INTERNATIONAL July/August 2022—Vol.45 No.7 A GLOBAL REVIEW OF GLASSMAKING WWW.GLASS-INTERNATIONAL.COM 2022July/AugustInternationalGlass See how we are driving the industry forward. Visit us at glasstec 2022 – Stand B38, Hall 15. DESIGNED FOR PERFORMANCE. ENGINEERED FOR ENDURANCE.

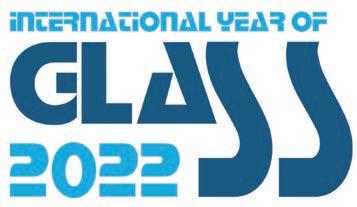
eme.desorg.desks.net
For 150 years, the SORG Group has consistently delivered performance and endurance, resulting in sustainability for glassmakers in over 80 countries. Our three world-leading brands provide a single source for all batch, melting and service requirements. All these years later, we are still a family business, and we are still committed to driving the industry forward.
A century and a half of innovation Five generations of the Sorg family have led our business since 1872, ensuring that we always do the right thing and strengthen relationships through unbeatable service and support. In the continued pursuit of innovation to provide our customers, industry and planet with ever-improving solutions, we believe in creating partnerships that last for decades, built on enduring respect and trust. This has been our approach for the last 150 years and we are committed to this for the next 150.
The Power of 3 Nikolaus SORG, EME and SKS work relentlessly to make the glassmaking process more efficient and sustainable. Combining our unique strengths allows us to provide optimal furnace design, glass melting, glass conditioning and installation, as well as lifecycle support for furnaces, batch houses and cullet return. The ‘power of three’ depicts our belief in a turnkey approach for major projects and our commitment to provide market-leading technology, service and support. Everything we do is designed for performance and engineered for endurance.
See how we are driving the industry forward. Visit us at glasstec 2022 –Stand B38, Hall 15.


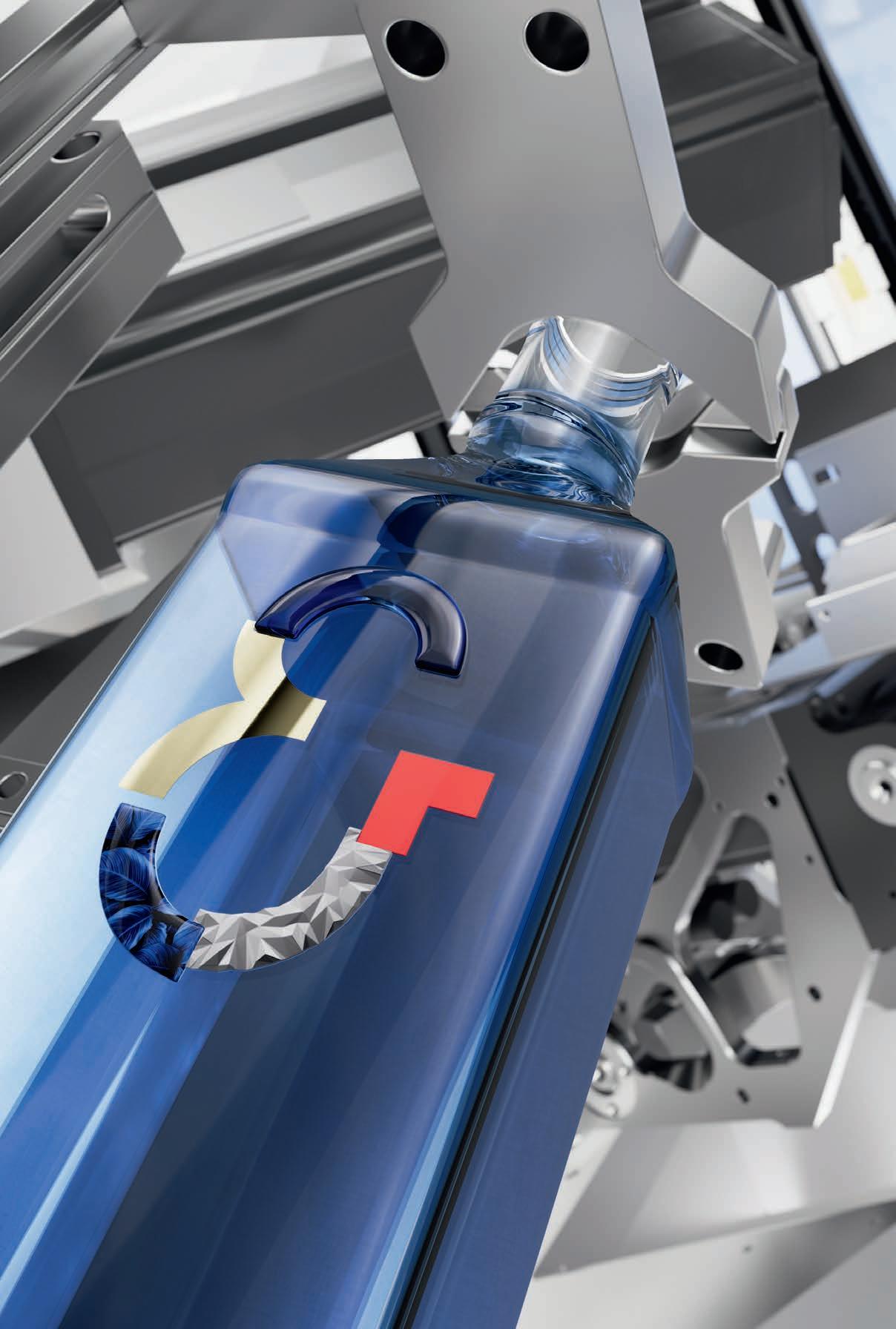
See you at the Glasstec 20. – 23. September | Hall 12 Booth B33 Uniting inks and substrates to create a uniqueness, which is incomparable.Wekammann.deprintyour world


855154 Email:
Editor: Greg Morris Tel: +44 (0)1737 gregmorris@quartzltd.com
855132 Email:
Deputy Editor: Jess Mills Tel: +44 (0)1737 jessmills@quartzltd.com
Chief Executive Steve Diprose Chairman: Paul
Officer:
Subscriptions:JackMichaelHomewood Tel: +44 (0)1737 855028 Fax: +44 (0)1737 855034 Email: Website:Email:Tel:SurreyQuartzPublishedsubscriptions@quartzltd.combyQuartzBusinessMediaLtd,House,20ClarendonRoad,Redhill,RH11QX,UK.+44(0)1737855000.Fax:+44(0)1737855034.glass@quartzltd.comwww.glass-international.comGlassInternational(ISSN0143-7838)(USPSNo:020-753)ispublished10timesperyearbyQuartzBusinessMediaLtd,anddistributedintheUSbyDSW,75AberdeenRoad,Emigsville,PA17318-0437.PeriodicalspostagepaidatEmigsville,PA.POSTMASTER:sendaddresschangestoGlassInternationalc/oPOBox437,Emigsville,PA17318-0437. Official publication of Abividrothe Brazilian Technical Association of Automatic GlassMemberIndustriesof British Glass Manufacturers’ ChinaConfederationConfederationNationalAssociation for Glass Industry Glass International annual subscription rates including Glass International Directory: For one year: UK £205, all other countries £268. For two years: UK £369, all other countries £482. For three years: UK £408, all other countries £563. Airmail prices on request. Single copies £53. Printed in UK by: Pensord, Tram Road, Pontlanfraith, Blackwood, Gwent NP12 2YA, UK. Glass International Directory 2021 edition: UK £206, all other countries £217. Printed in UK by: Pensord © Quartz Business Media Ltd, 2022 ISSN 0143-7838 2 Editor’s Comment + International news 10Digital glassmaking: Stoelzle Where the glass is always greener 15Decarbonisation: BOC Industrial Gases Is hydrogen the answer? 18Decarbonisation: Glass Futures How hydrogen can help meet net zero goals 23 Personality profile: Zippe CTO focuses on sustainability 27Decarbonisation: NSG Decarbonising the flat glass process 31Refractories: SEFPRO A focus on decarbonisation 34Digitalisation: Siemens 39 Personality profile: Tiama The hot end specialist 44 Personality profile: Heye’s MD A partner for a smart plant 47Decarbonisation: Exxergy 51Decarbonisation: HVG 57 Recycling: FEVE What will it take to close the recycling loop? 61Decarbonisation: British Glass 65Recycling: Grupo Vical Closing the glass loop in Central America 70 Financing: IFC 73 Furnaces: Electroglass Increasing the strength of glass 79Glass conditioning: Horn 83Digital glassmaking: PVAG Digital twin in water-saving systems 86Decarbonisation: Schneider Electric A carbon-free future 89 Glass Packaging: CETIE 95 Lubrication: 101Refractories:CondatRath From refractories to hot gas filtration 107Furnaces: Ametek Land Imaging camera provides insights 111Decarbonisation: GEA 115Measurement: Marposs Flexible automatic measurement 118 Palletising: Thimon 127 Quality control: ChemiTek 15 31 39 44
Contents Glass International July/August 2022 www.glass-international.com 1 Plus find us on LinkedIn and www.glass-international.comTwitter. @Glass_Int July/August 2022 Vol.45 No 7 www.glass-international.com
Sales Executive: Manuel Martin Quereda Tel: +44 (0)1737 manuelm@quartzltd.com Director Tony tonycrinion@quartzltd.comCrinion
855117 Email:
855023 Email:
Designer: Annie Baker Sales Director: Ken Clark Tel: +44 (0)1737 kenclark@quartzltd.com
Managing
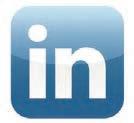
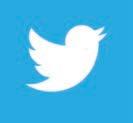









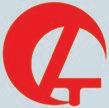

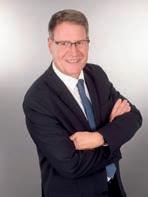
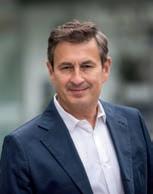
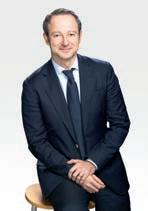
for daily news updates. www.glass-international.com 2
International News GREG MORRIS, EDITOR Be first with the news! For breaking, up-to-date news
Construction is proceeding on schedule at the new Ard agh Glass Packaging factory in Wyszków, Poland. The glass manufacturer chose Forglass, a European supplier of glass melting tech nologies, to design and deliver the batch plant for its green fieldTheproject.newbatch plant will be joined with a new, 400 tpd fur nace that Forglass is also con structing.Forthis project, Forglass has designed and fabricated raw material and cullet storage si los, dosing, mixing and batch transport equipment, as well as the cullet return system, in cluding two of the company’s innovations: Selectable Grain Crusher and SmartScraper.
Forglass on track to deliver batch plant to Ardagh Glass Packaging
FRONT COVER www.sorg.deIMAGE: Glass International 2022
July/August
Heinz-Glas will use fibre cast packaging from renewable raw materials to protect its premi um glass bottles in transit in Upper Franconia, Germany. The fibre cast packaging was developed with the co logne-based companies PA PACKS Sales and Coty. The 3D printed transport bowls are more dimensional ly stable and shock-absorbent than their plastic predecessors and guarantee improved pro tection.Theinnovation is based on 100% renewable fibres such as cellulose from trees and in dustrial hemp. This alone will significantly reduce the CO2 footprint of the packaging. According to the zero-waste principle, the fibre cast trans port packaging can either be recycled as wastepaper in the green cycle system or rot as bio compost within six weeks. The cast fibre transport packaging is also robot com patible, and can be adapted to individual customer require ments in a cost-efficient and flexible manner.
www.glass-international.comVISIT:
Heinz-Glas plastic-freeusespackaging
All set for glasstec Another peculiar northern hemisphere summer. After last year’s apocalyptic rain, this year most of Europe has been drenched in sunshine, enduring what seems like a never ending heatwave and subsequent droughts and water shortages, even in temperate UK. The climate had a knock on impact on industry, with water levels in the River Rhine in Germany dropping to such low levels that ships were forced to reduce their cargo.The river was so shallow in parts that companies were forced to consider switching freights to rail or truck for their important industrial elements, such as chemicals and components, which is costl an inefficient t a time of high inflation a global supply-chain crunch and a looming gas crisis, low Rhine levels are another headache for industry to have to contend Decarbonisationwith. is a major topic at next month’s glasstec trade show in Dusseldorf. It is the main subject of the parallel conference, while a number of exhibitors will be highlighting their latest technology. Some of those exhibitors are highlighted within these pages where they unveil their latest innovations to help fight climate change t ill be the first time in four years that glasstec has taken place and Glass International will of course be exhibiting as well as distributing the magazine. It will be wonderful to see so many of you again both during the show and after hours.We’ll also be able to see first han if ater le els ha e risen in the Rhine by then.
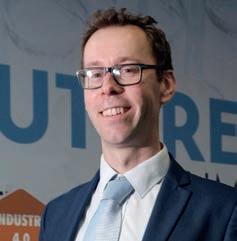
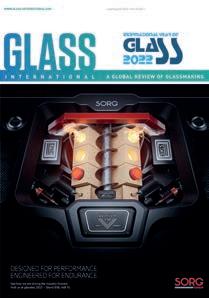
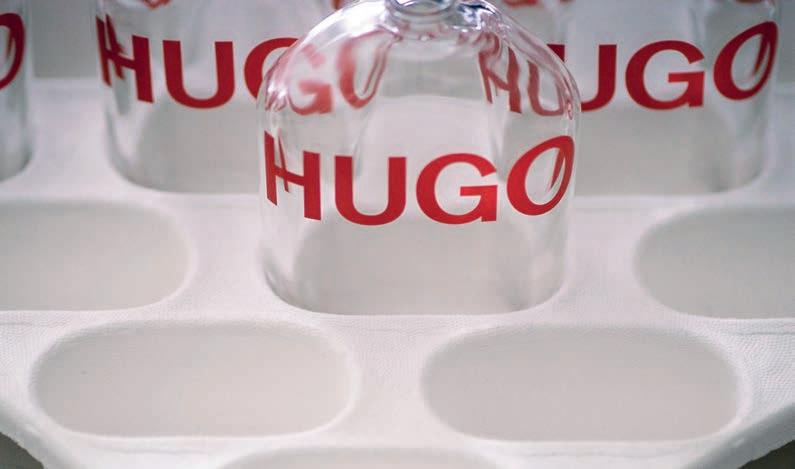
Schott forstand-aloneestablishescompanypharmaindustry
After 41 years with Sorg Keramik Service (SKS) Werner Frankenberger is retiring. Mr Frankenberger joined the company in 1981, and became Technical Manager in 1996.Hisretirement plans are simple yet fun – to cycle more: “I’ll miss my colleagues and customers, but I look forward to investing more time in riding a bike.”
Verallia is investing in the electrification of its Cognac plant in France with all-elec tric melting technologies pro vided by Fives. Global glass bottle packager Verallia signed a partnership with industrial engineering group Fives to reduce carbon emissions through all-electric melting technologies. This new investment is part of Verallia’s strategy to modernise production capa bilities with a view to longterm growth, particularly in France, the historical birth place of Verallia.
Sorg manager FrankenbergerWernerretires
Pilkington Brazil part ners with Warner Bros. Pilkington Brazil, a part of the NSG Group, has secured a partnership with Warner Bros.TheEntertainment.BlindexPower Box line exclusively features designs of the main Warner Bros characters printed on glass. hese range from official prints on the windows to personalise finishes on accessories, offering customers numerous possibilities for customising shower enclosures. O-I to construct glass manu facturing facility in Bowling Green, Kentucky, USA.
The new plant will be the first facility purposely built for O-I’s MAGMA technology. The company plans to invest up to $240 million in multiple expansion waves over time and create approximately 140 new jobs in the region. The production facility will set new standards in sustaina ble glass manufacturing by us ing renewable electricity, gasoxy fuel and other innovative solutions.
Andres Lopez, CEO of O-I Glass, said: “O-I is determined to be the most innovative, sus tainable and chosen supplier of brand-building packaging solutions. The new plant is an important milestone as we continue the pursuit of our expansion plan in the US and globally, building a bright fu ture for the company and its stakeholders.”TheMAGMA melter, and its footprint, are significant ly smaller than a legacy glass furnace. A smaller system size and alternative materials used in its construction allow the MAGMA melter to reduce waste and construction mate rialsTheneeded.newfacility will serve the Premium Spirits category. The proximity to key custom ers in Bourbon country will re duce logistics and further en hance O-I’s customer service, flexibility, and sustainability. Start of the first production line is expected mid-year 2024 followed by up to two more production lines to serve the growing market and contin ued development of MAGMA. News
Patrice Lucas, CEO of Veral lia, said: “Electric furnaces of such capabilities have never been implemented in France, or even in Europe, for food packaging glass and we are very proud to be pioneer in thisThearea.”project includes design and supply of Prium E-Melt cold-top vertical melters, one of the most advanced technol ogies available to significantly reduce CO 2 emissions at the plantThelevel.melters will have the capacity to produce 150 to 200 metric tonnes of glass per day, which makes them the largest all-electric furnaces for food packaging in the world. The melter design has been formulated based on Fives sig nificant electric melting oper ational experience. The development is fully in line with Verallia France’s intention to fulfil its environ mental commitments made at the group level, targeting a 46% reduction in its CO2 emissions by 2030 to lim it global warming to 1.5°C (scopes 1 and 2) and reach car bon neutrality by 2050.
Verallia to electrify Cognac plant in Fives partnership O-I to build $240 million MAGMA facility in Kentucky, USA
Sisecam contracts Zippe for batch plant project Sisecam has contracted Zippe to execute three batch plant projects in Turkey and Hungary.Zippe will execute one container glass plant and two flat glass pro ction facilities Zippe will supply the entire technology for these plants in the fiel of batch an c llet Completion for the projects will be mid-March 2023.
Glass International July/August 2022 NEWS IN BRIEF www.glass-international.com 3
Schott has legally established a stand-alone company for its pharma business to advance its growth strategy. The pharma business will operate under the new name Schott Pharma AG & Co. KGaA as of August. The company is also investing €450 million to meet worldwide demand. The carve-out will be completed by the end of year.
International
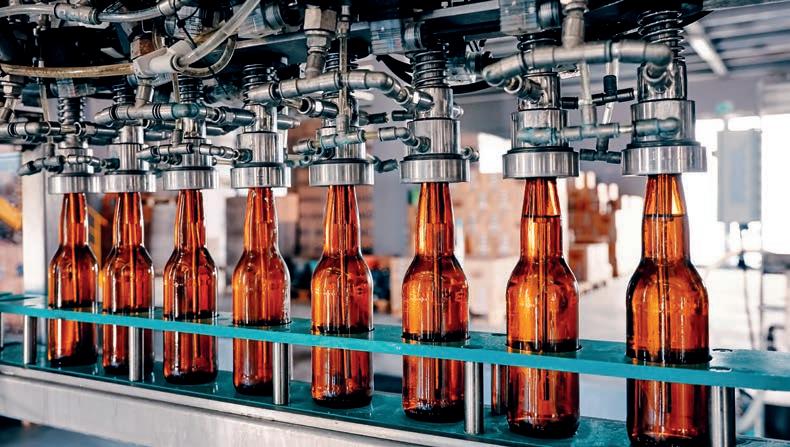
NSG to invest in Malaysian solar glass production line
NSG Group is to invest in production capacity of TCO (transparent conduc tive oxide) coated glass in Malaysia to support the growing solar market. A float line at the Johor Bahru factory of NSG’s Malaysian Sheet Glass will install online coating ca pacity soon and start ship ping TCO glass for solar panel manufacture after the facility is in operation. It is anticipated that the supply from the convert ed line will commence in March 2024. The investment is to support the expansion strategy of NSG partner, First Solar a global manu facturer of thin-film solar panels.Inaddition to its exist ing facilities in Vietnam and Malaysia, First Solar is constructing a new man ufacturing plant in India, which is expected to be commissioned in the sec ond half of 2023.
Need to boost energy input to your air-fuelred regenerative glass melting furnace? Air Products’ Clean re® HRx™ Synchronized Boosting System is an innovative and coste ective solution. This patent pending, commercially-proven technology is added to your furnace and synchronized with air-fuel ame reversals for optimal ame stability and luminosity. Bene ts includes: • Ultra-low NOx emissions • Reduced energy consumption • Higher glass quality • Enhanced productivity • Increased furnace capacity • Remote performance monitoring To make glass better, put Air Products in the mix. Cleanfire® HRx™ BoostingSynchronizedSystem © Air Products and Chemicals, Inc., 2021 (43776) All the boost you need, perfectly synchronizedtell me 800-654-4567,airproducts.com/HRxmorecode13639 International News Glass International July/August 2022 AGC Glass Europe will cre ate a new glass range with a significantly reduced carbon footprint, to be launched by the end of 2022.Following advanced testing and successful pro duction trials, the compa ny will be producing a new low-carbon glass range, with the possibility of de livering the first orders by the end of 2022. Further details of the range will be provided at a press conference at glass tec 2022 in Düsseldorf in September.Theimplementation of combined measures at sev eral recently upgraded fur naces has made it possible to reduce the carbon foot print of part of the group’s production.DavideCappellino, Pres ident of AGC Architectural Glass Europe & Americas Company, said: “I am very proud to announce that, with our continued pro gress in decarbonisation, AGC will launch its first low-carbon glass product range by the end of 2022. This represents a key mile stone in our roadmap to carbon neutrality.” AGC has already an nounced its commitment to carbon neutrality by 2050 and its interim tar get to reduce direct and indirect CO2 emissions by 30% by 2030. The roadmap includes many actions for the com ing years, based on an in tegrated approach – from research and develop ment, sourcing and pro duction, moving through the entire supply chain and transportation, and closing the loop according to the Cradle to Cradle ap proach.Thecompany will focus on switching to new key technologies, sustainable raw materials, alternative energies and increased glass recycling to avoid process-related and indi rect emissions.
AGC to produce lowcarbon glass range
NSG Group started op eration of the second ded icated float line for solar glass in Vietnam in Janu ary 2020, and a new plant in Luckey, Ohio, USA has been operating since No vember 2020. The glass produced in these plants is exclusively supplied to First Solar.
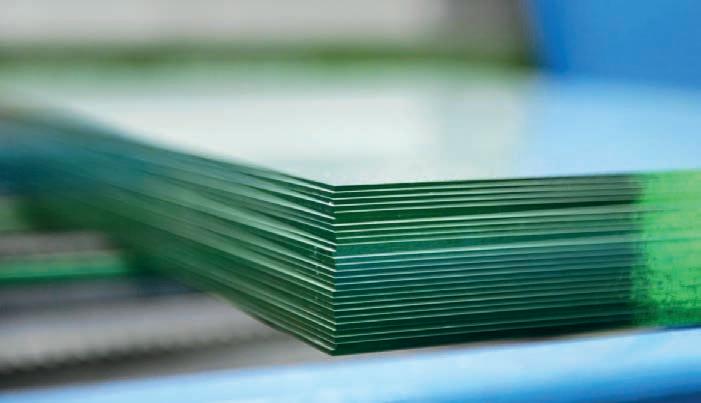
PSR CORD DISPERSAL SYSTEM Proven and www.parkinson-spencer.co.ukguaranteed.
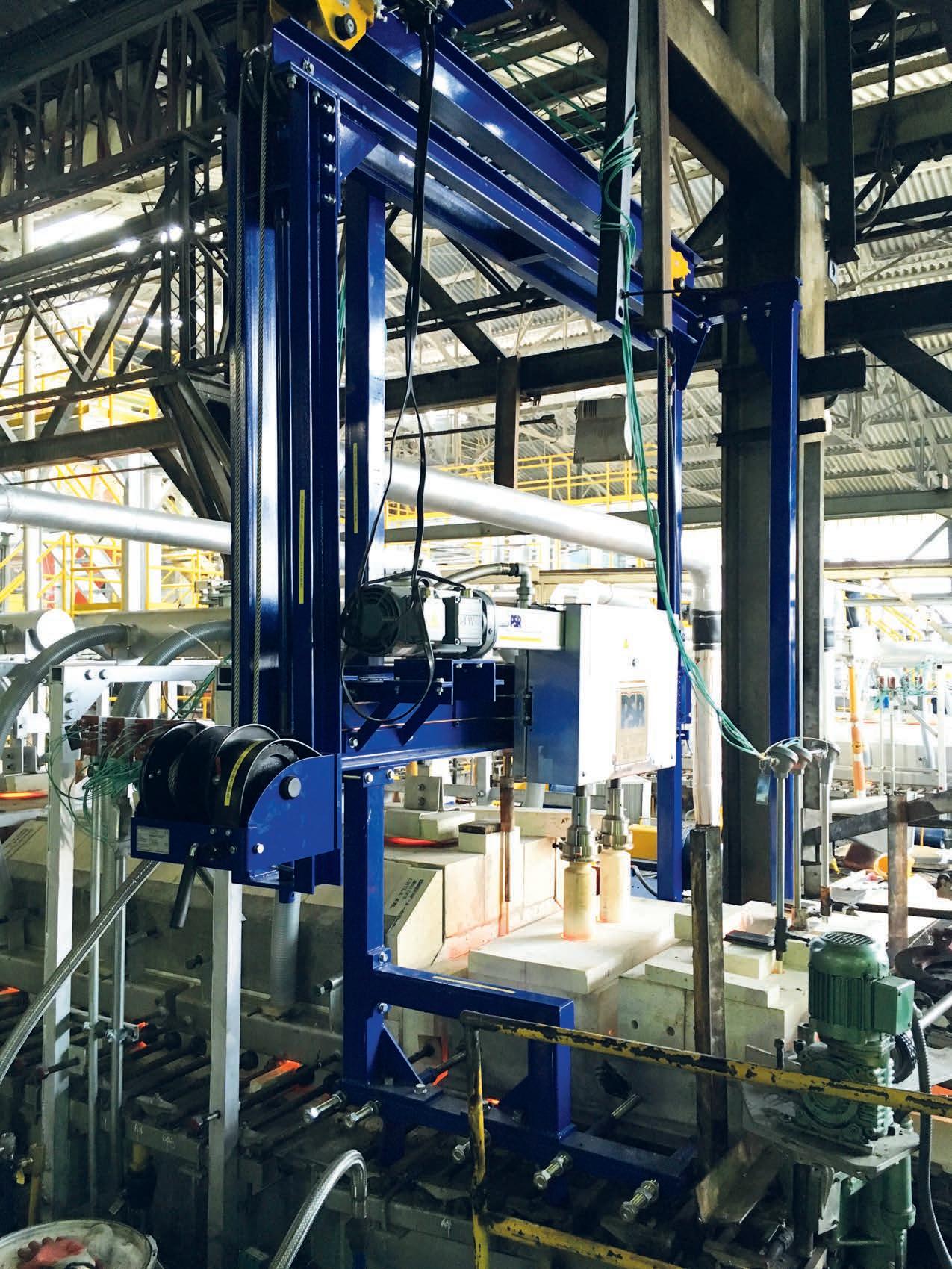
Our most popular news over the past month, asdetermined by our website traffic. full stories can be found on our website.
� 2. O-I to build $240 million MAGMA facility in USA � 3. Record year for container glass production
Strong revenue growth at AGI Greenpac Indian packager AGI Greenpac reported a strong growth in re en e in its latest financial note due to an increase in glass container packaging volumes.ForQ1FY23, revenue from Operations increased from crore to crore registering a strong growth of 78% on a y-o-y basis. Operating EBITDA stood at crore registering a growth of 57% on Y-o-Y basis with margins of 18%.
Maison Lillet has won the Millésime Eco-Design award for its sustainable packaging created with O-I. French distillery Maison Lillet, a subsidiary of Pernod Ricard, worked with O-I to create more environmentally friendly Thispackaging.included a glass bottle which contained 35% recycled glass and was 110g lighter than the previous version.
� 7. Heinz-Glas uses plastic-free packaging � 8. Stoelzle completes €45 million Polish glass investment
Turkish glassmaker Sisecam is to build a frosted glass furnace and processing line in Mersin, Turkey.Sisecam’s new frosted glass furnace will operate with a capacity of 600 tons per day and along with an energy glass processing line with a capacity of 20 million m2 per year in the Tarsus Organized Industrial Zone (OIZ). The total investment worth will be approximately TL 3.4 billion ($193 million), including working capital. With its new investment, Sisecam said its aims to close the supply gap that may arise in the energy glass sector and to contribute to the country’s economy by utilising export opportunities.SisecamChairperson and Managing Director Ahmet Kırman said despite the increased energy costs, the cost of electricity generation from solar energy has decreased and the sustainability sensitivity of the global arena has increased which offers new opportunities to glass industry. “When the investment reaches full capacity, it will reach €120 million ($122 million) in annual sales revenue, it will direct approximately 30% of its sales volume to export markets and it will create more than 1,000 jobs.”
All
� 9. NSG secures funding for syngas glass project
� 4. Verallia to electrify Cognac plant in Fives partnership
PHP Float Glass to double production PHP Float Glass Industries is set to double its production capacity to 300 tonnes a day in two years to meet growing local demand in Dhaka, Bangladesh.Thefactory currently man fact res float glass with thickness ranging from 2.5mm and 12mm and will be able to produce up to 15mm glass after the expansion. The expansion will also allow the factory to take on an additional 700 employees. Vidrala to electrify Spanish PV plant Vidrala will begin the electrification of its photovoltaic (PV) plant located at its factory in Crisnova, Castilla La Mancha, Spain. The PV plant is the largest solar project of the glass industry in Spain. The plant will produce 100% of the electrical energy of the production centre at times of maximum intensity, reducing around 9,000 tons of CO2 per year. First bottles produced by Revimac IS machines in Asia Myanmar Golden Eagle (MGE) has pro ce its first bottles using Revimac IS machines at its plant in Myanmar, Asia. Four IS forming machines supplied by Revimac to MGE, under the contract signed at the end of 2019, were commissioned several months ago. stories in the news
www.glass-international.com 6 Glass International July/August 2022 NEWS IN BRIEF
Lillet and O-I collaboration wins sustainable packaging award Sisecam to build $193 million Turkish glass facility
International News For
� 5. Indian company changes name � 6. Sisecam to build $193 million Turkish glass facility
� 1. Scotch whisky brand switches to glass bottles
The new packaging earned them this year’s Millésime Eco-Design award, which is run by AdelpheAdelphe.is a non-profit eco-organisation that aims to develop the recycling of household packaging from companies in France. Launched in 2020, the Millésime competition aims to reward companies in the wine, champagne, spirits, beer and cider industries that are committed to improving the environmental impact of their packaging.
Top 10
� 10. O-I Canada secures $21 million funding for glass investment the latest Industry News scan the QR CODE using your iOS or Android device

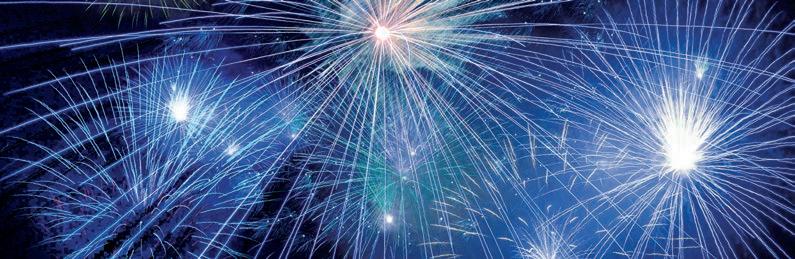
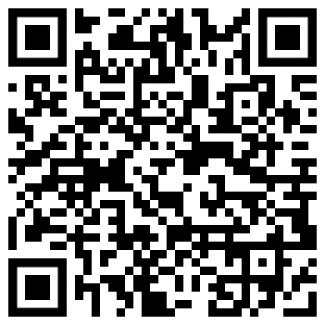
GLASS SERVICE
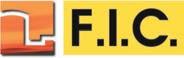
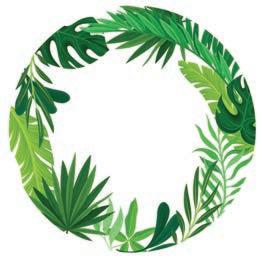



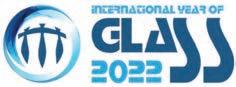
Dubai-based glass container manufacturer Ammat Glass chose the Sorg Group to deliv er a single source for its recent furnaceAmmatrebuild.Glass Industries wanted to improve its hot end processes to lower energy and maintenance costs, expand ca pacity and enhance the quality of glass Nikolausconditioning.Sorgwas respon sible for the design and en gineering of a new furnace. The furnace had to have a 140 m² melting surface and 450 tpd melting capacity for flint, green and amber glasses. The furnace incorporat ed Deep Refiner technology, which increased the residence time of the glass in the furnace to improve the glass quality. Nikolaus Sorg installed three 340S+ forehearths to supply three IS 12 section triple gob machines to increase produc tion capacity, with the ability to add a fourth forehearth in the future. Boosting was also used throughout to assist with melting, thermal barrier boost ing and throat boosting. EME improved the efficien cies and capacity of the batch houseAftersystem.auditing the batch plant, EME worked out a con cept to upgrade the facility. The main goal was to increase the plant’s capacity and im prove the dosing and weighing accuracies.EMEreplaced pieces of equipment to enhance accu racy and installed a new high duty pan mixer. The company also supplied a new cullet re turn system, including a single forked-link chain scraper con veyor for a capacity of 450 tpd. The electric control system was upgraded to a more modern system controlled by the PLC. SKS supervised the construc tion of the steelwork for the furnace rebuild and provided support with the refractory in stallation, with more than 100 workers present on-site at any one time. SKS also guided the heating and commissioning of the furnace.
Ammat Glass chooses Sorg Group
Konatic has released an app which allows mobile phones and tablets to read datamatrix codes on glass bottles. For many years, Konatic has been working on an app to read the datamatrix code on bottles. The app uses artificial intel ligence (AI) to ‘scan’ a bottle, which can then display the following information on any smartphone: � Date, hour, minute and second of production � Section and cavity number (new) � Plant number and line Until recently, localising the code with the smartphone was time consuming. But the new algorithm with AI can detect the code automatically and read it faster. The app, called Konatic Reader, is available on Android or Apple store free of charge with a limitation of two read ings per day. There is also an option to purchase a yearly li cense with unlimited readings (send request to Konatic). Konatic will be at glasstec Hall13D16.
European & UK glass containers recycling rate hits record high Average EU27 + UK collection for glass packaging recycling hit a new record rate of 80% in 2020, according to data from FEVE.This represents an increase of 2% points compared to 2019, with nine countries already achieving over the 90% collection target.
More than 23.4 million tonnes, or 83.3 billion bottles and jars, were produced for the European and global markets in 2021.
Heinz-Glas launches in visible glass protection Heinz-Glas has launched a protective coating to shield its products from danger. ra iation is filtere to protect the sensitive ingre ients refine glass surfaces ward off bacteria and viruses, and an optical fingerprint ens res the authenticity of the products.
for turnkey solution Schott to construct US facility
Record year for container production Container glass production was at its highest ever level in 2021, according to data released by FEVE – the European Container Glass Federation.Industry production volume of glass packaging for the food and beverage sector increased strongly by 5.0% compare to fig res
Stoelzle completes €45 million Polish furnace investment Stoelzle Czestochowa recently celebrated the successful rebuild and expansion of its t a flint f rnace The new furnace will have fi e more efficient pro ction lines, melting output will be more efficient an the amount of energy used in the melting process will be reduced by at least 10% per ton of Improvedglass. E-boosting will also use more green electricity to reduce the consumption of natural gas.
NEWS IN BRIEF www.glass-international.com 8
Glass International July/August 2022 International News
Konatic app reads damatrix codes
Schott Minifab, a subsidiary of Schott, will open a new man ufacturing facility in Arizona, US to serve the diagnostics market.Thefacility will open this fall in Phoenix, Arizona, offer ing diagnostic and life sciences companies an end-to-end solu tion to design, develop, manu facture, and scale-up their con sumable devices. Greg Wolters, CEO of Schott Minifab, said: “The facility will play an important role in our unique service offerings and provides companies a partner to advance the manufactur ing of consumable devices, empowering patients and pro viders to get diagnoses quicker and more accurately. “Rather than managing doz ens of suppliers, companies can partner with Schott Minifab to handle the complete lifecycle of product development un der one roof so they can focus their efforts on innovation and reduce the total cost of goods.” The purpose-built facility further enhances Schott Mini fab’s service offerings and sig nificantly increases Schott’s manufacturing capabilities in the United States to serve its global customer base. The services will include best-in-class high density array printing following Schott’s ac quisition of Applied Microar rays Inc (AMI) in October 2021.
GLASS SERVICE l l l l l
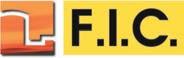



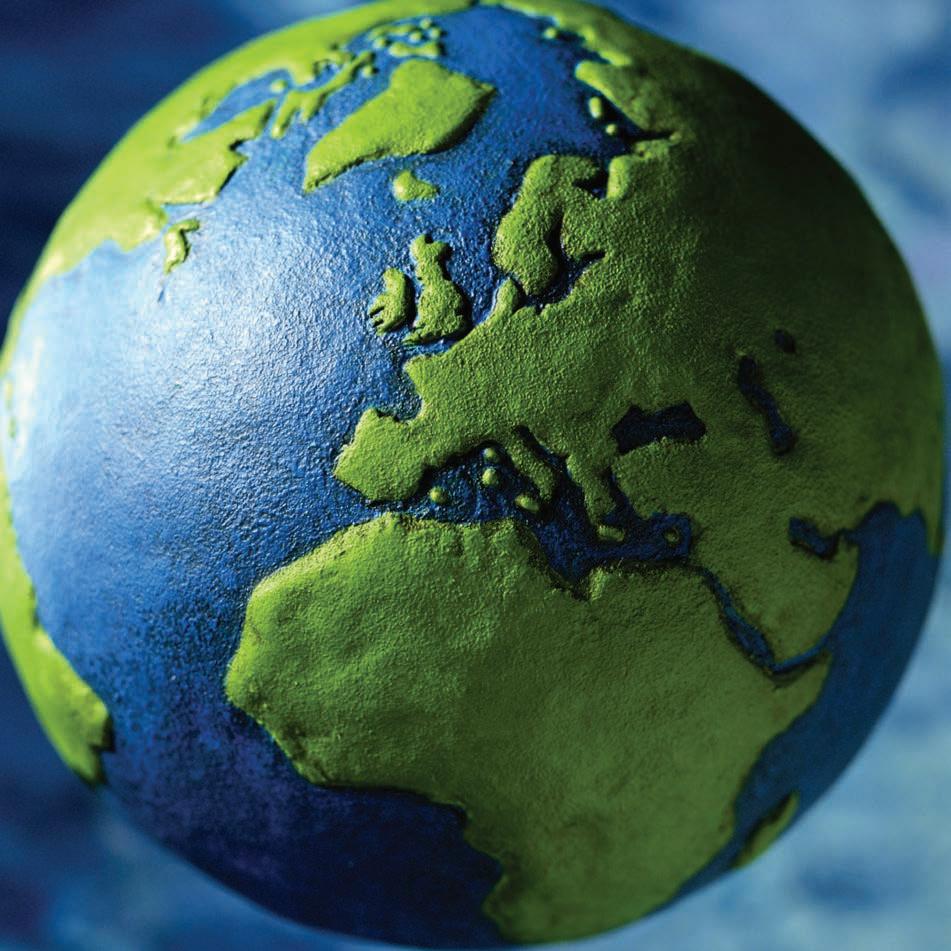
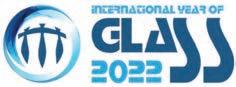
Typically, colleagues manually combined measured values on an Excel spreadsheet and drew decentralised conclusions from this data. “There were no standardised KPIs, nor could they be automatically calculated,” says Roschitz about the initial situation. “Due to the ever-stronger connection between IT and OT, a uniform strategy for the infrastructure of all the factories had to be developed.” Thomas Mayrold knows what that means on-site in a factory like K flach. He’s been Energy Manager at headquarters for approx. four years. “At that time, it was impossible to link energy and production data,” says Mayrold. “In general, it was extremely difficult to identify correlations using data. For example, how do we determine what amount of energy is needed to produce one tonne of glass ” But we already knew the energy-intensive areas: furnace, feeder, and annealing lehr. Procedure Stoelzle decided to bring Siemens on board at the beginning of 2020. In joint workshops, energy-efficiency and carbonrelated KPIs were developed and the most relevant potential savings prioritised. A metering concept was then developed and the overall requirements for an energy management system were translated into a call for bids –based on the premise that all these actions contribute to an energy policy for the entire group and fit into the overall sustainability concept. This concept stipulates prioritised fields of activity that systematically bring Stoelzle closer to achieving its energy-efficiency and carbon goals: process and energy
Digital glassmaking Glass International July/August 2022 100 www.glass-international.com
The Stoelzle Glass Group, with headquarters in K flach, Austria, is a trailblazer when putting sustainability agendas into practice. “If you want to survive on the market, you have to demonstrably improve your environmental performance – for example, by reducing energy consumption and carbon emissions,” says its CEO Georg Feith. Stoelzle’s plans for its seven global production sites and its annual output of around 3.8 billion bottles is a 20% reduction in power consumption, an initial 50% reduction in carbon emissions by 2030, and finally, carbon-neutral glass production by 2050. The well-known frame of reference for measuring this across industries is Scope 1, 2, and 3. The ‘corporate carbon footprint’ encompasses all the emissions generated by a company’s activities in one year, and the goal is a reduced carbon footprint. The ‘product carbon footprint’ alone encompasses all the emissions generated by one unit of a product across the entire value chain and throughout its entire lifecycle. If we look at current practices, there’s a slight shift in priorities underway. “Everyone knows that the whole industry wants to reduce its energy costs sooner rather than later. They used to make up about 10% of our operating costs, but in the current situation they’re up to 30%,” says Feith, and highlights yet another challenge: “Using the latest technologies, furnaces the size of ours need gas.” A lot of effort is also being invested in the area of recycling and raw material substitution, where Feith sees potential energy savings of about 10%. “Depending on the colour of the glass, the desired haptics, and the weight, however, everyone hits natural limits when it comes to recycling, and when carbon-neutral secondary raw materials like process soda are used, availability plays a role,” Feith explains, although he also notes that a 10% increase in the use of cullet reduces carbon by about 5% and energy consumption by 3%. The CEO is considering a conversion to green electricity and alternative fuels. “The infrastructure for green fuels like hydrogen still isn’t there. Hydrogen first has to be produced, and this has to be done using solar or wind energy if it’s going to be green.”
The strategic challenges at the company’s management level are directly reflected in the factories. Taking a sustainable approach, Stoelzle created the new position of a group-wide Energy Manager in autumn 2020. Since then, it’s been Alexander Roschitz’s job to translate major guidelines into concrete actions. “We recognised early on that we needed an energy management system on the group level. There were metering points but not enough, and none that were interconnected – neither in the individual factories nor across factories.”
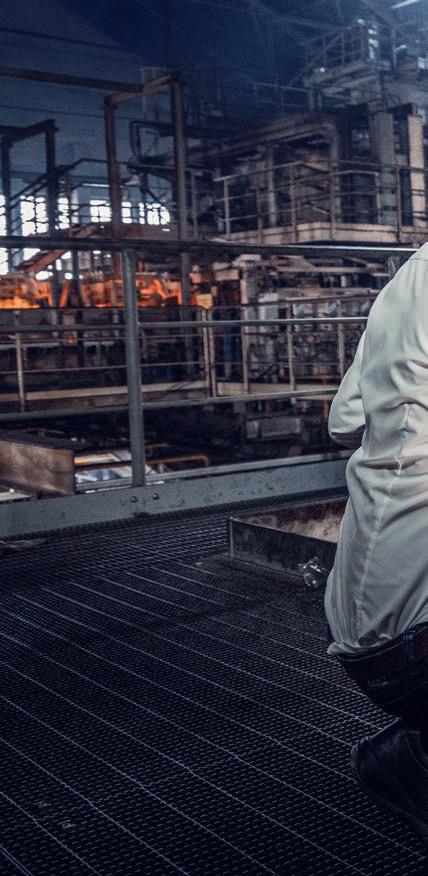

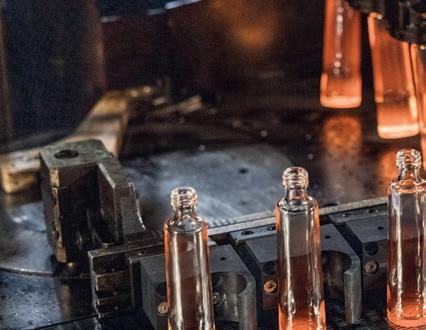
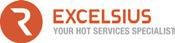
Where the glass is always greener
Continued>> optimization, PCR and raw material substitution, and green electricity and sustainable fuels. As a key project for process and energy optimisation, management at Stoelzle identified the rapid introduction of an appropriate power monitoring and management system. Goals In its selection and implementation of an energy data management system, Stoelzle combined a range of objectives: “What we needed was software that could be used group-wide for acquiring, recording, and evaluating data and for visualizing it in a variety of ways and deriving actions,” says Roschitz.“Wecan draw the right conclusions much more reliably on the basis of data – for example, we can identify process deviations because we’re making energy consumption transparent. That’s extremely interesting for us, because Stoelzle always has two factories with the same portfolio,” says Roschitz. The overriding objectives are always to improve energy efficiency and reduce energy costs. In concrete terms, improving energy efficiency means being able to identify inefficiencies and deviations early on and track and evaluate trends and changes in energy consumption. “It could be that the production volume is being increased, furnaces are aging, or the composition of the batch is changing. With the software, corresponding measures can be defined and implemented and their effect can also be measured,” Mayrold explains. Requirements When examined more closely, the requirements Stoelzle defined for the software can be boiled down to four quality characteristics: transparency, data quality, standardisation, and reporting. The following goals were specifically linked to these characteristics:
Stoelzle Glass Group plan to reduce energy consumption at its seven production sites by 20% and cut its carbon emissions in half by 2030. The centerpiece of this is an energy management system from Siemens which is responsible for up to 5% of its energy savings. Rudolf Traxler* discusses.
Glass International July/August 2022 www.glass-international.com 11
Digital glassmaking
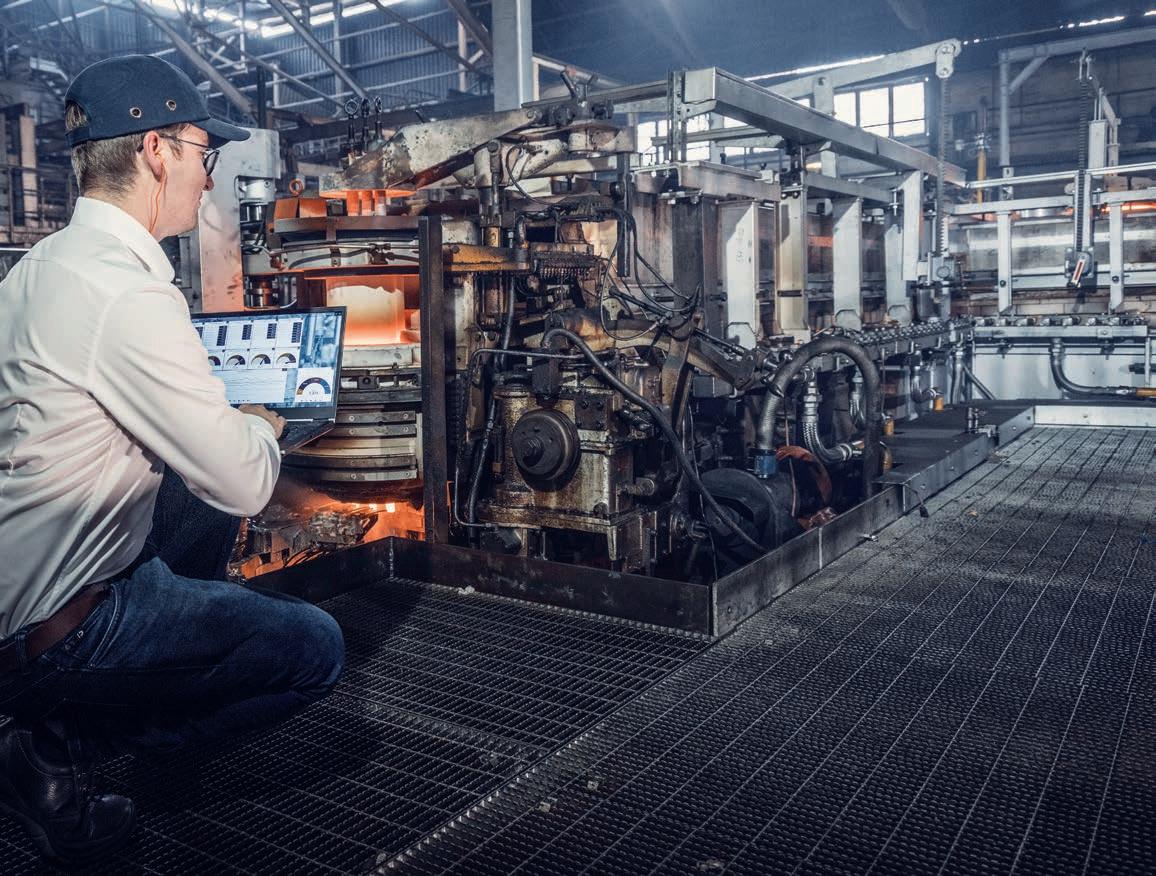

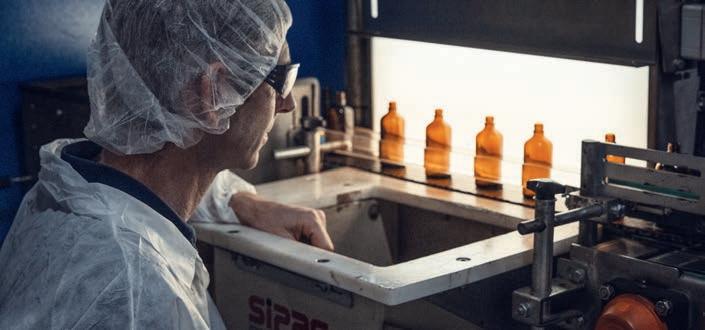
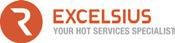
Transparency: Full transparency of all energy data, meaning gas, electricity, CO2, water, and compressed air on different aggregation levels including machine plant, line, factory, and even group. In particular, making carbon emissions transparent is essential for certificate management. The goal is to reliably determine what’s influencing energy consumption.
Data quality and standardisation: KPIs define and identify standardised comparability and tracking. They’re the only way to establish benchmarks and the only way factories can learn from one another. With high-quality valid data, it’s also much easier to prove and uniformly document compliance with all the relevant statutory regulations. Reporting: What’s needed is a more detailed analysis and the elimination of time-consuming manual evaluations.
Glass International July/August 2022 120 www.glass-international.com
� Annealing lehrs: With better temperature control, the generator sets can use 20% less natural gas.
*Head of Software Applications, https://www.siemens.com/global/en.htmlSiemens, Stoelze Glass Group, Köflach, Austria, https://www.stoelzle.com/
Since the project was launched in early 2021, all seven factories have been taking steps to connect to the energy management system, with the K flach site leading the way. By the end of 2022, all the other European factories will be connected via the company-wide WAN, and the US location, which has been part of the company since March 2021, will follow in 2023. The services provided by the Siemens team include the engineering, supply, installation, and commissioning of the electrical and non-electrical metering points and connection to SIMATIC Energy Manager PRO. For example, water metering: Siemens selected SITRANS FS clamp-on ultrasonic flow meters with non-intrusive sensors that could be installed during operation without having to cut the pipe. Another example is the vortex flow meters: Siemens chose SITRANS F 330 flow meters due to their accuracy and low pressure losses. “Siemens also provided support for other important steps, including the initial data-point list with a target actual table – and then the connection of IT, the above-mentioned provision of meters and instrumentation, installation, and wiring,” recalls Energy Manager Mayrold about the start-up project in K flach. “Siemens managed to perform the conversion during ongoing operation brilliantly, implementing most of the metering points within eight months and almost all the data interfaces since January 2022. It’s a living system, so to a certain extent it’s never finished,” Mayrold says. For those who love numbers: in K flach alone, 1,800 data points were integrated via seven interfaces in process and production systems and 70 new metering points were added depending on the importance of the media: gas, electricity, compressed air and water. As a result, the connection of other locations has been almost easy. “Because the data is acquired decentrally but we designed a centralised EDMS infrastructure in K flach, connecting internationally was very manageable and easily to do for a project of this size,” says Roschitz. Because K flach was the first to use the new system, initial options for energy and process optimisation have already been verified and resulted in concrete measures: � Water: Monitoring revealed that the amount of municipal water used can be reduced by 50% at the K flach location.
� Compressed air: Thanks to the software, Stoelzle can now measure compressed air consumption at each machine and detect leaks.
olution an customer enefits Stoelzle ultimately realised that these multifaceted requirements would be met best by the SIMATIC Energy Manager PRO energy management system from Siemens. “We chose Siemens because the company is a single-source supplier with international experience and glass expertise that was offering a turnkey solution from the field level to the management level. So we weren’t just impressed by the excellent software itself, but also by the coupling of hardware expertise – from energy meters, process instrumentation, and automation and communication components to a groupwide energy management system,” says Roschitz.
The goal is a standardised, flexible, needsbased presentation with reports that are harmonised factory-wide and even groupwide. This is the only way to link energy and production data and make this data usable for controlling (for example, energy balance, cost center accounting, verification of energy bills, evaluation of energy and CO2 KPIs, and tracking of energy-efficiency measures).
Mr Feith says: “We made the right choice with Siemens, because we were impressed by the company’s turnkey solution from the field level to the management level. We’re now looking forward to the international rollout and other collaborative steps that will make Stoelzle a glass manufacturer that’s successful on the market while being verifiably energy-efficient with demonstrably low emissions.” He is keeping a constant watch on the interconnection and expansion on all Scope levels over the next few years: Scope 1 covers direct emissions from sources owned or controlled by Stoelzle. Scope 2 covers indirect emissions from the generation of electricity, steam, heat, and cooling that Stoelzle buys and consumes. Scope 3 is all other indirect emissions produced by Stoelzle’s value chain. Siemens has developed SiGreen for this purpose: it’s an ecosystem-based approach for exchanging emissions data that makes it possible to exchange emissions data along the supply chain and, by making this data available in Simatic EnMPRO, combine it with the data from its own value creation to produce a true product carbon“Thisfootprint.alsocounts in Siemens’ favour: future requirements are going to be increasingly complex and interconnected, and the solutions are already available today,” says Feith. �
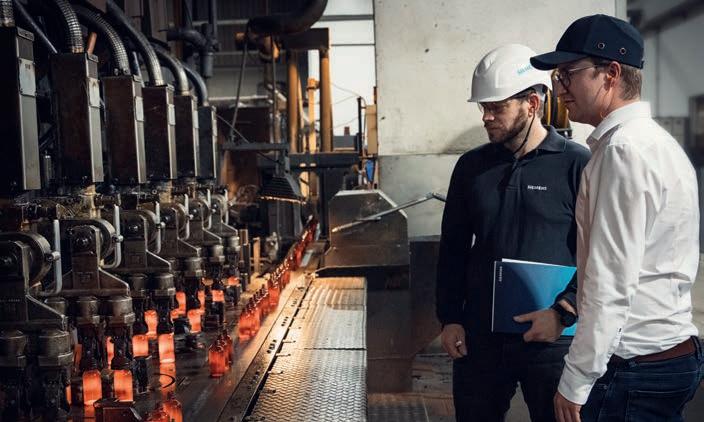
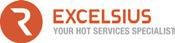
Dynamic Duo Meet Vol SW and Vol SSB. Side Wall and Sealing Surface & Base Take the smart approach to your glassware inspection with our tandem SW and SSB Volcano units. These team players lock up your toughest defect issues with the power of innovative machine vision and adaptive technology. Inspection problems solved! Simply Smart Machines SM SW + SSB Simple + Smart =

www.heye-international.com MAXIMISE YOUR PROFIT +High production speed +Fast job COMBINE+Clean+Robot+ReducedchangesdowntimesoptiondesignSPEEDAND FLEXIBILITY WITH SUPERIOR LIFETIME Hi WE`LL MEET AT GLASSTEC!HALL14,C18
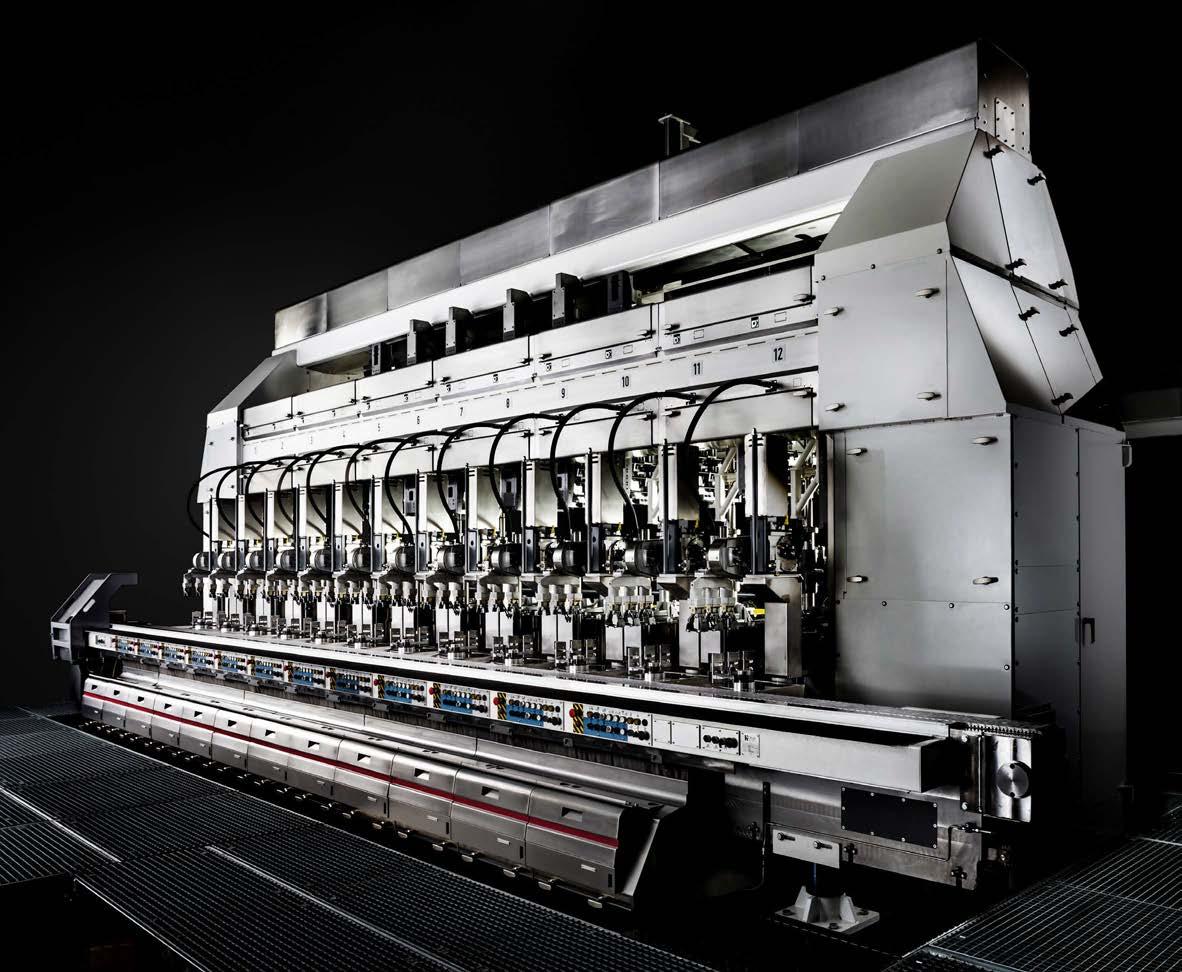


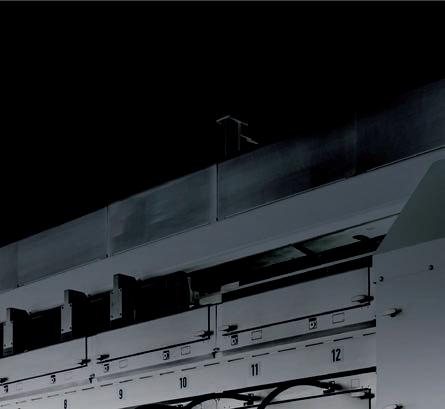
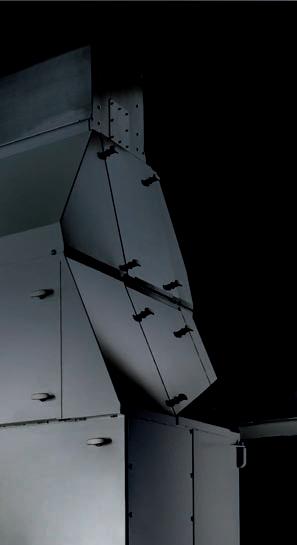

Can hydrogen solve the sector’s decarbonisation plans?
Flat glass manufacturer NSG group recently completed successful hydrogen trials at its Pilkington plant in St Helens, UK. The trials lasted for three weeks and had the aim of firing the furnace with 100% hydrogen with the quality of the manufactured glass unaffected. The trial resulted in a world first – the production of float glass using hydrogenThetrials were part of the Hynet Northwest Fuel Switching Scheme - a UK-government funded scheme - to demonstrate the feasibility of switching several industrial processes from natural gas to Pivotalhydrogen.tothesuccess of the trial was the reliable supply of hydrogen from gas group BOC. The company is part of the Linde group and operates the largest network of gas production facilities across the UK. It operates five hydrogen production sites, in Margam, Barry, Newport, Teesside and one close to the NSG glass manufacturing facility in St Helens. BOC’s role in the trial was to demonstrate that it could deliver enough hydrogen on a large scale for NSG. The organisation had to mobilise its supply to provide enough hydrogen for the entirety of the trial. At one point, when demand for hydrogen from the glass plant was at its peak, BOC provided a truckload of hydrogen to the facility every hour. As Wayne Bridger, BOC UK and Ireland’s UK sales manager of decarbonisation and hydrogen applications, states, no other company in the UK would have the capability to mobilise a supply chain to do the trials and deliver what it did. The group had been involved in hydrogen trials in other sectors such as cement, minerals and wine before but the one at NSG was its largest. At its peak, NSG required about 3000 m3 an hour of hydrogen. The hydrogen was supplied from BOC’s production sites to NSG in its trucks, which have a typical capacity of 2800 m3. The company has 75 trucks in the UK so mobilised about 100 trucks from its European division to keep up with demand. The trial presented several engineering challenges. BOC’s trucks had to be converted to carry 10 bar instead of operates fi e h rogen pro ction facilities in the
The company mobilised 100 trucks to supply the NSG facility for its hydrogen trials.
Decarbonisation Glass International July/August 2022 www.glass-international.com 15 Continued>>
Industrial gases company BOC is a key provider of the UK’s hydrogen needs for industry and recently took part in successful trials at NSG Group’s St Helens, UK glass manufacturing plant. Wayne Bridger* describes how hydrogen could be the answer for glass’s problems, but it may take at least 10 years before adequate infrastructure is in place.
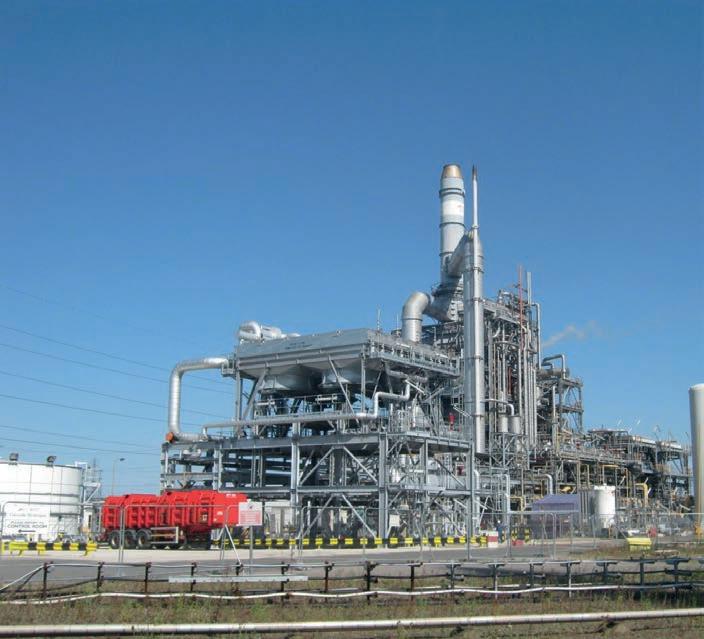
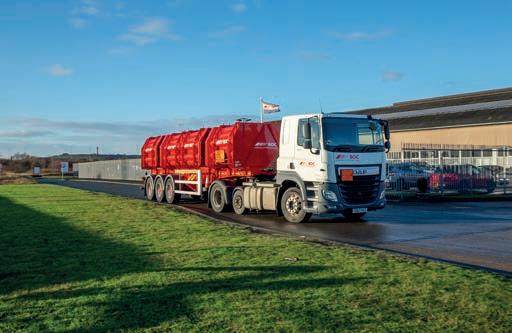
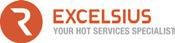
“When I speak to industry there is this concern about a no regrets pathway, it seems industry doesn’t want to make regretful decisions about where it invests. It doesn’t want to put CAPEX into one technology which goes in one direction only to find that another technology has gone in another direction. That is paralysing industry to some extent, it is not making any decision because it doesn’t want to make the wrong decision.
*UK Sales Manager-Applications at the Linde Group, BOC Industrial Gases, www.boconline.co.uk/en/index.htmlUK “
Wayne Bridger
�
“While hydrogen is part of the future we contend that other, well established technologies should be the early part of the“Thesolution.UKindustry will be reliant on a range of things and I guess the danger is that some of that is big, complex, expensive and long term so it needs to act now because the clock is ticking.
“People are talking about significant steps by 2030 to achieve that, so there is not a lot of time for experimentation and development, you have to start to rely on proven technology to move forward. That is the position we are advocating.”
Glass International July/August 2022 160 www.glass-international.com their usual 228 bar gas. Inside NSG’s facility, two seven-metre-high skids were constructed to help with ventilation due to hydrogen’s dispersal rate and flammability characteristics. Mr Bridger said discussions about the trials started in 2018 and did not start until 2021 – although this was partly due to the pandemic. Planning of the trials took over a year “If a company is considering embarking on a decarbonisation journey, it is worth saying the engineering and interface discussions for the trial lasted at least a year. These are not quick decisions, it is a thoughtful process. We were in the fortunate position where we could dedicate a small engineering team to the project because it requires a substantial engineering effort to do these things well.”Headded: “Summarising that journey, you need a lot of resources, and a lot of production, distribution and engineering capability to enable substantial trials to go ahead.” Future Looking ahead, Mr Bridger said BOC currently had enough hydrogen capacity to help run two or three average sized container glass plants in the UK. “It gives you a sense of the scale in infrastructure required. I talk to a lot of people in industry and I repeatedly hear the weight of expectation in the future. There is almost a utopian view of the future where hydrogen will come along and solve our problems.”
“There is no single silver bullet to all of this, there are pathways which involve a number of technologies.
“It is a journey and we think the industry should be building more data and operating experience to begin to think how to begin this journey. It is lengthy and requires a lot of input from both sides but there are steps the industry could and should be taking.
But this utopian view is challenged by increased energy price volatility, likely higher energy costs and the cost of carbon compliance in future, he said. “There is a gap in my mind between this utopian future of hydrogen that says ‘don’t worry it will be okay’ because there is lots of low cost hydrogen coming, while all the business models for hydrogen and carbon capture and carbon pricing are still in “Also,debate.nothing is built yet. We have got this long horizon where all of this will come together but we have problems today. Somehow we have to survive this gap period between where we are today and what the future promises. “I hear what people are quoting as the future cost of hydrogen and, well good luck, because it is going to be a long time coming. What we do know is that hydrogen is likely to be more expensive.
Summarising that [decarbonisation] journey, you need a lot of resources, and a lot of production, distribution and engineering capability to enable substantial trials to go ahead.”
“We have options for the decarbonisation of industry such as hydrogen, biofuels, electrification and carbon capture but no of those are free and all require large infrastructure investment.”Hebelieves that, in the long term, renewable electricity will be the energy source to power the glass manufacturing industry but until then will be a bridging period where a variety of technologies will be used. Initially fuel efficiency should be a focus, with the use of oxy fuel technology and waste heat recovery before medium term technology such as hydrogen and carbon capture come into use. Paralysis He suggests business needs to take action quickly if they are to decarbonise their facilities in the near future.
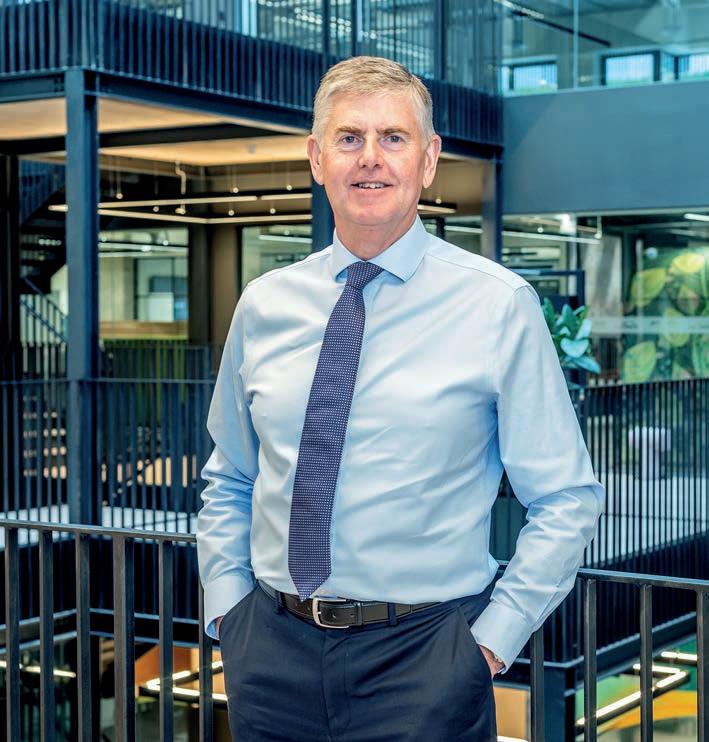
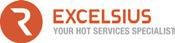
+44
Improving combustion can enable you to increase glass production, reduce fuel consumption, enhance glass quality, and reduce emissions, such as NOx, SOx, CO₂, and particulates. Let Air Products’ in-house modeling and melting experts help you get there. For more than 70 years, we’ve delivered safe oxygen solutions, from our very first oxygen enrichment applications to our continuously evolving portfolio of low-emissions Cleanfire® oxy-fuel burners. Our industry-leading burner systems can now utilize hydrogen as a fuel, for a lower carbon footprint. You can count on Air Products for reliable gas supply and to help optimize your production— just like we have done for hundreds of furnaces all over the world. Contact us to put the skills and experience of our global team to work for you. Optimal melting takes one key ingredient: Us. To make glass better, put us in the mix. U.S. +1 800 654 4567 Europe (0) 800 389 0202 Asia 400 888 7662 610 706 4730 +44 (0) 1270 612708 21 3896
tell me airproducts.com/furnacemore Chemicals,
+86
© 2021 Air Products and
+1
Inc.
2000 Air 2022CelebratesProductstheInternationalYearofGlass

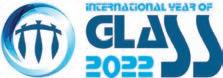
Hydrogen is my passion. Before Glass Futures I studied this molecule and worked on developing technology to produce green hydrogen using electrolysis and renewable energy. As we face a climate emergency, I’m a firm believer in hydrogen as the flame of the future and I’m convinced it can play a key role in decarbonisation of the glass industry.Weknow glass is really carbon intensive. Internationally, glass manufacturing produces at least 86 million tonnes of CO2 annually. But most of this can be eliminated when glass is recycled, and existing technologies could turn glass manufacturing into a mostly carbon-free process. And there lies the challenge to make it clean. To find a solution suitable for everyone in the world including countries where glass isn’t recycled. Many countries have committed to global net zero targets. In the UK alone, the government has established a 78% carbon reduction target by 2035, with the net zero target by 2050. Globally, there’s the Paris Agreement, committing countries to limit global warming to well below 2°C, compared to pre-industrial levels. To achieve these goals we need to do something different right now, as Einstein said “insanity is doing the same thing over and over again and expecting different results”. Disrupting the industry To be able to make the necessary changes, there’s no longer room for small improvements. At Glass Futures
12
Dr Palma Gonzalez Garcia* discusses the advantages and pitfalls of the use of hydrogen in glassmaking.
Glass International July/August 2022 180 www.glass-international.com
How hydrogen as a fuel can help us to meet global net zero goals

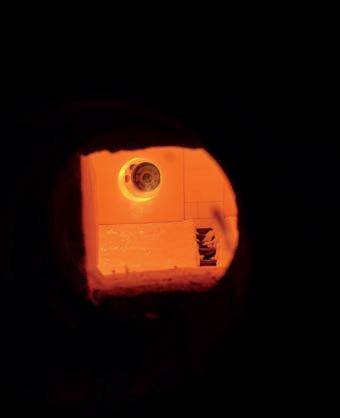
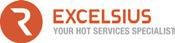
our aim is to become disrupters through collaboration and technical innovation delivering the necessary changes to create markets for change, creating a space where industry and academia can experiment and test new technologies. The technology readiness level of commercial scale furnaces is high, to suit market demand. Glass furnaces are built from scratch and will operate for around 20 years non-stop, so it’s really difficult, practically impossible, to test new technologies which could improve the glass making process and make it more sustainable. This would pose too high a risk for industry, losing production for a day or longer would mean losing millions of pounds. Our sector, as well as other heavy industries is highly risk averse.
We looked into biofuels, electric boost and of course hydrogen including different hybrid fuels by combining some of these fuels. We looked at: � the efficiency of the fuel in combustion and performance, the effect on glass melting and if any modifications are required to the industrial fuel delivery systems due to the properties of the fuel such as corrosion, density, flashpoint � the cost of obtaining fuels such as green hydrogen versus grey/blue plus availability � whether the fuel is safe to handle and any health and safety requirements for storage etc and � its environmental impact including emissions after the combustion process.
Fig alma present ring the flat glass biof el trials at il ington t ro p for the F Phase 3 programme Fig at ral gas flame in the Fig alma in front of the omb stion est e Fig alma t rning on the gas ring the fire p of the 3 4
What about hydrogen and other fuel sources? In 2020, we received £7.1m for the Industrial Fuel Switching (IFS) programme funded by the Department of Business, Energy and Industrial Strategy (BEIS) in the UK. The programme ran between January 2021 and March 2022 bringing together those all-important partners from industry, the supply chain and academia. The soul of the programme was to find suitable alternative low carbon fuels to enable the decarbonisation of the glass sector and, potentially, the rest of the foundation industries.
On the other hand, the technology readiness level of academia is low. They mainly build research prototypes focused on finding solutions for a specific problem and often have little commerciality. Therefore, you can see there’s a gap, but how do we bridge it? Our new Global Centre of Excellence in St Helens will provide a 30 tonne per day glass facility bringing people together to implement ideas and new technologies at industrial scale. This testing of prototypes and research into different energy sources and raw materials will give industry the confidence to introduce new sustainable solutions in their furnaces without the risk of losing production.
As part of the IFS project, we ran several pilot-scale tests looking into the effects of hydrogen in glass melts, oxyfuel and hydrogen tests. We also investigated a range of fuels including pure hydrogen in our 350kW combustion test bed. The full results are being published in conjunction with BEIS this summer. The combustion properties of hydrogen are substantially different from those of natural gas because of its calorific value and its high velocity and diffusion rate. Adapted nozzles and burners showed stable combustion and at input powers of up to 275kW the flame shape is very similar to natural gas. The experiments showed negligible hydrogen concentration in the flue, which indicates complete combustion. NOx was detected due to air ingress in the furnace. Overall, they showed that with optimised combustion to limit the NOx emissions, new burner technology will enable hydrogen and oxygen combustion on an industrial scale. In terms of the impact of hydrogen in glass melts, we used different raw material recipes to investigate the impact of hydrogen combustion on the foam build up and stability in glass melts. Preliminary melts showed glass foaming seems to be enhanced by the presence of water in the atmosphere. The programme also saw us carry out the first large scale trials using 100% biofuel in two industrial plants, Encirccontainer glass and NSG Pilkington - float glass. Both were a major success showing biofuel as an alternative low carbon fuel for the glass sector.
Decarbonisation Glass International July/August 2022 www.glass-international.com 19 Continued>>
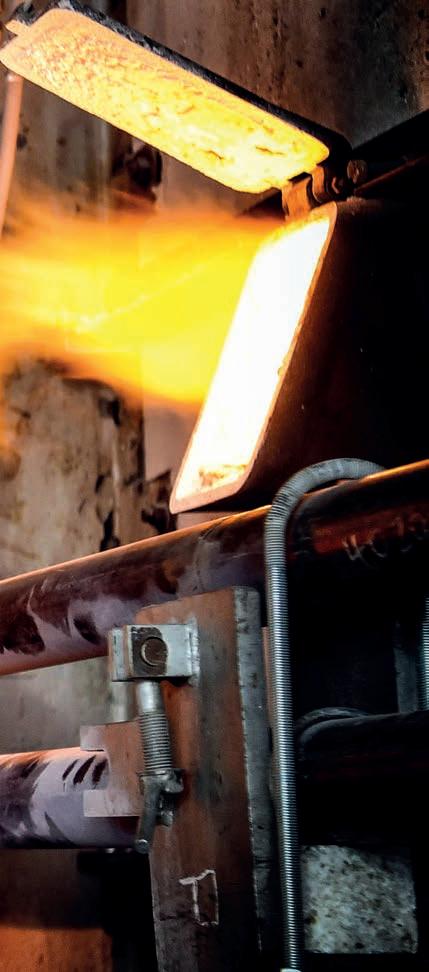

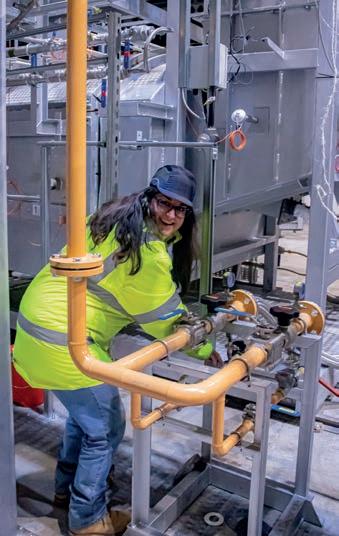
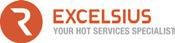
Essentially there will be no net zero without carbon capture and hydrogen. Yet, however promising hydrogen is there are several challenges that still need to be overcome.
The four-week flat glass trial made NSG Pilkington the world’s first flat glass manufacturer to fire its furnace on 100% biofuel. One of its furnaces was powered on a sustainable biofuel made from organic waste materials, creating 165,000ft2 of the lowest carbon float glass ever made. The fuel emits circa 80% less*1 CO2 than traditional natural gas used in theHydrogensector. advantages and pitfalls: � Despite being the most abundant molecule it can’t be found in Earth’s atmosphere on its own so has to be produced.
� People have a fear of hydrogen because it’s flammable so is perceived by many as dangerous. � Clean production is still a challenge. Today, 95% of hydrogen is produced from wood or fossil fuels, mainly by steam methane reformation, meaning the hydrogen is far from green or blue. Steam methane reformation with newly developed carbon capture technologies can produce relatively clean hydrogen, known as blue, which is a good solution as green hydrogen is still in the early days of development.
During the three-week trial at Encirc, UK multinational beverage alcohol company Diageo used its Black & White Scotch whisky brand to produce a total of 173,000 bottles using 100% recycled glass. More than 1 million bottles of Carlsberg were also made, reducing the carbon footprint by 90%.
� Hydrogen at high pressure causes embrittlement which can cause breakages to pipework/storage if stainless steel with 12% plus nickel isn’t used.
� It’s highly dense. It contains the largest amount of energy by mass with greater efficiency than the majority of fossil fuels. � It’s a clean fuel that produces only water as a by product. Hydrogen is a flexible energy source which supports the global net-zero strategies with the potential to abate 80 gigatons of CO2 by 2050, according to the Hydrogen for Net Zero report. Clean hydrogen (both renewable and low carbon) offers the only long-term, scalable, and cost-effective option for deep decarbonisation in sectors such as steel, maritime, aviation, and ammonia.
� It’s non-toxic. Hydrogen produced from alternative energy sources such as solar and electrolysis provide clean and environmentally friendly energy due to recyclability of its generation and combustion � It can be stored in bulk for long periods and be easily produced and transported.
� It can easily leak through flanges and fittings so existing transport networks and tanks will need upgrading.
� Distribution is tricky. Depending on the site, delivery can be difficult and the size of a furness/facility might not make an on-site hydrogen production plant feasible. Long-term outlook We know hydrogen is clean but during testing we’ve seen that NOx levels can be problematic when burning pure hydrogen. This means, that NOx control technologies must be developed and implemented to mitigate noxious nitrogen emissions. We also need to see what the longerterm effects are on the furnace refractories with such high water content and understand how hydrogen combustion affects the furnace atmosphere and glass chemistry and quality long-term. Despite the challenges, I’m convinced that hydrogen will hold the key to decarbonisation in the foundation industries.Yes,thechallenges are many, but they’re the challenges we’ll be able to overcome through working together globally. Research and development will be the key to finding solutions, that’s why we’ll use our new pilot plant to work on radical, disruptive new programmes with our partners in search of the best technologies for our sector and beyond. �
Fig omb stion est e in rins orth otherham hich ill be transporte to the lobal entre of cellence once operational
� The ability to produce large amounts of green or blue hydrogen is limited as large amounts of inexpensive and carbon-neutral electricity is needed. Within the UK we simply don’t have enough wind, tidal and solar electricity to make green hydrogen production viable.
� The cost of electrolysis is still very high compared to other ways of hydrogen. Alkaline electrolysis in the UK (including capex) producing 12.53/kg, based on PEM electrolysis production is around £14.86/ kg, while blue hydrogen production by autothermal reforming is £4.81/kg (including capex, CCS and carbon). As time goes by, it’s expected that the cost of green hydrogen will decrease.
*Combustion Technical Lead, Glass Futures, St Helens, https://www.glass-futures.org/UK
Glass International July/August 2022 200 www.glass-international.com

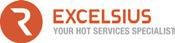
Hall 15,
Markus Gruber Senior Vice President Business Unit Glass, Grenzebach Maschinenbau GmbH Let us be your guide through the world of glass
We look forward to your visit glasstec, Düsseldorf - 23.09.2022, Booth 15B23 glasstec 2022, the central get-together for the international glass industry, will once again take place in Düsseldorf. At Grenzebach, we can hardly wait to meet our customers, partners and interested parties at the fair! Visit us and experience exciting technologies, new products and a special atmosphere live again. It’s especially worthwhile to discover our innovations –such as the redesigned annealing lehr, the dross box, the new conveyor technology and our SERICY digitalization platform. We look forward to seeing you!
20.
www.grenzebach.com


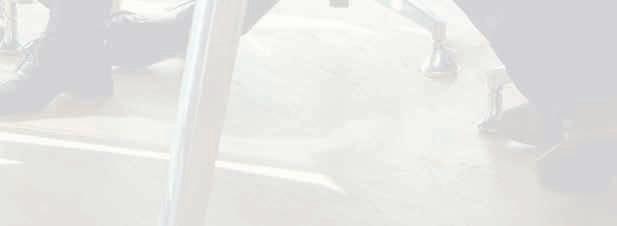

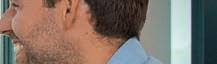
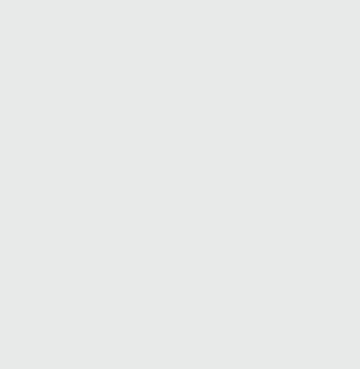
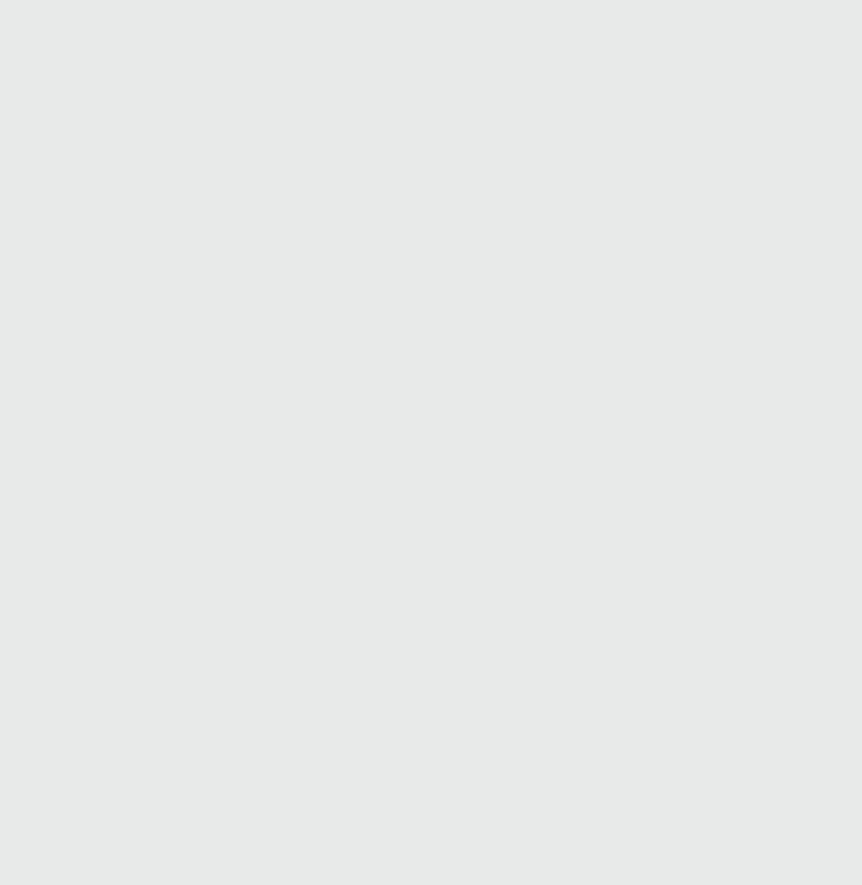
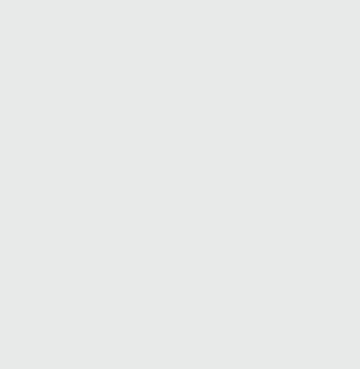

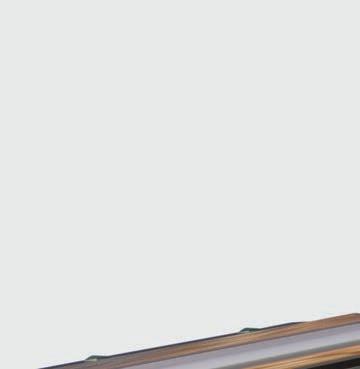
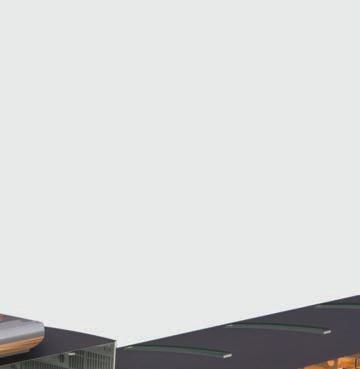
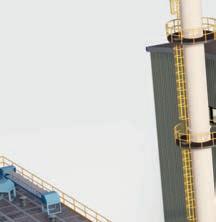


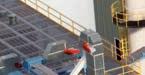

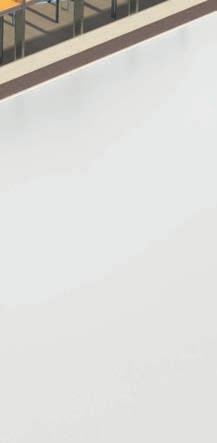

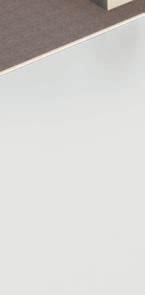
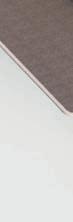


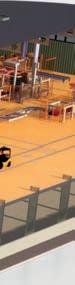

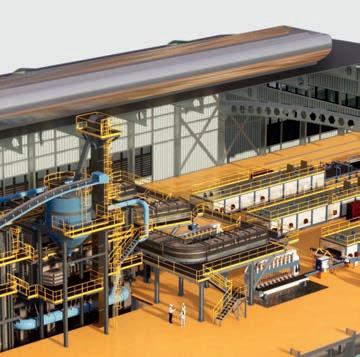
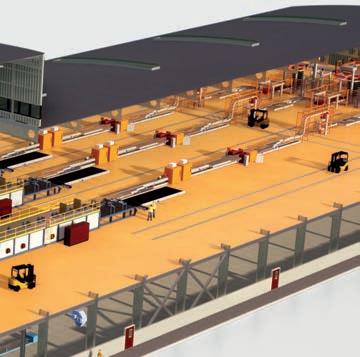
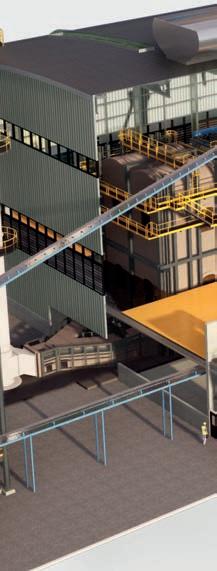

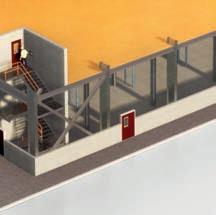
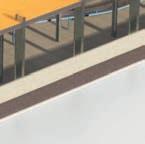
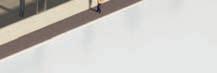

