
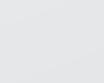
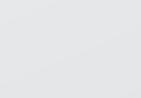

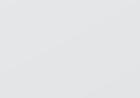
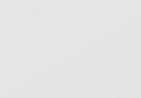
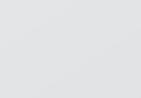
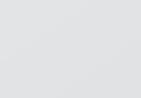

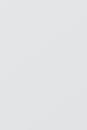
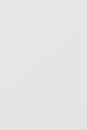

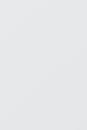
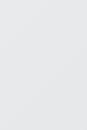


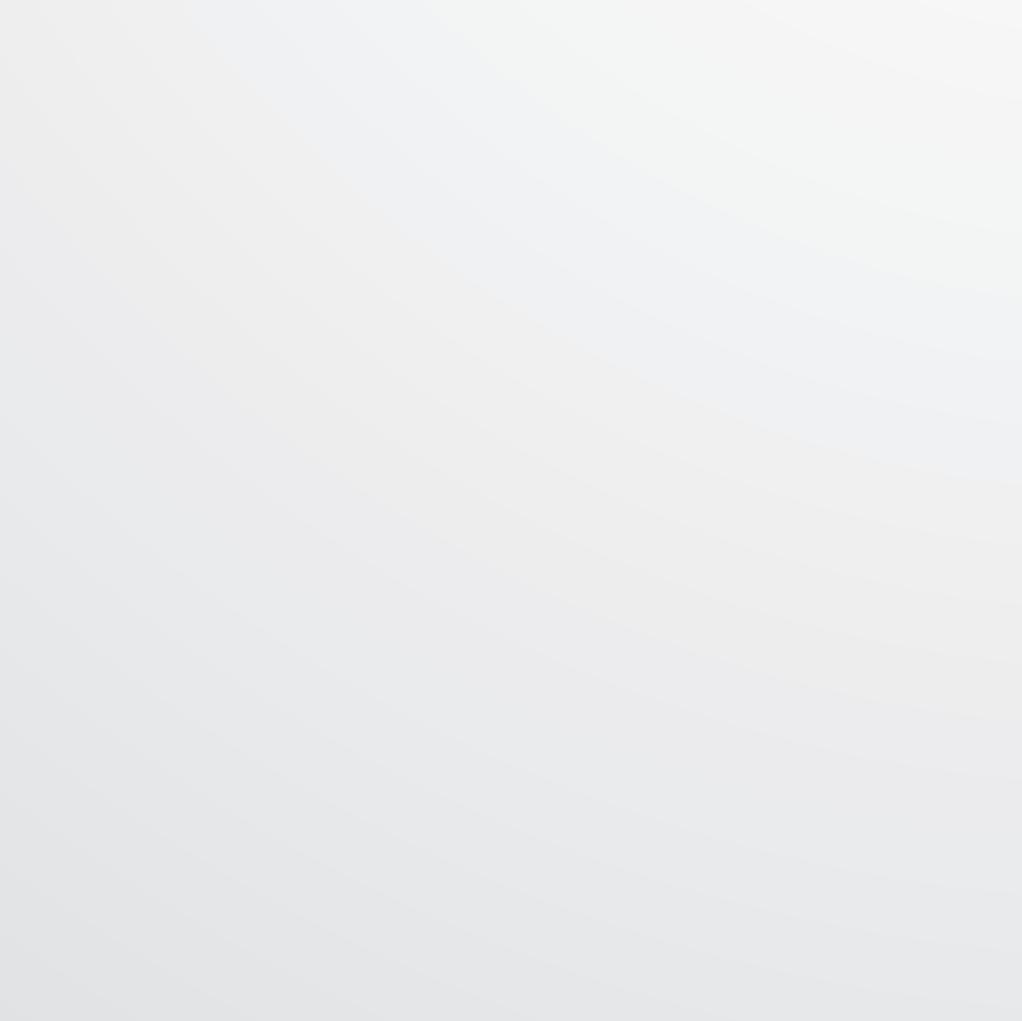

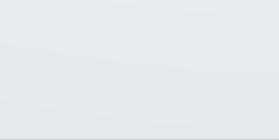


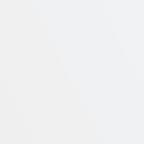
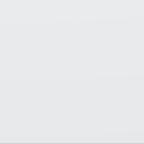
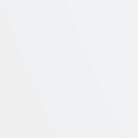
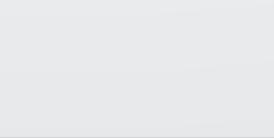
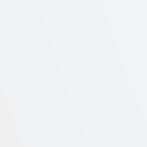

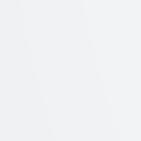
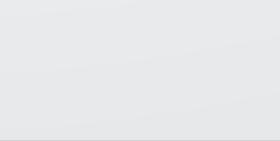
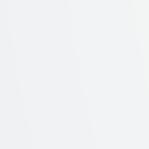
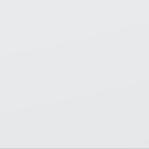
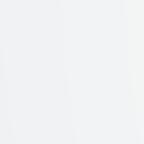
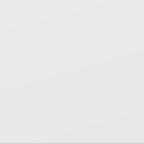


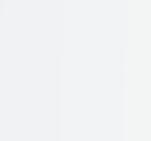
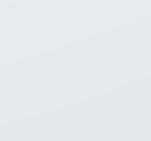















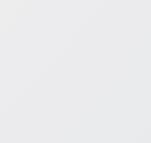
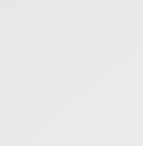
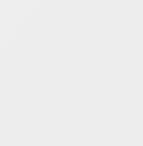

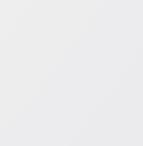
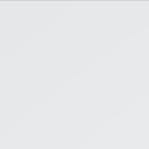
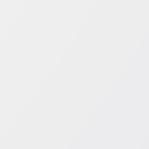

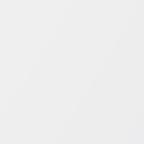
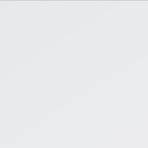
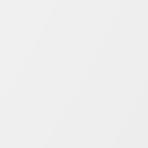
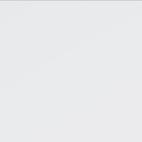

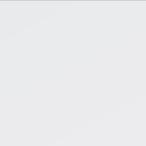

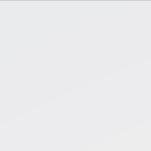

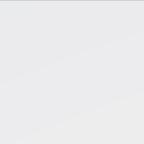
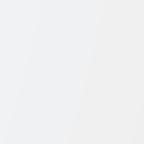

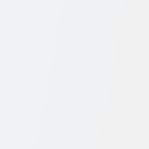
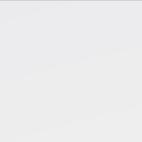
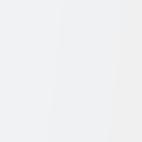
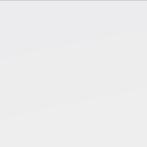
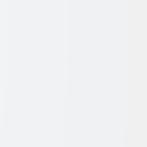
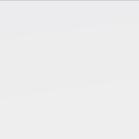


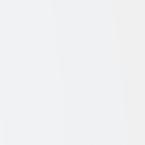
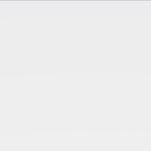

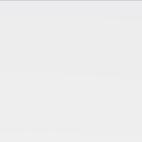
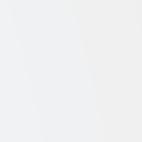

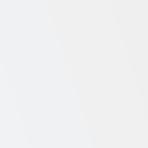
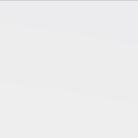
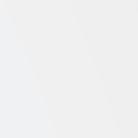
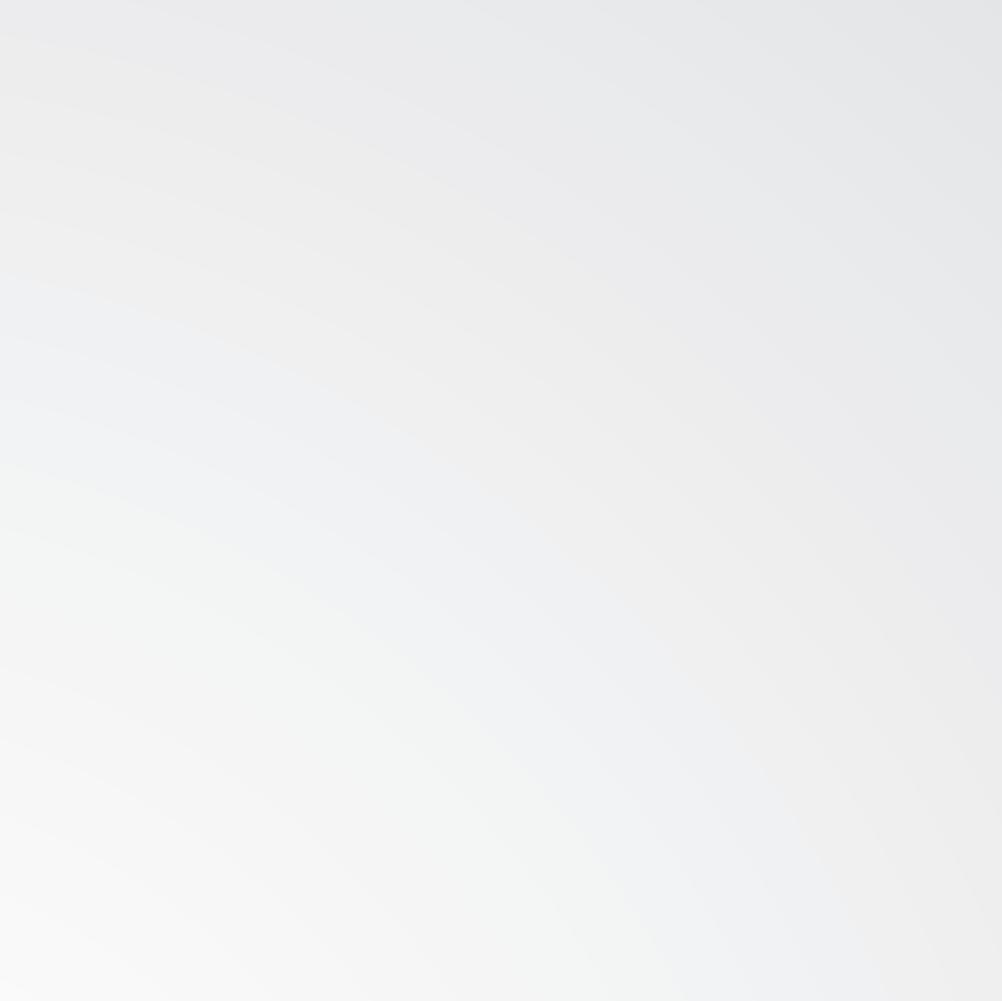
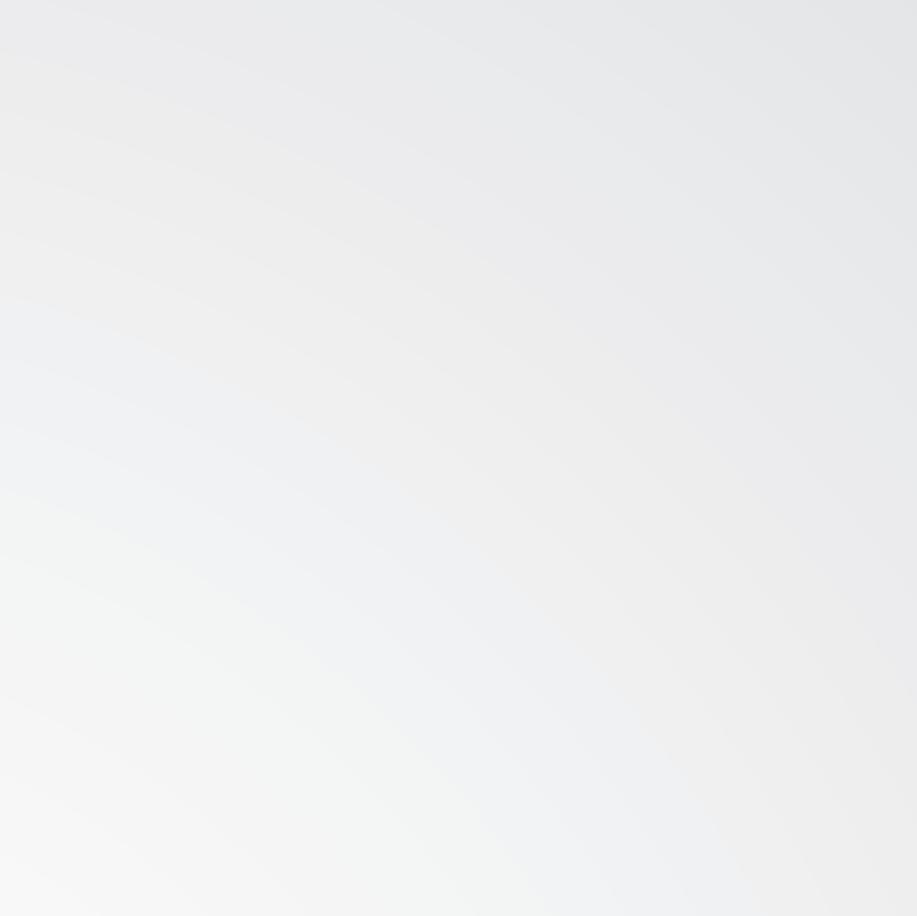


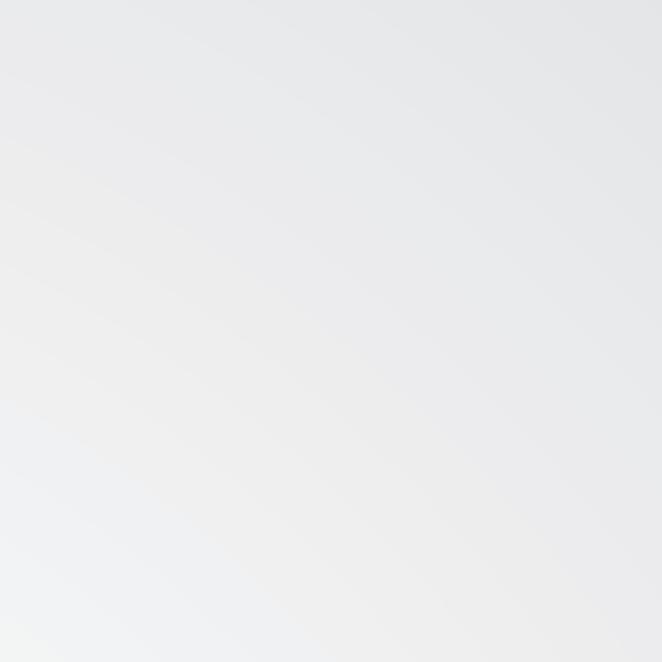

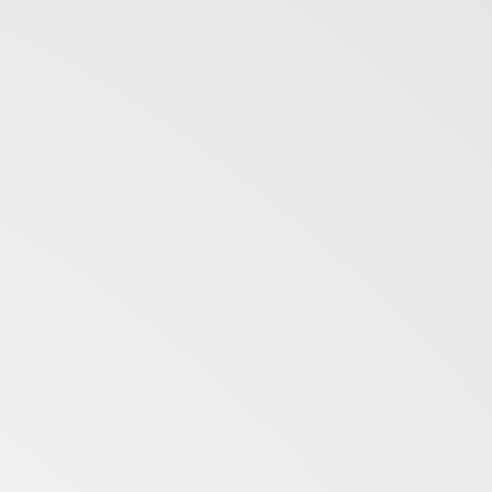
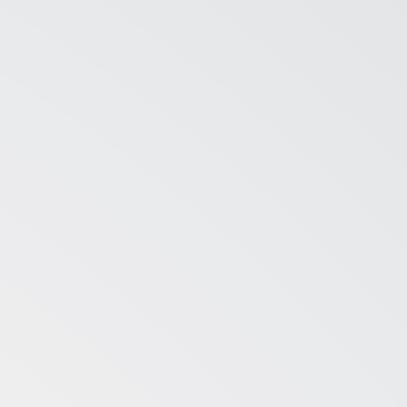
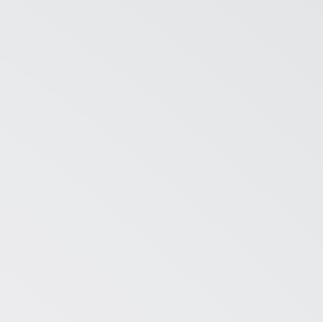
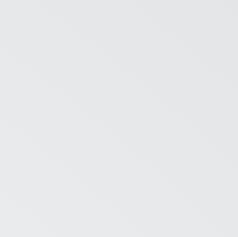
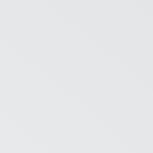






























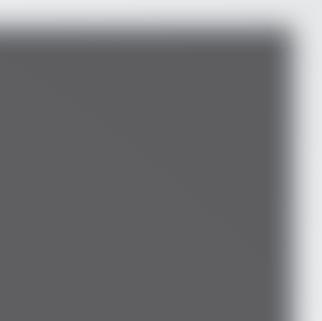
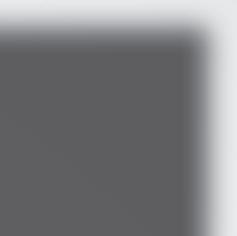
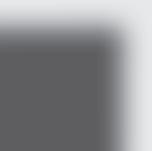













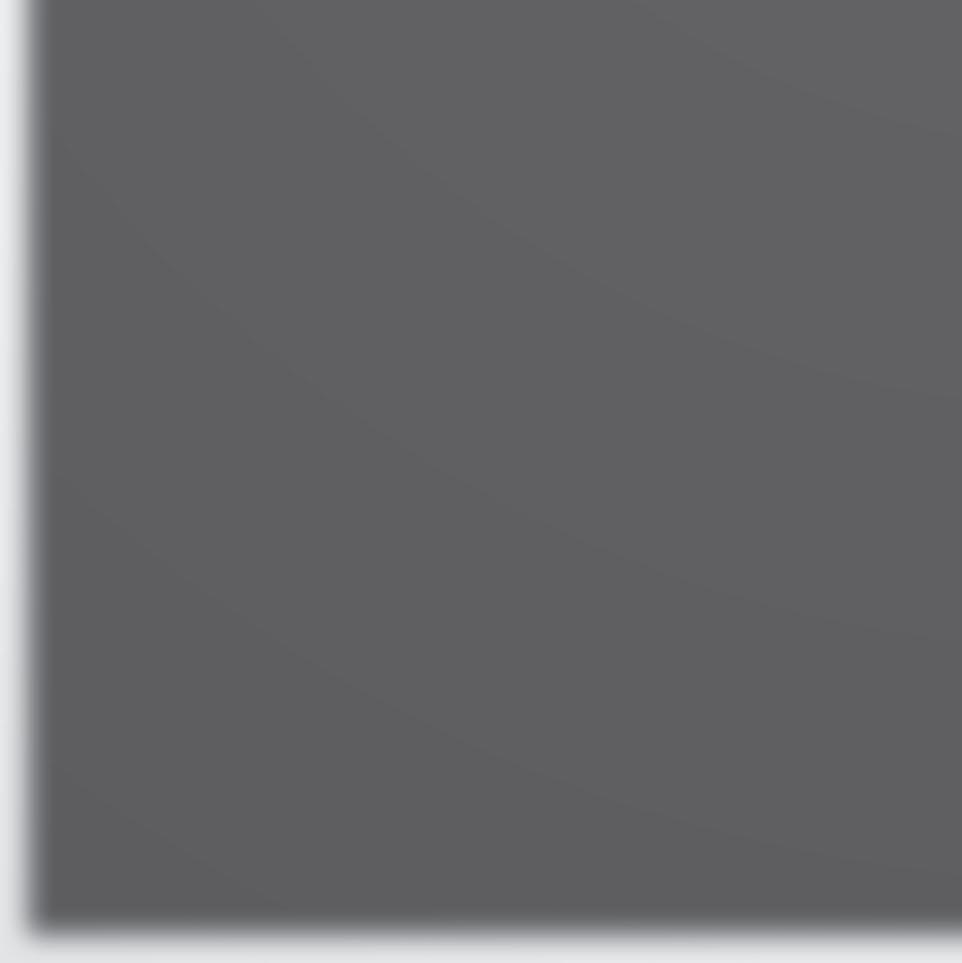
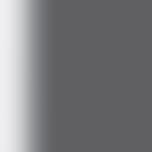
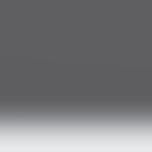

