to
Skills
Net Zero
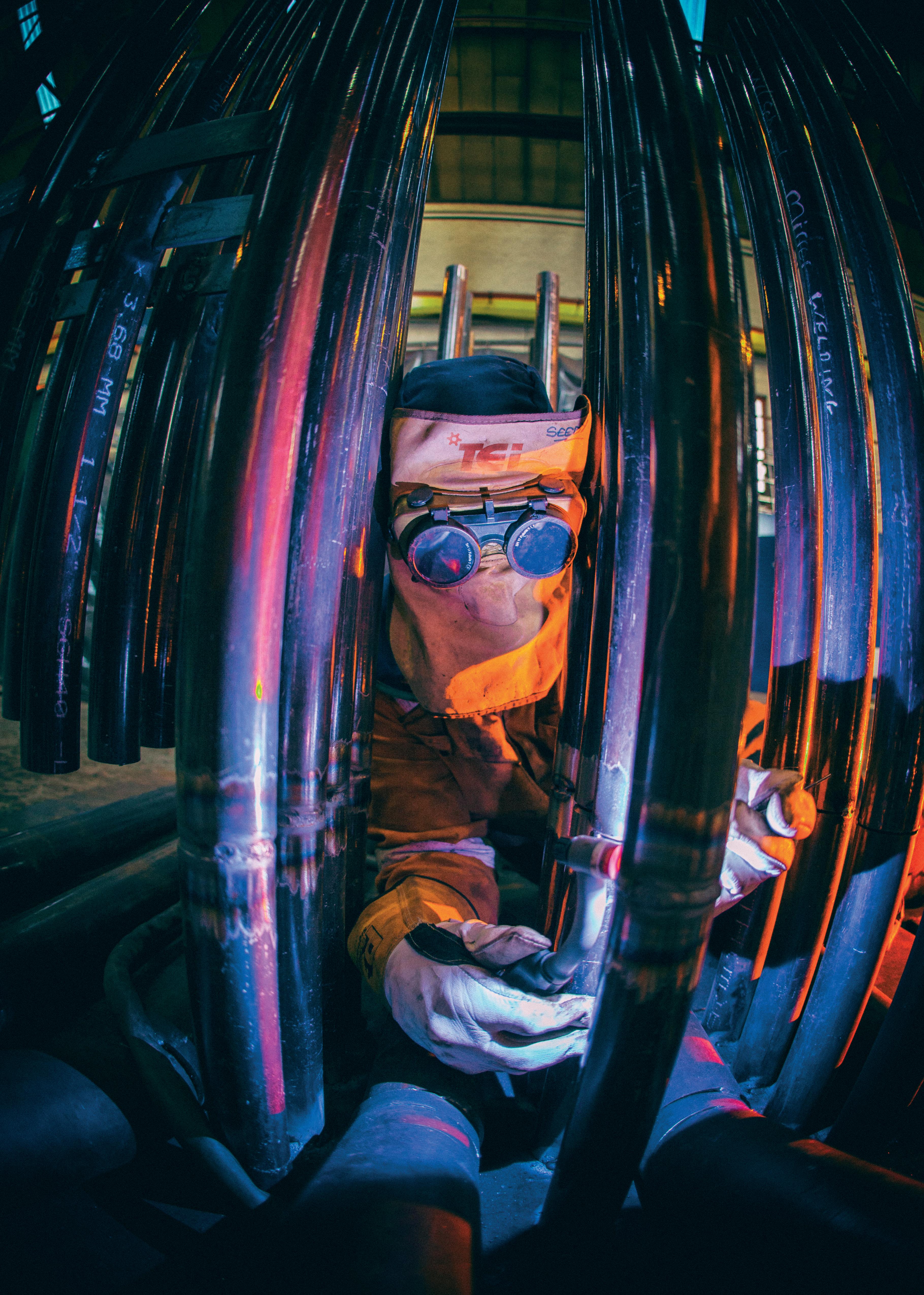
CEO Andrew Schofield
Group COO Joe Woolsgrove
Creative Director Tom Vince
Data & Insights Director Jaione Soga Editor Libbie Hammond
Assistant Editor Mary Floate
Content Editors Daniel Baksi, Alex Caesari, Danielle Champ
Editorial Administrator Amy Gilks
Managing Art Editor Fleur Daniels
Art Editors Paul Gillings, David Howard, Charlie Protheroe, Lee Protheroe
Artwork Administrator Rochelle Broderick-White Sales Director Alasdair Gamble Project Director Philip Monument Head of Client Services Callum Arneil Head of Content Management Adam Blanch Head of Global Media Programs Mark Cawston
Project Managers Lewis Bush, Jo-Ann Jeffery, Natalie Griffiths, Ben Richell, Laura Thompson
Content Managers Mark Cowles, Jeff Goldenberg, Melanie Joyce, Tarjinder Kaur de Silva, James Page, Wendy Russell, Richard Saunders, Kieran Shukri
Media Sales Executives Jessica Eglington, Will Gwyther, Sam Surrell
Marketing Manager Matt Bone
Social Media Co-ordinator Rosie Clegg
IT Support Iain Kidd
Administration Natalie Fletcher, Rory Gallacher, Ibby Mundhir
© 2022 Finelight Media Group
Corporate Head Office
Cringleford Business Centre, 10 Intwood Road. Cringleford, Norwich NR4 6AU U.K.
T: (312) 854-0123 T: +44 (0) 1603 274130
US Office
2240 West Woolbright Road, Suite 402 Boynton Beach. FI 33426 T: (561) 778-2396
Hello and welcome to the October issue of Construction & Civil Engineering We’ve given the magazine a bit of a refurbishment – what do you think of our new look?
This month, our features look at Skills, Net Zero, and Technology – all of which remain at the top of the agenda across the sector. The first topic hones in on talent in Building Control – maybe not an obvious career choice but a pivotal one if we are to build the number of new homes we need.
To achieve Net Zero, the right insulation is critical, and to ensure construction can keep up with future demands, technology such as BIM and AI have to be embraced. Find out our authors’ perspectives inside.
story this
delves into
operations at TEi. Alan Waddington, MD, offers readers an insight into what makes the business tick.
Turn to page 18 to learn more.
lh@finelightmediagroup.com
The Covid 19 pandemic has blown the UK housing gap wide open, with many people suffering from overcrowded, insecure and inadequate housing. According to the National Housing Federation, 8.4 million people in England alone are living in unaffordable or unsuitable accommodation, at the same time, the BBC’s Housing Briefing states 1.2 million fewer homes have been built in the UK than required by the population, a situation that experts say could take 15 years to rectify.
Housing isn’t the only gap we’re experiencing. The construction sector is facing an ongoing skills shortage, which threatens to stall any plans made to accelerate housebuilding. One significant part of this shortage lies in Building Control. Approved Inspectors (AIs), the experts with the ability to sign off a building or a renovation at the point of completion, are decreasing in numbers with no sign of a significant influx of new talent to the sector. This is something that could cause a major bottleneck to the construction and subsequent occupation of these much-needed homes.
