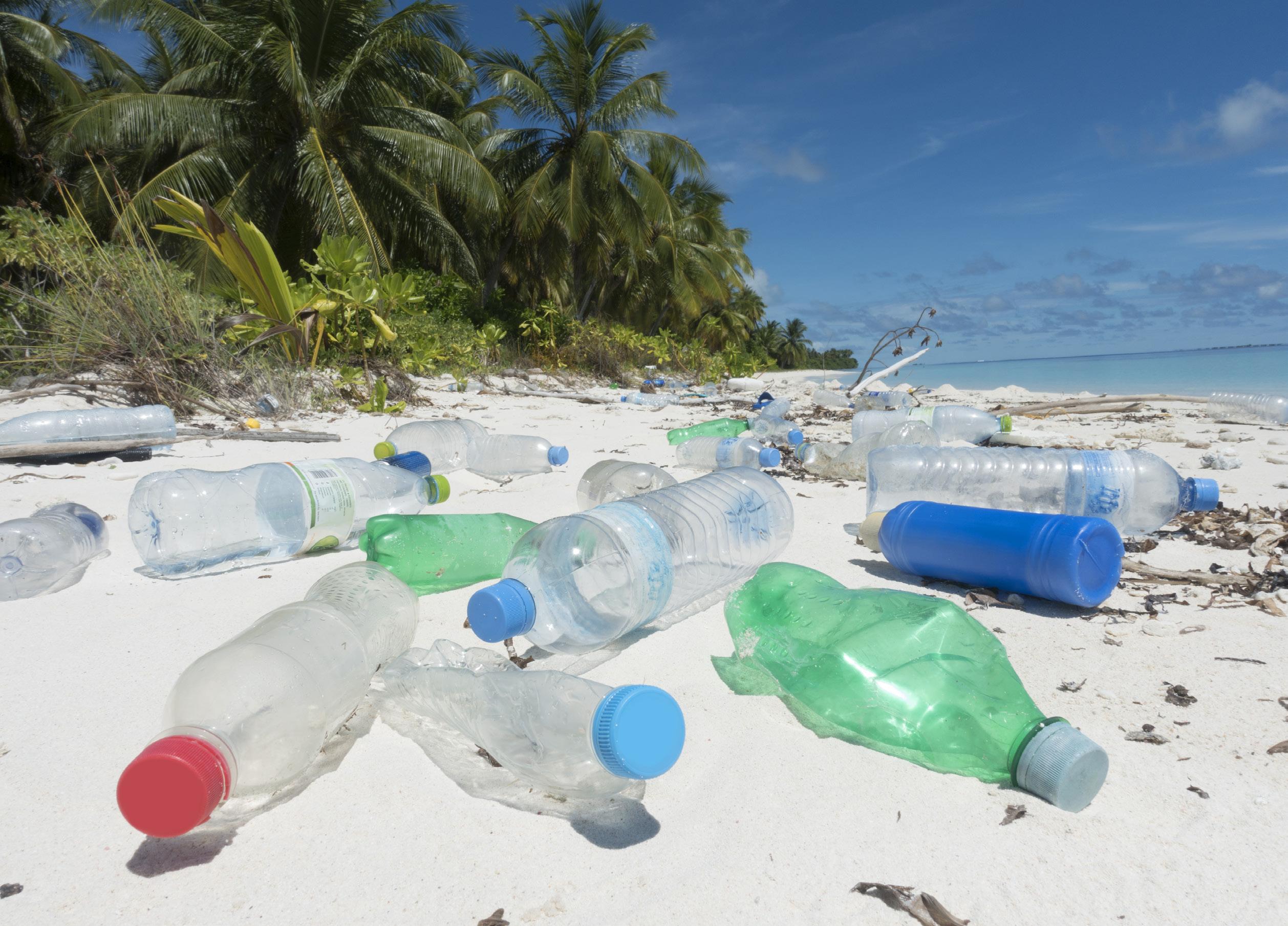
Meeting the Challenge of Sustainability in Plastics
Plastic pollution has become one of the greatest challenges facing our planet. Min Zhu, PhD, Senior Director, Technical Services and Operations, US & Canada Softlines at SGS, explores the issues and asks what are the drivers for change and what solutions are available to businesses who are committed to plastics reduction and sustainability?
The issue with plastics
In 2022, the Organization for Economic Co-operation and Development (OECD) published ‘Global Plastics Outlook: Policy Scenarios to 2060.’ They predicted that by 2060, global plastic use would triple from 2019 levels. In turn, this could potentially also triple the levels of plastic waste, although improvements in waste management and recycling could mitigate this down to just double.
The publication also predicted plastic leakage into the environment would double to 44 million tonnes (Mt) a year. Stocks of accumulated plastics in our rivers and oceans would more than triple, from 140 Mt in 2019 to 493 Mt in 2060. At the same time, greenhouse gas emissions (GHG) from the plastics life cycle are expected to more than double.
On the positive side, recycled plastic use is predicted to double, but this would still only account for 12% of the total plastics being used in 2060.
As the publication put it, a “business-as-usual outlook is unsustainable.” 1
Plastic waste is a problem because, once it enters the environment, it obstructs food chains and causes devastation to the natural environment. Toxins within the plastics will also concentrate as they move up the food chain, causing a variety of health concerns in humans, including neurotoxicity, dermal irritation and organ inflammation.
It is clear to consumers, governments and industry that we must now aggressively respond to the issue of plastic use and pollution.
