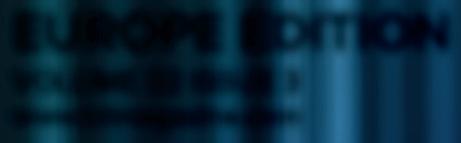
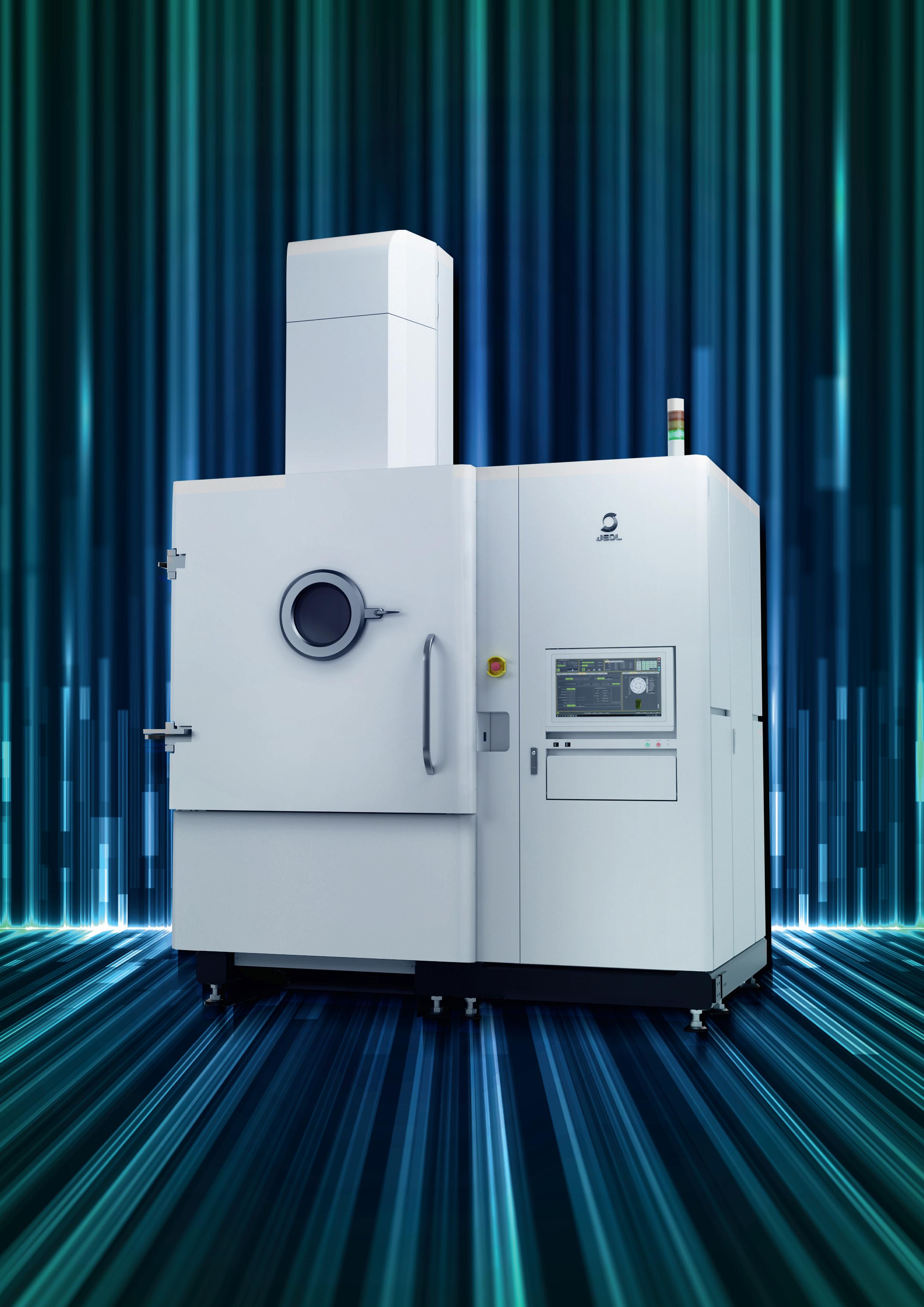
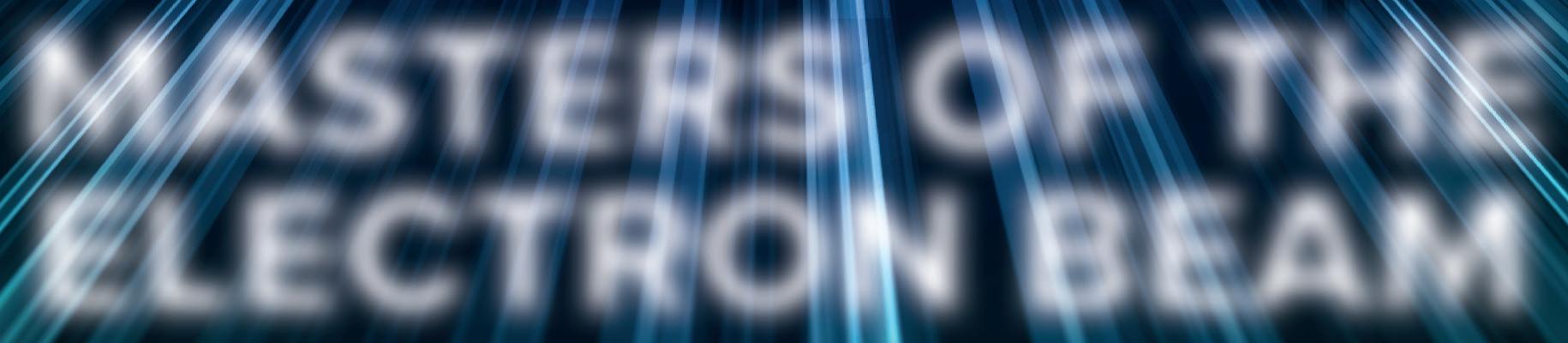
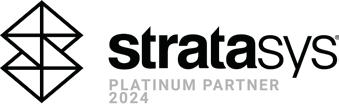
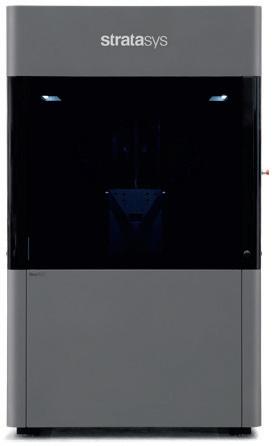
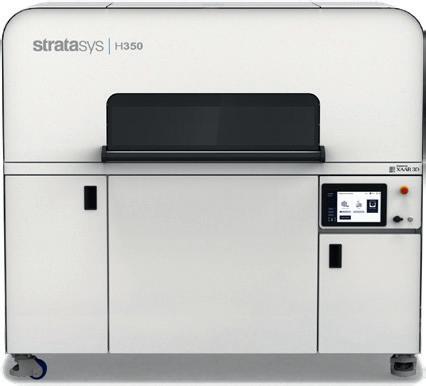
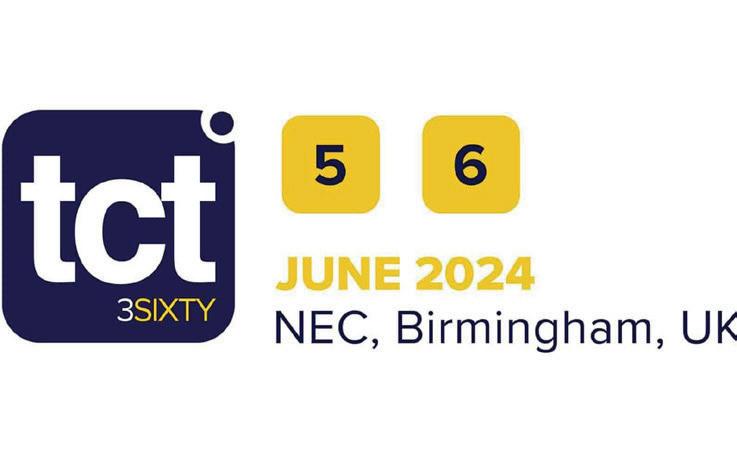
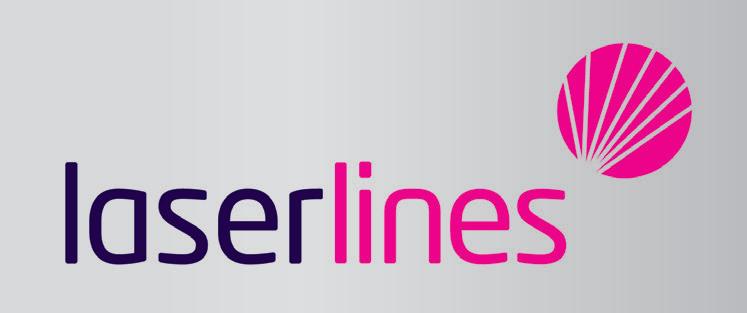
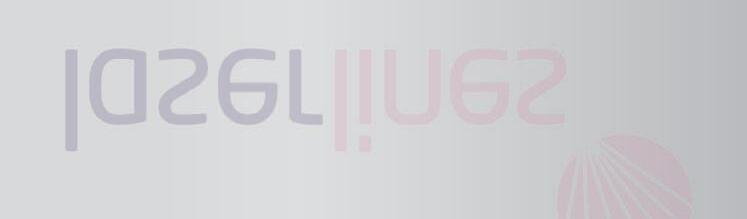


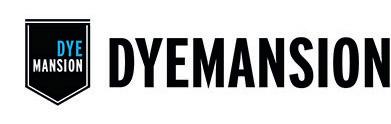
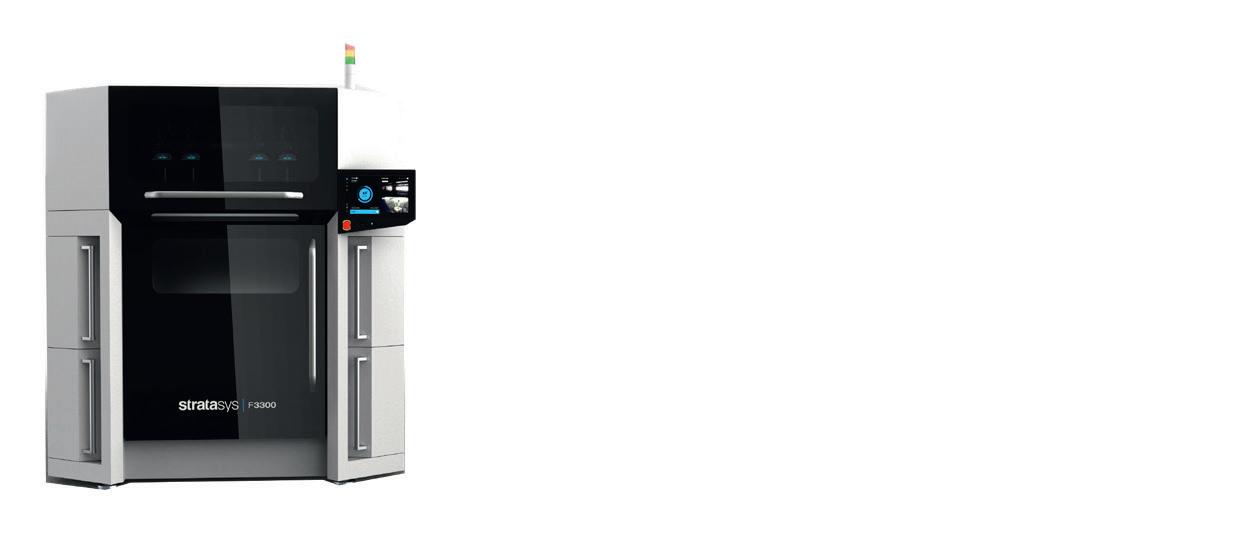

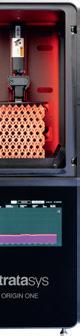
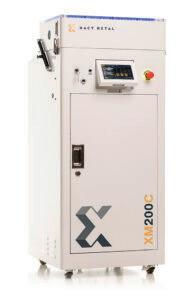
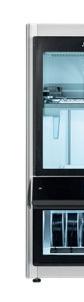
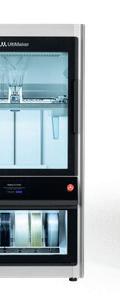
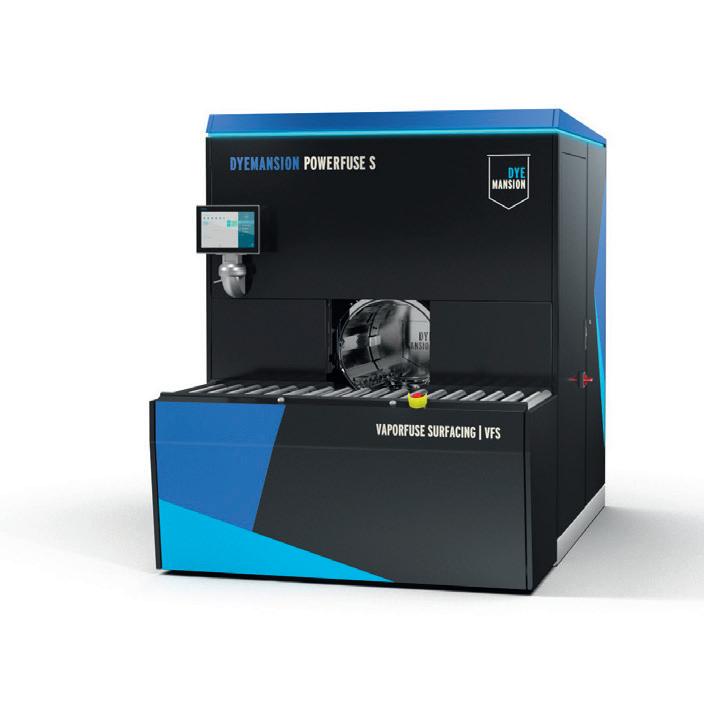
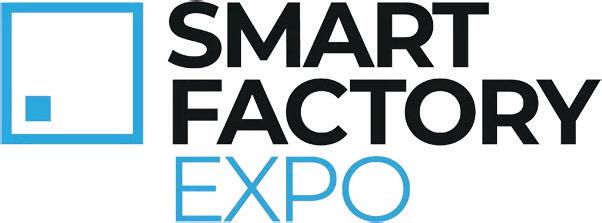
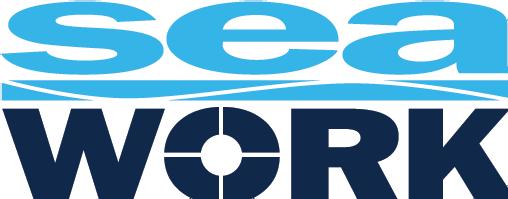
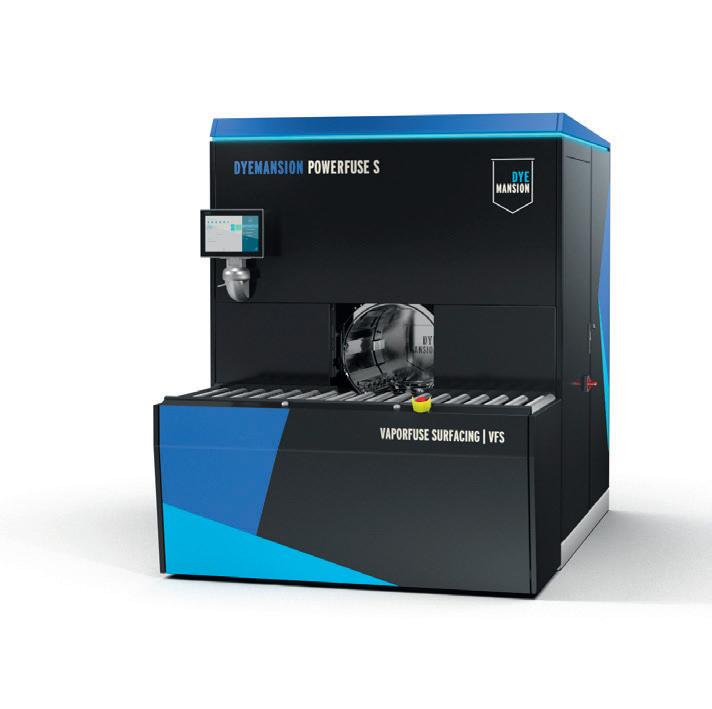
EDITORIAL
HEAD OF CONTENT
EDITORIAL
HEAD OF CONTENT
The countdown is on and has been for some time. Messages are coming in every day, the mark on the calendar draws ever closer, the to-do list has hardly had a dent.
