

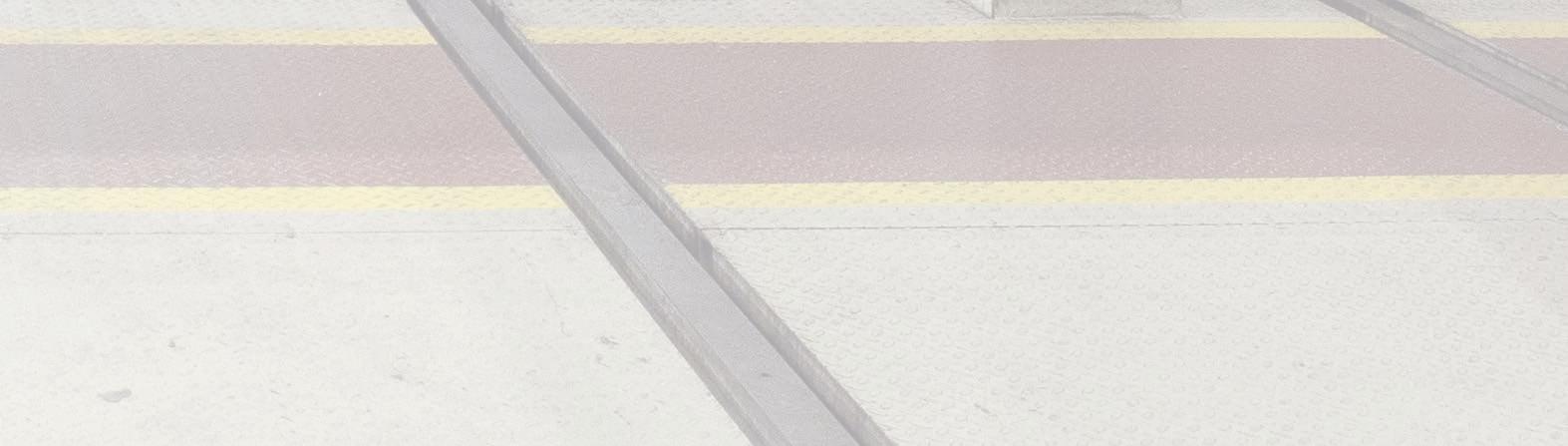
Tebulo Robotics specializes in the design and supply of innovative robotic solutions that operates under extreme conditions. With our many years of experience, knowledge in technology and driving forward advancements in engineering and robotics, we are able to offer a wide range of superior solutions that accelerate industrial processes.
Tebulo Robotics creates high quality robot applications that are the solution for making industrial processes faster, better, safer, cleaner and more productive.
You have in your posession the official programme for the Future Steel Forum 2023 and in it you will find an exciting programme of presentations from experts in the field of steelmaking and digitalization, not to mention a collection of articles reflecting some of the themes to be discussed over the next two days. You will hear from steelmakers, academics, plant builders and specialists in the field of AI, a subject receiving a lot of bad publicity, as the world gets to grips with the technology. Whenever I think of AI, I think of the HAL computer in Kubrick’s 2001: A Space Odyssey, but here’s hoping it’ll be a little more helpful. Perhaps one day we will live in a dystopian world like that envisaged by legendary science fiction writer, Philip K Dick. We might all have Dr. Smile the suitcase psychiatrist at our sides, and we might all be locked in our apartments and sued by our front doors if we don’t pay our rent. As Jon Voight’s character in Deliverance said to Burt Reynolds’ character, “You make that sound rather shitty, Lewis”, and let’s face it, who knows what the future might bring? But let’s hope that AI will do more good than bad and will aid steelmakers in their quest to produce greener steel.
��t����������te����e��e�������������e����te�e������� te�h���������������e����� ��e�����av��� e�e����� �����e��������������e���������
����t��tee���e�h������e� ����������e��� ����e������t��������������t������he������ ���t���e����e�e�����������e������������t����e��
08:30
Welcome to the Future Steel Forum by Matthew Moggridge, Programme Director and Editor, Steel Times International
08:40
Opening Keynote Address by voestalpine: An overview of the company’s HPM (High Performance Metals) Division, its sustainability strategy and its digital transformation by Dr. Michael Eder, Chief Digital Officer, and Philipp Horner, Chief Sustainability Officer, voestalpine, HPM Division.
Opening Themes – Professor Dirk Schaefer, Head of the School of Engineering, University of Lincoln, United Kingdom.
09:20
New challenges in the steelmaking industry – digital transformation by Dr. Jeasook Chung, Group Leader/Research Fellow, Control and Instrumentation Research Group, POSCO South Korea.
09:50
A New Approach to Implement Industry 4.0 Concepts in the Steel Industry by Dr Thiago Turchetti Maia, Executive Vice President, Centre of Excellence, SMS Digital.
10:20
Tea & Coffee Break
10:50
The Steel Decarbonization Challenge and Digitalisation by Dr. Klaus Peters, Secretary-General, ESTEP, and Costanzo Pietrosanti, Chairman of the Smart Factory Focus Group, ESTEP, and Dr. Valentina Colla, Assistant Professor of Metallurgy, Scuola Superiore Sant’Aanna.
Digitalisation in Action – Session Chair: Dr. Klaus Peters, Secretary-General, ESTEP
11:20
Industrial Cybersecurity – Using Artificial Intelligence to Improve Risk Management by Carlos Russell, Chief Business Compliance Director, Ternium, Argentina.
11:50
Cyber-Physical Systems and Robotics Applications in Intelligent Steel Works by Osamu Yamaguchi, General Manager, Strategy, JFE Steel, Japan.
12:20
Forge a Future-Proof Steel Company by Going Digital, by Stefan Koch, Global Lead, Metals Industry, SAP.
12:50
Lunch
Decarbonization and Digitalization – Session Chair: Rutger Gyllenram, CEO & Founder, Kobolde & Partners.
14:00
Saving Energy and CO2 Emissions Through Synchronized Scheduling of Continuous Casting and Hot Rolling Operations by Dr. Falk-Florian Henrich, Founder and CEO, Smart Steel Technologies.
14:30
Defining the Green Steel Premium by Stanislav Zinchenko, CEO, GMK Center, Ukraine.
15:00
Tea Break
15:30
What Will it Really Take for a Decarbonized, Digitized Future-Fit Steel Sector? By Caroline Ashley, Director, SteelWatch.
16:00
Digital Manufacturing and Decarbonization – Panel Discussion
• Caroline Ashley, Director, SteelWatch.
• Jean-Paul Nauzin, Technology & Innovation Director, Fives Group
• Maria Salamero Sansalvadó, Head of Sustainability, CELSA Group.
• Dr. Valentin Vogl, Steel Industry Analyst at ARIA.
• Osamu Yamaguchi, General Manager, Strategy, JFE Steel, Japan.
• Sanjeev Manocha, Director of Business Development, Lanzatech
Panel chair: Rutger Gyllenram, Founder and CEO, Kobolde & Partners, Stockholm.
16:45
Life Cycle Information Management, Scrap Processing and the Recovery of Alloys by Rutger Gyllenram, Founder and CEO, Kobolde & Partners, Stockholm.
17:15
Green Steel: A New Frontier for In-Space Manufacturing and Circular Economy by Professor Mini C Rai, Global Chair in Robotic Engineering and Head of Space Engineering Research, University of Lincoln, UK.
17:45
Closing Remarks.
17:55
Conference Closes.
08:30
Welcome to the Future Steel Forum by Matthew Moggridge, Programme Director and Editor, Steel Times International
08:40
Opening Keynote: CELSA’s approach to Industry 5.0 as an enabler of circular value chains by Anna Doménech Abella, Corporate Innovation Manager, CELSA Group.
Digital and AI Solutions – Session Chair: Sanjeev Manocha, Director of Business Development, Lanzatech
09:10
How Digitalization is driving Sustainable Steelmaking at AFV Group Beltrame and BM Group, by Ion Rusu, Research and Development Manager, Polytec BM Group.
09:40
AMI Artificial Intelligence Developments for Stainless Steel Production in Aperam Genk by Emmanuel Placier, Business Development Manager for Europe, Middle East and Asia, AMI Automation.
10:10
Tea Break
Digital and AI Solutions continued – Session Chair: Sanjeev Manocha, Director of Business Development, Lanzatech
10:45
Integrated Sinter Pellet Operation Control at Tata Steel Jamshedpur, India, by Bikash Kumar Chatterjee, Head of Sinter Plant Operation, Tata Steel Ltd, and Vikas, Head Client Partner, Iron Making, Tata Steel India.
11:15
Challenges and Strategies for Decarbonizing the Steel Sector by Dr. Aliyu Aliyu, senior lecturer in Sustainable Energy, University of Lincoln, UK, and Professor Dirk Schaefer, head of the School of Engineering at the University of Lincoln.
11:45
Digital Solutions for the support of the EAF operation by Assistant Professor Dr. Vito Logar, Faculty of Electrical Engineering, University of Ljubljana.
12:15
Three Ingredients of Successful AI Projects by Giovanni Bavestrelli, Director of Data Science, Tenova.
12:45
Lunch Break
Business Models – Session Chair: Holger Stamm, Partner, Energy and Natural Resources and Operations, Oliver Wyman
14:00
A Friend in Need – a Friend Indeed! Challenges with AI-based Decision Support by Kurt Herzog, Head of Industry 4.0, Primetals Technologies, Austria.
14:45
Strategies for Sustained ML Use in Steel Production: A Real-World Case Study by Pamir Ozbay, Head of Operations and Co-founder, Fero Labs
15:15
Tea Break
15:45
Using a Digital Twin in Virtual Commissioning of an Automated Warehouse and Logistics by Tony Leikas, CEO, Pesmel Corporation.
16:15
Decision Intelligence Solution for Quality Management in Steel Manufacturing by Luca Cestari, Senior Manager, Process and Quality, Danieli Automation DIGI&MET.
16:45
Energy Consumption Forecast to Cash in on Profits from Short-Term Market Price by Dr. Stefan Albers, Business Consultant and Global Solution Architect, PSI Metals.
17:15
Advanced Modelling to Enhance Product Quality, Increase Productivity and Prevent Human Error by Alexandre Gauche, Steel Digital Factory Director, Fives Group.
17:45
Closing Remarks
17:55
Conference Closes.
Matthew Moggridge has been editor of Steel Times International since January 2014, having previously edited Aluminium International Today, both published by the UK-based Quartz Business Media. During his time on both titles he has travelled extensively around the world interviewing and writing about leading figures in the metals industry and covering international steel and aluminium conferences. In addition to working as a journalist in many different industrial sectors, he is also the creator and driving force behind the development of the Future Steel Forum.
Matthew’s career as a business journalist has spanned many leading titles covering other industrial sectors including food processing, foodservice, foreign direct investment, bulk handling and transportation and computers.
Dr. Jeasook Chung is the group leader of the control and instrumentation research group at POSCO. He has studied the steelmaking process for over two decades. With his domain expertise, he has been trying to shift the industry’s focus from traditional knowledge-and-experience-based improvements to AI-based smart manufacturing in the steelworks. Jeasook received his PhD in mechanical engineering from POSTECH. He has been a researcher at the POSCO Technical Research Lab for 26 years.
Pamir Ozbay is the head of operations and co-founder of Fero Labs, an industrial machine learning software company based out of the US and Germany. His team of industrial data scientists is committed to maximizing customer value through the implementation of explainable ML. Pamir’s career commenced in 2009 within GE’s industrial automation division, following the completion of his M.S. in electrical engineering from Columbia University. Over the years, he has undertaken diverse roles across engineering, sales, and consulting at industry leaders including TMEIC and Siemens, with a primary focus on the steel industry. He remains heavily involved in Fero’s steel deployments across the globe.
Stanislav Zinchenko is the CEO of the GMK Center, chair of the Committee for Environment and Sustainable Development of the European Business Association, and president of the Council of Supply Chain Management Professionals’ Ukraine Roundtable. For the last five years, Stanislav has provided consulting services for Ukrainian iron and steel companies, specializing in sustainability issues, supply chains, CAPEX policy, and market analysis. He has 15-years of experience in consulting for manufacturing companies and expertise in operational management and supply chains as a team leader, consultant, and analyst in international projects in the field of entrepreneurship, operational efficiency, and logistics infrastructure. Stanislav has a master’s degree in international economics from Kyiv National Economic University.
As part of the AMI team based in Europe, Emmanuel Placier is responsible for business development in Europe, the Middle East and Asia. After graduating from the Monterrey Institute of Technology, Emmanuel obtained a master’s degree from the Czech Technical University in Prague for mechatronics and control engineering. He has since focused his career in the steel industry, specializing in electrode regulation and EAF optimization. Since 2014, Emmanuel has focused on developing business opportunities for AMI after having worked as a regulation engineer.
Alexandre Gauche has been working at Fives since 2017, starting as a digital and innovation director in the energy division, then becoming a service and digital director in the steel and glass division. He has a master’s degree in engineering, science and technology from École Polytechnique in France and a master’s degree in science and executive engineering from École Nationale Supérieure des Mines de Paris, France.
