REAL-TIME PERFORMANCE FOR A PERFECT BATCH Visit us at glasstec 2022. Stand B38, Hall 15. eme.de INTERNATIONAL September 2022—Vol.45 No.8 A GLOBAL REVIEW OF GLASSMAKING WWW.GLASS-INTERNATIONAL.COM 2022SeptemberInternationalGlass

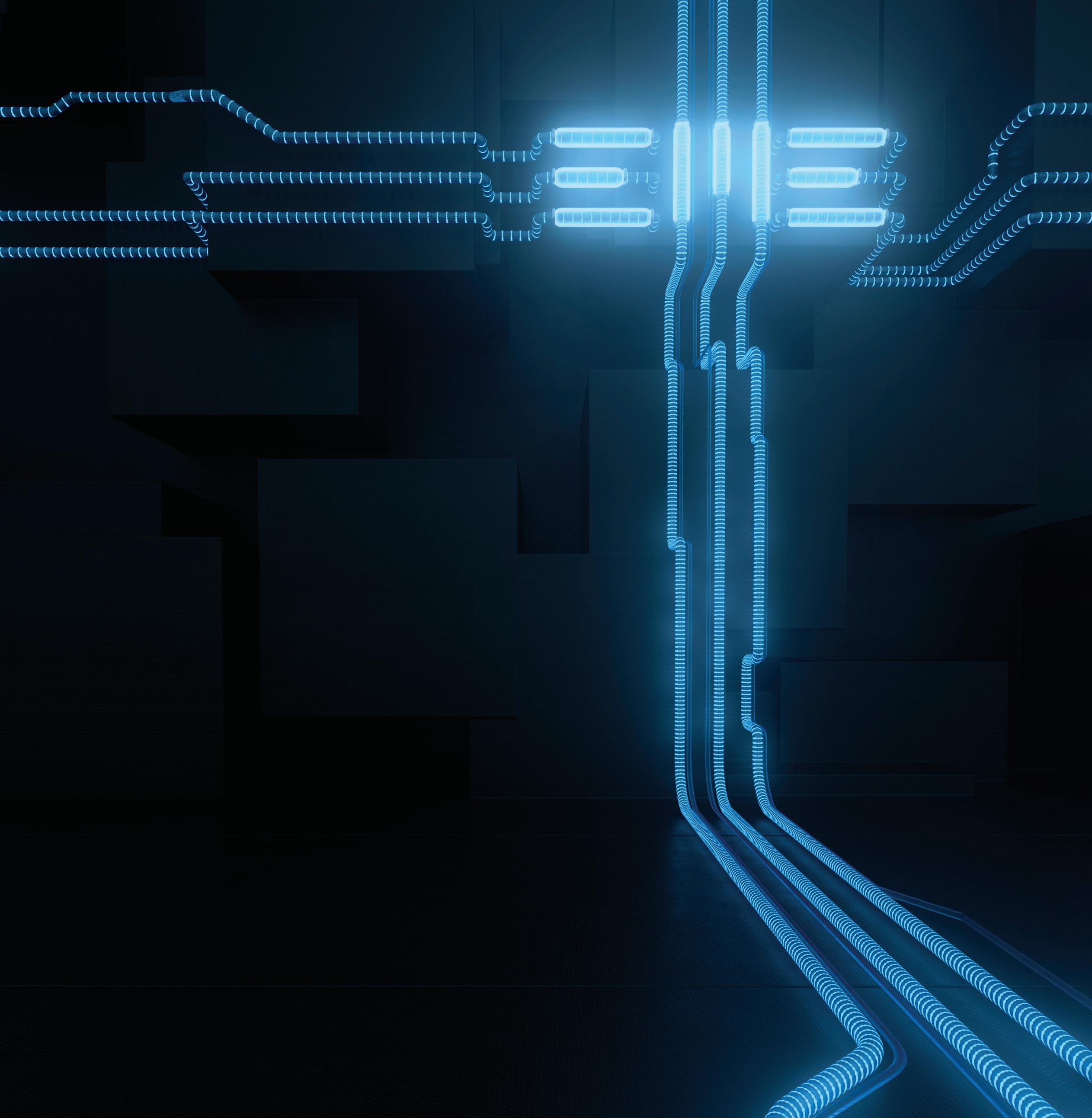
New logo . . . same smart machines

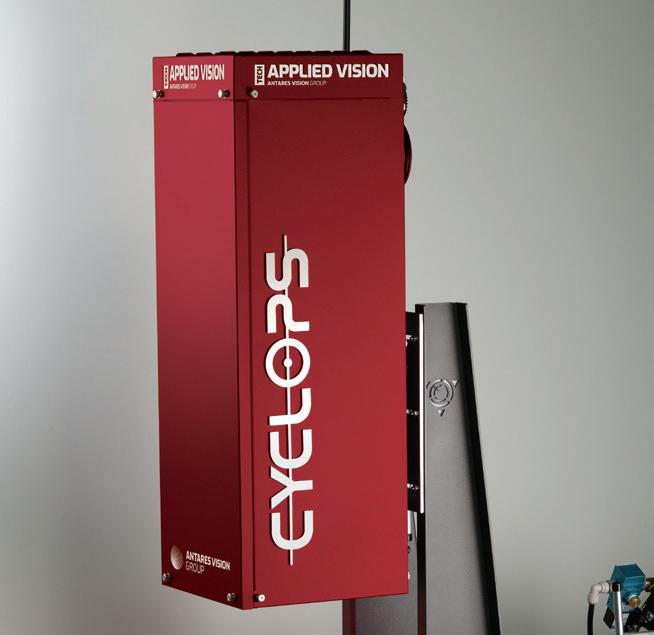
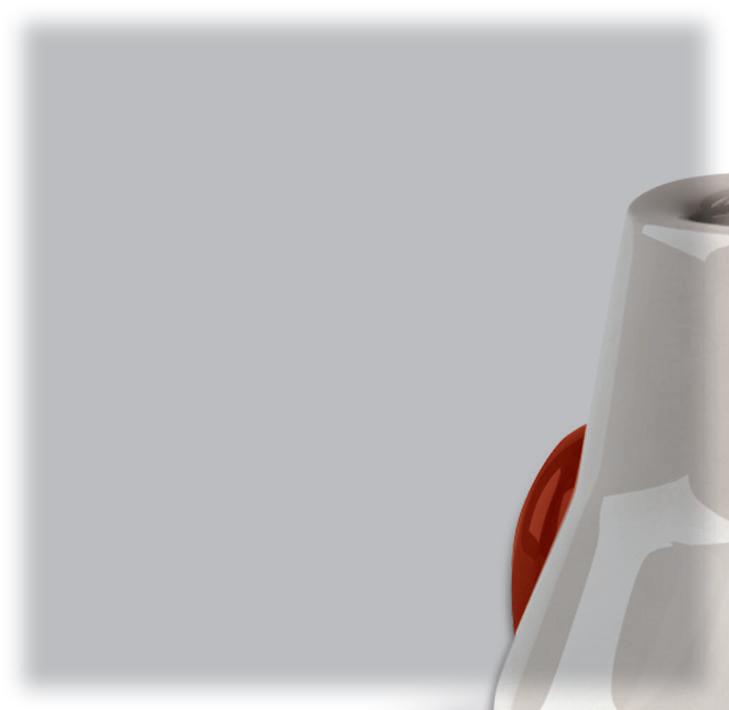

Applied Vision Corporation now doing business as At Applied Vision, we’ve changed our logo to Antares Vision Group, but we have the same machine vision inspection equipment known for durability and defect detection with best-in-class after-sale solutions. Also, as part of Antares Vision Group, we now offer track & trace, digital factory and supply chain transparency as complements to our inspection capabilities.
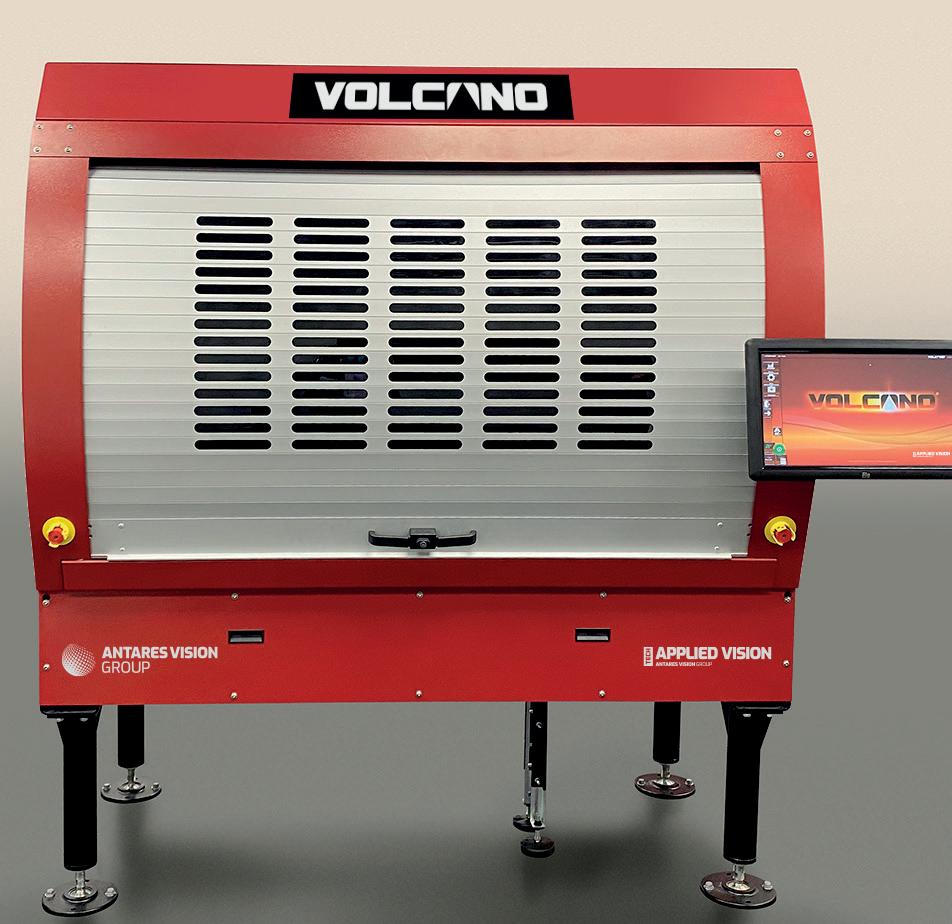
71
Chief Executive Officer: Steve Diprose Chairman: Paul Subscriptions:MichaelJackHomewood Tel: +44 (0)1737 855028 Fax: +44 (0)1737 855034 Email: Website:Email:Tel:SurreyQuartzPublishedsubscriptions@quartzltd.combyQuartzBusinessMediaLtd,House,20ClarendonRoad,Redhill,RH11QX,UK.+44(0)1737855000.Fax:+44(0)1737855034.glass@quartzltd.comwww.glass-international.comGlassInternational(ISSN0143-7838)(USPSNo:020-753)ispublished10timesperyearbyQuartzBusinessMediaLtd,anddistributedintheUSbyDSW,75AberdeenRoad,Emigsville,PA17318-0437.PeriodicalspostagepaidatEmigsville,PA.POSTMASTER:sendaddresschangestoGlassInternationalc/oPOBox437,Emigsville,PA17318-0437.
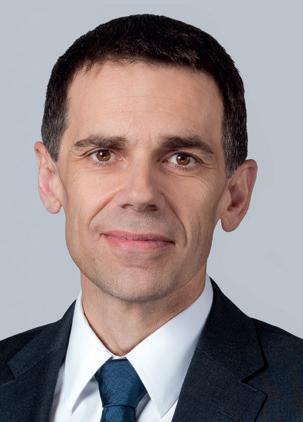
29
19
38
54
70
25
42
Abividrothe Brazilian Technical Association of Automatic GlassMemberIndustriesof British Glass Manufacturers’ ChinaConfederationConfederationNationalAssociation


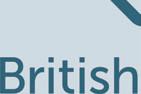

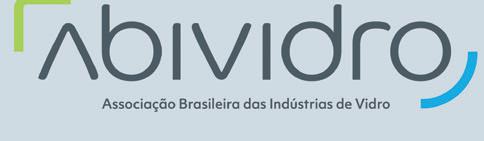
47
58
77
2 Editor’s
Contents Glass International September 2022 www.glass-international.com 1 Plus find us on LinkedIn and www.glass-international.comTwitter. @Glass_Int September 2022 Vol.45 No 8
www.glass-international.com
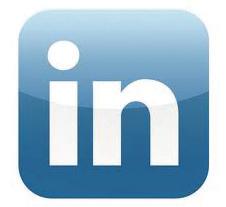
Editor: Greg Morris Tel: +44 (0)1737 855132 Email: gregmorris@quartzltd.com Deputy Editor: Jess Mills Tel: +44 (0)1737 855154 Email: jessmills@quartzltd.com
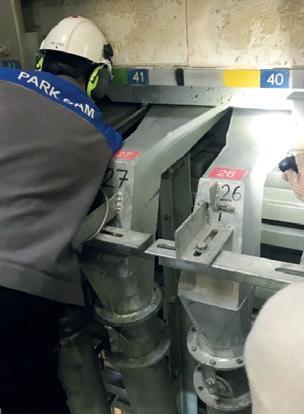

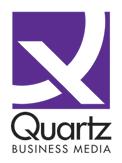

for Glass International annual subscription rates including Glass International Directory: For one year: UK £205, all other countries £268. For two years: UK £369, all other countries £482. For three years: UK £408, all other countries £563. Airmail prices on request. Single copies £53. Printed in UK by: Pensord, Tram Road, Pontlanfraith, Blackwood, Gwent NP12 2YA, UK. Glass International Directory 2021 edition: UK £206, all other countries £217. Printed in UK by: Pensord © Quartz Business Media Ltd, 2022 ISSN 0143-7838 Comment + International news Company profile: Fusion Y Formas Mexican glassmaker with a personal touch People profile: Emhart Glass President Embracing digital technology Overview: Chemical Market Analytics An overview of the soda ash market Decarbonisation: NSG Group NSG’s hydrogen trials Decarbonisation: TECO True carbon neutrality in glassmaking Decarbonisation: Sisecam Recycling in a circular economy perspective Decarbonisation: Krysteline A deep dive into recycling Decarbonisation: Schott Decarbonising the speciality glass sector Furnaces: Celsian Furnace simulation to assist operations Furnaces: Sefpro Electrical boosting of refractories Digital Glassmaking: Vertech Eco-responsible glassmaking with SIL Company profile: Techglass An all round furnace provider Furnaces: Sorg Electrifying the industry Inspection: Dr Gunther A marketplace of inspection solutions Inspection: Iris Inspection machines 20 years of inspection solutions Refractories: Paneratech Park Cam refractory success Forming: Siemens & Sklostroj Pulling out all the stops Inspection: Antares Vision Group Change of name for Applied Vision Furnaces: Neil Simpson Reducing the impact of CO2 in furnaces
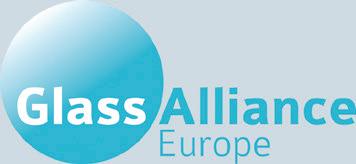
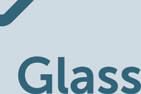
56
14
Designer: Annie Baker Sales Director: Ken Clark Tel: +44 (0)1737 855117 Email: kenclark@quartzltd.com Sales Executive: Manuel Martin Quereda Tel: +44 (0)1737 855023 Email: manuelm@quartzltd.com Managing Director Tony tonycrinion@quartzltd.comCrinion
14 68 71 77
61
68

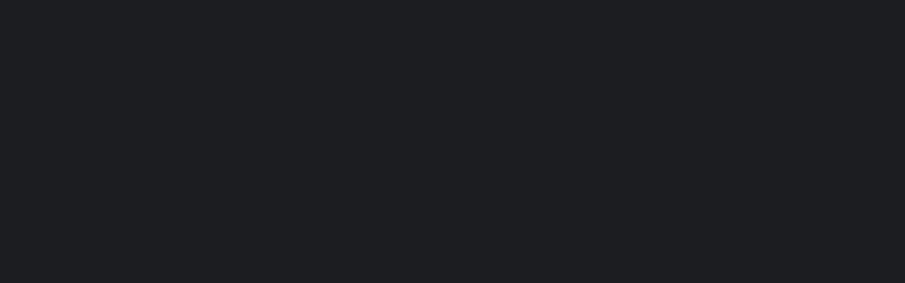
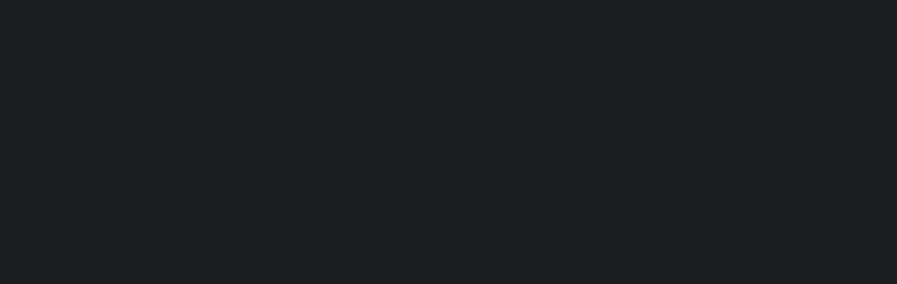
Official publication of

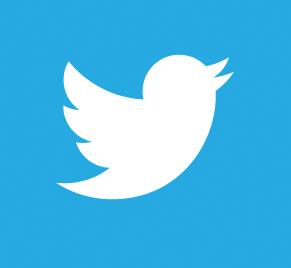
44
Glass Industry
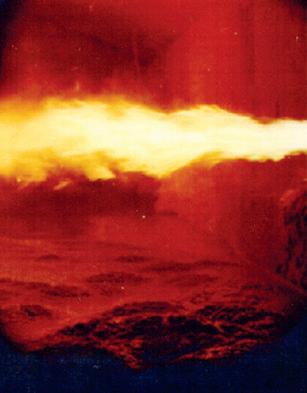
33
10
50
www.glass-international.com

International News GREG MORRIS, EDITOR Be first with the news! For breaking, up-to-date news www.glass-international.comVISIT: for daily news updates.
GLASSMAKING 2022SeptemberInternationalGlass FRONT COVER www.sorg.deIMAGE:
INTERNATIONAL
Gerresheimer to invest
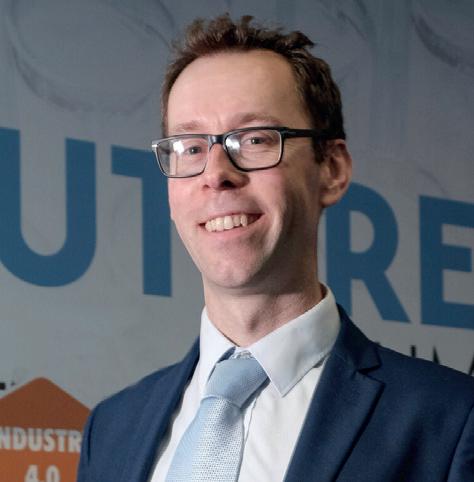
When will the energy crisis end? Container glassmakers may be enjoying an unprecedent ed boom in demand for their packaging but they face a severe headache that could hobbleLikeproduction.other heavy industries, glassmakers have been hit hard by soaring energy costs, which have been pushed up due to the Ukraine war. This combined with snarled-up supply chains and the continued fall-out from the pandemic have exacerbated fears of a global recession over the winter months. Industry - like households have already felt the pain. Companies in other industries as diverse as aluminium and fertilisers have already reduced or stopped production altogether due to Russia’s squeeze on supply of gas. One German glassmaker, Heinz-Glas said it faced a 10-20% increase in energy costs and suggested it was being pushed to the brink. The shortage of Russian supply coincided with Europe’s worst drought in 500 years which also impacted industry. Alternative sources of power such as nuclear and hydropower were impacted as a result of low water levels, which in nuclear’s case could not be used to coolTherereactors.areof course plans in place to rely on energy sources other than Russian gas but the conversion of this will take time, with mid2024 an optimistic forecast. The question is how long can industrial manufacturers last? It could be a long winter.
Gerresheimer is to invest in the rapid expansion of its manufacturing, supply and logistics capability for glass vi als in the US. The investment will expand Gerresheimer’s capacity by new vial forming lines, includ ing dimensional inspection, annealing, cosmetic inspec tion and packaging. The existing facility in North Carolina will be en larged by the installation of new modernised vial forming lines and a new warehouse. The project is supported by the Biomedical Advanced Research and Development Authority (BARDA) office in a 70/30 cost-share co-oper ative agreement. The office has agreed to provide up to approx. $66 million to Gerres heimer for the project. Under the agreement, Ger resheimer will increase its annual production capacity in Morganton, NC with vials that can be used in vaccina tion campaigns against infec tious diseases, such as Cov id-19 and others.
2
$94 million in US facility
Mexican glass manufacturer Vitro discussed the construc tion of a flat and container glass plant in Egypt during a meeting with authorities.
The Mexican container and float glass producer wants to invest in a 350,000m2 flat glass factory and a 150,000m2 container glass facility under a free zone framework, with a total investment of $400 mil lion.The discussion took place in a recent meeting between Vit ro CEO, Adrian Sada, Counsel lor Mohamed Abdel Wahab, CEO of the General Authority for Investment and Free Zones, and Jose Octavio, Ambassador of Mexico in Cairo. If approved the investment would lead to the creation of 1500 jobs.
Vitro discusses $400 million Egyptian glass plant investment
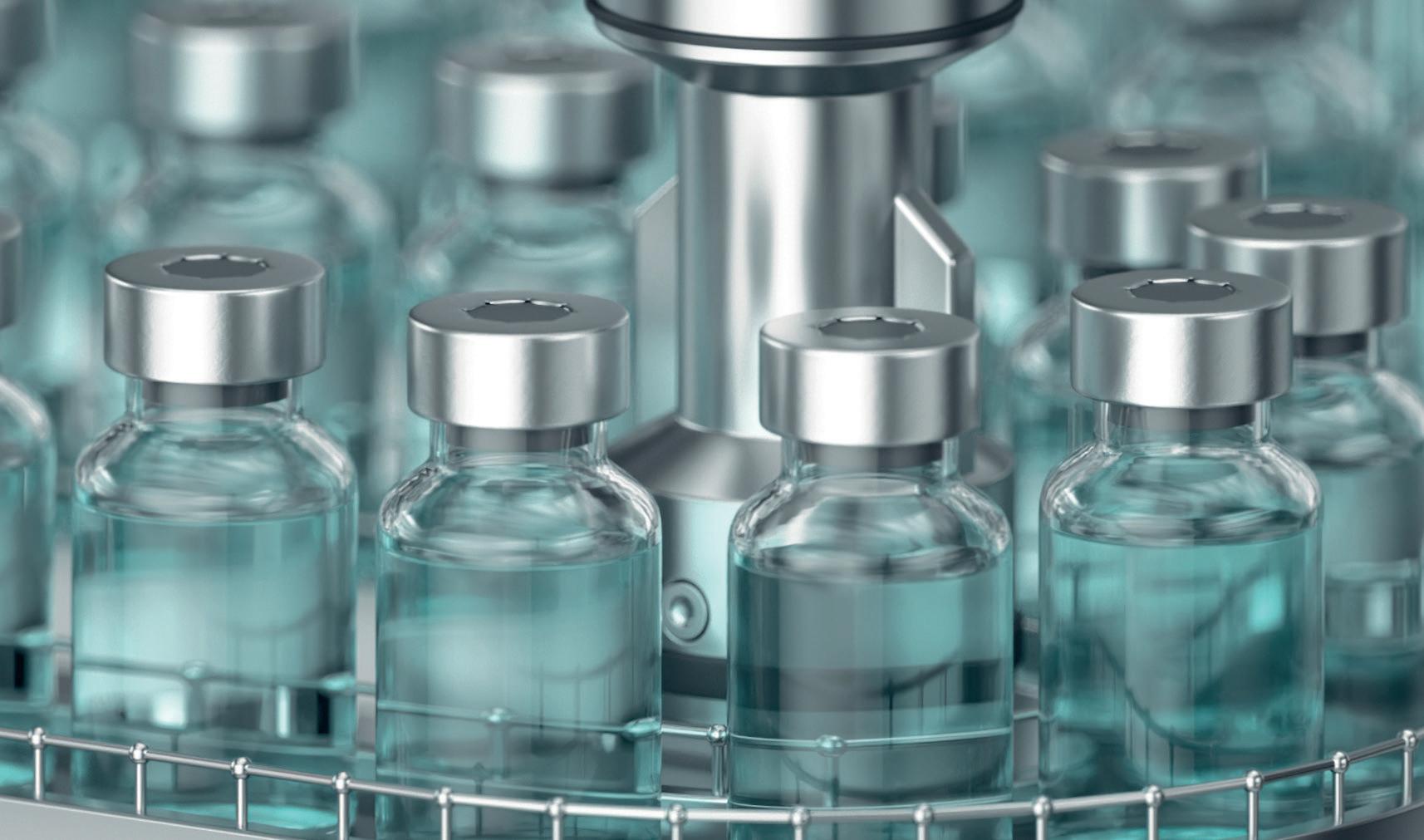
REAL-TIME PERFORMANCE FOR A PERFECT BATCH A GLOBAL REVIEW OF Glass International September 2022

A low radiation conductiv ity of the melt will result in a poor melting rate of the batch and thus in a low furnace pull rate.The method for determin ing kR(T) has a sound scientif ic basis and can be applied to any silicate glass without or with (a combination of) the colouring ions Fe, Cr, Cu, Co, Mn and Ni. Links *) https://doi.org/10.1111/ ijag.15111 **) 00:1-12. https://doi. org/10.1111/ijag.16603
Decarbonisation technologies aided by new study
The Vetropack Group sold 2.69 billion units of packaging glass in the first half of 2022. Due to the absence of capac ity at its Ukraine plant, sales volume was 6.9% below the prior year’s figure of 2.89 bil lionTheunits.war damage in the plant meant that a value adjustment of CHF 46.5 million had to be debited to the half year, so the Vetropack Group is posting a loss of CHF -9.7 million (prior year: 40.4 million). Damage also led to the loss of jobs at the facility in May.
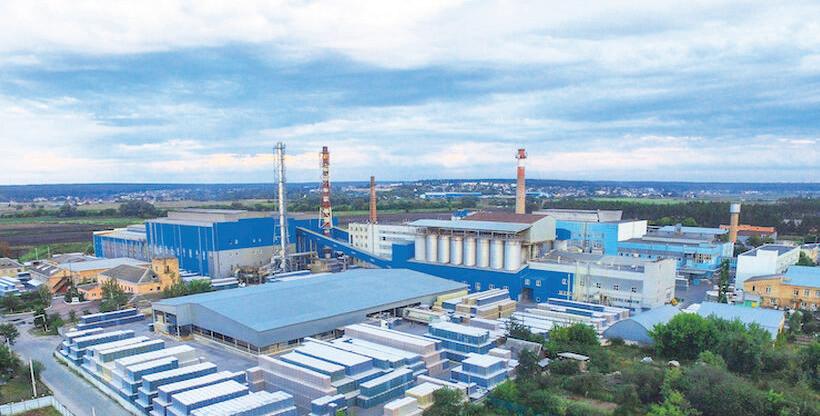
International News
Two articles on thermal ra diation conductivity of glass melts have been published to aid in the design of low carbon glass melting technologies.
Ukraine war damage impacts Vetropack’s glass sales
Germany’s Institut für Glasund Rohstofftechnologie (IGR) has changed address. The institute for glass and raw material technology is an independent provider of analysis and advice for all things related to glass. Its new address is: Institut für Glas- und Rohstofftechnologie (IGR), Else-Krengel-Strasse 9, D-37079 Göttingen, Germany.
Accurate data is available on the viscosity behaviour of practically all industrial glasses. However, the existing data on the thermal radiation conductivity of glass melts is scarce and often unreliable. But the guessing of this es sential glass melt property is no longer necessary.
Two peer-reviewed arti cles with accurate models for quantifying the thermal ra diation conductivity kR(T) of industrial silicate glass melts were recently published, see: Faber AJ et. al. in Int J Appl Glass Sci (2020*) & 2022**)), a journal of the American Ce ramic Society. For designing any industrial glass melting process, includ ing low carbon melting tech nologies, by CFD modelling, the thermal transparency of the glass melt is a key property, next to viscosity. For example, in electric glass furnaces, the transfer of the heat generated around the electrodes to the cold batch on top of the melt is strongly limited by the radiation con ductivity of the melt.
German instituteproductionglassresearchchangesaddress
Glass International September 2022 NEWS IN BRIEF www.glass-international.com 3
Horn secures Vetropack glass furnace contract Vetropack has contracted Horn Glass Industries for a furnace repair at its Czech Republic glass production facility.Furnace 52 at the Moravia plant in the Czech Republic will be repaired in 2023. Equipped with the latest technology from Horn in the areas of gas heating, electrical control and e-fusion power boosting, the furnace is expected to go into operation in November 2023.
Scotch whisky brand switches to glass bottles Scotch whisky brand Royal Salute is to switch to sustainable glass bottles. The brand’s porcelain flagon - which has been used since its inception in 1963 – has been exchanged for a recyclable glass bottle. The bottles will result in a 70% reduction in the carbon footprint of the brand’s primary packaging. War damage to Vetropack’s plant in Gostomel, Ukraine resulted in a reported loss of CHF 9.7 million ($10.04 mil lion). In its latest financial note, the glass container manufac turer said three major devel opments were dominant dur ing the first half of 2022: the ongoing Ukraine conflict, in creases in energy and produc tion costs, and sustained high demand for packaging glass. Sharp increases in energy and production costs led to major market price adjust ments in the packaging glass industry.Vetropack managed to com pensate for most of these ad ditional costs with an energy surcharge that is transparent for customers. Nevertheless, unabated high demand for glass pack aging and capacity reductions caused by the shutdown of the Ukrainian glass industry have already led to a number of bot tlenecks in meeting customer demand throughout Europe.
HFT adds Senior Manager to safety team HFT has expanded its safety team with the hiring of safety veteran David Melendez. Mr Melendez will serve as Senior Safety Manager and brings more than two decades of worldwide safety experience across multiple marketSafetysectors.isat the forefront HTF’s operations, with a fundamental imperative of zero incidents.
Durable anticorrosive glass launches in the UK
The range has been exten sively laboratory tested at high temperatures and levels of hu midity, where it demonstrated that it resists corrosion far bet ter than untreated glass. It meets stringent EN 1096-2 standards, which certifies the products as able to withstand challenging outdoor weather conditions and abrasion.
Zippe starts construction of Vetropack plant Zippe has started the construction of a batch house for Vetropack in Boffalora, near Milan, Italy. The plant will supply two melting furnaces and two cullet return systems. The plant is expected to go into operation in spring 2023.
4
The glass has a wide range of residential and commercial applications, such as shower cubicles or back plates against cooking surfaces in kitchens.

Glass International September 2022
The highly transparent glass is easier to keep clean due to its special pyrolytic anticorrosion coating which acts as a barrier on the surface of the glass.
Canpack Group reveals new headquarters Canpack Group has relocated its corporate headquarters to a new address in Kraków, Poland. The offices are located in a modern MK29 complex in the heart of the city. The offices will encourage co-operation and integration, encompassing new technology and befitting Canpack’s culture.www.glass-international.com
Pilkington OptiShower, a range of anticorrosive and du rable glass by the NSG Group, has launched in the UK to sup port designers specifying glass for use in high-moisture envi ronments.Thedurable, clear glass is specifically designed to pre vent surface corrosion when exposed to water, moisture and humid environments.
Pilkington OptiShower’s anticorrosion properties also make it suitable for marine ap plications, such as aquariums and maritime vessels.
Kirk Green, Regional Sales Manager at Pilkington United Kingdom Limited, part of the NSG Group, said: “We’re ex cited to launch this product in the UK to help new customers identify applications where the glass can deliver long term durability, no matter the con ditions.”Therange is coated ‘online’, meaning the anticorro sive coating is applied while the glass is still hot, rather than as a post-manufacture spray like many other prod ucts on the market with simi lar properties. This makes the product easier to process, as well as harder and more robust when in use.
NEWS IN BRIEF
Pilkington provides glazing for Elizabeth line project Pilkington UK, part of the NSG Group, supplied 5,000 high performance glass panels to the Elizabeth line project in London.Intotal, Knorr-Bremse Rail Systems UK installed almost four kilometres of high performance glazing across eight Elizabeth line stations in central London. The glazing comprises two pieces of advanced toughened glass, addressing the current risk requirements including barrier safety and blast resistance. Sisecam Conference to celebrate IYOG Sisecam’s 37th International Glass Conference will take place in Istanbul, Turkey on 17-18 November 2022. The conference will be held in hybrid form, both virtually and in-person, at the Sheraton Grand Istanbul Atasehir Hotel. The event will acknowledge the significant role and technical potentialities of glass with this year’s theme of ‘Inspiration for Tomorrow’.
International News
Mexican and Andean demand boosts O-I’s glass results
Strong demand for glass con tainers in Mexico, the Andean countries and southwest Eu rope boosted O-I’s results. The world’s largest contain er glass manufacturer report ed a1% increase in shipments in the second quarter of this year, which comes on top of an 18% improvement in the prior year quarter. Volume was up nearly 1% in both Americas and Europe, said the company’s CEO An dresItsLopez.balance sheet is now in the best position since prior to its acquisition of O-I Mexico in 2015, he Year-to-dateadded.shipments were up 3% about 5% in Europe and 2% in the Americas. Mr Lopez said market trends clearly favour glass resulting in the strongest market funda mentals in over 20 years. He said: “Across Latin Amer ica, a structural shift in de mand is driving sustainable growth. “Customers and consumers increasingly favour premium products and our customers are localising international brands that had been success fully imported to these mar kets for several years. “Premiumisation favours one-way glass containers, while consumer affordability and sustainability consider ations are prompting greater use of returnable bottles. “For example glass now holds 50% market share in the Brazil beer category as both one-way and returnable glass gain share.”
PSR SYSTEM 500 FOREHEARTH Achieves the best glass thermal homogeneity and energywww.parkinson-spencer.co.ukefficiency.
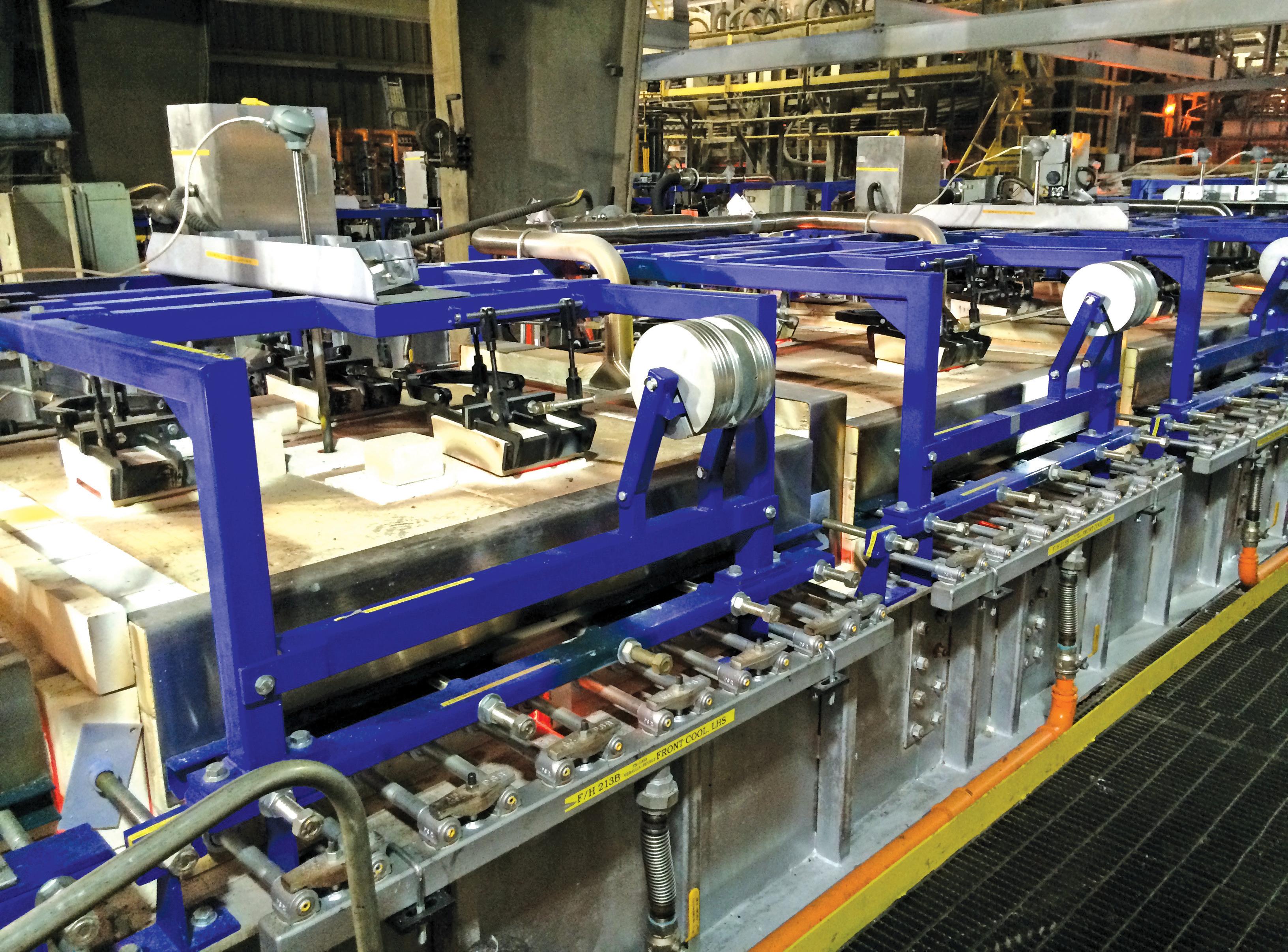
Vetropack’s glass sales International News For the latest Industry News scan the QR CODE using your iOS or Android device
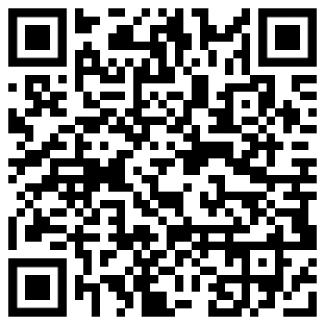
� 1. O-I to build $240 million MAGMA facility in USA � 2. Soda ash company bids to acquire Indian glass manufacturer � 3. Vitro discusses $400 million Egyptian glass plant investment � 4. Verallia to electrify Cognac plant in Fives partnership � 5. Gerresheimer to invest $94 million in US facility � 6. Glass leak at Vitro’s Wichita Falls facility � 7. Sisecam contracts Zippe for triple batch plant project � 8. Grenzebach and Sorg form glass technology company for impacts
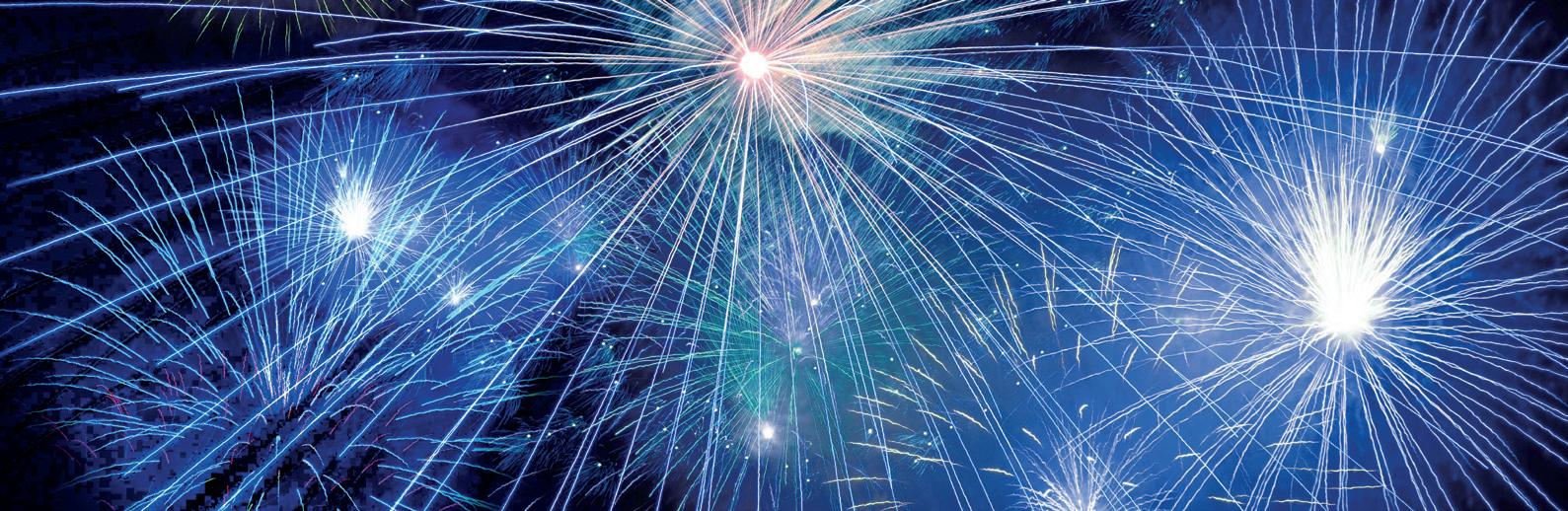
Forglass performs hot overcoating at flat glass manufacturer
www.glass-international.com
Forglass has partnered with one of the world’s largest producers of automotive and architectural glass to perform a hot overcoating of its float furnace in Europe. Hot overcoating of a large float furnace is one of the most demanding types of furnace repair, requiring organisation andDuringteamwork.therepair, the furnace is kept around its operating temperature, so those working around the furnace must wear special equipment to protect them from exposure to extreme Schedulingheat.this type of work also has to account human endurance while working in extremeTeamsconditions.mustwork in short intervals giving them time to rest and cool off. Hot overcoating of a large float furnace is planned to minimise glass-to-glass time and there is no room for delay. Detailed planning is key, allowing exactly the right amount of time to complete each task.
double Mexican capacity in $116 million investment Saverglass is to double capacity at its Guadalajara, Mexico, production facility and increase its decoration capability.The $116 million investment will include a 200,000 tonnes a year furnace capable of manufacturing 200 million bottles in three colours: extra-white, antique green, and dark yellow. Agr to introduce new measurement systems at glasstec 2022 Agr International will feature its high-precision laboratory dimensional measurement system at glasstec 2022 in Düsseldorf, Germany. Agr will display several new product developments in quality management equipment for glass containers at glasstec.
can be found on our
6 Glass International September 2022 NEWS IN SaverglassBRIEFto

alliance � 9. Schott establishes stand-alone
All full
Our most popular news past month, by website traffic. stories website.
Italian glass manufacturer Vetrerie Riunite has began reconstruction work on its second furnace, known as the Centauro, in order to increase its production capacity. The vault, superstructure and regeneration chamber of the old structure have been maintained.Allglassconditioning and distribution channels, and other parts of the furnace in direct contact with the glass, are under Tecsiglassconstruction.handledthe design, demolition and reconstruction, as well as the updating the software, along with Fila termoidraulica, which executed the construction of the compressed air, methane and technological water systems. C.D.M. undertook the heavy carpentry and Alca handled the upgrading of the electricalThesystem.reconstruction of the furnace will allow the production of 190 tons of glass per day, instead of 175, so as to be increasingly competitive in theInmarket.thisway, Vetrerie Riunite consolidates its position in the global market for glass doors for washing machines and dryers.
Italian glass manufacturer increases furnace capacity
our
over the
as determined
Sefpro and Tecsiglass form partnership Sefpro has formed a strategic partnership in Italy with Tecsiglass.Therecently founded company Tecsiglass is managed dynamically by experts with more than 25 years of experience in furnace design, reconstruction and project management. As Sefpro agent, Tecsiglass will further improve the company’s customer proximity with customers in the Italian market and work closely with its European Customer Service. Gerresheimer to invest in North Macedonian facility German pharmaceutical company Gerresheimer is to invest in a new factory in the beginseriesquarterTIRZonSkopje,DevelopmentTechnological-IndustrialZones(TIRZs),NorthMacedonia.Thestartofconstructionitsexistingpremiseintheisplannedinthethirdofthisyear,whileproductionshouldin2024.
pharma industry � 10. Ukraine war damage
The efficiency and quality of work has to be 100%, as there is no time to redo a mistake.
Top 10 stories in the news
We printyour world Koenig & Bauer Kammann GmbH Weidehorst 80 | 32584 Löhne kammann.de Uniting inks and substrates to create a uniqueness, which is incomparable.
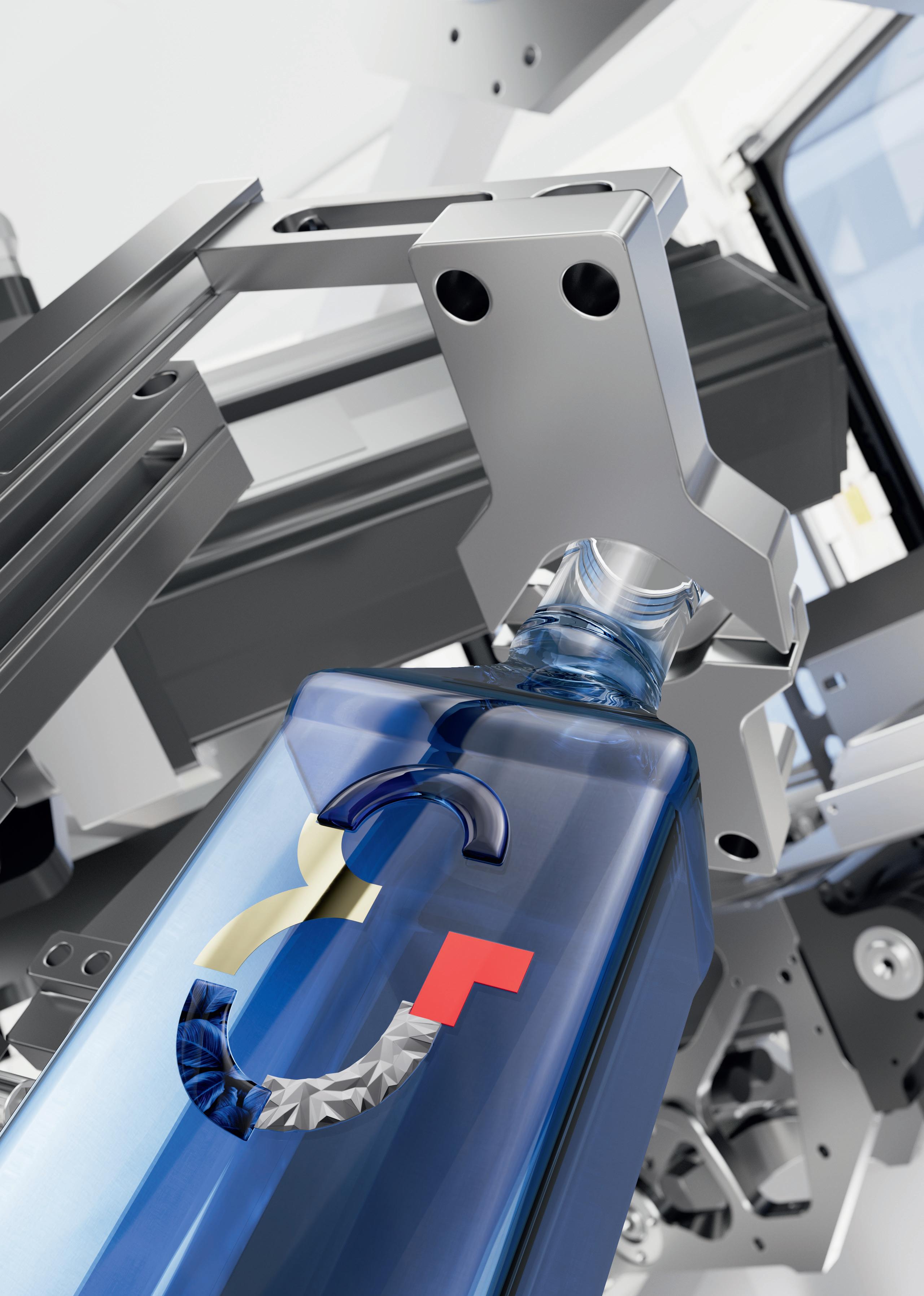
SGD Pharma appoints former Verallia boss as CEO Global glass primary packaging supplier SGD Pharma has appointed Olivier Rousseau as its new Chief Executive Officer. Mr Rousseau joins the business after four years as CEO & President of container glass manufacturer Verallia France, and with 30 years experience in the industry.
Brazilian flat glass manufacturer Vivix is to build a BRZ1.3 billion ($248.1 million) production factory. The site in Goiana, Brazil, will be constructed next to its current glass manufacturing facility and be fully operational in the second half of 2025 and have a capacity of 1000t/day. This will make it the largest in operation in Brazil. The plant, the company’s second, will increase the organisation’s total capacity to 1900t/day and become the second largest float manufacturer in the domestic market.
French hydrogencompletesmanufacturersuccessfultest
British Glass Focus Awards dates This year’s British Glass Focus awards will take place on November 17. The annual celebratory event of the glass industry’s achievements over the year will be held at Sefton Park Palm House, Liverpool, UK.
Glass International 2022
NEWS IN BRIEF www.glass-international.com 8
French borosilicate glass manufacturer La Maison Française du Verre has completed its injection tests of up to 20% (in power) of hydrogen mixed in natural gas at its Châteauroux site. The company was able to validate this approach to decarbonisation at a true glass melting scale with a full load. The first results were very encouraging.
September
O-I Glass partners with Ivalua
Vivix to manufacturingBrazil’sconstructlargestglassfurnace
International News
Soda ash company bids to acquire Indian glass manufacturer futronic bids farewell to two long-time companions Two long-serving colleagues at glass production technology company futronic, Johannes Dimmler and Bernhard Kubik, haveBernhardretired. Kubik was with futronic for almost 37 years and Johannes Dimmler for 38. Both of them had become part of the furniture, as it were, and they’re already sorely missed. Dimmler and Kubik played a crucial role in the develop ment of the CIMOG machine control system. Without them there would also have been no EPRO, no FMT24S and no EPRO Upgrade Kit. They’re both people who know a tremendous amount about the complex process es involved in container glass production.It’sfairto say that without Johannes Dimmler and with out Bernd Kubik, futronic would be a different company.
India’s largest container glass producer by capacity, Hindu stan National Glass Limited (HNGL) may see a new owner and management soon. Soda ash producer, Nirma has submitted an INR 16,500 million ($206 million) plan to acquire the bankrupt com pany.Africa-based bottle maker Madhvani Group and con tainer glass producer AGI Greenpac have also submitted separate resolution plans for theDanishcompany.beer maker Carls berg, private equity funds Oaktree Capital and SNJ Dis tilleries are among a dozen en tities that have shown interest in acquiring the company. At a committee of creditors meeting recently, HNGL lend ers rejected an INR 12,50013,000 million ($156-162 million) one-time settlement (OTS) offered by the promot er.The resolution profession al Girish Juneja, backed by EY, has admitted INR 33,280 million ($416 million) claims from financial creditors. HNGL has made several at tempts since 2018 to settle the loans, but the negotiations did not progress due to the promoter’s inability to tie up funds.Inits latest attempt a year ago, HNG offered an INR 14,000 million ($175 million) settlement over ten years and a conversion of the INR 5,000 million ($62.5 million) loan intoHowever,equity. the settlement offer was not unanimously ap proved - a precondition to the deal. Edelweiss ARC, which holds 21% of the debt, reject ed the proposal claiming it to be below expectation. In 2019, an OTS backed by Carlsberg could not be con cluded after it failed to get ap proval from the Competition Commission of India. HNGL was admitted for in solvency proceedings in Octo ber 2021 based on an applica tion filed by DBS Bank.
O-I Glass has selected Ivalua to streamline its Global Direct and Indirect Source-to-Pay (S2P) Processes O-I Glass chose Ivalua after assessing technology and pro cess gaps related to strategic sourcing, supplier relation ship management, category management, vendor quality, sustainability, and compli ance.O-I Glass also intends to pro vide an optimised buying pro cess with catalogues, guided buying, and an Amazon-like userSupportedexperience.by Ivalua’s solu tion, O-I’s strategic S2P initi ative aims at generating sig nificant cost-reduction across several key business process areas including savings on indirect categories through process standardisation and spendFurthermore,consolidation.the project will deliver an improved user experience throughout the buying process, a reduction in administrative activities and, crucially, an optimised supplier base driven by a com prehensive assessment of sup pliers.Lastly, Ivalua will ensure seamless integration with O-I’s existing ERP platform, as well as several third-party solutions.
Your
info@hft.comBooth C48-1 / Hall 13
For 75 years, HFT has developed a reputation as a leading EPC contractor to the global glass industry. What you might not know is in that time, HFT has completed over 300 EPC projects in 47 countries for Float Glass, Container Glass, Fiberglass, and more. Whether it’s a greenfield glass factory in a far corner of the globe or a major facility reconfiguration just up the road, HFT has consistently delivered quality, efficient, and innovative project solutions. This performance, plus our commitment to customer satisfaction makes us the clear single-source choice to take your next project from concept to completion. vision. Our expertise. The perfect partnership. www.hft.com |

Somethanaresolutionsclearerothers.
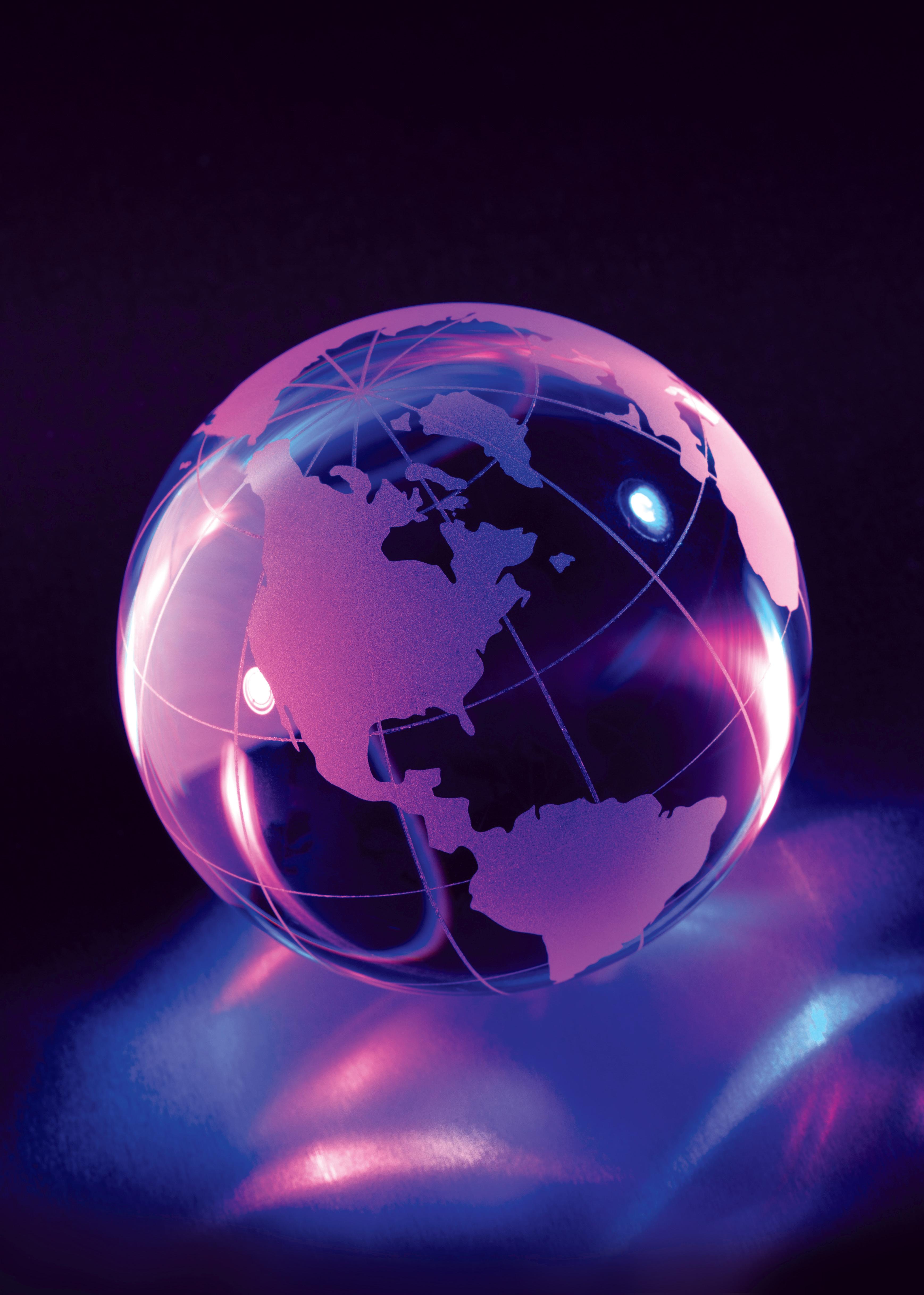
Fusion Y Formas’s success is linked to the increase in popularity of tequila.
“This customer came in who wanted to make tequila a premium spirit, which was a new idea at the time. It took us 10 months to do it and as the Andres Hernandez
tequila industry changed, the business grew.”
The glassmaker’s origins were founded upon the production of bottles for a single tequila brand local to Jalisco state. In the subsequent 25 years since its inception the company has grown to supply more than 200 customers around the world. And this growth is set to continue. The company recently completed a furnace investment which has increased the daily capacity at its 3600m2 facility in Zapopan, Mexico. The company is managed by the Hernandez family, who have glassmaking in their DNA.
Both Fusion Y Formas and the tequila spirit are located in the famous Jalisco state, Mexico and over the last 25 years the two brands have grown considerably.Therisein the popularity of tequila in recent years has been spectacular and it is now the second most popular spirit in the USA, only behind vodka.
10
Cesar decided to form Fusion Y Formas which would focus exclusively on making tequila bottles using a semi-automatic process. After 20 years he handed over the management to sons Andres and Pablo who changed to the production to an automatic glass manufacturing process.Theorganisation’s focus lies in the craft of glassmaking. Rather than making lower cost, generic and mass-produced glass, it specialises in the production of small batches of approximately 10,000 bottles and upwards. It will work closely with customer to design a bottle with personality
www.glass-international.com The evolution of Mexican glassmaker Fusion Y Formas has mirrored that of one of Mexico’s most famous exports in recent years.
Father Cesar founded the company while working for his own father at the family’s handmade glass factory back in 1998. The company was formed when Cesar was working in his father’s handmade glass factory when a customer requested a tequila bottle.
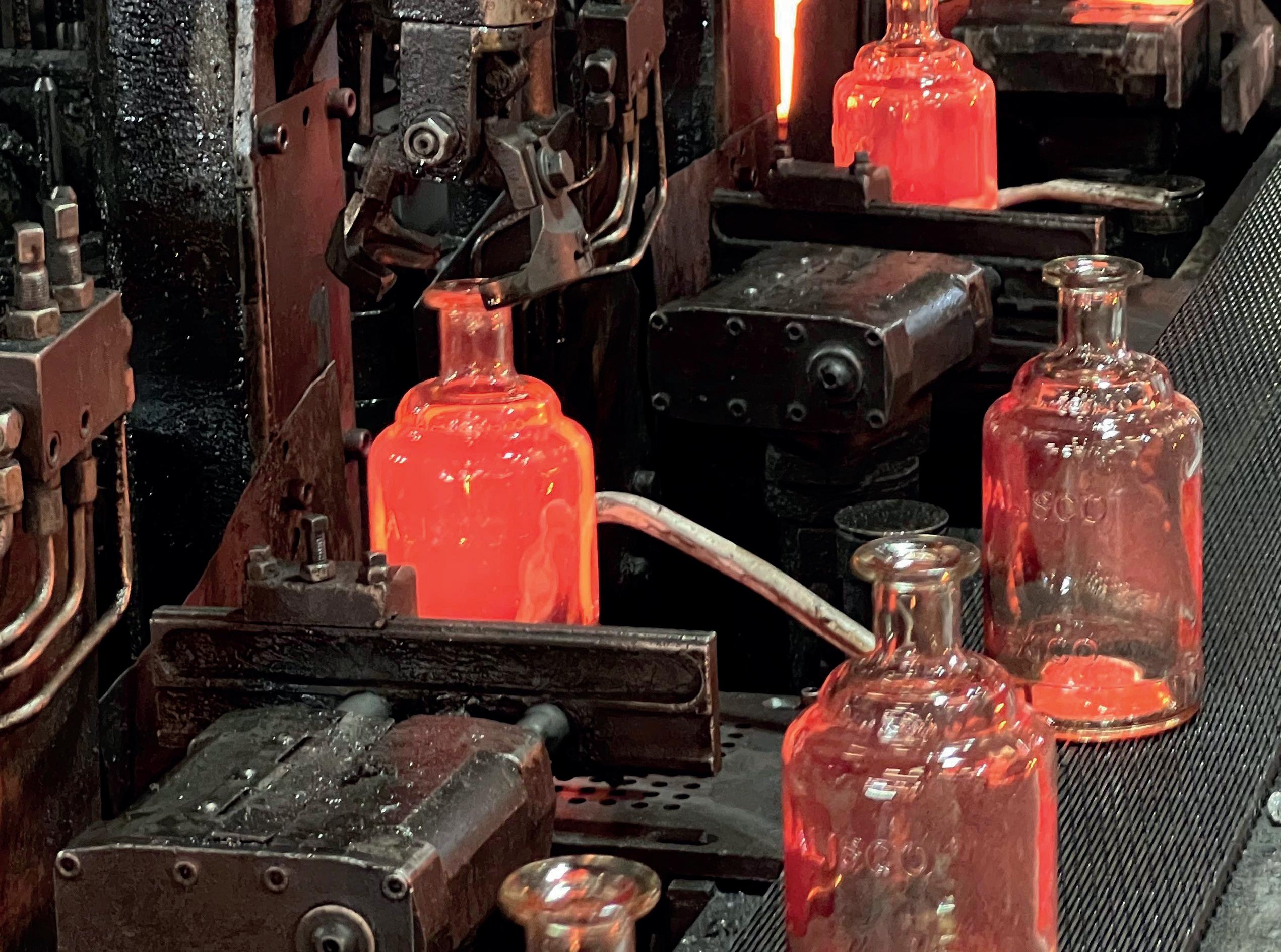
Company profile: Fusion Y Formas Glass International September 2022
““We have industryinnovate,continuouslytotheisfamouslyrigidbutwithinthatcontextweinnovateevenifsometimesitisbyaccident.Innovationisoneofthosethingsthatyougettodowhenalone,whennooneistellingusthatitcannotbedone. ”
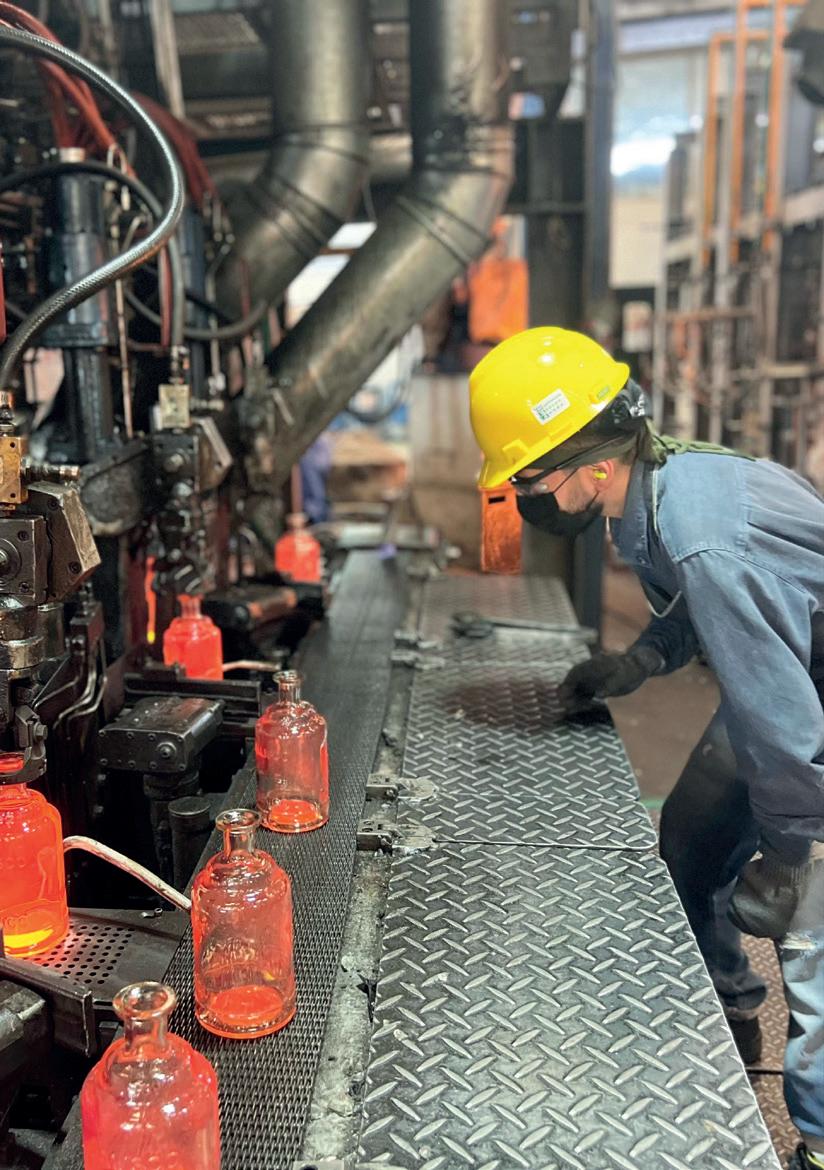
Recycled glass

The majority of its glass is in flint but it has the
Key to the development of the factory has been colleague Victor Pedraza, the company’s production director who Andres and Pablo both cite as a huge influence. He has been with the group for 22 years and has worked in all areas of the business. Not only is he technically minded but has also consulted on the design of bottles.
Pablo has worked on more than 100 bottle and jar designs, working on elements such as engraving, holes in the bottle and asymmetric shapes. His favourite remains his first design for that of a small Mezcal bottle.
companyitsFusionaglassmakerMexicanwithpersonaltouchyFormasislocatedinthesameregionofMexicoastequila.Thankstostrongcustomerfocus,thefamily-runthrivesinbuildingrelationshipsandincraftingglassbottlesthathavepersonality.
As a smaller, family run company it has to continuously be creative. In the past it has created water-based mould cooling technology and added seeds to Andresglass.says: “We have to continuously innovate, the industry is famously rigid but within that context we innovate even if sometimes it is by accident. Innovation is one of those things that you get to do when alone, when no one is telling us that it cannot be done.”
adaptability to produce in other colours too.
One of its stand-out points is it manufactures from 100% recycled glass. While there is currently a strong trend on the environment, the company has used 100% recycled glass for as long as Andres can remember. Its furnaces also use an oxy combustion process to help prevent solid discharges into the atmosphere and to minimise the generation of CO2 Andres says: “The main difference between us is we use 100% recycled glass to make our bottles and are the only factory in Mexico that produces this way.“We have used recycled glass from the beginning. At the time it was not appreciated that using recycled glass could help the environment, we just did it. Today energy saving and helping the environment is a big subject, but we have been doing it since our grandad’s factory, it is in our bloodline if I can say that.”
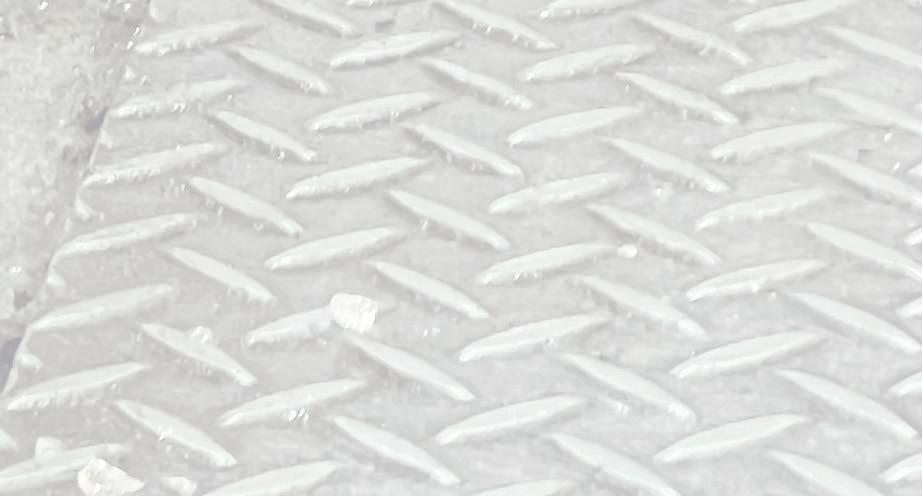
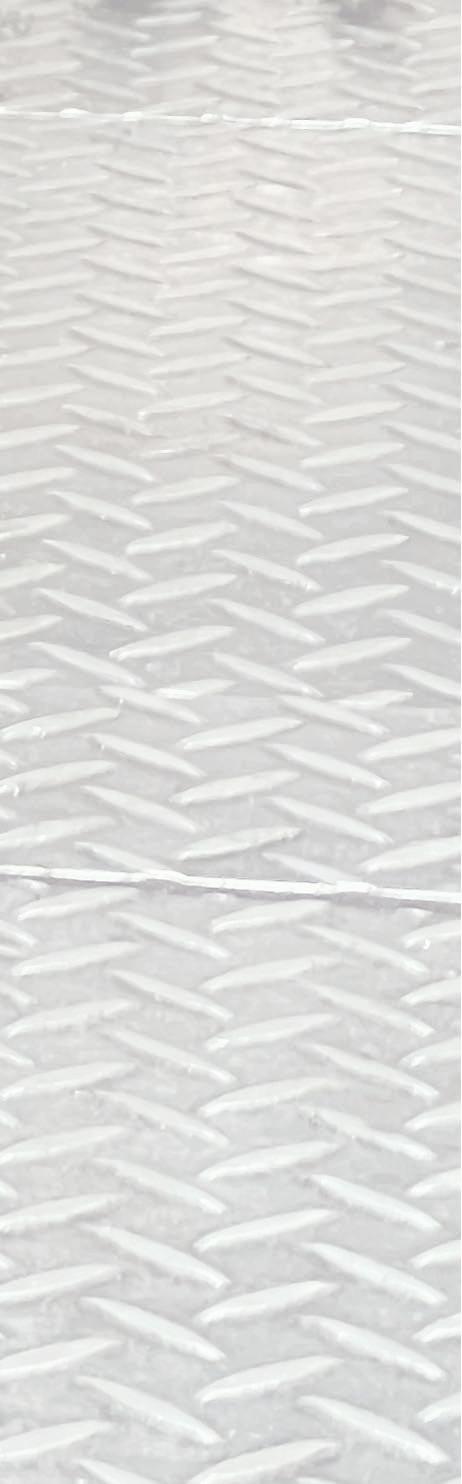
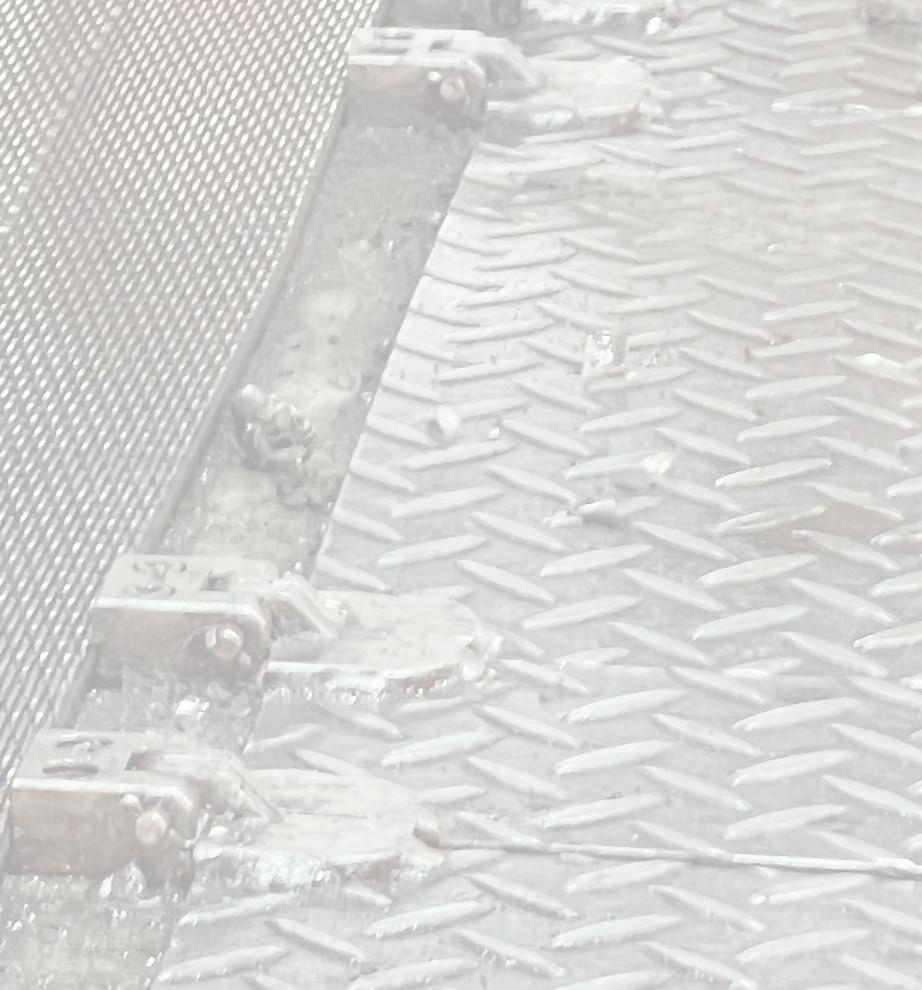
Its bottles and jars are shipped from Jalisco to all around the world so when Pablo is in discussions to design the bottle he has to consider the impact of transportation and of the temperature in its final destination, for example.
The company is involved in the design phase of the bottle and aims to add personality to every brand it works with. Andres said: “We work with customers from the design to the production phase and then afterwards we open the doors of the factory – we want customers to feel part of the product, it is theirKeyfactory.”tothedesign of the bottles is brother Pablo who is responsible for the engineering behind the design ideas. He will talk with a customer, take their idea and then add his own creativity to the design.Andres says: “There are always guys that want to push the limits and try to do something crazy but Pablo is the guy who brings them down to Earth. We want to offer something more realistic and he will describe what can and cannot be done and the risks“We’reinvolved.focused on the long-term relationship and we always say that if you want to do something with us then they should also discuss something with another factory to see if they can do it.”
Company profile: Fusion Y Formas Glass International September 2022 www.glass-international.com 11
“It was a diamond shape in a cylindrical bottle which was difficult to engineer. It also had an unusual texture which I liked about it.”
Andres states: “In my opinion, he is an artist who can see things before everybody else. He plays a unique role and has been involved in many aspects of the factory.
“He has put a lot of sweat into the company and Continued>> and one which will maximise its impact on the shelf. Given its proximity to the tequila distilleries of Jalisco, it naturally specialises in the manufacture of bottles for the spirits sector but also caters for the food and olive oil markets. Its size of bottles range from 25ml to 3 litres. As Managing Director Andres Hernandez says: “Our main market is Mexico, but our bottles are also in Europe, USA and South America - they are shipped all over the world.”
“I have seen the company grow with more machines and a larger oven. I thought it would stop at a second machine but once you’re in the glass industry you cannot stop. I hope my sons continue working here for as long as they want.” �
Company profile: Fusion Y Formas
Fusion Y Formas, Zapopan, Jalisco, Mexico http://fusionyformas.com/en
Plamasso worked on Fusion’s recent 38t/ day furnace investment, which saw its capacity increase to 53 tonnes a day during a 30-day construction programme. The glassmaker has two furnaces and went through the furnace rebuild after the previous oven reached the end of its life. It has two semiautomatic forming machines with plans to possibly increase to three machines in future. History Both Andres and Cesar’s links to glass were forged at a young age, when both would spend weekend in the glass factory as youngsters.
www.glass-international.com puts the company before himself sometimes. He lives and breathes the company.” It was Victor who developed the water-based mould cooling technology and who played a key role in the optimal layout of its production area.
Family company The benefits of a smaller, family company means it is quick to respond to customer questions and make rapid decisions. “Our biggest strength is our flexibility, we are a family-owned business and are always close to the customer. If we make a decision we don’t have several layers of people to go through. I’m in charge of the commercial area and it is always nice to form relationships and form friendships and build that close knit trust.” It has forged strong links with several other companies which have a similar, family run profile. One of its strongest ties is with Spanish furnace designer and manufacturer Hornos Plamasso. The companies have worked together for 15 years and are now more like friends than suppliers.
12
Cesar said: “For me it was aged 10 or 11 when my father would take me to his factory on a Saturday to give my mum a break! I would help wrap the glass figurines but I never related it as a place of work, it was just somewhere where I would help out.”
Andres would spend the weekend at the factory as a teenager, just hanging out. It was only after finishing university aged 21 when he began to work for the company that he began to fully appreciate the magic of the glassmaking process.
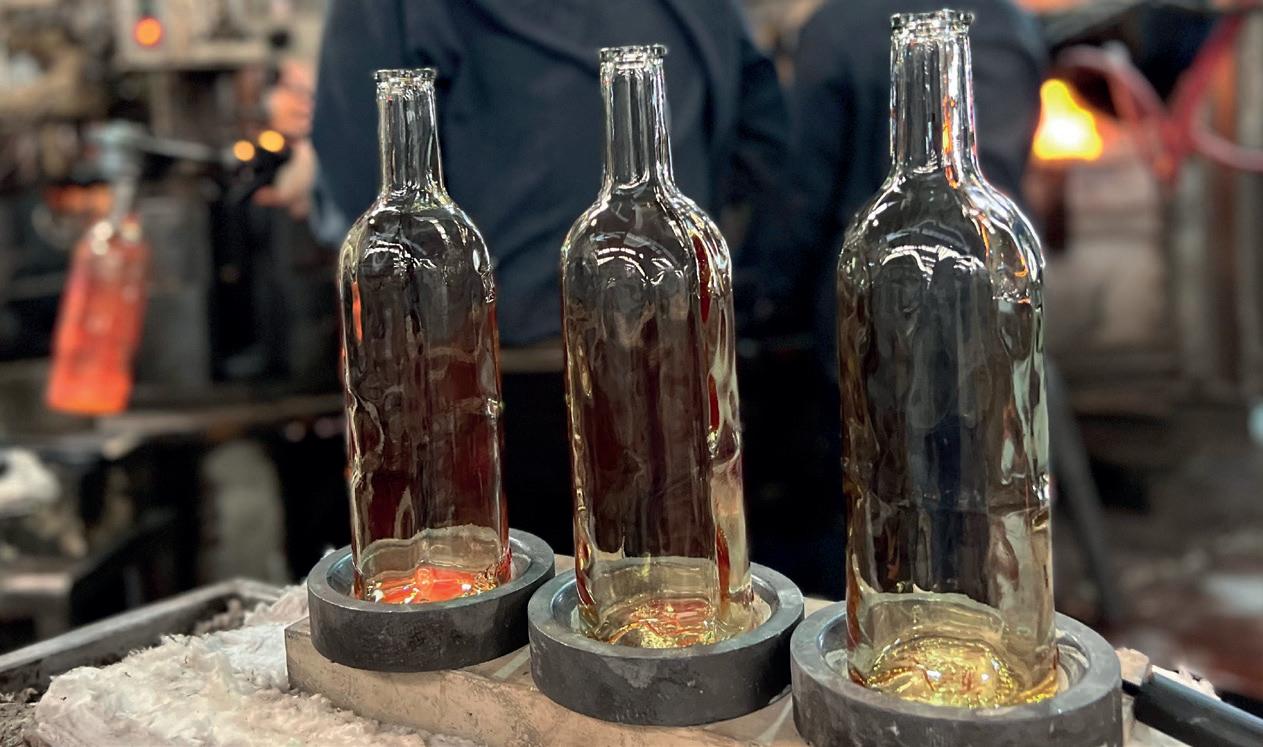
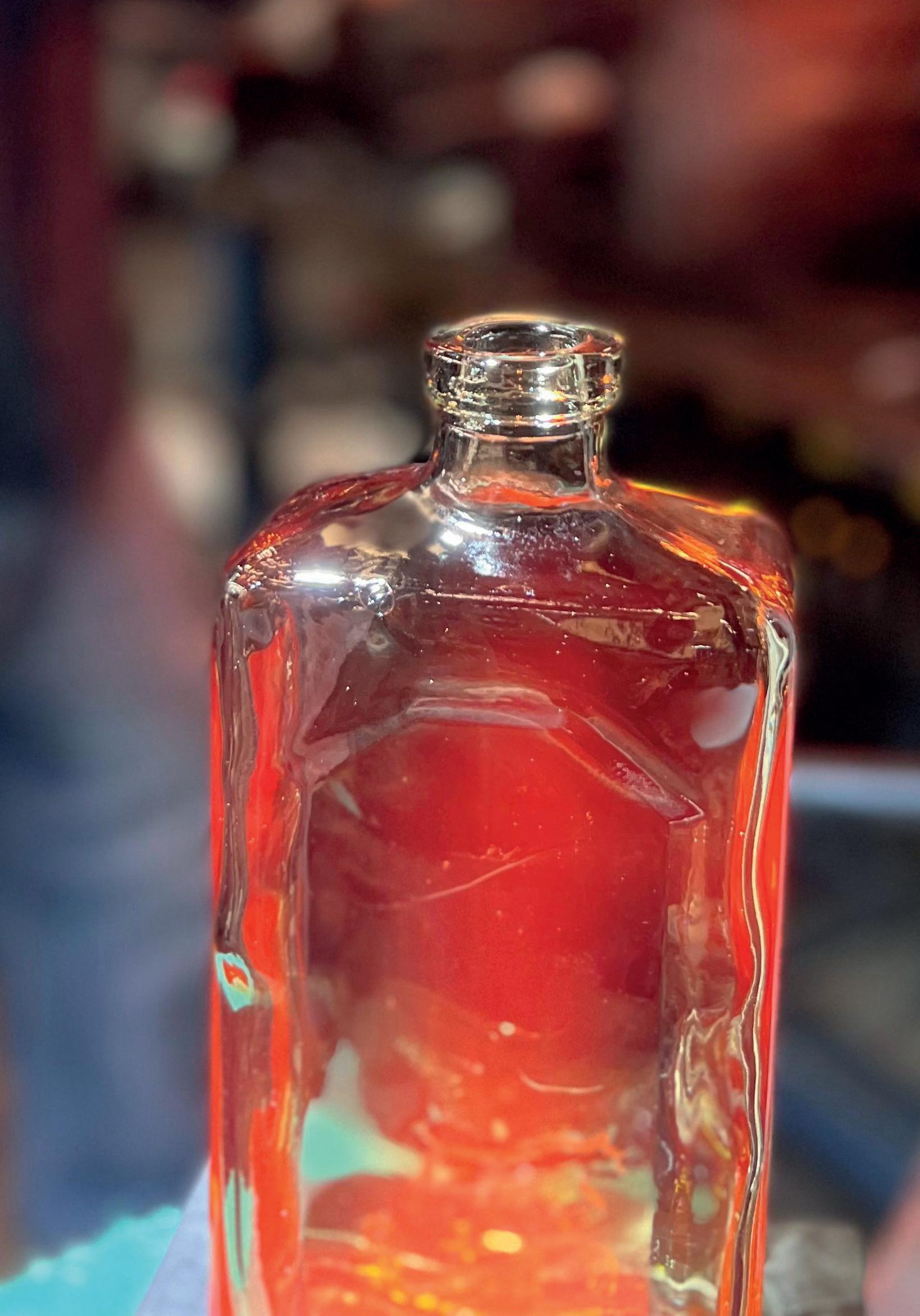
“In Mexico there is saying that once you are in glass industry you make a crystal widow – you get fully absorbed in the industry! For me I started in moulds and have worked in maintenance, furnace production etc to see the whole factory. Lastly I worked in the administrative part such as accounting and HR and then took the commercial side of the company. It has allowed me to get a wider view of the company and to see every element of how the factory is run.”
While Cesar has handed over the management reigns to his sons, he still retains a consultancy role and is open to any questions his sons might have about the business and glassmaking. He is proud of what his family has achieved so far.
“They are a family-owned company, are similar ages to us so we have a lot in common. It is a really human and easy-going relationship.”
GLASS SERVICE Are you looking to the future for CO2 reduction? Then look no further than FIC... Tying Technology Together The eventual solution is hybrid fur naces operating at up to 80% electricity BUT small steps increase electric boost to reduce the CO2 then superboost. GS and FIC are THE companies to supply CFD modelling of your flexible future fur naces. FIC ...the pathway to a cleaner future www.fic-uk.com +44 (0) 1736 366 962 The World,s Number One in Fur nace Technology FIC (UK) Limited Long Rock Industrial Estate, Penzance, Cornwall TR20 8HX, United Kingdom