This morning, one message read simply: ‘28 days!’ That’s 28 days until I step off a plane to be slapped by a wave of heat and pushed onto the nearest sunbed, with only cocktails and books in reach. All of which would be quite exciting if it didn’t mean that in 21 days, I’d be en route to the National Exhibition Centre in Birmingham for the annual TCT 3Sixty show.
That’s not to say one isn’t excited by our flagship event – quite the contrary, as you’ll come to understand once reading the rest of this issue – it’s just that putting together an event the size and scale of TCT 3Sixty can be a tad stressful. And as someone who sits in the editorial
Laura Griffiths e: laura.gri ths@rapidnews.com t: 011 + 44 1244 952 389
GROUP CONTENT MANAGER
Samuel Davies e: samuel.davies@rapidnews.com t: 011 + 44 1244 952 390
ADVERTISING
HEAD OF SALES TCT PORTFOLIO
Carol Cooper e: carol@rapidnews.com t: 011 + 44 1244 952 386
TELEPHONE SALES EXECUTIVE
Amy Gilham e: amy.gilham@rapidnews.com t: 011 + 44 1244 952 373
PRODUCTION
Sam Hamlyn Matt Clarke Robert Wood MANAGEMENT
C.E.O. / PUBLISHER
Duncan Wood
department for the company’s media arm, I don’t know the half of it.
What I do know is our operations, sales, marketing, and project management teams are running full pelt towards June 4th, when our second UK User Group kicks off, proceeding the two-day 3Sixty trade event that sandwiches our seventh annual TCT Awards ceremony.
It is all systems go. But we're not the only ones. There are hundreds of exhibitors, dozens of speakers, and thousands of visitors all working to get their booths prepared, presentations rehearsed and agendas in order.
In preparation, the TCT editorial team has been speaking to many of our exhibitors and speakers for this latest issue of TCT Magazine. In some cases about what they’re showcasing at the
SUBSCRIPTIONS
PUBLISHED PRICES
event, in others about what challenges they’re looking to solve and what opportunities they’re looking to pursue.
Our coverage does not end here, though. We will be continuing these conversations at the show, absorbing the insights shared across our conference stages, and networking with the AM industry at our User Group event, TCT Awards ceremony, and our end-of-day-one exhibitor party. There’s already whispers of several product announcements and UK debuts to report on too.
All of that is to say, I can’t wait to have my feet up in 28 days’ time. But before I get there, do make sure to follow TCT’s media channels in the coming weeks, and if you can, join us in Birmingham from June 4-6. All the details can be found at www.tct3sixty.com.
TCT North America Print Subscription - Qualifying Criteria
US/Canada - FREE UK & Europe - $249 ROW - $249
TCT Europe Print Subscription - Qualifying Criteria UK & Europe - FREE US/Canada - £249 ROW - £249
Subscription enquiries to subscriptions@rapidnews.com
Read this and back issues for FREE on Issuuwww.issuu.com/tctmagazine
The TCT Magazine is published bi-monthly by Rapid News Publications Ltd No. 3 Office Village, Chester Business Park, Chester, CH4 9QP. t: 011 + 44 1244 680222 f: 011 + 44 1244 671074
© 2024 Rapid News Publications Ltd While every attempt
6. MASTERS OF ELECTRON BEAM
JEOL details how it is bringing its legacy electron beam technology sophistication to additive manufacturing.
9. I PRINT, THEREFORE I-DAMP?
Sam Davies speaks to Hyphen Innovations CEO Onome ScottEmuakpor about the company’s inherent Damping via Additive Manufacturing Processes technology.
13. PUSHING HORIZONS
Stratasys Global Director of Aerospace Foster Ferguson provides insights on the implementation of AM in aerospace.
17. CASTING CALL
America Makes Program Manager
Litsa Rubino explains how America Makes is driving the integration of additive across sand casting.
19. WHAT NEXT?
3D Systems, Nexa3D, Formlabs and BASF open up on the progress being made to develop more highperformance materials for resin 3D printing technologies.
23. ON THE VERGE
Laura Griffiths speaks to KraussMaffei about the plastic fabrication company’s additive manufacturing offering.
27. THE JIG IS UP
Laura highlights the opportunities for gains in the 3D printing of jigs & fixtures, with insights and examples from several industry players.
30. A NEW ARC
WAAM3D CEO Filomeno Martina discusses WAAM3D’s unique capabilities, how to create value in supply chains, and an upcoming product launch.
32. ZEROING IN
Sam reports on how 3T AM is working towards its Net Zero goals as it continues to scale its manufacturing output.
35. TCT 3SIXTY PREVIEW
Technology highlights, Q&As and conference picks ahead of the UK’s definitive AM event.
50. PLAYING THE LONG GAME
3D technologies consultant Steve Cox asks the question: where are we now when it comes to adoption of AM in the UK?
For over 75 years, JEOL has been synonymous with innovation in electron beam technology. The name JEOL stands for “Japan Electron Optics Laboratory,” and is a testament to JEOL’s commitment and mastery of the electron beam.
Established in Tokyo in 1949, the company initially focused its expertise on electron microscopy, with its development of transmission electron microscopes as well as scanning electron microscopes, semiconductor photomask production and lithography solutions. To this day, JEOL is synonymous with instrument accuracy, reliability and excellent customer support. However, in 2014, JEOL embarked on a groundbreaking journey into a new industry, additive manufacturing (AM), culminating in the development of its latest innovation – the JAM-5200EBM metal 3D printer.
This machine not only highlights JEOL's rich history in sophisticated electron beam technology, but also represents the culmination of decades of precision engineering and beam steering expertise now applied in the dynamic realm of metal 3D printing. This expertise, combined of JEOL’s comprehensive service support network of 180 field service staff across the United States with a median staff tenure of 17.5 years, helps ensure minimal downtime and optimal machine performance. In fact, JEOL USA’s standard warranty and service contracts guarantee a machine uptime of at least 90% along with an onsite response time of 48 hours after an issue has been reported.
The JAM-5200EBM distinguishes itself through its cutting-edge Electron Beam Powder Bed Fusion (EB-PBF) technology. Equipped with a robust 6kW electron beam, this machine operates at speeds a thousand times faster than conventional lasers used in similar technologies. This phenomenal speed and power advantage drastically reduces production times and circumvents the need for several postprocessing steps that are traditionally necessary in metal 3D printing, such as
stress relief heat treatments and wire electrical discharge machining (EDM). The JAM-5200EBM’s electron emitting source has a lifetime of >1500 hours, which is the highest lifetime source in the EB-PBF market.
Ensuring the powder used in the printing process meets strict compositional and particle size specifications in accordance with standard AMS7011, which is for Ti6Al4V Grade 5 produced with EBM technology. This is vital for maintaining the integrity of the final printed products.
plate. This capability, unique to EB-PBF, allows for the largest quantity of parts to be built in a single run to meet higher production quantities.
EB-PBF is known as a “hot process” as the powder bed is maintained at an elevated temperature using the electron beam prior to melting at each layer. This is known as the “preheat” step and achieves several advantages, including enabling parts to be printed anywhere within its build envelope, even without connection to the build plate. This capability, unique to EB-PBF, allows for the largest quantity of parts to be built in a single run to meet higher production quantities.
the stringent AMS7032
reaffirms its ability to produce aerospace-grade materials with outstanding reliability and
underwent rigorous testing and quality assurance
In late 2023, JAM-5200EBM achieved compliance with the stringent AMS7032 standard, a milestone that reaffirms its ability to produce aerospace-grade materials with outstanding reliability and precision. The JAM-5200EBM underwent rigorous testing and quality assurance protocols to evaluate its ability to produce parts with consistent mechanical properties, chemical composition, and material properties across multiple production cycles.
“A culmination of decades of precision engineering and beam steering expertise”
evaluate its ability with consistent mechanical and material
Compliance with AMS7032 standard involves several key
Compliance with AMS7032 standard involves several key factors:
● Process Stability and Control: Demonstrating the JAM-5200EBM can consistently produce parts with the same high quality over repeated runs and under varying operating conditions. This includes maintaining precise control over the electron beam parameters and environmental conditions within the build chamber.
SHOWN: Inauguration of JEOL’s JAM-5200EBM at Cumberland Additive in Neighborhood 91
● Consistent Mechanical/Material Properties: Conducting extensive mechanical, material, and chemical composition testing on printed specimens to verify that they meet or exceed the performance criteria set out in the AMS7011 standard, which includes requirements for Ti6Al4V Grade 5 material produced with EBM technology.
The successful compliance with AMS7032 not only highlights the robust performance of the JAM-5200EBM but also positions JEOL as a pivotal player in sectors where the precision, material properties, and repeatability are of utmost importance. For aerospace manufacturers, this compliance provides the assurance that AM parts meet stringent safety and performance standards, for critical aerospace applications.
Demonstrating compliance with AMS7032 is not just a technical accomplishment for JEOL, it is a testament to the company’s commitment to quality, reliability, and industry leadership. It opens doors to new market opportunities where compliance is a prerequisite and enables JEOL to engage more deeply with key industry players who require the highest levels of assurance in material and build quality.
The strategic introduction of the JAM5200EBM at Cumberland Additive in Pittsburgh’s Neighborhood 91 was more than just a product launch within the North American market; it represented a significant stride in JEOL’s global strategy. Neighborhood 91 is designed as a comprehensive ecosystem for AM, enhancing synergies by connecting all phases of the printing supply chain. This setting is ideal for showcasing the JAM5200EBM’s capabilities, emphasising its quick setup and operational excellence.
The collaboration with Cumberland Additive, a contract manufacturer specialising in AM, enables JEOL to leverage Cumberland's extensive expertise in producing high-quality parts for aerospace, energy, defence, and space industries. This partnership not only demonstrates the capabilities of the JAM-5200EBM but also serves as a beacon for the potential of EB-PBF technology in critical sectors.
Bill Freyvogel, Chief Commercial Officer, Cumberland Additive, comments: "We have developed a unique partnership with JEOL as their presence within our N91 facility enables us to a collaborate and expand access to new materials for our customers. We are making solid progress towards supporting our aerospace and defence customers with serial production parts and we view this as just the beginning.”
As JEOL continues to push the boundaries of what is possible in AM, the company remains committed to enhancing the functionalities of the JAM-5200EBM.
Efforts are ongoing to expand the range of compatible materials, potentially including high melting point and refractory alloys which could open new avenues in sectors such as aerospace, defence, and energy. Recently, JEOL developed a process parameter set for Pure Tungsten, which notably has a high melting point and is challenging to manufacture from a conventional machining standpoint and printing using laser-based powder bed fusion processes.
Another example of enhanced functionalities of the JAM-5200EBM is the imminent release of JEOL’s Back Scattered Electron Imaging system, a game changer for in-situ process monitoring. Using already established technology developed on JEOL’s Scanning Electron Microscopy, the JAM-5200EBM is capable of scanning and detecting the backscattered electrons emitting from the powder bed and forming an image of the layer. This image allows for potential defects within the melted layer to be detected and reported, resulting in a highly effective process monitoring and quality control process. Future developments of this technology will allow for defects detected to be repaired in-situ, allowing for improved material quality produced by the JAM-5200EBM.
Future initiatives also include deepening collaborations with leading industry partners and research institutions to explore novel applications of EB-PBF technology. In April JEOL installed a JAM-5200EBM at the Technical University of Munich, which is deeply engaged in AM research and aims to drive further innovation using JEOL’s EB-PBF technology. These kinds of collaborations are expected to drive further advancements in design and material science, expanding the potential for AM to meet complex and evolving industry needs.
The JAM-5200EBM stands as a testament to JEOL’s commitment to innovation and excellence in metal 3D printing. By seamlessly integrating decades of expertise in electron beam technology with the latest advancements in AM, JEOL is not only following industry trends but actively setting them, offering new levels of efficiency, quality, and reliability in metal production.
As JEOL looks to the future, it is poised to continue its efforts in transforming the landscape of AM with solutions that meet current demands but also anticipate and shape future developments.
3D printing in premium quality: highly productive and compact
With the next generation of the TruPrint 1000, we are continuing our success story The metal 3D printer fits perfectly for dental applications with lower part costs through preform, multiplate and hybrid, digital process chain But the machine is also impressive in the R&D area or in small series production More information at www trumpf com/s/truprint-1000
So, a little about myself,” begins Onome Scott-Emuakpor.
A college basketball player turned mechanical engineer turned founder/CEO, Scott-Emuakpor is talking ahead of his second appearance as a speaker at TCT 3Sixty. His first, in 2022, saw him present on behalf of the U.S. Air Force Research Laboratory (AFRL), delivering a talk that focused on the development process for verifying the integrity of additively manufactured (AM) parts. Two years on and he’ll be demonstrating how a technology called i-DAMP can enable the binder jetting of a superalloy for high-pressure turbomachinery and aerospace applications. In between, he picked up the TCT Aerospace & Defence Application Award less than a year after setting up the Hyphen Innovations business that has brought i-DAMP to market.
i-DAMP, or Inherent Damping via Additive Manufacturing Processes, is the result of years of AM research and engineering. ScottEmuakpor has around 20 years of experience in structural mechanics, structural dynamics assessment, and their correlation to turbine engine structural integrity. He first started working with AM about 12 years ago.