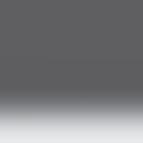
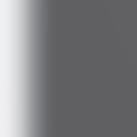
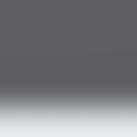
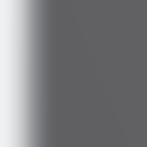
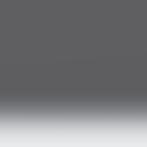
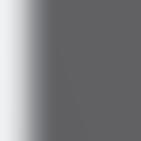

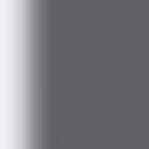

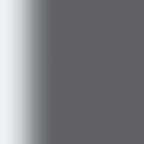
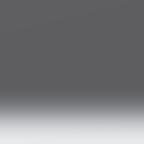
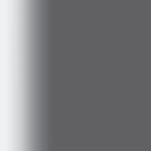

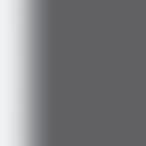


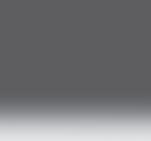































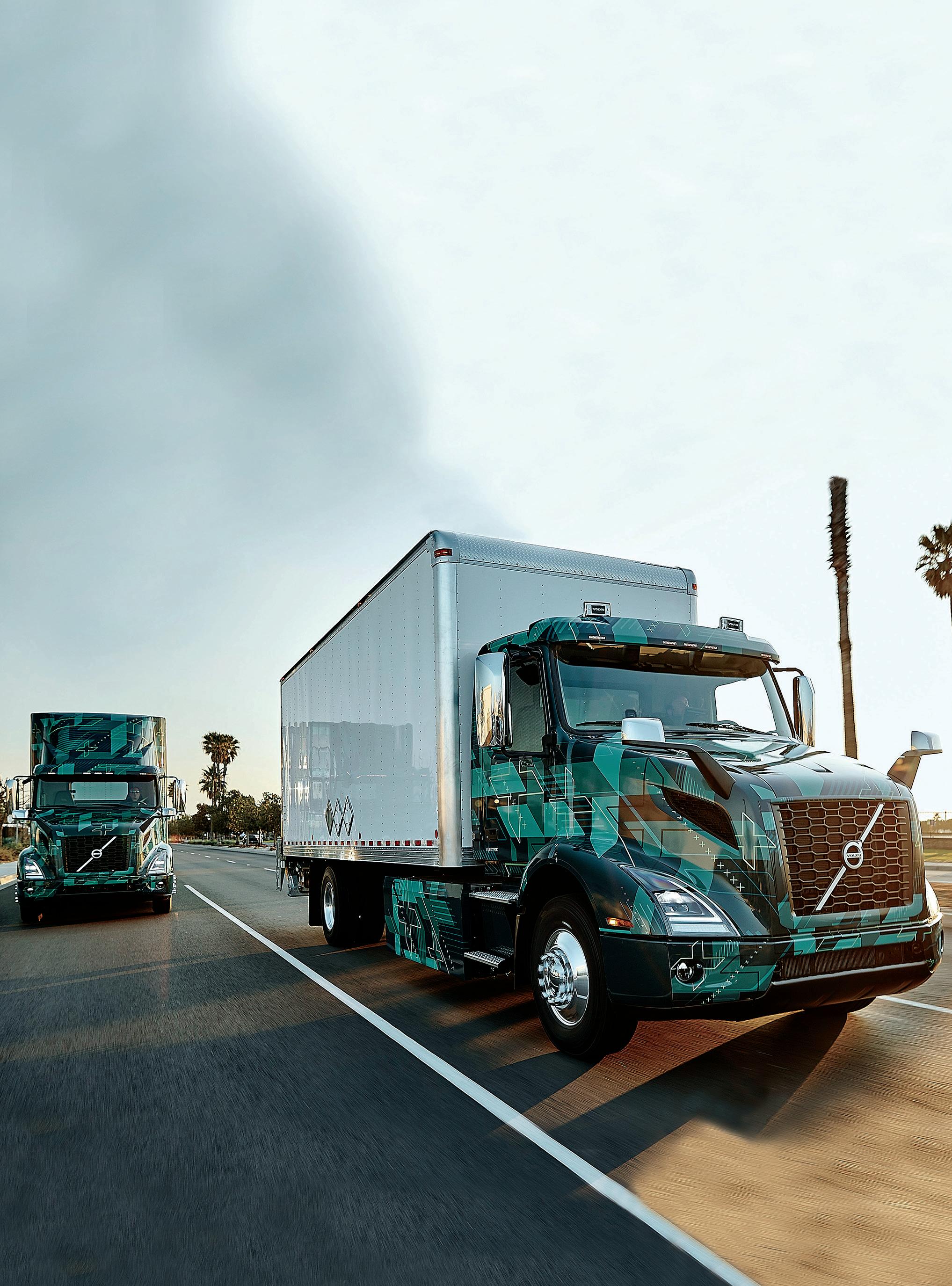
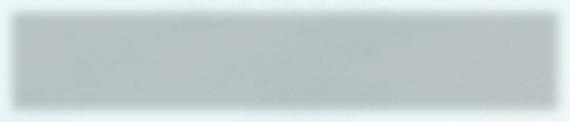
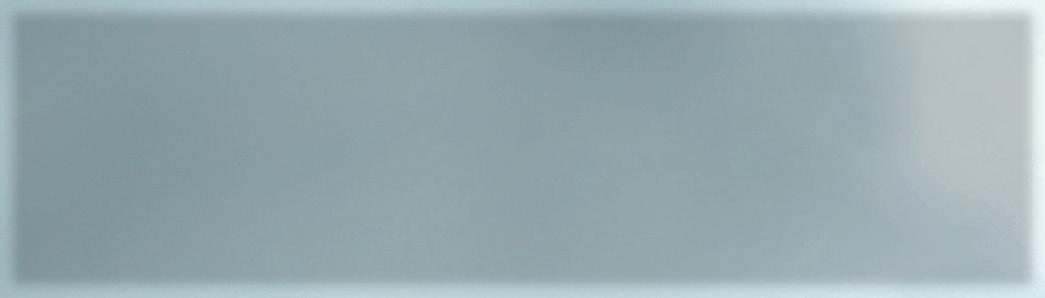
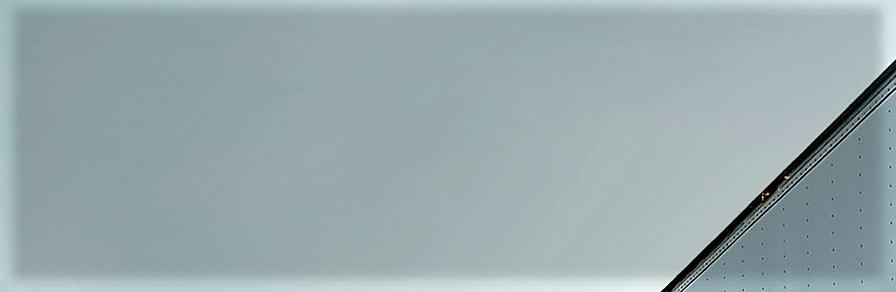










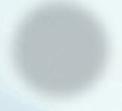
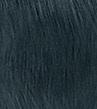
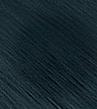
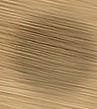
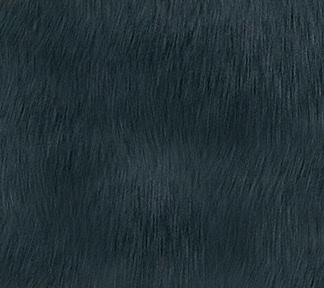
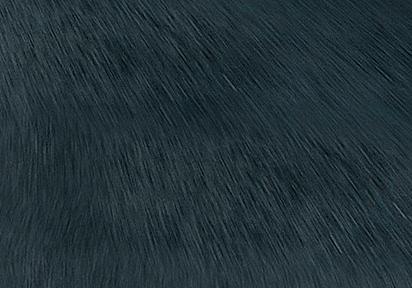
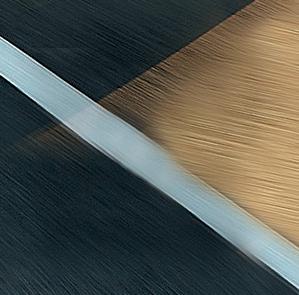
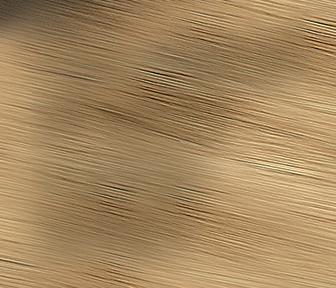
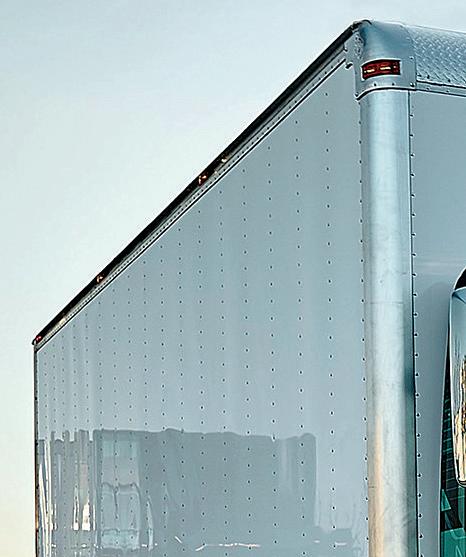

