22 minute read
Progettazione e Tecnologie dei Materiali Compositi per Sistemi Lancio
Next Article
a cura di:
Ing. A. Mataloni (Avio)
L’azienda Avio di Colleferro, un’eccellenza a livello mondiale nel settore dello spazio, impiega correntemente materiali di nuova generazione e tecnologie di Advance manufacturing. L’utilizzo dei materiali compositi per i sistemi di lancio è consolidato da decenni di applicazioni nel settore. La maggior parte delle strutture primarie del lanciatore sono oggi in materiale composito, in particolare per la parte alta del lanciatore, che ha un impatto più pesante rispetto al carico utile del vettore. Tra queste strutture, gli involucri per motori a propellente solido e l’interstadio 2-3 del lanciatore Vega-C sono esempi di componenti basati per larga parte su materiale composito ad alte performance (Figura 8).
Per ciò che riguarda l’involucro, il vessel e le skirt sono realizzati in carbon-epossidica ad alta resistenza a fibra lunga, con tecnologia del filament winding per il tow e Automated Tape Laying per il tape. Le interfacce sono realizzate in lega di alluminio. Sono presenti anche componenti elastomerici tra skirte vessel, in previsione delle differenti dilatazioni provenienti dalla pressurizzazione (Figura 9).
Test a livello full scale vengono fatti sia in fase di sviluppo e qualifica, che per l’accettazione. Si verifica il comportamento delle strutture in pressione, sotto carichi meccanici o in cicli simultanei di pressione + carichi meccanici (es. strutture di primo stadio lanciatore). Sono necessari banchi prova dedicati e l’adozione di un sistema di monitoraggio spostamenti e deformazioni adeguato. Il comportamento globale del motore viene invece verificato da prove a fuoco su banchi statici (Figura 10).
L’ interstadio 2-3 è un progetto nato da una collaborazione per lo sviluppo tecnologico tra Avio e il CIRA (Centro Italiano Ricerche Aerospaziali). È in materiale composito posizionato tra il secondo e terzo stadio del lanciatore Vega-C. È composto da due sezioni (superiore e inferiore) tra le quali avviene la separazione dello stadio a fine combustione e il resto del lanciatore. Le interfacce esterne, come nel caso degli involucri motore, sono in lega di alluminio (Figura 11).
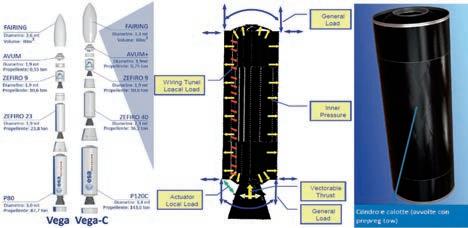
Il processo realizzativo avviene attraverso avvolgimento di fibra secca di carbonio in una preforma e successiva infusione di resina. Il processo di infusione e cura avviene in autoclave. Seguono estrazione del mandrino, intestazione del composito e integrazione delle flange di interfaccia. Tutte le fasi, dal design al processo realizzativo e alle fasi di testing per la qualifica, vengono interamente gestite in Avio. Per ciò che riguarda l’involucro, Avio ha ritenuto strategico formulare e produrre al proprio interno una linea di prepreg base di fibra di carbonio, con caratteristiche focalizzate sulle proprie applicazioni (Figura 12). a cura di:
Ing. P. Carlorosi Dallara (Dallara)
L’impossibilità di eseguire manutenzioni su un satellite post lancio di un vettore richiede una maggiore accuratezza nell’esecuzione dei vari componenti e l’avere un’alta confidenza che i componenti abbiano una durata almeno uguale a quella necessaria per il completamento della missione. In maniera analoga, l’ottimizzazione delle forme e l’utilizzo dei materiali al limite delle loro proprietà meccaniche per avere una maggiore leggerezza strutturale sono aspetti di grande interesse per le applicazioni aerospaziali. Considerando questi tre aspetti, si può dire che il settore dello sport racing è simile a quello dell’aerospazio. In quest’ottica di cross fertilization, ovvero di trasferimento tecnologico di processi da settori diversi, la sezione di controllo non distruttivi (NDA) è stata presentata da rappresentanti della Dallara Automotive. Da oltre 40 anni, Dallara progetta e produce alcune tra le più sicure e veloci vetture da competizione e da strada al mondo. Le competenze distintive Dallara sono quattro (Figura 13): la progettazione utilizzando materiali compositi in fibra di carbonio, l’aerodinamica, la dinamica del veicolo e la produzione prototipale.
Dallara è in grado di produrre fino a 200 vetture da competizione l’anno: è presente in tutti i campionati Formula 3, è il fornitore unico di vetture ai campionati IndyCar, Indy Lights, Formula2, Formula3, Super Formula, realizza inoltre cellule abitacolo e parti strutturali per la Formula E, il WEC
(World Endurance Championship), l’ELMS (Electric Motorsport) e l’IMSA (International Motor Sports Association). Negli ultimi anni l’attività di ingegneria e produzione si è ampliata notevolmente, sia per quanto riguarda le vetture da competizione, sia per le vetture stradali ad alte prestazioni. Recentemente l’attività di ingegneria ha anche rivolto il suo target all’aerospazio visto l’aumento dell’interesse in questo settore. Nell’ottica della sicurezza e affidabilità dei componenti il reparto Controllo Qualità svolge in Dallara un importante ruolo di monitoraggio e controllo dei prodotti e dei processi, con focus particolare su quelli che sono definiti ‘’processi speciali’’, come le tecnologie realizzative per prodotti in materiale composito, prevalentemente costituiti da fibra di carbonio / vetro e resine termoindurenti, leghe leggere. Per verificare la conformità strutturale e quindi la buona adesione delle parti in materiale composito è necessario:
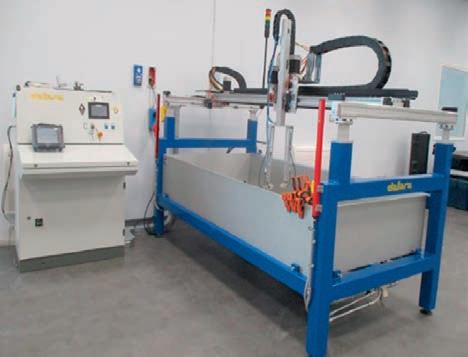
• utilizzare il più opportuno metodo diagnostico;
• rendere ripetibili i controlli;
• poter registrare il risultato del controllo;
• poter confrontare il risultato del controllo durante la produzione della serie (che può durare anche diversi anni).
