The Turkish steel industry is weathering the storm. The importance of machine learning and big data.
Steelmakers push ahead with green steel technologies.
Danieli discusses its award-winning Rotoforge.
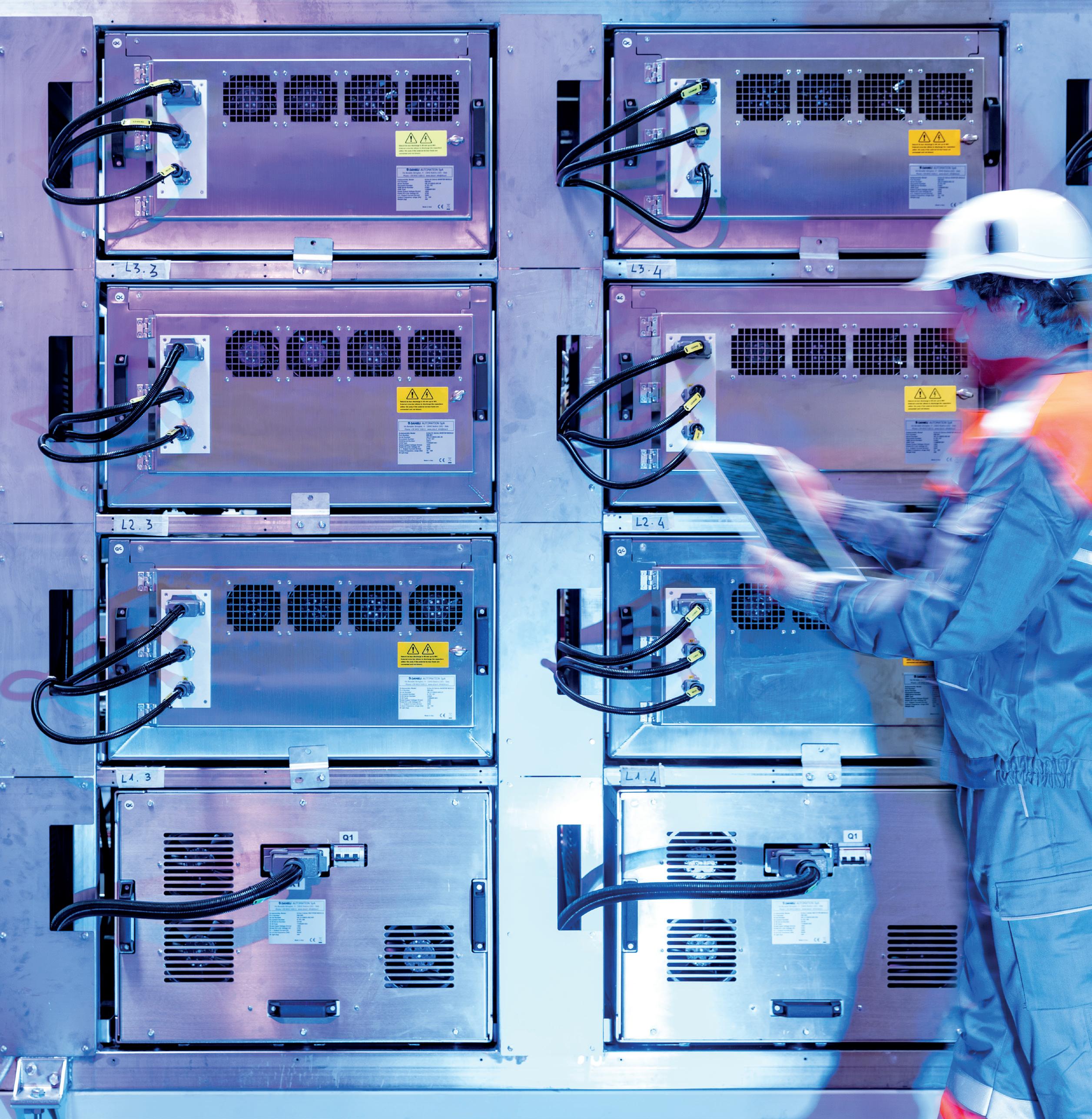
The Turkish steel industry is weathering the storm. The importance of machine learning and big data.
Steelmakers push ahead with green steel technologies.
Danieli discusses its award-winning Rotoforge.
solutions to improve your productivity
TotalEnergies Lubrifiants provides a comprehensive range of innovative steel rolling oils, casting fluids and maintenance lubricants. With TotalEnergies Lubrifiants you can:
• Improve product quality and safety standards
• Reduce overall operating costs (TCO) and CO2 footprint (TCO2)
• Significantly increase your productivity
• Decrease in maintenance failures
EDITORIAL
Editor Matthew Moggridge
Tel: +44 (0) 1737 855151
matthewmoggridge@quartzltd.com
Editorial assistant
Catherine Hill
Tel:+44 (0) 1737855021
Consultant Editor
Dr. Tim Smith PhD, CEng, MIM
Production Editor
Annie Baker
Advertisement Production
Martin Lawrence
SALES
International Sales Manager
Paul Rossage paulrossage@quartzltd.com
Tel: +44 (0) 1737 855116
Sales Director
Ken Clark kenclark@quartzltd.com
Tel: +44 (0) 1737 855117
Managing Director
Tony Crinion tonycrinion@quartzltd.com
Tel: +44 (0) 1737 855164
Chief Executive Officer
Steve Diprose
SUBSCRIPTION
Jack Homewood Tel +44 (0) 1737 855028
Fax +44 (0) 1737 855034
Email subscriptions@quartzltd.com
There’s nothing like an interview request from the BBC to sharpen the mind. Whenever something big goes down in the UK steel industry, I know it’s only a matter of time before the phone rings and the small display next to the receiver shows the word ‘anonymous’. Yes, it’s the Beeb and they want to hear my views on whatever topic has hit the headlines.
Matthew Moggridge Editormatthewmoggridge@quartzltd.com
I was about to say I haven’t been interviewed by the BBC for some time, but then I remembered the story about plans to open a coal mine in Cumbria – Whitehaven to be precise – and the expressions of bafflement and dismay on virtually everybody’s faces as the penny drops and they realise that the UK is governed by a crazy and, some would say, out-of-control Tory Party – those who brought UK citizens the much-maligned Brexit, the unbelievable ‘Partygate’ and numerous unsavoury stories of corruption. Like a lot of people, I had already heard of plans to open a coal mine – specifically for the UK steel industry – but like everybody else, I couldn’t quite believe it, living as we are in a world obsessed with reducing carbon emissions and moving away from fossil fuels. Who else would open a coal
mine in these green times other than the UK? So, when the phone rings and ‘anonymous’ appears on the screen, it can only be the Beeb. This time it’s about British Steel’s decision to close down its coke ovens. Around 300 jobs are at risk, possibly double that depending on which newspaper you read, and British Steel is citing increased costs and a global recession for the bad news.
British Steel’s decision to shut down its coke ovens gave the BBC a chance to discuss the aforementioned coal mine again. There are four blast furnaces in the UK, two are owned by British Steel and two by Tata Steel in Port Talbot, South Wales. If the coal mine is destined to produce metallurgical coal for use in UK blast furnaces, then it has one less customer if British Steel’s coke ovens are to be closed and one assumes the company will import coke for ironmaking. It is most odd when I consider the amount of column inches I have devoted to the decarbonization of the steelmaking process, that a coal mine is on the agenda of our crazy politicians in power. While, in mobile phone parlance, the future is Orange, in the steel industry, the future is very much green.
The PROFILEMASTER® SPS is a light section measuring device for measuring contours and dimensions on profiles of all kinds in cold and hot steel applications.
Benefits:
Maximum measuring accuracy thanks to temperaturestabilized measuring systems
Shape fault detection (SFD) thanks to high sampling rate
High-precision measurements
Detects process problems at an early stage
Fast maintenance and easy cleaning
Digital Transformation impacts not only industry but also society and the relations between humans. By developing intelligent robots and advanced automation technologies, we make our skills available not only to upgrade production efficiency, but also the way of working, with the goal of improving quality of life as a whole.
Everyone at Polytec works with competence and enthusiasm to create a sustainable, people-centered industry.
Russian steelmaker and miner Severstal is set to invest $1.1 billion in a number of major projects in its Severstal Russian Steel and Severstal resource divisions in 2023. In 2022, the company was preparing to invest $1.6 billion, but spent $982 million, according to media company Kallanish. In 2023, the firm will continue to focus on key areas including information technology, industrial safety and the environment, but will also continue to develop and modernise its production.
Source: Kallanish, 2 February 2023
The first blast furnace that was idled at Hungarian steelmaker Dunaferr in the summer of 2022 is irreparably damaged and will not restart, sources close to the plant have stated. Workers at the site have been informed the other furnace will be restarted in the coming weeks, although it is not yet clear where the raw materials will come from. Liberty Steel has been supplying coal to feed the site's coke ovens since December 2022, when it entered liquidation.
Source: Argus Media, 2 February 2023
them to receiving less money than they might be entitled to under the scheme.’’
Source: Money Marketing, 7 February 2023
Baffinland Iron Mines Corporation (Baffinland) and Salzgitter Flachstahl GmbH - a subsidiary of Salzgitter AG - are strengthening their co-operation by signing a memorandum of understanding (MOU) to investigate the use of Nunavut high-grade iron ore in low carbon steel production. Baffinland and Salzgitter Flachstahl GmbH will consider which supply strategies regarding using iron ore produced by Baffinland are best suited to hydrogen-based steel production in a direct reduction plant. In addition, the companies will work together on optimizing the Scope 3 emissions of their shared value chains.
Source: Market Screener, 6 February 2023
3D printing technology developed by Arcelormittal at its research and development centre has been used by students at Nebrija University, who redesigned rally cars that took part in the 2023 Dakar Rally. A new part that connects the side box of the car with the bargeboard, achieving a 20% weight reduction below the limit set, was 3D printed at the ArcelorMittal laboratory. The Dakar Rally is the world’s toughest automotive competition from a mechanical standpoint and, therefore, constitutes one of the best environments for the deployment of disruptive technologies, such as 3D printing.
Source: Green Car Congress, 6 February 2023
The Financial Conduct Authority (FCA) has renewed its warning that certain firms are making unsolicited offers to former British Steel Pension Scheme (BSPS) members who have not made complaints, following over 1,000 former members of the scheme receiving unsuitable advice from financial advisers accused of ‘enriching’ themselves. The FCA stated: “We are concerned that this is a deliberate attempt to exclude former BSPS members from the scheme, binding
Felman Production, a New Haven, West Virginia-based metallurgy manufacturing company that employs over 100 workers, has announced that it has signed a five-year agreement to sell ferro-silicomanganese,
a key component in steel production, to a multi-billiondollar publicly traded steel and metal manufacturer based in the United States. The name of the mill was not disclosed.
Source: Steel Orbis, 8 February 2023
A father and daughter team have forged a new landscape feature in one of Northumberland, UK’s wildest locations. A 25ft long steel goat has been constructed in the Whitelee Moor national nature reserve, with its installation by the Revitalising Redesdale Partnership, led by Natural England, marking the conclusion of a five-year project to ‘celebrate the valley’s cultural heritage’. Stephen Lunn, one of the sculptors, said: “It represents a goat jumping down into water….a few months’ work have gone into it and we are pleased that it is in the public domain and can be seen by people.”
Source: Chronicle Live, 8 February 2023
As the metals industry transforms in pursuit of green steel, the future of sustainability demands pioneers and leaders with vision, courage, and a willingness to push the boundaries of innovation and eco-friendly metals production. Primetals Technologies is redefining sustainable metals production.
We’re making orange the new green.
A ‘significant milestone’ has been reached in the build programme for the Dreadnought ballistic missile submarine programme. In a ceremony in February, steel was cut on Warspite, the third of four new Dreadnought Class submarines, currently in build at BAE Systems’ Barrow-in-Furness, UK site. The manufacturing of the submarines will support ‘tens of thousands of jobs’ across the UK, says reports, in one of the most ‘complex domestic projects ever undertaken’.
Source: Naval News,
9 February 2023
A pair of global steel manufacturers have abandoned a nearly halfbillion-dollar deal after federal antitrust officials raised objections. Tenaris, a global steelmaker based in Luxembourg, last year announced plans to acquire a subsidiary of Austria’s Benteler that operates an advanced steel and tube production plant in Shreveport, Louisiana.
Tenaris hoped that the deal for Benteler Steel & Tube Manufacturing would bolster both its production range and its US manufacturing footprint. US antitrust officials, however, raised concerns about the proposal, and Tenaris recently announced that Benteler North America had terminated the deal.
Source: Manufacturing.net, 9 February 2023
Hydrogen’s utility as a reductant for steelmaking is the subject of a study by steel specialists who are using a simulated shaft furnace to help make the assessment. The team used laboratory simulations to get an accurate picture of how hydrogen and other materials behave in the extreme conditions of a furnace, as a first step towards piloting a new type of hydrogen-fuelled process. The study was a collaboration with the Steel and Metals Institute, based at Swansea University, and the Materials Processing Institute, based in Middlesbrough, UK.
Source: The Engineer, 10 February 2023
FTC Solar, a global solar tracker systems provider, and Taihua New Energy, a Thailand-based steel fabricator, have formed a joint venture agreement to create Alpha Steel, a manufacturing partnership dedicated to producing steel components, including torque tubes, for utility-scale solar projects. “This agreement will further enhance our domestic supply chain, and our ability to support our customers and the growth of the US solar market, with domestic manufacturing utilizing US steel,” said Sean Hunkler, CEO of FTC Solar.