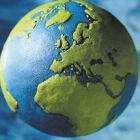
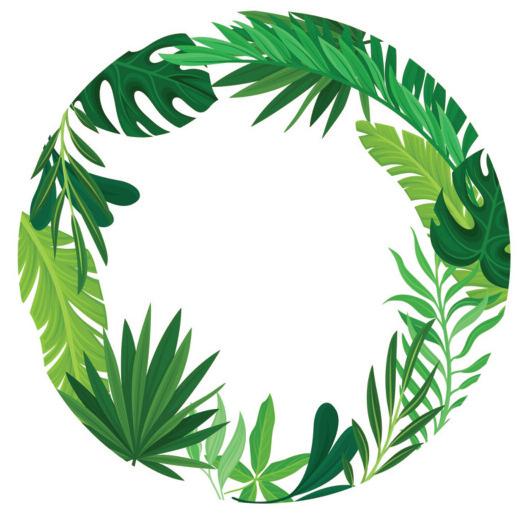
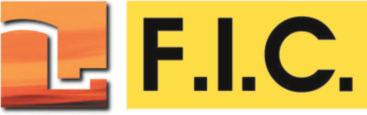
Embracing digital technology for glassmaking
“Getting the opportunity to lead Emhart, one of the technology leaders in the glass container industry, and being able to work with our great team was a fantastic opportunity.”Hehasretained the company’s focus on developing the end-to-end digital technology with which the company has become synonymous, as well as maintaining Emhart’s high levels of support to its glass customers around the world.
Emhart’s strategy is to take automation of the forming process to the next level. A prerequisite are machinesmodern Glass International September 2022
“It goes without saying that I was very excited and honoured to get this opportunity. I’d spent most of my career in the glass industry, and I started out at Emhart as a young engineer. I continue to be fascinated by glass production and the breadth of the technical disciplines and challenges it brings. On top of that, I love the spirit of the industry, and I really enjoy the collaborations with our customers. Put simply, hardly a day goes by when I don’t learn something new about glass manufacturing,” he states.
Personality profile: Emhart President www.glass-international.com 14
In his first major interview since being appointed President of Bucher Emhart Glass 18 months ago, Matthias Kümmerle explains how he intends to continue the company’s focus on digital technology. He believes not only does digital technology improve a glass plant’s production efficiency but it can also help with the climate challenge.
For Matthias Kummerle, the opportunity to lead the Swiss company was one that was too good to turn down. Prior to taking on the role of President, Matthias had worked in the glass industry for 15 years, the last 10 of which saw him leading Emhart’s Research & Development department. And during that time, he developed a passion for both glass manufacturing and the company.
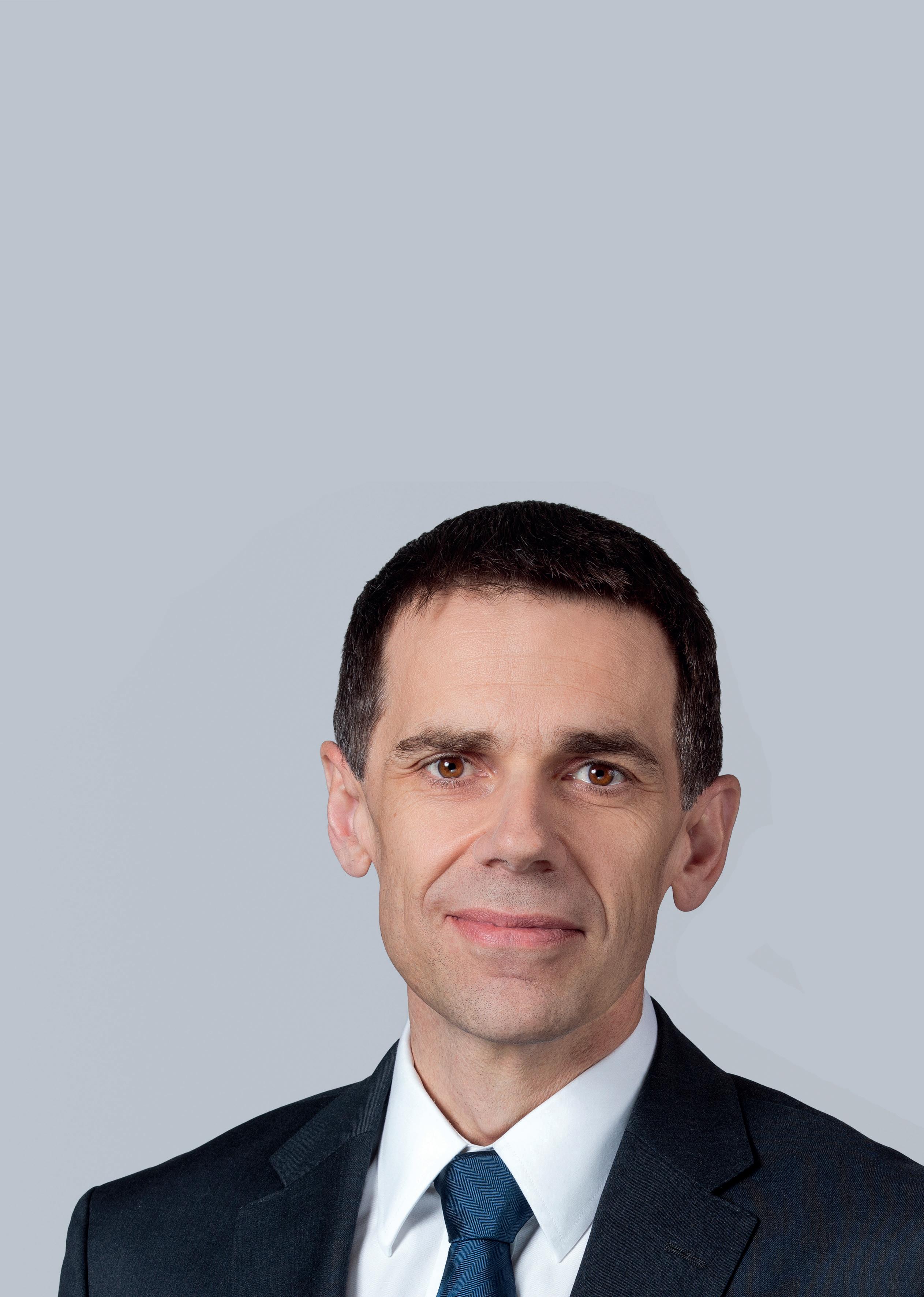
“For me,” he states, “the certain risk in such a situation is complacency. So, the issue here is to make sure that as an organisation we keep our feet on the ground, stay hungry, accelerate innovation, and try to improve every day so we can serve our customers in an even better way.”
Arguably the biggest challenge that Emhart and the industry as a whole are facing is that of energy and climate change and the fact that glass production has a large CO2 footprint. Companies such as Emhart and also furnace suppliers will be required to find even more ways of supporting the effort to reduce energy and CO2 emissions. The glass forming process has already contributed to the CO2 challenge by helping to improve pack to melt rates within plants and produce lightweight containers through modern forming machines and closed loop control.

Personality profile: Emhart President www.glass-international.com 15 Continued>> equipped with repeatable servo actuators and sensors that measure and acquire process data. This data is processed by advanced control algorithms and used to automate the forming process in the form of closed loops, automatic process control and robotic interventions. Emhart is investing substantial R&D efforts in all these areas.
One of the immediate focus areas is now on further reducing some of the complexity out of the advanced measurement and software systems.
“The energy and climate challenge is a topic that will not go away and it will put the glass industry, starting with Europe, and then everywhere else, under tremendous pressure. There isn’t much time left and the types of initiatives required will be complex so we must start to tackle the problem now. This will require collaboration, such as working closely with furnace suppliers and customers alike so we can find solutions together. Basically, there are no quick wins to be had. Instead, the challenge is to start developing technologies and work on initiatives now,” explains Matthias.
Leadership The move into leadership was not a leap into the unknown for Matthias. He had already been part of the Emhart Management team for 10 years and had previously led its Research & Development department. This meant Glass International September 2022
“Currently, we’re missing a simplification step that will enable people with regular skill levels to be able to work with these types of systems. In other words, things have become quite complex,” explains Matthias. “We need to further increase the reliability of these systems, and we must reduce the complexity at the user level. That is one of the challenges ahead of us and this is required now if want to ensure users get the full potential of this powerful technology,” he states. The second focus relates to customer support and securing even deeper collaborations with its partners to ensure even more successful projects. In tandem with its customers, Emhart is aiming to jointly identify and develop the best solutions for each specific case. With its own Research & Development centre in Connecticut, USA, it is able to jointly develop and optimise applications with customers. Matthias explains that with an increasing number of Emhart customers the relationships have evolved from collaborations into partnerships. “In every single case, we saw that such a situation became ‘win-win’ and created value for both sides. And this is our vision of how we want to offer our support to the market,” states Matthias. Challenges Matthias took on the role of President in January 2021 against the backdrop of the coronavirus pandemic and the various lockdowns being enforced in many countries around the globe. He admits the intervening months have proven to be something of a roller coaster ride and that more challenges lie ahead. Recalling his first days in the new role, he states:
“The main concern was how the market and business would develop. We had just started a new year and the order intake collapsed. Added to that, the market outlook was uncertain. We were looking at an L-shaped recession as being the most likely scenario at that time. Therefore, our immediate concern was whether there would be enough work for everyone or if we might have to consider restructuring,” he adds. This was the starting point for Matthias. However, pleasingly, the demand for equipment was proving to return much faster and stronger thanThisanticipated.meantthat Emhart very quickly found itself in the opposite situation and began to struggle to get enough capacity. Consequently, difficulties with the globally strained supply chains, logistics bottlenecks and massive inflation rates became the dominant Furthermore,topic.holding a solid market position and benefiting from a currently strong market environment, there’s the challenge presented by the possibility of complacency.
“It means we can follow the bottle for the entire process – by this I mean from the moment the bottle is cut to the moment it is read and inspected,” he clarifies.
“Glass producers that are going on this journey are changing how they operate and are becoming more data-driven and more analytical about their operations. They typically end up on an improvement trajectory that ultimately results in increased output,” explains Matthias.
Bucher Emhart Glass, Cham, Switzerland www.emhartglass.com/ he was familiar with Emhart’s organisation and processes, its technology, products, and services, and he’d already met many of Emhart’s customers, partners, and suppliers. And throughout his time at Emhart, he’s enjoyed working for the company. As he puts it: “I believe that if I didn’t enjoy it, I wouldn’t have been good at my job and I’d never have got the chance to take on this role. You have to like what you do if you’re going to do it well!”
“It means we need to entrust employees with a lot of responsibility and encourage them to move out of their comfort zones and accept that mistakes can happen. Actually, I’m convinced this has been the Emhart culture all along because this is how people grow. And we need to foster that because our people are the backbone of the company,” he adds. “And I believe my own style reflects that culture quite well.”
Personality profile: Emhart President www.glass-international.com 16 settings and sensor data, are linked with a unique identifier that allows them to be mapped.
Matthias cites Emhart’s former President, Martin Jetter, as being an influential figure in his career to date. It was Mr Jetter who originally appointed Matthias to lead Emhart’s R&D drive and he was the manager Matthias has worked the longest with. “He taught me the power of positive energy and the importance of believing in something and persevering with it. The power of partnerships and those resulting ‘win-win’ situations are a couple of examples of how working with Mr Jetter influenced me. Digital technology Emhart will unveil a large number of exciting new products and technologies at the forthcoming glasstec event in the areas of gob and container forming, end to end technology, cold end inspection and service offerings, aiming to address some of the aforementioned challenges.
Over the past two years, Emhart has developed applications and services that will enable the next level of process and control, process monitoring and provide full transparency over the forming and inspection process. Maybe most importantly, the availability of the data can assist a glass plant in its transformation process to become more data-driven and enable a data-driven culture.
Through the Advance Data Interface, Emhart can give customers access to the synchronised data, which can be fed into any plant management system or used for the customer’s own analysis.
The use of this data and digital technology also enables plants to become more efficient and gives them more control over the manufacturing process. Added to that, the concept of digital technology is a useful way by which young talent can be attracted to the industry.
Next steps Matthias believes there will be a modernisation wave in forming machines over the next 10 years that will see more flexible machines covering wider product ranges and machines that are better prepared for more robotic automation. The use of process control, sensors, and robotic interventions around the machines will also increase. Interconnectivity already exists between hot and cold end equipment but it will increase to include other areas such as furnace systems. Artificial Intelligence (AI) will also become more prominent in analysing the large data amounts, particularly in the area of glass inspection technology.
Matthias intends to continue the culture he’s already been nurturing internally at Emhart, which is one of a flat hierarchy with an open office space. He doesn’t have an office of his own and openly encourages colleagues to approach him directly if they need to talk to him. This is part of a company-wide effort to break down organisational silos and encourage cross-functional teamwork. Matthias doesn’t believe in managers simply telling people what to do. He wants people to take ownership of problems, come up with initiatives, and propose solutions.
“Inspection technology will be hard to recognise compared to what we have in place today. It will allow the automatic set-up and the reliable classification of defects based on AI, which is an area where we will see tremendous progress.
Emhart’s offering includes a focus on data collection and how the company now has the infrastructure in place to enable customers to collect synchronised data from the forming and inspection process to get full traceability. All includingparameters,productionmachine Glass International September 2022
“We are seeing algorithms based on AI that are far superior conventional inspection algorithms, and the results from the machine are now becoming more reliable than results determined by the “Inspectioneye. is an area where those technologies are already working well but we are just at the beginning. I’m pleased to say there is much more to come,” enthuses Matthias. �
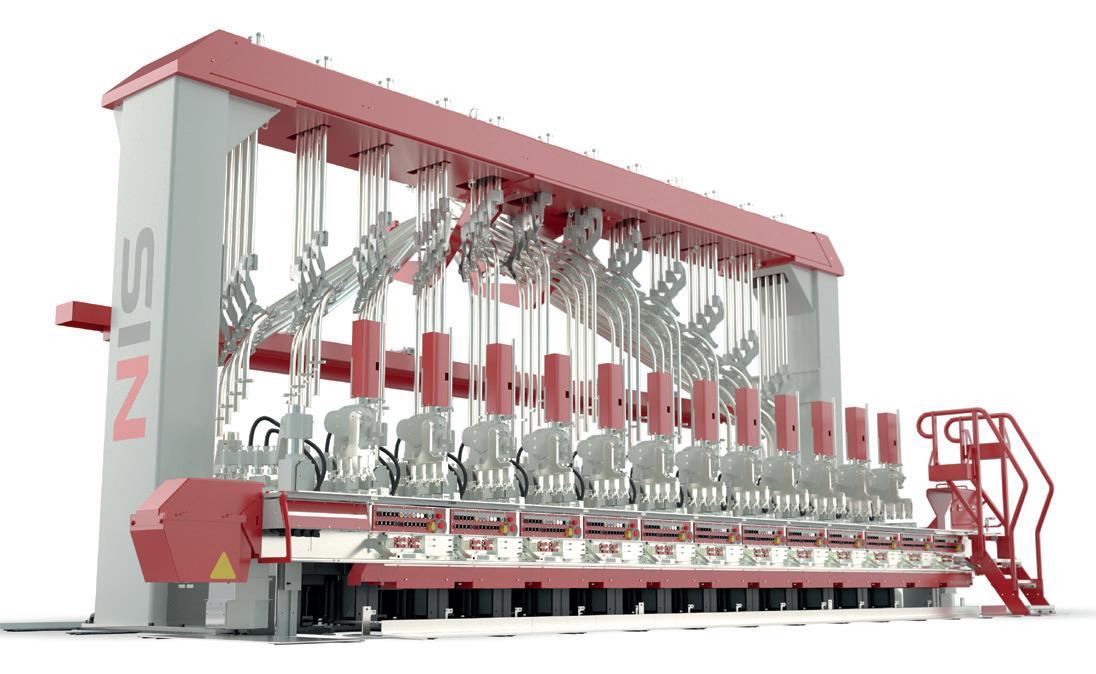
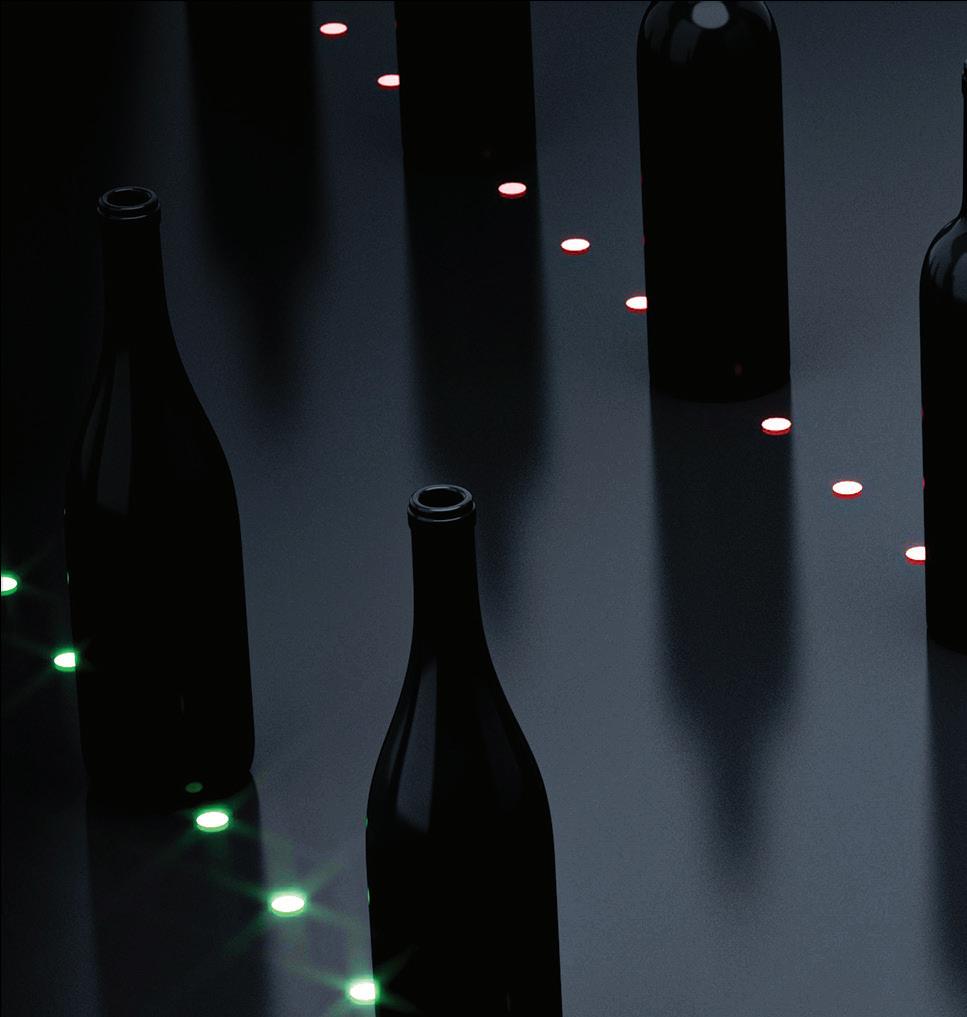
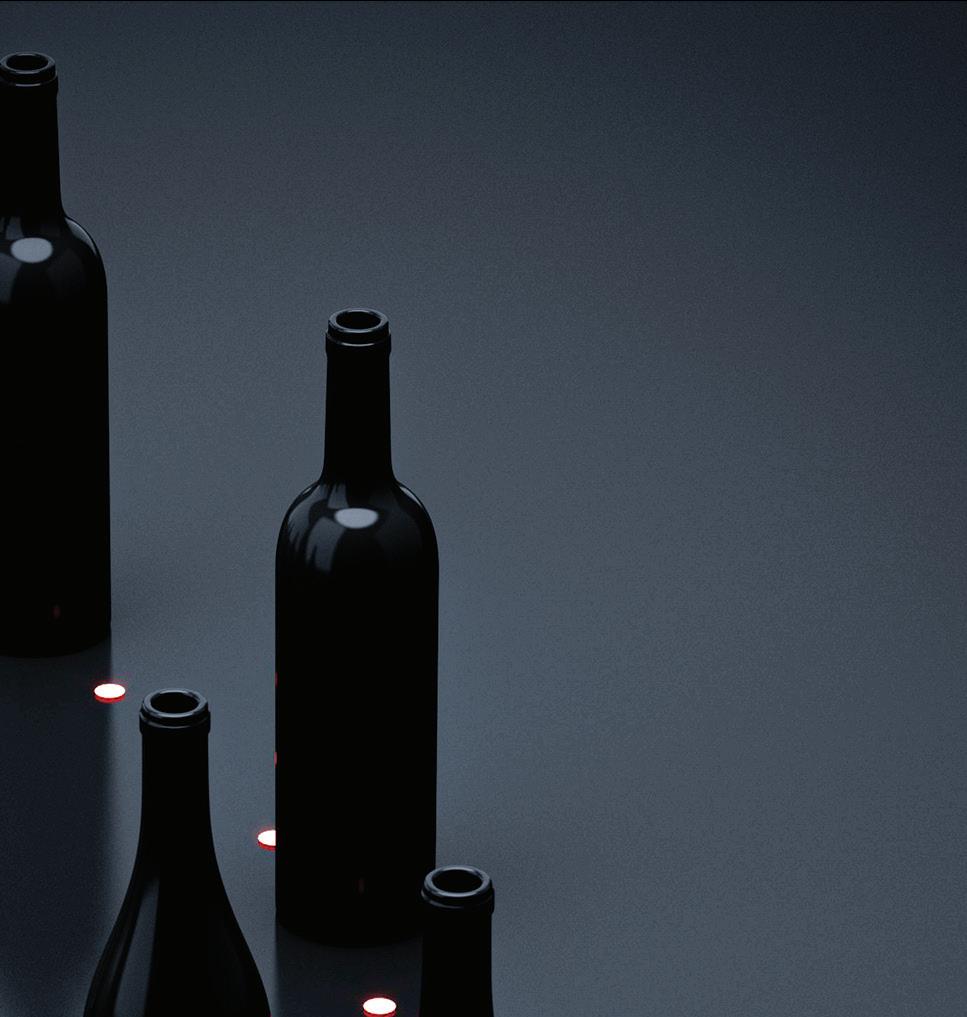



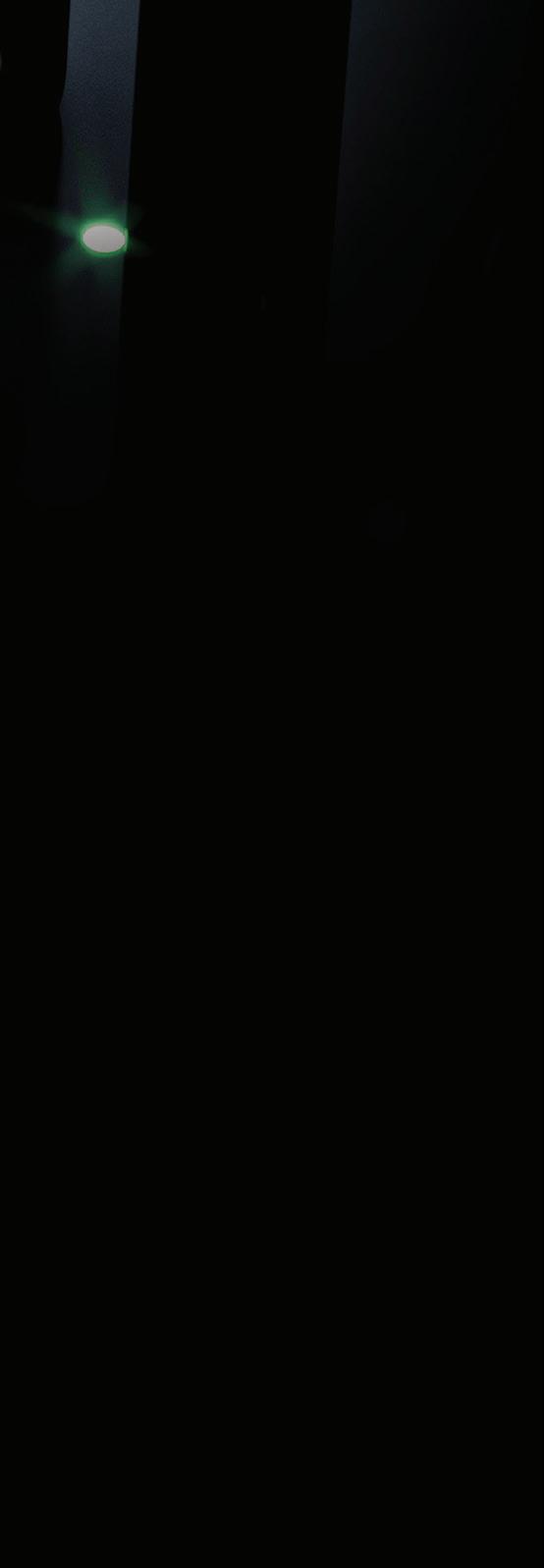
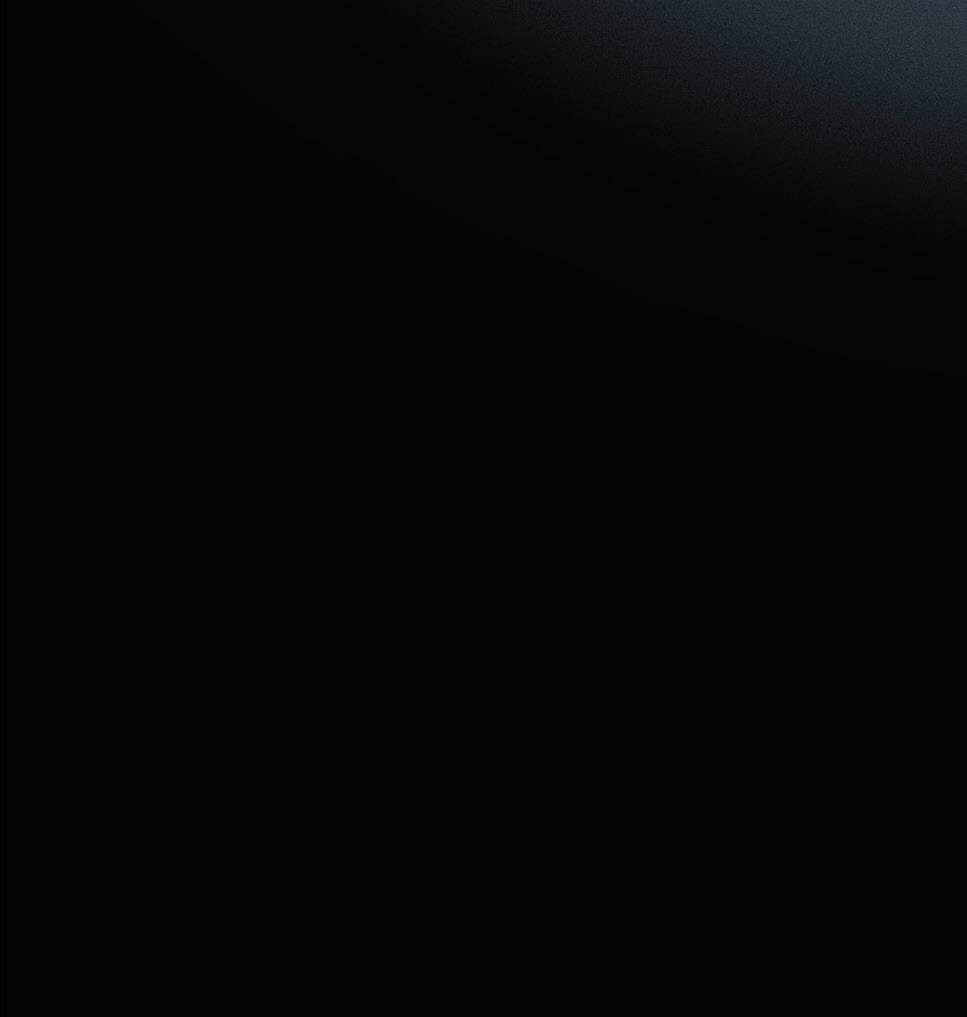
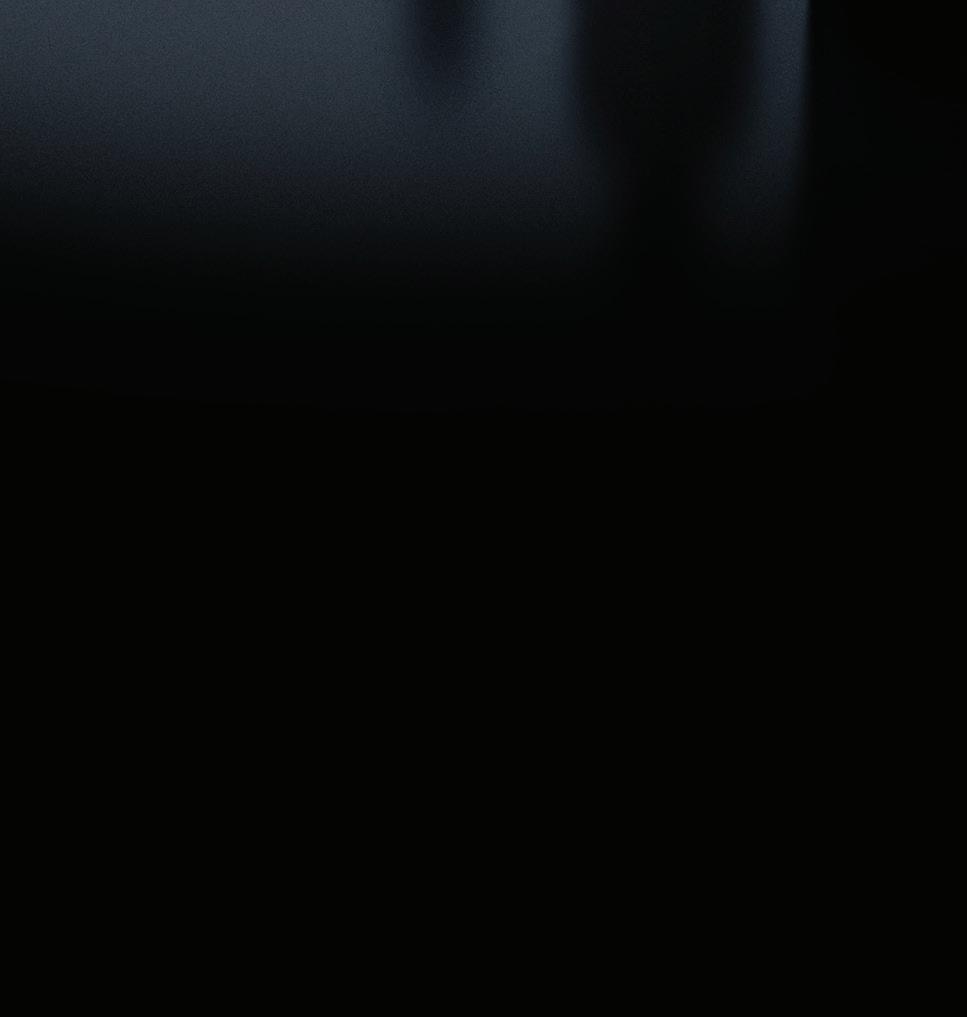
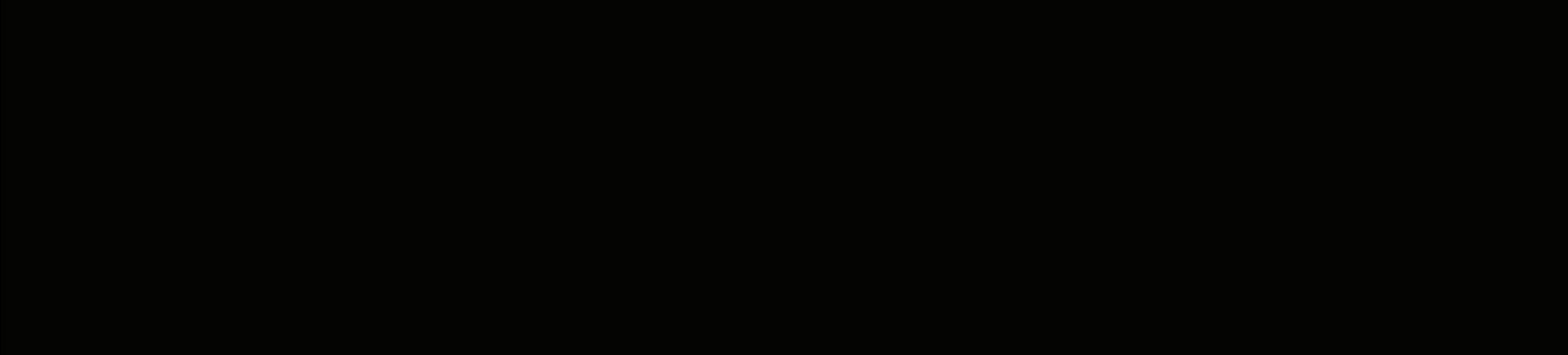

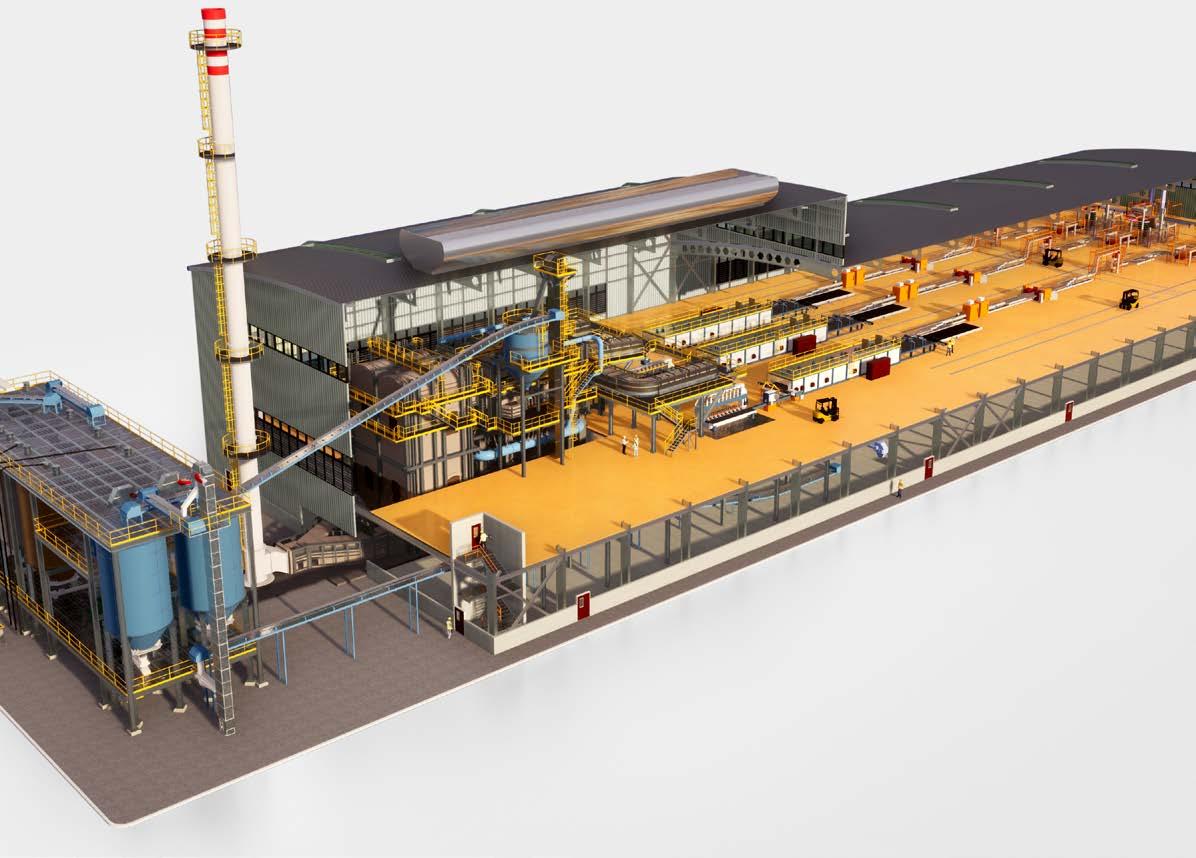
Logistical constraints, delayed vessel departures, port congestion, inland � Fig 1. World Soda Ash demand.
The US is the single biggest exporter in the world followed by Turkey in 2nd place. China and Bulgaria vie for 3rd place due to the fact that Chinese export volumes can swing significantly from year to year. Chinese exports can switch from over two million mt in a particular year to under one million mt in another year, as was the case last year.
MargueritemarketMorrin*discusses
The Covid-19 pandemic has been a major shock to the global system and defined by some as the most significant event in the 21st century. It has had often devastating consequences for our personal as well as professional lives. The soda ash industry has not been immune. Soda ash is a very basic chemical product with glass being the single biggest end use application, accounting for over half of total world demand. Other important sectors of demand include soaps and detergents, sodium silicates and metals and mining. When large sections of many economies were temporarily closed, in a bid to tame the spread of Covid-19 across the world, this had a substantial negative impact on demand.Despite some end use sectors faring better than others, overall demand fell by about 5.5%, year-on-year in 2020. This was followed by a strong recovery in 2021 to the extent that demand in 2021 exceeded pre-Covid levels. Our expectation for 2022 was that growth would continue. We were aware though that total world soda ash capacity was in decline with the total this year about 1.0 million mt less than the total in 2020. As such, we were anticipating tight market conditions this year. This has proved to be the case, but in fact, conditions to date have been even tighter than anticipated after yet another major world event occurred when Russia invaded Ukraine in February (Fig 1). Russia in itself is not a significant player in the global soda ash market accounting for just 4.3% of world demand and Ukraine even less significant at just 0.4% of the world total. The CIS (Commonwealth of Independent States) region is in fact quite self-contained. And while Russia is a major soda ash exporter, with exports averaging 720,000 mt per year in the past three years, these volumes are mostly destined for countries within the region. However, in today’s market when soda ash has been extremely tight, diminishing exports from Russia places extra pressure on markets like the India Subcontinent and Africa, which traditionally purchase regular spot volumes from Russia. We have very recently seen some renewed export activity from Russia, at fairly competitive prices, although to date the volumes have not been significant. However, while there has been some small impact from the Russia/Ukraine conflict on soda ash trade, the main influence of the war is on global energy prices and at times energy availability.
The Black Sea, is an important trade route for soda ash. Exports from Bulgaria via the Black Sea are at risk due to the Russia/Ukraine conflict, as well as imports from Turkey to Central Europe via the same route. To date there has been no known impact on trade via this trade route (Fig 2).
The trade patterns so far this year help explain the global market tightness.
A global overview of the soda ash
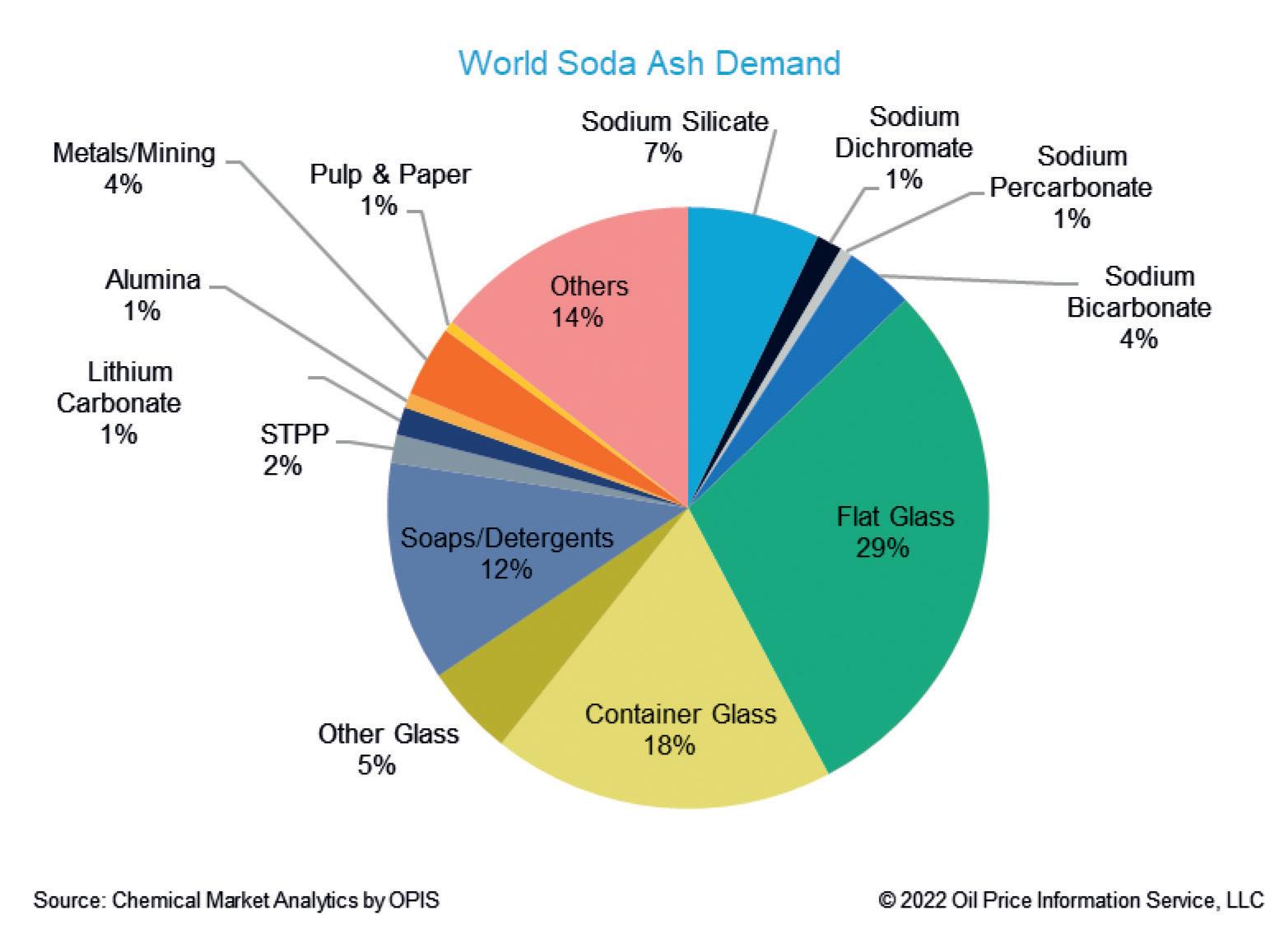
� Fig 2. World soda ash per capita demand. Trade In the soda ash industry a lot of product is shipped from where its produced to a different destination to be consumed, in fact about a quarter of production is moved to another region to be consumed.
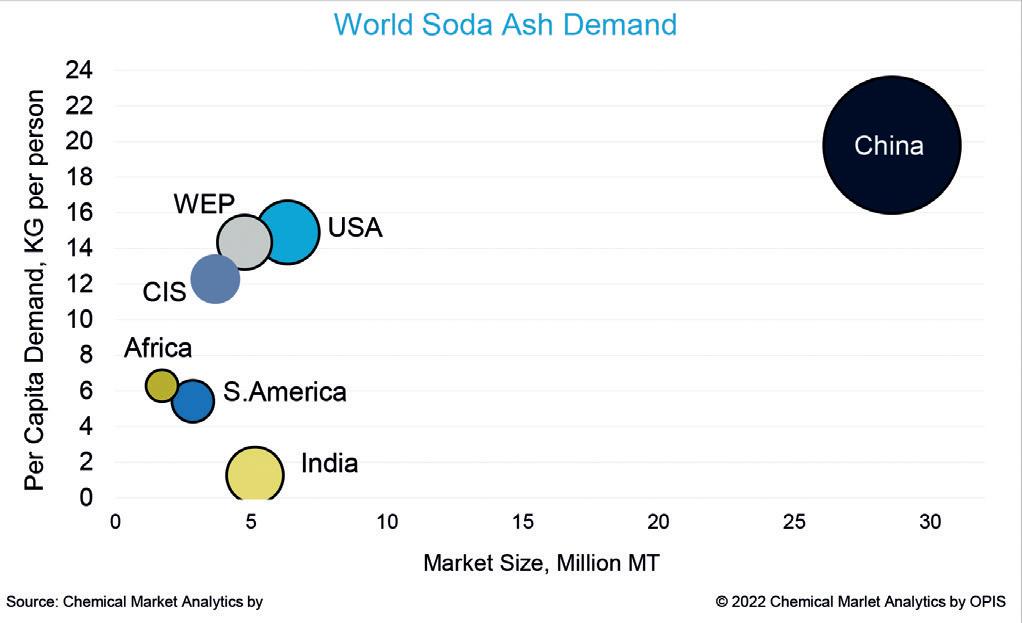
Soda ash update Glass International September 2022 www.glass-international.com 19 Continued>>
how recent global events have impacted the soda ash market.
As such trade developments are very important for the industry.
� Fig 5. Soda ash fuel sources
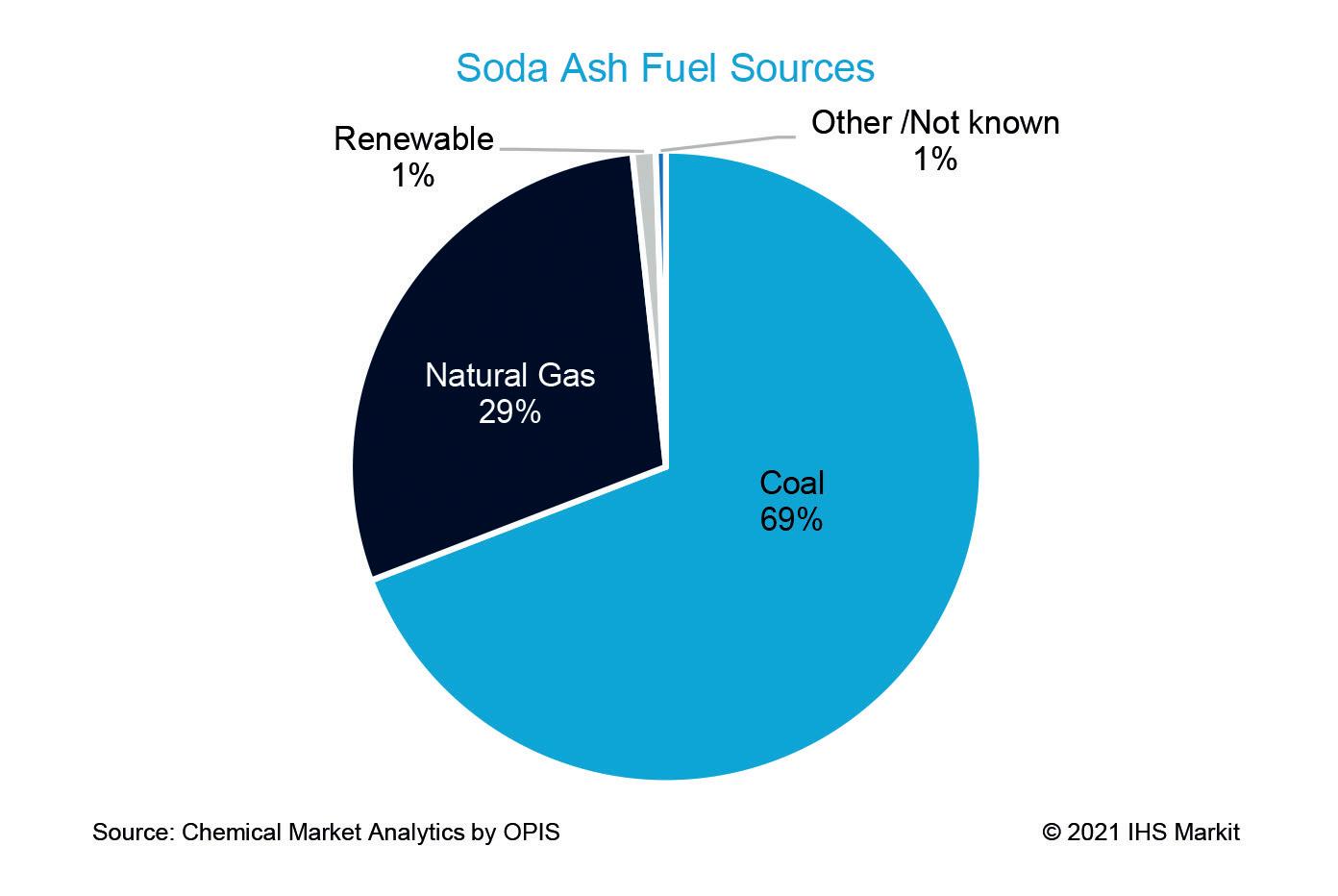
Soda ash production in West/Central Europe has been impacted indirectly by the conflict because of energy related issues which has at times forced producers to declare force majeure. The European Union has a ban in place on coal imports from Russia which became fully effective from the 2nd week in August. As a consequence a number of plants are expected to switch from anthracite to coke. In addition, the availability of coal/coke/anthracite, on top of likely continued high prices, will maintain pressure on the region. In addition to energy related operational issues the industry has also been plagued by plant problems. Two US producers have had to declare force majeure while there have also been plant issues in Argentina and Botswana. In addition, the largest soda ash plant in Iran had to temporarily shut recently following a fatal accident at the plant.
Prices Tracking China’s export prices provides a good barometer of the trend in global pricing. Chinese export prices fell considerably in 2020, in August 2020, in the midst of the COVID-19 pandemic, China’s export price average $161 per mt FOB. This weakness in China put pressure on other exporters to lower prices especially when annual 2021 contracts come up for renewal. This year we see very different market dynamics with record high prices being recorded globally. In June this year export prices from China averaged $417 per mt FOB, the highest export price on record (Figs 6 and 7).
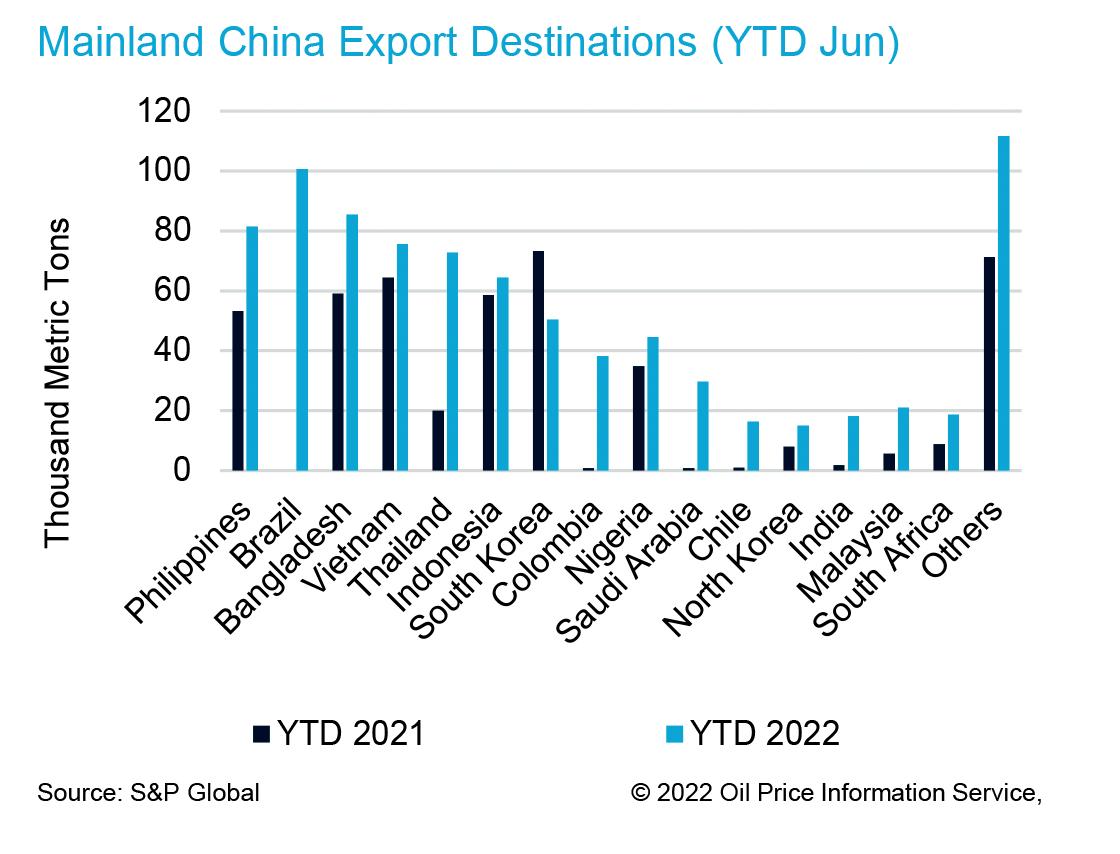
� Fig 3. Soda ash exports, YTD. � Fig 4. Mainland China export destinations, (YTD, June).
Soda ash update Glass International September 2022 0 Continued>> 20
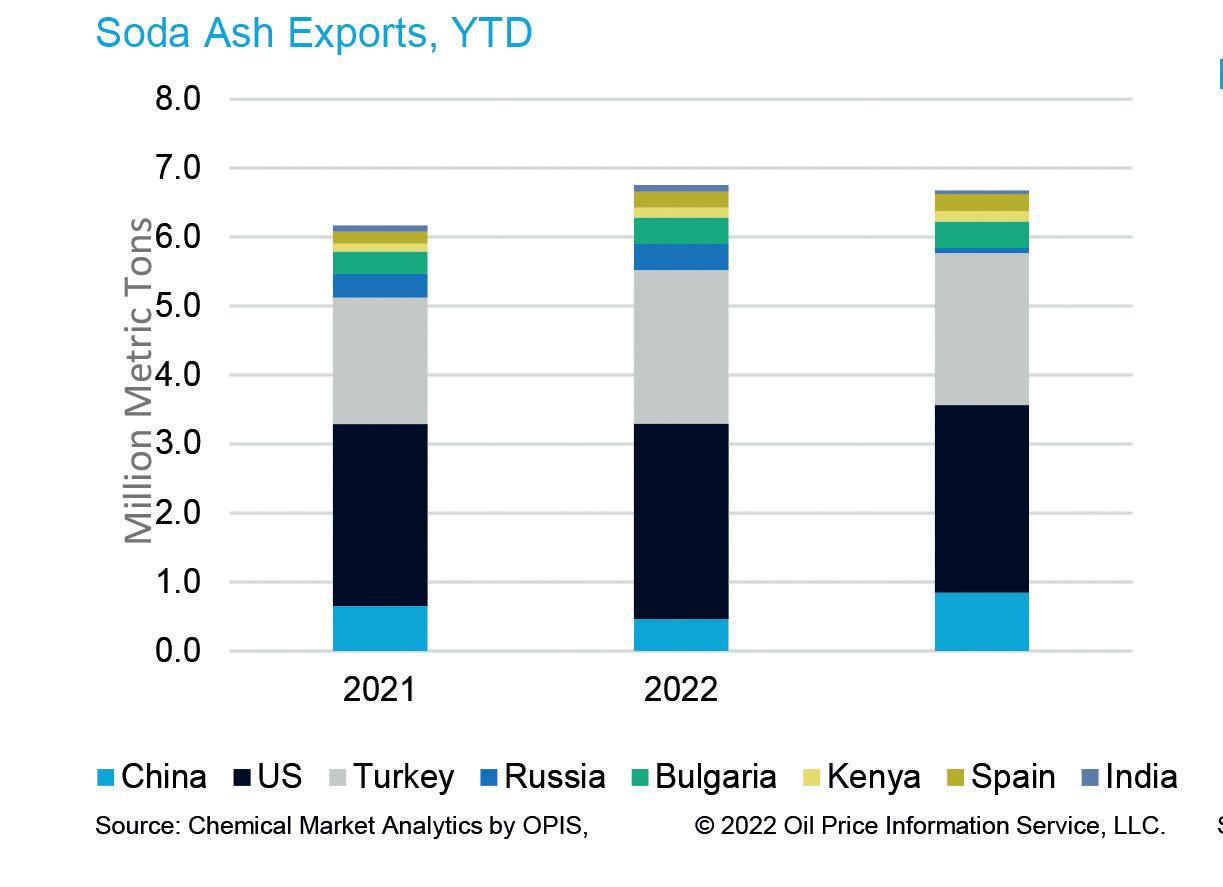
www.glass-international.com
China’s exports to the region to date have totalled 196,000 mt, while in JanuaryJune last year the total from China to South America was just 12,000 mt. In fact, in the first half of this year Brazil was the single biggest export destination for China. A lack of spot availability in South America has encouraged this shift in exports from China. Energy The Russia/Ukraine conflict is having a major impact on energy prices, especially in Europe. Energy availability can also be an issue. Soda ash plants typically use either coal or natural gas as energy sources with natural gas taking a bigger share than coal in West Europe (Fig 5). In addition, for the synthetic Solvay soda ash technology, either anthracite and/or coke are raw materials for the production process. Russia accounts for about 40% of West/ Central Europe’s natural gas supply. In addition, Russia is responsible for about 81% of global anthracite exports, 13% of global coke exports and about 16% of global seaborne thermal coal exports.
We are though recently seeing some weakness in China, both in the domestic market and also export prices. Freight rates have also softened which supports lower spot prices on CFR basis. It’s too early to understand if this recent softness in China is a temporary correction, or more of a structural change, and as such to understand the impact that this may have on other regions. At the some time though, producers in many parts of the world are dealing with historically high cash costs with little prospect that these costs will ease any time soon which will also underpin pricing going forward.
trucking issues and also various soda ash operational issues have slowed the growth in trade. To date exports from key sources are up by just 4% or 257,000 mt, year-onyear, which is mainly due to increased availability from China (Fig 3). Exports from the US, to date are down by 4% or 113,000 mt, year-on-year, and exports from Turkey are down by 1%, year-onyear. Another interesting observation in terms of trade is that for China the biggest increase in exports has been to South America, which is not a traditional destination for Chinese product (Fig 4).
™ THE FUTURE OF CONVEYOR CHAIN www.pennine.org sales@pennine.org +44 (0) 1484 864733
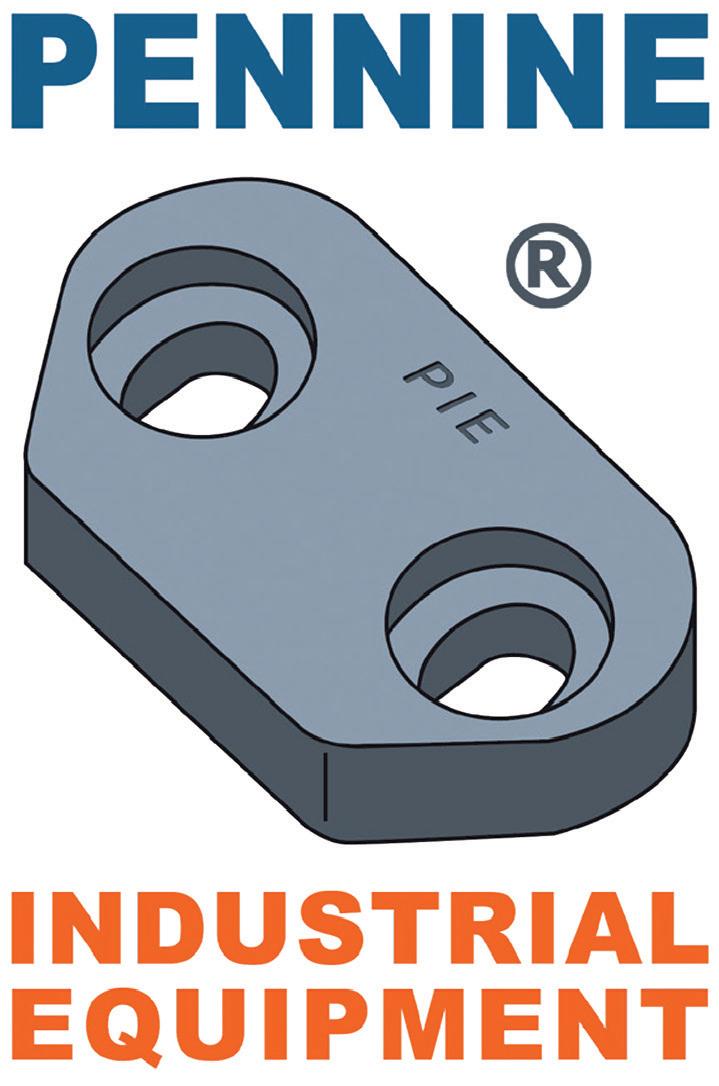
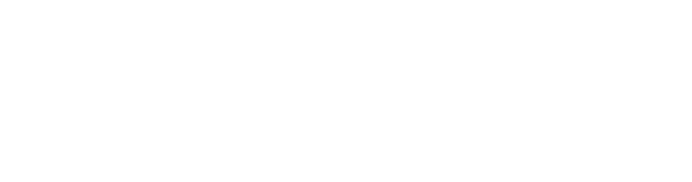


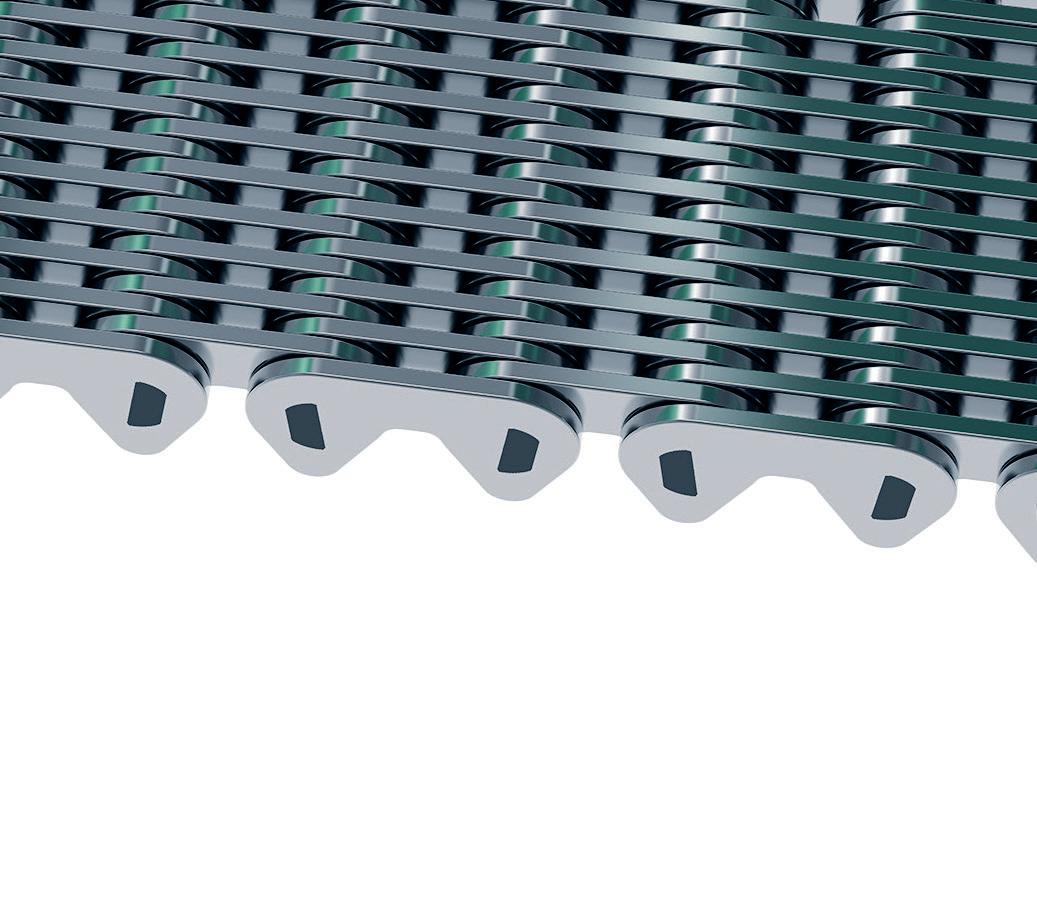
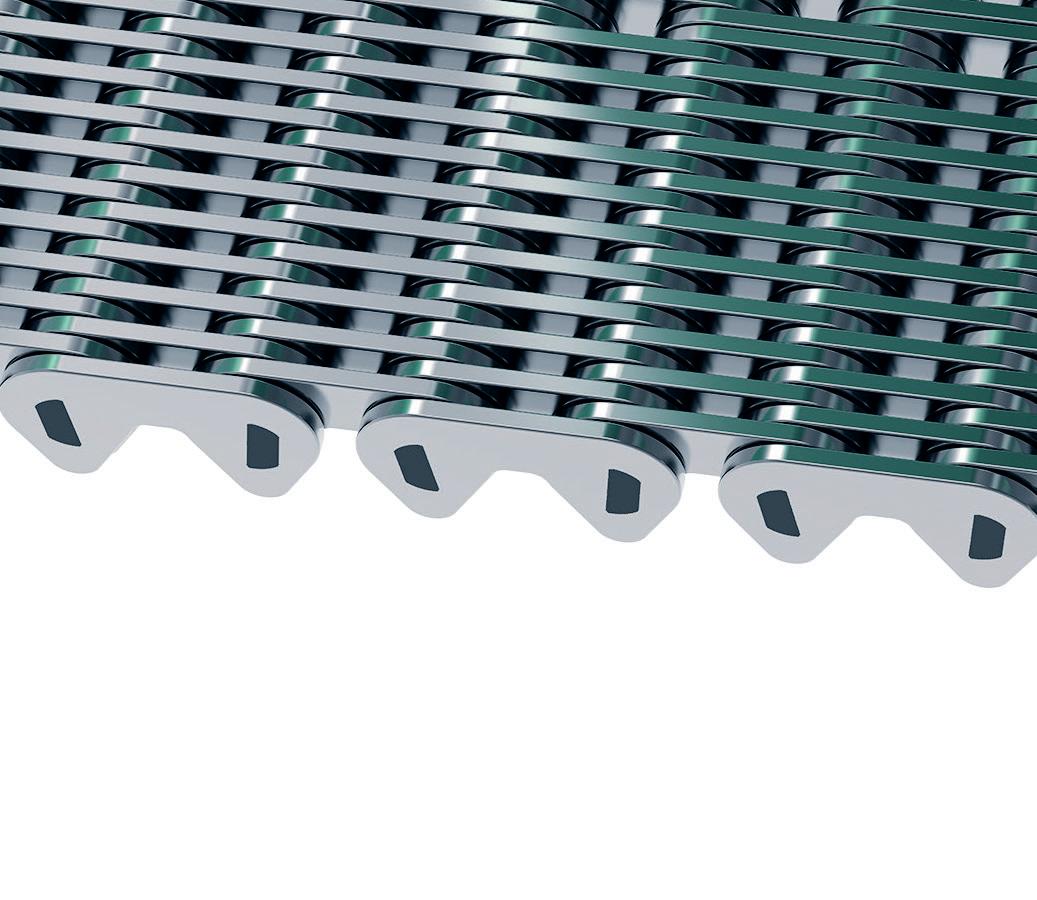