Il punto di partenza per realizzare quanto sopra descritto è creare progressivamente una cultura sullo sviluppo dei controlli non distruttivi (CND), integrando anche le tecniche così da definire la scelta del metodo più opportuno in relazione alla geometria del componente e alle tempistiche realizzative produttive e quindi dell’esecuzione di controllo.
Affiancata all’esperienza nei CND vi è quella della metrologia tridimensionale sia laser scan che a tastatura CMM (Coordinate-Measuring Machine). L’ultimo sviluppo relativo ai controlli ad ultrasuoni è quello della progettazione e realizzazione di una vasca per il controllo automatico ad ultrasuoni (Figura 14). L’impianto programmabile è in grado di essere flessibile all’analisi ultrasonica di vari componenti critici ai fini della sicurezza dei prodotti o producibili in futuro da Dallara, tale da fornire una mappa di conformità del componente in CScan per ampiezze e spessori.
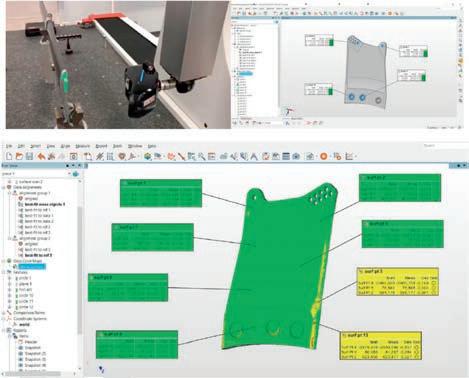
Il sistema di automazione che è stato progettato così da permettere il controllo dei componenti più larghi ipotizzati come oggetto di diagnosi (alettoni). L’impianto di movimentazione multi-asse è controllato da un sistema PLC (Programmable
Logic Control) digitale, concepito per eseguire controlli non distruttivi di tipo ultrasuoni su molti componenti. Con questa tecnologia è stata possibile l’automazione di controllo ad ultrasuoni permettendo quindi una riduzione dei tempi di diagnosi e un risultato di diagnosi più puntuale e facilmente consultabile. Le tecniche utilizzabili sono quelle a trasmissione e pulse eco.
A questo controllo si integrano i risultati dei controlli tridimensionali delle medesime parti anche in questo automatizzati grazie all’ausilio di una CMM. L’unione dei risultati degli output CND e dimensionali automatici consente di avere un pacchetto di risultati dimensionali e strutturali delle parti che potenzialmente potrebbero essere anche allineate sui medesimi RPS (Revolutions Per Second) anche con le relative matematiche teoriche (Figura 15).
Systems Engineering per sviluppo piattaforme sat in manifattura additiva
La presentazione ha affrontato direttamente, ma da un punto di vista non tradizionale, l’argomento del Design For Additive Manufacturing (DFAM) per le applicazioni spaziali. Il tema ha acquisito una rilevanza sempre più diffusa ormai da circa 10 anni a questa parte, per il settore aerospaziale e non solo, poiché dopo una prima, e in parte ancora in atto, lunga fase di prototipazione “artigianale”, le tecnologie di produzione additiva (AM) sono ormai sempre più una reale opzione progettuale e produttiva complementare, e non sostitutiva, delle più tradizionali tecnologie di manifattura a livello industriale. Mentre dunque la manifattura additiva è in una cruciale fase di transizione dalla ricerca e sviluppo (R&S) alle operazioni ingegneristiche “on the-shop-floor”, questo lavoro di ricerca ha affrontato un argomento, che seppur implementato in un ambito applicativo molto specifico, risulta essere molto rilevante, poco diffuso e le conseguenti questioni analizzate altamente critiche sia a livello progettuale che realizzativo, valide tanto per l’industria spaziale che per la comunità ingegneristica e scientifica in generale.
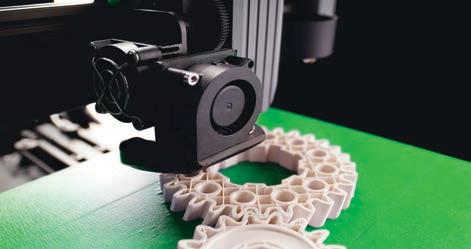
L’introduzione delle tecnologie AM per la produzione terrestre (on-ground) di sistemi spaziali, per definire fin da subito l’ambito applicativo al quale fa riferimento il lavoro, ha aperto tutta una nuova serie di quesiti in ambito R&S per la comunità accademica e industriale, tra cui: come è possibile ottenere il massimo beneficio applicando le tecnologie AM ai sistemi spaziali? Come è possibile ripensare le tradizionali architetture delle piattaforme dei veicoli spaziali all’interno di una mentalità DFAM? Come è possibile migliorare l’attuale approccio DFAM incorporando le metodologie di ingegneria dei sistemi esistenti al fine di gestire la maggiore complessità di progettazione? Come è possibile ridurre lo sforzo di progettazione e produzione dei prossimi futuri sistemi spaziali AM? A queste domande si è provato a rispondere attraverso un lavoro di ricerca congiunto tra Dipartimento di Ingegneria Meccanica e Aerospaziale dell’Univeristà “La Sapienza” di Roma, divisione strutture e materiali spaziali di Beyond Gravity (già RUAG Space, di Zurigo) e Agenzia Spaziale Europea (ESA), confluito in una tesi di dottorato industriale svolta dal 2015 al 2018 e che ha portato alla realizzazione di un primo prototipo di struttura multifunzionale, realizzata interamente in AM presso i laboratori de “La Sapienza” di Roma, di una porzione di pannello biomimetico (riduzione notevole della massa) di un sistema satellitare avente al tempo stesso capacità strutturali (supporto, resistenza e rigidezza), termiche (smaltimento calore attraverso heat-pipes integrati nella struttura) e di harnessing (accomodamento e distribuzione di cavi elettrici-elettronici). Inoltre, come ulteriore risultato del processo di progettazione, realizzato a Zurigo presso RUAG Space interamente con metodologia concurrent engineering, si è realizzato un tool operativo di ausilio alla progettazione real-time, successivamente poi proposto internamente da ESA come possibile tool da valutare come supporto per futuri studi di sistemi spaziali da realizzarsi in AM. Tale tool, sviluppato in Excel, permette la gestione a livello sistema della progettazione in concurrent engineering, ovvero attraverso l’interazione simultanea e sinergica di più domini tecnici, tramite un rigoroso processo sistemico (life-cycle vision) e sistematico (strutturato e metodologico) basato su modelli di rappresentazione, gestione e tracciamento delle opzioni, scelte, dati e variabili di design a partire dai requisiti cliente.