Source: Solar Power World, 10 February 2023
Luxembourg-based steelmaker ArcelorMittal has announced that it has pushed back the start-up date of a $150mn project at its Las Truchas iron ore mine in Mexico to 2024. The delay is due to slower progress in equipment deliveries and construction work, as well as holdups in obtaining the required construction permits, the company said in its 2022 report. The company said its Mexican subsidiary is investing around $150mn to
increase production of pellet feed by 1Mt/yr to 2.3Mt/ yr and improve concentrate grades at the mine in Michoacán state.
Source: Bnamericas, 10 February 2023
Tata Steel CEO and managing director TV Narendran said that the merger of seven subsidiary companies with Tata Steel is expected to be completed in 2023-24, news agency PTI has reported. The seven subsidiaries to be merged with the company are Angul Energy, Tata Steel Long Products (TSPL), The Tinplate Company of India, Tata Metaliks, TRF, Indian Steel & Wire Products, and Tata Steel Mining and S&T Mining Company.
Source: Mint, 12 February 2023
Nippon Steel has announced that it has invested a total of JPY123 billion in its facilities, to improve the capacity and quality of electrical steel sheets. In the first half of 2024, the production capacity of electrical steel sheets and high-grade electrical steel sheets was expected to rise by 1.5 times and 3.5 times compared to the current level, said the company.
Source: Yieh Corp Steel News, 13 February 2023
At SMS group, we have made it our mission to create a carbon-neutral and sustainable metals industry. We supply the technology to produce and recycle all major metals. This gives us a key role in the transformation towards a green metals industry.
Large steel mills in southern Turkey are expected to remain shut for weeks, with production lines idle and workers trying to cope with the impact of the massive twin earthquakes that shook the region. About a dozen facilities in Iskenderun and Osmaniye – close to the epicentre of the 6 February temblors – account for a third of national steel output, according to Veysel Yayan, secretary-general of the Turkish Steel Producers Association.
Source: Bloomberg UK, 13 February 2023
United States Steel Corporation will supply General Motors with its advanced and sustainable steel solution called verdeX steel, the steelmaker has announced.. The steel is manufactured with up to 75%
South Korea’s largest steelmaker POSCO has stated that it has discussed co-operation for a low carbon HBI project with the Western Australian government, in order to secure low-carbon steel materials in addition to other key materials like hydrogen, lithium, and nickel. “Australia has been a business partner since POSCO inception,” POSCO group chairman Choi Jeong-woo said. “We also need to co-operate in clean hydrogen and secondary battery materials sectors.”
Source: Pulse News, 14 February 2023
fewer emissions compared to traditional blast furnace production, is made with up to 90% recycled content, and is endlessly recyclable without degradation, the company says. US Steel’s verdeX steel will be manufactured at Big River Steel, a LEED Certified facility that also meets the ResponsibleSteel Standard site certification, along with a new advanced technology mill under construction in Osceola, Ark.
Source: Green Car Congress, 15 February 2023
The first foundation stone has been laid for a new green steel plant, set up by JSW Group, in India’s Kadapa district. The plant is expected to produce 1Mt/yr initially, which will then grow to 3Mt/yr. JSW has stated that necessary infrastructure, such as roads, power, and a water supply will be provided to the plant. The plant is expected to be commissioned within 24 to 30 months.
Source: Biltrax Media, 16 February 2023
Steelmaker Ternium is considering building a new $2.2 billion steel production plant near its current Pesqueria site in northern Mexico, the company's chief executive has announced, though a final decision has not yet been made. "We will disclose the location pretty soon," CEO Maximo Vedoya said in a call with analysts, adding the plant would be in the ‘USMCA region’, referring to the region covered by a trade pact between the United States, Mexico and Canada.
Source: Reuters, 15 February 2023
Four men have appeared in court accused of a conspiracy to steal from a UK steelworks. The defendants are accused of conspiring to steal £30,000 worth of copper from Liberty Steel’s Newport, UK site on 6 February. The defendants, whose ages range between 22-35, were remanded in custody after they appeared before Newport Magistrates’ Court.
Source: South Wales Argus, 16 February 2023
Tata Steel and Central Building Research Institute (CBRI), a constituent of the Council of Scientific and Industrial Research (CSIR), have signed an MOU to collaborate on research, academic growth, and sustainable solutions in mining. The MOU was signed by D B Sundara Ramam, vice president raw materials, Tata Steel, and Prof. R. Pradeep Kumar, director CBRI, a company press release stated. Under the agreement, CBRI will provide scientific inputs to Tata Steel on slope stability analysis and control measures in mining areas and affordable and sustainable green housing technologies for the rehabilitation and resettlement of families in mining areas. Source: Business Standard, 16 February 2023
British Steel has revealed its role in the £34m renovation of Middlesbrough Station, Northern England. Story Contracting is carrying out work on site for the second phase of the transport scheme, which will revitalise the station undercroft, and create new walkways and spaces for businesses. Steel bought from British Steel will be used on the overhaul, with its fabrication taking place at Middlesbrough-based CB Construction (Cleveland) Ltd. The steel is expected to arrive at the station this month, with 40 tonnes used to form part of the ticket hall, new staircase, wall structures and undercroft.
Source: Insider Media, 16 February 2023
Sanjeev Gupta, CEO of GFG Alliance, a global mining company, has sparked controversy over the administration of one of his biggest British customers after launching an attempt to take control of it. GFG Alliance has acquired control of a Singapore-based company called Aartee Group Pte Limited, an indirect
ArcelorMittal Nippon Steel India (AM/NS India), a joint venture between ArcelorMittal and Nippon Steel, will purchase two double-strand slab casters from Danieli, an Italy-based equipment supplier, for its Hazira plant. The new slab casters will enable AM/NS India to have an additional annual production capacity of 6Mt. The new installation will be put into operation in early 2025. The two casters will increase the plant’s product quality and efficiency, according to a company press release.
Source: Yieh Corp Steel News, 16 February 2023
Production at Tata Steel's Port Talbot site in Wales is being affected by a lack of domestically-produced hydrochloric acid, which is used in its pickling and annealing processes. UK industrial acid output has reduced by as much as 70-80% since energy costs soared in response to the war in Ukraine.The company is trying to establish fresh sources of the acid, most likely from continental Europe. The disruption affects output of all its products, with hot-dip galvanised being produced from annealed cold-rolled coil.
Source: Argus Media, 17 February 2023
Chemical engineers from Imperial College London have joined forces with the UK’s Materials Processing Institute (MPI) to develop a process that will produce hydrogen and valuable metals from steelmaking sludges. Nanomox, which is a spinout from Imperial’s chemical engineering department, have developed a patentpending process that uses green catalytic solvents at low temperatures to directly oxidise metals. If developed to commercial scale, the process would offer an alternative to energyintensive pyrometallurgical processes currently used to recover zinc from steelmaking wastes and so reduce the amount of material sent to landfill, the engineers have stated.Source: The Chemical Engineer, 17 February 2023
shareholder in two UK steel companies which recently collapsed into insolvency. Sources said that GFG was expected to issue a statement to confirm the purchase, and to say that it has filed a legal challenge to try to overturn the administration of Aartee Bright Bar Ltd and Aartee Bright Bar Property Ltd.
Source: Coast FM, 17 February 2023
After locals from Warren, Ohio, reported hearing a loud blast, rescue personnel arriving on the scene discovered an explosion at the ArcelorMittal Warren coke facility. Following the incident, a company representative gave a statement to 19 News stating that the factory would carry on with regular operations.
“A boiler failed at its Warren Coke plant this afternoon causing a loud noise heard throughout the adjacent areas to the plant. No employees were injured and the facility continues to operate normally with redundant boilers,” the spokesperson said.
Source: Opiyi Central, 19 February 2023
British MPs have teamed-up to back a plan which would create 16,000 jobs, boost Britain’s struggling steel industry and generate enough green energy to power 24 million homes. The scheme, which includes deepwater docks at Port Talbot, South Wales, and Milford Haven, would attract £5.5 billion investment, according to supporters. The project would see wind turbines and platforms manufactured at Tata’s Port Talbot steelworks and sailed into the Celtic Sea off West Wales to form a floating offshore wind farm.
Source: The Mirror, 26 February 2023
Tata Steel Mining Limited has signed a memorandum of understanding (MOU) with natural gas company GAIL for the supply of natural gas to its ferro alloys plant at Athgarh in Odisha's Cuttack district in India. According to the MOU, GAIL will supply the agreed quantity of natural gas through its pipeline from Gujarat to Athgarh. Signing the MOU, Tata Steel Mining MD Pankaj Satija said, “As a responsible mining company, we are committed to protect the environment by using cleaner fuels, and signing of the MOU with GAIL will further help us in this direction.”
Source: The Economic Times, 3 March 2023
Australian iron ore company Magnetite Mines has completed extensive metallurgical test-work studies for the Razorback Iron Ore Project in South Australia, determining the processing flow sheet and optimising for ore body variability. The company’s studies estimate iron ore grades above 68% iron from this flowsheet, above the direct reduction (DR) cut-off of 60% iron.
“Razorback will produce Direct Reduction pellet feed (DR Grade) products that are needed to make steel using methods that generate lower carbon emissions’’, Magnetite Mines CEO Tim Dobson confirmed.
Source: Proactive Investors, 28 February 2023
On 1 March, Arabian Pipes Company has signed an agreement with Aramco, a Saudi Arabian oil company, with an estimated value of SAR 62 million, according to a company filing. Under the 11-month contract, Arabian Pipes will provide Aramco with steel pipes from its factories. Last September, the two entities teamed up for a supply deal worth around SAR 155 million.
Source: Zawya, 3 March 2023
It is with great sadness that I announce the passing of one of Steel Times International’s regular History page writers, Harry Hodson.
Harry was always a pleasure to work with and had a great sense of humour, which brightened the day whenever he called the office to discuss one of his excellent and wellresearched articles.
Ukrainian mining and metals company Metinvest has launched a project at its Kryvyi Rih plant in which workers are building underground shelters for front-line troops. Steel workers are assembling prefabricated materials into underground shelters using a Soviet-era design. Each shelter requires nearly two tons of steel, with the bunkers being built to withstand projectiles with calibres of up to 152 millimetres, and the space for six soldiers.
Source: Scripps News, 4 March 2023
India’s Jindal Steel and Power (JSPL) has firmed up plans for a capital expenditure of $1.22 billion to construct a 3Mt/yr greenfield mill project in South-East India, a company official has announced. The official stated that a memorandum (MOU) of understanding will be signed shortly with the local government. The steel mill will be part of the company’s investment in the area, which includes setting up a port and constructing a slurry pipeline.
Source: Steel Orbis, 6 March 2023
While I have worked with Harry on History pages since 2014, when I was appointed editor, he was already a force to be reckoned with when I arrived on the scene. My predecessor, Dr. Tim Smith, himself a regular contributor to our popular History pages, commented: “One of his achievements was to come up with a theory on how the Iron Bridge at Coalbrookdale was erected. [A paper on the subject is held at the Institute of Civil Engineers]. He even built a model of the bridge which is there at the museum in the toll booth at the end of the bridge, and he appeared on TV about it too.” Each part of the model was uniquely cast and then assembled in the same manner as the bridge itself.
After leaving school aged 15, Harry started work alongside his father at John Grundy Ltd, Iron Foundry. He worked in the iron and steel industry for most of his life and became fascinated with the history of it, particularly the Iron Bridge at Coalbrookdale.
One thing is for sure: Harry will be sorely missed by his friends, family and work colleagues as well as his many readers on Steel Times International
Our innovations aiming at decarbonizing the steel industry: CO2-free steel production process Siderwin, Furnace Electrification, Carbon Capture, Heat Recovery, Jet Vapor Deposition (JVD), E-Qual® Electrical Steel Processing Technologies
Innovation is part of our Group’s DNA. For over 200 years John Cockerill Industry has demonstrated its ability to think differently and its capacity of seeing things from another angle. Still today, we are combining talent and technology, history and modernity, engineering and services. Virtues that help us to accompany our steelmaking clients in their digital transformation journey and their transition to responsible, zero carbon steel making.
johncockerill.com/industry
The most technically advanced coil joining equipment available. Period.
Guild International can design and build the welding machinery you need to keep your coil processing lines up and running smoothly and profitably. We are the world leader in supplying highly-engineered coil processing equipment known for reliability and performance. Contact us today to begin designing the perfect coil joining equipment for your processing lines.
For more information, visit our website at www.guildint.com or call +1.440.232.5887
World Leader in Coil Processing Equipment for the Steel Processing, Tube Producing and Stamping Industries Since 1958
A REVIEW of 2022 shows that while steel imports were held in check and showed a modest 2% decline, finished steel imports jumped some 11% in 2022. The American Iron and Steel Institute (AISI) reported that US imports in 2022 amounted to 30.8Mt of finished and semi-finished steel in 2022, down from 31.5Mt in 2021. But finished steel imports, as many steel pundits had predicted, rose 10.9% to 25.2Mt in 2022 up from 22.8Mt of finished steel in 2021.
