8 minute read
New technologies to push the recycling agenda
Next Article
Recent industry developments in recycling technologies and collaborations are focused on improving recycling rates and recycled material quality, and increasing recycled content in products, says
Angelica
Buan
in this report.
Wastes still rising even with recycling
Whenever the staggering amount of waste plastics is mentioned, recycling comes to mind as a solution. No doubt that recycling offers the sweet spot in reducing wastes.
Recycling conserves resources by converting used materials into new products, reducing the need to consume natural resources; it saves energy because manufacturing with recycled materials requires significantly less energy than manufacturing new products from raw materials; it reduces the need for raw material extraction, which pollutes the air and water; and it conserves energy while lowering greenhouse gas emissions.
However, it is clear that current recycling rates have not kept up with the rate of plastic waste production.
Citing data from the UN , the production of 400 million tonnes/year of plastic waste is only the tip of the iceberg when it comes to the enormous environmental problem that must be addressed.
Single-use plastics (SUPs) contribute to the mounting waste. Every minute, 1 million plastic bottles are purchased globally, and up to 5 trillion plastic bags are used annually. All of these will almost certainly be discarded after use.
According to the OECD's Global Plastics Outlook report, only 9% of plastics are successfully recycled today, with the remaining 22% being mismanaged. Of that, 15% is collected for recycling, but 40% is discarded as waste.
According
Some plastic materials are not recyclable
Recycling, according to Greenpeace USA , is a "dead end street" in terms of reducing the amount of plastic waste in the environment. Or, in the case of most plastics, recycling is ineffective. Circular Claims Fall Flat Again, a report released in October 2022, stated that a majority of plastics cannot be recycled.
No type of plastic packaging in the US meets the Ellen MacArthur Foundation's New Plastic Economy (EMF NPE) Initiative's 30% recycling rate criteria to be classified as "recyclable."
Commonly used resins in bottles and containers in the US, PET #1 and HDPE #2, and previously thought to be recyclable, have reprocessing rates of 20.9% and 10.3%, respectively. Every other type of plastic has a reprocessing rate of less than 5%.
Similarly, mechanical and chemical recycling of plastic waste have failed because plastic waste is difficult to collect and sort for recycling, is environmentally hazardous to reprocess, often consists of and is contaminated by toxic materials, and is not economically viable to recycle.
According to the report, paper, cardboard, metal, and glass do not have these issues, which is why they are recycled at much higher rates.
Also is the fact that post-consumer recycled (PCR) plastic from household waste poses toxicity risks and is not produced on a commercial scale for food-grade uses anywhere in the world, including the US. As a result of its findings, the organisation deemed that the real solution is to switch to reusing and refilling systems.
Advanced sorting for flexible packaging
Choosing which plastic items are accepted in recycling facilities or can be recycled is a difficult task in itself. That is why, sorting plastic waste is critical if recycling rates are to improve, with high purity rates that are free of contaminated and nonrecyclable items. Advanced sorting technologies enable more efficient and effective sorting that is less complex and uses less energy.
The EU-funded Circular FoodPack, which addresses the challenge of recycling flexible packaging with multilayer composites, is one of the most recent developments in the European recycling sector.
The Circular FoodPack project, which started in June 2021 and will end in November 2024, will be implemented by 14 businesses and research centres from six different European nations, with the Fraunhofer Institute for Process Engineering and Packaging serving as the project coordinator.
Flexible plastic packaging is used in food and personal care because of its ability to meet safety and hygiene standards. However, modern sorting and recycling processes are incapable of reliably sorting and recycling flexible packaging with multi-layer film structures.
As a result, the majority of multi-material composites are disposed of in landfills or used for energy recovery. Furthermore, EU legislation prohibits the use of recyclates in food packaging applications.
Circular FoodPack's Tracer-based sorting systems are being further developed to separate food from non-food packaging as well as improve mechanical and physical recycling processes. The project is also developing ecodesign innovative mono-material food and personal care packaging that is easy to sort and recycle.
