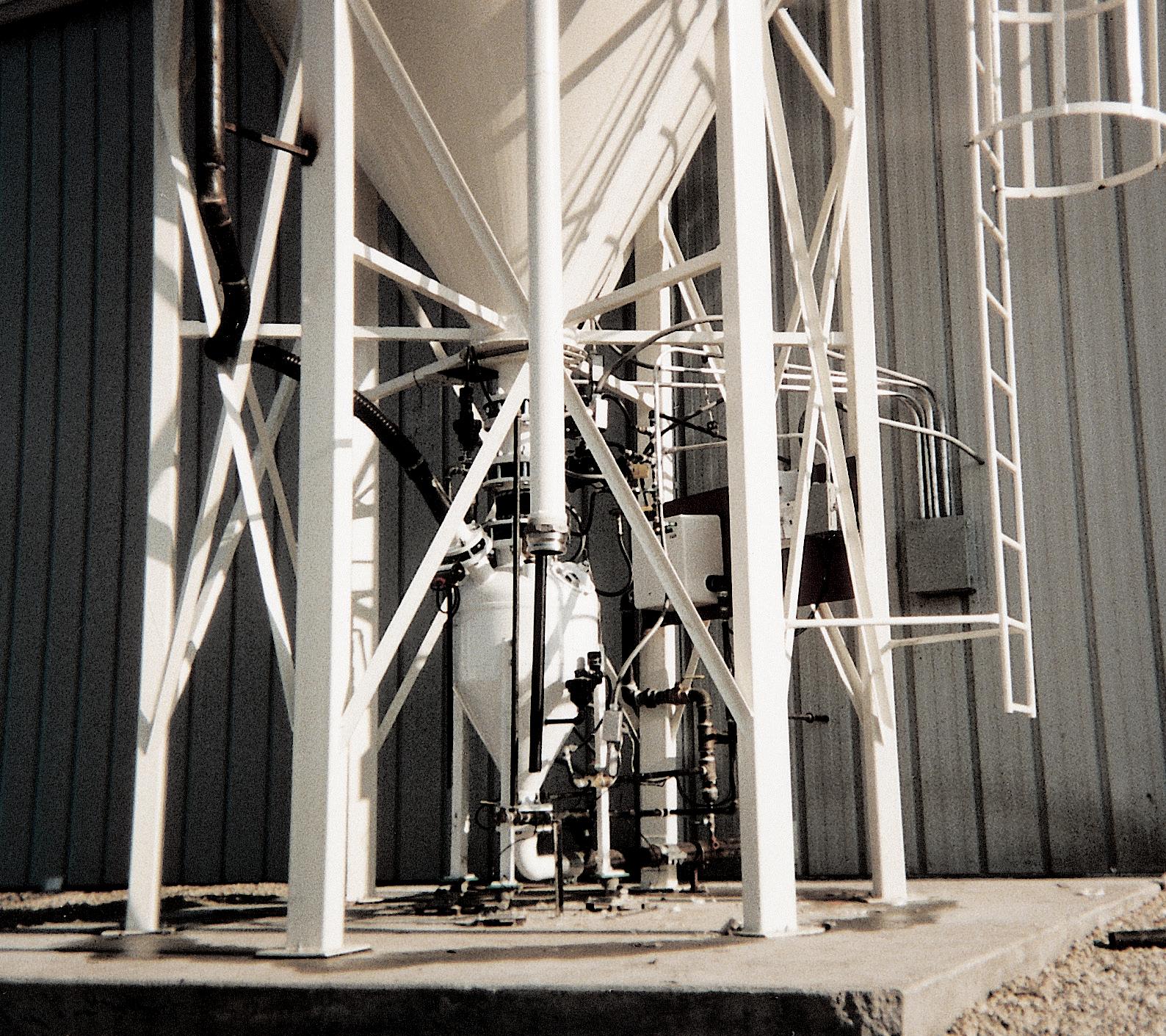
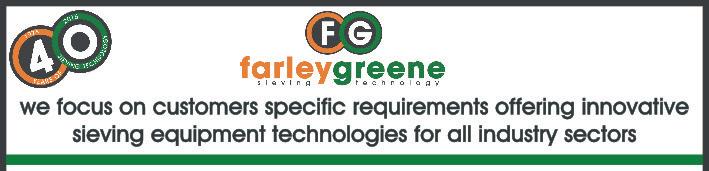

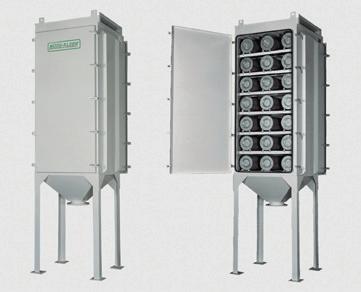
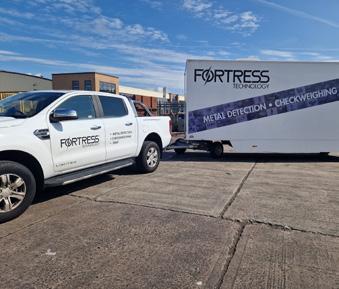
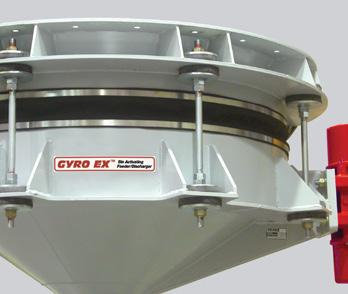
From micron sized powders to large pellets and everying in between, Dynamic Air can move your dry granular materials gently, reliably and with significant reductions in product degradation and/or system wear.