The three biggest foreign suppliers in 2022 were Canada, Mexico and the European Union (EU), whose combined supplies made up roughly 54% of total US imports. Other major steel suppliers to the US in 2022 included South Korea, Brazil and Japan. China’s steel exports to the US rose 38.7% to 651kt, despite negative sentiments about Chinese steel production which is said to contribute to carbon emissions and pollution.
Sustainability and, with it, the emphasis on producing ‘green steel’ seems to be gaining ground in the US.
Massachusetts-based Boston Metal announced an investment of $120 million to produce what some industry experts are touting as ‘clean’ steel that is much less harmful to the climate than traditionallyproduced steel. Boston Metal’s initiative is backed by ArcelorMittal.
Boston Metal, which is deploying
renewable electricity to convert iron ore into steel, will use the funds to increase its production at its plant in Woburn, near Boston, besides its production operations in Brazil.
Environmentalists, arguing that traditional steel production greatly pollutes the environment and contributes to climate change, have been pointing out that some 75% of global steel production entails the traditional method of burning large quantities of coal to heat the blast furnaces for the release of pure iron from ore.
Tadeu Carneiro, Boston Metal’s chief executive, has been quoted by the US media as saying that his company’s technology specifically targeted the decarbonization of steel production ‘at scale’. The technology, developed at the Massachusetts Institute of Technology, does not rely on burning coal. Boston Metal claimed that it can eliminate all carbon dioxide from its steel production, hoping to increase production to millions of tons by 2026. The company said that it can extract metals from slag normally considered waste.
ArcelorMittal announced recently that it was investing $36 million in Boston Metal. The investment, ArcelorMittal said in a statement, is the company’s largest single initial investment to date through its XCarb® Innovation Fund, launched in March 2021 with the goal of ‘investing in the best
and brightest technologies’ that hold the potential to play a meaningful role in the decarbonization of the steel industry, a process ArcelorMittal intends to lead.
Indeed, as ArcelorMittal said, this investment had led a $120 million Series C fundraising round undertaken by Boston Metal. Other participants in the round included Microsoft’s Climate Innovation Fund and SiteGround Capital, which joins Boston Metal’s existing shareholder register which includes Breakthrough Energy Ventures, mining majors Vale and BHP, BMW Ventures and several clean-tech venture capital funds.
Boston Metal is developing and commercializing a patented Molten Oxide Electrolysis (MOE) platform for decarbonizing primary steelmaking. The MOE which uses electricity to produce molten steel through a direct, one-step process, is capable of processing a wide range of iron ore grades through high temperature electrolysis, producing relatively impurity-free liquid steel with no accompanying carbon emissions, according to a statement. As a fully customisable steel manufacturing solution, the modular MOE cells can be scaled until desired production capacity is reached. ArcelorMittal said that Boston Metal had raised over $200 million in three fundraising rounds and grown from a team of eight employees in 2018 to
over 100 today. The company planned to commercially use its technology by 2026. ArcelorMittal’s CEO, Aditya Mittal, said that ‘we have been impressed by the passion and vision [Boston Metal] has to contribute to the decarbonization of steelmaking’.
Much of the steel produced in the US is made by melting old steel; this is done in electric kilns and emits a fraction of the gases that affect the environment and climate compared to the production of new steel.
Indeed, alliances have been formed to produce cleaner steel. Nucor, for instance, recently announced that it planned to manufacture heavy-grade steel at a new $1.7 billion plant in Brandenburg, Kentucky. Electric arc furnaces will be used to produce new steel from scrap metal. The product, according to the company, is meant for use in the offshore wind industry which provides in part an option to fossil fuel-burning electricity and thus becomes crucial for the goal of controlling climate change. This will require huge quantities of steel, as some 90% of an offshore turbine is made of steel and each turbine, including the base, needs some 180 tons of steel per megawatt.
Electric arc furnace steelmaker Nucor’s chief executive, Leon J. Topalian, during a recent fourth quarter earnings call, said that the company expects its expanded Gallatin flat-rolled steel mill in Kentucky to raise its full capacity in the second quarter of the current year, resulting in further delay for the mill.
While emphasis on producing cleaner steel grows, there are also fears that such plans could possibly be put on hold if, as some Cassandra cries convey, the country is heading towards a recession. Recession fears have also restrained demand for steel and led to a price surge. Nonetheless, steel demand is expected to be fueled by urbanization and automobile electrification.
While some experts believe that these factors would not greatly mitigate the negative effects of the recession, others are confident that these will soften the blow usually dealt by an economic downturn. There are also those who are confident that the Infrastructure Investment and Jobs Act (IIJA) would further boost allocations for building infrastructure such as high-steel consuming roads and bridges.
The industry, happy about the prospect of good business resulting from the huge demand for steel used in infrastructure building with a provision of $1 trillion, also derives satisfaction from the requirement that only US-made steel would be used in infrastructure projects, thus not allowing foreign suppliers to reap the windfall business from the projects.
Paul Scott, president of the Alliance for American Manufacturing, has said that the requirements would allow the US to lessen its reliance on foreign steel alternatives.
The IIJA is also intended to prioritize domestic manufacturing and create jobs for American workers. Starting 14 May, all federally-funded infrastructure projects will have to use iron and steel produced in the US under the administration’s ‘Buy America’ requirements. However, exception to this
general requirement can be made if the purchase ‘would be inconsistent with the public interest,’ if the needed materials are not produced ‘in sufficient and reasonably available quantities or of a satisfactory quality’ or ‘if the material increased a project’s cost by 25% or more’.
The recession, if it is already there as some industry observers claim, could curb the spending enthusiasm of the average American to buy new vehicles – electrical or otherwise.
Meanwhile, the North American steel industry faces another challenge: a bankruptcy reorganization for the Radnor firm Phoenix Services may affect US steel production, according to The Philadelphia Inquirer.
Phoenix Services, which recycles molten slag that accumulates during steel production at the nation’s largest steel plants, is in its sixth month of bankruptcy reorganization while tons of waste it normally handles are piling up at its clients’ plants.
Phoenix has 1,700 machines that clear hot waste at mills owned by Nucor, US Steel, ArcelorMittal, Cleveland Cliffs and other big steelmakers; the recycled waste is then sold for construction and road materials. Phoenix lawyers said that the company needs to charge the steel mills higher prices because of inflation, Fed rate hikes, the Ukraine war and many other factors.
But some argue that Phoenix and its financiers, are using economic conditions to break contracts and pass rising financial costs to the steelmakers.
Nucor has warned that the growing backlog of could force production cuts, threatening shortages or price hikes on carmakers and other manufacturers. �
THE German tubemaker Mannesmann established its Brazilian subsidiary in 1952. It constructed a new mill in Belo Horizonte, the capital of Minas Gerais state, which at that time had a population of 352k. Nowadays, considering the area as a whole, the population has exceeded six million. Since the beginning, the project specialised in the production of seamless tubes. The plant was inaugurated in August 1954, by the country’s president Getúlio Vargas, and later gained historical significance as the location of Vargas’ last public appearance before he committed suicide amid a political crisis.
Mannesmann’s mill was established in the Barreiro district, with an initial nominal capacity of 100kt/yr crude steel. The decision to invest in a greenfield mill focused on seamless tubes was strongly connected with the discovery of oil in the Bahia state. Therefore, the project was erected nearer to the raw materials (iron ore, in particular) rather than to its
main customer. It was ultimately the right decision, because the state of Rio de Janeiro turned out to be the largest oil producer in the nation. The Barreiro mill is located some 470km away from the city of Rio de Janeiro.
The Brazilian subsidiary of Mannesmann improved its crude steel capacity to 290kt/yr in 1965, then to 550kt/yr in 1975 and later to 955kt/yr in 1990. As can be observed in Graph 1, its crude steel production
* Professor in Economics, Federal University of Uberlândia, Brazil. E-mail: germano@ufu.br
increased from 442kt in 1974 to 723kt in 1980 and to 842kt in 1986, reverting partially to 503kt in 1990, when the country faced a severe recession when GDP dropped by 4.4% year-on-year.
Pig iron output expanded from 257kt in 1972 to 685kt in 1986, then retracted to 390kt in 1990. Meanwhile, the respective figures for seamless tubes production were 125kt, 370kt and 228kt. The long steel products (medium bars and profiles) were equivalent to 179kt in 1972, 241kt in 1977 and 92kt in 1990. It is worth noting that while Mannesmann Brazil was originally focused on seamless tubes, at least in the period 1972-1978, its production of such products was lower than medium bars and profiles.
Mannesmann Brazil engaged in considerable modernisation projects throughout its long history. For example, it commissioned a BOF in 1978. Two years later, it modernised its automatic rolling mill for seamless tubes that started-up in
1956. Nevertheless, as of 1990, production became complex.
At that time, the plant had two blast furnaces and two submerged arc furnaces (SAF), combining for a 720kt/yr pig iron capacity. The SAFs came on stream in 1960 and 1961. It is interesting to stress that blast furnace #1 was commissioned in 1963, based on coke, but was converted into charcoal and then reverted to coke. Blast furnace #2 was started-up in 1986 and, from the beginning consumed charcoal.
The steel shop consisted of one BOF (700kt/yr capacity) and three EAFs (255kt/ yr) in 1990. Beside the conventional casting, it had a 550kt/yr continuous casting machine (started-up in 1986). The seamless tube lines comprised of an automatic rolling mill with mandrel (tubes from 140 to 323mm, capacity of 225kt/yr), a hot pilgrim rolling mill (tubes from 60.3 to 168.3mm, which started-up in 1978, with a capacity of 120kt/yr), and two mechanical extrusion presses (tubes from 33.4 to 88.9mm, installed in 1954 and 1961, with a joint capacity of 70kt/yr). In addition, it had a 140kt/yr medium bar and profile rolling mill, processing special/alloy steel.
Besides the Barreiro mill, Mannesmann had two other plants in Brazil in the early 1990s. The Garulhos mill, located in the metropolitan area of São Paulo city, had a 84kt/yr capacity of welded tubes (eight to 120mm), with its main customers being the automotive, machinery and equipment, and household appliance sectors. The São José dos Campos mill, also in the state of São Paulo, had a 60kt/yr drawing machine for fabricating wire. The other plant was acquired in 1986 from Fi-El, but resold in 1994, to Gerdau.
Indeed, it can be verified that at the beginning of the 1990s, Mannesmann Brazil had a relatively complex production structure, because it operated with two different technologies – both for producing pig iron (blast furnace and SAF) and steel (BOF and EAF). Moreover, despite the fact
that it focused on seamless tubes, it also fabricated welded tubes, bars and profiles, wire rods and drawn products.
Another important characteristic of Mannesmann Brazil relates to vertical integration, as in 1955, Mannesmann Mining was founded, and in 1961 the Pau Branco Mine, which is still in operation, was acquired to supply the internal iron ore supply needs. In 1969, a Forestry division was created with the goal of producing charcoal.
In the first half of the 1990s, Mannesmann Brazil made relevant changes in its production structure. The implementation of a 200kt/yr ladle furnace and vacuum degassing equipment, in 1993, had three goals: a) to improve final product quality; b) to provide flexibility to the steel shop; c) to increase the BOF’s productivity, allowing the EAF’s deactivation (the first two EAFs were installed in 1956 and the third one in 1961). As a result, the steel shop had its capacity diminished from roughly 1Mt/yr to 800kt/yr in 1994.
A new continuous rolling mill (tubes from 32mm to 117mm), at a cost of $80M, was commissioned in 1995. The underlying logic was the same as that of the investment in the steel shop. It allowed the production of better-quality tubes (especially with regard to the dimensional issue) and the removal of outdated equipment (two mechanical extrusion presses and hot pilgrim rolling mill). As a result, total rolling mill capacity was reduced by 35kt/yr.
It is understood that Mannesmann Brazil interrupted the production of long steel products (bars and profiles) in 1999. Thus, it became fully focused on tubes. In the same year, the company produced 368kt of pig iron, 365kt of crude steel, 293kt of seamless tubes and 2kt of longs. The company’s trajectory in the current century, when it became a subsidiary of Vallourec, will be examined in the next part of this feature. �
In the first part of this ongoing feature, Germano Mendes de Paula* examines the establishment of the Brazilian subsidiary of German tubemaker Mannesmann, which later became a subsidiary of Vallourec.
The government, however, withdrew export duty on some products and rationalised the same on others in November 2022, which came as a major relief for Indian steel producers.
In addition to a boost in domestic consumption, the export duty abolishment
on finished products encouraged Indian steel producers to further pursue the penetration of global markets and thus, exports were boosted.
The Indian steel industry was plagued due to a massive export duty levied in May 2022 which was later withdrawn. The government reversed the export duty on iron ore with grades below 58% which had been 50%, while the tax on iron ore above this threshold was cut to 30% from 50%. The export tax on pellets was rolled back to nil from 45% and that on pig iron, hotrolled/cold-rolled alloy and non-alloy flat steel products of 600mm or more in width was slashed to zero from 15%.
Further, the Indian government reinstated an import duty on coking coal, anthracite
coal and ferronickel to 2.5% from nil, and that on coke and semi-coke was restored to 5% from nil.
The six-month-old levy was abolished when the slowdown in the global economy affected domestic demand for steel which eventually resulted in a meltdown in steel prices throughout the world, including India.
Until duty revocation, imports turned favourable as inward shipments from China were cheaper than sourcing from domestic producers. As a consequence, China overtook a large portion of the Indian steel market in India as well as abroad.
