INTERNATIONAL PSR SUPPLEMENT - September 2022 PSR – Celebrating a Centenary Year WWW.GLASS-INTERNATIONAL.COM
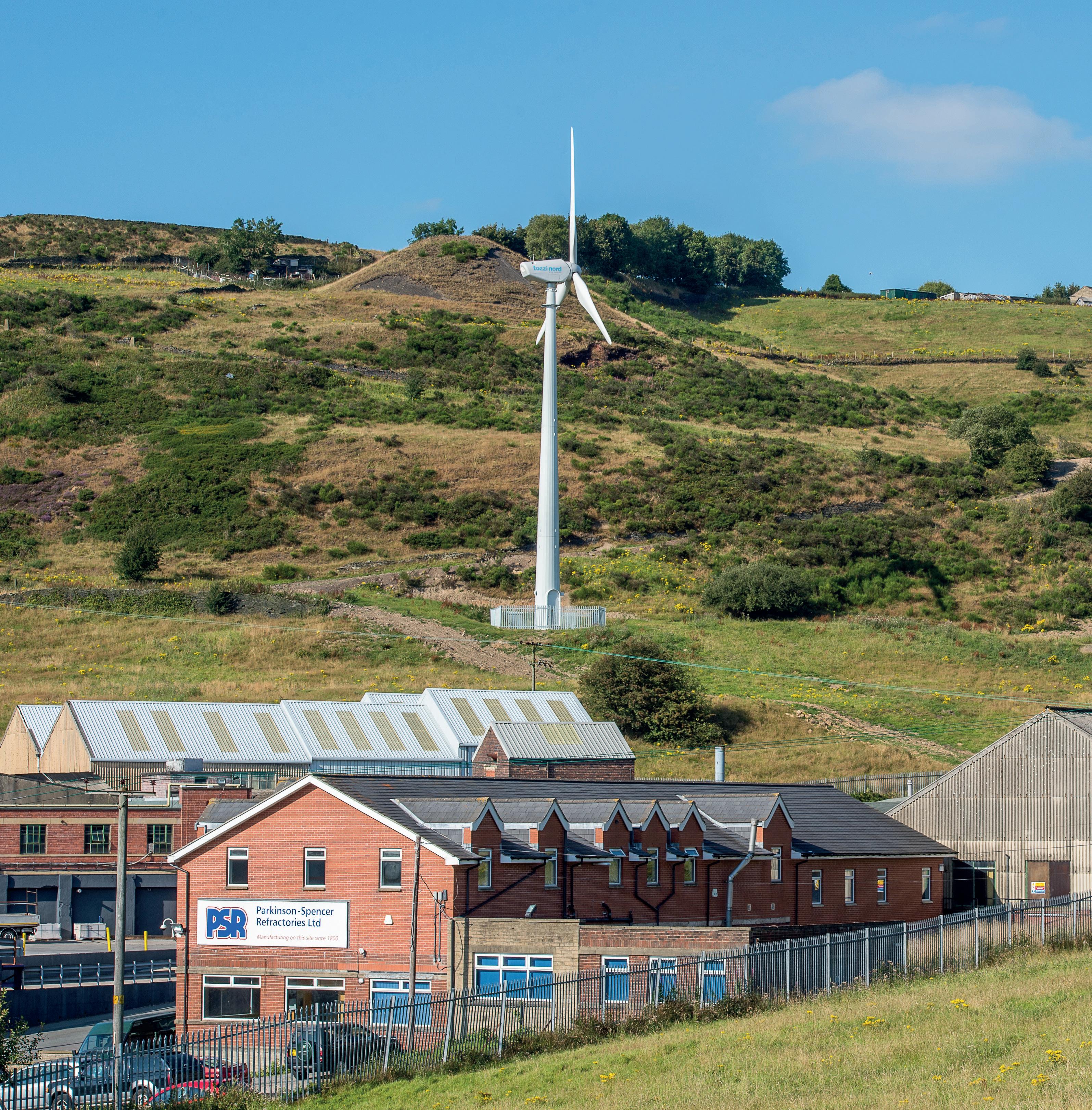

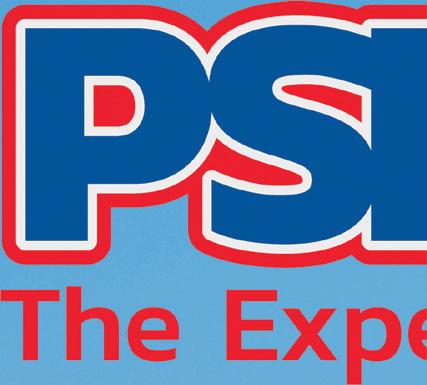
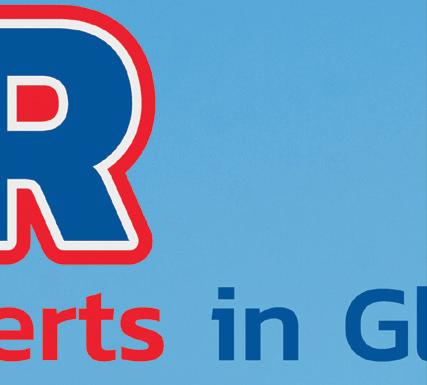
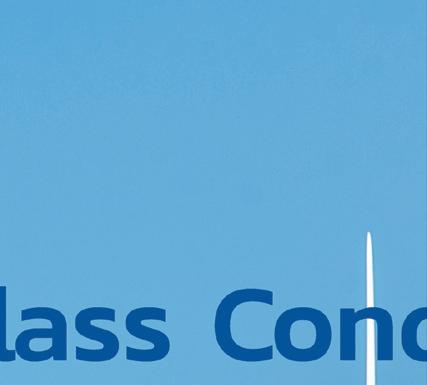
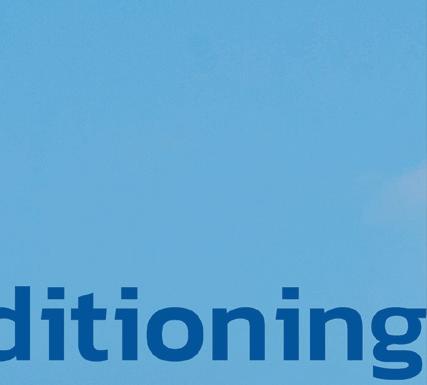
Simon Parkinson, Managing Director at Parkinson-Spencer Refractories
What do you think has been key to the company’s longevity? Well, I think it’s a case of evolution and not revolution. It has been essential for PSR to evolve alongside the industry; moving from traditional fireclays to modern refractory materials, from glasshouse pots to feeder expendables, and developing our Technical Services division to enhance and supplement our services to the industry. We are always innovating to develop and enhance refractory materials and engineered solutions with improved performance to benefit our customers’ operations. We never stand still, and innovation is something that we embrace and is key to our future success. Our R&D teams help ensure we remain at the forefront in the market with the best refractory solutions and glass conditioningCollaborationequipment.andbuilding strong relationships have also been key and we take pride in nurturing our teams, partnerships, agents, and customers. We collaborate with institutes and universities, combining our industry expertise with academic capabilities to develop new refractory materials and processes.
