4 minute read
Rubber Journal Asia
According to Grand View Research , the primary drivers of the market are an increase in patient demand for medical tubes to administer fluids and medications, as well as an increase in the incidence of respiratory diseases like asthma, lung cancer, and pulmonary fibrosis.
Silicone tubing is used in a range of medical devices, including catheters, drug delivery systems, intravenous sets, and other items due to its efficacy and safety.
A major player in medical tubing space is contract design and manufacturing provider to the medical device and pharmaceutical industries Freudenberg Medical . It has expanded its new cleanroom manufacturing operation in Massachusetts, US, to include custom silicone extrusion and tube processing.
Silicones
gamma irradiation, X-ray, and e-beam; and is a more environmentally friendly option than silicone and can be recycled.
Growth prospects in Asia
According to Orion Market Research , the AsiaPacific medical grade silicone market will grow at a 5.8% CAGR from 2021 to 2027. The surge in demand for disposable devices, as well as the popularity of cosmetic surgeries due to changing lifestyles and beauty standards, is primarily driving this growth for medical grade silicone.
Simultaneously, changing health needs and demographic shifts, for example, the rising geriatrics population in the region are driving the adoption of medical grade silicone. Citing data from Qualtech research, Asia will have 60% of the global population by 2030, with a quarter of that population being over the age of 60.
Moreover, adoption of universal health coverage in the region not only promotes affordable access to safe, effective, and highquality medical products, but also bodes well for the medical devices and diagnostics markets.
Southeast Asia, with its burgeoning economy, is expected to see healthcare and medical device market expansions, with revenues projected to reach nearly US$10.9 billion in 2023, growing at a CAGR of 7.9% to 2027, according to Statista .
Thailand takes the lead in the region’s market growth
Freudenberg Medical has added HelixFlex high-purity thermoplastic tubing to its existing pharma portfolio of silicone tubing and components
It said that production of silicone tubing began in January, and additional capacity will be installed in the first quarter of the year to better serve customers. In order to meet the highest quality standards for medical applications, the material focus is on platinum catalysed addition-cured silicones.
On the other hand, while silicone has always been a go-to material for biopharma applications, with silicone material in short supply in recent years, Freudenberg Medical started offering its global customers another single-use tubing option.
As a processor of custom medical and biopharma tubing including multi-lumen, complex single lumen, and micro extrusions, Freudenberg Medical has expanded its existing pharma portfolio of silicone tubing and components with the launch of its HelixFlex highpurity thermoplastic tubing last year.
According to the company, HelixFlex tubing is sterilisable via a variety of methods, including autoclave,
Thailand’s medical device industry is among the most developed in ASEAN, ranking first among ASEAN peers.
Aside from government incentives that support the country’s medical device sector, Thailand has an abundance of raw materials used in the production of medical devices, particularly single-use items such as rubber and plastic. Furthermore, some institutions and regulations, ranging from the R&D processes to intellectual property protection, ensure that the goods produced can be commercialised.
As a result, Thailand is an attractive destination for manufacturers providing the medical and healthcare sectors. This is a reason that silicones and specialty solutions company Momentive Performance Materials is preparing for its most recent growth investment, a new manufacturing facility in Rayong, Thailand.
This new facility, Momentive’s second in Rayong, is expected to drive Momentive’s manufacturing capacity expansion targets in order to meet the growing Southeast Asian market demand for specialty silicones in industries such as healthcare, beauty and personal care, automotive, energy, and agriculture.
Silicones
China, a hotspot for medical devices China continues to be the market leader in medical devices. The country’s medical device market revenue is expected to more than double to RMB800 billion in 2020, up from RMB308 billion in 2015.
According to a Deloitte report, China’s medical device industry, which has 26,000 manufacturers, accounts for 20% of the global medical device market.
The Chinese medical device market is envisioned to grow, possibly exceeding previous years’ growth rates and according to Fitch Solutions , it will grow at a CAGR of 8.3% between 2021 and 2026, reaching US$48.8 billion by 2026.
To capitalise on the vast market opportunities in China, US materials firm DuPont is expanding production capabilities for its Liveo pharma silicone tubing by adding manufacturing capacity in eastern China, to meet demand for high-performance biopharmaceutical tubing.
During the drug manufacturing process, one of the largest surface areas in direct contact with drug substances and products is tubing. As a result, it must meet stringent regulatory and quality standards. The tubing produced in eastern China will be manufactured in a facility that adheres to the same quality principles as DuPont’s materials site in the US.
DuPont Healthcare, in addition to its long-running facility in the US and the new Chinese site, is pushing the envelope further in terms of capacity building. Liveo has established a second US manufacturing facility in South Carolina to produce tubing.
Meanwhile, Legenday , a Shenzhen-based manufacturer of LSR and (high consistency rubber) HCR parts, is foraying into the promising next generation of healthcare and medical products by developing conductive silicone parts that provide the necessary flexibility, safety, biocompatibility, and electrical conductivity. The firm says the components are made of high-quality silicone that contains electrically conductive and inert particles, with optional EMI shielding.
