9 minute read
Building a zero-net waste solution for EV batteries
With the automotive sector’s eventual transition to electric vehicles (EVs), sustainable manufacturing and recycling of EV batteries has become a focus, according to Angelica Buan in this article.
From charging stations to batteries: EV concerns
The global market for electric vehicles (EVs) is booming, especially following the downturn in the automotive sector during the pandemic period. The first half of 2022 saw more global sales of EVs than the six months before, according to an audit by European consultancy Roland Berger
Meanwhile, according to a Goldman Sachs Research , EVs will account for 50% of new vehicle sales globally by 2035, with EV sales expected to reach 73 million units in 2040, up from around 2 million in 2020. Meanwhile, IDTechEx predicts that EV markets on land, sea, and air will generate US$2.6 trillion by 2042, with a double-digit annual growth rate.
The rapid adoption of EVs has created a gap in charging infrastructure. In Roland Berger’s third edition EV Charging Index report, which polled over 15,000 customers in 30 countries, representing more than 93% of global EV sales, insufficient charging infrastructure was cited as the top concern by more than half of respondents (53%).
In Southeast Asia, however, a decline in the global EV-to-charging point ratio from 2 to 1.8 in the first half of 2022 suggests that the region’s sector is able to meet the level of demand at this time.
On the other hand, EV batteries are categorically becoming a barrier for wider EV adoption. According to consultancy McKinsey in its Race to Decarbonise Electric Vehicle Batteries report, while global demand for electric mobility has resulted in significant increases in battery production, with over 5 terawatt hours (TWh) of gigafactory capacity expected by 2030, more waste is also being generated as a result of this growth.
Similarly, some experts have disputed the environmental friendliness of EV production, pointing out that the production footprint of an internal combustion engine (ICE) vehicle is roughly twice that of an EV.
Factors ranging from the manufacture of the vehicle’s body to the source of electricity used in the EV’s production and fuel cycle emissions all contribute to the embedded emissions of EVs.
Decarbonisation of battery sector
McKinsey also mentions the carbon footprint of EV batteries, adding that producing a typical EV (with a 75-kWh battery pack) emits more than 7 tonnes of CO2 emissions just from the battery.
As well, McKinsey estimates that the average EV battery today emits up to 100 kg of CO2 equivalent per kilowatt-hour (CO2e/kWh).
Meanwhile, the materials and energy required to manufacture EV batteries account for the majority of the batteries’ carbon footprint. Mining raw materials such as lithium, cobalt, and nickel is not only labourintensive, but also harmful to the environment because it necessitates the use of chemicals and massive amounts of water and it can result in contaminants and toxic waste.
Hence, the market for lithium-ion batteries is anticipated to be driven by the electrification of vehicles. Because of their small size, ability to be recharged, ability to be recycled, and high-density energy output, lithium-ion batteries are already used extensively.
For this reason, demand for nickel will rise because it is required in the production of lithium batteries. Higher-nickel-content batteries are also preferred because they provide more energy and storage at a lower cost, allowing EVs to travel farther.
China dominates EV battery market; Indonesia catching up
The majority of EV batteries are manufactured in Asia, with China accounting for 70% of the market share, according to Global Supply Chains of EV Batteries report by the International Energy Agency ( IEA ).
According to Deloitte, China dominates the global battery and mineral supply chains because it produces almost 75% of all lithium-ion batteries. It also accounts for 70% of cathode production capacity and 85% of anode production capacity, which are both important components in batteries. Furthermore, it has more than half of the processing and refining capacity for lithium, cobalt, and graphite.
Global supply chains, however, have recently been disrupted, and a number of new players are making a difference, with Indonesia, positioning itself as an EV battery hub due to its abundance of nickel.
CO2e/kWh, or up to nearly ten times less than the current most emission-intensive OEMs.
To reduce carbon emissions while producing more EV batteries, recycling end-of-life batteries is being promoted as a practical, circular approach. Batterygrade materials such as graphite, nickel, cobalt, copper, manganese, aluminium, lithium, and other valuable metals can be recovered from used EV batteries through recycling.
