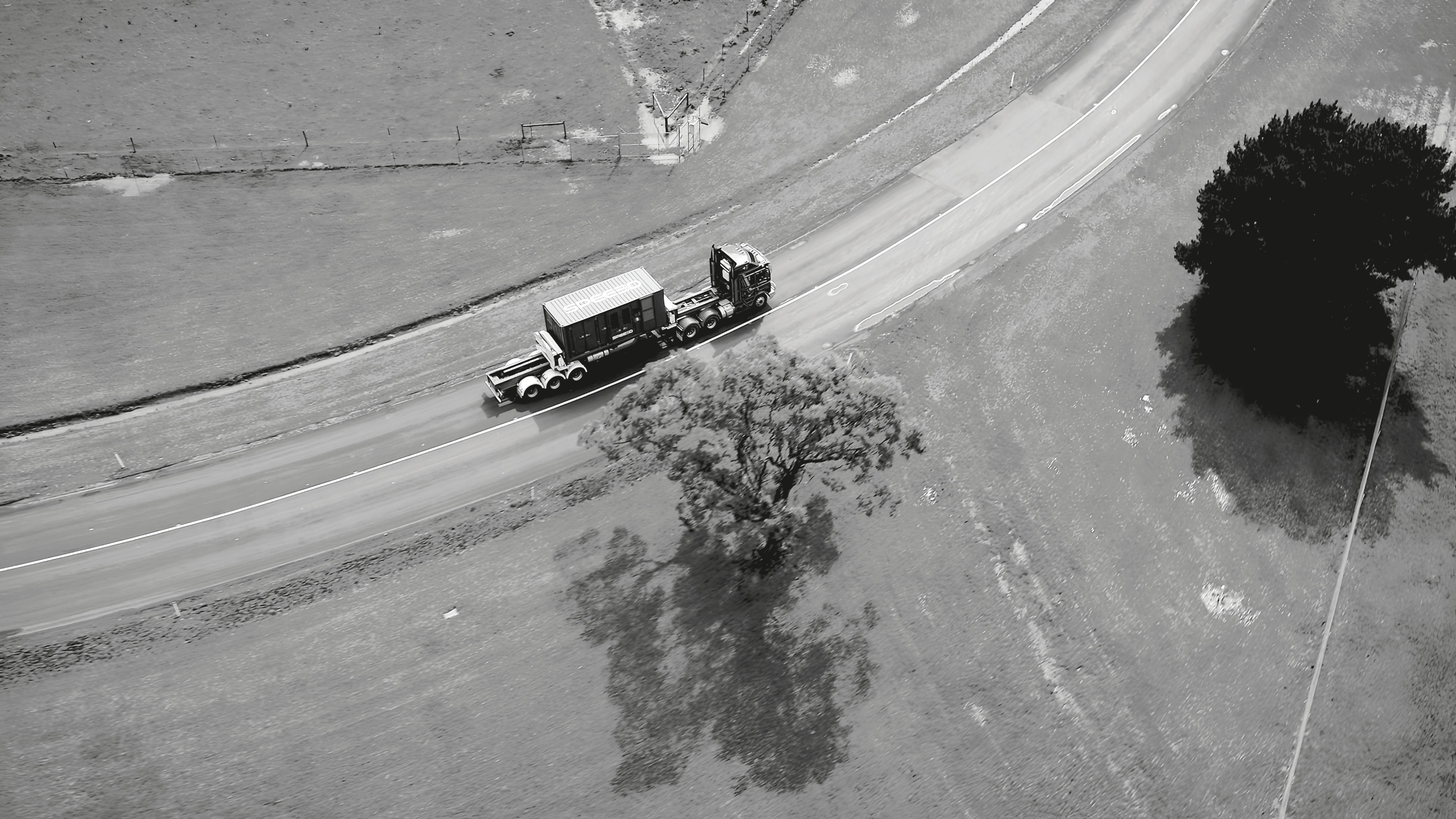
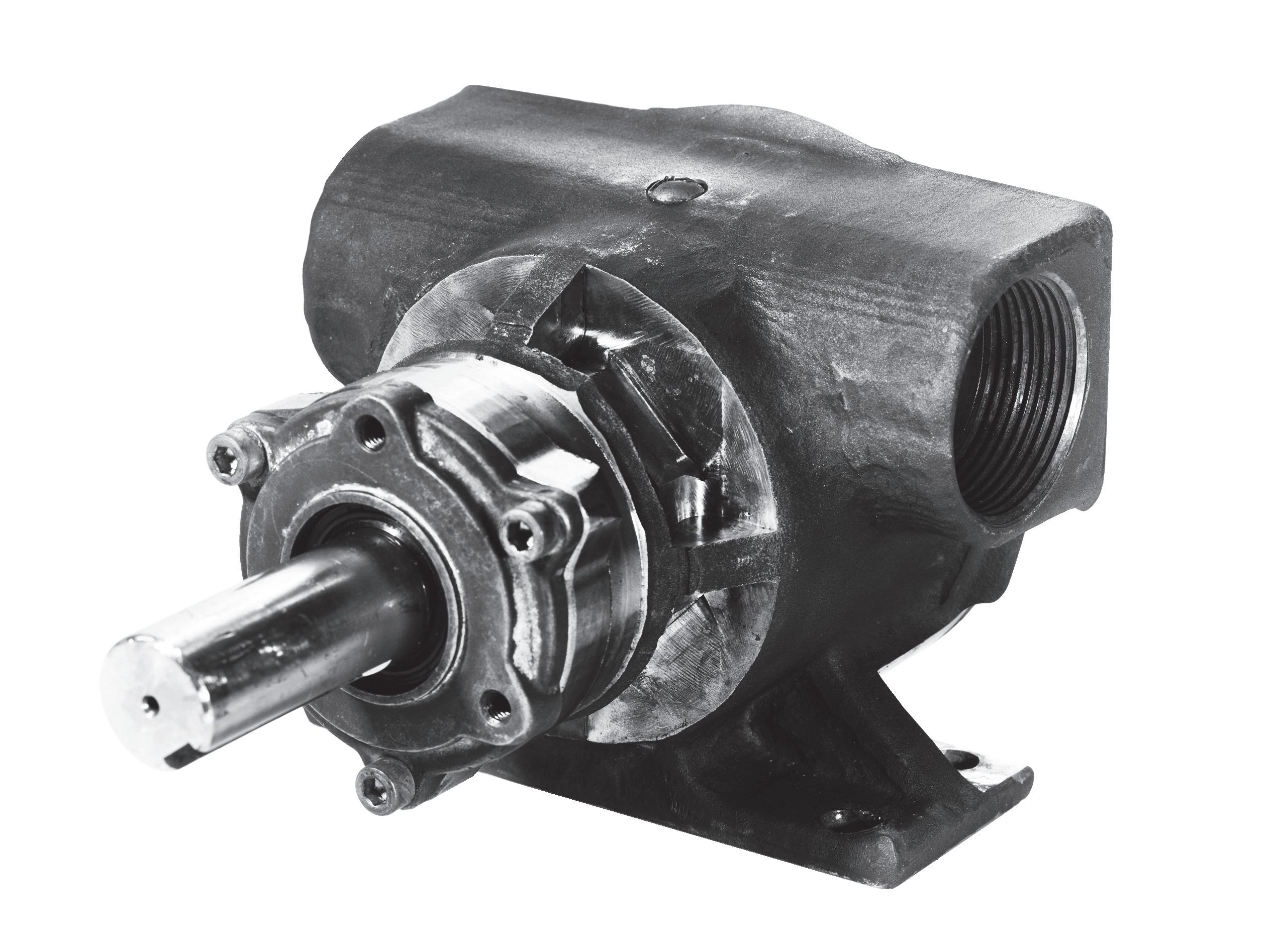
Your search for a 3D printer capable of producing complex & creative models in up to 10,00 0,00 0 colours is over . T he new Mimaki 3DUJ-22 07 delivers extraordina r y detail in full colour.
E xplore a wor ld of colour for just
£ 3 4,995
EDITORIAL
HEAD OF CONTENT
JUNIOR CONTENT PRODUCER
Oliver Johnson oliver.johnson@rapidnews.com
ADVERTISING
HEAD OF SALES TCT PORTFOLIO
Carol
PRODUCTION
Sam Hamlyn Matt Clarke Robert Wood
MANAGEMENT
C.E.O. / PUBLISHER
Duncan Wood
ISSN 1751-0333
SUBSCRIPTIONS
PUBLISHED PRICES
TCT North America Print Subscription - Qualifying Criteria
US/Canada - FREE
UK & Europe - $249 ROW - $249
TCT Europe Print Subscription - Qualifying Criteria
UK & Europe - FREE
US/Canada - £249 ROW - £249
Subscription enquiries to subscriptions@rapidnews.com
Read this and back issues for FREE on Issuuwww.issuu.com/tctmagazine
The TCT Magazine is published bi-monthly by Rapid News Publications Ltd No. 3 Office Village, Chester Business Park, Chester, CH4 9QP.
t: 011 + 44 1244 680222 f: 011 + 44 1244 671074
© 2023 Rapid News Publications Ltd
While every attempt has been made to ensure that the information contained within this publication is accurate, the publisher accepts no liability for information published in error, or for views expressed. All rights for The TCT Magazine are reserved. Reproduction in whole or in part without prior written permission from the publisher is strictly prohibited.
I can't think of many scenarios that would bring together additive manufacturing (AM) users from major companies like Stryker, GKN Aerospace, Alpine F1 and Thales for a frank, open dialogue about the state of the industry – but that’s exactly what we got at this year’s inaugural TCT UK User Group day.
Calls for a UK-based user group have been sounded for a while but this year, weeks before our 2023 TCT 3Sixty event in Birmingham, we decided to heed them and invite a select group of UK-based end-users to spend a day together at the NEC and hash out the industry’s key challenges – because what’s one more event when you’re on the last stretch of the run up to your flagship trade show?
The day homed in on three areas: AM repeatability, economics, and enterprise-wide adoption; the conversation that flowed was refreshing, enlightening, and at times, challenging.