Drivers for change
In addition to the indisputable impact our use of plastics is having on the planet, there are a number of other drivers now impacting industry to make positive changes. Firstly, governments and regulators are introducing stricter rules to address plastic pollution – UN Plastic Treaty (2022), EU Green Deal’s plastic tax, US EPA National Strategy on Plastic Pollution (currently being drafted), and EU restrictions on microplastics introduced under REACH.
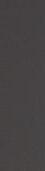
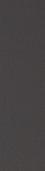
Secondly, many governments are moving to closed-loop systems for their economies. These circular economies incorporate recycling and upcycling strategies within the life cycle of a product, replacing the linear model of manufacture, use and discard. Instead, products are designed for reuse and recycling, reducing our reliance on virgin plastic.
Thirdly, institutional investors and shareholders are beginning to focus on environmental performance. Areas they will consider when making investment decisions include the use of renewable plastics, recycling, waste management and the use of non-petrochemicals and bio-based raw materials.
Finally, consumers are actively looking for products that can demonstrate sustainability. An increase in consumer understanding and demand means there is the potential for market growth for companies committed to sustainability.
The demands of the environment, governments, investors and consumers indicate change is on its way. At the same time, technological innovation is providing us with tools for making positive changes, such as advances in materials science, recycling technologies and biodegradable alternatives and the incorporation of new waste management and circular economy systems to simplify the process of becoming more sustainable.
Industry responds
SGS recently conducted a survey that involved global businesses in all consumer product sectors, from automotive to furniture. This survey found that 90% of businesses currently use plastics in their products and packaging. However, 87% were seeking to make their products and packaging more sustainable, with 52% looking for improvements in recyclability, 52% looking for alternatives to plastics and 89% actively working to reduce plastic packaging and transition to more sustainable alternatives.
When looking at the barriers to change, the survey found the primary challenge was cost (26%), followed by sourcing sustainable materials (21%), lack of knowledge (18%) and issues with regulatory compliance (17%). To achieve their sustainability goals, these companies felt they needed technical assistance and guidance, help sourcing sustainable material suppliers, and access to research and industry insights.
Four pillars
Consumer products manufacturers and suppliers must respond in four areas – four pillars.
1. Reduction and prevention – remove macro- and microplastics from the environment, reduce their presence in the environment and prevent leakage into the environment
2. Plastic packaging – assessment of recyclability, comparable property evaluation of alternative materials, verification of recycled content and assistance with material selection and/or redesign
3. Recycled and recycling – focus on the three primary methods for recycling:
• Mechanical recycling – verification of recycled content through testing and chain of custody
• Chemical recycling – recycled polymer quality and compliance testing and verification of recycled content
• Enzymatic recycling – intermediates and final recycled polymer quality and compliance assessment and verification
4. Process/product certification – build trust in products and processes with verification against a wide range of internationally recognized certification schemes, including:
• SGS Green Marks – covering environmental attributes such as industrial compostability, biodegradability, bio based, hazardous substances presence, recycled content and PVC-free content
• International Sustainability & Carbon Certification (ISCC) Plus certification
• Global Recycled Standard/Recycled Claim Standard (GRS RCS) certifications
• EU Ocean Cleaning Standard (OCS) certification
This four-pillar approach provides guidance for industry actions and helps businesses meet their commitments to reducing plastic use, especially in relation to disposable plastic packaging. It will also support businesses in achieving their long-term sustainability goals, help build consumers’ trust in their products and processes and enable competitive advantage in increasingly complex markets.
SGS solution
SGS’s comprehensive range of services, built around the four pillars, supports forward-thinking businesses as they address environmental concerns. Alongside testing and certification solutions, we also provide consultancy services for eco-design, material selection and recycling and waste management strategies, helping organizations to achieve a closed-loop system with less reliance on virgin plastics.
With SGS Green Marks, businesses can demonstrate the sustainability of their products in a way that is trusted and verified, and which overcomes the perils of a consumer base that is increasingly cognizant of the threat of greenwashing. Certification is only achieved following an independent, scientific assessment of the product against internationally recognized standards for a range of environmental attributes.
References 1 Global Plastics Outlook : Policy Scenarios to 2060 | OECD iLibrary
To find out more about SGS Green Marks https://www.sgs.com/en/services/sgs-green-marks
Magnavale Easton Development, set to support food security in Lincolnshire, approaches finish line

Magnavale is pleased to announce that its highly anticipated Easton-based temperature-controlled storage facility is approaching the finish line and is set to open in Q3 2024. This advanced development represents a significant step forward in supporting food production and strengthening food security in the Lincolnshire region.
In recent weeks, the facility, based just South of Grantham, Lincolnshire, has witnessed remarkable progress, with the installation of crucial components such as refrigeration pipework, cladding, roofing, and the refrigeration plant. These milestones bring the facility closer to becoming a cutting-edge solution for sustainable and efficient cold storage.
Amanda Cogan, Magnavale’s Chief Operating Officer, commented:
“We recognise the critical role that our automated temperature-controlled facility will play in supporting food production in Lincolnshire, minimising food waste and ensuring product safety. Easton has been designed with the cold chain in mind. With the integration of cold chain solutions, such as contract packing, the facility will allow partners to cut out unnecessary steps in their cold chain, reducing transport costs and reducing carbon emissions.”
The Easton development underscores Magnavale’s commitment to sustainability and environmental responsibility. Powered by renewable energy sources, the facility aims to reduce its carbon footprint while incorporating advanced automation technologies to minimise unnecessary transportation and associated costs.
Working with some of the best equipment suppliers in the industry, the facility has been designed to prevent disruptions during peak operational periods like the Christmas season, with multiple pallet ingress and egress points to avoid bottlenecks as well as built-in redundancy planning with no single point of failure.
