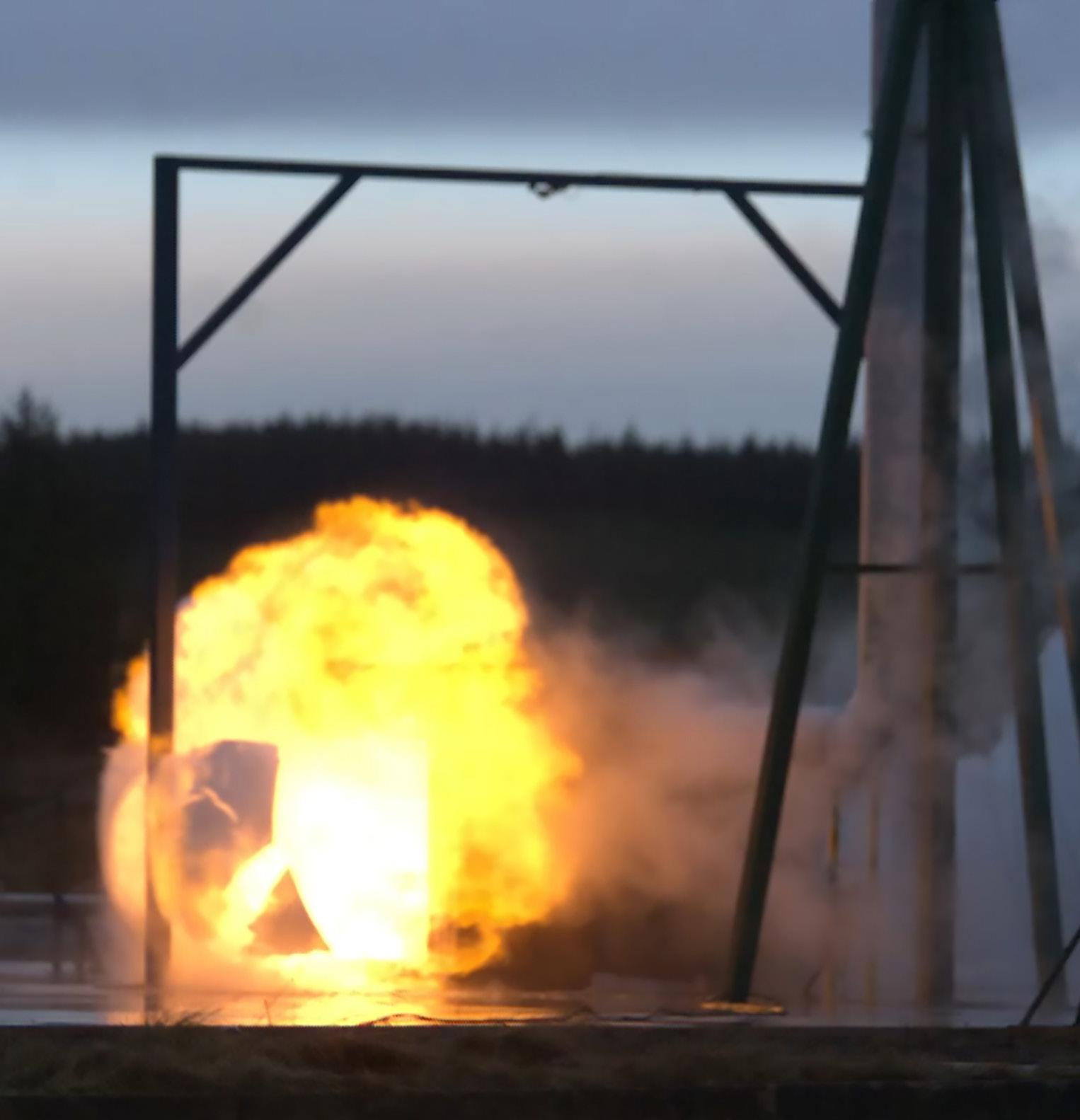
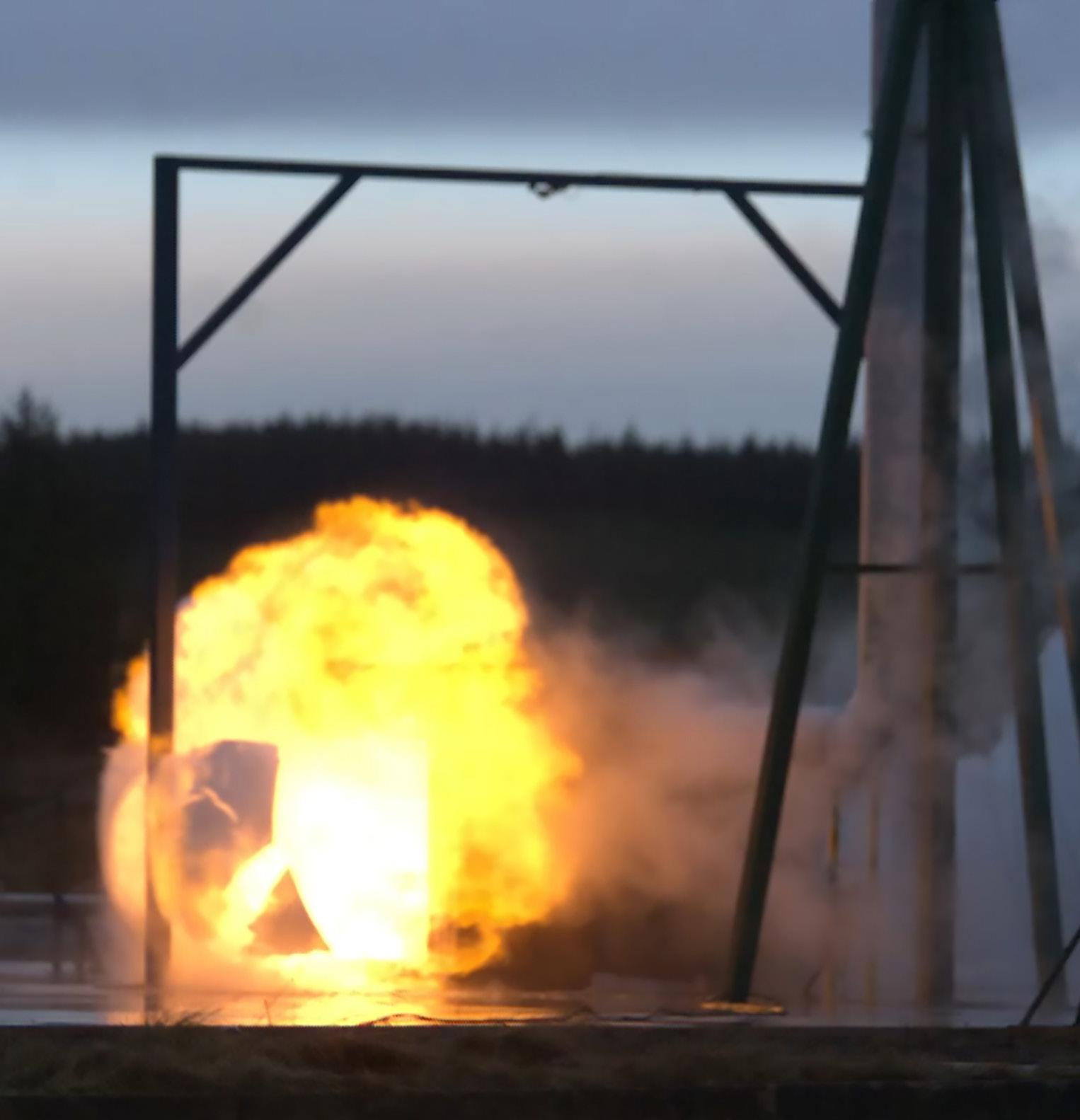
LifEx, the
in the

We have reduced the size, lowered the weight, shortened the time of installation, removed any type of risk, reduced any maintenance intervention, avoided 70% of the components and saved tons of CO2. We have also eliminated the possibility of improving it.
