+1-800-918-2600 | gcinfo@grancoclark.com | www.grancoclark.com Hydraulic Free : Fully Electric System. GRANCO CLARK’S ALL NEW Non-Hydraulic System utilizes servo actuators and pneumatics instead of hydraulics. This includes the Log Lift, Log Pusher, Pullers, Stretchers, Hot Saw, ECS Saw and many others. Our Hydraulic Free Systems are quiet, quick, powerful and boast incredible new features. Now that your energized, let’s talk! 1-800-918-2600 Tired of Maintaining Hydraulics? INDUSTRY NEWS ALFED 60TH ANNIVERSARY DECARBONISATION THE JOURNAL OF ALUMINIUM PRODUCTION AND PROCESSING www.aluminiumtoday.com September/October 2022—Vol.35 No.5 NO5VOL.352022SEPTEMBER/OCTOBERTODAYINTERNATIONALALUMINIUM INDUSTRY UPDATES +1-800-918-2600 ı gcinfo@grancoclark.com ı grancoclark.com
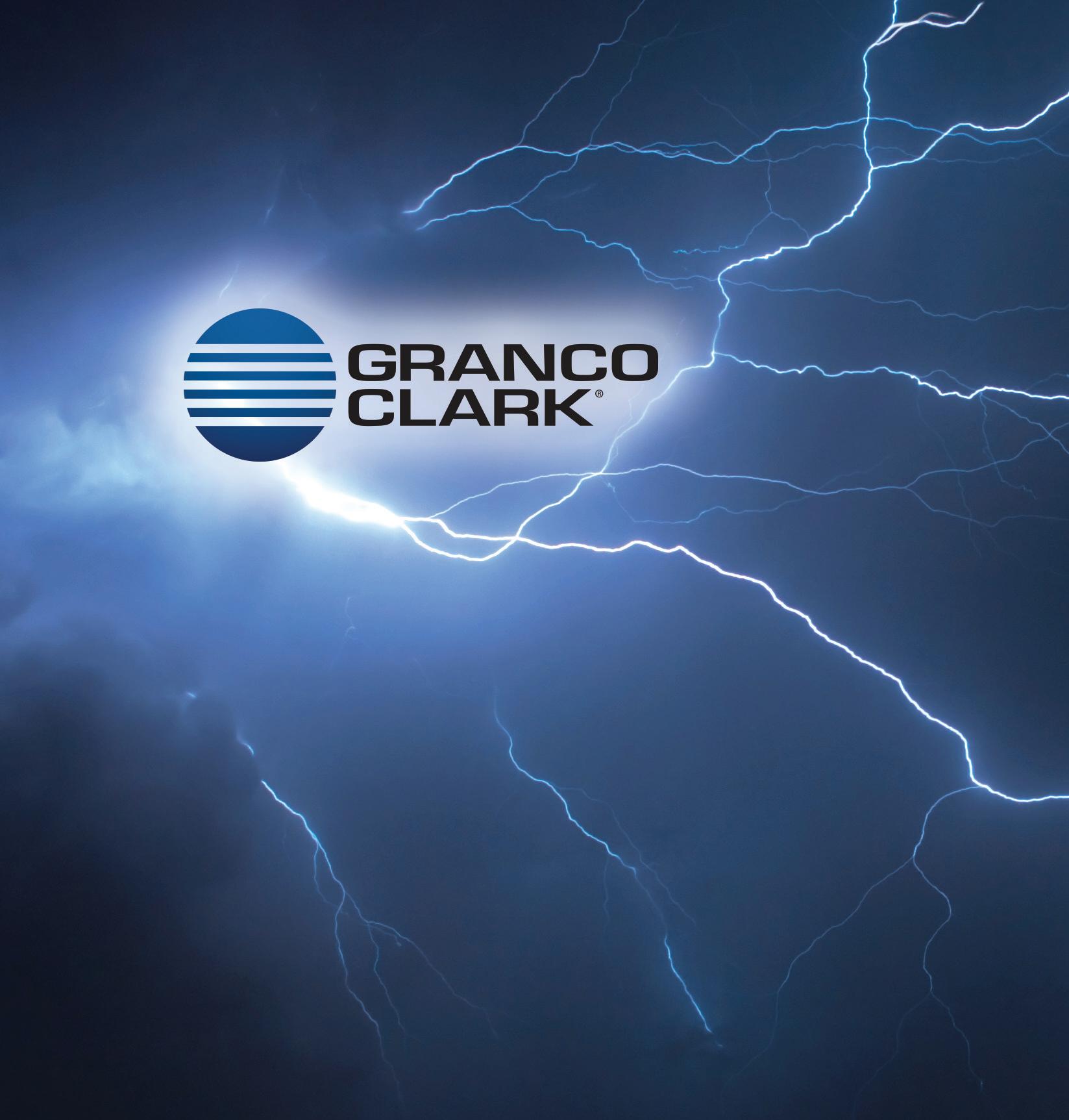

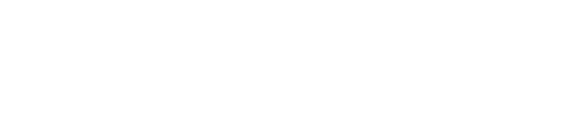















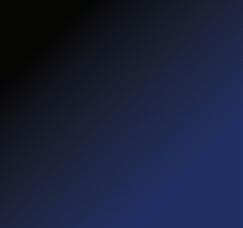

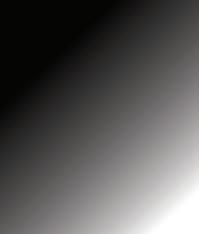


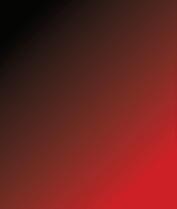
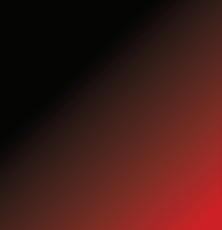
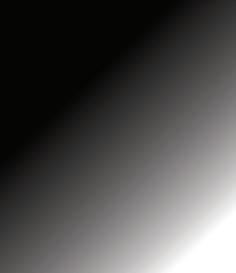
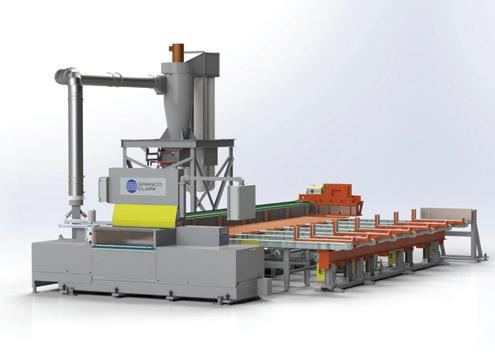
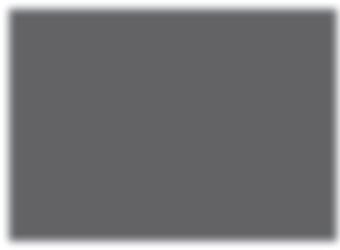


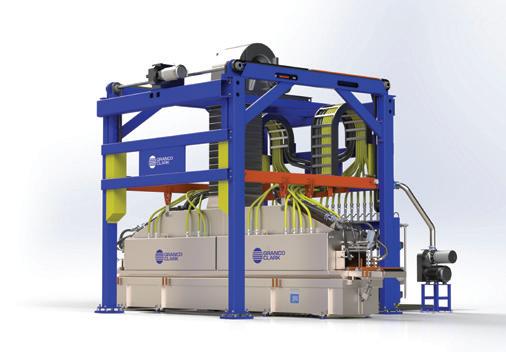
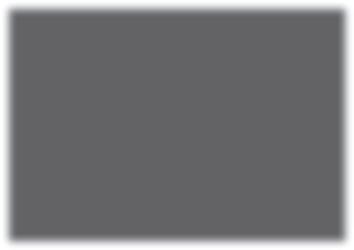
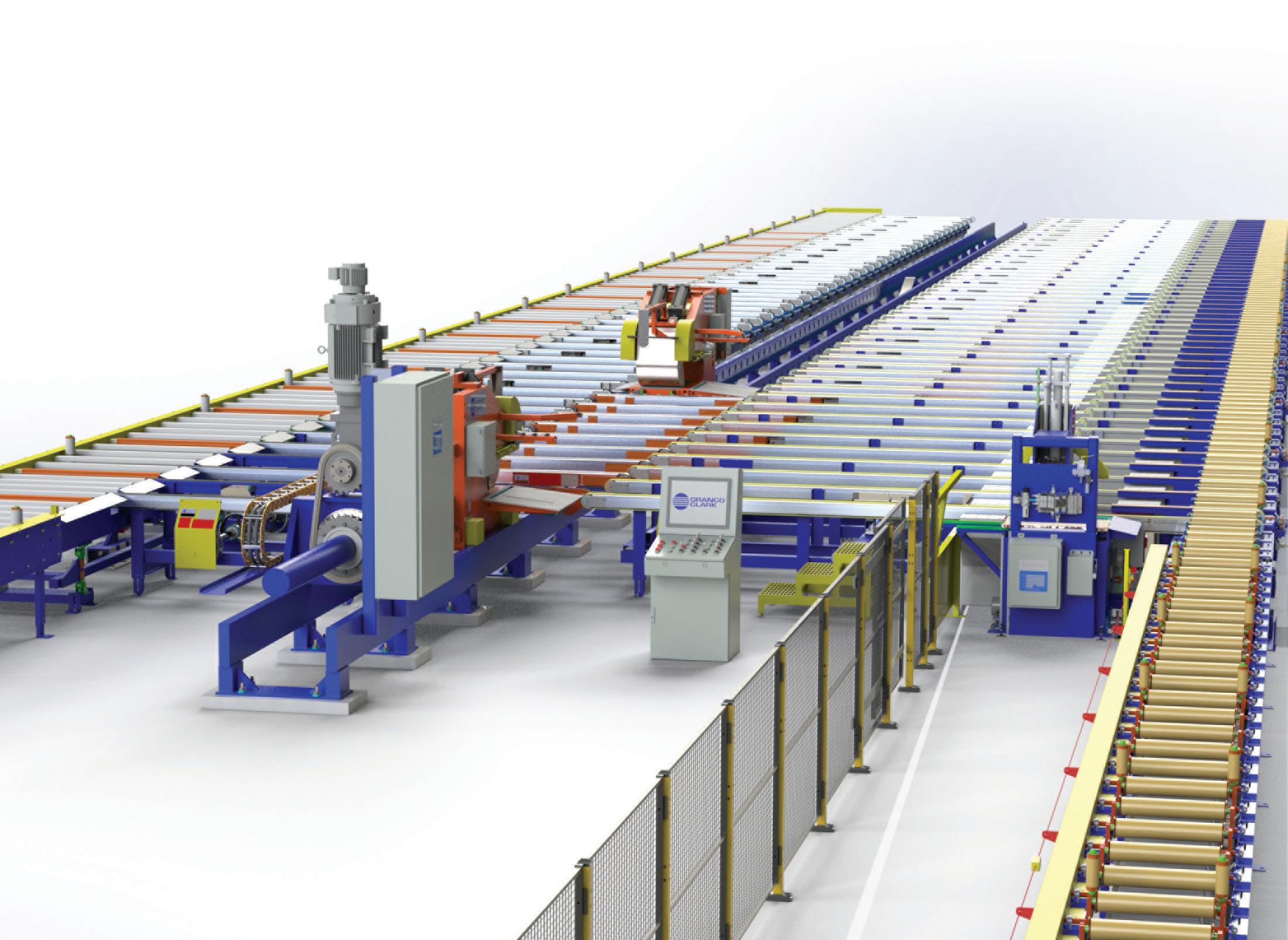
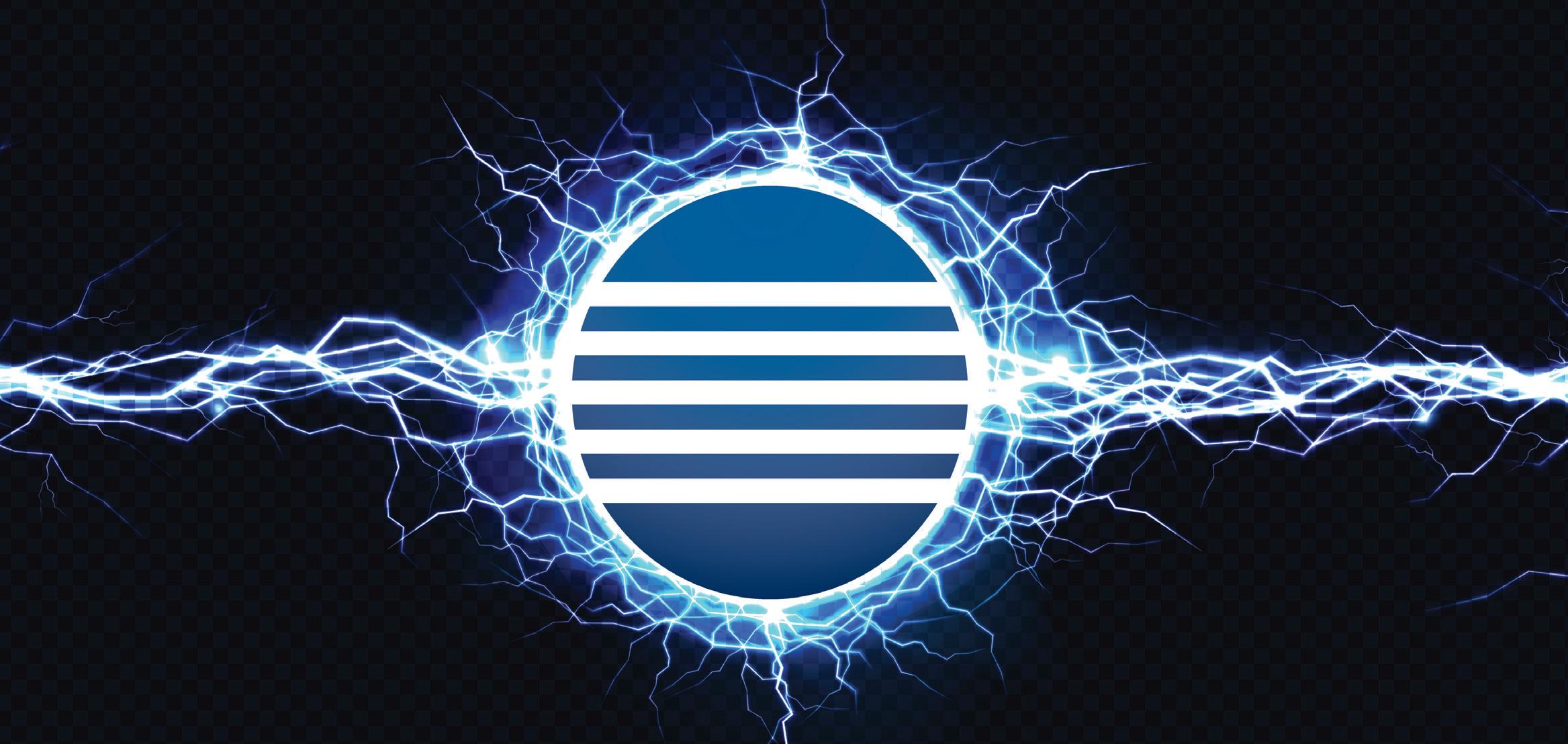
CONTENTS 1Aluminiumwww.aluminiumtoday.comInternationalToday September/October 2022 2 LEADER 2 NEWS Volume 35 No. 5 – September/October 2022 COVER Cover picture courtesy of Granco Clark Editorial Editor: Nadine Bloxsome Tel: +44 (0) 1737 nadinebloxsome@quartzltd.com855115 Editorial Assistant: Zahra Awan Tel: +44 (0) 1737 zahraawan@quartzltd.com855038 Production Editor: Annie Baker Sales Commercial Sales Director: Nathan Jupp Tel:nathanjupp@quartzltd.com+44(0)1737855027 Sales Director: Ken AdvertisementTel:kenclark@quartzltd.comClark+44(0)1737855117Production Production Executive: Martin Lawrence Managing Director: Tony Crinion CEO: Steve JackCirculation/subscriptionsDiproseHomewood Tel +44 (0) 1737 855028 Fax +44 (0) 1737 855034 email Annualsubscriptions@quartzltd.comsubscription:UK£257,allother countries £278. For two year subscription: UK £485, all other countries £501. Airmail prices on request. Single copies £47 ALUMINIUM INTERNATIONAL TODAY is published six times a year by Quartz Business Media Ltd, Quartz House, 20 Clarendon Road, Redhill, Surrey, RH1 1QX, UK. Tel: +44 (0) 1737 855000 Fax: +44 (0) 1737 855034 Email: aluminium@quartzltd.com Aluminium International Today (USO No; 022-344) is published bi-monthly by Quartz Business Ltd and distributed in the US by DSW, 75 Aberdeen Road, Emigsville, PA 17318-0437. Periodicals postage paid at Emigsville, PA. POSTMASTER: send address changes to Aluminium International c/o PO Box 437, Emigsville, PA 17318-0437. Printed in the UK by: Pensord, Tram Road, Pontlanfraith, Blackwood, Gwent, NP12 2YA, UK © Quartz Business Media Ltd 2022 ISSN1475-455X Supporters of Aluminium International Today SEARCH FOR ALUMINIUM INTERNATIONAL TODAY 6 86246337 +1-800-918-2600 gcinfo@grancoclark.com www.grancoclark.com Hydraulic Free : Fully Electric System. GRANCO CLARK’S ALL NEW Non-Hydraulic System utilizes servo actuators and pneumatics instead of hydraulics. This includes the Log Lift, Log Pusher, Pullers, Stretchers, Hot Saw, ECS Saw and many others. Our Hydraulic Free Systems are quiet, quick, powerful and boast incredible new features. Now that you’re energized, let’s talk! 1-800-918-2600 Tired of Maintaining Hydraulics? INDUSTRY NEWS ALFED 60TH ANNIVERSARY DECARBONISATION THE JOURNAL OF ALUMINIUM PRODUCTION AND PROCESSING www.aluminiumtoday.com September/October 2022—Vol.35 No.5 NO5VOL.352022SEPTEMBER/OCTOBERTODAYINTERNATIONALALUMINIUM INDUSTRY UPDATES +1-800-918-2600 gcinfo@grancoclark.com grancoclark.com 77 6 IAI GLOBALANNIVERSARYUPDATE 13 Aluminium Outlook 17 CRU GREENERQ&A ALUMINIUM 21 Opportunities for the UK Metals Industry 24 Solar Steam decarbonisation 29 The role of regenerative burners 32 Every step matters on the path to zero 34 The Turla RFK’s new heaters range RECYCLING 37 New generation X-TRACT 41 Coffee capsule recycling 45 Focus on Podback US OUTLOOK 49 US aluminium capacity changes 55 ALFED 60th ANNIVERSARY DIGITAL MANUFACTURING 63 Behind the digital transformation mindset GRAIN REFINEMENT 69 The grain refinement phenomenon LUBRICATION 73 Matrix Speciality TECHNOLOGYLubricants 76 Roll texturing for the aluminium industry FURNACE SAFETY 77 Carbon bake house efficiency FURNACE TECHNOLOGY 81 Lowering aluminium melting operating costs TRANSPORT & HANDLING 86 Vehicle and stationary equipment EVENT REVIEW 88 MECSPE/METEF
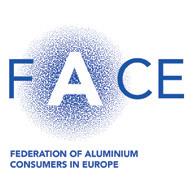
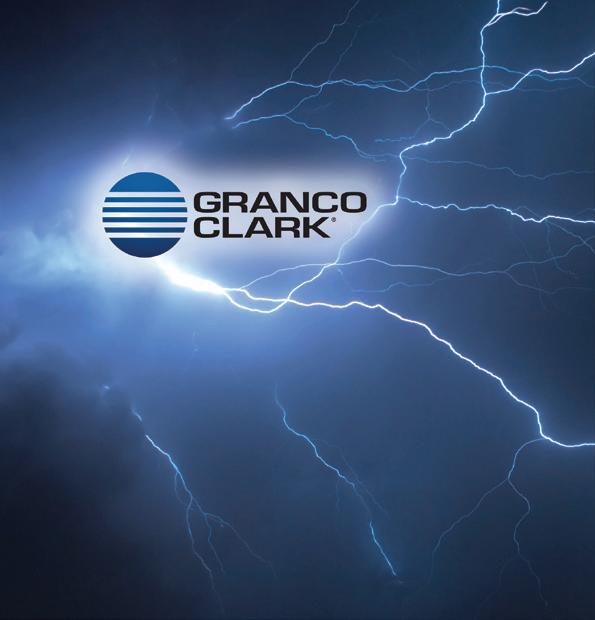




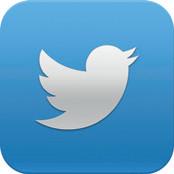
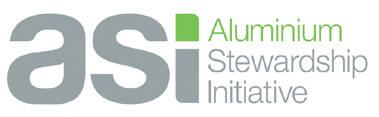
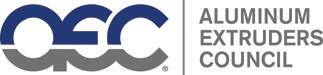
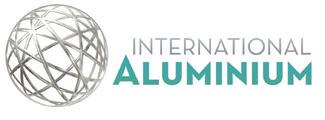
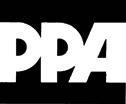
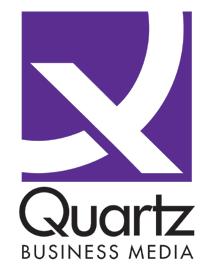
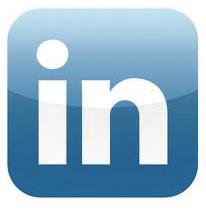
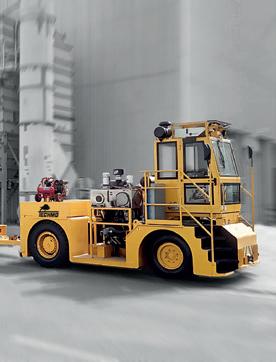
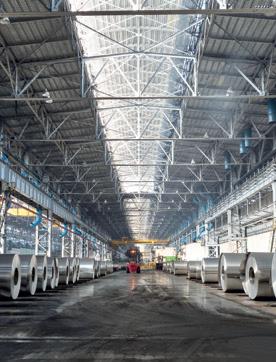
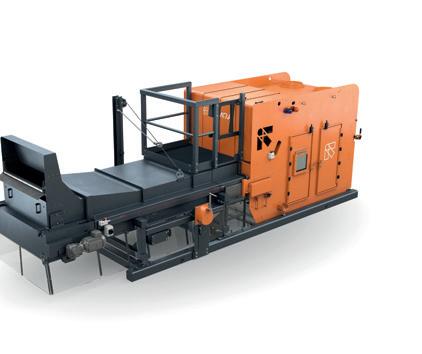
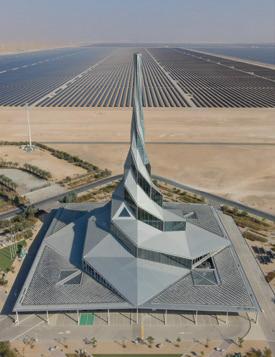


Slovalco to stop primary aluminium production
BEGINNINGS
September/October 2022
COMMENTNEW2
The Sept/Oct issue always sym bolises getting back into routine and returning hopefully feeling refreshed from a summer holiday or Thattwo!‘back to school’ feeling never seems to leave you and I will be treating myself to a new pencil case and stationery in or der to take on a new role as the Membership and Sustainability Manager at the UK Aluminium Federation (ALFED) from 1st September.Aluminium is ideally posi tioned to help UK industry as it moves towards more sustainable supply chains and I am excited to announce that my new position will see me helping to outline ALFED’s Sustainability Strategy and adhere to the 2050 Roadm ap, while working with members on programmes which directly impact the future of a circular economy.Iwillstill maintain my position of Editor on Aluminium Interna tional Today, so not much will change on that front! Some of you may even have to see more of me in the future and with the events season also around the corner, I will be wearing both my AIT and ALFED hats across a number of conference and panel sessions.Inparticular, I will be hosting the Digital Manufacturing Ses sions at the Innovation Plaza at the ALUMINIUM Show and look forward to hearing from those leading the way with new tech nologies and helping to create the smelter of the future. This issue is also full to the brim with articles and I hope you are reading this after picking up your free copy from our booth at the ALUMINIUM Show! Enjoy! nadinebloxsome@quartzltd.com
Hydro’s majority owned Slovalco aluminium facility in Slovakia has decided to close the primary alu minium production at the plant. The closure will be completed by the end of September 2022. The decision to terminate pri mary aluminium production at Slovalco comes in response to adverse framework conditions and high electricity prices, which show no signs of improvement in the short term. The casthouse in Slovalco will continue its recycling operation, serving customers in the region with 75,000 tonnes of recycled aluminium annually. “Slovalco is a well run and mod ern primary aluminium plant, well placed to serve European custom ers with high quality aluminium products. I regret that it has not been possible to secure continued operation of the primary produc tion at the plant,” says Ola Sæter, head of Hydro’s primary produc tion and chair of Slovalco’s Board of “SlovakiaDirectors. has not implement ed the competitive EU CO2 com pensation framework. This has prevented Slovalco from entering long term power contracts and the plant’s current contract ex pires at the end of 2022. Due to the current Slovak framework con ditions and the European power prices, Slovalco would incur sub stantial financial losses if it contin ued its operation beyond 2022,” saysSlovalcoSæter. curtailed 40 percent of its 175,000 tonnes per year primary capacity in late 2021 and early 2022, and is currently run ning at 60 percent of its capacity. The primary production lines at Slovalco will be mothballed and may resume operations at a later stage if the market and framework conditions allow. The closure pro cess will commence shortly and be completed no later than the end of September 2022.
International Today
TOP STORIES Rio Tinto expands low-carbon billet production in Canada Rio Tinto is investing US$188 million (CA$240 million) to in crease the production capacity for low-carbon, high value aluminium billets at its Alma smelter in LacSaint-Jean, Quebec by 202,000 metric tonnes. The existing casting centre at Rio Tinto’s Alma plant will be expand ed to accommodate new stateof-the-art equipment, including a casting pit and furnaces, allowing a larger portion of the aluminium produced to be converted to high er value billets. Construction will begin in May 2023, after complet ing detailed engineering and pre liminary work, and commissioning is expected in the first quarter of 2025.
The investment will strengthen the supply chain in North Ameri ca and allow Rio Tinto to be more agile and flexible to support the critical growth of North American manufacturers for a variety of high value-added products, primarily in the automotive and construction industries. Aluminium billets are extruded through a die and the resulting profiles are used to make various products like bumpers and roof rails for cars as well as doors and window frames. The investment is expected to generate nearly US$160 million (CA$200 million) in economic benefits for Quebec. The project will create around 40 new per manent jobs and help to support the 770 existing jobs at the Alma plant.Sébastien Ross, Managing Di rector of Rio Tinto Aluminium’s Atlantic operations, said: “This expansion of our low carbon alu minium billet production capacity in Quebec will allow us to better meet our customer’s growing de mand for high quality alloys and value-added products made with renewable hydroelectricity. This new capacity will help to strength en the position of our Alma smelt er and we are proud to work with our employees, clients, Quebec equipment manufacturers and partners to bring this much antici pated project to fruition.”
multi-functionalhighly-automated,cranesinJebelAliEmiratesGlobalAluminium(EGA)hasannouncedthecompanyistoinstallhighly-automated,multi-functionaloverheadcranesinJebelAliinasteptowardsfullautomationofcranesusedforreductioncelltending,andsecuringoperationsfordecadesahead.EGAisreplacing16cranesthathavecompletedtheir25-yearusefulliveswithjust14newmodelsthatincorporateauto-positioningandadvancedsensingcapabilities.Theincreasedautomationcapabilitiesofthenewcraneswillim
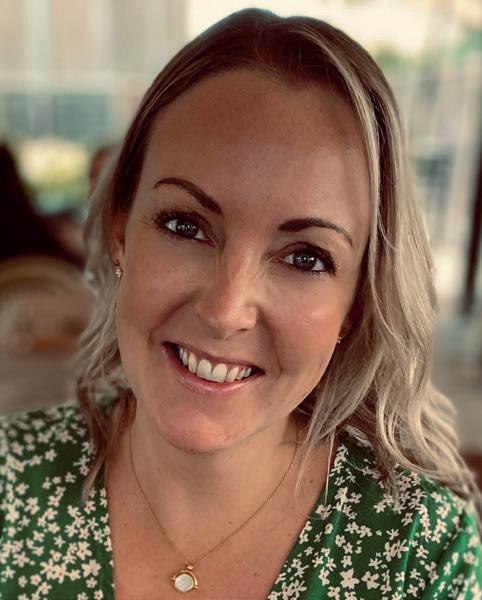
prove safety, efficiency and relia bility. The technology brings closer EGA’s future ambition of operat ing cranes remotely from a central control room and ultimately ful ly-autonomous crane operation. EGA has contracted Fives, a French industrial engineering group, to supply the new cranes. The first new crane is expected to be delivered before the end of 2023 with all 14 new cranes in op eration by the beginning of 2025.
EGA to install
Aluminium
3 NEWS IN BRIEF NEWS Dynamic Concept and EPIQ Machinery enters into partnership Dynamic Concept and EPIQ Machinery have announced a breakthrough in robotic solutions. Indeed, the two Quebec-based equipment manufacturers have combined their forces to cocreate a robotic equipment that will improve the maintenance operations of molten metal furnaces for primary and secondary aluminium smelters. This innovative, energyefficient robot will automate furnace tending operations such as: skimming, dry cleaning and stirring through programmed sequences.
ASI’s Performance Standard V3 (2022) has been conditionally approved as a recognised alignment-assessed standard by the London Metal Exchange (LME), for Track A of their Responsible SourcingAnRequirements.independent standard alignment assessment has confirmed ASI’s 2022 Performance Standard is OECD-Aligned. LME Brands for aluminium can use ASI Certification against the 2022 Performance Standard to demonstrate compliance with the LME’s Responsible Sourcing requirements. Full, unconditional approval will be assessed after the implementation portion of the alignment assessment is complete.

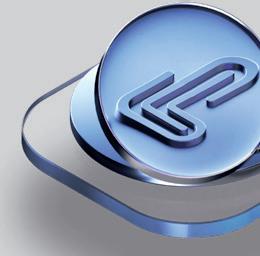
“Our partnership with Sortera will allow Novelis to continue to increase the amount of recycled content in our automotive alloys and subsequently reduce our carbon footprint,” said Derek Prichett, Senior Vice President, Corporate Development at Novelis. “It also aligns with our goal of becoming a fully circular business, as we will be able to keep more automotive aluminium in our supply chain and re-direct it back into the same products.”
New standardaluminiumintroducesCoin,Luminiumdigitalcommodity-backedtoken,an Luminium Coin, a project setting a global “aluminium standard,” announced its official launch with more than $100,000 in token sales.The Miami-based start-up was established by Dr. Richard W. Rahn, former chief economist at the U.S. Chamber of Commerce and former member of the Cayman Islands currency board. In 1999, he predicted the crypto boom in his book, The End of Money and the Struggle for Financial Privacy. AMAG and thyssenkrupp Aerospace extend their cooperation The partnership between AMAG Austria Metall AG and thyssenkrupp Aerospace has existed since the very beginning of AMAG’s aviation history. The strong cooperation has now been extended for a further six months in the coming year with the signing of a new supply contract. thyssenkrupp Aerospace has thereby secured the procurement of premium aluminium for the coming year through AMAG.
“ASI has done an excellent job translating the text of the OECD Guidance into practices for the aluminium value chain that producers can both implement and be audited against”, said Nicole Hanson, Responsible Sourcing Manager, LME. “We’re pleased to take on the responsibility of integrating the OECD Guidance into ASI’s Certification program for the aluminium value chain, and collaborating with LME on their Responsible Sourcing requirements. Using a risk-based approach to harmonise due diligence across multiple sectors adds value for all stakeholders”, said Fiona Solomon, ASI CEO.
The partnership supports Novelis’ sustainability goals to reduce its carbon footprint by 30% by 2026 and to be carbon neutral by 2050 or sooner. Using recycled aluminium as input material requires approximately 5 percent of the energy used to make primary aluminium, thus avoiding approximately 95 percent of the carbon emissions associated with production.“Weare thrilled to work with Novelis, the global leader in sustainable aluminium solutions,” said Michael Siemer, CEO, Sortera Alloys. “Together with existing investors like Chrysalix and Breakthrough Energy Ventures, and now Novelis, we are poised to disrupt the global aluminium recycling space while cutting global emissions and driving a more sustainable industry.”
AlloysNoveliswill take advantage of Sortera’s advanced sorting technologies, including data analytics and advanced sensors, to recycle and re-use higher amounts of both automotive post-production and post-consumer scrap. Today, when different aluminium alloys are mixed, either after the automakers’ stamping process or when a vehicle is disposed of at the end of its lifecycle, they cannot be re-separated into the individual alloys. As a result, the higher value alloys are downgraded into lower value uses. With the use of the Sortera technology, Novelis will be able to effectively separate the mixed scrap into individual alloys and recycle them back into the same product, closing the loop. This will allow Novelis to meet original equipment makers’ exacting needs for performance, durability, safety and design.
capabilitycastingincreasesAlcoaAlcoaCorporationhas
LME recognition of ASI Performance Standard V3
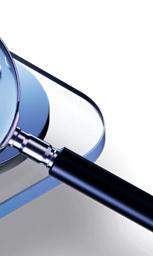
announced that construction will soon begin on a project to increase the casting capabilities at its Deschambault smelter in Canada to include standardTheingots.new casting equipment will be constructed in an existing building, with the project fully complete in the first quarter of 2023. The output from the approximately $8 million return-seeking capital investment will complement the site’s two existing vertical casting pits, which exclusively cast T-bar ingots.Adding standard ingot casting to the site’s capabilities will allow greater flexibility for alloying in smaller batches to meet customer needs for value-add products such as foundry alloys for the automotive industry. Each standard ingot weighs approximately 10.5 kilograms.
Novelis announces partnership with recycling start-up Sortera
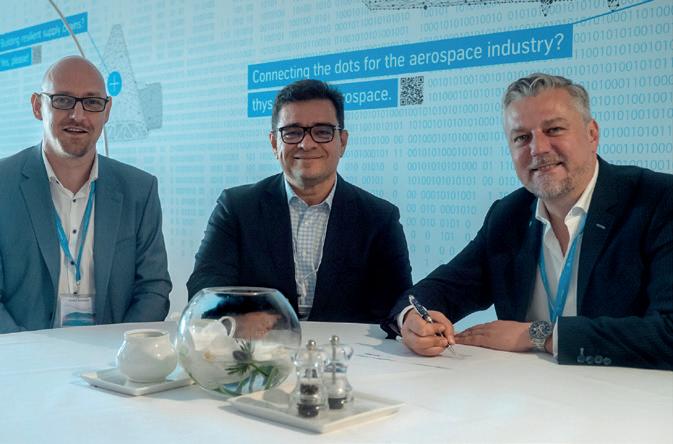
10th - 14th 40th International Conference and Exhibition of ICSOBA ICSOBA (The International Committee for Study of Bauxite, Alumina & Aluminium) mission is to organise the annual Technology Conference with a scope covering upstream aluminium activities from mine to metal. Held in Athens, www.icsoba.org/2022/Greece
CANPACK Group to invest in greenfield beverage can plant
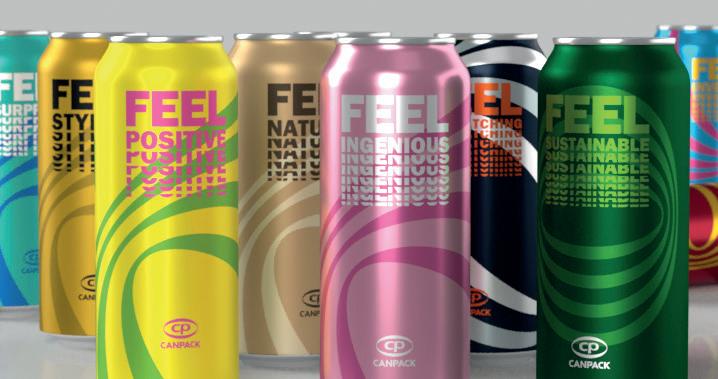
The Conference aims to position the South African aluminium industry as a premier supplier to the continent and the world. Held in Cape Town, South Novemberwww.afsa.org.za/Africa
Time has come to re-energise our industry after all the detours, distractions, disruptions, inflations, shortages and imbalances of recent months and years. Held globalconsulting.comwww.conference.az-virtually
4
Hydro invests in Henderson plant to expand recycled aluminium production
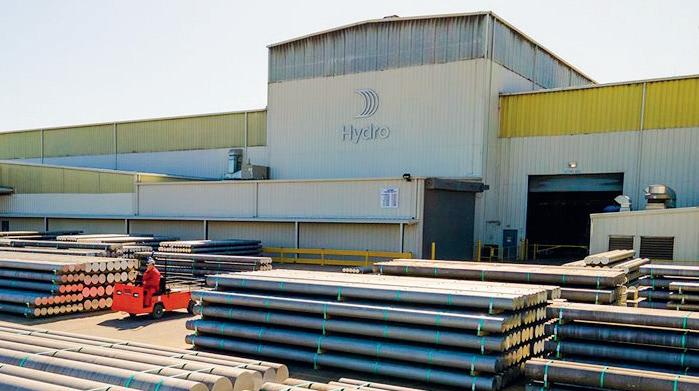
Aluminiumwww.aluminiumtoday.comInternationalToday
September 27thALUMINIUM29th
GREENER NEWS
Hydro is investing NOK 150 million ($15 million) into its Henderson facility in Kentucky, U.S. to deliver certified recycled aluminium prod ucts to the automotive industry. The investment will both enhance Hydro’s position as the leading producer of low-carbon, recycled aluminium in North America and further reduce the environmental impact from production. As the automotive industry in Kentucky is expanding, the invest ment will enable the plant to pro duce industry-leading advanced alloys for automotive applica tions, including the proprietary advanced material, Hydro CIRCAL, creating an opportunity to supply Hydro’s most progressive, sustain ability-focused customers with this cutting-edge product. The investment will support two key projects. To meet the specifi cations of the growing U.S. auto motive market, Hydro will install a new homogenization furnace to improve the plant’s recycling capabilities. This will enable the Henderson facility to produce a greater volume of advanced alloys using recycled metals with a lower carbonHydrofootprint.willalso install a new baghouse – a state-of the-art dust and gas collector for reducing air emissions. This will allow the plant to use greater volumes of post-consumer scrap and explore new, more difficult types of scrap, like material with paint or other contamination, which requires ad vanced equipment to recycle. The new baghouse will also improve the air quality inside the plant and reduce the overall environmental footprint from operations.
The world’s leading trade show and B2B platform for the aluminum industry and its main application industriesthe show focuses on solutions for automotive, mechanical engineering, building and construction, aerospace, electronics, packaging and transportation. Held in Germany. Octobercom/en-gb.htmlwww.aluminium-exhibition.
26th - 27th AFSA - International Conference & Exhibition
8th - 10th AZ Global Aluminium Conference
CANPACK S.A., has announced it will increase its manufacturing capacity of aluminium beverage cans with a new production facili ty in Poços de Caldas, in the State of Minas Gerais, Brazil. Officials from CANPACK along with state and local officials and economic development leaders jointly an nounced the new facility following the approval of the project, with economic development incentives provided by both the state and lo calWithgovernments.atotalinvestment of ap proximately BRL 710 million (USD 140 million), this new facility represents CANPACK’s continued commitment to developing the Brazilian packaging sector. The announcement of this new plant takes place only a few months after the company committed to investingBRL360 million (USD 70 million) in an aluminium beverage can ends production facility in Manaus (Amazonas). The total value of both investments exceeds BRL 1 billion.Construction of the facility in Poços de Caldas is expected to begin in the last quarter of 2022, and the plant operation is slated to commence in the first quarter of 2024. The installed initial to tal capacity of the new plant will be approximately 1.3 billion cans per year, and its volumes will be geared towards meeting the de mand of Brazilian customers. It is expected that the new produc tion plant will bring around 140 high-qualified direct jobs to Poços de Caldas region.
On the path to complete the de carbonisation of the AMAG Ran shofen site, the substitution of fos sil energy sources, and therefore also solar electricity production, is an essential element. Following the successful commissioning of Austria’s largest rooftop photo voltaic system with 55,000 square metres of collector surface in au tumn 2021, the first expansion has now been undertaken. With another 5,000 square me tres on the roofs of the new logis tics hall, the entire plant now cov ers an area of nine football fields or 60,000 square metres. Annual production increases to 7.3 GWh with the expansion. This amount of energy could supply around 2,000 households with electrici ty. The green electricity generated is used exclusively at AMAG and supplements the electricity mix, which has already consisted of 100 per cent renewable sources for several years. With the expan sion of the rooftop photovoltaic system, AMAG is taking a further step towards CO2 neutrality, which is being supported by ongoing technological improvements and innovations to increase energy ef ficiency.
AMAG expands Austria’s largest rooftop photovoltaic plant
29th - 1st December ARABAL 2022 ARABAL has announced that the 24th edition of ARABAL (the Arab International Aluminium Conference and Exhibition) will be hosted by Egyptalum. Held in www.arabal.comEgypt2022DIARYForafulllistingvisitwww.aluminiumtoday.com/events

precimeter.com
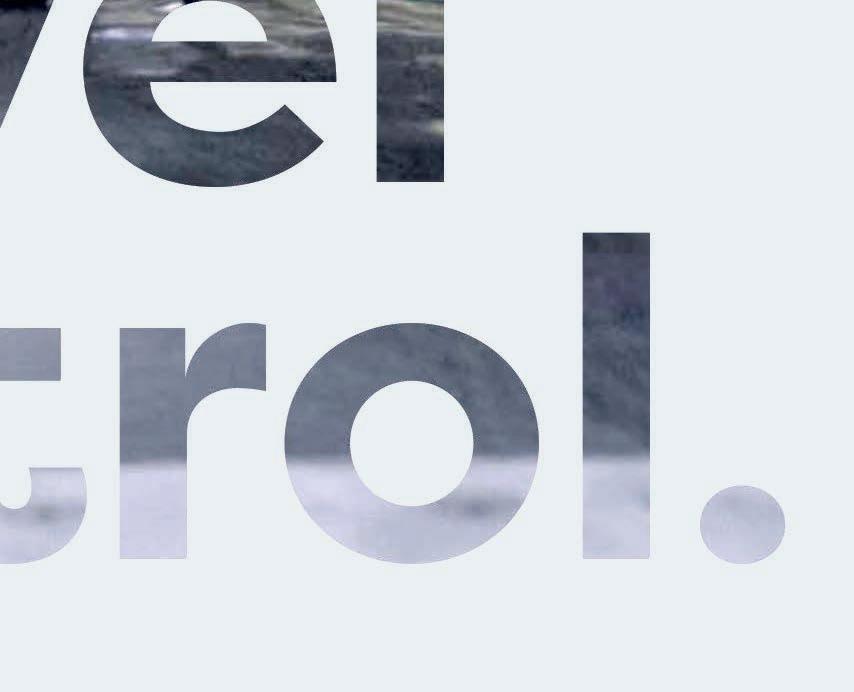
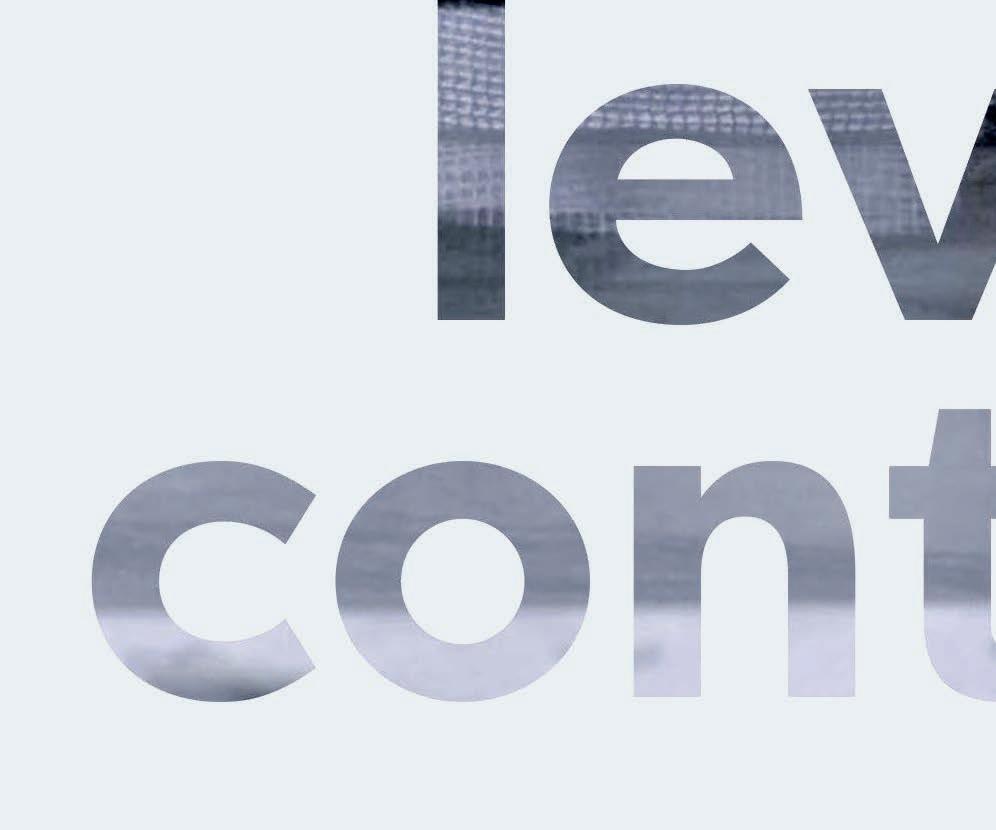
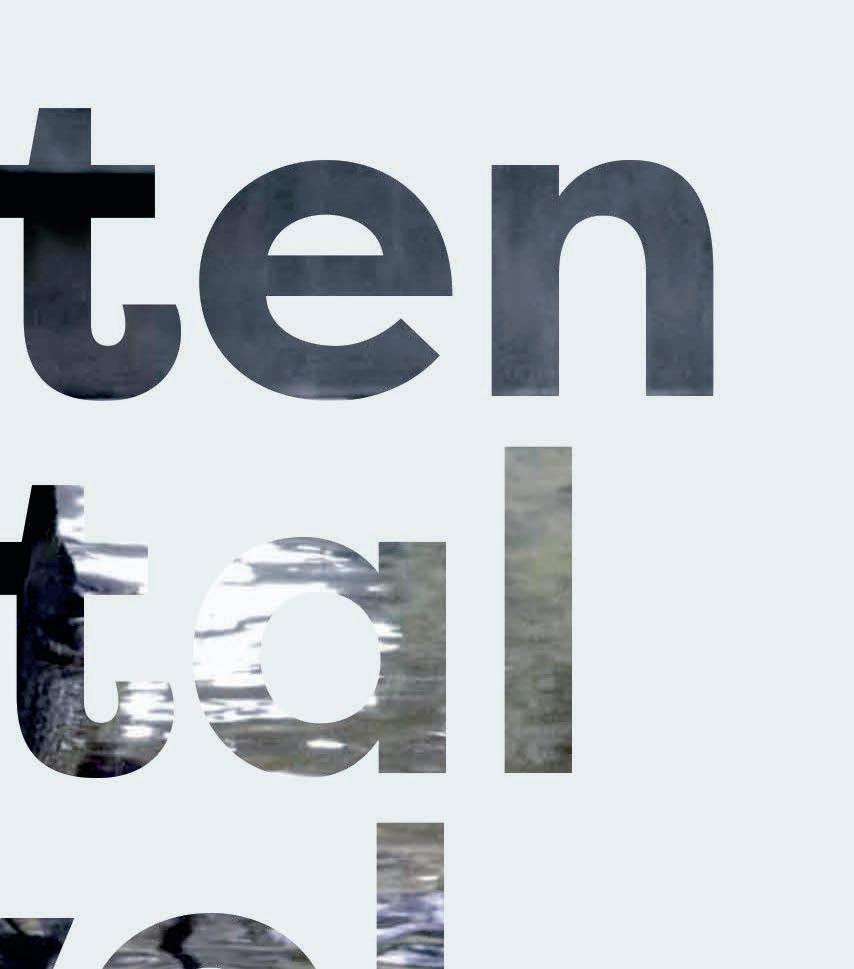
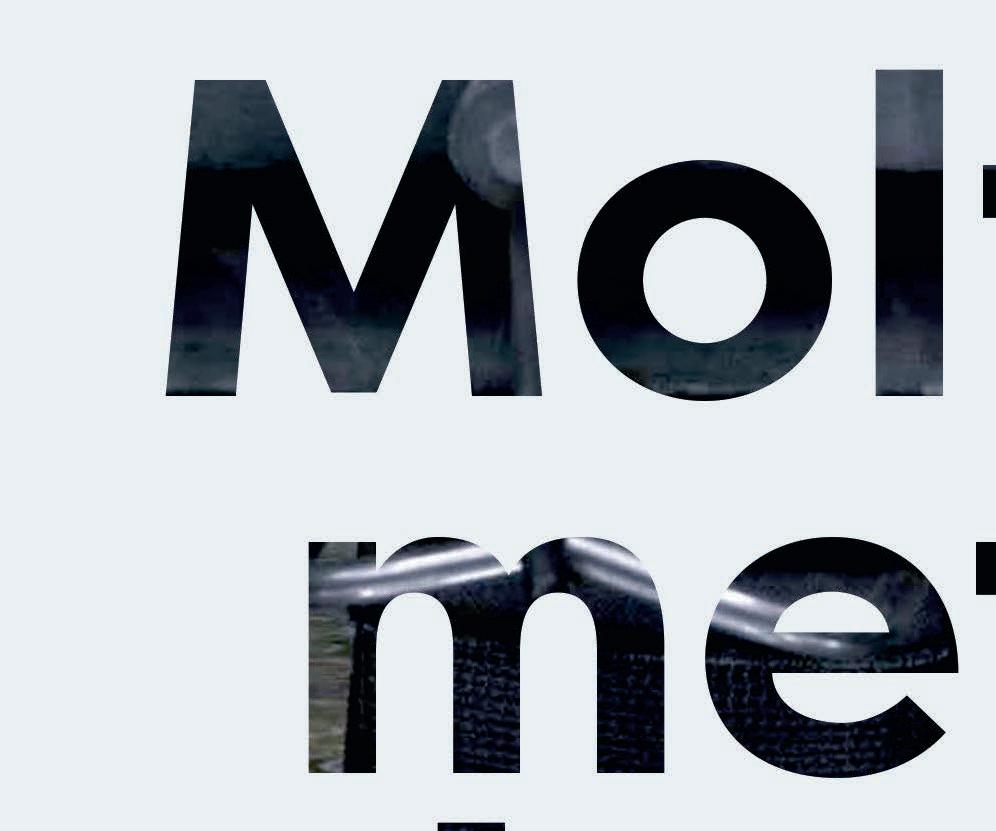

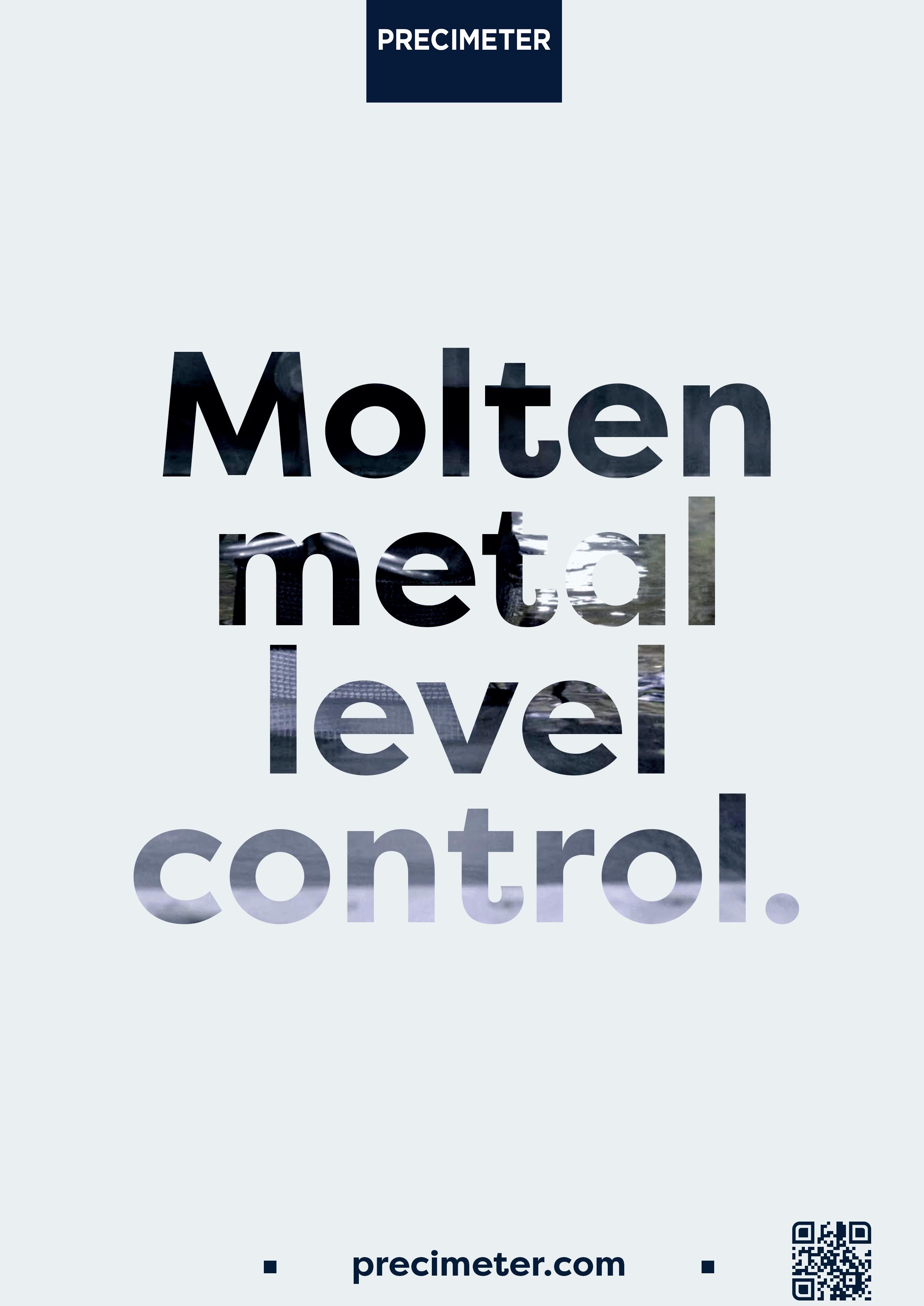
Advancing the aluminium inHowbettersustainabilitysector’sforatomorrowIAIissupportingthealuminiumindustryimprovingitssustainabilityperformance
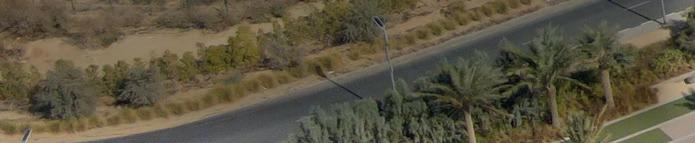
Aluminium International TodaySeptember/October 2022 IAI ANNIVERSARY6
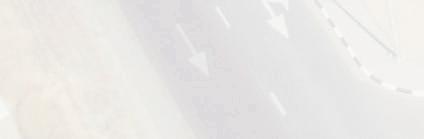
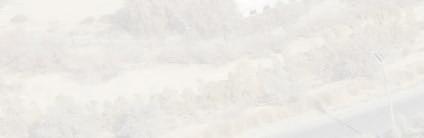
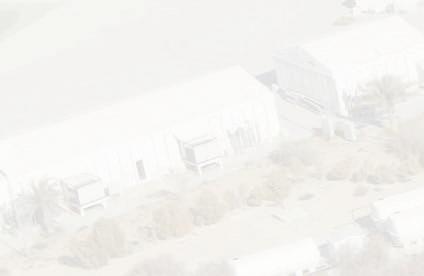

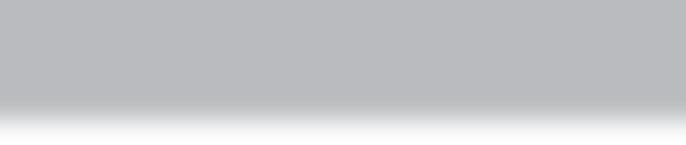

“Along with the exciting market opportunities that will arise for aluminium from a focus on sustainability, the expectation on industry to produce sustainably will remain a requirement **Editor, Aluminium International Today aluminium demand based on the shift Recent across the industry and a move towards “Sustainability the context of choices between materials, this
Rising to the challenge While the aluminium sector is mindful of the impact of increased production on sustainability in terms of GHG emissions Lightweight, durable, and infinitely recyclable, aluminium remains one of the most important and useful materials in existence and plays a central role in achieving the sustainability ambitions of multiple sectors. This adaptability continues to fuel demand, particularly from automotive manufacturers and the construction sector. In our final article in this collaborative series with International Aluminium Institute (IAI), we look at how the IAI has provided a forum for leading the industry in improving sustainability performance and demonstrating the benefits of aluminium products. It is well-known across the industry that the demand for aluminium is set to increase, driven by consumer demand for environmentally friendly solutions in transport, infrastructure, energy, and food security. Nadine Bloxsome* speaks to longstanding IAI members to discuss aluminium’s future prospects and how this is driving the sector to progress its sustainability in producing the metal.
to deliver continuous improvements in performance. The aluminium industry is well placed to deliver on these expectations. Through the IAI, the industry has both an excellent track record on delivering improvements and has well developed plans for how key issues – such as bauxite residue and greenhouse gas emissions – can be addressed.”
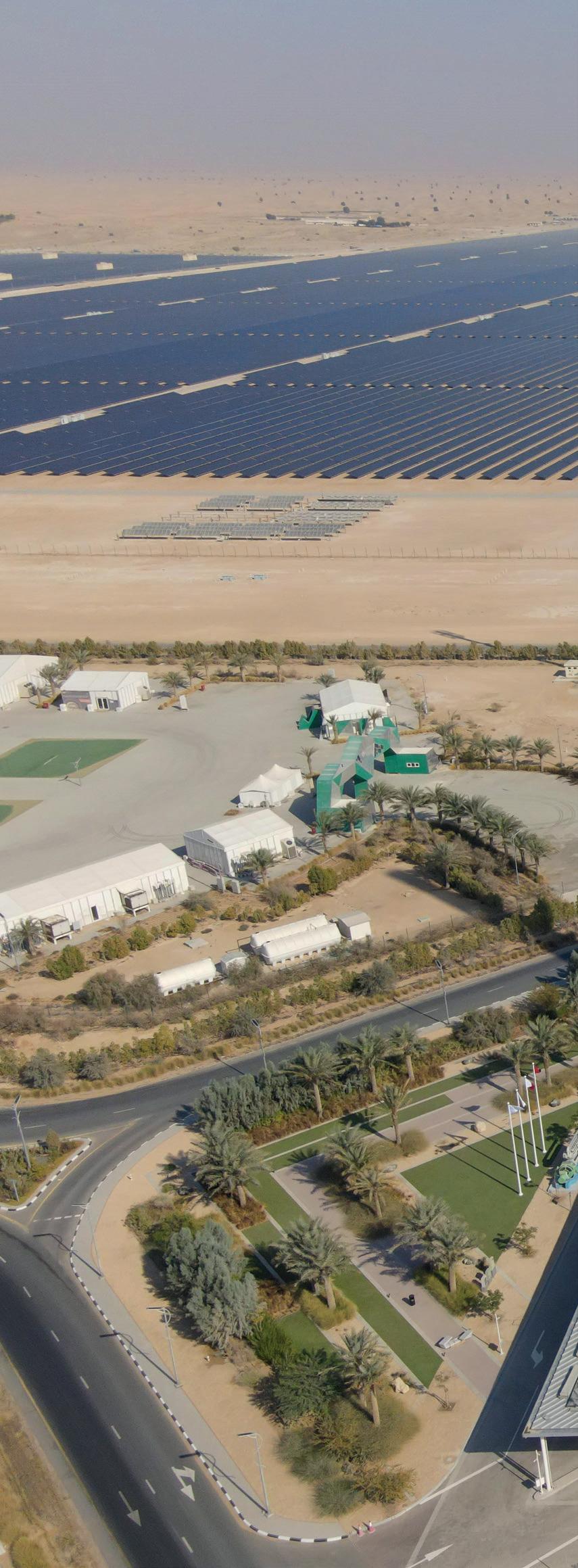
“The suitability of aluminium in a world that values sustainability has been demonstrated, for example, in IAI’s recent work examining the choice between aluminium, plastic and glass for beverage containers. Aluminium out-performs the other materials in all aspects of recycling and circularity – from collection rate, to recycling rate and particularly closed loop recycling.“However, we also see similar conclusions in the work of others, such as the findings of the International Energy Agency on the role that aluminium will play in future electricity infrastructure as part of the transition to clean energy. A role that is underpinned by aluminium’s electrical conductivity, light weight and abundance.“Anditis increasingly happening in real world purchasing decisions such as the increased use of aluminium in motor vehicles as part of the larger trend toward electric vehicles. Aluminium will deliver more sustainable cars with better performance and longer range.
“We are witnessing a permanent change in how consumers choose products and suppliers,” says Miles Prosser, Secretary General,“SustainabilityIAI. aspects of the production process are now explicitly part of sourcing decisions along with technical specifications and price. In the context of choices between materials, this shift benefits aluminium. The inherent characteristics of aluminium – particularly lightweight and recyclability – will skew purchasing decisions toward our metal.
The benefits of aluminium are also wellknown; it is lightweight, strong, durable, and infinitely recyclable, making it the sustainable material of choice. As we strive for a more energy-efficient future, aluminium continues to provide innovative solutions and competitive advantages for businesses and consumers.

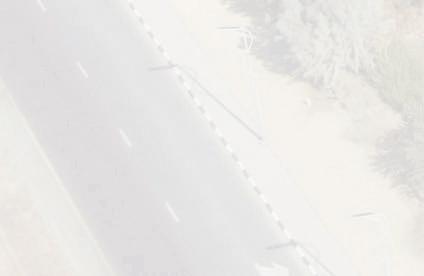
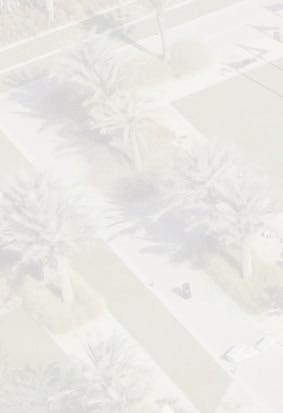

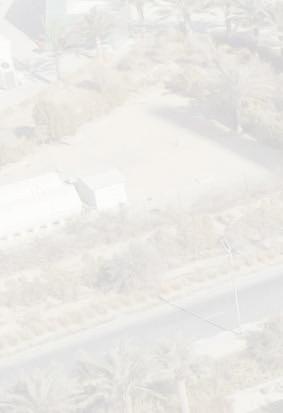
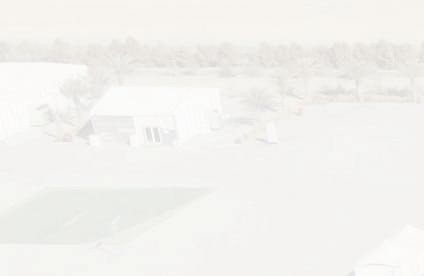
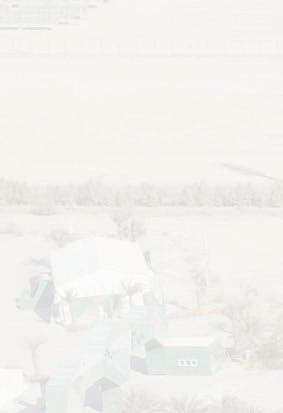
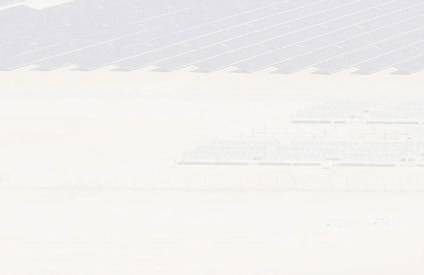
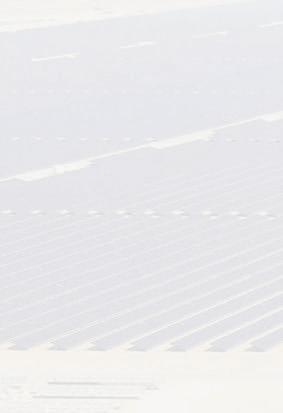
Sustainability is a key factor in driving aluminium demand based on the shift to electric vehicles, electric renewables investment and recyclable packaging that doesn’t end up as marine litter or in landfill.Recent years have seen a huge shift across the industry and a move towards creating a sustainable supply chain, a move in which the International Aluminium Institute (IAI) has played a pivotal role when it comes to challenging and supporting its members.
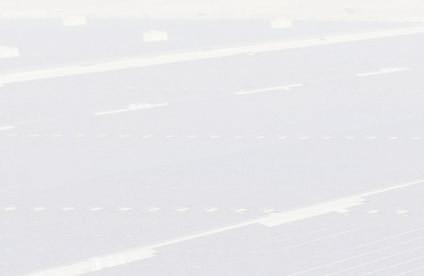
Cleaner means greener This eagerness for change is echoed across the industry and in numerous other projects already underway across the supply chain. Emirates Global Aluminium (EGA) is also committed to producing cleaner, greener aluminium and was the first manufacturer to announce in January 2021 that it had produced aluminium from the power of the sun1 In cooperation with Dubai Electricity and Water Authority (DEWA), EGA introduced ‘CelestiAL’ aluminium to the world, a vision supported by HH Sheikh Mohammed bin Rashid Al Maktoum, Vice President and Prime Minister of the UAE and Ruler of Dubai, to make Dubai the most sustainable city in the world and to take the lead in the development and application of scientific and technological advances in the energy sector.
DEWA supplies EGA’s smelter with at least 560,000 megawatt hours of solar power yearly from the Mohammed bin Rashid Al Maktoum Solar Park, a development which the IAI Board recently saw first-hand, and the scale of which was a sight to behold.
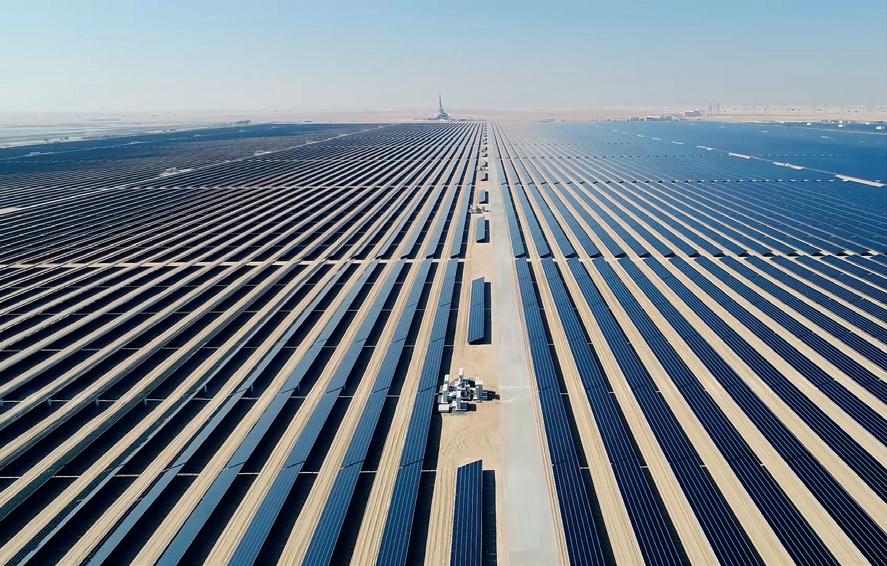
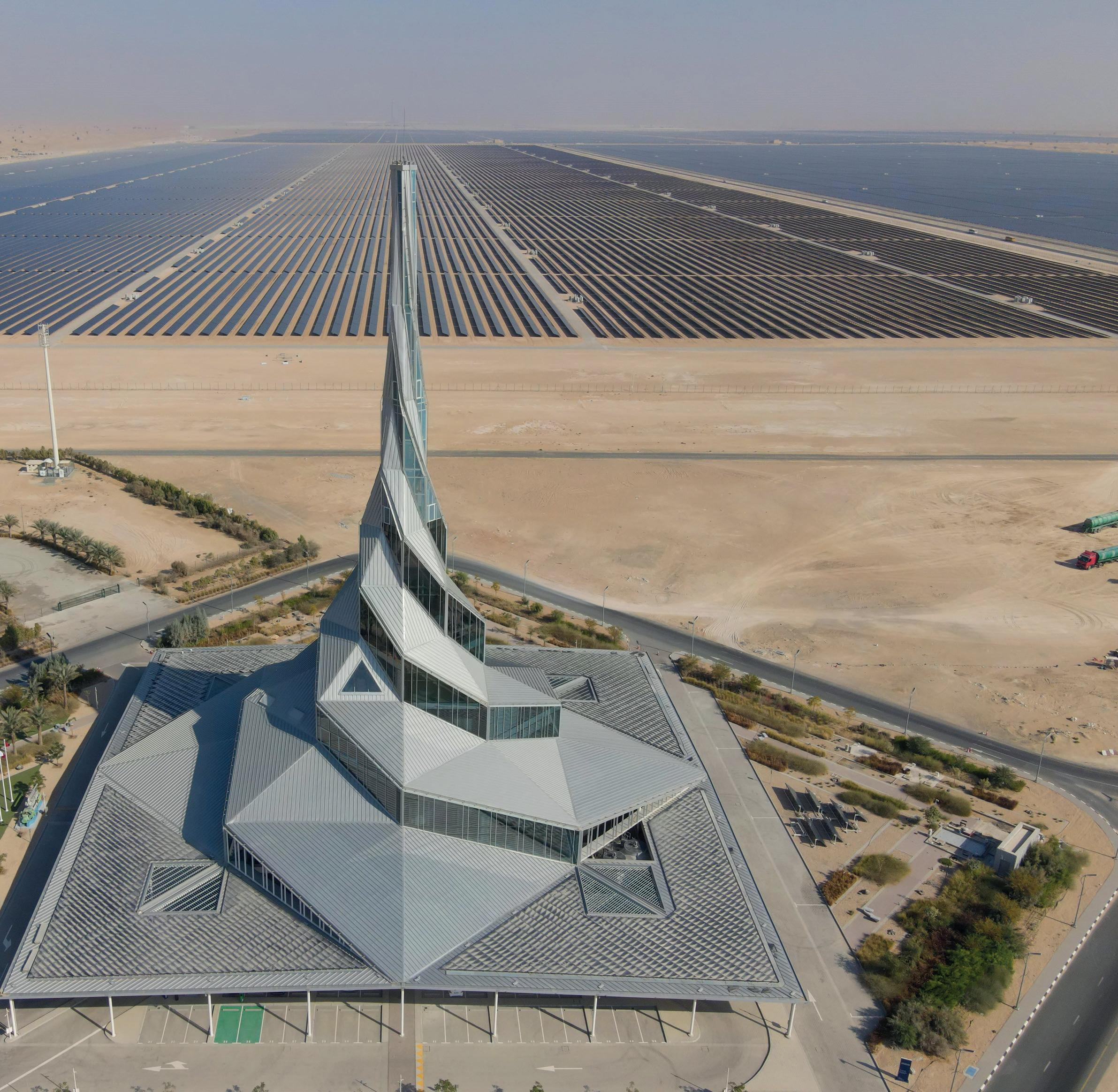
Salman Abdulla, Executive Vice President EHSS & Business Transformation Mohammed Bin Rashid Al Maktoum Solar Parkcredit Dubai Electricity and Water Authority
IAI ANNIVERSARY 7 Aluminium International Today September/October 2022 and impacts on the local environment, there are issues that require commitment and management through sector and value chain collaboration, which is key to meeting the challenges for a better tomorrow.Indiscussing these challenges with IAI members, there was an overwhelming want to present opinions and views on how individual companies are working to reinvent specific areas of the industry, which will have a greater impact on the way aluminium is produced, recycled and contributes to a more sustainable world.
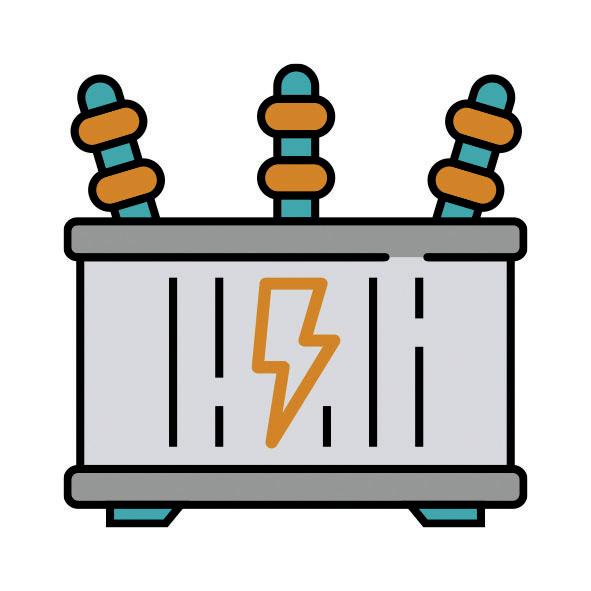
Therefore, this article is slightly different to the others in the series, as it not only includes a selection of interesting interviews with industry representatives, but also breaks off into independent opinion pieces from member companies.
The first contribution comes from Ben Kahrs, Alcoa Executive Vice President and Chief Innovation Officer, and looks at how technology, specifically the ELYSIS joint venture and the Refinery of the Future project, is planning to fundamentally change the aluminium production process.
THE TIME TO REINVENT THE ALUMINIUM INDUSTRY FOR A SUSTAINABLE FUTURE IS NOW:
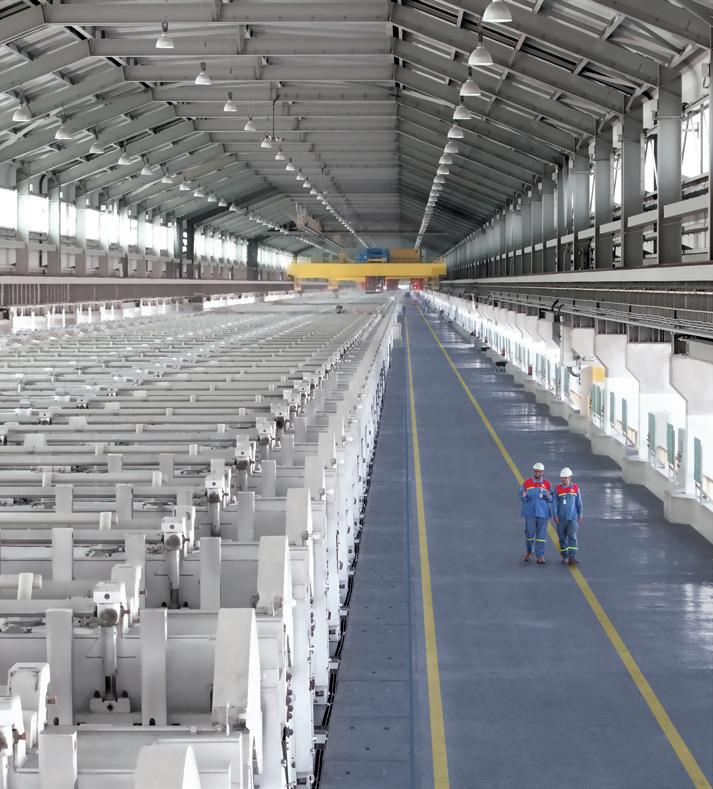
“IAI’s data collation capabilities are amongst the best for any industrial association. This means we are able to fairly and reliably benchmark our performance against whole industry data, and that drives performance improvements. A key example for us is safety. IAI’s data also provides transparency on the industry to our sector’s stakeholders,” says Mr Abdulla.
“More recently, I have been working as part of the sub-committee on the Mission Possible Partnership for sector transition efforts. I am also an active participant in other IAI Committees including the Health Committee and Safety Working Group. I am also involved in the project approval process, where EGA is an actively engaged.
The aluminium industry has a critical role to play in the low carbon future. It can replace both heavier metals and plastics across a wide range of applications. Perhaps most importantly, it’s infinitely recyclable, and it’s no surprise that aluminium demand will continue to grow for decades to come. According to the International Aluminium Institute (IAI), global demand for aluminium will increase by up to 80 percent by 2050. In order to fulfil its potential as a linchpin of the sustainable economy, however, the industry will need to rapidly decarbonize. According to the IAI, the industry would need to reduce greenhouse gas emissions intensity for primary aluminium by more than 85 percent from a 2018 baseline to meet a Beyond 2 Degree Scenario defined by the International Energy Agency. To achieve decarbonization at scale will require breakthrough innovation that can fundamentally transform the energy requirements of our industry. Furthermore, reaching the 1.5 Degree Scenario requires a 97 percent reduction in greenhouse gas emissions intensity. Both scenarios include a 340 percent increase in post-consumer scrap utilization. At Alcoa, we’re working on technologies that have the potential to decarbonize aluminium smelting and alumina refining, as well as unlock new possibilities for post-consumer scrap recycling. These projects align with our vision to reinvent the aluminium industry for a sustainable future and will help us achieve our net zero 2050 ambition for scope 1 and scope 2 emissions. Transforming the aluminium production process to decarbonize smelting and refining Our technology roadmap includes two initiatives that can fundamentally transform aluminium smelting and refining – our ELYSIS joint venture and our Refinery of the Future project. ELYSIS is a joint venture built around a zero-carbon smelting technology invented at Alcoa’s Technical Center near Pittsburgh. This technology represents the first major smelting breakthrough in more than 100 years, reinventing the Hall-Héroult process first developed by Alcoa’s founder in 1886. ELYSIS replaces the carbon anodes used in traditional aluminium smelting with inert, proprietary materials, to eliminate all greenhouse gas emissions from the smelting process, instead emitting pure oxygen. This new process can deliver an estimated 15 percent savings in production costs, as it eliminates traditional operating expenses associated with items such as calcinated coke, coal tar pitch, anode baking furnaces, and more. It also has the potential to increase production by 15 percent compared to traditional processes. Here’s the most exciting part: ELYSIS is already producing zero-carbon metal today at its Industrial Research and Development Center in Quebec, Canada. And that metal has already been used in commercial applications from companies ranging from Apple and Audi. The joint venture is on track to have a commercially available package for the broader aluminium industry from 2024. ELYSIS is a critical lever to decarbonize the industry, as smelting represents a majority of the emissions in the aluminium manufacturing process. However, it’s equally important to address carbon emissions in the alumina refining process. Unveiled in 2021, our Refinery of the Future project aims to both reduce the capital cost of developing a refinery and enable decarbonization of the alumina refining process through a combination
“IAI is a great enabler for our industry, bringing together peers to address shared global challenges. Obviously, we must make progress separately as competitors, but IAI provides whole-ofindustry knowledge and analysis which both supports and spurs our individual work. Sustainability is an area where this is particularly helpful. For example, EGA was able to build on past learnings provided through IAI membership in our own work to develop re-uses for spent potlining. The same goes for healthrelated issues, and now we are discussing gender diversity in our industry. Of course, the big sustainability topic is greenhouse gas emissions where IAI has not only developed its GHG mitigation pathways but also partnered with organisations such as the Mission Possible Partnership for sectorial transition.”
BY BEN KAHRS
As touched upon in the previous articles in this series, the IAI provides data that assists the industry in making informed decisions on key issues. One such issue surrounds untreated bauxite residue and EGA recently announced the construction of a pilot plant to convert bauxite residue into soil products that can be used for greening and other purposes in the UAE2 According to reports, this pilot plant is thought to be the first of its kind in the world and follows five years of research & development by EGA and The University
Aluminium International TodaySeptember/October 2022 IAI ANNIVERSARY8 at Emirates Global Aluminium is also a member of the IAI Environment & Energy Committee (EEC). He comments, “At EGA, we work with IAI at multiple levels. I have been member of the EEC for over six years. Together as an industry through this Committee, we have done some very important work including on the re-use of spent potlining and defining greenhouse gas reduction pathways for our sector.”
Enabling Pilot Projects
Potline 3 at EGA’s Al Taweelah site Image courtesy of EGA
While some industries experienced severe shutdowns and shortages during the emissions. The process also allows 100% of the steam generated by the calciners to be captured and reused, significantly reducing water use. Electric calcination also allows heat to be delivered via a thermal storage system, enabling the refinery to act like a battery to support activities to stabilize the grid. We are proud that Australian governments are investing to assist in the testing and development of the technologies. Unlocking new possibilities for post-consumer scrap recycling Research shows that the world’s increasing demand for aluminium will need to be met by an increase in recycling, and Alcoa is working to develop technology that can unlock more of our metal’s infinite recyclability.
As members, we will play our full part to ensure IAI can continue playing its important role for decades to come.”
“IAI has supported the development of the industry for the past 50 years.
Demand growth
of ELYSIS
EGA’s Bauxite Residue R&D Group has created a portfolio of additional novel applications that are at an advanced stage of development, with further pilot-scale trials expected.
Reinventing the industry for a sustainable future
Our ASTRAEA metal purification process, the third major component of Alcoa’s technology roadmap, is designed around a new electrolytic process. It can take any post-consumer aluminium scrap, regardless of alloy combination, and beneficiate it up to high purity that exceeds the purity of primary aluminium produced at most smelters today. We are targeting the millions of tons of aluminium scrap contained in low-value automotive shredded scrap. This type of scrap is composed of impurities and alloys that contain other trace metals, making it difficult to recycle today. But our ASTRAEA process can change that, unleashing the potential of underutilized aluminium. The purified metal created from lowgrade scrap could then be usable for rigorous applications such as aerospace.
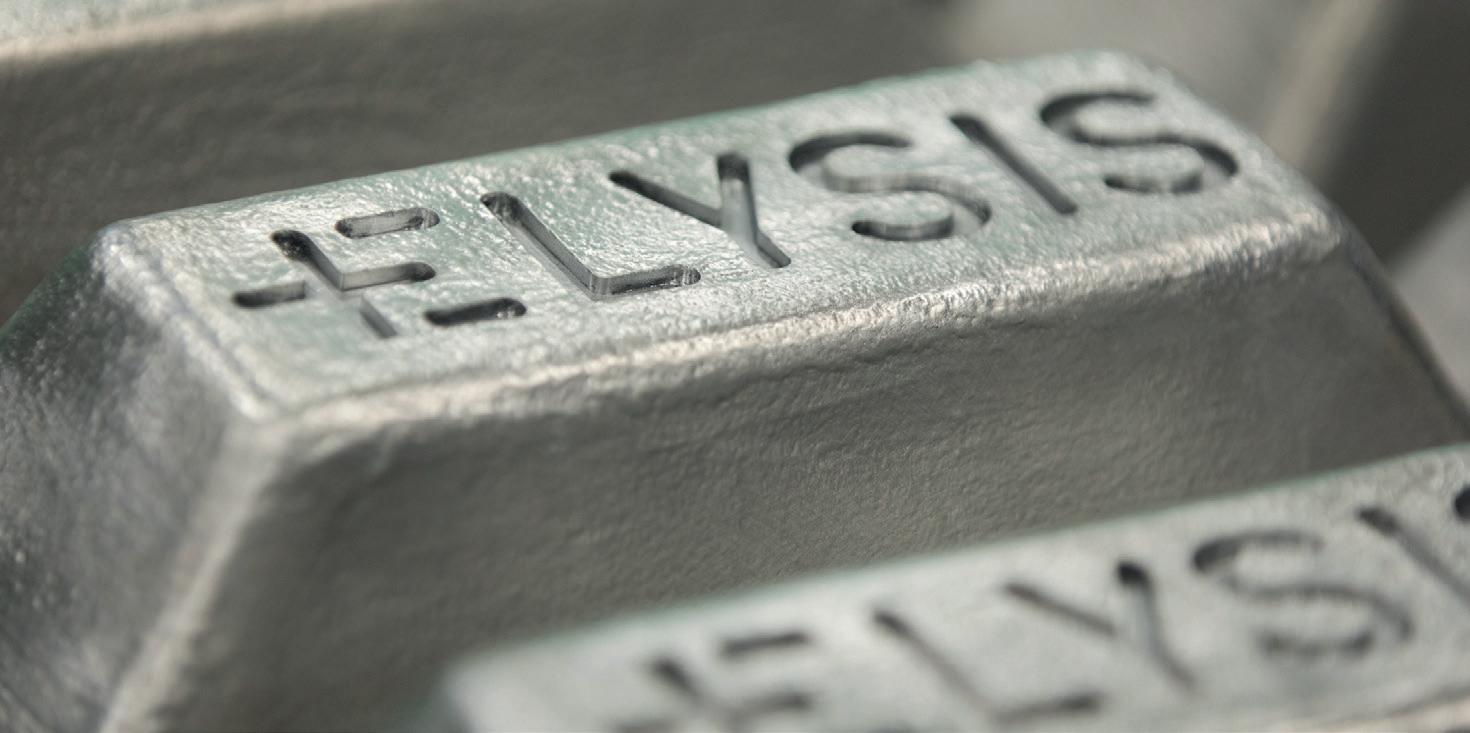
9 Image
International Today September/October
Aluminium 2022 of processes and technologies, including mechanical vapor recompression (MVR) and electric calcination. With support from partners such as the Australian Renewable Energy Agency, Alcoa is adapting these proven technologies for use in alumina refining. Together, these technologies have the potential to cut 98 percent of emissions from the refining process and reduce fresh water use by up to 70 percent. With MVR, compressors powered by renewable energy turn waste vapor into steam that can be used to provide refinery process heat. Low-pressure steam is captured before it reaches liquid phase and re-compressed back to the highpressure steam needed for digestion. This would avoid significant energy losses and save water. In fact, MVR alone has the potential to reduce an alumina refinery’s carbon footprint by 70 percent and eliminate up to 35 percent of freshwater usage.Electric calcination is a direct replacement of a traditional, direct-fired calcination plant. Calcination is the final stage in the refining process. Currently, calciners are powered by fossil fuels, but with electric calcination renewable energy will drive the calciner, eliminating carbon of Queensland’s School of Agriculture and Food Sciences. EGA’s ‘game-changing’ process converts bauxite residue in its entirety in hours into an environmentallybenign, plant-friendly soil. Industry experts estimate that at least 150 million tonnes of bauxite residue are produced worldwide each year and less than two percent are currently put to productiveAbdulnasseruse.Bin Kalban, Chief Executive Officer of Emirates Global Aluminium, said: “The productive use of bauxite residue has been a global challenge since the dawn of the aluminium industry more than a century ago. We believe that our Turba process is a breakthrough, and our pilot plant will enable us to learn how to apply it on a large-scale. This and other potential solutions we are developing hold out the prospect of an end to new bauxite residue storage this decade, whilst creating products useful in the UAE.”
EGA has already developed re-uses for other waste streams from its industrial activities. These include spent pot lining, a by-product of aluminium smelting, which is re-used as an alternative feedstock and fuel by the UAE cement industry; carbon dust, which is also used as a fuel in cement manufacturing; and dross which is processed to recover aluminium. EGA’s long-term aspiration is to send zero process waste to landfill.
Ben Kahrs is the former IAI Chair of the Board courtesy
“Aluminium is an essential material for decarbonisation economy-wide and it also matters how sustainably aluminium is made,” says Mr Abdulla. “The companies in the industry have begun this journey from different starting points, largely determined by the energy sources that were most cost competitive when their facilities were built decades ago, rather than climate change considerations. Each company will proceed on this journey in its own way and at its own pace. The big challenge we share is that aluminium will lose its competitiveness as a material if our industry does not make sufficient progress quickly enough.
The work to decarbonize the aluminium industry is just beginning, but the path for Alcoa is clear. Working with partners across the value chain, we are advancing a series of technologies that align with our vision to reinvent. The industry is ready and eager for change. And so are we.
IAI Board visit to DEWA’s Solar Park, ImageUAEcourtesy of Dubai Electricity and Water Authority
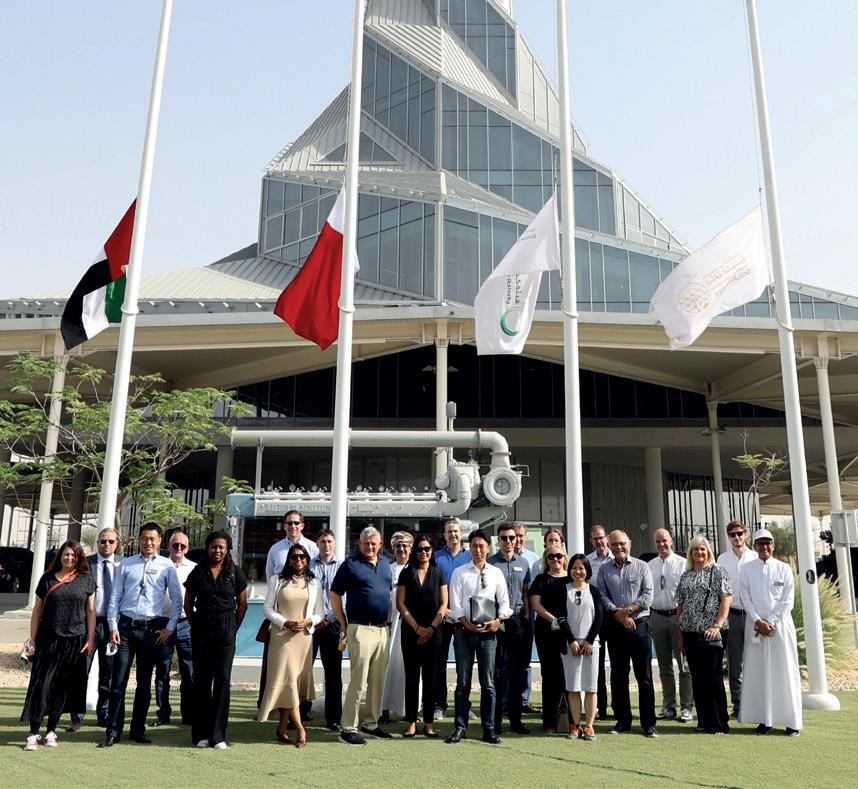
Box A: Final Conclusion by Pernelle Nunez
COVID-19 pandemic, the aluminium industry, although not without its struggles, came out of the other side to a demand forecast to grow by 33.3 Mt in the following decade, going from 86.2 Mt in 2020 to 119.5 Mt in 20303.

