A GLOBAL REVIEW OF GLASSMAKING

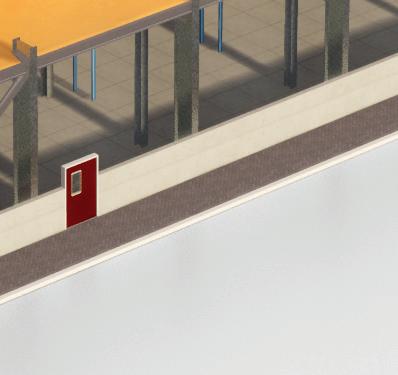
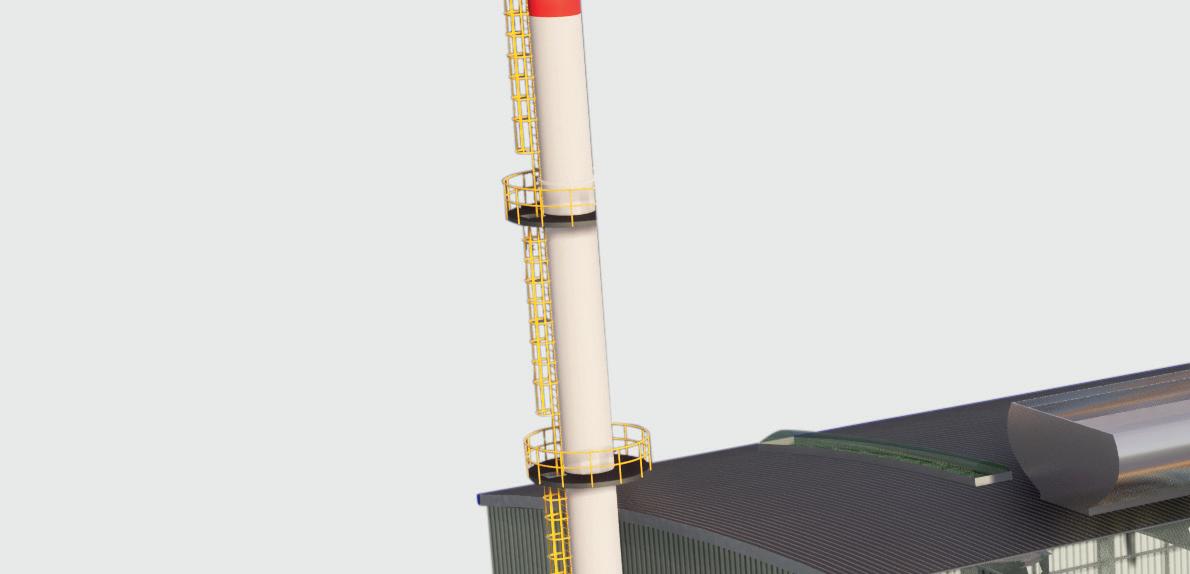


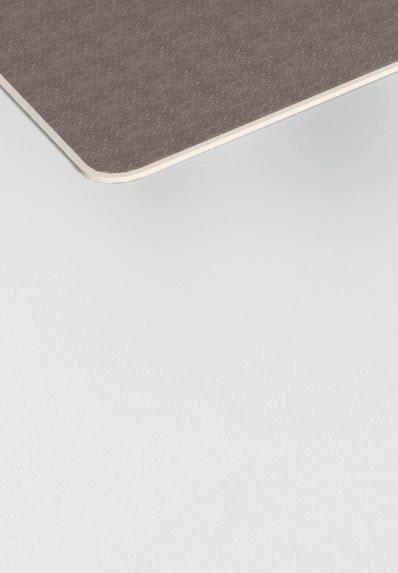

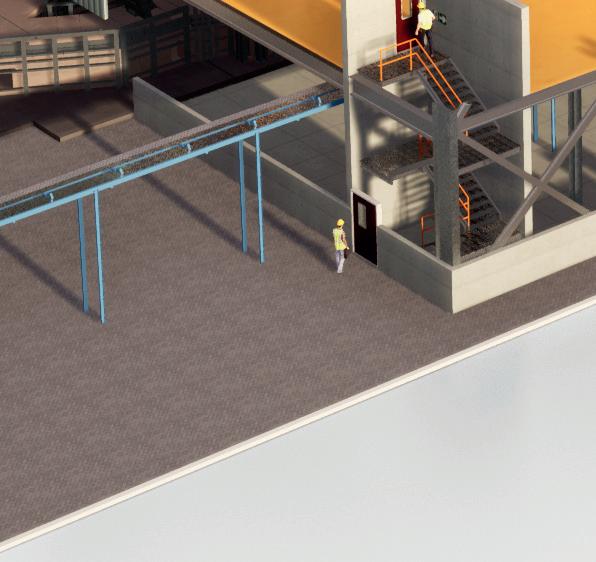

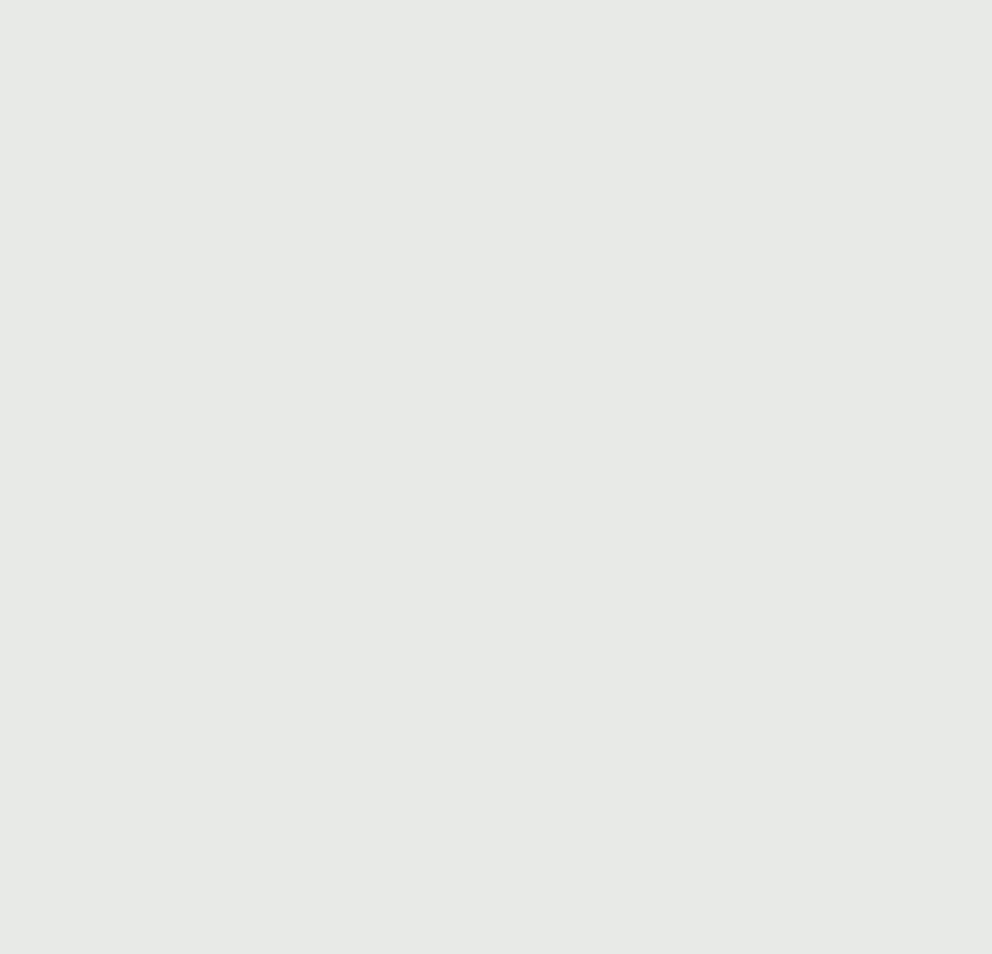
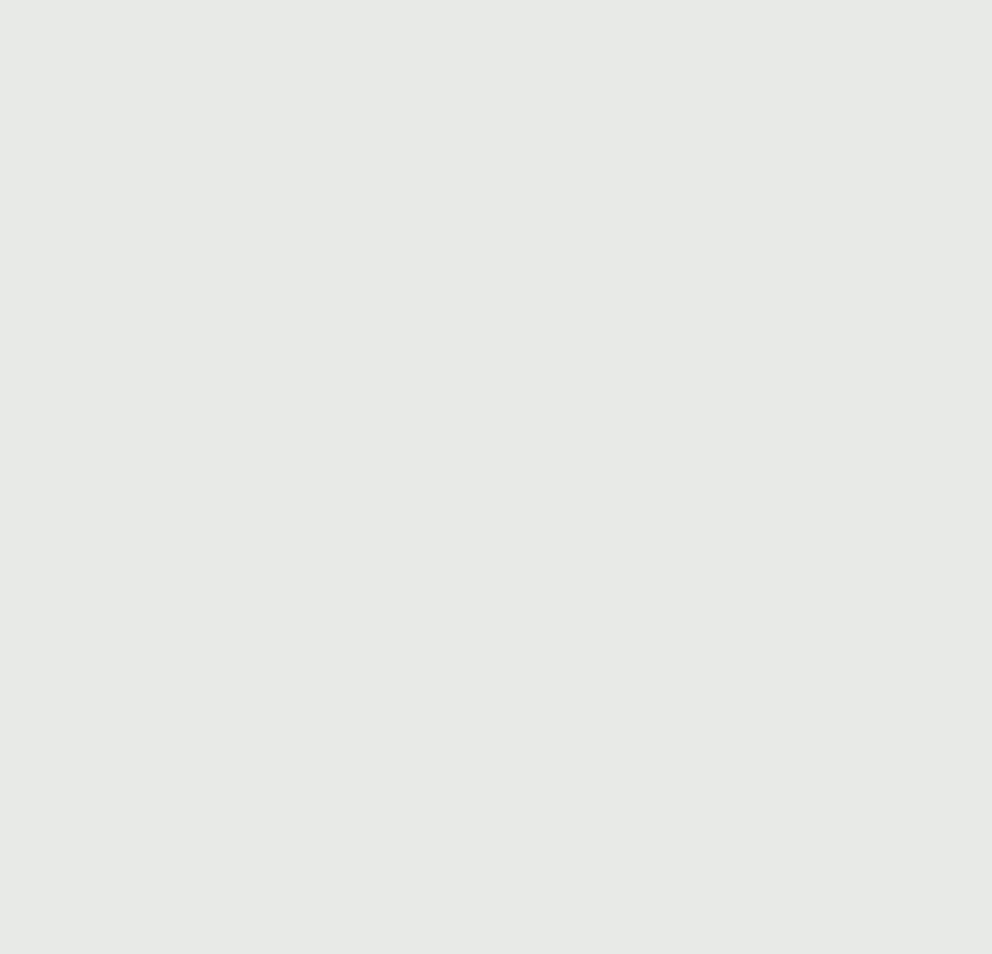
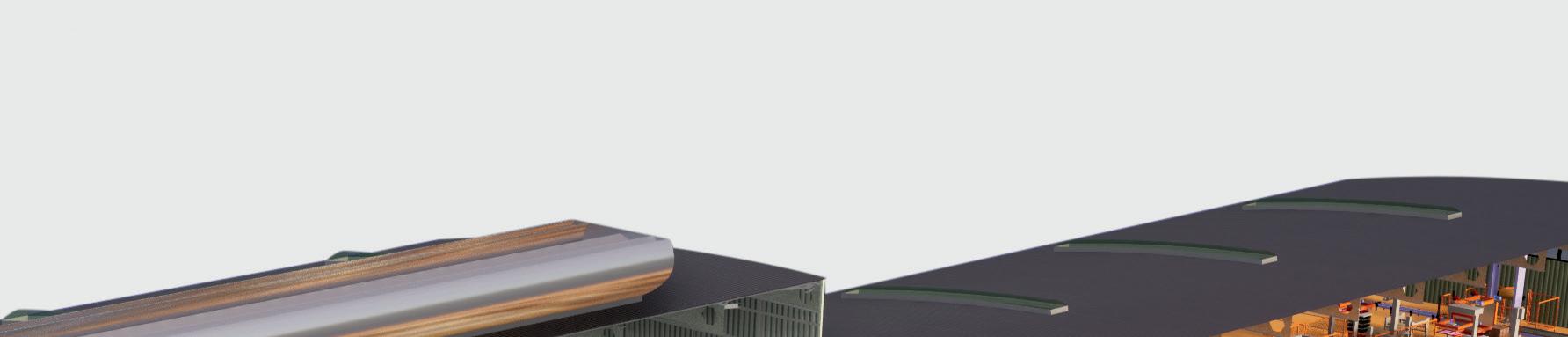
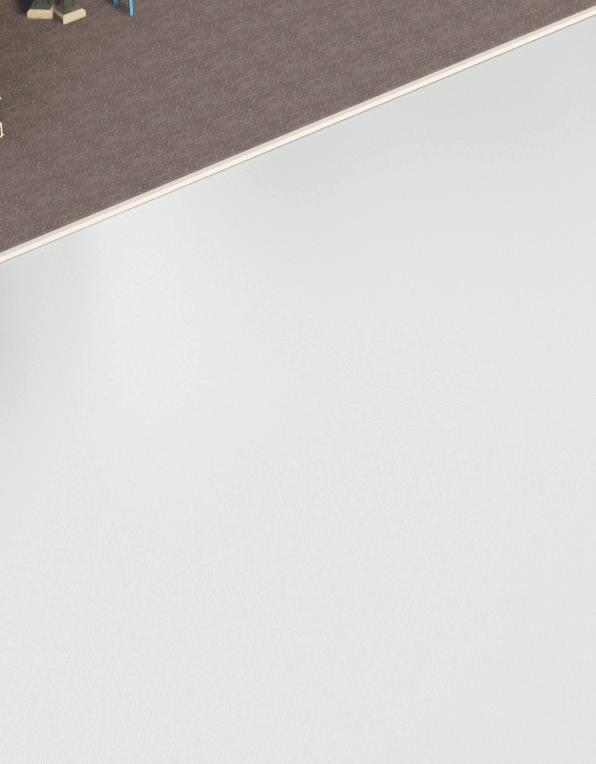
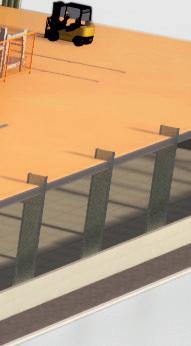


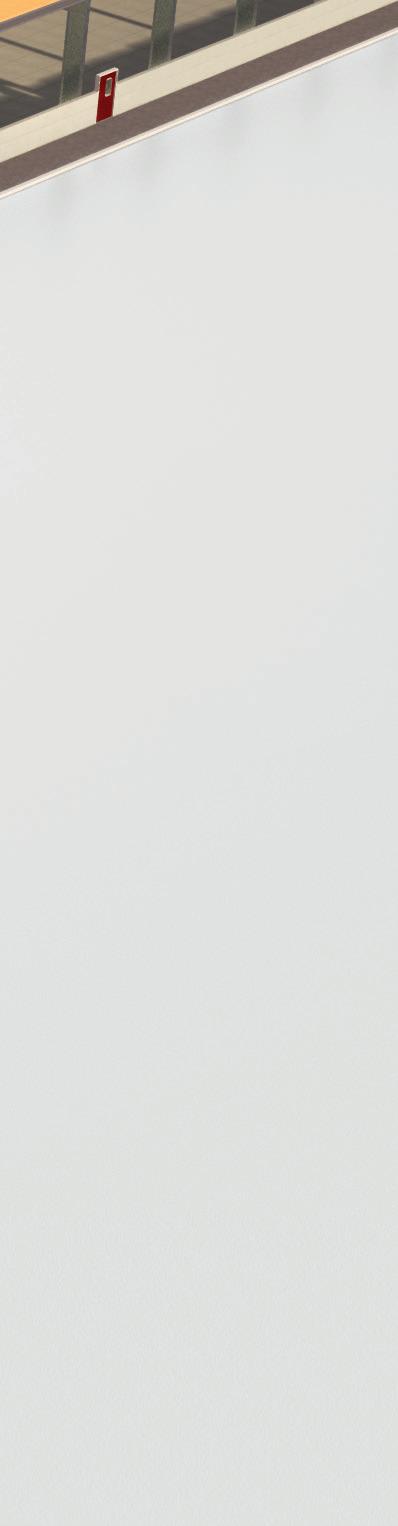

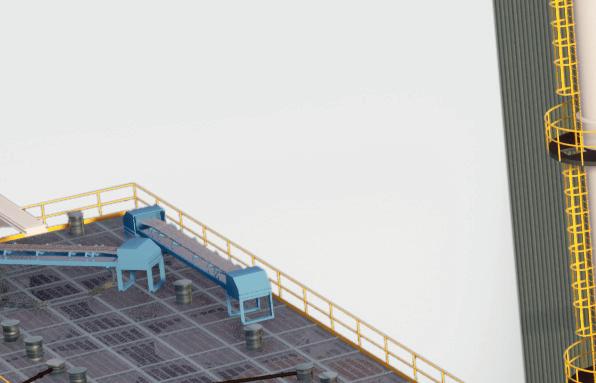
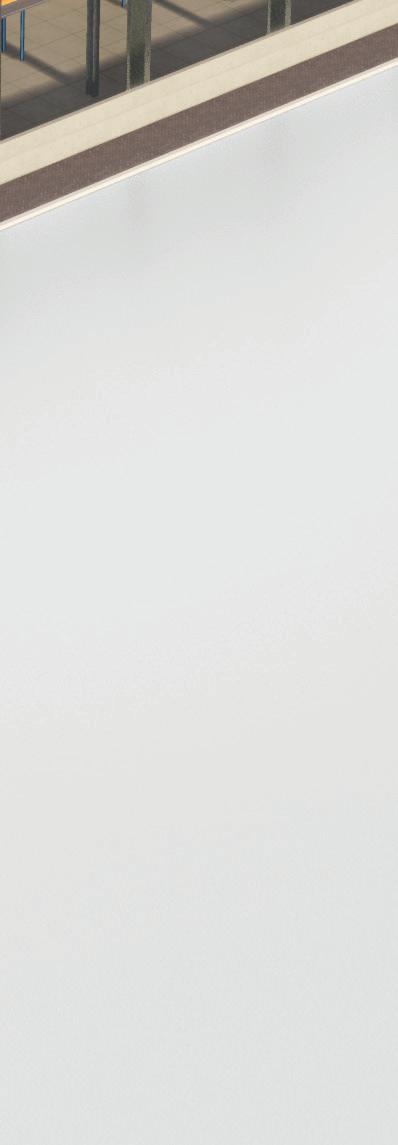
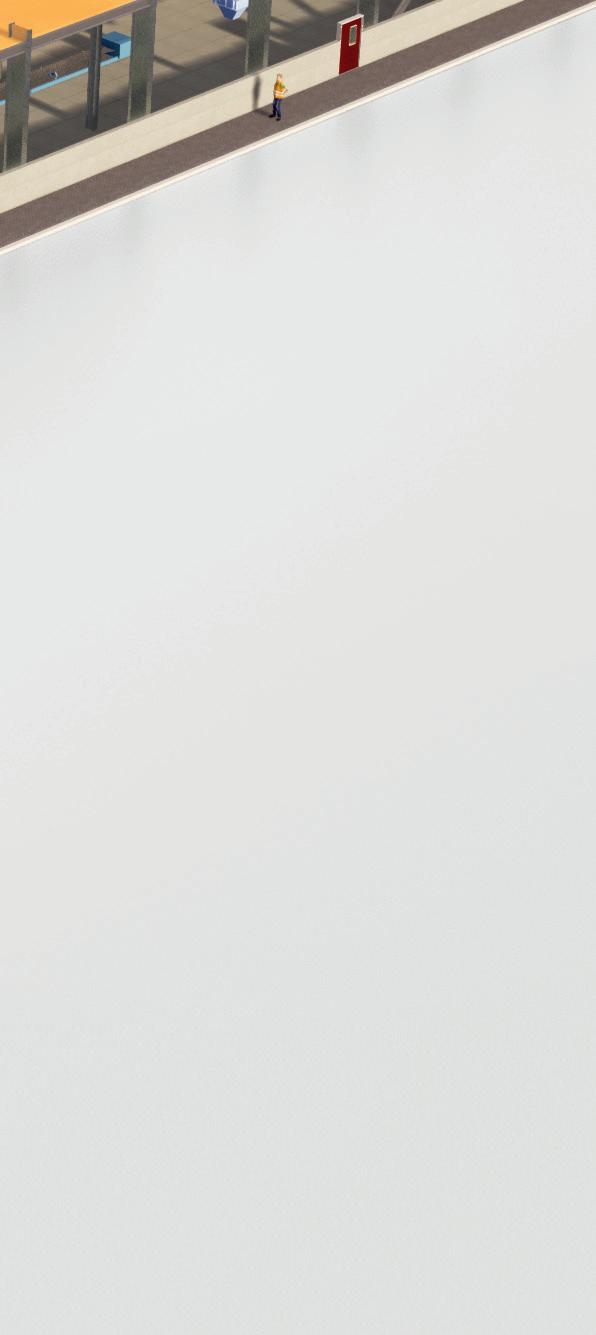
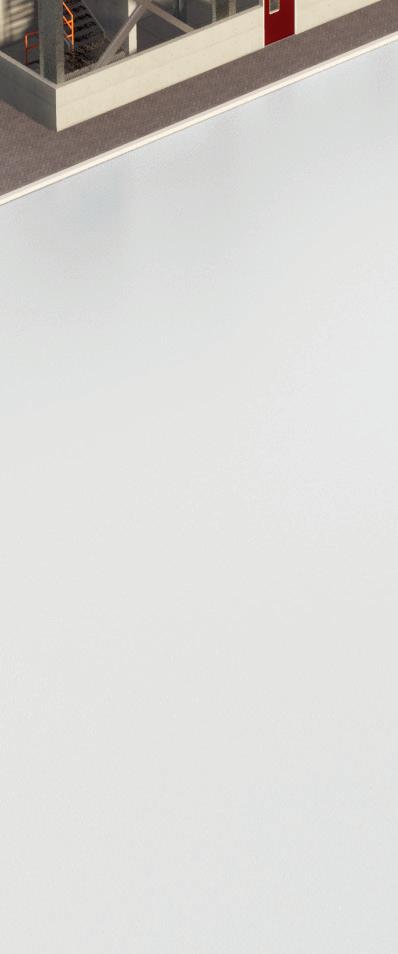
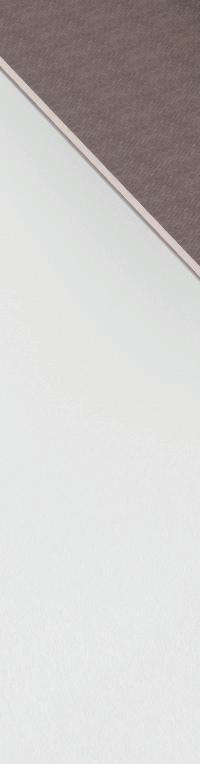

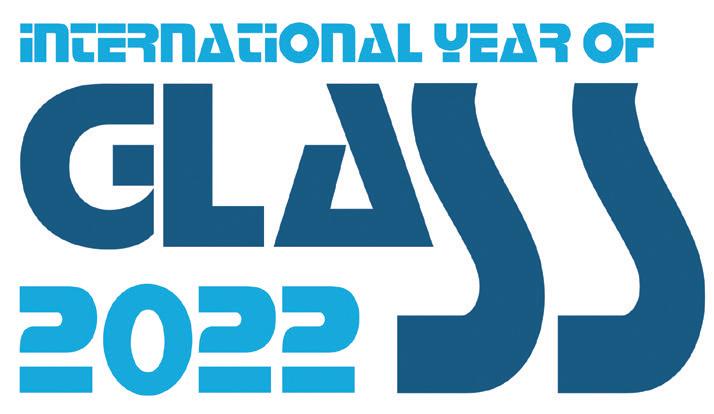
EME is changing the face of the glass industry. As a world-leading batch and cullet treatment specialist, our vision is simple. To design and engineer the most effective batch and cullet processing technology that endures the most demanding production environments in the world. Our cutting-edge digital dashboard is the first web-based batch system for the glass industry. We support batch handling, recipe management and predictive maintenance by providing real-time data performance. Access our user-friendly monitoring and analysis system anytime, anywhere. For optimal batch production, partner with EME.
Editor: Greg Morris
Tel: +44 (0)1737 855132 Email: gregmorris@quartzltd.com
Deputy Editor: Jess Mills Tel: +44 (0)1737 855154 Email: jessmills@quartzltd.com
Designer: Annie Baker
Sales Director: Ken Clark
Tel: +44 (0)1737 855117 Email: kenclark@quartzltd.com
Sales Executive: Manuel Martin Quereda Tel: +44 (0)1737 855023 Email: manuelm@quartzltd.com
Managing Director
Tony Crinion tonycrinion@quartzltd.com
Chief Executive Officer: Steve Diprose Chairman: Paul Michael
Subscriptions: Jack Homewood
Tel: +44 (0)1737 855028 Fax: +44 (0)1737 855034 Email: subscriptions@quartzltd.com
Published by Quartz Business Media Ltd, Quartz House, 20 Clarendon Road, Redhill, Surrey RH1 1QX, UK. Tel: +44 (0)1737 855000. Fax: +44 (0)1737 855034. Email: glass@quartzltd.com Website: www.glass-international.com
Glass International annual subscription rates including Glass International Directory:
For one year: UK £205, all other countries £268.
For two years: UK £369, all other countries £482. For three years: UK £408, all other countries £563. Airmail prices on request. Single copies £53.
Printed in UK by: Pensord, Tram Road, Pontlanfraith, Blackwood, Gwent NP12 2YA, UK.
Glass International Directory 2022 edition: UK £206, all other countries £217.
Printed in UK by: Pensord
Glass International (ISSN 0143-7838) (USPS No: 020-753) is published 10 times per year by Quartz Business Media Ltd, and distributed in the US by DSW, 75 Aberdeen Road, Emigsville, PA 17318-0437. Periodicals postage paid at Emigsville, PA. POSTMASTER: send address changes to Glass International c/o PO Box 437, Emigsville, PA 17318-0437.
© Quartz Business Media Ltd, 2022 ISSN 0143-7838
FRONT COVER IMAGE: www.falornitech.com
It feel like things have returned to pre-Covid normality in recent weeks with a flurry of industry-related events.
Sector professionals were spoilt for choice with networking events in Thailand, Turkey, Belgium, UK and USA.
These get-togethers enabled executives to at last see each other face to face for the first time in years.
Glass International attended as many events as feasible and - as always - it was a pleasure to reconnect.
One of the key themes around the world was that of collaboration.
The industry faces many challenges, particularly in its aim to reduce emissions from the production process, and many leaders acknowledge this will only be achieved by working in partnership with others.
This was exemplified at the recent Glass Problems meeting in the USA. Scott Cooper, President of event organiser the GMIC, unveiled an alliance between several glass manufacturers which will focus on using green hydrogen to power the melting process.
And this was no lastminute plan as part of a speech to impress conference delegates.
The organisation had gained the ear of politicians several months beforehand during meetings in Washington D.C who had urged the organisation to seek further funding.
The industry is at last on the radar of senior figureheads, which in turn has opened inroads into funding to help enable the sector to decarbonise.
Coca-Cola Beverages Sri Lanka will put a family-sized glass bottle back on the market to encourage reusable packaging and aid consumers in the currency crisis.
The Big Buddy Pack branded 750ml glass bottle is priced at 180 rupees, compared to 150 rupees for a 400ml PET bottle and 380 rupees for a 1.5 litre pack at supermarkets.
Sri Lanka is currently experiencing the worst currency cri-
ses in the history of its intermediate regime central bank.
Sri Lanka’s rupee collapsed from 200 to 360 to the US dollar in 2022, triggering monetary instability.
Annual inflation is now running at around 70%. Food prices, which respond faster to money printing, are up to over 90% over the last year.
Panjak Sinha, Managing Director of Coca-Cola (Sri Lanka and Maldives), said: “It [the
product] is affordable in these trying times and is differentiated with a unique refillable glass bottle, paper labels and aluminium cap.”
Despite the latest bout of monetary instability, the firm will not leave the country.
The firm said it had invested $99 million in the country in the last decade and has built distribution network with 80,000 plus outlets.
French automotive glass manufacturer Holophane has requested to enter receivership after a spike in energy costs.
Its energy costs will be 250% higher this year.
It will be €10.5 million this year compared to an average of €3 million over the past three
years.
The glassworks based in Andelys, Normandy, France specialises in the production of automotive fog lights and optics.
It also said demand for automotive lighting had declined in recent years in favour of
plastic, which enables lighter vehicles.
By being in receivership the company can protect creditors as well as possible while continuing to look for a buyer.
According to the receivership notice, it has 241 employees at the facility.