Raised hands popped up from tables to flag the chicken and egg situation that AM finds itself in – we want repeatability to get to high volumes, but we need high volumes to prove out repeatability – and asked if, in a bid to turn AM into a reputable production method, we hold the technology to too high a standard compared to established processes. As one vocal participant shared – if you were to visit a traditional casting house and saw how the sausage is made, you might never get on a plane again …
Yet one theme that continued to crop up no matter the subject was the need for more open communication and sharing of knowledge, as you’ll read from another proactive attendee in our expert column on page 38. No one expects a global aerospace firm, for example, to give away its AM secret sauce, but there is much to be gained by sharing not only our success stories but how they came to be, and similarly, how our failures taught us to grow.
There are themes from the User Group peppered throughout this issue: in a visit to the Natural History Museum which calls for greater collaboration to further conservation and science (P. 32); in the column from a UK technology provider which looks at how AM can bridge the UK’s oil & gas skills gap (P. 29); and in the column from experts at the Manufacturing Technology Centre which looks at a global challenge through a UK-3D printing lens (P. 13).
I must say a huge thank you to our UK-based TCT Advisory Board members who helped steer the direction of the day and kickstart those necessary conversations. This is just the beginning and I feel energized, as I hope those in the room did, to build on this in the years to come and create an active platform for UK AM users. Because you know what? As anyone in that room could concur - we’re actually really good at it.
An open material system means users are not restricted by the usual parameter constraints, this offers the ability to utilize any 355 nm hybrid resin chemistry
engineered throughout using state-of-the-art technology, proven components and aesthetic
The Neo produces highly accurate parts with unparalleled industry quality Optimising the machine design and utilising the latest cuttingedge technology available for laser and scanners, our beam delivery system produces exceptional layer-to-layer alignment repeatability The printed parts are dimensionally accurate, with exceptional sidewalls and crisp feature resolution.
08. NEED FOR SPEED
Metal 3D printing firm SPEE3D discusses AM for production, manufacturing in the field, and sustainability.
11. RENEW AND REUSE
On the back of a visit to 6K Additive in Pittsburgh, Sam Davies explores the company’s sustainability efforts.
13. SUSTAINABILITY AND AM
Additive manufacturing experts from the Manufacturing Technology Centre in the UK discuss the sustainability credentials of AM.
16. GREEN GAME CHANGERS
Laura talks to Siemens Digital Industries’ Eryn Devola about digital transformation, sustainability as a business metric, and more.
19. INFINITY ON HIGH
Oli Johnson takes a look at IperionX’s ‘infinitely recyclable’ titanium offering.
21. DOES IT HAVE TO BE METAL? A look at the proliferation of highperformance polymers for end-use parts.
25. MAKING THE FUTURE
Sam speaks to Merit3D CEO Spencer Loveless about the company’s additive manufacture of one million epoxy hanger products.
27. NEW TERRITORIES
Seurat Technologies discusses the use of its Area Printing technology to produce 59 tons of Siemens Energy turbine parts.
29. 3 WAYS AM COULD DESKILL OIL AND GAS PRODUCTION
Dave Moore from UK reseller Tri-Tech details how AM can address the skills shortage in the energy space.
30. TAKE ME OUT TO THE BALL GAME
Wilson Sporting Goods and Nexa3D share how their collaboration is reducing cost and time in the development of baseball bats.
32. WELCOME TO JURASSIC PRINT
Laura reports back from a behind the scenes tour of the Natural History Museum.
35. HI, MY NAME IS…
Oli speaks to Evo3D about the launch of Rapid Fusion and receiving 1.1 million GBP in funding from Innovate UK.
38. I'LL SHARE MY BANK CARD & PIN BEFORE I SHARE AM DATA Rob Higham, CEO of Additive Manufacturing Solutions, shares his thoughts on data and IP.
When you last spoke with TCT, you remarked that ‘when you get into production, it's all about speed.’ What else makes for successful adoption of AM for production?
BYRON: Speed and cost are the obvious ones – but there’s also usability. Can you put the technology in a factory or out in the field and rely on it to produce strong, reliable parts without a team of experts operating it? When we launched the XSPEE3D, which comes in a 20-ft container and is made to be transported into the field, we called it expeditionary technology. I like that term, but I also think usability is a good word – our process doesn’t have restrictive safety constraints so it can sit almost anywhere. It also has software built in that enables the user to generate parts without going through iterations of prototyping. It’s built for production, not for the lab, and I think that makes a huge difference in adoption among our customers.
DAVID: Vision is key. This is where our defence partners have excelled and moved the adoption needle quickly and effectively. They focused on an objective and took the steps to get themselves there. Adoption happened relatively quickly as a result and the adoption base continues to expand. Defence hasn’t cut any corners – there’s been rigorous engineering and qualification along the way – but all of that happened to deliver a common vision.
Compare this to other industries where I think we sometimes forget to set a vision or objective or forget that we’ve set one. A lot of activity takes place, but that activity gets stuck in the technical weeds. Little progress is made and therefore adoption is stifled.
The company launched in 2017 and since then you’ve introduced multiple solutions to the market based on metal cold spray technology. How would you describe the journey so far?
BYRON: Like with most new technology, the path taken was not the one initially envisioned. Coming from a manufacturing background, Steven (Camilleri – co-founder) and I focused our development around that sector. Soon after the first version was released, we were approached by the Australian Army with the request to deploy. We jumped at that opportunity and have grown substantially from that point onwards. Next steps are into parallel sectors: mining, oil & gas, and heavy industries. The manufacturing sector is still our passion, though, and those applications are starting to evolve. Stay tuned…
SPEE3D’s technology has been widely adopted by customers in defence. Why do you think SPEE3D has had such interest from this sector?
DAVID: A combination of the pandemic and global insecurity (Ukraine for one) has caused defence, military, and government to think differently about supply. Commercial industry has had the same issues, but the potential impact has not been as severe for them to act with the pace and vigor defence has.
Why SPEE3D? Well, our technology simply meets the technical, commercial, and operational challenges being faced by defence – a need for larger metal parts of simple geometry on demand at the point of need from a financially viable and technically sound source.
You describe the recent XSPEE3D as “the next generation of deployable metal manufacturing.” Can you elaborate on that and your ambitions there?
BYRON: Our vision is bold – to have a printer less than two hours from anywhere. As you push the boundaries, SPEE3D will be there. As a soldier, miner, oil rig operator, manufacturer, or space explorer you need access to metal parts, now. To do this, you need technology that is robust, reliable, and above all, useful. XSPEE3D, a fully transportable solution, is enabling this vision to become a reality.
DAVID: SPEE3D’s ambitions are straightforward; to make manufacturing as easy as possible.
Listening to the market, they wanted a solution which could be moved anywhere and operated quickly by relatively inexperienced technicians. XSPEE3D is a fully containerised production cell that delivers precisely that capability.
We also know that for those clients of ours where operating tempo matters (e.g., defence, natural resources) having the production facility at the point of need adds value in an order of magnitude.
Could that deployable AM concept apply to other industries where on-demand manufacture is needed?
DAVID: Absolutely. We are talking in terms of technology and knowledge transfer here, not concept development.
Defence has shown that Cold Spray Additive Manufacturing (CSAM) and mobile CSAM can be an effective and safe component of an AM strategy.
The competitive edge mobile CSAM offers industry is significant; lower costs, higher productivity, less downtime, release of capital, decarbonisation, etc. We see greatest utility in industries like energy and mining where the cost of production outage is high, where capital is tied up in physical spare parts most of which are never used, and where carbon emissions and environmental impact is hard to abate.
This issue of TCT is all about sustainability. What are your general thoughts on AM’s sustainability claims?
“SPEE3D technology less than two hours from anywhere.”SHOWN: SPEE3D'S ROCKET NOZZLE & SIX-AXLE ROBOTIC ARM
BYRON: Before SPEE3D, AM still relied on centralised manufacturing, followed by distribution. By manufacturing only what you need at the point of need, you not only minimise waste inherently, but you eliminate shipping and storage, which translates into a significant reduction in the carbon footprint –not to mention freed-up capital to reinvest in your operations.
DAVID: Generally speaking, AM offers manufacturing a great way to decarbonise. The most sustainable part is one you never make; AM’s ability to produce within a digital warehouse system rather than traditionally physically warehouse parts is the most obvious example of this.
On that, what would you say is unique about SPEE3D’s technology in terms of offering a sustainable manufacturing process?
DAVID: We are learning more every day but SPEE3D has two clear differentiators:
Point of Need: around 17% of CO2 emissions of any part is associated with shipping. By manufacturing at or close to the point of need you can eliminate a huge footprint here.
Low energy/CO2 process: An internal study demonstrated CSAM emits 60% less CO2 and consumes 33% less energy than the equivalent part made in casting.
Generally, SPEE3D is more sustainable from being a “cold” process. Any process which requires heat, lasers, etc. will involve high energy. CSAM relies on kinetic energy, so it’s a bit like keeping the heating in your house down or putting on a cooler wash. Eliminate the temperature/heating issue and you’re instantly being more sustainable.
Are you undertaking sustainability initiatives in-house?
BYRON: As an Australian business, we see the effects of climate change in extreme weather like seasonal bushfires and flooding; our colleagues in Europe and the US are experiencing similar issues and we are committed to do our part. We’re in the process of measuring and benchmarking current processes, and then following this, we will do a review and subsequent implementation of key opportunities.
We have implemented some early initiatives, such as the eradication of single use materials in our product packaging. Items such as polystyrene are banned, and we will be using recycled/reclaimed
materials that can be further broken down and recycled/reused again. A SPEE3D ESG team has been formed to compile more initiatives where we will measure and promote our success, and as we grow, I expect this will accelerate.
We have also joined the AMGTA (Additive Manufacturing Green Trade Association) to ensure we play a leading part in how our technology can be a sustainable and environmentally responsible solution.
You’ve previously described your vision to take AM to production. In your view, what’s been the most limiting factor standing in the way of that so far?
DAVID: An absence of vision and an obsession to overcomplicate technical processes. Done correctly, vision dictates what technical steps need to take place. Right now, technical processes hold vision for AM hostage. Until this model is broken, AM will sit in the R&D department. This is dangerous because when the economy is squeezed, it will be the R&D budget that gets cut. If we are serious about AM, it’s time to get serious about vision-led adoption strategies. This is what I spend a significant amount of time speaking to industry about.
This is not the same as saying we should skip steps or compromise quality, quite the opposite in fact.
What do you see as the biggest misconception about additive manufacturing technology today?