In particolare, il contributo specifico di tale lavoro è stato quello di dimostrare la tesi che per massimizzare realmente i benefici dell’AM per i sistemi spaziali è necessario adottare un approccio olistico sia per il sistema spaziale che per il suo flusso di lavoro di progettazione e sviluppo (Figura 16). Il presupposto critico principale, infatti, è stato che partendo da una semplice riprogettazione di singoli componenti (ad esempio strutture terziarie o di supporto) sia possibile ottenere solo miglioramenti marginali (ad esempio riduzione di massa), mentre ripensare la metodologia progettuale tradizionale all’interno delle innovative logiche DFAM con un approccio di Systems Engineering (SE) è l’unico vero modo per raggiungere vantaggi davvero dirompenti e multidominio, che incidono fortemente sulle tradizionali architetture dei veicoli spaziali. Pertanto l’obiettivo è stato quello di mostrare come l’introduzione di metodologie di SE avanzate, in particolare processi, metodi e strumenti di progettazione concurrent, aventi un’accurata prospettiva di tutto il ciclo di vita del sistema, un coinvolgimento diretto e real-time di più domini, tecnici e non, e gestito in maniera strutturata e basata su modelli, dovrebbe necessariamente essere adottata al fine di consentire una riprogettazione efficace ed efficiente e la realizzazione di componenti complessi, unità e sistemi AM, con riferimento diretto alle strutture primarie dei veicoli spaziali. Ciò consente un duplice miglioramento: a livello di componente/unità e a livello di sistema, ovvero sulle prestazioni dell’unità stessa e a beneficio dell’intero sistema. Di conseguenza consentendo di trarre i massimi benefici dall’AM, di gestire la maggiore complessità del DFAM e infine di avvicinarsi correttamente a una riprogettazione della piattaforma di un veicolo spaziale a partire dalle strutture primarie ma riprogettate in ottica di sistema satellite.
Tale obiettivo di ricerca è stato così declinato in alcuni specifici passi realizzativi, poi opportunamente soddisfatti e rappresentati da relativi lavori scientifico-tecnologici proposti e pubblicati:
• Indagine sulle relazioni tra DFAM, sistemi di veicoli spaziali e metodologie di Systems and Concurrent Engineering (SE/CE).
• Proposta di un nuovo approccio DFAM che integri le metodologie SE/CE (metodi, processi, strumenti).
• Applicazione e validazione della metodologia proposta per una piattaforma satellitare (obiettivo metodologico)
• Realizzazione di un innovativo sistema spaziale attraverso tecnologie AM come benchmark di progettazione (obiettivo tecnologico).
• A conclusione del lavoro le peculiari figure di merito misurate sono state:
• Performance del prodotto in termini di integrazione multifunzionale: numero di funzioni integrate.
• Sforzo progettuale in termini di costi e tempi di progettazione (programmazione) con riferimento all’approccio tradizionale.
• Impegno produttivo in termini di costi e tempi MAIT (programma) con riferimento all’approccio tradizionale.
Pertanto, sono stati sviluppati primariamente due casi studio abilitanti al resto del lavoro, volti a comprendere, testare e dimostrare le relazioni tra approccio DFAM e sistemi di veicoli spaziali (con particolare attenzione alle strutture primarie di piattaforma) e quindi tra sistemi di veicoli spaziali e Metodologie SE/CE rispettivamente. Si è in particolare ideato e realizzato un primo prototipo concettuale di Cubesat (piccolo satellite di dimensioni 10x10x10 cm) la cui struttura è stata ottimizzata topologicamente e la sua configurazione ripensata, al fine non tanto di ridurne la massa, ma di poter effettuare le operazioni di assemblaggio-integrazione-test (AIT) del sistema finale in maniera più efficiente. Perciò, si è prima realizzata una configurazione in cui il CubeSat è stato decomposto in due parti (Figura 17), facilmente integrabili e realizzate però in un unico job di lavorazione additiva e poi si è pensato di realizzare una unica struttura apribile attraverso una cerniera collegante le due parti. Tale ultimo concetto è stato poi successivamente analizzato in dettaglio e sviluppato in un ulteriore lavoro di ricerca, attraverso un’altra tesi di dottorato nello stesso gruppo di ricerca, a cura dell’ing. V. Cardini. Questo primo step progettuale (caso studio) è stato necessario per approcciarsi e comprendere meglio sinergie e limiti tra DFAM e un sistema spaziale completo (seppur con focus primariamente sulla struttura primaria), volutamente piccolo da essere gestibile in termini di volumi e complessità. Il secondo caso studio ha riguardato la progettazione per uno studio di fase 0 (fattibilità ingegneristica) di un sistema spaziale completo (spacecraft) per una missione spaziale interplanetaria attraverso l’utilizzo di una metodologia (metodo + processo + tool) concurrent, basata su Excel come strumento di scambio dati, elaborazione della configurazione, etc.
Successivamente l’approccio metodologico adottato per affrontare il caso studio principale, è stato quello del Through-life Integrated Concurrent Engineering (TICE), concetto proposto a livello teorico già anni fa dall’ing. Marco Lisi a proposito del corretto approccio sistemico da adottare in merito alla progettazione e gestione di grandi infrastrutture satellitari, come ad esempio le mega-costellazioni, e impiegato per la prima volta a livello pratico. Dunque, abbinando le caratteristiche del DFAM con i metodi, i processi e gli strumenti del Systems and Concurrent Engineering (SE/CE), attraverso una proficua collaborazione con RUAG Space, grande azienda manifatturiera di sistemi spaziali che tra le prime si è dedicata anche allo sviluppo di soluzioni relative all’AM, è stato implementato l’approccio TICE per la riprogettazione di un pannello radiante integrato multifunzionale per veicoli spaziali, scelto come punto di riferimento rappresentativo di un sistema completo di veicoli spaziali. Grazie a questo caso di studio è stato possibile raggiungere completamente gli obiettivi metodologici e tecnologici entro i tempi comunque limitati di una tesi di dottorato. Come principali risultati, le attività di ricerca hanno portato in primo luogo alla definizione di un innovativo Concurrent Design Tool adatto per integrare soluzioni in AM (Figura 18) in grado di facilitare il processo di tradeoff e alla definizione concettuale di un sistema AM e in secondo luogo alla realizzazione di un prototipo ingegneristico AM innovativo di un pannello radiante multifunzionale biomimetico per applicazioni spaziali (Figura 19). a cura di: Ing. C. Melzer (Beyond Gravity)

Tale lavoro di dottorato ha voluto rappresentare uno studio esplorativo con il fine di sviluppare e validare nuove metodologie ingegneristiche non solo per la riprogettazione di parti innovative di veicoli spaziali AM, ma per spingere AM e DFAM ad affrontare un obiettivo ancora più sfidante: capire meglio come influenzare le tradizionali architetture dei veicoli spaziali grazie al DFAM.