India’s steel trade imbalance
The Joint Plant Committee, under the
By Dilip Kumar Jha*
INDIAN steel mills have seen a sharp turnaround in business sentiment over the last two months following the withdrawal of the export duty which coincided with the ensuing seasonal demand from the construction and infrastructure sector. Normally, the new season’s construction activity begins in November and stretches up to May the following year, with demand moving up, irrespective of price. But, India’s steel demand picked up almost three weeks later than was expected this year, on account of the export duty levy which dented consumer sentiment. Also, the delay in demand pickup was attributed to consumers’ expectations for a price cut as inventory continued to rise across all major factories.
Ministry of Steel, showed India’s overseas steel trade remained skewed in favour of imports during the tax period as Indian products lost competitiveness in the world market due to the export levy. Between AprilDecember 2022 alone, India’s overall steel exports plummeted by a staggering 54% to a mere 4.74Mt from 10.33Mt reported in the corresponding period last year. In December 2022, India’s steel exports plunged by 45% to 442kt from 798kt reported in the comparable month in 2021.
During April – December 2022, however, India’s steel imports shot up by 27% to a nearly three-anda-half-year high of 4.4Mt from 3.46Mt reported in the same period last year. In December 2022 also, India’s steel exports jumped by a phenomenal 65% to 653kt from 395kt imported in the same month the previous year.
India’s steel producers ramped up their output in the last few weeks amid expectations of an improvement in domestic and overseas sales in the coming season. Positive sentiment emerged after the government withdrew the export duty and also reaffirmed its commitment to support infrastructure growth.
Indian steel mills are witnessing an increase in consumer demand which was also supported by restocking from wholesalers. The Centre for Monitoring Indian Economy (CMIE) estimated over a 10% increase in India’s steel consumption during the OctoberDecember 2022 quarter compared to the same period last year. Tata Steel reported a 2% increase in steel output during the same quarter with a robust increase in output reported by other players too.
A sustained rise in domestic demand has prompted steel mills to raise their product prices by INR 1,500 a tonne, leaving room for a further increase by at least INR 3,000 per tonne in the near future. The market has already absorbed earlier increases and is now gearing up for the next round of rising prices.
Unfortunately, the price increase may not yield the desired profitability to Indian steel mills due to rising raw material prices. Since a large portion of approximately 90% of Indian steel mills’ coking coal requirement is met through imports, largely from Australia, the sudden spurt in its prices may dent India’s steel producers’ profit. Also, iron ore prices surged in the last few weeks to squeeze steel mills’ margins even further.
Amid recessionary fear in the global economy, India is looking to ensure raw material supply for long-term future plans. While the government has already announced a production-linked incentive (PLI) scheme to support India’s steel industry, the next major plan of the government is to secure more minerals and coking coal for long-term business plans in 2023. The Indian government is also working out a strategy to identify new reserves of coking coal within and outside India, and sign partnership agreements with potential suppliers for the future. �
• Preparation of pellets and micropellets
• Sinter mix preparation
• Recycling of valuable residues like dusts, ashes, sludges, slurries
• Fine grinding
• Preparation of carbon paste for graphite electrodes, anodes, cathodes
• Coal preparation
• eirich.de
Multiple approaches exist to improve your business by the application of modern technologies such as machine learning and big data. At Arcadia Steel, we believe that many steel companies have only started to acquire data-driven techniques.
HOW much can one gain from digital transformation? From our experience, a 3-7% improvement in productivity or a 2-3% reduction in costs is a realistic outcome when we are talking about the implementation of a data science solution directly for a production unit. We reckon that focusing on a bottom-up transformation, where the main effects are derived from operational improvement on a production unit’s level, can significantly benefit steel producers.
In the steel industry, we operate in a highly expertise-oriented sphere. Experience and practical knowledge provide us with
By Boris Voskresenskii* and Kseniia Kingsep**an understanding of how to run a steel factory efficiently, but it is only valid to an extent. From our experience, data might not support up to 50% of expertise-based hypotheses.
Moreover, it is a common phenomenon. Modern medicine, for example, has had huge success due to a shift from an expertise-driven approach to a data-driven approach. Medicine prescriptions we receive help us not because one brilliant doctor stated this in a book 25 years ago, or because the consulted doctor has once treated a similar patient and prescribed him the same pills. Drugs work because
thousands of patients go through highly sophisticated, statistically significant trials before a particular medicine is released to the public. Nowadays, data science is also used by pharmaceutical companies to create more effective treatments. And with a similar approach, steel producers can operate factories more efficiently.
We suggest you build a solid but simple methodology for creating digital products to achieve this. From our experience, a digital product should pass through the following steps:
1. Evaluate an idea and data availability
2. Estimate an expected economic effect
3. Create a minimum viable product (MVP)
4. Pilot the MVP to evaluate the model quality and the economic effect of the product in real life
5. Develop a stable version of the software and release it and provide support
6. Regularly re-evaluate the economic impact (we suggest quarterly evaluations)
7. Deactivate the software if it stops
Every step for a successful product is essential, but many ideas may not last long enough to live, even to the first stable version. Some will terminate on an idea discussion step, some – after the data cannot be gathered, and some – at the time of economic estimates. The crucial idea here is that the order of the steps is of great
importance, and one cannot start the next step until the previous one is completed (except for step 5, because usually, a pilot lasts for about three to six months and during this pilot, the team continues to develop software).
The second step has a critical significance. Without economic effect evaluation, a team should not proceed with product development. We believe that there are
only two exceptions to this rule: safetyand ecology-oriented initiatives; but even for those, the goal should be measurable. Furthermore, ecology often goes together with the economic effect of cost reduction. In other cases, if the potential economic impact of the product is unclear, then there is no reason to start the project.
But how can you evaluate a product before a MVP is created and the proof of concept has already successfully been left behind? Especially when there are so many essential tasks at the factory for which machine learning and neural networks could be used!
We advise you to apply the following principles:
1. An evaluation is just an evaluation – it is not a commitment to the stakeholders. The actual impact can be much less or much more. An evaluation only helps to decide which project to start next and compare the project’s effect against its costs (usually, in data science projects, costs are much lower than the effect; a good project has a 10x ratio).
2. Check the data from your production process. Some volatility in efficiency will provide insights into what can be achieved
if the process becomes more stable and efficient with the help of data science.
3. We can usually say that a 1% increase or decrease is achievable with visible inefficiencies in the production process. From our experience in cost reduction, you can typically achieve a 2-3% cost reduction and a 3-7% production increase with machine learning instruments. There is another exciting hint – if the expected effect is under doubt and it seems to be less than 1%, we suggest not starting the project at all because, for the industrial processes, it is sometimes hard to reliably measure such a small effect based on the existing data. And if there is no way to measure an effect, it should be assigned a zero value.
The following essential step is the regular quarterly re-evaluation of the economic effect of the data product. One of the goals of doing this is to create a portfolio of valuable digital products for the company. All products have their lifecycle. There is a high chance that after a pilot, without focus, the impact of the product will gradually diminish (for example, personnel from the factory can begin to use the software less and less). Regularly monitoring
and updating the digital portfolio helps to see such cases on time and allows you to evaluate how much value all your digital products contribute to the company.
Next, let’s discuss how to organize a team. There are several approaches to how this can be done. The main two are:
1. A distinct product team with full-time members in it
2. A delivery IT team with a customer from a business
In our opinion, these two approaches do not work well for digital product creation in the steel sector. The classical customerdelivery approach is unsuitable because it is time-consuming and does not grant the team enough product ownership to create an innovative product. A distinct product team is suitable for a massive product with many features and long development but is not the best for many medium-sized products because of the costs of such a team and the scarcity of rare specialists. Also, creating a product owner role who can also be an effective project manager for data scientists and developers is often complicated and, in most cases, not the best way to use your product owner.
Therefore, we suggest this team configuration to create digital products:
1. A factory team with a product owner coming from a business side. The product owner is a person who believes in this product, sees its benefits, and is ready to devote more than 50% of their time to it. They are a steel process expert and have connections with various people across the factory, enough authority to add people from operational processes to a team, and an advocate for digital products in a factory. Other factory team members will include domain experts, automation specialists, operators and so on.
2. A digital team with a project manager as the leader of this team. Team members will be data scientists, software developers (front-end and back-end), data engineers, DevOps, and support engineers. In this
Let us introduce a simplified example of what a typical process might look like based on a real case from our practice. The story begins at the point where a pickling shop starts to bottleneck and a flat steel product owner shapes the need to increase the output of the shop as a digital project aimed specifically at increasing the speed of one of the pickling lines (start of step 1).
The idea is challenged by the factory team members, including technology experts and shop management. The team carefully examines external limitations like coil yard capacity and logistics and internal limitations like unit technical state, including the ability to run steadily at a higher speed. They spend some time looking for non-optimality examples and find several. As a result, this investigation shows that the main potential of the output
At this point, the product owner requests to allocate resources for the project, providing a brief introduction to the digital team management. As the preliminary work was performed thoroughly and the economic effect was significant and clear, the project hit the top of the ranking and is quickly accepted into the development. Step 3 begins.
An experienced data scientist and a project manager are appointed to create an MVP. A data engineer is temporarily engaged at the beginning to retrieve the data from multiple original data warehouses with limited storage volume and stores this data on Hadoop. The data scientist carefully examines the data and dives into the technical specifics of the pickling process with the support of a pickling technology expert and the product owner. Together, they come up with an idea to create a mathematical model to calculate each second’s speed. The model design requires a few more helper blocks to be developed, so a second data scientist is appointed to the project to parallelize development (it makes sense as the economic impact is high). After all the models are ready, a software developer joins the project to productize the solution. Later, the product owner invites an automation specialist to the project to implement integration with the process control system. Here, everyone hopes the MVP is ready (end of step 3).
configuration, only the data scientist should work full-time on this product; the others can be allocated when necessary and one project manager can lead three to five projects simultaneously.
To achieve results, these two teams, of course, should work in a close partnership. There is no division on customer or delivery parts; everyone works together towards a common goal. Also, there is no strict technical description at the start of the project. The product is continuously being shaped in the development process and no one can tell you how exactly it would look from the beginning in detail. Such a flexible approach allows the whole team to experiment and use creativity to devise the most suitable solution to tackle the initial problem.
increase could be revealed if the speed control of the second transport unit of the pickling line is improved. In the process of analysis, the product owner also inspects data warehouses to ensure that there is enough historical data for future detailed analysis and is assured by the automation specialists that a third-party software could control the speed. Still, it will require some additional work for the integration. The idea of direct control arises as nonoptimalities and is often linked with lags in the operator’s actions. Here, step 1 is completed.
The economic impact of the increase of the line output is vast and is based on both the market state and plant development plan – all the calculations support this decision and are approved by the financial controllers (step 2).
The product owner, with the support of the pickling shop management, starts test launches. It requires some training of the unit’s operators to know how to interact with the new software. Typically, the first test launches last 15 to 60 minutes and allow us to see the behaviour of the software in real life, which might differ from the one seen during the offline simulations. In this case, the behaviour differs from the expected, so the product owner and data scientists analyse the reasons and conclude that there is one more crucial technological feature that was not properly considered. One of the modules requires significant changes. The data scientists start working on those changes and two weeks later, the software is ready for further tests. This time, the test launches are successful. Thus, step 3 is completed and the pilot begins (step 4).
While the new software operates the pickling line for a decent amount of time, there are still specific steel assortments that require additional logic to be added
to allow 24/7 pickling line control by the model. One data scientist continues working full-time to deliver those additions. Meanwhile, there is already enough data to make conclusions about the impact of the product on the most typical assortment. The data scientist develops a simple tool which the product owner uses to compare unit productivity across different periods before and after the model launch and calculates the overall profit obtained using the model. It is 5% on the typical assortment and a couple of months later, the team sees approximately the same increase in total for all assortment groups. By that time, the stable version is released, an extensive monitoring system in Grafana is deployed with the help of support engineers, and the pilot is completed (end of steps 4 and 5).
Later, given the significant economic impact, version 2.0 is also developed, which utilizes reinforcement learning (RL) and gives additional productivity increase. It is inspired by the data scientists who
notice the pickling process uncertainties are not addressed by the mathematical model and see the pickling line as an appropriate environment for an RL agent. Several additional blocks are designed for that version: pickling line digital twin, generative adversarial network to provide RL with enough steel sheet data (history is limited), the RL agent itself, and a few helper modules. Three data scientists in total work on this part to deliver it as soon as possible. You can see more details about the RL approach in our article1
This version is successfully released and starts working 24/7. The new version is a separate project with its economic evaluation, MVP, and effect assessment. Otherwise, new tasks and ideas can arise every week and the project will never come to an end.
In the course of a few years, the situation in the market and at the steel plant changes, but the evaluation of the model is performed quarterly, allowing users to see the role of the product in the
1. https://arxiv.org/abs/2008.06933v2
company’s digital portfolio, interact with the shop management and operators to control model use, and to make decisions regarding digital resource allocation, when required (this might happen, for example, if the process control system is altered or the technical state of the unit has some major changes). Step 6 is life-long.
Generally, we do not expect digital products to get obsolete and reach the end of their lifecycle until some critical changes hit the production unit. The model might be deactivated if a production bottleneck is avoided by some other more effective means, for example, by building a new unit or by a complete reconstruction.
In other cases, if the target is still applicable, the model can catch up with the new circumstances by retraining or introducing some changes.