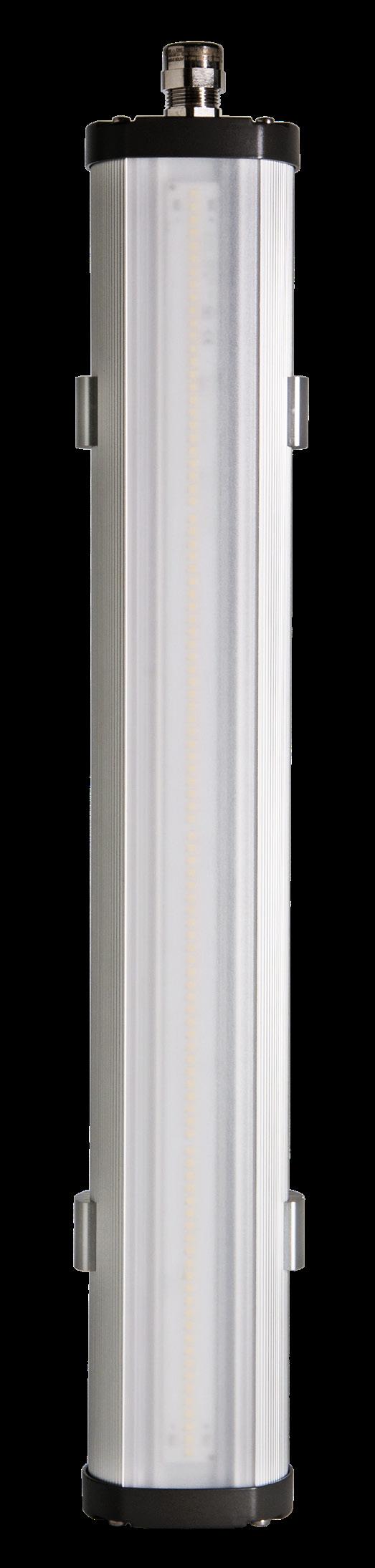


The advent of hydrogen into the global energy mix has been difficult to miss. A flurry of recent funding announcements and planning applications is evidence of hydrogen’s viability as an energy source on an industrial scale. With the UN’s Climate Conference (COP26) set to take place between October 31 and November 12, it is likely that that hydrogen, especially ‘green’ hydrogen produced from renewables, will receive further endorsements and support.
Taking the UK as an example, there have been recent moves to develop renewable energy infrastructure. In July, several companies including BP, Equinor, Orsted, Shell, and RWE submitted bids to build offshore wind projects off the coast of Scotland, the first round of seabed leasing in Scottish waters for over a decade.
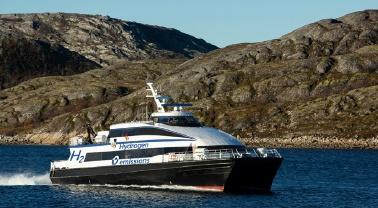
Elsewhere, SSE Thermal and Equinor submitted a planning (DCO) application for two first-of-a-kind, low-carbon power stations in the UK’s Humber region,which could triple the UK’s hydrogen output.
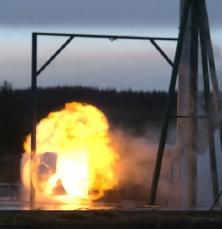
However, it is important to remember the need for safety. As discussed on page 13, although renwables and environmental initiatives such as carbon capture are often perceived as being green, clean and therefore safe, the risks are frequently overlooked, and often not dissimilar to those seen in the oil and gas industry.
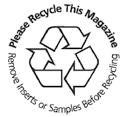

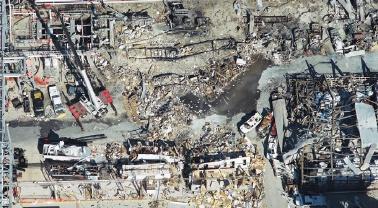
While renewable energy isn’t a new concept, hydrogen and carbon capture on an industrial scale certainly are, so it is important that the industry remains aware of the risks involved and keeps safety at the heart of the journey towards net zero.

…Alistair Hookway, Editor, Hazardex alistair.hookway@imlgroup.co.uk

Serious regulation breaches identified from investigation into December 2020 incident at Equinor plant
The Petroleum Safety Authority of Norway (PSA) announced on June 24 that it had completed its investigation into the December 2020 incident involving a turbine breakdown and subsequent fire at Equinor’s Tjeldbergodden methanol plant. The regulator said serious breaches of the regulations were identified, and that Equinor has now been given an order to identify, initiate, and follow up a number of safety measures.
