THE
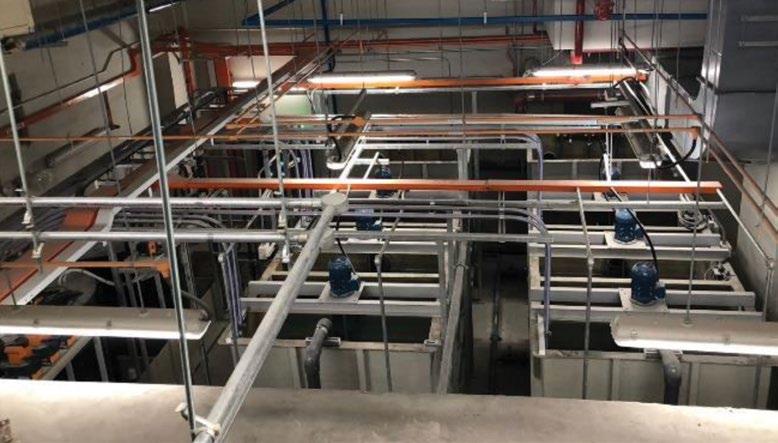
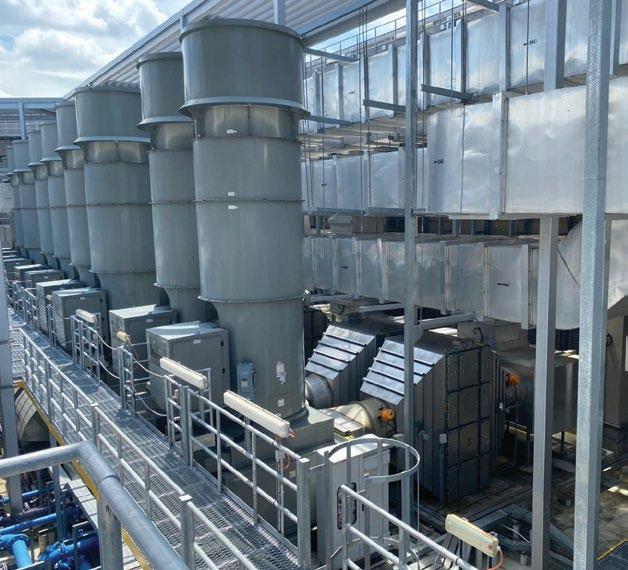
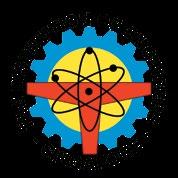
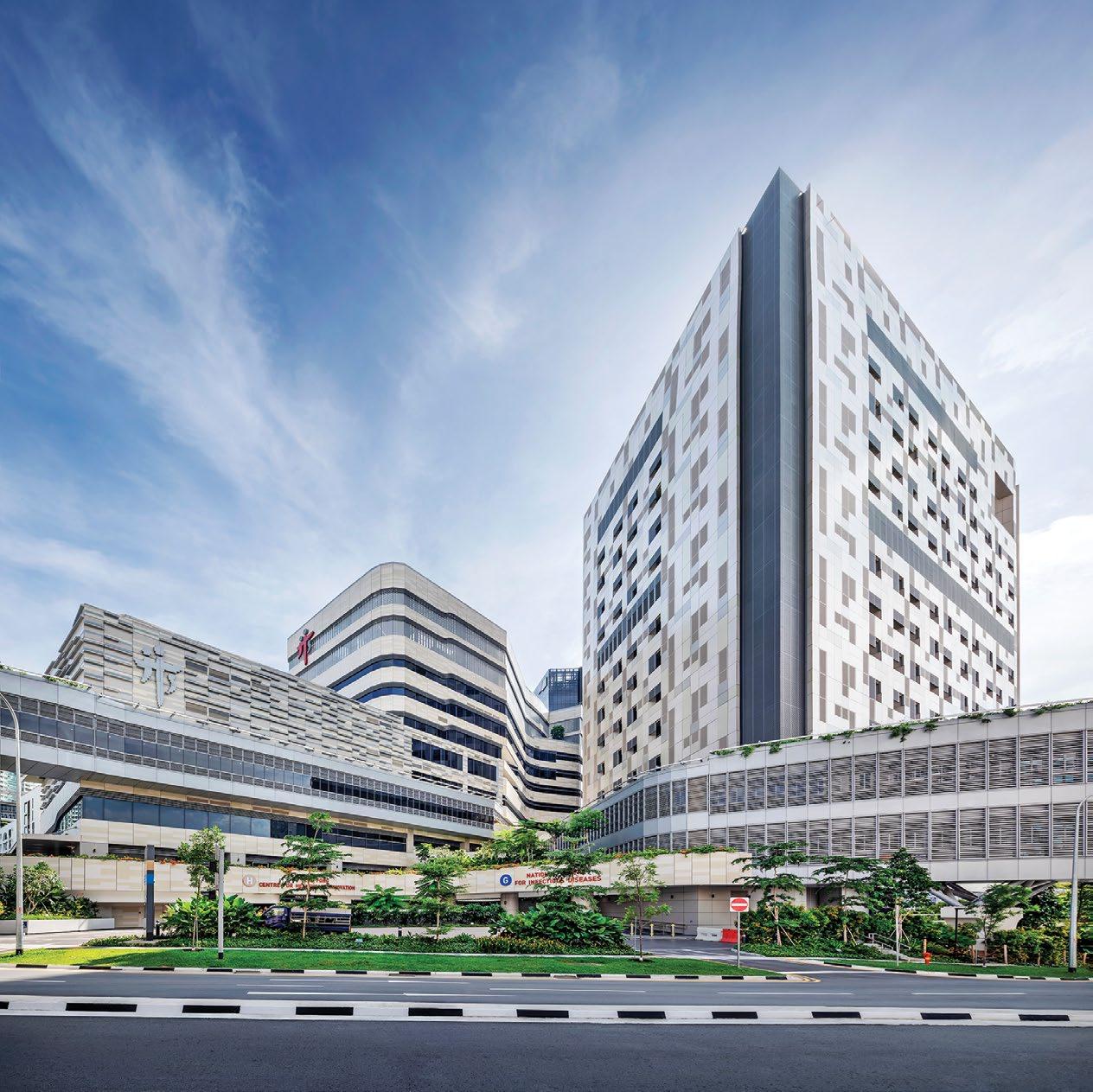
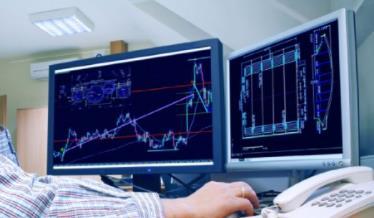
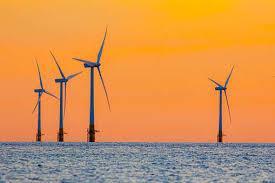
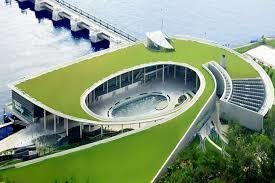
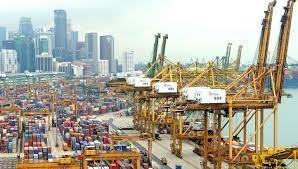
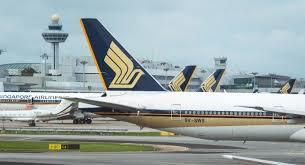
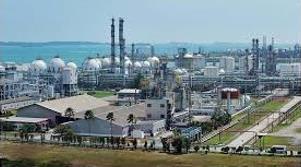
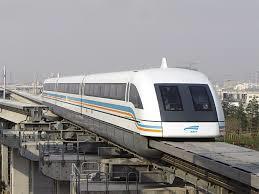
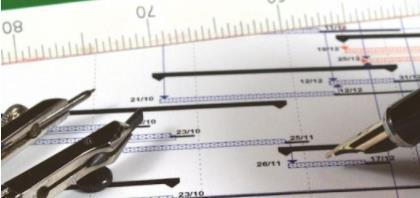
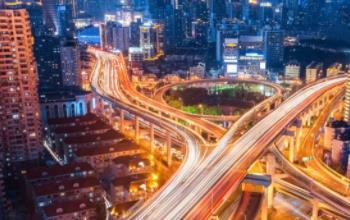
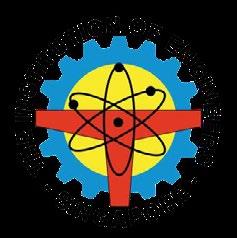
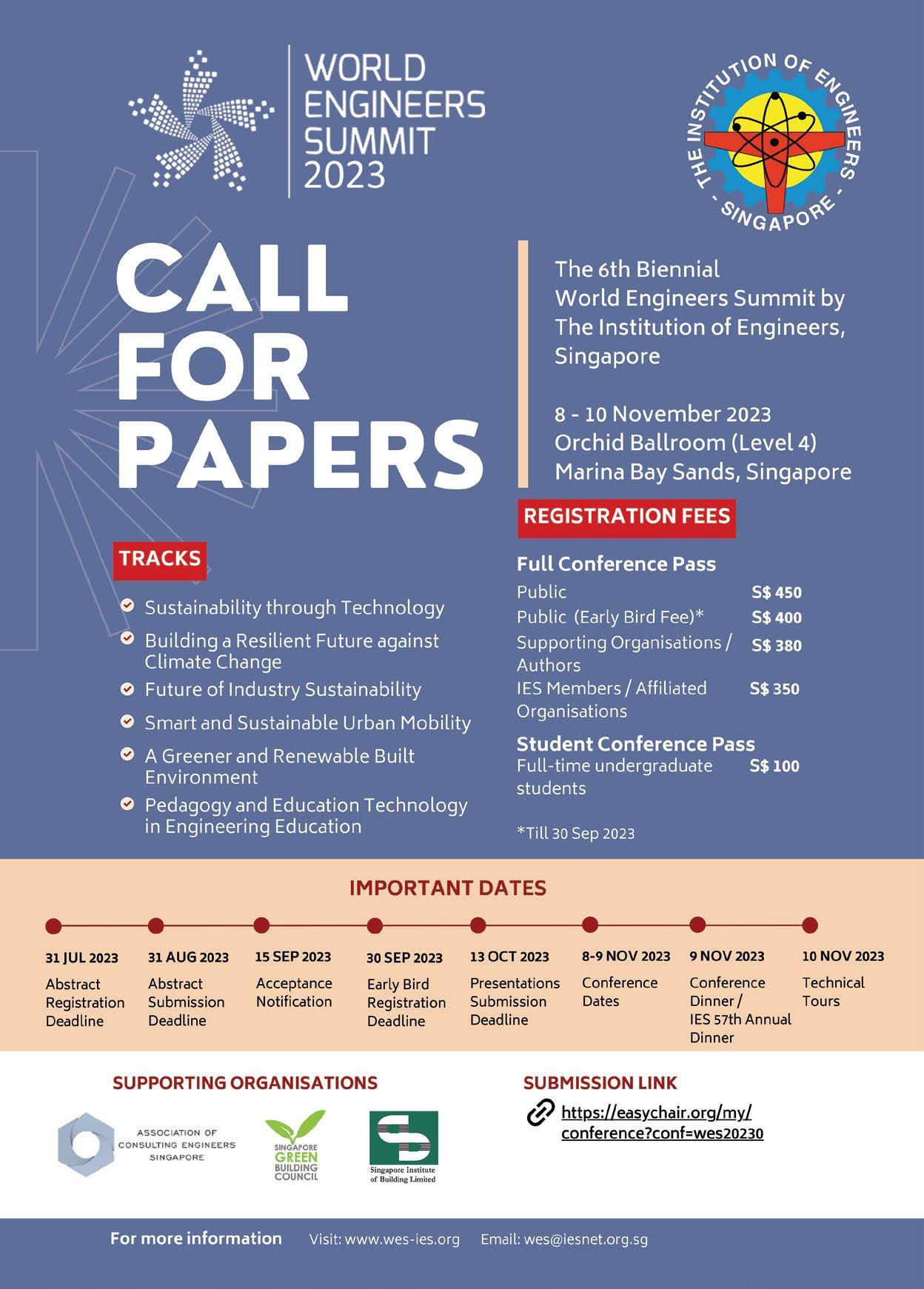
16 Designing healthcare facilities for infectious diseases
Some of the challenges and solutions are described.
