5 minute read
RECYCLING Recyclingfabriek voor vervuild staal geopend
Next Article
Recyclingfabriek voor vervuild staal geopend
De eerste recyclingfabriek voor vervuild staal ter wereld is eind september geopend in Delfzijl. Purifi ed Metal Company kan hier staal dat bijvoorbeeld is vervuild met asbest of chroom-6 een nieuw leven geven. Er is zoveel interesse om schroot in te leveren voor recycling dat het niet bij deze ene fabriek gaat blijven.
Dagmar Aarts
CO2- en grondstoffenbesparing
Door staal te recyclen tot nieuw staal hoeft er geen nieuw staal geproduceerd te worden via delving en opwerking. Per kilo Purifi ed Metal Blocks (PMB’s) bespaart PMC ruim twee kilo primaire grondstoff en (1,4 kilo ijzererts, 0,8 kilo steenkool en 0,3 kilo kalksteen), vergeleken met het delven en opwerken van nieuw staal. Daarnaast bespaart het bedrijf per kilo geproduceerde (en dus gerecyclede) PMB’s de uitstoot van één kilo C02, vergeleken met het delven en opwerken van nieuw staal. Tijdens het recyclingproces worden verschillende verontreinigingen met de rookgassen meegevoerd. In het zeer geavanceerde rookgasreiningssysteem worden deze onschadelijk gemaakt. De verontreinigingen (minder dan één procent van het binnenkomende vervuilde staalschroot) worden verzameld en vervolgens gestort. In Nederland komen jaarlijks tienduizenden tonnen vervuild staalschroot vrij, bijvoorbeeld van gebouwen, treinen, schepen en industriële installaties. Dit staal wordt nu gestort, waardoor een waardevolle grondstof verloren gaat. Of het wordt schoongemaakt, een lastig en kostbaar werk. Voor chroom-6 is er op het moment zelfs geen andere goede oplossing dan de nieuwe fabriek.
Proces
Het gepatenteerde proces van Purifi ed Metal Company (PMC) is vrij simpel. Het normale proces van staalsmelten gebeurt bij temperaturen boven de 1500 graden Celsius, het smeltpunt van staal. Bij die temperatuur zijn alle asbestvezels al lang vernietigd. ‘Wit asbest gaat al kapot bij 700 graden en andere vezels hebben een iets hogere temperatuur nodig. Bij 1040 graden Celsius zijn alle vezels vernietigd’, zegt Jan Henk Wijma, CEO van PMC. ‘Door verhitting vallen alle asbestvezels uiteen in zand, glas en magnesiumoxide. Drie schone grondstoff en voor hergebruik.’ Belangrijk is echter wel dat er geen asbestvezels of andere vervuilingen in de lucht terechtkomen. Daarom heeft de fabriek een volledig gesloten verwerkingsproces. Luchtsluizen, onderdruk in de fabriek en speciale fi lters voorkomen dat asbestvezels, chroom-6 en andere gevaarlijke stoff en bij het transport, de overslag en de verwerking vrijkomen en zich kunnen verspreiden. Ook de rookgassen uit de fabriek zijn volledig schoon.
Chemische samenstelling
Uiteindelijk is het verontreinigde staalafval na het proces omgevormd tot Purifi ed Metal Blocks (PMB). Deze stalen blokken worden gegoten in een baksteenformaat en zijn volledig vrij van vuil. Door het compacte formaat kunnen de PMB’s effi ciënt en gericht worden ingezet in productieprocessen in staalfabrieken en gieterijen. De Purifi ed Metal Blocks worden in batches van twintig ton verkocht. Elke batch heeft een unieke chemische samenstelling. Deze hangt af van wat er aan de voorkant de fabriek is ingegaan. ‘Dat kan verschillen van RVS tot constructiestaal’, legt Wijma uit. ‘Pas nadat het gesmolten is, kunnen wij zien wat de samenstelling is.’ Die verschillende chemische samenstellingen kunnen een voordeel zijn voor staalfabrieken en gieterijen. Zij kunnen kiezen welke batch voor hen interessant is. Wijma: ‘Ze kunnen zelfs nuttig gebruikmaken van de legeringen die erin zitten. Dat kan namelijk een besparing opleveren. Nikkel is daar een mooi voorbeeld van. Het is ontzettend duur materiaal. Als er een
De fabriek in Delfzijl kan, eenmaal op maximale capaciteit, 150.000 ton schroot per jaar verwerken (vergelijkbaar met vijftien Eiffeltorens).