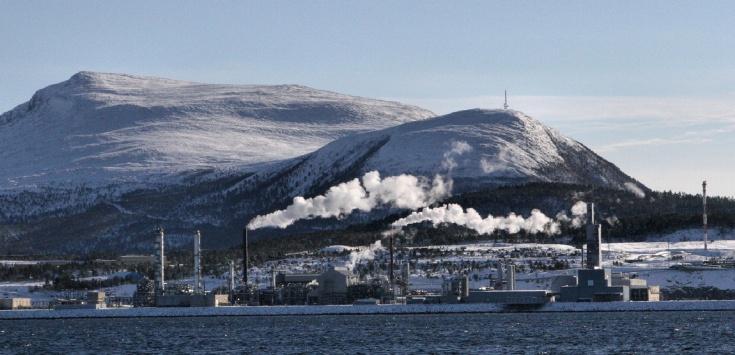
The incident occurred on 2 December 2020 in a compressor house, which forms part of the methanol plant and contains equipment for compressing synthesis gas (a blend of hydrogen, carbon dioxide and carbon monoxide) as well as a steam turbine generator with associated support systems.
During work to adjust the parameters of the regulator which controls steam admission to the turbine generator, a process shutdown (PSD) had to be initiated manually owing to an unexpected response from the control system.
When PSD is initiated, the generator must be disconnected from the power grid and the turbine isolated from the steam network. In this case, isolation from the steam
network failed and the backflow of steam at the intermediate pressure level increased turbine rotation. This faster speed caused turbine blades to come loose from the rotor, which then became wedged and stopped abruptly. That caused the shaft to snap between turbine and gear. One result of this breakdown was that components from the turbine shaft and a flexible coupling on the shaft were flung about with great force.
These objects struck piping for the turbine’s lube oil system, which broke and caused a lube oil leak that then ignited. The resulting fire lasted around an hour, but did not spread to other systems in the compressor house. About 1,000 litres of lube oil are estimated to have leaked out.
The PSA’s investigation found that the incident had the potential to become a major accident and could have caused serious personal injury or death as well as substantial financial loss. No physical injuries were sustained as a result of the incident.
A statement from the PSA said that in the event of a turbine trip, plant operators are supposed to make a physical check of the turbine generator. Had they or other personnel been in the compressor house when the breakdown occurred, they could
have been struck by flying components. The latter was also hurled with great force through the walls of the compressor house and could have hit people outside the building.
Flying components also hit the synthesis gas plant located in the same building. Had this caused a synthesis gas leak, the outcome could have been an explosion and/or a large fire.
The direct cause of the turbine breakdown with subsequent fire was that isolation from the steam network at the intermediate pressure level failed to function as intended during an PSD of the system.
The investigation also identified several elements which have or could have been significant for the incident occurring. These included:
- Information used as a basis for classification - Failure to handle an impaired barrier function - Maintenance - Failure of a system review to pick up design weaknesses - Technical documentation
Four nonconformities were identified by the investigation, related to:
- Identifying safety functions and barrier follow-up
- Follow-up of the system - Documentation - Safe distance from the fire scene
Two improvement points were also identified in relation to:
- Unclear how the Tjeldbergodden fire appliance was used
- Unclear performance standard for personnel check (POB) in the plant.
As a result of the investigation, the PSA has ordered Equinor to “identify, initiate and follow up measures to ensure that equipment with a safety function is identified and classified to ensure correct follow-up of its function and proper handling of impairments in order to secure safe operation.” The deadline for compliance with the order is 31 December 2021. The plan for complying with the order must be submitted to the PSA by 15 September 2021.
Oil company fined £400,000 for North Sea platform gas leak
Offshore oil company Apache has been fined £400,000 after it failed to provide written safety procedures for the depressurisation of an oil well, which led to the release of more than 1000kg of hydrocarbon gas at its Beryl Alpha production installation in the North Sea.
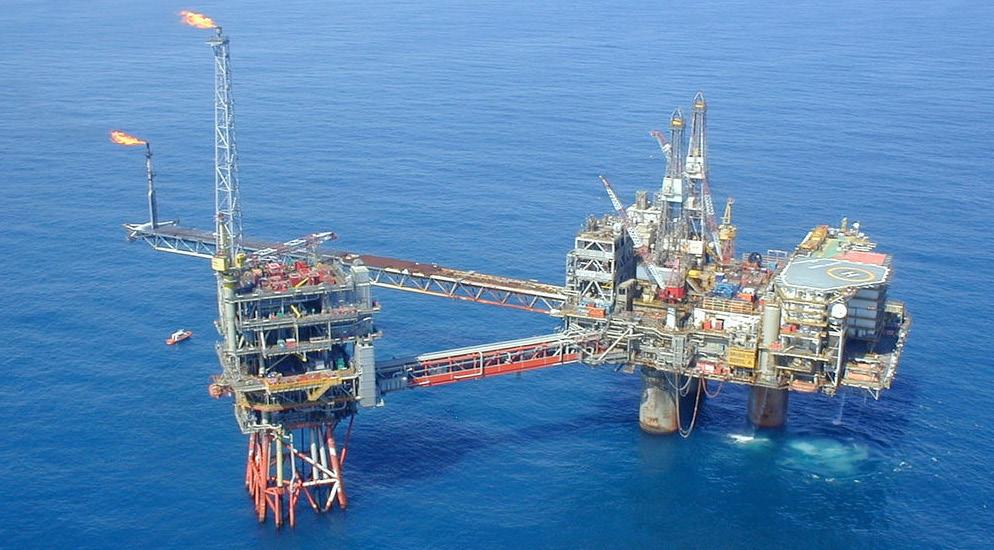
Aberdeen Sheriff Court heard how on 2 June 2014, Apache had allocated a production technician to carry out a depressurisation task on one of its oil wells, which he had performed on previous occasions. However, Apache failed to provide him with any written safety procedures, expecting him to carry out this complex task from memory.