Düzce Cam is to build a 600 t/day solar glass production line at its Bilecik Plant.
O-I Glass reported strong third quarter results for 2022 as higher average selling prices boosted sales by $221 million.
O-I reported its financial results for the third quarter which ended September 30, 2022.
Andres Lopez, O-I Glass CEO, said: “O-I reported strong third quarter perfor mance which exceeded guid ance driven by solid net price realisation as we began imple mentation of our third price increase this year in Europe.
“Our glass shipments in
creased slightly compared to the prior year period, as ex pected. Elevated asset project activity contributed to higher operating costs, as we commis sion much needed new capac ity to support future growth.”
Net sales were $1.7 billion in the third quarter of 2022, up from $1.6 billion in the prior year quarter.
Higher average selling prices boosted sales by $221 million.
Shipments (in tons) im proved nearly 1% but a less favourable mix resulted in a $4 million decrease to net sales.
Segment operating profit was $266 million in the third quarter of 2022 compared to $243 million in the prior year quarter.
Mr Lopez said the company would continue to deliver on key transformation initiatives.
O-I expects operating costs will be higher in the fourth quarter of 2022, due to incre mental expense for expansion project activity.
However, this should be par tially offset by benefits from the company’s ongoing Mar gin Expansion initiatives.
Israeli glass manufacturer Phoenicia will become carbon neutral by converting its CO2 emissions to soda ash, which will be reused in production.
Phoenicia signed an agree ment with Airovation Tech nologies to install a unit that transforms CO2 emissions from its Yeruham plant into minerals that can be used in the glass production process.
After a decade of research at the Hebrew University of Jerusalem, Airovation has de veloped a method to capture sodium carbonate (soda ash) from CO2 at the point where the latter is emitted.
Extracting soda ash from CO2 is done by a patented
chemical invention that uses Superoxide Radical, the most powerful oxidiser in nature.
Under the new partnership, Airovation will run a twophase scale-up process, even tually leading to the first fully commercial unit at the Yeru ham plant.
This will reduce Phoenicia’s global warming carbon emis sions, contribute to a circu lar economy, and reduce the company’s dependence on soda ash imports, an Airova tion statement said.
Phoenicia CEO Michel Ben Simon said: “Phoenicia is thrilled to support an Israeli start-up and to co-operate in the execution of this pilot.
“The pilot represents a cru cial step toward turning Phoe nicia into the operator of the greenest factory in the State of Israel.
“It is also the country’s only factory capable of recycling broken glass bottles that are collected in accordance with the national deposit law, as well as a factory that works on natural gas, as we have built a natural gas power plant that should start working within two months.”
He continued that Phoeni cia installed another facility a ten years ago to prevent the emissions of particles and ni trogen oxides.
It signed an agreement with Chinese plant builder CTIEC to build the facility.
The site currently hosts a 300t/day solar line and will have a capacity of 900 tonnes when the new line is in place.
Fiskars Group will invest €10 million in electric furnaces for its Iittala glass factory in Hämeenlinna, Finland.
The investment will reduce the factory’s CO2 emissions by approx. 10,000 tonnes a year (74%) and decrease energy consumption of the melting furnaces by 67%.
The project will start next year and be completed in 2026.
Researchers at the Freiberg University of Mining and Technology in Germany are investigating how to melt amber glass with green electricity instead of gas.
The goal of the research project, which officially starts on 1 January 2023, is the stable and reliable production of brown glass with green electricity from renewable sources.
The research project will be organised and funded by the project management organisation AiF-IGFForschungsvereinigung for the next two years.
Verallia has appointed PierreHenri Desportes as Chairman of Verallia France.
With extensive experience in the industrial sector, Mr Desportes took over as head of the group’s French subsidiary on November 2, 2022.
Verallia Group CEO Patrice Lucas wished him success in his new role.
O-I Glass
by
million in third quarter O-I Glass sales increase by $221 million in third quarter
Verallia Group and Spanish beer brand Mahou San Miguel have partnered to reduce CO2 emissions at their plants in Burgos, Spain using thermal energy recovery systems.
The two companies’ energy efficiency project uses untapped heat from glass production at Verallia’s plant to generate steam at Mahou’s brewery.
To date, Verallia has saved 175 tonnes of CO2 per year by using steam.
SEFPRO’s furnace cooling systems at its SEPR plant in Le Pontet, France will reduce its gas consumption and CO2 emissions by approximately 500 tons.
The systems for furnace cooling, as well as a dust collector, will reduce the SEPR’s plant water consumption by at least 100,000m3 per year.
Fives has put forward more than 16 annealing lehrs into operation for a photovoltaic (PV) manufacturer in China over the last few months.
The annealing lehr for extra-large glass ribbons, features Fives’ technology and engineering efforts of the local team in China.
It has a production capacity above 300 MT per day.
Vidromecanica has relaunched its website to reflect its different equipment ranges.
The updated site’s new design allows customers to find the equipment they’re looking for more easily and provide online feedback.
The website provides information for glass plant managers and directors, from hollow glass to tableware glass factories, looking to supply their plant.
The NSG Group and SaintGobain have started a manu facturing furnace in Argenti na.
Its Argentine subsidiary, VASA Vidrieria Argentina launched the furnace on Sat urday October 8 at the week end at its Planta Cardales site.
