7 minute read
Improving global carbon emissions, one package at a time
Next Article
Designing consumer product packaging to reduce carbon footprint is a win-win for global sustainability causes, adds Angelica Buan in this report.
In 2022, global CO2 emissions from energy increased by 0.9% or 321 tonnes, setting a new record of more than 36.8 gigatonnes. According to the International Energy Agency ( IEA )’s CO2 Emissions in 2022 report, emissions from energy combustion increased by 423 metric tonnes (Mt) while emissions from industrial processes decreased by 102 tonnes.
Meanwhile, the Climate Collaborative (comprising a community of businesses joining forces to tackle climate change) says that packaging contributes significantly to greenhouse gas emissions (GHG) because it typically consumes 5% of the energy used during a food product's life cycle. Furthermore, some goods' packaging has a greater impact on climate change than the fuel used to transport them to market.
As noted in UNEP's Emissions Gap Report 2022 , only an immediate system-wide transformation will result in the significant reductions in GHGs required to meet a 1.5°C target by 2030, or by 45% compared to current policy projections.
Current policies predict a 2.8°C temperature rise by the end of the century, well short of the Paris Agreement target of keeping global warming well below 2°C.
As a result, adopting the circular economy model is expected to accelerate progress toward these goals.
The Carbon Collaborative defines circular economies as systems that "eliminate waste and pollution, keep products and materials in use, and regenerate natural systems."
A company's bottom line can benefit from adopting a circular ethos, and brand reputation and leadership can be strengthened as a result, it adds. To accomplish this, circular product packaging has to be designed, and resources invested in materials and methods to close resource loops.
Packaging
Tackling rising carbon emissions with circular packaging solutions
With these figures obviously on the uptrend, rising carbon emissions is seemingly becoming out of control. And that seems to be the case, because authoritative institutions like the United Nations Environmental Programme ( UNEP ) are issuing dire warnings after new findings that emissions are not going down significantly.
Meanwhile, by utilising advancements in design and end-of-life systems, the World Economic Forum has estimated that 50% of the world's plastic packaging can generate income even after its initial use, amounting to as much as US$3 billion annually across all OECD countries, including the US.
Thus, awareness to circular packaging has reached fever pitch and currently, industry leaders, brands and manufacturers are collaborating in efforts to improve the carbon footprint of packaging.
True sustainable packaging with rPLA
Consumers consider the packaging's ability to be recycled and biodegraded as well as its sustainability. The amount of recycled content in a packaging also matters today, so companies are increasing the amount of recycled content materials in their products.
Packaging
Consultant McKinsey 's True Packaging Sustainability report provides these insights on sustainability, which it claims can be divided into three main components, namely, removing packaging leakage into the environment, increasing recyclability and utilising recycled content in packaging, as well as minimising packaging's carbon footprint.
Closed-loop economy with rPET PET is the most recycled plastic in the world, and its recyclable, flexible, safe, and lightweight properties are driving sustainable growth. Due to rising demand from the food and beverage industry, the recycled PET (rPET) market size is anticipated to surpass US$ 17.2 billion by 2030 at a CAGR of 7.6%, according to Acumen Research Investments in rPET are also increasing, as indicated by partnerships to produce more rPET materials and rPET-based packaging.
Thailand-based chemical firm Indorama Ventures ( IVL ) is collaborating with Evertis , a producer of mono and multilayer semi rigid barrier films, on the development of a PET film suitable for use in food packaging trays based on recycled PET flakes.