23 New survey reveals five pressing themes reshaping the security industry Sustainability, mobile IDs and a changing workforce continue to be among top concerns.
24 Only with appropriate measures can AI technology be truly transformative
It has great potential but also the possibility of being misused.
25 Challenges for network security in the hybrid work era
The findings of a survey conducted across nine countries in the Asia Pacific region are summarised.
26 How cobots could help make the most of ‘Asia’s food-bowl’
Across Asia-Pacific, a thriving food and beverage industry has been among the first to turn to collaborative automation.
28 Fire safety of electrical transformers in underground structures
This article provides a practising engineer’s viewpoint on the fire safety and mitigation measures for electrical transformers in underground structures.
36 High-purity cleaning of industrial parts and components
The objective is to achieve a high level of component cleanliness by focusing not only on the actual cleaning solution but also on the entire process chain and the ambient conditions.
www.ies.org.sg
President Mr Dalson Chung
Chief Editor T Bhaskaran t_b_n8@yahoo.com
Publications Manager Desmond Teo desmond@iesnet.org.sg
Publications Executive Nuraini Ahmad nuraini@iesnet.org.sg
Editorial Panel Dr Chandra Segaran
Dr Ang Keng Been
Mr Jaime Vega Bautista Jr
Dr Victor Sim
Mr Soon Ren Jun Dr Alexander Wiegand
Media Representative Multimedia Communications (2000) Pte Ltd sales@multimediacomms.sg
Design & layout by 2EZ Asia Pte Ltd
Cover designed by Irin Kuah
Cover image by CPG Consultants
Published
The Singapore Engineer is published monthly by The Institution of Engineers, Singapore (IES). The publication is distributed free-of-charge to IES members and affiliates. Views expressed in this publication do not necessarily reflect those of the Editor or IES. All rights reserved. No part of this magazine shall be reproduced, mechanically or electronically, without the prior consent of IES. Whilst every care is taken to ensure accuracy of the content at press time, IES will not be liable for any discrepancies. Unsolicited contributions are welcome but their inclusion in the magazine is at the discretion of the Editor.
On 15 June 2023, The Institution of Engineers, Singapore (IES) announced the call for nominations for the IES Prestigious Engineering Achievement Awards 2023 and the inaugural IES Sustainability Awards 2023. The two awards will recognise individuals and organisations for their exceptional achievements in pushing the boundaries of engineering to support Singapore’s development and transformation towards a green, climate-resilient and sustainable future.
Since 2013, the IES Prestigious Engineering Achievement Awards have served as an ode to excellence in engineering projects. The awards are presented to individuals or organisations that demonstrate outstanding engineering skills, enable engineering progress and enhance quality of life in four categories:
• Applied Research and Development: research and development projects before commercialisation.
• Engineering Project: engineering projects which have been successfully implemented.
• Technology Innovation: technology or product invention which has been successfully commercialised.
• Student Awards – ‘IES Young Creators’ Award: innovative ideas on applications of science. The awards will underpin efforts to elevate public appreciation of engineering.
IES conceived the Sustainability Awards as a key initiative of the IES Green Plan 2030, launched in January 2023, to create greater impetus amongst engineers to advance Singapore’s sustainable development agenda.
The IES Sustainability Awards recognise outstanding achievements of engineering projects and initiatives that promote sustainability and innovation. The awards are given to individuals or organisations responsible for outstanding engineering projects that demonstrate sustainability. The awards comprise three categories:
• Completed engineering projects with sustainability features and practices: demonstrate the use of sustainable features and practices, including green buildings, renewable energy installations, or sustainable infrastructure.
• Innovative solutions for sustainability: reduce environmental impact and carbon footprints via new technologies, products, or services that promote sustainability.
• Promising start-ups for sustainability: potential and level of innovation in their products or services.
“The awards seek to applaud engineers whose exemplary work is making a huge impact on our economy, society and environment, yet often go unnoticed. IES hopes to spotlight these engineers as role models to spur them to scale new heights and inspire the next generation of engineering talent to
sustainable nation,” said Mr Dalson Chung, President of IES.
Nominees for both awards will be put through a rigorous evaluation process. Nominations will close on 28 July 2023.
Nominations should be submitted via the following links:
For the IES Prestigious Engineering Achievement Awards
https://bit.ly/Engineering-Achievement
For the IES Sustainability Awards –https://bit.ly/IPEAA-Sustainability
For categories and submission criteria for both awards, please scan the QR code:
More information may be obtained from the IES website, Facebook, Instagram, LinkedIn and Youtube. The winners will receive their awards at the IES 57th Annual Dinner on 9 November 2023, to be held in conjunction with the World Engineers Summit (WES) 2023. Each winning team will receive a
Makino Asia Pte Ltd, a leading provider of machine tools, recently commemorated 50 years of its presence in Singapore. The Singapore office serves as the company’s Asia-Pacific headquarters.
Achieving the milestone of SGD 1 billion in annual revenue last year, the Asia-Pacific business currently contributes more than 40% to the group’s consolidated revenues.
At its Jubilee Celebration, held earlier in the day, Makino Asia unveiled its latest innovation, the S50 Vertical Machining Centre (VMC) which is designed to optimise production efficiency and provide consistent quality for precision metal-cutting in the aerospace, medical, automotive and semiconductor industries.
Mr Gan Kim Yong, Minister for Trade and Industry, was the Guestof-Honour at the event.
Makino Asia’s SGD 75 million International Research and Development (IRD) Centre here, stands as the only one of its kind outside Japan. The facility spearheads the design and development of industry-leading machine tools for fast-evolving industries, including New Energy Vehicles (NEVs). These Singapore-designed and Singapore-made machines are currently being used by customers in over 40 countries across the world.
In 2019, Makino Asia launched its advanced machining factory in Singapore, as a model machining factory incorporating advanced automation technologies, rivalling those in other technologically advanced countries like Germany, Japan and Switzerland. The advanced machining factory continues to play a pivotal role in the innovation and implementation of new solutions, achieving a 60% increased output per employee by streamlining processes and automating repetitive tasks.
With its proprietary Manufacturing Operations Management (MOM) system being fully digitalised, Makino Asia ensures end-to-end traceability and seamless inter-process information-sharing, empowering informed decisions and a swift resolution to operational challenges. This digitalisation and automation of manufacturing processes enables advanced data analytics and drives holistic efficiency improvements beyond individual optimisation.
In addition, Makino Asia is also actively exploring opportunities to invest in Additive Manufacturing, recognising its potential to com-
plement conventional subtractive processes and revolutionise the future of manufacturing.
Makino Asia partners with various government agencies and actively collaborates with educational institutions such as ITEs, polytechnics and universities, as well as industry players at both local and global levels, in support of nurturing and developing a robust talent pool.
“Makino Asia will continue to design advanced technology products with high performance and reliability for the manufacturing needs of the future. Empowering our customers to reach their maximum
dation of our success, and it will continue to be our driving force. Today, we have 13 technology centres across the Asia-Pacific and we are also exploring and investing in Additive Manufacturing to complement conventional machine tools and product development,” said Mr Neo Eng Chong, CEO and President, Makino Asia Pte Ltd.
“In pursuing our responsibility towards the environment, we currently have application technologies for our customers to reduce energy consumption through using their machine tools more efficiently. In the decades to come, we will make a concerted effort towards pursuing environmental sustainability in all Makino Asia products,” he added.
In recognition of its responsibility towards environmental sustainability, the company strives to ensure sustainable production while designing machines optimised for specific materials. In Singapore, Makino Asia’s advanced machining factory uses chilled water to regulate temperatures, leading to a 25% reduction in power consumption, while its solar panels provide 20% of the electricity consumed, thereby reducing the overall carbon footprint.
“Makino has been a long-standing partner of Singapore in advancing
our ambition as a global manufacturing hub and supporting talent development efforts in the sector. Over the last 50 years, Makino has not only grown its manufacturing footprint in Singapore, but also expanded its local capabilities across its headquarters and R&D functions. Makino’s significant presence here has enriched our manufacturing ecosystem and supported the growth of other companies in the aerospace, medtech, semiconductor and automotive industries. Its strong focus on environmental sustainability is also commendable and will serve its operations well in the long term,” said Mr Lionel Lim, Vice President & Head, Technology Hardware & Equipment, Singapore Economic Development Board.
Headquartered in Japan, Makino is a world leader in advanced CNC machining centres.
Since its incorporation in 1973, Makino Asia has been growing as a market leader in machine tool technology, introducing innovative solutions that boost productivity and profitability to its customers. Its operations span across China, India, Vietnam, Thailand, Indonesia, Malaysia and the Philippines, with 1,700 employees, including about 20% focused on research and development, and application functions. There are six manufacturing plants, located in China, India, Malaysia and Singapore, producing a wide range of machining centres and EDM machines for the global market.
Temasek Polytechnic (TP), together with the Environmental Management Association of Singapore (EMAS), and industry partners, LS 2 Holdings Limited (LS2), Republic Power Pte Ltd (Republic Power), Cleantools Pte Ltd (Cleantools), Karcher Singapore Pte Ltd (Karcher), and Nilfisk Pte Ltd (Nilfisk), recently launched Singapore’s first Enviro Tech Innovation Hub (ETIH@TP). This innovation hub will serve as a pioneering ‘living laboratory’ dedicated to the advancement of public hygiene and integrated facilities management.
A first in Singapore, the hub will serve as a platform for developing capabilities, and co-creation and test-bedding of innovative solutions in the cleaning industry.
ETIH@TP will be housed within TP and will operate under the coordination of TP, EMAS and LS 2, in collaboration with a consortium of Enviro Tech partners including Republic Power, Cleantools, Karcher and Nilfisk, and with the support of the National Environment Agency (NEA).
The seven organisations jointly signed a Memorandum of Understanding (MoU) recently, at the CleanEnviro Summit Singapore (CESG) Catalyst 2023 event at Sands Expo and Convention Centre, Marina Bay Sands Singapore.
The MoU signing was witnessed by Mr Ng Chun Pin, Deputy Chief Executive Officer (Planning, Corporate and Technology) of NEA and Mr Aw Tuan Kee, Deputy Principal of Temasek Polytechnic.
The ETIH@TP will officially open its doors at the end of 2023 and will be accessible to all cleaning industry partners and thereby support the transformation of the Environmental Services (ES) industry.
ETIH@TP will also promote training and skills development through joint Continuing Education and Training (CET) courses.
Mr Song Kwok Yuen, Director, School of Engineering at Temasek Polytechnic, said, “Temasek Polytechnic is committed to support the transformation of the environment industry. ETIH@TP will curate and offer customised workforce upskilling courses and programmes that are validated collectively by government agencies, IHLs and trade associations, to meet training needs in the environmental services industry.”