Although incorporated as a company in 1921, PSR has come a long way since the original formation of the company over 200 years ago, whilst going nowhere at all.We are still based on the same site as when we were founded in 1800, when two farmers began extracting fireclay from the local countryside and founded the Parkinson and Spencer partnership. We’ve been in the same industry, serving the same glass container market since the company began all those years ago. Of course, the landscape of that industry is now unrecognisable from what it was back then. The container glass industry is always changing, and with it the operations of the business have changed completely. The final ties to our clay mining past were brought to an end, firstly with the closure of the last of the clay mines in 2012 and then with the end of our glasshouse pot making business in 2016. Instead PSR has evolved into a leading supplier of forehearth, distributor and feeder expendable refractories, and engineered solutions and services for the entire glass conditioning process.
PSR – CELEBRATING A CENTENARY YEAR Glass International September 2022 0 1 www.glass-international.com
PSR – Celebrating a centenary year UK refractory and glass conditioning company PSR celebrates 100 years since its incorporation as a Limited Liability Company. Simon Parkinson* discusses the company and its role in the glass industry.
The actual date of our anniversary was July 2021, and due to the Covid-19 pandemic, it really wasn’t practical or appropriate to arrange a major celebration to mark the event at the time. It’s been a difficult couple of years for everyone, but thankfully we’ve now started to travel once again and pay some visits to our customers this year. This culminates in a long overdue Glasstec event, where we hope our friends in the glass industry around the world will visit us and help mark the anniversary in some way.Joanne Parkinson, my sister and Commercial Director, is also working on a new employee engagement strategy. As part of this she will be looking to arrange some celebratory employee events.
Tell us about the company today: how many staff do you employ and what do you manufacture at your site? We are still based in Halifax, in the foothills of the Yorkshire Pennines, and have approximately 90 employees. Our people are highly skilled in what they do and remain our biggest asset. About 50 of our employees are skilled craftspeople involved in the manufacture of PSR refractories. About 15-20 are part of our Technical Services department as Project Engineers and Draughtspeople, with the remainder spread across our Laboratory and Administrative support functions. Our core business is the manufacture of feeder expendables and forehearth and distributor refractories, alongside the design and supply of forehearth systems and auxiliary glass conditioning solutions.Refractories for the glass industry has been the foundation of the business throughout our history, and it’s a tradition that lives on to current times. Our legacy refractory products include feeder expendables, channel blocks and distributor blocks, forehearth refractories and furnace blocks, and each year we produce up to 1,500 tonnes of refractory products, still using traditional slip cast methods.
How has the company evolved since its inception?
Congratulations on your milestone anniversary! Do you have any plans to celebrate or to mark the occasion?
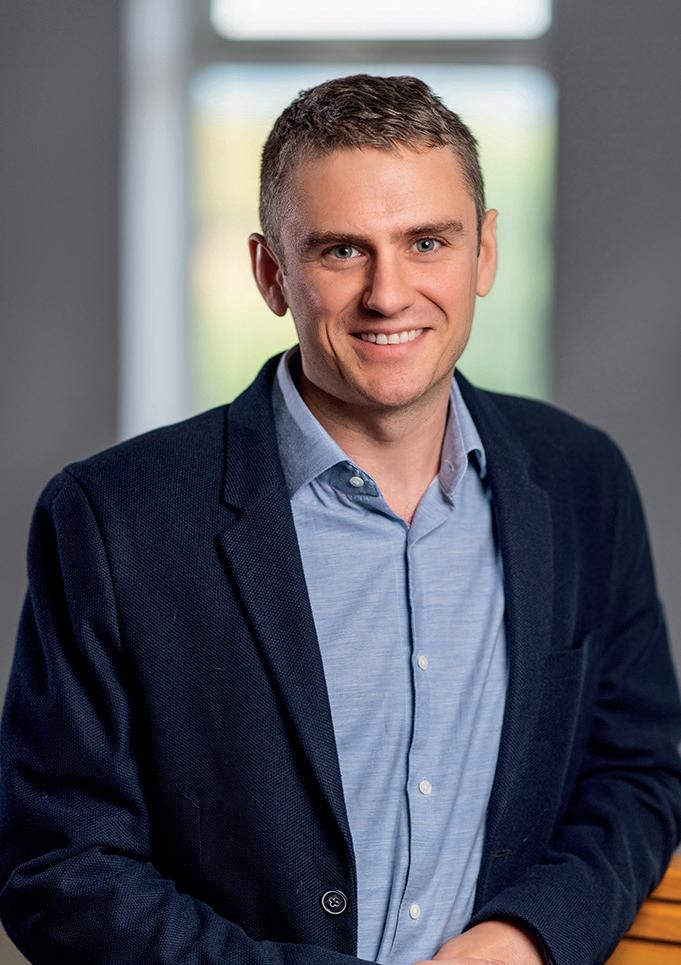
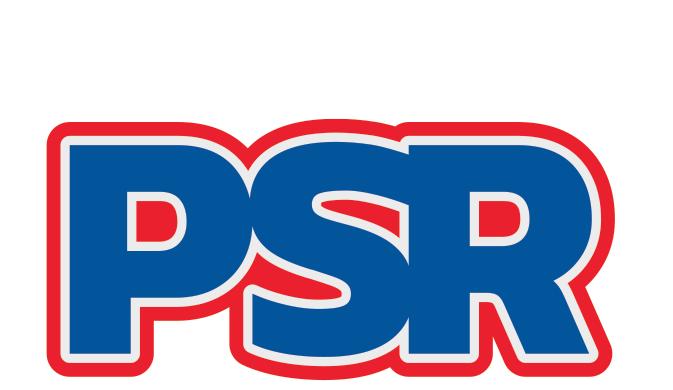
We are the experts in glass conditioning, with all our products and services forming vital parts of the glass conditioning and gob forming process.