Beyond Gravity (ex RUAG Space) è stata dal 2014 in poi (Figura 20) tra le prime aziende ad occuparsi di utilizzo delle tecnologie additive per applicazioni spaziali. Tanto che ad oggi può vantare un know-how e un heritage di notevole importanza nel settore, unitamente alla già riconosciuta expertise a livello mondiale in ambito manufacturing per strutture, meccanismi e componentistica aerospaziale.
La produzione con tecnologia di Additive Manufacturing ha un elevato potenziale di innovazione per soddisfare le elevate esigenze degli elementi flessibili ma anche delle parti strutturali nelle applicazioni spaziali, offrendo vantaggi quali una maggiore libertà di progettazione, topologie ottimizzate per resistenza e massa e nuove topologie cinematiche monolitiche. In questo quadro, è necessario controllare l’intera catena di sviluppo (Figura 21) per strutture realizzate con tecnologia AM qualificate per il volo spaziale.
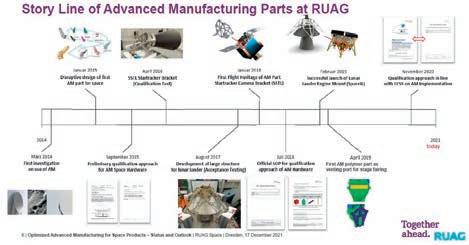
Dopo la selezione del processo produttivo e del materiale più idoneo, nella fase di concept design dovrebbe essere avviata la definizione di un processo produttivo end-to-end su misura. Ciò include la verifica della materia prima, l’ottimizzazione dei parametri di produzione, la caratterizzazione dei materiali, lo sviluppo del progetto, compreso il lavoro di ricerca e ottimizzazione topologica del componente sulla base della distribuzione degli stress e della sua funzionalità, la produzione, il trattamento termico, la finitura superficiale e la qualificazione fino alla verifica delle esigenze ambientali e di durata del prodotto spaziale. L’elevata rugosità superficiale e la bassa precisione geometrica delle geometrie prodotte con tecnologia AM dipendono principalmente dalle dimensioni della polvere e dalla dimensione del raggio laser focalizzato. Queste ultime in particolare possono avere conseguenze critiche sulle prestazioni meccaniche e sulla durata di elementi specie se soggetti a carichi a fatica. Per superare tali ostacoli, l’attenzione deve essere posta nella post-produzione (post-processing) della superficie di componenti flessibili specie se aventi pareti sottili, multidimensionali e se caricati dinamicamente.
La validazione del processo end-to-end consente non solo l’applicazione del processo per utilizzo spaziale, ma anche l’utilizzo di parti prodotte con AM (Figure 22 e 23) con tutti i suoi vantaggi e le opportunità di superare le sfide nelle attuali strutture spaziali e nello sviluppo dei meccanismi. Beyond Gravity, date le elevate esigenze tecniche e scientifiche nel settore spaziale, per accelerare lo sviluppo e la creazione di tecnologie di produzione avanzate nello spazio, utilizza le tecniche di AM più avanzate e opportuni processi progettuali e realizzativi sempre all’avanguardia. In questa maniera, l’azienda multinazionale svizzera sta contribuendo sempre più a
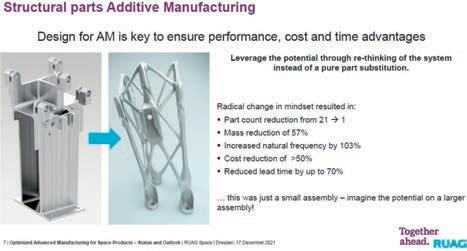
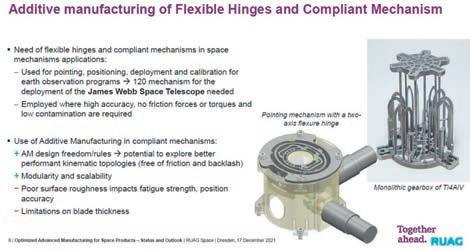
Il Flap Interface del progetto VIEWS (Validation and Integration of Manufacturing Enablers for Future Wing Structures) sviluppato da GE Aviation nel 2016 in collaborazione con il consorzio Airbus capeggiato da GKN, può essere un esempio di applicazione di Additive Technologies in ambito aeronautico la cui tecnologia può essere direttamente trasferibile ad un contesto spaziale. Il processo di colata in cera persa consiste in una stampa 3D di uno stampo in cera per supportare la creazione di uno stampo ceramico in cui il metallo fuso viene iniettato sottovuoto o con iniezione da centrifuga e quindi lasciato solidificare. La parte prodotta dopo l’iniezione è poi trattata superficialmente tramite pressatura isostatica a caldo e quindi macchinata localmente per produrre il componente finale. Utilizzando questo processo, in opposizione al metodo più convenzionale di lavorazione a fresa da billetta, produttori e progettisti possono creare forme più complesse. In tal modo, è possibile combinare componenti diversi facenti parte dello stesso assieme prodotto e ridurre il numero di elementi per il fissaggio delle parti. in ultima analisi, si aumenta la continuità nella struttura complessiva e si consegue una riduzione del peso.
Più in dettaglio, con riferimento al componente preso in esame, la precedente soluzione prevede l’utilizzo di nove parti distinte realizzate in lega di alluminio (Al7049) e lavorate a fresa (Figura 24).
La soluzione alternativa invece prevede l’utilizzo della colata in cera persa con lega di Titanio (Ti6Al4V) e permette di realizzare un componente che metta assieme tutte le nove parti in un unico pezzo (Figura 24). Il componente finale ottenuto da colata in cera persa dopo ottimizzazione del design mostra una potenziale riduzione del 20% del peso complessivo dell’assieme, riducendo il numero di elementi di fissaggio utilizzati e ottimizzando il layout finale. Vista da una prospettiva di processo, la colata in cera persa del titanio per la specifica applicazione del componente analizzato ha ridotto lo scarto di materiale del 60%, oltre a ridurre il numero delle nove parti come da iniziale design a una sola parte ottenuta per colata.
La validazione è stata eseguita al calcolatore ed in maniera empirica in test house. La Figura 25 riporta il modello FEM (Finite Elements Method) del componente in colata in cera persa di lega di Titanio utilizzato per l’analisi a fatica. La Tabella 1 riporta l’analisi comparativa del modello FEM dell’assieme in lega di Alluminio (Al4049) lavorato a fresa e quello di colata in cera persa in lega di Titanio (Ti6Al4V).