With an engineering degree in machine automation, Tony Leikas has held various positions in the technology industry areas of engineering, sales, and management. He has 25 years of working history in Pesmel and since 2011 has held the position of chief executive officer. His experience in sales combined with the firm technical background has given him a strong basis for leadership of the company. Tony has been a member of the management group of Pesmel for over a decade. He is also chairman of the board of Pesmel Taiwan and the other subsidiary companies.
Kurt Herzog completed his master’s degree in industrial automation at the Technical University of Vienna and his MBA at the Linz Management Academy. In 1997, he began working for VAI, a predecessor company of Primetals Technologies, in the area of process automation, and held several management positions in electronics and automation as well as in engineering. Since 2016, he has been responsible for the Industry 4.0 portfolio of Primetals Technologies.
After working for four years as the head of production planning and IT at a PSI Metals customer, Stefan Albers joined PSI Metals in 2007, working in various positions as a software engineer, solution architect, project manager and business consultant for planning, scheduling, and execution. Stefan holds a PhD in electrical engineering from TU Dortmund.
Professor Dirk Schaefer is the head of the school of engineering at the University of Lincoln. He is a professor of mechanical engineering and an international thought leader in research on cyber-physical systems for production engineering (Industry 4.0). Dirk also directs the Industrial Digitalisation and System Intelligence Research Group in the school of engineering.
Dr. Falk-Florian Henrich is the founder and managing director of Smart Steel Technologies. The company offers AI-based software products to optimize steel production. Prior to founding Smart Steel Technologies, Dr. Henrich built the high-tech company CeleraOne (2011-2018) and established it as the market leader in the paid content sector before selling it to Axel Springer SE. Dr. Henrich holds a PhD in mathematics and contributed substantial research to the theory of loop spaces of Riemannian manifolds and artificial intelligence.
Dr Aliyu Aliyu is a senior lecturer in sustainable energy at the University of Lincoln and is a member of the Sustainable Energy and Power Research Group within the school of engineering. He has interests in low-carbon technologies such as the production of biofuels and green hydrogen and has worked with companies to assess the deployment of low-carbon technologies.
Professor Mini C. Rai is the global chair in robotic engineering and heads space engineering research at the University of Lincoln. In partnership with industries and stakeholders, she leads various projects on robotics, AI, automation, and control within the Lincoln Centre for Autonomous Systems.
Rutger Gyllenram is a Swedish metallurgist and entrepreneur. He has an MSc in process metallurgy and materials science and a Licentiate degree (Dr-ing) in metal production technology from the Royal Institute of Technology, KTH, in Stockholm. He is the founder and CEO of Kobolde & Partners AB, working with raw material and process assessment, which is crucial for decarbonization in the steel industry.
Carlos Russell is the business conduct compliance and cybersecurity director for Ternium. Over the last 10 years he has built Ternium’s cybersecurity programme, including industrial cybersecurity, privacy, and technology risk management concerns. Prior to joining Ternium, Carlos spent 20 years dealing with complex business and technology transformation programmes in various industries, working for global management consulting companies such as PwC, Capgemini Consulting and EY in the UK. Carlos holds a BSc in computing and information systems from Goldsmiths College (University of London) and is certified in Cybersecurity (CISSP, CISM), IT Audit (CISA) and IT Governance (CGEIT).
Caroline is the inaugural director of Steelwatch, the first international civil society organisation exclusively focused on driving decarbonization and transformation in the steel sector. She is an experienced leader, systems-thinker and change-maker. A socio-economist by background, her career has spanned work in INGOs, policy research, policy making, consultancy, community development, business innovation and impact investment.
Prior to SteelWatch, Caroline led global programmes at Forum for the Future, exploring the transformations needed for a just and regenerative future, including how businesses can be future-fit. As Economic Justice strategic lead at Oxfam GB she led a global team supporting communities and challenging business around the world for socio-economic transformation and climate resilience. Rooted in international development, Caroline has lived and worked in multiple African and Asian countries. She worked in the Namibian government shaping post-apartheid environmental management, initiated approaches to address poverty within the tourism industry internationally, catalysed innovation with over 100 businesses in DFID-funded challenge funds, and worked with multiple development banks on their development impact.
Giovanni Bavestrelli graduated from the Politecnico di Milano, Italy, with a master’s degree in software engineering, after attending high school in Johannesburg, South Africa, for five years. He joined Pomini Tenova in 1994, working on roll grinder automation, developing and commissioning software systems for running roll shops in steel plants. He later joined Unisys Corporation in 2000, leading the development team for the Hermes editorial system. He went back to Pomini Tenova in 2004 as a software engineering director and has since worked for Pomini Tenova, leading the software development team. In 2016 he contributed to Tenova’s Digital Transformation initiative and later joined the new Tenova Digital Team as director. He currently holds the posiiton of data science director, focusing on AI applications and working with all of Tenova’s business units.
Dr Klaus Peters obtained a doctorate in engineering in 1993 and gained a state doctorate (Habilitation) in 1998 (RWTH Aachen), starting his industrial career with thyssenkrupp Steel Europe (tkSE). His senior experiences include production, sales, quality and research and development both on a national and international level.
From 2011, Dr. Peters joined several working groups and committees of the European Steel Technology Platform (ESTEP) and oversaw international research projects and European funding of tkSE, becoming secretary-general of ESTEP in 2015. He is a member of the Steel Advisory Group (SAG) of the Research Fund for Coal and Steel (RFCS) and board member of the public-private partnership Processes4Planet. He is also the executive director of the Horizon Europe Clean Steel Partnership.
Vito Logar is an assistant professor at the faculty of electrical engineering, University of Ljubljana. His research field consists of modelling, simulation, and optimization of electric arc furnace (EAF) processes. He has been involved in this field for 15 years and has published numerous papers in scientific journals and conferences describing different areas of EAF-process modelling as well as optimization approaches. He was a leader of several projects (domestic, EU, and industrial) addressing different aspects of EAF efficiency, the latest being the EU Horizon 2020 SPIRE project: Inevitable (GA. 869815).
Jean-Paul Nauzin began his career as a metallic material expert at ArcelorMittal France in 1996, where he worked for five years, before becoming a metallic material expert at PSA Peugeot Citroën (France). Jean-Paul Nauzin held this position for over a decade, before he joined Fives as an automotive steel expert and CEO of Fives KEODS, Fives subsidiary. Today, he is Innovation & Technology Director of the Steel & Glass Division at Fives. Jean-Paul obtained a Master’s degree in Materials Science and Forming from the Université Nice-Sophia-Antipolis, France, as well as an Engineering degree in Materials Science and Processing from the École des Mines de Nancy, France.
Anna Domènech is an experienced industrial engineer with a master’s degree in international business management. With over 12 years in funding and innovation management, she has held the position of corporate innovation manager at CELSA Group since 2020. In this role, she coordinates innovation initiatives across all business units spanning Spain, France, UK, Poland and the Nordic countries.
Previously, Anna gained valuable expertise during her six-year tenure as a consultant in Brussels, assisting industrial clients in navigating the European innovation ecosystem. Before joining CELSA, she spent four years managing Nissan Europe’s participation in public funding programmes, supporting innovation initiatives across their factories, research centres, and business units throughout Europe.
Luca Cestari is product portfolio manager at Danieli Automation Digi&Met, with a passion for developing digital solutions that leverage datadriven process and quality control in the steel industry. Prior to this position, he gained considerable experience as a software engineer and innovation manager on multiple research and development projects, introducing innovative concepts and technologies in the fields of smart sensors, robotics, data science, and mathematical modeling and simulation of industrial processes.
Luca holds a master’s degree in electronic engineering from the University of Padova and a degree in metallurgical engineering from the University of Udine.
Osamu Yamaguchi worked in JFE Steel’s steel laboratory from 1992 to 2022, focusing on process control and optimization for production schedules and logistics in steelworks.
Currently, he is working in the data science project department of the company, specializing in planning, installing and education in data science technologies. Osamu graduated from Kyoto University and holds a master’s degree in control theory.
Dr. Thiago Turchetti Maia is the executive vice president for SMS digital’s Center of Excellence. He has 20+ years of experience in leading technology companies focused on industrial digitalization. He founded Vetta and Viridis, two companies later incorporated by the SMS group. He has led software industry associations and served on different supervisory boards. He holds a PhD and an MSc in electrical engineering, a BSc in computer science, and an MBA in finance.
Sanjeev Manocha is the business development director of LanzaTech Inc headquartered in Chicago, USA. He joined LanzaTech earlier this year, having developed a passion to decarbonize industries. He is leading steel, cement and energy-intensive industry sectors. In terms of his wider career, Sanjeev is a metallurgical engineer with an executive MBA, who started his working life in the iron and steel industry, having served in various executive positions across Europe, Asia Pacific and North America. In the later part of his career, Sanjeev moved to the lime industry. He also served as a board member with various businesses and institutes.
Bikash is a metallurgical engineer from NIT Durgapur, with18 years of experience in iron ore sintering and pelletization, operation, design and engineering. Bikash specializes on the sintering process, controlling stack emissions, pelletizing process, drying and grinding process, and has a wide understanding of plant machinery. He has worked with Tata Steel Limited since 2010 as head of operation, sinter plant.
Vikas is an electrical and electronics engineer from BIT Sindri, with an MBA from IMT Gaziabad. Vikas has 18 years of experience in the IT sector of SAP. He has worked for Tata Steel since 2005 as a head client partner in iron making, charged with driving digital transformation.
Michael Eder is global chief digital officer of the voestalpine High Performance Metals Division and the managing director of voestalpine High Performance Metals Digital Solutions GmbH. He started his career as an automation engineer in the iron and steel industry, responsible for implementing technological control systems for rolling mills. Before joining voestalpine, he worked for a leading management consultancy, performing operational improvement as well as strategy engagements. He holds an engineering degree in telecommunication engineering, and a master’s in business science from Johannes Kepler University. His PhD degree from Leopold-Franzens University focused on ‘The impact of family influence on company volatility and performance: the case of German public companies’.
Holger Stamm is a partner in Oliver Wyman’s global energy and natural resources practice. For more than 20 years, he has assisted global clients in the steel and chemical industries with their transformation. His consulting focus ranges from strategy development to operational transformation and performance improvement programmes. Holger has extensive expertise in business and governance model optimization, value-based and sustainable procurement, as well as on topics such as green steel and ESG transformation issues. His goal is to support customers in challenging transformations and manage the path to green steel and thus making an active contribution to the decarbonization of society. He studied physics at the Rheinisch-Westfälische Hochschule in Aachen and has worked in the process industry and in consulting.
Ion is responsible for project development in the research and development department at BM Group Polytec S.p.A. He holds bachelor’s and master’s degrees in electronics and automation engineering from the University of Brescia. During his employment, he followed the design and commissioning of innovative robotic installations in different applications at several steel plants around the globe. Currently he manages the development of ongoing research and development projects at BM Group Polytec S.p.A.
We understand how it is important to efficiently extract and process precious metals and minerals.
You save valuable resources while keeping your employees and the environment safe.
Liquiline CM44 and CPS11E: Versatile transmitter and Memosens pH sensors ensure reliable measurement and safe calibration in the lab.
FieldPort SWA50: Intelligent Bluetooth or WirelessHART adapter for the easy connection of all HART field devices to the Netilion Cloud via Edge Devices.
Do you want to learn more? www.de.endress.com/primaries-metal
Cerabar PMC71B: Absolute and gauge pressure transmitter combining measurement accuracy with IIoT functionalities.
Philipp Horner is chief sustainability officer at voestalpine’s HPM division. With over a decade of experience in logistics, automotive sector, and metals, he has held his current role since 2022. Philipp is a member of multiple advisory boards, and completed his education at the Technical University, Graz, specialising in industrial engineering and automotive technology.
Costanzo started his career at Centro Sviluppo Materiali S.p.A. in 1979, becoming department manager and director in 1992. He has significant experience in the fields of finite element analysis and modelling, fracture mechanics, and plant erection management and quality control.
Costanzo is currently a research and development project evaluator at the RFCS (Research Fund of Carbon and Steel), a chairman of the Smart Factory Focus Group of the European Steel Technology Platform (ESTEP) and a member of the task force and the implementation group of the Clean Steel Partnership. Since May 2015, he has held the position of senior consultant in the steelmaking sector for Danieli Automation.
Valentina Colla is the assistant professor of metallurgy and responsible for the Information and Communication Technologies for Complex Industrial Systems and Processes research team (ICT-COISP) of the TeCIP Institute of Scuola Superiore Sant’Aanna. Her research activity concerns simulation, modelling, management, and control of industrial processes via traditional and artificial intelligence-based techniques. She has considerable experience in the development of solutions to improve energy and resource efficiency in the steel sector, including by-products characterization treatment and valorisation. She participated in 75 EU-funded projects (11 as project co-ordinator) as well as many projects funded by private companies. Valentina is an active member of ESTEP, where she is vice-chair of the focus groups entitled ‘smart factory’ and ‘circular economy’. She has co-authored about 400 papers published in international journals and conferences.