Dynamic Air dense phase pneumatic conveying systems have been proven in over 15,000 installations worldwide. They handle a wide range of materials and bulk densities at rates from less than a hundred kilograms per hour to 400 tonnes per hour, over distances exceeding 1500 metres.
Each Dynamic Air system is custom designed from one of our sixteen different conveying concepts. So you get a conveying solution that fits your process perfectly, without compromises.
Our high material-to-air ratios reduce energy and compressed air requirements. Our low conveying velocities provide significant process savings in both operation and maintenance.
Issue
Sales Director: James Scrivens
Production: Sarah Daviner
Accounts Manager: Avery Hudson
Office Manager: Katie Brehm
BULK SOLIDS TODAY is published 6 times a year by Abbey Publishing Ltd
ADVERTISING & EDITORIAL
Please contact us at:
Tel: 01933 316931
Email: editorial@bulksolidstoday.co.uk advertising@bulksolidstoday. co.uk
Web: www.bulksolidstoday.co.uk
Twitter: www.twitter.com/
BulkSolidsToday
CIRCULATION
To receive a copy free of charge, please send your details to subs@bulksolidstoday.co.uk
No part of this publication may be reproduced by any means without prior permission from the publishers. The publishers do not accept any responsibility for, or necessarily agree with, any views expressed in articles, letters or supplied advertisements.
ISSN: 1365/7119
All
Parker Hannifin’s Filtration business has reached a major milestone on the journey towards mass production of hollow fibre membrane technology for fuel cell humidification applications, a vital step towards reducing carbon emissions.
By enabling optimal moisture levels, hollow fibre membrane technology allows fuel cells to last longer and to perform more efficiently and reliably. It supports the transition from fossil fuels, accelerating the shift to fuel cell electrical vehicles in the next five years.
Parker announced the successful completion of the specialized test rig which is to validate products by Parker OEM (Original Equipment Manufacturer) customers. This new technology enable Parker to test the membrane technology in ways that are much more advanced and aids to develop robust system solutions for fuel cell. It was produced in partnership with the Fraunhofer Institute for Microengineering and Microsystems (IMM), a Germany-based non-profit for scientific research.
Burkhard Hartmann, R&D Officer at Parker’s Engine
Mobile Filtration Europe (EMFE) Division, said: “The results speak for themselves: This has been an outstanding collaboration with the Fraunhofer Institute. It moves us all towards better, more efficient, more reliable fuel cell electrical vehicles, a vital step towards a cleaner, better tomorrow.”
Dr. Gunther Kolb, Representative from the Fraunhofer Institute for Microengineering and Microsystems, said: “Fuel cell technology is key to reduce
Bulk Solids Today is the bi-monthly digital journal covering the storage, processing and handling of materials ranging from fine powders to the heaviest raw materials. To subscribe to Bulk Solids Today magazine or for more information, please feel free to visit www.bulksolidstoday.co.uk
emissions worldwide. The partners are confident that the hollow fibre membrane technology will be further improved, the service life of the fuel cell humidifiers will be extended, and their efficiency will be increased for the customers.”
Learn more about Parker’s Filtration solutions at:
https://promo.parker.com/ promotionsite/engine-mobilefiltration-europe/gb/en/home
Food safety specialist Fortress Technology is taking to the road with its new demo van. Bringing a selection of its metal detection and checkweighing technology, along with industry inspection expertise, direct to UK food factories.
For food processors pressed for time, yet eager to explore future machinery, data packages and training tools to support their food safety strategy, the Fortress demo van is equipped to help. From getting to grips with the equipment first-hand, to exclusive live demos and detailed metal detection and checkweighing test reports, employees can visit the van without disrupting production. Saving food factory managers time and money.
Arranged by appointment only, Fortress colleagues simply park the van close by – space allowing in the company car park - and open the doors.
“Listening to our customers, the real struggle for many is dedicating the time to view inspection equipment. Visiting trade shows or our Banbury production facility and showroom can add more stress to people’s already busy schedules. It also limits the number of people, departments and decision makers who might want to input into investment decisions. Bringing the technology to manufacturing sites solves this,” explains Phil Brown, managing director at Fortress Technology Europe.
Demonstrating the technology on site also reduces the collective carbon footprint, highlights area sales manager Jaison Anand, one of the masterminds behind
this initiative. “Most exhibition venues are clustered a good couple of hours away from manufacturing sites. Attendance, including overnight stays, adds to this cost. The beauty of the Fortress demo van is it can fit around everyone’s needs, production schedules and project timelines,” adds Jaison. Staff enquires can all be addressed in a single visit. One trip also enables the engineering, technical, quality, finance, procurement and management departmentssome of whom rarely influence investment decisions – to view the equipment and ask practical questions. Without information overload and exhibitor distractions.
Currently equipped with a retail-spec Vector conveyor metal detector and Raptor checkweigher, a Combi system is being added soon. Already, Jaison and the team have visited several food processors
to deliver quick presentations on retailer codes of practice, hygiene, audit, integration guidance, and more.
The feedback following its first trip to a customer facility was extremely positive. Jaison reflects: “It was so much more productive and useful having Fortress travel to the customers site. In two hours more than four team members from three different departments popped out to see the equipment. They really valued the experience and getting the chance to view the machinery first hand. The uptake for bookings confirms this is a great idea which supports our customers pressures and pain points.”
Part of the new service package launching at PPMA 2023, booking slots are now open. Email marketing-fte@ fortresstechnology.com to set a mutually convenient time for a demo.