In conclusione, la colata in cera persa è una valida alternativa in alcune applicazioni in cui la complessità delle geometrie è elevata ed è necessaria una maggiore continuità strutturale senza l’utilizzo di fastener di giunzione. In Figura 26 si mostra il prototipo in lega di Titanio e la soluzione in nove parti in lega di Alluminio. La Tabella 2 sintetizza i maggiori vantaggi dell’utilizzo della colata in cera persa per specifici usi legati alla complessità geometrica ed alle richieste di maggiore resistenza meccanica.
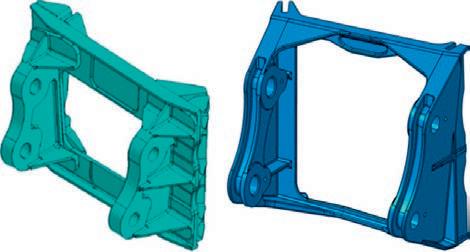
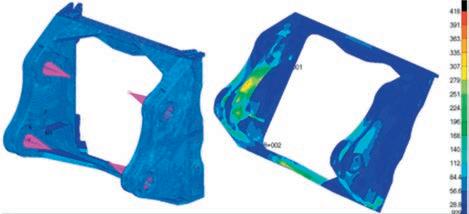
Applicazione di Additive Manufacturing Extraterrestri
a cura di: Z. Zhu
L’epoca in cui viviamo ci permette di sognare e di puntare ad una sfida ambiziosa, cioè quella di stabilire un insediamento permanente sulla Luna e Marte (Sherwood, 2011; Woerner, 2016). La creazione di tale ambiente richiede però tecnologie sofisticate ed efficaci per venire incontro alle condizioni avverse come la gravità alterata, il vuoto e di conseguenza mancanza di aria, l’esposizione alle radiazioni, l’instabilità chimica e fisica (Porter & Bradley, 2016). A tale proposito, K. Kennedy ha proposto una suddivisione di abitazioni extraterrestri in 3 classi (Figura 27), secondo lo sviluppo ed evoluzione della tecnologia in ambito aerospaziale (Kennedy, 2002):
• Classe I: abitazioni pre-integrate, prodotte sfruttando l’industria terrestre, complete di sistemi di supporto e pronte all’uso.
• Classe II: abitazioni prefabbricate, prodotte sfruttando l’industria terrestre, utilizzabile previa installazione, assemblaggio, o dispiego.
• Classe III: abitazioni costruite in-situ, richiedendo capacità manufatturiera locale. Le prime due classi, seppur dotate di alte prestazioni nell’affrontare le condizioni al contorno, sono però fortemente vincolate alla capienza dei sistemi di lancio e non possiedono capacità di espansione. Per questo motivo, le agenzie Spaziali e la comunità scientifica sono alla ricerca di metodologie costruttive in grado di instaurare una industria manufatturiera in un ambiente extraterrestre (National Research Council, 2014).
Tra queste, spicca il ruolo della manifattura additiva in combinazione con l’utilizzo di risorse locali. In particolare, l’ESA ha sperimentato una tecnica brevettata chiamato “D-Shape” in grado di “stampare” il guscio esterno delle abitazioni sulla Luna, utilizzando il terreno locale chiamato “Regolite” (Cesaretti et al., 2014).
D’altro canto, il materiale locale adoperato in questo processo può essere anche l’acqua, se posta nelle condizioni in cui riesce a raggiungere il suo stato solido. È questo il concept vincitore della “Centennial Challenge”, promossa dalla NASA nel 2015 (Morris et al., 2016). L’utilizzo del ghiaccio, Figura 29, come materiale di costruzione ha molteplice vantaggio come la salubrità chimica, la schermatura naturale alle radiazioni e nello stesso tempo, essere permeabile alla luce visibile creando un ambiente interno più confortevole. Le metodologie citate, seppure promittenti, sono tutt’ora in fase di sviluppo e perfezionamento. Infatti, sono in corso studi sui materiali utilizzati in quanto ad oggi gli esperimenti sono stati effettuati in laboratorio, sotto condizioni controllate richiedendo l’intervento e la sorveglianza umana. Inoltre, il processo costruttivo richiede integrazione tecnologica come quella impiantistica ed energetica. Ciononostante, queste innovazioni in ambito di automazioni nel processo costruttivo potranno portare notevoli benefici anche sulla Terra, come nel caso di alloggi low-cost, nelle soluzioni abitative a basso impatto energetico, e nelle situazioni di post calamità.
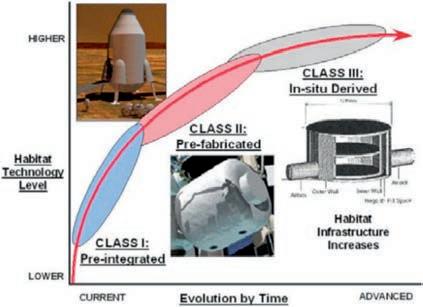
Sitogra a
• www.avio.com
• www.dallara.it
• Revisiting the configuration of small satellites structures in the framework of 3D additive manufacturing. https://doi.org/10.1016/j.actaastro.2018.01.036
• A Preliminary Design of a Mission to Triton: a Concurrent Engineering Approach. https://doi.org/10.1007/s42423-018-0001-9
• Building components for an outpost on the Lunar soil by means of a novel 3D printing technology. https://doi.org/10.1016/j. actaastro.2013.07.034
• The vernacular of space architecture. https://doi.org/10.2514/6.2002-6102
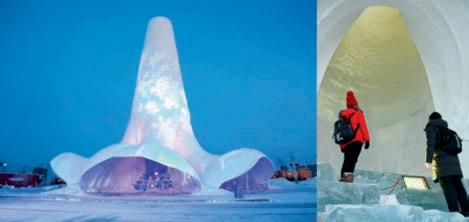
• Mars Ice House: Using the Physics of Phase Change in 3D Printing a Habitat with H2O. https://doi.org/10.2514/6.2016-5528
• 3D Printing in Space. https://doi.org/10.17226/18871
• Architectural Design Principles for Extra-Terrestrial Habitats. https://doi.org/10.5281/zenodo.202160
• Inhabiting the solar system. https://doi.org/10.2478/s13531-011-0004-y
• Moon Village: A VISION FOR GLOBAL COOPERATION AND SPACE 4.0. https://www.esa.int/About_Us/Ministerial_Council_2016/Moon_Village
Bibliogra a
• R. C. Rice1, J. L. Jackson1, J. Bakuckas, S Thompson, “Metallic Materials Properties Development and Standardization (MMPDS)” Issue 1, Jan 2003.
• MSC.Software Corporation, “Quick Reference Guide - MSC.Nastran 2005 r3”, Feb 2006.