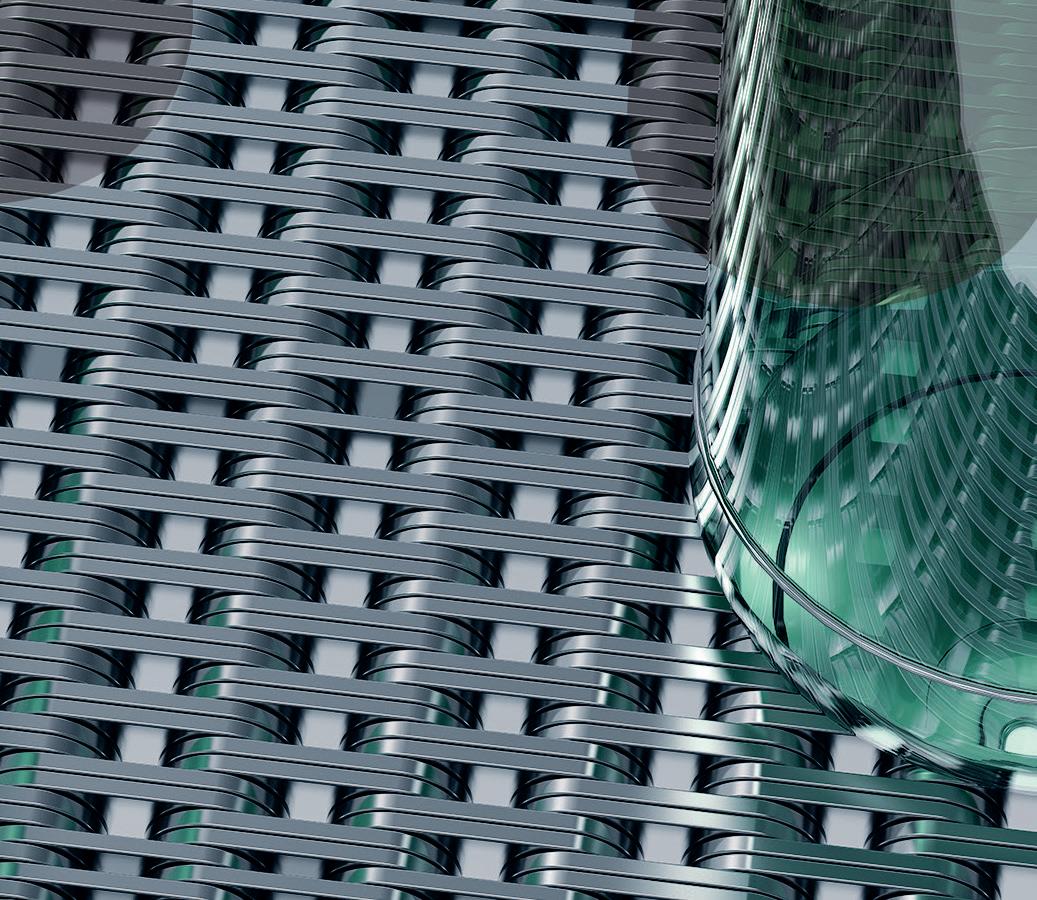
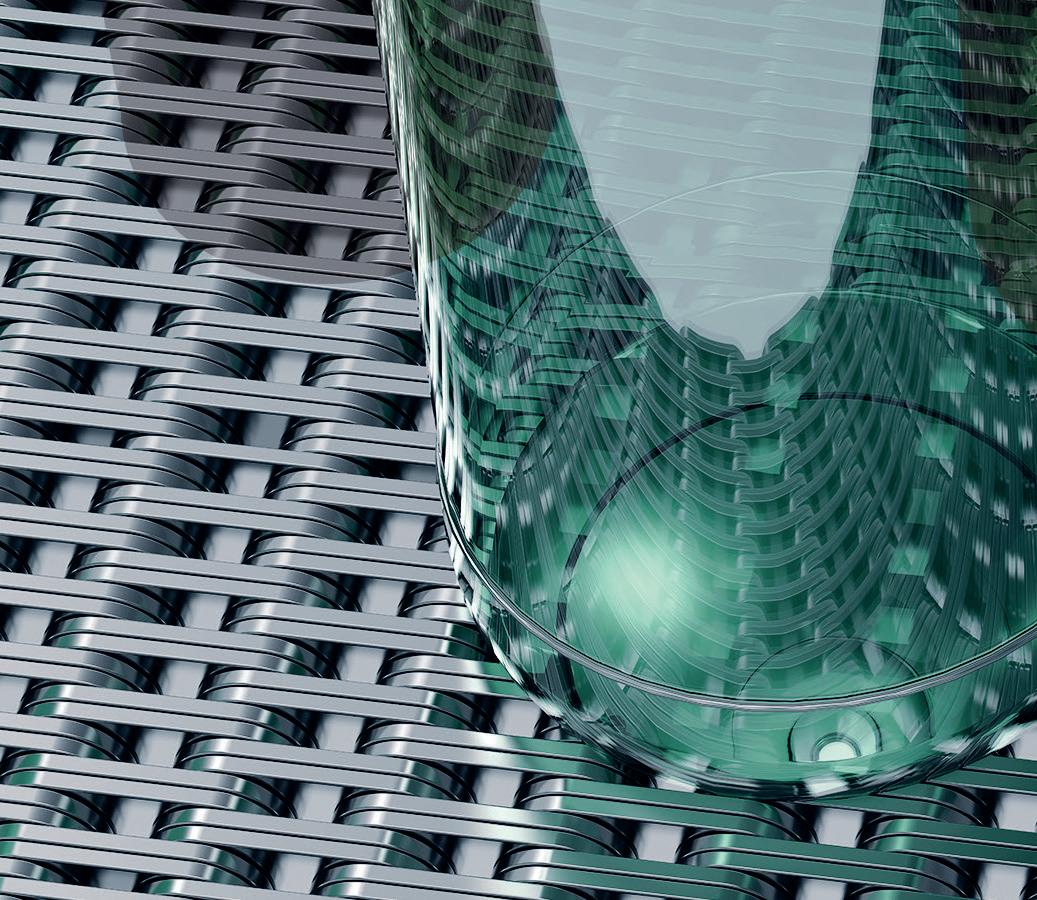
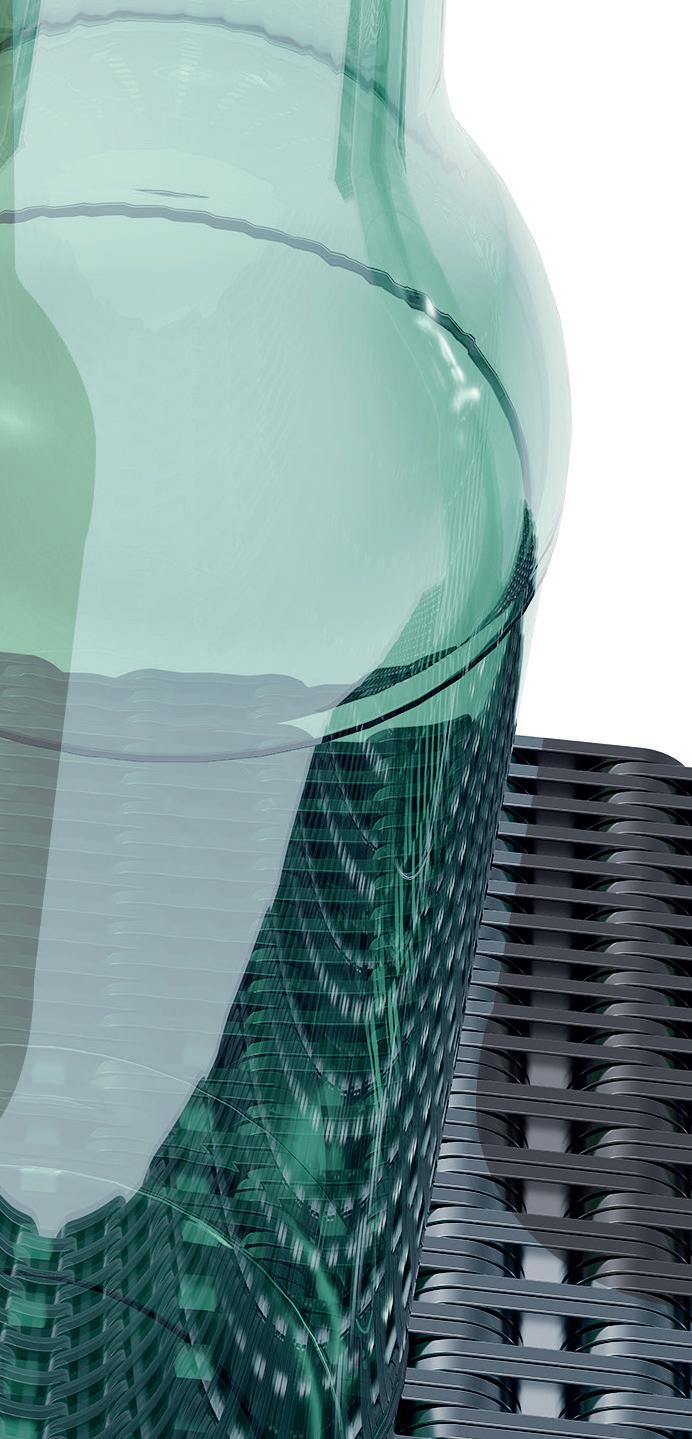
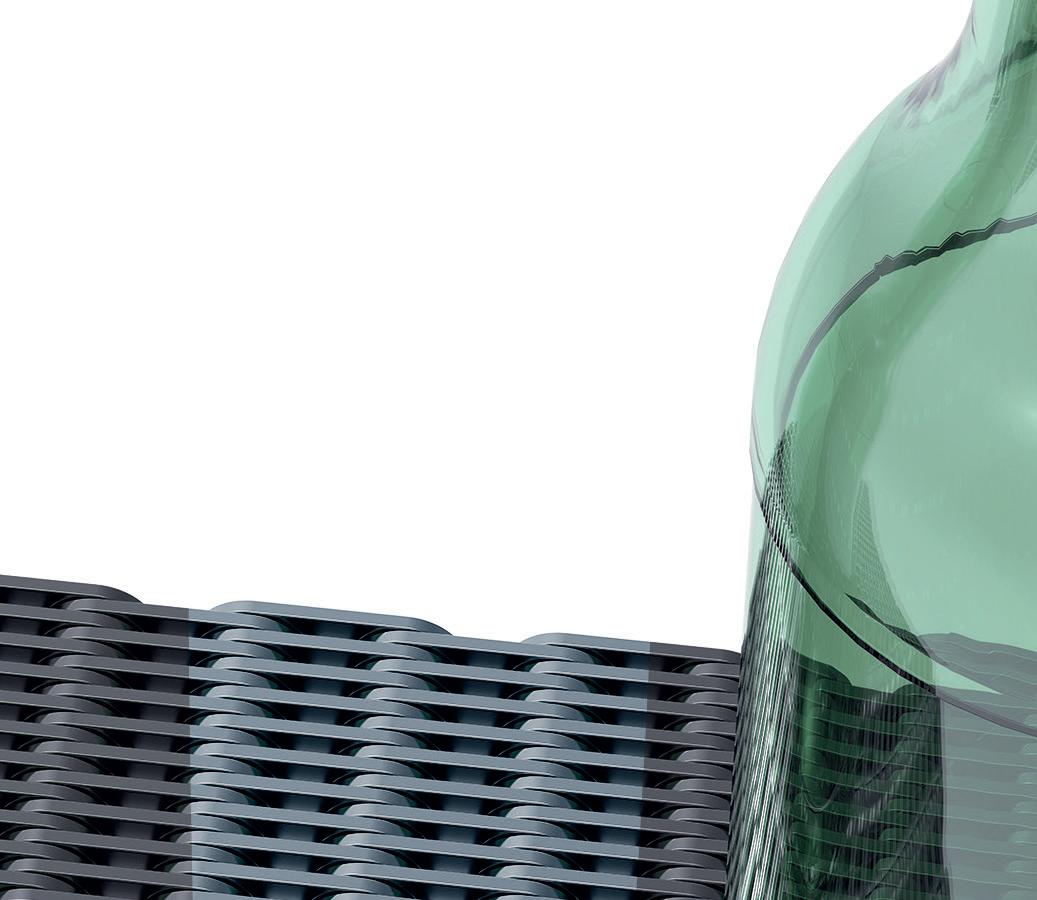
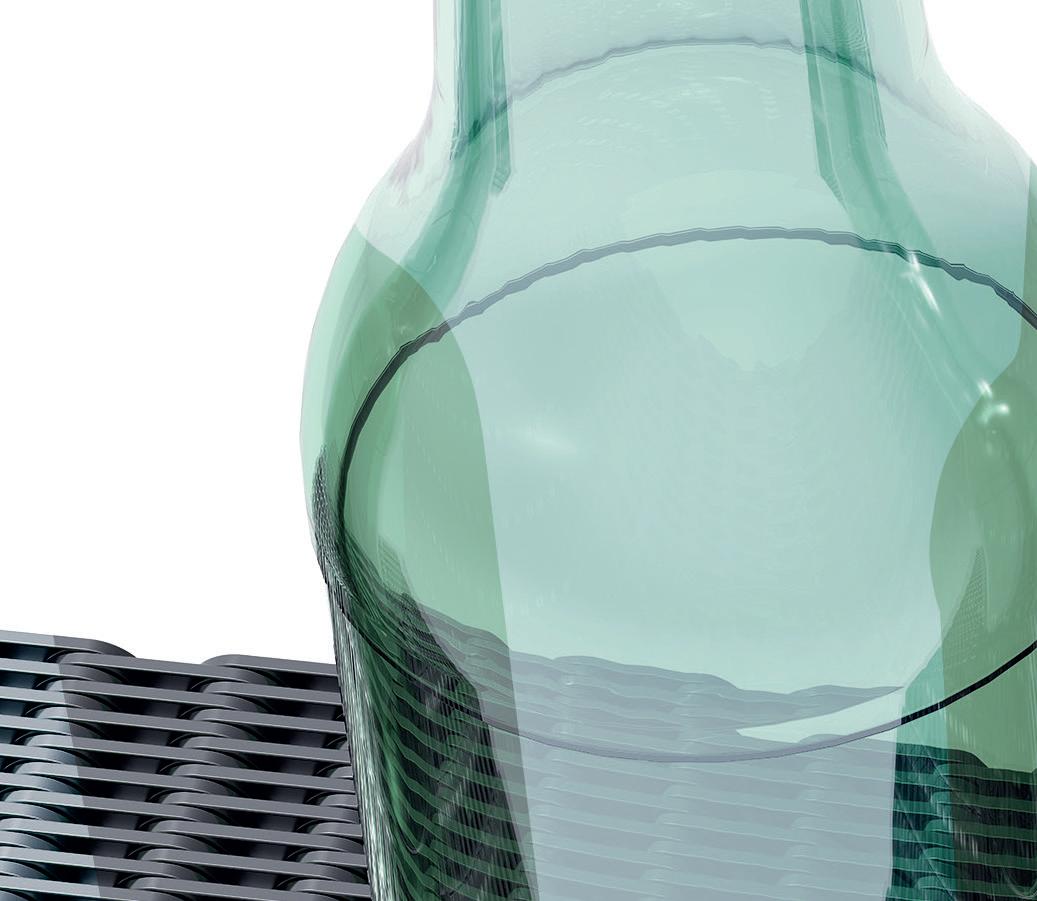
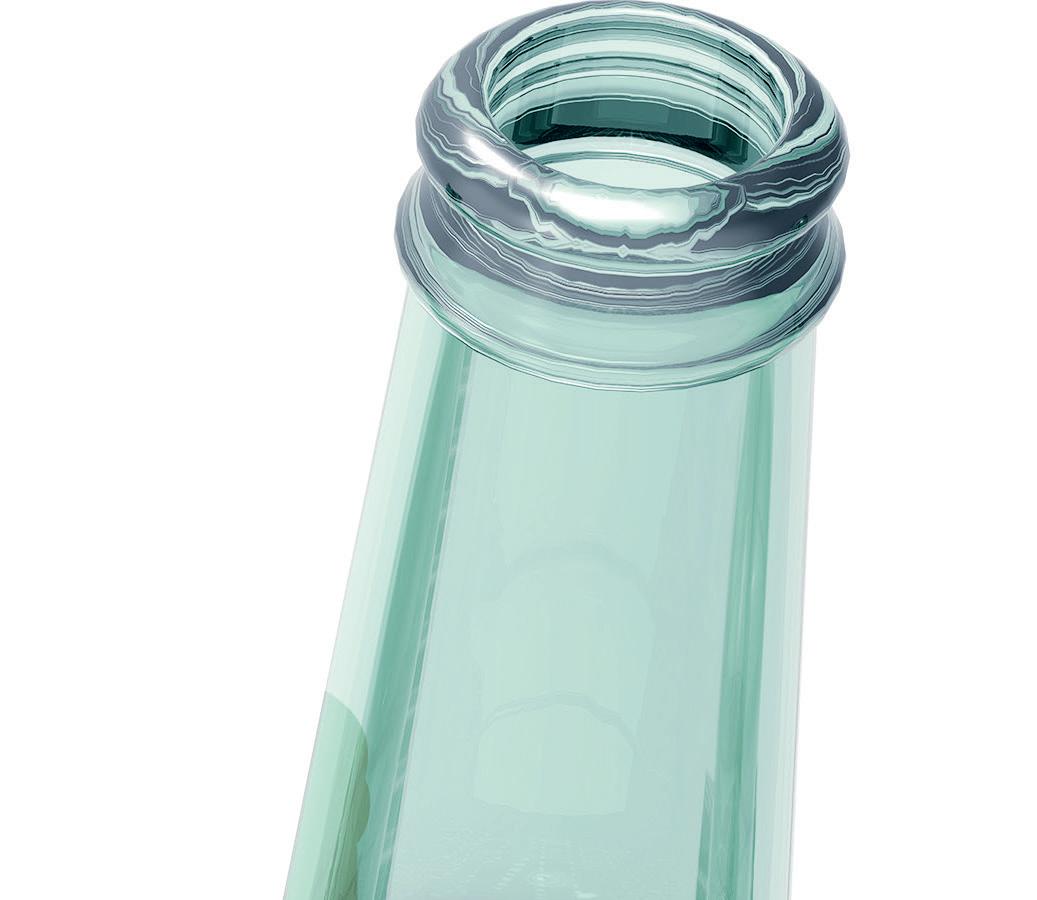
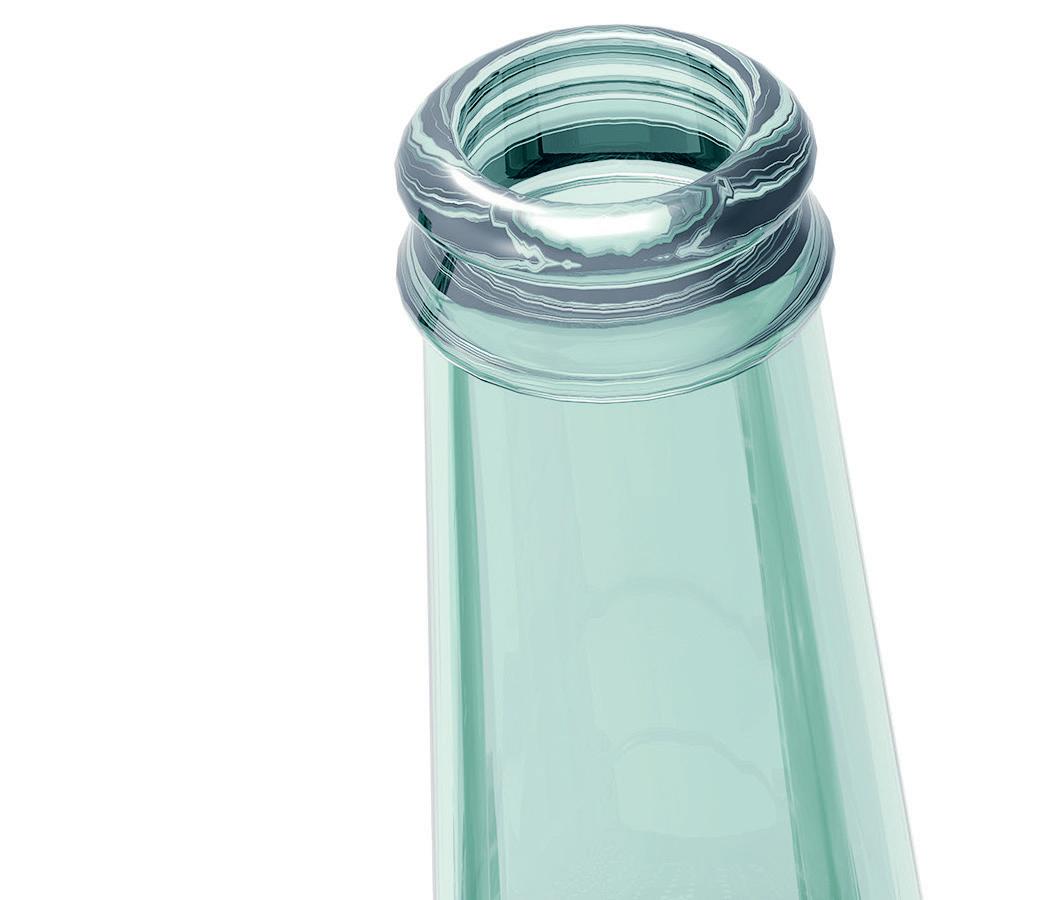
In April 2020, the US producer Genesis Alkali idled its trona based plant, located in Granger Wyoming. Meanwhile, the expansions announced in late 2019 were pushed back. These included an expansion by Solvay scheduled for the end of 2021, Genesis Alkali, planned for Q2 2022 and Ciner (now Sisecam Wyoming) planned for 2023. These expansions were also due to be followed in 2025 by the opening of two large greenfield projects in the US by Ciner/Sisecam (now majority owned by Sisecam). Genesis is now the first US producer set to bring on stream additional capacity, which is scheduled for early/mid next year and includes the restart of its idled capacity in Granger as well as the addition of new capacity. All other projects have been delayed to the 2024/2025 time period, or even later. Soda ash capacity in China has been in decline since 2021. None-the-less, there are ambitious expansion plans for China. However, these plans are dominated by one single project, a huge natural soda ash plant in Inner Mongolia. Phase I of the Inner Mongolia project is set to have an annual capacity of around 5.0 million mt. This was to come on stream by mid this year but was delayed until July 2023. However, the exact scope of phase I of the project, including its timing and initial size are being widely debated, even locally in China. Meanwhile, outside of the US and China, there are also projects underway in a few other regions, albeit on a smaller scale, including in Saudi Arabia, Turkey and India.
In recent decades China has dominated capacity expansions and since 2000 has built around 22 million mt of new capacity, which was primarily to meet its own rapidly growing domestic demand. However, the pace of expansions in China has slowed recently. This slowdown in expansions in China has been accompanied by renewed interest to build capacity in other parts of the world. In the second half of 2019, a number of capacity expansions were announced, as soda ash demand in the medium term was expected to steadily increase. This time much of that extra capacity was planned for the US and scheduled over the 2021-2022 time period, with further expansions due to come on stream in 2025. However, since then the soda ash market saw a major impact from Covid-19 with a drop in both demand and prices. In response, soda ash producers were also forced to rethink their future plans.
Soda ash update Glass International September 2022 220 www.glass-international.com
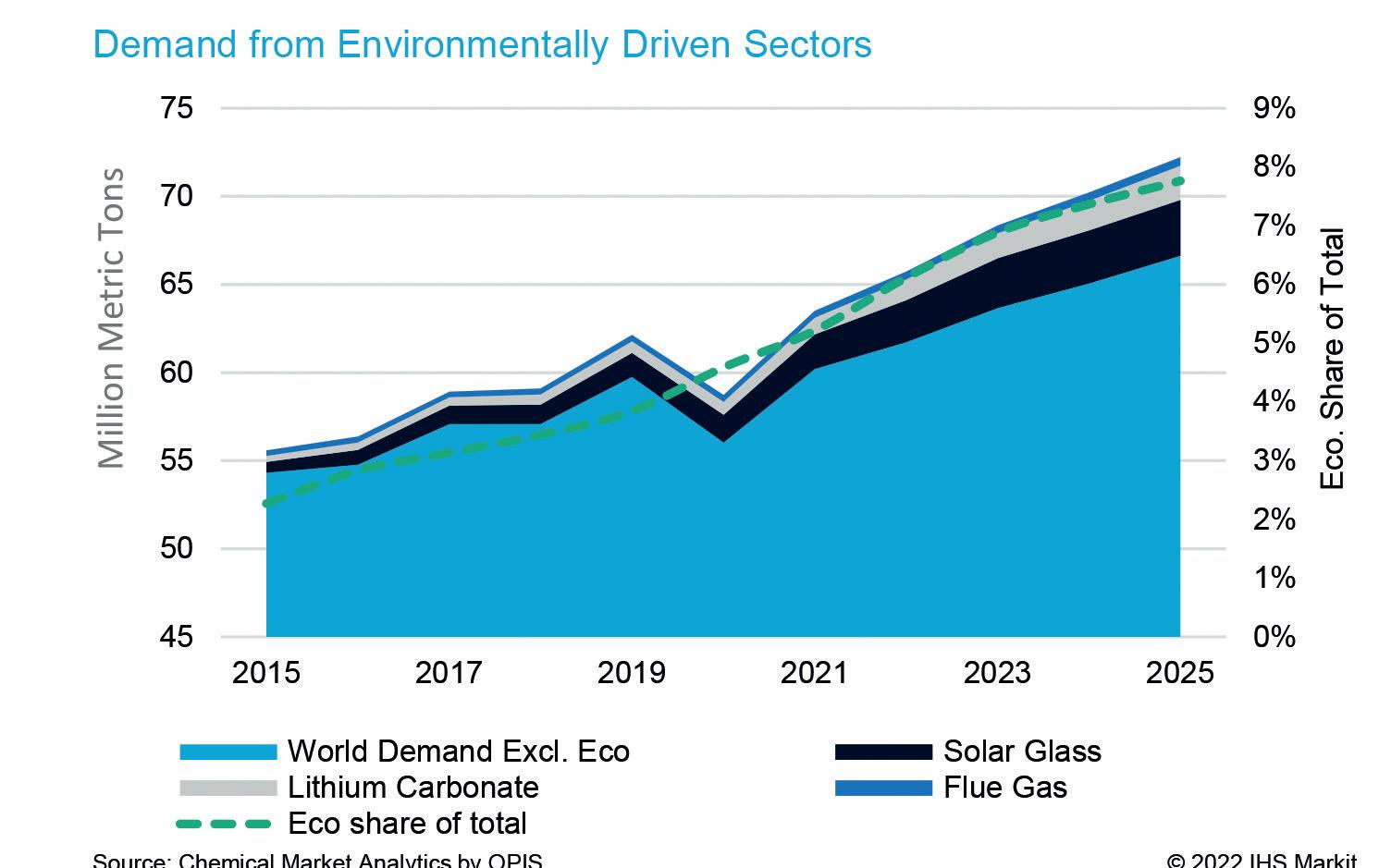
� Fig 6. Soda ash export price comparison. � Fig .7 Chinese weekly soda ash prices (including VAT).

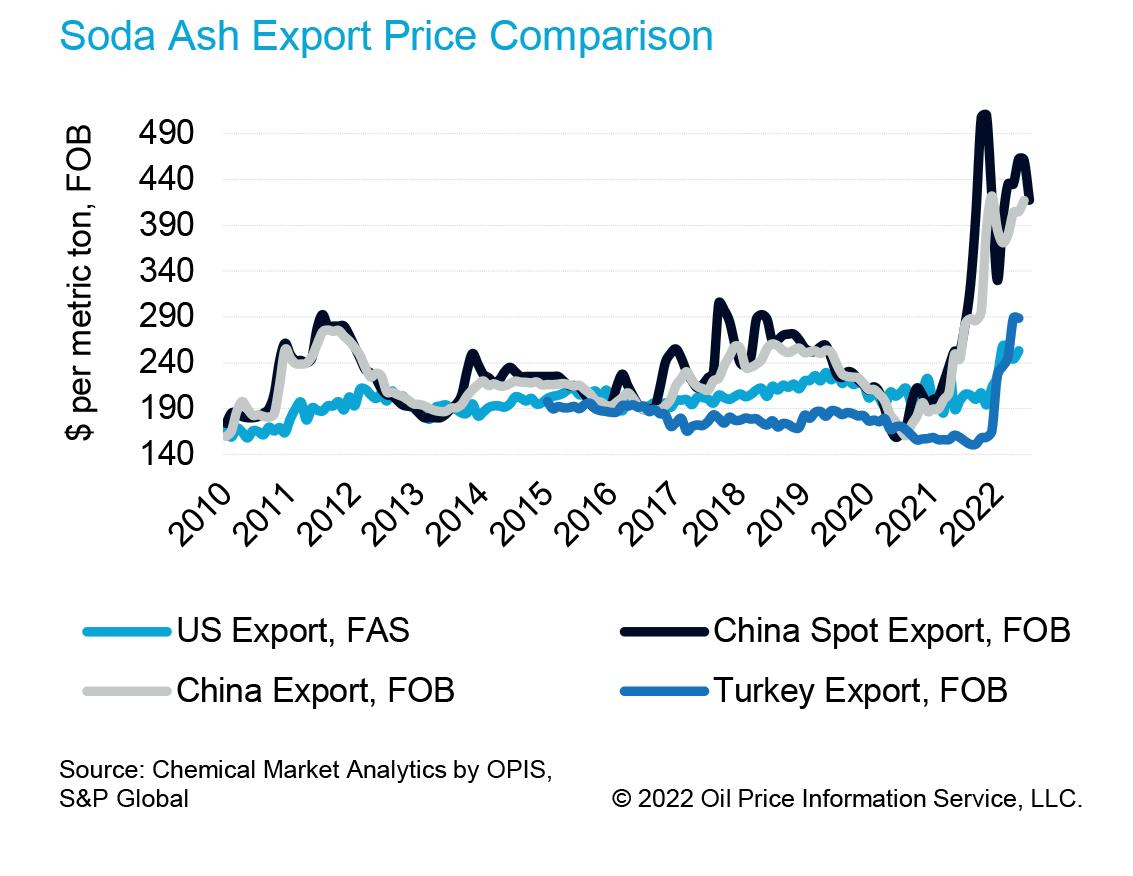
A prolonged Russia/Ukraine conflict is likely to lower soda ash demand growth over the medium term, as a result of a slowdown in global economic growth and demand destruction in the conflict region. However, with the exception of the CIS region, any significant demand erosion has not been noticed yet. Glass plants around the world, including in West/Central Europe appear to be
� Fig 8. Chinese soda ash demand indicators, YTD May.
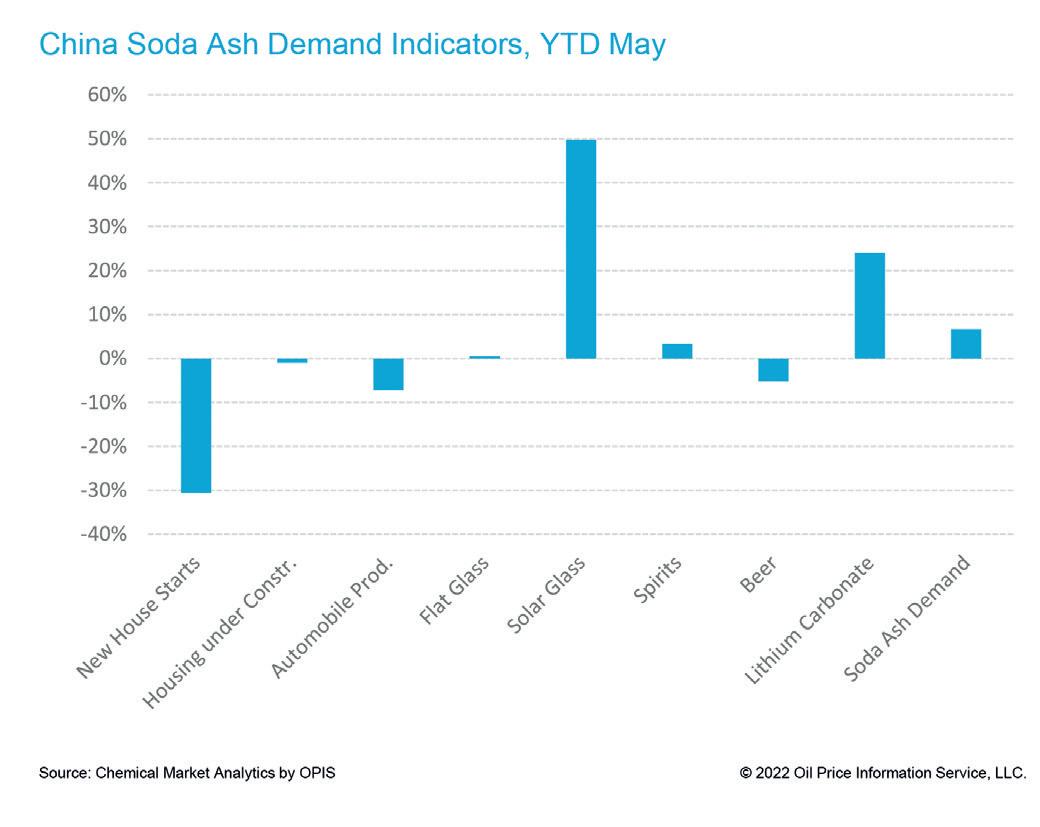
Demand drivers
� Fig 9. Demand from environmentally driven sectors.
Capacity plans
*Executive Director, Global Soda Ash Services, Chemical Market Analytics by OPIS, London, UK Marguerite.morrin@chemicalmarketanalytics.com
Summary Soda ash demand recovered well as Covid-19 restrictions eased with demand to date being strong across most key regions. However, the situation in China, the biggest soda ash market in the world is mixed.
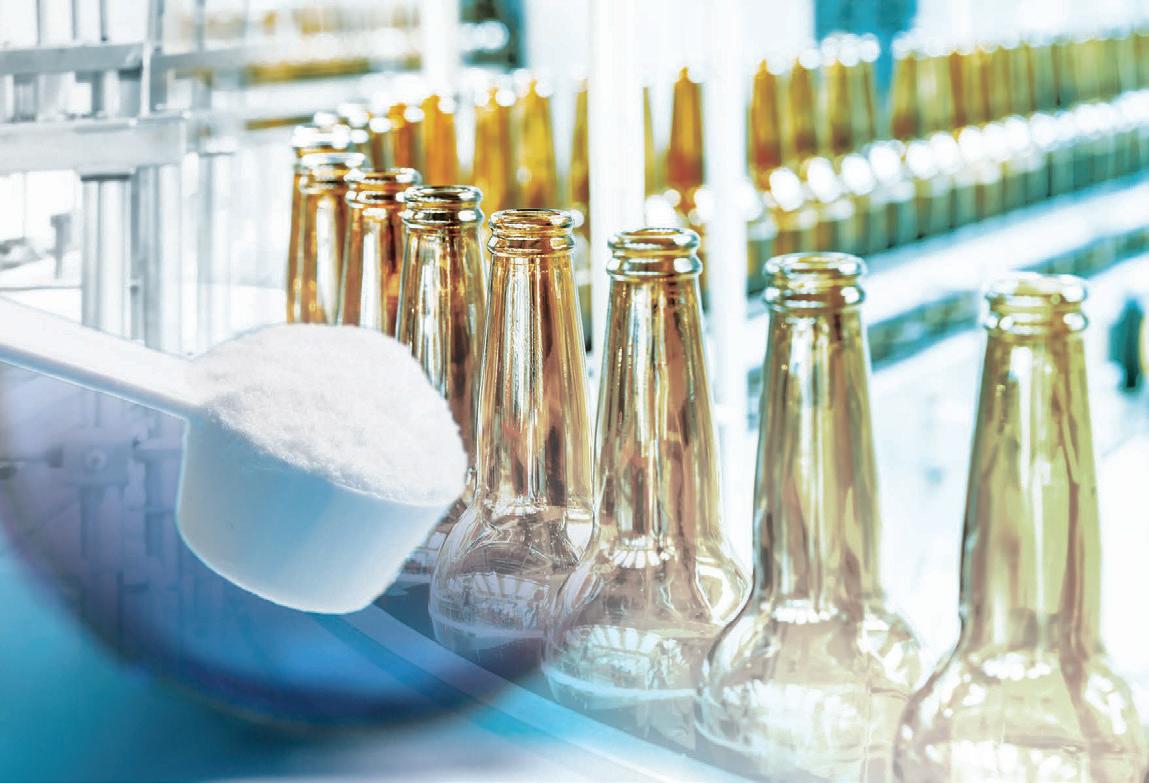
In addition, while demand in general in the rest of the world has been strong, some companies expect a challenging environment in the second half of the year and into 2023, due to inflation and macroeconomic uncertainty From the supply side there is also uncertainty. Supply issues have been problematic to date with the potential for further disruptions, especially in Europe due to its reliance on Russian coal and natural gas. In terms of prices, we have seen record high soda ash prices across the world and acute shortages, in some cases undermining demand.Recently though there has been some softness in prices in China which could spill into other markets. Cash costs though in most parts of the world remain extremely high with no ease in sight. As such, the outlook is mixed with clearly some clouds on the horizon. To get further insight into the outlook for soda ash please join us at our forthcoming conference. Chemical Market Analytics by OPIS, a Dow Jones Company (formerly IHS Markit), is hosting its annual World Soda Ash Conference October 1113. The conference will be held in person in Sorrento, Italy, and include speeches from the industry’s leading companies, as well as experts from Chemical Market Analytics. �
SU PPLY CHAI N CONFID ENCE 5 LOCATIONS ACROSS UK AND IRELAND • Soda Ash • Sodium Sulphate • • Feldspars • Chrome • Barium Sulphate • Sodium Nitrate SPECIALISTS IN THE GLASS INDUSTRY +44 (0)20 8332 Contactsales@newport-industries.com2519us:+44(0)20 8940 6691
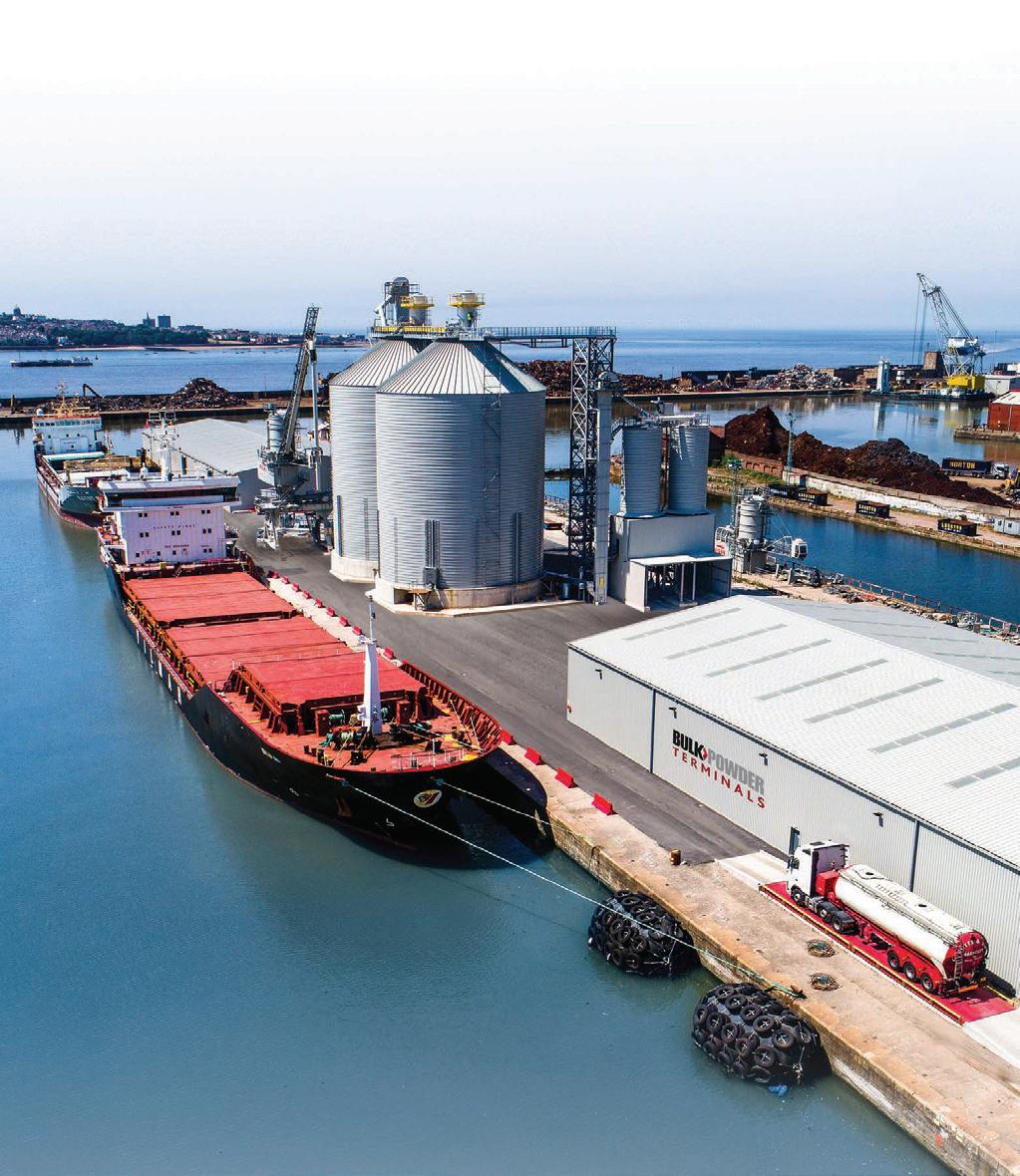
Lithium carbonate, a key component in some batteries, is also supporting growth in soda ash demand, especially in South America but in China as well. Sodium bicarbonate also has a growing environmental application, which is for flue gas desulphurisation (Figs 8 and 9).
Solar glass has the potential to provide new demand for soda ash. In the wake of the war in Ukraine, the shift to green energy is no longer just about environmentalism, it is also now about energy security. This global trend will accelerate the use of solar power in the coming years and hence, it will create additional demand for solar glass. China is dominating the PV (photo voltaic) and solar glass space. Chinese solar glass capacities under planning would alone consume an additional 20 million mt per year of new soda ash demand, if approved. Such glass proposals do seem excessive, and much more than the PV industry appears to require, nonetheless, it indicates the opportunities and also the lack of transparency in terms of what this ultimate demand opportunity may be. India also has ambitious expansion plans for solar glass while Southeast Asia has become a bit of a hub for this type of glass.
Soda ash update Glass International September 2022 www.glass-international.com 23 operating at full capacity with demand said to be robust. There is though concern about very high stocks of flat glass in China. Meanwhile, one demand category which may be less influenced by economic factors, and thus cushion the blow from slower economic growth, is the environmental category. This sector of demand includes lithium carbonate, solar glass, and sodium bicarbonate which were each immune from the negative impacts of the Covid-19 pandemic.
DESIGNED FOR PERFORMANCE. ENGINEERED FOR ENDURANCE. Our history spans 150 years of delivering countless innovations to propel the global glass industry forward. Nikolaus SORG has designed advanced furnaces with unrivalled performance and asset lifetime. EME has engineered batch and cullet processing technology to endure the most demanding production environments. SKS is the world leader in furnace rebuild and lifecycle services. Together, we form the SORG Group, and our new positioning line represents what the invincible power of three can do for our customers in the race to build a more efficient, more sustainable future. See how we are driving the industry forward. Visit us at glasstec 2022 – Stand B38, Hall 15. eme.de sorg.de sks.net

� Fig 1 - Hydrogen trailer. At full flow, a tanker of hydrogen was used every 40 minutes during the Port One Trials.
� Pilkington’s Greengate furnace at St Helens, UK.
The scale of the trials meant that we needed to co-ordinate across the teams each day to cover modifications to the burners as well as monitoring the furnace behaviour during the trials. Above 70% hydrogen the flames became invisible, which was expected but still new (Fig 3).
I have worked on furnaces for many years,
� Andrew Keeley, Principal Technologist at NSG Pilkington, led the hydrogen trials.
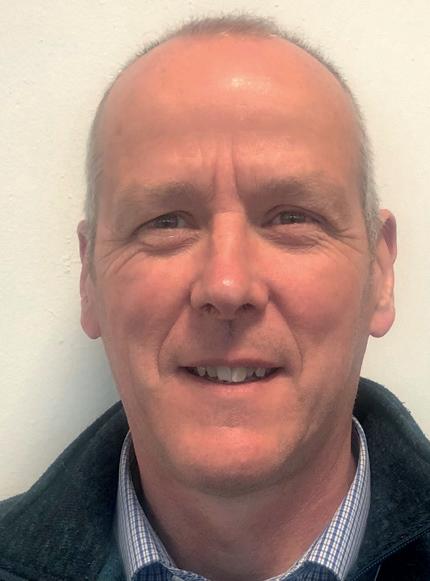
As part of our decarbonisation strategy, we are investigating low carbon fuels as part of our commitment to reduce our CO2 emissions by 30% by 2030 and to achieve net zero by 2050. We have been working with the HyNet project for a number of years on the feasibility of using hydrogen as a fuel to fire our furnaces.
Site installation started in January 2021 and generally went very well. The main challenge was installing pipework for the trial around a live furnace and ensuring that it was all gas tight as fully welded was not practical for a temporary installation.
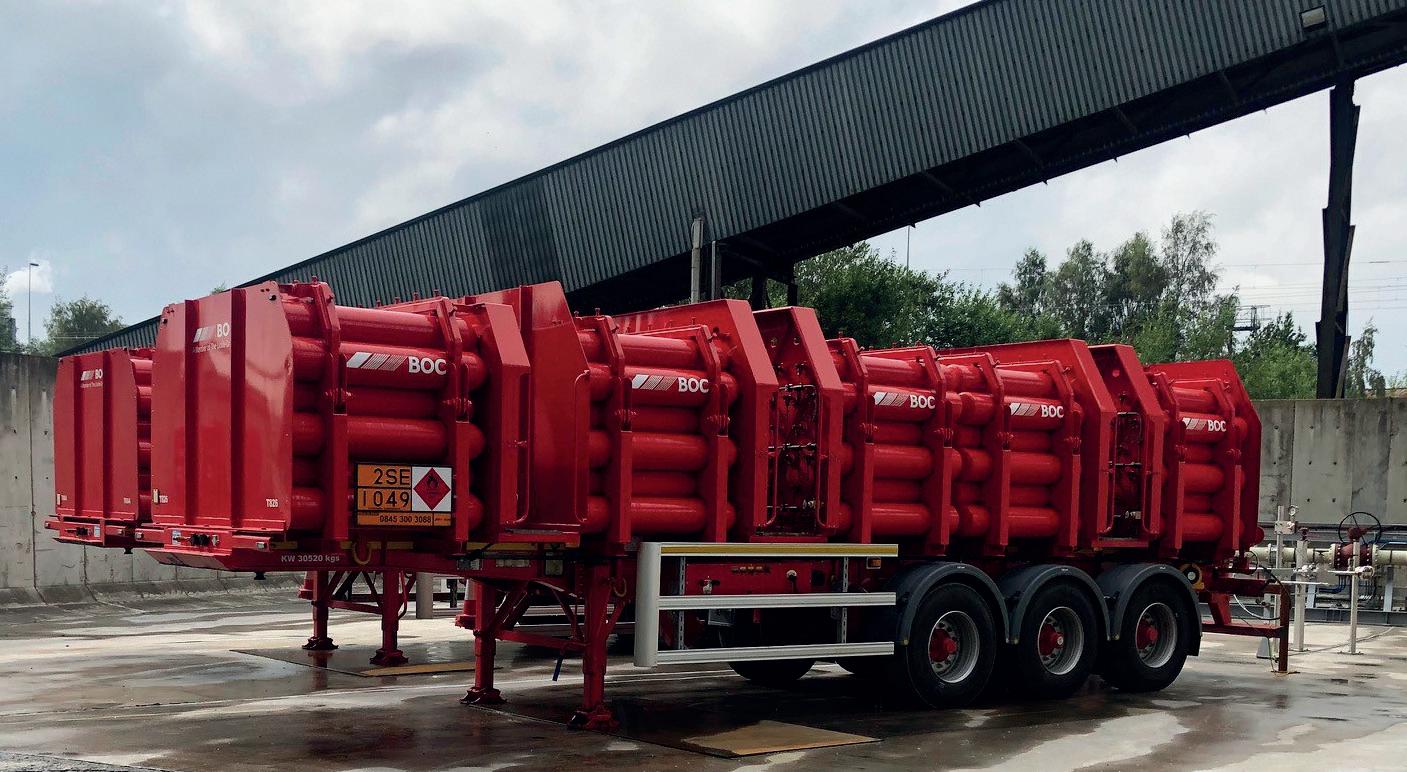

I was the NSG project manager for the hydrogen firing trials at our Greengate Works in St Helens, UK. The role involved working with Otto Simon, the installation project lead, site engineering and our central engineering team during the installation phase and then working with the R&D and operations teams during the trials as well as with BOC, who supplied the hydrogen for the trials (Fig 1).
The hydrogen firing trials were funded by the UK government as part of the Industrial Fuel Switching Programme. The HyNet consortium applied for funding under this programme for a series of trials at industrial sites in the North West including ourselves and Unilever, the UK-based household goods maker. Hydrogen looks to be one of the most favourable alternative fuels for flat glass manufacturing although other fuels such as biofuels also have good potential.
Decarbonisation Glass International September 2022 www.glass-international.com 25 Continued>>
It was a great opportunity to lead this project but really it was a team effort overall. The site team (Fig 2), R&D team, Otto Simon and subcontractors all worked well together and delivered the project.
The Port One trials took place over a threeweek period. The first challenge was that this project kicked off in May 2019 and we then ran into Covid which led to some delays due to restrictions on travelling.
Andy Keeley* shares his experience of leading NSG Pilkington’s recent hydrogen trials in St Helens, UK. The trials aimed to demonstrate that the furnace could run safely at full production without impacting product quality as part of the manufacturer’s plans to decarbonise.
NSG’s successful hydrogen trials
Trials
*Principal Technologist, NSG Pilkington, Lathom, Lancashire, https://www.pilkington.com/en-gb/ukUK
� Fig 3. Natural gas flames compared to the invisible hydrogen flames in glass furnace.
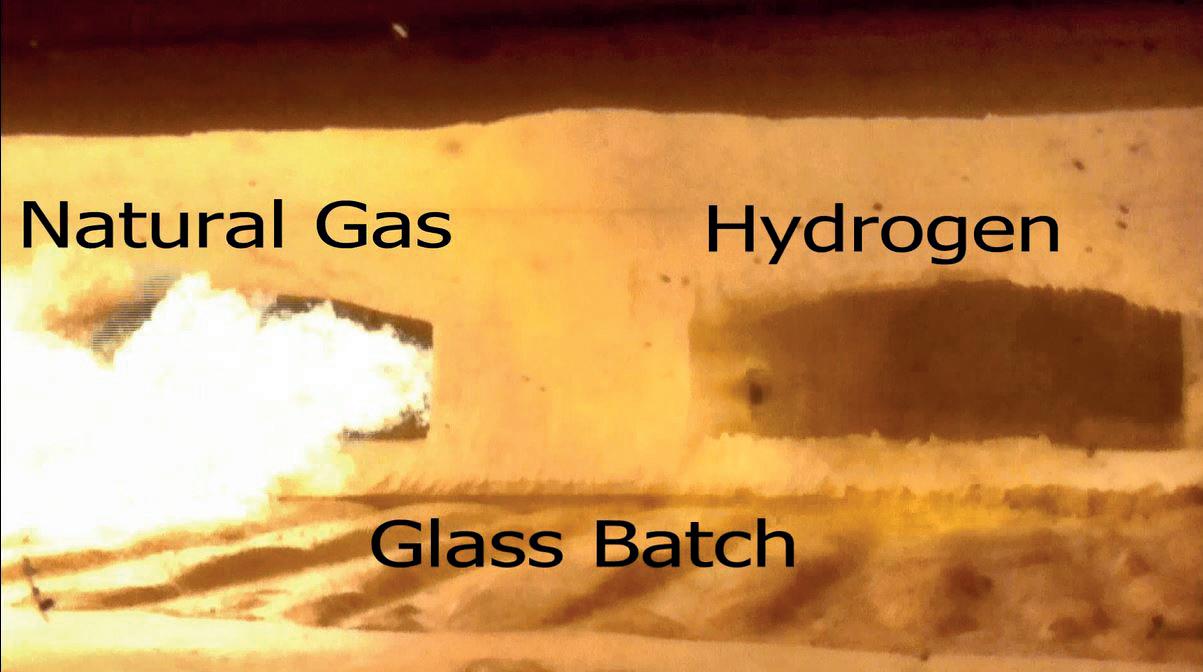
Decarbonisation Glass International September 2022 260 www.glass-international.com but this was the first time I have been involved in such large-scale R&D trials. During the trials, we monitored the furnace closely and were able to produce high quality glass throughout. Apart from the change of fuel on the port firing hydrogen, we were able to operate the rest of the furnace the same with no other process changes being required.
The main outcome of the trials was that we could fire 100% hydrogen on the furnace and get effective melting of the batch. Based on these results, we have confidence that we could convert the upstream part of the furnace to 100% hydrogen and then progressively move downstream once we have assessed the impact of firing hydrogen on foam clearing and glass chemistry. If we could convert the furnace to run on 100% hydrogen, we could reduce our Scope 1 CO2 emissions by more than 65%, with the remaining CO2 coming from the raw materials.
Green hydrogen could prove particularly challenging for the following reasons: � Getting reliable and cost-effective access to sufficient renewable electricity and water. � Physical space on or close to our sites. � Cost – green hydrogen is currently much more expensive than grey or blue hydrogen. � Capex if directly investing or finding a suitable third party.
Challenges On the upstream ports, the main challenge is heat transfer while downstream you are clearing foam and heating the glass for refining. For downstream ports, the higher water content in the atmosphere can lead to more foam. It has not been possible to test this at scale due to the limited availability of hydrogen. We will only be able to test this when we have large volumes of hydrogen available in the future when the HyNet project goes live.Wayne Bridger of BOC said at Furnace Solutions there is unlikely to be enough hydrogen infrastructure in place to meet industry requirements for at least 10 years.
So, the question is how will furnaces be fuelled in the intervening years? In the North West of England, we are lucky to be close to the HyNet cluster which is quite advanced and so I believe hydrogen is a realistic fuel for this site. For other sites in the group, we would have to assess the options based on what was available.
Fuel of the future?
In reality, we expect to use a mixture of electricity and low carbon fuels to fire our furnaces with the choice of fuels dependent on what is available and commercially viable locally. We also expect to use an increasing proportion of cullet to reduce our overall energy requirement. We believe we have carried out sufficient trials to allow us to fire hydrogen on our furnaces, at least on the upstream ports, so we are not planning any further largescale trials. The next major step will likely be when the HyNet project goes live and we have a hydrogen pipeline to site.
�Fig 2. The site team for the hydrogen trials.
Hydrogen is one of the potential low carbon fuels we could use for the future. We also carried out trials in February 2022 firing 100% bio-oil on the same float furnace which was also a world first.
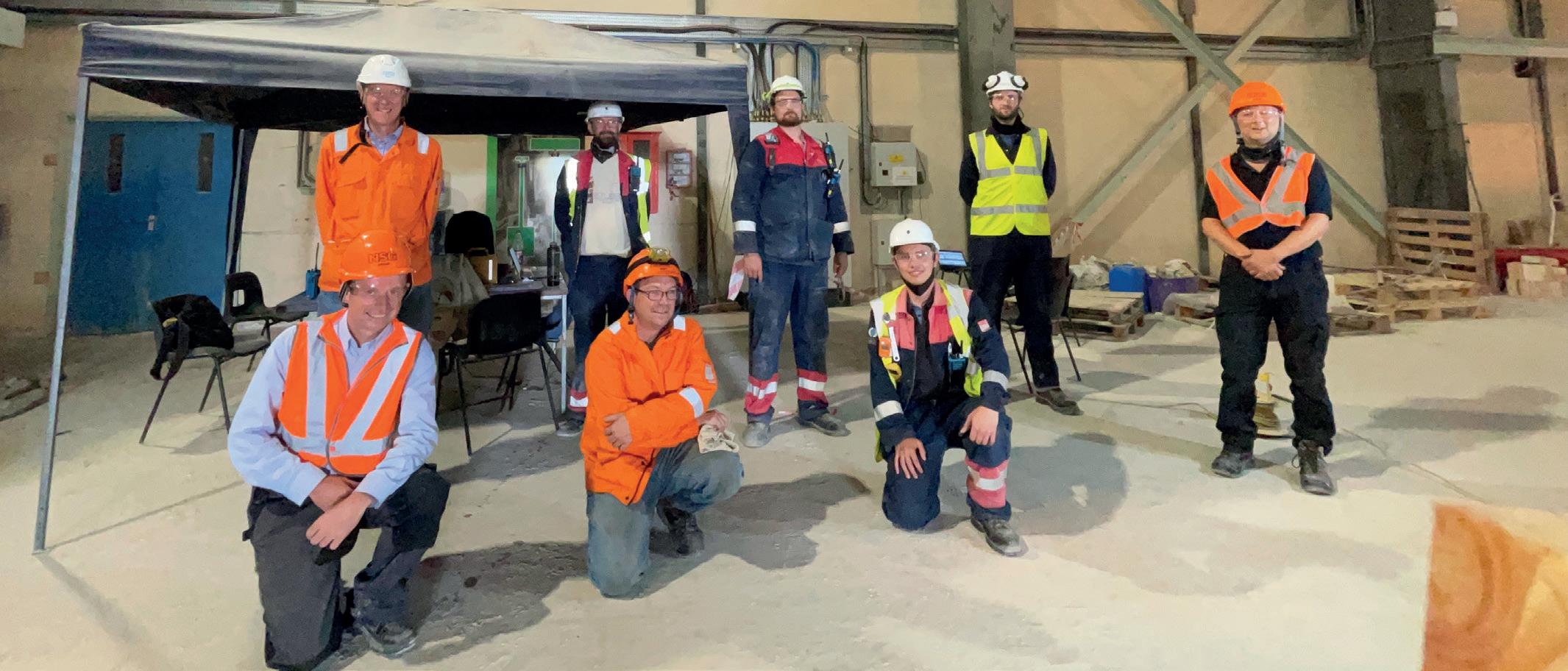
See you at Glasstec, hall 13, stand A31 Batch Plants | Cullet Plants | Automation | Modernization | Engineering | Factory Cullet Recycling Glass Recycling | Batch Charging | Glass Level Controlling | Preheating | Maintenance & Service ZIPPE INDUSTRIEANLAGEN GMBH | Alfred-Zippe-Str. 11, 97877 Wertheim, Germany | T: +49 9342 804-0 | zippe@zippe.de | www.zippe.de
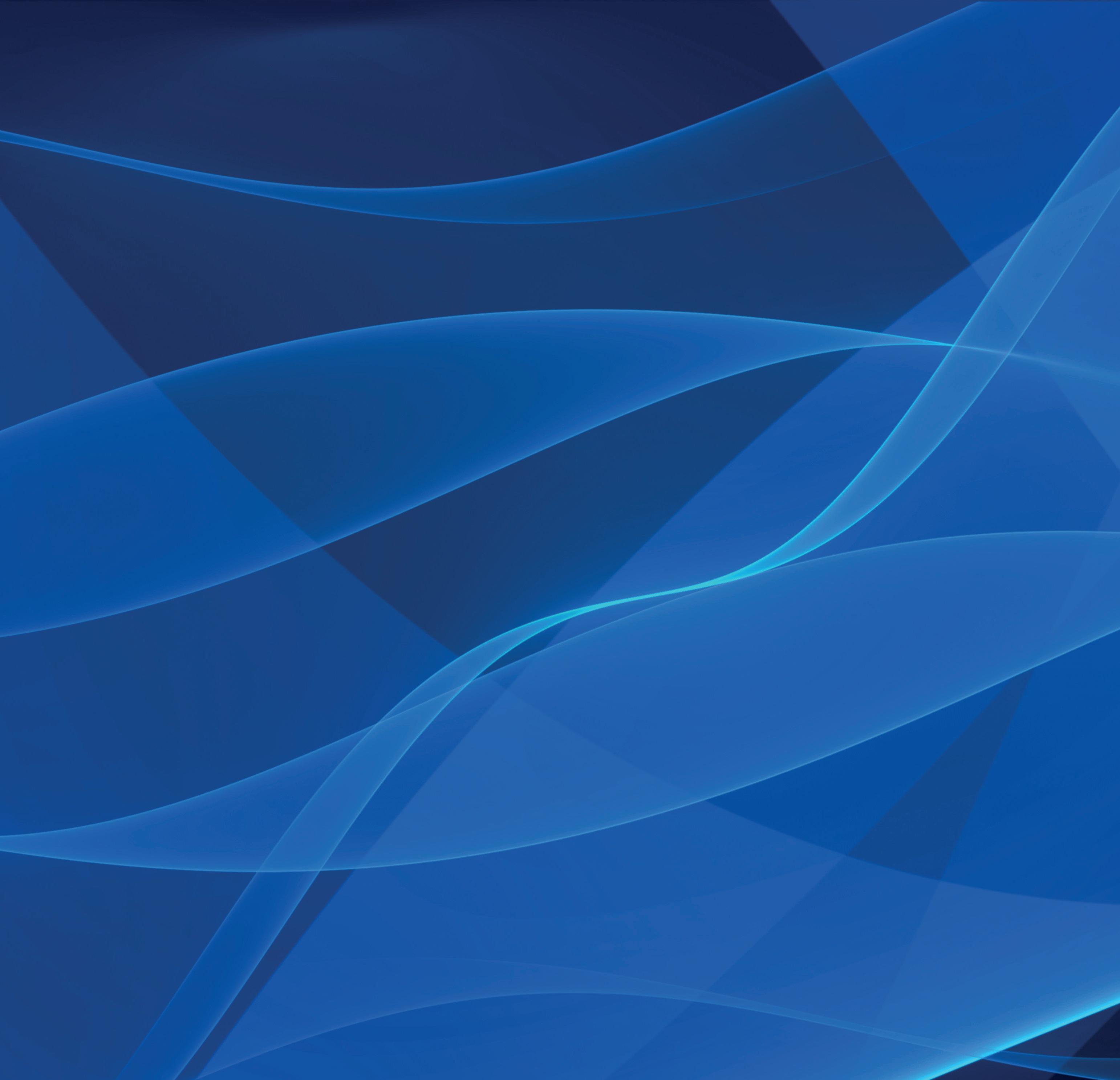
® TOLEDO ENGINEERING / TECOGLAS / ZEDTEC / KTG ENGINEERING / KTG SYSTEMS / EAE TECH DESIGNING,www.teco.comBUILDING AND MODERNISING YOUR FURNACES, FOREHEARTHS AND FURNACE EQUIPMENT A KTG fact... Did you know that KTG screw batch chargers are custom built to handle loads of up to 120TPD each? YOURCHARGINGBATCH
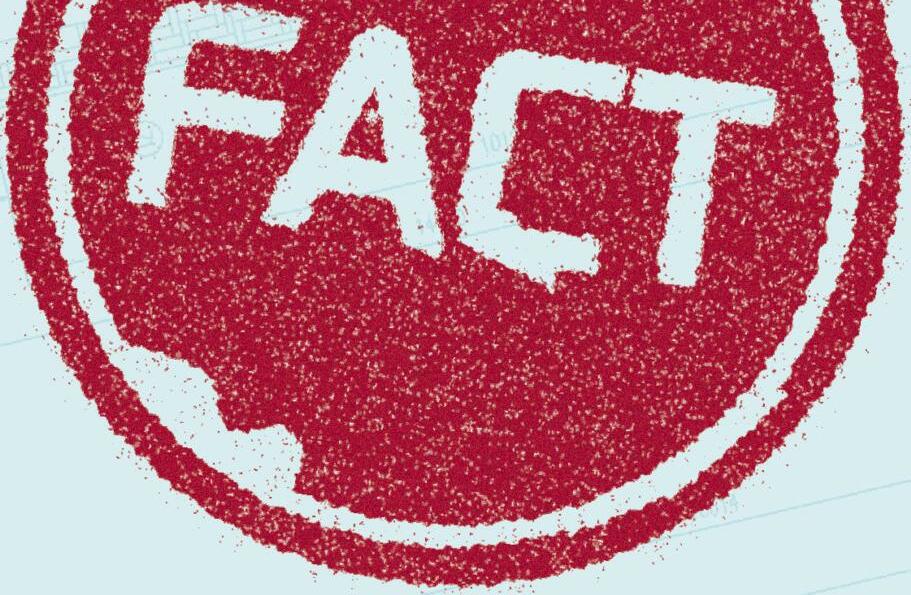
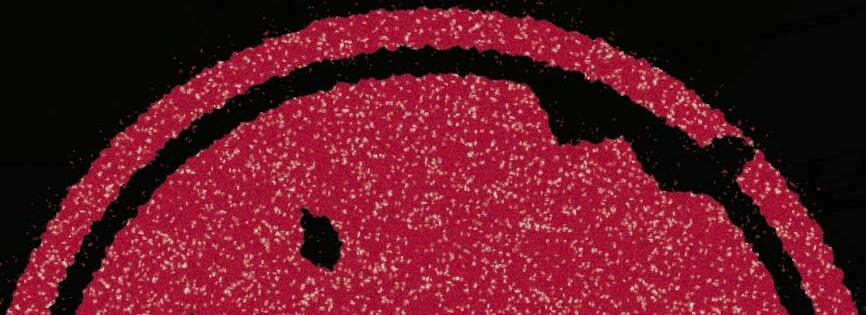
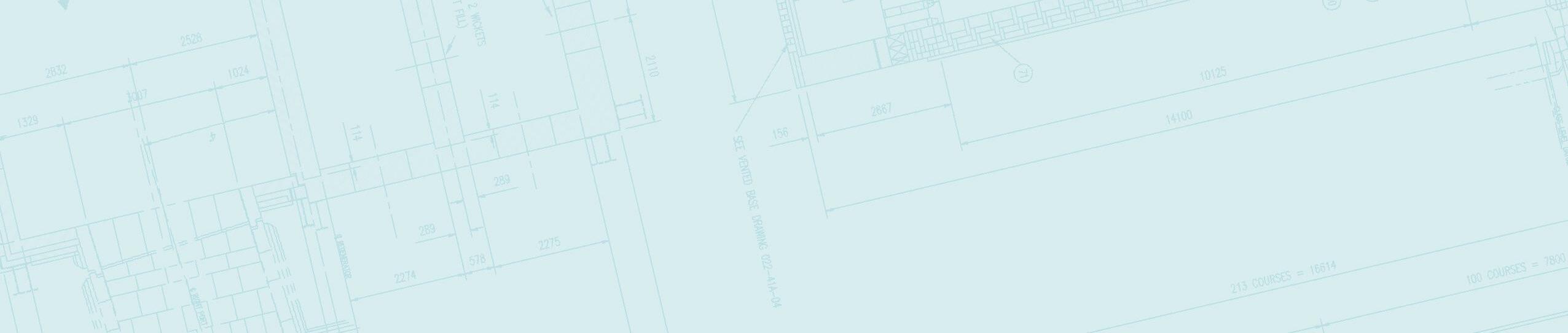