Moreover, product safety is a paramount concern at Magnavale Easton. With planned systems such as oxygen reduction in place, the risk of fires is almost eliminated, ensuring that stored products remain protected from fire and the water damage associated with traditional sprinkler systems. This innovative approach to safety further solidifies Magnavale’s commitment to preserving the integrity of its partners’ stock.
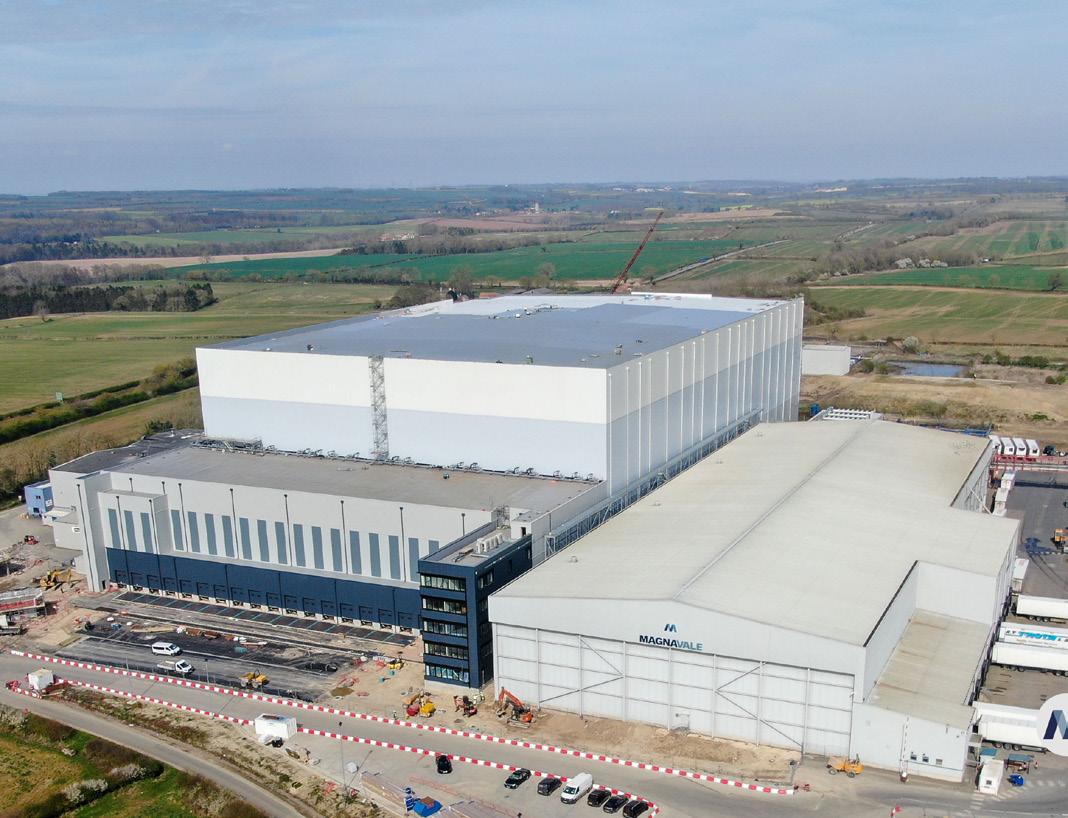
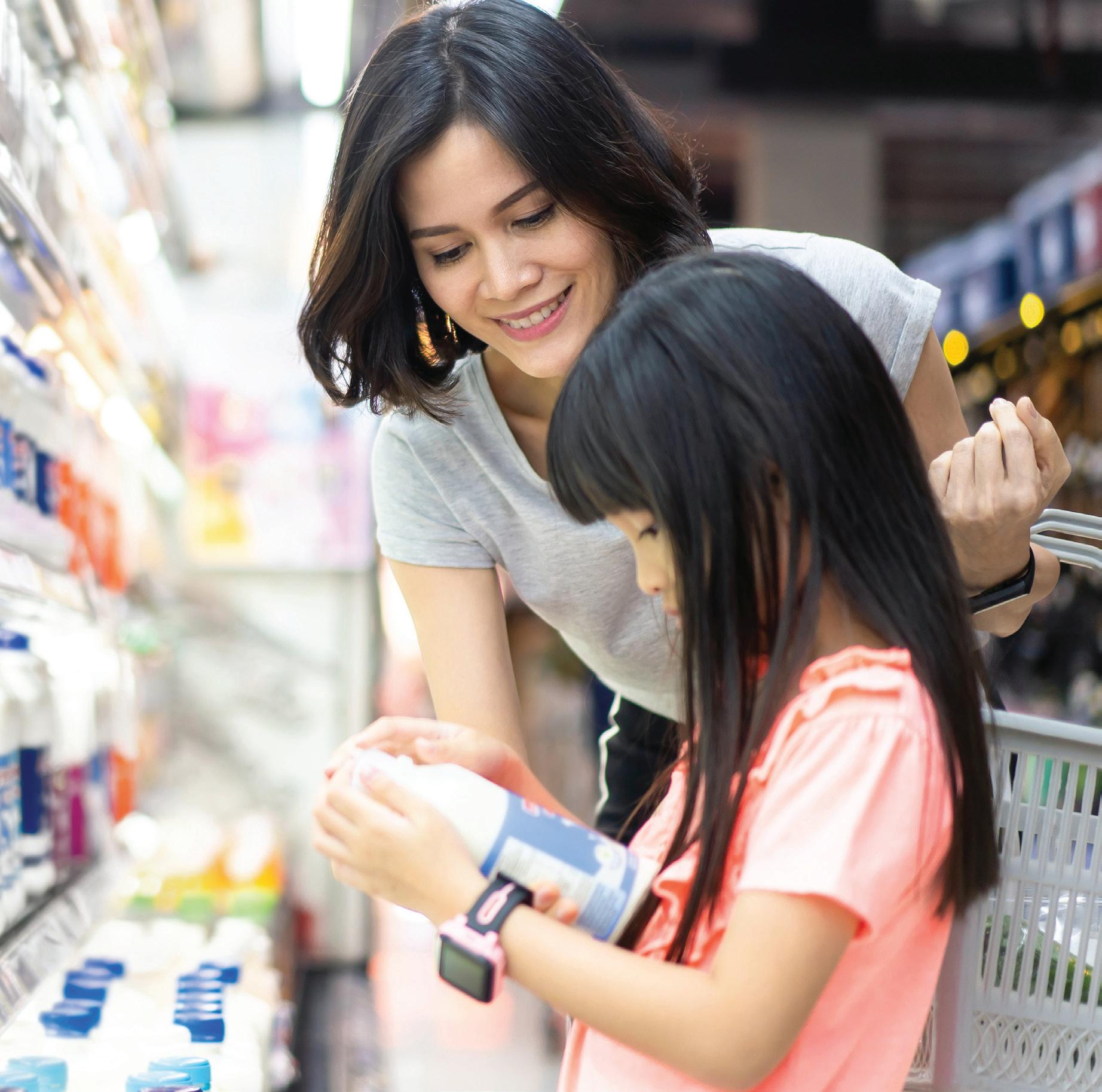

The 2D code revolution is here. Are you ready?