• A. Boschetto, M. Eugeni, L. Bottini, V. Cardini, G. Graterol Nisi, L. Pollice, P. Gaudenzi, “Introduction of Innovative Additive Manufacturing Technologies into the Nanosatellites Design and Realization”, Italian-Israel – ASI-ISA Conference on Nanosatellites, Italian Space Agency, Rome, 9-10 April 2018
• L. Pollice, P. Gaudenzi, R. Usinger, M. Gschweitl, V. Cardini, M. Eugeni, G. Graterol Nisi, “Systems Engineering and Systems Architecting Approaches for Innovative Additive Manufactured Spacecraft Structures”, ESA-ECSSMET, Noordwijk, The Netherlands, 28 May – 1 June 2018
• R. C. Rice1, J. L. Jackson1, J. Bakuckas, S Thompson, “Metallic Materials Properties Development and Standardization (MMPDS)” Issue 1, Jan 2003.
• MSC.Software Corporation, “Quick Reference Guide - MSC.Nastran 2005 r3”, Feb 2006.
Lo spazio, una nuova economia: una rete di Piccole
Medie Imprese come strategia di sviluppo in un settore che si è avvicinato “anni luce” alla nostra vita quotidiana
Lo spazio è sempre stato un ambito dedicato alla scienza, alla ricerca, all’implementazione delle nuove tecnologie, nuovi materiali ecc. Oggi lo spazio si è aperto ad un pubblico variegato, con un linguaggio più comprensibile, realizzando servizi che sono vicini alla quotidianità di ognuno: le vacanze spaziali, un film di fantascienza fino a pochi anni fa, oggi una realtà. È necessario fare una riflessione su come sta cambiando rapidamente questo settore e capire quanto impatti sull’economia reale e sulla geopolitica, quest’ultima oggi sotto i riflettori.
Il territorio italiano è storicamente legato ad una tradizione culturale spaziale iniziata già all’inizio degli anni 60: ricordiamo che siamo stati la terza nazione a mettere un satellite in orbita ma anche tra le prime a creare infrastrutture come, ad esempio, il Centro Spaziale di Telespazio, nel Fucino (AQ) in Abruzzo, che è attivo dal ’63. Le regioni italiane legate a questo tipo di attività economica si suddividono in 12 Distretti Spaziali nei quali ritroviamo numerose realtà imprenditoriali in grado di manifestare competitività anche a livello internazionale. L’Italia, infatti, presenta una grande capacità industriale in ambito Spazio frutto proprio di tradizioni culturali che hanno poi lasciato in eredità competenze e tecnologie all’avanguardia. Nel tempo, ad ereditare questa ricchezza di idee e di esperti con un elevato livello di formazione non sono state solo le Grandi Aziende Spaziali, quelle che in prima persona costruiscono e mettono in orbita satelliti o che partecipano alle grandi missioni scientifiche, ma anche di un vero e proprio ecosistema di PMI che forniscono prodotti e servizi specialistici oltre che di costruttori di veri e propri satelliti di piccole dimensioni, oggetti tanto piccoli quanto ultramoderni che consentiranno a tutti di accedere allo Spazio con facilità crescente e di godere dei servizi da esso offerti. L’America, ha chiaramente dato un grosso impulso allo “sdoganamento” di questo settore, prima di nicchia, oggi di tutti, e noi Italia non possiamo che implementare ciò che abbiamo sempre rappresentato in questo settore. Per le Piccole e Medie Imprese le ambizioni oggi sono paragonabili a quelle delle grandi realtà industriali italiane del settore dello Spazio, perseguendo in simbiosi con esse, missioni specifiche sia di tipo commerciale, sia scientifico che educativo.
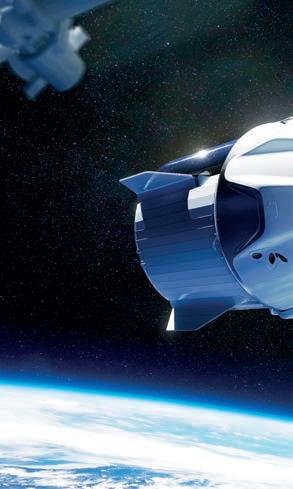
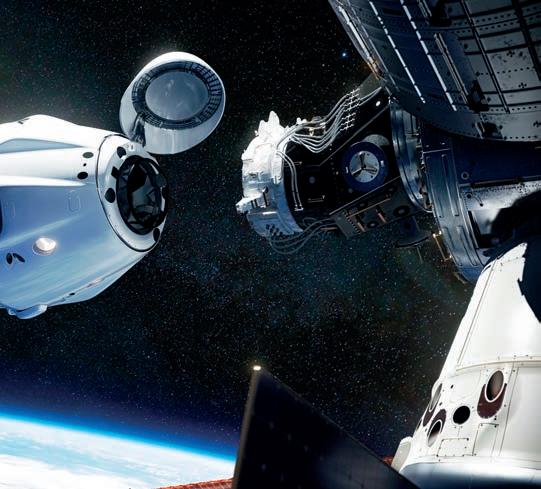
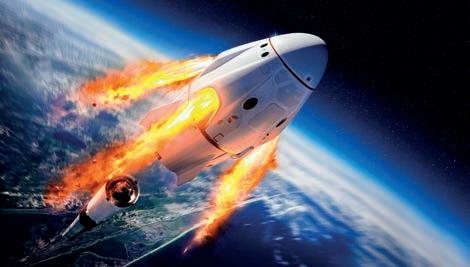
Questo sistema di Piccole e Medie Imprese costituisce una sorta di rete sul territorio legandosi alle Grandi Imprese Spaziali ed alle Università e Centri di Ricerca1. Il gioco messo in atto da questo sistema di attori, in cui le imprese locali si sentono coinvolte, è una strategia in azione e che sta già portando vantaggi, basti considerare l’interesse che le PMI hanno rivolto, negli ultimi tempi, all’impiego dell’orbita bassa (LEO), opportunità che porterebbe queste aziende ad avere un ruolo sempre più centrale in quello che può essere definito un vero e proprio mercato spaziale. I servizi derivanti dall’implementazione ed il lancio di questi satelliti sono: il monitoraggio del territorio, la meteorologia, i servizi internet, studi scientifici, ecc. Potendo contare su un numero maggiore di dati rispetto alle costellazioni tradizionali, queste ultime ovviamente danno dati di maggior pregio. Ma grazie alla grande quantità di dati (big data) che si possono ottenere si è capaci di fare importanti passi in avanti tecnologici.