However, for a model to last long and continue to generate real impact, we always need proper monitoring, close contact with the factory team, and regular reevaluations. �
2023
The Future Steel Forum, now in its SEVENTH successful year, is heading for Vienna this September to examine the important relationship between digital manufacturing and the decarbonization of the steelmaking process. Come and listen to experts from the two most important areas of global steelmaking at present. This is a must-attend conference for anybody with an interest in the fast-developing world of Industry 4.0 technologies and those responsible for sustainable steel manufacturing.
CONFIRMED SPEAKERS FOR FUTURE STEEL FORUM IN VIENNA INCLUDES:
The Industry 4.0 paradigm shift in the late 2010s triggered smart automation and data exchange in manufacturing technologies and processes, bringing about increased applications of Artificial Intelligence in the industrial sector. This article explores how steelmakers were impacted by the digital transformation, and the innovations that have led to smart products, processes and supply chains.
THE enablers of the fourth industrial revolution are automation, increased computing power, availability of real-time data and analytics, AI and machine learning (ML) models. The generation of big data in the manufacturing industry resulted in increased digitalization of all processes, generating large amounts of data that were integrated in modern industrial plants.
From these technological developments in automation technology, real-time data collection, and visualization, digital twins emerged. These use real-world data and analytics, simulation, or ML models, to glean information and make production and quality decisions. Digital twins are used to answer what-if questions and give intuitive insights. Simulations are equally possible and are used for process design
and enhancements.
In the metals industry, digital twins are currently available not only for production lines but also for consistent data collections of material units along their production route. Additionally, digital twins are used for transports in the stockyards, enabling transparency and efficiency along the whole production process.
One of the key benefits of digital twins is the ability to harvest new knowledge out of data, supported by ML models. Such models are generated out of historical data and results for a process. This way, they are trained, validated and can be used to predict future results based on new data inputs.
However, conventional ML is often perceived as a ‘black box’ and unreliable, especially for steelmakers. For industrial applications, ‘white box ML’ is required and progressing quickly. In explainable ML models, correlations among features are recognized, weighted, and presented to the user to explain process behaviour. In some cases, the hypotheses made by the domain experts can be validated and quantified. In other cases, the model itself might suggest new dependencies. It is the continuous interaction between transparent data science and domain knowledge that is expected to leverage the potentials of ML in the steel industry. For this goal, ML needs to become a commodity to the industry, available when needed, easy to ‘consume’, and to deploy.
Smart supply chain – the next generation of supply chain Digital steel production management will increasingly involve close collaboration between human agents like a scheduler or yard operator, and smart autonomous agents. These agents are small pieces of software that focus on a very specific set of problems. They can make independent local decisions and notify human agents or
supply chains. The human decision-makers will have immediate visibility on any supply chain event. With the support of digital twins and smart agents, they will have access to predictive and prescriptive services and the ability to perform fast ‘what-if’ scenario benchmarking. In this way, they will make faster decisions aligned with key performance indicators’ priorities.
Finally, AI will allow the system to continuously learn and self-improve from events and to capture non-linear and complex system dependencies, leading to a better understanding of defects, process deviation and root causes.
Smart processes and products emerge
Single solutions have been developed in the past years to leverage the potentials of Industry 4.0 in different areas of steel production.
At the melt shop, Online Heat Scheduler (OHS) by PSI Metals manages and optimizes the detailed work schedules for the heats. Based on dedicated work plans, it schedules all required treatment and transport steps, and assigns production lines and operating equipment based on available capacity in real-time. It gives an overview of the current versus planned progress for all heats. OHS always ensures the seamless delivery of heats and sequences to the caster and reacts in case of any disruptions or breakdowns. Using AI models, PSIqualicision AI is integrated into the OHS and is designed to optimize the process quality by means of intelligent data collection, analysis and balance between goal and criteria conflicts.
algorithm would be called to suggest for each material unit the best possible downstream parameters, in order to react to the identified deviation risk and nudge the material to the possible best result according to the available knowledge. This is done systematically and dynamically after each selected production step.
A powerful example of quality prediction is the prediction of surface defects that can appear on cold-rolled coils towards the end of their production route. A ML algorithm can be trained on historical data of finished coils and identify the casting conditions under which a subsurface defect is created in the slab and later on discovered on the coil. After validation, the algorithm can be used to evaluate the slab after the casting process with respect to the risk of defect appearance in the downstream process. It might indeed be able to predict which type of defect will appear after rolling and how severe it might be, long before the slab is processed.
In addition to processes, metals products themselves are becoming smart. PSI Metals’ partner coilDNA developed a technology that gives metal an identity. The technology turns it into an intelligent product by allowing you to track its history.
even other smart agents working together to solve larger problems by communicating together in Multi-Agent Systems (MAS). Such agents can be incorporated as part of business process workflows and can be enhanced through AI in order to detect changes in their environment, learn from the impact of decisions and adapt their behaviour accordingly.
Through real time availability of big data from the end-to-end supply chain, computational power, digital twins, and ML algorithms, we have all the ingredients to build smart supply chains. That is, supply chains that are able to take faster and better decisions. Reducing latencies in decision-making and reacting to flow disruptions are some of the biggest potential benefits of the digitalization of
This AI-based decision support by OHS/ PSIqualicision involves three simple workflow steps structured to optimize process quality. These include the automatic analysis of inputs, set up of constraints and business goals, then the running of the solver and the analysis and balancing of KPIs with PSIqualicision AI and finally, the iteration, comparison and heat schedule release supported by PSIqualicision AI-based scenario management.
In Quality Control, predictive algorithms are used to evaluate the risk of deviation of a target feature at any stage of production. Feeding the algorithm with as-is real input data for the upstream process and the necessary expected input values of the downstream process enables the use of the algorithm at any stage. In case of out-of-range prediction, a prescriptive
Using cloud communication, the manufacturer requests a unique DNA sequence for the produced parent material, and can print this code on the material’s surface during production. All relevant MES data linked to the material and its DNA code is sent back from the manufacturer to coilDNA where it is saved in a dedicated repository. The unique printed DNA sequence along the length of the material is the reference for retrieving information about the material composition, the manufacturer, the position within the parent product, properties, or qualityrelevant production parameters, including carbon footprint data. With a dedicated app on a mobile device, customers can scan the printed DNA on any steel sheet and retrieve the available information from the coilDNA repository.
To capture opportunities and manage smart material and process flows, production management systems need an Industry 4.0 upgrade. There are some building blocks required for such a production management 4.0 system upgrade.
The first step would be to break the traditional automation levels pyramid as shown in Fig 1.This structure has two main limitations:
• Communication: Generally, one level can only communicate with the levels directly above or below it.
• Data abstraction and/or translation: This occurs when passing from one layer to another, limiting data to certain layers and not to others. This makes it difficult to integrate or connect a ML service that would require data from different levels.
The next would be for a production management 4.0 system to provide an open platform architecture that enables a flexible orchestration of business process flows. More specifically, a dedicated workflow management service should support configuring customized and adaptive business processes. This may involve native functions from different business areas such as quality control or production planning, but could also integrate external systems and services such as an ML-based defect prediction service.
Such service-oriented architecture should further support different database management systems, and the replication and mapping of data where relevant through dedicated audit trail services.
In addition to core advanced production
scheduling and manufacturing execution system services, a P M 4.0 system needs to provide state-ofthe-art embedded business intelligence, UI configuration, authentication, authorization, and event notification services. One such system is the PSImetals Service Platform shown in Fig 2
With the PSIbus, flexible communication and data integration enables loose coupling among registered services in a peer-to-peer way. An API integration layer and dedicated adapters allow external services to register to the platform and be integrated into workflows. The integration bus also allows seamless and direct connection of services that use data from different layers of the traditional automation levels pyramid, bypassing the earlier mentioned data losses that may occur due to abstraction and transfer in-between layers.
As an example of how different digital services can be integrated by a modern production management system (PMS), let us look at a hot rolling schedule adaptation required by a non-conformity occurrence. In case of one or more slabs showing issues in terms of quality, logistics or production, dedicated planning services will de-schedule the slab(s) and check the feasibility and quality of the remaining rolling sequence. Depending on the answer, the check flow might end or continue with the search for alternative slab candidates. A dedicated workflow management service enables designing and adapting material flows as needed. For instance, a third-party defect prediction service could be plugged in in
order to support the quality check of the slabs to be newly allocated to the order with open demand.
In an e-commerce platform, many functions of the PMS could be called a service. Using the buyer’s data as input, a dynamic rule-based order dressing could answer feasibility inquires, including first-time inquiries. The Due Date Quoting planning function could then use the results of the production order elaborated by order dressing to estimate the delivery date. And after the purchase, all material data could be retrieved by calling the quality management service. For this, the e-commerce platform needs to be securely connected to the PM services, via PSIbus.
In a KPI-driven PMS, it might be possible to balance classical KPIs like quality, throughput, stock or due date, with new KPIs like efficient energy consumption and reduced CO2 emissions. This way, not only the best scenario could be identified, but the impact on sustainability of any decision would become clear, enabling sustainable steel production.
It is clear that the ongoing digital transformation promises to make steel material and production workflows smarter and greener. We anticipate more improvements in the planning and production process.
As AI takes on more repetitive and datadriven tasks, the role of human agents will switch to focus on tasks that AI is not yet capable of performing, like creative thinking, innovation, scenario assessment and people management. A new generation of PM 4.0 Systems is needed to support this paradigm shift, to connect human and AI agents and build a service platform designed to provide the required visibility, reactivity and flexibility. �
Metal is the backbone of our society. It’s in the structures we ride, work and live on every day. That’s why you’ve trusted the detection technology inside every ARL iSpark for over 80 years to ensure every piece of steel and metal you produce is safe. With so much riding on that, why would you choose anything else?
Over the past year the US energy pipe and tube market was even stronger than expected, albeit at varying degrees different product segments. While both have seen double digit year-on-year growth, the rate for oil country tubular goods (OCTG) has been outpacing that for linepipe.
“LIKE for most markets, energy pipe had a dramatic recovery from Covid,” Kurt Minnich, vice president tube & pipe for Argus Media observed, maintaining, “With its rapid increases both in 2021 and 2022, it is currently looking even better than it did pre-Covid, given its extremely high growth rates. He noted that last year OCTG demand jumped about 60% and linepipe demand increased by an also very impressive 25% year-on-year. And while even at the beginning of 2022 demand was already on the upswing, Paul Vivian, a partner at the Preston Pipe Report, noted that demand for both products just continued to improve as the year progressed.
In fact, Philip Gibbs, a metals equity research analyst for KeyBanc Capital Markets, said that the energy market was the biggest demand driver for the US steel industry last year and the only major enduse sector that saw substantial growth. “With the rising interest rates, construction
was overall stable to down slightly. Automotive output didn’t grow very much and most industrial markets were generally flat.
But even with its big jump last year, Stephen Landes, a research analyst with S&P Global Market Intelligence, noted that drilling activity, therefore energy pipe demand, still remains lower than it had been pre-Covid, and while there is still potential for a little bit more growth this year, he said that he believes that demand for OCTG and other energy pipe demand could be close to peaking. A national OCTG distributor, however, said this isn’t a reason for concern. “Volumes and prices will remain strong,” he said, noting that it is just that the turbocharged market, fuelled by the panic buying last year amid the unprecedented tightness of supply, is starting to calm down. That isn’t that surprising, especially given the concerns about inflationary tailwinds and a possible
By Myra Pinkham*recession and the vulnerability that the energy sector has to such geopolitical forces as the war in Ukraine, Philip Bell, president
of the Steel Manufacturers Association (SMA), pointed out.
“Uncertainty has always been a part
of the oilfield business, but the current combination of economic uncertainty and increased volatility has made operating in the oilfield even more challenging than usual,” Minnich said. “And the energy pipe markets need to navigate everything that has been going on including supply disruptions, regional issues, the tight labour market, ESG (environmental, social and corporate governance) issues and the wide band of uncertainty around forecasts for oil and natural gas prices.”
He noted that such uncertainty makes it very difficult for exploration and production (E&P) companies to develop their drilling programmes or to get financing. In fact, Vivian said that with West Texas Intermediate (WTI) oil prices coming down to $70-$80 per barrel from $90-$100 and with natural gas prices flatter than expected due to a milder than expected winter, the E&P companies have been cautious and patient about their investments even though they are cautiously optimistic that at some point energy prices will move higher again.
Given that oil and natural gas drilling activity is seen as being a direct driver for OCTG demand and an indirect driver for linepipe, a lot of attention tends to be paid upon Baker Hughes’ US drill rig count. While it has been stagnating and even easing slightly month-on-month, at 760 active rigs in mid-February it was still up 17.8% from 645 rigs a year earlier and up considerably from the height of the Covid pandemic when the count dropped to
Leppold, head of steel research at Fastmarkets, noted that the uncertain economic outlook is affecting operator plans meaning that there is potential for drilling investments to come off over the near term until the E&P companies get a better view of what is going on, especially given that such investments are getting more expensive with the cost of pipe and the steels used to make that pipe rising at
creates a big challenge,” he said, “Because we are a commodity following another commodity.”