Career Dr Emrich has spent a substantial part of his career in diferent functions at Bosch Rexroth, first at its site in Lohr am Main, and then in Witten, both in Germany. He then had a spell at Weiss GmbH as a Vice President involved in its global operations. His previous experience dealing with topics such as assembly, logistics worldwide, purchasing, supply chain or lean management means he is in a good position for the job at Zippe. Since starting the role of Chief technology Officer at Zippe on July 1 last year, Dr Emrich has spent the past 12 months rapidly getting up to speed on the main industry topics and talking points, from digital glassmaking to sustainability. He has visited different Zippe customers in glass facilities around the globe and gained an understanding of the specifics of the glass manufacturing sector. He recognises the sector has become more concentrated in recent years, which provides opportunities for Zippe. For companies with facilities globally it is often difficult to find a global standard for each site. It takes time for global companies to change. Zippe, with its flexibility, speed and agility, is in a position to help if required. “Here at Zippe we can decide in hours. We have the advantage that we are agile, flexible and fast.”
Dr Emrich took advantage of the easing of restrictions to spend some time with his colleagues from Lahti in Finland in order to help accelerate the integration process. A successful PMI of decades-long competitors is hard work and not self-running. He has also spent time listening to Zippe’s own staff to discover its strengths and work out areas for improvement.“Theemployees here were open from the beginning and gave me the big picture about what works well and other things that have potential. It was important for me to get an overall picture. It is important for me to hear these opinions because we can only offer good solutions if we work together. I regard myself as a team player and it is important to integrate all the different groups.”
Chief Technology Officer focuses on sustainabiliy
Andreas Emrich is an industrial expert. While he may be a newcomer to the glass industry he has spent the majority of his career working in a variety of industry sectors. He aims to bring this experience and know-how from other sectors to Zippe to help continue the company’s growth. “Zippe has a large tradition with lots of experienced, skilled employees. But on the other hand, most have not experienced anything other than Zippe or the glass industry. So it could be an advantage to have someone with no experience of the glass industry to bring other experience, new ideas and impulses to the business,” he states.
erson it rofi e e hno o fi er Glass International July/August 2022 www.glass-international.com 23
Continued>>
Communication He sees his new role as comprising of two components: the internal and external. Internally he sees his role to optimise and accelerate process within Zippe and to change the mindset in some issues. For example, after the acquisition of Lahti by Zippe in 2018, the integration of the companies was delayed by the Covid-19 pandemic and the various travel restrictions and reduced personal contact.
Zippe’s new chief technology officer believes the future of the batch plant specialist lies in sustainable manufacturing technology. Here Dr-Ing Andreas Emrich outlines how this technology will drive the company forward.
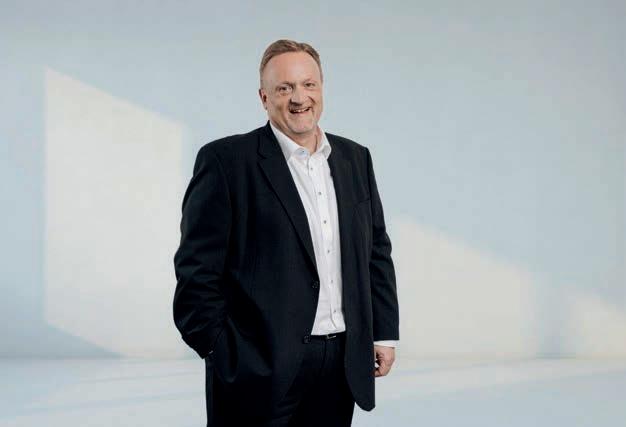
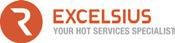
Chief Technical Officer, ippe, ertheim, Germany zippe de
“If our customers know in advance when they have to do something, then the situation does not come as a surprise and is easier to handle. “If we can support our customers in this regard, for example if we can check and control the drives or machines and can give them information about a change in behaviour, then a customer can prepare.”
Dr Emrich is impressed by Zippe’s global customer base as well as the amount of in-house knowledge the company has in specialist subjects. He has already witnessed Zippe’s strengths.
Similarly, he sees the rise in Industry 4.0, digital technology and components such as Virtual Reality and AI and being fundamentally important to the glass industry. While the subject of maintenance may not be top of everyone’s lists, Dr Emrich believes the rise of digital technology can have sweeping changes in this regard. The integration of VR means equipment can be installed and systems updated over the internet, rather than a member of staff undertaking a physical journey to a glass plant.
he anticipates the use of oxy-fuel and electricity in furnaces to increase. To meet this anticipated increase in demand Zippe is working on a oxy-fuel optimised batch preheater (BPH) and, together with one of the big global players in flat-glass on the first BPH for float.
Withincommitments.theglassindustry
“Here at Zippe we are working on solutions which meets all the specific requirements of our customers. For example, we can use our system in Wertheim to look on the systems of our customer and provide the necessary update.”
“In my experience in other sectors, we will implement good solutions and experiences from other industries which I believe can work here at Zippe and throughout the glass industry.”
“It is good to hear the needs directly from the customer and to discover what they expect from Zippe. We always aim to be better and to provide smart solutions. We want the customer to say that working with Zippe brings them added value and best life cycle costs.”
In-house knowledge Despite only being in the glass industry a short time, he believes he can bring fresh ideas from his time outside the sector.
“For example, Zippe has experience of materials globally. Its customers are around the world, but not all of them use the same sand for example. So there are very large differences depending on the region and Zippe has experience of handling all these different materials around the world. From my point of view this is a huge advantage compared to competitors.”
He adds: “Predictive maintenance based on knowing what will happen from my experience it is not such a problem for the customer but unexpected downtime and maintenance is a problem - and nobody likes that!
Dr Emrich will raise his profile in the glass industry even further over the next few months: he spoke at the ICG conference in Berlin in July, and will be at glasstec in Dusseldorf. This will give him the opportunity to integrate himself even further into the industry and discover further customer needs.
Digital glassmaking
“The glass industry is already started to change with its commitment to sustainability. But when you look at the discussions about climate, CO2 reduction, renewable energy and sustainability, I think we will see many more changes in the future. “It will be tough for many industrial companies but it also offers opportunities and is a good circumstance to change.”
Another advantage is it can source a large share of mechanical equipment from its own site. The mechanical department is next to the electrical department, each with more than 40 staff.
He has already had a similar experience when he was at Bosch. He was part of a team tasked with helping increase its energy-efficiency and reduce its global CO2 footprint in its production sites at 20 facilities around the globe. The company trialled and installed a variety of solutions at the various sites. While the company experienced pain in the short term in terms of terms of internal acceptance and willingness to change because of the transition, but in the long term it improved the company’s reputation and boosted its Environmental, Social and Governance (ESG)
“We have all these departments close by so can offer good solution with a combination of all these technologies and you can’t drive anything better or faster than your own company,” he states.
erson it rofi e e hno o fi er www.glass-international.com 24 Decarbonisation
Externally, he sees the main priority as decarbonisation, efficiency and the changing face of the glass sector as it faces up to the challenge of climate change and a more sustainable world. While he agrees it will be tough for many industrial companies to have to adapt to a world of renewable energy and reduced emissions, he believes Zippe is already far ahead in this respect.
�
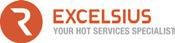
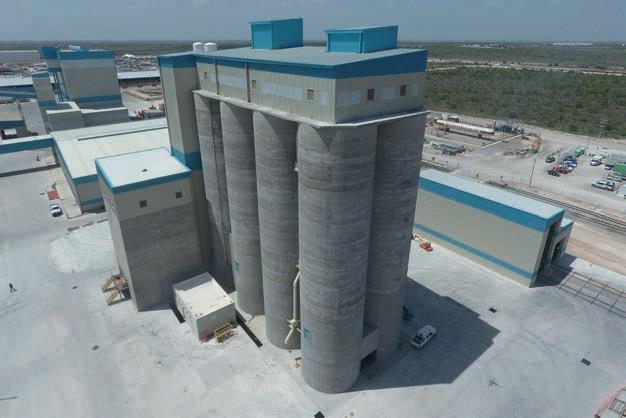
See you at Glasstec, hall 13 stand A31 Batch Plants | Cullet Plants | Engineering | Preheating | Factory Cullet Recycling | Glass Recycling Batch Charging | Glass Level Controlling | Modernization | Automation | Maintenance & Service ZIPPE INDUSTRIEANLAGEN GMBH | Alfred-Zippe-Str. 11, 97877 Wertheim, Germany | T: +49 9342 804-0 | zippe@zippe.de | www.zippe.de
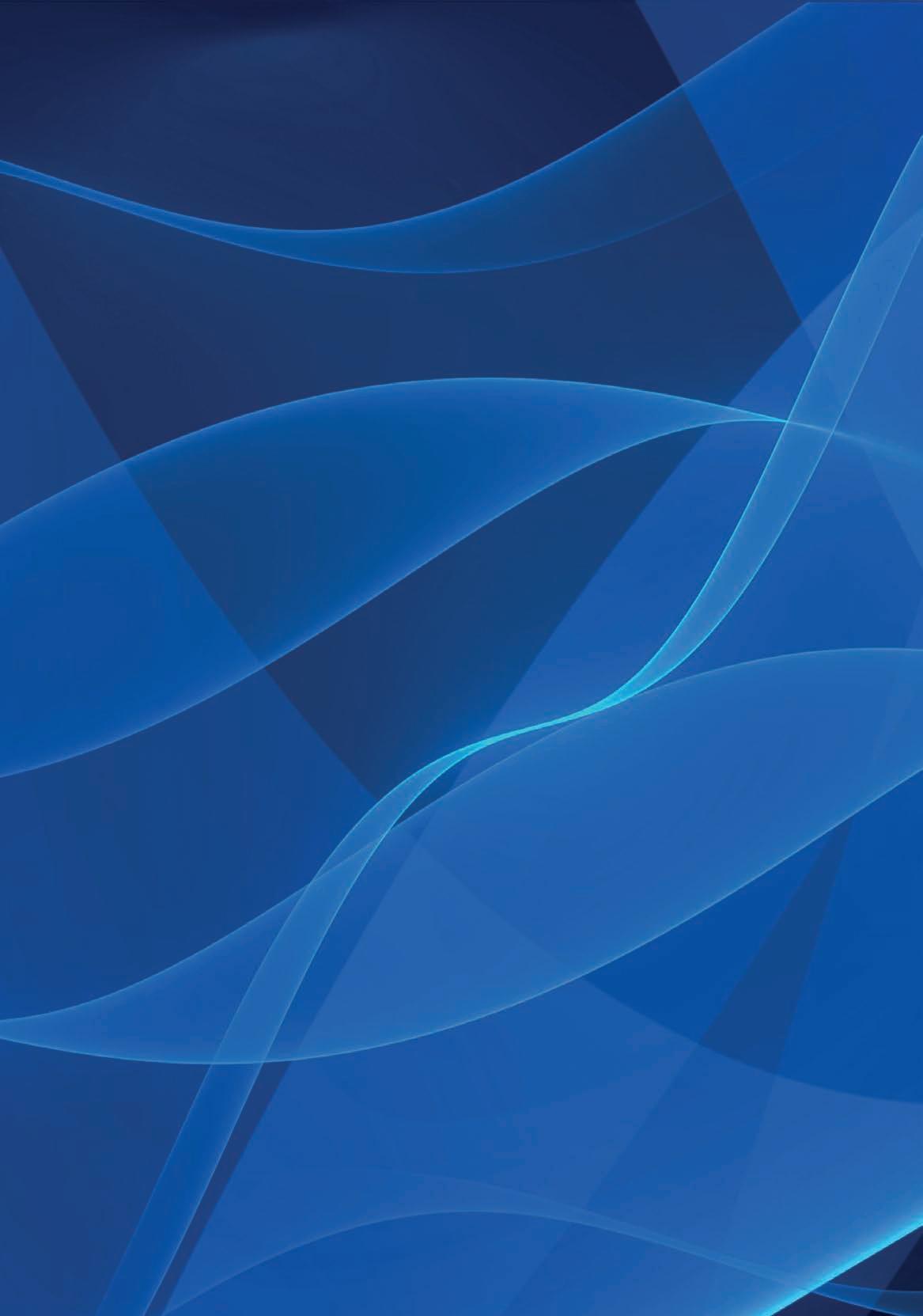
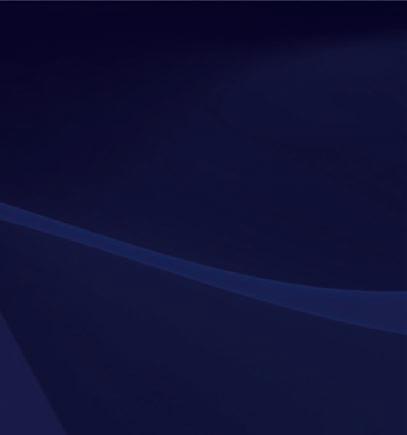

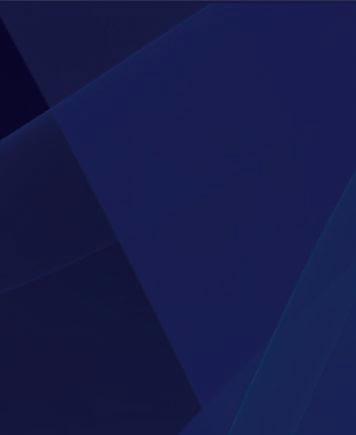
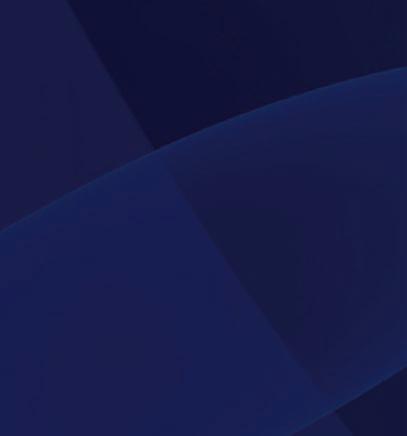
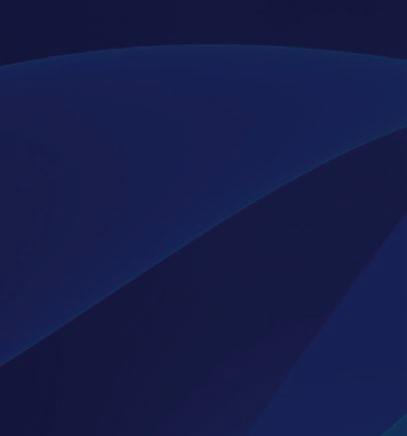



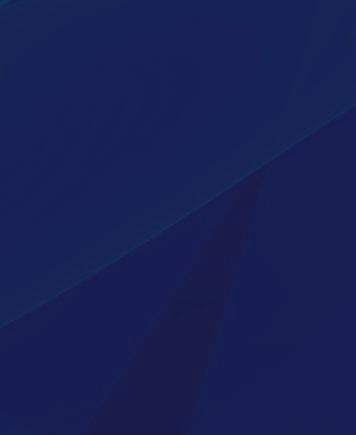
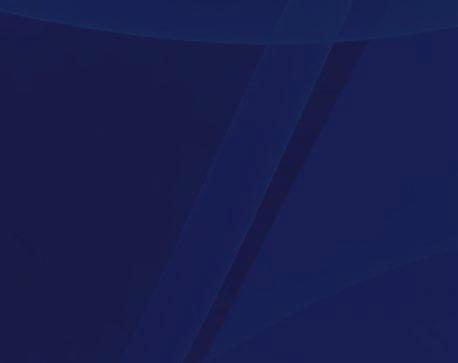
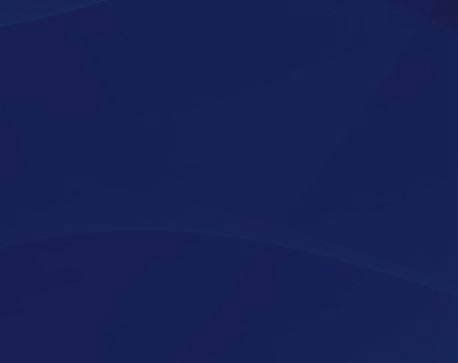
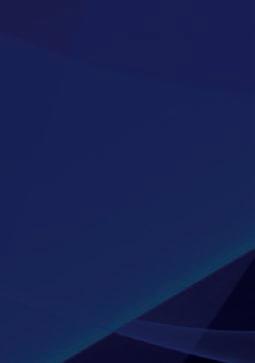

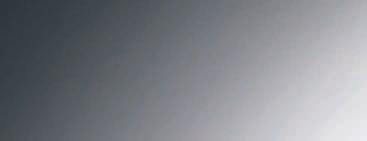

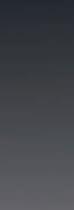

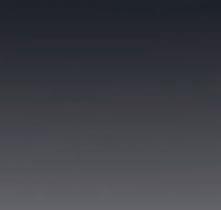
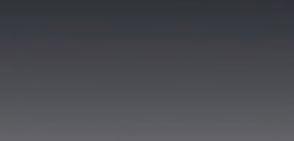
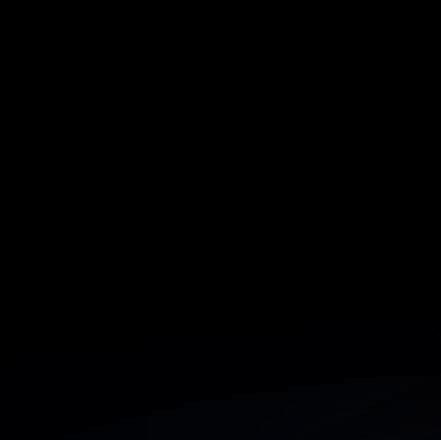
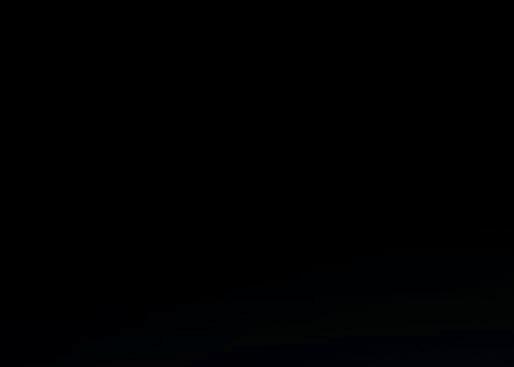
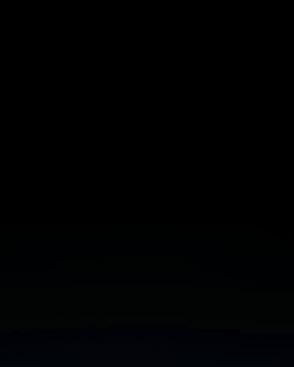
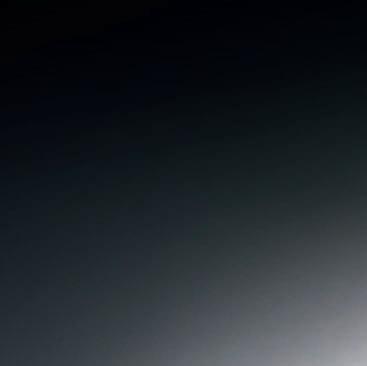
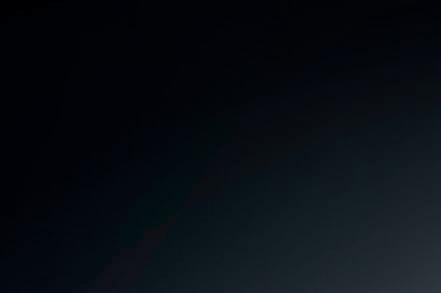
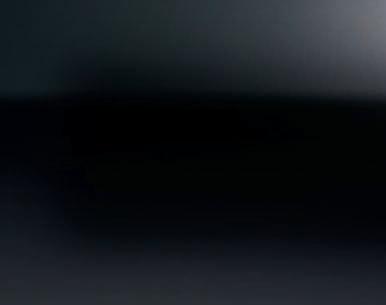
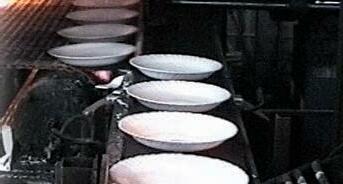
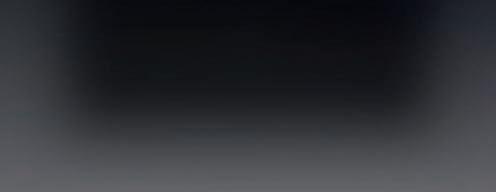

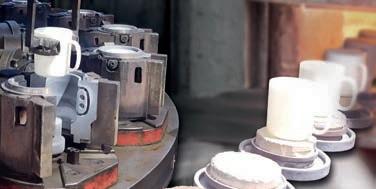
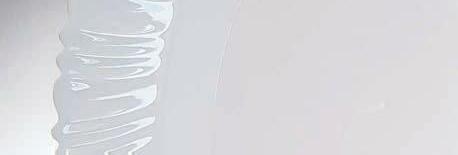
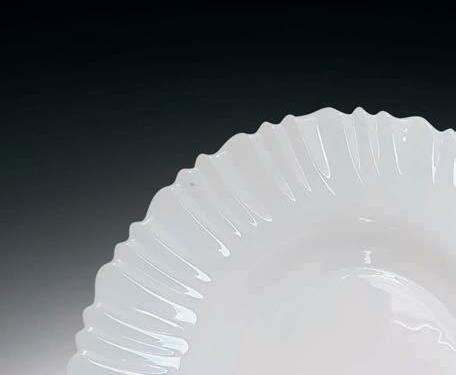
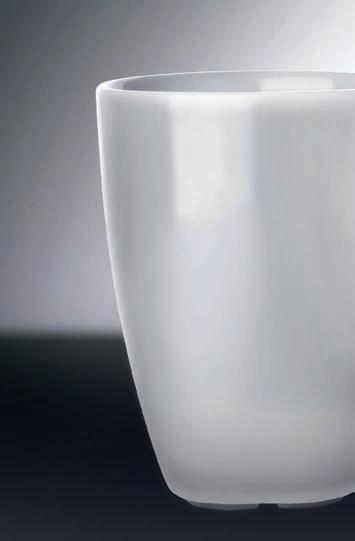
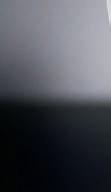
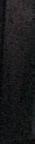
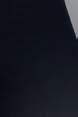
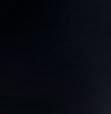



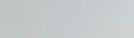
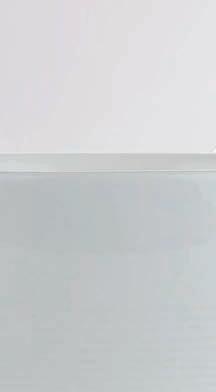

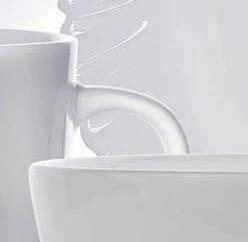





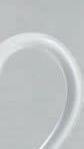

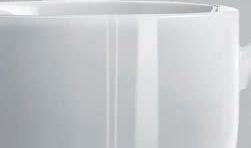

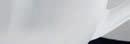
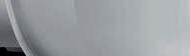

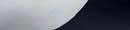

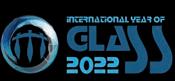
The same fuel was previously trialled successfully on a container glass furnace also co-ordinated by the UK’s Glass Futures. Active collaboration within the private sector, but also with the public sector, will help to drive innovation and progress as shown with the hydrogen and biofuel trials which were supported by the UK’s Glass Futures and funded by UK government as part of the Industrial Fuel Switching programme.
A second world-first trial was also undertaken in St Helens in early 2022 with the use of biofuels made from organic waste materials which powered the float furnace entirely for four days creating 165,000ft2 of the lowest carbon float glass ever made.
very little has changed in the flat glass manufacturing process since Sir Alastair Pilkington pioneered the current ‘float’ process for Pilkington (now part of NSG Group) in 1952. Improvements since then have incrementally improved efficiency and also supported new environmental legislation. Enhancements have been made on product development including revolutionary coating technologies such as Pilkington K Glass, Pilkington Activ and NSG TEC. These products, and many others, have supported energy efficiency globally by improving the thermal efficiency of buildings, reducing vehicle weight as well as supporting the generation of renewable electricity through solar power. But there is a recognition that in addition to the strong contribution of flat glass products in the fight against climate change, the manufacturing processes themselves also need to change, and quickly. There is much debate about how best to achieve this transition. NSG Group’s ambitious 2050 carbon neutrality target is now being actively pursued through a range of solutions and following a number of successful world-first trials over the last 12 months NSG Group is well placed to lead the way towards fully decarbonised flat glass manufacturing.Lastyear,NSG Group successfully manufactured float glass using hydrogen instead of natural gas at our float glass furnace in St Helens in UK, the very place where Sir Alastair Pilkington made his ground-breaking discovery in 1952. The world-first trial was a key step towards decarbonising the operations and demonstrated that float glass could be manufactured using an alternative, more sustainable fuel, without impacting the high quality and reliable production levels that can be expected from NSG Group. The trial was split into two separate trials. The first saw a part of the furnace fired on 100% hydrogen. The second saw a full-furnace hydrogen blending with 15% hydrogen combined with 85% natural gas.
Flat glass manufacturing is an energy intensive process which utilises mainly fossil fuels such as natural gas to achieve furnace temperatures of around 1600°c.
Decarbonisation Glass International July/August 2022 www.glass-international.com 27 Continued>>
Decarbonising the at glass process
The need to decarbonise the production of flat glass is no longer debated but exactly how this transition will take place is still very much up for debate within the sector.
Most of the emissions from the flat glass manufacturing process come from these furnace operations which typically operate continuously for 15 to 20 years before being Fundamentallyrebuilt.
Chris Dye highlights roup’s efforts to decarbonise the at glass manufacturing process which included successful hydrogen and biofuels trials at its il ington facility in t Helens.
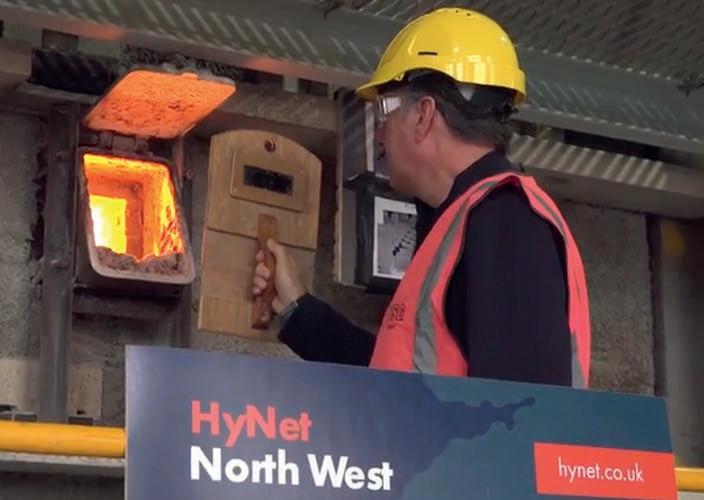
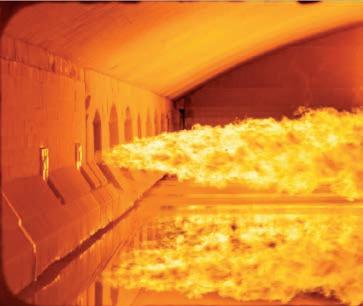
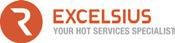
For 75 years, HFT has developed a reputation as a leading EPC contractor to the global glass industry. What you might not know is in that time, HFT has completed over 300 EPC projects in 47 countries for Float Glass, Container Glass, Fiberglass, and more. Whether it’s a greenfield glass factory in a far corner of the globe or a major facility reconfiguration just up the road, HFT has consistently delivered quality, efficient, and innovative project solutions. This performance, plus our commitment to customer satisfaction makes us the clear single-source choice to take your next project from concept to completion. vision. expertise.
The perfect partnership. www.hft.com | info@hft.comBooth C48-1 / Hall 13
Our
Somethanaresolutionsclearerothers.
Your
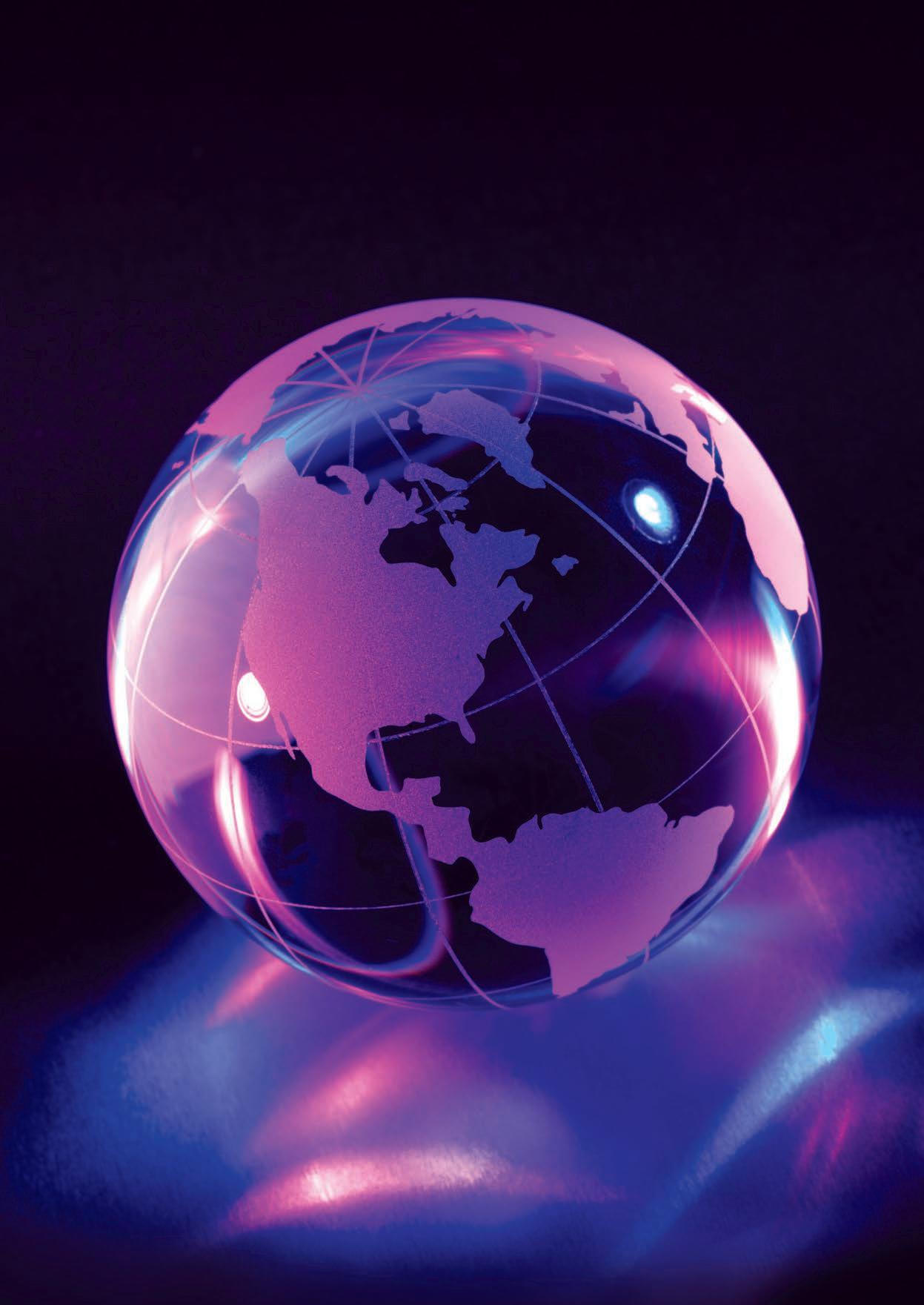
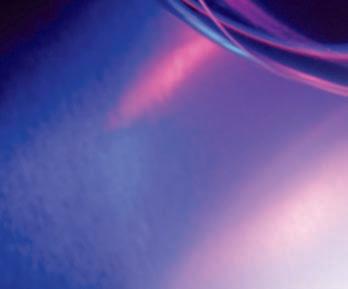

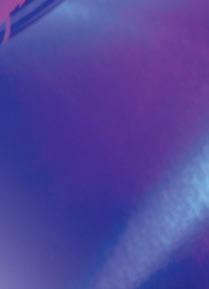




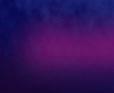



These alternative fuel projects are complemented by NSG Group’s renewable electricity strategy which seeks to deliver 50% of global electricity from renewables by 2024. A key milestone towards this target was the introduction of the group’s first Virtual Power Purchase Agreement in 2022.
The successful initial trials undertaken recently provide confidence that decarbonised solutions can be identified. The most appropriate furnace fuel is likely to differ regionally due to local factors such as fuel availability, cost and competition for such fuels. Of these, cost is discussed most of all, however the flat glass manufacturing’s scale presents both an opportunity and a threat. The large, constant demand for reliable and consistent fuel is crucial. Switching between fuels will need to be possible and this form part of the future planning and testing in addition to scaling up firing trials. But of course, cost is of crucial importance especially to avoid any risks of carbon leakage. Here, national governments must play an important role during the initial transition to financially support industries such as flat glass manufacturing to invest or commit to such decarbonised alternatives. By supporting wider rollouts of renewable energy and carbon dioxide infrastructure, both crucial to support decarbonised glass manufacturing, it will be possible to see quicker and deeper progress. Such an approach has been widely successful in the renewable electricity markets and has now led technologies such as wind and solar to become the lowest cost of generation in many countries. By providing such support, it should be possible for governments to work within a safer environment and therefore transition at a faster pace. Of course, efforts continue to reduce the amount of fuel needed. Here cullet will play a crucial role due to its low embodied carbon content. Increasing the percentage of cullet will help to reduce the need for any fuels and should help to produce lower carbon end products.
Given that the furnaces due to be rebuilt in the early 2030’s will still likely be operational by 2050, NSG Group’s carbon neutrality target date, the challenge becomes more immediate. There are many options available including further efficiency, carbon capture, cullet and alternative fuels. It is likely that all of these are likely to be needed and that we will see more variability between furnaces than currently.
The progress that NSG Group has made in pioneering firing trials during the last 12 months has given confidence to the glass sector that such targets can be achieved. �
Decarbonisation Glass International July/August 2022 www.glass-international.com 29
SU PPLY CONFIDENCECHAIN 5 LOCATIONS ACROSS UK AND IRELAND • Soda Ash • Sodium Sulphate • • Feldspars • Chrome • Barium Sulphate • Sodium Nitrate SPECIALISTS IN THE GLASS INDUSTRY +44 (0)20 8332 Contactsales@newport-industries.com2519us:+44(0)20 8940 6691
The agreement signed with Spanish utility EDP Renewables will see approximately 100 GWh’s of renewable electricity supplied to NSG Group’s European operations reducing carbon emissions by approximately 80,000 tonnes per year. Such projects in combination with electro-boost projects can help to further decarbonise NSG Group processes.
*Renewable Energy Manager, Pilkington UK, NSG Group, St Helens, UK www.nsg.com
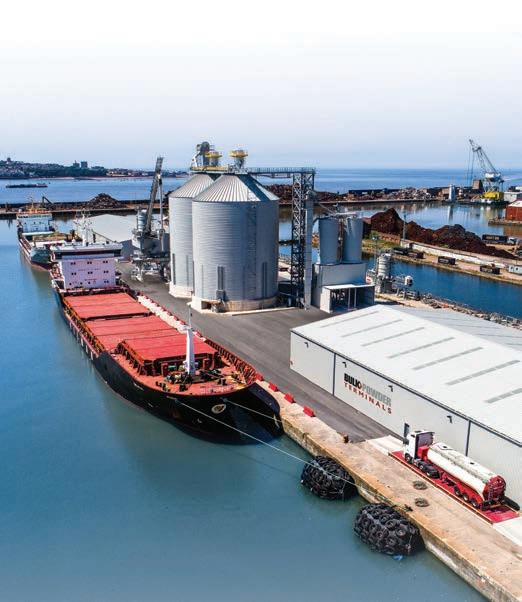
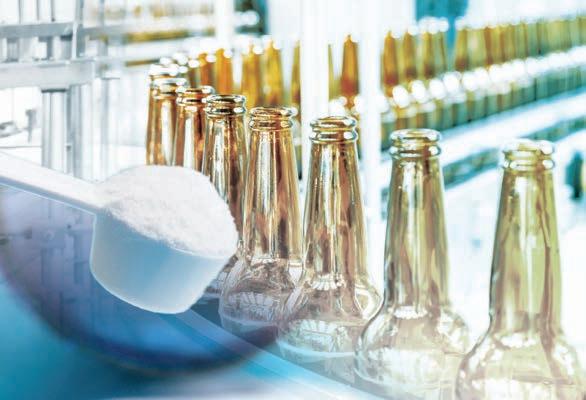
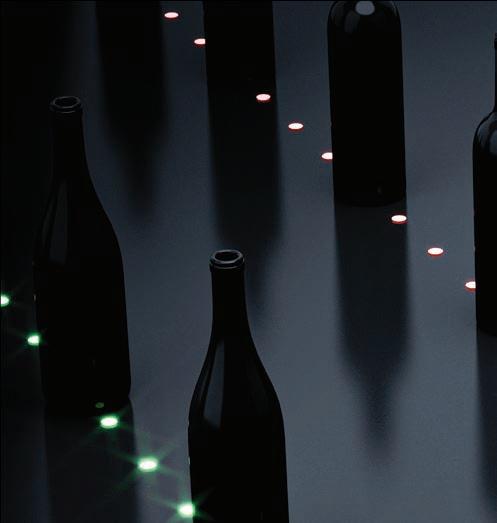

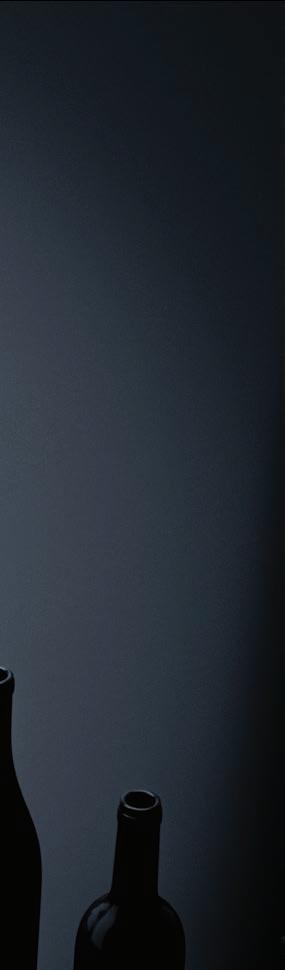
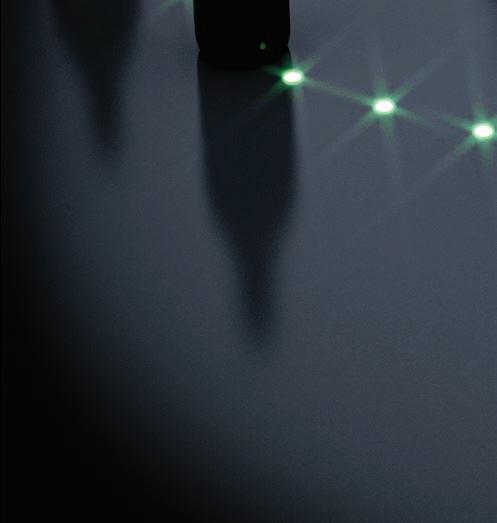

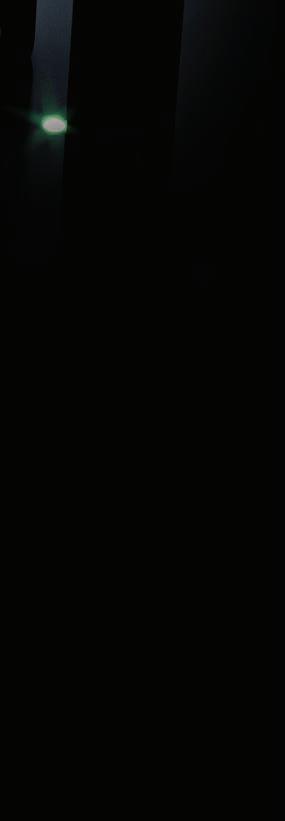


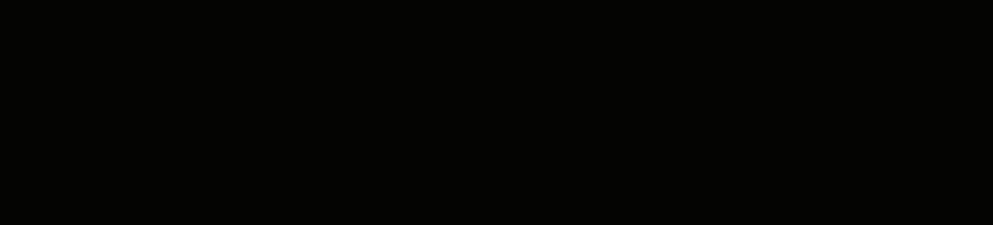
The glass industry is entering a new era where new key challenges are Whilearising.innovation within the glass industry has always been core to its success, whether by continuously enhancing energy and furnace performance, glass quality or promoting circularity, we see a radical paradigm shift related to carbonneutrality.Thisshift
A focus on decarbonisationLaurentCohen-Scali* shares his insights into how SEFPRO’s refractory solutions have a key role to play in the decarbonisation of the glass industry.
Refractories Glass International July/August 2022 www.glass-international.com 31 Continued>>
is the greatest challenge faced by the world today. As a specialist refractory solution provider to the glass industry, Sefpro has a key role to play. Helping our customers to meet those new strategic challenges and combine performance with carbon neutrality at each step of furnace life is the essence of our vision: together ‘we shape a carbon neutral glass industry, for a brighter future’. A future made of zerocarbon glass for the generation to come. Carbon-neutrality is our clear objective and we will continue our efforts, step by step, one furnace at a time, thanks to the commitment, determination and knowhow of our Achievingteam.carbon neutrality also means coming together as an industry, combining efforts with all stakeholders. Our refractory solutions have a key role to play in the decarbonisation of the glass industry, but it is only a part of the journey.Weare developing partnerships with major glassmakers and industry partners to support the transition to carbon-
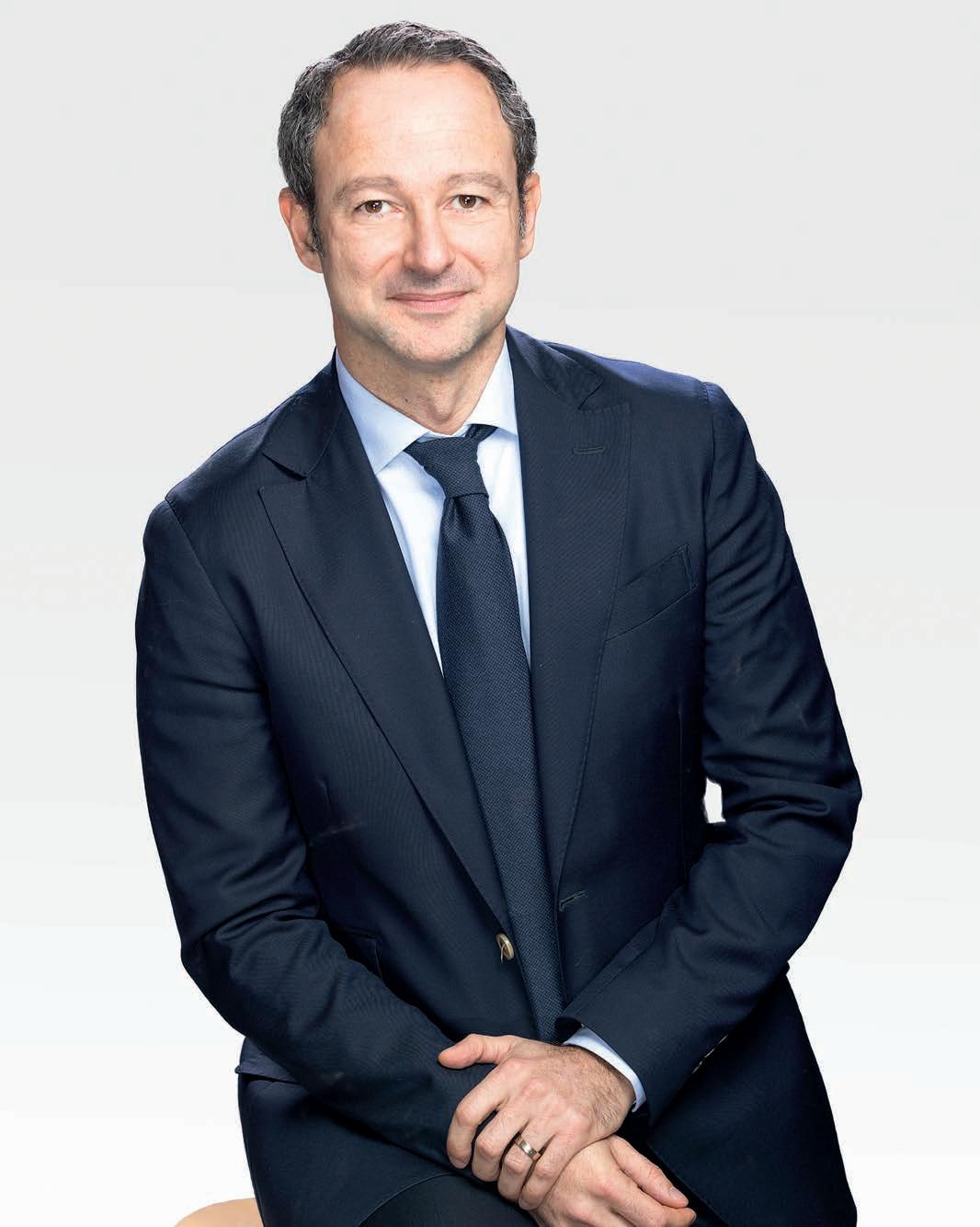
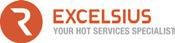
WE SHAPE A CARBON-NEUTRAL GLASS INDUSTRY FOR A BRIGHTER FUTURETheglassindustry is entering a new era. The industry must come together to achieve a common goal. We are fully dedicated to and streamlined for the special requirements of the glass industry. SEFPRO offers you high-quality refractory solutions and services for your entire production process and beyond. For a brighter future, we are there for you with innovative products and services for the furnace lifecycle and beyond. Let‘s shape the future together. at Convention Center Düsseldorf, Germany Booth: 13A47 September, 20-23, 2022 Visit us at: www.sefpro.com
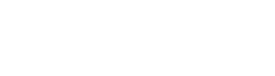

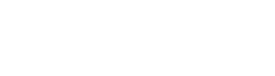

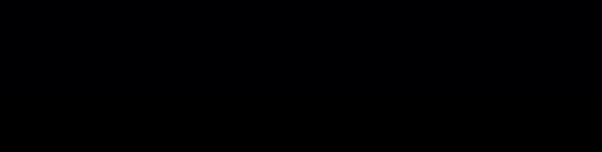
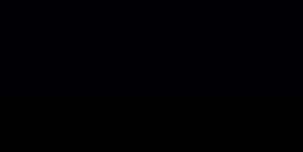
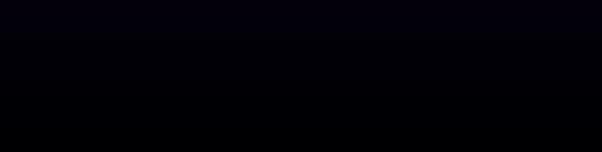
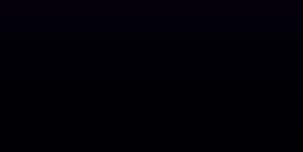

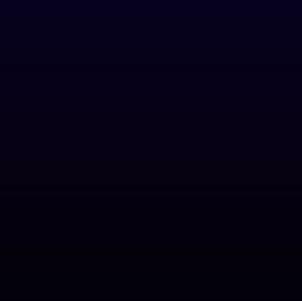

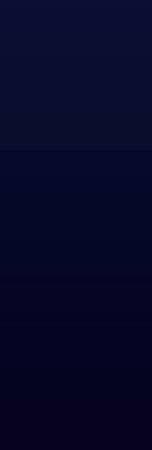

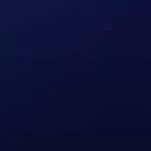
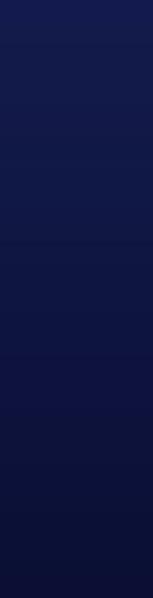


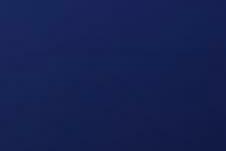
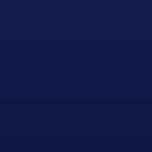


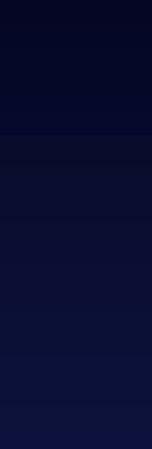

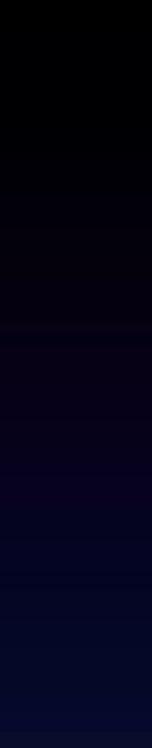
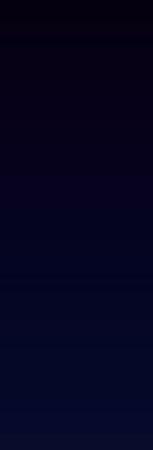
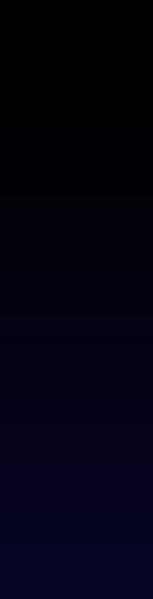
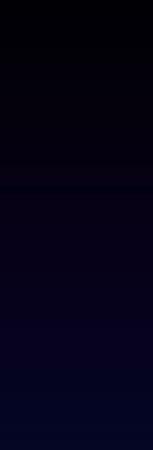
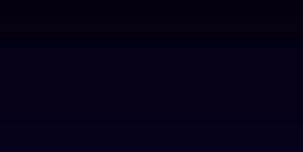
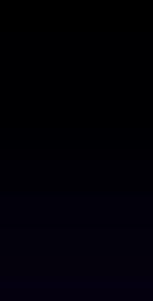

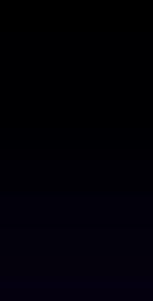
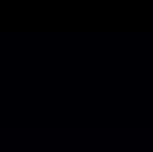


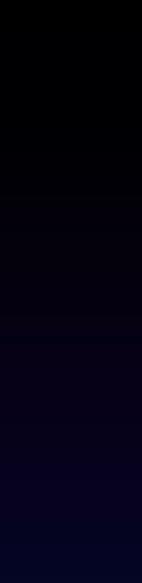
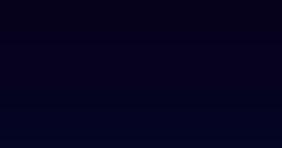

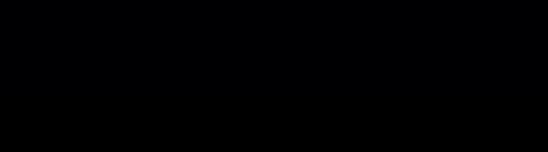

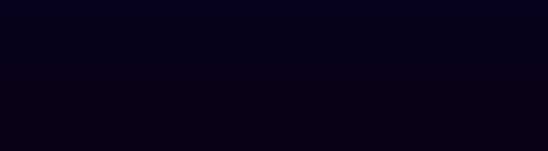
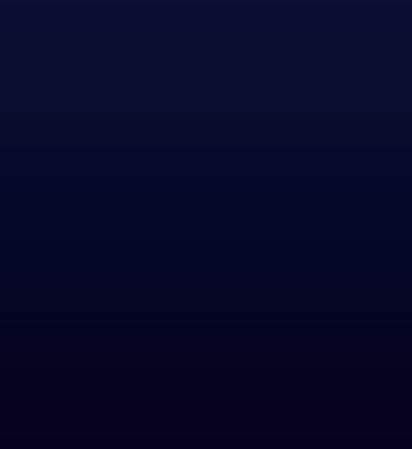

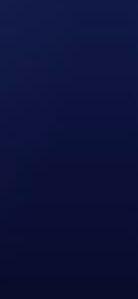
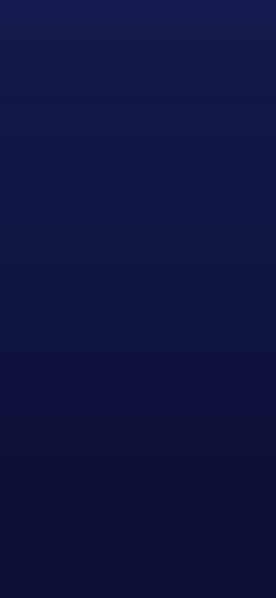
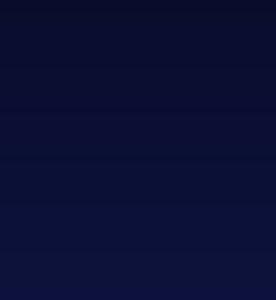
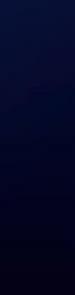

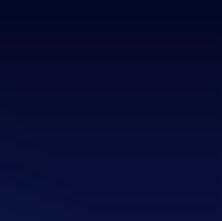
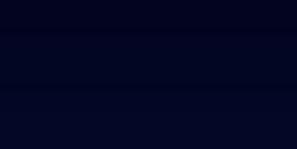
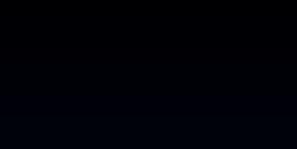
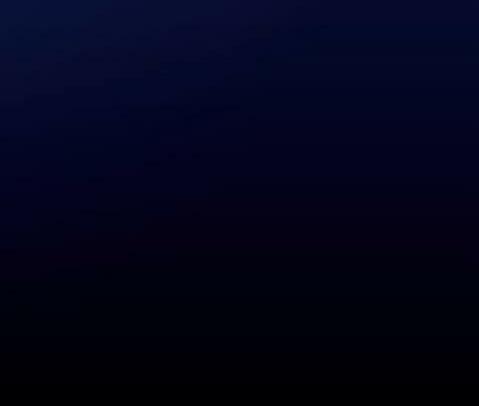
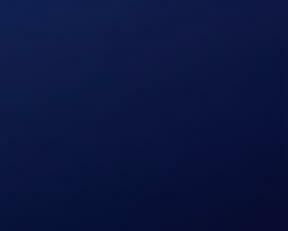

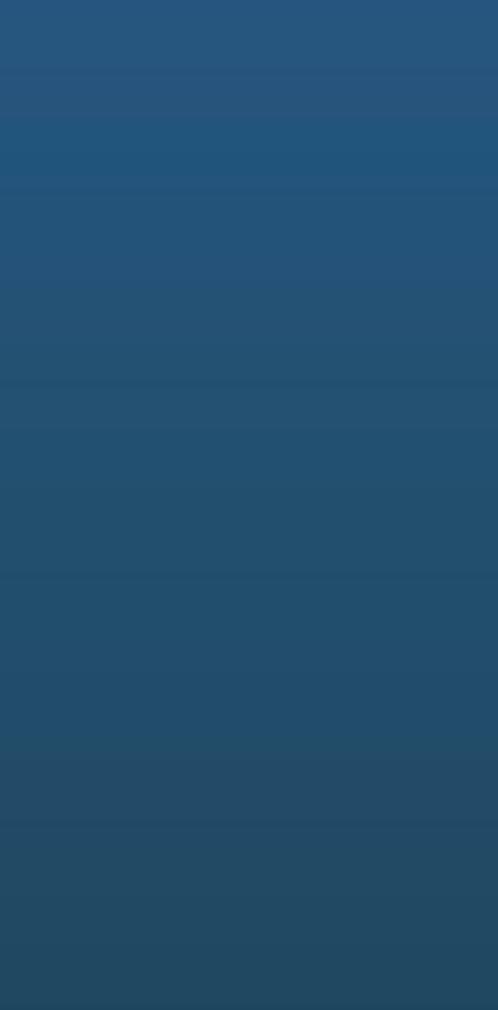


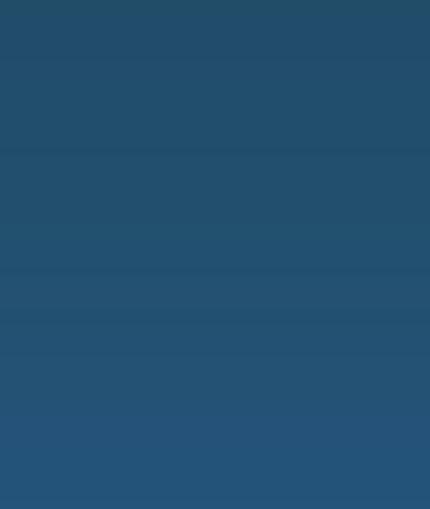
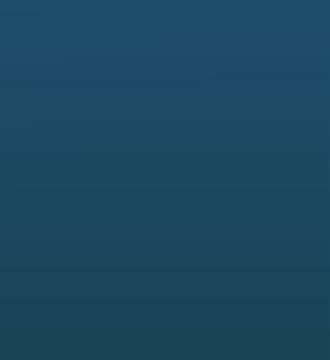

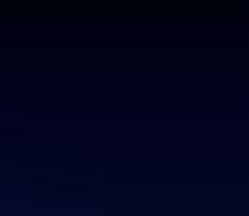
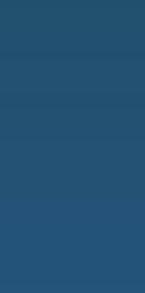
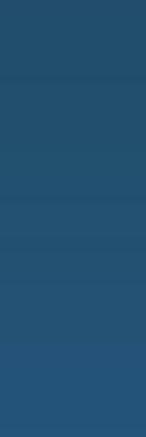
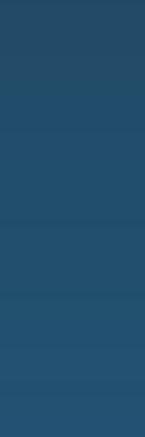
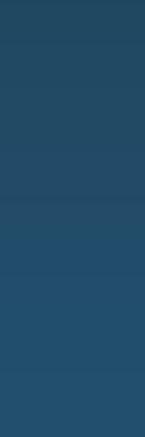
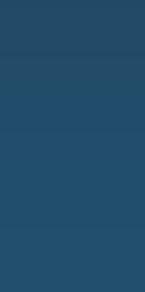
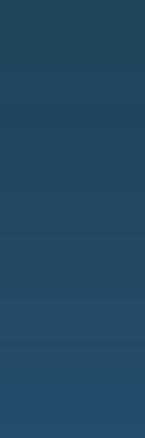
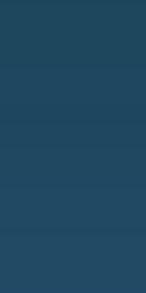
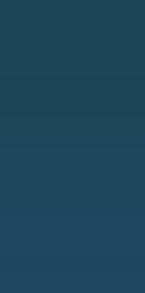
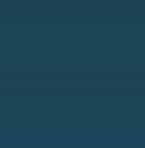
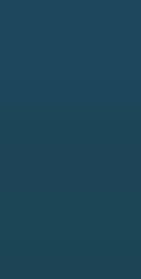
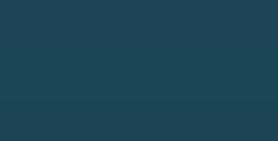
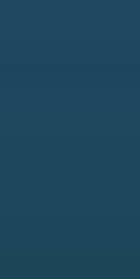
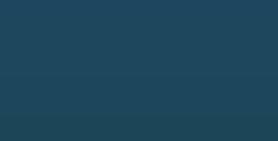
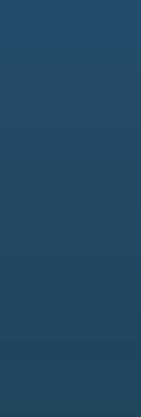

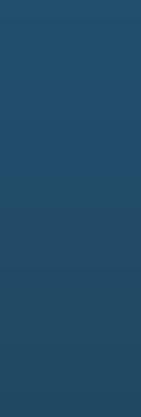
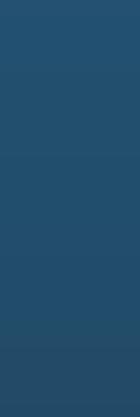

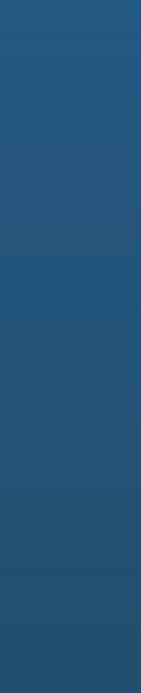

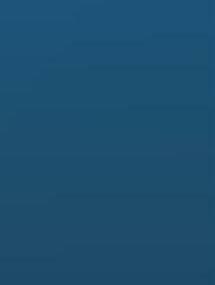
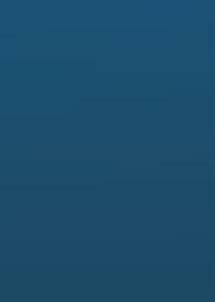

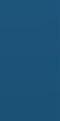
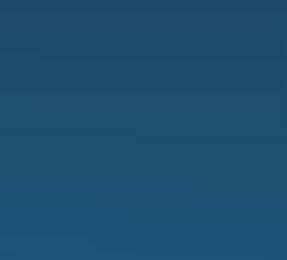
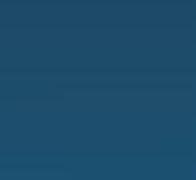
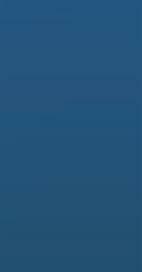
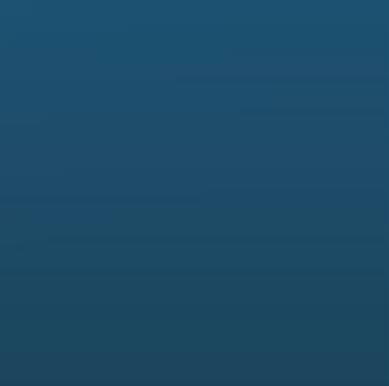
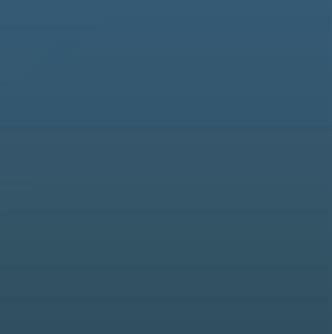
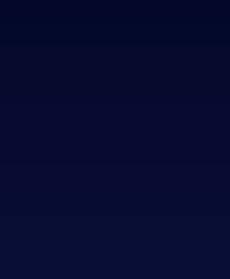
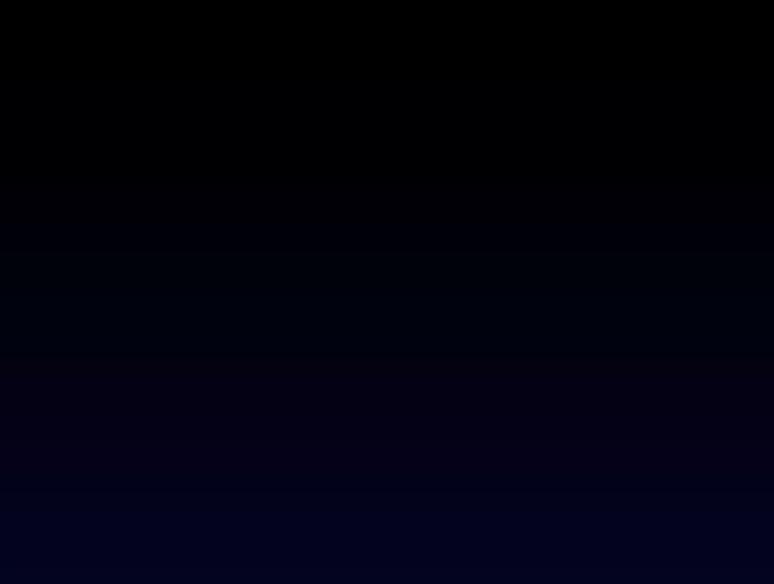

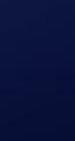
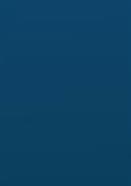

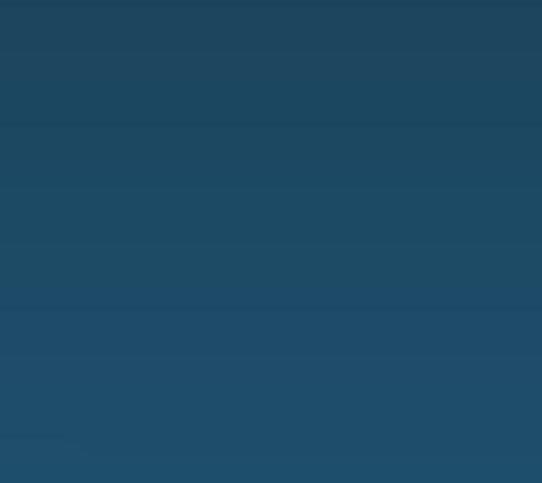
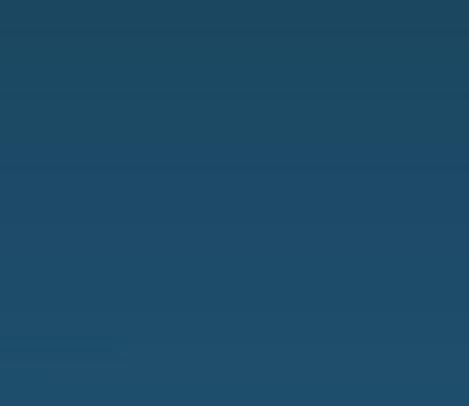
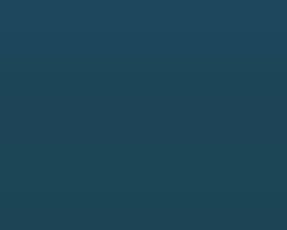
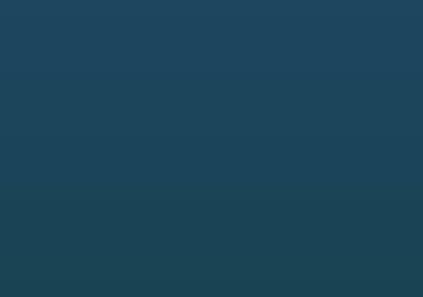
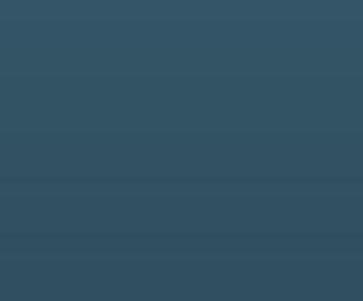
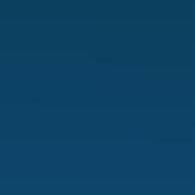
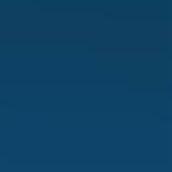
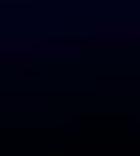

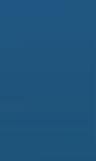
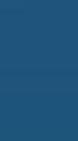
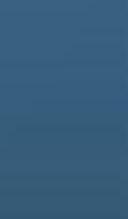
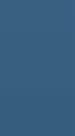
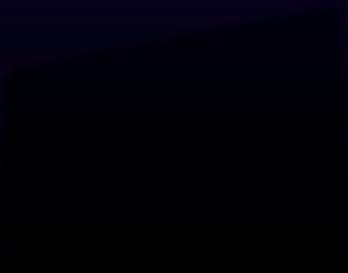
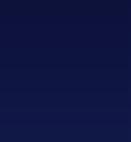
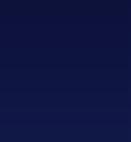
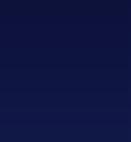

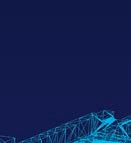
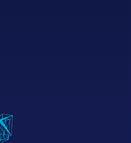
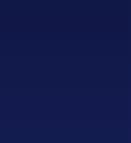
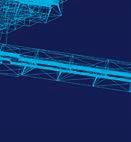
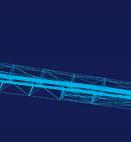
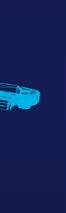
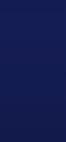


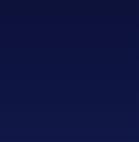

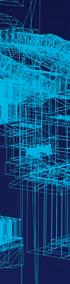

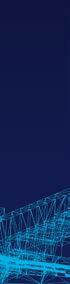
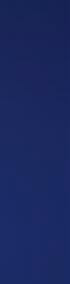
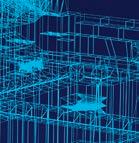
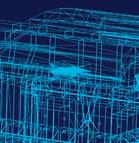
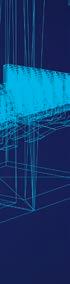

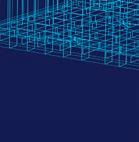
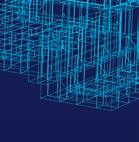
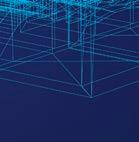
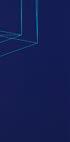
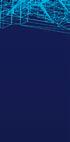
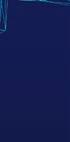

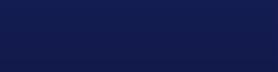

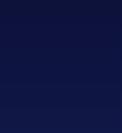

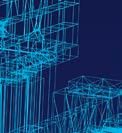
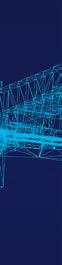
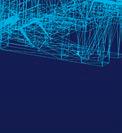
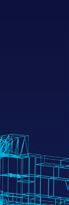
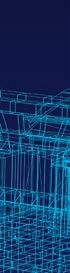
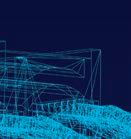

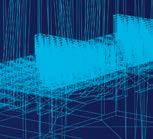
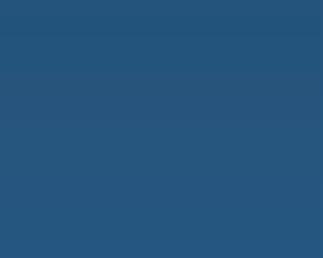
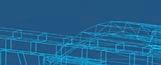
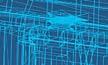
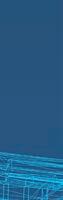
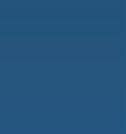



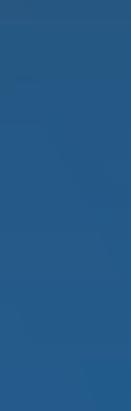
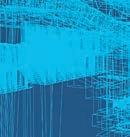
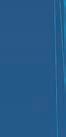

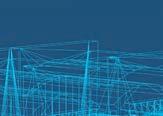
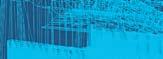
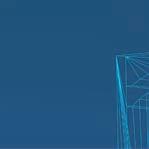

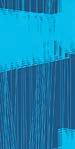
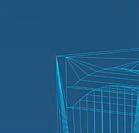
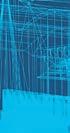
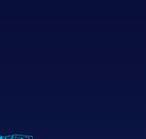
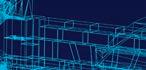

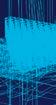
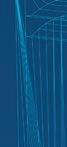
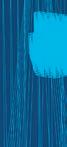
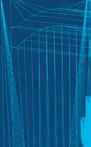
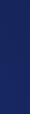


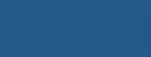
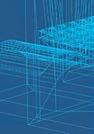
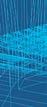
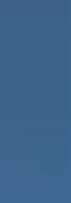


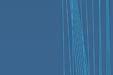

Another area of development is real time monitoring of regenerator plugging and of sidewall corrosion. Acquisitions We are delighted to welcome Monofrax and AFR to the team. Beyond new products and capacity, they bring a new perspective and customer knowledge which will enhance our ability to serve our customers locally. Thanks to these acquisitions, our footprint is truly global, which allows us to optimise our supply chain and continually be at our customers’ side to co-develop new solutions for carbonneutral glassmaking. glasstec glasstec is a major event for the glass industry and the ideal place to share our new vision. It is also a great opportunity to present our new solutions, demonstrate the expertise of our team and finally meet again with our friends and colleagues of the glass world. �
Refractories neutrality. We are collaborating with PaneraTech to help glassmakers optimise use of their refractory assets and accelerate digitalisation of their furnaces. Actions and commitments We acknowledge that, as a key supplier to the glass industry, we weigh on our customers’ scope 3 carbon footprint. Our environmental impact must also be limited to ensure health and safety of our employees, our partners and neighbouring communities. Our sustainability roadmap is clear: be carbon neutral by 2050, with objectives to complete by 2030 on water usage, CO2 emissions, circular economy and product stewardship. In five years, we have already made substantial progress towards achieving these objectives. For example, we managed to reduce water withdrawal by 20% in our plants, reduce our non-recoverable waste by 84% while production increased, and our efforts allowed us to cut 82,000 tons of CO2 emissions on our sites. From the first fused cast refractories in Modane in 1929, Sefpro has supported glassmakers in all of their challenges. All along our history, we have developed solutions for the most demanding glass applications such as pharmaceutical or display glass, this experience and expertise is invaluable today to keep developing new solutions. Achieving carbon-neutrality will mean going beyond providing the highest performance and quality refractory blocks to becoming an enabling partner to our customers. Decarbonisation developments Some of our existing solutions remain relevant to address these challenges. Once developed for the display market, Xilec being the highest resistivity refractory on the market is a great choice for electrode blocks in furnaces with increased electrical boosting. Our fused cast alumina ranges will prove essential to hydrogen and oxygen furnaces. Services – from numerical simulation to 3D scans – will support customers in making the best refractory choices for their furnaces. Our teams are also working on new solutions and new business models. XiROC – a new refractory material combining the best of AZS and high zirconia- was launched this year.
*Vice-President SEFPRO, France www.sefpro.com

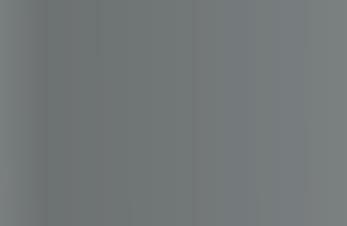
Digitalisation Glass International July/August 2022 340 www.glass-international.com
The Siemens Glass Team is based in Karlsruhe, Germany. The team is refreshingly different and united in its passion for glass and glass manufacturing. What motivates us is the fact that we’re able to make a difference in the industry. By “us” I mean a complex network of international colleagues. For example, colleagues in Erlangen, Germany, who provide machine builders in the glass industry with perfectly customised automation and drive solutions. Siemens is in constant contact with stakeholders who are similarly motivated, which includes glass manufacturers, processors, machine builders, plant section suppliers, planners, system integrators, technology companies, and even representatives in research, science, and professional associations. Innovations can only be advanced and implemented in the broader context of the entire glass industry ecosystem. At Siemens, we’ve summarised this approach in the motto: “Clear view on glass.” Our approach is to interact with all industry representatives on an equal footing. To do this, we need to acquire a clear view of what the individual stakeholders are concerned about, drawing on our profound knowledge of the industry and as experts in the fields of automation, digitalisation, and security as interdisciplinary issues. The “clear view” also means an increasing reliance on data rather than experience. In other words, clarity through data, which first must be collected, then evaluated, and finally interpreted. In the International Year of Glass, we’re looking forward to having attention drawn to an essential industry whose products are often taken for granted much like the air we breathe – or are even totally unknown. We all drink without putting too much thought into the glass we drink from; we all look out the window – but the fact that an airbag has a glass seal or that a space telescope relies on this same miraculous material isn’t common knowledge.We’realso hoping to highlight many technological refinements, from the nano effect and integrated electronic shading and targeted light to radio wave transparency in panes and all the different types of glass. It’s also more important than ever that as representatives of the industry we call attention to how sustainable glass is, especially through recycling. Close to 100% of the material can be reused in the manufacture of new glass products, and recycled glass currently accounts for up to 90% of the raw material used in a glass melt. This also significantly reduces energy requirements.
Digitalisation could provide solutions for the industry’s sustainability goals
The glass industry is focusing sustainabilityon more than ever, and on saving energy in particular. situation.industrycandigitalisationautomationinsightsWachtmann*Tobiasprovidesintohowandsolutionsstrengthentheinitspresent
Digitalisation Over the past few years, in-person Tobias Wachtmann, Head of Glass & Solar business at Siemens. Image source: Siemens.



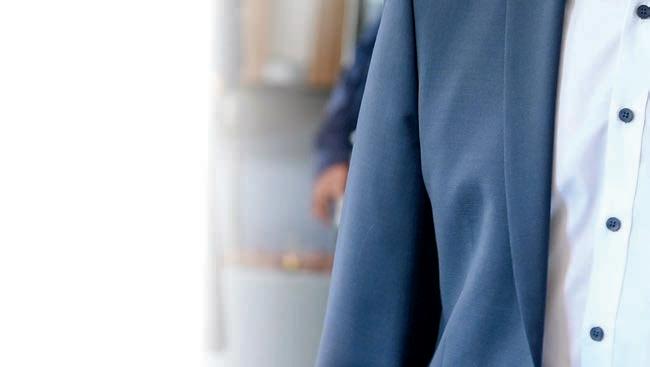

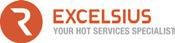
Digitalisation Glass International July/August 2022 www.glass-international.com 35 Continued>> meetings have become rare. However, rather than hindering Siemen’s business activities, this period inspired a lot of activity. It acted as a catalyst for practicing new and even more digitally-oriented processes.Ourregular interactions with customers, partners, and professional associations are essential to our everyday work. They’re the only way we can translate desires into solutions. There are two sides to interacting on a screen. On the one hand, we no longer had to prepare for trips, and travel time was eliminated, which made us more flexible andOnefficient.theother hand, our work intensified: a project meeting with Chinese customers in the morning, virtual participation in a glass conference in England in the afternoon, and countless team meetings in Thebetween.challenge was to provide the usual depth of information, because the length of video calls is usually limited and their content is often fixed. If we wanted a thematically flexible and creative conversation like those we might have at a watercooler or at business lunches, we had to schedule a separate meeting. Digitalisation solutions are also delivering measurable benefits for customers. For example, specialty glass manufacturer Schott was planning a new construction to expand plate-glass production at its site in Bolu, Turkey.
Using simulations, the company was able to rethink and calculate processes, material flows, logistics workflows and, most importantly, all what-if scenarios beforehand. The experts benefited from their own experience and from Siemens’ Tecnomatix Plant Simulation software. With a virtual twin of an entire production plant, Schott was able to prevent misdirected investments and save resources.Another example from Schott is when the company linked numerous simulation tools together prior to building a new machine. Before the loader of raw glass for the ceramic-glass cooktop production process was built, Schott used digital twins to simulate engineering and control as well as a behavioural model, kinematics, and machine commissioning. The abundance of benefits that resulted are literally paying off. This project was the first time Schott linked its existing and proven Process Simulate robotics simulation software to Create MyVirtual Machine/Operate software, which was new to SimitSchott.software from Siemens – which already had a long track record at Schott – served as the link between Create MyVirtual Machine/Operate and Process Simulate. More developments by the machine builders and plant engineers themselves ensure that glass manufacturers can take advantage of significant innovative advances, as the examples of Forvet, Sklostroj, and Fama demonstrate. Automation To conserve energy, all improvements must be based on a consistent, endto-end, state-of-the-art technological foundation of production. Integrated automation is practically a necessity –it’s not optional. For example, WiegandGlas, which is located in Schleusingen, Germany, and is one of Europe’s most advanced container-glass factories, relies on an integrated automation concept that employs Siemens’ Simatic PCS 7 process control system. With this foundation, a variety of software-based solutions can be implemented: for example, to increase energy transparency and efficiency. This isn’t applied across the board as a panacea but only after an analysis is performed. Each company has its own goals and requirements, so our aim isn’t to sell specific software but rather to provide our customers with comprehensive advice on what technological resources make sense given their objectives. With so many options, finding the right solution for customers can be a complex issue. We recommend that our customers start by taking part in what we call Digitalisation Consulting. We meet in workshops and closely examine the company’s goals and market requirements. Are they looking for more flexible production Greater efficiency Reduced costs Higher quality and or sustainability Our teams apply all their experience in a comprehensive discussion of these issues. They combine industryspecific knowledge on everything from raw materials to the finished product with expertise that extends to the field, automation, process, and corporate management levels and includes specific associated IT requirements. Our customers also benefit from a broad-based partner network. Just look at the examples of Horn Glass, Zippe, and Grenzebach, with whom we’re working closely on future issues. The above consulting results in the creation of a digitalisation roadmap that examines, highlights, and evaluates specific requirements, business models, and existing infrastructures (IT and OT). The digital transformation can then proceed based on the roadmap’s plan. In addition to digitalisation options,
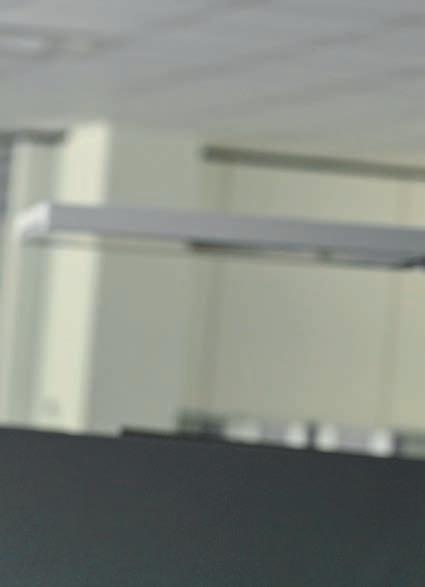
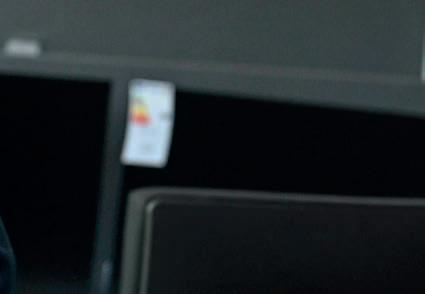
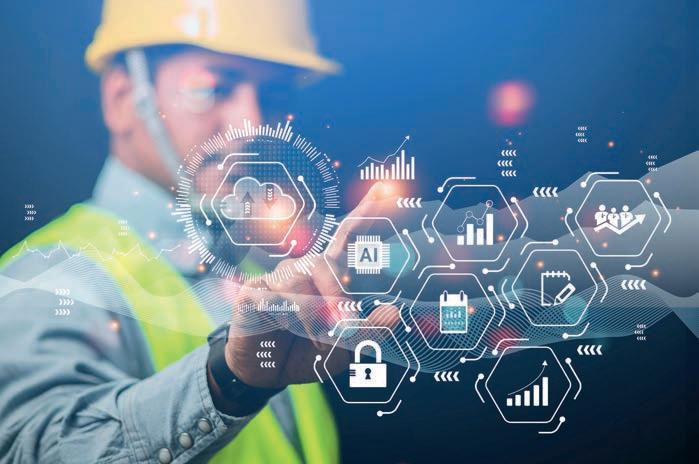
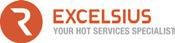
Image Siemenssource:
* Head of Glass & Solar business, Siemens, Karlsruhe, https://www.siemens.com/global/en.htmlGermany
Decarbonisation
The glass packaging manufacturer Vetropack, for example, wanted to implement a uniform and connected energy management system in addition to energy procurement. Its requirements ranged from planning and strategic procurement to recording consumption and auditing, all of which could be covered by our holistic approach using the Simatic Energy Manager PRO energy management system and add-ons for the structured procurement of energy. The Austrian glass manufacturer Stoelzle is having similarly positive experiences with the software. The company’s goal was to reduce energy consumption by 20%. According to Stoelzle, knowledge provided by the system alone was responsible for a three to five percent reduction.
Digitalisation Glass International July/August 2022 360 www.glass-international.com it also contains ROI calculations. The completion of the roadmap signals the transformation into a digitally operating glassOncompany.ourpart and at the customer’s request, we offer an integrated solution portfolio comprised of hardware, software, communication, security, and services. Many customers have already traveled this path with us, including Guangdong Huaxing Glass in China and Steklarna Hrastnik in Slovenia.
Decarbonisation is essential. It’s important that we actively develop melting technologies that aren’t dependent on gas or oil. A carbon-free economy requires a consistent conversion from fossil fuels to alternative energies without endangering the security of supply: for example, by making sure that storage media are available. This is an extremely complex task. Take the examples of our customers WiegandGlas and Heinz-Glas in Bavaria: HeinzGlas assumes that it could become less dependent on the energy market if it owned 10 wind turbines. Although this sounds realistic on the surface, it hits a wall in terms of scaling. Based on its own data, WiegandGlas calculates that it would need 100 wind turbines. Taken together, the glass companies in the region around HeinzGlas and Wiegand-Glas alone consume enough electricity to power a city of 400,000 inhabitants. Because these furnaces operate around the clock, wind energy also needs to be stored to cover windless days. This is where hydrogen comes in, Tobias Wachtmann has overseen the global Glass & Solar business at Siemens in Karlsruhe, Germany, since June 2020. The 46-year-old began his career with the company in 2000. After training in industrial technologies, he occupied many positions in sales at the Siemens subsidiary in Cologne. In 2012, he transferred to the process industries headquarters in Karlsruhe, where he began enthusiastically supporting customers in the glass industry. Since 2017, he’s worked in Vertical Glass & Solar, specialising in Account Development. although its production also requires electricity from renewable sources or natural gas. Despite the obstacles, this was the path chosen by our Slovenian customer Steklarna Hrastnik. The company uses solar energy to generate green electricity for producing and storing hydrogen, which is added to the natural gas used for the glass melt. Steklarna Hrastnik’s goal is to replace 50% of its primary fuel with hydrogen, which would reduce its greenhouse gas emissions by about 20% in the medium term. We see these as promising initiatives that need to be promoted in collaborations with research, business andSustainabilitypolitics. also means safeguarding jobs. The German machine builder Waltec is an example of how a win-win situation can be turned into a win-winwinForsituation.decades, the company has been innovating its glass presses side by side with Siemens. As a result, it’s been able to offer glass tableware manufacturers like Trend Glass exactly what they need: sustainable concepts like fully electric e-servo presses. Since Trend Glass has been using the fully electric version, employees have been working in a healthier environment, thanks to the absence of oils. They’re also finding it much easier to operate the less complex machines. Emissions software Siemens developed an ecosystem-based approach for exchanging emissions data. At the end of 2021, we launched our first solution for querying, calculating, and transferring information on the actual product carbon footprint (PCF). SiGreen makes it possible to exchange emissions data along the supply chain and combine it with data from a company’s own value creation to obtain a product’s true carbon footprint. To achieve this, Siemens initiated the open, cross-industry Estainium network with the goal of enabling manufacturers, suppliers, customers, and partners to exchange trustworthy PCF data. With SiGreen to support them in tracking their product carbon footprint, companies can take targeted reduction measures that deliver a quantifiable effect. Because the fact is, the supply chain accounts for a major proportion of product-related emissions. Scope 1 covers direct emissions from sources that a company owns or controls. Scope 2 covers indirect emissions from the generation of electricity, steam, heat, and cooling that the company buys and consumes.Scope3 is all other indirect emissions produced by a company’s value chain. To limit global warming to 1.5° Celsius, Siemens is committed to a science-based reduction pathway along our entire value chain. This is how we’ll ensure that our climate protection efforts are in harmony with the Paris Climate Agreement’s highest level of ambition. Our goal is clear: all Siemens production facilities and buildings worldwide will achieve a net zero carbon footprint by 2030. We’re already developing energy-efficient products with a low carbon footprint, from energy-saving motors to fan-less electronics modules and the corresponding procurement of components with an optimised footprint.�
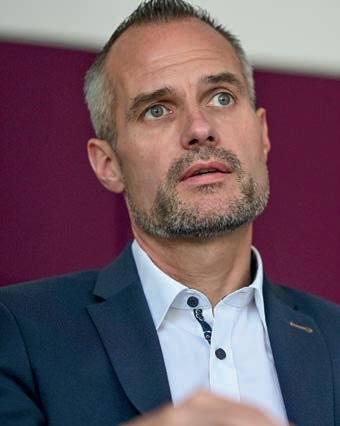
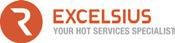
High-performance printing machines for glass hollowware www.isimat.com VRGS-A10016-00-7600_AZ_Glas_Mittelstand_A210x120-EN_1.indd 1 03.02.21 15:04
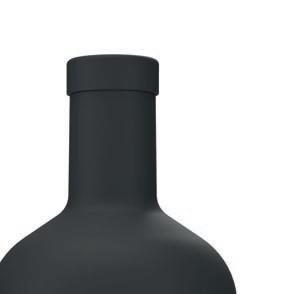
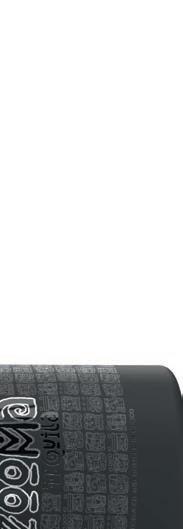
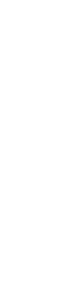
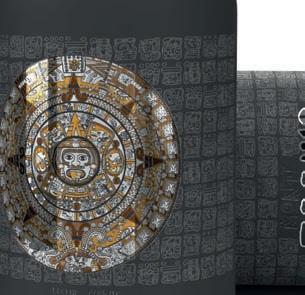
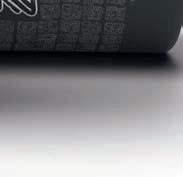
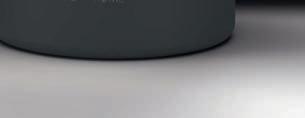

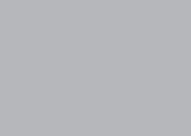

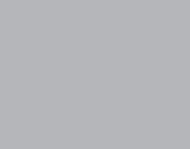



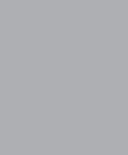








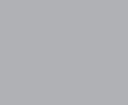







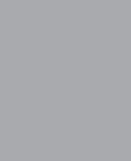























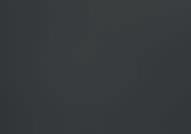














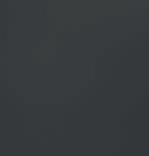







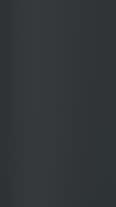





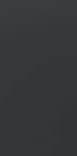



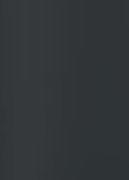



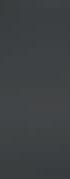


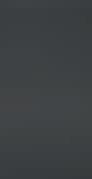
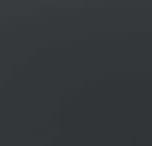
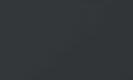




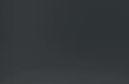


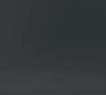











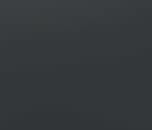
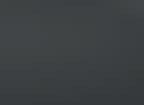















































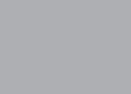

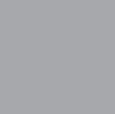













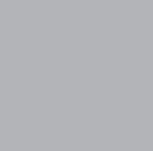




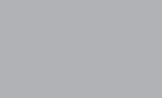

















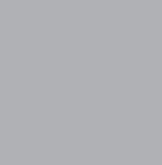

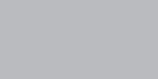
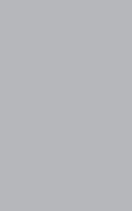






















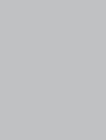
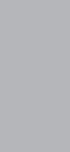


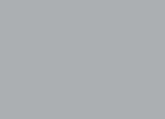

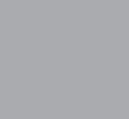
















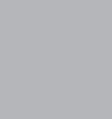




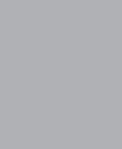













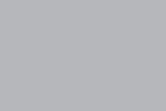
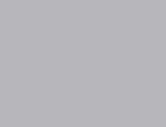



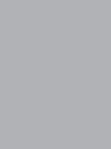

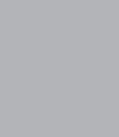
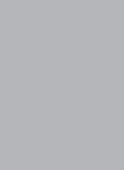

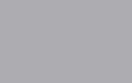

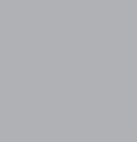






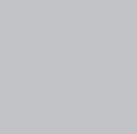
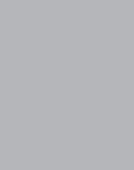
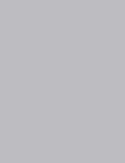
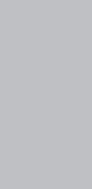






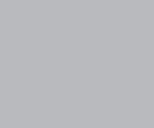










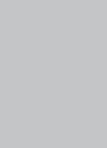



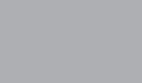



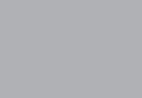

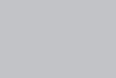
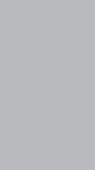