Battery cell, module and pack level charge/discharge cycle testing solutions designed to provide high accuracy measurement with advanced features. Regenerative systems recycle energy sourced by the battery back to the channels in the system or to the grid.
Battery simulation for testing battery connected devices in all applications to confirm if the device under test in performing as intended. Battery state is simulated which eliminates waiting for the charge/discharge of an actual battery. Real time test results include voltage, current, power, SOC%, charge/discharge state and capacity.
To learn more about our Battery Test Solutions visit chromausa.com
chromausa.com | 949-600-6400 | sales@chromausa.com © 2022 Chroma Systems Solutions, Inc. All rights reserved.
NI announces its highest-performing EV battery cycler to date
Li-Cycle opens battery recycling facility in Alabama
COMSOL’s Multiphysics software adds tools for vehicle electrification
Skeleton Technologies launches supercapacitor/battery
AM Batteries secures $25 million in financing for its dry-electrode technology
New DC-DC converter features GaN Systems power transistor
Avery Dennison introduces two new adhesive products for EV batteries
Bosch begins motor production at Charleston plant
LG Chem to build major cathode plant in Tennessee
MAHLE Powertrain to open EV test facility in Michigan
Keysight Technologies launches new DC emulator for testing EV fast charging
ZF’s new e-axle for pickup trucks features 800 V SiC inverters
AMP raises $17 million for its energy management platform
Metis’s Battery Safety Sensor earns ISO certification, enters UK production
Interplex releases new stackable multi-row board-to-board connectors for EVs
Piedmont Lithium wins $142-million DOE grant for Tennessee lithium project
Fleets tested Volvo VNR Electric Class 8 tractors for three years: Here’s what they learned
Amazon to invest a billion euros to electrify its fleet in Europe
Bollinger and Wabash to develop last-mile refrigerated delivery truck
EU confirms 2035 zero-emission sales mandate for new cars and vans
Electrify America launches a new brand-neutral EV marketing campaign
Mercedes-Benz unveils electric trucks for construction site applications
Automakers and infrastructure providers ask UK government for ZEV mandate
Rental agency Sixt to buy 100,000 BYD EVs for European market
Komatsu presents 20-ton-class Proterra Powered electric hydraulic excavator
EPA announces first grants from School Bus Program to 389 school districts
VinFast secures $135 million for electric public bus fleet
Deutsche Post DHL orders 2,000 electric delivery vans from Ford Pro
Foxconn launches new pickup and crossover EVs
Buick to introduce its first Ultium-based EV in China
New Mercedes eSprinter delivery van demonstrates 300-mile range
Volta Trucks and Siemens partner on Truck as a Service offering
Domino’s to roll out fleet of 800 Chevy Bolts nationwide
CHARGED Electric Vehicles Magazine (ISSN: 24742341) October-December 2022, Issue #62 is published quarterly by Electric Vehicles Magazine LLC, 2260 5th Ave S, STE 10, Saint Petersburg, FL 33712-1259. Periodicals Postage Paid at Saint Petersburg, FL and additional mailing o ces. POSTMASTER: Send address changes to CHARGED Electric Vehicles Magazine, Electric Vehicles Magazine LLC at 2260 5th Ave S, STE 10, Saint Petersburg, FL 33712-1259.
PG&E to offer vehicle-to-grid export rate for commercial EVs
Electrify America unveils megawatt-level battery energy storage system
Shell acquires German commercial EV infrastructure provider
Franklin Electric introduces switchgear for DC fast charging stations
NAPA collaborates with Qmerit to offer EV charging solutions
GSA expands contract with Eaton to include EV infrastructure
Québec charging network launches heavy vehicle charging pilot
Fermata launches new V2X bidirectional charger
TeraWatt to build truck charging corridor along I-10 from Long Beach to El Paso Electric Era’s new turnkey EV fast charging solution for convenience stores
Delta Electronics demonstrates 400 kW solid-state transformer-based charger
FLO to provide up to 40,000 chargers for GM’s dealer charging program
SAE International launches initiatives centered on EV charging station reliability ev.energy’s new Pando is a cloud-based EV charging management platform
ADS-TEC’s ChargeBox Dispensers provide battery-buffered indoor charging
Our flexible printed circuits do more than link battery cells to EV electronics. They flex during charging cycles, creating a sleeker, lighter solution that boosts miles per charge.
Put our long history of technical knowledge and consultation to work for you. From engineered materials to innovative circuitry, our vertically integrated solutions are uniquely created to help your concepts take shape.
sheldahl.com
For Letters to the Editor, Article Submissions, & Advertising Inquiries
Contact: Info@ChargedEVs.com
1. PUBLICATION TITLE: CHARGED ELECTRIC VEHICLES MAGAZINE. 2. PUBLICATION NUMBER: 18170. 3. FILING DATE: SEPTEMBER 29, 2022. 4. ISSUE FREQUENCY: QUARTERLY 5. NUMBER OF ISSUES PUBLISHED ANNUALLY: 4. 6. ANNUAL SUBSCRIPTION PRICE (IF ANY). 7. COMPLETE MAILING ADDRESS OF KNOWN OFFICE OF PUBLICATION: CHARGED ELECTRIC VEHICLES MAGAZINE, 2260 5TH AVE SOUTH, #10, ST PETERSBURG, FL 33712. CONTACT PERSON: CHRISTIAN RUOFF. TELEPHONE: (727) 522-0039. 8. COMPLETE MAILING ADDRESS OF HEADQUARTERS OR GENERAL BUSINESS OFFICE OF PUBLISHER: CHARGED ELECTRIC VEHICLES MAGAZINE, 2260 5TH AVE SOUTH, #10, ST PETERSBURG, FL 33712. 9. FULL NAMES AND COMPLETE MAILING ADDRESSES OF PUBLISHER, EDITOR, AND MANAGING EDITOR: PUBLISHER, EDITOR, AND MANAGING EDITOR: CHRISTIAN RUOFF, 2260 5TH AVE SOUTH, #10, ST PETERSBURG, FL 33712. 10. OWNER. FULL NAME: CHRISTIAN RUOFF. COMPLETE MAILING ADDRESS: 2260 5TH AVE SOUTH, #10, ST PETERSBURG, FL 33712. 11. KNOWN BONDHOLDERS, MORTGAGEES, AND OTHER SECURITY HOLDERS OWNING OR HOLDING 1 PERCENT OR MORE OF TOTAL AMOUNT OF BONDS, MORTGAGES, OR OTHER SECURITIES: NONE. 13. PUBLICATION TITLE: CHARGED ELECTRIC VEHICLES MAGAZINE. 14. ISSUE DATE FOR CIRCULATION DATA BELOW: #61, JULY-SEPTEMBER 2022. 15. EXTENT AND NATURE OF CIRCULATION. A. TOTAL NUMBER OF COPIES (NET PRESS RUN). AVERAGE NO. COPIES EACH ISSUE DURING PRECEDING 12 MONTHS: 11050; NO. COPIES OF SINGLE ISSUE PUBLISHED NEAREST TO FILING DATE: 11,650. B. LEGITIMATE PAID AND/OR REQUESTED DISTRIBUTION (BY MAIL AND OUTSIDE THE MAIL): (1) OUTSIDE COUNTY PAID/ REQUESTED MAIL SUBSCRIPTIONS STATED ON PS FORM 3541: 9469; 9562. (2) IN-COUNTY PAID/REQUESTED MAIL SUBSCRIPTIONS STATED ON PS FORM 3541: 0; 0. (3) SALES THROUGH DEALERS AND CARRIERS, STREET VENDORS, COUNTER SALES, AND OTHER PAID OR REQUESTED DISTRIBUTION OUTSIDE USPS: 0; 0. (4) REQUESTED COPIES DISTRIBUTED BY OTHER MAIL CLASSES THROUGH THE USPS: 0; 0. C. TOTAL PAID AND/OR REQUESTED CIRCULATION (SUM OF 15B (1), (2), (3), AND (4)): 9469; 9562. D. NON-REQUESTED DISTRIBUTION (BY MAIL AND OUTSIDE THE MAIL): (1) OUTSIDE COUNTY NONREQUESTED COPIES STATED ON PS FORM 3541: 0; 0. (2) IN-COUNTY NONREQUESTED COPIES STATED ON PS FORM 3541: 0; 0. (3) NONREQUESTED COPIES DISTRIBUTED THROUGH THE USPS BY OTHER CLASSES OF MAIL: 132; 55. (4) NONREQUESTED COPIES DISTRIBUTED OUTSIDE THE MAIL: 895; 829. E. TOTAL NONREQUESTED DISTRIBUTION [SUM OF 15D (1), (2), (3) AND (4)]: 1027; 884. F. TOTAL DISTRIBUTION (SUM OF 15C AND E): 10469; 10446. G. COPIES NOT DISTRIBUTED: 581; 1204. H. TOTAL (SUM OF 15F AND G): 11050; 11650. I. PERCENT PAID AND/OR REQUESTED CIRCULATION (15C DIVIDED BY 15F TIMES 100): .9045; .9153. I CERTIFY THAT 50% OF ALL MY DISTRIBUTED COPIES (ELECTRONIC AND PRINT) ARE LEGITIMATE REQUESTS OR PAID COPIES. 17. PUBLICATION OF STATEMENT OF OWNERSHIP FOR A REQUESTER PUBLICATION IS REQUIRED AND WILL BE PRINTED IN THE ISSUE OF THIS PUBLICATION: ISSUE 62, OCTOBER-DECEMBER 2022. 18. I CERTIFY THAT ALL INFORMATION FURNISHED ON THIS FORM IS TRUE AND COMPLETE. CHRISTIAN RUOFF, PUBLISHER, SEPTEMBER 29, 2022.
We’ve made some major changes to the Charged web site (www.chargedevs. com), including a long list of cosmetic and substantive improvements. e main change you will notice is in how we now organize our content.
For over ten years, Charged has covered the EV industry in-depth in three general areas: e Tech, e Vehicles, and e Infrastructure. Now that the world is nally starting to catch up with our EV obsession and we see rapid acceleration in deployments of large-scale EV and charging projects, we’ve decided to start grouping our content into two main buckets: EV Engineering and EV Fleets & Infrastructure.
e simple goal of the site update is to show readers more relevant content based on the speci c topics they are interested in.
So, for example, when engineers visit our site to watch a webinar about the latest in battery testing technology or how to unleash SiC power device e ciency, they’ll be shown more content suggestions related to those elds of engineering.
Similarly, when a municipal project manager visits our site to read an article about common mistakes to avoid with electric transit buses or managing a eet’s charging schedule to maximize uptime, they’ll see more content related to deploying EV eets and infrastructure.
e new site changes are not just about organization—we’re also greatly expanding our content o erings. e bigger and better format re ects the explosive growth of the EV industry—there’s so much going on that we had to increase our coverage.
Our strong suit has always been our original content, including interviews with experts, opinions, deep dives, and, increasingly, material in webinar and video formats. You can expect to see a lot more of this in the new year. For example, in addition to our EV Engineering virtual conference and webinar series, which has grown enormously popular, we’re also expanding the eet electri cation video series to help those out in the world who are struggling to deploy various EV and charging projects quickly.
As we move into a new Year of the EV, things are moving quickly on multiple fronts.
• Electri cation of heavy-duty vehicles is a hot topic, and industry players are getting together to map out a new transport ecosystem—see John Voelcker’s article on the nal presentation of the Low Impact Green Heavy Transport Solutions project, page 52.
• Meanwhile, charging station manufacturers are o ering products that revolutionize the process of installing infrastructure—see our Q&A with the CEO of Beam Global, page 72.
• Even as vehicles and infrastructure evolve rapidly, engineering remains at the heart of it all—Je rey Jenkins o ers a technical discussion of high-power interconnects and disconnects, page 22.
• One of the biggest near-term challenges our industry faces is building out the battery manufacturing capacity in time to meet short deadlines—on page 28 you will nd six tips for creating high-throughput battery production in record time.
EVs are here. Try to keep up.
Battery labs need power—lots of power—in order to test batteries by cycling them over and over. NI, a provider of automated testing and measurement systems, keeps turning up the voltage. e company has just unveiled its highest-voltage EV battery cycler to date, the High Power System-17000.
is 150 kW battery cycler is designed to support existing EV architectures “while leaving room for future higher-voltage variants as technology continues to evolve.” It features new synchronization capabilities, as well as a modular design that’s designed to o er battery labs increased layout exibility and lower maintenance costs.
In order to support applications beyond battery cycling, such as inverter testing and dynamometer applications, the HPS-17000 has standardized power- and application-speci c breakout sections in the cabinet. is is also designed to enable local service technicians to act quickly should a malfunction occur.
Time-sensitive networking technology allows multiple HPS-17000s to synchronize down to the microsecond, so cyclers positioned tens of meters apart can reliably operate in parallel. is synchronization also extends to high-accuracy current and voltage sensor units, so battery design and test engineers can readily correlate cycler actions with external measurements at microsecond-level resolution.
Additional features include: modes ranging from 400 V to 1,500 V; high-frequency test signal production; support for EIS and ACIR applications; parallel operation via time synchronization over Ethernet; and time-stamped setpoint streaming for large, distributed deployments.
Battery recycler Li-Cycle has announced that its Alabama Spoke plant in Tuscaloosa has started commercial operations.
e Alabama Spoke uses Li-Cycle’s patented technology to recycle and directly process full EV battery packs without any dismantling through a submerged shredding process that produces no wastewater. Li-Cycle says its full pack processing capability improves e ciency, and can process the growing variety of EV battery architectures, including cell-to-pack formats that have limited options for dismantling.
e Alabama Spoke is strategically located to support the recycling needs of the company’s growing battery supply customer base in the southeastern US, where several battery and automotive manufacturers are establishing operations. is growth is expected to produce a signi cant amount of battery production scrap and endof life batteries that will require recycling.
“Li-Cycle is creating an essential domestic supply of recycled material to support EV production and assist automakers in meeting their domestic production content requirements,” said co-founder and CEO Ajay Kochhar.
Together with its two other North American spokes— located in Kingston, Ontario and Rochester, New York—Li-Cycle now has a total input processing capacity of 30,000 tons per year, or the equivalent of batteries from approximately 60,000 EVs. By the end of 2023, the company expects to have a total of 65,000 tons per year of processing capacity across its Spoke network in North America and Europe.
e primary output product of Li-Cycle’s Spokes is black mass, consisting of valuable metals, including lithium, cobalt and nickel, which the company will convert into battery-grade materials at its rst Hub facility, which is under construction in Rochester. Li-Cycle expects the Hub to be capable of processing 35,000 tons of black mass annually, with battery materials equivalent to approximately 225,000 EVs. Li-Cycle aims to begin commissioning the Rochester Hub in 2023.
Skeleton Technologies has introduced a new product that combines supercapacitors and batteries, and has joined a coalition of nine members, including oil giant Shell, that aims to electrify mining equipment.
e SuperBattery doesn’t use any cobalt, copper, nickel or graphite. e company says it can last for 50,000 cycles. It is currently being used or tested in hybrid and fuel cell vehicles and charging infrastructure.
“Skeleton’s patented Curved Graphene material allows for 100 times faster charging compared to standard lithium-ion batteries,” says the company. “Used in o -road vehicles, SuperBattery can be charged in less than a minute, therefore requiring much less charging time spent per day: less than an hour, whereas 6.5 hours are needed with a lithium-ion battery.”
Skeleton says it plans to begin mass production of the SuperBattery in 2024.
“We are proud to work alongside Skeleton—and our consortium members—to develop a new pilot o ering of electri cation solutions for o -road vehicles and to demonstrate how partnership and close collaboration can help mining businesses meet their environmental goals,” says Shell VP Grischa Sauerberg.
“ e pilot o ering combines ultra-fast charging with Skeleton’s new SuperBattery, in-vehicle energy storage, and power provisioning and microgrids,” says Skeleton.
AM Batteries (AMB), a pioneer in lithium-ion dry-electrode technology, has closed a $25-million Series A nancing round led by Anzu Partners. Other investors include TDK Ventures, Foothill Ventures, Toyota Ventures, Zeon Ventures, SAIC Capital, VinFast, Doral Energy-Tech Ventures and Creative Ventures.
AMB will use the funding to expand its team and accelerate its commercialization e orts, advance its roll-to-roll manufacturing pilot line to a production-grade line for customers, and extend its dry-electrode manufacturing platform to new battery chemistries and technologies such as solid-state batteries. Massachusetts-based AM Batteries was founded in 2016. e company says its dry-electrode manufacturing technology allows for the coating of Li-ion battery electrodes with no need for harmful solvents or energy-intensive evaporation. Compared to the conventional slurry casting approach, AMB’s dry-electrode process “completely eliminates solvent recovery and electrode drying, which reduces energy consumption of a battery plant by 50%, saves 40% of capital equipment in electrode manufacturing and potentially produces higher-energy, faster-charging and lower-cost lithium-ion batteries.”
To manufacture battery electrodes, AMB uses an electrostatic spray deposition technique by which the cathode and anode active materials are electrostatically charged and deposited onto metal foil current collectors, which are then processed to their nal state.
“One of the fundamental problems for battery manufacturers today is re ning manufacturing techniques to remove the toxic solvents used in wet-coating of electrodes,” said Yan Wang, AMB co-founder and CEO. “ e progress we have made at AMB is a major step forward in solving this problem.”
A new DC-DC converter from Renesas Electronics includes a GaN-on-silicon power transistor made by GaN Systems.
e GS61008P is a 100 V enhancement-mode power transistor that provides a 46% reduction in system size, according to GaN Systems.
Renesas’s new DC-DC bidirectional converter is designed for 48 V mild hybrid vehicles and electric motorcycles, and includes an automatic phase drop function, an ISL78226 PWM controller and a half-bridge driver.
“A combination of GaN with the automatic phase drop function achieves highly e cient power conversion even at low loads, exceeding 94% power e ciency over a wide load range of 400 W to 3 kW,” says GaN Systems. “ e half-bridge driver ISL78420/444 provides an easy and cost-e ective method of driving GaN transistors.”
GaN Systems says the converter enables “a 46% reduction of the PCB area by leveraging the excellent switching capabilities of GaN Systems’s transistors—enabling a high-e ciency power converter with a high switching frequency of 500 kHz. is allows the use of very small 1.3 µH inductors, which leads to a signi cant decrease in size and weight.”
Tape and adhesive company Avery Dennison Performance Tapes has introduced some new tape and rubber adhesive products for EV applications.
e single-sided, conformable and dielectric tape can provide electrical insulation for EV batteries.
“ is dielectric material uniformly maintains its thickness, and the polyurethane facestock prevents electrical arcing, which can lead to shorting and res in the battery pack,” says the company. “ e single-coated tape design is durable and creates an instant bond, eliminating the need for cure or dry times.”
e Flame Tough Rubber adhesive is a ame-retardant and halogen-free adhesive which is recommended for runaway barrier, compression pad and electrical insulation applications. e adhesive meets the UL 94 VTM and UL 94 standards. It’s part of the Flame Tough rubber adhesive product line, and the company says it has higher tack and adhesion than the line’s acrylic and silicone adhesives.
e new adhesive will be available in transfer tape and double-coated versions.
Bosch has begun production of electric motors at its Charleston, South Carolina manufacturing facility. e company plans to invest an additional $260 million to further expand production of electri cation products at the site.
Bosch is producing rotors and stators, and assembling the motors, in a building where diesel powertrain components were once made. e company announced in January 2020 that it would wind down production of diesel components, and work to expand its electri cation-related business.
Now the company says it has secured additional electromobility orders that require expansion at the plant—an additional 75,000 square feet will be added to the existing 200,000-square-foot facility to make room for future production. e expansion, including the deployment of new high-tech manufacturing equipment, is expected to be complete by the end of 2023.
Bosch’s range of motors can deliver anywhere from 50 to 500 kW of power, and 150 to 1,000 Nm of torque. Voltages range up to 850 V, and applications include passenger cars and light commercial vehicles.
“We have grown our electri cation business globally and here in the North American region,” said Mike Mansuetti, President of Bosch in North America. “We’ve invested more than $6 billion in electromobility development, and in 2021 our global orders for electromobility surpassed $10 billion for the rst time. Local production helps to advance our customers’ regional electri cation strategies, and further supports the market demand for electri cation.”
As part of the site transformation, Bosch has provided reskilling and upskilling opportunities to associates to prepare for the production of electric motors. e company is also collaborating with local schools to add electrication topics to the curricula. e Bosch Community Fund has made $2.5 million in grants for STEM education in the Charleston area since 2013.
Image courtesy of BoschLG Chem has signed a memorandum of understanding to establish a new cathode manufacturing facility in Clarksville, Tennessee.
Manufacturing plants for batteries and other EV components are popping up all over the country these days, and the announcements invariably mention President Biden’s In ation Reduction Act, which o ers incentives for companies to establish supply chains here in the good old USA. LG Chem says its new Tennessee facility will allow it to “proactively address the changing dynamics of the global battery material market and with legislation such as the In ation Reduction Act.”
“LG Chem’s decision to invest $3.2 billion in Clarksville is a testament to Tennessee’s unmatched business climate, skilled workforce and position as a leader in the automotive industry,” said Tennessee’s Republican Governor Bill Lee. “I thank this company for creating more than 850 new jobs.”
e 420-acre plant is expected to have an annual production capacity of 120,000 tons of cathode material by 2027—enough to power 1.2 million EVs. Construction will begin in the rst quarter of 2023, and mass production is expected to start in the second half of 2025.
e new facility will produce NCMA cathode materials containing nickel, cobalt, manganese and aluminum for next-generation EV batteries. LG Chem says the plant will incorporate its most advanced production technology, including the ability to produce more than 10,000 tons of cathode material per line. e company plans to automate the entire production process, and to establish a quality analysis and control system that will be “the benchmark for all other cathode plants in the world.”
LG Chem says the new facility will rely completely on renewable energy provided by solar and hydroelectric power.
MAHLE Powertrain is planning to establish a new EV powertrain testing facility at its engineering center in Plymouth, Michigan.
e company is investing $4 million in the facility, which is designed for testing, developing and calibrating two- and four-wheel drive platforms.
“As well as full powertrain testing and calibration work, the facility will enable the development of powertrain systems, the calibration of transmissions, hybrid and battery-electric powertrain con gurations, Real Driving Emissions (RDE) measurements and electric vehicle range determination,” says MAHLE.
e facility will include dynamometers for up to 7,000 Nm of instantaneous torque per wheel with an average torque response time of 0.5 ms, a 623 kW battery emulator with a future expansion capacity of more than 1 MW, a test cell for ADAS assessments, and a testbed for US and EU emissions rules.
e facility will be able to accommodate a maximum wheelbase of 4.5 meters, and will be capable of testing at temperatures from -10° to 40° C.
“ is investment underscores our determination to provide world-class services to our clients through the provision of state-of-the-art facilities and expertise,” says Managing Director of MAHLE Powertrain USA Hugh Blaxill. “ e new facilities will extend our unique capabilities to cover client requirements both in the US and globally, and will prove an invaluable resource for light-duty and heavy-duty manufacturers alike. Crucially, this means we are able to conduct a signi cant amount of development and validation work without requiring a large number of prototype vehicles to be built by the manufacturer.”
Test and measurement technology company Keysight Technologies has introduced a new DC emulator product series, which is designed for EV fast charging applications.
“Our next-generation high-power DC emulators, based on silicon-carbide technology, are greater than 96% e cient and provide more power and higher voltages in less space, when compared to similar systems,” says Keysight VP omas Goetzl. “When combined with the SL1047A Charging Discovery System, it enables our customers to test all aspects of high-power DC fast charging in their labs.”
e SL1800A series Scienlab Regenerative DC Emulator can emulate EV batteries up to 1,500 V and up to 900 A, and can accommodate DC charging testing up to 270 kW.
e company says the emulator also has a “regenerative system that returns power to the grid when acting as an electronic load during EV battery emulation/ charging tests.”
Superior lifecycle thermal protection combined with the mechanical performance of a compression pad.
Ultrathin, Lightweight Solutions
Optimum thickness for maximum energy density.
PyroThin can accommodate thermal and mechanical requirements of pouch and prismatic cell architectures.
ZF has introduced an e-axle designed for Class 1-6 pickup trucks in the North American market.
e eBeam Axle is composed of a motor, transmission, solid axle, and the company’s 800 V SiC inverters. It is intended for 400 and 800 V systems, and is capable of supporting up to 350 kW and 16,000 Nm per axle.
“ e eBeam Axle allows for the same level of performance as traditional internal combustion engine-powered pickup trucks, speci cally in towing capacity, torque and smooth acceleration required for hills or steep inclines, while providing quiet operation, one-pedal driving, unchanged ground clearance and the ruggedness expected from a pickup truck,” says the company.
EV energy management specialist AMP has closed a Series A funding round that raised $17.25 million. e funds will be used to speed up the development of ampOS—a connected energy management platform composed of the company’s ampCloud, battery management system and a bidirectional onboard charger. e company says its technology is aimed at accurately assessing the health of battery packs, providing improved battery pack management, supporting V2G and informing nancial services involved in warranties and insurance for EVs.
“Our company’s technology will shrink the upfront and operating costs of both the mobile and stationary battery sectors,” says AMP CEO Anil Paryani.