You have recently become managing director – how has the transition been and how are you finding it?
Having been on the Board of Directors since 2015, and previously working with our Technical Services Division, I was already involved in looking at the overall picture of the business and carried out many of the day-to-day activities I’m involved with today. David has also remained involved in the business as Chairman and always been available as a mentor to me, providing guidance and support along the way. I’ve also started to work with a professional business coach to support my development and the growth of the PSR business.
What advantages are there to being a family-run company? Stability and longevity, but also flexibility and the ability to adapt quickly to changing circumstances. We are fortunate to have had eight generations of the family with the ambition and commitment to carry on the family business and drive the company forward, and I’m always proud to hear from customers about the relationships that they enjoyed over many years with my father, David, and even, on some rare occasions, with my grandfather, Henry. A strong family ethos and values remain at the heart of our business, and some of our existing employees have worked with myself, my father, and grandfather. We also have some local families with multiple generations having worked for the business and with the Parkinson family. This loyalty, expertise, and our approachability, is something highly valued by our customers and partners.
Internally, new methods and technologies for producing refractories in a more sustainable way are going to be essential. We are now at the start of a project, in collaboration with the British Ceramic Confederation and Sheffield Hallam University, to develop low-carbon refractories by reducing firing times and temperatures through novel additive technologies.
How can the company help glass manufacturers meet the challenges of today? Our customers include some of the world’s leading container manufacturers and our technical knowledge and expertise allows us to provide sustainable solutions to meet their glass conditioning problems.
Our forehearth systems are proven to provide the best thermal homogeneity and lowest energy consumption over the widest operating range, our Cord Dispersal Systems are the only guaranteed solution to the common, and costly, defect of “cat scratch” cord, whilst our feeder expendables are proven over many decades to provide the best operating life and reliability in service. This comes from our vast knowledge and experience in what we do, learnt over two centuries of service to the glass industry and the continuous improvement and development of our processes and products. For example, over the last few years we have developed new feeder expendable materials to provide improvements in operating life from 50% up to 300%.
As part of the ceramics and glass industries, we are involved in very energy intensive processes, and it is vital that businesses strive to achieve the best operational and environmental efficiencies to allow them to operate ethically and sustainably. We help our customers to do this. How do you see your technology evolving in the future? Clearly the drive to a sustainable future is going to be critical to the PSR business and the entire glass industry. The UK government target is for all sectors of the UK economy to be decarbonised and to be net zero by 2050, and new technologies involving new fuels and different methods of production will be required to address this enormous challenge.
In 2019 I took over the reins when my father, David, retired as Managing Director. There have been interesting times since then; with the pandemic and other economic and geo-political events. You might say I’ve been somewhat thrown in at the deep end! That said, the transition felt very natural because it’s something that I’d been working towards for some time.
PSR - THE EXPERTS IN GLASS CONDITIONING Glass International September 2022 www.glass-international.com 2 What does the company specialise in and what do you consider are its strengths?
We are currently working with Glass Futures to design the forehearths and distributor for their research and development facility, producing 30 tonnes of glass per day. Amongst other trials, the switching of fuels between natural gas, biogas, oxy-fuel, hydrogen, or oxy-hydrogen will form a part of the research taking place in the facility. This will help guide the industry towards the solutions for the future.
Can you indicate any future plans for the company? The future of the business is going to revolve around the continuation of our development activities to improve our services to the glass industry whilst transitioning towards a low-carbon future. Over the past decade we have developed and introduced new refractory compositions to the glass industry and we have plans to continue this process with the emphasis on our engineered products and sustainable solutions for the future.
*Managing Director, PSR, Halifax, UK www.parkinson-spencer.co.uk/
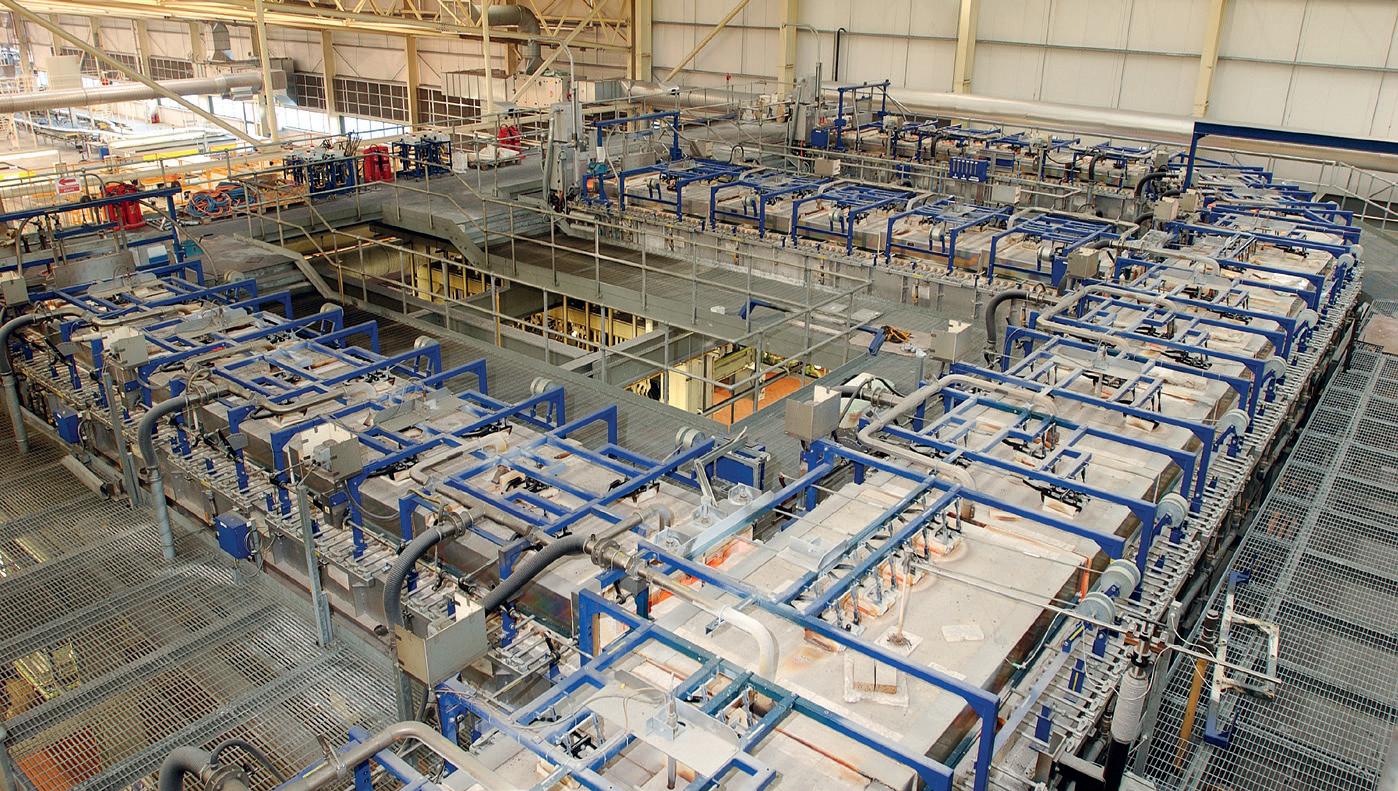
History has demonstrated the wisdom of Caleb’s decision to focus on the glass industry and although we no longer manufacture any of the fireclay products from Caleb’s time, we continue to specialise in products for the glass industry.TheSpencer family remained as shareholders in the business until 1997 although their participation in the running of the business ceased in the early 1900s. In 1976 the name of the company was changed to Parkinson-Spencer Refractories Ltd and the reference to Ambler Thorn Fireclay Works was dropped in order to better represent the nature of the business.