The plant, located, approx imately 70 kilometres north-
west of Buenos Aires, will have an estimated production of 900 tonnes per day.
It will supply architectural glass for the domestic market as well as export to countries in the region.
Founded in 1938 and the re sult of the association of two of the largest glass manufactur ers in the world: NSG Group –
Pilkington and Saint-Gobain, VASA implements advanced technology in the manufac ture of a range of products.
VASA contains around 500 employees and is present with operations in four countries: Argentina, Bolivia, Paraguay and Uruguay.
Vidrala plans to raise the price of its bottles after soaring nat ural gas costs hit its profitabil ity in the first nine months of the year.
Vidrala’s net profits have fallen due to increasing natu ral gas prices.
Despite its revenues rising 24% in January-September
from the same period a year ago, its net profit per share fell 37%.
The company said the high er bottle prices will help grad ually raise its operating mar gin in the fourth quarter.
Vidrala expects earnings before interest, taxes, depre ciation, and amortisation to
represent 20% of sales in the fourth quarter up from 15.6% in the first nine months this year.
Higher bottle prices will feed into Spanish inflation, which has dipped over the past two months from a three-decade high of 10.8% in July.
A UK glassworks has secured planning permission for the installation of an air separa tion unit.
The O-I Alloa facility, UK said the unit will separate air into oxygen, nitrogen and
argon using a distillation pro cess with storage on-site.
Much of the oxygen will be piped straight to the glass works to fuel upgraded oxy-fu el furnaces. The move will reduce carbon emissions and
ensure the viability of the business, which employs hun dreds of people.
The unit will be installed by Air Products industrial gases group.
GMIC director says farewell to industry
Bob Lipetz said farewell to the glass industry after 12 years at the helm.
Mr Lipetz, the Executive Director of the Glass Manufacturing Industry Council (GMIC) in the USA, said goodbye at the 83rd Glass Problems conference held in Columbus, Ohio, USA.
He will be replaced by Kerry Ward, who will join the organisation in January.
The everyday milk bottle has been voted as the most iconic glass packaging in the UK.
As part of the IYOG celebrations, experts from the worlds of packaging, retail, manufacturing and plasticfree living were brought together to choose the UK’s top 10 glass bottles and jars.
The single pint reusable glass milk bottle won due to its instantly recognisable shape, perfectly suited design and sustainable, made-to-bereused credentials.
AGI Greenpac reports 66% revenue increase
Indian glass packager AGI Greenpac reported a 66% increase in revenue in its latest financial report, driven by improved efficiencies.
In its financial results for the second quarter ending September 30, 2022, revenue from Operations stood at 513 crore, registering a growth of 66% on Y-o-Y basis.
Wheaton Brasil to use biogas for production
Wheaton Brasil will use biogas as an energy source for its glass manufacturing processes.
According to the manufacturer’s estimates, using biogas will reduce its annual CO2 emissions linked to the production of glass by approximately 7,000 tonnes.
This is equivalent to more than 50,000 trees planted over a period of 20 years.
Ardagh Glass Packaging Africa (AGP – Africa) will invest in a third furnace at its Nigel production facility in Gauteng, South Africa.
The investment in a third furnace (N3) follows the recently commissioned Nigel 2 (N2) expansion and will further increase the facility’s capacity.
The expansion is expected to be commissioned in late 2023, well ahead of current
standard lead times.
Following completion, the Nigel production facility will be the largest glass container production facility in the AGP - Africa network, and on the African continent.
N3 will be a replica of the N2 expansion completed earlier this year and will similarly incorporate a new furnace and additional production lines.
It will also provide significant energy, water efficiency
and environmental benefits, representing another important step in AGP – Africa’s journey to decarbonise the glass production process and reduce emissions.
This capital investment will further bolster the government’s economic recovery plans in Ekurhuleni, Gauteng, offering additional job opportunities and increased ancillary supply-chain benefits in the community.
The Knauf Group will increase its mineral wool production capacity in Central and Eastern Europe with a €135 million investment.
As well as retrofitting the existing plant, which was acquired earlier this year, Knauf Insulation plans to expand its presence by building an addi-
tional insulation facility.
The investment will allow the company to increase its annual production output to 75,000 tonnes of mineral wool every year.
The new facility is scheduled to be completed by 2024.
It will create more than 100 new jobs and hundreds
of additional jobs for regional suppliers, contractors and vendors.
The existing Romanian plant in Târnaveni, MuresCounty, has already undergone a series of upgrades and has been brought up to date in line with Knauf Insulation’s manufacturing standards.
Steklarna Hrastnik, through its Swiss owner GlobalGlass, is set to take over the SFS Paracin factory, in Serbia.
The Paracin factory was in bankruptcy before the takeover and was the subject of a national programme for the revitalisation of the glass industry in Serbia.
The GlobalGlass group will increase its production capacity (by around 300 tons/ day) and its range of products.
The glass industry in Germany is cautiously optimistic following the release of an Interim report of the Gas Commission in Berlin.
BV Glas President Dr. Frank Heinricht is now hoping for a timely implementation through politics.
Watlow completed its acquisition of Eurotherm from Schneider Electric on October 31, 2022.
Eurotherm said Watlow’s industrial technology and its own precision control would offer complete thermal control loop solutions.
Watlow will establish Eurotherm’s sites in Worthing, UK and Dardilly, France as Advanced Development Centres for its electronics and controls product offering.
Ardagh plans to commercialise its Briquette Project, which will create more usable material for furnaces and reduce CO2 emissions.
The project is now in the final stages of being commercialised, and should be fully commercial by 2023.
Using cullet could help Ardagh reduce its Scope 3 emissions, of which 53% come from producing soda ash.
Visy broke ground on its $500 million glass recycling and remanufacturing factory out side Brisbane, Australia.
The facility, which repre sents the largest investment Visy has ever made, will recy cle up to 200,000 tonnes of Queensland’s glass annually to produce 1 billion bottles a year.
The site is expected to be op erational in 2025.
Visy Executive Chairman Anthony Pratt said: “Recy cling is an important weapon
against climate change and the technology employed in this factory will help Australia to go from an average of 30% recycled glass content in bot tles to 70%, which is moving towards world’s-best practice.”
The facility, in Stapylton just south of Brisbane, will be built next to Visy’s current box factory and beverage can plant.
It will support approximate ly 200 green collar manufac turing jobs once operational, and will bring Visy’s Queens
land workforce to more than 1000 people.
The project will also create over 600 jobs in construction.
The project is underpinned by a long-term partnership with Asahi Beverages, and agreements with Visy cus tomers including Lion, Bund aberg, and Coca-Cola.
This facility brings Visy’s to tal investment in Australia to over $11 billion.
Visy will relocate its glass remanufacturing operations from South Brisbane in 2025.
Duralex put its only furnace on standby on November 1 due to soaring energy prices.
The furnace, located in La Chapelle-Mesmin, in the Loiret, France will remain on standby for at least five months.
José Luis Llacuna, President of Duralex, said: “The price of energy usually represents 5% to 7% of our turnover. Today, it is around 40%. It is not ten able.”
The company said its energy bill had gone from €3 million
euros last year to €12 million this year.
Duralex announced the site’s standby at the beginning of September.
The time between the an nouncement and its imple mentation is explained by the complexity of the operation: in theory, a glass furnace nev er stops to prevent being dam aged.
“The oven will not be stopped purely and simply, but we will keep it at temper ature so that we can restart it,”
said Mr Llacuna.
As the company now has sufficient and quality stocks, it believes that it can continue its commercial activity nor mally during this period and thus continue to serve its cus tomers satisfactorily.
Therefore, the site will con tinue to operate, with full ac tivity resuming next year.
“We have a tariff cover al ready contracted on electric ity, which will allow produc tion to resume in the second quarter of 2023.”
French glass packager Verallia is to acquire Allied Glass in a £315 million agreement.
Established in 1874 and headquartered in Leeds, Allied is a UK-based manufacturer of glass packaging containers for the premium spirits, food and drinks markets.
It has four furnaces and 600 employees.
It has modern extra-white, bespoke colour and decora tion capability, with a strong focus on sustainability, based on an ESG policy with clear targets across all areas and a market leading use of cullet
across all products.
Verallia said the acquisition will enable it to benefit from Allied’s expertise in premium glass bottles, specifically in the Scotch Whisky and Gin sec tors, and from its established position on the UK market.
With nearly 50 locations and over a 125-year history, we process a variety of glass in the U.S., Canada and Mexico. We partner to recycle deposit, single-stream MRF, soda lime, borosiliate, plate and more. Contact us today to explore a glass recycling solution: info@smi.com
Italian pharmaceutical glassmaker Bormioli Pharma recently completed the refurbishment of its Bergantino, Italy furnace, which is dedicated to the production of type II glass containers. Davide Faverzani, Head of Engineering at Bormioli Pharma, discusses the project.
The Bergantino furnace refurbishment took 60 day from glass to glass. The project started with the complete demolition of the old furnace, together with the dismantling of two production lines and the cullet conveyor system.
After this, we continued with the construction of the new furnace, the installation of the new lines and the most advanced vision systems.
Moreover, the project included the installation of a new insulation system, which allows us to increase energy performances and furnace life.
As far as the issue of continuity of energy and gas supplies is concerned, Bormioli Pharma has taken a number of mitigating measures to keep the risk of supply
interruption to a minimum, so limiting the impact also on this project.
We have binding contracts in place with international energy production and distribution companies who do not foresee the risk of a reduction in supply in the next 12 months unless highly disruptive geopolitical event occur.
Government and European Institutions are issuing recommendations aimed at limiting energy consumption through targeted actions (e.g., reduced use of air conditioning or heating systems) and, at present, there are no specific measures in place that have a major impact on industrial companies.
Moreover, the sector in which Bormioli Pharma operates, namely pharmaceutical & healthcare, has been identified, both at a National and European level, as an
‘essential’ supply chain.
Sustainability was a consideration during the works. We have installed a special insulation system which allows to reduce consumption, thus allowing for a more sustainable production.
The new furnace relies on a mixed technology, which use both electric and natural gas power. Moreover, an extra power boosting system has been introduced to guarantee the opportunity to increase the melting performance in the future.
Other investments took place within the plant at the same time.
Within the new furnace refurbishment project, we have replaced the medium voltage substation with a new monitoring
power system. Moreover, at the Bergantino plant we are revamping the parking area and the entrance building and we expect to close the project by the end of this year.
Digital technology was also a consideration during the investment. Digitalisation is an aspect we always consider when making new industrial investments. In the case of the new furnace, we have connected all the production equipment – from furnace up to palletizer – with a special Industry 4.0 supervisor system.
The new furnace will contribute to reinforce the positioning of our Bergantino plant as the biggest European production site for pharmaceutical moulded glass.
In this plant we produce 1.8 billion glass vials every year, which reach more than 100 countries. More specifically, the new furnace will be mainly dedicated to the production of modern type II glass containers, thus meeting the growing demand for this kind of product.
The first campaign started last September producing different Type II
glass product formats, from small glass vials up to 1000 ml infusion bottles.
Demand in Italy’s pharmaceutical industry has been impacted by Covid-19. Going back to the 2019-2021 period, the packaging market has been impacted as the economy as a whole by the Covid-19. Nevertheless, other than for the enormous shortage of glass vials, which has been addressed by the industry and aside from some anti-cyclical development of certain diseases (as flu and other seasonal diseases) as well as the delay in therapies due to the stay-at-home
policies implemented in many countries which slow down or stopped for one year the demand for specific packaging products (such as syrups bottles), the Covid-19 only slightly affected the macro trends of the market which is projected to grow at mid-single-digit up to 2026, in line with the pharma market.
We expect that Italian market will reflect the same European trends described above. �
Bormioli Pharma, Italy
https://www.bormiolipharma.com/en
Engineering project management group cm.project.ing has grown to 90 permanent employees since its formation 15 years ago. CEO Dr Daniel Schippan* provides an overview as well as its expansion plans into flat glass.
Cm.project.ing serves the glass industry with engineering project management and design services.
This includes: project feasibility; FEED (front end engineering and design); detailed engineering; securing financial options to procurement and contracting; design-build general contracting; project management; project execution; architectural design; interface engineering, utility, and process engineering; commissioning and performance; and global start-ups.
Therefore, I would say we are deeply involved and have an excellent global footprint in the glass industry.
I have an extensive background in glass. I studied at the RWTH Excellence University of Aachen, the University of Glass Science and Technology.
My doctoral thesis was done at BSN Glasspack, which was created from the merger of the glass container businesses Danone and Gerresheimer. BSN Glasspack was later acquired by O-I in 2004.
I have worked with glass all my life. After university, I had several stages in the container glass industry, then the glass wool industry, before returning to the container glass industry.
I have worked as the Head of R&D, Head of Glass Technology, Head of Growth Investments, Plant Manager, and CPO.
My experience in different positions in the international glass industry gave me vast technological and management experience,
which allowed me to build an extensive network in the glass business.
My experience in the glass industry encompassed growth and CAPEX investments. When I oversaw these, I was searching for a company that could give me a holistic approach to green and brownfield projects.
There was a lack of holistic companies that could offer those services with a focus on electrical engineering, architecture, HVAC (heating, ventilation, and air conditioning), utility, and technical project management.
The difficulty with most companies is that they have good people with good process technology, but this doesn’t make a project successful in all disciplines. This was the inspiration for our company to serve the glass industry with all of these disciplines, to make CAPEX and investment projects successful.
In the beginning, it was very difficult to sell our services and get international customers. The main challenges involved were: getting the business off the ground; making the company popular; forming an experienced team; getting the office equipped; and running, and having, all the interfaces in place.
Today, the company is at its best after 15 years and we are constantly challenged to be on the leading edge of technology.
I wouldn’t say there was one significant moment that we knew we had made it in the glass industry. Our focus was to go step-by-step.
We first got projects in Germany, then had successful projects in Europe, and then had successful projects internationally.
Next, we were successful with different suppliers. This built up from newcomers to midsized customers, up to large leading customers.
One factor that goes into success is reliable and knowledgeable employees. This is essential for an engineering office; we put a lot of effort to find good people who fit well in our team structure.
We also work innovatively, which means we always try to be up to date or even ahead with tools and software. We aim to have all that is currently available produce the best engineering services possible: to be brave - to go a step beyond normal engineering offices. (Pic 1)
We have 90 fixed employees, unlike engineering offices which work with a low number of fixed employees - when they have a project, they’re working with external sub-suppliers. That is not our strategy. We need to co-operate.
With fixed employees, we can work in the same office building. This allows for daily discussions to address grey areas within the servers to work on. These are definitely factors of success. We take great pride in our reputation, and will continue to improve and innovate.
It was impossible to start right from the beginning with 90 employees, so we had to produce many ideas to build, develop and grow the company.
Architecture and HVAC were not services right from the beginning. During the last 15 years, we have been able to develop our own architecture, construction team, and HVAC team.
We have developed a lot of new and modern software. We have created a CFD (computational fluid dynamics) approach for an optimised design, and, at present, we can offer the whole and complete holistic scope of services in-house.
We don’t offer a product: our product, or service, is our engineering.
� Pic 1 – cm.project.ing’s site in Jülich, Germany.
At Glasstec, we presented new designs, especially the part of our BIM (Building Information Modelling), which is normally used in the construction industry.
We converted it into a holistic BIM for the glass industry, which integrates process engineering, so we highlighted these tools as well.
The fair, after four years, had a positive atmosphere and was a great success. We had a lot of global and new customers at our booth.
I was pleased to see where the glass industry is going in terms of sustainability for the environment, in terms of CO2 neutrality, innovation, new technology, and new capacity for glass against plastic. I believe the industry is on the right path.
We have already accomplished many things and are on the right track. However, we also need to consolidate, despite having a lot left to do.
We have footprints in the flat glass industry dating back some years, and we are looking forward to exploring more special glass applications in the future, such as for solar photovoltaic glass.
Therefore, we aren’t just starting out, we’re currently in a consolidation phase. We want to grow sustainably and intelligently.
To ensure the future, it is necessary to continue to develop skilled people, to have successful projects, to be innovative, and to expand again.
As a company, we must ensure excellence in work. That means we must provide our customers with added value, and we must work in a highquality manner.
I have been thinking for some time about expanding into similar industries, such as steel and aluminium. We were never in a position to expand in those fields because we were always very busy in the glass industry. This is definitely on the agenda for the next 10-20 years.
This is something we are looking at on a longterm basis. Perhaps for my children, it will be on their agenda to serve in the steel and aluminium industry with our added value engineering expertise. �
*CEO, cm.project.ing, Jülich, Germany https://www.cmprojecting.de/home
Peter J Firth* examines the technology enablers in the glass industry and suggests that, rather than being competitive, there can be a symbiotic relationship between suppliers that can benefit the glass manufacturing sector.
For quite some time now, I have had in mind to put my thoughts on this topic into an article.
Let me point out, before we go any further, that the use of the term ‘GUYS’ is not a sexist statement by me. In using ‘GUYS’, I am meaning that in the most liberal sense, embracing both sexes. Of course, I think we all know we need more talented women in the glass industry.
That said, let’s continue with the main topic.