procentje in zit, is dat al bijna honderd euro per ton waard. Dat is echt waardevol voor bedrijven.’ Nog een voordeel voor de staalproducenten is dat ze door het gebruik van de blokken van PMC 75 procent minder CO2 uitstoten dan fabrieken die staal uit ijzererts maken.
Opgespaard
De nieuwe fabriek kan al rekenen op veel interesse. Verschillende Nederlandse bedrijven, zoals BASF, Shell, DOW en Prorail, hebben zich al gemeld om hun schroot in te leveren.
‘We willen kosten voor de samenleving verlagen. We willen het recyclen niet duurder maken dan het storten.’
JAN HENK WIJMA CEO PURIFIED METAL COMPANY
Wijma: ‘Ik heb van een aantal bedrijven begrepen dat ze het afgelopen half jaar hun schroot hebben opgespaard, zodat ze het niet naar de stort hoefden te brengen in afwachting van onze opening. Dat is heel mooi nieuws.’ Zelf heeft PMC op twee locaties ook al een paar duizend ton vervuild schroot liggen. ‘Dat is gelijk serieus’, zegt Wijma. Ook bedrijven uit andere Europese landen en de VS weten PMC al te vinden. ‘Het laat zien dat de kern van het probleem in westerse landen identiek is’, zegt Wijma. ‘Onze oplossing is daar een milieuvriendelijk alternatief voor dat kosten bespaart. Dat zijn onze drivers. We willen kosten voor de samenleving verlagen. We willen het recyclen niet duurder maken dan het storten.’
Meerdere fabrieken
De fabriek biedt werk aan dertig mensen. Wanneer ze op volle capaciteit draait, komen daar nog eens 35 arbeidsplaatsen bij. Met de bouw van de fabriek is een investering van zeventig miljoen euro gemoeid. De fabriek in Delfzijl kan, eenmaal op maximale capaciteit, 150.000 ton schroot per jaar verwerken, equivalent aan het gewicht van vijftien Eiffeltorens. Daar wordt in drie jaar tijd naartoe gewerkt. Met die capaciteit kan PMC het vrijgekomen staal uit Nederland recyclen, aangevuld met wat staal uit België en Duitsland. Voor het schroot uit de andere geïnteresseerde landen is nu dus eigenlijk geen plek. Daarom heeft het bedrijf al plannen voor meerdere fabrieken wereldwijd. In Duitsland heeft PMC zelfs al een locatie in de omgeving van Leipzig op het oog.
Financiering
De financiering voor deze volgende fabrieken zal een stuk gemakkelijker gaan dan de eerste fabriek in Delfzijl. ‘De Europese investeringsbank vond ons eerste project veel te risicovol’, zegt Wijma. ‘Maar ze heeft nu aangegeven een rol te willen spelen in meerdere van onze fabrieken.’