The Beryl Alpha rig has 40 well slots and some of its oil wells are gas-lifted to increase production efficiency. The use of gas lift means that there are large inventories of pressurised hydrocarbon gas. Any uncontrolled release of these inventories is a potential major hazard event.
At approximately 19:40 local time, four flammable gas detectors had detected gas in the area and automatically activated the platform water deluge system. The general platform alarm sounded, and all 134 workers went to their muster stations. The gas release continued, and the installation remained at
muster station for more than six hours.
An investigation by the UK Health & Safety Executive (HSE) found that deficiencies in Apache’s safety management system (SMS) led to a release of more than 1000kg of hydrocarbon gas. Apache had failed to carry out a risk assessment for depressurising gas lift wells, which meant there was a lack of suitable written procedures. The use of a formalised written procedure by Apache would have ensured that this task was carried out correctly in a safe and consistent manner across all staff shifts, preventing the safety critical emergency shutdown system from being disabled during well depressurisation. The prolonged duration and magnitude of the release was a direct consequence of the inadvertent defeating of the emergency shutdown system in this instance.
Prosecutors said that over 100 members of staff were exposed to the risk of serious injury or death if the gas release had ignited. Given its reported 2019 turnover of £400 million, Sheriff Philip Mann said a £600,000 fine was appropriate. This was lowered to £400,000 as a result of Apache’s guilty plea.
Sheriff Mann told the court: “This was a serious breach of health and safety responsibilities which had the risk of serious
injury, but fortunately that risk was low. However, there was a system in place which, if it had been followed, would have prevented the situation from occurring. The company has a good health and safety record, no previous convictions and has fully cooperated with steps to remedy the situation.”
Speaking after the hearing HSE principal inspector Dave Walker said: “Although the offshore industry has managed to reduce its overall number of hydrocarbon releases, it is still the case that in most years there are several, which are of such a size that if ignited would result in potentially catastrophic consequences.
“At more than 1000kg, Apache’s Beryl Alpha’s hydrocarbon release was the largest reported to HSE in 2014. It occurred during complex work on a well, which used a large volume of high-pressure gas to improve production rates, the hazardous nature of which had been highlighted in specific HSE guidance.
“The depressurisation of an oil well is a safety critical task, and so should have been formalised in a written procedure to set out a specified sequence of operations to perform the task correctly and prevent potential fatal consequences.”
The images of the fire, which happened on the ocean surface to the west of Mexico’s Yucatan peninsula, were shared around the world on social media and drew widespread criticism from environmentalists. No one was injured in the incident and the fire was eventually extinguished after five hours.
On July 5, PEMEX said in a statement on its website that an electrical storm forced the company to shut down pumping equipment on the nearby Ku-C offshore platform. At the same time, a leak on a 12” underwater pipeline caused a build-up of natural gas on the ocean floor which was then most likely ignited by a lightning bolt as it rose to the surface.