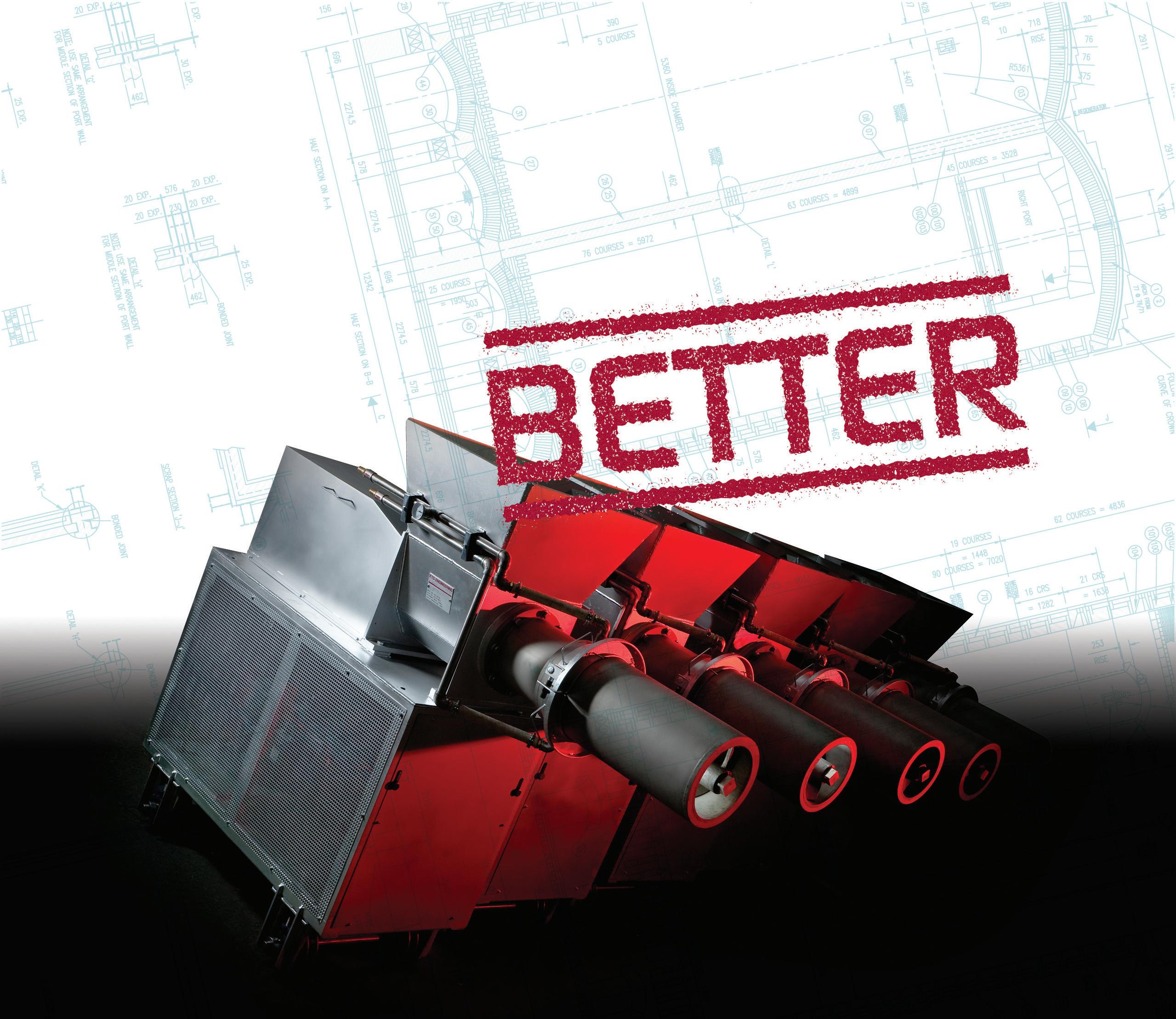
� Fig 2. Carbon Dioxide flows in exhaust due to batch materials. � Fig 3. CO2 emission from glass (batch) and fuel by furnace type and cullet level
Silicate Glass + CO2
Decarbonisation Glass International September 2022 www.glass-international.com 29 Continued>>
Increased cullet and elimination of carbonate materialsThepaths are not mutually exclusive, they can be combined to increase the reduction in CO2 emissions Interestingly, the second item, alternative fuels, does not address CO2 emissions from the batch. So, carbon capture would still be required and/or the use of carbon credits. In this article, the economics, more specifically the operating expense (OPEX) considerations are going to be limited to alternate fuels, specifically hydrogen (H2) and batch materials (Fig 1).
� Carbon Capture/Sequestration � Alternative Fuels - Hydrogen, Biogas, Blends, Electricity � Batch Modifications
Fig 2 shows some typical volumetric (normal) and mass flows of exhaust CO2due to batch.
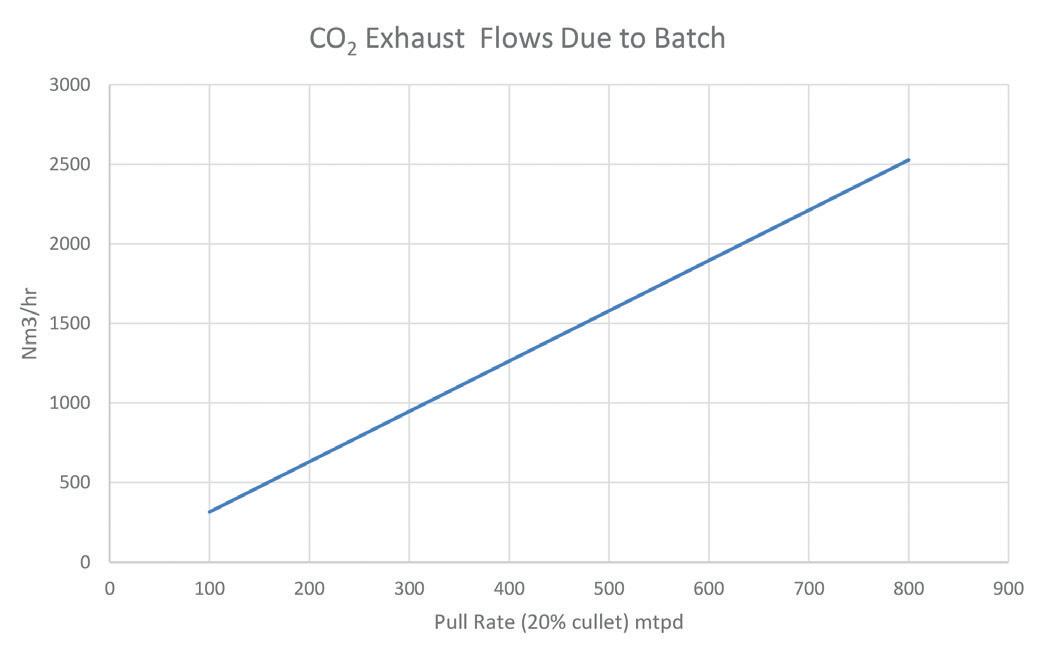
True carbon neutrality in glass
Chris Hoyle* and Brian J. Naveken** discuss the various pathways the glass industry needs to take to decarbonise.
There is an English expression known as ‘the elephant in the room’ which refers to an important or enormous topic that is obvious, where no one mentions or discusses it but needs to be addressed. In the case of carbon neutrality in glass, it is the economic considerations. There are basically three paths to carbon neutrality for glass manufacturing. These being:
At 20% cullet approximately 35% of CO2 emissions from the production of glass is from the melting of the batch materials and has not received the attention that emissions from fuel has gotten. Other CO2 emissions by cullet percentages are represented in Figure 3.
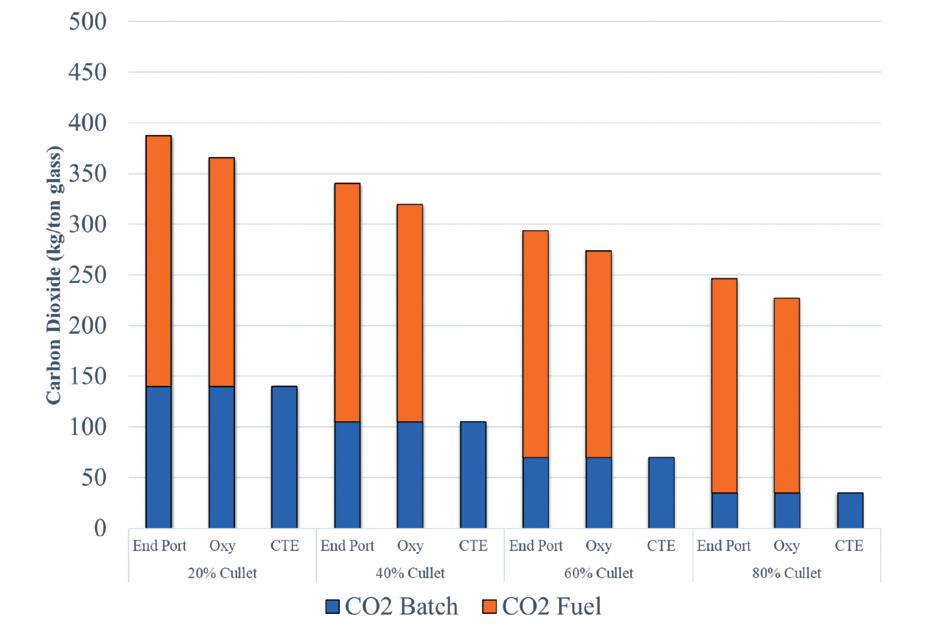
In a basic equation for the production of SiOglass,2+ Na2O + CaO Soda Lime Silicate GlassThere contains no carbon dioxide (CO2) product formation. The formation of CO2 is a product of using the carbonate forms of the Na2O and the CaO more commonly known as soda ash (Na2CO3) and limestone (CaCO3). The resulting equation now becomes, SiO2 + Na2CO3 + CaCO3 Soda Lime
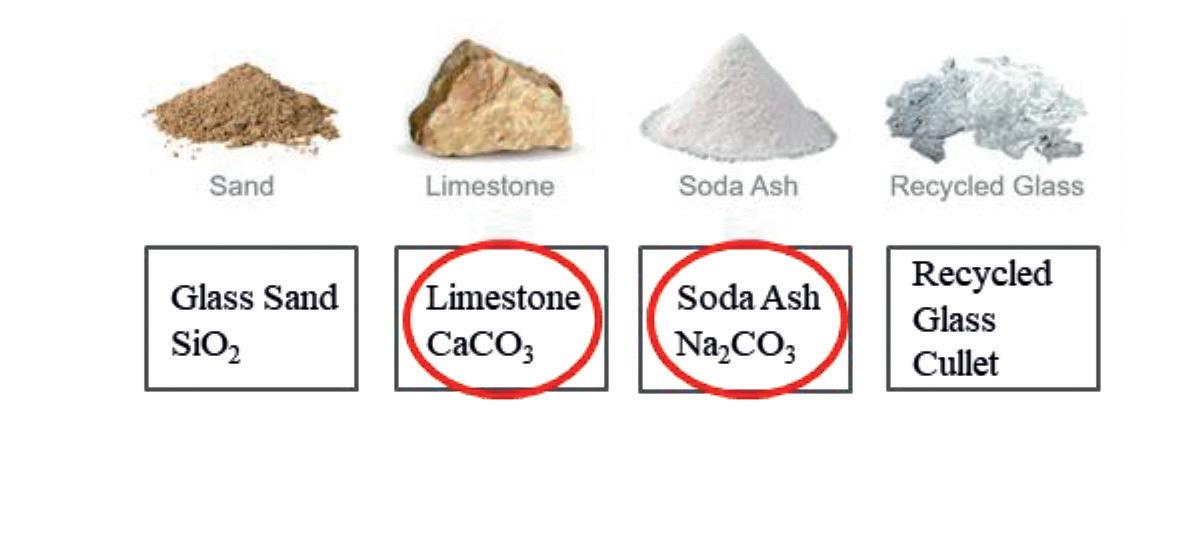
There are two main reasons why the carbonate form of the raw materials is used. These being the abundance of the raw materials, which also results in a lower cost, and secondly the melting of batch takes less energy. By using soda ash and limestone, this reduces their respective batch material cost by approximately 4-5 and 1.5-2 times. Alternatively, batch materials from recycled sources, such as water treatment waste and fly ash, can be used but this
� Fig 1. Basic batch materials of Soda Lime Silicate glass.
The basic equation for the combustion of natural gas using air or oxygen is, CxHy + zO2 xCO2 + (y/2) H2O Natural gas is primarily made up of methane which combusts as, CH4 + 2O2 CO2 + 2H2O Now, if we look at hydrogen, the CO2 product gets eliminated. 2H2 + O2 2H2 O Perfect! The H2 combustion eliminates of 100% of the CO2 from the gaseous energy source for melting and refining glass (note: all electric melting does the same). But let’s look a bit closer. The heating value of natural gas is ~36.73 MJ/ Nm3 as compared to hydrogen’s ~10.78 MJ/Nm3. What this means to glass melting is: � Will need ~3-3.5x the volume of hydrogen than natural gas � Will have to account for the effects on distribution and storage of H2 � Will produce ~1.5x more water vapour in exhaust � What effects will the water have on glass and refractories? � Will need 25% less oxygen (economic advantage over Oxy-Fuel furnaces) � Exhaust mass flow and velocity negligible � The higher flame speed of H2, higher permeability, and hydrogen embrittlement will require greater safety measures Figure 5 shows the comparison of a container and float furnace using air-gas or oxy-fuel and replacing the fuel type with hydrogen with all other inputs remaining the same. The economic practicality is constantly changing and will continue to change due to energy prices and the processes used to generate hydrogen.
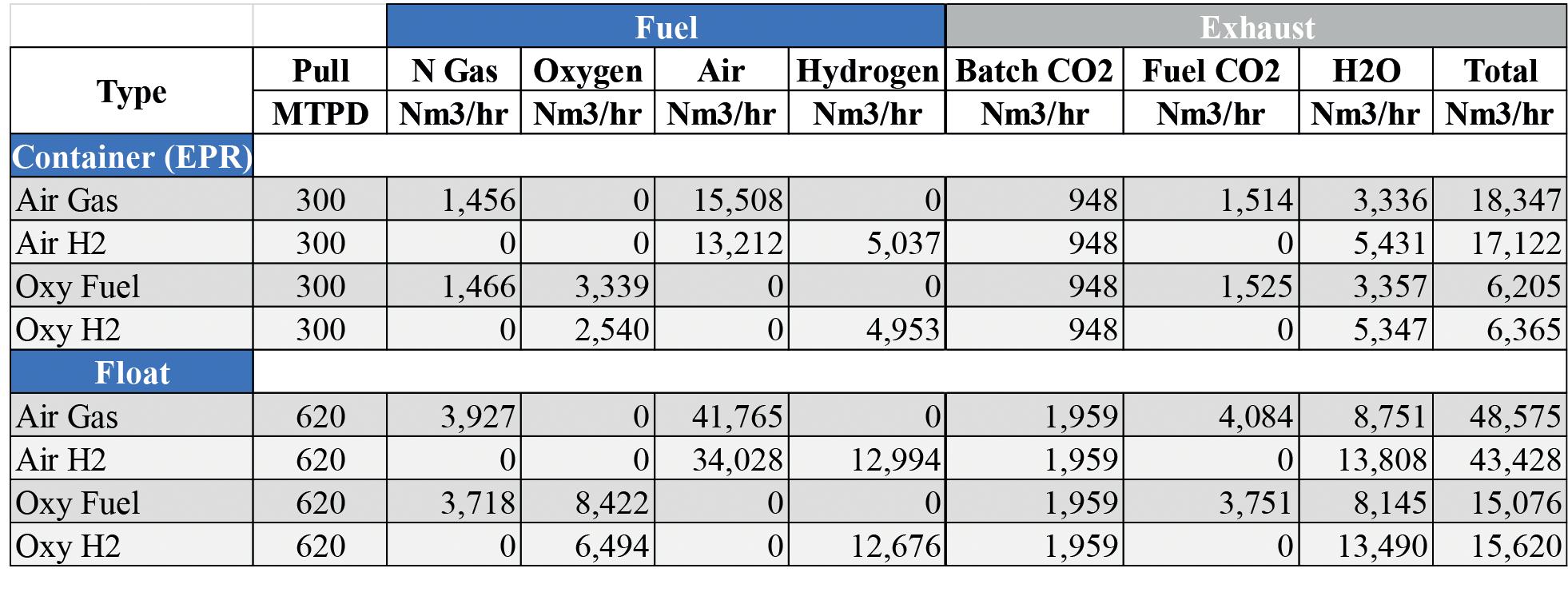
Alternative Fuels
Technical Feasibility of Hydrogen in Glass Furnaces
The first questions for the success of hydrogen combustion is how will the hydrogen be generated, transported, stored and ultimately combusted in existing glass furnaces? Or will all new furnaces designs be needed? Or just modifications to existing furnaces?
When looking at carbon neutrality, hydrogen (H2) looks to be the most viable candidate, and this can be seen in the research and the billions of dollars in potential funding for hydrogen hubs and infrastructures.IntheUnited States alone there is a Department of Energy funding opportunity of $8 billion for the fiveyear period encompassing fiscal years 2022 through 2026 for the development of regional clean hydrogen hubs that demonstrate the production, processing, delivery, storage, and end-use of clean hydrogen.Thisconcept is presented in Figure 4
� Mechanical Systems The molecular weight of hydrogen is 2 and methane is 16 which means hydrogen is a smaller molecule and considerations for materials to reduce leaks at valves, gaskets, etc. need to be met.
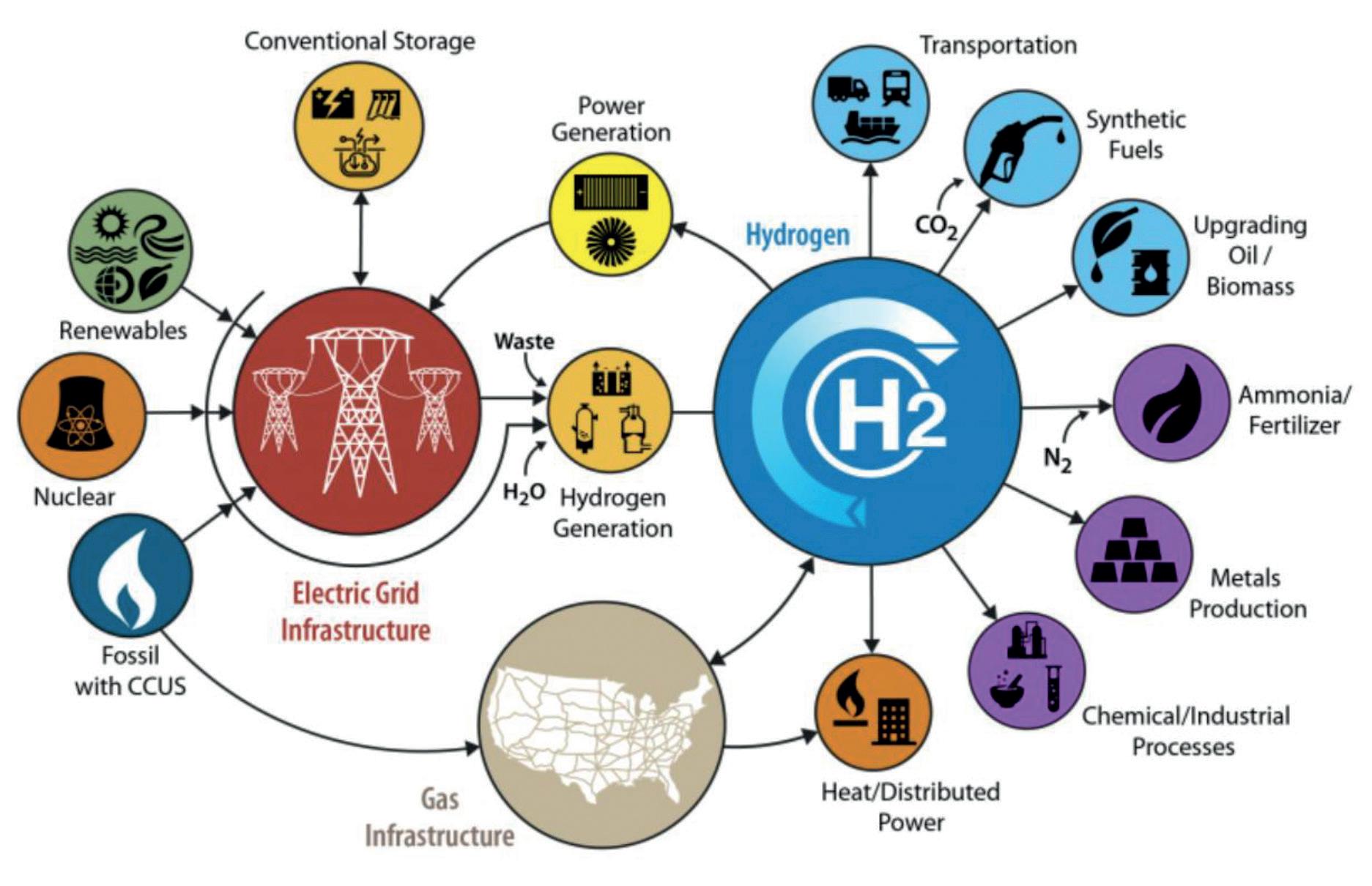
� Fig 4. H2@scale U.S. Department of Energy (www.energy.gov/eere/fuelcells/h2scale).
If hydrogen cost gets comparable to natural gas on a volumetric basis, which currently it is two to three times higher, one’s energy cost would still be triple due to the increased volume of hydrogen needed.Toput the volume of hydrogen into a bit more perspective, for a float furnace to convert their port 0 oxy-fuel burners to hydrogen would require five times more hydrogen than what they use to operate their tin However,bath.by 2050, the natural gas economic advantage may disappear with the addition of carbon taxes (Fig 5).
Taking the first bullet point from above, in order to get the same melting energy from hydrogen you need to increase the volumetric flow of hydrogen by three to three and half times.
� Fig 5: Fuel flows and specific species exhaust flows.
Some of the considerations for furnace conversions from natural gas to hydrogen are:
Decarbonisation Glass International September 2022 300 www.glass-international.com will only reduce the carbon footprint by 4-10%.Toget to complete neutrality, carbon capture/sequestration would still be needed (Fig 3).
EAE Tech provides industrial automation engineering services and custom control systems. � *Senior Vice President-Technical Director, **Mgr. of Technology & Technical Sales, TECO https://teco.com/Group,
Electrical Furnaces With all electric furnaces CO2 emissions are eliminated to same degree as hydrogen combustion and has been a production proven and economical method of melting glass. The biggest drawback is glass quality but with the same degree of effort and innovation that hydrogen combustion is receiving, the fining/refining issues should be able to be overcome.
Air Products is blazing a new trail for oxy-fuel burner technology . . . Boost your performance and productivity for better glass with the Cleanfire® HRx ™ burner! tell me airproducts.com/HRxmore© Air Products and Chemicals, Inc., 2022 Upgrading your oxy-fuel burners, adding burners to boost production, or converting your air-fuel furnace to oxy-fuel? The patent pending Cleanfire HRx burner offers you expanded functionality and flexibility with unmatched performance. It can deliver: • Increased flame radiation for high fuel efficiency • Ultra-low NOx emissions • Foam reduction capability for higher-quality glass • Enhanced productivity • Optional remote performance monitoring feature • Integrated high efficiency oxygen supply system This burner is the latest innovation in the long line of industry-leading Cleanfire® burners for the glass industry, which are now able to utilize hydrogen as a fuel, for a lower carbon footprint. To learn more or to schedule a demonstration in our state-of-the-art lab, call 800-654-4567 (code 10868) or visit airproducts.com/HRx
As part of the TECO Group, Toledo Engineering, Tecoglas and KTG Systems can offer total furnace capabilities in glass furnaces of all types, with KTG Engineering supporting this activity as glass plant equipment manufacturers. Zedtec are the TECO Group specialists in forehearth and working end technology.
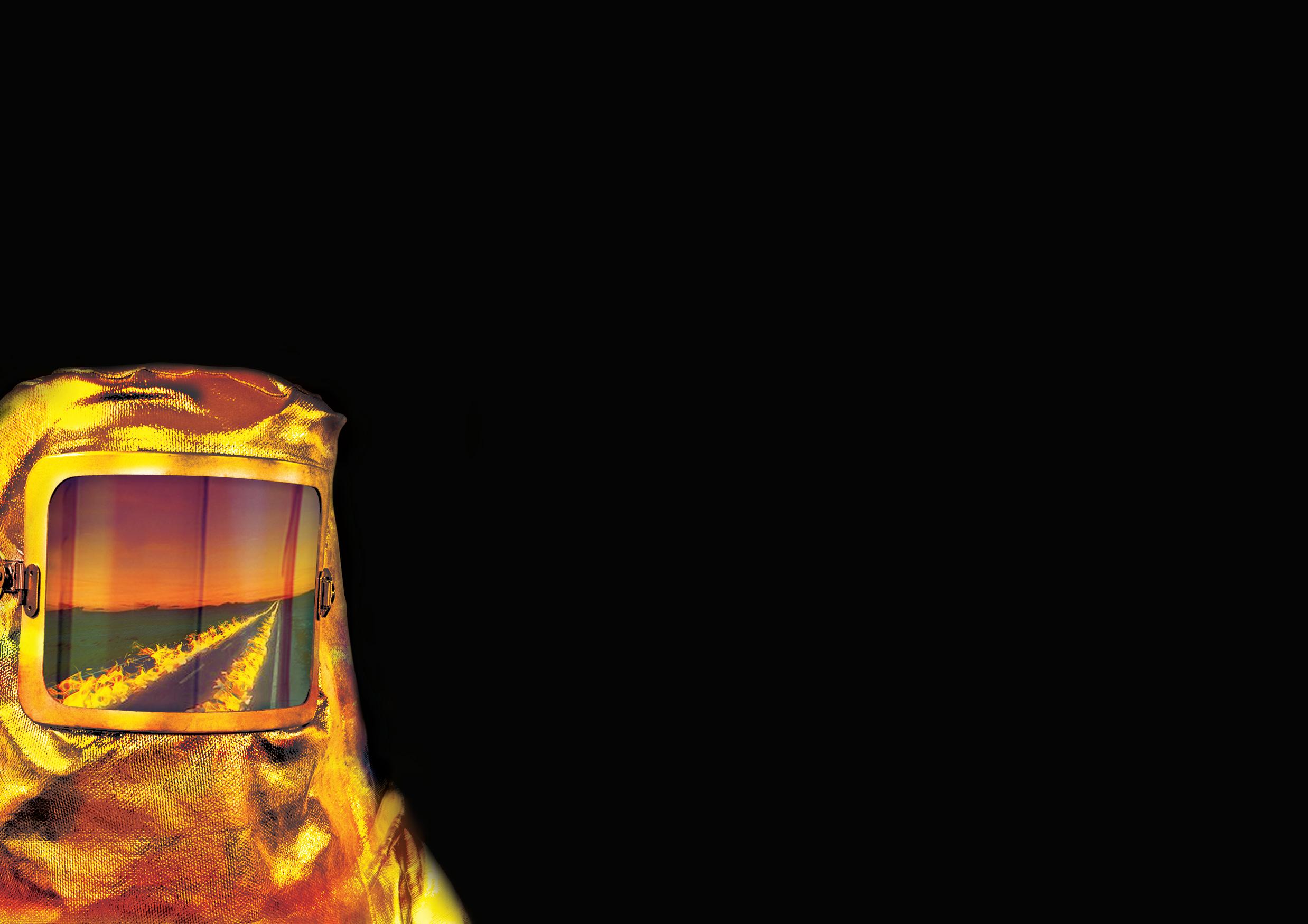
Decarbonisation Glass International September 2022 www.glass-international.com 31 � Effects on refractory due to increased water in the exhaust � Flame control and speed � Heat transmittance over the batch blanket as well as glass due to the lack of carbon in the fuel which lowers the flame luminosity and affects radiant heat transfer
Conclusion Carbon emissions from batch materials is significant. At 20% cullet it accounts for approximately 35% of the CO2 Non-carbonate forms of soda ash and limestone will need to addressed while considering economic and supply considerations.Usinghydrogen as an alternative, the price of hydrogen needs to be reduced considerably in relation to natural gas. All electric furnaces from a fuel standpoint produce no CO2 like H2 and have been production proven for many years by the leaders in all electric melting, The TECO Group. More innovation into the refining and fining of glass using all electric may ultimately make the most economic sense.Internationally there is a considerable decarbonisation effort going on within the glass community as well as other industries. Hydrogen trials in glass furnaces have begun and will continue. Refractory companies are conducting tests for increased water content in the exhaust and burner companies are developing new designs for hydrogen combustion.Thechallenges to decarbonise glass production are numerous and demand innovation along multiple paths, from raw materials to adaptation of hydrogen combustion, to advances in all electric melting.TheTECO Group companies are uniquely positioned to solve clients’ issues, in this case decarbonisation, by delivering solutions that creates value through innovation within a framework to manage risk.
WE CAN PROVIDE YOU SOLUTIONS, NOT ONLY PRODUCT. WANT TO KNOW HOW? IT’S COOL STORY. LWN LUFTTECHNIK as a leading company in IS Machine Cooling systems can accelerate your production portfolio! We connected all three factors: knowledge, trust, efficiency. Due to our more than 25 years experience we were able to deliver and provide IS Machine Cooling to glass plants all around the world. We are chosen one, because we can provide complex solutions, beginning of design, through manufacturing and finishing on the assemblingVisitprocess.us: Hall 13 / C96 We’re at 20-23 September 2022 Düsseldorf | Germany
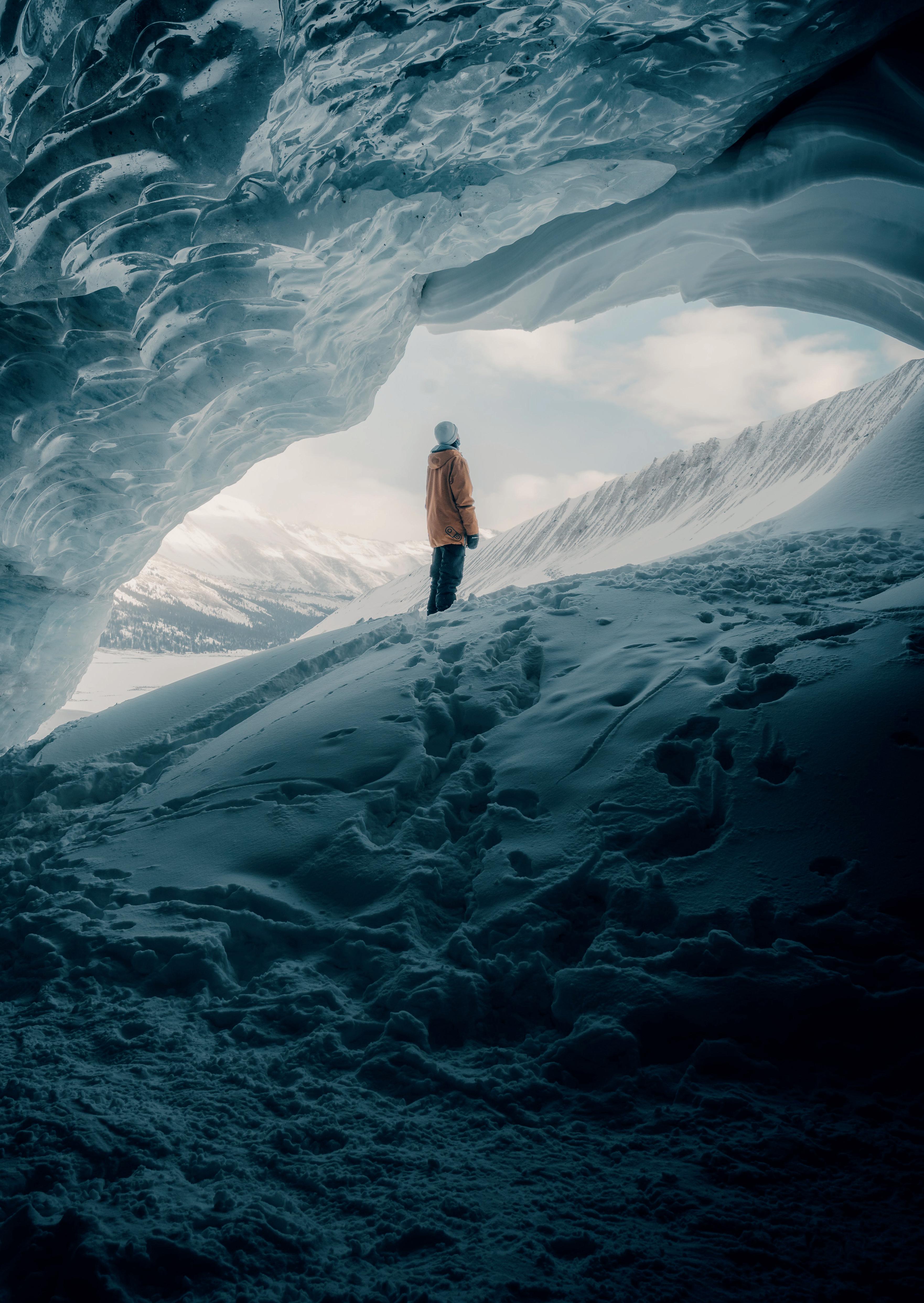
Economic analyses show that, implementing circular economy principles in fundamental productions of modern industry, may support the solution of many important problems such as climate change, water crisis, landuse and employment.
The other advantage of using cullet is that the same amount of cullet is � Fig1. Standard soda lime and recycled glass products (increase in cullet ratio from 25>95%).
Sisecam Recycling Glass International September 2022 www.glass-international.com 33 Continued>>
The importance of recycling from a circular economy perspective
Recycling should and will have a place in daily life for all people.
To explain with an example, giving cost saving chances to a company, supporting the environmental gain with reduced environmental impacts and creating versatile job opportunities, are some of the benefits of recycling. But the most important impact is that all benefits are sustainable for recycling. If recycling could be a lifestyle for society, all benefits on recycling may occur.
The circular economy is defined as an economic system that is restorative or regenerative by intention and design. It replaces the ‘end-of-life’ concept with restoration, shifts towards the use of renewable energy, alternatively reusing, recycling and recovering materials. It also eliminates the use of hazardous compounds and aims for the elimination of waste through the superior design of materials, products, systems in production/distribution and consumption processes.
With its 100% recyclable nature, eco-design and modern production technology glass is a perfect example of today’s circular economy concept in action.The recycling period begins with a separation and separation collection at the end of a product’s lifetime. It is then continuous with those separated processing steps. The last step for recycling is using the recycled material for new production instead of virgin material. Recycling is a win-win game where it has some benefits in diverse platforms.

CO2 emission revision
By using cullet, production can capture significant benefits; decreased raw material consumption, reduced energy consumption and emissions. Approximately 1t cullet replaces 1.2t raw materials and 1t cullet using avail 0.67t CO2 emission reduction. When production is applied using 100% cullet, up to 25-30% energy saving can be reached. Sisecam has processed 1.2-million-ton cullet since 2011; therefore, the amount of carbon emission that is equal to 442.021 cars’ emission for one year is prevented via using cullet.
Packing material has two versions of recycling. One of them is downcycling (downstream recycling) and the other is closed – loop recycling. With downcycling, material turns into another product with known loss in the quality of product. Transformation of plastic bottles into a new type of fabric in textile industry can be given as an example for downcycling. On the other side, material can be recycled to same product without any loss in quality via closed-loop recycling. Glass recycling in our case is an example for closed-loop recycling. Hence, glass is a material that can be recycled infinitely many times while protecting its quality and form. The process can be continued in endless loop.
Arca Iyiel* and Efe Caglayan** discuss Sisecam Environment Systems project to boost glass recycling in Turkey and to create a resource-efficient circular economy.
Fostering glass recycling Sisecam prioritises the use of raw materials, natural resources and other production inputs that are sourced from recovery practices and the outputs of other industries, thus localising the supply chain, decreasing emissions from transportation and production, and reducing our environmental footprint. Sisecam believes that circular economy practices will change the production and waste removal processes, starting from the design phase, and will initiate an important industrial transformation by ensuring the products and waste are recyclable.Inline with the circularity vision, Sisecam established its Sisecam Environment Systems to boost glass recycling in Turkey and to create a resource-efficient circular economy. In addition to carrying out waste glass recycling processes at its two facilities, Sisecam also purchased the cullet of alternative suppliers who provides cullet that are ready for the furnace and production step. Sisecam has already increased postconsumption recycling capacities by directly and indirectly investing in four waste-glass recovery plants with an aggregate recovery capacity of 790K tons/year. Sisecam has been carrying out our Glass and Glass Again project since 2011, in co-operation with its various stakeholders. The project aims to support the transition to a recycling society by effecting social behavioural change. Glass and Glass Again has three main objectives: � Raising public awareness on glass packaging recycling � Developing the infrastructure for the collection of glass packaging waste � Modernising the facilities where glass packaging waste is collected and processed, and separating glass packaging waste from household waste before landfilling Social framework Since the launch of this initiative, more than 250,000 primary school students have received instruction on recycling, more than 20,000 glass collection containers have been made available to municipalities, and 1,562,000 tons of glass waste have been recycled. This effort has prevented greenhouse gas emissions equivalent to eliminating 562,239 passenger vehicles from traveling 10,000 kilometers. Energy savings from recycling has amounted to the equivalent of meeting the heating and hot water needs of 65,595 homes for a year. In addition, carbon dioxide emissions have been reduced by an amount which is equivalent to having 48,220,678 trees a cleaning the air for a Theyear.use of cullet in 2021 was 26%, and Sisecam continues to work towards increasing the percentage up to 35% by 2030. To increase this rate even further, Sisecam is developing projects, and social, communication campaigns promoting the use of recycled cullet in production. In addition to glass packaging production, Sisecam is pushing the possibilities of using cullet at the maximum rate for other glass production processes, depending on quality and type of Asglass.a result of Glass and Glass Again efforts, Sisecam produced the world’s first glassware collection in 2020, the Aware

� While setting up the deposit fee, it should attract the consumer but also be reasonable in terms of selling costs.
prevented to be sent into a landfill For operators, finding internal cullet is generally not a problem. In fact, the scarcity of internal cullet is an indication of high productivity. However, some fundamental problems may be encountered in the supply of external cullet.Composition, colour, and redox conditions of external cullet may differ to internal cullet. Contaminants such as ceramics and metals have to be removed to obtain a suitable cullet, heavy metal containing glass cullet should comply with the limits. Grain size and grain size distribution should match the specifications. Addition to those, recycled cullet must be able to compete with the cost of raw materials and should offer advantages in terms of environmental taxes and emission restrictions if there is any. Otherwise, the recycling of glass will never be attractive for the operators. Consequently, as well as finding enough cullet, finding cullet in suitable conditions is an obstacle that needs to be well managed.Basically, it is critical for an effective recycling system to meet the following conditions:
� Management should be centralised, but in practice, regional conditions should also be considered for the operation step.
� First, the installed capacity of sorting & recycling infrastructure should be sufficient. � To be financially viable, covering all packaging types is important. Therefore, it is possible to finance waste with another.
� Support mechanisms should be considered, at least in the early stages of the system.
� The involvement of all stakeholders is essential and better to support the voluntary initiatives and to plan joint actions with the policymakers.
� It is also critical that the system is supported in social terms (such as individual and commercial participation.)
� The system should be governed and controlled by strict regulations, direct or indirect obligations should be defined, and effective targets should be set.
� Optimising logistics is important, recycling facilities can be built close to or attached to production facilities.
Sisecam Recycling Glass International September 2022 0 Continued>> 34
www.glass-international.com
The future we see through. Innovation, technology and versatility make the BDF IS Machines the ideal solutions for high productivity, low maintenance effort and considerable energy saving. bdfi ndustriesgroup.com IS ANGULAR ADV 1050-8050 6-8-10-12 SECTIONS AND TANDEM IS 4 1/4”: SG-DG -TG 3”-TG 3 1/8” IS 5”S: SG-DG-TG 85MM IS 5 1⁄2”: SG-DG IS 6 1/4”: SG-DG-TG 4 1/4” 8-10-12 SECTIONS AND TANDEM IS-P: DG 6 1/4”-TG 4 1/4” IS PARALLEL ADV 8050
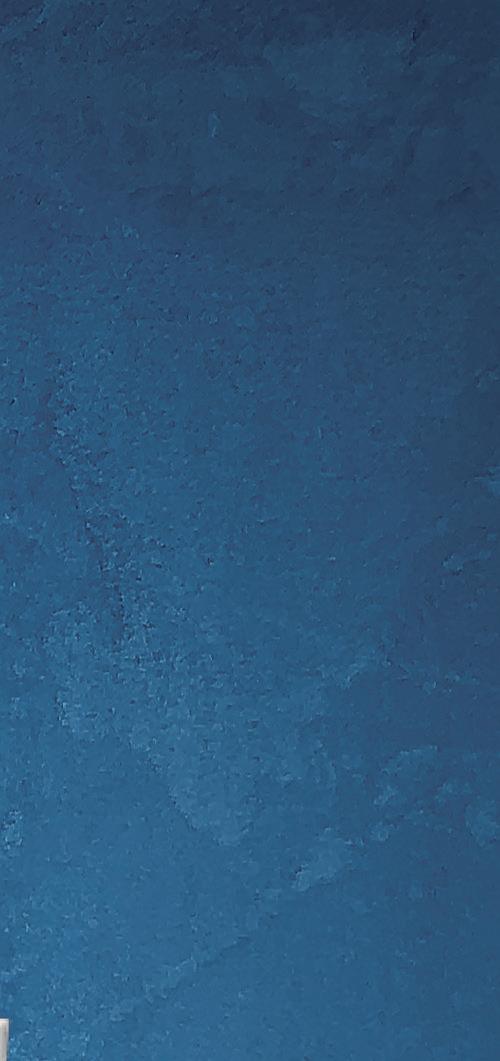

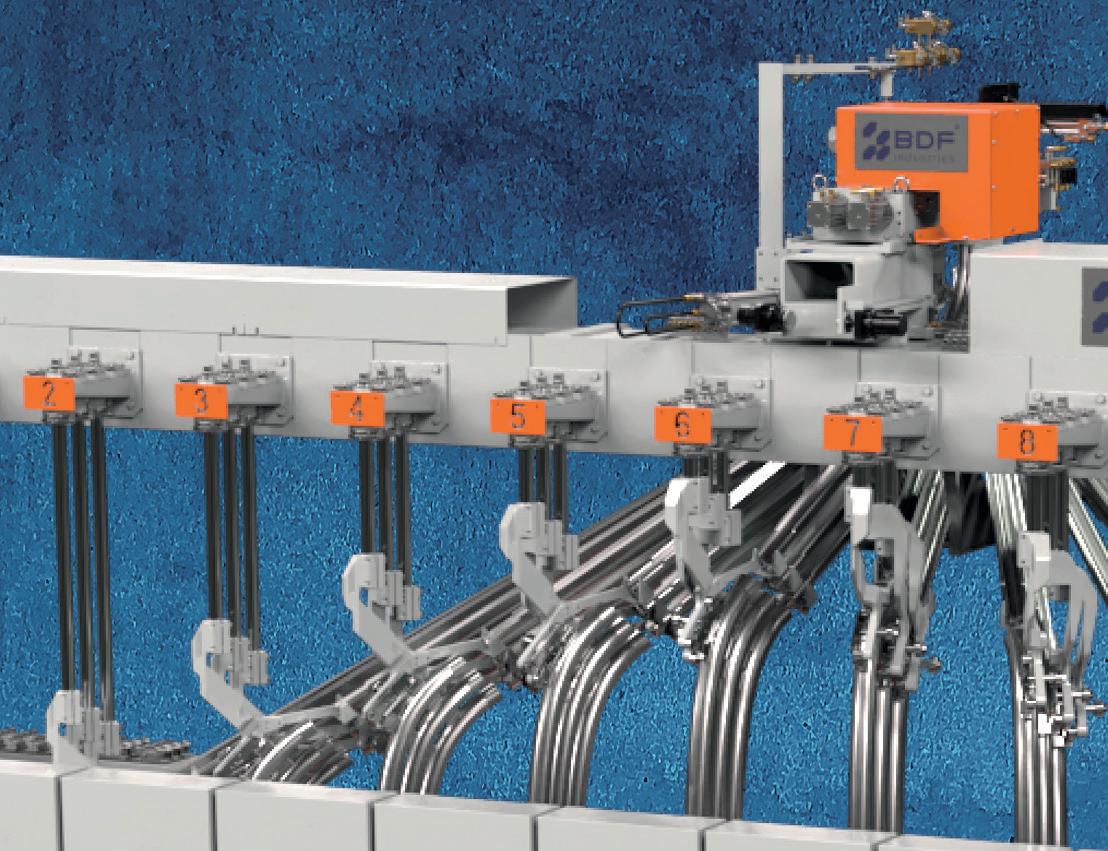

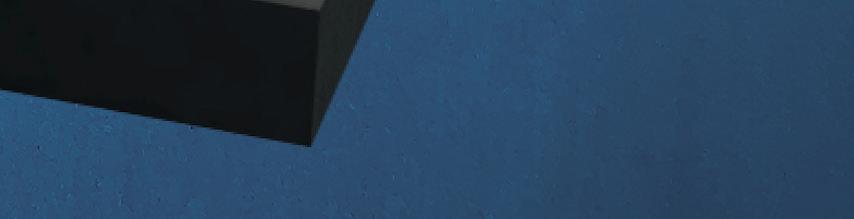

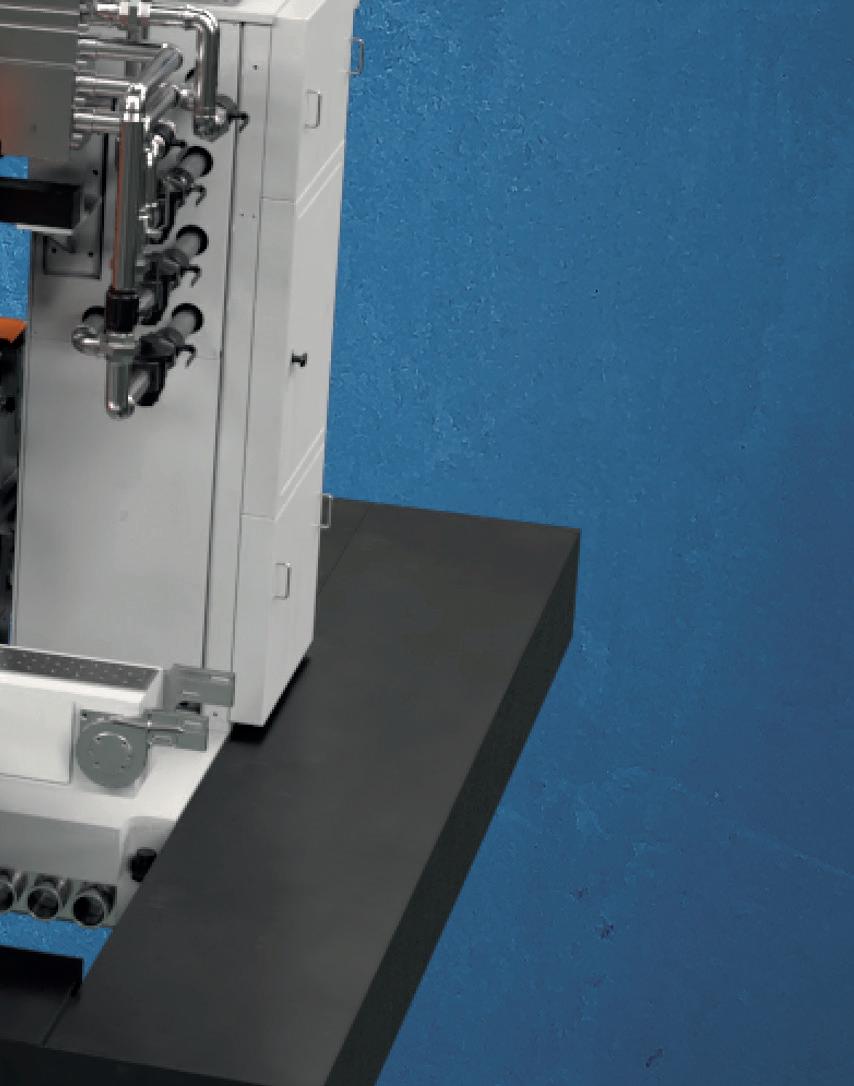

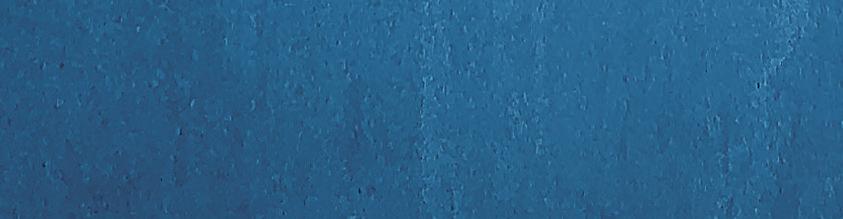

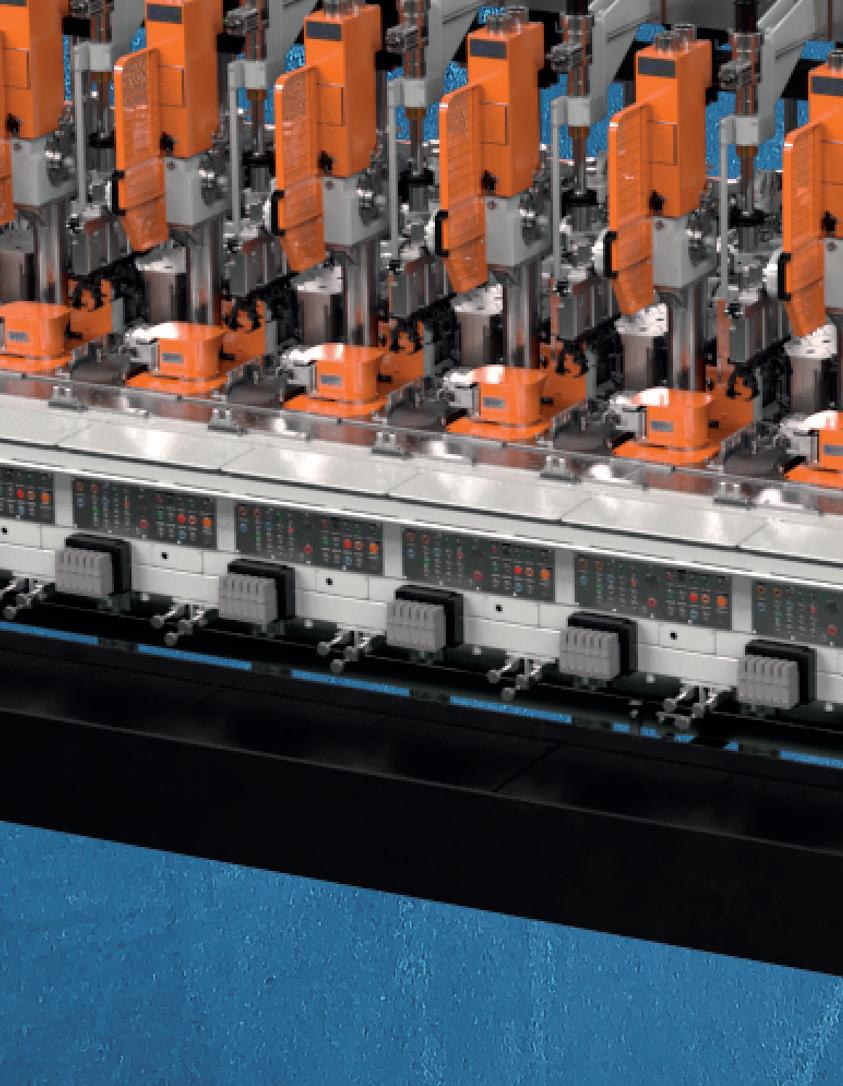
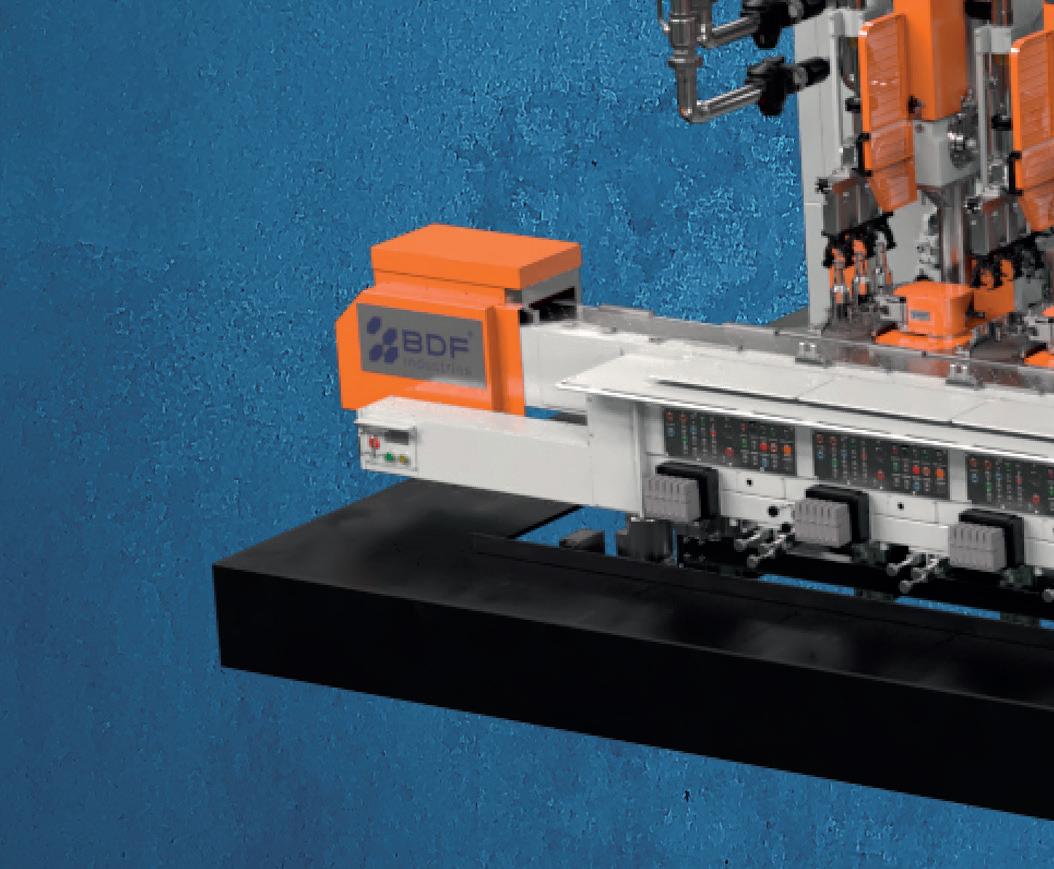

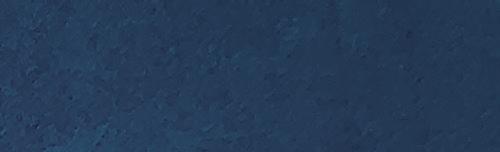

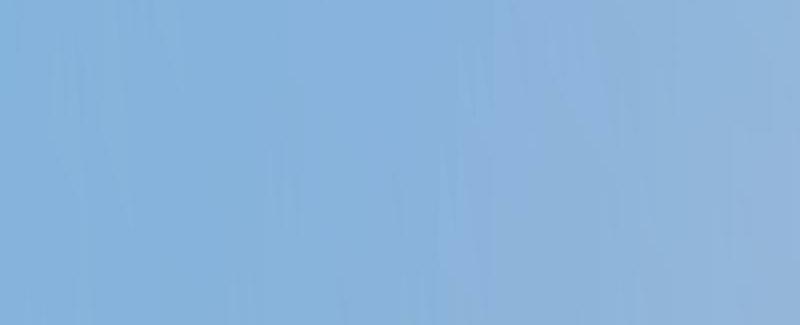

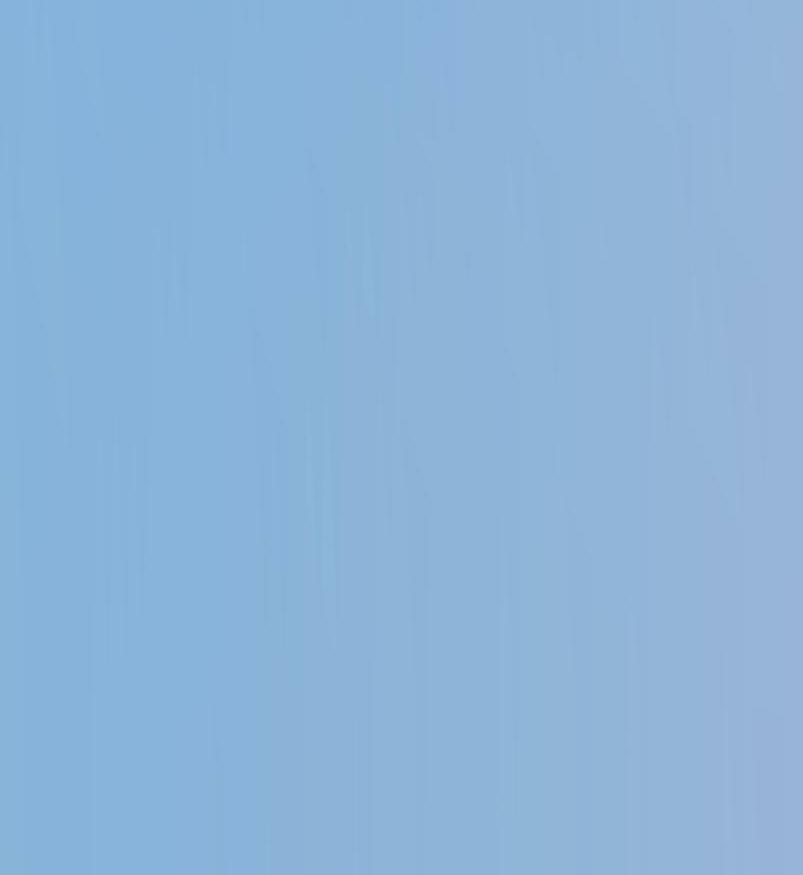
� Contamination in cullet should be kept under control, especially for metals, ceramics, stones, glass ceramics.
� Particle size distribution is also important to prevent bubble forming potential and refractory corrosion
� The most important issue was the composition unstability in cullet mix � Fe2O3 % change in cullet made colour control harder, the change in the ratio of alkaline earth metals may cause workability harder
Recycled glass production practice
� If cullet contains different coloured and composition glasses, some operational interventions should be applied in the batch and the furnace, as previously discussed.
On the other hand, production with 100% cullet, strengthens awareness by decreasing raw material usage, reducing energy requirement and 0.423-ton CO2 / ton of glass emission. �
Glass International September 2022 360 www.glass-international.com Collection, by collecting and recycling the glass that has been used at least once before with the vision of leaving a better world for future generations. The Aware Collection eliminates the need for new raw materials, while supporting the circular economy and reducing the amount of carbon footprint and industrial waste. Through solving the transparency and colour problem of recycled glass in conventional recycled glass production, quality of Pasabahçe is reflected in the collection. Sisecam customers are invited to support the recycling movement of glass waste and to be a part of sustainability (Fig 1).
Apart from these analyses and tests, glass products were evaluated for thermal analysis, CTE, dishwasher resistance, corrosion test, bubble ratio and bubble analysis and striae. When recycled glass composition was compared with normal soda lime production in terms of viscosity values, it was found that both compositions have similar properties at high and low temperatures.Cobaltisadded to have stable colour. Colour difference of recycled and standard soda lime glasses can be seen in figure 1.
One of the most important motivations of the project is to increase the awareness of recycling. As mentioned in previous sections, our world should be protected by saving resources and taking action to decrease CO2 Productionlevel.yield is almost 100% in recycled glass whereas with traditional raw materials, batch yield is only about 83-85 %. This means, global resources can be saved by using recycled glass instead of using batch materials. At the beginning of the project, previous experiences were reviewed, and a literature survey was performed for evaluating possible quality risks. After planning the laboratory studies, cullets which were coming from different sources with various colourants and compositions were analysed. Afterwards, melting was done by sole and by mixing different ratios of cullets to analyse their effect on colour and workability. As a final step of laboratory studies, characterisation studies were carried out to differentiate the effects of cullet on glass properties Then pilot trial was planned in one of the pot furnaces to evaluate different melting conditions and cullet qualities. Glass samples obtained in pilot trial showed that redox of the cullets and contaminants in the cullet have huge effect on colour. Reduced conditions and colored contaminants decrease brightness and lead to change in color parameters. Also, characterisation study was performed on the samples. Finally, some analysis and tests, such as chemical homogeneity, colour homogeneity, optical parameters, dishwasher resistance and mechanical properties were done to compare different cullet sources and compositionsAfterlaboratory studies and pilot trial, another trial in bigger scale process conditions was done in May 2020. In this trial production, different cullet ratios and compositions were evaluated. During that period, furnace pull increased by 30% and cullet ratio increased from 25 to >95 %. Only small number of raw materials added to normalise glass composition. With this trial, >95% cullet usage in glass production parameters reevaluated � Cullet quality limits � Colour tolerance � % usage � Energy advantage � Production conditions � Real samples for quality control tests.Energy requirement for melting changed drastically. Natural gas requirement for melting tank decreased By using 100% cullet, energy saving in the melting end reached up to 31%, which is a remarkable decrease in NG requirement.Someproduction operations were reconsidered for 100% cullet usage. Cullet sorting and choosing representative analysis are important issues for stable production. Cullet ratio should be increased gradually for batch blanket control. Furnace atmosphere control is important especially for glass redox that affects glass colour. Because of lack of knowledge in terms of furnace reaction, cullet quality and ratio are evaluated carefully. For glass products quality, chemical analysis and colour parameters were monitored, periodically. Mechanical properties were also tested, and some actions were taken to improve the quality.
Summarising the main challenges of recycled production:
*Glass Properties Manager, **Environmental Sustainability Manager, Sisecam, www.sisecam.com.trTurkey
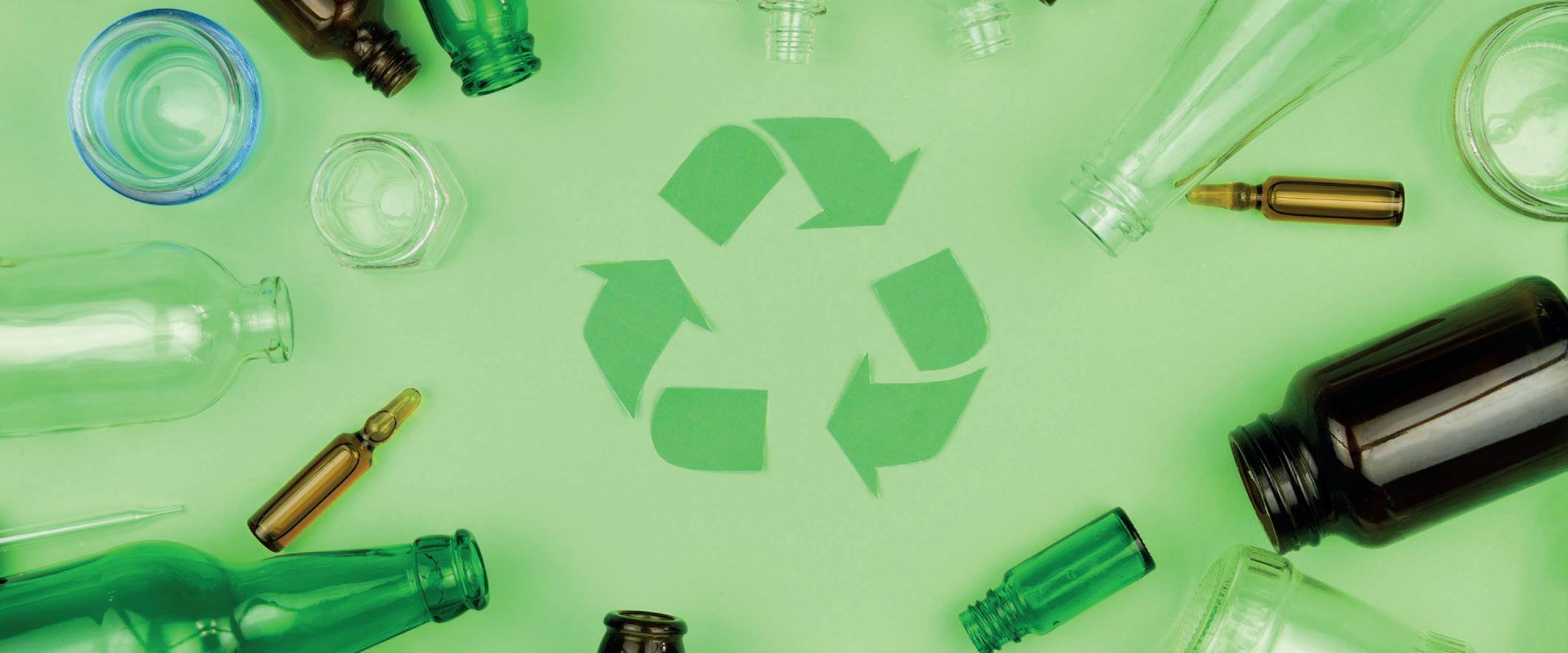
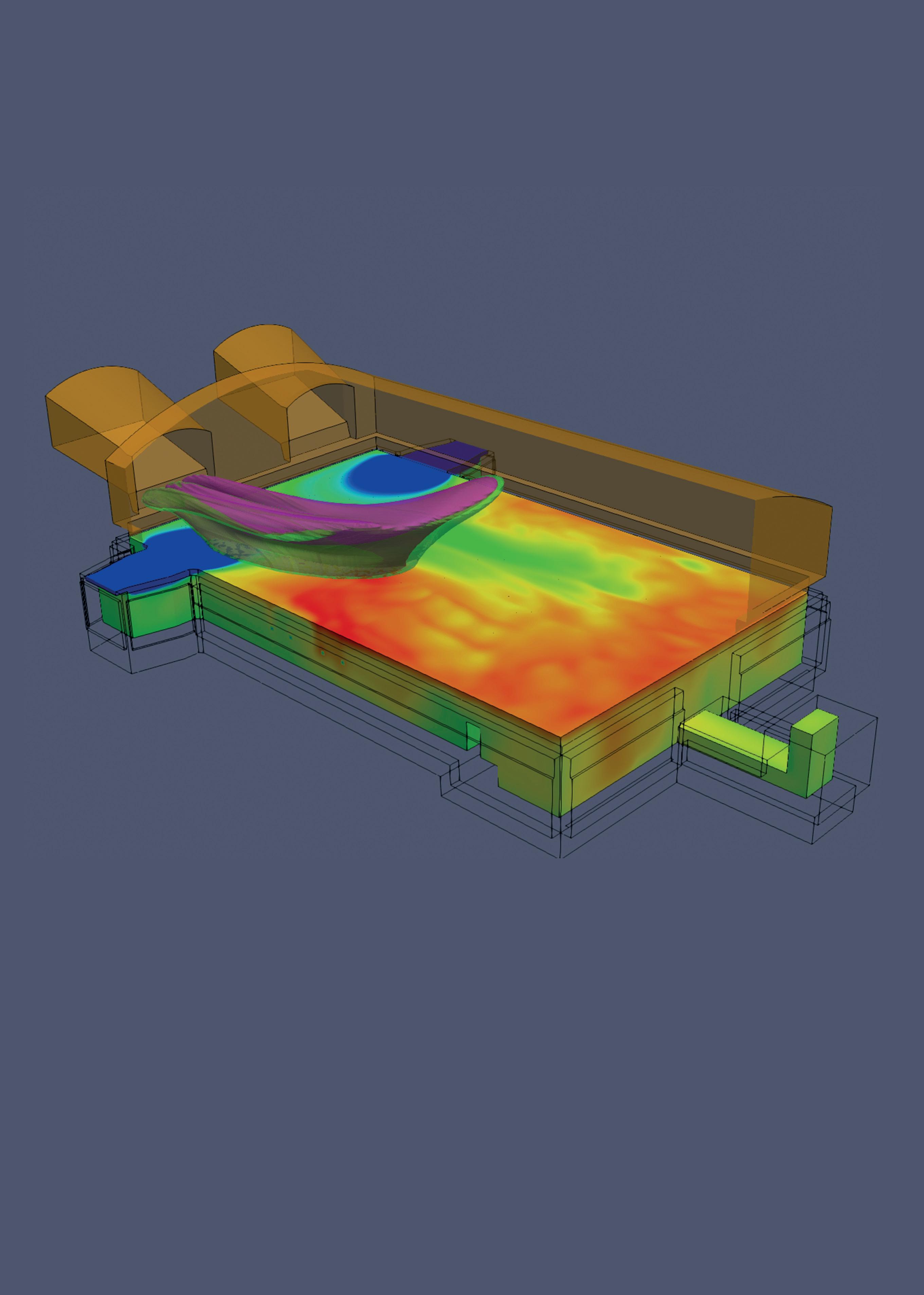
More than 50 million tonnes of container glass are landfilled an nually around the world. Steve comprehensiveinvestigatesWhettingsteel*howamoreCO2strategycouldcreateaninclusiverecyclingsystemfocusedonglassrecoveryandreuse.
Economics has always been one of the main challenges for the recycling industry when it comes to glass, balancing the high cost of recovery and processing with the proportionally low value of cullet. However, arguably a greater challenge for glass recycling is the long chain CO2 cost of delivering glass to a furnace, in many cases the true cost of CO2 is not appreciated or understood, since the claimed CO2 benefit of using cullet does not account for its recovery, recycling, transport, nor the disposal to landfill of the glass which is not suitable for remelt. These CO2 losses can be significant, in the region of $2.64 billion a year globally, in the container glass sector alone.More than 200 million tonnes of glass are produced globally each year, yet less than 40% is re-used for new glass production (remelt or glass wool) due to limited furnace capacity and locations, quality or colour disparity of the glass, 1
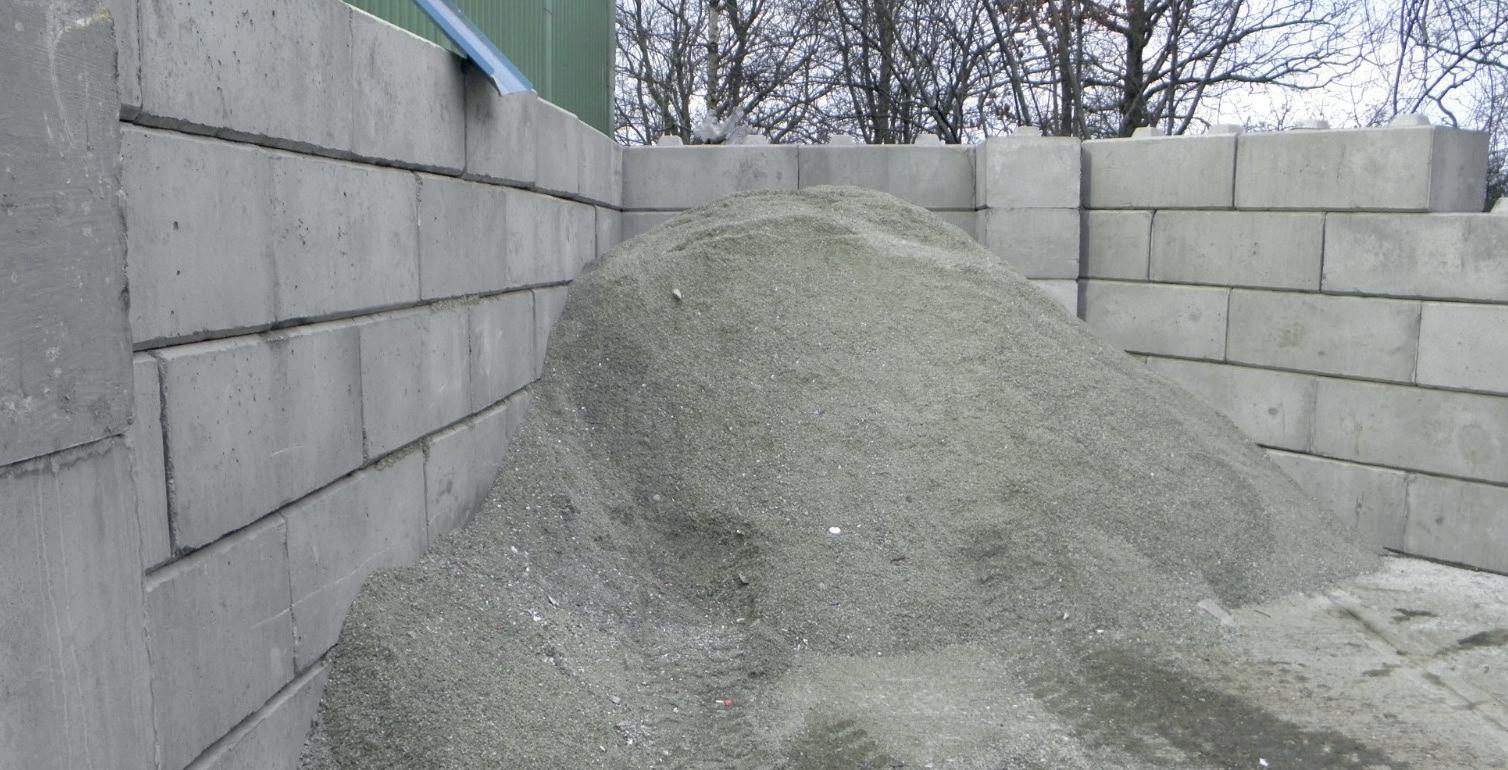
Recycling Glass International September 2022 380 www.glass-international.com
A deep dive into sustainable glass recycling
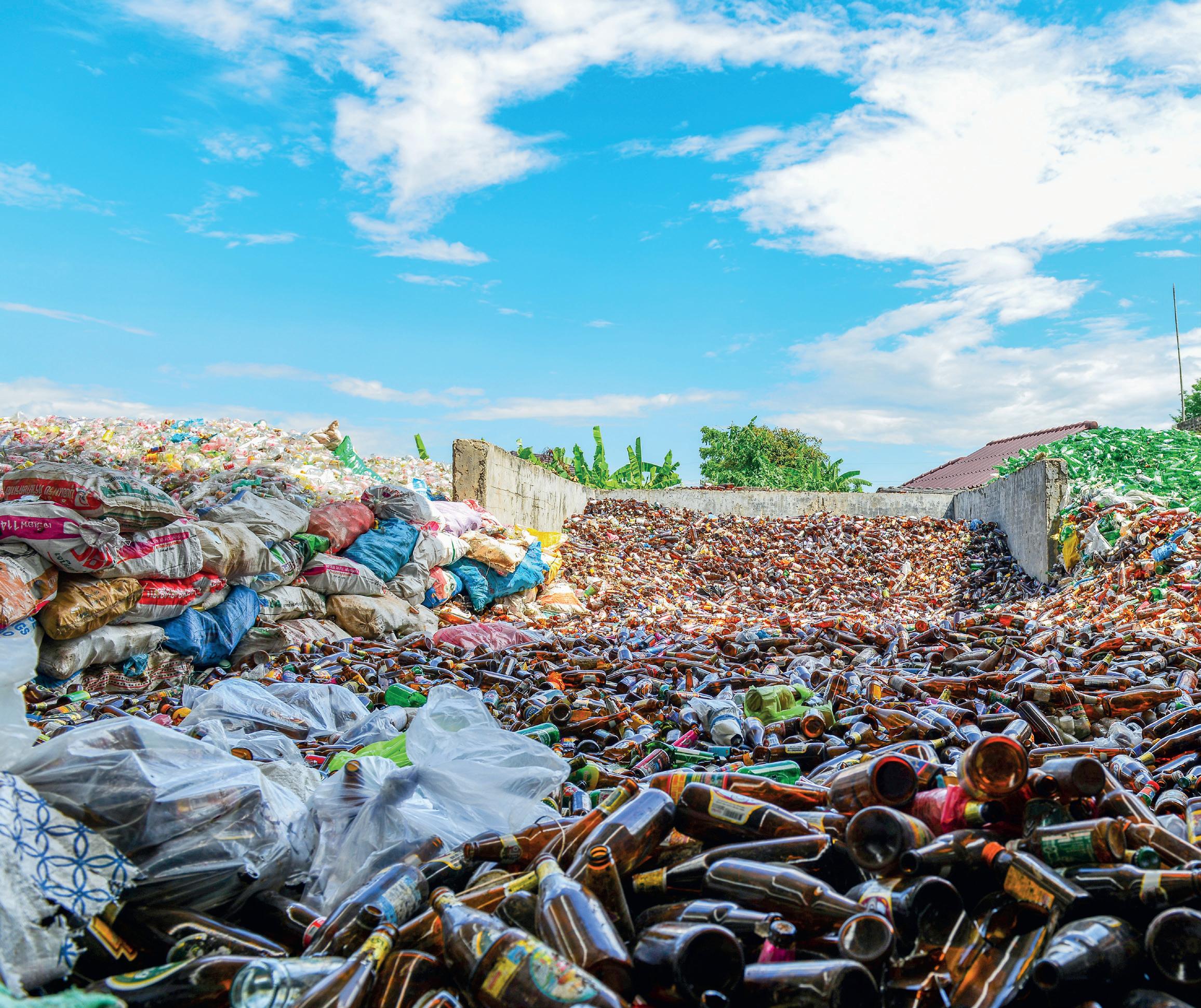
Recycling Glass International September 2022 www.glass-international.com 39
Fig 4. Lettuce crops, suitable for glass-based silicon fertiliser.
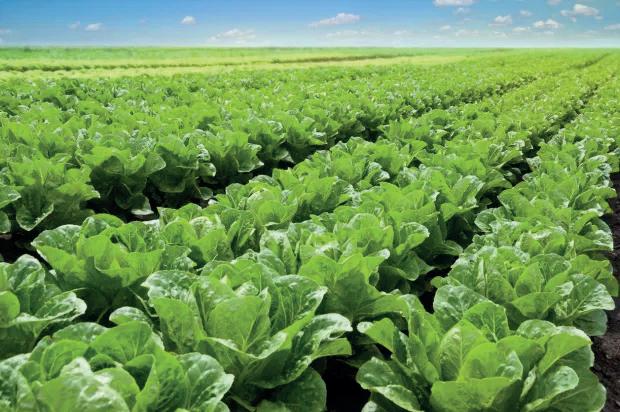
Fig 3. Photovoltaic (PV) cells in solar panels.
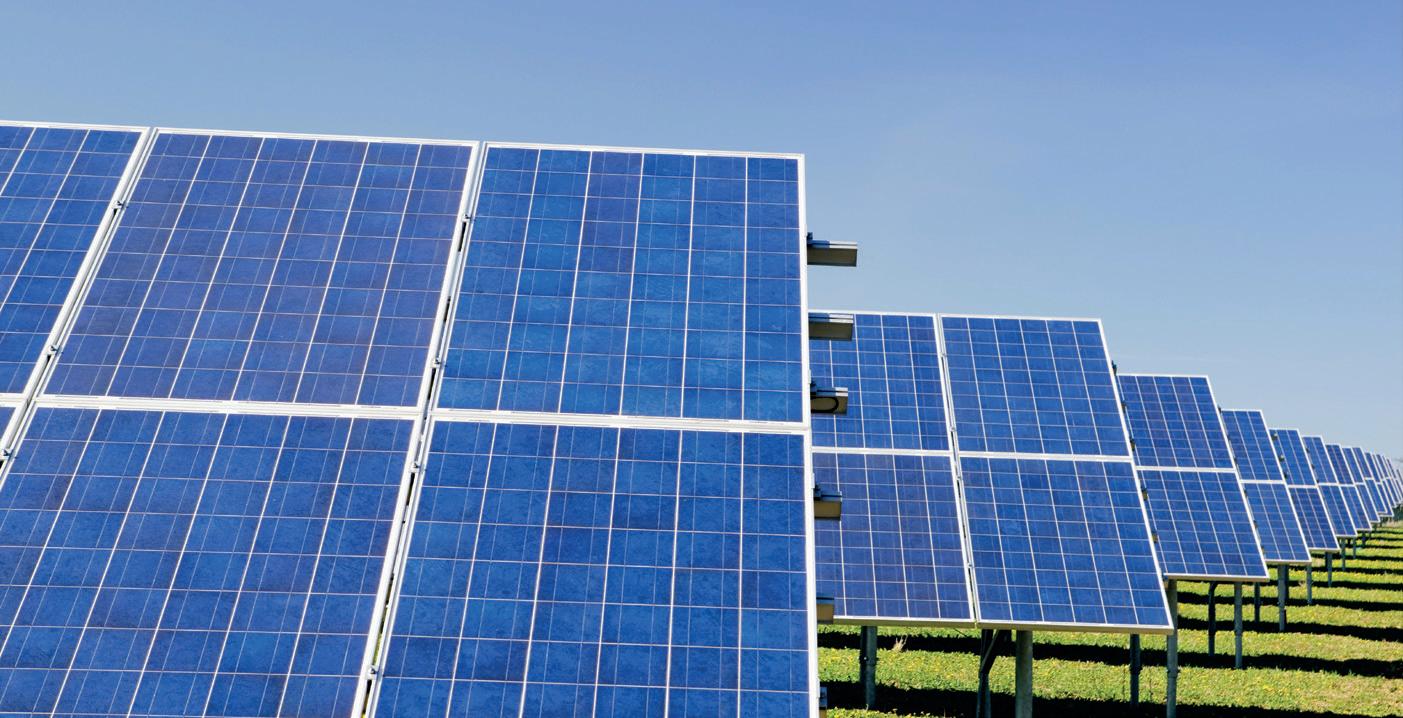
Research & Development
One of the simplest ways to reduce the CO2 associated with glass recycling is to avoid hauling the product around. This is often achieved by locating lots of different activities on the same site. For example, not only glass resizing and processing to separate cullet from different fractions with re-sell potential, but also having a waste-to-energy plant on site or recycling facilities for paper/metal. Larger installations of this kind, where other pieces of the materials’ recovery process might be located alongside or nearby, eliminates the need to continually haul the materials around to processing plants in different locations. (Fig 2)
Firstly, we need to look at the CO2 costs involved in the various stages of collecting, sorting, and recycling glass: from the point where it might be collected from kerbside, transported to a central recycling point, and taken to different locations for segregation or colour sorting.
Considering glass recycling within a more encompassing strategy, such as this, will provide a greater quantity of high-quality cullet across a broader marketplace, while providing ultra-low CO2 materials for multiple diverse markets which are both technically and commercially viable, decreasing the glass industry’s overall CO2 footprint and meeting the challenging 90% recycling target.
The technology is already available to do things differently, and the glass that cannot be used in remelt can be less carbon-intensive than cullet, in addition
More than 50 million tonnes of container glass are landfilled annually around the world. That’s $36 billion of lost carbon credit and $100 billion of lost revenue opportunity. This deep dive will consider how a more comprehensive CO2 strategy will evolve a more inclusive recycling system, one focused on Fig 1. Glass that is unsuitable for remelt due to size and quality will traditionally be sent to landfill, or used as low value aggregate substitute.
Low CO2 For a truly sustainable glass recycling system to exist, low CO2 solutions for 100% of glass entering a recycling facility are required, not just a focus on producing cullet for remelt. By increasing the demand for these alternative low CO2 uses of glass across a broad spectrum of markets, the economic value of waste glass will be enhanced, which in turn will stimulate investment across the entire glass recycling landscape.
maximising glass recovery and reuse. When a system is based on glass location, quality, and market options, while understanding the complexities and market dynamics, a fair and logical approach can be established for improving cullet quality and quantity plus an increase in revenue and investment opportunities of glass historically landfilled or used in low value markets.
Continued>> and the perceived economics. As a result, the rest of the material ends its life in landfill as daily cover or used as a low value aggregate substitute (Fig 1).
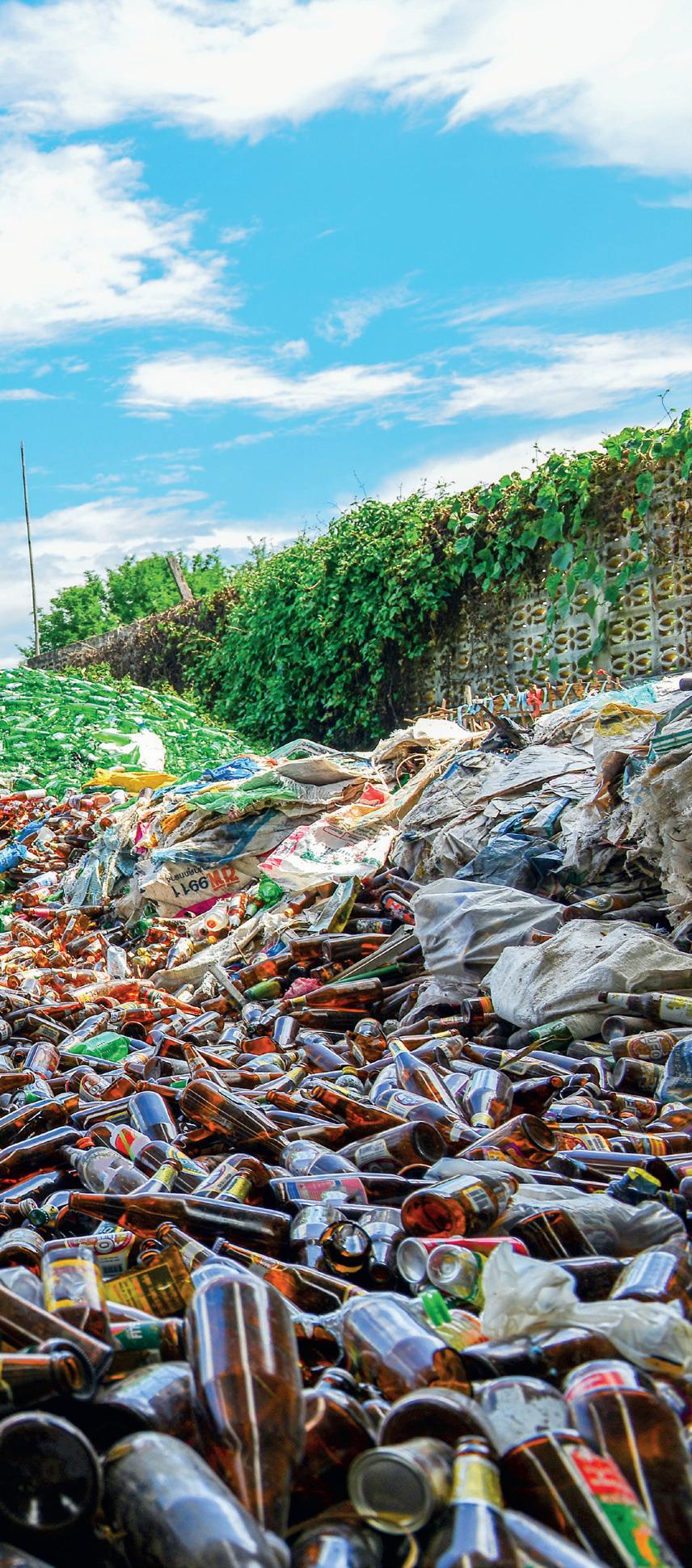
2 3 4
The transportation of waste and the accompanying CO2 is even more of an issue for islands or remote/rural communities, as their waste is traditionally transported or exported elsewhere to be sorted and processed, or sadly sent to landfill due to the cost. Therefore, low CO2 solutions for glass recycling are not only good for the health of the planet but also often financially beneficial too.
A recent EU announcement to increase recycling rates to 90% is a significant and progressive step, one which challenges the industry to consider its strategy and drive investment. Innovation has always challenged the recycling industry to evolve, never has there been greater focus on science and innovation to achieve more with less. Innovation and progressive thinking are developing a clearer strategy for glass recycling, one focused on CO2 and the recycling of all types of glass including containers, flat glass, pharmaceutical borosilicate and photovoltaic (PV) cells (Fig 3).
Fig 2. CO2 in the atmosphere.