Solids handling specialist, Ajax Equipment, has supplied equine nutrition specialists, Saracen Horse Feeds, with a lump breaker for reducing the size of caked sugar beet pulp from big bags. Saracen Horse Feeds has over 200 years’ experience of supplying nutritional products and expertise.
To determine the specification required Ajax fed samples of the sugar beet through a test machine. The lump breaker used in tests and now in operation at Saracen Horse Feeds uses a combination of a profiled rotor and grille bars to break down the material to a predetermined suitable size. The spacing of grille bars in a lump breaker allows a maximum particle size to be set to meet the requirements of the process.
“From the initial conversations to completing the installation, Ajax understood our manufacturing brief and have delivered to expectation. As a
premium horse feed manufacturer it is imperative that our stringent manufacturing processes are met at every stage of production and the new installation supports the use of complex ingredients designed to support the nutritional needs of horses and ponies,” said Joe Lydiate, senior operations manager, Saracen Horse Feeds.
Commenting, Eddie McGee, managing director at Ajax Equipment, said, “Many materials become set in lumps when stored and require processing before they can be used. The adaptability of design and ease of operation make Ajax’s lump breakers an ideal choice for breaking down a wide range of materials including those for animal feed, chemical production and waste to energy processes.”
For more information on Ajax Equipment lump breakers call +44(0)1204 386723, email: sales@ ajax.co.uk and visit www.ajax.co.uk.
PACE Mechanical Handling will be joined by Spanish packing machinery giant Innova at this year’s PPMA Total Show.
PACE was appointed as Innova’s first-ever UK representative last year and has exclusive access to the company’s range of end-of-line strapping and wrapping packaging machinery, including its Stretch Hood system.
Unique to the UK market, the Stretch Hood system guarantees total protection against humidity, rain and dust due to the tightness of the wrapping and properties of the Stretch Hood film, which envelopes palletised products from above to the base.
As well as being the only system that delivers completely waterproof protection, Stretch Hood uses the minimal amount of film possible, reducing material and energy costs.
Stretch Hood is the only system that prepares the film precisely to the size of the load to be packaged. The tubular film is slightly smaller than the contour
of the load as the Stretch Hood machine stretches and applies the film to fit the dimensions of the load, sealing it completely.
Innova, which was established in 2001 and is headquartered in Castellón, Spain, says that the film used by the Stretch Hood system is one of the most advanced materials available, being a multilayer LLPDE polymer composition, offering waterproof protection and exceptional stretching capabilities.
The Stretch Hood system complements PACE’s range of automated packing machinery, which includes the Gemini twin head weigher, Orion Weigher, Orion Weigher and sack placer and the CBC sack placer and stitcher line, all of which will be promoted at the PPMA Total Show. As well as its own machines, PACE has a long-standing partnership with Motoman of Japan, allowing it to offer a wide range of robots, from pick and place up to specialist heavy lifting models.
“We are really looking
forward to the PPMA Total Show. Having Innova on our stand will give visitors a fantastic opportunity to learn more about the Stretch Hood system and our ability to develop bespoke automated packing solutions,” says Nick Cesare, PACE’s managing director. “2023 has been fantastic for us so far, and it’s looking like it will be a recordbreaking year. In the first eight months of 2023, we have beaten our previous best year, which was 2018, when we saw turnover reach seven figures.
“I think we’ve benefited from several factors. Most industries are currently looking for ways to cope with labour shortages, and they’re looking to pack more quickly and effectively. Automation and robotic packing and palletising are therefore increasingly popular with them.”
To learn more about PACE Mechanical and its automated solutions and the Stretch Hood system from Innova, visit stand G14 at the PPMA Total Show or www.robotpalletizing.co.uk.
If you would like to subscribe to receive a regular copy of the digital edition of Bulk Solids Today magazine, you can subscribe on our website - www.bulksolidstoday.co.uk
If you are interested in advertising within Bulk Solids Today magazine or supplying editorial content, please feel free to get in touch using the details on our website or below.
Bulk Solids Today is sent to our digital readership of over 9,000 Chief Engineers, Operations Managers and Technical Managers from within sectors including Chemicals, Food & Drink, Mining, Quarrying, Transport/Distribution, Recycling & Waste Management and more.
www.bulksolidstoday.co.uk
The Modu-Kleen downdraft dust collector developed by Dynamic Air is an automatic self-cleaning dust collector that offers significant advantages over conventional dust collectors with regard to performance, efficiency, filter access, energy, noise, maintenance and space requirements. With the ModuKleen downdraft dust collector, dirty air enters at the top of the dust collector housing and flows downward to the cartridge filters, improving the filtering process and the material-to-air ratio. Air velocities are much lower than
those with a conventional dust collector, reducing the load on each filter cartridge and extending filter life. Cartridge filters are positioned horizontally, requiring less floor space, and making filter removal easier.
Personnel never have to enter the filter housing for general maintenance or for cartridge filter removal, making the process much safer and quicker. For fast and easy inspections, a large, quick-opening door allows maintenance personnel to closely inspect each cartridge when required and any single
cartridge can be removed without disturbing adjacent cartridges. Because each cartridge filter has a unique built-in quarter turn bayonet mount, no tools of any kind are required for cartridge removal.
https://www. dynamicair.com/products/ dustcollector681.html
Dynamic Air Ltd.
Milton Keynes, United Kingdom
+44 1908-622344
E-mail: sales@dynamicair.co.uk
www.dynamicair.com
If you would like to subscribe to receive a regular copy of the digital edition of Bulk Solids Today magazine, you can subscribe on our websitewww.bulksolidstoday.co.uk
If you are interested in advertising within Bulk Solids Today magazine or supplying editorial content, please feel free to get in touch using the details on our website or below.