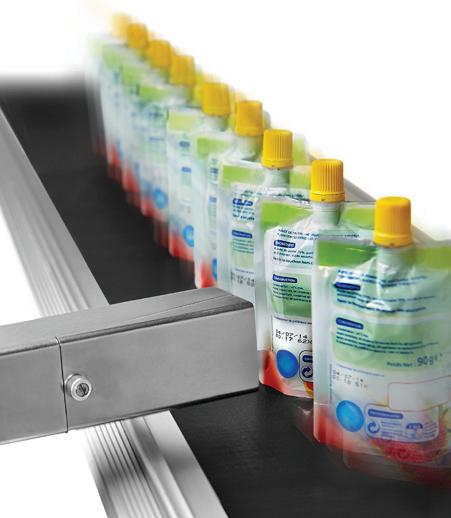
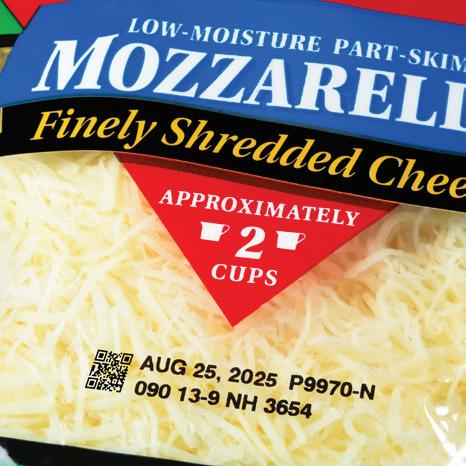
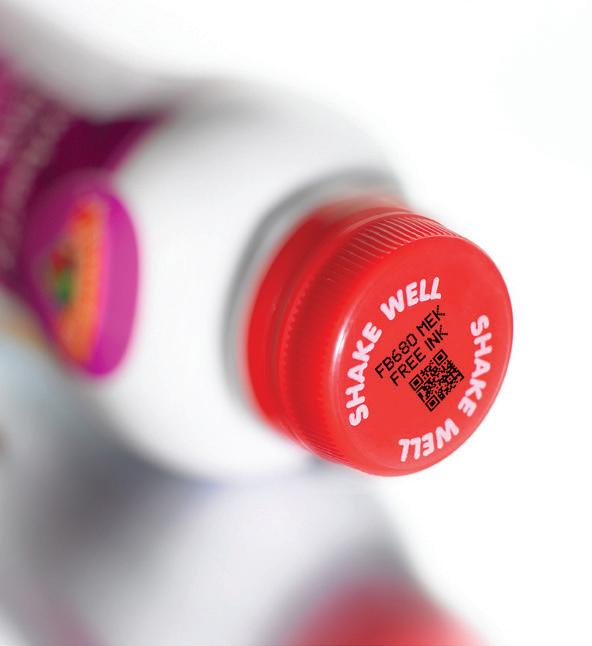
Markem-Imaje is the leading provider in marking and coding dynamic QR and 2D codes, producing durable codes at high-speed on any surface. By connecting your brand from factory to your consumer, we protect your brand.