“Once I got to the point in my professional career that I started working on figuring out ways to improve performance of individual components,” Scott-Emuakpor explains, “it was clear that additive manufacturing was a viable path to take leaps and bounds in being able to make components that just couldn’t be made any other way.”
He just had to figure out how to expedite the implementation of AM in a safe and repeatable way. Scott-Emuakpor was lucky that, at the AFRL, he had access to true stateof-the-art technology, giving him insights not just into the challenges of metal AM, but the potential solutions too.
“We’re able to suppress vibration enough that it’s not a concern.”
The challenge that Scott-Emuakpor wanted to sink his teeth into was that of vibrations and vibration fatigue. Vibrations occur, of course, in any product or system that has a motor, from bread makers to cutting tools to turbine engines. At best, they cause a racket or mean a less pleasant ride, and at worst, they can cause critical failures. In 2018, a mother of two on Southwest Flight 1380 died after debris from an engine failure smashed a passenger window on the 14th row, partially sucking her out of the window and delivering blunt trauma to her head. It was caused by severe vibrations in the left engine.
“The thing with turbine engines is that, once a crack initiates and it starts to propagate, the time it takes for that to happen can be within minutes. So, it’s not one of those things where [you can] land the plane in 30 minutes and try to figure it out. Once it happens, it’s done and the damage is there. Because of that, there’s a lot of inspection that goes on, a lot of free understanding of the material and the component before everything’s been assembled, and so, in general, it’s good to reduce vibration.
“Then, when you incorporate additive manufacturing, you incorporate the fact that the variations in manufacturing for additive are significantly more than the variations in manufacturing from forging or machining or casting. For us, we thought, what if you just got rid of the vibration completely? Then, all of a sudden, the stresses are so low that the variation in the material property that you’re concerned about is no longer an issue. That philosophy, that thought process, was the birth of i-DAMP.”
Xenia® Materials engineers and manufactures high-performing thermoplastic composites, offering a wide choice of carbon and/or glass fibre compounds as well as ultra-light structural materials based on dedicated thermoplastic polymer matrix, optimised for Fused Granulate Fabrication (FGF) additive manufacturing.
Focusing on mechanical performance and lightweighting, Xenia® offers a dedicated range of materials that open up a series of applications in key vertical markets, including aerospace, automotive, oil & gas, and tooling.
Boasting high stiffness, dimensional stability, low density, low thermal expansion and high durability, Xenia’s product families have been developed to enable the rapid prototyping of finished parts and the production of composite tooling that requires dimensional stability while achieving the lowest CTE (Coefficient of Thermal Expansion) value.
These materials are essential for the development of applications such as:
• Direct lamination moulds
• Jigs
• Lamination masters
• Thermoforming moulds
• Rapid prototyping
The use of Xenia® materials compared to the traditional processes for making tooling composites results in significant benefits, starting with a material saving from optimized design around the 50% among with only 25% of the time needed for the actual production of the tool compared to the traditional processes.
We'll explore further how the company's 3D printing granule materials offer versatility across various applications. Whether end users seek lighter, more cost-effective substitutes for metal, a durable composite for tooling, or a flexible, lightweight
option for sports equipment, these materials can meet a broad spectrum of needs.
XECARB® 3DP ⊲ Thermoplastic composites reinforced carbon fibre (up to 50%)
Xenia’s XECARB® 3DP family of materials is based on its standard XECARB® product range for injection moulding and consists of highly selected base polymers all reinforced mainly with carbon fibre. The XECARB® 3DP portfolio includes materials that cover engineering polymers, such as HDPE, POM, ABS, PET-G, PC and high-performing ultra-polymers, such as PEI, PESU, PEEK, PPS, with a carbon fibre reinforcement that goes up to 50%.
This group of materials is the broadest in Xenia’s portfolio and it is known for delivering superior mechanical features, low density, and low thermal expansion. Also offering minimal warpage risk and high quality surfaces, it is ideal for metal replacement and tooling applications.
The greatest demand from LFAM 3D printing end users today is for composite tooling applications, and the XECARB® 3DP range of carbon fibre reinforced thermoplastics is ideally suited to this application area. This is not only due to the toughness of the composites, but also the fact that the fibre reinforcement minimizes the risk of warping throughout the printing process resulting in high-fidelity dimensional parts with a high-quality surface finish, especially in curing processes.
• Minimal warpage risk
• Lower CTE value achievable
• High-quality surface
Xenia® offers a range of composite materials optimized for different temperature ranges, each suited to specific applications in industries such as aerospace, motorsport, nautical and design manufacturing where the thermal stability during the process and the quality surface is essential.
For low temperature applications, up to 110°C of curing temperature, Xenia has developed 3 grades reinforced carbon fiber:
• XEGREEN® 23-C20-3DP (rPET-G)
• XECARB® 28-C20-3DP (ABS)
• XECARB® 52-C20-3DP (PC-ABS)
These materials are ideal for rapid prototyping, trim tools, jigs, holding fixtures, layup tools, as well as low temperature master models and moulds. Each composites provide the necessary durability and printing precision for the most complicated designs without the need for high-temperature processing.
In the context of curing processes applications that needs to handle temperatures up to 140°C, Xenia offers the following materials:
• X ECARB® 52-C20-3DP (PC-ABS base polymer)
• XECARB® 40-C20-3DP (PC base polymer)
These materials are essential for producing more robust and thermal resistant components such as trim tools, holding fixtures, thermoforming moulds, layup tools, room temperature tooling, and medium temperature master moulds. The higher temperature tolerance of these materials allows for their use in environments that are slightly more demanding than those suitable for low temperature materials, allowing to obtain laminated carbon parts that require more complicated geometries.
For high temperature applications that needs to go up to 210°C in curing temperature process, the indicated materials are the one on the higher part of the polymer pyramid:
• XECARB® 15-C20-3DP (PEI base polymer)
• XECARB® 51-C20-3DP (PESU base polymer)
• XECARB® 5-C20-3DP (PEEK base polymer)
These materials are specifically engineered to withstand harsh conditions and are typically used in the production of trim tools, holding fixtures, as well as high temperature tooling and master moulds. These highperformance composites maintain structural integrity even under extreme heat, making them perfect for high-stress and long life applications in demanding aerospace and motorsport sectors.
Xenia Materials will exhibit at the TCT3Sixty event in Birmingham on June 5-6, 2024, showcasing their advanced composite materials at Booth J30
i-DAMP was developed at the U.S. Air Force, with the technology using automated computational code to examine finite element results and strategically place voids in areas of printed parts that avoid high stresses. These voids trap unfused powder within them, which helps to dissipate energy when the part starts to vibrate, suppressing the overall vibration of the system. The unfused powder, then, is performing much the same role as a pendulum does in the middle of a building that has been constructed in a city susceptible to earthquakes.
Scott-Emuakpor says that the technology opens the door for redesign opportunities, reducing the weight of a part or creating more fuel efficiency, but he also notes that there are immediate benefits when using i-DAMP without changing any external geometry. One project with the Air Force has seen i-DAMP deliver a 10x improvement when it comes to damage resistance without any need to tweak the external geometry of the part.
Hyphen Innovations also sees great opportunity in the consolidation of components by combining i-DAMP with AM. Typically, monolithic parts are considered to be more susceptible to vibration than multi-part assemblies because there are no connecting interfaces to dissipate energy during vibration. So, manufacturers would on the one hand enjoy the weight reduction and fuel consumption improvements enabled by part consolidation, but the part would be more susceptible to failure as a result of the high stress during vibration.
“Some people accept that, if there’s a costbenefit and they can easily track it, but if we do something like incorporate i-DAMP into this system now, not only were you able to consolidate the parts, reduced costs and all these other things, we’re also able to suppress vibration enough that it’s not a concern.”
Though early in its journey, Hyphen Innovations has already engaged in projects with the U.S. Air Force and sees plenty of long-term potential in i-DAMP within the aerospace and defence sectors. Such are the lengthy qualification and certification processes in those industries, however, Hyphen Innovations is also hoping to make a more immediate mark on other markets, such as automotive, maritime, tooling and household appliances.
The company is a small outfit though, and so as it looks to broaden its horizons must think differently about how it approaches each project. Currently, the modestly-sized Hyphen Innovations team engages on a personal level with each use case that presents itself. But the goal is to take a step back from every development process, and instead provide a software tool that has much of the knowledge baked into it.
“Right now, if an aerospace company is interested in this, they have to reach out to us and then we’re involved in the development process, we have to tell them where to put their unfused powder voids and how to redesign and so on. It can be a bit cumbersome and not quite done in a timely fashion,” says Scott-Emuakpor, before citing nTop’s development of an ‘intermediate step’ that automates elements of part design. “We’re trying to create this intermediate step where you create your initial design. You say, ‘well, I want to increase damping and I want to be able to optimise this for weight,’ and all of a sudden, this software does that for people in an automated fashion and now we’re able to leverage the full strength and capability of i-DAMP.”
It is the next step of a venture that is, in one way, years in the making and, in another, centuries. As an engineer with a passion for technology, the decision to leave the AFRL and go his own way was a hard decision to make. But as a Black American fascinated by entrepreneurship and technology development in the black community, it was an easy one.
Citing the U.S. Census, Scott-Emuakpor notes how the white community has ten times more resources available to them than the Black Community, and when you look at the history books, members of the Black Community were for a long
time denied the right to own intellectual property. When that was eventually legalised, they were often priced out. Even today, the Black American community makes up around 14% of the US population but only accounts for around 2% of current patent awards.
The challenges for Black American entrepreneurs throughout history, then, have served as an additional motivation for Scott-Emuakpor, who not only wants to address the challenges in additively manufactured industrial parts but also to be an inspiration to other Black entrepreneurs and engineers.
“From an entrepreneurial perspective, you had obstacles where if you started a business, your biggest concern wasn’t that you may go bankrupt, your biggest concern was that you may literally lose everything, like your family, your entire neighbourhood could get burned down. Despite those significant obstacles, we had so many people from the Reconstruction Era to the Jim Crow Era who developed businesses with that fear and still went through it.
“My only obstacle is that my business might fail. And that’s it. If my business fails, I take myself and my PhD and my experience and go get another job. It’s not a genuine obstacle. If not somebody like me, with the background, with the understanding, to go out and start my own business, then why should I expect someone else to have confidence? I feel like me doing this is honouring the sacrifices that were made by people before me who were putting their lives on the line to come up with new technology and to start businesses. It feels like a natural calling to go out there and take a chance that was much less of a chance than those who came before me.”
Onome Scott-Emuakpor will present at TCT 3Sixty on Wednesday, June 5th, 2024.
You're always contending with trying to make sure that you have the best readiness for your vehicles and equipment,” explains Foster Ferguson, Global Director of Aerospace at Stratasys, and a retired Lieutenant Colonel for the United States Marine Corps.
It was there where Ferguson, having spent two decades in supply chain logistics, and as a former Commander for a maintenance battalion with a mission focused on intermediate level repair for everything from trucks to optics to radios and ground equipment, began thinking about additive manufacturing (AM).
“We started on that journey knowing that there was pretty substantial capability out there and we started looking around and trying to find out who we could partner with,” Ferguson says of how the mission brought them to Stratasys. “We trained a team of about ten Marines, supply guys, warehouse guys, machinists and technicians. We quickly learned that these mechanics that are working on these things day in and day out know the areas that they need to affect. Additive was just this wonderful alternative.”
As the US Department of Defense's curiosity in AM heightened, policy was being created, but Ferguson was nearing a crossroads: to stay in the military or retire. Instead, Stratasys wanted to hire him to support its government military activity, and the AM journey continued.
Ferguson describes the current state of AM adoption in the aerospace, space and defence industries as being at an inflection point. The Lockheed Martins, Boeings, Northrop Grummans and Blue Origins of the world are taking a digitised approach to production and designing with additive in mind, where it makes sense. Ferguson believes there is great opportunity for AM, primarily around supply chain, localised manufacture, and sustainability, but more could be done to encourage adoption.
“Those days of being a generalist are gone.”
“Awards should have some sort of additive component,” Ferguson suggests. “Policy and awards will drive that if it's written into the language for organisations to really think critically about it. We have to force ourselves to move into the future.”
Global events and pressures have undoubtedly played a role in forcing companies to innovate. We witnessed this at the height of the pandemic when 3D printing experienced a fresh surge as its banner ability to manufacture locally and on-demand seemed like a silver bullet in a world of supply chain disruption. But is AM really having the profound impact on the aerospace supply chain that was promised? Ferguson shares an example from a recent visit to an unnamed defence prime manufacturing parts for space in the U.S., and describes being ‘blown away’ by the volumes being churned out of a fleet of seven F900 FDM systems.
“It was everything from production support to design iterations, into the full end of that spectrum for production parts fully integrated into the platform. That's happening in a lot of locations,” Ferguson says. “I think that if an organisation is not considering additive as part of their strategy for manufacturing, then they're behind, and I really feel that we've crossed that chasm where we've had the early adopters and now we're getting into this early majority.”
A decade has passed since Stratasys made headlines with its 1,000 3D printed parts for an Airbus A350 XWB aircraft. Each of those parts was printed using Stratasys' flagship FDM technology in Airbus certified ULTEM 9085 as part of a schedule risk production activity to increase supply chain flexibility. Since then, Stratasys has expanded its polymer technology offering through a number of acquisitions and internal developments and now counts five core technologies alongside a catalogue of advanced materials. Ferguson believes that polymers, in particular, have provided agile ground for aerospace innovation to happen, especially for in-field defence manufacturing where the barrier can be much lower than metals.
The Next Step in the SLA Evolution New Formlabs 3D Printer - Form 4
Choose new Form 4. Unmatched Speed, Accuracy, and Reliability to Redefine you 3D Printing
• Industry-Leading Dimensional Accuracy
• New applications
• Expansive Materials Catalog
• High-Volume Reliability and Consistent Success
Partner with UK based supplier of Formlabs 3D Printers. Streamlne your processes. information@advent3d.co.uk 01295 672600
“When you get into high-performance thermoplastics with our FDM technology, they're filled with different types of materials,” Ferguson explains. “We have a nylon material that's 35% chopped carbon fibre, it's essentially the same mechanical strength as aluminium. I can go from 140 parts on an assembly down to 16. That changes the weight, and of course the speed to design. When you're talking about how much it costs to send a rocket into space, every kilogramme has to be measured. That's where polymer additive is nicely positioned.”