Tracer-based sorting identifies packaging items that contain unique printed, fluorescent tracers that emit an unambiguous signal when exposed to laser light, resulting in the assignment of a material-specific sorting code.
The mechanical and physical solvent-based recycling process cascades will allow Circular FoodPack to purify the recyclates, resulting in a reduction of contaminants, colour, and odour.
A promising deinking technology that can remove all types of inks while also ensuring deodourisation will be scaled up in the existing mechanical treatment cascades. The cleaned material is then recycled using solvents through the patented CreaSolv Process for separation
Improvements are being made to the mechanical and physical recycling procedures as well as the separation of food packaging from non-food packaging using Circular FoodPack's tracer-based sorting systems into various material components such as fillers, additives and PE.
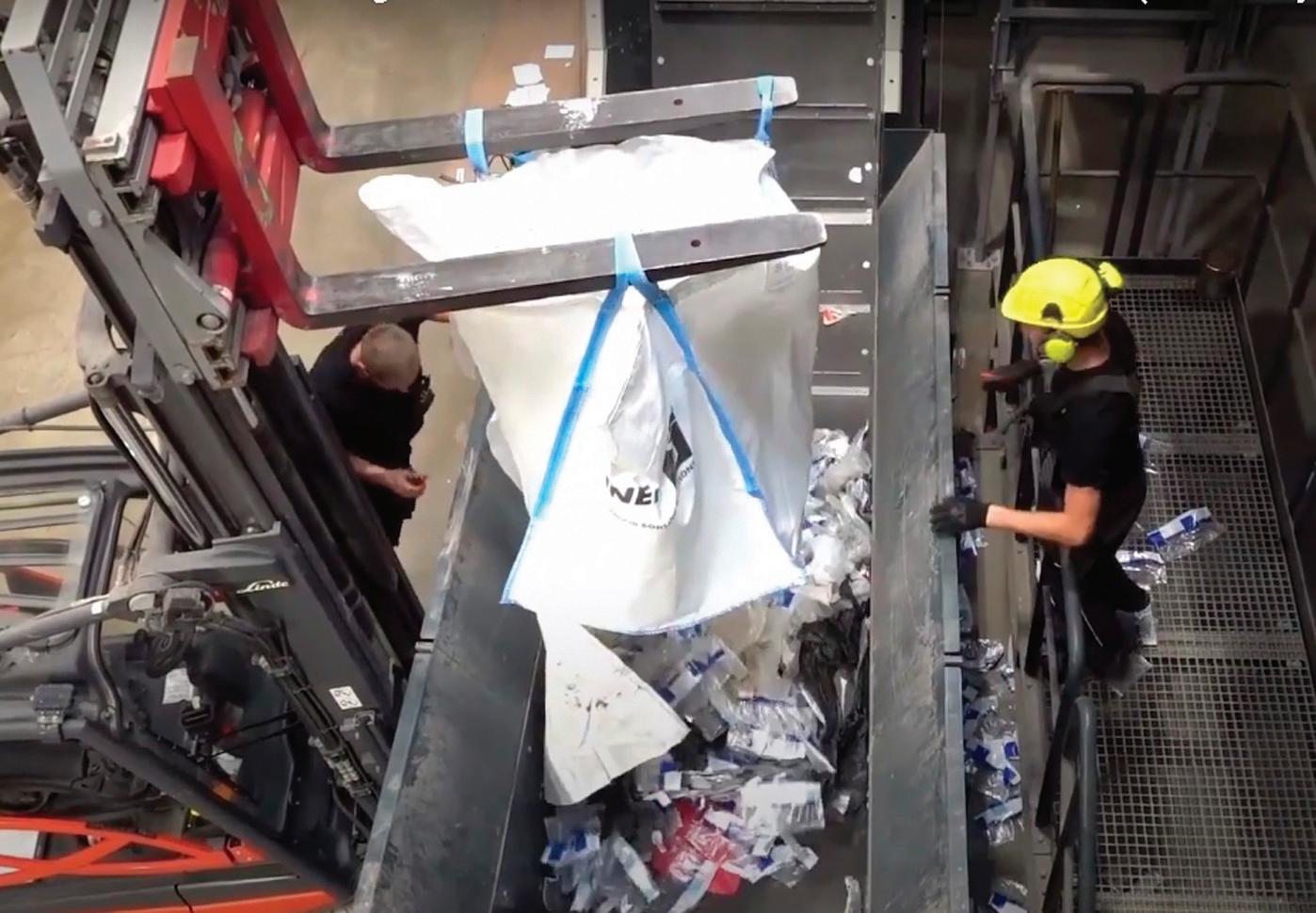
At the same time, the project aims to create a recyclable and reusable packaging material containing at least 50% PCR materials, with applications in dry food packaging, home care, and personal care packaging.