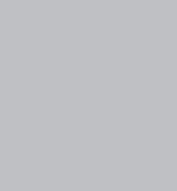

















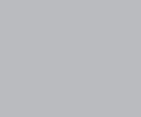





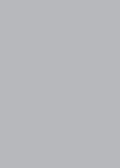



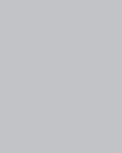
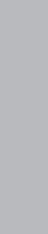

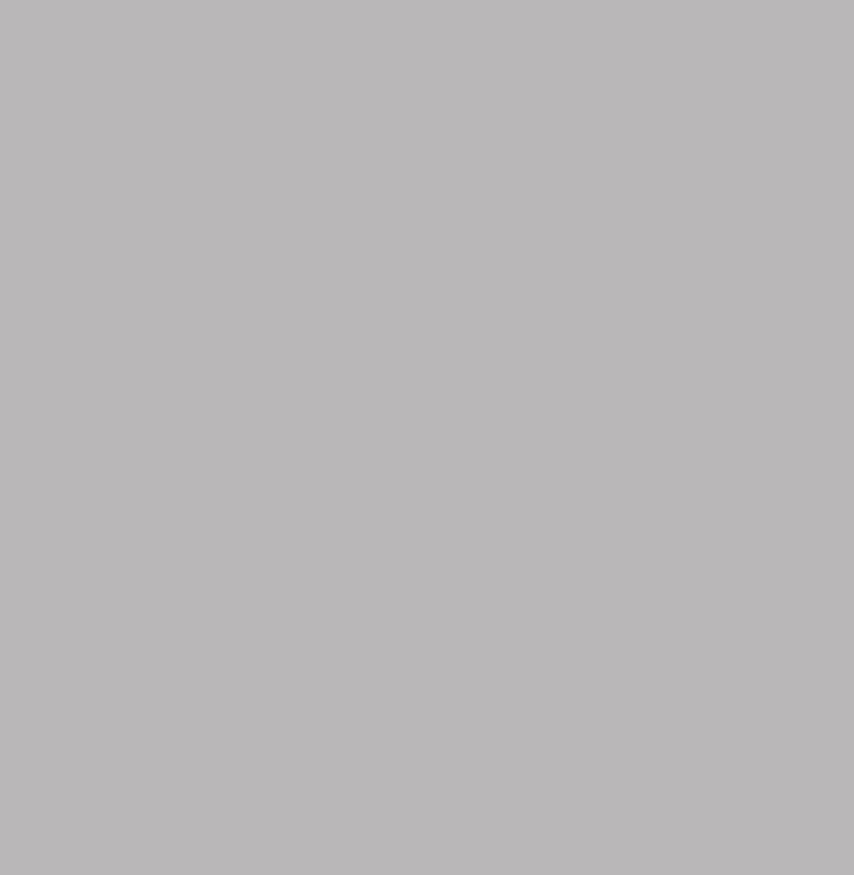
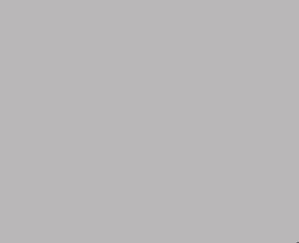
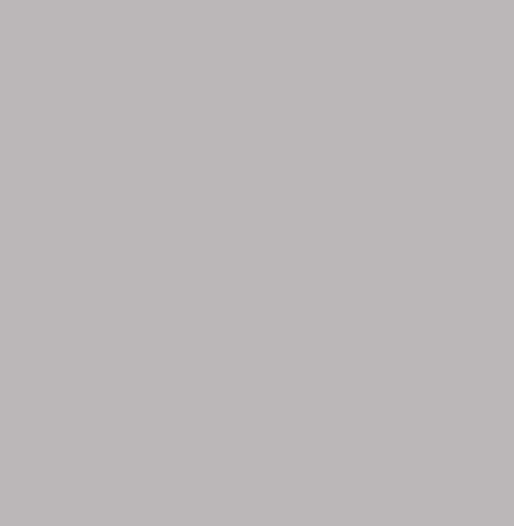
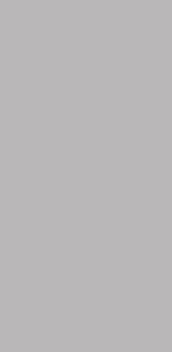
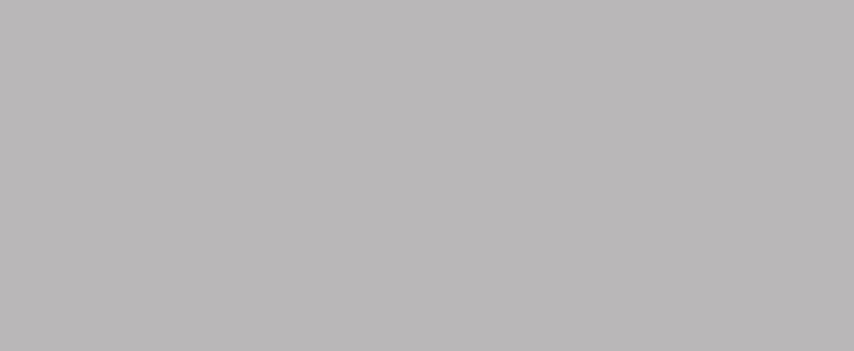
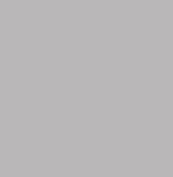





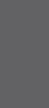







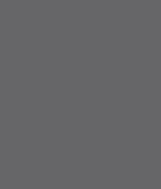

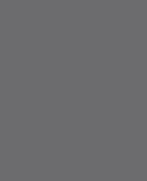
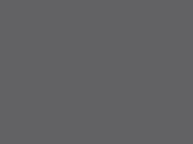
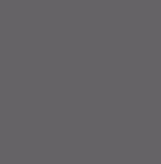
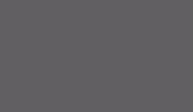
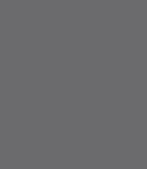
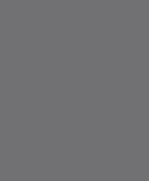
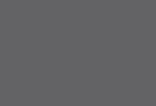
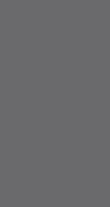
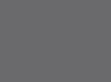

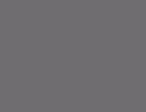
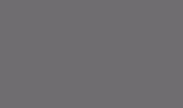
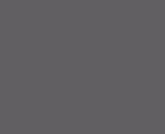
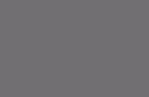
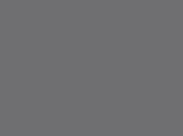
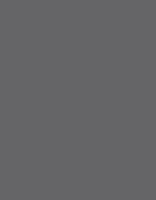
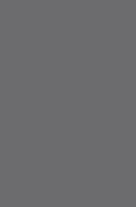

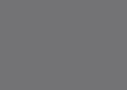
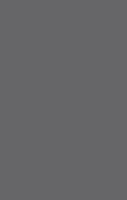
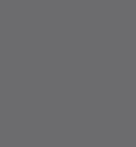
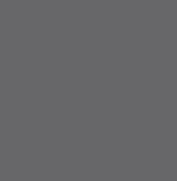
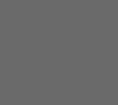
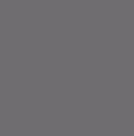

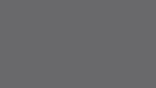
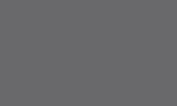
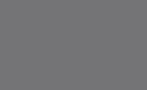
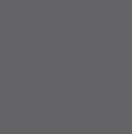
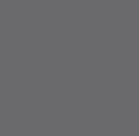
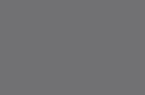

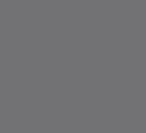
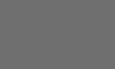
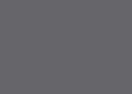

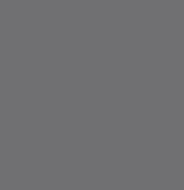
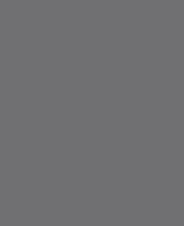
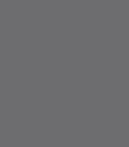
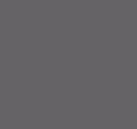

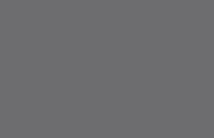


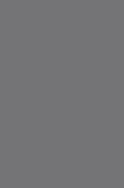
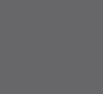
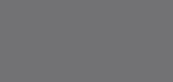
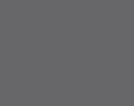
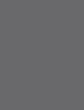

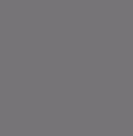

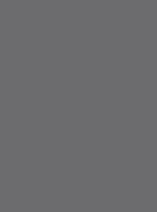

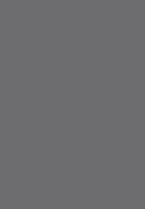
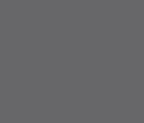
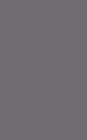
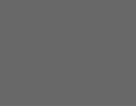
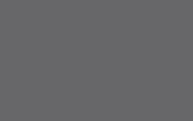

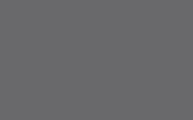

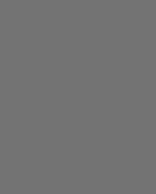
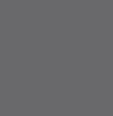
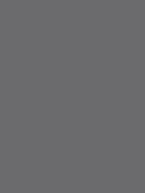
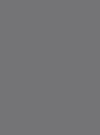
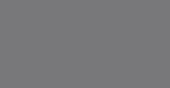


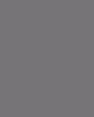
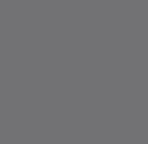
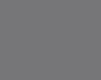



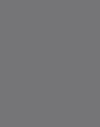



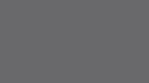
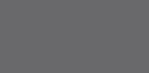
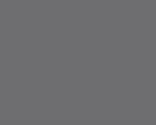
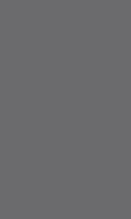

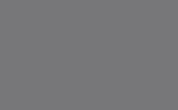
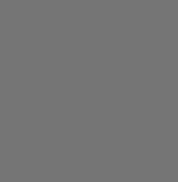
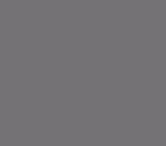
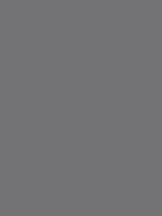
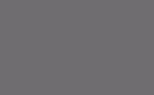
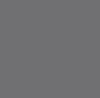
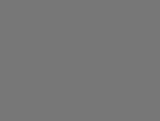
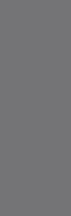
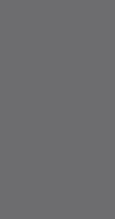
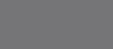

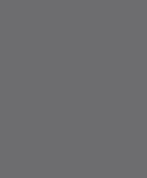
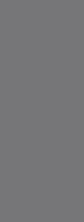
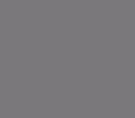
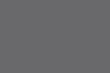
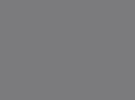
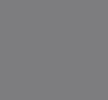
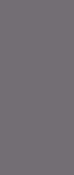
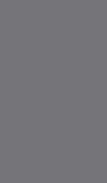
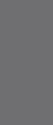

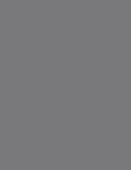
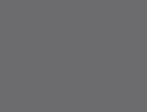
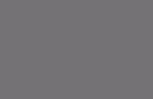
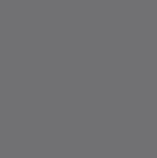
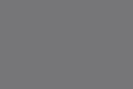


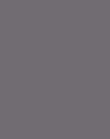
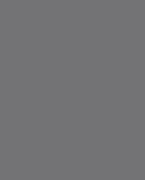


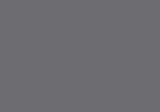
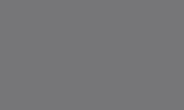

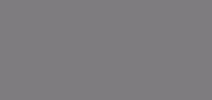
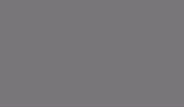


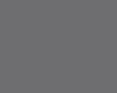
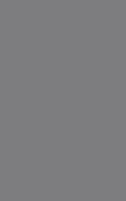
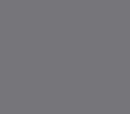

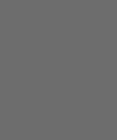
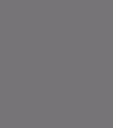
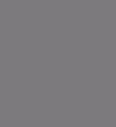
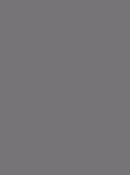
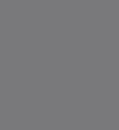


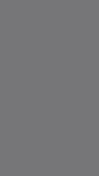
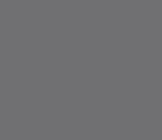
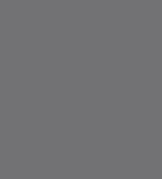
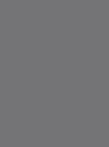
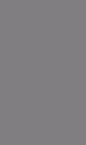
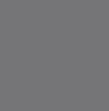
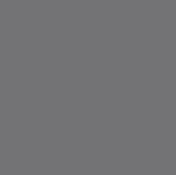
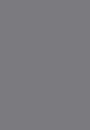
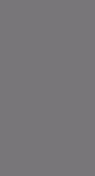

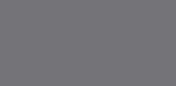
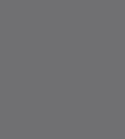

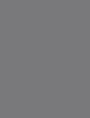
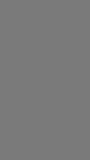
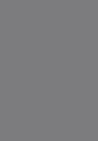
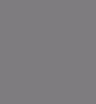

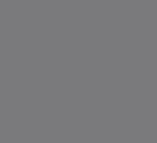
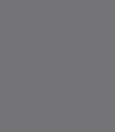
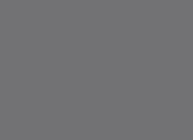
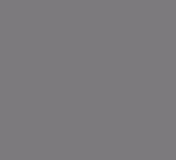
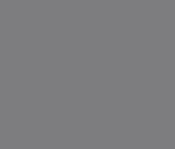
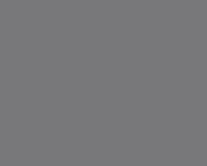

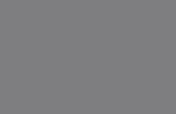
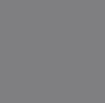

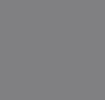
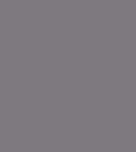
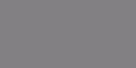

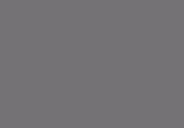

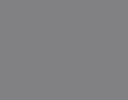
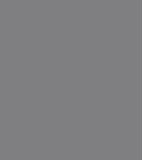
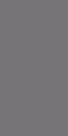

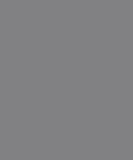
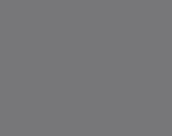

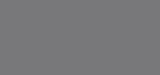
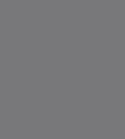
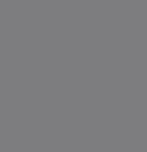
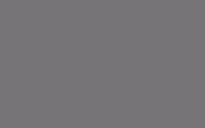
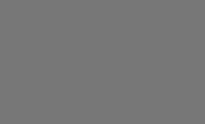
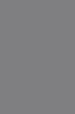
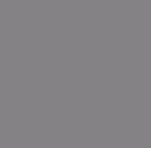

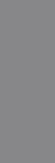

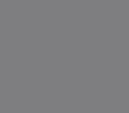




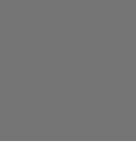

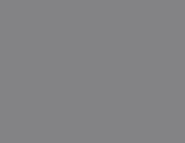
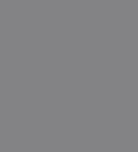

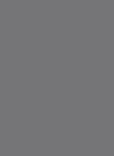
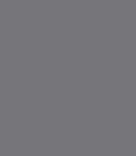
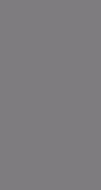
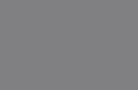

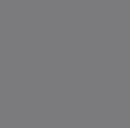
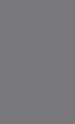
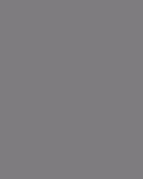
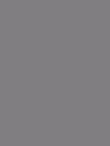
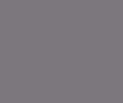
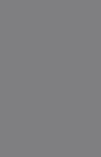

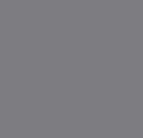
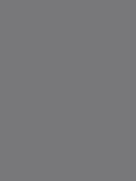
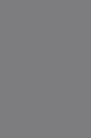
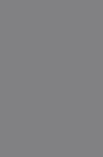
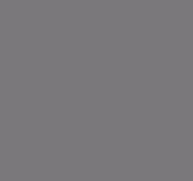
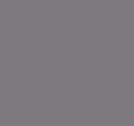

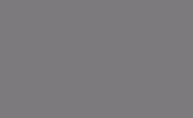
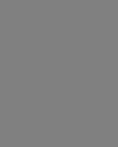

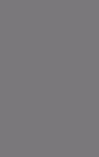
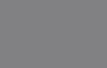

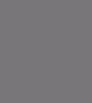
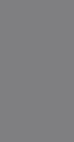
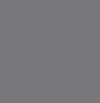

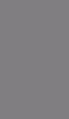
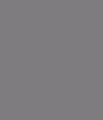


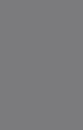
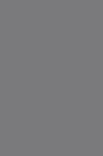
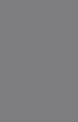
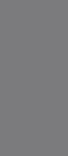





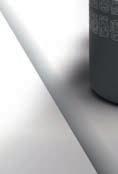









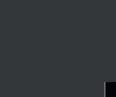




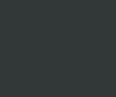





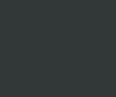














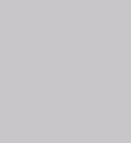

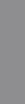
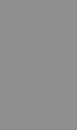

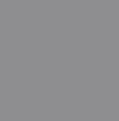

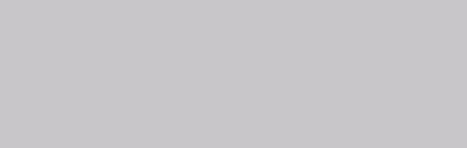

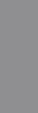
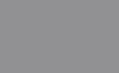


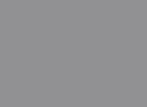

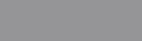
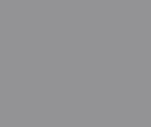
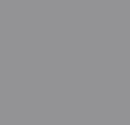
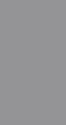
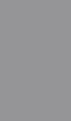


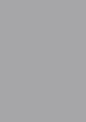
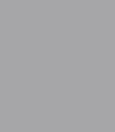



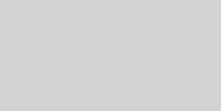


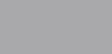
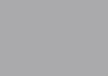



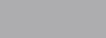


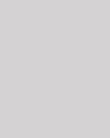

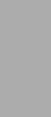
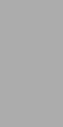
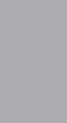












































































































































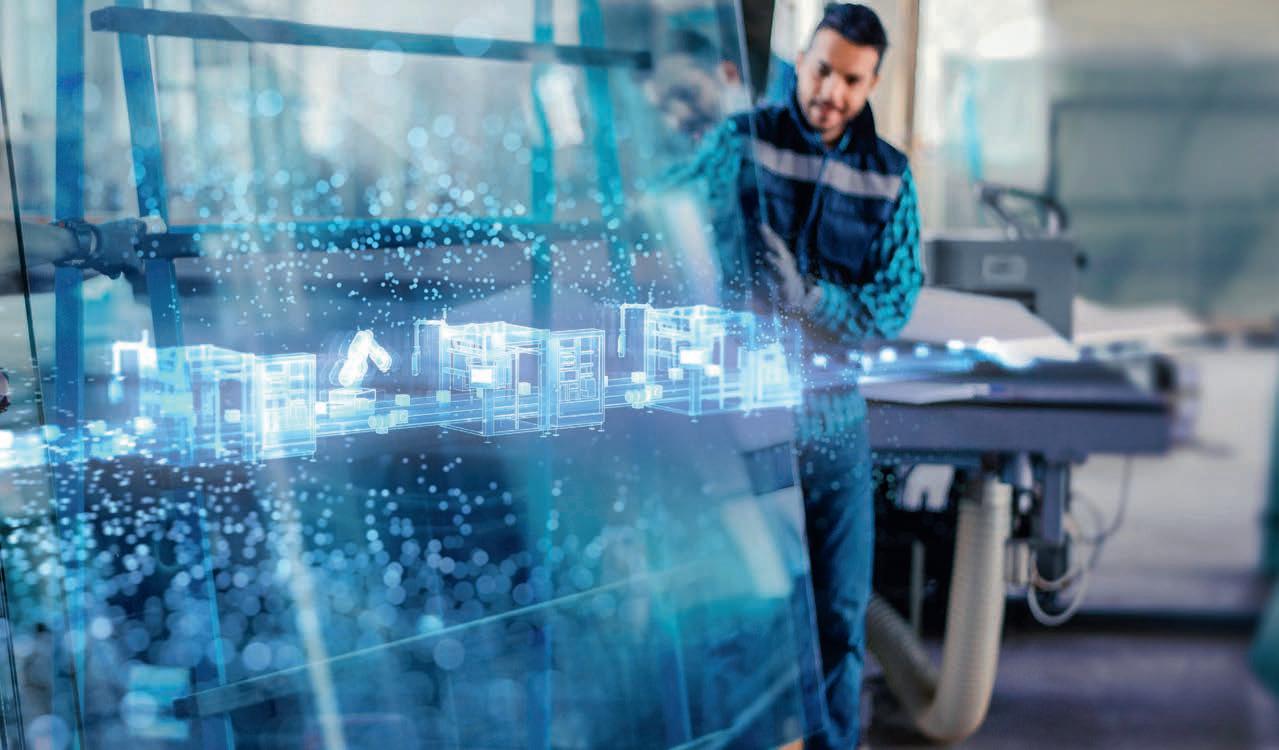
ServingtheGlassCommunityformorethanacentury
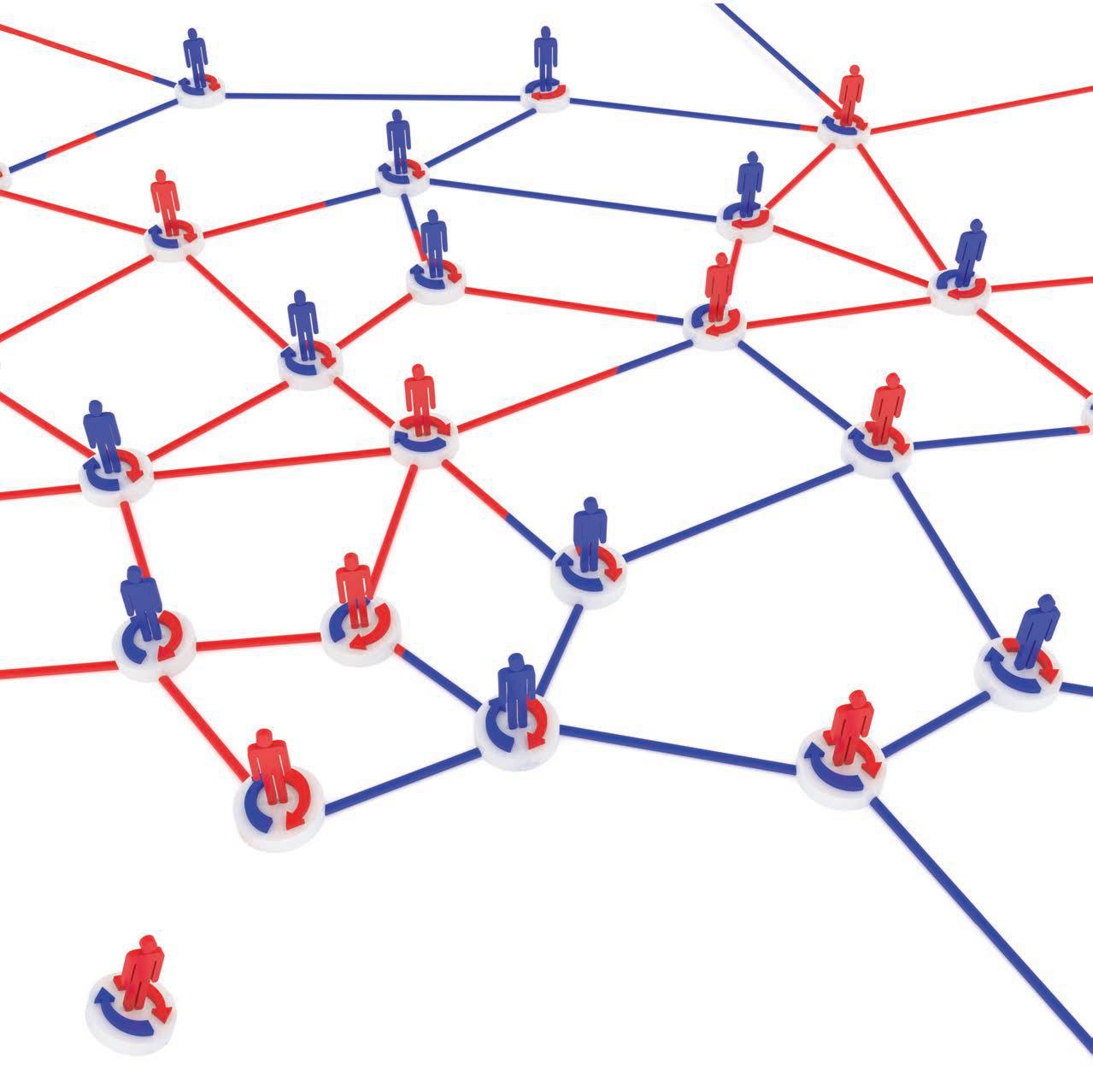
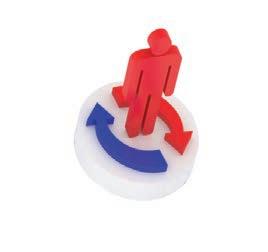

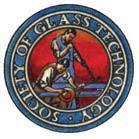
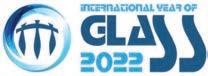
For more than 15 years now, Tiama has gradually invested in the development of process sensors dedicated to the hot end. Tiama’s Hot End business unit, which is now well structured and strengthened by a doubled developer staff, is 100% focused on supporting the hot end operators in the factories. Our historical ‘vision’ know-how, coupled with our growing hot end expertise, enables the company to provide real technological responses to our customers’ needs, and to evolve these responses to the constant and changing challenges of the factories. The quest for performance and quality is at stake for all glassmakers, especially today in the global context of inflation and the environmental challenges.Weare,and will be, more and more present to develop the appropriate tools to help our customers to better understand their process, but also to better anticipate drifts and thus improve their performance. This is the heart of our ambition. Finally, everything we do now and tomorrow in terms of products developments within the hot end business unit fits perfectly into our Tiama ecosystem strategy and allows our customers to complement their overview of their production, already fuelled by all cold end and laboratory equipment data. The correlations thus possible, the cross-alerts are all key means made possible by what we do and want to do within the hot end business unit.
2. HOW HAVE TIAMA’S HOT END SYSTEMS EVOLVED SINCE THEIR ORIGINAL LAUNCH?
The hot end specialist Michel Carpentier was recently appointed head of Tiama’s Hot End business unit. He reveals his plans for the unit and how it can help glass manufacturers as well as describing his 25-year career in the glass industry.
Hot end systems were launched 15 years ago to meet a glass industry need to monitor productions directly at the output of the IS machine, rather than waiting for the cold end information. An infrared analysis of the articles was an obvious response in the process monitoring, so Tiama launched the I-CARE system, which became well known to the glass industry. Quickly, it became clear that we had to go back up the process and come up with a gob monitoring solution, where everything starts. Thus, after the acquisition of the company Gedevelop, our product range expanded to include our Hot Mass, based on a two-dimensional acquisition of the images of the gobs. This was, for Tiama and what was going to become the business unit hot end, a major breakthrough in the conquest of the hot end process. Then things got faster. After the development of the I-CARE and the feedback of our customers, we understood that a more modular approach to the monitoring of the IS machine output process was a real need. Moreover, with our cold end expertise, the logic of integrating a ‘vision’ machine into the hot end has emerged as a great opportunity to create a hybrid solution, combining the best of both worlds, with infrared analysis and visible light analysis, and at the same time allowing us to differentiate ourselves from our competitors, based solely on infrared technology. This is how our dual system, Hot Eye/Hot Form, was born, supplemented by our Hot Move solution for tracking the alignment of articles on the IS conveyor. Today, we are in a dynamic of intense development: we will officially present at glasstec 2022 our new gobs monitoring system, the Hot Mass II, based on a 3D analysis of the gobs, with extreme precision and stability of measurements. We are integrating the evolution of the technologies available at the core of our equipment, both in the soft and the hardware side, with increasingly powerful systems and HD cameras. Tools available today such as artificial intelligence, machine learning, big data are opportunities to increase the performance of our products, to meet the still existing and numerous field expectations.
erson it rofi e i he r entier Glass International July/August 2022 www.glass-international.com 39
Continued>>
1. HOW CAN TIAMA’S HOT END UNIT HELP A GLASS COMPANY’S HOT END OPERATIONS?
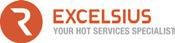
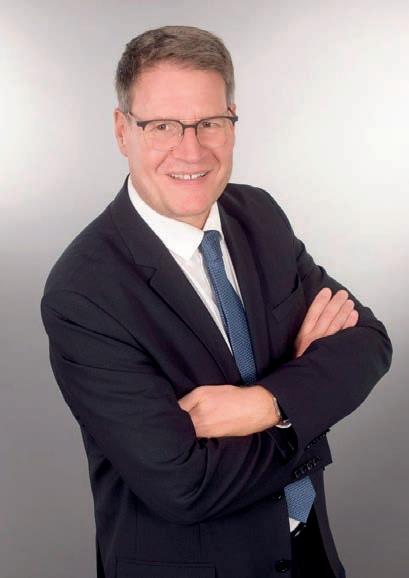
erson it rofi e i he r entier Glass International July/August 2022 www.glass-international.com 40
Our major ambition within the Business Unit Hot End is to provide our customers with systems which will give them real-time information, or even top-level regulation. All this contributes to improve performance and overall stability of the lines, with undeniably increased responsiveness and accuracy in the corrective actions implemented. Each bottle, each small container thus saved by this improved performance, is in fact an economy made in terms of carbon footprint and thus contributes directly to the sustainability of the glass industry. Since the global average glass yield is around 85% of PTM, the margin for progress of this carbon footprint is enormous and we are with our customers’ sides to contribute actively to it.
5. CAN THE HOT END UNIT HELP WITH A COMPANY’S SUSTAINABILITY PLANS?
First of all, a few words about GlassFORM.ai: This company was born at the end of 2021 from a common and convergent view of both Tiama and Bottero on the future of the hot end. The conviction was, and remains, that this future depends on data management and automation for many reasons. GlassFORM.ai is now operational and about to release its first product, the GOBexpert, and will soon start the development of the FORMexpert product. These software programmes will operate on the same principle: collect real-time data from everything that is accessible on the production lines (feeder, IS machine, hot end sensors, cold end machine inspection systems, etc.), build a dynamic database that will be used by the GlassFORM.ai platform, which will implement artificial intelligence, machine learning modules to refine pre-established models that will finally enable regulation models to interfere with the feeder mechanism, on the IS machine, tomorrow on the feeder and more. GlassFORM.ai software will be standalone solutions, connected to a data collection architecture implemented on each production line, and connected to production systems, to help our customers improve their performance and quality, through a more stable and controlled process.
3. HOW WILL THE GLASSFORM.AI SOFTWARE BE USED IN THE HOT END UNIT?
4. HOW ELSE WILL THE HOT END SYSTEMS DEVELOP/USE INDUSTRY 4.0?
There are two answers to this question. On the one hand, we consider hot end products to be stage 1 of industry 4.0. Indeed, all our sensors, connected to a data structure through our Tiama ECO-system solution, provides in real time bulk information that will be collected, analysed and correlated as with our Tiama DataMine tool to bring back relevant and delayed information to the teams on the production lines, and/or will be used in the GlassFORM.ai tools to bring a true ‘loop’ to the heart of the glass process. On the other hand, our hot end sensors are capable of providing a huge amount of crucial information which can be treated with artificial intelligence to become even more useful to the hot end teams, such as the recognition and monitoring of critical defects directly at the output of the machines. This is already a major contribution that is totally linked to what we call industry 4.0.
The hot end business unit is in a strategic development cycle. On the one hand, we are strengthening our internal skills so that we can better meet our ambitions, and on the other hand, we are working to make our organisations evolve to be more reactive. Our goal is to improve our time to market. Finally, we want to develop our business by relying first on some strong mature products, which provide a solid ground to ensure our capacity to develop new products. The ambition is strong and the means to achieve it are being implemented! The challenges facing our customers are opportunities for us to support them and develop ourselves.
In a nutshell, I had the chance to discover the world of industrial glass as part of my engineering training. Since day one, I have been fascinated by this industry, which is little known but so complex What I find extremely attractive and fascinating in this industry is that, on the one hand, it is impossible to go around it, you learn about it every day from morning to evening until the end of your career, and, on the other hand, you are confronted to all the techniques and technologies of the industry, and they evolve very quickly. To finish on the process side, each time I see a gob falling remains for me a pleasure that all the glassmakers know well. It is the magic of glass! On another side, and this is the main one, this job is hard! You do not count your hours, but the teamwork with women and men who have the same passion is so rewarding, that you end up forgetting your difficulties. The successes are won together. In short, the world of glass is a ‘small family’ in which it is a good place to live, and that is what driven me since day one!
7. WHAT DO YOU ENJOY ABOUT WORKING IN THE INDUSTRY?
Continued>>
6. ARE YOU ABLE TO INDICATE ANY FURTHER PLANS TO DEVELOP THE UNIT?
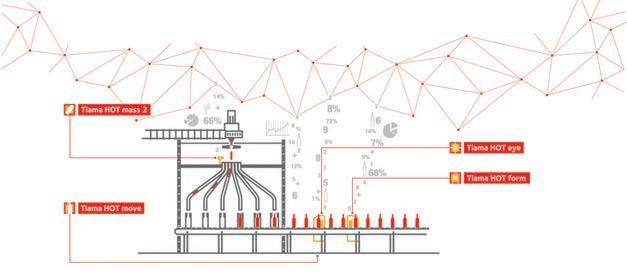
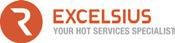
® TOLEDO ENGINEERING / TECOGLAS / ZEDTEC / KTG ENGINEERING / KTG SYSTEMS / EAE TECH DESIGNING,www.teco.comBUILDING AND MODERNISING YOUR FURNACES, FOREHEARTHS AND FURNACE EQUIPMENT A Zedtec fact... Did you know Zedtec’s Rapid Cool technology is considered to be the most effective forehearth cooling system on the market? COOLING FOREHEARTHYOUR
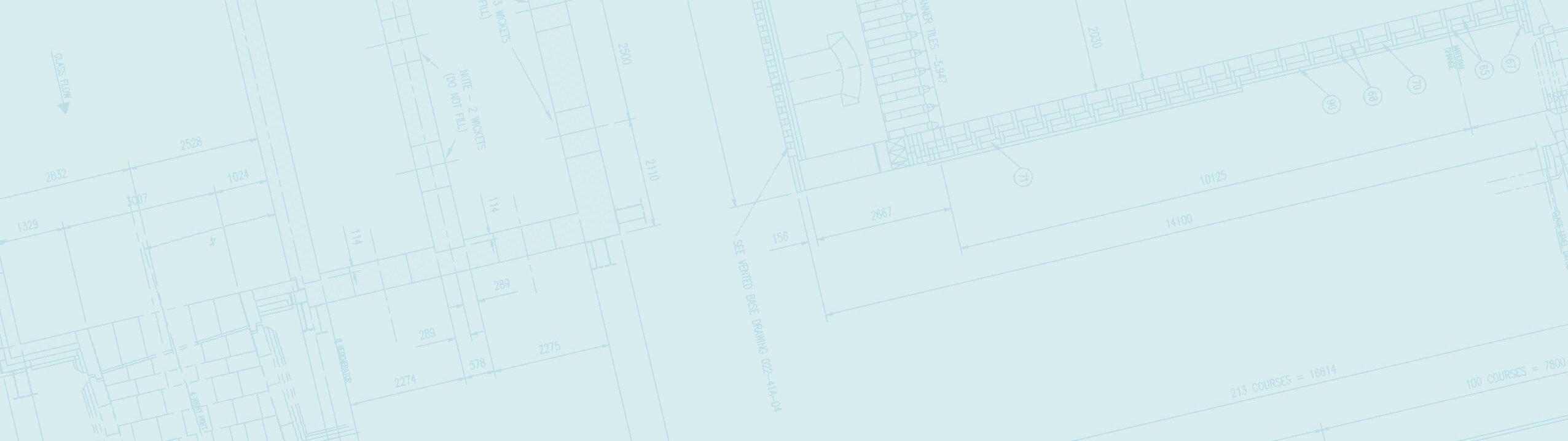
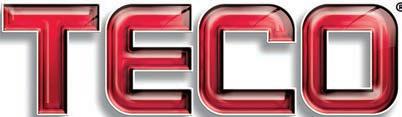

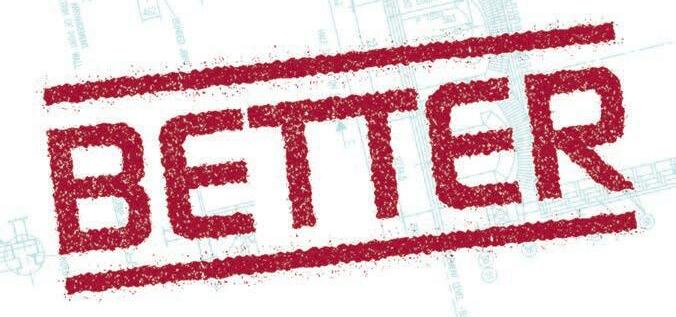
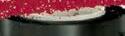
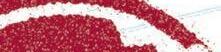
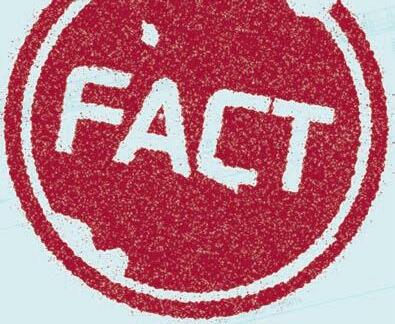
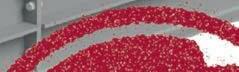
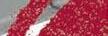
Having spent 21 years in the glass industry, 100% in the factory, when I was contacted by Tiama to take the lead of the Hot End business unit, I immediately saw the logic and coherence for me to take up this challenge. Indeed, what is more important for the development of this activity, with a young learning team, than knowing the world of glass from the inside, so that we can share on a daily basis what is important and what is not, and to be able to guide the solutions to be implemented in the future in order to meet a single objective: help the glassmakers to improve their lives with improving performance.
All my experience today, with all the hot end team, helps me to be particularly careful not to develop only “Nice to have Products”, but “Must have products” that really meet factory expectations that I faced myself in the past.
erson it rofi e i he r entier Glass International July/August 2022 42 8. HOW HAS THE INDUSTRY EVOLVED IN THIS TIME?
Since I began my career in the glass world in 1997, I have witnessed several profound transformations at the heart of the factories. First of all, although the glass process has remained unchanged for many years, the production tools have been thoroughly modernised. The digital age has come, and the machines have gradually integrated servo-drives, offering unrivalled setting and control possibilities. Quality control tools at the cold end have also undergone a major change with the age of digital and camera vision control. In addition, production supervision tools have also been completely reviewed with an impressive amount of real-time information that can now be obtained.
10. WHAT DO YOU BELIEVE TO BE THE MAIN CHALLENGES IN THE GLASS PACKAGING INDUSTRY?
Coming from this industry also allows me to enhance the understanding of our customers, speaking the same language, so that we can go straight to the goal and move faster. There is still a lot to do in our business unit and being a former glassmaker from training and from the heart is an asset I will use to make the most of my new position!
To follow on the previous question, through our tools, our ability to stand by the plants, our ability to innovate, our ability to adapt and build the appropriate dynamics, as with GlassFORM.ai. We are fully aware of these challenges and are fully committed to addressing them. These are in fact challenges that concern all of us, whether you are a glass producer or a supplier of technology such as Tiama. Tiama, Saint-Genis-Laval, France www.tiama.com
In conclusion, I would like to highlight one last point which has become a growing problem for the glass world. Indeed, over the past two decades, it is undeniable that a loss of skills has occurred in factories as a result of the retirement of experienced glassmakers, as it is increasingly difficult to recruit and retain good profiles. Thus, a race against the clock has begun between this challenge of competence in factories and the technological development which must now and in the future compensate, with increasingly intelligent sensors, with regulation systems based on artificial intelligence. It is clear that man will remain at the heart of the glass equation, but the tools must be at his side, adapted to the challenges of tomorrow.
Overall, the control of the process has been considerably strengthened, in order to meet the quality requirements of bottler customers who have nothing to do with what they had even 10 years ago, or 20 years ago. The procedures, the control of materials, moulds, equipment, etc. all contribute to a major structural change in the glass world: We have moved from a time when glass was ‘magic’, when empiricism was the standard to a much more scientific, more Cartesian approach, to fact-based, data-driven approaches which are now the daily work of factories, even though much remains to be done!
In short, I would like to mention the following four major challenges, which are completely interrelated: Technical performance, economic performance, environmental performance around a key issue related to people knowhow... In a context in which the quality of production has been considerably improved and can still be improved, it is clear that these four subjects are at the heart of the glass world’s attention. The current global context and the succession of crisis we face only reinforce the weight of these challenges, and that is where Tiama, with its HE Business unit, can and must help its customers in the coming years.
9. HOW HAS YOUR EXPERIENCE OF THE INDUSTRY INFLUENCED YOUR NEW ROLE?
The answer to that question is obvious to me.
11. HOW WILL TIAMA’S NEW HOT END UNIT HELP CUSTOMERS FACE THESE CHALLENGES?
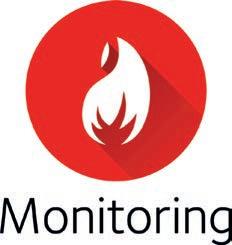
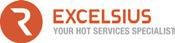
Smart Factory is approaching and, thanks to the YOUniverse, it has become far easier to prepare for. It’s also cost effective because the Tiama Hot-End Monitoring System is modular: you choose what you need and when you need it, building the YOUniverse that suits you. … and they can take action autonimously – now that’s Smart! So, whatever choice, it will knowledge
your
improve your
of the process and it is backed by our service, support and training, along with constant research. For more information visit youniverse.tiama.com HOTTIAMAMASS For gob weight control, gob shape and temperature monitoring HOTTIAMAMOVE Article managementpositioningwith early warning to avoid jam HOTTIAMAEYE For critical defects detection and recognition, dimensional measurements HOTTIAMAFORM For infrared radiation monitoring and real time statistics Data – the deciding factor Prepare for the future it’s less expensive than you think. Monitoring www.growth-group.com
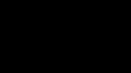
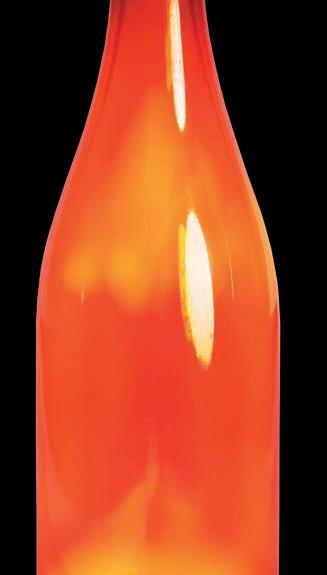
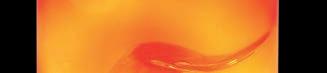












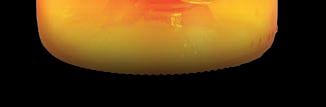
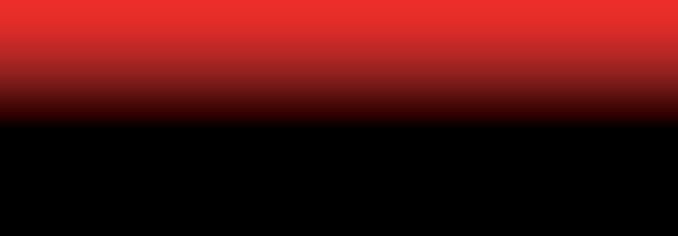
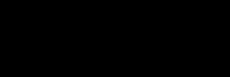
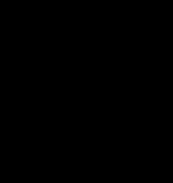
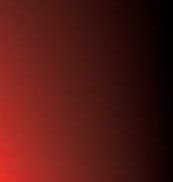
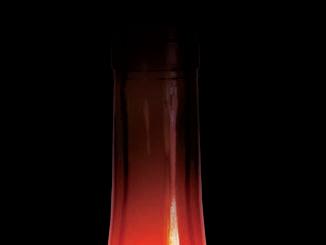



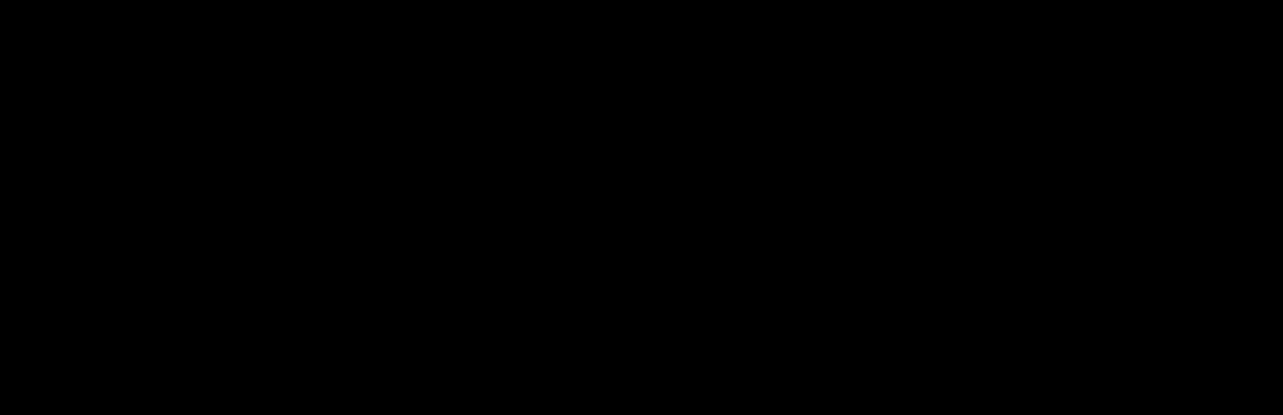
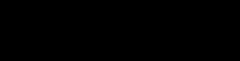

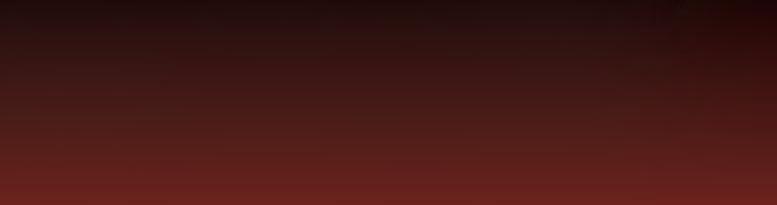
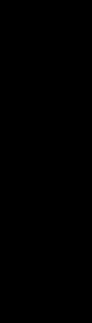
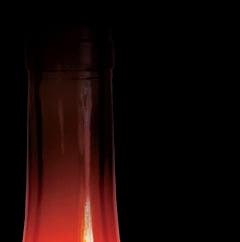

erson it rofi e e e ntern tion Glass International July/August 2022 www.glass-international.com 44
A partner for a smart plant
I was at a stage in my career where I was ready for a new challenge. When I looked at Heye’s portfolio, and the developments and opportunities in the glass industry, I saw the possibility to contribute to new ideas and support further progress in the sector. Heye International provides technical support and solutions to its customers and has a lot of new ideas and innovations in the pipeline, which I am committed to supporting to commercial development.
ns eter er MachineInspectionSmartLine
1. HOW EXCITED ARE YOU TO BE APPOINTED AS MD AT HEYE INTERNATIONAL? Thank you. After some months in the role and having had the opportunity to develop a good understanding of our market, our business model and our capabilities, I am indeed very excited to have joined the Heye International team, who have greatly impressed me with their dedication, their knowledge and experience. I am confident that Heye is well positioned to achieve further success, to address our industry challenges and to continue to grow our customer base, our service network and our product portfolio.
2. WHAT WAS IT ABOUT THE ROLE THAT APPEALED TO YOU?
Heye International appointed Hans-Peter Muller as Managing Director earlier this year. He outlines his vision for the company and how digital technology will remain at the forefront of its portfolio.
Heye International, Obernkirchen, Germany www.heye-international.com
3. YOU WERE MOST RECENTLY MANAGING DIRECTOR AT DIETRICH PROCESS SYSTEMS. WHAT SKILLS AND EXPERIENCE WILL YOU BRING FROM THIS ROLE TO HEYE? In my former role, I had global responsibility for a business line. I had the opportunity to adapt the existing organisation to future market requirements and opportunities. This included the development of new business models and strategies to cover market cycles, looking at new and enhanced applications and solutions as well as implementing a greater focus on innovation processes and development projects.

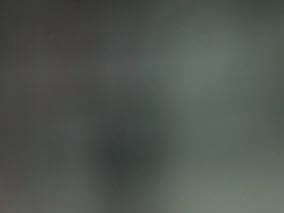
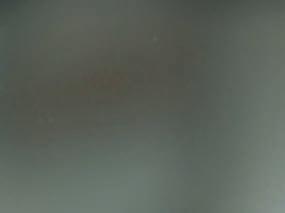
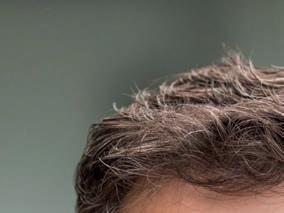

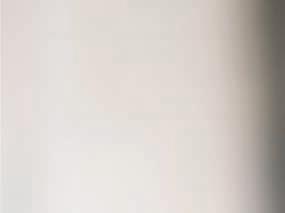
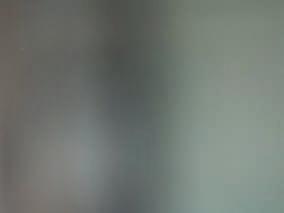


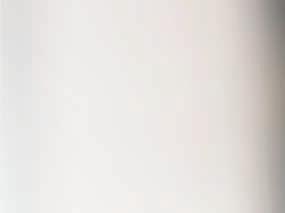
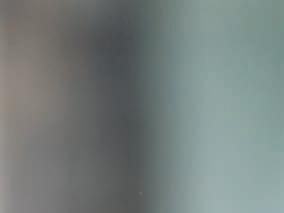

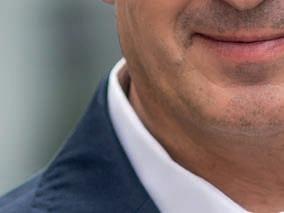
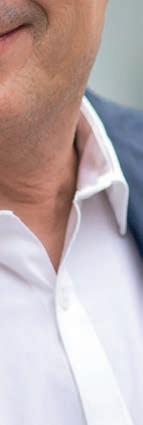

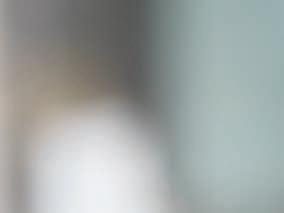

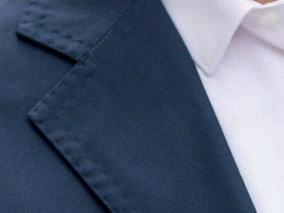


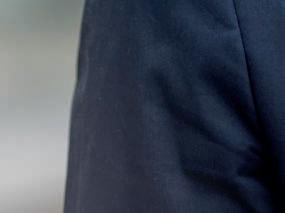
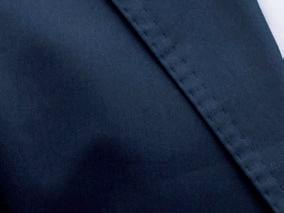
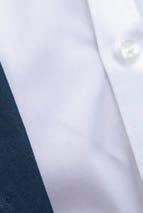
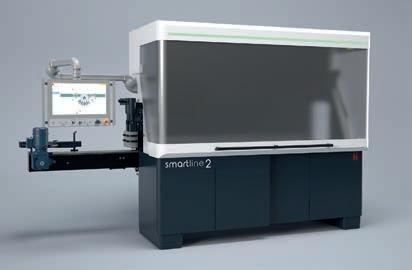
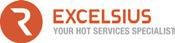
Yes, I do, and I enjoy working with my team. I try to be clear and consistent about my expectations and combine this with open and honest feedback. I trust in people and their abilities and believe in empowering my team to take ownership and accountability. Every employee has an important role to play in achieving our objectives and reaching our targets, my door is always open whenever support is needed. As a leader I strive to build a positive culture, in an environment where my team feel empowered. In this way, we can best work together, to bring new solutions to our customers.
6. WHAT IS THE BIGGEST CHALLENGE FACING HEYE?
7. WE HAVE SEEN THE EXPANSION OF DIGITAL TECHNOLOGY IN RECENT YEARS IN GLASS MANUFACTURING. HEYE HAS BEEN AT THE FOREFRONT OF THIS. HOW WOULD YOU LIKE THE COMPANY TO EXPAND ITS DIGITAL OFFERING?
erson it rofi e e e ntern tion Glass International July/August 2022 www.glass-international.com 45
The main target for the coming years for Heye is to further enhance our position as the technological leader in our sector. This requires a focus on structured innovation in our development process, and increased efficiency in manufacturing, including shorter throughput times and optimised capacity. We will also focus on strengthening our global presence and improving our capabilities to provide local service and support, as well as attracting and retaining young talent.
8. WHAT BENEFITS DOES DIGITAL TECHNOLOGY BRING TO THE INDUSTRY? Today, boosting efficiency is a key challenge in the glass production sector. To optimise both costs and performance factors such as PTM (pack to melt) or mould life, an overview of all relevant production data is needed.Oursystem gives a complete overview of production performance. The data collected includes diverse inputs, including from the laboratory, the article counter, the inspection machines, the IS-machines, together without input from the operator. We offer our customers a fully supported partnership on their individual path towards a smart plant, resulting in the creation of a highly automated and cost-effective glassworks. ee ine hine “A particular area of concern is the lack of skilled labour, especially in the technical functions.”
4. DO YOU ENJOY BEING A LEADER? WHAT IS YOUR LEADERSHIP STYLE?
5. CAN YOU GIVE AN INDICATION OF WHAT IS YOUR VISION FOR HEYE UNDER YOUR LEADERSHIP?
The big target is certainly to make better links between the hot and cold end of the process and to develop machines which are smart enough to learn from and avoid defects, by predicting them and taking preventive actions.Thevision is an intelligent and completely closed machine with very limited operator input, which is self-learning and can independently set itselfDigitalup. technology will also help to further reduce the consumption of raw materials, energy and will help to further improve the sustainability of glass packaging.
After a challenging period through Covid 19, where our employees demonstrated a high level of commitment and discipline, we are now, like many other companies, facing major challenges in the supply chain. This not only means significant price variations and longer delivery times, but it also requires flexibility and creativity in finding alternative solutions and sources. A particular area of concern is the lack of skilled labour, especially in the technical functions. This, in line with ongoing demographic change, however, this serves to focus us on attracting and recruiting new technical talent which is crucial to our future success.
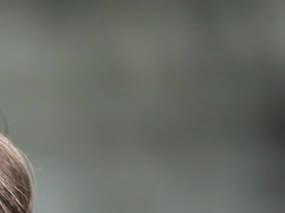

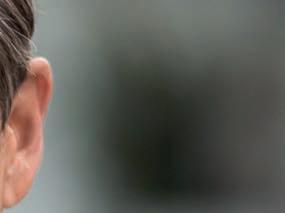
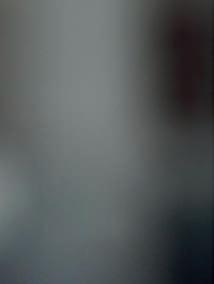
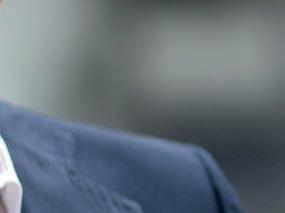
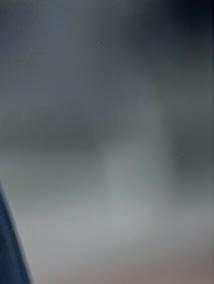
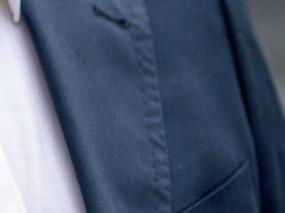
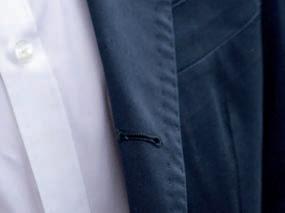
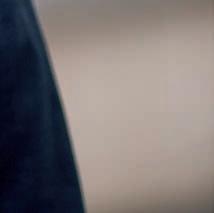
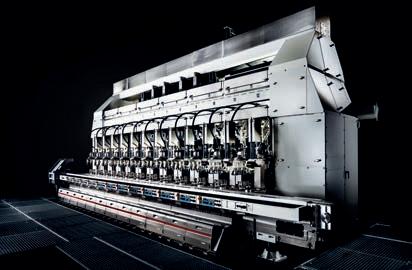
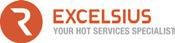
For humans, it’s obvious. For NEO too. NEO Artificial Intelligence for defect recognition
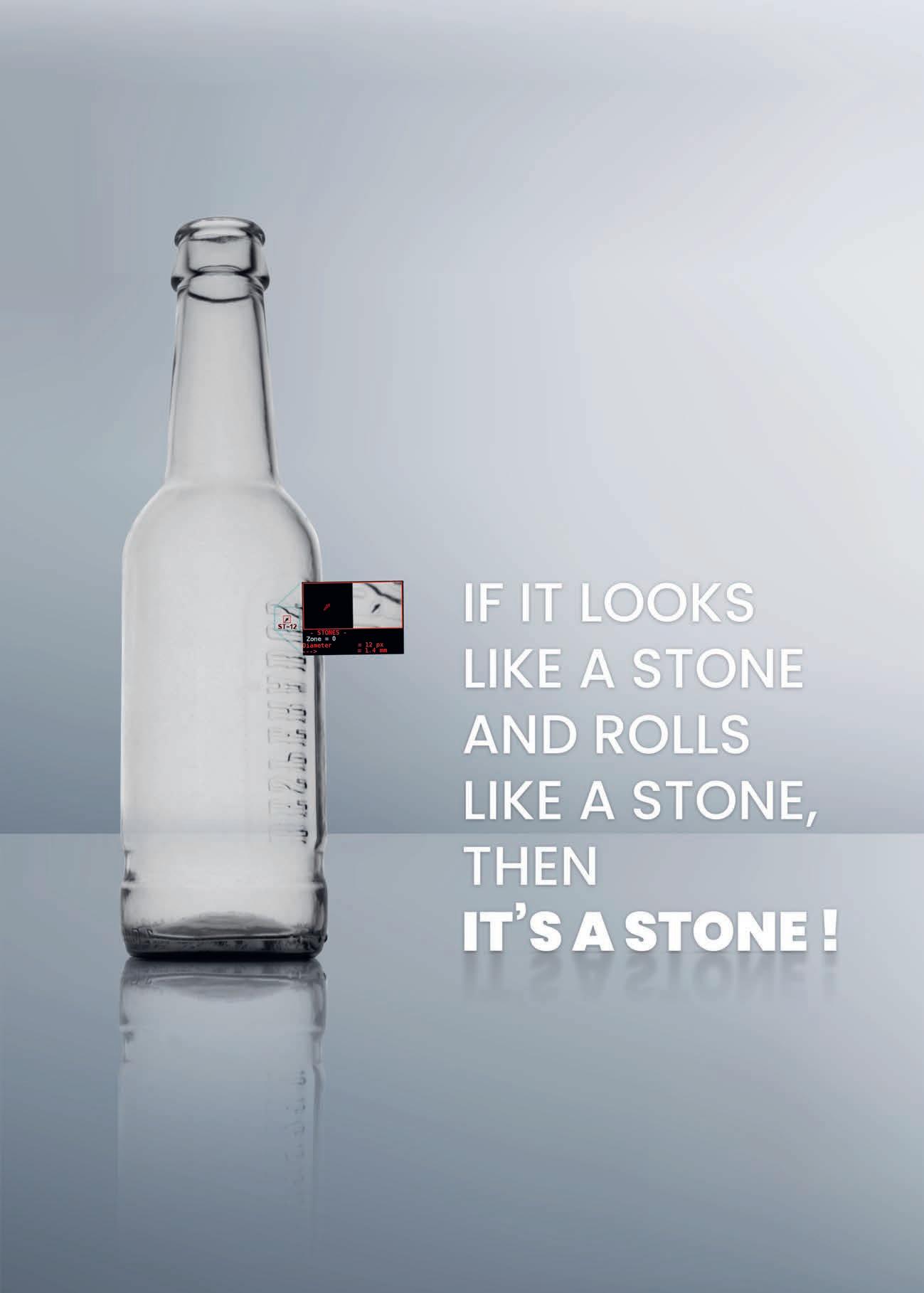
Context The glass industry is under pressure to decarbonise due to its high energy demand in the production process. This is particularly true as energy prices soar, and in addition, the cost of CO2 certificates is on the rise as well. Glass strength drops drastically after glass is exposed to atmospheric moisture and to high forming temperatures. At high temperatures, above 900°C, water is highly chemically reactive. During forming, the newly formed glass surface is rapidly attacked by water hydrolying the Si-O-Si network forming terminating Si-OH groups (Fig 2). When it is freezing outside there are an order of 1g/m³ water vapour in the air, and when it is humid in the heat of the summer approximately 40 – 50 g/m³ water vapour. Water is everywhere on this planet, and it is corrosive at high temperatures. A discovery by Dr Yoldas within the past four decades changed our historical definition of glass as a material that must be formed at high temperatures. Every crack ever studied in glass has hydroxyls concentrated at the crack tip. These OH groups continuously drive the crack tip deeper into the bulk glass. The deeper, the weaker the glass is to stress and breakage. If glass has a strength of about 3.4 GPa (500,000 psi), it has flaws at a depth of only 10 – 50 nm. There is a relationship between flaw depth and measured strength. Now if that reaction was catalysed by water for a chemistry like the glass with the crack, the crack could be healed and the depth of the crack could be reduced increasing the mechanical strength. The limitations of glass strength and brittleness have been concerns for centuries. As an example, besides being a world famous artist in the 16th century, Michelangelo was also intrigued with glass. He found back in the time that if he redrew rods of glass to smaller and smaller diameters – strength would increase after each redrawing. He reasoned that the cause of failure was surface flaws and by redrawing he was diluting the flaws. Nearly 100 years ago, Griffith explained why glass failed to achieve its full theoretical strength. It can be reasoned that the above mechanism describes at least one if not the prevalent mechanism why at least conventional mass produced glass such as typical container and sheet glass achieves only less than 1% of the theoretical strength of the Si-O-Si bond. Be it as it may, one possible approach to reduce carbon footprint might be given by increasing the mechanical strength of glass, which would allow reducing the wall thickness of glass substrates while still achieving the design strength. Today, the glass industry uses various methods to improve glass strength, mostly imposing compressive stresses to bury the surface defects, including ion exchange (chemical toughening), thermal toughening, or lamination of low expansion glass over high expansion glass. All of these methods have various shortcomings and limitations. For example, the widely used methods of ion exchange and thermal toughening do not work below certain glass thicknesses and have compositional limitations. In the past, no one has ever produced a process to heal the surface flaws described above. A new glass surface treatment approach is currently under development approaching the stage gate of technology readiness level (TRL 4). This contribution will discuss intermediate results from lab tests. The approach Several recipes have been designed creating a combination of (1) chemical Fig implifie mo el of initial s rface fla formation Fig implifie mo el of crac propagation b creation of terminating gro ps
Increasing the strength of glass
Bulent E. Yoldas, John T. Brown, Thomas C. Sauer* and Sabine Schweizer, Lalitha Subramanian, and Ian Flynn** discuss a collaboration including Ardagh and Diageo to lightweight glass bottles.
D
uring COP26, a collaboration between Ardagh, Dassault Systèmes, Diageo and Exxergy was announced to develop lightweighting solutions for container glass. The collaboration was initiated through the Diageo Sustainable Solutions programme with the purpose to demonstrate the potential of this proof of concept.Thisarticle outlines results particularly from the theoretical and physical testing. The virtual twin part of the project has been sponsored by Ardagh Group and performed by Dassault Systèmes based on one of Exxergy’s recipes, with Diageo supporting Exxergy’s laboratory work. While there is still further work ongoing, a paper was presented at the International Congress on Glass (IGC) in Berlin in ExpandingJuly. and furthering the results presented at IGC, this article deals with preliminary results from both, the virtual twin as well as initial lab test results.
Decarbonisation Glass International July/August 2022 www.glass-international.com 47 Continued>>
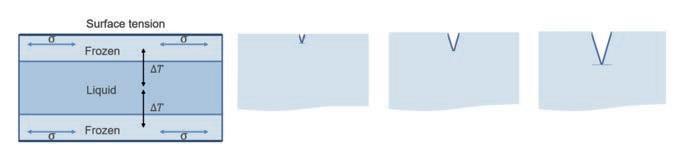
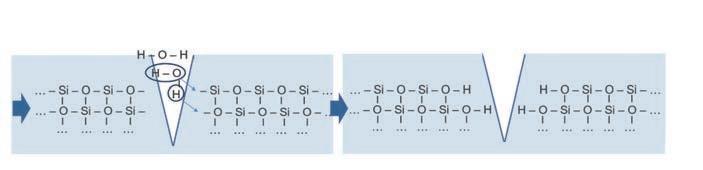
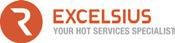
Fig oating la er on the glass s bstrate Fig emplar brea age test res lts Fig emplar res lts from intentionall pre amage glass.
Fig irt al t in mo el of the coating on glass. Fig left an Fig right oome in ie s of the coating glass interface
Decarbonisation Glass International July/August 2022 0 Continued>> 48 www.glass-international.com compounds and (2) process settings that result in a chemical reaction of the reactive groups of these chemical compounds with the terminating OHgroups of the glass surface. The resulting reaction creates covalent bonds bridging into the Si-O matrix by repairing the covalent bonds cracking the terminating OH-bonds and recreating new covalent bonds. With this approach, the previously cracked Si-OH/HO-Si terminal groups are bridged by creating a new Si-O-X-OSi covalent bond, X being the reaction product after the chemical compound has reacted with the H- or OH-groups on either end of the terminal OH-groups. The primary goals of this approach are to heal the surface defects at least partially and to reduce surface brittleness by increasing ductility. As a result of achieving these goals, as the stress capacity and the ductility increase the wall thickness can be reduced and as a result, raw material and energy savings may be achieved. The main task currently is to provide proof of concept in theory and in practice. Initial results from simulations To provide critical insights from chemical point of view, a virtual twin of the coated glass surface was modeled at molecular level using Materials Studio and Pipeline Pilot. The coated glass surface was modeled by subjecting the reactants to a proprietary stepwise procedure. The condensation reactions between the reactants of the coating formulation among themselves and with the surface exposed hydroxyl groups of the glass surface have been simulated. The finally obtained model (see Figs 3-5) shows indeed (1) a polymerised and cross-linked coating layer, which is (2) covalently bound to the glass surface Fig 3. shows a 3D simulation box of the glass substrate with the coating on top. Zoom-in-views of the interface are shown in Fig 4 and 5 Covalent bonds between coating and glass are highlighted in Fig 4. Water from the condensation reaction is shown in blue. Fig 5 illustrates a zoomed-in-view after NPT molecular dynamics simulations and after removal of the by-products. Not all –OH groups have reacted. These –OH groups can, in turn, react in a self-healing process. To explore the impact of surface oome in ie after b il ing crosslin e coating co alentl bon ing to the glass s rface oome in ie after e ilibration tmosphere Coating layer lass s bstrate
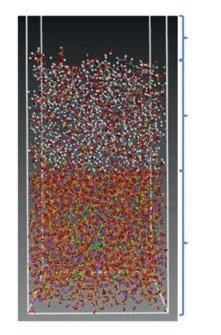
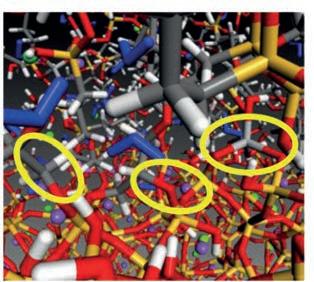
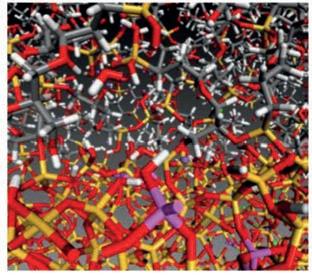
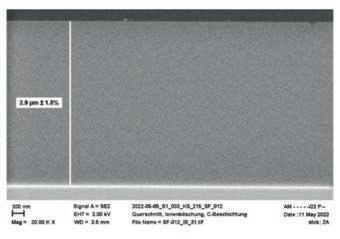


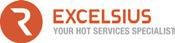
Preliminary results from the lab After mixing, the chemical compound is applied to the glass substrate surface as a coating to the surface and then cured at a set temperature and time. Several recipes (composition of the chemical compound, times, temperatures) have been tested to find the best suiting combination. One crucial aspect is naturally economics, and therefore, an optimised coating thickness. As can be seen in Fig 3, a few layers are sufficient. In the current lab setup, the coating thickness is significantly larger, depending on the application to a thickness of ~1.4 to 3.0 µm, see Fig 6 Following the analysis of the physical properties of the coating, it was applied to flat glass samples, and after the curing procedure exposed to different mechanical stress testing procedures. The results from the breakage tests can be seen in Fig 7. Three different glass thicknesses have been tested, 4 mm, 3 mm, and 2 mm, soda-lime glass as well as borosilicate glass. The test results for the 4 mm glass have been stressed using a 4-point probe, the other glasses with a ring-onring method. As can be seen in the figure, the average increase ranges from 84% to 144% depending on the glass thickness. The standard deviation is significant, the reason for which is currently under investigation.Inafurther test, mechanical damage has been imposed onto the glass surface by using a Vickers imprint test using 10 and 20 N force resulting in diagonals of approximately 40 – 50 µm. In Fig 8, the breakage can be seen on microscopic level on the left hand side. Following the intended surface damage, the samples were coated again. On the top right, an image of the sample after coating illustrates that the previously applied damage can hardly be seen anymore.
The breakage test results using a standard 4-point probe method proofs that the original strength can be recuperated, in some cases even exceeded.
� er , Gr el ,
Decarbonisation Glass International July/August 2022 www.glass-international.com 49 defects and the self-healing properties of the coating, additional simulations were carried out. Models with defects were created and subjected to the simulation protocol. The analysis of the simulations showed that the coating can fill scratches and form covalent bonds, even if the coating has been applied prior to the damage. Fig 3 shows the modeled structure of the glass substrate near the surface and the topping layer of the coating that has created the covalent bonds to the glass matrix as can be seen in Fig 4
Conclusions In conclusion, given the results of the virtual twin as well as the laboratory tests provide the evidence that the chemistry works. That said, further studies are currently in progress advancing the coating technology to pilot scale and to industrial scale. There is an opportunity to make a step change in the sustainability of glass, by reducing the materials and energy required to produce it and to make the glass itself more robust lending it to refill and reuse models of consumption. The technology opens a suite of new applications; an opportunity to win terrain back that has been lost to PET containers by means of establishing lightweight bottles; and new repair options. Further results may become available at Glasstec in September. Ger s
a assault S st es, https
co GLASS SERVICES SHEARING We make shear blades. So you can make hollow glass. www.pennine.org sales@pennine.org +44 (0)1484 864733 A division of:



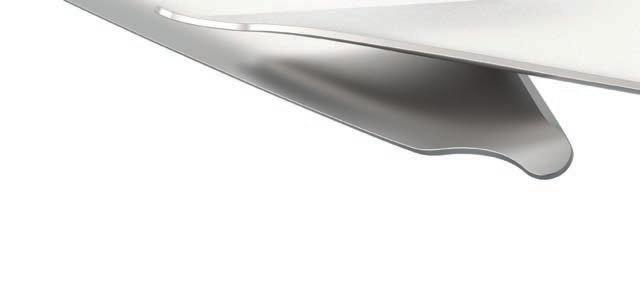
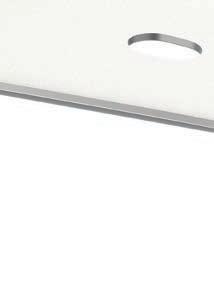



13B92GLASSTEC DISCOVER MORE AT FIVES’ STAND 20-23 September, www.fivesgroup.com2022 Forit’syoutimeto Greenerget

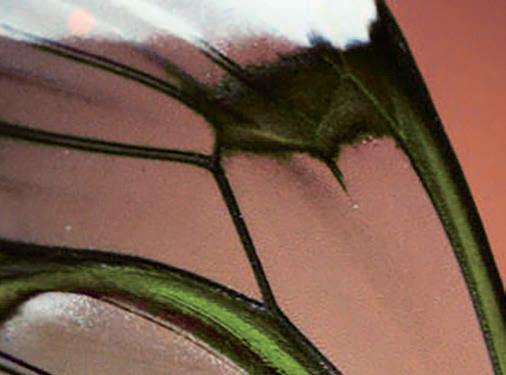

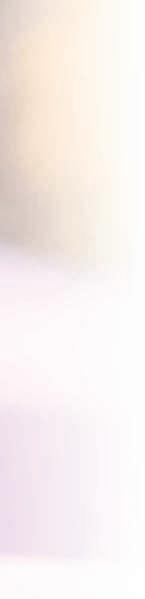
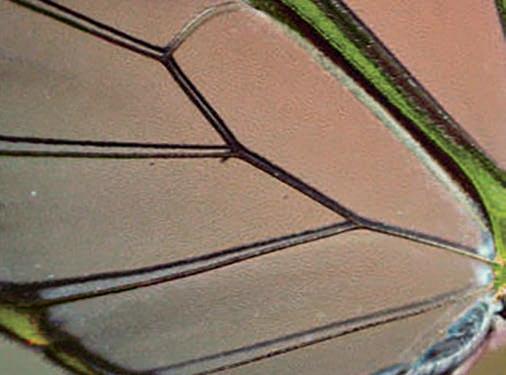


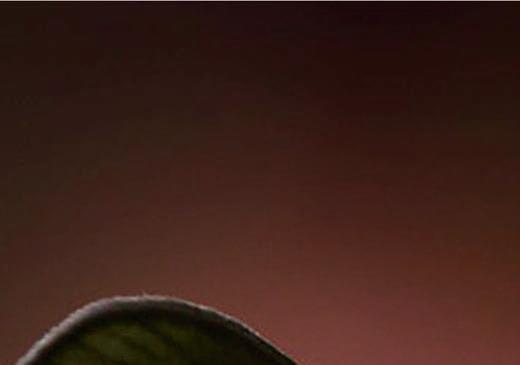
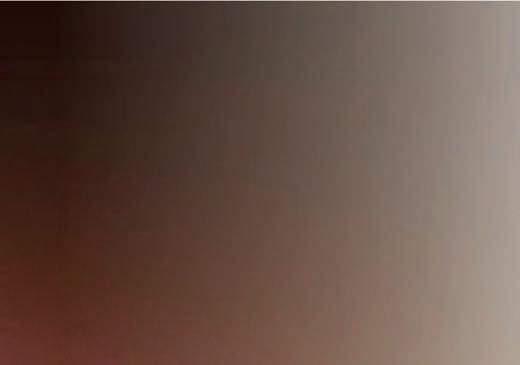
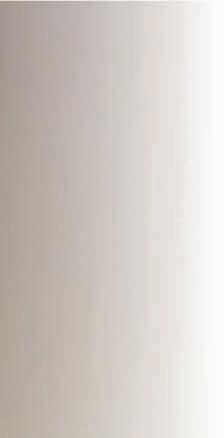
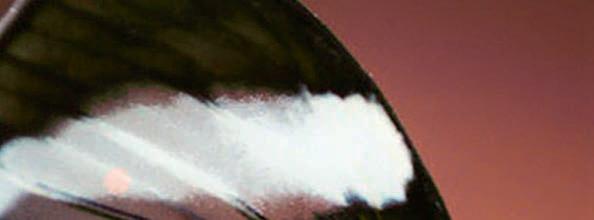


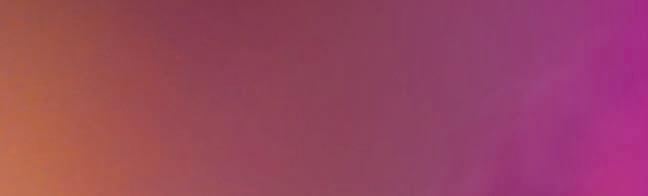
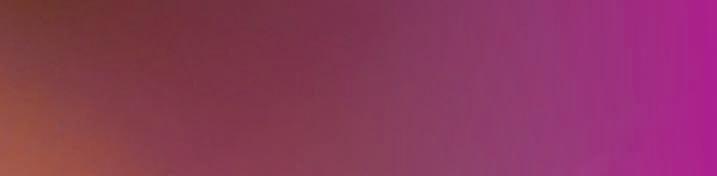
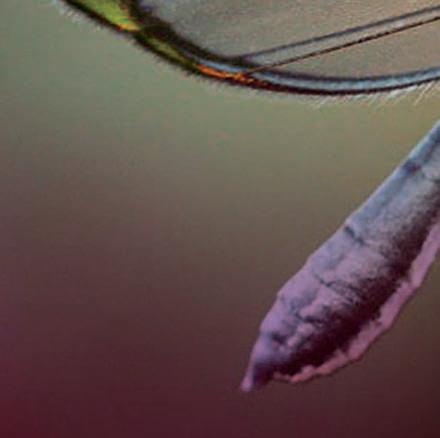
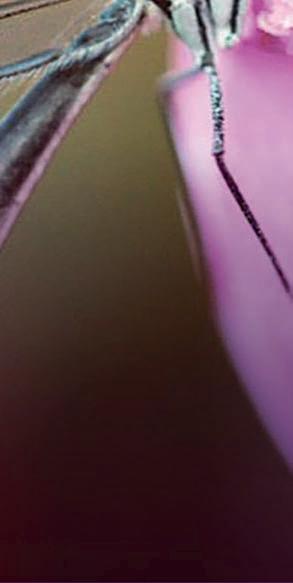


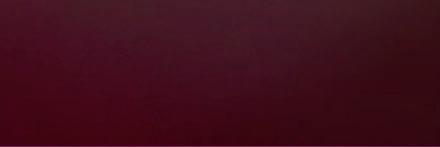

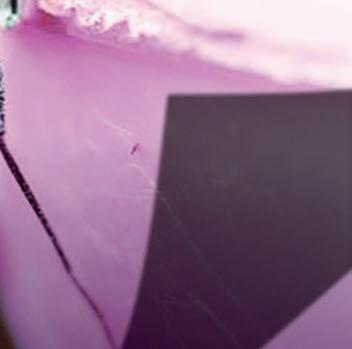
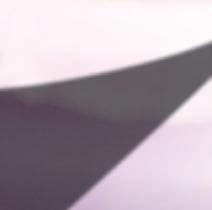


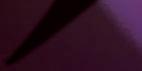
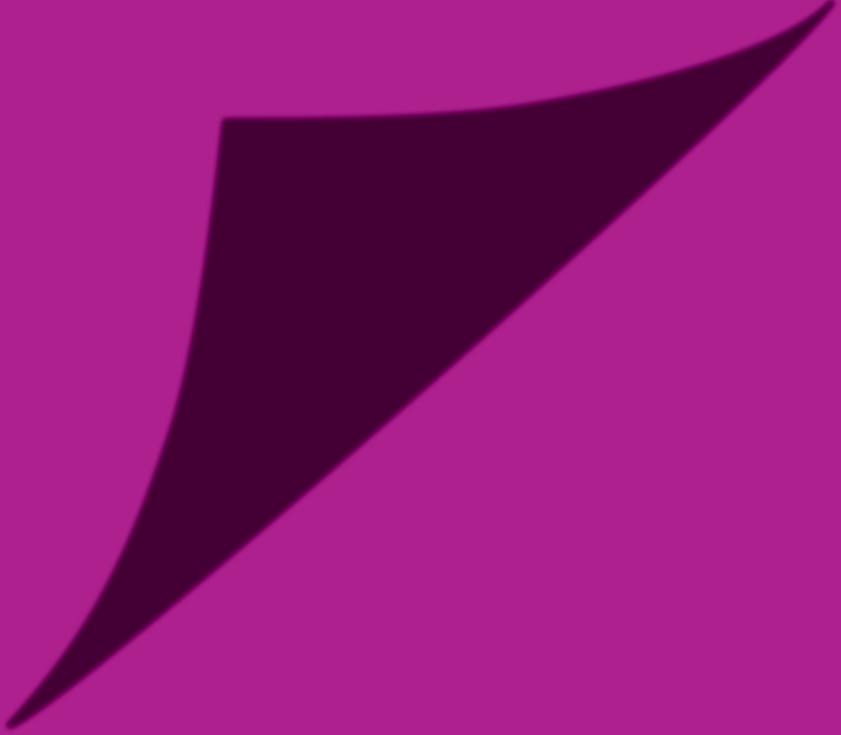
Emission measurements have become important as the glass industry aims towards carbon neutrality. HVG’s Henrik Gustmann* and Karlheinz Gitzhofer* explore the current challenges for glass manufactures and measuring institutes in Germany.
Emission measurements in Germany
Decarbonisation Glass International July/August 2022 www.glass-international.com 51 Continued>>
The Research Association of the German Glass Industry (HVG)[1] has been active in research and served the glass industry for more than 100 years. The HVG has also been able to perform emission measurements for its members and customers since 1975. In the last decades, environment and climate protection has become important for the society and the glass industry. Hence emission measurements have become a priority for HVG (Fig 1). In this paper, general regulations and requirements for the emission measuring institutes, like HVG, are presented. Laboratory norms, accreditation, notification and interlaboratory tests have changed the way we work and improved the quality of institutes. Although all these regulations are blurring the difference between several institutes, HVG stands out due to its specialisation and focus on the glass industry. Background knowledge of the process, years of experience and onsite analytics are just some aspects that make HVG the respected partner of glass manufactures.Theresults of HVGs emission measurements are also a valuable dataset for several own research and development projects. Moreover, the knowledge and the data are inputs to the discussions on national and international standards and Team of the HVG emission measuring institute.