Bulk Solids Today is sent to our digital readership of over 9,000 Chief Engineers, Operations Managers and Technical Managers from within sectors including Chemicals, Food & Drink, Mining, Quarrying, Transport/ Distribution, Recycling & Waste Management and more.
www.bulksolidstoday.co.uk
bst@abbeypublishing.co.uk
Tuf-Lok ring grip pipe and tube couplings are rugged, heavy duty, self-aligning and self-grounded couplings with a high end pull. They can be used for almost any application where pipe or tube ends need to be connected. The Tuf-Lok self-aligning couplings install quickly and easily with little effort. Features
• Self-aligning
• Self-grounding
• High pressure rated
• Full vacuum rated
• Stainless or mild steel
• Usable on thin or thick wall pipe or tube
• Low cost
• Reusable
• Absorbs vibration
• Externally leakproof
Leading materials handling specialist, Spiroflow, an Automated Handling Solutions (AHS) company, has launched a next-generation twin-line bulk bag filling system. Following extensive research and development, the new system addresses the limitations of slow, outdated equipment that was prone to spillages and excessive product and dust emissions.
Introducing several key features that significantly enhance production capacity, weigh accuracy and operator ergonomics, the twin-line system is able to handle up to 20 x 500kg bulk bags per hour on each process line - a total of 40 bulk bags. Weigh accuracy is a key aspect of the new system as it achieves an impressive -0/+500g per bulk bag - this precision ensures consistent and accurate filling of each bag, minimising product waste and optimising inventory management processes.
One of the system’s notable design innovations is the incorporation of a raising and lowering filling head, specifically engineered to improve the ergonomic load of empty bags for operators. This feature aims to enhance operator comfort and safety, reducing the risk of workplace injuries.
The integration of auto-release hooks and roller conveyors streamlines the entire filling process, allowing for seamless and automated transfer of full bulk bags from the filler to the conveyors. This automation minimises the need for manual intervention, further enhancing efficiency.
With a strong emphasis on housekeeping, each filler is equipped with an integrated and independent dust extraction and filter system. This ensures that product and dust emissions are minimised, maintaining a clean and safe workspace for both operators and the environment.
The system includes a customised platform design that complements its functions and facilitates operator workflows to optimise operational efficiency. This design consideration ensures smooth operations and enhances the overall performance of the filling system.
The inclusion of an automated roller conveyor system enables the smooth transfer of full bulk bags throughout the entire system, significantly reducing the need for manual handling and increasing overall throughput. In addition, the auto-dispensing pallet
system efficiently places the pallet in position before loading the empty bag, simplifying the bag-loading process and saving valuable operator time.
Safety is a top priority in the design of the new bulk bag-filling system. The equipment is fully enclosed with safety fencing and features interlocked access gates to prevent unauthorised access while ensuring that the equipment operates safely and efficiently.
The new bulk bag filling system combines enhanced production capacity, precise weigh accuracy, ergonomic design, automation, safety features, and customised platform design to create a state-of-the-art filling solution that optimises efficiency, minimises waste and ensures a safe working environment.
“We are excited to introduce this revolutionary double bulk bag filling system, which addresses our clients’ needs for increased productivity, accuracy, and safety,” said Spiroflow’s Rhodri Jones. “This advanced technology not only enhances operations, but also contributes to a more sustainable and efficient working environment. The new system is currently in use with a powder manufacturing company, where it has considerably improved throughput, safety and efficiency.”
Automated Handling Solutions (AHS), is set to join forces with Advanced Material Processing (AMP), integrating Kason Corporation and Marion Process Solutions, to showcase their material processing equipment and solutions on stand F54 at the PPMA show, at Birmingham’s NEC, UK and on stand 4-309 at POWTECH, Nuremberg, Germany, both between the 26 - 28 September.
Swedish hair and beauty specialist Lyko has chosen Vanderlande to automate its new warehouse in Vansbro, Sweden. The two companies signed a contract for the installation of Vanderlande’s FASTPICK goods-to-person (GtP) order fulfilment system, including robotic item picking. Lyko needs a new solution to cope with rapid growth and to meet its ambition to break into emerging European markets.
Vanderlande’s FASTPICK was selected because it meets the company’s need for greater efficiency and capacity, and can be installed on a limited footprint. The greenfield warehouse is scheduled to open in 2025 and will be Lyko’s largest automation project so far. The scalability and flexibility of Vanderlande’s solution provide the opportunity for further extension.
The system includes the ADAPTO automated storage and retrieval system (AS/RS): 216 ADAPTO shuttles will be able to access more than 152,000 product locations across 27 levels and 40 aisles. The innovative system will be capable of handling 45,000 orders every day.
The contract also includes 15 GtP workstations, three of which are equipped with robot item pickers from Vanderlande’s portfolio of Smart Item Robotics. In addition, all the manual workstations, including those for decanting, are height adjustable to minimise lifting duties for operators. The system also includes Vanderlande’s POSISORTER shipping sorter.
The state-of-the-art solution is driven by Vanderlande’s digital suite of software services. During the entire process, the system handles items as gently as possible, which makes it an ideal solution for Lyko, with its stock of fragile and expensive products, such as bottles of perfume.
“This solution gives us the capabilities we need to scale our business in a cost-efficient way – it will therefore support our plans for growth and help us expand into Europe,” says Rickard Lyko, Lyko’s CEO and founder. “By increasing our capacity and providing us with the efficiency we need through integrated robot technology, Vanderlande has shown that it best understands our needs.”