Metis Engineering has earned ISO certi cation for its Production Battery Safety Sensor, which designed to monitor the health of a lithium-ion battery pack and detect cell venting. e sensor was developed using ISO26262 processes, and has been tested to ISO Automotive Standards by Applus+ 3C Test, an independent testing house.
Manufacturing of the production version of the Battery Safety Sensor has begun in the UK to ll orders from OEMs and Tier 1 suppliers, which are using them in ASIL B applications.
“Our Battery Safety Sensor measures pressure change and volatile organic compounds (VOCs) for the detection of cell venting, which is an early stage of thermal runaway,” said Metis Engineering Managing Director Joe Holdsworth. “It also monitors humidity, dew point and air temperature parameters to ensure that the battery continues to operate in optimum conditions.”
e sensor is designed to pick up a range of environmental parameters to ensure that the battery continues to operate in optimum conditions, and has an optional accelerometer to record shock loads. is data can be used to crosscheck with other inputs, such as cell temperatures, to check for cell venting. e sensor relays the data over a con gurable CAN interface to a control unit, such as the vehicle’s ECU, to alert the driver that cell venting has occurred. e sensor can also trigger a process to cut the circuit to the battery pack, allowing it to cool down and prevent thermal runaway.
Metis says its Battery Safety Sensor typically detects venting within seconds.
“ e early detection of cell venting is vital to the safety of the vehicle’s passengers and everything in the immediate proximity. We hope that this sensor o ers an a ordable part of the solution,” said Holdsworth.
Interplex, a manufacturer of interconnect products, has released a new product that allows multiple connector units to be stacked together.
e company’s Multi-Row Board-to-Board (BTB) connector product features a proprietary “snap-in biscuit design.” According to Interplex, this allows interconnections to be appropriately sized, eliminating the need for custom-built units.
e new BTB connectors feature copper alloy 0.4 mm miniPLX press- t pins with low levels of contact resistance (<1 mΩ) and a 3 A current-carrying capacity.
e new connectors are available in board stacking heights from 7 mm to 30 mm, and can have between one and six rows, with up to 30 contact terminals per row. According to the company, they’re capable of withstanding high humidity levels (8-hour cycling up to 10% RH), shocks (35 g for 5 to 10 ms across ten axes) and vibrations (8 hours per axis). ey support a working temperature range of -40° to 150° C (-40° to 302° F).
Interplex expects its new BTB connectors to be used primarily in EVs—speci cally for electric power steering and ECUs.
Piedmont Lithium has been selected to receive a $141.7-million grant from the DOE, one of the rst wave of projects aimed at expanding domestic supply of battery raw material funded by the Bipartisan Infrastructure Law.
e funding will support the construction of Piedmont’s Tennessee Lithium project, which has a budget of approximately $600 million and a goal of establishing lithium hydroxide production capacity of 30,000 metric tons per year.
e Tennessee Lithium project is located in McMinn County, Tennessee. e aim is to produce lithium hydroxide from spodumene concentrate using a process developed by Finnish rm Metso Outotec, which Piedmont says will deliver lower emissions than traditional processes.
Construction is to begin in 2023, and production expected to commence in 2025.
Piedmont is also developing projects in Quebec, Ghana and North Carolina. When its current portfolio of lithium assets becomes fully operational (by 2026), the company expects to be producing 60,000 tons per year of lithium hydroxide in the US. Piedmont estimates that the new US battery plants currently in the pipeline will require a collective 600,000 tons per year.
“ e US government is putting investment dollars behind its policies to support energy independence and national security, and we are grateful to be selected to help spur critical, domestic development of the EV battery supply chain,” said Piedmont CEO Keith Phillips. “Over 80% of lithium hydroxide production today occurs in China. is grant will accelerate the development of the Tennessee Lithium project as a world-class lithium hydroxide operation, which is expected to more than double the domestic production of battery-grade lithium hydroxide in the US.”
e subtle—and entirely informal—di erence is that an interconnect is directly or manually operated (inserting a plug into a jack, for example) while a disconnect is indirectly or automatically operated, for example the moving contacts in a light switch, circuit breaker or contactor, or the fusible link in a fuse (which is “operated” by opening up from overcurrent). is might seem to be a distinction without (much of) a di erence, but a notable one is that the typical interconnect uses contacts that slide past each other, whereas most disconnects use contacts that meet (or pull apart) directly, with minimal to no sliding component to their motion.
Generally speaking, the four main design objectives for high-power interconnects and disconnects are: 1) minimizing contact resistance; 2) resisting mechanical wear from each operational cycle; 3) preventing contact degradation from all operational and environmental causes (e.g. arcing, corrosion, etc.); 4) maintaining safety during both normal and abnormal (fault) conditions.
One of the rst considerations is how to bring the contacts together to close the circuit (i.e. the “make” operation), and how to pull them apart to open it (i.e. “break”). In the case of plug and socket type interconnects which conform to a standard, such as CHAdeMO or J1772 for EV charging stations, these details are going to be dictated to the design engineer, with precious little room for deviation even in those all-toofrequent cases in which the standard doesn’t quite anticipate all the challenges imposed by physical reality.
e next parameters to consider are the circuit conditions, primarily: the voltage and current to be handled; whether it is AC or DC; and whether the circuit is predominantly resistive, inductive or capacitive in nature. While it’s probably obvious that making or breaking under heavy load should be avoided if many cycles of operational life are desired, it’s perhaps less well appreciated that contacts designed for high current can become progressively more
In the electrical/electronic world, the terms interconnect and disconnect both refer to a means of joining two sides of a circuit together.
resistive from repeatedly making/breaking under no-load conditions (aka “dry switching”). is is due to the buildup of sul des and/or oxides on the contact surface, which requires either a su cient current ow during the make operation to punch through them (read: a su cient voltage di erence), or a strenuous sliding/wiping action, which will itself result in accelerated wear of the contact surfaces (a case in which the cure is arguably as bad as the disease). Otherwise, when circuit conditions are predominantly inductive, it is the break operation that is most stressful, because of the arc that will jump across the opening contacts if it is not suppressed with a snubber of some sort (e.g. a metal oxide varistor, resistor-capacitor circuit, etc.).
Conversely, when circuit conditions are predominantly capacitive—as typically applies to the input to a charger or an inverter—then it is the make operation that is most hazardous, due to the extreme current which will ow if the voltage di erence is not reduced with a pre-charge circuit just prior to closing the contacts (with, for example, a smaller relay and resistor wired across the main contacts).
e nal circuit condition that greatly a ects interconnect/disconnect design is whether AC or DC is being switched. AC of a given power level is far easier to deal with, because the voltage and current periodically cross through zero (e.g. 100/120 times per second for 50/60 Hz, respectively), which will tend to extinguish any arcs that might form during the break operation (there is less bene t to switching AC during the make operation, since it is practically impossible to synchronize the closing of a contactor—much less a human inserting a plug into a socket—with the zero-crossing of the AC voltage waveform). Note, however, that at a high enough voltage and/or with an insu cient contact separation distance (exacerbated by
separating the contacts too slowly during the break operation), mains-frequency AC will happily re-strike an arc 100/120 times per second. Two solutions o en employed in higher-voltage disconnects are magnetic blowouts, in which magnets placed on either side of the contacts push the arc away as they separate; and lling a sealed contactor with sulfur hexa uoride, a gas with a dielectric strength approximately 2.5 times higher than air (however, it is a potent greenhouse gas—the “no free lunches” rule strikes again).
As is so o en the case in engineering, optimization of one parameter comes at the expense of another, and so it is with electrical life vs mechanical life vs corrosion resistance for the contacts in an interconnect or disconnect. For plugand-socket interconnects (by far the most common type), the contact surfaces will almost certainly slide past each other during the make/break process, and this is where the heartache of mutually exclusive goals begins. e rst pair of contradictory goals is that minimizing the contact resistance requires the contacts in plug and socket to meet with high force, but that then makes the plug too di cult to insert or remove from its mating socket. For plugs/sockets that are only infrequently mated—such as for a dryer or electric range—straight blades in the plug that must force apart curved leaf-spring contacts in the socket are acceptable, despite requiring 10 kg or more of force to mate in the case of dryer and range interconnects.
An AC charging station port on an EV handles a similar maximum amount of power to an electric range (i.e. 240 VAC / 50 A), but requiring a similar 40+ pounds of force to insert the plug into its charging port would not be welcomed by any EV owner (to say nothing of the fact that the combo would wear out a er 100 or so uses). One practical solution is to use round pins that mate with sockets that are
It’s perhaps less well appreciated that contacts designed for high current can become progressively more resistive from repeatedly making/breaking under no-load conditions (aka “dry switching”).Eaton’s ‘Breaktor’ device for EVs combines the high-voltage protection device functions of fuses, pyro switches and contactors into a single coordinated device Image courtesy of Eaton
a cylindrical hyperboloid in shape (strongly resembling a “Chinese nger trap”), as this will achieve a much higher total contact area between each pin and socket, while requiring even less insertion/removal force. A cylindrical hyperboloid socket is much more expensive to manufacture, of course, but this is a case in which the less expensive solution—straight blade interconnects—is simply unworkable, rather than merely not as good.
To continue the theme of tradeo s, improving the mechanical and/or corrosion-resistance properties of a contact material tends to come at the expense of lower conductivity, so it is very common to make the contact out of one metal or alloy, and then plate another metal/alloy onto it. For contacts that can be protected from the atmosphere (e.g. inside a sealed contactor), the emphasis can shi from achieving the highest corrosion resistance to minimizing both metal transfer from arcing and contact resistance, but the contacts in the plugs and sockets of EV charging stations must contend with all three requirements: good corrosion resistance; good mechanical fatigue and wear properties; and low contact resistance (albeit with less need to minimize material transfer from arcing…or that should be the case, anyway).
e highest conductivity (aka lowest bulk resistivity) is obtained with silver, of course, but the best corrosion resistance is obtained with the platinum group metals, or gold. While silver can be a good choice of contact material inside of a sealed contactor, or for bolted-together connections (such as
bus bars), it too readily forms oxides/sul des (aka tarnish or patina) if exposed to the atmosphere/pollution, and it is also quite a so metal in its pure form, so it wears poorly and tends to deform, rather than spring back, from impact, meaning it’s not the best choice, whether contacts come together directly or slide past each other. Alloying silver with copper greatly improves the mechanical properties compared to either pure metal, but then the conductivity drops below that of pure copper (around 92% IACS for sterling silver). Of the platinum group metals, palladium is most commonly used both in alloys and as a plating for contacts, as it has excellent corrosion resistance and decent hardness without being too brittle, making it a preferred choice for sliding contacts. On the minus side, its conductivity is much worse than that of pure copper (16% IACS) and it is exceptionally expensive, of course. Rhodium has better conductivity than palladium (about 38% IACS), and is much harder as well (about 3x to 4x), but that also means it is more brittle, so perhaps it’s an even better choice for sliding contacts, rather than those that meet with considerable impact force.
e nal consideration is operational and environmental safety, which mainly consists of not exposing live conductors, if applicable, and not catching on re due to overload, an external ignition source, arcing, etc. e latter objective can be met by only using materials which are non-combustible and which won’t melt at too low a temperature. Operational safety can be much more di cult to achieve for interconnects that are handled by a person, like the charging plug for an EV fast charger, compared to devices located inside a charger or inverter, such as a contactor or a fuse. A decent—if not foolproof—solution is to simply shield the contacts on the live side of an interconnect in two dimensions (so that sliding along the third axis is still
possible). is is the strategy employed by every electrical outlet found in the home, a er all, and though it has arguably stood the test of time, it is still possible to stick a foreign object into the outlet terminals, or only partially insert the plug into the outlet, thereby exposing the live circuit to a child’s (or a fool’s) ngers. Consequently, a more thorough solution is to use retractable shutters over the pins, sockets, or both, which automatically retract upon insertion of the plug into its receptacle.
Lastly, the means by which wires are terminated into their respective contacts is critical to overall safety (and e ciency). At low currents, a spring-cage, or “screwless,” clamp is a very reliable solution, as the spring ensures that the wire strands are pressed against the terminal cage despite vibration or cold- ow displacement of the copper. Screw clamps are used at current levels from a few amps up to around 10 or so, because they can apply far more compressive force for a given housing volume. From 10 amps to several hundred, crimping a lug onto a stranded wire cable is the termination of choice, as it has the lowest possible resistance, good resistance to vibration, and good to excellent corrosion resistance. For extra longevity and corrosion resistance, lugs can be lled with dielectric grease before inserting the cable and crimping it. e grease is forced out from every interface between the cable wires and the lug wall, e ectively sealing o the crimped area from air, liquids, etc. Much the same would be accomplished by soldering the cable into the lug, but that is never done—at least not for cables that will be subjected to exing or vibration—because the solder causes embrittlement and fatigue cracking of both itself and the copper wires over time. De nitely not something you want happening to a DC fast charger cable carrying a few hundred amps!
Two solutions often employed in higher-voltage disconnects are magnetic blowouts and filling a sealed contactor with sulfur hexafluoride, a gas with a dielectric strength approximately 2.5 times higher than air.Sensata Technologies’ GXC and MXC series of smart contactors Image courtesy of Sensata Technologies
Batteries represent nearly one third of the total price of a typical EV, and there’s a push to get that down to 20% or less by the end of this decade. In an e ort to lower costs and accelerate production, the EV industry has been searching for ways to make the assembly process more e cient and to decrease the time it takes to create a battery assembly line. New highly-automated battery assembly lines usually take months to develop. Can that be accelerated?
In 2020, precision automation company DWFritz needed to develop a complex battery production line for a leading North American battery manufacturer. e requirements included high speeds, a tight footprint and an accelerated development time.
Considering the complexity of the project and the short development time, DWFritz decided to form a strategic partnership with automation supplier Bosch Rexroth. Together, the two companies operated in a concurrent engineering environment, allowing for rapid design iteration
and accelerated execution.
“In the past, we would have used several di erent suppliers,” explained DWFritz President Mukesh Dulani, “but just to start the collaboration between di erent suppliers, in this case, would have taken us at least 10 to 15 weeks. For this project, we only had 12 weeks of design and engineering time and 8 weeks for procurement, so we had to work with a partner like Bosch Rexroth who could supply the technology and the engineering support for us to be successful.”
No matter the cell size or form factor, battery manufacturing is a complex, multistep process that brings together dissimilar materials to form the battery’s cathode and anode, then combines them with the insulator into a nished package.
“ e line had to operate at very high speeds,” said DWFritz VP of Sales Chris Povich. “Space was also a challenge. Even though the line is more than a hundred feet long, it had to be designed to t into a very tight
footprint. And the motion platform had to handle very robust motion-control demands—one system alone had in excess of 50 axes of motion.”
Together, the two partners say they managed to create a new battery manufacturing line that met the client’s requirements and set a new benchmark for building out production capacity.
To learn some tips for creating new production lines quickly, Charged recently chatted with Bosch Rexroth’s Mark Ziencina.
Q Charged: With all the new activity and incentives for local production in EV manufacturing, demand must be pretty high for your automation expertise.
A Mark Ziencina: e demand is absolutely incredible. I’m the Vertical Manager for Battery and EV at Bosch Rexroth, the automation division of Bosch. I have 28 years of factory automation experience in components and capital equipment, and what we’re experiencing now is through the roof. Our group specializes in solutions for the battery and EV segments, drawing from our past experience with battery technology and working with a variety of partners and customers in the battery and EV markets.
e challenge is to keep up with the demand, and I’m not even talking about the chip shortages and other supply chain issues. Everyone agrees that globally, this market is going to be growing at about a 23% compound annual growth rate. However, in North America, we see it growing a lot faster than this, because we’re trying to catch up with China and other Asian countries who jumped into the market early.
With all the incentives and new requirements, as well as all the money pouring into the EV market, everybody
needs equipment now. Everybody wants batteries. ey all want it at the same time. So, it’s a good problem to have, and with enough experience you can learn how to get it done with available resources.
Q Charged: Rexroth recently published a case study about its partnership with DWFritz, detailing how you were able to cut time to implementation for new cell production. What do you think are the most important tips to accelerate time to market?
A Mark Ziencina: DWFritz was looking for an automation supplier for that cell project that had all of the various solutions that they needed, such as material transfer conveyors, Cartesian systems, and linear actuators that had high precision, extreme reliability, and the ability to work in cell assembly environments. ey were also looking to execute the project in a very short time frame, as opposed to the standard 12-month execution time.
ey chose us, and we became an extension of their engineering department. Our applications engineers worked side-by-side with their design engineers to shrink the design time through concurrent engineering, multiple iterations, and a lot of back and forth.
Tip #1: Limit the number of strategic partners and suppliers to form a small group with experience operating in a concurrent engineering environment to allow for rapid design iteration and accelerated project execution.
Tip #2: Use a digital twin design that allows you to test the systems while you’re waiting for the hardware to arrive and be installed.
For all of these manufacturers, time to market is critical right now. Partnering with the right equipment builder and the right automation supplier will help to meet those goals, as opposed to managing a basket of di erent suppliers who do not have the holistic view of the project and may or may not have the depth of experience in these applications and processes.
On this project, a completely virtual development environment enabled the team to create a digital twin of the communication platform between Manufacturing Execution System (MES), the so ware that runs manufacturing operations in a factory, and automation controllers, saving an enormous amount of time.
Q Charged: How did the footprint requirements of the manufacturing line a ect the development time?
A Mark Ziencina: Small footprints can create a lot of challenges that delay design time if the team doesn’t have the right experience. For example, we used our MTpro layout so ware to design conveyors that t into the tight machine footprint and also provided the machine-to-machine connection. In some instances, the machine was so jammed with automation—40 to 50 axes of motion in one frame—that there was not enough space for a control enclosure to t all of the drives. So, we went with our cabinet-less technology, which has motors with onboard servo drives, to eliminate the need for a huge box full of servos. Everything was distributed throughout, which facilitated a more compact system.
Q Charged: In terms of length of the projects, what has been the historical development time for a standard cell line, and what is the industry pushing towards now?
A Mark Ziencina: Depending on the complexity of the project, typically, it was 12 to 14 months to execute an entire line, maybe a year and a half. Now everyone wants to
Tip #3: Use an open machine control architecture that allows real-time data access and machine-to-machine communication. This keeps all of the production modules in sync and allows operators to monitor and control the processes.
shrink this down to 6 to 8 months or less. So the challenge is, what can we pull from our past experience? What modules and solutions do we have in our product portfolio that could shrink that design time?
We work on the design side as well to o oad that from the customer’s and the manufacturer’s plates. Drawing from our knowledge of cell, module and pack assembly applications, we choose solutions, customize them for the particular product, and shrink that down.
We also pool all of the raw materials required for our products. We can closely estimate how many conveyors, for example, will be required for a project and have them in stock so we’re not waiting on parts. So, while the design is still ongoing, we bring in the materials, and then as soon
Tip #4: Work with automation and equipment suppliers during the product design stage to address the subtle design details that affect the assembly development process.
as the design is complete, we can start sending the nal drawings to the manufacturing oor. We do everything we can to shrink the design window and the production execution window by working very closely with the customer.
Q Charged: What are the most common material bottlenecks that typically delay a project?
A Mark Ziencina: Everything is in short supply—even small
Multiphysics simulation helps in the development of innovative battery technology by providing insight into mechanisms that impact battery operation, safety, and durability. The ability to run virtual experiments based on multiphysics models, from the detailed cell structure to battery pack scale, helps you make accurate predictions of real-world battery performance.
» comsol.com/feature/battery-design-innovation
Tip #5: Choose suppliers that are well-versed in multiple open-protocol technologies and customizable offthe-shelf modules. This allows users to write their own application-specific modules, avoids the need to design everything from scratch, and provides the ability to reuse the modules in future product lines.
things like T-nuts for aluminum framing. But most commonly, it’s the chip shortage that’s really impacting all the automation suppliers. Lead times on motor controllers can be 12 months or more. Worldwide, there is no manufacturing sector that is isolated from the chip shortage. Preparing, planning ahead, and reserving that capacity ahead of time is key, because it can really impact the installation and ramp up of these new lines and new capacity.
Q Charged: What other factors are important to assure a successful execution?
A Mark Ziencina: It’s really important to pick reputable suppliers that have a global footprint and a local presence, plus experience in the battery manufacturing
space. Additionally, experience with standardization to open protocols is key because you have to bring many solutions under the same umbrella. is assures compatibility without tying you to one particular supplier. ere are so many manufacturers with di erent platforms for control architectures, and every manufacturer tries to lock their customers into their speci c ecosystem. We went directly against that with our ctrlX open architecture controller design, for example, which can be programmed in any of the common languages. It’s compatible with anyone’s products. It includes apps that users can write themselves, so they’re not locked into a certain programming environment. You don’t have to nd specialists who know a speci c language or development platform—you can get programmers to program in Python, C/C++, Java, or whatever they like, to get the entire automation executed. Our controls directly communicate all the way up to the MES. It’s important to pick the right architecture and standardize so you don’t have to support and stock a lot of di erent products.
Tip #6: Use Industry 4.0 technology such as smart sensors, vision algorithms and component tracking systems to perform inspections throughout the assembly process.