After observing the glass container industry for many years, as a long-term employee of a major glass manufacturer, I have come to my particular opinion and I would like to share it with others in the industry.
As an employee, it is not so easy to share opinions widely due to potential conflict with an employer’s point of view. However, now that I am operating as an independent consultant to the glass container industry, I am free to openly share my thoughts with you.
Firstly, who are the suppliers I am thinking about?
For me, it is mostly about the equipment suppliers that provide us with the tools and equipment to carry out our business using the best available technology. However, my logic also extends and applies to other suppliers, such as those for raw materials, utilities and any other services to the glass industry.
Therefore, please realise that, as I write, I may hold equipment suppliers in mind, but it also applies to any suppliers to the glass industry. Equally, I write in the context of glass container manufacture, as I write this from my experience in the glass container industry, yet the same thinking can equally apply to other areas of glass manufacture.
Before I reveal exactly what I mean by the GUYS and the GIANTS, I would
like to point out that these two different categories of suppliers occupy the same space in the market. To most people, the only apparent difference is the size of the company. However, further consideration will reveal the differences go much deeper than that.
By now, you might be painting a picture in your mind as a ‘David and Goliath’ situation; with the little ‘guy’ having the objective of slaying the ‘giant’. However, nothing could be further from the truth, as you will find out soon. In fact, there is a relationship between the two that can be very productive for all concerned.
Now let us explore some background behind the specific naming of these acronyms. This should paint a better picture of exactly what we are talking about here. I tried to have a bit of fun with the naming, so here goes:
I hope that clarifies what we are talking about. I also hope you see the distinction straight away in a fun and easy way to remember.
In case you need a little help to clarify, the GIANTS are easily recognisable and they literally are the ‘Giants’ of the glass industry suppliers; widely-known to many with a large installed base of equipment, typically over many years. In a glass equipment supply context, a few company examples would be Horn, Emhart, Heye International, Zippe and Tiama. If you go to the glass exhibitions then these companies would likely be the ones with the largest and most glamorous stands, including separate meeting and hospitality rooms, not to mention the quality of the welcome refreshments
on offer (which I personally welcome during a busy day at a glass equipment exhibition).
On the other hand, the GUYS are much smaller businesses that might not be known to some people, even though they have been in the industry for some years. The GUYS may have their equipment installed quite widely in certain companies in particular parts of the world, but not widespread across the entire international glass industry. Furthermore, certain glass companies who have adopted their equipment might even have come to rely upon it. To those companies, it is necessary to support their current level of operations in terms of quality and efficiency.
In these cases, even though the equipment provided by the GUYS may be making a significant contribution where it is installed, they are simply not as widely recognised as the equipment supplied by the GIANTS. Also, the level of business is much smaller than that of the GIANTS.
Please note that the term ‘Young’ used in the acronym of ‘GUYS’ is used very loosely, since every company matures at a different rate, and not necessarily measured by years in business alone.
We can conclude this section with actual examples of such GUYS. The ones that come immediately to mind for me are Pro-Sight from the UK, Konatic from France, and Socabelec from Belgium, to name a few.
So much for the distinction, now for my main point: As glass container makers, we need a nice balance and mix of both of these distinctly different kinds of suppliers. If we can recognise that, as well as act up on it, we will help our industry survive and thrive in partnership with all our suppliers.
The GIANTS are needed to provide the large volumes of equipment that are required to serve the mainstay of our basic operations in the glass business. To do this, such companies are necessarily highly structured, with specialists assigned to each area of detail in their operation. However, with that comes a management and operational structure that is difficult to respond quickly to the demands of our changing industry.
The GUYS, on the other hand, are necessarily much less structured and their employees may have to take on several distinctly different roles. Additionally, their Managing Director (CEO, or the like) will probably be very much customer-
facing on a daily basis and may have a certain level of a hands-on role in the business. This means these companies can easily adapt to the voice of the customer and with that bring innovations to the glass suppliers much faster than the GIANTS are able to do.
The GUYS also have to use innovation as a competitive advantage, because simply following in the GIANTS footsteps will not provide them with the business they need to survive. The GUYS will also have the time to focus on innovation and meeting the detailed requirements of their customers. This is helped by the fact that they don’t have the challenges associated with the large volumes of equipment supply to lose any sleep about.
technically challenge the GIANTS. The GIANTS may then respond by addressing the same issues as the GUYS, albeit with some further delay in getting those developments to market. Without the GUYS, however, such developments by the GIANTS may never have come at all, or at least not so quickly. In this case, the glass industry, as their customer, will suffer in the sense of not performing to the level they could otherwise have done.
In recent times, it has been seen that some of the GIANTS adopt the development work of the GUYS directly. Ideally, this is done via a licensing agreement with the GUYS or occasionally a buy-out of the GUYS’ business to integrate their technology into the GIANTS’ offerings. (In more aggressive cases, it might seem more like copying which is unfortunate and is just not cricket, to coin an old English phrase.)
The GUYS are the ones that need our support the most in order to foster the beneficial relationship described above. When we invest in the GUYS we invest in the development of the wider industry. The GIANTS on the other hand are there to meet our demands on a larger supply scale, as already mentioned. That is not to say they don’t do any development work of course, as many GIANTS invest heavily in the area of R&D. However, it is good to have ‘our’ GUYS there to keep the GIANTS on their toes.
� On a plant installation visit with Gregory Duez of Konatic.
The GUYS, therefore, tend to be at the forefront of many new developments, although their work development work might not be broadcast as loudly and as widely as the GIANTS’ offerings are.
You would now be forgiven if you are thinking that there is a strong competitive nature between the GUYS and the GIANTS. As stated at the outset, this is not actually the case. Rather, they have a somewhat symbiotic relationship and the main beneficiaries of that relationship are the glass plants as customers of their equipment. If we, in our glass operations, can recognise that, we can decide to act in a way that supports and fosters the development of the relationship already described, to our ultimate benefit.
Let us look at how that relationship works between the two, in case it is not already obvious.
In the case of the GUYS, they are creating developments that may
Due to my personal reach on LinkedIn (request to connect with me if you are not already in my network by using the QR Code at the end of this article), a number of the GUYS have asked me if I can support them in some way. Well, let me say I am not a salesman by any stretch of the imagination, and those who personally know me will vouch for that, I am sure. I won’t say I am too honest to be a salesman, but by saying that you might know what I mean. No offence intended to any salesperson of course, I respect your craft but, personally speaking, I could not do it.
I was recently told by someone that the moment I come down in support of one particular supplier, I will lose a lot of my following on LinkedIn. Whether that is true or not is up for debate. However, I have seriously considered this point and think I should show some support to ‘our’ GUYS. That is especially because it creates the benefits to the glass industry I have already described above. That would then meet my principles of trying to support the glass container manufacturers, which
�
is where my roots are.
Having said that, I can of course only point to the real benefits that any of the GUYS bring to the glass manufacturing operation, as anyone coming to market without such a benefit has no contribution to make. There is absolutely no chance of any salesman ‘gloss’ from me!
Many of you will probably already know about my LinkedIn Groups of ‘Glass Container Defects and Production Matters’ and ‘Glass Jobs 4 Glass People’. These two groups are aimed at supporting the glass industry too, no gloss, just fact (or honest opinion, maybe I should say).
In conclusion, when you are looking at the range of suppliers in the glass industry, make a distinction between the GUYS and the GIANTS. In some cases, the GUYS can give you process benefits faster than the GIANTS. Because of that, don’t pass them over if you are interested in optimising your manufacturing process. Also remember that on a longer-term basis, by supporting the GUYS you are supporting the future development of the industry, as surely the GIANTS will later adopt or integrate the development direction that the GUYS are currently paving the way for.
Let’s hear it for the GUYS! �
*Peter J Firth Glass Container Manufacturing Consultant Glass Container Manufacturing Consulting Ltd www.linkedin.com/in/ peterjfirth-glasscontainermanufacturingconsultant
P.S. To access the early development of a LinkedIn Page Post dedicated to the GUYS, type bit.ly/MEETOURGUYS into your browser (exactly as shown, like you would for a password). Alternatively, use your phone camera on the QR Code given for it here.
Ihave taken a detailed look at the Konatic Smart Gob system to appraise its benefits to the Glass Container Industry. This included a review of technical documentation as well as a visit to a glass plant to see the system in operation and get hands-on experience.
I conclude that there are significant benefits apparent both in process control as well as energy and raw material savings that should enable most glass plants to get a payback on their investment within a year... and that is what the accountants like to hear!
Firstly, about the payback that is most easily justifiable. This comes from the fact that the weight variation is controlled very closely to a few grammes by the system automatically adjusting the tube height as it sees a change in the size of the gobs (using two cameras). That means the weight of a job can be run more closely towards the lower end of the tolerance specification in Blow Blow (BB) and Wide Mouth Press & Blow (PB) production (which normally have wide tolerances). Just imagine a few grammes saved on average on each container made!
Note that the main benefits are realised in Blow Blow and Wide Mouth Press Blow production. This is because with Narrow Neck Press & Blow (NNPB) production, there should already be a closed loop weight controller which will be part of the plunger pressing control system to maintain the tight gob weight control required for that forming process.
Now back to using the system with BB and PB production... If the system is set up to save glass, then the payback is in the form or savings in glass and energy required to make each container. If you know your cost per tonne of glass then it will be easy to calculate how much money will be saved over the course of a year, whilst still making the same amount of containers to sell. There is more about that if you want to join the LinkedIn Group for the Konatic Smart Gob.
The Smart Gob will also prevent the lost production that can occur quite easily on BB and PB production, as typically there is normally no automatic weight control system being used. Usually, these forming
by Peter J Firth*.processes still rely on the IS Operator to make the manual adjustments. However, the operator typically only checks the job weight every 15 - 20 minutes, depending on the plant procedures. If there is an upset in the flow or temperature of the glass in the forehearth then out-ofspecification weight will result. But with the Smart Gob, the adjustment would have been made to the tube height to compensate and maintain weight control.
Another disturbance that is quite typical in most plants comes from job changes on neighbouring lines. During this period, the weight can be affected unless there is a system like the Smart Gob installed. In this case, the variations in the temperature of the glass and the glass level in the forehearth, which could be caused by the neighbouring job change, can be compensated for automatically by the Smart Gob system.
Gob shape is another requirement for control that is often talked about. You hear well-known sayings like having the right ‘gob for the job’, which is very true.
Once you have the right gob shape then the Smart Gob imaging system will save the images so that it is easier to reproduce in future.
The variation in gob shape from one job run to another has often been cited as being the reason that some job runs are good and others are not so good, even though all other setups seem the same. We can therefore remove that variable and have more consistently good production runs.
From a quality control point of view, there is 100% weight checking of the containers for correct weight specification
and this is all done in a non-contact way using the two cameras looking at the gobs.
Additional benefits come in some specialised areas of production too. Take for instance the production of jars where the push-up control is particularly important. In this case, the consistency in weight control leads to a more consistent base thickness which means the push-up depth control is more easily maintained.
In another similar example where the base thickness is important in cosmetic container production, a similar benefit is gained as the base thickness of those containers is directly affected by the variation in gob weight. A reduction in such variation, therefore, means the bottom thickness is more easily held in specification.
It all makes you wonder how we managed all these years without such a system. Well, the answer is we haven’t managed, we have just suffered and lived with it in my opinion. The technology now exists to solve our previous such problems and the Smart Gob can give the glass plant the benefits described above.
If you want to know more, simply join the GUYS LinkedIn Group for the Konatic Smart Gob by using the link below. �
*Glass Container Manufacturing Consultant, Glass Container Manufacturing Consulting Ltd
This group is only for Glass Container Company people: https://www.linkedin. com/groups/12727457/
Alternatively, if you want to contact me direct about anything in this article, or need any further information, please email me at peterjfirth@gmail.com
For humans, it’s obvious. For NEO too.
After 60 years in the glass industry, Dr Arun Varshneya has become the Society of Glass Technology’s first president from overseas. His plans for his presidency include expanding the society’s global reach and focusing on the sustainability of glass.
The Society of Glass Technology (SGT) is a nonprofit organisation based in Sheffield, UK.
The society provides a communication network for the industry by publishing journals and textbooks, and organising meetings and conferences on glass related topics.
Dr Arun Varshneya said he was honoured to be the society’s 58th President. He succeeds Stuart Hakes, Chief Executive at FIC, who held the position between 2019 and 2021.
Dr Varshneya is President and CEO of Saxon Glass Technologies, and was a Professor of Glass Science & Engineering at the Alfred University in New York, US for 28 years.
He has 45 years’ experience in research on ion exchange strengthening, and has authored several key publications and patents dealing with the process.
Dr Varshneya cited his father as his inspiration for
joining the glass industry. His first thought was of him upon hearing he was SGT’s new president.
“My first reaction was to thank my late father who pushed me to study glass at the Dept of Glass Technology, University of Sheffield, under the chairship of Professor RW Douglas way back in 1962.
“I have always had pleasant interactions with the SGT, beginning from my first week in Sheffield, and so it was quite an honour to be asked to become its 58th president.”
Dr Varshneya has been associated with the society since his studies began in 1962, and said that the relationship never faltered when he returned to the US in 1965, after completing his degree at Sheffield.
“In early days, I used to admire the SGT staff for their hard work abstracting for the Society Transactions.
“I appreciate the desire of the SGT Council to attempt to internationalise the Society and pick me as their first overseasdomiciled leader. ”
“Now it has come around in full circle! I have presented invited lectures at society meetings, published in the journal, and have delivered a short course on glass, sort of giving back.” (Pic 1)
Dr Varshneya believes his experience in the industry has given him a unique skillset for his role as SGT president. From his education to being an industrial scientist, to a professor and finally an entrepreneur.
“The full 360° experience along with business skills and fundraising skills for non-profits will perhaps provide a broader vision of the SGT.”
As the first SGT president from overseas, Dr Varshneya believes his connections to American and Indian organisations will help him to expand the society’s global reach.
“I appreciate the desire of the SGT Council to attempt to internationalise the Society and pick me as their first overseas-domiciled leader.
“My strong attachment to the American Ceramic Society as a distinguished life member can greatly help me carry that mission, in addition to building up our strength as a glass professional group providing a service to the benefit of mankind-atlarge.”
Despite being based in America, Dr Varshneya is
� Pic 1. SGT members at an International Commission on Glass (ICG) meeting in London, 1968. Including Dr Varshneya (right) and the late Professor Guenther H Frischat of ClausthalZellerfeld, Germany (left).
� Pic 2. Dr Varshneya (back row, last on the right) as a final year honours student at the Department of Glass Technology, University of Sheffield, 1965.
� Pic 3. EpiPen and chemically strengthened glass cartridge.
optimistic that he will be able to stay connected to the membership and the leadership of the society using online media. He said that ‘the pandemic has taught us how to work remotely’. However, he will visit the UK from time-to-time.
Dr Varshneya said he had five goals for his time as president:
�1) Build a bridge across the Atlantic. He would like to put the SGT in closer working relationship with the American Ceramic Society. Since he also has good relations with the Indian Ceramic Society, the All India Glass Manufacturing Association, he dreams of building a ‘Glass Alliance’ - much like the ‘Star Alliance’ of airlines.
� 2) Increase its individual and corporate membership.
� 3) Increase journal content and impactfactor, for example by improving the h-index (number of citations) of the journals. To this end, Professor Alastair Cormack has become the Editorin-Chief of two SGT journals: ‘Glass Technology’ and ‘Physics and Chemistry of Glasses’. Professor Cormack is well recognised in glass sciences, as a
Join the worldwide network of interests centred on making glass great
The Society of Glass Technology exists to serve people who are interested in the production, properties or uses of glasses, whether from a commercial, aesthetic, academic or technical viewpoint. It is a non profit making organisation serving a worldwide membership publishing jour nals and text books, organising meetings and conferences on glass related topics.
You can now join the SGT by going to www.sgt.org and selecting your jour nal choice and appropriate package. You will also be able to see the comprehensive history and activities of the society
Professor of Ceramic Science and Founding Dean of the Inamori School of Engineering at Alfred University.
�
4) Add a focused ‘Sustainability with Glass’ as a regular feature alongside our other technical symposia each year. He may also consider adding named symposia.
faculty member, Dr Varshneya set up Saxon Glass Technologies as an entrepreneurship. This was to fill the market need for a chemically strengthened glass cartridge for EpiPens (Pic 3). These devices combat anaphylaxis shock caused by severe allergic reactions.
5) Expand SGT interaction with trade shows such as Glassman, Glass Performance Days, Glass Problems Conference and with trade magazines. He said a glass industry professional should have a seamless access or transition between moving from one to the other by providing cross-links.
�
Dr Varshneya said he would be happy if he could achieve three out of the five goals.
After his initial education at Agra University (India), Dr Varshneya started his education in glass with Professor Douglas at Sheffield (Pic 2), and then with Professor Alfred R Cooper in Cleveland, US.
He enjoyed 12 years as an industrial research scientist at Ford and GE Lighting before being invited by Alfred University in 1982 to join faculty rank. During his time as a teacher and researcher, he took the time to write the textbook ‘Fundamentals of Inorganic Glasses’.