DAVID: That it is not ready for industrial adoption. SPEE3D’s automated approach means process and quality control is attainable. The pace of the system means throughput can be achieved in volumes viable for industry; and not just for prototyping/premanufacturing.
Most recently we’ve seen SPEE3D’s expansion into the European market. What’s next?
BYRON: SPEE3D technology less than two hours from anywhere!
Treating customers as its suppliers, 6K offers buyback agreements as part of its long-term supply contracts that means, as long as the user has good traceability on their parts, 6K will take back their scrap and offer, for example, 15% off their next order. There are also strategic relationships in place with some of the US’s largest processing facilities to upcycle material from failed builds, support structures, condensate, and out of spec or used powders to turn them into powder or ingot.
Aplume of microwave-based plasma is engaged. Powder particulates previously loaded into hoppers are injected from two points. And the particles flow into the heat zone, melting quickly before the surface tension of the molten metal causes it to form a perfect sphere.
“Microwave-based plasma – that’s basically the secret sauce,” says 6K Additive President Frank Roberts. “With the UniMelt [process], you’re using microwaves as your energy source. Energy is passing through a waveguide, and they’ll intersect a torch stack. In the torch stack, that’s where we’re applying gas. The result is, instead of having your electric field be concentrated on the OD (optical density), the electric field gets dispersed pretty evenly through the core of your plasma.”
After TCT visited 6K Additive’s facilities in Pittsburgh earlier this year, there will be a deeper dive into the company’s UniMelt process – the central piece in a process that is delivering high-quality metal powders to additive manufacturing (AM) users – in a later issue of the magazine. But here, the focus is on how 6K Additive is ensuring its method of material manufacture is as sustainable as it can be. Not just in the control of energy as it spheroidises its powders, but in the way it procures raw material at the front end and recycles it at the back end. For while quality is the top priority for 6K Additive, sustainability of its products is a close second. It has been since day dot.
To underscore the company’s sustainability claims, 6K Additive commissioned a third party – Foresight Management – to conduct lifecycle assessments on its nickel and titanium powders. These powders currently represent around 95% of what flows through the company’s factories, and as
detailed in a TCT Magazine cover story last year, were shown to use much less energy and emit much less carbon than conventional techniques. With nickel, 6K Additive was using 6,265MJ of energy and produced 301kg C02-eq for every 100kg delivered – a 91% energy reduction and 92% carbon emissions reduction. Titanium, meanwhile, was using 56,268MJ of energy and produced 2,748kg C02-eq for every 100kg delivered – a 74% energy reduction and 78% carbon emissions reduction.
“This is twofold,” Roberts says of how 6K is able to deliver these numbers.
“It’s the efficiency of UniMelt, so how effective we’re able to put energy into that machine and generate plasma – it’s highly efficient from 99% coupling power into plasma creation – and then the other big mover is yield. You only put in what you want to get out. All that energy goes into prime product, not in waste. That’s what makes this meaningful data.”
6K Additive is keen to point out that, thanks to UniMelt, its yield tends to be much higher than the 25-50% yield delivered by conventional atomisation processes. That 6K can save so much material from going straight to landfill is a good start, but 6K is also incentivising its customers to recycle material once used, bringing the front and back end of its processes together to close the circle.
Before a decision is made on whether 6K uses the incoming metals for its powder business or its alloy business, it goes through a ‘complicated decision tree’ that considers quality, economics, and efficiency. Since powder is the company’s biggest value stream, 6K will hope to get most incoming scrap metal through that business, but the alloy side of the company will pick whatever isn’t feasible for the powder side.
“Let’s say you had nickel 718 solid, some sort of big ring out of a jet engine, it will never make sense to take something that large and turn it into turnings and then the turnings into powder,” Roberts explains. “The most efficient thing you can do with that is immediately take it to some wrought product or application. The goal is nothing that was on any one of these value streams leaves this site and goes to a landfill. We’re looking at ways of upcycling everything.”
As of this summer, that looks set to include materials previously used in hip, knee, and shoulder joint replacement surgeries in partnership with Surgical Metal Recycling.
“If you generate a used powder, chances are we will be able to rejuvenate it,” assesses Roberts. “You can really see true scrap-to-powder-to-part-to-scrap-to-powderto-part, and just continuing this infinite loop without the need for things like ore coming from Russia, [for example.]”
Reshoring the production of metal materials is also on the agenda at 6K Additive. Its Pittsburgh facilities currently boast four UniMelt bays, but the company is in the process of expanding that to ten. At the point at which those bays are operational and 6K Additive is manufacturing a wider range of materials at the volumes its producing nickel and titanium, expect more lifecycle assessments to follow, and more incentives for its customers to recycle their material.
Sam Davies reports on 6K Additive’s sustainability efforts after going through the doors at its Pittsburgh headquarters.
“We’re looking at ways of upcycling everything.”
1 2
One of the most impactful changes in 3D printing is to switch to renewable energy. At Materialise headquarters, we’ve maximized the number of solar panels and operate all our processes on green energy — drastically reducing our carbon footprint.
Create more transparency.
Today, there is insufficient transparency to make blanket statements about the sustainable nature of 3D printing. That’s why we are committed to creating more and more diverse life cycle analyses (LCAs).
3
Innovate and invest.
Materialise introduced Bluesint PA12, a rapid prototyping material that lets you print with 100% re-used powder. With Bluesint PA 12, powder that would typically be wasted can get a second life to make new parts.
Making 3D printing more sustainable will require building a shared commitment to make a difference.
With sustainability gaining traction, manufacturers are seeking innovative and eco-friendly solutions to reduce environmental impact. Additive Manufacturing (AM) offers an opportunity for sustainable practices to overcome this challenge. The AM industry grew 18% in the last year (Wohlers Associates, 2023) emphasising the need to explore sustainable ways of using the technology. This requires moving towards a circular economy, aiming to eliminate waste through circulating resources and balance environmental, economic, and social factors. This article explores AM’s current state, benefits and challenges in the circular economy context, and provides strategies and opportunities to enable AM as a sustainable manufacturing technology.
AM’s sustainability advantages over conventional technologies include:
• Material efficiency – Lower buyto-fly ratios and tooling elimination.
• Energy conservation – At the manufacturing stage, thanks to reduced material sourcing and design optimisation, and at the operation stage enabling a more efficient energy or fuel consumption during operation.
• Reduced transport –Distributed manufacturing enables on-site manufacturing, reducing goods and materials movement.
• Life extension – Through highly optimised or customised parts that have the potential to extend product life, and through assembly component repair or replace, reducing waste.
While these benefits suggest AM offers greater sustainability, key challenges remain to fully understand its true impact. These include materials, energy consumption, data availability and knowledge-related challenges to make the industry aware of their contribution to a circular economy.
The extraction and processing of AM materials contribute to environmental degradation and greenhouse gas emissions. While some polymers are derived from natural sources, most AM materials require mining or are derived from oil. Furthermore, each AM technology has specific material requirements, such as melt flow characteristics, viscosity, and thermal properties, hindering the development of standard sustainable materials for all processes. This diversity limits material scalability and leads to issues around recovery and recycling, where unique material compositions make it challenging for conventional waste streams. An additional challenge is identifying materials, which requires specialised equipment for composition analysis and recovery route definition.
AM processes require energy for heating, melting, and fusing materials, whilst removing support structures, surface finishing, and applying coatings require additional energy, time, and resources. Capturing and assessing sustainability metrics is more difficult due to continuous part changes. Additionally, energy for one part per build differs compared to multiple, limiting the ability to calculate energy consumption on a component basis.
While AM shows great potential for smallscale production and customisation, scaling up for mass production remains a challenge. Enhancing AM machine throughput while maintaining quality is necessary to make AM competitive with traditional manufacturing in terms of efficiency, leading to energy reductions.
Understanding the environmental impact of AM faces two crucial challenges: data availability and how to use it to validate AM’s sustainability. Databases like Ansys’ Granta are resource pools for materials, however, the differences between AM processes hinder assigning generic data for comparison. The agile nature of AM leads to a varied processing and destination for parts, reducing the data uniformity. The sheer volume of data needed for reliable and accurate product and machine lifecycle assessments continues to be an ongoing challenge in identifying AM’s true environmental impact.
As an AM designer, it may feel like there are limited opportunities to impact its sustainability, however, design is understood as a circular economy driver and there are already common design strategies to promote a sustainable mindset. These are some prominent sustainable design strategies and their potential use cases in AM, starting with those that are most effective at reducing environmental impact:
AMEXCI, founded on the 1st of December 2017, has since been a vital force within the Nordic Additive Manufacturing (AM) ecosystem. Our multinational team, now 30 strong, has extensive expertise in AM fields such as design, parameter development, manufacturing, prototyping, research, and education. With operations in both Sweden and Finland, we supply various industries and are certified in delivering
services to aerospace and defense (AS9100D) sectors, and we recently achieved a certificate of conformity in accordance with IATF 16949, positioning us to produce serial parts for the automotive industry. This diverse skill set allows us to manufacture parts of consistent quality and continue to advance in our field.
concern in today's manufacturing industry, and AMEXCI is charge in promoting environmentally responsible practices
Recently, AMEXCI, along with its shareholders, made the decision to build a new factory and invest in
As one of the industry users, AMEXCI recognizes that the practices is essential for ensuring the long-term viability of the needs of a changing world.
approach to argon, and understand information alreduce our in turn footprint. consumption, assessment (LCA) and miniactivities. The environof our decisions optimization, and environmental footexample possible lowering we can only an applications but the insustai-
First and for proresources manufacturing potential industries, from automotiensure
OUR PROCESS TOTAL ENERGY (KWH)
PRINTING TIME (MIN)
The importance of responsible practices –Building a sustainable future with AM
more capacity to become a leading player in AM in the region. The move was motivated by the increasing demand for this technology, and the need for a more efficient and sustainable manufacturing process. In the current landscape of industry challenges—ranging from disrupted supply chains and component shortages to geopolitical complexities— there is a pressing need for digitalization and improved resource efficiency to minimize the environmental impact of production. This calls for an innovative approach, and AM has a significant role to play. Although AM should not be viewed as an universal solution or a replacement for traditional manufacturing, it does offer substantial advantages over conventional production methods when applied appropriately.