Maria Salamero Sansalvado has worked within the Abgar Group, a water utility business, for 25 years. She has undertaken different functions and positions in the fields of operations, technology, research and innovation and communication in the water sector. Maria has led the creation of technology centres and knowledge transfer and training at an international level. In the last five years, she has been the director of sustainability at Aigües de Barcelona, activating, among others, the first Sustainability Committee of the Board of Directors and the company’s 2030 Agenda. Since September 2022, she has held the role of head of sustainability at Celsa Group, a family business created in 1967 that produces circular and low carbon steel, being the first industrial company in the steel sector in Spain and the second in recycling in Europe. Maria is currently president of the Industrial Engineering Association of Catalunya, holding the role of engineering for sustainable progress.
Dr. Valentin Vogl works as a steel industry analyst at ARIA, an organisation doing research and analysis on climate and energy issues. Before joining ARIA, Dr. Vogl completed his PhD thesis titled ‘Steel Beyond Coal: Socio-Technical Change and the Emergent Politics of Steel Decarbonization’ at Lund University. Dr. Vogl’s current research interests are the industrial politics of green steel and of coal industry decline. Dr. Vogl has published widely on matters of steel decarbonization and has been advising on matters relating to the steel industry within the International Energy Agency and other organizations and companies.
Stefan has worked for more than 20 years in the manufacturing industry and IT with a focus on the metals industry. He has a wide knowledge of supply chain and manufacturing solutions and their use throughout the metals industry.
Other developments & technologies aiming at decarbonizing the steel industry:
VolteronTM: CO2-free Steel
Production Process
Furnace Electrification
Carbon Capture
Heat Recovery
The JVD line introduces a technological breakthrough in the steel coating of advanced high resistant steel grades difficult to galvanize by hot dipping. This genuine alternative to Electro-Galvanizing and Hot-Dip-Galvanizing considerably reduces the cost of galvanized steel and provides multiple advantages when it comes to quality, speed and OPEX. Developed for ArcelorMittal with the help of our experts, John Cockerill is in charge of commercializing this unique technology worldwide.
Our E-SiTM equipment and processing lines are designed for the production of strong, ultrathin, lightweight, and highquality Non-Grain Oriented (NGO) steel grades essential for the future of e-mobility.
High-performance Acid Regeneration supporting responsible steel making and the circular economy
John Cockerill Industry’s ARPs come with smart plant control systems, provide waste energy recovery and drastically reduce pickling process plants’ fresh acid demands and waste streams in general. What is more, they are providing the lowest emissions in the market.
ABB
Website: www.new.abb.com/metals
Email: karen.hildebrandt@se.abb.com
ABB’s products, solutions and services help to ensure safe, reliable and efficient operations across the metals industry, while its team of technologists are always working on the latest solutions to help take the industry to the next level.
Phone: +528110014050
Website: www.amiautomation.com
Email: info@amiautomation.com
AMI Automation is an international automation and control solutions company with a focus on designing, manufacturing, and implementing innovative technology solutions to provide process improvements that help make companies more efficient. Industries it serves include steel, mining, cement, pulp and paper, and oil and gas.
The company combines its 30+ years of experience with automation and controls including artificial intelligence to assist its customers with the challenges of implementing and upgrading to new technology solutions. In addition to new equipment, AMI can add updates to older existing equipment for cost-effective process improvements. AMI can provide repairs and spares as well as preventative maintenance programmes. The company’s team of experienced, specialized engineers is available for consulting, custom design, training, and technical support.
AMI Automation consists of two groups: the Industrial Systems Group’s focus is on drive solutions while the Meltshops Solutions Group is focused on electric arc furnace optimization.
Email: jan.matthias@beda.com
BEDA Oxygentechnik is a supplier of safety oxygen lancing solutions for steel plants and foundries. The company supplies optimized solutions for blast furnaces, converters, EAF meltshops, casting areas and scrapyard applications. Highest safety and best cost efficiency are its unique commitments to its worldwide customers.
BEDA is offering leakage-free argon stirring solutions, contributing to process stability and quality in secondary metallurgy and delivering substantial savings in operating costs. With various products for oxygen and carbon injection, BEDA contributes to the safety and productivity of EAF operations.
Website: https://combilift.com/
Email: info@combilift.com
Combilift is the largest global manufacturer of multi-directional forklifts and an acknowledged leader in long load handling solutions. Innovation, Flexibility and Service is the ethos on which Combilift’s success is built and has seen it become the world’s fastest-growing forklift manufacturer, exporting to more than 85 countries and with more than 60,000 trucks in use worldwide.
No other manufacturer in the world can deliver the same level of customisation and adaptability, or cater so effectively to the diverse needs of every individual customer, whether their enterprise is large or small.
Phone: +41 61 715 7700
Website: www.endress.com
Email: jens.hundrieser@de.endress.com
Phone: +49 (0) 2102 - 910 914
Website: www.beda.com
Endress+Hauser is a leading supplier of products, solutions and services for industrial process measurement and automation. It offers comprehensive process solutions for flow, level, pressure, analysis, temperature, recording and digital communications across a wide range of industries, optimizing processes with regards to economic efficiency, safety and environmental protection.
The company focuses on seven strategic industries, one of them being the metals industry. With more than 60 years of experience, Endress+Hauser helps its customers to improve their processes regarding efficiency, cost savings, plant safety and sustainability.
As one of the most innovative companies in the field of measurement instrumentation, Endress + Hauser owns more than 6,500 patents and spends approximately 7% of sales on R&D. To enable customers to take the first step towards Industry 4.0, the company supports them along three axes:
• Along the value creation chain
• From the field to the control level
• From planning to maintenance
Phone: +1 (428) 461-9286
Website: www.falkonry.com
Email: info@falkonry.com
Falkonry is an AI software platform for time series data, enabling steel manufacturing companies to improve operational productivity, reduce risk, and put an end to unplanned downtime. By analyzing high-speed real-time machine and sensor data, Falkonry AI applications identify developing faults earlier and better than would ever be possible with manual systems. This patented AI is automated, requires no set-up, and securely scales across the enterprise in both cloud and edge environments. Maintenance and operations teams use Falkonry applications for faster troubleshooting and taking timely actions that keep production processes running smoothly.
STAND TBC
Website: www.ferolabs.com
Email: info@ferolabs.com
Fero is factory optimization software that enables manufacturers to stay ahead of ever-changing production conditions. With intuitive software guiding them, your engineers can confidently take informed action that gets
results without wasting time or resources. Powered by machine learning that makes decisions clearer, Fero gets leading global manufacturers – including Covestro and Celsa – better production results in less time. With Fero, you see every situation – and every solution – more clearly.
STAND 22
Phone: +33 1 45 23 75 75
Website: www.fivesgroup.com/
Email: steel@fivesgroup.com
Fives is an international industrial engineering group, whose activity in the steel industry dates back to 1867. Today, Fives’ steel business line provides steelmakers with turnkey solutions, process expertise and technologies for the carbon, stainless and silicon steel sectors in long and flat products, as well as tube and pipe, including strip processing, reheating and rolling.
As a provider of turnkey solutions and a full range of equipment, Fives offers:
• Metallurgical intelligence and competitive strategy development
• Design and supply of strip processing lines and reheating furnaces
• Thermal and mechanical technologies and proprietary equipment
• Automation systems
• Smart maintenance
Since its foundation, Fives has always put innovation at the core of its development strategy, by investing into R&D to design and create pioneering technologies that meet the performance requirements of industrial companies in a broad range of sectors. Fives has also adopted a collaborative approach, built on partnerships and joint ventures with public and private players (start-ups, major groups, laboratories and research bodies, universities, etc.) to contribute to building the factories of the future.
Fives combines its process expertise with digital tools to offer industrial companies solutions that facilitate production system management and maintenance: data and flow management, modelling and simulation of production line equipment, digital control and robotization, and smart maintenance.
Phone: +49 (2324) 207-0
Website: www.koeppern-international.com
STAND
Website: https://haverniagara.com/
Email: info@haverniagara.com
Haver & Boecker Niagara is a leader in screening and pelletizing. Its mission is to deliver the best of these technologies to customers in the mining, minerals, aggregates, cement, construction materials, fertilizers, salt and recycling industries.
With deep roots and years of experience in these industries, the company uses innovative and shared technologies to effectively meet the needs of customers around the world.
STAND
Website: https://johncockerill.com
Email: welcome@johncockerill.com
John Cockerill Industry supplies sustainable innovative technologies for cleaner and smarter steelmaking aiming at producing more sustainably and decarbonizing the steel industry. For over 200 years, JOHN COCKERILL (formerly CMI) has endeavoured to improve the performance of production facilities while making them more resourceefficient and environmentally friendly. Its offering for the steel industry comprises of reheating furnaces, pickling lines, acid regeneration plants, cold rolling mills, strip processing lines and automation.
John Cockerill’s vast experience in the fields of engineering, international project management and sourcing enables it to provide innovative and global technical solutions tailored to the needs of your industrial complex, or specific equipment. The company operates all over the world and offers customized life-cycle services: design and set-up, after-sales services and spare parts, transformation and upgrading, and training and remote support.
Email: info@koeppern.de
Maschinenfabrik Köppern is specialized in the development and fabrication of roller presses as well as engineering services for complete roller press-containing plants. There is a wide range of applications for presses by Köppern in the metallurgical industry. They are used for briquetting the fine fractions of caustic lime, coke/coal, ores, metallurgical residues, feed materials in reduction processes, cold application of direct reduced iron with binders or hot applications at approx. 700°C (HBI). High-pressure ore and minerals sizing technology has been a new field of application for roller presses for about 25 years.
Phone: (UK) +44 (0) 1684 892456
(NL) +31 (0) 546 534 444
Email: salesinfo@malvern.com
Malvern Panalytical technologies are used by scientists and engineers in a wide range of industries and organizations to solve the challenges associated with maximizing productivity, developing better quality products, and getting them to market faster. The company’s mission is to create superior, customerfocused solutions and services to deliver tangible economic impact through chemical, physical, and structural analysis of materials. Malvern Panalytical is a leader in the materials characterization market, developing expert analytical solutions which deliver superior actionable insight.
Underpinned by extensive industry knowledge and technical and applications expertise, Malvern Panalytical instruments help users better understand a wide variety of materials, from proteins and polymers to metals and building materials. The technologies enable the measurement of parameters such as particle size, shape and zeta potential, biomolecular interactions and stability, rheological properties, elemental concentrations, and crystallographic structure. Highly reliable and robust characterization of these properties is fundamental to predicting how a product will behave during use, to optimizing its performance and achieve manufacturing excellence.
Phone: +32 3 650 2211
Website: https://omp.com
Email: LBongaerts@ompartners.com
OMP helps companies facing complex planning challenges to excel, grow and thrive by offering the best digitized supply chain planning solution on the market. Its Unison PlanningTM concept has a unique approach, handling all supply chain planning challenges in a unified way, and synchronizing planning stages, horizons, functions and roles. The combination of services and technology boosts collaboration throughout any value chain. Unison PlanningTM is a cloud-based, out-of-the-box solution for industry-specific challenges. Customers in consumer multiple industries utilise Unison PlanningTM in order to make the right decisions at the heart of their business.
Phone: (603) 766-6060
Website: www.optris.com
Email: sales@optris-ir.com
Optris was founded in 2003 and has since established itself as one of the leading manufacturers of non-contact temperature measurement devices.
The product portfolio comprises of stationary infrared thermometers and online infrared cameras as well as accessories and software for industrial applications and research and development.
Phone: +49 (0) 7243 604-0
Email: info@polytec.de
Website: https://www.polytec.com/eu/velocimetry/areasof-application/steel-aluminum-metals
For over 50 years Polytec has provided high-technology,
optical measurement solutions to researchers and engineers. Its commitment is to provide the most precise and reliable optical instruments and sensors available for non-contact measurement of vibration, length, speed and surface topography. Polytec instruments help to solve pressing application challenges in R&D, engineering and manufacturing quality and process control and help customers to maintain a leading position in their field. The applications range from micro system technology to large-scale mechanical engineering for the automotive sector, aerospace and steel industry, medical technology and biomedical sciences.
Non-contact length and speed measurement in production processes in the steel, aluminium and metal industry is the domain of Polytec LSV Laser Surface Velocimeters – made in Germany. High-precision measurement with laser accuracy in harsh conditions is what these optical sensors were made for. LSV provides reliable measurement data for feedback on machining processes, process control and process optimization. LSV optical sensors help users with a wide range of sensors, offering the optimum stand-off distances for measurement application. Polytec experts offer measurement services at their own test centres or at customer sites.
STAND 10
Phone: +44 (0)20 8996 4300
Website: www.primetals.com
Email: contact@primetals.com
Primetals Technologies, headquartered in London, UK, is a world leader in the fields of engineering, plant building, and the provision of lifecycle services for the metals industry. The company offers a complete technology, product, and services portfolio that includes integrated electrics and automation, digitalization, and environmental solutions. This covers every step of the iron and steel production chain— from raw materials to finished product—and includes the latest rolling solutions for the non-ferrous metals sector.