The quantity of vials being produced for Covid vaccinations is immense, and innovative technologies, such as Krysteline’s Imploders, can remove aluminium or rubber stoppers, separate and return them, providing the secure destruction of the units.
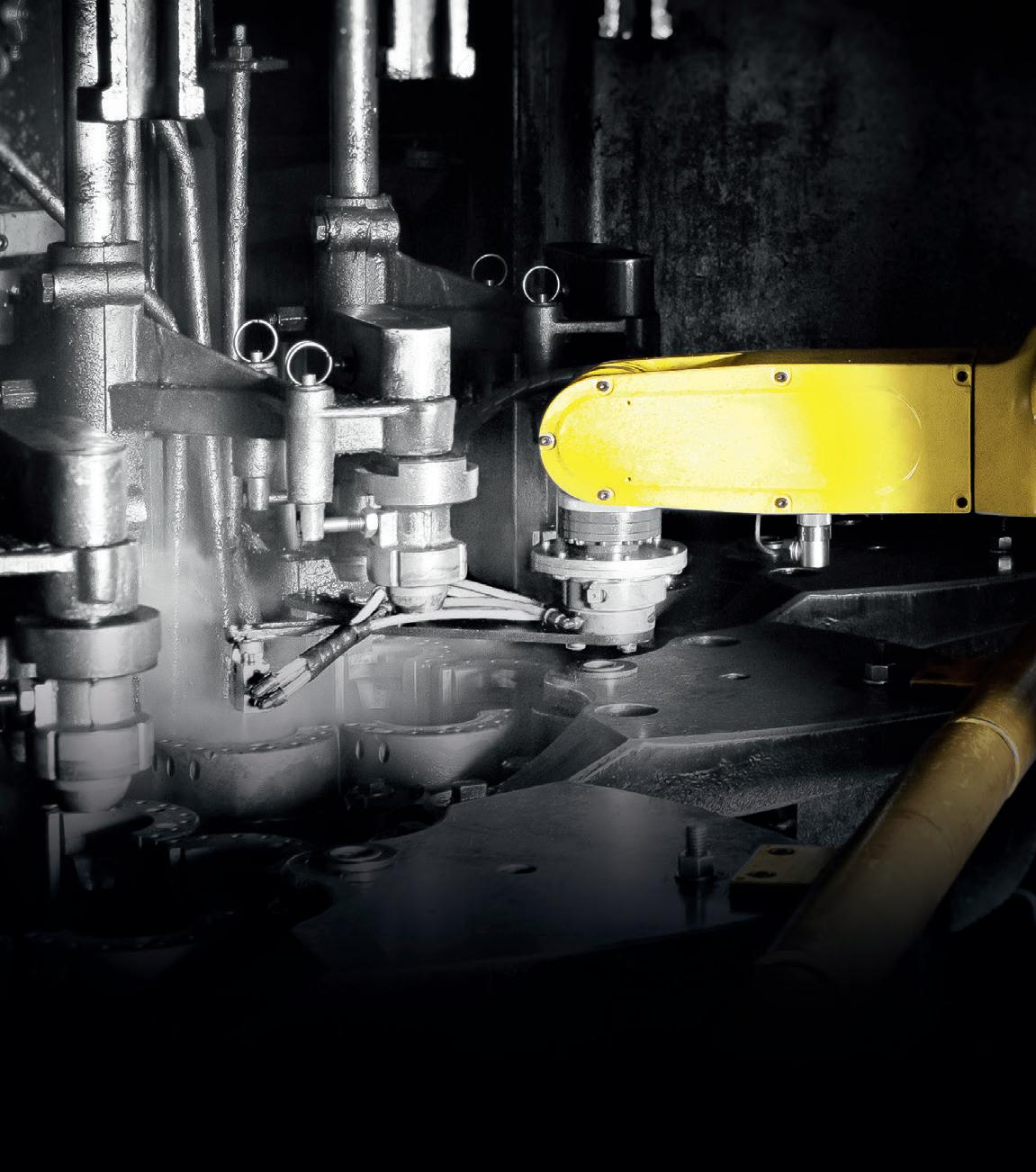
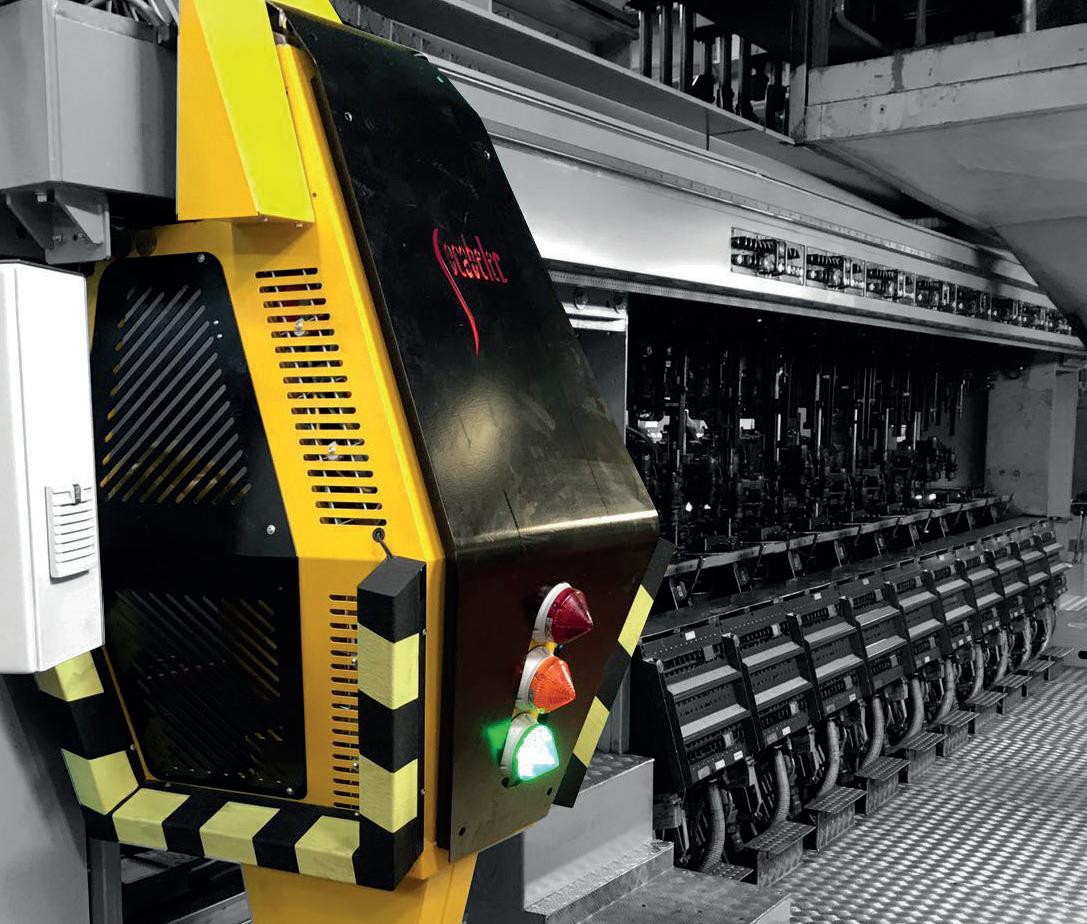
Another recent patented innovation is a glass-based silicon fertiliser. This can be added to compost, with the consequence of silicon leaching out which enhances the growth of certain plants or crops such as salads, rice, and plantains (Fig 4).
*CEO, Krysteline Technologies, Southampton, https://www.krysteline.com/UK
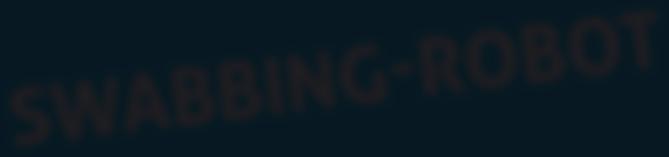
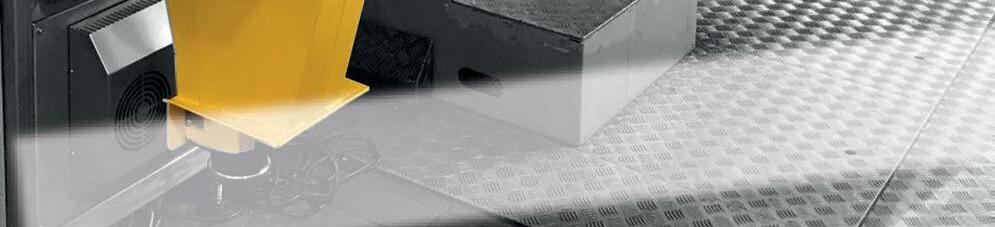
High Value – Low CO2 Solutions
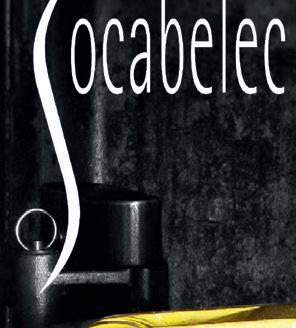
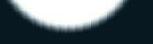
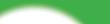

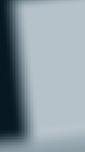

International universities are playing a substantial role in Krysteline’s progress towards a sustainable glass recycling strategy. They provide credible R&D activities in the processing of special types of glass (PV cells, borosilicate, wind turbine blades for example) for recycling and establish revolutionary innovations for the processed glass spanning agriculture, construction, and art.
Higher-value end products include foam glass, a lightweight aggregate-based material which is often used in airport runways and construction sites, and its CO2 cost is extremely low compared to the lightweight materials it replaces.

Krysteline Technologies is proud to be taking part in the UN’s International Year of Glass 2022. Our CEO, Steve Whettingsteel, will be speaking at events throughout 2022 on the topic of sustainable glass recycling as part of the International Year of Glass including the upcoming XX Brazilian MRS- Materials Research Society Meeting (XIII BrazGlass symposium) in September and the International Year of Glass Closing Ceremony in Japan in December. �
The feasibility of approaching High Value – Low CO2 solutions for glass recycling and recycled glass is based on the re-sell value acquired by the <10mm waste glass fractions (and other glass unsuitable for remelt) after they have been extracted from comingled material, processed, and prepared – and readied for any one of a number of alternative end markets.
International Year of Glass
Krysteline’s research partnership with the University of Sherbrooke has led to the development of a product for concrete production, a Green Ultra-High Performance Glass Concrete (UHPGC) that is fully approved to the ASTM global standards. As the world’s recycling industry understands more clearly the CO2 footprint of its products at each part of the collection and repurposing process, it is likely to play a more significant role in identifying low CO2 uses for glass and other materials. Krysteline is well placed to provide sustainable markets across a broad spectrum of locations, all considerate of their CO2 footprint.
Each research project is vital in disseminating knowledge across marketplaces, assessing and developing the market, generating reliable CO2 data, and enhancing technology for cost-effective production.

Glass International September 2022 to potentially acquiring a higher re-sell value if handled appropriately.Oneareawhere there has been a rise in demand recently is in the de-packaging and recycling of pharmaceutical containers.

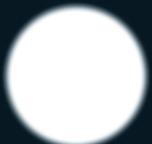
Germanyin2017Julyininstalledswabbing-robotlatest*



*
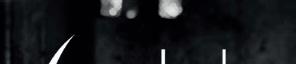





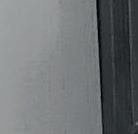
The Society of Glass Technology exists to serve people who are interested in the production, properties or uses of glasses, whether from a commercial, aesthetic, academic or technical viewpoint. It is a non profit making organisation serving a worldwide membership publishing jour nals and text books, organising meetings and conferences on glass related topics. You can now join the SGT by going to www.sgt.org and selecting your jour nal choice and appropriate package. You will also be able to see the history and activities of the society of Glass Technology
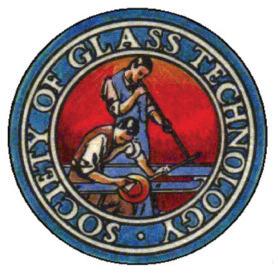
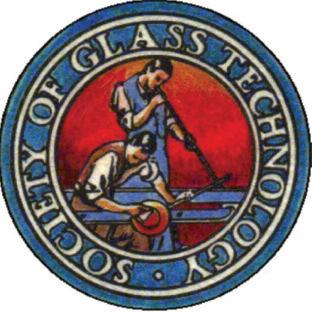
comprehensive
Serving the Glass Community for more than a century www.sgt.org +44 (0) 114 263 4455 9 Churchill Way, Chapeltown, Sheffield, S35 2PY, UK
Society
Join the worldwide network of interests centred on making glass great

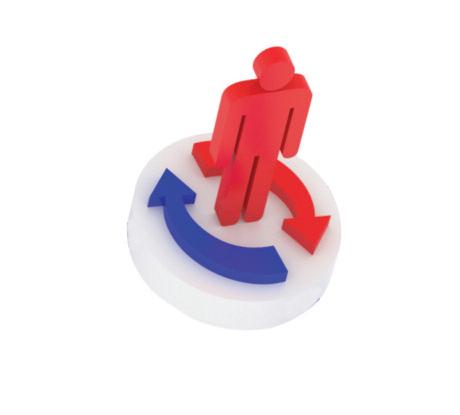

Decarbonisation Glass International September 2022 420 www.glass-international.com
Dr. Matthias Müller*, discusses how hydrogen and electrification of fur naces could help Schott become a climate neutral glass manufacturer.
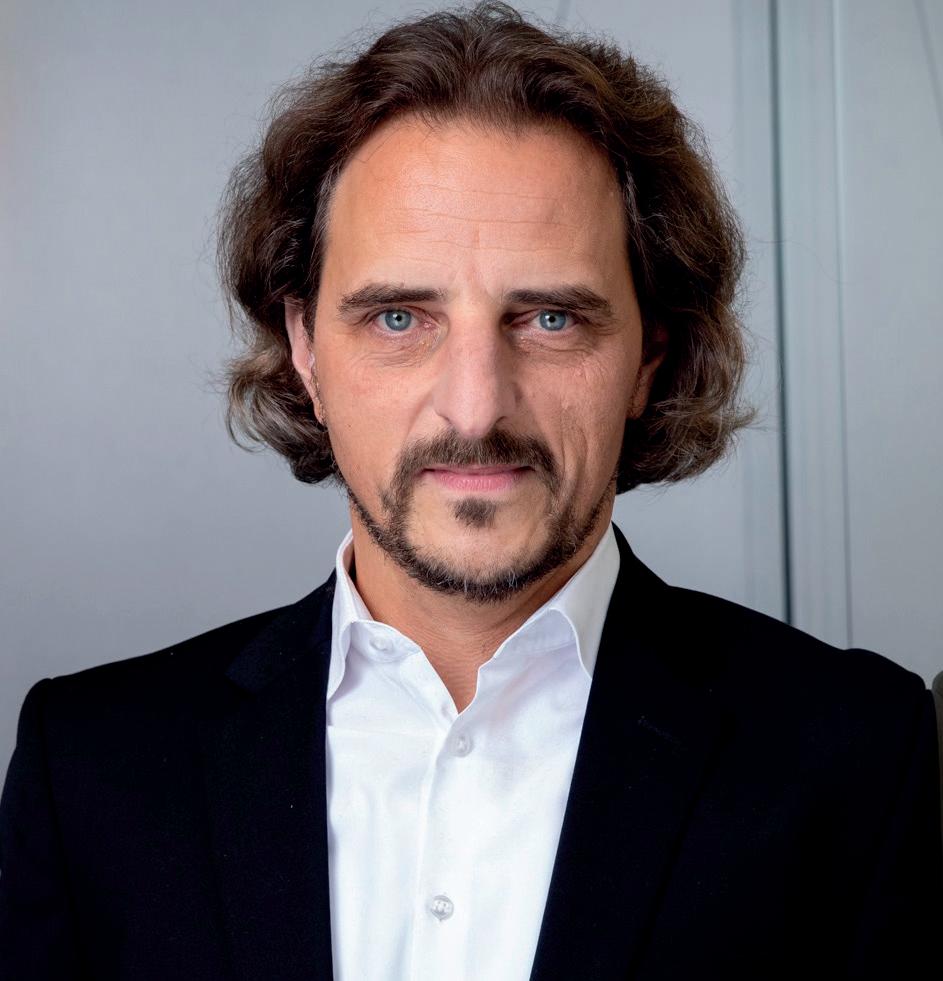
Glass plays a substantial role in modernising our society, but it is also energy-intensive to produce, requiring temperatures of up to 1700° C to melt raw materials in tanks 24 hours a day, 365 days a Today,year.natural gas is primarily used to heat the huge melting tanks - sometimes the size of a house. This in turn produces high carbon emissions. Only a switch to new technological solutions based on renewable energies can remedy this situation. Climate protection Climate change is one of the greatest challenges of our time. The continuing reliance on use of fossil fuels will further deteriorate the environment, and society has a responsibility to tackle this. Everyone, from politicians to private companies, must work together to reduce carbon emissions and combat these dangerous effects.
The change in the climate can be felt in many regions of the world and has led to the fight against climate change moving high up on the agenda of many countries and companies. Furthermore, the current international energy crisis has emphasised the requirement for a strong, diverse energy portfolio that is more independent from fossil sources. In 2020, Schott set itself the goal to become climate neutral by 2030 (based on Greenhouse Gas Protocol scope 1+2). The company is initially focusing on the emissions it can influence itself, but intends to include the other Scope 3 emissions from the upstream and downstream supply chain in the medium term.Based on the Avoid – Reduce –Compensate principle, Schott is pursuing an action plan with four goals: technology change, increasing energy efficiency, switching to green electricity, and as a last step compensating remaining greenhouse gasses by investing in climate protection projects certified to strict standards. We are all aware that making glass production carbon neutral is a huge challenge with many open questions. However, I am deeply convinced that it is the right challenge to tackle.
Speciality glass has enabled the advancement of science through landmark technology like microscopes and telescopes. Other uses of speciality glass often go unnoticed despite their societal impact.
Flagship projects
Decarbonising the speciality glass industry
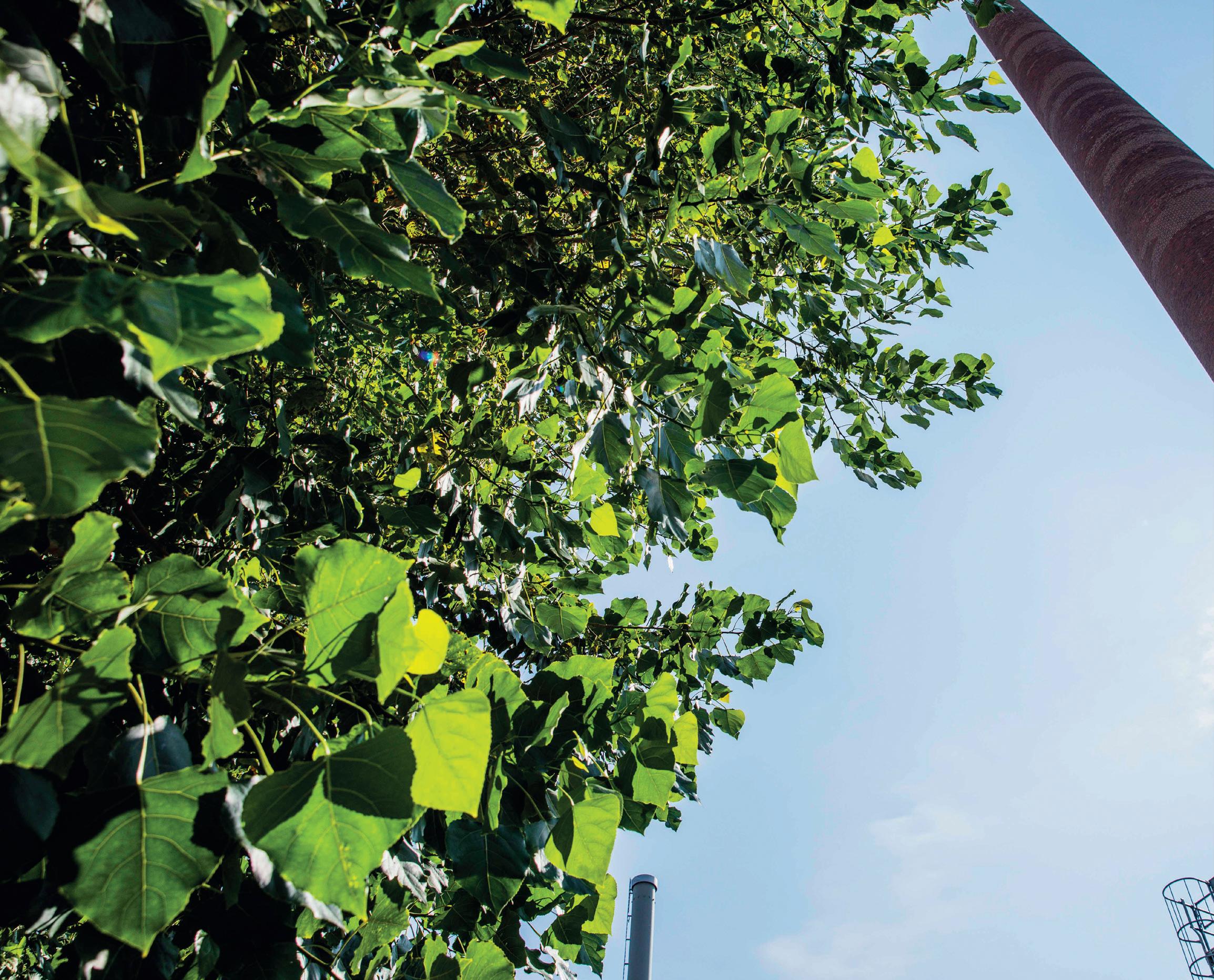
One of the biggest challenges is transforming the production process. In the long term, Schott aims to abandon the use of fossil fuels wherever possible. This change requires rethinking glass production fundamentally. Glass melting is a complex and sensitive process. Different glass properties and qualities require different raw material compositions, melting aggregates, melting methods and forming processes. Different interactions must also be taken into account within the melting technologies currently available. Therefore, depending on the type of glass and product, different scenarios for CO2 neutral or CO2 free production must be developed with solutions that fit exactly in each case.
For example, glass empowers some of the world’s most powerful microchips, stores life-saving medications safely, and enables the lab-on-a-chip devices that have revolutionised healthcare.
Furthermore, the industry needs subsidy programmes to bear the high investment costs that arise during technological change. In addition to funding for research and investments, we also need support for the additional costs incurred by using alternative energy sources, such as green electricity.
Collaboration
However, such a challenge is far too great to master alone. This tour de force can only succeed through collaboration between policymakers and industry players. To manage this change, the glass industry will need reliable framework conditions, especially for the success factors that lie outside their sphere of influence.
*Executive Vice President R&D and New Ventures at www.schott.comSchott,
Over the course of a month, the ratio of hydrogen in the natural gas/hydrogen mixture will be gradually increased to up to 35% by volume in three test phases lasting around 10 days each. Schott will use these experiments to learn more about not only the effects of hydrogen in glass melting processes, but also how we might use higher percentages for production. The tests are planned to take place in the fall of 2022.
The path to carbon neutrality is greatly accelerated by digitisation. Schott currently relies on artificial intelligence and Big Data solutions to make the melting process more efficient. Thanks to new sensors and technologies, mass data recorded at the melting tanks can be better structured, analysed automatically and used to achieve greater process improvements. As a result, engineers and technicians can recognise the complex interactions in the melting tanks more quickly and intervene in a more targeted manner, resulting in greater stability, higher yield, and an overall increase in efficiency.
Decarbonisation Glass International September 2022 www.glass-international.com 43
The Planet 1 project concerns industrial research into the complex interactions in the melting process for speciality glasses for technical applications when the electrical heating component is increased to over 60%. The projects are supported by funding from the Decarbonisation in Industry grant programme of the German Federal Ministry for the Environment. In both new technologies, only green electricity will be used to reduce carbon emissions. The development work is planned in such a way that the first pilot plants can ideally be set up from 2025 onwards. In the case of hydrogen, Schott launched a new research project at its headquarters in Mainz, Germany, to gradually test hydrogen-natural gas-blends in large-scale melting trials at a furnace.
In this trial, R&D experts will gradually replace natural gas with hydrogen.
Now we need to turn our efforts towards modernising our own production process and making it more sustainable.
In the Prospect project, experts develop a concept for a pharmaceutical tubing glass melting process in which the melting units are almost entirely heated using electricity instead of the fossil fuel natural gas.
A better future Glass has existed for thousands of years, but we have only scratched the surface of possibilities with this material. Our industry has already advanced countless products and technologies.

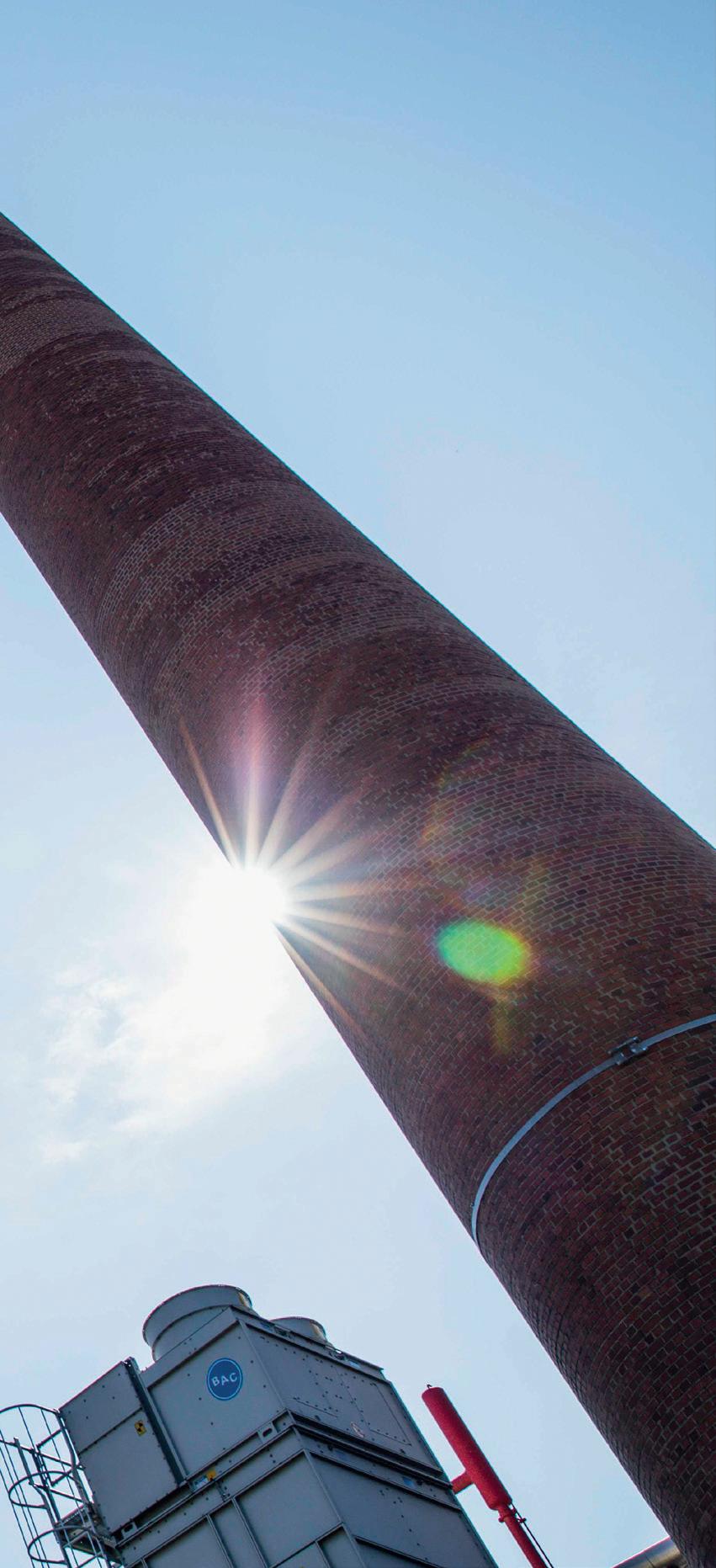
Due to the complex inter-relationships, the development of new technologies is associated with elaborate process simulations as well as considerable risks and uncertainties with regard to the production process, product quality and the necessary financial expenditure. Scientists and melting experts are working on different technological solutions in various development projects at Schott. The company is particularly focusing on hydrogen and electrification technology to heat its melting tanks. In the field of electrification, the company currently pursues two main flagships projects:
Fighting climate change and coming up with more sustainable solutions is a task to tackle for everyone. With the 2030 Agenda for Sustainable Development, the United Nations have set the table for change. Now, the whole glass industry needs to do their part to bring decarbonisation and innovation together to produce a more sustainable future and cutting-edge glass products. �
Technology change is the biggest obstacle on the way to climate neutrality. As a company, we are willing to make strong investments to improve the speciality glass manufacturing process.
The biggest hurdle for technology change in the glass industry is formed by external factors: The sufficient availability of green energy at competitive costs will be one of the most important success factors. We need to have a reliable, continuous and uninterrupted supply of green energy. This requires efficient transmission and distribution networks. Besides green electricity, green hydrogen and – as a bridging technology – bioenergy, are particularly needed.
Digitisation
We have been initiating this process for several years because we are firmly convinced of this transformation. We all know that research projects require stamina. However, I am confident we will be able to set important impulses to produce this fascinating material in a carbon neutral way.
Our initial research is already showing promising results and we are confident we can help to develop solutions for the glass industry. The transformation process toward climate neutrality can only succeed with groundbreaking technological innovations and a high level of development and investment.
Computer simulation started its development in the previous century. The initial goal was to have a tool that could help understand and predict heat and mass transfer, fluid flow, chemical reactions, and other related processes that occur in engineering equipment, in the natural environment, and in living organisms. The processes of heat transfer and fluid flow pervade many aspects of our life. Like in real life, the best approach to solve a complex problem is to divide it into smaller pieces and try to solve it piece by piece. One of the first simulation methods described was based on this principle and worked as follows: a process is cut into many small boxes, and for each box, the laws of physics are calculated.[1] For the complete process, there is information exchange between the boxes. This is the principle of computational simulation tools as we know them today (Fig 1).
Nearly all furnace designs are validated by mathematical furnace simulations. GTM-X is widely accepted simulation software and CelSian is proud that most furnace designers use GTM-X to improve current furnaces performances and work on new designs. The questions that � Fig 1. Example of an energy flow balance over a control volume (Patankar).
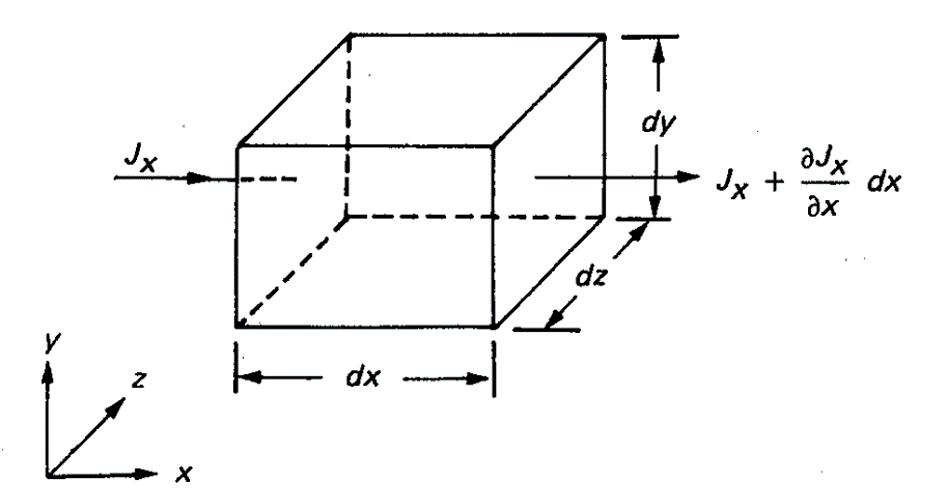
� Fig 2. US NOAA, a model based on the ocean and atmosphere interactions.
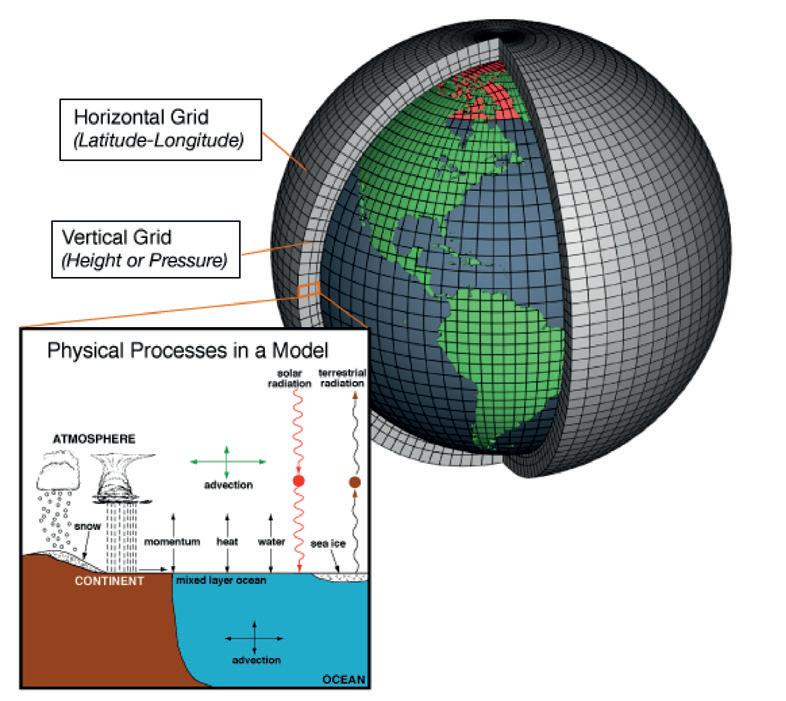
CelSian has developed a simulation software, GMT-X, for glass furnaces. Andries Habraken* outlines how the software’s dedicated models allow it to accurately describe the inside of a glass furnace.
Glass furnace simulation CelSian developed simulation software for glass furnaces. This simulation software, named GTM-X, is similar to the software used for the weather forecast or the one used in the automotive and airplane industries, but it is equipped with dedicated models that allow it to accurately describe the phenomena inside a glass furnace.
Furnaces Glass International September 2022 440 www.glass-international.com
Furnace simulations to assist in daily operation
Fig 2 shows an example of a climate model.[2] The Earth’s atmosphere is cut into a finite number of connecting blocks, and in each block, equations are solved to describe the local situation. The model includes all the basic components of the climate factors (atmosphere, ocean, land, and sea ice). The boundaries of this model lie in the energy coming from the sun and the heat losses toward the surrounding space.Weather forecast models are incorporated into our daily life. We use them to schedule activities or decide how to commute to the office for instance.
Data from laboratory experiments and many years of field experience is used to define and validate dedicated models like the model for the batch blanket[3] and the model to calculate the dissolution of sand grains.[4] CelSian’s laboratory is supporting the modelling of cold top furnaces, as the request for full electric furnace technology is rapidly increasing (Fig 3 This). simulation software is used inhouse by CelSian’s engineers to support process improvement projects, as well as by the engineering teams of several glass producers and furnace designers. Continuous developments are driven by feedback from the industry, like the implementation of a special radiation model needed for low iron glass melts.[6]
The weather forecast is a well-known example of a simulation tool that is used to predict wind, rain, and temperatures.
The simulation as described above is almost as fast as in real-time, but still too slow to steer the glass furnace directly. For direct control of the furnace, a much faster model is created from the CFD model, by performing a series of step tests on the digital twin. This method is safe
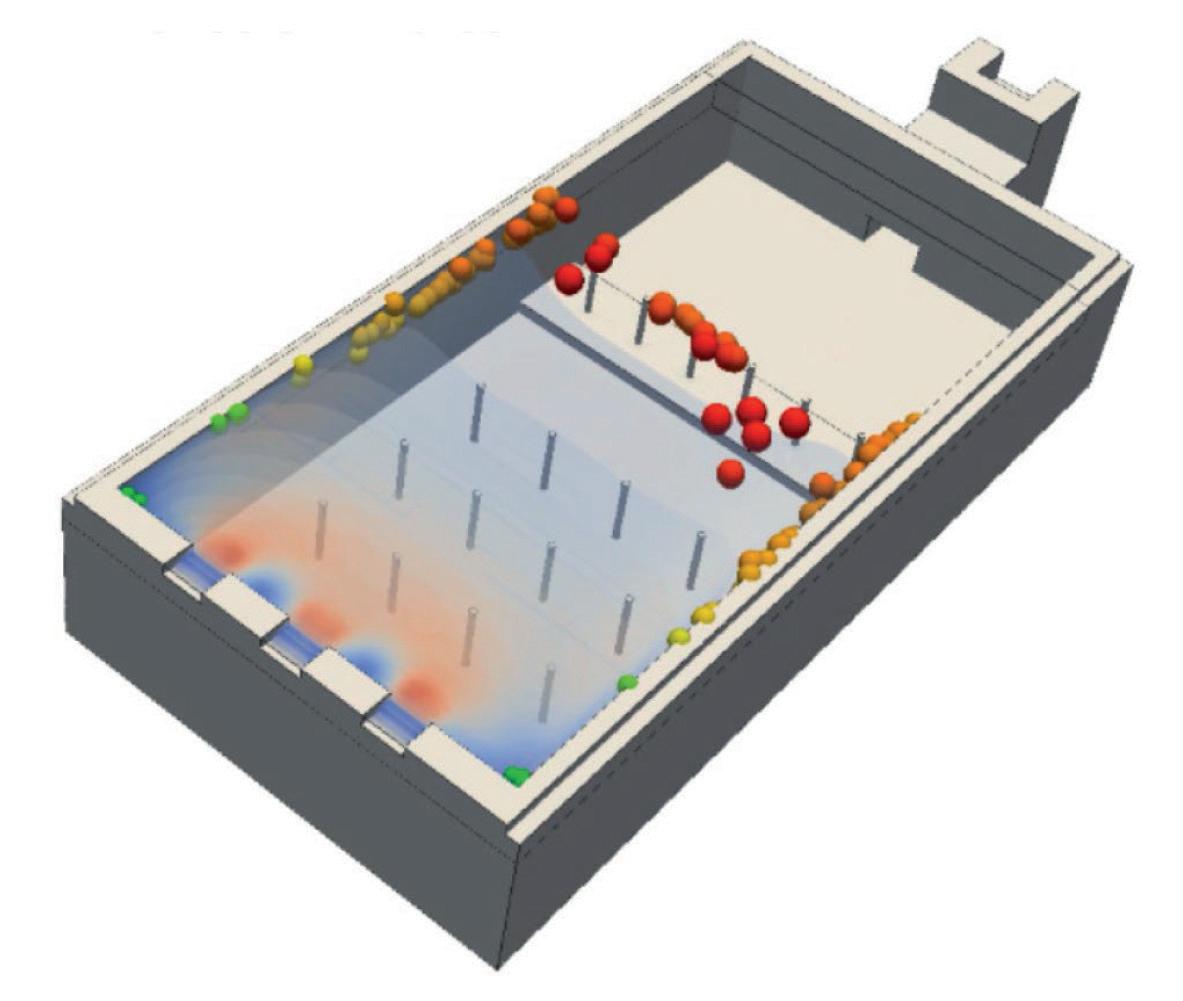
� Fig 4. Example of a hybrid furnace design (courtesy of Fives Stein).
� Fig 6. Time transient modelling of a colour change and the impact on temperatures.
Reducing carbon footprints is one of the largest challenges that new furnace designs will need to tackle. Current initiatives focus on reducing energy use and investigating alternative energy sources like biofuel, electrical energy, and hydrogen. Although the best choice will most likely be driven by availability, technical challenges can be solved by computerIncreasingmodelling.theamount of electrical boosting energy in a conventional furnace should not be done without carefully checking the impact on product quality. The flow of the glass melt is driven by temperature differences, and the wrong location of the electrodes can lead to production issues (Fig 4).
Having a time changing computer model opens the road to other applications. The model predicts how and when changes occur as a result of a change in the process. As the response of a glass furnace is very slow, it is difficult for a furnace operator to understand how the furnace responds. The dynamic computer model is a very helpful tool to support the operator. It is a digital twin of the real furnace, providing many virtual sensors beneath the melt surface.
Solid inclusions, bubbles, and blisters are investigated in a laboratory, and their source of origin can be traced via computer modelling. Once the cause of a defect is known, possible solutions are safely tested in the computer model, leading to the safest and most promising solution to be applied in the real furnace. This approach has been proven in hundreds of projects. For furnaces in which the product colour changes, it is profitable to reduce the time at which the product is out of the spec. Fig 6 shows a model of a float furnace that is in the process of a colour change. The simulation reveals the change in iron oxide in the glass melt, which affects the product colour but also the radiative properties of the glass smelt. These properties are important to consider as they have an impact on the crown temperatures in the furnace. The simulation shows how the energy needs to be corrected to prevent overheating the crown.
� Fig 5. Modelling and validation of hydrogen combustion.

Future-proof furnaces
Using an alternative energy source like hydrogen leads to questions like burner design, the impact on product quality, and the consequence on the furnace’s lifetime. Fig 5 shows the result of a project in which modelling is combined with lab-scale testing to look at the impact of hydrogen combustion on heat transfer.
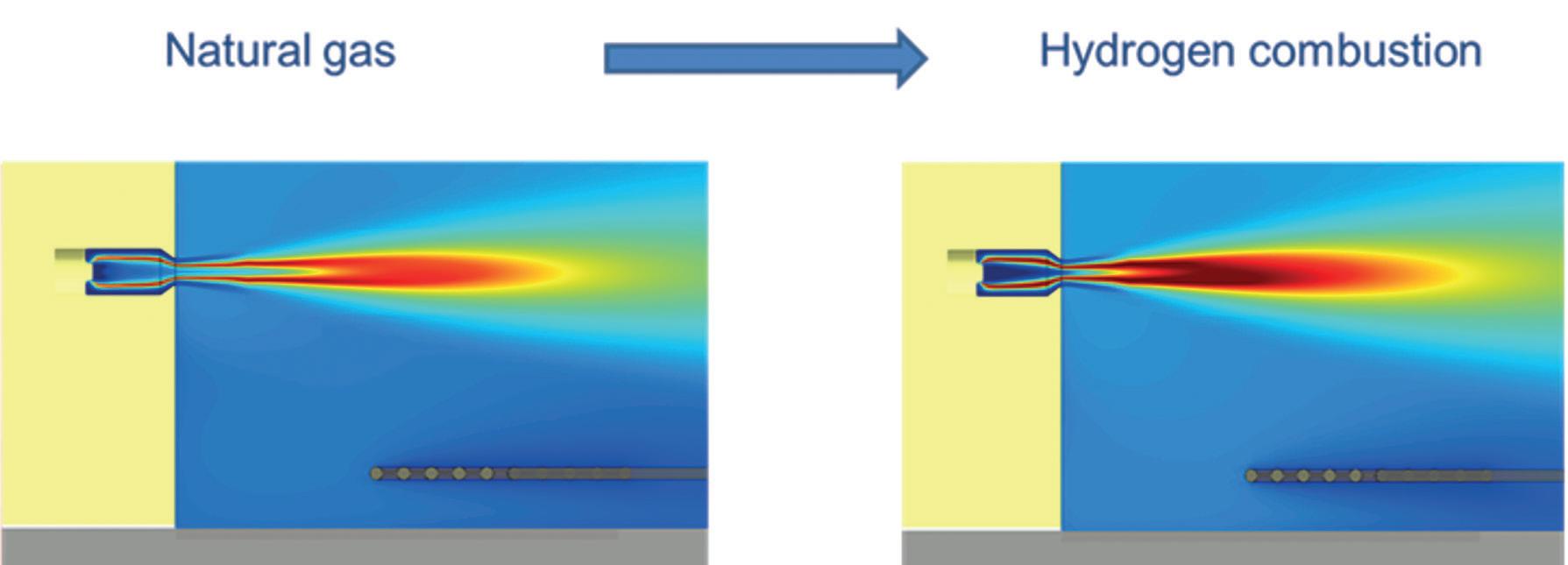

� Fig 3. The cold top furnace experiment in CelSian’s laboratory.
Support daily production
GTM-X answers are related to low energy use, good product quality, low emissions, and a long furnace lifetime.
Furnace control
Furnaces Glass International September 2022 www.glass-international.com 45 Continued>>
6) A.M. Lankhorst, L. Thielen, P.J.P.M. Simons, A.F.J.A. Habraken: Proper modeling of radiative heat transfer in clear glass melts. In: 73rd Conference on Glass Problems, ed. by S.K. Sundaram (Wiley, Chichester 2013) pp. 249–258
7) L. Huisman: Control of Glass Melting Processes Based on Reduced CFD Models, PhD Thesis (Technical University TU Eindhoven, Eindhoven 2005)
5) R.G.C. Beerkens: Analysis of elementary process steps in industrial glass melting tanks – Some ideas on innovations in industrial glass melting, Ceram. Silik. 52(4), 206–217 (2008)
Hill Book Company 2) National Ocean Service, a model based on ocean and atmosphere interactions, January 21, 2021.
Furnace support Process optimization Training and R&D
www.celsian.nl
Glass experts
3) A.J. Faber, R.G.C. Beerkens, H. de Waal: Thermal behaviour of glass batch on batch heating, Glastech. Ber. 65(7), 177–185 (1992)
Celsian’s aim is to minimize the cost of making glass for end users and the environment. We have an agile team of glass experts using proven methods like furnace modelling, laboratory measurements and practical furnace health checks to optimize glass melting processes. We also train operators and glass technologists through our standard course, dedicated programs and various e-learning modules. We strive to be the best partner for optimization of glass production worldwide.
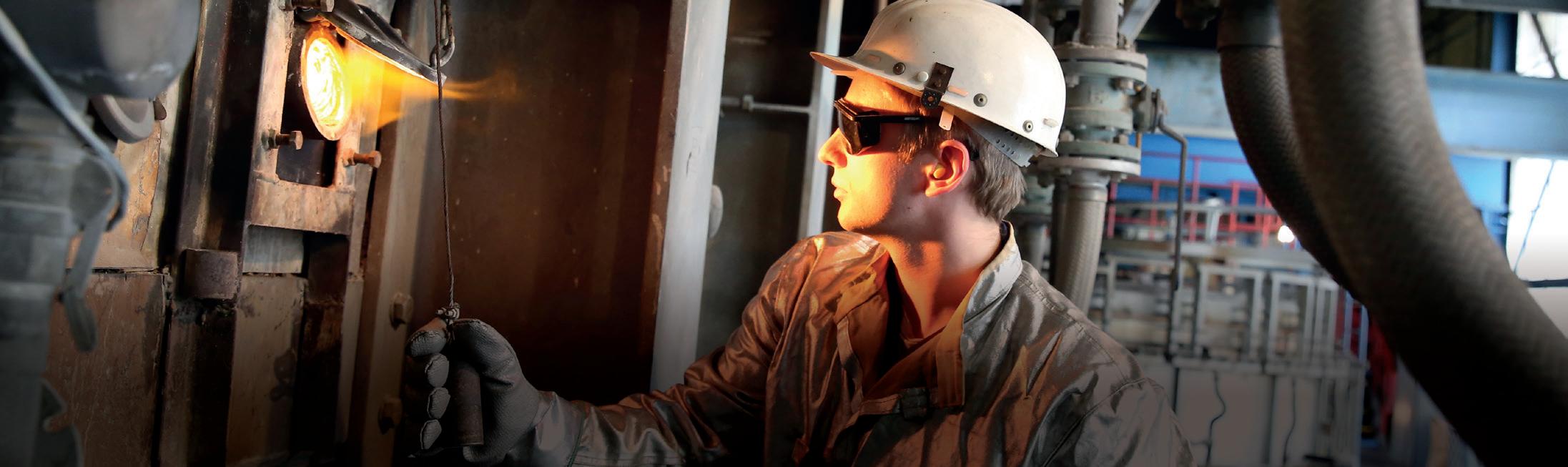
4) R.G.C. Beerkens, H.P.H. Muijsenberg, T. van der Heijden: Modelling of sand grain dissolution in industrial glass melting tanks, Glastech. Ber. 67, 179–188 (1994)
References 1) Numerical heat transfer and fluid flow, Suhas V. Patankar, 1980, McGraw� Fig 7. Using a detailed furnace simulation to generate a fast and accurate control model.
[7] By using this technique, it has been proven that the standard deviation for average glass melt temperatures reduced from 1° C to 0.25 °C. By using the controller, temperature stability is achieved and the unstable period after a large process change, like a job change, is reduced to a minimum. If you are interested in the services and software CelSian offers, please contact us and we will find the best solution together. �

Furnaces Glass International September 2022 460 www.glass-international.com for the furnace, does not impact product quality, and results in a control model without information from unknown disturbances.Thereduced model can be used directly in an MPC to estimate glass melt temperatures in the furnace, and change the setpoints to keep these temperatures stable and within the allowed bounds.
*Segment Leader of Process Optimisation, CelSian, Eindhoven, www.celsian.nlNetherlands
In alignment with their commitment to reduce energy consumption and environmental footprint, glassmakers are accelerating the transformation of their production tools to reach carbon neutrality. Depending on the market, type of furnace, glass quality requirements and the local availability of alternative energy sources to replace fossil fuels, the industry is seeking to increase the energy efficiency of furnaces and exploring new melting technologies. High electrical boosting could be used in multiple furnaces to decrease fossil fuel consumption and CO2 emissions. Recent trends suggest the proportion of electrical power in the energy mix of furnaces will increase in years to come (super boosting, hybrid furnaces…) and several glassmakers have switched to fully electrical furnaces.
� Fig 1. Corrosion behaviour of ER 1685 RR AZS in sodalime glass. � Fig 2. Effect of glass temperature profile on soldier block corrosion after 5 years
Electrical boosting on refractories
Corrosion of refractory materials
An increased electrical energy share in glass furnaces leads to an increase in glass temperature and velocity in the lower part of the glass bath. Such changes will have a significant effect on the corrosion of tank refractories. Thanks to an extensive database of dynamic corrosion tests results, and industrial experience and measurements, SEFPRO was able to establish specific corrosion laws, linking the corrosion rate of refractories in contact with glass with the temperature of the interface between the glass and the refractory material (Fig 1). The mentioned corrosion laws were then included in a broader 2D simulation model allowing to estimate the corrosion of sidewalls in glass furnaces.
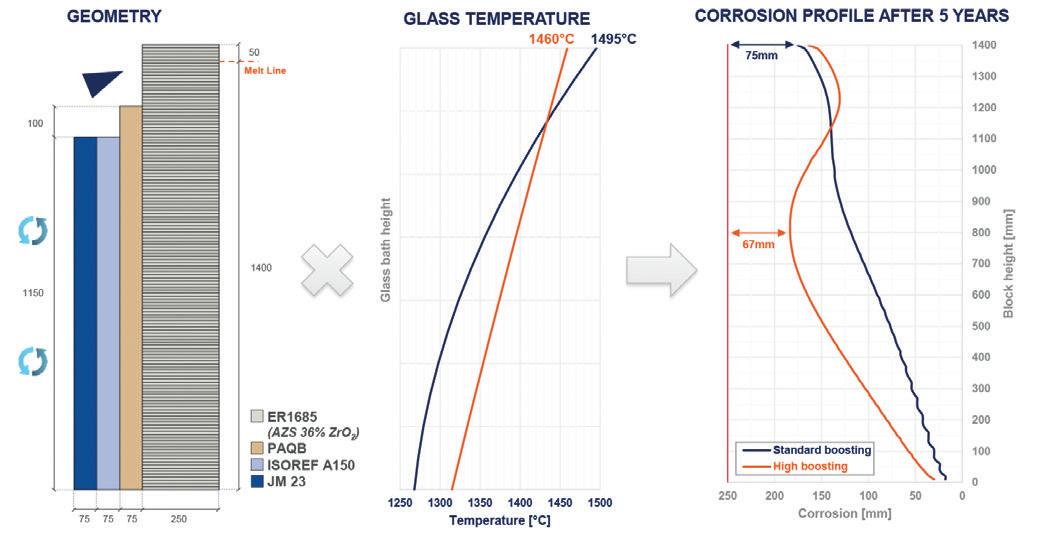
Scenario 1: Applying a larger patching tile during maintenance, covering the entire height of the block and removing insulation layer behind, allows to reach the 10-year lifetime target with a safe refractory thickness on the entire height of the block (Fig 4).
Nevertheless, removing the insulation
Stephane Schaller*, Michel Gaubil*, Isabelle Cabodi** and Pierrick Vespa**
Furnaces Glass International September 2022 www.glass-international.com 47 Continued>>
The model results were then validated through studies and collaborations with glassmakers, using industrial data (hook measurements, 3D scans) for different furnace architectures (end-fired, crossfired, cold-top), glass types (sodalime, opal, borosilicate) and refractory materials. The developed numerical tool could assess the modifications in refractory materials corrosion when varying their operational environment (glass temperature and distribution, insulation, air cooling).
In the case of high electrical boosting, with the evolution of glass – refractory interface temperature profile, the critical corrosion point is shifted toward the bottom of the block. After some time, a new critical point is located at about midheight of the block, below the area covered by the typical patching tiles, leading to a final refractory thickness of 34mm after 10 years of campaign, as illustrated in Fig 3, for the applied parameters of this specific study. Such changes in blocks’ corrosion highlight the necessity to adapt furnace design or maintenance strategy to maintain safe refractory thickness at sidewalls during operations. Both scenarios are simulated hereafter.

The following results assess the effect of high electrical boosting in a given configuration (adapted from sodalime end-fired furnaces) and their consequences on industrial operations and lifetime. Numerical simulation of soldier blocks’ corrosion According to simulation results, modifications of the glass bath’s properties due to electrical boosting leads to a change in the corrosion profile of the soldier blocks (Fig 2).
discuss how the increased use of higher electrical boosting in furnaces could impact refractories. Using numerical simulation, they found increasing the share of electrical boosting will have an effect on soldier blocks’ corrosion.
In standard conditions, the critical corrosion point is located at the melt line. The usual way to manage soldier block corrosion during campaign is to apply a patching tile on the top part of the block and pursue operations.
� Fig 5. Improved initial design with 350mm, ER 1711 RT void-free block & reduced insulation.
The simulation of this specific case highlights the importance of optimised initial design, specifically regarding insulation and block size. A well-designed insulation package kept for the entire lifetime of the furnace appears to be more efficient than running a bare block after over insulating during the first part of the campaign.Finally, high electrical boosting corrosion profiles point out that the use of a void-free block is mandatory to reduce the effect of shrinkage cavity on the corrosion rate. The corrosion model presented does not account for the effect of shrinkage cavity on corrosion rate. The actual corrosion of partially filled (RN or RR) refractory blocks during operations might therefore be higher than anticipated, specifically in the bottom part of the block.
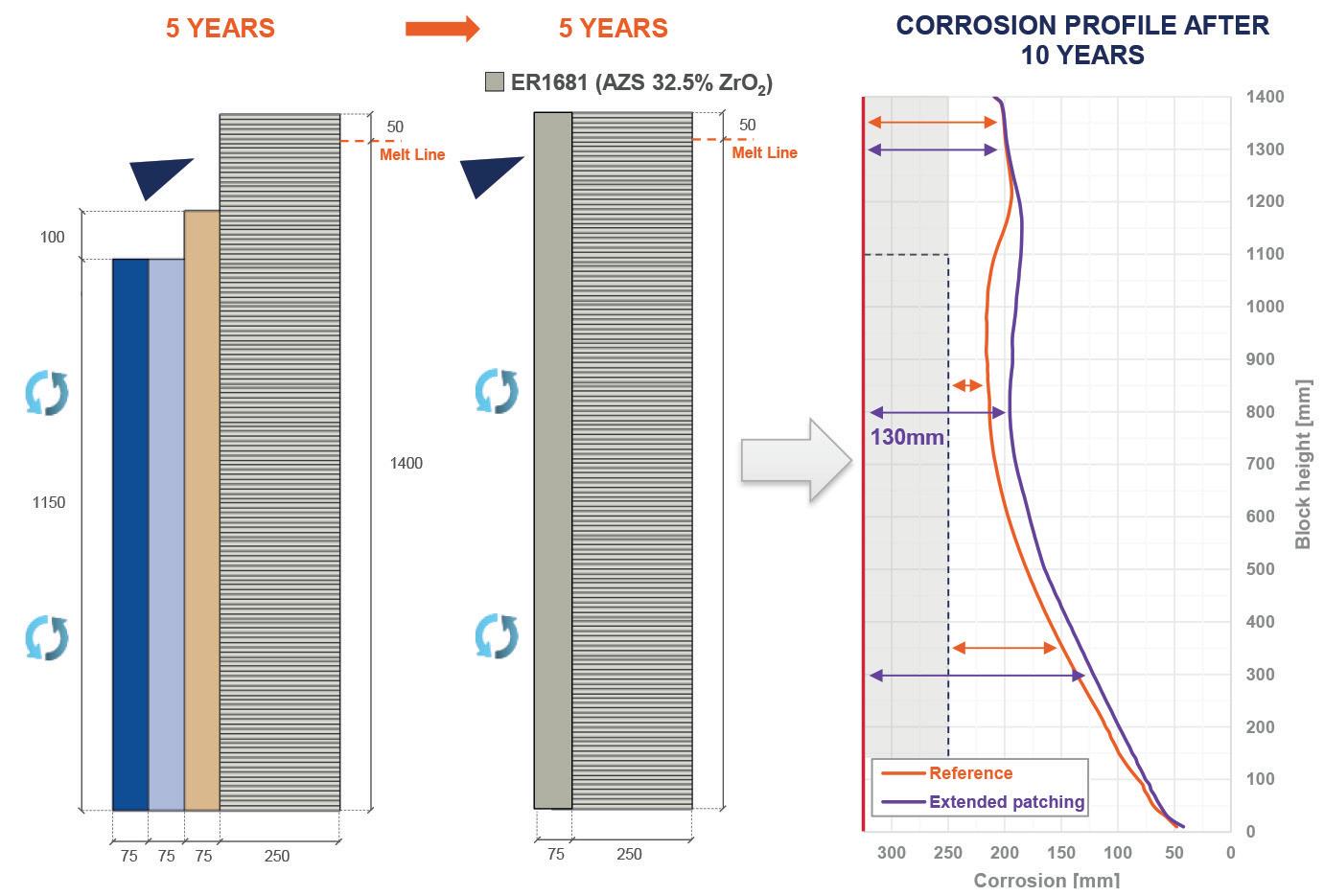
The cases studied represent only two options among the vast range of possible alternative designs. Every furnace being unique, SEFPRO can provide calculations for specific sets of operating conditions to reach the best compromise between energy losses, investment cost and furnace lifetime. �
*SEFPRO, France, www.sefpro.com **Saint-Gobain Research Provence � Fig 3. Effect of glass temperature profile on soldier block corrosion after 10 years. � Fig 4. Application of a larger patching tile & insulation removal.
Furnaces Glass International September 2022 480 www.glass-international.com in the bottom part of the block results in an increase in thermal losses for a total of 855 MWh/m² over the 10 years of operations in the study’s calculation conditions. The additional losses will need to be balanced by increasing energy consumption and, therefore, operational costs and CO2 emissions.
Scenario 2: A second option to increase lifetime of the soldier block assembly consists in modifying the initial design of the block. The example presented here (Fig 5) shows a thicker block (350mm vs 250mm), made of a higher AZS grade and void-free casted. The initial insulation package is also reduced by removing the third layer present in the initial design.
The final residual thickness at the critical corrosion after 10 years is safe (80mm). Moreover, by running the entire 10-year campaign, keeping insulation layers, thermal losses are reduced by 66% (292 MWh/m²) compared to Scenario 1 (855 MWh/m).
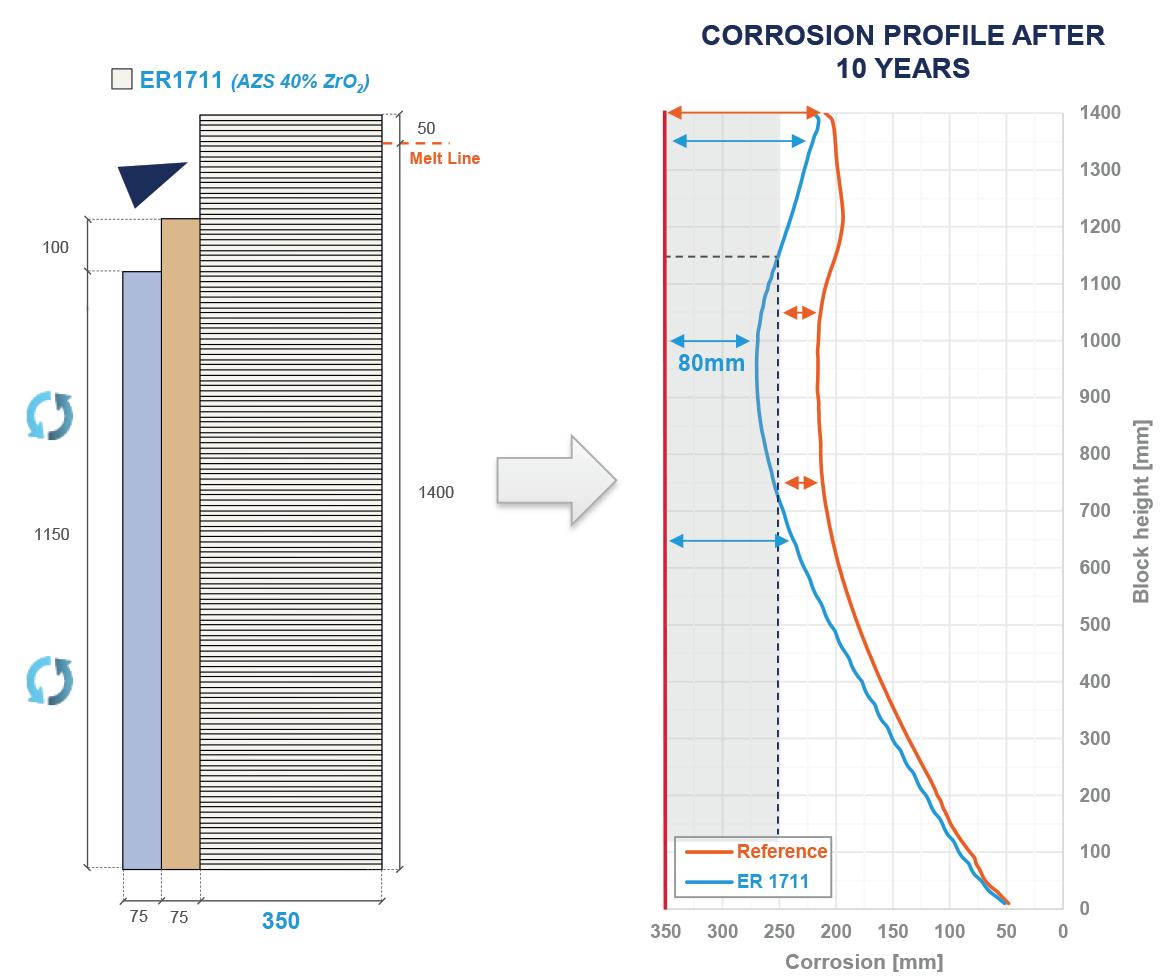
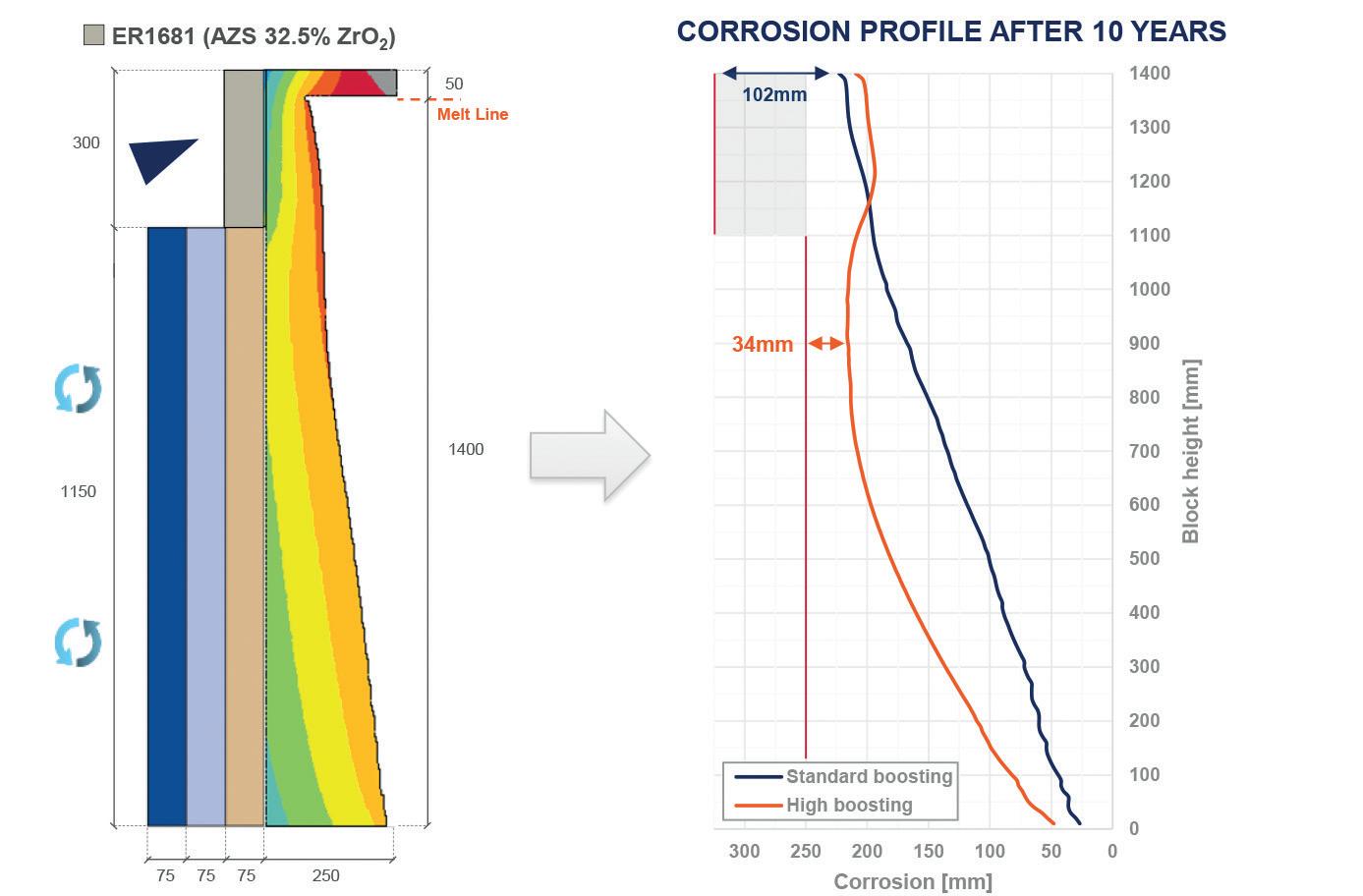
Conclusions Industrial measurements and numerical simulation show that increasing the share of electrical boosting inside glass furnaces will have a significant effect on soldier blocks’ corrosion. It typically translates in the emergence of a second critical corrosion point located lower in the height of the block. The simulation performed on a fictional sodalime furnace shows that modifications are necessary to maintain the lifetime of the furnace’s tank. Two examples were presented, allowing in both cases to reach the same lifetime as the reference (10 years). For the first case, the same initial design is considered and the maintenance strategy is adjusted. By applying a larger patching tile, covering the entire height of the block and removing the insulation behind, the targeted lifetime is achieved with safe residual thickness at every point of the block. However, the insulation removal necessary to apply the overcoating leads to an increase in thermal losses, reaching a total of 855 MWh/m² after 10 years.
The second approach allows to maintain an insulation package for the entire campaign, leading to total thermal losses of 292 MWh/m². Thanks to the modification of the soldier block’s design (thicker block, higher zirconia content, void-free product), the bottom of the block is secured while offering a 66% reduction in specific thermal losses compared to the previous case.
Choosing blocks exhibiting improved filling (RT or RS) would lead to increase safety of operations and improved agreement between simulation results and actual wear of the refractories.
It is a material with a real opportunity for the future. Recycling is the first step, but we have to go further. The glass industry has to find way in order to make its production process even cleaner, to reduce consumption, to drastically diminish its CO2 emissions. Production supervision and technology have also a great role to Glassmakersplay!are looking for solutions to produce articles using maximum quantity of cullet. They are constantly looking on how to produce the strongest and lightest articles. But the ecology is another big challenge for them. The use of sustainable and decarbonisation technologies to reduce the carbon footprint is a must today. Investing in the renovation of premises or in new machines could be one solution; but this costly measure wouldn’t be enough. The whole process must be daily controlled, in terms of energy consumption for example, in order to provide glassmakers with all the keys to make suitable decisions. Glass manufacturers need to collect, record, extract, exchange and display data coming from all over the plant. The digitalisation of manufacturing is transforming the operations, processes, acting on energy footprint of factories and supply chains. This modern paperless solution, allows a faster exchange of information and data between all plant sectors, making production requirements efficient, increasing performance and production quality. Fig 1. Plant Scheme
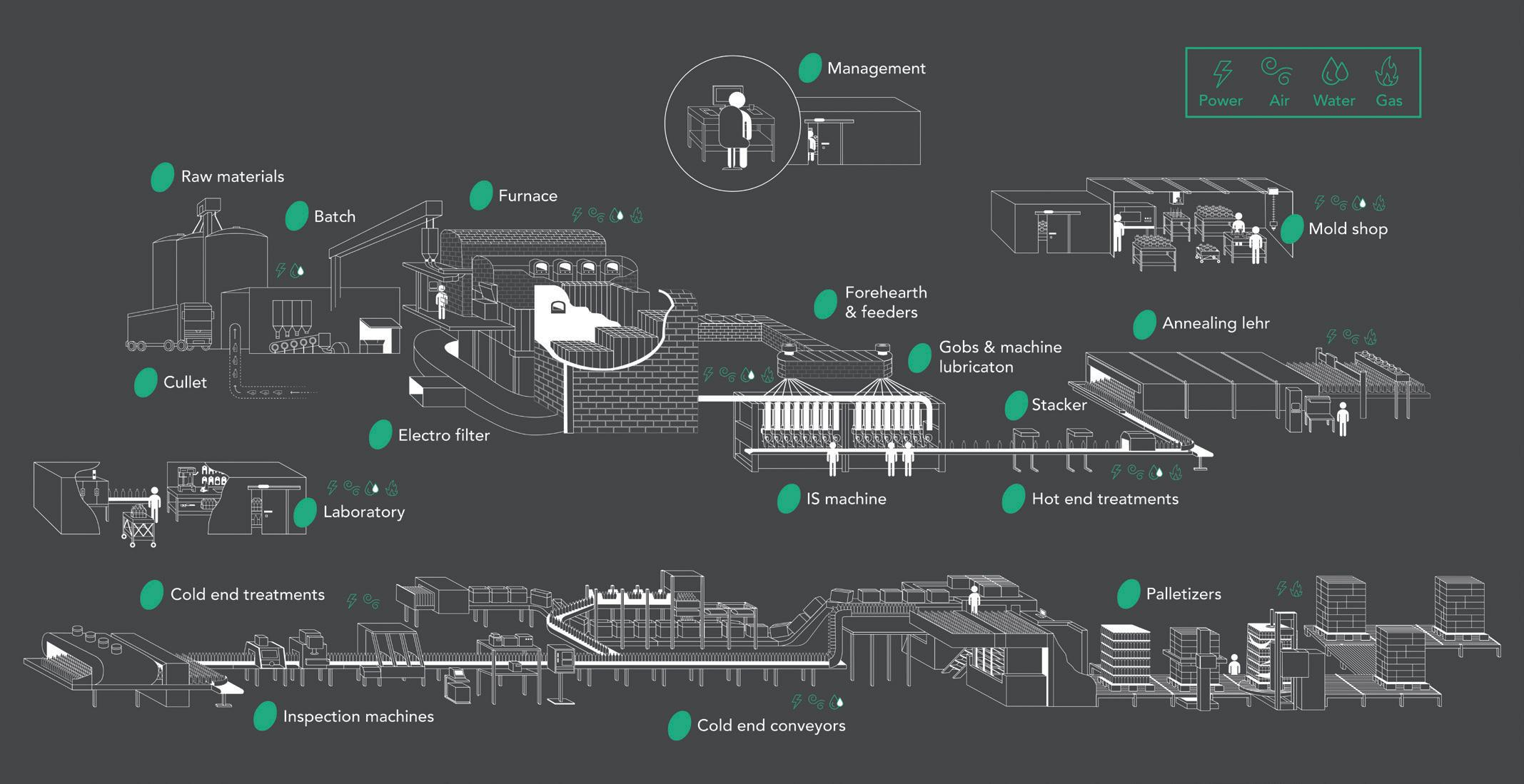
Digital glassmaking Glass International September 2022 500 www.glass-international.com Continued>>
Technological innovation through Industry 4.0 is essential for the glass industry to overcome ongoing technical, economic and ecological challenges. Ulas Topal* explains how it is possible to successfully deal with these matters. According to Global Footprint Network, today the 7.9 billion people on Earth are using more resources than it can provide. By 2050 we will require three Earths in order to supply our needs, if we don’t change our habits by making our consumption sustainable. As a result of global warming generating natural disasters, the commitment to reduce CO2 emissions is more than necessary. Currently one of the most challenging concerns for industry is to continue to produce faster higher quality articles at the lowest cost but, at the same time, to be environmentally friendly. Glass, as container, is definitely a lasting and sustainable material when comparing with single-use plastic. It can actually be used and reused. Glass is 100% and unlimitedly recyclable.
Eco-responsible glassmaking with SIL digital solutions
Example of Industry 4.0

Faced with big ecological challenges, glassmakers need to consider technologies and industry 4.0 as excellent opportunities. Monitoring Key Performance Indicators has become essential for glassmakers: first of all, so that they are aware of their energy consumption; secondly so that they have consistent data for analyses and decisionmaking.Also,digital era represents a revolution both for managers and for operators. Thanks to digital solution, operators are not linked to their terminal any more. For instance, a quality controller can follow up setouts on the production line, working on a smart device with a full web application managing quality controls.
On the path to reduce the footprint of glassmakers, the first step consists in measuring, thus controlling, energy consumption. This step is absolutely essential to carry out an effective energy policy. Vertech’ developed SIL4.0 to this end, to meet glassmakers’ needs. Regarding energy consumption, SIL4.0 is connected to key spots in the plant like to the furnace, where it can get real-time temperature; to the electro-filter, where it can get real-time green-house gas emissions; to the annealing lehr, where it can get real-time temperature curve throughout the lehr. All the places on the production line where SIL4.0 is able to be connected are reported on schemes.
Optimising cullet is of big interest from both ecological and economic points of view. Using cullet to produce new articles implies a much smaller use of raw materials, more especially sand.
SIL includes indicators related to statistical process control, like the Gaussian curve. At a glance, glassmakers can see deviations from a standard value allowing them to anticipate on measures to be taken for continuous improvement of the production process.
All these possibilities are key tools for managers to debrief on past actions and make appropriate decisions.
Digital glassmaking Glass International September 2022 www.glass-international.com 51 Continued>>
Energy consumption, temperature in the furnace or in the lehr or the stock of raw materials: all this information can be displayed on one screen. KPIs of several plants within one same group can even be simultaneously displayed. Real-time KPIs are displayed on fully customisable dashboards displaying data on furnace, forehearth, cooling system temperature, daily CO2 emissions, consumption, etc.
comparisons.Utilitiessuch as electricity, gas, water and air are used in the glass production process. Glass is warmed at a high temperature in the furnace. Once the article is produced, glass is warmed one more time before being progressively cooled. As a consequence, a significant amount of greenhouse gas is rejected, particularly through fumes, which makes glass production a polluting activity.
For glassmakers, sand constitutes a real problem, economically and ecologically. Indeed, raw materials need to be paid and transported to the plant. But most importantly, like any other resource on Earth, sand is not unlimited. All kinds of sand are not suitable for glass production; for example, sand from deserts would be too regular. Therefore, sand must be extracted implying heavy ecological consequences: destruction of ecosystems, shore erosion, or even sometimes desalination.Byusing more cullet, all these problems can be reduced. Likewise, using some materials like soda and lime allows reducing the fusion temperature, which is of high interest regarding energy consumption. As controlling composition and raw materials is extremely important, SIL provides all the KPIs to do so.
To go into further details, data can be extracted and handled as glassmakers wish. In the form of pivot grids, datasheets, grouped, timeline or stock charts… Everything is possible with SIL!
Vertech’, a pioneer in digitalisation for the glass industry, accompanies glassmakers on their trip to climate neutrality and to consumption sustainability. With SIL solutions, technical parameters and economic interests meet ecological requirements. SIL is a Manufacturing Execution System supervising production of the whole glass plant. With SIL the productivity increases and the workflow becomes smoother. SIL can be installed everywhere in the glass plant: from the batch to the palletiser, through the mould shop and the quality laboratories.Theprinciple is simple: SIL connects and collects real-time data everywhere where sensors can be connected. From the batch to the palletiser, points are multiple. Once data are collected, SIL displays them on fully customisable dashboards: SIL collects data, and the glassmaker chooses which KPIs it wants to display.
With all these KPIs, glassmakers will have a perfect overview of their energy consumption. By exactly knowing the quantity of greenhouse gases they reject, glassmakers will be able to control their Fig 2.
The innovative SIL4.0 software, is the company’s answer to the challenges currently faced by the glassmakers. The multitude of real-time data gathered throughout the glass plant is essential for analysing the past and for foreseeing the future.Theaim of SIL4.0 is the glass plant and its production processes digitalisation from raw material to finished product. Collected KPIs are crucial for the production process monitoring and for quick decision making. A dashboard can simultaneously display data even from several plants, facilitating cross-plant
The future of glassmakers cannot be considered with serenity without a supervision system as complete as the SIL. �






































































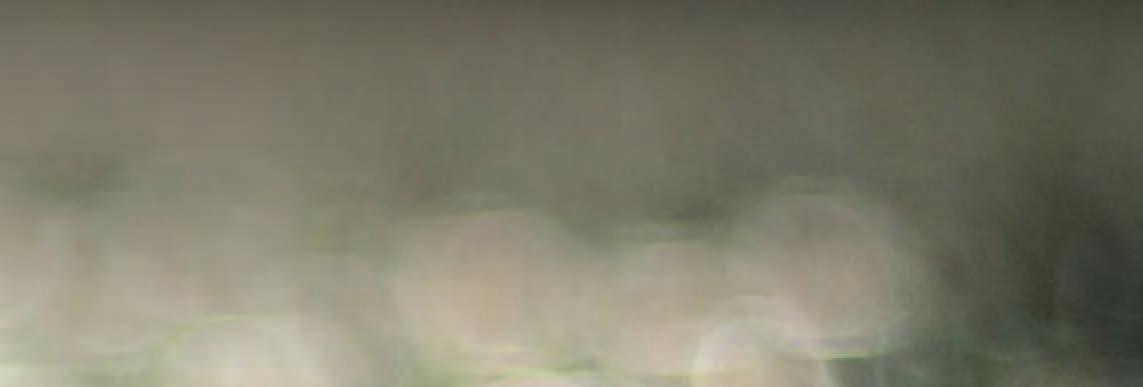
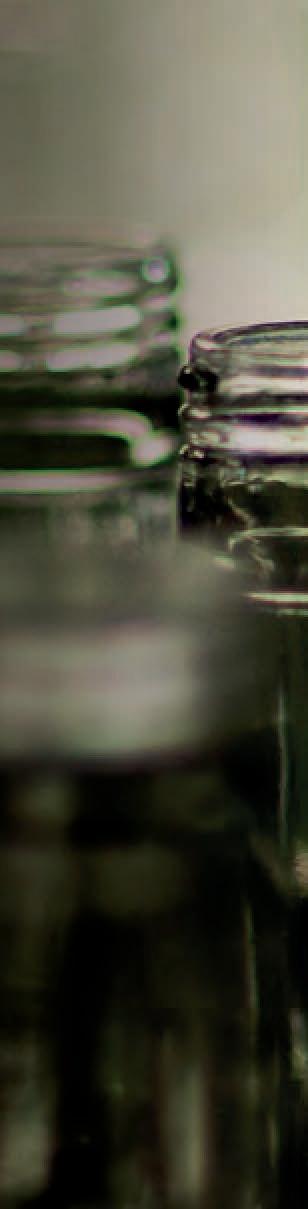
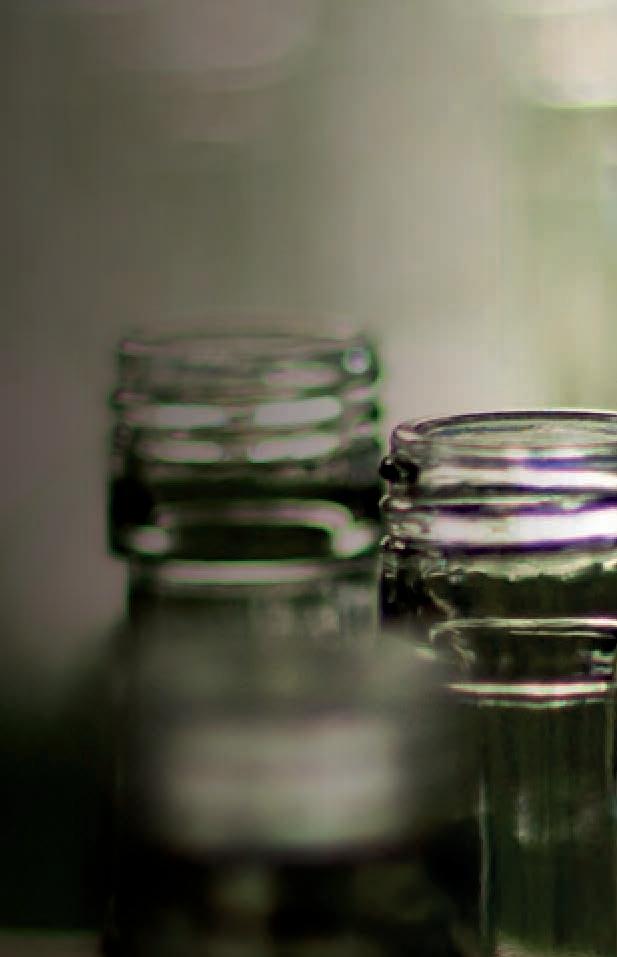
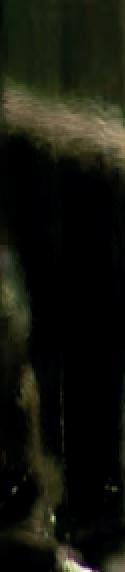