Rather than merely replicating conventional manufacturing processes, AM opens new opportunities to solve previously insurmountable challenges like complex geometries of functional parts at one go, low volume productions in short lead times, design/ material iterations on demand and many others. It all begins with envisioning the function of a particular component, product, or system and translating this into specific geometries. This is where a company like AMEXCI can provide expert guidance, helping you understand what is achievable and how to proceed in adapting to AM.
the sustainability implications of AM.
This isn’t just about reducing environmental impacts of producing parts. AM methods help reveal new possibilities for sustainable innovation - from manufacturing lightweight parts to reducing the carbon footprint of logistics through localized production. The very nature of AM, with its layer-by-layer approach, encourages more efficient use of materials and therefore, holds immense potential in driving sustainability in production processes.
AMEXCI is at the forefront of exploring and implementing responsible production practices for a more sustainable use of AM. We see AM in this regard not solely as a manufacturing tool, but as an integral component of a comprehensive, forwardthinking, and sustainable industrial strategy.
USING AN EFFICIENT DESIGN
REDUCTION OF TRANSPORT WAYS
Furthermore, AM allows Original Equipment Manufacturers (OEMs) to contemplate production on demand, eliminating the need for large inventories, allowing swift product version changes, and offering potential logistical benefits by producing closer to the end customer. The defense market, e.g., is keenly exploring these benefits, alongside the wider implications for supply chain resilience. It’s important to note that there’s no one-sizefits-all approach as every case is unique.
ENVIRONMENTALLY PRODUCTION
After establishing the intended function, our next focus is an in-depth analysis of the associated energy consumption, material use, and other resources required in the additive manufacturing process. This crucial step helps us measure the environmental footprint of producing these components on a serial basis. Where appropriate, this can be compared to the environmental footprint of conventionally manufactured components to understand
If you’re interested in exploring how AM could benefit your particular use case, don’t hesitate to reach out to AMEXCI. We’re here to work with you and guide your journey into the future of manufacturing.
that these advancements are made in a way that is responsible and sustainable.
In addition to the environmental benefits, sustainable practices can also lead to financial benefits, such as reduced costs for materials and energy. By reducing our consumption of resources, we can minimize waste and increase efficiency, resulting in a more cost-effective and profitable operation.
Further information: www.amexci.com
As an industry leader, AMEXCI is committed to promoting sustainable practices in additive manufacturing,
and we believe that this commitment long-term success of the industry. efforts to measure our resource a life cycle assessment tool, with our network, we hope industry and inspire others and responsible future for AM.
“We are committed to understanding the environmental impact of AM and how these technologies can be used to lower the resources and energy needed to manufacture parts.”
• Design for life extension – Topology optimisation or generative design can enable highly functional parts which can prolong life. Customisation offered by AM can improve desirability and emotive connection, also linked with prolonged life.
• Waste source reduction design –Lattices or topology optimisation can reduce material usage whilst retaining the structural integrity. Part consolidation can reduce material usage and assembly steps.
• Design for material substitution – When options are available, the environmental benefits of different materials should be considered.
Material substitution of high-density materials with low-density materials can reduce energy use in transportation and more efficient operation.
• Modular design – Where there is difference in life span, only defective parts need to be replaced, saving energy and resources compared to remanufacture of the entire component. Distributed manufacture ensures spares are available on demand.
• Design for reusability – Standardising certain aspects of the design may allow for re-use in future products.
• Design for disassembly – Considering how the assembly could be dismantled into individual materials ensures each resource can be recovered at end of life.
• Design for recycling – Recycled and recyclable materials should be considered where possible. Ecolabelling practices should be used to identify materials for easier recycling such as embossing material information or QR codes.
• Design for energy recovery – Materials that give off toxic fumes should be avoided if incineration is the disposal method.
• Design for disposability
– The use of toxic materials should be minimised or eliminated. Consider biodegradable materials which can be composted.
As the technology progresses, it is important to understand how AM can develop its sustainability credentials. Finding alternative materials that are renewable, bio-based, recycled and recyclable is crucial for reducing the environmental impact of AM, however, sustainable materials must also balance these requirements without compromising function. Expanding production and supply chains for sustainable materials and making them economically viable will be essential for their widespread adoption.
There are limited options for recycling AM waste due to poor waste infrastructure, incentives to recover material and material identification issues. Further research is required to establish suitable waste management strategies and develop the infrastructure to recover return to recycled feedstock. There is also currently no standard practice for labelling AM parts, making it difficult to identify and recycle AM materials. Although labelling tools would enable designers to combat this issue as individuals, a more widespread solution would require legislating the use of environmental labelling. Labelling practices could simplify material identification and maintain specific material compositions or alloys through the recycling process as opposed to being mixed with other grades which would prevent them being re-circulated back into AM feedstock. Overcoming these material-related challenges in AM requires collaboration between material scientists, AM technology developers, and industry stakeholders.
To fully understand the sustainability of AM, data needs to be collected and assessed. Life Cycle Analysis is a prominent tool used to assess product or process sustainability therefore it should be more widely used in AM. Widespread and reliable data relating to the environmental impacts of AM materials and processes is needed beyond individual case studies and research to enable the leverage of such tools.
To improve AM’s sustainability in the future, every stage of the design for AM workflow and its supply chain must engage with the concept of the circular economy. Since the topic of sustainability is still relatively new, it cannot be expected that everyone involved will have prior experience. Therefore, it is important that the necessary education is made available relevant to the role. Training and guidance will help to shape the mentality of the industry and transition it towards a circular economy.
As a disruptive technology AM has the potential to lead the way in sustainable manufacturing and promotes benefits such as material efficiency, energy conservation, reduced transport, and life extension. However, the challenges, such as the environmental impact of materials used, variable energy consumption, and lack of standardised data for sustainability assessment limit its current potential. Designers can adopt sustainable design strategies to make an immediate impact on their components, however, the future of AM sustainability depends on developing renewable and recyclable materials, establishing effective recycling practices, and promoting education and training in the circular economy for the industry.
References Wohlers Associates. (2023). Wohlers Report 2023: 3D Printing and Additive Manufacturing Global State of the Industry.
“AM has the potential to lead the way in sustainable manufacturing.”
TCT: What role do you think sustainability has to play in the context of digital transformation?
ED: Sustainability is an important outcome of digital transformation. Today, companies are looking for ways to bring more innovative products to market, faster than the competition, at a competitive price point. In addition, they have to pay attention to their environmental impact. The only way to do that is to be more deliberate in balancing all of these requirements. Becoming a digital enterprise is a key enabler for sustainability.
TCT: How is Siemens supporting that?
ED: Siemens is uniquely positioned to combine the digital and real worlds to help industries drive the outcomes mentioned above. Our Digital Threads enable companies to connect their whole value chain, from design to production, in use and end of life. Comprehensive Digital Twin technologies, including simulation results, production data, material information, supplier carbon footprint data, and product carbon footprint data help executives make smarter and betterinformed decisions for sustainability. In addition, Siemens helps businesses drive a circular and continuous design and manufacturing optimisation process based on data from the real and digital world.
TCT: You recently hosted a panel featuring perspectives across automotive, agriculture and space. Given the variety of these industries, was there a key takeaway that could apply to most if not all industries?
ED: Some key takeaways that can be applied to all industries: First, speed is important. Companies need to be able to plan for different scenarios without expelling physical resources. #2: Start small, and then scale with the right tools and skillset to capitalise on your investments based on your biggest sustainability needs. #3: And this makes me hopeful – while our challenges around sustainability and the environment are huge, industry has brilliant people tackling them from all different angles and in all different industries.
TCT: You recently shared in a report how nearly 80 percent of a product’s lifetime environmental impact is determined during the design phase. What considerations do manufacturers need to be making and how early do they need to start making them?
ED: Manufacturers and in particular design engineers can no longer put all their focus on traditional drivers of product performance, quality, and cost. Today, many designs still fail to live up to their promise for sustainability because of the design strategy used. Putting sustainability first means designers need to start looking further upstream and downstream of their products. The products of tomorrow need to be designed with sustainability in mind from the earliest development stages – designing and building for reuse, using fewer materials or less energy in manufacturing, remanufacturing and recycling, or incorporating carbonfree technologies. Digitalisation and automation are game changers to achieve these goals.
TCT: How can simulation help with determining sustainability impact in those early stages?
ED: One of the biggest advantages of simulation is that it allows people to try more things digitally before building physical prototypes. In the 1980s or 90s, when you were developing products, you had to move to the most probable designs - those that you intuitively thought would work. Simulation gives us freedom to test hundreds or thousands of designs that don't seem intuitive at first but might be really effective in the long term. Being able to test without boundaries is impactful. It brings innovation to life in a more reliable, dependable and sustainable way.
TCT: One solution is to deploy sustainability as an additional business metric. In your experience, how seriously are businesses thinking about sustainability when making key decisions?
ED: For multiple reasons, sustainability is becoming a key factor in making
decisions. We call them the carrot and the stick approach. In places like the U.S., with the Inflation Reduction Act (IRA), there is a lot of funding for sustainability (the “carrots”). Understanding the positive impacts of sustainability can help decision-makers secure funding. The other space, the “sticks”, can be found in places like the EU: the legislation that you're required to comply with. Using rules and regulations to really weigh in as a factor in your decisions is important. In addition, the Corporate Sustainability Reporting Directive (CSRD) requires companies to not only disclose what they're doing for sustainability, but to also have a strategy and a plan, to understand their impact. For the UK specifically, the Financial Conduct Authority (FCA) Sustainability Disclosure Requirements enforce product – and entity-level sustainability reporting in the U.K. as well as for product naming and marketing. The good news is, more and more companies are looking at
“Industry needs to start rethinking their make, take, dispose strategy.”
sustainability as long-term profitability. They realise if they don't start acting now, they will be left behind.
TCT: More and more companies are carrying out lifecycle analysis to assess environmental impact of parts and products. How important is it to connect all parts in the designto-manufacture ecosystem to ensure we manufacturers fully understand the impact and where improvements can be made?
ED: I actually held roles in quality management before moving to sustainability. One of the old mantras you often hear is “You can't control what you don't measure”. Being able to control your sustainability impacts first depends on your ability to see and understand the data. Lifecycle impacts depend not only on what happens within the manufacturing facility, but also in the supply chain. Getting and analysing the right data helps you make choices about how to minimise your carbon footprint, reuse material etc. This requires people to work together in ways that they never have before. It requires looking at data holistically and outside of your own manufacturing facility to leverage all that collective intelligence that’s out there. Your ecosystem plays a big role in it, because you need to be able to share information with your partners and supply chain, customers and consumers, to understand the downstream effects and work together on the solutions.