‘Opportunities for aluminium in a post-Covid economy’ proposes possible routes for the IAI to influence and further promote the consumption of aluminium in selected sectors and regions. Commissioned by the IAI, the main focus of this study was to identify key regions and sectors that will drive demand growth going forward, guiding the industry’s response on key issues and opportunities.
This is an understanding that positions the industry well to supply a sustainable metal for the future.
“Sustainability is at the forefront of development across the aluminium industry,” says Zaid Aljanabi, Head of Aluminium Consulting, CRU. “It is interesting that since the establishment of IAI, 50 years ago, there have been a number of different identifiable phases. In the 1980s, there was a period of shortage and squeeze, which was followed by the break-up of the Soviet Union and a lot of metal entering new markets, which changed the dynamics of the industry.
Aluminium International Today
September/October 2022 IAI ANNIVERSARY10
“Then, in the early 2000s, we saw China becoming a large net importer, followed by structural overcapacity, followed by the 2008 financial crisis and prices collapsed. I
At the beginning of this year, CRU worked with IAI on a report, which was prepared to deliver an overview of the aluminium demand growth for different sectors, future trends, and policies and developments that will drive this growth over the coming years.
Looking ahead is an inherent part of sustainability – it is after all about the future and ensuring that something is able to continue over the long-term. This is the motivation behind the next phase of the IAI’s sustainability work program which explores what an industry Sustainability Roadmap might look like to 2050. This project aims to provide a detailed action plan for the industry, working towards a shared vision on key issues across the sector. It continues to be an important step towards establishing sustainable aluminium, or a sustainable aluminium industry, as one that is greater than a single issue. It emphasises that in order for aluminium to be truly sustainable there is work to do across a broad suite of interlinked issues, much like the UN SDGs provides a blueprint for society. This comprehensive approach also encourages the industry to continue to strive for solutions that are multi-faceted and most importantly not detrimental to other sustainability ambitions or areas of development. In establishing this shared vision and roadmap, it’s been interesting to look back at the past few decades - a time where the aluminium industry landscape has been revolutionised. The aluminium industry has, in a relatively short space of time, shifted from a fairly homogenous industry where the majority of primary producers had a similar level of organisational maturity, operations were similarly sized and managed, hydropower was the main energy source, sustainability challenges and external pressures were all fairly well aligned across a few key producing regions.
Today, the industry is much more diverse, new regions have emerged as key production centres with different drivers, sustainability challenges and solutions. The supply chain is more fragmented, there are a greater number of global companies, and every site is operating in a uniquely complex ecosystem. This environment can make the development of industry-level action plans particularly challenging with diverging views, priorities and specific situations rarely making for cohesive and united efforts. Despite these differences, and perhaps accelerated in some ways by the shared experience of the covid-19 pandemic and recovery, the industry is rallying behind a shared sustainability vision and has started to see that there is far more that unites them than perhaps initially thought. There is broad agreement on the major sustainability challenges facing the sector: climate change, impacts on people, circularity, biodiversity, water, waste and emissions. There is also an understanding that different pathways exist to reach the same end point and to satisfy ever-growing expectations.
As we continue to develop the industry’s Sustainability Roadmap at the IAI, we hope that stakeholders recognise the importance of continuing to work together. This will be key to enabling aluminium to be a sustainable material of the future; one which is produced with minimal impact on the environment and communities, and effectively used in applications that benefit the environment and broader society.
Sustainability has been at the core of much of the IAI’s work over the past 50 years. It is also a concept that has gained significant momentum across businesses and broader society over the past decade, developing into an integral part of the corporate agenda. The IAI’s early dalliances with sustainability were mostly related to environmental data – something which continues to be a linchpin for our organisation. The sustainability program has continued to develop over recent years to now encompass a much broader range of projects covering key challenges facing the industry including climate change, waste management, land management, circularity, occupational and community health and safety. This year the IAI has looked at sustainability through the well-known lens of the UN Sustainable Development Goals – understanding how the industry, and aluminium as a metal, contributes to the achievement of these ambitious, interlinked national-level aspirations. What has been promising to see is that aluminium has a contribution across all 17 goals – yes, some have a greater link with the industry, or the material compared with others, but there is something being contributed across all 17 goals which is a fantastic achievement, and one which really demonstrates the breadth of benefits delivered by the industry’s sustainability activities and efforts.
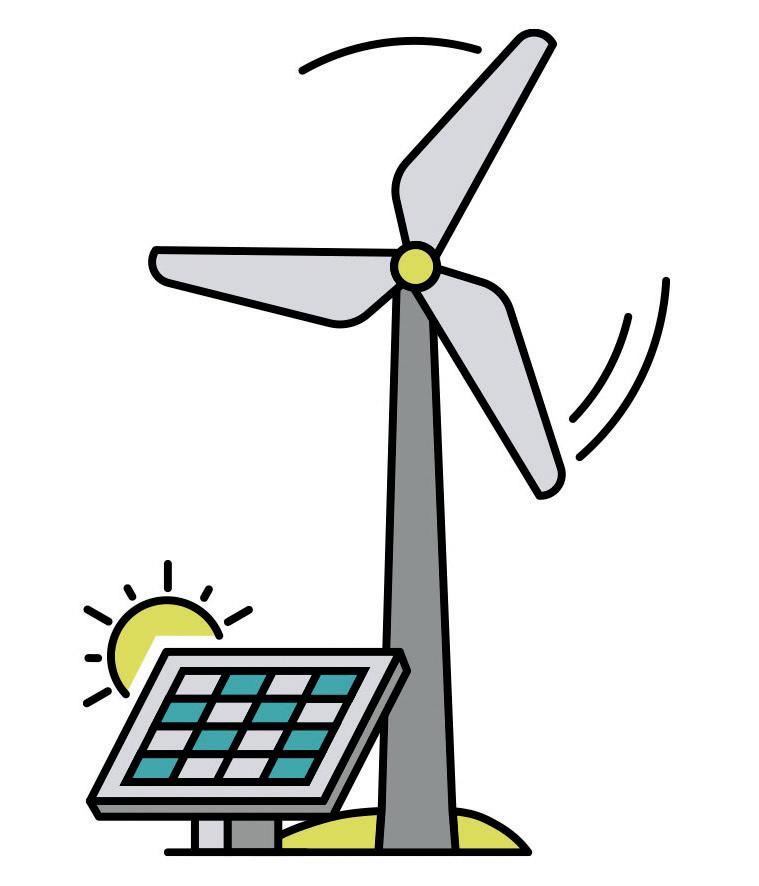
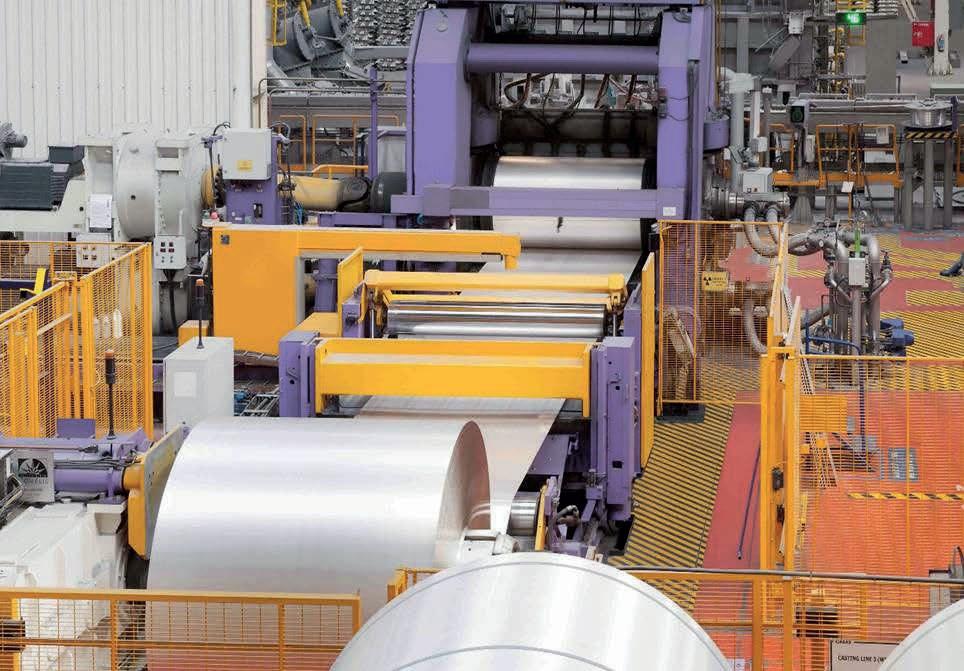

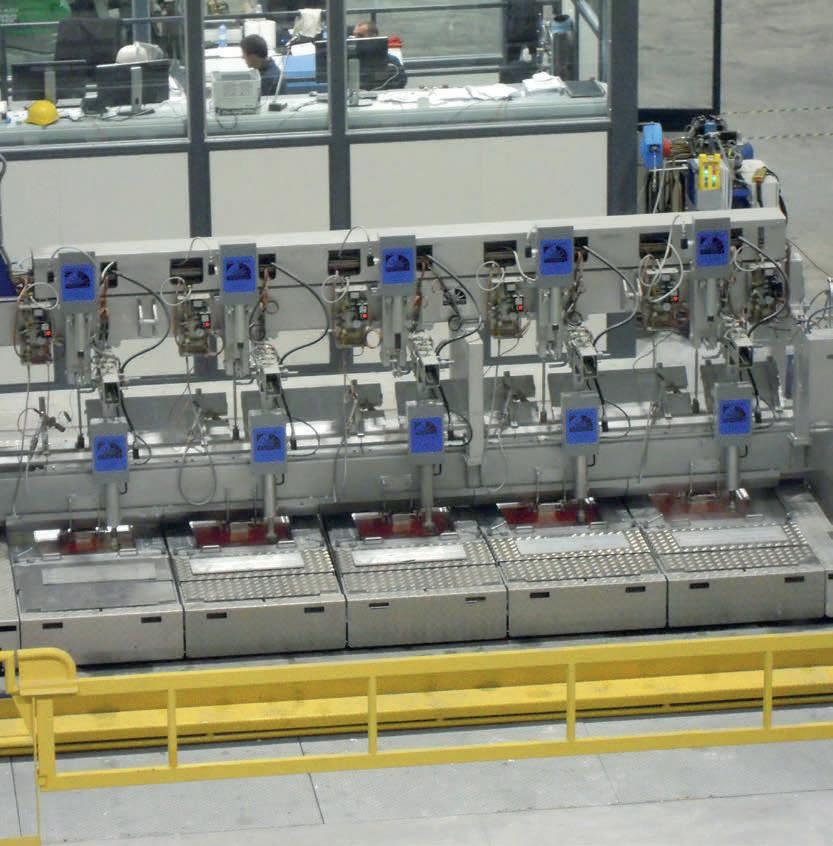
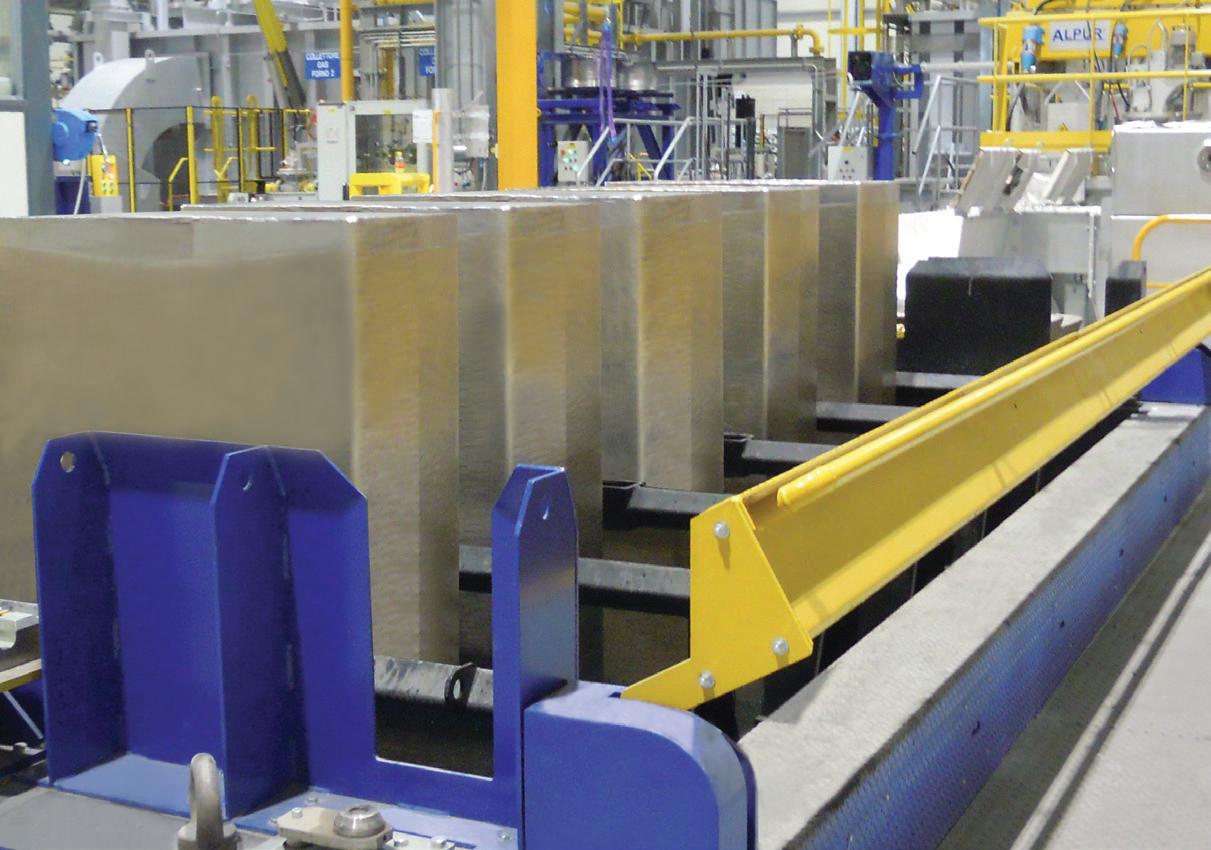
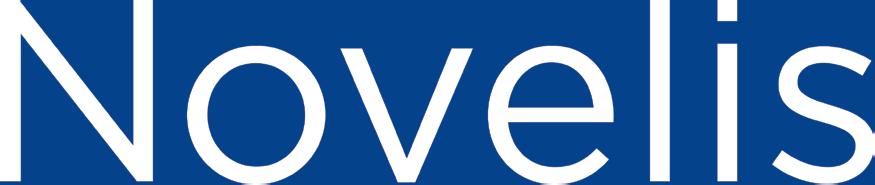
Aluminium International TodaySeptember/October 2022
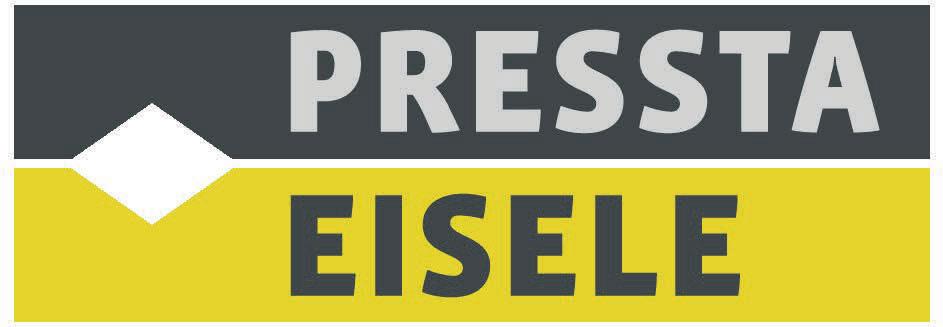

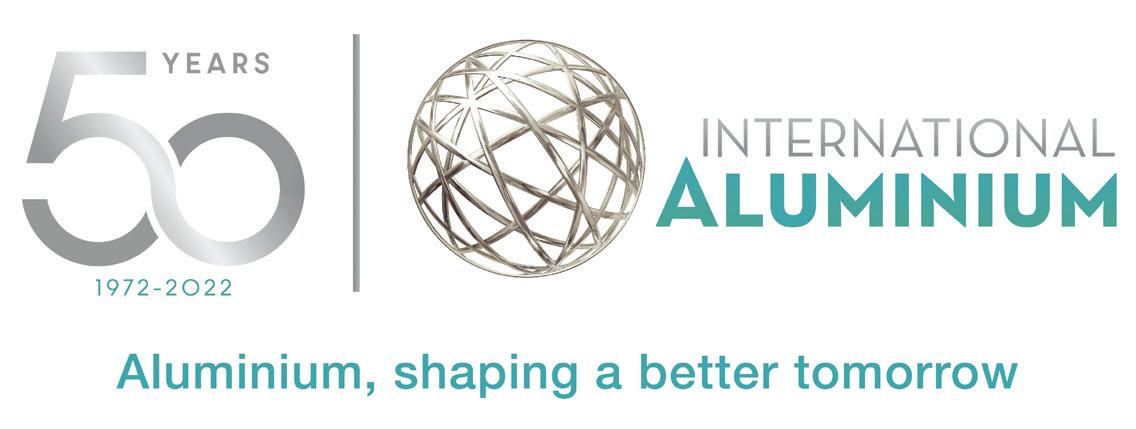
IAI ANNIVERSARY12 think now, coinciding with the COVID-19 pandemic, we are entering a fifth phase, which is the emissions era.”
“Some end-use sectors are interlinked,” continues Zaid. “Our study highlights transportation as a key sector, as it combines highest growth and is part of the energy transition story. However, I think that in a way, it also relates to the electrical sector and its infrastructure which will accompany and support this transformation.”
Sustainability Roadmap and future initiatives To offer a final conclusion on the current and future work of the IAI when it comes to supporting the industry through this transition, Pernelle Nunez, Deputy Secretary General, Director – Sustainability at IAI, looks at how best to establish this shared vision and roadmap across the sector. (See Box A)
� 1. 2.the-sun/to-produce-aluminium-using-the-power-of-make-the-uae-the-first-country-in-the-world-https://media.ega.ae/ega-and-dewa-https://media.ega.ae/ega-to-build- 3.waste-stream/breakthrough-on-use-of-globally-challenging-pilot-plant-to-make-soil-products-after-rd-Opportunitiesforaluminiuminapost-Covideconomyreport,CRU,IAI,2021
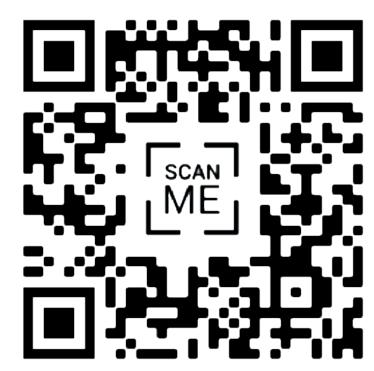
One area highlighted in the report as a main driver for aluminium demand is the electrical sector. The report states that this will be, ‘driven by the rise of renewable energies and the expansion of the power grid.’‘Although both wind and solar power are substantially more aluminium intensive than traditional energy sources, solar power uses, on average, more than four times the amount of aluminium per megawatt than wind technologies. Supporting solar power projects through alliances with designers and manufacturers, working closely to ensure supply chains are streamlined and solar power remains competitive, is a good starting point to making the most of aluminium’s exposure to the nonconventional renewable energies sector.’
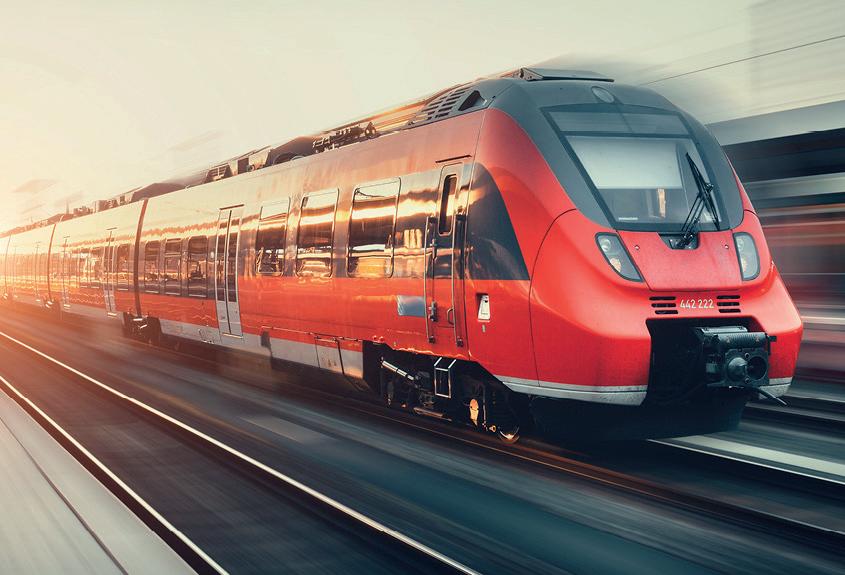
In a decarbonising world, given its qualities, aluminium is a key material to reduce global carbon emissions. However, the paradox is that the production of primary aluminium itself requires significant amounts of electricity. This is likely to lead to two key developments, which are already underway and are expected to accelerate over the next five to 10 years. By Andrew Wood* and Liping Li** *Alumina Limited
Looking at the medium term, outside China, between 4 and 6.4 million tonnes per annum of growth in primary aluminium production is expected over the next five years, as shown in the graph below. The majority of this growth is expected in Asia (excluding China), the Middle East and Latin America. This growth would require between 8 and 12 million tonnes of extra alumina production in the next five years.
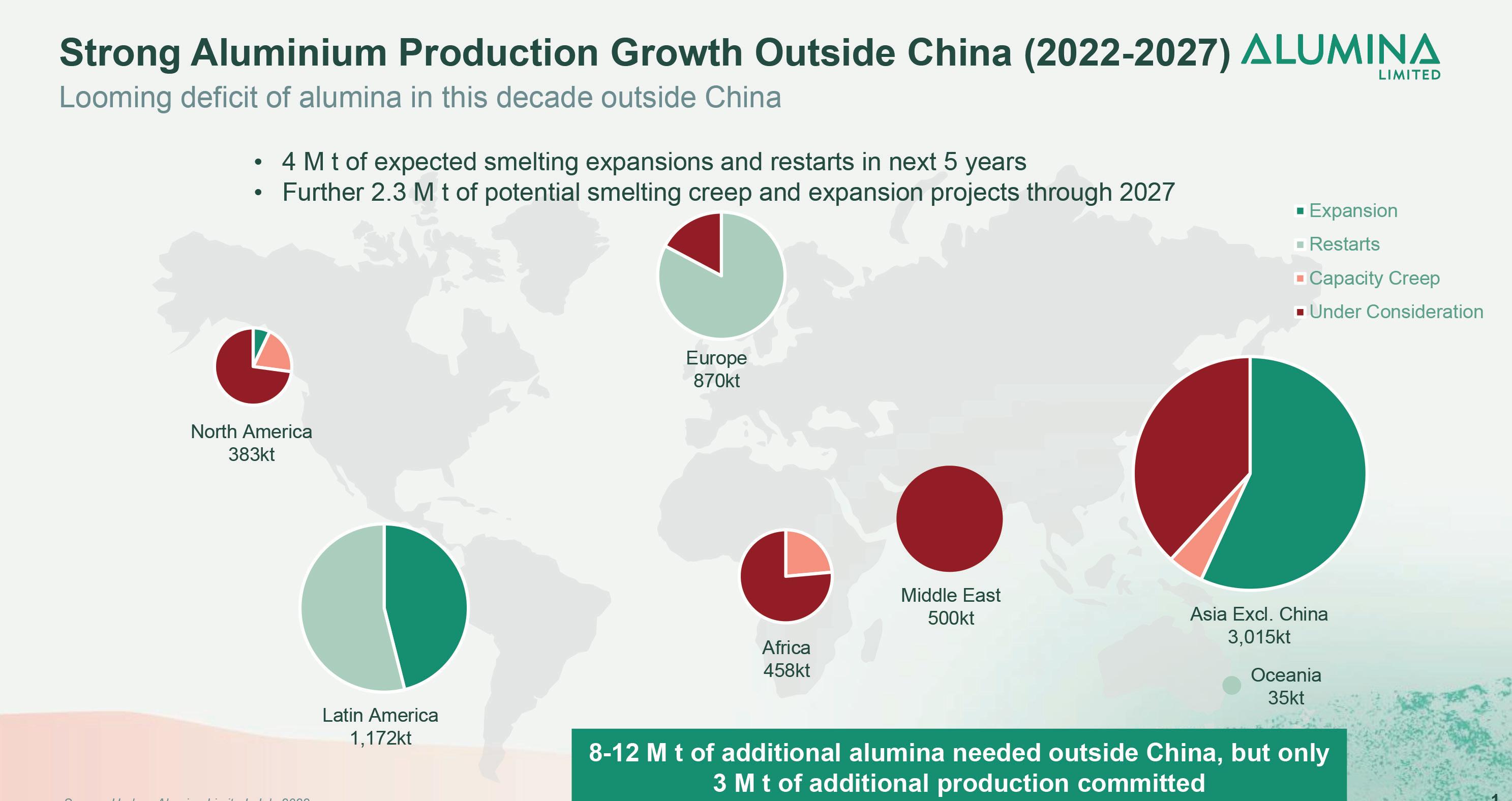
The first is a migration of fossil fuel smelting hubs to areas where renewable energy is more prevalent, whether existing or with great potential. As a transitional measure, some smelters have commenced reducing average emissions by purchasing some renewable electricity or constructing their own generation assets
The second is an increase of investments by aluminium producers in aluminium recycling, whether greenfields or brownfields developments or mergers and acquisitions or simply buying more scrap aluminium. This is a prompt way, using existing technology, for primary smelters to average down their emissions intensity, as recycling uses around 5% of the energy used to make primary aluminium. For future greenfields, or large brownfields, expansions, in either smelting or refining, it is likely that there will be considerable pressure from countries, investors, lenders, communities and other stakeholders for a more sustainable development from an ESG perspective than has been the case in the past. This is likely to include low carbon emissions in absolute terms, rather than a transition or incremental pathway, which may be more tolerated for existing assets.
It has been forecast that global aluminium consumption is expected to grow by over 33 million tonnes from 2020 to around 120 million tonnes in 2030 (CRU). The main volume growth is expected in the transport (electric vehicles), electrical (power transmission and solar and wind power), construction (infrastructure and urbanisation, particularly in Asia outside China) and packaging (beverage containers) sectors. To meet this growth, a higher proportion of recycled aluminium will be used than is currently the case. As a result, of the 33 million tonnes of forecast extra production by 2030, around 20 million tonnes are expected to come from recycled aluminium and 13 million tonnes from primary aluminium. This would require an additional 25 million tonnes of alumina production globally.
Aluminium Outlook
GLOBAL UPDATE 13 Aluminium International Today September/October 2022
Other important ESG factors, particularly for new developments, are likely to include the need to minimise waste, take into account more fully community issues, robust and relatively prompt rehabilitation, minimisation of environmental footprint and water usage and compliance with more stringent government approvals.
Aluminium International TodaySeptember/October 2022 GLOBAL UPDATE14 The identification and likely timing of specific smelting expansion projects is relatively foreseeable, even in a lower aluminium and premium price environment due to their likely cost curve position. However, the timing and location of alumina growth outside China is harder to predict. Beyond some production ramp ups underway in India and Indonesia, and some potential refinery restarts, particularly once energy prices abate, no alumina growth projects have been committed to publicly. There are many alumina growth projects outside China on the drawing board, and most have been projects for many years but not committed to. Past problems have included perceived difficulties in making an adequate financial return given relatively high capital costs, borrowing limitations, political risk, distance from good quality, low-cost bauxite and the unavailability of low-cost, long-term energy. Adding to those constraints today in a world which wants to decarbonise, is the need for low carbon, reliable energy sources – and the other ESG constraints referred to above. Even if some of those projects were committed to today, it is highly unlikely that sufficient production would be available to meet the required extra demand for alumina outside China over the next five years. In this scenario, what is likely to happen? Does that mean the smelting growth projects are unlikely to proceed without an anticipated reliable source of alumina? What is likely in such circumstances is that Chinese refineries would be able to supply any shortfall in the short-term, by restarting their high cost or inefficient unutilised capacity. This can be accommodated because Chinese refiners are more flexible and in a number of cases see advantages in being able to flex production up or down. This may be based on market conditions, such as margins between price and cost, availability of bauxite, comfort in having spare capacity etc. However, Chinese refining production has on average higher operating costs than outside China so to export they need high alumina prices in the rest of the world. That is why China is unlikely to be a net alumina exporter throughout the commodity cycle. The only two times in history when China has been a net exporter of alumina were 2018 and 2022. This was when there were severe, prolonged shortfalls in alumina supply outside China, and, in both periods, they led to spikes in the alumina price, relieved only when supply/demand equilibrium was restored.Chinese primary aluminium production is capped at 45 million tonnes per annum. Installed capacity is around 44 million annual tonnes and the current operating annual run rate is around 41 million tonnes. For alumina, installed capacity is around 96 million annual tonnes and the current annualised operating rate is 82 million tonnes. The Chinese aluminium production cap, carbon policies and other environmental factors are likely to slow growth in new aluminium and alumina capacity. So, over the next 10 years, the demand outlook for primary and secondary aluminium and alumina looks positive. And, in the next five years there are some likely alumina supply constraints outside China. � www.aluminalimited.comContact SALES.PRECISION@IMASCHELLING.COM WWW.IMASCHELLING.COM Visit us at the ALUMINIUM 2022 in Duesseldorf and see our Saw-Robot-Solution live in action! Booth 3E22 27. - 29. September „PRECISION2022 IS OUR PASSION“
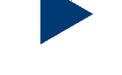

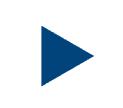
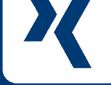
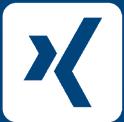



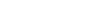
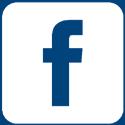
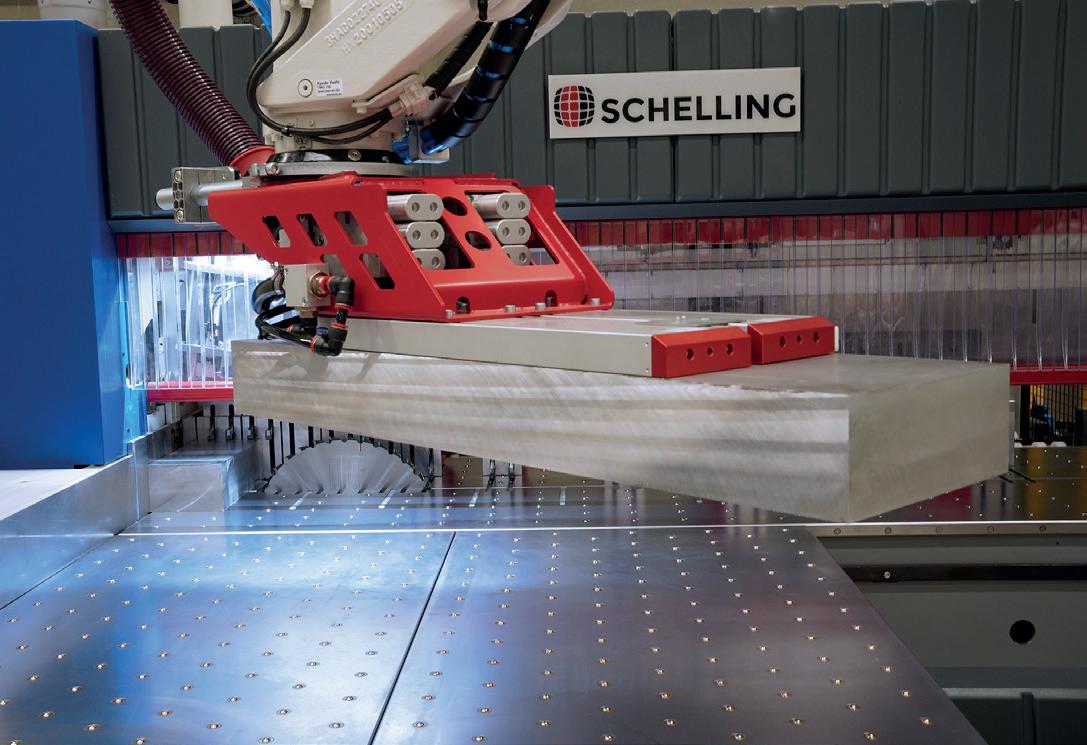
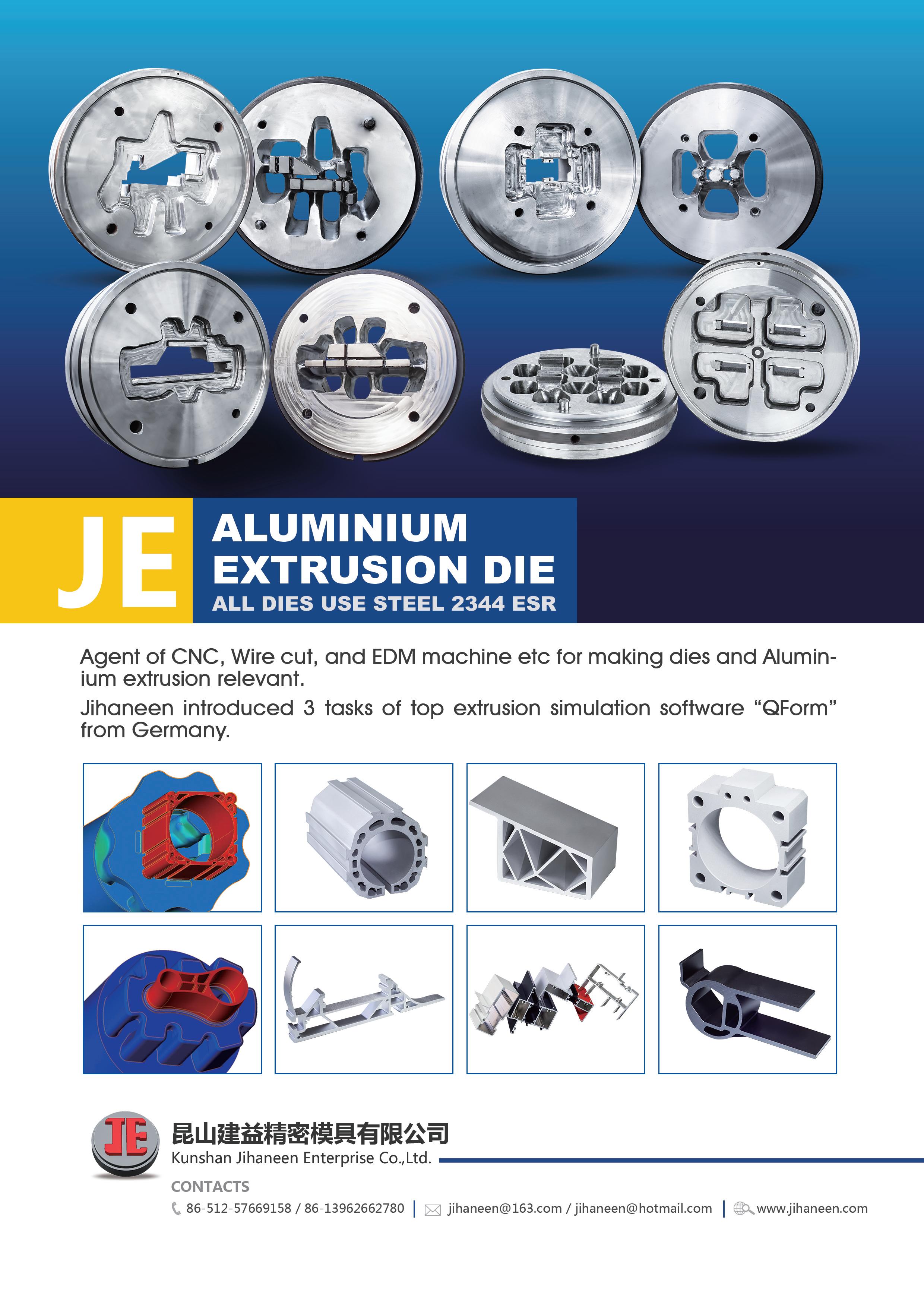
TotalEnergies 552 006 454 RCS Nanterre - France. Photos: 123RF - Design: lubricants.totalenergies.comms.industry@totalenergies.com TotalEnergies Industry Solutions processingAluminum fluids Hot & cold rolling mills Expertise and technical support for all applications
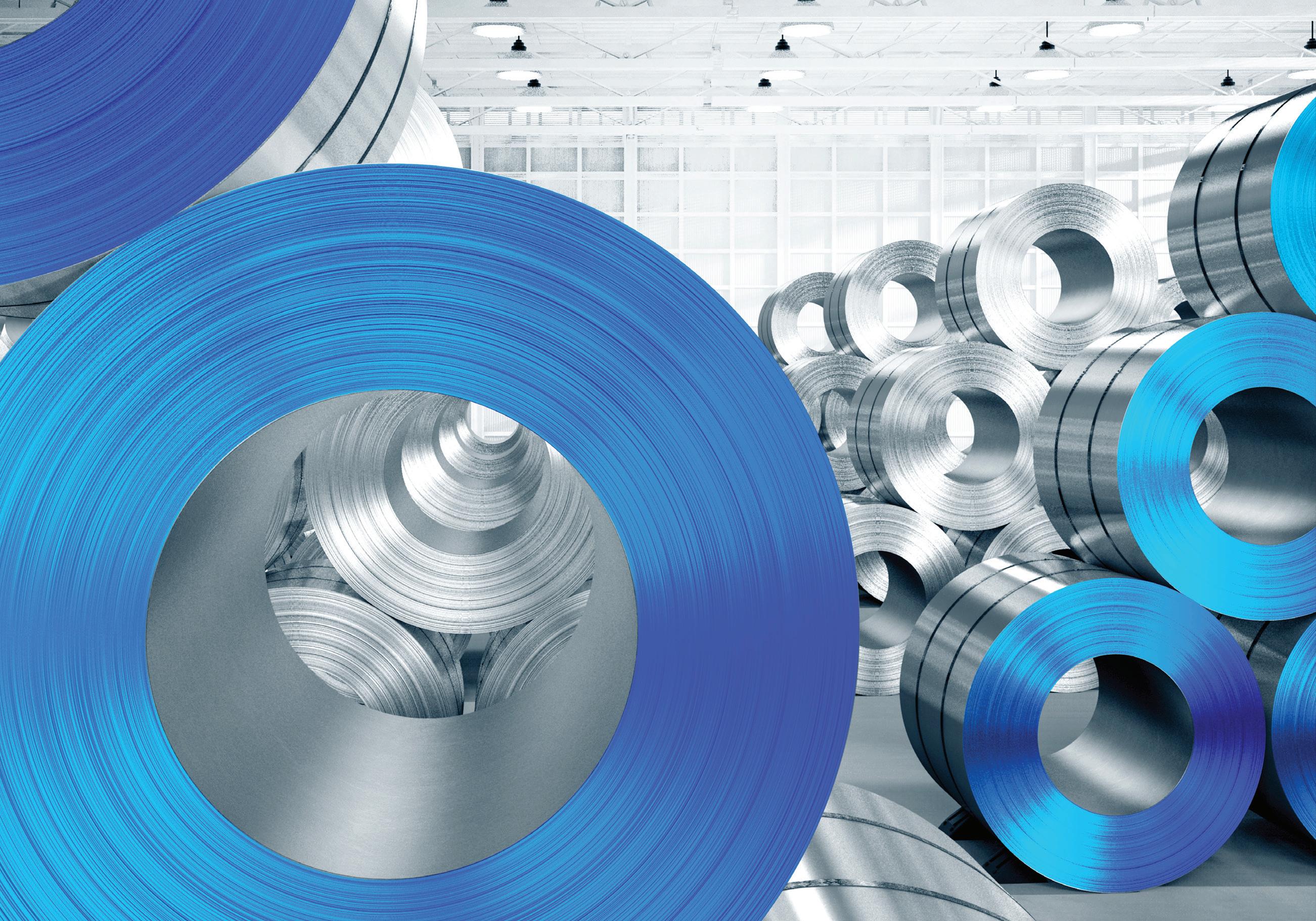
Spokesperson: Paul Williams* *Head of Aluminum at CRU Group
The market currently � So far, 2022 has been a year of market volatility and ongoing uncertainty, how have these shocks impacted aluminum demand, and the overall market? The aluminium industry has been buffeted this year from the war in Ukraine, continued supply chain disruption, rising energy costs, and weakening demand prospects.LMEaluminium prices have tumbled by approximately 40% from their peak at just over $4,000 /t earlier this year, when the concern was whether aluminium supply would be hit by the war in Ukraine, to the recent low of $2,310 /t in July 2022, as concerns over demand and higher Chinese primary output took over. SHFE aluminium (Chinese) prices have also suffered from domestic demand weakness due to lockdowns in China, and a very weak construction sector. Looking back to the beginning of the year, the market was gradually tightening as demand was growing healthily; but supply, especially outside China, was constrained. Then after the war began in Ukraine, prices surged on fears over supply, whether from Russia with the threat of sanctions, or elsewhere from rising energy prices. However, a dramatic turnaround occurred in Q2 as we saw plummeting prices, as with other base metals, with multi-decade high inflation in Europe and the US, and rising interest rates heightened fears of a global recession. The market had seemed set for another substantial deficit in 2022, but we now expect the market to be in modest surplus over H2 2022. Indeed, while there have been further closures in the world ex. China of smelter capacity due to rising power costs, the loss of demand growth from weakening economic growth outweigh this. After near three-decade highs in price volatility this year, we expect aluminium prices to start a recovery over the remainder of this year, aided by production cuts in China and Europe, and a subsequent demand rebound in China. However, any recovery in price is likely to be slow, and demand could continue to disappoint in key regions such as China and Europe.
� Prices have fallen more than 40% from their peak earlier in the year. Given the demand and recession fears, is the price decline justified?
The decline in prices may have overshot however, at least for aluminium. Even as demand weakened in the first half of this year, global stock levels continued to drop.
Total stocks outside China (incorporating both reported and estimates of unreported stocks) are estimated to have
CRU Q&A
As highlighted, there has been a dramatic drop in prices. And not only in aluminium, but prices across base metals on the LME have declined. This reflects a change in investor sentiment towards metals and concerns that the US and Europe will enter recession.
Data: CRU Aluminium Smelting Cost Mode
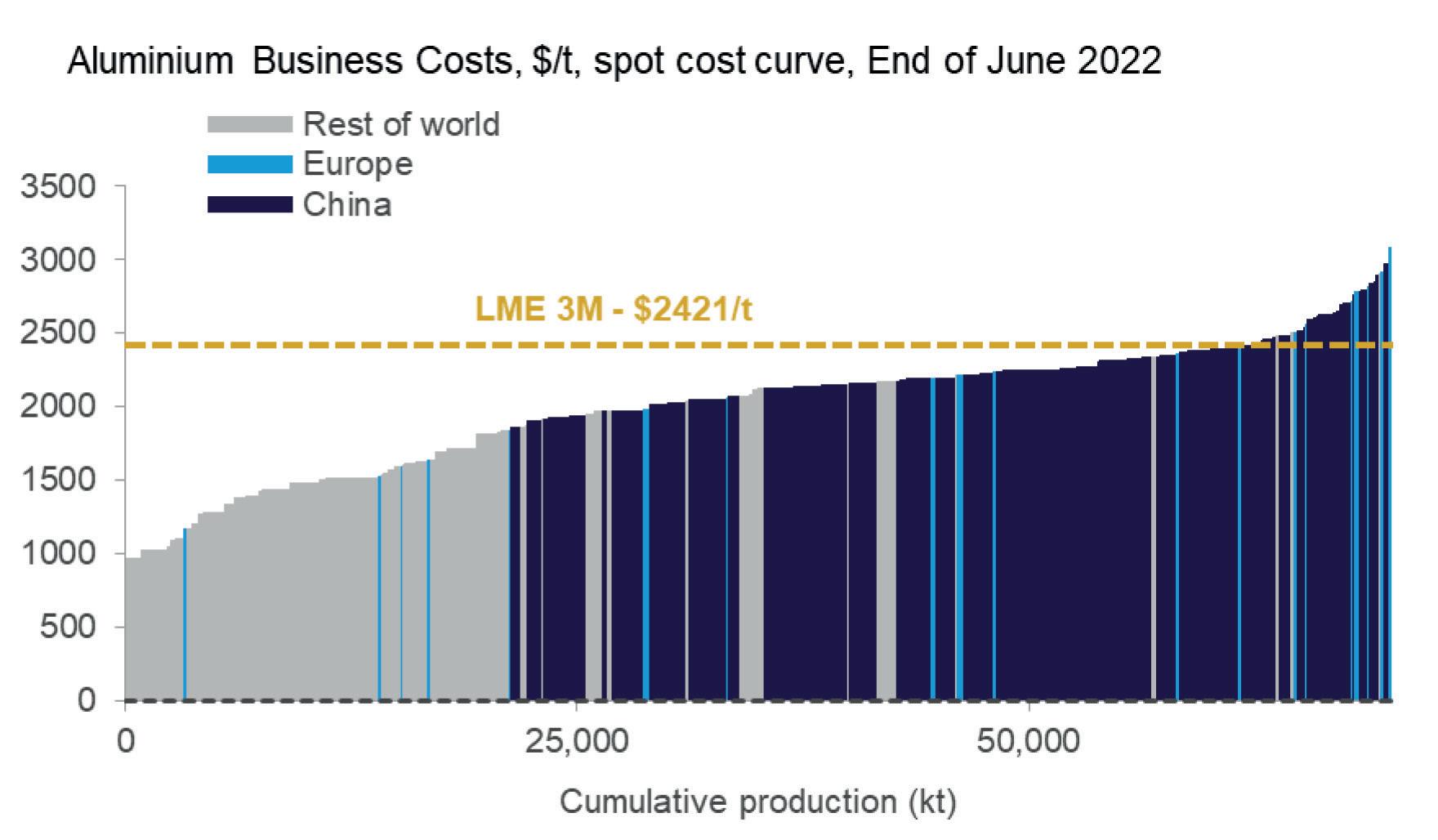
GLOBAL UPDATE: Q&A 17 Aluminium International Today September/October 2022
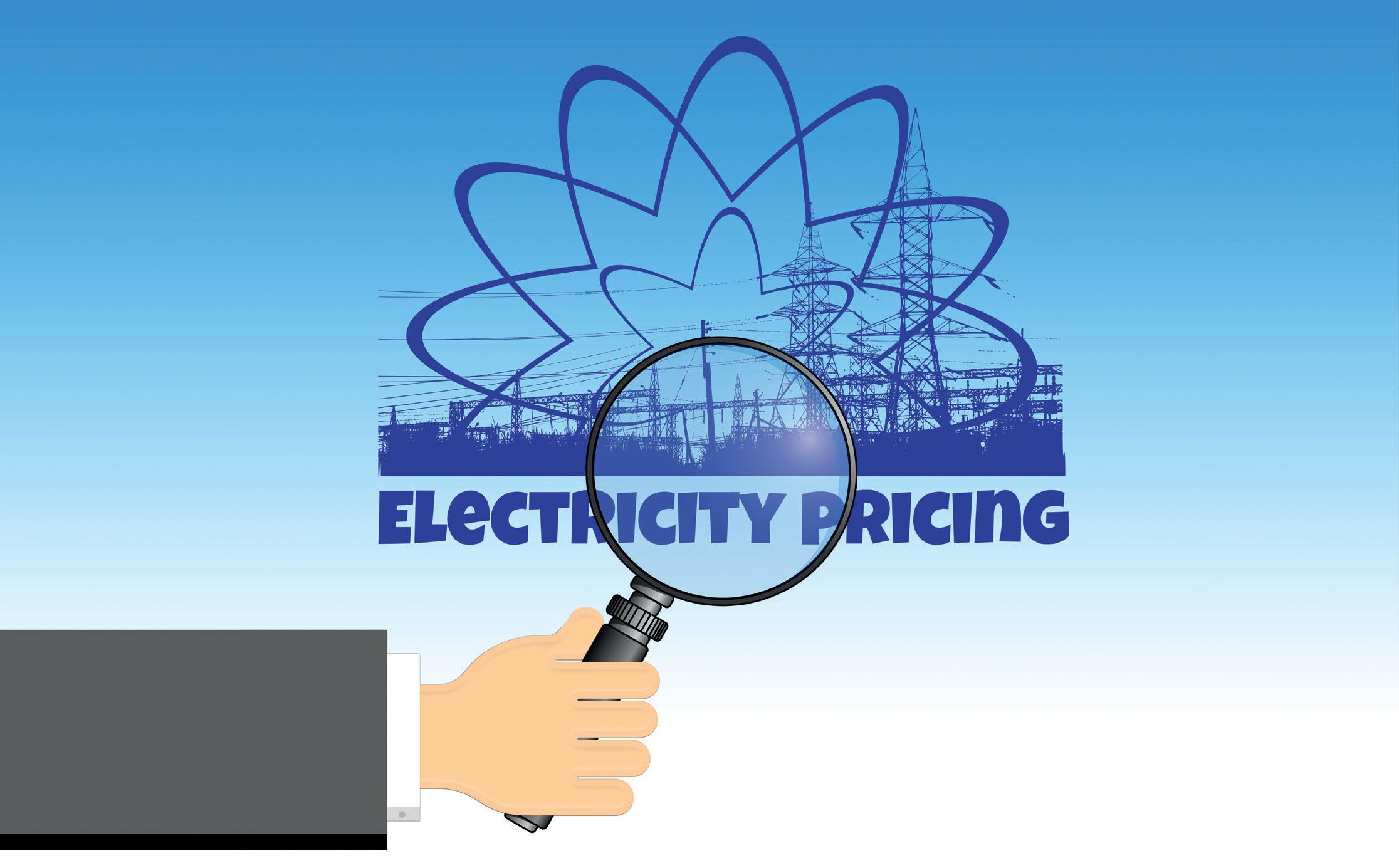
Aluminium International Today

� Currently, energy prices are having a large-scale impact across all industries, how is it impacting aluminum? High energy prices have been impacting the aluminium industry significantly. Aluminium smelting is a highly electrointensive process and power costs represent around 30-40% of total costs. However, as aluminium smelters are extremely large power consumers, many benefit from low-cost hydropower and/ or long-term electricity contracts which shield them from market prices. Some smelters also have hedging mechanisms in place. The rise in energy prices mostly impacted European smelters where some production was curtailed to avoid losses, some smelters in the US, and smelters in China where most smelters rely on coal. Between the end of June and mid-July, a large share of Chinese smelters went under water due to decreasing metal prices. More recently, Indian smelters have also faced cost pressure due to rising coalDueprices.tohigh power costs, the aluminium primary industry can be significantly impacted by carbon pricing mechanisms. Smelters relying on coal and gas power sources, but also those exposed to market prices, are the most at risk. However current carbon pricing mechanisms are implemented progressively and the impact on industrials is mitigated, this is likely to be the case for future mechanisms in other countries.
� What will be the key drivers impacting aluminum demand in 2023?
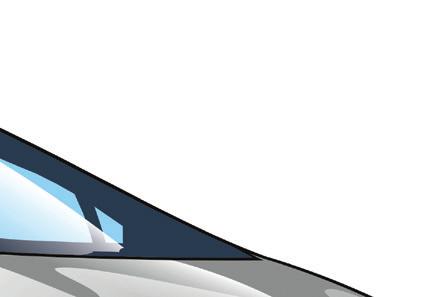
As noted already, the recovery of the Chinese economy and the stabilisation of its construction sector are crucial for aluminium demand in 2023. Outside of China, the market will continue to be buffeted by high inflation that will hurt sectors such as building and construction and consumer durables. High inflation will also impact auto demand, but this market has seen its build rates impacted more by supply chain shortages, such as in semi-conductor chips. Easing in supply chain issues should support rising auto build rates through late 2022 and into 2023.The packaging market has been performing better than other sectors, with beverage cans continuing to grow globally, although inflationary impacts have begun to slow growth in the US in some segments. Foil in packaging is also performing strongly across many regions, but over time it will be other foil applications such as battery foil that will take over the growth in this sector. Battery foil will grow as the vehicle industry transition towards electric vehicles and away from traditional internal combustion engines in the auto sector accelerates. �
� More generally, how has changing demand for vehicles impacted the aluminum industry? The transition to electric vehicles (EVs) is being aided by the array of new models being released. We have seen the great success of the all-electric Ford F-150 in North America, which will be released in 2022, but has already pre-sold capacity. In Europe, following the popularity of the Nissan Leaf, the company released an SUV, the Nissan Ariya, to compete with Tesla Model Y, and VW ID4. Whereas BMW’s i4 will compete with the Tesla Model 3. More affordable options have also hit the market, such as Vauxhall Corsa-e, and Fiat 500e. Not forgetting the European favourite Renault Zoe which continues to sell well. Despite efforts to compete with Tesla, the Tesla Model 3 remains the fastest selling electric car in Western Europe, given its long range. Tesla has recently opened a giga factory in Germany – the first in Europe – which signals their desire to expand sales and production in the region.Ouranalysis found that Plug-in hybrid electric vehicles (PHEVs) have the biggest net gains in terms of total aluminium content. Moving from ICE to PHEV results in a loss of 44 kg of aluminium per vehicle, but a gain of 124 kg, resulting in a net gain of 80 kg/vehicle. BEVs which are structurally similar to PHEVs are the second biggest net gainer, with a net gain of 63 kg/vehicle. This is lower than PHEVs because BEVs have bigger weight losses from engine blocks and transmissions. Finally, hybrid-electric vehicles (HEVs), currently the most popular choice amongst consumers, have the least aluminium net gain (~21kg/vehicle), because they have lighter, smaller EV parts.
� Thinking about the rest of the year, what can we forecast for the rest of 2022? In the world ex. China, we think LME prices have probably stabilised, but demand will continue to struggle in some regions, especially in Europe. And the key forecast for H2 is the recovery in demand in China. While we expect demand to pick up by Q4, it will be more moderate than the last time the economy emerged from self-imposed Covid lockdowns. Indeed, we see demand continuing to fall in China in Q3 y/y as current market conditions across many end-uses remain soft, before consumption grows by over 5% y/y in Q4 aided by the modest impacts of stimulus and recovery in the auto sector. Even with this recovery in demand, the Chinese market should be in surplus given the rise in production we are seeing in the country from the previous restarts of capacity and ramping up of new capacity that was delayed from 2021 when there were energy shortages in the country. Thus, we still expect closures in China to occur given their position on the cost curve. The concern is that there will be little to no recovery in demand in H2 especially as the problems in the construction market have intensified in recent months and attempts by authorities to stabilise the market may prove fruitless. A failure of demand to pick up before year end would plunge the Chinese market into a very large surplus, leading to lower prices and even more closures of capacity than currently expected.
GLOBAL UPDATE: Q&A18 fallen a further 429,000 tonnes in the first six months of the year, with stocks on the LME falling to below 300,000 tonnes. Also, worth considering this point, which we will go into in more detail later, is that the fall in price, coupled with rising energy costs, is leading to further smelter closures. In recent weeks prices have stabilised around the $2300-2400 /t level given risks of more closures. If demand weakens further the price could drop more, but this only increases the risk of further smelter closures outside China.
Looking to the future
� There is a growing trend towards
September/October 2022 EVs – with not just consumer demand rising, but governments increasingly setting ambitious EV targets – how will an increase in demand for EVs impact aluminum?

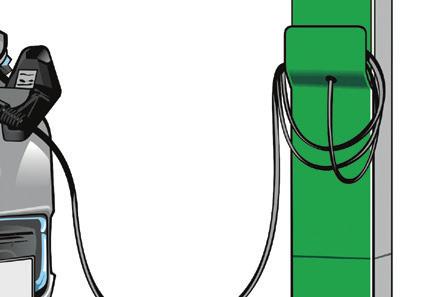
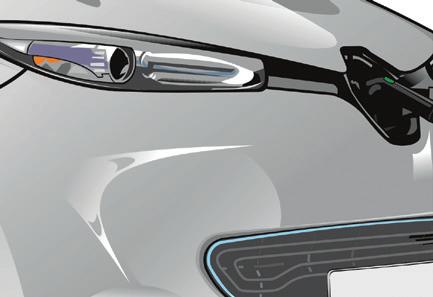




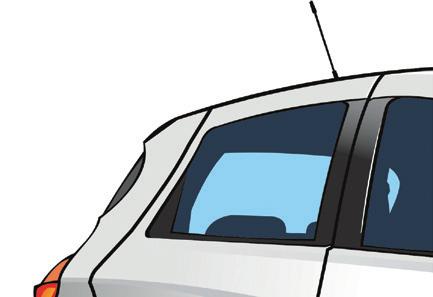
THE NEXT DIMENSION IN GRAIN REFINEMENT Up to 85% less grain refiner needed for cost savings 120% relative efficiency compared to high efficiency refiners Reduced particle count consistently increases melt quality Made with low carbon aluminium +44 (0) 121 684 0175 | info@mqpltd.com | www.mqpltd.com
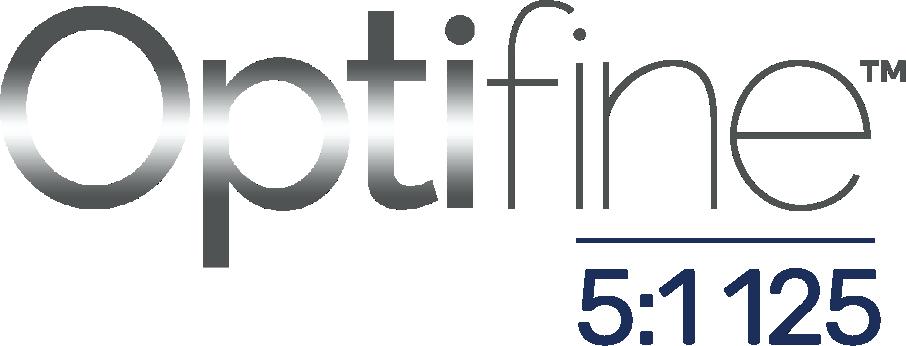
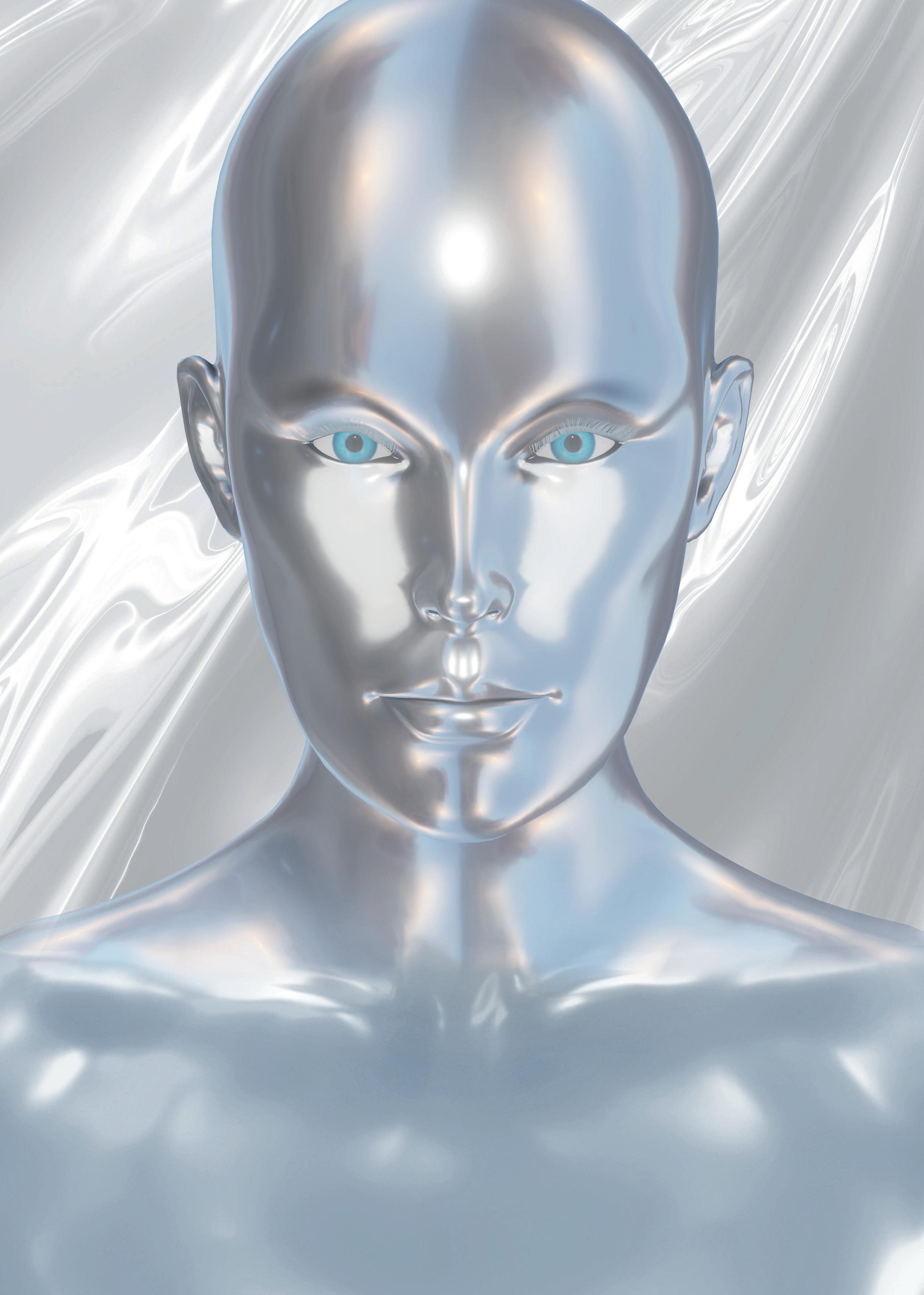
WE CARE.
At the ALUMINIUM 2022, we would like to exchange ideas with you on the subject of refractory technologies in 2022. We always keep a close watch on the needs of our customers: Smart refractory solutions and services for the aluminium industry. Visit us from September 27 to 29 at our stand: Hall 6 / D41. www.refra.com
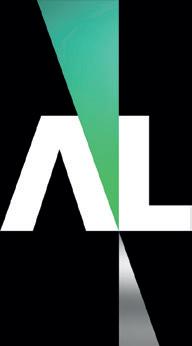
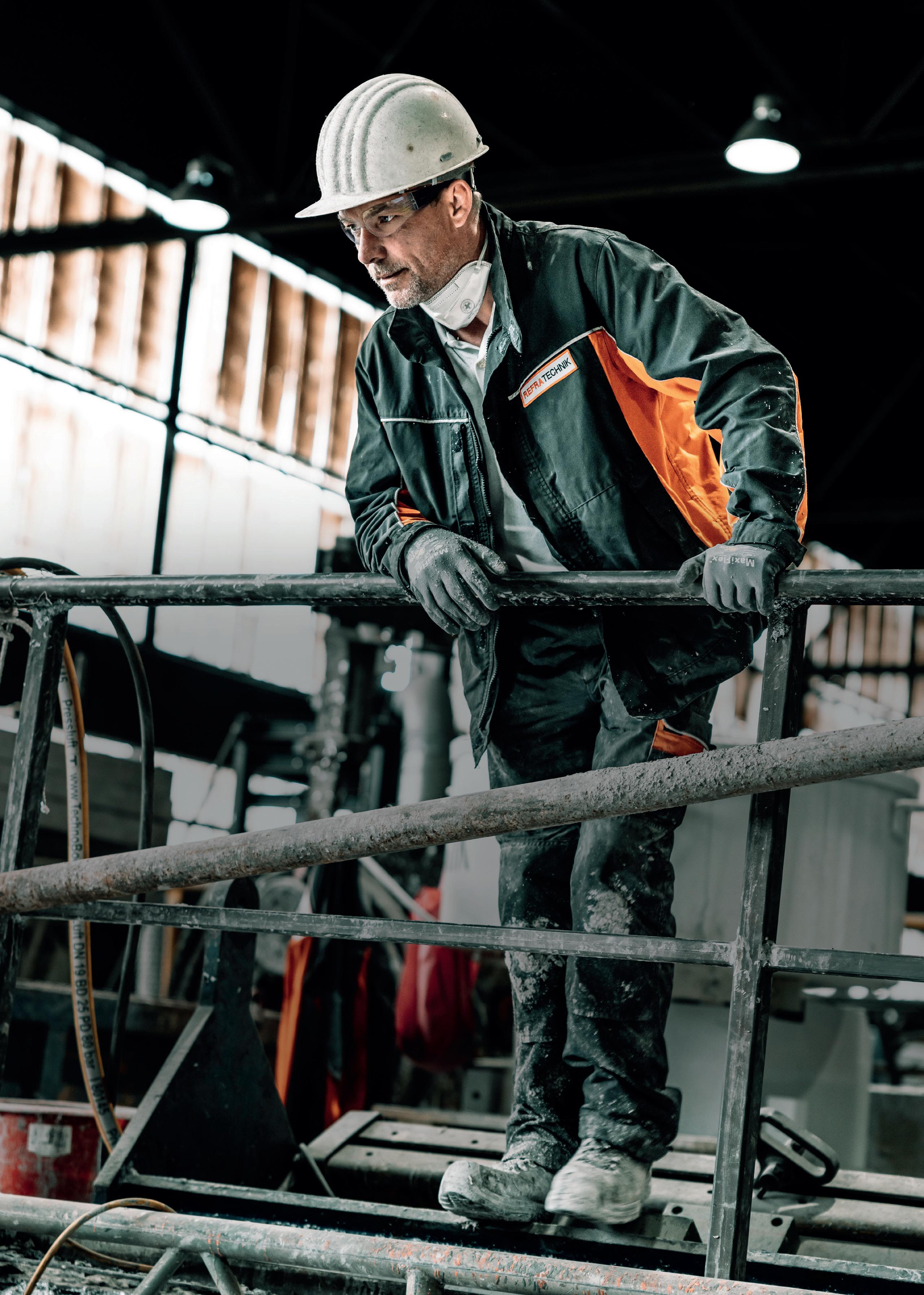
Socio-political issues are also having a significant impact on the supply chain.
GREENER ALUMINIUM 21 Aluminium International Today September/October 2022
By Alan Banks* *Ford Motor Company UK Innovations Supervisor
The effects on the global supply chain in recent years have been profound; COVID, the crisis in Ukraine but also the issue with the ‘Evergiven’ being stuck in the Suez Canal have highlighted the fragility of our ’just in time’ lifestyle. Sourcing globally for the lowest landed cost has served us well for many years – it has lowered operating costs, enabled us to take advantage of lowcost country production that consumers have benefitted from since its inception. Supply chains in Eastern Europe and the Far East were able to be exploited for easy to ship, high labour content commodities to keep costs down for the collective good. We could argue that job losses in local economies that made way for globalisation have been the price we’ve paid but by and large, this was driven by consumer demand for less expensive goods. Consumer pressure generally wins against any argument to the contrary – and for many of these products, price sensitivity is high. Recently however, global sourcing for the lowest cost has been called into question. Primarily driven by the sensitivity of the supply chain itself seen highlighted by the global pandemic, issue with ocean freight, and the need to cut greenhouse gas emissions and CO2 in particular. The raw material markets have been particularly under scrutiny, as sourcing globally for the lowest cost typically means in less developed economies, who often use fossil fuels in their manufacture, and coupled with the distance of shipping this has led to higher embedded CO2 in raw material production, rather than driving GHG reduction. Consumers today are more environmentally conscious demanding improvements, and in some instances, they are willing to pay more for greenerDemandgoods.for recycled materials and sustainable products is only likely to increase going forward – regardless of legislation that is put in place. We could be in a position whereby public expectations out-perform legislation with the aim to reduce CO2. As OEM’s become more environmentally astute, the transition to lower embedded CO2 materials and products will become a requirement. It is unlikely that high-polluting (and low cost) countries today will be able to transition to zero-emission countries tomorrow, which will leave the supply chain vulnerable to unexpected and rapid legislation changes and potential shifts in consumer demand. In the auto industry this is likely to be very important as the push for zero-emission vehicles has a time limit. By 2035, all vehicles sold in the UK must be 100% zero-emission. But if the embedded carbon in the manufacture of these vehicles isn’t addressed – including how that vehicle is recycled at end of life – then it could be argued that the industry has only done half the job in reducing GHG.
The impacts of the Russian gas supply to Western Europe, to the grain supply from Ukraine itself, have all contributed to huge price rises across all markets. But before this, the global Covid Pandemic also cause supply issues – such that the global pricing was adversely affected.
Similarly, demand for materials used for Battery Electric Vehicles (BEV’s) such as Cobalt, Nickel and Lithium have increased exponentially and were already on short supply prior to the war, and Russia has one of the world’s largest nickel mines is in Siberia, which is now sanctioned so the situation will be exacerbated as demand for BEVs continues to grow, so we must look at better solutions to recycle and reuse these materials both to improve the CO2 footprint but all to secure supply.
Opportunities for the UK Metals Industry
The CO2 required to produce material from recyclate is minimal compared to virgin. For instance, the CO2 output per tonne of aluminium generates approximately 20 tonnes for coal-based production. The European average is 6.7 tonnes of CO2 per tonne of aluminium. But this compares to less than 0.5 tonnes of CO2 to make aluminium from recyclate Fig 1. For the UK auto industry alone, this would equate to 8.25 million tons of CO2 reduction if the UK produced its own aluminium with 50% scrap (Fig 1). For
The war in Ukraine has given the world shortages in ways nobody anticipated.
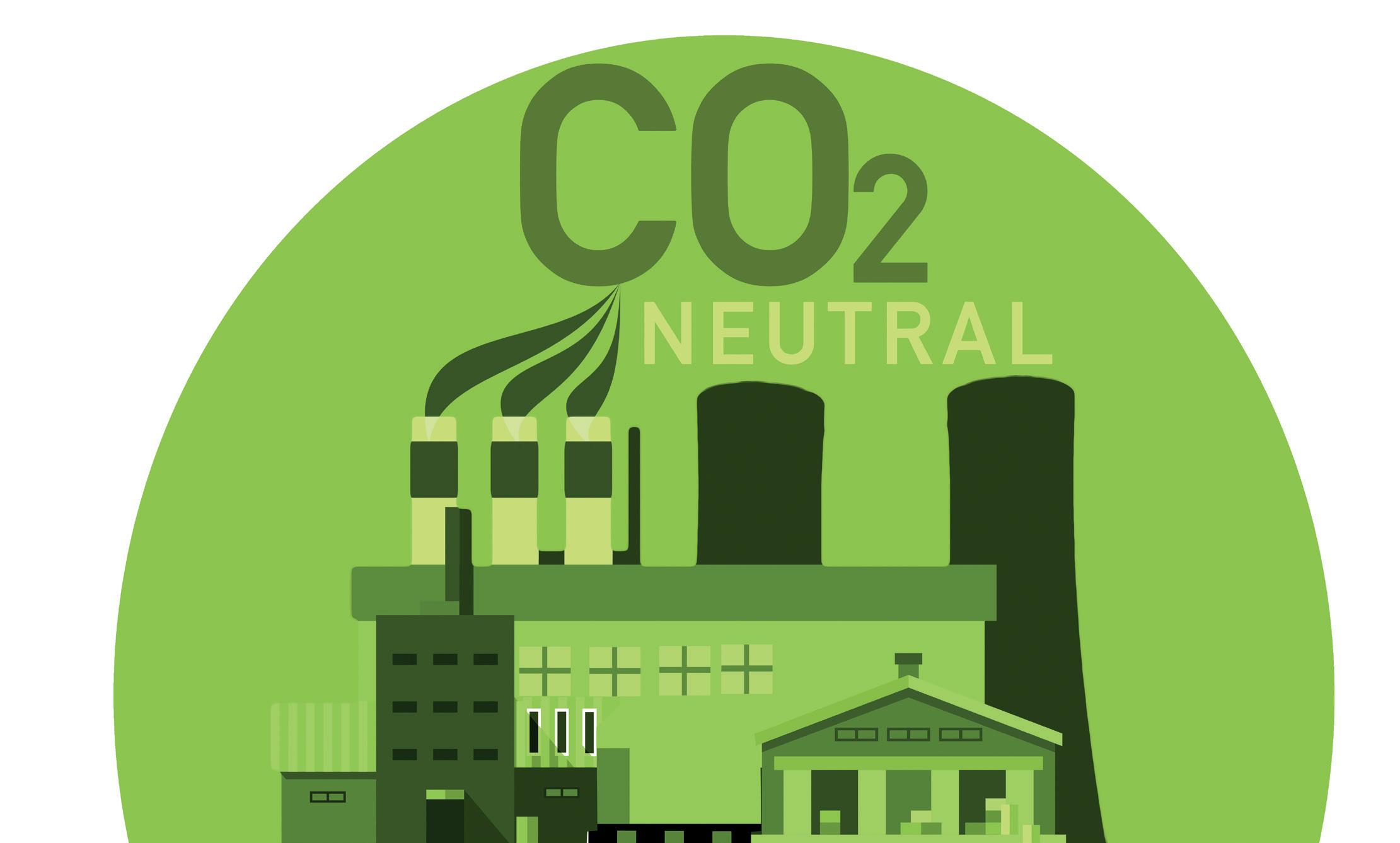
17.0
� Anchors industrial innovation here in the UK (ultra high strength steel) 2,730 Direct Jobs Plus 4,290 Indirect - Total 7,020
in the metal mixAIofper/TonCOofTonsAIofper/tonCOofTons22 20.05.0
The Department of Business, Energy and Industrial Strategy (BEIS) could use on-shoring of recyclate to incentivise businesses to invest in UK materials using repurposed scrap as the base-line for a materials strategy. Incentives for business (not just direct funding) are the key for businesses to invest if they see long-term potential for their investment. Establishing security of the supply chain is a priority in the current and future markets. With uncertainty around longterm supply due to the war in Ukraine and the uncertainty around Taiwan, it is in the interests of the UK business sectors to understand and take advantage of any opportunities that exist. As the world evolves, so must the way we do business. In the post Cold War era, the economics of local supply in a global market mitigated against the local economies. In the current market, especially with CO2 reduction as a requirement, the market opportunities may well be favourable for a re-think on the way we do business. Earth overshoot day (the day in which humanity has used up all of the biological resources that the planet can naturally regenerate) gets earlier every year (Fig 3). In 2022, that date is July 28th. In the UK alone, the date was May 19th. Whilst the issue ‘could’ be resolved by decarbonising high polluting material sources, this will not resolve the fragile supply chain and the UK will lose the job creation and wealth improvement opportunities that on-shoring would provide. �
Aluminium International TodaySeptember/OctoberGREENER2022ALUMINIUM22
As the UK doesn’t have a remelt facility, the UK low value scrap is exported to be repurposed into high value (and high cost) material. This is the kind of opportunity that exists for anyone who can make a business case for material on-shoring. The UK steel industry has a similar CO2 equation as the Aluminium industry and would also benefit (Fig 2).
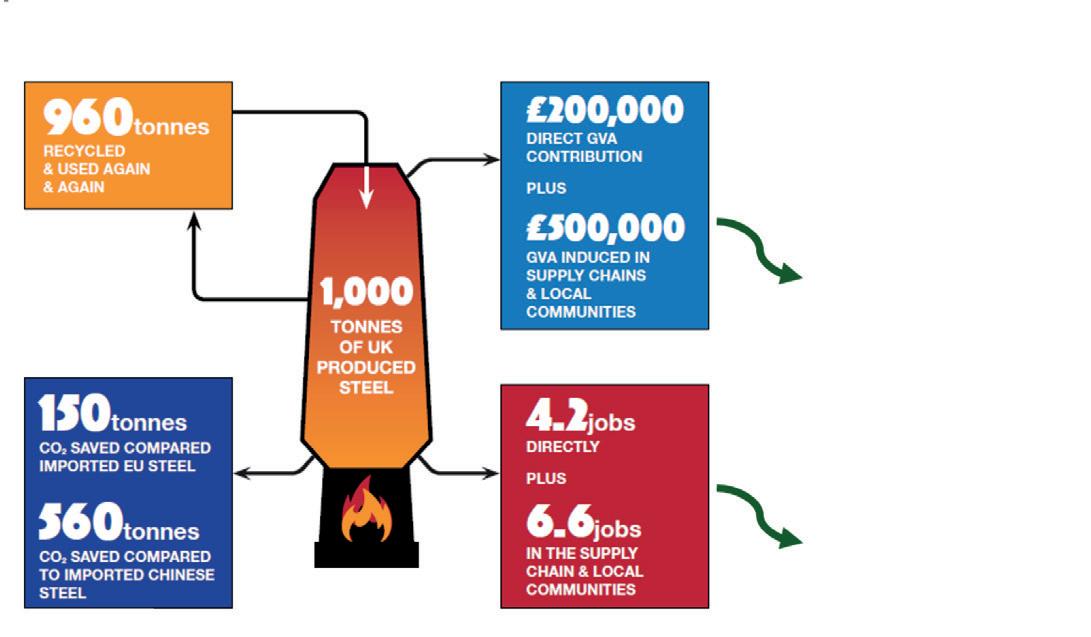
Fig 2. CO2, GVA for the UK Auto Steel Industry (UK FigSteel)3.Earth
Fig 1. Embedded CO2 Comparison for Aluminium Production (ALFED)
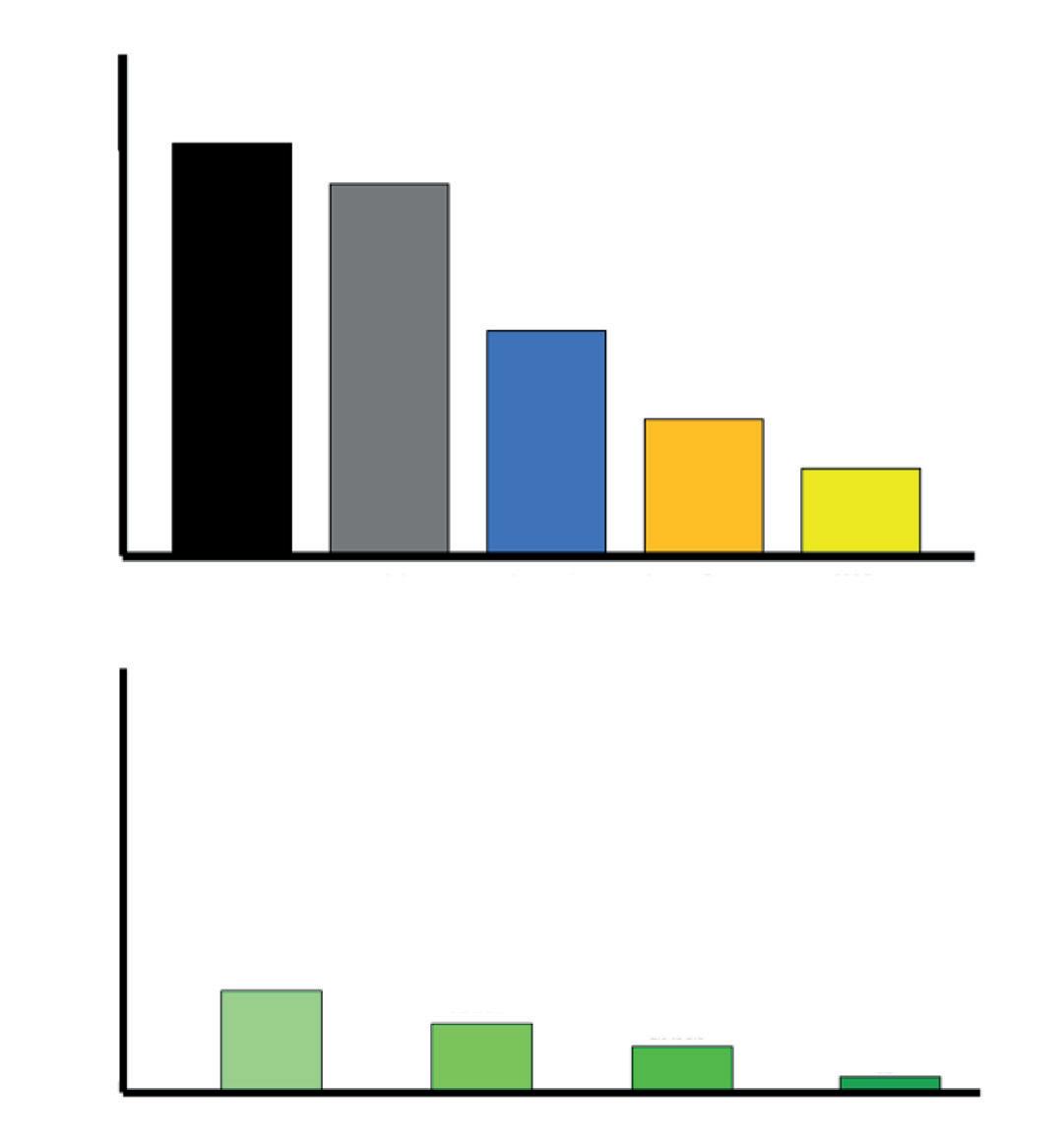
electricityfree
� Opportunity to show global leadership as first country to commit to decarbonised steel sector � Transforming jobs into green jobs in areas the Government want to level up � Provides £2.5 billion to UK economy with significant growth opportunity (in excess of 650k tonnes annual production450k domestic & 200k export) � New production methods and innovation will lead to significant competitive advantage
Aluminium origin importance, re-cycling & carbon footprint Green house gas emissions of primary aluminium production % Post consumer scrap to 7.0 3.5 to 5.0 2.0 to 3.0 0.5
reference, the UK scraps 100k tonnes of aluminium a year. The UK auto sector is healthy and is likely to grow as the demand for zero-emission vehicles intensifies. To protect UK supply chain, the raw material opportunities for manufacture within the UK can help with the resilience to outside influences and global insecurities. As well as the CO2 reduction, the business case behind the on-shoring of raw material is compelling. To be selfsufficient for the UK auto industry for Aluminium, Steel, Carbon Fibre and Glass fibre would:� Reduce global CO2 by 137 tonnes of CO2 per tonne of material produced � Over 13 million tonnes annually � Create over 13,500 jobs � Generate over £5bn for the UK economyWhilst this potential should be industry led, the foundations of the opportunities could be underpinned by Government strategy starting with the Department of the Environment, Farming and Rural Affairs (DEFRA) wo would own the recycling strategy for materials. Encouragement to prevent off-shoring (and thus generating a huge amount of CO2 in the process) to recycle scrap material would set the agenda for materials to be made in the UK. DEFRA would need to work with the environmental lobby to demonstrate that although CO2 output from the UK will increase in the short term, the global reductions would be a compelling argument.UKCO2 output would be mitigated in the longer term by investment in green energy. Scotland, for instance, is already powered by 98% renewable energy and as the other UK countries decarbonise, so to will the CO2 output diminish.
Coal-basedproduction25%Postconsumerscrap 50% consumerPostscrap 75% consumerPostscrap 100% Post recycled process averageGlobal ImportsEuropeto
Overshoot Day
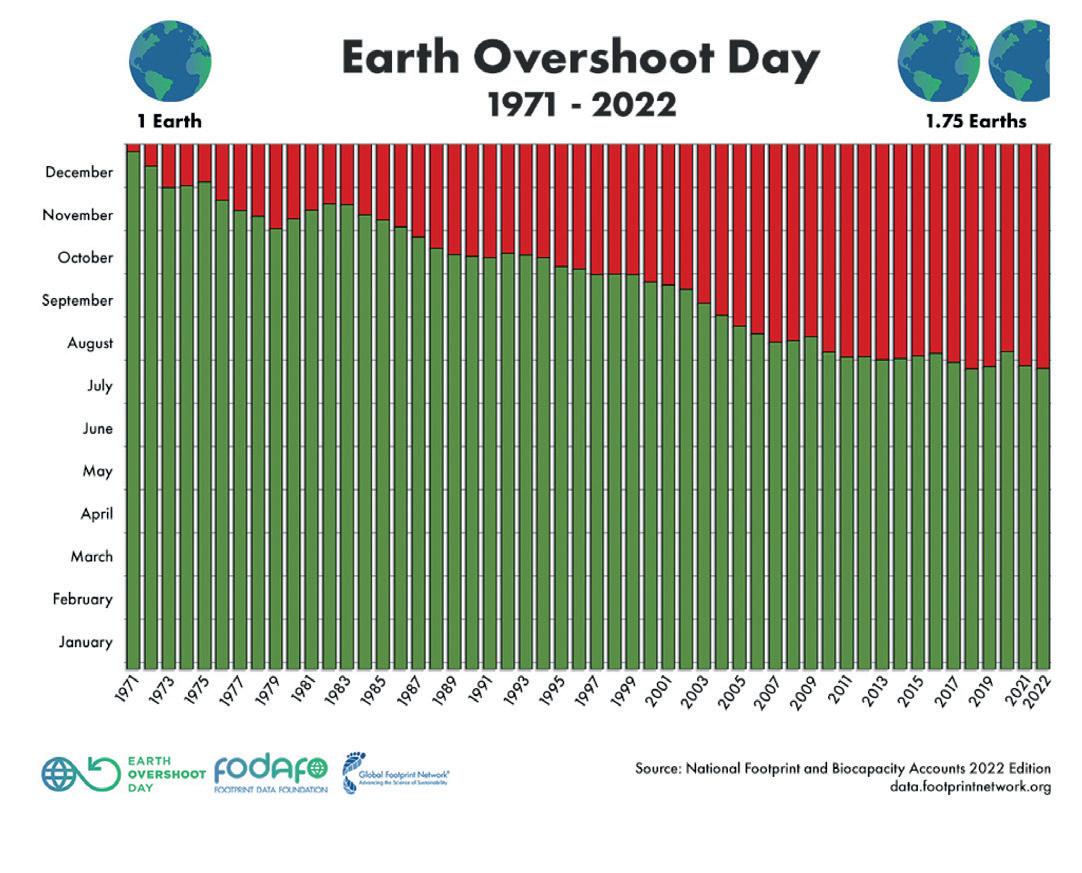
and Job Creation Opportunities
Primary(gateRecyclingtogate)Aluminium(cradletogate) 0.5 tons of CO2e can be reduced to <0.2 tons CO2e by the use of green hydrogen for melting, etc CO2productionEuropeanAverage 10.6 6.7 4.0 to 4.5


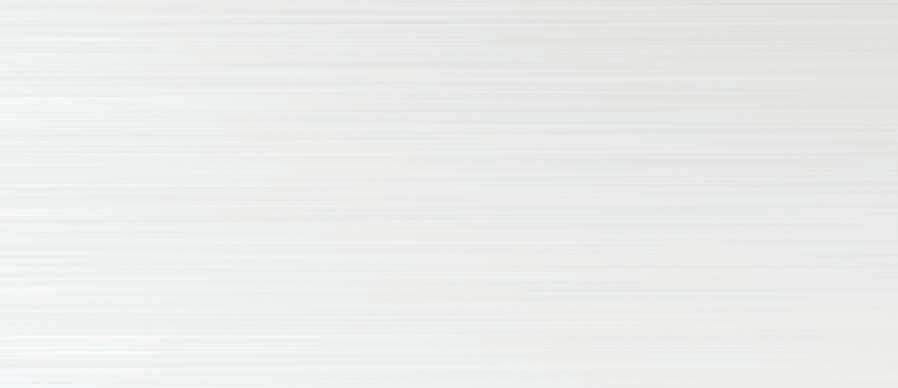
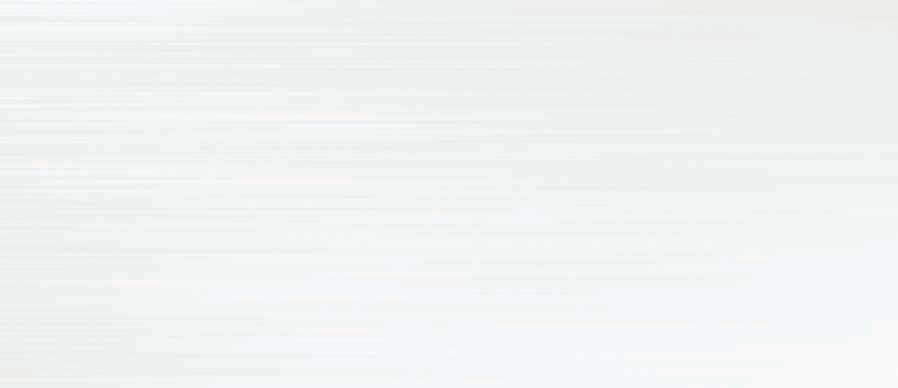

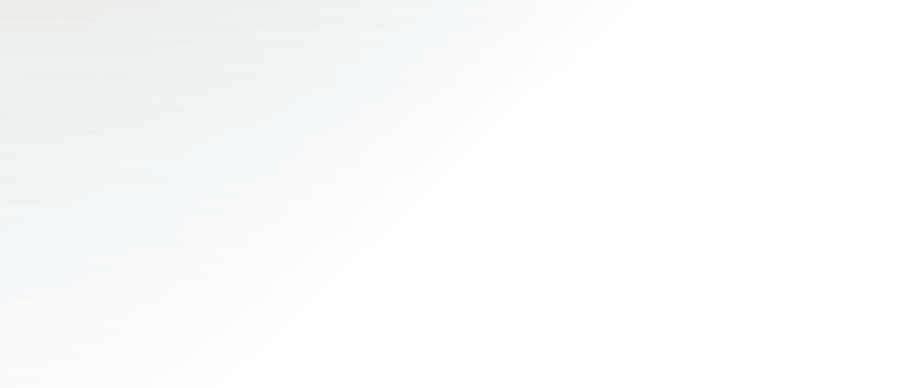
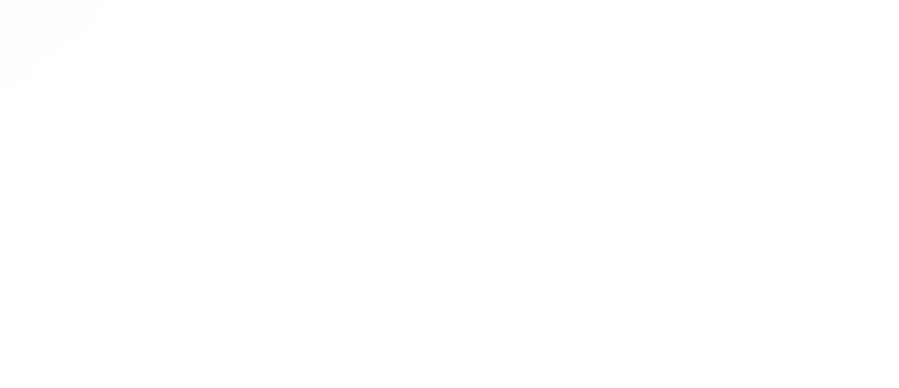
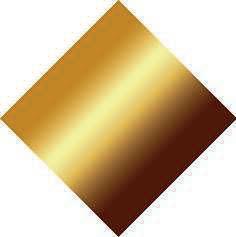
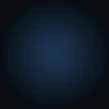
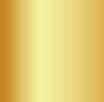






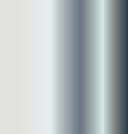

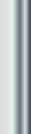
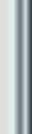
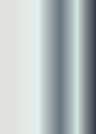
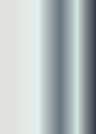
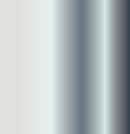
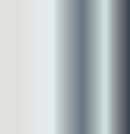

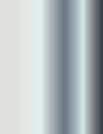
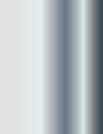

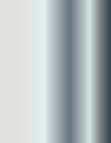
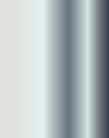
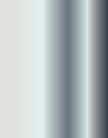
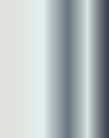
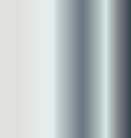
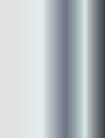
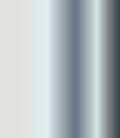

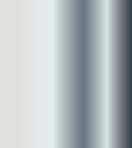
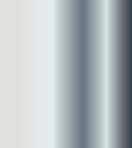
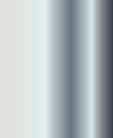
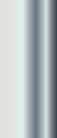

By Rod MacGregor*
Decarbonising Industrial heat is essential to combating climate change Industry consumes over 32% of all the energy used worldwide. That’s more than transportation, residential, or any other sector. Three quarters of the energy industry uses is in the form of process heat, and only one quarter is used as electricity. That makes industrial process heat one of the largest energy markets in the world, and as a result one of the largest emitters of greenhouse gasses. Therefore, we won’t make progress combating climate change unless we address emissions from industrial process heat.
We all live on the same planet, sharing the same atmosphere, so the motivation to decarbonise is for the common good of all people, companies and countries. However, those industrial companies that take a leadership position and decarbonise first, will reap substantial economic benefits. Emitting CO2 is now associated with actual financial cost in many parts of the world, ranging from cap-and-trade systems in Europe, Australia and the US to some regions imposing a carbon border tariff on imports of goods based on their embedded carbon content. Over time, of GlassPoint Solar
* CEO
How Solar Steam helps decarbonise the aluminium industry
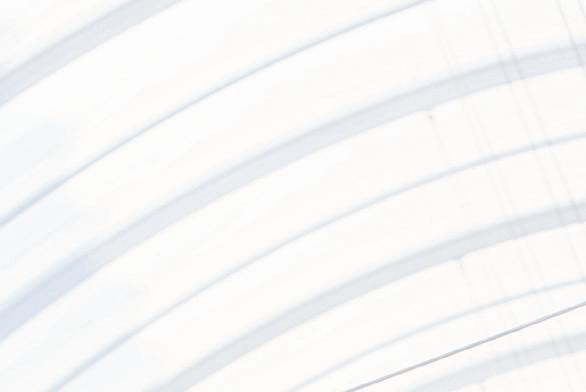
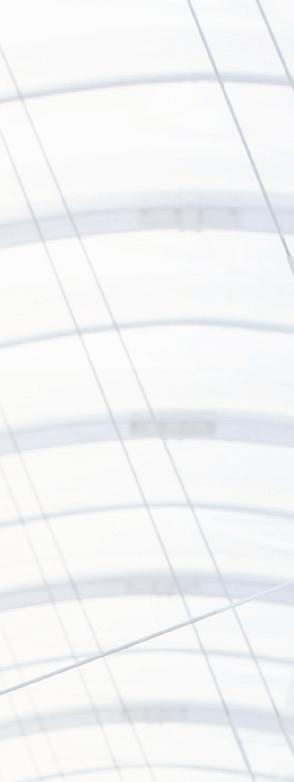

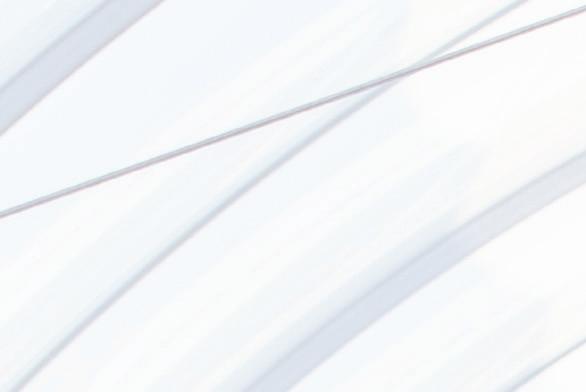
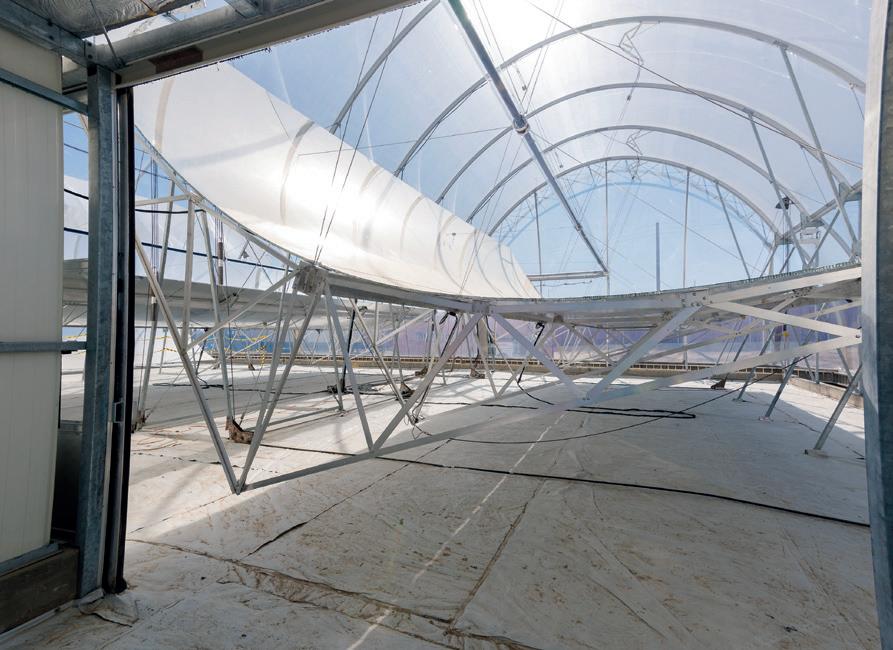
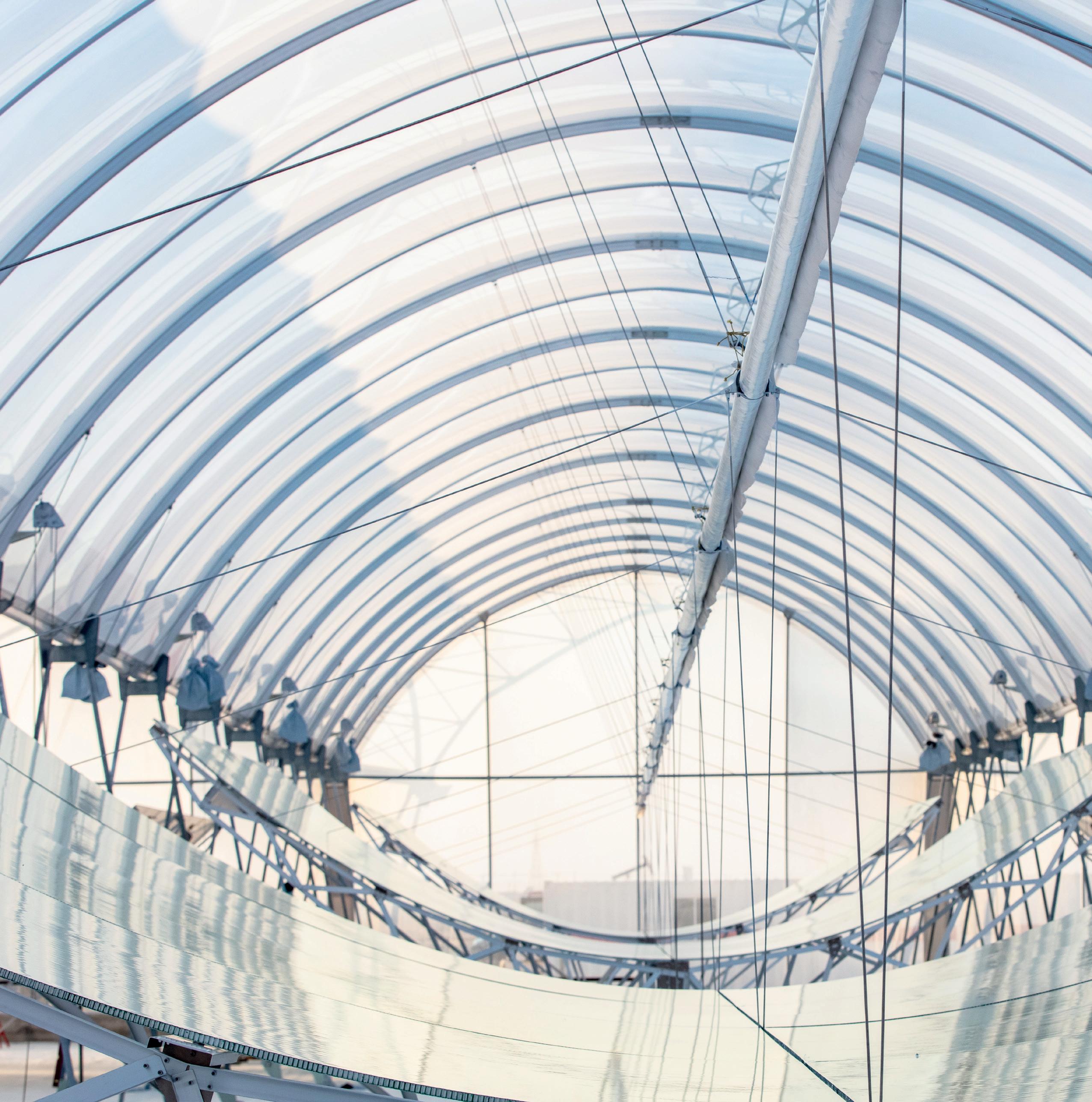
Aluminium International TodaySeptember/OctoberGREENER2022ALUMINIUM24
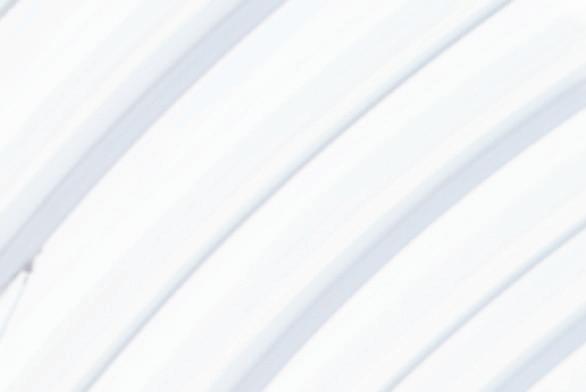
Aluminium production alone generates more than 1 billion tons of CO2 a year, according to data from the World Economic Forum, and a substantial portion of that comes from fuel burned to make process heat.
Benefits of decarbonising
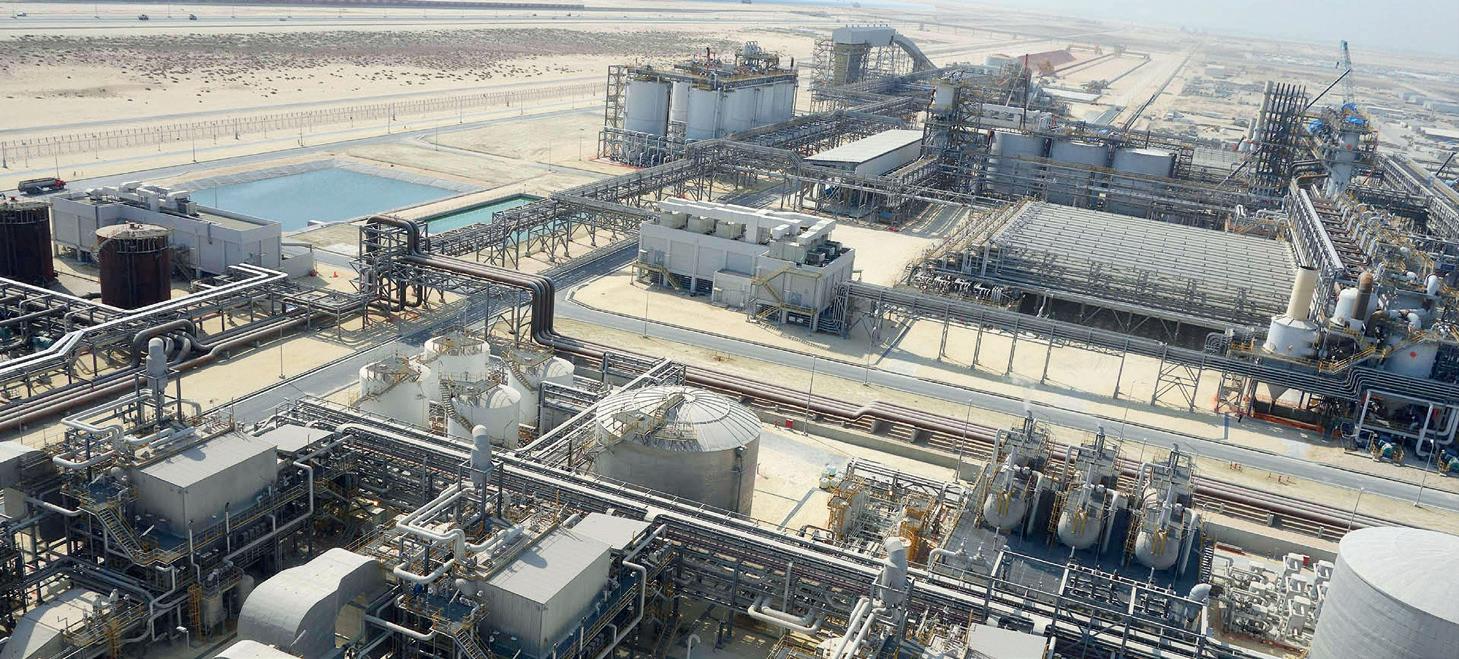
Decarbonising industrial process heat is difficult Companies whose emissions come primarily from electrical loads have a number of proven technologies they can readily deploy to reduce their emissions. Solutions range from installing solar panels or wind turbines, to simply purchasing renewable energy from the grid.In contrast, decarbonising industrial process heat is much more challenging due to the lack of proven technical solutions, massive scale, and lack of any shared infrastructure. There is no national steam grid. For example, consider the process heat required for a Bauxite refinery that converts Bauxite to Alumina, the precursor to Aluminium. In a typical refinery, just one of the process steps “digestion” requires over two GW of energy. That’s more than the energy consumed by a city like Washington, DC. It is exceedingly rare to find renewable energy installations of that size, and those that exist cover a vast amount of land.
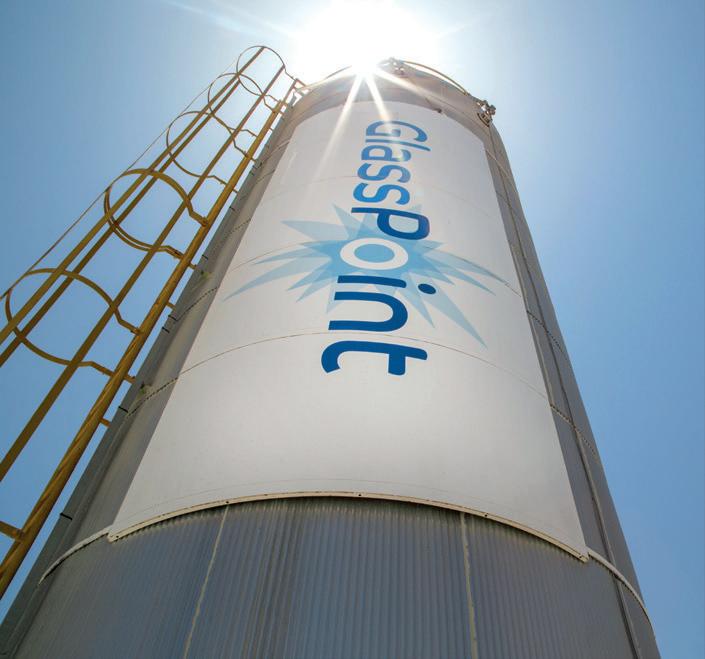
More than half of the 3,000 CEOs responding to a 2022 survey by IBM cited sustainability as their greatest challenge when looking ahead two or three years. That was up from 32% only a year earlier.