“We hope to grow awareness and upskill workers to adopt new technologies such as robotics and automation, Internet of Things (IoT) and data analytics in environmental services. We will also develop training programmes to support those in new job roles, such as integrated
facility specialists and sustainability specialists,” he added.
Mr Tony Chooi, EMAS President, said, “Through consultation and joint effort with the National Environment Agency, TP and EMAS, together with Enviro Tech consortium partners (such as LS2, Republic Power, Cleantools, Karcher, Nilfisk etc), the hub will plan and carry out initiatives for workforce upskilling, talent development and test-bedding of new solutions. EMAS and Enviro Tech consortium partners will also provide consultancy on outcome-based contracting, to help address the issues of manpower constraints and to boost efficiency and productivity in the fast-changing environmental cleaning landscape.”
Mr Alvin Ong, CEO of LS 2, said, “With the ETIH@TP, we are able to support and expedite the skills and capabilities transformation of environmental cleaning industry players and help them to undergo the relevant digital transition to manage ongoing challenges whilst enabling them to take on fresh opportunities, not just in Singapore but also in global markets.”
The launch of ETIH@TP aligns with the goals of the Environmental Services Industry Transformation Map (ES ITM) 2025 which aims to enhance ongoing industry transformation initiatives.
parts2clean 2023, the 20th inter national trade fair for industrial parts and surface cleaning, will be held from 26 to 28 September 2023 at the Stuttgart Exhibition Center, Germany.
The event will provide a platform for the exchange of information on all the latest trends, innovations and benchmark applications in this field.
“The exhibitors at this year’s parts 2clean will present ideally adapted and future-oriented solutions to meet these stiffer requirements. These include developments in the area of wet chemical processes and dry cleaning technologies, as well as for improved energy and resource efficiency, greater cost-effectiveness and flexibility, and the integration of component cleaning into connected manufacturing processes,” said Christoph Nowak, Project Director at Deutsche Messe, organisers of parts2clean.
A novelty at the event is the addition of the ‘High Purity’ theme to the parts2clean core areas, which addresses special solutions for the semiconductor supplier industry, medical technology, sensor technology, electronics and numerous applications related to electromobility.
The exhibitor presentations across industries, technologies and materials will be complemented by a supporting programme which is adapted to the current challenges in component cleaning.
“With knowledge and expertise as well as approaches to solutions for process design, adaptation and optimisation, the focus is on competition-relevant topics which are not covered anywhere else to this degree,” Nowak added.
The bilingual technical forum at parts2clean has been one of the highlights of the international trade fair, for many years. Renowned experts from research and science, as well as from associations and industry, will offer knowledge and expertise, as well as benchmark solutions, in simultaneously translated presentations (German to English and English to German) on a number of topics, at this year’s event.
• ‘The basics of industrial cleaning processes’ will include presentations on the mode of action of cleaning processes and media, drying processes, special features and the suitability of product carriers, and component design that is optimised for cleaning.
• ‘Monitoring and controlling cleaning processes’ will focus on process automation, the use of AI (artificial intelligence) for cleaning and analysis processes, and its integration into factory automation systems.
• ‘Cleaning for electrical engineering and electronics’ will feature practical examples and special solutions will be presented, along with fundamental challenges, and
both the opportunities and limits involved in cleaning technology.
• ‘High purity applications –challenges and solutions’ will address applications for, among other things, EUV lithography, semiconductor manufacturing, microtechnology, medical and pharmaceutical technology, while also highlighting actual innovations.
• ‘Monitoring and analyzing cleaned surfaces’ will provide detailed information and solutions for verification of the technical cleanliness achieved.
The special show on ‘Technical Cleanliness’, organised as a joint project with the CEC (Cleaning Excellence Center) will present the path to and the implementation of innovative technologies for component cleanliness as well as the accompanying quality assurance.
The Fachverband industrielle Teilereinigung (FiT) association will once again be represented with a special showcase and an attractive programme.
Drawing on its long experience in infection control projects, covering planning to engineering, Singapore-based CPG Consultants describes some of the challenges and solutions.
Over the last couple of decades, infectious diseases seem to be evolving, with the resulting requirement for different forms of treatment and containment procedures. Highly infectious diseases are mostly viral and bacterial infections that are easily transmissible from person to person, cause a life-threatening illness with no or few treatment options, and pose a threat to both healthcare personnel and the public. Thus, with every infectious disease outbreak, the preparedness of the healthcare sector is put to the test.
In healthcare settings, early detection of infectious diseases plays a crucial role in all treatment and prevention strategies. An infectious disease facility should be designed to be able to screen, isolate and treat patients with different types of infectious diseases, with the flexibility for future adaptation to suit different forms of treatment, whilst all the time remaining functional and friendly for users such as staff and patients.
The Healthcare Division of CPG Consultants has extensive experience in the medical planning and designing of facilities for treating
patients with infectious diseases. In the past, the division designed isolation rooms for major hospitals in Singapore such as the Singapore General Hospital, National University Hospital as well as Changi General Hospital, just to name a few. At the height of the SARS crisis in 2003, Singapore’s Ministry of Health requested CPG to put together additional isolation facilities for SARS patients on the open grounds of the Communicable Disease Centre (CDC) at Tan Tock Seng Hospital (TTSH), as well as renovate the old buildings on TTSH premises.
It is important to ensure that the design of healthcare facilities for infectious diseases will allow for measures to isolate suspected cases for investigation and management to be done swiftly and effectively. Infectious diseases could be airborne, or spread by droplets, or by contact with blood or body fluids. They can be spread person to person, or indirectly, through a medium, via a carrier or transmitted by contact with a surface which has been contaminated by another person. Careful medical planning of the facility, in terms of workflow and adjacencies, is critical to ensure the safety of patients, visitors and staff.
A healthcare facility for infectious diseases should be designed to provide appropriate isolation and intensive care units for inpatient care. Four types of patient rooms (Cohort room, Isolation room with no ante-room, Isolation room with ante-room, and Intensive Care Unit) are designed, based on a modular template, with similar sizes and similar toilet cores, regardless of the type of patient room.
This makes it easier to convert a room from one room type to another, should the need arise. For example, if more rooms with ante-rooms are needed, renovation would be much easier with rooms based on a modular template, than if the room structures were very different, to begin with. Every room must also to be tested for air-tightness, at the completion of construction.
A Cohort room with four beds in the same room is designed to be naturally ventilated and can house patients with the same infection. This could be a case of family members or patients of the same gender. This design is more space-efficient as it houses more patients (four patients instead of two) than
if they were single-bed rooms. In most cases, patients in four-bedder Cohort rooms are also less ill and gathering them in the same area helps save on staffing resources.
The typical Isolation room (without ante-room) is designed to house a single patient who is more infectious than those in the four-bedder Cohort room. Negative air pressure and single-pass air conditioning in the room aim to reduce the risk of infection spreading to other people. Working on the National Centre for Infectious Diseases (NCID) project, the CPG Healthcare team initiated an improved design where, instead of the traditional design with the toilet closer to the ward corridor, the design includes maximum glass frontage from the ward corridor, in
The National Centre for Infectious Diseases (NCID) is a 330-bed, purpose-built facility designed to strengthen Singapore’s capabilities in infectious disease management and prevention.
NCID houses clinical services, public health, research, training and education, and community engagement, under one overarching structure. In addition to the functions of the Communicable Disease Centre (clinical treatment of infectious diseases and outbreak management), the new
functional units of NCID include the National Public Health and Epidemiology Unit, the National Public Health Laboratory, the Infectious Disease Research and Training Office, the Antimicrobial Resistance Coordinating Office, and the National Public Health programmes for HIV and Tuberculosis.
Benchmarked to international standards and best practices for treatment and safety, NCID will better enhance Singapore’s ability to respond effectively to infectious outbreaks.
order to allow staff to supervise the patient.
Isolation rooms with ante-rooms are similar in design, but with the addition of an ante-room, to house patients with even more highly contagious or air-borne diseases. An ante-room serves to control contaminated air. Upon leaving the patient room, one enters the anteroom which is a negative air pressure environment. This means that the air in the patient room cannot flow out into the ward corridor outside. Medical workers can also remove their personal protective equipment (PPE) here so that it does not contaminate areas outside of the patient room. In normal hospitals, the Intensive Care Unit (ICU) does not come attached with ante-rooms, if there is no need to handle infectious patients. For an infectious diseases facility, however, the ICU would have to come with ante-rooms, not only to cater to severely infectious patients who are critically ill and need more medical support but also to ensure that the infection does not spread. In a certain type of ICU design, CPG introduced the additional design feature of a pass-through hatch between the ante-room and the patient room. Supplies can then be passed without the need for a staff to enter the room, thus reducing the exposure of staff to infectious patients.
In addition to the Cohort, Isolation and ICU rooms mentioned above, for patients with infections that are highly virulent and which can be spread from person to person, a special type of High Level Isolation Unit (HLIU) ward has been designed, that can provide the best care for such patients. During the Ebola outbreak, the CPG Healthcare team had visited hospitals in the US, which handled Ebola cases, to study the requirements needed. Subsequently, the HLIU design was conceived.
The HLIU unit consists of:
• The patient room with ensuite toilet and shower.
• A Clean Donning room for staff.
• The Dirty Doffing room together with staff shower.
• A Dirty Utility room.
• A viewing area, outside, that can be used by staff, or by the patient’s family members.
The HLIU unit is also designed to manage the movement of staff, patients, visitors and materials, so that cross-contamination can be avoided.
Staff flow: Staff would already have put on their first level of PPE when they enter the ward. Before entering the patient room, there is a clean area for donning additional PPE (Donning & Support room). Typically, staff serving the patient would stay in the patient room for a few hours. If they need additional supplies, these can be passed to them via the pass-thru hatch. When staff exit the patient room, there is a separate Doffing room where they can remove the outer PPE, then enter the staff shower area and put on clean PPE before returning to the ward.
Material flow: All equipment is brought into the Dirty Utility room and cleaned before leaving the unit. Patient waste will be treated with chemicals, double bagged and put into bins before being brought out. They will subsequently be brought to the decontamination area to be autoclaved before leav-
ing the ward.
Patient flow: Patients are masked and protected, and are wheeled into the HLIU via designated routes which would be decontaminated immediately. After the patient is brought into the patient room, the trolley would be decontaminated in the Dirty Utility room before being brought into the ward.
Visitor flow: While visitors are not encouraged, due to the risk of infection, research evidence has shown that patients recover better with the presence of their loved ones. Therefore, in order to accommodate visitors, yet ensure their safety, patient and visitor routes are clearly separated. Patients are brought into the patient room via the Doffing room. A restricted number of visitors will be permitted to enter the ward and communicate with the patient through a viewing window.
The five types of rooms mentioned above, were designed by the CPG Healthcare team and successfully adopted by the NCID.
Rooms are also designed such that, during an escalated outbreak of infectious diseases, the number of beds can be increased flexibly, to house additional patients with
the same illness. The supply of medical gases and other support facilities have been designed to take care of the additional patients. With flexibility in these designs, it is estimated that the number of beds can be increased by 30% to 40%, during a major outbreak.
In addition to designing rooms to accommodate an increase in the number of beds, room types can also incorporate convertibility. A four-bedder Cohort room, which is designed to be naturally ventilated, can be converted to two Isolation rooms by installing a partition, closing and sealing the windows and air-conditioning the room (with checks to ensure that the designed air pressure is achieved).