The project ensures that all newly developed process steps and (by-) products are subjected to comprehensive sustainability assessments that take into account the entire life cycle, including environmental, economic, and social impacts. This will allow evidence of the new packaging's sustainability to be compared to advance multilayer multi-material packaging.
Plastic waste recycling presents a number of challenges in terms of collection, sorting, and reprocessing, whereas other materials do not, which explains why they have higher recycling rates
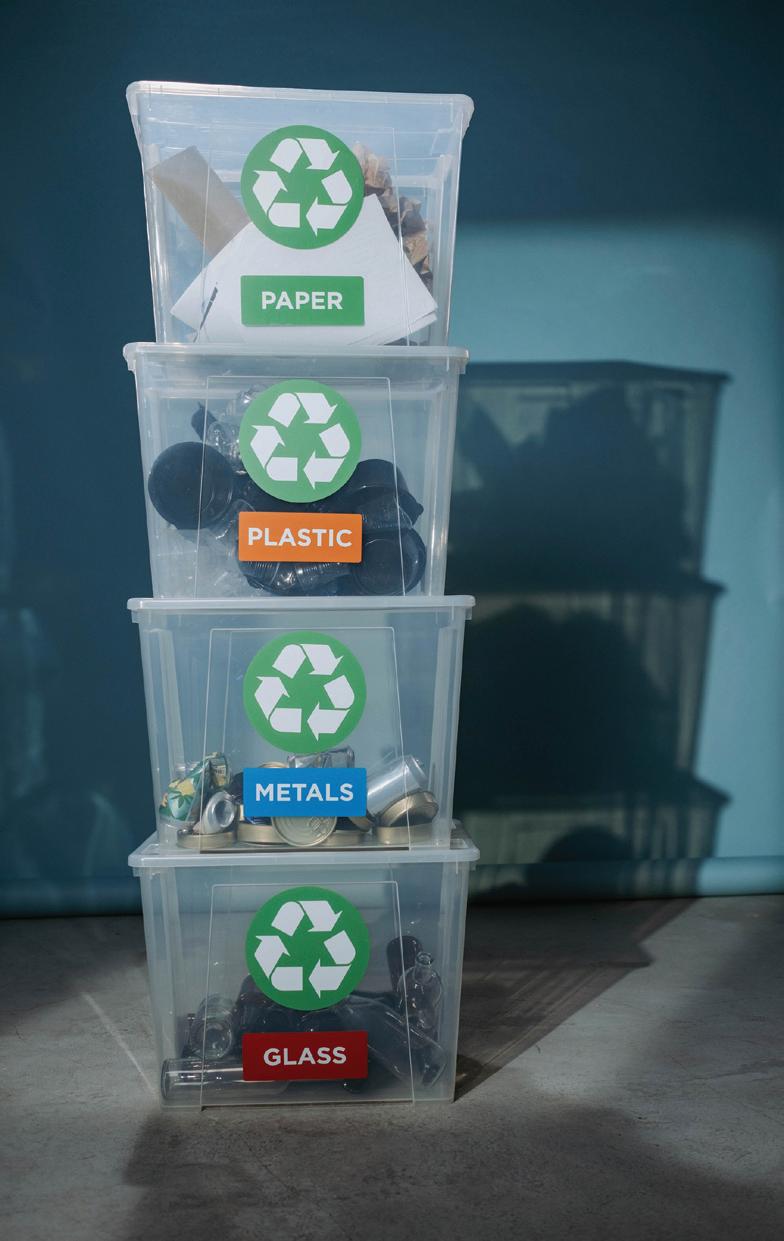
Pushing waste out of incineration waste streams
Incineration is thought to be effective at reducing waste volume by up to 95% and solid waste volume by up to 85%, depending on the components of the solid waste. However, incineration neither promotes recycling nor waste reduction. It is also said to emit toxic compounds and particulates that are hazardous to human health.