Homes constructed in the UK will always require the involvement of building control whether this comes from the local authority or the approved inspector network. As AIs, we act in an advisory capacity to developers and homeowners when it comes to ensuring the house is compliant with all of the current regulations. In a situation where there is a shortage of people with this expertise and qualification, we will begin to see an increase in valuable empty homes that could be used to improve the welfare of vulnerable people.
Will the building control skills gap expose the housing crisis further, or can we build a bridge to a better future? Iain Thomson reports.
At the same time, instead of ensuring property owners make their return on investment, they could instead be facing costly insurance premiums to protect the work at point of sale.
In 2015, the government committed to building 300,000 homes a year by the mid2020s. But this can only happen if building control is able to acquire more skills to the sector. The challenge is that building control is not a leading career of choice for most. More often than not, we find that people’s perceptions of those working in building control is that of an introverted analytical type, only there to cause roadblocks to the success of a project. This is something that the industry must work on changing.
The truth is that building control officers have a vital role to play in the future of the built environment and our housing market. The day-to-day of the role is dynamic, social and significantly influential. Without building control officers and the knowledge that they bring to the table, construction projects will face uncertain futures or even end up being occupied without the correct compliance in place – a risk that nobody should be prepared to take. Understanding that these careers can play a huge part in alleviating the housing crisis could be just the thing to drive a younger wave of people towards a career in building control.
The building control industry needs to take responsibility for changing these misconceptions. It is vital we shift the focus towards it to being about people who care deeply for the future, safety and security of the UK’s housing. In reality there is a true consultative value that building
control offers to the clients they work with. Our role can involve anything from working with architects to plan from the first stages of drawings to completion of the project. It can involve consultation with a homeowner and their builder to ensure that an extension is built to the best possible standards. Or it can be about adding value to a developer to enable them to create more thermally efficient homes to command greater resale values. But this isn’t something that building control can do alone. The wider construction sector should be publicly backing the importance of building control officers, instead of seeing them simply as a hurdle than needs to be overcome.
There is an absolute necessity that housebuilders and developers can ensure safety in their buildings. Without the inspection of buildings by competent, qualified personnel, there is the potential for increased risks and major tragedies.
We as a society need building control officers to ensure the homes that we live in meet the required regulations. We need them to help challenge developers to build better housing and to work alongside architects to encourage them to create sustainable and energy efficient housing. We need them to support the creation of new methods of construction with offsite manufacturers, helping speed up the housebuilding process. And we need them to advise property owners about how a race to the bottom on price could put the building occupants at greater risk.
“ “
Now is the time to advocate the work that building control does, to help grow our industry and build those allimportant houses for years to come
“ “
Building control officers are working on behalf of the final occupants, ensuring they are safe and secure. At the same time, they are protecting the reputations of all the people involved in the project. Now is the time to advocate the work that building control does, to help grow our industry and build those all-important houses for years to come.
It is vital therefore that the building control sector, spanning across private and local authority, works in unity to ensure the misconceptions of the industry are changed. This can be achieved through open lines of communication with educational establishments, ensuring that the next generation can see the opportunities of a career in building control. Both sides of the sector must also invest in skilling up its workforce, creating a ‘one voice’ training method available unilaterally across the sector. The wider construction sector can play its part by creating stronger relationships with building control, establishing them as extensions of their own teams and not seeing them as a roadblock to their projects success. Finally, it needs to come from the UK Government and the newly appointed Building Safety Regulator, who should be ensuring their policy supports competent building control professionals, empowering them to develop their skills, to allow for talent pool large enough to work across the myriad of structures within our built environment.
Iain Thomson is CEO of Assent Building Control. Assent is a wellestablished UK-wide corporate Building Control Approved Inspector that provides a complete solution for all building control services. Founded in 2005, Assent is at the forefront of building control in the UK and has an excellent reputation, offering a very high level of service, building strong long-term relationships with its clients and is dedicated to adding value.
Building for the future with legacy in mind is a major challenge for the whole construction sector. Faced with the ambitious Net Zero target for 2050, the sensible approach is to make the right choices that not only meet but exceed regulatory targets for thermal efficiency without compromising on materials. Simon Storer, Chief Executive of the IMA, explains why a fabric-first approach to design is the way forward and a key measure to reducing heat loss, improving energy consumption, and cutting carbon emissions.
The role of PIR and PUR insulation in achieving energy efficient buildings and a sustainable future cannot not be underplayed. Good insulation is essential if homes and buildings in the UK are to become more energy efficient and sustainable and off-set some of the increasing energy costs and climate change conditions. The fabric-first approach to energy efficiency prioritises insulation within the building envelope, significantly restricting air leakage, which in turn prevents heat loss.
Using PIR insulation with high thermal efficiency will make a big difference between a building’s success or failure and is one of the simplest and most cost-effective ways to reduce energy demand and cut CO2 . The thermal performance of a building envelope makes a significant contribution to reducing the overall building energy usage – so tighter U-values in walls, floors and roofs will help to deliver the standards required.
With lambda values as low as 0.021 W/ mK, PIR insulation is available as boards, blocks and composite panels, and PUR as spray and cavity injected insulation. Performance can be achieved with products that are thinner than many other commonly used insulants. In short, designers can achieve the highest insulation values from the minimum thickness of material, which in turn maximises floor space. PIR insulation products are widely used on residential, commercial and refurbishment projects because of their exceptional insulating properties, high strength and light weight.
Whilst many more affordable homes need to be built to an overall higher performance level to reduce costs and emissions, all homes need to be finished to a much better build quality. We must reduce or better still eliminate the ‘performance gap’ between design performance and what is built.
If the housing stock is to meet long-term performance standards, then we must have more thermally-efficient building envelopes “ “ “ “
This is why competency in installation is vital, because when a high performing product such as PIR/PUR is not installed correctly, the thermal performance will not be maximised and the full benefits not realised.
Contractors need to make sure that not only the levels of site supervision are of a good standard, but the manufacturer’s installation instructions are followed to avoid issues around potential cold thermal bridges and awkward details.
Once the high-quality building fabric has been completed there should be no need to worry about it over the life of the building.
If the housing stock is to meet longterm performance standards, then we must have more thermallyefficient building envelopes, which in turn will result in improved comfort for occupants. Getting the fabric of the building properly insulated should always be the starting point. It is a fundamental step towards achieving the net-zero target as well as compliance with the energy performance requirements of the revised Building Regulations Part L.
By considering the fabric from the outset of a project, it is estimated
to cost just one-fifth of the total cost of retrofitting to the same quality and standard at a later date. Homes should be built that solve today’s challenges and provide long term solutions, as it would be scandalous if homes being built today become the homes in 2050 that need to be retrofitted.
Within the new Part L requirements of the building regulations, all new homes will be expected to produce 31 percent less carbon emissions through a combination of fabric improvements, low carbon heating technologies and PV panels. This 31 percent reduction is the first step, but by 2025, new
housing will be expected to produce 75-80 percent less carbon emissions compared to current standards. Achieving higher Fabric Energy Efficiency Standards (FEES) in specifications will be crucial for housebuilders in order to pass SAP and comply with Part L. Looking ahead to the Future Homes Standard in 2025, boilers might be replaced with air source heat pumps or some other low carbon technology, but the fabric targets of the building are expected to remain. As we have said, getting the fabric right in the first instance, is not only a sustainable approach but also a tried-and-tested way of limiting heat loss within the building.