Convertibility not only helps an infectious diseases facility to deal with major outbreaks of disease, it will also make the functioning of the facility more economically viable, when required to switch between the different modes of use.
In a nutshell, infection control in a healthcare facility is imperative in maintaining a safe environment for everyone. Medical planning, as part of an important strategy used under infection control, should consider room designs that can increase bed count flexibly, effectively isolate patients for treatments, provide adequate staff support facilities, as well as provide facilities which can be adjusted to cater to new medical protocols in future.
These planning considerations, when combined with well-trained healthcare workers, effective mechanical systems and adherence to strict medical protocols befitting outbreak of disease situations, can help to achieve a more optimal environment for patient care, which will help more people embark on the journey to recovery. Every infectious disease outbreak will bring about new challenges, but a well-designed infectious diseases facility will provide the foundation necessary to meet these challenges.
The emergence of COVID-19 has subjected hospitals around the world to unprecedented strain and put the spotlight on the healthcare sector, globally. Effective management and prevention of infectious diseases become significant, with a focus placed on healthcare facilities that can achieve ‘infection control’. A key component of infection control is the creation of infectious disease control facilities, with good medical planning and safe mechanical systems installed within the premises. Coupled with a strict set of medical SOPs (standard operating procedures) and good medical teams, infection control can be accomplished.
As discussed earlier, good medical planning can strengthen the capacity of an infectious diseases facility to isolate and treat patients with different types of infectious diseases.
The discussion can now be directed towards how safety designs in mechanical systems help to protect the occupants in a healthcare facility.
While protective measures and PPEs are essential for ensuring the well-being of the medical team, mechanical systems act as vital organs in a healthcare facility, providing fresh air, water and other important elements that keep the facility running efficiently and safely. Thus, the consideration of whether the air-conditioning and mechanical ventilation (ACMV) systems as well as waste management systems are designed for use, safely, is paramount to the prevention of nosocomial infections (infections contracted in the healthcare facility).
The majority of nosocomial infections are caused by factors such as poor hygiene and surface-to-surface contamination. However, there is some risk of infections spreading via AC systems. The design of AC systems within an infectious diseases healthcare facility is thus motivated by a desire to reduce infections via air transmission.
One method of reducing the duration of exposure, or the number of microbes which a person is exposed to, is by increasing the rate of dilution ventilation with the flow of clean air into a space. For instance, when the CPG mechanical engineering team was working on the NCID project, the air in the patient rooms was constantly purged at a minimum rate of 12 times the room volume, per hour, that is, 12 ACH (air changes per hour). This air setting reduces the duration of exposure to microorganisms within the room and dilutes the air, for the safety of the medical staff and patients.
The pressure relationships help in mitigating the spread of infections. Within healthcare facilities, many rooms require various pressures relative to that required by adjacent spaces. The intent of pressurisation is to move potentially infectious particles from the cleanest areas to less clean areas. It is important that the rooms are designed with negative pressure. That means the supply of air from the Air Handling Units (AHUs), which is used to re-condition and circulate air as part of the air-conditioning system, is less than the air exhausted from the room, thereby creating a minimum negative pressure of -2.5 Pa in relation to the ward corridors.
In this way, the air inside the patient room would not flow out into the corridor. To facilitate the movement of the medical staff into the room, an ante room is provided. The inner and outer doors are interlocked such that only one door would open at any one time. This minimises the air movement by keeping opened channels to a minimum.
For more complicated layouts, such as the High Level Isolation Units (HLIU) and operating theatres, the air pressures for adjacent rooms and the interlocking of doors have to be considered carefully, to ensure that contaminated air does not flow to the cleaner areas.
While the basic requirements do not seem complicated, the design and construction of a ward with, say, 15 or more patient rooms and supporting facilities, would require substantial design and detailing considerations. To ensure that the correct amount of air enters each room, normal VAV (variable air volume) control would not be sufficiently accurate. Instead, venturi valves, which help to create constrictions in pipes to vary the flow characteristics of air, are used to control the flow rates of the air supply and exhaust.
With the movement of medical staff through the ante rooms and other operation rooms, the air pressure changes. The venturi valves, which control the air supply and exhaust, constantly adjust themselves, to maintain the air flow and pressure requirements. Within a patient room, the air is supplied from the ceiling near the foot of the patient’s bed. The air exhaust is at a lower level, near the head of the bed. In this way, the contaminated air from the patient is removed as soon as possible and the medical staff is better protected with clean air.
To maintain the comfort and quality levels of the air-conditioning, the temperature and humidity levels should be at 24 ± 1o C and 55 ± 5%, respectively. The AHUs are provided with coils which first cool and then heat, to meet the temperature and humidity requirements, based on psychometric calculations. Heat pumps are provided to save heating energy which is substantial for the air flow involved.
The safety of the areas around the wards cannot be neglected, either. In fact, the exhaust air from the ward rooms has to be cleaned using the High Efficiency Particulate Air (HEPA) filter. As an added safety measure, the air is disinfected using UV lights. High plume fans then further dilute and jet the exhaust air into the atmosphere, above the roof.
Other than patient rooms, the infectious diseases facility also includes other amenities used to treat and administer checks on infectious patients. These include operation theatres and radiology centres etc. In the case of more serious outbreaks, screening centres and clinics housed within the facility are available to manage the potentially larger number of
patients. It is important that the air flow and pressure regime in these areas are controlled.
Especially with regard to supporting facilities, such as laboratories where bodily samples from infectious patients are drawn and tested, the air flow and pressure regime in each of these areas have to be tailored to meet the layout and operation requirements, while preventing contamination.
An example is the operating theatre. Pressure regimes are required to manage the air flow between the operating theatre, the patient preparation room and the scrub room. Usually, the design is such that the air will flow outwards to the corridor. However, where infection control is needed, the situation is different. In the case of an infectious diseases facility, the
Testing of the operation theatre to ensure that contaminated air does not flow out.
air in the supporting rooms around the operating theatre would have to be let out via air exhaust ducts, so that contaminated air will not
flow to the corridors as well as to patient and staff areas outside the operating theatre suite, in order to ensure infection control.
When implementing air flow and pressure regime designs, it is important to ensure that everything is based on design calculations. Even during the construction stage, the rooms have to be tested for air tightness of the walls, the floors and the soffits as well as the pipes, ducts and wiring into the rooms. This is to make sure that the settings are in accordance with the calculations.
For the testing and commissioning of the completed installation, besides performing the usual operation tests, failure modes of the systems are also checked and fine-tuned. For example, if an AHU or high plume fan fails, it may cause contaminated air to flow out from the patient rooms and into the clean areas. Thus, mitigation measures are devised for each failure scenario, including the anticipation of control network failure. Failure scenarios are also tested for other areas, such as laboratories and clinics, which require infection control.
Apart from the control of contaminated air, sanitary waste from the patient areas is disinfected before being discharged to the public
sewer. The process involves a dedicated set of sanitary pipes leading to collection tanks. From the tanks, the waste is pumped in batches to dozing tanks where sodium hypochlorite is used for disinfection. The treated waste is further chemically balanced to the correct acidity levels before being discharged into the public sewer.
Designing mechanical engineering systems for infection control can be complicated. In engineering for safety, there are many considerations with regard to testing, redundancy, failure control and compliance with operational requirements.
Many have said that COVID-19 is not a black swan event and the possibility exists for another pandemic.
CPG Consultants has long experience in infection control projects, covering aspects from medical planning to mechanical engineering for safety. Through these projects, the firm continues to hone its skills and increase the understanding of transmission prevention strategies, in order to successfully meet the next challenge within the healthcare sector.
HID, a worldwide leader in trusted identity and physical security solutions, recently announced its inaugural State of the Security Industry Report, which gathered responses from 2,700 partners, end-users, and security and IT personnel, across a range of titles and organisation sizes representing over 11 industries.
By looking at what is driving the next innovations and the technology that supports them, the security industry is empowered to create more value for its organisations and its people. Conducted in Q4 of 2022, the survey reveals the following five common threads:
• Nearly 90% of respondents acknowledge sustainability as an important issue
End-users are increasingly demanding that suppliers provide footprint transparency, in terms of their operations, product sourcing and research and development practices, with 87% of respondents stating that sustainability ranks as ‘important to extremely important’. Mirroring this trend, 76% said they have seen the importance of sustainability increasing for their customers.
To support this growing demand, security teams are leveraging the cloud and the Internet of Things, even more, to optimise processes and reduce resources. Additionally, new products and solutions are being strategically developed to address sensible energy usage, waste reduction and resource optimisation.
• Most organisations still need to fully embrace ‘identity as-a-service’ (IDaaS) to support hybrid work
The majority of survey respondents – 81% of them – stated they are offering a hybrid work model. As an
example, 67% of respondents state that multifactor authentication and passwordless authentication are most important to adapting to hybrid and remote work, while 48% point to the importance of mobile and digital IDs.
Interestingly, the survey also reveals almost half of the organisations are not quite ready to implement a comprehensive IDaaS strategy.
• Digital IDs and mobile authentication to propel many more mobile access deployments
Identification and authentication are more commonly completed via mobile devices, including smartphones and wearables. The growing popularity of digital wallets from major players such as Google, Apple and Amazon is a key driver of this trend.
And expanded capabilities allow smartphone users, for example, to add keys, IDs and digital documents directly in the wallet app. These include, but are not limited to, drivers’ licences, verifiable COVID-19 vaccination information, employee badges, student IDs and hotel room keys.
Commercial real estate companies (40%) are outpacing other verticals, as large commercial real estate firms are leveraging mobile access as part of their larger tenant experience apps, according to the HID survey.
• Nearly 60% of respondents see the benefit of contactless biometrics
Biometric technologies represent a major break from more conventional means of access control. Using biometrics as an additional authenticating factor (e.g. biometric scans to verify an individual’s physical identity) can help organisa-
tions eliminate unauthorised access and fraud.
The importance of this trend is exemplified in the survey data, which shows that 59% of respondents are currently using, planning to implement, or at least testing biometric technologies in the near future.
• Supply chain issues continue to be a concerning factor but optimism begins to emerge
According to the survey, 74% of respondents say they were impacted by supply chain issues in 2022, although 50% are optimistic that conditions will improve in 2023. The most affected are commercial real estate companies, with 78% citing supply chain problems as their main concern.
More than two-thirds of organisations with fewer than 1,000 employees indicate that they were highly impacted by supply chain issues in 2022, but they are also the most optimistic that these issues will be resolved in 2023.
By better understanding the above topics, security professionals will be better prepared to adapt faster, deliver exceptional digital plus physical experiences, and capitalise on breakthrough innovations in solutions and services.
US-headquartered HID provides trusted identity solutions that give people convenient access to physical and digital places and connect things that can be identified, verified and tracked digitally. The company works with governments, educational institutions, hospitals, financial institutions and industries.
HID is an ASSA ABLOY Group brand.
Sustainability, mobile IDs and a changing workforce continue to be among top concerns.by Rebecca Law, Country Manager, Singapore at Check Point Software Technologies
It has great potential but also the possibility of being misused.
Artificial intelligence (AI) has the potential to be a transformative technology that can significantly impact our daily lives, but only with appropriate bans and regulations in place to ensure AI is used and developed ethically and responsibly.
AI has already shown its potential and has the possibility to revolutionise many areas such as healthcare, finance, transportation and more. It can automate tedious tasks, increase efficiency and provide information that was previously not possible. AI could also help us solve complex problems, make better decisions, reduce human error or tackle dangerous tasks such as defusing a bomb, flying into space or exploring the oceans.