A partnership between chemical firm LyondellBasell and the European thermal waste treatment company EEW Energy from Waste GmbH ( EEW ) takes waste reduction to the next level by extracting and recycling plastics from incineration waste streams using advanced sorting technology.
This agreement could include the development of waste pre-sorting facilities at or near EEW incineration plants to remove plastics from waste streams destined for incineration, as well as investment in advanced sorting facilities to further sort and refine the plastic that has been removed.
This collaboration is also expected to close the loop on plastics sent for incineration by sorting them for use as feedstock in mechanical and advanced recycling processes. EEW will first construct a sorting facility to recover plastics for the raw material cycle.
LyondellBasell also announced a partnership with Kirkbi A/S , Lego brand's family-owned holding/ investment company, to invest in APK , a German company that specialises in a solvent-based recycling technology for LDPE.
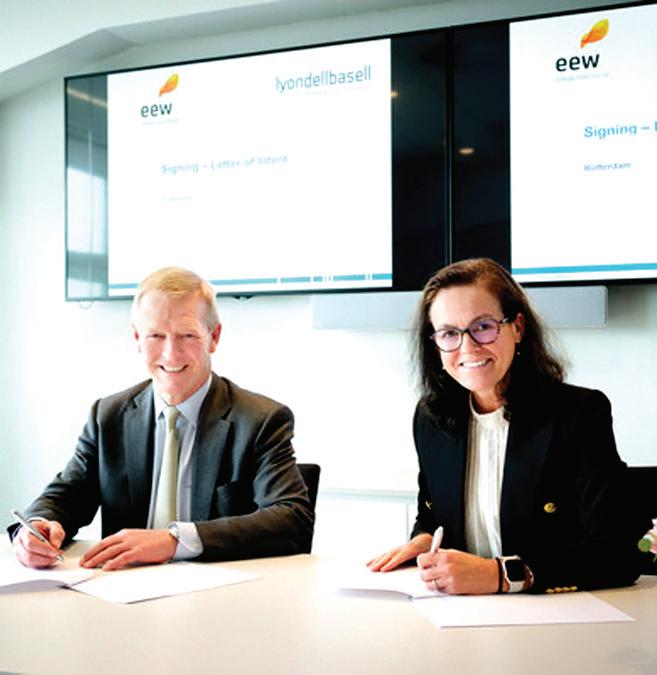
APK aims to increase the recycling of multi-layer flexible packaging materials, which currently account for the majority of mixed plastic waste from the consumer sector. APK’s solvent-based Newcycling process separates the different polymers of multi-layer packaging materials and produces recycled materials with what is said to be “a high degree of purity” suitable for new packaging materials.