Primetals Technologies is a joint venture with Mitsubishi Heavy Industries and partners, with around 7,000 employees worldwide.
STAND 11
Phone: +49 39203 512 0
Email: tobias.knape@promecon.com
PROMECON specializes in the design and manufacture of high technology measurement systems for monitoring and optimization of thermal processes for various industries – the power generation industry, the cement industry, and the metal smelter industry.
Especially for furnace analysis in the steel melting industries, PROMECON’s McON IR, a 3rd generation off gas analyzer, provides operators with lower tap-to-tap times, high energy savings and increased process safety.
By measuring the velocity and the composition of the furnace, off-gas operators get detailed process data, such as CO/ CO2 ratio and water content. The infrared measuring principle is aware of drifts and requires minimal maintenance.
Phone: +352 4970 – 2840
Website: www.sms-group.com
Email: anne.marmann@sms-group.com
The SMS group unites global players in plant and machinery construction for processing steel and non-ferrous metals, operating under the roof of SMS Holding GmbH. The family-owned company – now run by the fourth generation – stands out with its strong market position and corporate culture of responsibility, together with highperformance products and services tailored to individual customer requirements.
The SMS group combines the flexibility of medium-sized company units with the vast resources of a global group. The company builds on the continuous training and comprehensive expertise of its employees to develop groundbreaking technologies, as well as electrical systems, and automation services.
The SMS group is your partner for new plant and machinery as well as modernisations and upgrades.
STAND 13
Phone: +49 30 403673720
Website: www.smart-steel-technologies.com
Smart Steel Technologies is the category leader for AI in steel. The company’s development team, consisting of top metallurgists as well as AI, data and software experts focuses exclusively on one industry: steel.
Based on its unique Steel AI Platform, the company delivers ready-to-use AI software packages for the optimization of every aspect of steel manufacturing. Smart Steel Technologies’ software products merge data live across production steps, solve the surface inspection problem, drastically optimize continuous casting quality, hot rolling quality, energy consumption in steelmaking and cross-process productivity.
Leading European steelmakers, including both, large integrated plants and specialized EAF facilities run Smart Steel Technologies’ software successfully in production.
Phone: +31 72 20 05 500
Website: www.tebulorobotics.com
Email address: info@tebulorobotics.com
Tebulo Robotics is the leading and innovative specialist in high-tech robot integration, working closely with major players in the steel, aluminium, and heavy industry.
With its specific expertise in R&D, engineering, assembly, and commissioning, Tebulo builds and maintains high-quality integrated robot applications.
The company’s expert and multi-disciplinary teams surprise customers with their approach, advice, realization, service and aftersales. With its flexible and high-tech solutions, customers are assured of a significant improvement in safety and productivity. This allows customers to capture and/or maintain a leading position.
In addition, the company offers sufficient support during the entire life cycle as well as tailor-made solutions for nonrobotic automation problems.
Tebulo is an ambitious and motivated employer and offers its team a challenging work environment with room for personal
input and development. Taking responsibility and constantly improving is in the company’s DNA.
STAND 6
Phone: +44 (0)3300 58 44 60
Website: www.tmeic.com/industry/metals
TMEIC is an industry leader in steel mill automation and drive systems, with almost 100 years of experience in process control and automation technology for hot mills, cold mills, long products, and processing lines.
Technical capabilities include complete engineering and design, mill modernisations and revamps, simulation and testing, and comprehensive project management. Site services include mill audits, start-up, and commissioning.
TMEIC’s complete range of steel mill automation products includes large AC and DC main drives and motors, auxiliary drive equipment, level 1 controllers, level 2 process models, and HMI systems.
STAND 18
Phone: (+49) 16096863960
Website: www.tvarit.com
Email: vikas.goel@tvarit.com
Tvarit GmbH is a Frankfurt-based industrial AI company with a vision of sustainable and zero-waste manufacturing. With a proven track record of leading ROI-driven end-toend AI and Industry 4.0 transformations, Tvarit has achieved a 50% reduction in scrap and an 8% reduction in energy consumption for metal manufacturers. Maintaining a sharp focus on reducing scrap and energy consumption, Tvarit is reshaping the landscape of the steel industry through innovation. At the heart of Tvarit’s success lies its ‘Hybrid AI’ technology that merges the intricacies of the steel domain with the cutting-edge prowess of Deep Learning. Tvarit stands out with its streamlined approach to data science and machine learning, achieving implementation in both a fast and cost-effective manner, while maintaining 100% accuracy in select cases. Tvarit offers a unique combination of reliable technology, customized solutions, and customer-
focused consulting, ensuring both rapidity and top-notch service.
Tvarit is backed by top-tier German VC firms and customers across nine countries actively use its solutions. Tvarit specializes in shop floor digitalization, Industry 4.0, AI, analytics, scrap reduction, and energy waste reduction.
7
Phone: +49 2522 75-0
Website: www.venti-oelde.com
Email: info@venti-oelde.de
Air is the medium Venti works with. Research and development, planning and consulting, manufacturing and service, whatever the company does, the emphasis is on innovative air technology. Venti Oelde plants and components are used for collecting, handling and filtering of air, vapours, gases, dust and airborne solids.
As long ago as 1930, Venti Oelde was planning, developing and manufacturing in its North-Rhine-Westphalian location, Oelde. Apart from industrial fans, its manufacturing programme includes dust collection and process gas cleaning plants, exhaust air treatment plants, ventilating, heating and air-conditioning plants, recycling and waste treatment plants as well as plants for surface technology. Maintenance, servicing, inspection, repairs as well as plant upgrading, rationalisation and enlargement complete the available services. Experienced specialists in a large number of outside offices and agents ensure expert support all round the world and quick contact to all business partners.
1. HAVER & BOECKER NIAGARA GMBH
2. COMBILIFT LTD
3. MALVERN PANALYTICAL B.V.
4. POLYTEC GMBH
5. ENDRESS + HAUSER GMBH
6. TMEIC INC
7. VENTI OELDE GMBH
8. SMS GROUP GMBH
9. BEDA OXYGENTECHNIK GMBH
10. PRIMETALS TECHNOLOGIES GMBH
11. PROMECON GMBH
12. FALKONRY INC
13. SMART STEEL TECHNOLOGIES GMBH
14. ABB
15. FERO LABS
16. OMP
17. JOHN COCKERILL
18. TVARIT GMBH
19. TEBULO ROBOTICS B.V.
20. KÖPPERN GMBH & CO. KG
21. AMI AUTOMATION INC
22. FIVES S.A.
23 OPTRIS GMBH
With all of the hype around artificial intelligence, expectations of its potential uses have soared. Some of these expectations are unreasonable and can stand in the way of successful AI projects. By
I have observed a general assumption that if you put together a lot of data, one or more smart data scientists, and some fancy algorithms/tools/technologies, then you can solve almost any problem with AI.
This assumption is a gross oversimplification.
Don’t get me wrong. A wealth of data is important. Skilled data scientists are instrumental. Algorithms/tools/technologies are indispensable. These are all necessary ingredients, but in and of themselves are not sufficient for a successful AI project. Especially at the onset of a project, focusing mainly on these elements may prove to be ineffective.
I believe there is a different set of three ingredients that are fundamental to an AI
project, and focusing on them right from the start can set the project in the right direction and increase its probability of success. Though I base my assertions on direct observations of AI applications in manufacturing, I believe the same set of ingredients would be useful to other AI projects, in different industries.
The first of these three ingredients is a clear target. A goal. A problem which, if solved, will bring value to stakeholders. I find it amazing how many projects start with solutions in search of problems and not the other way around. “Here’s an amazing tool or technology, let’s use it!” This is not a good start. First, we must identify a valid target, and define the problem that blocks us from reaching it. This problem should be well-
*Director of data science, Tenova
defined, and it should, when solved, address real issues. It must also be compatible with what AI can do at the time, or at least in the very near future. Identifying a specific target, and establishing that it is worth pursuing and compatible with current technology is a great start, even before finding any data, employing data scientists, or writing a single line of code.
While the second ingredient does concern data, I believe the industry’s focus on ‘big’ data can be misleading. Our focus should be on good data, even if said data fits on a single machine. There is much we can do with a limited amount of good data. Rather than buy into the assumption that more data is always better, we should focus first on the quality of data available. Ask yourselves how
dependable and representative your data is. How was it gathered? If by sensors, how reliable are they? What is the level of noise in the measured signals? Can it be reduced? Are better sensors needed? Are more sensors needed? Should better processes to track data be established? What should humans do differently to make sure data is reliable? What could be done to improve the integrity of data? What are the ramifications of any holes in the data? Or outliers? Is any data noticeably missing? Would said data prove useful? Where can it be found? How should it be interpreted? Likewise, how should the results of models be interpreted?
Which brings me to the third ingredient of successful AI projects: domain experts, i.e., people who know the industry, the process, the problems, and the customers we hope to address with our AI solution. It is not necessary that these experts know anything about AI. What is necessary is that they approach the project with curiosity and an open mind.
Speaking from experience, it is not always easy to convince domain experts that AI solutions can bring value. They are rightfully confident in the value of their knowledge. They have years of experience that have served them well. Then along comes a young data scientist who knows nothing about their business and yet thinks they can improve upon it? No way! In this case domain experts might feel threatened. They may privately worry that AI is rendering their skills obsolete, and yet nothing could be further from the truth. Even once an AI solution has been developed and has produced results, it will still need to be deployed, commissioned, tuned, serviced, re-evaluated, retrained, and updated in time. This maintenance depends on the expertise of skilled insiders and their continued commitment to the project. Only these experts can evaluate the worthiness of a solution beyond what a percentage of accuracy can tell a data scientist. For a data scientist who does not understand the process
being addressed, data is just strings and numbers. For a domain expert, that data holds knowledge and meaning, which can lead to better ideas and solutions. On their own, data scientists can have a lot of fun with data. They may even come up with interesting models. Domain experts meanwhile could continue to go on as they had before, and with a certain degree of success, but this is not the way to innovate. Together, data scientists and domain experts can work to create impressive AI solutions.
AI is a fascinating evolving technology, and I am privileged to work in it with a dynamic team in a company that believes in its huge potential. Harnessing that potential is a complex and rewarding challenge, one that I believe is better navigated with an eye on the indicators described above: establishing a clear target, prioritizing good data, and collaborating with domain experts. May these guidelines prove themselves valuable to your own AI projects. �
Cyber-Physical Systems (CPS, Fig 1) means using AI to analyze sensor data collected from the actual manufacturing process (physical), reproducing advanced virtual processes (cyber) in digital space using state-of-the-art technologies, and connecting the two in real time. Virtual processes make it possible to understand the internal state of facilities that cannot be seen in real time, and to predict future conditions. By feeding back the results of health monitoring and control strategies to operational actions in the actual process, stable operation can be realized, and productivity improvement can be expected by making process bottlenecks visible. In addition, process innovation through virtual experiments and the mechanization of knowledge and know-how can lead to work style reform.
A blast furnace is a piece of equipment that removes oxygen from iron ore to extract pig iron and is considered the heart of a steelworks. It has a significant impact on costs in the steelmaking industry, and stable
and highly efficient operation is extremely important. On the other hand, operating conditions change from moment to moment due to the nature of the raw materials charged into the blast furnace, and it is difficult to directly observe the inside of the furnace. In response to this situation, JFE has developed and introduced technology that can predict the heat inside the blast furnace eight to 12 hours in advance, which is important for stable operation and detecting anomalies that may cause serious problems in the blast furnace. Furthermore, we have built a
guidance system for operators to provide the most appropriate actions to take in response to the predicted results and lead to stable operation and production. (Fig 2)
With the aim of saving energy, reducing CO2 emissions, and minimizing costs, JFE Steel has developed a guidance system to assist operators.
Since the steelmaking process requires a large amount of energy, it is important
to optimize the operation of the fuel and electricity used in order to save energy, reduce CO2 emissions, and improve cost competitiveness.
In steelworks, by-product gases generated in the upper processes such as blast furnaces, coke ovens, and converter, as well as electricity and steam obtained from energy conversion facilities such as power generation and waste heat recovery, are effectively used in the plants within the works. The shortfall in the supply of fuel and electricity to meet the plant’s demand is compensated for by purchasing from external sources (Fig 3).
Based on the CPS concept, the newly developed guidance system (Fig 4) uses a vast amount of real-time measurement data and detailed production plans for each plant to model the physical phenomena to be forecasted and perform supply and demand forecast calculations to accurately forecast supply and demand conditions from the present to the future. Then, taking into account the operational constraints, characteristics, and contract information of various power generation facilities within the steelworks, the optimal operating conditions that minimize external purchases are determined through fuel and power simulations, and the results are provided to the operator as guidance.
In contrast to conventional operations based on the experience and capabilities of operators, the new system enables even more
efficient operations, saving energy, reducing CO2 emissions, and lowering fuel and electricity costs.
We developed the world’s first autonomous ultrasonic inspection robot for thick plates. By introducing this robot into the plate off-line inspection process and automating manual inspection work, we have achieved further improvements in inspection reliability and work efficiency.