But at the same time, we see massive use of AI technologies to develop cyber threats as well. Such misuse of AI has been widely reported in the media, with select reports around ChatGPT being leveraged by cybercriminals to create malware.
Overall, the development of AI is not just another passing craze, but it remains to be seen how much of a positive or negative impact it will have on society. And although AI has been around for a long time, 2023 will be remembered by the public as the ‘Year of AI’. However, there continues to be a lot of hype around this technology and some companies may be overreacting. We need to have realistic expectations and not see AI as an automatic panacea for all the world’s problems.
We often hear concerns about whether AI will approach or even surpass human capabilities. Predict-
ing how advanced AI will be is difficult, but there are already several categories. Current AI is referred to as narrow or ‘weak’ AI (ANI - Artificial Narrow Intelligence). General AI (AGI - Artificial General Intelligence) should function like the human brain, thinking, learning and solving tasks like a human. The last category is Artificial Super Intelligence (ASI) which can create machines that are smarter than us.
If AI reaches the level of AGI, there is a risk that it could act on its own and potentially become a threat to humanity. Therefore, we need to work on aligning the goals and values of AI with those of humans. To mitigate the risks associated with advanced AI, it is important that governments, companies and regulators work together to develop robust safety mechanisms, establish ethical principles and promote transparency and accountability in AI development. Currently, there is a minimum of rules and regulations. There are proposals such as the AI Act, but none of these have been passed and essentially everything so far is governed by the ethical compasses of users and developers. Depending on the type of AI, companies that develop and release AI systems should ensure at least minimum standards in terms of privacy, fairness, explainability and accessibility.
Unfortunately, AI can also be used by cybercriminals to refine their attacks, automatically identify vulnerabilities, create targeted phishing campaigns, socially engineer, or create advanced malware that can change its code to better evade detection. AI can also be used to generate convincing audio
and video deepfakes that can be used for political manipulation or to produce false evidence in criminal trials, or trick users into paying money.
But AI is also an important aid in defending against cyber attacks, in particular. For example, Check Point uses more than 70 different tools to analyse threats and protect against attacks, more than 40 of which are AI-based. These technologies help with behavioural analysis, analysing large amounts of threat data from a variety of sources, including the darknet, thereby making it easier to detect zero-day vulnerabilities or automate patching of security vulnerabilities.
Various bans and restrictions on AI have also been discussed recently. In the case of ChatGPT, the concerns are mainly related to privacy, as we have already seen data leaks, nor is the age limit of users addressed. However, blocking similar services has only limited effect, as any slightly more savvy user can get around the ban by using a VPN, for example, and there is also a brisk trade in stolen premium accounts. The problem is that most users do not realise that the sensitive information entered into ChatGPT will be very valuable if leaked, and could be used for targeted marketing purposes. We are talking about potential social manipulation on a scale never seen before.
The impact of AI on our society will depend on how we choose to develop and use this technology. It will be important to weigh the potential benefits and risks, whilst striving to ensure that AI is developed in a responsible, ethical and beneficial way, for society.
Only with appropriate measures can AI technology be truly transformative
Fortinet, a global cybersecurity leader driving the convergence of networking and security, recently unveiled the findings of a new Asia-Pacific SASE (Secure Access Service Edge) survey that it had commissioned and which was conducted by IDC.
The report is based on the survey conducted by IDC across nine countries in Asia Pacific and explores cybersecurity leaders’ perspectives on hybrid work, particularly how it impacted their organisations in the last year and their strategies to mitigate the security challenges arising from the adoption of hybrid work. Key findings from the survey include:
• The rise of the ‘branch-office-ofone’: According to the survey, 92% of respondents in Singapore have a hybrid or fully remote working model, with more than two-thirds (68%) having at least 50% of their employees working in hybrid mode. This shift to remote work has resulted in employees becoming ‘branch offices of one’, working from their homes or other locations outside the traditional office. Consequently, 64% of respondents in Singapore anticipate managed devices to surge by more than 100% over the next two years (with some expecting growth of 400%). Additionally, 76% in Singapore expect unmanaged devices to grow by over 50%. This is expected to compound the complexity and risk of security breaches, placing additional strain on already overburdened IT security teams.
• Unmanaged devices pose a risk: With cloud computing and remote work becoming more prevalent, an increasing number of users, devices, and data are located outside of enterprise
networks. Currently, over 30% of devices connecting to networks in Singapore are unmanaged, raising the possibility of security breaches. Survey respondents in Singapore expect this figure to rise, with 76% predicting a 50% increase by 2025.
• The need to secure cloud: With hybrid work increasing, employees require multiple connections to external systems and cloud applications, to remain productive. Survey respondents indicated that their employees in Singapore need more than 25 connections to third-party cloud applications, increasing the risk of security breaches. Hundred percent of respondents in Singapore expect this number to double, over the next two years, while more than 70% feel that this number will triple, exacerbating the risk. Maintaining network security while ensuring employee connectivity to third-party and cloud-based services is a significant challenge, as traditional security measures are inadequate.
• Increased security incidents: Hybrid work and the growth in managed and unmanaged connections have caused a significant rise in security incidents, with 48% of surveyed organisations in Singapore reporting more than triple the number of breaches. According to the survey, 70% of respondents in Singapore have experienced at least a 2X increase in security incidents. The top security incidents include phishing, denial of service, data/identity theft, ransomware, and data loss. However, only 49% of organisations across Asia have dedicated security personnel, which leaves them more vulnerable to security incidents and breaches.
• SASE – a game-changer for hybrid work: To tackle the challenges of hybrid work, many organisations across Singapore plan to invest in a single-vendor SASE solution to improve their security posture and provide consistency in the user experience for remote employees. The need for a comprehensive solution that offers a consistent security posture for users on and off the network while simplifying security policy management and enhancing the user experience for remote employees is driving many organisations to explore SASE.
• The preference for a single vendor: As organisations adopt SASE to manage networking and security services, they are seeking a converged platform to streamline their operations. According to the survey, 66% of respondents across Singapore prefer a single vendor for networking and security capabilities, with 74% consolidating their IT security vendors. About half (50%) of the respondents prefer a single vendor for cloud-delivered security services and Software-Defined WAN (SD-WAN), citing benefits such as reduced security gaps, improved network performance, ease of deployment, and ability to address integration and scalability challenges.
The survey was conducted among 450 cybersecurity leaders from nine different locations across Asia (Hong Kong, India, Indonesia, Malaysia, The Philippines, Singapore, South Korea, Thailand, and Vietnam).
Survey respondents came from nine industries, including manufacturing (14%), Retail (13%), Logistics (14%), Healthcare (13%), FSI (10%), and Public Sector (11%).
Across Asia-Pacific, a thriving food and beverage industry has been among the first to turn to collaborative automation.
Countries across the Asia-Pacific region have been synonymous with the export of agriculture and the manufacturing of food. Southeast Asian countries like Thailand and Indonesia as well as Australia and New Zealand, representing Oceania, all have long and proud histories as agricultural exporters. In fact, Thailand is responsible for roughly 34.5% of the world’s rice exports, and Australia alone produces enough to feed 80 million people, despite having a population of just 26 million.
Taking a micro look into Australia’s food sector, it has been smashing records for production, exports and farm income. The country’s food and drinks are exported all over the world, notably to the US and other parts of Asia, with China being a major end-customer. From the likes of seafood and meat to grains, dairy and wine, Australia’s and New Zealand’s agriculture, along with their food and beverage industries, make a major contribution to employment, and their economies (USD 71 billion in Australia). Currently, over 243,000 people are employed in the food and beverage manufacturing sectors, in Australia.
Elsewhere, Singapore is home to a thriving food manufacturing industry supplying safe and quality food products for local consumption and export around the world. Consisting of approximately 1,000 food manufacturers across 10 sub-sectors, it houses established MNCs, homegrown brands and an increasing number of food-tech start-ups. In 2018, the food manufacturing industry had about 50,500 employees and contributed more than SGD 10.7 billion.
As dainty as everything sounds, food production is extremely labour-intensive and a thriving industry is heavily dependent on having a large workforce to prepare and package food and drink, for both domestic consumption and export. Currently, the APAC sector is facing the tightest labour market in decades, due to immigration slowing down since the start of the COVID-19 pandemic, despite borders opening up and businesses getting back in the saddle.
Collaborative automation lightens the workload with the smaller workforce, by performing repetitive tasks and allowing them to focus on other tasks that require the human touch. When the workforce slowly repopulates, the addition of collaborative automation to more manpower only makes businesses more efficient and effective.
In fact, it has been estimated that, by 2030, one in three new jobs created in the agriculture industry will be technology-related. Singapore is a prime example of a country with a workforce decreasing rapidly. The United Nations estimates a decrease of about 600,000 workers between 2023 and 2043, in Singapore. Ultimately, collaborative automation will aid the declining labour force in the decades to come.
As with the trends globally, automation has acquired an important role, supporting businesses of all sizes and it is no different in the food industry. The most recent World Robotics Report has indicated that 26% of industrial robot installations in 2021, within Australia and New Zealand, were in the food
industry. In the midst of labour shortages, collaborative robots (cobots) are well placed to support Australia and New Zealand’s food and beverage sector, with solutions that include packaging and palletising its output.
Ageing populations and the effects of COVID-19 are driving labour shortages. The pandemic forced businesses to source for different solutions to address the lack of manpower, and automation was found to be a viable solution. Over the last couple of years, industrial robots have been steadily gaining popularity amongst manufacturers, throughout the region, especially with handling and assembly tasks.
With the increased payload of the UR20, the latest model from Danish cobot developers, Universal Robots, palletising products in bulk, in particular, will become possible, giving businesses alternatives to spending big on industrial robots. The cobot is useful especially in the packaging of beverages.
The field of automation has much untapped potential, as both Australia and New Zealand are way under the global average ratio of industrial robots to manufacturing employees. The adoption rates of automation in other Asian countries have been slow, as well, with developed countries such as Singapore installing only 3,467 new robots in 2021 –which is 35% lower than in 2020.
Though the food and beverage industry is rapidly taking steps towards automation, it remains important to ensure that opportunities are not just for conglomerates in the industry but are also available for companies of all sizes. Robotics should be not only for large-scale
operations which are accompanied by significant capital investments, but also for local companies, to help them stay competitive and remain relevant in the fast-paced and ever-evolving industry.
Robots are starting to play a key part in many businesses across various industries and they are becoming increasingly common in the workplace. With that, it is important for the future workforce to be well-versed in robotics, to fit seamlessly into future vocations. Educational institutions in Australia have seen this, and are now including relevant technical training in their curriculum. Universities and vocational training centres are offering robotics education, including exposure to real world applications such as palletising.
Collaborative robots are commonly used in the classroom as a part of this training. Currently there are approximately 150 cobots installed across educational institutions in Australia. With the increasingly important role automation is starting to carve out in various industries, it is vital that the emerging workforce is well-versed in their ins and outs, for a seamless transition from
school to the workplace.
In due time, the ability to under stand automation and work together
The World Robotics Report 2022, released in October 2022, shows that an all-time high of 517,385 new industrial robots were installed in 2021, in factories around the world. This represents a growth rate of 31% year-on-year and exceeds the pre-pandemic record of robot installation in 2018, by 22%. As at October 2022, the stock of operational robots around the globe hit a new record of about 3.5 million units.