Investors are also increasingly pressing companies to reduce their carbon footprint and, in some cases, refusing to invest in industries with high emissions.
Apple, Tesla and BMW to name a few, have recently stated their future preference and made statements about their future intention to only source aluminium with lower embedded carbon.
Electrification is Not the Answer
More than seven in ten said that board members were pressuring them to do more, and 5 % said they were receiving pressure from investors to shrink the company’s carbon footprint. Industrial leaders are responding to the challenge – last year 28 of the world’s top miners vowed to reach net zero by 2050. That amounts to a third of the global mining industry with operations spanning 650 sites over 50 countries, and includes industry leaders like Anglo American, Rio Tinto and BHP.

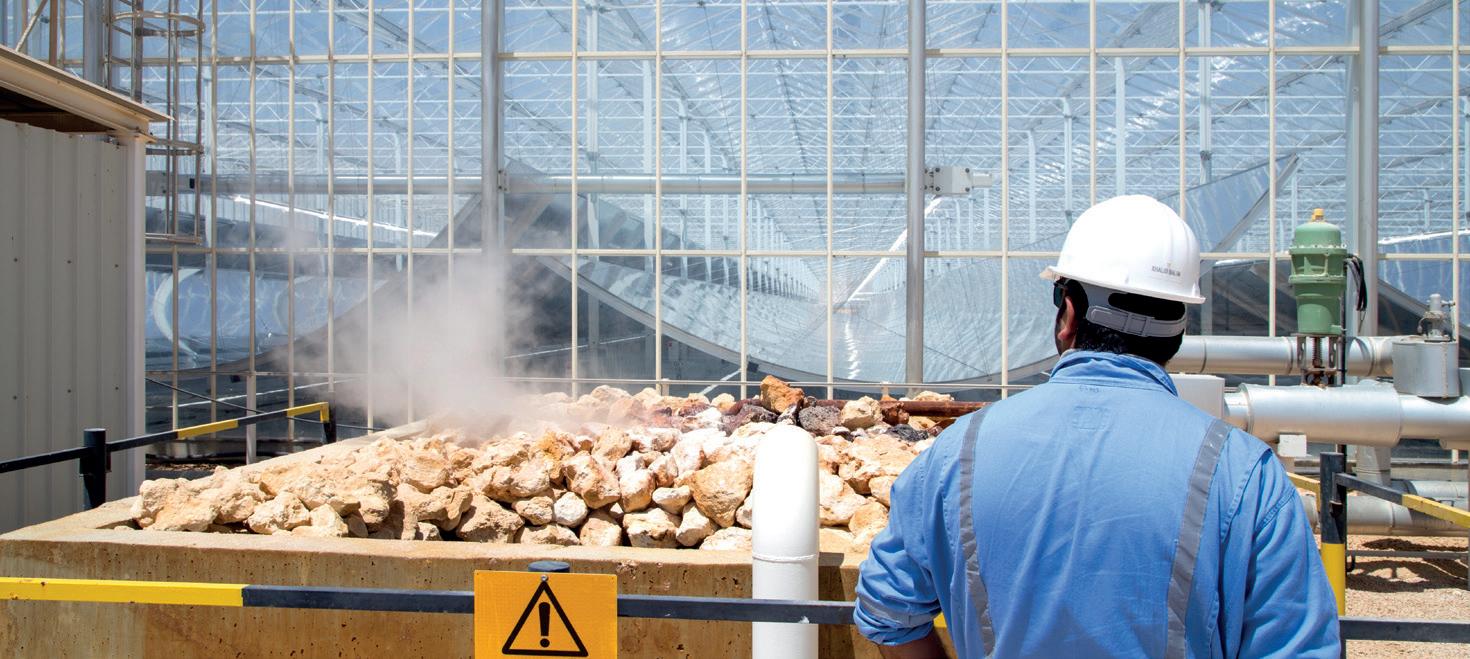
Fortunately, there is a technology that has already been deployed at scale that can produce process heat with zero emissions, both day and night. The basic idea has been around for centuries. Sunlight is
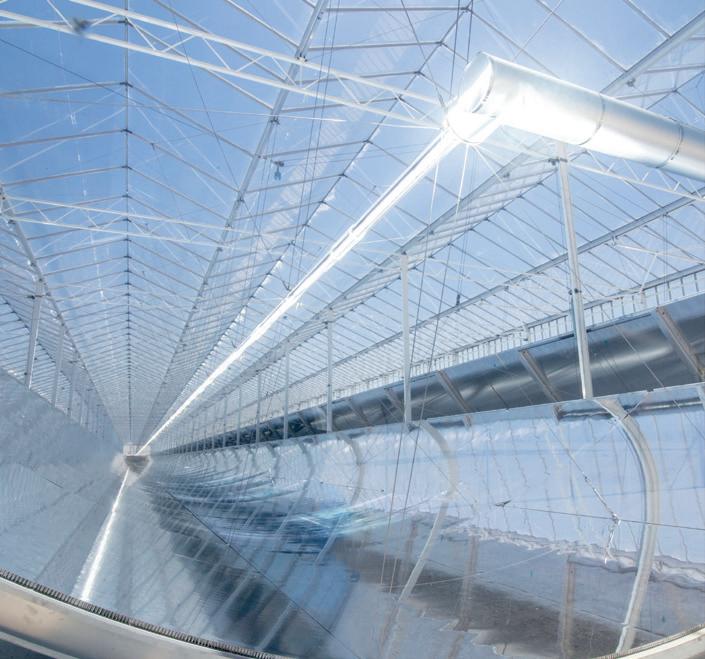
GREENER ALUMINIUM 25 Aluminium International Today September/October 2022 those companies with lower embedded carbon will increasingly enjoy lower operating costs than their higher emitting peers.On the demand side, customers are increasingly expressing a preference for materials with lower embedded carbon.
Proven Technology Deployed at Scale
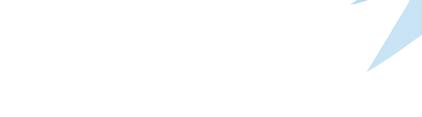
The idea of using electricity to decarbonise process heat is not a viable solution, due primarily to some basic laws of physics. A power station burns fuel to make heat, and that heat is then used to spin a turbine that makes electricity. Due to the laws of thermodynamics, only half the energy in the fuel becomes energy in the electricity. When that electricity is then converted back to heat for use in an industrial process, more than twice as much fuel would have been burned, and hence twice the emissions generated, compared to just burning the fuel locally. This means that electrifying by using power from the grid, will approximately double CO2 emissions. Even if the grid was powered from 20% renewable energy sources, the other 80% would still come from fossil fuel sources that emit at twice the rate when compared to burning fuel locally. This would lead to a 160% increase in emissions overall. Even if the grid was powered from 50% renewable sources, day and night, emissions would be the same as burning fuel locally. Of course, a 50% renewable grid will take many decades to achieve in most countries.
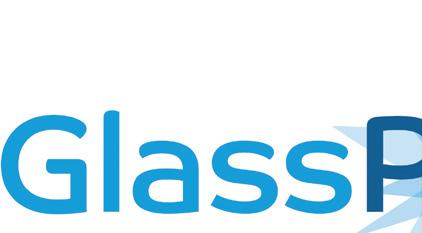
focused to produce heat in much the same way as a magnifying glass can be used to focus sunlight to burn wood. This direct conversion from sunlight to heat is highly efficient and so uses a fraction of the land area that a traditional solar plant designed to produce electricity would occupy.
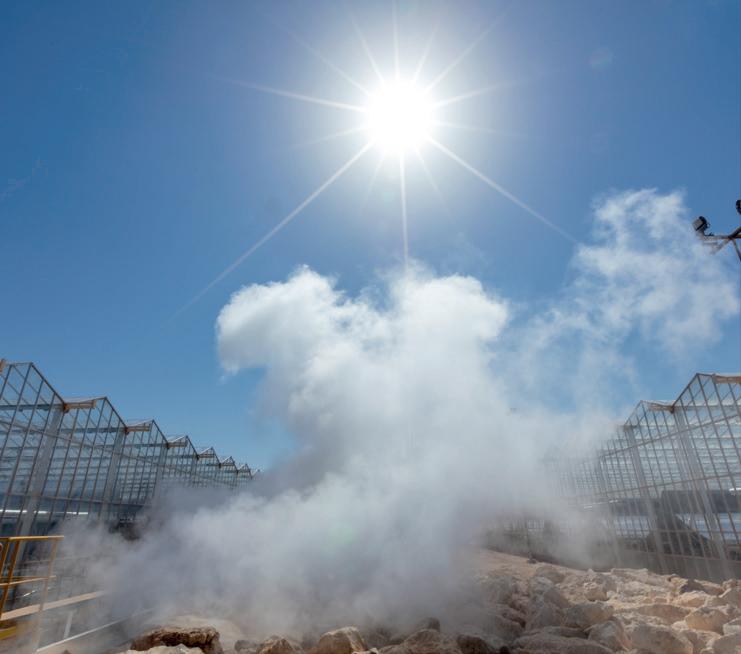
GREENER2022ALUMINIUM
GlassPoint has been deploying solar thermal process heat systems for the last ten years, and now represents more than half of the installed base of solar industrial process heat worldwide. We have built projects in North America and the Middle East, including one giant plant in the desert of Oman that boils over 2,000 tons of water every day to produce high pressure steam.
26
The GlassPoint system consists of giant curved mirrors that focus sunlight onto pipes containing water. The heat boils the water creating steam that can be used in an industrial process. The mirrors are housed in massive greenhouses to protect them from the elements, and automated washing units clean the greenhouse roof at night (capturing and reusing water to minimise waste).
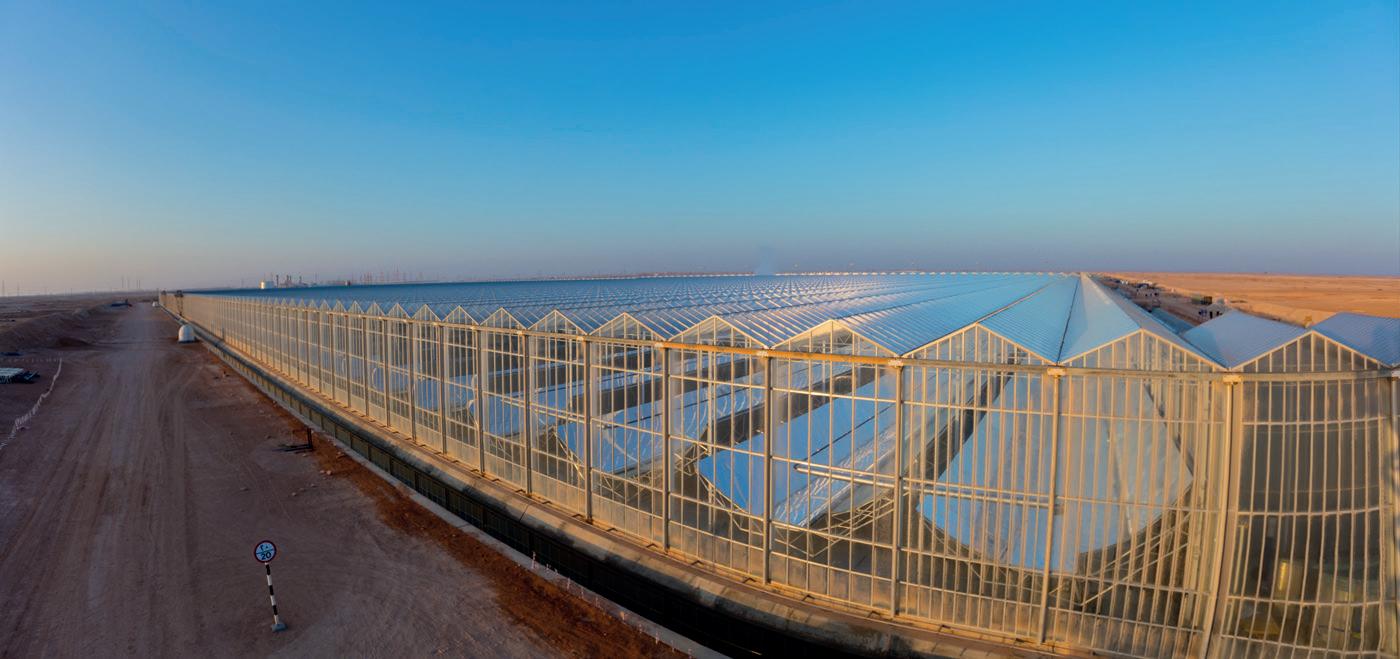
A massive opportunity Aluminium facilities circle the globe in sun-heavy locales ideal for solar steam –from the sunbelt in the US to Australia to the Middle East. Producers don’t need to change their infrastructure, simply build solar steam facilities alongside their own. Beyond aluminium, solar steam is an ideal match for a range of industrial processes that rely on heat – from food production to paper mills to virtually any industry you can think GlassPointof. solar steam is the only solution proven at scale today, and is a critical asset in helping alumina refineries, and other users of process heat meet their net-zero commitments. �
Aluminium International TodaySeptember/October
Ma’aden taking the lead in the Alumina sector In June 2022, we signed a memorandum of understanding with Ma’aden to build a giant 1.5-gigawatt solar thermal project in Ras al Khair, Saudi Arabia, for use in the digestor phase of their Bauxite refinery. When completed, the project will rank as the world’s largest solar process project and one of the largest of any kind on the planet. Currently the refinery uses gas to produce steam; when it switches over to solar, Ma’aden will produce 600,000 fewer tons of CO2 a year, representing just over half of their total emissions at this one facility. And as Robert Wilt, the CEO of Ma’aden, said, “This significant development will dramatically reduce our carbon footprint and bring us closer to our mandate of carbon neutrality by 2050.” Solar steam may not be the least expensive fuel option, but it is the cheapest way of producing emissions-free heat. We sell steam in long-term purchase agreements, saving our customers from diverting capital from their core business functions. With solar steam, a company can lock in their price of energy for 25 years – no small advantage given the volatility of energy prices that will only increase as the energy transition progresses.
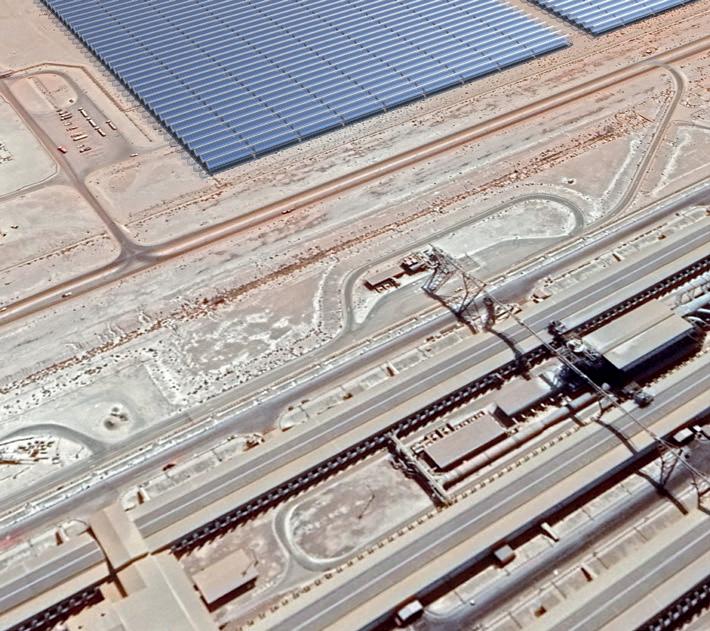
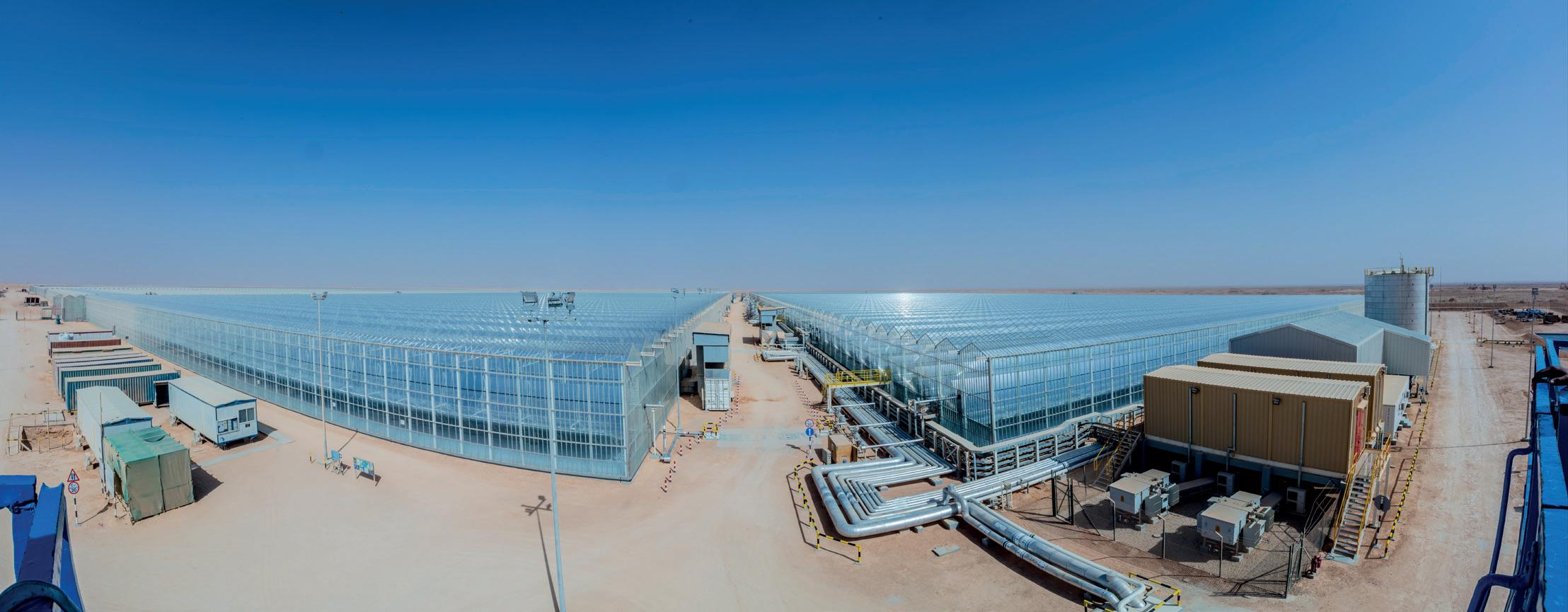
If you’re looking for all-round improvements in efficiency and sustainability across your entire plant – as well as a lower carbon footprint – then ALTEK’s complete, end-to-end Dross Management Solution is the answer. It recovers, recycles, reduces and repeats – creating the perfect circular economy. With no more need for specialist treatment centres or landfill. Even the Non-Metallic Product (NMP) becomes a valuable resaleable resource. ALTEKadvance: end-to-end Dross Management Solution. Altek Europe Limited, Lakeside House, Burley Close, Chesterfield, Derbyshire, S40 2UB, UK +44 (0) 1246 383737 altek-al.com/advancedsolutions Partnering | Thinking | Insight | Solutions
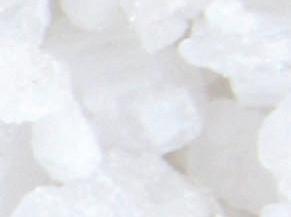
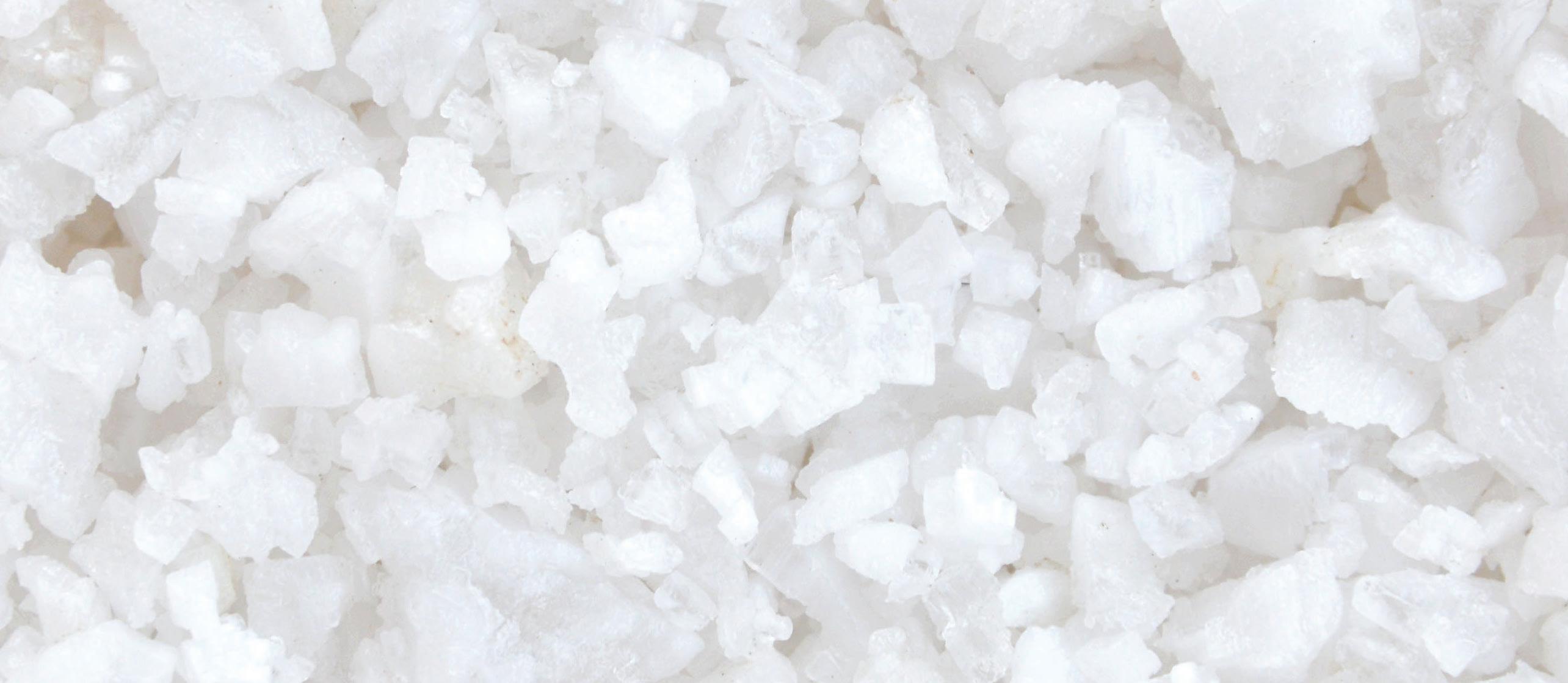
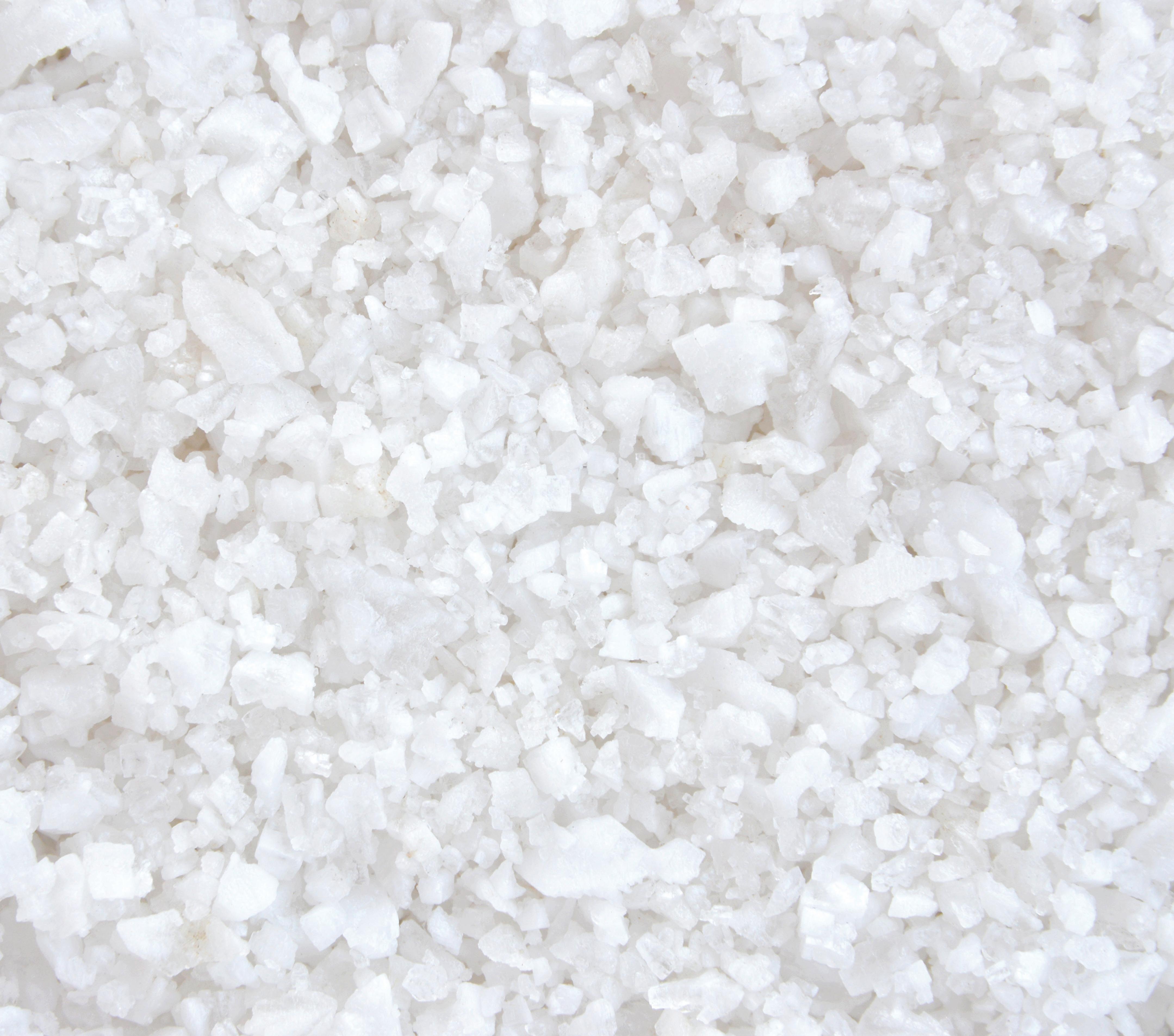
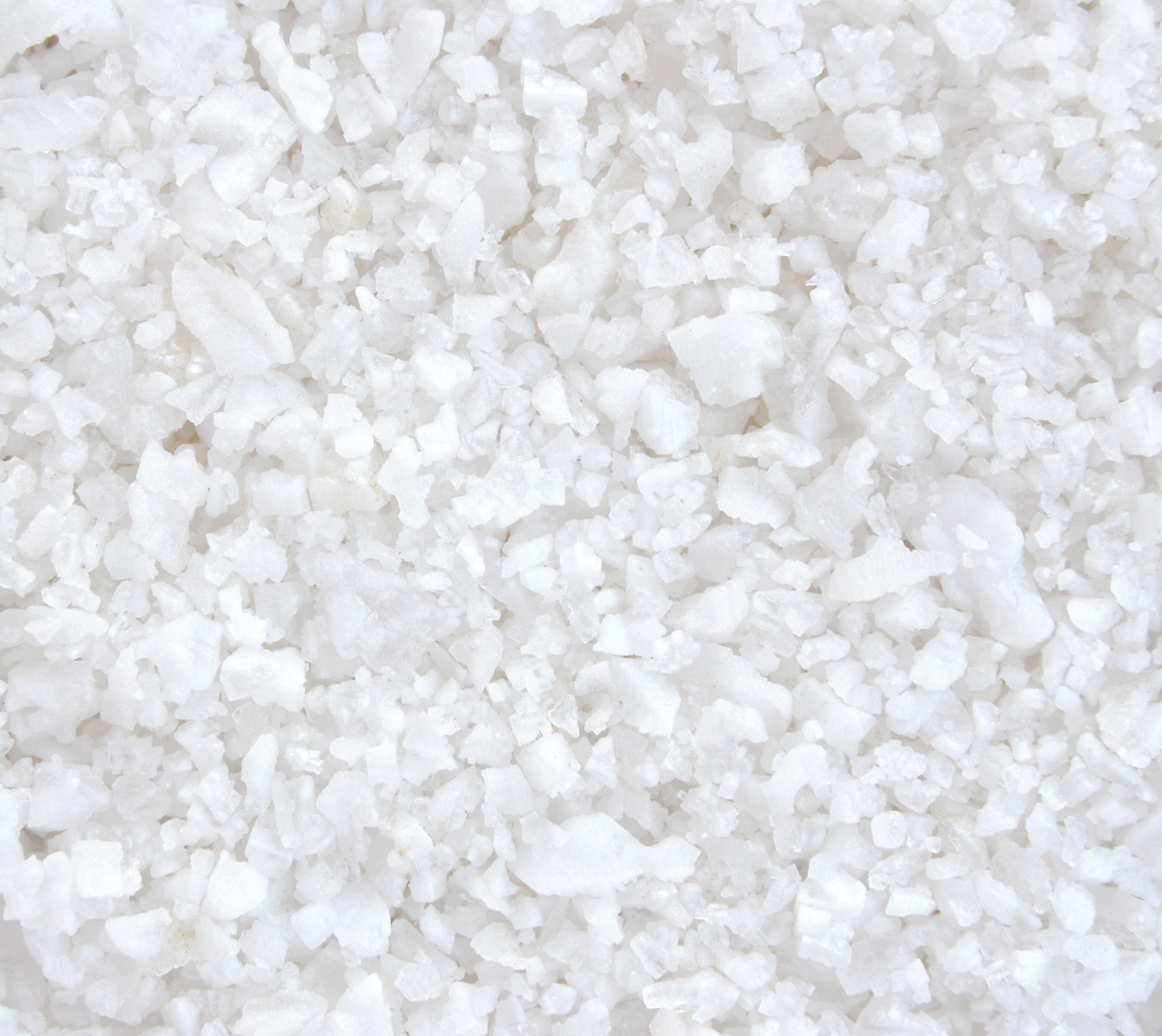
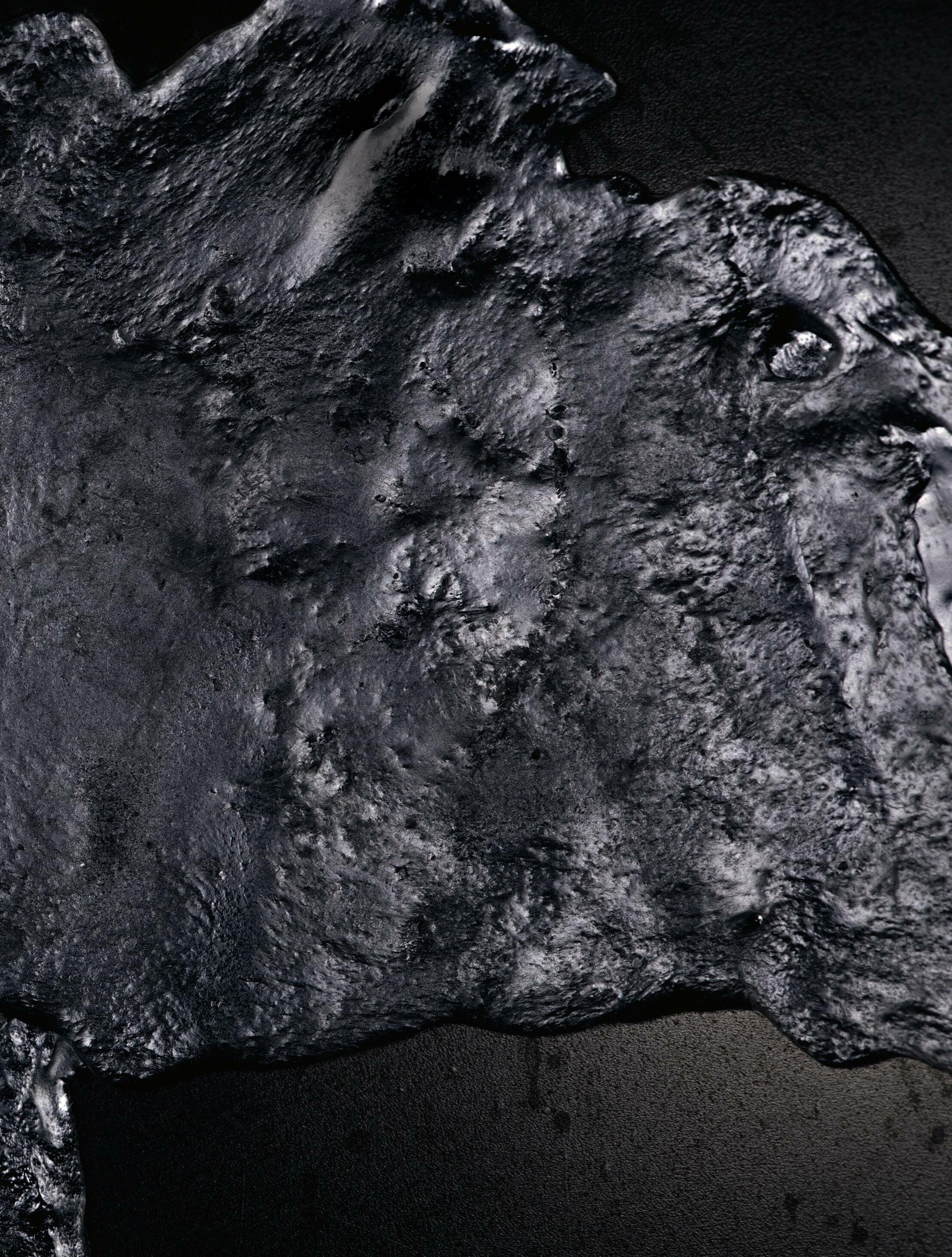
Carbon Area Our carbon area plant solutions and technologies are designed for excellent reliability and availability. We can provide a complete range of technologies and process solutions in both greenfield and brownfield project environment.
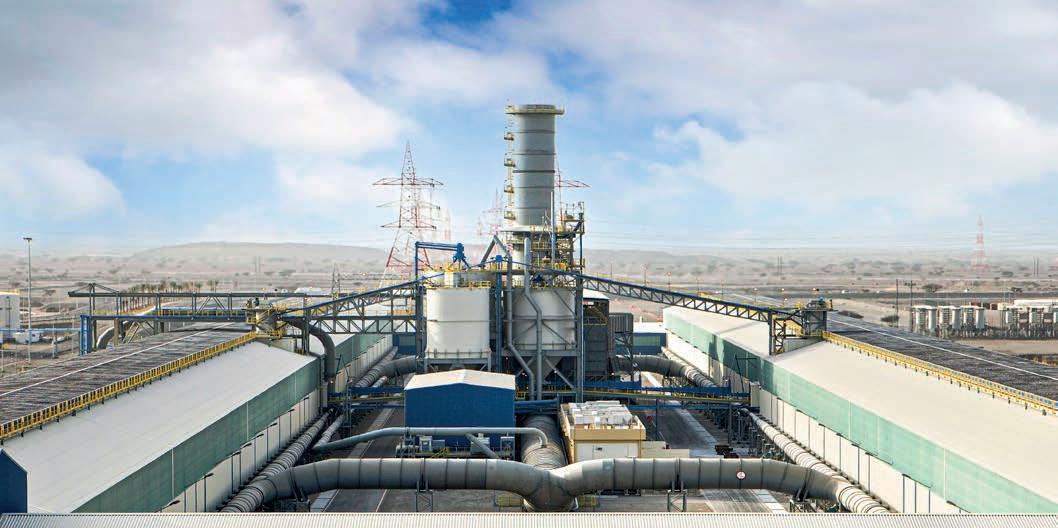
TOGETHER TOWARDS PERFORMANCE
Electrolysis and Environmental Solutions Offering a unique combination of know-how, state of the art and proven technologies we stand ready to help our clients with their metal production and environmental concerns. With a culture of innovation we also support them in their emission control.
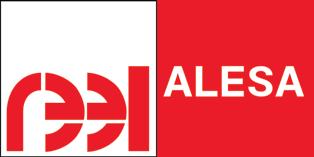
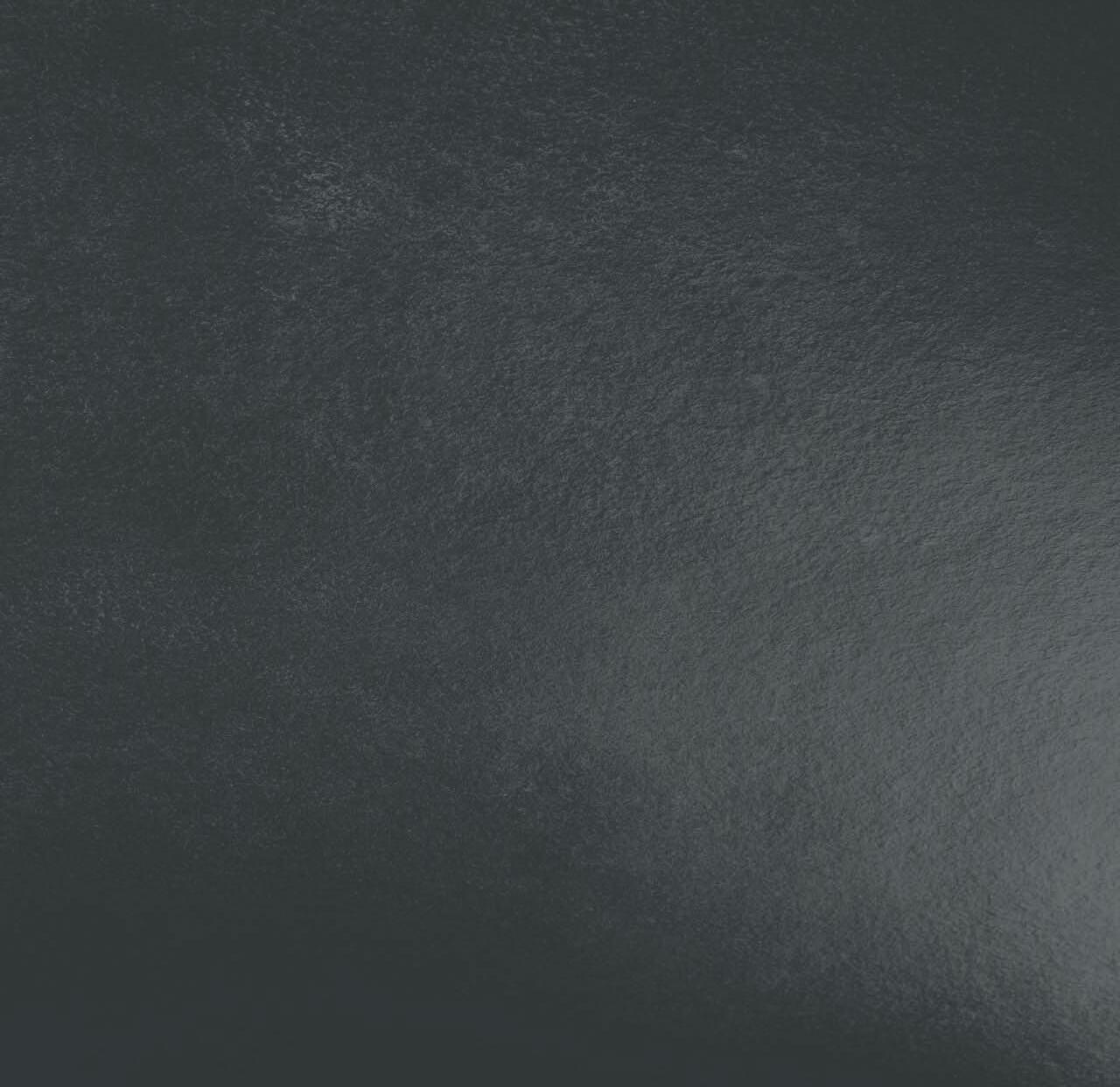
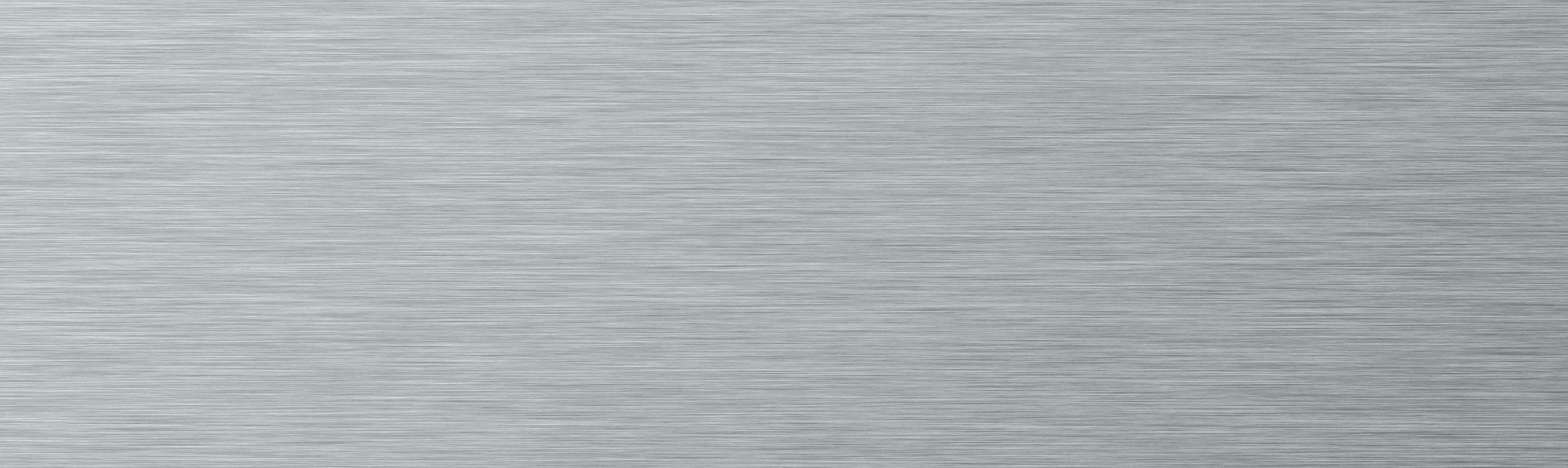
Port Area From incoming material delivery, to conveying, storage and transport to the smelter, we have been supporting the Aluminium Industry with premium solutions for decades.
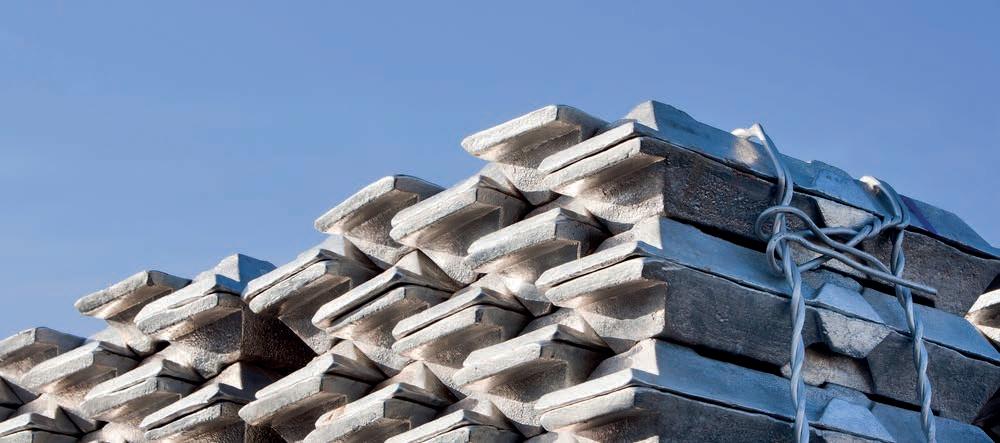
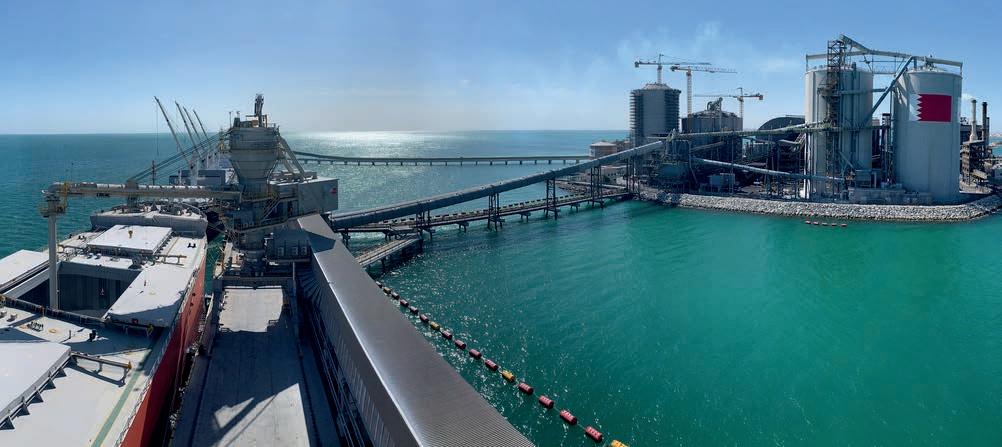
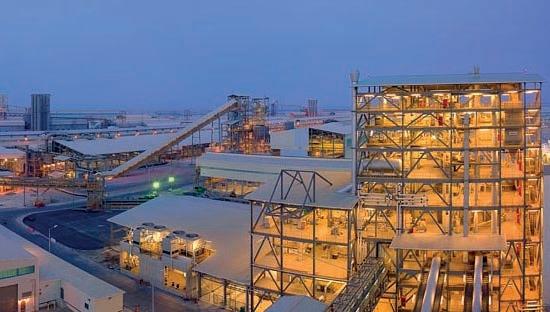

www.reelinternational.com

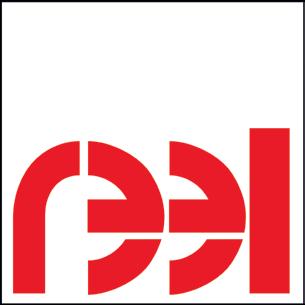
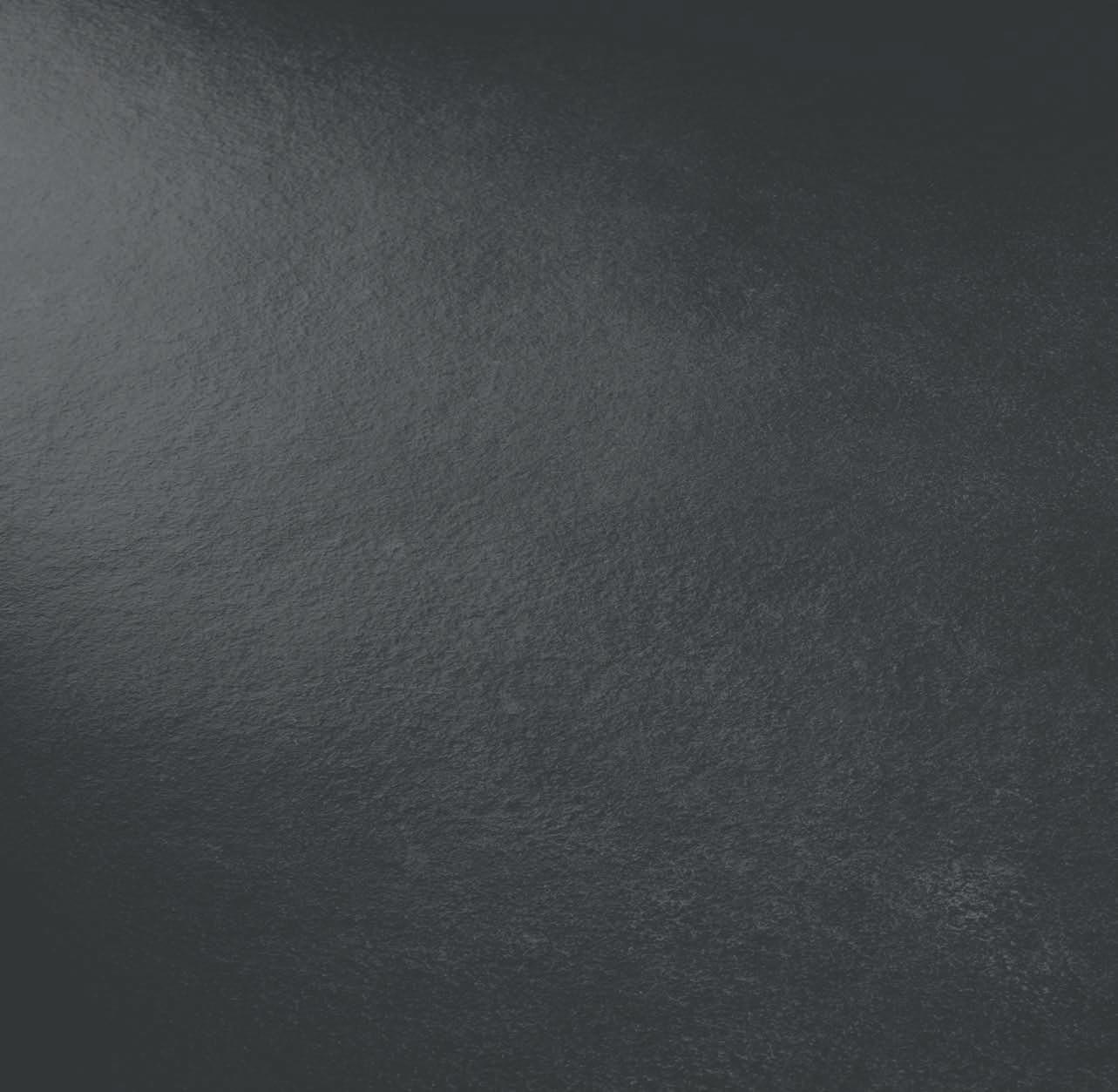
Casthouse REEL international is a leader in the design, fabrication, and supply of casthouse equipment for today’s highly competitive and quality-driven Aluminium Industry.
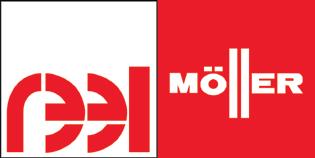

Although the historic implementation of regenerative burners has been focused on increasing production and minimising fuel cost while maintaining ultra-low NOx emissions, the current drive towards decarbonisation has given regenerative burners a new purpose in the industry – lowering the carbon footprint of aluminium production.
GREENER ALUMINIUM 29 Aluminium International Today September/October 2022
How is CO2 Formed and How Can It Be Reduced?Untilrecently, the main focus of emissions reduction in industrial thermal processing has been NOx emissions. However, the need to decarbonise the industry has shifted the focus to decreasing CO2 emissions. Unlike NOx, CO2 is a major species in the combustion of hydrocarbon fuels, as given by the following general reaction for the combustion of any
Fig 1. Illustration of North American TwinBed™ II regenerative burner operation Fig 2. Illustration of LNI technology with a North American TwinBed™ II regenerative burner
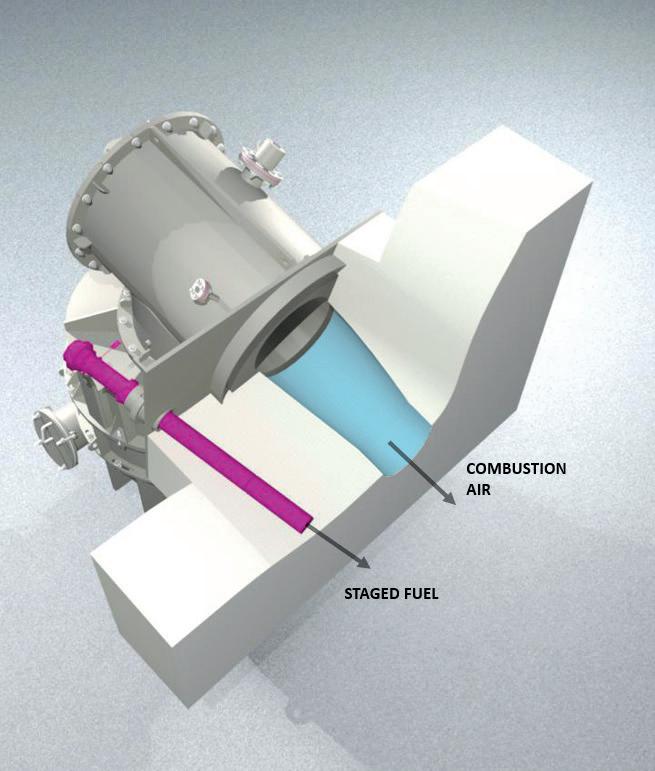

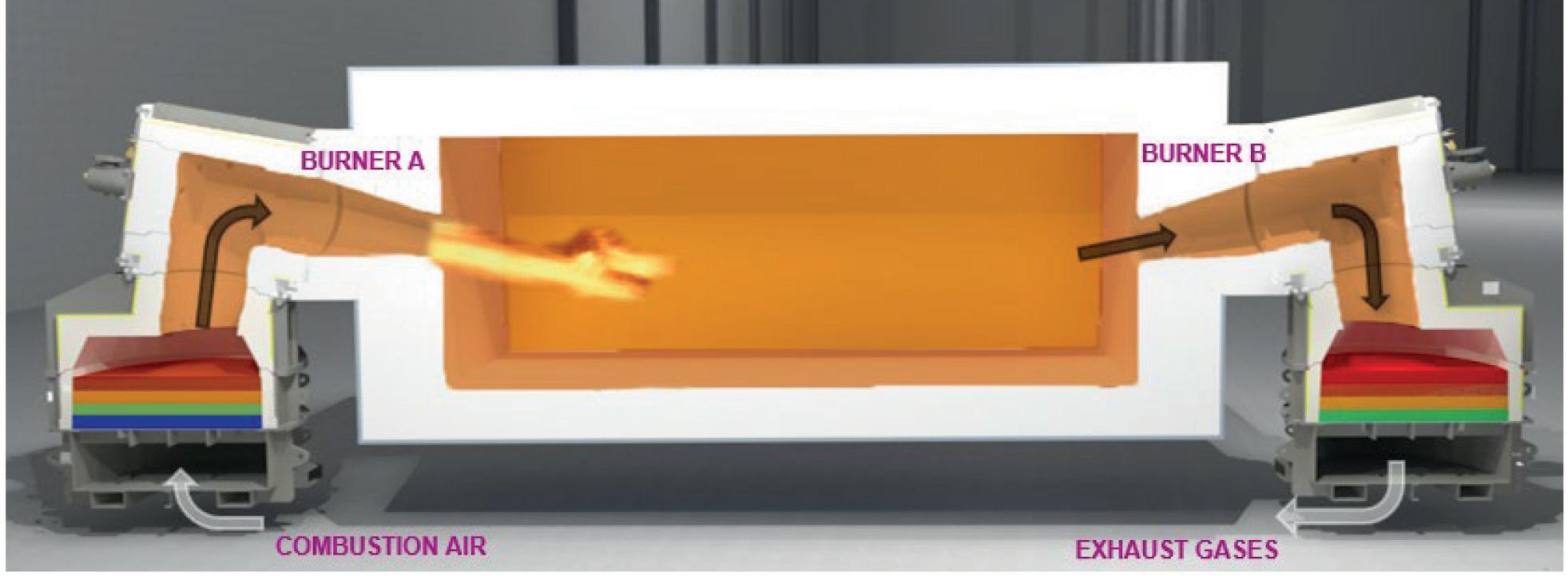
Overview of Regenerative Burners and LNI Technology
The role of regenerative burners and Low NOx Injection Technology
Regenerative burners have played a significant role in aluminium melting for many years due to their ability to increase production and lower fuel cost. By reclaiming heat from the furnace exhaust gases and using it to preheat the combustion air, regenerative burners reduce the amount of fuel needed to melt the aluminium. Regenerative burners operate in pairs, which can be seen in Fig 1. Burner A begins firing while burner B is extracting hot furnace gases through its regenerator. The heat from the furnace gases is stored in the ceramic regenerative media of burner B, and the gases exit the regenerator at a much cooler temperature than the furnace temperature. The burners then switch operation, and burner B, which was previously exhausting the furnace gases, now operates in firing mode. Cold combustion air enters through the regenerator of burner B and reclaims the stored heat from the media. This process increases combustion efficiency by up to 45% compared to a conventional cold air combustionAlthoughsystem.preheating the combustion air improves efficiency and reduces fuel consumption, it also leads to an increase in NOx emissions. NOx emissions are strongly dependent on temperature, local oxygen concentration, and residence time. In order to mitigate the rise in NOx emissions caused by high combustion air preheat temperatures, regenerative burners can be paired with Low NOx Injection (LNI) technology. With LNI technology, fuel and preheated combustion air are injected separately into the furnace once it’s above the autoignition temperature of the fuel. This is done by using an outboard fuel injector that is independent of the main burner body. This allows the fuel and air to entrain and mix with the furnace gases prior to mixing with each other. The result is flameless oxidation and a high volume, low intensity, low temperature combustion process with low local oxygen concentration. This technology provides an 80 percent decrease in NOx emissions compared to conventional high efficiency burners. (Fig 2)
The Sankey Diagram in Fig 5 shows that available heat is equal to the gross heat input minus all flue gas losses, and it represents the sum of the heat to the load and all other losses. By extracting energy from the exhaust gases and using it to preheat the combustion air or furnace load, heat recovery minimises the amount of gross heat input required, and, therefore, increases the percent available heat to the Regenerativeprocess.burners use heat recovery to provide up to a 45% decrease in fuel consumption and CO2 emissions compared to a cold air, natural gas system. Achieving the same reduction in CO2 emissions without heat recovery would require 72% hydrogen by volume blended with natural gas. Regenerative burners can be relatively easily retrofitted to an existing furnace, and compatibility with LNI ultralow NOx combustion technology means that NOx emissions performance will not be sacrificed for low CO2 emissions. However, if the goal is to eliminate any CO2 emissions from the combustion system, hydrogen will eventually need to be introduced. Regenerative burners with LNI technology conveniently provide solutions to some of the most challenging realities of hydrogen fuels – high cost, fast flame speeds, and high flame temperatures. The most significant benefit of regenerative burners is the reduction in fuel consumption, which results in lower CO2 emissions as well as improved fuel
Aluminium International TodaySeptember/OctoberGREENER2022ALUMINIUM30
hydrocarbon in air: CX Hy+a(O2+3.76N2) xCO2+(y⁄2)H2 0+3.76aN2
Regenerative Burners: Decarbonisation through Heat Recovery and Hydrogen Fuels
From a decarbonisation perspective, heat recovery provides a significant benefit as it simultaneously decreases CO2 emissions and fuel cost by improving process efficiency. Furnace efficiency can be expressed in terms of percent available heat, which represents the best possible furnace efficiency. % Available Heat=100%((available heat)⁄(gross heat input))
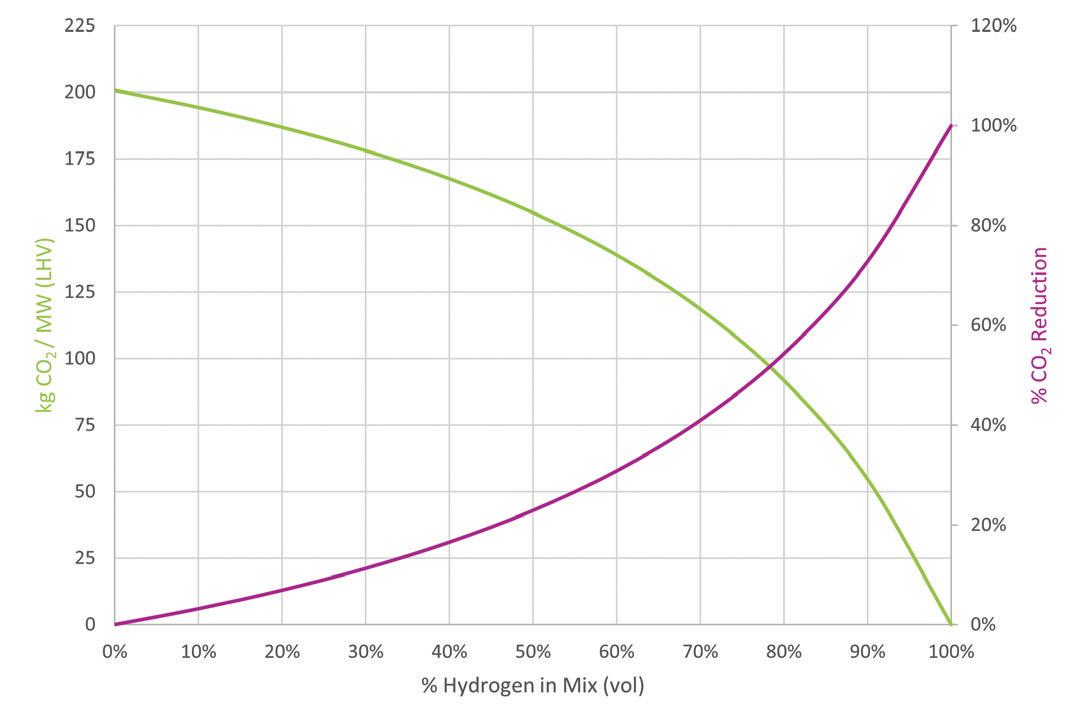
The amount of CO2 produced is directly proportional to the number of carbon atoms in the fuel. Therefore, the amount of CO2 formed in the combustion process depends only on the fuel composition and the amount of fuel consumed by the process. The combustion system CO2 emissions can therefore be reduced by improving efficiency and/or using an alternative fuel with lower carbon content. Process efficiency can be improved through maintenance and operational practices, such as maintaining proper air/fuel ratio, effective furnace pressure control, regularly inspecting and repairing furnace refractory, doors, and seals, and optimising operational practices. Heat recovery can be used to further increase efficiency by reclaiming heat from the exhaust gases and using it for useful heating, either in the same process or in another process within the plant. This can be done by strategically designing the flow of products of combustion within a furnace, diverting flue gases to another process within the plant, or using a heat recovery device, such as regenerative burners.Other than improving process efficiency, the only other means of reducing the CO2 emissions from a combustion system is to use an alternative fuel with lower carbon content, such as hydrogen or hydrogenenriched natural gas. Although hydrogen is a high-quality fuel, firing burners with hydrogen poses several challenges compared to natural gas, including hydrogen’s higher flame temperature and faster flame speed. The flame temperature of hydrogen is 150-200°C hotter than a methane (the main constituent of natural gas) flame across all air/fuel ratios. This implies elevated NOx emissions when firing hydrogen fuels with conventional burners. The flame speed of hydrogen is also significantly faster than methane, especially when operating under rich conditions or with minimal excess air. This fast flame speed means the likelihood of flashback of a premix flame into the burner body greatly increases. Rather than using pure hydrogen as a fuel source, there is also the option of blending hydrogen with natural gas to lower CO2 emissions. For most properties, the impacts of blending hydrogen are nonlinear. For example, Fig 3 shows the flame temperature for different levels of hydrogen blended with natural gas. While there is a near-linear region between 0-30% hydrogen content, the flame temperature rises rapidly as the hydrogen level increases beyond that point. Achieving significant CO2 reduction requires blends that are in the steeper nonlinear regions. As shown in Figure 4, achieving only a 25% CO2 reduction will require 50% hydrogen blended with natural gas and a 50% CO2 reduction will require 76% hydrogen blended with natural gas. (Fig 4) Therefore, a combustion system decarbonisation strategy focused solely on hydrogen fuels can potentially require significant changes to the burner and system design to combat the challenges associated with firing fuels that contain large amounts of hydrogen. The high level of hydrogen content required to achieve significant CO2 reduction, and the design challenges and steep fuel cost associated with hydrogen fuels point to heat recovery with regenerative burners as a logical step on the path towards decarbonisation.
Fig 4. CO2 reduction as a function of hydrogen volume blended with natural gasFig 3. Adiabatic flame temperature for different levels of hydrogen blended in natural gas
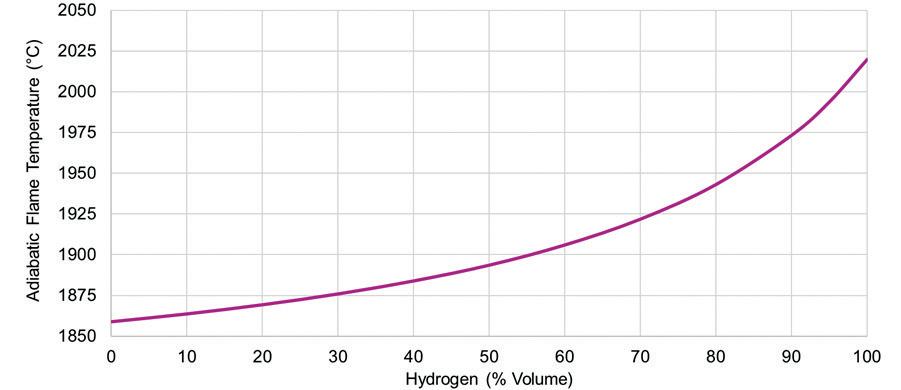
�
Conclusion Reducing the CO2 emissions of aluminium melting furnaces is essential to the decarbonisation of the industry, and it can be done in several steps. The first step is to maximise the efficiency of the existing furnace by improving air/ fuel ratio and furnace pressure control, repairing any damage or degradation, and optimising operating practices. Next, a regenerative combustion system can be retrofitted to an existing furnace to provide up to an additional 45% decrease in CO2 emissions without sourcing any alternative fuels. Finally, the regenerative combustion system can be relatively easily retrofitted for operation with pure hydrogen to eliminate CO2 emissions.
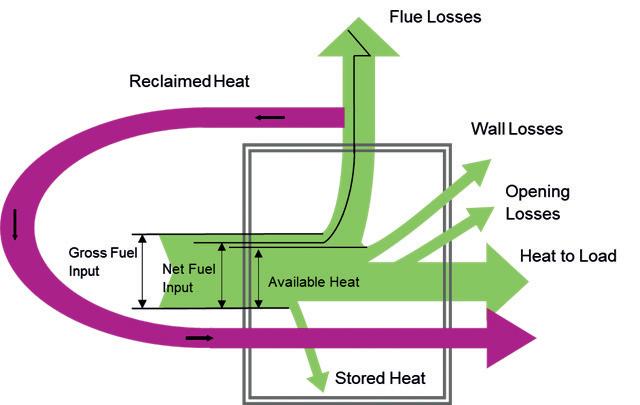
One of the reasons for this result is that burning pure hydrogen eliminates any prompt NOx formation that occurs when burning a nitrogen-containing fuel like natural gas. The absence of prompt NOx, combined with the suppression of peak flame temperatures due to entrainment of the products of combustion, results in a significant overall NOx emissions reduction at typical aluminium melting furnace temperatures. (Fig 7)
A new fuel injector and hydrogen fuel train with the proper materials of construction can be fabricated and installed without any need to change the burners or other system components.
Operating regenerative burners with hydrogen fuel and LNI technology will accomplish decarbonisation goals, while simultaneously minimising NOx emissions and mitigating the increase in operating costs.
Firing pure hydrogen with regenerative burners and LNI technology eliminates CO2 emissions, resolves the flashback concerns of hydrogen fuels, decreases NOx emissions compared to natural gas, and minimises the high cost of hydrogen by maximising combustion efficiency.
GREENER ALUMINIUM 31 Aluminium International Today September/October 2022 costs. Fig 6 compares the cost range of CO2 reduction with hydrogen fuels on a cold air system (pink) and the cost range of CO2 reduction with hydrogen fuels on a regenerative system (grey). With relatively minimal hydrogen blending, regenerative burners can provide a significant decrease in CO2 emissions. For example, a hydrogen blend having a median fuel cost of $100 per MW available to the process would improve CO2 emissions by about 10% for a cold air system but 65% for a regenerative system. Furthermore, as the level of hydrogen in the fuel increases, high efficiency regenerative burners mitigate the progressively high fuel cost. (Fig 6 From) a burner design perspective, one of the most challenging characteristics of hydrogen fuels is the potential for the hydrogen flame to flashback due to the fast flame speed. Flashback occurs when the flame speed exceeds the feed speed of the fuel and combustion air mixture in a premix burner. Because many burners, even nozzle mix burners, operate with some amount of premixing of the air and fuel, careful consideration needs to be taken when evaluating if the burner design is suitable for hydrogen firing. When using LNI technology with a hydrogenfired regenerative burner, the possibility of any flashback is eliminated because the air and fuel are injected separately into the furnace allowing combustion to take place inside the furnace volume, rather than in the burner tile. Furthermore, because LNI relies on entraining the products of combustion into the oxidant stream, it is a solution to manage the high flame temperatures of hydrogen fuels. In fact, lab tests firing pure hydrogen with LNI on a pair of regenerative burners have shown LNI NOx emissions are lower with pure hydrogen than with natural gas. For example, at a furnace temperature of 1150°C, NOx Fig 7. Comparison of LNI NOx emissions with a pair of North American TwinBed™ II regenerative burners operating on natural gas and hydrogen
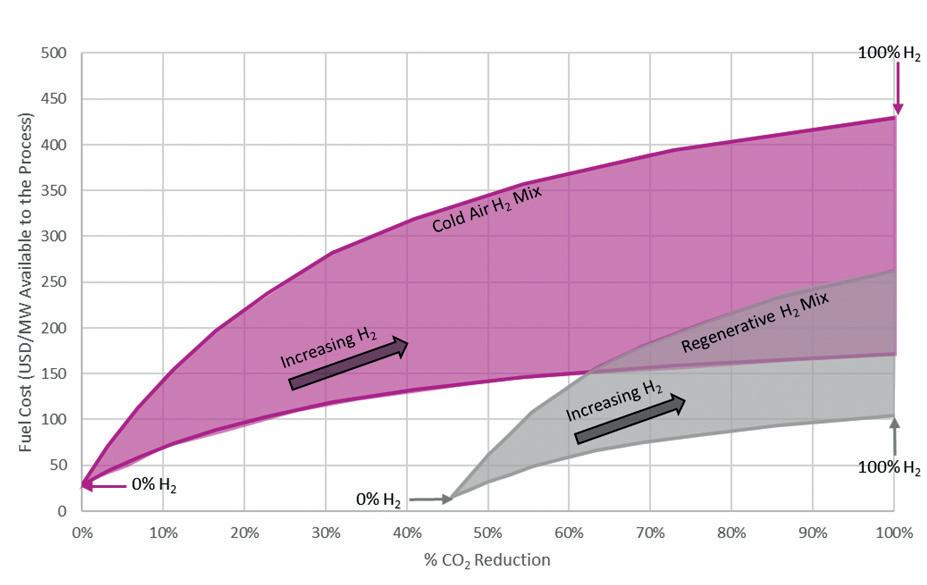
Fig 5. Sankey Diagram showing the heat balance in a furnace Fig 6. Comparison of fuel operating expense with cold air and North American TwinBed™ II regenerative hydrogen-fired combustion systems emissions with natural gas are roughly 0.035 g/MJ whereas NOx emissions with hydrogen are roughly 0.02 g/MJ.
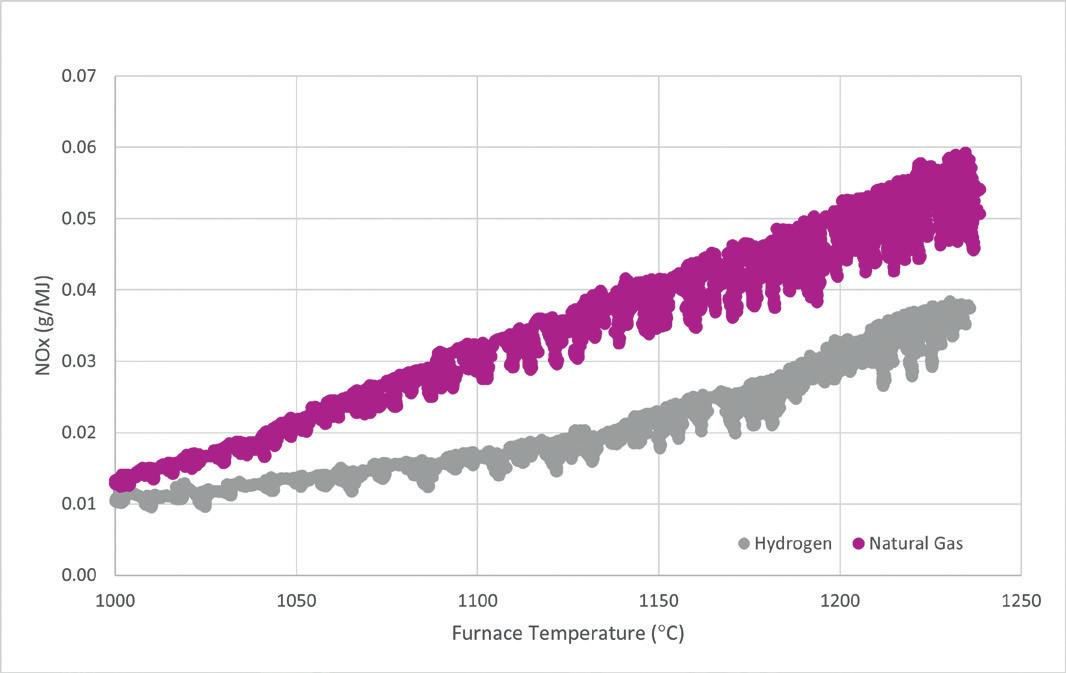
Aluminium International TodaySeptember/October
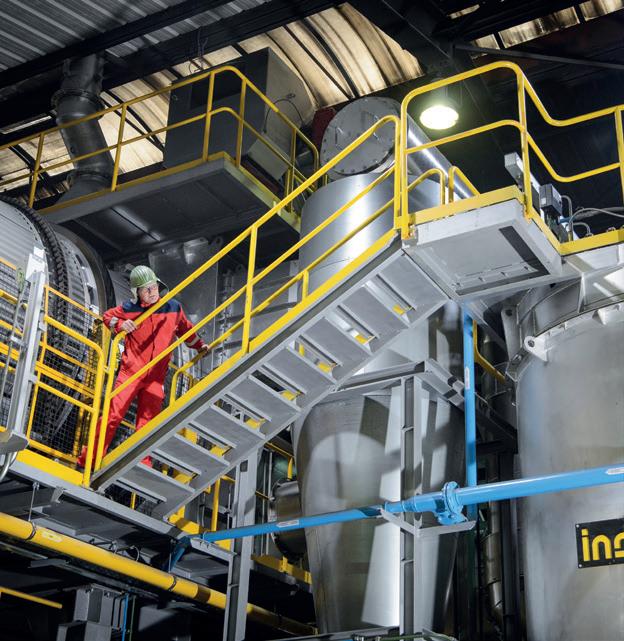
It would be terrific if we could, but the appetite we helped develop is not going to be fed by recycling alone. We need more primary aluminium. Which implies more mining and energy use, and potential harm to the environment. We need more primary capacity because scrap metal is returning to the market too slowly. Predictions by the International Aluminium Institute, CRU Aluminium and others indicate a need for several tens of millions of tonnes of new capacity until 2050.We can look at this as an opportunity to help soften the environmental load, we as an industry. We can look at this new primary aluminium capacity and say that it is going to be built with carbon capture and storage technology, or zerocarbon technology. Getting all the way to zero-carbon, however, also depends on our ability to decarbonise our casthouse operations (through use of green hydrogen, biogas or direct electrification of casthouse furnaces) and in bauxite and alumina. Decarbonising aluminium casthouse operations As aluminium producers – we are not the only one – fight to be first in our race toward zero-emission production, we need to step back for a few minutes and recognise that there are no quick fixes. That this is going to take some time. That all the small steps matter.
GREENER2022ALUMINIUM
Every step matters on the path to zero We call aluminium the metal of the future because product designers are using more aluminium and in new and better ways, and they have been for years. Strong and growing is how we can describe the market pull for our light metal. The future! But from a sustainability perspective, we shouldn’t forget the irony here: That finding new and better ways of using aluminium means we need more aluminium.
In theory, it is easy to just feed your burners with hydrogen rather than natural gas. But in practice, you might need to modify the burners because the flame is different, both in temperature and size. That isn’t all. You also must upgrade the supply and storage of H2 due to safety issues, including your routines for checking gas leakages – H2 is inherently explosive. You need to ensure the same metal quality, too, because moisture or H2 can be absorbed in the metal. And you will need to provide a supply chain for the hydrogen and agree with the customer on accepting the process change and paying for the additional cost. That said, the decarbonisation of our casthouses is very much possible. I just mentioned hydrogen. Hydro is today using natural gas to remelt scrap and ingot. This can be replaced by hydrogen or biogas, or direct electricity for inductiontype furnaces. This is more or less known technology and not hard to abate.
The devil is in the detail. Take our use of hydrogen in the casthouses as an example.
Decarbonising bauxite and alumina operations I work a lot toward more sustainable primary aluminium production, toward our zero-carbon target in Hydro. Decarbonising bauxite and alumina operations should not be forgotten, however, in the bigger picture. In general, the push for decarbonisation *Chief Technology Officer and Head of Corporate Technology Officer Below. Hydro Aluminium Clervaux, in Luxembourg. This is Hydro’s largest recycling plant in Europe in terms of capacity.
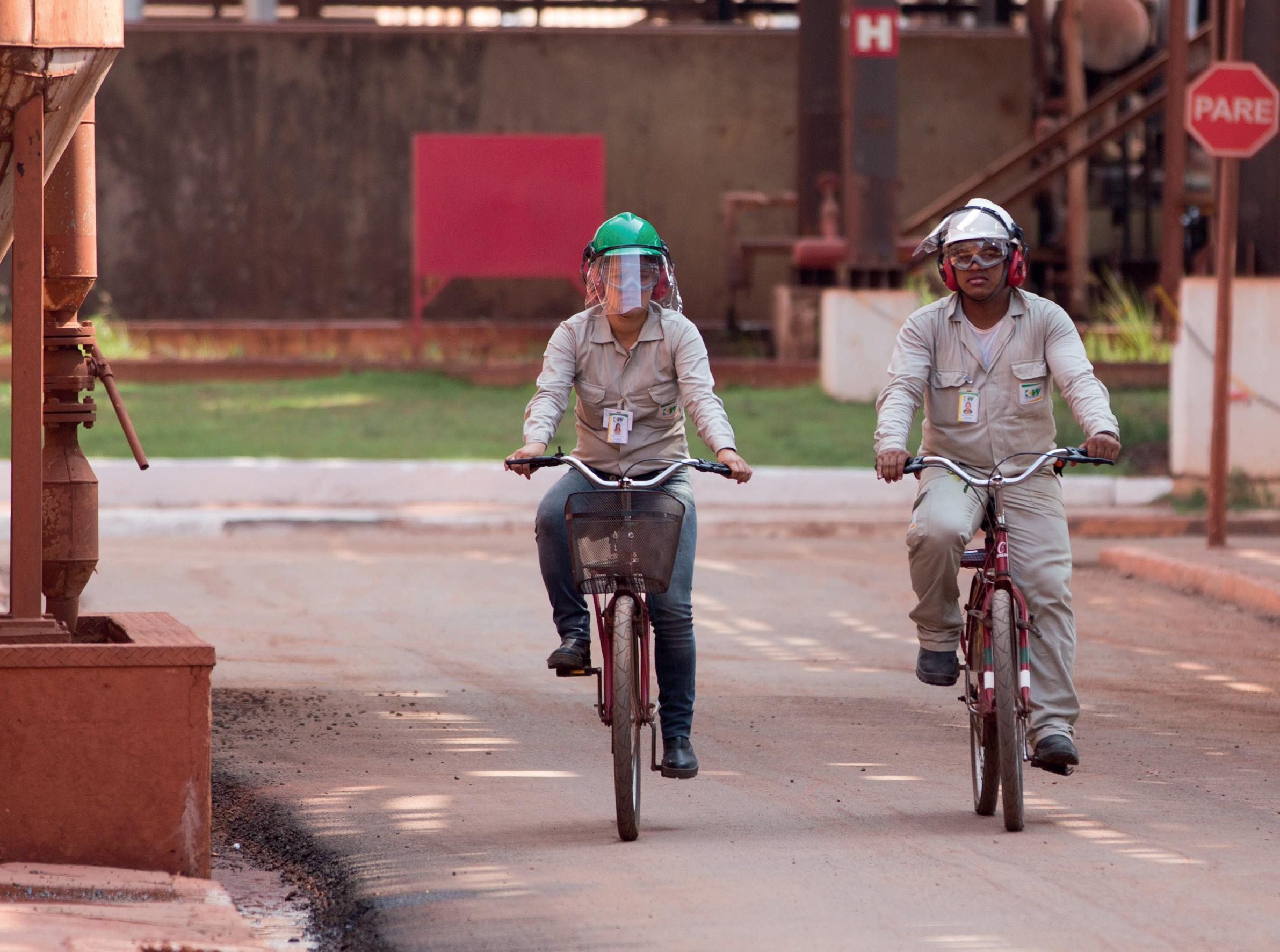
By Hans Erik Vatne*
32
GREENER ALUMINIUM 33 Aluminium International Today September/October 2022 in this area has not had the same intensity as with primary aluminium production, probably due to all the myths and public relations focused on inert anodes. But it is Bauxitecoming. is where our aluminium value chain begins. It is not a mineral but a rock that is composed largely of one or more aluminium hydroxide minerals. Aluminium oxide – or, alumina – is one of its main components, so we refine bauxite to produce the alumina that we need to produce primary aluminium. In 1888, the Bayer process was invented. It is a four-step process – digestion, filtration, precipitation and calcination – for refining bauxite into alumina, and improving this process is where I feel the decarbonisation work should start.
The process goes like this: First, we mix the bauxite either with caustic soda or sodium hydroxide, and then heat this under pressure. The sodium hydroxide dissolves the aluminium oxide and forms sodium aluminate, in solution. The iron oxide and other caustic insoluble impurities are then separated by decantation and filtration. The end result is alumina. Where would we start with decarbonisation? Well, we use a lot of steam in the Bayer process, and this is traditionally made by burning coal. It can be converted to electrical boilers, and is already being done in some cases. In addition, we use coal and heavy oil for calcination while drying the alumina at >1000 degrees Celsius.
The calcination part is harder, but I can see hydrogen as a likely long-term solution while natural gas could be used as an intermediate step in the improvement.
1 2
� Hard-to-abate emissions will require brand new technology and the development of new production processes. These will be either inert anodes (non-carbon anodes that do not actively react with alumina in the cell but catalyze the splitting of alumina into aluminium and oxygen) or Hydro’s own HalZero process, where we first react alumina into aluminium chloride and then do the electrolysis on the aluminium chloride. � China is key because the power used for most of its primary production is coal-based. I will say they are looking more and more into inert anodes and CCS, and this is very positive with regard to decarbonisation. � More collaboration with our industry as well as others is also a key theme. With regard to the latter, Hydro just joined a common EU R&D project where we are actually collaborating with the glass industry on how to use hydrogen in melting processes – for casthouses, not smelters. And CCS is a topic where we are working with external partners and looking to other industries. In the aluminium industry, we are getting better.
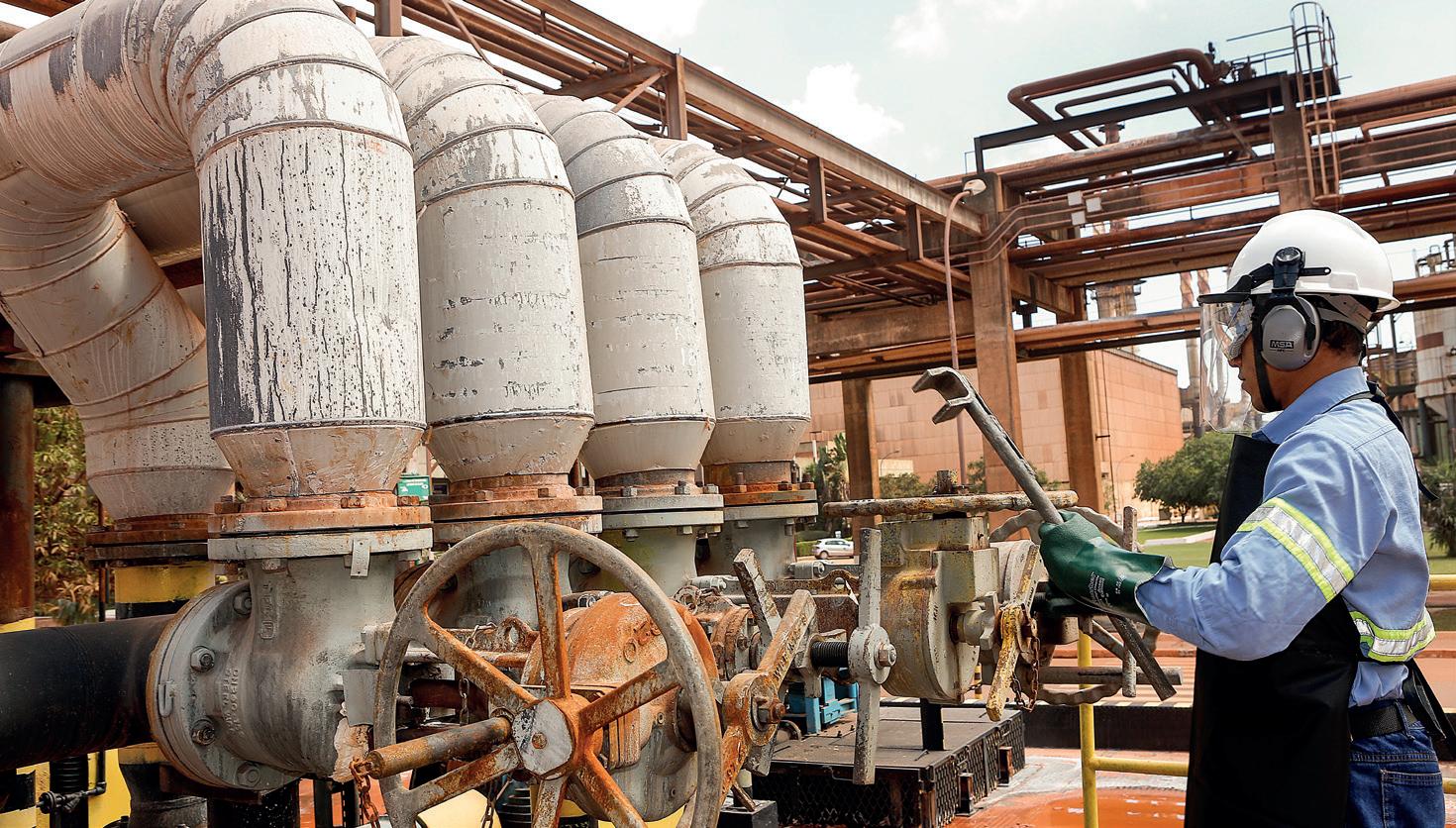
Zero-carbon aluminium is an awesome target, but critical in the perception of aluminium as a sustainable material – in green premiums, our license to operate, our work to create a more viable society.
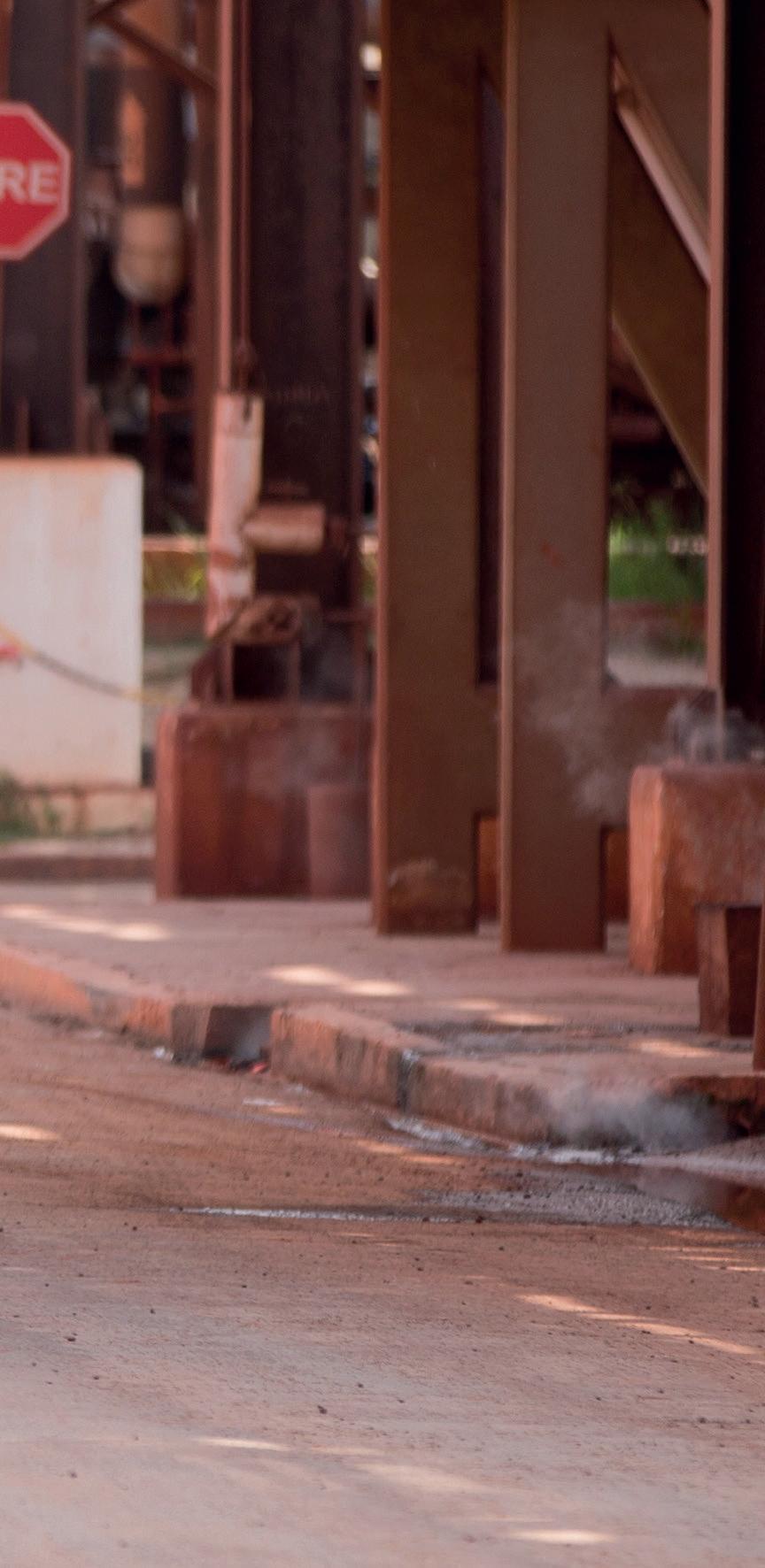
An awesome target
Hydro colleague standing in front of a casting mold in Portland, Oregon, USA
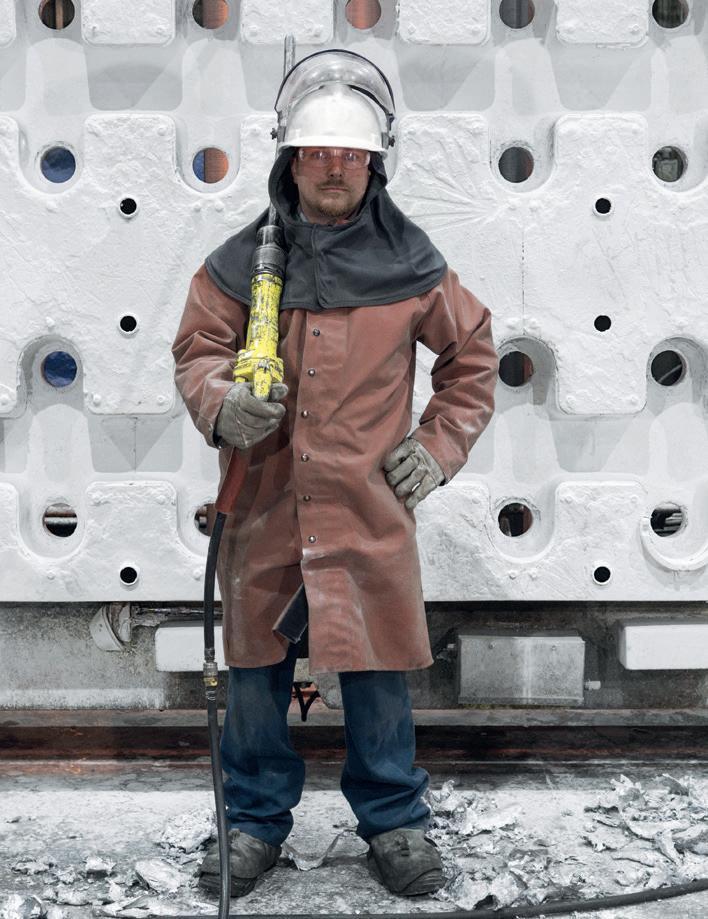
For some metals, such as iron, it is possible to do this by reacting with hydrogen, which produces water as a byproduct in addition to the iron.
Elysis is a good example of collaboration, with Alcoa and Rio Tinto joining forces to commercialise a new smelting process with inert anode technology. And we are in discussions with peers to collaborate on parts of our own roadmap to zero. Collaboration with public and private partners is vital. We usually don’t talk about the costs related to this work, but I once heard the estimate for the whole industry on inert anodes, and it was relatively high. Hydro has said that we plan to spend NOK 2.3 billion on decarbonisation efforts in our upstream business area, through 2026. Then you have to industrialise this work, followed by implementation. But instead of focusing on the costs, I would rather that we emphasise our need for partnerships as we work toward this great, and achievable, goal. We should also not forget that while decarbonisation is probably the most important action our industry is facing to strengthen the competitiveness of aluminium, it is only part of our sustainability ambitions. Sustainability in our industry also means protecting biodiversity and securing our license to operate and making improvements to the communities where we do operate. � Alunorte alumina refinery in Barcarena, Brazil. Erik Vatne