This helps to pinpoint problematic areas and provides upstream feedback that can bring about production line changes to account for incoming material variability, precision assembly tolerances and high-throughput demands.
Learn more Considering the extent of current e orts to ramp up EV production capabilities and source battery components made in North America, we can expect to see a number of manufacturers trying to fast-track their assembly lines.
ey may want to take a lesson from the DWFritz/Bosch Rexoth partnership.
ese two companies recently presented at the 2022 Charged Virtual Conference on EV Engineering. To learn more about the project, check out the webinar recording.
Battery disconnect unit featuring Breaktor®
Power levels in electric vehicles are increasing. EVs need to drive farther and charge faster. What does this mean for system safety? Expertise is critical when managing, distributing and protecting electrical systems. Eaton’s advanced battery disconnect units (BDUs) feature integrated Breaktor® circuit protection technology, enabling EV manufacturers around the globe deliver the safest vehicle systems possible.
Because that’s what matters.
Learn more at: Eaton.com/eMobility
We make what matters work.
Engineers are always looking for cost-e ective ways to get the most range out of an electric vehicle’s battery pack. Exro Technologies is triangulating on a solution with three core concepts: motor control, battery charging and powertrain optimization. Exro’s patented Coil Driver technology took home the Gold in the 2022 Edison Best New Product Awards in manufacturing, logistics and transportation. e original idea has now launched its own spin-o technology that enabled fast AC charging, eliminating the vehicle’s onboard charger and facilitating vehicle-to-everything (V2X) capabilities.
Exro’s newest partners include Vicinity Motor Corporation, which is piloting Exro’s high-voltage Coil Driver in its Lightning eBus, and evTS, which will use Exro’s low-voltage Coil Driver starting in 2023. Exro has innovation and manufacturing centers in Calgary, Phoenix and Ann Arbor, and a growing list of partners and products.
Charged recently chatted with Josh Sobil, Exro’s Chief Commercial O cer, to learn more about the company’s technology, its history and its vision for the future.
Q Charged: Exro started with an idea for a unique motor control system. Can you tell us how it works?
A Josh Sobil: Electric motors are designed to deliver either high torque or high speed, depending on the way in which
the coil windings are con gured. Applications that need both torque and speed usually require either a motor/gearbox combination or more than one motor, adding weight, cost and complexity to the system. Exro’s core technology is a unique motor control system, the Coil Driver, in which the motor coils are wound so that they can be recon gured on the y to e ciently provide the requisite torque or speed, without the need for a gearbox or multiple motors. e theory behind the Coil Driver is the ability to drive the machine in two di erent con gurations. You can start the machine in a series con guration, which provides a high current density and a very high torque. en it can switch to a parallel situation, which reduces the impedance of the coils and delivers more power while maintaining the motor’s e ciency. e key advantage is the ability to expand that e ciency map or that torque envelope, and get more out of the same frame, so we can reduce the machine’s cost and improve its performance. e Coil Driver gives the engineer another option to tweak the design of the powertrain and get more out of the machine.
ere are cases where we use smaller machines to get the same amount of power and torque that’s required out of a given drive cycle, or we get rid of components like the twospeed gearbox in applications that only need a low gear to provide ve to ten seconds of very high starting torque. We see a lot of that in the commercial vehicle space. Any time you can remove components and improve e ciency, it’s an advantage to our customers [because] they can either reduce the size of the battery or remove other components that might be more costly.
Exro Technologies is building a future in which an EV’s motor, drive, gearing and AC charging system are integrated into one highly compact and efficient system.
You can start the machine in a series confi guration, which provides a high current density and a very high torque. Then it can switch to a parallel situation, which reduces the impedance of the coils and delivers more power while maintaining the motor’s effi ciency.
“ ”
A Josh Sobil: It shi s in about ten milliseconds. We have noticed a little kick, but in a commercial vehicle or a car, it wouldn’t even register because the inertia would just absorb it. On a motorcycle or something small, there might be a little kick, but we can program it so you don’t feel it.
at’s part of our secret sauce—the ability to switch very quickly without a torque interruption, especially in commercial vehicle applications. Having a torque interruption is quite a big deal because you’ve got so much inertia to overcome. Anytime you’re on a hill and you interrupt the torque it’s just more work that you have to do, and more stress and strain on the actual system. So, the faster you can switch, the more advantageous it is.
Q Charged: Where did the Coil Driver idea come from? What’s the history behind it?
A Josh Sobil: It’s kind of your classic startup story. e founder, Jonathan Richie, was a garage inventor, as they say, with an interest in wind power. He was looking at the fact that windmills generated power at various torques and speeds, only a few of which would be at the optimal setting. At one time, it might only be working at 85% e ciency, versus 96% e ciency at exactly the right load. So he thought, “If I could change the circuit inside the machine [on the y] then maybe I could get di erent operating
points to have higher e ciencies [across the whole operating curve]. If I could start to meld those together, then I could see an overall increase in generator e ciency.”
As a startup in a garage, the challenge was breaking into a wind generation market that’s working with megawatt-level machines. Designing products for that market was prohibitive from the start. at’s not to say that it’s not a good use case—I think it will be, but there was also an EV market opportunity that was building. An EV motor has a pro le where, if you look at a machine’s torque curve and then plot all of the operating points that an EV actually operates under, it almost lls the entire torque map. So we determined that this is probably a more accessible market, just from a commercialization standpoint. For example, we could design a hundred-kilowatt inverter for an o -highway application, which is a lot less stringent than even an automotive application or a wind power application. So there are ways to get into the
Q Charged: Can you feel the shi when you switch the topology of the drive, like shi ing gears?Images courtesy of Exro Technologies
EV market, although the barriers to entry are absolutely massive. We’re looking to our partners to help bring us into the bigger automotive sector.
Q Charged: ere must be a cost-bene t analysis that you work through with the di erent applications, like o -highway or commercial trucks. What’s the main application that you’re working on right now?
A Josh Sobil: We’re looking at urban and highway applications, which require a very high peak e ciency across the entire operating range—what’s called an e ciency island—and that’s exactly what the technology does. So if the vehicle is operating at low speed, we can deliver the torque to get started, maybe to climb a very steep incline. at might provide a new route that a garbage truck can take in the city, improving the e ciency of the overall operation. And there’s an expansion of that curve so that the e ciency is better at highway speeds as well. at’s de nitely where we see the Coil Driver shine. ere are applications that require a lot of torque down low, but they also need power at highway speeds. at’s a very typical trade-o in any electric machine. A gearbox gives high torque, but it can’t increase power. So we’ve seen a lot of interest in the o -highway sector, and even in
motorcycles, which need a lot of power at the high end, but also want to be light. e powertrain is a key component of the vehicle’s weight—the battery and the motor are going to be very heavy components. If we can lightweight the motor and still deliver the power and torque, then it’s a good application. We’re also working with partners in the passenger car sector. By removing the onboard charger and integrating three-in-one con gurations, we’re reducing both cost and weight. And that’s what we’ve seen the OEMs wanting. When you show an e ciency bene t, they’re going to ask,
We’re looking at urban and highway applications, which require a very high peak effi ciency across the entire operating range—what’s called an effi ciency island—and that’s exactly what the technology does.
“ ”
“How much smaller can I make my battery?” at’s the dollar factor that they’re going to apply.
Q Charged: You mentioned removing the onboard charger. How does Exro’s technology a ect battery charge control?
A Josh Sobil: at feature was a byproduct of the way the topology was built up. What’s interesting is the ability to do this with an AC frequency, so you don’t need a DC supply to charge quickly. If you have a very high continuous power that you can send through the powertrain, you can charge at a considerably higher power than what you might get out of a DC fast charger. It’s something that we’ve been testing and proving out, and we’re expecting to release it in our second generation of drives. We’ve now got a patent pending for the ability to charge through the Coil Driver.
All of our high-voltage products can accept this, so you could use it in a passenger vehicle as well. We’ve demonstrated charging above 20 kW right now, just with the standard Coil Driver. Once we move to the higher powers, then we have continuous power ratings up into the hundreds of kilowatts, so this is something you could put on a passenger car. You would need to look at the infrastructure and ensure that the plug was appropriate, but it would replace the EV’s onboard charger.
E ectively we’re using the drive itself as the onboard charger. It’s a four-quadrant drive, so we can run power in both directions. e same way you would regenerate while you’re braking, you can convert AC power to DC power through the drive. And that’s fundamentally all we’re doing. An inductive component is needed to do that, so we use the motor’s inductance.
Q Charged: Why doesn’t everyone design a motor drive that can also be used as the onboard charger?
A Josh Sobil: Good question. Fundamentally, because the motor would produce torque, so you can’t use the machine unless it produces no torque. If you were to apply the current through a typical motor, it would naturally start turning. With the Coil Driver, since we can control the individual coils, we apply the current in an opposing fashion, so the torque cancels itself inside the machine. You have to make sure to cool the drive,
obviously, because you’re going to have current and you’re going to have losses, but those are the main di erences.
And I should also [point out that] there are others that have looked at doing this with a six-phase drive by opposing three of the phases. So we’re not the only ones that can do this, but it’s an added feature to what we’ve been able to do with just the topology of the drive itself and the way that we connect it to the machine. We don’t change anything in the drive, and fundamentally a drive can connect as a recti er in that same way, but it’s the way that we connect that allows us to produce zero torque out of the machine. at’s a native advantage to the technology that, in all honesty, we realized a bit a er the fact. We were focused on the torque envelope and e ciency and then we thought, “ ere’s discussion out there about using the drive as a charger, so could we use this?” So we made sure it worked and about a year ago we applied for the patent. Now it’s becoming a focal point because it’s a huge cost-saving feature.
Powertrain optimization Exro o ers engineering services to help its customers design or modify motors to accommodate its Coil Driver technology. e company provides a co-development platform to customize inverter controls that reduce the need for multiple motors and/or gearboxes and optimize battery usage.
Q Charged: So when you call it a three-in-one system, what three components are you referring to exactly?
Effectively we’re using the drive itself as the onboard charger. It’s a four-quadrant drive, so we can run power in both directions. The same way you would regenerate while you’re braking, you can convert AC power to DC power through the drive.
“ ”
A Josh Sobil: e term three-in-one system refers to the drive, motor and gearing as an integrated drive unit. ey’re known as e-axles or integrated drive units on the automotive side. And then you can imagine how much more compact it is without the charger, so you can do everything with that integrated drive system. at’s our vision—our roadmap for the future is really around being able to integrate everything in the EV’s powertrain. Trying to lightweight, downsize and make everything more compact at a system level has a desirable impact on cost.
Q Charged: Suppose you’re talking to a potential customer and they just want to increase the e ciency of an electric garbage truck. As a general example, how would you estimate the potential e ciency gains with your Coil Driver system?
A Josh Sobil: What we’ve been simulating—and it obviously depends on the drive cycle a little bit—shows that commercial trucks tend to have around a 3-4% range increase. If you can remove 4% of a 200 kWh battery, at $135 a kilowatt-hour, then you’re saving roughly $1,000. Or you can keep the same size battery and get 4% more range at no extra cost.
We’ll be starting some real-world drive cycle testing this winter. We’re excited about that. It’s coming with one of our partners for an e-axle on a commercial truck.
Q Charged: So, you have the custom power electronics design and you couple that with a custom-wound motor. Will you always supply that combination as a package?
A Josh Sobil: Depending on the customer, yes, we’ll sell it as a system. Some customers will design their own machine and we will couple the inverter to their motor.
Fundamentally, we are not a motor manufacturer, but the technology requires that in some cases we have a machine to sell. We are not changing the magnetic design of the machine—we’re changing the way we connect to its coil groupings. It’s more of a mechanical interface for the cables. e drive itself just replaces a standard inverter, but what you would see are twelve connections—four per phase—going into the machine.
Q Charged: e fundamental hardware di erence is that you have an inverter with a lot more switches than a standard one, right?
A Josh Sobil: Exactly. We’re still using standard switching devices—the topology of the drive is what’s di erent. e circuit is unlike any other drive that’s out there because we’re driving individual coils, so it doesn’t look like a typical three-phase drive. But we still use silicon carbide (SiC) devices. In our high-voltage inverter, we’re using a standard PCB design and manufacturing methods. Eventually, we’ll get to a bare die construction on the drives.
Q Charged: What phase of commercialization are you in now? What are the next steps for Exro?
A Josh Sobil: Right now, we’re in our launch phase starting in ‘23. We have some early partners that have placed orders for equipment. ey want to see samples at the end of this year so they can start to validate into the next year. We’re building a drive manufacturing facility in Calgary and plan to produce drives for commercial and o -highway applications by the third or fourth quarter of next year.
A Josh Sobil: Fundamentally, the company is focused, obsessed and passionate about power electronics. We are also working on ways to optimize power on the battery side. We’ve developed a battery control system that manages individual cells, very similar to managing individual coils, so it’s taking that granular philosophy and transferring it over to the storage side. It’s in our R&D pipeline, and we’re going through the UL approval process on that storage unit.
Q Charged: Do you have any other products in addition to Coil Driver?
The circuit is unlike any other drive that’s out there because we’re driving individual coils, so it doesn’t look like a typical threephase drive.
“ ”
Amazon is moving full speed ahead to electrify its European vehicle eet. e delivery diva will invest a billion euros ($975 million) over the next ve years in electric vans, trucks and low-emission package hubs in Europe.
Amazon said the plan is to expand its electric van eet in Europe from the current 3,000 vehicles to over 10,000 by 2025, but didn’t say what percentage of its last-mile delivery eet those gures represent.
e company also hopes to purchase some 1,500 heavy-duty electric trucks (such as the Tesla Semi, Freightliner eCascadia or Volvo VNR Electric) to move goods between ports and logistics centers.
Amazon didn’t say what brands of EVs it’s looking at, but it has ordered 100,000 electric delivery vans from Rivian, and a few of these have been spotted on the streets making deliveries. e retail leviathan has also ordered EVs from Mercedes, Lion Electric and Volvo.
In addition to purchasing new vehicles, the online octopus will deploy thousands of additional EV chargers at European facilities, and will double the size of its European network of “micro-mobility” hubs. Amazon currently makes deliveries via electric cargo bikes or on foot, using centrally located hubs in 20 European cities.
Bollinger Motors (now a subsidiary of Mullen Automotive) has teamed up with truck body and trailer manufacturer Wabash to develop a refrigerated truck body on an electric chassis.
Wabash has developed a lightweight composite technology called EcoNex Technology, which it says will seamlessly integrate with Bollinger’s Class 4 electric chassis cab and deliver signi cant weight savings, leading to increased payload capacity and lower costs.
EcoNex is made with a high-e ciency foam core, encapsulated in a polymer ber-reinforced shell and a protective gel coat. Wabash says it can boost thermal performance by up to 30%, while reducing weight by up to 20%, and that the structural strength eliminates the need for metal or wood.
“Wabash’s EcoNex composite technology reduces the amount of electricity needed to maintain cold temperatures,” said Mark Ehrlich, VP of New Business Development at Wabash. “ e all-electric truck we’re developing with Bollinger Motors will be highly e cient, with more uptime and less charging compared to conventional construction.”
“I’m excited to help green up the journey from farm to table,” said Robert Bollinger, founder and CEO of Bollinger Motors, who was inspired to start the company while he owned a farm in upstate New York.
Amazon to invest a billion euros to electrify its fleet in EuropeImage courtesy of Amazon Image courtesy of Bollinger Motors
e European Commission has agreed to set a zero-emission sales mandate for new cars and vans by 2035. As the average age of passenger cars in the EU is just under 12 years, this policy should put the bloc on track to reach the target of converting its eet to zero-emission-only by 2050, the date by which capitals have agreed to be net-zero. Separate legislation covering CO2 standards for trucks and heavy vehicles is on the agenda for next year.
“ e agreement…sends a strong signal to industry and consumers: Europe is embracing the shi to zero-emission mobility,” said EU Green Deal Chief Frans Timmermans.
Politico expressed surprise that the decision was reached so easily. “Previous EU e orts to regulate incremental improvements in vehicle fuel e ciency standards dragged on for years, with acrimonious lobbying and demands for exemptions and special conditions. is time around, it’s taken just over 15 months since the legislation was presented in July last year to nalize the 2035 phaseout target.”
“ ere is a huge consensus” within the car sector that it’s time to move, one industry executive told Politico. “Nobody is questioning that there needs to be an increase in the targets…Instead it’s just the how and when.” is doesn’t mean there was no wrangling: France lobbied to exempt plug-in hybrids from the ban; Italy sought to protect its luxury supercars; Renault, BMW and Volkswagen said they need more time; and Hungary, Italy, Romania and Slovakia, along with Germany’s Free Democratic party, pushed for a loophole that would allow sales of vehicles running on e-fuels to continue. In the end, these proposals were rejected, and a deal con rming the 2035 target was reached.
Critics of the mandate raised a number of concerns. Some quite rightly pointed out that making the 2035 target work will require massive investments in charging infrastructure and securing sources of raw materials. Others fear that, as ICE vehicles are phased out Europe, they’ll simply be shipped to developing countries.
Some opponents warned of various nightmare scenarios. German conservative MEP Jens Gieseke fears that the high prices of EVs might lead to a “Havana e ect,” saying, “A er 2035, our streets might become full of vintage cars, because new [electric] cars are not available or not a ordable.”
Other naysayers fear that the EU rules will bene t up-and-coming Chinese carmakers. At the recent Paris Motor Show, China-based brands such as BYD and Great Wall unveiled new EVs aimed squarely at the European market. With that issue in view, the Commission plans to take a lenient stance when it dra s new Euro 7 regulations that will cover non-carbon pollutants such as nitrogen oxides, ammonia and particulate matter.
Electrify America has launched a new brand-neutral marketing campaign titled “As Seen on EV.”
Modeled a er popular streaming television content, “As Seen on EV” aims to correct common misperceptions about EV ownership, particularly those related to driving range and charging access, by highlighting the day-to-day advantages of driving electric.
“Spanning TV genres from dramas and reality-dating shows to telenovela, the campaign showcases the bene ts of driving electric by making EVs the star of the show,” says EA.
EA describes its upcoming videos:
• Reality dating show theme—highlights EV attributes of sporty styling and quiet driving along with the ability to charge an EV at home or on the road
• Historical drama theme—spotlights the instant torque and fast acceleration that EVs provide along with generally lower routine maintenance requirements than gas-powered vehicles
• Western theme— showcases range capability and interesting features only found in EVs like the trunk in the front or “frunk”
• Telenovela theme—informs viewers that EVs have zero tailpipe emissions
• Courtroom drama—focuses on the wide variety of models and styles of electric vehicles to suit di erent needs
“Just as streaming TV rede ned how people watch television, EVs are rede ning transportation,” said Misti Murphey, Director of Brand Strategy and Integrated Marketing at Electrify America. “ e As Seen on EV campaign allows us to meet consumers where they are— in the now-familiar medium of streaming TV—to build consumer con dence about EVs.”
Mercedes-Benz Trucks presented several battery-electric trucks for construction site applications at this year’s bauma construction industry trade show in Munich. e manufacturer showed a “concept prototype” of the eActros LongHaul, which features an electric power take-o for semi-trailers such as tippers, making it suitable for deliveries to construction sites. Mercedes has already been equipping the eActros, which went into series production in 2021, for heavy-duty distribution with the appropriate electric power take-o .
Together with partners, Mercedes is also presenting a battery-electric prototype of the Arocs construction site truck as a mixer, featuring high ground clearance and o -road capability.
Mercedes-Benz says about 20% of the trucks it sells in Europe are in the construction site segment, making it the second most important market segment for the manufacturer a er long-distance transport.
“We are working on a completely CO2-neutral portfolio, including the demanding construction segment,” said Karin Rådström, CEO Mercedes-Benz Trucks. “Particularly versatile, robust and powerful trucks are in demand here. It is also a very complex area for electri cation due to the wide variety of applications. Partnerships between vehicle manufacturers and bodybuilders are therefore crucial to o er our customers the right solutions.”
“A lot of CO2 can be saved by complete electri cation. At the same time, low-noise e-vehicles can make a signi cant contribution to noise reduction, especially at construction sites in urban areas. e social and political pressure on our customers is signi cant,” said Stina Fagerman, Head of Marketing, Sales and Services.
It’s anybody’s guess where the UK government stands on e-mobility and clean energy these days. At the moment, UK government policy calls for phasing out ICE vehicles by 2035. But 13 years is a long time, and some in the EV industry apparently fear that the actual implementation of this policy could end up being “not quite the thing.” An ICE ban may sound like a drastic move, but if it doesn’t include interim targets (as California’s Advanced Clean Cars II regulation does), then automakers could delay taking action for another decade, and infrastructure providers and other industry players might have little incentive to invest.
A group of industry stakeholders, including Ford, ChargePoint and battery manufacturer Britishvolt, recently sent an open letter to the UK’s Secretary of State for Transport and Secretary of State for Business, Energy and Industrial Strategy, asking them to resist pressure to water down the proposed ICE ban.
e letter reads, in part:
e decision to ban the sale of new petrol and diesel cars and vans from 2035 puts the UK on track to be one of a G7 country [sic] to transition to electric vehicles. What matters now are the policy levers and enablers to support manufacturers and customers in making that switch. An ambitious Zero-emission Vehicle (ZEV) mandate would guarantee a minimum proportion of electric vehicles on the road from 2024 and provide a clear signal and trajectory to infrastructure investors to accelerate the charge-point roll-out. We understand that the design and ambition of mandate is still being discussed within government and a consultation response is due imminently. We urge the government to move quickly and bring forward legislation to ensure the mandate is operational from 2024, as originally intended.
e bene ts of the UK Government’s leadership on this issue are already visible. High-pro le investments to support the EV transition in the UK have created and safeguarded thousands of jobs, with the prospect of many more to come. e Government’s own assessment estimated that 40,000 extra jobs will be created by the EV transition. From research and vehicle design, to chargers and so ware; to energy