Improving the quality of steel products is an important issue, and we have been developing and introducing various inspection systems to provide defect-free products to our customers. For ultrasonic flaw inspection inside thick plates, on-line automatic flaw inspection has been applied. Off-line manual inspection by skilled workers has been used in some cases due to restrictions on plate thickness and other factors. However, manual inspection has limitations in terms of accuracy in moving inspection equipment on steel plates, accuracy in recording inspection results, and work efficiency, making further improvement of inspection reliability and work efficiency an issue.
To address this issue, we have developed our own robot that combines a self-propelled robot and an ultrasonic flaw detector. The robot is equipped with an indoor high-
JFE Steel is actively promoting CPS-based development to stable operations, save energy, reduce CO2 emissions, and improve our cost competitiveness. Here, we will provide an overview of the technology and the benefits obtained from our developed items.Fig 2. CPS for blast furnace Fig 3: Flow of fuel and electricity in steelworks Fig 4. Guidance system for fuel and electricity
precision self-position recognition system, which enables it to recognize the difference between its own position and the target position on the plate, and to perform ultrasonic flaw detection while automatically moving along the target route. Since the process from flaw detection to pass/fail judgment can be automated, the system not only improves inspection reliability to the same level as on-line automated flaw detection, but also automates and streamlines the process (Fig 5). In addition, inspection results are automatically stored as digital data, contributing to improved traceability and simplified quality trend management. The robot itself has been made small and light enough to be lifted and carried by one person, greatly improving usability (Fig 6).
Coil products manufactured at the steelworks are packed and temporarily stored in a product warehouse near the shipping wharf. On the day of shipment, they are removed
from the warehouse by cranes and loaded onto carriers or trucks for shipment to customers. Because coil loading/unloading in the warehouse is performed under extremely complex operating conditions with many cranes moving in parallel, crane operators have traditionally had to make decisions about the order in which to load and unload coil products while checking the shipment status on a screen. As a result, there were cases where coil products had to wait to be unloaded, and shipping efficiency was not sufficiently high.
In order to deliver products to customers without delay, we have been working to
improve the operating efficiency of our cargo handling facilities. In particular, since the operation of product warehouse cranes has a direct impact on shipping efficiency, we developed a smart operation system.
The smart operation system automatically optimizes the work order based on the operation and shipping plans using Scheduler Functions (Fig 7), thereby improving the efficiency of warehousing and shipping operations and making them unmanned. Furthermore, the Scheduler Functions’ ‘Coil relocation scheduler’ (Fig 8) rearranges coil products into an ideal arrangement while there is no urgent work, thereby avoiding the time-consuming digging work that occurs when another coil product is on top, and significantly reducing the waiting time for warehousing and shipping. This system can be applied to three-tiered coil warehouses and warehouses with no unloading area and limited space.
This optimization system with JFE’s automatic crane (Fig 9) significantly improves shipping capacity. �
To be the leading partner for our customers in this transformation, SMS group bundles all competencies from electrics/automation, digitalization, and technical service. Our goal is to maintain and expand the performance of our customers' plants throughout their entire lifecycle. Together with our customers, we develop integrated solutions specifically geared to the customer's use case. In doing so, we focus on crucial KPIs such as plant availability, product quality, productivity, or delivery reliability but also on increasingly relevant topics such as sustainability and safety.
In primary and secondary steel mills, operators rely on industrial scales to weigh metallurgical vessels. Ladles and tundishes filled with liquid steel and slag can weigh tonnes and are often carried on moving frames, such as rail-cars, swivel turrets, and raising/lowering platforms. At Metallurgical Sensors, Inc., (Metsen) we spend a lot of time in mills working with steelmakers. Many of them have told us that they find conventional electro-mechanical (strain-gauge) type load cells to be inadequate.
Nearly every mill we visit has an abandoned weighing system that failed to meet its intended purpose. Alternatively, steelmakers resort to estimating weight for liquid metal or slag based on freeboard and
weighing shredded scrap steel or slabs and billets based on shape. They are compelled to take this approach due to several critical deficiencies observed in conventional weigh systems.
First, conventional weigh systems rely on load cells, which are a type of mechanical force transducer exposed to the rigours of daily operations. As a result, the load cells must be overdesigned to meet the anticipated shock loads. Unfortunately, resolution and accuracy are sacrificed in the design.
Conventional load cells also require micro-volt sensitive electrical wiring and
connections rated for extreme heat, grease, oil, and fluids. To meet safety requirements and maintain reliability, this requires frequent recalibration and unscheduled repairs that disrupt production.
The commissioning calibration of a conventional weighing system processor requires multi-point calibration to formulate a best-fit polynomial to describe the physical characteristics of multiple load cells working in unison. If a load cell is stressed beyond its yield point, residual stresses remain, and the original polynomial no longer reflects the new physical characteristics. Unfortunately, multi-point recalibrations are rarely performed in the field, so this frequent error is seldom discovered. In the end, readings and
By utilizing a range of ‘unconventional’ systems, the steel industry can improve production accuracy, and eliminate guesswork, says Lucas Demysh*
values are often incorrect with the exception of the zero and the single point derived from the test weight.
After commissioning, the common procedure for recalibrating the weighing system is to adjust the zero and span to match a known test weight (two-point calibration).
The assumption is that the polynomial describing the physical characteristics of the combined load cell system remains unchanged. However, conventional load cells, by design, are limited to single-axis measurements. Side loads are deadly. The readings cannot be trusted when one or more conventional load cell is overloaded due to dynamic shock loads. And diagnosis is impossible until a system recalibration with a test load is performed.
Also, a weighing system can be inaccurately recalibrated and stuck due to debris. This can continue undetected for weeks or months.
The hydraulic weighing system is unconventional and completely different from conventional weighing systems for several reasons.
First, hydraulic load cells are dynamic, which means they can be stowed for protection against shock loads and deployed as required. The hydraulic pressure is coupled to a custom high-precision digital pressure transducer located in a safe environment away from the production area via small diameter (1/4”) hydraulic tubing and flexible hoses wherever movable joints are desired. Each measurement transducer has a minimum accuracy of 0.010% = approx. ±32 lbs, a precision of 0.0015% = approx. ±5 lbs, based on a max load of 317,816 lbs per
transducer. The typical hydraulic weighing system configuration uses four independent transducers, providing a combined system accuracy of approx. ±64 lbs, and a precision of approx. ±10 lbs, based on a maximum evenly distributed load of 1,271,200 lbs per system.
The system can also be remotely cycled (exercised) at any time, especially during normal production, making it inherently selfcorrecting. This prevents binding, keeping it highly functional and dependable.
In summary, the hydraulic weighing system offers steelmakers several advantages. It is simple. The pressure multiplied by the piston area equals the load, so no complex polynomial is required. The hydraulic weighing system never drifts out of calibration, which ensures reliability. The system employs pressure transducer redundancy. Multiple pressure transducers can be installed on a single circuit to provide independent cross-checks, ensuring the true pressure is continuously measured. When all the samecircuit transducers do not report the same values, a warning is presented to investigate.
The hydraulic load cell can be designed so that the side-load capacity is almost the same as the vertical load capacity. This is impossible with a conventional load cell. The hydraulic load cell is relief-valve protected from overload conditions.
New environmentally-safe fire-resistantapproved hydraulic fluids can be cooled and cycled through the cell for high-heat applications.
By design, the hydraulic load cell has higher resolution than conventional load cells, and special materials and exotic surface treatments are applied to minimize internal friction.
The Hydroweigh System developed by Metsen was created for extreme environments like those found in steel mills. It addresses the deficiencies of the conventional electromechanical type load cells. The Hydroweigh system can be used in a cantilever or fully supported dead-lift configuration. In a cantilever configuration, part of the load is supported on a fulcrum, and the hydraulic weigh cell supports the remaining portion of the load. A single hydraulic weight cell circuit and a plurality of cell circuits can be used.
In a fully supported dead-lift configuration, the complete load is supported by numerous independent hydraulic weigh cells. Instead of a conventional electrical summing junction, the total weight is calculated by simply adding together the individual hydraulic weigh cell measurements in the PLC. There is no limit to how many cells can be used to measure the load.
In conclusion, the industry now has a solution to maintain accuracy, eliminating guesswork and time-consuming, productiondisrupting calibration checks. �
This article presents the technological challenges in recovering and reusing steel and other high-value materials floating around the earth’s orbits, as well as the state-of-the-art additive manufacturing in space, the technological gaps, and the step towards manufacturing green steel from space debris.
By Mini C. Rai*, Dirk Schaefer*, Manu Nair*, Mithun Poozhiyil*, Shan Dulanty†Since the launch of Sputnik in 1957, chrome and nickel steel alloys have been widely used for building satellites and launchers for manned and unmanned missions. Their high resistance to extreme temperatures makes them ideal for spacecraft heatshields. The James Webb Space Telescope used steel molds to construct its 6.5m primary mirror containing pressed beryllium powder. Steel tubes are also used for building a telescope’s cooling system. Likewise, solar sails use steel booms to ensure proper deployment. Various other sub-systems on board the International Space Station and other spacecraft are made of steel and other high-value materials.
These examples give an insight into the application of steel and its unprecedented needs in the booming space industry. A great economic and technological opportunity exists here regarding scavenging the failed satellites/components and using them to manufacture new parts.
Satellites are made of materials that resist, without failure or excessive distortion, the static, dynamic, and thermal stresses that occur during launch, deployment, and service[1-3]. Structurally, a satellite can be divided mainly into two parts based on the
material used and its functionalities. The primary structure comprises of components designed to transmit loads through the spacecraft, attachment points for payloads and other associated components. The secondary structure includes the rest of the parts, such as solar panels, thermal blankets and electronics. Aluminium and its alloys are the conventional primary structure material used for flight structures of all types and, therefore, in space debris. Main materials used are 2000/7000 series aluminium for tanks, silicon, lithium, manganese, magnesium, aluminium alloys, particularly aluminium-coated polyimide and Kevlar™ for
shielding. Aluminium is not strong on its own; conventionally, it is converted into alloys with other metals for increased strength and weight reduction.
For small spacecraft structures focusing on 1U – 12U platforms, the primary structure follows a Monocoque design (Fig 1); most are machined from 6061-T6 or 7075 aluminium. Several commercial off-the-shelf (COTS) CubeSat structures are machined from Al 5052-H32, which range in size from sub-1U to the larger 6U – 12U SUPERNOVA structures. The Endurosat CubeSat structures are mostly made of aluminum 6061-T651.
The common aluminium alloys used in space applications are shown in Table 1 The present and future spacecrafts also use special materials [2] for their various components; for example, aluminium-lithium alloys, polymer-matrix composites, carboncarbon composites, and metal-matrix composites are popular. The aluminiumlithium alloys (WeldaliteTM, alloy 2090, alloy 8090) offers weight reduction of 7-20% to the components manufactured in comparison
with the conventional aluminium alloys. These low-density alloys offer increased stiffness and higher strength and are used in liquid oxygen and liquid hydrogen fuel tanks. Polymer-matrix composites are another class of materials used in flat panel components, structural truss members and propellant tanks of spacecraft. Among the well-used polymer-matrix composite fibres, for example, glass, Kevlar™ and graphite epoxy, the most commonly used polymer-matrix composite for primary spacecraft structures is graphite epoxy. The polymer-matrix composites are subjected to environmental degradation effects, and the strength of the components is threatened by the three-to-five years of exposure to the space environment. Carboncarbon composites are another material used in spacecraft components that are exposed to extreme temperatures, typically up to 1650°C. These materials are used in the tails and wings of airframes, the leading edge of the nose and over the parts of the fuselage along with titanium-matrix composite.
In order to reduce the cost, metal-matrix
composites (MMC) are becoming available with applications to spacecraft frames and components. MMCs such as B/Al, Gr/Al, Gr/Mg, and Gr/Cu have been manufactured for spacecraft components such as tubes, plates, and panels. Aluminium alloys reinforced with silicon carbide, alumina, boron particulates or fibres offer increased stiffness and strength; however, these materials are more expensive than conventional alloys. The boron-aluminium MMC is used in primary structures for space transfer vehicles and silicon-carbide particulate-aluminium alloys for cryogenic tanks. Other successful applications of continuous-fibre reinforced MMC are rib truss members in the mid-fuselage section of Space Shuttle Orbiter and Gr/Al composite in a high-gain antenna boom for the Hubble Space Telescope [5]. Using these, a 45% weight savings over the baseline aluminium design for the mid-fuselage section of Space Shuttle Orbiter was achieved. Furthermore, the desired stiffness and Low Coefficient of Thermal Expansion (CTE) to maintain the position of the antenna during space manoeuvres for the Hubble Space Telescope was made possible. Discontinuously reinforced aluminium MMCs, for example, SiCp/Al and cast Grp/Al, are used for electronic packaging applications in spacecraft and satellites. These components are significantly lighter than metal alloys and are cost-effective.