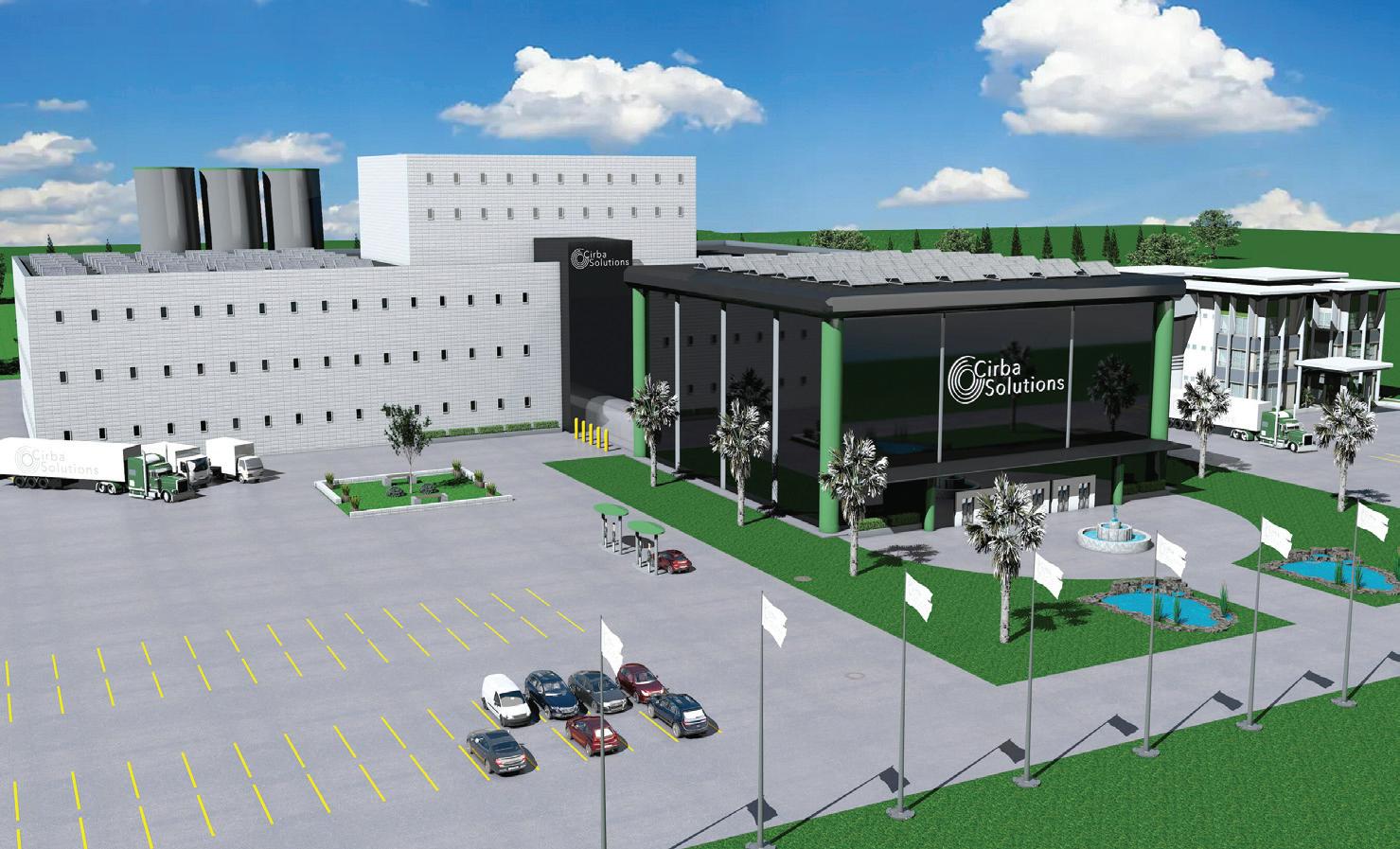
In addition, it is well known that the extraction of lithium from the earth results in significant water usage in addition to environmental damage to the land and soil that are being mined.