Founded in 1800 as a partnership between the Parkinson and the Spencer families the early business operated as a partnership for four generations until Caleb Parkinson joined the company. Caleb was born in 1889 and joined the company in 1903 at the age of 14. His father had died two years earlier when Caleb was only 12 years old, so Caleb’s mother Agnes became his guiding influence and a hugely important figure in the history of PSR. Caleb understood the potential of the early business and had a skill for locating and securing the all-important fireclay deposits on which the group depended.
A HISTORY OF PSR Glass International September 2022 0
Caleb’s notes as chairman of the first Annual General Meeting of the shareholders in 1922 also show how important the glass industry was to him. He said this to the shareholders.
A history of PSR 2021 was a centenary year for PSR, representing 100 years since the company was incorporated as a limited liability company. PSR Chairman, David Parkinson reports.
www.glass-international.com
Caleb Parkinson (far right) with his wife Edith at the 1948 British Exhibition in Copenhagen
Today the company is solely owned by the Parkinson family. 7th generation David Parkinson is largely retired but retains an interest in the business in his position as Chairman. Brother and sister Simon and Joanne Parkinson are the 8th generation with Simon at the helm as Managing Director and Joanne in support as Commercial Director.
Simon, David and Joanne Parkinson
He also realised that in order to move the organisation forward, investment would be required in modern plant and machinery and, with the support of his mother Agnes, proposed that the business be converted into a limited liability company.Theeffect of this would be that instead of the family members being liable for any or all the debts of the business they could invest in the new company safe in the knowledge that the extent of their liability would be no greater than the value of their investment, otherwise known as their shareholding. Caleb had two elder sisters and a younger brother and with the support of Agnes they all became shareholders in the new company that was established in 1921 as Parkinson & Spencer Limited. In addition to the five Parkinson shareholders there were also five Spencer shareholders, although the Spencers only held one third of the shares as compared to the two thirds of the Parkinsons. The company at that time was very different to the business it is today and reference to a letterhead of the period illustrates Caleb’s ambition. The company’s principal products were identified as firebricks and other general fireclay based refractory items but highlighted as specialities were “Glasshouse Potclay and Tank Blocks”.
“This is the first time I have ever had the pleasure of presiding at a company meeting so please forgive me if I make a few blunders. I shall not trouble you too long with my report as I am sure you are all well acquainted with the position of our firebrick trade. Since our meeting last August we have experienced some very bad trade and I am afraid the prospects are not too good for the remainder of “The1922.chief reason for the bad trade is the slump in the Glass trade, the high taxes on spirits and beer which means the call for ordinary bottles is very low, and no tariff on imported common bottles. “Taking the brick trade throughout the country I am confident we are getting our share.“Atpresent we are not working full time but we are hoping for better times.”
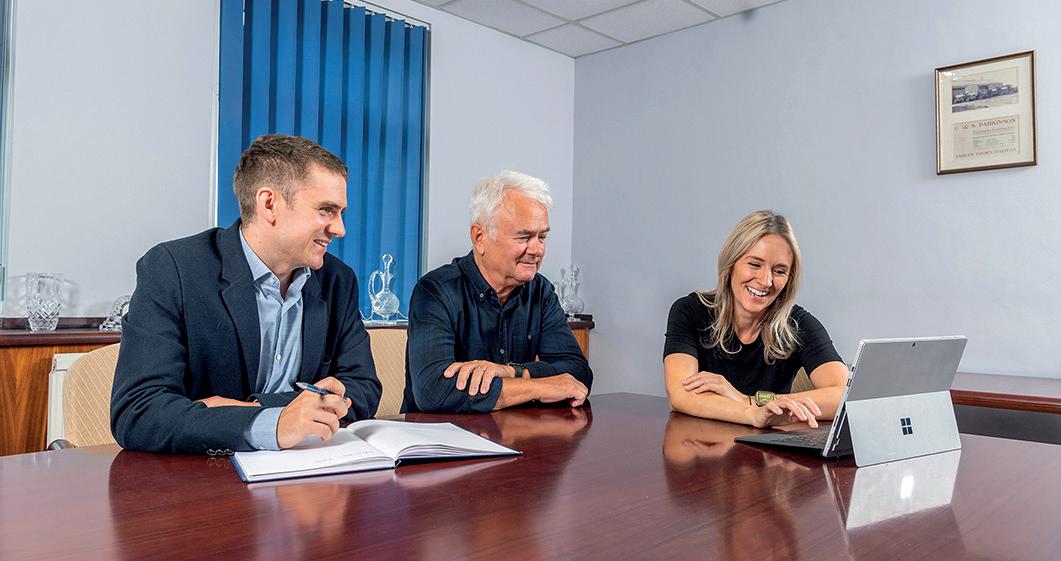
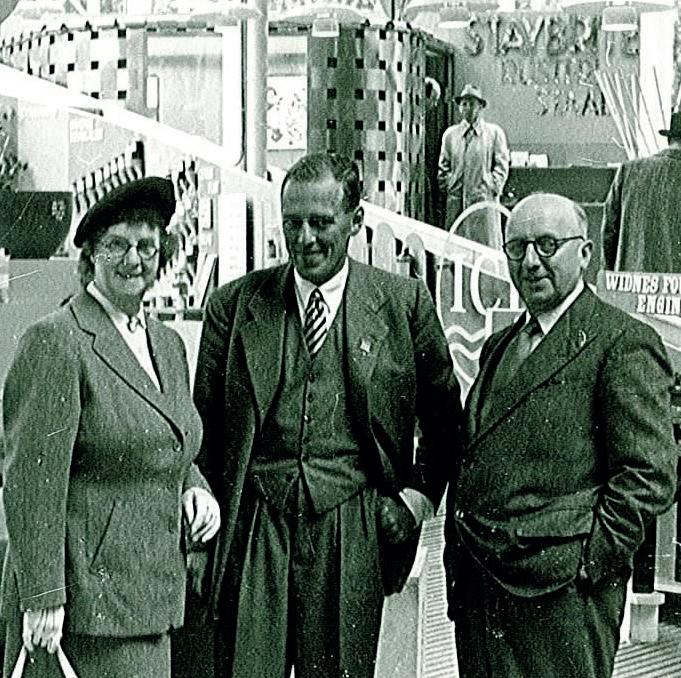
PSR - GLASS FUTURES Glass International September 2022 www.glass-international.com 4
The
From the 900 tonne per day furnace, distributor and seven forehearth layout at Encirc Elton, thought to be the largest in the world, to the 30 tonne per day design at the Glass Futures pilot plant, our distributors and forehearths can cover the widest possible range of glass conditioning requirements. We look forward to working closely with the Glass Futures team as the project is realised. PSR will take a keen interest in the next generation glassmaking trials which will be taking place at the Centre for Excellence in the coming years.