This gave him a global reputation from students and glass professionals: “As a result of my textbook, I have often been called the ‘Glass Guru’, which brings smile to my face.”
Dr Varshneya’s recent area of study has been the chemical strengthening of glass, but he has explored with composition-property-structure relations, molecular dynamics calculations of glass structure, non-oxide glasses, natural glasses, industrial issue such as glass inhomogeneity, and glass-to-metal sealing.
“After spending 60 years in glass, I could say, I am one of the more thoroughbred horses in glass on the globe.”
In 1996, while still a full-time university
The “little strengthened glass business” has supplied 0.5 billion cartridges since 1996, helping save thousands of human lives each year with a near-zero probability of glass fracture during administration.
Dr Varshneya is now retired from his Alfred University professorship, but still remains actively involved with glass R&D at Saxon Glass.
Dr Varshneya said that creating glass products to benefit others was the most enjoyable aspect of the industry for him. For example, knowing that his glass cartridge for the EpiPen could potentially save a life. More recently, Saxon Glass has also provided glass specific to Covid-19 vaccine storage needs.
“I enjoy working on glass topics which would make our precious planet liveable for generations to come. We must look at the issues relating to glass in sustainability, healthcare, and communications.”
He continued that he had always taught his students to focus on glass products and processes that would bring benefits to humankind (Pic 4).
“Working on issues of zero-carbon glass melting, recycling, conservation of resources, toxic waste immobilisation and, of course, glass in healthcare and in communications should bring joy to anybody.”
Moving forward, Dr Varshneya hopes to unite with likeminded individuals through the SGT.
“I invite individuals who are as excited about glass products as I am to come forward with outreach efforts and organise symposia and webinars which discuss cutting edge concepts to students and professionals alike in an instructional manner.” �
It‘s having ALL the right data, at the right time, at the right places. YOUniverse gives you more process control and helps you to foresee problems early and to take the right decisions quickly, With open-protocol software solutions, linking hot and cold end sensors to your production machinery, you make the most of the data in your plant, you improve glass quality, you reduce wastage and increase productivity. Make your life easier - with YOUniverse.
Visit youniverse.tiama.com to arrange a demonstration
After being postponed due to the pandemic, the World Soda Ash conference took place last month at the Hilton Sorrento Palace Hotel in Italy.
The event was the largest World Soda Ash conference in 10 years with over 300 attendees and 20 speakers from approximately 35 countries and 200 companies.
Keynote speakers included glassmakers Sisecam, NSG and Ardagh, as well as soda ash industry expert Marguerite Morrin (Fig 1), Executive Director of Chemical Market Analytics by OPIS.
The last three years have proven eventful for the industry, with the price of soda ash skyrocketing due to a shortage of raw materials and increasing energy prices.
However, demand for glass, and
consequently soda ash, remains strong. In her talk, Ms Morrin said 59% of world soda ash demand comes from the glass industry.
Unsurprisingly, many companies are looking at renewable energy sources to save costs and reduce emissions.
Recent events have had a huge impact on the market. Ms Morrin said no-one could have predicted what was to come at the last World Soda Ash conference in 2019. A global pandemic, the Russia-Ukraine war, the risk of global recession and climate change have resulted in some of the highest soda ash prices on record.
She said: “Soda ash markets this year have been the tightest we’ve ever seen.
We’ve seen some of the highest prices on record, even heard of spot prices $1000 per million tonnes - something unheard of for this industry.”
Europe was relying on Russian gas for 40% of its supply, which has resulted in record high natural gas prices and crude oil prices – but the consequences are still not fully known.
This has also increased the risk of global recession due to rampant inflation, interest rates rising sharply, and currency volatility. The Chinese economy is also slowing for the first time since the 1990s.
Although Ms Morrin said some consequences were due to the Great Recession, which occurred from 2007 to 2009, post-2009 much soda ash capacity
closed around Europe.
In total, this was approximately over 2 million tonnes, including West Europe, Central Europe, and the Commonwealth of Independent States (CIS). The biggest net impact was in West Europe.
West Europe had a net loss of capacity
of approximately 1 million tonnes. In Central Europe capacity losses have been offset by other capacity gains, with a similar situation in the Commonwealth of Independent States (CIS).
In 2023, there will be 1.5 million tonnes less capacity in the United States (US) than predicted. In 2027, this will increase to 300 million tonnes.
However, there has been a 6 million tonne increase in capacity in the Middle East. Much of the increase has been in Turkey (mostly natural soda) with some capacity in Iran also.
1.1 million tonnes of capacity is planned for the coming years, including 800,000 tonnes in Turkey and a synthetic plant in Saudi Arabia. Meanwhile, India will remain a net importer of soda.
Elsewhere, China dominates with capacity expansions. In recent decades, China has added 30 million tonnes of capacity, mostly to meet its own domestic demand (Table 1).
The most ambitious Chinese expansion is an 8 million MT per year natural soda ash project in Inner Mongolia.
Overall, natural soda ash is taking a bigger share of the total world capacity. In 2017 it was 25%, which has increased by 3% this year. Based on what’s scheduled, this will increase to 38% by 2032.
Ms Morrin said the total world soda ash demand is expected to be 65 million metric tonnes (MMT) this year, with the
demand growth, and will remain a driver in the forecast period as well. It will account for the second biggest volume of new demand by 2027 at an approximately 2.1 million net increase in terms of soda ash.
Ms Morrin said total world soda ash demand is projected to grow by 2.4% in 2023, and has grown by just over 2% this year.
In the world excluding China (ROW), 1.1 million tonnes of new demand is predicted per year until 2027. While China has 660,000 tonnes of growth predicted per year out to 2027.
Meanwhile Russia accounts for 4% of world demand per capita, but this is mostly self-contained in terms of supply/ demand dynamics.
Flat glass has remained important for all regions. It has grown about 4% per year in the historic time period, and will grow by approximately 2% growth in forecast period. There has been a net increase in demand of approximately 2 MMT, so it is still a very important demand driver.
China is by far the biggest flat glass producer in the world. Flat glass has driven demand growth for soda ash in China, which has influenced world demand overall.
Construction (not including solar glass) is the main driver, with 1.7% growth even during the pandemic (from 2020). Construction spending is slowing
glass industry dominating at 59%. (Fig 2)
While flat glass has the single biggest end use at 30%, solar glass has become an important growing application at 5%. Meanwhile, container glass accounts for 19% of total world demand.
Flat glass has been a larger driver for
down next year, although the long-term potential is still positive.
Meanwhile, global automobile production accounts for less than 10%
The largest World Soda Ash conference in 10 years took place in Sorrento, Italy. As the energy crisis threatens the industry, the conference focused on decarbonisation and cost reduction through renewable fuels. Jess Mills was in attendance.� Fig 1. Marguerite Morrin, Executive Director of Chemical Market Analytics by OPIS. � Fig 2. World soda ash demand.
of world demand for soda ash, although it has seen a 3.8% growth post-pandemic.
Container glass production has not grown as fast as flat glass. The expected growth for container glass through the forecast years is a modest 1% per year, and a net increase in soda ash demand of about 600,000 tonnes. (Fig 3)
However, Ms Morrin said container glass had seen a ‘renaissance’ in recent years, with West Europe being the biggest producing region.
She said many believe container glass to be a better packaging material relative to plastics due to its environmentally friendly properties, such as its infinite recyclability.
Europe has the highest recycling rates in the world at approximately 80%. There have also been recent movements to increase recycling in Australia, which has gone from 30% to between 50-60%.
However, in the US, production has
shown a decline year on year and its recycling rate of 31% has hardly budged. Although some states have particularly high rates, such as Oregon at 73% and California at 67%. The US target is to reach an average recycling rate of 50% by 2030.
There is also an ongoing effort globally to use more recycled glass, which has lowered the consumption level for soda ash. For example, a 10% cullet increase will reduce CO2 emissions by 5% and energy consumption by 2.5%.
Ms Morrin estimated that if there was no recycling in West Europe, the region would consume an extra 1.5 million tonnes of Soda Ash.
She said: “We could say [recycling] is bad for soda ash, but it’s clearly good for container glass demand, because we see container glass as a packaging material still growing in Europe.”
She also believed soda ash production correlated with the regions responsible for the most CO2 emissions. China, the US, West and Central Europe, and India are responsible for approximately 85% of world soda ash production. In comparison, China, the US, India, and the EU account for 50% of global CO2emissions.
Ms Morrin said solar energy was one of the fastest growing sources of renewable energy, if not the fastest. Photovoltaic (PV) installations grew last year and even during the pandemic, which resulted in a growth of 22%. This year, demand growth has surged to 44% year over year.
Despite many companies signing up to the Paris Agreement, pledges to date
� Fig 6.The location of Sisecam’s projects in Wyoming, US.
still fall short of what’s needed to meet net zero. However, high energy prices have given an incentive to transition to renewable energies, as well as a new focus on energy security after the RussiaUkraine war.
Fossil fuels still account for 80% of the world’s energy, but solar energy is widely available.
Ms Morrin said estimates suggest that the amount of energy that shines on the Earth for an hour is more than enough to supply demand for all energy requirements for the world for a year.
However, to reach net zero, PV installations would have to grow at a rate of 25% per year to 2030. This would equate to soda ash requirement of 17 million tonnes.
There remains a lot of uncertainty
+60,000
+200,000
+700,000
in Europe. Coal and coke availability remains a problem, and anthracite is no longer available.
Russia was responsible for approximately 90% of anthracite. Since August 2022, the EU banned imports from Russia. This meant many plants switched to coke, leading coke prices to become
any of them.
This year, the market had lower capacity in the world than last year, which resulted in net loss of approximately 600,000 tonnes of soda ash. This, combined with positive demand growth, caused world
its sustainability targets.
Annually, Sisecam produces 5 million tons of soda ash and 5.6 million tons of glass. Of the soda ash produced, 55% goes to glass manufacturers.
Sisecam doubled its soda ash capacity after acquiring the rights to the Sisecam Wyoming business in 2021, which was
incredibly high and less available.
Ms Morrin said this has left natural gas-based plants exposed due to the high energy prices.
In West Europe, 46% of plants use natural gas for soda ash fuel production, while coal accounts for approximately 70% of world soda ash fuel sources.
Ms Morrin said that while some companies may be able to switch back to coal, in terms of CO2 emissions, more sustainable fuel sources should be used instead.
She continued that the 8 million MT Inner Mongolia plant could export soda ash to Europe cheaper than the European natural gas producers, and in-line with the US natural gas producers. Meanwhile, Turkey would remain competitive, and coal-based producers would remain competitive.
Although producers in China are less competitive Turkey and America, she said the new Inner Mongolia plant had the potential to be more competitive than
operating rates of the highest on record, which is why the market fell so tight. (Fig 4)
Looking at forecast period, Ms Morrin thought that this year would peak for world operating rates.
In China, the Inner Mongolia project could ramp up quicker than expected. Also unconfirmed capacity in China could come on stream, which would pull operating rates even further down.
Without Chinese capacity, operating rates will come down to almost to what they were prior to this year’s peak.
Overall, she believed it was unlikely that the market would return to normal in the short term.
However, she concluded that sustainability was the one certainty for the soda ash industry.
Ertugrul Kaloglu (Fig 5), CEO of Sisecam Chemicals Resources, spoke on Sisecam’s soda ash expansion project in the US and
previously owned by Ciner Resources.
To further increase its capacity, Sisecam will make a $4+ billion natural soda ash investment (Pacific Soda) in the US together with Ciner Group (60% Sisecam and 40% Ciner off take agreement). (Fig 6)
With this starting investment, Sisecam will manage 10 MMT per year of global soda ash production.
Sisecam is expected to become the world leader in soda ash production with the additional soda ash capacity that will be produced by the Pacific Soda Ash Project.
The investment includes the establishment of the largest soda ash production facility in a single location. Consequently, Sisecam is expected to be the largest natural soda ash producer in the United States. By 2028, it plans to supply 7.8 million tonnes of soda ash to the global market.
Sisecam will manage ~40% of the global planned new capacities (including expansions) until 2026. Excluding China, it will operate ~70% of the global new natural soda ash capacities (including expansions) until 2026.
Of the company’s planned global capacity expansion until 2026, >80% is natural soda.
Production related to CO2 intensity in natural soda is ~70% lower in comparison to synthetic soda ash, while energy usage is ~60% and water usage is ~85% lower.
John Sadlier (Fig 7), Chief Sustainability & Procurement Officer of Ardagh, discussed the group’s plans to reduce its GHG emissions.
The Furnace of the Future Project was a consortium of 19 EU glass container manufacturers which was initiated by Ardagh with the help of FEVE, the European Container Glass Federation.
The project aimed to develop a fullsized container glass furnace that would run on 80% green electricity and 20% natural gas.
The furnace would reduce CO2 emissions by up to 50%, and allow for amber and green glass production –which would not be possible with a fullelectric furnace.
However, the project was unsuccessful in its grant application. Despite this setback, Ardagh plan to continue the project by finding a way to make it themselves or as a smaller consortium.
Mr Sadlier said another alternative was to use green hydrogen. He said the group was highly considering deploying a 5MW hydrogen electrolyser at one of its sites as a pilot project.
The electrolyser would use 100% renewable energy, which would generate 1,000 m3 of green hydrogen per hour.
This would reduce natural gas consumption by 20% in the furnace (This is the Limmared furnace news story we published last week) .
The aim would be to go live with the pilot project in 2023.
Mr Sadlier said Ardagh was initially focused on Europe for the project, but the recent Inflation Reduction Act of 2022 in the US offered a more attractive alternative.
The Inflation Reduction Act will make a down payment on deficit reduction to fight inflation, invest in domestic energy production and manufacturing, and reduce carbon emissions by 40% by 2030.
The act makes hydrogen a more competitive fuel in North America, and in states with low electricity cost, green electricity is more readily available.
Mr Sadlier said that Ardagh believes in hydrogen as a future fuel, and is looking to be part of future hydrogen pipeline projects.
He continued that the group’s next steps would be to replace the 20% natural gas used in the Furnace of the Future with hydrogen.
This would create a furnace with zero CO2 emissions from fossil fuels in the combustion process, and contribute to the Ardagh’s overall goal of reducing its Scope 1 and 2 GHG emissions by 42% by 2030.
WE (West East) Soda is the UK incorporated holding company for the global soda ash operations of Ciner. The company’s CEO, Alasdair Warren (Fig 8), revealed WE Soda’s latest greenfield project, Project West, at the conference.
Project West will be located near the Green River in Wyoming, US. It is in addition to the company’s participation in the Pacific Soda project with Sisecam, in which WE Soda has a 40% interest.
The project is expected to produce ~3 million mtpa of initial production capacity, and will then be scaled over time to meet growing global demand.
It is export focused, given the profile of demand around the world, and will export through new facilities that WE Soda are developing in California, US. The project will target the markets of Asia and Latin America in particular.
WE Soda plans to target production by 2030, which means Project West will target the ~3-4 million tonne gap in supply between 2028 and 2030.
The project will use solution extraction, which will target the largest deep trona beds. This is the same technology currently being used for the company’s plants in Turkey, and which will be deployed for the Pacific project.
For the first time, WE Soda believes it has the technical capability to develop a project which utilises up to 100% renewable energy.
Mr Warren said Wyoming had characteristics that would allow WE Soda to create solar and wind power generation, as well as solar steam.
Together with existing projects, We Soda will invest ~$4 billion and add over 6 million mtpa capacity by 2030.
Philippe Kehren (Fig 9), President of Solvay’s Soda Ash & Derivatives, outlined Solvay’s projects to increase soda ash capacity and achieve carbon neutrality.
Mr Kehren highlighted the need to transition out of coal and gas to achieve decarbonisation, suggesting that trona based production units could increase capacity sustainably.
Trona-based soda ash is less CO2 intensive, due to it being a mix of solution and mechanical mining.
However, there are only three reserves in Wyoming, Inner Mongolia and Turkey - all of which would have to be exported. Based on this, Solvay predicted that tronabased soda ash would grow up to 38% by 2030.
Overall, Mr Kehren believed exploiting trona would not be enough to meet global demand.
Therefore, Solvay will pilot a new soda ash manufacturing process at its plant in Dombasle, France which will cut its CO2 emissions by 50%.
The technology, based on electrochemistry, has been in development for the last 30 years. It will preserve natural resources by using 20% less water and salt, 30% less limestone consumption and eliminate limestone residues.
Once validated, the process will be implemented across all Solvay sites, including Spain, Bulgaria, Italy, France and Germany.
Further environmental initiatives include Solvay’s plan to use biomass boilers at its Rheinberg plant in Germany. The boilers will use discarded woodchips to produce steam and electricity, which will replace coal.
This will make Rheinberg the first soda ash plant in the world to be powered primarily by renewable energy. Solvay plans to use 100% of renewable energy at the site by 2025. This will reduce the plant’s emissions from 1 to 0.3 tonnes of CO2 per tonne of soda ash.
Also in Dombasle, Solvay will use a locally sourced, non-recyclable waste to fire up RDF (Refused Derived Fuel) boilers. This means it can cut its imported fossil fuels and create a new outlet for local waste (400 tonnes) currently going into landfill. � www.chemicalmarketanalytics.com
The 83rd Conference on Glass Problems included a two-day conference, exhibition, short courses, a one-day seminar focused on Energy Decarbonisation in Glass Manufacturing as well as plenty of networking opportunities. Greg Morris was there.