Asia remained the world’s largest market for industrial robots. Seventy-four percent of all
newly deployed robots in 2021 were installed in Asia (in 2020, it was 70%). Installations for the region’s largest adopter, China, grew strongly by 51%, with 268,195 units shipped. Every other robot installed globally in 2021 was deployed here. The operational stock broke the 1 million unit mark. This high growth rate indicates the rapid speed of robotisation in China.
Japan remained second to China as the largest market for industrial robots. Installations were up 22% in 2021, with 47,182 units. Japan’s operational stock was 393,326 units in 2021. After two years of declining robot instal-
which will aid everyone to become more efficient and effective in delivering the results needed.
lations in all major industries, numbers began growing again in 2021. Also, Japan is the world’s predominant robot manufacturing country. Exports of Japanese industrial robots achieved a new peak level at 186,102 units in 2021.
The Republic of Korea was the fourth largest robot market, in terms of annual installations, following behind the US, Japan and China. Robot installations increased to 31,083 units in 2021. The operational stock of robots was computed at 366,227 units.
The World Robotics Report is published by the International Federation of Robotics (IFR).
This article provides a practising engineer’s viewpoint on the fire safety and mitigation measures for electrical transformers in underground structures.
Introduction
As Singapore drives the optimisation of land use, more and more electrical substations are being located in underground structures, to make way for ground level connectivity and higher economic value usage through commercial developments. It is therefore important that building owners, architects and consulting engineers are aware of the fire risks associated with oilfilled transformers in underground structures.
This article focuses on the fire risk and mitigation measures for underground 22 kV/400 V and 6.6 kV/400 V oil-filled transformers, as these constitute the bulk of distribution transformers installed in Singapore.
On 1 September 2022, the Singapore Civil Defence Force (SCDF) issued the 11th batch of amendments to the Code of Practice for Fire Precautions in Buildings 2018 (Fire Code 2018). Included among these amendments are the amendments to the fire safety requirements for electrical transformer rooms in underground structures, which have become mandatory from 1 March 2023.
In Labrador, Singapore, SP Group is building Southeast Asia’s first largescale underground substation, and more buildings are locating their transformers and substations in basement structures. So, one may ask “What is the fire risk for oilfilled transformers in underground structures and are the statutory fire safety requirements adequate
to mitigate the risk of transformer oil-generated fires?”
Risk is a product of probability and impact. The probability of occurrence of an oil-filled transformer fire is extremely low, but the impact can be severe when transformer fires do occur, if adequate fire safety measures are not in place. To mitigate the risk of an underground transformer catching fire, we need to understand why and how a transformer fails and an oil-generated fire occurs.
A transformer fails because its insulation system is no longer able to withstand the electrical stresses generated during operation, or the failure is caused by electrical disturbances such as lightning surges, switching impulses, overloading, ferro resonance, short circuits, line faults etc. When the transformer insulation fails, a large short circuit current will flow through the transformer, resulting in an arc flash. Until the electrical protection isolates the fault, the arc flash will
trigger a cascade of increasing damage to the transformer, from rapid pressure buildup in the oil tank to tank rupture, oil spill, oil ignition and sustaining of the oil-generated fire.
Power transformers are commonly used in power transmission and distribution to reduce transmission and distribution losses. In Singapore, most 22 kV and 6.6 kV distribution transformers are oil-filled transformers, for reasons of cost and efficiency. Compared with dry type transformers, oil-filled transformers generally cost less and are more efficient and tolerant to overheating during an overload. Because oil has significantly better heat conductivity than air, it results in lower electrical losses and maintenance costs. An oil-filled transformer essentially comprises an electrical circuit, magnetic core, dielectric insulation, oil tank, bushings and accessories, as shown in Figure 1.
The electrical circuit comprises the primary and secondary windings on the magnetic core which provides a continuous magnetic path for voltage transformation. During normal operation, the alternating current in the primary windings generates a varying magnetic field which permeates through the magnetic core. Concurrently, the varying magnetic field in the magnetic core induces an alternating current in the secondary windings, in accordance with Faraday’s law of electromagnetic induction. The voltage transformation is in accordance with the turns ratio of the primary and secondary windings.
A transformer is only as strong as the weakest point in its dielectric insulation. Its capacity is limited by the temperature the dielectric insulation can tolerate. The weakest point is usually the oil dielectric insulation between the conductor windings and between the windings and the transformer tank. The oil also serves to cool the heat generated in the windings and reduces the temperature rise during normal operations and when faults occur. The oil dielectric insulation in the windings typically begins to deteriorate at around 100° C, in accordance with IEEE Standard C57.91-1995. Hence the transformer must be operated with its ‘hottest spot’ lower than this temperature, otherwise its useful lifespan may be affected.
In general, transformer dielectric insulation can be classified into three types:
• Flammable fluids (such as mineral oil)
• Less flammable fluids (fire point > 300° C, such as silicone oil and vegetable oil)
• Insulating solids and gases (such as in dry type transformers)
Mineral oil is a combustible material that has traditionally been widely used for electrical insulation and cooling in transformers. Its popularity is due to easy availability and relatively low cost, as well as its excellent properties as a dielectric and cooling medium. Less flamma-
ble fluids were developed to withstand the large amounts of arc energy and they offer advantages of a higher flash point and fire point. Commonly used less flammable fluids include synthetic and natural ester-based oils and silicone-based fluids. Dry type transformers have their core and windings cooled using air convection, instead of being immersed in a fluid.
To assess the risk of a transformer fire, we examine the basics of how fires start in transformers. The fire triangle, shown in Figure 2, illustrates three key elements that are required to initiate and sustain a fire – heat, fuel, and oxygen with a concentration of more than 16%.
If any one of these three elements is absent, a fire will not start. Similarly, if any of the three elements is removed after a fire has started, the fire will be extinguished. In the
context of an oil transformer, the three key elements are:
• Heat – produced from electrical and chemical energy
• Fuel – transformer oil
• Oxygen – normally absent in the transformer oil tank
There are two sources of heat energy in a transformer, namely, electrical energy and chemical energy. The electrical energy always present in the transformer during normal operation produces resistance heating, induction heating and dielectric heating, as shown in Figure 3.
Transformer primary and secondary windings and electrical connections generate heat proportional to the square of the current passing through. However, the heat can become excessive due to poor connections, transformer overload or cooling system failure.
Induction heating occurs in transformer tanks and structures, due to varying magnetic fields from leakage fluxes and it can become excessive due to overloading and deteriorated cooling.
Dielectric heating occurs at the transformer bushing and terminations. It can become excessive and reach thermal runaway, due to ageing and increased moisture levels.
The chemical energy inside the transformer oil is normally zero
during operation. The chemical energy of the oil will be released when the insulation of the transformer breaks down, causing an internal arc flash or external arc flash. The insulation can break down by electrical disturbances due to the following reasons:
• Inter-turn insulation failure due to manufacturing damage, water infiltration, long-term overload and over voltages, mechanical movements of turns and obstructions in oil flow.
• Water contents in oil or sludge in oil, leading to winding tank insulation failure.
• Thermal faults caused by overloading of transformer, poor electrical connections or poor oil flow.
• Prolonged partial discharges due to cavities in insulation, moisture in insulation and poor connections.
• Excessive eddy current heating in magnetic core due to magnetic circuit failure, large negative or zero sequence currents, or circulating currents in the tank and core.
• Voltage surges with high rate of rise of current, short circuits in the secondary windings and rapidly fluctuating load currents.
• Explosion of load tap changer due to accumulation of combustible gases.
• Arc flash due to poor contacts at bushings, loose springs in tap changer contacts, pitted contacts of tap changer, poor maintenance and poor condition monitoring.
An internal arc flash in an oil-filled transformer will cause a high temperature in the arcing gases and the surrounding oil, but it cannot start a fire inside the tank without access to oxygen. The oxygen dissolved in the oil is not accessible to start a fire. If the current feeding a high energy arc is not disconnected rapidly, the tank may rupture if the weakest part of the tank fails. The high temperature gases and oil then get access to oxygen and will ignite if it reaches the flash point or if it makes contact with metal sufficiently hot to cause an ignition, resulting in catastrophic damage to the transformer.
The possibility of this scenario being created is slim due to the multi-tier electrical protection and robust transformer design. Multi-tier electrical protection is programmed to isolate the insulation failure of the transformer and cut off the current feeding the internal arc fault of the transformer. And the transformers are usually built and tested to international standards, such as IEC 60076.
An external arc flash can occur when the insulation of high voltage bushings fails. High voltage bushings are constantly subjected to high electrical field stress during voltage transformation, abnormal lightning and switching voltage surges. The bushing insulation will deteriorate due to inherent impurities, surface contamination and moisture deposits. Prolonged partial discharge, external leakage and tracking may eventually lead to catastrophic failure of the bushing insulation.
If the flash over causes the bushing to collapse into the transformer oil tank, it may result in an oil spill. The high temperature arc will ignite the oil spill and start a fire. Bushing failures can cause violent explosions and could be the main cause of transformer fires.
When the transformer insulation fails, the electrical resistance is limited only by the source impedance. The circuit for normal transformer operation and the equivalent circuit during a short circuit are presented in Figure 4.
Mathematically, the short circuit current approaches infinity as source impedance approaches zero. The large short circuit current will generate tremendous arc flash energy, typically in mega joules, with the temperature reaching few thousands of degrees Celsius.
The arc will continue until it is extinguished either by the removal of the short circuit by the electrical protection or by the dielectric fluid, due to the increase in arc length.
Effects of transformer fires in underground substations
Once the tank ruptures during an arc fault, air rushes into the tank and provides the oxygen to the burning oil and this completes the fire triangle for ignition to occur. The oil will explode and result in a blast with intense radiation, scattering flaming oil, steel parts, gaseous decomposition, burning insulation and melted conductor, onto the surroundings. When this
occurs, heat released from the initial burning of combustible gases may vaporise and burn the dielectric fluid close to its flash point. If the heat of combustion continues to vaporise the fluid, it will result in a sustained fire on top of the liquid. At this stage, the fire point characteristics of the dielectric fluid becomes paramount, as a higher fire point will require more combustion heat to sustain the fire.
The oil tank explosion will likely ignite neighbouring transformers and cause more damage. The temperature of an oil fire is likely to exceed 1000° C. The duration of a transformer oil fire can exceed 4 hours, depending on the transformer capacity, which in most cases is the time it takes to burn out the transformer oil.
Traditionally, the predominant dielectric coolant has been mineral oil. While exhibiting good dielectric properties, mineral oil typically does not provide an adequate margin of fire safety during transformer failure. With a fire point of 165° C, mineral oil requires significantly less heat to hit its fire point as compared to less flammable fluids like natural or synthetic ester-based fluids.
If a fire occurs due to transformer flashover and the oil spill gets into contact with air, it will result in the following:
• Generation of fire gases – The transformer oil and insulation will burn to generate carbon dioxide, and carbon monoxide if air supply is restricted. Other corrosive gases will be released from burning cable insulation.
• Generation of smoke – Smoke will likely reach untenable levels before the temperature does. This is especially so when fire occurs in a basement. Smoke can cause damage to the respiratory system and impair vision, thus reducing the ability of the occupants to escape.
• Generation of heat – Transformer oil fire generates intense heat which can cause burns. Intense radiant heat can cause instant death.
• Loss of Oxygen – Fire consumes oxygen. During an underground transformer fire, the oxygen level in the vicinity of the basement will drop significantly, impairing the judgement of the occupants and their ability to escape.
In addition to the above, there is a risk of pollution from an oil spill and contamination of the environment.