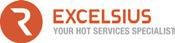
regulations)(BImSchV)BundesimmisionsschutzverordnungenAct).(BImSchG)Bundesimmisionsschutzgesetzthe[2](FederalImmissionControlFurthermore,thereareseveral[3](FederalemissioncontrolaswellastheTA-Luft[4]whichsetemissionlimitsaswellastheboundaryconditions.Basedonall
Fig amples of the ne limit in mg m al es for con entional heate container an flat glass furnaces.
Glass International July/August 2022 0 Continued>> 52 www.glass-international.com regulations or on regulatory limits (e.g. boron-emissions, mercury-emissions).
Regulations As previously mentioned, there are also several current challenges for the glass industry regarding emission measurements. One of these is the socalled new TA Luft[4,5], which became effective in December 2021. One new regulation is, that the authorities can now impose semiannual emission Fig 1.Mobile HVG emission measurement laboratory on a trailer.
These contributions were beneficial for the glass industry, as can be seen in the second part of this paper, in which current challenges for the German glass industry due to the growing requirements and regulations in field of emission measurements are summed up. Germany Emissions measurements in Germany are regulated by
these, the authorities, like state offices for example, were able to create a notice of approval for the maintainer of a site. In these notifications, the emission limit values, restrictions etc. can be found. The maintainer must prove that it complies with the limit values with the help of discontinuous or continuous emissions monitoring. Therefore, an independent notified (after §29b BImSchG) test institute is needed. The institute performs discontinuous emission measurements, calibration of the automatic measuring system and functional tests. The results of the measurements are reported to the maintainer, which in turn reports to the authorities. To be officially notified the institute must be accredited by the national accreditation body DAkkS. There is an information exchange between DAkkS and the competent authorities of the institute. Based on the accreditation, the competent authorities can notify the institute. Nevertheless, there is a constant monitoring and regular quality control of the institute through the DAkkS and the authorities. So, the institute must prove that it complies with the statutory provisions, which is a current as well as a constant challenge for every institute. Accreditation As already mentioned, an official emission measuring institute in Germany needs an accreditation. Therefore, a quality management system after DIN EN ISO/IEC 1702:2018 must be implemented. That means, for example, that operation instructions (SOPs) for every process are needed. Moreover, gapless documentation, a detailed risk evaluation and constant quality control are some major points for a full quality management system. This system is monitored by experts of DAkkS with the help of audits every 18 month. Moreover, the accreditation must be renewed every five years. Here the institute must face a big reaccreditation audit. To comply with the accreditation, the institute is only allowed to use standard reference methods. Of course, the methods must be validated and constantly verified. Therefore at least two interlaboratory tests have to be performed for each method within five years. The institute must be an independent company with competent, experienced and constantly trained personal. Furthermore, the test institute has to maintain an own chemical laboratory for all analyses. The only exceptions are the highly toxic components like dioxins and furans. Moreover, the institute is only allowed to use certified measuring equipment for official measurements. If the institute complies with all these requirements, it will get an accreditation by DAkkS. Based on this, the authorities can notify the institute for official emission measurements. Like the accreditation, this notification must be renewed every five years. So, there is an additional review of the accreditation, of the results of the interlaboratory tests, the competence of the personal etc. by the authorities.
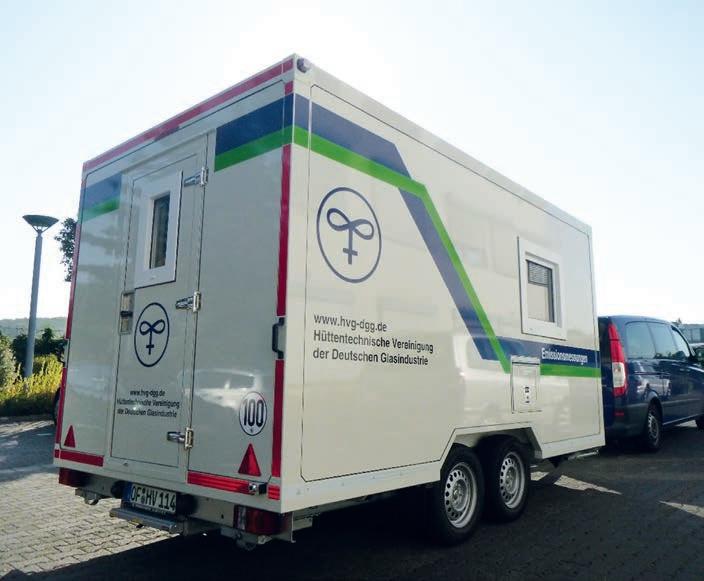
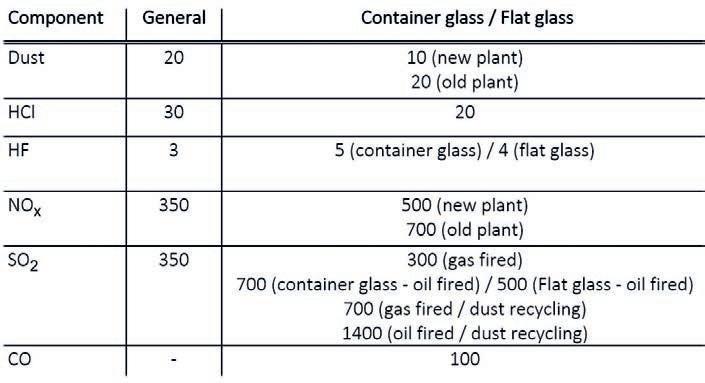
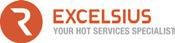
As an innovative technological leader in the global glass industry, we have a crucial responsibility towards the future of our planet. Therefore an environmentally friendly platform for electric boosting is available: E-Fusion – HORN Power Boosting.
HORN’s answer to the future way of glass melting focuses on our environment by creating a new boosting world which takes electric boosting to a whole new level.
HORN has bundled its forces to use sustainable energy in order to reach less CO2 emissions. Our specialists and comprehensive service package ensure a highly efficient performance of the plant over the entire life cycle.
ADVANCED LEVEL OF ELECTRIC BOOSTING
WWW.HORNGLASS.COM
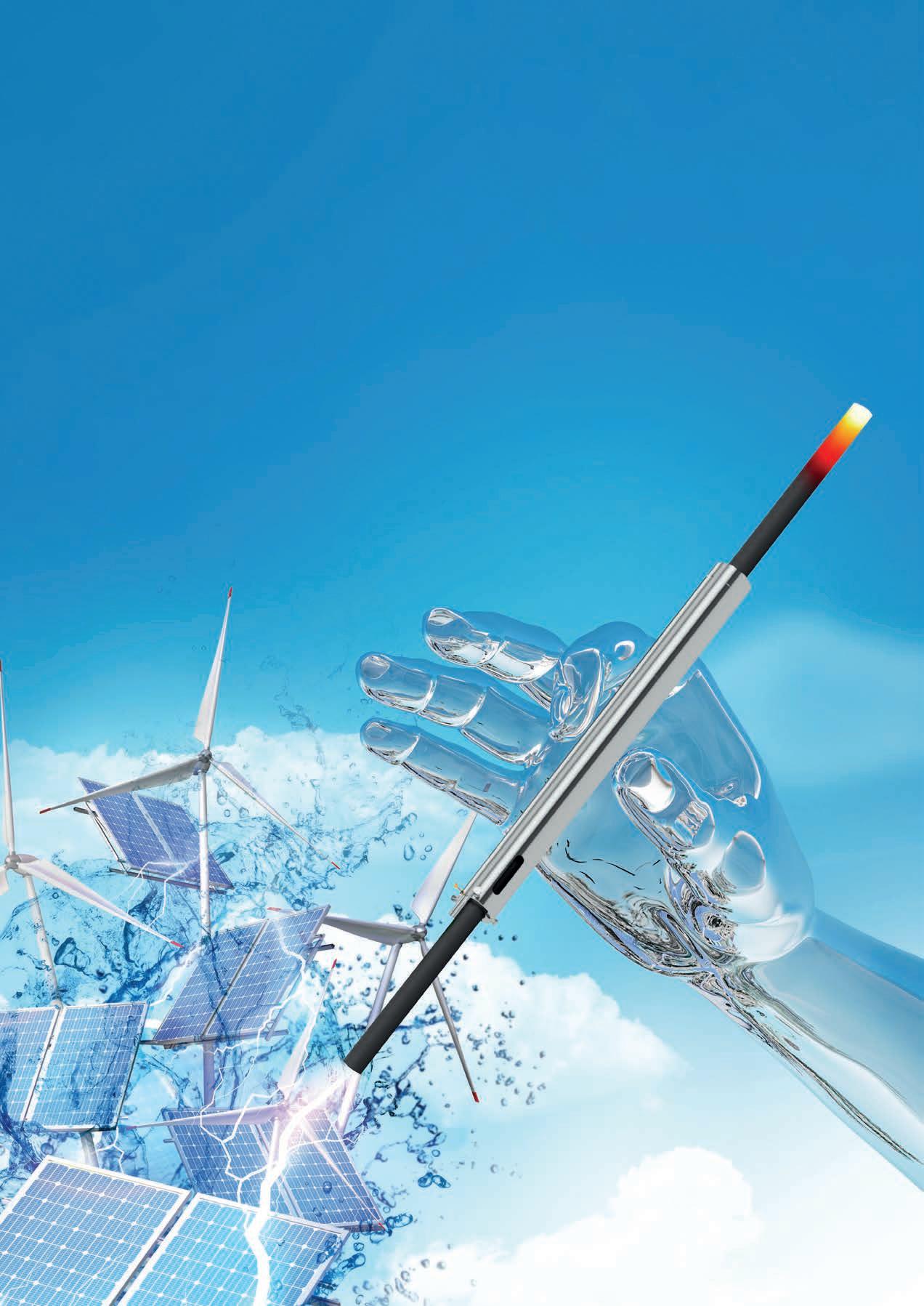
2. 3.bimschg/https://www.gesetze-im-internet.de/https://www.gesetze-im-internet.de/bimschv_44/4.http://www.verwaltungsvorschriften-im-internet.de/bsvwvbund_18082021_IGI25025005.htm5.https://www.lai-immissionsschutz.de/documents/lai-auslegungsfragenkatalog-44-bimschv-mit-schaubild_1643987733.pdf *Research Associates for Environmental Protection, Hüttentechnische Vereinigung der Deutschen Glasindustrie (HVG), Offenbach am Main, http://www.hvg-dgg.de/en/home.htmlGermany Fig 3 - Exceptions of limit values (in mg/m3) for some sectors of the glass industry. Fig 4. Probe for dust measurements.
Naturally, in the glass industry the discussions most of the time revolve around subjects like burner technologies, glass properties and investments. But the change in exhaust composition is also worth discussing. For example, in case of H2-Oxy-fuel furnaces, one will get lots of water vapour and less nitrogen. This leads to new challenges in terms of emission monitoring and measurement technologies.Inthecaseof all-electric furnaces (AEF), HVG already has a sufficient dataset with the possibility of direct compression to conventional furnaces. Thus, it is possible to sum up some general remarks on the typical emissions of all-electric furnaces. As expected, the emission properties of AEFs differ from fossil fuelled furnaces. In case of cold-top-furnaces HF, HCl and B (gas and dust) emissions are reduced due to absorption within the batch cover. On the other hand, dust-, NOx and organic emissions can emerge directly from the batch (Fig 4). In case of NOx emissions, this could be problematic because it is not possible to reduce NOx via reductive conditions in an AEF. Furthermore, the flue gas temperature is typically too low for an efficient NOreduction via SCR. Moreover, organic and highly toxic emissions can be problematic especially in the case of cold-top furnaces and use of recycling cullet. Dioxins and furans (PCDD/PCDF) can be formed due to the so called de novo synthesis in the temperature range between 250°C and 450°C.Thus, one could conclude that, allelectric furnaces are providing several advantages regarding emission reduction in case of some compounds (e.g. HF, HCl and B). Simultaneously, other compounds like NOx and organics become a new challenge. Therefore, it is possible that an adaption of measurement methods and surveillance concepts (e.g. limit values) is needed. � References 1. www.hvg-dgg.de/emt
Decarbonisation Glass International July/August 2022 540 www.glass-international.com measurements if no continues emission monitoring is installed, which is still the case for many glass-production sites. Furthermore, there are new and strict limit values (Fig 2). However, the new limit values as well as new measurement intervals must be imposed by authorities. So, pre-emptive obedience by the maintainer of a site is not necessary. There are separate specific tonnagerelated limit values for oxy-fuel furnaces and electrically heated furnaces, for systems with raw material preheaters and for systems with nitrate purification. Each glass sector must be considered separately, as individual emission limit valuesMoreover,differ. due to the research of HVG in co-operation with BV Glas and Federal Environment Agency (UBA) there are still several exceptions for some sectors of the glass industry (Fig 3). Some exceptions like for SO2, NO2, Pb, Se, As and Cd had been established already for the ‘old’ TA Luft. It was possible to preserve these regulations. There are also new exceptions for the glass sector which can be traced back to HVG-research projects. For example, it was possible to hinder a tightening of limit values for mercury from 0.05 mg/m3 to 0.01 mg/m3 if recycled cullet is used. Furthermore, based on HVG research projects, it was possible for the glass industry to avoid a strict and most likely not compliable limit of 1 mg/m3 for boron (classified as toxic to reproduction) emissions. Power generators Among others the revision from 2019 of the 44. BImSchV[3] regulates emission measurements on emergency power generators which were also wildly in use within the glass industry. So, power generators of 1 MW or more have now to be registered and approved by the authorities. Emission measurements are mandatory for new generators since 2019 and for old systems starting from 2024. In a big difference to the regulation of the TA Luft, the new rules of the 44. BImSchV need not be announced or imposed by local authorities. That means the maintainers of the generators are instantly responsible for the registration of their systems as well as for the demanded emissions measurements. Alternative melting technologies Climate change, as well as the urgent gas-shortage, requires an energy transition. Therefore, alternative melting technologies such as H2-Oxyfuel-, hybrid-, all-electric and water-cool furnaces are currently being discussed. Furthermore, energy saving technologies like preheating of recycling cullet as well as downstream use of heat are interesting.
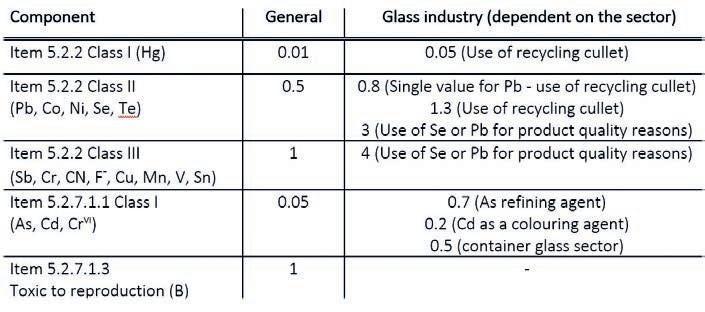
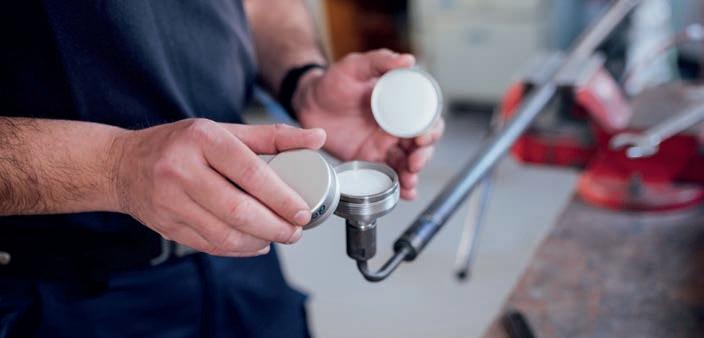
www.excelsius-global.comExcelsiusGlobalServicesGmbH Bgm.-Dr.-Nebel-Straße 14 D-97816 Lohr am GermanyMain Telefon +49 (0)9352 6044-0 Telefax +49 (0)9352 6044-19

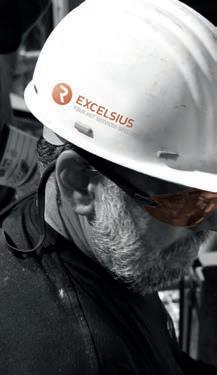

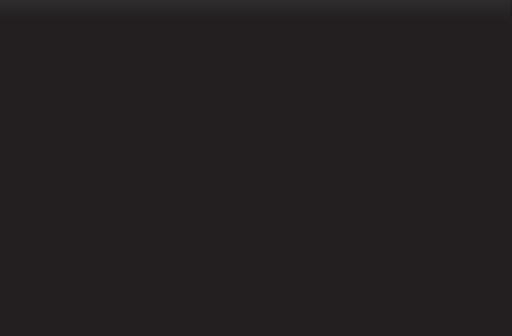
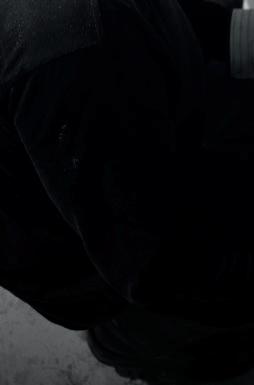
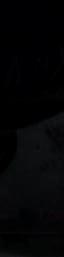
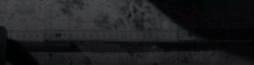
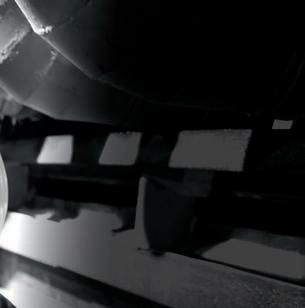
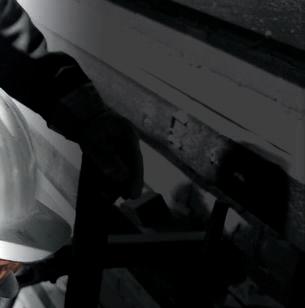
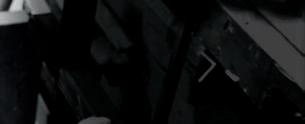

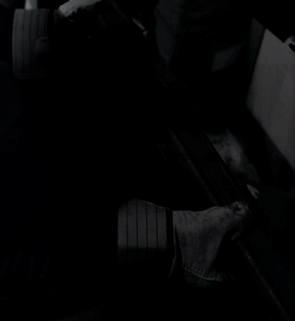
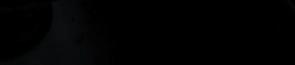


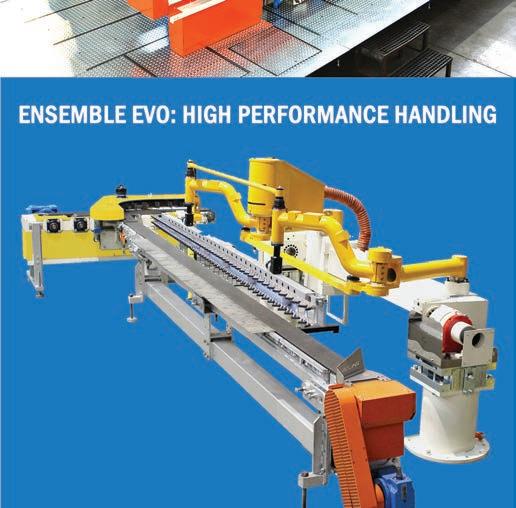
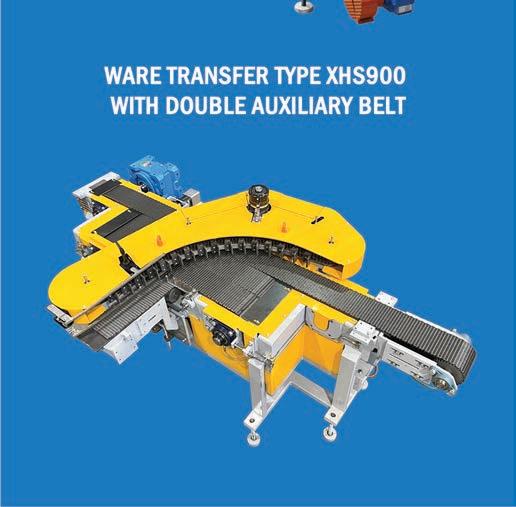
M ONEY Discover more and arrange your individual presentation: WALTEC MASCHINEN GMBH GERMANY KRONACHER STR. 2A 96352 WILHELMSTHAL +49 9260 99010 INFO@WALTEC.DE WALTEC.DE/ESERVO SUSTAINABLE HOT END PROCESS OPTIMIZATION BY COMPONENTSPERFORMANCE Boost the output of your press process up to 20%, consume up to 80% less energy, reduce compressed air up 130 m³/h and improve your sustainability footprint. Deliver process power only when really needed Driving substantial savings in energy and compressed air Higher efficiencies, more precise movements and optimized process repeatability Improved operator health and safety through less in-air oil pollution and residues Industry 4.0 compliant E SERVO performance components from WALTEC are compatible with almost all in-market press lines, including machines from other suppliers and can be used to upgrade your existing press line. Made Germanyin
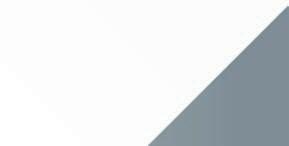
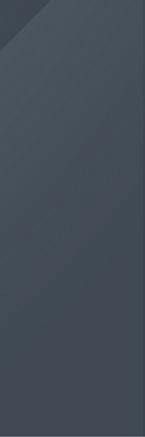

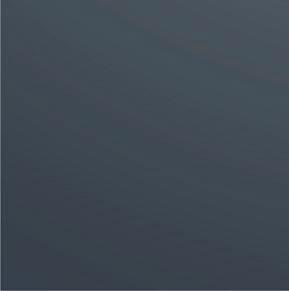
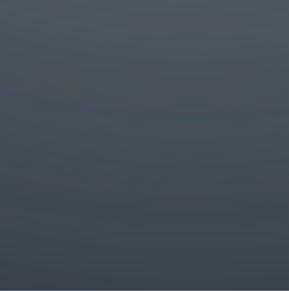
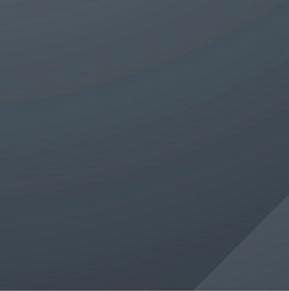
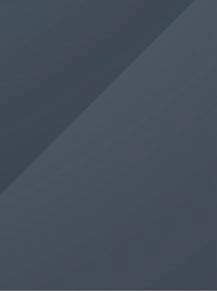
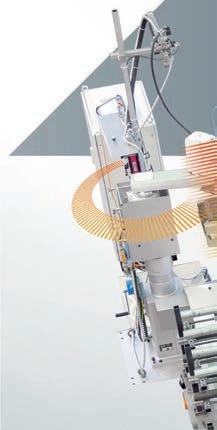
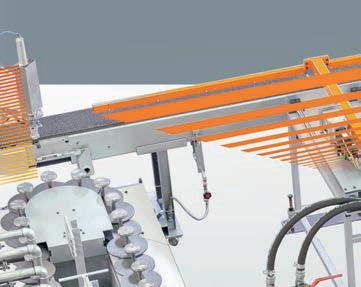
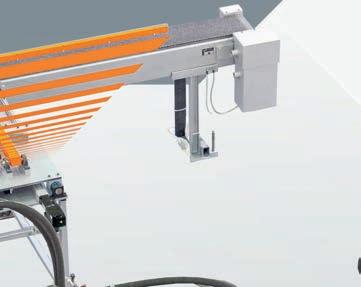
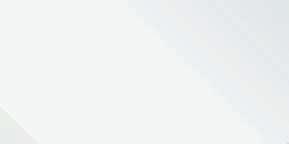
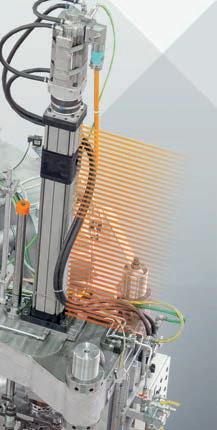
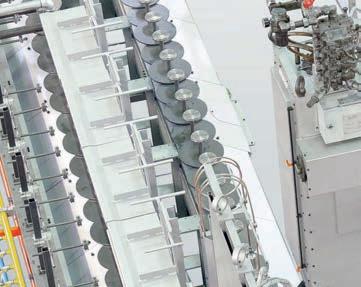
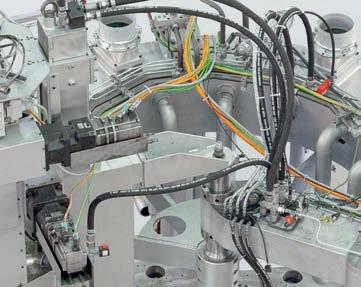
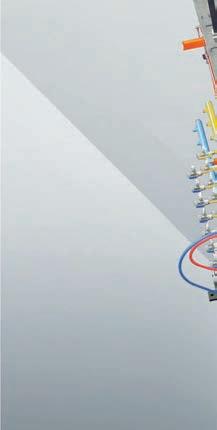
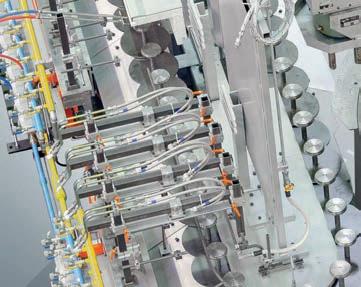
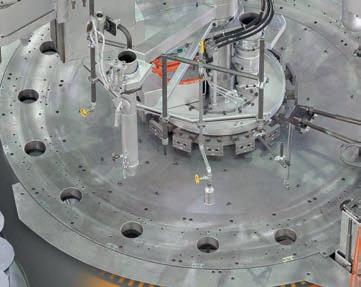
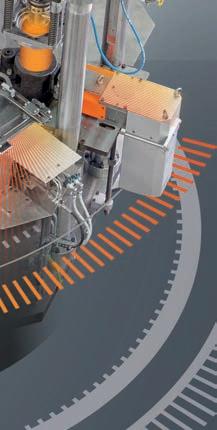

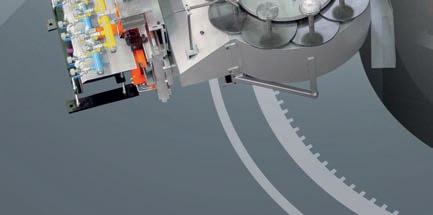

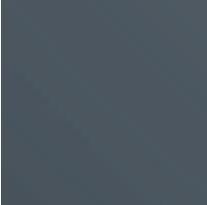


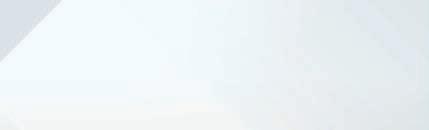
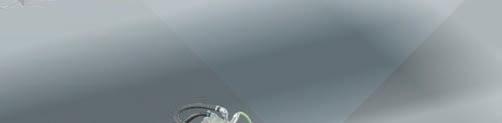
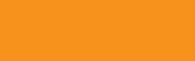
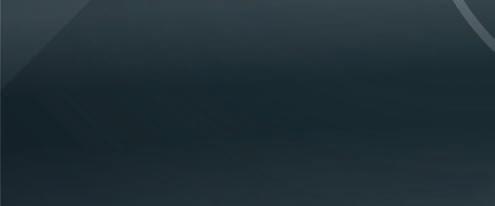
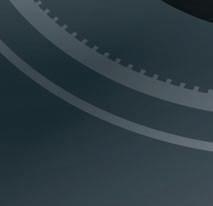




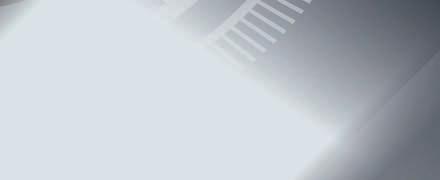
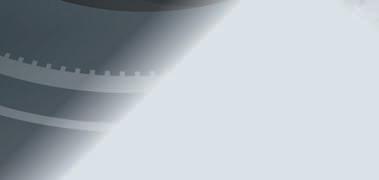


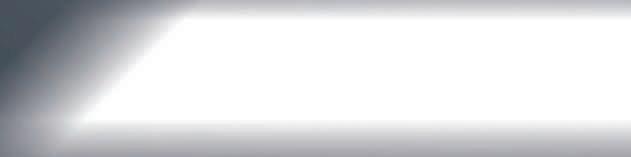
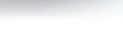


At the Sustainable Industrial Manufacturing Europe 2022 conference, Adeline Farrelly* shared how recycling is a key part of the glass industry’s decarbonisation pathway combined with making the energy transition. Glass is healthy, reusable and infinitely recyclable, it is the hidden gem in a carbon neutral future, said Nature – the international journal of science.1 By addressing our biggest challenge – the CO2 footprint–the glass industry can offer a future-proof packaging that is healthy, circular and climate-neutral – one that can sustainably meet growing consumer demand. We are living in a very difficult period with gloomy global warming forecasts, the war in Ukraine, the COVID crisis and the economic fallout from all this, the future has never felt more uncertain. Even in this uncertainty, people are more than ever demanding businesses and policy makers to ensure we foster a more sustainable world for the next generation. They are more attentive to the environmental challenges and demand that circularity and responsible production be high on the agenda and no longer empty buzzwords. Glass meets this demand for true circularity: it is a permanent material that can be endlessly recycled in a closed bottle-to-bottle loop without loss of its intrinsic properties it is inert and always remains healthy and safe for food grade packaging no matter how many times it is recycled. It is the beating heart of an industry that is strategic for the EU economy because it services the essential EU food, beverage, and pharmaceutical sectors as well as cosmetics and perfumery in the EU market, but also for the export of high-end products across the world. And figures speak for themselves. In 2021, the European production for the food and beverage sector increased by 5.0% in weight and 3.0% in unit terms, reaching its highest level ever recorded. More than 23.4 million tonnes or 83.3 billion bottles and jars were produced for the European and global market. Likely, in 2021 the production of flacons for the perfumery, cosmetics and pharmaceutical segments knew a strong growth by 2.2 % to reach 13.7 billion units.2 According to 2019 figures, the sector exports around €1.2 billion (empty bottles and jars) and enables extra EU exports of around €250 billion if you take into account filled products. More than 125,000 people work in the glass packaging value chain across Europe, guaranteeing a resilient local supply chain. On average, more than 70% of raw materials used in container glass production travel less than 300 km prior to being used in a glass furnace. Likewise, glass plants deliver more than 50% of their products within 300km. Every year €610 million is invested in upgrading plants for better energy efficiency and reduced CO2 emissions (i.e. a significant 10% of the operational and maintenance costs).However, producing glass requires a lot of energy and if produced with fossil-fuels such as gas, CO2 emissions are produced. The industry has been constantly working to make glass production more energyefficient and less pollutant, and it has made major steps forward by increasing
What will it take to close the recycling loop?
Recycling Glass International July/August 2022 www.glass-international.com 57 Continued>>
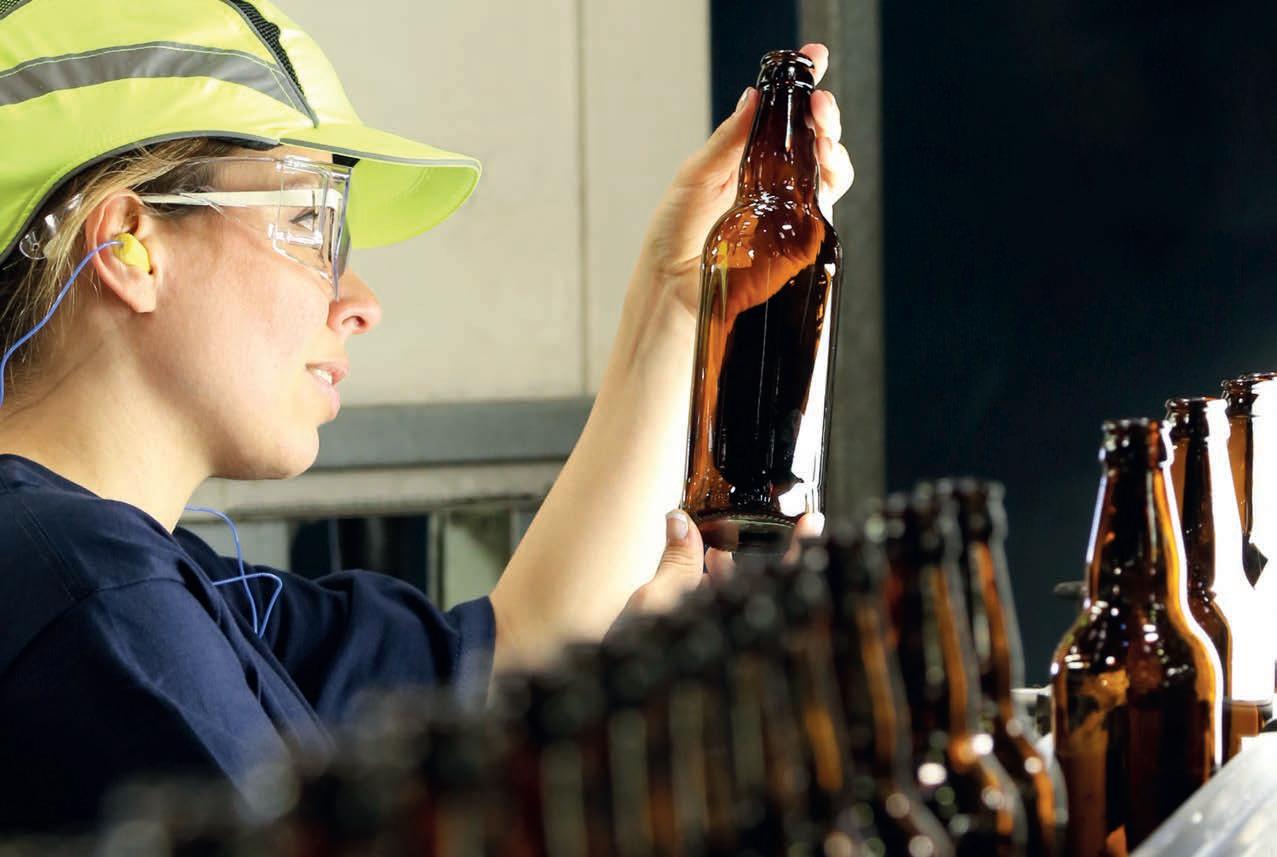
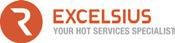
Recycling Glass International July/August 2022 580 www.glass-international.com the quantity of recycled glass in the batch and innovating the production technology. But this is not enough. As an important economic powerhouse of the EU economy, we’re committed to the UN 2030 Sustainable Development Goals (SDGs), and by 2050 we want to achieve a major revolution, starting now, in the way we produce glass that is fit for a circular and climate-neutral economy. This will secure the future of the sector and the jobs that depend on the industry within important value chains. To help secure the future of the European glass industry in a circular and climate-neutral European economy, many ‘disruptive’ paths for decarbonising the production process are needed, as technologies and systems are not yet commercially available. Transitioning to climate-neutral production requires huge capital and operational expenditure public sector support and funding is therefore important to helping industries to deploy the new, disruptive technologies to be on track to meet the decarbonisation targets set by the Paris Climate Agreement and the EU climate law: measures under discussion aim for more than a 60% CO2 reduction by 2030 compared to 2005 and net carbon neutrality by 2050. We have a twofold CO2 reduction strategy: addressing the 80% of CO2emissions through an energy transition for melting technologies and addressing the remaining 20% through closing the glass loop to recycle more, enabling more recycled glass cullet to be used in place of virgin raw materials, to make our circular economy work better. Energy transition and melting technologies To address the first pillar, in the last two years the European container glass industry jointly worked on the ‘Furnace for the Future’ project to get a grant from the EU Innovation Fund, but it didn’t succeed. However, in its initial phase it has allowed the industry to design a breakthrough technology to massively reduce CO2 emissions from container large-scale glass furnaces by replacing natural gas with up to 80% renewable electricity. Based on the know-how the industry has acquired by preparing the application, glass manufacturing companies continue today individually to invest in designing the breakthrough technology and the scaling up of electric melting on a commercial scale. When created, these hybrid electric furnaces will overcome existing technological barriers, and will be capable of melting reduced (amber) glass, as well as flint and green glass, together with high levels of recycled glass. With this new hybrid technology, the industry will be able to cut 50% of current CO2 emissions from our factories. These more efficient “Furnaces for the Future” are already on the horizon, with cleaner energy, improved hybrid technology and more use of recycled glass than ever before. Combined with other innovations and sustainability initiatives, these new technologies will reduce carbon emissions from glass production significantly. Our industry continues to invest in improving existing technologies and exploring other solutions (biomass, hydrogen etc.) and at company level there are many more sustainability initiatives.
Closing the glass recycling loop The remaining 20% of CO2 emissions come from the melting of virgin raw materials in the furnace. But if replaced with recycled glass (cullet) these emissions are eliminated. Every tonne of recycled glass saves 1.2 tonnes of virgin raw materials, with a 3% energy reduction for each 10% of glass recycled in the furnace and a 5% reduction of greenhouse gas emissions.Glassis Europe’s most recycled, closed loop food and beverage packaging material – latest figures put the collection rate at 80%.3 Most recycled glass ends up back in the production loop: the average batch mix contains 52% recycled content. However, while 80% of glass put on the market is collected, 20% is not. To close the loop, glass depends on a whole system of stakeholders working together to collect more and better-quality glass for recycling.Thecontainer glass sector initiated Close the Glass Loop – a multi-stakeholder platform to unite the glass collection and recycling value chain, and to establish a material stewardship programme that will result in more bottle-to-bottle recycling. Our aim is to have people recycling more and better. This platform brings together local authorities, cities, brands, recyclers, extended producer responsibility schemes and producers to achieve a 90% collection for recycling target by 2030.
� Saverglass and Verescence are industrial partners in VERCANE, the consortium formed by ENGIE, Fives, Saverglass and Verescence to study different carbon-neutral energy systems that could be compatible with the glass melting process: hydrogen, bioresources and process electrification.
� O-I and Dalkia, a company that specialises in energy solutions, have joined forces to recover heat for the neighbourhood’s homes, through a district heating network.
� Verallia is investing in electric furnaces at its site in Cognac as it strives to meet its ambitious CO2 reduction targets. The furnaces are set to come on-stream in 2023-2024 and will produce extra-flint glass for wines and spirits.
� The Federal Association of the German Glass Industry (BV Glas) is partnering with the GWI institute in Essen to research hydrogen as a substitute for fossil fuels in the glass production process and has received funding from IN4climate.
� Wiegand-Glas announced the production of the new Eco2Bottle, a wine bottle made of guaranteed 93% recycled glass and with climate-neutral electricity from 100% hydropower.
� Ardagh implemented a Tesla Battery Storage System in Irvine, Scotland.
*Secretary General of the European Container Glass Federation (FEVE), Brussels, Belgium, www.feve.org (1) glass-value-chain-reaches-major-milestone/(3)(2)d41586-021-02992-8https://www.nature.com/articles/https://feve.org/year2021productionhttps://closetheglassloop.eu/europes-
� Encirc has worked with Glass Futures and have pioneered the use of biofuel during a test production on one of Encirc’s furnaces.
Here below just some examples:
Close the Glass Loop action plans are being developed at EU level and in several countries - see www.closetheglassloop.eu The industry is committed to enabling the transition to a resourceefficient and low-carbon economy and ensuring the long-term sustainability of manufacturing. By doing so, the industry will ensure actions and business goals are in line with global commitments to the UN 2030 Sustainable Development Goals. In fact, the UN has made 2022 the International ear of glass a perfect opportunity to show how glass in all its applications can contribute to achieving these Sustainability Goals and glass packaging with its project to be climate neutral and fully circular is a key part in achieving these aims. �
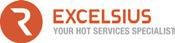
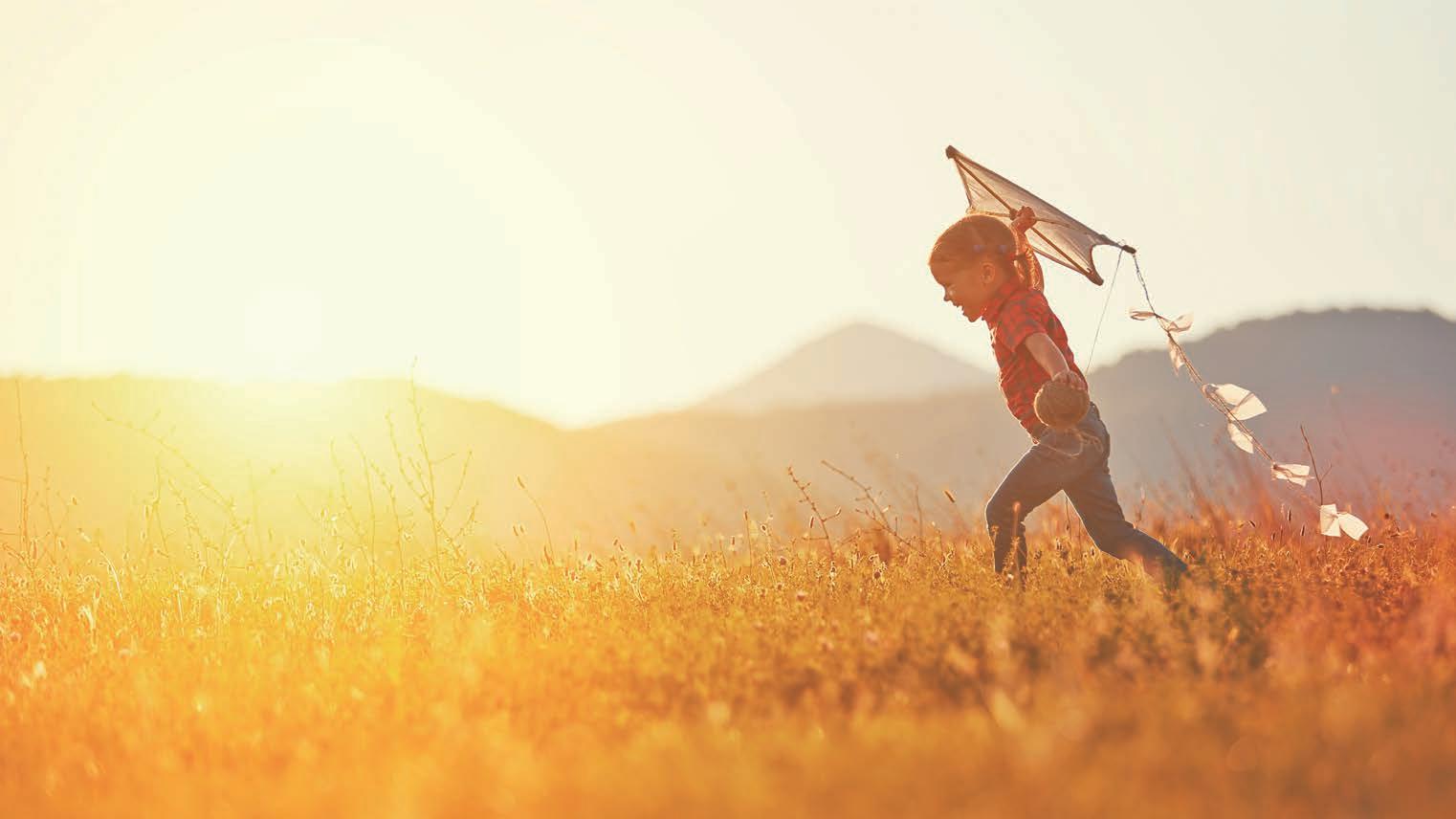
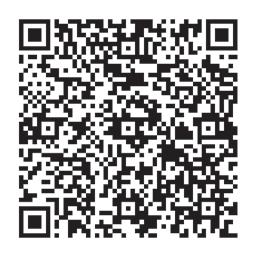
53035 MONTERIGGIONI (SI) ITALY - Strada di Gabbricce, 6 Tel +39 0577 304730 ifv@fonderievaldelsane.com www.fonderievaldelsane.com


Mark Pudner* discusses the UK glass industry’s route to net zero. While technologies such as hydrogen and carbon capture storage will play a part, renewable electricity is believed to be the main energy source for glass manufacture. In 2021, British Glass published the UK Glass manufacturing sector’s net zero strategy to demonstrate that net zero can be achieved by 2050, and set out a range of policy measures required to enable that transition. The publication followed many years of working with government and publishing the glass sector decarbonisation roadmap in 2014, which was closely followed by the BEIS glass sector decarbonisation strategy in Since2015.then, there has been rapid growth in decarbonisation research in the UK and EU, and much of the technologies, such as hydrogen and carbon capture storage, which were originally dismissed in 2014, are all now looking promising to help achieve net zero. Routes to net zero Several possible routes to achieve net zero have been considered, however the sector is currently limited in how much progress it can make as much of the infrastructure is not yet available and alternative low carbon fuels are not cost competitive. When considering the coming years, we assumed that several measures would be implemented: furnaces transitioning to oxy-fuel melting, short term use of biofuels and sites installing waste heat recovery.Theuptake of biofuels will be largely dependent on cost and availability. If a sustainable source of competitively priced biofuel could be made available, some glass manufacturers could reduce a large proportion of carbon emissions, though this is viewed as a transitionary measure. Longer term, we expect electricity will be the main energy source used for glass manufacture, which will be supplemented by some hydrogen where a full switch to all electric melting is not viable.Using electricity for glass melting is a far more efficient use of energy and is also associated with very low emissions of other pollutants. This is important as we will be expected to significantly reduce other emissions such as NOx and SOx by 2050. For float glass there was uncertainty over the amount of electricity that could be used so a much lower proportion of electricity was applied in the modelling. It was assumed that longer term hybrid furnaces will gradually switch from natural gas to hydrogen and outstanding technical issues are addressed to allow furnaces to be future proofed to allow for theSomeswitch.blue hydrogen is expected to be available from the mid-2020s, but it will be 2035 and beyond before it is available more widely.
Reduction of process emissions
Decarbonisation Glass International July/August 2022 www.glass-international.com 61 Continued>>
Process CO2 emissions will be the most difficult to abate, however it is assumed that there will be a reduction due to increased cullet use and research is ongoing with the use of alternative raw materials from waste (Glass Technology Services led EnviroAsh project) and calcined raw materials. However, there are challenges with the recovery of postconsumer flat glass and quality cullet availability.Overall,our data shows that between 2002 and 2018 the average CO2/tonne packed for the sector (including emissions from electricity generation) has reduced by 23%. This is due to improvements in
British Glass explains the UK’s net zero strategy
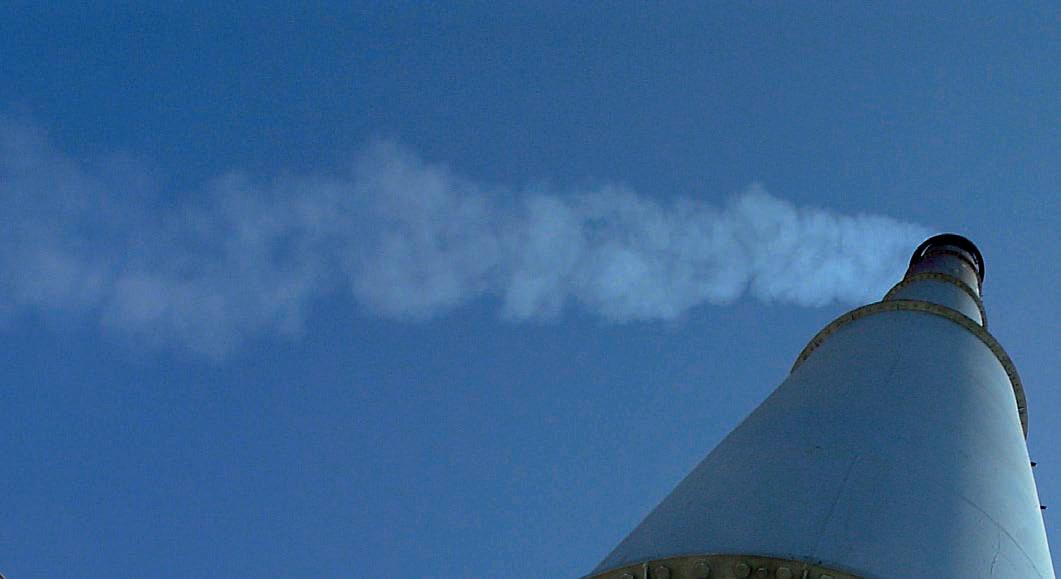
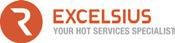
� *Senior Technical Advisor, British Glass, hapelto , She el , K https://www.britglass.org.uk/
Decarbonisation Glass International July/August 2022 620 www.glass-international.com energy efficiency, increased cullet use, and decarbonisation of the electricity grid.As Fig 1 shows, we believe the sector can go carbon negative by 2050 due to the negative grid emissions. Further savings could be made if the carbon savings of products, such as energy efficient glazing, are included.
Abolishing the CPS is a simple measure that the government could take to help reduce everyone’s electricity costs. Overall, while there is still progress to be made in the short and long term for both policy and infrastructure to allow the glass sector to achieve net zero, we still believe this is possible by 2050 and we will continue to work alongside industry and government to pave the way to carbon free glass manufacturing. To read the UK glass industry net zero strategy visit –publicationsuk/knowledge-base/resources-and-www.britglass.org.
Fig 1. Potential route to net zero by 2050.
A key part of the strategy are the policy recommendations that will enable the transition to net zero whilst ensuring that our sector remains competitive and is protected from carbon leakage. Without a secure supply of competitively priced low carbon fuel the sector will not be able to decarbonise whilst remaining competitive. Under our energy cost policy recommendations, we propose establishing a funding mechanism to support operational, as well as capital costs associated with switching to low carbon fuels. This could be, for example, through a government business model that encourages the electrification of industrial heat by supporting the additional cost of electricity. This would protect first movers and accelerate the decarbonisation of the sector.We also recommend reforming electricity pricing to reflect the much lower costs of supplying low-carbon electricity and that our sector is exempt from additional policy costs which are likely to be added to the cost of natural gas in the Underfuture.the recommendations for infrastructure, we advocate upgrading and future-proofing electricity capacity and networks to enable electrification of glass manufacturing. Alongside this, we recommend support for the high cost of upgrading site electricity connections for electrification of glass manufacturing. For dispersed sites it will also be important to ensure that hydrogen infrastructure allows connections as early as possible. Whilst we are making good progress on solutions for decarbonisation, we still need government to continue support for deep decarbonisation innovation projects and introduce funding for large scale industrial demonstration projects. In terms of policy on circular economy, our strategy recommends improved consistency across UK container glass recycling and for support for innovation in the recycling system to increase yields of glass available for remelt. This year we were successful in keeping glass out of the English deposit return scheme, which would have decreased the volume of glass going to Althoughremelt.there are established schemes for the collection of pre-consumer flat glass, most of the post-consumer glass from construction projects will end up in landfill. To address this issue, we recommend the recycling of flat glass is written into public sector contracts, reforming building regulations on design for end of life to increase recycling of flat glass and raising awareness of the circular options within the construction industry. At British Glass, we recently responded to the UK ETS consultation which proposed aligning the number of CO2 allowances distributed through the scheme each year to 2030 with net zero. Whilst we support the government’s commitment to achieve net zero by 2050, the reduction in allowances to 2030 is not achievable as it does not align with other government decarbonisation policies on infrastructure and availability and cost of low carbon fuels. This will dramatically increase carbon compliance for our sector whilst we will be unable to react to reduce ourAnotheremissions.key area of work is electricity costs. UK glass sites have higher electricity costs than equivalent sites in the EU. Sites in Germany and France benefit from a reduction in network costs due to the valuable contribution they make to the grid in providing a stable base load. We have been pushing for this for a while and later this year we are expecting a consultation on reducing network charges.Another element of the electricity charge that could be reduced for our sector are the indirect carbon costs. The carbon cost is made up of the UKETS cost and the carbon price support (CPS). The CPS is an outdated policy which was introduced when carbon prices were very low to support the move away from coal fired generation. Now that carbon prices in the UK ETS exceed £80/tonne we no longer see a need for this policy, especially given the recent electricity prices.
Impacting policy
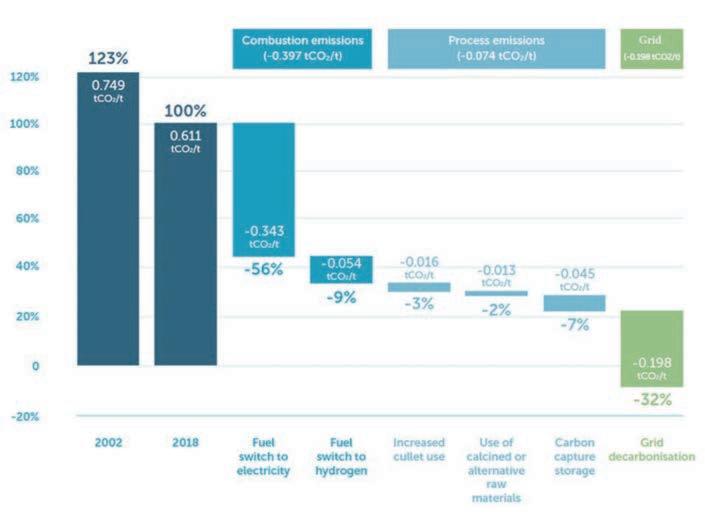
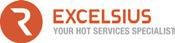
infodesk@celsian.nlFollow us on Your partner for future-proof glass Visit us at Glasstec 2022 20-23StandSeptember15B13
using proven methods like furnace modelling, laboratory measurements and practical furnace health checks to optimize glass melting processes. We also train operators and
the
through our standard course, dedicated programs and various e-learning modules. We
Celsian’s aim to minimize cost agile team of glass experts glass technologists strive to be the best partner
of making glass for end users and the environment. We have an
for optimization of glass production worldwide. Furnace support Process optimization Training and R&D
is
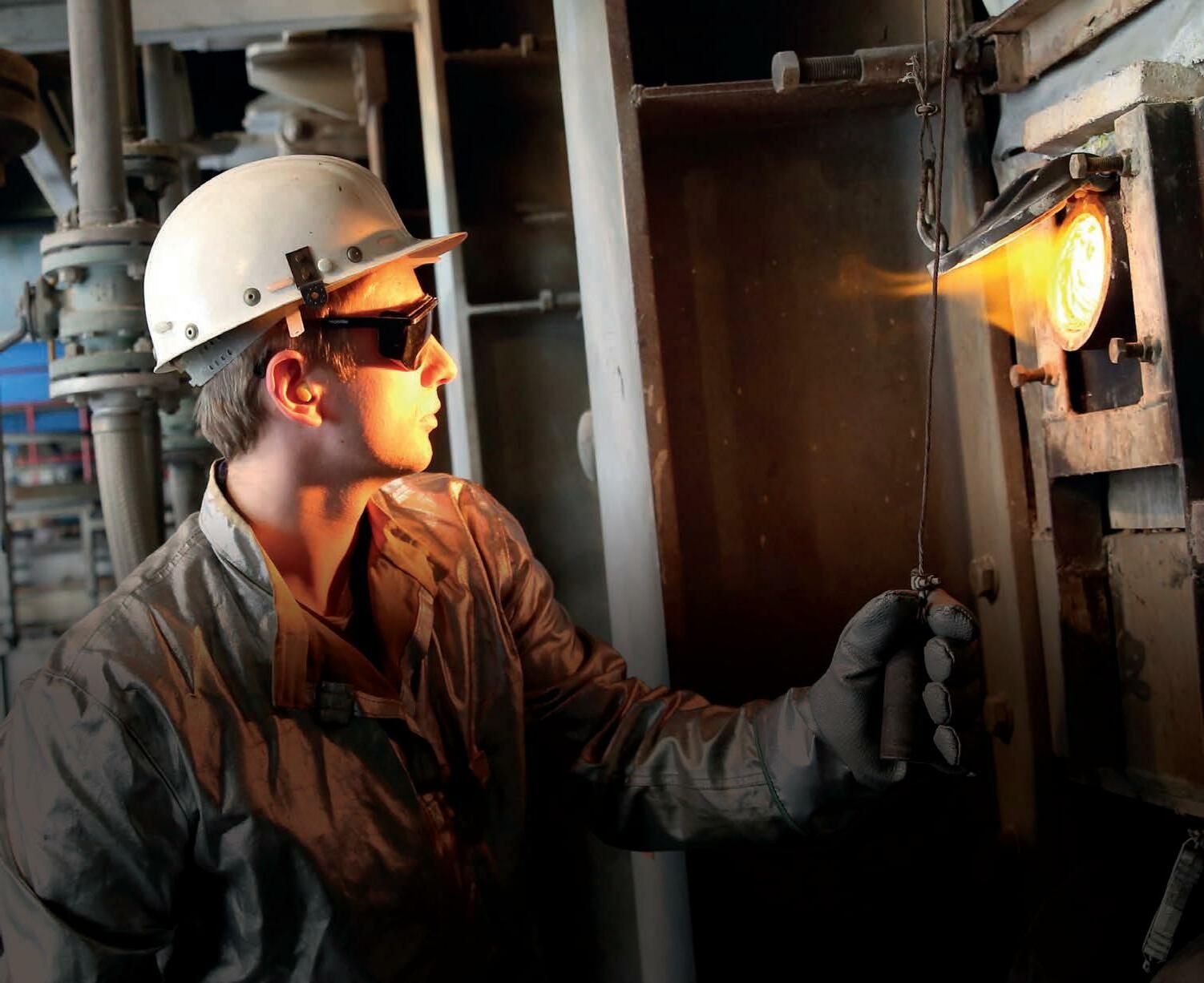

Grupo Vical is the largest recycler of packaging material by weight in Central America. Eduardo Ordoñez* discusses the manufacturer’s waste picking scheme, which has seen a recycling rate of up to 80% in Costa Rica and 90% in Guatemala.
Grupo Vical started the operation of its production plant in Guatemala in 1964, becoming the first glass container manufacturer in Central America. In 1978, the second production facility was added in Costa Rica thanks to the markets demand.
Recycling Glass International July/August 2022 www.glass-international.com 65 Continued>>
Grupo Vical has two production plants with two furnaces each, and 12 production lines with a total daily capacity of about 900 metric tons. Our current flint production is mainly done in Guatemala with five production lines and an in-line colouring feeder. The colour production (amber and green) is basically carried out in Costa Rica with seven production lines. Our facilities have an unbeatable geographical position, being strategically located in the North and South of Central America, serving within our geographically natural market and abroad over 200 clients in more than 20 countries. Grupo Vical currently supplies containers for the food, pharmaceutical, beer, soft drink and liquor industries. Regarding our strengths, we are focused on providing: the best possible quality an outstanding service to our customers while being committed to environmental protection and occupational health and safety for our 1500 employees. These goals are achieved thanks to our well qualified staff with a 100% service and results-oriented attitude, as well as the great commitment to the acquisition of technology and automated quality control systems, together with quality and food management systems. Certifications also assure the quality and safety of our products and the efficiency of our plants. Due to these investments in technology, our processes and systems result in versatility to produce all types of glass containers. Recycling The company started recycling glass from the beginning, receiving cullet mainly from glass shops and a few glass pickers. During the early eighties, we started getting glass from some providers of the municipal dump. However, said activity was reorganised at the end of the nineties, starting a slow growth that exponentially accelerated the last 10 years. At the time, we received cullet from every country in Central America, and countries in the
Closing the glass loop in Central America
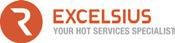
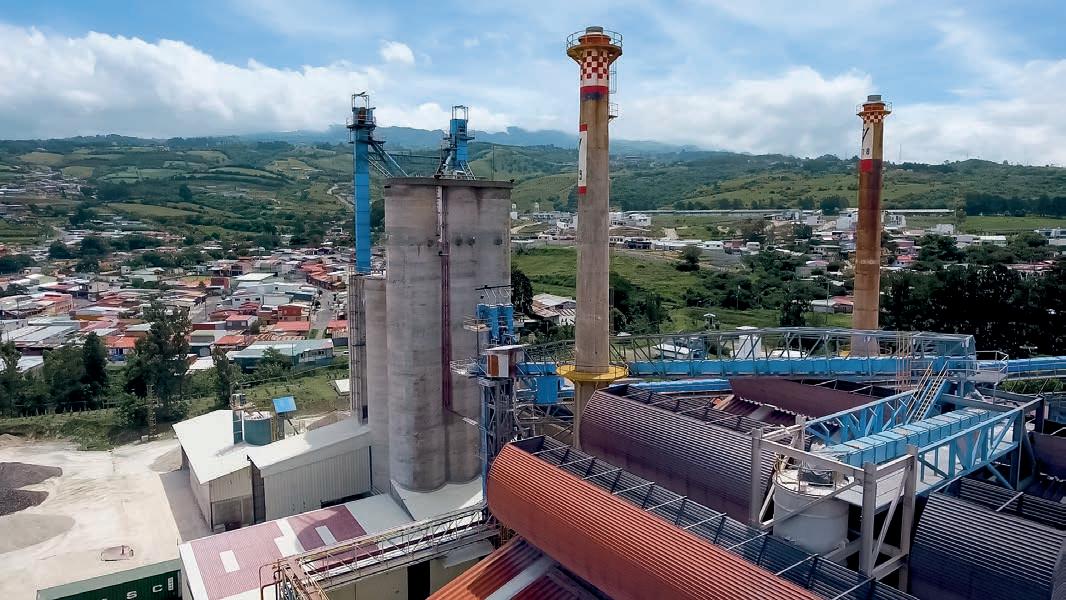

Forming a network
*Head of Communications & Corporate Affairs, Avenida Petapa, central-american-glassmaker-group/http://grupovical.com/en/vical-Guatemala.
Before the scheme started, we didn’t pay that much attention to cullet since we had an abundance of raw materials, to the point that we had a global recycling rate of only 4% by 2005. Glass recycling was irregular, practically confined to a few glass shops and a couple of glass pickers, until, as said, it became necessary to assure a stable and efficient operation.
Caribbean since we are committed to bringing back as much cullet as possible from the countries in which we sell our products.Though Guatemala and Costa Rica (where our factories are) had large deposits of silica, feldspar, and limestone, they were located relatively far away from our production facilities. Guatemala was suffering from social upheaval that made it difficult to get raw materials without delays. Another problem was that, during the same period, the train service ceased to exist at the same time in both countries, so this made it even more difficult to transport those materials in an efficient way. Finally, the energy (fuel and electricity) costs also raised during that time. Hence, taking advantage of glass recycling turned out to be something practical and profitable, as well as the right thing to do in relation with the environment. We developed a network of waste pickers to bring back waste glass into our factories.
Recycling Glass International July/August 2022 660 www.glass-international.com
It was hard work to organise the network of waste pickers since it was something new for the region. There was practically no information, less education, and no legal support in that regard. No one had the idea of what revaluing, residual value, and recycling was. It was just trash. No one wanted to pick anything from the garbage, collectors just threw everything away into the dump. We started by convincing some pickers that selling cullet could be a good income for them and started organising the cullet recovery first from the rural region, since there were more people in need that would appreciate that income. A little time later we moved to San José Cartago and Guatemala City to do the same with an increasing success, and finally we started doing the same in the rest of countries of the region. We currently have more than 1100 collection centres throughout Central America and the Caribbean. These provide around 2000 direct and many indirect jobs, and has become a real parallel industry, which only the last year had an economic spill of more than $14 million. That makes Grupo Vical the largest recycler of any material by weight in the region. We buy every amount of cullet the pickers bring to us in a fair and stable price. We also provide knowledge on the best way to collect it, supply safety equipment so they can do their job in a better and safe way, and in some cases, we give them some basic equipment like glass crushers so they can do a more efficient work. Sustainability The scheme has been successfully implemented in parallel in both plants. Hence, we have reached an average quantity of 118,000 MT of glass in the last five years, managing to reach important recycling rates like the one of Costa Rica with an 80% and Guatemala’s 90%. It is important to have such high recycling rates because we can reduce the pressure on natural resources reducing the amount of raw material needed to produce new glass. We also contribute to reduce the amounts of waste that go to the landfills, the emissions to the environment, and diminish the need to transport of both raw materials and waste. In short, by recycling glass we save 50% in emissions and 30% in energy during the new glass production process and of course a lower carbon footprint. Currently, we do also recover glass from the other countries of the region that has made us reach between 40% and 50% of recovery rate in the region the last five years, making, as said, Grupo Vical the largest recycler of any packaging material in the region by weight. Fuel consumption has decreased, while the life of the furnaces has been extended. Another important point is that our dependence on virgin raw materials has been reduced, becoming an example of circular economy in the region. The scheme has helped raise awareness of the importance of glass recycling among the countries in Central America and the Caribbean, since our scheme is based on education and relationship with a lot of stakeholders. So, with both our collection system and our educational communication platform, Por un mundo limpio como el vidrio (For a world as clean as glass), we have managed to position glass as an environmentally friendly material, and of course a recyclable one, in the region. Mr Ordoñez also spoke at CGL’s twoyear anniversary event. See his talk via https: youtu.be lBZzDsc 3dk t 5622�
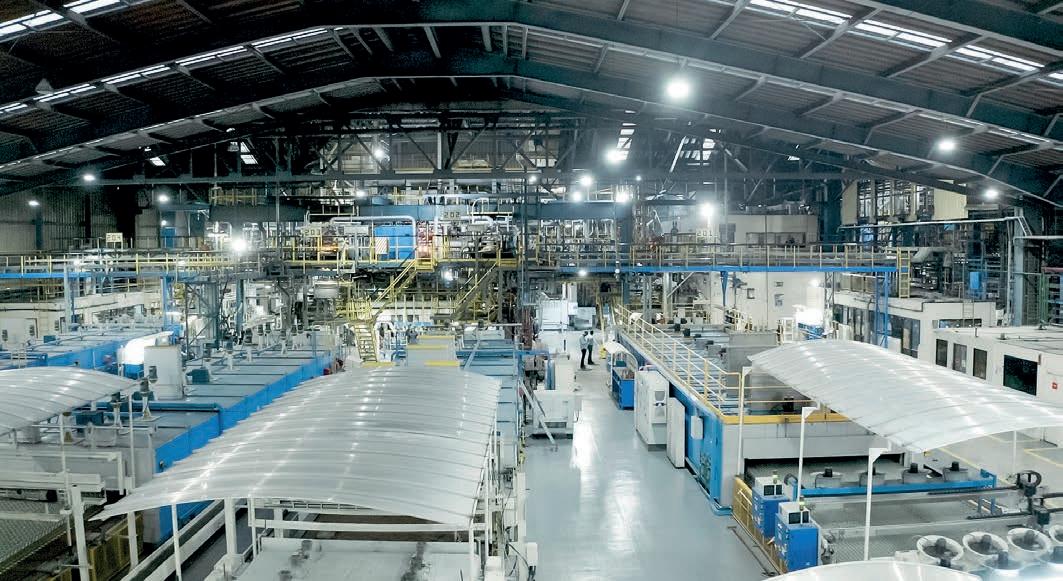
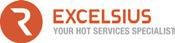
Celebratingglassforitsinfinite formsandinfiniterecyclability MONOFRAXLLC FALCONER,NY,USA info@Monofrax.com www.Monofrax.com Phone1-716-483-7200 refractorypartnerYourfusedcast

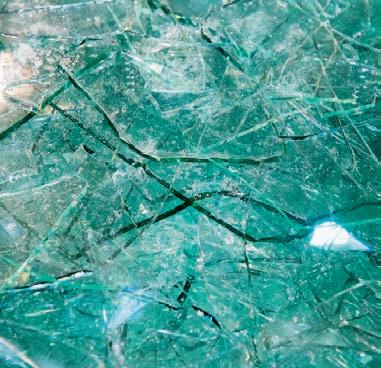
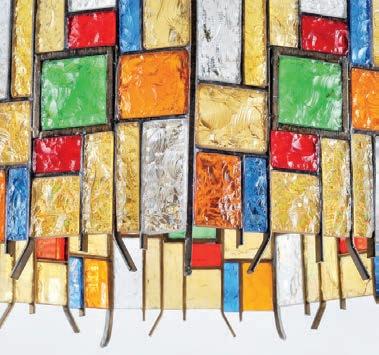
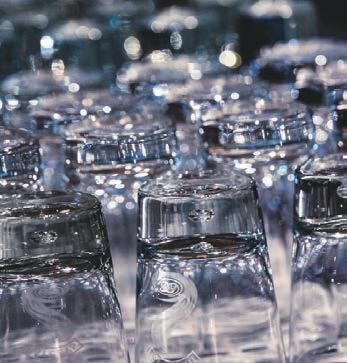
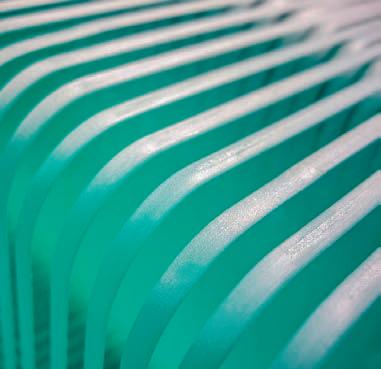
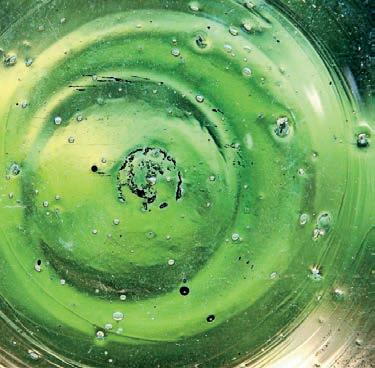

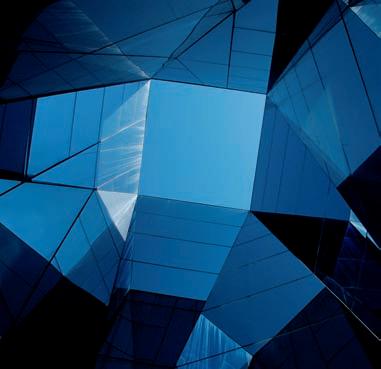

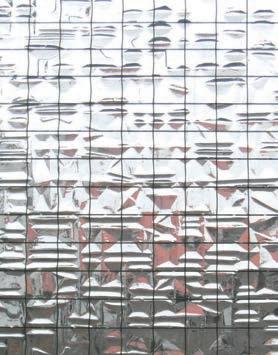
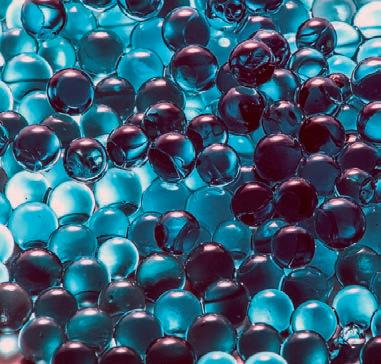
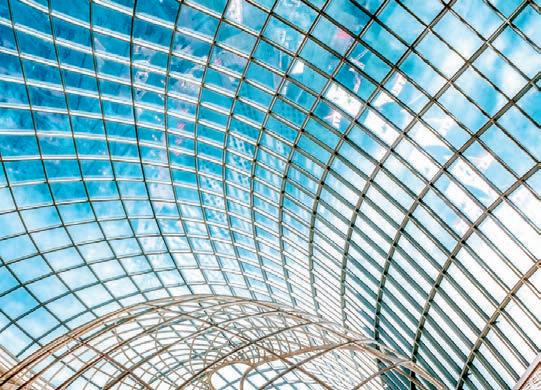

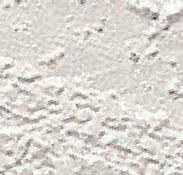
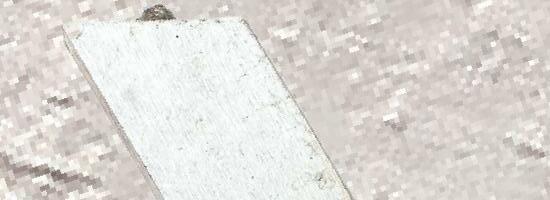
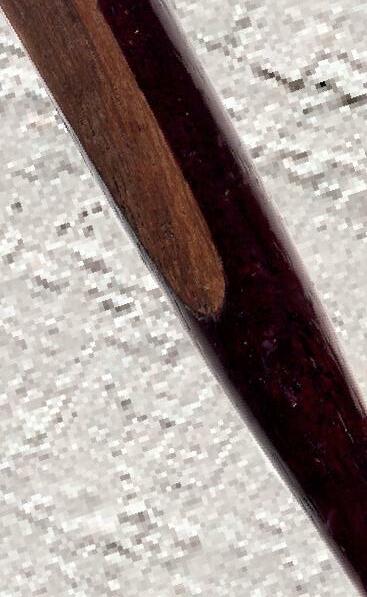
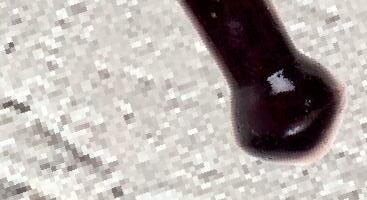
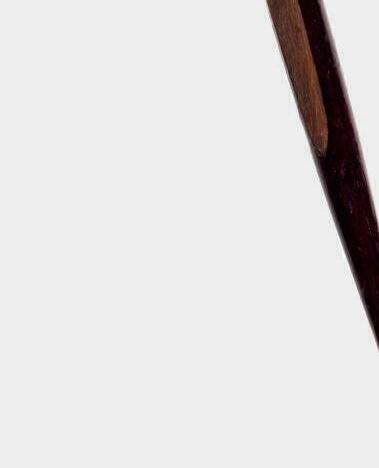
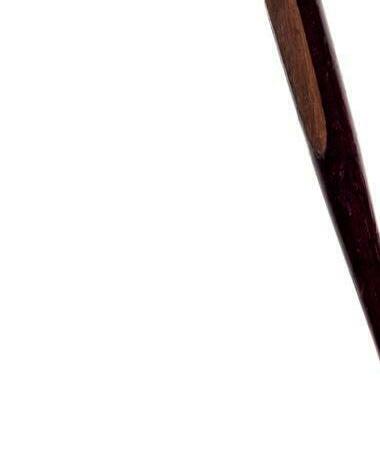
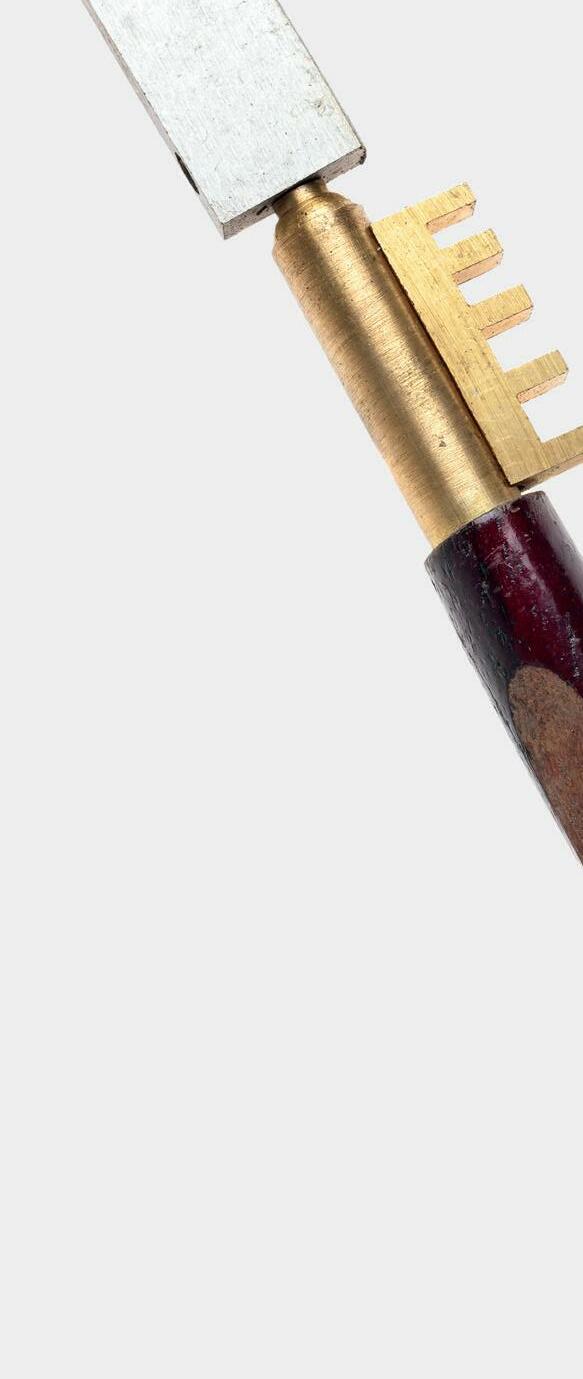
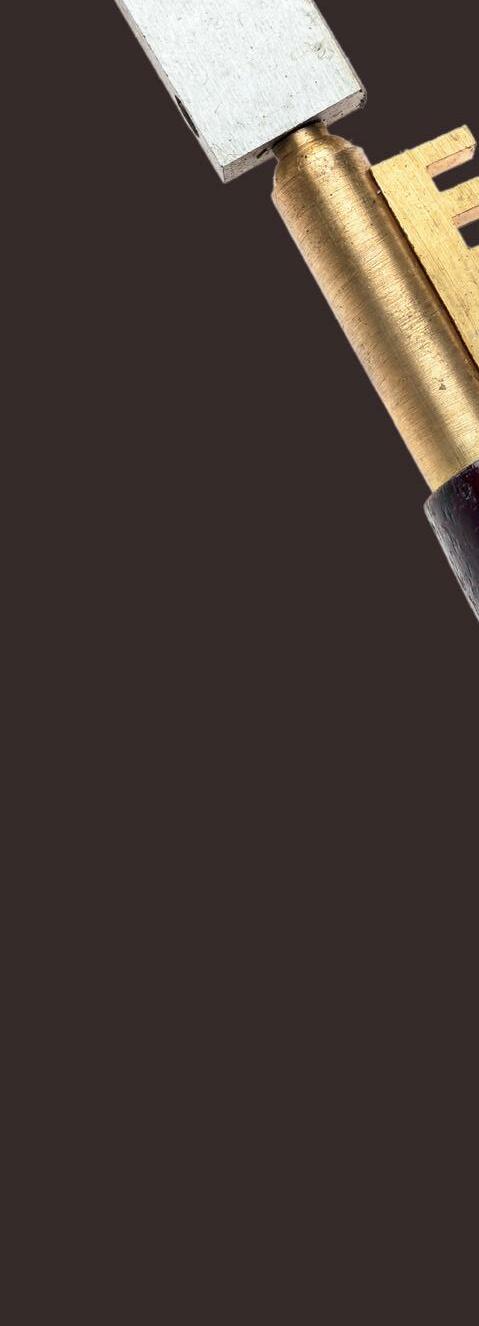
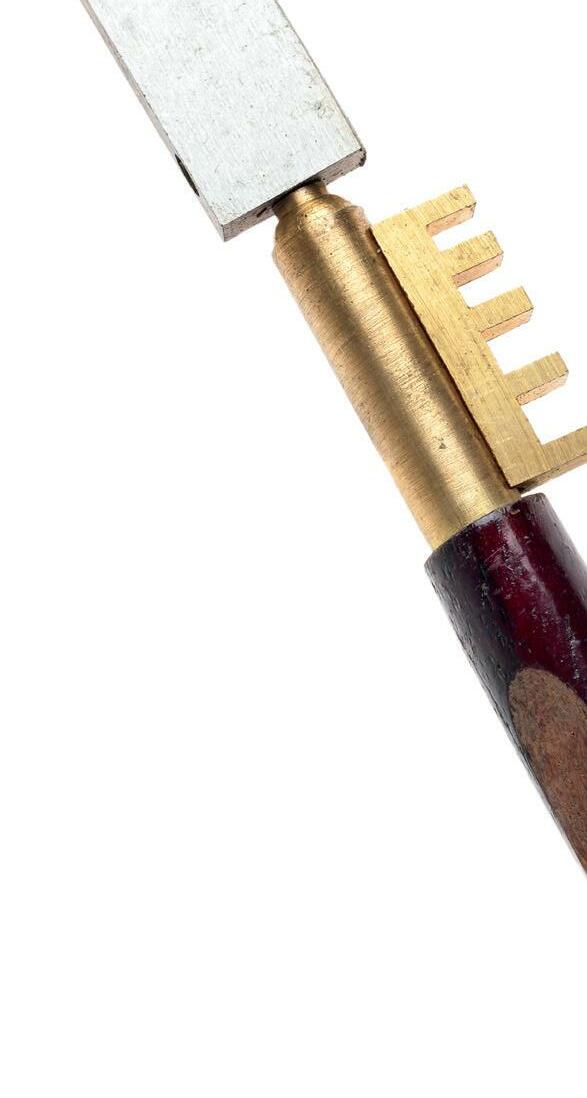
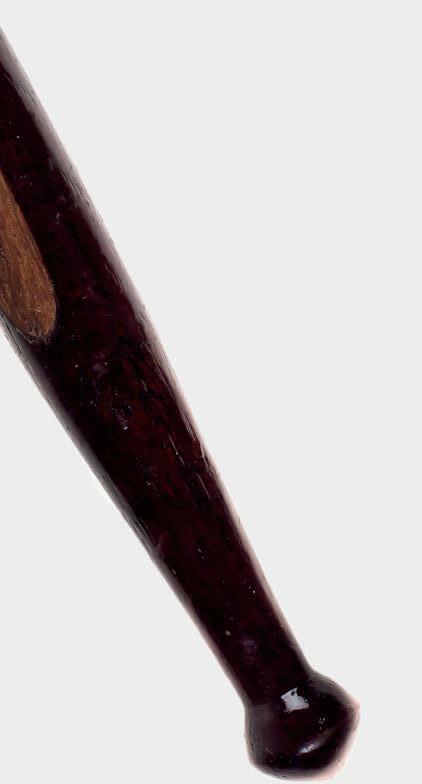
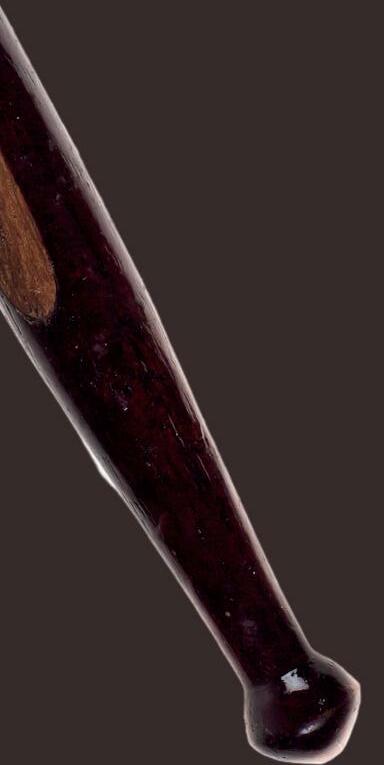
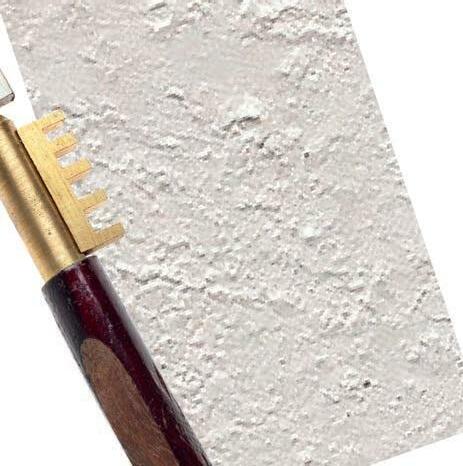

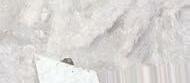
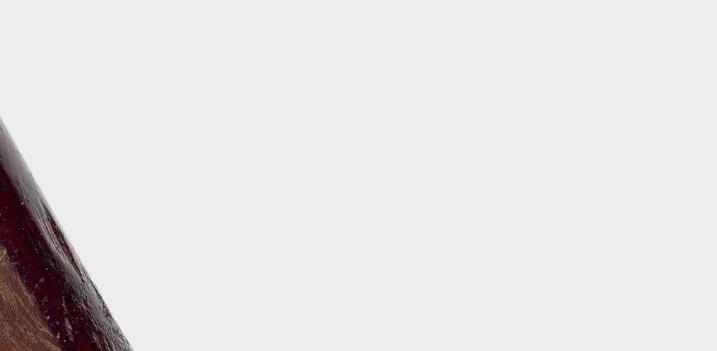


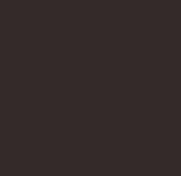
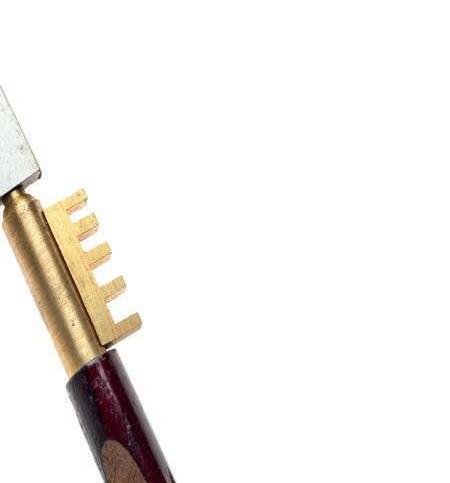
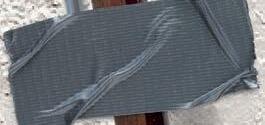
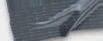

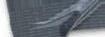



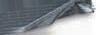
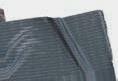
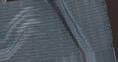

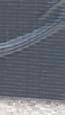
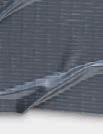
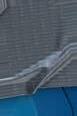


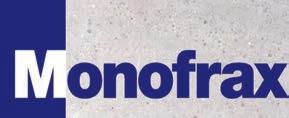




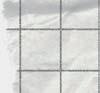

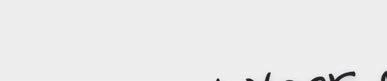
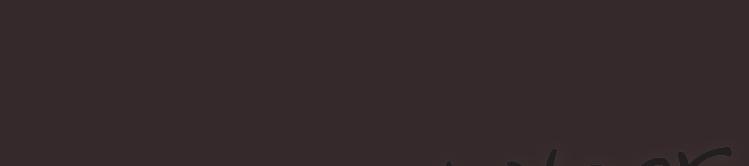

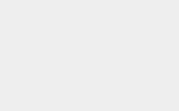
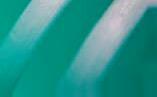


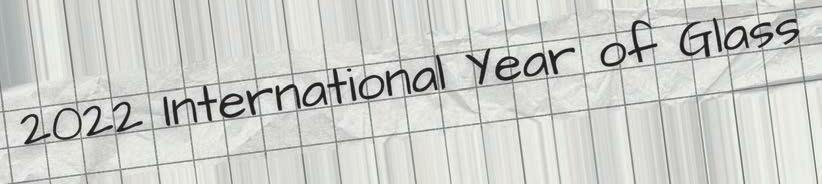







EXPANDING THE SYSTEM The possibility of expanding the system depending on the needs.
HOW CAN WE HELP YOU? WE KNOW HOW TO MAKE YOUR BUSINESS COOLER. AND WE MOULD LIKE TO HELP.
MOULD COOLING Cooling of the molds by high e iciency, energy saving fans. AUTOMATED CONTROL SYSTEM With ofandparametercontinuouscontrolself-correctionconditions.
COOLING EFFICIENCY Own cooling e iciency selection program for your molds. FAN SELECTION Due to a productionspecificportfolio. STABLE OPERATION For many years. World is changing. In the same time we have to face several challenges. According to newest technical trends and best knowledge, we are improving our solutions and products for your business. We know how important it is to have trust and confidence with all actions with your business partners. We also know that you require highest e iciency in all kind of works. We connected all three factors: knowledge, trust, e iciency. Due to our more than 20 years experience we were able to deliver and provide IS Machine Cooling to glass plants all around the world. We are chosen one, because we can provide complex solutions, beginning of design, threw manufacturing and finishing on assembling process. Mould Cooling.
REAL-TIME MONITORING OF FAN Monitoring of fan operating parameters, with suggestions for improvements for the operator.
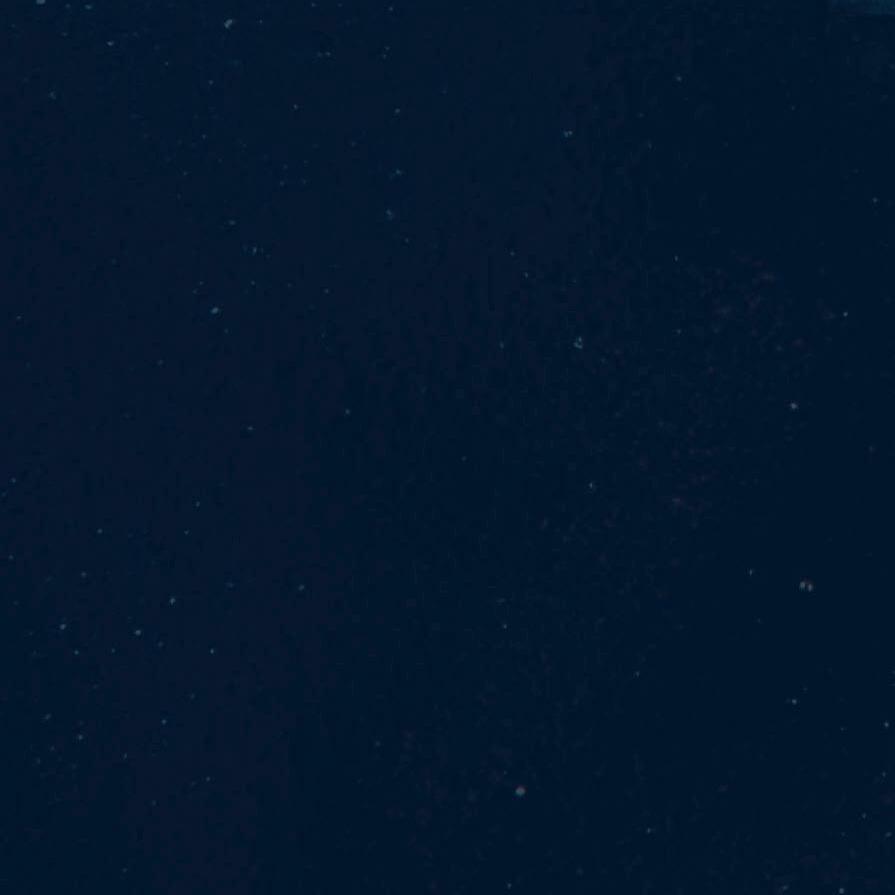
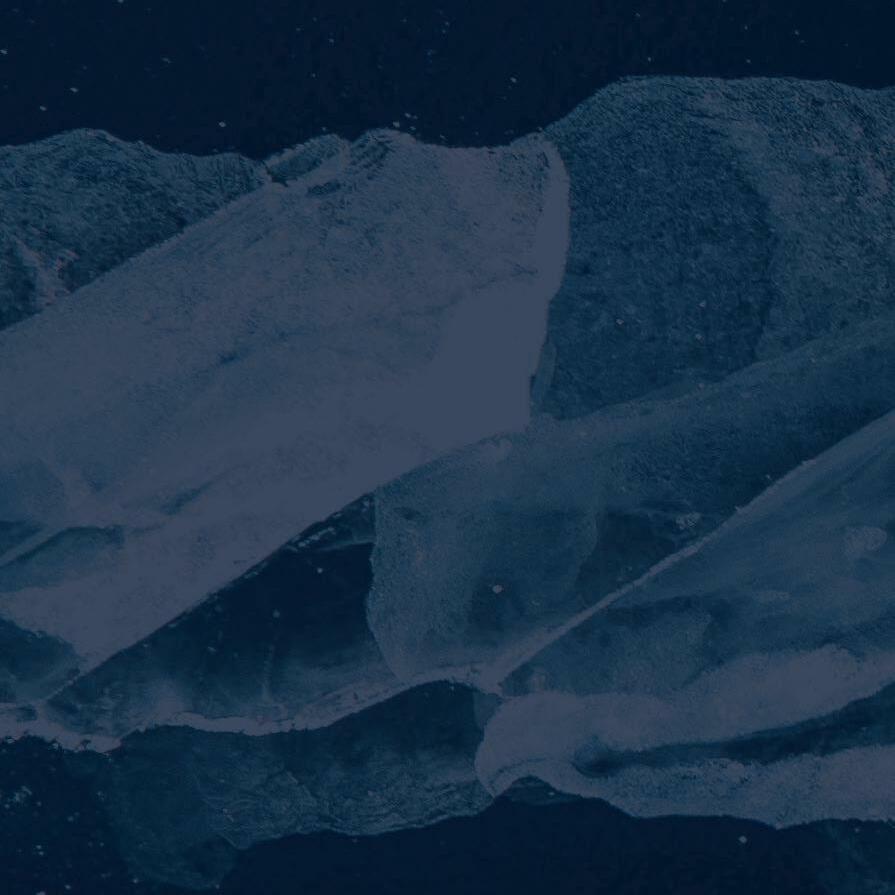
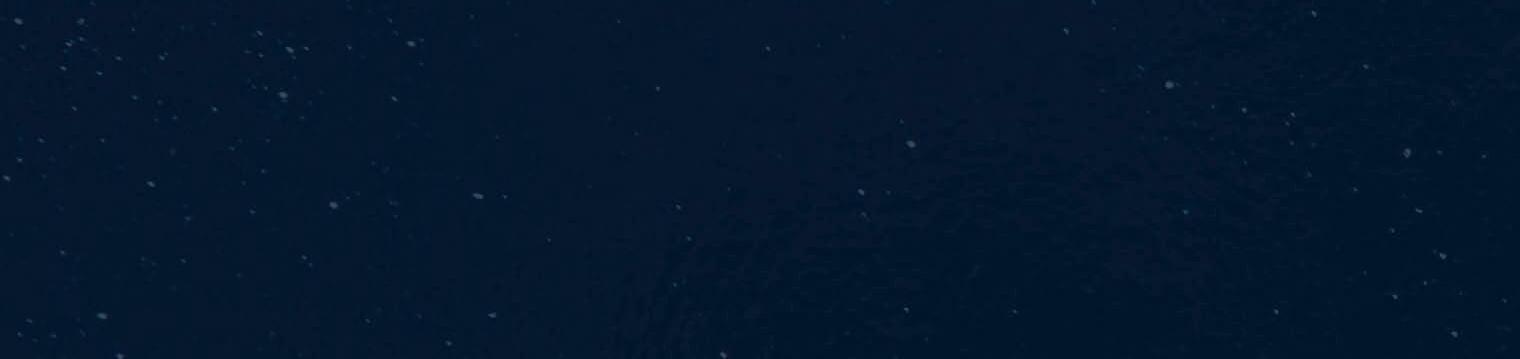
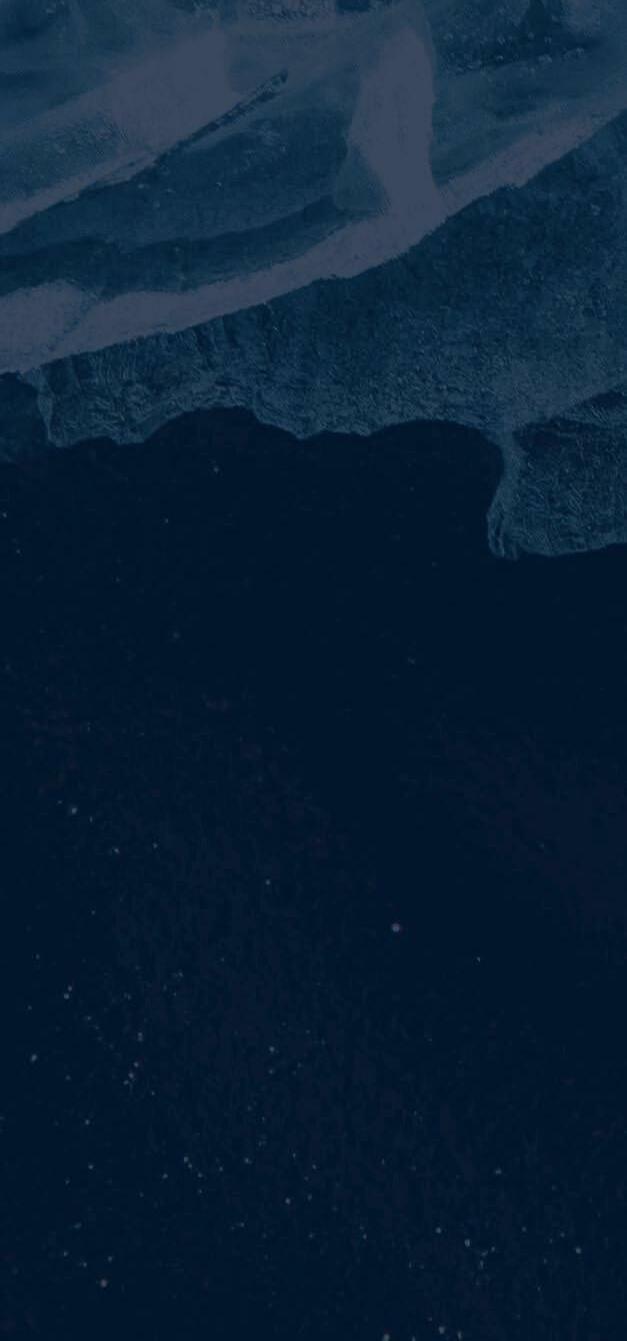
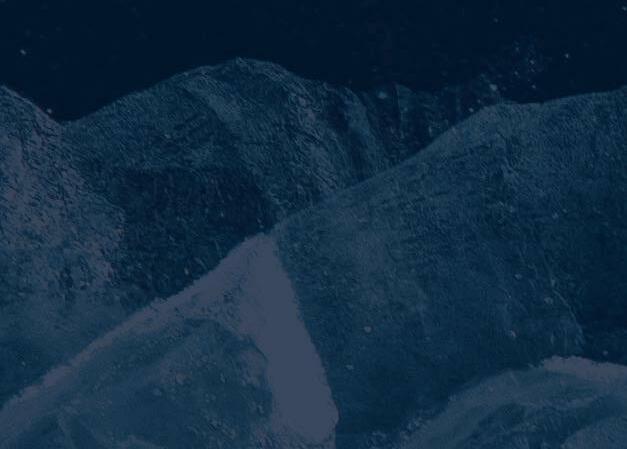
We are producing fans. But our fans, are not just a machine. Due to our own selection program, which was developed by our Research and Development Department, we can fit all factors directly for your current production portfolio on IS Machine. Because of this, we can save energy and still have possibilities to improve production speed! With us, your fan will never stop, long time stable work is one of priority. We can control your system. Fan is just the begging of whole process. We know how to menage with air. Conditions are changing, but cooling process should be stable. We developed control system for your needs. Fan and cooling parameters will be adjusted automatically. Moreover, control system will inform you about possible disadvantages during work and will propose any changes. We can deliver whole system. Dead plate, conveyor and servomotors cooling. Including ductings, pneumatic valves for Blank and Blow Side, stainless steel compensators, oil reduction system, manual valves and many di erent parts. Good thing is that your system can be extended anytime you want! We will assist you. Beside of guarantee system, we can o er much more. We are doing maintenance and service also. Let us know, maybe we can upgrade your current fan? Full research and analysis. Speak with us, we can provide you full analysis of your current IS Machine cooling system. We will let you know about any weaknesses and then, we can o er our solution!
WE CAN PROVIDE YOU SOLUTIONS, NOT PRODUCT. WANT TO KNOW HOW? IT’S COOL STORY
Get in touch with us, and you will stay cool!
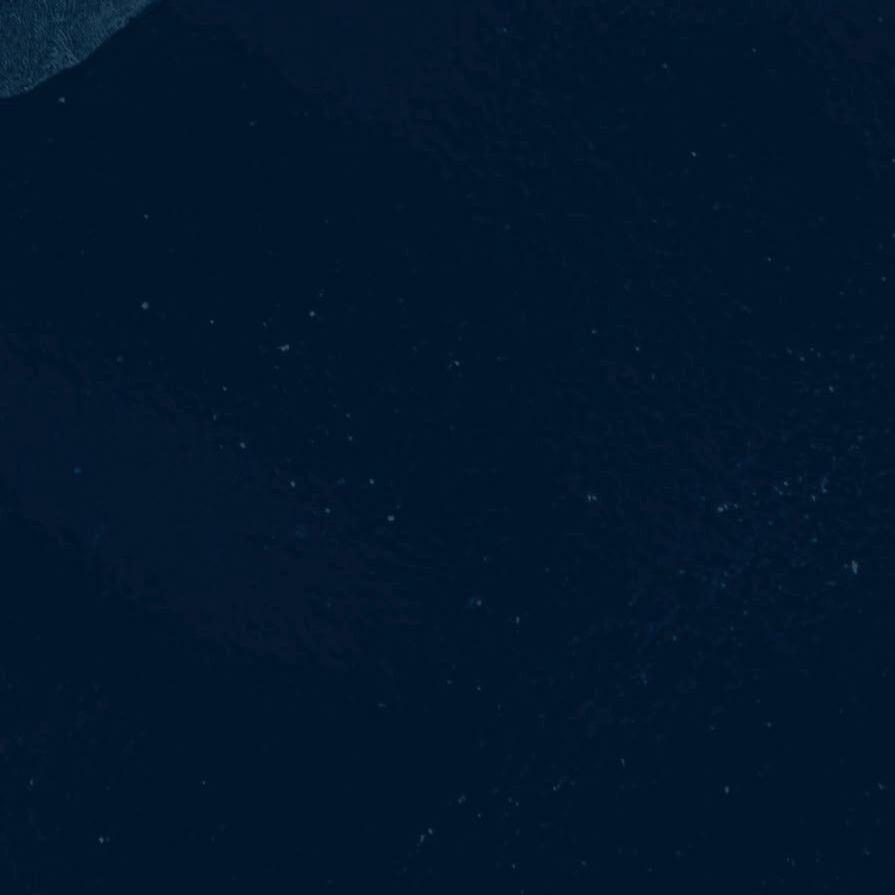
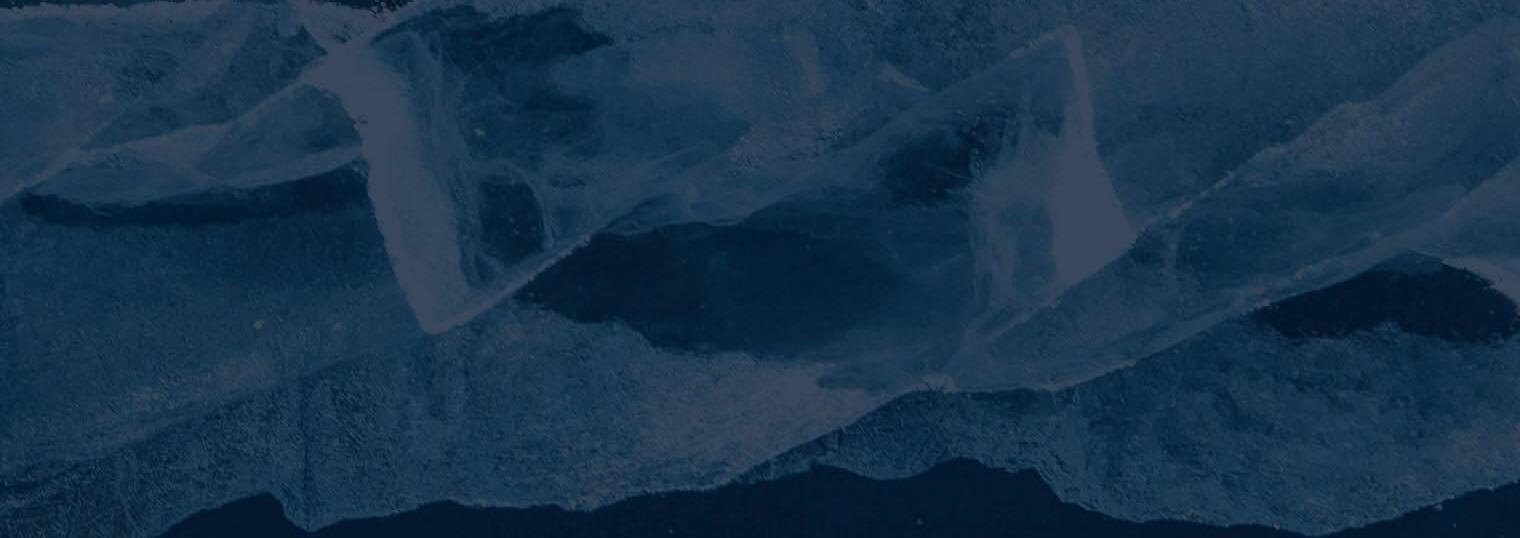
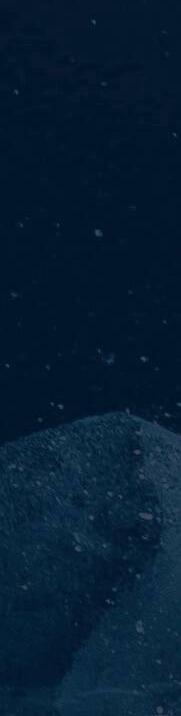
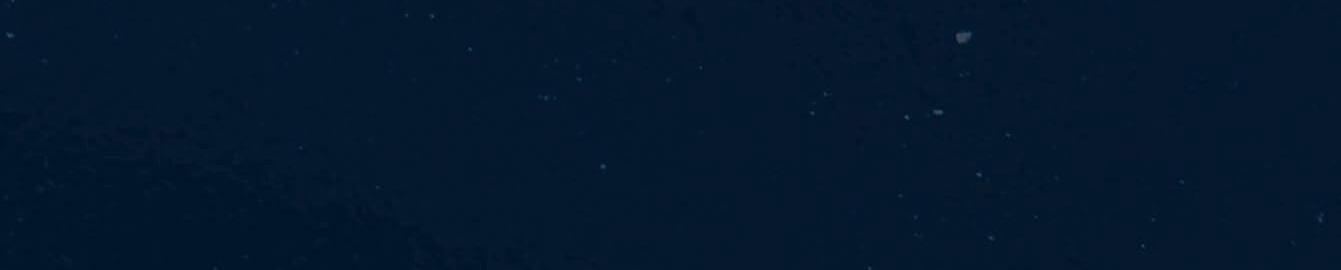
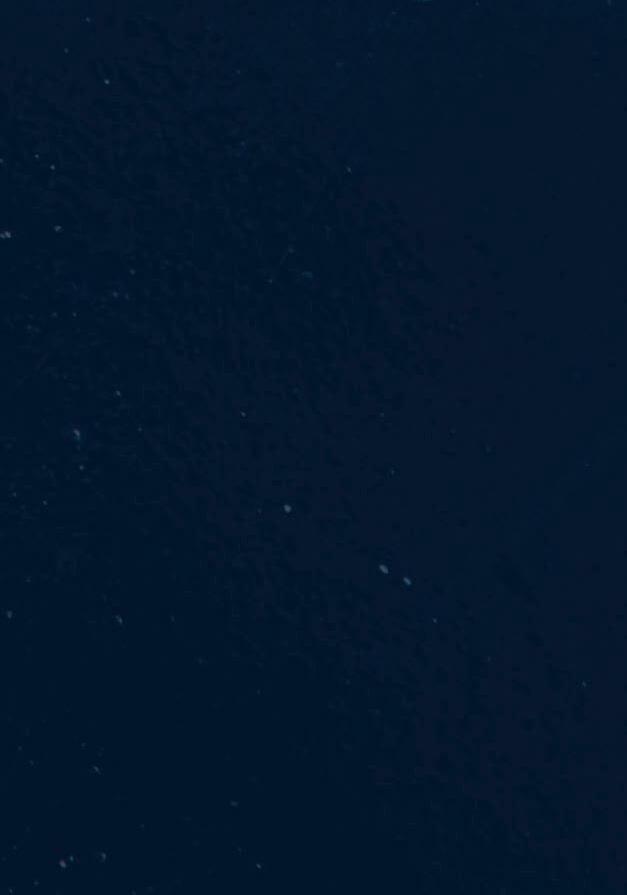
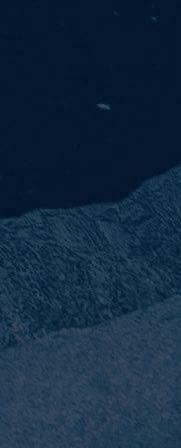
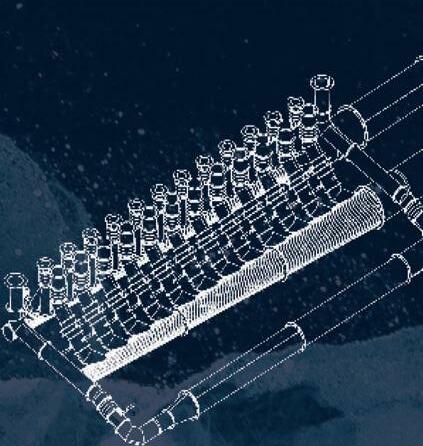