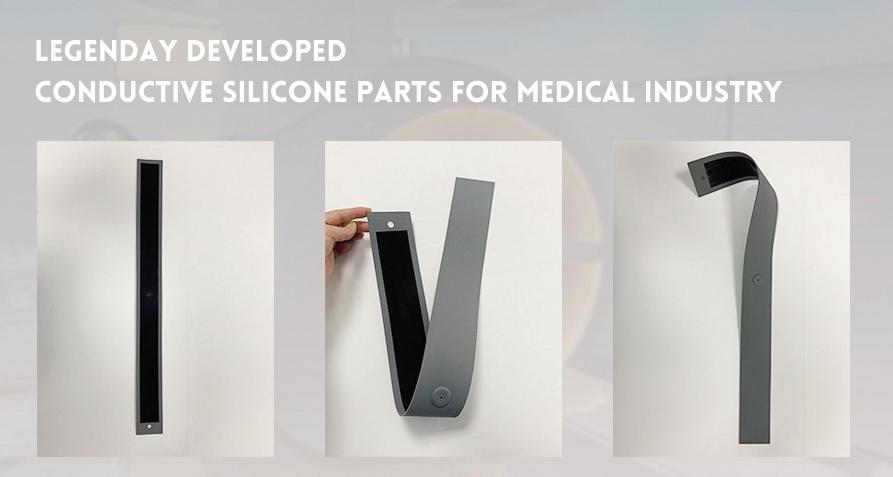
LegenDay will use conductive silicone with low volatility and ion content for more sensitive medical electronic systems. This makes the silicone parts suitable for hermetically sealed, vacuum, or high-heat conditions.
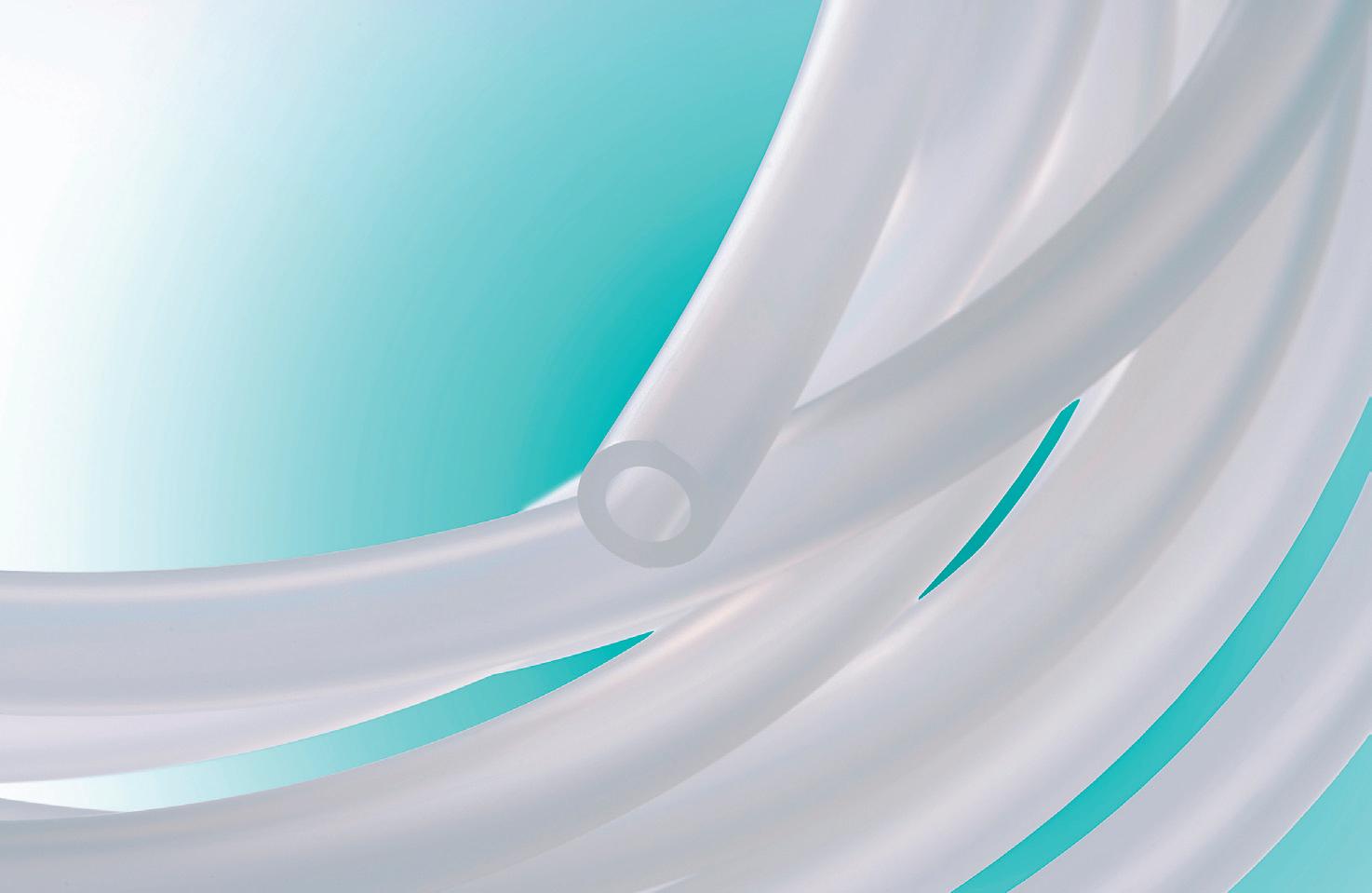
The conductive silicone parts, which have passed safety testing validation and requirements as outlined by the US FDA, vary from large to miniature medical electronic components; and are made from HCR or LSR.
Developing electrically conductive silicone parts is a breakthrough in the medical industry, according to Legenday, which currently is one of the few companies that claim to offer this capability.