TotalEnergies Corbion, Posco International, and Esol have joined forces to improve PLA recycling infrastructure and technology in South Korea
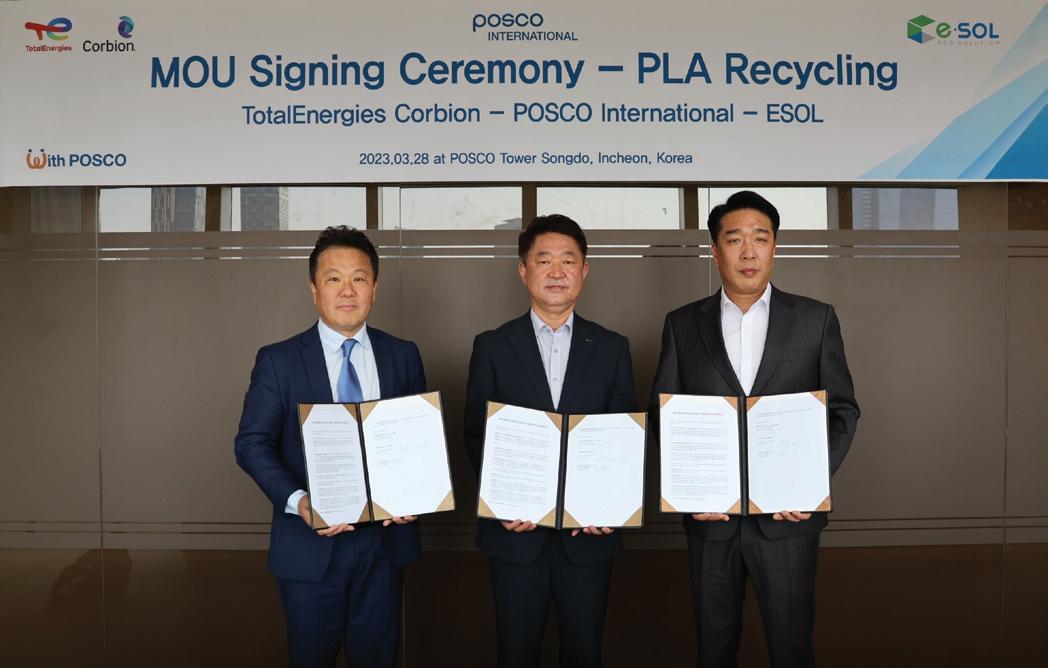
Building on growing carbon neutrality initiatives worldwide, TotalEnergies Corbion , Posco International , and Esol formed a partnership to advance polylactic acid (PLA) recycling infrastructure and technology in South Korea, which is pushing its five-year National Strategy for Green Growth strategy to decarbonise and achieve net-zero emissions by 2050.
Posco, South Korea’s largest trading company, intends to expand its green portfolio by entering the biobased plastic recycling sector. While Posco will manage and finance the project, Esol, also from South Korea that already produces PLAbased products in the country, is in charge of retrieving the post-consumer recyclate (PCR) PLA waste and advancing the technology to collect and sort, purify, clean, and rework the PLA.
The partnership will enable TotalEnergies Corbion, which is already supplying its Luminy brand of rPLA to the South Korean market, to leverage its existing advanced recycling technology and infrastructure to establish a recycling infrastructure throughout its supply chain for a more sustainable use of plastics in the country’s growing PLA market.
PLA, a low-carbon-footprint alternative to traditional plastics, is quickly becoming a popular material for bottles, containers, and other food service and packaging products. Luminy's mechanical and advanced recycling is increasing PLA demand in the food packaging sector, adds TotalEnergies Corbion.

After six years of R&D, IVL is now commercially producing rPET flakes from PCR trays in Verdun, France, that are comparable in quality to flakes derived from bottles, it adds. The Deja carbon neutral PET pellet, the latest addition to its Deja portfolio, is said to be the world’s first certified carbon neutral PET pellet solution.
The tie-up will support Evertis’s target of an average incorporation of 50% recycled content in its films by 2025, helping it to further meet its sustainability goals. Plus, Evertis adds that the new technology also protects and preserves food, reducing about 154 million tonnes/year of food waste costing EUR143 billion across the EU.
IVL says its new recycling technology has the potential to divert over 50 million post-consumer PET trays from landfills or incineration each year, and supports the EU’s plastic collection and recycling targets.
Packaging
Global-scale sustainability with rPET PET producers and chemical companies are likely to support a technology that enables true circularity for PET by using alternative feedstock to petroleum-based monomers and is fully compatible with existing polymerisation plants. Carbios, a French company in the field of biochemistry, offers brand owners a way to comply with expanding regulatory standards and achieve their sustainability goals for using rPET in their goods and packaging.