Here in the UK, Senior Aerospace BWT, a supplier to regional, military, private jet, and rotorcraft markets, is using a pair of Stratasys Fortus 450mc 3D printers from Tri-Tech 3D to produce interior components for low-pressure air ducting systems and air handling in aircraft interiors. After delivering its first duct for flight use on regional passenger jets in 2018, the company has supplied hundreds of lightweight, flight-ready interior aircraft parts. More recently, BAE Systems installed the first two Stratasys F3300 systems in the UK via Laser Lines. The F3300 was launched last year to provide a ‘step change’ in print speed with rates up to twice those of current highproduction FDM systems. BAE Systems plans to use the technology to drive product improvements, while reducing time to market across the company’s Air sector products. At the time, Steven Barnes, Additive Manufacturing Lead for BAE Systems Air sector, commented that the machines are giving the British defence company the ability to “rapidly prototype new parts,” and “stand ready-toproduce one-off spare parts at the touch of a button.” Without going into detail, Ferguson concurs that BAE Systems’ engineers are “very visionary” in their plans for the technology.
“It's a completely new platform,” Ferguson says of the F3300. “We've designed a lot of sensors and information flow, so that will continue to evolve, and I think that the user will have a very informative experience, and certainly when it's integrated into their other systems, it'll be a real asset for them.
“It's been a lot of work over the years, but we built this in collaboration with our customers.”
Stratasys reseller Tri-Tech 3D’s Robert Pitts recently described 'AM utopia’ as the ability to print functional, end-use parts. That 1,000 parts on an aeroplane figure from 2014 is now more like 2,500, but that doesn’t mean we’ve quite reached utopia yet. At the recent AMADS Conference in the UK, in a conversation about AM in defence, John Sneden, the Air Force Director of Propulsion at the US Air Force Life Cycle Management Centre, commented, “If I’m at war and it takes 6-9 months to deliver the part, how useless is that?” The last time TCT spoke to Stratasys about aerospace in 2021, the takeaway was that AM confidence was an ongoing challenge. And much like the supposed silver bullet in supply chain, digital inventories, often lauded as the holy grail for AM in a production capacity, are far from easy to implement. Though, according to Ferguson, aerospace organisations very much want to.
“Going back to the days of being in the Marine Corps, taking these large defence logistics agencies that have warehouses of stock and contracts that aren't responsive to the needs,” Ferguson recalls, “how do we position a digital inventory, but then of critical importance is, how do you secure it from a cybersecurity perspective?”
The aerospace sector is, naturally, risk averse. You cannot have failures at 33,000 feet in the air, nor on the ground in a combat zone, and while the sector has led the way for a lot of AM adoption, that aversion can be limiting. Yet, in addition to clear avenues like lightweighting and MRO, Ferguson feels there is room for the aerospace sector to leverage AM to address further challenges.
“I think that there's an opportunity to address quality issues with additive,” Ferguson explains. “When you're getting into testing and quickly developing fit function checks, the things that might be required through a quality inspection, quality assurance inspection, additive is a great tool for that. Quality and safety are major issues. Stratasys has got a great opportunity here to help these engineers with quality and inspection.”
Aerospace, space and defence are often grouped together, but they each have very different demands. While aerospace may practice more caution with time tested standards, the space industry is fast moving, and there’s no blueprint for how things should be done. Stratasys recently provided 3D printed samples that will be brought to the lunar surface in a series of Northrop Grumman sponsored experiments as part of Aegis Aerospace’s first Space Science & Technology Evaluation Facility mission. Whether it’s on the moon, on a commercial airliner or in combat, focusing on each of those unique opportunities will be key to ensuring meaningful adoption continues.
“Aerospace is unique because you generally have a lot of innovation. You're going to push the horizons of technologies, software and materials,” Ferguson says. “Those days of being more of a generalist are gone. We very much have a vertical focus with our customers – it's helping pull us all forward.”
Visit Stratasys at TCT 3Sixty:
Tri-Tech 3D Hall 1 | G30
Laser Lines Hall 1 | H43
SYS Systems Hall 1 | C11
Additive manufacturing (AM) technologies are known to provide benefits for lowvolume, high-mix casting production. They offer advantages for tooling design and opportunities to improve productivity rates in upstream or downstream operations from the casting process. As such, the U.S. government, and the Department of Defense (DoD) recognise the need to prioritise AM integration in casting applications.
Although AM promises to augment the casting industry, its current limited utility, especially in defence and sustainment, prohibits full integration. Additionally, a decline in U.S. foundries exacerbates an existing workforce shortage, further hindering progress.
Nonetheless, AM's potential to improve the casting sector is enough to draw on the broader industry for innovative solutions with America Makes, the national additive manufacturing innovation institute, at the helm. Tasked by the DoD, the Institute, in partnership with Deloitte Consulting, developed a multi-year technology roadmap to create and deploy AM capabilities in the casting and forging (CF) industry. This roadmap assessed issues affecting the CF industry, identified AM opportunities to mitigate these issues and determined the investments needed to support AM integration into manufacturing operations. Based on these findings, a portfolio of projects and their corresponding execution plans were defined and are now being deployed to drive AM usage in the casting and forging industry.
The need to scale sand printing capabilities was a high priority, high impact project that emerged from the roadmap activities. To address the immediate need, America Makes released a project call to meet market demand.
Aerospace industry leader, Honeywell was awarded the project, and in October 2023 began working on the two-year endeavour to improve the casting quality of parts produced with AM sand moulds and cores.
Areas of focus included:
● Evaluating and implementing measures to improve surface roughness.
● Identifying methods to minimise dimensional variations.
● Determining cause and identifying methods to reduce porosity caused by sand mould outgassing.
● Developing methods to disseminate findings and best practices to industry.
NAVIGATING PART QUALITY PAIN POINTS IN AM SAND CASTING COMPONENTS
Binder jetting is among the AM techniques used for creating sand moulds and cores. However, like other AM technologies, its limitations currently restrict usage due to its influence in critical part applications.
These include:
● Surface roughness (caused by stepping where finished metal parts retain the layered texture of the 3D sand mould).
● Dimensional inaccuracies.
● Porosity due to mould outgassing during the casting process.
The project explores the application of AM sand moulds and cores to produce Honeywell's gearbox housings, covers, and inlet housings for the Chinook Helicopter T55-714C engine. Working in tandem with project partners ExOne, Hoosier Pattern, Ohio Aluminum, and Chicago Magnesium, Honeywell is evaluating the current processing parameters for AM sand moulds and cores. Cast part assessments based on design requirements will ultimately identify quality gaps and gauge technological improvements.
The success of this project will provide a new baseline of recommendations for improving AM sand moulds/cores for the broader sand casting industry.
AM technologies provide an opportunity for greater profitability, new markets, and new business models, but without an expansive understanding of how to address workforce gaps and limited capacities of small-to-medium-sized foundries, the industry will remain at a crossroads.
“A high priority, high impact project.”
LITSA RUBINO
Program Manager at the National Center for Defense Manufacturing and Machining (NCDMM)
In her role, Rubino manages the National Additive Manufacturing Innovation Institute’s technology projects and is also responsible for leading internal strategy development and formation of new project efforts that focus on integrating additive manufacturing into casting and forging technology.
A second layer of this project is to support small and medium-sized foundries lacking the necessary data and models for their casting operations, which is crucial to mitigate business risks while competing in the bidding process for low-volume or high-mix products.
These efforts, led by the American Foundry Society (AFS), include developing training materials and courses for domestic sand casting industries. The objective is to promote best practices and methods to improve the quality of cast parts produced with sand-printed moulds and cores. Additionally, industry events will feature presentations that highlight technology improvements and best practices for additively producing sand castings.
America Makes recognises that transitioning from AM usage to wide adoption requires a joint effort to assure the needs of the larger market are met. The ongoing project demonstrates the Institute's commitment to staying ahead of innovative solutions, providing practical steps that create a significant impact.
This project lays the groundwork to enhance the quality of sand-cast parts, accelerating AM adoption across tooling for sand casting applications. From a broader perspective, leveraging the America Makes road-mapping efforts to identify and address CF industry gaps presents a significant leap in AM maturation, ultimately enhancing national security.
● Stereolithography (SLA)
● Stereolithography (SLA)
● Metal Additive Manufacturing (DMLS)
● Metal Additive Manufacturing (DMLS)
● Selective Laser Sintering (SLS)
● Selective Laser Sintering (SLS)
● Fused Deposit Modelling (FDM)
● Fused Deposit Modelling (FDM)
● Multi-Material Printing
● Multi-Material Printing
● Vacuum Casting
● Vacuum Casting
● CNC Precision Machining
● CNC Precision Machining
● CMM Inspection & 3D Scanning
● CMM Inspection & 3D Scanning
● Traditional Modelmaking
● Traditional Modelmaking
Market leading in-house technology combined with a skilled, experienced team ensures that CA Models
Market leading in-house technology combined with a skilled, experienced team ensures that CA Models
● Specialist Painting and Finishing
● Specialist Painting and Finishing
Precision Prototyping services continually surpass customer expectations across the UK and Internationally.
Precision Prototyping services continually surpass customer expectations across the UK and Internationally.
01786 464434
01786 464434
sales@camodels.co.uk www.camodels.co.uk
sales@camodels.co.uk www.camodels.co.uk
We are dedicated to providing an excellent service
– from rapid quote to on-time delivery
– producing high-quality components at the right price.
· Stereolithography
· Selective Laser Sintering
· Vacuum Casting
· Two Shot and Over-moulding
· Silicone Components
· Silicone Tooling
· Reaction Injection Moulding
· Water Clear Lenses
· Traditional Model Making
· Model Finishing
Sam Davies explores the progress being made in the development of highperformance materials for resin-based 3D printing technologies.
The sight of a stereolithography (SLA) part gradually turning brown while perched on a worktop is a familiar one for many long-time users of the technology.
So too is the same part dispersed into a hundred pieces on the floor seconds after being handled by a butter-fingered colleague.
But these instances are increasingly becoming a thing of the past, as materials, processes and knowledge all continue to improve.
Many people point to different developments as the turning point. The introduction of alternative photopolymer 3D printing technologies, the entry of industrial material suppliers or the endeavour of leading end-users in dental, healthcare, consumer goods and beyond. Did materials follow machines or vice versa? Did the big, industrial chemical giants introduce better products and higher standards? Have customer demands forced innovation?
Whichever it is, the quality of resin-based 3D printing turned a corner somewhere along the way, and those manufacturing machines and developing materials are now looking to hit the accelerator.
Formlabs recently made headlines with the introduction of the latest generation of its Form SLA 3D printing series, the Form 4. But it was not only bringing to market a machine capable of delivering
maximum vertical print speeds of 100mm per hour inside a build volume that is 30% bigger, but a set of General Purpose Resins with 2x improvement in elongation at break and a 1.3x increase in impact strength compared with the previous generation of materials too. These improved general purpose materials are supplemented by, for example, a Rigid 10K grade that boasts 88 MPa ultimate tensile strength and a heat deflection temperature of up to 238°C (0.45 MPa), and a Flame Retardant Resin that has certification for UL 94 V-0 at 3 mm thickness.
3D Systems has taken the same approach, and points towards the Figure 4 platform as a key enabler of its progress on the materials side. The Accura AMX Durable Natural is highlighted by 3D Systems Technical Fellow Marty Johnson as a material that, because of its 80% elongation at break and 64 joule per metre impact measurements, is suitable for tooling, jigs and fixtures applications with property deviations less than 10% over eight years for indoor applications. Its flame retardant grades – Accura AMX Tough FR V0 and Figure Four Tough FR V0 – are flame retardant at 2mm thickness with property stability for up to five years.
Nexa3D, meanwhile, offers materials like the xPRO1100-Black which features a Shore D hardness of 84, tensile strength of 71 MPa and heat deflection temperature of 112°C (0.45 MPa). Among BASF’s line-up is the Ultracur RG 3280, with its heat deflection temperature of >280°C and high stiffness of around 10 GPa.
BASF’s entry into the market through its AM Solutions business was a validation of the additive manufacturing industry. This chemicals giant is so used to having clients work at such high volumes, its minimum order quantities would be a tough ask for most users of AM to match. So, for a company like that to see opportunity in AM spoke volumes. Yet, having operated in the space for coming up to a decade now, the company speaks of a change of mindset when working with AM clients, and still sees prototyping and product development applications as the driving force on the resin side of its 3D printing business.
“DLP technology is evolving, and SLA technology, yes we are going to applicationspecific, but from what I’ve seen in the market the majority are still using it for
prototyping-type applications or sacrificial parts,” said Meisam Shir Mihammadi, Business Development Manager at BASF AM Solutions. “You’re making your part, it has to be accurate enough or good enough, it gets the job done.”
That’s where the industry stands today, but there is motivation in each of these companies to push the envelope with materials development and continue opening the doors to production applications. After all, that’s where the scale is.
“It’s no secret,” Johnson said. “How do we get into more low-volume production, bridge production, how do we get in to help the production driven customers? How do we get in with your service bureaus so that they can do low volume production? How do we get to the things that help you to that full solution?”
Those are some billion-dollar questions. And it’s a case not only of technical proficiency, but business case too. It’s not just what the machines can handle and what the chemists can come up with, but what businesses can afford to do. Because developing materials is one thing and having them qualified, certified or verified is another, but who pays for those processes at the front end is a dilemma.
Shir Mihammadi reckons it’s the biggest hurdle when discussing how the AM industry can deliver more high-performance materials. He used application-specific materials, something many in the industry have called for, as an example.
“The demand is there, and we have that manpower, it’s just usually those markets –if you’re going to application specific – take longer to develop the material, and who is going to pay that development cycle cost is always the question. If the business case is not there, or there isn’t confidence, it’s always going to be hard.”
“Who is going to pay that development cost?”
Tuning chemistries to suit a specific application is fundamentally a good idea on paper, but a manufacturing company is always going to want assurances on the volume it can guarantee before undertaking a potentially lengthy and costly development process.
For 3D Systems, a company with over 30 years in the game, it’s a case of speaking to a broad range of customers and truly honing in on the properties required. At Nexa3D, meanwhile, it points to its hybrid approach that dips into its internal expertise and that of the likes of BASF.
“We have an outreach to a lot of customers and we funnel that back in and start looking at how we take those requirements and satisfy the main customers that we’ve got, because we know there’s people that are after those materials,” Johnson explained.
“The ability of having this hybrid approach [allows us] to collaborate with everybody, piggybacking on the R&D investment of the likes of BASF and Henkel, and periodically where we see an interesting niche that is not being currently fulfilled, we will formulate it ourselves,” Nexa3D CEO Avi Reichental offered.
The open vs closed approach to material development and availability is long-held debate in the additive
manufacturing industry. Nexa3D and BASF highlight the pros of knowledge and risk share that comes with the open mindset, while 3D Systems and Formlabs will note how their less collaborative efforts give them control over the development process. Reichental, who has experience of both models, notes how a closed approach can ‘reinforce what you can do, but not necessarily what you can’t do,’ but Kyle McNulty, SLA Product Lead at Formlabs, believes: “Formlabs has a distinct advantage of being one of the only vertically integrated companies in 3D printing. We are formulating and manufacturing our resin in-house, and have direct capacity to quickly scale up innovative new formulations while controlling costs.”