Leppold pointed out that while looking at the rig count is still very useful, there are also other factors that need to be considered when determining true OCTG demand. For example, she noted that because of increased well depths and lateral lengths and the efficiency of the rigs, there is actually a need to use more pipe per well. In fact, Leppold said that as of the second half of last year the consumption of casing and tubing per rig had already grown to over 600 short tons per rig per month, which is a substantial increase from 2019 when their consumption was about 400500 tons per rig per month. Minnich said that this has been a long-time trend, noting that several decades ago rigs had consumed somewhat less than 200 tons of pipe per month. However, the expected restarting of some of the older, less efficient rigs that were idled during the pandemic could affect the average OCTG consumption per rig.
the same time as labour issues are affecting both the cost and availability of workers. S&P Global’s Landes noted that this is coming at a time when E&P companies are refocusing their capital structures and looking to increase their cash flow as opposed to taking on more debt and drilling more oil and natural gas than they need to.
“But no one really knows what the US rig count will be later this year,” said an
Also, OCTG consumption has been impacted by moves to locate wells closer together on pads, Leppold said, explaining that this has enabled those wells to be connected by laterals and utilize horizontal or directional technology. She noted that while this isn’t a new trend, it is one that has been increasing over time.
Vivian said that another reason for the pick-up in OCTG demand has been the huge amount of drilled but uncompleted
about 250 active rigs, and Minnich said he believes that the number of rigs could pick up later this year, bringing the rig count up to the low 800s.
That, however, isn’t a given. Kimberley
OCTG distributor who wished to remain anonymous, given the wide range of potential WTI oil prices – which, he said, could be anywhere between $30 and $167 per barrel. “That uncertainty and volatility
(DUC) wells being completed over the past year, there is a need for more new wells to be drilled. Gibbs noted that during the pandemic, and even a year or so before that, the number of DUCs were at historic
highs, and once the energy sector began to recover, operators started to uncap their DUCs in the second half of 2021 and continued to do so aggressively throughout 2022 to get oil and natural gas flowing before any new drilling took place.
In fact after hitting a high of 8,800 in mid-2020, Minnich said that over the past year DUC inventories had been essentially cut in half and are now at what operators in most regions of the country consider to be at a good support level. Given that, the anonymous OCTG distributor said he doesn’t expect those inventories will be worked down further. In fact, he said it is possible that they could slowly increase this year as new wells are drilled.
The story, however, is different – and somewhat mixed – for linepipe, Leppold said, noting that while small diameter linepipe used for oil and natural gas gathering lines, is supported by similar dynamics as OCTG, demand for large diameter pipe for transmission pipelines hasn’t been as strong.
But even demand for large diameter linepipe has been somewhat mixed. There have been certain governmental policies and environmental challenges, including pushes by environmentalists to stop certain pipeline projects from being approved. Some projects have either been rethought or cancelled and this has had a negative impact. Vivian said that recently there has begun to be at least a mild improvement in companies being able to get pipelines built. Much of that, according to Devon Jobagy, vice president of supply chain and technical sales for MRC Global, is being driven by liquefied natural gas (LNG) activity, particularly the resurgence of new LNG projects – largely in Texas and Louisiana – since the start of the war in
Ukraine. He noted that with US companies looking to service Europe with LNG, the amount of LNG-related quotation activity by E&P companies is massive, resulting in a significant number of planned projects that are either in the feasibility or funding stages. That will require an increased amount of linepipe to gather and transport natural gas to the LNG facilities.
gas drilling since it is used for gathering purposes. “But given the large number of suppliers of that type of pipe, its supply isn’t that tight and its prices haven’t been as strong as those for OCTG.
And while there is currently more quoting activity for large diameter linepipe than there had been over the past few years – albeit more for DSAW pipe than ERW pipe – and several new pipelines in the works, Jobagy said it isn’t anywhere near as strong as it was four or five years ago when there was a big build-out in the Permian basin (a large sedimentary basin in the southwestern part of the USA). Leppold agreed stating that with most of the projects either being for short distance new pipelines or expansions or replacements of existing pipelines – while improving – is still in oversupply, particularly when it comes to seamless linepipe. Jobagy said that this is because of a kneejerk reaction by pipe distributors last year, who double and triple bought seamless linepipe when domestic seamless mills were almost exclusively producing OCTG.
At the same time, he noted that there are a number of major projects related to carbon capture technologies that will fuel hundreds and thousands of miles of pipelines, therefore tying up a lot of linepipe production capacity. But Leppold said it was still a long way off, and the same is true for hydrogen transportation.
According to Leppold, the largest percent linepipe demand is for small diameter –under 16-inch outer diameter (OD) pipe – which tends to trend with oil and natural
“Overall we saw the energy pipe and tube sector claw its way back last year, buoyed by higher energy prices and rising rig counts,” SMA’s Bell pointed out. In fact, Gibbs noted that volumes, prices and profitability had been stronger than anticipated. He said that while it is possible that that market had recently peaked, he said that it should be able to sustain itself at least through the first half of this year. What will happen in the back half of the year will depend on what happens with energy prices and the US economy. “It should remain robust even if energy prices moderate,” the anonymous OCTG distributor said. “But if they pick up, there could be another scramble.” �
Ready to invest in carbon capture?
Munters has the expertise and equipment to support your project. We have decades of experience in Mass Transfer and Mist Elimination – Clean technologies that are essential to any successful carbon capture project, no matter the industry. You can count on Munters proven solutions to support your carbon capture project.
Clean technologies by Munters
Amid harsh instability of energy pricing, natural gas shortages, and slumps in the construction sector, the Turkish steel industry is learning from the present to prepare for the future. Catherine Hill* attended Steel Orbis’ New Horizons in Steel Markets conference in Istanbul, Turkey, to uncover how one of the largest global steel industries was weathering out a storm that shows no signs of clearing.
WITH only a few minutes left until my flight from London Heathrow to Istanbul lands, the muffled crackling of the pilot’s intercom sounds; ‘‘Welcome to Istanbul; the meeting point of the world’’. I disembark, go through the winding queues of passport control, and then message my airport pick-up who I’ve already missed four calls from while attempting to connect to the airport Wi-Fi. He tells me he is waiting in level four, and sends me a photo of what looks like painted green walls. I leave the airport and spend the next 40 minutes blindly stumbling around what seems to be a car park from the movie, The Matrix, with
no people and no cars, just endless rows of empty grey spaces. Every few minutes he video calls me in exasperation; ‘I AM HERE. WHERE ARE YOU??’. After we establish that he isn’t even in the same car park, let alone the same level, I get in a lift, and start feverishly pressing buttons in a random order. Finally, the doors open and I see a glimpse of green walls, and a bright white sign reading; ‘Level 4’. I message him; ‘I AM HERE. WHERE ARE YOU?’. I have arrived in Istanbul, the meeting point of the world.
The financial district where the Steel Orbis Conference I am attending is based is a mixture of pastel-cake blocks of apartments,
*Editorial assistant, Steel Times International
and skyscrapers that look like the helm of a ship from the future. Pavements are narrow and undulating; you are either racing toward a pothole, a crack in which a root of a tree emerges, or the road where drivers sleepily approach their 9 to 5 with the window cranked down and a cigarette artfully drooped between nicotine-stained fingers. The conference venue, Marriott Hotel Asia, is a vision of sunken lights, swirling carpets, and huge swinging doors that reveal a waiter carrying a tray of precariously stacked glasses. The conference title – New Horizons in Steel Markets – is an unsubtle gesture toward a country
that has defied expectation in its growth, with the Turkish steel industry being the largest producer in Europe, and the seventh in the world, having showed the largest production growth in 2011 and 2012 post the global financial crisis of 2007. Turkey’s geographical location presents it with an easily accessible, large-scale, high-value export market, and with most of its steel capacity being located close to a coast, producers are able to switch between supplying domestic and export markets as required. However, its positioning does not provide immunity against the current crises that are harrowing the steel market across the world: rising energy costs, natural gas shortages, slumps in the construction sector, and scrap pricing. In fact, Turkey’s consistent success despite a history of global challenges makes the fight even more important – there is a case to make of reputations, and of set standards, that have become not only valuable to uphold, but essential in securing a viable future.
The conference began with an overview of the Turkish steel industry from Dr. Veysel Yayan, secretary general, Turkish Steel Producers Association. Yayan cited the ‘huge surge in energy prices’, saying it is ‘impossible’ to keep up with the pricing, and the industry ‘being urged to compensate is unnatural’. ‘‘People assume [Turkey] is in a good financial situation, we are not, but the [Turkish] ministry said we thought you were, and we thought you could compensate the surging cost, but it is impossible – it is an experience we have faced for the first time’’. According to Yayan, domestic production has dropped by 9%, and finished steel consumption has declined by 2.5%. There has also been, continued Yayan, a ‘shrinkage in Turkey’s flat steel consumption’, although he predicted that in 2023, the construction sector will pick up, boosting consumption
levels. Yayan then spoke on the energy crisis, saying that ‘Turkey and the EU are differentiated in terms of the crisis’, and that ‘a price difference exists between Middle Eastern countries and Far East countries.’ ‘‘It is difficult for us to compete at the moment,’’ Yayan said, ‘‘because our margins are decreased – and a bottleneck has been created.’’ For this to change, Yayan called for a re-balancing in pricing, and the global steel sector as a whole to fight for this – ‘‘we should win together’’, he summarized.
Uger Daldeber, general manager of Colakoglu Metalurji then followed, beginning his presentation by stating: ‘‘each year we try and make estimations for the sector, but the world is changing very fast – by the time I’ve finished my speech what I’ve said may not be true.’’ Turkey was recovering post-pandemic, Daldeber said, but then the Ukraine crisis came; a conflict that in his words was ‘unlike Iraq or Afghanistan, with deeper impacts for [Turkey] and the world’. In short, he stated, ‘‘we were not prepared.’’ In terms of the eponymous markets of the conference, Daldeber commented that it was a case of ‘survival’, rather than ‘success’. ‘‘Right now, we cannot compete with European countries because of these conditions’’, he continued, ‘‘we are losing our competitive edge; how is this loss going to be financed?’’ According to Daldeber, Turkey is currently paying the highest energy tariff in the world – while other countries have had a 50% price increase, Turkey has faced a 70% increase. ‘‘Sustaining an advantage can only be done by sustaining local production’’, he concluded, although allowing for the fact that the domestic steel industry still had ‘homework’ to do in terms of renewable energy, raw materials, and digitalization. This aspect of protectionism was a frequently implied, if not outwardly
stated topic within the conference; the external issues Turkey faces appear to have created a drive that is inwardly directed. To boost its economy that has been driven down by global factors, it must address what it can control; domestic imports and exports, tariffs, and investments.
Next to the stage was Baris Ciftci, head of raw materials markets analysis at worldsteel, who spoke on the expectations and developments within the global steel industry. ‘‘In 2018, the status was good for the steel industry after China’s exportation normalized,’’, he said, but then came the pandemic and Russia’s invasion of Ukraine which disrupted the expectation of ‘normalization’. Since 2021, said Ciftci, 20Mt of steel production globally had been lost. However, he predicted that there will be a 1% recovery in 2023, compared to the 2.3% decline of 2022, thanks to the robust American economy. ‘‘Structurally speaking,’’ Ciftci stated, ‘‘we are sure of one thing; China is now required to change its economic model, as its model has become dependent on real estate investments. When it declines, it has severe repercussions.’’ The ideas of ‘established global orders’ were raised, with Ciftci commenting that the disruption has challenged these orders, which in turn creates transformation. In his eyes, this will lead to widespread digitalization, and optimized processes despite the difficult conditions in the short term. In terms of the automotive sector, Ciftci said that it is currently facing a ‘perfect storm’, with waves of disruption via on-demand mobility (car shares, taxis etc.), smart EVs, and autonomous mobility. To weather out the market volatility, the industry must grow with it, he concluded, embracing ‘smart and digital manufacturing and carbon neutral ecosystems’. This way, not only will the steel industry survive, but it will be
transformed as a result of its challenges.
The conference closed with a panel of five steel industry executives; Metin Tayfun Iseri, business development and international affairs director at Çolakoğlu Metalurji, Kerem Çakir, general manager at Borcelik, Mehmet Çakmur, general manager at M Steel Dis Ticaret, Kemal Saraç, general manager at Yucel Boru, and GÖkhan Demiruz, chairman at Gokmetal AS.
The moderator began the panel by asking the panellists to name the most important factors affecting the industry and the market, and after a short pause, Iseri stated that the world has been ‘divided in two in terms of energy prices, with Turkey on the expensive side.’ ‘‘However,’’ he added, ‘‘energy pricing is not the problem of today; it is the problem of the last 78 years due to bad handling of inflation.’’ Cakir acknowledged Iseri’s statement, citing the difficult conditions, and expanded on the issue of declining demand; ‘‘We don’t know about the future – we try to make sales for January-March, but the price is not certain. Steel, iron, and glass have to pay exponentially more than other industries – I’m not criticizing policy, but we need to
work together.’’
On the Ukraine crisis, Cakmur stated that since the invasion, ‘Turkey had lost its biggest suppliers, while Chinese exports to Russia actually increased with demand’–which in his eyes, was a manipulation of a complex geo-political environment, utilizing fissures in the market to expand. Iseri echoed this statement, as he raised the ‘double standard’ that was at play in the industry, with companies not selling Russian steel, but still exporting. The topic of protectionism then returned, with Iseri continuing to criticize the ‘Build America, Buy America’ scheme established in 2021 in the US, which requires that all iron and steel, manufactured products and construction materials used in covered infrastructure projects are produced domestically. In Iseri’s view, the policy drives ‘hardships on the Turkey industry’, as a result of its limiting effect on exports. Tension quicky arose after this statement, as Sarac rebutted Iseri, saying that ‘buy Turkish is not going to save us; we have to shake hands with these markets’. The panel culminated with a discussion on the green transformation currently taking place within
the global industry, with Sarac saying: ‘‘I think the green transformation is going to be most important thing to happen, and I’m not just talking about green of the trees, I’m talking about green of the dollars.’’