www.markem-imaje.com
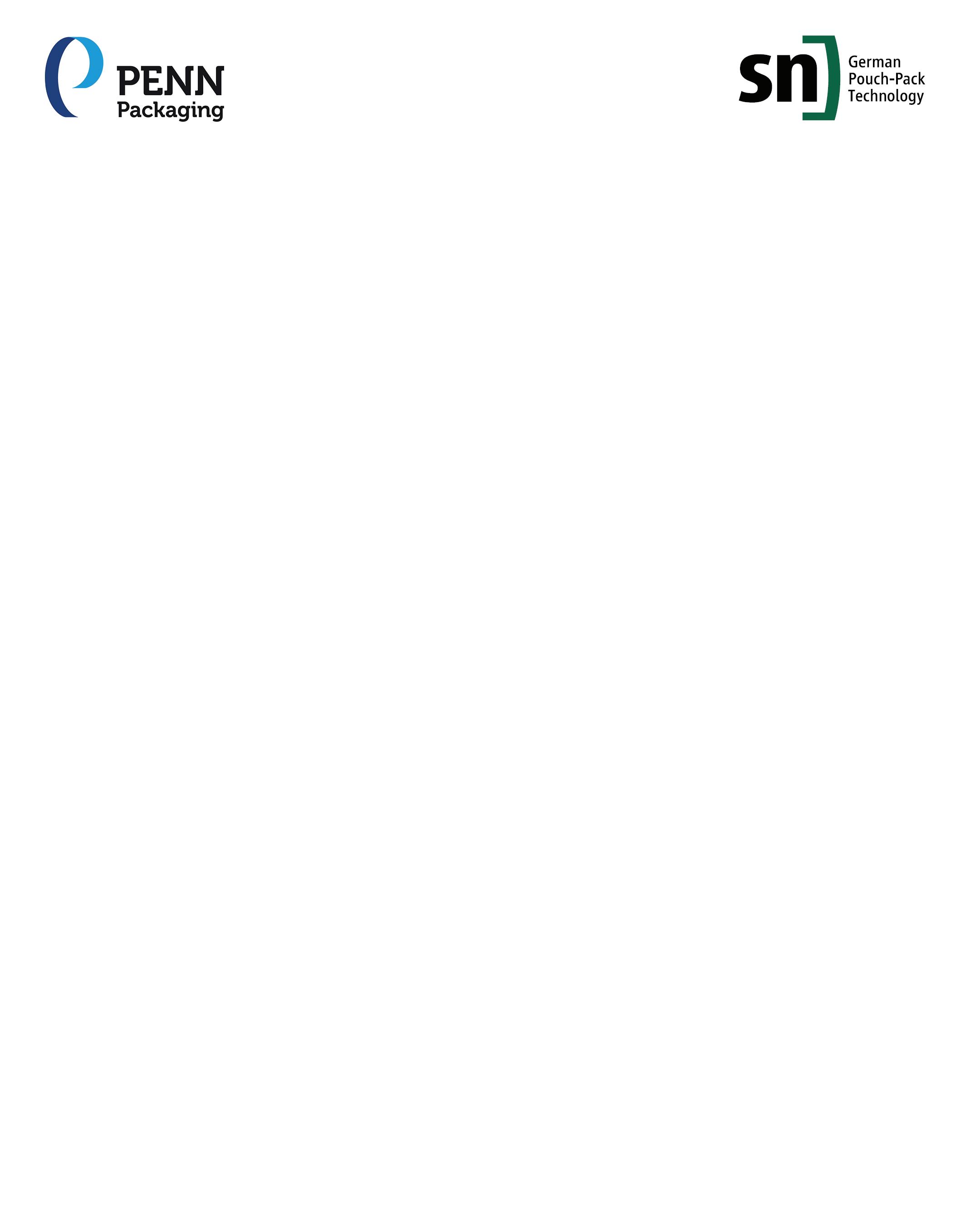