Meanwhile, EV battery recycling is also a lucrative market, as stated by Meticulous Research ’s 2030 global forecast report. It adds that the recycling market is expected to be worth US$15.8 billion by 2030, growing at a CAGR of 32.1% from 2023.
With today’s technologies, the carbon footprint of recycled battery materials has been significantly reduced: the carbon footprint of recycled batteries is typically four times that of raw materials derived from primary sources.
Indonesia is positioning itself as an EV battery hub, as it has the world’s largest nickel reserves, totaling 21 million tonnes and accounting for approximately 23.7% of all known nickel reserves
Indonesia has the largest nickel reserves in the world, totalling 21 million tonnes and accounting for about 23.7% of all known nickel reserves. These reserves are mostly concentrated in the east of the nation, particularly in Sulawesi and Halmahera. Deloitte cited that 30% of these nickel reserves are under the control of Indonesia’s state-owned mining industry holding company Mining Industry Indonesia ( MIND ID ) and its subsidiary, PT Aneka Tambang
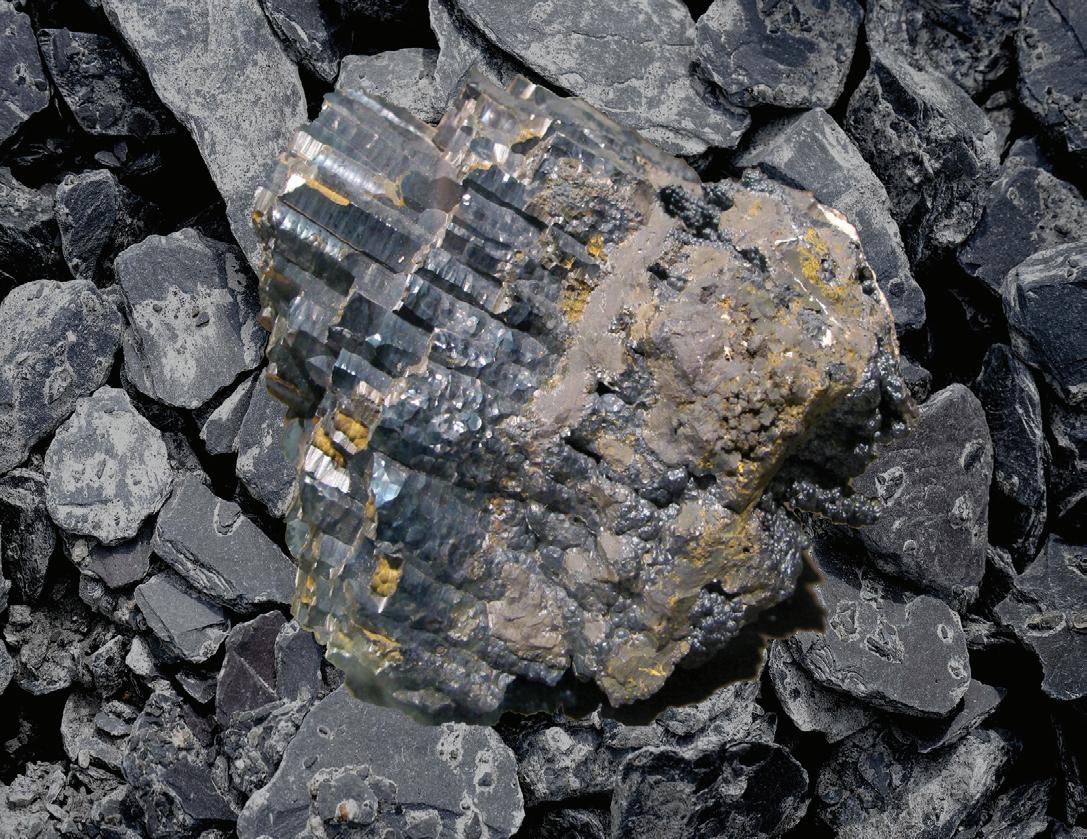
As reported by Deloitte, Indonesia expects 2.2 million EVs to be in use by 2030, necessitating approximately 31,000 battery swapping stations and charging station points. According to its EV roadmap, 600,000 EVs and 2.5 million electric motorcycles will be produced by 2030.