Depolymerisation technology to produce rPET
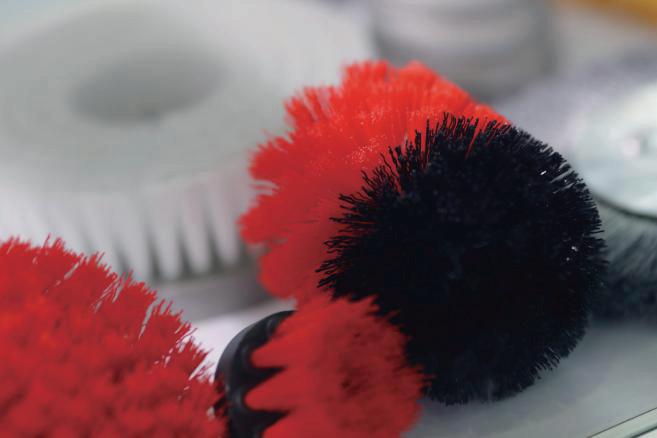
PET bottles have the advantages of convenience, low cost, and design flexibility, but have a short shelf life (around 6 months) and are likely to end up in landfills due to their single-use characteristic.
Despite the fact that PET is fully recyclable, only 7% of the PET produced globally is recycled bottle-to-bottle.
LyondellBasell and EEW's collaboration is expected to close the loop on plastics destined for incineration by sorting them for use as feedstock in mechanical and advanced recycling processes
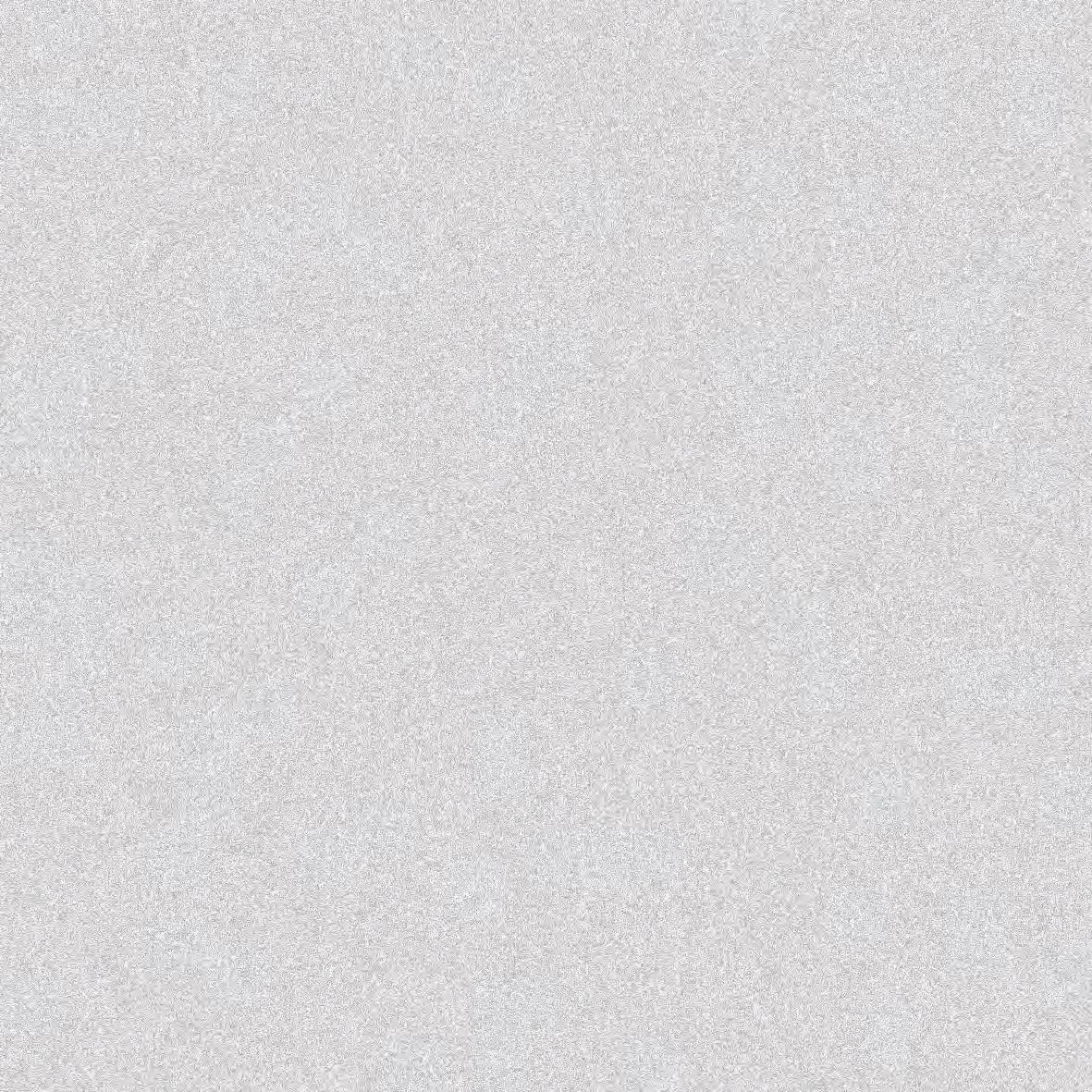
According to the European Chemical Industry Council ( Cefic ), this is partly because mechanical recycling, the current technology, is unable to remove colours from PET waste and also has an adverse effect on the material's quality after each cycle.
Low quality recycled materials have always been a concern for manufacturers adopting more recycled content in their packaging.
A recent collaboration between Italian oil firm Saipem, and Garbo , an Italian chemical company, focuses on improving recycled PET quality. ChemPET is Garbo's proprietary depolymerisation technology that converts PET waste, into new PET that has high value in the chemical and food industries, it says.
European plastics supply chain push for higher legal certainty of recycled content
With the recent meeting of 31 trade associations for the EU to be clear on how it legally views chemical recycling and how recycled content is tracked in plastic products, the tracking of recycled content is a major issue with industry pressing for the legal acknowledgement of a mass balance approach.
Essentially, this is push for policy support from the European Commission and EU member states for chemical recycling that could help speed investment and add more overall plastic recycling capability.