Whatever your opinion on the approach, that some of the biggest names in resin-based 3D printing are confident of their capacity to deliver high-performance formulations is encouraging for users of the technology.
At Formlabs, the focus continues to be on improving durability, temperature stability, tensile strength, flexural strength, and impact resistance to enable more and more end-use parts. 3D Systems is along the same lines, but also seeks to emphasise its expertise in print process and how the company can work with customers to find the right combination of material and parameters for their application. For BASF, its looking to improve things like shrinkage control, sustainability, and ensuring that, for example, clear materials stay clear for longer. And Nexa3D has its sights set on ‘probably the single most obvious gap out there.’
“Temperature plus toughness,” finished Nexa3D COO Kevin McAlea. “We have some tough materials today in our industry, and they’re very useful, and they’re among the best-selling materials that we have, but there are temperature limiters of perhaps 70-80°C. There are a lot of opportunities for a tough material that gets you into the 100-150°C range, whether it’s automotive, whether it’s eyewear, a whole host of applications. We can’t quite do that today. That’s one of the trade-off s that we are trying to overcome.”
Exhibiting at TCT 3Sixty: 3D Systems Hall 1 | D2
Nexa3D Hall 1 | D30
Formlabs Hall 1 | D50
BASF Hall 1 | G10
Abold piece of orange plastic furniture inside KraussMaffei’s Additive Manufacturing Tech Centre in Munich stands as an indicator as to how the plastics processing company is approaching its AM offering - where it makes sense.
The full-scale 3D printed meeting hub, complete with functional desk and seating, was extruded into existence following demand from staff who needed a quiet place to work amid the bustle of its AM development and services. But it also served as an internal demonstrator, and validation of its polymer 3D printing productivity. The other big motivation was to start a conversation, “food for thought,” around what can be done with large-scale AM, and one that will continue to reverberate at TCT 3Sixty this year where KraussMaffei, along with its meeting pods, will exhibit for the first time.
“We are offering products and services across mainstream technologies from injection moulding to extrusion, and the latest one is additive manufacturing,” says Rolf Mack, KraussMaffei’s Vice
President Additive Manufacturing, of the company’s practical approach. “This brings us a unique position to actually consult the customer on the best matching technology for their needs.”
Last year, KraussMaffei celebrated its 185-year history, which found its footing as a German maker of locomotives. By the 1950s, the company would enter a new industry, plastics, where it would quickly establish itself in the development of injection moulding machines and plastics machinery. In 2022, another emerging market, which KraussMaffei had watched slowly develop in parallel to its own polymer activity over the three decades prior, was beginning to materialise.
“In the last 20 to 30 years, additive [manufacturing] has established itself to become the gold standard for rapid prototyping and small series production,” Mack explains. “I believe the market matured and the judgment of KraussMaffei was, at the decision point to enter the market, that we are on the verge [of becoming] a widespread adopted technology.”
KraussMaffei recognised that an AM solution, engineered to deliver reliability and commercial viability, offered “big potential for growth."
At K Show 2022, the company declared it wanted to be a part of ‘opening up additive manufacturing technology for industrial production.’ It introduced two machines, the powerPrint and precisionPrint, based on plastic granulate fused deposition and stereolithography technologies, and designed to meet optimum cost per part and quality assurance whether printing prototypes or parts in series.
“It's not only about the system or the machine,” Mack said. “We are having an end-to-end approach and we are application focused to ensure we have this good fit between the tool and the specific use.”
To KraussMaffei, ‘end-to-end’ means design optimisation, exploiting AM’s design freedoms and understanding its limitations; right through to post-processing, finding the best milling parameters to turn large-format near-net shapes into finished parts with the required surface quality.
“We are still a manufacturing company of machines and systems so we put particular focus on ensuring that we get absolute process control when printing,” Mack says. “We want to have reliability in terms of quality, but also ensure when we are printing a part the first time, there's a good part coming out, and therefore you need to precisely control the printing process. We accomplish this with a heat-resistant build chamber, extensive sensorics and a thorough qualifying process.”
KraussMaffei perhaps knows better than most that in order to be successful, AM production systems need to become more like other industrial technologies. It knows this because it has decades of experience designing, manufacturing and servicing industrial machinery.
“This was an excellent starting point and based on our experience across the technology, we hold fundamental and widespread knowledge about how to process polymers,” Mack says. “We saw a strong fit and matching this market opportunity and our capabilities together to make an offering and push the adoption in the market.”
“We want to raise the bar, day by day.”
As the AM industry has developed, the entry of known companies, from household technology brands to chemical giants, has ratified the notion of AM as ‘the next big thing.’ But KraussMaffei, according to Mack, is not interested in hype. Trust, on the other hand, is paramount, and Mack acknowledges that the AM industry is still reeling from the overpromises that were made over the last decade.
“I think it's essential to make clear what is the best fit application for the technology and its capabilities, but also clearly state what cannot be done at this point of time,” says Mack. “We are still in an evolution. It doesn't mean it cannot be done in the future, but it's important, I think, to build the trust in AM and our solution first. It's like a tool. It's for a specific purpose. We are discussing an industrial grade solution to enable mass adoption and there's somehow still the narrative going around that AM can solve it all and I believe this is just not the case. There is not something like an AM Swiss Army knife, which can do it all.”
But KraussMaffei is confident in its offering. Part of that confidence has come from maintaining its ethos that the first part that comes out of a machine must be right, but also from spending the last two years immersed in the AM market, working with existing customers in sand casting, tooling and pipe and fitting industries, to help them understand where additive can add value.
“Since we have become active with additive, we are getting requests from our customers, from injection moulding, from extrusion, and from other areas because they see the opportunity now to address certain demands they were not able to do in the past,” Mack explains. “For example, our injection moulding customers, they are looking for volume business, and if there are small volumes, they were not able to address it because it was not commercially SHOWN:
viable. Now we are offering something to them where they can make a commercially viable offering to their customer.
“Injection moulding, extrusion and all toolbased have a huge advantage. It's about scale. It's about volume, but there's also a certain lead time related to it. If you want to try a new design, additive is perfectly suited to do that. It’s not one way or the other. We are seeing that we can optimise across technologies and this is always founded in our experience that we can consult and make a good recommendation to the customer, which technology or combination best suits their demand.”
Since commencing sales, KraussMaffei has increased the productivity of the PowerPrint by about 50% by optimising its output process control, and is also ramping up its service business capacity to meet demand. Its first sold systems are set to become operative soon, and Mack says the company expects “many more” in the coming weeks and months.
“We want to raise the bar day by day, week by week, year by year,” Mack says, and that means continuing to explore large-scale applications where additive
is the best fit, and doubling down on those drivers of reliability and commercial viability to ensure AM is at the same level of already established production technologies.
“We definitely entered a market with the ambition to become a market leader with our PowerPoint solution,” Mack concludes. “Obviously this will not fall into our lap so we need to now actually live up to the promise we made with this reliable, commercially viable solution. Within the next five years, it's all about bringing the maturity and the productivity of the solution on a level we are used to in injection moulding and extrusion.
“The potential is clear. We see the demand, and our ambition is unwavering. We aim to become the most reliable and commercially viable solution for largescale additive manufacturing, driving the mass adoption of this technology.”
KraussMaffei will exhibit at TCT 3Sixty: Hall 1 | C40 & C49
It has been almost ten years since Todd Grimm stood up on stage at TCT Show and encouraged us all to ‘embrace the mundane.’ Gesturing towards manufacturing aids like jigs and fixtures, and tooling, his call went against the grain of the 3D printing projects that were otherwise filling up keynotes in the hazy days of 2014.
Embrace it, people did. Cutting guides and work holding devices might seem ‘boring’ but their impact has been far from it for large companies like Volkswagen, L’Oreal, and Heineken, which have reportedly saved substantial time and money over the last decade by printing these often-overlooked applications. But are they overlooked or did the boring just become, well, normal?
Industry consultant Kevin Ayers believes tooling to be one of AM's most neglected applications. Instead, he thinks these parts should represent around a third of the technology’s applications by volume. According to the 2023 Wohlers Report, jigs and fixtures made up just 7.4% of AM applications worldwide, while end-use parts counted for just over 30%. That’s great news for the march towards production applications but it also means there is likely a lot of low hanging fruit that just isn’t being picked.
“While we have made tremendous progress towards printing [tooling, jigs and fixtures], I still see a huge opportunity,” Luis Rodriguez, Application Engineer, UltiMaker told TCT. “I say that because I help companies, daily, discover that 3D printing is a viable alternative to traditional manufacturing."
Those companies include the likes of IME Automation, North American Lighting and ERIKS, which have each used its desktop polymer systems to rapidly produce components like packaging jigs, nesting blocks and welding jigs. It was also UltiMaker machines which allowed Volkswagen Autoeuropa to achieve 98% cost and 89% time savings by bringing its tooling, jigs and fixtures production in-house. Though, Rodriguez says some companies face a key hurdle: they simply don’t know where to start.
“If a company doesn’t commit a person to focus on this a few hours a week then adoption will never happen,” Rodriguez explained. “UltiMaker tries to make this easier by creating an ecosystem of hardware, software, materials, and services that just work. We don't want engineers to waste time tweaking, we want engineers saving time and making money with our printers.”
WORDS: LAURA GRIFFITHSOne of the biggest barriers to AM adoption in general is often application discovery, and fundamental learnings from low-risk applications like jigs, fixtures and tooling –additive design considerations, limitations, for example – can be used to influence further adoption in other areas across a business.
“When we assist companies with site scans, we focus on high-gain, low-complexity applications first, leaving high complexity or low gain applications for last,” Rodriguez said. “These are indeed low hanging fruit because they have a big impact in a short amount of time. Why is this? The geometry is simpler, easier to design. The environment they operate in doesn’t expose them to high-temperatures, chemicals, or cleaners. This means we can use standard or engineering grade materials that are easy to print. This allows any company to prove out the technology, gaining confidence to tackle additional areas like spare parts for MRO storerooms/ tool rooms or parts within end-use products can even be re-designed in CAD to not only replace but update and improve their function.”
Florian Reichle, Commercial Managing Director at trickle3D, a Berlin-based developer of software solutions for additive manufacturing, agrees.
“We've noticed a clear trend. Once a company discovers a successful 3D printing application, they quickly realise broader potential for 3D printing in their operations, leading to a 'why didn't I think of this before?' moment,” Reichle told TCT. “FDM 3D printers are getting cheaper and easier to use every day, so it’s easy for the newcomer to achieve ROI from day one.”
“These applications remain a hot topic among experts.”
in the design. To that end, the company has developed software tools that enable users to design their own components. Its fi xturemate tool, for example, simplifies the design process for users, including those with limited CAD skills, allowing them to design custom fi xtures in under 20 minutes. The technology has been adopted by several players in automotive and transport. Ford Motors has automated its design process, taking design time down from 2-4 hours to 10 minutes. This represents a 95% effort reduction and enables those without CAD expertise to design tools independently with a userfriendly interface. Similarly, Audi, which was already using 3D printing for fi xture production, has reportedly been able to design a greater number of fi xture designs for the rollout of a new performance Electric Vehicle, cutting design time for tools by 80%.
"You could say 3D printed fi xtures, jigs, and other tooling are the 'killer app' of 3D printing,” Reichle said. “Process simplification and accurate machining are some of the qualities maintained by jigs, fi xtures and other tools, and these qualities are always in demand.
“The benefi ts are clear: Compared to traditional manufacturing, lead times are shorter, and there’s more control over the entire process, leading to better productivity. It also enables production staff to refine the tools they use, improving aspects such as ergonomics.”
Similarly, Heineken, which trialled Ultimaker S5 printers in its Seville plant for a year, was able to reduce costs by 70-90%, and decrease its delivery time by 70-90% by designing and replacing old parts with new optimised designs. Meanwhile, UltiMaker’s Method X and Method XL 3D printers have been used by IME Automation to produce numerous parts for its systems, including jigs, fi xtures, and end of arm tooling. With UltiMaker's recently launched Factor 4 system, the company is choosing to focus on light industrial applications, which includes functional prototyping, manufacturing tool and bridge parts in production operations.
“Every single application has a return on investment calculation,” Rodriguez said. “For 3D printed applications we analyse lead time and cost. How fast can we print this part and how much does it cost to produce? When pitted against traditional manufacturing, ordering lead times, and minimum order quantities, 3D printing applications every time, especially with low quantities. We say that with an UltiMaker on your production floor, you have your own in-house production. You are ordering from yourself, getting a jig, fi xture, spare part in hours vs weeks and for a fraction of the cost.”
The hopeful end game of any generally hyped-up technology is that it gets to a point where it’s so widely accepted, it’s simply not worth talking about anymore. The word
is out, and these applications are evidently being implemented by brands big and small, but any noise and excitement from the industry seems to favour those applications in end-use parts and serial production. The AM industry talks a lot about maturity, and maybe jigs, fi xtures and tooling have reached it. But if AM overall is still only scratching the surface of possibility, and jigs and fi xtures currently represent just a small fraction of that adoption pie, new users may risk missing out on key low-risk, high-value opportunities that could then set further applications in motion.
“We often say that complexity is free, but that doesn’t mean it has to be complicated,” Rodriguez concluded. “While there is a time and a place for finite element analysis, topology optimisation, or generative design, the simplest of brackets can have a tremendous impact for any production environment. Every company, no matter the size or budget cannot afford to have anything in the production line down.”
Reichle added: “Any company focused on success aims to enhance efficiency and cost-effectiveness, and adopting 3D printing for production tooling offers an easy implementation with immediate cost savings. While it might appear that these applications have faded from regular discussion, they remain a hot topic among enthusiasts and experts.”
Born out of a decade of pioneering research into Wire
Arc Additive Manufacturing (WAAM) by a team at Cranfield University, WAAM3D, a UK-based developer of large-scale metal 3D printing technologies, has spent the last seven years developing and commercialising an AM process that is geared towards the manufacture of largeformat metal parts for aerospace and heavy industries. Filomeno Martina, CEO and co-founder of WAAM3D, talks to TCT about WAAM3D’s unique capabilities, creating value in supply chains, and an upcoming launch.
TCT: Can you remember the first time you saw 3D printing or the first time it clicked with you?
FM: I was a double degree student at Cranfield and I wasn't particularly excited by any of the group projects that had been offered to us. In fact, it was our individual master's thesis project and I ended up walking past the lecturer, and he had this metal artifact on his desk.
It was a twisted column, made by WAAM, as I then found out. I was captivated straight away. So, even though I was in Cranfield to do a master's in production, I ended up doing my thesis on the very first trials of titanium deposition using plasma, which is one of our signature features. That was 14 years ago, and I've never looked back.