Da questa visione sistemica nasce la necessità di valorizzare sempre di più le PMI nazionali e gli enti della formazione a vantaggio dopo tutto anche della grande azienda, per mantenere un presidio tecnologico elevato. Questo è il perno su cui ruota l’intero “mercato spaziale” di cui si faceva cenno e che, attraverso la promozione di progetti di formazione per tecnici e ingegneri del domani, potrà evolvere portando ad uno sviluppo del settore spaziale nazionale che avvicinerebbe ancor di più il Paese ad una posizione di potenza, di autonomia e di vantaggio strategico internazionale.
Lo Spazio è quindi considerabile un settore strategico e molto dinamico, un mercato in espansione. È un’economia stabile che basa il suo successo sulla cultura che si riesce a creare intorno ai progetti. Inoltre, lo scenario è internazionale e la competizione è aperta. Infatti, il prossimo futuro porterà, grazie a questo sistema, alla costruzione di Stazioni Spaziali Commerciali così come la colonizzazione della Luna.
Piccole aziende sentono di potersi mettere in gioco, senza sentirsi in ombra rispetto alle grandi imprese, perché vantaggiose a queste ultime grazie al contributo attivo che hanno nelle grandi missioni spaziali: guardare alla vita fuori dal nostro pianeta madre, investire in prodotti e tecnologie per rendere lo Spazio una realtà fruibile per i viaggiatori del futuro, missioni spaziali robotiche in grado di riportare sulla terra frammenti e parti di pianeti e corpi celesti. Insomma, grazie all’intervento laborioso ed è il caso di dirlo, indispensabile, delle
PMI nel settore spaziale, si può immaginare un futuro vissuto nello spazio ove è garantito il confort a bordo di stazioni orbitali o su altri pianeti. Tutto questo è qualcosa di straordinario.
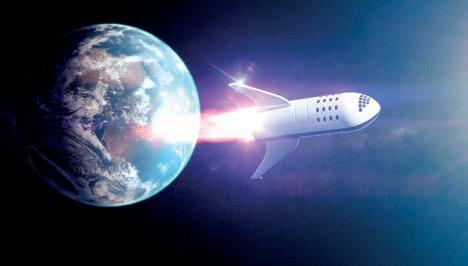
L’obiettivo è quindi dare il giusto ruolo centrale alle PMI, cosa di cui si occupano i distretti spaziali prima citati. Un esempio, lo SPARC Cluster nato per le aziende Abruzzesi e Laziali che operano in ambito Spazio. L’aggregazione totale permetterà di spostare in avanti la frontiera spaziale grazie alla messa a sistema delle competenze e delle capacità. D’altro canto, come nelle grandi missioni spaziali si prevede la collaborazione di varie agenzie spaziali e di conseguenza la cooperazione delle grandi aziende, allo stesso modo anche le piccole missioni vengono affrontate dalla collaborazione di più aziende. Ma, per perseguire questo obiettivo, la cooperazione deve preservare le competenze sviluppate da ciascuna azienda, e il “fairplay” è un elemento necessario.