PSR designs forehearths for Glass Futures
Having served the glass industry for over 200 years, we have seen periodic transformations within the sector as processes, materials and products have changed beyond recognition. It is imperative to stay at the forefront of technological advancements as we look to the future of glassmaking. Therefore, it is with great pride that we are collaborating with colleagues at Glass Futures to design flexible and innovative forehearths at the Global Centre of Excellence for Glass, which is the Glass Futures pilot plant under construction in the historic glassmaking town of St Helens.
The not-for-profit research and development facility will feature a 30 tonne per day glass melting furnace as well as raw materials and cold-end processing to support research and development projects with the container, flat glass, fibreglass and tableware industries. Clients will be able to use the plant to bridge the difficult gap between the lab and full-scale manufacturing. PSR has designed the distributor, colourant alcove, container forehearth and rolled plate forehearth as well as a drain forehearth for the pilot plant. At the heart of this project is the flexibility to switch seamlessly between research and development initiatives. This has led to the implementation of a number of interesting features. For example, the forehearths must be able to switch between maximum and minimum tonnage operations on each line. To accommodate this, we have been able to revisit some of our past designs for a forehearth casing jacking system to address the problem of head loss at high pull and low operating temperatures and the unwanted increase in glass depth that occurs if the forehearth casing remains sloped down at low pull and high operating temperatures. This enables the forehearths to operate efficiently under a wider range of production conditions as necessitated by the vast array of possible projects demanded by clients.
In addition to incorporating some of our past developments into the design, we have implemented elements which are new to PSR, such as the design of a rolled plate forehearth. A colourant alcove will feed the container line, while the rolled plate line will have its own colourant system.
As with all our forehearths, both lines will be constructed ready for the future installation of a PSR Cord Dispersal Stirrer system in the event that this is required to combat the common cat-scratch cord defect.Aswe transition to a low carbon future, more research is needed on alternative combustion methods, such as hydrogen firing, swapping to biogas or oxy-fuel and oxy-hydrogen.Wewereable to draw on oxy-fuel combustion technologies which PSR developed in the 1990s, but for which until now there has been little demand, to meet the design requirements of the pilot plantWhileforehearths.oxy-fuel forehearths have not gained much market popularity in the past 30 years, we are excited to see renewed interest amid tightening emissions regulations. In view of this, we are looking to design burner blocks with flexible fuel capability, which will enable further development of combustion systems for glass conditioning in the forehearth. We can take this knowledge forward to future designs of PSR combustion systems to ensure that plants built today will be ready for the fuels of the future. This project has been an opportunity to demonstrate our expertise and capabilities as a manufacturer of glass conditioning machinery and forehearth refractories. Designing such a flexible system has not been without its challenges, but we have been presented with an opportunity to envision something which has never been done before and to contribute to the future of our industry, just as we have contributed for the past 222 years.
Alex Packer, Sales Engineer at Parkinson-Spencer Refractories, highlights PSR’s role within the Glass Futures project. Global Centre of Excellence, St Helens
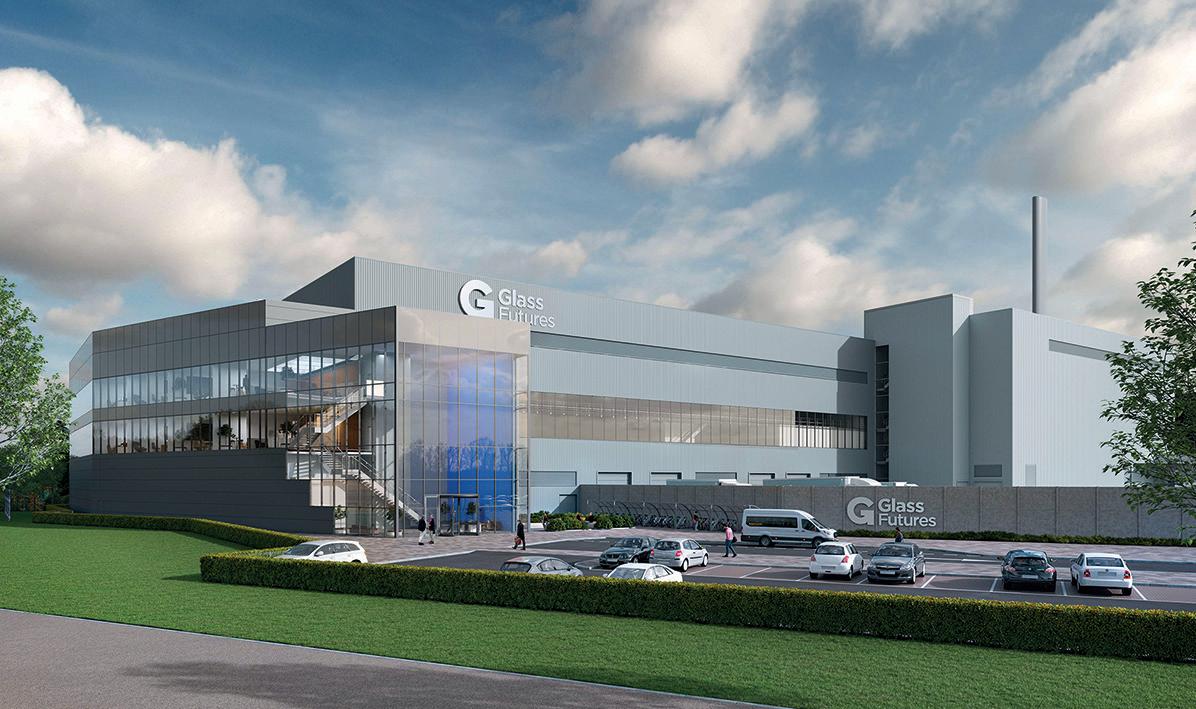
Creating PSR Project and Design Engineers
Les Gaskell, Technical Director, explains PSR’s successful policy of recruiting young, talented engineers.