“We listened closely to what the Lyko project team needed, and we’re delighted that they chose our state-of-the-art technology to help realise their expansion plans,” says Vanderlande’s Executive Managing Director Warehouse Solutions, James Cotton. “The FASTPICK solution offers the company the flexibility and sophistication it requires to handle an extensive range of products and deliver orders
to customers as quickly as possible. We look forward to the installation and forging a long-term partnership with this dynamic company.”
Company profile of Vanderlande
Vanderlande is a market-leading, global partner for future-proof logistic process automation in the warehousing, airports and parcel sectors. Its extensive portfolio of integrated solutions –innovative systems, intelligent software and life-cycle services – results in the realisation of fast, reliable and efficient automation technology.
The company focuses on the optimisation of its customers’ business processes and competitive positions. Through close cooperation, it strives for the improvement of their operational activities and the expansion of their logistical achievements.
Vanderlande’s warehousing solutions are the first choice for many of the largest global e-commerce players and retailers in food, fashion and general merchandise across the globe. The company helps them to fulfil their promise of same-day delivery for billions of orders, with nine of the 15 largest global food retailers relying on its efficient and reliable solutions.
As a global partner for future-proof airport automation, Vanderlande’s market-leading baggage handling systems and related passenger solutions are capable of moving over 4 billion pieces of baggage around the world per year. These are active in more than 600 airports, including 12 of the world’s top 20. In addition, over 380 of Vanderlande’s security lanes are installed at checkpoints worldwide.
Vanderlande is also a leading supplier of process automation solutions that address the challenges in the parcel market. More than 52 million parcels are sorted by its systems every day, which have been installed for the world’s leading parcel handling companies.
Established in 1949, Vanderlande has more than 9,000 employees, all committed to moving its customers’ businesses forward at diverse locations on every continent. With a turnover of 2.1 billion euros, it has established a worldwide reputation over the past seven decades as a global partner for future-proof logistic process automation.
Vanderlande was acquired in 2017 by Toyota Industries Corporation, which will help it to continue its sustainable profitable growth. The two companies have a strong strategic match, and the synergies include cross-selling, product innovations and research and development.
www.vanderlande.com
Conveyors are among the most dynamic and potentially dangerous equipment in bulk handling. The operational basics of belt conveyor systems regarding the hardware installed and the performance required from the components are too often a mystery to many employees. This knowledge gap also creates a safety gap. Since personnel are the single most important resource of any industrial operation, to meet workplace safety standards, the consensus among safety professionals is to design the hazard out of the component or system, which historically yields more cost-effective and durable results.
Designs should be forward-thinking. This means exceeding compliance standards and enhancing operators’ ability to incorporate future upgrades cost-effectively by taking a modular approach. This method alleviates several workplace hazards, minimizes cleanup and maintenance, reduces unscheduled downtime and extends the life of the
belt and the system. Before the drafting phase, designers should:
1) establish the goals of reducing injuries and exposure to hazards (dust, spillage, etc.);
2) increase conveyor uptime and productivity, and;
3) seek more effective approaches to ongoing operating and maintenance challenges.
To meet the demands for greater safety and improved production, some manufacturers have introduced equipment designs that are not only engineered for safer operation and servicing but also reduced maintenance time. An example is the Martin® QC1™ Cleaner HD/XHD STS (Safe-toService) primary cleaner and the Martin SQC2S™ STS secondary cleaner, designed so the blade cartridge can be pulled away from the belt for safe
access and replacement by a single worker.
The same slide-out technology has been applied to impact cradle designs. Systems like the Martin Slider Cradle are engineered so operators can work on the equipment safely, without breaking the plane of motion. External servicing reduces confined space entry and eliminates reach-in maintenance while facilitating faster replacement. The result is greater safety and efficiency, with less downtime.
An example of a safer belt cleaner is the CleanScrape®, which received the Australian Bulk Handling Award in the “Innovative Technology” category for its design and potential benefits. The revolutionary patented design reduces the need for bulky urethane blades altogether. It delivers extended service life, low belt wear, and significantly reduced maintenance, which improves safety and lowers the cost of ownership.
Unlike conventional belt cleaners that are mounted at an angle to the belt, the CleanScrape is installed diagonally across the discharge pulley, forming a threedimensional curve beneath the discharge area that conforms to the pulley’s shape. The novel approach has been so effective that in many operations, previously crucial secondary belt cleaners have become unnecessary, saving further on belt cleaning costs and service time.
Although the policy is generally not explicitly stated by companies, the “LowBid Process” is usually an implied rule that is baked into a company’s culture. It encourages bidders to follow a belt conveyor design methodology that gets the maximum load on the conveyor belt with the minimum compliance to regulations using the lowest price materials, components and manufacturing processes available.
When companies buy on price, the benefits are often short-lived, and costs increase over time, eventually resulting in losses. In contrast, when purchases are made based on the lowest longterm cost (life-cycle cost), benefits usually continue to accrue and costs are lower, resulting in a net savings over time.
Engineering safer conveyors is a long-term strategy. Although design absorbs less than 10
percent of the total budget of a project, Engineering / Procurement / Construction Management (EPCM) services can be as much a 15 percent of the installed cost of a major project, additional upfront engineering and applying a life cycle-cost methodology to the selection and purchase of conveyor components proves beneficial.
Safety-minded design at the planning stage reduces injuries by engineering hazards out of the system. The system will likely meet or exceed the demands of modern production and safety regulations, with a longer operational life, fewer stoppages and a lower cost of operation.