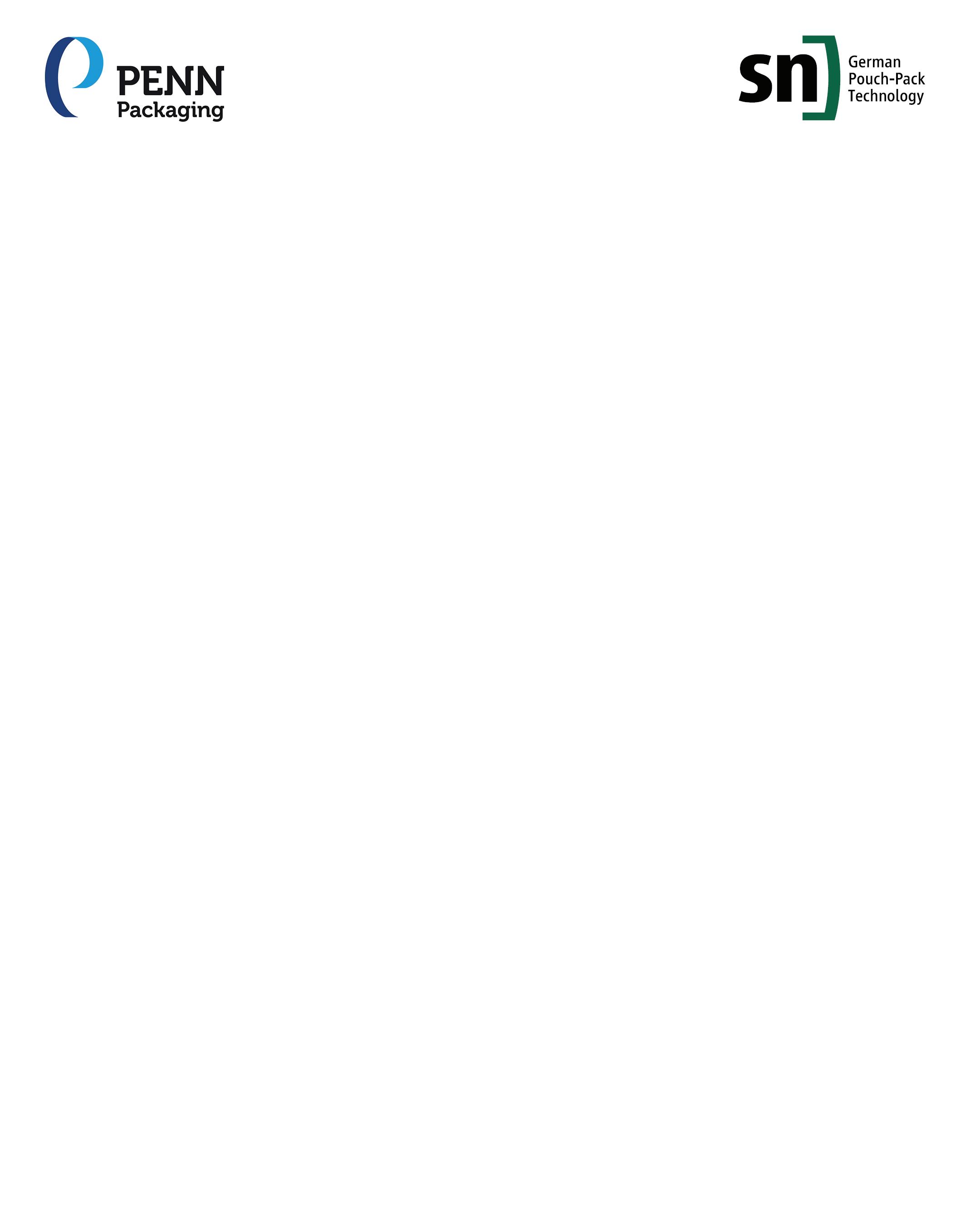
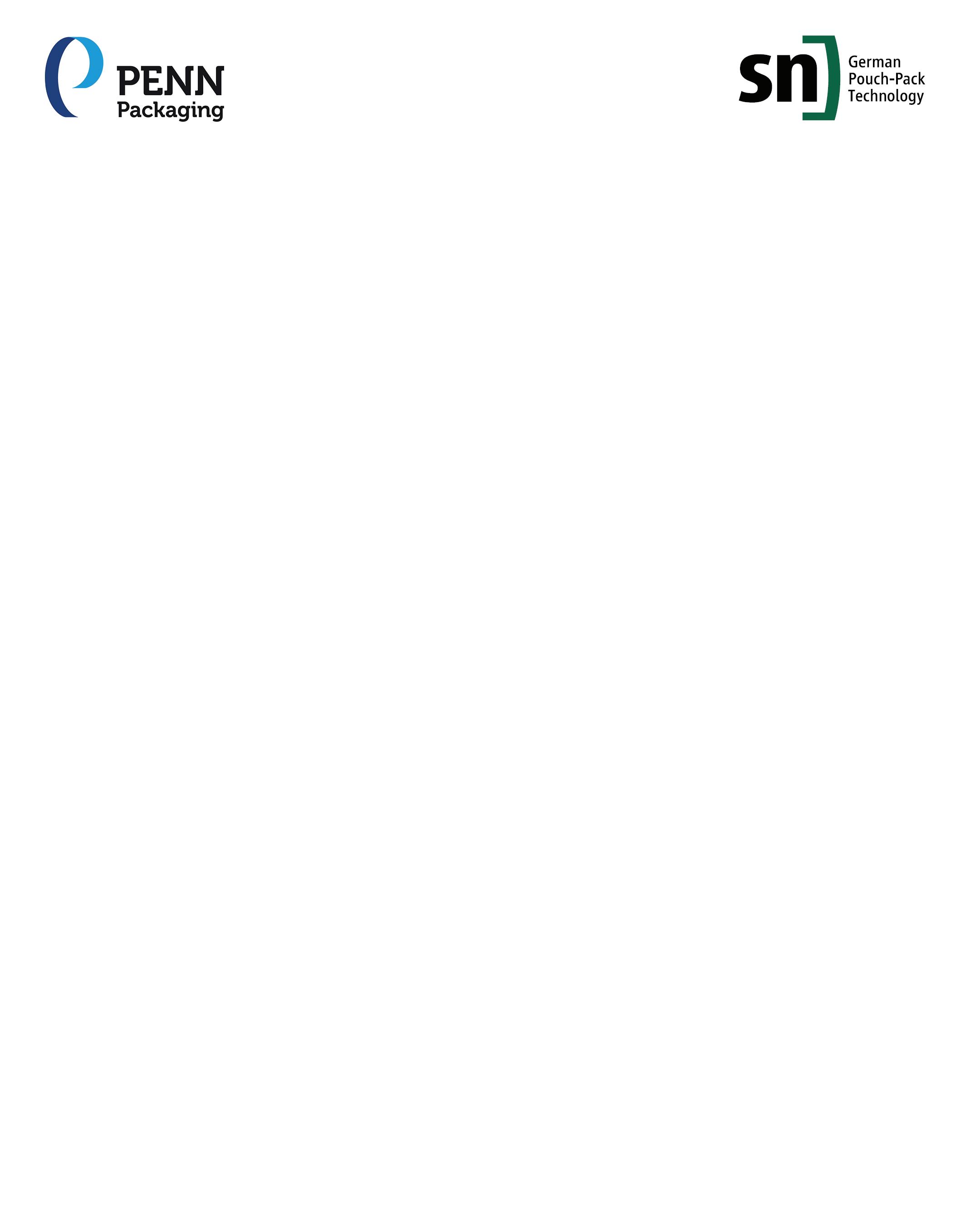