Additive manufacturing techniques are becoming popular in space applications, driving the new era of in-space manufacturing. Additive manufacturing has the advantage of printing parts of various shapes and forms which could not be produced by conventional techniques. The three-
dimensional printed parts offer reduced mass, increased complexity, better performance and reduced printing time. There are diverse techniques available with different advantages and challenges for printing satellite parts [6, 7]. A few examples are (a) cavity and flow path creation of EQUULEUS CubeSat thrusters from the aluminium alloy AlSi10Mg (b) thermal management system for high power CubeSat (ALSat#1 mission) (c) powder-bed fusion of the metal alloy Inconel®718 for the redesign of NASA’s thruster (d) stainless steel 316 L and CoCr for liquid rocket engine injector head (e) direct metal laser sintering of AlSi10Mg to prepare antenna feed arrays (f) selective laser melting of permalloy to prepare magnetic shields for fibre optic gyroscopes.
The space industry provides immense value to life on Earth by deploying satellite and space infrastructures facilitating communication, navigation, real-time global-scale monitoring of Earth and space, and supporting other technological developments. However, the satellite reaches end-of-service or becomes derelict in space due to end-of-lifespan or various technical malfunctions. Millions of space debris, large and small, orbiting Earth threaten the space ecosystem. There is a growing concern over the increasing number of space debris heavily affecting sustainable space operations. According to the study by Ryan et al., a total mass estimate of ~ 7kt is calculated for space debris having a net
worth of ~$600 billion[8]. These findings triggered the quest for harnessing highvalue materials in orbit to establish a circular economy for space.
To address this alarming issue, many businesses, regulators and insurers have stepped in to support Active Debris Removal missions to clean up space. However, the current approach is to deorbit space debris, but the remnants returned to Earth are nonbiodegradable objects, polluting the oceans and affecting marine life. Space trash, an immense resource, should be reused and repurposed for manufacturing newer systems in orbit. According to current literature, the value of orbital debris suitable for re-use is estimated at $1.2 trillion [8]. As a result, there is an increasing interest in reusing the parts and materials from derelict satellites in orbit as a step towards additive manufacturing in space. For debris capture, recycling and reuse, it is important to understand the materials used for satellite construction[9] and the factors affecting its material characteristics[10]. This is because the material characteristics change due to various extreme environmental factors once the spacecraft reaches its end-of-service or becomes derelict in space. In 2021, a study by Yalung et al. described a material classification methodology for In-Orbit Debris using ESA’s DISCOS (Database and Information System Characterising Objects in Space) and other sources [11]. Initially, a classification system based on the shape of objects was developed, and later material properties of each object category were
added.
The feedstock needed for on-demand manufacturing of new or replacement parts and components can be produced by recycling materials in orbit, including those previously used for packaging or current space debris. This includes the abundance of steel and other metals on the orbiting space debris. However, research on recycling space debris and additive manufacturing in space is still in its infancy, hindering the goal of achieving an in-space circular economy. Understanding how much is potentially re-usable (whether materials and/or components) for future space initiatives is not wholly understood and given the resources required for manufacturing and launching spacecraft on earth, fully maximising their lifecycle in space needs to become an essential part of the In-Orbit Servicing, Assembly and Manufacturing (ISAM) field. The ability to evaluate and assess orbital debris and then categorise the potential for re-use (and then re-purpose and recycling including re-manufacture) should be an essential capability for establishing in-space manufacturing and a circular economy in space.
Further, extending to the manufacturing domain, and in step with the on-earth waste hierarchy, are the principles of circular manufacturing (manufacturing products which are long-lasting, easy to repair, refurbish, remanufactured and recycled) and remanufacturing (where previously sold, worn, or non-functional products can be rebuilt and recovered through the disassembly, cleaning, repair, and replacement of worn out and obsolete components). To truly maximise the waste hierarchy for orbital debris and to regenerate green steel in orbit, these approaches must also be considered. An artistic illustration of the evolving OrbitSweeper concept that will facilitate in-space manufacturing and a circular economy in space is shown in Fig.2
A paradigm shift toward in-space manufacturing aligns well with our curiosity to continue to explore the universe and improve lives on Earth while achieving a sustainable circular economy on Earth and in space. Such capabilities will significantly reduce launch costs and carbon footprint by
Amazing performance, extensive battery life and unrivalled ergonomics combined with all the advantages of the Combi-CB range make the CB70E the most powerful, compact multidirectional forklift yet.
The new COMBi-CB70E electric forklift is the most compact 7,000kg counterbalance truck on the market. It is loaded with a host of features that greatly enhance operator comfort, including excellent all-round visibility, a spacious gas-strut suspension cab, independent electric traction and our newly developed Auto Swivel Seat which intelligently swivels 15 O in the direction of travel.
Contact Us Today combilift.com
To find out how Combilift can help you unlock every inch of your storage space.
For 50 years, Köppern briquetting machines have played a key role throughout the world in the production of HBI for DRI processes.
And HBI is still in demand, as demonstrated by the new HBI plants equipped with Köppern roller presses at LEBGOK (Russia), ArcelorMittal (USA), CLIFFS (USA) and upcoming installations, reducing the CO2 footprint of the steel industry.
» State of the art technology
» Experts in process technology
» High plant availability
» Long-lasting equipment
Köppern – Quality made in Germany.
www.koeppern.com
decreasing the number of launches and the need for ground-based fabrication. Considering the importance of net-zero manufacturing on the ground and in space, recycling materials from space debris for on-demand manufacturing in orbit would be environmentally friendly and economically profitable. �
References
[1] Kopacz, J.R., Herschitz, R. and Roney, J. Small satellites an overview and assessment. Acta Astronautica 170 (2020): 93-105.
[2] National Research Council. Technology for small spacecraft. National Academies Press, 1994.
[3] Weston, Sasha, Cameron S. Miller, Joshua E. Ingersoll, Bruce D. Yost, Elwood Agasid, Roland Burton, Roberto Carlino et al. State of the art: Small spacecraft technology. NTRS - NASA Technical Report 2018
[4] Abd El-Hameed, Afaf M., and Y. A. Abdel-Aziz. “Aluminium Alloys in Space Applications: A Short Report.” Journal of Advanced Research in Applied Sciences and Engineering Technology 22, no. 1 (2021): 1-7.
[5] Rawal, Suraj P. “Metal-matrix composites for space applications.” Jom 53, no. 4 (2001): 14-17.
[6] Blachowicz, T., Ehrmann, G. and Ehrmann, A., 2021. Metal additive manufacturing for satellites and rockets. Applied Sciences, 11, 12036 (2021): 1-15.
[7] Sears, Patrick J., and Koki Ho. “Impact evaluation of in-space additive manufacturing and recycling technologies for on-orbit servicing.” Journal of Spacecraft and Rockets 55, no. 6 (2018): 1498-1508.
[8] Leonard, R. and Williams, I.D., 2023. Viability of a circular economy for space debris. Waste Management, 155(2023): 1928.
[9] Finckenor, Miria M. Materials for spacecraft. American Institute of Aeronautics and Astronautics, 2018. No. M16-5055.
[10] Gonzalo, J., Domínguez, D. and López, D. On the challenge of a century lifespan satellite. Progress in Aerospace Sciences, 70 (2014): 28-41.
[11] Yalung, F., Thompson, A.D., Toomer, C.A. and Bolouri1d, A., Modelling of the Materials Classification of In-Orbit Debris using DISCOSweb and other sources. Reinventing Space Conference, 28-30 June 2021.
Steel Times International is the key publication for the steel market, reporting on iron and steel making issues from all corners of the globe.
The Steel Times International Directory is the essential guide to steel manufacturers, producers, suppliers of plant equipment and services to the steel industry. Order your print or digital copy priced from £105 or subscribers.
Packed with information on the steel industry and continually updated with news for steel professionals, www.steeltimesint.com features special articles and interviews with leading industry gures.
A round-up of the top news stories is sent to more than 7,000 industry professionals each week. You can register online to receive the weekly newsletter and keep up-to-date with the latest news from across the steel manufacturing industry. www.steeltimesint.com/e-newsletter
For the production of green steel (steel made without using fossil fuels) to reach commercial scale, CAPEX in excess of €2 trillion to €3 trillion will be required, based on our calculations. This is the case even though most of the technology needed to produce green steel already exists in pilot form at least. That amounts to an average investment of €1,000 to €1,500 per ton of steel produced.
It is unlikely that any steel producer or even the entire industry en masse would be able to supply that magnitude of CAPEX until 2050. But steel can pool resources with industries that will also benefit from steel’s conversion. Ultimately, the key to transformation will be partnerships, joint ventures, and alliances with other industries involved in steel production including energy, mining, chemicals, and private capital — as well as end users such as automotive, transportation, and construction companies.
To be a survivor over the long run, a steel producer will need to create or join this kind of ecosystem. Otherwise, it would likely go out of business or become so peripheral to what will eventually become a global
green steel market that it might as well be defunct. But by creating these new economic ecosystems, steel can become a global economic model for decarbonization and have a hand in reducing emissions across the industrial spectrum as carbon-intensive steel becomes green.
The next seven years will be make-orbreak, given how long it will take to build these ecosystems and transition the industry. This push to change is due to demand increasingly shifting to green steel and the possibility that governments will impose increasingly strict mandates for green steel content use. Banks and institutional investors — on their own quests to decarbonize portfolios — are already raising the cost of capital to carbon-intensive businesses, meaning growth or even operational improvements may come at a steep price. Eventually, some banks could cut off access entirely.
Where conventional steel uses highcarbon coal called coke in blast furnaces
to produce the intensive heat necessary to make steel, green steel production relies on renewable energy both to create green hydrogen and to run electric arc furnaces. Hydrogen has been identified as probably the best replacement for coke because it burns hot enough for the direct reduction of iron ore (DRI), with only water as its emissions. The CAPEX funds for steel production would be used to construct sufficient hydrogenbased DRI capacity, as well as to replace blast furnaces with electric arc furnaces.
The reward for early movers could be considerable. Besides creating a global market for green steel, leaders in decarbonization will also spawn trading in commodities used in green steel production. On the energy side, these might include green hydrogen, synthetic gas, and biomethane — all low-carbon energy sources that will not reach commercial scale without sufficiently developed marketplaces.
Raw materials used in green steel production like high-grade iron ore and scrap metal would also get a boost. Finally, and perhaps most importantly, it will generate the
Strong demand for steel is incentivizing decarbonization initiatives. However, costs, logistics, and technological requirements for industrial transformation will not only rely on the steel producers themselves, but partnerships that allow resources to be pooled.*Partner, energy and natural resources, operations, climate and sustainability, Oliver Wyman ** Partner, energy and natural resources and operations, Oliver Wyman
demand necessary to justify extensive new capacity in renewable energy and storage, whether it’s solar, wind, hydro, nuclear, or thermal.
Meanwhile, the industry must deal with a shortage of renewable energy — probably the biggest immediate obstacle to steel’s efforts to decarbonize. The International Energy Agency (IEA) has stressed that the period between now and 2030 must become one of an unprecedented clean energy investment of about $5 trillion. For
solar and wind, the addition of some 630 gigawatts (GW) of photovoltaics and 390 GW of wind will be necessary. That would be four times the size of the record-level expansion in 2020. Today, the largest sources of low-carbon energy are provided by hydro and nuclear power, which also need to be expanded.
Without expansion of renewable energy, industries like steel will end up competing with each other for what’s available, leaving the losers with only fossil fuels to meet demand. Take Europe. By 2030, producing 32Mt of flat green steel in Europe would consume 12% of the region’s renewable energy, while still only satisfying about 30% of the demand for steel. By 2050, to produce 95% of the projected European green steel demand would require the industry to consume more than 40% of Europe’s available renewable energy, creating a huge imbalance between the supply and demand for renewable energy.
While part of that imbalance will likely be addressed with imports of green hydrogen as well as synthetic gas and biomethane, Europe may not want to create an unhealthy energy dependence on other regions. The only way to reduce that potential dependence would be for Europe to dramatically expand its current renewable capacity, beginning today.
(Fig 1).
Companies that intend to lead the industry must, first, identify the appropriate stakeholders with which to form alliances. This could mean joining forces with automotive manufacturers as H2 Green Steel in Sweden did when it partnered with Mercedes Benz or as Boston Metal in the United States did with an investment from BMW. The advantage for
sizable end users is the ability to guarantee a source of green steel through pre-arranged supply deals in the early days when green steel will be in short supply.
Both green steel start-ups also received sizable investments from some of the world’s largest steelmakers: ArcelorMittal in the case of Boston Metal, and Kobe Steel in the case of H2 Green Steel. Mining giant BHP also invested venture capital in Boston Metal.
But given that energy is the component most elusive in green steel production, smart partnerships moving forward should consider bringing deep-pocketed energy producers into their ecosystems to help ensure sufficient green power. For example, Hitachi Energy invested in H2 Green Steel in 2022. Finnish power company Fortum has signed an agreement to supply H2 Green Steel carbonfree electricity generated primarily from hydro and nuclear power. But those pushing forward in green steel are still outliers today.
(Fig 2)
Steel is an economic building block of the global economy. It is a key commodity in the production of cars, ships, trains, agricultural equipment, machinery, appliances, and aircraft as well as in the construction of everything from factories and skyscrapers to societal infrastructure.