The enormous challenge of achieving a Net Zero carbon-built environment must be woven into what many are now saying must be a ‘green economic recovery.’ Good insulation clearly has a role to play and by taking the fabric-first approach, specifiers will be taking the direct route to achieving the Net Zero target. ■
Insulation Manufacturers Association (IMA) is the Trade Association that represents both the Polyisocyanurate (PIR) and Polyurethane (PUR) insulation industry in the UK. Its members manufacture rigid insulation that provides around 40 percent of the total thermal insulation market in the UK. IMA’s membership comprises all of the major companies in the industry, including manufacturers of finished PIR and PUR insulation products, as well as suppliers of raw materials and associated services.
Insulation Manufacturers Association www.insulationmanufacturers.org.ukIt’s been 21 years since Steven Spielberg’s film A.I. Artificial Intelligence was released. At the time, many of us watched with disbelief that we could ever become so reliant on technology.
Fast-forward to now, and AI technologies are hugely prevalent across all industries. The construction industry has historically been quite behind with the use of technology, instead relying on traditional skilled tradesmen to do the job.
However, AI is slowly infiltrating the sector with the introduction of 3D printing and bricklaying robots, building information modelling (BIM) systems, intelligent HR systems and much more.
Bricklaying robots built an entire house in High Wycombe in just 33 hours last year and the creators believe that time could become up to four times faster.
So, what does this mean for the industry? Sharing his opinion on the subject, Parm Bhangal, Managing Director for Bhangals Construction Consultants, commented: “In the construction business, it’s all about strategy and planning. We always plan 12 months,
three years, five years ahead and look at how our business is going to evolve
“As part of that forward planning, it’s important to make sure that you are making the most of any opportunity that comes your way. Perhaps you’re a bricklayer, and you could ensure that you are trained on the operation of any new equipment as soon as possible. That way, you’ll be at the forefront of pioneering approaches to modern construction, as they come along.
“It’s important for us to train our workforce on new modern
“Bricklaying robots could mean loss of jobs for a skilled workforce, but I believe there is room for both. Robots are probably doing more straightforward builds rather than technical builds and there is no substitute for well-honed expertise and craftsmanship passed from one
“However, introducing this type of automated technology could speed up a build, provide less waste days and allow more efficiency. And of course, it could be a vital way of combatting the continued materials and skills shortage that the construction industry is now facing.”
▲ Parm Bhangal discussing strategies with the team
Another type of AI which is becoming more prevalent in the construction industry, is building information modelling (BIM). This process imitates the construction process in a virtual environment, meaning an entire project can be scoped and costed before a single shovel of dirt is turned.
This intelligent software modelling process means that architects, engineers and contractors can collaborate on a building’s design, construction and operation, in a more risk-free and cost-effective setting.
According to Dodge Data and Analytics, users of BIM systems report benefits such as an improved ability to manage complexity, improved design quality, reduced errors and reworks, better ability to meet customer and design requirements and increased stakeholder buy-in.
Parm believes BIM systems have been a game-changer for the construction industry. “It’s the foundation of digital transformation within the industry. It means that we go into each project fully prepared and with a comprehensive understanding of scope and cost.
“Quite often, a problem that could have derailed the whole build will be solved before construction work on a project has even started.
“BIM is an absolutely vital piece of AI technology which is improving the way we build across the world. I am confident that we will only see this type of technology become more prevalent in the coming years.”
AI technology can also be used to alter the design itself. Parametric design is the practice of using AI to alter design parameters and achieve staggering design feats. AI analyses
thousands of blueprints as source material for a project, then designs its own concepts with this new knowledge. This can lead to innovative design elements based on ‘best practice’ designs from across the world.
But AI technology isn’t just confined to scoping out projects. It can also help when hiring the skilled people who will deliver these projects. AI HR software supports quality recruitment efforts by analysing applicants, an essential cog in the construction industry machine.
AI technology can also keep a detailed personnel record, enabling the software to predict employees who might be inclined to lead or employees that may be close to leaving. This can inform management’s decisionmaking for taking the appropriate actions to form teams and help employees grow.
The uses of AI in the construction industry don’t end there. It is predicted that technology such as surveillance drones, wearable tech that learns workers’ habits and schedules to personalise safety alerts, 3D printers which detect and repair structural design flaws, and autonomous equipment which perform heavy-duty tasks which are unsafe or unreachable for humans, will all become a more commonplace sight in years to come.
Parm said: “The future uses of AI in the construction industry are countless, and we’re seeing new technologies emerge all the time. I do not believe that this means redundancy or lack of opportunity for an average construction worker. Rather, AI exists to make projects more streamlined, stress-free and safe.
“So what are the downsides? Quite often, the initial upfront cost for purchasing one of these types of AI is prohibitive, and may put many business owners off. Also, some can
be put off by the lack of human intervention. After all, the industry was built on human relations – right from the teams who plan out a building project through to the workers who build them.
“However, we are facing a labour shortage which cannot be underestimated, and AI technology could play a vital part in alleviating those concerns somewhat. I would encourage business owners to do their research on AI technologies and make an informed decision.
“With all new technology and incoming trends, it is vital to look at how it will affect you and your business and plan accordingly for that, ensuring you adapt to stay strong in the market.” ■
Parm Bhangal www.bhangals.co.uk Parm Bhangal is Managing Director at Bhangals Construction Consultants.Parm is a regular on Business and Construction podcasts as well as writing articles about the Construction industry. In 2019, he won ‘Entrepreneur of the Year’ and ‘Employer of the Year’.
Bhangals Construction Consultants offers quantity surveying and estimating services to builders, architects, property developers and homeowners to support them with their renovation and development works. It can supply one service or complete project management. It talks to customers and help them to make the most out of their budgets and keep their construction project costs down.
Quite often, a problem that could have derailed the whole build will be solved before construction work on a project has even started
“ “ “ “
Though TEi has been trading under its three-letter moniker since 2004, the company’s history goes much further back. In the 1980s and through into the 1990s, the company was what we might call an amalgamation; multiple engineering companies, including well-respected names such as Greens Economisers, The Senior Group, and Foster Wheeler, came together as one overall entity in the engineering and construction sector. Therefore, as a company that unites these various commercial and historical strands, TEi can actually trace its formation all the way back to 1845 as the original Greens Wakefield.
The founder of that company, Edward Green, patented the Economiser boiler and, up until this very day, TEi continues to design, fabricate, and install the product and its various pressure parts. With a strong presence in Wakefield, a city in West Yorkshire, UK, which is made up of a head office, metallurgical laboratory, and numerous workshops, the Greens-now-TEi name has been and remains a key one in the local community.
How TEi’s more than 150-year story is informing its model for sustained success
Today, the company is recognised as a leading specialist welding company with experience in major construction turnarounds, turnkey project management, and repair and maintenance frameworks. A broad overview of the services offered by TEi is as follows: a nationwide operations division providing on-site project delivery and client support; a UKAS-accredited metallurgical laboratory offering on-site assessment and labbased mechanical testing; a heat exchanger division to support on-site eddy current testing of shell and tube heat exchangers, workshop refurbishments, and on-site explosive cleaning; and a technical services division comprised of an in-house design team that supplies pressure vessel design, piping design, pipe flexibility analysis, structural steel design, and on-site inspection.