TCT: How did WAAM3D come about?
FM: We were born in 2018 as a Cranfield University spinout company to create a commercial supply chain for the process which Cranfield had been investigating really since the early 1990s, but definitely with renewed vigor since Stuart Williams, who is still the head of the centre and one of the founders of the company, joined Cranfield around 2006.
We were doing a lot of high-profile demonstration work with a bunch of aerospace companies, but at that point in time there wasn't any kind of commercial provider, so we set out to create value in our customer supply chains, leveraging the WAAM process.
TCT: The UK is known for its AM research, but has a bit of a hard time when it comes to translating that into business. WAAM3D managed to take that leap. How challenging was that?
FM: If we compare the approach that the UK takes versus the US, there are some differences in the way spin outs are managed, but the UK is getting better at that. The big problem that we've had, and I think a lot of other companies will face in the UK, is the much smaller funding pots that we can access compared to other countries, and the fact that in the eyes of a VC type of operator or a private equity firm, at the end of the day, we
are just one of the many opportunities that they will test. We've been very lucky because we have a partner in Accuron Technologies that has been supporting us since the very beginning and with several subsequent cash injections. They are a corporate venture, so they've got much more patience than other investor types. And at the same time, they see a use for our technology in other companies that they have in their portfolio. So the partnership is being delivered over several dimensions.
On top of that, you have to have a clear understanding of what the future holds. The market may not be aware of their needs, or they may be aware of their needs, but the product must serve a clear purpose. I think in 3D printing, for a long time, there was a lot of debate on where the technology could actually be used and could deliver its full potential, and I think by now, over the last 15 years, we've got a pretty good understanding of what that means.
TCT: So why WAAM? What is it good for?
FM: From the point of view of a technology in a production environment or in manufacturing operations, you must be able to demonstrate a way or two, or as many as possible, to create economic value for your customer. And when we look at the way this can be manifested in one, we've got things that can go from prototypes to serial production to supply chain shortening. There's quite a lot of boxes that
can be ticked. And this, in terms of the total addressable market, I believe, is a much bigger share compared to other processes which are of course limited in terms of the size that they can really target. But with WAAM, as the build rates keep growing, we are being asked to look at parts that are much bigger, much more complicated, in a growing range of materials.
TCT: Wire arc additive manufacturing seems to have gained more traction recently. Why do you think that is? And how do you remain competitive?
FM: You have a basic technology, which, at its core, is based on fully off-the-shelf technological elements. Really, that's part of our own narrative. If you go back to the kind of academic publications that we were doing in the middle of the 2000s, late 2010s and so on, we always advocated for the lower barrier to entry.
Our key differentiator is really how we've been able to take those off-the-shelf components and add a bunch of newly designed bespoke sensors, safety devices, control, and to make the machine a lot more capable, underpinned by software, which we've been developing over the last 15 years now. Because back in the day, you have the robot and you have the power source, but we had no means to actually program it. So, we started from there. Then we created a bunch of algorithms to calculate processes automatically. The layer height not being fixed, actually getting the geometry right is where we take a lot of responsibility as a supplier of machines and technologies by adding algorithms that do the calculation automatically for you, for a bunch of different materials, for a bunch of different geometries, and then obviously the control system.
Really do your due diligence, make sure you come prepared from a technical point of view. I think, like all new technologies, you have a bunch of firms that really know what they are doing and others that are sort of riding the hype and the marketing excitement. Sometimes it's tricky to distinguish between the two groups. The only way to do that is to understand the subject matter, and understand that 3D printing is just another tool in the arsenal of the modern engineer. It's not a panacea for all problems in manufacturing. It needs to be used tactically and cleverly.
We're trying to push ourselves as a slightly premium provider, with machines that can be customised to suit all budgets, capabilities, but on the higher end range of the of the specification and we've got some pretty unique features, the least of which that we have been talking about for the last year, this new high productivity WAAM variant which moves 15 to 16 kilogrammes an hour, which is something that we have patented, and that's unique to us.
TCT: In your 14 years in the industry, what is one thing that you think will be useful for anybody new to additive to understand now that would save them a lot of pain and a lot of time in the future?
TCT: WAAM3D will be at TCT 3Sixty on 5-6th June. I hear you’ll be launching something. Can you give us any hints at what that may be?
All I can say for what's coming at TCT 3Sixty this year is we're going to show and release something new on the hardware side, which will probably be seen by our friends out there as a bit of a departure compared to what we've been traditionally associated with.
There'll be some more teasing happening over the next couple of weeks on social media, but if you want to see what's new, you've got to be at the show in June.
This interview has been edited for brevity and clarity. Listen in full on the Additive Insight podcast.
Exhibiting at TCT 3Sixty: Hall 1 | G50
Sam Davies on how 3T AM is working towards its Net Zero goals as it continues to scale its manufacturing output.
Drop the mic, exit stage left. Have I convinced you?”
3T AM CEO Dan Johns has stopped speaking. For now.
He stands in the 3T AM production facility, not on a stage and not with a microphone – yet – but he’s doing a lot of convincing. Johns has already spent a couple of hours articulating why 3T considers additive manufacturing as a tool for outputting billets rather than parts, and now his attention is turning to how the company will achieve Net Zero status by 2032.
But before he continues, a pit stop to make sure his audience is keeping pace. Is it making sense? Are there any questions? Do you believe?
Of course, none of that really matters, so long as Johns, his colleagues, and 3T’s customers are on the same page. And it seems, such is the health of the company’s books these days, that they are. Johns freely admits that he’s no carbon accounting expert, but he won’t ignore what’s working.
The phrase Net Zero followed by a number in the relatively early 2000s is a common goal in the 21st century for companies and countries alike. The magic number for the UK, for example, is 2050. For 3T AM, it’s 2032 – ten years on from the new management’s first year at the helm of the company.
Ten years, it was felt, would be a good runway. Far enough into the future for it to seem realistic, but soon enough to focus minds. “We’re not doing it because of external forces, customer directives, legislative targets, we’re doing it because we believe in it,” Johns says. “Now that the legislation is consolidating and customers’ CSR and ESG agendas are strengthening, it has become a perfect storm.”
3T AM has seen staff – whether they’re 30 minutes into their career or 30 years – fully engage with these efforts. Meanwhile,
clients like Rolls Royce are said to have noted how, merely by having a vision, 3T AM is ahead of many of its other suppliers when it comes to achieving Net Zero.
That vision is being enacted already. From the installation of LED lighting to the incorporation of renewable energy, to the electric van, to its lean manufacturing philosophy, 3T AM is already making strides towards its 2032 goal.
Metal additive manufacturing technology is proving quite important to those ambitions. As documented in the previous issue of TCT Magazine, earlier in his career, Johns commissioned studies into the potential of additive manufacturing to deliver reductions in mining, feedstock, and machining. One study assessing the additive manufacture of an Airbus A350 bracket found three times less of the former, thirteen times less of the latter, and five times of the one in between.
Johns has now applied the same maths to the 10,000 components 3T AM is contracted to manufacture throughout 2024. If each of those components was made the traditional way, machining from a billet of material, 3T AM would create 45,000 kilogrammes of waste. Using AM to produce a billet at near-net shape that will then be machined? It’s just 1,000 kilogrammes. In terms of mining, it’s 13,000 tonnes of rocks that need to be extracted compared to 45 tonnes.
“I’ve normalised the actual mass of the parts to standardise it to create a model, I’ve used that same maths and scaled it,” Johns says. “When we start to look at it through that lens, it’s just bloody obvious.”
Metal AM is one of the foundations of 3T AM’s approach to sustainable
manufacturing at volume. In the years since the BEAMIT acquisition in 2021, the company has implemented a three-pillar strategy that has seen it build out something of a one-stop shop that encompasses the core elements of the manufacturing value chain post-mining. It has then sought to digitise, developing a digital twin of the entire factory, and automate processes as much as it can –when it does its breakdowns, labour amounts to less than 10% of the cost of a part.
These pillars will ensure many things – one of them is consistency, which will be essential for the company to deliver on its Net Zero 2032 ambitions. Data capture and data analytics are also going to be important facets, so 3T AM is in the process of applying energy monitoring technology to every piece of equipment involved in the manufacture of components, from printing through machining through inspection. This will allow each piece of machinery to be audited, with 3T AM able to first monitor how much energy will be expended as parts move through the workflow, converting that into kilogrammes of CO2 per part, and second, to hopefully be able to put a Net Zero digital certificate against every part that goes out the door.
“That, in the end, is the vision. Every part net zero,” Johns says. “Our consciousness about this is about setting the sustainable manufacturing standard. That’s it. Our mission is to be net zero by 2032 – and as a consequence of the success we’re having – and be greater than 150 million [GBP] in revenue. The reality is, I never have visions or missions around revenue, but I’m not the only one who sets the vision and mission, I work with my team, and we created a purpose. We’ve instilled our values into 3T. Net zero is the focus. And if we get that right, the revenue comes.”
What does net zero really mean, though? In essence, it’s the balance between the greenhouse gases that are produced and the greenhouse gases that are removed from the atmosphere. In manufacturing, to produce anything with zero emissions will be a tough ask, so it’s instead about doing as much as you can to reduce the carbon value of a part and off setting the rest via a carbon exchange programme.
3T AM has recently carried out a study on a part that was previously manufactured the conventional way and now leans on additive
manufacturing. The original component tallied 106 kilogrammes of carbon per part. Once additive manufacturing was incorporated, that came down to four kilogrammes per part. A 102kg per part reduction, which would leave just four kilogrammes to be off set. And this is with further improvements to 3T’s lean manufacturing practices still to come.
“This is where we start to know that we are going in the right direction,” Johns says. “Anybody in manufacturing needs to be buying AM printers and getting into this. If you don’t, you’re not going to be in the future. It’s as powerful as that because the corporates are going to be challenging their supply chain strategies and they’re going to hit something called Scope Three. Scope Three is having to have net zero through the supply chain. If you’re a supplier in that supply chain and you do not have a net zero agenda or you’re not doing the things that help achieve carbon emission balance, they won’t use you anymore.
“If companies like us don’t figure out how we’re going to demonstrate that we can reduce our carbon emission, we will end up with a carbon tax and therefore prices go up, and it goes to the customer. So, either the customer pays it, or they find somebody else that’s doing it, and then we’re out of business. You have to future-proof yourself because this is coming. And it’s coming really, really fast.”
Eight years ago, a spirit of innovation and practical problem-solving is what President Barack Obama described as essential if the challenge of climate change was to be taken on before he performed what may be the most famous mic drop ever at his final White House address.
Eight years into the future and Johns will be hoping such spirit has seen 3T AM reach the kind of milestone that Obama was calling for. The kind of milestone that is required for the future of the planet, of manufacturing and of business. The kind of milestone that Johns will advocate when he picks up the microphone as a keynote speaker at this year’s TCT 3Sixty.
Dan Johns will deliver his keynote presentation at TCT 3Sixty on Thursday June 6th, 2024. Register at TCT3Sixty.com.
Exhibiting at TCT 3Sixty: Hall 1 | D9
In the dynamic world of 3D printing, staying ahead means not just keeping up with current trends but pioneering new technologies. At IPFL (Industrial Plastic Fabrications Ltd), our commitment to innovation is reflected in over 55 years of excellence in bespoke plastic manufacturing and a noteworthy 21-year journey in additive manufacturing (AM). Founded in 1969 and introducing our first 3D printer in 2003, IPFL has remained at the forefront of the 3D printing industry.
Our journey began with investments in Polyjet technology and rapidly expanded to encompass Selective Laser Sintering, FDM, Stereolithography, and Multi Jet Fusion. Most recently, we've embraced the groundbreaking Projection Micro Stereolithography (PµSL) from Boston Micro Fabrication. With a resolution as fine as 10µm and 2µm, these micro 3D printing solutions allow us to deliver unmatched detail and precision, which are
indispensable in applications ranging from microneedle arrays and microfluidics to complex components in medical devices and electronics.
Adam Bloomfield, our Head of Additive Manufacturing, emphasizes that "our wide scope of manufacturing services serves a huge range of industries. We get a lot of custom because of our versatility." This versatility is a testament to our broad portfolio of manufacturing equipment and our unwavering commitment to regularly invest in new solutions.
IPFL’s prowess particularly shines in the field of micro 3D printing. "It keeps us evolving," Bloomfield notes. "We constantly have new technologies becoming available to support our customer requirements." At IPFL, we're not just adapting to changes;
we're creating them, leading innovations that set new industry standards.
This year at TCT 3Sixty, we are highlighting our investment in PµSL technology, which uses UV light projection to cure liquid photopolymer resins layer by layer, forming high-quality parts with exceptional detail and accuracy. IPFL were early adopters of the micro 3D printing method as the first bureau in Europe to add the 10µm system to its portfolio and now the only service with both the 10µm & 2µm systems. The introduction of PµSL has expanded our capabilities in microfluidics, where we integrate microfluidic channels into medical or drug testing devices as a single, seamless part. This has developed from our advanced microfluidics work in diffusion bonding.
Our early adoption of the MicroArch S240 and the subsequent integration of the MicroArch S230 2µm system from BMF's series into our workflow, makes us the only service provider in Europe to operate at these resolutions.
This unique capability allows us to undertake proofing and development work that transitions into batch production for unique pieces that can't necessarily be produced in any other way.
Looking to the future, IPFL is committed to advancing our technology and expanding our capabilities. Whether it's through the continuous improvement of our existing technologies or the pioneering of new ones, our goal is to ensure that our clients always have access to the cutting-edge solutions they need to stay ahead.
Innovation, precision, and versatility—these are the pillars that define IPFL in the world of 3D printing. As we celebrate over two decades of additive manufacturing expertise, we invite you to explore how our advanced micro 3D printing services can help bring your next project to life. With IPFL, you're not just building layers; you're building the future.
Visit us at TCT 3Sixty: Hall 1, Booth E35 between June 5-6, and learn more at www.ipfl.co.uk.
TCT 3Sixty is the UK’s definitive event for additive manufacturing and industrial 3D printing. On 5-6th June, the NEC Birmingham will be the place to see the latest machines, materials, software and applications, alongside a programme of content designed to inspire, educate and increase the adoption of AM technologies. Here, we bring you a selection of previews, conference picks and Q&As with key exhibitors.
What will SPEE3D be showcasing on its stand at this year’s TCT 3Sixty?
SPEE3D will be displaying metal parts manufactured with our patented cold spray process in four of our approved materials – aluminium 6061, aluminium bronze, copper, and stainless steel 316. We will have information about our printers and case studies of customers who are using our technology to make parts for defence and commercial industries.
What manufacturing challenges is SPEE3D helping to solve?