I left the venue, having narrowly avoided being run over by a truck lurching out of a kebab house car park. As I approached my hotel, it began to rain, and I looked at the blotted grey clouds hovering in the sky, heard glimpses of an exasperated conversation between a woman and her phone, and saw a businessman pick a huge yellow leaf off the sole of his shoe. I felt like I could be anywhere. Maybe it was the trapping air of the financial district, sucking things in and turning them into an impassive global language. Maybe it was the rain.
When I returned to the UK, I found a single half burned Camel cigarette in my suitcase. I don’t smoke, and I’m not sure how it got there, but I realised that my sole memento of the trip was a used American cigarette butt of unknown origin and not knowing what that meant, or if it meant anything, I went to bed. �
Combilift is the perfect fit for the steel industry. Our multidirectional forklifts, straddle carriers and mobile gantry cranes are perfect for handling long product, allowing you to maximise your storage, efficiency and safety.
• Safer product handling
• Optimised production space
• Improved storage capacity
• Increased productivity & output
• Enhanced profits
Granulometry is the measurement of the size distribution in a collection of grains and must be carefully controlled to produce the desired properties in sinter of low RDI, high RI and a suitable distribution of porosity. Results of laboratory trials show that incorporating sufficient fine ore, below 100µmsize, to provide adhering particles for the sinter constituents and larger particle sizes of 1-3mm to provide nucleation sites for porosity, is essential.
By S Acharyya, S Dhara, Dr G M Chowdhury, M K Singh, R K Ram & A MallickTHE steel industry in India is increasingly facing challenges in producing good quality sinter due to the depletion of high grade reserves of hematite ore. The Eastern region of India is characterised by an abundance of high loss on ignition (LOI) iron ore as well as high gangue content generally of grain sizes between 0.5mm to 3.0mm.
The production of sinter has an important role in an integrated steel plant both to provide a permeable charge material and to recycle plant fines. The materials available
to sinter can vary to a wide extent, from iron ore fines to plant dust for recycling, fluxing agents, coke breeze and undersize sinter. The natural resources of iron ores vary considerably depending on the mineral composition and mining technology applied to produce the sinter feed. Therefore, it is vital to assess the characteristics of the available raw materials and ascertain the ratios of blending to meet the sinter quality requirements for blast furnace operation. The Reduction-Degradation
Index (RDI) and Reduction Index (RI) are the two most important sinter qualities for blast furnace operation. In general, they share an opposite relationship; sinter with a low RDI tends to have a high RI. High RDI is detrimental as too high a strength allows gas to pass too freely up the furnace stack and thereby increase fuel use; a value below 30% is thus aimed for, while a value above 65% is the target for RI. It is thus important to keep the RDI and RI values within these ranges for smooth
The authors are with the Research & Development Centre for Iron & Steel, Steel Authority of India, Ranchi, India. Corresponding author S Acharyya. e-mail: sudip.acharyya@sail-rdcis.com/gmail.com, telephone: 8986880192.
operation of the blast furnace. Pores in the sinter play an important role in influencing its properties[1,2,3]. Porosity is formed at the interfaces between flux (limestone & dolomite) and coke particles, after their assimilation and combustion[4]. Hence a good distribution of these two important raw materials is required to achieve an evenly distributed network of porosity. Researchers also report that a good nucleus for porosity results from including high quality dense adhering fines during granulation and also results in the required high RI and low RDI values[5]
To improve sinter quality in terms of high RI (>65%) and low RDI (<30%) values, a technique of differential and selective granulation of high loss on ignition (LOI) and low LOI iron ore has been applied.
Two types of iron ore have been used; one with high LOI (>4%) and the other of low LOI <4%. The ores were mixed with high grade limestone, calcined lime and dolomite as fluxing agents. Coke breeze was added to meet the fuel requirement. Details of the granulometry and chemical analysis are as given in Tables 1, 2, and 3
The sinter charge consisted of approximately 36% high iron bearing ore, (63-64% Fe) of a particle size greater than >3mm. The silica content was low at 2-3%.
For sintering, the 1 to 3mm size fraction is the prime constituent to aid the formation of nuclei for pore generation during granulation. A size fraction below <1mm is needed to produce adhering fines. These are the key for melting. Increasing the quantity of the adhering fines results in improved melt quality. To increase the sinter charge with adhering fines part of the +3mm size fraction was crushed to <1mm and mixed with the existing <1mm size fraction. Two grades of iron ores were granulated; size fraction 1 to 3mm of high LOI ore for the nucleation of porosity
and low LOI ore enriched by crushing to below <1mm size fraction to increase the proportion of adhering fines.
Laboratory trial
Five pot sintering experiments were carried out using different fractions of nucleating and adhering fines combinations. The laboratory scale sinter pots used were 310mm in diameter with a bed depth kept at 650mm. Suction pressures were 1200 to 1300mmWC.
For experiments number 1, 2 and 3, varying proportions of Low LOI iron ore
GSM200tocapacityandGFM100tocapacity inoperationatNAF,NewCastle/PA
GLAMAMaschinenbauGmbH
Headquarters: Hornstraße19D-45964Gladbeck/Germany
Fon:+49(0)204397380
Fax:+49(0)2043973850
Email:info@glama.de
GLAMAUSAInc.
60HelwigSt.,Berea,Ohio44017
Fon:+18774526266
Email:sales@glama-us.com
May23–25,2023 CLEVELAND,OHIOUSA HuntingtonConventionCenter
Visitusatboothno.: 213
GIR-P1tocapacity inoperationatStandardSteel,Burnham/PA
GFM150tocapacity inoperationatScotForge,SpringGrove/IL
Table 5. RDI, RI and porosity distribution of sinter sample were used as adhering fines and high LOI iron ore for nucleation of porosity. For number 4, only high LOI iron ore was used as both adhering fines and nucleation agent. For number 5, high LOI iron ore provided the adhering fines and low LOI ore for nucleation.
The green mix was prepared in three stages.
1) All the fine iron ore (<1mm size fraction), flux and coke was mixed.
2) The required additions of high or low LOI ore of 1mm to 3mm size fraction for pore nucleation were added along with sinter returns and 30% of total water, each batch being mixed by shovel.
3) Finally, with the exception of batch No 2, each mixture was brought to 70% total water and charged to a mixing and balling drum to agglomerate to grains.
No water was added to number 2 mix and mixing was carried out manually at all stages. In all other experiments the end water content was 7.5 wt% of the dry mix charge. The chemical basicity of the sinter mix was kept within 2.15 to 2.2 and MgO within 1.75 to 1.8%. In mixture 4, low LOI ore was absent, instead the mixture contained a total of 60% high LOI ore of which 45% was below <1mm in size for use as adhering fines and 15% in the size range 1-3mm to act as a nucleus for porosity.
In mixture 5, high LOI iron ore below size <1mm was used for adhering fines and Low LOI ore of size 1-3mm was used for nucleation.
The constituents of each experimental mixture is summarised in Table 4
The sinter samples from each pot trial were subjected to RDI and RI (JIS-M-8713)
tests and internal porosity characterised by X-ray Computed Tomography as a nondestructive test.
porosity was also examined. A range of three porosity sizes are shown in the table. From the result we observe:
1. The total volume of porosity ranges from 6.77 to 9.71% and does not show any direct relationship with RDI or RI value.
2. There is no clear relationship between porosity in and around an un-reacted nucleus and the RDI value for porosity between 16 to ~18.5%. In case number-4 the pore volume in and around a nucleus is much higher (~27%) and a very poor (high) RDI value, but also high RI value are present.
3. Sinter samples of experiments numbers 1 and 5 generally show similar porosity networks throughout each sample as well as in and around iron ore nuclei. In contrast, comparing number 5 with number 2 shows a difference in the porosity network in number 2 which has a non-uniform distribution of pores. This could result in weak points in the sinter and thus the inferior RDI value for No 2.
4. In experiment No 3, <100µm pores are generally distributed throughout the sintered mass and pores larger than >100µm make up part of the pores of the high LOI ore nuclei.
Table 5 indicated the results of the RDI and RI and porosity tests. Only closed porosity can be measured by Computed Tomography, the distribution being calculated using the equivalent diameter of a sphere of similar pore volume. Porosity distribution was determined as Total closed porosity and closed porosity adjacent to an ore nucleus. The area surrounding an unreacted iron ore nucleus showing closed
5. In experiment number 4, in spite of its very poor RDI value, the RI value is very high. Careful observation in the porosity network reveals that there is not only a non-uniform distribution of porosity but the vol% of <200 µm sized pores in and around the iron ore nuclei are greater than in the remainder of the sample.
Since there was no difference in the mixing method of all samples except
number 2, the flux and coke particles have all been mixed properly with the adhering fines. This has resulted in a more homogeneous melt formation across the sinter bed and thus better values of RDI and RI. In the case of No 2, the difference in mixing procedure may have resulted in selective concentration of flux and coke in the granulated mix which may have formed an inhomogeneous bonding phase across the sinter bed resulting in a poor RDI value.
In the case of experiment number-4 where a very high (poor) value of RDI resulted, this may be due to the higher alumina content of the high LOI ore which was the only ore used. High alumina in the melt and subsequently in the bonding phases may have resulted in the high RDI value.
The following can be concluded from the above discussion:
1. To achieve the desired high RI and low RDI values, proper iron ore granulometry and mixing of fuel and flux with the ore plays a very important role. Low LOI iron ore acting as adhering fines is characterised by high quality and dense
sinter which helps in creating the right quality and quantity of melt for bonding. High LOI iron ore of a porous nature characterised by a low melting temperature can be bounded with the sintering melt.
2. Intensive mixing between adhering fines, fuel and flux is required for a chemically homogeneous mix required to generate melting and an even porosity network distribution.
3. With restriction of >200µm size pores within 35% in the sinter will result in the desired RI value of >65%. For a suitable RDI value, the size fraction >200µm needs to be within 25% to achieve <30 RDI.
4. Better RI and RDI values can be achieved if <100µm sized pores are mostly distributed in the sintered mass while 100 to 200µm sized pores are associated with nuclei (as in case of experiment number-3).
5. Heterogeneous distribution of porosity between the ground mass and in and around unreacted nuclei will result in weak point generation and heterogeneous expansion during the reduction process and lead to a poor RDI value as in experiment number 4). �
The author thanks his co-author and RDCIS for technical and financial support and IIT Kharagpur’s central research facility for 3D characterization of sinter samples using X-ray computed tomography.
[1] N. V. Y. Scarlett, M. I. Pownceby, I. C. Madsen and A. N. Christensen: Metall. Mater. Trans. B, 35B (2004)
[2] C. E. Loo and W. Leung: ISIJ Int., 43 (2003), 1393; X.Lv, C. Bai, Q. Deng, X. Huang, G. Qiu: ISIJ Int, Vol.51 (2011), No.5, pp. 722-727
[3] H. Kimura, T. Ogawa, M. Kakki, A. Matsumoto and F. Tsukihashi: ISIJ Int. (2005), 506; 42. S. Machida, K. Nushiro, K. Ichikawa, H. Noda and H. Sakai: ISIJ Int. (2005), 513. [4] Yang et.al. ISIJ International, Vol. 31 (1991), No. 5, pp. 468 477.
[5] Ishikawa, Y. Shimumura, Y. Sawaki, M. Hida, Y and Toda, H., Nippon Steel Corporation, Japan.
The introduction of Danieli’s award-winning Rotoforge system to ABS’ special steel plant in nearby Udine, Italy, has put the Italian steelmaker streets ahead of its competitors in the production of finished bars (of up to 500mm) for the energy, automotive, nuclear and oil & gas sectors.
DANIELI’S Rotoforge is an alternative solution to the production of high-quality material through forging, with the efficiency and profitability of a rolling mill.
The Rotoforge system produces products with, it is claimed, the same internal quality as cast materials, and this is possible because of a new ‘RF’ design of heavy-duty stand that imparts the same tensile strength to the core of the bloom that is found in materials produced by a forging process.
The Rotoforge can be found inside the ABS special steel plant in Carngnacco, Udine, Italy, where 1.1Mt/ yr of long products are produced, out of a total capacity of 1.5Mt/yr. There, a technologically-advanced, new 190-millionEuro facility that produces 500kt/yr of special steel and automotive application wirerod is also in operation (see Steel Times International September 2022).
ABS gains benefits in productivity by feeding the Rotoforge with high-quality, 850-mm diameter blooms produced by an adjacent continuous casting machine (CCM #3).
The Rotoforge plant was started up on 12 September 2015. After a smooth hot test run it entered industrial operation. The arrival of the Rotoforge at the ABS plant was widely regarded as the most important step in the plant’s upgrading of its ‘Marte’ plant, a project started in 2013 with the step-by-step replacement of the facility’s ‘800’ reversible mill and continued a year later with the installation of the new ‘1000’ blooming mill.