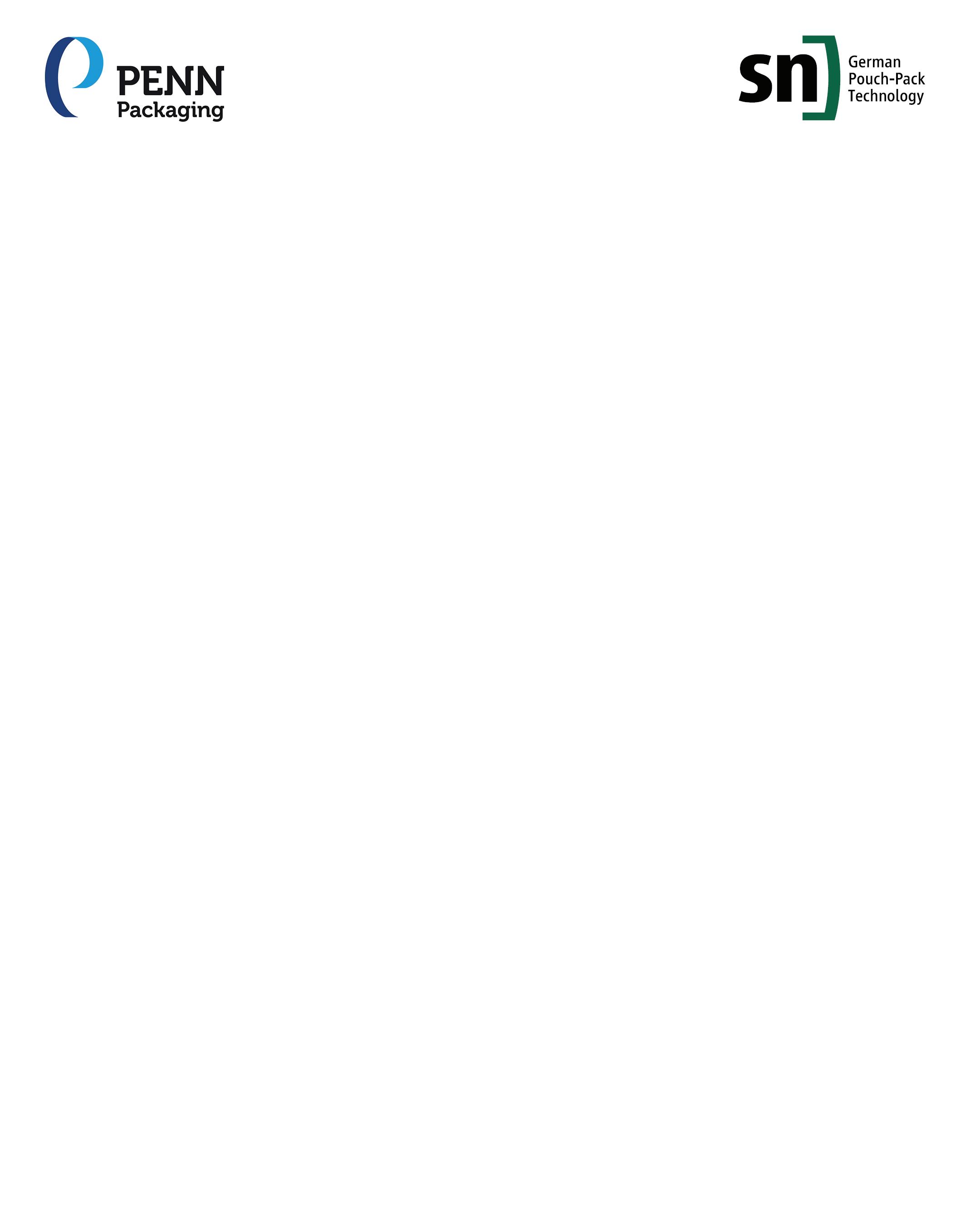