Our goal is to make manufacturing metal faster and bring it closer to the point of need, so downtime is reduced. SPEE3D’s patented cold spray additive manufacturing (CSAM) process enables our customers to make strong, dense metal parts faster than ever thought possible – in hours and days vs. weeks and months for traditional casting. In addition, our printers are mobile and can be used in the factory or the field for on-demand printing at the point of need, and the process
Through its work with the likes of the Australian, UK and US Armed Forces, what has SPEE3D learnt about the capability of its technology and how it can be applied?
Working with defence led us to develop our expeditionary printer, the XSPEE3D, which is housed in a shipping container and can be easily transported to the point of need. Additionally, we have a complementary unit, the SPEE3Dcell, which is also in a shipping container and has everything required for post-processing, including a heat treatment furnace, a CNC three-axis mill, tooling, and testing equipment.
Defence – like most industries – strives for efficiency and aims to avoid costly downtime. Bringing the manufacturing capability right to
tct3sixty.com
What opportunities do you see in the UK market for SPEE3D's technology? We work with the Manufacturing Technology Centre (MTC) in the UK and recently completed trials with the UK Army with our XSPEE3D and SPEE3Dcell. We see many more opportunities to partner with commercial industries like Oil & Gas, Maritime, and Manufacturing in the UK to help them solve supply chain bottlenecks and innovate new solutions. We hope to have some of these conversations at TCT 3Sixty!
itself is sustainable and does not require extensive training.
the point of need has been a gamechanger for them.
The German pioneer of direct metal and polymer selective laser sintering technologies will be on hand to discuss its latest developments, including the EOS M 300-4 system, equipped with four 400w precision fibre lasers, and Fine Detail Resolution (FDR) technology, which is opening up new application opportunities for delicate structures with very fine surfaces and thin walls. Furthering its recent developments in demanding materials like Aluminum Al5X1 and copper, EOS recently co-launched a UK Centre of Excellence for Additive Manufacturing at the University of Wolverhampton, which will be used for knowledge exchange and research commercialisation activities, with a particular focus on copper.
Formlabs will present Form 4, the latest iteration of its flagship desktop stereolithography 3D printers, for the first time. With the Form 4 –and the dental-focused Form 4B – the company believes it has set a new standard, harnessing a new and proprietary Low Force Display print engine which helps to deliver ‘unmatched’ print quality and print speeds that are two to five times than the Form 3+. The Form 4 machines are also said to achieve maximum vertical print speeds of 100mm per hour and can also deliver up to 40% lower cost per part with 33% lower resin pricing and a 3.5 times higher throughput.
TCT 3Sixty will see the unveiling of ADDiTEC's new Hybrid3, which the company describes as 'a revolutionary marvel' in metal AM. This machine combines two advanced 3D printing technologies— Liquid Metal Jetting (LMJ) and Laser-Wire Directed Energy Deposition (LWDED)—with precise CNC machining. This multi-faceted approach not only enhances production quality but also accelerates production speeds, propelling industries into a new era of manufacturing efficiency and versatility.
The Hybrid3 is designed to guarantee superior accuracy, dramatically reduce turnaround times, and effortlessly handle a diverse range of materials. ADDiTEC believes its integration of cuttingedge technology with meticulous engineering make it a transformative tool for any industry.
HP aims to bring together new systems, data intelligence, software, services, and material innovations to enable users to scale their 3D production with efficiency, precision and repeatability. Since launching its polymer Multi Jet Fusion technology in 2017, HP has expanded its additive offering with new platforms, materials and automation solutions that have been leveraged by companies in automotive, healthcare, sporting goods and more for end use parts in their millions. HP recently announced the launch of its new polymer PA 12 S material in collaboration with Arkema, which is said to offer a reusability ratio of 85%, thought to be the highest on the market.
What can we expect from the Matsuura stand at this year’s TCT 3Sixty?
On the “Additive by Matsuura” stand at TCT3Sixty, visitors can expect to witness the very latest innovations for mass manufacturing 3D printing and post-processing from our portfolio of class-leading 3D printing technologies. This includes Desktop Metal, HP, ROBOZE, DyeMansion and Lumex Avance.
We know Matsuura will be unveiling something special at the event. What can you share with us so far?
Additive by Matsuura is proud to announce the first UK exhibition appearance of an Roboze Argo-500 3D printer, delivering components in a myriad of materials and ushering in the era of customised industrial production with super polymers.
Can you tell us about an application that will be a mustsee for visitors on the show floor?
Live metal 3D printing no longer exists in the realms of science fiction, with Matsuura LUMEX and Desktop Metal it is a commercially viable reality – as we will demonstrate at TCT3Sixty. Designing components in metal for 3D printing that simply cannot be produced by conventional subtractive CNC machine tools is becoming a routine production method for our UK customers.
From your experience providing AM solutions to the UK market, how would you describe the UK's AM opportunity?
Matsuura has experienced phenomenal growth in our Additive business over the past 5 years, so much so that our investment in our state of the art Additive Manufacturing Centre in Leicestershire truly reflects what we see as the continuing growth cycle and steepening investment curve for additive manufacturing technologies at the heart of the shop floors of mass producers of components in the UK.
Nano Dimension will showcase its flagship manufacturing system, application samples and materials at TCT 3Sixty this year. Among the products the company will be highlighting at the event is its industrial-level micro-AM technology from its Fabrica Giga suite. This technology is able to capture the most intricate details of any design and enables the fast and effective production of miniature and complex components, from electronic connectors to moulds.
The company will also present the advanced attributes of its Admatec series for R&D and industrial serial production needs. With a large build volume and the ability to print both complex ceramics and metal geometries, Nano Dimension will show how the Admaflex 300 4D printer can undertake the mass production of silica shells and cores for high-precision casting.
AiBuild software provides flexibility with intelligent automation of the entire additive manufacturing process.
It's flagship AM platform is acclaimed for its advanced toolpathing capabilities and AIpowered interface, catering to both SMEs and Global Enterprises with tier 1 clients in Aerospace, Automotive, Construction, Energy, and Marine across 20 countries.
With an extensive AM platform range and flexibility, the UK-based company says users can push the boundaries, expand their AM applications and understand the parameters that will deliver predictable, high quality outcomes that support high return on investment, accelerated adoption and scalability.
AiBuild collaborates with AM hardware and materials partners to seamlessly integrate the unique properties of these systems and materials into its software, ensuring users experience a fully cohesive AM system.
Backed by first class investors including Boeing and Nikon, AiBuild is ISO 27001, GovCloud certified and won the TCT Software Award in 2023, underlining its industry-leading status.
At TCT 3Sixty, Laser Lines will explore a curated selection of cuttingedge technologies from Stratasys and other partners. Featured solutions include products from...
Stratasys: As a platinum partner in the UK, Laser Lines will highlight the latest advancements, including SAF technology in the H350 printer, along with Origin One, Neo800, and a variety of reliable and adaptable FDM 3D printers.
Post Processing Machines: The latest innovations in post-processing technology from DyeMansion, designed to enhance workflow and elevate final product quality.
Genera: 3D printing systems and post-processing units that have been designed to work together optimised to increase repeatability.
Xact Metal: Affordable metal 3D printing technology from Xact Metal, unlocking new possibilities for manufacturing endeavours.
Ultimaker: Exceptional quality of FDM printing, renowned for its reliability and precision in project execution.
Bentec Ltd will be showcasing products from both Impossible Objects and Prey.
Impossible Objects is a 3D printer and materials company pioneering advancements in the additive manufacturing and composites manufacturing industries. Visitors interested in composite parts with aluminium-like properties at half the weight are encouraged to stop by the stand to learn more.
Prey UPI, meanwhile, revolutionises automated final product inspection, delivering a universal, user-friendly, accurate, flexible, repeatable, and comprehensive solution across various industries.
Central Scanning is the only Artec Ambassador & Gold Certified reseller in the UK and is a leader in its field, providing scanning equipment and related software. It is also part of the Zeiss/GOM #HandsOnMetrology network and can provide sales, training, and ongoing support.
In addition to 3D scanning capabilities, Central Scanning offers a comprehensive 3D printing service utilising inhouse 3D printers from Stratasys, MarkForged, UltiMaker and Prusa. The company can print in a wide variety of materials, including full-colour multi-material printing on the Stratasys J750.
Whether you are looking to purchase equipment or accessories to enhance your own capabilities or to commission 3D Scanning and 3D printing as a service, Central Scanning is a must-visit to assist your engineering requirements.
Kerstar offers a wide range of UK manufactured, ATEX-rated, high-performance industrial vacuum cleaners which are trusted by leading operators in a wide range of industries - including additive manufacturing.
Some additive manufacturing processes can create nonconductive combustible plastic powder dust which must be safely removed once the process is complete. Having equipment in place to effectively clean up dust will help to protect operators from harmful particulate, prevent explosions, maintain machine functionality, and improve product quality by preventing cross contamination.
Kerstar manufacturers a number of ATEX-rated vacuums which are certified for use in Dust Zones 21 & 22. A selection of these vacuums will be on display at TCT 3Sixty where visitors can see them in action with live demos. Experts from the Kerstar team will also be on hand to take any enquiries.
For over 70 years, Ogle has been a leading industrial modelmaking, prototyping and low volume production company. With a human-centred approach, the Ogle team works with customers to bring concepts to reality, utilising a range of processes such as large industrial 3D printing (SLA, SLS), CNC machining, industrial model making, vacuum casting, paint and finishing facilities.
The company supports the design and development process for a wide range of industries including aerospace, architectural, automotive, defence, film and TV, medical, product design and renewables.
From your initial enquiry through to the delivery of models or parts, the team at Ogle has the skills and extensive knowledge to ensure your project is delivered on time, to the highest standards. Visitors will also be able to take advantage of the Ogle consultation process where you can meet with the team to discuss your project requirements in detail.
Dyndrite provides high-performance software tools that give its users the power, freedom and control necessary to deliver next generation additive manufacturing solutions. Dyndrite LPBF Pro is a powerful new application empowering metal 3D printing professionals with previously unattainable speed, part printing capabilities, and cost savings. Unlike legacy Additive CAM software, Dyndrite LPBF Pro provides production-oriented tools, specifically those focused on materials and process development.
What will BMF be showcasing on its stand at this year’s TCT 3Sixty?
BMF will be showcasing its newest printer, the microArch D1025, the first platform in a new hybrid resolution technology series. Powered by PµSL and based on BMF’s new hybrid resolution technology, the microArch D1025 prints in dual resolution in 10µm and 25µm single-use modes and within the same print layer. The microArch D1025 delivers improved builtin automation, which enables greater efficiency – saving time, resources and cost. Delivering the same ultra-high resolution, accuracy and precision BMF is known for, the new D1025 will revolutionise the prototyping and production of parts requiring micron-level precision and repeatability.
What manufacturing challenges is BMF helping to solve?
Since BMF’s inception in 2017, our key focus has been developing and manufacturing micro 3D printing platforms that deliver a faster, more affordable solution to traditional manufacturing methods for miniaturised parts that normally would need to be micro moulded or, in some cases, impossible to produce in another way. BMF’s PµSL technology continues to enable manufacturers across various industries, such as medical devices, electronics, optics, and microfluidics, to develop and produce innovative micro-scale products and components with unprecedented precision and design flexibility.
What opportunities do you see in the UK market for PµSL technology?
The UK has a thriving medical device industry, with a growing demand for customised and high-precision components for applications such as surgical instruments, implants, and prosthetics. PµSL technology can enable the production of intricate and patient-specific medical devices with exceptional accuracy and biocompatibility. The UK also has a wellestablished precision engineering and manufacturing industry, with companies operating in fields like aerospace, automotive, and industrial equipment. PμSL's high resolution and accuracy could be leveraged for producing micro-scale parts and components with complex geometries for these industries.
Finally, the UK is home to numerous prestigious universities and research institutions that are actively involved in various fields of science and engineering. Last year, The University of Nottingham’s Centre for Additive Manufacturing selected BMF as an advisor for an EPSRC grant-funded 3D printing project where researchers are developing a playbook for standardising 3D printing in medtech and life sciences applications. More recently, our CEO, John Kawola, was asked to serve on the advisory board for another project based in the University of Nottingham’s Biodiscovery Institute following a grant to focus on designing bio-instructive materials for translation ready medical devices.
@LERT lab and the University of Liverpool are proud to present project SCAFFOLD (Smart Cooperative Agents For Fabrication Of Large Designs).
This is our vision for a union between swarm robotics and additive manufacturing: Using many robots capable of navigating the object they are 3D printing to remove limitations to size by removing stationary motion systems. These robots will be able to achieve this with minimal feedback and computation by embedding scaffolding in the object.
At our booth we will be displaying the first proof of concept prototype for the system, an FDM robot that can climb on the part that it is printing. This project is still in its infancy and we are eager to interact with industry and academia so that they can help shape this technology and vision from its very beginning, so that it can meet the ever evolving needs of modern manufacturing.
CDG 3D TECH are UK experts and suppliers of 3D printing, 3D scanning, additive manufacturing and post-processing products and services, with over 20 years of experience and nationwide support. Its product offerings include SLS 3D printing with 3D Systems SLS 300 and Sinterit Lisa X, plus vapour-smoothing of parts via AMT’s PostPro SFX solution. The company also offers resin 3D printing via its ProJet MJP and Figure 4 capacity, as well as filament 3D printing from manufacturers such as Fusion, Omni3D and Intamsys. Its binder jetting 3D printing partnership with CONCR3DE, meanwhile, provides an open-source powder 3D printer for technical ceramics, foundry sand, stone, stoneware, and bio for recycling. Post-processing solutions are provided in partnership with PostProcess Technologies, covering support removal, part cleaning and surface finishing, while CDG also offers reverse engineering and metrology services through its 3D scanning capacity.
Micromeritics presents the AccuPyc and FT4 instruments, setting new standards in precision measurement. The AccuPyc ensures unmatched accuracy and efficiency in density determination, while the FT4 offers in-depth insights into powder flow characterisation. Both instruments are meticulously crafted to enhance research, manufacturing, and quality control processes. With precise measurements and user-friendly interfaces, the AccuPyc and FT4 redefine excellence in their respective fields. Join Micrometrics to experience firsthand the transformative capabilities of these instruments. Explore their advanced features and discover why Micromeritics remains the global leader in particle characterisation.
Tri-Tech 3D is one of the UK’s leading experts in 3D printing. Off ering the complete range of Stratasys Polyjet, FDM, SL & SAF 3D printing technologies, as well as One Click Metal, X-Jet and UltiMaker systems, the company serves a variety of diff erent industries including manufacturing, engineering, design developments, automotive, aerospace, healthcare, dental and many more.
Tri-Tech 3D provides a comprehensive service from advice on initial specifi cation and supply of 3D printing hardware to on-site installation, staff training, and on-going product support.
Whether you need precision tooling, rapid prototyping, or production parts, its expert team will be on hand to offer guidance and support at every step, to ensure that you harness the full potential of advanced 3D printing technologies no matter your application.