Recycling for circularity, material recovery
According to McKinsey, a number of industry giants are already working to reduce emissions below 20 kg
Recycling lithium-ion batteries is viable. In order to produce, recover, and recycle lithium, cobalt, nickel, and manganese, US petrochemicals firm ExxonMobil , for instance, has developed a solvent extraction technology that can assist raw material suppliers, EV battery manufacturers, and recyclers.
When compared to other recovery processes, Escaid diluents from ExxonMobil for solvent extraction (SX) for battery recycling can enable +90% recovery of the rare metals at +95% purity with costeffective capital investments, high material selectivity, low energy consumption, and without toxic fumes.
Automotive
Partnerships for end-of-life batteries to meet rising demand
Recycling of EV batteries is also being accelerated by two new developments. In South Carolina, Cirba Solutions , a US battery materials and management company for end-of-life batteries and gigafactory scrap, is developing a world-class EV battery materials facility that will supply enough battery grade materials for more than 500,000 EVs annually.
Over the next five years, the company intends to invest more than US$1 billion in the sector.
Beginning the first phase of a US$300 million investment in the state’s flagship lithium-ion EV battery recycling facility, Cirba will have its eighth operational facility in North America, and its fourth strategically located in South Carolina.
This flagship will bring critical battery materials to the US, focusing on the extraction of critical materials such as nickel, cobalt, and lithium from end-of-life hybrid and EV batteries, gigafactory scrap, and end-of-life consumer batteries. Groundbreaking is scheduled for this year, with operations set to begin in late 2024.
Elsewhere, Li-Cycle , a US-based lithium-ion battery recycler, is collaborating with Kion Group , a German provider of industrial trucks and supply chain solutions, in a global lithium-ion battery recycling partnership. The company is developing a new lithium-ion battery recycling facility in Harnes, France, where large global automotive OEMs have an established presence, and where plans to build three battery gigafactories have recently been announced.
Under the partnership, Li-Cycle will recycle lithium-ion batteries from Kion’s global brands using its proprietary submerged shredding technology, which it says is safe, environmentally friendly, and cost-effective. The agreement, which is for an initial period until 2030, has designated Li-Cycle as Kion’s preferred global recycling partner to ensure that Kion batteries are recycled sustainably.
According to Kion, which currently has a global fleet of more than 1.7 million industrial trucks, including forklift and warehouse trucks, and is the largest industrial truck manufacturer in the EMEA region, Li-Cycle’s sustainable process allows up to 95% of the mass of a lithium-ion battery to be recovered and the critical minerals contained in those batteries to be used to manufacture new batteries.
Li-Cycle’s facility in France will be constructed in an existing building site with access to renewable energy. The plant is expected to have initial processing capacity of up to 10,000 tonnes/year of lithium-ion battery material, with option to expand to up to 25,000 tonnes/year. It is expected to leverage Li-Cycle’s ‘Generation 3’ Spoke technology, which has the capability to directly process full EV and energy storage battery packs without any manual dismantling.
The French facility is expected to become operational in 2024 and is expected to bring Li-Cycle’s future planned capacity across its global network to more than 100,000 tonnes/year of lithium-ion battery material.
Li-Cycle’s first European facility will be located in Germany and is expected to be the company’s largest facility to-date, with processing capacity for 30,000 tonnes/year of lithium-ion battery material, including main line and ancillary processing capacity.