More collaboration on steps to zero Several major themes related to decarbonisation bear repeating.
1 and 2. Hydro
Hans
And in our competition with other materials, some of which have an easier way to decarbonisation than we do. Metals in their natural condition bound to oxygen, as aluminium in alumina and iron in iron oxide. We need to split this compound, most commonly by reacting the oxygen with carbon to produce carbon dioxide and the free metal.
The world is moving more and more towards the path of sustainability and energy saving. Need made more urgent after the increase in raw materials and energy bills. Turla rfk has been working hard focused on solutions to apply on its machinery that are voted as much as possible towards energy saving and sustainability. Thanks to research and development, it has achieved cuttingedge results, The new heaters proposal is a shining example of this effort. The new oven will offer the possibility to boost production and to dramatically reduce the emission thanks to its incredible efficiency. Particular attention has been done on how the fumes are managed and re-used and thanks to the new electronic devices applied on the different zones controls. STEP, The name acronym as our furnaces are worldly know “Super Thermal Efficiency aimed for Production” have now reach a new higher level, meeting the word, planet symbol, GREEN The environmental friendly heater match the last requirement in terms of pollutions and care of the future of the planet. There are many financial subsidies available for the replacement of old heating systems with new modern systems that are more attentive and respectful of the environment. The Heaters require furthermore low maintenance costs in terms of labour, parts, production stops to carry out maintenance procedures etc... The new range of Heaters provide a real time production optimisation. Most of the heaters today in the market, or we can say all of them, are controllable through temperature setting, not via its real power, that is, its amount of gas in each zone of the heater, The New STEP_GREEN is fully controllable.Theheater is extremely simple and easy to be used. It provides you with the highest possible hourly production: thanks to its outstanding efficiency, the heater is shorter or produces more tons per hour if compared to any other log heaters today. To require the lowest operating costs on the market means that not just the gas consumption is very little, but that spare parts costs much less, maintenance operations have to be carried out less frequently and quickness, with the best interface with the whole production system and with the best connection with press requirements and so on.
4. smoke extraction chimney: New Special Type of extraction fan. The furnace is very robust and can be accessed easily for maintenance. Each zone of the oven can be opened (unless still hot) within 5 minutes! The insulation inside the furnace is made so that 90% of the furnace can be touched without hazard risk. The oven is engineered so that maintenance operations are very limited to the control of the thermocouple pins sharpness and their cables regular replacement, in other words the furnace is engineered to dramatically reduce the necessity to open the log heater for inspection.Thelast heaters produced have the possibility to extract each roller singolary to make an inspection without open the furnace, just simply sliding the roller out from the side.
The fundamental bases in the new Heaters range are: 1. insert to divide the air flow: from the first insert with machined plates, rollers, and air coupling, we moved on to a very simple small separator that limits the contact of the billet with the containment plates.
3. modification of heating heads: The new burner heads have a swirl effect which allows a better heating uniformity and avoids localized functions (hot spots) on the billet.
Like all modern systems respectful for the environment, such as hybrid cars, alternate energies etc. also this Turla furnace STeP_GREEN model can be driven in two modes:
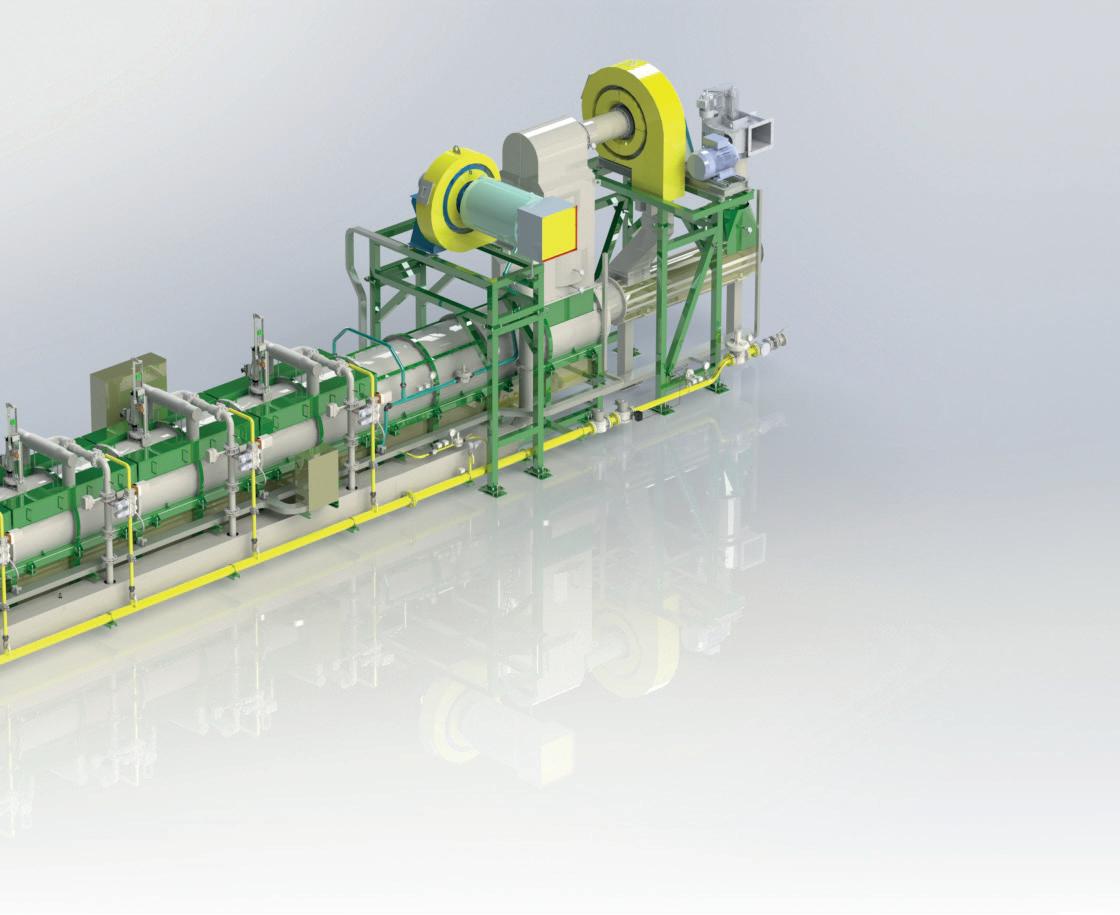
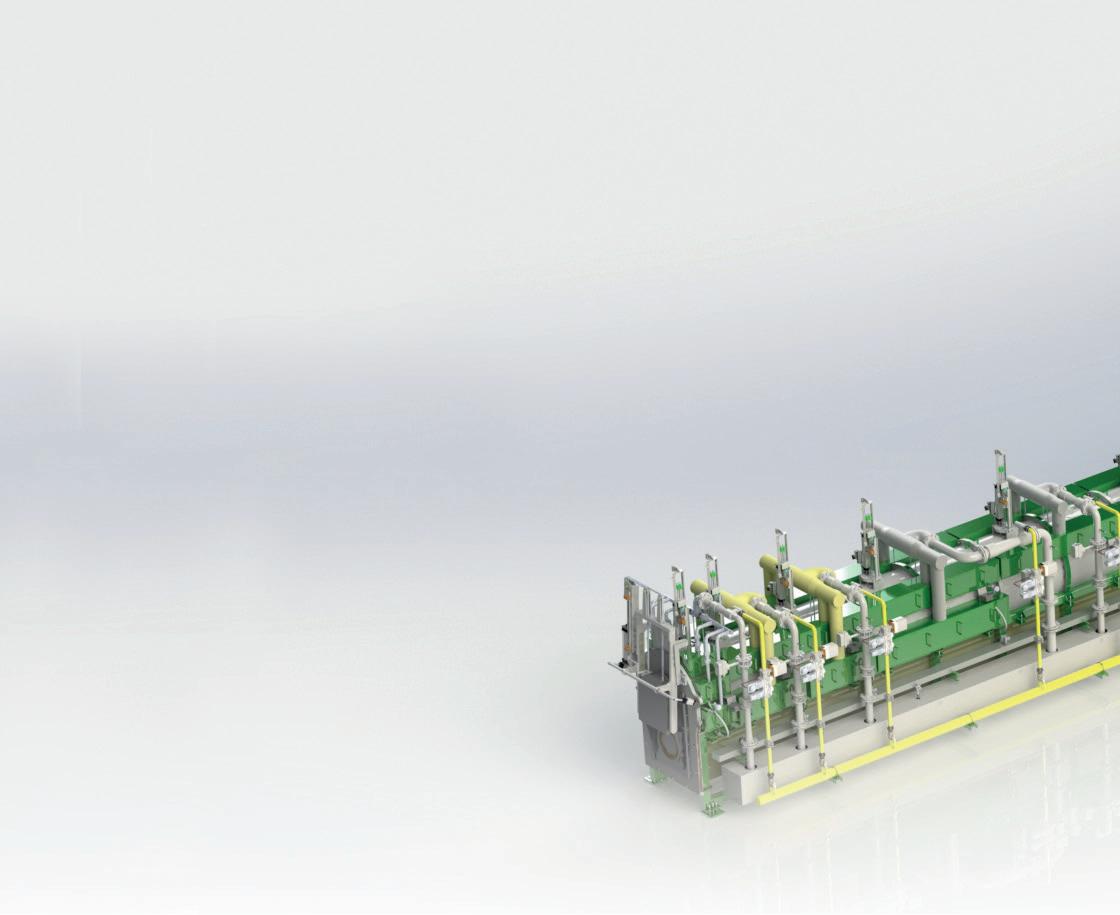
Green sustainability:
Particular attention in the design also for maintenance, upper and laterals walkways where maintenance workers can work safely and with the right spaces, thermocopies with double cylinders to be replaced in the shortest possible time and special transparent to infrared and visible for thermographic inspection inside electrical boxes where all the electronic devices for each area are supplied, to be able to easily identify and quickly test or replace them.
2. conical at the furnace outlet: from the conical made of sheet metal, normalized etc, we have passed to a conical in masonry by installing swirl effect burner heads.
1. Energy saving MODE: the operator can decide to set an upper limit to the oven consumption. The oven will automatically run at a given rate but will never exceed the consumption limit set by the operator. A warning signal will inform the operator that the required production cannot be reached if, before that, the maximum consumption limit is reached. The operator can also see in REAL TIME the gas consumption PER EACH ZONE of the oven and, in full environmental responsibility, he can chose to give more or less power to each zone, therefore affecting and influencing the behavior and consumption of the oven in each condition he would like this to happen.
Aluminium International TodaySeptember/OctoberGREENER2022ALUMINIUM34
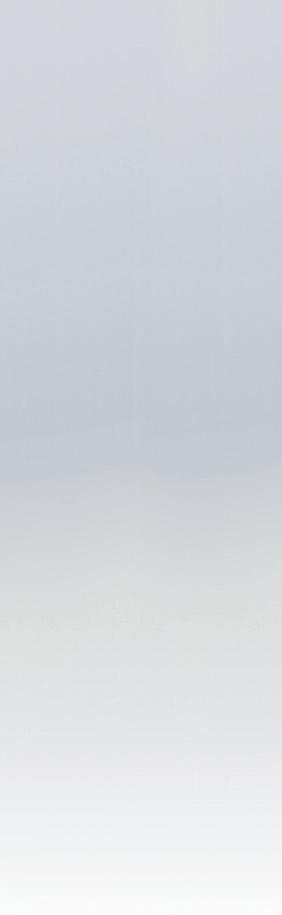
2. Full production MODE: This machine is engineered to deliver the maximum throughput the customer purchased the furnace for. The consumption, compared to other furnaces on the market remains incredibly lower but, the system, in this mode, will take care of delivering just the required amount of tons per hour. �
The Turla RFK’s new heaters range
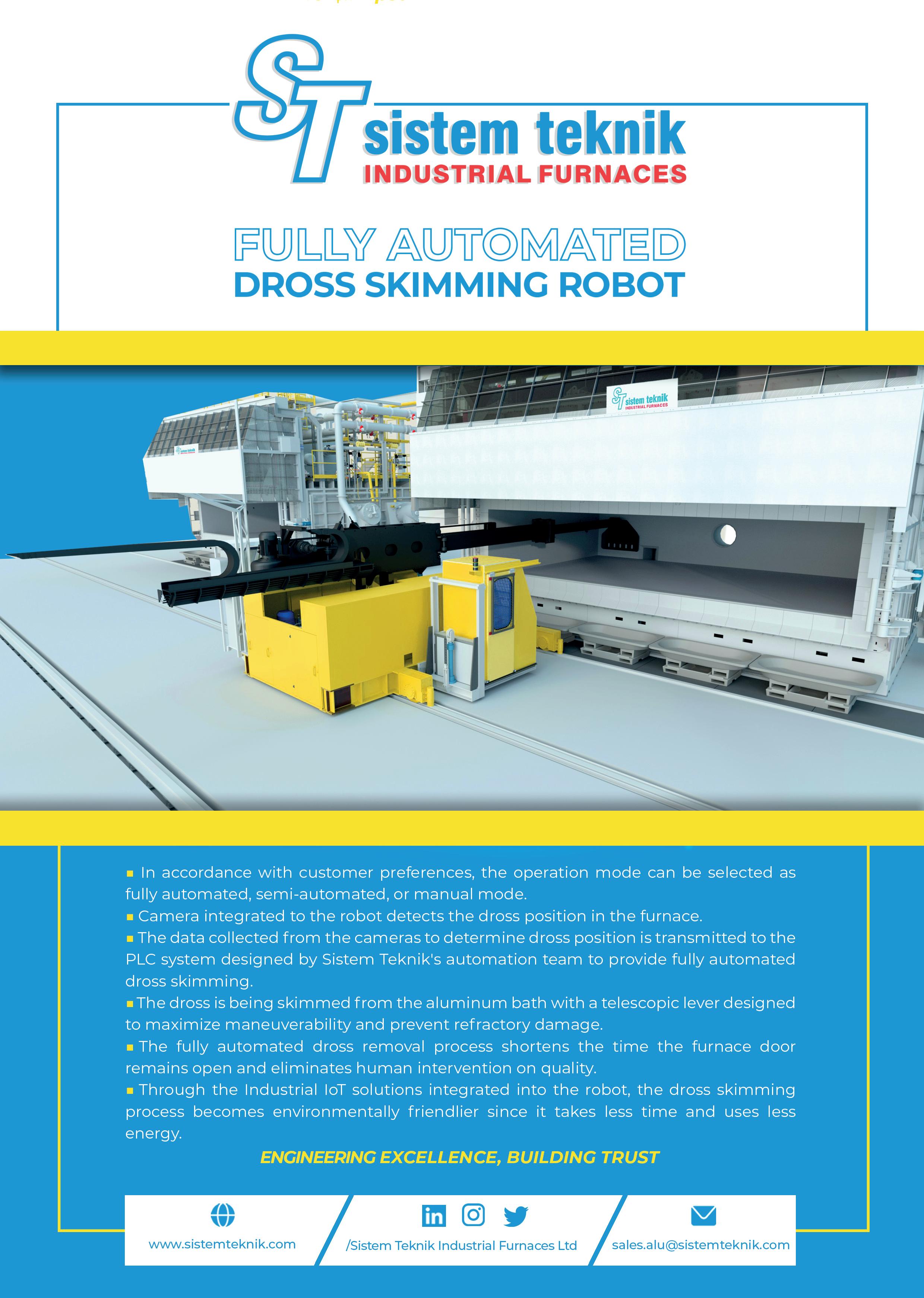
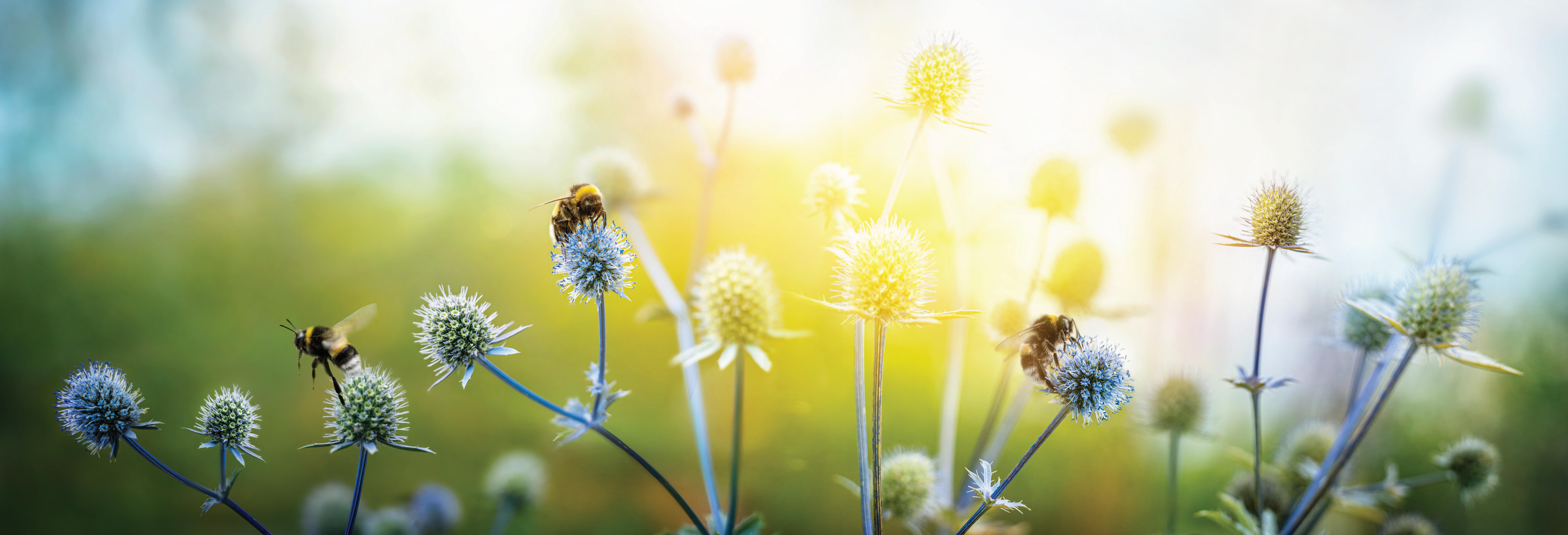
Alutrade, the UK’s largest independent aluminum recycling company and extrusion specialists was the first company to trial the new X-TRACT and could reach purity levels in aluminum sorting of up to 99%.
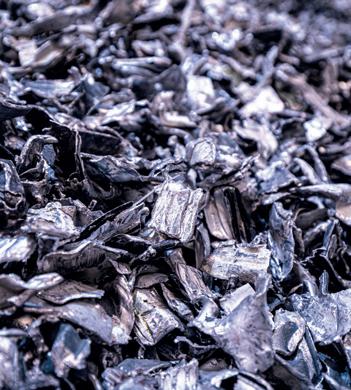
Enhanced Capability and Flexibility
TOMRA Recycling launches new generation X-TRACT
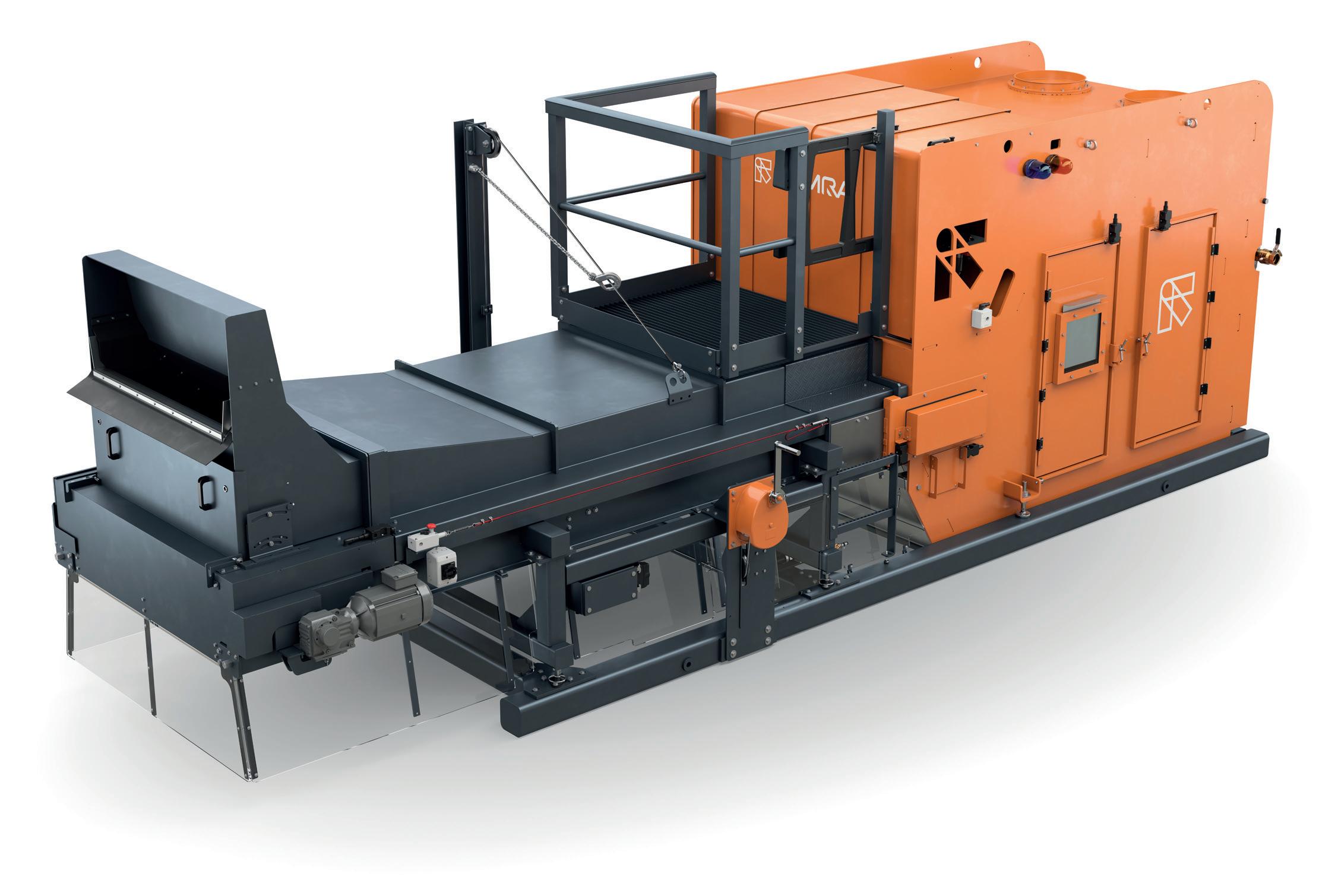
RECYCLING 37 Aluminium International Today September/October 2022
Faster, more precise detection Offering groundbreaking innovations and high-speed sorting capability, the new X-TRACT features Dual Processing Technology, which increases the capacity per meter width. Its simultaneous single object and area processing allows operators to choose between high purity and high recovery sorting. Even adjacent, overlapping, and composite materials can be instantly identified and separated using data-driven decision making. The highthroughput sorting system features a nextgeneration DUOLINE XRT sensor with two independent line scans positioned close to the input material for high precision detection and faster processing. Due to its close proximity to the material, the sensor also effectively detects copper wires and ultra-thin objects to reduce material loss and maximize profits. Its new x-ray source offers variable power with up to 1000w supply for high-throughput processing of multiple applications and grain sizes, from large fractions to fines (>5mm).
The new generation X-TRACT is now capable of sorting with higher belt speeds ranging from 2.3 - 3.8 m/s, to maximize throughput and yields at the same time. To accommodate the faster belt speeds and higher throughput, TOMRA designers extended the sorting chamber and added new extraction ports to remove dust and reduce air turbulence. With improved image capturing, the new X-TRACT delivers unrivaled sorting accuracy and its new intensity scale feature measures the relative thickness of objects. This eliminates the need for additional sensors and improves the detection of specific material groups like printed circuit boards.While the previous generation of XRT metal sorting systems from TOMRA offered models that varied by application, the new X-TRACT is based on a modular machine concept. This gives operators the choice between high resolution or high sensitivity sensor systems and different valve blocks, but also enables more operational flexibility and easy upgrades to minimize long-term capital expenditures. Machine trials in a production environment produce 10-30mm sized aluminum fractions with 99% purity levels.
For more than 15 years, TOMRA Recycling has been a global leader in the advancement of aluminum recycling and processing. Only recently, TOMRA Recycling introduced the next generation of X-TRACT with a new design and breakthrough innovations. New X-TRACT’s enhanced capabilities and machine intelligence offer major advancements in the high-throughput sorting of complex mixed metal streams to produce high purity, furnace-ready aluminum fractions. With a multitude of brand-new and enhanced features, the next generation X-TRACT sets the stage for accelerating the production of circular metals as the industrial sector moves toward a lowcarbon future.
New X-TRACT is also enabled for cloud-based monitoring, data-driven optimization tools, and remote access with the add-on TOMRA Insight service. With the ability to connect to the machine through online monitoring and digital services, TOMRA’s service team can identify potential issues before they arise and provide remote support to ensure low downtimes. �
Manage your aluminum more safely and more productively using less space with Combilift’s materials handling solutions combilift.com • Safer product handling • Optimised production space • Improved storage capacity • Increased productivity & output • Enhanced profits Safety Storage Efficiency A. Today Liz A5 May 2022.indd 1 22/04/2022 10:34:49
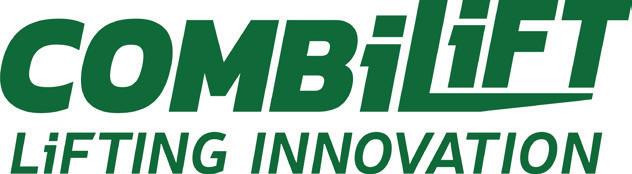
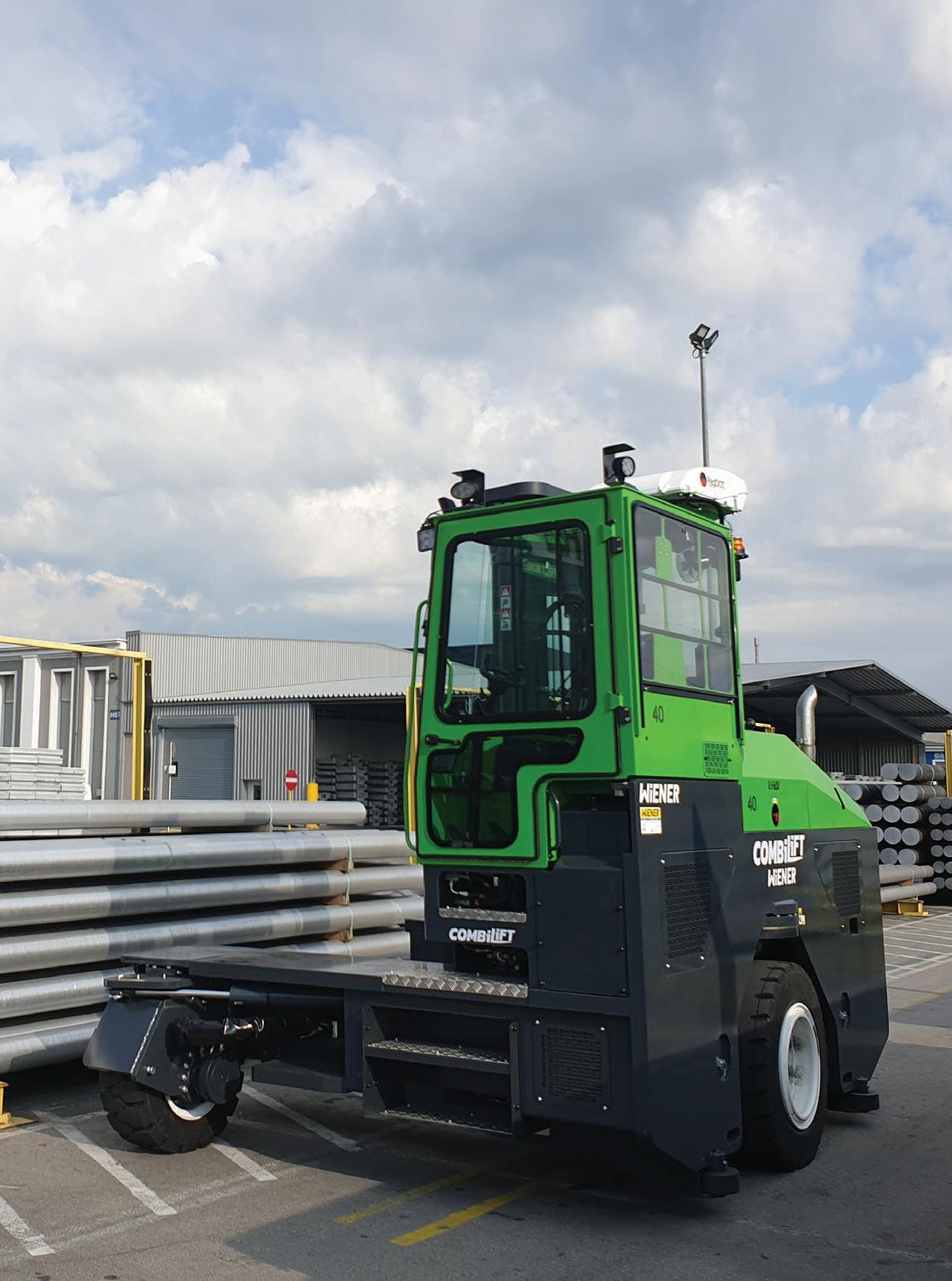
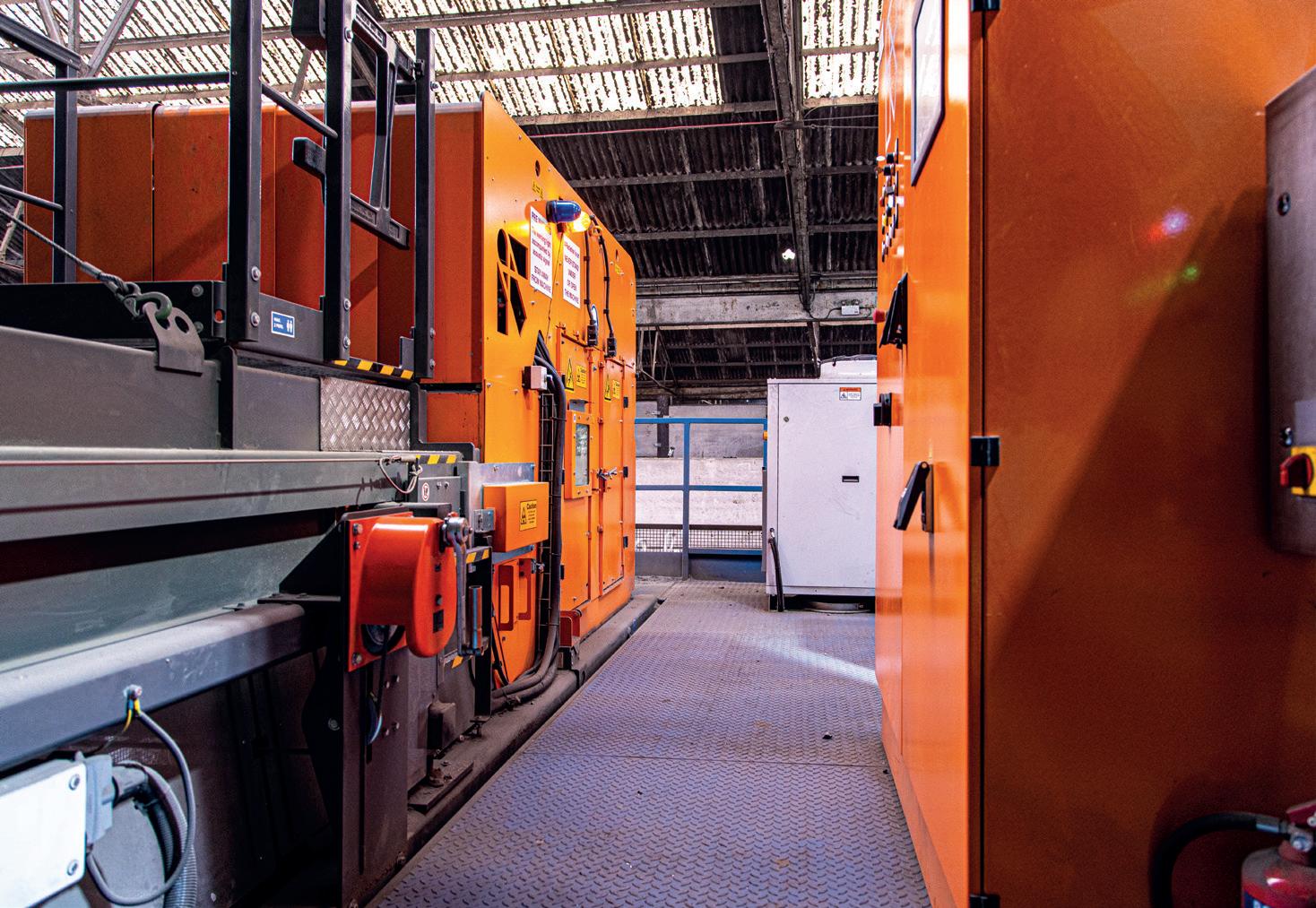
Designed with the Future in Mind The proven and robust design of X-TRACT has long convinced the most prominent industry players worldwide. Developing a new machine to meet the future needs of the industry involved collaboration with customers, design engineers, aluminum processing experts, metal application specialists, and service teams. To extend the lifetime of the machine, the designers added enhanced sensor shielding in addition to its top-mounted x-ray source to protect its most valuable components and provide extra stability. The new sorting system that separates aluminum from heavy metals and super lights in a single step even comes with a 4-Year extended warranty on the x-ray source and XRT sensor to consistently meet high-performance standards and service levels.
Aluminium International TodaySeptember/OctoberRECYCLING202238


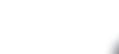
For more details about X-TRACT and highlights from the machine trials, please visit: www.tomra.com/xtract
Terence Keyworth, Segment Manager Metals at TOMRA Recycling emphasized: “New X-TRACT gives recyclers and smelters opportunities to increase their revenues with high-purity aluminum fractions while lowering their carbon footprint and having enough material on hand to meet the market demand. The automotive and construction sectors rely on recycled aluminum to lower their carbon footprint – it’s a matter of being fast enough to supply the surging demand.”
Tom Jansen, Segment Manager Metals at TOMRA, explained: “Our partners in the aluminum industry rely on the lowest downtimes and long-term performance. X-TRACT’s new design makes it faster and safer for plant operators to replace parts due to normal wear and tear with as little downtime as possible.” The machine’s new catcher hood allows for easier access for maintenance, whether performed by a service team or on-site staff that has been trained by TOMRA.
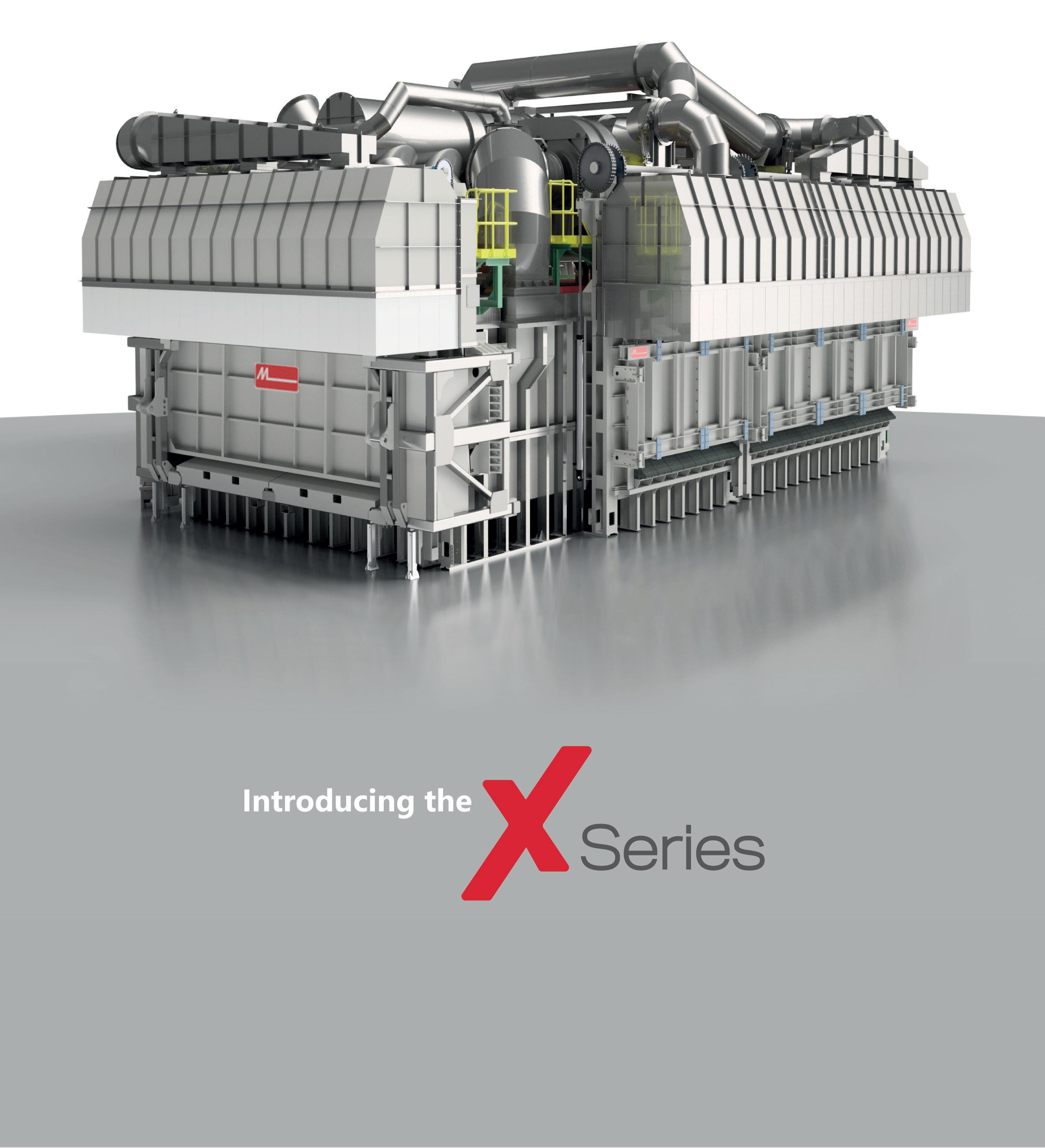


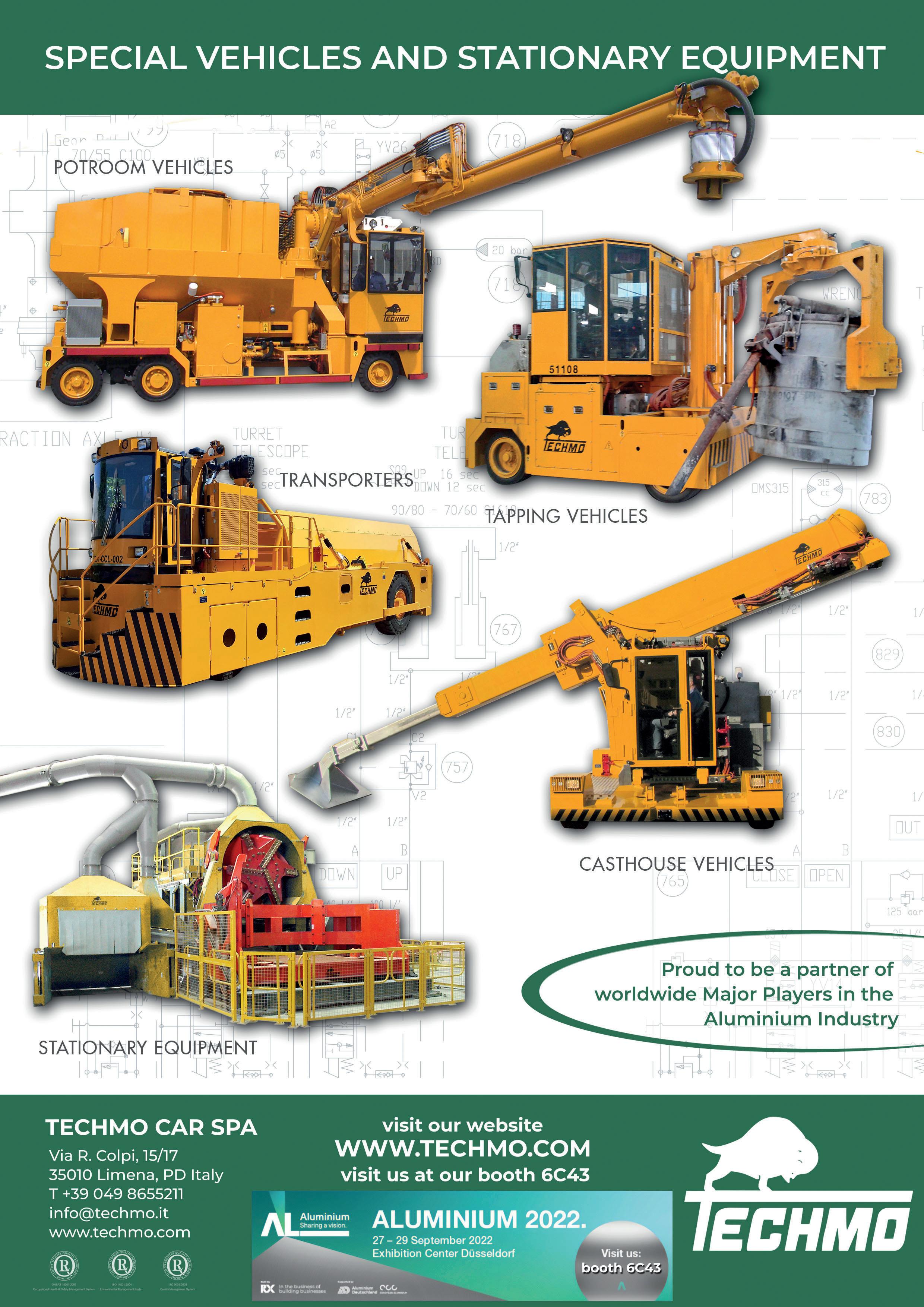
As consumers become more aware of the benefits of recycling their aluminium coffee capsules and there are new variations added into the market, the demand and need for recycling will only continue to grow. To meet this everincreasing demand Tandom can run the equipment on extended shifts explains Mike.
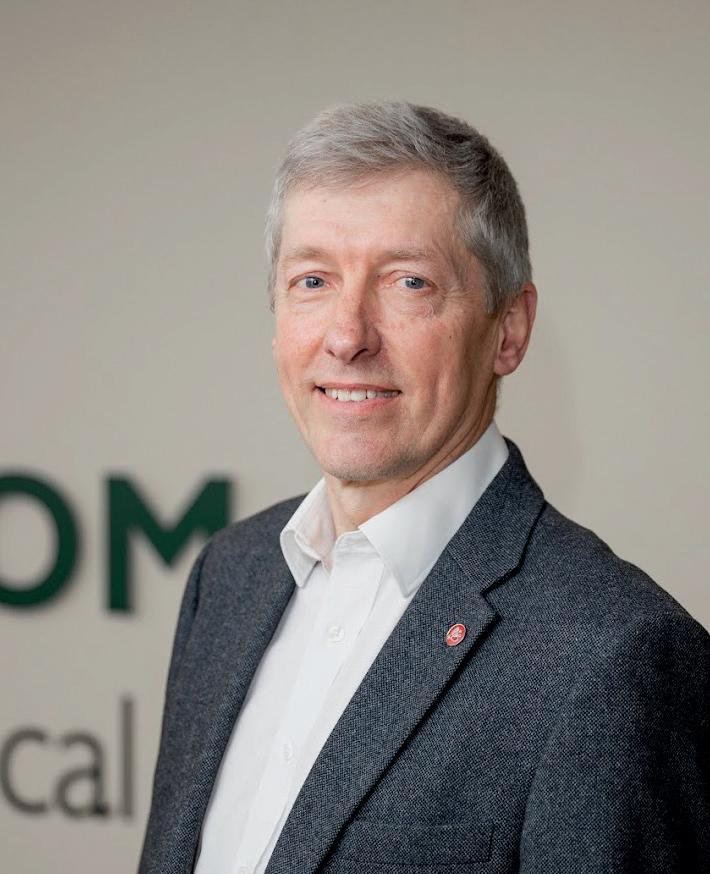
Coffee Capsule Processing
One of the main reasons Aluminium International Today was recently invited to visit the Congleton facility was to see the coffee capsule processing system in action! This relatively new system has developed significantly since it was introduced in 2020 and with the support and help of organisations such as Alupro, Nespresso and more recently the launch of the Podback scheme, Tandom has seen huge growth in the number of aluminium capsules now being processed daily.
“It’s a great success story,” continues Mike. “The sales of coffee capsules are predicted to be going up and up, so we need recycling schemes in place to support this. Tandom has been engaged from the very beginning and we were willing to try and find a solution. It’s not always been easy, with several trials and painful procedures along the way, but it’s great to be part of this collaboration and success story.”
Industry challenges
“We have a number of key targets including zero landfill and year on year
As with all manufacturers, Tandom has had to face a number of challenges over the years, but more recently, the rising energy costs and salt slag recycling capabilities have led to necessary operational changes and monitoring systems being implemented.
RECYCLING 41 Aluminium International Today September/October 2022
The initial idea for this scheme started back in 2008, with engagement from Nespresso and Alupro following the bad press that aluminium coffee capsules were receiving from the media and the genuine desire from Nespresso to have a recyclable product.
“In the early days it began as a very labour-intensive process, with the bags having to be cut open by hand and the capsules loaded into the shredder before separation would take place with the coffee going one way and aluminium the other before being melted in the furnace.
*Editor, Aluminium International Today **Director, Tandom Metallurgical Group & President, ALFED Mike Dines
Wake up and smell the coffee capsule recycling
“As time went on, we started to see the tonnage growing and the Pilot scheme was such a success that we decided we needed to automate the process and in 2020, we installed bespoke equipment that can take the bagged capsules and separate out all the individual components of Aluminium, Coffee and Plastic.
With sustainability efforts high on the agenda for the aluminium industry and consumers, Tandom Metallurgical Group is leading the way with new recycling processing technologies. Nadine Bloxsome* recently visited the company’s Congleton, UK, site to see these processes first-hand and speak with Mike Dines** about the challenges currently facing the recycling sector. Tandom Metallurgical Group (Tandom) was formed in November 2008, bringing together AL Resources Ltd and Integrali Ltd. In 2009, Tandom acquired the assets and premises of FE Mottram Ltd, one of the largest aluminium ingot producers in the UK. From there, the company grew and this financial year will report a turnover of approximately £140 Million, up from £20 Million in 2010. Significant investment was also made into the Congleton, UK site in 2013/14, with the purchasing of new furnaces and pollution handling systems. Today, the company offers a whole range of processes for aluminium, nonferrous metals, stainless steel, and ferrous scraps from two sites within the UK. It is responsible for processing scrap metals from a wide range of industries including aerospace, automotive, building and food; handling materials as diverse as coffee capsules, used beverage cans, drosses, turnings and cuttings.
“There was coverage on the TV including The One Show at the time, which led to the handling of aluminium coffee capsules receiving criticism, as the belief was that the majority of capsules were ending up in landfill,” says Mike Dines, Director, Tandom.“Webecame involved very early on because we had already had the equipment on site that could process and handle the capsules they were generating, it started out as a Pilot Study to see how well we could separate out the coffee from the capsule and to understand the challenges that it posed. We certainly didn’t expect the tonnages we are seeing today that has been as a result of the successful scheme that Nespresso introduced; this growth continues with the development and introduction of the Podback scheme.
“We are also a very diverse business and work with scrap, trading, and aluminium melting. While this is all recycled material, it still consumes a large amount of energy, so we have recently had a Carbon Trust survey carried out to challenge parts of our business and look at how we can be more efficient, how we use energy and whether we could improve our furnaces and general operational procedures. It has also encouraged us to look at renewable energy and whether solar panels would be beneficial plus any energy saving technologies from simple things such as LED lighting to the more difficult heat recovery systems. The first part that we had to do was to fully understand where we consumed our energy and as such, we have introduced live time monitoring of all our“Everyequipment.piece of equipment now has live, real-time data that’s gathered from it, so we can drill down into each component and see things like which motor is consuming the most energy on the shredding line. This is the first part of our sustainability drive; to understand where we use it and where we can look to reduce our consumption, either doing more with the same or doing the same with less.”
Aluminium International TodaySeptember/OctoberRECYCLING202242 energy improvement targets.” says Mike. “As a recycler, we are already sustainable, but it is our goal to now look at other solutions to make sure we are doing as much as we can to deal with industry issues as well as those that we have internally.”
� 2012 Tandom Metallurgical (Midlands) Ltd opens � 2013 Master alloys section developed � 2014 Rotary furnace and filter plant operational � 2015 Induction furnace and Filter plant commissioned � 2016 Midlands operation moves to larger yard in Brownhills � 2017 Dross processing facility commissioned � 2018 Construction of new yard at Congleton � 2019 UBC Recycling yard opens � 2020 Automatic Coffee Capsule processing installed � 2022 New shredding line installed
Tackling salt slag It’s not just rising energy prices that are creating challenges for the industry, there is also a significant need to successfully process a growing amount of salt slag. “The salt slag we produce has always been dealt with effectively, but unfortunately, due to a fire at one of the main processing plants in Germany, there are now restrictions on processing volumes across Europe and this is putting a big pressure on the whole of the industry,” says Mike. “Everyone is looking at how we can manage this situation.”
As new data continues to feed into the model, machine learning technology also improves its predictions over time. “We wanted to find a solution that would enable us to achieve greater efficiencies, while also making sure that we could achieve as high a yield as possible,” says Mike. “Working closely with Air Products, we collected a substantial amount of base data before the 4.0 technology was added to the furnace, this then demonstrated the benefit and impact of the digital twin. We were really pleased with the result, as it not only improved our yield, but also reduced our energy usage too - reducing carbon emissions by 15 per cent and achieving the same amount in energy savings.”
“Whether the UK will see a player come into the market to build a salt plant, we don’t know, but we are also looking at how to tackle the issue further upstream, with better melting technologies in the rotary furnace and producing less salt slag at this stage of the process. “We invested a couple of years ago in a mill that removes non-aluminium parts prior to melting so we are experimenting with whether we can mill more and reduce the volumes of material that actually go into the furnace with the result of less salt slag being generated. It’s a huge challenge for the industry but one that Tandom is facing head on.”
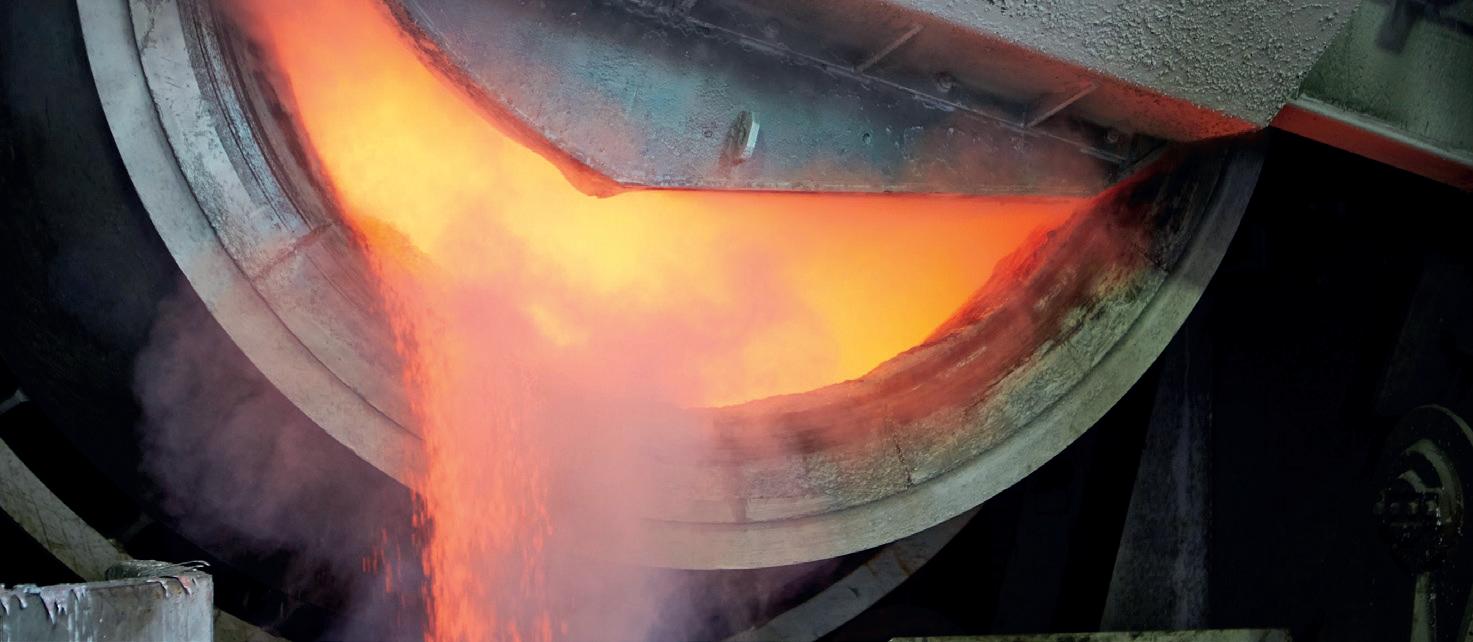
� 2008 Formed - Bringing together AL Resources Ltd and Integrali Ltd under one trading name.
Futureproofing Going forward, it looks very likely that there will be more effort made towards partnerships and activities linked to sustainability; and it is clear that Tandom’s willingness to engage with the industry and explore new methods will keep the business at the forefront of theseWhiledevelopments.itisanoptimistic time for futureproofing and investing in new technologies, there are substantial challenges on the horizon that could affect not only this business, but the UK aluminium industry and supply chains in general. �
One specific area in which Tandom has explored new technology is by teaming up with industrial gas company, Air Products, in creating a digital twin of the remelting process.In2020, Tandom embarked on a 10-month study with Air Products to explore how the introduction of smart technology, such as equipment sensors and associated analytics, could generate data, which could be used to boost efficiency and productivity. The digital twin model of the equipment or melting process uses data to determine the efficiency of the melting process, calculating exactly when the metal inside has reached optimal melt conditions. Real-time closed or open-loop feedback is provided to operators, either automatically shutting down the burner or alerting them that the metal has reached the required temperature for tapping.
� 2009 Tandom purchased the assets of FE Mottram (NF) Ltd.
� 2010 Ingot production commences. � 2011 Tandom purchased the land and buildings of FEM (NF) Ltd
“A big challenge we are focusing on is residual plastics within aluminium packaging and how to separate this. There are technologies out there that can assist with this, such as Microwave Pyrolysis, so this is one aspect we are looking at.
Digital Twin Technology
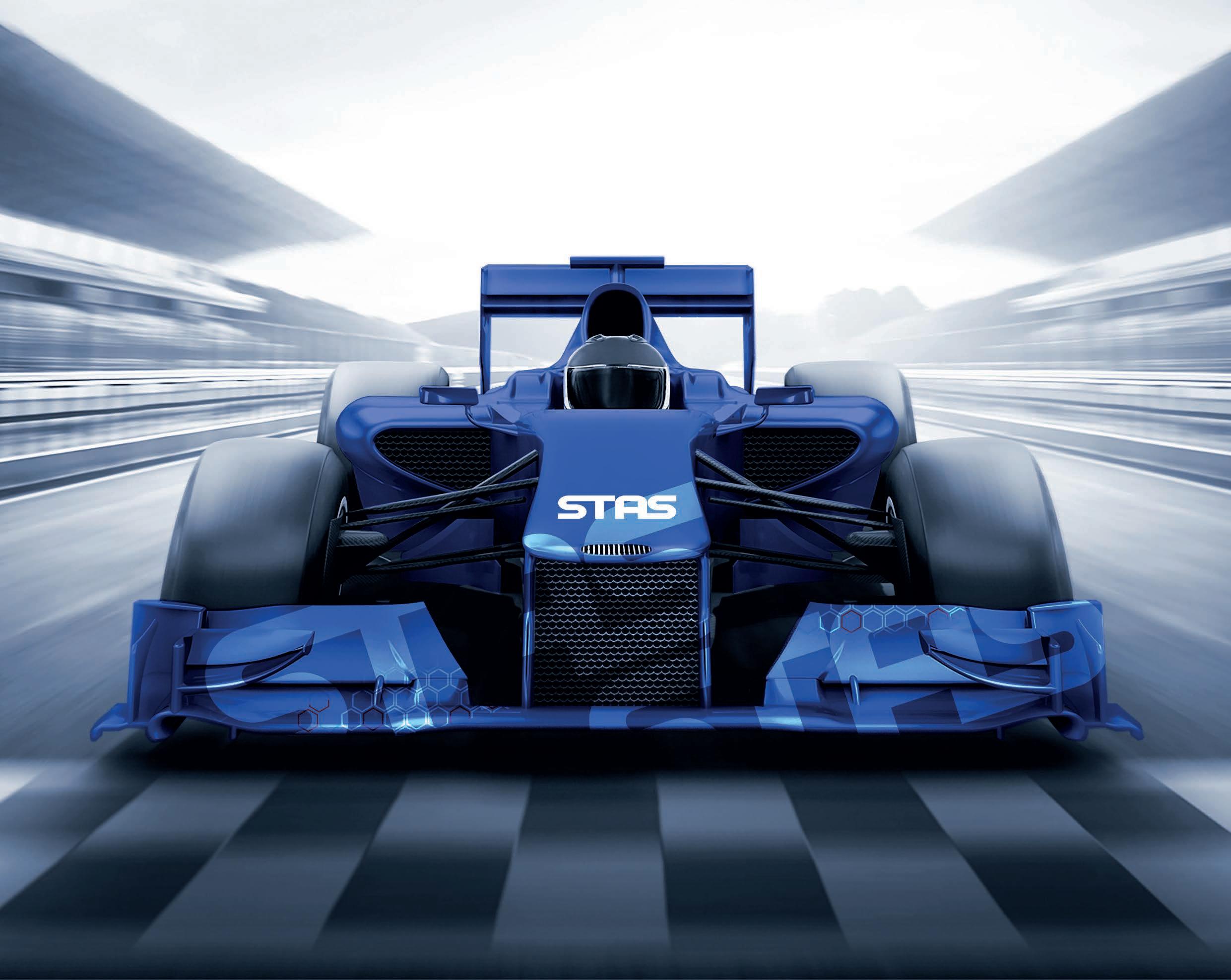

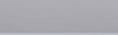
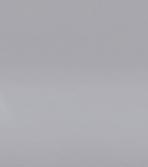


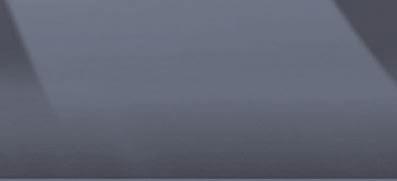
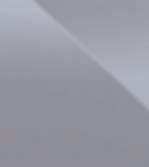

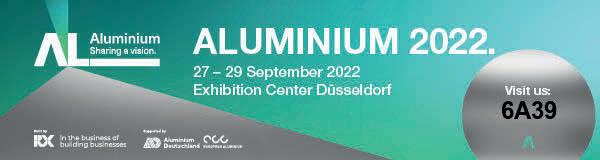
Sarclad UK sales@sarclad.com sarclad.com World leading technology solutions for Aluminium rolling mills Roll inspection Roll texturingsurface World leader in EDT texturing of rolls for strip supply into the highest grades of exposed automotive and white goods Surfaceapplications.andcoreroll defect detection for aluminium and steel rolling mills, utilising eddy current, compression and creep wave technologies. Sarclad North America sales@sarcladna.com Sarclad China sales.china@sarclad.com Sarclad India sarclad.india@sarclad.com

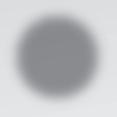

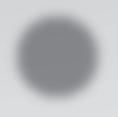

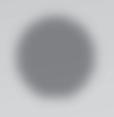

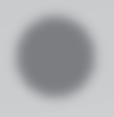
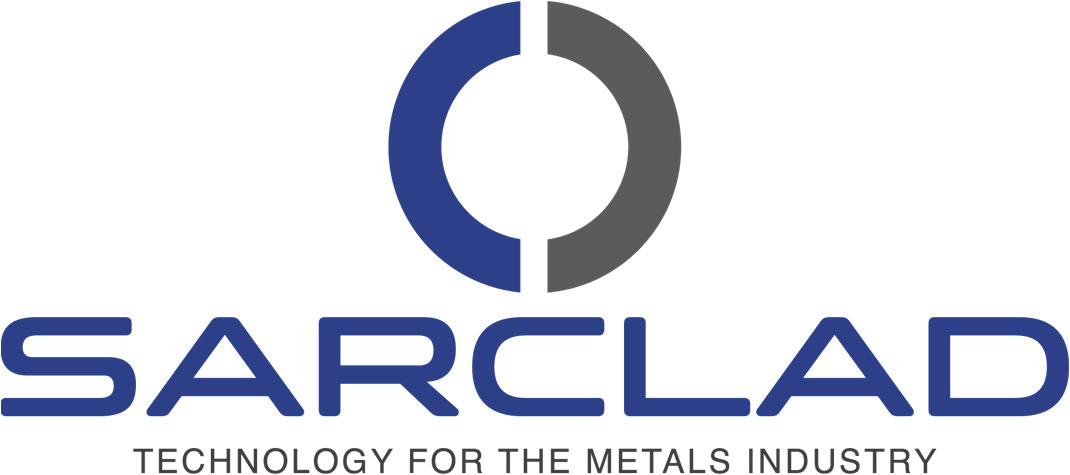
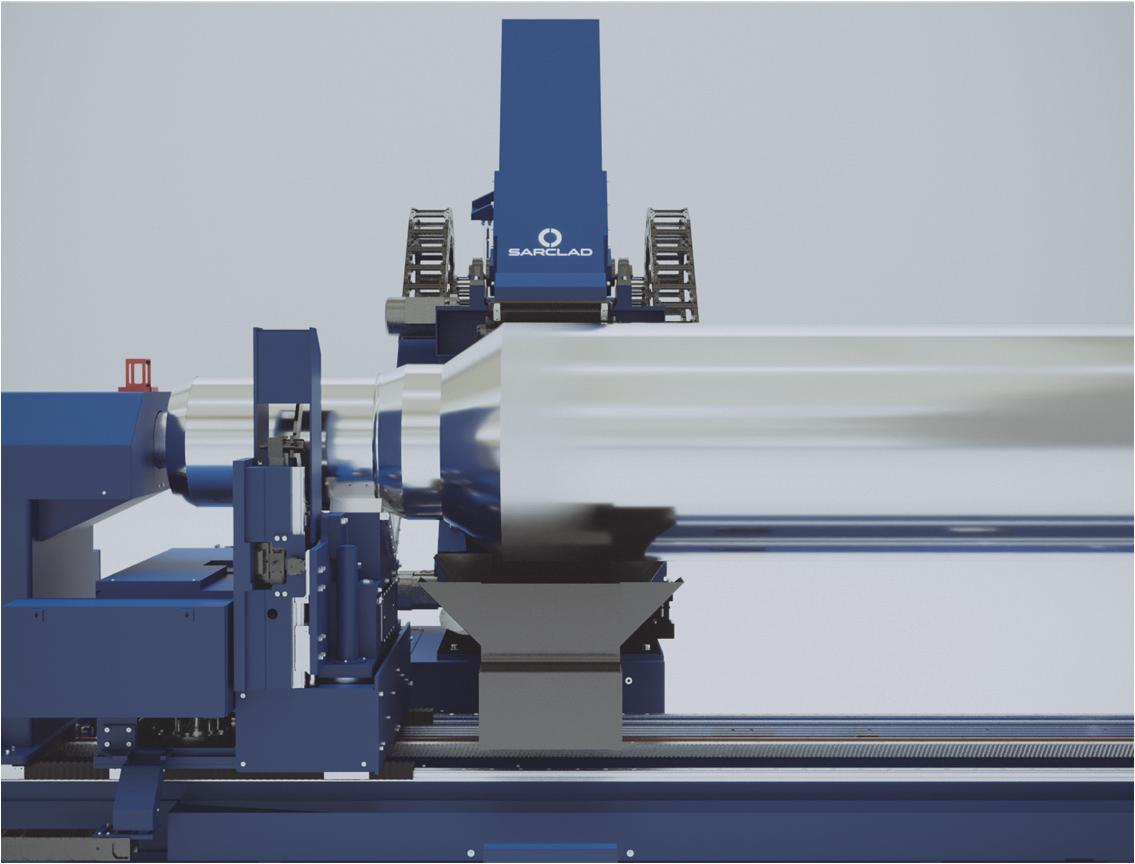
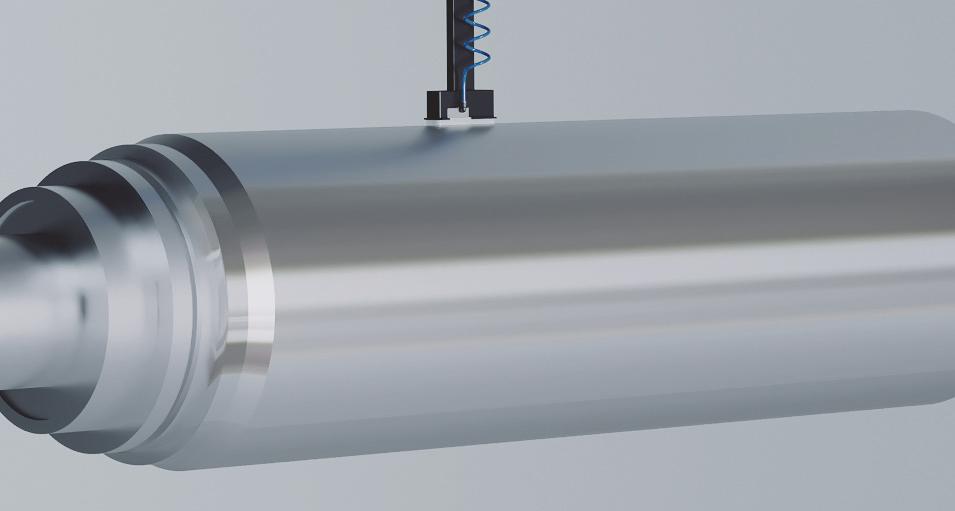
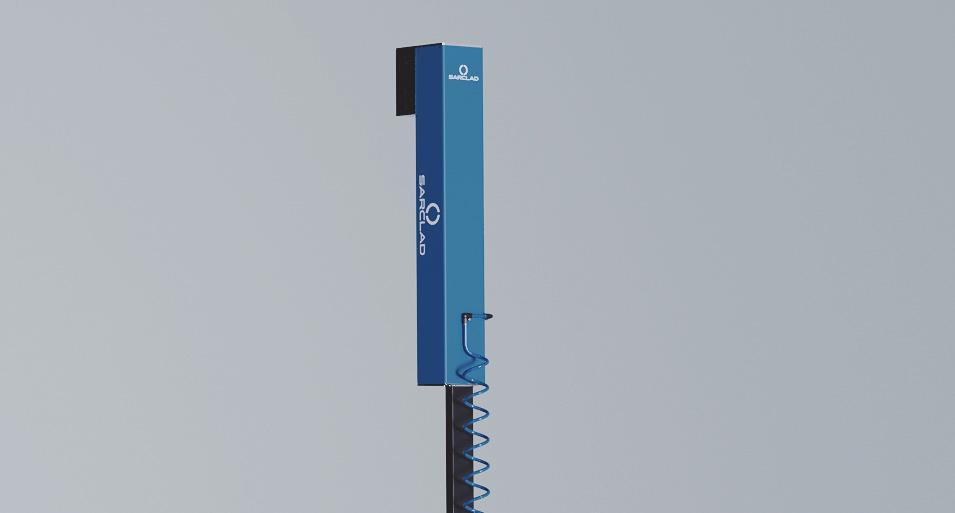
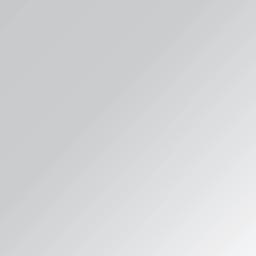
2. Polling of 4,323 adults conducted by YouGov on behalf of Podback, (9-11 September 2020)
Podback became operational in April 2021. We currently have kerbside collections in eight local authority areas from Exeter to South Derbyshire; meaning that more than 495,000 households
1. Viridor’s Recycling Index, carried out by YouGov (22 September 2020)
The entire pod recycling process takes place within the UK. Aluminium pods are recycled at Tandom Metallurgical Group in Cheshire, where they are shredded to remove the coffee grounds, then melted. The recycled metal is used in the manufacture of packaging and automotive components. Plastic pods undergo a similar process at Bright Green Plastics in Yorkshire, with recycled polymer used in the manufacture of a range of durable packaging for the grocery and agricultural sectors. The coffee grounds are sent for anaerobic digestion, producing biogas and soil improver. Bags are recycled by a specialist film reprocessor.

In recent years, we’ve seen an increasing focus on improving waste and recycling systems, with UK governments taking action and public opinion on the responsibilities of business also strengthening. In fact, polling of consumers has shown that 64% of UK adults believe that manufacturers should bear the cost of recycling the waste that is generated by the items that they sell1 Coffee pods are just one of the everyday items that are regarded as ‘hard to recycle’: not only do they contain organic material, i.e., coffee grounds; but also their size and light weight make them too small to be effectively captured and reprocessed through established recycling systems. To address this, individual beverage pod producers initially developed their own recycling schemes. Recognising the need to improve recycling of pods across all materials, the two biggest pod machine manufacturers, Nestlé and Jacobs Douwe Egberts UK, joined forces to develop a cross-industry solution. Launched in November 2020, Podback is a not-for-profit joint venture, and supported by their brands, which together account for 80% of the pod coffee market. This is the first time these competitors have teamed up in this way to try and tackle a shared challenge. Podback provides consumers with simple and convenient ways to recycle aluminium and plastic beverage pods. With 90% of consumers saying that they would like to be able to recycle their coffee pods through their usual household recycling service2, our priority is to work with local authorities to make this a reality. Podback is entirely funded by the brands that support it, meaning that councils implementing the scheme are able to provide kerbside collections at no extra cost to themselves or residents.
*Executive Director, Podback,
Focus on Podback
Following on from the focus on Tandom Metallurgical and its coffee capsule recycling capabilities, Rick Hindley*, highlights the importance of these partnerships and plans for growth.
RECYCLING 45 Aluminium International Today September/October 2022
Flexibility and efficiency HMR Hydeq – your preferred partner in the metal flow
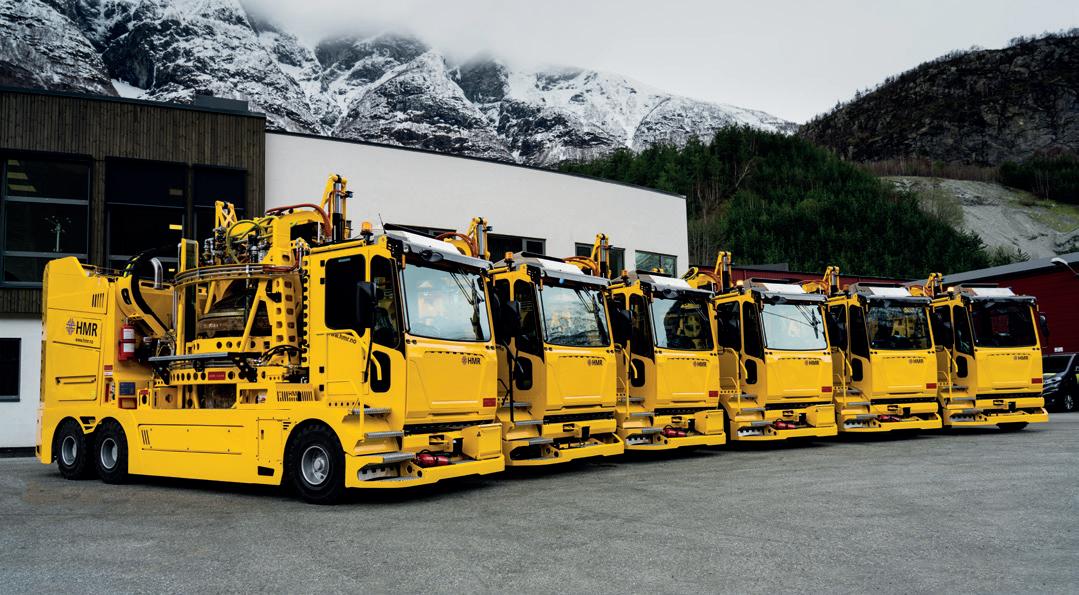
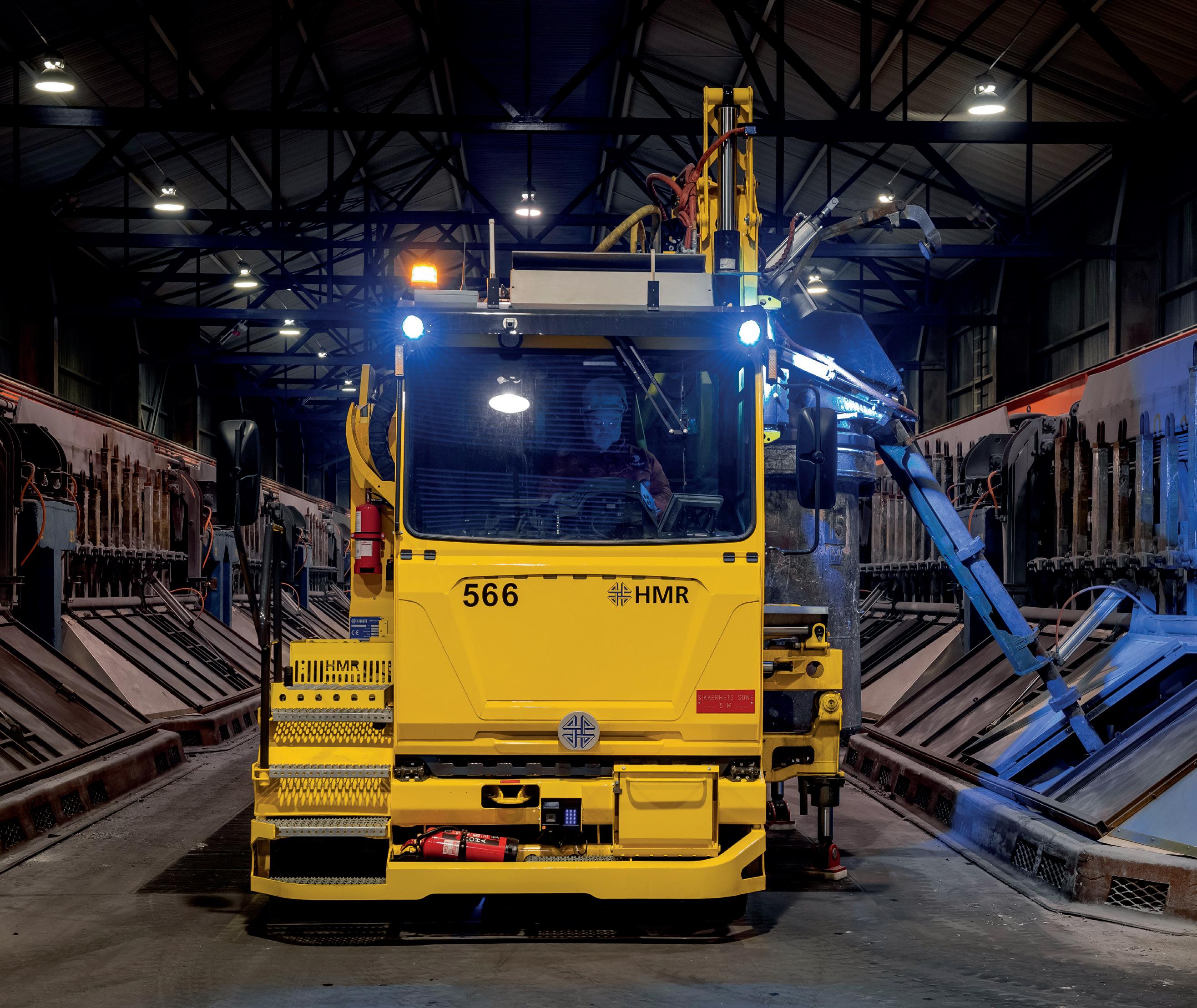
SætreØyvindPhoto:
Our one-man operated, vehicle-based metal transfer concept is the most efficient and cost-effective way to move molten aluminium from the pots to the cast house. HMR’s concept ensures cutting-edge technology for mobile transfer equipment. Industry 4.0 technology for connected equipment and autonomy for operation of metal transfer are our vision. www.hmr.noHMR Hydeq AS | N-6884 Øvre Årdal, Norway | E.: hmr.hydeq@hmr.no
USA OUTLOOK 49 Aluminium International Today September/October 2022
“When our company considers making investments, we look further out than any specific economic cycle,” Boney said, noting, “While we are cautiously aware of certain short-term issues that could mute demand somewhat and manage our business to reflect that, we are optimistic about the mid- and long-term prospects for aluminium demand.
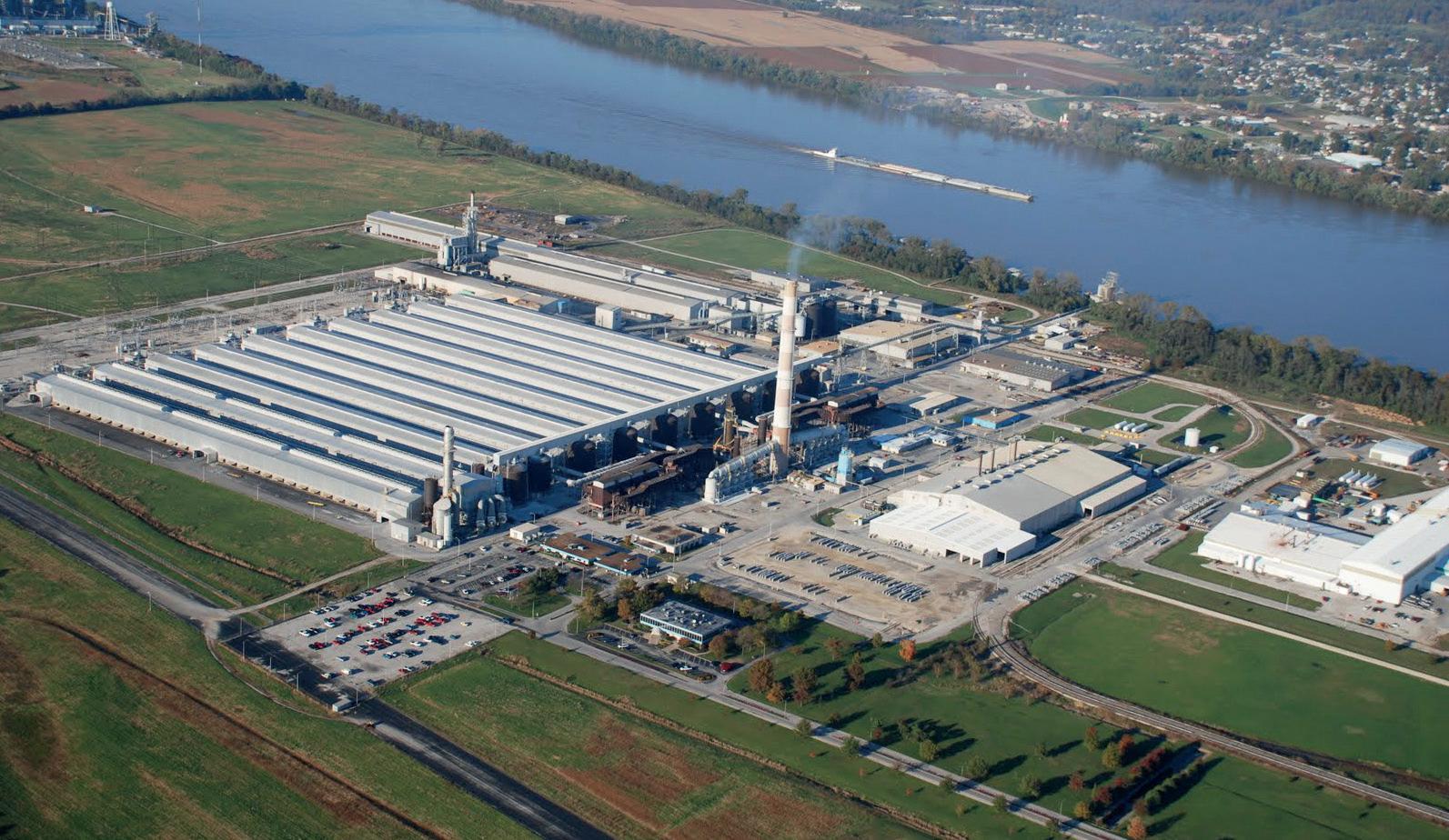
US aluminium capacity changes
Also, he noted that late in May investment firm Manna Capital Partners and Ball Corp., a leading global provider of aluminium beverage packaging products, announced plans to construct and operate a 1.2 million tonne greenfield aluminium can sheet rolling mill and recycling center in Los Lunas, New Mexico, which they originally intended to bring online by 2025 or 2026 although that might be pushed back given the deceleration in customer beverage can demand late in the second quarter.Thisis in direct contrast to some recent moves by US primary aluminium producers – most notably the decision late in June by Century Aluminum to temporarily idle its Hawesville, Ky., smelter,
Recent changes in US aluminium production capacity have been quite different depending upon where a company is in the value chain. While several primary aluminium companies are at least temporarily idling capacity at some of their US smelters, it is quite a different story downstream with the announcement of several sizable rolling mill and extrusion mill investments, including the plan for steelmaker Steel Dynamics Inc. (SDI) to build both a greenfield aluminium rolling mill and two supporting satellite recycled aluminium slab centers in cooperation with Unity Aluminum Inc. (formerly Braidy Industries).Clearlythe long-term trend has been and continues to be a push by companies to reduce their carbon emissions and to support a more circular economy. Daria Efanova, a research associate for Sucden Financial, said that as a result of this, it is likely that there will be further investments by US companies aimed at expanding their capacity to produce low carbon, recycled aluminium and to improve recycling technologies.Butshenoted that with aluminium prices falling at the same time as energy prices rallied over a very short period of time, in the second quarter of 2022, some primary smelters decided to temporarily close some production capacity, primarily to save input costs.
Gregory Wittbecker, an aluminium advisor for CRU maintains that this has been due to the continuation of the same problem that the US primary aluminium industry has been struggling with for the past 40 years, which is the availability of competitive electricity. He said that started when the US federal government began to regulate its power markets in the early 1990s. “That is what led to the wholesale closure of aluminium smelters in the Pacific Northwest and to the problems the US primary aluminium market is facing today,” he declared. Overall, however, Tom Boney, president of Novelis North America, termed 2022 – like the past couple of years – as being an exciting time for the US aluminium industry. He said that three fundamental drivers supporting investment in the market – especially the downstream market – has been strong demand for sustainable, low carbon aluminium; an increased interest in more robust supply chains; and that long-term underlying demand is expected to remain strong.
Mike Stier, vice president, finance and strategy for Hydro North America, agreed, noting that not only has the demand from such major aluminium-consuming sectors as automotive and building and construction recovered from the decline it experienced at the height of the Covid-19 pandemic, but customers’ desire for greener, recycled aluminium products has also been growing, seeing that as a way for them to meet their own sustainability ambitions. “As a result there have been several investments announced that target remelt and recycling facilities to increase recycled content and to reduce the industry’s overall carbon footprint,” heInsaid.addition to those investments coming from conventional mid- to downstream aluminium producers, there have been a few by other types of companies. In fact, Wittbecker termed the July 19 announcement by SDI as the first US entry into aluminium by a low-cost, wellrun steel player, although he noted that SDI’s ownership Omnisource – the largest US nonferrous scrap recycler – gives the steelmaker unique upstream sourcing capabilities for aluminium scrap.
By Myra Pinkham*
*US Correspondent Photo courtesy of Century Aluminum
Efanova noted that also, due to certain operational challenges, Alcoa Corp. curtailed one of the three potlines that were still online at its Warrick, Ind., smelter since it idled two other potlines in 2017.
“These investments are all predicated on strong domestic demand, which is currently at near record levels, and a projected strong demand picture going forward,” Meenan said.
Novelis Guthrie
TomBelow:Boney - Novelis EVP and President
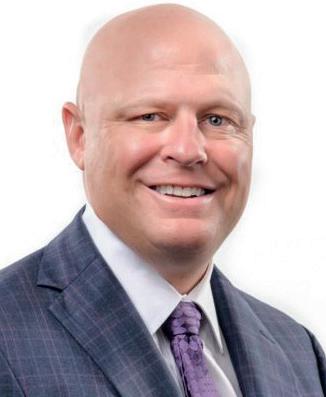
The 650,000 tonne a year flat-roll mill with onsite melt and slab casting capabilities, to be located in the US Southeast, is expected to start-up in
He said that the fully integrated Bay Minette facility, which while being largely focused upon the demand for can sheet will also sell into the automotive and specialties markets, will have an initial capability to produce 600,000 tonnes of finished products when it comes online in 2025. Boney said that it is Novelis’ intention for it to be Scope 1 and 2 carbon neutral with the facility to not only use higher percent recycled content inputs, but to also be powered by renewable energy sources and to use recycled water.
Groundbreaking - 5.2.2022
Meanwhile, Matt Meenan, a spokesman for the Aluminum Association, said that there has been unprecedented growth in mid- to downstream investments, noting that over the past 12 months there were not only more than $3.5 billion in US aluminium investments by Aluminum Association members alone. That doesn’t include the announcements by SDI and Manna Capital/Ball.
“Recycling is a big part of downstream aluminium investments, especially as companies try to achieve their emissions goals,” Efanova noted, pointing out that recycled aluminium uses 95% less energy than primary aluminium. She said that many of these investments are quite sizable. For example, she maintained that Novelis’ May 2022 announcement to build a $2.5 billion rolling mill and recycling facility in Bay Minette, Ala., is the largest single US aluminium investment in a couple of decades.
And this is just one of Novelis’ many announced investment projects, including several that are already in motion, Boney said noting that the company has recently announced about $4.5 billion worth of global investment opportunities, including over $3 billion in North America.
Aluminium International TodaySeptember/October 2022 USA OUTLOOK50 most likely for 9-12 months, taking approximately 200,000-250,000 tonnes out of the market. This, according to John Mothersole, a director of S&P Global’s market intelligence unit, is particularly troubling given that Hawesville is currently the only US aluminium smelter producing military specification aluminium.
The company is also on track to expand its recycling capabilities at its Greensboro, Ga., facility to enable it to recycle more types of aluminium scrap more efficiently and to upgrade its hot reversing mill motors, drives and hot finishing mil cooling system in Oswego, NY.
During the company’s recent earnings conference call Steve Fisher, Novelis’ president and chief executive officer, said that he views SDI’s announcement that it will be entering aluminium as being positive as it validates the view of the long-term strength of the US, and global aluminium demand.
While this comes at a time when aluminium prices have fallen back down to about $2,400 per tonne after peaking at nearly $4,000 per tonne in March considering the widespread supply concerns following Russia’s invasion of Ukraine and China’s pandemic-related lockdowns, there are also other factors at play, particularly high electricity prices. In fact, according to Matt Aboud, the company’s senior vice president for strategy and business development at Century Aluminum, electricity costs have gone up 300-400% over the past year, and given that the primary aluminium industry is such a huge consumer of electricity, any company that doesn’t have their energy prices fixed are facing cost issues. “That is why we had to curtail production at Hawesville.”Similarly, Mothersole noted that while venture capital group Blue Wolf Capital Partners has expressed interest in restarting and modernising the Intalco smelter in Ferndale, Wash., which Alcoa shuttered in 2020, its plans are at least temporarily on hold given that to date it hasn’t been able to get a power deal from the Bonneville Power Authority. As far as Hawesville, Aboud said that Century Aluminum plans to restart that smelter once energy prices return to a more normal level. While it is hard to say exactly when that would be, he said that, based on the energy market’s forward curve, it could potentially occur as soon as in April Wittbecker2023. said that if power prices remain elevated for another six to nine months there is some potential for additional rationalisation of US smelter capacity with Alcoa Warrick and Magnitude 7 New Madrid at the greatest risk.
Automotive Recycling Center
Upon announcing the project, Mark Millett, chairman, president and chief executive officer, said that aluminium sheet had been on SDI’s radar for many years and that, given the metal’s significant and growing supply deficit, he believes that this is an ideal time to penetrate the market with the production of high-quality, low-carbon aluminium. He said he believes this is a low-risk move given it will broaden SDI’s ability to serve existing and new customers and will provide further mitigation of market cycles, adding, “It should be considered as an adjacent business to our steel operations with considerable overlap in process and operational knowhow.”
Also, in May, Novelis broke ground on a $350 million auto recycling centre in Guthrie, Ky., adjacent to its automotive sheet finishing line there – an investment that Boney said is expected to reduce the company’s carbon emissions by over 1 million tonnes and will enable it to grow its closed loop recycling relationships with its customers.
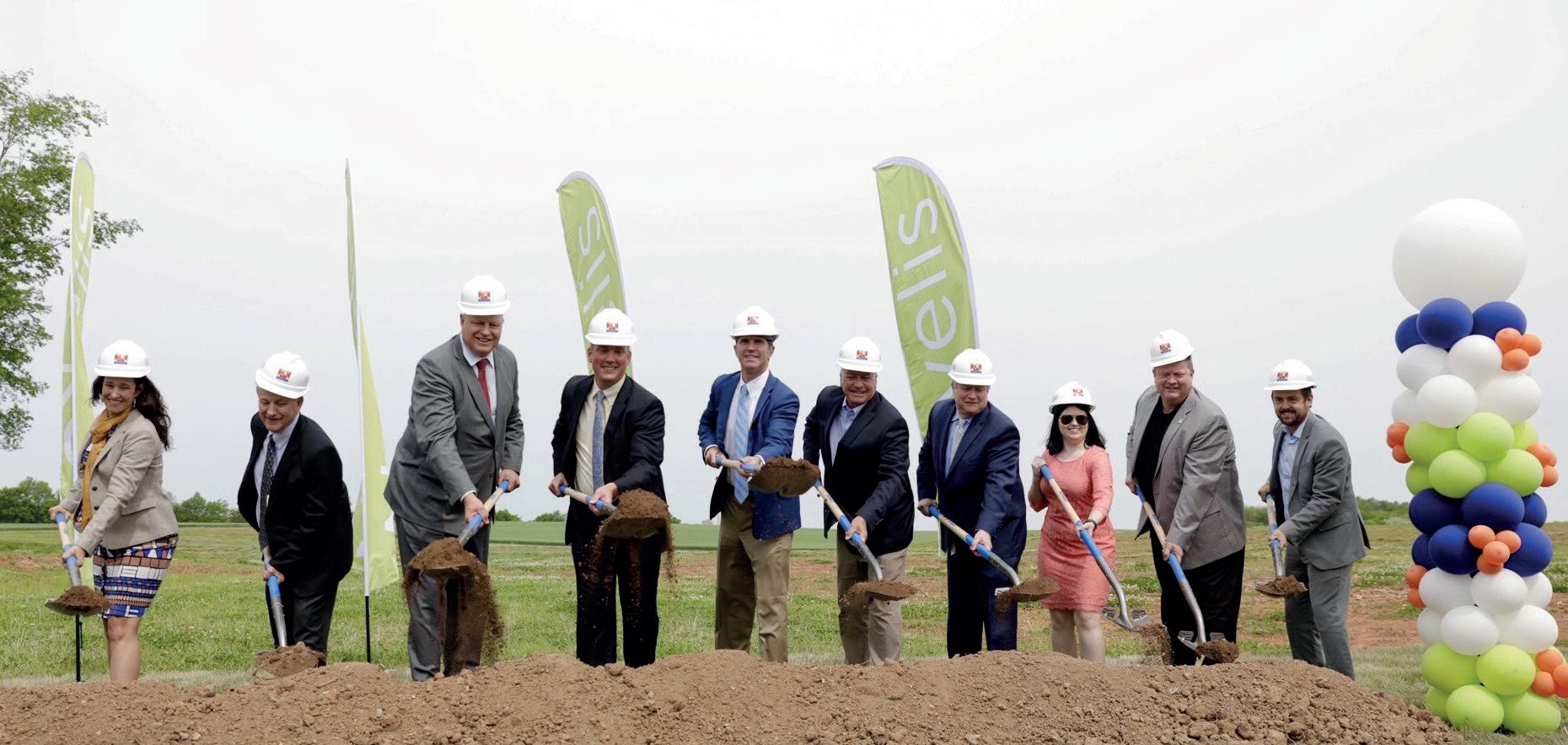
AUTONOMOUSCHARGING&SKIMMINGMACHINES