Dynamic Air dense phase pneumatic conveying systems have been proven in over 15,000 installations worldwide. They handle a wide range of materials and bulk densities at rates from a few hundred pounds to 400 tons per hour, over distances exceeding 5,000 feet. The HDP 4000 Full-Line Concept dense phase pneumatic conveying system has many advantages over more traditional dense phase concepts with regard to degradation and energy consumption. The system utilizes the DC-5 Air Saver technology to achieve an optimum pressure balance while counteracting forces of friction. The Full-Line Concept system conveys materials at low velocity and high density while utilizing very low air consumption. The enclosed system is clean and can be fully automated to convey to packaging or process bins. Very few moving parts are utilized, as the prime mover is standard plant compressed air at 100 PSIG. Dynamic Air Full Line Concept systems have proven to be very low in maintenance and are very flexible with regard to space and various custom plant situations
https://www.dynamicair.com/systems/hdp4000. html
Dynamic Air Ltd.
Milton Keynes, United Kingdom
Phone: +44 1908 622344
E-mail: sales@dynamicair.co.uk
• Premiere: new NX Series feeder for poorflowing bulk materials to debut at Powtech in Nuremberg, Germany
• First joint product development: NX feeder combines proven Kubota design with proven Brabender Technologie components
• NX feeder as well as other Kubota Brabender Technologie highlights in Hall 4, Booth 225
A large number of international process, bulk materials and conveying technology experts are set to convene at POWTECH in Nuremberg (Germany) from September 26 to 28, 2023. Kubota Brabender Technologie GmbH will again be there this year and showcase many of its proven products - and unveil a new one: the enhanced NX Series feeder.
Premiere: NX feeder
An NX Series feeder in the medium feed capacity range that handles poor-flowing, sticky powders as well as fibers and pellets will be showcased for the first time. What makes it special is that it combines the proven mechanical design of one of Kubota Corporation’s most innovative gravimetric feeders with Brabender Technologie GmbH’s proven load cells and motors. The result is a feeder featuring a special negative angle wall hopper geometry and an diagonal agitator that prevents bridging and ensures optimal bulk material flow into the screw. In combination with other innovative components, mass flow is optimized and a uniform screw fill level is achieved.
This makes the feeder the first jointly developed product that showcases Kubota Brabender Technologie as “One Company”. Other exhibits that the company will be showcasing include Generation 2.0 twin and single screw feeders, demonstrating the modular design and easy accessibility of the equipment, and the Flexwall 40, which provides live insights into its operation through its transparent hopper. The MiniTwin feeder including ionizer and the FDDW liquid feeder will also be exhibited.
First joint product development milestone
Kubota Brabender Technologie is one of the world’s largest providers of gravimetric and volumetric feeding systems and discharge devices. The company’s products are used in various sectors and industries for both batch and continuous production. Almost exactly one year after integration, the company has reached the first joint product development milestone with the new NX feeder - the first German-Japanese product under the new Kubota Brabender Technologie brand that complements and rounds out the company’s portfolio. “Our ambition is to harness the synergies of both companies and to jointly develop successful, high-quality products for the global market,”
Bruno Dautzenberg, Managing Director of Kubota Brabender Technologie, explains.
Visit Kubota Brabender Technologie at Powtech from September 26-28, 2023!
Our experts look forward to speaking with you.
You will find us in Hall 4, Booth 225
For nearly 40 years, family-owned business Campbell Contracts has been extracting sand and gravel from its Letterbailey quarry in County Fermanagh, Northern Ireland. More recently, in response to market demand, the company commenced blasting to increase the supply of its sand, gravel, decorative gravel, crushed rock, rock fill and screened topsoil.
In 2019, the Campbell family partnered with CDE to support them to grow the business and diversify its portfolio of high-quality quarried aggregates. The final solution allowed the company to process three new materials it previously categorised as waste from its quarrying operations: clay-bound sand and gravel, primary scalpings and crushed rock fines.
THE PROBLEM WITH PONDS
Increased tonnage, however, and subsequent pond maintenance resulting from Campbell Contracts expanding its operations put additional
pressure on labour availability on site.
In pursuit of a solution, a detailed site audit conducted by CDE engineers revealed pond cleaning was consuming up to 15% of total operational hours and that improved water management practices would help to alleviate labour pressures.
Following a competitive tender process, CDE proposed its AquaCycleTM thickener for primary stage water management to efficiently manage silt content and address the shortcomings typically associated with settling ponds.
Delivering competitive advantage to its customers, CDE’s AquaCycle accelerates return on investment by maximising production efficiency, improving output product quality and reducing water and energy costs.
Traditional wash plants use a series of ponds to recycle water and for the natural settlement of suspended solids and silts. As wash plant technology
has advanced and tonnages have increased, the area needed for settlement ponds has dramatically increased and these are often a source of significant operational and logistical challenges.
Accounting for the increase in material throughput alongside fuel and labour costs, ongoing pond management costs £5 per tonne on average.
CDE’s technical pre-sales manager William Melanophy said: “We consistently invest in research and development with the aim of enhancing the capabilities of our water management and recycling equipment, and the AquaCycle – a single, compact and user-friendly unit that can be applied to high and low tonnages across many markets – is at the forefront of this effort.”
An alternative to water extraction and the costly process of pumping water to the plant, CDE’s AquaCycle minimises water consumption by ensuring up to 90% of process water is recycled for immediate recirculation.
After feed material has been washed and classified, waste is sent to the AquaCycle thickener tank. Here, a small amount of polyelectrolyte flocculant is added to the water via an automatic dosing station which forces fine particles to settle on the bottom of the thickener tank. It helps to maximise the settlement of solids in the smallest possible space as waste sludge is thickened and discharged to the holding pond, resulting in a lower total volume of material being sent to the pond which drives down
maintenance costs and manual labour requirements.