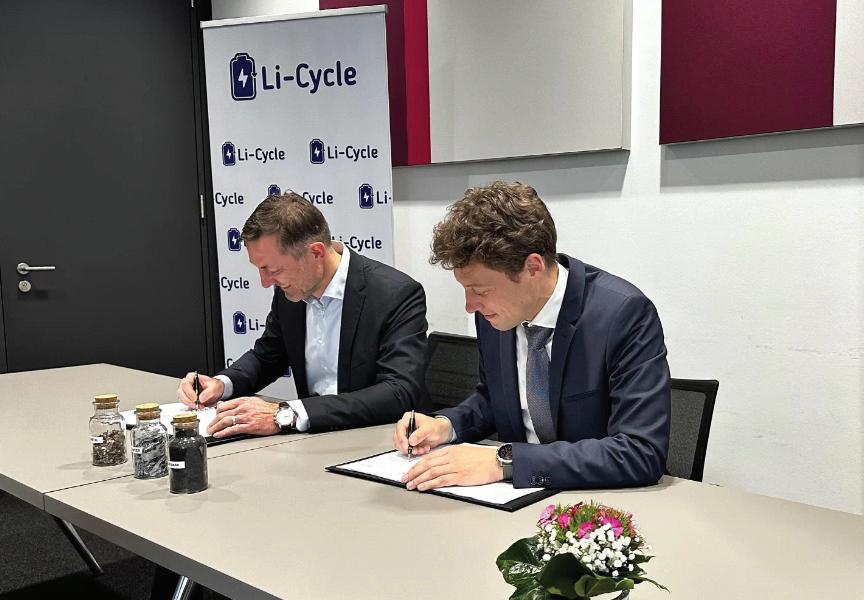
Li-Cycle is also developing a facility in Norway, which is expected to have processing capacity of up to 10,000 tonnes/year of lithium-ion battery material.
Ascend Elements , a US-based battery recycling and engineered materials company, has entered into an agreement with Honda Motor to collaborate on stable procurement of recycled lithium-ion battery materials for Honda EVs in North America. Use of recycled battery materials in new EV batteries can dramatically reduce the carbon footprint of electric vehicles.
Ascend Elements has recycled used lithiumion batteries for American Honda Motor Co. since 2021. The new agreement is an important step toward creating a closed-loop supply chain for recycled battery materials – including lithium, nickel, and cobalt – leveraging the efficiencies and environmental benefits of Ascend Elements’ patented Hydro-to-Cathode direct precursor synthesis process. Ascend Elements’ commercial products include recycled lithium, nickel, and cobalt, as well as sustainable cathode precursor (pCAM) and cathode active materials (CAM) – all made from used lithium-ion batteries and gigafactory manufacturing scrap.
It adds that several peer-reviewed studies have shown Ascend Elements’ recycled battery materials can perform as well as virgin sources while reducing carbon emissions associated with mining.
Based in Westborough, Mass., Ascend Elements is a provider of sustainable, closed-loop battery material solutions. From EV battery recycling to commercialscale production of lithium-ion battery pCAM and CAM, Ascend Elements says it is revolutionising the production of sustainable lithium-ion battery materials.