Then there is TEi’s fabrication workshop, which is EN1090-accredited and has the capability to be tailored to any project requirements. It is predominantly utilised to support the firm’s major contracts and projects. Next up, and rounding out an overview of services offered, is TEi’s EN38342-accredited welder training school, which is primarily used for training and qualifying core welders. However, the school can also be utilised for external clients to produce welding procedure qualifications and to train and qualify welders in specific techniques.
With more than 150 years’ service to the energy, process, manufacturing, and construction industries, it is clear that TEi, particularly through its training school, intends to give back to the next generation of professionals and tradespeople. “TEi is a service organisation,” begins Alan Waddington, Managing Director at TEi, who recently sat down with Construction & Civil Engineering to offer our readers an insight into the longstanding company. “As such our people are our strongest asset. We have a staff headcount of approximately 250 (which can increase during high demand).
“Even though the numbers are fairly high, employees often describe TEi as feeling more like a family-type of company, and one in which people are treated with respect and due care,” he goes on. “Our culture is based upon team effort with consultation and collaboration in effect across management, all the way from the shop floor spokespeople to our safety representatives. Moreover, we utilise an internal committee network and questionnaires, which are delivered to employees across the organisation to help us gauge a consensus of opinion. We consistently invest in training across all levels of management, appraise performance, set objectives, and reward good performance. If TEi succeeds, then collectively we will reap the benefits of that success.”
Provincial Safety Services (Provincial) has been supplying PPE for 40 years, and has gained vast experience in supplying personal protective products into the heavy industrial and construction sector. From headto-toe protection, Provincial will provide the best solution. Offering a bespoke garment manufacturing service is also a strong part of our service, and gives you the opportunity to stand out wearing garments that you want, as opposed to what we have. We are proud, and thank TEi for choosing Provincial to supply its PPE requirements. For any of your future PPE needs, please consider Provincial Safety Services as a potential supplier.
At no point was a strong, unified workforce more important than during the Covid-19 pandemic and the disjointed, unnerving world it created for employees and businesses alike. As TEi services the energy and petrochemical industries, its personnel were considered key workers and subsequently the company was fortunate enough to continue trading.
As Alan elaborates: “The pandemic did present us with the issues of lockdown and a restriction in working at office locations, however we kept going. Strict site protocols were put in place to ensure the health and safety of our employees on contract sites.
“All main operational support services are controlled from our head and regional offices, and therefore implementing working from home effectively was certainly a learning curve for us, but one that was embraced quickly and, in the end, ensured that our operations continued,” he explains. “During the lockdown, we invested in and improved IT and office equipment for all staff at TEi. One simple thing we did was utilise Office365 to better enable flexibility in both software and hardware. This has ensured we can continue with our flexible working and has benefitted our ability to react to both market and national issues with little disruption to the business.”
Commercial dynamism of this kind is always important in times of adversity, but for TEi it has seemingly become a new way of life – and that has paid dividends. Since the pandemic, the firm has seen various new framework contracts established with key clients like Drax, EPUKI, ExxonMobil, Uniper, and RWE – just to name a few. “We work closely with all clients and our repeat custom and framework agreements stand as a testament to the strong client relationships we hold throughout the UK and across the majority of the country’s prominent energy infrastructure assets,” notes Alan. “This year has seen us successfully deliver large contracts at the PX Chemicals Park, plus installation of a US Boiler System, and work on major outages for Triton Power.
Contractor Accommodation Services (CAS) is proud of its longstanding partnership with TEi, sourcing, and managing accommodation when the company’s teams stay away from home.
“For the past four years, CAS has consistently supplied me and the TEi team with accommodation across the UK and Europe, from Central London and the countryside of west Wales to Dublin to Rotterdam.
“CAS is quick to follow up on enquiries, understand our requirements and needs, while providing a great service. This partnership has not only assisted TEi in delivering projects within budget during a challenging economic climate, but has also provided the team with comfortable, quality accommodation,” says Jake Parker, TEi Area Manager.
“So, in short, some major milestones for us – and there is still a good part of the year left to go,” he says. “We have also been instrumental in installing Original Equipment Manufacturer (OEM) apparatus for existing gas stations, bringing them back online to ensure national supply meets demand. In addition, we have been working with major clients to enable sites that facilitate the government’s upcoming Net Zero drive for carbon sequestration and hydrogen production in the East Coast Cluster.
As mentioned previously, an ethos of constant improvement is essential to TEi’s company outlook. It is for this reason that the firm runs its own training school, encouraging future generations to see an exciting new career path in an industry that they might have otherwise overlooked.
Yet TEi also wants to improve its own standards, always looking at methods of bettering its services and output for clients. “We continuously look to improve our productivity on-site and, as such, we have developed numerous strong relationships with industry renowned institutes including The Welding Institute (TWI) and welding specialist contractors,” expounds Alan. “In turn, this helps to ensure we are utilising the best available technologies and consumables to deliver a quality product to our customers. Furthermore, our welding school acts as a Research and Development (R&D)
base for welding trials, often with project mock-ups created to make sure the best technology is utilised and trialled before TEi reaches site.”
The company has also developed an internal web-based application to help administer sections of its Integrated Management System (IMS). As Alan goes on to explain: “The application assists our site teams in producing timesheets and purchase orders to improve the processing time for our head office’s purchasing and accounts departments. The application can also give us realtime costs allotted to contracts and it provides us with a performance dashboard. Now, however, our attention is turning to a number of energy efficiency schemes involving waste heat recovery technology.
“With the current instability in the energy market and the high demand, that is now more important than ever,” he concludes. “TEi remains a strong prospect within the UK energy market. The availability and sourcing of skilled labour has proven difficult in 2022, and this will likely continue in the near future. However, we will look to invest in the development of our core capabilities to minimise the effects of this. We strongly believe there are growth opportunities to be had in the UK and abroad in the next five years –and we intend to take them.” ■
www.tei.co.uk
How Celsa Steel UK is becoming a leader in sustainability for the construction industry
With more than 9000 employees and a turnover of over €5 billion, Celsa Group is the second largest recycler and manufacturer of long products in Europe. The family-owned company, with over 50 years’ experience in the steel industry, has pushed itself to become one of the most diversified and integrated producers of reinforcement steel within the construction industry.
Celsa Group produces eight million tonnes of steel per annum from its melt shops based in Spain, the UK, Poland, Norway, and France. In addition to this, it also owns and operates downstream fabricators and upstream scrap operations. This month, Construction & Civil Engineering hears from the Head of Sustainability and Strategy of its UK branch, Chris Hagg, about the development of the company’s British footprint, and how it is determined to grow its operation.
Celsa Steel UK (Celsa) has been producing in the UK for nearly 20 years, and is one of the largest recycling companies in the country. It produces all its products exclusively through an Electric Arc Furnace (EAF) process, using scrap metal as the raw material. Based in Cardiff, Wales, the business’ EAF capability can produce over one million tonnes of steel per year. Adjacent to the steel production, Celsa also has its Rod & Bar Mill capable of producing 900,000 tonnes per year of reinforcing and wire rod products, and its Sections Mill capable of producing 350,000 tonnes per year of merchant bar and sections. At its facilities in Cardiff, Celsa employs over 900 people, and has an annual revenue of over £500 million.