services and the vital ongoing task of installing, supporting and maintaining the vehicles and networks: every corner of the UK has the opportunity to bene t from the transition.
In September, 17% of new cars sold were fully electric. With 11.6% and 6.6% for 2021 and 2020 respectively, we see an impressive level of growth that puts the UK within sight of the 22% oor for 2024 set out in the ZEV mandate consultation. Bringing forward this legislation will provide a clear and dependable signal to infrastructure providers on EV supply, de-risking chargepoint investment decisions. is signal is crucial to help accelerate the weekly installation rate of new public charging infrastructure. Front-loading the chargepoint roll-out is essential to boost consumer con dence, especially where customers do not have access to home or work charging infrastructure. As manufacturers bring more EV models to market and sales continue to climb, any risk of oversupply of chargepoints becomes negligible.
Given the success of the UK government’s approach in driving take-up of electric vehicles thus far, we would encourage ministers to protect the current ZEV mandate trajectory by limiting the exibilities allowed under a ZEV mandate, to avoid watering down the impact of the investment signal. Allowing manufacturers to “borrow” extensively against future deliveries of electric vehicles, thereby dampening delivery in the early years of the mandate, will weaken the targets and planned CO2 reductions and slow infrastructure roll-out due to the lower number of EVs being brought to market. Such an approach would forfeit the hard-won gains that the UK has made by moving further and faster than the EU on this issue.
A er a decade of talking about renting EVs, major car rental companies (including Hertz, which announced plans in October to order up to 175,000 GM EVs) are now starting to place serious orders. is is excellent news, because o ering EVs to rental car customers could have a multiplier e ect—who’d want to go back to their gas-burner a er driving electric for a week? e latest rental giant to get charged is Sixt, a Germany-based company that operates in 100 countries, including the US and Australia. Sixt plans to buy at least 100,000 EVs from China’s BYD between now and 2028. e deal is a big boost for BYD, which recently began selling EVs in Europe.
Under the rst stage of the agreement, Sixt will order several thousand EVs, the rst of which will be available to customers in Europe, beginning in Germany, France, the Netherlands and the UK, in the fourth quarter of this year. e rst model to be o ered will be the BYD Atto, a compact SUV.
BYD and Sixt will also explore opportunities for cooperation in other regions of the world.
Komatsu showed o a 20-ton-class electric hydraulic excavator at the recent bauma trade show in Munich.
e machine is powered by a lithium-ion battery system from Proterra. Since January 2021, the two companies have been jointly developing electric medium-sized hydraulic excavators, and have been conducting proofof-concept tests on research machines at customers’ construction sites.
Komatsu says the new excavator has achieved digging performance and durability equivalent to those of engine-driven hydraulic excavators. “Hydraulic excavators are the most versatile type of construction equipment, and the mid-size class, in particular, is used in a wide range of job sites and applications, mainly in earth excavation and loading operations, requiring power and durability to withstand heavy-load work,” says the company.
is model integrates Proterra’s Li-ion battery technology with Komatsu’s components, such as the hydraulic pump, controller, and electric motor for work equipment operation. Komatsu has developed a robust cage structure to provide additional protection for the battery packs.
e machine weighs 24,000 kg, and features a 123 kW powertrain. e 451 kWh Proterra Powered battery system enables operation for up to 8 hours when fully charged.
e excavator is scheduled to be introduced to the Japanese and European markets in 2023.
e Clean School Bus Program, part of President Biden’s Bipartisan Infrastructure Law, makes $5 billion in rebates available over ve years for school districts to purchase electric or low-emission school buses.
In May, the EPA announced the availability of $500 million for the rst installment, but because of the overwhelming demand from school districts across the country (and perhaps, the urgency of getting the money out before a new regime on Capitol Hill can kill or cripple the program), the agency increased that amount to $965 million. e application period closed in August, and now the agency has selected (through a lottery system) 389 applications totaling $913 million to support the purchase of 2,463 buses.
Some 95% of these will be electric buses (others have LNG or LPG powertrains), and 99% of the school districts that were selected are in “priority areas,” serving low-income, rural and/or Tribal students. EPA will distribute awards to school districts in all 50 states and Washington DC, along with several Tribes and US territories. More applications are under review, and the agency plans to select more in the coming weeks, to bring the full amount of funding in this round to $965 million.
Recipients can now proceed with purchasing new buses and eligible infrastructure, a er which they must submit Payment Request Forms with purchase orders documenting their investments. e EPA is partnering with the departments of Energy and Transportation to provide school districts with technical assistance to ensure e ective implementation.
e administration plans to make another billion for clean school buses available in scal year 2023, so districts that didn’t get selected in 2022 can try again.
“As many as 25 million children rely on the bus to get to school each day,” said EPA Administrator Michael S. Regan. “ anks to the Biden-Harris Administration, we are making an unprecedented investment in our children’s health, especially those in communities overburdened by air pollution. is is just the beginning of our work to build a healthier future, reduce climate pollution, and ensure the clean, breathable air that all our children deserve.”
e Asian Development Bank (ADB) has arranged a $135-million nancing package for EV manufacturer VinFast. e funds will support the company’s e orts to establish an electric public transport bus eet and a national charging network in Vietnam.
Established in 2017, VinFast is a subsidiary of Vingroup, Vietnam’s largest private enterprise, and some boosters have predicted that it could become “the next Hyundai.” In 2020, the company announced plans to launch eets of electric buses in several Vietnamese cities. Earlier this year, VinFast raised $4 billion to support market launches in Europe and the US. It has opened six stores in California, and is building a $2-billion manufacturing plant in North Carolina.
e climate nancing is certi ed by the Climate Bonds Initiative, a scienti cally-based standard for labeling debt instruments that contribute to addressing climate change. Institutions involved in the nancing package include Export Finance Australia, the Finnish Fund for Industrial Cooperation, the Austrian Development Bank, and responsAbility.
“ is project delivers a high-impact, sustainable transport solution for Vietnam while helping it meet its climate goals and supporting the growth of climatenance in the region,” said ADB Private Sector Operations Department Director General Suzanne Gaboury. “Asia and the Paci c is the frontline of the global ght against climate change, and private sector projects like this one with innovative partners such as VinFast are crucial to help its countries decarbonize their economies.”
Deutsche Post DHL Group is going electric—the German logistics giant plans to invest some 7 billion euros in electri cation between now and 2030, by which date it aims to make 60% of its delivery vehicles zero-emission. e company currently operates a substantial number of Ford EVs at several locations around the world.
Now DHL has announced plans to buy more than 2,000 electric delivery vans from Ford by the end of 2023. Ford Pro, the automaker’s eet division, has already handed over several E-Transits under the agreement, which will join DHL’s last-mile delivery eet in several countries. e order volume concentrates on E-Transit panel vans designed for handling express shipments in the Americas and Europe.
e agreement also includes a suite of eet management products and services, including Ford’s connected E-Telematics so ware and charging solutions.
“Ford Pro and Deutsche Post DHL Group share the vision of greater sustainability and a commitment to electri ed solutions,” said Hans Schep, General Manager, Ford Pro Europe. “E-Transit is the top-selling commercial EV in North America and since June is also the best-seller in its segment in Europe, meaning the all-electric 2-ton van is already making big strides to support this ambition.”
“Electri cation of last-mile logistics is a major pillar to decarbonize our operations” said Anna Spinelli, Chief Procurement O cer and Head of Mobility at DHL. “Adding the new Ford E-Transit to our global eet of around 27,000 electric vans further strengthens our capability of providing green delivery services worldwide.”
Everybody seems to be getting into the EV game these days, but Foxconn, which is famous as a contract manufacturer for Apple, is no newcomer to the eld—it has been working to produce an EV since 2014.
In 2021, Foxconn made a deal with Lordstown Motors, under which it bought a chunk of the latter’s factory, and will help it to produce EVs. Foxy is also building EV plants in Wisconsin and ailand.
Also in 2021, the Taiwanese titan unveiled an EV called the Model C, which was later renamed the Luxgen n7, and is being produced in partnership with Taiwanese automaker Yulon Group.
Now the company has unveiled two new EVs that will…wait for it…eventually be sold in the US! e Model V pickup and Model B crossover hatchback are aimed squarely at the hottest stateside vehicle segments.
e former has a double-cab, 5-seat con guration, a payload capacity of up to one ton and a towing capacity of three tons. e company plans to manufacture it in Taiwan, ailand and the US.
e Model B, which was designed in partnership with Pininfarina, is “based on the Model C platform, but with changes to the platform size and a new body design.” At this point, it’s described as a “concept prototype,” and few specs are on o er, other than a range of 450 kilometers and a 2.8-meter wheelbase.
Foxconn doesn’t appear to have any plans to establish its own brand—rather, most industry pundits expect it to follow its successful model, and manufacture the new vehicles for other automakers. In fact, at the recent unveiling event, Chairman Liu Young-way said that his company hopes to eventually be building a huge share of
the world’s EVs, and even spoke of striking a manufacturing deal with the Big T.
“Based on our past records for the PC and cellphone markets…we’re at about 40-45% of the overall market share,” said Liu. “So, ambitions-wise, hopefully we are able to achieve the same kind of achievement like in the [IT industry], but we will start small, which is about 5% [of the EV market] in 2025. I hope one day we can do Tesla cars.”
If Foxconn could help OEMs alleviate some of their troublesome supply chain problems, that would be a big selling point. “Supply chain resilience has always been Foxconn’s DNA,” said Liu. “Our global footprint in 24 countries gives us a huge advantage to meet EV industry demands.”
As far as a Tesla deal, EV cognoscenti consider it unlikely. Tesla relied on contract manufacturing for the Roadster, but has moved steadily in the opposite direction since those days. Indeed, the company has invested much in perfecting production processes at its Gigafactories, and has touted “the machine that makes the machine” as a product in itself.
Buick will introduce its rst EV developed on GM’s new Ultium platform later this year in China. Deliveries of the ve-seat SUV will begin in the rst half of 2023 and will be followed by a second Ultium-based EV by the end of next year.
Buick’s Ultium-based EV will be equipped with a battery cell made speci cally for the Chinese market, along with GM’s “nearly wireless” battery management system. It will also feature the enhanced Super Cruise driver assist technology, as well as the Virtual Cockpit System jointly developed by GM and PATAC (GM’s automotive engineering and design joint venture in Shanghai).
Buick plans to open up to 58 Buick EV City Showrooms across the country, and more than 600 Buick NEV Zones across its dealership network. e best-selling GM brand in China also plans to install over 400,000 charging poles across the country by the end of 2023.
“With the Ultium platform at their core, the new models will play a strategic role for Buick in China’s highly competitive EV market,” said Cesar Toledo, General Director of Buick Sales and Marketing at SAIC-GM.
Mercedes-Benz is preparing to release an improved version of its eSprinter electric delivery van, and—hurrah!— will start selling it in the US.
e current-generation eSprinter, which is sold only in Europe, manages a mere 93 miles of range. A pre-production prototype of the new version recently took a road trip from Mercedes HQ in Stuttgart to the Munich airport, through the mountains of the Swabian Jura. e van nished the 295-mile journey with about 12 miles of range le in the tank, and logged an average e ciency of 2.8 miles per kWh (no other technical specs have yet been released).
e prototype was tted with the largest of three battery pack options that will be available at launch, and Mercedes says this is the pack that will be included on eSprinter models built for the American market.
e next-gen eSprinter will make its o cial debut in February 2023, and will go on sale soon a er that. Production will begin at two plants in Germany in February, and in Charleston, South Carolina in the second half of 2023.
Commercial EV manufacturer Volta Trucks has signed a letter of intent with Siemens Smart Infrastructure, outlining a partnership to o er a Truck as a Service package that includes so ware control systems, facility electrication, charging infrastructure, energy management, building equipment and project nance.
Siemens will oversee the technical infrastructure of the charging installations, including the hardware and so ware required to operate the charging and power distribution infrastructure for eets of Volta Zeros. Volta Trucks’ customers will also bene t from the Siemens performance management platform, which uses analytical and simulation models and considers factors such as eet duty cycles, charging times, battery life, optimal utilization and costs, and asset management.
e Volta Zero is a purpose-built 16-ton commercial EV designed for urban distribution. It features a range of 150-200 km (95-125 miles), as well as “an innovative, safety- rst approach to cabin design, providing unrivalled visibility for its driver and [enhanced] safety for other road users.”
“To deliver the electri cation of urban logistics at pace and scale, we need operationally e cient electri cation infrastructure aligned to the exact requirement of each eet,” said Volta Trucks CEO Essa Al-Saleh. “In Siemens, we have a world-class partner with the innovative technical solutions our customers will expect.”
Domino’s Pizza has announced a new order of 800 2023 Chevy Bolt EVs. e custom-branded Bolts will arrive at “select franchise and corporate stores throughout the US” over the course of several months.
Domino’s says EVs provide several advantages for the pizza use case. e Bolt o ers enough range for “days of deliveries,” and is expected to have lower average maintenance costs than legacy vehicles. “Electric eet vehicles also provide more opportunity to attract delivery drivers who don’t have a car of their own.” e delivery giant’s US eet currently includes some 112 EVs, and the count is to reach 855 by the end of 2023. e company also uses electric bikes and/or scooters in 24 international markets.
It may be a while before you see a Bolt in Domino livery however, as the new EVs will be distributed throughout the US—according to an interactive map, California will get 105 of them, and Florida will get only 6 for now.
Domino’s is partnering with Enterprise Fleet Management, which will provide local account management, vehicle acquisition, nancing, telematics solutions and maintenance for the EVs.
“Domino’s launched pizza delivery in 1960 with a Volkswagen Beetle [and has] tested autonomous pizza delivery with cars and robots,” said CEO Russell Weiner. “Domino’s has always been on the cutting edge of pizza delivery, and electric delivery cars make sense as vehicle technology continues to evolve.”
“With an a ordable price, fun driving characteristics, and a 259-mile range, the Chevy Bolt EV is the future of Domino’s electri ed deliveries,” said Ed Peper, Vice President of GM Fleet.
Large commercial trucks and other heavy equipment have run on diesel fuel for many decades now. Requirements for more aggressive emission a er-treatment and the hardware to achieve that add cost and complexity for eet operators. Rising fuel-economy standards during the 2020s will do the same. But today, heavy trucks remain a diesel world.
at’s about to change. e far higher volumes of carbon dioxide per mile from heavy trucks make them an obvious target for zero-emission powertrains. Some makers suggest hydrogen fuel cells will be the way to go; the most promising application seems to be long-haul trucking with few or no stops.
However, heavy-duty electric trucks from traditional makers have started to hit the market. Publicity magnet Tesla said it delivered its rst battery-electric Semi tractor on December 1. It has now received a Certi cate of Conformity for the Semi from the EPA. Among its rst announced customers, back in December 2017, was Pepsi, which reserved 100 of the trucks and plans to use them in the California regions of Modesto and Sacramento.
Volvo Trucks (now a separate entity from the carmaker Volvo owned by China’s Geely) knew several years ago it wanted to get into the electric truck business. Its rst model was an electric adaptation of its conventional dieselpowered VNR tractor. It had a 264 kWh battery pack powering the tractor’s twin motors with more than 4,000 lb- of torque and a range estimated at up to 150 miles.
To gure out how to make electric trucks work in practice, the manufacturer, the state of California, and a wide array of partners—more than a dozen all told—launched the Volvo LIGHTS (Low Impact Green Heavy Transport Solutions) project in 2019 to test its rst electric Class 8 tractors with multiple Southern California operators.
e goal was simply to gure out, for a small number of trucks in di erent uses, what worked, what still needed work, and what practical hurdles existed for battery-electric trucks in a previously all-diesel eet.
Altogether, the group’s nal presentation lists 18 insights Volvo and its partners gained from the project. Many were covered in detail during a day of presentations and site visits for partners and media held this past August in Ontario, California.
e overall lesson, repeated frequently, was that multiple entities must come together for electric heavy trucks to succeed—including many that eet operators haven’t dealt with before—and that this has to happen early in the planning process. Put another way: Plan rst, order trucks second.
e rst lesson, one that may seem obvious, is that electric trucks are better suited to some routes than to others. “Identifying ideal routes is key to success,” says the LIGHTS group’s nal report, and the learnings were underscored by the eet operators taking part.
e starting point was routes of 80 to 150 miles a day, but more factors came into play than sheer range. Topography (lots of hill-climbing or mountainous terrain) and weather (extreme heat or cold) have signi cant impacts on an electric truck’s e ective range. In this case, Southern California has fairly temperate weather, and parts of the region are quite at. But the eet operators need to work
Pre-planning and coordination among many partners proved critical to integrating heavy-duty electric trucks into fl eets. While benefi ts are clear, costs remain a challenge.
The group’s fi nal presentation lists 18 insights Volvo and its partners gained from the project.
together with the truck-maker and its dealerships to identify the most promising initial routes for electric trucks.
Driving style also matters. Experienced diesel drivers will need training for electric trucks to maximize use of regenerative braking, which can recapture 5 to 15 percent of a battery’s energy. While semi drivers can be a conservative group, those willing to become the rst EV drivers in their eets soon came to appreciate some side bene ts of electric trucks.
Driver Elvis Alvarado and eet manager Hector Banuelos openly discussed the pros and cons of the rstgeneration VNR Electric tractor tested by NFI. Among its advantages were smooth power delivery, lack of continuous gear shi ing, less vibration (“I could write on my notepad,” marveled Alvarado), and the ability to retain cabin cooling or heating when parked in no-idle zones. Also, he noted, he needed much less time to check over the truck’s powertrain before runs—and he didn’t smell like diesel fuel a er the workday.
As for challenges: e VNR Electric tractors were quiet enough that yard and port sta o en didn’t hear them coming, requiring extra alertness on the driver’s part.
Range anxiety was a continual factor, and Banuelos suggested it could be hard to get the quoted 150 miles to cover two round trips to a port and back in a 10-to-12-hour shi . He expects the 250-mile range of second-generation VNR Electric tractors to provide a comfortable margin in many more circumstances.
Driving style also matters. Experienced diesel drivers will need training for electric trucks to maximize use of regenerative braking, which can recapture 5 to 15 percent of a battery’s energy.Images courtesy of Volvo Trucks North America
It’s crucial that any operator have at least one person charged with the responsibility of coordinating all aspects of adding electric trucks to a eet. He or she should be prepared to work closely with primary contacts at the electric utility, perhaps multiple government agencies, any contractors hired to upgrade electric service or install charging equipment, and more.
While a truck-maker and its dealer can help in identifying suitable routes and matching them to electric trucks, that’s only the start of the process. Shepherding the planning, permitting and construction of the needed infrastructure, training for eet operators and drivers, and ensuring that trucks don’t arrive until their charging is live...all of those tasks should be centralized in one person with clear authority and lines of reporting.
It can well become a big, complicated, sprawling job. But for ambitious eet sta , it’s experience that can make them far more attractive to future employers.
Electricity is everywhere, including in or near the eet depots and parking lots where heavy trucks spend much of their time. But the time and cost of installing the needed charging infrastructure for electric trucks can vary enormously: “from a few thousand dollars for lower-power
chargers to millions of dollars for high-power chargers” that can deliver up to 1 megawatt each.
It’s hard to generalize on costs and e ort, but factors include a eet’s electrical load pro le (how much power needs to be delivered, and when), the size and cost of the chosen charging hardware, the existing electrical infrastructure at the sites chosen, and even the distance of a site from high-voltage service lines.
It’s crucial that any operator have at least one person charged with the responsibility of coordinating all aspects of adding electric trucks to a fl eet.Images courtesy of Volvo Trucks North America
One major tradeo is what level of DC fast charging is required to allow trucks to ful ll their duty cycles. A 150 kW charger may recharge a battery pack to 80 percent in about 2.5 hours, while a 250 kW unit can cut that to 1.5 hours—at the cost of longer installations, more infrastructure work, and higher charging station costs. It all depends on the needs of the routes being covered by the electric trucks.
As the report notes, "A more powerful charger may entail longer installation timelines and higher capital investment costs in the form of civil and electrical upgrades that are di cult to justify during an early demonstration stage but can provide a faster charging experience."
Faster charging is typically more expensive because it requires an electrical system to operate at peak power, for which utilities levy higher demand charges, since it puts more stress on the electric grid. However, these higher energy costs can o en be managed through a sophisticated EV service platform for smart charging.
For eet operators, concepts like demand charges and charging management so ware are entirely new. When it comes to diesel fuel, the only signi cant variables are how far away it is and what it costs per gallon. e small number of operators who run mixed-fuel eets (diesel and gasoline, or diesel and natural gas) will understand these tradeo s better.
Starting out, eets may want to mix high- and low-power DC fast charging to see which meets the needs of di erent duty cycles and routes. But if asphalt must be trenched, electrical service must be upgraded, and new cabling must be run into parking lots, it’s crucial to plan for future upgrades—by wiring for higher power or more stations than needed at launch—to prevent the need to retrench and add wiring down the road.
With luck, not every electric truck launch will take place amidst a global pandemic, as the Volvo LIGHTS project did. But the process of installing charging infrastructure will inevitably encounter delays, as all the participants stressed. e earliest possible contact with both the electric utility and local land-use and permitting authorities is crucial, especially if this is the rst local project with megawatt-scale charging.
The time and cost of installing the needed charging infrastructure for electric trucks can vary enormously.
It’s crucial to plan for future upgrades—by wiring for higher power or more stations than needed at launch—to prevent the need to retrench and add wiring down the road.Images courtesy of John Voelcker
ose early meetings will help “calibrate expectations” for the eet operator about how fast a project can realistically progress.
e LIGHTS partners advised EV eet adopters to build in extra time before the vehicles themselves are scheduled to be delivered—because a large electric truck without the ability to charge it is little more than a parking-lot paperweight.
Emissions come way down, and so does cost, but ... ere’s no longer any question that electric trucks have signi cantly lower lifetime carbon footprints than any trucks running on fossil fuel. Furthermore, like passenger EVs, their carbon emissions per mile will fall over their lifetimes as the grids they’re charged on decarbonize.
e LIGHTS team had the Volvo VNR Electric tractor assessed by a team at the University of California, Riverside on a heavy-duty dynamometer. Combined with a life-cycle