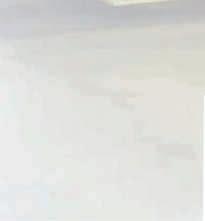
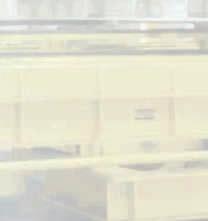
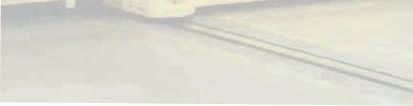


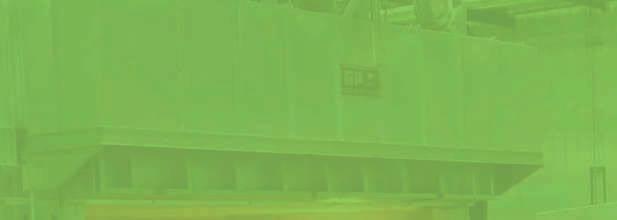
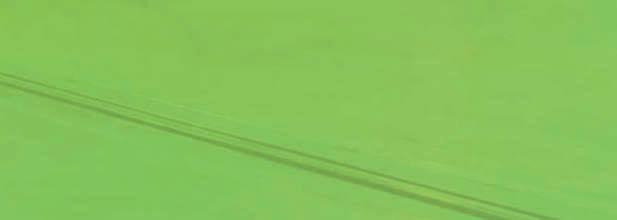






Efanova said that despite what has occurred recently with smelters, in the long-term there will be a need for more aluminium production capacity, especially given rising demand for aluminium for electric vehicles. But even with recent closures (and downstream expansions), companies aren’t struggling to find enough primary aluminium.
“We not only have to be excellent when it comes to closed loop recycling, but we have to be wonderful urban miners so we don’t have to go into the ‘good Earth’ to get all of our natural resources.” Kelly Thomas, Alcoa’s executive vice president and chief commercial officer, agreed, observing that the aluminium industry as a whole is working to deliver more sustainable solutions, including decarbonising aluminium production and accelerating the development of new recycling technologies. �
USA OUTLOOK52 early 2025. Additional slab supply will be provided by the new satellite slab casting centres – one in north central Mexico and one in the US Southwest. The mill’s recycled aluminium requirements will be supplied by SDI’s Omnisource subsidiary, which currently handles 500 million lbs. of aluminium scrap. “We believe that through our Omnisource recycling platform we can increase the scrap content,” Millett said. Aluminium companies haven’t just announced new US flat-roll related investments. Wittbecker noted that there has also been a big wave in new extrusions capital investment with about 40 new extrusion presses in the process of being added in the US, Canada and Mexico. That, he said, could add at least 800 million lbs. of new extrusion capacity. Efanova said Norsk Hydro alone plans to produce an additional 120,000 tonnes of aluminium extrusions per year for a variety of transportation, construction and consumer applications. Stier noted that Hydro has recently announced a $27 million investment in its The Dalles, Ore., recycling facility to expand its remelt and billet casting capacity and to increase its use of post-consumer scrap; a $50.6 million investment in its Cressona, Pa., extrusion facility to expand its recycling capabilities, including remelt and extrusion billet casting, to increase its use of post-consumer scrap and to source 100% of its electricity needs from a local solar farm; and a $15 million investment at its Henderson, Ky., recycling site to both add a new homogenization furnace and bag house and to enable the facility to produce a greater volume of advanced alloys using recycled materials including Hydro CIRCAL®, an aluminium billet made with a minimum of 75% recycled, post-consumer aluminium scrap. In addition, Hydro’s Spanish Fork, Utah, extrusion and recycling facility has joined its Montreal, Quebec, plant in being 100% powered by renewable energy.
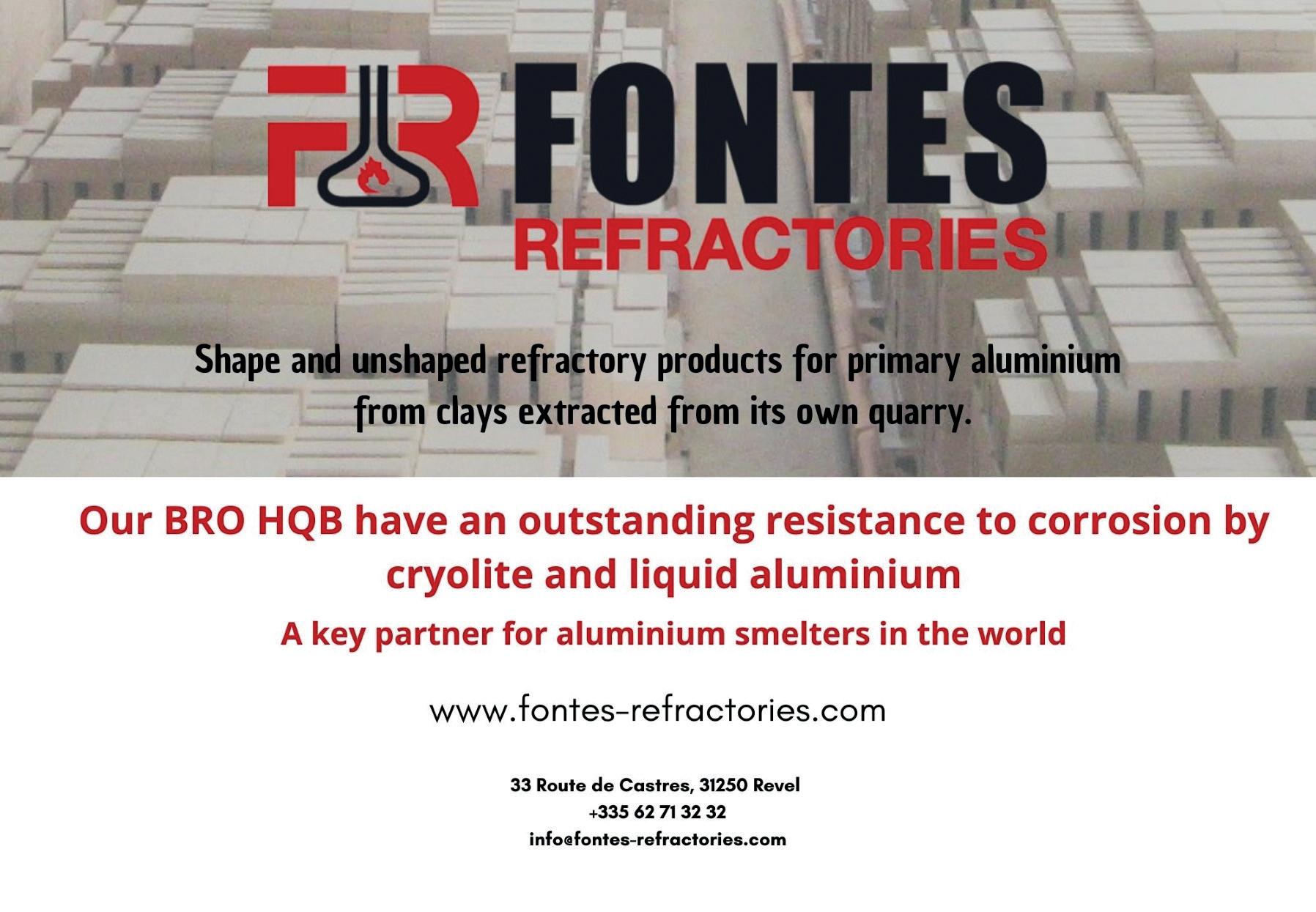
Century’s Aboud said that over the longterm he is optimistic that downstream demand will support growth upstream, “But I’m a little concerned about the overall US energy policy and how energy prices have skyrocketed. That could be unsustainable.”Boneysaid that while mid- and downstream producers will need primary aluminium for a very long time, the push to use more recycled content will continue.
On the other hand, Mothersole noted Kaiser Aluminum declared force majeure at their Warrick, Ind., rolling mill that they acquired from Alcoa because they haven’t been able to get enough magnesium to meet their contractual obligations. While still operating, the mill is expected to produce at about 50% of its capacity through the end of the third quarter.
Mössner develops and builds machines for cutting aluminium slabs, blocks and plates. Adapted to customer requirements, the special machines are individually equipped with a variety of components for an optimal solution to specific work processes. Visit us: Aluminium 2022, 27-29 September 2022 Düsseldorf, Hall 5 Booth 5C37

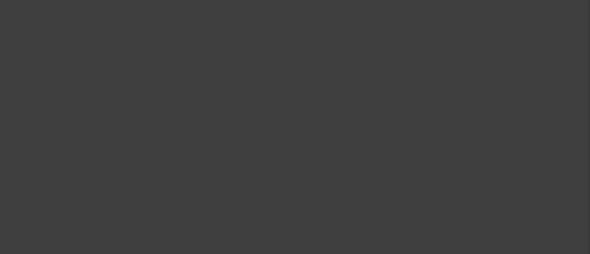
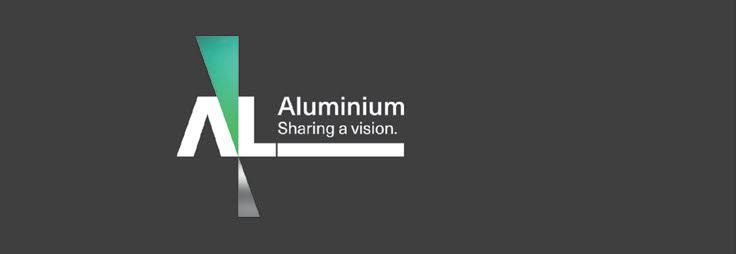
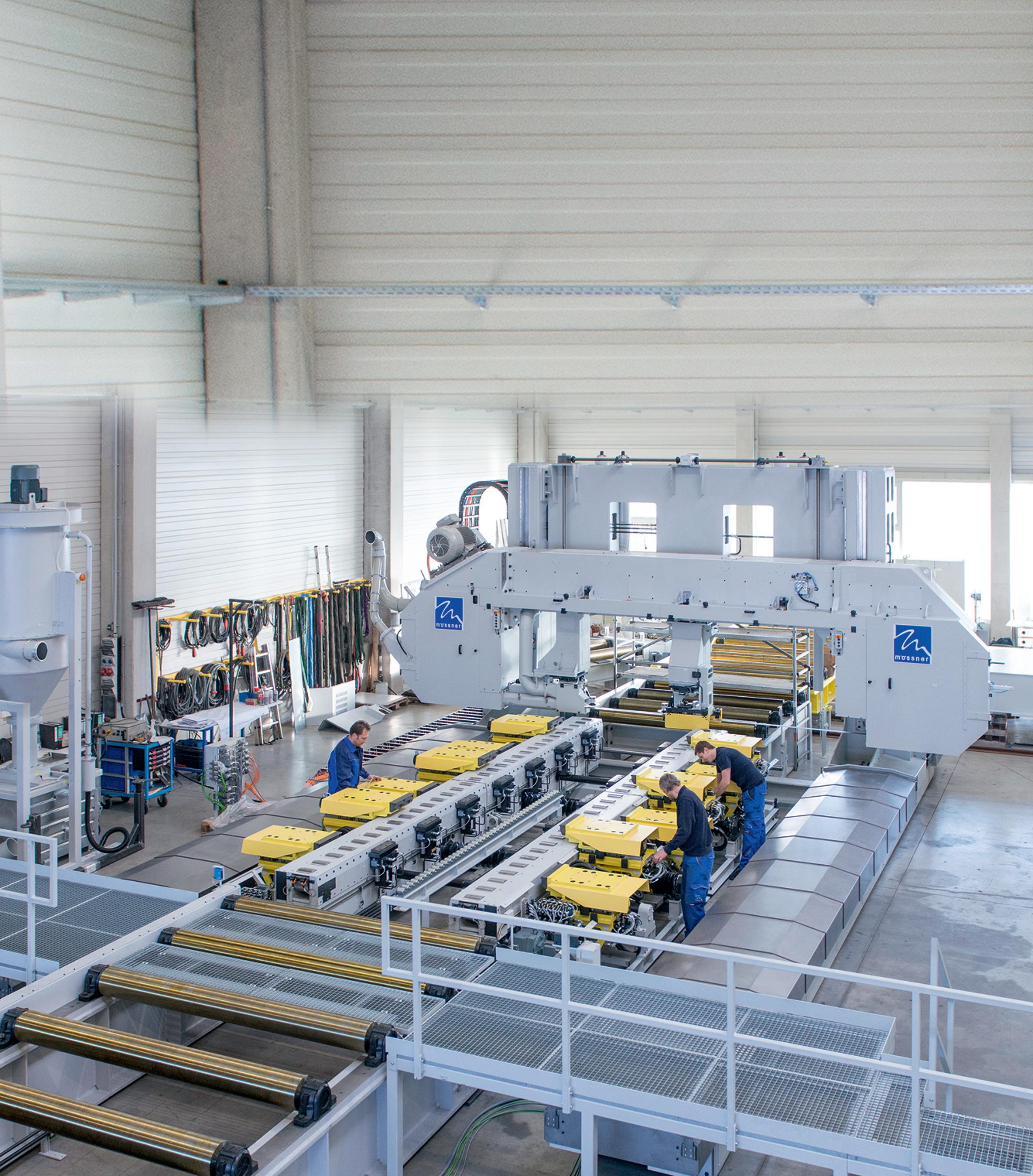
Mössner ingot saws are in operation worldwide. Adapted to different customer requirements, rolling ingots and T-bars are reliably cut to size. The sawing technology is used in primary and secondary aluminium production.
If panels of different thicknesses are to be produced from one ingot, the Mössner horizontal saws are suitable for this. The horizontal saws are able to precisely produce blanks as panels in different sizes. This reduces the over-milling of the slab to a minimum and the customers receive more marketable material.
At the “Aluminium” trade fair in Düsseldorf from 27 to 29 September 2022, August Mössner GmbH + Co KG will be showing application examples of the wide range of its solutions for the aluminium industry. These include sawing, testing and handling of aluminium.
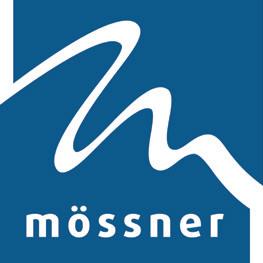
Mössner offers a comprehensive portfolio of saws for processing T-bars, rolling ingots, plates, blocks and billets. The saws are unique in their solid steel construction, the precise cutting process and the long saw blade life.
“With our turnkey, fully automated plate production, which also includes the process steps of milling, foiling and handling, our customers are always one step ahead,” explains Oliver Vogt, Product Manager in the Aluminium Division at Mössner.
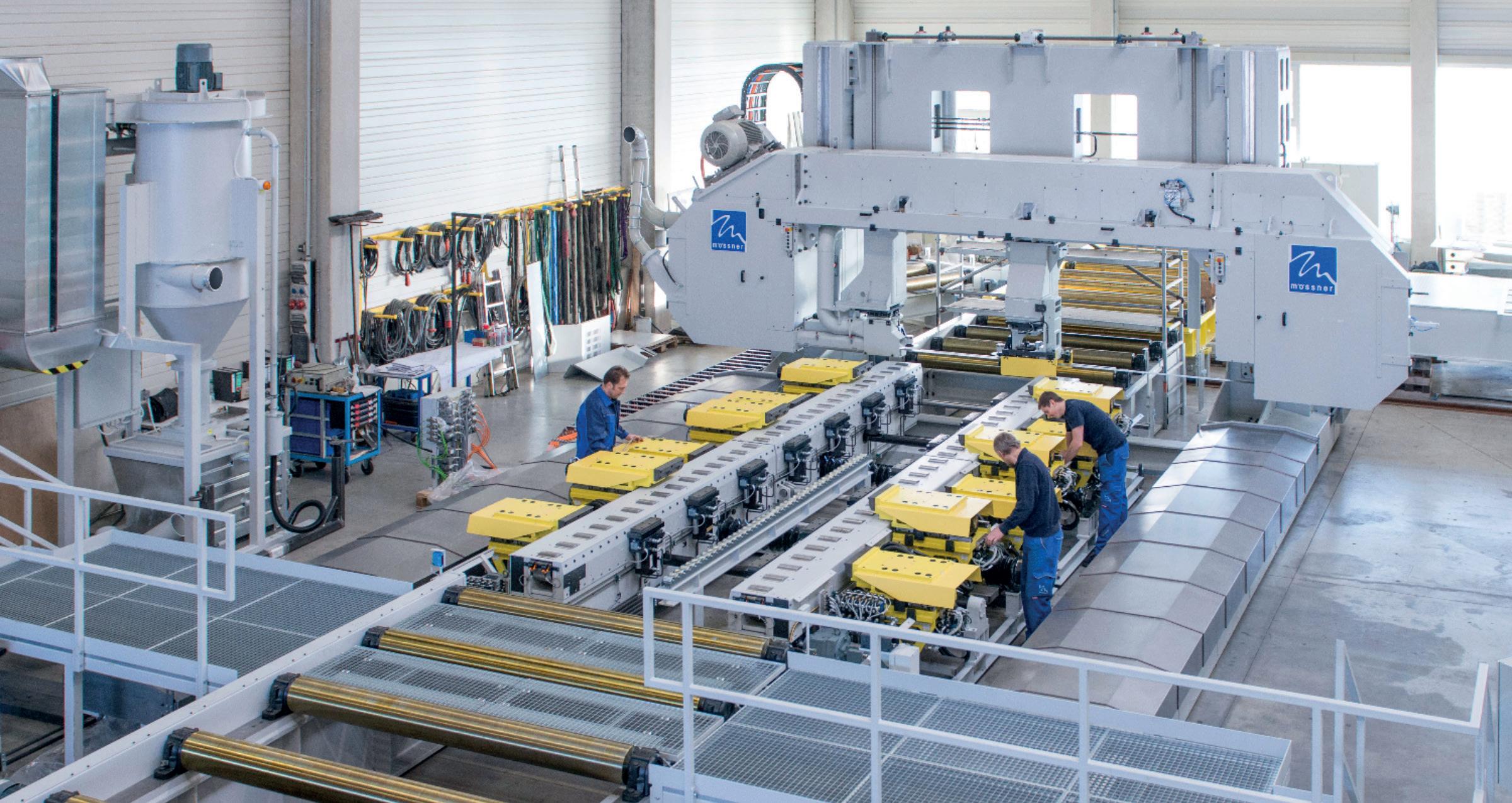
Mössner’s ingot saws are available in various configuration levels. Depending on the customer’s needs, the ingots are imported, for example, by a downender. Heavy-duty shuttles then transport the ingots to the sawing area or, alternatively, stow them in the designated buffer area. Innovative handling systems and automated scrap, head and foot cut disposal allow for almost autonomous operation. After weighing and marking, the rolling or T-bars to be processed are ready for removal.
You can see Mössner’s systems “in action” at any time on Mössner’s YouTube channel: UC00-LMwa6fuoEhxwFVhTTjg.https://www.youtube.com/channel/
Mössner offers further innovative products for aluminium technology: � Contour saws � Vertical block saws with optional saw blade rotation � Circular saws for the production of aluminium circles � Circular plate saws � Saws for the aerospace industry � Conductivity testing systems
Higher efficiency and energy savings through high saw blade life and low chip waste
For the perfect production of aluminium blanks August
Aluminium International TodaySeptember/October 2022 54 ADVERTORIAL
Phone
Mössner develops and builds special solutions in the fields of mechanical engineering, automation technology and robotics. With its 140 employees, Mössner is also able to handle larger projects without losing the necessary flexibility for special solutions. At its site in Eschach, Mössner develops, manufactures and assembles the systems and commissions them for its customers worldwide. In the field of aluminium technology, Mössner offers precise sawing and milling systems for primary and secondary aluminium production. These enable the processing of rolling ingots, T-bars, blanks, contours, circular blanks, samples, blocks and plates.� Mössner GmbH + Co KG | Hohenstaufenstraße 3 | D-73569 Eschach +49 (0)7175 99806-0 | Phone +49 (0)7175 99806-35 0 | www.moessner-kg.de 0 | post@moessner-kg.de URL Link: www.moessner-kg.de
“Planning, development, assembly and commissioning are carried out by our expert staff. The experience and knowhow from 125 years of mechanical engineering flows into the development. Our customers worldwide appreciate the turnkey delivery of the plant technology “, explains Christian Kunz, Managing Director and Sales Manager at Mössner.
Over the last 60 years, the Aluminium Federation (ALFED) has emerged as the voice of the UK aluminium industry.
ALFED, like European Aluminium and IAI, represented a longstanding trend within global aluminium for cooperation.
The Aluminium Federation, 1962 – 2022: Forging a Voice for UK Aluminium

was constituted on 14 May 1962 assuming the mantle of its predecessors the Aluminium Development Association (ADA) and the Aluminium Industry Council (AIC). During its formative decades, the Federation’s council reflected the structure of the aluminium industry both nationally and globally, dominated as it was by the large first mover vertically integrated multinational aluminium producers (Alcoa, Alcan, and British Aluminium), some large downstream rollers and extruders, and sectoral associations. (Figs 1-3)
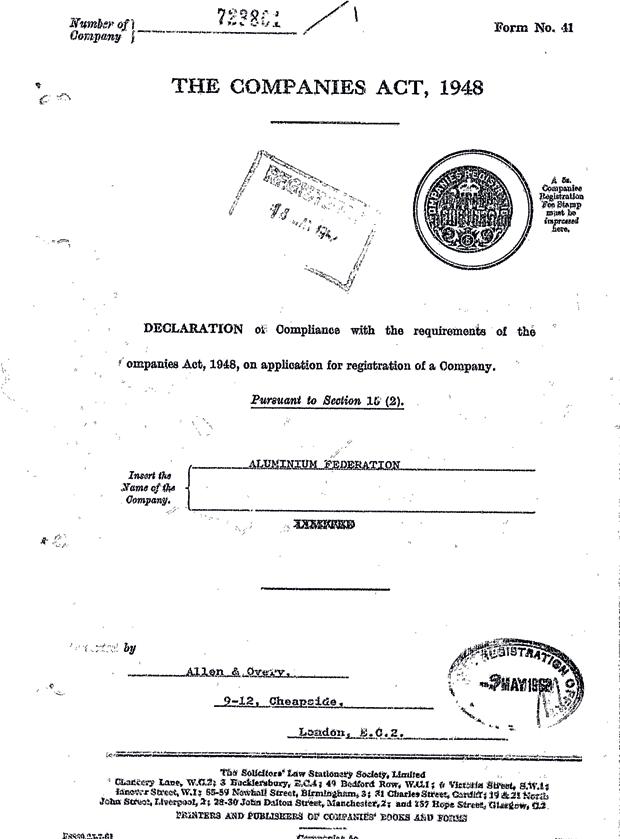
Fig 1. Articles of Association, Companies House Fig 2. Fig 3. *Professor and Head of Management Group, Edinburgh Napier University **Professor of Business History and Entrepreneurship, Adam Smith Business School, University of Glasgow, Scotland. ***Senior Lecturer, Otago Business School, University of Otago, New Zealand. 39,000 jobs to the UK economy (and spill-over benefits of 104,000 jobs and £7.4bn in GVA). As well as reviewing documentary evidence, the project has involved interviewing current and former ALFED office holders (past presidents and general secretaries/ chief executive officers).ALFED
ALFED’s history, like that of European Aluminium and the International Aluminium Institute (IAI) (both celebrating significant anniversaries over 2021-2022), is that of both the domestic and global aluminium industry. ALFED has evolved since its formation to build upon its original knowledge and skills in technical advice and guidance to develop its capabilities in networking, consultancy, technical education, and above all in advocating for and lobbying on behalf of the industry. The Aluminium Federation: Our History, Our Heritage, 1962-2022 project was conceived of by the project team of aluminium and energy historians, in conjunction with ALFED, both to chart the Federation’s history and to provide an organisational and strategic resource for the future, for an industry which currently directly contributes £2.9bn in GVA and
From the outset, these bodies developed real coordination and valuable knowledge exchange on marketing, research and development and transportation that continues into the current day. The AAC collapsed in the late 1930s principally under pressure from Nazi Germany’s rearmament programme. However, after 1945, this was succeeded by a variety of European initiatives intended to foster cooperation, including the Centre international pour le développement de l’aluminium (1950), the European Wrought Aluminium Association (1953),
ALFED ANNIVERSARY 55 Aluminium International Today September/October 2022
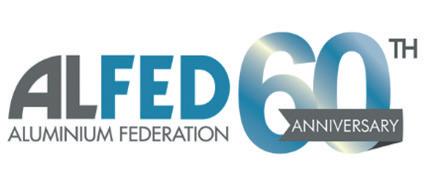
The first truly successful demonstration of cooperation within the global industry being the Aluminium Association (formed in 1926 and superseded in 1931 by the Alliance Aluminium Company (AAC).
By Andrew Perchard*, Niall G MacKenzie**, and Duncan P Connors***
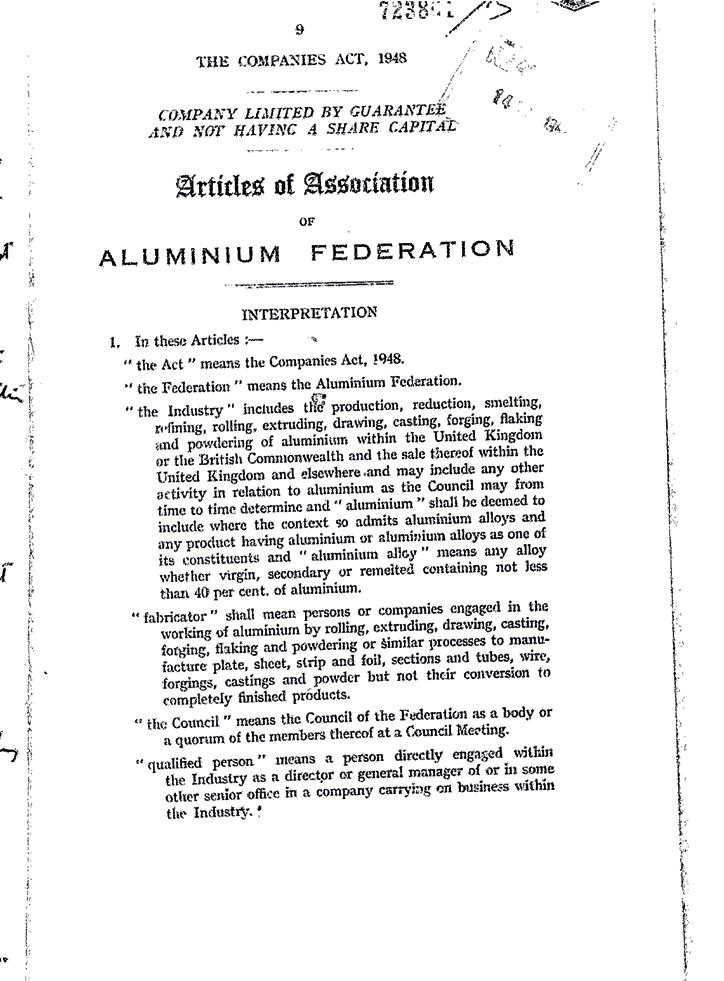
1. ‘Aluminium Federation Ltd’, (UK) Board of Trade files (1966-1975), BT328/96, UK National Archives.
Figs 4 & 5. Promoting Aluminium. Images, Financial Times associations, ALFED’s new secretarygeneral (1972-1988) Paddy Matthews implicitly addressed the overdue need for a renewal to make it more relevant and sustainable for a changing industry and membership, remarking to the Financial Times in July of the same year: ‘The broader base of the federation will also enable it to speak and act authoritatively, both nationally and internationally, on behalf of the industry as a whole.’3 (Fig 6)
Aluminium International TodaySeptember/October 2022 ALFED ANNIVERSARY56 and the Organization of European Aluminium Smelters for the Secondary producers (1960). This represents one of the enduring features of the industry; the capacity for coopetition that has extended not just amongst the producers but in other external relationships as well. Like many industry associations, ALFED’s history is one of a changing membership and bringing together diverse and, at times, divergent interests in the industry.
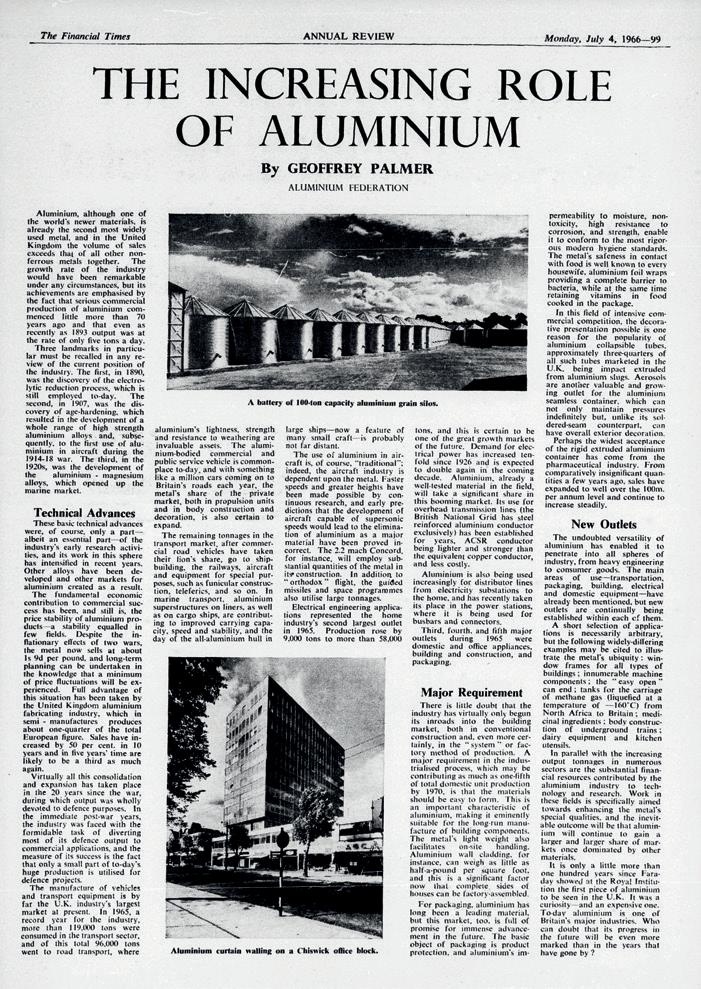
The experiences of the 1980s and 1990s both reinforced the benefits of ALFED’s reconstitution and underlined the need for constant renewal and assiduous acuity to change in the industry. Coming on the back of greater price volatility and uncertainty for primary producers following aluminium’s launch on LME, the UK industry was confronted by a
The UK and global aluminium industry was already changing fast, as were markets and society around it. In the years leading up to the formation of the Federation, both nationally and globally, the country club atmosphere of the first movers amongst global aluminium producers was shaken to its core by relative newcomer Reynolds Metals (the Virginia-based US producer) and Tube Investment’s hostile takeover of the British Aluminium Company Ltd in 1959. The “Aluminium War”, as it became known, as well as rocking the foundations of the industry and firmaments of the City of London (while dividing the then UK Cabinet), also demonstrated the increased competition in the industry after WWII. In the decades that followed ALFED’s formation, the industry was confronted by further important changes in the economic and political landscape. Harold Wilson’s Labour government (1964-70) sought to address the longstanding balance of payments problems, primary aluminium supply and cross-subsidise the next generation of nuclear reactors (the Advanced Gas-cooled Reactor) with a competition for a new slate of aluminium smelters in 1967, with mixed success. Whilst the UK’s admittance to the EEC in 1973 provided welcome access to continental European markets, increased global competition and the fuel crises of the 1970s led to further uncertainty. The global industry was about to experience a major disruption with the launch of the metal on the London Metals Exchange in 1978; between 1980 and 1982, global aluminium prices fell by 40%.
2. Otto Realf Norland, The Magic of Merchant Banking (Oslo, 2022), 278. ‘Aluminium Federation’, Financial Times, 9 July 1973, 11.
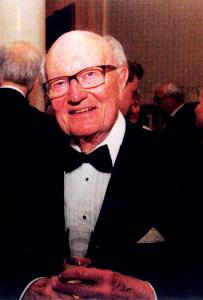
3. ‘Aluminium Federation’, Financial Times, 9 July 1973, 11.
ALFED’s council and chief officers was dominated in its early decades by those from the large first movers in the industry and engineers reflecting its essentially technical and promotional brief taking over from its predecessors the ADA and AIC. The focus on technical matters, education and promotion of the metal was undoubtedly helpful to the sector. It also involved close technical cooperation with and in leveraging support from government, such as over the reduction of emissions from the secondary industry that had grown rapidly during WWII but was by then in pressing need of modernisation especially after the introduction of the Clean Air Act of 19561. ALFED’s activities were timely and purposeful in promoting aluminium as an industry and product against growing consumer demand (in such areas as construction, transport and household products) and competition (Figs 4 & 5). These attempts also reflected increased competition from downstream producers in continental Europe as the formation of ALFED had in some respects anticipated with the UK still outside of the European Economic Community (EEC). The specific objectives also reflected the dominance of the aluminium majors who had no additional need of public affairs capabilities which they either managed in-house or through agencies. However, in a clear indication of their recognition of the value of the organisation, they deployed some of their most senior managers who brought broader global business and political networks. Otto Realf Norland, who joined ALFED’s council after he became Alcoa GB chairman in 1978 and was concurrently a managing-director of merchant bank Hambros, recalled the composition of the Federation’s governing body at that time: ‘… I was also automatically appointed to the Council of the Aluminium Federation. Alcan and British Aluminium were the biggest aluminium companies in the UK, followed by Alcoa, and many large manufacturing companies were also represented by their managing director or chairman. The Stockist Federation and other specialist associations had one representative each, and the council totalled around 18 men, half of whom were old industrial hands and pipe smokers.’2 ALFED’s early governance structure and strategic outlook (and dominance by the majors) became increasingly incompatible with the changing membership and context of the industry. Following the reform of its constitution in 1973, including the co-option of the 10 product-based trade Fig 6. Otto Realf Norland, ALFED Vice President,1981,President,and1982
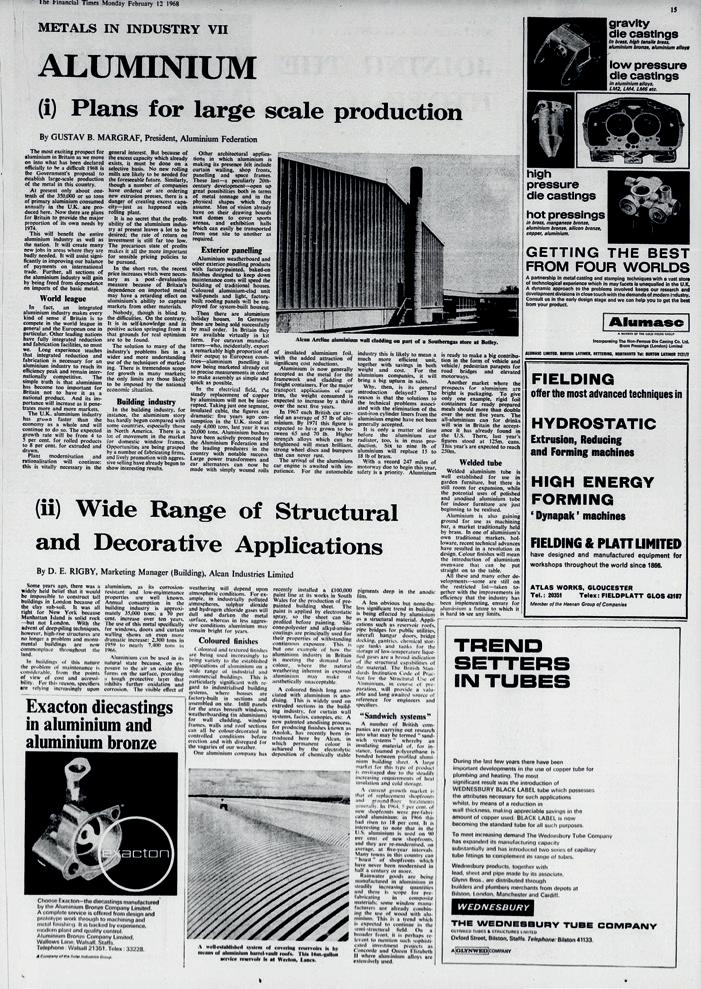
GLAMAMaschinenbauGmbH Headquarters: Hornstraße19 D-45964Gladbeck/Germany Fon:+49(0)204397380 Fax:+49(0)2043973850 email:info@glama.de glama.de Costeffectiveheavyduty mobileequipment foraluminiumindustries... always thedurable solution GLAMAUSAInc. 60HelwigSt.,Berea,Ohio44017 Fon:+18774526266 Email:sales@glama-us.com

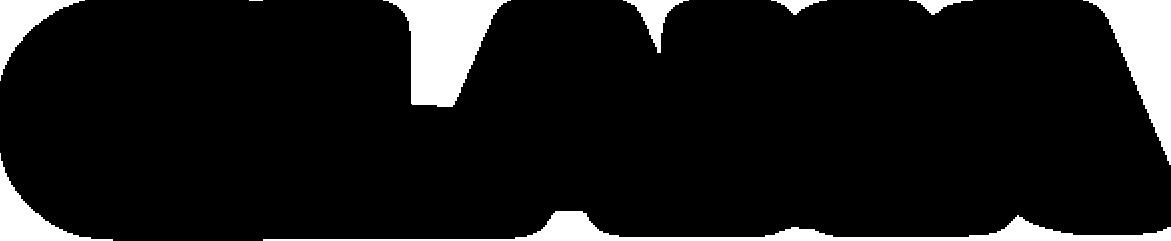
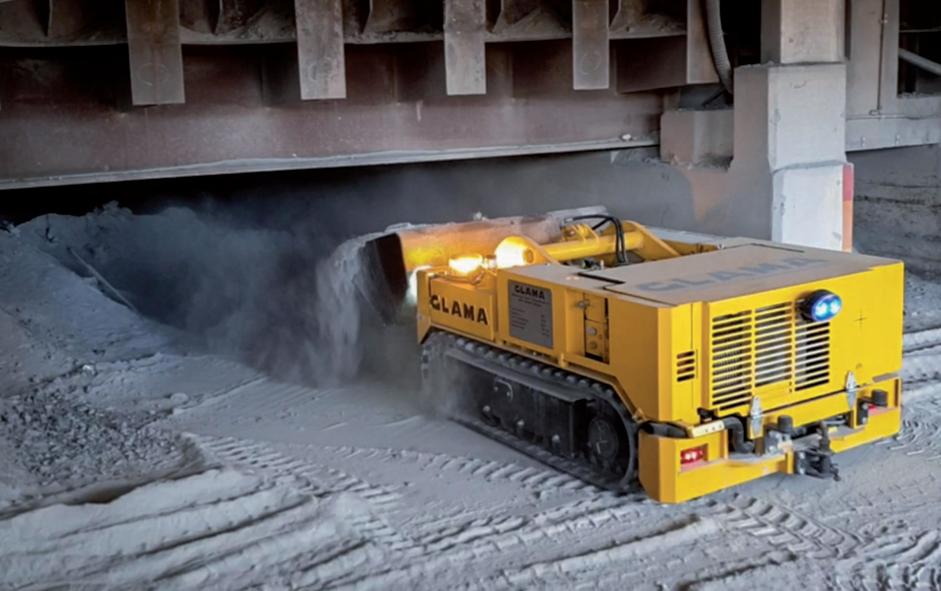

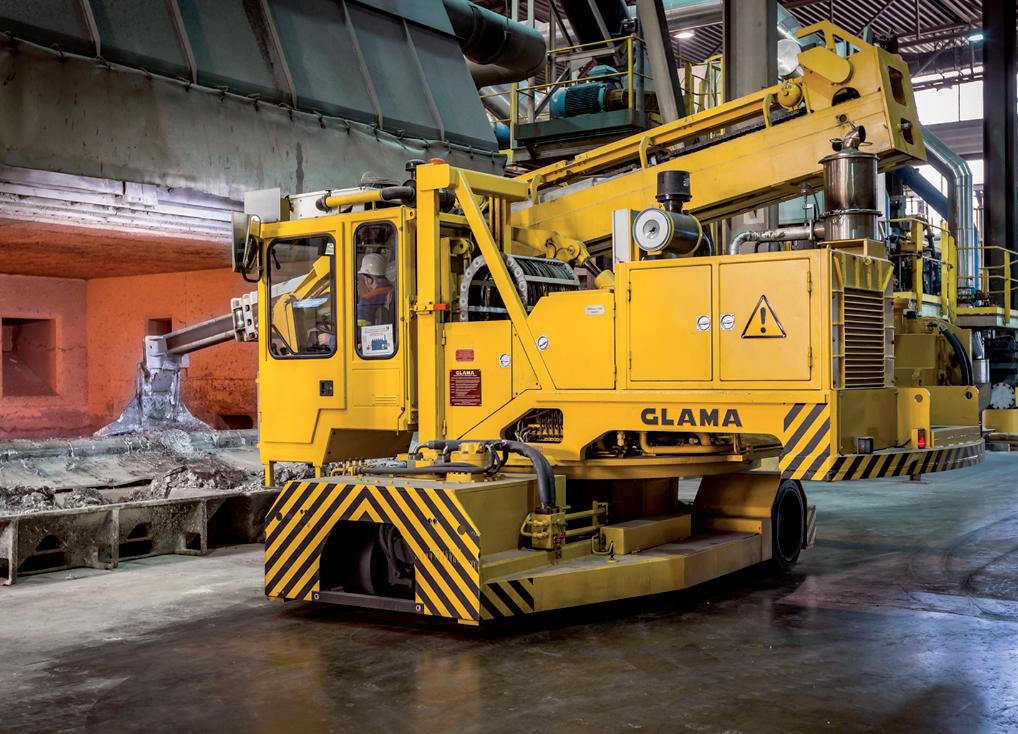
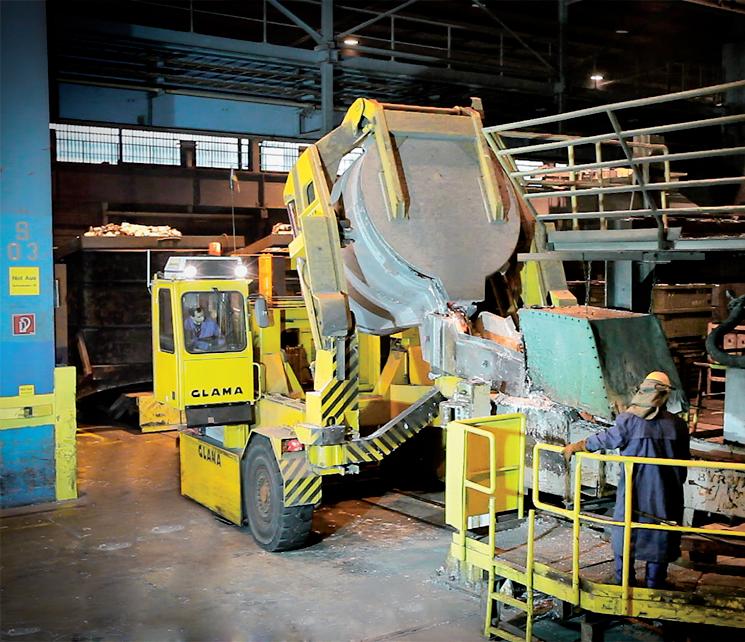
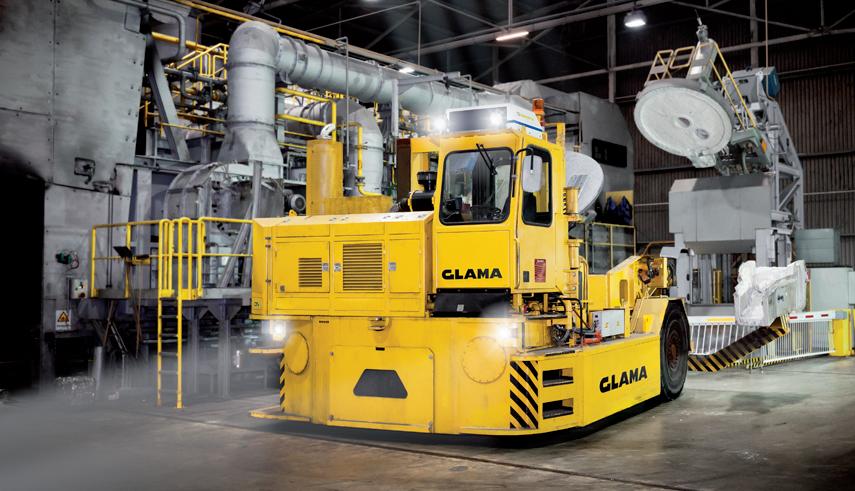
The collapse of the Soviet Bloc introduced increased challenges with a glut of cheap and subsidised aluminium flowing into global markets, alongside the rise of other new aluminium producers from other BRICs countries, such as Brazil, India and South Africa, and Middle East producers. In the latter, ALFED became a significant template and mentor for the development of producers’ associations. (Fig 8) Within the first decade of the millennium, the UK and global aluminium industry had changed markedly with the disappearance of many of the first mover global majors. As ALFED secretary-general and then chief executive (2005 –2017) Will Savage reflected in an interview with Light Metal Age in 2015. An increased and diversification of ALFED membership and changed context required greater acuity and the need for change within the organisation. New opportunities and challenges for the aluminium industry once again underlined the need for constant renewal of ALFED’s governance, organisational capabilities, and national and transnational cooperation not just within the sector but across sectors, such as through the UK Metals Council.
Fig 7.British Aluminium Company Ltd, Invergordon smelter, October 1975, British Alcan collection
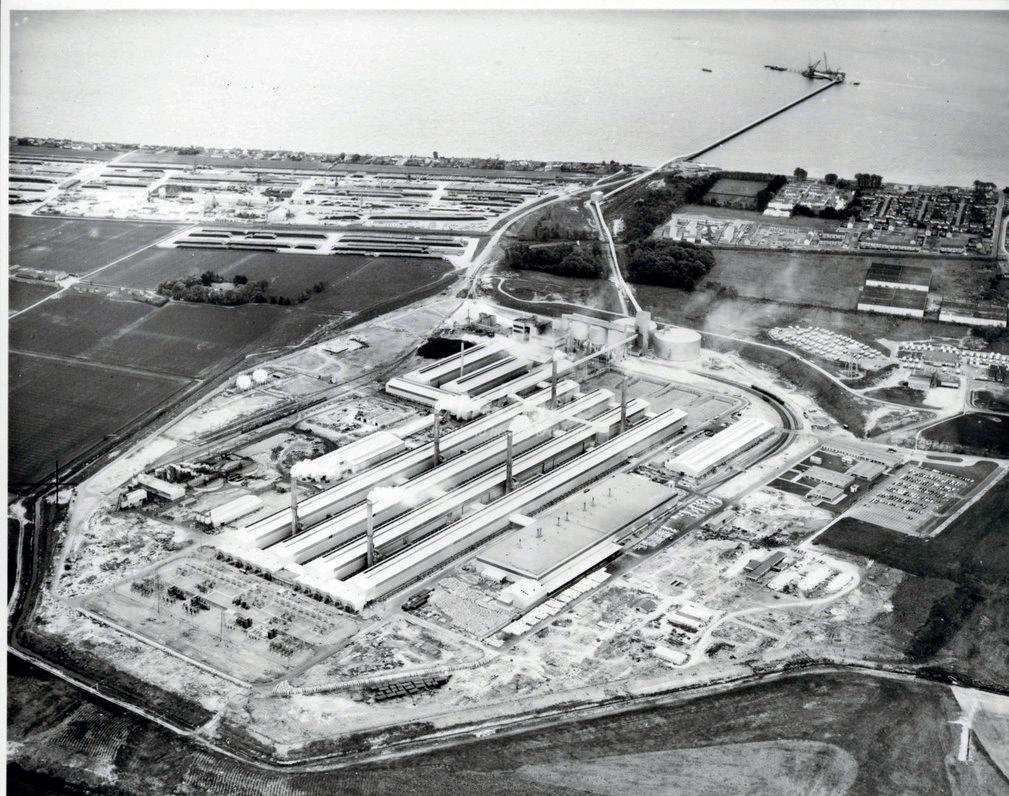
Packaging Ltd, Nick Kendal, outlined in his speech to the Federation’s House of Lords lunch in May 1992: ‘It is currently estimated that less than 5% of the UK population are active recyclers; so any initiative can be successful there has to be a major education campaign which will persuade the public to recycle waste – legislation and economic instruments alone will not provide the incentive.’
4. Ministry of Defence, The Falklands Campaign: The Lessons, (Cmd.87), 1982, p.19; Crum et al, ‘Advances in Aluminium Relative to Ship Survivability’.
Aluminium International TodaySeptember/October 2022
5. Perchard, Aluminiumville; Morel, Histoire technique de la production d’aluminium.
Consumer recycling remained significantly behind that of industry; while recycling in sectors such as construction and transport had risen to 70% and 90% respectively, household recycling hovered around 5% still by the late 1990s, leaving the UK one of the poorest performers amongst the EU15 at the time. However, combined publication education campaigns and investment in recycling points, had significantly improved this by the 2000s.6
ALFED has responded with revitalising its producer groups, and a vastly increased membership, as well as its strengthening of links with government. In ALFED’s diamond year, the greatest challenge facing the industry and society both now and for future generations will be in showing leadership on sustainability, as well as the legacies of Brexit and supply
ALFED ANNIVERSARY58 number of shocks of market, political and public relations nature. British Aluminium, one of aluminium’s global first movers who had dominated the UK industry for almost a century, bankrupted by crippling energy costs from its Invergordon smelter (arising both from poor strategic decisionmaking and the failure of new nuclear generating capacity and the refusal of the new Conservative government to mitigate the effects of these energy prices) was compelled to merge with Alcan Aluminium UK in 1982. That same year, the UK aluminium industry confronted adverse news stories following the sinking of the Type 42 destroyers HMS Coventry and Sheffield and Type 21 Frigates HMS Ardent and Antelope during the war in the Falkland Islands about aluminium and fire, which made connections with the fire on board the US Navy cruiser USS Belknap in 1975 in which the aluminium superstructure had collapsed and erroneously claimed that aluminium had caught fire. The subsequent Ministry of Defence enquiries repudiated these claims, supported by subsequent naval engineering research, that attributed the fire and sinking of these vessels to aluminium but it necessitated the industry to develop a coordinated public relations response to defend the industry4 Similarly, controversies over poorly informed stories around aluminium and Alzheimer’s disease, both underlined the importance of the Federation’s building up its public affairs capabilities. These were reflected in the increased development of an All Party Group on Aluminium within the Houses of Parliament, the recruitment of staff at ALFED with public relations experience, and more determined profile for aluminium in public fora. These efforts were led after 1988 by ALFED’s new secretary general Dr David Harris, alongside Labour peer Lord Shackleton and a significant number of other parliamentarians. Out of this also prospered the longstanding ALFED House of Lords lunch, which remains a highly important date in the Federation’s calendar and demonstrated the importance of the organisation’s network activities. This also impressed the importance of ever closer international ties with fraternal organisations, particularly European Aluminium and IAI (formed in 1981and 1972 respectively). (Fig 7) By the 1990s rising energy prices and pressure to reduce emissions also underlined the importance to the industry of devoting far greater attention to sustainability. Both issues became increasingly significant for ALFED over the ensuing decades. While the aluminium industry globally had been an early leader in end-of-life recovery (initially for the purposes of reclamation in war economies and increasingly as a result of rising energy costs) and recycling (notably firms like Reynolds Metals and their partnerships with drinks manufacturers), industry emissions, especially from primary and secondary production had become a pressing issue for regulators and producers requiring a major step change. Technological advancements in furnace technology, such as those led by Pechiney, made significant improvements to primary production in emissions reduction and washing in the 1980s, with the modernisation of the British Aluminium’s (and then Alcan’s) Lochaber smelter between 1978 and 1983 being a notable example. And firms like the newly amalgamated British Alcan placed an increasing emphasis on cleaning up its act between the 1980s and 1990s, specifically prioritising reducing energy costs, tackling acid rain, and scaling up the recycling of aluminium cans, including expending £28 million (around £64m in 2021 real prices) on the 55,000mts recycling plant at Warrington.5
The challenges and opportunities presented by championing sustainability also underlined the importance of ALFED and the industry cooperating with others to promote a change in consumer behaviour over recycling, as the MD of Alcan’s Ecko
6.Nick Kendal speech to the ALFED House of Lords Lunch, 19 May 1992. Lord Shackleton Papers. Houses of Parliament Archive; Perchard, Aluminiumville.
+1-800-918-2600 | gcinfo@grancoclark.com | www.grancoclark.com Hydraulic Free : Fully Electric System. GRANCO CLARK’S ALL NEW Non-Hydraulic System utilizes servo actuators and pneumatics instead of hydraulics. This includes the Log Lift, Log Pusher, Pullers, Stretchers, Hot Saw, ECS Saw and many others. Our Hydraulic Free Systems are quiet, quick, powerful and boast incredible new features. Now that your energized, let’s talk! 1-800-918-2600 Tired of Maintaining Hydraulics?
















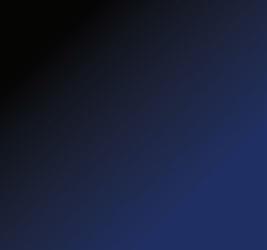
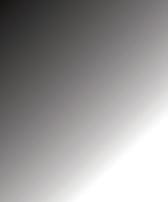


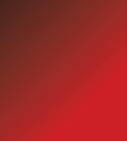
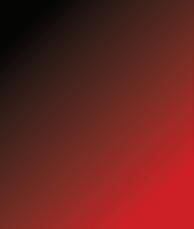

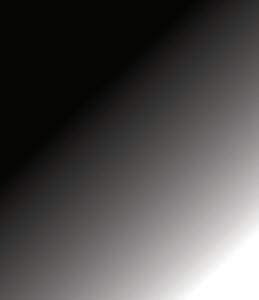
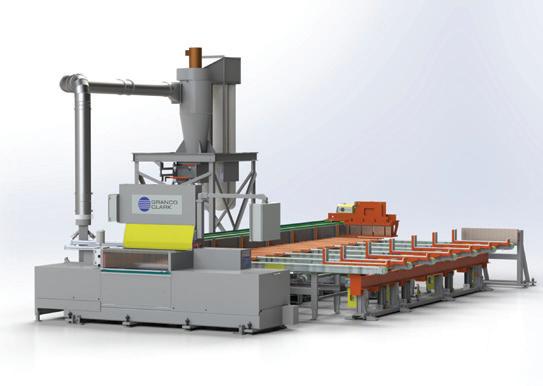
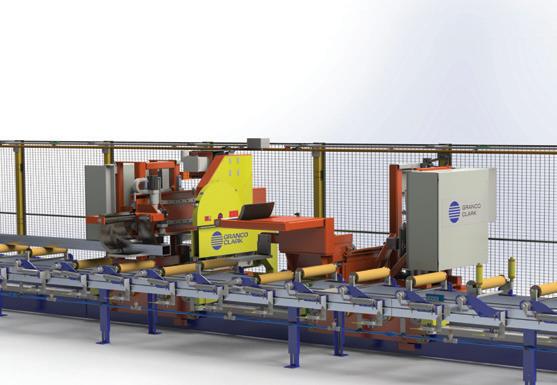
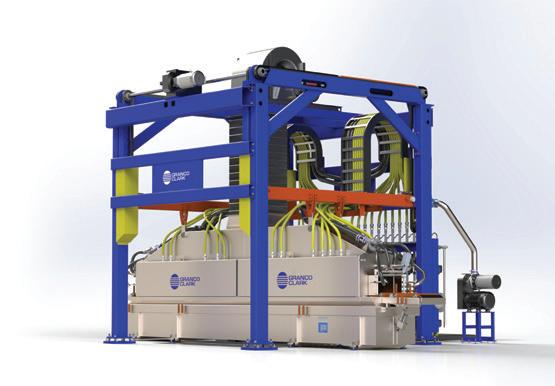
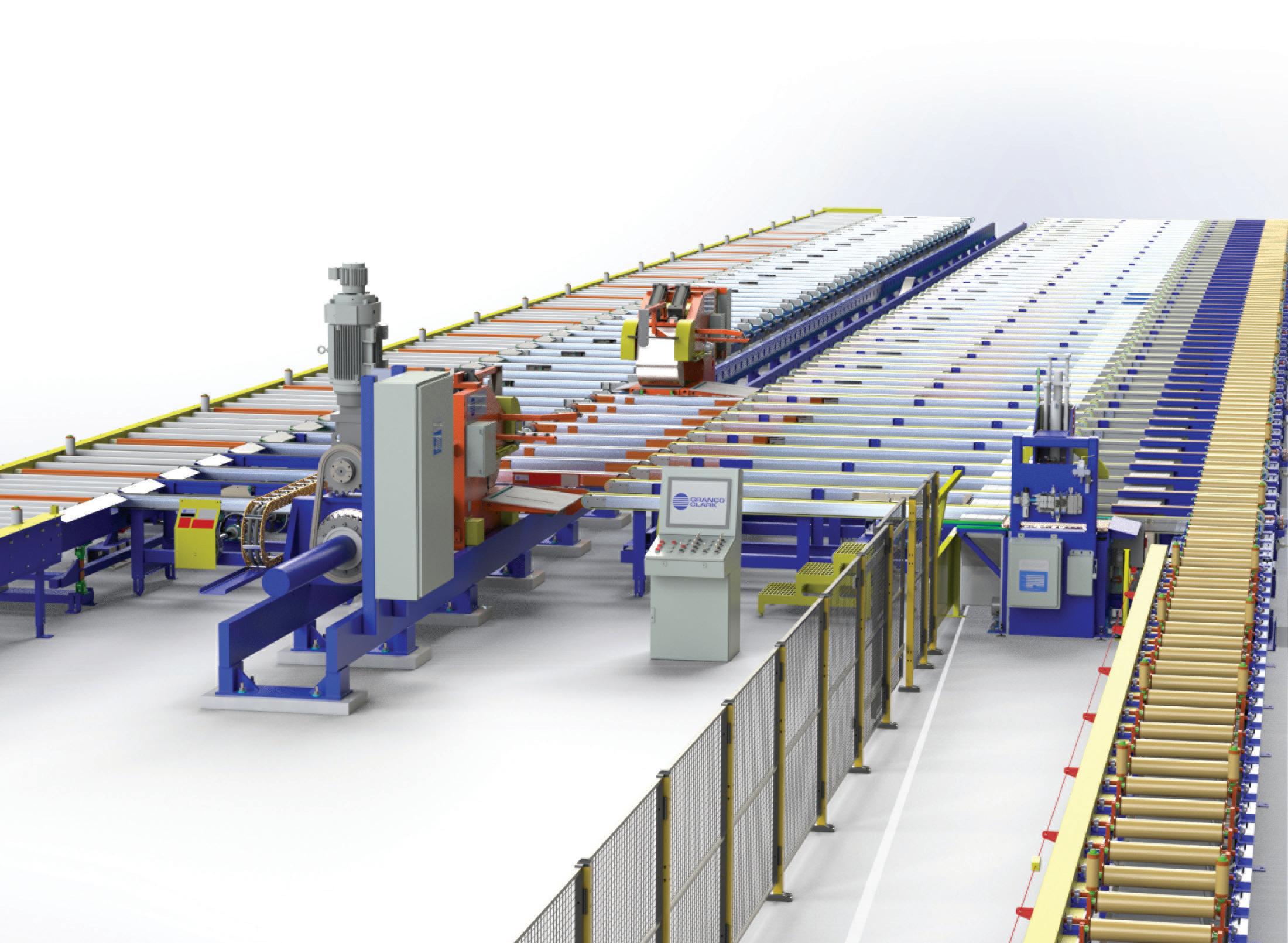
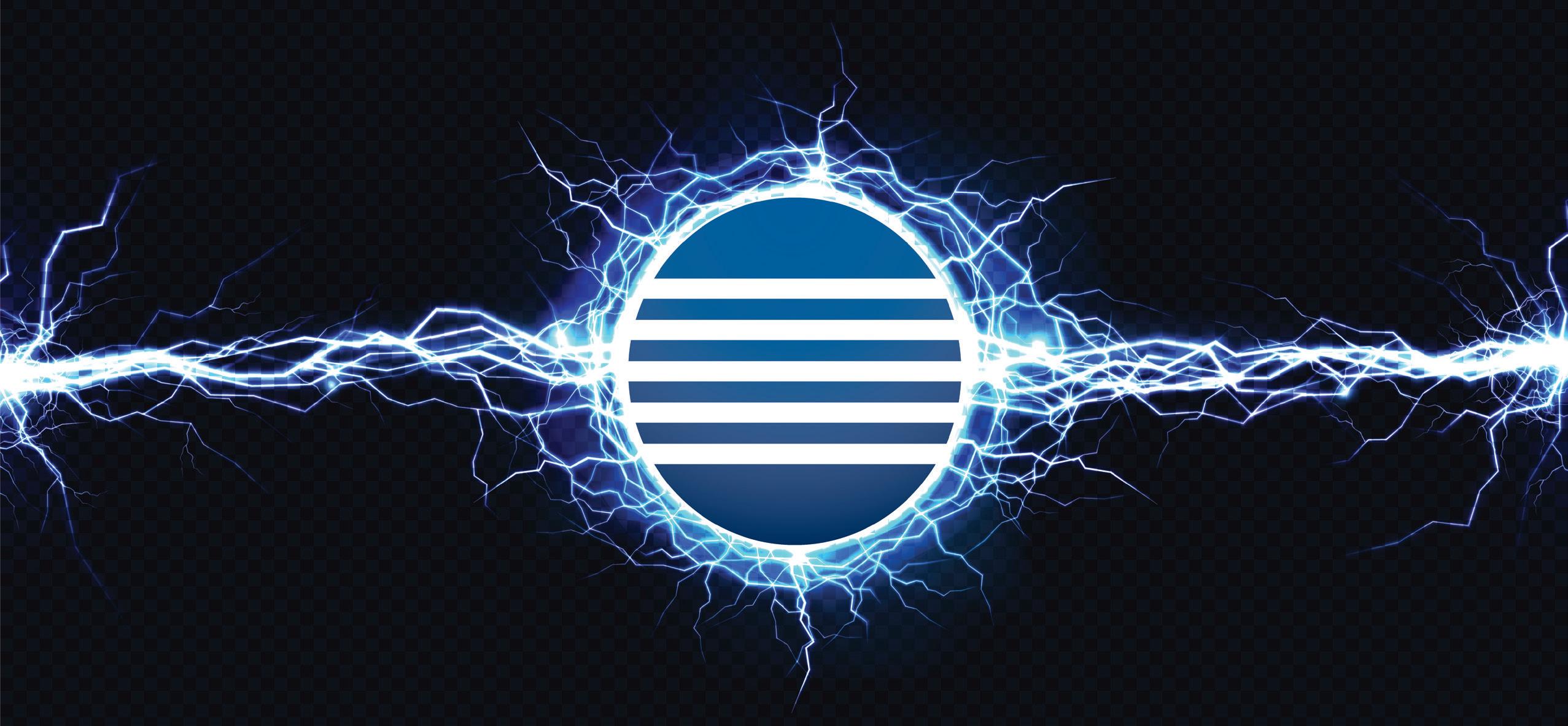
Phillipe Morel (ed.) Histoire technique de la production d’aluminium (Presses Universitaires de Provence, 1992).
Aluminium International TodaySeptember/October 2022
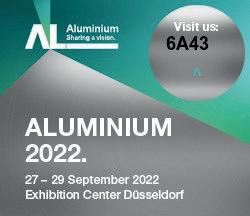
Andrew Perchard, Aluminiumville: Government, Global Business and the Scottish Highlands (Carnegie, 2012).
Novak, ‘Advances in Aluminium Relative to Ship Survivability’, Naval Engineers Journal 124 (2), pp.105-114. Ministry of Defence, The Falklands Campaign: The Lessons, (Cmd.87) (Her Majesty’s Stationery Office, 1982).
Niall G. MacKenzie, ‘Be careful what you wish for: comparative advantage and the Wilson Smelters Project, 1967-82’ In Hans Otto Frøland and Mats Ingulstad (ed.) From Warfare to Welfare: Business-Government Relations in the Aluminium Industry (Tapir Academic Press, 2012), pp.163-198.
Kyle A. Crum, Jerri McMichael, and Milsoslav
ALFED ANNIVERSARY60 chain disruptions. Here ALFED, as the voice for UK aluminium, can look to historical precedent to lead and support the sector. ALFED, like the industry, has risen to such challenges in the past with innovation. Throughout ALFED’s 60-year history, the challenges and opportunities facing the industry through changing circumstances have prompted cooperation and renewal. That has required bold and clear sighted leadership within ALFED at pivotal moments to reform the Federation and its governance, to reorientate its strategy, and to equip it with the capabilities to meet fresh challenges and opportunities.�
ALFED/ Fraser of Allander Institute, The Aluminium Industry in the UK (ALFED, 2022)


Otto Realf Norland, The Magic of Merchant Banking (Oslo, 2022).
Fig 8. ALFED 1998 Cover
Marco Bertilorenzi, The International Aluminium Cartel: The Business and Politics of a Cooperative Industrial Institution, 1886 – 1978 (Routledge, 2016). Marco Bertilorenzi, Aluminium’s Advocate: The Historical Evolution of a European Trade Association, 1981 – 2021 (European Aluminium, 2021)
RIEDHAMMER carbon@riedhammer.dePhone:KlingenhofstraßeGmbH7290411NürnbergGermany+4991152180www.riedhammer.de ANODE BAKING FACILITIES CARBON BAKING TECHNOLOGY DESIGN > MANAGEMENT > TURN -KEY PROJECTS The RIEDHAMMER anode baking facility is a key component in a modern anode production plant. Our plants offer many advantages such RHSafeFlexibleHighLowExtendedExcellentCustomisedas:designanodequalityfurnacelifetimeenergyconsumptionproductivityequipmentsupplyoperationmaintenancestrategy 98 YEARS OF INNOVATION
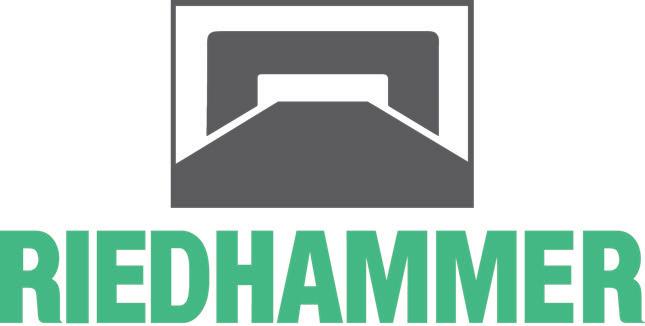
Andrew Perchard, ‘This Thing Called Goodwill: The Reynolds Metals Company and Political Networking in Wartime America’, Enterprise & Society 20 (4) (2019), Andrewpp.1044-1083.Perchard and Niall G. MacKenzie, ‘Aligning to Disadvantage: How corporate political activity and strategic homophily create path dependence in the firm’, Human Relations 74 (7) (2021), pp.978-1006.
References: ‘The Changing Shape of the U.K. Aluminum Industry: An Interview with Will Savage, ALFED’, Light Metal Age (February 2015), ‘Thepp.58-9.Aluminium Federation: More than a fifty year story’, Aluminium News 3 (December 2019), pp.14-16. ALFED/ Fraser of Allander Institute, The Aluminium Industry in the UK (ALFED, 2021)
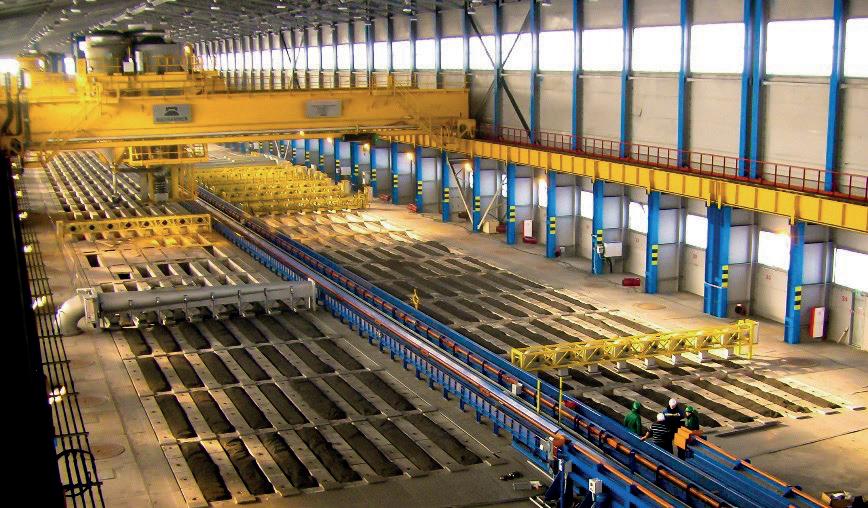
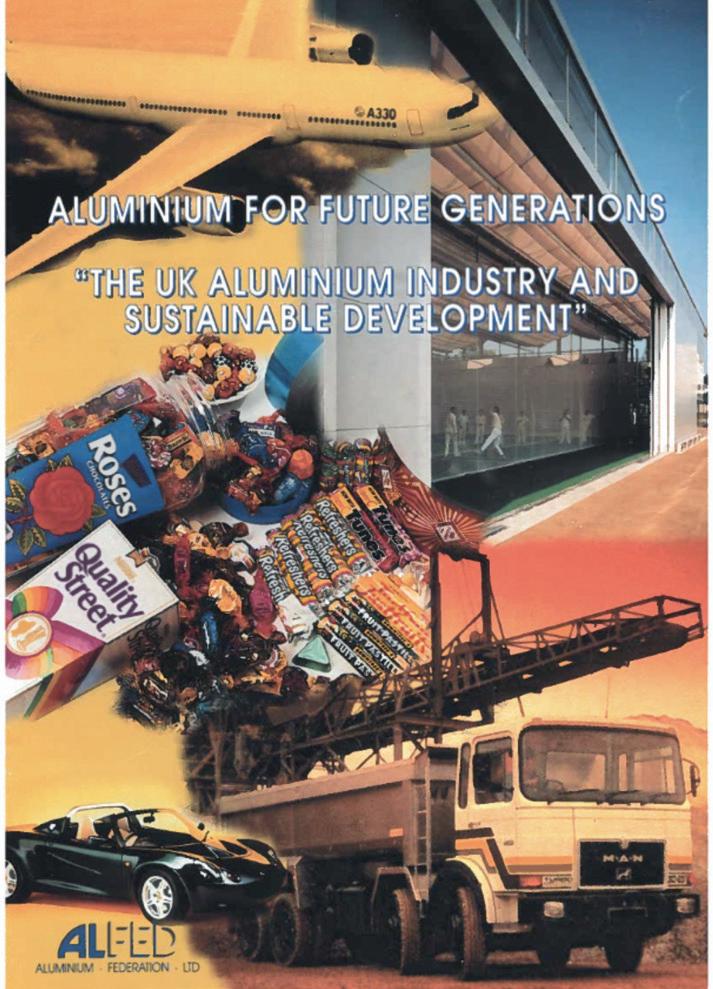
PSImetals empowers sustainable operations for generations to come www.psimetals.com/ Software Excellence for Steel & Aluminium Producers
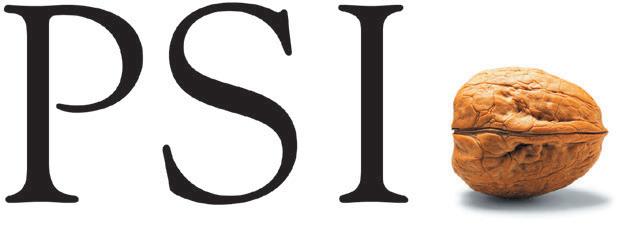
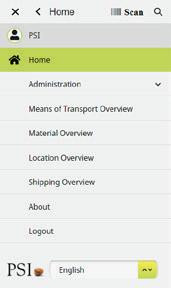
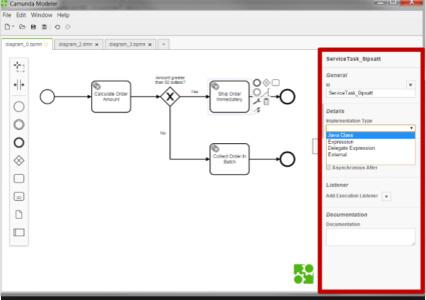
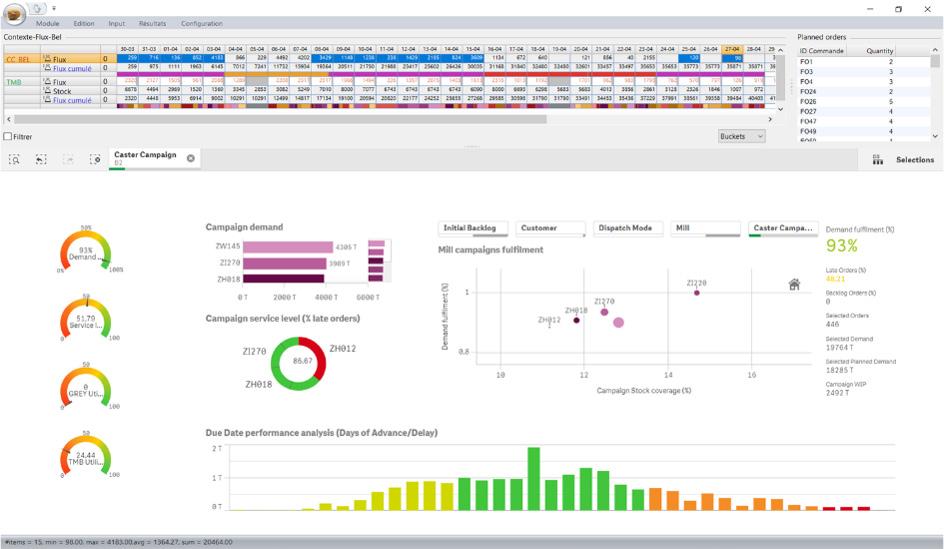
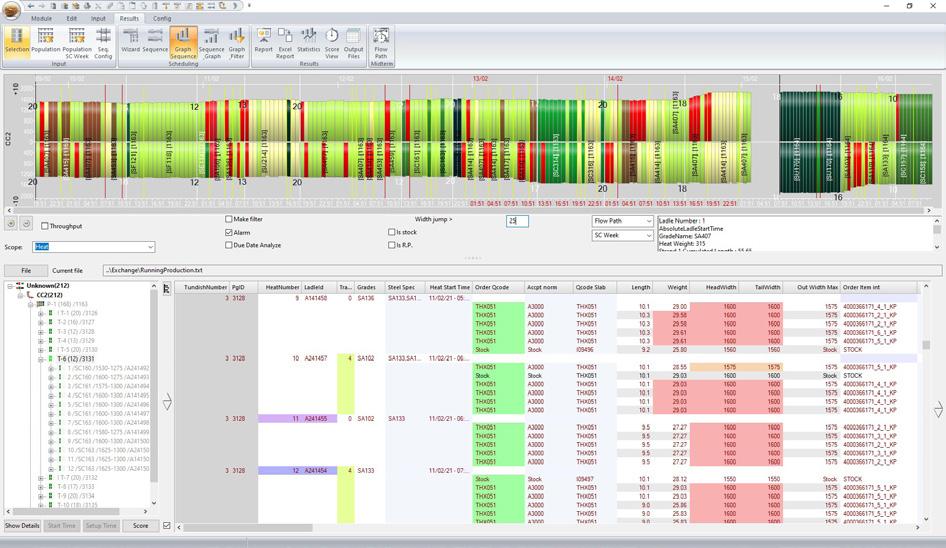
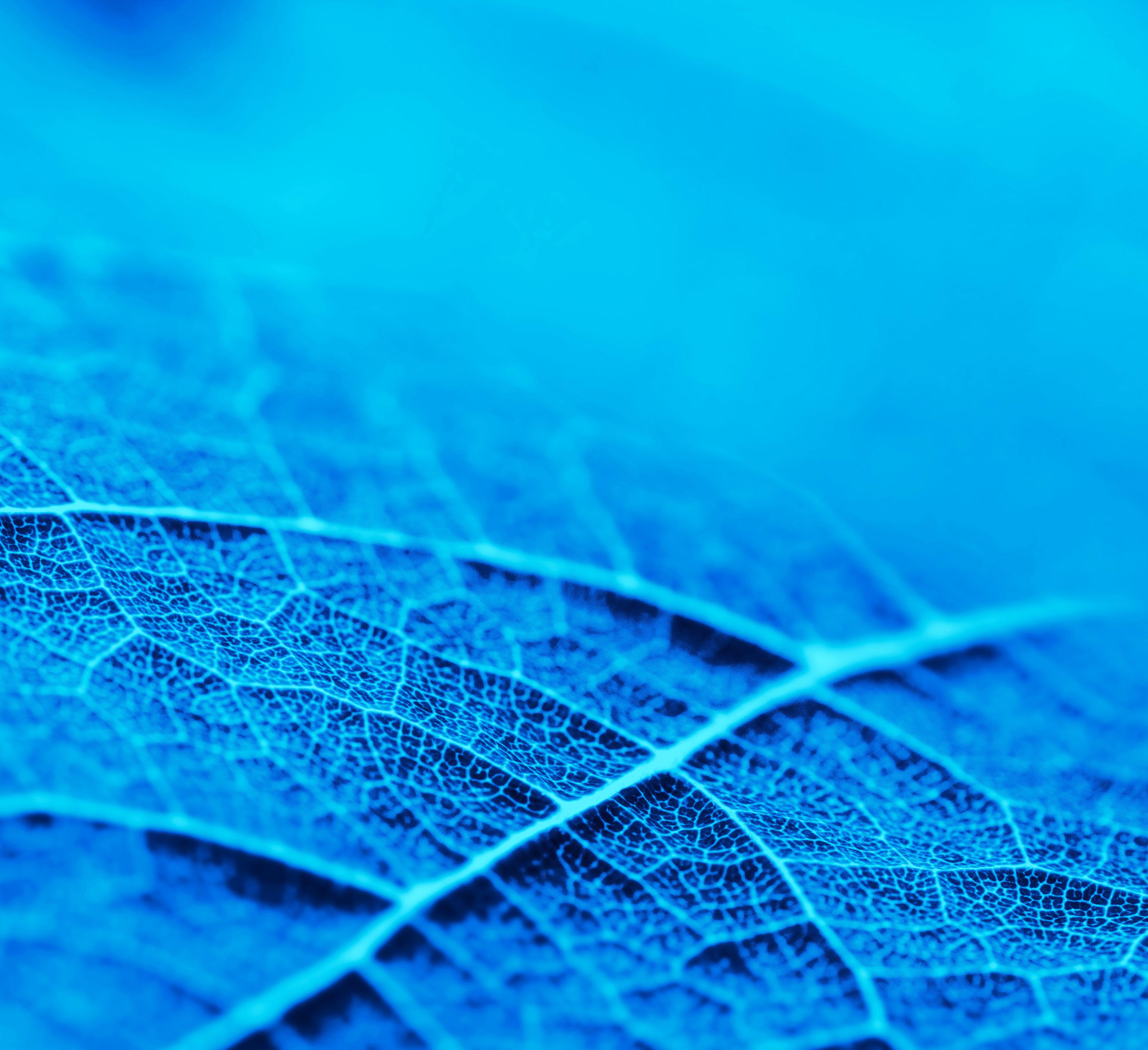
The next dimension in grain refinement Up to 85% less grain refiner needed for cost savings 120% relative efficiency compared to high efficiency refiners Reduced particle count consistently increases melt quality Made with low carbon aluminium +44 (0) 121 684 0175 | info@mqpltd.com | www.mqpltd.com
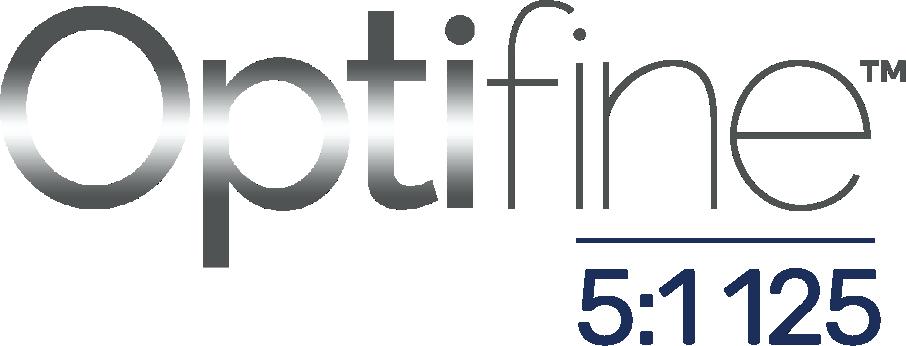
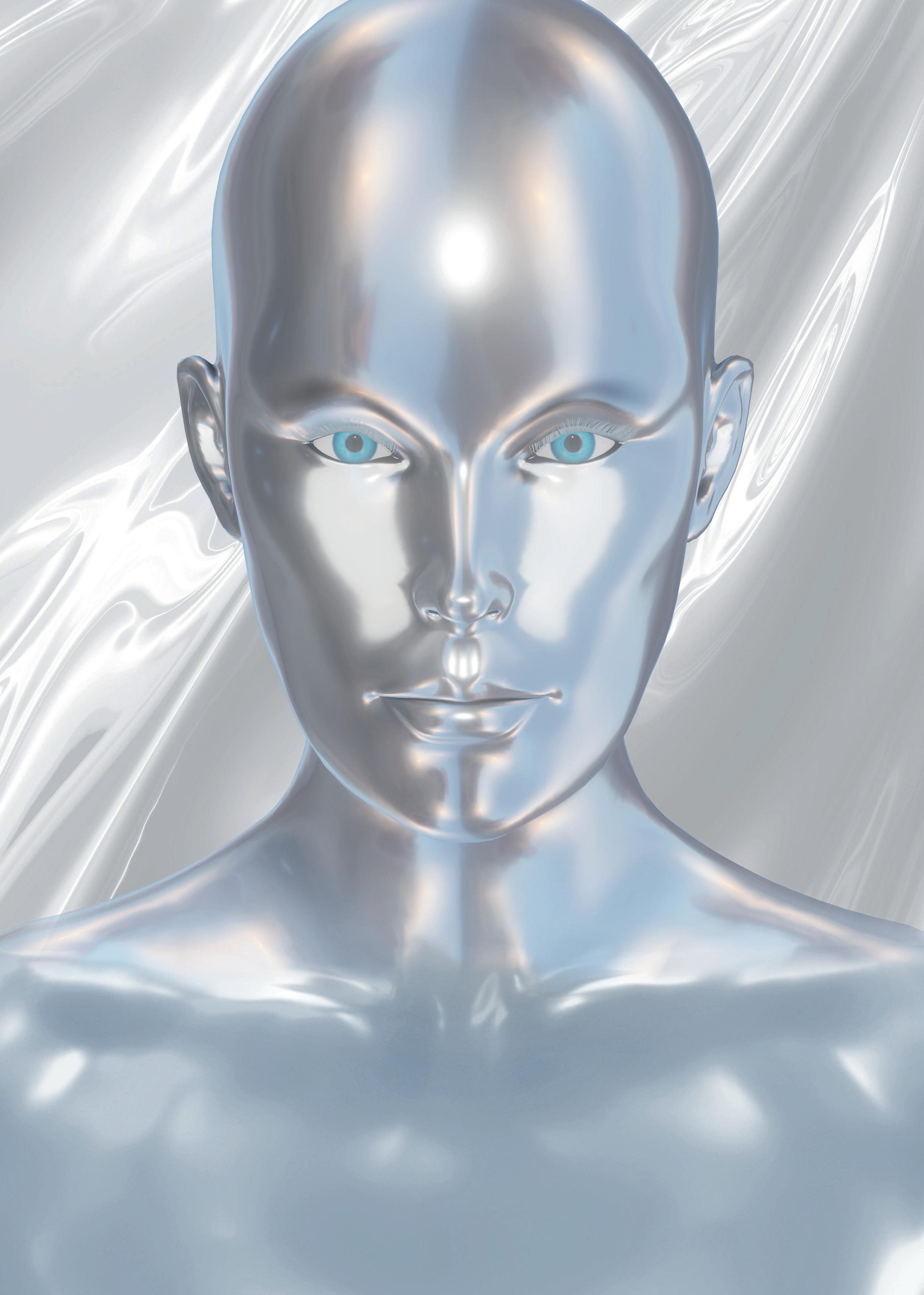
The digital transformation journey is already underway in countless businesses around the world. It is on even many more executives’ minds who, for many valid reasons, have yet to execute their plans to embrace digitalization. In fact, 72% of over 1,300 manufacturing executives that were surveyed by BCG in 2022 have said they consider advanced analytics to be more important now compared to how they felt just three years prior. With continually increasing uncertainty, this change in outlook has happened–and continues to happen–at an extraordinary pace. Depending on the size and maturity of your company, you have probably considered going digital because operations have simply become too complicated and dynamic to sustain them manually. Perhaps they have even started to occur at a larger scale. Such cases necessitate technological solutions, not just for profit, but simply to keep the motor running. Others may find that their goals are standing just out of reach and just need to find the right stepping stool. This is true even for many who have already started their digital journey. McKinsey’s latest Global Survey provides us with a reliable framework for where attention in the transformation process should be given.
With so much ongoing buzz around AIbased solutions in business planning, what can we expect to change in the coming years for the aluminum industry? More importantly, how will we be required to change with it? By 2023, organizations across all sectors are predicted to invest close to $6.8 trillion in digitalization efforts. The initial reason for this push is quite obvious: automation of business operations leads to higher accuracy and saves time. Zeroing in on the nuance of these motivations, however, can tell us a much more detailed story–one that can help us discern effective targets to aim for when undergoing the digital transformation process. Because businesses are made up of many variables, ensuring that any upgrades you make are worth the investment requires consideration of more than just the end result. To discover what will work best for your manufacturing business, there are a few questions that will help shed light on some of the overall aspirations that drive the digitalization mindset as well as a few of the biggest foreseeable challenges that can hinder maximum potential. By exploring these facets of such sizable business decisions, gauging where your company lies in the process will become clearer. This assures your organization can take confident and decisive next steps.
Why are so many going digital?
Behind the digital transformation mindset
The Case of Heiniger Heiniger, a leading metalworking manufacturer focused on high-quality animal sheering equipment, faced a challenge in its sales planning due to scattered data and cumbersome manual, repetitive processes. In the span of a mere eight weeks, Heiniger implemented a mobile-based data integration solution that both digitized its sales planning efforts as well as allowed multiple departments to * Regional Vice President, Channel for Jedox, Inc
DIGITAL MANUFACTURING 63 Aluminium International Today September/October 2022