Expansion of the global economy would not be possible without steel. Thus, its decarbonization will automatically reduce the carbon footprints of other major industrial sectors, as the introduction of green steel should result in a sizeable cut in emissions for its end users as well.
Globally, the demand for steel is expected to expand 30% by 2050, according to
the World Economic Forum (WEF). Given that the steel industry is the largest-emitting manufacturing sector, producing 7% of all man-made greenhouse gas emissions, a significant increase in production would be disastrous for global warming without substantial conversion to less carbon-intensive steel. (Fig 3)
Because of higher production costs, green steel will cost more than conventional steel. While that’s an obstacle to adoption, green steel does offer the added value of helping users reduce their emissions. For producers, value-added green steel offers an opportunity to decommoditize their products and protect
their margins — especially given predictions on downward pressure on prices for conventional steel.
The first green steel volumes in 2025 are expected to cost up to 20% more than highcarbon steel, depending on the quality and product differentiation. The question: will end users and consumers pay the premium without
regulations forcing them to? For a car, the extra cost of green steel might add as much as €500 to €800 to the price tag. While electric vehicles use less steel, the average vehicle is more than 50% steel.
But not all regions will experience rising costs for steel equally. Access to cheaper green energy, such as hydro power, could give certain steel-producing regions an advantage. For instance, Boston Metal is building its first full-scale green steel facility in Brazil, the second largest producer of hydropower by installed capacity. H2 Green Steel already benefits from Scandinavia’s cheaper hydro energy.
Starting in 2025, as the first substantial quantities of green steel enter the market, most of Europe will be supplied by the operations in the Nordics, such as H2 Green Steel and SSAB. Salzglitter, Germany’s second largest steelmaker, was recently awarded €1 billion of government funding for its SALCOS hydrogen-based steel production project. But competition will spring up eventually in
places like the Middle East. Nordic countries, for example, would likely enjoy an 11% cost advantage over Germany. The Middle East would have a 22% to 25% cost advantage. By 2030, the equivalent of one big European steel plant’s production will be replaced by green imports such as slabs from places in the Middle East. (Fig 4)
The future leader in steel will be the producer that can create and manage new industrial ecosystems that can build the necessary infrastructure to foster the transition. Not only must steel executives shift their mindset from managing one company to managing a network of cross-industry relationships, they will also need to decouple their companies’ steel production from steel rolling and manage different transformation paths. They will also have to accelerate their own programmes for sourcing green hydrogen and renewable energy, relying on partners in the energy and chemicals industries.
The green transformation will take decades and it will be costly. Given the many challenges that need addressing, the efficiency of investments will ultimately determine the leaders of the new industry. Greenfield players have an advantage initially because of the absence of legacy elements of the old steel in place and their ability to locate near renewable energy production. While first movers and start-ups will gain useful knowledge and scoop up partnerships, legacy players can catch up by going all-in with a green transformation strategy that is likely to result in higher CAPEX efficiency and a faster transformation.
The undeveloped green steel market offers opportunities for an ambitious steel company to grab the pole position.
The suppliers with the fastest ramp-up curve, technical leadership for decarbonized production, and the most efficient partnerships for renewable energy and green hydrogen are likely to turn the industry rankings upside down. �
An increased utilization of alloys from scrap will either require increased regulations, higher alloy and clean scrap prices, demands on low scope 3 emissions in steel, improved opportunities to utilize small amounts of scrap with specific analysis, optimized information management throughout the life cycle, or a combination of all. This article contains scenarios developed in the Swedish research project; ‘Scrap precision’.
The development of the steel industry is today characterized by two ambitions, namely the abatement of greenhouse gas emissions and the conservation of resources. Both are addressed in the concept of circular economy, where recycling of steel results in new steel with a lower carbon footprint compared to steel from the blast furnace route and a reduction of the consumption of iron ore to what is needed to compensate for iron losses in the recycling process.
The aim of this article is to outline how digitalization and the use of AI-technology can support resource conservation and abatement of greenhouse gas emissions in the circular economy of alloys. This is based on scenarios and research questions used in the project ‘scrap precision’, which was completed by five Swedish steel producers. The aim of scrap precision is to further develop models to assess scrap quality, increase the knowledge about certain scrap types, and in the long run, to suggest methods to increase the quality of scrap. The work is financed by the Swedish Innovation Agency, Vinnova. This article is based on logic reasoning from what is perceived as common
knowledge in the steelmaking domain, hence no references are given.
Steel is an alloy of iron (Fe) and up to 2% carbon (C), plus a number of other alloying elements like manganese (Mn), chromium (Cr), nickel (Ni), molybdenum (Mo), vanadium (V) and silicon (Si) to mention some of the most frequently used. Copper (Cu) and phosphorus (P) are alloying elements in some rare cases but are most often unwanted. Most steels have a ferritic structure and are magnetic whereas stainless steels with a high content of nickel and molybdenum have an austenitic structure and are not magnetic. Furthermore, steel is often coated with materials such as zinc (Zn), aluminium (Al) chromium, and nickel. Alloys and coatings make it possible to give a specific steel type its desired strength, hardness, heat resistance, corrosion resistance and other important properties. The percentage of alloying elements can typically vary from under 1% for simple construction steels to 2-10% for special steels, and above that for stainless steels. Elements that are not part of the specification
By Rutger Gyllenram*for the steel type are considered tramp elements and can be harmful and tolerated only up to a certain level. Apart from the chemical composition and the coatings, steel products are given their final properties by metal working and heat treatment.
Production of alloys is more costly and emits more greenhouse gases than production of iron – and on top of this, the ores are often considered critical raw materials by the EU. Making full use of the alloys in steel in the recycling process is, therefore, also an important factor in the circular economy.
Using steel in products
Customers, like the automotive, machine and appliances industries, source their material mainly based on physical properties, ESG-properties, and price – and do not necessarily know the chemical analysis of the steels used in a product. A complex product like a car or a dishwasher contains a multitude of steel types with different alloy compositions, together with other metals like aluminium and copper in wiring. However, for cars there exists at least one database where
producers in the automotive industry can register what materials are included in their products, and for constructions, Building Information Management systems, BIM, contain material information which may be used in a deconstruction phase at the end of the building’s life.
Historically, scrap alloys have been handled as impurities, apart from high-alloy scrap where the alloy price justifies more accurate sorting and trading rules. Scrap quality is dealt with in EU regulation 333/2011, which contains a description of scrap classes and requirements in order for a material to cease to be wasted according to the waste directive. As far as ferritic scrap is concerned, there are restrictions on the maximum content of alloys that can be included, as they are seen as impurities. Apart from ferritic stainlesssteel scrap with alloy contents above 10%, there are no ferritic scrap classes that have minimum values for alloys and where these are thus seen as valuable metals.
In life cycle calculations, regardless of whether they follow LCA standards or new types of initiatives, primary alloys are handled as scope 3, i.e., processes in upstream steelmaking that contribute to the emission of greenhouse gases – and the higher climate footprint resultantly affects the product. Scrap and alloys in scrap, on the other hand, have no impact upon most standards and initiatives apart from their contribution to greenhouse gas emissions that transport and handling processes for scrap involve.
In environmental declarations according to standards EN 15804 and prEN17662, the environmental value of recycling can be stated as additional information. According to the standards, the reduced value of not using the entire alloy value must appear in the declaration – but that is questionable if it is done in practice.
Steel scrap can be of different origins and is here divided into three groups:
� Home scrap collected within the borders of a steelmaking facility
� New prompt scrap collected from rerollers and manufacturing facilities
� Old scrap from demolition sites or collected obsolete products
Both home scrap and new prompt scrap
have the potential to be recycled in a way where the information about the alloy content is preserved if this feature is included in the design of the production equipment. This, however, is not always the case. Scrap where information about the steel code is lost, which is standard for old scrap, can be analysed with a hand-held X-ray analyser. This is regularly done when there are larger amounts of similar material. Shredded, magnetic and non-magnetic scrap are separated into two streams. For non-magnetic scrap, in some facilities, stainless, which has a high alloy value, is sorted into two groups – one with molybdenum, and one without. For magnetic scrap, the alloy value is today not considered high enough to justify automatic sorting. The maximum levels of tramp elements in the
increasing the oxygen potential in the steel, other elements are lost. Elements with lower affinity to oxygen, like nickel and copper, stay in the steel and have to be diluted if the levels are too high. In some cases, it is possible to melt under reducing conditions to retain the alloys in the steel. This is done, for example, with steel with high levels of manganese. Foundries use induction furnaces without oxygen, which is why these can make better use of alloys in scrap, but in return are dependent on clean raw materials without impurities.
Four factors determine how well alloying elements in steel can be recovered so that they retain their value as alloys: identification,
magnetic stream are, therefore, controlled by blending the input material in order to dilute the mix so restrictions can be contained. This means adding a certain amount of low alloy material together with each dishwasher-type product in order not to exceed the maximum level for chromium. Copper, while being nonmagnetic, often follows the magnetic stream as copper wire trapped in magnetic steel, which is why it has to be separated manually by personnel at the conveyor belt.
Steel production in both converters and electric arc furnaces is generally done under oxidizing conditions. Oxygen creates a foaming slag, removing any excess of carbon and abates impurities such as phosphorus. Part of the manganese, chromium, vanadium, iron, and other elements with higher or equal affinity to oxygen as iron are also oxidized into the slag. This means that when the contents of a tramp element are abated by
sorting costs.
Identification: When steel is cast, it has a steel code that says what it contains. The longer the steel code can be linked to the material, the better. In a steel mill and in manufacturing processes further down the chain, the steel code is known when internal scrap occurs during turning, punching, cutting and grinding, etc. This information follows the material back to whoever is to mix the scrap and creates a new melt and a new casting. Improving this capability requires (in many cases) investments in both control and logistic systems. Sorting of shredded ferritic scrap has high potential for improved alloy recovery if the dilution philosophy is abandoned and complex products with alloyed ferritic steel are shredded in plants with advanced technology for identification like laser technology (LIBS), X-ray methods or image
recognition combined with robot technology or other means of diverting streams.
Sorting: A steel mill may have hundreds of different steel codes on its production programme but has significantly fewer storage locations for home scrap. Typically, a plant with 100 steel types may use 10 groups of home scrap. The ability to keep different materials apart in a cost-effective way is a key issue in the entire steel product life cycle. An automatically sorted flow of fragmented ferritic scrap in different alloy classes poses a logistical challenge but may strive to fit into the sorting patterns for home scrap.
Recycling method: The utilization of alloying elements in steel scrap requires that whoever is to melt the scrap has a flexible production apparatus that can keep track of the alloy content in various scrap lots and optimize production so that the alloy content is fully utilized.
Covering costs for sorting: Improved identification and sorting creates both a large scrap flow that is cleaner than the inflow of unsorted scrap, and several smaller outgoing flows of alloyed scrap. Both represent a higher specific value than the unsorted scrap. If the total added value is higher than the costs of identification and sorting, then the costs can be covered without external intervention. Much indicates however, that this is not yet the case, which is why other models to cover the costs must be sought to guarantee circular alloy flows, which likely means some form of regulation (or we can assume that the demand for abating greenhouse gas emissions will change the rulebook.)
Three factors govern how the market will affect alloy recovery, namely: the cost of diluting tramp elements, the cost of using primary alloys, the cost of increased identification and sorting and logistics.
When integrated plants are closed and replaced with electric arc furnaces, the demand for clean scrap and DRI will increase. Most OECD countries have a scrap surplus, and export materials are not used locally. This may, however, not have the quality used for high-end steel and steel normally produced in the BF-BOF route. Furthermore, production of DRI with low emissions of greenhouse gases
will have a higher cost than iron from blast furnaces, which makes it more expensive to dilute tramp elements.
With increased costs for CO2 allowances, it is reasonable to believe that alloys will be more expensive in the future. Raw material scarcity and global availability are other aspects that may play a role in the future. A factor perhaps closer in time is the environmental value. When companies reduce their greenhouse gas emissions for ironmaking towards zero, the carbon footprint of primary alloying elements will no longer be negligible. This increases the market cost for using primary alloys alongside the value of alloy scrap –even if the content of the alloying element is low.
2) The cost for dilution of tramp elements increases, but the cost of primary alloys remains as it is now
3) The cost for dilution of tramp elements remains as it is now, but the cost of primary alloys increases
4) Both the cost for dilution of tramp elements and primary alloys increases
In the first scenario nothing will happen unless legislative measures are implemented. A possibility is to make it mandatory for companies that make products with a certain complexity and alloy content to ensure that their products are reprocessed so that alloys are recovered to their full value. In the second scenario it is important to implement measures to take care of the streams of low alloy scrap that may occur on the market and that carry extra costs for logistics that are not covered by the value of the alloys. In the third scenario the value of the alloys will cover the logistic costs and the resulting cleaner scrap will be used as ordinary scrap without extra costs. Finally, the fourth scenario is probably what the steel life cycle will finally look like and may not need extra legislation or support.