“All Celsa’s products contain 98 per cent recycled content and conform to the latest British Standards,” Chris states. “Information relating to quality assurance, test certificates,
We’re the original asphalt recycling company; developing, and manufacturing highperformance asphalt products since the 1960s. With 95 percent of our asphalt recycled, we are leading the way with our sustainable roadmaking solutions. Our unique asphalt recipes, and tailored services add superior value wherever there’s an environmental challenge. We’re dedicated to creating firstclass products, matched by our commitment to innovation and sustainability.
properties of the steel, and deliveries can be supplied digitally, directly to the customer. An additional benefit that we provide is all our rebar output is grade B 500 C, nuclear grade, suitable for nuclear power station construction, as well as multiple iconic projects throughout the UK. Our rebar is easily recognisable with UK stamped on every bar.”
Keeping in step with the company’s recycling initiative, there are a variety of strategies in place for the business to remain committed to sustainability. Chris acknowledges that in many instances, particularly given the cost requirements of the construction industry, this is not an easy
task. However, Celsa incorporates innovation to ensure that it contributes to minimizing its carbon footprint. “We are a very energy intensive company with low margins for our products,” he insists. “However, we are always looking for ways to improve our energy efficiency, productivity, and cost effectiveness. We have many continuous improvement projects in place to reduce the amount of both electricity and gas used, such as hot charging, energy recuperation, oxygen enrichment, and a new SVC.
“We are already a low-carbon steel producer with emissions that are less than a quarter of alternative steelmaking routes,” he adds. “Our decarbonisation pathway is clear.
To reduce our direct scope one emissions, we need to have an alternative to natural gas for our reheating furnaces in particular. Currently, it appears the most likely alternative is hydrogen, and we are in discussions with a number of potential hydrogen suppliers. Eliminating our carbon emissions from natural gas would reduce our emissions by over 60 per cent. Our scope two emissions are dependent upon decarbonisation of the national grid or alternative arrangements (for example, Power Purchase Agreements) for provision of renewable electricity. We have identified our scope three emissions, and they will be worked on in conjunction with suppliers in the future.”
The pandemic hit the construction industry particularly hard. Fortunately, Celsa is equipped with a dedicated and hardworking team, and was able to pivot quickly to ensure the security of its operation. “Unlike
Jaga Brothers is a general haulier in South Wales that has been trading since 2006.
As a business, we specialise in steel and construction deliveries across the UK. We are also accredited with FORS Bronze certification, and are adamantly working towards a Silver.
Jaga Brothers has had a partnership with Celsa Steel UK since 2009, but it is only the last five years that we have taken our partnership to a greater scale. We deliver approximately 180,000 tonnes a year for Celsa, and are due to increase these volumes to 250,000 tonnes a year.
We believe Celsa Steel UK to be a key business within the construction industry, and we are proud to be a key partner in the company’s success.
many business in the UK, Celsa did not cease working during the pandemic,” Chris reflects. “Whilst demand for our products was immediately affected, and for a period of time it was only a third of our normal rate, the resilience and loyalty of our workforce meant that we were able to continue production.
“Having provided all those who were capable of working from home with the necessary resources a full week in advance of the national lockdown, we were well prepared to continue,” he adds. “Unfortunately, the impact on our business was such that we needed intervention to be able to support everyone. We were immensely grateful for the government’s financial help, which came in the form of a loan under the bespoke arrangement of the Birch Scheme for the exceptional circumstances of ‘a company of strategic importance’.”
Despite these challenges Chris acknowledges that Celsa did not compromise on quality and project delivery for its
customers. “We continually consult with our clients and ultimate end users about potential new requirements,” he says. “The construction industry has often been slow to adopt new standards and opportunities to innovate. We remain ready and willing to offer higher strengths grades and new sizes for projects.”
In conjunction with this, the business is also proud of the team with which it works. Celsa’s company culture is one that is committed to the growth and development of its people. The business has invested substantially in training and development to ensure that it prioritises the safety, wellbeing, and vocational growth of each individual within the business. As a result, it has crafted a dynamic group that has served as the cornerstone of its overall prosperity.
Part of the company’s success is also driven by the excellent relationships maintained within its supply network. The synergy in this regard has meant that products can reach the company’s customers
in pristine condition and in a timely manner. Commitment to this goal has meant that the business is able to fulfil projects to the best of its ability. “The most successful contracts are those where the supply chain is consulted and aligned,” Chris argues. “In recent experience, the most progressive have been major projects where there was great dialogue between us, our partners, and customers to achieve optimum results.”
As businesses adopt best strategies to help navigate their supply chain difficulties, Celsa remains on course for a positive result in 2022. This has been a successful journey for the company. However, it has not been without its challenges, and currently, according to Chris, the largest is the turbulence of the supply chain, both in terms of raw materials and energy. “Because we are committed to improve our circularity, we want better segregation of materials within the scrap we receive, so we can separate out the non-ferrous (aluminium, copper, rare
earths) from the ferrous scrap suitable for our production,” he explains.
Chris expresses that there are some exciting developments in the pipeline that will serve as a fantastic springboard for the company’s continued growth. “We are looking at the best opportunities to help increase our economic stability,” he concludes. “From my perspective, it is important that the UK Government fulfils its promise to address the disparity between electricity costs in the UK and near competitors. Once this has been resolved, that will place us in a stronger position to secure our longevity. Beyond that, when I think about our five-year plan, we are determined to further reduce our carbon footprint in the coming years to supply a near net zero product to the construction market.” ■
www.celsauk.com
Switching it up: how a rejuvenated ParkerSteel is establishing itself as one of the steel industry’s strongest players
erformance with purpose,” states Dylan Alexander, the Managing Director at ParkerSteel. It’s an ideal that for the last few years has led the way for the company – one of the UK’s largest suppliers of structural steel –amidst the challenges of both Brexit and Covid-19. “Profitability alone was how we measured success in the past,” he goes on. “But that’s not enough in today’s world. We also have to look at the environmental and social impact of our operations.”
In 2020, Dylan identified a need for ParkerSteel to shift its focus towards a new purpose: creating a better future for its employees, customers, and the surrounding community. As a result, he developed an innovative business model, SWITCH, designed to address global issues across every level of the company through six distinct channels: Sustainability, Waste, Information, Technology, Community, and Home.
“Rather than sign up to a pledge, we want our results to speak for themselves,” Dylan explains. “SWITCH’s holistic approach to creating change encourages real solutions to real problems that have already proven beneficial. ParkerSteel has been a part of the Canterbury landscape for over 100 years, so we have strongly established roots here. Therefore, improving the wellbeing of the community is equally important to improving the performance of our company.”
Although SWITCH has only recently been rolled out within the company, a number of initiatives have already
ParkerSteelbeen implemented, including a £2.5 million upgrade of ParkerSteel’s delivery fleet to lowemission vehicles. “Our fleet covers in excess of 20,000km daily, so this change to greener vehicles is going to substantially reduce our carbon footprint,” Dylan continues. “We’ve also switched to paperless deliveries, which will save over 300,000 pieces of paper every year.”