The Rotoforge offers an alternative to forged products, obtained by rolling, but combines the best features of both forging and rolling technologies:
• High internal quality, comparable to a forged product
• Improved size tolerances and quality
• High reduction ratio for the entire product range (>1:3) for rounds up to 50mm and equivalent square
• High productivity
• Short lead-time and fast response to market demand.
The solution outlined by Danieli required
a rolling stand that was capable of imparting to the material the same strain ‘to the core’ that is applied by a forge. As a result of the high degree of drafting on each pass, ‘Rotoforged’ material has a fine grain size and very low soundness (FBH < 2 mm), while the rolling process ensures excellent surface characteristics and high
productivity, hence a dramatic reduction in transformation costs as no additional machining is required.
During the Rotoforging process the bar is rotated at every pass (as in the forging process) to increase the isotropic grain characteristics of the final product.
To minimize investment costs and
quicken the return on investment, ABS and Danieli installed the Rotoforge stand upstream of the two reversible stands in operation at ABS’ ‘Marte’ plant. ‘Marte’ is the name given to the plant’s big bar line, which incorporates Rotoforge and blooming.The installation gave rise to a new challenge: a rolling mill with three
2-high reversible stands offering maximum flexibility in terms of production and quick changing times – all very important features for a SBQ mill, where production lots are small and require frequent stand changes.
The high reduction ratios needed to produce quality large rounds entailed enlarging the cross section of the feedstock coming from upstream processes.
During the summer of 2014 the CCM #3 ‘Hercules’ Conticaster was revamped to produce round blooms of up to 850 mm. From 2015 onwards, ‘RF 13’ and ‘RF16’ ingots were cast, the first of a series of ingots with a shape developed for rolling in the Rotoforge, and to ensure a minimum reduction ratio of 1:3.6 up to 500mm rounds.
A larger ‘RF 18’ ingot will be produced in the future, to further increase the minimum reduction ratio to 1:4.
The plant layout was developed to maximize flexibility of operation:
• Cast blooms are heated at a rate of 100 tph (cold charge) in a Danieli Centro Combustion new walking-beam reheating furnace, with the additional possibility of hot charging directly from CCM #3.
• Ingots are heated in six existing pit furnaces directly connected to the Rotoforge via a transport trolley.
• The three reversible stands are arranged ‘in cascade’, each one specialized in finishing a set range of rounds and equivalent squares: round 110-230 mm (Reversible 800), round 230-405 mm (Blooming 1000), round 360-500 mm (Rotoforge 1800) and equivalent squares, ensuring the best final product achievable in terms of quality and tolerances.
The new stands design operates in fully automatic rolling mode, connected to a higher level of automation and enabling
Times International is the key publication for the steel market, reporting on iron and steel making issues from all corners of the globe.
Packed with information on the steel industry and continually updated with news for steel professionals, steeltimesint.com also features special articles and interviews with leading industry figures.
A round-up of the top news stories is also sent to more than 8,500 industry professionals each week. You can register online to receive the weekly newsletter and keep up-to-date with the latest news from across the steel manufacturing industry.
the introduction of control algorithms that make the process steady and repeatable, with benefits for head and tail deviation and bar straightness.
The perfect rolling set-up is guaranteed thanks to hydraulic capsules installed in all stands on the bottom roll and a flexible in-line adjustment system of rolls and guides. The rolling guides are designed to be removed together with the roll chocks through the stand housing, to further reduce the already quick roll-change operations time.
Another important element of the Marte plant upgrade was to put in line all the finishing operations for rounds up to 260mm (higher product mix volumes): quenching, sandblasting, chamfering, nondestructive testing, stacking and binding, to deliver to the discharge table a final product ‘ready for the truck’. The revamp started in 2013 from the finishing end and the smaller of the existing finishing stands to take a decisive step forward in final product quality and presentation and drastically reduce off-line reworking operations.
To increase the quality of rolled products, the revamping continued over the following
two years with the Reversible 800 and the Blooming 1000 stands (the larger of the two existing stands), and during summer 2015 with the installation of the new re-heating furnace and Rotoforge 1800, without stopping the plant other than during scheduled yearly maintenance shutdowns. The new technology resulted in better production control of bars with outstanding quality characteristics.
Since then, ABS has been supplying
end users with products offering high mechanical performance, superior metallurgical characteristics and improved tolerances/straightness.
ABS is committed to continuous improvement to maintain its leadership in the SBQ sector, and to provide a tailored service to satisfy customer needs in terms of quality, reliability, repeatability, and flexibility. The Rotoforge has given the company an edge over its competitors. �
The main threat to the steel industry, aside from understanding the requirements of green steel, is ‘wishful thinking’ says Rutger Gyllenram*. In his eyes, legislation needs to support decarbonized production, rather than offer a framework that hinders it.
1. How are things going at KOBOLDE & PARTNERS? Is the steel industry keeping you busy?
Today’s focus on sustainability has made it really rewarding to be in the metallurgy business. There is a lot to do everywhere; the industry has to abate greenhouse gas emissions, and metals as materials offer customers high-performing, lightweight recyclable materials that are necessary in their transformation work
2. What is your view on the current state of the global steel industry?
There is global confusion. Companies know where to go but we do not know the rules of the game. What should be the requirements for ‘green steel’? Furthermore, investment in new technologies is combined with tremendous risk, which in some cases is hidden by governments. This is questionable if it is done to save jobs. We have tried that during the energy crisis in the 1970s, and it did not go well.
3. In which sector of the steel industry does KOBOLDE & PARTNERS mostly conduct its business? We work with process and raw material assessment in all kinds of steelmaking and in the ore, scrap and alloy segments.
4. Where in the world are you busiest at present?
Our main topic now is to work with scrap quality and find ways to deal with the situation in Sweden when all blast furnace plants are replaced with electric arc furnaces.
5. Can you discuss any major steel contracts you are currently working on?
Kobolde is involved in the FerroSilva company that will start production of DRI reduced with biogenic syngas. A number of companies have worked together on
this for the last couple of years and now plans are starting to materialise. With the captured biogenic CO2, we will create a carbon sink which is a welcome change in the industry. Hopefully we can start production 2026 in smaller scale at a steel plant and later on we will scale up.
KOBOLDE & PARTNERS to offer them solutions in terms of energy efficiency and sustainability? If so, what can you offer them?
Our two main off-the-shelf offers are raw material optimisation and post-mortem analysis (from old process data) of raw material quality. Very often we do the analysis ourselves since companies today have lean organisations.
9. How quickly has the steel industry responded to ‘green politics’ in terms of making the production process more environmentally friendly and are they succeeding or fighting a losing battle?
It depends on how you define the battle. Some companies have been very successful in decreasing the carbon footprint by investing and making production more efficient.
6. Where does KOBOLDE & PARTNERS stand on the aluminium versus steel argument? Both are great materials and you should use the material that gives the lowest life cycle emissions based on greenwash-free assessments.
7. What are your views on Industry 4.0 and steelmaking?
It is all about standardisation. We need to make it possible to connect equipment and systems from different suppliers – perhaps we are close but I do not think we are there.
8. In your dealings with steel producers, are you finding that they are looking to companies like
10. Where does KOBOLDE & PARTNERS lead the field in terms of steel production technology? Process and raw material assessment and DRI production from ore and biomass are the areas we focus on and where we are on the frontline. We are also engaged in standardisation which will be even more important in the future.
11. How do you view KOBOLDE & PARTNERS’s development over the short-to-medium term in relation to the global steel industry?
We are constantly getting more and more partners and collaboration projects concerning the transition to steel with low emissions of greenhouse gases. We intend to continue that work.
12. What is KOBOLDE & PARTNERS’s experience of the Chinese steel industry?
We had a project on scrap quality with
USTB in Beijing and began a discussion on raw materials, but we were perhaps too early.
13. Where do you see most innovation in terms of production technologies – primary, secondary or more downstream?
I think that we need to work more on the reformation of the blast furnace in line with what was tested in the ULCOS project. Hydrogen will no doubt come in the future but I am afraid that politicians are underestimating the time for decarbonizing the electricity grid and making the process competitive. In the meantime, we have to rely on an oxygen blast furnace with top gas recycling and CCUS.
14. How optimistic are you for the global steel industry and what challenges face global producers in the short-to-medium term?
I think the main threat to the steel industry is wishful thinking and over-ambition from the politicians when it comes to the transition to steel production with low greenhouse gas emissions. Rules that harm companies that have already done their homework are detrimental and must be stopped. When it comes to the abilities of our engineers, I am very optimistic if they are given the right tasks and tools.
15. What exhibitions and conferences will KOBOLDE & PARTNERS be attending in over the next six months? Early April it will be Green Steel World and in May, Fastmarkets International Iron Ore. Then, of course, the webinars and conferences of Steel Times International
16. KOBOLDE & PARTNERS is headquartered in Sweden, but what’s happening steel-wise in the area?
I think an important trend is the development of powder production and additive manufacturing where Sweden has a leading role. Our connection to that is raw material assessment which is important since you require minimal variations in the steel analysis.
17. Apart from strong coffee, what keeps you awake at night?
Russia’s war in Ukraine and the situation in Iran.
Apart from the human aspects which are horrendous, the three countries can play really important roles in the future abatement of greenhouse gases for more than one reason.
18. If you possessed a superpower, how would you use it to improve the global steel industry?
I would restore trust in global trade and multi-national supply chains. �
The Romans occupied much of present-day Britain during the period 43AD to 410AD. The attraction to possess this far outlying region from Rome was its mineral wealth of iron, tin, lead and copper.
By Tim Smith*OF particular interest to the Romans was the abundance of iron ore close to the coast of southern England in the region known as the Weald, the area first occupied by the Romans. Here relatively rich iron ore, as iron carbonate, assaying at 40-50% Fe content, along with plentiful supplies of timber to make charcoal, had led to the development of smelting during the pre-Roman Iron Age. Today, excavations reveal that small ‘Bloomery’ shaft furnaces built of clay, probably standing some 1m high, and with hearth diameters of 0.3m or so, were used to smelt iron ore. The furnaces were heated with charcoal, high temperatures being reached by using bellows to blow in air, through a hole in the furnace wall, located 0.3m or so above the base of the furnace. When a high enough temperature was reached, broken ore that had previously been roasted to convert the carbonate to the oxide, was added along with the charcoal. Carbon monoxide from combustion of the charcoal reduced the ore to a solid mass of spongy iron, known as the bloom. When sufficiently large, this was extracted from the furnace and hammered while still hot to consolidate it. This forging procedure was carried out a number of times by reheating the mass of iron and hammering. It is important to note that normally the iron was never molten, only the waste material from the other constituents of the ore became molten and could be tapped from the furnace during smelting as a slag.
The iron produced in this labour-intensive way was very valuable, in particular it was used for making weapons, armour, nails and horseshoes, and, in the Roman era, much was exported from the Weald to Europe to serve the Roman armies there.
The value of raw iron makes it a rare find during excavations of bloomery sites.
However, in the early 1960s, at a site near Cranbrook in Kent, in the eastern part of the Weald, such a piece of metallic iron weighing 0.7kg was found. Known as the ‘Cranbrook Bloom’ – but strictly a billet since it had been consolidated – this was subjected to metallographic examination by G T Brown of GKN, and the results published in the official journal of the former Iron & Steel Institute of June 1964 (JISI 202 No6 pp502-504). His findings are summarised below.
The ‘bloom’ (Fig 1a) had been forged in antiquity to a squarish section measuring 3.1 x 3.1cm, tapering to 2.2 x 2.2cm and of length 14cm. It proved too hard to cut with a saw. Spark erosion was used to take samples for examination and a high speed slitting wheel employed to section the iron along its full length. Metallographic examination of samples along its length
showed it to be inhomogeneous, and chemical analysis at three points showed the carbon content varying from 1.16w% to 1.46w% (Table 1).
Macro-examination of the polished and etched longitudinal section showed extensive cracking from a slag inclusion (Fig 1b). Micro-examination showed areas of high carbon and areas of low carbon content. The structure mainly consisted of very fine pearlite (Fig 2) with varying amounts of free cementite as an intergranular network nucleated on previous austenite grain boundaries and as individual blocks and transgranular needles (Fig 3). There were also isolated areas of ledeburite – the austenite – iron carbide eutectic (Y-Fe3C) (Fig 4) indicating incipient melting at a temperature more than 1147°C. Small areas of martensite were also observed, (Fig 5) particularly around the periphery, indicating the iron had been quenched. These areas also showed retained austenite (Fig 6), despite this being a metastable phase at ambient temperatures, it was still present after some 1850 years.
In conclusion, the Cranbrook ‘bloom’ appears to have been rejected by the smiths
soon after the smelting stage when they found they could not produce a malleable iron for the manufacture of products. Hence, it remained at the bloomery site to be found 1850 years later.
Two further ‘blooms’ were found elsewhere on the Weald and are the subject of another paper and will be examined in a later issue of Steel Times International �
Micrographs are published by permission and are copyright of the Institute of Materials, Minerals & Mining, London UK
#itsmorethanjustamachine
3-ROLL TECHNOLOGY FOR SBQ SIZING. A Reducing & Sizing Block for long products keeping its promises. Achieve your goals with KOCKS RSB®
VISIT US
12.-16.6.2023
up to 160mm
finishing size in round or hexagonal dimensions
Hall 1 / Booth A79
up to 20% up to 10% energy savings in the mill line
increase in production