We have recruited 14 engineers over the years in this way. Their one year placement experience allows them to hit the ground running when they start full time employment at PSR. Of the four ex placement students still working at PSR:
When PSR first set up its Technical Services Division to supply complete forehearth and distributor systems in the early 1990’s it recruited suitably experienced engineers from the glass industry to develop, sell and supply these new products as well as fulfil customer requirements for on-site engineering services to supervise the installation and commissioning of these systems. However, as our customer base increased in this specialist area, the need for more engineers to fulfil our project management requirements, as well as on-site service expectations, meant PSR had to recruit and train the engineers we needed ourselves as they were not readily available in the glass industry, and experienced engineers recruited from other industries were not adaptable to our needs.One of our most successful methods of recruiting suitable engineers over the years has proven to be the employment of students studying for an engineering degree for which an industrial placement year is part of their four year degree course. The idea for employing placement students came from an engineer we recruited in the mid 1990’s as a Project Engineer who had completed a Mechanical Engineering degree at Sheffield Hallam University and had also done a placement year with United Glass (now O-I Glass) as part of the course. We commenced employing placement students in 1999 and up to the present time we have employed 44 students over these 23 years with two additional students commencing their placement year with us in August, 2022. Each year we tend to have between two and four students.Placement students are employed as Technical Assistants to augment our team of engineers responsible for the design, manufacture, supply, installation, commissioning, servicing and development of our forehearth and distributor systems. They carry out work as required in our drawing office, assisting our design engineers in designing 2D and 3D layouts for projects. In the workshop they assist in the assembly; checking, testing, labelling and packing of superstructure bracing and cooling control steelwork, combustion equipment, temperature control equipment and systems and stirrer systems. We also provide them with the opportunity to work on site with our engineers in the supervision of the installation, set-up, testing, warm-up and commissioning of the systems so they see the final product producing glass. As typically 95% of our business is export all over the world this invariably involves them travelling abroad. Over the year, students gain a broad perspective of the work we do from design to commissioning and experience the working conditions inside a glass factory. In turn, we gain an insight into the student’s character, interests, abilities and potential.Asaminimum, placement students fulfil the requirements for their degree and leave us with good industrial experience and an insight into working in the glass industry. For students that show particular interest in our work as a possible future career, we maintain contact and sometimes sponsor them for their final year; particularly if they carry out their final year project based on a subject to further develop our systems.
PSR - CREATING ENGINEERS Glass International September 2022 0 5
� Bryon Doan (2011-12) with nine years’ service is now our Project Development Manager responsible for Project Design and Development and for general recruitment and supervision of our placement students.
� James English (2015-16) with five years’ service is currently a Project Engineer.
www.glass-international.com
� Tom Foster (2008-9) is now our Project Sales Manager with 12 years’ service and responsible for Project Management and Sales.
� Fahim Zwan (2019-20) is a new Project Engineer with one years’ service. With many of our Technical Services personnel having been placement students themselves, they are always involved in training placement students. This has helped us develop our in-house training and ensure engineers gain the specialist knowledge and experience they require. It has also helped us to successfully recruit and train new Project and Design Engineers that had not benefitted from a placement year at PSR.