The greatest loss of maximum potential benefits when undergoing a digital transformation occurs most often in the implementation stage. Understandably, fear of making costly mistakes is why many are still seeking useful guidelines to achieve transformation and optimize value creation across the enterprise. In addition to these motivations, another major impetus for digitalization is harnessing the power to face unpredictability. Businesses have had to make peace with the fact that supply chain disruptions aren’t ending any time soon. For example, among some of the top supply chain threats manufacturers are expected to face in 2022 are demand unpredictability and supplier risks and delays. To address the difficulties that companies are facing with regard to planning and forecasting, many have begun to implement AI-based solutions for these reasons alone.
By Christian Ritter*
In doing so, you may discover that the digitalization process does not necessarily require dramatically expanding your resources. Quite the contrary, it may even unveil new ways of condensing existing systems or processes. The advantage to this method is, of course, augmenting the power of the resources you already have without having to trade valuable, straightforward usability for those who will be transforming alongside the company itself. Will your solution be ‘one-size-fitsall’ or something more personalized? Unique circumstances come with unique demands. In addition to the external factors that influence the day-to-day operations of your business–think supply chain disruptions, for example–there are just as many internal factors that should be considered as you are making the digital leap. Your industry, type of workplace–whether it is a traditional office space, completely remote, or more often than not, a hybrid of the two–and all the personalities and skill sets that make up your workforce are some of the key determinants in deciding how best to move forward in the digital transformation journey.
64 perform self-service analysis with instant mobile access to customer data any time of day or night. Their seamless sales planning process has greatly reduced time while supporting improved profitability.
Steinart’s example illustrates how taking a personal inventory and developing deeper awareness of your unique situation can lead to simplicity without sacrificing sophistication. One-size-fits-all models for automated solutions can absolutely serve an adequate role in business enhancement and should be considered as part of the transformation process. Once your company is enabled by the gains it has already made, then it may be time to reassess if more fine-tuned updates are necessary to meet your needs.
The carrot dangling in front of us can block what is up ahead if we don’t take a holistic approach to systemic change. If companies are singularly focused on day-to-day output as opposed to the big picture, they may discover not long after implementation that the new tools are not as intuitive as they thought for their users. This means that for any company-wide changes, it is important to prioritize userfriendly options that are, at the baseline, easy to navigate and learn. Not only will this approach lead to the immediate gains that one expects with automated processes, but ensure smooth business continuity during the transformation. Any progress is still progress
sitting on your checklist as of today, ask yourself how these goals coincide with each other.
At times it can be overwhelming not only to parse out what solutions are out there, but also which of the many options offer the greatest value-add Sometimes it is important to take a step back and remind ourselves that planning for something as wide-ranging as a complete digital transformation takes time and requires patience. Discussing is progress. Research is Theprogress.results from the aforementioned McKinsey Global Survey reflect this truth very well. It reports that companies experience success in correlation with the number of actions that comprised its transformation process, not by following a specific subset of actions. Such a finding should empower executives to take any plans they have for change out of storage and bring them to the forefront of their business planning. By extrapolating personal insights from this list of questions, you can feel confident exploring new terrain in your digital transformation journey, with no hiking gearOrientingrequired.your company’s mindset towards digital transformation through even the smallest steps you can take will bring you closer towards adaptable and scalable processes that simply your business complexities. The hype and buzz around digital transformation may try to push you in specific directions. Delve into a personal inventory of what is benefiting your company today and what will add value tomorrow. Those answers will be what successfully advances your digital transformation journey. Christian Ritter is the Regional Vice President, Channel for Jedox, Inc., an award-winning provider of Enterprise Performance Management solutions. With more than 20 years in supply chain and technology, he brings a unique expertise to helping organizations understand how to achieve a culture of decisiveness and confidence and outperform expectations again and again. � http://www.jedox.com
Feeling stuck in the digital transformation process?
A common stumbling block businesses encounter in the digital transformation process is prioritizing power over implementation. To reiterate, McKinsey’s Global Survey has indicated that the implementation phase is where most of the maximum potential benefit is lost. Without understanding the human cost of implementation, e.g. the time and effort required of all workers who will be using the new systems, there will be additional roadblocks that delay or minimize success.
The Case of Steinert Consider the success of Steinert, a leading mechanical engineering firm in magnet and sensor sorting solutions. As the world’s only full-range provider of sorting and separation technologies, they needed to undertake a more granular search for ways to accommodate business growth. Recognizing where operations became increasingly more complex, they set out for a new method of monitoring a wide range of long-term projects that require close, accurate supervision. With the implementation of a new, integrated solution that can draw from a centralized pool of data, Steinert’s management accountant can now adapt to new business developments swiftly and independently. By seeking to replace unnecessary complexity with an easyto-use integrated system, they were also able to increase the speed of their global reporting by five times. Companies that are diverse in functionality and require vast amounts of flexibility may need to look into prioritizing accessibility of information that can, in turn, enhance both the output and the experience of its workers.
Aluminium International TodaySeptember/OctoberDIGITAL2022MANUFACTURING
What’s on your digital transformation checklist (so far)? Clearly, optimization of time management and accuracy of data is one of the main driving forces that has drawn so many towards automated solutions. Some may strive for more robust collaboration potential between departments by improving lines of communication between decision makers and those with necessary information. Other times, businesses may prioritize flexibility in decision-making when daily fluctuations influence their large-scale operations. These motivations are inextricably linked to each other, particularly in optimizing the ability to collaborate with accurate, real-time data. From this particular angle, we can observe how taking an integrated approach to building your digital transformation checklist can be beneficial in the search for a solution that will lift your company’s operations and improve businessWhateverperformance.maybe
For those that have already waded into the waters of technological advancement and have found themselves treading in the deep end, it is important to reevaluate the perspectives that have informed their transformation journey. While this sounds like you may want to know what is going on at the top, oftentimes it is the opposite. You need to look at your processes from the ground up.
Zero Friction Aluminium Induction Billet Heaters • Specialist Frictionless Billet Handling • Bespoke Made to Measure Systems • Tapered Heating using Multi-Zone Coils • Precise Closed-Loop Temperature Control • Increased Productivity and Temperature Accuracy • 50 Year History Serving the Extrusion Industry Call +44 (0)1256 335 533 Email: www.inductothermhw.cominfo@inductothermhw.co.uk AIT 2020 - AD-1.indd 1 18/12/2019 15:43:43 Our premium steels TQ1, CS1, Q10 and HP1 are characterised by particularly high heat resistance and high toughness: ∙ Optimal for highly loaded extrusion tools Long lasting tool life In addition, we offer numerous premium services such as: ∙ Modernisation of tool technology FEM analyses to improve performance Visit us at Aluminium 2022 in Düsseldorf, Hall 3 Stand A71 Premium Steel and ExtrusionServicesPremiumfor Kind & Co., Edelstahlwerk, GmbH & Co. KG Bielsteiner Str. 124-130 D-51674 Wiehl Fon. +49 (0) 22 62 / 84-0 Fax +49 (0) 22 62 / 84-175 info@kind-co.de www.kind-co.de
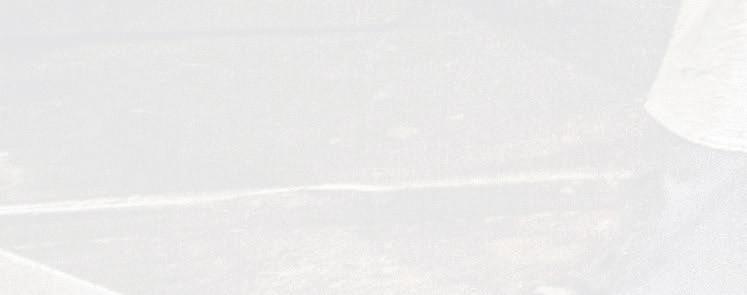
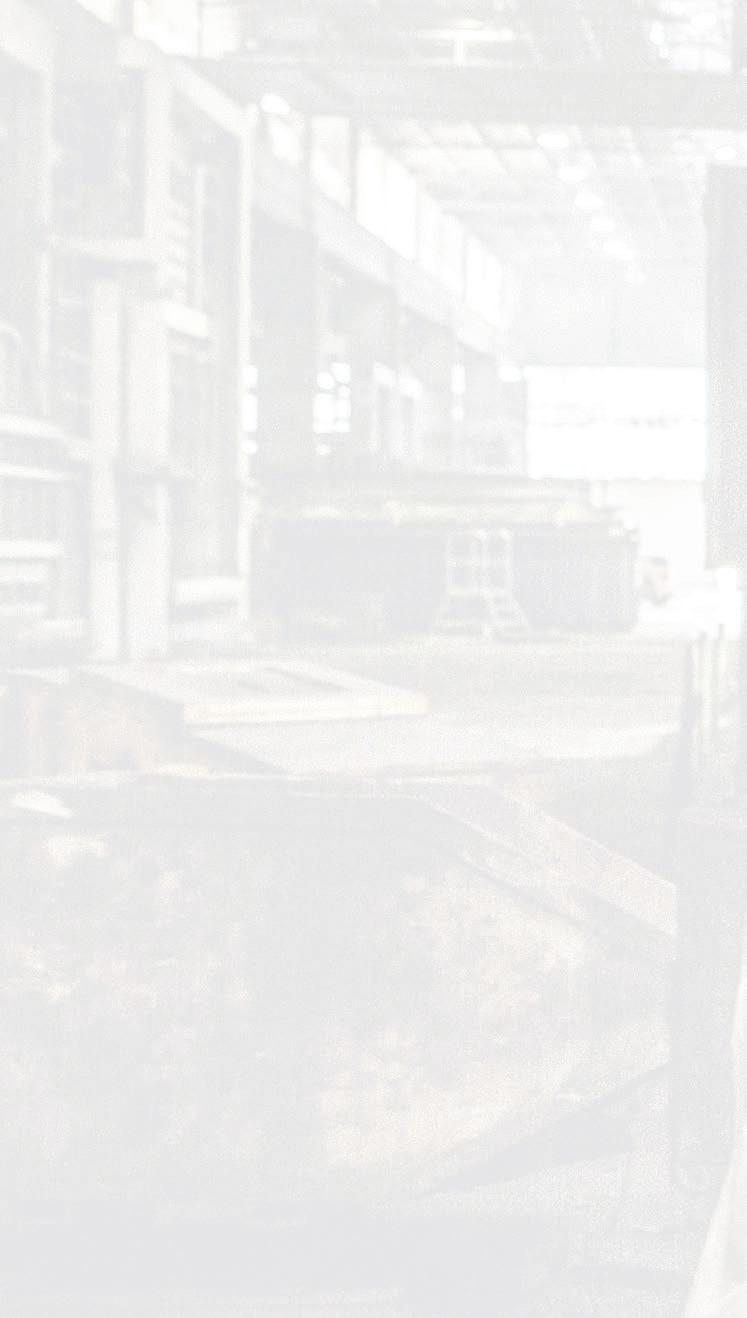
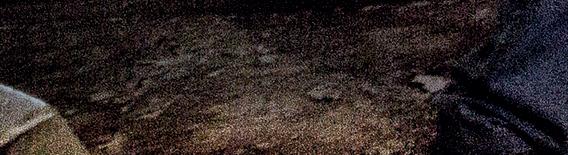

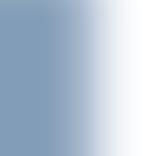
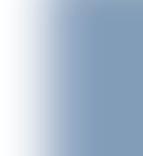
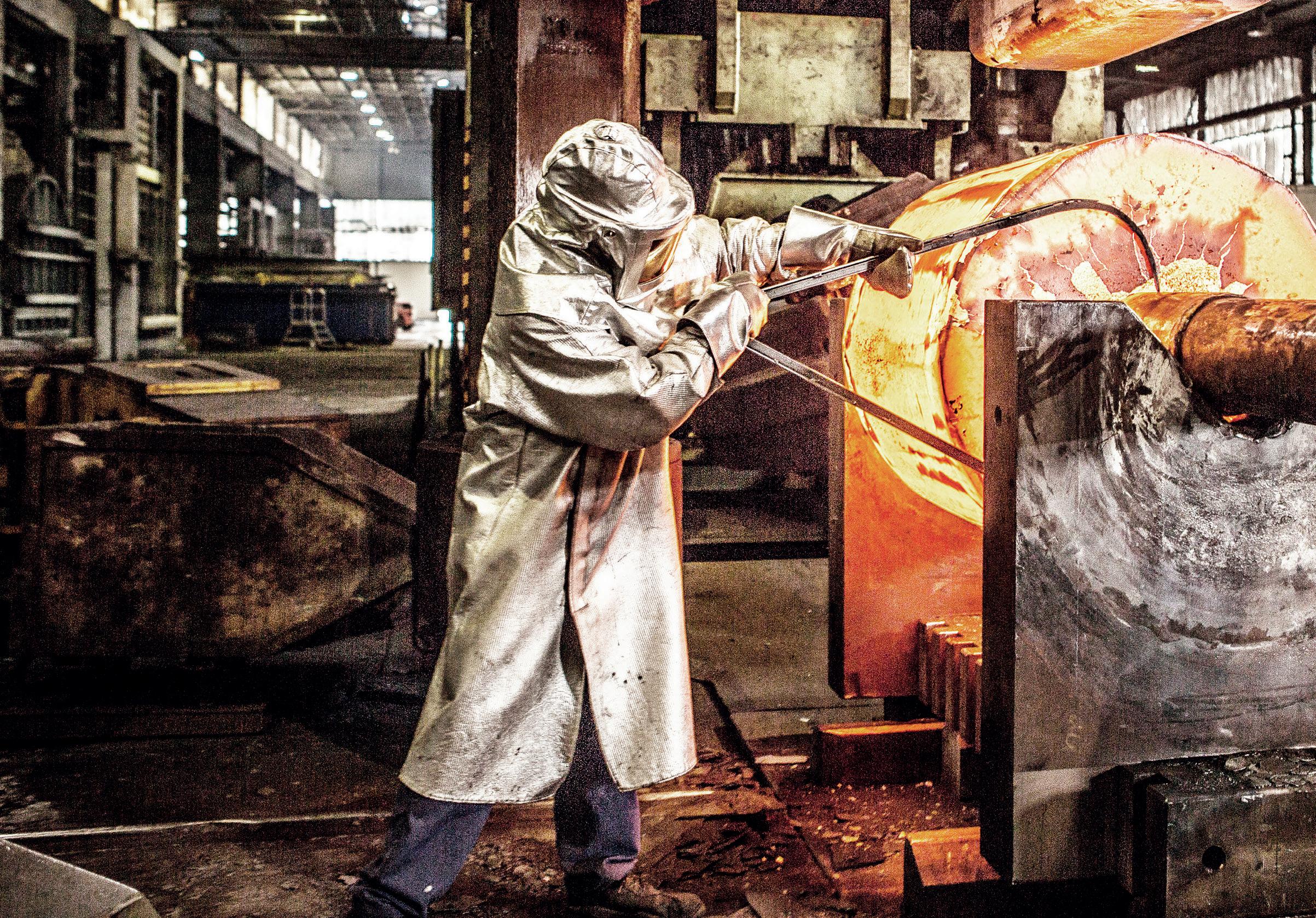
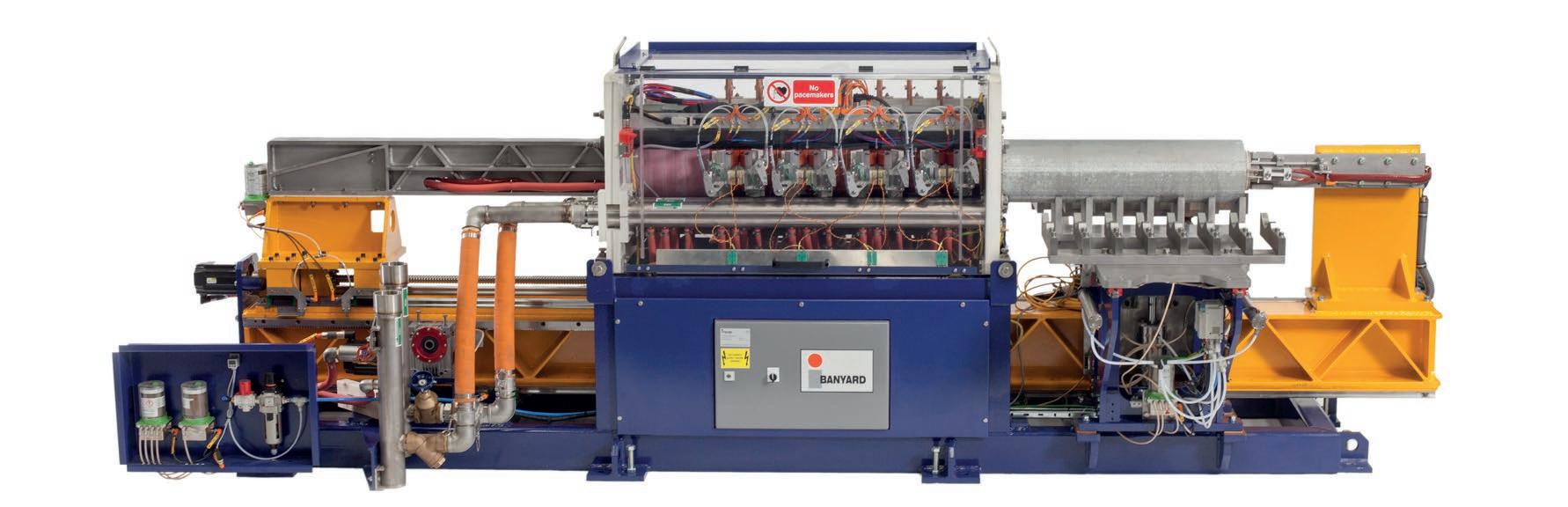
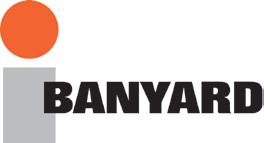
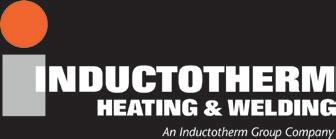
danieli.com DanieliTwenty answers to be a step ahead 01. Sustainability 02. CO2 reduction 03. 4.0 intelligent plant 04. MIDA ECR 05. QSP DUE 06. Digimelter 07. Energiron DRI 08. Long-life BF 09. Quality slab casters 10. Pickling and cold mills 11. Galvanizing / Air knives 12. Billet casters 13. Billet welders 14. Wirerod mills 15. Rail and section mills 16. The Drawer sizing block 17. Reheating systems 18. Seamless tubes 19. Extrusion lines 20. Aluminium mills

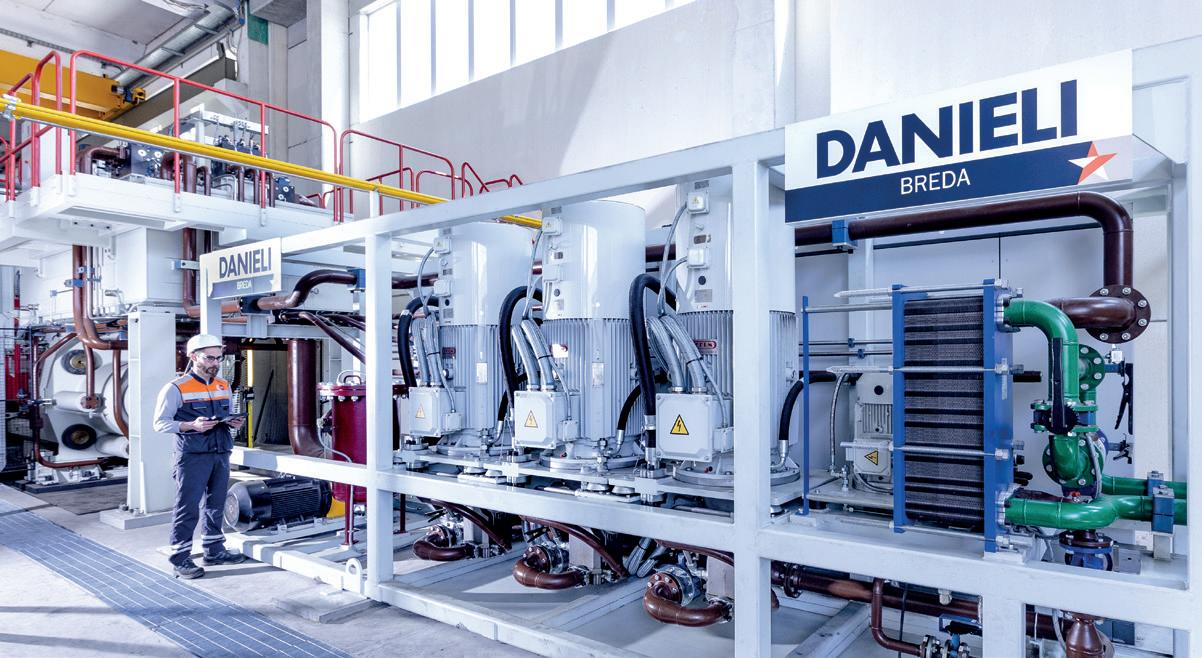

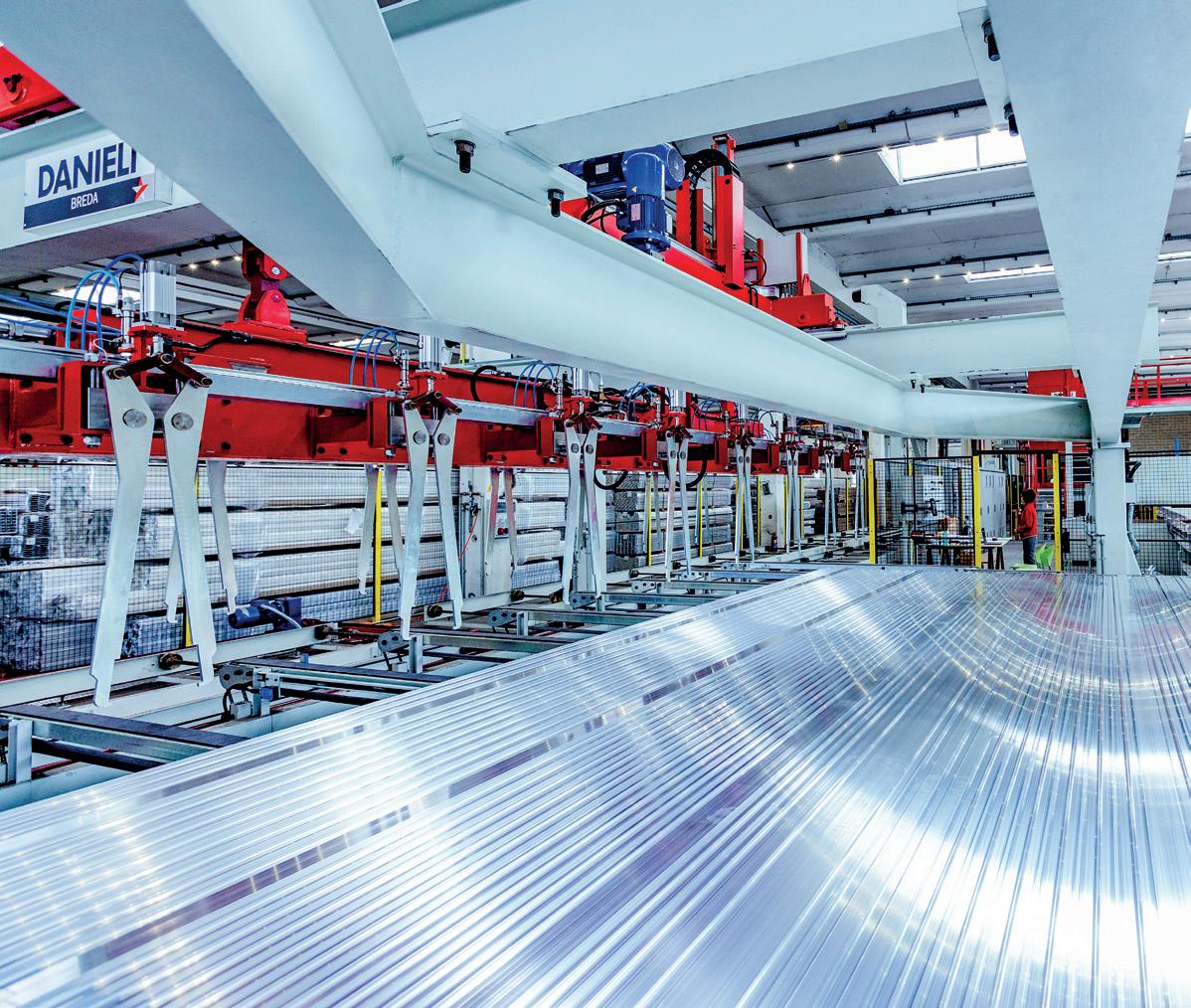
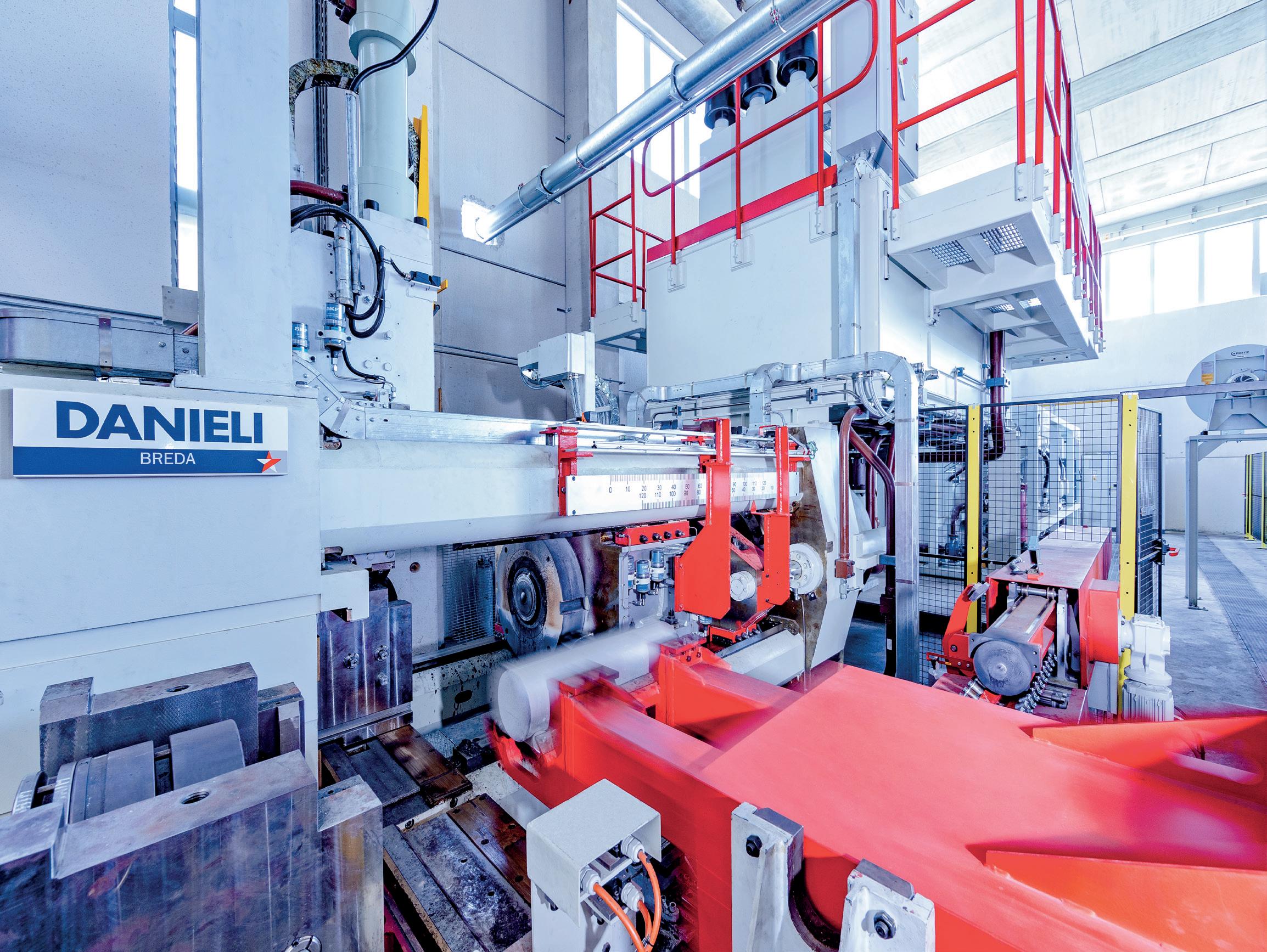
The patented Ecoflame gas billet-heater minimizes heat loss from the exhaust fumes and reduces gas consumption per extruded ton up to 30-35%, depending on the product mix. Accurate taper heating of the billet is achieved through new-design burners. Multivariable transducer controls correct the stoichiometric gas and air mixtures, reducing maintenance and manual adjustments. In the downstream area, a patented electrical stretcher allows a more accurate repeatable stretching stroke while reducing maintenance operations.
Danieli patented solutions cover the upstream, extrusion and downstream technology areas, for lower energy consumption and lower OpEx, whilst allowing production flexibility through proprietary automation control systems featuring HMI remote-control via tablets.

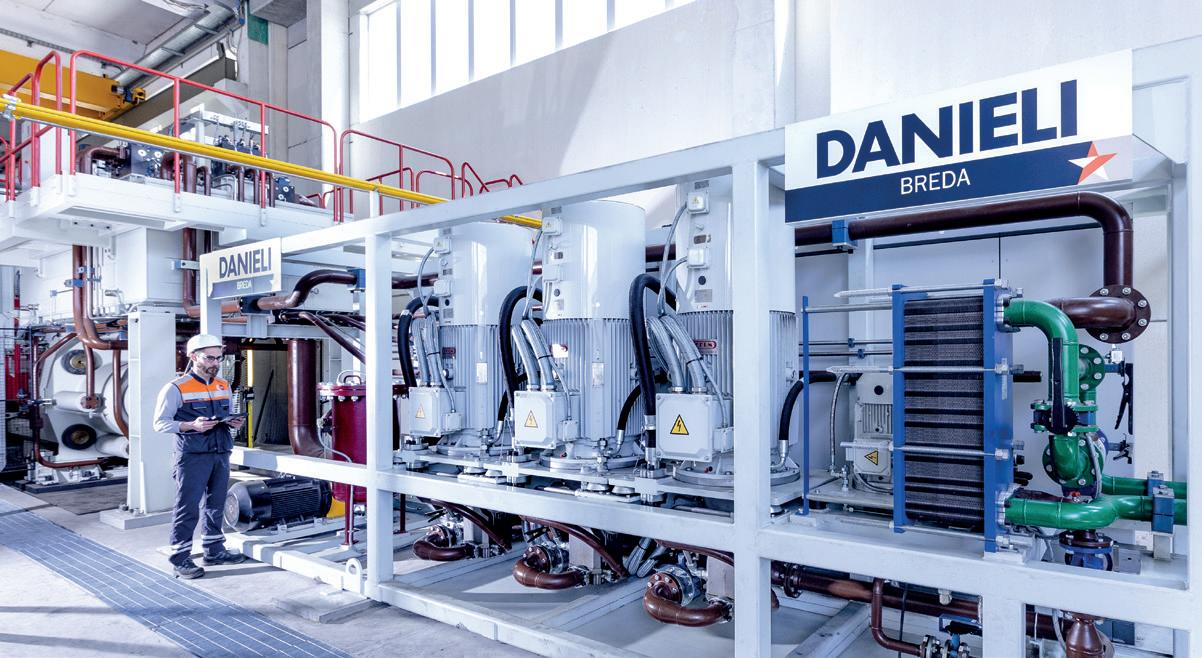
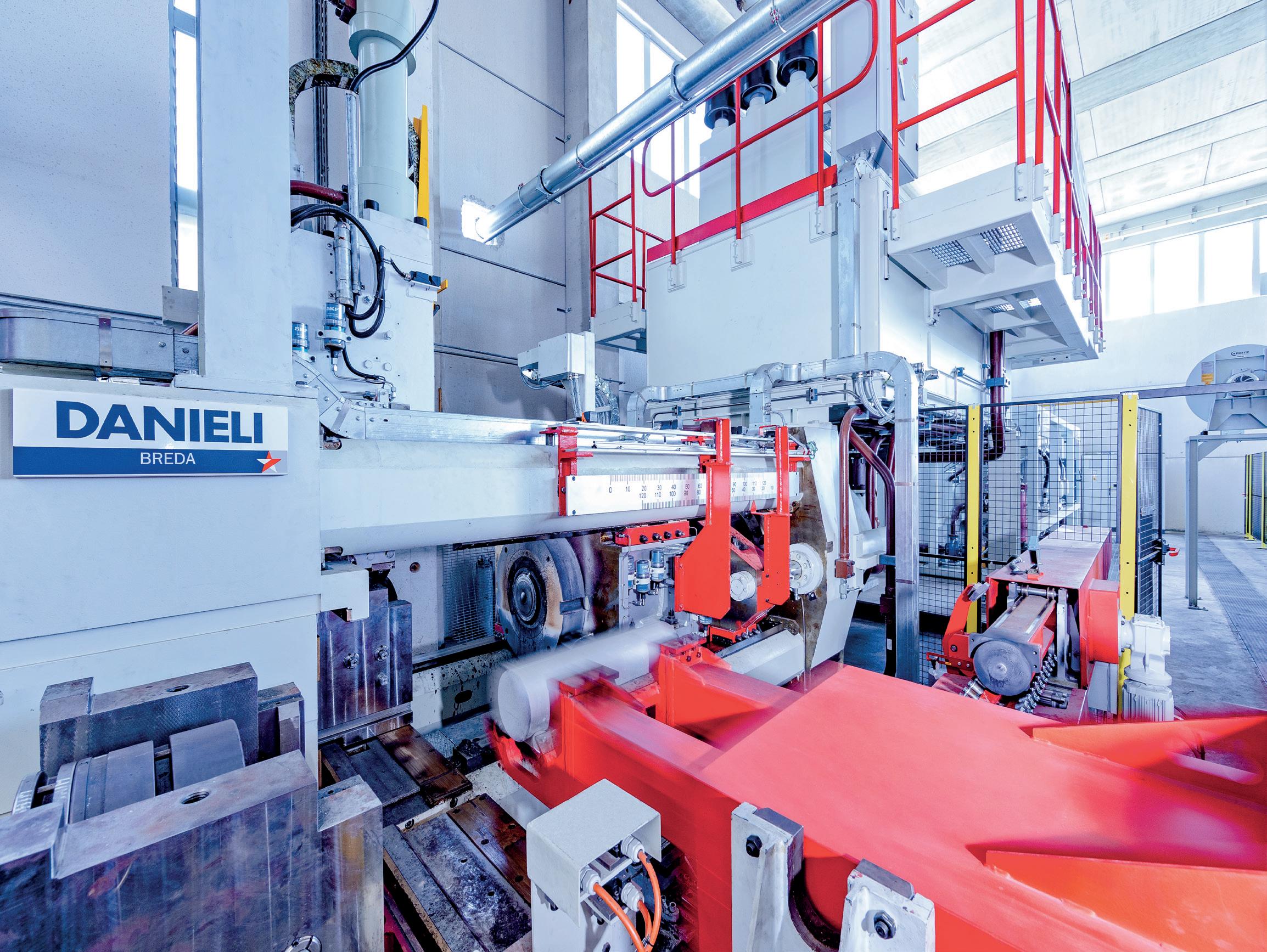
ESED 4.0 is the Danieli-patented energy-saving solution for extrusion presses, achieving average energy savings of 25-30% compared to traditional systems.
Energy-saving, higly-efficient solutions for integrated extrusion plants
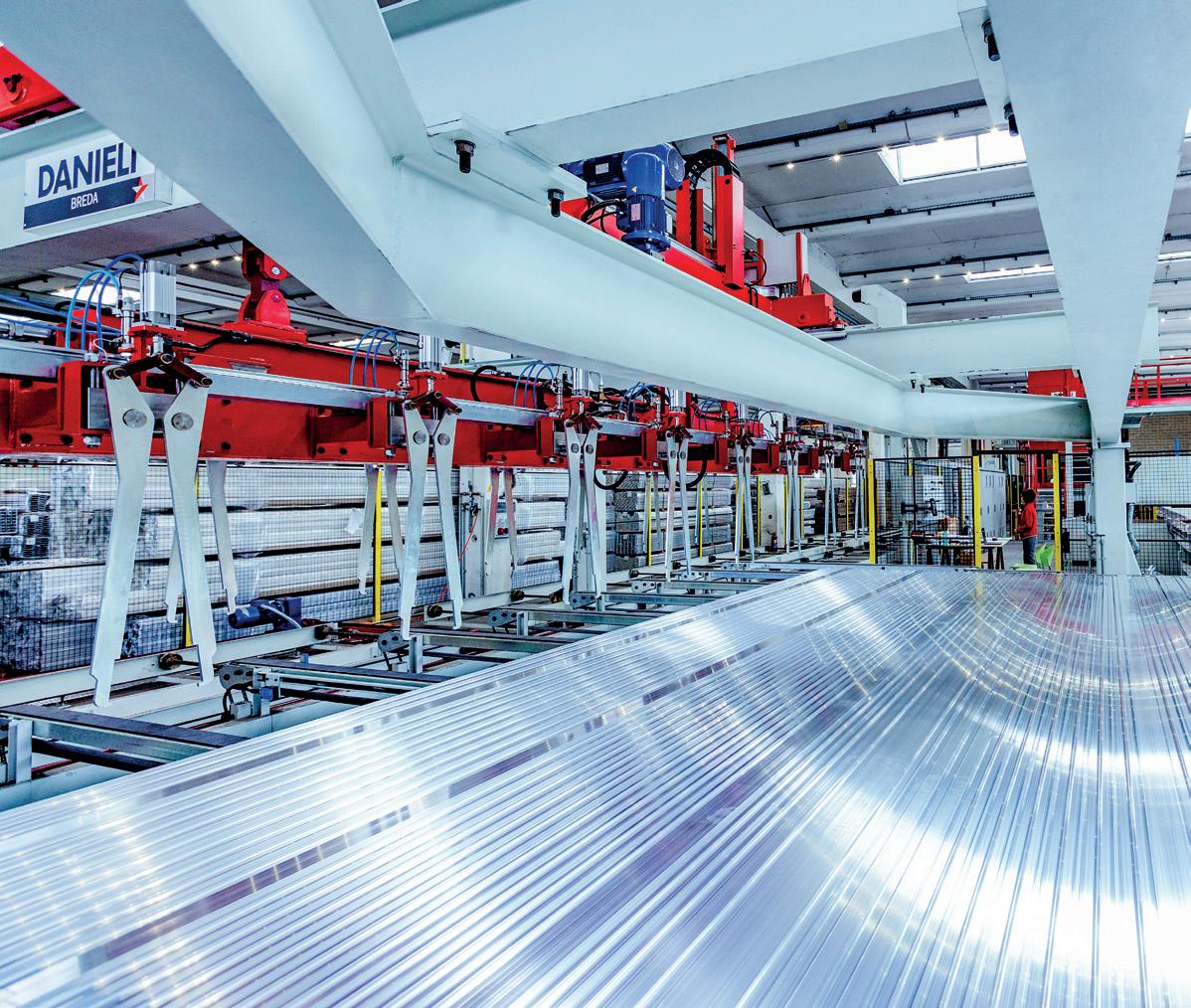
The new, “nimble crab” fully electric billet loading, handling/transferring the billets directly from the heater to the press, reduces the billet heat/energy loss significantly and improves billet temperature accuracy by 5-7%.
19ANSWERaheaatoaDanielinswersbestepD
Danieli breDa extrusion benchmark technology
In the primary aluminum business, part traceability protects manufacturers, buyers and sellers by providing a set of authentic and valid data. By tracking each individual product, the information can be narrowed down to a specific batch or production process. Laserax’s laser technology is the most widely used marking method to identify and guarantee the origin of sustainable aluminum. We are proud to work with leading primary aluminium producers around the world to drive a meaningful change for product transparency and sustainability.
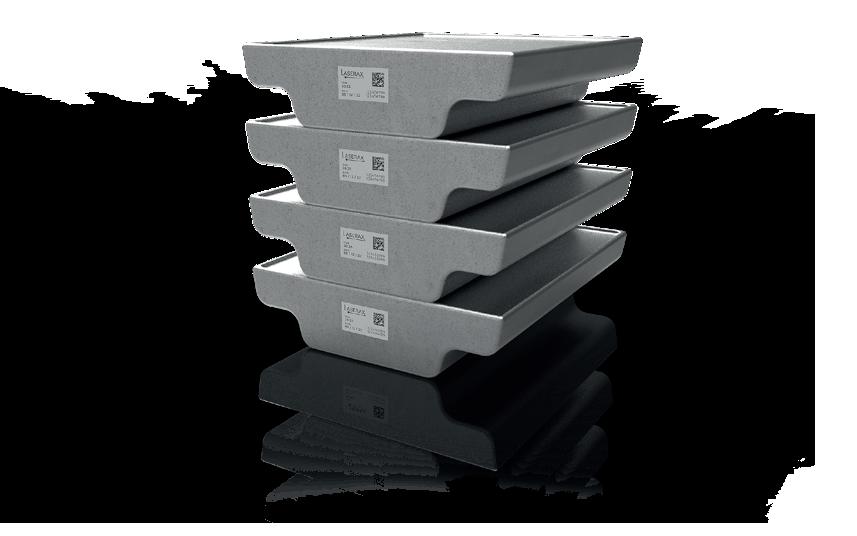
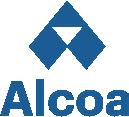
BEST OF THE BEST LASER SOLUTIONS FOR APPLICATIONSTRACEABILITYFORTHEALUMINUMINDUSTRY
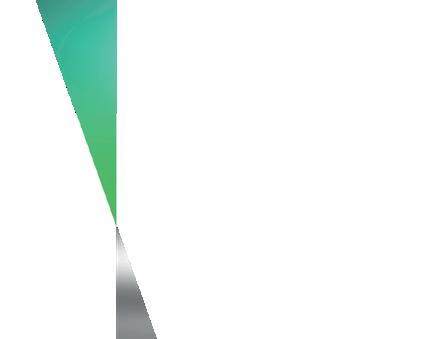
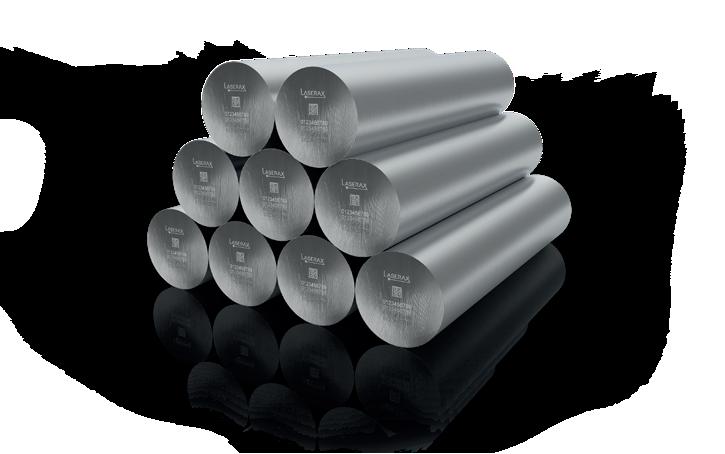
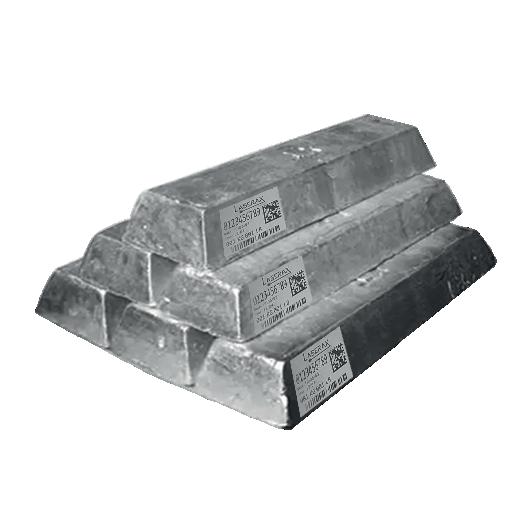
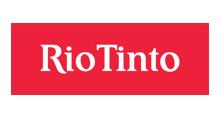
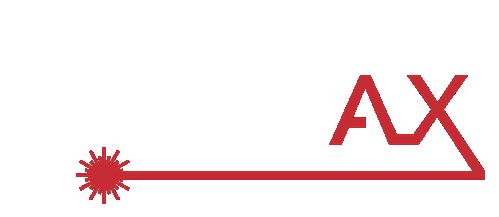
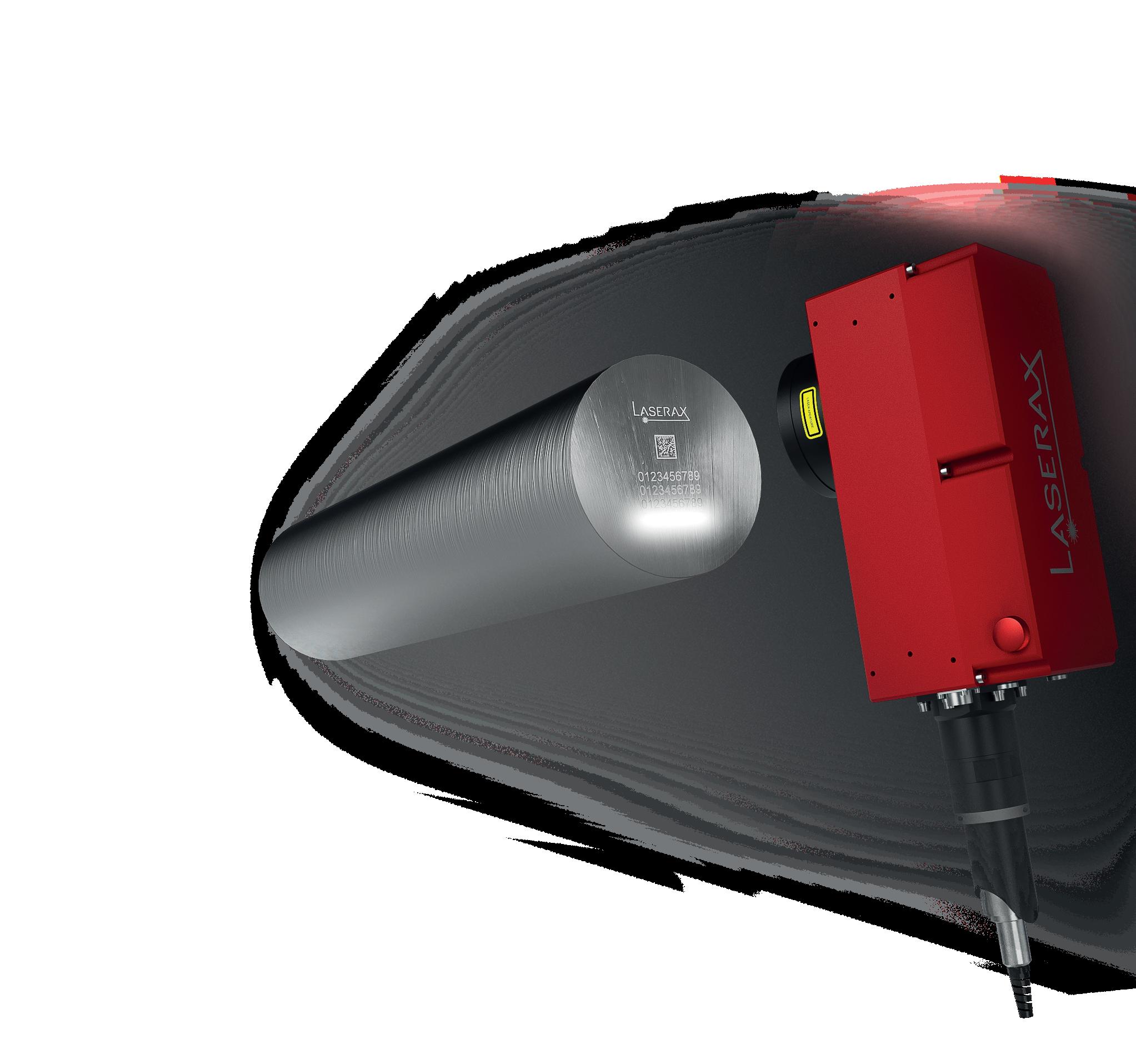
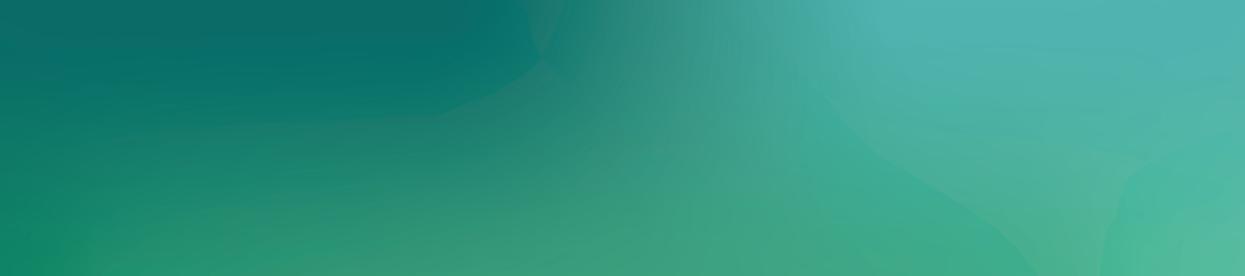
Serialize products and accurately identify billets to automate extrusion process and meet new extrusion requirements from major automotive OEMs. Stop spending on expensive labels that fall off. Laser etch a high-definition identifier label directly on the sow’s surface to obtain foolproof traceability and inventory management. Ensure heat resistant traceability with laser marking and unlock industry 4.0 features with individual ingot serialisation and bundle automated labeling.
LASERAX.COM MEET LASERAX AT ALUMINIUM 2022. 27 - 29 September 2022 Exhibition Center Düsseldorf
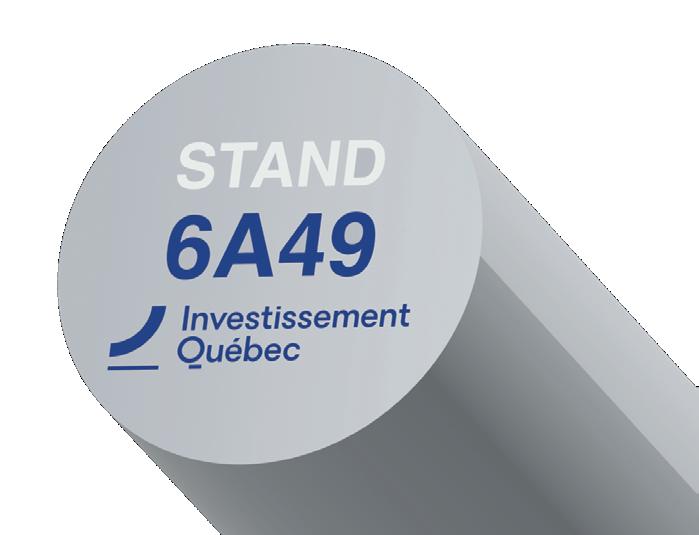
GRAIN REFINEMENT 69 Aluminium International Today September/October 2022
The grain refinement phenomenon
Located in Rotherham, South Yorkshire, AMG Aluminum’s UK manufacturing plant began operations as London & Scandinavian Metallurgical Company (LSM) in 1938, where production of aluminium master alloys began in 1954, and the development of titaniumaluminium-boron grain refiner alloys in coiled rod form followed in 1978.
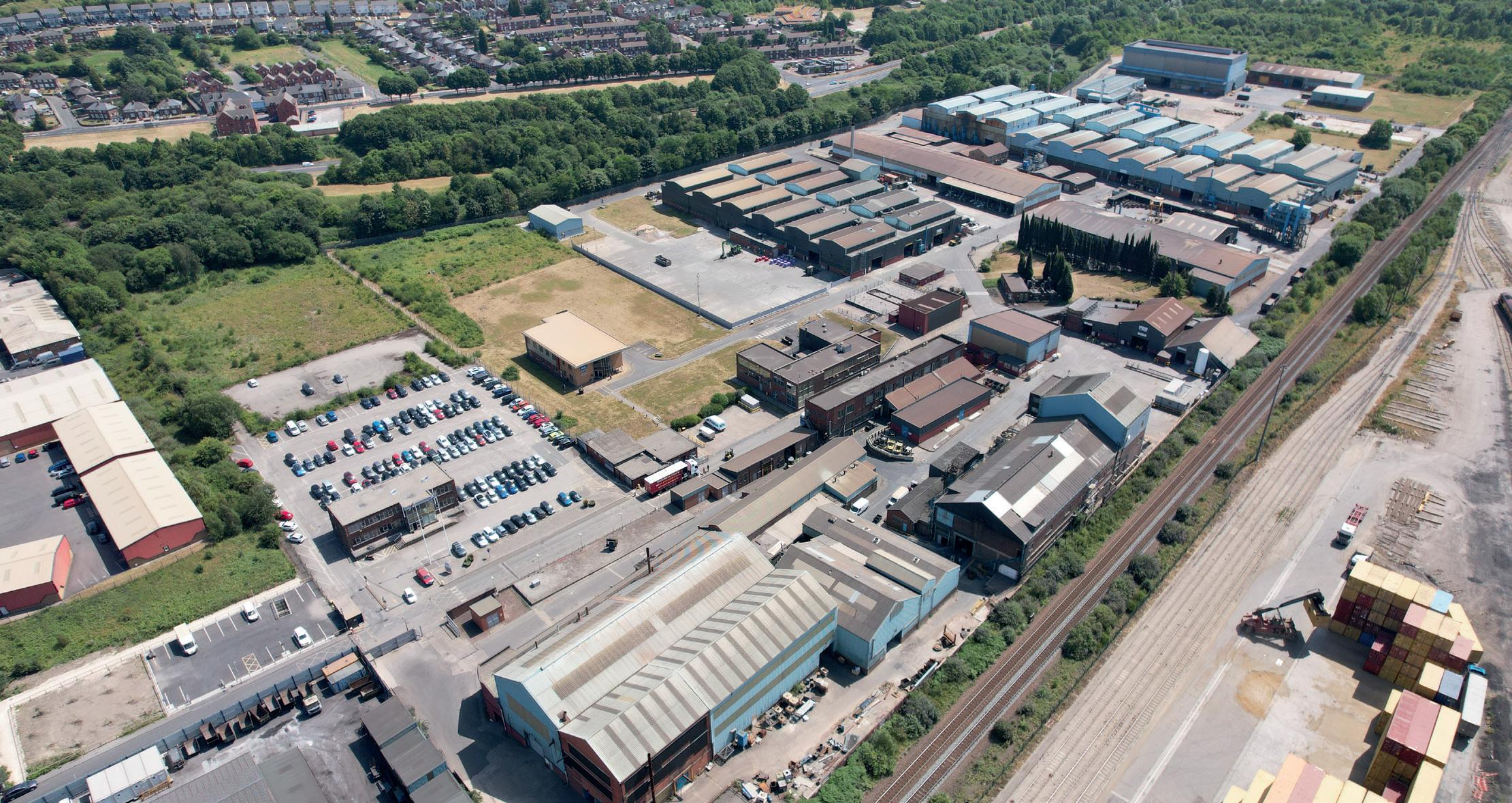
The AMG Aluminum group was formed in 2011 from KB Alloys (USA), LSM (UK) and Companhia Industrial Fluminense (Brazil), and now has over 350 employees, five ISO 9001 manufacturing sites, and a production capacity of over 35,000 tonnes. What is Grain Refinement? When metals solidify they form individual crystals or “grains”. In aluminium castings without grain refinement, grains can be of the order to 5 to 10mm in size. Large grains are undesirable as they can be the cause of casting defects e.g. cracks and hot tears, or can lead to issues when the casting undergoes downstream thermomechanical processing e.g. rolling, drawing, extrusion. Grain refinement is the phenomenon of decreasing the size of the aluminium grains that are formed duringMicron-sized,solidification.insoluble particles (e.g. TiB2) can be added to molten aluminium to act as nucleants from which aluminium grains can form and grow. Theoretically, the greater the number of nucleants particles present during solidification, the Typical aluminium-titanium-boron grain refiner alloy microstructure (100x magnification) showing matrix of aluminium with TiB2 (smaller particles) and TiAl3 (larger particles) greater the number of aluminium grains formed – and, therefore, the finer the grain size. [It should be borne in mind that, in practice, this is not the case!]
What is TiBAl ADVANCE™? As casthouses continue to demand increasing quality standards for critical products, research into grain refiners continues at a practical and fundamental level. AMG Aluminum has developed a
AMG Aluminum is a world-leading provider of grain refiners, master alloys, fluxes, compacted additives and rod feeders to the aluminium industry, and is one of the business units of the Advanced Metallurgical Group N.V.
Once aluminium grains have nucleated, grain growth occurs. Most impurity/ alloying elements found in aluminium exert a grain growth restriction effect. By doing so, they give more opportunity for further nucleation events in the region ahead of the solidification front. In other words, growth restriction slows down the rate at which these newly-formed grains consume and solidify the surrounding liquid aluminium, and therefore it helps keep more liquid available from which many more grains can form. In general, but there are exceptions, the more highly alloyed the aluminium, the easier it is to grain refine. Titanium is the most effective growth restriction element; its role in grain refiners is thus two fold: it contributes to both nucleation (as TiB2) and grain growth restriction (when dissolved as an alloying element).AMGAluminum’s aluminium-titaniumboron grain refiner rod is designed to introduce a controlled amount of titanium (in the form of soluble TiAl3 particles) and insoluble TiB2 particles into molten aluminium. The rod is typically injected into the flowing metal stream between the casting furnace and the caster.
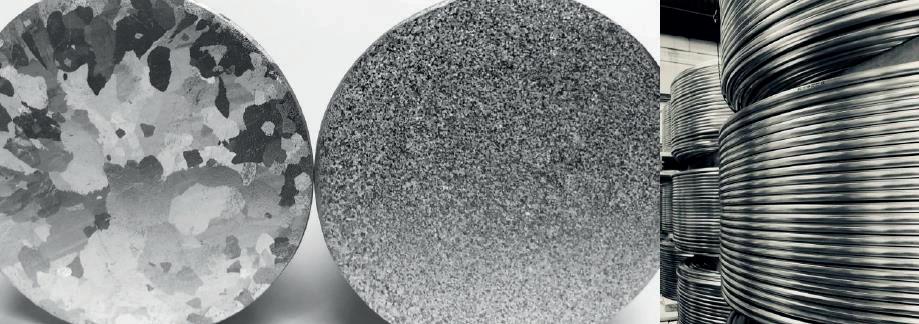
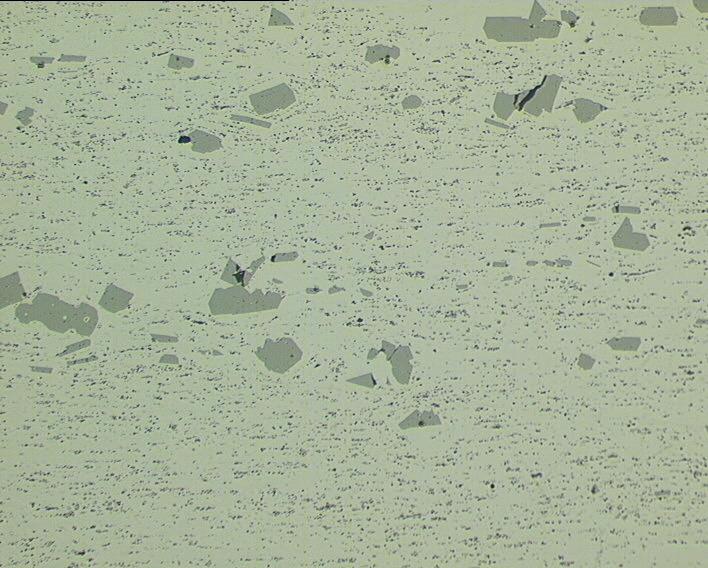
Aluminium International TodaySeptember/October 2022 GRAIN REFINEMENT70 new, improved and more efficient grain refiner – TiBAl ADVANCE™. TiBAl ADVANCE™ is an Al-3%Ti-1%B alloy that can be used with confidence at much lower addition levels than other grain refiners – while consistently meeting the demands of the casthouse in terms of grain refinement of the as-cast structure.
Increasing the amount of dissolved titanium, prior to the addition of grain refiner, can contribute to a profound decrease in overall grain size. and highly active TiB2 particles, free from agglomeration, essential for the most effective grain refinement. Utilising proprietary DC casting simulation technology, TiBAl ADVANCE™ is subject to a rigorous test regime to guarantee a controlled grain refining response, even at extremely low addition levels.AMG Aluminum carries out tests commensurate with casthouse addition rates, which demonstrate reliable consistency of the product in terms of grain refinement response – i.e. a uniform distribution of equiaxed grains and freedom from twinned columnar growth. [Note that the general trend of grain sizes obtained in AMG Aluminum’s laboratory tests is somewhat coarser than those obtained in the casthouse.]
Green Aluminium Reducing global CO2 footprint is at the forefront of AMG Aluminum’s ethos. Aluminium used for the production of TiBAl ADVANCE™ is sourced from smelters using renewable energy, with emissions less than 4 metric tonnes CO2 per metric tonne of aluminium (approximately 4 times less than that typically from smelters that use energy derived from coal). Additionally, through the adoption of TiBAl ADVANCE™, the casthouse can benefit from an increase of up to 300% in casting output per tonne of grain refiner. This means that the raw materials used to produce this tonne of TiBAl ADVANCE™ have been up to four times more effective than they would have been had they been destined for a standard grain refiner. Reduced grain refiner consumption also means a reduction in the energy and costs associated with global logistics. In 2021, AMG Aluminum was proud to have been awarded a GOLD rating for sustainability by EcoVardis.
Grain refiner rod fed into launder
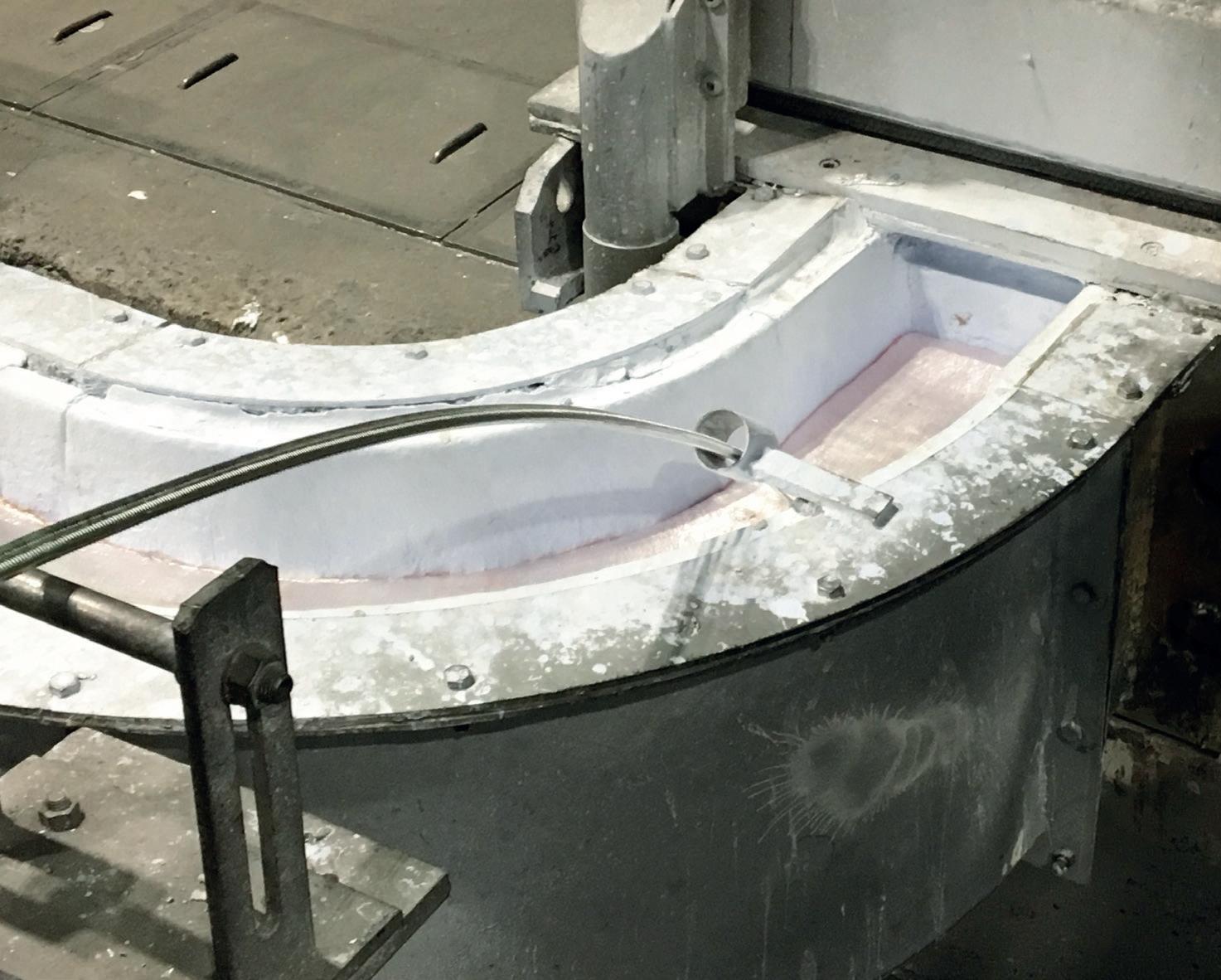
The benefits of a lower grain refiner addition rate include reduced grain refiner inventory, less frequent coil changes, and a significant reduction in the likelihood of deleterious chemical and metallurgical interactions related to grain refiner particles.Theperformance of conventional grain refiners is generally not tested and certified at lower addition levels. The level of grain refinement experienced in the casthouse can vary greatly between different batches of grain refiner due to inconsistencies in quality. This can result in adding more than necessary for safety, which leads to increased chance of introducing particle defects and a higher usage cost; or worse, adding too little, which may lead to cracked DC castings, or high centre line segregation in twin roll casting – which can result in entire casts being scrapped. Deleterious TiB2 agglomerations can be tens or hundreds of microns in size, and may interact with other inclusion species, such as oxides, causing issues such as premature blocking of filters leading to impeded metal flow; or worse, scrapped products due to catastrophic inclusion defects. In addition to problems with inclusions, poorly formed or agglomerated TiB2 particles vastly reduce the efficiency of the grain refiner. AMG Aluminum’s production technology promotes the formation of well-dispersed, uniform
Considerations of TiBAl ADVANCE™ To realise the maximum value-added potential of TiBAl ADVANCE™ AMG
Laboratory trials comparing different grain refiner samples at different addition rates can validate the benefits of TiBAl ADVANCE™ and demonstrate the possible reduction in grain refiner addition rate.
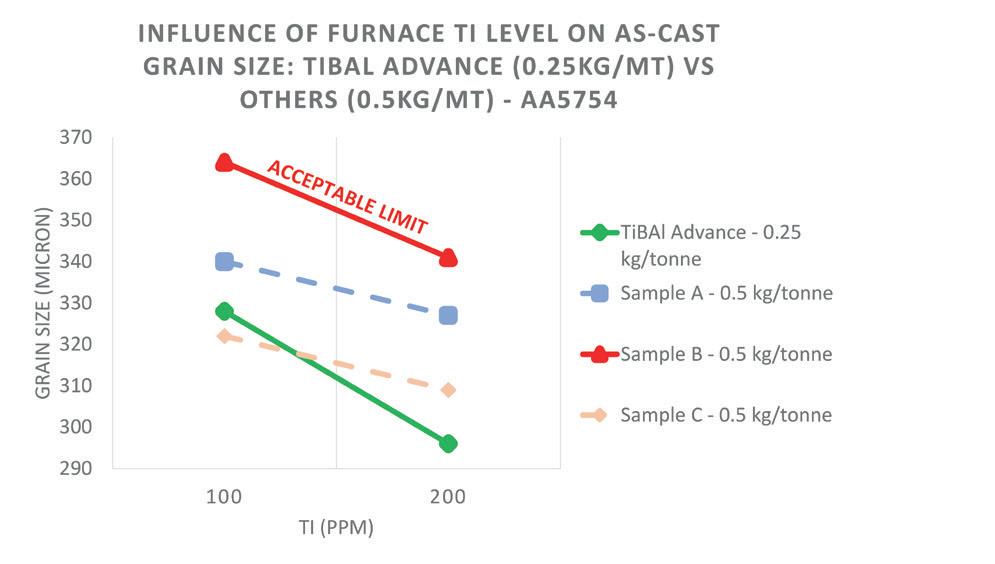
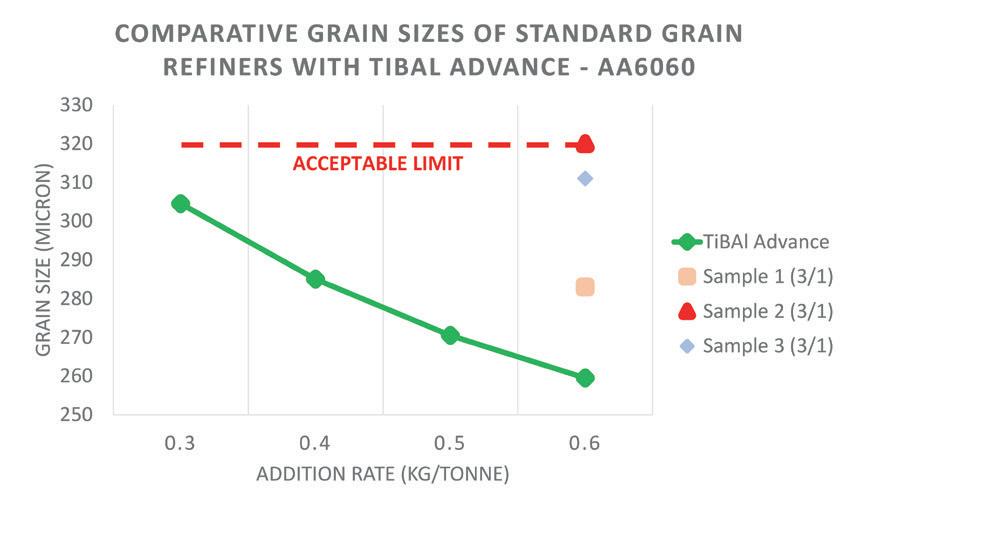
The success of the aluminium industry is dependent on technologies that innovate. For example, the use of novel alloy compositions for lightweighting in the automobile industry; or electromagnetic casting technologies to reduce shell thickness and scrap from rolling ingots. The continued development of grain refiner and master alloy technology contributes to the sustainability of the aluminium industry, meeting the needs of producers for aerospace, automotive, construction and packaging industries, to name but a few.” – and remove indentation.AMGAluminum continues to supply superior performing products at a consistently high quality. �A coil of TiBAl ADVANCE™ - ready to grain refine 100s of tonnes of aluminium
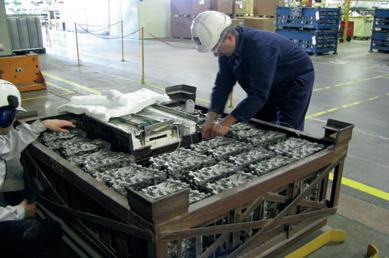

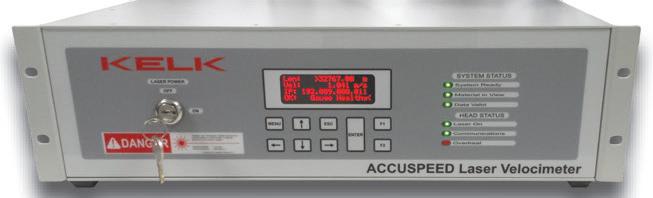
Aluminum offers bespoke application advice, with consideration given to specific details of the casting setup such as advice on optimisation of grain refiner addition level, alloy composition, furnace Ti content, grain refiner feeding technology and grain refiner addition point.
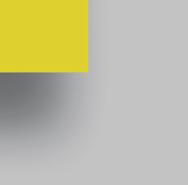
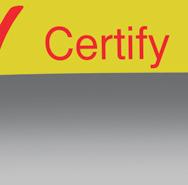
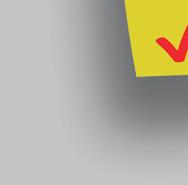
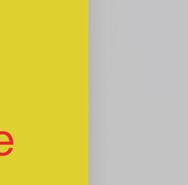
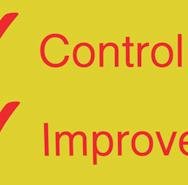
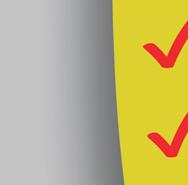
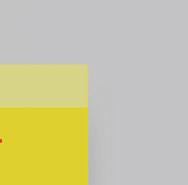
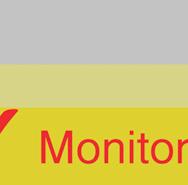

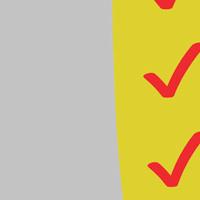
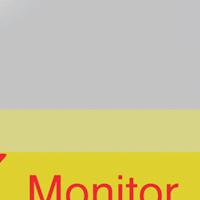
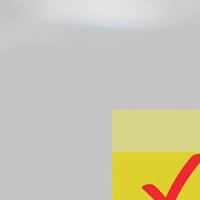
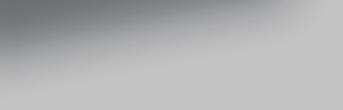

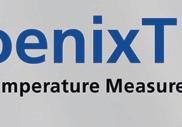
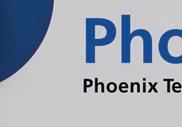
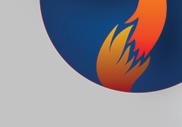
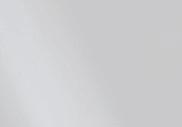
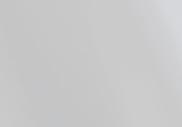
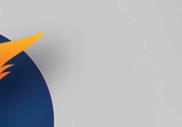
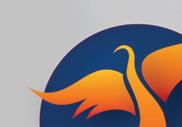
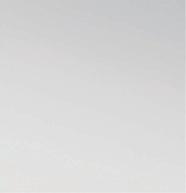
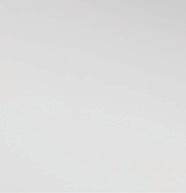
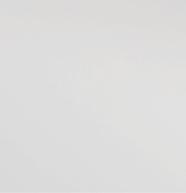
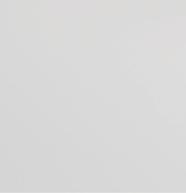
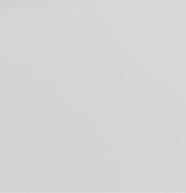

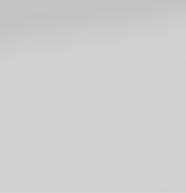
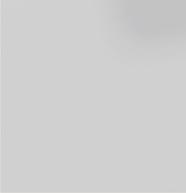
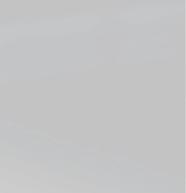
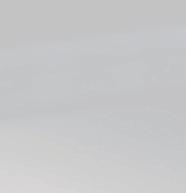

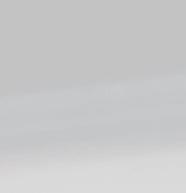
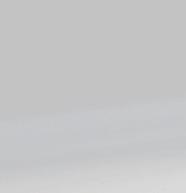
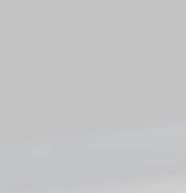

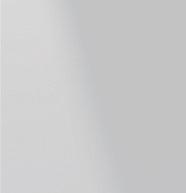

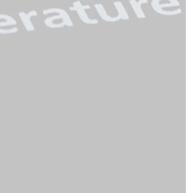
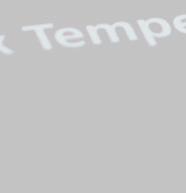
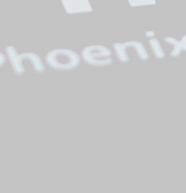
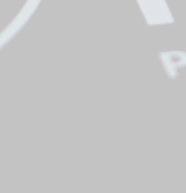
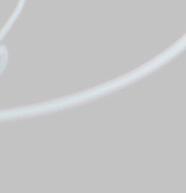

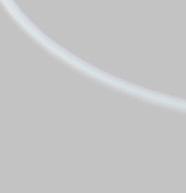
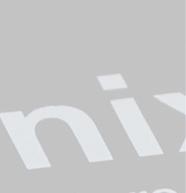
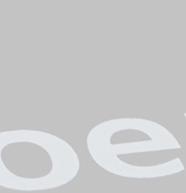
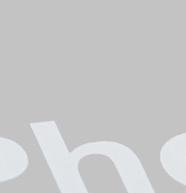
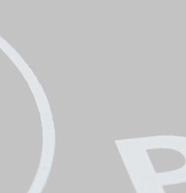
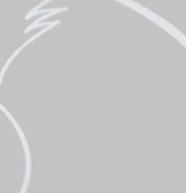
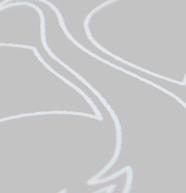
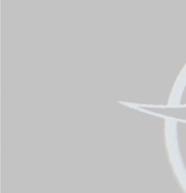
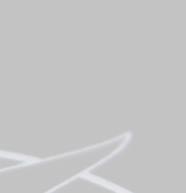
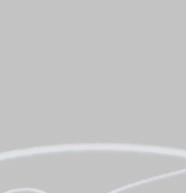
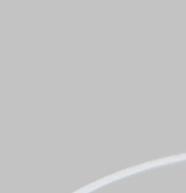

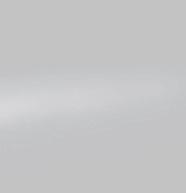
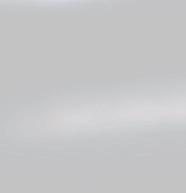
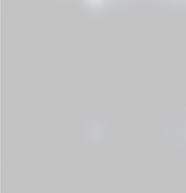
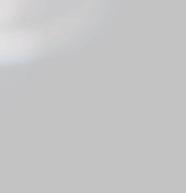

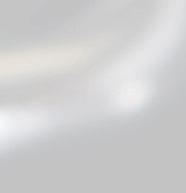
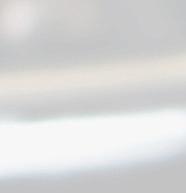
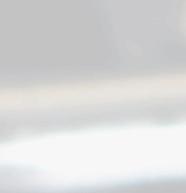
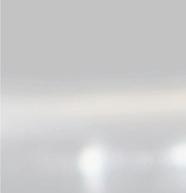
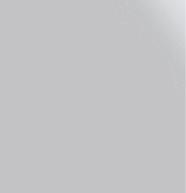


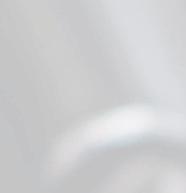
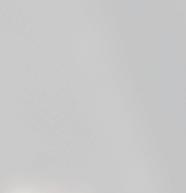
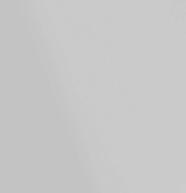
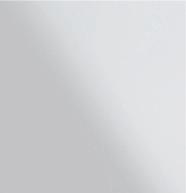
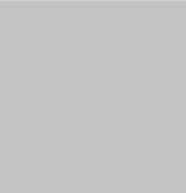
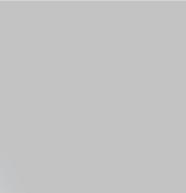
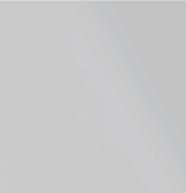
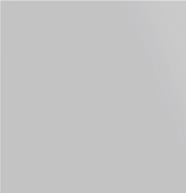
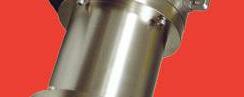
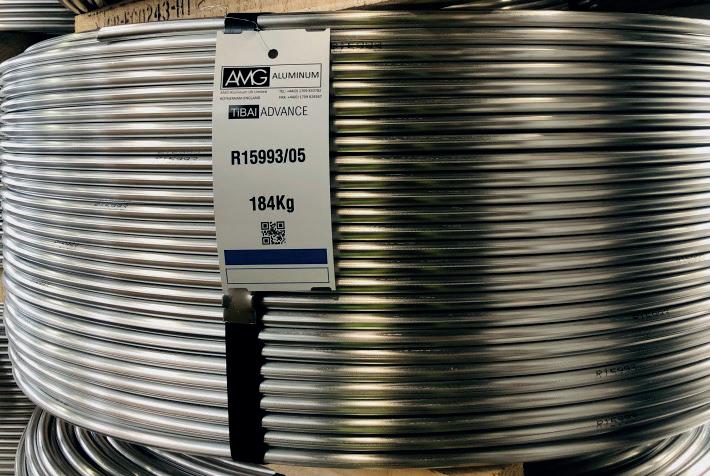
International Today September/October
GRAIN REFINEMENT 71
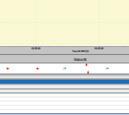
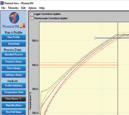
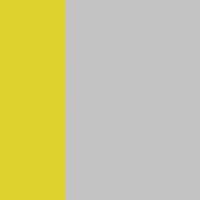
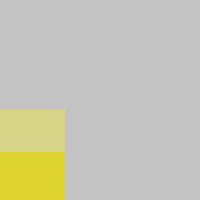
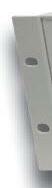
AMG Aluminum’s casting technology laboratory can be used to demonstrate the grain refinement effect in a wide range of casting conditions: � Any alloy composition (including a range of Ti levels for a given alloy) � Range of cooling rates and thermal gradients � Range of grain refiner types, manufacturers and addition rates. Engaging with the casthouse at a technical level is key to measuring the success of any trial. To validate the benefits of TiBAl ADVANCE™ it is recommended, firstly, to carry out laboratory trials in an analogue melt of the desired alloy composition(s); and secondly, with support from a global team of dedicated and experienced casthouse support advisors, to verify the results in controlled trials on site. A typical approach is to make comparative tests between i) the current grain refiners in use - i.e. the “benchmark samples” - and ii) AMG Aluminum’s TiBAl ADVANCE™. The results will demonstrate the addition rate reduction that can be realised, whilst still achieving the desired grain size. Multiple benchmark samples are suggested due to the likely variability from batch to batch, delivery to delivery, and supplier to supplier. In some cases, equivalent grain sizes can be achieved with TiBAl ADVANCE™ at addition levels over 75% lower than conventional grain refiners; however, additional titanium solute may be necessary in the case of low grain refiner addition rates in certain alloy systems. A consequence of lower grain refiner rod addition rates is that greater control must be exercised over the addition rate into the metal flow - especially at the critical tolerances required at the low addition rates possible with TiBAl ADVANCE™. AMG Aluminum also offers a range of rod de-coiling and feeding solutions to meet the demands of the casthouse.
Forkelk.comSteeland Aluminum Rolling Industries Improved measurements of shiny material due to better sensitivity control Better length accuracy in cut-to-length applications as a result of faster acquisition and Improvedtrackingnoise immunity with Digital Communications from the Optics Head Accurate elongation and mass-flow control with improved signal processing and synchronization Enhanced I/O for better integration with modern automation systems For details call +1-416-445-5850, or kelk.sales@vpgsensors.com ACCUSPEED Laser Velocimeter 13012-EN_Feb20 Temperature Profiling and Surveying Solutions in the Aluminium Industry Process Monitoring solutions for • Homogenizing • Solution Heat Treatment T5/T6 • Ageing • Brazing (CAB & Vacuum) • Powder Coating …...and many more Comprehensive Passes through furnace with the product. • Complete product temperature profile • Measurement at up to 20 points • Live 2 way radio communication option Safe No Trailing thermocouples so quick, safe, system installation without production delays. Easy Fully compliant AMS2750 or CQI-9 TUS reports with only a single Click! PhoenixTM GmbH Germany info@phoenixtm.de PhoenixTM Ltd UK sales@phoenixtm.com ... where experience counts ! PhoenixTM LLC USA info@phoenixtm.com www.phoenixtm.com
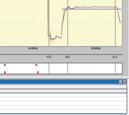

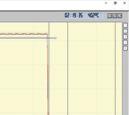

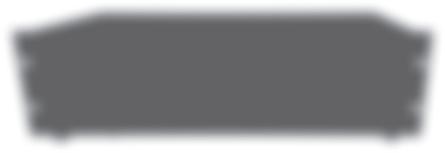
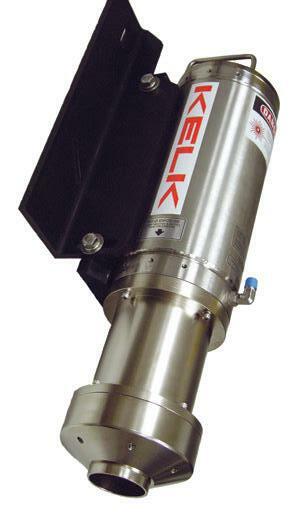
Aluminium 2022
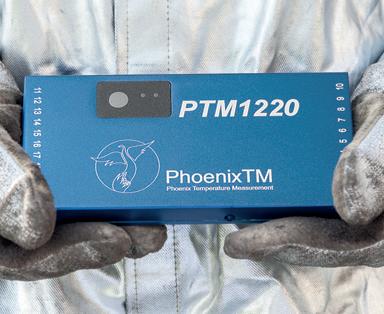
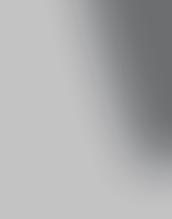
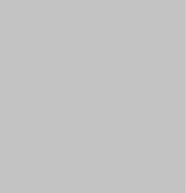
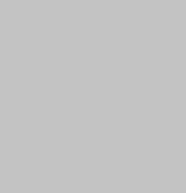
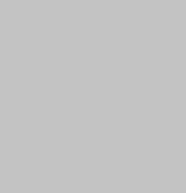
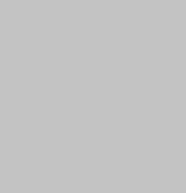
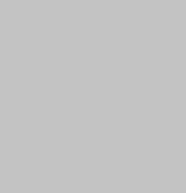
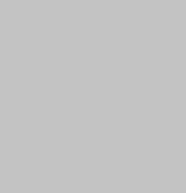
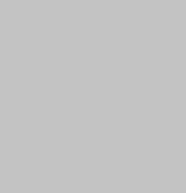

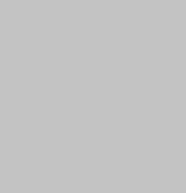
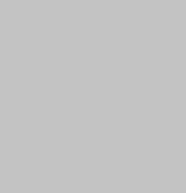
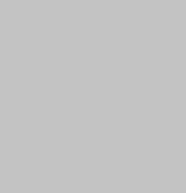
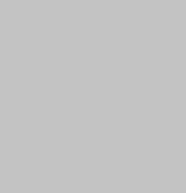
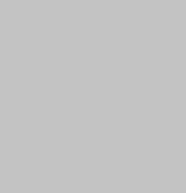
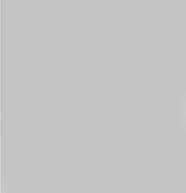
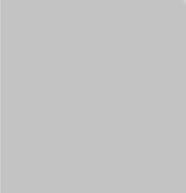
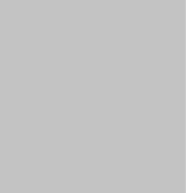
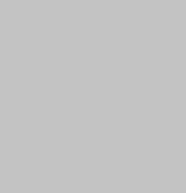
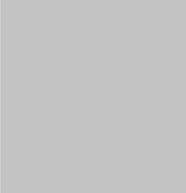
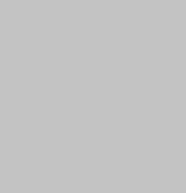
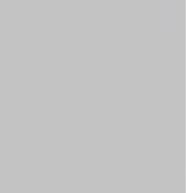
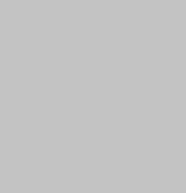
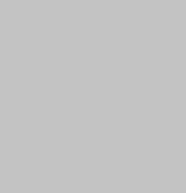
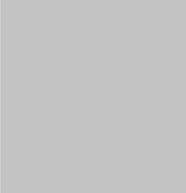
marketthealuminiumHigh-qualityforconsumer www.fivesgroup.com ALUMINIUM For you, industry brings innovation to life. Behind lightweight and recyclable cans, is an industry that produces the finest quality of aluminium, using high performance manufacturing Fromtechnologies.designing process equipment to supplying complete installations and services, Fives is one of the world’s leading aluminium industry suppliers, improving performance, the environmental footprint and quality of its customers’ products. Each day, Fives demonstrates that Industry can do it
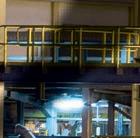


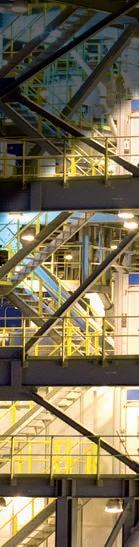
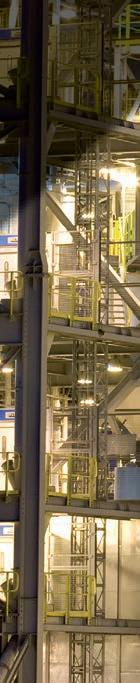

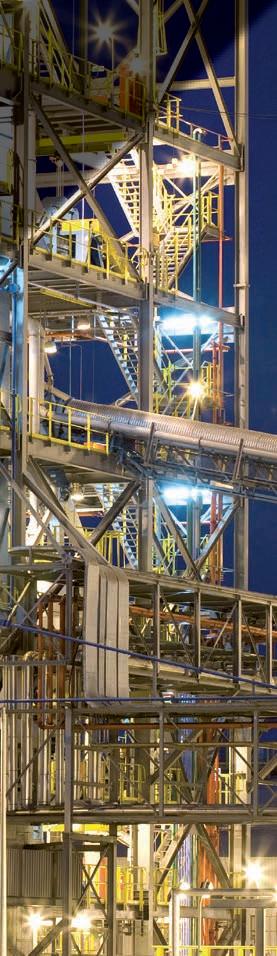

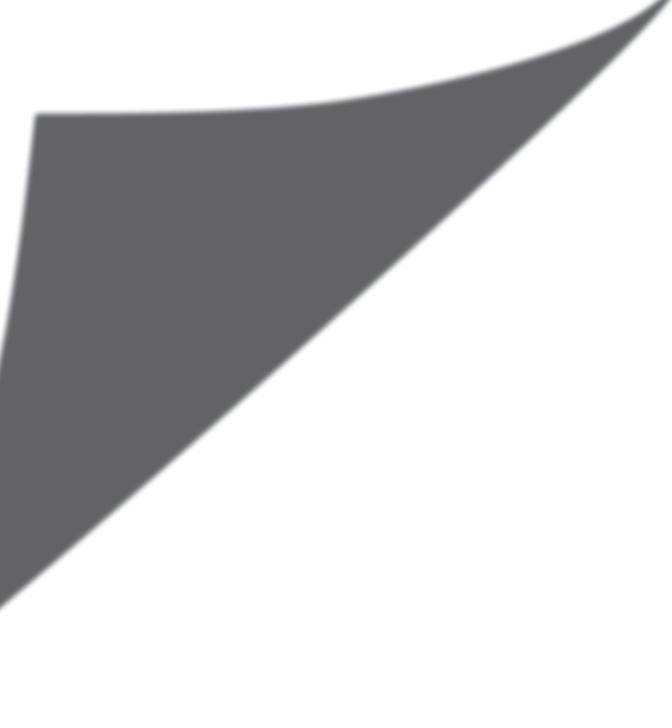
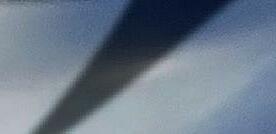
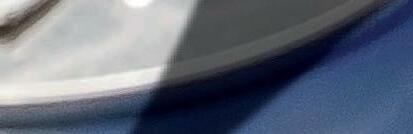
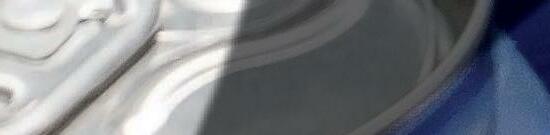


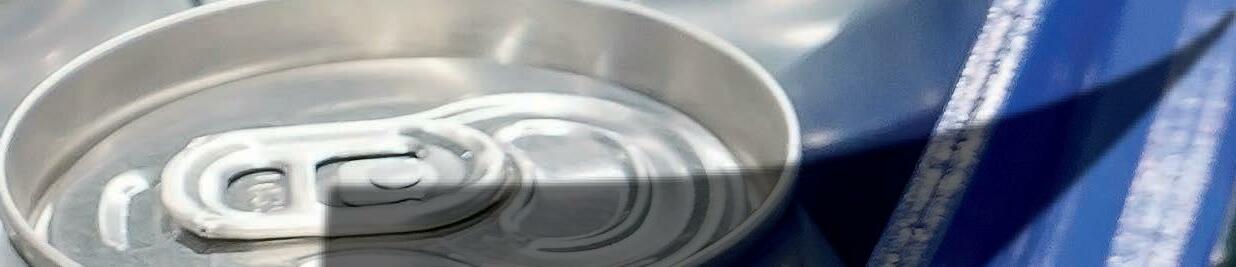
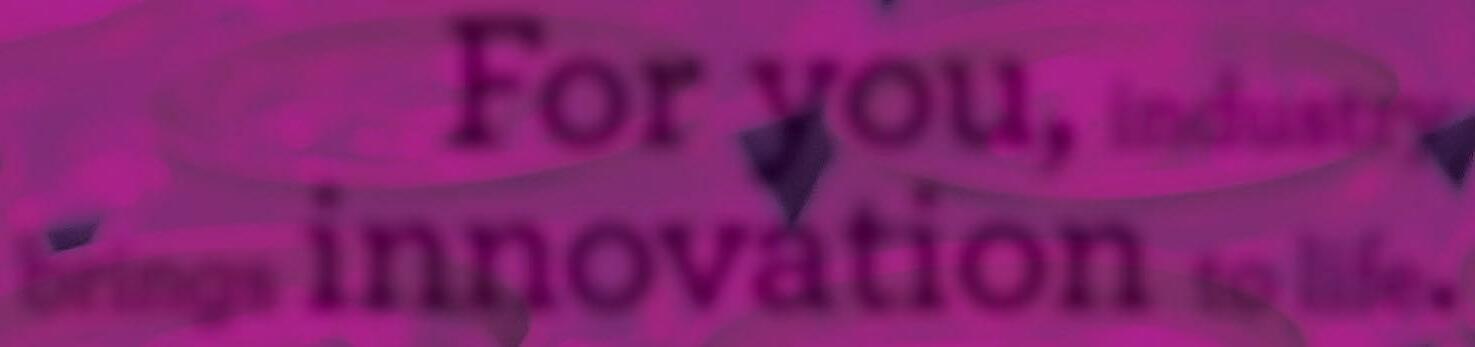
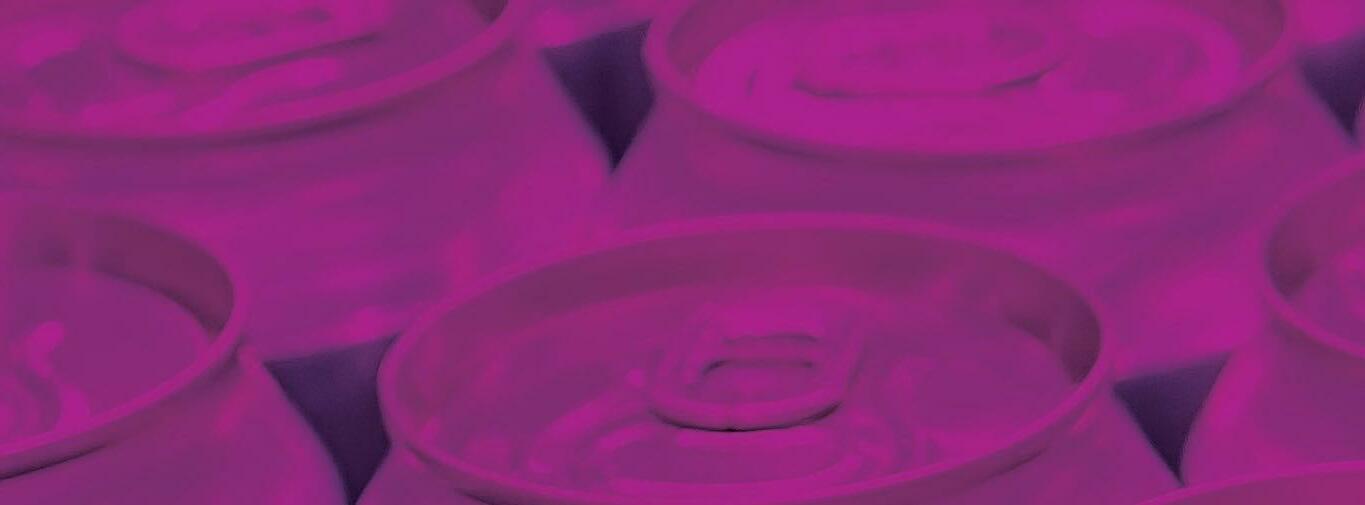


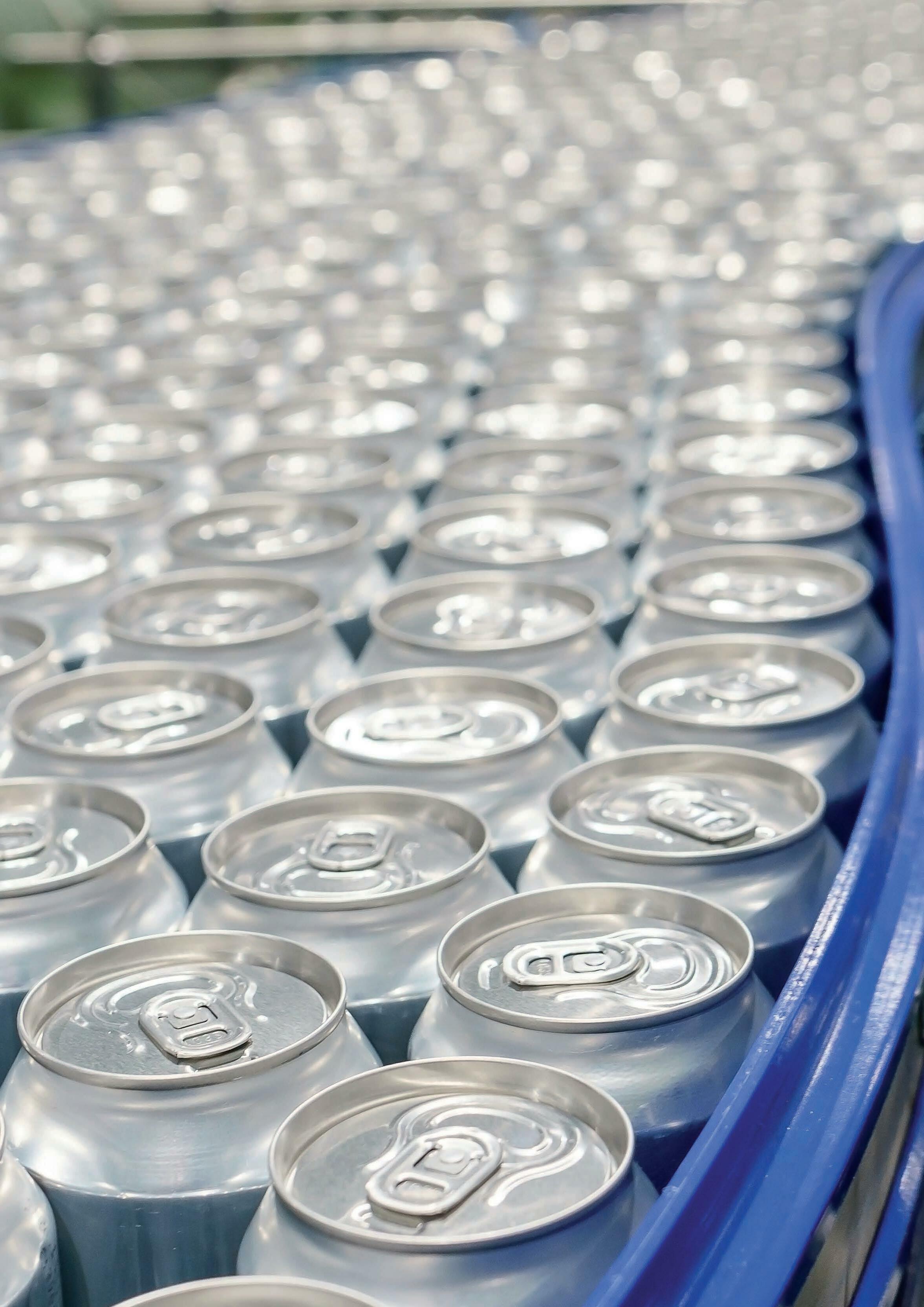
*CEO Matrix Speciality Lubricants Assistant Aluminium
�
What was the inspiration?
�
and
�
LUBRICATION 73 Aluminium International Today September/October 2022
Why did you experiment with coatings?
Matrix Speciality Lubricants: An interview with the CEO
What makes the coating different to other coatings? How does it work?