TCT: What would you say is the most overlooked or forgotten factor when it comes to assessing sustainability impact in manufacturing?
ED: Maybe not overlooked, but certainly complex is the concept of circularity. Industry needs to start rethinking their make, take, dispose strategy. While recyclability and remanufacturing are important, extending the life of the products that we already have and making sure that we're driving maximum use out of them is the clearest path to circularity.
It requires rethinking business models in a fundamental way.
TCT: How concerned do we need to be about so-called greenwashing in design-to-manufacturing?
ED: Greenwashing can be concerning. Well intended people continue to look at their small piece of the puzzle unless they can understand that full value chain from cradle to next cradle. It's hard to understand exactly what those impacts are and disclose them. We need to continue to be mindful especially when there aren’t universally understood and accepted standards yet. CSRD is aimed at ensuring transparency, and the Green Claims Directive in the EU will give clear criteria on how companies should prove their environmental claims and labels. It’s expected to go into effect in 2024.
TCT: Across the business, Siemens is a major adopter of additive manufacturing (AM) technologies. For example, Siemens Energy is using it in the manufacture of flexible-fuel gas turbines. Is AM viewed as an enabler when it comes to Siemens’ sustainability goals?
ED: AM is one of the big trends we see in manufacturing as it allows creative thinking. Similar to simulation, parameters around how you manufacture a product can be eliminated with 3D printing. For example, what is the best way to lightweight a product? How do I make sure that I'm getting the functionality with the least amount of material? AM allows engineers to rethink design. In our own plants and factories, we have been able to reduce 70% of the overall weight of a part because we discovered it didn’t have to be produced in a conventional machining way. This can only be done with AM technology. It's a huge enabler for sustainability.
Traditional processes in the titanium metal supply chain lead to significant carbon emissions. According to IperionX, the supply chain is also very complex and leads to high refining and end part costs due to high scrap generation. What IperionX was built to do is bring low cost and sustainable titanium metal production to the world, as the company told TCT.
“Taso” Arima explained: “The whole concept and vision of IperionX is to build a sustainable and low cost titanium metal supply chain. Now, taking a step back, the titanium industry is both high cost and highly carbon intensive, and is not 100% circular.”
Arima described what is known in the industry as a “buy to fly” ratio: “A significant amount of waste generated for every ton of product that we produce. The reason for that is titanium metal is a relatively young metal, it was only first commercially produced in the 1940s and 1950s, as opposed to, say, steel, which has been around for a lot longer, and aluminium. They’re a couple of hundred years older. Titanium is relatively young and is challenged by the way you refine it, which led to the Kroll process [a titanium production process] being the only commercially available process to make titanium metal from the mineral.”
Arima says that the titanium industry has been challenged to develop sustainable and low cost titanium due to the Kroll process, and that 3D printing has attempted to address the issue with the shape of certain parts, taking away the machining process. An issue that arises with using titanium in 3D printing however is that in powder bed fusion, it typically uses a spherical titanium metal powder, which according to Arima is scrap intensive.
While using typical titanium metal powders in 3D printing can reduce the buy to fly ratio, users end up with a higher cost powder that is also carbon intensive says the CEO. The way IperionX aims to solve this issue is by deploying the same process whatever the titanium metal is made into, whether it be bars, plates or powder. IperionX uses processes that are low carbon, and fully circular, allowing for the creation of fully recyclable titanium metal.
IperionX uses two processes, one being the HAMR process developed by Dr. Zak Fang that allows for titanium to be manufactured from scrap or from titanium minerals. HAMR stands for the Hydrogen Assisted Metallothermic
Reduction process. According to IperionX, this process can take almost any form of titanium or scrap titanium alloy feedstock, and produce either commercially pure or alloyed titanium powders at low energy intensity. The other process used by IperionX is the Granulation-Sintering GSD process, also developed by Dr. Fang, which is a thermochemical process for producing spherical alloy powder that combines low-cost feedstock material with high-yield production.
Speaking about IperionX’s “infinitely recyclable” titanium, Arima told TCT: “You can take a product, put it into our process and it gets made into a new part. There’s no degradation. In the steel industry today and in the aluminium industry, but especially in steel, when there is a product with paint on it, typically these are downcycled before being recycled. Titanium doesn’t corrode, it could be left in the ocean for a hundred years, you can take it out and recycle it in our process and it would come back out as brand new titanium. With our process, it is unique that it can be infinitely recyclable because of the metal, the properties of being corrosion resistant, but in the current industry, you can’t just take scrap and recycle it, you always have to blend with minerals that can’t get a 100% recycled product. With our process and the properties of titanium put together, you have an infinitely recyclable supply chain of titanium metal.”
7 – 10.11.2023
Demand for increasingly complex and customized parts is rising, product cycles are becoming shorter, established supply chains are being called into question and sustainability is playing an ever greater role.
In short: Industrial production is becoming more demanding. Additive Manufacturing offers solutions to meet these challenges and inspire your customers.
Be ahead of your competition: Visit Formnext, the international expo and convention for Additive Manufacturing in Frankfurt am Main, Germany.
olymer 3D printed parts have long been bound by preconceptions around their feasibility for enduse applications. But after three decades of materials science, hardware improvements, and real world applications to learn from, much of those preconceptions around tricky layer lines, brittleness, and ‘only good for prototyping’, have shifted to mere misconceptions. In fact, in many cases, they’ve proven to be viable alternatives to traditionally manufactured parts – even metals.
"One misconception is that polymers lack the strength and durability for demanding applications,” Nirup Nagabandi, Ph.D., Vice President of Materials and Process Engineering at Essentium said. “However, advancements in high-strength 3D printed polymers have closed this performance gap, allowing plastics to match or exceed the mechanical properties of certain metals.”
Nagabandi offers the example of soft aluminium tooling which some Essentium customers have replaced with parts made using carbon fibre variants of its highspeed sintering powders. One customer was able to manufacture injection moulding inserts using PPS-CF to successfully produce 150 parts, while another, a contract manufacturer, replaced its production aids with parts made with Essentium’s PA-CF which were three times lighter than its aluminium counterparts and about seven times lighter than steel tools.
“Advanced 3D printed polymers like reinforced nylon, PEEK, PEKK, and PPS have mechanical properties that rival certain metals, allowing them to be effective replacements in various applications,” Nagabandi continued. “High-strength 3D printed plastics can offer enhanced corrosion resistance, chemical compatibility, and electrical insulation properties, which can be advantageous in various industries
and applications, such as in aerospace and consumer electronics, which are already extending their use of 3D printed polymers beyond prototyping and into full-scale manufacturing.”
Nagabandi also suggests that greater awareness is needed around suitability of polymers in extreme high- and lowtemperature environments. While some polymers do struggle, materials such as Essentium’s Duratem high-impact, hightemperature thermoplastics have been designed for demanding rail, automotive and aerospace applications.
Perhaps directly comparing polymers with metals isn’t entirely fair. Speaking to an anonymous source with over 30 years’ experience in AM polymers, there is an argument to be made for polymers that, while not perfect, are in many instances “good enough” to get the job done. Yet to deepen the adoption of AM in end-use applications, testing and benchmarking against traditional standards is crucial.
“We have to use the same test methods and standards that the plastics industry uses – and test for all environmental factors: heat, light, cold, humidity, water, as well as UV,” they said. “These strict tests are why metal replacement has been so successful in many industries –especially automotive.”
Last year Toyota Racing Development (TRD) established a partnership with Stratasys to expand its use of AM in end-use parts for its TRD-branded vehicles and racing cars – some of which may have traditionally been made in metals.
“There are a few reasons to look at replacing metal parts with high-strength 3D printed plastic (carbon infused),” Nelson Cosgrove, Executive Engineering Director, TRD explained. “One is to reduce mass in an area where the part strength can be managed with the use case. Another reason is when you need to make modifications to the part for additional requirements. Various brackets with clever
printing have made it possible to combine different materials within a single printed part, creating complex, multi-functional components with tailored properties.
Ilaria Guicciardini, Head of Marketing at Roboze, which specialises in high-performance AM polymers and composites, says for industries such as aerospace and energy, replacing a traditional metal part with highstrength 3D printed plastic can be a strategic choice.
“While metal has been traditionally favoured for its strength and durability, advancements in 3D printing technology have led to the development of highperformance plastics that can rival some metals in terms of strength and other properties,” Guicciardini said.
Earlier this year, Roboze introduced Carbon PA PRO, a PA 6 reinforced with carbon fibres, which it claims to be its strongest composite material to date, and Carbon PEEK, a PEEK matrix reinforced with carbon fibres. The latter was deployed to manufacture a metal replacement pump impeller for an oil and gas customer, which resulted in an 85% lead time reduction, decreased energy consumption, and 5-6 times lower weight compared to steel.
“These kinds of materials can withstand harsh environmental conditions including corrosion, erosion, and high temperatures,” Guicciardini explained. “The main advantages are the reduced maintenance of the components required thanks to the chemical resistance of the Carbon PEEK, lower mass which translates into safer handling and greater efficiency, dimensional resizing of the valves without necessarily creating special molds and digital warehouse.”
Newcomer Axtra3D made a splash at Formnext 2021 with its Hybrid PhotoSynthesis technology which combines the benefits of three polymer processes: SLA, DLP and LCD. Promoting speed and injection mould-like quality, the company agrees we should't be so quick to judge polymer capabilities.
“There is a misconception that 2-part materials that require post print thermal curing are the only materials that are “good enough” for production," Paul Spoliansky, founding member and Chief Revenue Officer at Axtra3D said. "There’s been a revolution in single part material development by all the large formulators and there are materials quite capable of meeting the demands of some end use applications.”
With the launch of its two X1 Series printers last year, Axtra3D believes it is taking photopolymerisation to ‘the next level,' while major materials developments have also helped propel the polymer industry as a whole.
“There have been major investments made in R&D from some the biggest resin formulators such as Henkel, BASF, 3D Systems, Spectra, Evonik and others,” Spoliansky added. “This has led to much better mechanical performance and long-term stability which is what’s been needed to enable production of end use parts. The rate of innovation has increased substantially, and I believe we’ll continue to see more capable materials being released at a fast pace.”
What that may look like, Guicciardini has an idea, and Roboze has recently commenced construction of a new lab for the development of new ‘super materials.’