Left to right: James English, Bryon Doan and Fahim Zwan discussing a project design at PSR
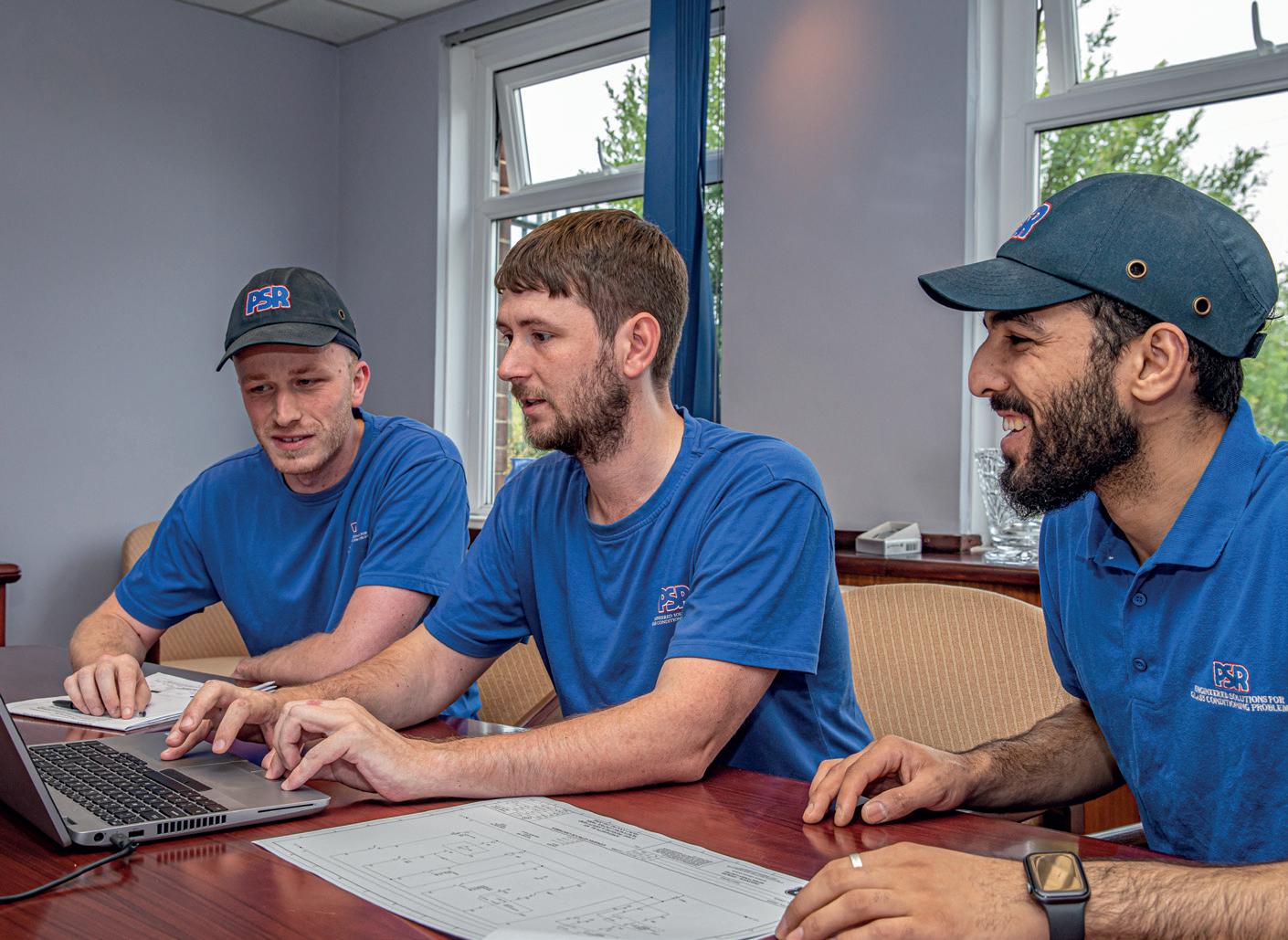
Low carbon refractories for the future
Feeder expendable refractory compositions
The addition of dopants to densify the material will be investigated to enable firing at lower temperatures or for shorter times, reducing energy consumption and CO2Basedemissions.onaliterature review we believe that >10% savings are achievable.
There are potential savings across the UK and global refractories industries if this technology were licensed and applied more widely. A 10% energy and CO2 saving across the relevant products within the global refractories industry would save up to an estimated 5 MT / year.
“BCC is delighted to be supporting PSR and Sheffield Hallam University with their project to develop novel additive technologies to enable faster and / or lower temperature firing of refractories. We look forward to supporting the dissemination about both the project and wider learning about the funding landscape to the UK ceramics sector,” said Jon Flitney, Energy & Innovation Manager at BCC.
This project, in collaboration with Sheffield Hallam University (SHU) and the British Ceramic Confederation (BCC), aims to find a cost-effective solution to reduce energy consumption in the refractory manufacturing process.
Jafar Daji, Technical Manager, discusses a project to reduce energy consumption in the manufacture of ceramic refractories.
PSR has been successful in its application for support for a Small Scale R&D project as part of the ‘Transforming Foundation Industries’ (TFI) Challenge fund from the UK Government’s ‘Industrial Strategy Challenge Fund’ (ISCF).
PSR - RESEARCHING REFRACTORIES www.glass-international.com 6
The project will benefit PSR through knowledge transfer with partners, and opportunities to co-create new concepts; transfer best practice through industry and academia partnerships; and improve the energy efficiency of the manufacturing processes.
PSR-930 – 24.9% ZrO2 PSR-930 is the latest material development to come out of PSR’s research and development department. It has a higher zircon content, but of equal importance is the particle packing density which we were able to achieve through detailed analysis of the refractory microstructure. With a porosity as low as 13% and a density as high as 3200 kg/m3, we were able to achieve excellent glass corrosion resistance whilst maintaining the thermal shock resistance inherent in our traditional refractory compositions. Results to date have shown an increase in the life of feeder expendable parts of 30-50% over our standard refractory compositions in most standard soda lime container glass operations. Our full range of feeder expendable refractories are now available in PSR-930 material.
“SHU is pleased to be supporting this project designed to enable our foundation industries to achieve their important decarbonisation goals, via new and novel technologies for more rapid, lowerenergy firing cycles,” said Paul Bingham, Professor of Glasses and Ceramics, SHU. After comprehensive development, in collaboration with the School of Chemical and Process Engineering at the University of Leeds, followed by extensive testing and field trials, PSR are now able to offer the following feeder expendable refractory compositions.
PSR-925 – 24.1% ZrO2, 74% Al2O3 PSR-925 was developed initially as a spout insert material as an alternative to other options such as fused cast AZS inserts or, more common in recent years, Chrome-Oxide inserts. Using Zirconia, a highly refractory material, as the base for the material (as opposed to the usual ingredient Zircon, more accurately known as ZirconiumSilicate) and adding only alumina grains and powders, we were able to achieve exceptionally high corrosion resistance. By manufacturing the material ourselves, using our usual slip-casting method, we are able to cast PSR-925 as a single piece ‘uninserted’ spout. This eliminates the joint which would otherwise be present between the spout insert and the spout body, and ensures the entire spout bowl is highly resistant to glass corrosion. PSR-925 spouts have proven to operate for in excess of 4 years in most typical soda-lime container glass applications, matching or even surpassing the life expectancy of a chrome-oxide inserted spout.With none of the potential drawbacks of Chromium containing refractories (such as glass discolouration and environmental considerations) PSR-925 represents the optimum solution for a spout bowl at a fraction of the cost.
As a manufacturer of refractories for the container glass industry, PSR falls within multiple energy intensive foundation industries (ceramics and glass). Current refractory manufacturing methods include long firing cycles where substantial energy savings and corresponding reduction in CO2 emissions could be achieved by reducing the lengths of firing cycles.