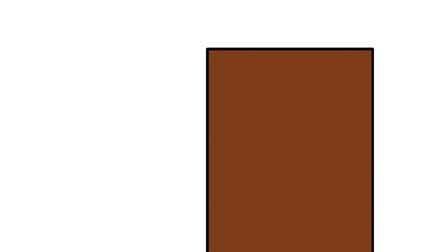
Our D-Max GW ASX is a very stable dispersion. The dispersion is developed from several components which warrants optimal conductivity and therefore a lower voltage drop between the anode stub and the carbon block. This lower voltage drop generates the largest savings on electricity consumption and ultimately a lower carbon footprint of the aluminium melting facility. We create a gel like structure in the dispersion which keeps the graphite in dispersion without settling down for a long time. This gives a dispersion which is not only stable and rarely needs agitation (savings on electricity), but also warrants a coating on the anode stub which always contains the same (amount) of material. Manual cleaning of dipping tanks is history using this type of dispersion. Besides the above mentioned benefits the coating also provides easier release in the timble press resulting in less deforming of the Anode stubs. Our specially formulated colloidal dispersion graphite coating contributes to an easier rod cleaning, less stickers, a very stable dispersion which does not allow the graphite to settle down and therefore does not need agitation.
How does one control friction, optimise machine accuracy, extending life of equipment, shock absorption? Changing the gears when driving or checking the time with a mechanical watch, lubrication is key to maintaining the life and efficiency of machinery. It is essential in the processing of aluminium into its usable form. Perry Peters* spoke with Zahra Awan** on the challenges and future of lubricants in the industry. A brief history on Matrix Speciality Lubricants Matrix Specialty Lubricants is a relatively young company and was founded by people who have workedin the lubricants industry for a long time. The founders expected, especially the major oil companies, to go back to their core business and pull out of the specialty Lubricants business. The Lubricants business requires a lot of problem solving, engineering and development, with relatively small volumes of end product. Matrix has dedicated themselves to always work towards their mission and vision which is; “the right lubricant for the right application.” Many people and companies use products for a long time for various reasons but do not realise that there might be better products. Often, we see that the “issues” they experience are accepted because they have been using the product a long time, these “issues” have become “normal” for them. It takes a company like Matrix to show and teach them that different chemistry and another approach might provide a performance that they were not aware of.
Given the fact that we are always looking for optimisation, we found that a coating was used for many years in Rodding Shops around the world. This coating has a primary function which is the release of remains of the carbon block and the remains of the timble. When we looked into the application and the products used in the market we found out a couple of things. There were many practical issues with the coatings, most of the products were very unstable and therefore, the graphite used settled in dipping tanks and hardened at the bottom. This resulted in regular manual cleaning of the dipping tank, loss of active material and a poorer quality of the actual coating. We also found that nobody looked at what the coating was doing. It created a layer between the anode stub and the timble and many products appeared to have a very poor conductivity. Since electricity plays a large role in the cost of the production of aluminium, minor increases in savings result in large financial benefits, and even more important is the reduction of the carbon footprint of an aluminium smelter.
** Editorial
�
�

The difference between D-MAX GW-ASX competitive products: Competitor: Deposit cleaning in tank required on a regular base Hard layer in tank to be removed Irregular coating High fluid consumption Waste material need disposedcostly Graphite at the bottom, (black/grey water at the top) dipping mainly in water. Consumption of water
International Today
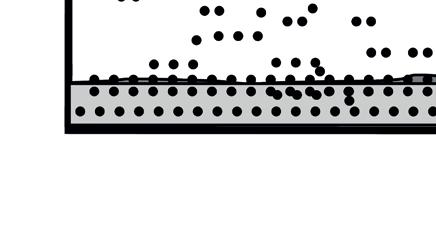
What are the benefits of using Matrix’s coating over traditional solutions? (Sustainable, environmental etc)
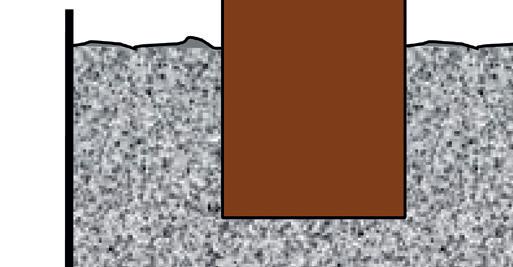
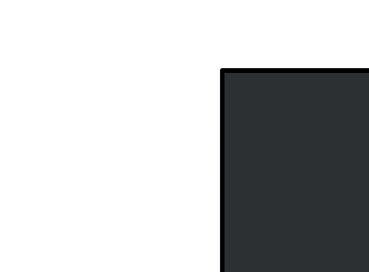
� No or very little deposits in tank � No cleaning of tank � Perfect coating of stubs
Arching: electrical corrosion and air burn shortening the stub life
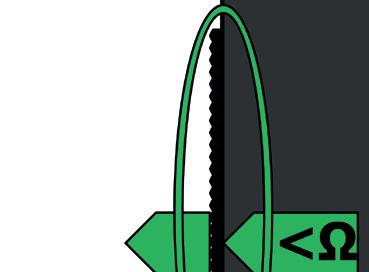
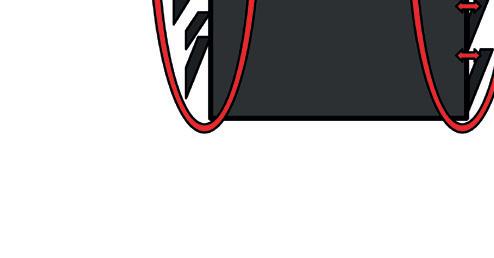
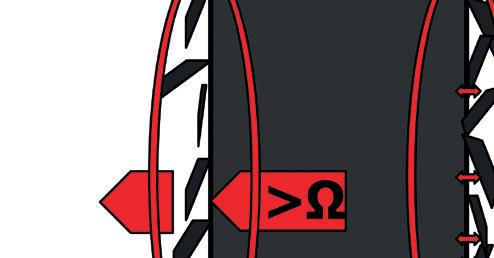

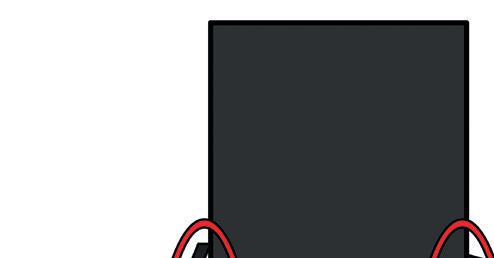
D-MAX GW-ASX � Extremely small solid particles � Stable dispersion � Regular coating � Best conductivity � Reduced electricity loss (lower electrical resistance Ω) � Good release of the cast iron thimble from the stub � No dust � Optimized coating usage � Nonflammable � Coats inside cracks and pores � Longer stub lifetime � Extended working life in dipping tankand water warrant good coating and consumption of the complete mixture
5- >10 Mv electricity savings thanks to improved coating conductivity
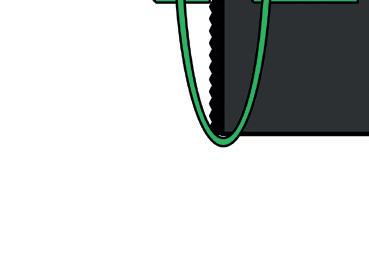
The difference between D-MAX GW-ASX and competitive products: Competitive coatings � Particle size distribution � Irregular coating � Poor conductivity � Electricity loss (higher electrical resistance Ω) � Poor release of the cast iron thimble from the stub � Arcing (shorter stub life) � Highly flammable � Unstable dispersion (heavy sediment in tank) � Requires continuous mixing and recirculation � Regular tank cleaning and refills
� Low tank maintenance � No need for constant mixing of coating material
As mentioned above there are several benefits but the main one is energy efficiency and therefore lower carbon footprint. This contributes in a relatively easy way to the “greener” production of aluminium. The use of this coating can be seen as changing from conventional lights to led lights. Quick fix, quick results. How can the coating improve the overall production chain of producing aluminium? Interestingly enough, we see that some aluminium smelting companies often see the Rodding Shop as a separate business unit with their own budget and responsibility. Besides the benefits the stable emulsion brings for them, such as: no manual cleaning, no agitation needed, easier timble press release and less deformed anode stubs, the main savings on energy consumption and lower carbon footprint are seen in the production process (pot cells). It requires a helicopter view approach to add all savings together justify the purchase of a more expensive product like D-Max GW-ASX. When taking all savings into consideration, the actual higher purchase price for the product becomes completely irrelevant. As well as the financial picture, there is of course the contribution to a better planet. Homogeneous suspension of graphite and water warrant good coating and consumption of the complete mixture
Loss of electricity due to poor coating conductivity
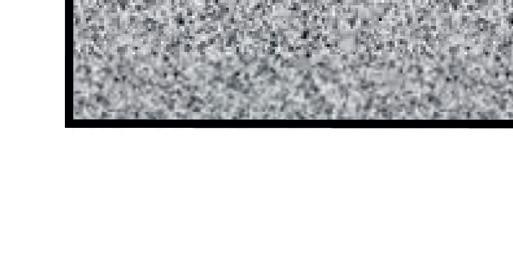

D-MAX GW ASX: � Stable dispersion � Extreme small graphite particles in a good dispersion give a very regular coating

Are you working on anything/ future projects? We are continuously improving the formulations and are now working on the next generation coating with even a higher conductivity. We also offer the aluminium smelting industry other products which save energy for compressors, vacuum pumps, hydraulic systems, gearboxes and more. These products all provide substantial energy consumption reduction compared to conventional products in the market.
Is there anything else you would like to mention? We hope to get in touch with the people responsible for energy savings and sustainable production of aluminium in the primary aluminium smelting industry who are not using our anode stub coatings and lubricants. We can offer them relatively quick and easy savings which can be seen as low hanging fruit. �
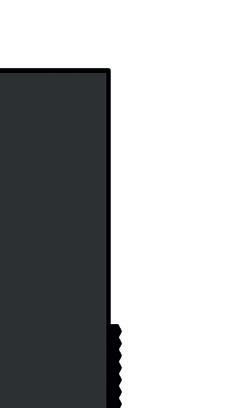
Aluminium International TodaySeptember/OctoberLUBRICATION202274
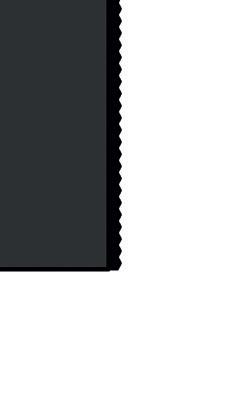
Proven energy saving from 15–60% Typical heat dross reduction abaut 20% Low NOx /reduced CO2 emissions High bath coverage Custom configuration Quadraflo© Sweep Aluminum Melting System ® Tel.: +41 (0)71 649 20 90 www.hotwork.agcontact@hotwork.ag Reliable briquetting machines from the world market leaderwww.briquetting.comMore information THE BRIQUETTE.The Original. VISIT AMBAluminiumUS!Düsseldorf27.09-29.09.2022Hall5,SF50Stuttgart13.09-17.09.2022Stand8C45 RUF_M_10_AIT_185x61_GB_AMB-Alu.indd 1 23.06.22 08:31 It’s down to us to make a difference. Sustainable manufacturing starts with great partnerships. A shared vision to make good products that are good for people and good for the planet. Let’s work together. CONSULTANCY, TECHNICAL SUPPORT AND TRAINING FOR THE ALUMINIUM INDUSTRY ENQUIRIES@INNOVALTEC.COMINNOVALTEC.COM UK size V4.indd 1 11/07/2022 10:25 www.dewinterengineering.com SURE, WE COULD TALK ABOUT THE EFFECTIVE, TAILOR-MADE AND TURN-KEY SOLUTIONS WE REALISED ... But honestly? We´re engineers ... New furnace issues to tackle just interest us more. So, challenge us! New 60 t furnace with ultralow energy and maintenance costs Furnace upgrades: bath capacity, temperature control, fume extraction, door systems. etc. Pressure regulation E E E E
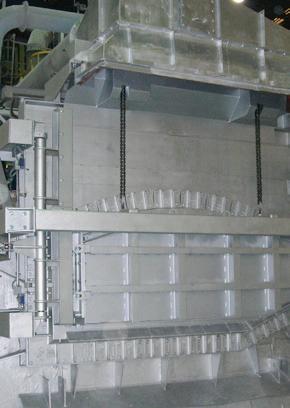
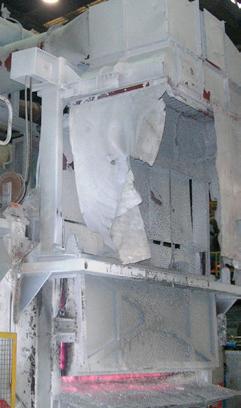
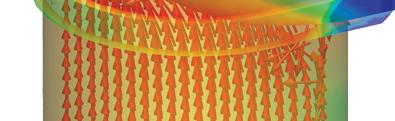
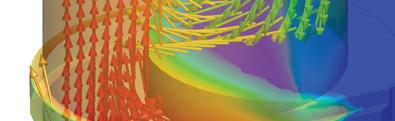

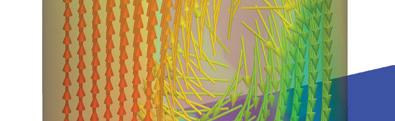
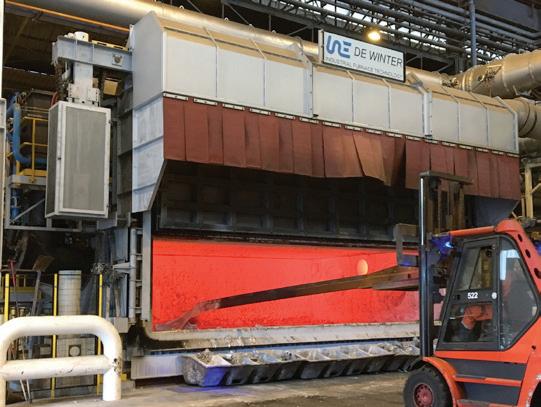
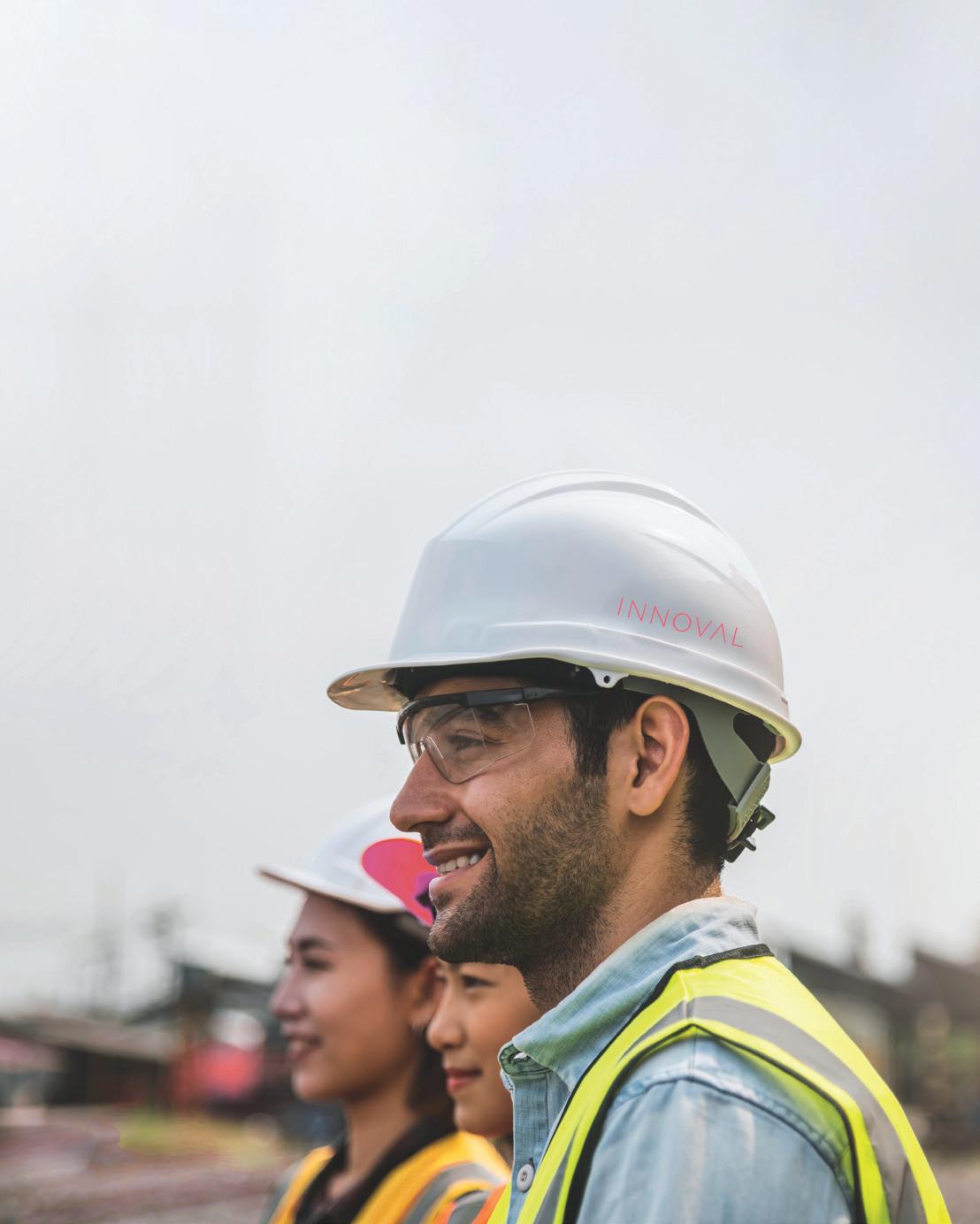



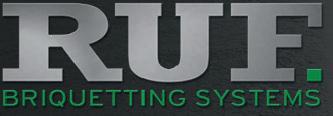


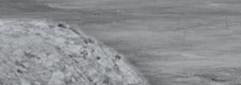

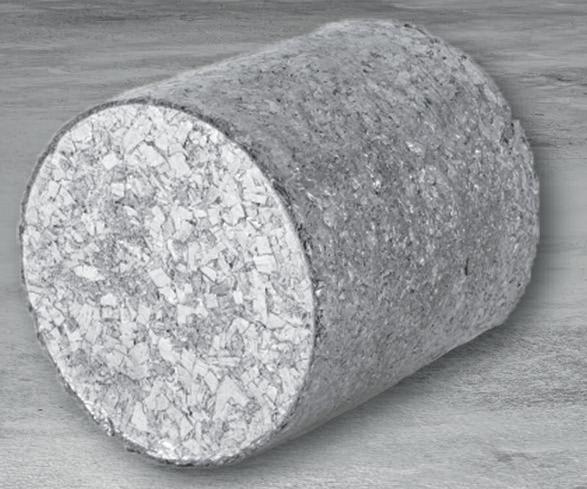
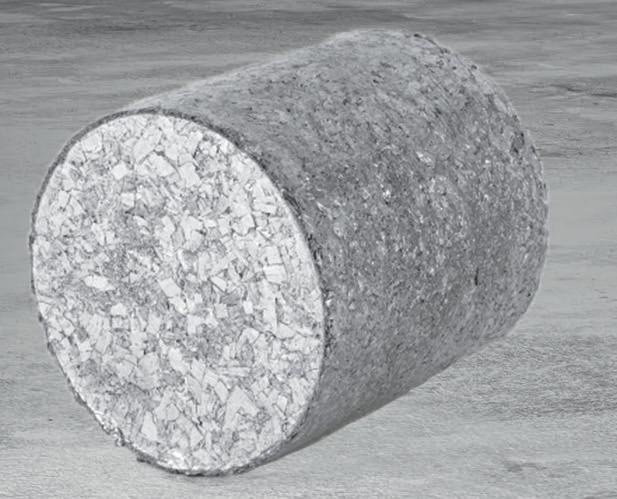
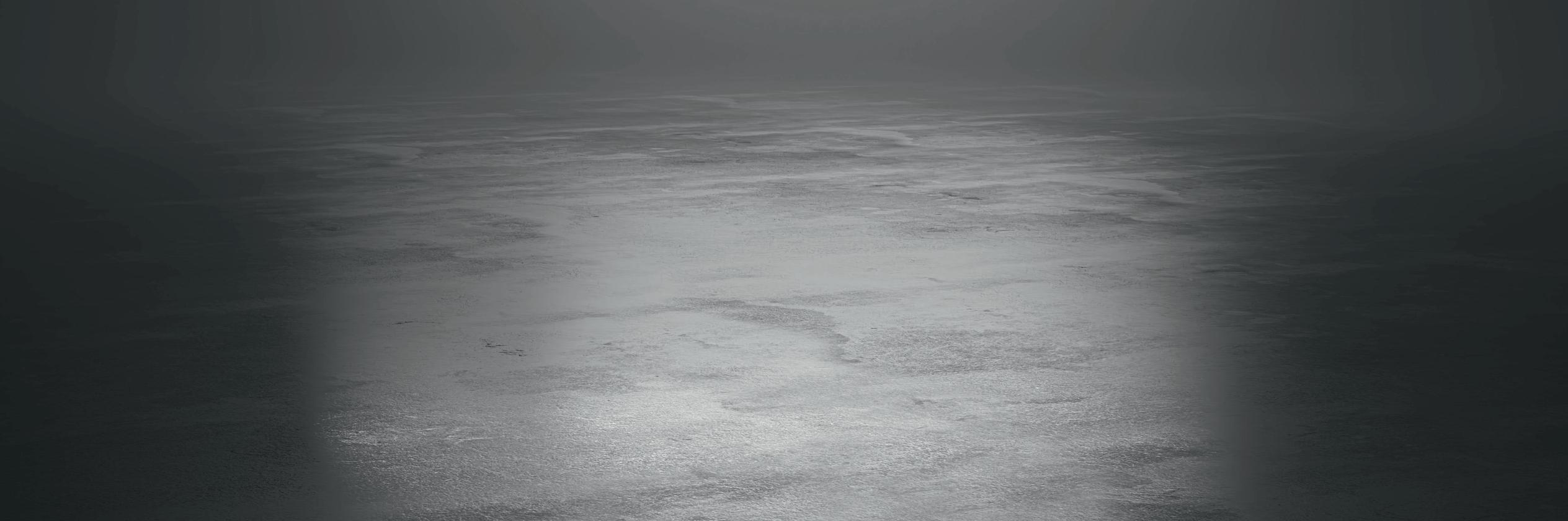
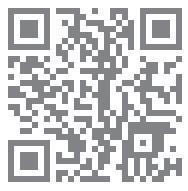

� Removes minor strip defects or imperfections
Roll texturing for the aluminium industry

The benefits of the Sarclad Rolltex Eco variant: Strip surface preparation for coating
� Reduces flow friction in the press
Aluminium International TodaySeptember/OctoberTECHNOLOGY202276
Microscopic image of a 1.2Ra EDT texture - The typical roughness for the Aluminium industry demonstrating the above texturing characteristics
� Retains even coating of lubricant for the press
For surface critical applications such as Automotive external panels and white goods, Sarclad’s Electro Discharge Texturing (EDT) technology ensures the optimum textured finish is transferred on the strip from the rolls. The Rolltex ECO (12 electrode texture head) has been specifically designed for the aluminium industry, providing precision texturing for up to 1,000 rolls per year. With aluminium consumption in automotive body in white applications increasing year on year, it is imperative that the rolls are optimally textured to imprint the required roughness and peek count onto the aluminium strip. These textured rolls are critical in the production of aluminium strip for body in white automotive panels, where the texture is ‘imprinted’ to provide lubrication for forming and an aesthetic appearance suitable for the highest surface critical applications.TheSarclad Rolltex ECO provides textures that are both stochastic (i.e. random, without lateral pattern) and isotropic (i.e. not varying in magnitude when measured in different directions). These characteristics are inherent in Sarclad EDT texturing, nut not laser texturing and are critical in ensuring consistency of body panel appearance through the stamping process.
� Offers better strip surface “keying”, aiding better bonding of surface coatings

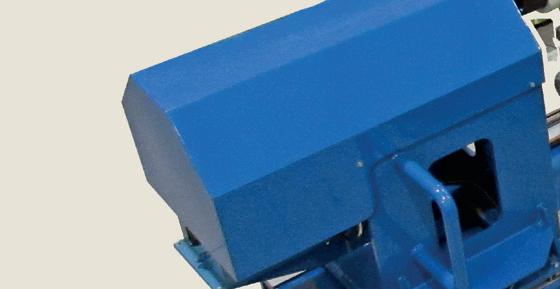

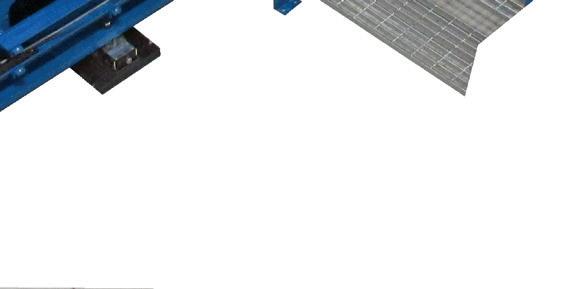
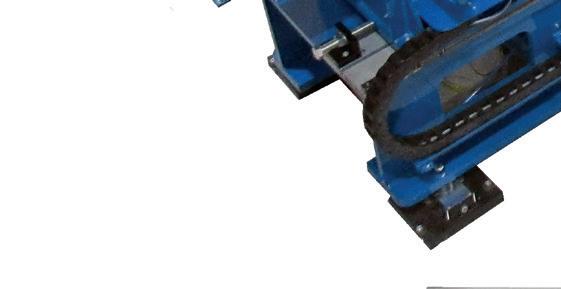
Rolltex ECO - The preferred industry solution for Aluminium mills.
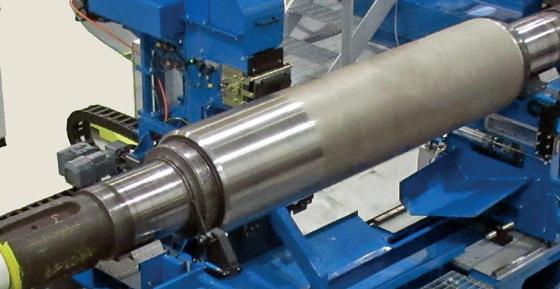

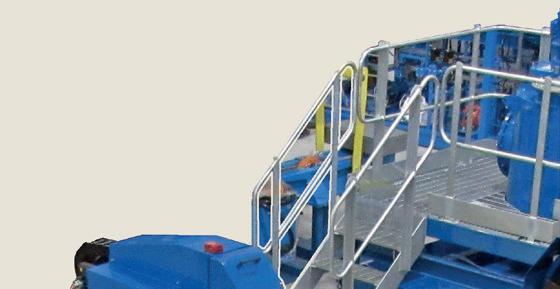
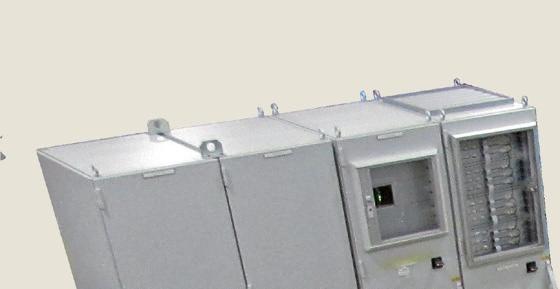
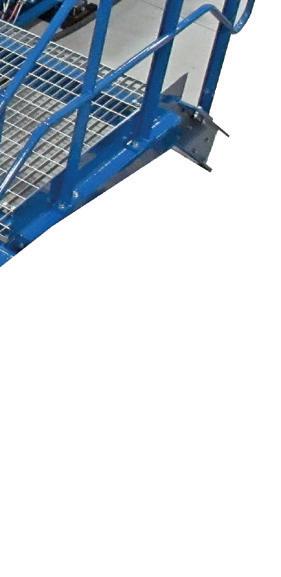
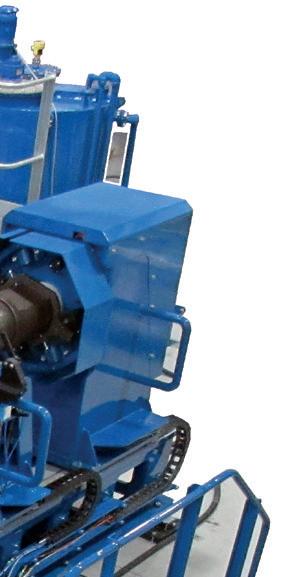
Further information available at: sales@sarclad.com | sarclad.com
� Achieves the highest quality strip appearance (stochastic & isotropic) Strip formability improvements
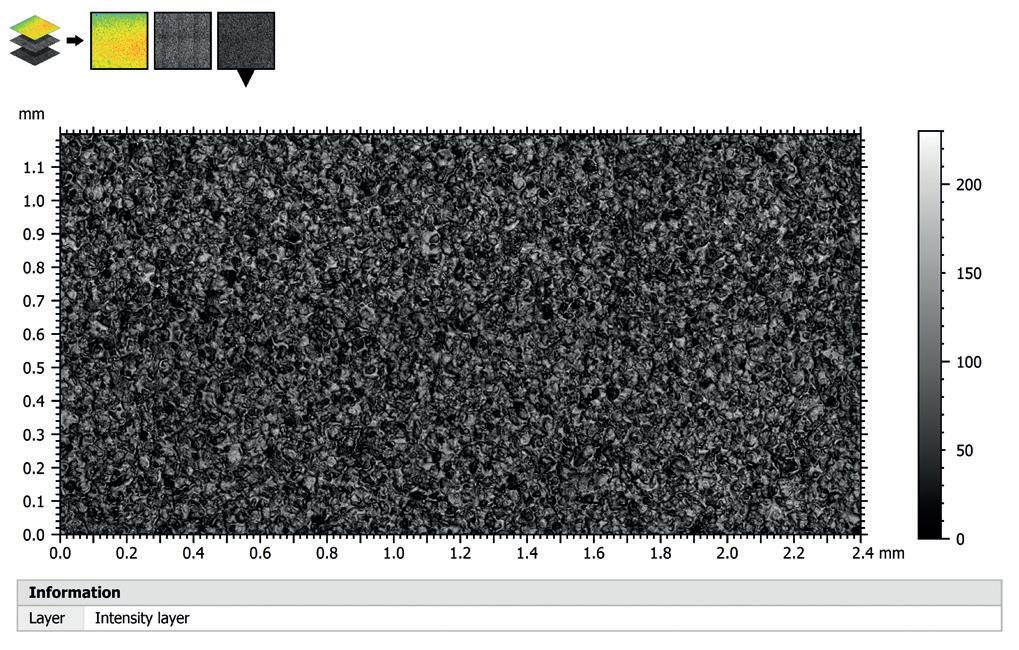
Total Aluminium content history & forecast, lbs / vehicle Sarclad Rolltex ECO
� Retains surface appearance after forming
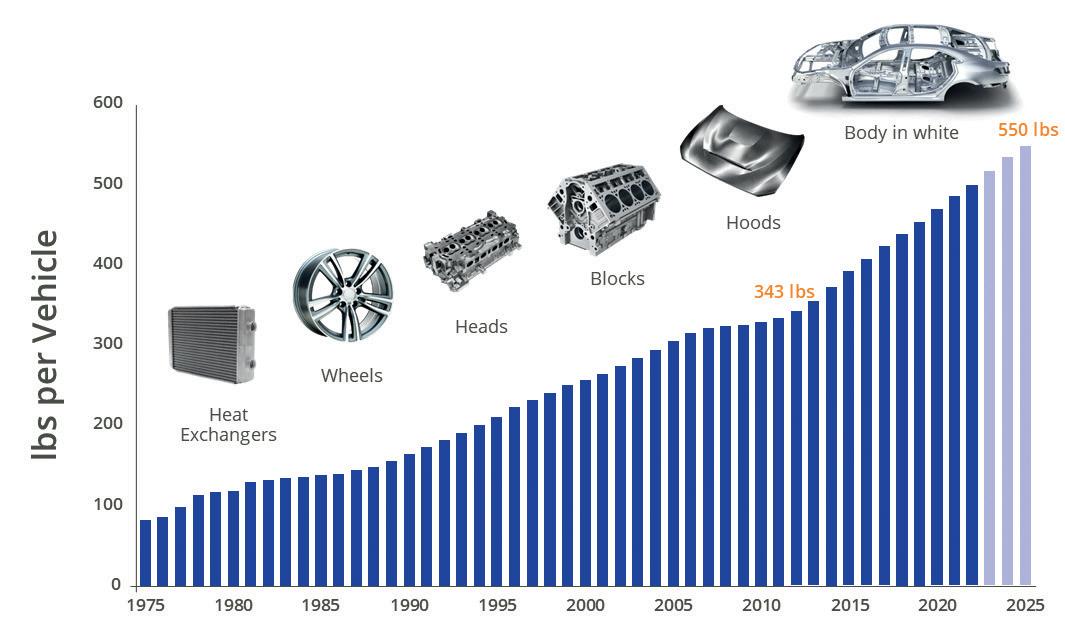
Farra has built many aluminium smelter pit platforms since designing and manufacturing the first one for the Tiwai Point smelter, near Bluff, in New Zealand, with equipment now operating in smelters across New Zealand, Australia, the Middle East, Africa, South America.
FURNACE SAFETY 77 Aluminium International Today September/October 2022
*
Farra’s team of 100 are doing big things when it comes to innovation regarding safety and efficiency in the maintenance of carbon bake furnaces for Aluminium Smelters globally. Based in Dunedin, New Zealand, Farra has leads this global niche market in supplying access equipment for the world’s aluminium smelters with purposebuilt pit maintenance platforms.
By Andrew Martin* Head of Sales,
Enhancing carbon bake house furnace safety and efficiency
Being proven and experienced with deep understanding of smelter bake house requirements and having over 25 years designing, manufacturing, and installing equipment for the aluminium industry Farra Engineering is the partner of choice for your pit maintenance machinery needs.
Farra PMU Dubal Test Jeannie 3
Pit platforms are hung over deep slitshaped pits, which make the anodes used later in the aluminium manufacturing process. Cages are lowered by wires from drums and maintenance workers descend into the pits. The complete equipment is rated up to 65°C. “It is a particularly hostile working environment. says Thomas Schweitzer, Manager of Design and Innovation. “Our design team understand
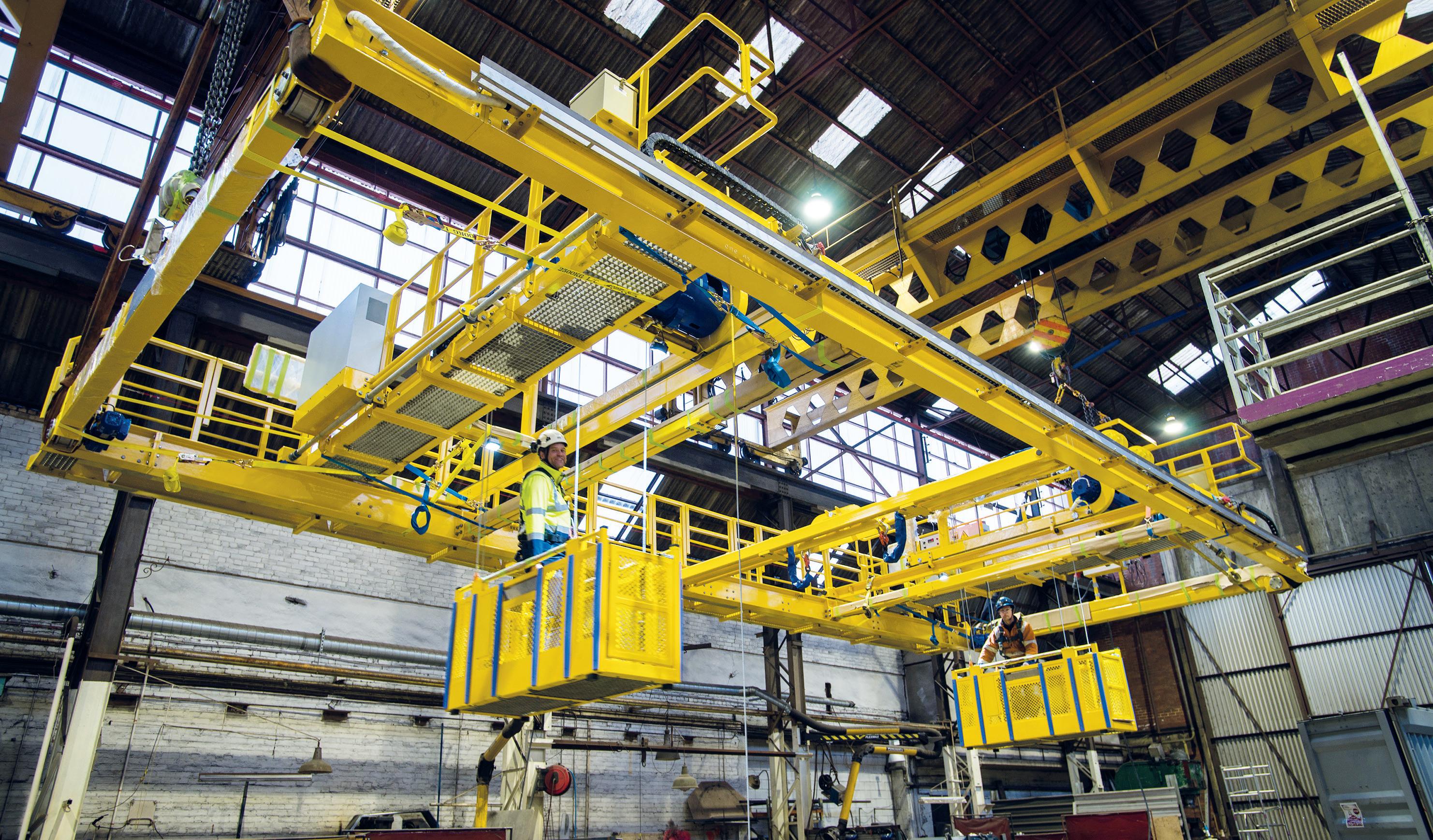
But there’s more to getting it done right than you might think. Only experience and learning from extensive testing and trials in the workshop and real-life applications can give you that insight”.
what it takes to design to be safe and efficient without cutting corners. “We have had others try to imitate what we have created and they have failed. On the surface it looks simple, and it should be.
Farra are committed to ensuring their products encourage safer work environments and increased bake house efficiency. Units typically allow safe access to up to 8 pits at a time for regular maintenance and work and are customised to each smelter, are built to
Farra’s pit maintenance units (PMU) create a safer and more efficient method for their aluminium smelter staff to access their carbon bake furnaces. Farra first created pit maintenance units for the Mozal smelter in 2002. In 2017, after 15 years of service, the well-used units were set to be retired. The two new PMUs were custom designed to match the layout and dimensions of the Mozal smelter and incorporated the newest innovations for PMUs. Other features installed included trackless relocation and dual gantry cages. Trackless relocation of the PMUs enabled the units to be driven with a remote between the Mozal Smelter’s carbon pits, saving time and freeing up their FTA crane for other essential smelter operations. The Mozal PMUs were designed to have dual gantry cages to double productivity. Each gantry cage had a safe working load of 350kg and was suspended by four corner wire ropes, connected to a single layer hoist and was fitted with two independent brakes to ensure the safety of the user.
Aluminium International TodaySeptember/October
The most recent bespoke option is Farra’s patent-pending Pit Wall Brushing Cages. These proprietary brushing units are added to the base of the PMU cages. They can remove the need for operators in the cages whilst cleaning of the pit is being undertaken. Sprung brushes can be activated every time the cage is used used manned or unmanned ensuring regular cleaning of the walls. There are several real benefits to this - No need to deal with cumbersome external cleaning units reducing the need to invest in additional equipment, It does not use the FTA, so it can be used for production improving fuel efficiency which has never been more important with rising costs, emissions, and the drive to meet the UN sustainable goals, and most importantly, it keeps your workforce healthy avoiding shoulder injuries caused by scraping the carbon off manuallyThisBrushing Cage one of the many features that have been embraced by Mozal Aluminium Smelter in Mozambique.

The delivery platform provides an area to store bricks and allows a delivery trolley to run to and from the main frame. A seventon emergency recovery hoist retrieves workers in the event of a wall failure.
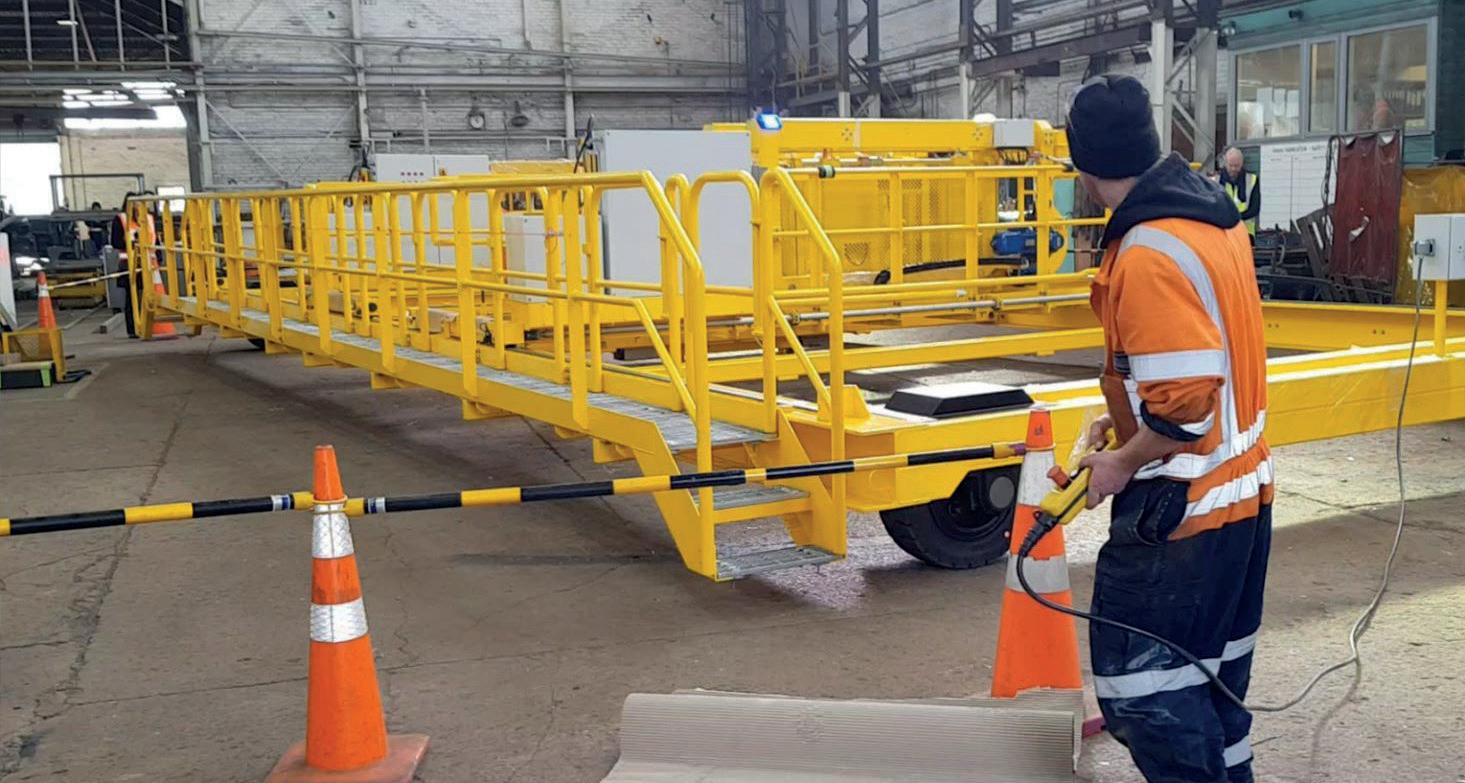
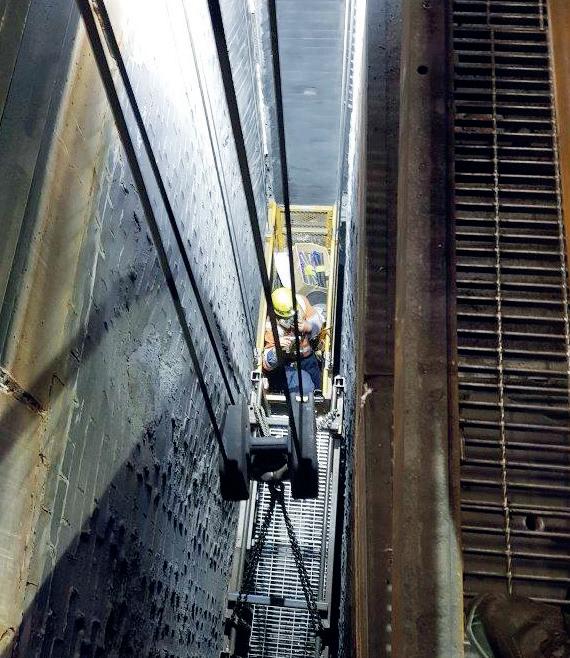

Lastly, the Hoist and Work Platform is open sided allowing unrestricted access to the flue wall and has a flexible floor to adapt to the shape of the pit. Brick removal and delivery are achieved with the use of an overhead monorail fitted with twin electric chain hoists. “The options are endless and this is a just taste of the difference Farra has made for others. We pride ourselves on building great relationships with our clients ensuring they get a quality outcome and what they actually need” says Farra CEO Gareth Evans. “We like to think that’s what brings our clients back to us. Because we understand what their operation needs to be better, safer and more sustainable”. � Farra www.farra.co.nzEngineering Brush cage deformation Mobile PMU Brush cage model Cage down hole
78
FURNACE2022SAFETY
last, and designed to work 24/7. Clients can choose from options like single or dual gantry, fresh air supply for the cage, CCTV in the cage for enhanced health and safety of staff, electric or pneumatic motion control supply for supply to the cage, a low profile 1650mm height, or a lightweight option less than eight tonnes to name a few.
The two cages allow the Mozal staff to work on multiple pits at the same time. Other major carbon pit safety innovations include Farra’s Flue Wall Building System (FBS) and Flue Wall Repair Unit. The FBS allows quick and accurate assembly of new flue walls away from the pit using the mechanically driven building platform. These can then be delivered into the pit fully built, saving your operations team time. The Flue-Wall Repair Platform (FRP) is designed to provide convenient access to the pit while protecting workers using the platform. The FRP consists of three platforms: The FRP Platform or main frame sits on the pit ends which provides protection in two ways and helps to stabilise the flue wall and protect workers in the event of a wall collapse.
BRUSHINGFUEL-SAVINGWWW.FARRA.CO.NZPITWALLUNIT Utilising the Pit Wall Brushing Cages: • Helps to avoid the build-up of carbon pieces, blocks and leftovers. • Ensures regular cleaning of the walls. No need to deal with cumbersome external cleaning units. • Does not use the FTA, so the FTA can be used for production. • Keeps the workforce healthy avoiding shoulder injuries caused by scraping the carbon off manually. • Has the potential for autonomous cleaning. RefractoryTechOL1/4 pg.qxp_Layout 1 2/17/22 3:06 PM Page 1 603.352.1415 info@polyonics.com INTRODUCING They thrive on the punishing temperature ranges encountered throughout the metal manufacturing process. From production through delivery of completed goods to customers, they take the heat every step of the way. polyonics.com/highdegree Labels & Tags for Metal Manufacturing
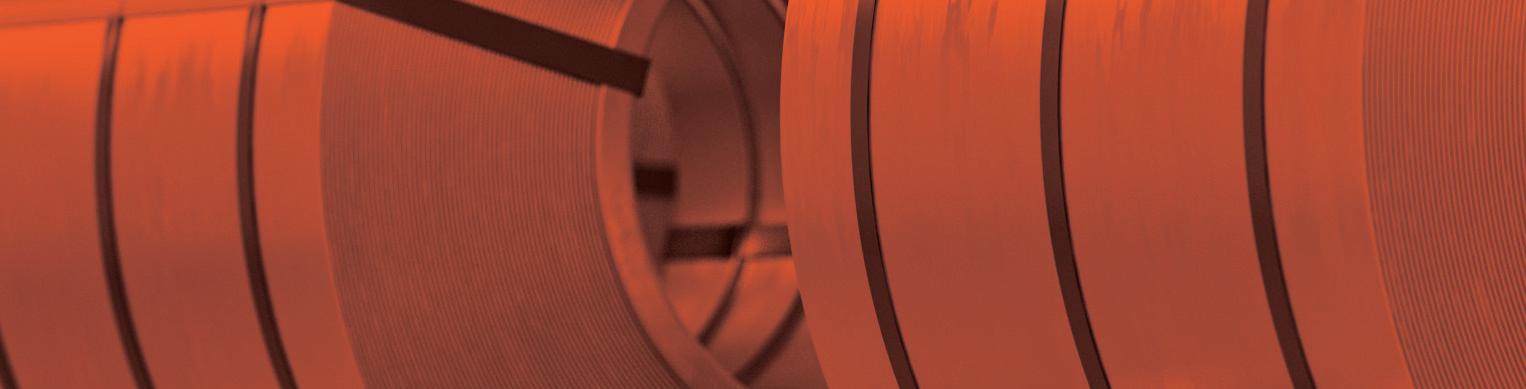


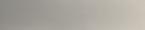




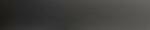





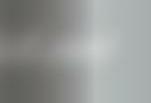

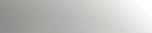
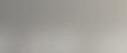


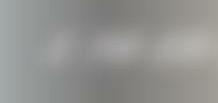
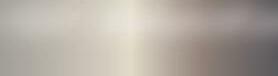
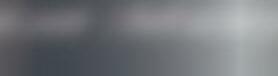

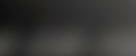

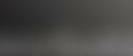

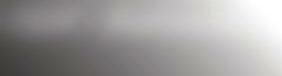
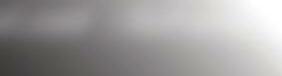
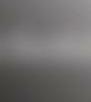

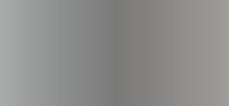
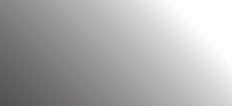


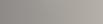
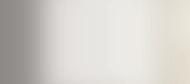
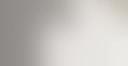
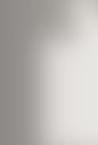

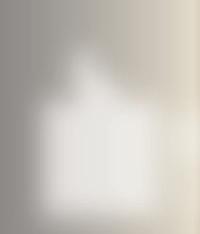
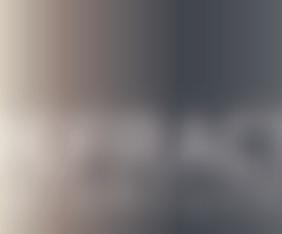
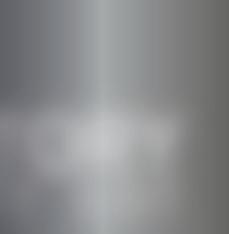


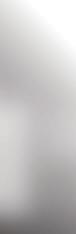
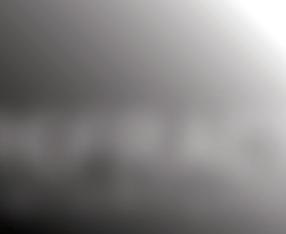
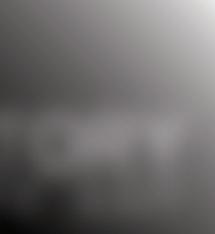












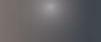
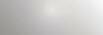

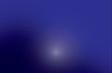
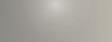
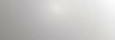

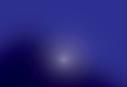
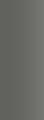
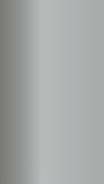
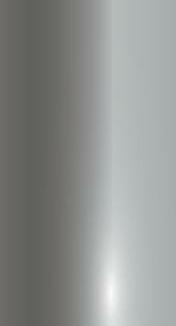
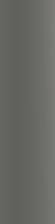
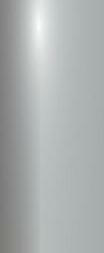

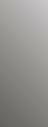
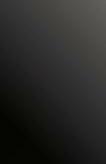
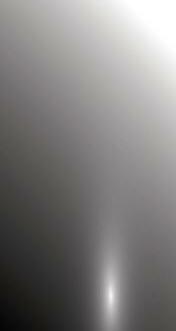
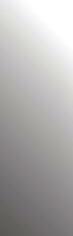
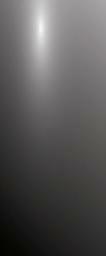

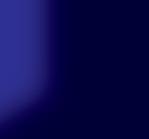
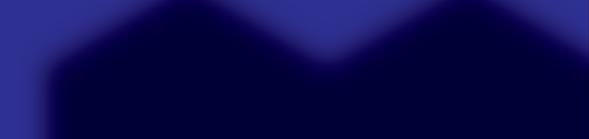
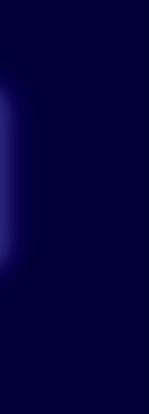
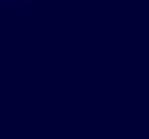
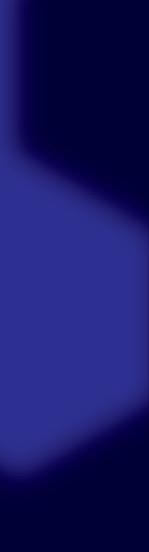
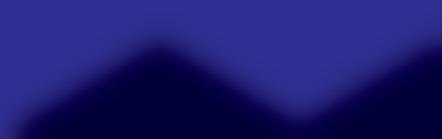
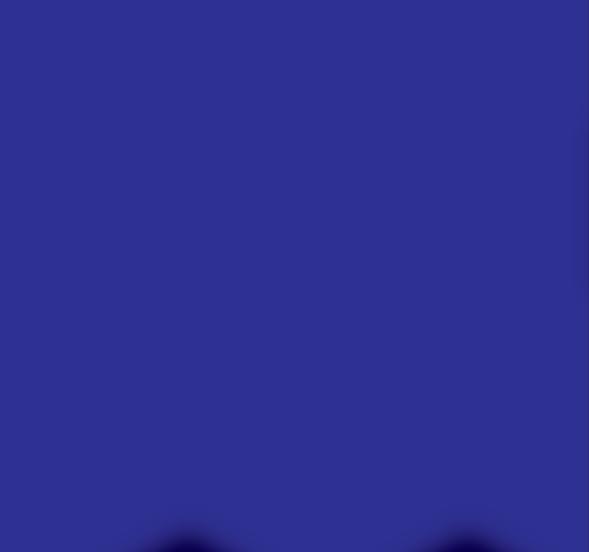

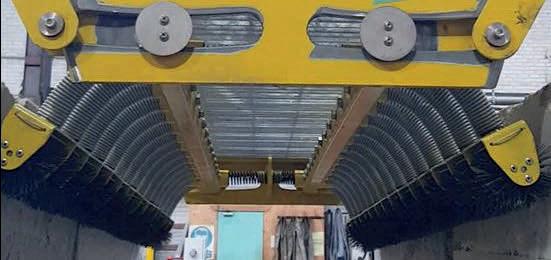
Automation-controlledflexiblerollingfaceseliminatebuttswellUniquedesignfeaturesallowoneAPEXmoldtocastmultiplesizestocastmultiplesizes














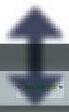




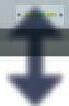


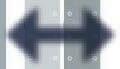


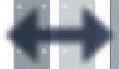
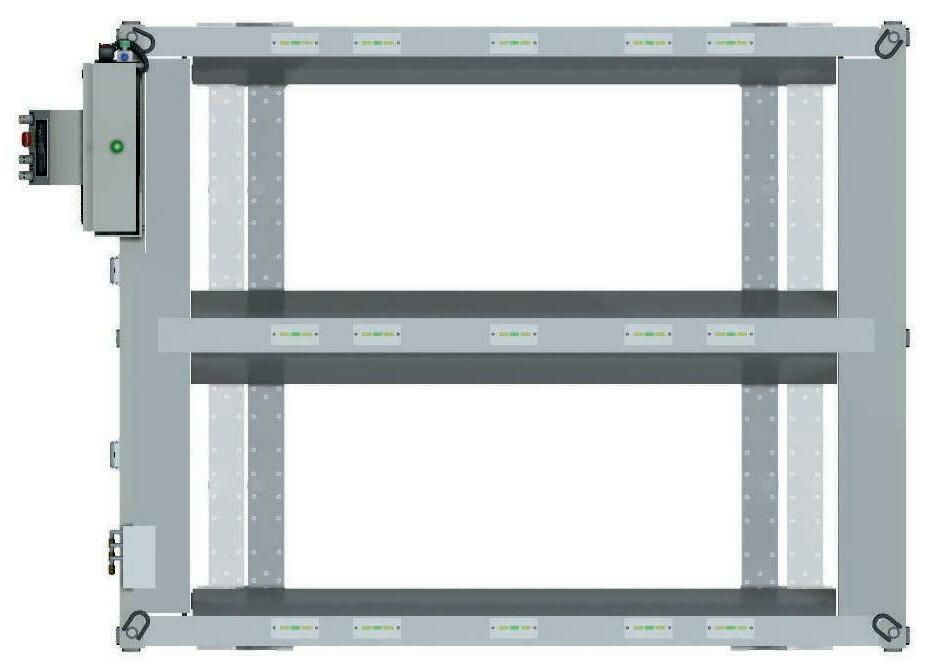
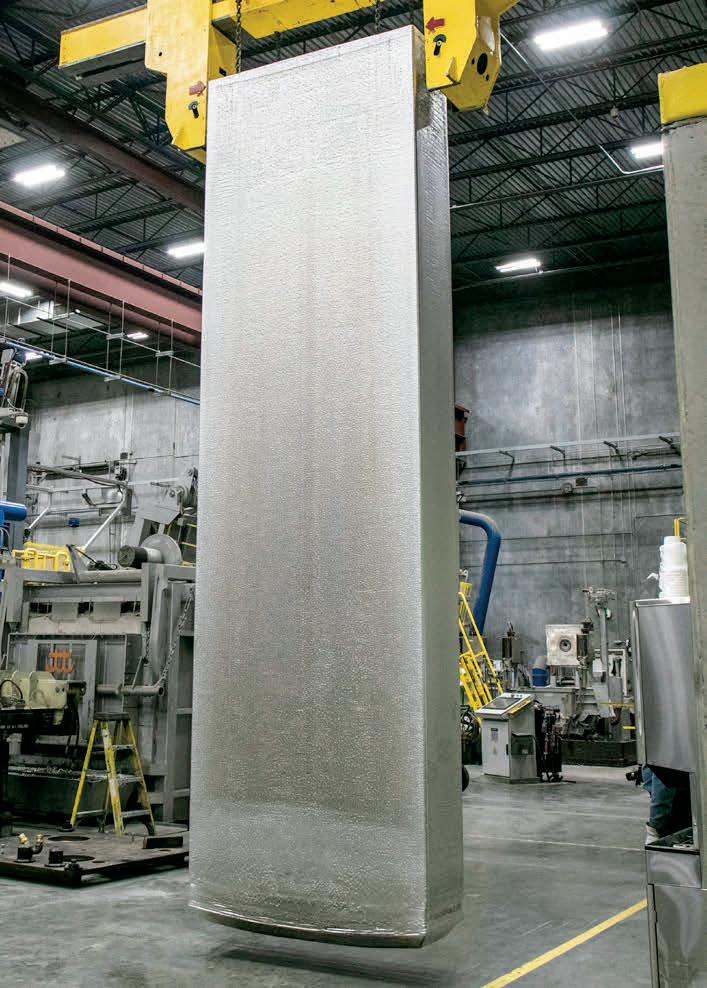






















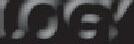








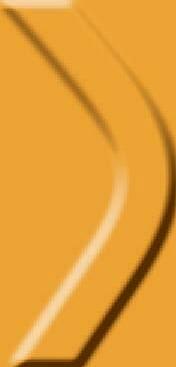

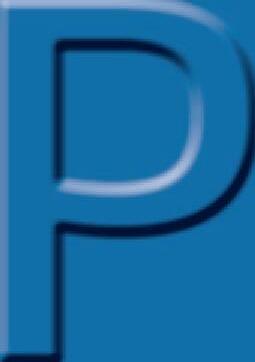
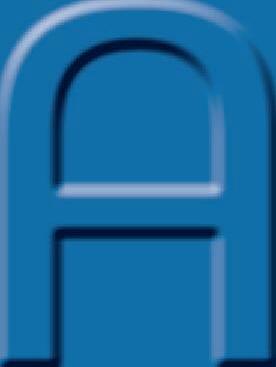
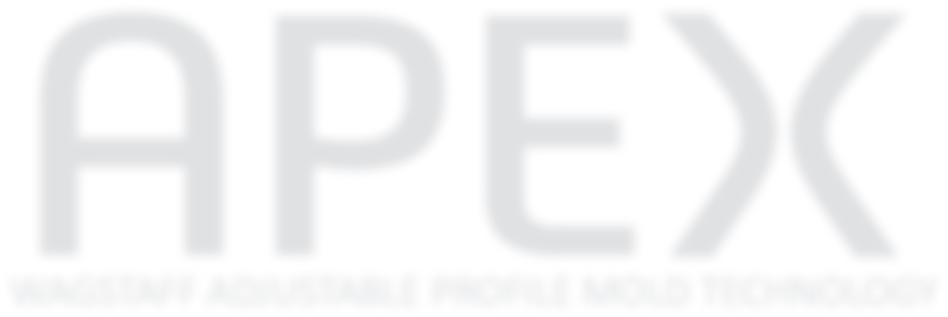
b) Theoretical flame Temperature for the stoichiometric combustion of natural gas plotted against the oxygen concentration of the combustion air
Flameless oxy-fuel combustion is an additional tool in the optimisation of aluminium furnaces. Air-fuel, traditional oxy-fuel and flameless combustion Fig 1 plots the theoretical flame temperature for the stoichiometric combustion of natural gas versus oxygen enrichment. It can be concluded that even low oxygen enrichment increases produce higher flame temperatures and improve combustion efficiency. In addition to the higher thermal efficiency of oxy-fuel burners over air-fuel, oxygen enrichment also improves the rate of heat transferred to the melt, e.g., increases heat flux.
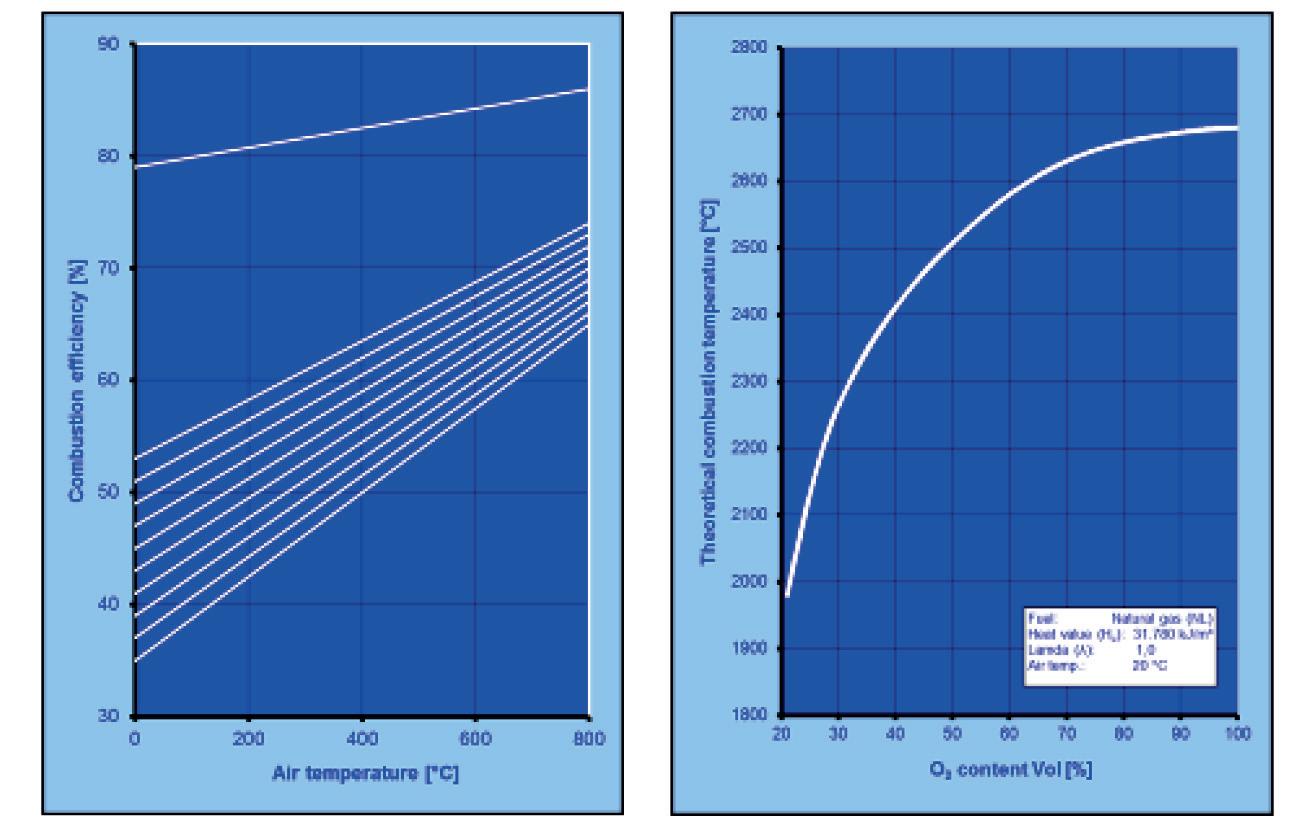
Flameless combustion employs both convective and radiative methods of heat transfer. With increasing temperature, the proportion of the radiation rises compared to convection. In addition, the radiative energy in an oxygen flame is due to the products of combustion from oxygen: triatomic molecules. Air-fuel combustion produces a majority of diatomic molecules, such as N2 and NO species, while oxy-fuel produces higher content of the triatomic molecular gases, CO2 and H2O as well as the lowers NO x level in the exhaust gas.
Thermal NO formation is controlled by 1) the flame temperature, 2) the oxygen concentration in the reaction zone, and 3) the residence time of the products of combustion in the high-temperature zone of the flame. As fundamental research has proven, thermal NO formation tends to be negligible for normal industrial gas burner residence times as long as the flame temperature does not exceed 1,600°C/2,840°F. Therefore, burners must be designed to avoid peak temperatures above 1,600°C/2,840°F in high-oxygen zones of the flame. Staged combustion, flue gas recirculation and flameless combustion are techniques which can reduce NO x emissions substantially. (Fig 2)
Fig 1.a) Influence of the combustion air temperature and the oxygen concentration on combustion efficiency.
Introduction In 1930, F.W. Davis wrote these prescient words, “All nonferrous metallurgy will be benefited by the use of cheap oxygen... the application of oxygen will revolutionise the art of smelting and it will probably change the whole operation and equipment.”
1. MPOT GmbH, Kaerntnerstrasse 45, A-8700, Leoben, Austria 2. MPOT LLC, 1003 N. West Street, Wheaton, IL, 60187, USA 3 PCI, LLC, 12201 Magnolia Ave, Riverside, CA, 92503
Fig 2. Principle of flameless / Flameless combustion [2]
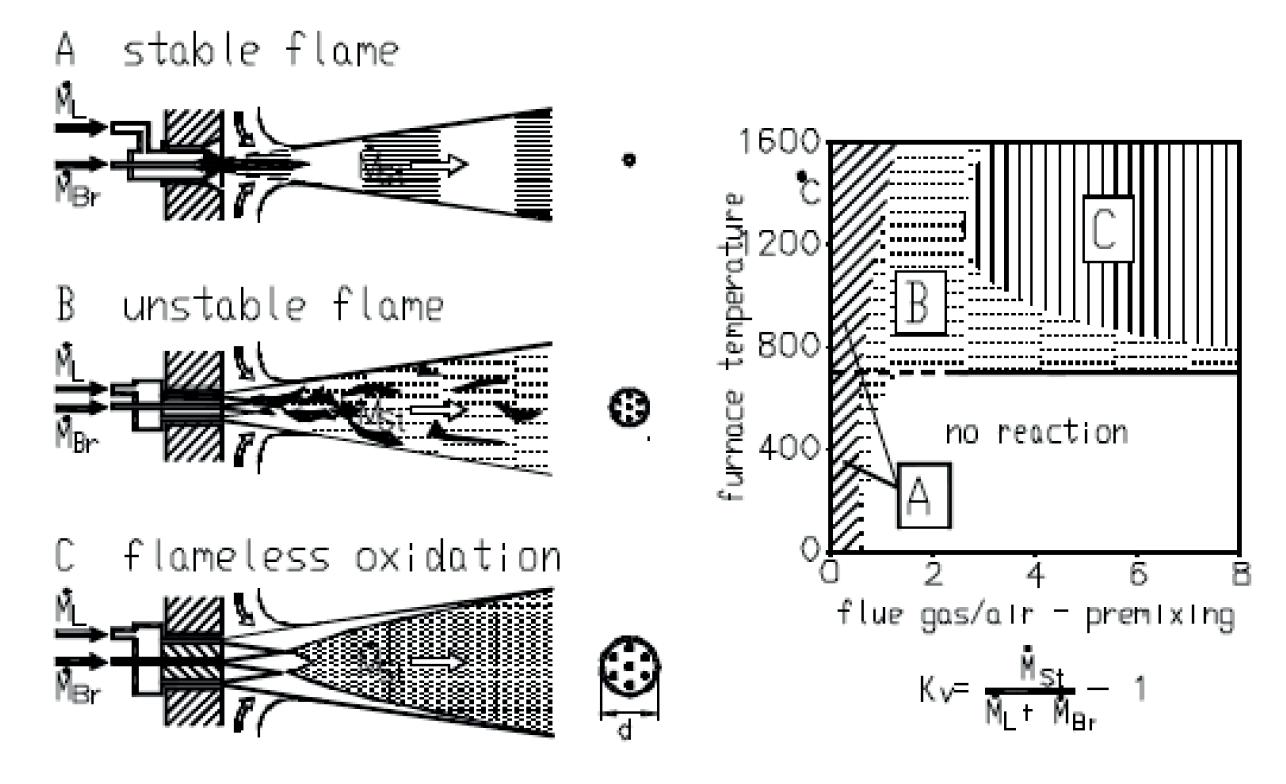
FURNACE TECHNOLOGY 81 Aluminium International Today September/October 2022
By Michael Potesser1, Curt Bermel2, Ali Saputra3, Pedro Nava3
Lowering aluminium melting operating costs
Lowering OpEx by using just enough pure oxygen participation Benefit of 100% pure oxygen participation is a more stable flame, higher melting efficiencies, higher productivity, and lower POC’s, if used at a lower AFT. However, the negative of all that pure oxygen is that you have to pay for it. Let’s be candid; margins in aluminium melting are tight, and every cast house must ruthlessly measure, monitor, and manage their operating expenses (OpEx) to remain healthy and profitable. MPOT’s mission provides cast houses the most efficient and lowest OpEx systems available. Our path to having customers for life: provide what you promise and service what you
Nothing could be more true in the arena of profitable aluminium casting. Are you continuously measuring your reverb’s pressure? Negative furnace pressure of 0.15” WC or worse. This is a huge amount of waste, both in fuel, productivity, margin, and emissions… literally going up the stack. Our solution is simple: manage furnace pressure with one moving part! (Fig 5). The circular sleeve acts as a blade, controlling the suction from the melter using a circumferential air knife, allowing the sleeve to raise and lower as the measured pressure changes. No damper, period! In Fig 6 is an estimate on the additional fuel and loss of productivity furnaces experience because they don’t measure and control positive pressure.
Aluminium International TodaySeptember/October
Application examples (Figures 3 & 4).
The stretch metric is empirical, based on hundreds of conversions with similar operating conditions. Below are the conversion results (Fig 3) on an already productive reverb melter.
Integrated pressure control unit Peter Drucker famously said, “You can’t manage what you don’t measure.”
� 58% overall decrease in natural gas (Btu/lb) � Homogeneity improved from an average of +/-25°C to 7°C, a 72% improvement MPOT®-Air-Oxy-Fuel Burner: Results: This melter was optimised using just 70% pure oxygen participation. Elimination of waste means $’s in the owner’s pocket! The MPOT®-Air series adjusts the burner to different oxygen enrichment levels of the oxidant (oxygen+air). This burner series is mainly used in reverberatory,
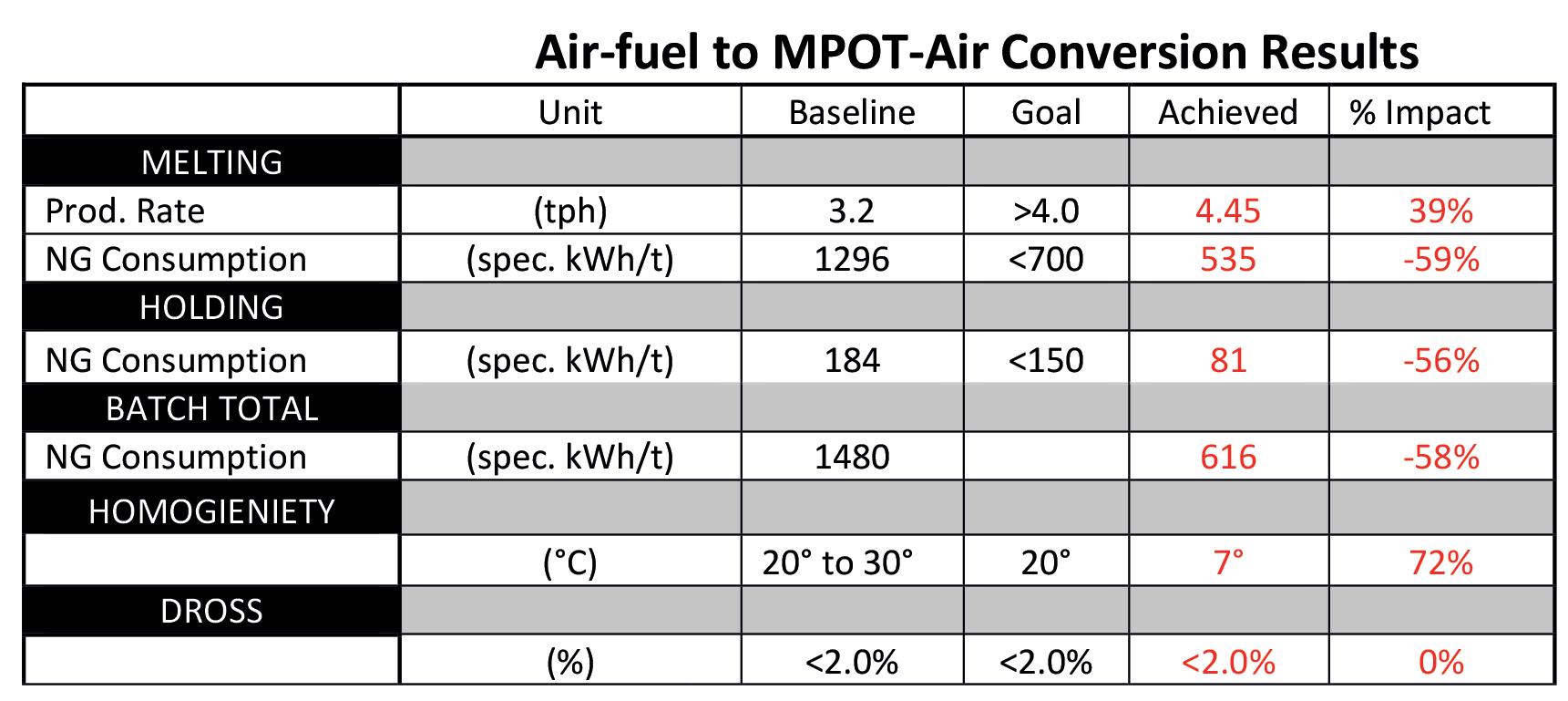
rotary and tilting furnaces in aluminium and copper cast houses. Additional Benefit: If melting 24/5 or 24/6, use higher oxygen participation on melting days, and on weekends, use 100% air! Why use pure oxygen when it is not required?
FURNACE2022TECHNOLOGY82 sell. The first step to controlling OpEx is taking a miserly approach to the two highest OpEx costs: fuel and pure oxygen. When we quote a combustion system, we guarantee our system’s performance, as well as offer an “expected stretch metric.”
Highlights: � 39% increase in productivity (mtons/hr) Fig 3 and below. Application of MPOT® Air burners on a reverb furnace Fig 4. MPOT® flameless combustion stage development, 400°C, 600°C, and 900°C, which is flameless mode
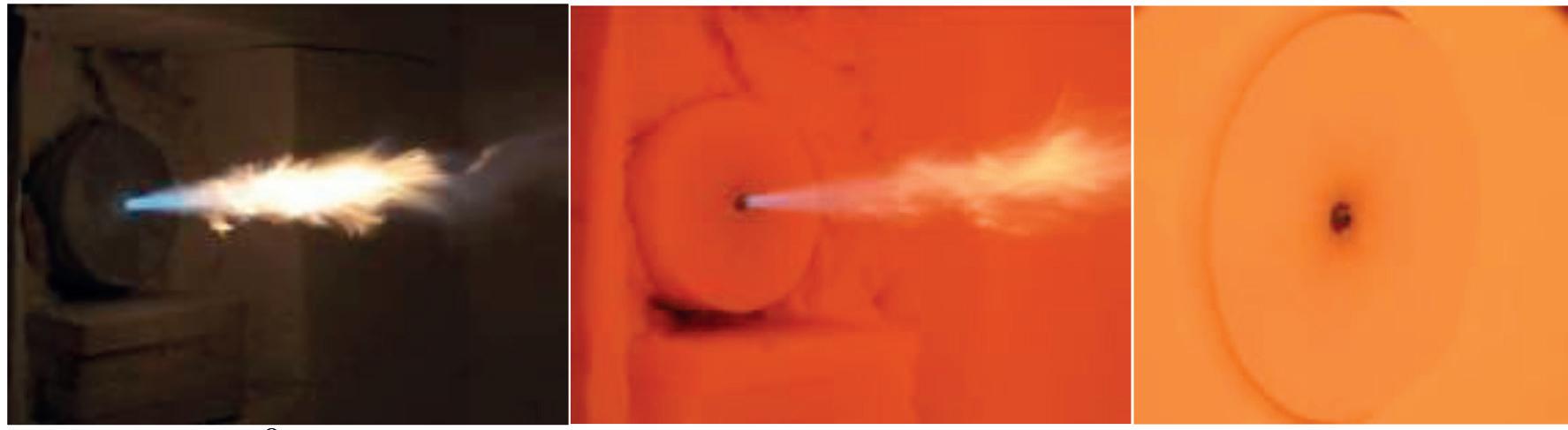
Alternative fuels In the case when natural gas supply is limited which causes unpredictable price swings, cast houses may consider alternative fuel sources such as LPG, Propane, and LNG as well as liquid fuels such as Marine Fuel Oil, Diesel fuel, Bunker C fuel, etc. MPOT has burners for each of liquid fuels to replace natural gas. For LPG, Propane, and LNG, the same burner and regulation control skid can be used. For liquid fuels, a liquid metering skid would be required, with a simple exchange of burners on the furnace. Having alternative combustion options provides an enormous benefit for cast houses in an energy market that is unpredictable. Advantages of onsite VSA oxyben Comparison of the two prevailing non-cryogenic onsite technologies are pressure swing adsorption (PSA) and vacuum swing adsorption (VSA). VSA is shown in Fig 7 Both technologies deliver oxygen 90% to 95% pure, and both use a molecular sieve (adsorption). Main differences are the central operating components and the operating pressures. Fig 8 highlights key differences between PSA and VSA technologies. This data is from an energy study on behalf of a SoCal municipality, comparing life cycle costs between PSA and VSA for a two separate lift station odor control projects. Each lift station
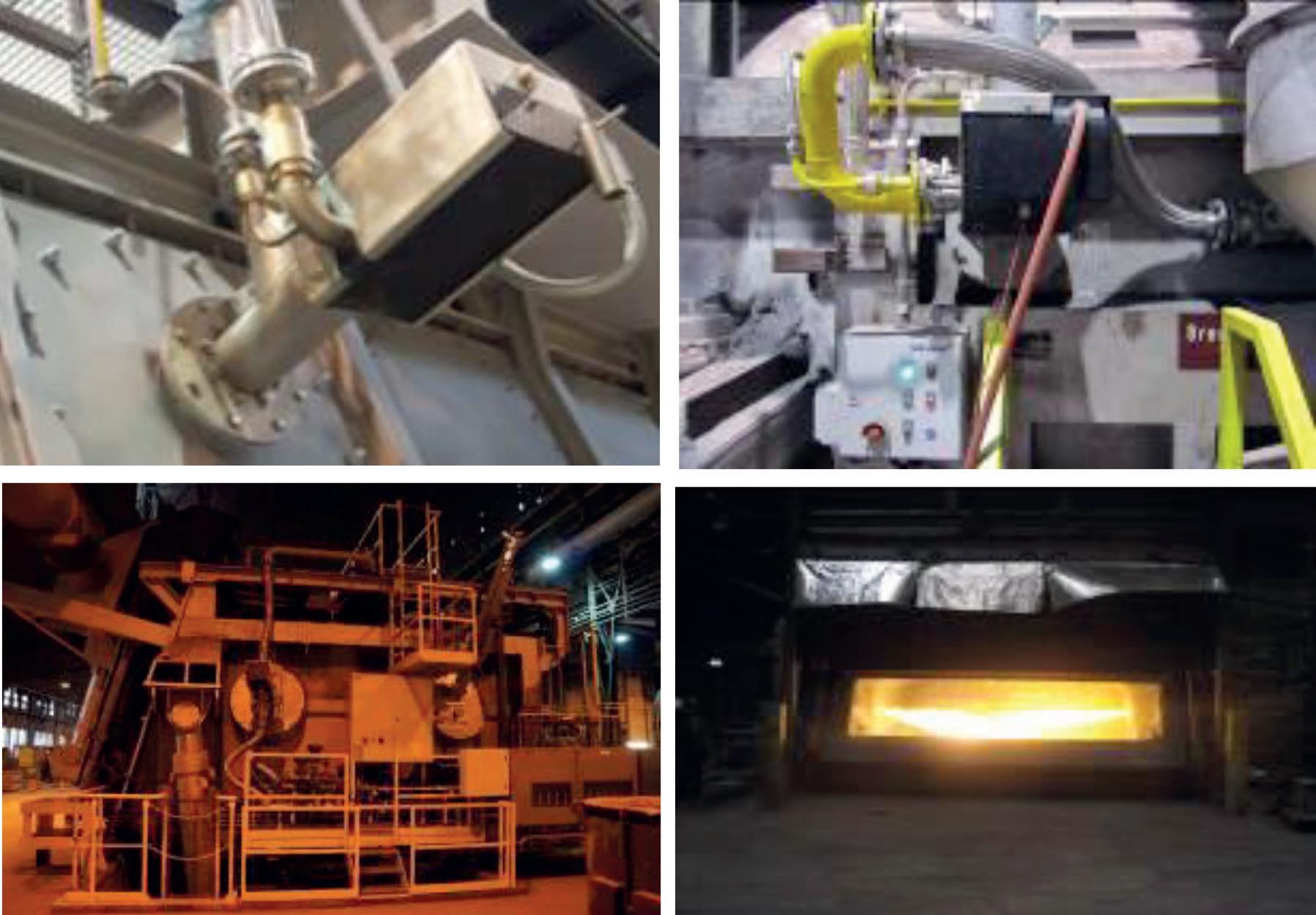
ST. LOUIS, MISSOURI, USA 800 325 7075 | www.gillespiepowers.com | 314 423 9460 ✓SINGLE CHAMBER / MULTI CHAMBER FURNACES ✓SCRAP DECOATING SYSTEMS ✓TILTING ROTARY MELTING FURNACES ✓SCRAP CHARGING MACHINES ✓LAUNDER SYSTEMS ✓CASTING / HOLDING FURNACES ✓HOMOGENIZING OVENS ✓COOLERS ✓SOW PRE-HEATERS ✓REPAIR & ALTERATIONS
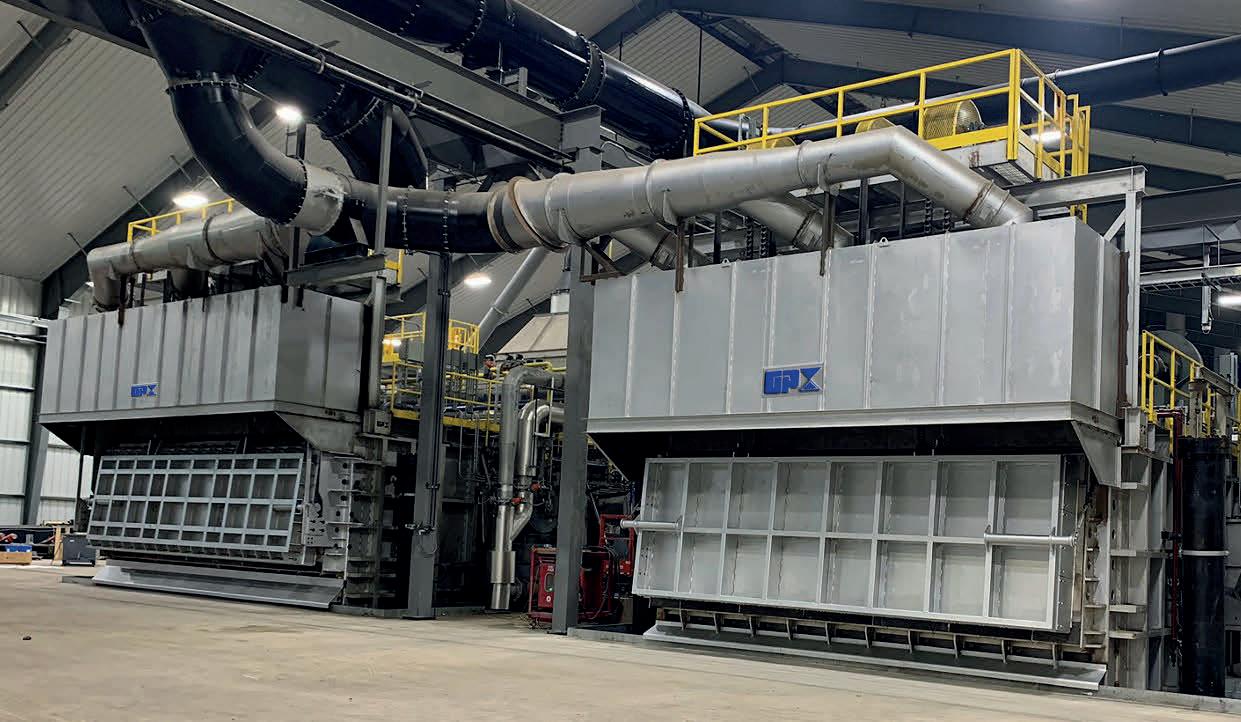
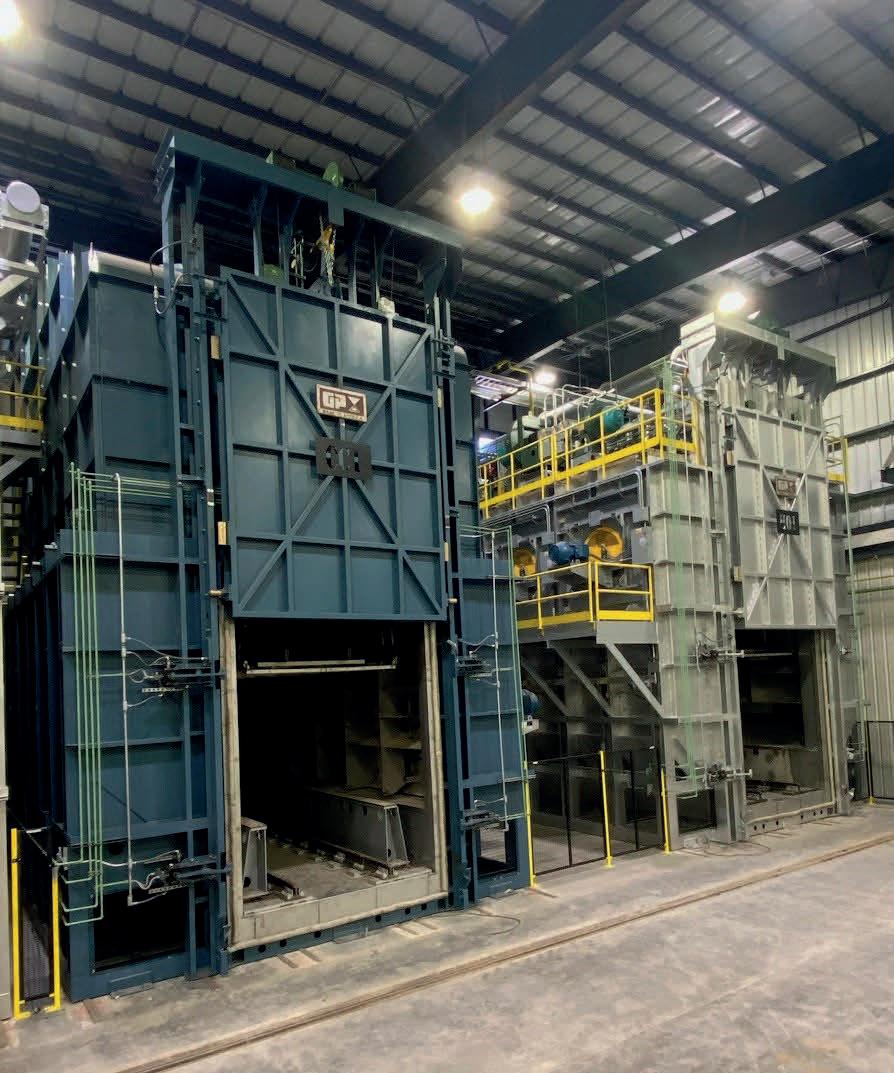
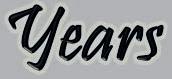
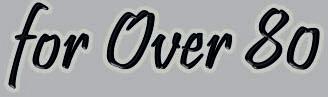
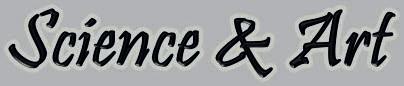
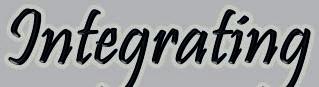