“Our further step will be the rapid progress in the development of alternative materials to petroleumbased super polymers, favoring the use of bio-based reinforcing fibers and matrices. The challenge lies in researching new materials and technologies that can on the one hand reduce the generation of carbon dioxide (responsible for the greenhouse effect), and on the other hand achieve the properties of the super polymers available today in the replacement of metal parts.”,
“The rate of innovation has increased substantially.”
Taking the reins of an industrial vacuum manufacturing business established in the late 1980s, Spencer Loveless was at a crossroads.
Father Mike, who founded Dustless Technologies, had passed away. Mum Colleen, who helped to run the company, was stepping back into retirement. And Spencer had the responsibility of moving the business forward. His father had engineered a vacuum initially to address the nuisance that was cleaning out a coal- and wood-burning fireplace, but soon expanded into industry. As Spencer took over, he was never perturbed by the ash, dust and slurry that needed hoovering up from a myriad of industrial settings, but instead with how the equipment was manufactured.
“I don’t like, almost hate, injection moulding,” Spencer tells TCT, “because every time a customer says, ‘Can you change this vacuum? Can you add a handle on top? Can you make this part bigger?’ The answer is always no even if their idea was great and made sense.”
Though the company manufactured its systems through conventional means, it had been prototyping with a Stratasys 3D printer since 2006. It was seeing the agility this added to product development that led Spencer to foster a mindset of continuous improvement.
In 2020, he founded Merit3D, harnessing 3D printing to make parts in the tens of thousands, hundreds of thousands, and even millions.
“We have to find how [to] benefit the customer,” Spencer says. “How is that manufacturer going to bypass overseas suppliers? How are they going to be very agile? How are we going to change the future?”
Posing those questions, an Abraham Lincoln quote comes to Spencer’s mind. ‘The best way to predict the future is to make it.’ Spencer, then, has been determined to prove additive really can be used to make the future, doing so in a way not many people project.
In May, the company announced an order for one million hanger components which connect two epoxy tubes to a mixer nozzle. But getting there hasn’t been without its challenges. Merit3D’s first order was for 1,000 phone cases. It took 30 days to complete, with Spencer
describing the process as ‘brutal’. But his team got better. Last year, Merit3D received orders for multiple batches of binocular tethers. A first order of 5,000 soon grew to an order of 60,000. Feeling confident, Spencer pushed his team to additively manufacture the components in a single day, despite a typical turnaround time being closer to two weeks.
All the stars – materials, machines, people power – had to align, but Merit3D proved it could be done. To go at such a pace every day would not be sustainable without automation at the back end to cycle the parts through post-curing, but when Henkel Adhesive Technologies came with a demand for its epoxy product hangers, Merit3D was not deterred.
Adhesive Technologies turned to Merit3D in response to supply chain issues. Harnessing a fleet of Photocentric LC Magna machines, with their 510 x 280 x 350 mm build volumes, and a set of approved materials (including BASF’s durable Ultracur EPD 1006 material), Merit3D can print 400 parts per 225-minute build, delivering 40,000 units a week. At 30,000 pieces, Merit3D implemented its first significant but subtle design changes. It did another at 100,000 pieces, and another is set for when they reach 500,000 pieces.
It is this continuous improvement that makes it more affordable for Merit3D to additively manufacture the hanger parts rather than injection mould them, and also helped to increase the initial order from around 600,000 units to one million.
“Having the customer back AM is key,” Spencer says. “Good enough should happen but you should always have a continuous improvement mindset.”
Merit3D does, not just of the application, but the processes that facilitate it. As the company powers its way through tens of thousands of units a week, it has learned more about what it takes to manufacture at those numbers, post-process at those numbers and control quality at those numbers. Automating post-processing is now a focus, as is traceability, as is the evolving design of the parts. Merit3D is fighting to prove additive as an option for high-volume manufacturing, and has been now for three years.
“Within a week, we had a first design, we gave it to them, and it broke,” Spencer explains of the one-million-part order. “And they’re like, ‘it doesn’t work for our application’ – which we hear every single day – and we said, ‘wait, wait, wait, just give us another chance. Tell us some of your more in-depth design parameters, what do you need this thing to do, how do you test it?’ It took that moment of, ‘hey, just give us a chance, let’s figure this out.’”
“You should always have that continuous improvement mindset.”SHOWN: THE HENKEL ADHESIVES EPOXY HANGER PRODUCT, 3D PRINTED USING PHOTOCENTRIC LC MAGNA TECHNOLOGY BY MERIT3D
Scale up your in-house print production with the Form 3L, an easy-to-use large format 3D printer for reliable production of prototypes at an unprecedented value.
No specialized technicians required. The Form 3L offers automatic resin dispensing, simple print preparation software, and an interface anyone at your company can use.
Get started now Formlabs 3D printers are ready to plug and print right out of the box, no specialized training required.
The Form 3L has a build volume of 33.5 × 20 × 30 cm, it can typically print up to 20 nozzles in a single build. Find out how the Form 3L can improve your production performance, call 01295 672600.
It was 18 months ago when Seurat Technologies began to detail to Siemens Energy the capabilities of its proprietary Area Printing powder bed additive manufacturing process.
As it did, the company shared how development continued on the parameters of its process, and its ability to print stainless steels, Inconels and tool steels. By May of this year, Seurat was ready to announce that it will manufacture 59 tons of parts for Siemens Energy turbines, with each side pushing the other into new territory. When they commenced discussions last year, Seurat hadn’t yet qualified Inconel 625 and Siemens had never considered additive manufacturing (AM) for these turbine parts.
Together, though, they will be ramping up the additive production of sealing segments for Siemens Energy turbines, starting at an annual rate of two tons and eventually climbing to an annual rate of 15 tons by the final year of this initial contract.
“This is a six-year agreement,” Seurat CEO James DeMuth says, “but that doesn’t mean this isn’t something that as we demonstrate capabilities that can be renewed and renewed and renewed. Really, this is all speaking to long-term production agreements to make parts. This was not a part that they had ever previously conceived to do via additive manufacturing. It was not a fit until we came along.”
Seurat caught the attention of Siemens Energy with its Area Printing technology, which it is intending to use to manufacture parts in mass volumes via a parts service offering. Area Printing is a powder bed 3D printing process which has been packaged into machines that currently print at 3kg/ hr across a 450 x 450 x 450 mm, with Seurat working to grow these capabilities to 1,700kg/hr and 9.6 x 9.6 x 9.6m by 2030. Siemens Energy has been so impressed by this roadmap, that it has also decided to become a strategic investor in Seurat. And as the conversation developed over the last year and a half, the pair worked together to assess potential applications, with most of Siemens Energy’s current roster of 3D printed parts considered too
low volume to make production with Area Printing economically viable. Concurrently, Seurat was working to develop and qualify materials. Qualification of 316L stainless steel was completed early, with Seurat next working through the qualification of Inconel 718. Deeming this to be more challenging than the qualification of Inconel 625 – a material suitable for the production of turbine sealing segments – Siemens Energy had identified their first application.
“We identify this as a great opportunity for us to expand their thinking and expand their mindset based on new capabilities,” DeMuth says. “They’re driving us to a new material. There’s qualification work we have to do, but as soon as we can get that buttoned up, they want parts as fast as they can get them because they have a need right now.”
What Siemens Energy needs is to install 250 of these parts per turbine. The segment component is a ring that thermally expands as the turbine spins before sealing, and has been a part manufactured by Siemens Energy for decades. Shifting a portion of the part’s production to Seurat, the metal AM company will see the capacity of one machine taken up for the next six years.
Though Siemens is beginning to leverage an AM process for the production of this part, the design of the component will remain largely the same with only small tweaks made to achieve efficiency gains.
“We often talk about how we can make a part and not do any design changes on it,” DeMuth says. “Well, Siemens can’t help themselves. They've already thrown in a couple of tweaks here and there to leverage additive because they can. Cost is justified and then we're bringing on additive features and capabilities to improve efficiency, improve performance, improve assembly.”
As production commences, Seurat is confident that the additive manufacture of these parts is just the start. They are currently ‘deep diving’ into the Siemens part catalogue to assess the suitability of components for the current Seurat machines, as well as future generations.
“We found this part,” DeMuth finishes, “but that doesn’t mean it’s the best part. Not by a longshot.”
With four Nylon powders to choose from, 3D print productionready, end-use parts on the Fuse Series.
The Fuse 1+ 30W printer's inert gas environment ensures that you'll get industrial quality parts, every time, while the user-friendly workflow enables anyone to take ownership over production.
With a more powerful laser and enhanced scanning speed, the Fuse 1+ 30W delivers parts at up to twice the speed as previous generations, allowing designers, engineers, and manufacturers to go from design to finished part overnight.
Take control of your design and production process with Formlabs’ fastest, most powerful SLS 3D printer yet.
The skills shortage in the oil and gas market is well-documented — in December 2022, Offshore Energies UK (OEUK), the leading trade body for the UK’s offshore energy industry, published a report highlighting an industry-wide skills gap. However, additive manufacturing (AM) could help firms overcome shortfalls in technical skills by largely automating design and production. Here Dave Moore, 3D print consultant at TriTech 3D, UK provider of Stratasys, One-Click Metal and XJet 3D printing solutions, explores three ways that AM could help deskill production.
AM offers speed and allows manufacturers to produce multiple iterations so that they can achieve the perfect part before manufacturing. With the addition of new materials and systems, AM is moving to the production line, and we are seeing greater use of printed parts for tooling. Offshore applications include investment casting, sand casting and composite layup tools. Even 3D printed holding fixtures and checking gauges for welded parts that would traditionally be hand fettled and made, are now additively produced in many offshore manufacturing facilities.
1. GREATER MATERIAL CHOICE
There is a growing range of increasingly sophisticated metals and thermoplastics available to oil and gas firms, meaning they can now additively manufacture durable, high-
performance end-use parts on demand. For example, manufacturers can use new high-performance carbon-filled materials to produce metal forming and bending tools, rather than having to wait for tools to be machined.
Material options for tooling and other offshore components include ULTEM 1010 resin, which has a good strengthto-weight ratio, and is flame, smoke & toxicity (FST) certified, for safe use in confined spaces. Meanwhile, ANTERO 840CN03 is a fused deposition modelling (FDM) PEKKbased electrostatic dissipative (ESD) thermoplastic. Both are high strength, heat resistant and offer exceptional outgassing capabilities.