The current volatility of the energy market has placed new emphasis on the need for energy security and consistency of supply, but under the guidance of its new business model, ParkerSteel seems able to stay one step ahead. In addition to installing LED lighting across all its facilities to conserve the maximum amount of energy possible, the company has conducted surveys in advance of installing solar panels on the roof of its Canterbury site.
SWITCH isn’t only about sustainability, however. A significant part of the model focuses on the health and wellbeing of ParkerSteel’s people and the creation of a positive workplace culture that empowers employees to take control of their own careers and discover a role at the company that suits their skills and aspirations. Last year, it invested over £100,000 in a variety of in-house training schemes that benefited over 300 employees, allowing them to upskill and improve their career prospects.
Like many industries, the construction sector is currently in the grip of a labour shortage, with younger generations increasingly overlooking the various opportunities it presents. To combat this longterm shift, ParkerSteel recently launched its graduate programme as a part of SWITCH:
the ParkerSteel Business Academy. Its purpose is to develop new internal and external talent and provide diverse and exciting career opportunities throughout the company’s commercial operations.
“The Business Academy is a one-year programme that enables candidates to gain in-depth knowledge across several areas of the business,” Dylan discloses. “The scheme has already attracted candidates with a range of backgrounds and skills, and we are pleased to say that we have made offers of employment to three people who started in September. We’re excited to see what new ideas they bring to the business.”
This isn’t the first time that ParkerSteel has taken the initiative to supply its own training programmes during a labour
crisis. During the nationwide shortage of LGV lorry drivers last year, Dylan implemented a 12-week Driver Academy programme to help solve this problem and assist LGV drivers in advancing their careers. “Adaptability is our strength,” Dylan notes. “We have the ability to evolve with each challenge we face and become stronger for it.”
The brunt of the pandemic may well be in the past, but for ParkerSteel, there are always lessons yet to be learned –not least, the importance of a robust supply chain as a means to mitigate delays and disruption. ParkerSteel was fortunate to have its supply chain strengthened when it joined the Taurani Group in 2019, a Dubai-based global conglomerate of companies within the steel manufacturing, scaffolding, and formwork industries. This partnership, in conjunction with
ParkerSteel’s port facility in Dover, put it in a strong position financially, as demonstrated during the pandemic and ensuing lockdown. Despite supply chain issues worldwide, its customers continued to receive first-class service and delivery with no interruptions.
This purpose-driven approach, in tandem with Dylan’s visionary growth strategy, has allowed ParkerSteel to flourish. Sustainable initiatives and strategic investments in people, quality products, and technology have seen the company’s revenue triple over the last three years, increasing by £30 million pounds during what remains a turbulent time for the industry.
Crucial to the continued financial success of ParkerSteel is Dylan’s continuous reinvestment into the company. In July 2021, it acquired Midland Steel Sections Limited (MSSL), which increased its customer base
and provided an important foothold into the Midlands, extending its reach into new markets. This acquisition has been supplemented by investment in additional technology and machinery across both sites.
“We’ve just added more saw and drill line machines, punching machines, and state-ofthe-art laser machines,’ Dylan comments. “All of these enable us to improve our existing services and provide our customers with an enhanced product offering.”
As ParkerSteel continues to grow exponentially, Dylan reveals the secret of its ongoing success, concluding: “Embracing purpose has strengthened our resilience in the face of challenges and increased the value we create for our customers and the surrounding community.” ■
MAC Trailers, as a brand of McCauley Trailers Ltd, is the longest established trailer manufacturer in Northern Ireland. We are committed to providing excellence in all areas of our operations, and as such, encourage the continuous training and development of our staff. In this way, we will continue to manufacture trailers, developed and built by employees who are skilled and effective at their jobs. We manufacture one of the widest ranges of trailers available for the transportation of plant and machinery. We have a standard range of agricultural and commercial trailers, and from this base, we can provide a wide variety of options to meet most customer requirements.
McCauley Trailers Ltd has an international market presence in more than 16 countries. All our trailers have been granted full European whole vehicle type approval, and have achieved ISO 9001:2015 quality assurance certification.www.parkersteel.co.uk
Founded in 2007 in response to a requirement from the UK-based supermarket chain Asda, Sigma Group (Sigma) has since gone from strength-to-strength, establishing itself as one of the country’s leading providers of full turnkey services for retail, leisure facilities, and commercial buildings. Going back to those humble origins, Sigma was brought in by Asda to support the nationwide chain’s property store operations and expansion programme with a dedicated kitting and logistics facility.
Fast forward to today, and the company has collaborated with household names like M&S, Boots, Primark, Asda, Sainsbury’s, Pets at Home, and Wilko. With that growing client list comes an increased demand for more expertise and infrastructure. Fortunately, Sigma was wellequipped to deal with such rising expectations. The firm’s scope of services rapidly expanded to include shop fitting installation projects, in-house mechanical and electrical systems, and construction. Subsequent expansion with clients has led to a strong portfolio of blue-chip customers in the grocery, fashion, home, pet, and DIY sectors.
Sigma now operates from a number of locations with over 500,000 square feet of consolidation facilities. As a result, the company can provide bespoke fixture demand management, consolidation, and pick-and-pack logistics services across the UK and around the globe. The company is keen to reduce end-toend costs for other businesses by streamlining what can often be disparate or independent processes, offering a more financially secure model for its clients.
Craig Bennet, CEO at Sigma, sat down with Construction & Civil Engineering to offer us an insight into the wealth of services offered by the company he so proudly leads. “We have five principal offerings, and it is our full end-to-end services that sets us apart from our competitors,” he begins. “First, there is our fixture and equipment division, focusing on conceptual and technical design and manufacture for global distribution. Then we have our consolidation, kitting, and logistics of Goods Not For Resale (GNFR) facilities to support retail operations, growth, and refurbishment programmes, as well as project roll-outs. In fact, we run dedicated facilities for Asda, Boots, Wilko, and M&S, plus additional shared user facilities for multiple retailers.
At Ace Door Systems Ltd (Ace Door), we work closely with SIGMA and offer a UK-wide design, supply, installation, and maintenance service for commercial and industrial doors.
Whether you need roller shutters, speed doors, fire doors and shutters, crash doors, PVC strip curtains or barriers, we have a solution for you.
We also have a team of highly qualified and experienced engineers, who are able to service and repair all types of commercial and industrial doors.
Our experience spans health, education, retail, engineering and many other sectors who have very specific needs.
Need a tailored solution? Our design team works with leading manufacturers to produce bespoke doors that meet industry standards.
“Then we have our projects,” he goes on. “These include equipment installation and planned asset maintenance services, all of which encompass a wide scope of ‘smaller’ works from project scheme roll-outs to warehouse flooring repairs, roofing works, pest control, and so on. Next up is Mechanical and Electrical (M&E), for which we have a dedicated in-house team supporting our projects and construction divisions while also undertaking their own roll-outs, which encourage store decarbonisation and energy reduction programmes. Finally, our construction unit is responsible for the full fit out of retail and hospitality environments and small construction works.”