The technology in this area has developed a lot in the last decade. The big challenges are to make the systems robust and cost-effective. In addition to this, an ability to co-operate between product companies, recyclers and steel companies is required.
Among commodity traders there is a saying: to be too early is to be wrong. It is likely that the market will support the development towards better alloy recycling, but at the same time, you should be prepared that it may take time. The third success factor is to some extent dependent on the first two. We can consider four scenarios for the near future:
1) Both the cost for dilution of tramp elements and primary alloys remains as it is now
In order to reduce the costs of identification, sorting and recycling, much needs to be done in the field of automation. This must be integrated into the digitization of the entire industry along with product manufacturing, scrap handling and recycling. It is possible that large-scale recycling of alloys will take some time, but development must not be hindered by developing systems based on the present practice of dilution of tramp elements and the use of primary alloys.
This article has described why alloying elements in steel often lose their function when steel is recycled and what can be done to preserve value. The steel industry’s transition to production with low emissions of greenhouse gases will affect how alloys are used and recycled. Digitalization and the use of AI have great potential to help abate greenhouse gas emissions, conserve resources, and decrease production costs in the decades to come. It is however important to assess the changes in business patterns as well as availability and quality of raw materials in order to create systems that do not conserve old practices but instead promote change. �
Since 1866
Steel Times International is a leading publication serving the global steel industry and offering its readers a strong focus on all aspects of the production process embracing both basic oxygen and electric steelmaking.
Choose your subscription package...
PRINT + DIGITAL SUBSCRIPTION
8 print copies and a printed copy of the Steel Times International Directory
Digital copy of the magazine delivered to your inbox every month
A digital version of our annual Steel Times International Directory
Access to our digital archive of past issues and webinars
Weekly Steel Times International newsletter
PLUS access to all digital issues of Furnaces International
DIGITAL ONLY SUBSCRIPTION
With a digital subscription you will receive all the benefits of the Print + Digital option, excluding print copies!
Contact us today
subscriptions@quartzltd.com to take advantage of our special subscription packages. WWW.STEELTIMESINT.COM
When investing in sustainability, the environment and safety are always high on the agenda in the modern steel industry. Important issues in this regard are the prevention of risky activities and improving ergonomics, for example when performing maintenance or refilling consumables. Recently, Tebulo Robotics has developed new robotic applications to significantly improve the working conditions of operators
In many cases, setting up a safe and ergonomic work environment may seem easier than it turns out to be in the steel industry’s daily practice. This is mostly due to space limitations while having to create sufficient distance between operators and hazardous processes in conjunction with the transport of steel coils. For example, it is still common practice for operators to enter a production line to replace consumables. Not only is this not ergonomic, it also leads to unwanted production losses. A similar situation occurs when performing maintenance on a strapping head, for example, where operators often find themselves in the line. Responding to this, Tebulo Robotics has, therefore, recently developed new robotic applications making it possible from now on to perform all the above activities in a safe working area.
The first demand for a plant, as described above, came during the pandemic from China’s Liangang hot strip mill. This plant processes about 5Mt/yr of steel. After rolling the hot sheet material, it is rolled onto coils that are always varying in diameter and width. Every hour, about 30 coils of steel must be fitted with three straps each, and in a time frame of no more than 120 seconds per coil (transport included). Besides applying the straps, performing maintenance on the strapping head is an unsafe if not impossible job for operators since the rolls are extremely hot. Tebulo Robotics was, therefore, invited to develop a so-called ‘Eye strapper’ for these hot rolls: A robotic installation fully integrated into the line.
Project
“A strapping head is an installation in itself and is purchased as a complete electropneumatic unit. The control of this part is integrated into the control system of the ‘eye strapper’, so that from a single PLC both the robot and the peripheral device
are controllable,” explained Rob Beentjes, director of Tebulo Robotics. It was one of the constraints ruling the development of the aforementioned 6-axes robotic system. In addition, when designing this configuration, careful consideration had to be given to the optimal method of feeding the strap material.
This was necessary in order to cope with the enormous variety of roll sizes. It was also important to make the strapping frame and robot tooling as compact and light as possible while taking into account the hot rollers’ high temperature. To cope with the latter aspect, Tebulo Robotics’ engineers drew on their experience with hot robotic marking systems. Since the strapping head and strapping frame together weigh about 500kg, ABB’s largest 6-axes robot was chosen. Beentjes added: “Because we were up against the weight limit with the chosen solution, it was decided to solve the usual solution for absorbing the transverse force robotically by incorporating its control in smart robot software.”
Compared to a conventional strapping machine, the strapping head on this robotized system can be made available to maintenance staff in various ways, outside the production line and behind heat shields, so they can easily access it at any time. Consider replacing the running and transport wheels. It is also worth mentioning that, depending on the employee’s availability of access, the strapping head can be adjusted to the proper working level. So, an employee no longer has to bend down or work above his or her height unnecessarily.
The above Chinese application was developed entirely in the Netherlands. It was then programmed and, together with the Chinese distributor, assembled on-site and commissioned remotely. This was realized by building a ‘remote access’ into the installation, so that Tebulo could remotely look into the software from the Dutch town of Warmenhuizen and provide support during commissioning. During final testing, a strapping cycle was first performed without hot steel coils. When this functioned as desired, the installation was put into further operation. The result is a robotic installation that has improved safety and working conditions.
Recently, Tebulo Robotics was asked by Tata Steel in the Netherlands to consider
a possible solution for replacing the existing strapping machines in ‘ Continuous Galvanizing Line 1’. To clarify, CGL 1 has two coilers, each with its own exit section and strapping machine. The new solution had to take into account the existing footprint, the limited space, and the already selected strapping/TIG welding head. It was also important to improve ergonomics and safety for operators. After conducting a feasibility study, Tebulo Robotics was awarded the contract. Not only had Tata Steel had positive experiences with Tebulo Robotics for many years, it was also inspired by the recently developed innovative dross robots at its CGL3 and out-of-the-box solution that Tebulo Robotics had realized in China.
At this installation the galvanized steel coils weigh dozens of tons. To perform regular maintenance and/or replenish consumables such as strap material, stickers, labels and ‘underlayers’, operators in conventional strapping installations have to stand in line, with all the risks that entail. Beentjes stated: “Tata Steel chose to set up both robot installations in such a way that the operators can safely carry out maintenance on the strapping heads outside the line and replenish the consumables. This was achieved
by ingeniously making use of the robot’s flexibility, combined with smart ‘tooling’ and peripheral equipment.”
Moreover, in the situation described above, our robot application offers a clear added value because, as with the Chinese application, multiple functionalities can be performed by one and the same robot. Although in principle the Tata Steel application could be performed with one robot installation, in this case the customer chose to set up two robot installations. Compared to the Chinese application, Tata Steel works with considerably thinner straps, making it possible to make do with a smaller strapping head and lighter robots. Engineering is now finished for the Tata Steel installations, with assembly having already started, and the testing is planned to take place in the upcoming months.
With the innovative out-of-the-box solutions described and detailed in this article, Tebulo Robotics is able to offer the new generation of operators a modern, safe, and pleasant work environment. This, in turn, aids production both ergonomically and in terms of safety. �
Combining readily available AI tools and techniques with sound risk management processes can better prepare an industrial operation to increase monitoring, reduce incident impact and launch automated remedial activities in near-real time, which in turn, can reduce downtime and improve resiliency capabilities of the operation.
Just so we are all on the same page from the beginning, the most generic definition of AI is the ability of machines or computer systems to perform tasks that typically require human intelligence, such as learning, reasoning, problem-solving, and decisionmaking. AI involves the development of algorithms and computer programmes that can analyse data, recognise patterns, and make predictions or decisions based on that data. It can be applied in a wide range of fields, from healthcare and finance to manufacturing and transportation, to automate tasks, improve efficiency, and enable new capabilities that were previously impossible.
AI is recognised as one of the
technological pillars of Industry 4.0 and beyond, with varying degrees of application across industrial manufacturing, and it is also considered an exponential technology, which means we will see enormous breakthroughs over the coming years thanks to AI. Whenever we incorporate industrial cybersecurity discussions to an industrial CEO agenda, we must discuss the triad of safety, integrity, and resiliency, together with the more traditional triad of confidentiality, integrity, and availability. This requirement fosters the right level of risk management coverage, as we embed operational technology (OT) with more traditional information technology (IT) into one integrated risk management framework.
AI can be instrumental in improving industrial cybersecurity risk management processes, by enhancing or complementing capabilities that may be already deployed and operational, on a case-by-case basis.
Let’s discuss some of the most obvious AI opportunities within an industrial cybersecurity programme:
� Threat detection: AI can help identify suspicious activity and potential threats by analysing vast amounts of data from various sources, including network traffic, system logs, and other security-related events. This can help security teams detect and respond to threats more quickly and effectively.
� Anomaly detection: AI can identify deviations from normal patterns of behaviour and flag anomalies that could indicate potential security risks. This can include identifying unusual user behaviour, network activity, or changes in system configurations.
� Predictive maintenance: AI can be used to monitor systems and identify potential vulnerabilities before they become exploitable by attackers. By analysing data from sensors and other sources, AI can predict when equipment is likely to fail, enabling maintenance teams to address issues before they cause downtime or security breaches.
When building a modern industrial cybersecurity programme, it is essential to factor the impact of Artificial Intelligence (AI) capabilities into reducing the cybersecurity risk on the shop floor. By Carlos Russell** Chief business compliance director, Ternium, Argentina.
� Incident response: AI can help automate incident response processes by providing real-time information about the nature and severity of a threat. This can enable security teams to respond more quickly and effectively, minimizing damage and reducing downtime.
� Threat intelligence: AI can analyse large volumes of threat intelligence data and identify patterns and trends that could indicate emerging threats. This can help organisations stay ahead of the curve and implement proactive security measures to prevent attacks.
� Security automation: AI can help automate routine security tasks, such as patch management, vulnerability scanning, and access control, freeing up security personnel to focus on more critical tasks.
AI capabilities can be deployed directly at the Security Operational Centre (SOC), either insourced or outsourced, to help enhance its capabilities, and, in turn, significantly improve key performance indicators such as mean time to incident remediation.
The case for simulation
AI and simulations are closely related because AI can be used to create, analyse, and optimise simulations.
Just to recap, simulations are computer models that imitate real-world scenarios and allow us to test different outcomes without having to physically perform the scenario. Simulations are used in many different fields, including engineering, finance, healthcare, and transportation, among others. AI can be used to analyse and optimise these simulations by creating algorithms that can learn from the simulation data and provide insights that may be difficult or impossible to discover through other means.
In a manufacturing plant, simulations can be used to predict how changes in the production process will impact efficiency and quality. By using AI to analyse the simulation data, it’s possible to identify the most efficient and effective way to make those changes.
Similarly, in the field of autonomous vehicles, simulations can be used to train self-driving car algorithms and test them in a safe environment before deploying them on public roads. AI can be used to analyse the simulation data to improve the performance and safety of the self-driving algorithms.
When we include simulations and AI in an industrial cybersecurity context, we can focus on the following examples:
� Attack simulations: AI-based attack simulations can help identify vulnerabilities in industrial control systems (ICS) and simulate attacks to test the effectiveness of existing security measures. This can help organisations proactively identify and address security gaps in their ICS networks.
� Threat intelligence simulations: AI can be used to simulate different types of cyber threats, such as malware, phishing attacks, and social engineering, and help organisations improve their threat intelligence capabilities. By simulating different types of attacks, organisations can better understand the tactics, techniques, and procedures (TTPs) used by attackers and develop more effective countermeasures.
of assurance over the programme, from the technical, process and people perspectives.
So, can hackers use AI tools to attack a company? Unfortunately, the answer is yes.
For example, Large Language Models (LLM) algorithms, such as the one used by OpenAI for ‘ChatGPT’ can alter and ultimately enhance wording on phishing e-mails, avoiding the usual tell tales of bad grammar to entice users to click on malicious links.
Hackers can also use AI to improve their ransomware code, improving their encryption protocols and even using chatbots with AI algorithms to negotiate ransom payments.
Finally, AI tools can also be used for ‘social engineering’, creating fake videos, or using voice cloning tools to recreate
� Network traffic simulations: AI can also be used to simulate network traffic patterns and identify anomalies that may indicate a cyber-attack. This can help organisations quickly detect and respond to cyber threats in their ICS networks.
� Cybersecurity training simulations: AI-based simulations can be used to train employees on cybersecurity best practices and prepare them for potential cyber-attacks. These simulations can help employees better understand the risks associated with their work and how to prevent and respond to cyber threats.
AI can enhance your ability to protect as well as to test your industrial cybersecurity implementation to provide a certain level
audio messages from company executives requesting urgent payments and attempting to entice employees to divert funds to fraudulent bank accounts.
AI is a powerful capability to develop across the industrial cybersecurity landscape, it helps to enhance our ability to defend, contain and recover quickly from an incident. It also helps to be better prepared and ready for cyber-attacks. By incorporating innovative cybersecurity strategies and continuously adapting to emerging threats, industrial organisations can mitigate cybersecurity risk and ensure the safety and resilience of their operations. �