Meanwhile, more systems, such as the Stratasys F900 industrial FDM printer, can accommodate a vast range of thermoplastics, and require less operator input than traditional CNC machines. Therefore, oil and gas manufacturers can create a wide range of reliable, heatstable and corrosion-resistant parts from one system without straining inhouse skills.
2. PUSHING BOUNDARIES
Unlike CNC machining and traditional labour-intensive manufacturing, AM systems require fewer raw materials,
can reduce waste and shorten supply chains. Furthermore, it can achieve this with minimal human intervention, which is critical when traditional machining skills are in short supply.
Manufacturers also have the freedom to additively manufacture various geometries sand configurations depending on the application, without worrying about the limits of the human hand and eye. For example, we worked with one business that used additive techniques to produce remotely operated vehicles (ROVs) for carrying out underwater inspections, and others have used this technology to print wellheads and subsea trees that control oil and gas flow.
3. SPEED AND ACCURACY IN ONE CNC machining allows oil and gas equipmentmanufacturing firms to produce heat exchangers and other components with precision and speed. Despite the industry now using 3D printing for factory floor production, many manufacturers still rely on CNC.
However, additive scores where complexity is needed — it gives manufacturers freedom of geometry and the ability to print bespoke highvalue parts cost-effectively and with little waste. From a skills point of view, it also eliminates the need for assembly and many systems are automated so they can run without someone standing next to them on the factory floor.
Although there is a glaring skills shortage in the oil and gas market, encouraging the transition to AM could help equipment-production firms streamline manufacturing while reducing pressure on already stretched in-house skills.
The ball game. Peanuts and Cracker Jack. The Great American Pastime. Baseball has been an integral part of American culture for over a century.
In Major League Baseball (MLB), the manufacturing process for bats has largely stayed the same since the late 1870s, but the design has changed numerous times, with the first major change coming in 1885 when a rule was introduced that allowed a flat side to the bats. This rule was later rescinded in 1893.
The first metal baseball bat was patented by William Shroyer in 1924, but would bend and dent if solid contact was made. Aluminium bats were not effective enough for mass production until 1970. In fact, MLB has never used metal bats, despite their popularity in lower levels of the sport such as Little League and college baseball, and still requires all MLB players to use wooden bats.
In 2023, however, Nexa3D and Wilson Sporting Goods are collaborating to bring further innovation to the baseball bat using additive manufacturing (AM). Wilson's R&D team, which recently caused a stir with its 3D printed airless basketball prototype, was seeking a more effective means to produce tooling for plastic injection mould prototypes, historically made with subtractive manufacturing technologies.
With a large print envelope and ultrafast LSPc process offered by Nexa3D’s NXE400 system, Wilson says it can now create a prototype in one working day, a process which could have previously taken months, and produce multiple design iterations in a single print batch. Wilson says the benefit of using 3D printing is that its R&D team can “afford to be wrong.”
In baseball, the part of the bat that hits the ball, the barrel, is a tube, normally
manufactured from a metal, or sometimes a composite such as carbon fibre. The handle is manufactured with a different material. According to Wilson, this is to tune the performance and feel of the bat. The plastic pieces of the bat include the end cap, a knob, a separate handle piece that goes inside the tube, and some internal technology to manage the performance. Some cosmetic elements, such as a grip that goes on the bat, can also be plastic.
Director of Advanced Manufacturing at Wilson Sporting Goods Glen Mason said: “It’s really interesting seeing the variety of technology that’s out there. And players have a preference, right? Because we do a lot of moulded parts, and we’re in a very high mix, low volume environment, meaning we might make millions of parts a year, but its thousands of this and hundreds of this and then 5,000 of this. We can tune each one of those components for the player. So, even though the bat that the college players are swinging and the 12-year-old players are swinging look very similar, and may even be branded similarly, they’re actually more than just a shorter version of the adult bat. We have tuned it specifically for that player to make it the best possible experience for them, and plastics allow us to do that.”
Mason told TCT that he doesn’t ever see wooden bats disappearing from MLB, partly due to baseball being a very traditional sport, but also due to the fact that the implementation of metal bats in MLB would change the game “significantly.” Mason added: “It would be easy to make a bat that hit the ball over the fence every time, that would not be the challenge. The challenge is making the game more fair, making more parity across the game.”
The standard in 2023 for the coefficient of restitution of a baseball bat is 0.5. Coefficient of restitution is the ratio of final velocity to the initial velocity between two objects after collision, or more simply put,
the percentage of speed a ball retains after hitting another object, such as a basketball hitting the ground, a tennis ball hitting a tennis racquet, or a baseball hitting a baseball bat.
Collisions in which there is no loss of overall kinetic energy is known as a “perfectly elastic collision". This collision has the maximum coefficient of restitution of e = 1. Collision where maximum kinetic energy is lost, is known as a “perfectly inelastic collision”, and has a coefficient of restitution of e = 0. If a ball was dropped from 10ft, and bounced back to 5ft, that would be a 50% coefficient of restitution, so would be measured as 0.5. Every baseball bat in the MLB has a stamp stating that it is BBCOR certified, meaning that the ball bar coefficient of restitution is 50%.
Mason told TCT: “Every manufacturer has to be at 50%. There’s no opportunity to be better, except there’s so much more to a bat than the energy. There’s the experience for the player, the way that the ball interacts with the bat, adding spin to the ball etc. If you’re hitting the ball faster or slower, you can have a different performance.
“We have a box, we have to play inside the box, but there’s a lot of room there, and I feel like its actually more than we even know because it’s constrained by the cost of tooling. Why don’t we have thousands of different models out there? Because they’re expensive to produce. If we really can zero in on these opportunities faster at lower costs, and can really identify some competitive advantage, which we’ve been doing since 1987 when DiMarini started, and we’re still doing it. This [3D printing] is just one tool along the way, but I’m personally really excited because in this advanced manufacturing role this is something I want to take advantage of.”
With 3D printing, Wilson is able to “fail fast and cheap” to innovate baseball bats.WORDS: oliver johnson
When Wilson first began using AM, it was to complement the use of injection moulding, with the brand liking the combination of the ease and the digital workflow of 3D printing, while still having access to the injection moulding feedstock that a lot of data had been built around.
Mason said: “In the early days I said, 'okay, this is just going to get me to digital tooling right? To faster moulds?' That was my walk in the door. I then realised quickly that it was far more than that because we have a different type of workflow where we can go from a CAD design to a moulded part with relatively low inputs. The time is so low that even if it just has the remote chance of being successful, why don’t we just try that? What’s the downside, right? We’re investing hundreds of dollars, and days, versus tens of thousands of dollars and potentially months. So, as the cost drops and the speed drops, all of a sudden, we are able to explore things that we weren’t able to look at before. So, initially, it was all about getting to a faster mould and now I’m realising it’s really more about a better workflow.”
Lasse Staal, Director of Business Development at Nexa3D told TCT: “I think what we’ve done in collaboration with Wilson is that the performance achievable with 3D printing has taken a leap forward. I’ve also been in touch with people interested in golf, and we’ve been making stuff for athletes in the Paralympics. One of the prohibitive costs associated with injection moulding used to be the tooling. To help people understand what is now possible, we need forward looking companies like Wilson who are able to and willing to take a chance with the technology. It may be only a little thing we are changing with this approach, but it does a world of difference to the workflow.
“What injection moulding is, first and foremost, is an incredible amount of tried and true materials that have been available for many years. It’s a lot of highly skilled suppliers who are used to working with those materials. We are on a mission to connect those manufacturers with a novel way of using injection moulding. I think the Wilson case is so powerful because it highlights exactly that. We are now changing the frame around injection moulding, moving it from having been a high volume to becoming a batch of one technology. With AM as the enabler, lets call it.”
“We're investing hundreds of dollars, and days, versus tens of thousands of dollars and potentially months.”SHOWN: A COMPLETED BAT WITH THE TWO HALVES OF THE MOULD SHOWN: A BATCH OF 3D PRINTED MOULDS ON THE BUILD PLATE
Typically, whenever I visit a new facility in search of a 3D printing story, I might be invited to handle a couple of prototypes, a fixture, maybe an automotive manifold. Today it’s a 60-million-year-old ammonite shell.
“It’s not just about dinosaurs,” Tom Ranson assures me as he places a box of fossils on a table at his lab inside London’s Natural History Museum. For a minute, I swear he can sense the Ellie Sattler fangirl in me but it’s merely a reminder of the scope of requests, from every imaginable angle of the museum’s 4.6 billion years of history, that arrive daily at the door of his 3D visualisation lab.
Whether it’s a squid crafted from a lost form of glassmaking, the skull of a living marsupial, or a close up of Charles Darwin’s personal collection – this is a day job where, genuinely, no two days are ever the same.
Tom’s four-year-old son has given him the premier title of ‘dinosaur doctor’ but his actual job title of ‘3D Visualisation Specialist’ finds him in a lab underneath the world-renowned museum, where dinosaurs, much like 3D technologies, are merely a gateway to a world of discovery.
Having spent a decade at the University of Suffolk in Ipswich where Tom was responsible for building out its 3D suite, he is now taking that same engineering and logical thinking and applying it to conservation challenges.
“I'm printing things that have been dead for 200 million years,” he jokes, acknowledging the juxtaposition between technological advancements at his disposal, and the fossils on his table.
Tom sees three big opportunities for 3D here: conservation, exhibition, and engagement.
The lab is kitted out with an arsenal of 3D scanners and 3D printers which
he believes places it right at the ‘front of the queue’ in terms of its 3D capabilities. There are portable handheld scanners from Creaform, a Faro ScanArm for larger specimens, and surface scanning equipment from Alicona which sit alongside a row of desktop printers from Ultimaker, Elegoo, Prusa and Formlabs – all benchmarked, not with your typical ‘3Dbenchy’ but rather a very on-brand Dippy the Dinosaur skull.
Requests come into the lab from just about anywhere – sometimes the other side of the world. The museum recently worked with Western Australia Museum to digitise a set of six marsupial skulls for further research – why fly 18 hours if you can study a digital model? As Tom explains, it’s all about asking conservationists what their problems are and opening them up to using 3D scanning and 3D printing technologies as a solution.
“It's very much a dream scenario because I just get to play with all of this kit,” he added.