Simply put, Sigma offers a holistic approach to the sectors it so robustly serves. An aspect of those services that Craig goes on to highlight is a current trial and roll-out across its M&E team to support carbon reduction within
Simply put, Sigma offers a holistic approach to the sectors it so robustly serves
“ “
each retail client’s property portfolio. Measures include features like LED lighting, handling and controller upgrades, and plant replacement.
Sigma’s growth is driven by both retailers’ nimbleness to react to changes in customers’ shopping habits, and through increasing its own client portfolio. This ensures that players in the market remain attracted to its full service offering and strong ability to support a business’ individual needs.
One recent example of this is the partnership between Sigma and M&S across its Cheltenham, Pollock, and Silverlink sites, where the construction and fittings specialist completed a range of works. Talking us through one of the extensive projects is Craig. “As an overview, we were brought in to improve the Cheltenham store for its customers,” he details. “We extended retail space in the clothing department to accommodate new concessions and improve the layout for M&S, while also refreshing the look of the whole store. Additions included
digital screens, new signage, and lighting fixtures. Then, we brought the food hall up to date by installing new selfscan tills and refitting the bakery.”
The project was a five-week scheme that required the Sigma team to carry out a wide range of tasks across the clothing, home, beauty, and food departments of the M&S store. All the while, Sigma had to keep within a set budget and ensure that disruption to customers and staff was kept to a minimum, thereby allowing the store to remain open and operational.
Sigma’s expertise was required to maximise the available space in the store before commencing the remodelling process. As part of the brief, the UK-based firm applied the refreshed format aesthetic, designed to uplift the store with an eye-catching appearance (keeping with the brand), and installed a range of new concessions and modern technologies to benefit the entire remodel.
“M&S Cheltenham is a large high street store and a prominent feature of the town centre,” explains Craig. “As a busy outlet, it was important that the work being carried out caused as little disruption as possible. A collaborative approach was therefore adopted between M&S and Sigma to make sure that all stakeholders were kept up to date with the planning and delivery of the project.
“ “
As a busy outlet, it was important that the work being carried out caused as little disruption as possible
“ “
In doing so, schedules were appropriately coordinated in line with the store’s needs.
“As part of this, Sigma’s just-in-time delivery methodology ensured that the equipment and fittings needed for the project arrived at the right time and as environmentally efficiently as possible,” he adds. “One of the aims of the project was to increase retail space at the store and improve the internal layout. In order for this to happen and before the installation of new features could commence, a soft strip out of the first floor was needed. This included the removal of the click and collect storeroom, as well as the till bank from the men’s clothing section, to create space for new concessions.
“To ensure that the store still had a sufficient number of checkouts to accommodate its customers, new tills were installed in an adjacent section,” he goes on. “The remodelling required brand updating of in-store concessions, including Per Una and Autograph. This involved the installation of new, illuminated signage for each brand,
which could be easily moved around if the store decided to modify its layout later on.”
Prior to the project, the signage in the beauty department was deemed ineffective by M&S; customers were having difficulty finding products and signs were not prominent enough. To remedy problems with this, Sigma installed new, visible, illuminated signs in keeping with the new aesthetic for the store. Aside from the remodelling of the home, beauty, and fashion departments, the team also carried out significant alterations in the food hall.
The largest aspect of that endeavour concerned the bakery. Sigma teams were responsible for tiling the walls, installing hygienic wall padding, laying new antislip flooring, and erecting a new frontage,
complete with new fixtures, lighting, and signage.
“To provide customers with more convenient ways to buy their groceries, the food hall upgrades also included the installation of self-scan tills at the checkouts,” Craig reveals. “Other areas that received modifications included the beer, wine, and spirits section by adding brick slips and illuminated signage above and behind the fixtures.”
Another aspect of Sigma’s work with M&S worth noting is its key improvements to the brand’s sustainability arrangements. Across several of the retail giant’s food stores, Sigma began a journey to improve energy efficiency, replacing over 200 obsolete belt-driven fans and motor assemblies for modern equivalents.
Another 50 fans are due to be installed later in the year. Compared to the older units, Sigma’s newly installed direct-drive EC plug fans will deliver important cost savings and, as Craig points out, will always run at 100 per cent efficiency.
Undoubtedly, M&S now has a Cheltenham store that better meets the needs of its customers and its staff. Craig remains proud of the fact that all the work was completed on budget, with minimal disruption, and within the agreed five-week timescale.
“Going forward, we will continue to expand our services and innovate to support our clients and distinguish ourselves as a customer-focused business, utilising the latest technology to drive and implement change,” he concludes ■
F ormed in 1994 by Mike Weaver, VolkerLaser began as a division of Worcestershirebased Laser Civil Engineering. Under Mike’s leadership, the business achieved Stirling Lloyd approved applicator status, becoming the first in the UK to offer a complete package of preparation, concrete repair, and waterproofing. From there, the company gained momentum, expanding its services, and winning a series of significant projects, including waterproofing work on the A14 Orwell Bridge in Suffolk, and numerous pilot framework schemes for the then Highways England (HE).
Since then, Mike’s goal has been to establish the company as the specialist contractor of choice. Work on the River Trent’s Cavendish Bridge, for which it received a Heritage Award, saw the company become the first in the UK to use a robot for hydro-demolition works, and the first to undertake gussasphalt (machine laid asphalt) and waterproofing applications on a steel bridge. Mike remained at the helm after its 2005 acquisition by VolkerWessels UK, which preceded its rebrand to VolkerLaser in 2009.
VolkerLaser now provides a tailored package of specialist works to clients all over the UK, including bridge deck waterproofing, expansion joints, concrete repair and cathodic protection work, steel repair and strengthening work, carbon fibre and temporary works, jacking and bearing replacement, and other specialised solutions. As Mike, now Managing Director at VolkerLaser, puts it, VolkerLaser has transformed into “an innovative contractor, with in-house expertise which we draw on to solve the most complex of logistical problems for our clients, developing unique methods and tailored packages of works to suit each individual project.”
To-date, the company has been responsible for work on several prestigious highways sites, including Reading Bridge, Woodhouse Tunnel,
“ “
“ “VolkerLaser now provides a tailored package of specialist works to clients all over the UK
Mersey Gateway, Queensferry Crossing, and the largest concrete repair project in the UK, the M5 Oldbury Viaduct. As part of the Viaduct’s second phase – a framework agreement direct award for National Highways – VolkerLaser was supported by its deployment of V-Deck™, an innovative under-deck access system for bridges, jetties, and ports, which offers a replacement for traditional suspended scaffolding.
“At the M5 Oldbury, part of the viaduct is situated over a canal, so traditional scaffold access was not sufficient,” Mike reveals. “Therefore, we proposed the use of V-Deck™ as an alternative and sustainable solution.
By working closely with National Highways and VTS, the manufacturer of the system, we undertook rigorous research and development to produce a strong and robust platform that could be installed quickly and safely. Not only did it create programme efficiencies on the project, but we also designed the system to be far less intrusive for the general public wanting to use the canal below.”
V-Deck™ isn’t the only solution that distinguishes VolkerLaser. The company is also the exclusive UK market provider of Fast Beam, a unique, safe, and extremely efficient access system designed to maximise working space and minimise traffic disturbance, whilst undertaking necessary parapet repairs, maintenance, or construction. Another replacement for conventional scaffolding methods, it’s a solution that reduces cost, time, manpower, and risk.