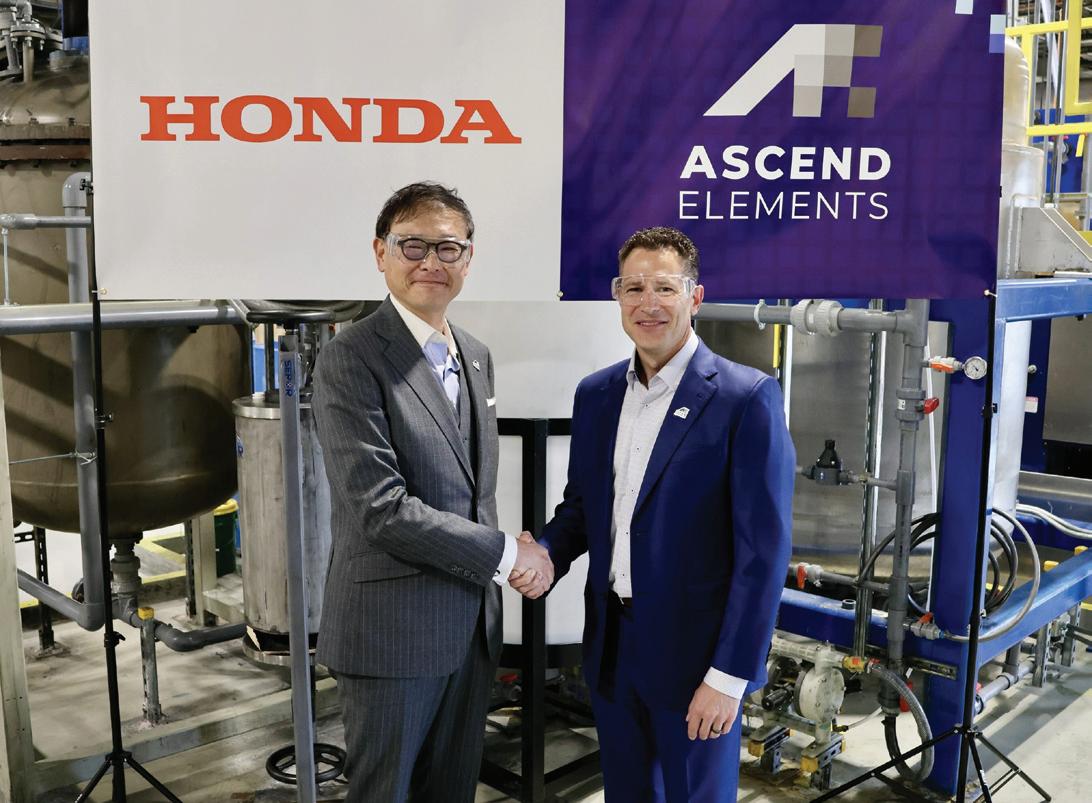
Its Hydro-to-Cathode direct precursor synthesis technology produces new CAM from spent lithiumion cells more efficiently than traditional methods, resulting in improved economics and lowered GHG emissions as well as with fewer batteries going to landfilling.
With lithium-ion rechargeable batteries increasingly powering up the automotive, energy storage, consumer electronics, and other industrial and household applications, there needs to be improved technology and supply chain innovations to better manage battery manufacturing waste and end-of-life batteries and to meet the rapidly growing demand for critical and scarce battery-grade raw materials through a closedloop solution.
Italian machinery sales reach a high in 2022; driven by exports
Against the backdrop of higher exports, Amaplast (Italian association of manufacturers of plastics and rubber processing machinery and moulds) said the year 2022 closed with a higher turnover of EUR4.67 billion, its second highest to be recorded. Sales were 5% higher than 2021 and the forecast of EUR4.5 billion in December was somewhat cautious, it added.
The association said the sales high was “satisfying”, considering the “numerous difficulties confronting the industry over the course of the year – some of which are having continuing effects – between export restrictions to Russia, raw materials and component shortages, and skyrocketing energy costs”.
Higher exports in 2022
With almost all of its machinery exported (70%), Amaplast said it reached a turnover of EUR3 billion from exports, despite the difficult geopolitical situation. Its exports increased to South America (+33% overall, with Brazil topping the sales but lower sales for Colombia, Chile, and Peru).
Meanwhile, sales to Asia went up by 9%; sales to India stood out at 24%, while those to China declined by 7%. In the Middle East, sales were up by 11% overall, with the driving forces being Saudi Arabia (36%) and the Emirates (58%).
Sales to the US were down by 3% but those to Mexico rose by 35%. Closer to home in Europe, sales were up by 8%. Plus, after a “most excellent” 2021, Amaplast said the domestic market remained relatively stable, with a less pronounced increment of 0.8% and turnover of EUR2.54 billion.
It also added that “contradictory signals are arriving from the Africa, contrary to what was observed for 2021”. Exports to North Africa fell by 24% on average while those to sub-Saharan markets have increased by a similar proportion.