Sustainable pathways for the industry
With an insulating layer of batch, or starting material, covering the surface of the glass in a continuous vertical melting process, a well-designed, all-electric melter can have a thermal efficiency of 85%, almost twice that of even the most energy-efficient fuel-fired furnaces. But major transformations in the glass manufacturing process, infrastructure, feedstock, and science and technology are still required to cut emissions on a much larger scale.
The International Finance Corporation (IFC) has funded several green initiatives to improve sustainability in the glass industry. Jinhuan Sun1, Marek Stec2, and Li Tu3 discuss how the organisation’s latest projects will target environmental issues facing the industry.
Strengthening sustainability IFC provides capital and advisory services to glass manufacturers operating in emerging markets to help them achieve optimal production and operations, including by moving up the production value chain, carrying out research and development, and adopting best practices to strengthen sustainability. IFC’s active portfolio in the glass industry, including its own and mobilised investments, was valued at $404 million in 13 projects across eight countries by end-2021.Keysustainability issues being addressed through IFC-funded initiatives include the following five areas: efficient energy consumption, emissions reduction, recycling, product innovation and sustainable finance.
Global concern about the impacts of climate change has led to increased attention on sustainability in manufacturing.Onefocusarea is the role of the glass industry in contributing to global emissions, and the steps that can be taken to create more circular processes that reduce emissions and waste. Given the importance of glass for construction, packaging and other products, its role in economic development is key, making it imperative that the private sector and development finance institutions look to incorporate circular economy principles into production, use and recycling of glass. The global glass manufacturing market was valued at $120 billion in 2020 and is expected to expand at a compound annual growth rate (CAGR) of 3.7% from 2021 to 2028.[1] Growth is mainly driven by the construction, automotive and packaging industries, where growing populations, rising disposable incomes and increased urbanisation and industrialisation are fuelling demand for housing, cars, health and beauty products, and packaged foods. In 2020, the five biggest exporters of glass—China, Germany, the United States, Hong Kong, and France— generated about half (49.5%) of globally exported glass and glassware.[2] While the industry’s high energy consumption remains a challenge, glass manufacturers in recent decades have introduced technology in the production process to reduce waste and boost efficiency. With support from the International Finance Corporation (IFC) and the private sector, the industry can continue strengthening the sustainability of its products while contributing to the ‘greening’ of other industries and meeting surging global demand.
ss fin n in Glass International July/August 2022 700 www.glass-international.com Continued>>
Challenges The two biggest challenges facing the glass industry are the large amounts of energy required in the manufacturing process and the large volume of combustion by-products emitted, including sulphur dioxide, carbon dioxide and nitrogen oxides.Inthe United States, energy accounts for an average 14% of total production costs.[3] The production process has substantial potential for improving energy efficiency by making changes in the energy-intensive melting and refining process alone, energy usage could be reduced by However,20–25%.[4]theactual amount of greenhouse gases emitted is directly linked to the type of glass produced, the type and amount of fossil fuels used, the energy efficiency of the manufacturing process and the use of recycled glass, or cullet. Melting furnaces contribute 8090% of the total air pollutant emissions from a glass production facility.[5] To reduce emissions, the industry is focusing on optimising the manufacturing process and exploring possible solutions such as carbon capture, utilisation and storage (CCUS) and increasing the use of cullet.Foryears, Europe has been researching and investing in product and process innovations, such as low-carbon technologies for flat-glass melting. Research is also ongoing into innovations that shift to carbon-neutral energy sources such as biogas, green hydrogen, and electricity generated from renewable energy. Another way to minimise emissions in the production process is through the adoption of electric heating technologies.
Efficient energy consumption Glass manufacturing is an energyintensive industry, and efficient energy use is a core area where IFC supports its clients.Strategies to improve energy efficiency include maximising cullet usage, introducing waste heat recovery techniques, controlling combustion,
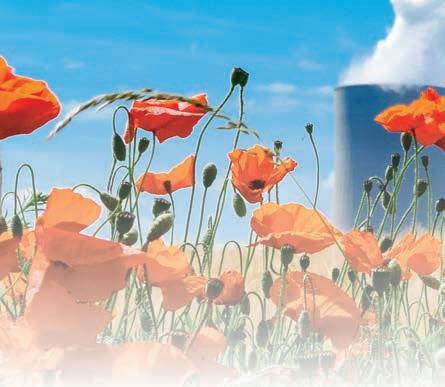
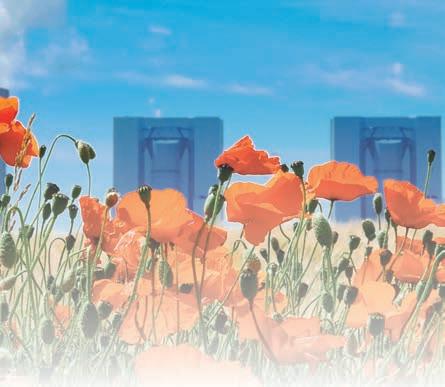

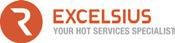
Conclusion Global demand for glass is projected to continue on an upward trajectory, along with growing pressure on the industry to further reduce energy consumption and greenhouse gas emissions. Over the last few decades, glass manufacturers have improved their sustainability through innovation, and they are expected to continue to do so through the rollout of new technologies and processes such as carbon capture.
� est e t cer, , SA greener-glass.html.ronment/renewables/the-75-percent-problem--making-[6].https://ww3.rics.org/uk/en/modus/natural-envi-production%20facility.cent,emissions%20to%20air%20from%20a%20glass%20contribute%20between%2080%20and%2090%20per-g&id=1323152002618#:~:text=Melting%20furnaces%20Manufacturing.pdf?MOD=AJPERES&CVID=jqeCVK-d98b-404d-91c2-2875f66fd63a/Final%2B-%2BGlass%2B-[5].https://www.ifc.org/wps/wcm/connect/e8c3b6d0-[4].Ibid. ty.without%20any%20loss%20in%20quality%20or%20puri-glass%20market%20was%20valued%20at,recycled%20cled-glass-market#:~:text=[8].https://www.alliedmarketresearch.com/recy-needed%20to%20recycle%20it.recycled%20glass,40%25%20more%20than%20that%20cling%20of%20Glass%20Saves%20Energy%20es-and-disadvantages-of-glass-recycling/#:~:text=Recy-[7].https://www.norcalcompactors.net/advantag-e%20e%20global%20recycled%20
a u acturi , A ri usi ess Ser ices ASSe ior ustr Specialist AS Glo al Sector ea a Se ior est e t cer AS ter atio al i a ce orporatio , ashi to
The sector also has a key role to play in boosting sustainability in other sectors, whether through lighter glass packaging or glass fibre used for wind turbine blades.
ssfin n in Glass International July/August 2022 www.glass-international.com
The biggest restraint to growth is lack of an established ecosystem, such as government support and infrastructure, to enable efficient collection, particularly in emerging markets. Glass breakage and contamination with other materials at recovery facilities increase processing costs. Moreover, procuring cullet in a clean, furnace-ready form requires a lot of processing that is usually done inefficiently, complicating the recycling process. Pro uct innovation Innovations in the design of glass packaging, such as through reduction in bottle weight and size, can help save raw materials and reduce carbon emissions from production and transport. IFC backs glass manufacturers’ efforts to develop products that are more sustainable or that contribute toward sustainability in the industry or in the broader economy. In 2013, IFC advanced credit to Sisecam, one of Europe’s largest glass producers based in Turkey, to finance its energyefficiency and other renovations. Sisecam focused on light-weighting its glass-packaging products, achieving a 14% reduction in emissions related to producing one bottle type simply by changing its design. In recent years, Sisecam has invested continuously on product R&D to create environmental and social benefits. As of 2020, it had more than 39 patented products that directly contribute to sustainability, such as its V-Block coating technology, which neutralises viruses and bacteria on glass surfaces. ustaina le finance IFC is a pioneer and leader in sustainable finance. Sustainable finance typically refers to “labelled” financial products that follow recognised market standards and principles. The two types of instruments include:
IFC will continue to partner with players to improve their energy efficiency, lower their carbon footprint and adopt circular economy strategies.
Associate
All these efforts will demand further investment in research and infrastructure, from waste-management facilities to collect and recycle end-of-life glass, to a guaranteed, steady supply of carbon-free electricity, to carbon capture transport networks and storage facilities.
i c or eferences php?id=12631.[3].https://www.eia.gov/todayinenergy/detail.%241.4%20billion%20%281.9%25%29.%282.1%25%29%2015%20Netherlands%3A%20of%20total%20glass%2Fglassware,%241.6%20billion%20na%3A%20US%2417.9%20billion%20%2823.4%25%20and-glassware-exports-by-country/#:~:text=1%20Chi-[2].https://www.worldstopexports.com/top-glass-ysis/glass-manufacturing-market.[1].https://www.grandviewresearch.com/industry-anal-
2. Target Driven, such as sustainability-linked financing, with pricing linked to achievement of environmental and social targets.
71 installing high-efficiency, low-energy compressors, and optimising furnace sizes. In 2019, IFC provided loans to Middle East Glass Manufacturing Company, a glass-containers producer based in Egypt, to rebuild its furnaces and streamline its cullet-processing operations to improve efficiency. IFC advised the company on developing an energy-efficiency plan which identified energy-efficiency measures to be adopted, a timeframe for implementation, and anticipated energy savings. Emissions re uction Glass manufacturing is a significant emitter of greenhouse gases, particularly carbonAboutdioxide.75–80% of CO2 emissions comes from burning fossil fuels to heat furnaces, so switching to a carbon-neutral energy source would represent a significant reduction.[6]IFCworks with clients to minimise emissions through such measures as deployment of air emissions-control equipment, melting control panels, and modern furnace designs installation of electrical boosters over melting chambers and of catalytic ceramic filters and use of low nitrogen oxides burners. In 2019, IFC extended financing to NSG Group to construct a greenfield glass production plant in Argentina. The project incorporates the latest technology to optimise fuel utilisation and recover heat in the production process, supporting the company’s decarbonisation ambitions. ecycling Glass is fully recyclable, and it can be reprocessed and reused in a closed loop. This contributes to lowering energy consumption, reducing industrial pollution, and conserving natural resources and landscapes. In the recycling process, used glass is crushed to form cullet, which melts at a lower temperature and uses about 40% less energy than is needed to make glass from scratch.[7] Glass recycling generates no processing by-products, and since the processing requires less heat, also extends furnace life. The global recycled-glass market is expanding quickly, with production forecast to reach $5.5 billion by 2025 from $3.5 billion in 2017.[8]
1. Use of Proceeds, such as green, social, blue, and sustainable bonds or equity, with dedicated use of proceeds focused on eligible categories, including climate adaptation, climate mitigation, ocean conservation, and social.
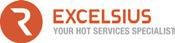
www.futronic.de the spirit of moving forward 1972 2022 50 years of futronic –At home in the heart of the glassmaking industry automation in a new dimension DATA STORAGESENSORS AUTOMATION jumo.es | jumo.de info.es@jumo.net +34 918 86 31 53 From GLASS PLANT to the CLOUD with designedSpecially More than sensors + automation
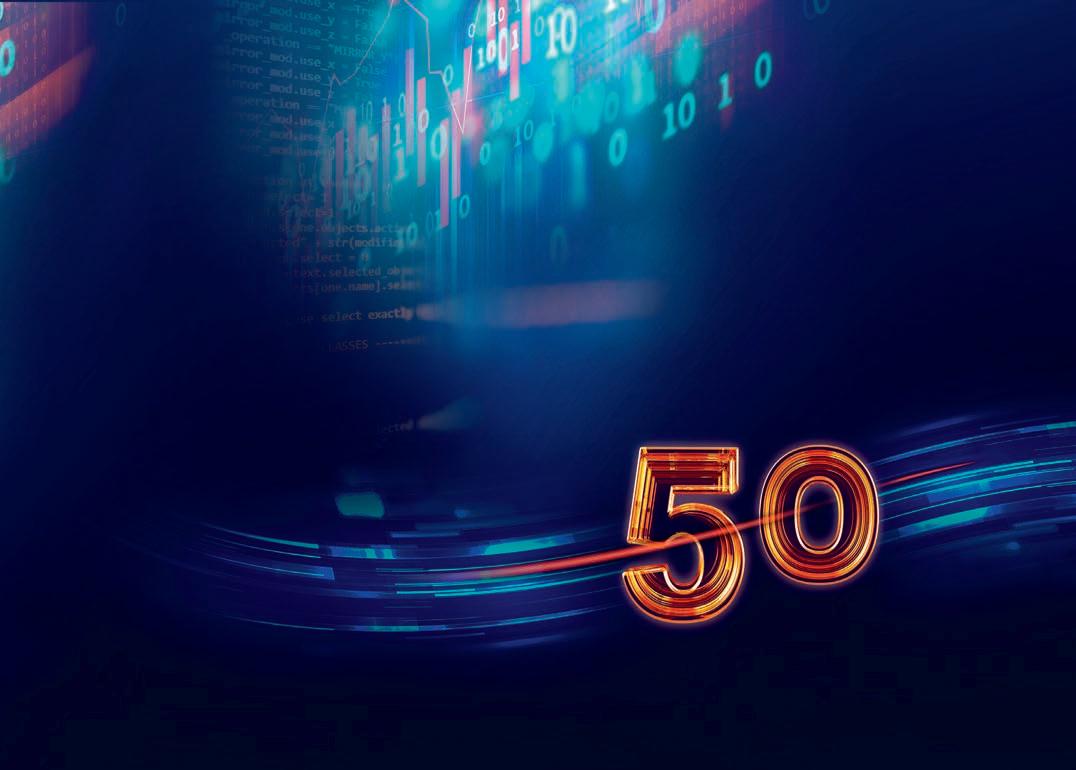
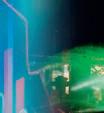
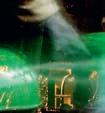
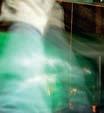

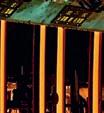
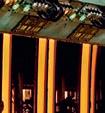
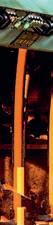
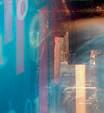
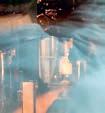
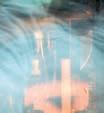
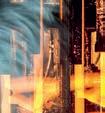

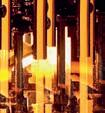
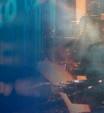
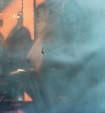
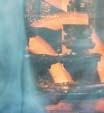


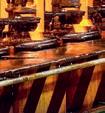
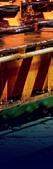

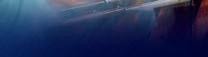
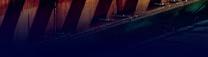

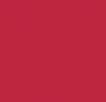

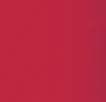
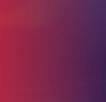
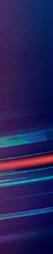
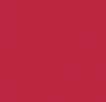
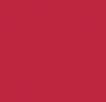


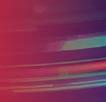


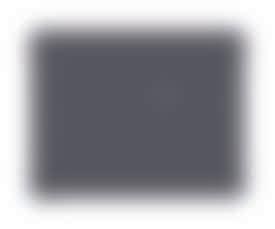
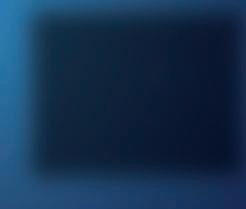

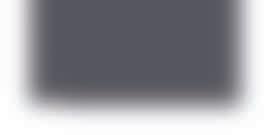
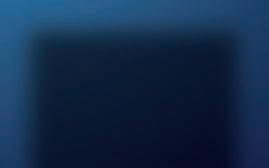
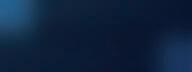


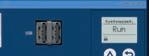
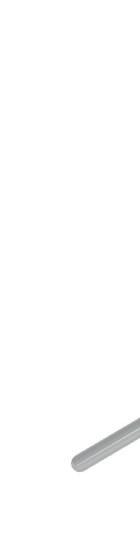

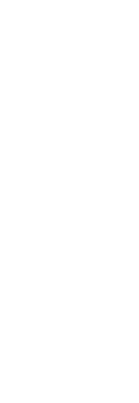
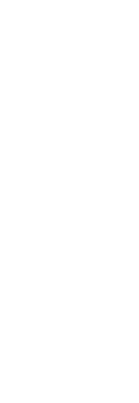


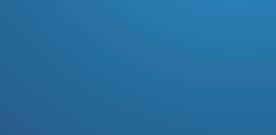

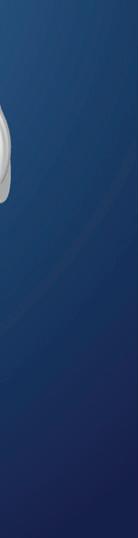
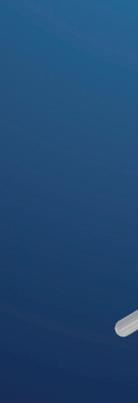
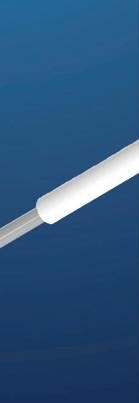
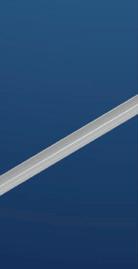
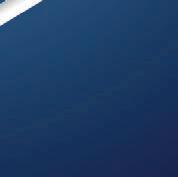
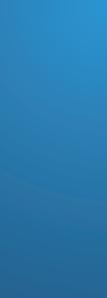

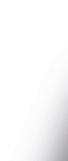
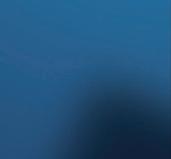




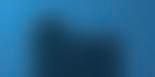
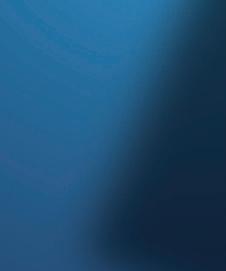
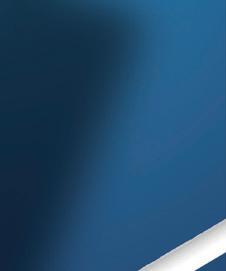
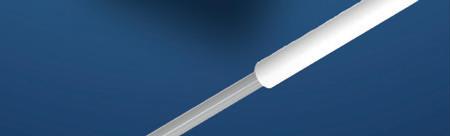























All Electroglass electrode holders feature external and internal low thermal mass insulation to minimise the heat extracted from the furnace whilst maximising the cooling around the electrode (Fig 1). Fig 1. A batch of Molycool holders ready for dispatch.
The purpose of the electrode holder Grahame Stuart* discusses the increasingly crucial role electrodes and electrode holders play in the industry’s aim to meet net zero goals. As the industry moves towards hybrid and all-electric furnaces to meet net zero goals and reduce reliance on fossil fuels, the part played by electrodes and electrode holders is becoming increasingly critical to operational success. Unsurprisingly, there is much to consider when selecting not only electrode holders but also the water system and the monitoring system.
Electrode holders for molybdenum electrodes provide physical support for the electrode and cooling that prevents glass seepage around the electrode. However, their primary purpose is the part they play in providing cooling to the molybdenum electrode where the electrode is not protected by a glass seal and would otherwise be subjected to atmospheric temperatures where oxidisation may occur. Oxidisation will lead to ‘necking down’ of the overall electrode diameter eventually leading to breakage. This ‘necking down’ results in increased localised temperatures, accelerated refractory wear and greater risk of glass leakage. Heat extraction The heat extracted from the furnace by the electrode holders must be considered when selecting these for any project as the objective is to cool the molybdenum electrode and not the surrounding refractory and glass. Excessive external cooling will not benefit the molybdenum electrode but will cause greater thermal stress on the electrode blocks leading to increased cracking and refractory wear as well as pulling heat from the melting process. Additionally, if an electrode holder design is employed that extracts more heat than is necessary, it is likely that a considerable amount of energy will need to be re-applied to the furnace to overcome this. For example, in a system with 24 electrode holders each extracting 2kw of energy more than is required, the nett melting energy to produce 2 tonnes/ day of glass is being lost - it is therefore easy to see why care must be taken when selecting electrode holders to ensure they are not creating an unseen operating cost.
Furnaces Glass International July/August 2022 www.glass-international.com 73 Continued>>

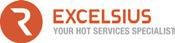
It is important that electrode advancing is not treated as routine maintenance with advancements taking place at timebased intervals rather than when wear has actually taken place. Routinely advancing electrodes that do not require it will result in over advanced electrodes that can Fig 3. Typical control and monitoring system
� Water flow monitoring to each individual electrode holder cooling coil/ circuit. � Needle valves and magnetic strainers at the entrance to each cooling coil/circuit.
Furnaces Glass International July/August 2022 0 Continued>> 74 www.glass-international.com
Dissimilar metal contact
Contact between dissimilar metals in glass can lead to a galvanic reaction and the generation of DC voltages which may result in the generation of bubbles at the junction between the two metals. These bubbles, typically of oxygen, can impact on glass quality, but more seriously can cause oxidisation to the molybdenum electrode at the point of generation leading to electrode failure.
Electrode advancing
All critical operating parameters should have alarm and trip set points to ensure any operational changes cannot go unnoticed and, where necessary the power to the transformers can be automatically stopped to prevent serious damage.
� A high-level header tank capable of storing sufficient water to gravity feed the electrode for a minimum of 25-30 minutes of normal operation.
It is recommended that the water within the system is tested weekly and that the pH, hardness, conductivity, and holding and header tank temperatures are recorded and any corrective action to keep parameters within recommended specifications be carried out. System monitoring Another area key to the success of any electrode heating system is monitoring of all operating parameters. Comprehensive metering, recording and associated alarm facilities are critical as is the operators understanding of this.
A well-designed monitoring and control system will give the operator an overview of system operation showing electrode holder temperatures, phase currents and voltages, status of transformers and key water system parameters such as individual water flows, pump status and tank water levels (Fig 3).
screens.Fig2.Typical
Maintaining correct electrode immersions is critical to ensuring efficient system operation whilst maximising furnace life. There are many factors that will determine how often electrodes require advancing. These include glass chemistry, temperature, power applied, electrical connection arrangement, electrode layout and current loading.
electrode holder water cooling system
Whilst a well-designed electrode heating system will minimise electrode wear, the oxidising properties of many glass compositions result in electrode wear and the need for periodic advancement of electrodes to compensate. The process of electrode advancing causes some degree of thermal shock on the electrode holder with the stopping and starting of cooling water flow and if the electrode holder is not designed with this in mind, holder life can be reduced. Design considerations such as continuous, unwelded cooling coils and compressed air-pre-cooling facilities help reduce the risk of electrode holder failure whilst advancing, as can proper operator training during commissioning by the manufacturer’s engineers.
It is important to consider electrode holders that have design features to prevent dissimilar metal contact helping to prevent DC voltage generation, as found on all electrode holders we produce.
The biggest risk to electrode holders is poor water system design and badly maintained water quality. It is always our recommendation that a separate dedicated cooling system be installed for the electrode holders. A good water system should have redundancies in-built in case of pump or power failure (Fig 2). As a minimum we recommend that all our electrode holder customers consider the following features on their electrode holder water cooling systems. � Duty and stand-by circulating pumps with automatic changeover.
� An automatic filling loop to provide city water in the event of prolonged power or pump failure
� A water softener operated on a loop to soften any top-up water or for use following any episodes operating on city water.
Other critical information that should be displayed and monitored includes individual electrode currents to ensure they are not exceeding design recommendations, earth current to ensure there are no earth faults within the system that may lead to localised heating and possible glass leak, and individual electrode volts-to-earth to help locate any earth faults and to assist with electrode immersion determinations.
Electrode determinationsadvancement
� A heat exchanger or chiller capable of extracting sufficient heat at the highest annual ambient temperature for the plant.
Water cooling
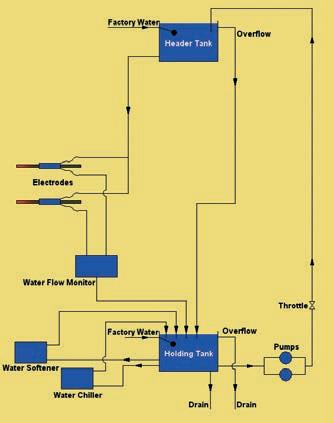

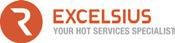
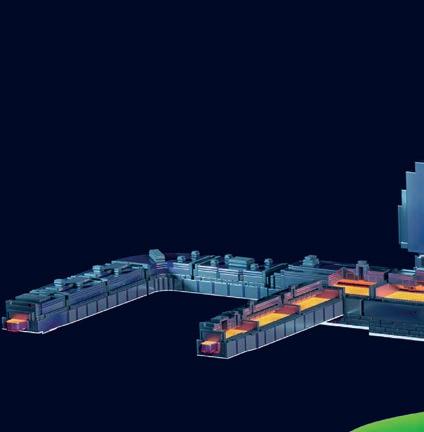


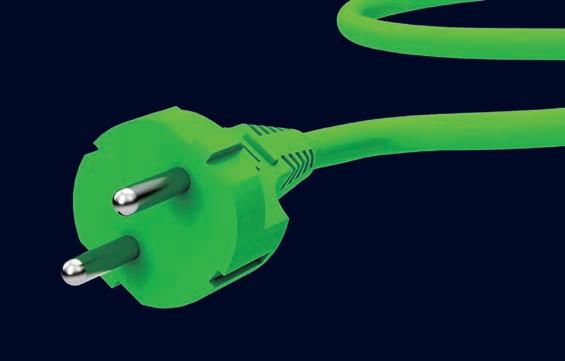
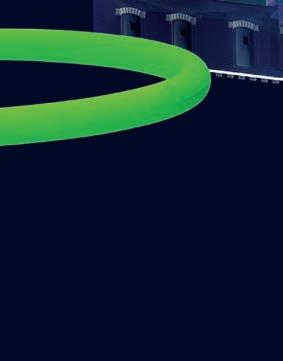
The VS range of holders is also recommended for applications where there are concerns about cooling water quality or consistency as they are extremely resistant to thermal shock and their internal construction means blockage of cooling ways due to calcium deposits is very unlikely.
Important choices All of the above are important points to consider when investing in electrode holders and can mean the difference between success or failure of the entire furnace project. With over 45 years’ experience in electrode holder development, design, and manufacture, and with several hundred produced each year for customers worldwide, Electroglass ensures that every holder it produces meets the exacting standards required to ensure reliability and long life. �
*Project Sales Engineer, Electroglass, e fleet, K http://www.electroglass.co.uk/ Fig 4. The use of physical modelling for electrode immersion checks. Fig 5. A holder undergoing manufacture in our own workshops in the UK.
Furnaces Glass International July/August 2022 760 www.glass-international.com
The VS splashguard holder
For glass types in which regular electrode advancement is expected we recommend the Vertical Splashguard (VS) range of holders. The VS range is manufactured to suit 50mm (2”), 63mm (2.5”), 76mm (3”) and 102mm (4”) diameter electrodes and features no welds on any of the cooling components and no sealed water-cooling circuits that could be ruptured by high pressure steam generated when cooling is re-applied following electrode advancing.
The HS splashguard holder Horizontal Splashguard (HS) holders are manufactured to suit 32mm (1.25”), 50mm (2”), 63mm (2.5”) and 76mm (3”) electrodes and feature weld-free cooling components, no sealed water-cooling circuits and a high level of resistance to thermal shock during water disruptions or following electrode advancing. Additionally, the HS range features removable cooling ways to allow the cleaning away of any sediment or calcium build up that might occur.
limit system power and possibly create convection that is detrimental to furnace operation leading to a reduction output and/or glass quality. A far better approach is to monitor operating data and plot changes in electrode current, amps-per-volt and volts-to-earth and advance by the correct amount per electrode only when required. However, there are other factors that that will affect glass conductivity and therefore must be considered before determining electrode immersions. These include changes in glass temperature and glass composition (Fig 4). At Electroglass we encourage our electrode heating system customers to work with us in determining electrode immersion and advancements by forwarding operating data on a regular basis. We will then review the various parameters and advise when and by how much to advance each electrode. Although this service is not unique to Electroglass the fact that we make no charge for it likely is. Our electrode holder ranges Electroglass offer three ranges of electrode holders to cover all melting situations. All of these are manufactured exclusively within our own workshops in England and every holder goes through extensive testing and inspection prior to its dispatch. Every holder can be customised in length to suit each individual installation with holders regularly produced ranging in length from less than 400mm to over 1650mm (Fig 5).
The molycool holder Our longest established electrode holder range is the Molycool which is primarily used for vertical and angled installations but can also be used for sidewall installations. It offers the lowest level of heat extraction from the electrode block through the design of its cooling coils and two stage thermal insulation. The Molycool range includes holders to suit 32mm (1.25”), 50mm (2”) and 63mm (2.5”) electrodes and, in common with all Electroglass holders features no welds on any of the cooling circuits. Molycool holders also incorporate an air-pre-cooling circuit that allows the use of a small volume of low pressure compressed air to initially cool the electrode holder prior to starting the cooling water flow, helping to reduce thermal shock on the holder’s cooling coil.
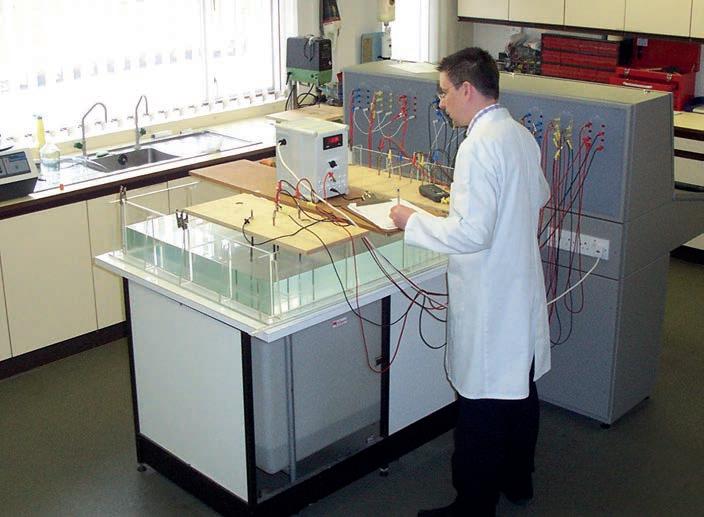

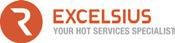
Checkadministration@novaxion.frforyourlocalcontactonwebsite www.novaxion.fr THE UNIQUE PATENTED SOLUTION FOR MOULD CLOSED SWABBING WITH 15 YEARS EXPERIENCE The new NX-VR-300 swabbing robot mounts on the valve blocks of all IS machines. Provides mould closed and neck ring automatic swabbing within the same section cycle. On the fly swabbing, no reject. NEW

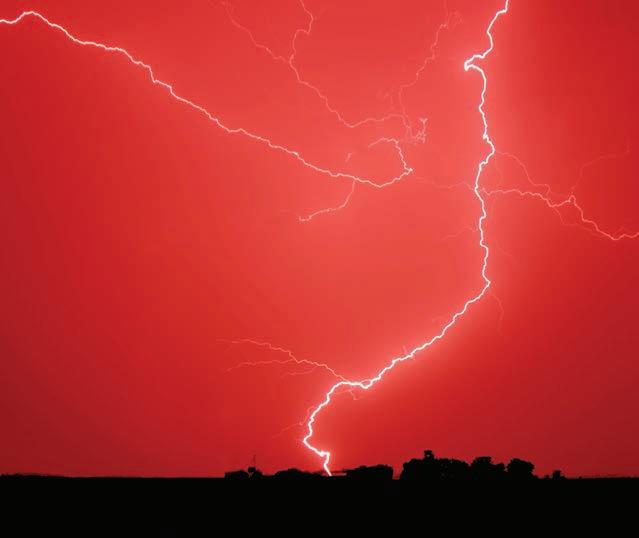
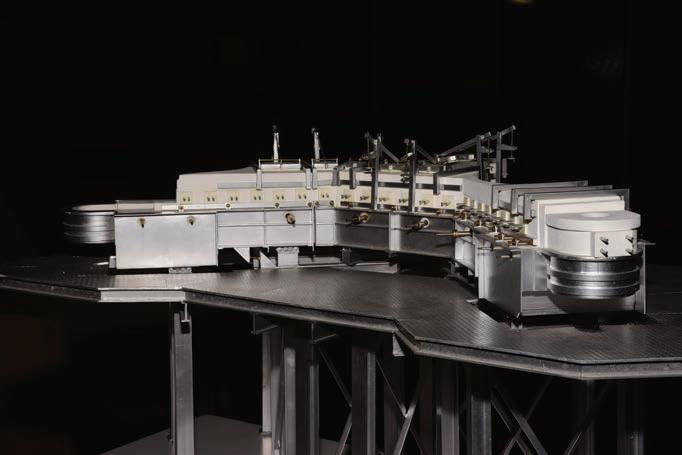
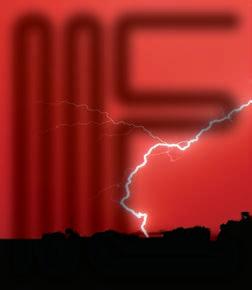
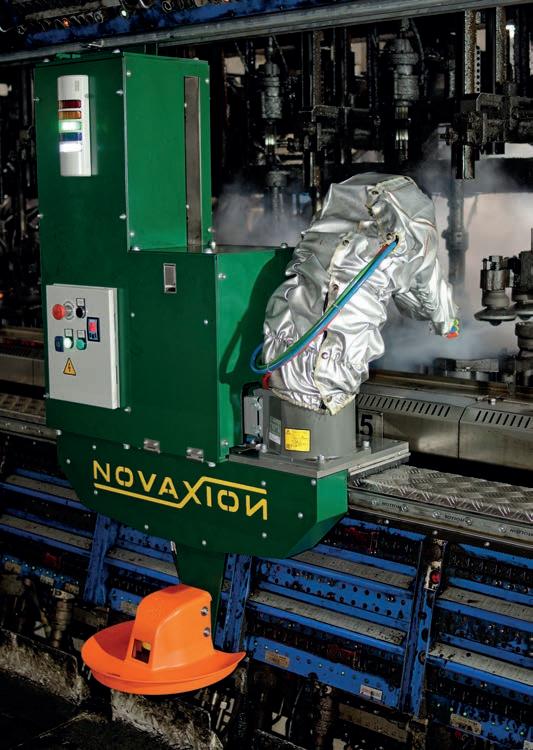
Our history spans 150 years of delivering countless innovations to propel the global glass industry forward. Nikolaus SORG has designed advanced furnaces with unrivalled performance and asset lifetime. EME has engineered batch and cullet processing technology to endure the most demanding production environments. SKS is the world leader in furnace rebuild and lifecycle services. Together, we form the SORG Group, and our new positioning line represents what the invincible power of three can do for our customers in the race to build a more efficient, more sustainable future. See how we are driving the industry forward. Visit us at glasstec 2022 – Stand B38, Hall 15. eme.desorg.desks.net
DESIGNED FOR PERFORMANCE. ENGINEERED FOR ENDURANCE.
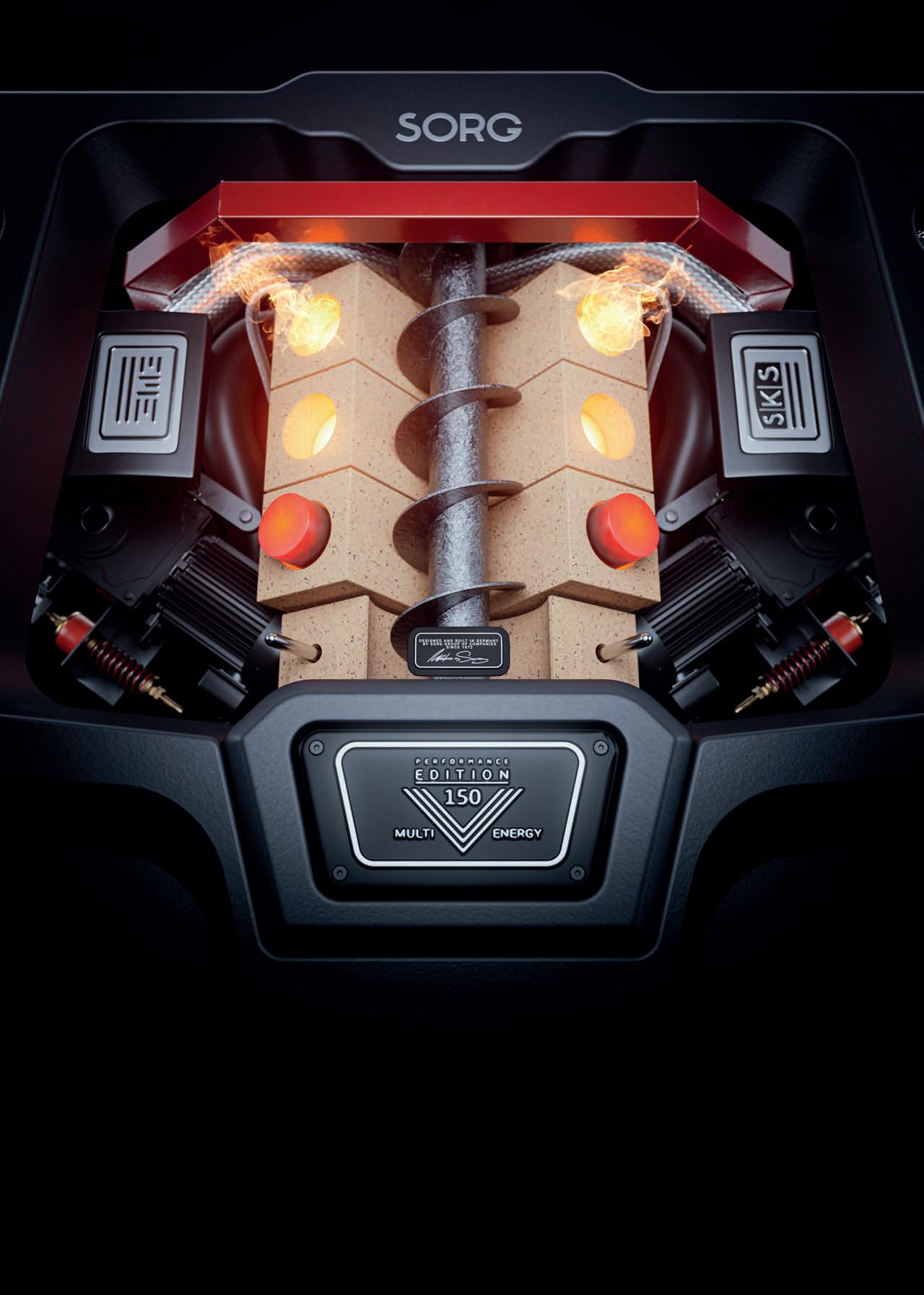
Tin baths To avoid glass defects and problems due to tin oxidation, it is necessary to monitor the atmosphere of tin baths in float glass plants. To protect the liquid tin from oxygen, a protective gas mixture of nitrogen and oxygen is continuously injected into the tin bath. To obtain a statement about the oxygen content, the dew point was measured from a sample of the tin bath atmosphere. Since water, hydrogen and oxygen are always in equilibrium, this is a reliable way to describe the state of the atmosphere.
Measuring the dew point to determine
Fig a im m specific ater content an calc late specific ater contentFig in tin o i e e ilibri m c r es an real meas re o gen partial press res
Glass conditioning Glass International July/August 2022 www.glass-international.com 79 Continued>>
Probes for extractive measurement
For eight years, Eurox Sauerstoff MessSysteme has been part of Horn Glass Industries and is now an integral part of its facilities. The measuring systems have many applications in the glass industry, which have been further developed in recent years. With the extractive measurements of Eurox, several measuring points can be measured with just one sensor. Together with a valve unit up to 12 measuring points can be analysed. The evaluation unit of the measuring system controls the valve unit, evaluates all measurement data and provides the results to the customer. Not only can the signals from the oxygen sensors be processed, but also information from the control system can be read in and thus enrich the evaluation of the measuring signals. With this system each measuring point of interest is measured one after the other, thus a quasi-continuous check of the system can be achieved. Depending on the application and the values of interest, different evaluation modes can be defined for the respective application. By default, visualisation takes place on the measuring unit itself, but it can also take place on the control system or on other output devices. The measuring systems are basically modularly expandable. There are measuring systems for glass conditioning, for tin baths and a mobile measuring unit for both applications. Glass conditioning The atmosphere in forehearths as well as in working ends has a great influence on the glass quality. Therefore, the combustion condition is an important influencing factor in glass conditioning systems. In reality, various parameters influence the combustion condition. So, the theoretical oxygen content in dry air is 20.9%. However, the exact O2 content depends, among other things, on the air humidity, which is often neglected in theoretical calculations. Therefore, a variation of 0.5% in the O2 content can thus lead to a change in the minimum air demand of 2%. The composition of the fuel gas is not stable, which has an influence on the heating value but also on the minimum air demand. This problem will certainly increase in the future. But there are also technical aspects that influence the stability of the combustion conditions. The non-linearity of the control valves, but also the hysteresis of the control system for setting the mixing ratio should be mentioned here. All these influencing variables are not large in themselves, but their influence can add up. Especially under near stoichiometric conditions, it is possible to change unnoticed from an oxidising to a reducing ratio and vice versa, which can lead to problems in glass production. The extractive measuring system of Eurox measures the real Lambda value of the premixed gas. For this purpose, it is catalytically decomposed in a reaction chamber and then analysed by a zirconium oxide sensor. Each measuring system is precisely calibrated to ensure a reliable Lambda measurement. Thus, the real combustion condition can be determined. Together with a control system, stable combustion can be achieved in all connected zones.
Eurox, a product line from Horn Glass Industries, has almost 30 years of experience with zirconia-based oxygen probes. Christian Reichl* discusses the line’s latest applications for the glass industry.
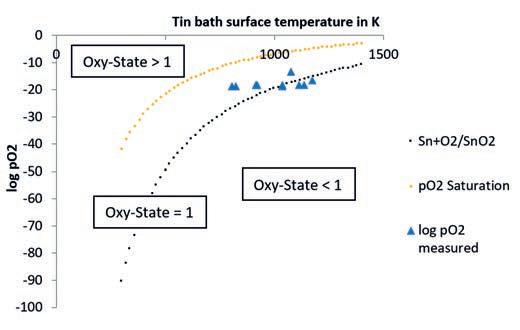
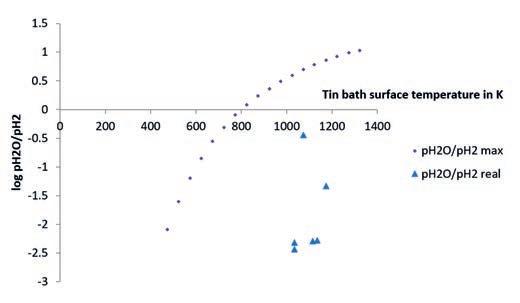
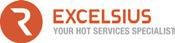
the state of the tin bath is still state of the art
The characteristic value describing the oxidation state of the tin bath surface (connection between liquid tin and tin bath atmosphere) is equal to one by definition when the measured oxygen partial pressure is on the black line. When the measured O2 partial pressure is lower than the equilibrium value, the equation Sn + O2 -> SnO2 is more on the educt side. The characteristic value is lower than one. When the partial pressure is higher, then the equation is more on the product side and the characteristic value is higher than one. As already described, there is an equilibrium in the equation 2 H2 + O2 -> 2 H2O. Also, the pO2 saturation curve has an influence on the calculation of the characteristic value. Thus, the value considers the formation of both 2- and 4-valent tin oxide. In reality, the measured O2 partial pressures along the tin bath are below the black curve at the glass inlet, and above the black curve when the glass belt leaves the tin bath under normal conditions, which indicates oxidation of the liquid tin, especially towards the end of the tin bath because of the lower temperature in this area. To obtain a statement about the gaseous 2-valent SnO, Eurox developed another characteristic value - the hydro state: SnO + H2 -> Sn + H2O. Here the H2O fraction calculated from the H2 O2 / H2O equilibrium is related to the H2 fraction in the atmosphere and compared with the maximum solubility of water in the atmosphere, which depends on temperature. By definition, the characteristic value on the saturation line is equal to one. When the measured specific H2O content is lower than the maximum solubility, the specific value is lower than one, when it is higher than the maximum solubility, it is above one. Fig 2 shows the calculated specific H2O content compared to the maximum specific H2O content in the atmosphere. The third output value by an extractive Fig De point temperatures along tin bath meas re ith ro meas re ment system.
Thetoday.extractive measuring system from Eurox can reliably determine the oxygen partial pressure even under extremely reducing conditions because, as already mentioned, there is always a certain residual partial pressure of oxygen due to the chemical equilibrium between water, hydrogen and oxygen. The measured oxygen partial pressure is given as a characteristic value. This value is formed by relating the measured oxygen partial pressure to the equilibrium of tin/tin oxide, which depends on temperature. Fig 1 shows both real measured O2 partial pressures (blue dots) and the Sn+O2/SnO2 equilibrium curve (black dots). A pO2 saturation curve is also shown (yellow dots), which is important for the formation of SnO (tin-2-oxide). The required measuring point temperatures are obtained from the temperature measurement in the tin bath.
Fig ortable p o nit ith accessories
measurement in the tin bath is the dew point and thus also the H2O content in theTheatmosphere.Eurox measuring system is calibrated in such a way that it also measures the dew point temperature correctly under normal operating conditions. Thus, it is also possible to notice a corresponding increase in the dew point temperature in the event of cooling water leakage, as the equation then shifts to the educt side due to the high H2O content. Fig 3 shows measured dew point temperatures with the Eurox measuring system. The temperatures on measuring point one and two are quite high, an air ingress was detected in this area. This means that there is not only a statement about the oxygen content in the atmosphere, but also about the water content and an estimate whether there is the right amount of H2 in the inert gas. A portable solution In addition to a stationary measuring unit for extractive measurements, Eurox has also developed a mobile measuring unit (Fig 4). The portable system can be used for measurements on glass conditioning systems and for tin bath atmosphere analysis. The measurement results can be visualised on a mobile device via WiFi. Together with the storage function, the measuring results can be archived over a longer period of time, analysed at a later date and compared with other measurements. �
Glass conditioning Glass International July/August 2022 800 www.glass-international.com
*Furnace Technology, Horn Glass Industries, Plössberg, https://www.hornglass.com/Germany
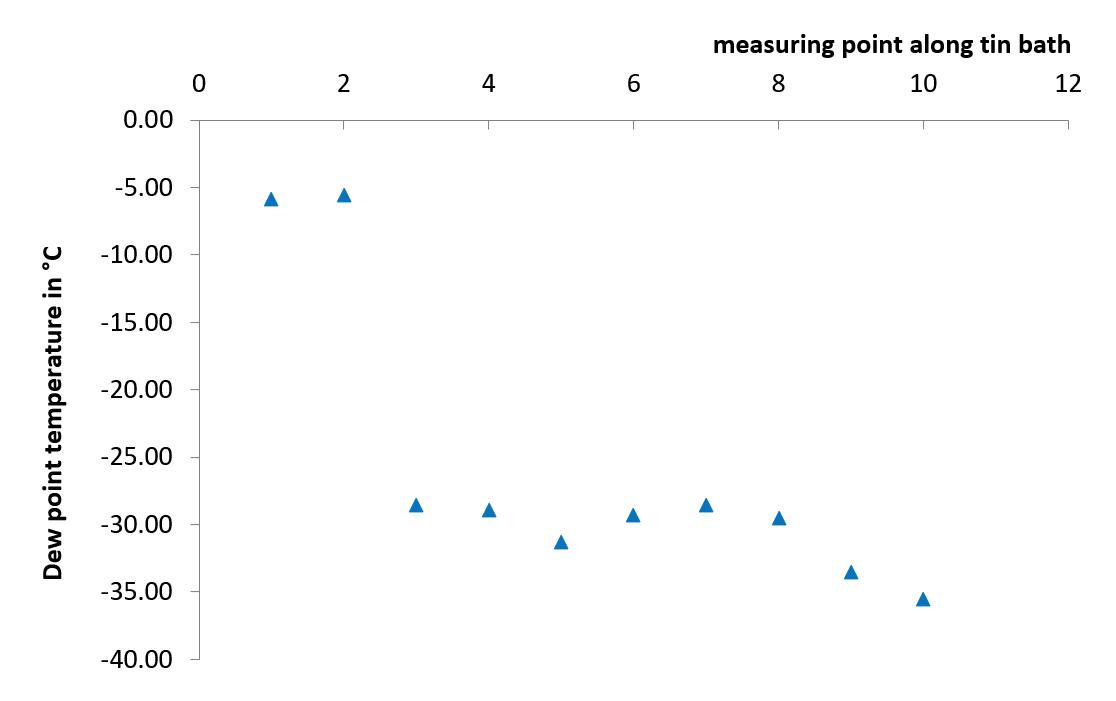
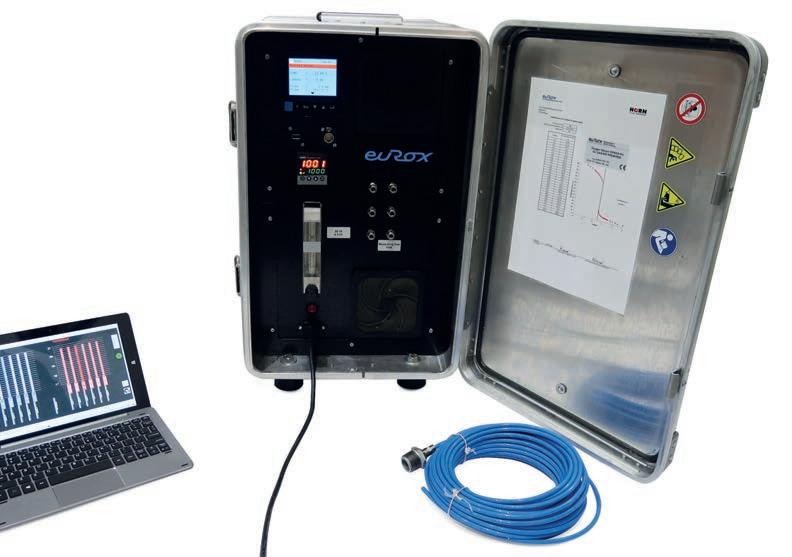
done,alwaysyou’vewhatdoalwaysyou“If got.”alwaysyou’vewhatgetalwaysyou’ll FordHenry handlingware
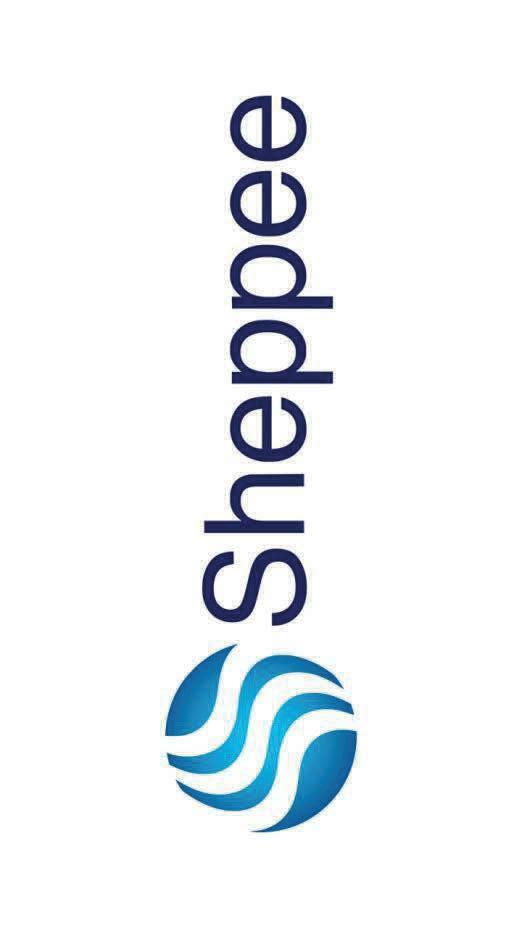
Holistic Glass Plant www.cmprojecting.deEngineering GLASS ENGINEERINGPLANT CO2 Reduction meets Producers Needs See you at GLASSTEC 2022 Hall 13 / Stand B34 CO 2 Reduction EnergySolar RecoveryHeat Wind Power Plant FuelHydrogenCulletRecycled
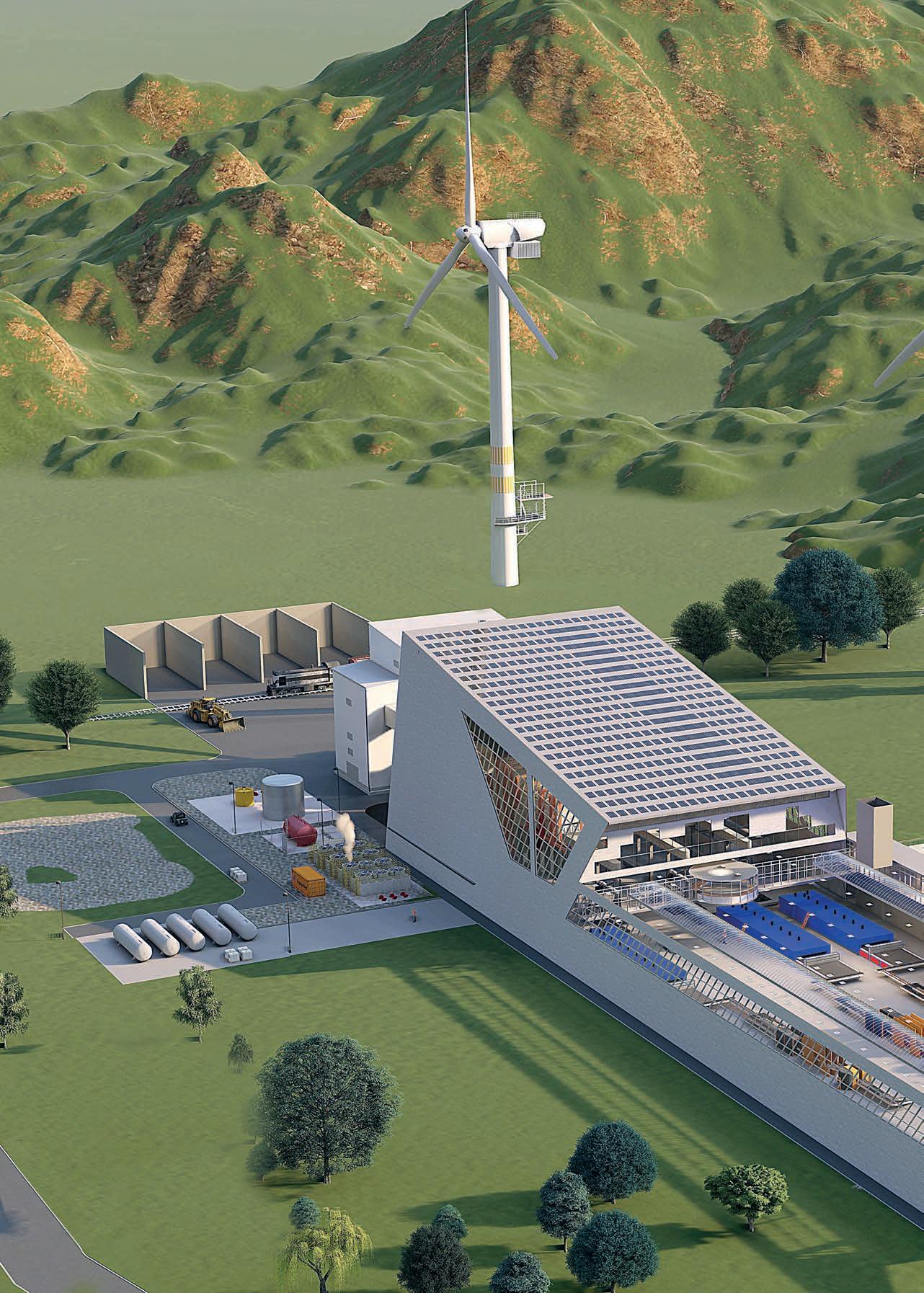
Digital twin in water saving and treatment systems Will an investment project deliver the required value? This major question is asked by each company when new equipment, repairs, or capacity extensions become necessary, reports Markus Franz*. To be able to answer this simple question, complex modelling must be carried out, which is costly financially and in time. To evaluate upfront the functionality and efficiency of a project, Industry 4.0 comes with several tools. Industry 4.0 is the current state of the art, and the technical revolution keeps advancing. New techniques enable mirroring the physical system with a digital version and to simulate infinite possible scenarios upfront without any impact on production. This visualisation of a system is the so-called ‘digital twin’.
Digital glassmaking Glass International July/August 2022 www.glass-international.com 83 Continued>>
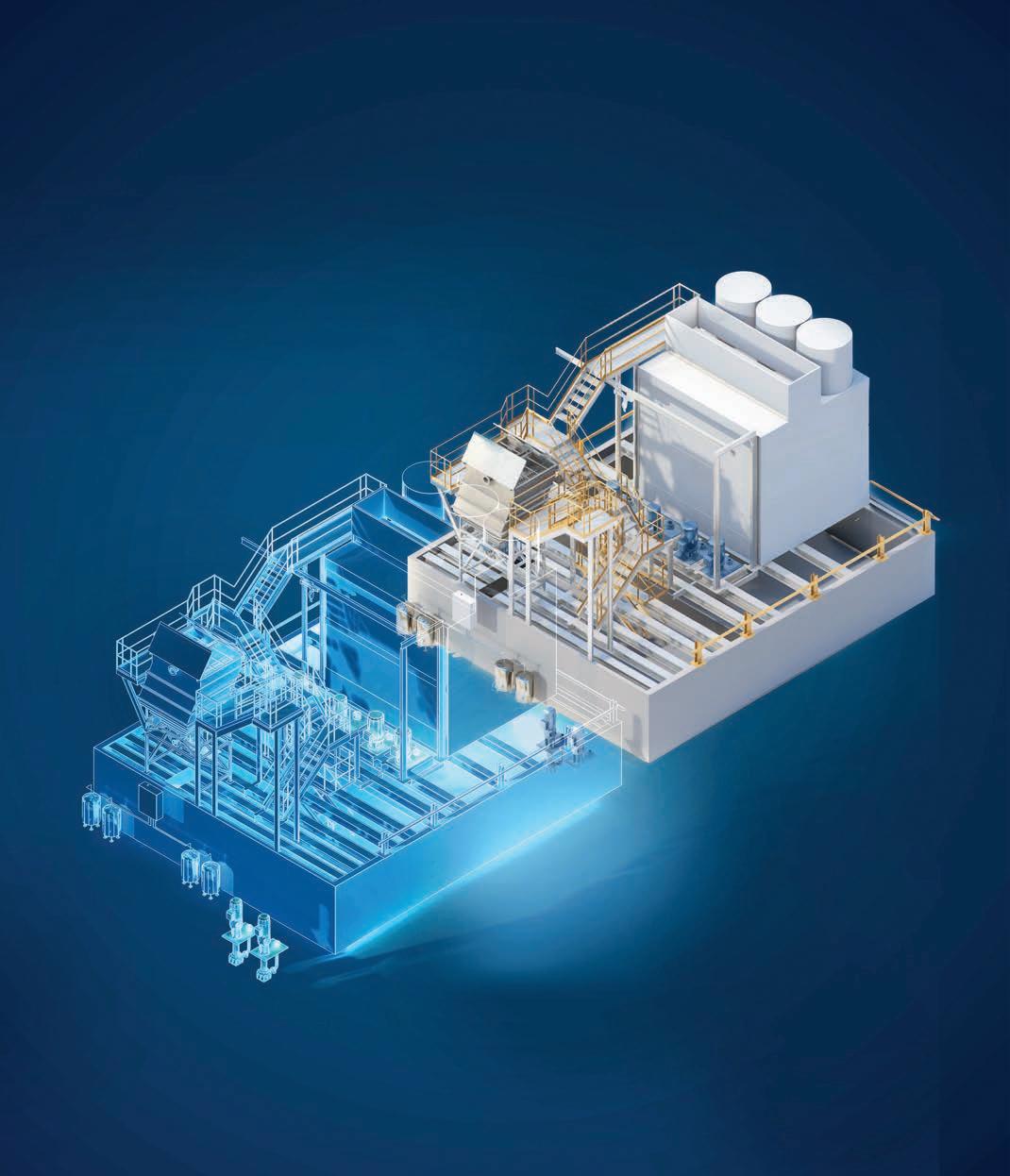
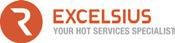

water systems WATER SAVING AND TREATMENT SYSTEMS Closed CustomizedLoopProgramming Solutions via Digital Twin Water System Design Predictive Maintenance Measures Optimization of Process HallSeewww.pvag-watersystems.deControlsyouatGLASSTEC202213/StandB34

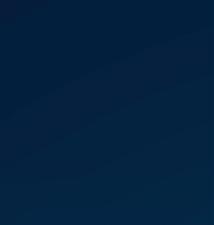
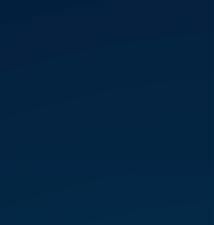
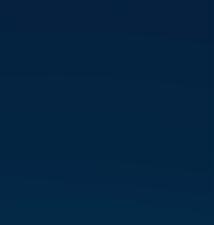
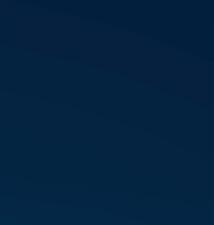
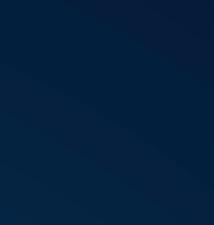
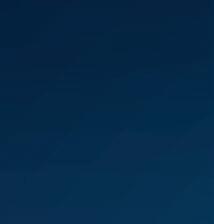
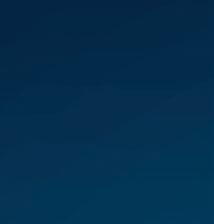
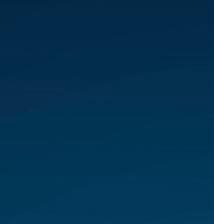

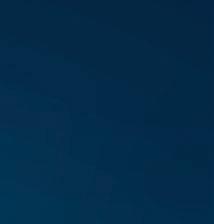
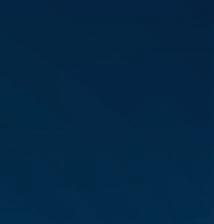
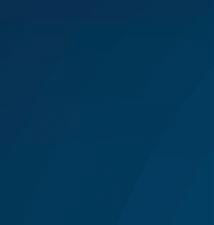
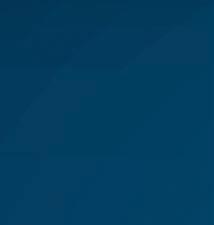
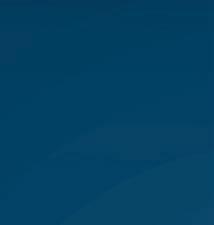
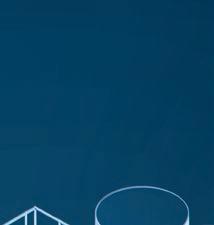
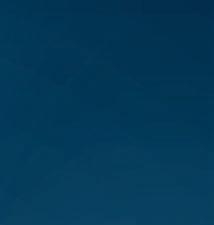
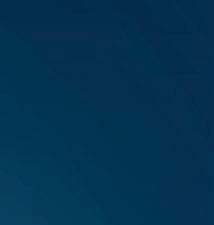
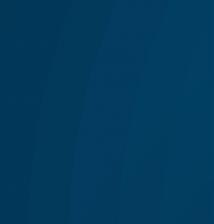

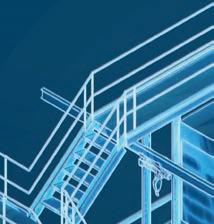
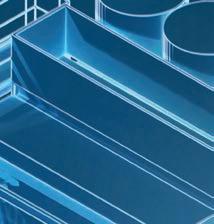


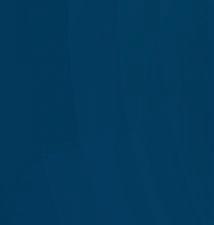
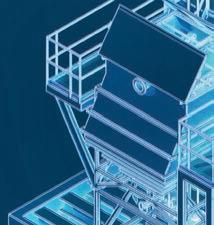
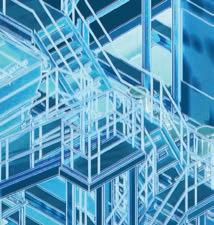

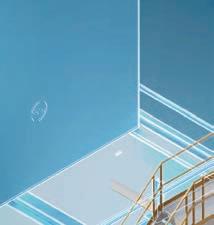
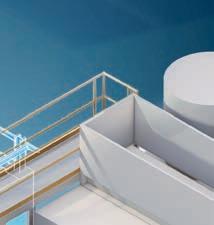
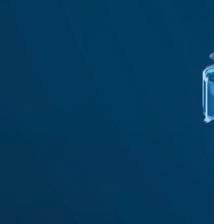
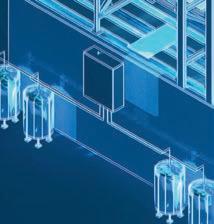

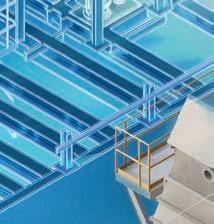
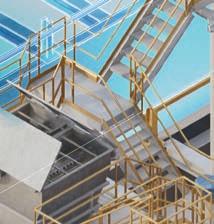
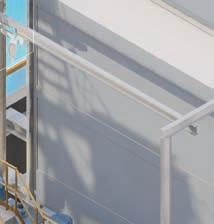
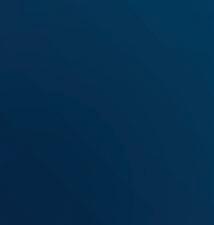
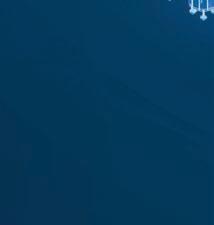
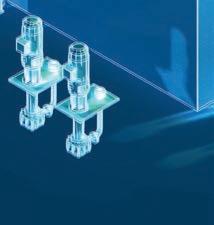
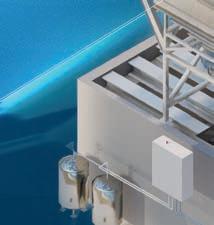
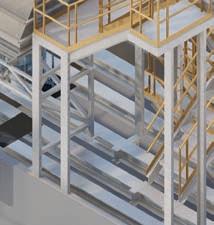
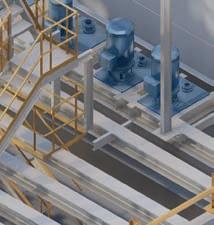
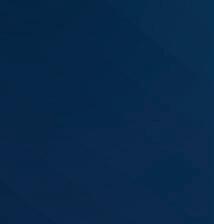
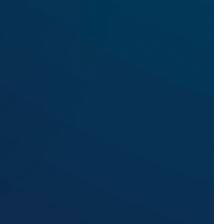

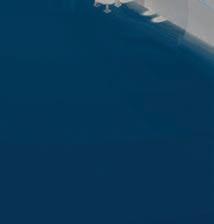
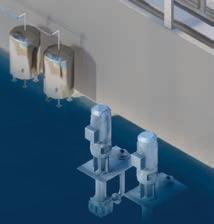

Germanyin2017Julyininstalledswabbing-robotlatest* *
The concept is based on the idea that existing processes or systems are used to implement a digital version. This provides a substantial benefit since the model can be optimised, by accessing a substantial database on how the system will react based on multiple variables.
Digital glassmaking Glass International July/August 2022 Digital twin
Important to note for a completely new process design, the digital twin cannot substitute the engineering process, but is complementary. The digital model in addition to the detail engineering shows the behavior of the process for different inputs, allowing the detail engineering planning to be adjusted or PVAGverified.water systems has been working with Siemens to develop and promote the introduction of the digital twin to the glass industry. For projects where current systems are to be optimised or for new designs of a cooling or water treatment system the digital twin is used to simulate the full potential of a system and to make the right engineering decisions for the processes. After a common understanding of what the system should look like and after basic engineering, a 3D model is set up to support the process planning. All necessary information like pump curves, equipment, valve data sheets, pipe routings, and specifications are included in the digital model.
Simulation tool The simulation tool SIMIT incorporates these data and is used to simulate the system’s different operating scenarios. The evaluation of the simulation is not only used to refine the detail engineering, however, also to improve customised programming solutions for each customer. Finally, after determining the most promising parameters to change with the model, they are used to change and optimise the physical model. Before implementing major changes to a current system, the operating team needs to be informed and trained on the new solution. Here the digital twin is also used, providing the operators with a virtual environment with real process visualisation and process behaviours to get familiarised with theDifferentchanges.scenarios like emergency cases can be trained for upfront, ensuring the operator knows better to react and feel confidently prepared for such incidents. Equipment damage and downtime can be reduced with this approach. To expand the implementation of the digital twin, PVAG water systems and Siemens will continue to work together. Especially inside the glass industry, there are substantial benefits to implementing this tool for improvements and reliability. Based on a distributed control system the digital twin can support predictive maintenance measures, improvements in logistics, and optimisation of process control. This advanced technology will enhance future investment projects.
During sensitivity analysis, the model will first be used to verify that the set-up is correct, and in a second stage to vary all parameters which can have an impact. In addition to varying input parameters like pressure or temperature, also complete equipment can be changed in the model to simulate the impact of the respective changes.
�
* Business Unit Director, PVAG water systems GmbH, Julich, Germany https://pvag-watersystems.de/en/
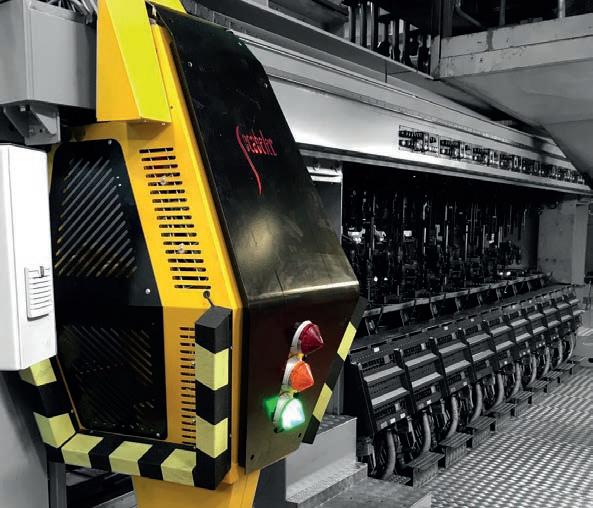




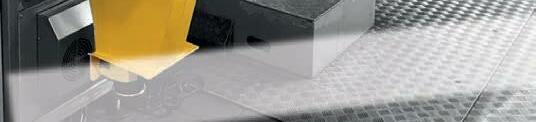





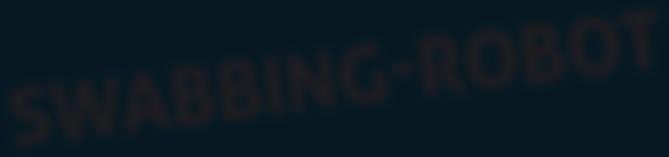


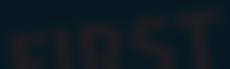

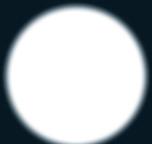

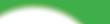
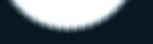
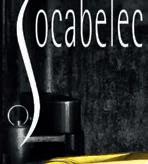

Electrifying carbon reductions 75-85% of CO2 emissions in glass manufacturing come from fuel combustion in the melting process. This provides a huge opportunity to slash emissions by replacing gas burners with electrical heaters. All-electric furnaces are quite a move away from traditional fossil fuel-fired smelter systems, not least in the massive reduction in carbon emissions. Compared to traditional fossil fuel heating at 1.1MWh/ton, net energy use for electric heating is around 35% lower; electric methods release no direct combustion-related CO2, thermal NOx, or SOx emissions. Also, when powered by green electricity such as solar or wind, the system can theoretically run without any CO2Theemissions.successof the electrical revolution in glass smelting is not purely theoretical, however. It is a proven and commonly used technology suitable for scaling up to meet large-scale systems. Even compared to the most efficient fossil fuel-fired smelter systems, electric furnaces are proving easier to control and maintain.
Decarbonisation Glass International July/August 2022 860 www.glass-international.com
Global glass manufacturing produces at least 86 million tonnes of carbon dioxide annually. It is an energy-intensive industry that relies on traditional processes and technologies but has also been traditionally risk-averse. However, coloured glass drinks bottles, for example, produce around 370kg CO2 emissions per ton1 – 150g in every bottle and 50%+ of CO2 footprint of the final product. As the world comes together to drive down carbon emissions, the time is ripe for the industry to change. Supply chain pressures in mobility, food and beverage and construction industries has already encouraged glass manufacturers to rethink existing glass production technology. However, this drive has accelerated to ensure the Paris 2030 and 2050 decarbonisation targets are met, reflecting growing consumer demand for sustainable products. To remain competitive, the glass industry must transform its processes quickly. This is where electrification and digitisation of the industry are coming to the fore, not only laying the foundation for sustainable production but also returning wider financial benefits.
When considered alongside a holistic electrification process and encompassing digitisation, the benefits are boosted even further. Holistic enefits Getting the most out of your plant assets while meeting sustainability goals is an increasing challenge that impacts both your profitability and the environment. The benefits of electrification are not limited to the furnace. Considering the complete power system and distribution architecture, from electrical grid to glass, it is possible to supercharge CO2 reductions. This can include integrating high-and medium-voltage distribution equipment, transformers, switchgears, VFD drives and other technologies across the process. This is a different way to incorporate power systems into process design, but one that can lead to significant savings of up to 20% CapEx, by improving the design and performance of the overall process.Forexample, electrical furnace design sees complete power systems optimised in terms of cost and reliability through modelling and simulation, using sophisticated digital twin equivalents that can assess whole systems rather than single processes. The result is greater streamlining, leading toward integrating renewables, microgrids, fuel cells, and battery storage technologies to provide resilient power grids and decarbonised energy transport and generation. Older plants were not designed with modern communications, data acquisition and analytical tools in mind so it can be a struggle to collect and collate information that drives improvements. To achieve maximum impact, electrification and digitisation go hand-in-hand. In an electrified plant, connected IoT devices can provide rich, real-time data that supports greater automation and effective decision-making. From design to maintenance, IoT technologies can ensure safety and efficiency, improve equipment reliability through predictive maintenance, simplify asset management through digital features, and enhance network security.
A force for change Efforts to elongate the lifetime of fossil-
How glass manufacturers can realise a carbon-free future How glass manufacturers can realise a carbon-free future

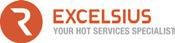
Glass International July/August 2022
*
References 1. Marscheider-Weidemann, F., Singer, N., Singh, R., & Eichhammer, W. (2009). Methodology for the free allocation of emission allowances in the EU ETS post 2012. 38235f971512_eneu/clima/document/download/1ec0de6a-0638-4297-b5cc-https://ec.europa.
fuel-burning furnaces are working against the industry. Most glass manufacturers only have one opportunity every 10 to 15 years to introduce a new innovative melting process, so it is not surprising that having to live with that decision leads to risk aversion. But the need for change is urgent. Almost every industry in the world has faced an ‘adapt or die’ moment, and now it is the turn of glass manufacturers to accept that change is here. This is not an easy truth, but any denial or delay in taking action will see the industry suffer. To thrive in an increasingly sustainability-minded environment, glass manufacturers must get clear on the need to challenge the old and embrace the new. While meeting global sustainability goals is justification in itself, the great news is that alongside carbon reduction, today’s electrical innovation drives business benefits that impact the bottom line - making the case for electrification crystal clear.
�
Germanyin2017Julyininstalledswabbing-robotlatest*
*Business Development Director - Mining, Metals and Minerals, Schneider Electric, Rueil-Malmaison, France https://www.se.com/ww/en/ rard e ouef ec discusses how the electrification and digitisation of the industry could help reduce carbon emissions.
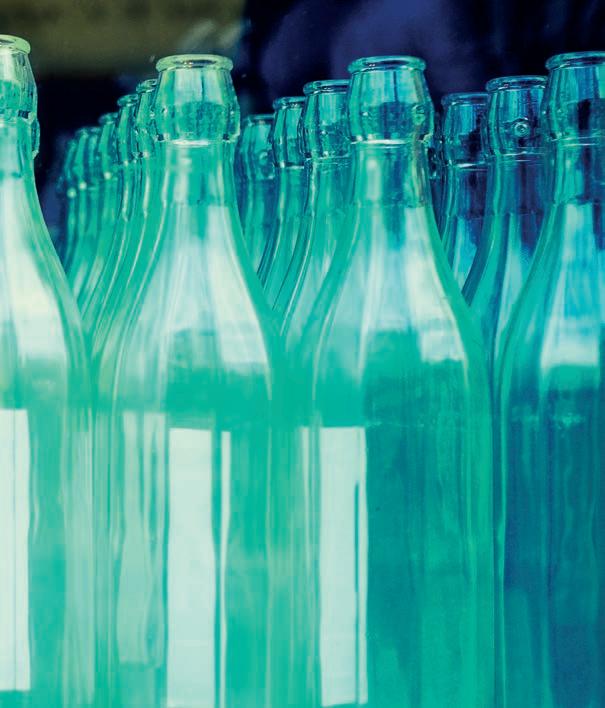
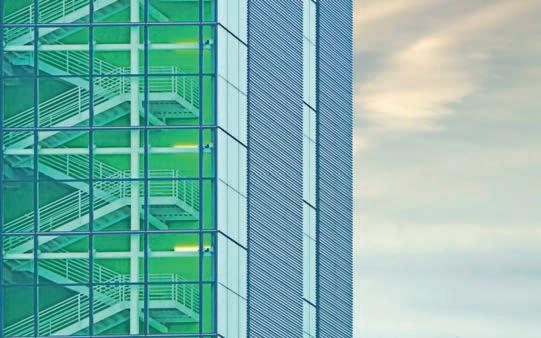
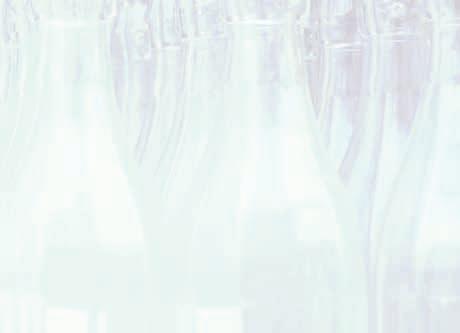
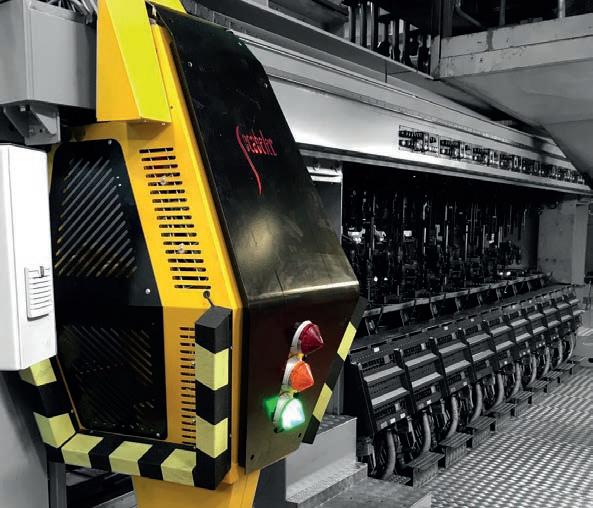