“Typically, 50 metres of Fast Beam access technology can be installed by a three-man team within an eighthour shift, whereas traditional systems can take up to two weeks to install,” Mike comments. “Traffic management can often be reduced to maintain traffic flow, and the system can also be used to provide a pedestrian walkway or cycleway during bridge repair works. The system can be hydraulically adjusted up or down by up to 1000 millimetres, either targeting specific individual access platforms or adjusted as a complete unit – and it can be installed alongside existing parapets, making it an ideal solution for rail bridge repair work and highways maintenance.”
Since 2018, VolkerLaser has been contracted to undertake bearing replacement works at the Port of Dover, culminating in its recent work at the East Cliff Viaduct. Originally constructed in 1976, the site consists of a 348-metre long, seven-span structure carrying a three-lane carriageway, which varies in width along the length of the route, and a two-metre-wide pedestrian walkway on each side.
“ “
Over the last few months, we have expanded our steelwork capabilities, blasting and painting services, and our concrete offering
“ “
“The project has drawn on our extensive temporary works capabilities, with bespoke and innovative access being designed by our in-house team to tackle the complex logistical problems we faced,” Mike reveals. “This involved designing two systems: a hanging frame solution, and a bespoke trestle system for the different piers across the structure.”
With VolkerLaser’s team now working on bearing replacements across all six piers, the project is indicative of the commitment to innovation that runs throughout the company as a whole. “As a business,
we never stand still,” Mike points out. “We’re always looking for new ways to extend our service offering and grow our business. Over the last few months, we have expanded our steelwork capabilities, blasting and painting services, and our concrete offering through the addition of P J Davidson (PJD), a specialist slipform contractor with a fantastic track record of success in the industry. Together, we will be able to provide a package of services unrivalled by any other specialist contractor.”
Largely unimpacted by Covid-19, VolkerLaser continues to undertake new challenges. The company
was recently contracted by engineering provider Amey to support works on a series of scheduled cable inspections on the M48 Severn Bridge. Having commenced in June, the works are set to run for a total of eight months, covering eight panels of the two 511-metre main suspension cables, as part of a routine inspection schedule to detect signs of corrosion.
“We’re carrying out the work in phases, using different access methods,” Mike indicates. “Those in the lower central area will be undertaken using scaffold access, and those being checked at the upper levels will use two specially designed gantries. These gantries will need to be installed using a crane and under a full closure of the bridge.”
Before we conclude, Mike is keen to emphasise the importance of the company’s team, which boasts a track record of dedicated service – including more than 30 employees more than a decade into their tenure. “It’s testament to our open and inclusive culture,” he concludes. “In recent years, we’ve really sought to concentrate on mental health and wellbeing, implementing initiatives to ensure that we’re taking care of our employees. Moving forwards, we’ll always be a business that concentrates on the development of our people, supporting them through their early careers, and aiding them in progressing through the ranks of the organisation.” ■
www.volkerlaser.co.ukFounded in November 2000 by Steve Hill and Nick Martin, Light Source began its life as a design house serving the telecommunications industry. In 2009, Kevan Egan joined the business to help develop a design and build model; since then the company has formed a reputation as one of the most respected Tier 1 delivery partners to key players in the telecommunications sector. A pioneer in the delivery of Fibre to the Home (FTTH), the company was responsible for building the UK’s first full-fibre city, Hull, and boasted a turnover close to £60 million in 2022.
Speaking to Construction & Civil Engineering, Steve Hill, Managing Director at Light Source, elaborates on the company’s range of services. “The business provides a full turnkey design and build solution,
in addition to maintenance and customer provisioning,” he explains. “We like to think that our agility is a key differential. The business is still privately owned, with a very engaging executive team, who make decisions quickly and follow them through with a hands-on approach.”
Despite employing more than 300 people, Steve maintains that the company has maintained a familyfeel. “From my point of view, every member of our staff and supply chain is part of the Light Source community, and without them we have very little to offer,” he insists. “A major initiative for me personally is inclusion and diversity, and I am accountable to ensure there is no racial or gender bias and guarantee an inclusive atmosphere right through the business. We run several initiatives to ensure there is constant collaboration
How telecoms contractor Light Source is helping to revolutionise UK villages, towns, and cities
furloughed, as was their choice,” Steve comments. “The transition to home working went well, even though a long-term working from home policy does not suit our operational model.
“Thankfully, we were well-prepared for the pandemic,” he adds. “We have a dedicated Risk Team and had previously prepared a ‘Business Contingency Plan’ for a pandemic, which we’d never thought we would have to use.”
In December 2021, Light Source celebrated the opening of a brandnew office in Spalding. It’s part of a strategy that has seen the company expand its operations throughout Lincolnshire and East Anglia. “Lincolnshire is a key area for the business where we will see huge growth in the coming years,” Steve confirms. “Our Spalding ‘super hub’
services three clients: Virgin Media O2, Netomnia, and Upp. Each client has separate security access with dedicated offices and warehouse space, and it is proving a very efficient method of delivery. We now hope to grow our Openreach business in this area, which will again create new jobs and internal opportunities.
“We class all our clients as genuine partners and have created some sincere friendships,” he continues. “We not only deliver and maintain their networks, but also work collaboratively to develop their network architecture and delivery methodology to ensure we mitigate any transitional stresses.”
With the fibre revolution well underway, companies within the sector are competing to pass new homes as quickly, economically, and as practically as possible. For Light Source, the challenge is to stay ahead of the competition, working with its technology partners to develop new ways of working, such as the use of drones to fly cable across rivers. To a similar end, the company is currently in the process of developing a pneumatic rocket launcher with the capability to fire cable over 150 metres across difficult-to-access terrain. But the rollout of fibre isn’t the only challenge facing the company.
“Probably the most challenging area for many businesses at the moment is balancing the investment required to reduce our carbon footprint with the efficient delivery of our services,” Steve notes. “Sustainability is fundamental to our on-going success and further growth. Previously, we have focused on understanding our impacts. Now, we are looking at viable ways to reduce our impact, which include investment, monitoring, and education. At the same time, we have, and will continue to focus on maintaining a healthy balance sheet and making measured decisions. This has meant taking the foot off the gas at times in order to reassess, regroup, and refocus, before moving on to the next stage of our growth.”
That ‘next stage’ is fast-approaching, thanks to a healthy order book for Light Source, and the scheduled opening of four more of the company’s super hubs: in the West Midlands, Leeds, Manchester, and Scotland. “In the coming years, Light Source will look at alternative utilities to diversify our service offering,” Steve concludes. “In addition, we’ll look to expand our telecommunications business with supplementary maintenance and customer provisioning work streams. Above all, we’ll continue to encourage our Light Source family to find ways to do more for our clients, become more valuable, do more, give more, serve more, and to inspire communities by connecting people.”
From bins and shelving to optimized mobile storage. From manual order picking to fully automated systems. All our products are modularly expandable, even to multiple floors. Our range includes the most diverse racking systems, which are fully tailored to your needs. Our experts have extensive experience in various industries. Make an appointment and discuss the possibilities for your warehouse equipment.