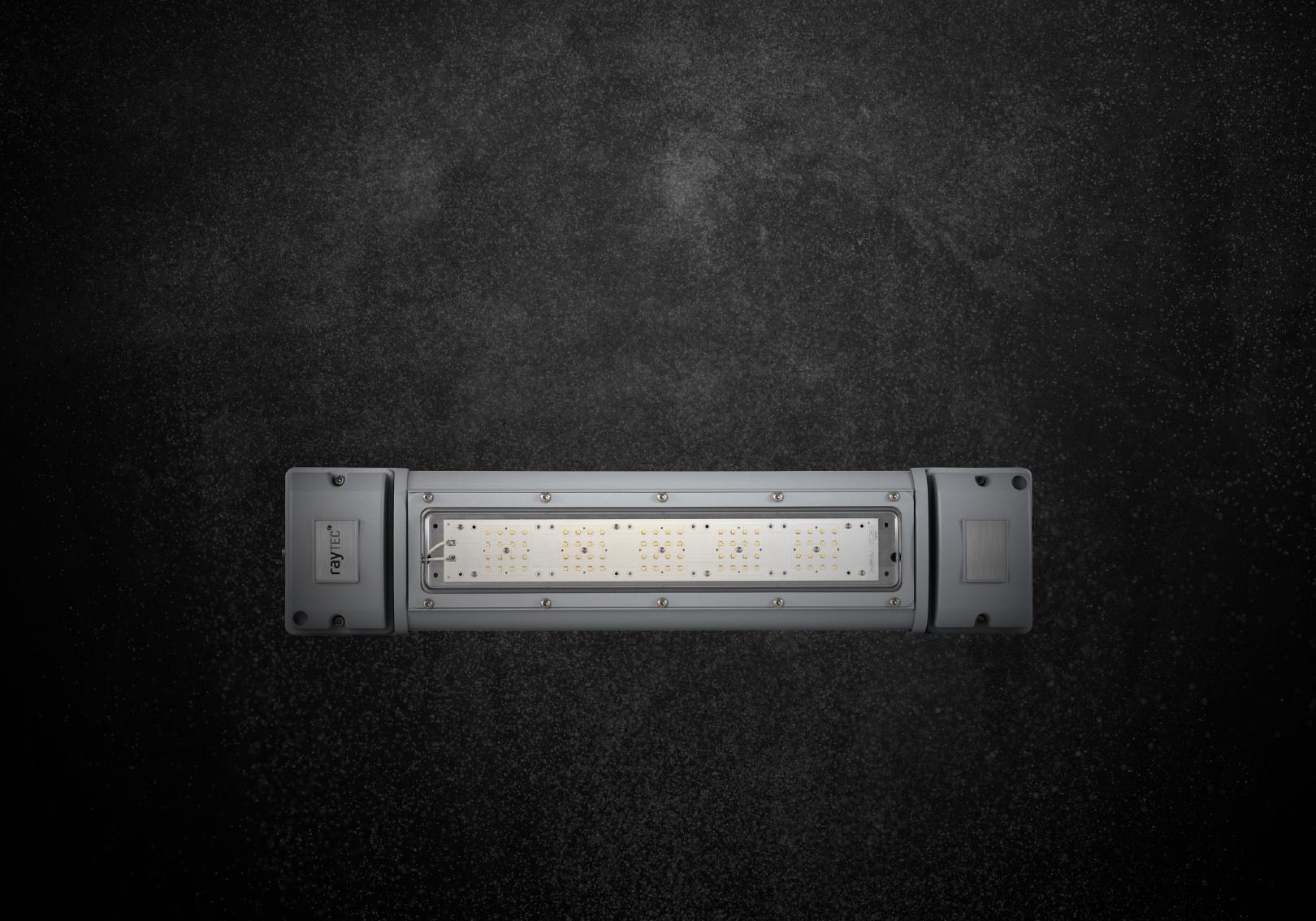
After five hours, the fire was completely extinguished by closing the submarine valve and injecting Nitrogen into the gas pipeline, PEMEX said. It added that there was no oil

‘Eye of fire’ in Gulf of Mexico caused by electrical storm, PEMEX says
TC Energy seeks over $15 billion in damages after US revokes Keystone XL permit
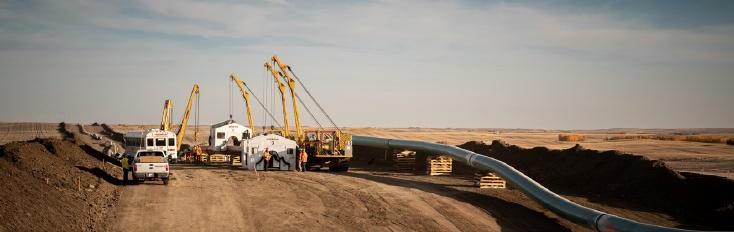
Canadian energy company TC Energy announced on July 2 that it is seeking over $15 billion (£10.8bn) in damages from the US after the Presidential Permit for the company’s Keystone XL pipeline was revoked on President Biden’s first day in office.