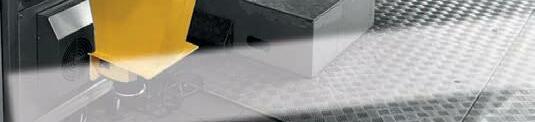





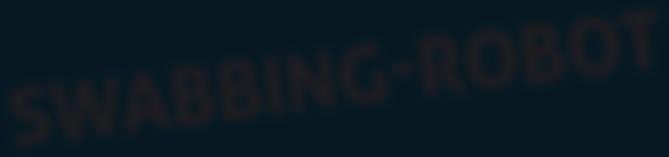


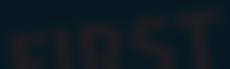

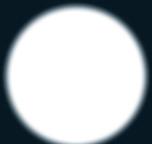

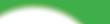
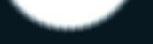
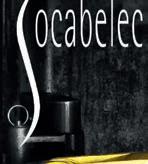
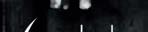
SAFINA Why Is Safina So Precious? • Flexibility • Express delivery terms • Customized production We Offer • Bushings • Labware • Thermocouples • Tubes and thimbles • Coating • Homogenizers • Outflow bowls • Sheets glasstec INTERNATIONAL TRADE FAIR FOR GLASS PRODUCTION • PROCESSING • PRODUCTS
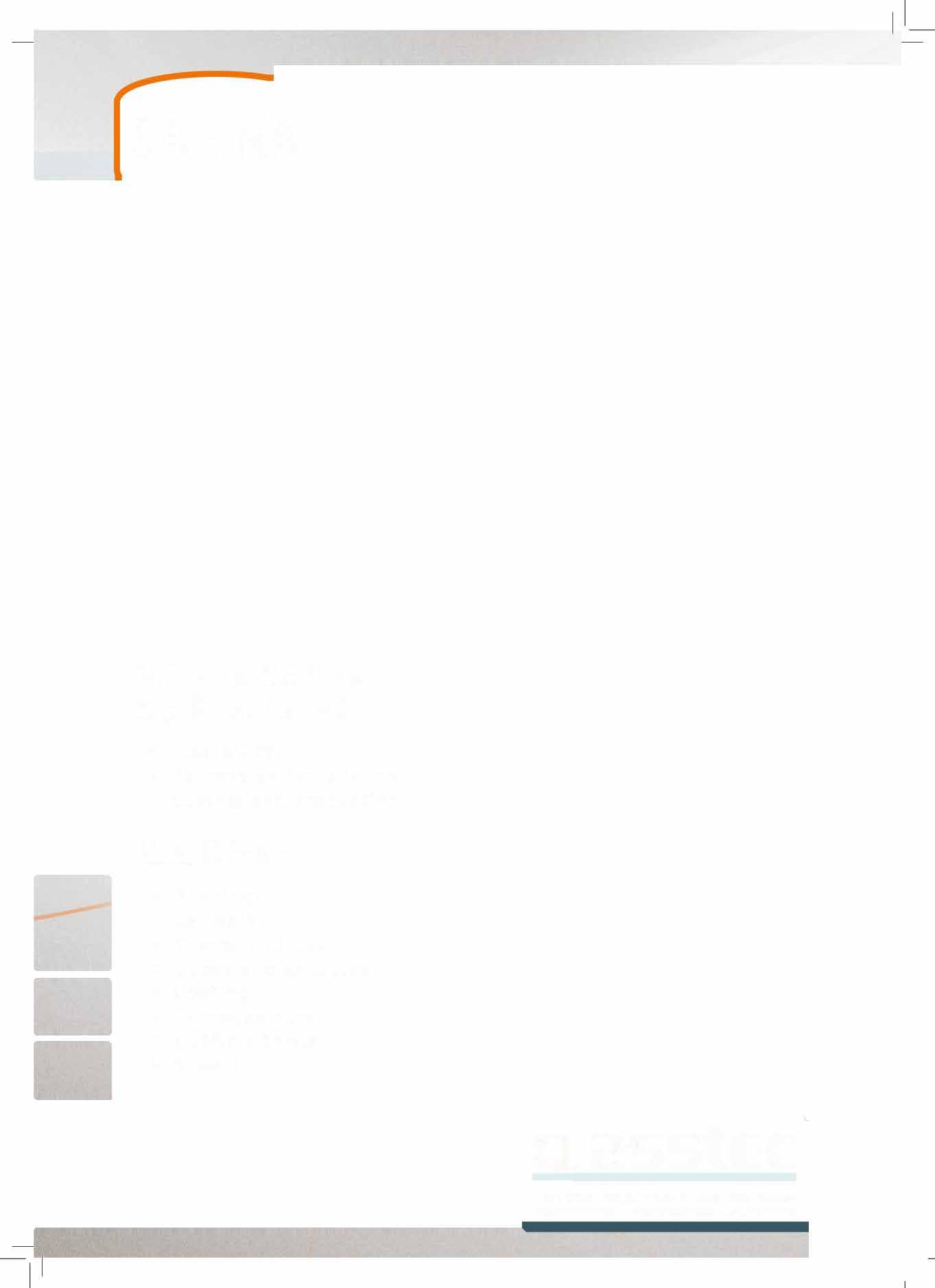
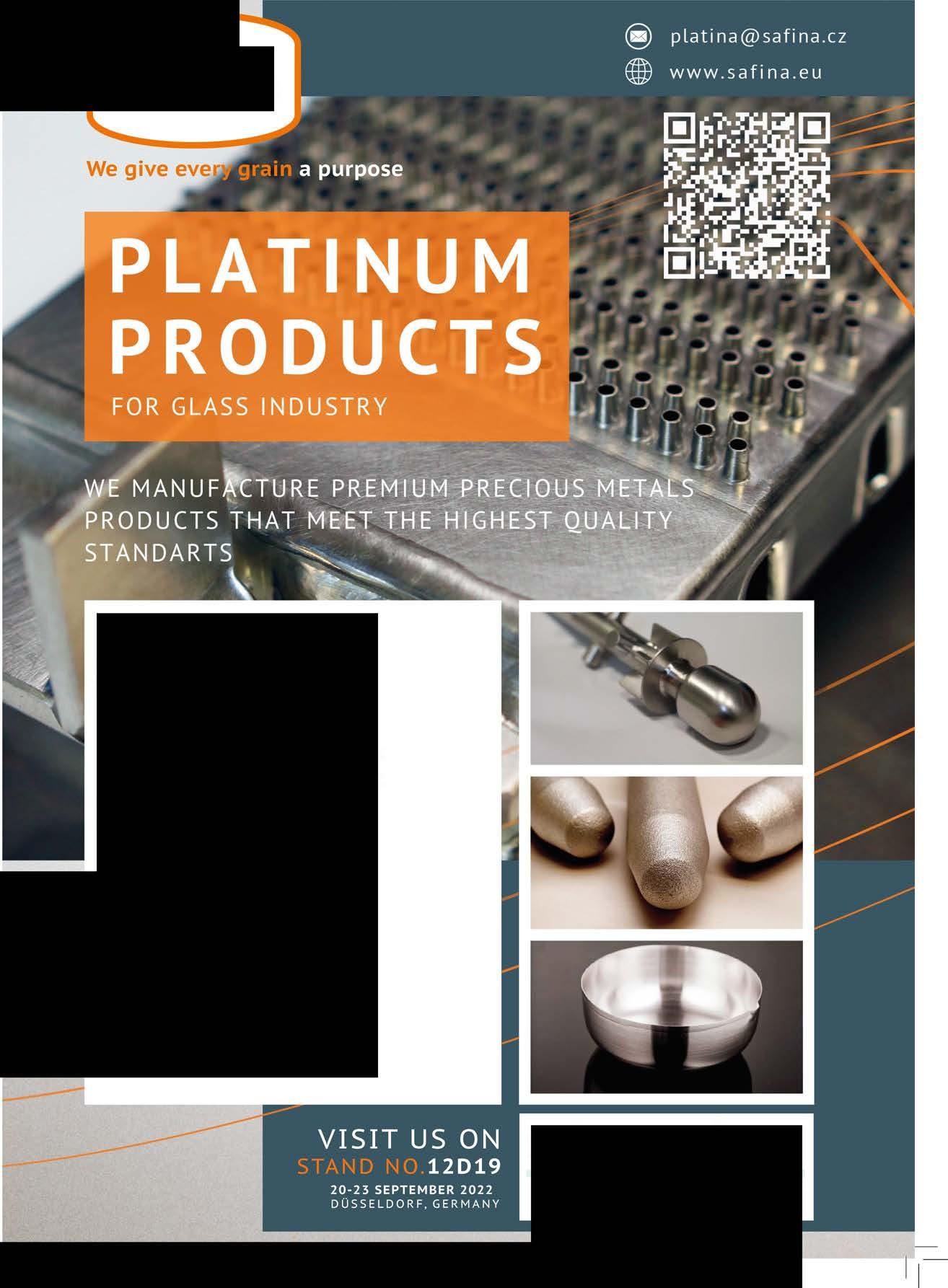
Harmonised perfumery solution To reduce their environmental impact, Josquin Peyceré, Cetie’s Secretary General for Glass Packaging.
Glass packaging Glass International July/August 2022 www.glass-international.com 89 Continued>>
� GUIDELINES N°17 - Specifications for aluminium screw caps for wines and alcoholic beverages.
This variant, which has been tested for several years in large-scale production, improves consumer safety when opening the cap. But it also requires excellent control of all the elements involved: � The bottle: geometry and surface finish
Cetie e plores the benefits of sustainable glass packaging Cetie has supported the glass packaging industry for over years providing technical reference documentation free of charge for its global audience. Josquin Peyceré* outlines how the organisation has begun to work on environmental issues. Cetie supports the glass packaging industry in its quest for performance, rigour, and quality by defining specifications and harmonising good practices, both in the glass manufacturing process and in the filling and capping operations. More recently, Cetie has been called upon to work on environmental issues.This year, the Cetie’s multidisciplinary working groups have made it possible to publish several reference documents, either in first edition or in revision and update, which are available free of charge to all users via its website.1 Food and beverages In the field of Food & Beverages, the main new developments concern the simulation test of label separation in the glass recycling process (DT41.00), and the guides for metal caps: � FS16.00 - Pressure resistance test procedures for products bottled with aluminium screw caps.
This variant of the finish was made official this year after multiple tests carried out within the Cetie framework to validate the range of possible dimensional tolerances. It complements the classic crown finish (defined by ISO12821 and 12822 standards), which remains the standard in cases where all the elements mentioned above are not under strict control or are likely to vary. A new group has also been established at Cetie this year, dedicated to the reuse of glass containers. This group focuses on bottles and jars that can be reused through a complete loop (use, return, washing, filling and sale again), and will work in particular on the cleanliness and physical integrity requirements that may be expected before a reusable container is put back into circulation, with a view to an outsourced washing service (not integrated into the filling chain).
� GUIDE N°11 - Metallic screw capping defects: identification and correction.
� The liner under the cap: hardness � The cap itself: metal thickness � The application of the closure onto the bottle finish, which must scrupulously respect the rules laid down in Cetie’s Guide n°4.
The crown finish, typically used on beer and unchanged for almost half a century, has seen a variant created. The GME13.10 (26 H 126 & 26 H 180 Crown Finishesalternative “P” point) is an option with a less sharp “P-point” for the cap to crimp onto the finish than the classic model.
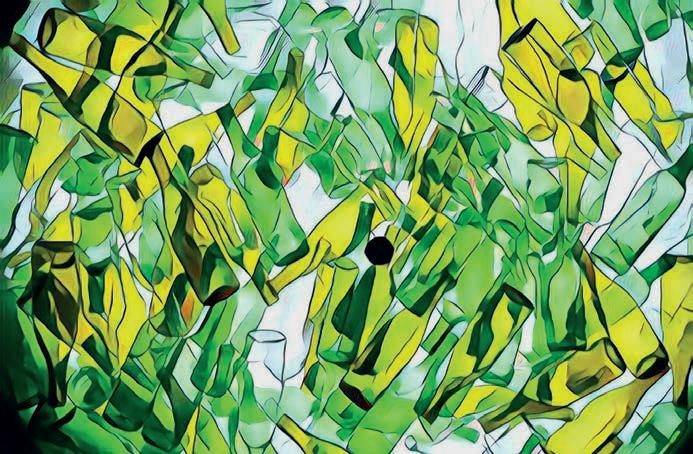
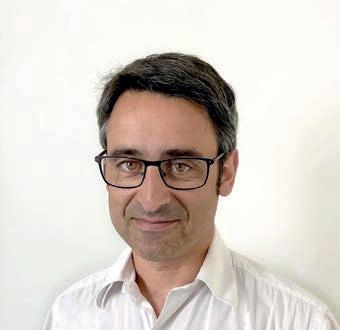
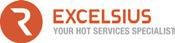
� GME40.20 – Flaconnagesustainable neck finishes: screw neck without additional bead.
� GME40.30 – Flaconnagesustainable neck finishes: interchangeable crimped finish with additional bead. International audience Cetie’s documents have a wide range of audiences. Some are intended for uality Managers or Development Directors, others are intended to be used directly by line technicians or even operators. To ensure that these documents are
perfumers have been confronted in recent years with the need to offer the consumer, in addition to the traditional “carnette” finish (flange finish) that receives a permanently crimped pump, a screw finish that allows the bottle to be refilled. Until now, of course, both types of finish have existed. But to make the two finish models live on the same bottle model required to create all the accessories (pump, pump cover, cap) in duplicate.Theperfumers therefore asked their bottle and pump suppliers to design a solution that would allow them to share the accessories and harmonise this solution to avoid each one having its own specific solution. This design was carried out at Cetie and, after cross-testing, resulted in a series of finishes with diameters of either 13, 15 or 17 mm, with closure elements compatible between the crimp version (carnette) and the screw capTheseversion.designs are free of charge, which allows the sector to limit the need for R&D, and to offer all the market players who have not yet switched to this type of finish the possibility of implementing the standard directly.
Glass International July/August 2022 0 Continued>> 90 www.glass-international.com
PUBLICATIONS
The list below is of Cetie’s publications from the last 12 months, which are all on the Cetie website1
available
GLASS CONTAINERS FOR FOOD AND BEVERAGES GME32.00MCA FINISHES GME30.11 FINISH ALSECO-ALCOA 28 GME13.10 26 H 126 & 26 H 180 CROWN FINISHESDIMENSIONS - ALTERNATIVE “P” POINT GME30.15BVP & BVS MINIMUM THROUGH BORE DT09.00 FACTORS TO CONVERT THE MASS OF WATER (in g) TO TRUE VOLUME (in ml), AS RE UIRED B THE MEASURING DIRECTIVECONTAINER(75 107 ECC) DT12.00 GENERAL GUIDELINES FOR THE PREPARATION OF GLASS CONTAINERS UALIT SPECIFICATIONS DT26.01 GLOSSAR OF GLASS CONTAINER VISUAL DEFECTS DT33.00 IMPACT TEST DT19.00 RECESSED LABELLING SPOTTING BAR GME21.10 FLAVLOCK FINISHES 26 - 38 mm GUIDE N°11METALLIC SCREW CAPPING DEFECTS - IDENTIFICATION AND CORRECTION FS16.00 PRESSURE RESISTANCE TEST PROCEDURES FOR PRODUCTS BOTTLED WITH ALUMINIUM SCREW CAPS DT41.00 SIMULATION TEST OF THE LABEL SEPARABILIT IN THE GLASS REC CLING PROCESS Guidelines N° 2.01PRESSURE SENSITIVE LABELING ON GLASS CONTAINERS GUIDELINES N°17SPECIFICATIONS FOR ALUMINIUM SCREW CAPS FOR WINES AND ALCOHOLIC BEVERAGES GLASS CONTAINERS FOR COSMETIC, PERFUMERY, PHARMACY DT36.01 TEST METHOD ON GLASS FLACON DECORATIVE ELEMENTS - ABRASION TEST - LINEAR ABRASER GME40.20FLACONNAGE - SUSTAINABLE NECK FINISHES: SCREW NECK WITHOUT ADDITIONAL BEAD GME40.25FLACONNAGE - SUSTAINABLE NECK FINISHES: INTERCHANGEABLE SCREW NECK WITH ADDITIONAL GME40.30FLACONNAGEBEAD - SUSTAINABLE NECK FINISHES: INTERCHANGEABLE CRIMPED FINISH WITH ADDITIONAL BEAD DT15.55 FLACONNAGE - TESTING PROCEDURE: VERTICALIT DT37.00 TEST METHOD ON GLASS FLACON DECORATIVE ELEMENTS - RESISTANCE TO BULK Glass container production line. Copyright: Shuttershock.
� GME40.25 – Flaconnagesustainable neck finishes: interchangeable screw neck with additional bead.
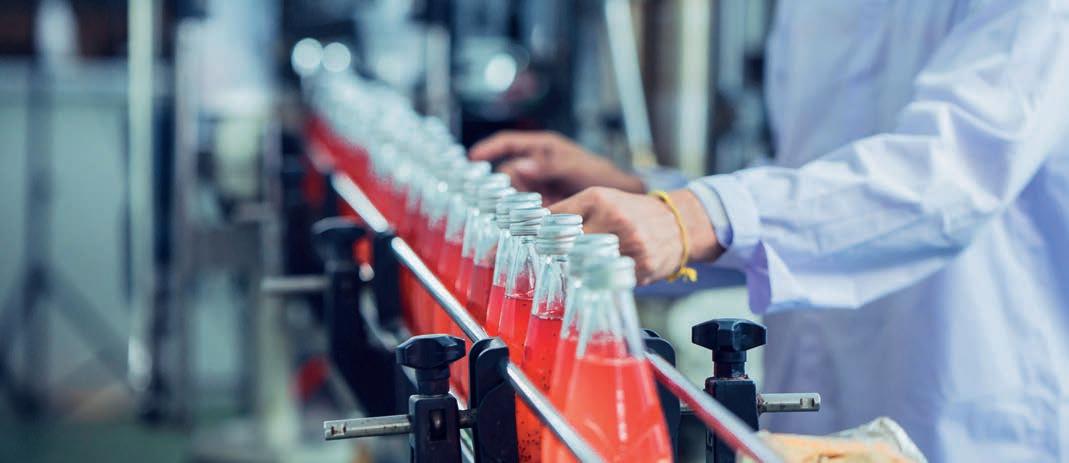
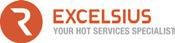
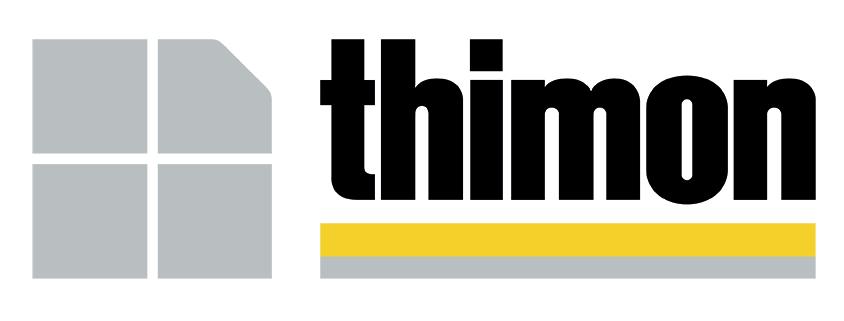

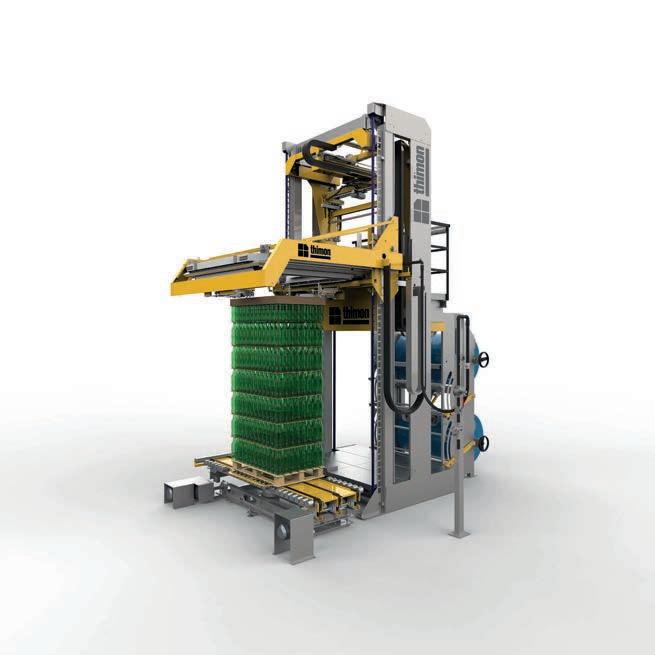

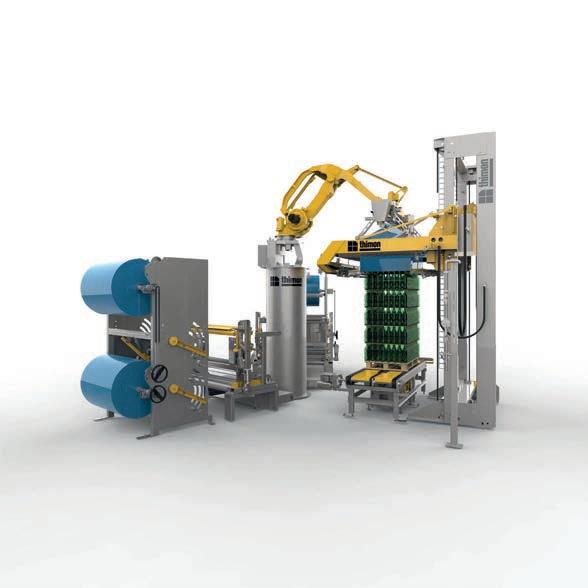
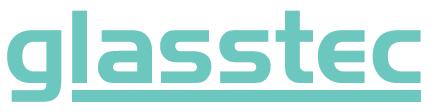
Cold End technology·Bottle conveying·Palletizing·Packaging·Handling·Software Complete Cold End from lehr to warehouse Sustainable intralogistics systems contributing to the protection of the MSKenvironmentEMSYsoftware for controlling and monitoring your Cold End Your reliable & sustainable partner for Cold End equipment COLD END FROM A SINGLE SOURCE MSK at Glasstec September 20 – 23, 2022 HallDüsseldorf13,Booth C32 MSK Covertech Group ·sales@msk.de·www.mskcovertech.com
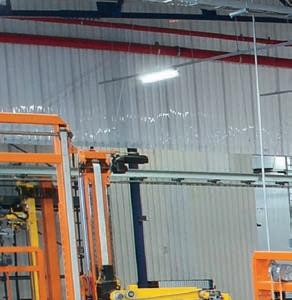
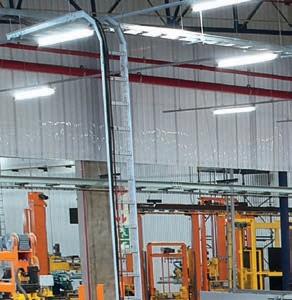

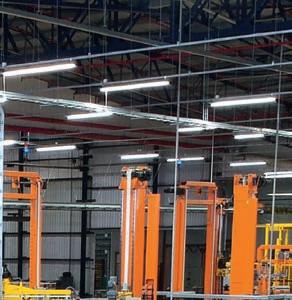
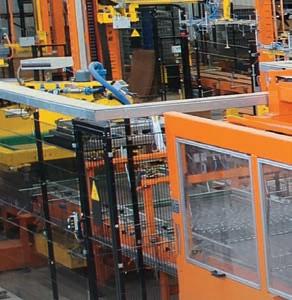
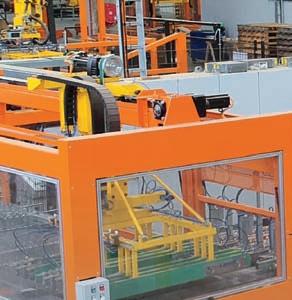
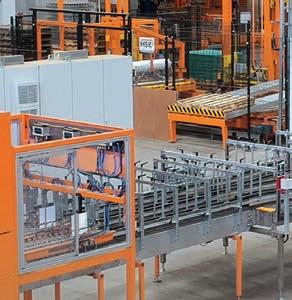

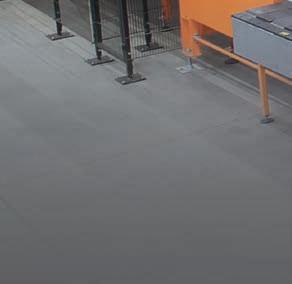
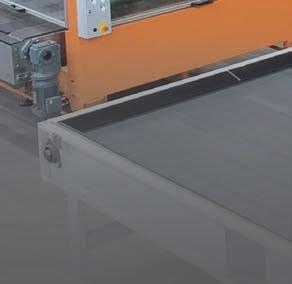
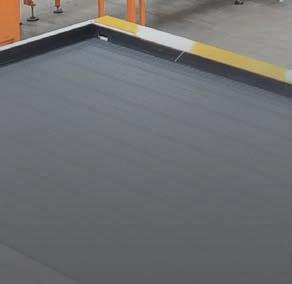

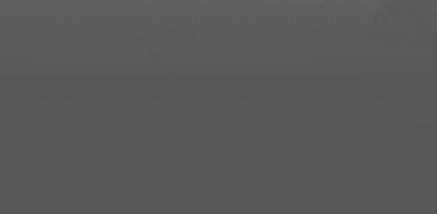
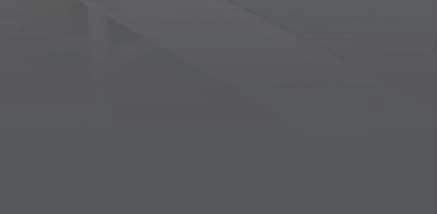
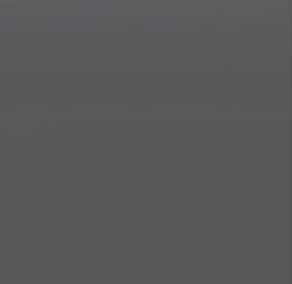
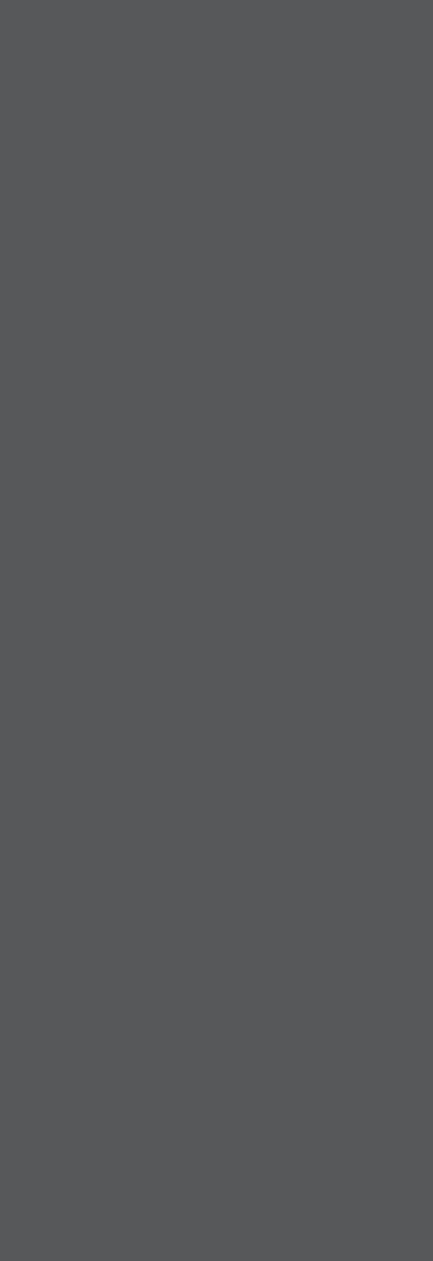
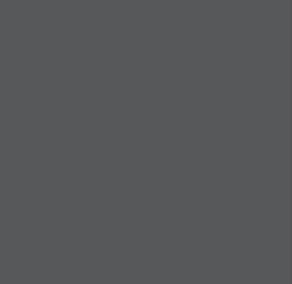
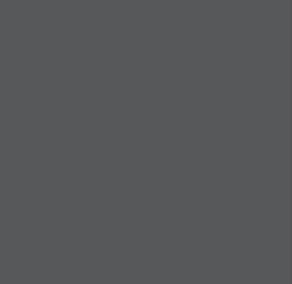
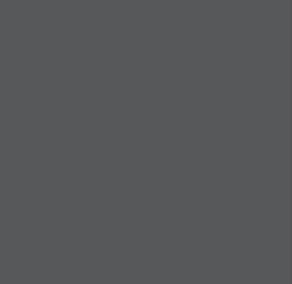
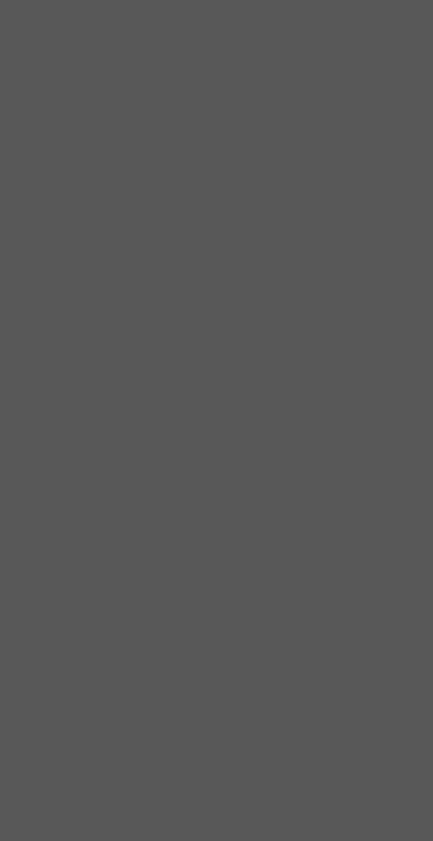

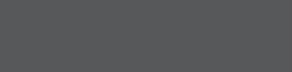
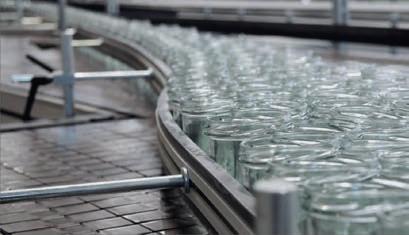
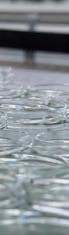
Glass packaging Glass International July/August 2022 www.glass-international.com 93 be proposed to European standardisation to replace the five existing standards. Challenges Regulatory developments, such as the laws on recycling or reuse, or the replacement of Directive 94 62 - Packaging & Packaging Waste (replacement to be published this year), require the sector to adapt in the best possible way, i.e. via solutions discussed and optimised by the consensus of the various players. Cetie’s international profile allows its members to benefit more widely from the experience of other colleagues or customers or suppliers. This sharing of expertise requires listening, rigour, but also responsiveness and agility. When a question cannot be answered immediately, test plans are launched, the results are shared, and conclusions are drawn together. This may require very close meetings. The Cetie team adapts the means and resources according to the urgency of the subject expressed by the working group. The team is also on the lookout for any question from anywhere in the world that could feed the group’s reflection, thanks to an online chat that is accessible to all: members, recurrent users of the website, or simple visitors arriving on the site for the first time. The dozens of documents currently being prepared testify to the enthusiasm generated by this type of collaborative work. �
vidromecanica@vidromecanica.com www.vidromecanica.com
available to as many people as possible, Cetie is making an unprecedented effort to translate its documents. In the last year, 34 translations have been carried out, mainly into German and French, but the first translations into Spanish have also begun. Some glossaries are even published in six languages. This means that a quarter of the world’s population will be able to read Cetie documents in their own language.
ChutesAutomatic CONVEYORSSCRAPER CRUSHERSCULLET
Revisions Document updates have also been important in recent months. Although some of these updates are improvements to the clarity of the content or readability, some of them are also major redesigns of the document. For example, the “MCA 28 mm” series of glass finishes for metal or plastic closures for carbonated beverages has been extensively revised. The working group has kept the nine existing finish versions, but has harmonised certain dimensions between the different versions and clarified certain points, such as the precise definition of the finish height. Finally, the nine versions are grouped in a single document, and this single document will
*Secretary General for Glass Packaging, Cetie, Paris, www.cetie.orgFrance
References: 1.https: www.cetie.org en the-cetiesdocumentary-database 122.html
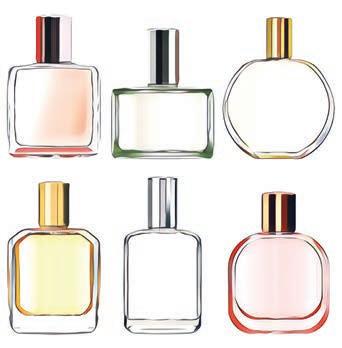
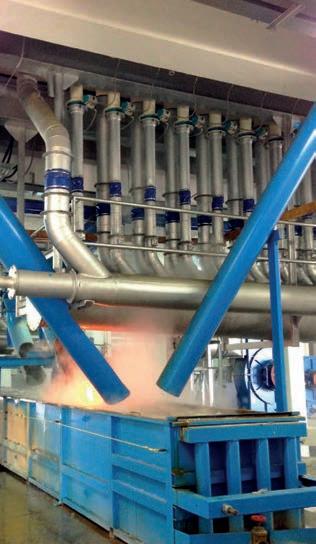




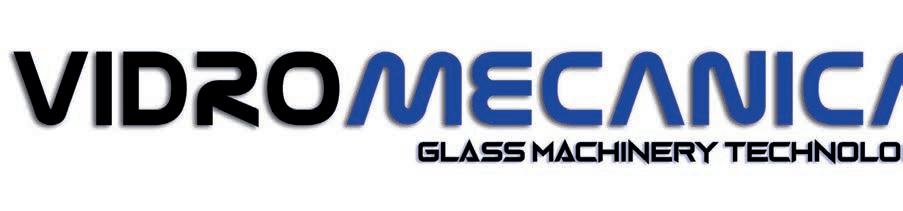
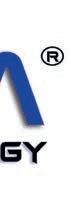

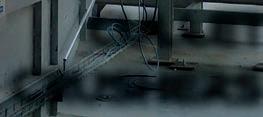

ware products lighter and stronger, produced with (almost) zero defects at higher speed and with minimum human dependency. The result is that the container and table ware industries are more competitive with other materials and more sustainable. Consequently together we create a better world! Bright ideas. Better glass. Better world.
Wewww.xparvision.comareworldleaderin table
the field of sensor and robot solutions for hot end inspection, quality assurance and closed loop automation. With our solutions we actively work together with glass producers on making containers and


















Swabbing greases: the right product for the right job
lorent uffino outlines why lubricants are an essential part of container glass manufacturing including how they can improve efficiency and create a safer wor ing environment.
Lubrication Glass International July/August 2022 www.glass-international.com 95 Continued>>
Swabbing greases are essential lubricants in the container glass manufacturing process to ensure a high and constant productivity. They provide a combination of several functionalities during the stage of glass forming like helping the molten glass to perfectly cover the mould surfaces and so avoid defects due to a bad distribution. Their releasing properties enable to easily remove the glass items from each mould which is essential to act against glassware checks. Finally, their lubrication performances will enhance moulds life and make them lastGraphitelonger. has been, for decades, a central element in swabbing greases formulations. It is a well-known raw material used for its lubrication properties in several industrial fields. Forging operations and tubes manufacturing are examples of other areas using it. Its origins can be natural (mining ore) or synthetic (full chemical process) and some of its characteristics like the carbon content, the particle size and its crystallography help Condat to select them for optimal performances.However,graphite is also at the origin of some well-known defects in glass making. A common issue is graphite transfer which leads to glass items dirtiness. This phenomenon is explained by the migration of graphite from the swabbing grease, applied to the mould, to the glass container. The second problem is graphite build-up. It mainly occurs in finish moulds where engravings are used. Graphite will concentrate in some areas and will last. The consequence is that the molten glass can’t reach them and block the mould covering. Marks are not fully printed, and production must be stopped. You can limit or overcome these defects by choosing the right swabbing grease for the right job or try a new technology, such as a white swabbing grease. Select the right grease Each segment of the container glass industry requires specific lubricants adapted to its production specifications: production rate, items cleanliness, types of glass, gob weights, items shape, etc. That’s why Condat decided to develop dedicated swabbing solutions depending on their customers application fields:
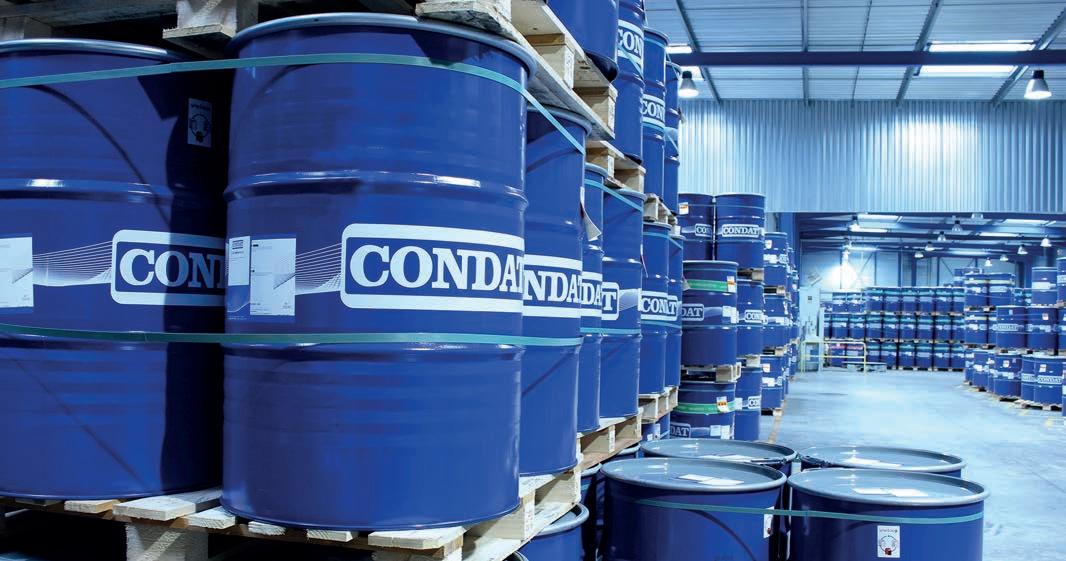
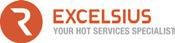
bottles
An Asian glass bottle manufacturer specialised in the production of light amber bottles used for energy drinks had been using a highly graphited swabbing grease for every mould in their 10 sections triple gobs IS Machines. Production yield was correct, but they were looking for more. After analysing the glass items manufactured and the material used for the mould, Condat glass experts suggested to test Condaglass 397, a lower graphited swabbing grease dedicated to the release of small glass containers. The product shows excellent wetting properties, while keeping good gob loading. Thanks to its high quality and minimum amount of graphite, Condaglass 397 helped the company to reduce the number of automatic rejects by 50% after swabbing.
� Spirit � Cosmetics & perfumes
� Indeed,Pharmaceuticalsdepending on the glassware being produced, a dedicated swabbing grease must be chosen. The use of a nonsuitable swabbing grease will lead to more rejects due to graphite transfer and graphite build-up. Each lubricant is also specified to a mould type. The needs of lubrication between the blank, the neck ring and the finish moulds are all different. Where high releasing properties are wanted in the first stage of the glass forming, swabbing the neck ring and the blank mould must be soft and light. Over-swabbing these areas will conduct to more glass checks.
Using a lower graphited grease
Less graphite also means less build-up! An essential feature which helped the company decrease its swabbing frequency by 33% and reduce the maintenance downtime of the moulds (Table 1) Over a year, this company could save more than 8 million bottles, together with a significant decrease of the swabbing grease consumption. But that’s not all. Besides productivity, safety was improved too. Less swabbing operations led to a decrease in the risk of operators’ injuries. Turn on white Made without graphite, Condat white swabbing greases avoid any graphite transfer. Automatic rejects after swabbing can be decreased and so millions of bottles are saved every year. As a result, glass manufacturers generate less waste and observe immediate productivity gains. Without graphite also means a cleaner working environment for the operators in the gob forming area. They do not handle graphited and blackened products when swabbing the blank, blow and neck ring moulds. And the same improvement occurs at the mould workshop. Condat’s objective is not only to replace graphite from swabbing greases but also to bring technical benefits in application. The lubricating raw materials used in their new technology have a higher thermal resistance which leads to increase the swabbing frequency. Companies that chose this solution were able to extend by two to four times their swabbing frequency. Thanks to this high performance, operators are also less in contact with the glass forming area and can be more focused on optimisation of the IS machine working parameters. Thus, white swabbing greases help to consume less, better and create a safer workingReducingenvironment.theenvironmental impact
Lubrication 960 www.glass-international.com Continued>> Glass International July/August 2022 � Wine & beer bottles
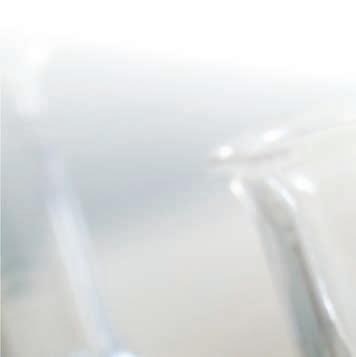
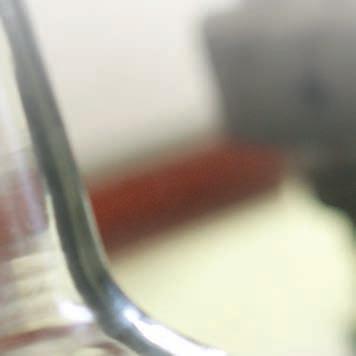
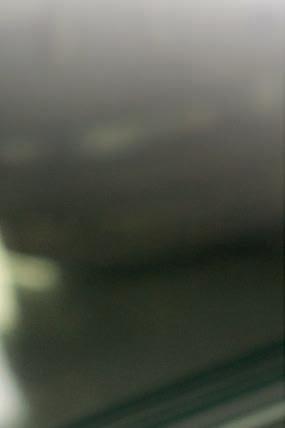

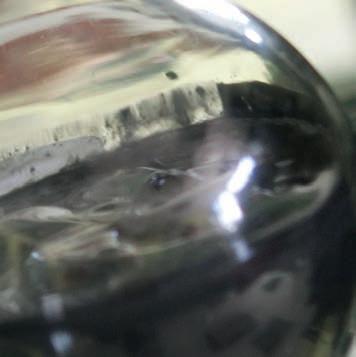
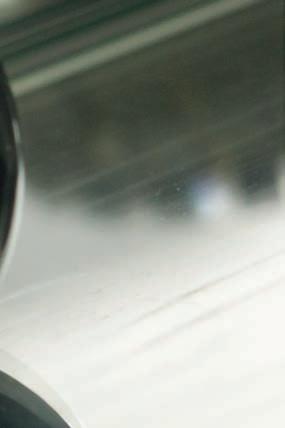
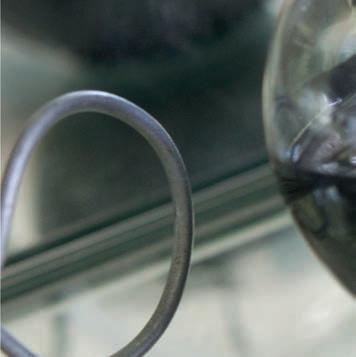
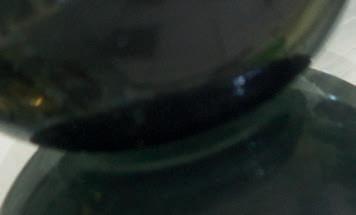
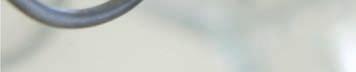
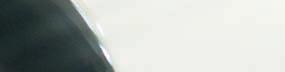

GAIN INSIGHT INTO GLASS MELT TANK THERMAL PROCESSES WITH ACCURATE REAL-TIME TEMPERATURE MEASUREMENTS The In-Furnace Thermal Glass Survey is AMETEK Land’s unique thermal optimisation solution for glass refractory applications, supplementing traditional inspections. It produces real-time and recorded images for analysis, helping to improve glass productivity with optimised pull rates, increased thermal and combustion efficiency, and lowered fuel costs. Protecting the refractory from damage and extending campaign life, the thermal glass survey also optimises the flame pattern to reduce energy consumption and helps ensure energy compliance. MARKET LEADING TECHNOLOGY - Live highresolution thermal images from the furnace, gas measurement and accurate data analysis. COOLING IDENTIFICATION – Reveal where there is too much or insufficient cooling to minimise emissions and corrosion. EARLY DAMAGE DETECTION - Identify small rat holes and other damage before it becomes apparent on the exterior. GET THE BENEFITS: SURVEY. ANALYSE. OPTIMISE. IN-FURNACE THERMAL GLASS SURVEYS LEARN MORE: WWW.AMETEK-LAND.COM | LAND.ENQUIRY@AMETEK.COM Confirming correct thermal profiles during reversal in a large furnace Identifying hot and cold spots during burning in a large furnace Verifying temperature of throat and front wall in an end fired furnace Determining peak flames in an end fired furnace


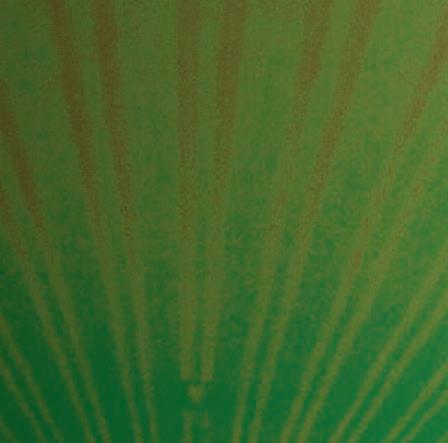
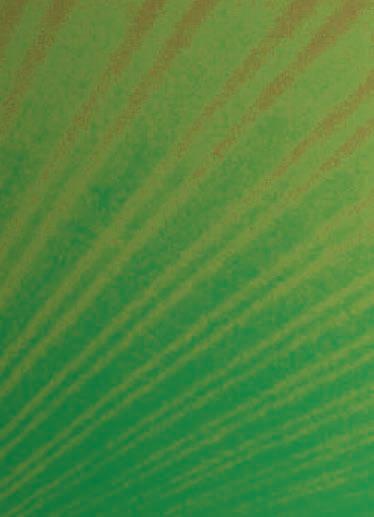
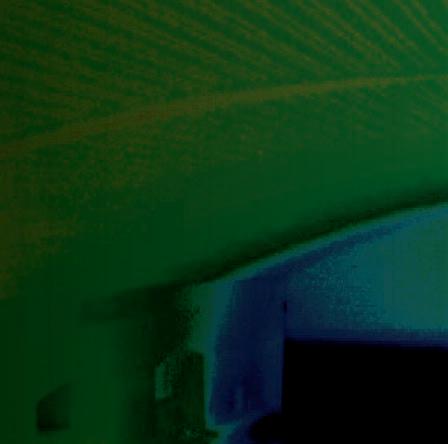
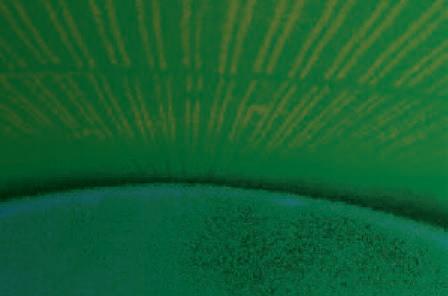
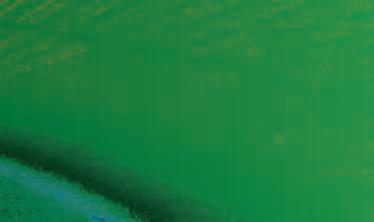
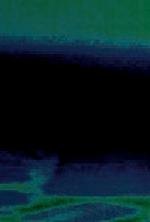
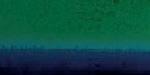
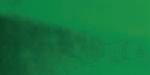


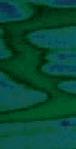

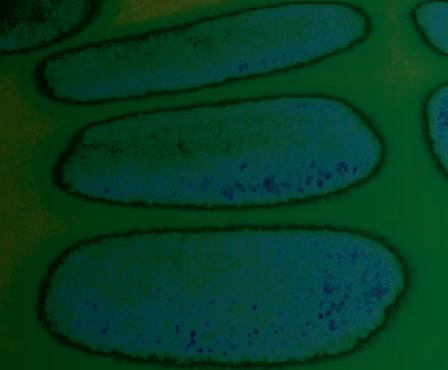

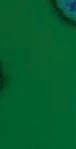
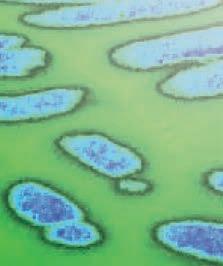
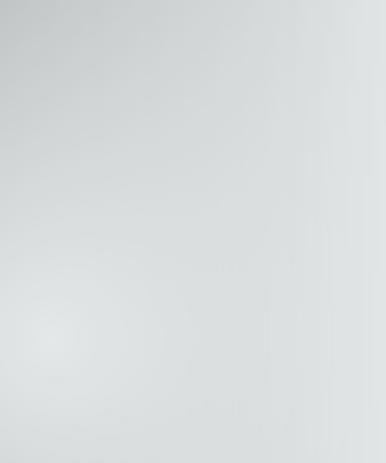

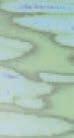
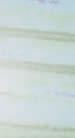

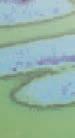
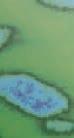
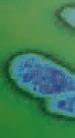

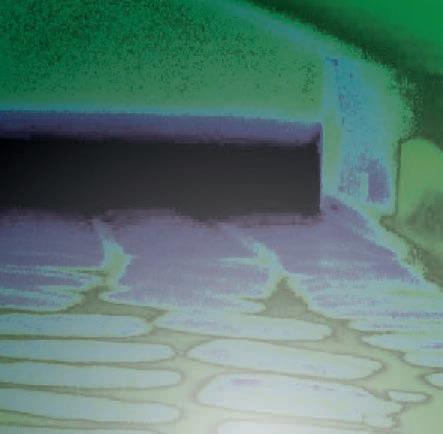
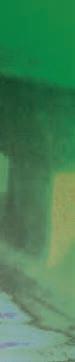





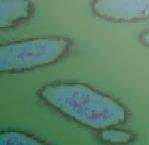


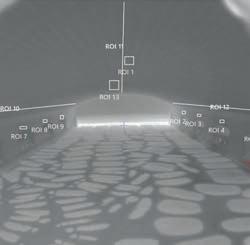
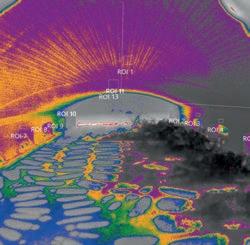
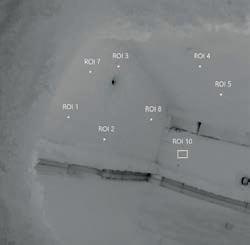
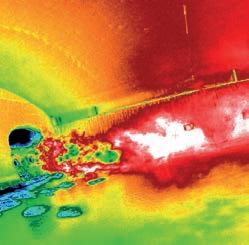
is an important topic at Condat. White swabbing solutions are made of a mix of renewable vegetable-based oils and recycled refined oils. Particular attention was also paid on end-users when developing the product, that’s why their Safety Data Sheet does not display any hazardous pictogram. Finally, thanks to their high flash point, Condat swabbing greases limit fire risk and ensure equipment and co-workers protection. Condat in glass making Condat has supplied and supported the container glass industry for more than 30 years by providing lubricating solutions. Around 200 customers around the world rely on it for their plant productivity and safety. All the glass production process is addressed with high valued solutions for the shears, scoops, deliveries, moulds and IS machine mechanisms. To know more about this glass lubricants offering, contact Condat at Glasstec Hall 14 stand B13. � *Product Marketing Expert, Condat Chasse-sur-Rhône, www.condat-lubricants.comFrance Lubrication Table 1: the maintenance downtime of the moulds.
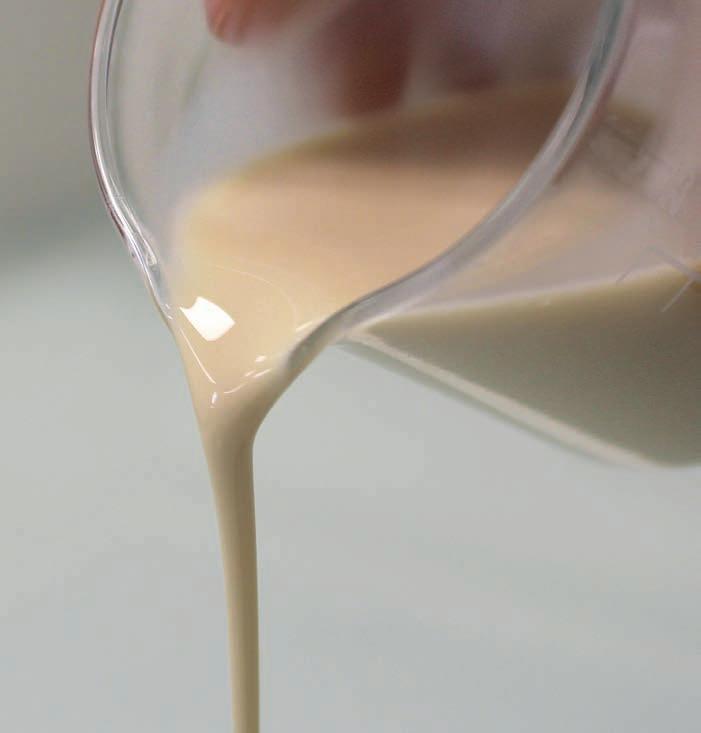


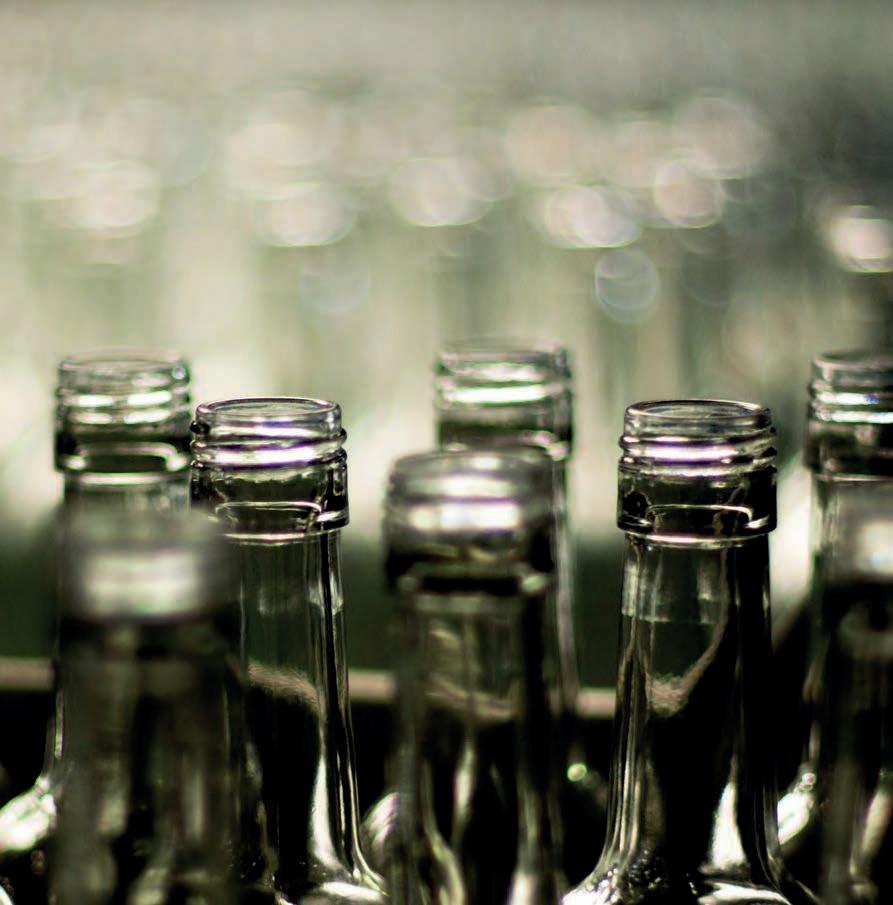
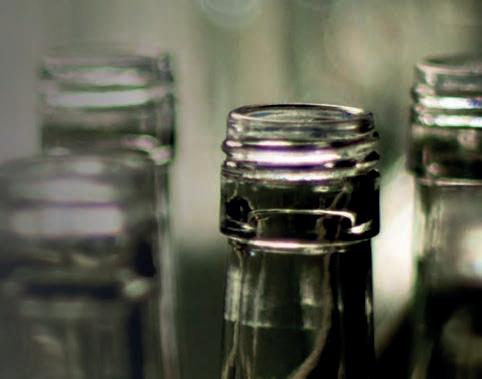

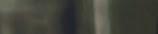

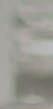
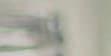




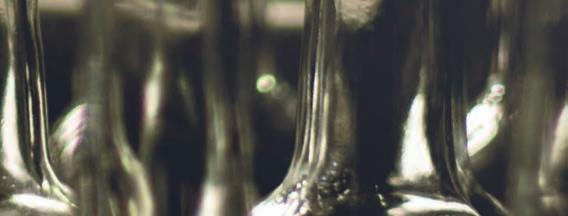
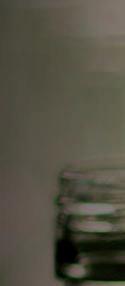
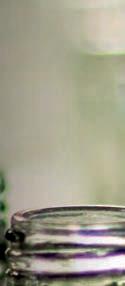



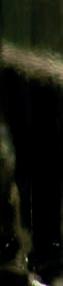
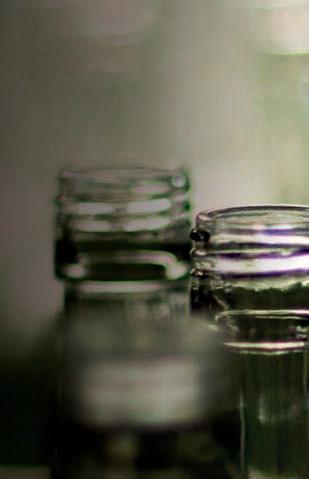
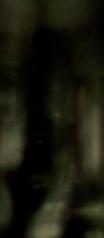

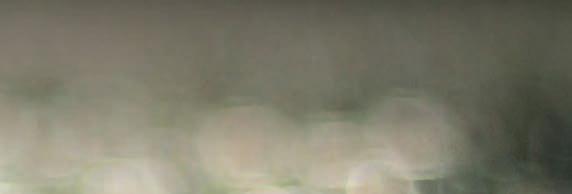

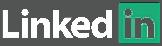
















































Conveying Ideas Inspiring Solutions Building Success Your global source for glass & fiberglass Major innovations for your future: •Over 120 years of combined experience in writing proprietary PLC control code for batch •Plug-resistantintegrityproprietary design standards for raw materials & batch conveying •Smart design with pre-fabricated modules •Easy improvement on existing batch plant •Air blending to replace mechanical mixers •Dust free systems •Patented air pollution control system free truck/railcar unloading automatic bootlift M529 NTE-Process Full scale testing at our Innovation Center RAW MATERIAL HANDLINGBAGHOUSE & ESP DUST HANDLING www.nte-process.com BLENDER TRANSPORTER 20-23 September 2022 Düsseldorf - Germany Visit us: hall 14, booth G41
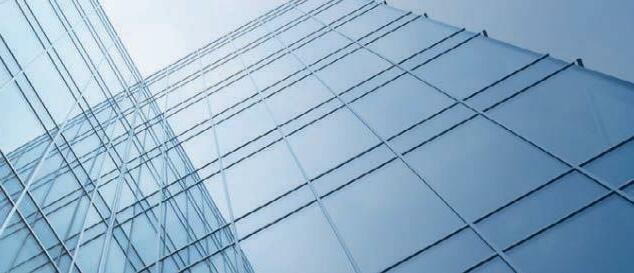

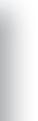
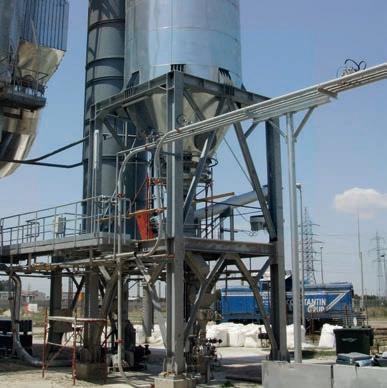


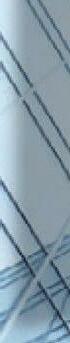
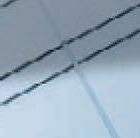
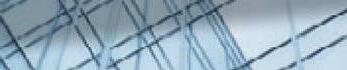
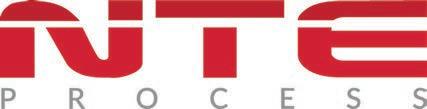

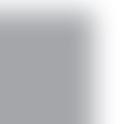
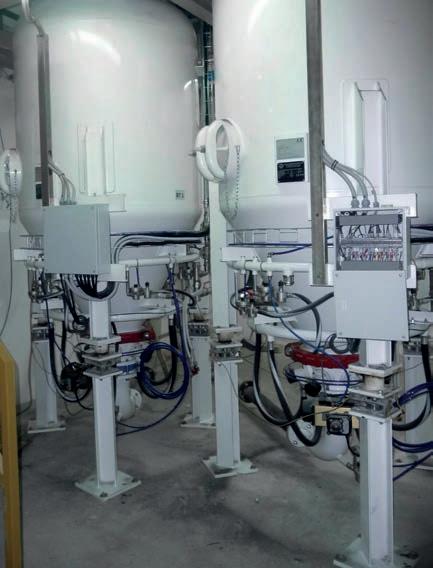



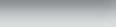
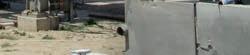

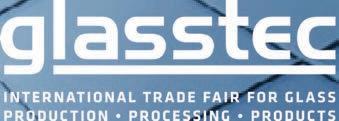
WE SHAPE A CARBON-NEUTRAL GLASS INDUSTRY FOR A BRIGHTER FUTURETheglassindustry is entering a new era. The industry must come together to achieve a common goal. We are fully dedicated to and streamlined for the special requirements of the glass industry. SEFPRO offers you high-quality refractory solutions and services for your entire production process and beyond. For a brighter future, we are there for you with innovative products and services for the furnace lifecycle and beyond. Let‘s shape the future together. at Convention Center Düsseldorf, Germany Booth: 13A47 September, 20-23, 2022 Visit us at: www.sefpro.com
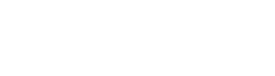

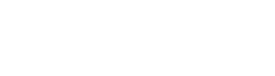

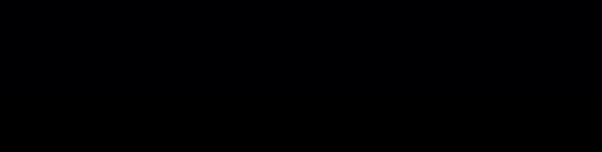
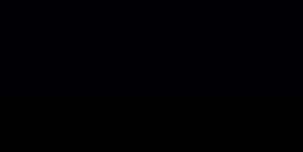
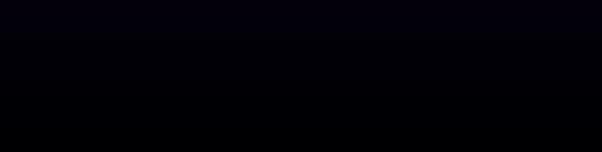
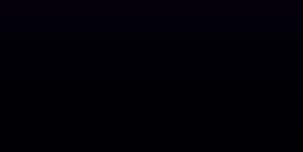

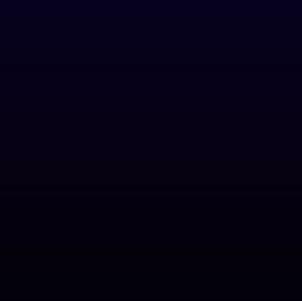

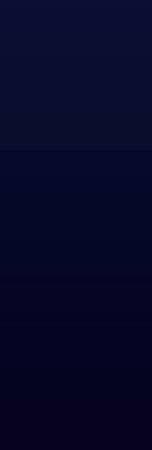

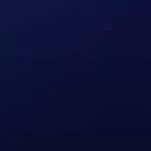
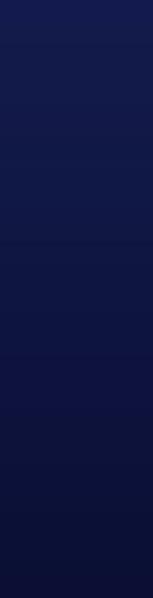


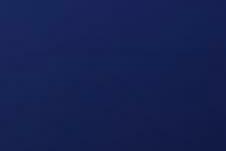
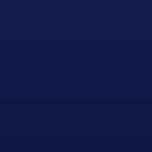


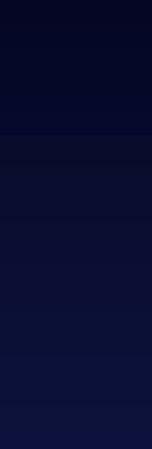

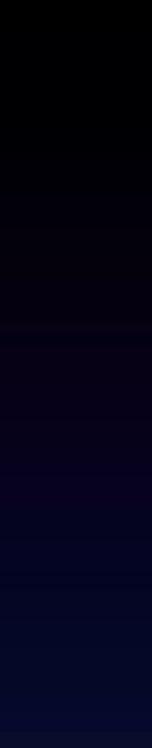
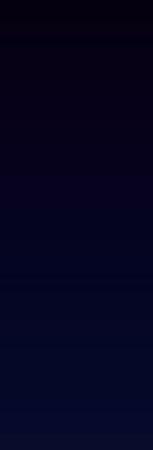
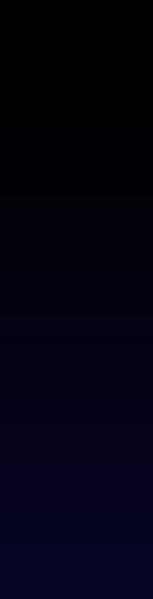
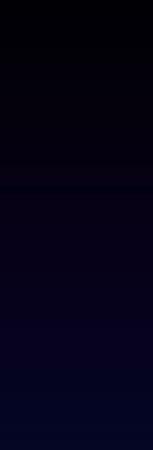
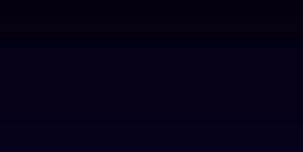
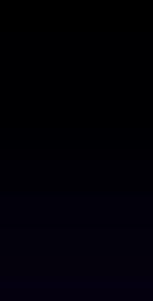

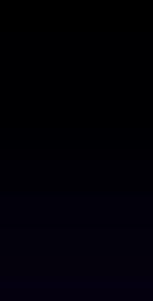
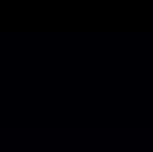


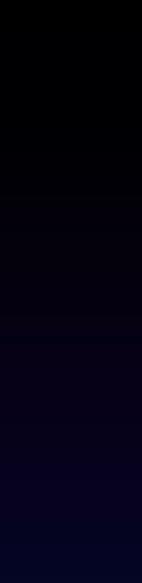
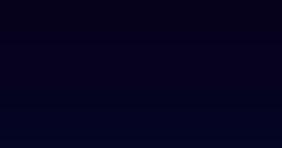

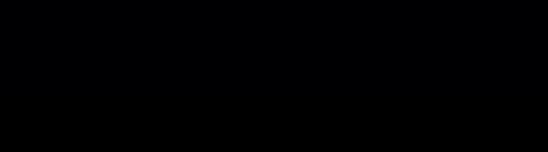

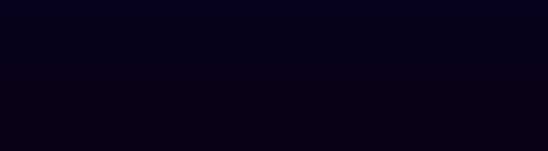
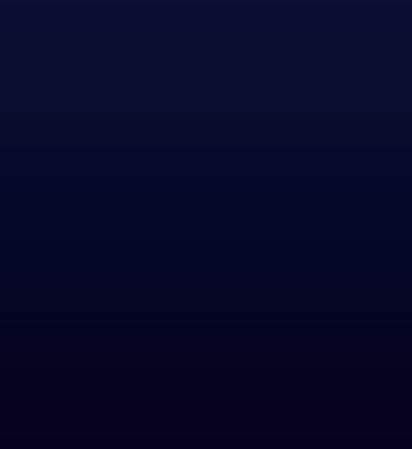

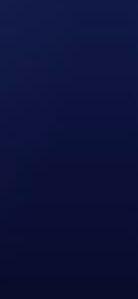
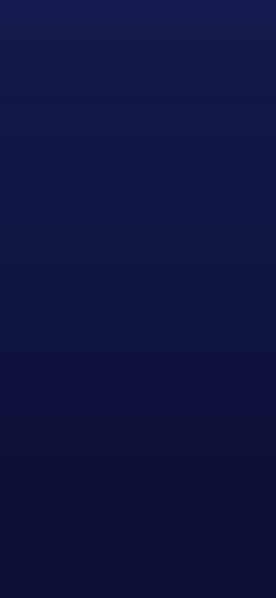
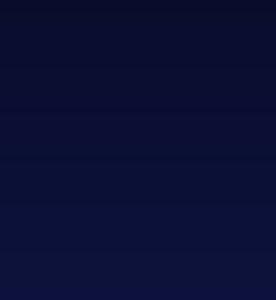
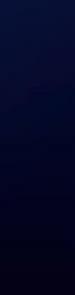

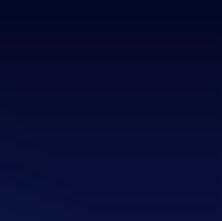
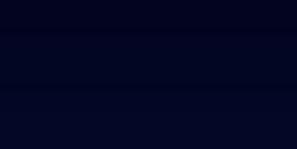
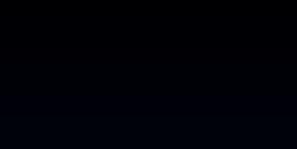
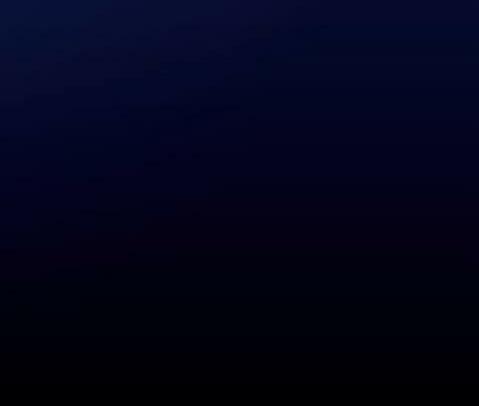
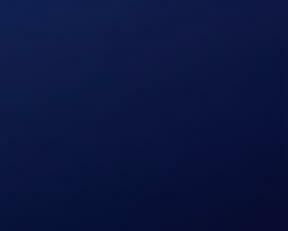

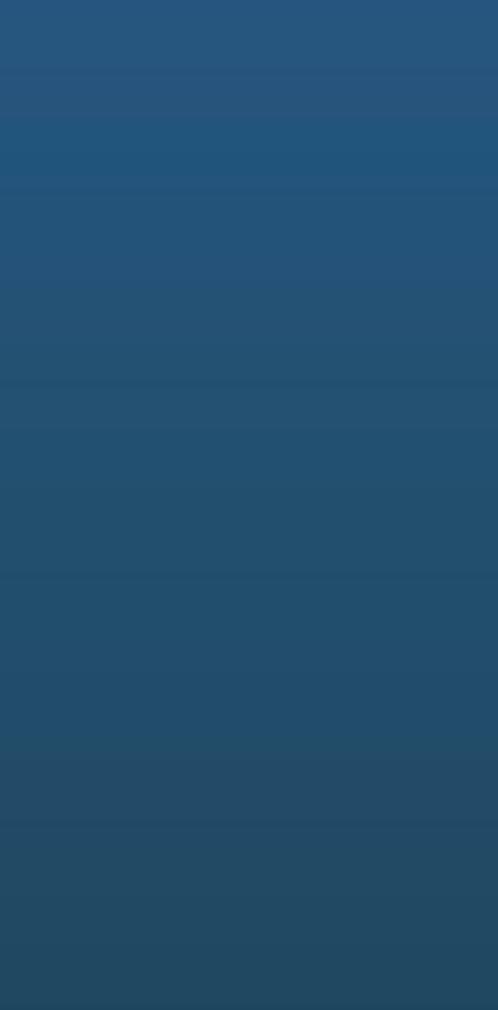


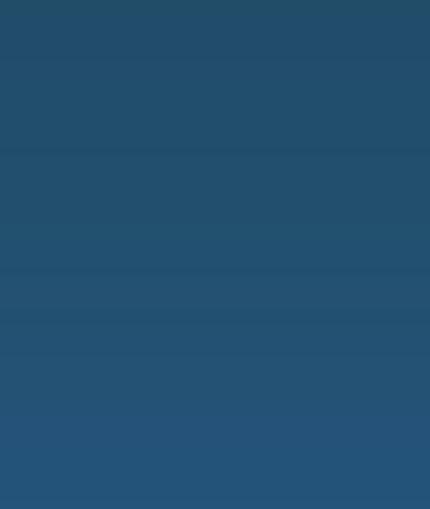
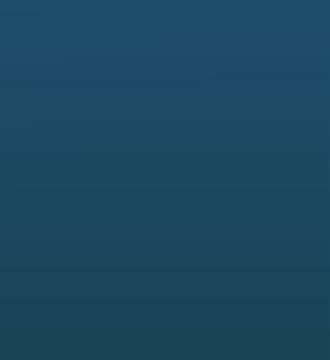

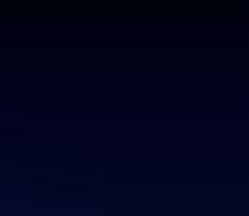
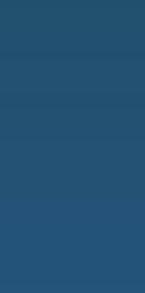
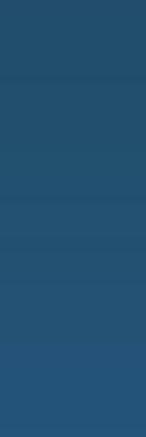
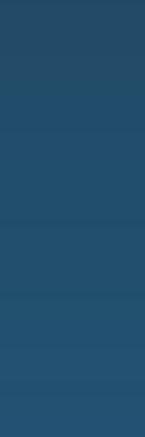
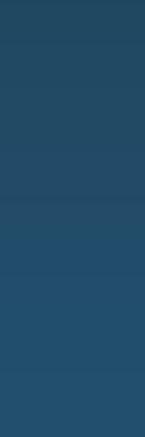
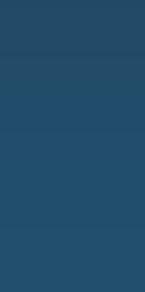
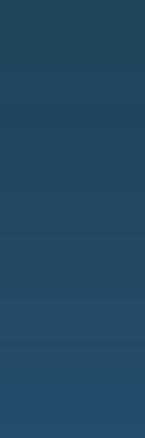
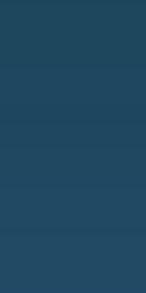
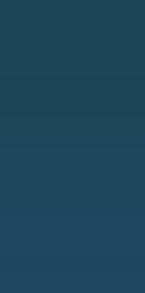
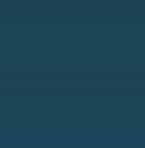
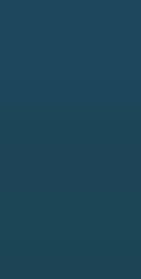
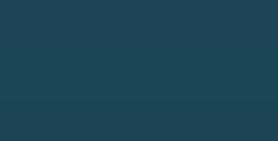
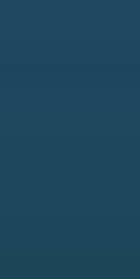
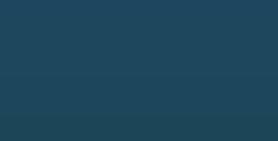
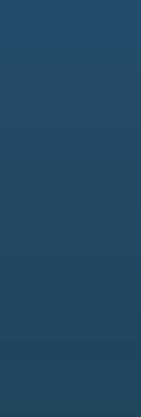

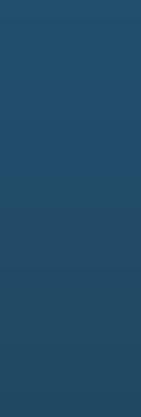
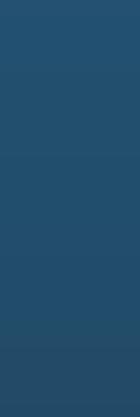

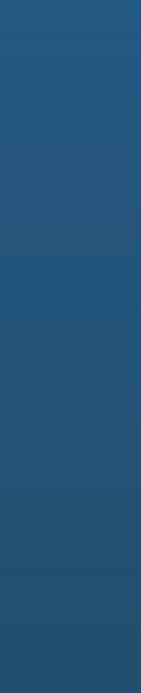

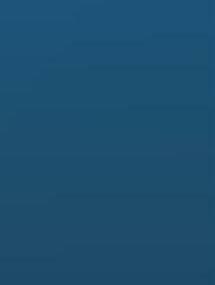
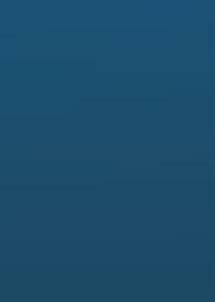

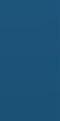
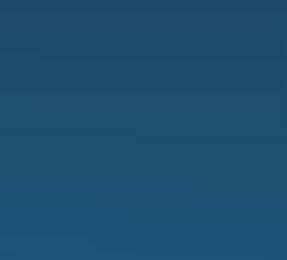
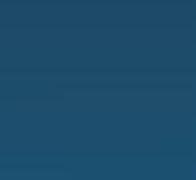
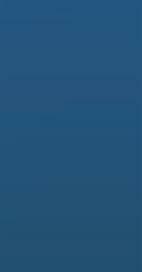
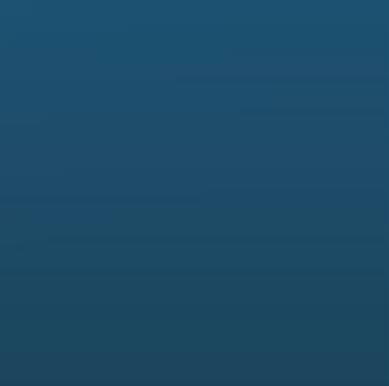
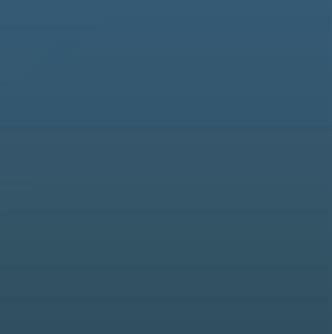
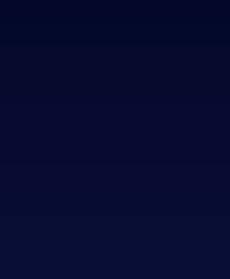
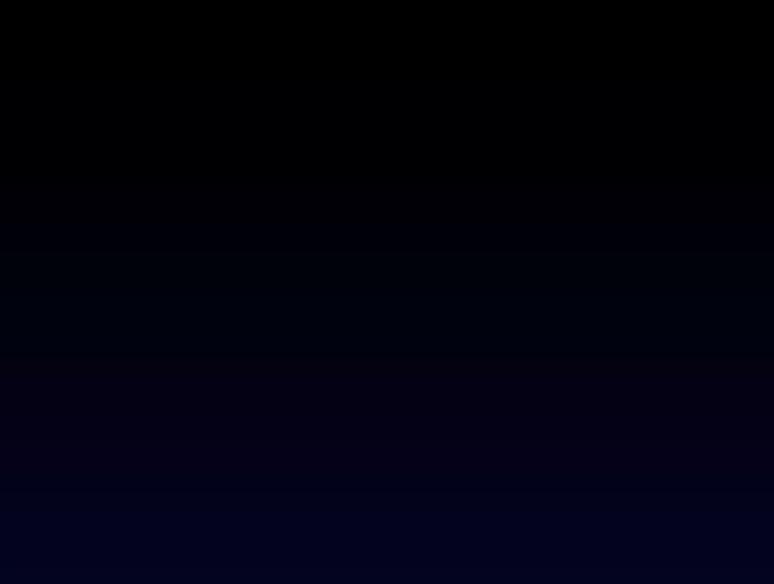

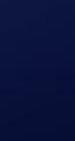
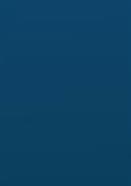

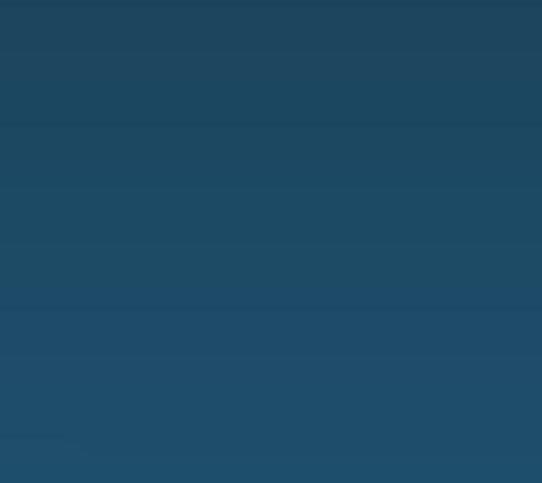
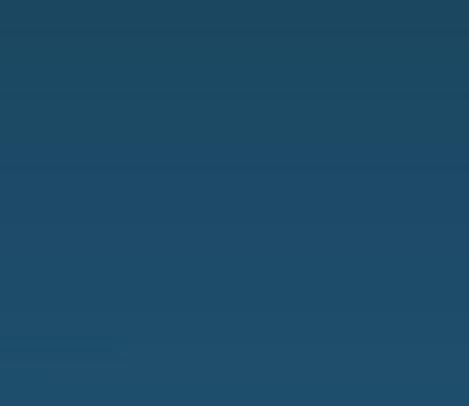
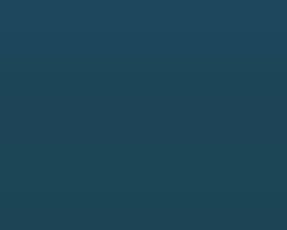
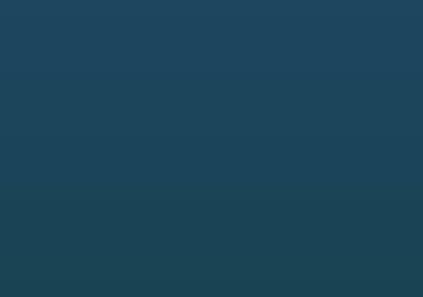
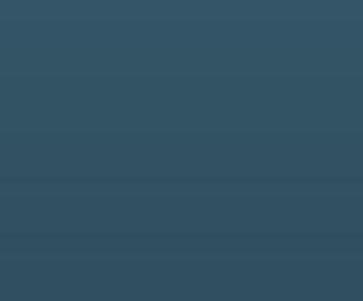
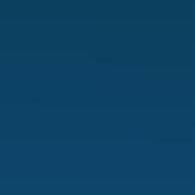
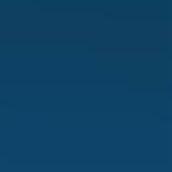
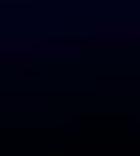

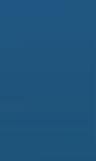
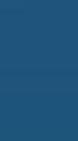
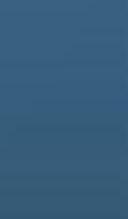
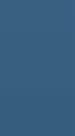
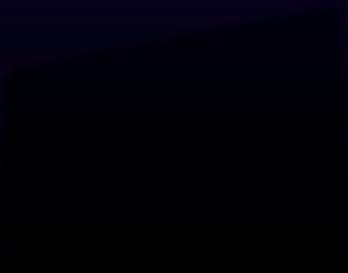
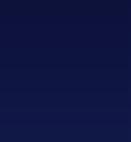
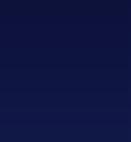
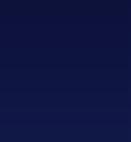

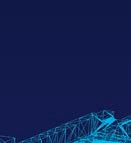
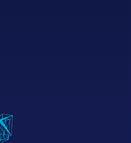
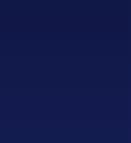
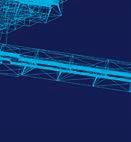
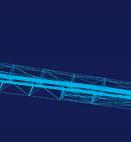
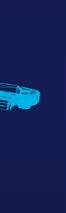
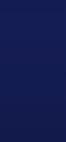


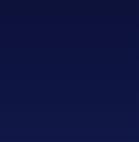

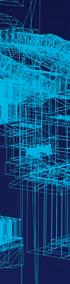

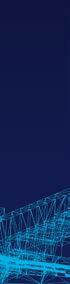
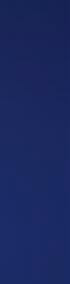
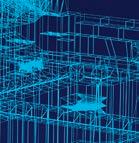
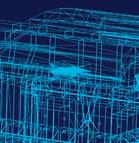
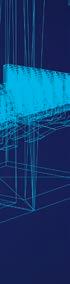

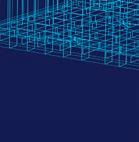
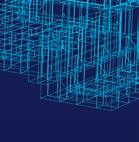
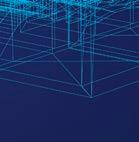
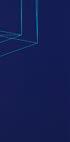
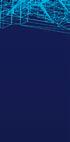
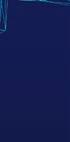

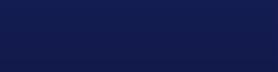

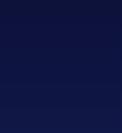

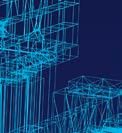
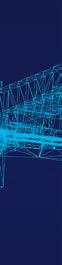
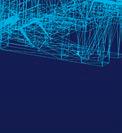
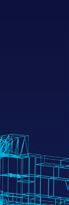
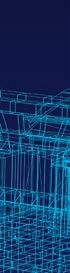
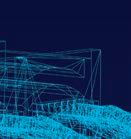

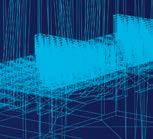
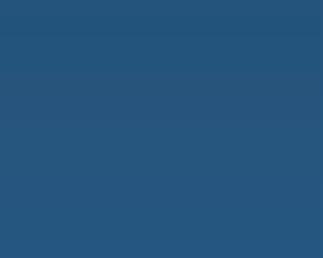
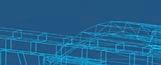
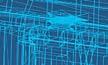
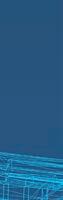
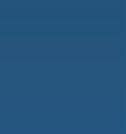



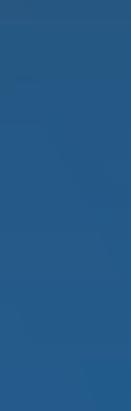
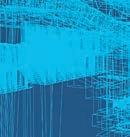
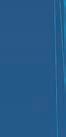

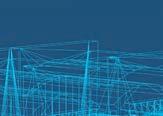
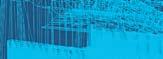
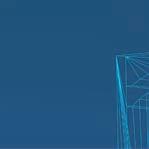

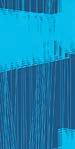
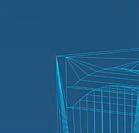
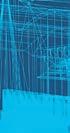
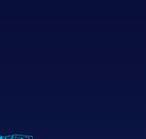
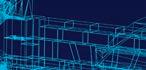

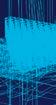
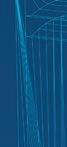
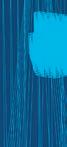
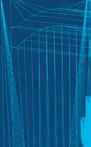
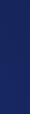


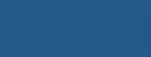
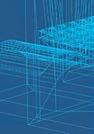
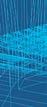
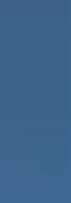