The event too place over four days and included a two-day conference.
Atotal of 423 industry professionals foccused on the glass manufacturing process at the recent Glass Problems conference (GPC).
A parallel exhibition included 60 glass and equipment suppliers exhibiting their latest innovations and technologies.
The two-day conference included 23 papers from glass manufacturers, customers and suppliers.
As well as two plenaries, themes focused on Quality, Melting and Controls, Refractory and Raw Materials and Combustion and Sustainability.
Opening the event, Bob Lipetz, Executive Director of the organiser, Glass Manufacturing Industry Council (GMIC) gave a love letter to American glass manufacturing.
Presented as a visual and oral poem homage to the glass manufacturing industry, it discussed the industry in the USA.
He said from the country’s earliest days
glass has enabled the growth and vitality of American society.
The can-do spirit of America, the great example of enterprise that is the American experiment is reflected in the mirror of American glass manufacturing.
It was the final year that Mr Lipetz will be executive director at GMIC and he was presented with a commemorative glass piece from GMIC president, Scott Cooper.
A further plenary talk was provided by Dutch-based organisation GlassTrend, which was the first time the group had spoken at GPC.
Speakers Bruno Purnode and Oscar Verheijen provided a paper titled ‘GlassTrend to Benefit Glass Manufacturing’.
GlassTrend was created in 2001 and now, more than 60 global companies co-operate in the field of smart and sustainable glass manufacturing.
Its recent emphasis has been on hydrogen combustion, process
electrification, and the use of low-carbon raw materials.
The presentation described GlassTrend as the globally acknowledged glass consortium with a focus on its members, its events, collaboration with other organisations and examples of joint industry projects.
Other speakers on the first day included NSG’s Andy Keeley discussing the hydrogen trials carried out in NSG’s Greengate, UK float glass manufacturing site in August last year (See Glass international September 2022, page 25) as well Leerdam’s Crisal Glass’ Marco van Valburg who discussed the company’s five-year operating experience with Optimelt heat recovery technology (see Glass International June 2022, page 10).
Further speakers were Celsian’s Andries Habraken discussing Modern controller and Sensor technology for energy efficiency, Vitro Architectural Glass, RHI Magnesita, Schneider Electric, and Stuart
Hakes of FIC UK discussing All Electric FH Design with Zero Emissions.
The opening of the second day saw Diageo’s Director of Packaging and Technology, Ronald J. Holmes discuss the challenges the company faces in its bid to use more recycled glass in glass manufacturing.
By 2030 the company wants 100% of its packaging to be widely recyclable or reusable/compostable. It wants to ensure glass is kept out of landfill and prevent it from being used as landfill daily cover. It wants to help improve recycling rates across the US. Recycling rates vary state to state but on average are about 30% compared to 50-60% in Europe.
Diageo is a board member of the Glass Recycling Foundation, co-founder of the Glass Recycling Coalition and has sponsored initiatives such as the Smirnoff Glass recycling in the Chicagoland area.
Day two speakers also included papers from TECO, the Czech Republic’s Glass Service, Sefpro, Robovent, Calcean, Linde, Air Liquide and Air Products.
TECO’s Edward Ferriera provided an update to a 2009 paper given at the conference titled ‘How Big is my Carbon Footprint’. This year’s paper discussed hydrogen as an emerging energy source and which has been added to TECO’s roadmap to meeting the future carbon emission requirements of glass melting.
To meet true carbon neutrality the industry must shift focus to create solutions to produce all types of glass products through all electric means, while meeting industry quality requirements. Mr Ferriera said electric melting has superior efficiency and energy can be obtained from geo thermal sources such as wind and solar.
Electric furnaces have a reduced furnace lifetime but that is not a negative – if a furnace has to be replaced every few years it allows glass manufacturers
the opportunity to upgrade with new innovations. This is particualry relevant today in such a fast paced environment and technology changes.
One of his final slides highlighted the cost of doing nothing.
In a worst case scenario, the slide provided the estimated total cost of damage to each US county.
Many of the southern states of the US would bear the brunt of climate change and force people to migrate to the north, leading to massive infrastructure investment.
Electric melting also came under the spotlight during Erik Muijsenberg’s talk, titled Glass Melting of the Future.
Mr Muijsenberg, Vice President at Glass Service in the Czech Republic, said the EU requires a 55% CO2 emission reduction by 2030 compared to 1990.
As well as legislative pressure, consumers are also demanding a reduction in CO2 now. There is also an added incentive to reduce CO2 – the price of CO2 has risen to €88 from its relatively recent low of €20.
Biofuel has potential to help the glass industry, with about 100 to 350kg required to melt a tonne of glass.
In 2016 Verallia successfully held a six-month biofuel trial to melt glass but at the time it was felt biofuels were not economically viable.
But many biofuels require water to grow crops and water could be at a shortage in future he warned. On top of this other industries, such as automotive, will also want to use biofuels, so supply to the glass industry might be an issue.
He also analysed the potential of hydrogen in glass melting.
While renewable ‘green’ hydrogen is crucial to meet the Paris Agreement goals by 2050, it will take 10 to 15 years to develop the appropriate technology on a mass scale.
Until then, hydrogen is likely to be
powered by fossil fuels.
While he forecast the majority of hydrogen will likely to go to other high-temperature industries, glass manufacturers should still prepare for its use. A significant advantage is it is easy to store and could be used as an energy source on those days when there is little sun or wind to power renewable energy.
He added it may make sense in future to locate a glass melting furnace close to the source of renewable power, such as a port or the coast where windmills are located.
At present the only way to get hydrogen to a plant is via trucks. Infrastructure to transport hydrogen via pipes would require the repurposing of gas pipelines or the construction of a completely new pipeline system.
He identified some of the benefits of electric melting compared to fossil fuelled melting, such as no emissions and dust, so no filter investment and costs for cleaning.
On top of that they are a lower investment, smaller in size with no or a simple crown and no regenerator or flue gas channels. They are currently sized at a maximum of 200/300 tonnes per day and the next challenge is the lack of experience with a larger furnace with higher pull rates.
He suggested for the next 10-15 years a hybrid furnace with boosting will be the safest choice of furnace with the gradual blending of biofuels.
The use of CFD modelling will be vital to support the design decisions and the upscaling of electric melting furnaces, he noted.
One solution to for glass manufacturers to help meet their sustainability goals may lie in the shallow waters of the Bahamas.
Alyson Myers, of Calcean discussed Oolitic Aragonite, which is a type of
biogenic calcium carbonate that forms naturally on the banks of the Bahamas.
Oolitic aragonoite forms during natural precipitation events called whitings, which appear as clouds in the water and been observed since the 1960s. Whitings occur when blooms of cyanobacteria enter the shallow waters of the Bahamas. During photosynthesis, carbon is
sequestered from the atmosphere and through a mineralisation process on the extracellular polymeric substance (EPS) of the cyanobacteria, bins with the calcium that is in the water, precipitating calcium carbonate.
Aragonite sequesters quantities of carbon from the atmosphere during its formation. The high purity of oolitic
aragonite means it has little or no iron, excellent for high clarity glass manufacturing.
The 84th Conference on Glass Problems will take place October 30 to November 4, 2023 at the Greater Colombus Conven tion Center, Colombus, Ohio, USA.
US GLASS MANUFACTURERS FORM HYDROGEN ALLIANCEUS glass manufacturers have been encouraged to join a glass industry hydrogen hub.
So far producers O-I, Libbey, NSG and Johns Manville alongside the GMIC have said they will take part in a proposed hydrogen for glass manufacturing hub in the Great Lakes region.
But if more companies express an interest in joining the scheme, the stronger the likelihood of securing up to $1 billion government funding for the project to go ahead.
Glass Manufacturing Industry Council (GMIC) President Dr Scott Cooper outlined the proposal at the Energy Decarbonisation in Glass Manufacturing seminar at the 83rd Conference in Glass Problems last week.
The US government wants to form hydrogen hubs in locations around the USA as part of the Infrastructure Investment and Jobs Act (IIJA).
It has allocated $8 billion for the development of these regional hubs to demonstrate the viability of the entire hydrogen value chain in production, processing, delivery, storage and end use.
As well as industry use, the hubs will meet demand from power generation, commercial heating and transportation.
Some of the supply side requirements
are that two hubs have to be in natural gas regions, and also that feedstock comes from renewables, nuclear and natural gas.
Dr Cooper, who is also Global Glass and Materials Science Leader at O-I, said about six to 10 hubs will be created with each one receiving between $400 million to $1 billion in funding.
The government was looking at a 50-50 cost sharing from outside government, and this could be from industry or as an in kind contribution.
So if a company were to put some equipment at its plant it would be regarded as an in-kind contribution.
The government has also made statements about job quality and diversity, and wants the hubs to be in areas of the US where manufacturing used to be located.
Dr Cooper said glassmakers came together on May 19 alongside the University of Toledo and representatives from furnace group Celsian discuss the proposal.
For the first time the GMIC had also visited Congressman in Washington DC during the National Day of Glass in April this year.
“It was eye-opening because we sat with Congressman and they listened. It showed that by coming together and
having one voice for the industry they will pay attention, particularly if they have glass in their district.”
There are 10 glass melting furnaces within 50 miles of Toledo with a potential of 200 t/day of hydrogen for glass making.
“My message is that if you want your organisation to be a part of this, it is not too late, it is not set in stone.
“The idea is to drive alignment behind the glass industry because we are not the largest gorilla in industry. Sustainability initiatives and decarbonisation are bigger than any one of us.
“Glass is not the biggest emitter on the block but it is substantial, we have to come together.
“My call to action would be if you’re a leader in manufacturing is to be telling your top leadership that we should be working together on this. If we move to the big ideas it will require investment but if we do it right we’ll get government help.”
Full proposals are due to be submitted to government by April 23.
Any glass manufacturers interested in joining the alliance should contact Dr Cooper or incoming GMIC Executive Director Kerry Ward.
A glass director said farewell to the industry after 12 years at the helm.
Bob Lipetz, Executive Director of the Glass Manufacturing Industry Council (GMIC) in the USA said goodbye at the 83rd Glass Problems conference held in Columbus, Ohio, USA.
He will be replaced by Kerry Ward, who will join the organisation in January.
Afterwards he said: “When I first accepted the offer to manage the Glass Manufacturing Industry Council some 12 years ago, I could not have imagined
what a remarkable journey it would be.
“It has been gratifying to see GMIC achieve its potential as the co-ordinator of glass manufacturing industry technical information, education, and initiatives.
“I discovered that it is a fascinating industry and I have made many friends along the way. You could say, ‘glass got under my skin’.
“The value of having the US glass manufacturing industry’s leading trade association organise the industry’s biggest conference was evident in the
� 423 – GPC
� 88 – Years since first conference (the conference took a hiatus during WWII)
� Two venues staging the conference (Greater Columbus Convention Center and Columbus Hilton Downtown).
� Five technical programmes (2 Plenary; Quality; Melting & Controls; Refractory & Raw Materials: Combustion & Sustainability)
excellence of the 83rd Conference on Glass Problems.
Speaking at the end of the conference, Mr Lipetz said: “All I try and do is listen to what the industry needs and try and put it together. We have an advisory board from manufacturing companies and the big suppliers who have their finger on the pulse and they tell me.
“You are the industry and what you do is really hard but people don’t realise that, it is not that simple, that is why this is called the Glass Problems conference.”�
� 24 – Speakers including 8 plenary session speakers
� Nine industry experts in the GMIC/Energy Star symposium, Decarbonization in Glass Manufacturing
� Two short course instructors: C. Philip RossBatch and Furnace Operations and Sjoerd Stelwagen - Electrical Glass Melting
� 60 – Exhibitors
� 18 – Hospitality suite hosts
RATH offers you the complete range of highest-quality refractory materials for the entire glass making process, including corrosion-resistant feeder expendables, forehearth systems and the original Emhart Glass System. Also benefit from our filtration of hot gases with our catalytic and non-catalytic filter elements. Contact our experts for your solution!
Denis First* discusses various applications of laser technology and describes the advantages this technology has brought to the glassmaking process.
Omco is a global specialist glass mould manufacturing for the hollow glass industry. The company has been in industry for more than five decades and has faced various challenges over the past.
From a small production facility we have grown to a multinational group, with today 2000 employees with eight production facilities.
Throughout its history, Omco has always investigated the latest available technologies trending on the market and taking the lead on these that were possible to apply into glass mould manufacturing.
The ones that could bring a higher standard of quality and/or product performance but also finding good economical return on other side.
Our R&D team would continuously follow on this, looking at how to apply any such pilot project idea into real industrial production practice.
Going some years back, one of such project was laser technology.
At the time, laser was already well present in other industries but not in mould making where Omco was the first to introduce it.
Today this laser technology is well established, not only up and running but also being one of the crucial part for operations, resulting with a higher standard of end product, glass moulds.
Today OMCO uses three different applications of laser technology; welding, engraving and measuring.
It is known that welding application on glass moulds is crucial for a higher lifetime, hardening the edges would allow bigger resistance to wear and damages delivering longer life on moulds and parts, however is not always good for the glass production (glass distribution) as such.
Any welded area running on glass machine, being exposed to high temperatures will behave differently compared to base material, due to different properties and different thermal conductivity.
Compared to other welding techniques, such as manual spray welding or the PTA (plasma transferred arc) method, laser
offers various advantages.
Laser delivers a constant thickness of weld layer, as well as enabiing a thin layer of welded area over the parting line on the mould allowing better thermal conductivity.
Due to the nature of the process there is no preheating required, with less heat affected zone in the welding area.
Therefore there is less chance to the deform metalographic structure of base cast iron material due to lower heat
tension.
Laser will also offer very good bonding of two materials (cast iron or bronze with nickel weld).
Therefore any mould properly welded by this method would have an advantage from the perspective of glass production performance and material durability and stability.
This welding became more of a controlled process compared to other methods and overall fast and efficient.
However, to get there, along with expensive investment into tailor made laser-welding units it was crucial to develop the right welding parameters and processes. Here Omco succeeded, bringing laser welding into strong industrial use, with six automated welding centres and delivering over 200, 000 laser welded moulds to the market.
Another important product for laser weld application commonly used today is also neck ring as part of the finish equipment where laser method offers various weld designs .
Thin layer of welding on edges (all edges or various designs of partially welded seams) compared to conventional method full profile weldings will offer bigger heat extraction on the finish of bottle and allow higher production speed.
Especially this will give good effect on bigger widemouth neck rings having less chances for ovality of the finish and overall better glass performance (Pics 1a, 1b, 1c).
Along with conventional CNC milling machining, laser engraving offers another level of approach into mould machining.
This method can be used for different kinds of engravings, decoration with
less limits compared to conventional 3D miling. As a machine works with laser light there is no restriction on tool, no limit on radius size compared to conventional methods.
Therefore with such method we can get another level of engravings offering various marketing ideas into the sale of bottles/end product.
If someone cannot put engraving ideas into a 3D model it can work just with a good quality photo; based on photo only, we can create a programme for laser engraving.
This method would also be used into various renderings/knurling on the mould cavity (Pics 2a and 2b).
Omco would use this technique for reverse engineering. If you want to replicate some of the mould shape, or this shape was made with old technology (for example if it was machined manually), laser can convert this into a proper format for the latest technology machining.
Laser is also used for different ways to measure during the machining process.
Quality control is crucial for Omco in order to get the highest standard of glass moulds where this measuring technology helps to assure this. �
*Group sales manager, Omco, Croatia https://www.omcomould.com/
Welding is a common word we usually find on Moulds drawings.
But what is behind this term?
Welding is used on glass moulds to protect critical areas, on their precise dimensions, or limit of the wear and fatigue during glass production, or resistance to the glass abrasion, and even sometimes to anticipate repair and maintenance.
Glass production is a question of heat transfer, the material used for mould parts and glass contact are often chosen for their thermal conductivity in priority and less for their mechanical properties.
Welding is an answer often chosen by mould designers, and mould experts to create a compromise between these problematics of heat transfer and higher mechanical properties.
For decades, and still today it is applied on cast-iron moulds manually, by blow torch using oxygen and acetylene gases. The material fused and applied is Nickel base.
Different types of torch and equipment can be used like projection fuse on
plungers and cylindrical parts.
Some automations were implemented on this process in the 90’s. But the waste of Nickel powder is high, as well as the reliability is not perfectly controlled.
This process has always mainly been manual. 25 years ago the used of PTA torch and automation was introduced.
This alternative welding method has drastically improved bounding control, and made easier applications on Bronze and steel parts, while reducing the waste of powder.
Approximately 10 years ago Laser welding came up and with automation only, reducing again the consumption of powder and reducing drastically time of application thanks to the possibility to apply welding without preheating.
HVOF (High Velocity oxy fuel) is also applied on mould parts and especially P&B and NNPB plungers.
Each coating process can be used in different and specific applications. Mould makers often need to invest in different equipment and processes to answer the variety of glassmakers expectations and requirements.