CDE business development manager Fergal Campbell said: “Our AquaCycle solution pumps directly to final remediation areas, meaning sludge does not have to be handled or transported. As well as increasing operational efficiency, it has helped to reduce labour and silt management costs while also extending pond life. This allows the Campbell Contracts quarrying division to better manage its labour resource by redirecting its team to high priority and value-adding tasks.”
Within the first year of operation, the reduced maintenance requirements and increased productivity enabled by CDE’s AquaCycle has contributed significantly to the company’s bottom line, driving down costs and supporting revenue generation.
“We are extremely happy with the results of our latest partnership with CDE,” Grainne Quinn, director of Campbell Contracts said.
“CDE’s AquaCycle has greatly improved operational efficiency on site which has allowed us to focus on generating new business and better serving our customers. The impact is unquestionable. We’re estimating the combined cost savings and new revenue brought about by the solution to be worth six figures to the business.”
For more information about CDE and its water management systems, visit cdegroup.com.
Located in the heart of England, Quarry Manufacturing and Supplies Ltd. (QMS) has since its formation in the 1980s grown to be one of the UKs leading suppliers of crushing, screening and stockpiling equipment. In addition to providing the hardware that makes the mineral processing industry tick, QMS has also supported aggregate and mining operations worldwide with the company’s extensive range of aftermarket crusher wear and spare parts.
QMS operates out of its purpose built facility (and two other sites) located in Leicestershire, England, and has established a robust and efficient network for supporting customers across the globe. Company service engineers have provided repair and maintenance to customers, which range from small quarries and recycling plants in the UK, to the largest quarrying and mining operations globally.
QMS has continually invested in new technologies, processes and supplier partnerships, consistently raising the bar, delivering high levels of customer service, product quality and value. In fact, QMS is now recognised as one of Europe’s premier manufacturers of bespoke aggregate plants, aftermarket crusher spares, wear parts and bespoke processing equipment. These have been designed
to meet the requirements of customers, with QMS always striving to exceed expectations.
With a hard won reputation for providing the equipment, parts and services the industry needs, QMS has recently finalised a bespoke sand and gravel plant for industry behemoth Cemex. Working in collaboration with principal contractor MEP (Mineral Engineering Processes), which supplied the specialist sand, dewatering and associated equipment, QMS was tasked with designing, manufacturing, installing and then supporting the new plant which is located near Burton upon Trent at Pyford Brook Quarry.
“We were initially contacted by MEP and Cemex with regards to collaborating with them regarding the new Cemex Pyford Brook sand and gravel quarry. MEP has a leading niche product range which has been designed to enhance sand and gravel production but required a partner to provide the aggregate plant knowledge and equipment to install the primary sand and gravel processing equipment. As the quarry needed a bespoke cost effective solution that had to be built and be made operational to a demanding time frame, and based
on our longstanding relationship, MEP and Cemex viewed QMS as the ideal partner,” explains company managing director Jonathan Beck.
“The Pyford Brook plant has been built to produce sand and gravel at a relatively high production rate of 250tph. As the quarry is brand new, and six months ago physically did not even exist, this meant that we had limited time to get the plant design right from the off, incorporating not only our equipment, but also the specialist MEP Hydrolig process. Our processing equipment had to not only be able to meet Cemex’s production targets, but also consistently produce the sizes required to make the quarry a profitable ongoing concern,” adds Jonathan.
The QMS plant at Pyford Brook has been designed with Cemex’s targets at its heart but has also been designed to take account of logistical and environmental concerns. Given the rural location of the quarry, and it being a new operation, these were important factors that had to be accommodated. In effect, the quarry (and its material processing equipment) had to be able to produce the products required with minimal disturbance to local inhabitants and the environment.
The design of the plant sees the initial feed material consisting of 150mm+ sand and gravel being loaded into a belt feeder through a hydraulic remote controlled tipping grid; this is then conveyed to a double deck polyurethane primary screen, with oversize material being returned to the QMS cone crusher. A double deck washing screen then further processes the material to produce a -20mm product. The end-product is then refined to be used in the manufacture of Ready-Mixed Concrete. QMS also supplied all the support structures, conveying and stockpiling equipment which are fully galvanised and were designed and manufactured in house to EN1090.
With Cemex’s Pyford Brook quarry now approaching full operational efficiency, the QMS equipment at the sand and gravel plant installation is only the beginning of the relationship. “Quarry Manufacturing and Supplies Ltd. has a reputation for equipment and plant design excellence. Our crushers, screens, feeders, support structures, conveyors and other associated equipment are now used throughout the world in some of the most demanding of applications,” explains Jonathan Beck.
“However, we don’t just make and install the equipment; we also support and upgrade all our plants, as well as providing aftermarket care on equipment made by other manufacturers. It is our
belief that when a QMS plant becomes operational that’s only the start of the story. We provide the expertise, know-how and drive to keep customers’ operations working at full efficiency as well as carrying a full parts inventory for maximised uptime.
“All at QMS take pride in making sure that our customers are able to be as efficient and productive as possible. We will continue to work with Cemex and MEP to ensure that the Pyford Brook Quarry provides the material for Cemex as long as there is a requirement to do so,” concludes QMS managing director Jonathan Beck.