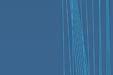

obert uss er discusses a feeder e pendable series e clusively developed and produced by ath which will be presented at glasstec .
The product range includes dense bricks and cast components, as well as refractories, dense low-cement, ultralow cement, non-cement, insulating, gunning and gunite castables, insulating Fig Filtrath filter elements ha e been speciall e elope for se in hot gas filtration p to
rom refractories to hot gas filtration
With more than 130 years of experience in refractory technology means Rath is at home wherever heat-resistant materials are essential – and thus also in the glass industry.Theinternationally operating Austrian refractories manufacturer offers a range of materials for the entire glass manufacturing process and specialises in hot gas filtration. It will present a new feeder expendable series at glasstec in September. There is also news from the Rath hot gas filter elements production facility in Meißen: the manufacturing capacities have been doubled by putting a new production line intoRathoperation.ownsseven production sites in Europe and the USA and operates in more than 30 countries. Refractory materials Including the original Emhart Glass designed feeder systems, Rath offers a range of quality refractory materials for the entire glass manufacturing process. High quality raw materials are used for all of Rath’s refractories, designed to achieve predictable density and resistance to erosion and corrosion. The organisation delivers refractory and insulating products for regenerator chambers, melting furnaces, distributors, forehearths and the original Emhart designed feeder expendables (including spouts, spout accessories, tubes, plungers, stirrers, rotor segments, orifice rings, etc.).
Refractories Glass International July/August 2022 www.glass-international.com 101 Continued>>
Having the original Emhart technical database and the widest mould park among the expendable suppliers, Rath provides the industry’s widest range of refractory feeder expendable compositions for all kinds of glass qualities. Its refractory spare parts are available in a variety of materials to address each customer’s individual needs. The bonded compositions include alumina silicates, AZS, zirconia, zirconia toughened alumina, fused-silica, calcined clay and clay flux materials. Glass manufacturing products Rath’s refractory products are designed for sectors such as container glass, float glass, C-glass, E-glass and tableware. It is also a supplier of glass house crucibles, daily pots, and accessories, such as gathering balls, rings, half rings, stoppers, furnace doors for art glass manufacturers.
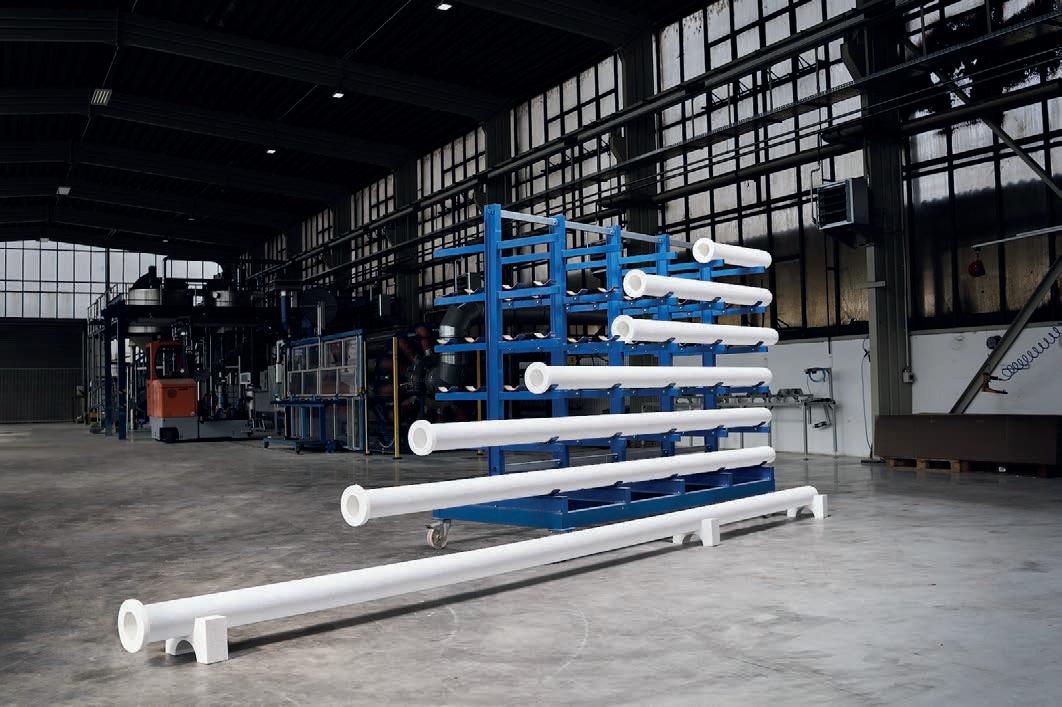
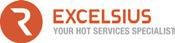
The Fourath 4xx feeder expendable series improves crack and thermal shock resistance, has extremely low impurities level, longer service life, higher glass quality and gob homogeneity. While the previous 3xx mixes – like the well-known 333, 315, 301, 338, 345 –were produced using the slipcasting technique, the Fourath 4xx mixes are produced using hybrid technology. Rath uses the same mould park, but casting is no longer done via slipcasting; instead, a special vibrocasting technology is used. “This brings advantages for our customers. For example, the new feeder series convinces with improved product quality – due to a more compact mix and better surface quality,” said Mr Nusszer. “We selected the highest quality raw materials to keep the impurity level to a minimum. Furthermore, with the new manufacturing technology – thanks to the much better dimensional tolerances we can keep – we can avoid the additional grinding, for example of the tube’s outer surface.”Thus,Rath can increase the service life. “The thermal shock resistance has also improved and the risk of cracking is lower than ever. The product remains in perfect condition until the end.” The new product is out now. Rath customers can easily switch to the Fourath 4xx feeder series. There are no additional costs for the moulds – the same part numbers are used as before, only the last three digits will change. The pricing of the new mixes is more or less the same; a price increase due to the improved quality is not Theenvisioned.followingproducts will be shown at glasstec: the already well tested and released 420 (a complementary mix of 333, 315) – tubes, plungers, orifice rings and stirrers as well as the new 473 zirconiainserted spouts; for the latter, Rath is still looking for candidates for operational Fig Filtrath filter elements ha e been speciall e elope for se in hot gas filtration p to
bricks and other insulation materials such as high-temperature insulation wool, vacuum-formed and microporous products.Furthermore, Rath produces special shaped products for the glass industry in its facilities in the USA and EU, such as burner blocks, peephole blocks, camera blocks, doghouse protection arches, lip blocks, restrictor tiles, tweels, mandrels, and fused-silica suspended and crown repair bricks. In addition, Rath provides refractory concepts for distributor and forehearth channels, including roof and burner courses, forehearth channels from different bonded high alumina and AZSbased refractory materials.
Refractories Glass International July/August 2022 0 Continued>> 102 www.glass-international.com
The further development of refractory compositions is a challenge that Rath is taking on. Robert Nusszer, Managing Director of the Sales Unit Glass, said: “We are constantly modernising the technology and our refractory compositions. The development of the new feeder expendable product family is a very important step ahead for all of us in the Rath Group.” After a five-year research and development process, the new Fourath 4xx feeder expendable series is ready for introduction at glasstec in Düsseldorf. Mr Nusszer continued: “We are pleased to present the next generation of our previous feeder series: a new product line based on a formulation which has been exclusively developed and produced by Rath.“The product has been put through its paces in our laboratories and has successfully passed the first glass factory trials in the last 1.5 to 2 years.”
Fourath 4xx
glasstec 2022
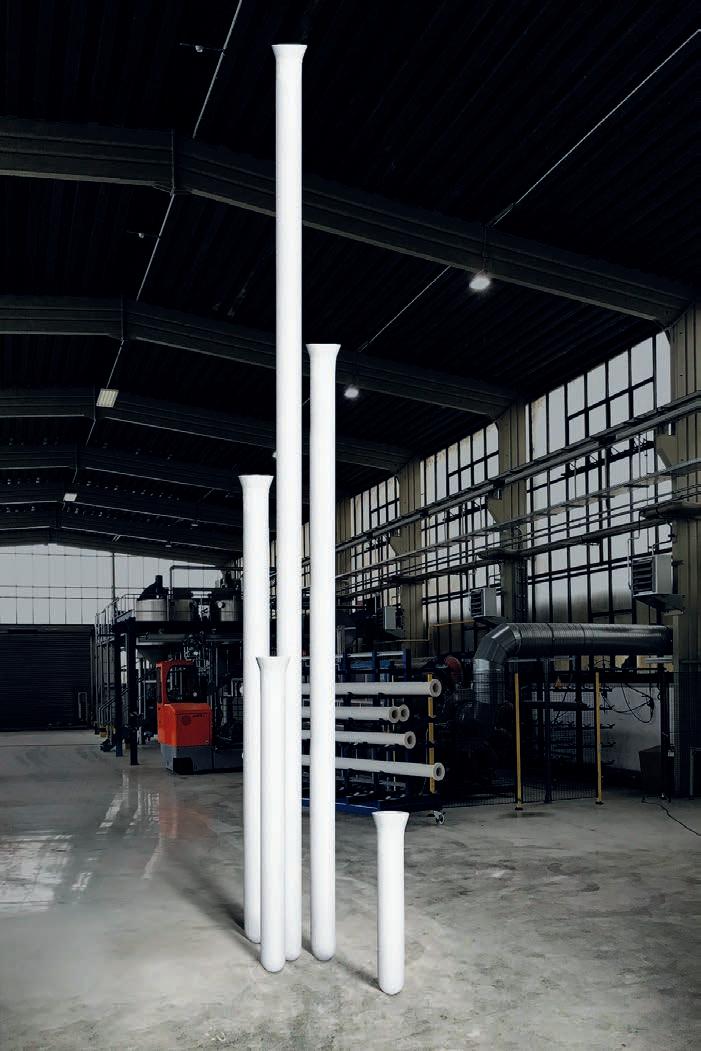
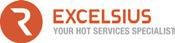
The future we see through. Innovation, technology and versatility make the BDF IS Machines the ideal solutions for high productivity, low maintenance effort and considerable energy saving. bdfi ndustriesgroup.com IS ANGULAR ADV 1050-8050 6-8-10-12 SECTIONS AND TANDEM IS 4 1/4”: SG-DG -TG 3”-TG 3 1/8” IS 5”S: SG-DG-TG 85MM IS 5 1⁄2”: SG-DG IS 6 1/4”: SG-DG-TG 4 1/4” 8-10-12 SECTIONS AND TANDEM IS-P: DG 6 1/4”-TG 4 1/4” IS PARALLEL ADV 8050
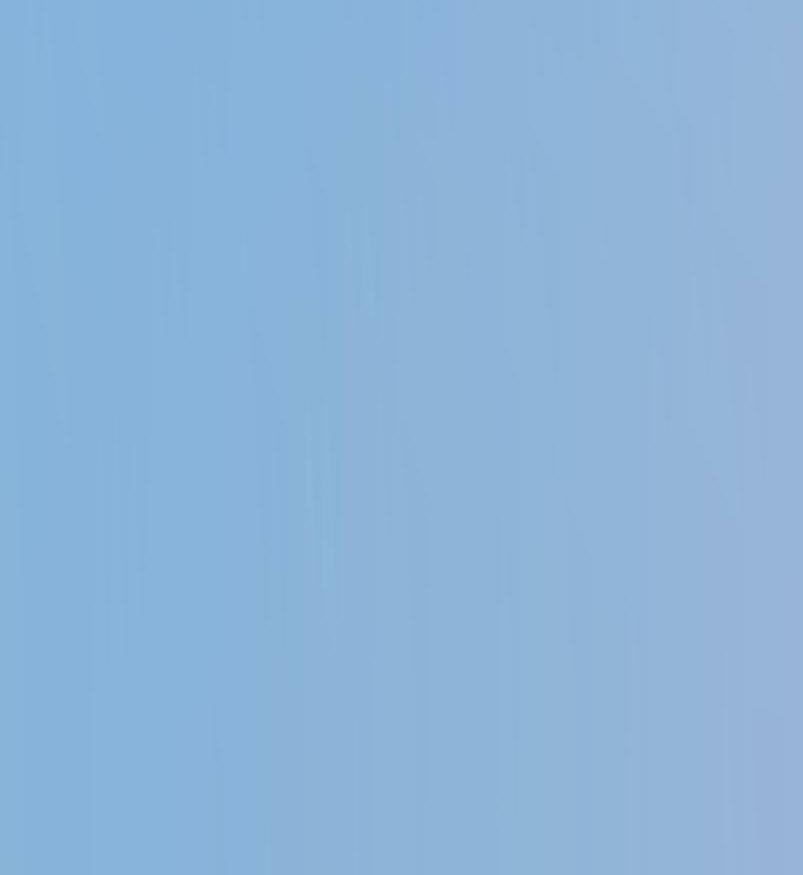
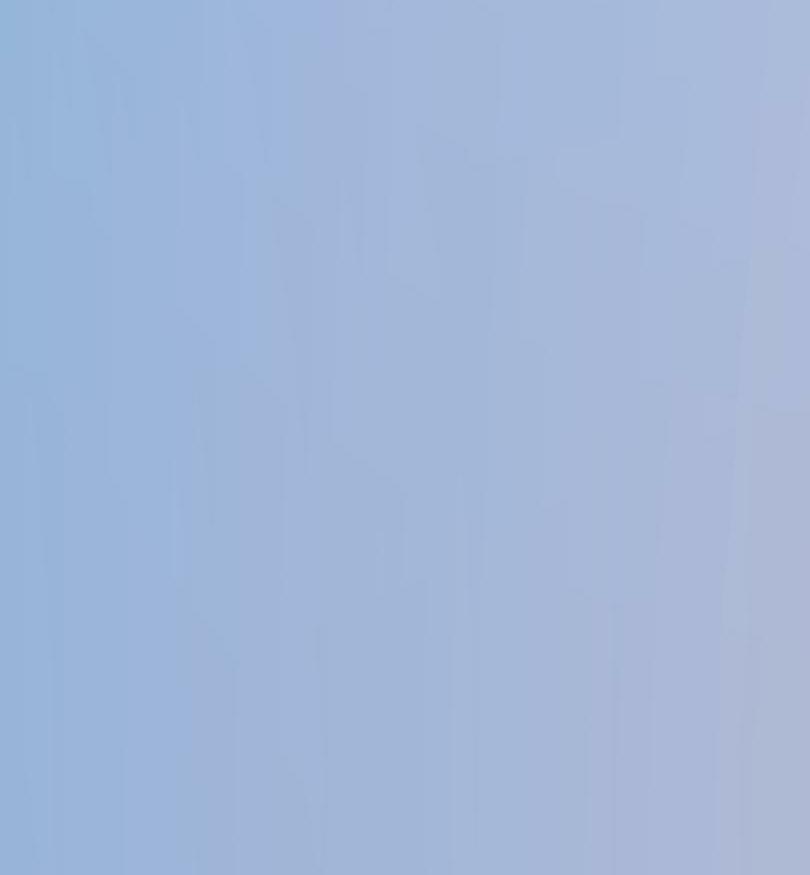
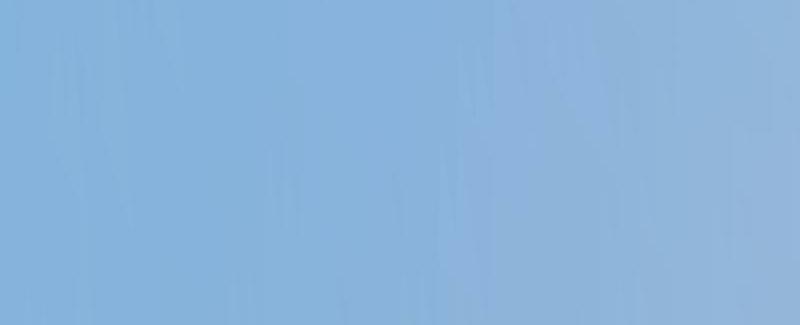
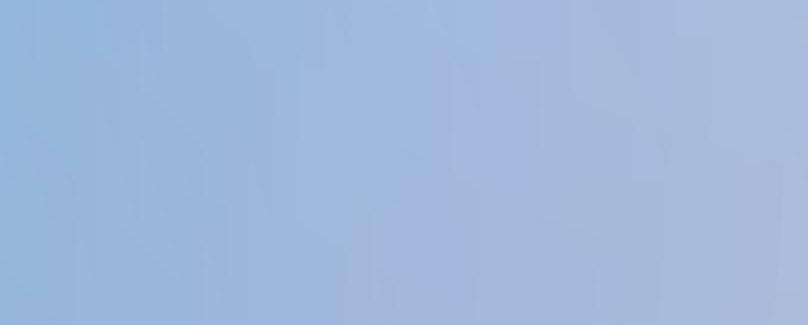
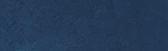


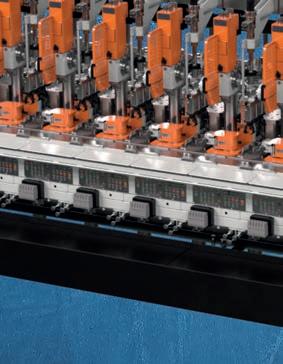

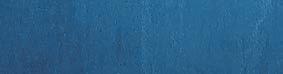

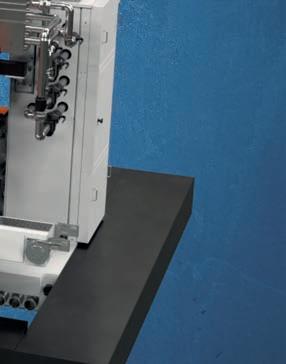
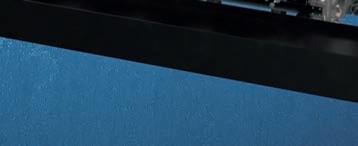
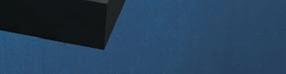
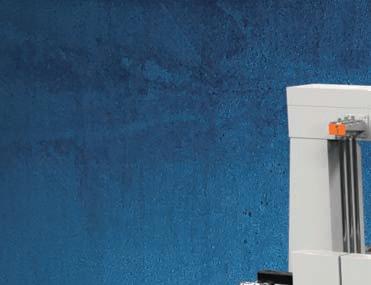
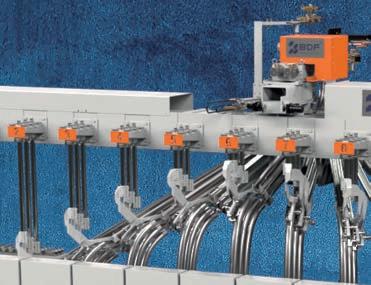
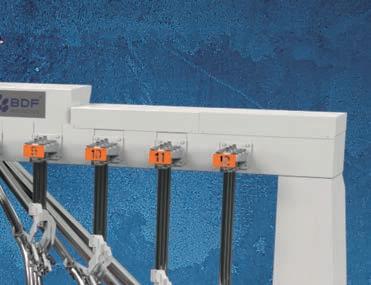
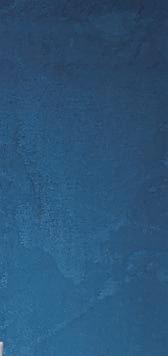
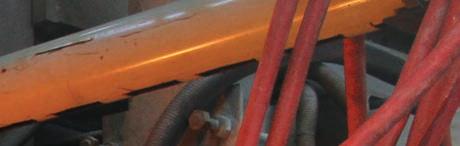
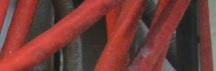


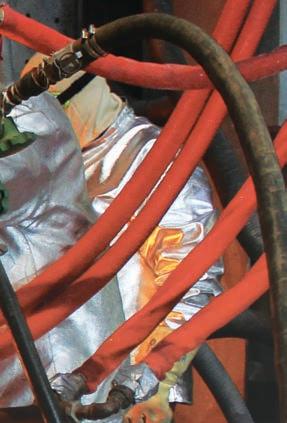





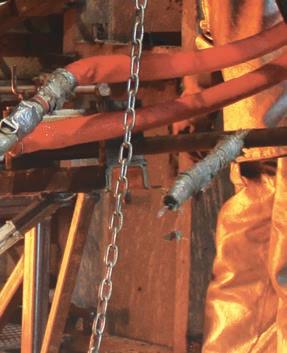
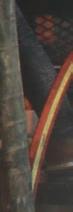

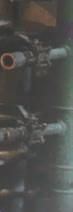


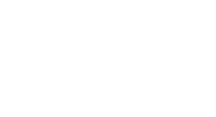

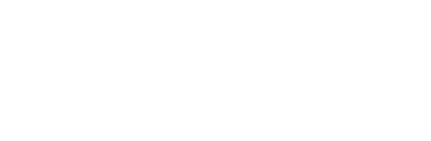
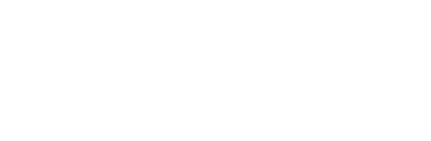
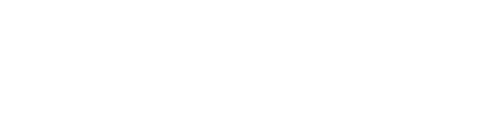
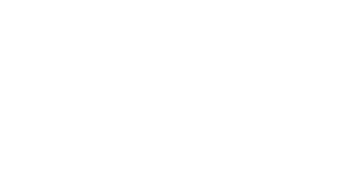
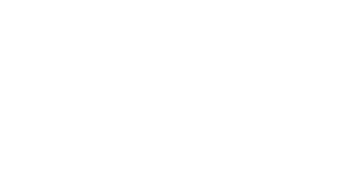
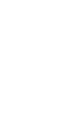


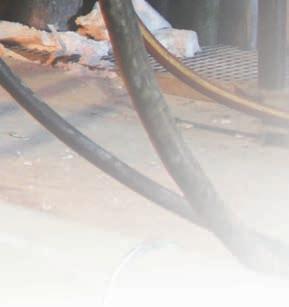
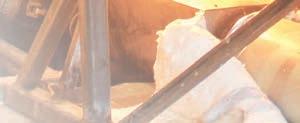


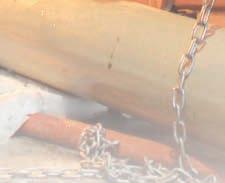
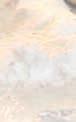
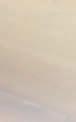

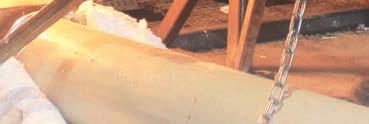
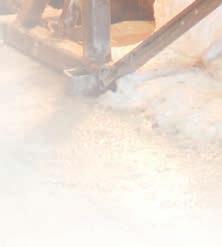
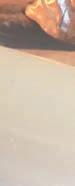
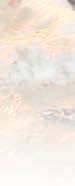
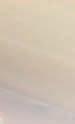
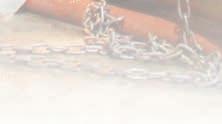
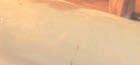
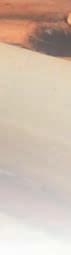
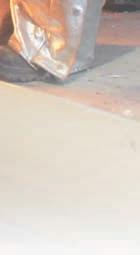


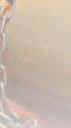
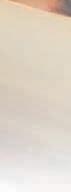



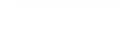

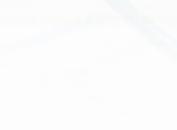

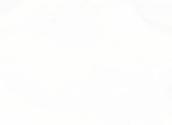









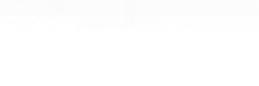




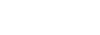
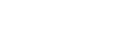
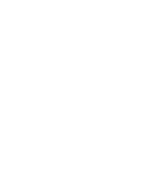
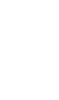
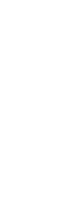

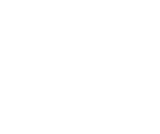



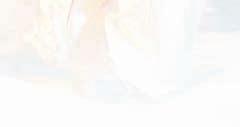



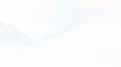


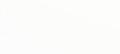

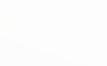


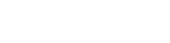
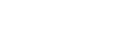
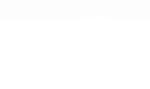






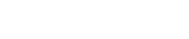
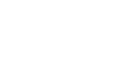




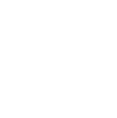








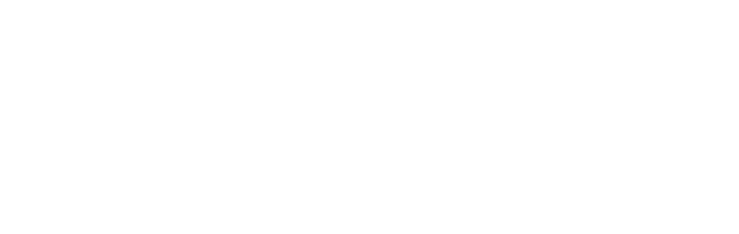


























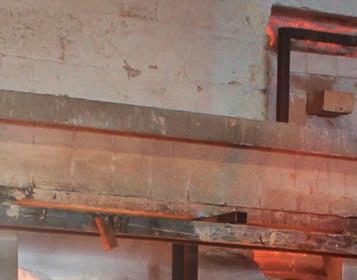
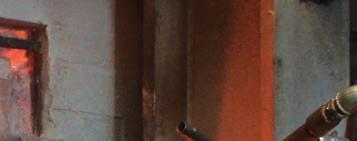
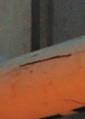
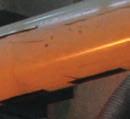
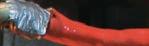

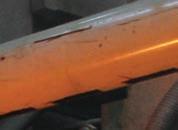
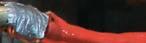
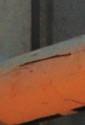


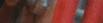
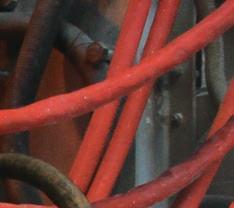
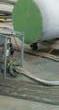
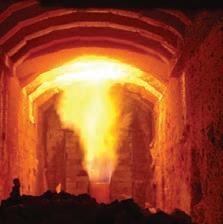
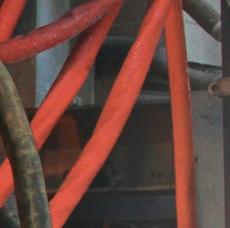



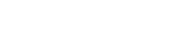
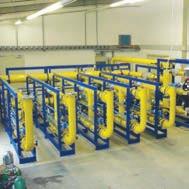
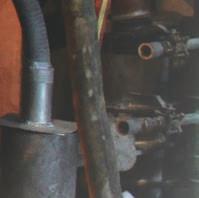
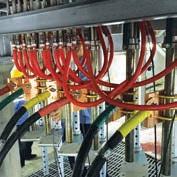
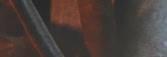
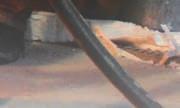
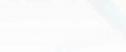


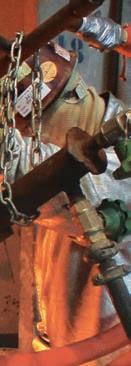


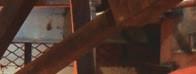
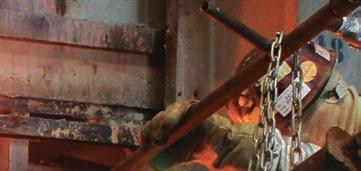
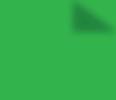
105 testing in glass factories. Hot gas filtration Whether fine dust, sulphur dioxide emissions or nitrogen emissions caused by high melting temperatures, all cause poor air quality. As a result, the glass industry – like many other industries – faces a big challenge: to filter and remove dust from flue gases and pollutants as efficiently as possible and to reduce emissions. Rath is rising to this challenge. As a company with extensive experience in refractory technology, it’s only logical that Rath also specialises in hot gas filtration. For many years, the company has been developing ceramic hot gas filter elements that make it possible to filter particle-laden industrial flue gases at temperatures up to 1000°C and reduce emissions of nitrogen oxides. Since 2016, all resources, capabilities and expertise in hot gas filtration have been pooled in Meißen, Germany. This research and production site of the company is now home to cutting-edge facilities for the manufacture of Rath’s Filtrath non-catalytic and Filtrath CAT catalytic filter elements (Figs 1 & 2). The latter were developed for pollutant emission control. These rigid yet highly porous and catalytically coated ceramic filter elements are used for multiple pollutant control of (fine) dust, acid gases, dioxins and nitrogen oxides in hot gas flows (at temperatures between 250° and 420°C) and can easily replace conventional textile filters. Rath also offers tailor-made solutions in terms of hot gas filter cartridge length. Using a specially developed ‘screw & glue’ connection, filter cartridges up to a length of six metres can be produced from several segments. The segments are assembled into a long filter element when the filter cartridges are installed on site. As of June 2022, Rath has doubled its manufacturing capacities when it put a new production line into operation at its Mei en plant. The filtration business line has seen a significant growth. “It has great potential since the glass industry has to drastically reduce its footprint on environmental pollution and the greenhouse effect. Rath is committed to advancing environmental protection and helping its customers in the glass industry achieve their ambitious environmental goals. Thus, Rath continuously develops and invest in this technology”, Mr Nusszer said. Glass know-how To meet the customers’ requirements in the best possible way, Rath has established a dedicated glass unit; all the resources and know-how in the field of glass are bundled in one global division. Rath’s engineers and technicians for industrial glass applications have an outstanding expertise, allowing them to develop powerful refractory materials that are tailored to the client’s individual requirements.Rathalso offers expert consulting services – from planning and installation to the maintenance and care of furnaces – and is a full-range supplier in the production of all required refractory materials for all layers in furnace construction. �
www.rath-group.com/glasstec A GLASS OF ITS OWN Refractories and Hot Gas Filtration for High Demands Visit us at glasstec Düsseldorf! Convince yourself live of the quality of our products. We’ll be on hand to showcase outstanding innovations from the following elds: • Refractories for the entire production chain • Crucibles for Art Glass • Hot Gas Filtration to ensure clean air JOINSept.DüsseldorfglasstecUS!20–23
*Managing Director of the Sales Unit Glass, Rath, Krummnußbaum, Austria www.rath-group.com/glass (Learn more about the new product line by visiting Rath’s glasstec booth D15 in Hall 13.)
Refractories Glass International July/August 2022 www.glass-international.com
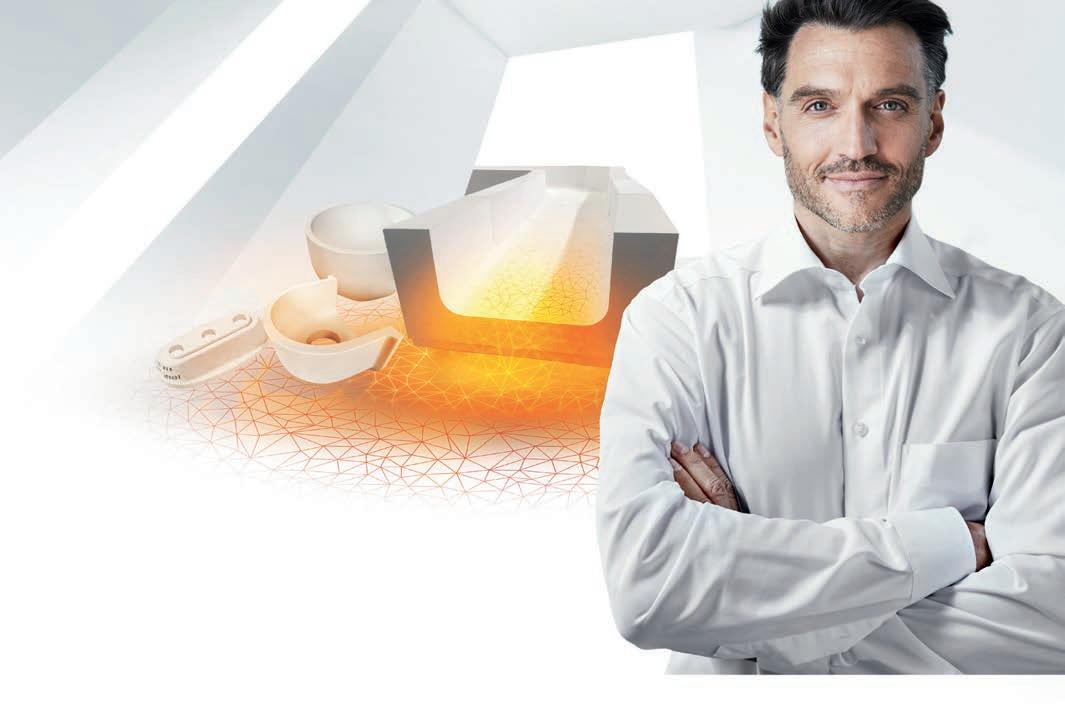
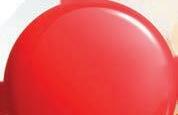
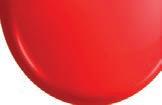
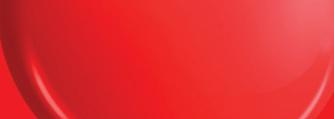
ALL ALL ALL ALL TRUST This means that Vimec inspection and control systems for syringes, vials, car tridges and ampoules deliver high speed, high precision, high reproducibility and hi-tech data monitoring and management along the entire production line thanks to years of experience, know-how and ongoing R&D. Customers trust Vimec quality because every sensor that we deliver, any where in the world, is validated with our own performance tests (far more rigorous than the market requires) and certified accordingly with service and support standards to match. FOR COMPLETE PHARMACEUTICAL GLASS INSPECTION AND CONTROL – WWW.VIMEC.NL – A MEMBER OF THE TIAMA GROUP. We know the challenges facing pharmaceutical glass makers because we focus only on your needs. at top speed the data
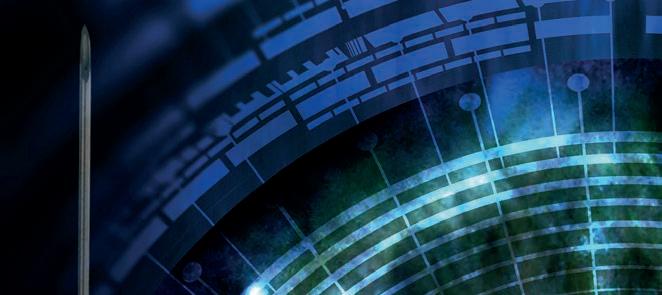
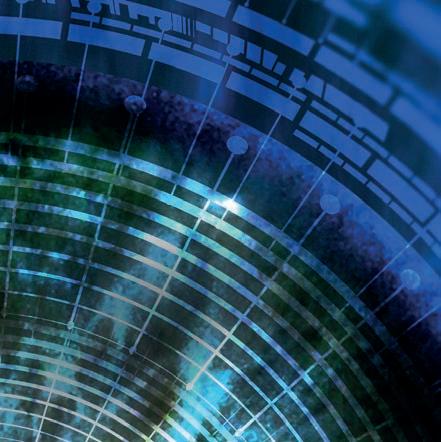
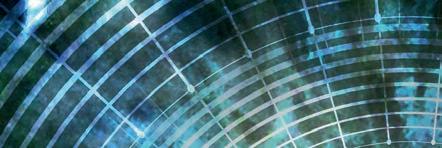
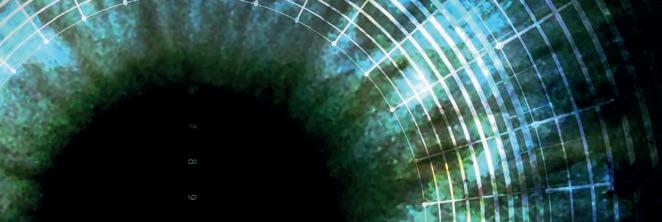
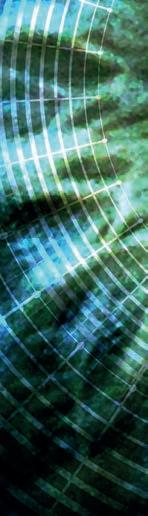

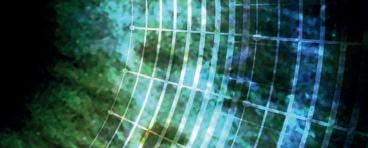

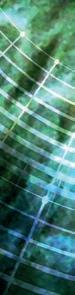
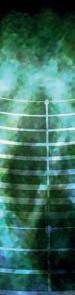
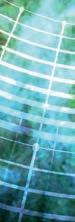
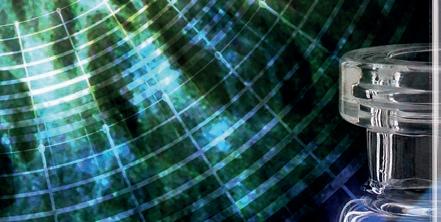
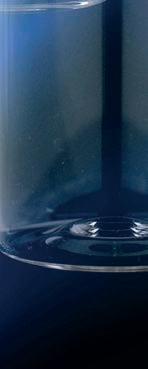

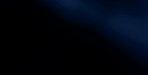
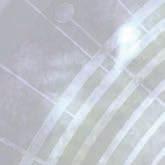
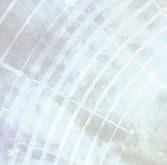
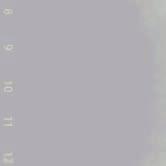
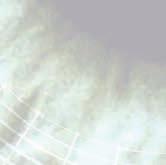







































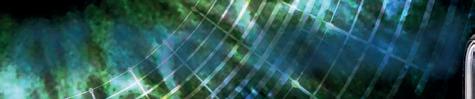





Float glass survey
In 2020, a float glass manufacturer attended one of Mr Simpson’s online training courses and saw the potential for a survey as part of its on-going asset protection plan. During Covid-19 travel restrictions, it was not possible to travel to the customer, so the NIR-B survey camera was shipped to the furnace site and remote online training provided by Mark Briggs, Ametek Land’s Global Field Service Engineer for Glass. The customer then made the measurements themselves and transferred the data to Ametek Land for remote analysis. This example was the first float glass survey to utilise the highdefinition NIR-B-2K camera with Image Pro software.
A high-definition imaging camera I - - offers . million points of measurements. eil impson outlines the recent surveys conducted by the camera as well as its benefits over previous models. Believed to be a unique service for the thermal optimisation of furnaces, in-furnace thermal glass surveys provide essential insights into the thermal processes within glass melt tanks. As everyone in the industry is aware, glass melt tanks are enormously energyintensive, and experience the highest temperatures of the glass production process. Thermal monitoring of the tank ensures the efficiency of the melt process and maintains consistent glass quality. Combining near-infrared borescope thermal imaging with portable multigas analysis, in-furnace surveys deliver accurate, real-time measurements to increase efficiency, productivity, and asset life in glass production.
The purpose of the survey is confidential however, previous reasons for such a survey include asset protection, quality/yield issues, energy reduction and environmental. The measured data can be used for validation of computational fluid dynamic (CFD) modelling, and it is often best to consider the analysis in a similar way to interpreting a CFD model. On a float survey, it is typical to start at the waist and on the side closest to the control room, in order to know the time of the furnace reversal. If there is a skimming pocket, then this is the best initial position to check signals before moving to the bridge wall peep hole, which is typically at a slightly higher elevation.Theskimming pocket typically gives a good view of the walls and is the best location for measuring the glass temperature using Ametek Land’s patented reflection compensation method. With sufficient manpower, it is possible to survey the four corner locations in the furnace on the first day. It is important to obtain the temperature when the flame immediately goes out. This is the highest temperature, since during the flame-out much of the temperature is lost. However, it is a calibrated temperature, since when the flame is present the emissivity is unknown.Theview from the waist is usually the best summary view, as this will show the suspended back or charging wall and whether it is symmetrical or closer to the firing or exhaust side. It should be possible to see all of the ports clearly on the opposite side and highlight which port is the hottest. With the NIR-B-2K and Image Pro Software, there is the potential to zoom in by 1600%, enabling refractory inspection for hot spots, cold
The Near-Infrared Borescope (NIR-B) imaging camera was developed by Ametek Land in 2012. Since then, more than 100 NIR-Bs have been installed by a variety of companies and are still operating successfully after eight or more years. Initial surveys The initial glass surveys were simply demonstrations, where an NIR-B was initially installed in a peephole in the bridge wall, as close to a preferred CCTV camera location as possible. One major glass manufacturer suggested that it may be beneficial to look in other peepholes too. The resulting survey and cool-down of Allied G2 were reported in previous Glass Problems conferences. It was only in 2019, when independent consultant Neil Simpson was struggling with flame optimisation for NOx in a float glass furnace, that the first full survey was performed by Ametek Land, this time including the regenerators. The survey of the regenerators through the target wall revealed there was refractory damage to the regenerator checker pack. A lifting or heaving of the pack had created an internal by-pass flue which resulted in too much air going down the right-hand side of port 4. The burner being used was a watercooled through-port burner which, typically, has the most adjustment, but with an in-balance of air the flame was deflected downwards. The survey was performed in 2019 using the original NIR-B-656 with 324,000 points of measurement.In2020Ametek Land launched the new 2K (high-definition) model of the NIR-B, which now offers 2.9 million points of measurements. This is equivalent to 2.9 million of Ametek Land’s Industry Standard Cyclops portable pyrometers measuring continuously. On a regenerative furnace, it is typical to take one optical measurement when the flame immediately goes out. If you were to take a Cyclops measurement every 20 minutes, you could take 72 point measurements in one day – so 36 on each side. It would take more than 24 years to get the image provided by one NIR-B-656, and 220 years to get the equivalent of a NIR-B-2K!
Furnaces Glass International July/August 2022 www.glass-international.com 107 Continued>>
Imaging camera provides essential insights for glass industry
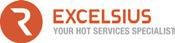
*Independent Consultant - Combustion, Energy and Glass, Ametek Land, ro el , ite Ki o www.ametek-land.com
Furnaces Glass International July/August 2022 1080 www.glass-international.com spots including holes, and areas at risk of NaOH attack. The worst-case scenario is a hole which requires welding. The zoom function enables users to zoom in on an existing thermocouple block location and highlight it as a region of interest (ROI) to verify temperature. Examples Fig 1 shows a float furnace example of an in-furnace thermal survey. By way of a key, left and right are relative to the glass flow. With no flames, the temperatures are calibrated. The red cross highlights peak flame temperature at a relatively low 1578°C. Fig 2 reveals the application of a simple isotherm below 1388°C is where there is a risk of NaOH condensation, which could cause corrosion to silica refractories. When the burners are firing, the indicated temperatures are not real since we do not know the emissivity of the flames. The application of relative isotherms offers the ability to see which flames are typically hotter and give an indication of the flame length. Generally, the higher the temperature the greater the risk of dissociating oxygen and forming thermal NOx, which is dominant in glass melting furnaces. While a flue gas analyser such as Ametek Land’s Lancom 4 can show which exhaust ports have the highest NOx, it may not indicate which of the burners is generating the most NOx. By positioning the NIR-B survey camera in the target wall peep hole, there is the opportunity to look at the flames (not shown) from both the firing side and the exhaust side to see the cause and effect. Typically, the integrator function (not shown) is best to use, since it averages the frames to indicate the dominant flows. While this was zoomed in to look at the flames, the 100% view (not shown) would allow inspection of the regenerator to check that a blockage is not creating the imbalance. Fig 3 shows the immediate frame following the flame-off. The temperatures are real. The 62-isotherm palette means that each colour is 4°. enefits Many large glass companies have invested in their own transportable NIR-B for their in-house survey teams. This offers the opportunity to have their technicians to send .erfx files to their refractory and combustion experts as well as validating in-house CFD models. Ametek Land also has some limited rental units available for hire. Typically, most customers start with a survey performed by Mr Briggs or one of Ametek Land’s survey team. Philippe Kerbois, Ametek Land’s Global Industry Manager of Glass, said: “An infurnace thermal glass survey is a valuable supplement to traditional refractory inspections. It helps glass producers to identify ways to improve productivity with optimised pull rates, increase their thermal and combustion efficiency, extend campaign life, refractory asset protection, reduce energy consumption by optimising the flame pattern, and ensure emissions compliance.” �
Fig F rnace from aist en of firing from left to right Fig F rnace ort en of firing from right left sotherms
Fig F rnace from aist en of firing from left to right ith areas of a con ensation
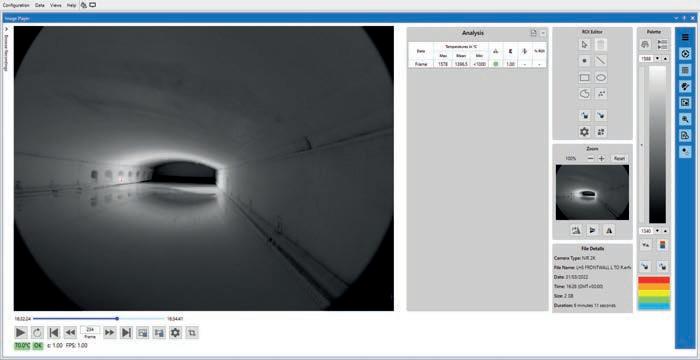
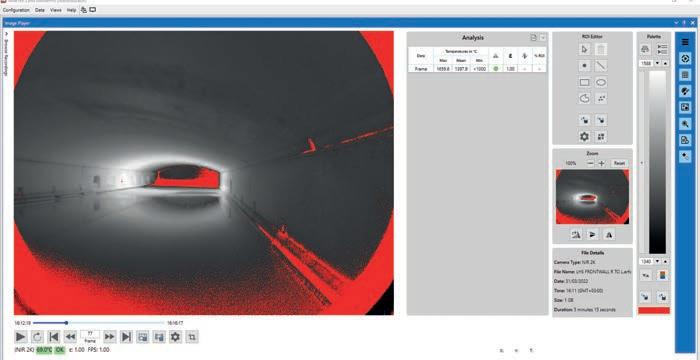

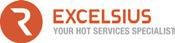

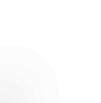


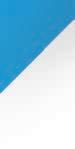


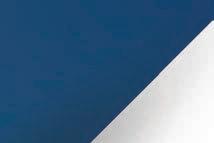
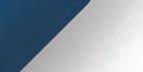

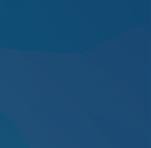
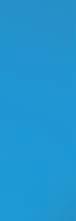
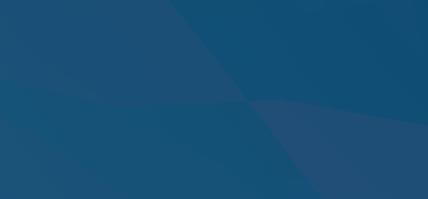
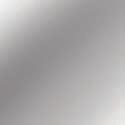
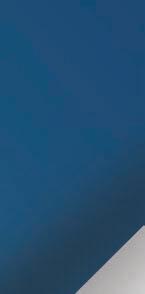

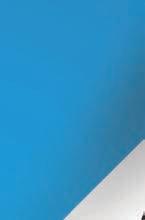


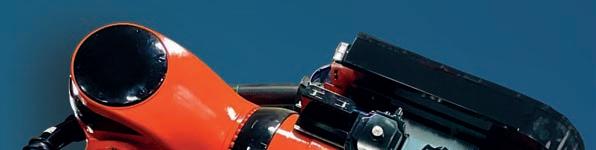

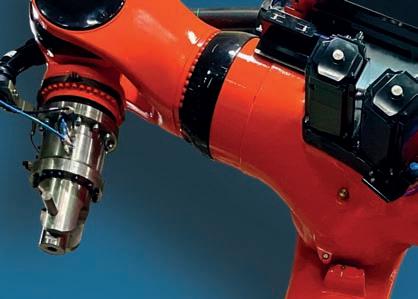
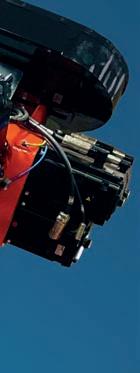
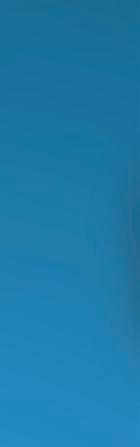
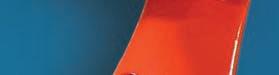
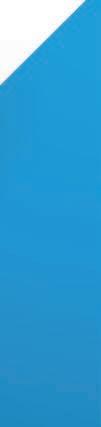
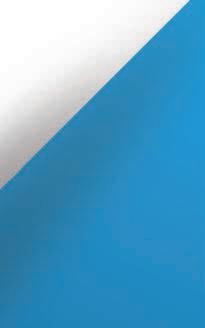
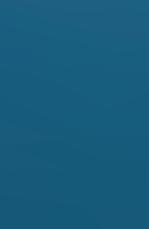


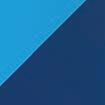

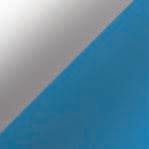

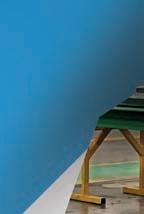
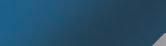

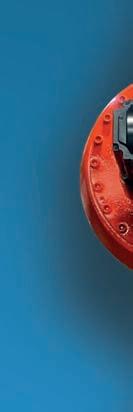
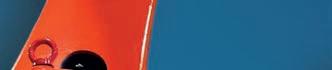


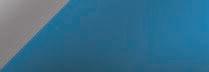
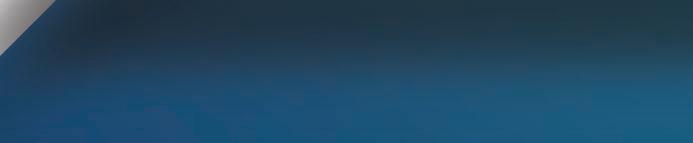


































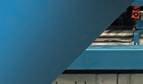
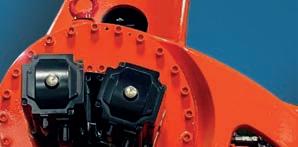
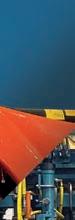
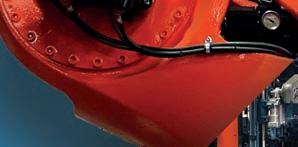
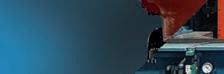

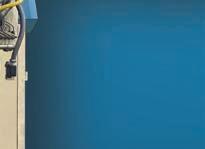
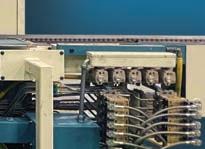

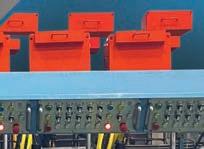


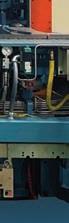


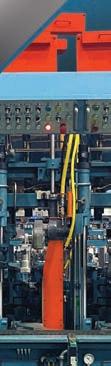


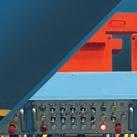
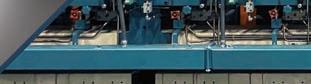

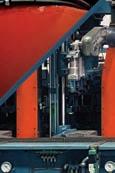
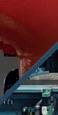

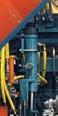
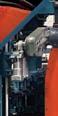
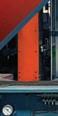

Contact Ramsey at www.ramseychain.com, sales@ramseychain.com, (704) 394-0322 Ramsey’s 100% Steel Sentry 2-Pin Chains: • Guard Links with Fully Recessed Pin Heads • 100% Hardened Alloy Steel Construction • Staked to Decrease Chain Elongation • Special Side Links For Easy Connection • Pre-Stressing for Reduced Chain Elongation • Available in ½” and 1” Extended Pitch SENTRY2-PI N CHAIN. FOR LONGERLIF E& HIGHE R SPEEDS ACTUAL PHOTOS OF SENTRY SINCE 1923 +1.724.482.2163AGRINTL.COM COLD END SUPERIOR MEASUREMENT AND TESTING FOR THE SAMPLINGON-LINELABORATORYTESTING PRESSURE & VOLUME DIMENSIONAL COATING PRESSURE DIMENSIONAL THEACCURACYHIGHEST ★ THE THROUGHPUTFASTEST ★ THE atVisitOVERALLBESTVALUEourboothglasstec Sept boothDüsseldorf20–2314C34
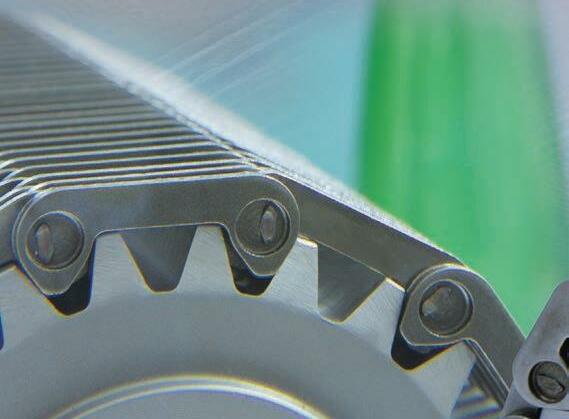
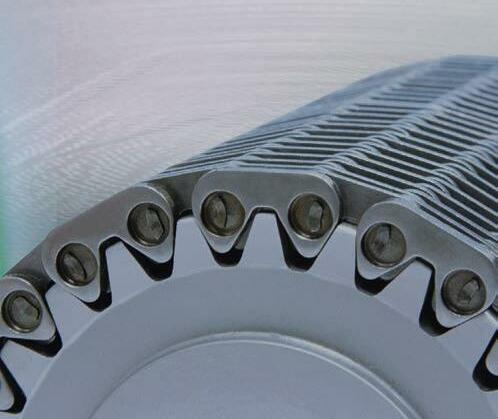

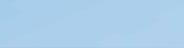
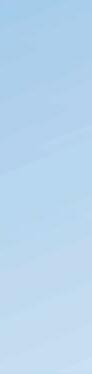
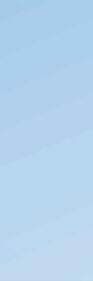
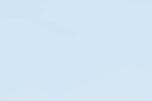

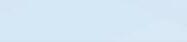


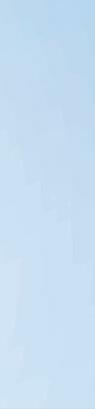

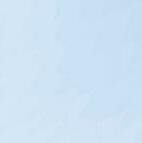




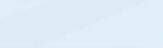
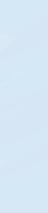
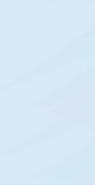
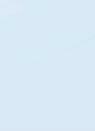




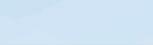
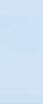


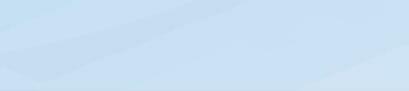


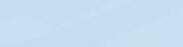

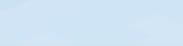

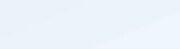
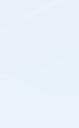


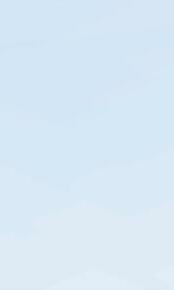
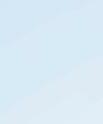

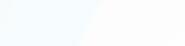


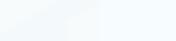



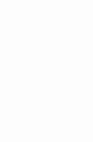
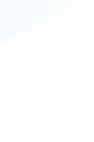
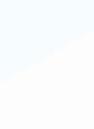


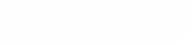



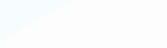
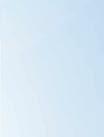
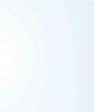









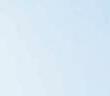


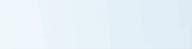



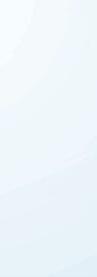



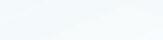


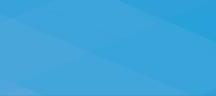

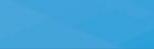


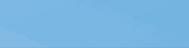
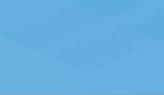
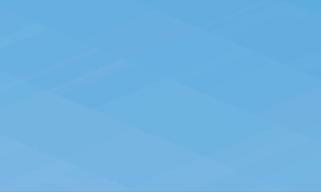
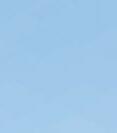

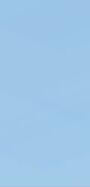
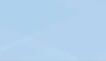
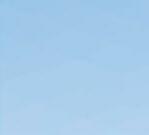


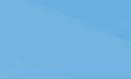


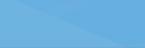
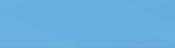

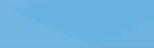

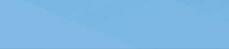
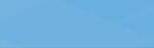
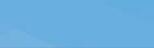
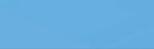
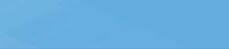

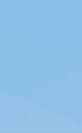







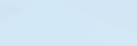
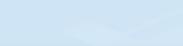

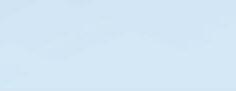


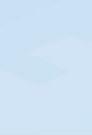



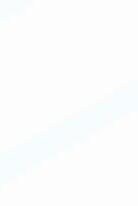
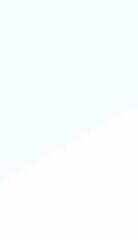


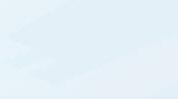
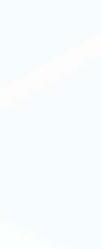
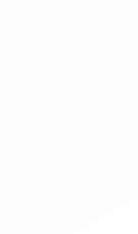
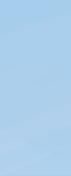



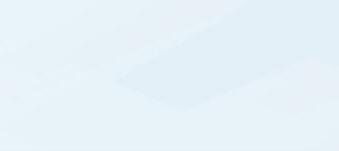
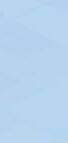
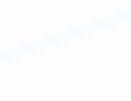
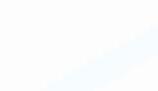






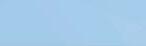


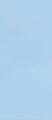

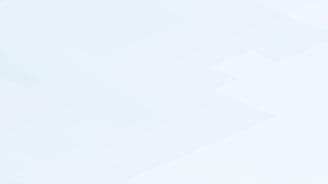


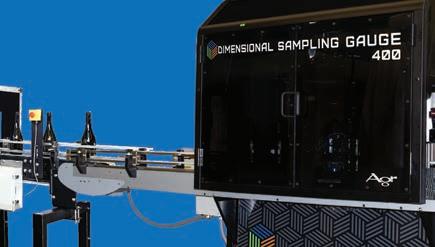
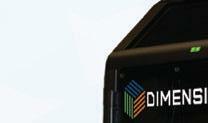










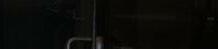
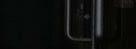

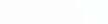


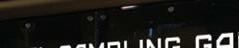
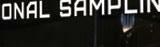



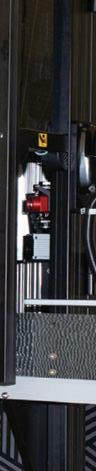


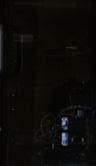

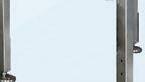

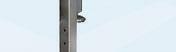

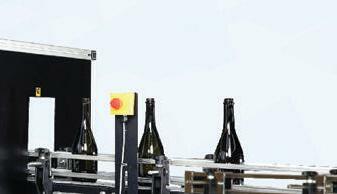
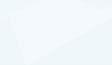

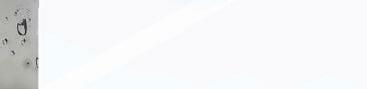
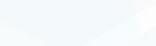

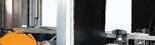

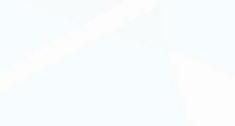

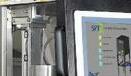
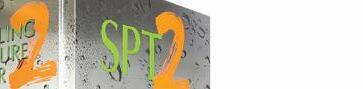


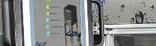

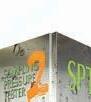

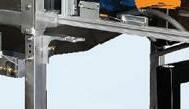
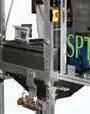



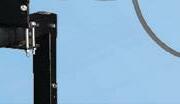
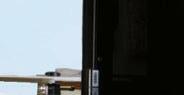
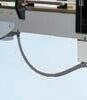





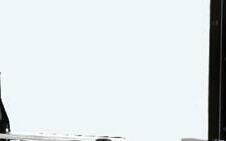

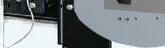


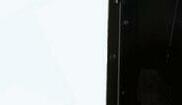
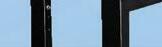
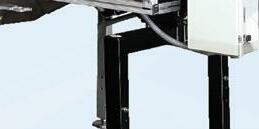
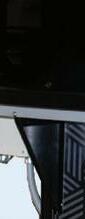

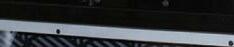
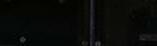



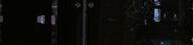

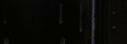











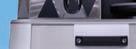


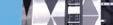


















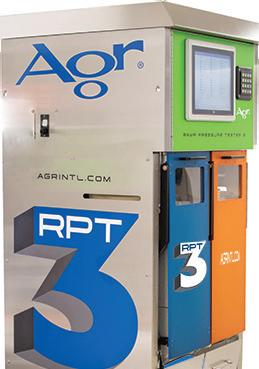
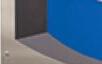
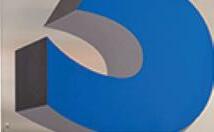
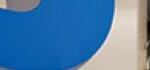




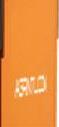
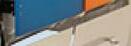



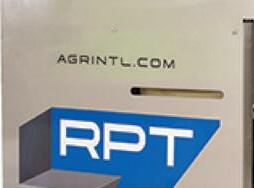
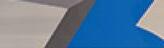
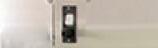













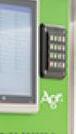




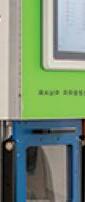
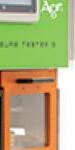




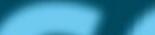



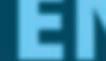

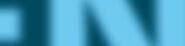
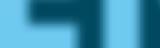






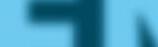


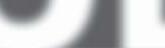
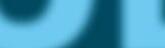
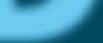






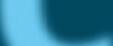
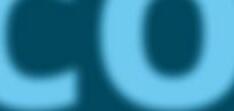




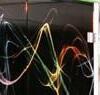



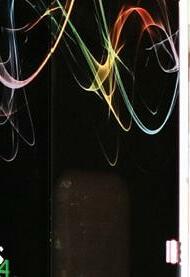
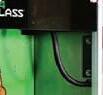

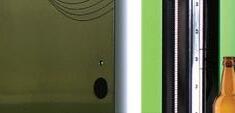
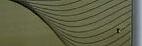

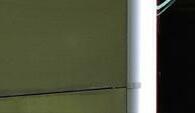




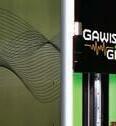


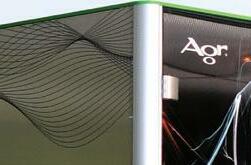
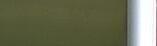

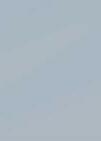
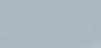

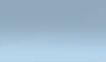
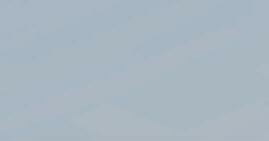



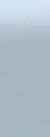



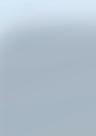
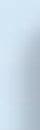
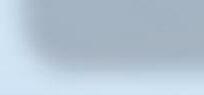
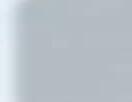

Energy efficiency The exhaust gas volume together with the available temperature level offer great potential for utilising thermal energy for various purposes. One example is the application of waste heat integration, which GEA Emission Control provides in its portfolio. Here, the gas flow is passed through heat exchangers where a heat transfer medium such as water or thermal oil is heated. In principle, heat exchangers can be positioned in the raw gas and/or the clean gas, depending on available thermal power from the furnace and the gas temperature, taking into consideration the needs of the emission control system e.g. for efficient desulfurization reaction. Through special design of the raw gas heat exchangers such as suitable tube pitches high dust loads can be handled without problems in continuous operation. Fig 1 shows an SCR system and a clean gas heat exchanger in vertical gas flow direction.
GEA’s solution approach to the net-zero strategy
Options for usage of the recovered heat include the provision of hot water or steam, drying of biomass such as sewage sludge, conversion to electricity or the generation of compressed air. In most cases the available heat is used to generate electricity with the help of an Organic Rankine Cycle (ORC). The transferred heat from the flue gas evaporates an organic medium, followed by the expansion of the organic steam in a turbine which is directly coupled to a generator. The physical properties of the organic media used enable flexible operation that can also compensate very well deviations in the amount of heat provided, e.g. due to different glass production campaigns or pull rates. As well due to the properties Fig 1. GEA’s vertical heat exchanger together with a SCR in a glass plant in Italy.
The re-orientation towards more sustainability and awareness of CO2emissions will have a significant impact on the design of e haust gas cleaning reports Dr. Marcel Zillgitt*. Since it is clear that only a drastic reduction of greenhouse gas emissions can stop global warming, the industry is facing an unprecedented challenge.[1,2] For the glass industry as an emitter of CO2 various approaches to emission reduction are available, which require a reconsideration of the exhaust gas purification section. Due to increased certificate costs [3] as well as national and international pressure to energy savings and emission reduction, the attention for this topic is as high as rarely before. GEA as a partner for emission control systems offers solutions for the long-term and sustainable orientation of a prospective exhaust gas cleaning, heat recovery and a broad range of applications to use CO2. Adaption to fuel switch To reduce CO2 emissions, of which 75% are attributable to fuel consumption in the glass manufacturing process,[4] natural gas was used instead of oil for firing. This cost-intensive conversion has an effect on the composition of the process gas but is not sufficient to significantly reduce CO2 emissions. A much-discussed approach is to substitute the fuel with hydrogen if produced climate-neutral. Renewable energies such as wind, biomass or solar energy can therefore be used. With the change of these new input conditions in the combustion process, a conversion of the existing glass plant becomes a prerequisite. This also affects flue gas treatment and purification, which must be considered as a mandatory part of the plant. Special precautions must be taken here with regard to the changed Wobbe index and thus the burner selection, as well as the risk of corrosion due to high flame temperatures. Also, the high proportion of H2O in the flue gas can lead to enormous condensation quantities. This is particularly the case if cooling is necessary for subsequent process steps such as a carbon capturing. In case of oxyfuel use for compensation of combustion air and thus nitrogen reduction, there is also considerable impact on the exhaust gas treatment. On the one hand, the reduction of the total volume flow means that plant sizes have to be reduced, for instance the filter surface load. On the other hand, the relative proportion of impurities in the flue gas increases. In addition to the higher CO2 content, an uplift for the acid dew point temperature is to be expected. [5] GEA is aware of this problem and offers special material combinations, for example to operate heat exchangers in the critical temperature range.
Decarbonisation Glass International July/August 2022 www.glass-international.com 111 Continued>>
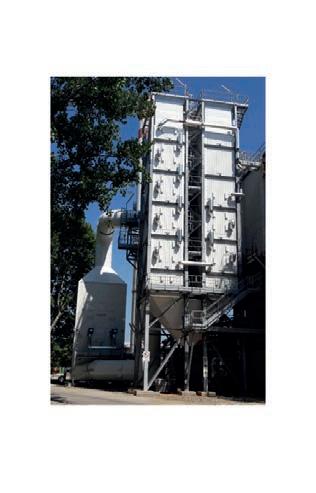
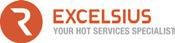
on 25 July 2022
GEA, as an expert for the entire exhaust gas cleaning line, adapts to this transformation and thus is currently starting up a pilot plant for investigation of specific operation conditions in the glass industry. Fig 3 shows the structure of the modular container of the CO2 pilot plant.With a capacity of 150 to 200 Nm3/h, up to 500 kg CO2 per day can be captured with GEAs mobile CO2 separation pilot, depending on the feed gas composition. For test operation, campaigns of three to six months should be targeted to demonstrate the functionality, evaluate the stability of the chemistry and to eliminate concerns related to gas contamination. In the near future, plant sizes covering entire glass plants will be engineered for capturing > 90 % of the total CO2 emissions. This is an essential step towards more sustainability and avoidance of greenhouse gas emissions in the glass industry. For this purpose, GEA offers adequate product solutions with regard to industrial exhaust gas purification to meet an efficient net zero strategy. Continuing the CO2 pathway, this also applies to liquefaction for transportation, conversion to carbonates or other chemicals as well as tailored CO2 utilisation support. With these reliable and target-oriented approaches, we are focusing on the new importance of waste gas purification in conjunction with its interrelated challenges.Withthese reliable approaches and in alignment with sustainability targets of our customers we are focusing on the new importance but also challenges related to waste gas cleaning, heat recovery and CO2 utilisation in glass industry.
[3] EU Emission Trading System (EU ETS) - Revision for phase 4
The technology comprises of several steps: after pre-conditioning of the gas stream by cooling and separation of impurities, the prerequisites for lowmaintenance CO2 separation are fulfilled. The gas then enters an absorber column where it is contacted with a lean amine solution, which is introduced at the top of the column in countercurrent flow. While passing the column the CO2 is absorbed into the liquid phase. From the sump of the absorber, the rich amine solution is transferred through a heat exchanger to a desorber column. Here, CO2 is released at high temperature by adding thermal energy and then further treated to the desired degree of purity. The lean amine solution is then conveyed back to the absorber column. A certain proportion of the required heat to regenerate the solvent can be obtained, for example, from the energy recovery of the high temperature processes in the glassAlthoughindustry.direct CO2 capture from the flue gas stream with amine scrubbing is state of the art, widespread application in the glass industry has not yet been implemented. However, the significantly increased costs for fossil fuels and the rising prices for CO2 certificates as well as the new awareness for sustainability could cause a re-evaluation of the use of this technology here. In particular, it is advantageous to specifically separate both process-related and energy-related CO2emissions, regardless of the fuel used.
5 Kather A., Kownatzki, International Journal of Greenhouse Gas Control, 5, 1, 2011, 204-209 [6] P. Loria; M. Bright, The Electricity Journal, 34, 2021, 106998 [7] International Energy Agency - CCUS technology innovation, lasttransitions/ccus-technology-innovation,iea.org/reports/ccus-in-clean-energy-https://www.accessedon27July2022 *Process engineer, GEA Bischoff, Essen, www.gea.comGermany Fig 2. Utilisation of waste heat. Fig 3. Container-sized mobile CO2 separation unit.
CO2 separation Chemical absorption by means of amine solution is recognised as a commercially proven tail-end solution for post-combustion carbon dioxide separation.[6, 7]
[2] E. I. Koytsoumpa; C. Bergins; E. Kakaras, The Journal of Supercritical Fluids, 132, 2018, 3-16.
Julyneutral-europe.pdf,uploads/2020/01/flat-glass-climate-https://glassforeurope.com/wp-content/[4]accessedrevision-phase-4-2021-2030_en,eu-emissions-trading-system-eu-ets/https://ec.europa.eu/clima/eu-action/(2021-2030),laston25July2022Flatglassinclimate-neutralEurope,lastaccessedon262022
Decarbonisation Glass International July/August 2022 1120 www.glass-international.com of organic medium the expansion takes place without critical droplet formation, which is why a long running time of the turbine blades is experienced. Condensation is achieved by recooling, with flexibility for the use of air-cooled condensers (ACC) or water cooling, based on boundary conditions at the respective plant such as available space or availability of water. Fig 2 shows the basic possibilities of waste heat utilisation for different applications as well as the schematic of the ORC cycle for electricity generation. By increasing the plant efficiency, energy can be converted in a meaningful way, so that the CO2 footprint and OPEX are reduced in the long term. For the future requirements on CO2 savings, which call for early action in view of rising certificate costs, the direct capture of CO2 from the waste gas stream must also be taken into account.
References [1] McKinsey Sustainability, sustainability/our-insights/how-the-www.mckinsey.com/business-functions/https:// emissions-at-net-zero-cost,european-union-could-achieve-net-zero-lastaccessed

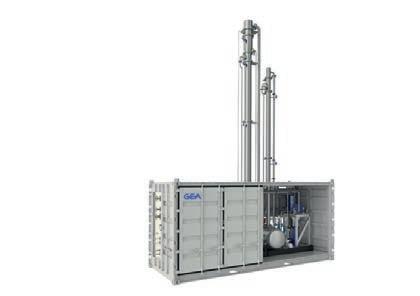
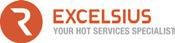
Handled With Care We believe what sets us apart is how we handle your business, marketing and brand. We have immersed ourselves in this fascinating industry, taking the time to understand its processes, technologies, supply chain and audiences. We love glass and are fortunate to be trusted by some of the leading brands. We care about every word we write, every mark we craft and every campaign we create. That’s what makes us di erent. wearearmstrong.com Over 1000 production lines are equipped with Graphoidal Shear Spray Systems. Contact us today to find out how our latest technology can help you. Tel: +44 (0) 1246 266000 Email: sales@graphoidal.com Fax: +44 (0) 1246 269269 Website: www.graphoidal.com Graphoidal Developments Ltd, Broombank Road, Chesterfield S41 9QJ, England
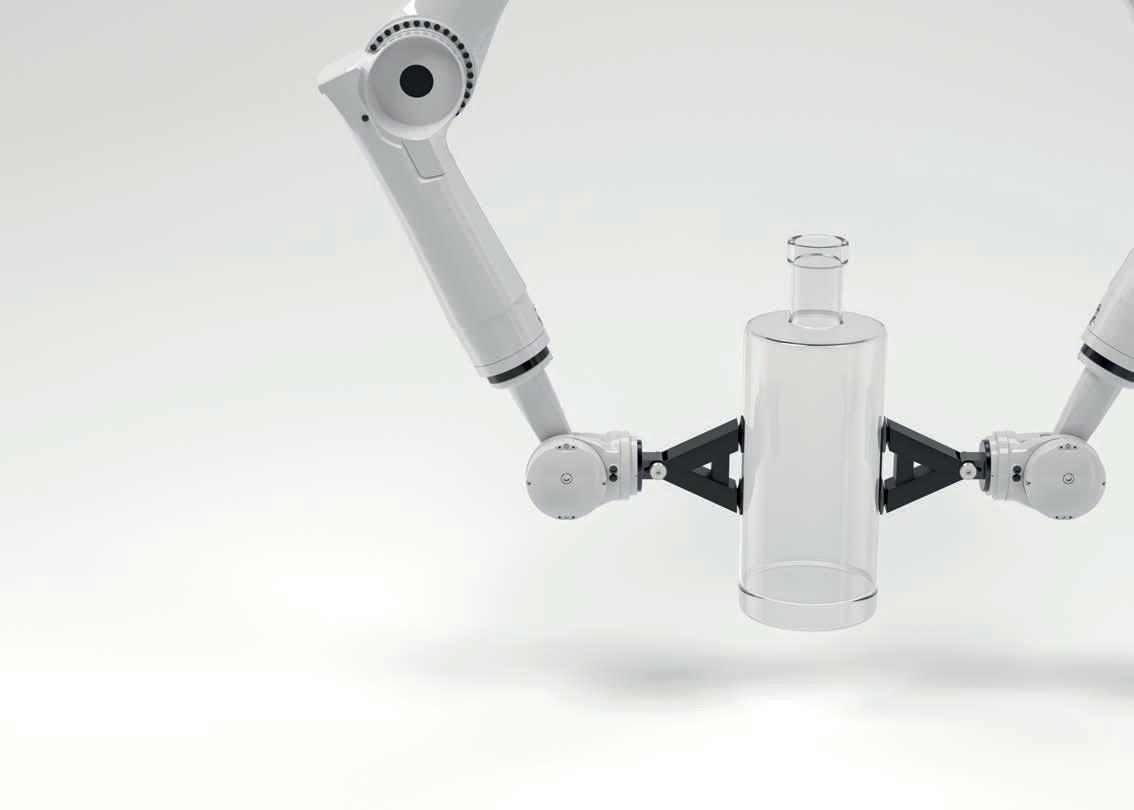
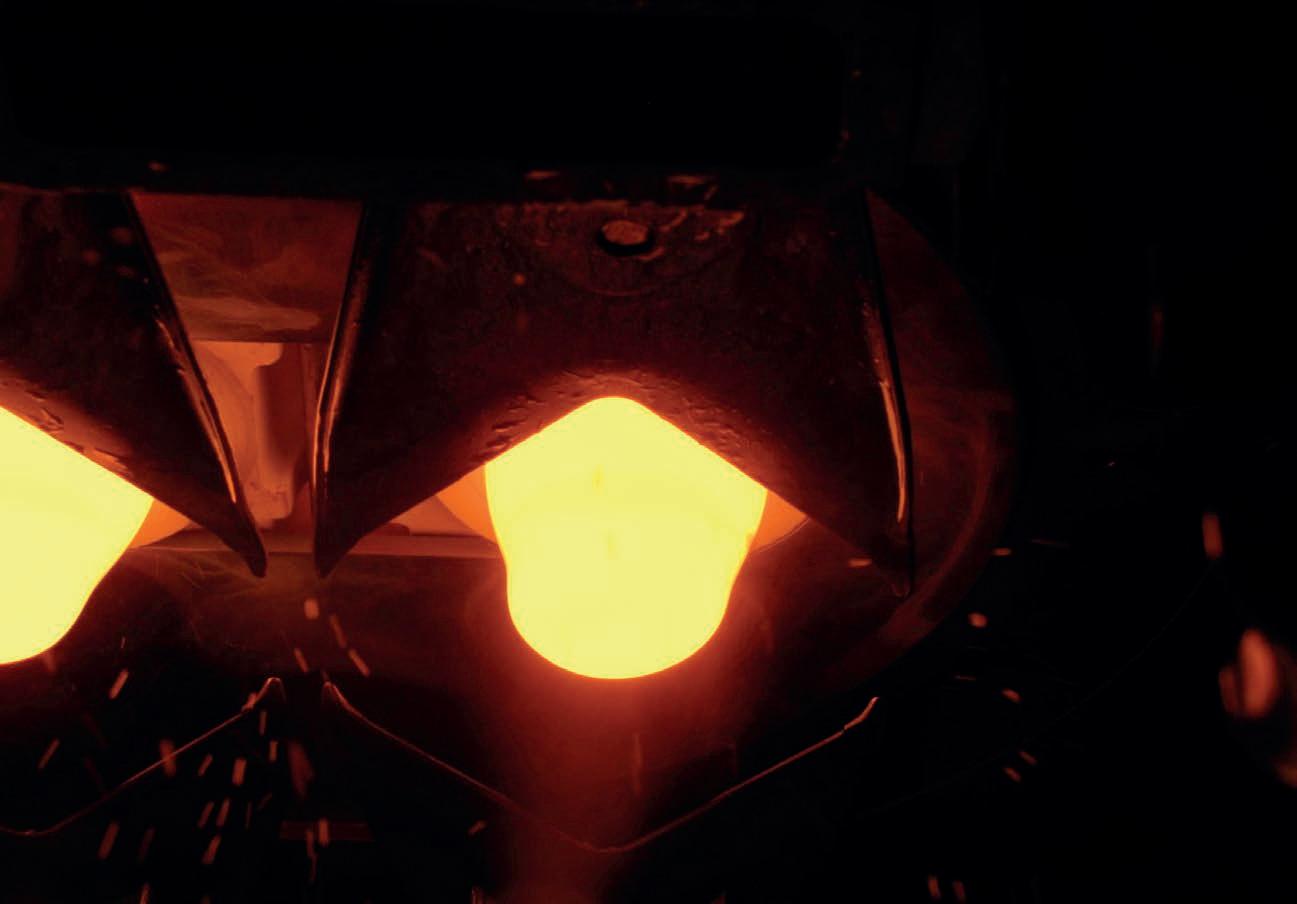
EVERY MEASURE IS POSSIBLE DIMENSIONEXTERNAL INSIDE DIAMETER AND PROFILE WEIGHT PUSH-UP THICKNESSWALL SINKSBULGESAND 71952 2022 visit us HALLC3814
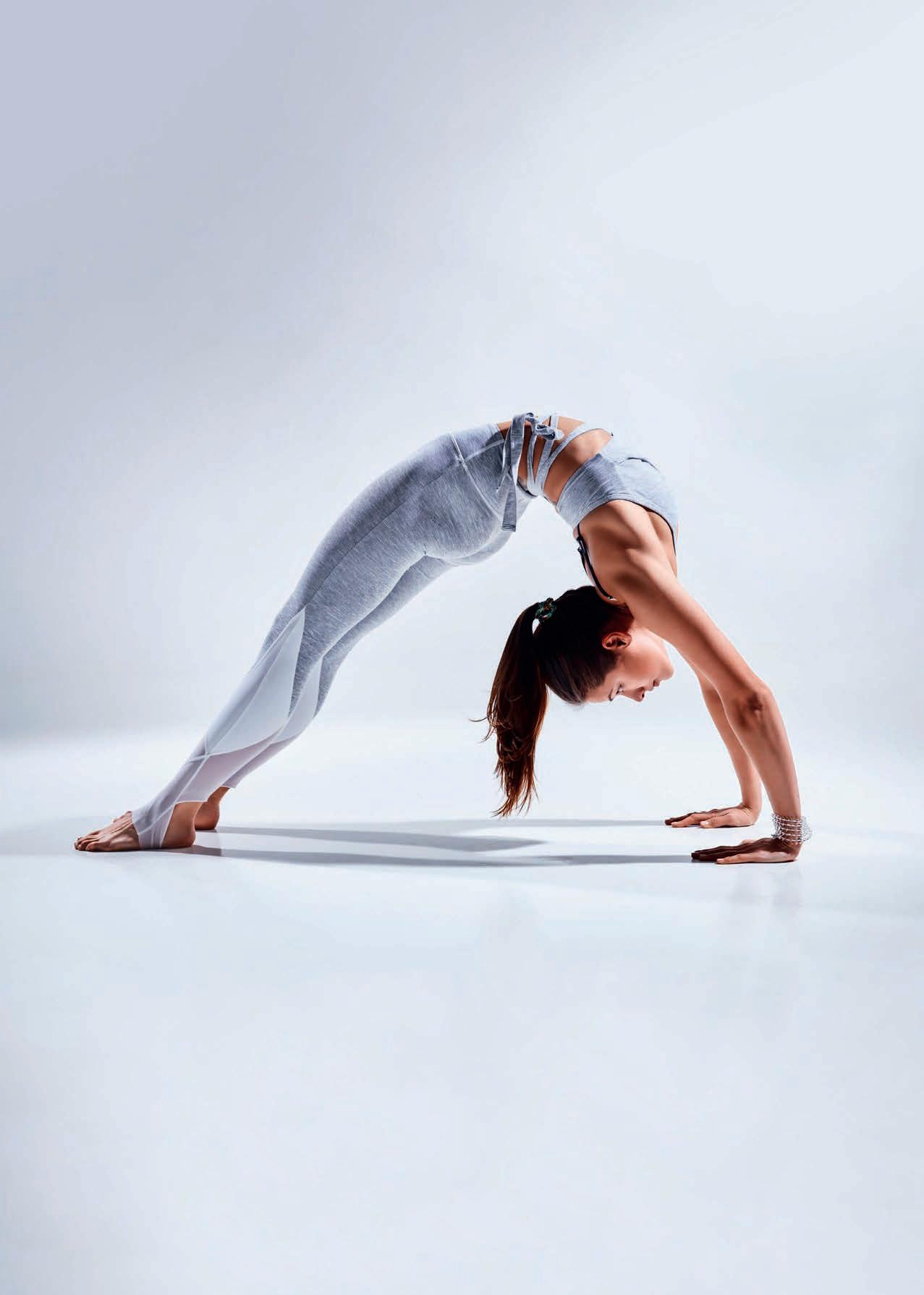

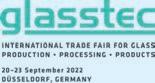
� Results relies on the operator’s skill.
� Define the level of automation required (fully automatic or semiautomatic). It should be considered that a fully automatic flexible machine, with multi-conveying systems, working 24/7 will dramatically reduce the need for manpower, thus leading to a very short return on the investment (ROI).
� Seek for alternative solutions and evaluate them carefully.
Outside the sphere of experts, there is somehow confusion on the meaning of “measurement” “inspection” and “testing”. Sometimes they are wrongly used as synonyms to generically indicate “controls” to be carried out on an article.
� Possibility of future upgrades allows
� No quantitative information available about the size of the problem.
� No data collection, no statistics, no process trends detection, no comprehensive information available to intervene on the process. In other words, if there a problem is detected, there is no comprehensive information to handle it. Most likely the consequence is a process not in control. For all these reasons and for others more, any glass container manufacturer will have to face, sooner or later, the decision to switch from manual to automatic measurement. When this decision is taken, the next step is to choose the solution, among those available in the market. It must be said that there is no “absolute best” solution. The best solution is the best one for the characteristics of the specific glassmaking plant and the range of articles produced. Then, what should be taken into account?
enefits of e ible automatic measurement in glassma ing
“Testing” is the process of checking the compliance with functional specification, also by destructive means. This article will be focused on measurement.Measurement is present at different phases of the glassmaking process, mainly, but not only, at the cold-end. It can be carried out near the manufacturing line, or in a Quality Control Laboratory, by means of go-no go or manual gauges or by means of flexible semi-automatic or automatic systems.
� A set of go-no go gauges is required for every article in production.
� A good suggestion is to take the time to think which are the necessary Fig isi ic a f ll a tomatic fle ible machine, with automatic handling. requirements.
� Manual gauging is a manpower intensive process.
� First of all, the investment in an automatic measurement system will last approximately 10 years. So, a wrong decision, can have a quite serious impact.
The use of go-no and manual gauges has several drawbacks.
� Costs related to purchasing, managing and periodically calibrating a very big number of hard gauges.
� Make sure the machine you are choosing really meets the needs. Do not look just at specification on the catalogues, but visit the supplier’s plant and make tests on the machine.
Let’s try to “Measurement”clarify. means checking dimensional and physical features, such as dimensions, shape, weight or thickness.“Inspection” means to check cosmetic features or the presence of defects, such as inclusions, cracks or other irregularities.
Measurement Glass International July/August 2022 www.glass-international.com 115 Continued>>
� Total flexibility, that is the capability to measure all the manufactured container without any job change, is a must-have feature.
� Easy and intuitive programming facilitate the use of the machine also from operators without too much experience.
Eleonora ordini discusses the advantages of introducing e ible automatic measurement systems in the glassma ing process. he suggests what should be ta en into account to choose the best solution from those available in the mar et.