Manual process was used for all applications on cast-iron based material; it has always been used for welding of mould edges, top and bottom matches, seams matches, and full cavity. It has also been used on steel and Bronze material but with some restrictions and/or specific know-how.
This process requires a high experience from welders before reaching a satisfying quality.
PTA process is welcomed for all applications on Cast-iron, Bronze and Steel mould parts, but dilution of the based material with welded powder is difficult to control perfectly. Bonding with based material is high.
The PTA process can be automatised and coupled with an induction preheating system.
Laser will be used for welding edges, top and bottom matches, as well as seam matches. So far it is not used widely for larger surface, but mainly edges welding. This process is fully automatised.
Laser welding can be applied to room temperature without any preheating, which leads to a really good advantage
and cost saving compared to manual
The manual welding process is not melting base material with the Nickel powder. The oxy-acetylene flux in combustion project the powder on the surface previously heated up to 800°C.
The bonding of the welded area is reached by the heating of the surface to weld with the torch, and the high temperature preheating resulting in enlargement of the grain structures spaces and hollowing the powder to enter in between the grains. When the mould part cools, the space between the grains closes and insures the correct attachment with the welded nickel material.
In order to facilitate the welding, a shot blasting is applied on the surface to be welded before preheating and improve the bonding.
The necessity to preheat at 800°C before welding on cast-iron requires an annealing treatment after welding application, in order to stabilise the cast-iron highly solicitated during this operation and releases the stress accumulated.
The PTA welding process (Plasma transfer Arc) is similar to TIG welding (Tungsten Inert Gaz) in regards to the creation of a ‘melting pool’ in proximity of the torch.
The PTA torch is composed of tubular anode in cupper in the centre of which a cathode in Tungsten stands. An Argon gas streams in between these two electrodes placed under electrical impulsions, and results in an ionization of the gas which can reach up to 15,000°C.
This process creates the pilot arc from the plasma gas at the nose of the torch and the anode is water cooled to avoid its melting.
The pilot arc melts the base material creating a melting pool and the powder is brought to this diluted bath. All the welding is protected by an inert gas through a separate channel.
The Laser process finds its energy through a laser beam, the welding process is similar to what is described with PTA, but the source of energy is different and more concentrated.
The torch is watercooled and lets the laser beam goes through, it brings the powder with shielding gas.
The quality of the welding is also protected via an inert gas to avoid any corrosion during the fusion.
With more than 40 years’ experience in designing, engineering, manufacturing, and repairing glass moulds for all processes and all type of glass, Meca-Glass Group offers its expertise in material and welding applications for industry moulds.
Recent developments have been made on coating applications, based on the expertise of the different processes described before.
MG-Group offers a solution to glassmakers with fully coated cavities moulds and blanks.
The entire glass contact is welded using the PTA process, specifics powders and specific welding gas.
For two years MG-Group has been manufacturing mould sets for perfume, cosmetics, and pharmaceutical glass containers using this new application. The results are showing significant advantages in heat control, glass appearance and lower seams marks.
The other advantages of coated moulds particularly ring in the ears of glassmakers concerned by Corporate social responsibility (CSR) offered swabbing reduction during the glass production. Shiny appearance, and lower seams marks lead in reducing burn off on the production lines and in consequence reducing the carbon fingerprint.
Finally, the reduction of swabbing
Stephane Franconville* outlines why welding remains such an important element of glass manufacturing.
processes.
results in lower the necessity of sorting glasses at the cold end.
All these benefits answer the economic, and environmental issues faced by the whole industry.
The luxury and cosmetics packaging makers are sensitive to these aspects to better meet their customer expectations.
MG-Group graduated in September 2022 Gold level with Ecovadis CSR evaluation.
The borosilicate glass used in pharmaceutical production is also taking advantage of the coating specifications and higher resistance to abrasion, resulting in glass moulds lasting longer during production cycle, and reducing the number of mould changes.
Current production tests are in progress on tableware moulds running very aggressive glasses such as Opal.
Our coating solutions can be adapted with different powder compositions to better answer each glassmaker problematics.
MG-Group is located in Normandy, France in the heart of the Glass Valley, and specialises in the design and manufacturing of glass moulds offering this coating solution, uses modern CNC equipment and has invested €2 million in new machines this year.
MG Group is composed of Somobresle, Meca Moules Services and Mouleries de la Bresle.
With over 90 employees, and around 50 CNC machines, our new group is leading the western Europe mould industry in cosmetics, and high-end perfume bottles, and will continue to invest in 2023 and will pursue its innovation strategy.
�
*Founder, MG-Group, Blangy-Sur-Bresle, France www.mecaglass-group.com
Marcin
The family-owned business Wikiera Uchman was founded in 1970 to support glass plants in the production and repair of machine parts, as well as the manufacture of mould components.
Good quality mould components and well-maintained forming machine accessories are mandatory to ensure stable productions of high-quality containers: not only it is a prerequisite for high production efficiencies, but it is also the base for setting-up best practice standards in a glass plant, and consequently reduce costly downtimes on the forming machines.
In today’s difficult economic environment, where energy prices are exploding, these production downtimes
must be kept to a minimum to save production costs.
For suppliers of parts, promised delivery times are becoming even more crucial to satisfy glass plants, and for Wikiera Uchman, this is no exception: offering glass container manufacturers a wide range of products at the best and promised delivery times is our mission.
Being in direct contact with glass during the forming process, special attention must be given to the quality and to the state of the mould equipment on the forming machine. This is obvious: how can you produce high-quality containers with bad quality moulds?
Thanks to our long experience in this
industry and to the trustful relationship we have with our customers, we at Wikiera Uchman are aware of that important aspect.
For that reason, we use the highest quality materials for each glass production application: various cast irons, steels and bronze as base material, depending on the type of container to be produced, always in accordance with our customer demands.
Neck rings (Pic 1), plungers (Pic 2), cooling tubes (for all forming processes: B&B, P&B and NNP&B) at the blank side, as well as bottom plates, blow heads and take-out graphite tongs at the blow side are our specialties.
With the use of the latest 3D design technology and with our latest computer numerical control (CNC) manufacturing machines, we supply our customers with best quality mould variables, and always keep to our promised delivery times.
Having good machine technology is not the only a requirement for high production efficiencies. Glass plants need to make sure that these machines are well maintained, which means being equipped with accessories and variables in best conditions.
It makes no sense to produce containers with high-quality mould equipment on old, unmaintained machine accessories and parts. Ultimately, old and/or poorquality accessories on the machine will ‘destroy’ the mould equipment, in particular the mould’s edges, leading in visible seams on the final produced container.
Wikiera Uchman is specialised with the repair of machine parts thanks to a very long relationship with one of the major worldwide glass producers located near our facilities in Poland.
For the last few years, our latest CNC technology allows us to manufacture brand new machine accessories, in particular components that ‘suffer’ the most on the forming machines: mould holder plates and mould holder inserts (Pic 3).
With a special treatment on the hanging mould contact surfaces, our plates and inserts are proven to last longer. In addition, we are producing connecting links and pins, and lately some specific mould cooling plenum chambers (Pic 4).
The pandemic was challenging for the whole glass industry. Glass manufacturers were under pressure to preserve a minimum number of personnel to operate the machines. The supply chain was also strained since all companies suffered the same issues with personnel and transport delivery.
Thanks to strict hygiene measures, at Wikiera Uchman we can proudly say that we were able to keep our activities at the top level, and none of our customers reported any delays. We were even able to gain some new customers thanks to our reliable delivery times.
Since February this year, the war in Ukraine is bringing new challenges for the container glass industry. Since our
company is located close to the Ukrainian border, a few months ago Wikiera Uchman supported the flow of refugees, by bringing food and goods at the border. Many of our employees also hosted refugees in their homes.
Today, the whole world is affected by this event, especially Europe. Energy prices (gas, electricity) are exploding. Consequently, the container glass industry is under pressure again, as
production costs are rising.
For Wikiera Uchman, there is no exception, and therefore, we implemented certain energy-saving measures to reduce the impact of the energy price increase.
The objective for us is to ensure the best competitive prices for mould and machine parts, always at shortest delivery times. �
*Co-owner, Wikiera Uchman, Kosina, Poland https://wikiera.pl/en/
when it comes to delivering quality.
When you need a batch plant or cullet treatment, come to the specialist. We are independent and dedicated entirely to producing the finest batch plants, cullet plants and associated products. Zippe has been on the cutting edge of technology for over 100 years and place this innovative spirit and expertise at your disposal.
Be it batch plants, cullet plants, automation, modernization, engineering, factory cullet recycling, glass recycling, batch charging, glass level measuring, preheating, as well as maintenance & service, with Zippe you’re right from the start!
right from the start
T: +49 9342 8040
zippe@zippe.de www.zippe.de
Merkad manufactures glass moulds, equipment and machine parts for the tableware glass industry all over the world.
The company has more than 36 years experience in manufacturing of tableware glass moulds. Today Merkad is a Tableware mould manufacturing factory specialist that offers Stainless Steel material with the ESR (Electro slug remelting) process, machining, design engineering for complete moulds, equipment and machine parts.
The company is located in Istanbul, Turkey with more than 80 employees and the latest machines. It continually researches and invests in new mould manufacturing technologies, machines, devices and design software to offer products with innovations with competitive prices and quick delivery.
Besides using high quality materials and day-by-day improving machining techniques, Merkad carries out continuous non-stop R&D studies, aiming at Free of Error’ manufacturing.
Behind Merkad’s growth and development, there is a focus on quality in every step of the production process.
Therefore, Merkad’s customers have the advantage of working with mould equipment that has a longer lifespan than its competitors and without the need of any extra processing during production.
Merkad has invested in technological Machining Centers in order to provide more capacity to its tableware clients who require high quality moulds for their glass production.
Merkad’s Production Department is equipped with 5 axis, 4 axis, 3 axis CNC High Speed Machining Centers, CNC Turn Milling Machines, CNC Turning Machines, 5 axis CNC Coordinate Measuring Machine, CNC Plasma Transfer Arc Welding Machine and other auxiliary machines.
Starting from the design phase, Merkad’s team collaborates with clients to find the best solutions, overcome possible difficulties in product design, finding and suggesting innovations and improvements, all by means of software simulations.
Merkad’s Engineering and Design department provides professional
service for glass production, such as pressing, blowing, stretching, spinning and stemware processes, right up to the design of articles with related technical drawings, and 3D modelling.
This means important details can be calculated and reflected to technical drawings, such as:
� Determining cooling profiles of plungers ;
� Identifying dimensions and the area of exhaust holes in blow mould cavities;
� Parison design and calculating the allowance of parison hanging in production of stretching stemware; and
� Obtaining homogeneity, glass thickness and ovality on spinning moulds.
The process for engraved moulds begins with a rough draft of the design required, which is then converted accurately into a 2D technical drawing. Dimensions and amounts of engraving on the mould are agreed after a discussion between Merkad and the client.
The next step is to convert the 2D image into a 3D relief using artistic CAD/CAM
software. A computer simulates different scenarios to test the overall design and feasibility of the mould once it is in use for production.
Being able to make all the balancing and homogenising glass volume distribution adjustments in this environment also guarantees a greater level of accuracy.
Regardless of how hard and how complicated glass designs are, all possible problems that could effect engravings are eliminated during design process.
After the design details have been finalised, Merkad submits the data, supplied by DWG, Step or IGS data, to clients for approval. After final confirmation, engravings are applied to the moulds.
These processes give Merkad and its customers the opportunity to address any design elements that might be incorrect or cause problems such as the glass product splitting when it leaves the mould. The procedure is primarily computer-based and therefore, any modifications can be made quickly and easily.
Merkad’s planning team also uses ERP software, in order to track all jobs through the production process. The production department keeps computerised schedules to stay ahead of each process and obtains current updates from all phases of production. This process enables the company to give and deliver its products on time to its clients.
The main target of Merkad development is to increase the efficiency and quality of the glass production of our customers with tableware moulds and equipment.
Merkad pays great attention to keep the quality of its products at international level and makes serious efforts to obtain further success of its brand, which has secured a special place in the glass industry.
As a result of these efforts, Merkad was awarded by the ISO 9001:2015 Quality Assurance System Certificate. Merkad also awarded with ISO 14001:2015 Environmental Management System Certificate & ISO 45001:2015 Occupational Health & Safety Management System Certificate.
Merkad’s quality policy is to achieve the following objectives: � To ensure customer satisfaction and exceed customer expectations, � Improve and enhance product and service quality with a risk-based approach, continuously, � Increasing the competencies of its employees by ensuring their participation and satisfaction, � To improve cooperation with customers, � To make affordable, sustainable and high quality production by investing in advanced technology and trained labour resources.
Merkad concentrates greatly on maintaining the quality of its products. Production is controlled by taking submeasurements after each operation, and after passing 100% quality control, each product is supplied with final control reports and material certificates.
Merkad also successfully utilises for relief creating is Reverse Engineering. With this particular method, a sample relief model is scanned and then copied into 3D. After making all necessary and requested changes on the model, Merkad carries out the precise wrapping of the relief on a new base surface.
The company has a 90% export rate which offers services to the world’s leading companies with our Design Center approved by the Turkish Republic Ministry of Industry and Technology. �
*Marketing Manager, Merkad, Istanbul, Turkey www.merkad.com
Sara Leoncini* highlights how the use of industry 4.0 can improve the production process of mould making.
The moulds for the production of tableware and technical articles present many complexities in the standardisation of production cycles.
The range of sizes of the articles -from perfume bottles or glass stem to insulators for power lines- and the various production processes used -press, blown, centrifuges, etc.- make it difficult to identify a common manufacturing process.
It is essential, therefore, to analyse each project with the utmost attention before starting the construction so that you can draw up a correct machining cycle that can allow you to realise the series of moulds with a good productivity.
To analyse the project it is necessary to have an integrated data management that can allow Production Managers to process work cycles that are based on historical data of similar processes and, at the same time, make it possible to check the progress of the work corresponds to what has been planned.
For production, it is essential to have multi-axis machine tools that are versatile and that allow to perform complex processing phases in a small number of placements with the aim of eliminating unproductive preparation times.
In fact, the company project of Officine concerns the innovation of the production process and aims to group various stages of machining on 5-axis machine tools that, reducing the time of equipment, have a longer automatic production time.
In this context, Officine is also equipped with data management systems that keep information under control, both from production and to production according to the principles of Industry 4.0.
The company’s goal is to achieve high productivity in a sector where standardisation and repeatability are
critical, thus developing the automation needed to be competitive in an increasingly selective market.
In the following photos, we can see the results with application examples of this project.
From a piece of raw material (the mould in photo 1), we directly obtain the finished mould (mould in photo 2) thanks to the union of various automated processing steps.
The work cycle includes turning, drilling and milling operations carried out in sequence on a 5-axis Machine Tool with double spindle in a single placement.
Working at high feed and cutting speeds, makes the choice of the tools used very important. These must perform both for the removal of material and for the duration and must allow the operator to
make the best use of the potential of the machine tool.
It has been calculated that the time taken to make the moulds with the new production cycle is 30% less than the time spent with the traditional machining cycle.
In this case, the piece of raw material is cut from the bar without further preparation (piece on top in photo 2).
The result is the finished mould holder ready for assembly (piece on bottom in photo 2).
Also in this case, the sequence of phases of drilling, turning and milling carried out at high speed allows to reduce the production time by about 30% compared to traditional processes.
The use of the new 5-axis Machine Tools in Industry 4.0 allows the review and often improves the production process of each series of moulds, regardless of the type of glass production to which they are addressed. �
*General Manager, Officine, Siena, Italy
https://www.officinesl.com/en
The British Glass Focus awards celebrated the achievements of the UK glass manufacturing sector over the past 12 months. Jess Mills attended.
The winners of the Glass Focus Awards 2022 were unveiled at a black-tie dinner hosted at the Sefton Park Palm House in Liverpool, UK.
Companies from across the glass supply chain gathered to celebrate the International Year of Glass and the milestones of the previous 12 months at the event which saw Pilkington NSG crowned Company of the Year for the first time.
The flat glass manufacturers also won the Health and Safety action award while Saint-Gobain Glass UK and Ardagh Glass Packaging were both double winners on the night. The former took home the Design of the Year – Flat Glass, and
Strengthening Business through People awards while the latter was awarded the Sustainable Practice and Marketing Impact categories.
Other winners included Beatson Clark’s Dana Godfrey winning the Rising Star award, Encirc securing the Innovative Solution prize and Stoelzle Flacconage’s One Gin coming out on top in the Design of the year – container award.
British Glass CEO Dave Dalton said:
“It has been another testing year for the glass sector and while many of the problems we have faced still persist, it is a great pleasure to gather everybody together at the Glass Focus Awards again to celebrate all the achievements our great
industry has accomplished.
“As always, the level of entries for each of the categories has been spectacular and wide ranging.
“From showcasing our talent for innovation and our status as pioneers on the journey towards net zero to the beautiful designs we see every day on our bottles and buildings and the unrivalled talent that makes up our workforce, it is a reminder of why the glass industry stands in a class of its own.
“We are all extremely proud of the work we have done over the last year and we look forward to continuing to build on our successes in 2023 and beyond.”