The fire triangle also demonstrates how transformer fires can be extinguished. Removal of any of the three elements of the fire triangle will extinguish the transformer fire.
The fire can be extinguished if heat is removed and the fuel is cooled to below its fire point. Water is an efficient cooling medium to extinguish external fires and protect adjacent assets from being heated to their flash point. Water is less efficient in extinguishing a fire burning inside a transformer. It is difficult to get water into a transformer tank. Oil will float on top of the water and continue burning. Water alone may not be efficient in extinguishing oil fires. Water with foam can be efficient as it excludes oxygen from the oil surface.
Removal of oxygen can be effective in extinguishing a transformer fire. A gas suppression system can displace or dilute oxygen (to ≤15%) and extinguish the fire. Gas suppression systems include FM200, INERGEN and Novec. However, occupants could be suffocated, if the gas is injected before all occupants have been evacuated.
Foam and high-pressure water mist can displace oxygen and reduce the concentration of oxygen to below 16%, to extinguish the fire. Foam can be effective for oil pool fires, but less effective where oil is spilling over vertical surfaces and it is difficult to get foam into a fire burning inside a transformer tank. A water deluge system and high-pressure water mist can dilute the oxygen and provide cooling.
Removal of fuel can be effective, but is often not possible. The strategy includes equipping the trans-
former tank with oil dump valves which can be opened by remote control. During a fire, the transformer oil can be dumped remotely into separation tanks or into gravel or crushed rock beds.
The first step in minimising the risk of a transformer fire, is to minimise the risk of transformer failure which can cause the fire.
First-step strategies are as follows:
• Improve transformer specification with better insulation levels and reduced temperature rise. Use type tested or similar transformers, where possible.
• Improve maintenance and monitoring of transformers. With effective maintenance and monitoring, anomalies and failure of transformer oil can be detected early, prior to their failure.
• Provide reliable electrical protection to clear electrical faults rapidly and protect transformers when faults occur. With fast protection, the arc energy is cut off quickly before it can cause an ignition of the transformer oil, in the event of spillage.
The second-step is to minimise the risk of a transformer failure developing into an oil fire, if a transformer failure does occur.
Second-step strategies are as follows:
• Use transformers with less flammable fluid as insulation and cooling medium.
• Use types of bushings with low explosion risk.
• Strengthen tank design to minimise the risk of tank rupture.
• Minimise uncontrolled release of oil and arcing gases.
• Avoid oil and arcing gases coming in contact with air (oxygen) if released.
Less flammable fluid is defined in NFPA70: NEC 450-23 as transformer dielectric coolants that have a minimum fire point of 300° C. The commonly used less flammable fluids are synthetic and natural
ester-based oils, and silicone oil. While such fluids cannot totally eliminate fire risk, they can significantly reduce fire hazards associated with transformers.
Unlike non-flammable fluids, less flammable fluids can still start a short-lived fire ball, if fluid is released as a mist and then ignited. But less flammable fluids will not support a long-burning pool fire and are unlikely to sustain a fire. Whilst these fluids can and will burn at sufficiently high temperatures, to the best of our knowledge, there have not been any reported transformer fire incidents involving less flammable fluids in this region.
Fire risk associated with different dielectric coolants
Experimental studies on the ignition and combustion behaviour of insulation fluids for transformers were conducted by researchers at Tokyo University of Science, Suwa in 2007, using a cone calorimeter. The fluids used in the experiments were mineral oil, synthetic ester-based fluid, natural ester-based fluid and silicone oil. Synthetic ester-based and natural ester-based fluids, and silicone oil, are less flammable fluids. The samples were heated in a conical, heat transfer apparatus and ignition was induced by applying a spark to the produced gas. The ignition time, heat release rate and smoke production rate were measured.
The correlation between time to ignition and radiant heat flux is shown in Figure 5.
The study indicates that when the transformer fluid is subjected to radiant heat flux, mineral oil ignites much faster than the less flammable fluids.
In terms of the smoke production rate, less flammable fluids emit much less smoke than mineral oil, as shown in Figure 6.
In terms of the heat release rate, mineral oil generates a much higher heat flux, compared to less flammable fluids, as shown in Figure 7.
It is evident from the study that less flammable liquids exhibit a fire risk far lower than mineral oil.
The lower risk in using less flammable fluids can also be quantified by examining the electrical process which is required to start and sustain a transformer fire. During short circuit failure of the transformer insulation, the arc energy required to start and sustain a fire in the transformer oil must come from the electrical fault energy that is feeding the arc, in accordance with the first law of thermodynamics. To understand the risk of transformer fire, it is necessary to determine the duration of arc energy required to start and sustain a fire in the transformer when using mineral oil and when using less flammable fluid, and compare the two results.
A simplified analysis can be carried out, with the following assumptions:
• Prospective fault level for 22 kV incoming service cable is 25 kA or 952.6 MVA (SP Group handbook).
• 22 kV/400 V 2 MVA transformer has 1,000 L of insulating oil (Schneider transformer data)
• Top oil temperature of 95° C (65° C rise over 30° C ambient) for corresponding hot spot temperature of 110° C.
• 100% of the arc energy goes into heating the fluid.
• Three-phase to earth, symmetrical, short circuit current occurs at the transformer, at the beginning of the high voltage winding. The worst case short circuit fault is 809.7 MW at 0.85 power factor.
A comparison of the duration of arc energy required for the transformer to reach fire point, when using mineral oil and when using less flammable oil, is given in Table 2.
The analysis is repeated using a 22kV/400V 1 MVA oil filled transformer with 760 L of insulating oil (Schneider transformer data). The results are shown in Table 3.
As compared with mineral oil, less flammable oil requires substantially larger amounts of energy through longer arc times to raise the temperature to fire point and sustain a fire. The arc time for a less flammable fluid-filled transformer is generally more than four times
that of mineral oil. In reality, the arc process is complex and the arc time is likely to be longer, as part of the arc energy will go into decomposing the oil into gases or the arc energy could be lower because not all phases are at fault or because of a high impedance fault. However, the safety margin will likely be similar.
Typical medium voltage switchgear protection for transformer short circuits is programmed to trip within 5 to 6 cycles at 20 times the rated current, to maintain network stability and minimise damage to equipment. For short circuits in mineral oil-filled transformers, 5 cycles in electrical protection trip-
ping time may let through enough energy to ignite and sustain a fire, in the worst case scenario. For less flammable oil-filled transformers, 5 cycles protection trip time is well within the arc time of 22 cycles before a fire can be sustained. In the event that the immediate electrical protection for the transformer fails, the upstream, medium voltage protection, in series with the transformer, will sense the short circuit current and isolate the faulty transformer within another 200 ms to 250 ms (or 10 to 12.5 cycles). The total protection trip time of 17.5 cycles is still well within the arc time of 22 cycles for less flammable oil-filled transformers to ignite and sustain a fire. Thus, the probability of arc energy to start and sustain a fire in a less flammable oil-filled transformer is electrically low. This may explain why less flammable oil-filled transformers have a flawless safety record.
US standards have already recommended the use of less flammable fluid-filled transformers in areas with higher risk or where a higher safety margin is required. The standards include the following:
• FM Global Standard 3990:2021 –Liquid-Insulated Transformers
• NFPA 70 – National Electric Code 2017 clause 450.23
• NFPA 850:2020 – Recommended Practice for Fire Protection for Electric Generating Plants and High Voltage Direct Current Converter Stations
According to FM Global Standard 3990 dated 2021, the transformer is filled with a less-flammable liquid to reduce the probability of ignition of the liquid. Less-flammable liquids, also known as high fire point or fire resistant liquids, are dielectric coolants that have a minimum fire point of 300° C, as per the ASTM D92 open cup test method.
The US NFPA NEC 450.23 recognises that the probability of a transformer fire occurring when filled with less-flammable fluid is much lower than when filled with mineral
oil. It therefore permits indoor applications of less-flammable fluid filled transformers, without requiring traditional fire compartments. The NFPA 850 clause 3.3.23 defines a high fire point fluid as a combustible dielectric fluid having a fire point of not less than 300° C.
On 1 September 2022, the Singapore Civil Defence Force (SCDF) issued the 11th batch of amendments to the Code of Practice for Fire Precautions in Buildings 2018 (Fire Code 2018), to mandate the fire safety requirements for electrical transformer rooms in underground structures.
The Code of Practice for Fire Precautions in Rapid Transit Systems 2022 has also incorporated these requirements under clause
9.8, so that underground station transformer rooms in rapid transit systems will be in compliance with these requirements.
The transformer oil should be tested to ASTM D92 or ISO 2592 standards, with the fire point exceeding 300° C. The use of less flammable fluids is in line with international standards to minimise the risk of transformer fire ignition and propagation.
The probability of oil-filled transformers causing a fire is low but not nil. The impact can be severe if a fire does occur and adequate fire safety measures are not in place. With increasing installation of transformers in basement
structures due to optimisation of building design, it is prudent for building owners and energy suppliers to provide transformers with less flammable dielectric oil (fire point exceeding 300° C). In the unlikely event that all things fail and transformers catch fire, a less flammable oil significantly reduces the likelihood of a pool fire and fire propagation. Fast electrical protection should be provided to protect the transformer against transformer faults and the faults should be isolated within 5 cycles, to reduce the arc flash energy and avoid ignition of the transformer oil.
In Singapore, fire safety measures should be provided to underground transformer rooms, as per SCDF Fire Code 2018 clause 9.6.7,
issued under the 11th batch of amendments.
For transformers in underground rapid transit systems, the fire safety measures should comply with the Code of Practice for Fire Precautions in Rapid Transit Systems 2022, clause 9.8. As Singapore continues to develop, with growing numbers of underground substations, less flammable oil transformers and the new SCDF fire safety requirements will minimise the long-term risk associated with catastrophic transformer failures.
Fire Code 2018, 11th batch of amendments
Code of Practice for Fire Precautions in Rapid Transit Systems 2022, Clause 9.8: Electrical Transformer Room in Underground Structures
IEC 60076 – Power transformers
IEC 60137 – Insulated bushings for alternating voltages above 1000 V
NFPA 70 – National Electrical Code, Article 450
IEEE 980 INT 1-3 – Guide for Containment and Control of Oil Spills in Substations
FM Global Standard 3990:2021 –
ASTM D92:2018 – Standard Test
Method for Flash and Fire Points by Cleveland Open Cup Tester
IEC 61100:1992 – Classification of Insulating Liquids According to Fire-Point and Net Calorific Value
Experimental study on ignition and combustion behaviours on insulation fluids for transformer using cone calorimeter, by Yamagishi and Suzuki (Er. Simon Lee, MSc, PEng, holds an EMA 22 kV Switching Licence. He is also a member of the SCDF workgroup on fire safety for underground substations.)
Earlier this year, Hitachi Energy, a global technology leader launched the next-generation TXpert Hub, a part of its ecosystem for the digitalisation of transformers.
The TXpert Hub enables monitoring by aggregating, storing and analysing the information received from a transformer’s digital sensors. It is conceived to simplify digitalisation of any transformer with enhanced connectivity and cybersecurity.
According to Hitachi Energy, digitalisation is becoming crucial to transformers, due to its pivotal role in enabling efficient, reliable and safe electricity networks, as well as managing power quality and flow control to fit the needs of today and tomorrow.
The next generation TXpert Hub, powered by the latest CoreTec technology, has been built from the ground up, to ease transformer digitalisation. It focuses on the following:
• Incorporating the operative experience from users of earlier versions of the system.