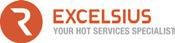
www.glass-international.com to have a machine able to safisfy future needs
*International Industry ManagerGlass Packaging, Marposs, Bologna, Italy bottles-and-glass-containersapplication/pharma-and-food-industry-https://www.marposs.com/eng/
� Do not limit your investigation to a single supplier.
Fig 2. VisiQuick-mini is a semi-automatic fle ible s stem ith man al container loading/unloading.
� Check the compatibility and level of integration with the manufacturing execution software (MES) used in your plant.
� Check the supplier’s references, credibility and, above all, experience in metrology as well as his after sales service capabilities.Marposs can supply solutions with different level of automation, to match the need of any customer and production environment.Thesolution with the highest level of automation and the widest number of available controls is VisiQuick, a fully automatic flexible machine, with automatic handling (Fig 1) It allows to measure, without any operator intervention, and without any job change, a wide range of containers irrespective of their dimensions, shape andVisiQuickcolour. can measure: � external dimensions with optical technology (cameras) � weight � push-up � mouth inside diameter and profile, with Marposs proprietary contact technology � wall thickness with chromatic confocal technology � labelling area profile (sinks and bulges), with a Marposs patented optical technology.VisiQuick can be supplied with all the above mentioned measuring stations or only with one or some of them, with possibility for future upgrades. Containers are feeded to VisiQuick by means on one or more conveyors. Multi-conveyor solution is very convenient and efficient, because it allows to measure different batches of containers without operator’s supervision.VisiQuick can be also feeded with samples diverted directly from the production line. An alternative solution to VisiQuick is Visi uick-mini, a semi-automatic flexible system, with manual container loading/ unloading (Fig 2). It can measure: � all external dimensions with optical technology (cameras) � weight, as an option Both VisiQuick and VisiQuick-mini are suitable to measure any kind of container like bottles and jars for beverage and food, pharmaceutical as well as perfumery or cosmetic containers. With a single system, glass containers manufacturers can perform accurately and automatically, all the controls that with manual gauges requires four to seven skilled operators and many more. With the additional advantage to collect data and detect in real time any production problem.BothVisiQuick and VisiQuick-mini are compatible with the most popular MES in theInIndustry.addition to these products, Marposs can support customers with training, maintenance programmes and an after salesMarpossservice.celebrated 70 years of activity and is present in 34 countries with its own sales and service organisation. �
Measurement Glass International July/August 2022 1160
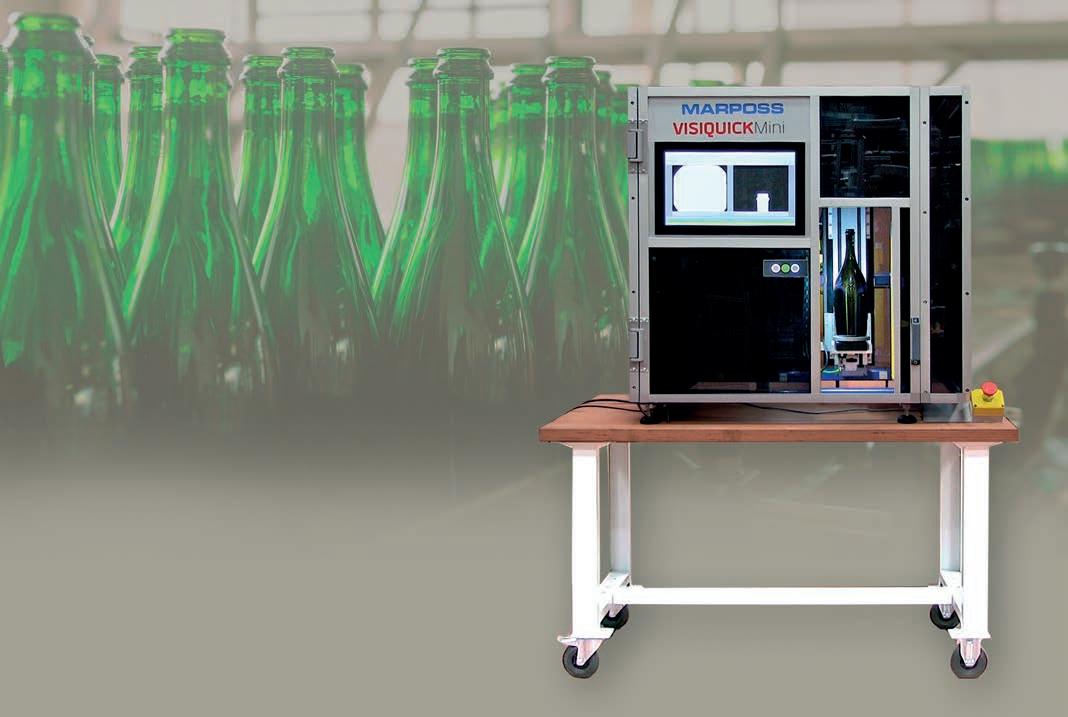
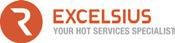
Curvink is exclusive agent for the glass bottle manufacturing industry worldwide for GmbHwww.rosarioc2c.com - www.curvink.com Rosario high speed screen printing machinery Palletizing- and depalletizing equipment for decoration lines We pleasedareto meet youat2022Glasstec Rosario-Curvink_Adv_180x127mm.indd 1 06-07-2022 15:08
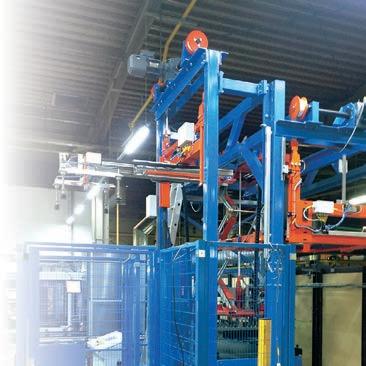

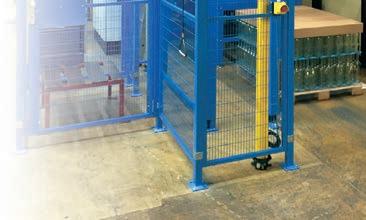
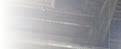
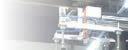


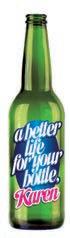


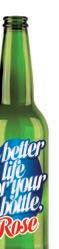
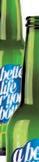
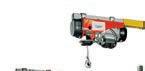
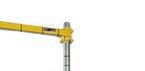
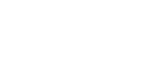
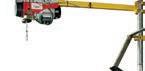
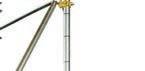
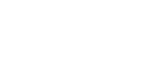
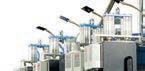
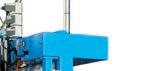
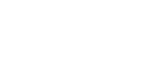

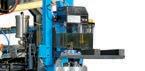
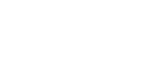
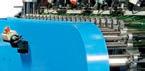

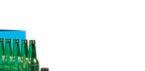
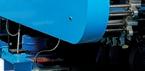
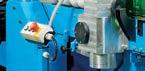
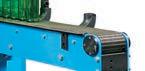
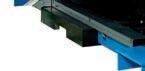
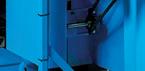
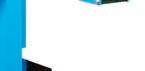

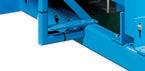
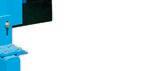

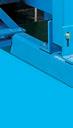
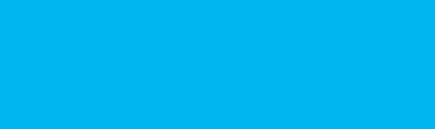

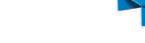

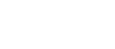
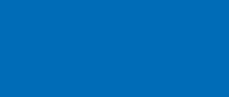

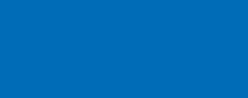


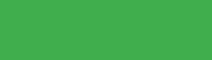
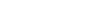
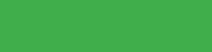

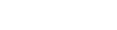
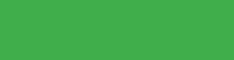




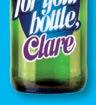
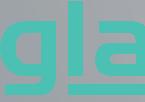
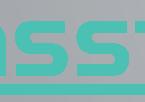
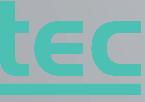
� Very low maintenance.
Empty pallets preparation lines
Taking charge of your entire end line Thimon* gives an overview of its products for packaging palletised loads and its automated shrink hooding machines developed for the hollow glass market.
The empty pallet preparation line is independent and is located upstream of the glass container palletisation. Its purpose is to place a floor mat (plastic film) on an empty pallet and to glue, staple or shrink-wrap it onto the pallet.This line can be equipped with an empty pallet destacker at the infeed and or a pallet restacker with floor mat at the outfeed. These pallets, equipped with their floor mats, are then moved to the palletisers (using shuttles). The floor mat is necessary because it provides a seal on all six sides of the pallet (Fig 1).
Thimon manufactures induction shuttles which main advantages are:
� No strain on forklift trucks and or operators (no ground or overhead supports).
Load and pallet centring devices
This equipment, which is fully automated and equipped with four mobile panels, is used to centre the products on a pallet to reduce defects linked to palletising or Fig 1. Pallets are e ippe ith floor mats to provide a seal on all six sides.
� No parts aging due to friction.
Founded in 1968, Thimon is a French manufacturer that designs machines specifically to meet customer requirements. We were the first company to create a machine capable of wrapping palletised loads, which made us pioneers in our sector. Today, the family company is above all a team of 70 people dedicated to creating end-of-line machines specifically designed to meet our customers’ needs. We manufacture every packaging solution existing on the market today. ou may know Thimon for its expertise in packaging palletised loads and designing automated shrink hooding machines.
The latter is developed for and particularly suited to the hollow glass market. But Thimon also manufactures many handling elements for your pallets. Because we have a multi-market experience, and we are developing our logistics know-how by accompanying our customers on this growing market for Thimon, we design lines that are more and more ergonomic and today offer efficient and intelligent solutions in general logistics. We can take advantage of this expertise for the handling of glass products. For example, we can integrate upstream and downstream of your hooding machine.
� No electrical risk as cables are buried and insulated.
Palletising Glass International July/August 2022 1180 www.glass-international.com
Shuttles Shuttles (one, two, four pallet places) allow empty or charged pallets to be moved automatically from the empty pallet preparation lines to the palletisers or from the palletisers to the hooding lines (Fig 2). It is also possible to move the pallets after hooding to the storage areas.
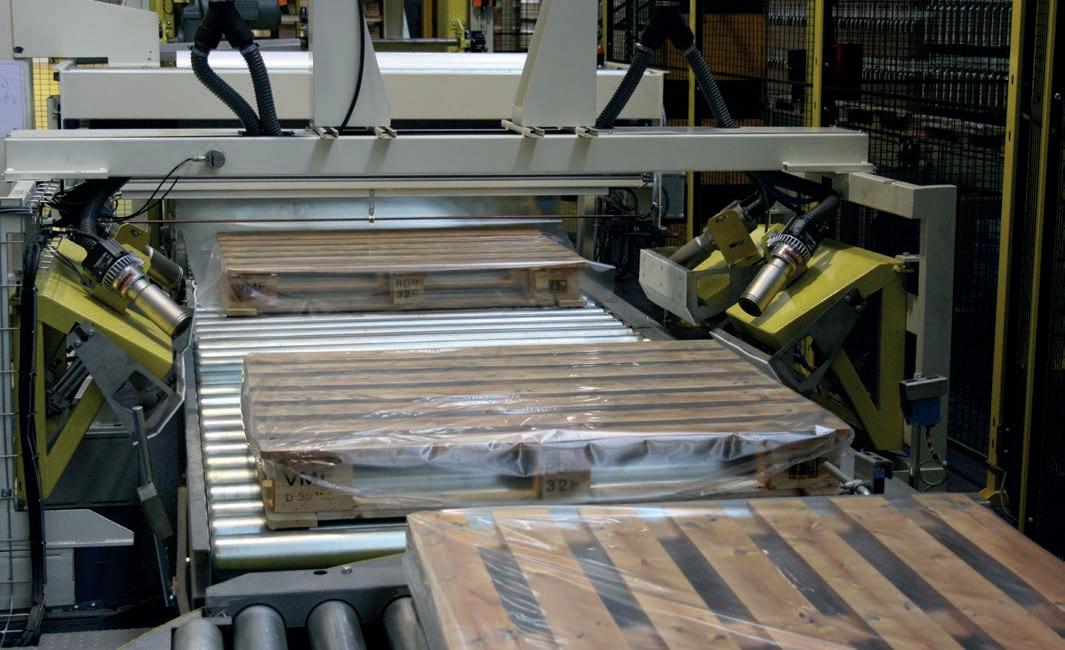
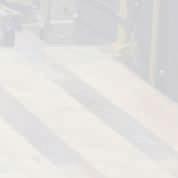
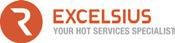
Palletising Glass International July/August 2022 www.glass-international.com 119
Fig 3. Thimon’s load and pallet centring device.
The top glass is installed just downstream of the shrink-wrapping machine.
� Broken glass collection bins under roller conveyors. � Shrinkage compensation options for ambient temperature. � Chain conveyor sidewall covers.
Top glass shrink top cover dispenser system
This type of equipment is very often used by glass manufacturers to add extra protection to reinforce the tightness of the packaging and to ensure perfect protection of their products. This process is very effective when stacking and storing pallets outdoors. Stackers The role of this element is to lift a pallet after shrink hooding and to automatically stack it on another pallet. Thimon stackers are equipped with fully secured retractable forks and lifting system. The stacking of pallets at the end of the hooding line optimises the flow and reduces and facilitates the operations of the forklift drivers in the storage areas. We also manufacture many handling elements common to all our customers’ markets, such as: � Lifts lowering devices. � Lifting tables. Fig 4. The top glass device is often used by glass manufacturers to ensure the protection of their products. � Conveyors. � Turntables. � Orthogonal transfer tables.
pallet handling (Fig 3). Used at the entrance of the hooding line, it allows to recentre the layers of glass containers on the pallet before hooding. The operation is done for all four sides at the same time, without any rotation of the pallet.
This is a device that allows a cover to be placed on the top of the pallet after a first complete hooding and to shrink the same film thanks to a heating frame (Fig 4).
� Raised or covered cable trays. As a reminder, in addition to its automated shrink hooders and the various handling systems presented in this article, Thimon has also developed robot machines, particularly adapted to the glass market. These shrink hooders are an excellent alternative for companies that want to offer themselves a high quality service. We know how to handle your pallet and the associated data (traceability, SSCC number, origin, etc.) throughout the entire cold end, from the exit of your palletisers to the loading of your products onto the trucks. More than 100 glass industry companies trust us to optimise their whole end of line. We have mastered all packaging technologies for all markets and offer the benefit of over 50 years’ experience. It is by accompanying our customers every day and by seeking out the best solution in every situation that we have constantly developed our expertise, with the sole aim of satisfying our customers. �
*Thimon, Méry, https://www.thimon.com/enFrance
Fig 2. Shuttles allow empty or charged pallets to be moved automatically.
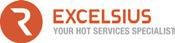


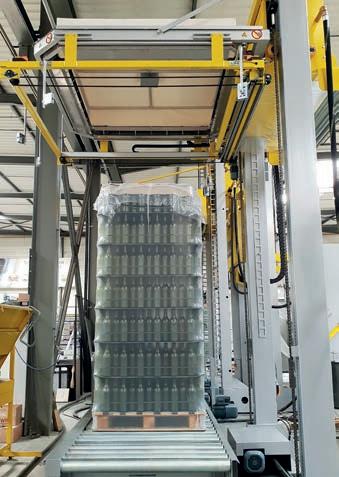
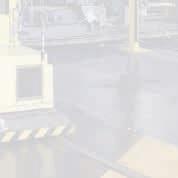
CONDAT -104 av. F. Mistral - 38 670 Chasse-sur-Rhône - FRANCE - Tel. +33 (0)4 78 07 38 38 - www.condat.fr - condat@condat.fr LUBRICANTS FOR GLASS INDUSTRY COMMITTED TO RESPONSIBLE PERFORMANCE CONDAT provides you glass lubricants allowing you to: • increase your productivity • reduce your consumption • respect people and the Environment Discover also our Eco-designed products for the Glass Industry! Visit us at: Hall 14 / B13
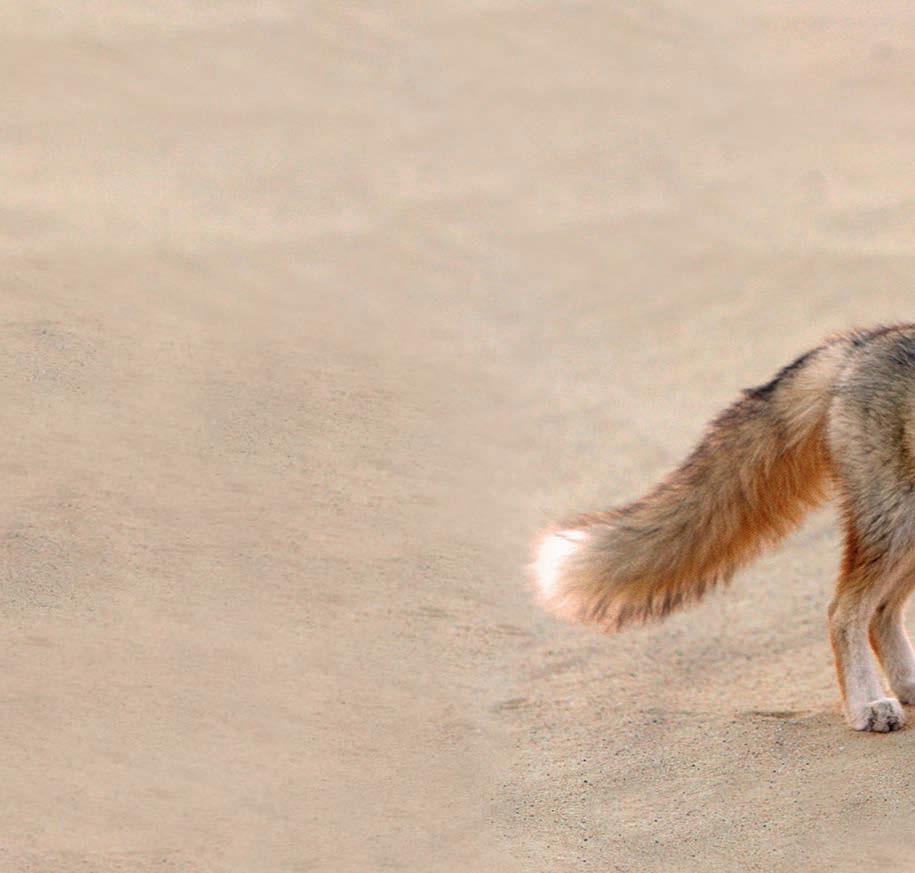
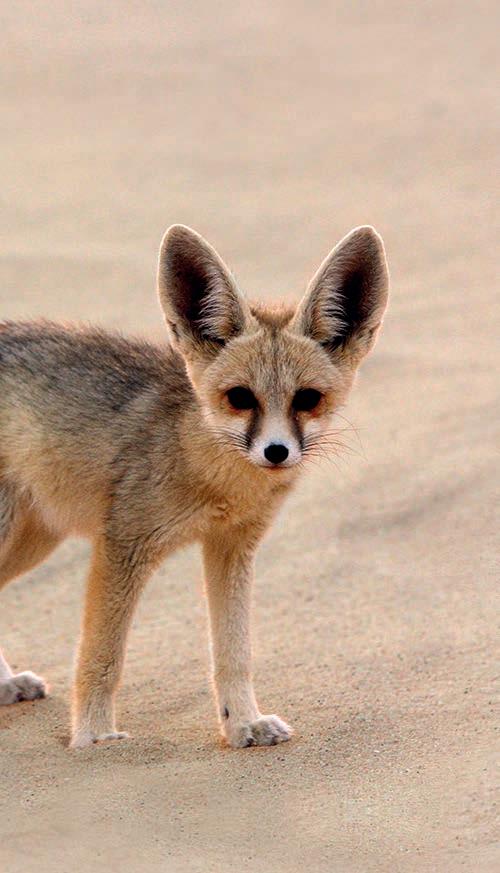

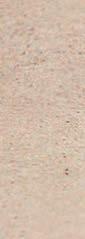


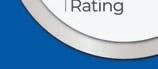
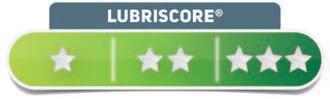
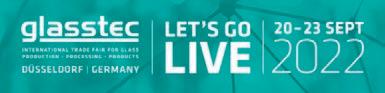


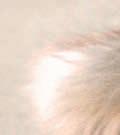
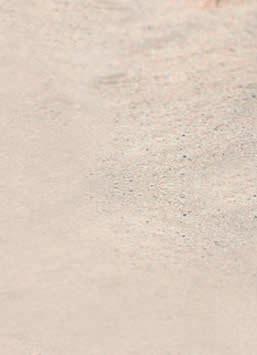

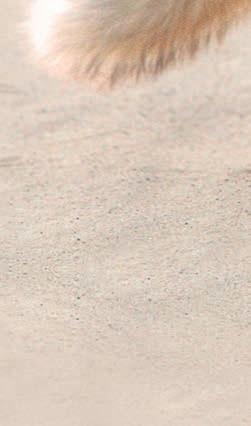

The event format is a niche trade exhibition where people can arrange meetings with a number of suppliers and industry experts in one place. Visitors and exhibitors can attend the free conference sessions to hear from industry experts. These exhibitions bring together international experts, hollow and container manufacturers and businesses that use glass containers, to discover the latest innovations which include energy efficiency, quality control, packaging, logistics and decorative possibilities. Go online to find out more at WWW.GLASSMANEVENTS.COM Ken Clark Sales Director +44 (0)1737 kenclark@quartzltd.com855117 Manuel Martin Quereda International Sales Manager +44 (0)1737 manuelm@quartzltd.com855023 glassmanevents.com/latin-americaglassmanevents.com/asiaLATIN AMERICA 2024 BOOK YOUR STAND TODAY glassmanevents.com/europe
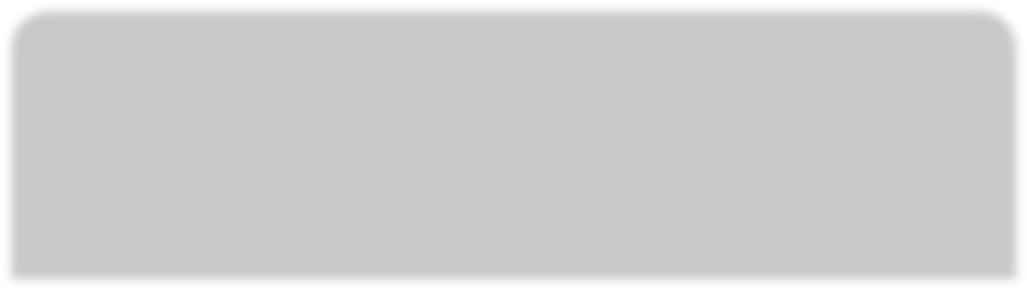
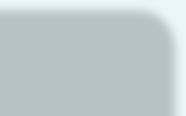

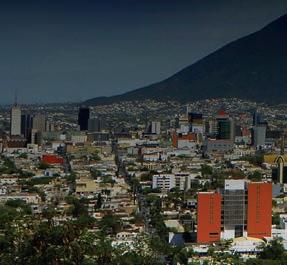

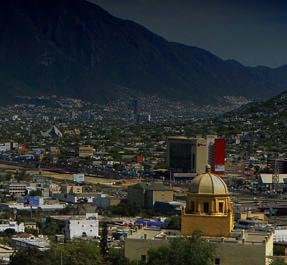
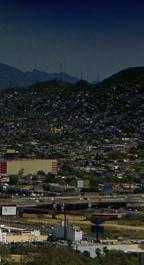

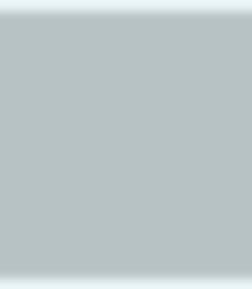
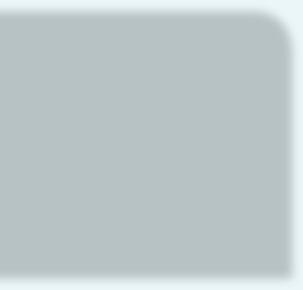
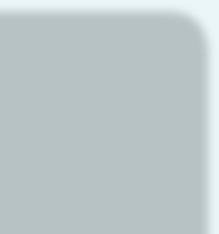
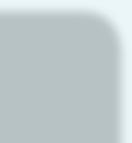

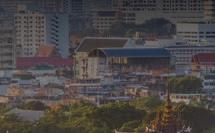
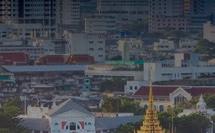


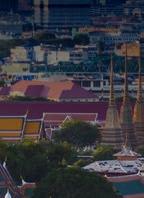
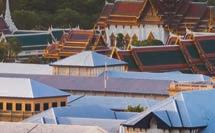
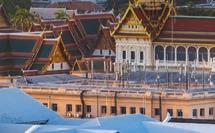
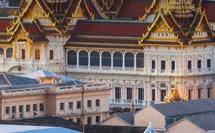
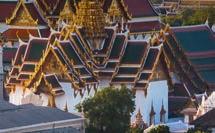
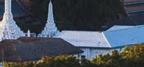


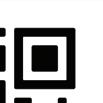



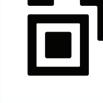


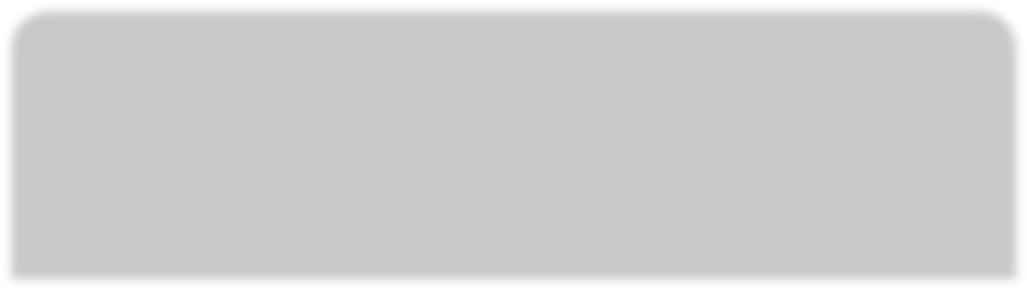
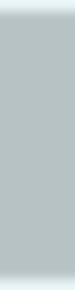
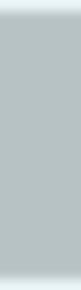
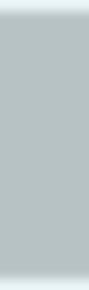

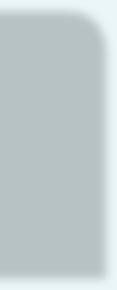
























































It has been repeatedly confirmed that good learning algorithms achieve better results than experts.
It took only 67 days from the glass drainage from the previous furnace to the start of the heat-up of the new one - three days less than originally anticipated. It is difficult to interpret this result without knowing the extent of the necessary demolition, construction and installation works.However, anyone who witnessed the situation before the drainage and then before the heat-up must consider this result to be Therecord-breaking.determinationand
Machine Learning
Forehearths,regeneratorworking end and furnace
Share of electric energy in melting up to 40% The furnace is designed to melt of up to 192tpd out of 480tpd by electric current. This allows the melting process to be optimized according to cost and availability of energy sources. It also offers the potential for dramatically greater reductions in CO2 emissions than standard solutions with electricity at an estimated 20%. The furnace was equipped with a combustion system with automatic individual burner control. This makes it easier to operate the system and, most importantly, reduces nitrogen oxide emissions and has a positive impact on energy consumption.
TECHGLASS is implementing a programme to introduce Machine Learning modules into control systems.
dedication of TECHGLASS employees have been recognised by the management of Stoelzle Czestochowa.
Massive
Short glass to glass time
Cooperation between TECHGLASS and Stoelzle Czestochowa dates back to the establishment of the Polish branch of this Austrian company, which took place in 2001.Todate, TECHGLASS has delivered there the furnace, working end and forehearths three times, and has completed more than 150 smaller orders. In 2020, the decision was made to implement a furnace with a pull of 480 tons per day with 5 forehearths, in a hall designed for a furnace with a 40% smaller melting area, the most ambitious option among those considered. The six-month tender process was completed in February 2021 with the victory of TECHGLASS. In house business model
Alternative fuels
The combustion system is designed for easy extension of LPG or oilThesupply.furnace control system ensures the stability of the combustion process, regardless of the amount of each fuel fed, reducing the impact on the production process to a minimum. This functionality becomes of vital importance in the current situation of uncertain natural gas availability and unpredictability of its price.
TECHGLASS ADVERTORIAL Glass International July/August 2022 1220 www.glass-international.com
TECHGLASS commissioningcelebratesof480tpd furnace
TECHGLASS has been designing and supplying completely equipped furnaces, working ends and forehearths for over 30 years. In July 2022 a 480tpd furnace was commissioned - the Stoelzle Group’s largest and one of the largest end port furnaces in Europe.
The execution of the project took place during the Covid pandemic and the war in Ukraine. Lead times for some components have been extended several times over. It has become common practice for suppliers to provide offers that are not binding in terms of neither prices nor deadlines. However, the TECHGLASS business model based on designing and manufacturing almost all of the systems in-house has helped address these challenges.Thestatus of each of thousands of orders was monitored in real time, allowing a quick response in case of any problems. This would not have been possible if production had been carried out by subcontractors.

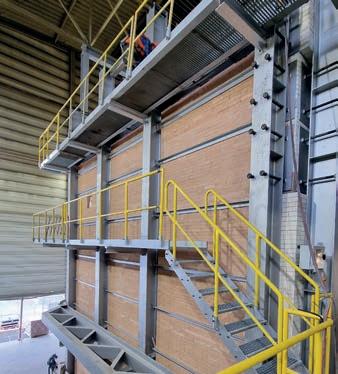
www.glass-international.com
TECHGLASS offers solutions for production of all types of glass
TECHGLASS ADVERTORIAL Glass International July/August 2022
TECHGLASS’ innovation
www.techglass.pl office@techglass.pl Left: Production hall. Right: Glass cubes production
The furnace supplied by TECHGLASS has exceptionally low energy demand, which is especially important with today’s rising gas prices and carbon dioxide emission costs.
To meet the customer’s very stringent requirements in this area, TECHGLASS has made a number of improvements. A very efficient transfer of energy to the melt from the furnace’s combustion space was achieved by equipping the furnace with two “extra wide” dog houses and four oscillatory batch chargers for excellent batch distribution. The furnace combustion system for CIECH Vitrosilicon was equipped, as in the case of Stoelzle Czestochowa, with automatic individual burner control. It is also designed for easy extension with LPG or oil supply.
TECHGLASS - GLASS INDUSTRY SOLUTIONS
TECHGLASS engineers are also working on applications of ML in other areas, such as optimising forehearths operation during assortmentObtainingchanges.evenasmall amount of energy savings from these measures is worth the effort put into them.
As part of the project, TECHGLASS also designed and supplied a batch house and three complete lines for producing frit in the shape of almost any size of cubes. Each of the three frit production lines is equipped with forming machines, conveyors, a cooling water system, all auxiliary systems, and a control system integrated with the furnace control system.
123 In the first stage, ML is planned to be used to minimize glass level disturbance after changing the combustion side.
Recently a TECHGLASS furnace of pull of over 300tpd for melting sodium silicate has been commissioned. The furnace is part of a project executed for CIECH Vitrosilicon S.A. which also covered engineering and supply of batch house and three modern production lines
Scope of supply
An important feature of the furnace design is to reduce the time between the production of products with different specifications, the so-called module. As a result, the amount of unwanted transient product is significantly reduced, which translates into savings and reduced environmental impact.
From left to right: Andrzej Skowiniak - President of TECHGLASS, Robert Janeczko - Chairman of the Board, CIECH Vitrosilicon. Hubert Domaradzki - Member of the Board, CIECH Vitrosilicon
CIECH Vitrosilicon is the biggest supplier of sodium silicates in Europe. It has two production plants in Poland. The company belongs to CIECH Group – an international, expanding group operating in chemical industry with strong global presence.
Reduced module
The standard is to transfer solutions for soda-lime glass, mainly container glass, to sodium silicate production. The innovative TECHGLASS furnace was designed from the ground up for melting this glass. This allowed the production of high-quality sodium silicate with energy efficiency unattainable with standard approaches and with very low NOX emission. The furnace can be operated without investing in and maintaining any secondary methods of reducing nitrogen oxides. Low energy demand
The execution of the project was such a success, that soon after its completion CIECH Vitrosilicon ordered a rebuild of the existing furnace with TECHGLASS. The rebuild was based on a significant modification of the furnace’s design.
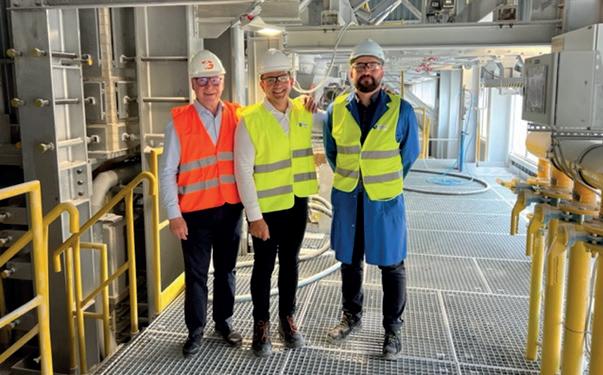
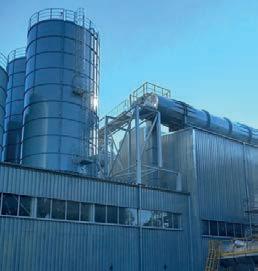
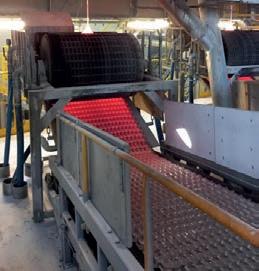
WWW.GLASS-INTERNATIONAL.COM Glass International offers readers the latest news from across the hollow, container, flat, and speciality glassmaking industry and is the official media partner for the global Glassman events. The magazine focuses on industrial, economic and environmental issues affecting the industry and includes articles discussing the latest developments and challenges in glass manufacturing. Regular features comprise of global news and events, company and country profiles, and previews and reviews of important industry conferences and exhibitions. COMPANYPROFILE:GERRESHEIMERDECORATIONUNITSPERSONALITYPROFILE:PHOENIXCHAIRMANFORMING INTERNATIONAL March 2019—Vol.42 No.3 A GLOBAL REVIEW OF GLASSMAKING WWW.GLASS-INTERNATIONAL.COM GlassInternationalMarch2019 If it’sinyourglass,we’llBrilliantly.inspectit. AppliedGlass.com INNOVATION TECHNOLOGY | SALES TRAINING SUPPORT AppliedVision_GlassInternational-April-2019.indd 3/7/19 10:59 March.indd 13/03/2019 10:29:25 CONNECTING THE GLASS MANUFACTURING INDUSTRY A round-up of the top news stories is also sent to more than 16,000 industry professionals each week as a free e-news bulletin. You can register online to receive the weekly newsletter and keep up-to-date with the latest news from across the glass manufacturing industry. www.glass-international.com/e-newsletter MAGAZINE NEWSLETTERWEB Join the InternationalGlassGroup @glass_int Packed with information on the glass manufacturing industry and continually updated with news for glass industryandalsowww.glass-international.comprofessionals,featuresspecialarticlesinterviewswithleadingfigures.
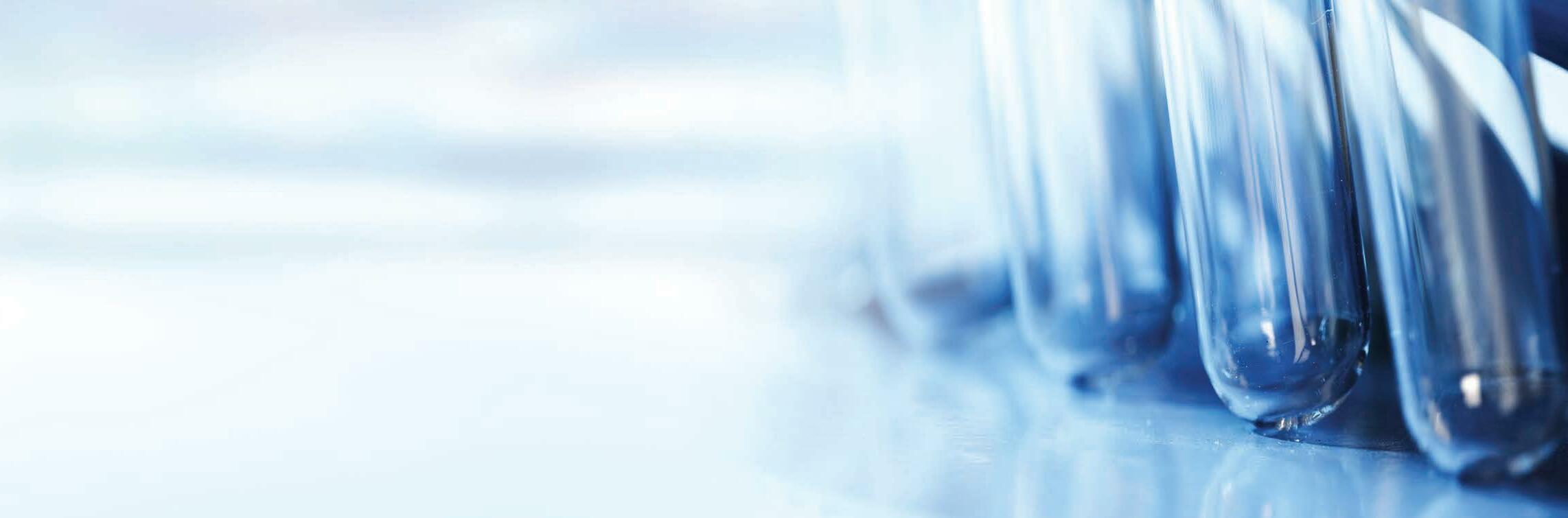
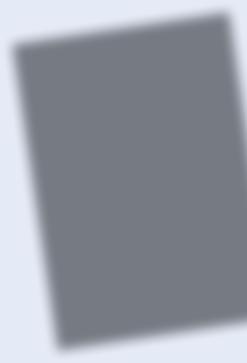


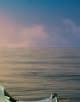



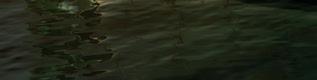
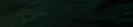


roviding state of the art batch oriented solutions to a vast range of industries like chemicals minerals construction and glass cmon s stems has gained a signi cant cross functional e pertise. his enables us to provide manufacturing solutions . from conceptual design up to nal deliver and from opera tions to information business la ers. he strategic partnerships with contractors like alorni ech have been providing us the opportunity to bid among best-inclass solution providers in the sector and to gain a signi cant market share, having already delivered successful projects on either brown or green eld basis to multinational glass manufac turers.proect milestone sealing the aforementioned partnership with the talian ngineering ontractor is the one at ulf lass actor in atar. high end mi ing plant for container glass production of tonnes per da . alorni tech is the contractor of the whole pro ect while cmon s stems is the one ensures the optimal batch and cullet distribution for two furnaces.cmons
Acmon
ACMON SYSTEMS
As a manufacturing solution provider for batch plants in glass industry 4.0 Systems o a o al oa the s a a . . o ta o as . . o@ac o .g . h ps ac o g o p.co Best in class batch house and cullet return solutions.
ACMON ADVERTORIAL Glass International July/August 2022 www.glass-international.com 125
stems is responsible for the entire process engineering of the batch plant which includes but is not limited to batch house, cullet returns both internal and external, mixers, silos for raw material storage building architectural la out and metallic sca old stud e uipment detail engineering manufacturing erection and installation supervision commissioning and pro ect hand over. he pro ect will be delivered full automated secur ing of trouble free operation et with direct connection to s stems and business intelligence la ers. ost sales services like training spare parts for two and ve ears operation are also including to cmon s scope of suppl . eorge oshakis ommercial irector of cmon roup said ver the last ve ears our main focus and commitment was to glass industrial sector a niche vertical which despite from initial challenges turns out to be the sector with the greater eturn on nvestment ratio throughout the entire organisation. he glass sector and more speci c batch plants and cullet return solutions is considered to be the industrial eld we will continue to invest in the ears to come. cmon roup is a world class enterprise providing industri al solutions on a turn ke basis in elds of material handling automation and process engineering robotics and conve ing s stems in real time connectivit with business la ers through industr . so ware pla orms. he s nergies created from three independent entities creates a uni ue blend of e pertise considered to be the one stop source for a wide range of indus trpecialisingverticals.in process technolog of powders particles and granules cmon s stems a member of cmon roup has been delivering customised and innovative solutions for raw materials automation.delivering added value to our customers we support a sus tainable industrial suppl chain and a smooth transformation to the digital factor of the future.
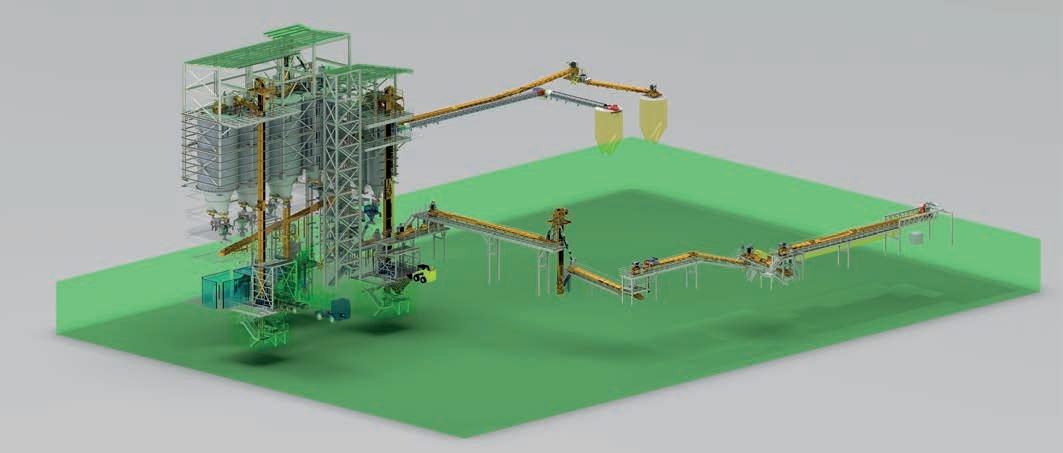
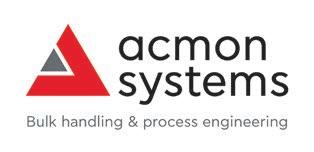
UNPROTECTED PROTECTED Innovativetreatmentforan easy-to-clean,alwayssparklingbathroom! Wonderinghowtokeepyourbathroomsparklingwithhalfoftheeffort? Joinglassmakers,architects,interiordesigners,cleaningcompanies,hotels,and housewivesusingIGPonits glass andothernon-poroussurfaces,suchas tilesand grouts, stainlesssteel and chromefixtures. Thistop-of-the-linetreatmentprotectsyourglassfrom limestonestains, soapscum,and dirtingeneral,withatrueperformanceguarantee. Aneasytoapplytreatmentthatwill cutcleaningtimeupto90% andreducefuture cleanings! Contactus: https://www.chemitek.pt/igp-industrialglassprotect info@chemitek.pt
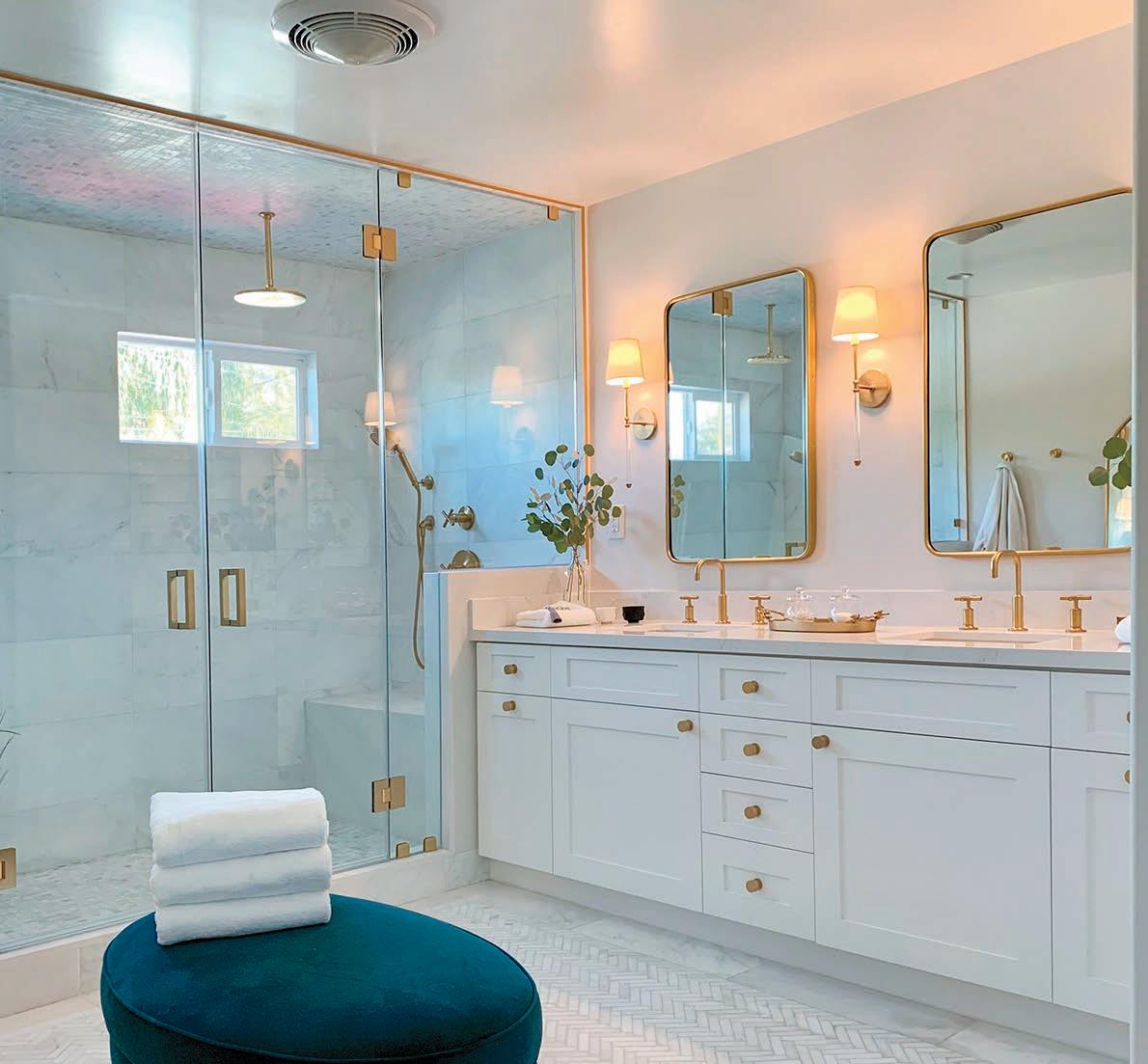
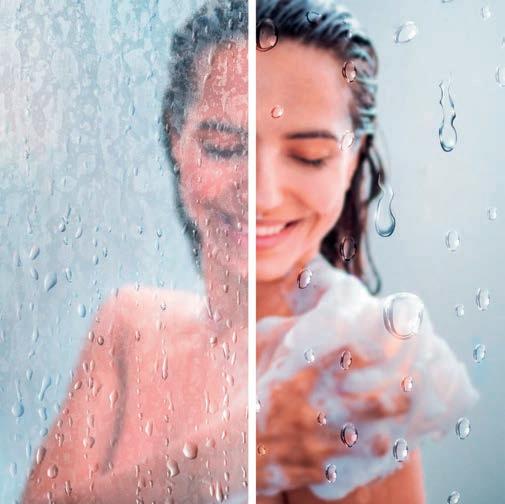

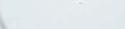
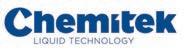
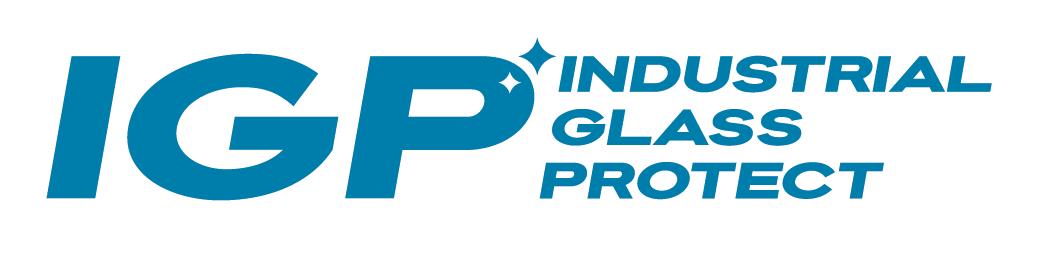
A solution to repel water and dirt from glass ChemiTek has broken new ground by entering into the cleaning and maintenance solutions for the HoReCa channel with Industrial Glass Protect (IGP).
Quality control Glass International July/August 2022 www.glass-international.com 127 Continued>>
Known as ‘one of the best hydrophobic coatings for stain-free glass’ IGP is a long-lasting treatment that repels water and dirt from glass, reducing cleaning time by up to 90%, eliminating glass deterioration as well as the need for toxic detergents for future cleaning.
IGP (Industrial Glass Protect) is an environmentally friendly, non-toxic treatment available for those looking to save time cleaning glass.
“After several studies in our laboratories, we developed the IGP as a coating for solar and non-solar glass. Thus, we innovated our product range by creating IGP PRO (B2B) and IGP Kit (B2C), two solutions that reduce glass maintenance and cleaning costs for both professionals and end consumers.”
César Martins, CEO and founder of ChemiTek, states: “We are a Portuguese company that develops, produces and markets easy-to-apply, innovative, efficient and environmentally friendly cleaning and maintenance solutions for the Solar, Glass and Automotive industries, with a special emphasis on the Solar“Inindustry.fact,when the IGP was developed, it was first thought of as a hydrophobic coating to facilitate the cleaning of solar panels.“However, observing the market trend of an increase in consumers interested in glass cleaning and maintenance items, time-saving cleaning tips and tricks and DIY guides, we came to the conclusion that there was a gap in the market for environmentally friendly and non-toxic hydrophobic treatments for glass.
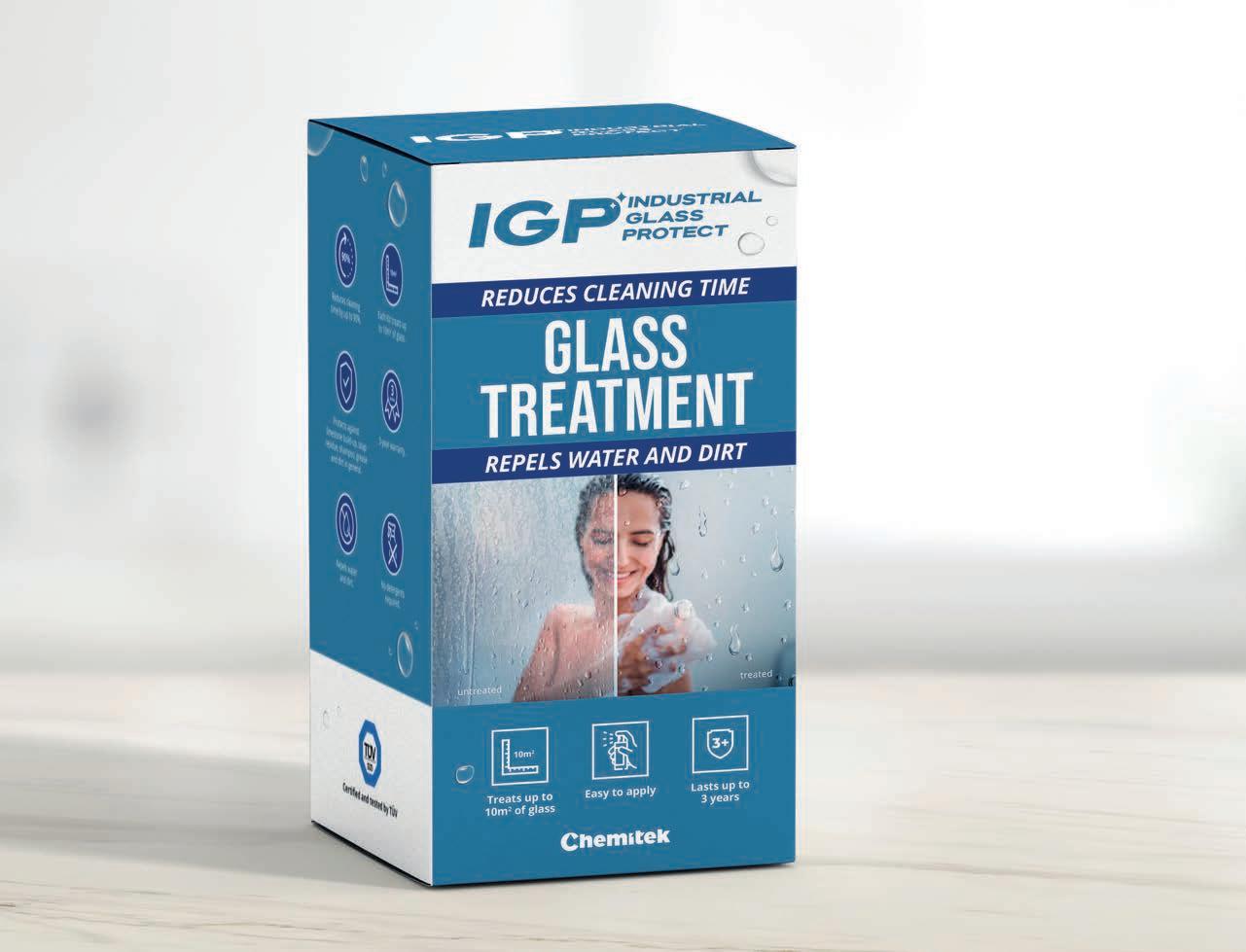
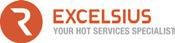
With a minimal cost per square metre, this coating can be applied by glass manufacturers or in-situ, as well as on most bathroom surfaces. It is not a glass cleaner, but a premium treatment to reduce cleaning time by 90% and facilitate subsequent cleaning!
Thanks to its hydrophobic properties, this treatment repels water and oil from the treated surface, minimising the adhesion of dirt and grease (such as soap, shampoo, dirt, dust, water, paint, etc.), but it does not eliminate the need to clean the glass, as it is not a self-cleaning product. Unlike other coatings, the IGP does not require daily cleaning products or revitalizers to maintain the coating. In addition to reducing cleaning frequency and time, the coating eliminates the need for aggressive and often corrosive/toxic glassDevelopedcleaners.
In September, ChemiTek will attend Glasstec, the world’s largest event for the glass“Glasstecindustry.isa market, trend, innovation and information platform for the global glass industry, and we are very pleased to present our coating and cleaning solutions alongside the world’s leading glass manufacturers,” says Mr Martins.
to last - with a real performance guarantee - up to five (IGP PRO) and three years (IGP kit), this product has a patented formula tested by the international laboratory TÜV Sud for use both indoors and outdoors, as it does not give off toxic odors or any type of vapors, and can be applied in shower cabins, mirrors, windows, glass facades, swimming pool glass seals, etc., facilitating future cleanings. Way more versatile than other coatings, which can only be applied on low-iron transparent glass, the IGP can be applied on all types of industrial glass (acidetched, digitally printed, patterned, tempered, laminated, curved, solar, etc.), as well as on stainless steel and chrome fittings (e.g. faucets, towel racks, etc.), tiles and grouts. This treatment also protects against limescale stains and reduces the need for glass replacement. These factors make the IGP an environmentally responsible product, the use of which reduces the cost of glass maintenance for a variety of reasons. This high-quality hydrophobic liquid coating technology is also highly appreciated and used by architects and interior designers, as it protects against cement dust, stains and etching on glass and metal surfaces during the construction phase. It also allows glass manufacturers to differentiate themselves from the competition by producing easyto-clean, low-maintenance glass that offers a value-added service and added value for customers, driving increased revenue.IGPPRO is available in 1, 2 and 5L canister formats for professionals in the HoReCa channel (hotels, restaurants, cafeterias and catering), cleaning companies and glassware and stainlesssteel material manufacturers. It is also available in the IGP kit format, which contains a 50ml bottle of IGP for end consumers who value their time and a clean home.
Visit ChemiTek in Hall 10, Booth B15, for expert advice and the latest information on all the features and benefits of IGP. � Chemitek, Esposende, Portugal Email: protectwww.chemitek.pt/igp-industrialglassinfo@chemitek.pt
Quality control Glass International July/August 2022 1280 www.glass-international.com
GGCGhazvinGlass Co. Float glass industry experts or international Float glass company Retired experts are called for collaboration with Ghazvin Glass info@ghazvinglass.comwww.ghazvinglass.comCompany. Legacy Continues...

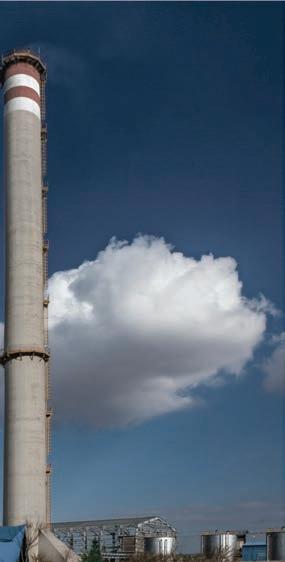
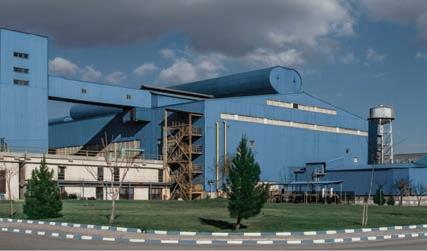
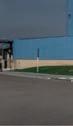
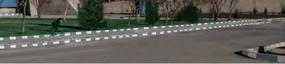

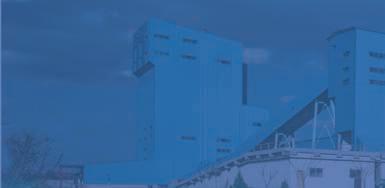



The IPGR group, International Partners in Glass Research, is offering the post for a project manager in research and development.
please send your
The International Partners in Glass Research (IPGR) is a research association founded 1984, based in Aachen, Germany IPGR is in close cooperation with the RWTH Aachen University. The members of IPGR are ten renowned international companies within the container glass industry The aim of IPGR is to create a vital, international research network and to conduct R&D projects for its members.
You are therefore a pro active, strategic thinking personality with a hands on approach and very good communication skills. Reporting is directly to the IPGR management board. We offer a highly motivated team, flat hierarchies, self dependent working and p roject responsibility. expertise, complete application preferably via email to: IPGR - International Partners in Glass Research Prof. Dr. Christian Roos christian.roos@ipgr.com
If you would like to apply your
Forckenbeckstraße 33 52074 Aachen , Germany www.ipgr.com BASF Temperature Sensing The Shape of Your Success Accurate, reliable, and affordable temperature sensing equals success for your plant. With the help of our proprietary Fibro ® wire, we will exceed your expectations in performance while reducing the cost of your temperature sensor. As a full loop precious metal provider, BASF can help you achieve more value by recycling precious metal outContactthermocouples.ustofindmore! catalysts.basf.com/glass BASF_CAT-003354_Visual_Components_AZ_180x127mm_RZ.indd 1 09.02.22 12:07
We are looking for a project manager for research and developmentin an international environment with high motivation for team orientated hands on working. The focus of the positionis on melting and conditioning of glass as well as energy and raw materials You lead and manage R&D projects from kick off to implementation in a container glass plant. After profound strategic and technical consulting you establish timelines, manage internal and external resources and conduct the R&D work together with the IPGR members. You impl ement derived results at our member companies. We are seeking an outstanding candidatewith sound scientific education, relevant working experience and a strong track record in the glass industry, preferably furnace operation and melting of glass. You are engineer or material scientist with focus on glass and you have a sound background in glass or ceramics , thermodynamics and kinetics of glass melting, and energy intensive processes.Project management and team coordination experience is required. Fluent English and willingness to travel internationally is mandatory.


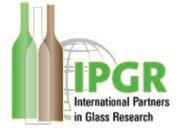
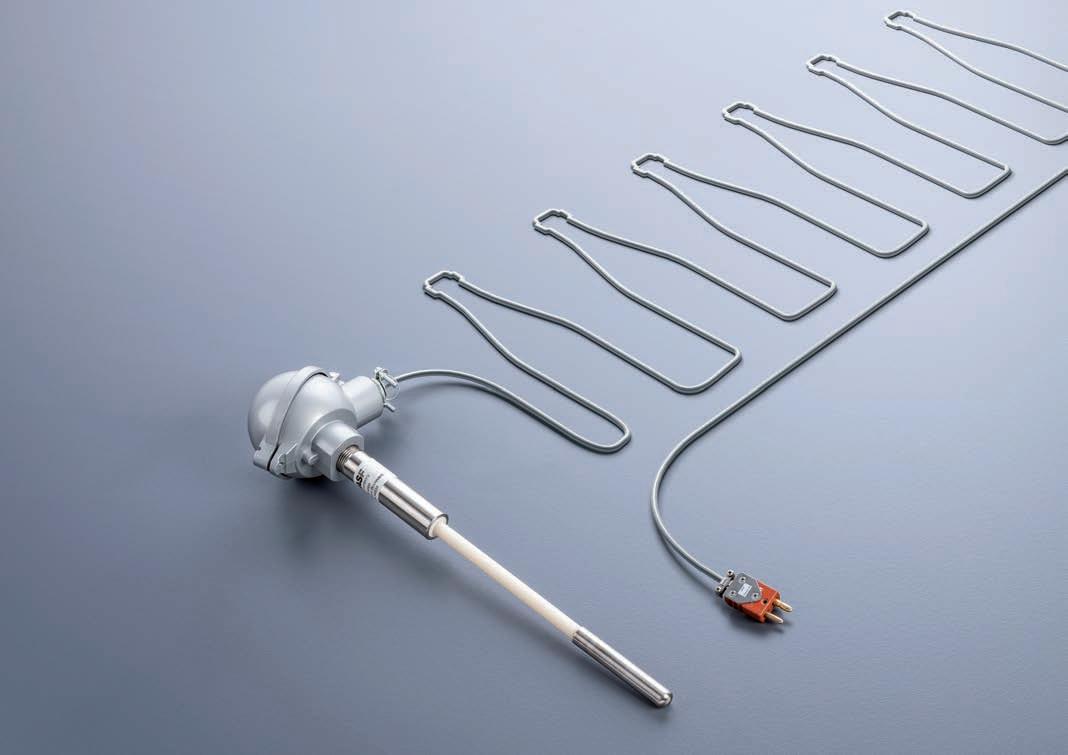
2023
2023
2023
REFRACTORIES
sste rofi es Glass International July/August 2022 1300 www.glass-international.com HALL 13/C34 HORN Glass Industries AG 95703BergstrassePloessberg, www.hornglass.comGermanyinfo@hornglas.de Some solutions are thanclearerothers. www.hft.comBooth 13C48-1
he event format is a niche trade e hibition here people can arrange meetings number of suppliers and industry e perts in one place. isitors and e hibitors the free conference sessions to hear from industry e perts. hese e hibitions bring together international e perts hollo and container manufacturers and businesses that use glass containers to discover the latest innovations hich energy e ciency uality control pac aging logistics and decorative possibiliti LATIN AMERICA | TURKEY he event format is a niche trade e hibition here people can arrange meetings ith a number of suppliers and industry e perts in one place. isitors and e hibitors can a end the free conference sessions to hear from industry e perts. hese e hibitions bring together international e perts hollo and container manufacturers and businesses that use glass containers to discover the latest innovations hich include energy e ciency uality control pac aging logistics and decorative possibilities. | TURKEY 2023 | KOREA he event format is a niche trade e hibition here people can arrange meetings ith a number of suppliers and industry e perts in one place. isitors and e hibitors can a end the free conference sessions to hear from e perts. hese e hibitions bring together international e perts hollo and container manufacturers and businesses that use glass containers to discover the latest innovations hich include energy e ciency uality control pac aging logistics and decorative possibilities. AMERICA 2024 | TURKEY 2023 | KOREA 2024 | MEXICO Turkey, Istanbul South Korea, Asia CAST Ltd . H-9200phone:TimföldgyáriMosonmagyaróvár,u.9-13.+3696574100fusedcast@motim.huwww.motim.hu
LATIN
HALL 13/F96 MOTIM SORG Keramik Service GmbH Stoltestraße 23 97816 Lohr am Main, Germany sks.net HALL 15/B38 FORYOUIT’STIMETOGET GREENER 13B92 SEE US AT GLASSTEC 20-23 September, 2022www.fivesgroup.comDüsseldorf Nikolaus SORG GmbH & Co. KG Stoltestraße 23 97816 Lohr am Main, Germany sorg.de HALL 15/B38 EME WockeratherGmbH Weg 45 41812 Erkelenz, Germany eme.de HALL 15/B38 Glass glasstecInternationalstandNo: Hall13/A81 Te�nolo�� for G�ss �du�ry 15F20www.gsl.cz 15F16www.flammatec.com Tomorrow,s Technology Today www.fic-uk.com 12F72 The Teco Group ecutive arkwa Toledo, Ohio 43606-2927, USA Tel +1 419 537 9711 www.teco.com HALL 13/B62 Electroglass Ltd. Brunel Road, Manor Trading Estate, en eet sse ngland. Tel +44 (0)1268 565577 info www.electroglass.co.ukelectroglass.co.uk HALL 13/A91
FUSED




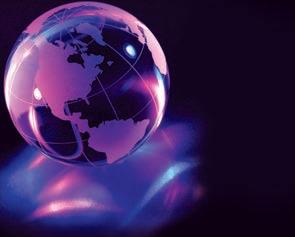

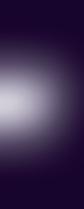
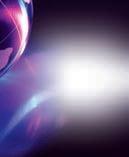

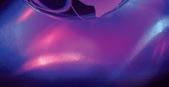


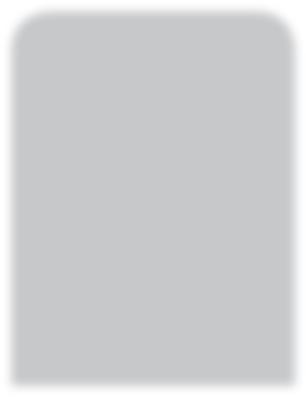
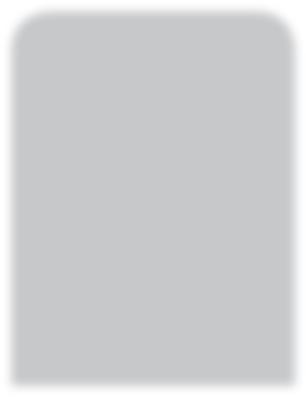
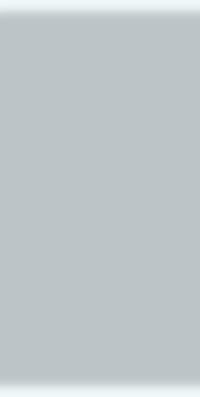
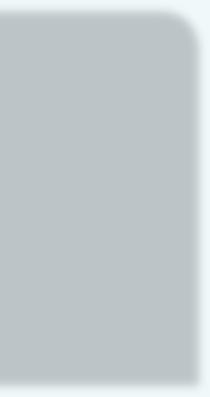

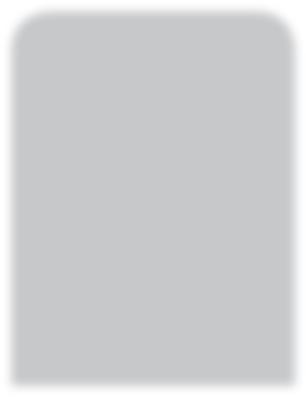
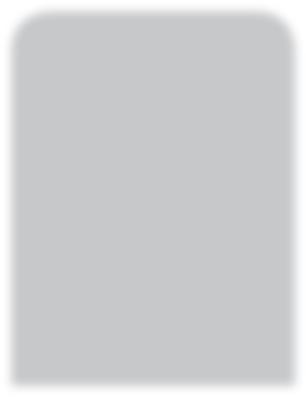
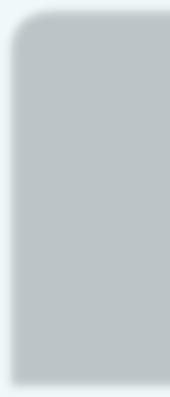
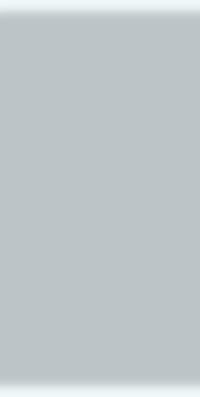
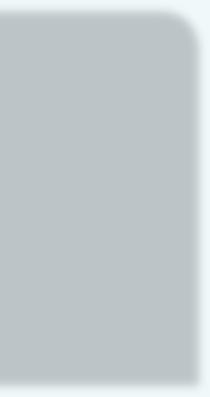

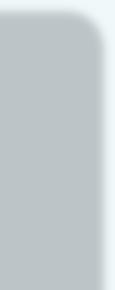
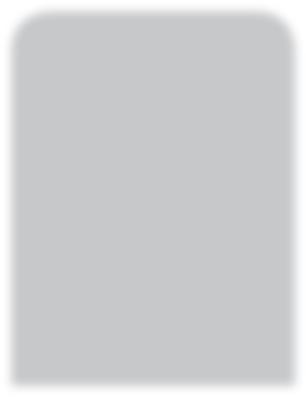
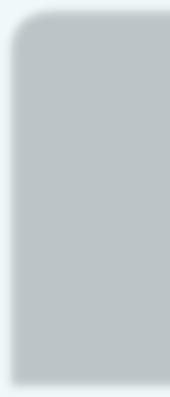
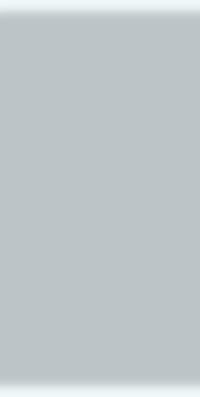
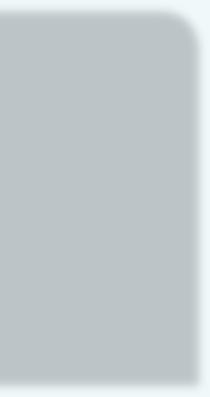

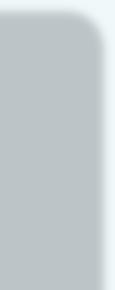
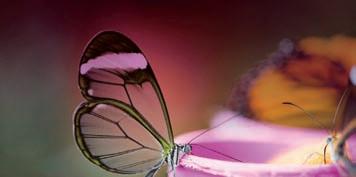


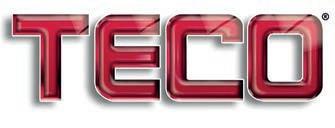
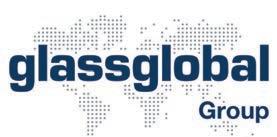
WSA2022 World Soda Ash Conference Hilton Sorrento Palace | Sorrento, Italy October 11-13, 2022 ����S��� ��� Volatility, Uncertainty, Sustainability: How will the soda ash markets navigate such challenging conditions? The global soda ash market commenced the year 2022 being extremely tight as the industry emerges from COVID-19. Demand has been robust across all end-use sectors and supply structurally short. However, the industry now faces new challenges following the Russia-Ukraine conflict on February 24th, raising several questions for soda ash markets. Ho� �ill un�olding sanctions against �ussia s�a�e global and �uro�ean energ� costs� �ill in�lation lead to de�and destruction� Ho� �ill en�iron�entall� in�luenced sectors contribute to global de�and gro�t�� ��at is t�e global su��l� and de�and outloo� �or co�ing �ears� Join us on 11 – 13 October for �orld Soda �sh �on�erence in Sorrento, Italy and gain the latest insights and deep analysis into the soda ash industry as you connect with the industry professionals and ��e�ical �ar�et �nal�tics experts. � Training Workshop: Commercial Impacts of Soda Ash Technologies Workshop � �� �ct� �ue •Technical overview of the Solvay Hou & Natural Process Economics •Structural Overview of the Chinese and Global Soda Ash Industries •Impact of Chinese Fertilizer Market on Hou Process •Global•RelativeEconomicsCompetitivenessTrade /Logistics •Role of Government in the Soda Ash Industry MEET US AT HALL 15 C14
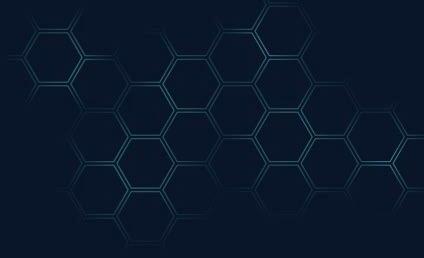

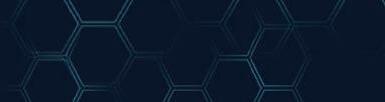
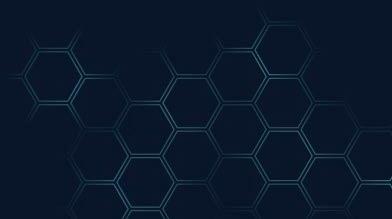
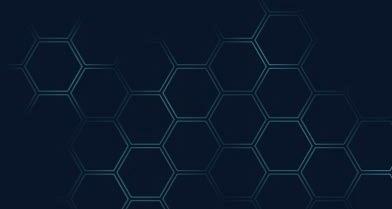
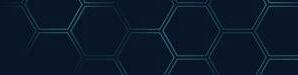
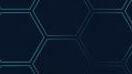
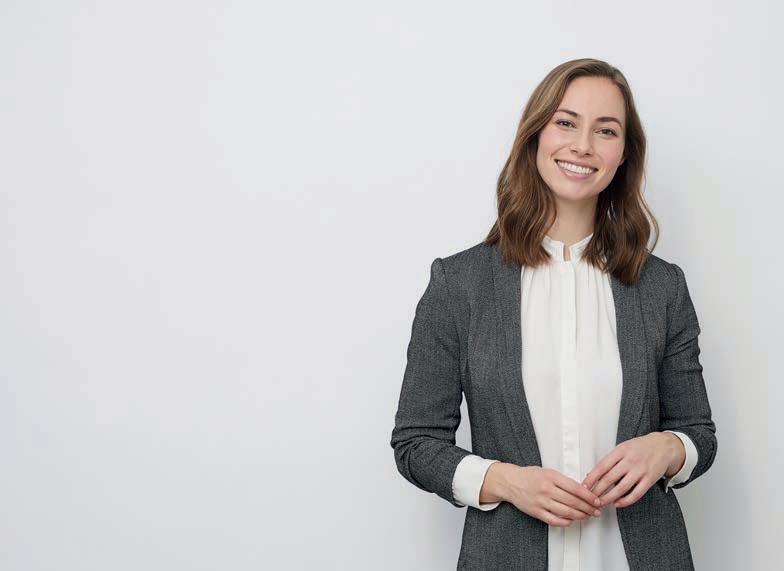
CLASSIFIEDS ANNEALING LEHR COLD-END COATING Global SystemsCombustion Total Support Unit 43, Evans Business Centre, Easter Inch, Bathgate EH48 2EH, Scotland, UK Tel+44 (0) 1506 657310 Fax +44 (0) 8704 799975 Email Sales@globalcombustion.com Web www.globalcombustion.com ZATIAMAdes Plattes, 1 Chemin des Plattes, 69390 Vourles, France Tel +33 (0) 4 37 20 15 00, Fax +33 (0) 4 78 07 94 50 Email: Website:www.tiama.commarketing@tiama.com ANNEALING LEHRS HEAT-UP SERVICES ELECTRICSYSTEMSHEATING Rio Tinto Minerals 2 Eastbourne Terrace London W2 6LG, UK Tel +44 (0) 207 781 1450 Fax +44 (0) 207 781 1851 Email: simon.cook@riotinto.com Web: www.riotintominerals.com RAW MATERIALSINSPECTION I NDUSTRIAL G AS E NGINEERS UNIT D2, BROOKSIDE BUSINESS PARK, GREENGATE,CHADDERTON, M24 1GS, ENGLAND TELEPHONE: 0161-654 7700 FAX: 0161-655 3812 E-MAIL: SALES@MONTSELAS.CO.UK WWW.MONTSELAS.CO.UK INDUSTRIAL GAS ENGINEERS Unit D2, Brookside Business Park, Greengate, Chadderton, M24 1GS, UK Tel +44 (0) 161 654 7700 Fax +44 (0) 161 655 3812 Email sales@montselas.co.uk www.montselas.co.uk MANUFACTURERS AND SUPPLIERS OF SELAS SQUARE PORT GAS & AIR VALVES GAS COMBUSTION EQUIPMENT SYSTEMS/BURNERSCOMBUSTION GLASS MEASUREMENTLEVEL Contact Esme Horn T+44 (0) 1737 855136 to book your space Low-Emission Oxy-fuel Solutions • Oxygen & oxygen flow control equipment • Global oxygen enrichment applications • Cleanfire® oxy-fuel burners • Start-up services Inerting Applications • Hydrogen, nitrogen & other gases • Enabling flow control equipment (39101) 800-654-4567 (code airproducts.com/glassgigmrktg@airproducts.com344) Bock Energietechnik GmbH Gösen 15 92685 GermanyFloss Tel: 0049 9603/1295 Fax: 0049 www.bock-energietec.deinfo@bock-energietec.de9603/2995 Electrical melting in perfection Special services - Engineering and modelling for boosting systems - Water-cooling Systems for electrode holder - Electrode holder for bottom / side / top - Power regulation / Transformers -Hot -Changedrillingofelectrode holder SCREEN PRINTING Bergkirchener Straße 228, 32549 Bad Oeynhausen, Germany kammann.de SCREENDIGITAL PRINTING HOT STAMPING FULLY MACHINESUNIVERSALAUTOMATICDECORATING KAMMANN GmbH
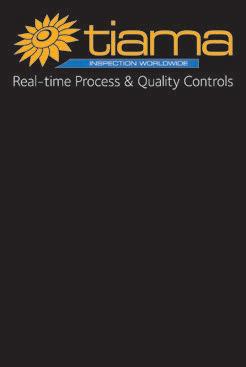
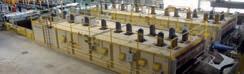
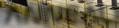
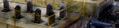




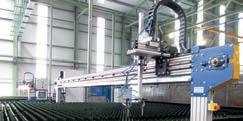
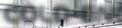

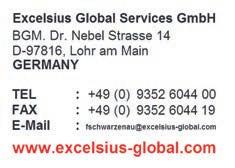


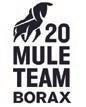














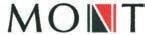
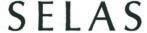


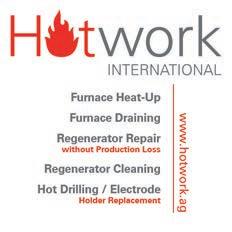
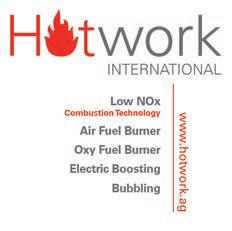
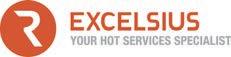
REFEL S.p.A. Zona Industriale Ponte Rosso 33078 San Vito al Tagliamento (PN), Italy T +39 0434 849 111 E info@refel.com
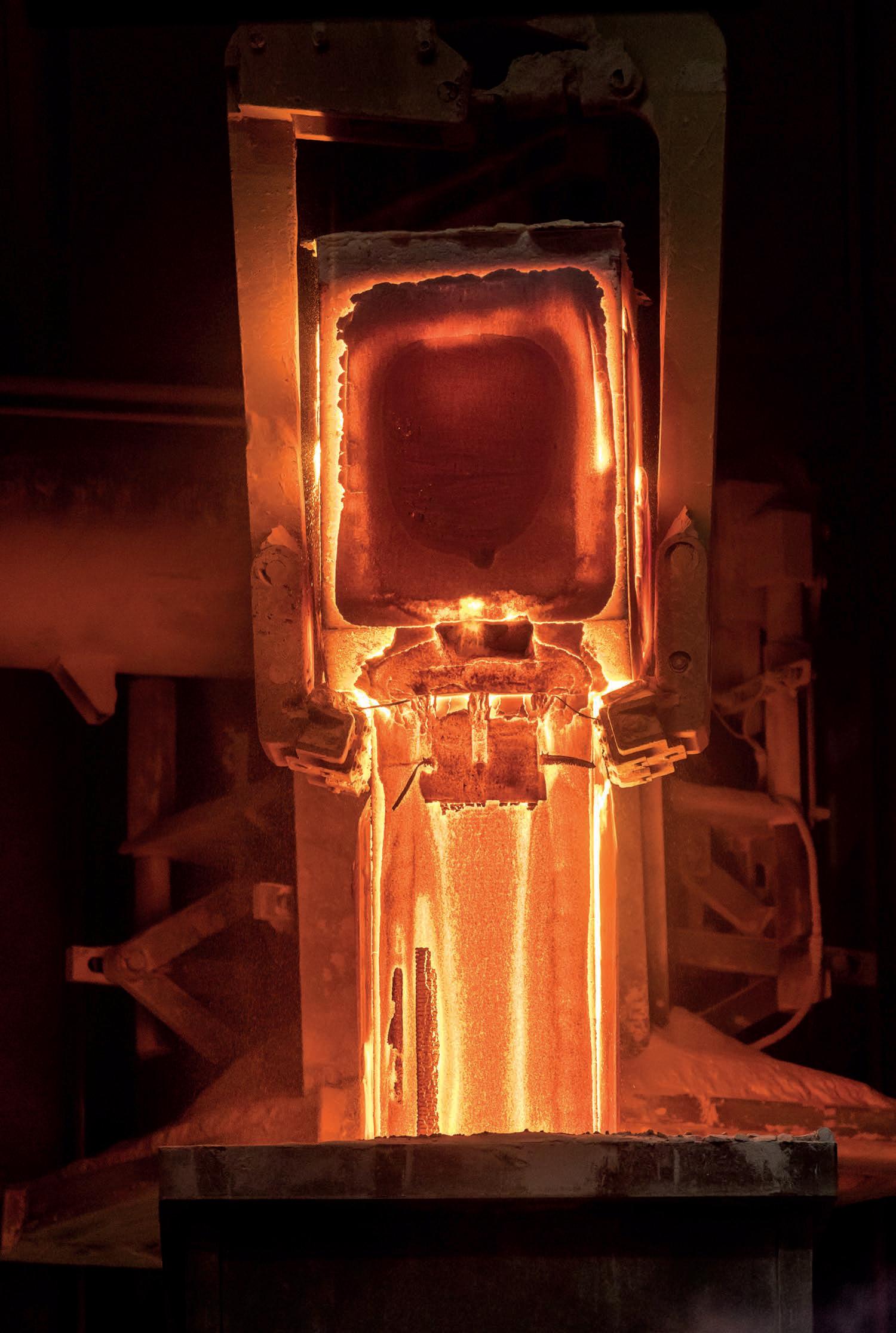
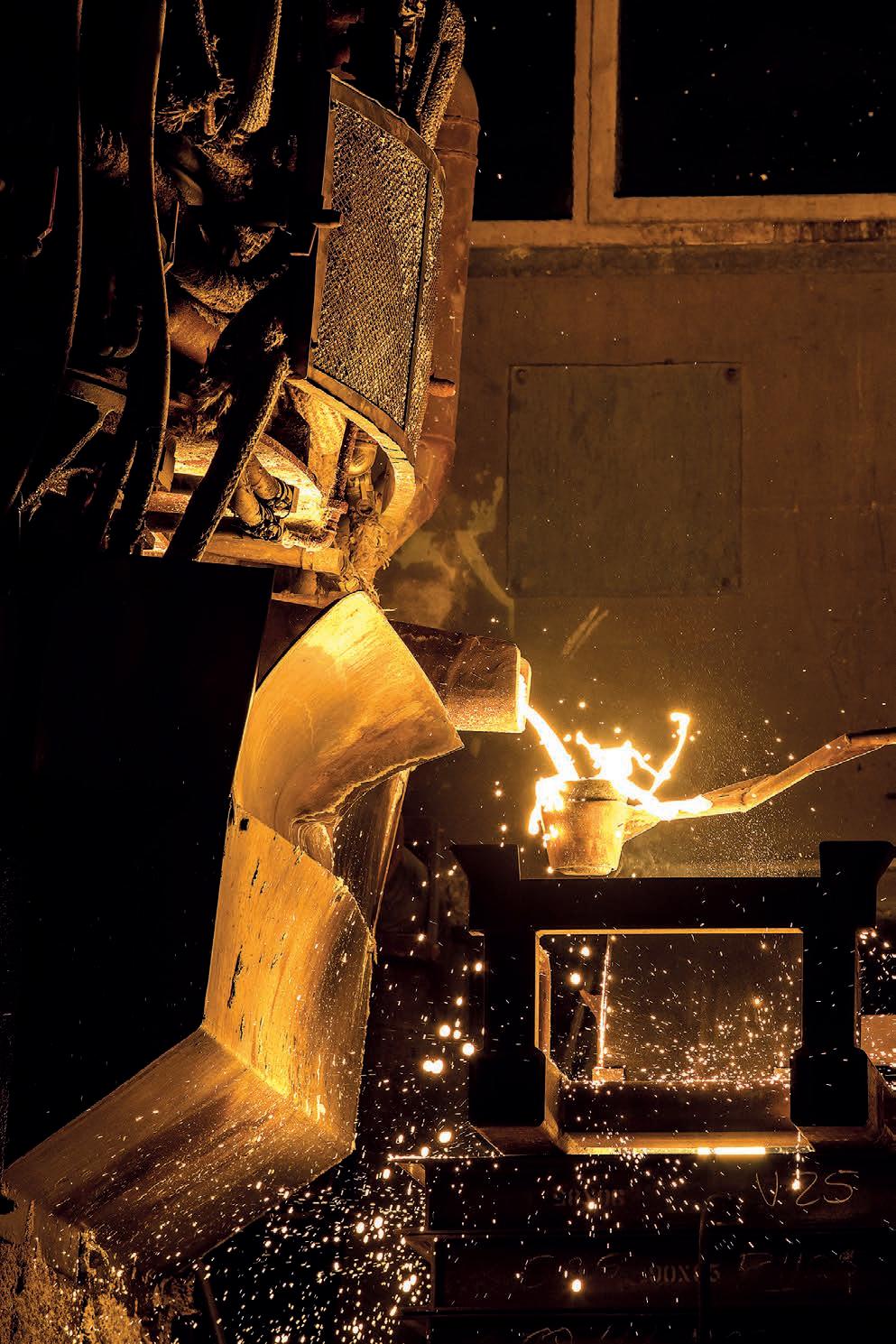
FUSED CAST REFRACTORIES REFEL 1532 REFEL 1334S REFEL 1240 REFEL 1334SC REFEL 1616ULX REFEL 1240 FVMo Excellence Made in Italy. This is the motto on which our company, manufacturer of high quality fused cast refractories material, bases its success. Our main focus is the highest possible customer satisfaction, understood as the ability to timely provide products and services that fully comply with the customers’expectations. www.refel.com
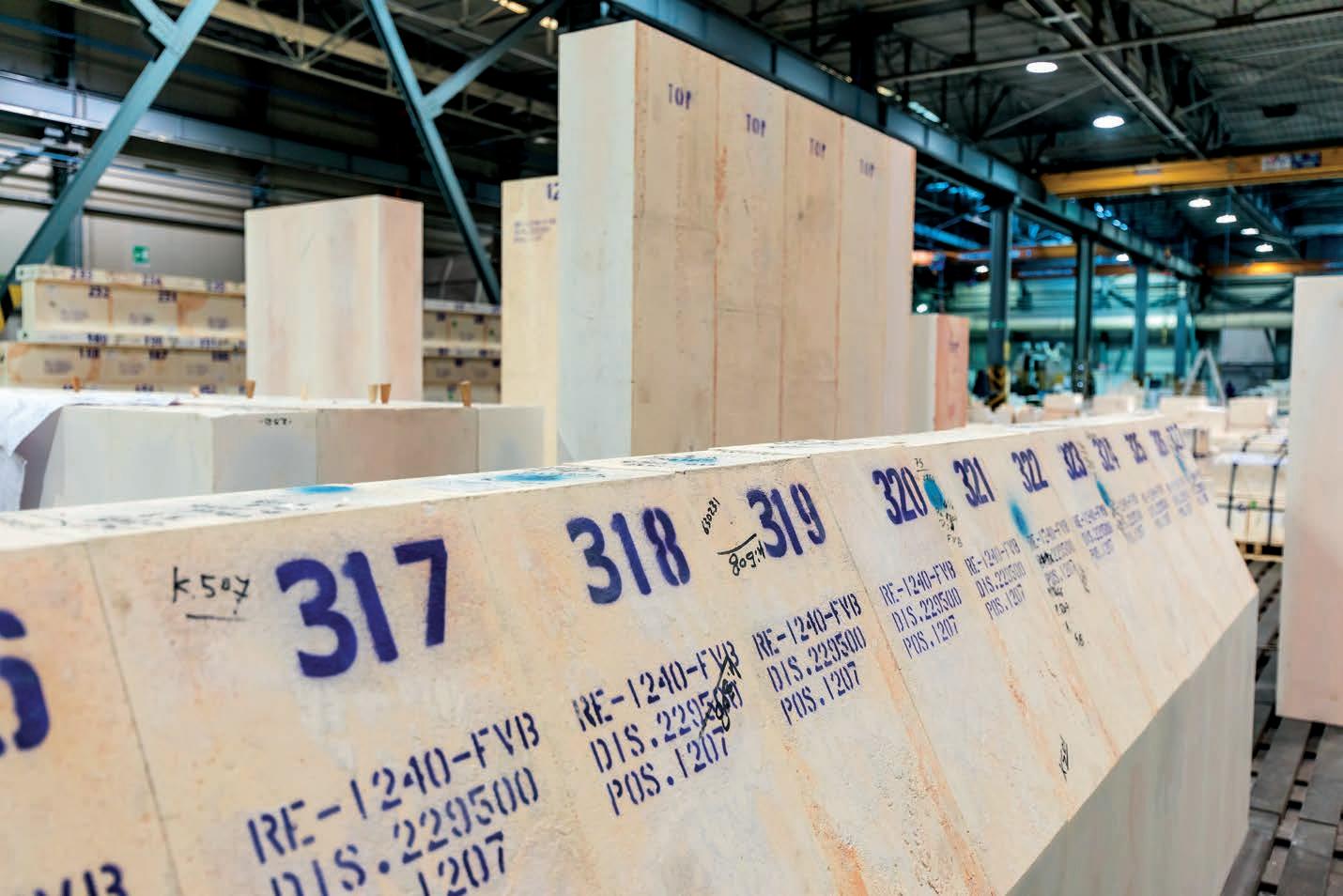
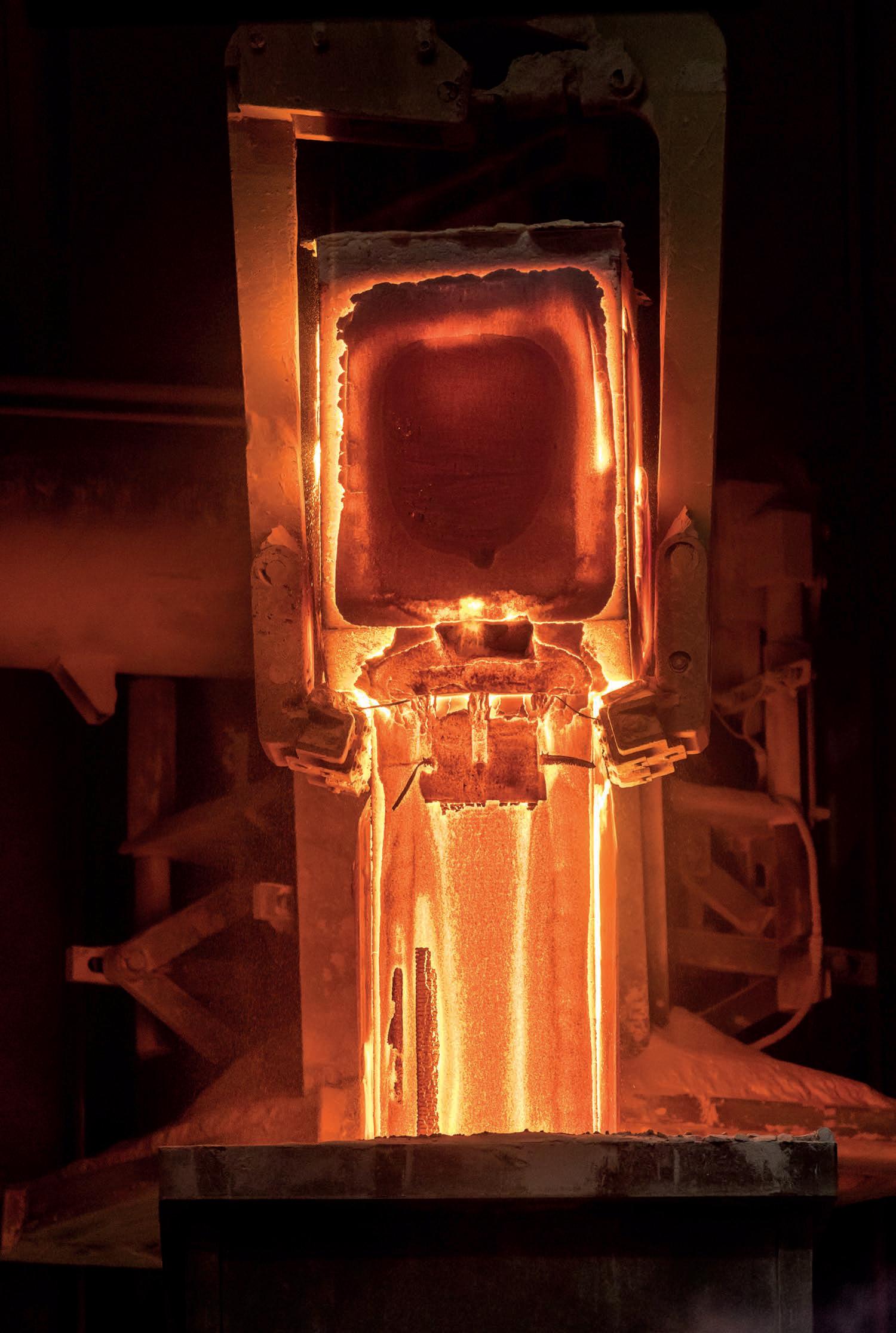
For details of our full range, please visit www.pennine.org
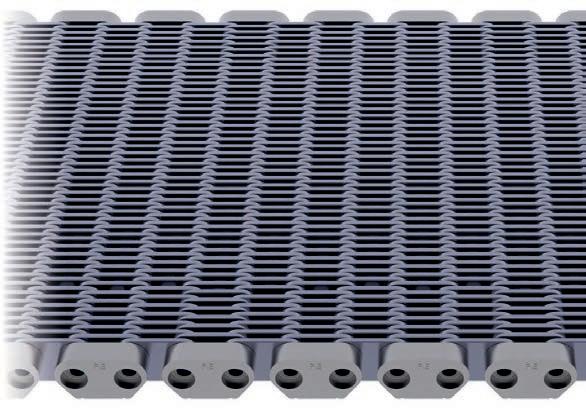
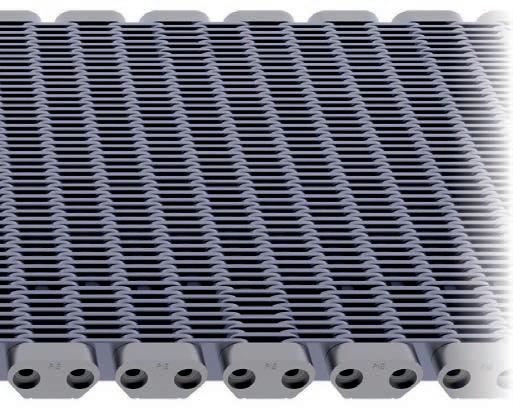


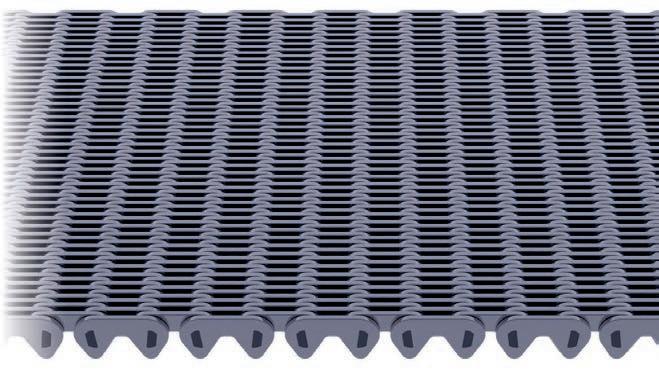


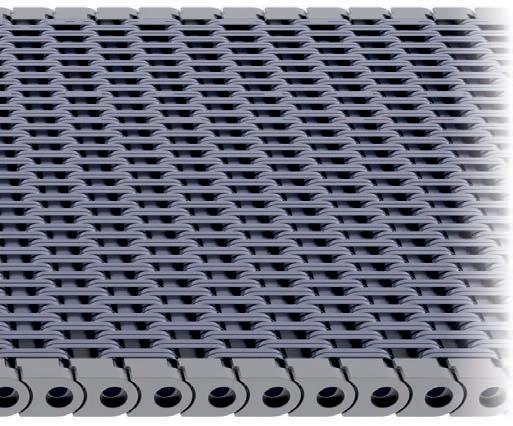
™ THE FUTURE OF CONVEYOR CHAIN www.pennine.orgsales@pennine.org +44 (0) 1484 864733
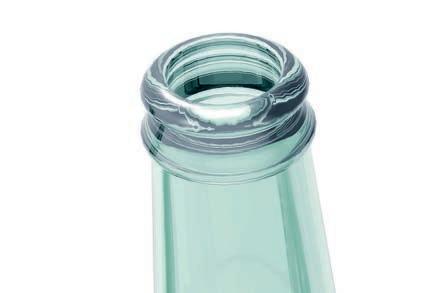
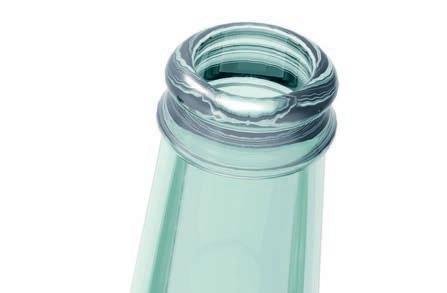
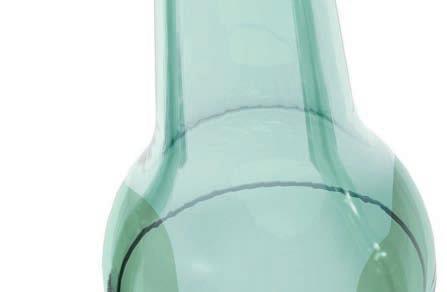
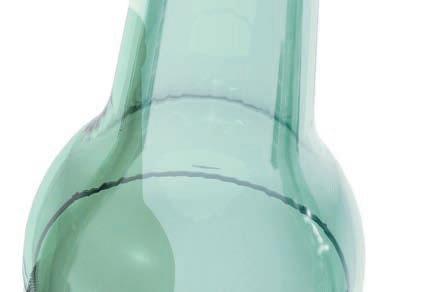
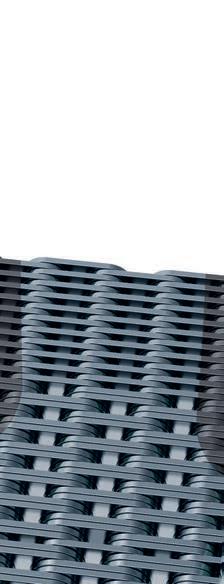
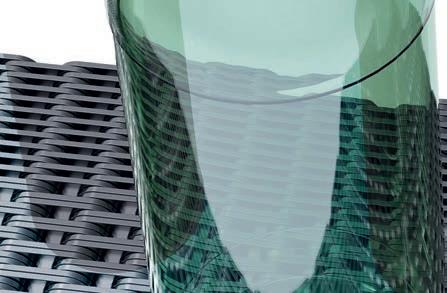
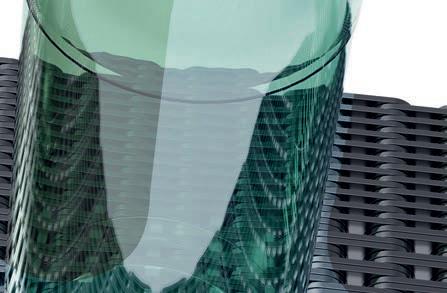
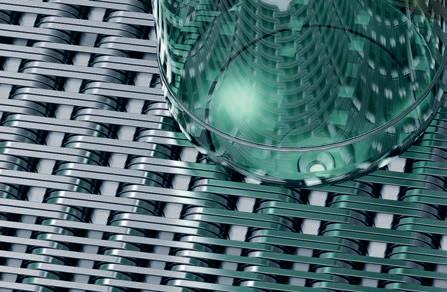
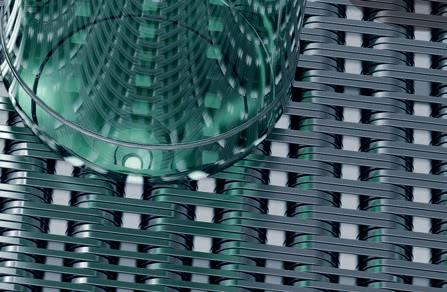
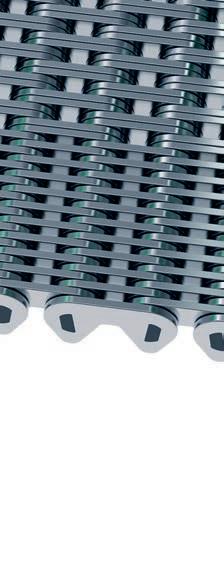

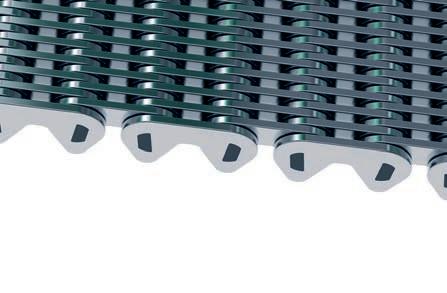
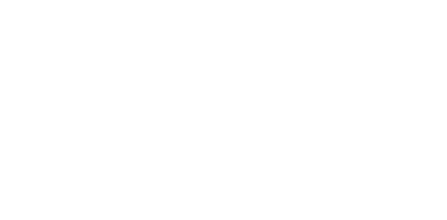
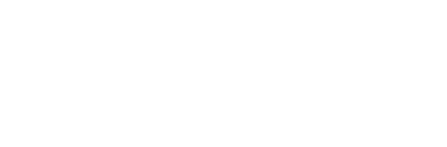
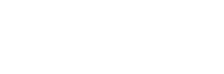
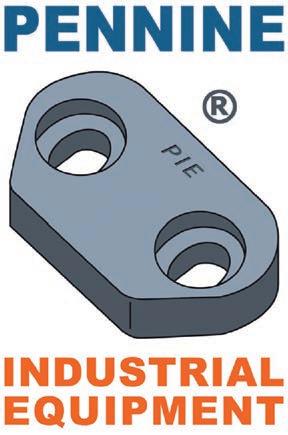