One Gin is a range of London Dry gins that make a difference. One Gin is the first gin brand to give back to a global humanitarian cause, with a share of profits going towards funding clean water projects in the world’s poorest communities.
The One Foundation has raised £25 million to date and has changed the lives of over 4 million people.
From the brand’s inception, the label was focused on the company’s signature butterfly, a symbol that reflects the brand’s ethical mission.
It’s been said that the tiny flutter of a butterfly’s wing can trigger a cyclone on the other side of the world. This belief – that small acts can lead to great change – is at the heart of what One Gin do.
When One Gin launched its first spirit, it was in a simple off-the-shelf bottle. The label design did all the legwork to inform the consumer of the quality of the liquid and drive the brand proposition.
One Gin’s ambition was to have its own bespoke glassware to communicate the brand
ethos, elevate its premium credentials and improve retail and back-bar stand out.
Research into the category and vintage glassware informed multiple concepts spanning shape, size, proportion, and colour. But with such a crowded marketplace, One Gin embarked on a mission to cut through the norm of what is expected from a gin bottle.
We envisioned a tall, elegant profile with art deco detailing, complementing the original label and being reminiscent of vintage glass bottles.
The strong shoulders are offset by delicate butterfly wings with tactile facets holding a variety of glass impressions enveloping the tapering, non-uniform hexagonal structure.
The new label is a simplified incarnation of the original, taking the body shape of a butterfly, with a sculpted mid-rift housing the wing connections.
Once the bottle is empty, its labels can be removed to reveal the word ‘water’ de-bossed into its front face. This is to promote a second life for the bottle as a water carafe.
The bottle was fully designed and manufactured at Stoelzle Flaconnage in Knottingley, UK.
One Gin said the manufacturer brought its vision to life with their technical expertise and credentials. The company’s aim was to use as little glass as possible in the context of a unique design.
The resulting bottle is below average weight for a premium 70cl spirits bottle. The closure is made from wood and natural cork and the label is made using recycled apple pulp, chosen for it’s a renewable and recycled credentials.
The Spark is part of the Helix in Newcastle, UK. It features a fully glazed façade with curtain walling and red aluminium cladding. Both building materials are 100% recyclable, which helps the business to attain the highest sustainability credentials.
The glazing includes Saint Gobain Glass’s (SGG) COOL-LITE SKN 144 II, a product designed to offer exceptional solar and thermal performance.
The Spark is a landmark office space, supporting both established and new businesses. It includes both exclusive
occupancy accommodation and large, open collaboration space.
Arranged over 12 floors, the 106,000 sq ft office building has been designed with the evolving needs of businesses in mind.
The office space is constructed to British Council for Office standards with a ratio of occupancy of one person per 8sqm NIA and to BREEAM Excellent with an EPC rating of A. SGG COOL-LITE SKN 144 II offers:
� A very low g-value of 0.23
� Optimum U-value of 1.1W/m2K
� Neutral appearance both in
transmission and exterior reflection
� Good levels of natural light transmission
COOL-LITE SKN 144 II can be used to improve the energy efficiency of buildings by considerably reducing overheating and the need for costly air conditioning in summer.
It is particularly suited to large areas of glazing where superior, solar control performance is required whilst at the same time noticeably reducing excessive heat loss in cold weather conditions.
Glazing specification: Heat strengthened laminate featuring solar control glass, designed to deliver safety and reduce the risks of solar gain.
STADIP PROTECT + COOL-LITE SKN 144 II (heat strengthened)/ 16 mm 90% Ar / 8 mm PLANICLEAR (toughened)
After finding the cooling process was falling below expected standards of efficiency, the team at Encirc’s Derrylin plant implemented several new processes.
The first was a new way of working around the container cooling process, which put in place a new dedicated system to monitor and manage energy expenditure.
The team then implemented a trial and improvement process, experimenting with different cooling hole diameters and fan configurations to achieve an energy saving of more than 60%, and a cost saving of up to £23,000 over the lifetime of each mould set.
Based on initial assessments in 2018, the traditional systems used to cool moulds at the site were found to use as much as 32KW of energy per tonne of glass made; the plant
Most people would assume the biggest danger in a glass factory would be the product itself. Glass has raw, sharp edges can cause a significant hazard, but the worst accident that an employee is most likely to suffer from is a severe cut requiring stitches to close the wound.
It is actually the vehicles used to transport the glass around the site, due to the size and weight of the product manufactured. This makes vehicle and pedestrian (V&P) safety NSG’s top priority.
The level of V&P safety can vary from site to site, country to country; many incidents involving internal site vehicles have been reported throughout NSG.
Therefore, the group developed a comprehensive GAP analysis tool to cover all aspects of V&P interaction.
These vary from the governing of vehicle speeds to segregation, and of course driver and pedestrian behaviours such as ‘signal for recognition’.
The aim is to implement a high level of safety throughout every NSG Pilkington site. Although there is a myriad of different
average was 24KW of energy per tonne.
vehicles, site configurations and processes throughout NSG’s business, a common approach was devised. The approach encompasses the following 10 elements:
1) Traffic management to reduce the number of vehicles on site.
2) Physical segregation and walkways to keep vehicle and pedestrian interaction to a minimum, and mark a safe way to get from A to B.
3) Limiting vehicle speed of internal vehicles to 5MPH max.
4) Vehicle design – a trial has now started at a St Helens site (UK) called ‘ZoneSafe’ which slows then stops a vehicle the closer it gets to an individual.
5) Vehicle maintenance
6) Hi-Viz clothing
7) Training for both drivers and pedestrians.
8) Behavioural safety programme
9) Safety Culture - managers will lead the V&P improvements.
10) Control of Change – this is to ensure that when a new process or area is changed that V&P safety takes a priority.
The GAP analysis actions are documented and submitted to NSG Group with % completion scores included.
The benefits are beginning to come through. Sites that show they have fully completed an element have been contacted to share their procedures, so that sites with a low score can implement these procedures. Toolbox Talks have now been shared to gain some commonality between sites.
New procedures have been devised like the VRM (Visual Reference Mark) on the mast of a FLT truck. If a load is higher than the mark, the driver must drive in reverse. This removes any ambiguity and is now a requirement on all FLT’s within the business.
Teams have also been formed from a cross section of the workforce to ensure the V&P safety procedures are met. This group includes drivers and people who visit the most areas on site on foot. The shopfloor employees are key as they have the best understanding and working knowledge of how vehicles and pedestrians interact on a daily basis.
It is still early days for this initiative, but the on-site impact has been “fantastic” so far.
After investigating the reasons for this high amount of expenditure, the team found the moulds were taking too long to cool. There was also no dedicated system in place to monitor and manage energy expenditure in the cooling process.
This exposed a need for improvement, in both the machinery and technology used at the plant, as well as the procedures in place around cooling.
The first step taken by the team was to standardise the cooling time for both the ‘blow and blow’ and the ‘press and blow’ processes, creating a consistent benchmark from which other parameters could be changed and the effect on efficiency could be measured.
To limit use of energy-intensive fans during cooling, the team used a trial and improvement process to find the most efficient cooling hole diameter. This was achieved by introducing different diameters each time they changed the sets on the machinery.
Comparisons were then made on a weekly basis to determine the optimum configuration. The team then took this information back to Encirc’s design working group who produced the sets with the next required cooling hole diameter.
This allowed the project to fit smoothly into established maintenance schedules, helping the team find the best solution without disrupting production.
The improvement process was executed manually at first, but the monitoring, feedback and response routine has now been incorporated with the rest of the plant’s systems and occurs almost automatically.
Where necessary, fans were then replaced during rebuilds to ensure that their contribution to cooling was powerful but efficient. Adjustable, automated fan systems that could be adjusted in
real time according to the needs of a specific machine were added to the lines.
These improvements have been shared with the Elton site, which uses the same machinery for its cooling process.
Thanks to the team’s efforts, the Derrylin site has achieved drastic improvements in efficiency, with energy expenditure dropping from an average of 24 to 10 KW per tonne of glass produced.
The new mould cooling process has laid the groundwork to support Encirc’s wider energy reduction goals and will help it meet ambitious Science-Based Targets, with annual carbon savings of 490.851 T/CO2e.
With businesses energy costs soaring and Encirc producing billions of containers every year, the savings from this project will only increase.
Reducing water consumption is a key part of Ardagh Group’s Sustainability Strategy. Its target is a 37% reduction for water usage by 2030.
To achieve this, Ardagh has invested in water reduction projects across its 20 sites.
These projects will save almost 900,000m3 of water, bringing Ardagh close to its 2030 target.
During 2021-2022, two such water reduction projects achieved substantial water savings: the Limmared Closed Loop Water Cooling Process and the Ujscie Water Reduction Project.
For years, the water supply to Ardagh in Limmared, Sweden, has come from the nearby river Månstadsån. Through a process of heat exchange, the river water cools high pressure compressors, vacuum pumps, furnaces and scrapers, which uses a lot of water.
By installing a two-step, closed loop air and water cooling system, air now replaces river water to cool the production process.
A small amount of river water is still used to cool the compressors in the cooling towers and in the flue gas treatment system.
The installation of air-driven, dry coolers reduces reliance on river water, which is used as back-up and during the warmest days.
This has delivered a 66% reduction in surface water in the first half of 2022 compared to 2021.
The Ardagh team in Ujscie has taken a major step to reduce water in 2021-22 by installing separate closed loop systems for clean and dirty water in place of using local groundwater (fresh water) to cool the IS machines.
The two independent loop systems support all three IS machines on-site.
In the clean water loop, water is circulated to cool the glass scoop to below 20°C, so glass doesn’t stick to it. In the dirty water loop, water is circulated to cool the ejecting pipes, where water is in direct contact with cullet or the glass drop.
Here, Ardagh uses two tanks: the first cleans the water of glass and oil particles, and the second acts as a buffer for the cleaned water, which is then used again in a loop, to cool the ejecting pipes.
After installation, the water loop delivered a 25% reduction in the first half of 2022 compared to the same period in 2021.
Together, these water reduction initiatives have reduced the group’s water footprint by
59% in the first half of 2022, compared to the same period in 2021.
These projects will improve production efficiency, and therefore competitiveness, and help to achieve Ardagh’s water intensity reduction target by 2030.
In Limmared, a new scraper water treatment plant was installed in June 2022 to clean the water from the scrapers for recirculation.
The next step is to check how well this is working and to monitor the reduction in water consumption since June; the goal for Limmared is to circulate the water infinitely.
Dana Godfrey, 19, joined Beatson Clark’s apprenticeship programme straight from school and has become an integral part of the team.
Ms Godfrey has already driven innovation at a historic glassworks and encouraged other young people to consider apprenticeships in the glass industry.
Beatson Clark partners with the AMRC in Sheffield to provide a thorough and industry leading apprenticeship program for its students. Ms Godfrey is shortly to finish the ‘Advanced Manufacturing Engineering Toolmaker Pathway’ qualification.
The first year of the apprenticeship is spent at the AMRC, with day release back to Beatson Clark’s workshop. Ms Godfrey excelled at AMRC, passing all the curriculum set her. After that first year, Ms Godfrey then embarked full time at Beatson Clark with day release back to AMRC.
In the Beatson Clark workshop, Ms Godfrey was set tasks to learn the various areas and skills required to be an all-round toolmaker.
Ms Godfrey quickly showed the manufacturer that she had a high propensity to learn, and perhaps most importantly, the ability to understand.
On the machining side, Ms Godfrey got involved with helping in the development of new techniques for inspecting the critical blank and baffle match on Beatson Clark’s mould equipment.
She was instrumental in the manufacture of the initial tooling and jigging as well as the maths involved, plus the subsequent trialling and testing carried out.
These jigs, tooling and techniques have been a revelation to the shop. Beatson Clark has passed the ideas on to its contractors, who have utilised the techniques to improve their own manufacturing consistencies and quality.
Ms Godfrey has also excelled in other areas. Beatson Clark introduced an advanced multisensor CMM into its shop for the first time. Ms Godfrey picked it up comfortably, as well as the rest of the inspection area, and is now cover for holidays in that section.
CNC turning, hand repairing the tools, welding, and milling are all areas Ms Godfrey can hold her own in and be trusted to carry out the work to a high standard. All the while, she has integrated seamlessly into the Beatson Clark team with her infectious easy-going nature and personality.
Ms Godfrey has also appeared in the British Glass video encouraging other young people to consider apprenticeships in the Glass Industry where her enthusiasm, integrity and confidence shone.
2021 was the year of the cold repair at SaintGobain Glass UK.
The event was more complex than the original site build, given the commercial business that needed to be maintained during this activity.
Saint-Gobain was able to maintain business services to its customers as promised through a safe and well executed plan, on a scale never been seen before in the UK flat glass industry. The four month outage was delivered within 48 hours of its original plan.
A large number of people delivered the plan, including those specially seconded into CR teams and those who incorporated it into their ongoing routines.
In preparation for its annual strategy deployment plan in 2020 and 2021, SaintGobain dedicated a whole strategic driver to the cold repair.
Individuals from Production and Engineering were given dedicated training outside of their daily roles to prepare for the work. This not only served to develop the skills of the individuals, but also the people that assumed their responsibilities.
The manufacturer’s logistics team used its recently implemented Class A, Integrated Business Planning (IBP) Tool to review customer demand, which was then matched to its stocks and planned imports from other Saint-Gobain sites.
The work covered the period of the production outage, as well as the year prior to ensure SaintGobain had built sufficient stocks. This was to keep its customers serviced during a lengthy period of no UK production.
The cold repair was delivered with a fraction of the usual European ‘expert’ assistance given Covid based travel restriction, such as that Saint-Gobain UK personnel had to assume an unexpected increase of responsibilities.
The glassmaking process is very technical by nature, and Ardagh often receives customer requests for a piece of media that explains clearly how glass is made.
This presented an opportunity to create an explainer video for customers, that could also be delivered to a wider audience. The aim was to bring a better understanding of glassmaking through a marketing campaign.
Most glass production videos are quite technical, long and uninspiring. Ardagh set out to change this with a short, fast-paced, modern video, which was shared widely in an integrated marketing campaign across Ardagh’s social media channels, achieving outstanding results.
The 90 second video1 was created to be easily shared on Ardagh’s website and across social media platforms: LinkedIn, Twitter, Facebook and Instagram:
Using upbeat music and a mix of filmed factory footage and animation, the video delivers the campaigns key messages.
It highlights the many benefits of glass packaging: purity, taste, quality, preservation,
reusability, and endless recyclability.
High quality footage takes viewers through the stages of glassmaking at Aradgh: from recycled glass cullet and raw materials to quality inspection.
Absolut Vodka bottles open the video and Johnnie Walker whisky bottles demonstrate the onward journey on the customer filling line. Clear white captions, animated to add impact, tell the glassmaking story.
The result is a fast-paced, modern, shareable video that reflects the Ardagh brand.
The video was shared widely in an integrated campaign across both Aradgh and Aradgh social media channels, as well as internally, and achieved exceptional results.
On all platforms, three videos were shared:
� LinkedIn: the videos increased Aradgh’s average impressions 2.7 times.
� Twitter: with targeted promotion, the videos generated a 206.7% increase on average monthly impressions.
� Instagram: achieved 1,000+ views and a 51.8% increase in accounts were reached
Over 1,200 contractors from 17 nationalities, including at its peak over 400 contractors per day, all had to be managed. This included adhering to a range of Covid based requirements to get people into the country and to safely supervise them once here.
Saint-Gobain also had to teach some of its shift team colleagues (managers and operators) to supervise works outside of their usual job requirements. This was because international colleagues from the wider group were unable to travel due to Covid restrictions.
The project was delivered on budget with customers recognising that Saint-Gobain had delivered its commitment. This included managing the import and large-scale transformation of over 50,000 tonnes of glass from six Saint-Gobain plants. This was included coping with disturbed supply chains from severe flooding in Germany
No major safety incidents occurred during the project, and the restart of production was within 48 hours of Saint-Gobain’s planned four-month outage.
Saint-Gobain described this as “exceptional” considering the complexity of the task, the challenges caused by the pandemic, and supply chain difficulties due to the lack of available shipping transport around the world at that time.
The manufacturer believed these challenges were overcome through the excellence of its people in training, preparation and execution.
after the reel was posted.
� Facebook: video posts generated 7,000+ views with a reach of over 11,000.
The posts also received comments from glass industry partners including Ripple Glass, Heye International, and the Glass Packaging Institute (GPI). Scott DeFife, GPI’s President, described the video as a “great way to tell the story of sustainable glass packaging”.
The video has been added to Ardagh’s website and online glass catalogue, to extend its reach. Ardagh has also created German and Polish versions for local audiences.
Further analysis of the video will go ahead, and campaign learnings will be taken forward into a forthcoming video campaign planned for November 2022.
Links: 1. https://www.youtube.com/ watch?v=LhVmTvR5VWg.
Unit 43, Evans Business Centre, Easter Inch, Bathgate EH48 2EH, Scotland, UK
Tel+44 (0) 1506 657310 Fax +44 (0) 8704 799975 Email Sales@globalcombustion.com Web www.globalcombustion.com
Choose only the best original parts for your machines.
emhartglass.com