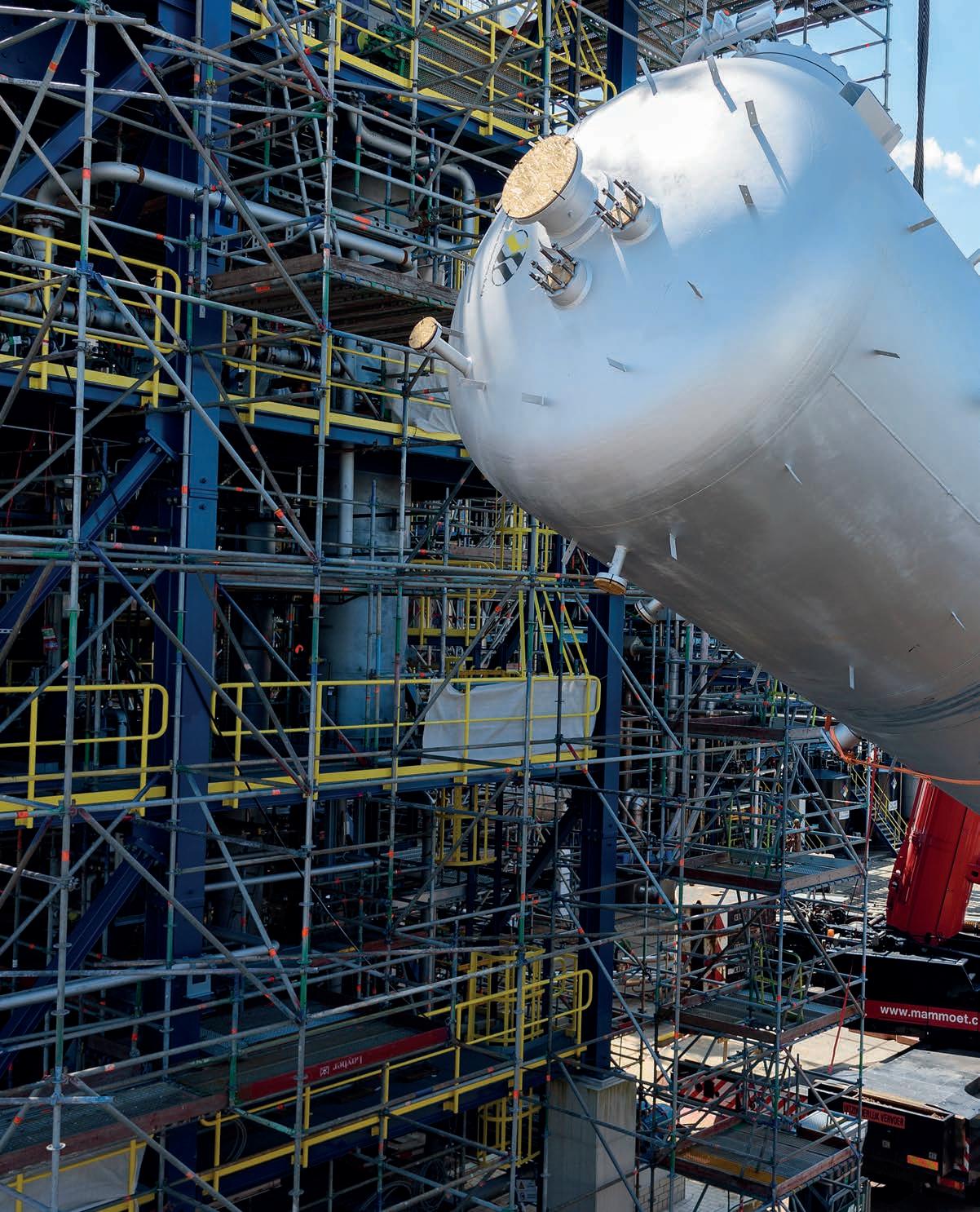
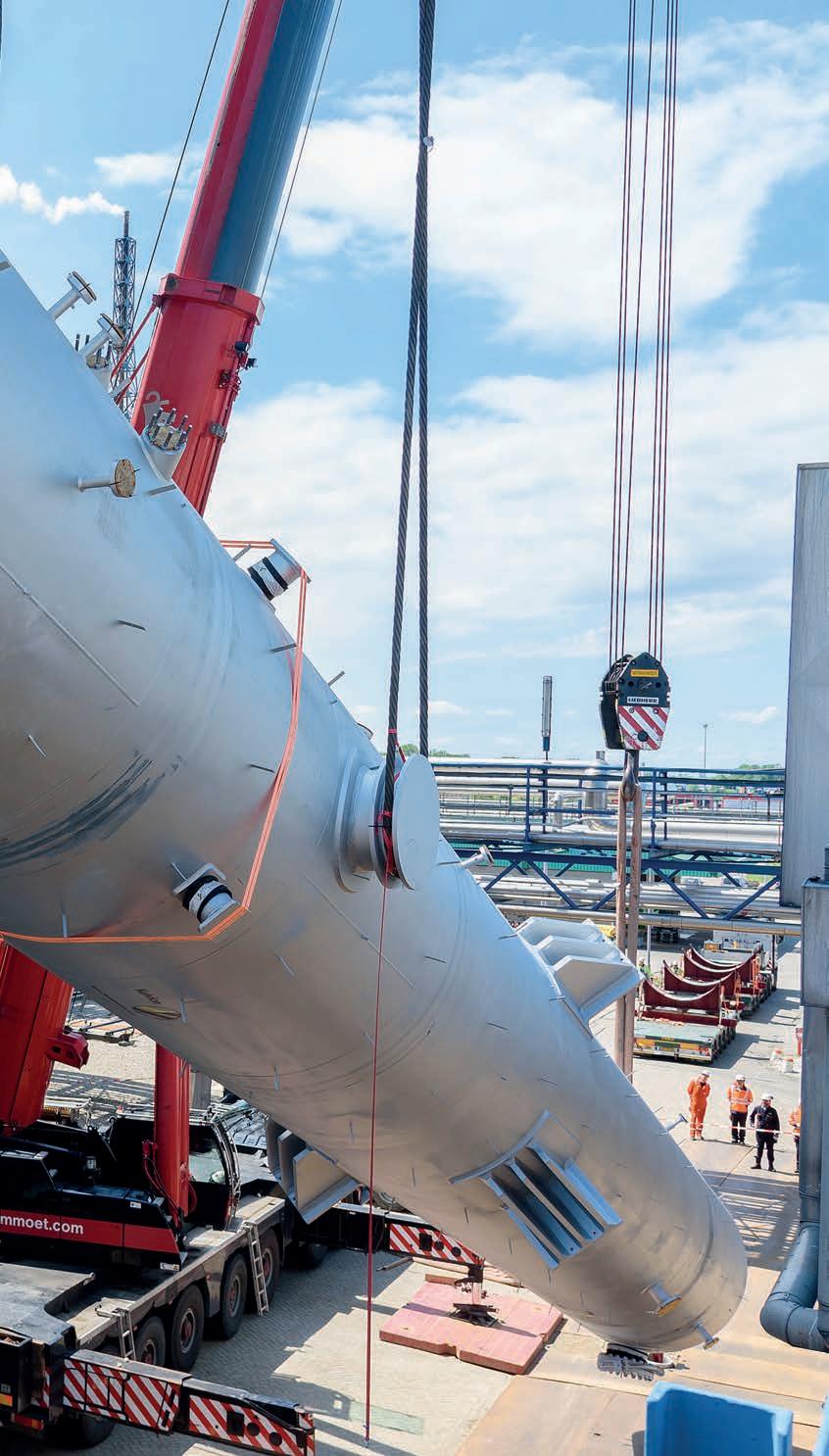
Delamine, producent van ethyleenaminen op het Chemie Park Delfzijl, heeft een nieuwe kristallisator
geplaatst. De 25 meter hoge en 84 ton wegende kolom gaat een processtroom verder indampen. Met de nieuwe kristallisator kan het bedrijf veel energie besparen. Dat komt door een slim ontwerp in combinatie met de juiste materiaalkeuze. Dit resulteert in een effi ciënt gebruik van de restwarmte in de opeenvolgende processtappen. Het oorspronkelijke plan was om de kritallisator al bij de voorjaarsstop in gebruik te nemen. De aanvoer van de installatie uit Spanje was vanwege corona echter vertraagd. Daardoor kon Delamine de kristallisator pas inhijsen tijdens de grotere stop in het najaar. Naar verwachting is de nieuwe installatie in november volledig operationeel.