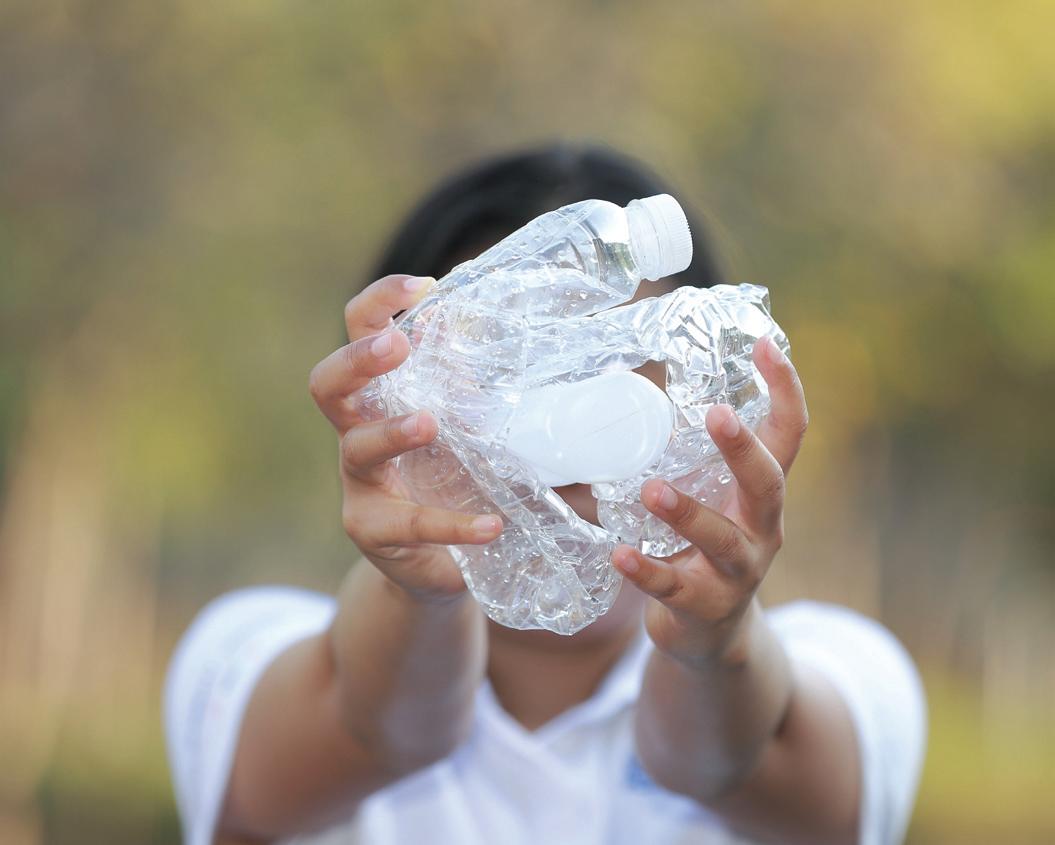
“The rules currently being developed for the SingleUse Plastics Directive (SUPD) implementing act will have a key impact on both mechanical and chemical recycling investments in Europe,” the associations said.
The timelines for targets set out in frameworks such as the proposed Packaging and Packaging Waste directive, which set out goals for chemical recycling capacity by 2030 and 2040, will require the sector to begin work on commercial-scale production facilities immediately, according to the associations.
“It is therefore key that policymakers set a precedent as to when and how a mass balance chain of custody in recycled plastics will be applied in the EU sooner rather than later,” the trade groups said. “This precedent should also set the direction of policy in non-packaging sectors such as automotive or construction, where recycled plastics targets are currently under discussion or may arise in the future.”
Saipem and Garbo have tied up to improve recycled PET quality. ChemPET is Garbo's proprietary depolymerisation technology that converts PET waste, into new PET resins
Saipem and Garbo will also cooperate on the industrial scale construction of Italy's first chemical plastic recycling plant, which will be located in Cerano, in the province of Novara.
ChemPET, according to Garbo, is based on a chemical recycling technology that, unlike the mechanical process, allows for the recycling of types of plastics, such as coloured plastics, for which there are currently no alternatives, and produces higher quality material. Furthermore, unlike the mechanical process, rPET from this process does not lose its properties during the recycling process.
ChemPET also makes process and by-product management easier while avoiding the use of flammable or hazardous materials.