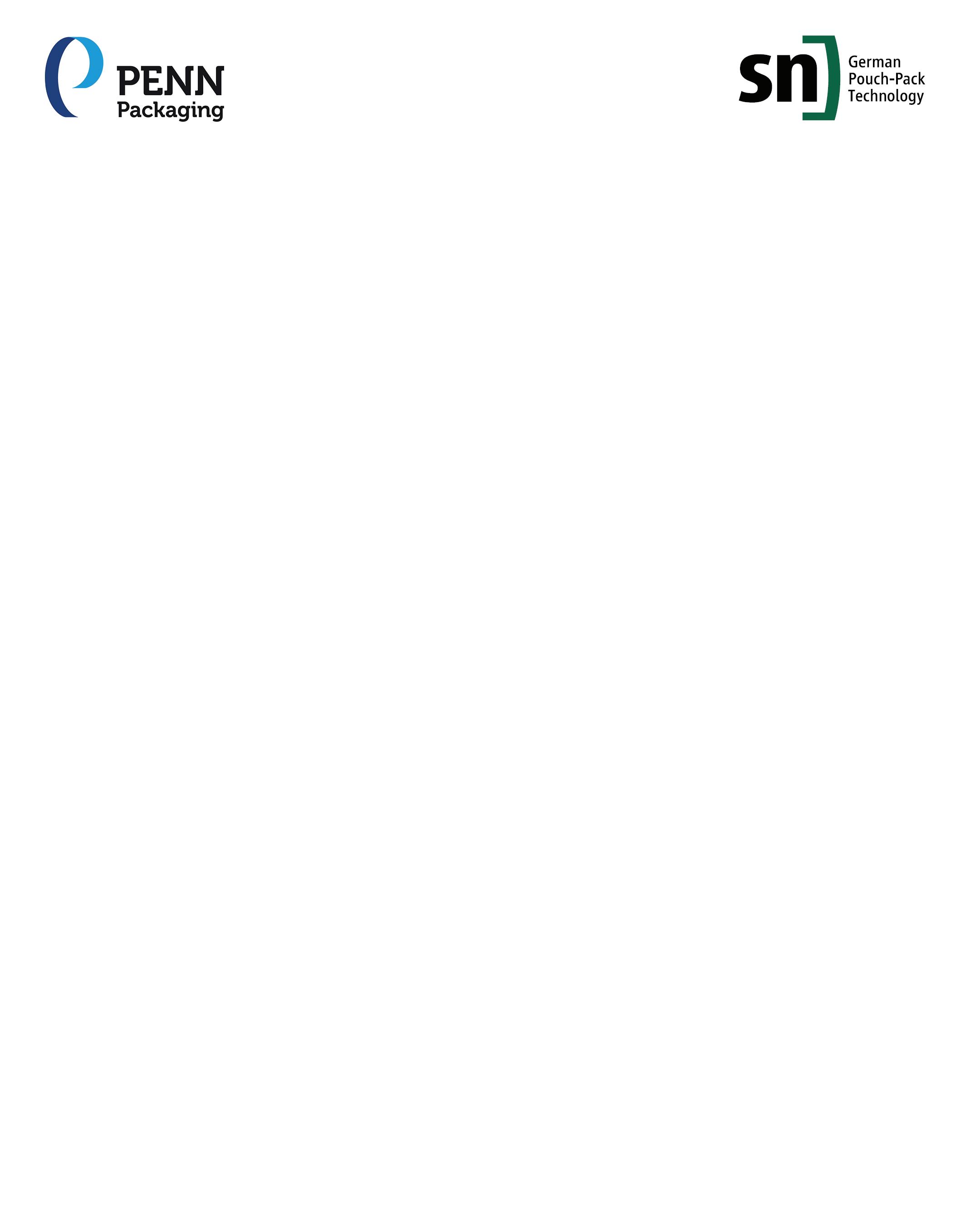
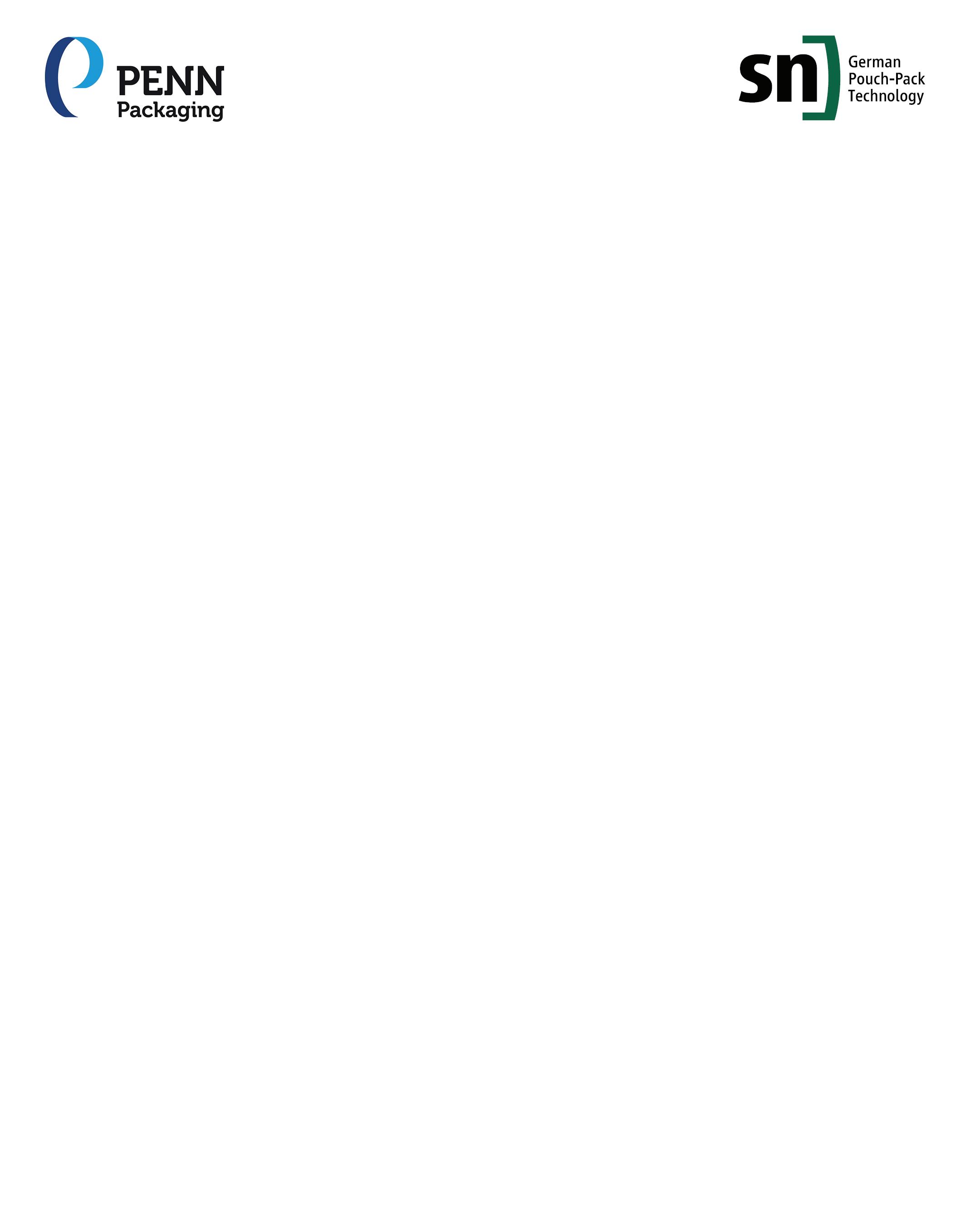