• Application of the latest technologies in communications and cybersecurity.
• Readiness for off-the-shelf retrofits.
The TXpert ecosystem TXpert is Hitachi Energy’s open, scalable, manufacturer-agnostic ecosystem for the digitalisation of transformers. It is designed to drive data-driven intelligence and decision-making in the operations and maintenance of transformers.
It is a complete suite of products, software, services and solutions, that work together and have the capability to integrate with new and existing digital equipment from other manufacturers.
TXpert upgrades and enhances the transformers to connect and integrate all the relevant data across many devices to deliver tangible impact and to realise digitalisation. It makes
the digitalisation of transformers easier, more effective and secure. Whatever the type of transformer – old, new, dry, or liquid-filled, transmission or distribution – the TXpert ecosystem would be relevant. With its solid grounding, built on the knowledge gained and intelligence developed through manufacturing and servicing large numbers of transformers, the TXpert ecosystem delivers actionable, data-driven insights that can help to reduce costs, optimise operations and extend life expectancy, thereby further enhancing the environmental performance.
The TXpert ecosystem includes TXpert-Ready digital sensors, the TXpert Hub monitoring system, Asset Performance Management software and TXpert advanced services.
The objective is to achieve a high level of component cleanliness by focusing not only on the actual cleaning solution but also on the entire process chain and the ambient conditions.
The enormously amplified and continually rising demands in many industries, on the performance and reliability of components and parts, also have an impact on parts cleaning. The term ‘high-purity cleaning’ is increasingly used, often as a synonym for ultra-fine and precision cleaning, in industries such as semiconductor supply, electronics manufacturing, electric mobility, optical and optoelectronics, sensor technology, photonics, thin-film technology, vacuum, laser, analytical technology, aerospace as well as medical and pharmaceutical technology.
The cleanliness requirements vary, depending on the product, area of application and company concerned. The spectrum of materials from which the components to be cleaned are made also varies greatly. It includes, for example, metallic materials as well as plastics, high-performance ceramics and glass materials.
The terms ultra-fine, precision and high purity cleaning, are closely related, because in all cases, extremely high levels of particulate cleanliness, in some cases, down to the nanometre range, and extremely stringent specifications, with regard to residual film contamination, have to be fulfilled.
And yet there are differences. For example, the term ‘high purity’ is often applied in connection with the semiconductor supply industry, including the manufacture of components for EUV lithography, as well as in high vacuum technology (XHV, UHV and UCV). In addition to particulate and filmic organic as well as inorganic contaminants,
hydrogen-induced outgassing (HIO) substances or elements must be taken into account here.
This means the component materials or the processing and cleaning media are not allowed to contain these so-called prohibited substances, because even the smallest amounts remaining on the components can lead to cross-contamination in a vacuum or limit the vacuum pressure. This would mean that the prerequisites for the flawless production of, for example, semiconductors and microchips as well as high-tech sensor and analysis systems, would no longer be met. This requirement does not usually apply in precision and ultra-fine cleaning.
The specifications for particulate cleanliness to be met during cleaning are given by specifying the corresponding surface cleanliness class (SCC). The filmic chemical (organic and inorganic) surface cleanliness is usually defined by individual specifications or works standards. In addition, outgassing rates are evaluated via mass spectrometers, where appropriate. These specifications are generally not available.
Focussing on the entire production process
These demanding cleanliness requirements cannot be met by a cleaning system alone. The focus, here, is much more on the entire
production chain, cleanliness-compliant parts handling and the ambient conditions, than is the case in classic cleaning tasks. One aspect of this lies in the upstream machining processes, which must support the cleanliness goal of high-purity, precision or ultra-fine cleaning. This is not the case in machining where, for example, components of the machining medium are worked into the surface in such a way that they cannot be cleaned off at all or to a sufficient extent.
Both chamber and ultrasonic multibath immersion systems, operated with liquid media with adapted process technology and drying, are used, as well as dry cleaning processes using CO2 snow jet technology, plasma cleaning and vacuum bakeout systems. When it comes to selecting the appropriate cleaning technology, the essential criteria are the cleanliness to be achieved, the contamination to be removed, and the material and geometry of the component. On this basis, it is possible to determine which and how many process steps, and which technology, are required. The optimum solution may also consist of a combination of different methods. Appropriate solutions are available for the frequently required monitoring and control of process parameters.
Regardless of which cleaning technology is used, the equipment must be designed to achieve the high level of cleanliness and to avoid re-contamination and cross-contamination. This includes, for example, selecting the materials and the plant components, as well as the processing. Welds, corners and edges, where even minimal amounts of dirt can collect, are counterproductive.
Compared to classic cleaning, in which a lot of oil, emulsion and chips often have to be removed, in ultra-fine, precision and high-purity cleaning, there are often only minimal residual amounts.
Depending on the contamination and cleanliness requirements, a solvent cleaner, usually a conventional modified alcohol, could be used. The situation is different with aqueous cleaners. These media are specially formulated to remove the last remaining contaminants from the surface while not adding new ones. Also, rinsing off the cleaner must be much easier. Overall, rinsing has a much higher priority here than in conventional cleaning with water-based media. Accordingly, the systems have more rinsing stages, and care is taken to ensure that the rinsing medium is not carried from one tank to the next.
The water quality used also differs. Appropriately treated water is used, adapted to the task. Reverse osmosis (RO) water, fully demineralised (FD) water and ultrapure water (UPW) are used.
Another essential aspect is the
environment in which high-purity cleaned components are handled. The parts are cleaned or dispensed in a clean room, depending on the cleanliness specification.
The clean room class is based on the surface cleanliness class to be achieved. In order to save costly clean room space, the cleaning system (equipped with appropriate air filter systems) can be placed in
a clean area and the parts can be sent through an airlock into the clean room. It is also necessary that appropriately trained and equipped staff are deployed here.
Especially when starting to produce parts with high demands on cleanliness, it can make sense to outsource the cleaning to an experienced and appropriately equipped service provider.
parts2clean 2023, the leading international trade fair for industrial parts and surface cleaning will be held at the Stuttgart Exhibition Center in Germany, from 26 to 28 September 2023. The event will present the latest developments in cleaning systems, alternative cleaning technologies, cleaning media, clean room
technology, quality assurance and testing procedures, cleaning and transport containers, disposal and reprocessing of process media, handling and automation, services, consulting, research and technical literature. A three-day technical forum will also provide a wealth of know-how on various cleaning topics.
Keysight Technologies Inc has introduced the PathWave Advanced Design System (ADS) 2024, an electronic design automation (EDA) software suite that gives chip designers new millimetre wave (mmWave) and subterahertz (sub-THz) frequency capabilities that accelerate 5G mmWave product design and anticipate requirements for 6G wireless communications development.
Developers of 5G and non-terrestrial network components are creating next-generation radio front-end modules using mmWave frequency bands that present significant design and simulation challenges. These frequencies are prone to signal loss due to propagation characteristics, atmospheric attenuation, complex packaging issues, and noise and dynamic range problems. Designing for 6G poses even greater challenges with sub-THz signals operating at higher frequencies.
Monolithic microwave integrated circuits (MMIC) and module designers are combining multiple semiconductor and III-V processes at mmWave frequencies, which requires multiple die assembly, module level interconnection and power considerations.
mmWave power amplifiers are built separately from the rest of the design to mitigate heat, yield and semiconductor performance issues. In addition, power amplifiers developed in gallium nitride processes handle higher current densities than silicon.
New semiconductor packaging techniques, such as flip chip bonding, achieve higher densities and performance. These packages also require co-design across multiple technologies
and processes because they concentrate challenges with internal crosstalk, electromagnetic interference (EMI), stability, and operating temperature.
The latest version of Keysight's industry-leading radio frequency and microwave (RF/uW) design software suite addresses these development pain points with algorithm, layout, electro-thermal, and workflow automation enhancements.
New PathWave ADS 2024 design capabilities include:
• Faster second-generation 3D-EM and 3D-Planar meshing and solvers – Delivers algorithm enhancements taking superior advantage of domain knowledge about microwave structures and processes. Mesh optimisation and layout and connectivity improvements reduce problem sizes for faster simulations. Solver enhancements also speed simulation by up to 10 times and require less specialised user expertise over a wider range of problems, including mmWave design at automotive radar frequencies of 79 GHz. Open workflows save database management and reduce overhead from
iterative, manual setup.
• Advanced layout and verification features – Enables design sign-off directly from ADS for LVS, LVL, DRC, and ERC for MMICs, as well as streamline productivity for module and multi-technology assembly. Wavetek is the latest foundry to fully support ADS for an end-to-end workflow.
• Electrothermal enhancements accelerate validation – Drives higher reliability and higher operating performance with validation of dynamic device operating temperatures under different bias and waveform conditions. Supports high-performance compute acceleration and up to 100 times transient speed-up using W3051E Electrothermal Dynamic Re-use, enabling higher test plan coverage and earlier insights in the design phase.
• Custom workflow support with expanded Python APIs – Increases flexibility and scalability. A load-pull data import utility, ANN modelling, and Python automation scripting for 5G power amplifier designers unlock new application potential to create targeted personalities of ADS.
New training technology, now available globally from Hexagon’s Manufacturing Intelligence division, leverages the power of its digital twins to help manufacturers train machinists and metrology specialists to use valuable shop-floor equipment. By combining hardware that realistically replicates machines with manufacturing simulation and operator’s software tools, it helps trainees gain practical experience without risking damage to expensive business-critical equipment, wasting materials, or tying up valuable production resources.
The HxGN Machine Trainer was developed by Hexagon to help companies and educational institutions attract and train the next generation of machine workers. This is important, with the industry facing a skills and labour shortage.
It is versatile because a digital twin can be created for the specific machine brand, type and configuration, that will be used.
Once trained, workers can easily move from the HxGN Machine Trainer to real machines, because the simulator is designed to be as realistic as possible – with hardware that replicates the look and feel of a real machine and a 43inch screen that displays accurate simulations of a large variety of machines and cutting tools. A light tower, physical CNC hand wheel and CMM joystick help to complete the experience, by enabling trainees to respond to issues and control machine movements exactly as they would on the shop floor. The agile training system also offers a range of digital twins for coordinate measuring machines (CMMs) to provide practical experience.
Each trainer unit can be equipped with up to three CNC controllers –including those by Fanuc, Heidenhain, and Siemens – on a single training console. The machine trainer utilises the latest version of Hexagon’s NCSIMUL CNC simulation software to simulate 3-axis, 5-axis, and mill-turn machine tools; and I++ Simulator software to simulate complete metrology processes.
Staff training to be machine-tool operators, machinists and, ultimately, CNC programmers, can use any of the three controllers to learn how to use its associated conversational programming language. Accompanying student exercises include instruction sheets that mimic typical manufacturing workflows and job specifications. These instructions list virtual cutting tools to be assigned to jobs and the CNC
program to be loaded to the trainer unit. In addition to troubleshooting and learning how to switch between manual and automatic run modes, as needed, students learn how to set machine-tool origins and tool parameters, and to determine cutting tool compensation.
HxGN Machine Trainer is available globally now, supporting 3-5 axis CNC machine tools, mill-turn machining and CMM training, with support for up to 3 CNC controllers on a single unit. It comes with a library of machine digital twins for Hermle, DMG and Fanuc machines. CMMs support includes the Hexagon TIGO SF, with support for other CMMs through the I++ Simulator, paired with either QUINDOS or PC DMIS metrology software. Customers can also request for a digital twin of any other machine.