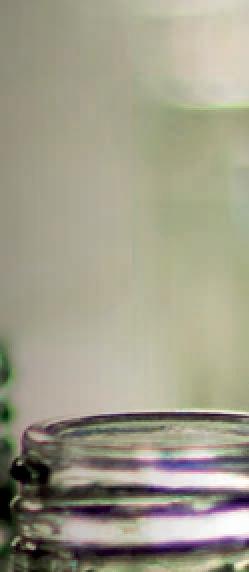
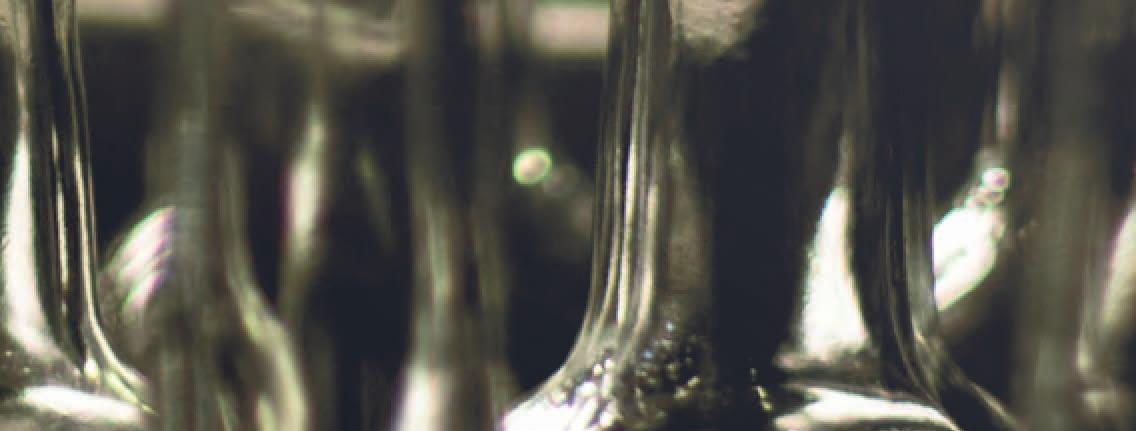
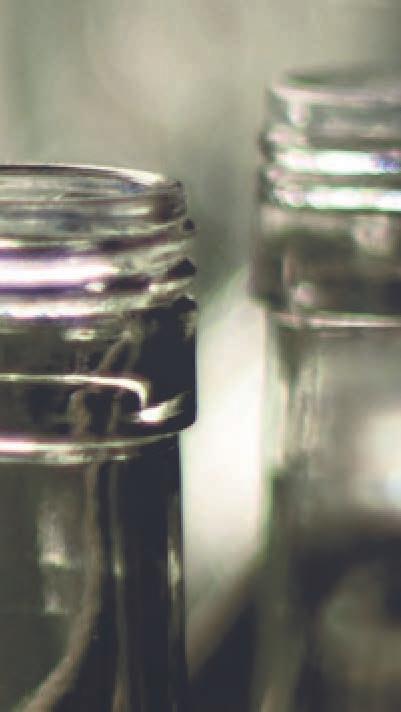


















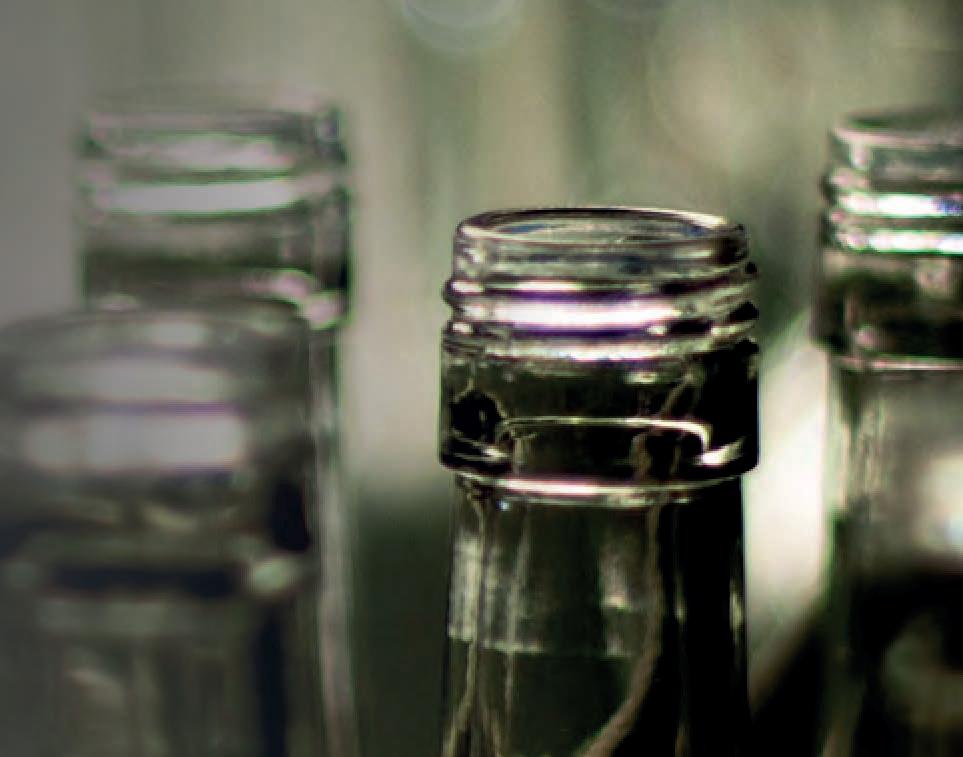
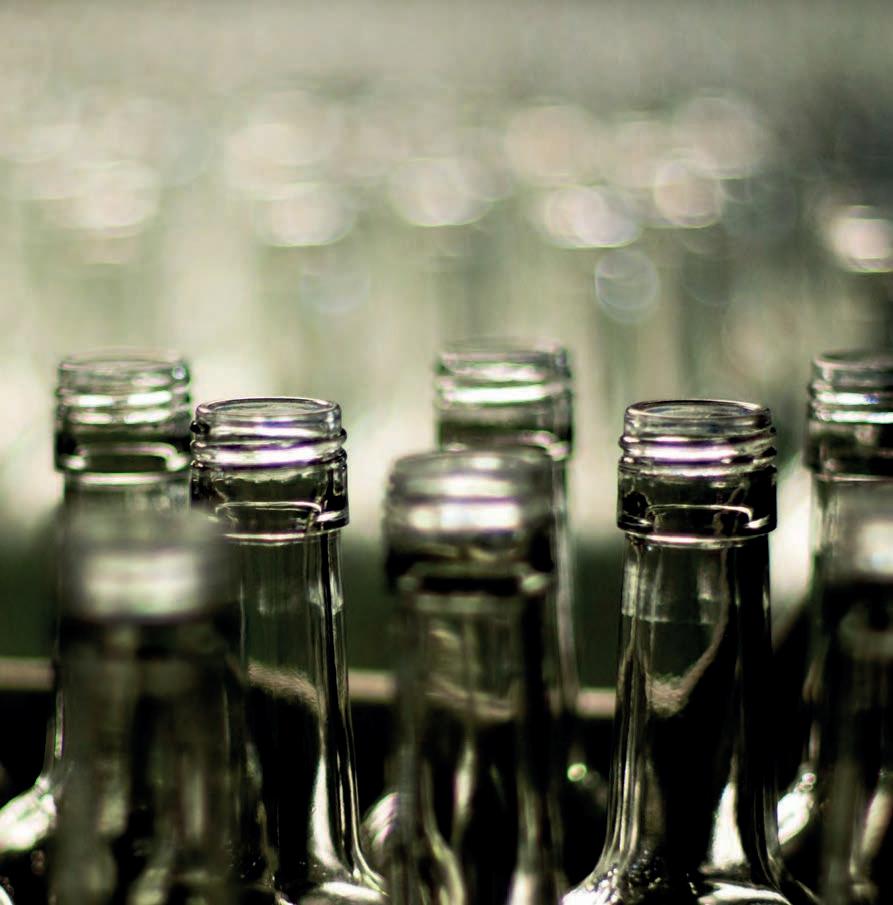
consumption by making decisions to reduce their carbon footprint and following the evolution. They will also have the consistent KPIs to take part in decarbonisation programs in order to compensate for their GES emissions.
Digital glassmaking




























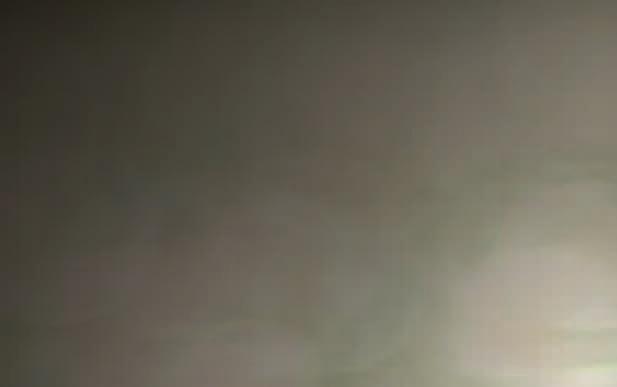
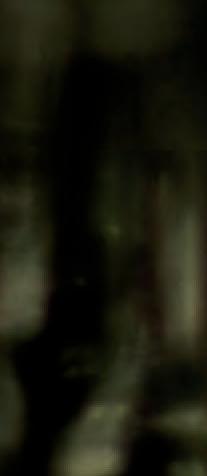
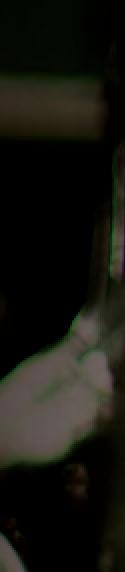

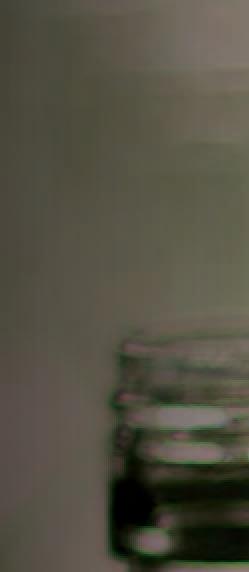

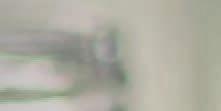








*Vertech, Chalon-sur-Saône, France www.vertech.eu Fig 3. SIL 4.0 Fig 4. SIL dashboards
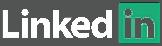
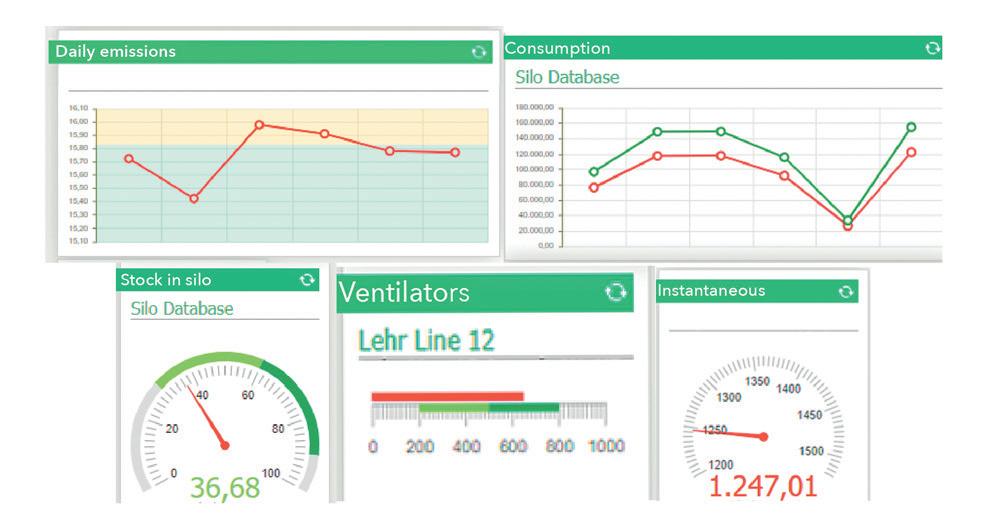
Vertech’ aims at going further and is constantly working on finding correlations in order to predict the future. Innovation has no limits and is the key to success for glass industry.




























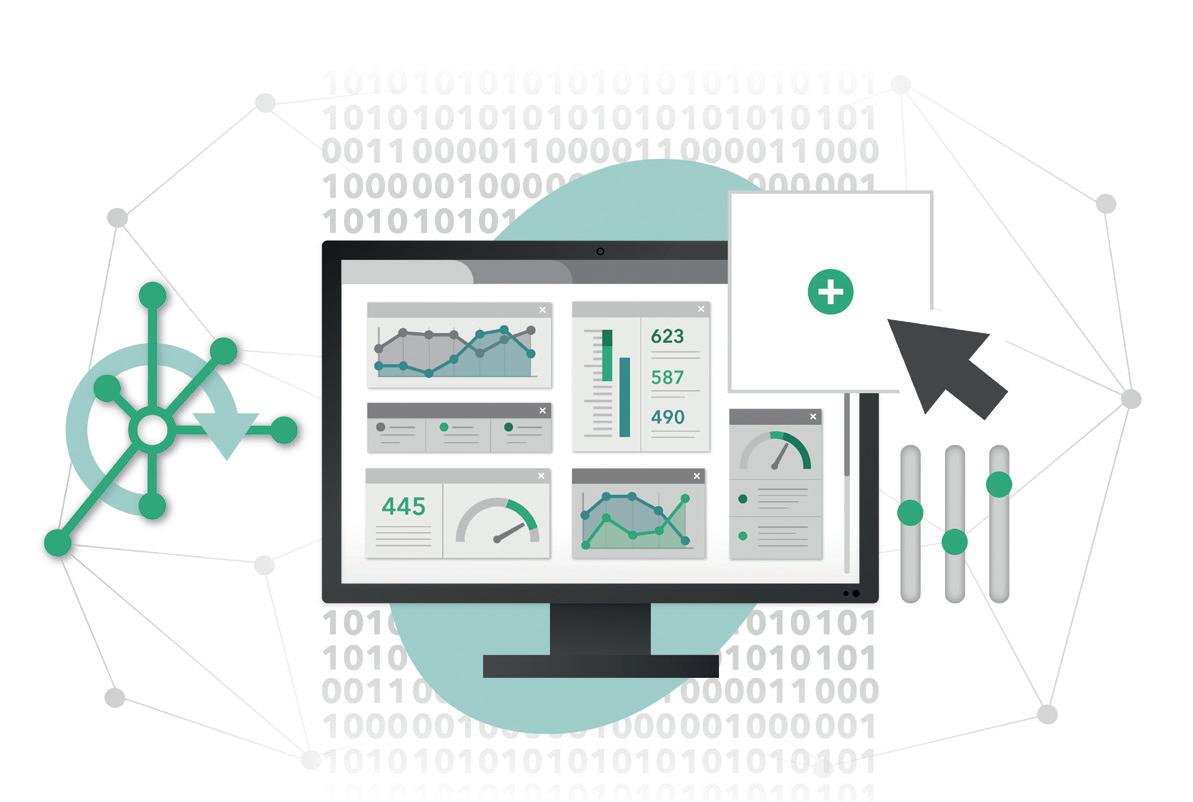
www.rath-group.com/glasstec A GLASS OF ITS OWN Refractories and Hot Gas Filtration for High Demands Visit us at glasstec Düsseldorf! Convince yourself live of the quality of our products. We’ll be on hand to showcase outstanding innovations from the following fields: • Refractories for the entire production chain • Crucibles for Art Glass • Hot Gas Filtration to ensure clean air JOINSept.DüsseldorfglasstecUS!20–23 MOULDs kilnspreheating ANNEALINGLEHRS www.vidromecanica.coM



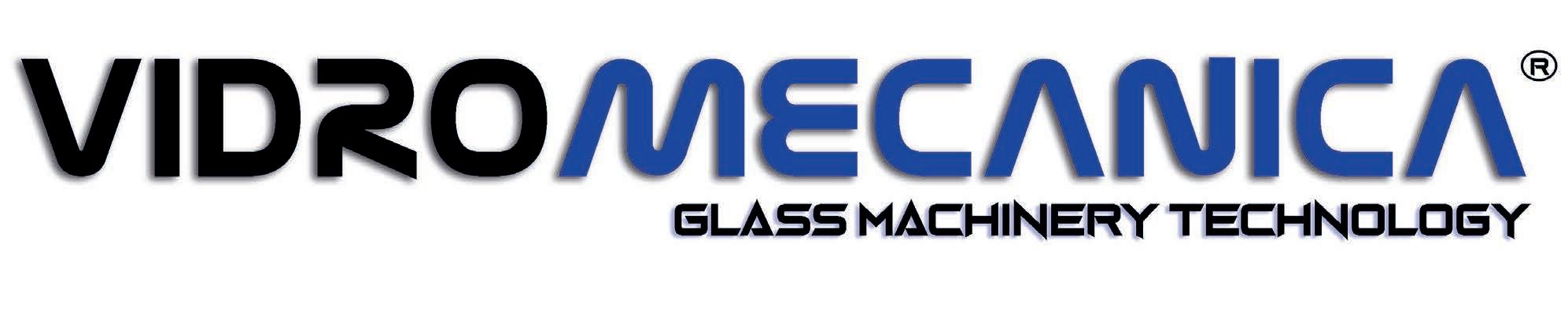
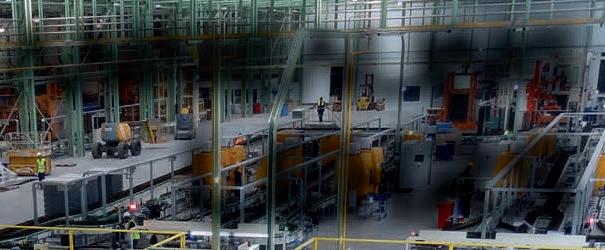


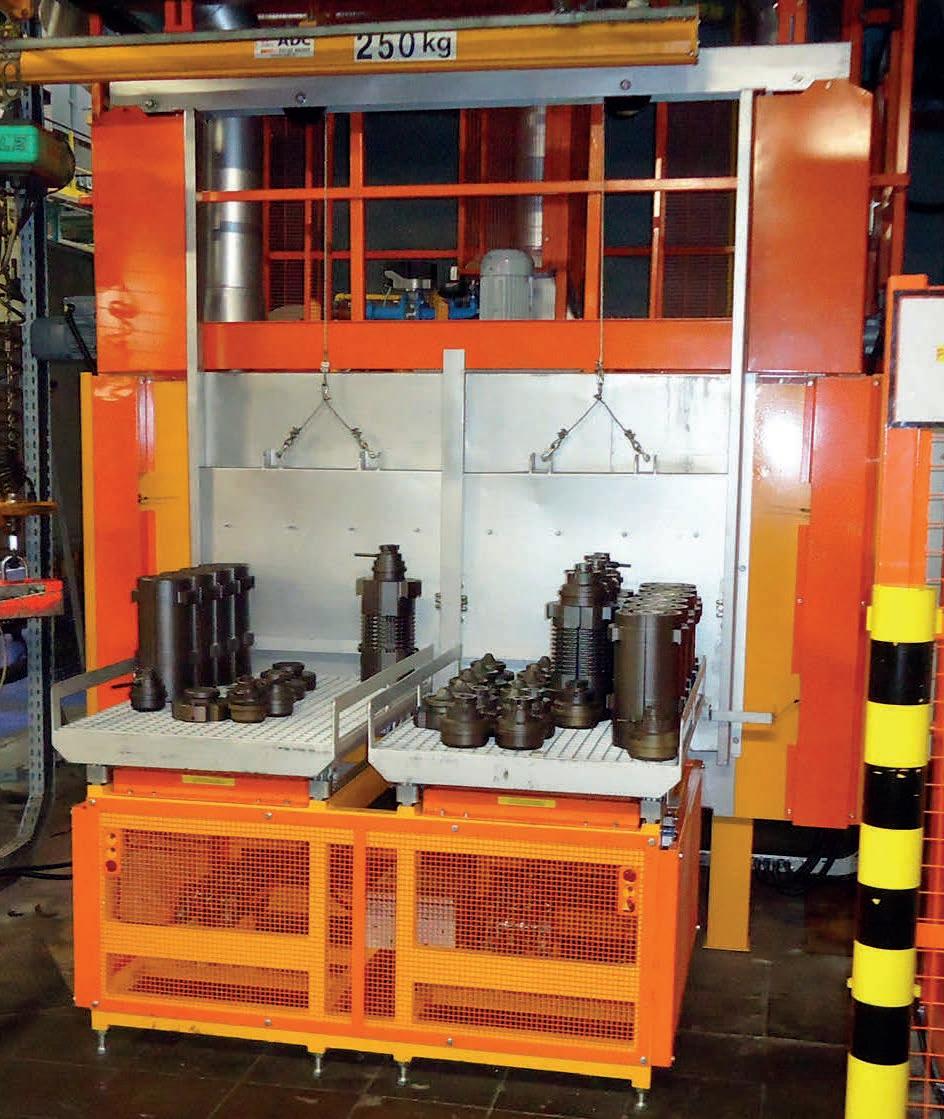

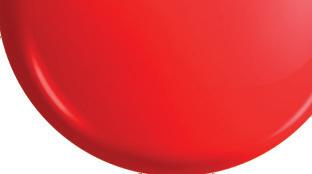

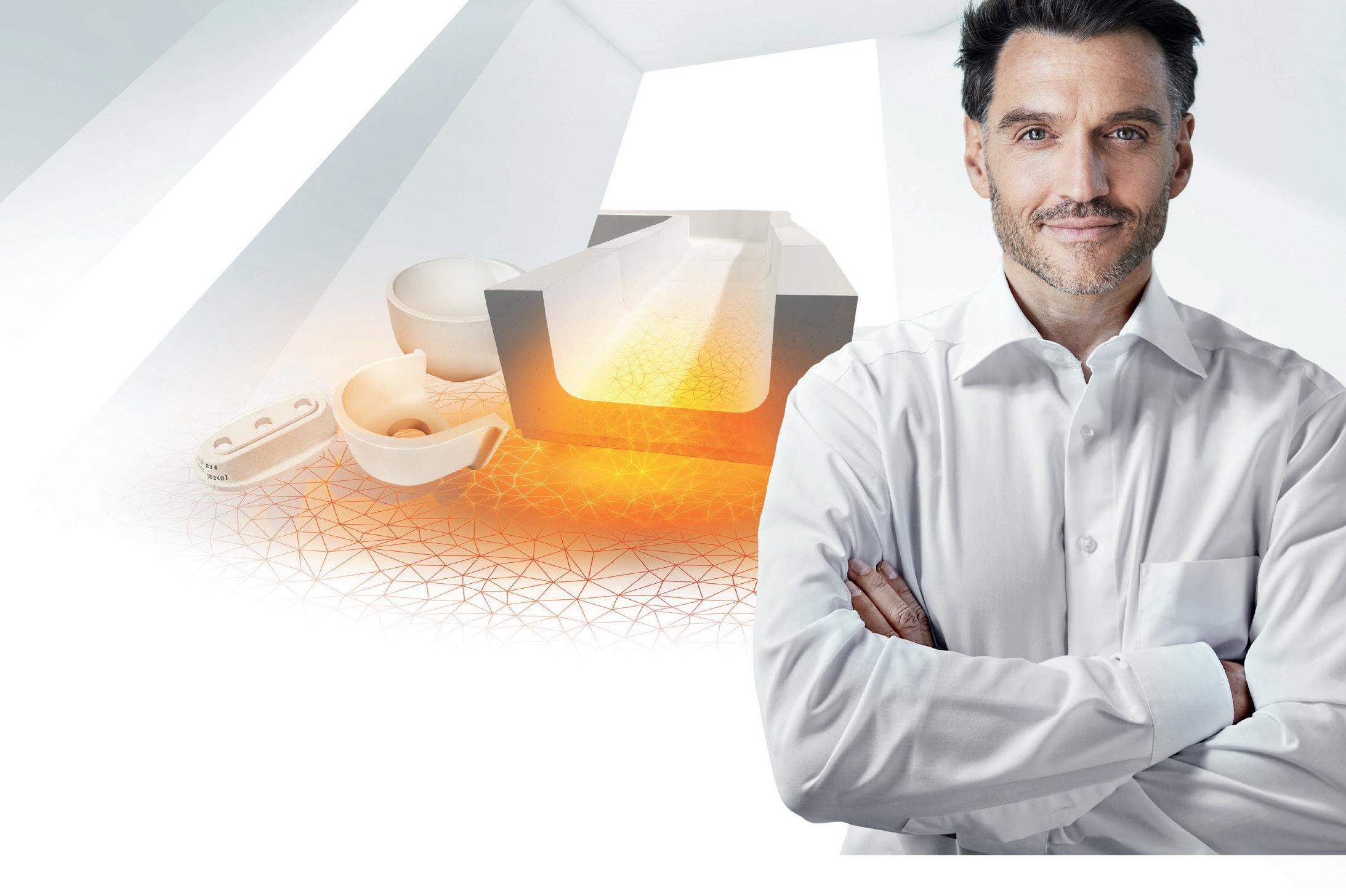
The furnace is an end-port regenerative, with the maximum pull of 480 tpd, working end and five forehearths. The combined length of all channels – working end and forehearths – is an impressive 85 metres. The production hall, in which the furnace has been installed, had been designed for a furnace smaller by 40%.
1 Congratulations of the recent furnace installation at Stoelzle. Can you describe the feeling of when the last brick has been put in place and you have completed the job? Thank you. Completing every big project is very satisfying, but this one was especially so as a combination of factors made it more challenging than any other we’ve executed before.Atthe pull of 480tpd the furnace is the biggest in our history, the biggest in Stoelzle Group and one of the largest end-port regenerative furnaces.Throughout the entire manufacturing process we had to manage unprecedented supply chain disruption. Some of our suppliers refrained from providing binding offers altogether!Attimes it was tough, but we’ve managed to solve every single problem that we encountered and here we are today – happy, satisfied and with a feeling of relief.
The new furnace is designed to be more energy efficient than the previous one - also supplied by Techglass. It was no easy feat as the technology of regenerative furnaces is mature and the progress in terms of energy efficiency is limited. The furnace can melt up to 40% of maximum pull by electric current, which is a lot, considering the industry standard at roughly half of that. This feature offers potential to dramatically reduce CO2 emissions, of course only if the electric current is generated from renewable sources.
An all round furnace provider
3 Have you worked with Stoelzle Czestochowa before? If so does that previous working relationship help when you start on a new project such as this?
c c
5 Stoelzle states the furnace will reduce the amount of energy used in melting. Can you tell us about the furnace’s environmental/ energy efficiency capabilities, as well as the improved e-boosting?
It was virtually the biggest furnace that fit there without any major modifications of the foundation plate.

4 What type of furnace was chosen for this job and why this particular furnace? What are its characteristics?
Continued>>
2 How long have you been working on this project for? When did discussions start with Stoelzle about the furnace, for example? Stoelzle started analysing possible variants of the new furnace a couple of years ago. That gave them plenty of time to meticulously check all possibilities. They settled on the most ambitious option and then the tender process took roughly five months. The project was awarded to Techglass in February 2021. The works on site started on May 9 with glass drainage from the existing furnace. The commissioning of the new furnace took place on July 27.
Company profile: Techglass Glass International September 2022 www.glass-international.com 54
� Techglass President Andrzej Skowiniak c
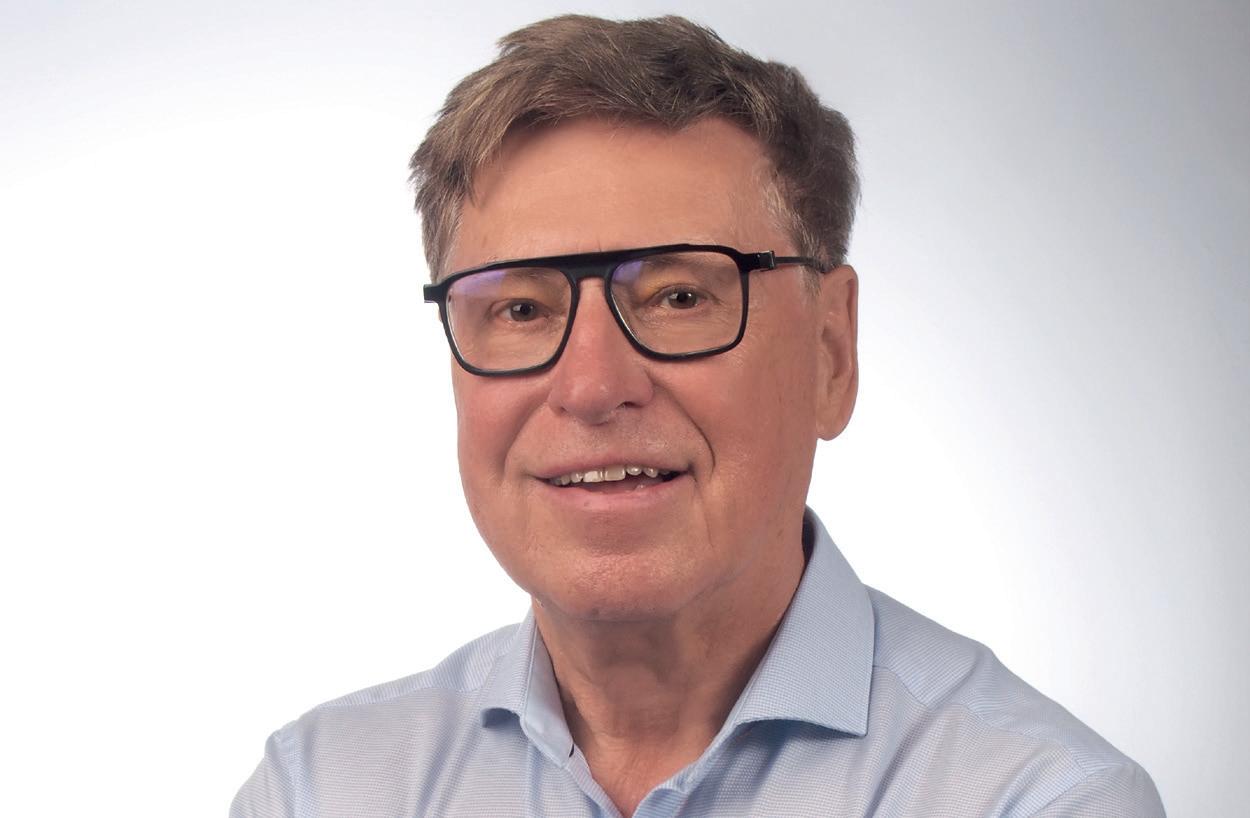
Fresh from installing its largest ever furnace at Stoelzle Czestochowa, Techglass President Andrzej Skowiniak describes the installation process of the energy efficient oven as well as the future prospects for the furnace industry in general.
Yes, we’ve been working with Stoelzle Czestochowa since 2001, that is since this Polish branch of the Austrian company was established. To date we’ve supplied three complete furnaces with working ends and forehearths and executed numerous smaller orders. We also supplied a furnace with working end and forehearths to Stoelzle’s Knottingley, UK plant. Naturally, the long-term business relationship helped us in being awarded this recent project. There is no way to predict the future, but the next best thing is to draw conclusions from experience. Based on the trust we gained over the last 20 plus years of working together, the decision makers in Stoelzle could be confident that we were able to execute this challenging project. And they were not mistaken.
8 Is the container glass industry the only one you operate in?
Currently, in September of 2022, the hottest topic among our customers is alternative fuels. There is a lot of uncertainty regarding the availability and prices of the natural gas in the months to come, especially in Europe. The good news is natural gas can be partially or fully replaced by LPG or oil for combustion in furnaces. We supply all engineering and systems required for this purpose.
The majority of our clients are container glass producers but we provide solutions for producers of all types of glass. Recently we supplied a batch house, a furnace of pull of over 300tpd and three frit production lines –that is a complete solution from raw materials to product - for the biggest producer of sodium silicate in Europe, CIECH Vitrosilicon. We were able to achieve very good operational parameters of the system, such as low energy demand and low NOx emissions, thanks to our engineering focused on the specific requirements of sodium silicate glass. The project was so successful, that soon after it had been completed, we were awarded another rebuild with modification project at the same customer.
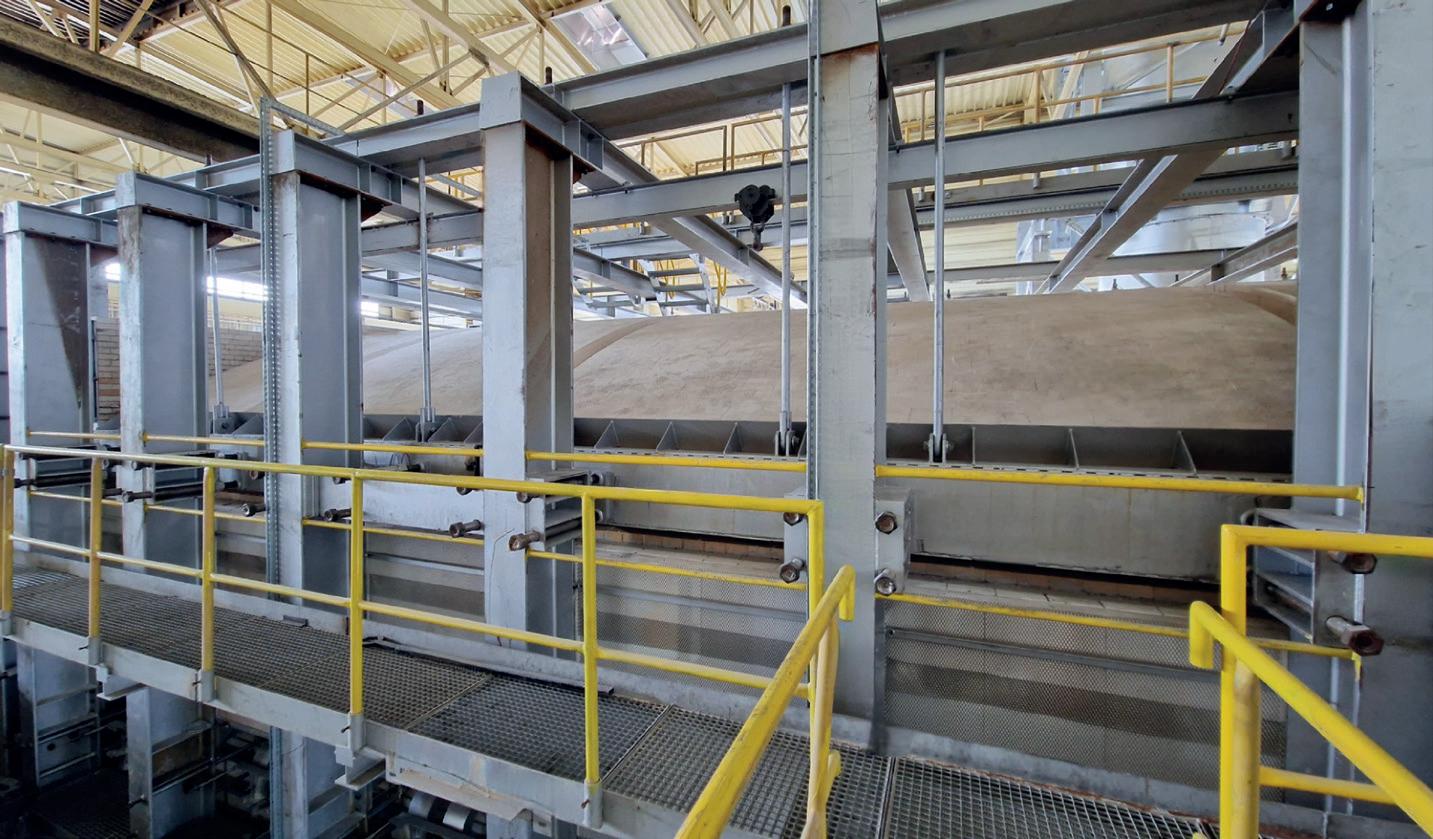
10 Finally, and more generally, there is a lot of talk about climate change and what the glass industry can do to improve on emissions in the melting process.
The other interesting topic is Machine Learning. Good algorithms fed by a lot of samples may yield results better and faster than even the best experts are capable of. There is a potential to improve many processes in the operation of furnaces, working ends and forehearths by ML. We invest in integrating ML-based solutions in our control systems and expect to see first successful applications next year.
Company profile: Techglass Glass International September 2022 www.glass-international.com 55
9 Hot topics in the industry
7 Tell us more about Techglass? Is Poland your main market or do you supply furnaces outside Poland? What are the company’s strengths? Techglass was founded in 1990. We supply furnaces, working ends and forehearths: all works and all supplies required. First, our engineers do all necessary designs, from refractory materials through steel structure to systems and equipment. Most of the projects in the glass industry are rebuilds with modification and therefore it is crucial to offer tailored solutions as we do, because the off-the-shelf ones do not account for the existing situations, different in each case. When all engineering is done, manufacturing starts. In Techglass the vast majority of systems and equipment is manufactured in-house. This helps overcome challenges of disrupted supply chains as it makes quick reactions for problems possible: the status of every order out of thousands is monitored in real time. When all deliveries are ready, we execute all works on site: drainage, demolition, installation, heat-up and start-up. We also provide a range of services for furnaces, working ends and forehearths. We are basically capable of doing everything but the ceramic welding.
6 Construction was completed in less than 70 days. What were the challenges and how did you overcome them? It took 67 days from the start of drainage to the start of heat-up. If someone says that it is not record-breaking, they surely either haven’t seen the situation before or after the works or both. The types of problems encountered on site are always the same, only this time it was all more difficult due to the complexity of the project. There is certainly no secret formula for overcoming the challenges. What makes this possible instead, is a team of skilled and hardworking employees who are all solutionoriented and solve problems one by one as effectively as possible.
*President, Techglass, Krakow, Poland www.techglass.pl
Many ideas are indeed being discussed regarding decreasing the negative impact of the glass industry on climate change: from relatively easy to implement, through very demanding to straight bizarre. The fact of the matter is that the more reduction in CO2 emissions a concept promises, the more expensive and demanding it is to implement. We believe that a radical decrease of the CO2 emissions is possible through transformation to all-electric furnaces. This would, by all means, be a massive undertaking, but since the required technology is there, it should in our opinion be considered as the most realistic way forward. Of course, it is not the role of the glass industry but rather the governments to create conditions to make the change possible. A step in this direction is to use electric power to melt 40-50% of total pull, just like in the furnace we designed for Stoelzle Czestochowa. It goes without saying that the electric power should be generated by renewable sources and should be at the very least no more expensive than other available fuels. At the end of the day, the glass producers need to make a profit. c
The only gas stream generated is a relatively small amount from the decomposition of raw materials in the batch, as well as water vapour from raw material humidity. This waste gas stream can be removed from the furnace superstructure, cleaned by means of a small baghouse filter and released into the environment without any further treatment – resulting in emission-free melting.
Furnaces Glass International September 2022 560 www.glass-international.com
Challenges in all-electric tonnage Zero emission melting through allelectric furnaces would have been widely adopted by glass plants if it wasn’t for the limitations on furnace size. In addition to producing no emissions, the Sorg VSM can comfortably operate at 200 tpd and offers a host of benefits to glass plants in terms of energy and maintenance reduction. The challenge in scaling the current VSM furnace design is the distance between opposite electrodes – either from top to bottom electrodes or from electrodes on one side of the furnace to the other.
Surge in sustainable melting
We have seen great steps forward for glass, with industry and governmentfunded organisations such as Glass Futures and FEVE making great inroads with research and development projects that will advance the sector in due course.
Around the world, every energy intensive industry is seeking low carbon alternatives to fossil fuels to stop climate change. Governments and organisations are uniting to tackle a global crisis of unimaginable consequences if action is not taken right now.
Sorg has offered all-electric melting since 1971. Its latest furnace has been increased to reach tonnage levels of up to 1200 tpd and could answer many of the challenges float glass manufacturers face.
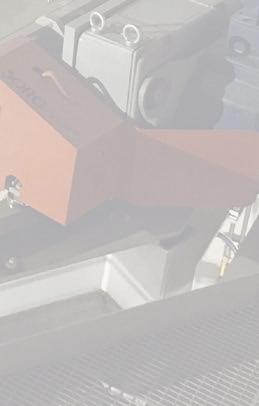
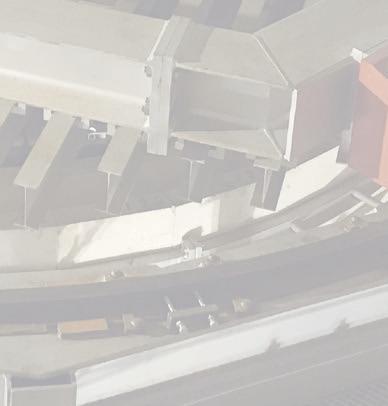
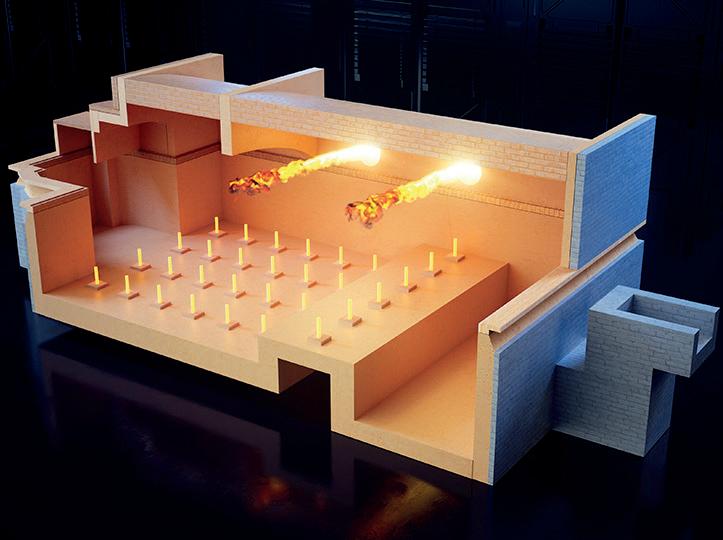
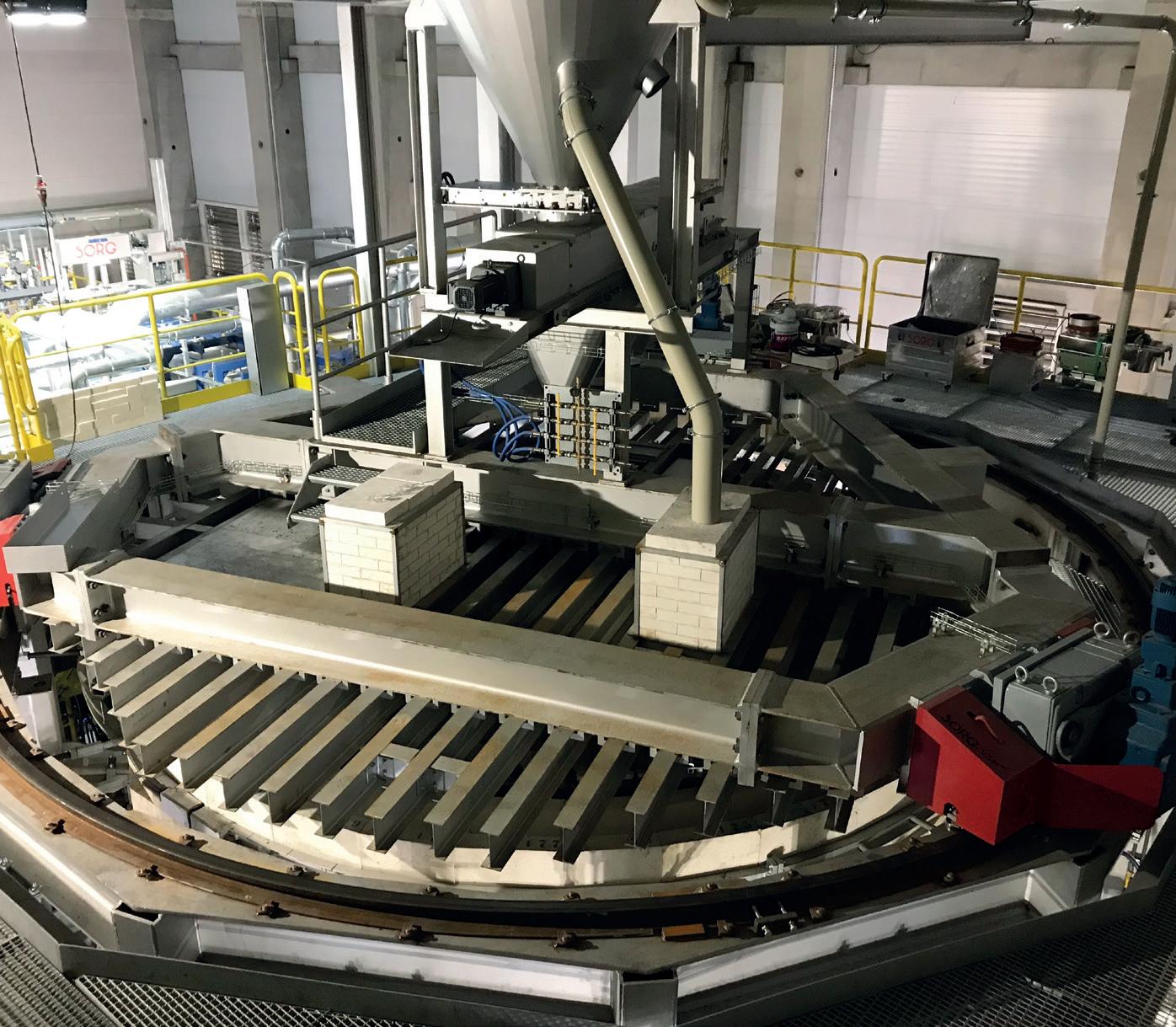
In recent years, extensive research and discussions on hybrid melting concepts and alternative combustion fuels, such as hydrogen, have been underway. These developments still have a long way to go –and due to the high capital cost and long lifetime of glass melting furnaces, the process is slow.
Electrifying the industry
Other leading technology brands in the Fig 1. The VSM ensures low waste and a dust-free factory environment for glass plants around the world Fig 2. Below: The Clean Melter hybrid furnace combines electric and combustion technologies to achieve up to an 80% electric share.
Nikolaus Sorg has led the way in allelectric melting since 1971 when its first VSM (Vertical Super Melter) was built. A radical furnace design with a rotating crown applied raw materials from the top to cover the entire surface of the glass bath with raw materials, forming an insulating blanket. Heinz-Glas was the first company to realise the potential of this new melting technology, using it to produce opal and flint glass flacons and jars. In 1972, the now widely recognised VSM received its patent and since then more than 100 ‘Vertical Super Melters’ have been supplied, producing all kinds of glass, especially high-quality glassware. With only one moving part and an enclosed superstructure, the VSM ensures low waste and a dust-free factory environment for glass plants around the world. It also reduces energy consumption. With no combustion, no energy is lost from large quantities of waste gasses unlike other traditional methods (Fig 1).
The conservative glass industry is hesitant to advance in these new fields without research and development support from governments to incentivise the use of more expensive low carbon alternatives like hydrogen.
Camera for bore diameter Detection of the inner bore diameter has been done with mechanical solutions in the past, causing high costs for tooling andDrmaintenance.GüntherInspections (DGI) has developed a solution that can be used as stand-alone retrofit machine, or integrated into a standard bottom/ mouth camera inspection machine (BMF type).The inspection unit consists of a camera above the bottle and a light source, mounted below the bottle. In addition to the inner bore diameter, spikes and also ovality problems are detected as well. Optional for the stand-alone unit is a second camera, allowing inspection of the outer diameter and checks in the mouth rim (Fig 4).
Cracks in the finish, an unfilled or overpressed finish and a wire edge are among the most critical defects. Camera-based check detection becomes a good alternative to sensors for check detection in star-wheel inspection machines.Formany container types, the check detection can be transferred to the camera sidewall inspection machine (CSWI) and the bottom/mouth inspection machine (BMF), which the Günther team is presenting during the glasstec exhibition. With new features, booth machine types cover a wide range of the inspection needs of a modern glass plant. The combination of both machines and the unique camera/light source design allows several images from different positions, but all with the same optical conditions. This paves the way for the detection of defects in the mouth, body and bottom of the container.
Two-camera inspection for planity and finish breakouts When inspecting for planity (flatness) and tightness, the wider the mouth, the greater the challenge. Dr Günther offers an improved solution integrated into the standard camera sidewall inspection machine (CSWI) or as stand-alone solution.Twocameras survey the mouth rim. Even smallest deviations (±20 microns) can be found and as a result, dip or saddle deviations or breakouts are detected. Any containers with a critical tightness defect are eliminated by these two camera solutions. The machine’s footprint is just 550mm x 650mm and it can be installed on existing conveyor belts with ease. The machine can be moved from one line to another; it is also available with wheels for easier re-positioning (Fig 1).
Data management
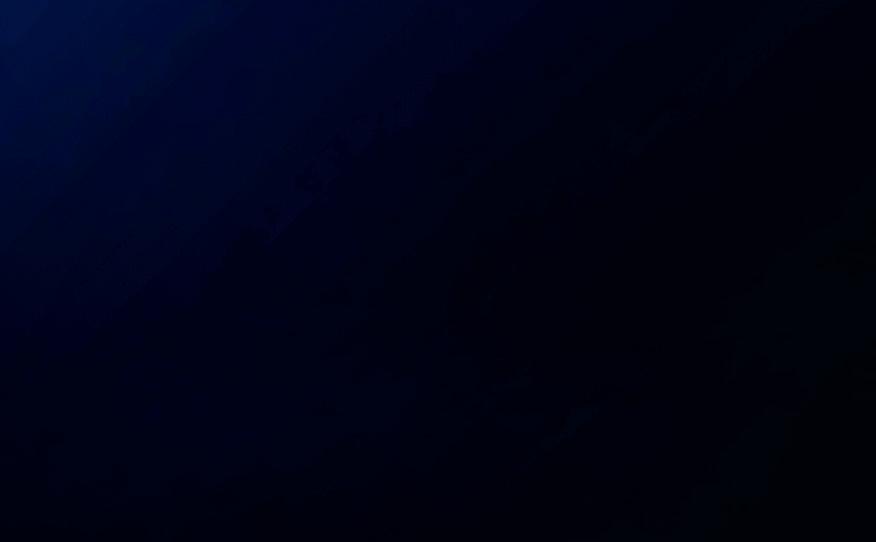
A marketplace of inspection solutions


Detecting wire edge and overpress
Among the most critical defects in glass container production are overpress and wire edge, particularly for narrow neck press and blow (NNPB) producers. An overpress is located on the inner rim of the sealing surface, like a fin of glass extending above the sealing surface. Wire edge is also a fin of glass but it is located under the inner ring of the sealing surface. The reasons for both defects lie in a toohigh gob weight or in problems related to the plunger movement. Dr Friedrich Günther, founder of the company, is proud to have been among the first to offer a technology solution for these critical defects in high-speed NNPB productions (Figs 2 and 3).
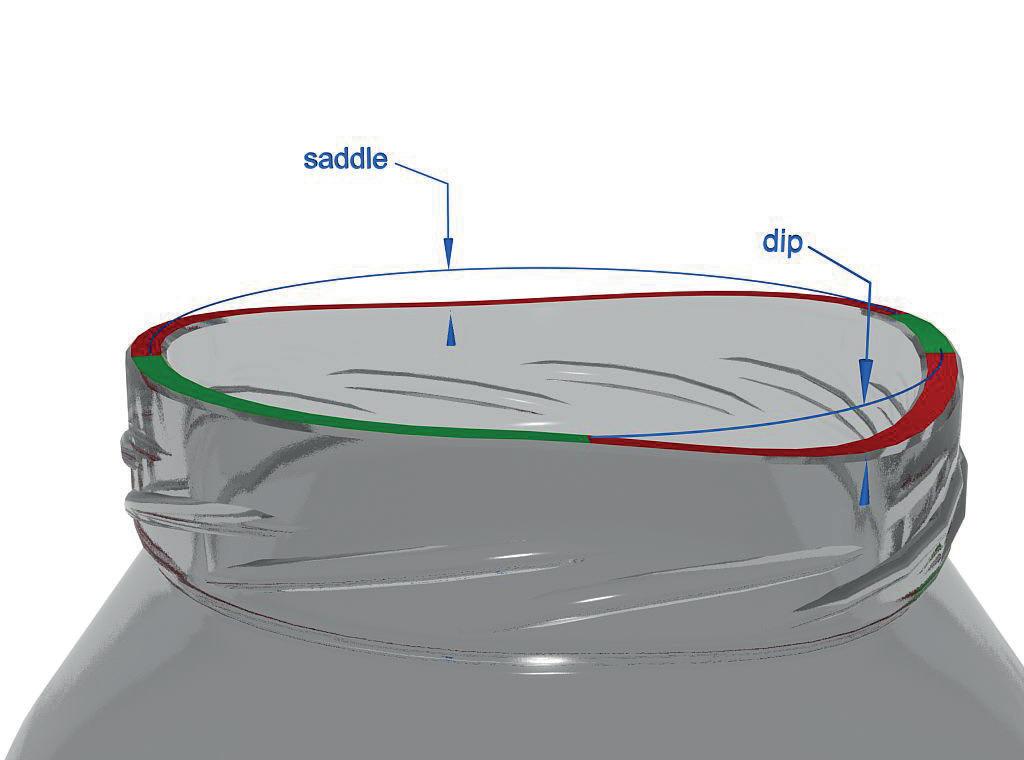
Inspection Glass International September 2022 580 www.glass-international.com
As container inspection technology progresses towards fully automated glass plants, the replacement of mechanical solutions is imperative. During glasstec’s exhibition, Dr Guenther Inspections will present a number of flexible camera inspection solutions for new cold end lines or re-engineering existing lines.
Multi-image inspection for high class cosmetics Recognition of the logo and engraving is essential today. Tilo Günther, R&D director of Dr Günther optical inspections, describes the complete solution package offered for this sector. “Smart lighting is a key component. For this reason, specific R&D investments have been made by the team. A special image processing module in the software makes even the smallest cosmetic defects visible. Checking washboards and folds of flacons is just as easy as checking for symmetry of the overall shape and the inner bottom contour.”
Innovative and user-friendly data management is crucial today. In � Fig 1. Dip and saddle detection.
Inspection addition to machine- and line-specific analysis tools, a central data and quality management tool is available. Among the latest developments is a user-interface with detailed, articlespecific reporting and data storage possibilities.“Withour new software module, the quality manager is able to improve the plant performance and to create customer-specific reports”, says Tilo. “Potential customers can have a look at our solution on the booth in Duesseldorf. “In summary, we see a big need for new, higher precise inspection systems. The extreme rise in energy costs force higher precision in inspection technology, to increase the pack-to-melt ratio while avoiding risks in the quality standard”, states Linda Günther, Commercial Director of the company. “We are happy to show all visitors our latest solutions � Fig 4. Bore diameter. during this year’s glasstec exhibition.” � Dr Guenther Inspections, https://www.optical-inspections.comGermany
� Fig 2. Wire edge. � Fig 3. Overpressed.
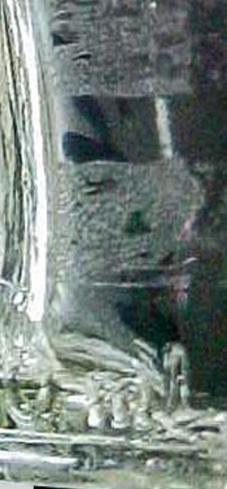
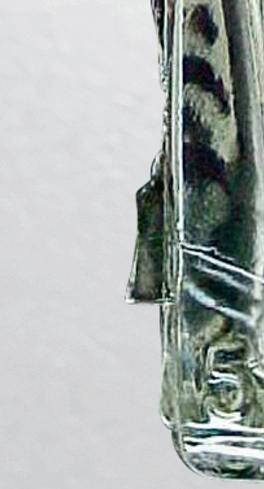

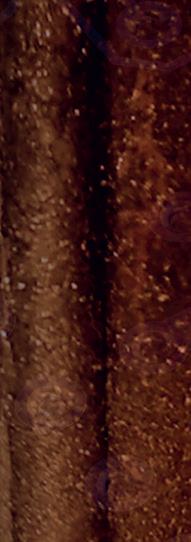
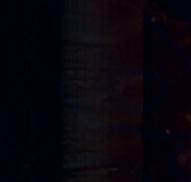

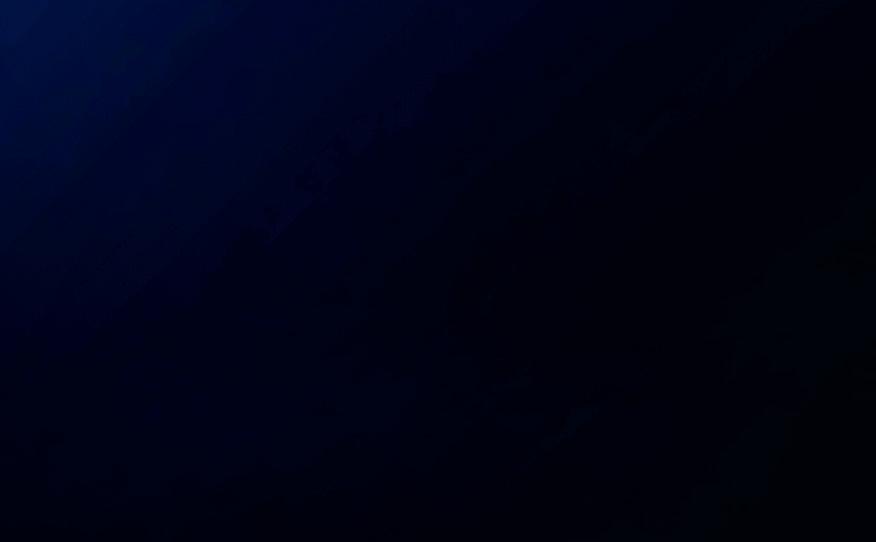
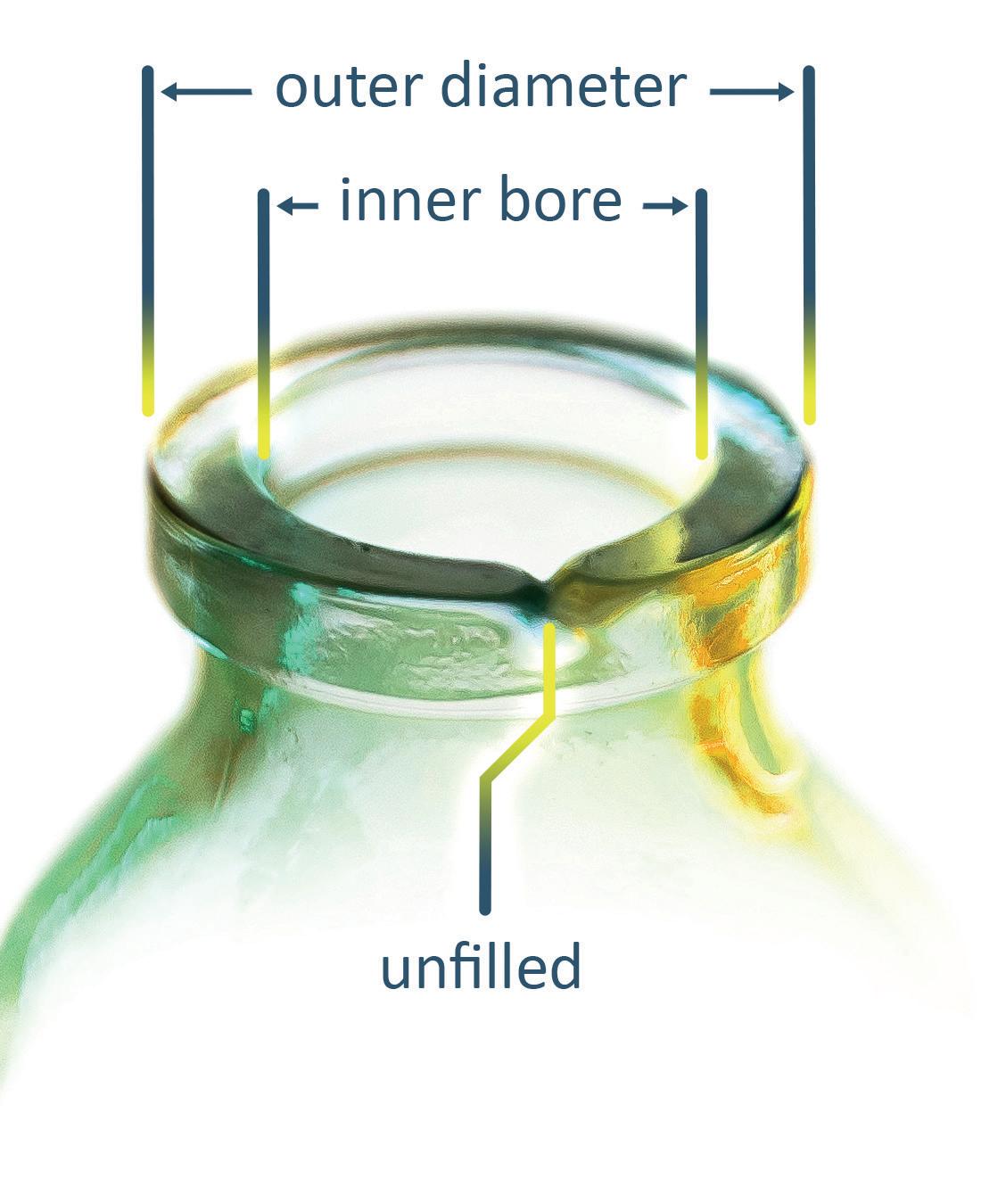
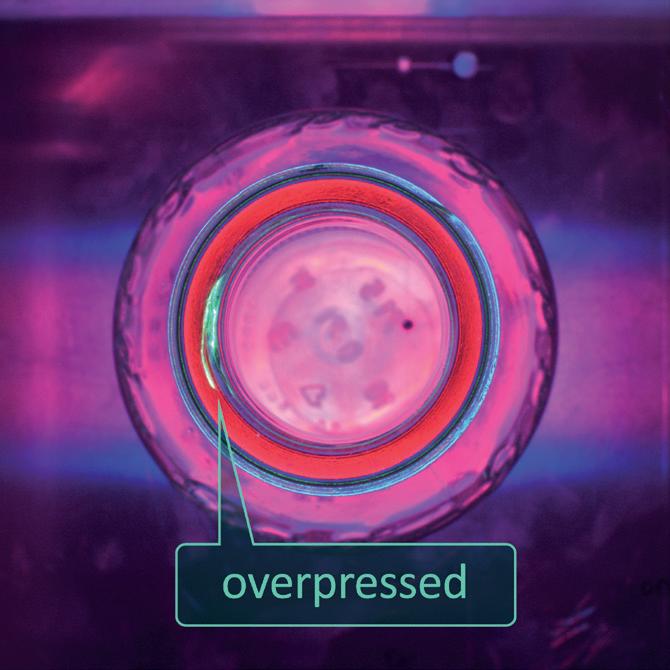
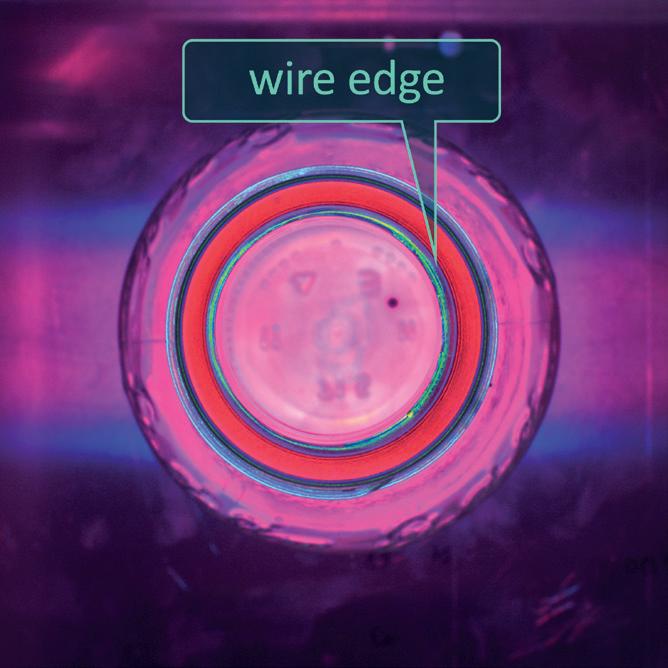
Zero defect quality in the vacuum process Vacuum Control System VCS www.futronic.de automation in a new dimension Inexpensive reject system Early detection of manufacturing and system problems Reduced error rate Significantly improved quality of products and production GermanyO-IPhotos:
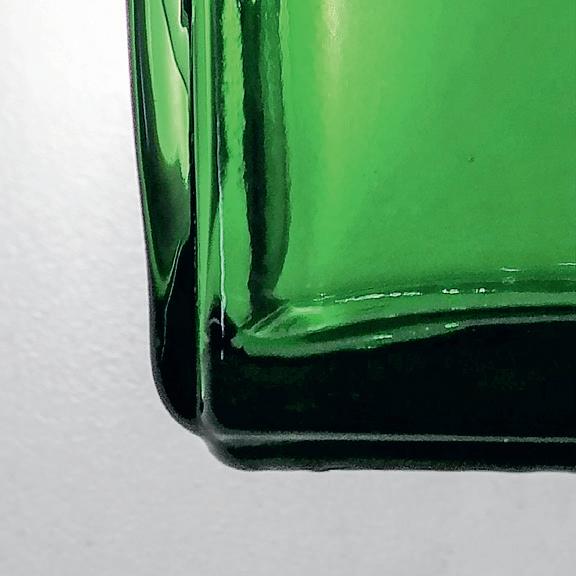
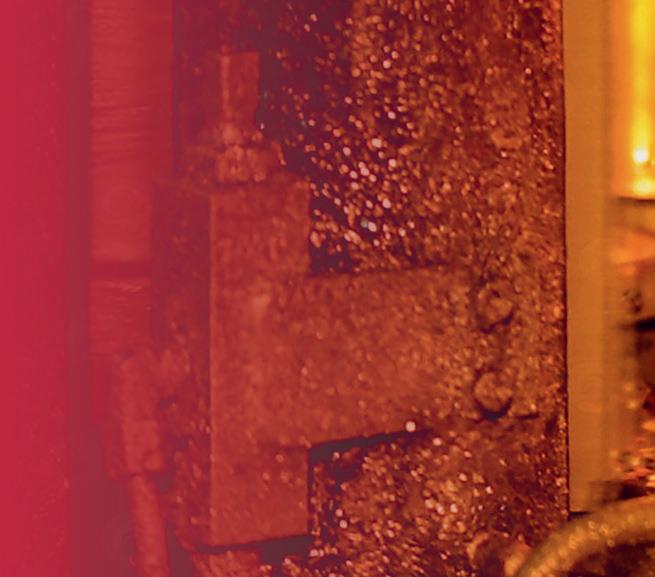


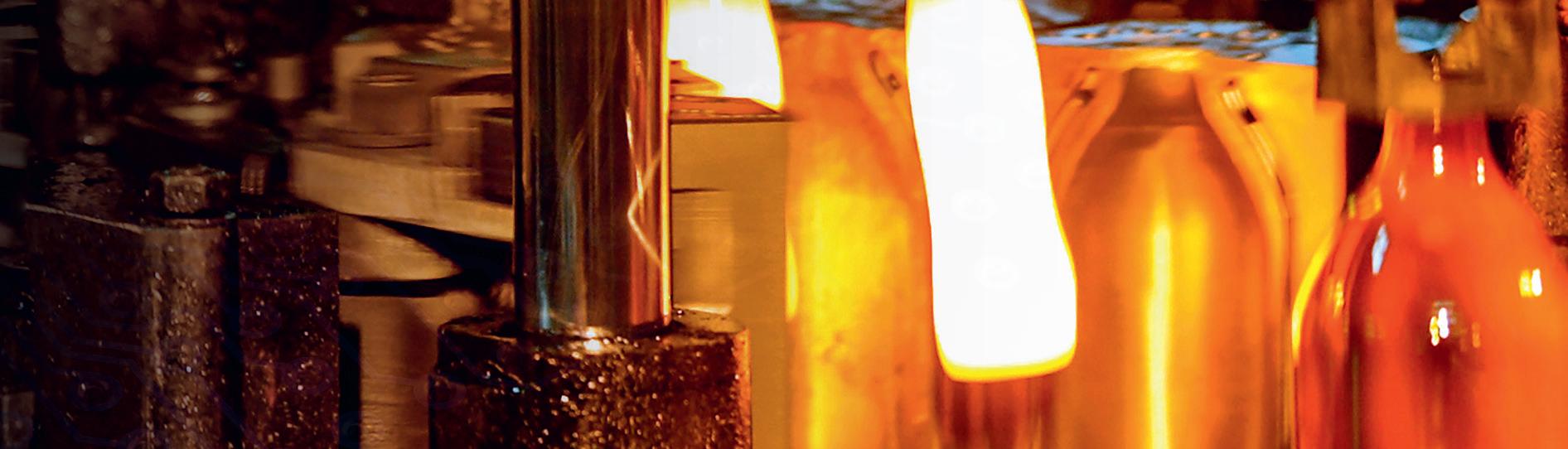

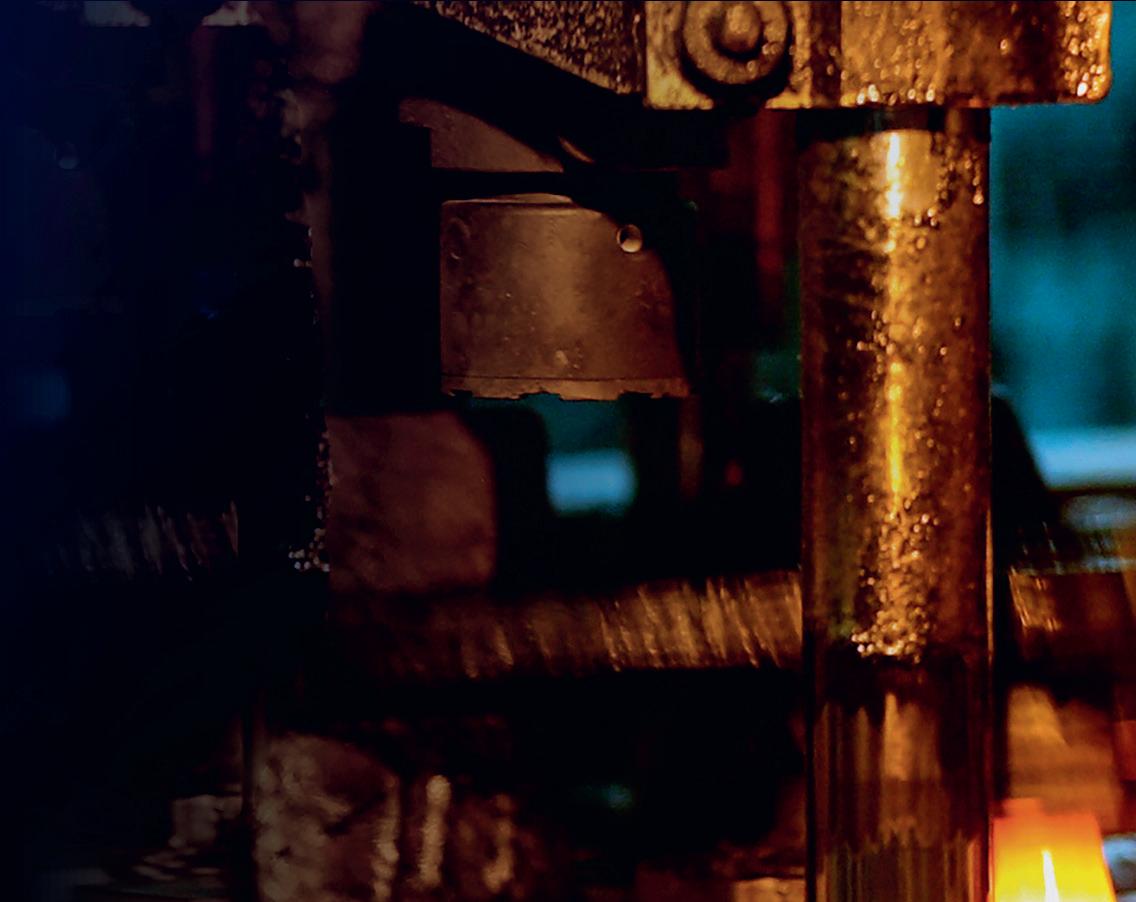
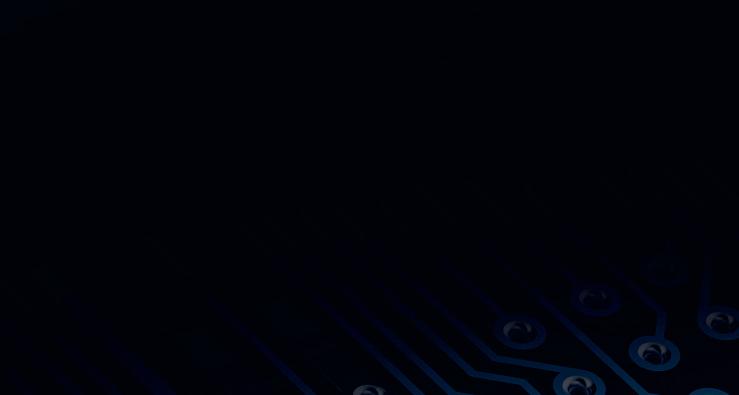


For humans, it’s obvious. For NEO too. NEO Artificial Intelligence for defect recognition
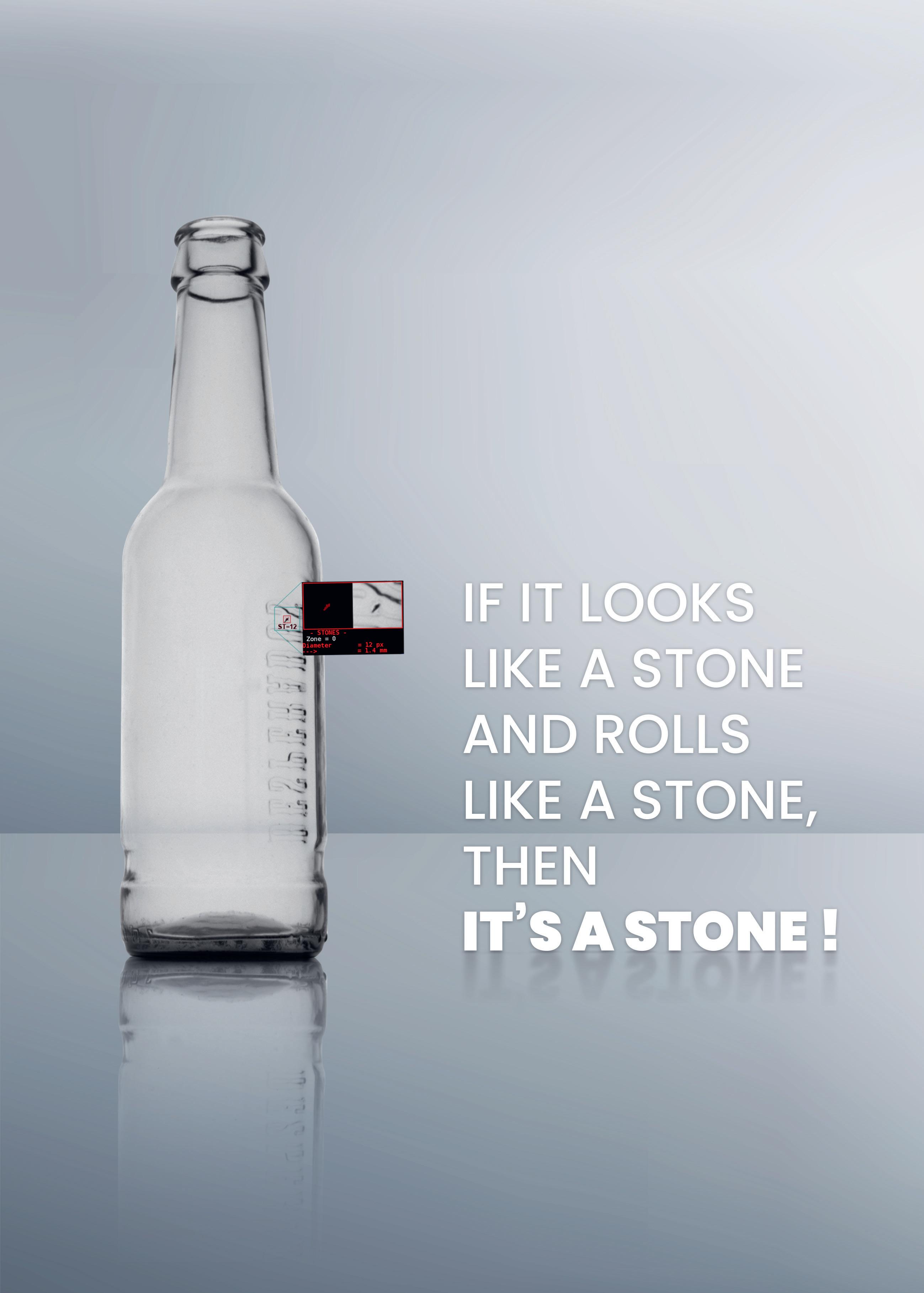
Developments
� Fig 1. Mr-Udomsak-Tangsaksathit (right) and Mr-Jean-Luc-Logel.
Established in the Auvergne RhôneAlpes region in France, the company provides turnkey inspection solutions for mass-produced glass containers of every shape, size and colour.