Some requests, however, can be a test of nerves, like the project currently under NDA which involved the surface scanning of five objects – the only five of their kind in the world – to record the most detailed surface models possible before destructive DNA testing. Or how about a pair of tiny 3mm herring ear bones, one calcified, one non-calcified, which were scanned using the Alicona Infinite Focus Microscope, and then scaled and printed at 15cm to better show wear and growth marks for display at a gallery in Finland?
When dealing with trickier specimens, 3D printing can come in handy. Tom is able to print ‘jackets’, traditionally made out of soft clay, to handle delicate objects – like the set of gemstones which were put under a microscope for chemical analysis but so small they needed a custom holder to keep them in place. Bigger pieces can benefit too.
“I was scanning a femur of an Iguanodontian, which are around 14 metres tall – so the femur is almost as big as me,” Tom explained. “But because your femur is designed to
attach to the hip and knee and to support weight in that direction, when you lie it on its side, it's not designed to do that. So, we've had a couple of them sitting in cupboards which just break and snap in the middle. When we make jackets for them, I feel a bit safer!”
3D printed mountings - the fixtures used to hold specimens during analysis - are another easy win and provide a better fit for objects and take less time to make. Traditionally cut to size from conservationapproved foam, Tom can instead scan a specimen using the Creaform GoScan if it’s in the field or the FARO ScanArm in the lab, and reverse engineer a custom mount using something like FARO’s RevEng toolkit and send for printing. What can typically take a month to produce manually now takes less than a day, depending on print time. Mountings can also be used to display artefacts in the public galleries, either as fully 3D printed custom mounts or 3D printed contact patches. Selecting and testing the right material however is crucial for stable,
long-term applications. So far only two materials out of 13 possible resins for the Formlabs Form 3 have passed Oddy testing for permanent use, while a further six have passed for up to six months use, which could potentially be useful for short term exhibitions or during transportation.
Then there are pieces like the 3D printed baryonyx claws, of which there are several in various materials across the lab – and another in my pocket to take home – that were 3D scanned and 3D printed to give visitors the opportunity to handle during public engagement demonstrations. 3D printed replicas are a way for visitors to get up close to specimens that would otherwise be too fragile or too small to be handled. And even better for Tom's nerves - if you drop a 3D printed replica, you just print another one, no problem.
There’s also a good chance if you’ve perused the halls of the Natural History Museum, you may well have already happened across some 3D printed parts in action.
“There are things out on display here that are 3D printed or that were cast from a 3D printed mould directly above us in the museum,” Tom said.
Sophie the Stegosaur, for example, lives upstairs and is the most complete stegosaur skeleton in the world – with the help of a few 3D printed elements. The museum is also currently working on a project with University of Cambridge to create the world’s first full fossil of an Ichthyornis. The data is being gathered
as part of a global effort which has resulted in a full 3D image of what researchers have determined the Ichthyornis looked like. Tom will help reconstruct it, using 3D printing, to deliver what will be the first physical example of the Ichthyornis that has existed since they were alive.
“I don't see any reason not to have a 3D printed element on display,” Tom argues. “It’s cool that there are fossils on display and there always will be, but completing the skeleton so that people can see what it looks like, with a 3D print, it's exactly the same thing.”
The centrepiece of the museum’s main Hintze Hall is a 23-metre-long blue whale skeleton. In fact, a massive project in 2015 to 3D scan Hope the blue whale during an ambitious move from the museum’s Mammal Hall, is one of the reasons this lab was created. But perhaps even bigger than a 3D whale scan are Tom’s ambitions: to build a digital library of everything in the museum. Today, that’s around 4 million specimens.
“I don't see any reason why we don't just digitise everything because it makes life so much easier,” he explained. “Researchers can say, ‘I want to see X specimens,’ and rather than it being a few weeks for them to find it in collections and bring it down to me, it could just be a library they download from and do their measurements. We can validate the model and the measurements so that everybody has confidence that what they've downloaded from us is absolutely accurate.”
If you caught Tom's talk at TCT 3Sixty this year, you'll know he is passionate about outreach, ensuring younger generations have a chance to not only learn about the artefacts inside the museum, but also the technologies bringing them to life in new ways. In a recent project, Tom 3D scanned a lizard from the museum’s spirit collection (specimens preserved in jars of spirits) and 3D printed a set for an experiment involving different strength magnets and a leaf blower to illustrate natural selection to a class of schoolchildren. It’s all about weird and wonderful solutions.
“I don't want there to be any barriers to anything because everyone's curious and everyone should be entitled to the same level of access,” Tom added. “The more people we can get involved, the more weird-like solutions we can come up with.
“If one kid then goes into science, then brilliant. My job's done.”
He is also keen to promote communication between different departments and further afield, collaborating with neighbouring institutions such as Imperial College London and the V&A museum to share knowledge and resources. Ultimately the lab could provide a valuable service for the industry.
“I just want to further science,” Tom concluded. “I want people to enjoy it and be able to do weird stuff. I don't want just one person saying, ‘I don’t know how to do that,’ to put a stop to some research.”
“I don't see any reason not to have a 3D printed element on display.”SHOWN: 3D PRINTERS INSIDE THE MUSEUM'S 3D LAB SHOWN: 3D PRINTED REPLICAS AND CUSTOM MOUNTS
At TCT 3Sixty 2023, Evo3D launched Rapid Fusion, its newest brand, and alongside it, announced the release of the Rapid Fusion PE 320 pellet extrusion system. Speaking to TCT a few weeks post-event, Director of Marketing and Development at Evo3D Jake Hand gave details on why the company chose to launch the brand at TCT 3Sixty, as well as giving an exclusive sneak preview of a big next step for Rapid Fusion.
TCT: What is Rapid Fusion?
JH: Rapid Fusion is a manufacturer and solution provider for large format additive manufacturing. Over the next two years you’ll see an extensive range of products come through that will allow us to offer well placed products into the market for the expansion of large-format 3D printing. So, in essence, we’ll only build products that complement that mission.
TCT: Why was the decision made to launch at TCT 3Sixty?
JH: TCT 3Sixty is the UK’s largest event for additive, and the timing aligned really perfectly for us to do it. It was a big push for us to get it ready to have it available at the show. The plan was that if we could announce it in what is the premiere UK event of the year, then that’s what we would do. And there was a massive amount of interest in Rapid Fusion at the event, and there has been a massive amount of interest since the event as well. We’ve had a lot of people get
in touch who wanted to work with us to test the product and to be a beta tester. TCT has got a big platform and it's pushing things forward in the industry.
TCT: What sectors will benefit from this technology?
JH: Anyone who requires moulds. We’re working with companies like Airtech and they’ve been in that space for a long time. This is a really quick way for people to create large forms and machine them and be able to utilise them in manufacturing really quickly. Anywhere you need to print something really quickly to a large scale you will see this become an option. Where we definitely see the first iterations in terms of industry, automotive is a big one, anything to do with engineering, production, manufacturing jigs for production lines, so it's not just the final use parts, sometimes it's going to be used to make parts
to go onto production lines that make the parts.
TCT: How long has Rapid Fusion been in the works for?
JH: Well, we realised there were gaps in the market. Products that needed to be produced weren’t coming to market quick enough for our liking. The plan to spin off and make Rapid Fusion has probably been about 12 months of work to this date. The extruder has taken that long to build, design and get ready.
TCT: What’s next?
JH: We’re going into a partnership to become the UK’s first manufacturer of large-format 3D printers. We’re building a printer and we’ve just had Innovate UK funding for the sum of 1.1 million GBP for the project. That’s going to see us build a very fast gantry style 3D printer. So, almost like a traditional 3D printer, but metre by metre with a pellet extruder. It’ll be modular, to switch from pellet extrusion to filament extrusion. It’ll be our own proprietary extruder and it’ll have a system on there that would be capable of some serious speeds. We’re working with Rolls Royce as part of that project, Baker Hughes, and National Manufacturing Institute Scotland are also involved. They’ve expressed interest in buying these machines as well when the project is finished, so that should truly put us on the manufacturing map. I think you can see that we’re here to stay and we’ve got lots of different things in the pipeline. The future looks quite exciting for the brand.
“I think you can see that we’re here to stay.”SHOWN: RAPID FUSION PE 320 PELLET EXTRUDER
Rob Higham, CEO of Additive Manufacturing Solutions Ltd, says we should stop and think about why we are so obsessed with classing our data as IP. Spoiler: your data isn’t worth the spreadsheet it’s written on…
Many before my time in AM, and many since, will have fallen into the trap of protecting what we believe to be valuable: our beloved data.
Let’s look at value by the Oxford Dictionary definition of “how much something is worth compared with its price.” You can see why we protect this data. If we are producing data via AM, it will inevitably cost a great deal to generate. However, there are numerous areas we are not thinking about.
Let us consider this example: you go for a family picnic, your aunt makes her “world famous” egg mayo sandwiches. Everyone loves these eggy delights; everyone also knows it is egg mayo. If we were to tell others it was egg mayo, could they simply go make their own egg mayo sandwiches? Of course. Could they make them identical or even better than your beloved aunt? Who knows. The recipe is key. Your aunt, the famous Colonel’s seven blends of herbs and spices, and maybe your own method for the perfect roast potatoes: this is IP. The ability to develop egg sandwiches, roast potatoes or primary structural titanium parts for aircraft all have a process as the secret weapon. This is what you have created with your investment. A process that allows repeatable world class sandwiches, spuds, or parts. This capability is your USP, your showcase capability that brings your customers great benefit and your shareholders their revenue. If the next time you make your special roast potatoes you decide it is a good idea to cover them in engine oil rather than your secret oil preference, are they still roast potatoes? Of course. Would anyone like to eat them? Unlikely. Your data is therefore the outcome of the process. So, if you are running Scalmalloy with the right, wrong or indifferent parameters, your materials data is how you close the loop. It is NOT of any value in isolation.
Here is perhaps the next obvious question: “okay, even if I get on board with this, the data shows our competition
what we are able to do and therefore gives them targets to exceed?”
Good. Competition is healthy, without competition you will stay still. Continual development is needed.
“What is the point in sharing data if it is not valuable?”
data, design values or an average from a project and some variation data. What does it show? Does it show your learning? What is the problem with sharing your learning?
Your current production data should show low variation across builds. Well done, making sure your customer sees that repeatability is crucial. Your competitors