What will MSA Manufacturing be showcasing on its stand at this year’s TCT 3Sixty?
For this year's TCT 3Sixty show we will be showcasing large format additive manufacturing (LFAM) 3D printing for industrial, engineering, architectural and design/creative sector applications.
That's end-use parts, prototype and proof of concept parts, series production parts, and mould tools from recyclable thermoplastic polymers, many of which are fibre reinforced.
We will be showing prints ranging from marine finished components, high temperature manifolds, tooling applications for the composites and GRP industries, to interior design and decorative items.
You will be bringing some interesting applications to this year’s event, can you share more?
Beyond industrial applications we will have several exciting design led pieces for furniture and architecture.
There’ll be a WILLO acoustic workspace tree plus an MSA printed Bench displayed in the entrance foyer of the exhibition venue. The tree trunk is made from recycled polymer, with oak branches and recycled felt leaves, they’re designed to break up space and absorb noise in working environments. Keep an eye out for
Xenia Materials engineers and manufactures highperforming thermoplastic composites, offering a wide choice of carbon and/or glass fibre compounds as well as ultra-light structural materials based on dedicated thermoplastic polymer matrix, functionalised for FGF (Fused Granulate Fabrication) additive manufacturing.
Xenia offers a dedicated range of materials optimised for LSAM production and high-precision manufacturing, focusing on the mechanical performances while achieving the lightest possible solution. The key properties of these products are high stiffness, dimensional stability, low density, low thermal expansion and high durability.
these as there will be an Instagram photo opportunity to win a special prize with that.
Plus, we'll also be showcasing some materials and finishing processes such as recycled cork, recycled metals, and recycled leather coatings applied to printed plastics, as well as gel coat and paint finishes.
What manufacturing challenges is MSA helping to solve and who are you looking to connect with at the event?
The technology and service we offer as a large format 3D print service bureau/ sub contractor means those without this technology – and that’s most as there are very few large format printers in then UK right now – can access our service and experiment with this amazing technology for applications in their sector, from prototyping to full series production.
LF3D sets the standard for large format additive manufacturing, delivering durability, unmatched speed, and uncompromising precision.
From rapid prototyping to end-use production, LF3D offers solutions that exceed expectations, whether for oneoff pieces or to support a full-scale 3D deployment.
MSA Manufacturing is proud and excited to be offering FLEXBOT LFAM as a cuttingedge 3D print service. This will enable
us to engage and partner in a wide array of projects. For example, in large scale moulded product sectors, outsourcing to finished part via 3D print technology is helping overcome availability of skilled labour, whilst simultaneously eliminating moulds in some instances. Where eliminating large mould tools is not feasible, printing these items reduces time to market significantly. In many cases, circularity is a driving factor in people’s initial interest in the technology.
Amazing things can be achieved with this combination of equipment and the wide variety of thermoplastics available. Now is the time to take the challenge and let your imagination run wild.
What will Arburg be showcasing on its stand at this year’s TCT 3Sixty?
Arburg will be taking part in TCT 3Sixty with two presentations. At the Introducing Stage on 6 June (1 p.m.), we will report on how Arburg has optimised its 750-3X high-temperature Freeformer for larger components and higher build speeds. The second presentation will focus on the reproducible 3D printing of implants made from resorbable and certified plastic granules. We will speak about innovations that hold the potential of revolutionise the way we approach implant surgeries. One of these is the development of resorbable implants. We will also be presenting a wide range of components manufactured using Freeformers and 3D printers from InnovatiQ at our stand B30 in hall 1. These include geometrically sophisticated air distributors for the aerospace industry made from the high-temperature plastic Ultem 9085, medical implants, but also grippers and operating equipment as well as functional components made from new materials and in hard/soft combinations.
Can you tell us about an Arburg AM application that visitors will be able to see on the show floor?
Another field of application that is of high interest for injection moulders are End of Arm Toolings (EAOT’s).
The TiQ 2 is particularly economical and also ideal as an entry-level additive manufacturing solution thanks to its open material system. Of interest to injection moulding plants is the possibility of using this 3D printer to produce individual EAOT’s, which can have resilient suction pads and mechanical grippers made of fibre-reinforced PA and PP, for example, with customised fingers for picking up parts. A recent example shown at our Technology Days in March 2024 were collecting flower pots with a wall thickness of around 0.45 millimetres produced on an electric injection moulding machine Allrounder 720 A. A Multilift V linear robotic system gently removed the thin-walled moulded
parts. The matching gripper, with its particularly lightweight design, was additively manufactured in advance using a hard/soft combination for a precision fit.
What opportunities do you see in the UK market for Arburg's AM technology?
In my view, the UK is one of the most innovative markets for AM technology. Additive Manufacturing technologies have ignited for example a transformative revolution in the healthcare sector. By leveraging advanced materials and design intricacies, 3D printed implants offer tailored solutions for complex cases. However, we are also seeing high demand for precise 3D printed functional parts and components in general. With our broad portfolio for additive manufacturing and injection molding, we offer "the right horses for the right courses" in the field of plastics processing. And many of our customers from the injection molding sector are also becoming increasingly involved in additive manufacturing. We will therefore continue to expand our AM activities in the UK market and take ourselves and our customers to the next level.
What can we expect from the Triditive stand at this year’s TCT 3Sixty?
We will be showing automation on the AMCELL 8300 production centric AM solution and our latest metal binder jetting system.
What makes the AMCELL platform unique?
The patented Automation, our unique EVAM software AM production workflow software.
As you explained, automation is a major feature of the technology. Can you tell us about the demand for greater automation in AM?
As the industry moves to meet production needs, manually handling AM parts has a major cost bearing on part production and prohibit the uptake of AM in many cases. There has never been a greater need to automate AM in order to meet production cost and supply requirements.
Can you tell us about an application that will be a must-see for visitors?
In the food processing industry where product is processed at high speed we supply many components for the production
lines which are quick cheap and easy to replace with minimal stoppage time but also FDA approved for the use within food and Pharma industries. We will be highlighting a number of case studies for Nestle at TCT 3Sixty.
You’ve seen what some of TCT 3Sixty’s key exhibitors are presenting at this year’s event, now it’s time to preview some of the presentations that will be delivered across our conference programme, starting with our keynote speakers and finishing with our editors’ picks from the rest of the agenda.
Manufacturing the Future, Needs You - Mike Curtis-Rouse, Head of In-Orbit Servicing & Manufacturing at Satellite Applications Catapult
Main Stage | Wednesday, 05 Jun 2024 | 10:30 - 11:00
Mega launchers are on the cusp of making getting to space as simple as getting the next train. Moving payload, product, and mass into space is going to be cheaper, faster, and more accessible than ever before. But exploiting the potential of this rapidly growing market is going to need new approaches, holistic and robust manufacturing supply chains, and active engagement from sectors which have focused purely on Earth. Manufacturing in space needs you!
Making the Shift to AM Production to Create High-Value Growth with a Net-Zero Focus - Daniel Johns, CEO at 3T-AM Ltd
Main Stage | Thursday, 06 Jun 2024 | 10:30 - 11:00
In this keynote presentation, CEO Dan Johns will explain how 3T AM plans to achieve its Net Zero targets by 2032 while scaling into serial production applications. The presentation will cover how the company has redefined where AM fits within its manufacturing value chain, how it has built its operational culture around manufacturing engineering first principles, and how it can use additive manufacturing to unlock its sustainable vision.
Digitalising AM Processes to Support Aerospace ProjectsSarah Everton, Manufacturing Engineer at ITP Aero UK
Main Stage | Wednesday, 05 June 2024 | 11:00 – 11:30
In Sarah Everton’s keynote presentation, the Manufacturing Engineer will explain the work of ITP Aero to introduce additive manufacturing technology into their aerospace projects. As it has integrated additive into a series of ongoing projects and products, ITP Aero has identified a number of challenges, as well as opportunities, which Everton will detail in her presentation.
Additive Manufacturing to Reduce Logistic Burden in Austere Environments and Reduce Supply Chain Obsolesce
Alexander Champion, Additive Manufacturing Lead Engineer at Ministry of Defence
Main Stage | Thursday, 06 Jun 2024 | 11:00 - 11:30
In the last of our keynote presentations, Alexander Champion will be providing insights into how the Ministry of Defence is adopting and implementing additive manufacturing technology across the UK armed forces and the country’s allies. Champion will discuss how additive manufacturing can be used to ease challenges in supply chain and logistics, with examples of applications and future opportunities for a series of additive manufacturing technologies.
Register for your free ticket and conference pass at tct3sixty.com
How Many 3D Printers Does it Take to Kill a Polar Bear – Assessing the Cradle-to-Gate Sustainability of 3D Printing - Phil Reeves, Managing Director at Reeves Insight Ltd
Main Stage | Thursday, 06 June 2024 | 11:45 - 12:15
In this presentation, Phil will look at some of the claims being made around sustainability and 3D printing before challenging some of the science - or lack of science - behind this latest marketing ploy. Phil will then discuss what is really involved in assessing the environmental impact of a 3D printing process, from the raw materials that go into making the printer to the hidden waste streams lurking at every corner.
Women in 3D Printing @ TCT 3Sixty: TIPE on Tour – Technology - Olga Ivanova, Director of Applications & Technology at Mechnano; Elena Lopez, Division Manager AM at Fraunhofer; Evren Yasa, Head of AM, University of Sheffield AMRC
Partner Stage | Wednesday, 05 Jun 2024 | 12:45 - 13:30
Our collaboration with Women in 3D Printing continues at TCT 3Sixty with a panel of three additive manufacturing experts coming together to answer the industry’s questions. This year’s theme will be based on the ‘technology’ strand of WI3DP’s annual TIPE Conference, and attendees will be able to submit questions in advance for our panel of leaders across AM materials, research and industrial applications.
Introducing the UK’s Aerospace Additive Manufacturing Strategy - Ruaridh Mitchinson, AM Technology Manager at The MTC – The National Centre for Additive Manufacturing
Partner Stage | Wednesday, 05 Jun 2024 | 11:30 - 12:00
The Aerospace Technology Institute (ATI) defines the technology strategy for UK aerospace aiming to transform the sector through technology and innovation. Recently, the ATI launched the creation of an updated strategy and roadmap for additive manufacturing (AM), led by the Manufacturing Technology Centre (MTC), which identifies the key challenges to wider AM adoption and industrialisation in the UK aerospace sector. This presentation will introduce the new AM roadmap, outlining the key themes, opportunities and way forward.
Futures?
Role of AM
Environmental
Jennifer Johns, Professor of Management at University of Bristol Main Stage | Wednesday, 05 Jun 2024 | 14:30 - 15:00
This presentation draws on academic work and industry examples to discuss the opportunities and challenges around the use of AM to create more sustainable business and environmental futures. It takes two perspectives. First, through the examination of how and where in the value chain/product life cycle of a product AM can be used as a tool to increase its sustainability. Second, via closer discussion of spare part production and the potentially transformative impact on warehousing and logistics.
Sales@3drp.co.uk
01438 487212
www.3drp.co.uk
We've tried 3D printing, it’s rubbish...." Whenever I hear that kind of statement it feels like a dagger right into the heart of what I do. As an independent consultant, I tell people that the only brand I really represent is that of “3D Printing & Additive Manufacturing,” and I want them to have the best possible experience.
You’ll probably already know that 3D printing is just another tool in the manufacturing toolbox and that it needs careful selection. So those people who have had that poor experience have either been sold the wrong technology, oversold the benefits or sold something that wasn’t ever going to be appropriate for what they want to do.
Using the toolbox metaphor, it’s akin to being sold a hammer when what you really need is a screwdriver: being sold a screwdriver on the promise it can build you a house, or being sold a hammer on the promise it can help take you to the moon. Vendors are sometimes complicit. They know the customer needs a screwdriver but what they are selling are hammers and will try to convince a customer that’s the right tool for them!
So, lots of careful work and due diligence is required when it comes to adopting AM and 3D printing to ensure success. I hope that’s where people like me come in, advisors who have no vested interest other than ensuring you see this technology in the best way and get the maximum benefit from adopting it.
So, where are we now with adoption in the UK, especially within industry? In my experience it’s a mixed picture and continues to feel like challenging work.
In my opinion there are some cultural barriers in the UK that I feel hold back adoption. Throughout my forty-year career working in engineering and manufacturing, it feels like short-term thinking is a mindset that exists in a lot of UK industry.
This technology is one that needs to grow over the long term and adopters, just like the stars of reality TV, tend to go on “a
journey” with it. That journey takes time. The way AM fits into a business develops and grows, which runs contrary to the short-term focus I see so often.
I often talk about personas when it comes to adoption. A key persona is someone I call “The Change Agent” who has the foresight to see the potential for 3D printing in a business. Very often this person is someone who is 3D printing at home as a hobby and has an appreciation for what it’s capable of. The other key persona is “The Banker” who needs to release the funds needed for adoption. What ensues is often a battle between the Change Agent, who perhaps has a long-term view, to convince The Banker of the benefits when they only see the short-term effect on the balance sheet.
on a successful trajectory to a longerterm relationship (and reward).
Working with adoption in the UK is not an easy gig, yet I know that it can put people on a path that can grow and scale over time. For that reason, it’s a part of my role that I find very rewarding.
I’ve seen many cases where the case made by the Change Agent is both compelling and backed up with good return-on-investment numbers, yet the short-term approach wins out in the end and the adoption stalls.
Another particular UK handicap is the lack of government support in this area, but as we have no overall industrial strategy at the moment, that’s not surprising. We can only cast an envious eye at the AM Forward programme in the USA that helps assist small companies in particular with adoption.
A further adoption challenge for a technology still seen as fairly new and developing is the number of hoops that a potential adopter will have you jump through to prove its initial use case. Producing endless samples, often free of charge, and lots of cost data seems par for the course. When the profit margins involved are sometimes slender, the amount of upfront effort and cost involved feels out of balance with the rewards.
Adoption is about playing the long game. You have to persevere and hope it puts people
“Careful work and due diligence is required.”
Our patented technology utilizes supersonic deposition to manufacture fast, strong parts suitable for industrial applications using 33% less energy than traditional methods.
The first forward-deployable and groundbreaking robot cell for reactive materials with Laser-Wire DED.
Enabling on-demand production, it effortlessly prints parts from any location, eliminating the constraints of traditional lead times.
Featuring advanced elements such as a 6kW fiber laser, closed-loop controls, and high deposition rates through LDED Technology.
Comprehensive solutions for end-to-end manufacturing needs.
Precision-driven performance through CNC machining, ensuring high accuracy and superior surface finishes to meet stringent tolerances.
Streamlined efficiency by eliminating the necessity to transfer parts between different machines or facilities, enhancing overall production efficiency.
Three cutting-edge technologies: LMJ for unparalleled resolution, LDED for rapid throughput, and CNC for meticulous finishing.