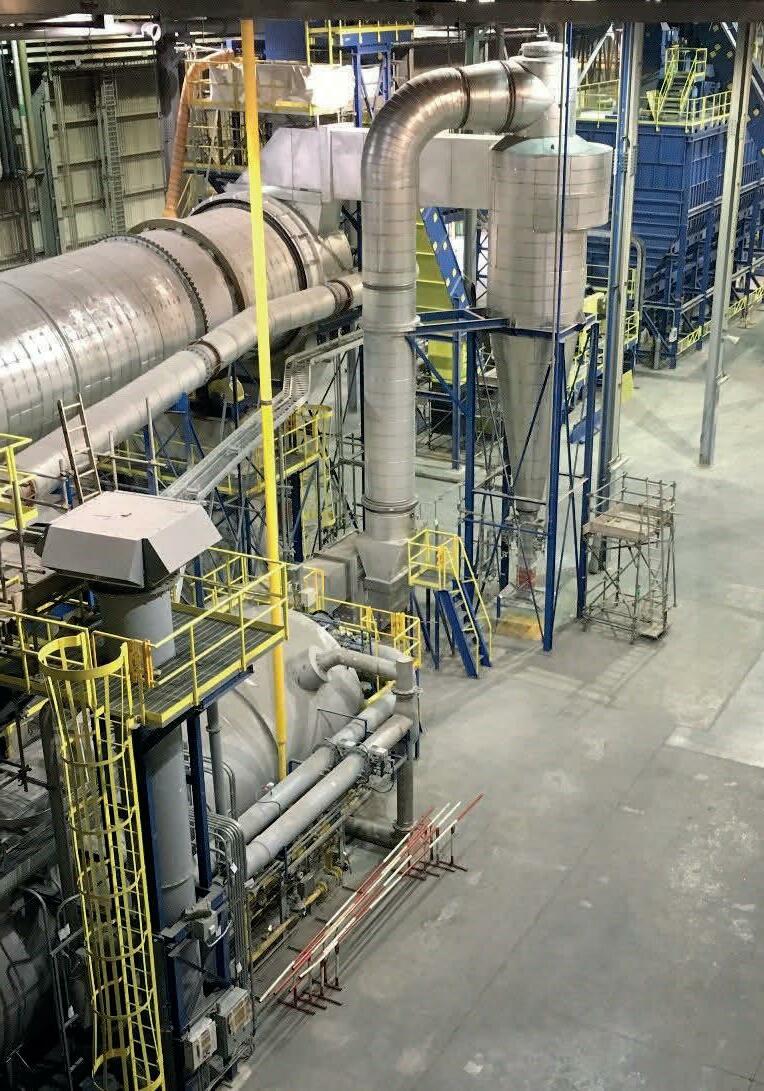

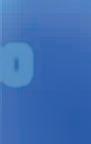
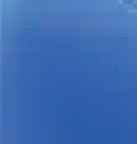




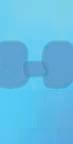

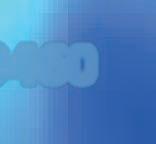
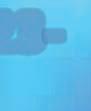



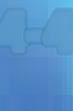






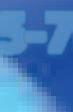



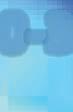




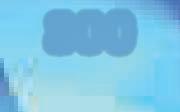
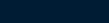
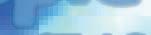



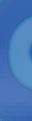
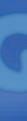
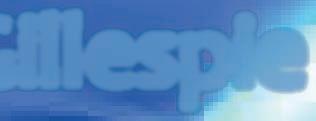
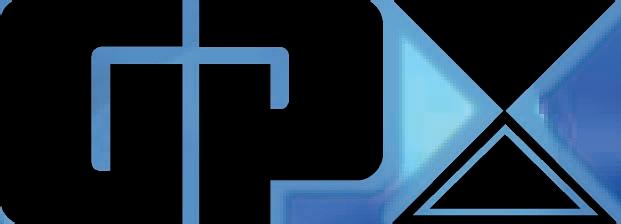
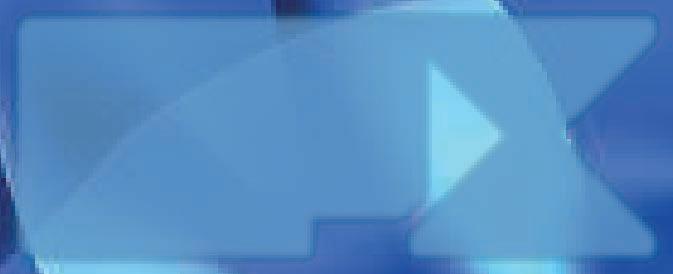
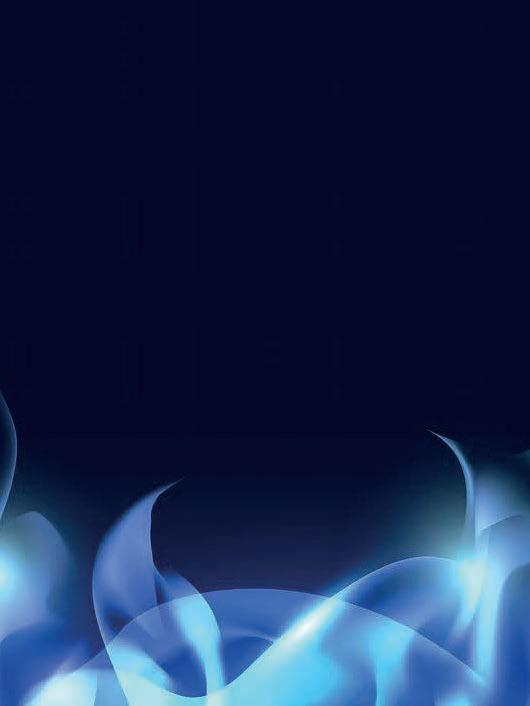
Aluminium International TodaySeptember/October
FURNACE2022TECHNOLOGY
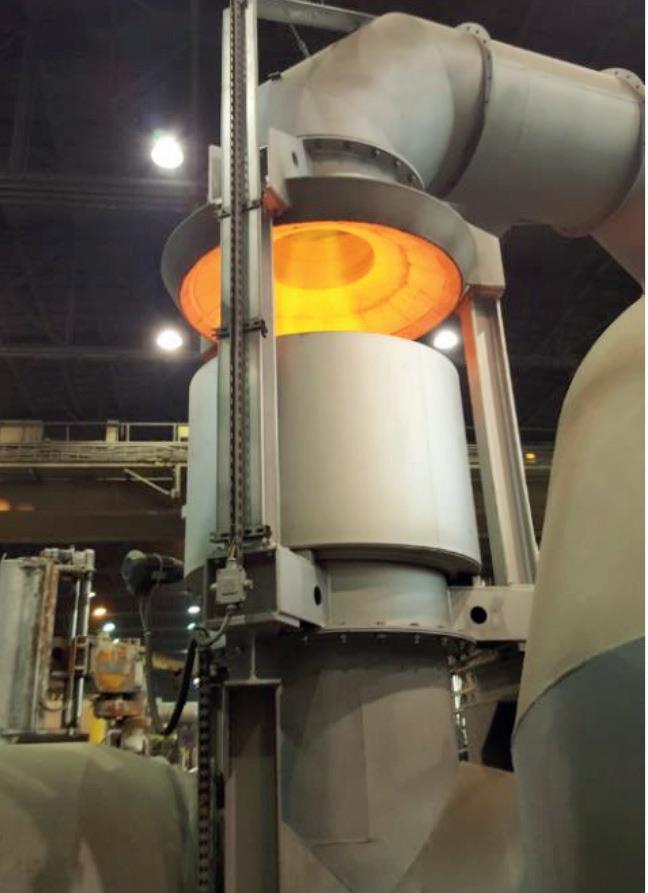
PSA’s also require a dryer to remove condensed water vapor that can foul the adsorbent. Because VSAs operate at lower pressures, water vapor will not condense on the adsorbent: no dryer required!
MPOT® IPCU Fig 6. Est. Value of Integrated Pressure Control Fig 7. Twin DOCS5000 Onsite O2 Generators Fig 8. Comparative Onsite O2 Generation Schematics
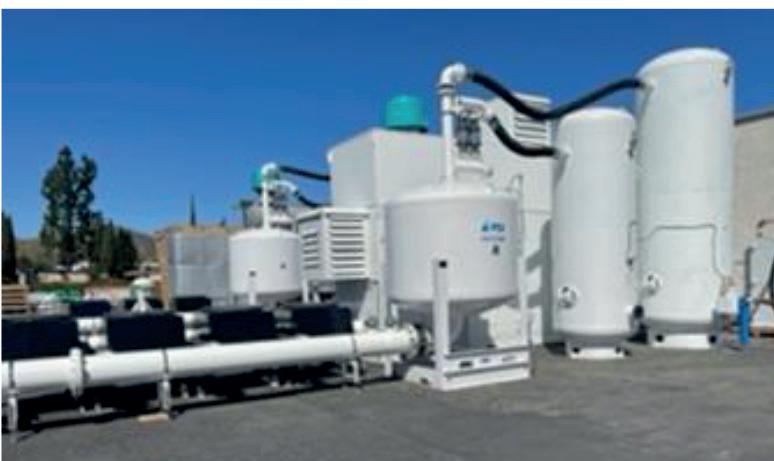
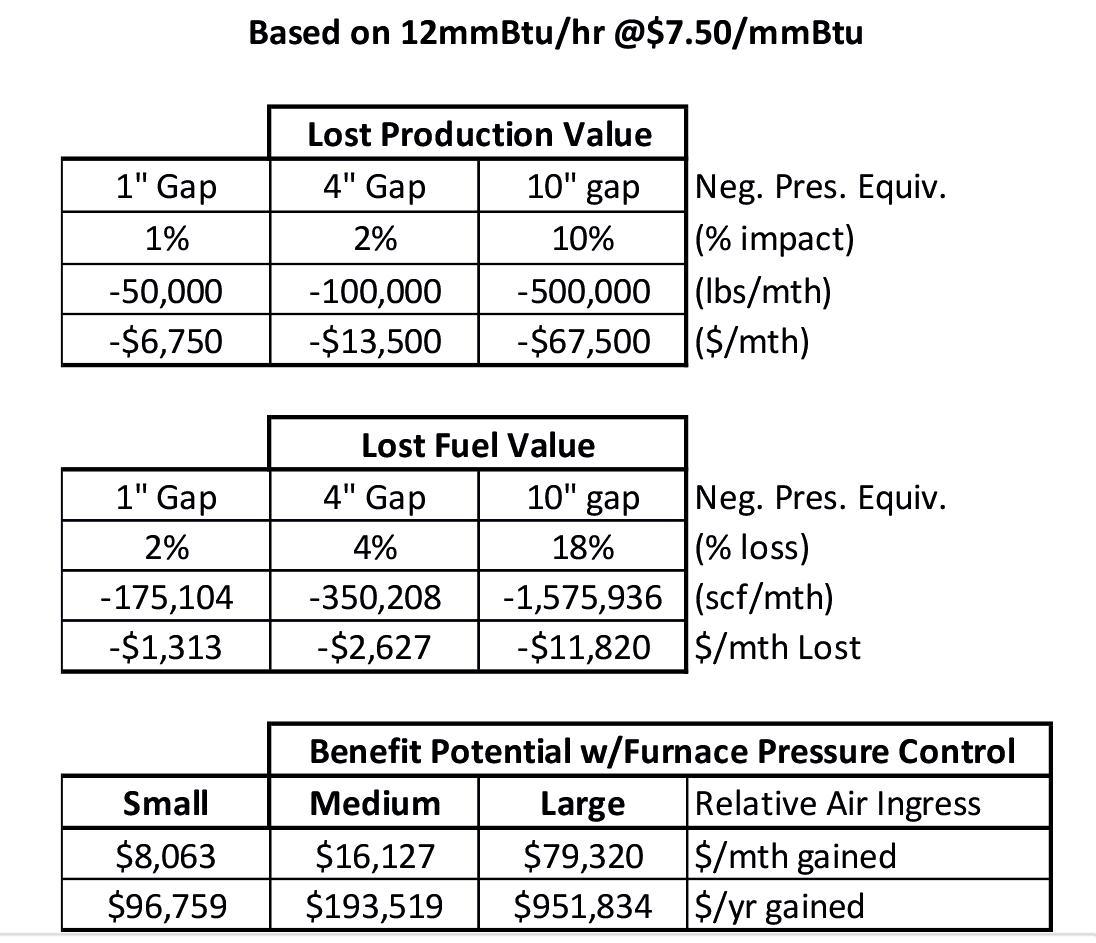
Aluminium is developing faster than any other primary metal. Couple casthouse efficiency improvements with the lowest cost, highest efficiency onsite oxygen molecules and you are establishing a successful casthouse to increase your output, increase your margins, and weather the storms that may come. Safe, dependable, reliable, environmentally conscious, and economically inviting technologies will transform the economic future of aluminium melting. We welcome your inquiries and look forward to working with you. References available upon request. �
Many PSA compressors utilise oilflooded screw compressors which lead to oil vapor mixed with the compressed air. This VSA uses an oil-free blower to eliminate fouling. The higher pressure swings associated with PSA systems lead to attrition of the adsorbent limiting their useful life. This VSA design with its lower operating pressures is designed so that the adsorbent material will last for the entire lifetime of the equipment.
The benefits of a VSA are summarised in the Table shown in the Figure above indicating the energy savings and reduced number of main component/valves. A VSA will save approximately 50% of the energy consumption over a PSA of equivalent size and delivered pressure. A VSA also eliminate 33% of the main components and 70% of the process valves which increase its reliability and significantly reduces its maintenance costs.
84 was supplied oxygen by its respective technology; Vacuum Swing Adsorption (VSA) and Pressure Swing Adsorption (PSA).This VSA design of the feed air system uses a reversible blower that operates at an order of magnitude lower pressure than the air compressor found in PSA’s. This results in significant energy savings because higher pressures are directly proportional to higher energy consumption.
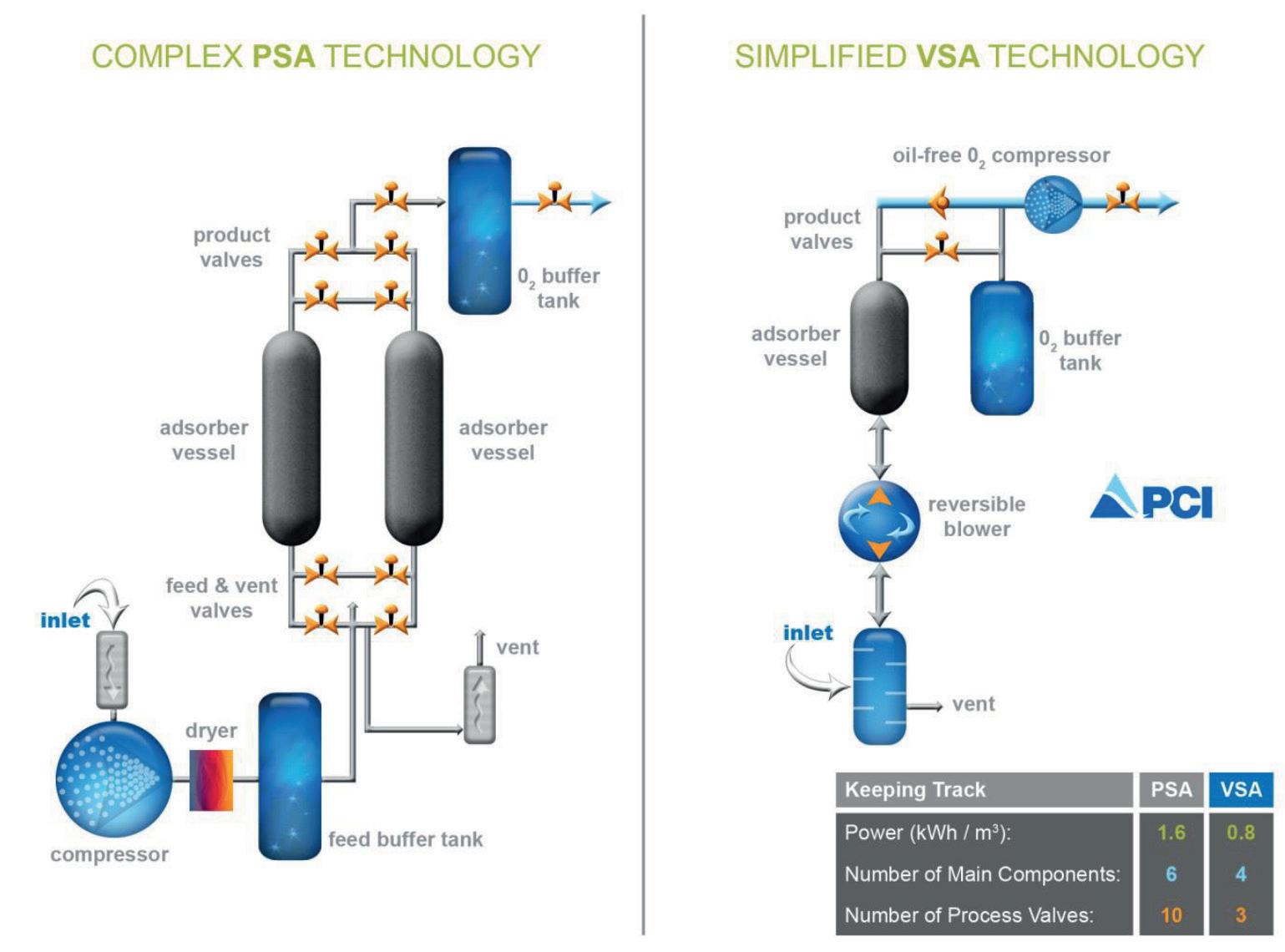
Fig 5.
Net Value Combining Air-Oxy-Fuel, Furnace Pressure Control, & VSA Oxygen Every furnace is unique and should be analysed and assessed individually. A broad stroke evaluation combining airoxy- fuel burners, pressure control, and VSA oxygen on a typical reverb melter, we estimate that the benefits could pay for the ownership of combustion equipment, installation, and onsite oxygen generation in ~1.5 years.
Conclusions
#IACE2022 2022OFEVENTALUMINIUMGLOBALPREMIUMTHEALUMINIUMFEDERATION OF AFRICASOUTH 26 - 27 OCTOBER 2022 Convention Square 1 Lower LongCapeStreetTown8001 ABOUT THE CONFERENCE The Aluminium Federation of South Africa (AFSA) will be hosting the International Aluminium Conference and Exhibition (IACE) this October. CAPE TOWN ICC WWW.ALUMINIUMSOUTHAFRICA.COM THEME Aluminium: Lightweight, Durable & Sustainable The conference aims to position the South African aluminium industry as a premium supplier to the continent and the world, and serves as a stepping-stone towards the vision of “Doubling Local Aluminium Demand by 2030”.

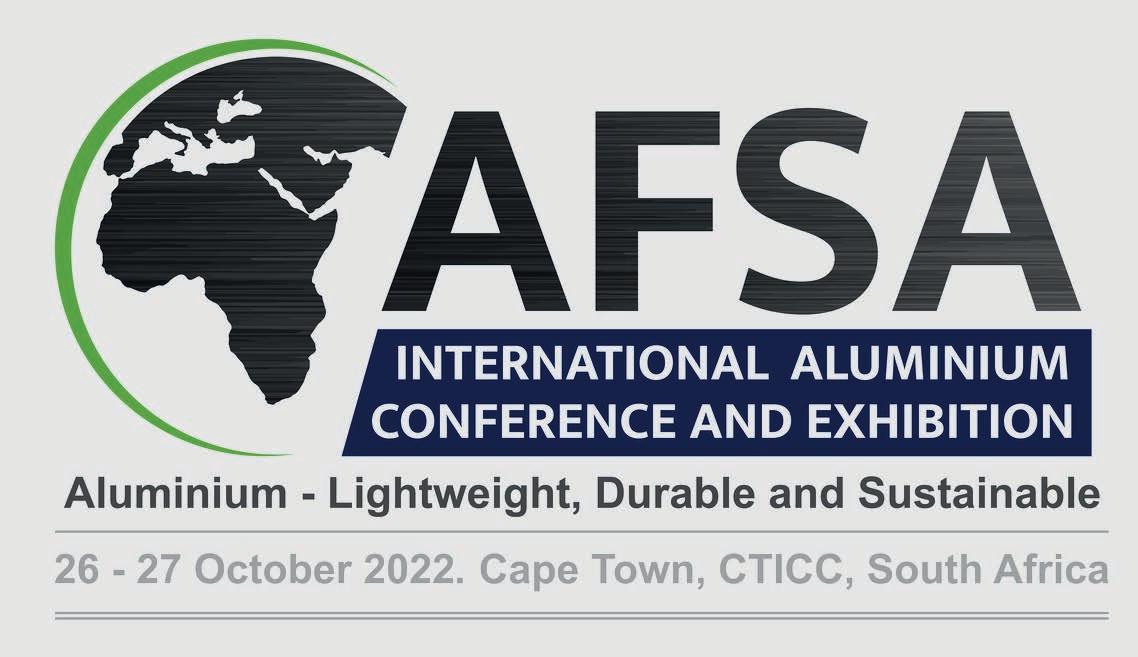
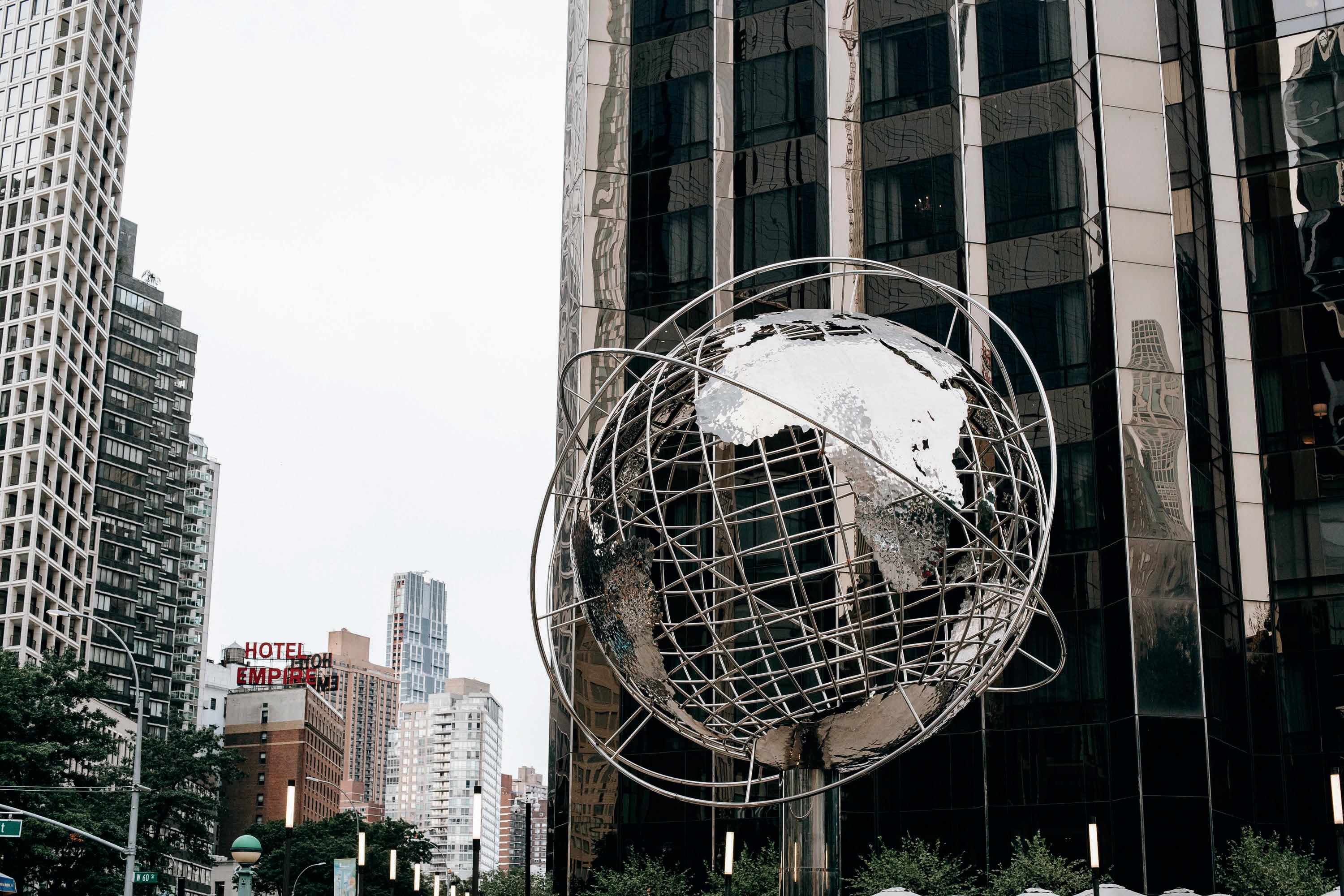
� The height of the trailer needed to be very low, to pass under the existing passages and equipment, with the pot assembly on board � The load bearing capacity of the roads needed to be respected even with the increased loads � towing and transportation along the plant became even more complex.
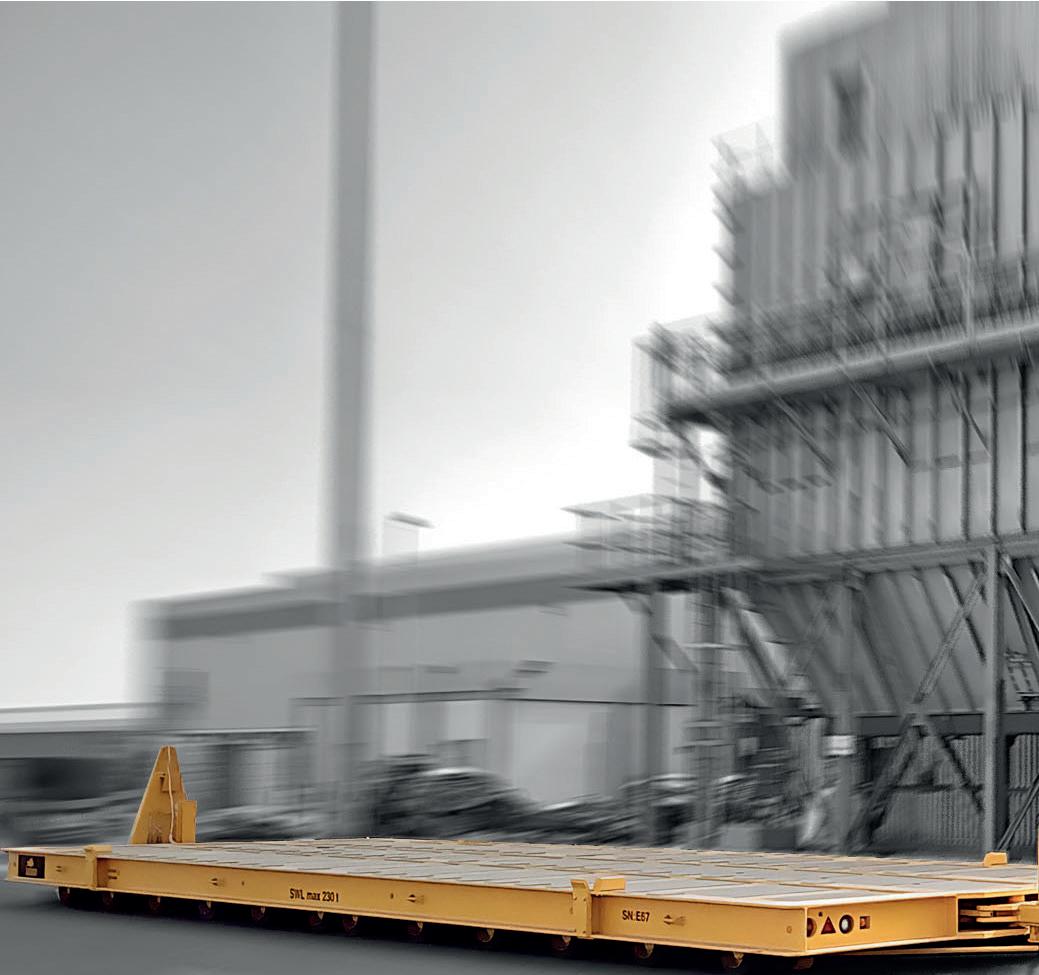
For several decades Techmo Car has been a major player in the design and manufacture of tailor-made vehicles and stationary equipment for the aluminium industry. Our team of experts who is focusing on the evolution of the market demand, allows Techmo to design and provide reliable and durable specifical equipment responding to the particularity and constraints of our customers, whether operational or maintainable. Our team’s taste for challenge, its flexibility and determination to find innovative technical solutions enabled Techmo to design and deliver tailor made vehicles with an unprecedented capacity.
As an illustration of our know-how, let us go back to a success story of the supply of a pot shell transport vehicle (towing tractor and trailer) for one of the wellknown smelters in the Middle East.
The specific above-mentioned campaign was planned in 2 years, with the refurbishment of more than 400 cells, a one-way transport distance of approx. 3 km; the cells had oversize dimensions, with a weight of 210 tons. But an additional need of the customer complicated the application: the pot cell must be transported together with its lifting beam, thus adding considerable weight and height to the assembly. It was not possible to find an equipment (towing machine + trailer) able to respect the existing constraints, in particular:
The overall weight to be towed by the tractor was 270 tons. The machine was designed, delivered, and tested at site within 12 months, then the campaign could start. Nowadays, the refurbishment of all the cells has been successfully completed within the planned period, with no breakdowns. The supplied tractor and trailer are currently ready for service and will be used in the next years for the refurbishment campaign of anotherThankspotline.toits expertise and knowhow, Techmo Car team continuously reinvents itself on each project in order to analyse customer’s problem in detail and to find the best solution, to meet the technical constraints of the aluminium industry. In addition, Techmo Car is currently working on various innovative projects in research and development, such as electric driven vehicles and AGVs. New evolution coming soon… � To discover some of our realisations or for any request, feel free to visit our website at www.techmo.com or contact us at info@techmo.it. We will be at ALUMINIUM 2022 in Dusseldorf from September 27th to 29th, 2022. Visit our booth 6C43
Designing and manufacturing vehicle and stationary equipment
Some years back, one of our main customers were organising a scheduled campaign of pot refurbishment. The work consisted of a series of operations to be performed on each cell of the potline: pot cell shutdown and removal, transportation to another facility of the plant for the relining, relocation of the renewed pot cells.
Techmo proposed to study a specific solution for the application
Aluminium International TodaySeptember/OctoberTRANSPORT2022 & HANDLING86
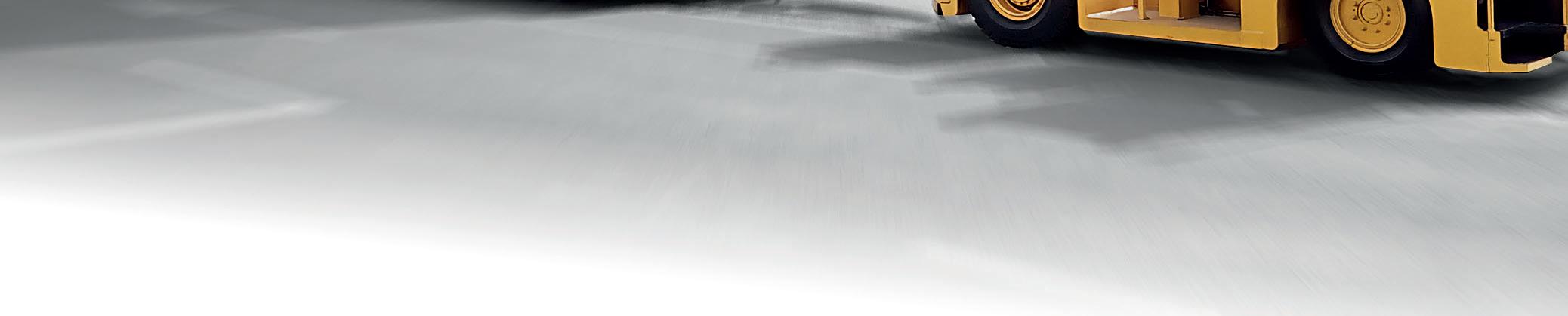
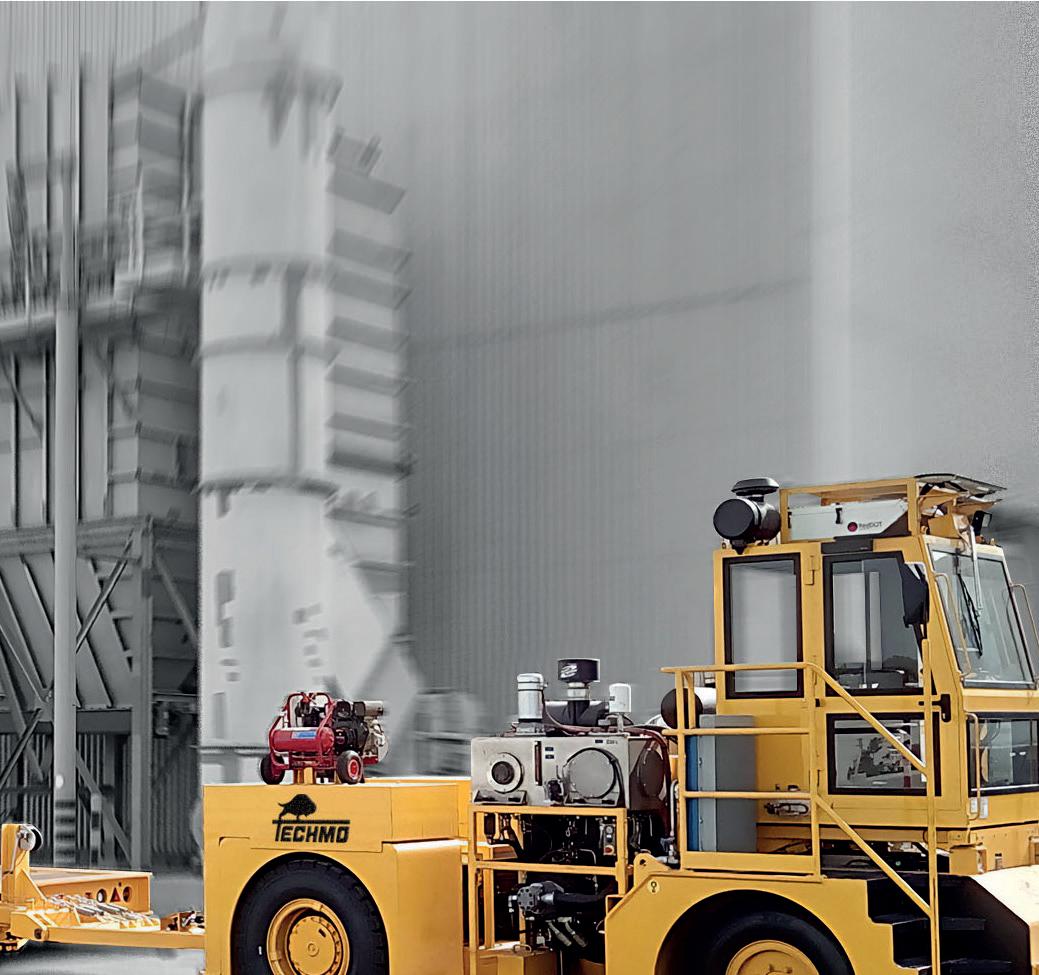
The tractor was equipped with a 305 HP diesel engine, with hydrostatic transmission, able to properly travel at a significant speed along the plant paths, curves and slopes when towing the loaded trailer. Moreover, the vehicle was designed for the specific plant environment, characterised by high temperature, dusts, intense magnetic fields. The trailer was designed with a very limited flatbed height. The support platform for the pot cell had unusual large dimensions in length and in width, with special pads and guides for the proper setting of the hot cell.
The wheel system needed a very accurate design, to allow the steering, while respecting the requirements for maximum height and maximum ground pressure. The final layout resulted with an impressive number of wheels, allowing the steering, with an adequate braking system for safety.
The Handling of a pot shell in a smelter is by default a complex activity: a pot has considerable dimensions and weight, and its maneuvering in the plant must be performed in a harsh environment, with several constraints along the path, and simultaneously with the potline production. The typical method for transportation is the use of the biggest available trucks in commerce, to tow special flatbed trailers on which the cells are uploaded.
Sustainable Industrial Manufacturing (SIM) is a global series of regional exhibitions and conferences supporting and facilitating the transition towards cleaner manufacturing around the LIGHTENINGworld. THE IMPACT OF HEAVY INDUSTRY SCAN ME TO JOIN THE MAILING LIST REGISTER TODAY www.SustainableIndustrialManufacturing.com EARLY BIRD TICKETS NOW AVAILABLE Organised by: Part of: FROM THE PRODUCERS OF: SECTORS COVERED GLASS STEELALUMINIUM CEMENT CHEMICALS
To support and facilitate the
Sustainable Industrial Manufacturing
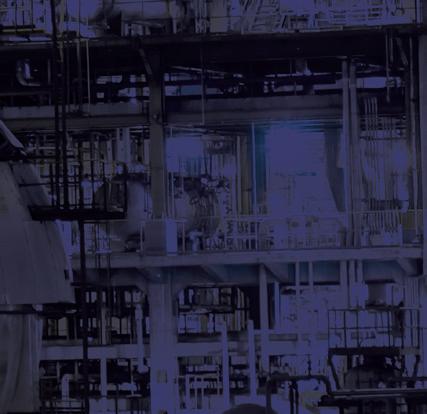
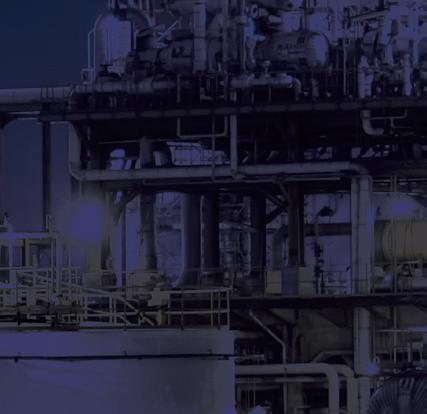
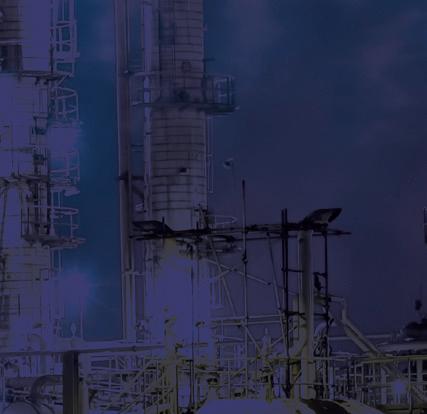
of industrial
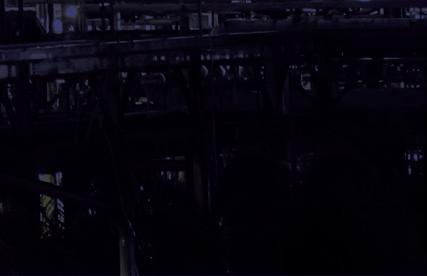

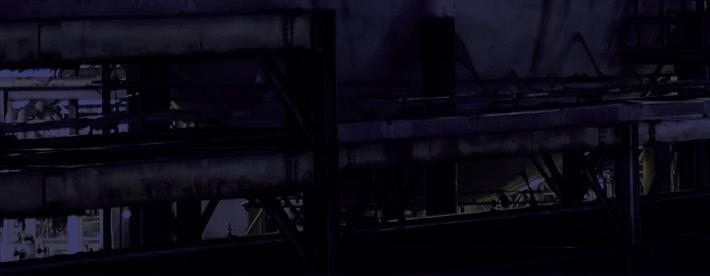
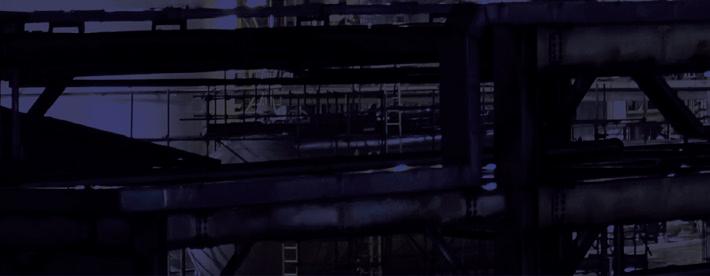
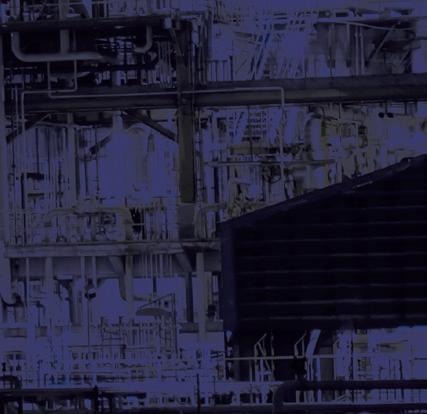

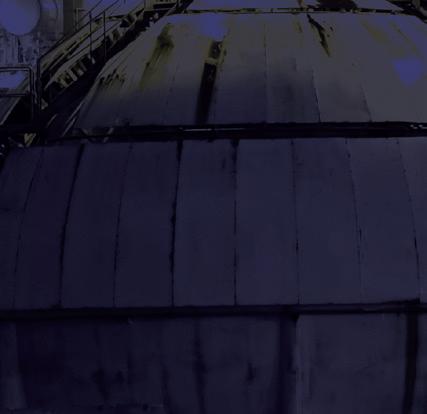
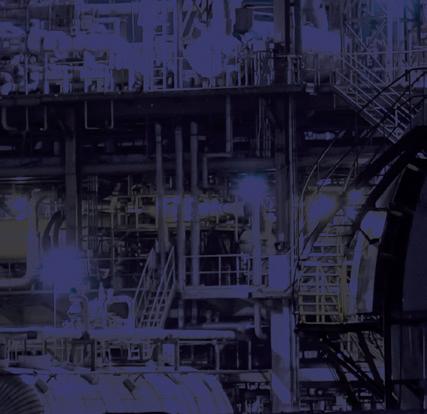
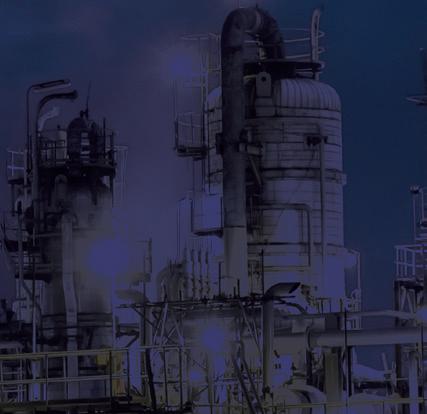
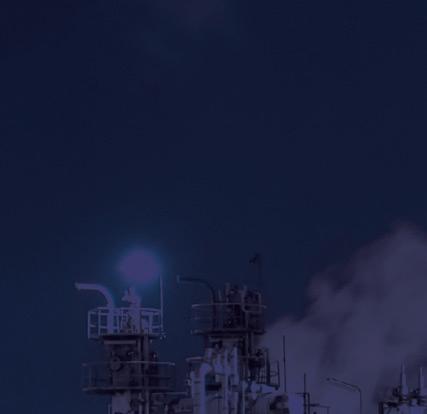
be
accelerate the
President Biden’s goal of a carbon-neutral economy by 2050 is dependent on the decarbonization of heavy industry. The 2021 Build Back Better Act, provides $4 billion for the deployment of technologies that can emission reductions facilities. transition USA, will staged Cleveland,
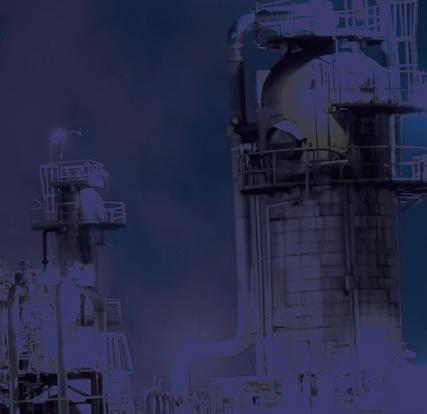
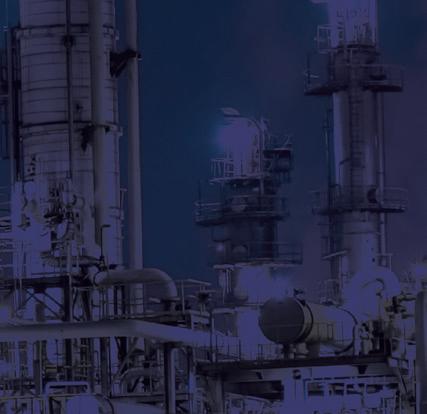
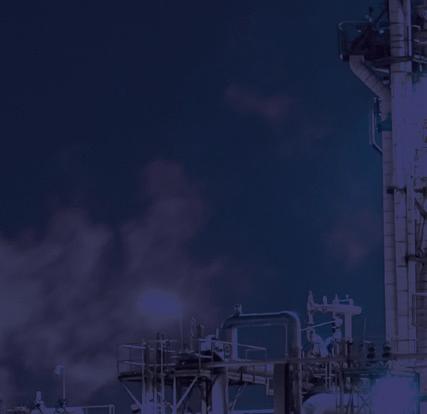
towards cleaner manufacturing in the
in
Ohio in December Hosting2022. leaders from industry, innovation, science, government and investment, SIM USA will bring together those responsible for driving sustainability across hard-toabate sectors. BUILD BACK BETTER FOR FURTHER INFORMATION ON EXHIBITING, SPEAKING OR ATTENDING SIM USA PLEASE SCAN THE QR CODE BELOW OR REGISTER YOUR INTEREST AT WWW.SUSTAINABLEINDUSTRIALMANUFACTURING.COM ROUNDTABLECONFERENCEEXHIBITIONDEBATES
*Editorial
39.348
AnMECSPE/METEF:interviewand review
The Green Aluminum Conference has stood out at METEF 2022, showing the metal’s potential on the circular economy and energy efficiency front. This edition has also marked the debut of the new Premio Pressocolata Italia awarded to Fondital due to the important contribution in the field of sustainability and innovation by its die-cast.
The 12th edition of METEF, the international expo devoted to aluminium, and the 20th edition of MECSPE, the exhibition on technologies and innovation for manufacturing, organised by Senaf took place simultaneously for the first time, from June 9th to June 11th, at BolognaFiere, closing with an actual success. The two events, whose inauguration was also attended by Deputy Minister of Economy and Finance Laura Castelli, have reflected the vibrancy of the market and also confirmed themselves as important hubs for the whole Italian and international industrial sector in 2022: suffice to say that 39.348 professionals have visited the 13 thematic halls and stands of the 2,000 exhibiting companies and participated in the many special initiatives and conferences organised in the halls, which have covered 92,000 square meters of exhibition space.
Aluminium International TodaySeptember/October 2022 EVENT REVIEW88
Manufacturing and aluminium supply chains get together in Bologna, to the satisfaction of operators: visitors and 2,000 exhibiting companies

Zahra Awan* interviewed Mr Conserva, president of METEF, to discuss the details of the past, present and future of aluminium and the METEF event. Mr Conserva was named as one of the top 50 people in the International Aluminum Institute’s celebrations. Assistant
Aluminium is among the key players of this transformation: it has been defined as the “metal of the future” because of its flexibility and endless re-usability, which are key features in making the industrial sector even more sustainable and efficient.
Mecspe, has thus relaunched its strategic role in pooling, comparing and promoting synergies between professional operators in the specialised mechanics and Industry 4.0 sectors, also thanks to the presence of foreign buyers. The program, rich in content and special initiatives, was developed along the three themes of digitisation, sustainability, and education, which are essential for business growth. The 20th edition also has also seen the debut of the Facilitated Finance Square, managed by Innova Finance, which organised some 50 meetings to show entrepreneurs the financial and fiscal tools available to businesses. As to Metef, great focus was placed on one of the most heartfelt issues in the business world, namely sustainability.
Mario Conserva: It is true, we are experiencing a complicated period, between Covid, the energy crisis, inflation, tensions on raw materials, ongoing conflicts. Metef is largely synonymous with aluminium, and the first observation to make is that in Italy the light metal market has recovered very well in 2021, positive prospects have been created for the aluminium industry even if the extraordinary fluctuations on the entire metal supply chain of raw materials has led to doubts and concerns about the future stability of the system. In any case, despite the many uncertainties of scenarios that are difficult to interpret, the return of Metef was a very positive fact, greeted with interest as the repositioning of a solid reference for the market, which just this year celebrated its 25 years of life. I like to remember that METEF, with its first edition in May 1997, was the first ever world trade fair dedicated to aluminium, it was ahead of its time and paved the way for photocopy events, such as Aluminium Essen in Germany, such as Alumex in the Middle East, then Aluminium in China, Turkey and many other countries, a clear sign of the growing importance of aluminium metal in the world economy and industry. Metef has restarted with new perspectives, a new organisational structure in a new location, with the support of Bolognafiere and Veronafiere, two of the main exhibition centers in Italy. In fact, Metef is now managed by Senaf, leader in technical publishing and the organisation of trade exhibitions and it has been relocated to the center of gravity in the Italian aluminium system that is Bologna and held in conjunction with MECSPE, the great Italian Exhibition dedicated to industrial manufacturing, now at its 20th edition with 2,000 exhibiting companies and 39,348 visitors (total of both exhibitions combined). So, the relaunch of Metef was positive, in any case an excellent result in terms of image and evidence of the strength of the Italian aluminium system in the international context thanks to the compactness and solidity of the collaboration with the main associations in the sector and institutions. We have very much oriented the relaunch of Metef by focusing on the eco-sustainability of prerogatives of aluminium, for some time now our magazine A&L Aluminium and its Alloys, born in 1988 and which has supported METEF since its birth, is subtitled with the appellation Aluminium for the Green Transition, and it is no coincidence that the main conference of this Metef 2022 in Bologna was centered on the eco-sustainability of aluminium, the metal of the future because it is an energy bank, because it is a champion in recovery and recycling, a fundamental point all the more in the European Union, where the production of primary metal is inexorably disappearing, and reuse is essential at least to solve some of the problems of critical metal deficiency, as we know we have to import more than 80% of our needs. We are therefore pleased to have brought these important characteristics of aluminium to the attention of all operator and decision makers by talking about new types of primary production, the major development of secondary aluminium, new technologies and new end uses focused on the possibility of eco-sustainability of the metal. Another positive element that we must underline in our event is the great role of the Metef Innovation Award, an historical pillars of our exhibition, and which once again highlighted the great creative intelligence of our system, in Italy and internationally. In this 2022 edition we had 13 very important participants in the competition for the Metef Innovation Award, a great result for the extraordinary quality of the applications, from equipment, to alloys, to processes, to system developments for a circular economy with our light metal at the center of attention, sensational results fully exploited by our jury. This is an element of merit because it indicates the great innovative trend that is in the spirit of aluminium applications.
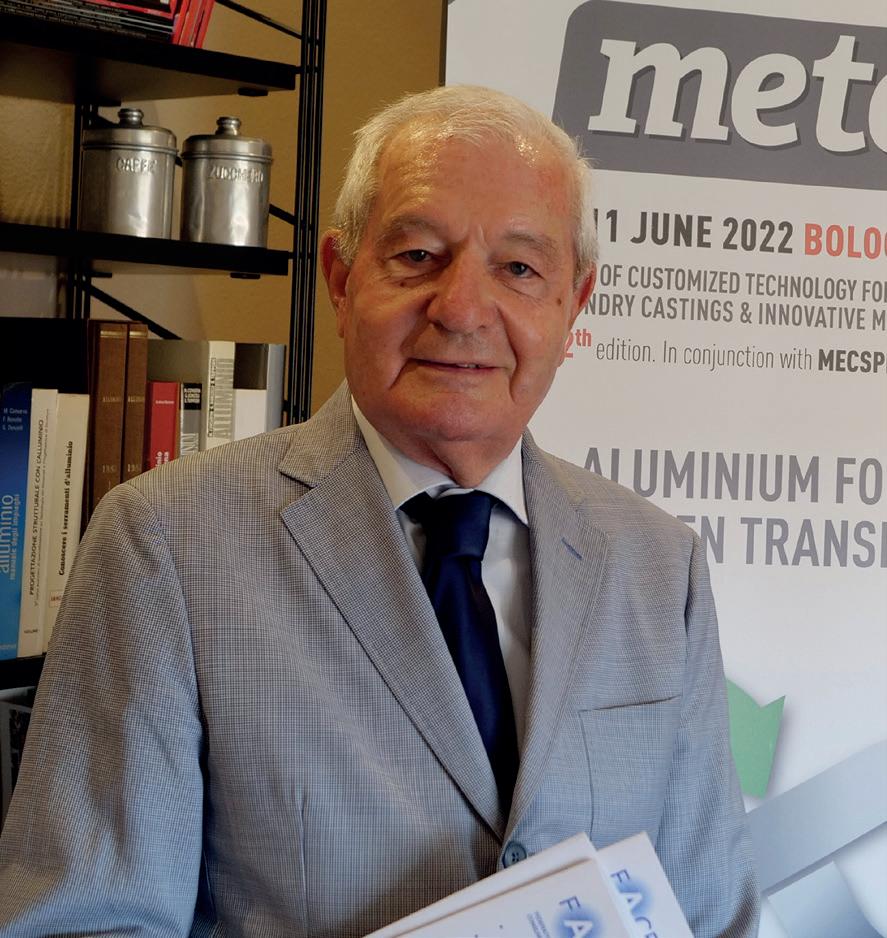
Anyway, I would like to mention all the names of the companies that have successfully participated in this award: Almec Tech Srl Altek Europe Limited Eural Gnutti S.p.A Extrutec GmbH FMB Srl - Gruppo OMR Foundry Ecocer Srl Hydro Aluminium / Norsk Hydro ASA Idra MeccanicaS.R.L Pi.Erre di Pederzoli R.E C. Srl NE.CE. SpA Raffmetal SpA Wagstaff, Inc. Zanardi Fonderie S.p.a.
EVENT REVIEW 89 Aluminium International Today METEF FINALLY RETURNS AFTER A FORCED BREAK OF 5 YEARS, HOW WAS THE RECOVERY IN THESE DIFFICULT TIMES?
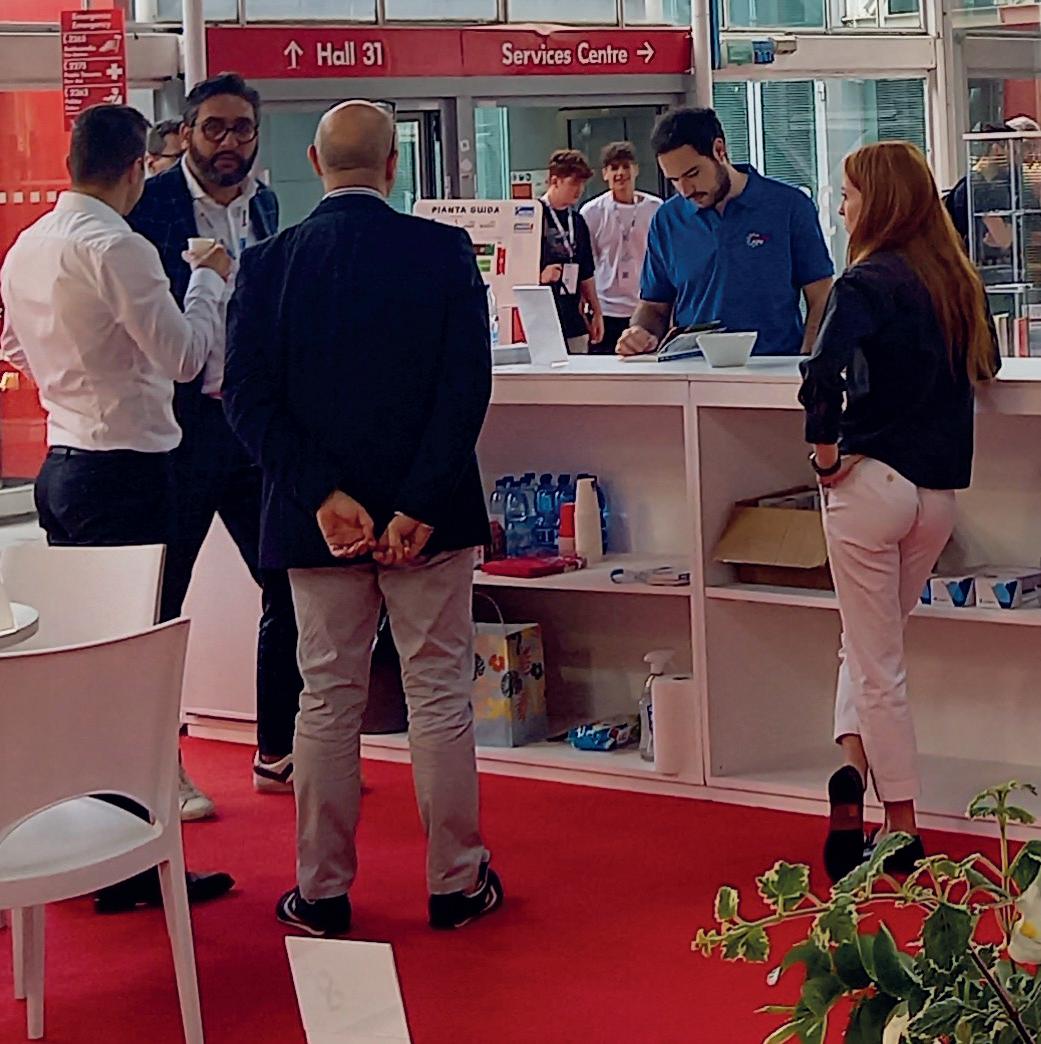
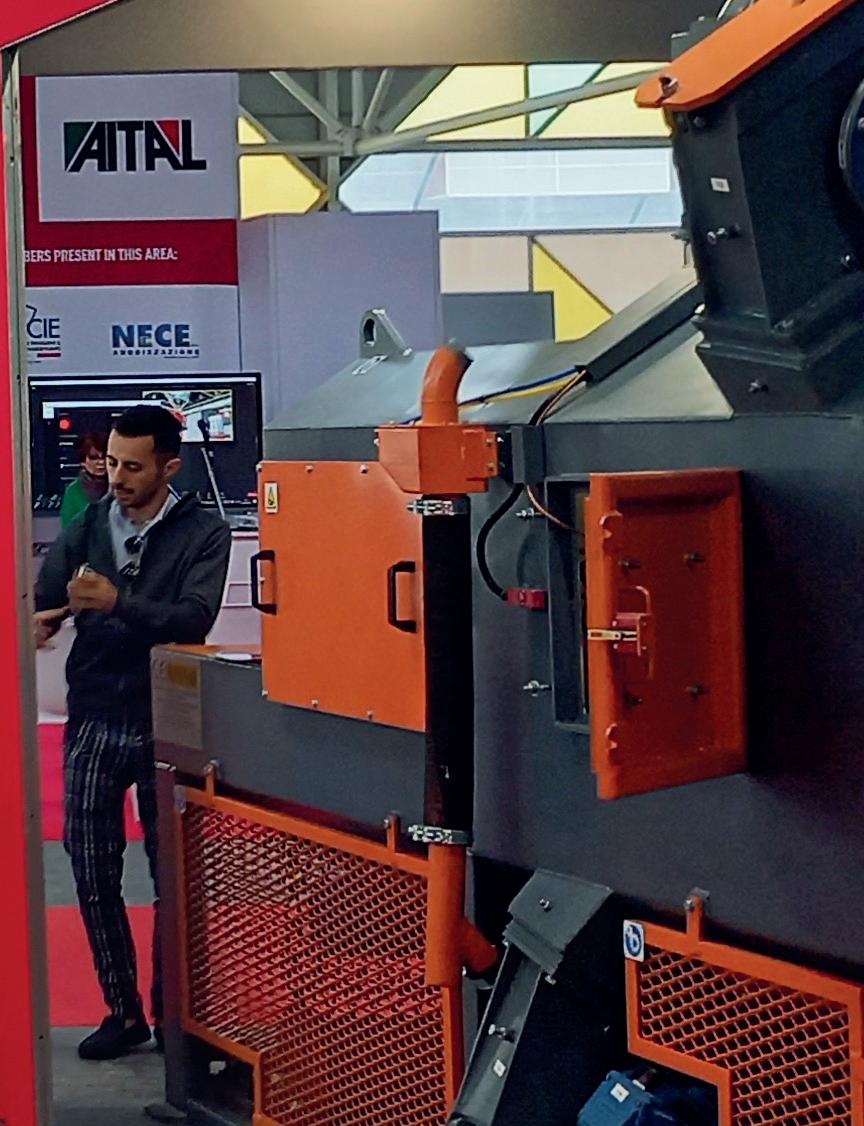
Potentially there are great opportunities, the big problem to be faced in Italy and Europe will be that of the primary aluminum supply chain. As I have already said, primary aluminium in Europe is steadily fading away, a process that began in the past, it was predicted, foreseen, and warned about, but never taken seriously. The recent “wake-up call” by Eurometaux at the end of 2021 was absolutely timely. The growth in the recovery of secondary aluminium is going very well, but the aluminium coming from recycling alone will never be able to make up for the total demand in Europe in the slightest. In Italy we have had zero primary production for years. For years as representatives of the needs of transformers and end users of aluminium, which represent 75% of the turnover in the EU and 90% of the workforce of the entire supply chain, we have denounced this dramatic situation, Metef has always been the bearer of these needs of the system, as we have been
WHERE DO YOU EXPECT THE ALUMINIUM INDUSTRY TO GO IN THE FUTURE FOR ITALY OR WHERE DO YOU WANT IT TO GO?
Aluminium International TodaySeptember/October 2022 EVENT REVIEW90

various countries, and in fact we have created alliance systems with the aluminium industry in North America in particular with the Extruders Aluminium Council since 1997, so too with aluminium in the Gulf when that new reality was developing, we have done the same with the aluminium industry in India, we have done it in Russia, in Poland, in Turkey. With a look at the world scenario, that today gives us great concern, we must underline in this regard the central role of Russia which is a large producer of primary aluminium and which feeds the markets of Europe for a significant part of metal with a low carbon footprint therefore also Italy. The role of Metef has been and is essentially also that of putting together these different systems, getting them to dialogue, from the associations of aluminium producers and transformers to the users of metal in its various forms, from automotive and transport, to packaging, to construction, mechanics, carrying forward the common image of aluminium as an important material for our future generations. Good aluminium to everybody.
The aluminium industry in Italy is an extraordinary vital segment and in fact, as I have already mentioned, it has reacted very well to the chain of negative events of the last three years. We have returned to a total use of metal in Italy of almost 2.3 million tons which is an all-time high, with a per capita consumption of around 40 kg which places us in a position of great interest worldwide. The industry is doing well, especially in extrusion and rolling, the foundry industry suffered a little due to the problems all over the world relating to the weakness of the automotive sector.
As we said before, fortunately in Italy and in Europe, we are working very well in the field of sustainability and in the recovery and recycling of aluminium, we have many companies in a cutting-edge position, some of these have had the right recognition of the Metef 2022 Innovation Award. It is a great merit that our industry has been fully committed to this segment. It is an important thing that undoubtedly helps a lot, but it is necessary to keep in mind very clearly that we lack the primary metal, we must find it of quality with a low CO2 footprint and it is essential to have it at competitive conditions in Italy and in the EU.
In this moment I have two strong feelings: first of all, I am very happy with the success to which we have reported this event born in 1997, unfortunately I regret not having been able to participate directly in the party, unfortunately Covid caught me, albeit in a light form at the moment I would have liked to be there with you all in Bologna. I would like to add one last thing. We have always considered Metef as a point of dialogue between the different aluminium systems in the IS THERE ANYTHING ELSE YOU WOULD LIKE TO ADD?
Metef’s global message is that the aluminium system is a lively, active, and proactive value chain, the existence in Italy of a reference point such as METEF, which gathers and brings together the main forces of the system, from production and processing companies to trade associations, universities, research, testing and control organisations, is a strong point of the system. Metef has always carried forward the message of aluminium not only for the aspects of the production chain, but also and above all towards the silent and often under-represented downstream segment, because inevitably the future of aluminium in particular in Europe will be mainly connected to transformations, processes and the growth of final applications.
repeating for years, it will be essential that our decision-makers in Brussels revise from the roots the issue of import duties in the EU on the raw material primary aluminium because it is not possible to hope that there will be a competitive future by keeping artificially and irresponsibly higher the level of the purchase price of raw aluminium in the European Union, with an absurd extra cost estimated by all analysts, starting with James King, Ecorys, Ceps, Luiss Studies and ending with the recent Fair Economics study in Germany, at over 2 billion euros a year, weighing on the shoulders of small and medium-sized downstream enterprises.
SUSTAINABILITY IN THE ALUMINIUM INDUSTRY IN ITALY WHAT IS THE FOCUS?
WHAT IS THE OVERALL MESSAGE OF METEF?
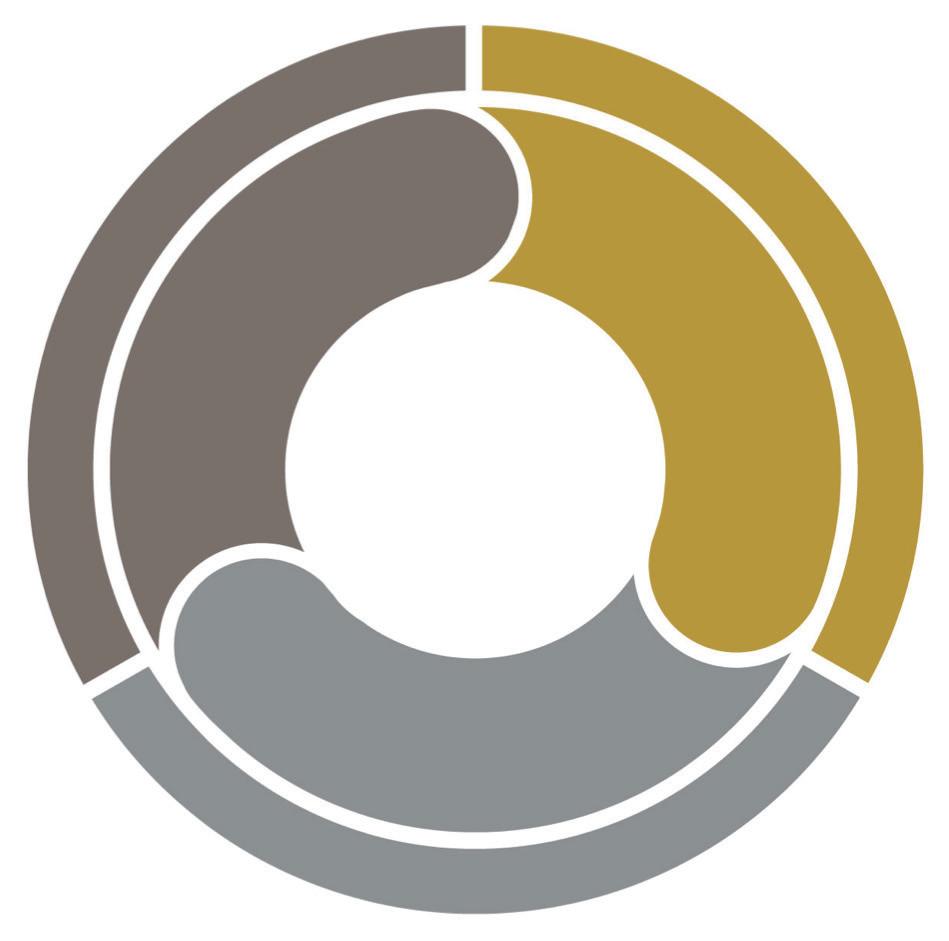
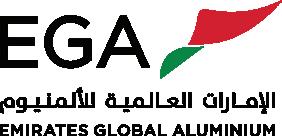
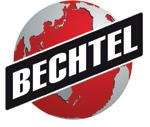
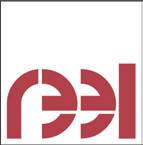

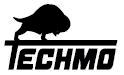
With global aluminium demand projected to increase 40 per cent by 2030, the aluminium sector will need to produce an additional 33.3 Mt – a reality only possible through the inception of streamlined technologies, digital manufacturing and sustainable solutions across the supply chain.
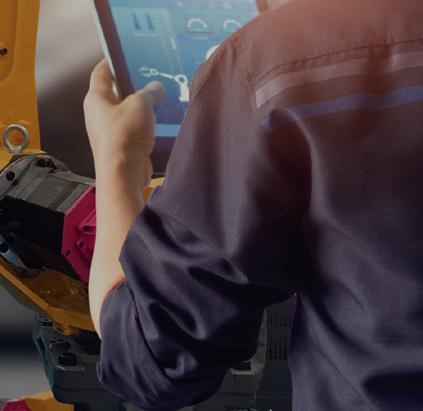
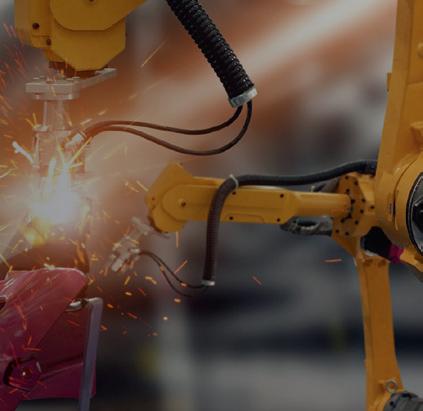
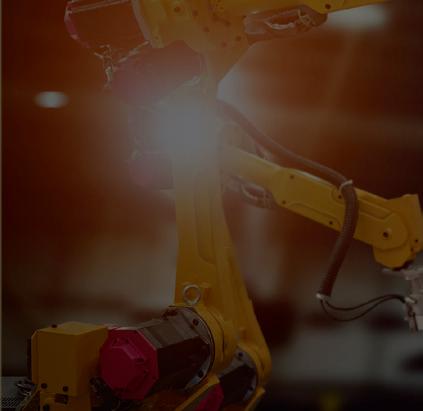
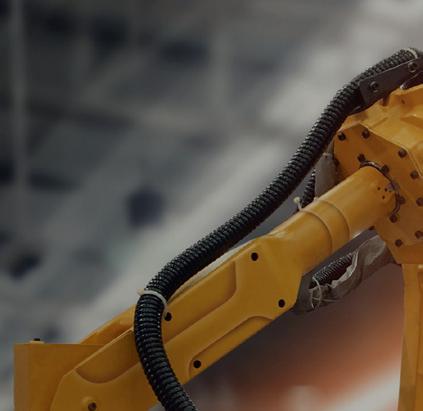
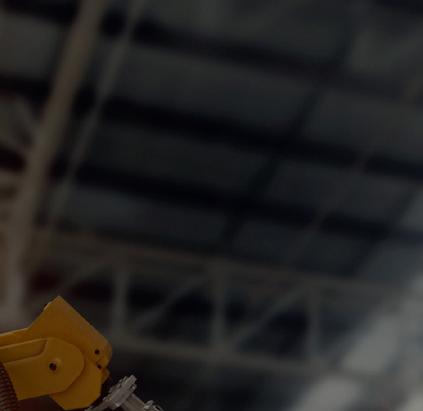
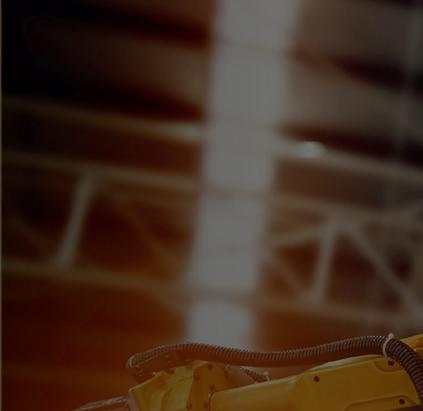
Join us at the Future Aluminium Forum to meet manufacturers rising to the challenge, focus on the opportunities that growth will bring, and prioritize time for your own learning and networking. In 2023, the Forum will return in a live format to Québec City, a region where the aluminium industry has existed for more than a century and is now seeing rapid change and collaboration between manufacturers, processors, suppliers and OEMs. Register your interest at www.FutureAluminiumForum.com @Alu_Forum
Aluminium International TodaySeptember/October 2022
For next year, MECSPE will go back to its historic dates and double the exhibition days: in fact, it will be held at the same time as METEF, from March 30 to April 1, 2023, in BolognaFiere. For the second time, MECSPE will also be held in Bari, from November 23 to 25 with “Focus Mediterraneo,” an edition devoted to the development of 4.0 technologies and a proposal increasingly focused on the sustainability and innovation of production processes. “We closed this edition with significant participation of manufacturing professionals: we can be really satisfied about it,” Emilio Bianchi, director general of Senaf, has commented, “The challenges that the industrial sector has shown itself capable of tackling in recent months have not affected the growth drive of companies, which continue to look to the future. The next steps will have to be taken in the direction of digital transformation and green transition; in this MECSPE, we will continue to develop innovative MECSPE/ METEF 2023? projects to support SMEs in the upgrading of the skills required for the proper use of new technologies and bring new generations closer to modern manufacturing. Therefore, choosing to return to Bari also in 2023, will be even more impactful: MECSPE will be held there for the second time, to continue the journey we have already started with local companies.”
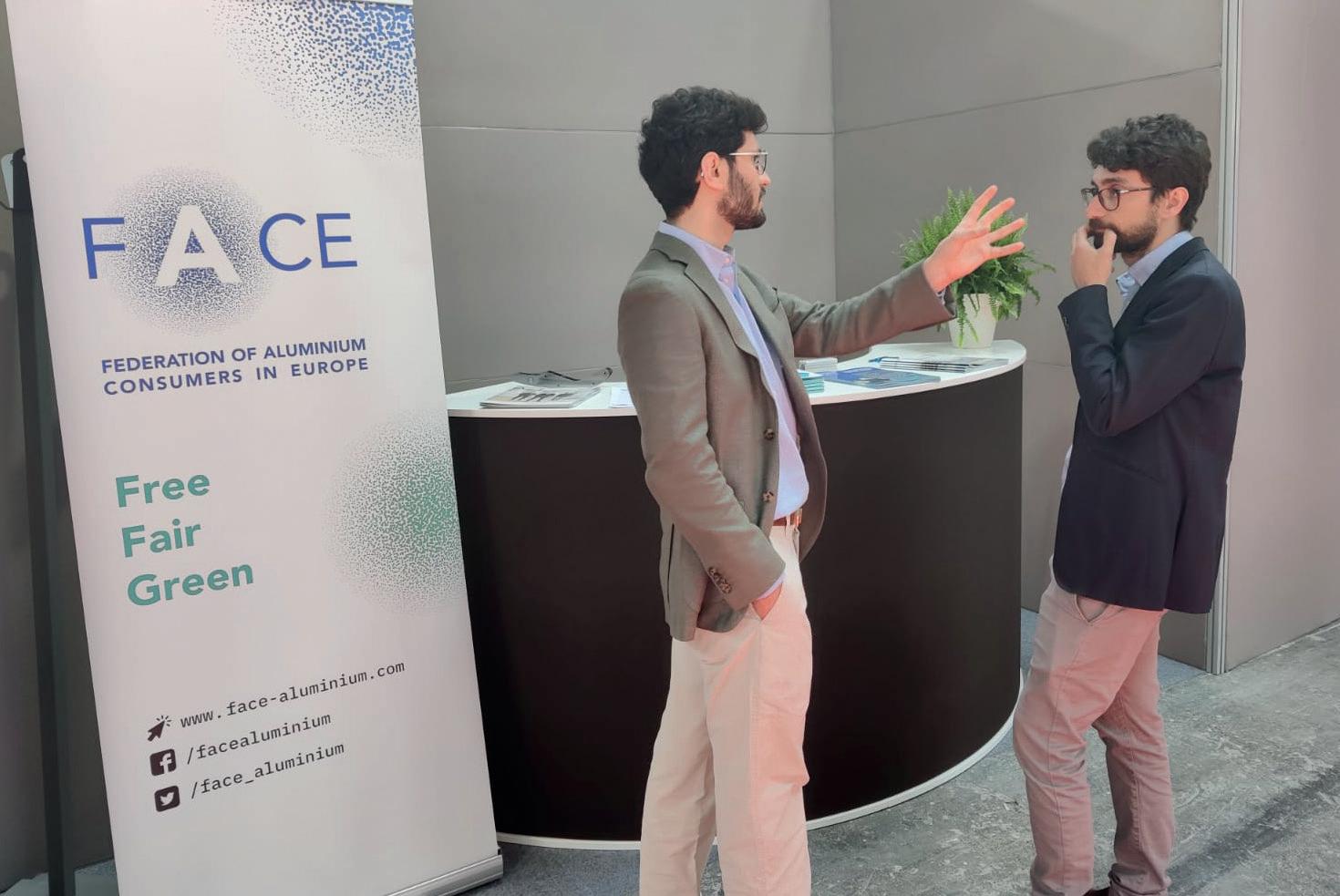
METEF REFIEW
To find out more about speaking contact: Nadine Bloxsome, Conference Director nadinebloxsome@quartzltd.com | +44 1737 855115
To find out more about stand and sponsorship opportunities contact: Nathan Jupp, Sales nathanjupp@quartzltd.comManager|+44 1737 855027 MAY 2023 Québec City, Canada O cial media partners: Supported by: FAF_23_HalfPageAd_185x128mm.ind.indd 1
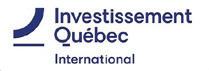
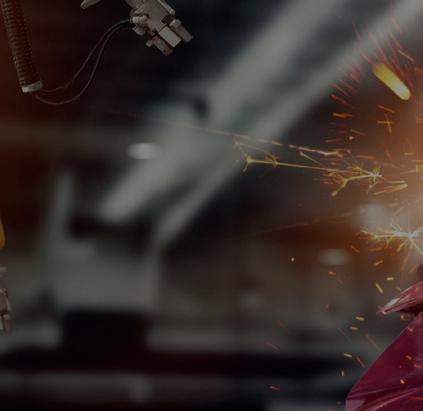
Future Aluminium Forum 2023: Meeting the Demand

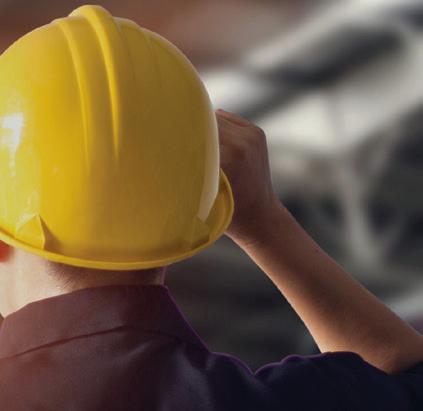

92
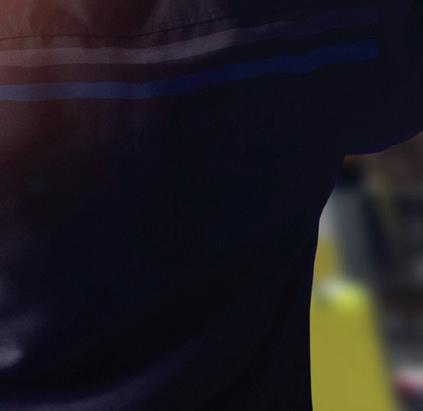
24/08/2022 11:13

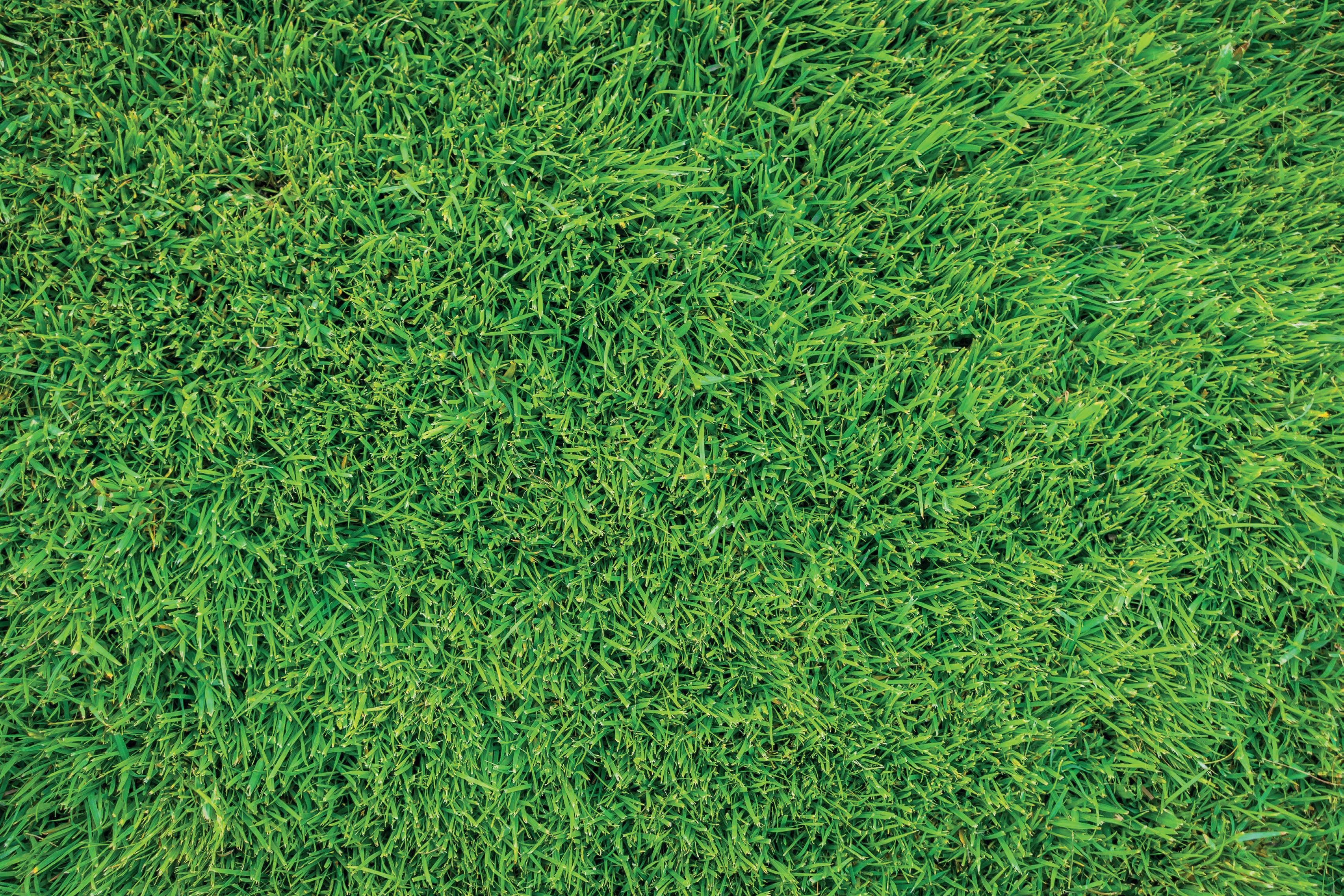
•
Come to booth #4C52 in hall 4 and experience our sustainability ambitions at the stand, exploring our exhibits, seminars and workshops.
hydro.com
•
Every step matters on the path to zero
ValetkaAlina/iStock.comPhoto:
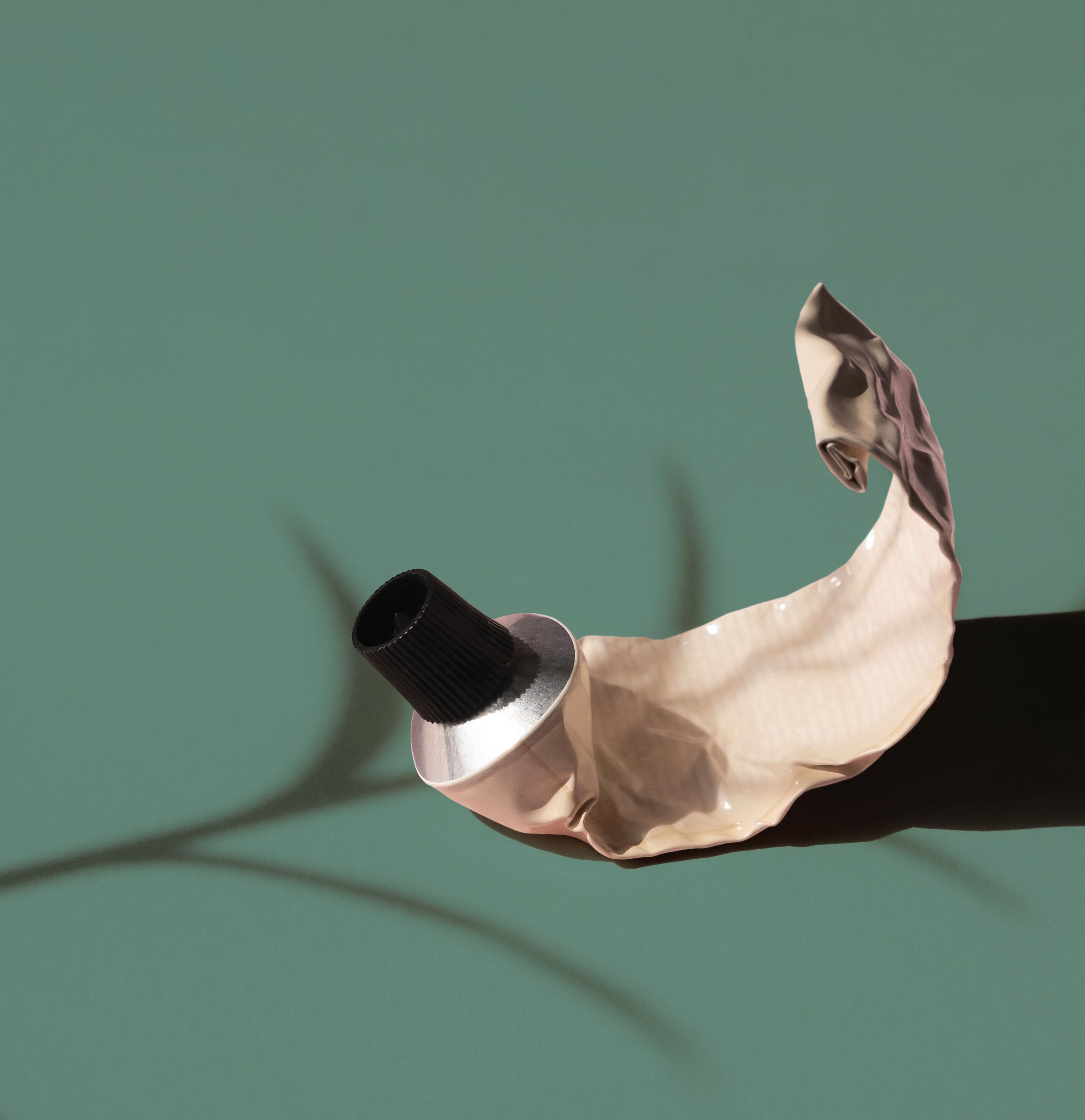
Achieving climate-neutral products is the next design challenge. Low-carbon aluminium ticks all the boxes. We can help your designs with: 100% recyclable material Eco design for your products EPD and full transparency, including all scopes, in our calculations Aluminium with a high percentage of post-consumer scrap Low-carbon aluminium There are many challenges ahead in producing in a way that will not harm our planet. We don’t have all the answers yet, but we can be your trusted partner in that everything we do works to create a fair and more circular economy with people and planet in mind. Contact us today to see what materials is most suitable for your next project.
•
•
•
Visit us at ALUMINIUM Exhibition 2022