L’industria Spaziale ha sempre puntato sulla valorizzazione di talenti indipendentemente da differenze somatiche, di genere, religiose o politiche ed ha rappresentato, soprattutto negli anni del dopoguerra, una competizione pacifica, dove poter dimostrare la propria superiorità tecnica attraverso il susseguirsi del raggiungimento di risultati ingegneristici, poi utili a tutta l’umanità. Questo è valido ancora oggi anche se la dimensione non è più solamente pioneristica verso requisiti e missioni sempre più impegnative ma anche tecnologica e industriale. Le opportunità di questo mercato sono tante. Fare squadra è la chiave del successo e l’Italia che è un player importante nel mercato internazionale deve rafforzare il suo ruolo, basti pensare che le basi di lancio, da sempre frutto di accordi internazionali, oggi risentono del conflitto russo-ucraino; pertanto, nuovi equilibri dovranno essere posti in essere. L’aereo di trasporto dei prodotti spaziali, l’Antonov russo è andato distrutto (Figura 1), quale sarà la sua sostituzione? L’Italia in una posizione geografica non favorevole ai lanci può fruttare l’ingegno ed il mare per poter continuare ad essere pioniera in un settore all’avanguardia? È necessario essere proattivi in un equilibrio che manca per essere una nazione che afferma la propria storia lavorando per il futuro.
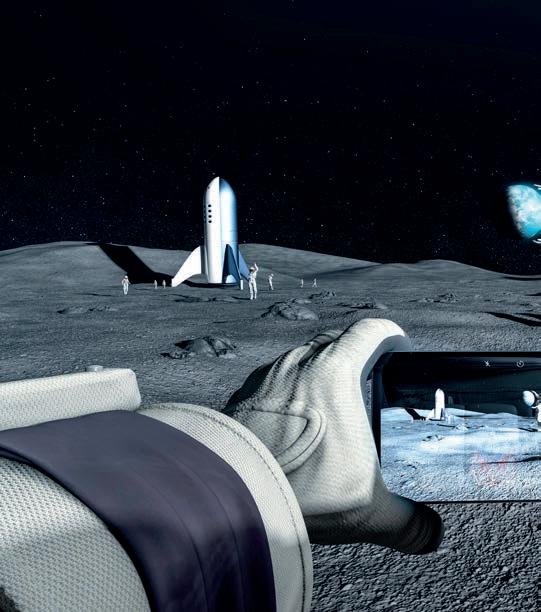
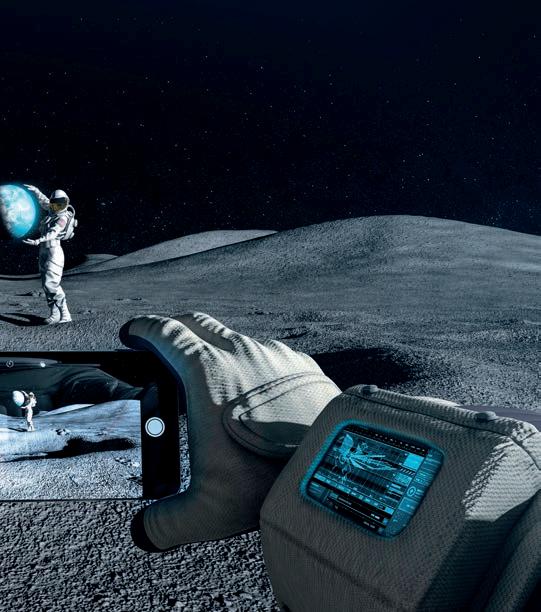
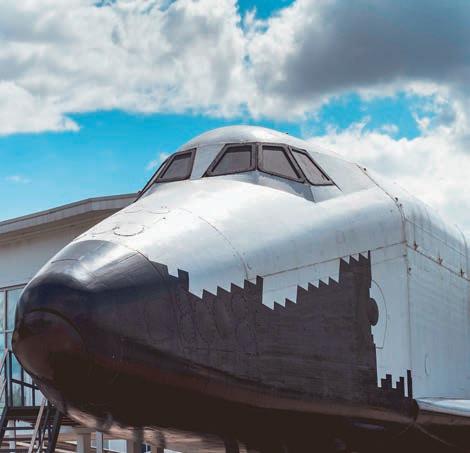
Note [1] Space Industry Catalogue, ASI, 2021/22 (https://www.asi.it/lagenzia/facilities/catalogo-dellindustria-spaziale-nazionale/)
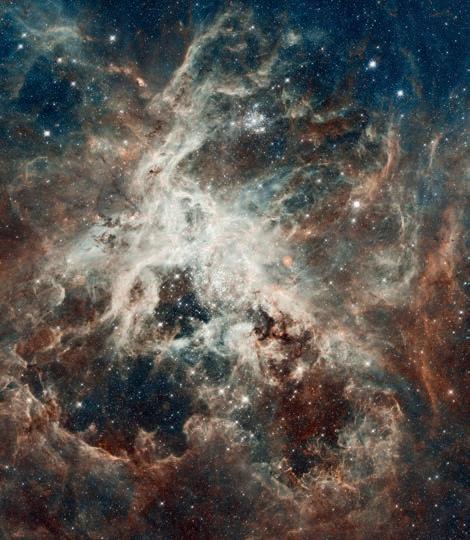
AREE DEL SITO WEB DELL’ORDINE
L’Homepage www.ording.roma.it
L’Albo degli iscritti https://www.ording.roma.it/albo-iscritti
L’Area degli iscritti https://area-iscritti.ording.roma.it/
I seminari https://www.ording.roma.it/formazione/
Sito della rivista https://rivista.ording.roma.it
Elenco delle Commissioni https://ording.roma.it/servizi-agli-iscritti/commissioni
Ordine Degli Ingegneri Della Provincia Di Roma
Piazza della Repubblica, 59 - 00185 Roma
Tel.: 06.487.9311 - Fax: 06.487.931.223
Cod.fisc. 80201950583
Orari di apertura al pubblico degli uffici
Lun 09:30/12:30
Mar
Mer
Gio 09:30/12:30 14:30/17:30
Ven 09:30/12:30
Sab 09:30/12:30
La Segreteria dell’Ordine chiude alle ore 16:00
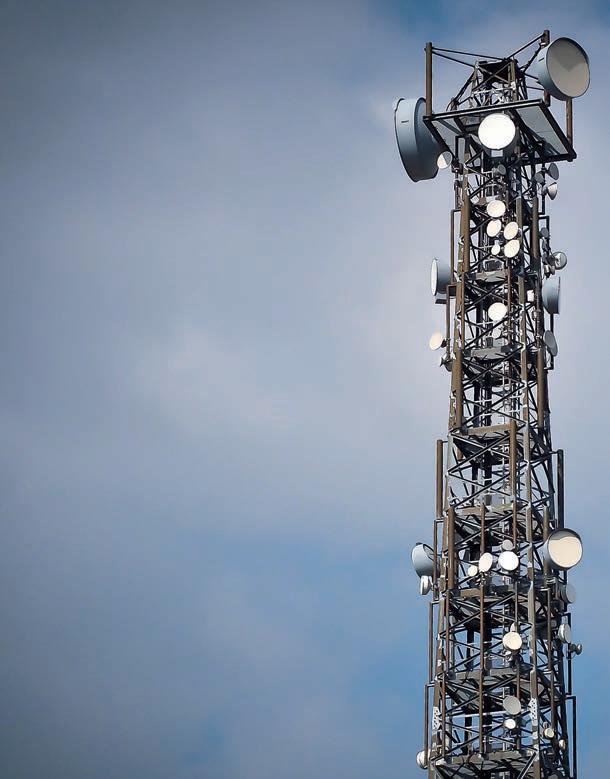
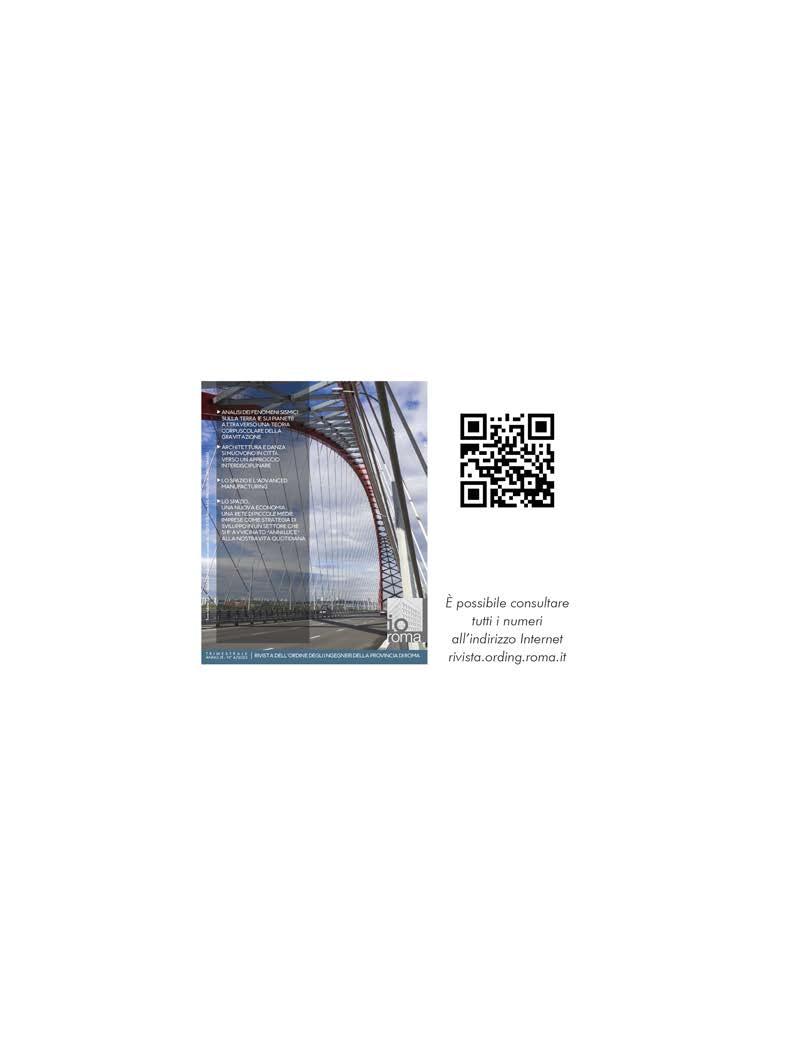