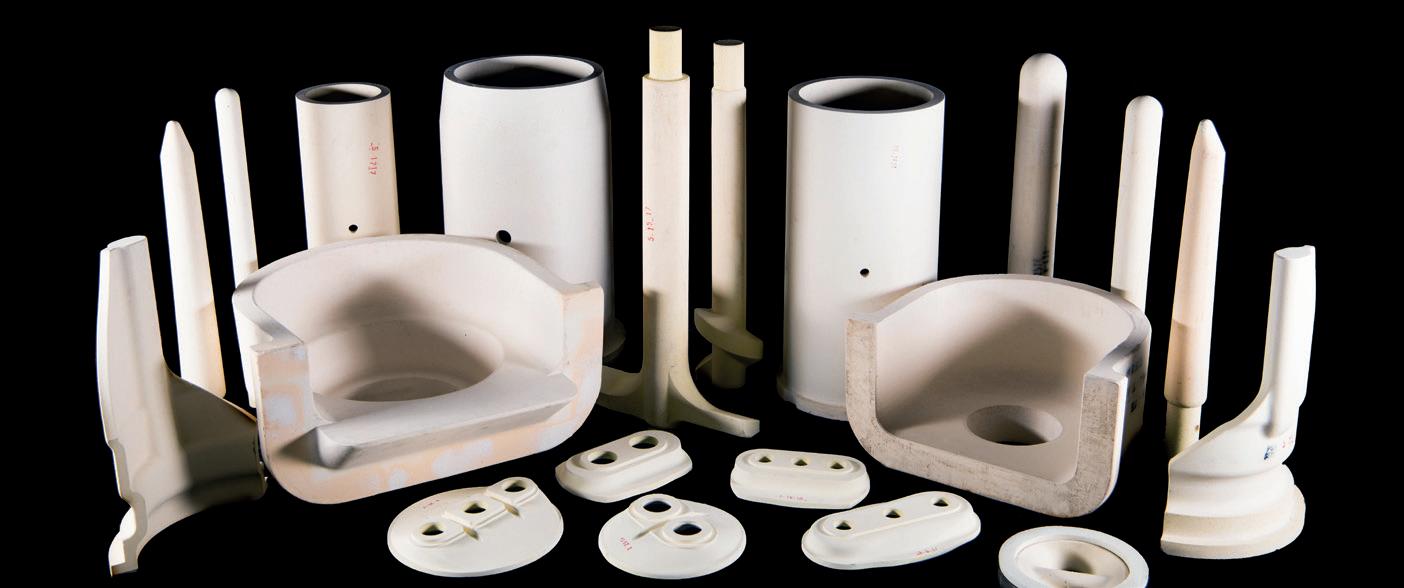
www.parkinson-spencer.co.ukMAXIMISEYOURPRODUCTIONCAPABILITIESWITHAPSRCOLOURANTFOREHEARTH.Comeandseeoursolutionon:StandA63|Hall13Glasstec.
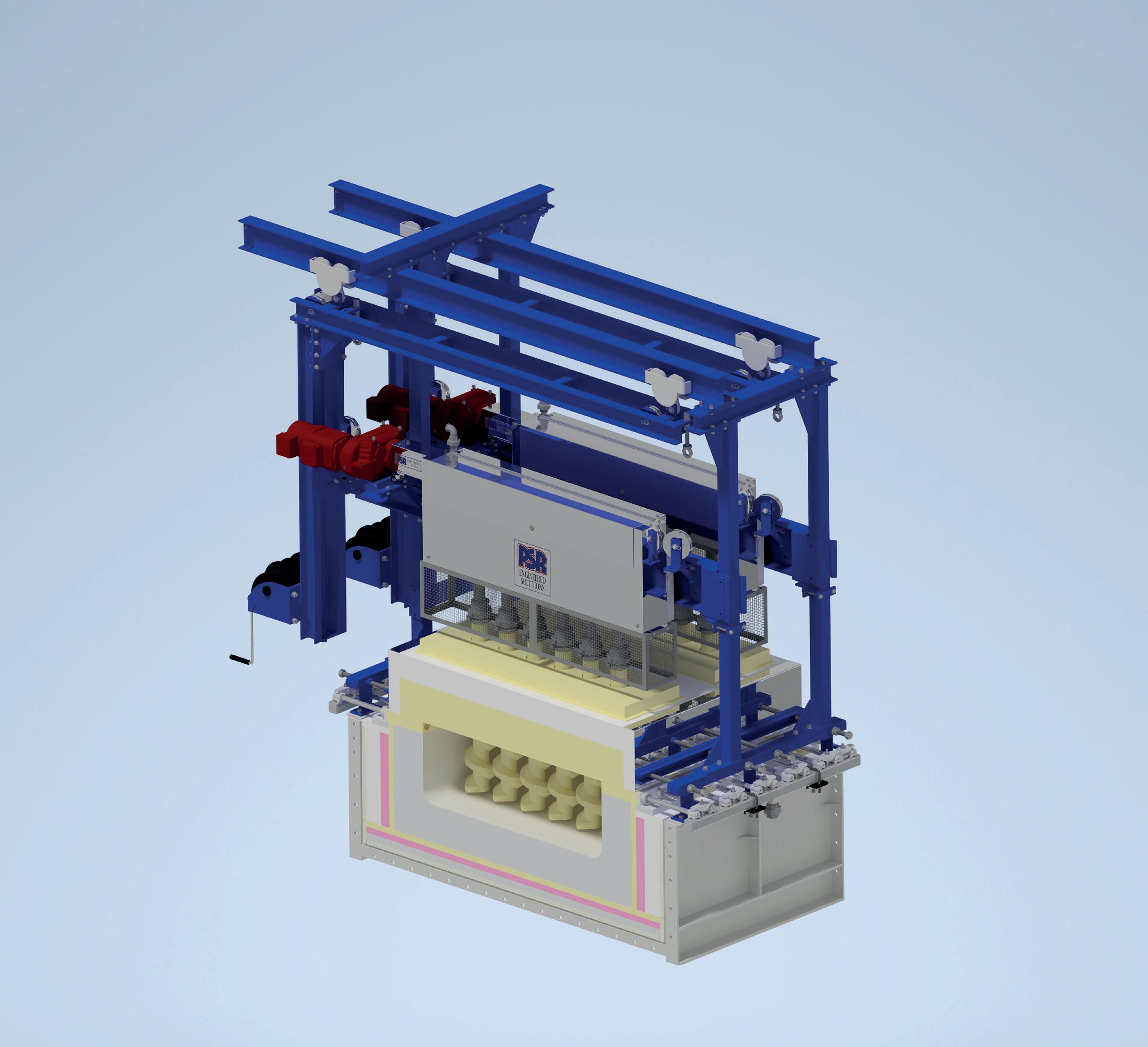