The full plant list QMS installed at the Cemex Pyford Brook Quarry consists of:
• Belt feeder – P/N FHB-20-1000, 20m3
• Cone crusher – P/N 13100_00, model B2
• Primary screen – P/N SVI-B02M, 1.83x5m double deck, polyurethane
• Secondary Screen – P/N SVIG02M, 2.4x6.0m double deck, wash screen
• Various galvanised steel support structures, conveyors and stockpilers
Founded in 1946, Santos Jorge has two facilities in the towns of Mollet del Valles (Barcelona) and Montblanc (Tarragona), where domestic glass and industrial glass are treated and recycled.
Thanks to the technology and versatility of the processes at these sites, they offer all kinds of recycled glass treatment services for different sectors such as glass manufacturing, water filtration, construction or abrasives, and are considered among the best in the European market.
Santos Jorge recycles around 100,000 tonne of glass per year, and the company recently added a Bobcat MT55 mini track loader to its machinery fleet, which due to its compact size is ideal for working in very confined spaces.
Manager at Santos Jorge, comments: “We needed to clean all the way to the corners under the belts that transport the glass and for this a super compact machine was essential, since we are talking about areas that are not too wide, with columns, and where a normal loader cannot access due to its size.
“Since we have been working with this Bobcat mini track loader, we no longer have to clean by hand with a shovel and brush, which has resulted in a comfortable, faster, more efficient and safer way of operating, and this also allows us to more easily keep cleaning and maintenance up-to-date, without accumulating glass debris.
“With the bucket on the loader we also load the glass waste into containers and with a custom-made stacker, we clean corners that it is impossible to reach with any other machine as the cabs would get in the way.
“Basically this is the only model that allows us to
access certain spaces in our facilities. And another noticeable advantage is that it is very easy to work with it.”
Currently, the Bobcat loader is performing maintenance on all the low and narrow corners of the recycling plant, performing maintenance on about 600 m2 of operating space.
The problems that Santos Jorge succeeded in solving with the Bobcat mini track loader are the same as those in aggregate plants and all of those industries that work with conveyor belts.
In the MT55, operators highlight above all its lightness, easy use, the compactness, manoeuvrability, its very good breakout force for a machine of this size, as well as its nominal load capacity of 254 kg.
Prior to the purchase of the MT55, Bobcat Of, the official Bobcat distributor, carried out a demonstration for Santos Jorge, showing the most suitable solution for their business. Improvement has been evident, with less labour for the same results and with greater efficiency and speed.
Antonio Hernandez added: “Whenever we have had a need, Bobcat Of has provided us with a good proposal, which is why we trust their team. They provide us with a good service both in advising us in the face of problems, and through their technical service.
“We also have a Bobcat S450 loader that has been in service for a few years now, equipped with a sweeper attachment, for other maintenance work in larger areas, with which we are also very satisfied.”
Bobcat skid-steer loaders are characterized by their small dimensions and great agility, combined with their amazing traction and lifting capacities - they overcome the difficulties of manoeuvring in confined spaces with ease and speed.
Bobcat has recently launched the company’s latest mini track loader, the MT100, with a rated capacity of 460 kg, a tipping load of 1314 kg, a powerful breakout force and a lifting height of 2057 mm. Its ISO joystick controls are ergonomically designed and offer very tight precision, for more comfortable control of the machine.
For more information about Bobcat and its products, visit www.bobcat.com.
• Henkel uses innovative EcoFloat® sleeve technology to improve the recycling of PET bottle bodies
• Technology enables easier separation of sleeve and bottle body in the recycling process
• CCL and Henkel were awarded for environmental contribution of new packaging design
CCL Label, a world leader in specialty label, security and packaging solutions, and Henkel announced today that they have won the AWA (Alexander Watson Associates) Award for their Best in Class Sustainable Design for Henkel’s Vernel brand fabric softener bottle.
AWA stated „The design was applauded for emphasizing recyclability and adhering to EPBP guidelines. The container, constructed from 100 percent recycled PET bottle materials and a low-density polyolefin sleeve, is designed for easy sorting and recycling“.
To improve the recyclability of the PET bottle bodies of its fabric softeners in Europe, Henkel partnered with CCL who has developed a new generation of floatable polyolefin material for shrink sleeves called EcoFloat®. This low-density material can be separated from PET bottle components during the sink-float separation process at recycling facilities. While the heavier bottle material sinks to the bottom of the water baths, the lightweight sleeve material floats to the top, even with full printed designs. This enables a clean separation of the PET and the label material, which is necessary to gain high-quality PET recyclate.
“The bottle body of our fabric softeners in Europe already consists of 100 percent recycled PET.
Using the new sleeve material, they are now also designed for recycling,” said Abdullah Mahmood Khan, Head of Global R&D Packaging for Fabric Enhancers at Henkel.
“Many consumers don’t remove the sleeve before discarding the bottle, which mostly means that
the bottle cannot be recycled either. We have now found a solution to enable the recycling of our bottle bodies in this case.”
Lukas Nachbaur, Account Manager Henkel at CCL Label, adds: „The collaboration with Henkel is a great example of what can be achieved by matching the product decoration with the primary packaging – making it a perfect fit for design for recycling. When Henkel was looking for the most sustainable solution for their Vernel bottle – we recommended EcoFloat, because it supports the recycling process of the PET bottle in every way.“
“When it comes to sustainable packaging decoration, we strive to be the industry leader – and we are proud to see this acknowledged by industry experts like AWA. The `Sustainable Product Family` is our portfolio of sustainable solutions for labels and sleeves that enables our customers to chose from different options, depending on what their sustainability goal is,“ says Marika Knorr, Head of Sustainability & Communication at CCL Label. „It is an integral part of our sustainability roadmap and we make sure that our products are in line with the official design for recycling guidelines of organizations like RecyClass in Europe and APR (Association of Plastic Recyclers) in the USA“.