assessment (LCA) of the electric truck’s well-to-wheel impact, the Volvo VNR saved 65 percent of total energy and 81 percent in fossil energy, and it cut lifetime greenhouse-gas emissions and criteria pollutants (hydrocarbons, nitrogen oxides, carbon monoxide and soot) by more than 80 percent compared to a baseline diesel truck.
e cost equation is trickier. Today, battery-electric Class 8 tractors still have a higher lifetime cost, due entirely to the initial purchase price of a heavy-duty vehicle with a huge battery (264 kWh for the rst-generation VNR Electric). An electric Class 8 tractor still carries roughly twice the price of a comparable diesel version. at in turn raises insurance costs as well. e LIGHTS team found that, once acquired, the electric truck had signi cantly lower operating costs per mile—but that didn’t make up for the higher purchase cost.
Several speakers highlighted the need for more federal, state and local incentives to encourage use of zero-emission heavy trucks.
From the report: “ e federal government and some states o er dedicated grant programs for BEVs and related infrastructure, but the funding currently available isn’t su cient to support widescale market deployment. In California, several utilities o er incentive programs to buy down the capital equipment cost for their customers, a model other states should consider emulating.”
Now that the Volvo LIGHTS program has o cially concluded, what’s next? Volvo has launched an updated version of its VNR Electric truck, with increased ranges of up to 230 or 275 miles from battery packs of 375 and 565 kWh. ose trucks are now arriving at selected dealers
in California and elsewhere. e company expects to sell hundreds of them, which will provide more real-world experience in a broader array of use cases.
Moreover, to expand beyond depot charging—the focus of the LIGHTS project—Volvo Group announced in midNovember that it would partner with the Pilot Group. at company, which operates more than 750 Pilot and Flying J travel centers across North America, plans to install highperformance charging infrastructure at selected locations over the next few years. is is a step that, so far, Tesla has not taken for its own Megacharger standard.
Mack Trucks, also owned by Volvo Group, updated its own electric tractor in March. e latest Mack LR Electric uses a standard 376 kWh battery, with twin electric motors producing 330 kW (448 hp) and identical peak
The LIGHTS team found that, once acquired, the electric truck had signifi cantly lower operating costs per mile—but that didn’t make up for the higher purchase cost.Images courtesy of John Voelcker
torque to the VNR Electric. e Mack electric truck is part of a $10-million program by the New York State Energy Research and Development Authority (NYSERDA) to reduce emissions by using zero-emission trucks in the Hunts Point neighborhood of the South Bronx, which su ers from some of the worst air quality in New York City.
Meanwhile, participants in the LIGHTS Project expect to continue experimenting with electric trucks. ey’ve seen some of the pitfalls, understand the process better, and are now considering how those experiences will let them scale from one truck to, say, ten, and then more. Stay tuned.
Participants in the Volvo LIGHTS Project were: California South Coast Air Quality Management District, Volvo Group, Dependable Supply Chain Services, trucking eet NFI, the Ports of Los Angeles and Long Beach, Southern California Edison, TEC Equipment, Shell Recharge Solutions (née GreenLots), University of California, Riverside College of Engineering, Rio Hondo College, San Bernardino Valley College, Reach Out and Calstart.
Funding of $90 million for the project came from the California Climate Investments, which contributed $44.8 million of Capand-Trade money. e balance came from the project partners. Volvo Trucks provided airfare, lodging and meals to enable Charged to bring you this rstperson report.
Paci c Gas and Electric (PG&E) has received regulatory approval to establish a vehicle-to-grid (V2G) export compensation mechanism for commercial EV charging customers in its California service area. e V2G export rate provides upfront incentives to help commercial customers o set vehicle costs, and enables these vehicles to export power to the grid during peak energy demand periods.
e California Public Utilities Commission (CPUC) adopted a settlement agreement with Electrify America and the Vehicle-Grid Integration Council (VGIC), an industry trade group, establishing a rate that will be available to charging equipment paired with stationary energy storage systems.
More than 420,000 EVs have been sold in PG&E’s service area, representing one in six EVs in the country. A wave of large EVs such as school buses and trucks is expected to hit the roads over the next few years, and the timing could be propitious. California’s grid is facing unprecedented challenges, and V2G-capable eets have the potential to be exible resources that can make the grid more reliable, e cient and a ordable.
VGIC, which is committed to advancing the role of smart EV charging, hopes that this new export rate structure in the nation’s largest EV market will serve as a guide for additional innovative rate structures across the country.
“ e CPUC’s decision is a strong step forward for Californians and in support of the state’s grid, implementing the nation’s rst dynamic export rate for EV charging customers,” said Ed Burgess, VGIC Policy Director. “Leveraging the capability of EVs as a grid resource will help integrate more clean energy into our power system, reduce energy bills for all utility customers, and support California’s ambitious decarbonization goals. We appreciate PG&E’s constructive approach to supporting this program, and believe it serves as a guidepost for other forward-looking energy providers to follow across the country.”
Charging network Electrify America has been at the forefront of a new trend: installing battery energy storage systems (BESS) at DC fast charging stations in order to manage energy costs and reduce stress on the grid. Now the company has unveiled its rst megawatt-level BESS. Battery energy storage, with or without local renewable generation (solar panels) acts as a bu er between charging stations and the grid. is can help operators to avoid expensive demand charges imposed by local utilities, and can also make it feasible to deploy fast chargers in more remote areas where adding additional grid capacity is di cult or impossible.
EA installed the megawatt-level BESS, along with a solar canopy, at its station in Baker, California. is site was chosen because of its remote location and utility capacity constraints. e BESS has a capacity of 1.5 MW / 3 MWh, and the solar canopy has a potential capacity of 66 kW. e expansion of the Baker station included the addition of four new individual chargers, bringing the total to twelve, some boasting 350 kW power levels.
“ e application of the megawatt-level energy storage is the latest example of how we are continuously innovating to tackle infrastructure challenges and meet charging needs today,” said Jigar Shah, Head of Energy Services at Electrify America. “As we expand the use of such solutions to more of our charging stations and also to our medium-duty and heavy-duty electric eet customers, we are positioned to enable continued transportation electrication even in the face of utility capacity constraints.”
Electrify America now has a total of over 30 megawatts of installed energy storage at some 150 locations. In California, 50 charging stations coupled with energy storage constitute the largest operating Virtual Power Plant (VPP) that can shi energy usage to o -peak hours in the California Independent System Operator’s wholesale energy market, CAISO.
Shell Deutschland, a subsidiary of global oil giant Shell, has acquired SBRS Charging Solutions, a provider of infrastructure products and services for commercial EVs.
SBRS, which is headquartered in Dinslaken, Germany, has a client base that includes municipalities, public transport operators and OEMs. “ e acquisition brings signi cant experience in electric bus charging and a material pipeline in electric truck charging,” says Shell.
SBRS is just the latest in a number of companies that Shell has acquired in the EV infrastructure segment, including ubitricity, Cable Energia, Next Kra werke, sonnen and LimeJump. e conglomerate currently operates over 100,000 charge points at Shell retail sites and other locations.
“ is acquisition will enable us to o er more charging solutions to business customers who need to electrify and decarbonize their eets or improve their depot charging capabilities,” said István Kapitány, Global Executive VP of Shell Mobility.
We pioneer motion
Being open to technological change is one of our biggest strengths. We consider the bigger picture and don’t hesitate to re-think convention. Together with our customers, we develop advanced systems that drive the vehicles of the future—and in the process—deliver smart, high-quality components that reduce fuel consumption, emit less carbon dioxide, and last longer. To learn more, visit: schaeffler.us
Franklin Electric has introduced a new switchgear product that supports up to four 150 kW DC fast chargers. It’s part of the company’s new NexPhase line of EV products.
“NexPhase is purpose-built to support the National Electric Vehicle Infrastructure (NEVI) formula program, helping to enable EV charging site owners to maintain NEVI’s 97% charger uptime requirements while minimizing installation, maintenance and operating costs,” says the company.
“By combining all EV charging electrical infrastructure into one enclosure, NexPhase eliminates the additional resources, time and supply chain di culties o en associated with designing, sourcing and installing a traditional mixed-manufacturer post-and-frame switchgear system.” e company also says: “Unlike common switchgear, NexPhase comes fully assembled, pre-wired, and factory tested, requiring only the utility and EV charger connections for installation.”
It also includes EV charger crash detection, ammable vapor monitoring, ood detection, pest mitigation and e-stop integration options, as well as a NexPhase monitoring system for outages, troubleshooting and cycling power to chargers.
e National Automotive Parts Association (NAPA), which operates 6,000 auto parts stores and over 17,000 service centers in the US, is collaborating with Qmerit, a provider of EV charging installation services.
NAPA will o er Qmerit’s turnkey EVSE installation services to charger buyers on NAPAonline.com. Customers can request an online estimate for their installation and connect with one of Qmerit’s certi ed installers. Qmerit’s network, which covers the US and Canada, is comprised of licensed electricians who are insured, background-checked and trained in EVSE installation.
“Alongside our existing commitments to increasing education and training for new technicians, NAPA is also committed to [providing] our network with the parts and accessories most crucial to maintaining an electric vehicle,” said Susan Starnes, VP of Emerging Markets at Genuine Parts Company.
“Combining our platform with the NAPA Network and its services in the a ermarket space will create a whole new channel for reaching consumers and businesses with the suite of services they need to make the transition to electri cation easier and more a ordable,” said Ken Sapp, Qmerit Senior VP of Business Development.
Eaton, a provider of “intelligent power management” products and services, has long done business with the US General Services Administration (GSA), the federal agency that manages the government’s property and physical assets, notably the massive federal vehicle eet.
Now Eaton’s contract with the GSA has been expanded to include EV charging infrastructure products and services (EVSE). e updated contract also provides a framework to support state and local government EVSE projects, including necessary upgrades to building energy systems.
Among other current projects, the VA is procuring Eaton Green Motion EV chargers for the VA Medical Center in Coatesville, Pennsylvania. Some of the newest Eaton solutions included in the GSA blanket purchase agreement (BPA) are the company’s smart-breaker chargers and energy storage solutions.
“For decades, federal agencies have relied on Eaton to advance sustainable, resilient electrical infrastructure projects,” said Jim Dankowski, Federal Government Marketing Director at Eaton. “Today, our longstanding government taskforce and energy transition team are also helping simplify every aspect of EVSE projects— from the charger to the grid.”
Québec charging network e Electric Circuit has launched a heavy- and medium-duty vehicle charging pilot project. As the number of electric trucks on the roads is expected to increase signi cantly over the next few years, the project aims to gain a better understanding of heavy-vehicle charging patterns in order to develop infrastructure that meets the needs of the market.
e pilot includes the installation of dedicated stations for heavy vehicles, designed with factors such as turning radius and trailer length in mind.
e rst charging station to be included in the pilot project is located on Rue Cunard in the town of Laval. It’s designed to be convenient for truck charging—heavy vehicles with trailers can park on either side of the two charging stations on site. e two stations have a combined power capacity of up to 350 kW, and feature both SAE Combo and CHAdeMO connectors. Other stations will be added by 2024.
“Although light vehicles were the initial focus of transportation electri cation, many other types of electric vehicles will be on our roads in the next few years,” said France Lampron, Director of Development of Energy and Mobility O ers at utility Hydro-Québec. “When it comes to charging, we intend to be ready to give the market the momentum it needs.”
Fermata Energy, a specialist in vehicle-to-everything (V2X) charging systems, has successfully deployed its FE-15 bidirectional charger on multiple commercial projects. Now the company has added a second commercial V2X-capable bidirectional charger to its lineup, the FE-20.
e FE-20 is a DC fast charger that can both charge and discharge the battery of a bidirectionally-enabled EV, creating opportunities for eet owners to earn revenue, while supporting grid resilience.
e FE-20 is made exclusively for Fermata Energy by Heliox. It’s available in ADA-compliant pedestal and wall-mount versions. e power level is 20 kW for both charging and discharging. UL certi cation is pending.
“Companies are facing increasing pressure to electrify their eets. Yet, at the same time they are looking for ways to manage costs,” said David Slutzky, CEO and founder of Fermata Energy. “V2X bidirectional charging actually allows them to both electrify their eets and earn revenue while their EVs are parked. Fermata Energy has pioneered bidirectional charging and now, along with our proprietary cloud-based so ware platform, we are introducing our second commercial bidirectional charger—the FE-20.”
Fermata Energy is now taking pre-orders for the FE-20 from eet owners and operators for Q1 2023 delivery.
TeraWatt Infrastructure has taken a big step toward realizing its vision of a network of charging hubs for eet vehicles—it recently raised more than $1 billion in institutional capital, which it will use to develop a string of charging centers for heavy-duty and medium-duty electric trucks along I-10 from the Ports of Los Angeles and Long Beach to El Paso.
e I-10 Electric Corridor will consist of multiple TeraWatt Charging Centers in California, Arizona and New Mexico. Each will feature “dozens” of high-power DC fast chargers, pull-through charging stalls and on-site driver amenities. e sites will be available both to longhaul truckers and local, last-mile delivery operations.
e Charging Centers will be located approximately 150 miles apart, a distance that supports the range of currently available electric trucks. Each site is located less than one mile from the nearest highway exit, and they range in size between 4 and 100 acres.
TeraWatt will manage all charging operations at the sites, and will incorporate advanced technology such as battery storage, on-site renewable energy generation and megawatt charging stations “as commercially appropriate.” e company will partner with local and state governments and utilities, and take advantage of whatever grants and incentives are available.
“Long-haul trucking electri cation represents a signi cant opportunity to reduce transportation sector emissions, but hinges on the rapid scale-up of specialized charging infrastructure,” says CEO Neha Palmer. “Our real estate and energy infrastructure development platform uniquely positions TeraWatt to solve the ‘charging problem’ for trucking operators, making freight electrication achievable within their operations. ere will have to be a lot of collaboration between stakeholders, including grid owners, operators, utilities, regulators and end users, to ensure that the grid can evolve alongside the shi to electric transportation.”
Electric Era, a developer of AI-driven storage solutions for EV fast charging, has launched a turnkey fast charging platform designed speci cally for the convenience store sector.
Electric Era says its PowerNode Platform enables convenience stores to meet the eligibility requirements for the National Electric Vehicle Infrastructure Formula Program without expensive grid upgrades or utility demand charges.
e PowerNode Platform is designed to predict and manage load, and uses battery storage to optimize charging, taking advantage of the most advantageous utility tari s. e company says it is capable of delivering 100 charging sessions per day at a standard convenience store.
Many see convenience stores as likely locations for DC fast charging. Fortune Business Insights estimates that some 28,000 convenience stores will o er charging by 2030.
“ e PowerNode Platform reduces grid requirements and demand charges by 3 times, while supporting the fastest charging speeds, allowing convenience stores to replicate the gas station experience while optimizing revenue and minimizing the costs of fast charging,” said Quincy Lee, Electric Era founder and CEO.
“Many of the 116,000 convenience stores across the country are planning to install EV fast charging capabilities in the coming decade using battery-supported EV fast charging technologies like the PowerNode Platform,” said Joe Montana, founder of investor Liquid 2 Ventures.
Delta Electronics (Americas) demonstrated a next-generation SiC MOSFET solid-state transformer-based 400 kW EV charger at a recent event attended by representatives of project partners GM, DTE Energy and NextEnergy.
Delta’s “extreme fast” EV charger uses a three-phase 13.8 kV medium-voltage SiC MOSFET SST topology. It provides 500 A of charging current, and the company claims grid-to-vehicle energy e ciency as high as 96.5%.
Delta says its next-generation SST technology o ers “essential capabilities for smart grid applications, such as reactive power compensation for voltage stabilization and improved power quality.” e new charger’s HVDC power architecture “enables connection with renewable energy and energy storage systems.”
“Delta continuously develops ground-breaking technologies and fosters long-lasting relationships with partners,” said Kelvin Huang, President of Delta Electronics (Americas). “ is is how Delta, a member of the RE100 and EV100 initiatives, has been able to deliver more than 1.5 million EV chargers worldwide over the past decade.”
“A key aspect of the new technology is the ability to connect directly to medium-voltage distribution and provide faster, more e cient charging compared to lower-voltage chargers,” said Richard Mueller, DTE Energy Technology, Standards and Interconnection Manager. “ is project will give DTE and its project partners signi cant insight into how these fast chargers can be integrated safely, reliably and with ever-growing numbers into the grid.”
GM has selected charging provider FLO as the supplier for the automaker’s Dealer Community Charging Program, which will install up to 40,000 public Level 2 EV chargers in local communities across North America.
FLO will provide its CoRe+ MAX chargers to participating dealers. ese new charging stations will join the FLO network and GM’s Ultium Charge 360 network, and will be available to all EV drivers.
FLO’s CoRe+ MAX charger delivers a maximum power output of 19.2 kW. FLO will manufacture the chargers for GM in North America, primarily at its new assembly facility in Auburn Hills, Michigan and at its plant in Shawinigan, Québec (both near Detroit).
One aim of GM’s Dealer Community Charging Program is to expand public charging access in underserved rural and urban areas. Participating dealers are eligible to receive up to ten Level 2 charging stations, which will be installed in key public locations including workplaces, multi-unit dwellings, event venues, colleges and universities. e rst chargers were recently installed in Wisconsin and Michigan at a park, library, sports complex and wellness center.
“With FLO’s collaboration and the support of our dealer community, we’ll signi cantly expand reliable and convenient infrastructure across the US and Canada,” said Hoss Hassani, VP of GM EV Ecosystem.
e abysmal dependability of public chargers is a major problem, and xing it is going to require some serious technical expertise and industry-wide cooperation. So it’s encouraging to see industry heavyweight SAE International, which calls itself “the oldest and largest technical society for engineers in the US, and the largest mobility standards organization in the world,” taking aim at the issue.
SAE has launched Sustainable Mobility Solutions, a new “innovation unit” focused on zero-emission transportation. e unit’s rst initiatives will center on the reliability of EV infrastructure, as well as partnerships for workforce development.
SAE has published “Charging System Performance Reporting,” a comprehensive study of charging failures along with a proposal for a system for evaluating those failures and nding solutions. “ e publication makes major contributions to reliability for EV drivers and represents the most comprehensive technical review of EV charging system performance, data reporting and reliability to-date,” said SAE Technical Consultant Craig Rodine.
Training has always been central to SAE’s mission, and the Sustainable Mobility Solutions unit will establish a couple of new training partnerships. DEKRA, a provider of testing, inspection and certi cation services, will collaborate on online training and certi cation in such areas as cybersecurity and safety. “Interoperability and seamless charging experiences are critical to the adoption of electric vehicles, but both require skilled technical workers who understand EV charging infrastructure, safety and cybersecurity,” said Fernando Rodriguez, VP of DEKRA Americas.
ChargerHelp!, a provider of eld-based EV charger technicians, will partner with SAE to certify the thousands of technicians needed to keep charging stations operational. “It is crucial that specialized maintenance technicians are well trained to help inform the industry how the so ware works together with the hardware, [to] support high uptime of the chargers, while practicing maximum safety,” said ChargerHelp! CEO Kameale C. Terry.
British EV so ware specialist ev.energy has launched a new cloud-based EV charging tool for business.
Pando is designed to enable charger manufacturers, distributors and installers to be fully compliant with UK Smart Charging Regulations. It provides load management, compliance testing and charger sharing as standard features. Following months of testing with 20 partners and over 20,000 chargers, Pando is now being rolled out to all ev.energy’s partners.
Every charger connected to Pando can be pre-commissioned, enabling faster installations. Installers can use Pando to check connectivity across their eets and delegate access to property managers, reducing returnto-site visits.
Other features include direct control of smart charging units, load testing capabilities and adjustable smart charging settings. Every charger is natively integrated into ev.energy’s EV ex platform, which enables smart and bidirectional charging as well as integration with grid exibility services.
“Our partners and early adopters have helped shape the service, and we’re now ready to roll this functionality out globally to property managers, installers, charger manufacturers and eets,” said Nick Woolley, CEO at ev.energy. “Pando will help ensure our partners and clients are not only compliant with the latest smart charging regulations, but they have the power to scale their business, with minimal e ort and full support from our team.”
ADS-TEC Energy has announced two new installation options for its battery-bu ered ChargeBox system. e ChargeBox Dispenser can now be installed indoors, and the associated ChargeBox Booster outdoor battery— which was previously installed partly underground—can now be completely installed at ground level.
e new installation options are available now in Germany, and are planned for other European countries and the US.
According to ADS-TEC, “Calculations at customers’ sites have shown that, in the long term, considerable savings potential can be achieved compared to a charging solution with corresponding new expansion of the existing grid infrastructure.”
e ChargeBox Booster can be installed up to 200 meters (656 feet) from the grid connection point and up to 100 meters (328 feet) from the ChargeBox Dispensers. e install requires only about 1.5 square meters (16 square feet) of oor or ground space. e system continuously charges up from the electrical grid, and can provide charging power of up to 320 kW.
e ChargeBox Dispenser can be installed in parking lots and underground garages, as well as in showrooms and halls.
“We have had a number of inquiries from large customers expressing the need for ultra-fast charging of e-vehicles inside buildings,” said Chief Sales O cer John Neville.
“Our ultra-fast charging systems, which are not dependent on large grid connections like conventional systems, far outperform in many use cases, and [deliver lower] total cost of ownership,” said omas Lächner, Head of Department Sales Representative EU.
During periods of rapid technological change, it o en turns out that certain new products have highly useful applications that few—perhaps not even their inventors—originally foresaw. is may well be the case with the EV ARC, a solar-powered o -grid charging station made by Beam Global.
When we rst covered the company, which was then known as Envision Solar, back in 2013, we immediately saw that its product would be handy for events, disaster relief and other applications requiring a stand-alone energy source that could be set up quickly. Since then, as charging stations both public and private have proliferated, a major challenge has emerged: installing chargers o en involves site preparation, trenching, upgrading utility service, permitting and regulatory approvals...the list goes on and on. Dealing with these requirements can end up costing more than the price of the hardware, and can cause delays of months or even years. e EV ARC neatly sidesteps all these hassles, and once it’s installed, it provides energy at no marginal cost, almost as a bonus.