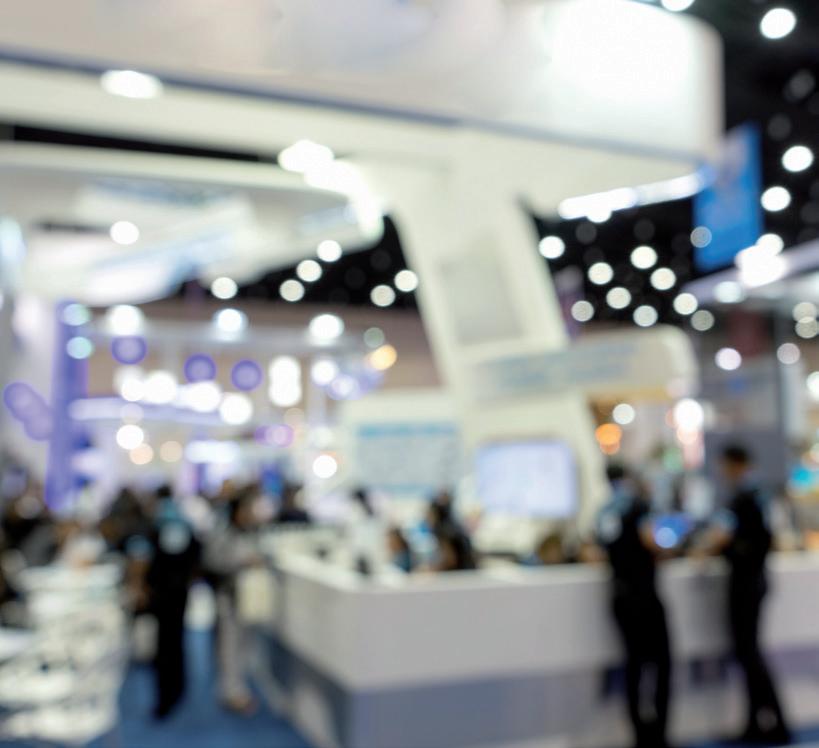
Carbios , which is preparing to commercialise its PET biorecycling technology on a global scale, said that the engineering basis and operational guidelines for units to be operated under license agreements are defined by the successful ongoing operations in its demonstration unit in ClermontFerrand and the advanced engineering study for its first commercial plant that is due to be commissioned in 2025.

Future Carbios licensees will be given all necessary process documentation to engineer, procure, construct, and operate their PET biorecycling plants under stringent HSE standards. Also this relates to high product quality, from technology promotion with the technical information summary to project development with a specific process design package and process book, it adds.
Carbios says it aims to reach out to other players in the value chain, such as waste management companies and public entities, by adding value to all possible sources of PET feedstock, including complex plastic packaging and textile waste.
Meanwhile, elsewhere, the Technical Committee of the Tray Circularity Evaluation Platform (TCEP) of PETCORE Europe has officially endorsed
Perstorp’s products have been endorsed in Europe for the design of circular thinwall food packaging solutions for hot-fill applications the use of Akestra 100 and Akestra 110, products manufactured by specialty chemicals innovator Perstorp , for the production of heat-resistant PET trays. Furthermore, the committee has recognised that the use of Akestra 100 and Akestra 110 do not have a negative impact on current European PET recycling streams.
TCEP is a voluntary European industry initiative that provides PET thermoforms design guidelines for recycling, evaluates thermoform packaging solutions and technologies, and facilitates understanding of the effects of new PET thermoforms innovations on the recycling process.
Akestra 100 and Akestra 110 enable customers to enhance rPET by adding heat resistance capabilities and also achieve sustainability targets by increasing recycled material content and enabling design for circularity.
With this endorsement, Akestra 100 and Akestra 110 are established to enable circular packaging solutions with high PCR content, and for being recyclable in existing recycling streams for tray-to-tray.
The products can also be used in Europe as replacement of linear traditional packaging made of PS or PP in the design of circular thinwall food packaging solutions for hot-fill applications.

Malaysia being developed as a biohub
In a related development, Hotpack Global , a Dubai-based food packaging manufacturer, is investing around US$90 million over the next ten years to build biodegradable packaging plants in Malaysia in collaboration with Free the Seed Sdn Bhd , a Malaysian manufacturer of biodegradable products from rice straw.
The company said that it aims to produce 70 million units/year of sustainable, fastmoving consumer goods (FMCG) packaging products, since the completion of the first plant. The project is being facilitated by Malaysian Bioeconomy Development Corporation (MBDC) and Malaysian Investment Development Authority ( MIDA ).
Construction of Hotpack Global’s 3,200 sq m plant, its first-ever manufacturing unit of in Malaysia and Southeast Asia, has commenced with a recently held ground-breaking ceremony in Gurun, Kedah. Construction will begin in May and is slated to be completed in August this year.

Malaysia is committed to environmental protection and meeting global targets with lower carbon emissions, as highlighted in its own 12th Malaysia plan and expected to become a leading biodegradable hub in Southeast Asia as a result of the project.
The project also allowed Hotpack Global to reach an agreement with local Malaysian farmers to ensure a consistent supply of agricultural raw materials.
The factory will make biodegradable food packaging out of agricultural waste such as rice straw, pineapple leaves, bagasse (the pulpy fibrous material left over after crushing sugarcane) and other agro-biomass materials.
In addition, as part of its 2025 strategy, the UAEbased company will be able to manufacture and supply a new line of biodegradable products for its global markets, including the Gulf Cooperation Council (GCC) countries, as well as establish a presence in Southeast Asia.
Eventually, the project is expected to position Hotpack Global as one of the world's top five producers of disposable food packaging products, within the next three years – an ambition that is going to accelerate the reduction of global carbon emissions.