�Fig 3. cosmeticdedicatedUltimateEvolutionNEOtodefects.
Jean-Luc Logel* looks back over Iris Inspection machines’ history and achievements since its inception 20 years ago.
In 2014, Iris continued to stand out with its ability to innovate and its strong R&D team, as well as the introduction of HD cameras.Increasing picture resolution and thus
On the basis of strong economic growth, due to massive investments in R&D and a diversified clientele, the company aims to increase its turnover and membership by 50% by 2025.
After ten years of experience in BSN glass manufacturing, which later became Danone Group, where they first met, Jean-Luc Logel (Fig 1) and Philippe Volay acquired Centralp in 2000, a company specialised in embedded electronic systems. They saw the latest technology developments, like the use of PCs in industrial environments and matrix cameras in industry, as a vast panel of opportunities. Investing massively in innovation, Iris has acted, from its beginning, as a pathfinder in designing the new concept of 16 cameras, previously six in glass inspection market.
Mr Logel, President of Iris Inspection machines, said: “This major innovation was the first marker of our company.
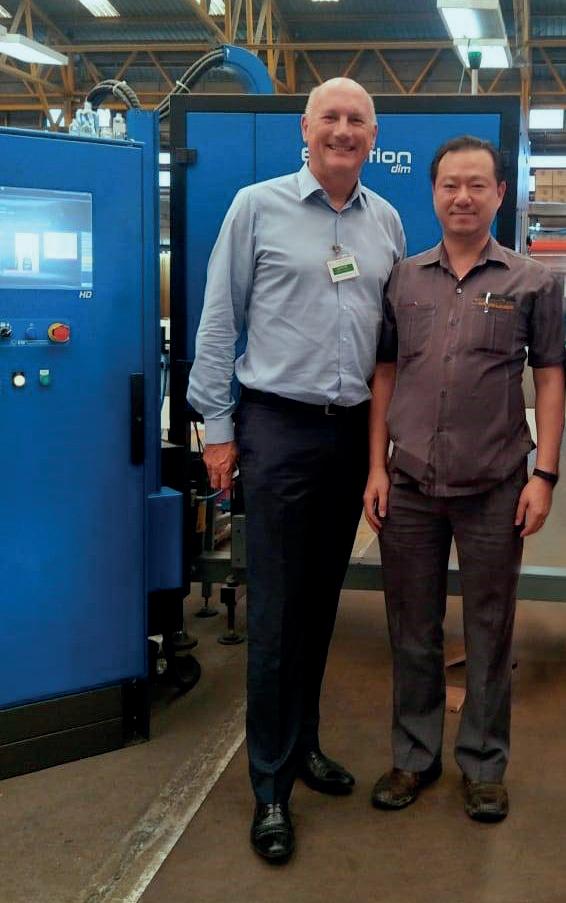
Celebrating 20 years of inspection solutions
As a specialist in the design and manufacturing of inspection robots to detect hollow glass defects, Iris Inspection has established itself as a global supplier for camera-based glass inspection solutions.
Inspection Glass International September 2022 www.glass-international.com 61 Continued>>
“The concept of 12 cameras (up to 16) provides 12 different angles of view, with two cameras positioned on a same vertical axis and taking two simultaneous pictures.“We’ve doubled the resolution, multiplied the angle of view, and thus can be two times more precise than a conventional approach.” (Fig 2).
Artificial intelligence
Inspection 620 www.glass-international.com the accuracy of defect recognition, the organisation continued to rise to the top of glass packaging inspection in Europe andInglobally.2018, the Evolution NEO range established Iris as the most innovative firm in glass packaging inspection market (Fig 3). Implementing artificial intelligence (AI) in this new range of inspection machines marks another step forward in glass defects. Based on learning process (machine learning), Evolution machines learn how to recognise and classify defects with the accuracy of the expert eye of glass people, and the repeatability of computer processing power. “It was a huge global success. Evolution NEO is a new era for glass inspection”, said Mr Logel (Fig 4).
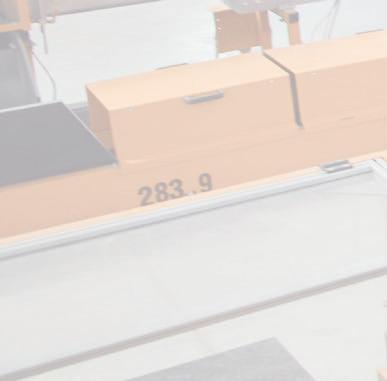

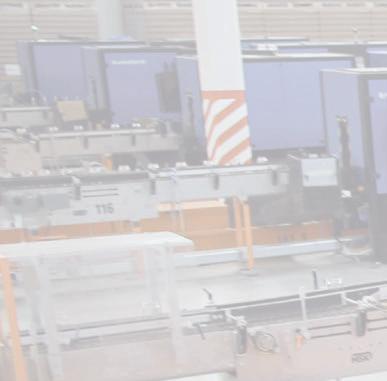
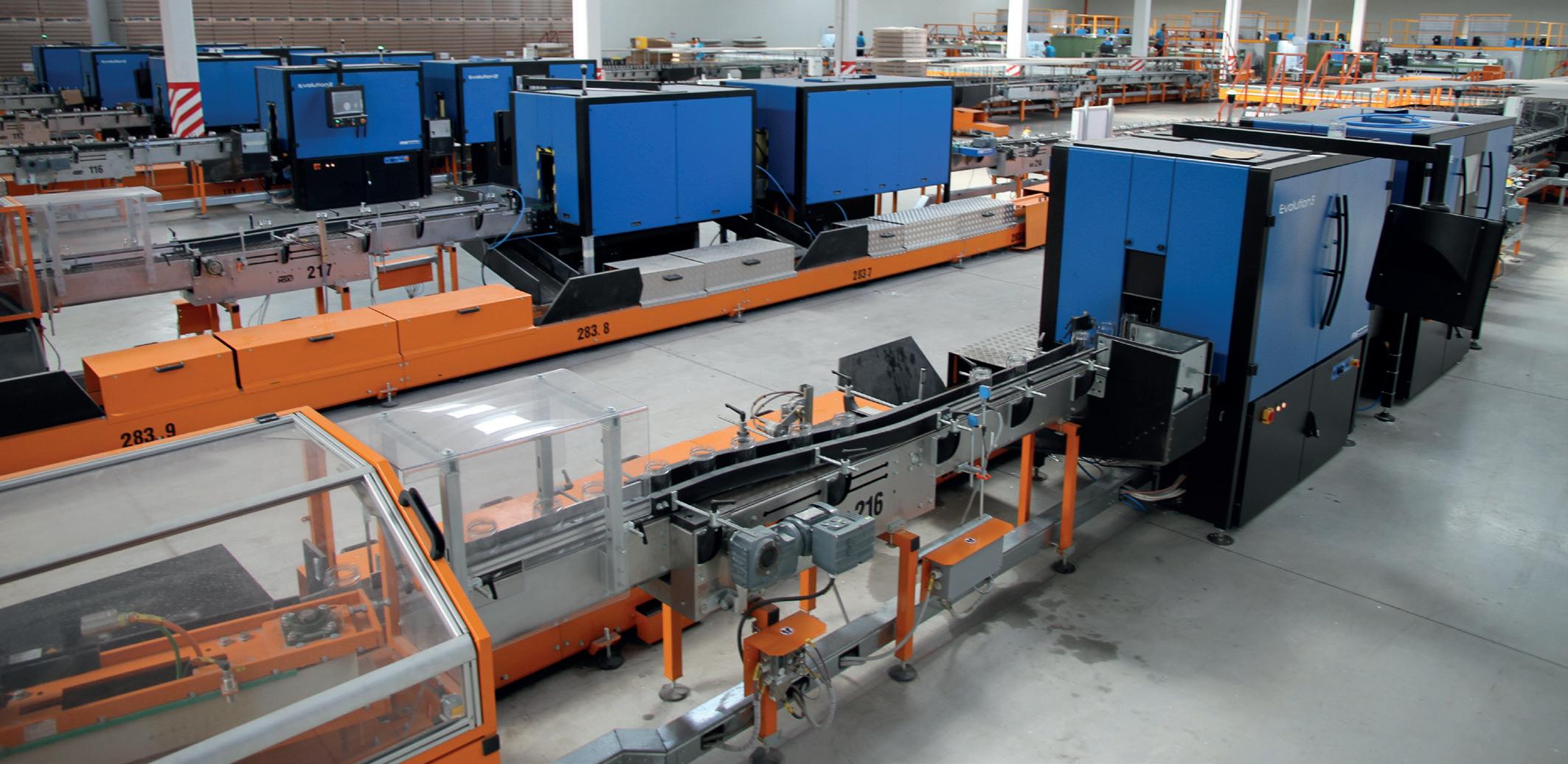
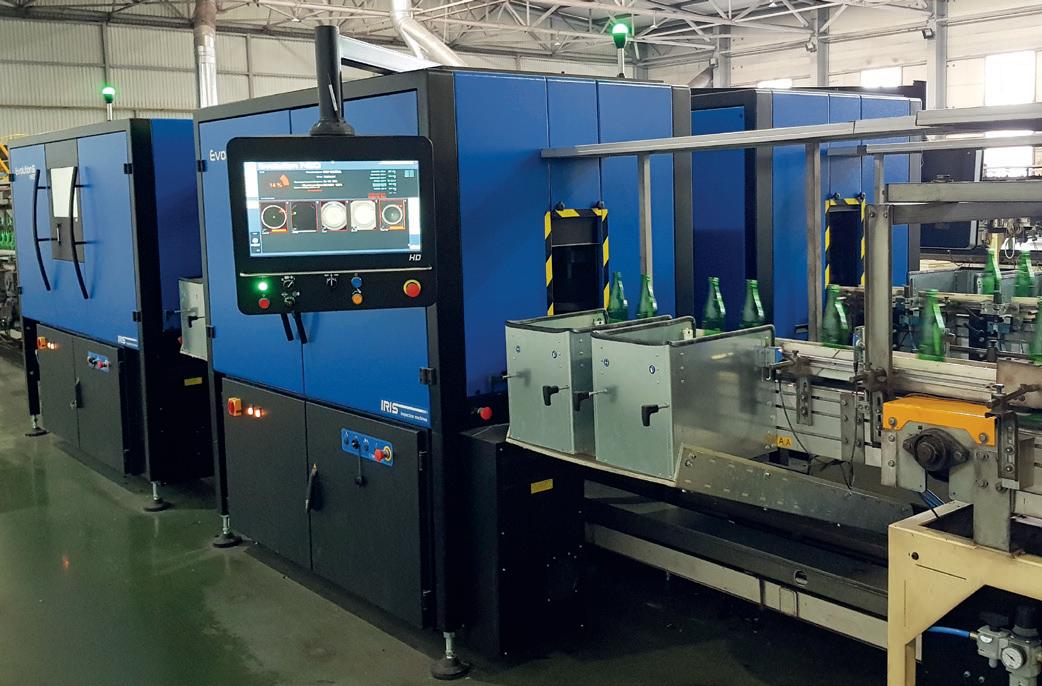

Strong ambitions With the shift taken by glass industry to reduce its carbon footprint and a high European market demand (3 to 5 million tonnes for Germany, Italy and France, against 4 million tonnes for USA and Canada combined), production will continue to grow over the next three years.
“We don’t produce enough glass for European demand. At Iris, we have a record high order book, and we can look to the future with confidence, backed by our transition to digital technologies. “In 2021, we sold 150 machines and we have some opportunities into the international market, in Turkey and Mexico, this seems to confirm that we will exceed the target. “I feel optimistic about the future of Iris, and of the market,” said Mr Logel (Fig 5). This optimism is reflected in the staffing projections. With a turnover of nearly €20 million, the group is anticipating turnover growth of 50% in the next three years. The same applies to employees: with 45 people currently, it is planning to increase its staff by 50%. With this expansion, IRIS will strengthen its customer service, dedicating more than half of employees to serve the client. Being closer to its customers through their expertise and being a pioneer in innovation is part of Iris’s DNA, which will drive the company to global success.
�Fig 5. One of Iris’s installations in Turkey.
As a pillar of the digital revolution, the Bron, France-based company focuses now on AI with the ambition to go even further.While AI can improve glass inspection, it will not replace glass expertise. Glass is a unique material, glassmakers’ knowledge and expertise are crucial to optimise the manufacturing process. Therefore, the new challenge for the team is to combine the power of their AI solutions with glassmaker know-how. “Innovation is a part of our DNA. We gave ourselves the means to become a pioneer and to be considered as a leading and ambitions player in Industry 4.0 with AI and its ability to improve efficiency, as shown by the 17% of investments in research and development,” said Mr Logel. Today, 5 to 10% of glass packaging manufacturing are destinated to become scrap/waste/loss. With AI, the technology specialist’s leitmotif is to work in close collaboration with glassmakers to reach the goal of “zero defect”.
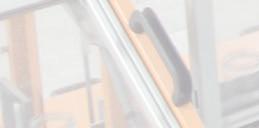
MACHINESINSPECTIONSATAGLANCE 45 people � €18 million turnover in 2021 � €40 million consolidated group turnover in 2021 (Wisetec Group) � 17% of turnover invested in R&D in 2021
�
� Fig 2. Easy-todeploy machineinspectionforan immediate efficiency. � Fig 4. Combining Evolution 12 NEO and Evolution 5 NEO to benefit from mould number correlated to sidewall defects.
� *President, Iris Inspection, Bron, France https://www.iris-im.com/ IRIS
Some solutions are clearer than others. Your vision. Our expertise. The perfect partnership. www.hft.com | info@hft.com Booth C48-1 / Hall 13


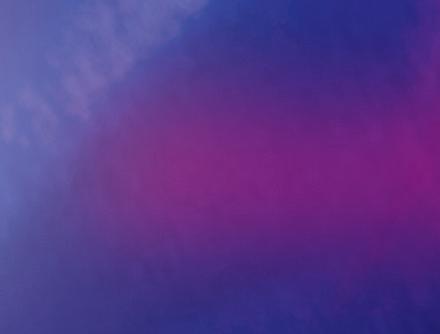
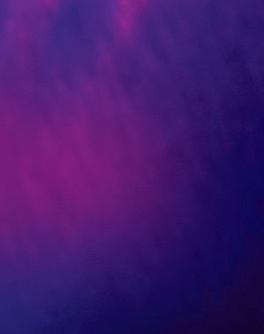

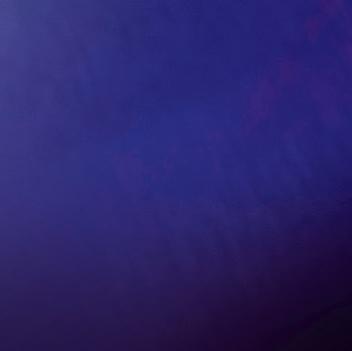
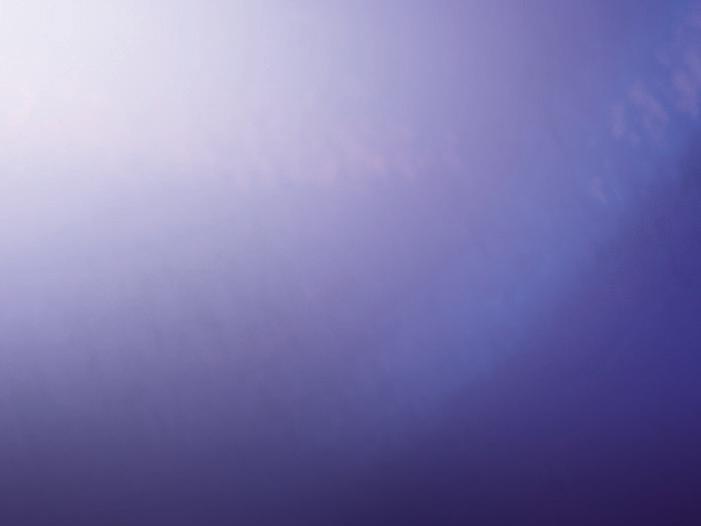
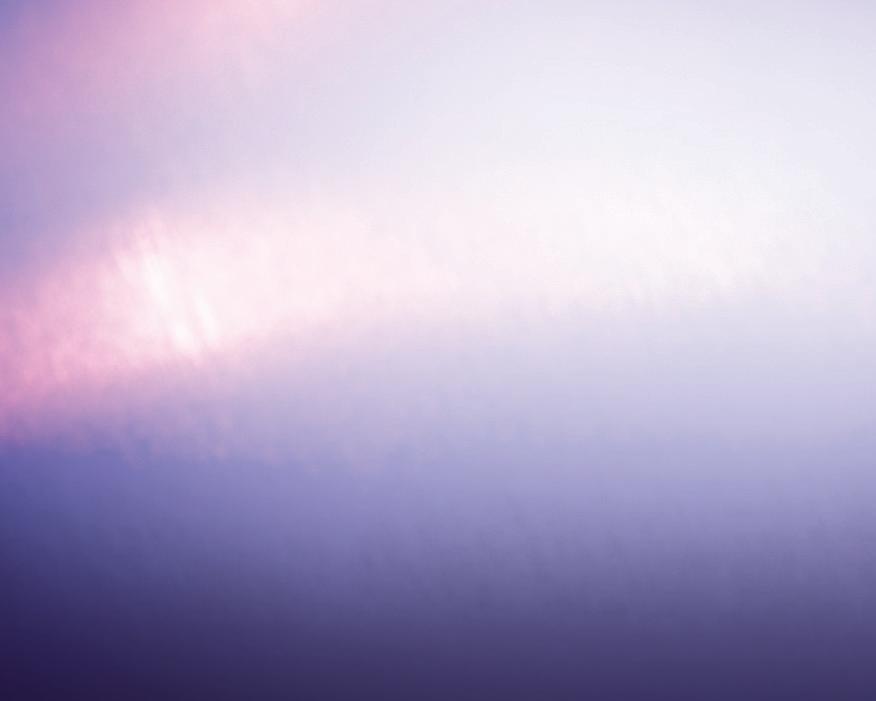

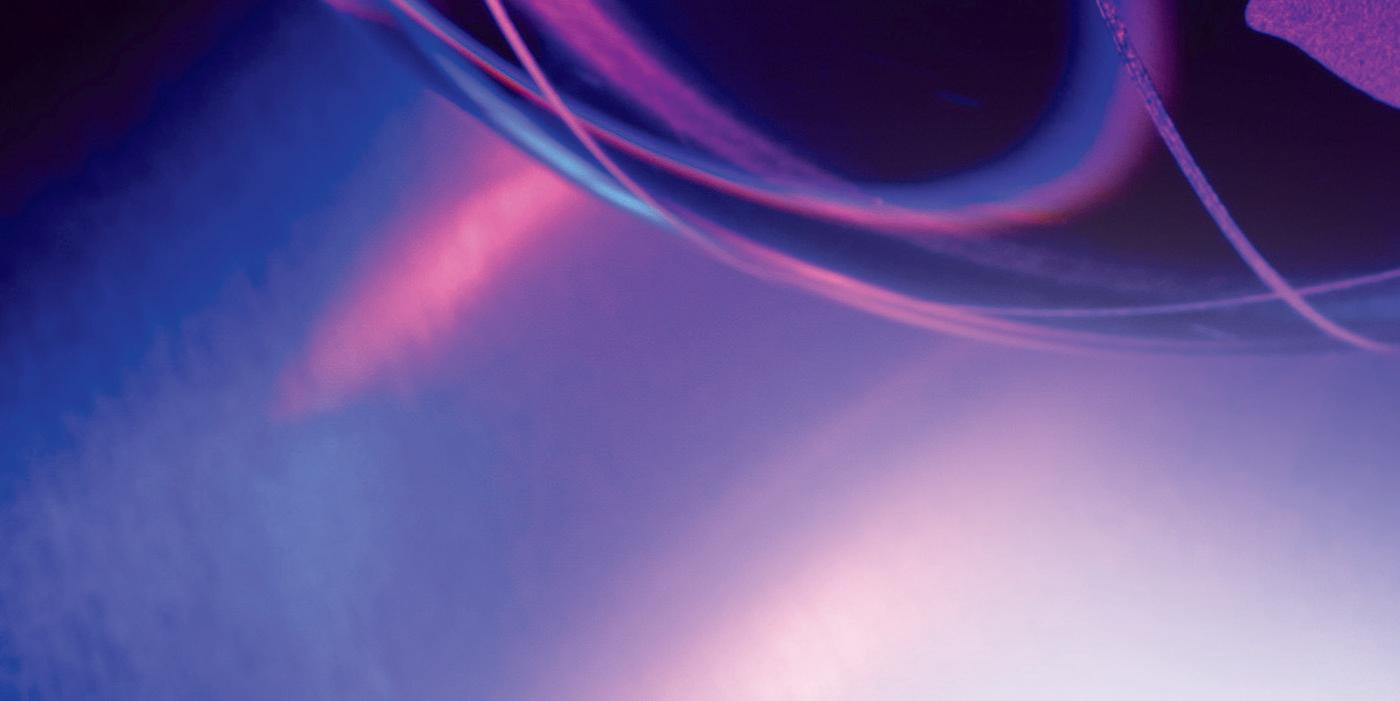

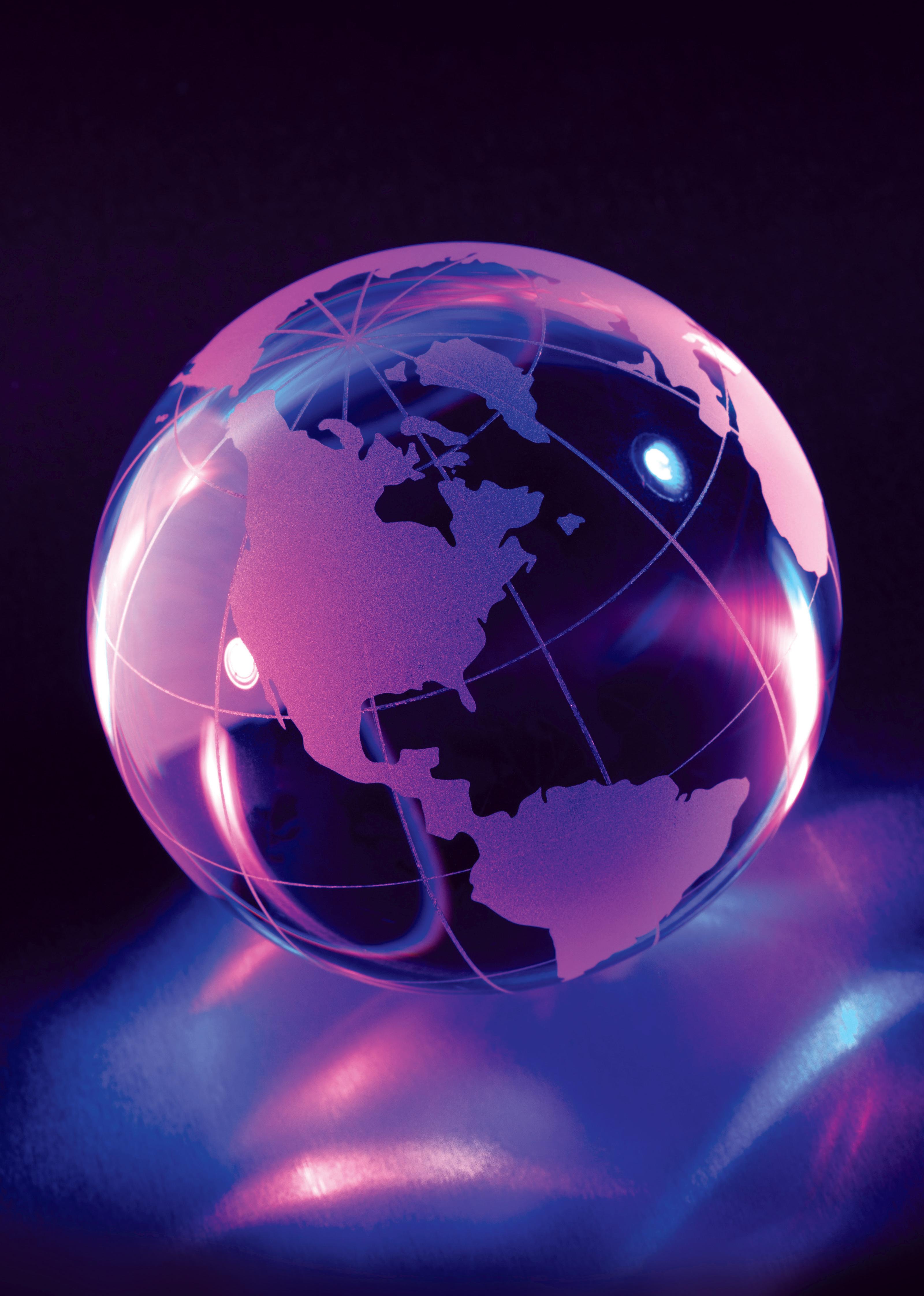
The co-ordination between process line and site buildings is always a key driver for a successful project. HFT brings together 500+ years of combined glass project and glass plant operational experience to ensure that all projects are approached diligently with a succinct understanding of the glass manufacturing process. HFT combines its glass production expertise with site, civil, buildings, and utilities to deliver a comprehensive, fully integrated and true single source project solution.
HFT’s expert glass team offers a combined 500+ years of experience in the turnkey design-build of world-class glass manufacturing facilities and glass process lines. HFT evolved from its container glass beginnings, to serving worldwide glass markets including float glass, rolled solar glass, container glass, fiberglass, tableware, pharmaceutical glass, sodium silicate, specialty glass and pressware. With more than 300 turnkey production lines delivered across 47 countries, the company takes great pride in its reputation and will continue improving and innovating to align with evolving client expectations. To further supplement its project execution capabilities, HFT incorporates in-house proprietary furnace designs.
HFT supports all stages of a turnkey project – from project feasibility reviews, FEED (front end engineering and decision) and securing financing options, to preconstruction, equipment and materials procurement, as well as design-build general contracting, project management, project execution, commissioning and startup.
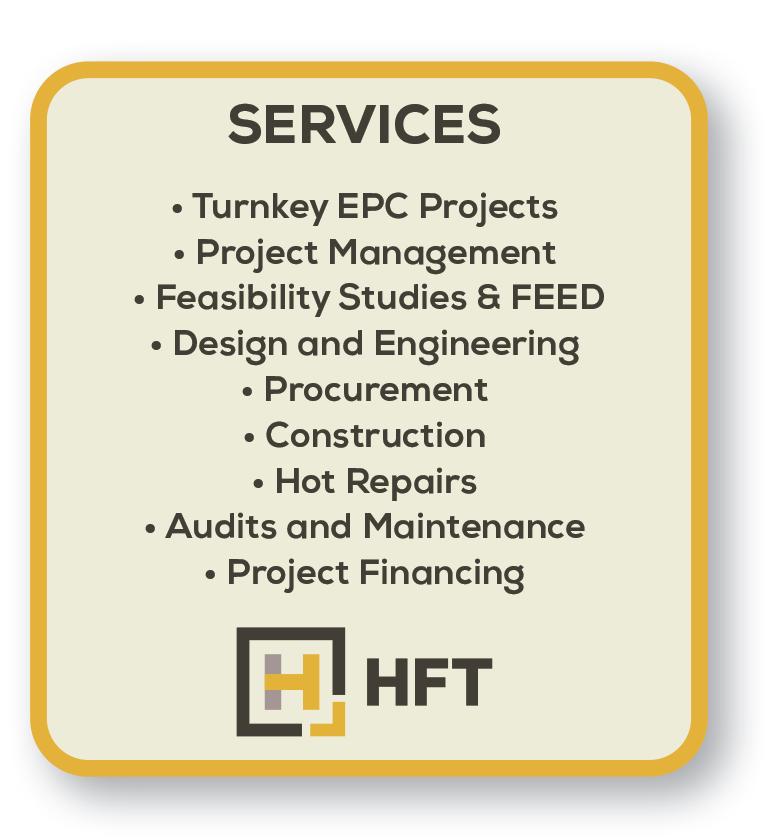
In addition to its global headquarters in suburban Pittsburgh, HFT has regional offices in the United Kingdom, China, the Philippines, Singapore, and St Croix. It’s all quite different from the days when one family directed the entire operation.
Advertorial: HFT Glass International September 2022 640
Seventy-five years may seem like a very long time … or, it may seem like just the beginning. For the company founded in 1947 by Henry F. Teichmann – known throughout the global glass industry as HFT – it’s clear the latter is true. Because, HFT is just getting started. “When I first came to HFT, 34 years ago, I couldn’t possibly have predicted where we’d be at our 75th anniversary,” says HFT President and CEO Mark F. Piedmonte. “Now, we’ve succeeded in navigating drastic technology changes during the past several decades, so as we move forward our challenge is to continue evolving and growing as our industry and the world do the same.” In 1947, the company’s primary focus was container glass furnace design. But a lot can change in three quarters of a century – and for HFT, it certainly did. Today, the company is among the world’s leading EPC (engineering, procurement, and construction) contractors.
HFT’s furnace technology includes oxy-fuel furnaces up to 600MTPD in operation for float and container glass, and regenerative air-fired furnaces up to 1,000 MTPD. Given ever-evolving compliance requirements, HFT is constantly challenged to be on the leading edge of technology. To that end, the company is currently working on an oxy-fuel float glass furnace design for melting over 800 MTPD. This brings some unique challenges. HFT will be drawing on its oxy-fuel float experience to mitigate risk, meet (and exceed) client expectations and deliver a quality and highly sustainable solution that will live up to the production demands of a large footprint oxy-fuel furnace while maintaining the expectation of furnace life. Going a step further, by incorporating its power generation group, HFT is able to offer leading-edge, sustainable solutions that includes the use of alternative energies, waste heat recovery, onsite solar generation, and other green solutions.
“The name of the company still says a lot about who’s most responsible for its 75 years of success,” says HFT President and CEO Mark F. Piedmonte. “Henry Teichmann, Sr., Henry Teichmann, Jr., www.glass-international.com
From glass furnace design to its current position as a leader in EPC in the glass industry, a lot has changed for HFT as it celebrates its 75th anniversary. It’s all about perspective.
After 75 years, global design/build engineering, procurement and construction leader HFT remains focused on the future
Continued>> Sheet glass, being drawn directly from the furnace during HFT’s early days. During HFT’s 20th anniversary celebration in 1967, Archie McIntyre (left), Henry Teichmann, Jr. (2nd from left), and Newton Teichmann (2nd from right) pose with colleagues.


A HFT team oversees batch mixing at Hsinchu Glass Works, Inc. in Taiwan on the early 90s.
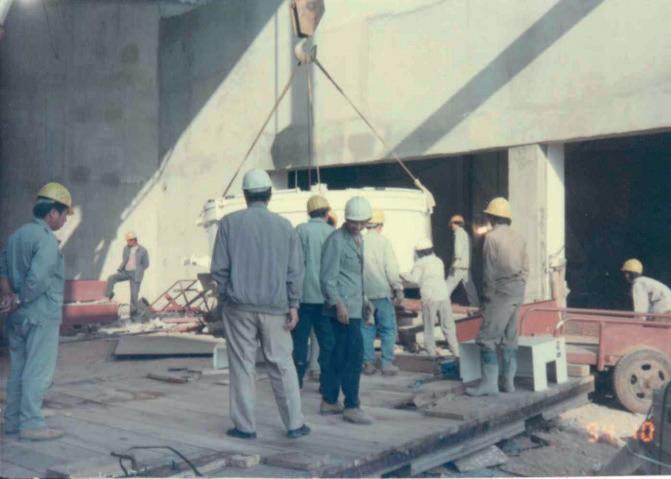
Advertorial: HFT Glass International September 2022 www.glass-international.com 65

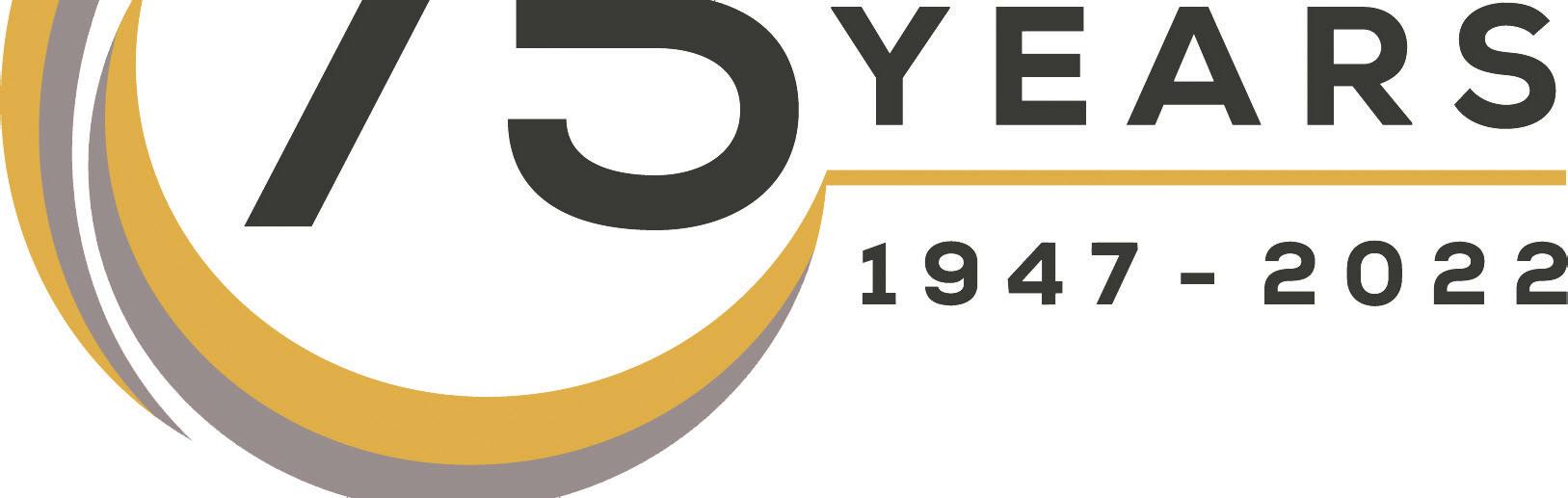
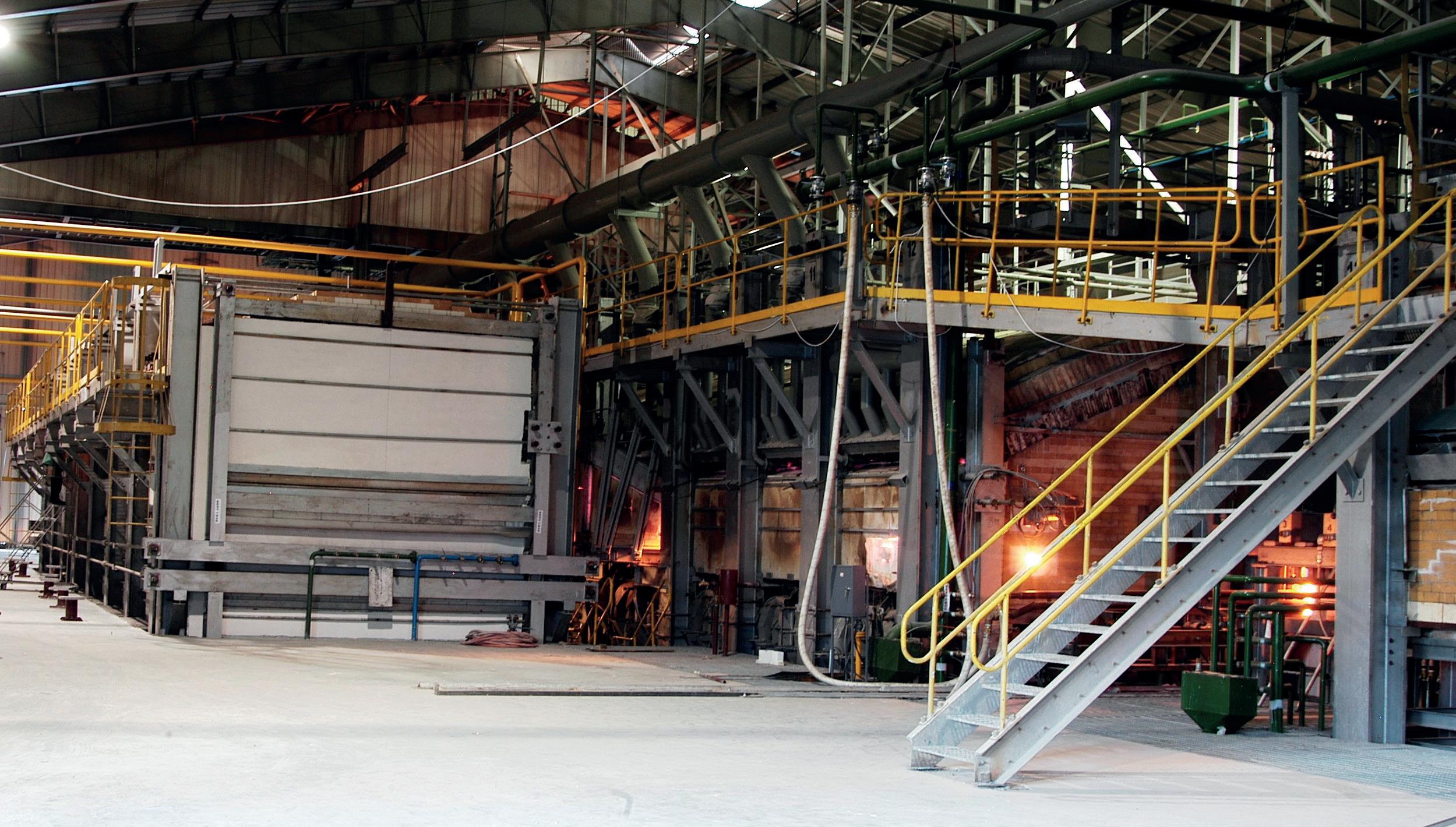
Chief Operations Officer Brad Hall sees the situation as an intense competition.
www.glass-international.com and Newton Teichmann all worked tirelessly to establish a world class engineering firm during the Pittsburgh’s industrial heyday. They set the standard of excellence that enabled us to survive, and then thrive. It’s that same standard we still pursue today.” Of the more than 2,100 projects HFT has completed, a particular milestone was the expansive, 2015-2016 redevelopment of an existing Mt. Zion, IL production site for long-time customer Fuyao Glass America. Complex and fraught with multiple risks, the project ultimately was completed both on time and on budget. Certainly, like companies the world over, HFT needed to overcome a slew of difficulties during the COVID-19 pandemic.“Thatwas a harrowing time within our industry, and we’re still dealing with multiple repercussions,” observes Chief Financial Officer Jordan Baker. “For example, there have been dramatic changes within the global supply chain and we’re also experiencing a renewed interest in localization. Growth will eventually come from this, and I’m also proud to note our company weathered the storm without layoffs or deferrals. We kept the entire HFT team intact, and that’s made us an even stronger company now.”One moment early in the pandemic stands out for Sam Leaper, the company’s director of Glass Business Development. “We’d changed ownership in February 2020, and the lockdowns came into force just a month later,” Leaper recalls. “We were engaged in rebuilding a pharmaceutical glass facility, and suddenly many of our employees were working from home, unable to actually go anywhere. We really needed to think on our feet, since this was entirely new. And then, there was an on-site outbreak of COVID. We needed to come up with a slew of creative solutions to keep everyone safe, while keeping the project underway.”Leapernotes that HFT has since completed a further four rebuilds for this client and is looking forward to more in the near future. One repercussion of the pandemic that seems to be impacting nearly every company and organization, wherever it operates, is a significant narrowing of the talent pipeline. It is a major issue in 2022, and one HFT is addressing in various ways, including the recruiting of young engineers through relationships with several leading universities in the northeastern U.S. “A big challenge right now is finding appropriately educated, skilled individuals to sustain the continued growth that HFT is enjoying,” says Kevin Yung, chief revenue officer. “We need to meet aggressive sustainability goals while innovating on a consistent, ongoing basis. To be successful, we need the right people. And they’re not easy to find.”
Advertorial: HFT Glass International September 2022 660

Chief Financial Officer Jordan Baker certainly emphasizes geography when he peers forward in time.
HFT, McMurray, PA, USA www.hft.com
“From the beginning, this company has consistently evolved to meet and exceed the needs of its clients,” he says. “That certainly won’t change. We’re strongly committed to becoming even more global, to refining and expanding the capabilities we offer, and to ensuring that our first-time customers always become repeat customers. From my perspective, the sky’s the limit.”
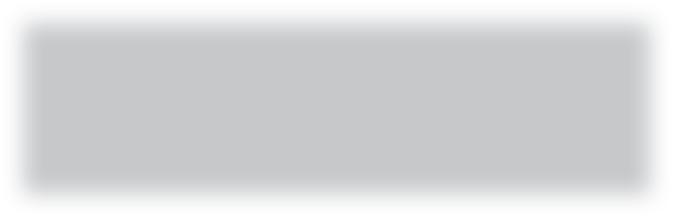
“What I envision when projecting a decade or so ahead is a company that’s more diverse in terms of the projects we complete,” Baker says. “I believe HFT’s major projects will be more evenly distributed around the globe, with a closer balance between the North America, U.K. and Europe, Middle East, andToAfrica.”Yung, it is clear technology will dictate the nature of the future – even looking ahead 75 years, to the company’s 150th“Evenanniversary.in2097,consistent steps forward in melting and production processes will be essential,” says Yung. “More than anything else, advances of this sort will enable us to dramatically streamline project capital requirements and the total cost of ownership. And that could very well transform our industry.”
For his part, Piedmonte is optimistic about HFT’s future.
“HFT is on the lookout for talent,” says Hall. “As a result, growing talent internally – along with careful planning for succession – is now the key to any organization’s success. There’s simply a shortage of qualified workers, and we’re committed to ensuring we attract and retain the specific individuals we need.” When celebrating 75 years of history, it’s natural to also look ahead and ponder what the future may bring. One key trend HFT is watching closely is the localization of glass manufacturing, in response to concerns about overall transport costs. Being as near as possible to customers is essential, and that suggests an expanding role for HFT Europe, which is headquartered in the U.K.
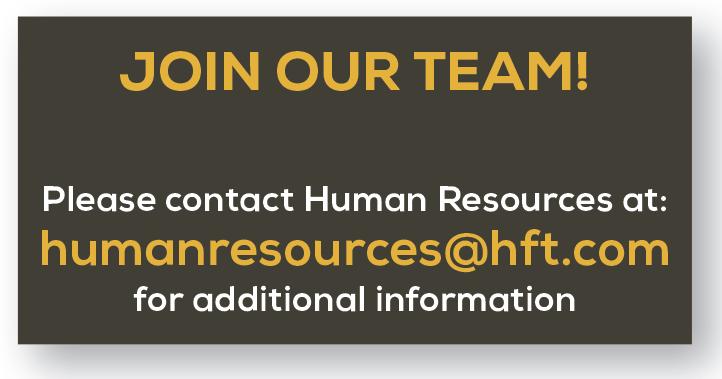
GGCGhazvinGlass Co. Float glass industry experts or international Float glass company Retired experts are called for collaboration with Ghazvin Glass info@ghazvinglass.comwww.ghazvinglass.comCompany. Legacy Continues... BASF Temperature Sensing The Shape of Your Success Accurate, reliable, and affordable temperature sensing equals success for your plant. With the help of our proprietary Fibro ® wire, we will exceed your expectations in performance while reducing the cost of your temperature sensor. As a full loop precious metal provider, BASF can help you achieve more value by recycling precious metal outContactthermocouples.ustofindmore! catalysts.basf.com/glass BASF_CAT-003354_Visual_Components_AZ_180x127mm_RZ.indd 1 09.02.22 12:07
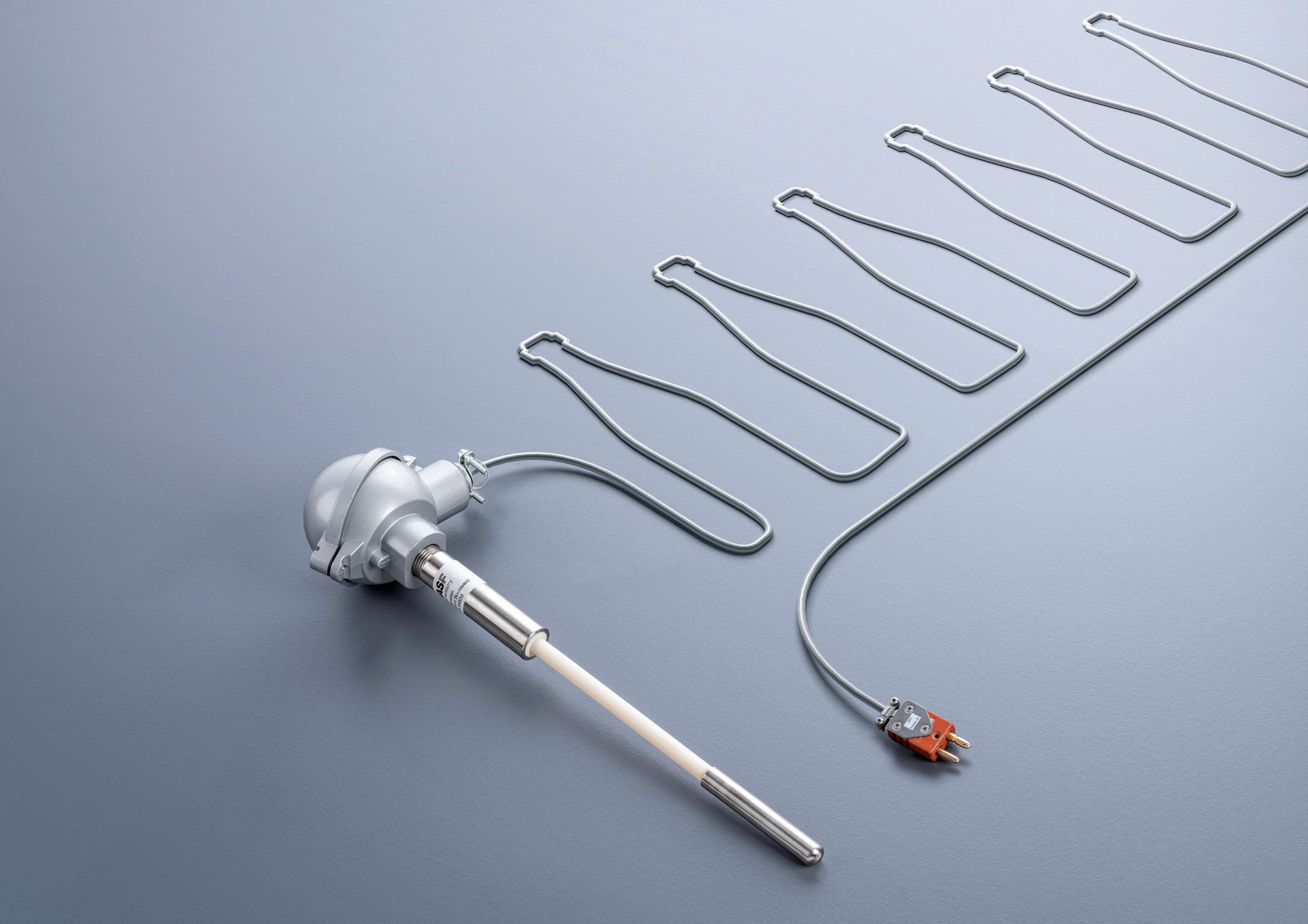

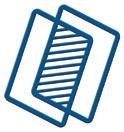
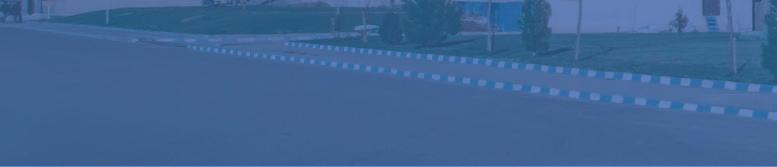
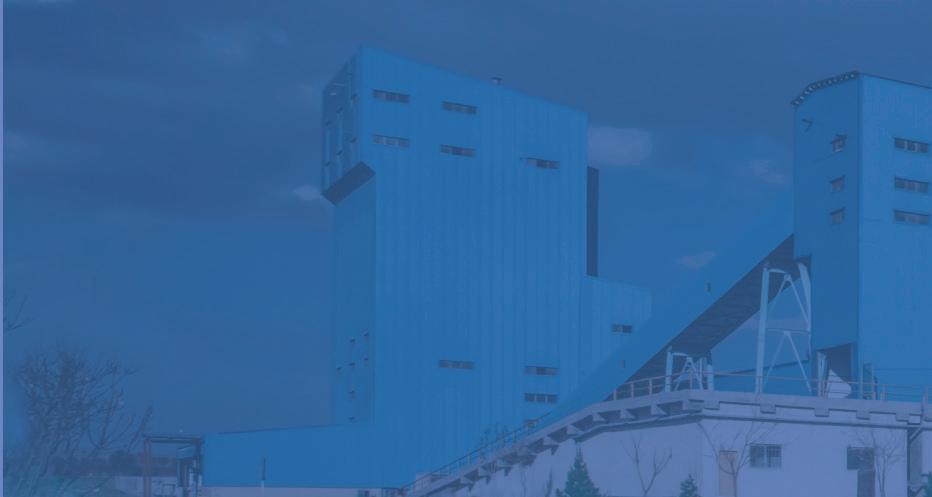


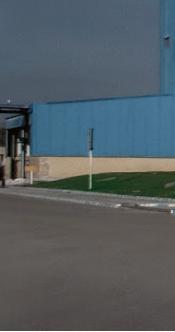
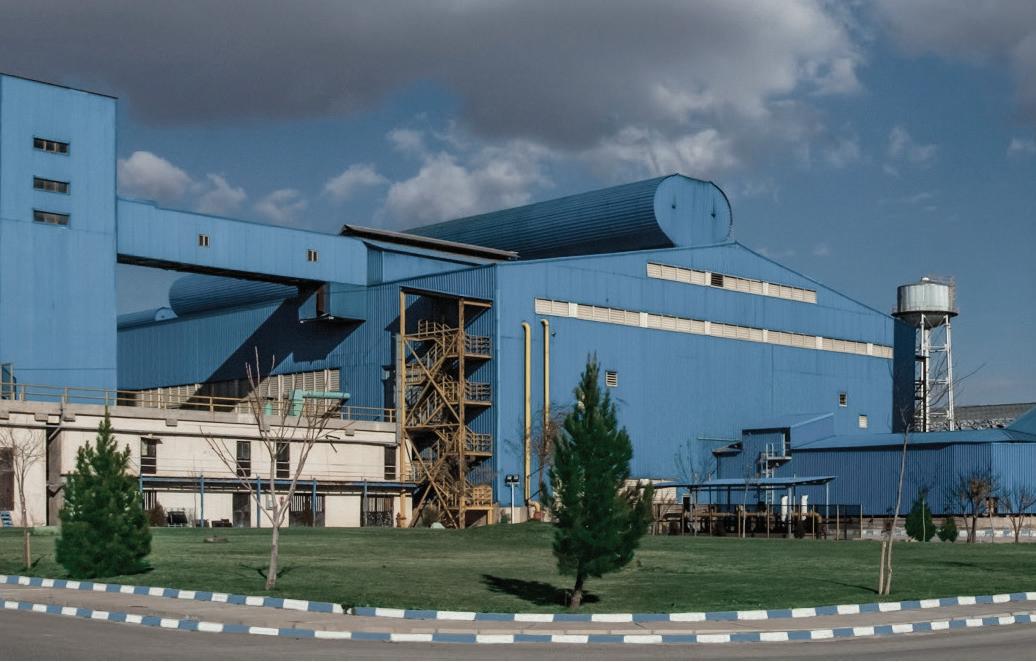
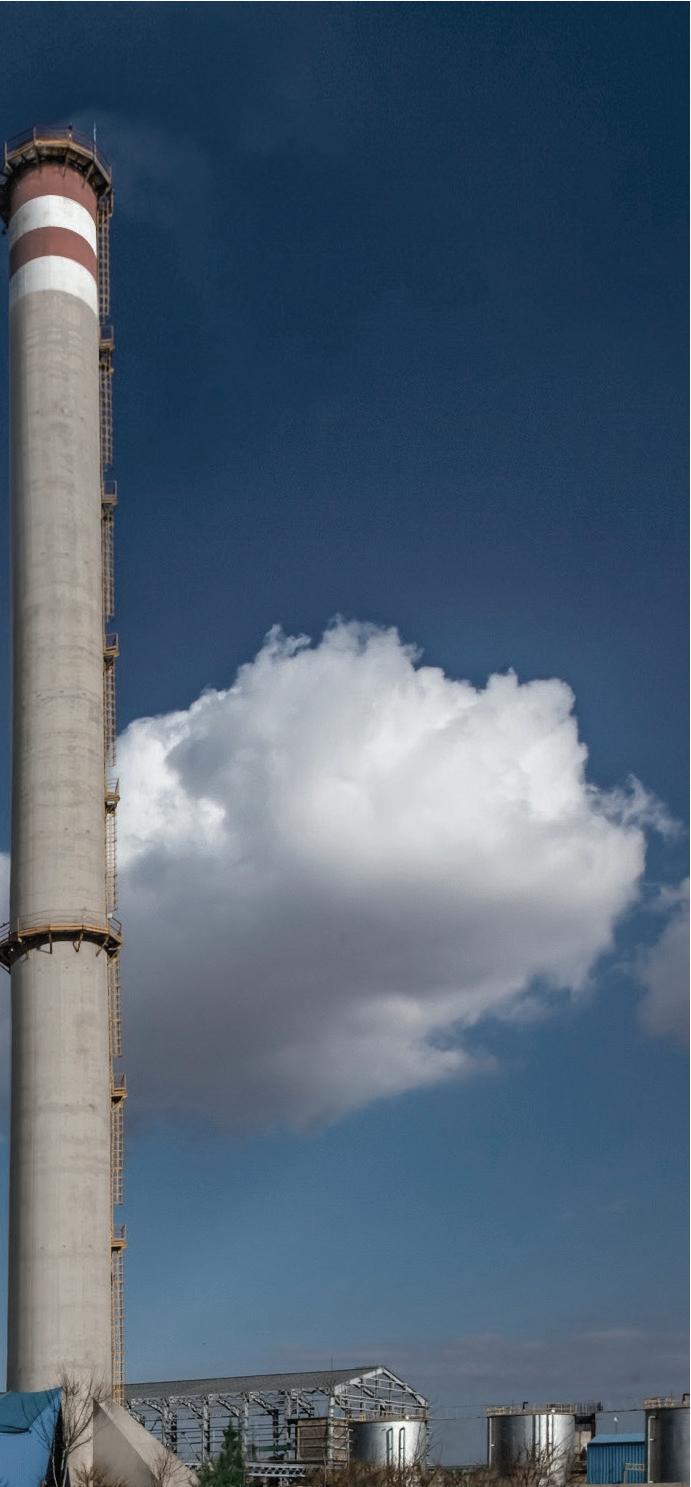
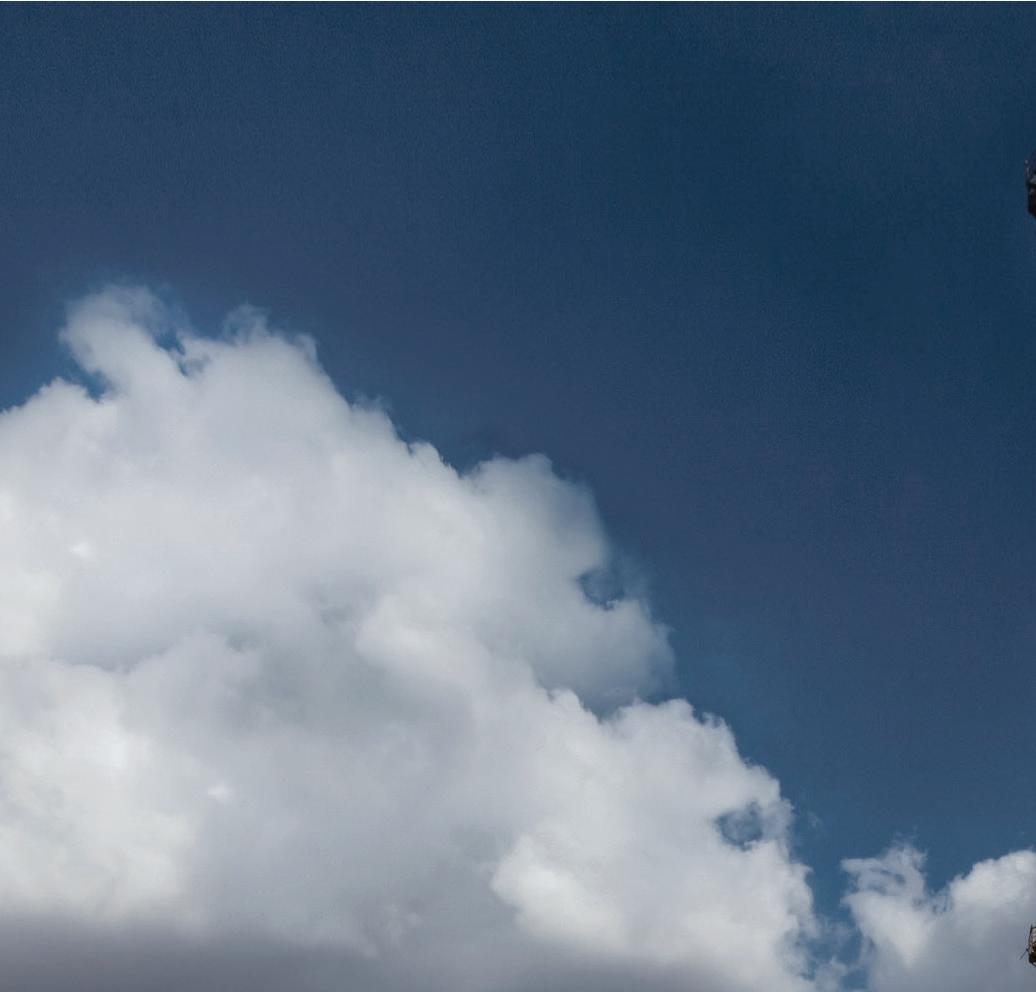
Refractories Glass International September 2022 680 www.glass-international.com
� Total refractory wear in the last 12 months is almost none when thickness is below 20mm.

� Data Collection on Park Cam Furnace 20
Park Cam recently made reality out of a glass industry dream. Working with PaneraTech to manage their furnace digitally, they were able to achieve zero refractory wear over 12 months while pulling at full capacity. This puts Park Cam one step closer to having the ideal furnace.
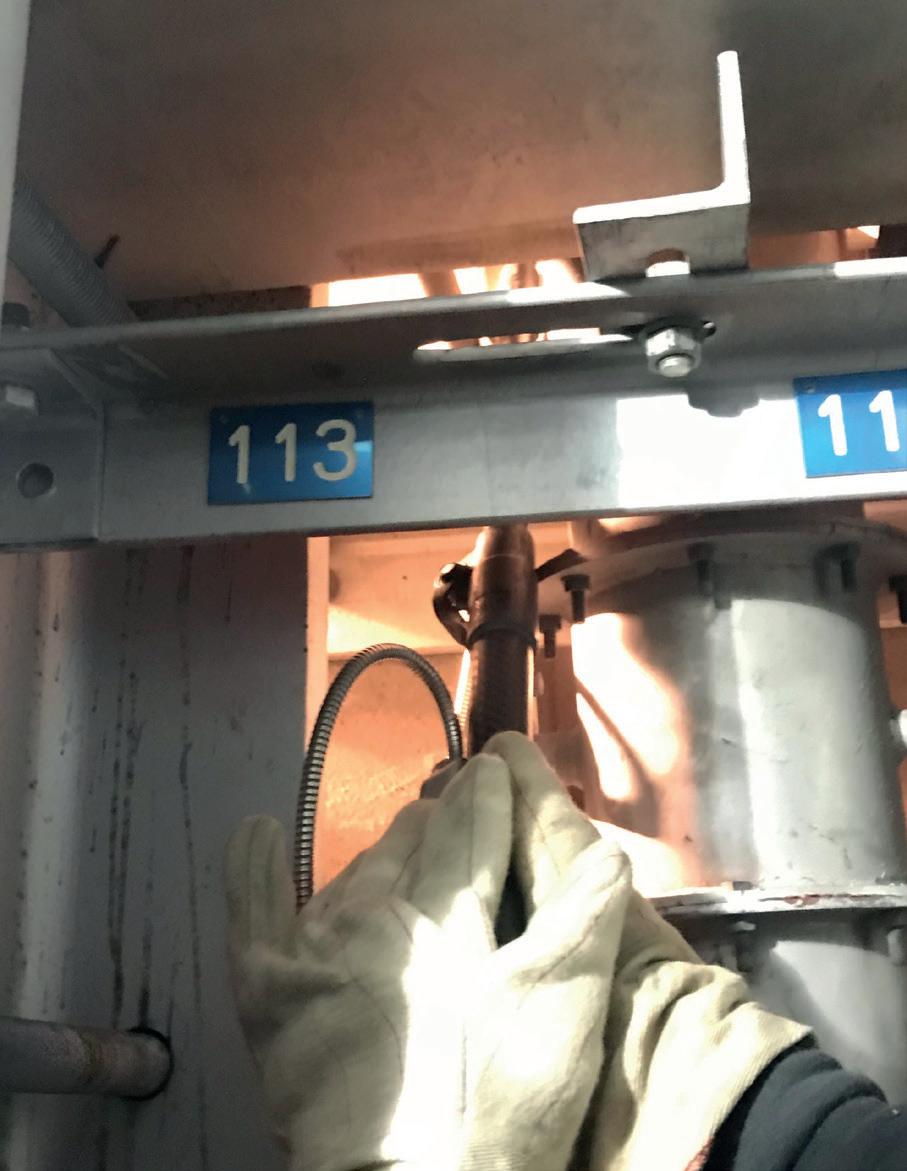
How Park Cam achieved zero refractory wear over 12 months
As the glass industry moves toward data-driven decision-making,
Park Cam is a container glass company based in Turkey with a production capacity of 365,000 tons per year. The furnace that achieved this milestone, Furnace 20, is located at Park Cam’s Bozuyuk glass packaging production facility.In2018, Park Cam began a multi-year furnace monitoring programme with PaneraTech to monitor the entire furnace with SmartMelter radar technology. The plant team collected data for SmartMelter inspections at least twice per year. These results were reviewed in a digital furnace model and discussed with the PaneraTech team. In its predictions, PaneraTech benefited from over half a million refractory measurements they had performed during this time. This allowed PaneraTech to make datadriven predictions when discussing the results with Park Cam. Park Cam used the data from the SmartMelter inspections to increase cooling wind at critical blocks and watch the area closely to ensure safe operation. The radar scans created a map that pinpointed the thinnest refractory areas. Once the critical areas were identified, the plant applied targeted wind cooling based on these reports. They also collected temperature data on a regular basis on these critical blocks. The plant continued to make adjustments based on recurring six-month scans. They were able to take the AZS to the limit of failure and ultimately past that limit to a controlled failure of the block which they were prepared for.By making data the heart of their decision-making process, Park Cam was able to have confidence in their actions. They were able to carefully manage risk while making financially rewarding decisions about their furnace. All glass manufacturers would like to optimise the life of their furnace; however, in the months that followed, Park Cam successfully took this goal to a new level.The industry typically overcoats when refractory thickness is 25mm (1 inch). However, Park Cam was able to operate without overcoating an additional two years after reaching 25mm. Once the thickness reached 18mm, the targeted cooling allowed the plant to operate 12 months with no additional wear on these blocks. Park Cam is the first glass manufacturer in the industry with a proven record of operating 12 months with virtually zero refractory wear at this stage. After this 12-month period, they decided to overcoat the refractory. This process extended the life of the furnace two years beyond typical industry practices.
To honour the International
Glass ad.indd 1 16/06/2022 11:16
to announce that we have
a commemorative yearbook that will celebrate the crucial role that glass plays in the 21st century and beyond. For more information or to order your copy
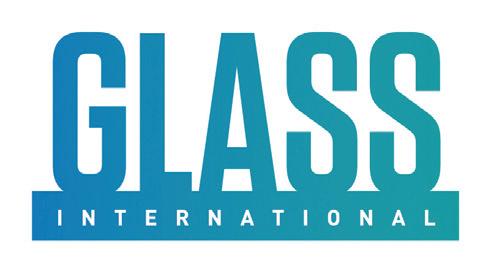

Glass, we are
Refractories Glass International September 2022 www.glass-international.com 69 advanced technology like radar-based sensors and digital tools to monitor and manage the furnace campaign are essential. PaneraTech has expanded their services to meet this need. To help more glass manufacturers optimise their furnace campaigns, PaneraTech now offers a full Digital Furnace Monitoring (DFM) programme. Over the last five years, after collecting more than 1 million points of refractory wear data in over 200 plants, PaneraTech is now able to put data at the centre of major decision-making for glass furnaces through the DFM programme. XSight software acts as the command centre for the programme, allowing managers to monitor their entire furnace portfolio in one dashboard. Furnaces in the DFM programme are digitally transformed so that furnace activities and records from radar scans, audits, temperature checks, and visual inspections can easily be viewed at the plant or corporate level.
SmartAudit is a key component of the DFM programme. SmartAudit is a traditional furnace audit that includes an 18-point radar spot check at eight data points on the metal line and ten points on high-risk areas to establish a health Index. Manufacturers can evaluate this radar sampling with KPIs such as pulled ton/ sqm to identify outlier furnaces early and take action before small issues become larger problems. A future addition to SmartAudit will be Digital Endoscopy, a service that upgrades traditional endoscopy with laser technology to measure the actual thickness of the super structure.Critical areas, such as the blocks that were carefully monitored by Park Cam, can now be monitored in real time with Polaris permanent IoT sensors. Polaris sensors can be installed anytime during the furnace campaign to monitor highwear areas closely. Polaris works especially well with electric or hybrid furnaces, as the sensors can monitor continuously without any interference with electrodes and with no disruption in production. However, the DFM programme is more than a collection of new tools. The data that is collected from this technology is used to create a refractory health index in the AI platform that was developed based on data from monitoring hundreds of furnaces. This index helps managers view data in the right context and prioritise maintenance actions. When a furnace is enrolled, PaneraTech creates a schedule of services for each year of the anticipated campaign life based on experience with hundreds of furnaces. Additional specific conditionbased monitoring on a narrower scope can be defined as necessary throughout the campaign life. PaneraTech also works with the plant team to develop a routine monitoring plan to complement this schedule, which can include furnace walks that are scheduled and confirmed in XSight software. Park Cam’s early interest in data-driven decision-making and their approach to refractory monitoring helped to establish a foundation for the programme that PaneraTech offers today. The partnership between these two companies proved that traditional ideas about furnace campaigns can be reimagined with advanced technology. � PaneraTech, Chantilly, VA, USA https://parkcam.com.tr/en/home/Parkhttps://paneratech.com/Cam,Turkey
� Data Collection on Park Cam Furnace 20. Year of proud released www.glass-international.com/gl-commemorative-yearbook-2022visit
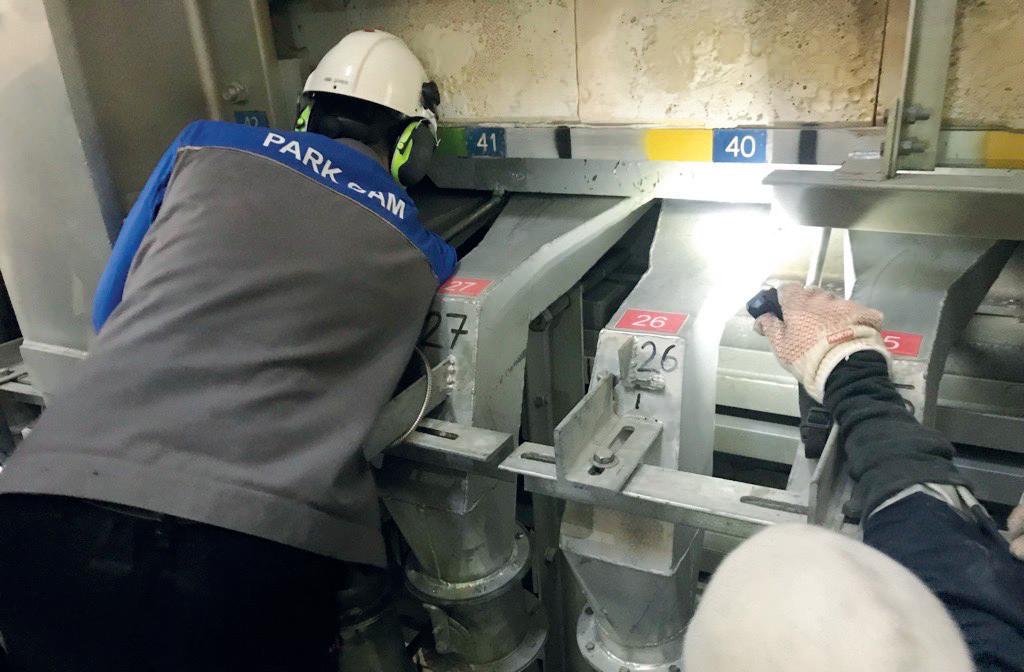
*Businesswww.sklostroj.cz/enDevelopment Manager for Production Machines, Siemens, www.siemens.com
“Servo technology would be more energy efficient, and compressed air is also extremely expensive,” says Ziegler. About every other IS machine from Sklostroj is delivered complete with servo technology. With the help of the Sinamics S120 converter, braking energy at the axes can be used to accelerate other axes at other stations. “In this context, we’re talking about DC or DC link couplings,” says Ziegler. Excess energy can also be transferred from machine to machine, thanks to regenerative AC/DC infeeds. A distributed Simatic fail-safe CPU with a fail-safe ET 200SP distributed I/O system controls higher-level and safety-oriented processes at the sections.
Energy-efficient actuators
“These are just three cornerstones among many in Sklostroj’s comprehensive strategy for making a substantial contribution to efficient and climateneutral glass production,” Ziegler affirms. “That’s why it’s all the more important to us that Siemens has stood by our side as a technology partner for over 15 years, providing consulting services and worldwide support in the areas of electrification, automation, and digitalisation,” he concludes. �
When people talk about energy efficiency in glass manufacturing, they generally mean potential savings from the glass melting furnace. But plant engineering and machine building companies like Sklostroj know that they also need to look at the forming process. “In the current energy policy situation – which will continue to challenge us all for some time to come –any process improvement is worthwhile,” says Mark Ziegler, Manager of Business Development and Marketing for the Czech manufacturer of IS machines and hot-end equipment.
Pulling out all the stops
When it comes to electrification, automation, and digitalisation, Siemens has been Sklostroj’s technology partner of choice for more than 15 years, states Radek Novotny* and Mark Ziegler**.
Forming Glass International September 2022 700 www.glass-international.com
** Sklostroj, Turnov, Czech Republic
As an engineer, Ziegler understands that in most glass factories, almost 10% of melting energy goes unused because the “pack-to-melt ratio” – the ratio of final packed glassware to the initial glass melt –is most 90%. “Everyone who works in the industry knows that the process is highly complex and that workers are increasingly difficult to attract,” says Ziegler. “So it’s important we realise the remaining 10%.”
A third strategic approach for achieving a sustainable forming process is the use of digital twins in engineering. “By simulating everything virtually in the development phase and commissioning the machines digitally on the computer, we shorten the conversion time, reduce downtime once again, and can prevent errors during ongoing operation,” says Ziegler. A good example is an upgrade to a new type of CPU that can be simulated without real hardware. “Operators can also be trained on the computer even before the machine is built.” Side by side
� In many of its machines and plants, the Czech company consistently relies on control and drive technology from Siemens.
With its 200 employees, the company is forging new paths in the field that it knows best, container-glass forming, which it has practiced for more than 70 years. Sklostroj (sklo = glass, stroj = machine), with headquarters in the Czech city of Turnov, exports about 95% of its precision machines. The engineering company supplies complete hot-end lines and plant components like IS machines, timing and drive systems, standalone systems including pushers, stackers, feeders, shears, and gob distributors, and much more.“The downtime of IS machines plays an important role in our approach to an energy-efficient forming process,” explains Ziegler. Preventive maintenance concepts have been a valuable part of the solution at Sklostroj. These concepts are based on the Drive and Timing Control System (SDT-10) automation platform jointly developed by Sklostroj and Siemens.Servo motors like the Simotics S immediately report deviations, such as higher torques caused by increased friction. With the added help of IoT platforms and at the customer’s request, the machines are becoming “smarter” thanks to AI, which makes them better and better at identifying data patterns. “At this point, glass manufacturers often become extremely concerned about data security, which is why we simultaneously developed appropriate security concepts,” saysAlongZiegler.with preventive maintenance, Sklostroj believes that keeping production changeovers and maintenance activities as brief as possible is another way to reduce downtime. With the SDT-10, for example, it’s possible to load all the parameters from an article database in a matter of seconds when a new job has to be programmed.
Reduced downtime
The second component in the energyefficiency concept involves traditional drive issues. An estimated 80% of the actuators in IS machines in glass factories are still operated by pneumatic cylinders.
The versatile digital twin
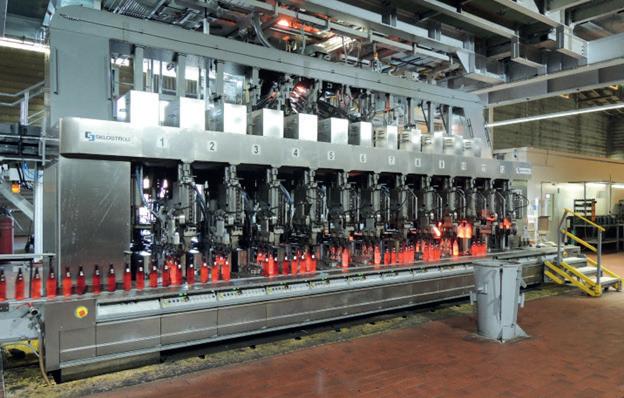
Centers of Excellence spread across the Antares Vision Group enterprise help to spur innovation that only happens when people, process and technology come together to discover what’s possible.
Antares Vision Group – Rigid Containers is also benefiting from the purchase that strengthens its own can and bottle inspection capabilities.
Jeff Hartung, V.P. of Sales and Customer Service for Antares Vision Group –Rigid Containers explains, this proven technology is now more accessible to customers.“Ourname is different, but our purpose of enabling quality inspections remains the same. We continue to build the tools that enable glass makers to increase their yields by accurately detecting and identifying defects,” Hartung said.
Applied Vision Corporation will begin operating under a new goto-market name – Antares Vision Group – Rigid Containers – as part of Antares Vision Group. It is a global provider of machine vision inspection systems, track and trace solutions and smart data management possibilities.Withtheacquisition
Glassmakers stand to improve product quality, brand protection, business growth, customer experience and sustainability with one reference partner.
Innovation Antares Vision Group – Rigid Containers, founded in 1997 and operating as Applied Vision Corporation until the fall of 2022, has developed vision systems for nearly 25 years based on patented optical, lighting and electronic image capture techniques combined with digital processing and AI algorithms that allow machines to adapt to normal process variation challenges.
Knowledge sharing between engineering and manufacturing disciplines – coupled with operational best practices within the group – means more mindshare is concentrated on solving for emerging needs. Often the inspection cameras, lighting and AI logic used by one manufacturer can address the challenges faced by another.
Applied Vision is now Antares
Creating Excellence Antares Vision Group – Rigid Containers is now benefiting from the synergy and collaboration between Antares Vision Group business areas that drive R&D and commercial advantages – everything from reducing the development time for new inspection solutions to expanding the options available to glass container manufacturers to applying serialisation on empty bottles.
The company now combines Applied Vision technology with digital solutions for product and supply chain visibility that enable efficiency improvements from sourcing and production to distribution. By leveraging team knowledge and digitisation tools across the Antares Vision Group enterprise, Antares Vision Group – Rigid Containers aims to help its customers build a clearer picture of their operations end-to-end.
Inspection Glass International September 2022 www.glass-international.com 71 Continued>>
Vision Group – Rigid Containers
of Applied Vision in December 2020, Antares Vision Group expanded its technological leadership to encompass a wider spectrum of inspection competencies and services in the food and beverage sector.
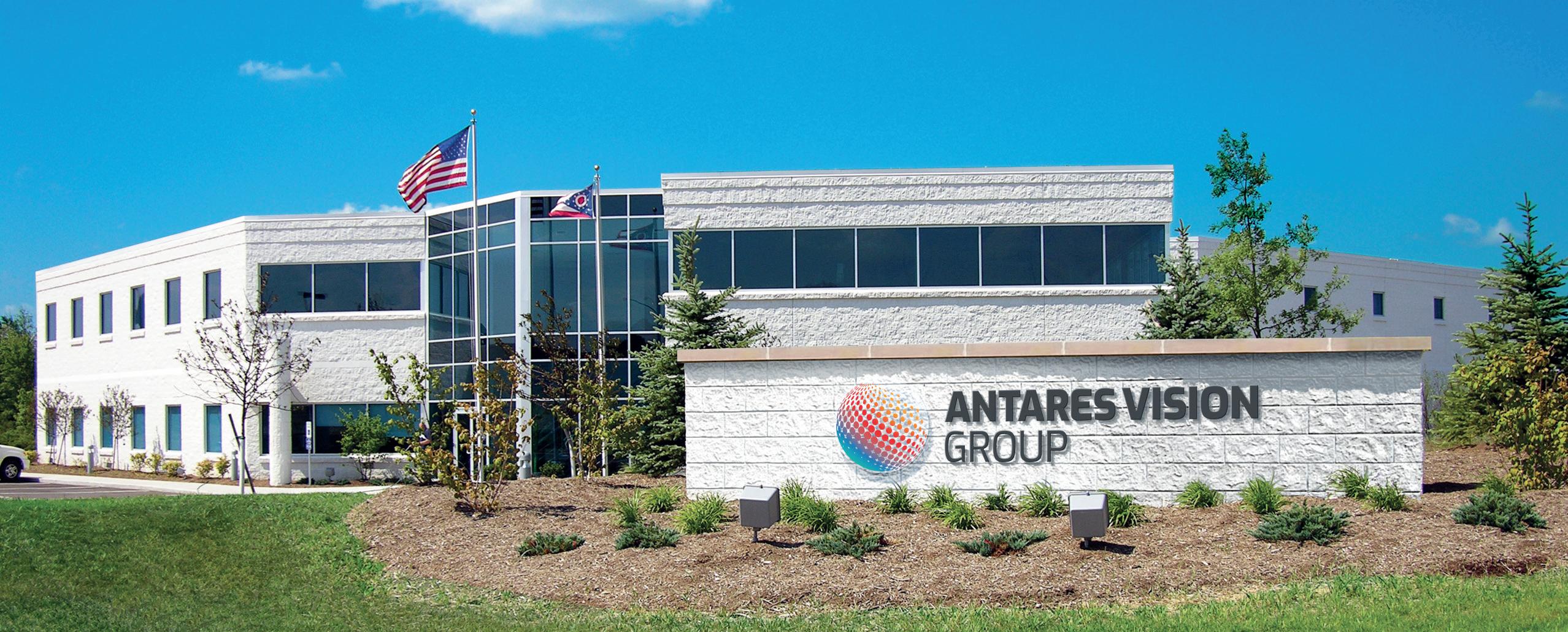
Capturing Data Hartung went on to say that moving forward, the company will serve as both a reference partner for quality inspections and for achieving high-quality standards across product and supply chains.
“As part of Antares Vision Group, we are dedicated to ensuring customers receive the excellent performance in quality products and services they deserve and making use of more world-class resources now available to us to accomplish our mission.”
As bottle makers continue to prioritise efforts around quality and safety, brand protection, and efficiency and sustainability, a partner that combines an ecosystem of relevant technologies into � Antares Vision Group – Rigid Containers is the new name for Applied Vision, owned by Antares Vision Group.
Growing Globally Thanks to Antares Vision Group’s considerable global footprint, Antares Vision Group – Rigid Containers has also expanded its customer service footprint in Europe, the Middle East, South America and across the Asia-Pacific region.
“Maybe you want eyes on goods and materials from the source to the shelf, or your concern is improving returnable container management or recycling, and we can support those activities with supply chain transparency that brings your physical and digital worlds together.” Same Inside Inspection systems from the company will incorporate the same Applied Vision technology that has always powered the company’s machines. Proprietary imaging techniques at the base of Applied Vision solutions, together with deeprooted technological know-how, allow Antares Vision Group – Rigid Containers to stand out in the marketplace according to “WeHartung.remain a US-based multinational leader that sets a high standard for quality inspection of glass containers,” he said.
“Other times it’s knowing that the treatments performed on line three are producing a great result, and how can I apply this to lines or machines in other plants?” Hartung said. “As part of Antares Vision Group, we can leverage more resources and expertise to help customers replicate the best results throughout their facilities, minimize waste from discarded bottles, improve recycling and take confident steps to fortify their operations against market uncertainties or the threat of a voluntary recall.”
Volcano systems using Applied Vision technology can provide mouldcorrelated statistics as well as image maps of defect locations without rotating glass containers. Simple setup and operation also support the efficient implementation of virtually any inspection sequence a plant requires.
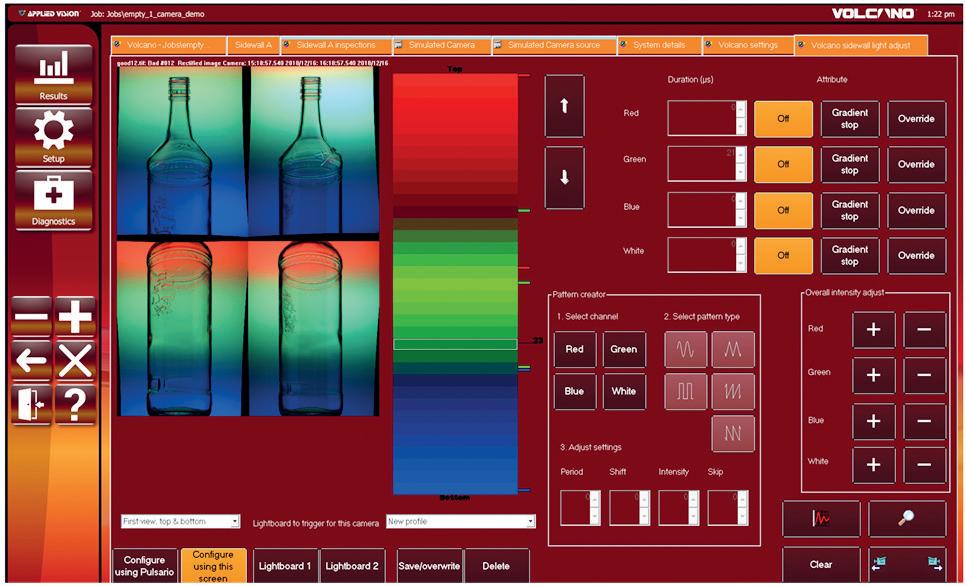
One Shared Vision Strategic acquisitions have made Antares Vision Group a technology partner for food and beverage, life science and cosmetics supply chains. By aggregating high-growth organisations of excellence that have demonstrated technologies at a global level, the group is striving to represent a technological hub of excellence that helps container manufacturers ensure the safety of product, profit, people and the planet.
rotatingdefectasmold-correlatedprovidestatisticswellasimagemapsoflocationswithoutglasscontainers.
Others will find there’s no one more qualified to improve their quality and production efficiencies through accuracy, reliability and speed.” � Antares Vision Group-Rigid Containers, Ohio, www.appliedvision.com.USA
“Our complete Volcano line includes Sealing Surface and Base, Sidewall and new Check vision systems for performing comprehensive inspections. “These systems can be electronically coupled to give plants a broader view of the container being inspected and a better idea of where problems may exist in the production process.”
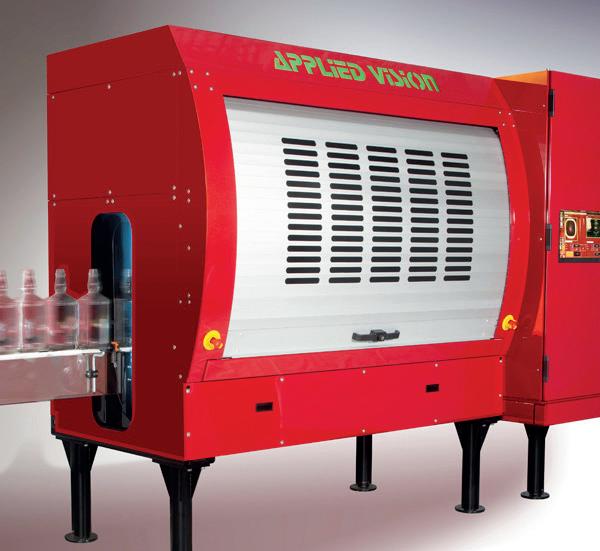
Inspection Glass International September 2022 720
inspection and control devices for bottling and packaging lines. This co-location initiative expands its presence in Europe and supports customers in the Middle East. The company is also moving forward to open a third service location to benefit South American customers. Based in Brazil, the centre will operate from the group’s local branch office that specialises in the inspection of life science and pharmaceutical applications while also delivering track and trace and smart data management solutions to a variety of industries.
www.glass-international.com one convenient offering can accelerate enterprise digitalisation and innovation goals.“Ifyou want to pinpoint the cause of dimensional flaws for lean, height or finish E&T for example, or you’re having trouble identifying the most problematic checks, we can offer a solution.
“We help ensure optimal inspection effectiveness on the fastest, most advanced production lines in the world, regardless of container complexity,” said Hartung.“Forthose who already know us, it’s business as usual but now there’s more to see. Let’s also talk about transforming your plant into a digital factory to better understand your product’s journey.
Hartung points to excellent aftersale service as a key contributing factor to the company’s past success. Antares Vision Group – Rigid Containers has traditionally hosted a service center within its US headquarters building to help customers get ahead of the curve with classroom training and hands-on instruction.“Sharing the knowledge that helps bottle makers eliminate error from their inspections is at the heart of what we do, and now we can offer our expertise to more customers as a member of the Antares Vision Group,” said Hartung. “From installation and troubleshooting assistance to getting parts to where they’re needed, we are localising our services in more places to provide an instantRecently,response.”Antares Vision Group – Rigid Containers opened a new service centre in Italy leveraging the group’s Beverage Business Area main office that provides �� Volcano systems using Applied Vision technology can
The event format is a niche trade exhibition where people can arrange meetings with a number of suppliers and industry experts in one place. Visitors and exhibitors can attend the free conference sessions to hear from industry experts. These exhibitions bring together international experts, hollow and container manufacturers and businesses that use glass containers, to discover the latest innovations which include energy efficiency, quality control, packaging, logistics and decorative possibilities. Go online to find out more at WWW.GLASSMANEVENTS.COM Ken Clark Sales Director +44 (0)1737 kenclark@quartzltd.com855117 Manuel Martin Quereda International Sales Manager +44 (0)1737 manuelm@quartzltd.com855023 Mexico City, Mexico glassmanevents.com/latin-america Seoul, South Korea glassmanevents.com/asia LATIN AMERICA 2024 BOOK YOUR STAND TODAY Istanbul, Turkey glassmanevents.com/europe