e EV ARC is not just a portable charging station—it’s an o -grid solar power system and stationary storage device that o ers EV charging as an option. Portability is one feature—the unit is transported on a custom-made trailer, and one of the company’s “deployment experts” can set it up in as little as a few minutes—but the system can also deliver multiple bene ts in permanent installations.
e EV ARC features a 4.3 kW sun-tracking solar
canopy, and battery storage options of 22, 32 or 43 kWh. It can be equipped with EV chargers of any brand. e whole thing ts in a single standard-size parking space.
Charged recently spoke with Beam Global CEO Desmond Wheatley, who has been with the company since 2010, about the surprisingly wide range of bene ts of the company’s EV ARC and Solar Tree systems.
Q Charged: We’ve been covering your company for some years, but it used to be called Envision Solar.
A Desmond: It’s exactly the same company, but we rebranded a couple of years ago. And the reason we did that is because Envision Solar was a very misleading name for us. Although we do use solar as one source of energy to power our products, it was a bit like calling Casio “Casio Solar” because they have a solar-powered watch. We make products that happen to use renewable sources of energy as opposed to connecting to the grid for the primary source of energy. I like Beam much better—a beam of energy, the structural beam.
Q Charged: When did you start selling the EV ARC?
A Desmond: It’s been ten years, and obviously we were a little bit crazy making a solar electric vehicle charging product ten years ago. ere were only about four EVs
(not just four models—I mean four vehicles) on the road at the time, but I was convinced that electri cation of transportation would take place. I was de nitely too early to the party. However, that party is really kicking into gear now, and all of the things that led me to come up with the EV ARC—my knowledge of what it takes to build infrastructure, go through permitting, environmental impact and also the understanding I had of the utility grid’s limitations—were what led me to build the product in the rst place.
For the rst eight years of our existence, it was hard to get people to really grasp that. Now they’re understanding it with a gusto all the way from the halls of power in Washington DC to corporate o ces across the country.
Q Charged: e more I read about your company, the more I’m struck by the many di erent applications and use cases.
A Desmond: With a couple of beers and a couple of hours, we could literally write a list two or three hundred items long.
Q Charged: For example, one of your customers has a site where they’re not allowed to do any digging because of hazardous waste. I would never have thought of that.
A Desmond: at’s, again, a lesson hard-learned by me in my past. I built lots stu in my lifetime, and there have been some instances where I was unfortunate enough to encounter subterranean hazardous materials. And the thing is, you end up owning it. In California, you end up having to clean, do remediation, and take all the spoils to Kettleman City [the site of a hazardous waste facility]. And that could be an end-of-project type of deal.
But the thing is, we knew that they would need EV charging in these types of environments—brown eld sites, nuclear waste sites. And frankly, at just about every airport in the country, you do not want to be digging up the asphalt, because most of the airports were built back in the twenties and thirties when the way you dealt with hazardous materials was to bury them under the concrete. So, the fact that we are able to deploy without digging for foundations or trenching or anything else means that we’re an ideal solution for those types of environments.
Many airports across the country will have a whole host of reasons why they do not want to get into that type of
construction project. One of those would be the potential for encountering hazardous materials, but there are many others. Of the 20,000-odd airports that there are in the US, about 15,000 of them are the smaller general aviation air elds, and they simply do not have su cient electrical circuitry to provide charging for terrestrial electric vehicles, far less for the wave of electric aviation that’s coming.
We were able to help set the world record for the longest ight of a production electric aircra last year, and the simple reason that we were able to do it where nobody else could was that we deployed charging infrastructure as this aircra island-hopped up Central California. Nobody else can do that. And in fact, when we rst contacted the airports and said we want to break this world record, they all said no, because we don’t want anybody digging, we don’t want the construction project, plus we don’t have enough capacity on our electrical circuits. And we said, we’ll send you a video and you’ll see why you don’t have to worry about any of that stu . e company that built the plane is called Pipistrel. ey have what certainly was at the time, and probably still is, the world’s only production electric aircra , meaning you could buy one. is is an o -the-shelf product—fantastic, by the way. We did [the record-setting electric ight] in conjunction with them and with another organization in central California that’s trying to rejuvenate these general aviation airports. California’s covered in them, and most of them are becoming disused because no one can a ord to keep aircra in the air. But the good news is, while it costs $40 to $50 an hour to keep a small plane in the air, the electric aircra costs $4 an hour—and even less than that, if you fuel it with sunshine as we did.
At just about every airport in the country, you do not want to be digging up the asphalt because most of the airports were built back in the twenties and thirties when the way you dealt with hazardous materials was to bury them under the concrete.
A Desmond: ere are three primary use cases for it.
e rst one is eet charging, and this is not just municipalities, this is the federal government, US Marine Corps, many others. ey’re charging their own eet vehicles. And when we talk about eet, of course that’s a very broad group. In New York City, the police department, animal welfare, you name it—every department that the city has, they’re now moving to electric vehicles, and they need charging infrastructure. In New York City, it takes an average of 24 months to put a grid-tied charger in the ground, by the time you go through environmental impact, permits, electrical work, everything. We do the same thing in less than one hour.
Beyond that, of course, in New York, like many other
jurisdictions, there is a lack of capacity on the utility grid.
is is why in August, when everybody turns up their air conditioning, ConEd turns the power o , because they do not have enough electricity to cover the current base load. As you electrify transportation, that problem’s going to become much more acute. Our products, of course, don’t require the grid, and therefore we’re able to deploy in New York without having capacity problems.
And then nally, New York is a target for terrorism and all sorts of other things, and the grid is a target. New York very sensibly wants charging infrastructure that will continue to charge their vital eet vehicles during any type of grid failure, whether that’s caused by a hurricane or because someone hacked into the grid or because terrorists knocked out a few substations, and our products solve that problem.
So that’s eet. en the next use case is workplace charging. We do that for both municipalities and the federal and state governments, but also for corporations like
Q Charged: I understand you have over a hundred US municipalities as customers. What are they using the EV ARC for?
In New York City, it takes an average of 24 months to put a grid-tied charger in the ground, by the time you go through environmental impact, permits, electrical work, everything. We do the same thing in less than one hour.
“ ”Images courtesy of Beam Global
Google, Johnson and Johnson and many others. en the third type of charging that the municipalities are o ering is public charging. ey’re trying to encourage people to clean up their carbon footprints, but they also want to encourage people to come into the city and spend money. So, if you provide EV charging, you get that EV driver who’s coming in pollution-free. EV drivers today are generally more a uent, so there’s more to spend.
Q Charged: So, the reason for choosing the EV ARC instead of a grid-tied charger is because it can be installed so much quicker and easier.
A Desmond: You’re absolutely right. e rapidity, the ability to deploy the infrastructure when you want it, not two years later when you’ve gone through planning and had the utility and everybody on board. at is absolutely huge. Many of our customers today, and this is increasingly the case, are taking possession of electric vehicles and they don’t have EV charging infrastructure, so they’ve got a lot of urgency. And because people have never done this before, they don’t understand that it’s going to take them a very long time to go through the permitting and construction and electrical work. We solve that problem for them because we can provide charging for them immediately. ere’s a lower total cost of ownership too, and that’s driven by the avoided costs associated with construction and electrical work.
We have hundreds and hundreds of locations deployed, and in almost every instance, the avoided cost of construction and electric work is greater than the cost of our product. So from day one you get [savings], because you didn’t spend money digging trenches and pouring concrete and doing all that sort of stu . And then of course you get a lifetime of free energy. If you avoid the cost of construction and electric work, you don’t even need to amortize the equipment anymore, and your cost of energy is zero. ink about that. Now you’re putting fuel into your eet vehicles as a zero unit. at’s the rst time that’s ever happened since horses, when the unit of energy was blades of grass, and even that wasn’t always free.
Grid vulnerability is increasingly on people’s minds. We have more blackouts and brownouts today than we have had at any time in our history, and yet we’re more reliant on electricity than we’ve ever been. And then nally, capacity. e grid itself has nowhere near enough capacity to electrify all of transportation. Transportation consumes
something on the order of 29 terajoules, and I think the grid delivers something on the order of 12 terajoules. So you can see right o the bat, there’s a huge imbalance there.
Even though EVs are more e cient, there’s nowhere near enough power on the grid. But it’s not just at the grid level, it is also at the substation level and even at the lot level. We have customers, for example, who have done the right thing—they’ve already installed grid-tied EV chargers, then more EVs come to their sites, so they need to put more chargers in. And they call their contractor and say, “Okay, you put 15 chargers in for me before, can you put in another 15?” and the contractor says, “We can’t do it, because you’ve already used up all your available circuit capacity on that site.” Most people don’t understand that electricity’s not just in nite, you can’t keep plugging more and more stu into it.
So then that customer is faced with either an incredibly expensive circuit upgrade—transformers, everything else, if that’s even possible. Or they’re going to go to the utility to upgrade at the substation. And of course, that only works until all the substations have too much capacity. So there’s a whole bunch of capacity reasons customers come to us. ey don’t have to worry about any of that. ere’s no planning, no permission. It’s like Lego—if you want more, just add more blocks.
A Desmond: ey start at $59,400. And remember that’s an all-in price, no construction, no permit process, and you’ll never get a utility bill. e average selling price is probably about $65,000. And the di erence is that we put di ering levels of battery storage in the products depending on what the customer’s needs are. Some customers need more battery storage than
Because people have never done this before, they don’t understand that it’s going to take them a very long time to go through the permitting and construction and electrical work. We solve that problem for them.
”
others. Our pledge to our customers, and we’re very proud of this, is that we will never sell them something that is more complicated or more expensive than they need. We try to sell them only the battery level that they need, because batteries are really expensive.
So, let’s say average selling price is $65,000. And again, in almost every instance where we’ve deployed across the US and even a little bit internationally, that was less than the cost of trenching, concrete work, planning, permitting, electrical infrastructure and everything else that would’ve been required to put the chargers where we were deployed. And then the unit of energy therea er is zero.
It has to be said that you can deploy EV charging less expensively than that. On a typical building, maybe there is an existing electric circuit which is close to a wall on the other side of which is a parking space. And in that case, all you really have to do is drill a hole, some minor electrical permitting, minor electrical work, and you’ve got an EV charger. at might exist in one or two locations on your property, but that low-hanging fruit quickly gets eaten up, and now you’re digging trenches and going through the landscaping and whatever else. With us, we don’t get deployed where the grid is available—we get deployed where people actually want charging. And those
locations are always much more expensive to [electrify] than the ones where the grid is available.
Q Charged: Your web site says the EV ARC is available with a Level 2 AC charger that can power up to 265 miles of EV driving per day, or with a DC fast charger that can power up to 1,100 miles per day.
A Desmond: In fact, we do all three charging levels. Level 1 [120 V AC] works terrifyingly slow if you’re used to the gas station model, but many of our eet customers drive less than 20 miles a day. In fact, some of the federal customers drive a lot less than that. So you can plug them in and charge them really slowly, but during ve or six hours, they’ll pick up all the daily range replenishment (we call that DRR) they need. In that instance, we’ll sell an EV ARC with six chargers and plug in six eet vehicles.
Eight out of ten commuters in the US drive less than 24 miles for their round-trip commute. So, we can plug six employees into a single EV ARC in a single parking space with no grid connection, and all of them will get their DRR while they’re parked there, or at least their commute replenishment. We also do Level 2 [240 V AC], and in that instance, we usually put one or two Level 2 chargers on an EV ARC. en nally, we do DC fast charging, and the way we accomplish this is not with one EV ARC but with four of them. For example, at a rest area we’ll deploy four EV ARCs. ey are all interconnected with an aboveground pre-engineered interconnection. Again, there’s no construction, permitting or electrical work. en we’ll connect a DC fast charger, and we use all four of the EV
In almost every instance, the avoided cost of construction and electric work is greater than the cost of our product.
ARCs, all of their generation and all of their storage, to provide that much higher charging rate, and more miles of course.
ere are also some very interesting things from a technology standpoint that keep happening. First of all, our product keeps getting better. Just last year, we announced a 12% increase in the energy delivered from our product because our engineers keep making it more e cient and essentially converting more sunlight to electricity, storing that electricity and then delivering it into a vehicle than before. e constant improvements in our products mean that the 265 [miles per day] used to be 240, before that it was 180, and so on. When I rst started doing this 10 years ago, believe me, they were nowhere near this good. But there’s another factor in the industry which is really helpful as well—electric vehicles themselves, not surprisingly, are becoming more e cient. When I rst started driving an EV 12 years ago, I was getting about 2.5 miles per kilowatt-hour. Today I can routinely get 5 miles per kWh. Now, I know how to maximize range, but it’s not driving slowly—I’m European, I’ve got a lead foot. But there are even car manufacturers now, like Lucid for example, I think they just announced 5.6 miles per kWh or so. e technology’s improving. So, if we tell you that an EV ARC will provide you 265 driving miles and we’re using 3.5 to 4 miles per kWh [as a benchmark], but in fact your vehicle is getting 5.5 miles, clearly the EV ARC is going to produce a whole lot more miles for you.
Q Charged: Tell me about disaster relief, because we just had a big hurricane here in Florida. I was down in Lee County a while ago, trying to help out. I understand that you have three EV ARCs deployed in Florida right now.
A Desmond: Yes. e fact is, whether we like it or not, these types of events are becoming more frequent and more severe, so we made some signi cant improvements to the EV ARC over the last couple of years. Previously, our electronics and our battery storage were mounted at ground level in an enclosure, which is common in the industry. We have migrated all of that into the canopy, which tracks and follows the sun, so now anything that matters on the EV ARC is 9.5 feet above grade. We can survive an inundation of 9.5 feet without any ill e ects to the product at all.
Furthermore, the product is currently independently rated for 125 mph wind speeds, and we’ll soon be rated for 150. But here’s the good news: We were in the Caribbean for Irma and Maria, and our products in those storms survived Category 5, 185 mph winds. It’s fantastically robust.
In disasters, the rst thing you lose is grid power. We also have emergency power panels built into the units and those are also 10 feet above grade. So rst responders, EMS, police can come and connect life-saving equipment to that emergency power panel—not just charge their vehicles, but also take power o the units to do other things like running ventilation, medical equipment, radios and other things.
is is not theory. is has taken place in several instances where rst responders and others have actually used EV ARCs during critical events. Most famously, the City of Oakland used the EV ARCs that they had deployed at their o ces during the height of COVID. No one was going to the o ce, so the EV ARCs were underutilized. ey moved them to COVID emergency medical centers and they got rid of the diesel generators—they
We don’t get deployed where the grid is available—we get deployed where people actually want charging. And those locations are always much more expensive to [electrify] than the ones where the grid is available.
”
used the EV ARCs to power the emergency centers and also charge their vehicles on those sites.
So it’s a very real application. I always joke that we’re a bit like Clark Kent. We’re sort of boring seven days a week, but if the shit hits the fan, the EV ARC pops into the phone booth, spins around and comes out as Superman and becomes even more valuable.
Q Charged: Any interesting new products coming up in the future?
A Desmond: We’ve got our streetlight replacement product, which is going to allow curbside charging. You take out the existing streetlight and replace with our product that has a light wind generator on the top of it, and a tracking solar array, and the column of the streetlight is full of our batteries (we make our own batteries and electronics). So we’ll be able to provide a meaningful EV charger on the curb. If you think about all the vertical cities, New York, San Francisco, Chicago, and then Asia and Europe, they don’t have big at parking lots like you have in Florida or we have in California. is will allow for curbside charging, but without doing any type of civil work or electrical work on it. It leverages the windmill, the solar and the streetlight circuit. We combine all three into our batteries and then we provide charging from that. We should be producing those next year.
And then right a er that, we have a patented product which is designed to recharge drones. We think there’s
going to be a big increase in the use of drones for package delivery and also military applications. e problem with drones is that they’re limited by their range and payload capacity, which is two ways of saying the same thing.
ey have to run home to recharge. In this instance, we will deploy networks of these things, and then the drones can island-hop without ever coming home. And we even have a modernized version of that in the patent. e US is launching drones o submarines, and now the submarine has to surface [to recharge the drones]. Our product will oat out there, GPS-stabilized, and drones can refuel and exchange data with the submarine.
Q Charged: You make your own battery packs?
A Desmond: We do. at was a very important thing to us—the safety, the energy density, and chie y our ability to make batteries in any shape that we want to. Most people are making batteries in squares and rectangles, and that’s just not very useful when you’ve got to try and t batteries in drones, in submersibles, in medical devices, in stationary devices...all sorts of things. It’s really important to maximize the e ciency of the real estate that you’re using, and sometimes that means not using a standard block-shaped battery. We are able to do that with our thermal management material that essentially is pretty unique to us, and we have lots of good patents on it.
Q Charged: And the EV ARC is charger-agnostic. You can use any kind of charger hardware and any charging network. Right?
A Desmond: Exactly. We don’t compete with those guys. We support them. We enable them.
“ ”
Images courtesy of Beam Global
growing number of countries and regions have enacted or proposed ICE sales bans, most of them for the 2030-2035 time frame. ese are meant to push automakers to accelerate their electri cation e orts, and we’re seeing a lot of evidence that it’s working. However, even if all new cars sold in 2035 are EVs, it will be a long, long time before ICEs disappear from the roads.
Leaving aside the question of whether ICE sales bans, most of which are non-binding “targets,” get watered down or circumvented over the course of the next 13 years, we need to remember that the average life of a car (in wealthy countries) is generally considered to be 10-12 years, and many linger for much longer.
Policymakers are well aware of this. When the European Commission recently announced plans to set a zeroemission sales mandate for new cars by 2035, it noted that this policy should put the bloc on track to reach its target of converting all cars on the road to zero-emission by 2050.
How is the “cars sold vs cars on the road” equation working out so far in places where EV sales are high? According to Statistics Norway (via e Driven), even in the world’s EV capital, where ICE vehicles now make up a small fraction of sales, 80% of total miles driven in 2021 were still powered by petroleum.
We also need to keep in mind that EV mandates, and EVs in general, have so far been almost entirely a phenomenon of the rich world. On a global scale, even a 2050 target for the end of oil may be overoptimistic.
By Charles MorrisAt least one US school district has stipulated that, as it replaces its diesel buses with EVs, the engine blocks of the old buses must be destroyed so they can’t be sold on. is should be mandated for all eets that are replacing buses, trucks and cars with EVs, but it will obviously make electri cation more expensive.
If, as some predict, resale values of ICEs plummet, will the problem solve itself? Remember when at-screen TVs caught on, and we started to see piles of unwanted CRT TVs sitting by the curb next to the trash cans? Could this happen with cars? I for one would love to see such a scene, but cars ain’t TVs. Consumer electronics makers didn’t ght the transition to at-screen TVs—they initiated it. In the auto industry, things will be messier. By all accounts, producing EVs is going to support far fewer jobs, and this has important political implications. Furthermore, the automakers aren’t likely to tamely write o their investments in engine and transmission plants as stranded assets. As EV mandates push ICE production and sales out of the a uent countries, some automakers may try to shi it to more southern locales. On the consumer side, if EVs aren’t attractive, drivers will nd ways to extend the lives of their tried-and-true dinosaur-burners.
EV mandates, and EVs in general, have so far been almost entirely a phenomenon of the rich world. On a global scale, even a 2050 target for the end of oil may be over-optimistic.
You and I may feel virtuous (and cool) zipping around in our Leafs and Bolts, but as long as millions of people are still driving ICEs, pollutants are still being pumped into the atmosphere, and if we don’t want to end up underwater, we need to get rid of the exhaust pipes a long time before 2050.
So, how to get these stinkers o the roads? A Cash for Clunkers program? Well, the US tried that back in 2008, and somewhere along the way it turned into a scheme to help auto dealers, not the environment—drivers traded in their old SUVs for newer, slightly less-polluting SUVs.
ere are doubtless much better ways to design a scrappage scheme, but these will only get us part of the way to the nish line.
How about ending the pipeline of old oil-burners from the Global North to the South and East? As people in the US and Europe replace their ICEs with EVs, where do the old ICEs go? To Central America, the Caribbean, Eastern Europe, Africa, etc, where they may ply the roads for another decade (and burn lthy, adulterated gas in the bargain).
Opponents of ICE bans have raised the specter of a “Havana e ect.” As one conservative German lawmaker put it, “A er 2035, our streets might become full of vintage cars, because new EVs are not available or not a ordable.” is must not be allowed to happen. e health of the planet, and of its human inhabitants, demand that legacy vehicles be politely ushered o the roads as quickly as possible. And the key to this is making EVs cheaper and more widely available.
Discouraging the export of polluting vehicles and instituting well-thought-out scrappage schemes would be welcome steps, but regulators can only do so much. Automakers have demonstrated that they can build compelling luxury-class EVs, and now they need to aggressively electrify the mass-market segments (and markets in developing countries).
e biggest barrier to EV adoption right now is not range, charging infrastructure or bogeyman auto dealers—it’s price. EVs can be, and must be, cheaper than legacy vehicles, and making that happen should be Job One for the industry right now. Achieving it is the only path to the glad day when we see the last of the gas-burners rusting in the rain ( guratively, of course—we really want to see them recycled).