This technology, as well as upcoming solutions, represents the industry's major push to increase not only recycling rates and recycled material quality, but also compliance with the regulations that plastic products must contain more recycled materials, and in the case of PET bottles, at least 25% recycled content, according to EU directives.
There are clear concerns over the mass balance approach to approximating the recycled content of individual plastic items and customer acceptance is critical. If recycling capacity is to grow however, and the move towards greater plastics circularity accelerated, then clearer policy support is required.
The industry view is that the mass balance model can be based on credible third-party verification and certification. Chemicals trade group Cefic says that process losses and outputs, consumed as energy, should not count towards the recycled content targets. At present the sector lacks a standardised approach, with the commonly-used methodology behind mass balance remaining contentious.
In mechanical recycling mass balance can also refer to the process of using a credit system to substitute the use of recycled material in one end-use for another in order to meet sustainability targets.
The concept of greenwashing is coming under increasing scrutiny in the EU, with regulators announcing a stronger push on eliminating the practice as deadlines to reach certain thresholds for recycling and carbon abatement draw closer.
At present, many of the systems for quantifying decarbonisation and waste-reduction remain fragmented, with McKinsey noting that the environmental, social and governance (ESG) space is currently similar to the state financial reporting was in a century ago.
Systems are likely to become more standardised over time, but the complexity of chemical – and even mechanical – makes the process a complex one, with few easy answers.