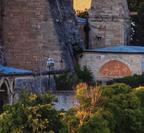
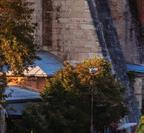
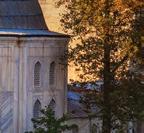

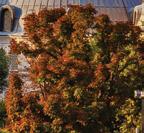
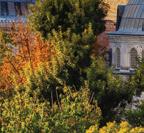
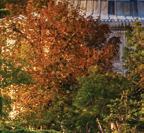

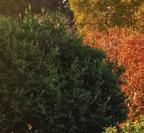
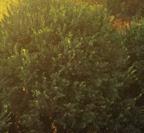
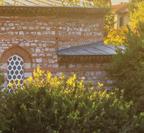
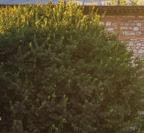
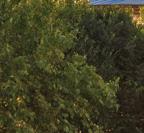


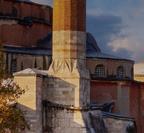
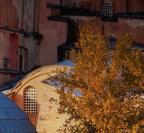
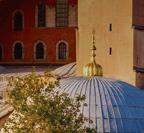
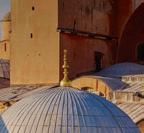
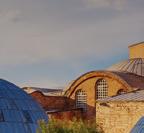
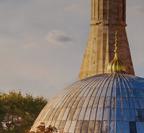
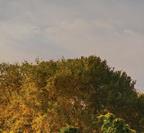
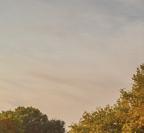
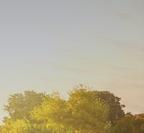

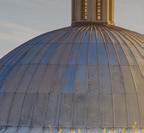
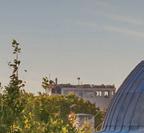
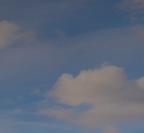
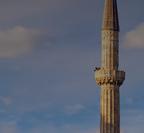
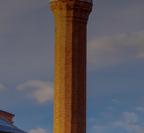
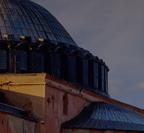
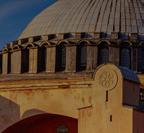
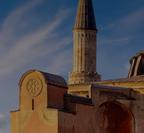
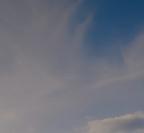
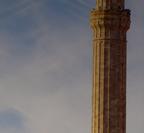

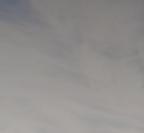
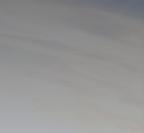
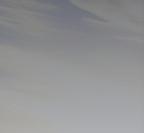
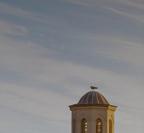
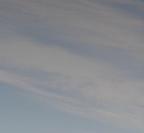
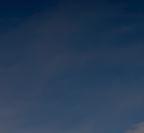
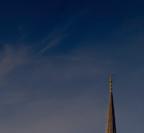

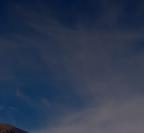
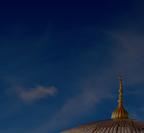
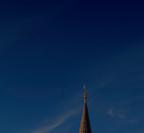




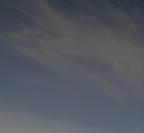
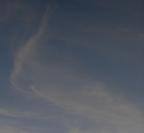
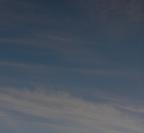
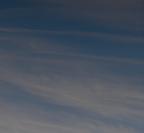

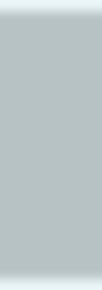
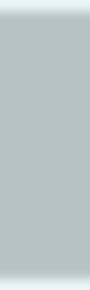
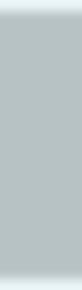
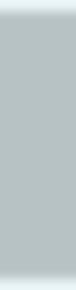
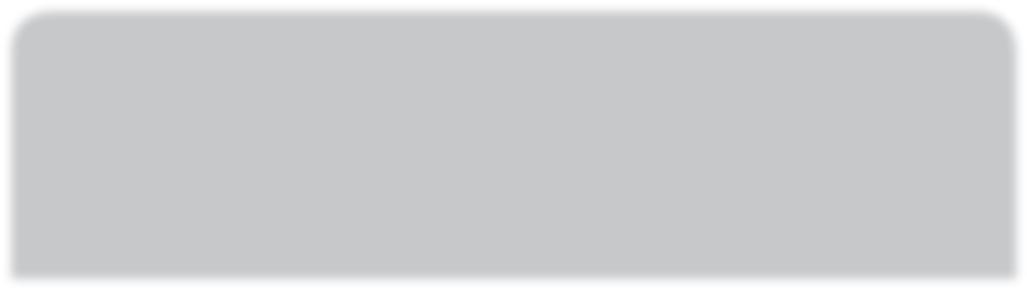
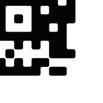
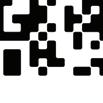

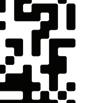
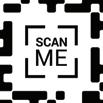

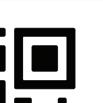
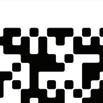
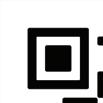
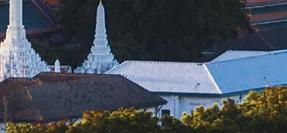
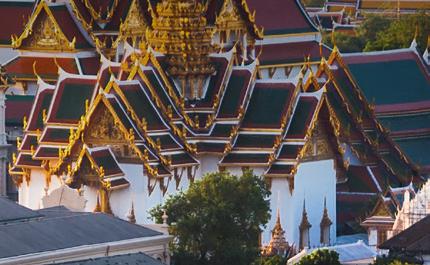
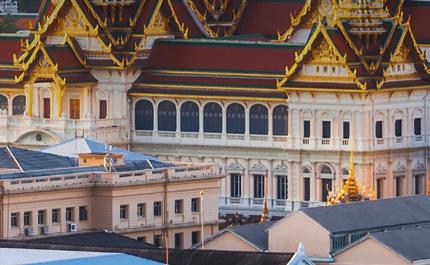
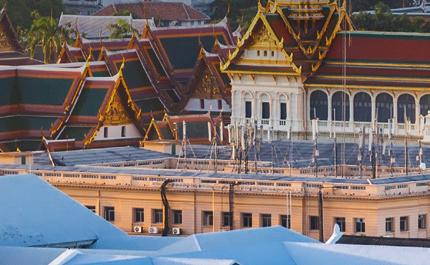
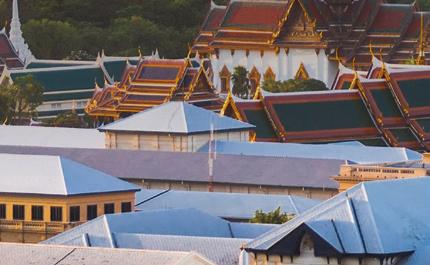
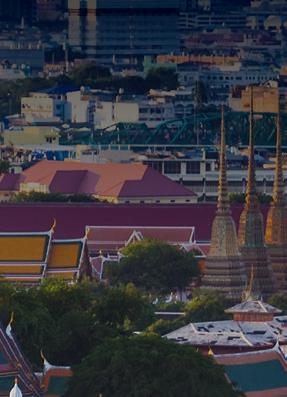

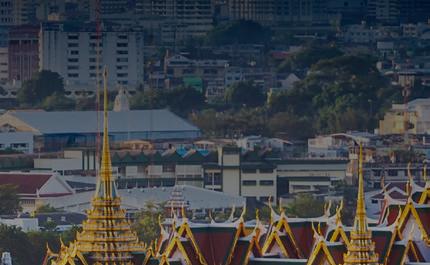
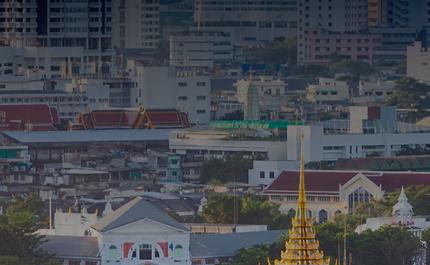


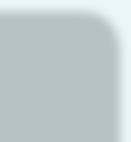


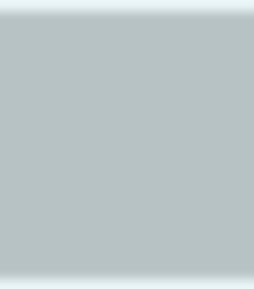
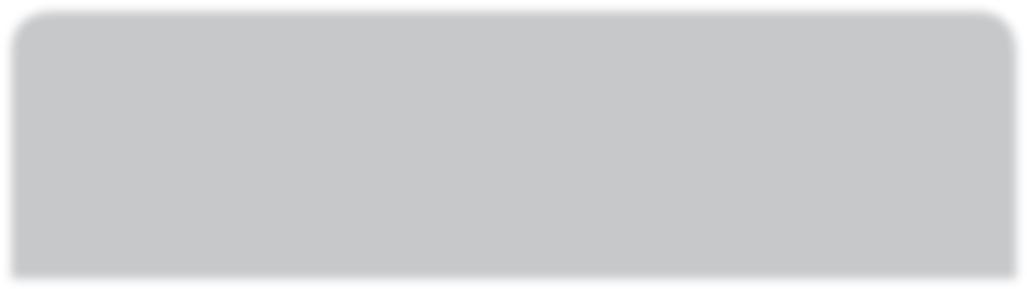
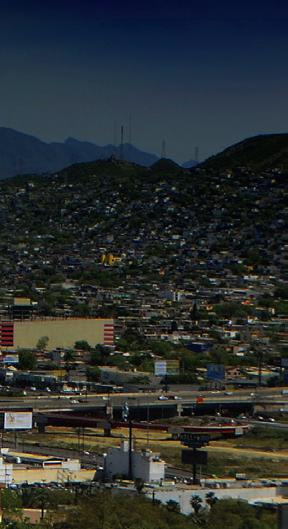
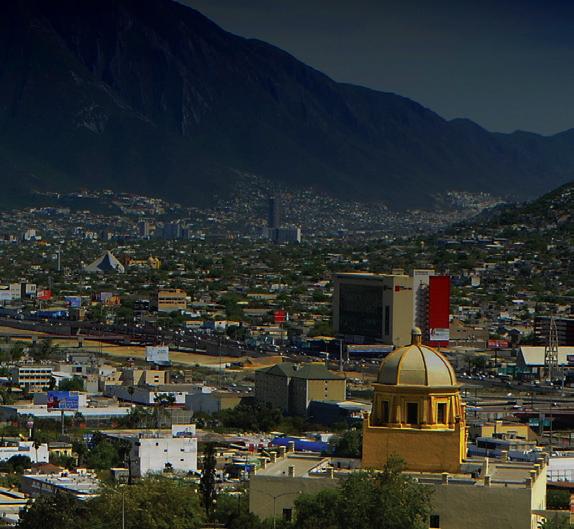
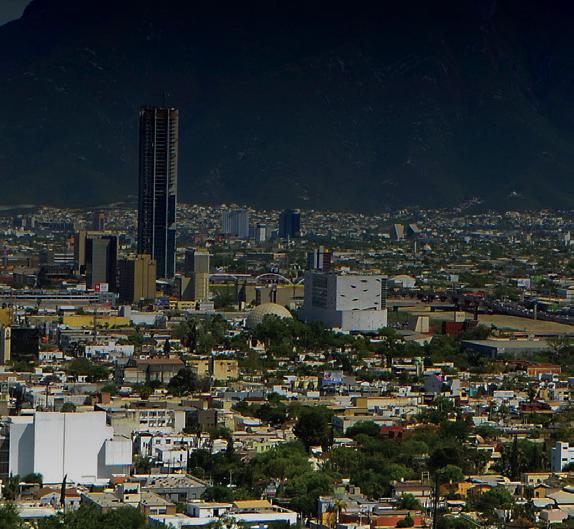


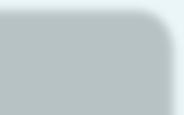
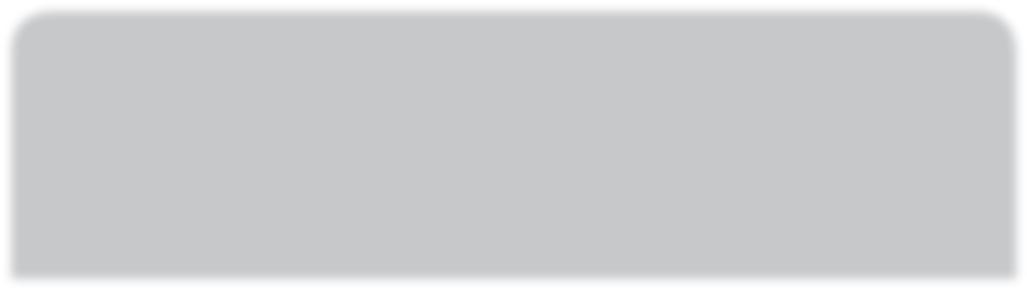
Machine Learning
Massive
Forehearths,regeneratorworking end and furnace
The combustion system is designed for easy extension of LPG or oilThesupply.furnace control system ensures the stability of the combustion process, regardless of the amount of each fuel fed, reducing the impact on the production process to a minimum. This functionality becomes of vital importance in the current situation of uncertain natural gas availability and unpredictability of its price.
The furnace is designed to melt of up to 192tpd out of 480tpd by electric current. This allows the melting process to be optimized according to cost and availability of energy sources. It also offers the potential for dramatically greater reductions in CO2 emissions than standard solutions with electricity at an estimated 20%.
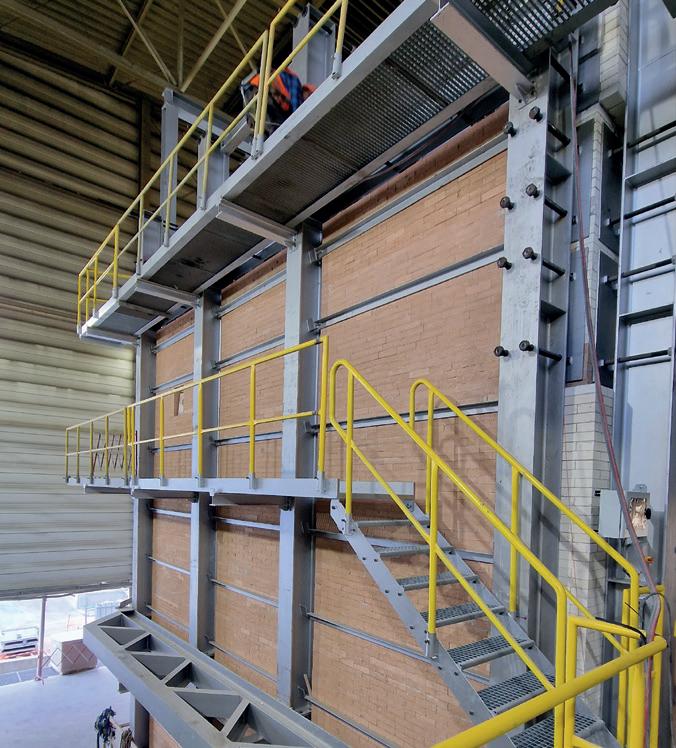
TECHGLASS is implementing a programme to introduce Machine Learning modules into control systems.
Short glass to glass time It took only 67 days from the glass drainage from the previous furnace to the start of the heat-up of the new one - three days less than originally anticipated. It is difficult to interpret this result without knowing the extent of the necessary demolition, construction and installation works.However, anyone who witnessed the situation before the drainage and then before the heat-up must consider this result to be Therecord-breaking.determinationand
TECHGLASS ADVERTORIAL Glass International September 2022 740
dedication of TECHGLASS employees have been recognised by the management of Stoelzle Czestochowa.
www.glass-international.com
TECHGLASS commissioningcelebratesof480tpd furnace
Alternative fuels
Share of electric energy in melting up to 40%
TECHGLASS has been designing and supplying completely equipped furnaces, working ends and forehearths for over 30 years. In July 2022 a 480tpd furnace was commissioned - the Stoelzle Group’s largest and one of the largest end port furnaces in Europe.
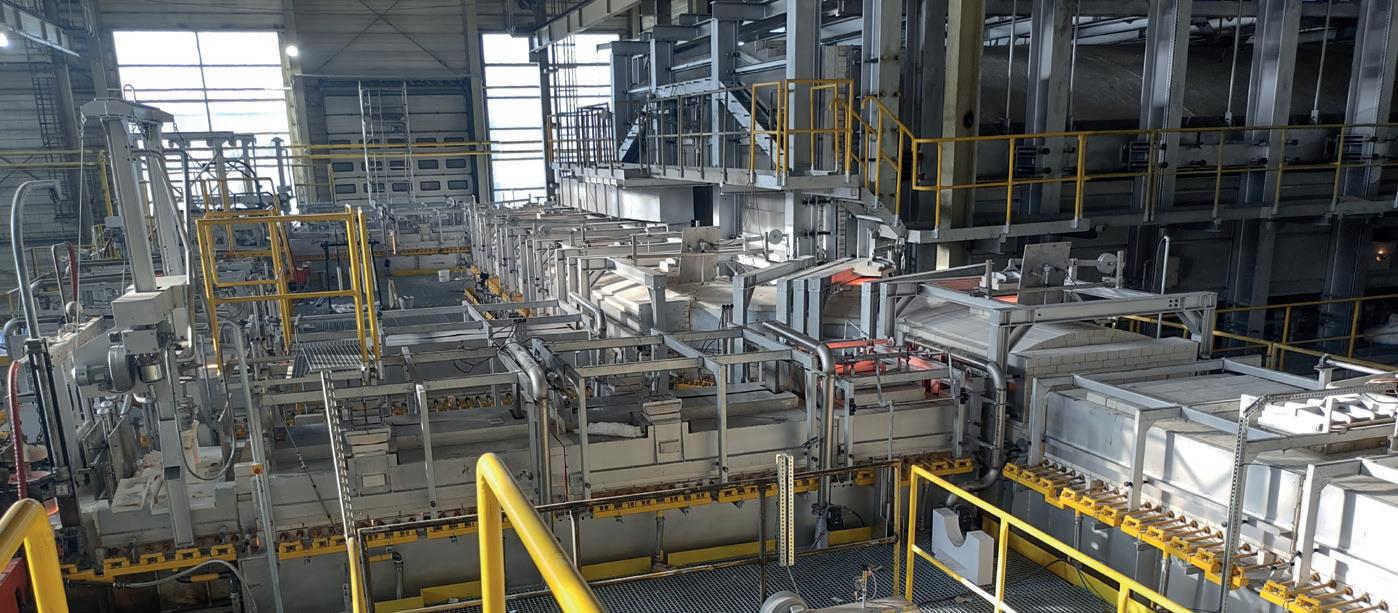
The furnace was equipped with a combustion system with automatic individual burner control. This makes it easier to operate the system and, most importantly, reduces nitrogen oxide emissions and has a positive impact on energy consumption.
It has been repeatedly confirmed that good learning algorithms achieve better results than experts.
Cooperation between TECHGLASS and Stoelzle Czestochowa dates back to the establishment of the Polish branch of this Austrian company, which took place in 2001.Todate, TECHGLASS has delivered there the furnace, working end and forehearths three times, and has completed more than 150 smaller orders. In 2020, the decision was made to implement a furnace with a pull of 480 tons per day with 5 forehearths, in a hall designed for a furnace with a 40% smaller melting area, the most ambitious option among those considered. The six-month tender process was completed in February 2021 with the victory of TECHGLASS.
In house business model
The execution of the project took place during the Covid pandemic and the war in Ukraine. Lead times for some components have been extended several times over. It has become common practice for suppliers to provide offers that are not binding in terms of neither prices nor deadlines. However, the TECHGLASS business model based on designing and manufacturing almost all of the systems in-house has helped address these challenges.Thestatus of each of thousands of orders was monitored in real time, allowing a quick response in case of any problems. This would not have been possible if production had been carried out by subcontractors.
From left to right: Andrzej Skowiniak - President of TECHGLASS, Robert Janeczko - Chairman of the Board, CIECH Vitrosilicon. Hubert Domaradzki - Member of the Board, CIECH Vitrosilicon
In the first stage, ML is planned to be used to minimize glass level disturbance after changing the combustion side.
www.glass-international.com 75
The standard is to transfer solutions for soda-lime glass, mainly container glass, to sodium silicate production. The innovative TECHGLASS furnace was designed from the ground up for melting this glass. This allowed the production of high-quality sodium silicate with energy efficiency unattainable with standard approaches and with very low NOX emission. The furnace can be operated without investing in and maintaining any secondary methods of reducing nitrogen oxides.
TECHGLASS’ innovation
The furnace supplied by TECHGLASS has exceptionally low energy demand, which is especially important with today’s rising gas prices and carbon dioxide emission costs.
As part of the project, TECHGLASS also designed and supplied a batch house and three complete lines for producing frit in the shape of almost any size of cubes.
Recently a TECHGLASS furnace of pull of over 300tpd for melting sodium silicate has been commissioned. The furnace is part of a project executed for CIECH Vitrosilicon S.A. which also covered engineering and supply of batch house and three modern production lines CIECH Vitrosilicon is the biggest supplier of sodium silicates in Europe. It has two production plants in Poland. The company belongs to CIECH Group – an international, expanding group operating in chemical industry with strong global presence.
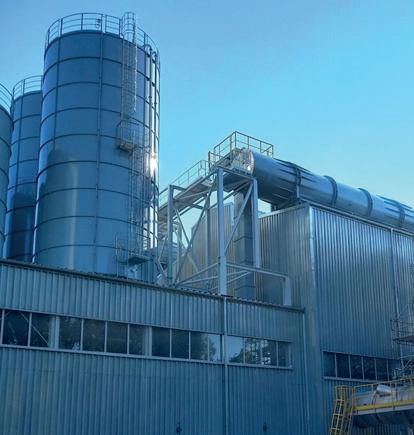
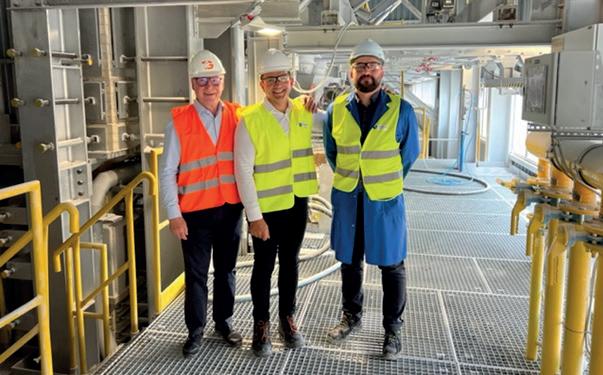
Each of the three frit production lines is equipped with forming machines, conveyors, a cooling water system, all auxiliary systems, and a control system integrated with the furnace control system.
Scope of supply
TECHGLASS - GLASS INDUSTRY SOLUTIONS
TECHGLASS offers solutions for production of all types of glass
An important feature of the furnace design is to reduce the time between the production of products with different specifications, the so-called module. As a result, the amount of unwanted transient product is significantly reduced, which translates into savings and reduced environmental impact.
The execution of the project was such a success, that soon after its completion CIECH Vitrosilicon ordered a rebuild of the existing furnace with TECHGLASS. The rebuild was based on a significant modification of the furnace’s design.
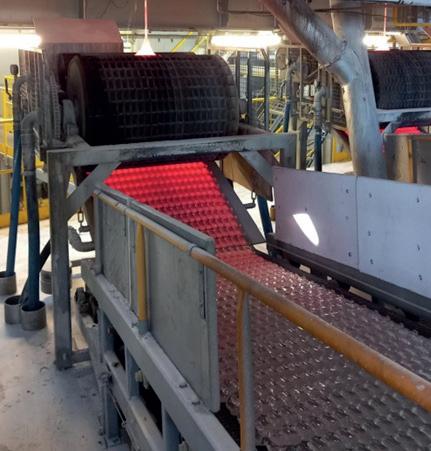
Low energy demand
Reduced module
To meet the customer’s very stringent requirements in this area, TECHGLASS has made a number of improvements. A very efficient transfer of energy to the melt from the furnace’s combustion space was achieved by equipping the furnace with two “extra wide” dog houses and four oscillatory batch chargers for excellent batch distribution. The furnace combustion system for CIECH Vitrosilicon was equipped, as in the case of Stoelzle Czestochowa, with automatic individual burner control. It is also designed for easy extension with LPG or oil supply.
www.techglass.pl office@techglass.pl
Left: Production hall. Right: Glass cubes production
TECHGLASS ADVERTORIAL Glass International September 2022
TECHGLASS engineers are also working on applications of ML in other areas, such as optimising forehearths operation during assortmentObtainingchanges.evenasmall amount of energy savings from these measures is worth the effort put into them.
WWW.GLASS-INTERNATIONAL.COM
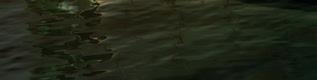


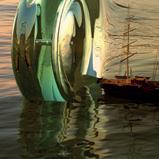
COMPANYPROFILE:GERRESHEIMERDECORATIONUNITSPERSONALITYPROFILE:PHOENIXCHAIRMANFORMING INTERNATIONAL March2019—Vol.42No.3 A GLOBAL REVIEW OF GLASSMAKING WWW.GLASS-INTERNATIONAL.COM GlassInternationalMarch2019 If it’sinyourglass,we’llBrilliantly.inspectit. AppliedGlass.com INNOVATION TECHNOLOGY | SALES TRAINING SUPPORT AppliedVision_GlassInternational-April-2019.indd 3/7/19 10:59 March.indd
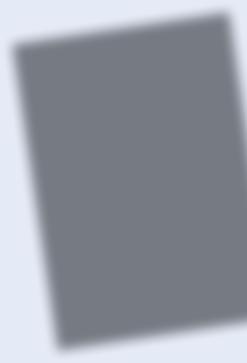
Glass International offers readers the latest news from across the hollow, container, flat, and speciality glassmaking industry and is the official media partner for the global Glassman events.
Packed with information on the glass manufacturing industry and continually updated with news for glass industryandalsowww.glass-international.comprofessionals,featuresspecialarticlesinterviewswithleadingfigures.

MAGAZINE
A round-up of the top news stories is also sent to more than 16,000 industry professionals each week as a free e-news bulletin. You can register online to receive the weekly newsletter and keep up-to-date with the latest news from across the glass manufacturing industry. www.glass-international.com/e-newsletter
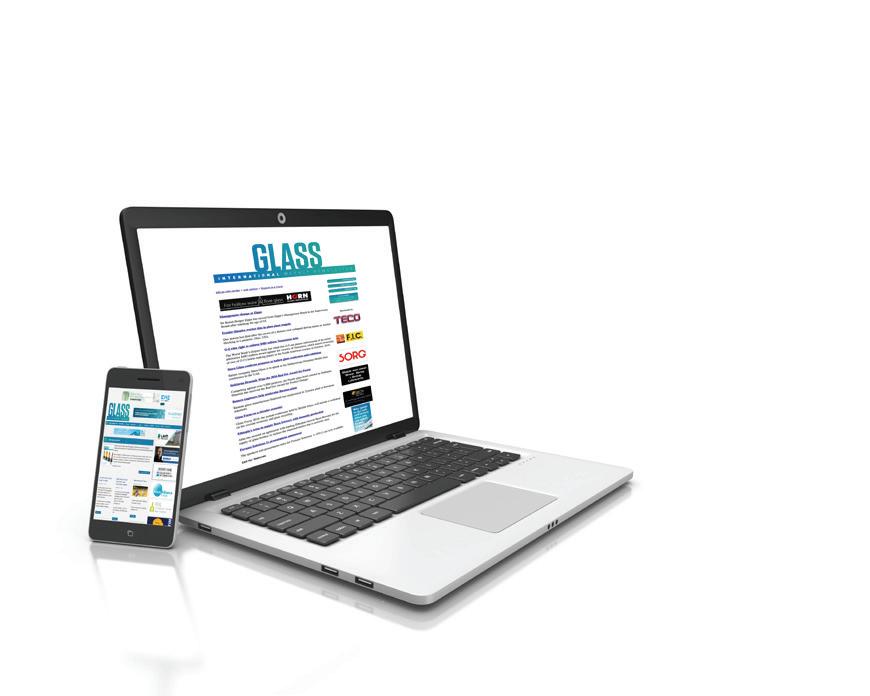
NEWSLETTERWEB
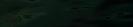
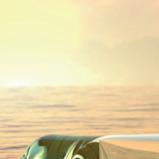
Join the InternationalGlassGroup @glass_int

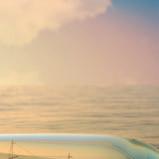
CONNECTING THE GLASS MANUFACTURING INDUSTRY
The magazine focuses on industrial, economic and environmental issues affecting the industry and includes articles discussing the latest developments and challenges in glass manufacturing. Regular features comprise of global news and events, company and country profiles, and previews and reviews of important industry conferences and exhibitions. 13/03/2019 10:29:25
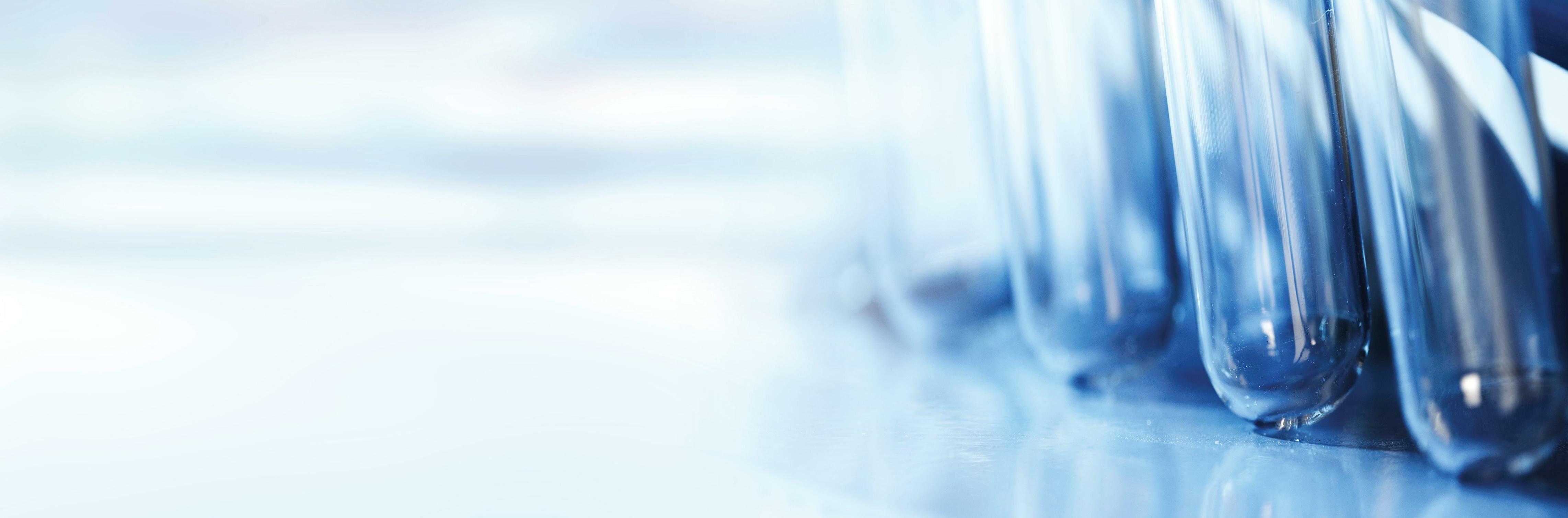
€100/tonne, if you save 1Nm3/h, it saves close to £1500 of CO2 credits PA plus the gas savings. Top Allowance % Uk Share 2 0.4% 9900584 25.3% 12 2.6% 21088628 53.9% 46 10.0% 30403257 77.8% 50 10.8% 30847839 78.9% 461 100.0% 39091102 100.0% CH4 + 202 CO2 + 2H2O CH4 = 16kg/kmol 1kmol + 2kmol 1kmol + 2 kmol O2 = 32kg/kmol Molar volume = 3 CO2 = 44kg/kmol 16 + 2*32 = 80 44 +2*18 = 80 mass balance H20 = 18kg/kmol 22.41 Nm3 CH4 gives 44kg CO2 1 Nm3 CH4 gives 1.96kg CO2 509.3 Nm3 CH4 gives 1 tonne CO2 Carbon
� Fig 3. Coal gasification was used for O-I’s three-port furnace in Alloa, Scotland, UK glassworks in 1950.

Starting with gas laws and the basics of combustion, we will look at the distribution/cost of carbon credits and lessons from the past. In part two we will look at techniques available today and simple financial models to justify investment in energy reduction and resulting emissions. From gas supply to stack, it will show how analysers, burners, control logic, training, and everything in between can be justified through CO2 and energy savings in a simple spreadsheet. Basics of combustions and formation of CO2
Reducing the impact of CO2 in furnaces
According to Rogers and Mayhew: � Molar volume = 22.41 m3/kmol at 1atm and 0°C = 22.41Nm3/kmol � Carbon dioxide [CO2] = 44 kg/kmol � Oxygen [O2] = 32 kg/kmol � => Carbon [C] = 44-32 = According to Rose & Cooper 1977: � Molecular weight of hydrogen H is 1.0079 See Fig 1 for basic combustion (ignoring nitrogen). For simplicity, assuming natural gas is methane, then if you save you Assuming is Credits
1Nm3,
Furnaces Glass International September 2022 www.glass-international.com 77 Continued>>
save 2kgCO2.
CO2
The 2021–2025 UK ETS Allocation is available to download from the UK government website.1 My analysis of the 461 sites (Fig 2) would suggest that the two highest sites have 25% of the CO2 allocation. The top 12 have over 50%, while the top 10% represents 46 sites which have 78%. Perhaps pure coincidence, but on the 21st of April 2021 the UK government enshrined a new target in law to slash emissions by 78% by 2035.2 It is when you get to the top 50 with 79% that we have first two glass plants. Looking at the 23 glass plants listed, it totals only 2.85% of the CO2 credits. If you utilise all your credits then you can buy more, however, if you can reduce through energy savings or use of cullet then you can transfer or trade on the open market. At the time of � Fig 2. Analysis of carbon credits by Mr Simpson of 461 UK sites. � Fig 1.Basic combustion (ignoring nitrogen).
12 kg/kmol
Neil Simpson presents a summary of his 2022 Furnace Solutions paper. He outlines how many m3/hr of gas it takes to produce a tonne of CO2 and how to justify the investment to reduce both.
Lessons from the past As someone who only has 30+ years of combustion experience, there are a lot of things which I have seen in the past and have heard of. Looking at the papers at Furnace Solutions in June and the ICG in Berlin in July, I am reminded of the 1990’s when all the industrial gas companies were promoting oxygen in a similar way that hydrogen is today. For decades I have been asked if I can burn hydrogen. Getting hydrogen to burn is not a problem, but making it combust where you need/want it is the skill! Beatson Clark to this day call their furnace operators “teasers” since one of the skills was to tease the gas from the coal. Most of the historic UK glass plants are close to coal fields since this was the fuel source. Whilst before my time, there was a short film made in 1950 to celebrate the 200th anniversary of O-I continuously making glass bottles in Alloa, Scotland, UK.3 The jubilee furnace had a capacity of 60 tpd and used coal gasification. Fig 3 shows a “well insulated crown” but is a relative term and probably was well insulated for the 1950’s. The threeport cross-fired furnace was fired with producer gas (produced on site). There is also an image of someone using a disappearing filament pyrometer which was a forerunner of the Cyclops. According to Rose & Cooper, typical produce coal gas was 50% hydrogen! The balance being methane 35%, carbon monoxide 10% and ethylene 5%. In 1950’s we could fire 50% hydrogen so higher should be possible. When I started at Laidlaw Drew in 1990, many of the UK glass furnaces were still operating on heavy fuel oil. My first gas burner conversion was at UG Peasley in 1993, which is coincidentally the site � Fig 5. Upcoming talks.
� Fig 4. Eclipse PF100 oxy oil operating on a fibreglass furnace.
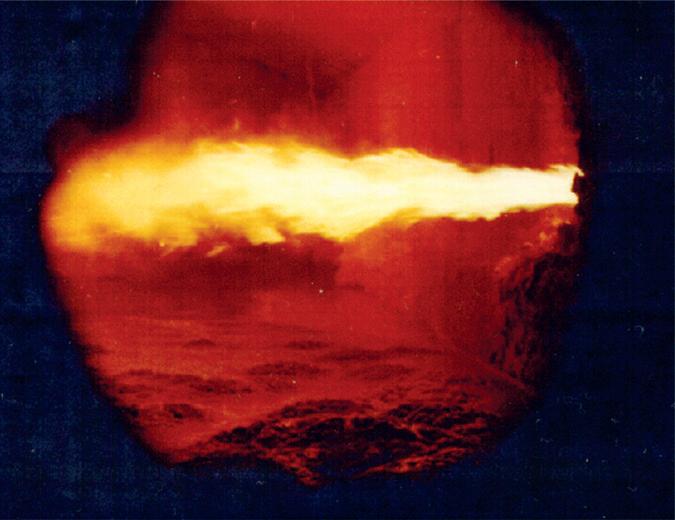
of the Glass Futures furnace and next to the Furnace Solutions event. My last oil to gas conversion was in 2019. The early 1990’s was the time when oxy gas and oxy oil were being developed. Oxy gas is relatively easy but oxy oil requires way more skill and care. When looking at the oil conversion of an EAF Rocket Burner to get a longer flame, we investigated the Laidlaw Drew archives and found the 1967 atomiser design jointly developed with Pilkington. Fig 4 is an Eclipse PF100 oxy oil operating on a fibreglass furnace and the shutter speed assumed (1000/s f16) has captured the sinusoidal/swirl effect of the oil atomiser. Ironically, biodiesel is seen as a possible route to decarbonisation and so is also a well-developed, but perhaps forgotten, combustion technology from the past. Since submitting the abstract - sadly due to the Russian invasion of Ukraine and resulting energy crisis - many glass companies are realising that their natural gas is not uninterruptible, and several are re-instating oil back-up systems. Upcoming talks All these topics are included in my Furnaces Glass International September 2022 780 www.glass-international.com submitting the abstract to the Society of Glass Technology Melting Technical Committee the cost was roughly €100 per tonne of CO2. It is now lower, but the cost of energy is now significantly higher. When looking at investment, Net Present Value [NPV] and Internal Rate of Return [IRR] should realistically be used on major and long-term capital investments. Payback is typically used for short-term energy savings. To date, including ESOS reports, I have never seen CO2 reduction included in the spreadsheets for payback or NPV. The Furnace Solutions presentation and this article are a first attempt to consider including carbon credits.
Industrial Combustion Decarbonisation 101.4 which can be run as bespoke. The next series of ½ day online training courses are scheduled for December 19th and repeated Tuesday 20th in afternoon. Two new oil courses are now included due to recent demand. On Wednesday 21st in the morning it will be the ‘Basics of oil combustion in glass furnaces’. Starting with the differences from natural gas will cover regenerative underport and through-port (conical/flat) and recuperative. On Thursday 22nd again in morning will be ‘Oxy oil combustion in glass furnaces’. Similarly, this will start with the differences between oxy gas and look at 100% conversion for temporary hot hold vs extended production, conical vs flat flame, with risks and possible mitigation. The course will cover methods developed in 1990’s for enabling regenerator repair andForboosting/recovery.detailsof courses (Fig 5) and registration scecombustiontraining@gmail.com.contact � * Independent Consultant, Simpson Combustion and Energy, Scotland, UK neilsimpsonfsgt@btinternet.com References: 1. https://www.gov.uk/government/ operators-of-installationspublications/uk-ets-allocation-table-for2. https://www.gov.uk/government/ slash-emissions-by-78-by-2035news/uk-enshrines-new-target-in-law-to3. https://www.youtube.com/ watch?v=8DVSaanSlAI

of industrial
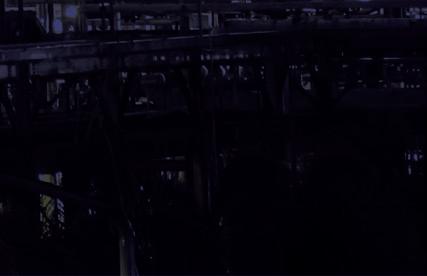


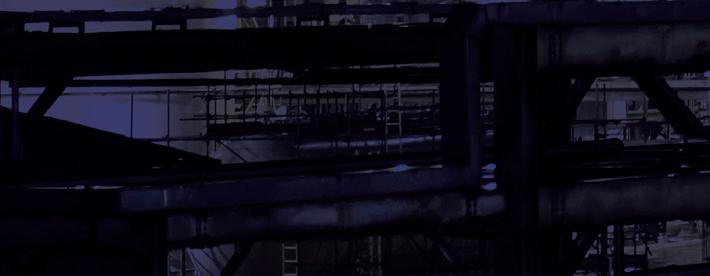
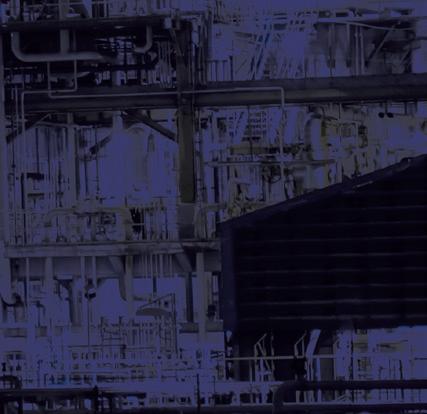
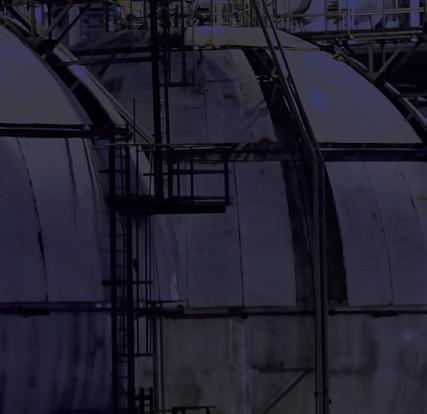
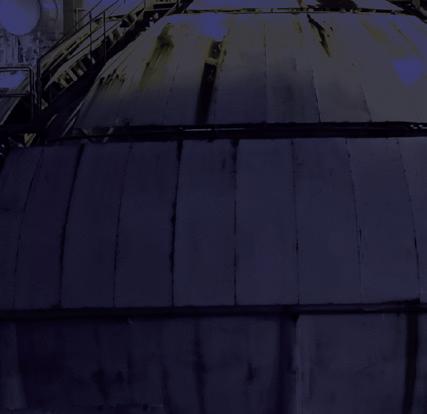
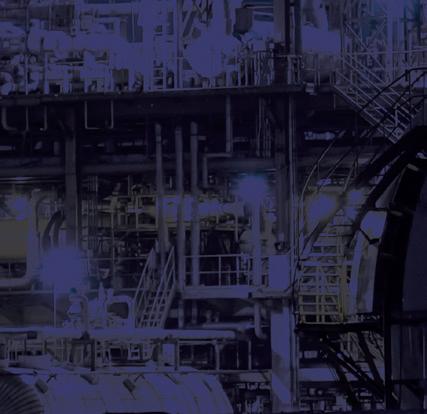

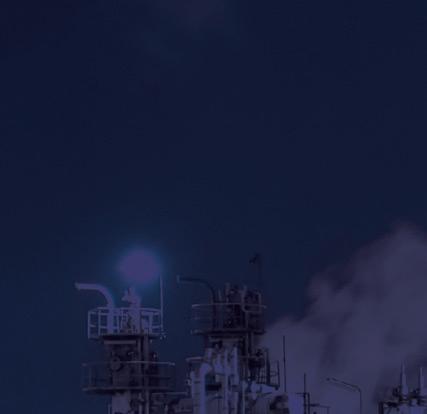
Sustainable Industrial Manufacturing (SIM) is a global series of regional exhibitions and conferences supporting and facilitating the transition towards cleaner manufacturing around the LIGHTENINGworld. THE IMPACT OF HEAVY INDUSTRY SCAN ME TO JOIN THE MAILING LIST REGISTER TODAY www.SustainableIndustrialManufacturing.com EARLY BIRD TICKETS NOW AVAILABLE Organised by: Part of: FROM THE PRODUCERS OF: SECTORS COVERED GLASS STEELALUMINIUM CEMENT CHEMICALS
Sustainable Industrial Manufacturing
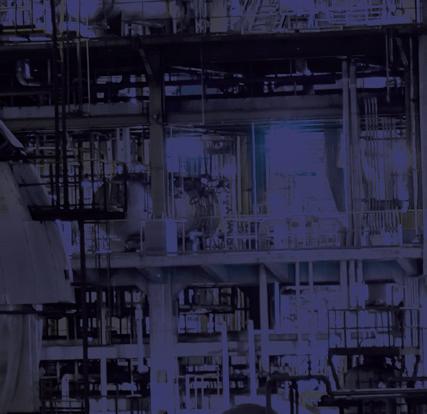


To support and facilitate the
Ohio in December Hosting2022. leaders from industry, innovation, science, government and investment, SIM USA will bring together those responsible for driving sustainability across hard-toabate sectors. BUILD BACK BETTER FOR FURTHER INFORMATION ON EXHIBITING, SPEAKING OR ATTENDING SIM USA PLEASE SCAN THE QR CODE BELOW OR REGISTER YOUR INTEREST AT WWW.SUSTAINABLEINDUSTRIALMANUFACTURING.COM ROUNDTABLECONFERENCEEXHIBITIONDEBATES
be
towards cleaner manufacturing in the
in
President Biden’s goal of a carbon-neutral economy by 2050 is dependent on the decarbonization of heavy industry. The 2021 Build Back Better Act, provides $4 billion for the deployment of technologies that can emission reductions facilities. transition USA, will staged Cleveland,
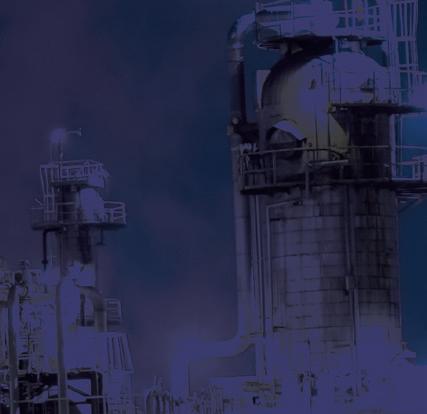
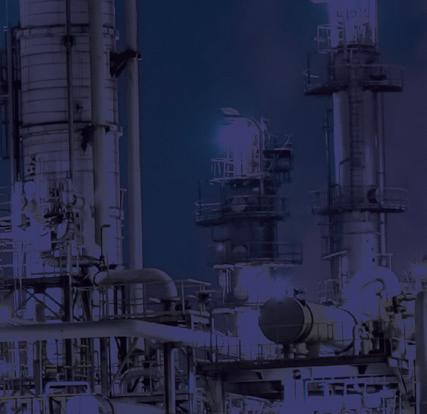
accelerate the
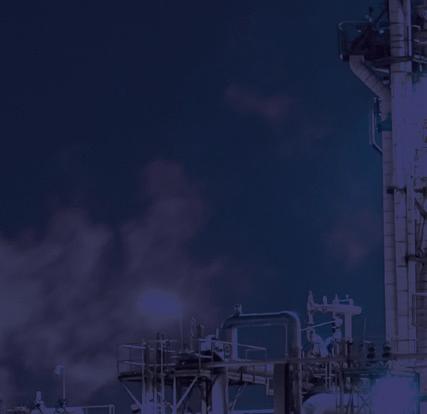
CLASSIFIEDS ANNEALING LEHR COLD-END COATING Global SystemsCombustion Total Support Unit 43, Evans Business Centre, Easter Inch, Bathgate EH48 2EH, Scotland, UK Tel+44 (0) 1506 657310 Fax +44 (0) 8704 799975 Email Sales@globalcombustion.com Web www.globalcombustion.com ZATIAMAdes Plattes, 1 Chemin des Plattes, 69390 Vourles, France Tel +33 (0) 4 37 20 15 00, Fax +33 (0) 4 78 07 94 50 Email: Website:www.tiama.commarketing@tiama.com ANNEALING LEHRS HEAT-UP SERVICES ELECTRICSYSTEMSHEATING Rio Tinto Minerals 2 Eastbourne Terrace London W2 6LG, UK Tel +44 (0) 207 781 1450 Fax +44 (0) 207 781 1851 Email: simon.cook@riotinto.com Web: www.riotintominerals.com RAW MATERIALSINSPECTION I NDUSTRIAL G AS E NGINEERS UNIT D2, BROOKSIDE BUSINESS PARK, GREENGATE,CHADDERTON, M24 1GS, ENGLAND TELEPHONE: 0161-654 7700 FAX: 0161-655 3812 E-MAIL: SALES@MONTSELAS.CO.UK WWW.MONTSELAS.CO.UK INDUSTRIAL GAS ENGINEERS Unit D2, Brookside Business Park, Greengate, Chadderton, M24 1GS, UK Tel +44 (0) 161 654 7700 Fax +44 (0) 161 655 3812 Email sales@montselas.co.uk www.montselas.co.uk MANUFACTURERS AND SUPPLIERS OF SELAS SQUARE PORT GAS & AIR VALVES GAS COMBUSTION EQUIPMENT SYSTEMS/BURNERSCOMBUSTION GLASS MEASUREMENTLEVEL Contact Esme Horn T+44 (0) 1737 855136 to book your space Low-Emission Oxy-fuel Solutions • Oxygen & oxygen flow control equipment • Global oxygen enrichment applications • Cleanfire® oxy-fuel burners • Start-up services Inerting Applications • Hydrogen, nitrogen & other gases • Enabling flow control equipment (39101) 800-654-4567 (code airproducts.com/glassgigmrktg@airproducts.com344) Bock Energietechnik GmbH Gösen 15 92685 GermanyFloss Tel: 0049 9603/1295 Fax: 0049 wwwinfo@bock-energietec.de9603/2995.bock-energietec.de Electrical melting in perfection Special services - Engineering and modelling for boosting systems - Water-cooling Systems for electrode holder - Electrode holder for bottom / side / top - Power regulation / Transformers - Hot drilling - Change of electrode holder SCREEN PRINTING Bergkirchener Straße 228, 32549 Bad Oeynhausen, Germany kammann.de SCREENDIGITAL PRINTING HOT STAMPING FULLY MACHINESUNIVERSALAUTOMATICDECORATING KAMMANN GmbH

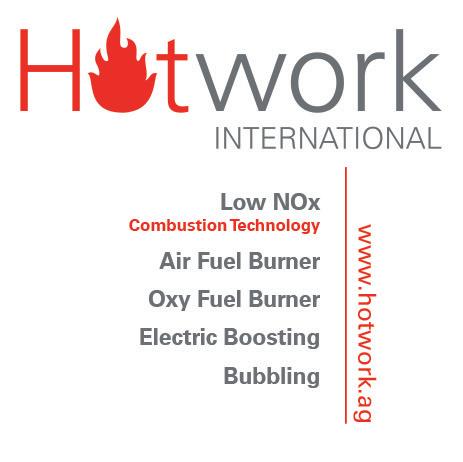
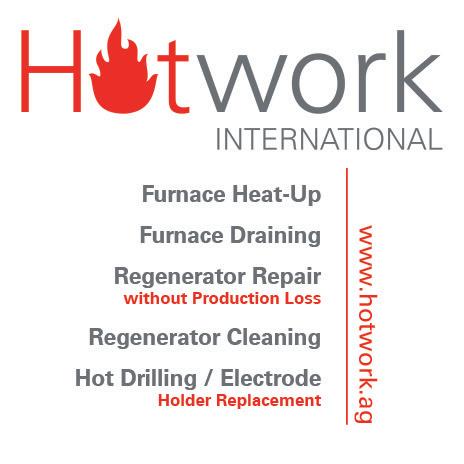

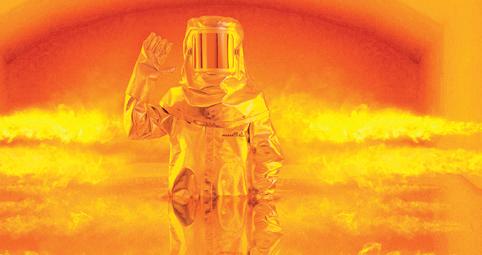
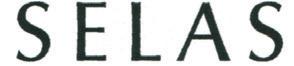

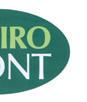
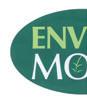

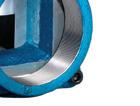
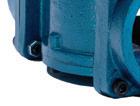

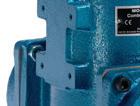
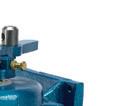
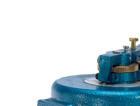

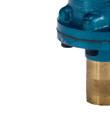
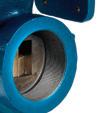

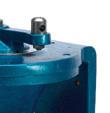
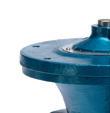

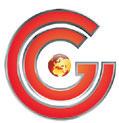
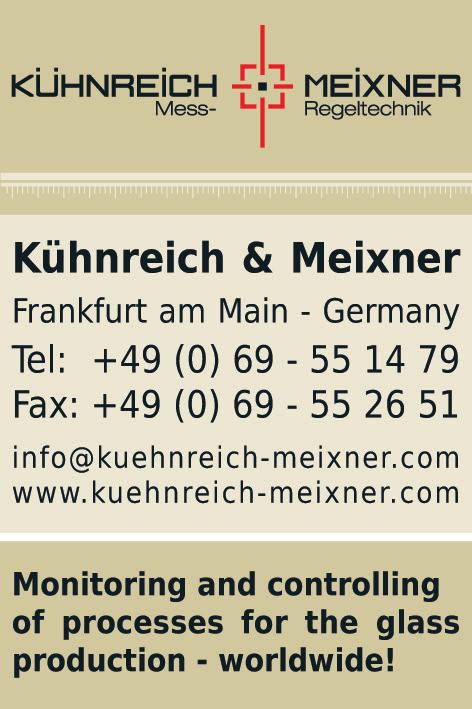
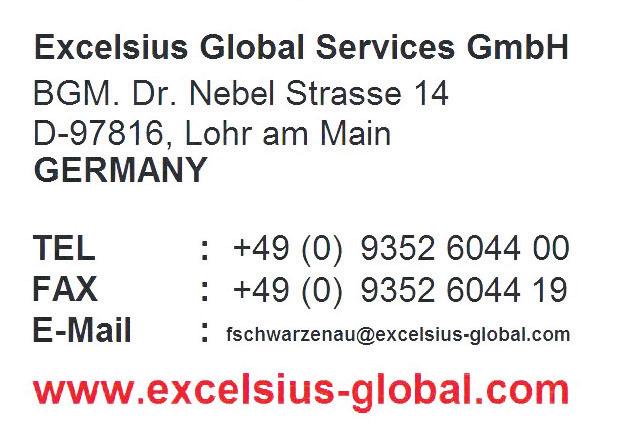
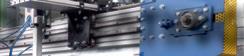
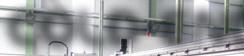
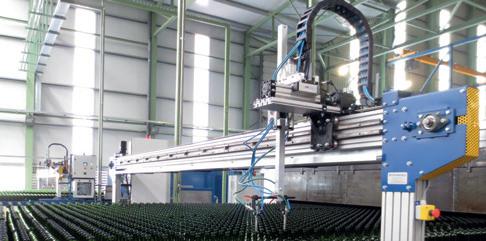
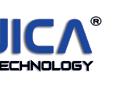


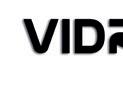
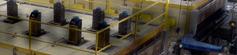
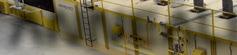
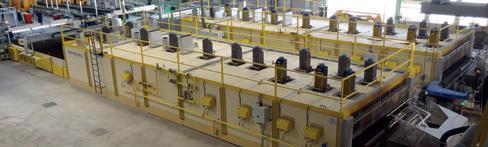
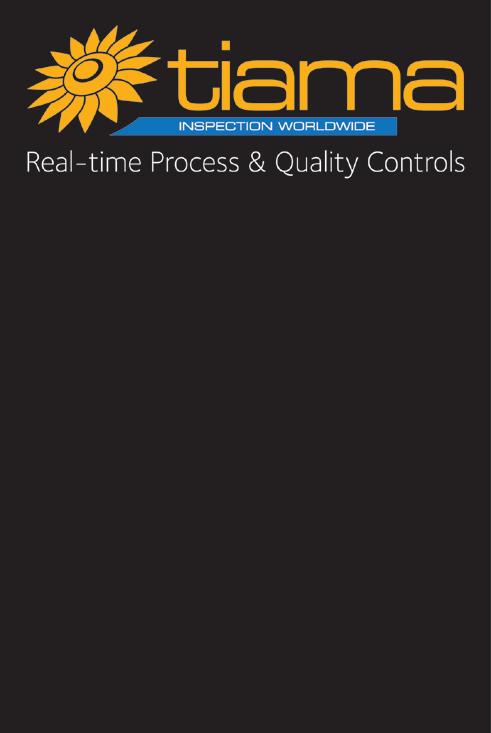
53035 MONTERIGGIONI (SI) ITALY - Strada di Gabbricce, 6 Tel +39 0577 304730 ifv@fonderievaldelsane.com www.fonderievaldelsane.com
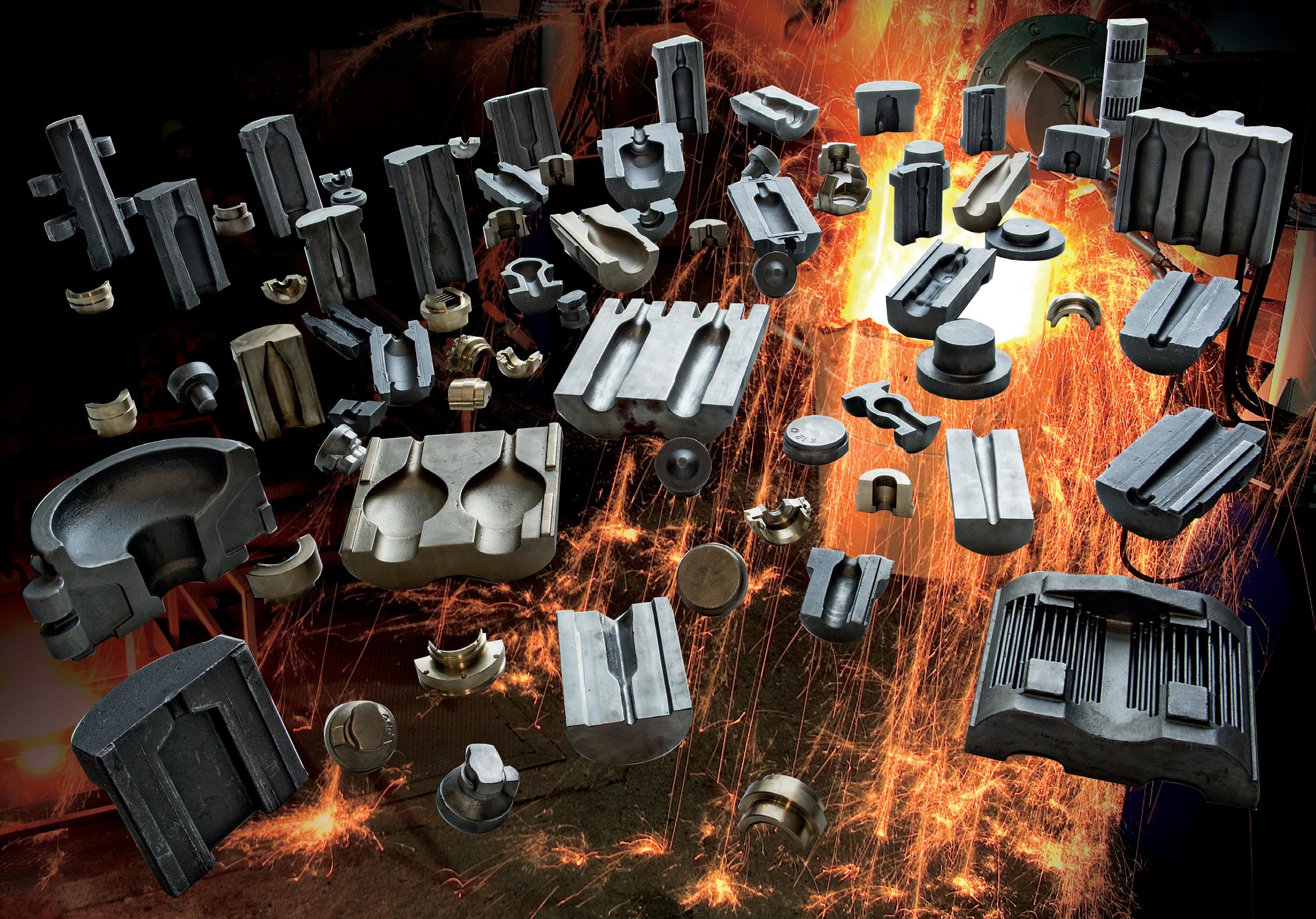
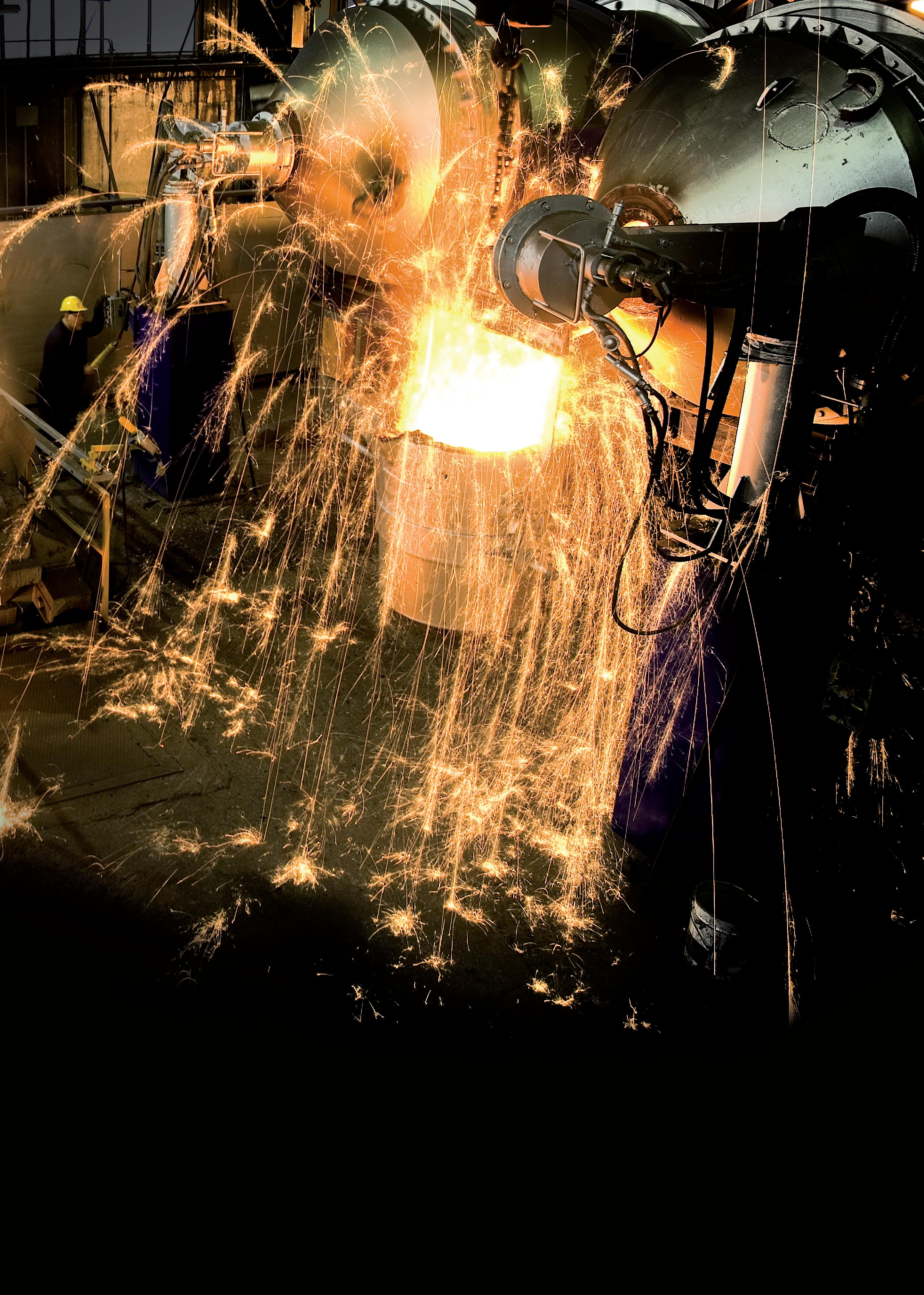
under control – all the time Data – the deciding factor Visit youniverse.tiama.com to arrange a demonstration It‘s having ALL the right data, at the right time, at the right places. YOUniverse gives you more process control and helps you to foresee problems early and to take the right decisions quickly, With open-protocol software solutions, linking hot and cold end sensors to your production machinery, you make the most of the data in your plant, you improve glass quality, you reduce wastage and increase productivity. Make your life easier - with YOUniverse.
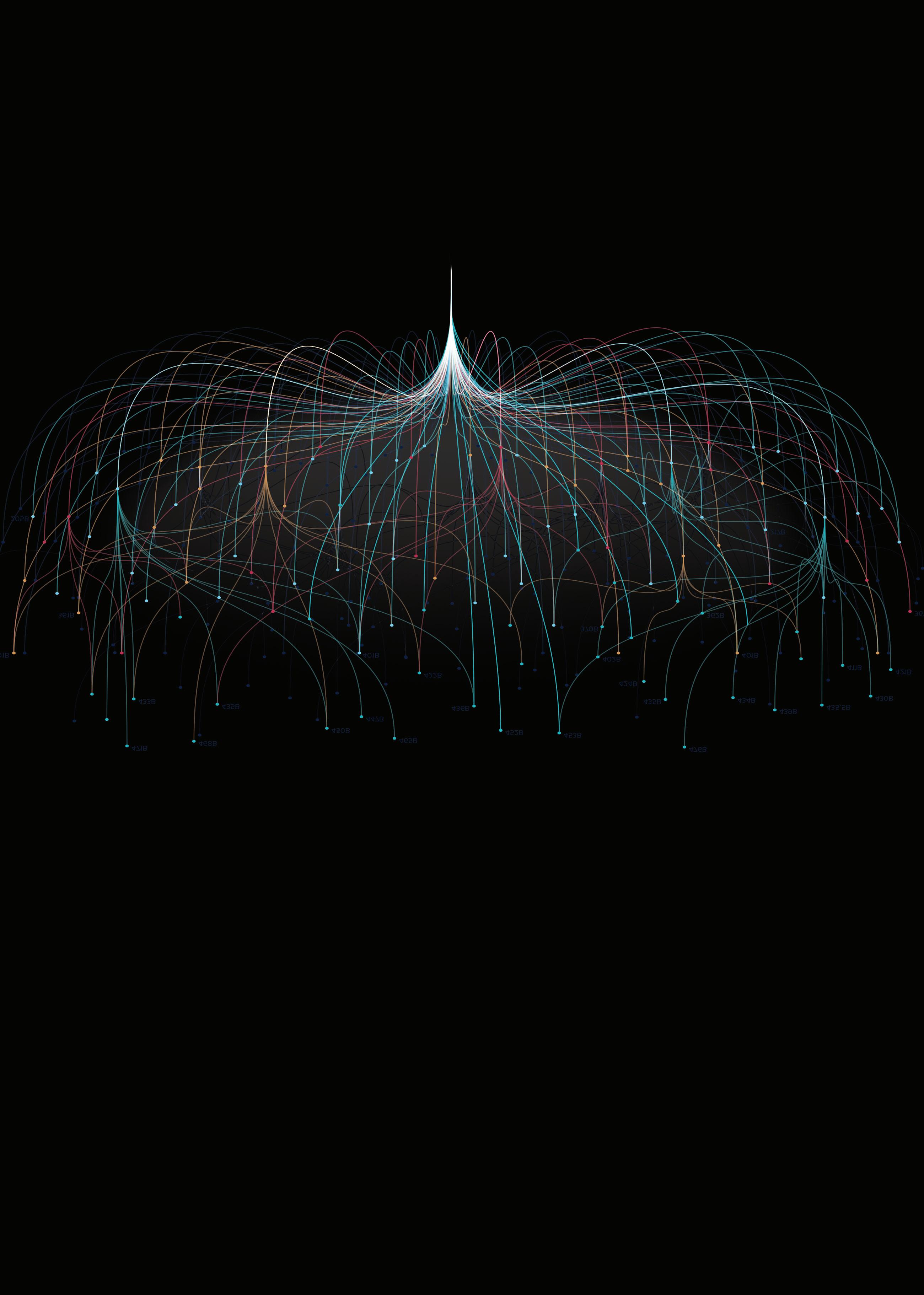