In a statement, TC Energy said it had filed a Notice of Intent to initiate a legacy North American Free Trade Agreement (NAFTA) claim under the United States-MexicoCanada Agreement to recover economic damages resulting from the revocation of the Keystone XL Project’s Presidential Permit. The company is seeking to recover more than $15 billion in damages that it claims to have suffered as a result of the US Government’s breach of its NAFTA obligations.
Revoking the Keystone XL’s Presidential
Permit was one of the first actions of US President Joe Biden following his inauguration on January 20. The Biden administration revoked the permit for the $8 billion project over concerns about fossil fuels contributing to climate change. In a statement announcing the cancellation, the White House said its decision followed an exhaustive review in 2015 conducted by the Obama administration which determined that approving the proposed Keystone XL pipeline would not serve the US national interest.
The review also cast doubt on the significance of the proposed pipeline for US energy security and the economy, saying its impact would be limited and that the US should instead prioritise the development of a clean energy economy, which would in turn create jobs. The analysis further concluded that approval of the proposed
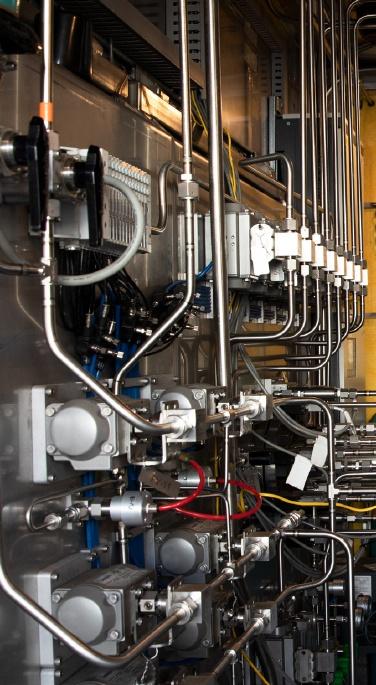
pipeline would undermine US climate leadership by undercutting the credibility and influence of the United States in urging other countries to take ambitious climate action.
The pipeline project, which would have been 1,210 miles (1,947 kilometres) in length and carried around 830,000 barrels of crude oil per day, was repeatedly delayed after it was first commissioned in 2010.

Keystone XL would have carried oil from Alberta to Nebraska but repeatedly faced opposition from US landowners, Native American tribes, and environmentalists. Biden was Vice President when the Obama administration rejected the project as part of its fight against the climate crisis. Keystone XL then became a central promise of Donald Trump’s presidential campaign who later issued a presidential permit for the project in 2017.
Following President Biden’s decision to revoke the Presidential Permit, TC Energy said the decision would “overturn an unprecedented, comprehensive regulatory process that lasted more than a decade and repeatedly concluded the pipeline would transport much needed energy in an environmentally responsible way while enhancing North American energy security. The action would directly lead to the layoff of thousands of union workers and negatively impact ground-breaking industry commitments to use new renewable energy as well as historic equity partnerships with Indigenous communities.”
Australian inquiry into 2020 mine explosion finds miners faced “unacceptable level of risk”
An inquiry into the May 2020 explosion at Anglo American’s Grosvenor coal mine in Queensland, Australia has found that production continued despite knowledge that the gas management systems were unable to cope with the rate of production. The Queensland Coal Mining Board of Inquiry report found that methane gas levels in the mine exceeded regulated levels 27 times in the lead up to the explosion which seriously injured five people.
The Grosvenor coal mine was closed following the blast but operations were restarted in May ahead of a staged restart following regulatory approval on April 22. The decision to restart operations had left miners “fuming” according to a union official who said that Anglo American had not kept workers informed about the plans to restart the mine,
a claim disputed by the company.
The explosion on May 6 seriously injured five workers with four of them being airlifted to hospital in critical conditions having suffered significant burns to their upper bodies and damage to their respiratory systems. The explosion was the second safety incident at Grosvenor in the span of 15 months.
The Queensland Coal Mining Board of Inquiry report, released on June 14, says that high methane levels resulted in the mine’s rate of production becoming higher than the capacity of the gas drainage system. It says that Grosvenor failed to take timely and meaningful action to control the explosive hazard posed by methane gas and that miners were therefore repeatedly exposed to unacceptable levels of risk.
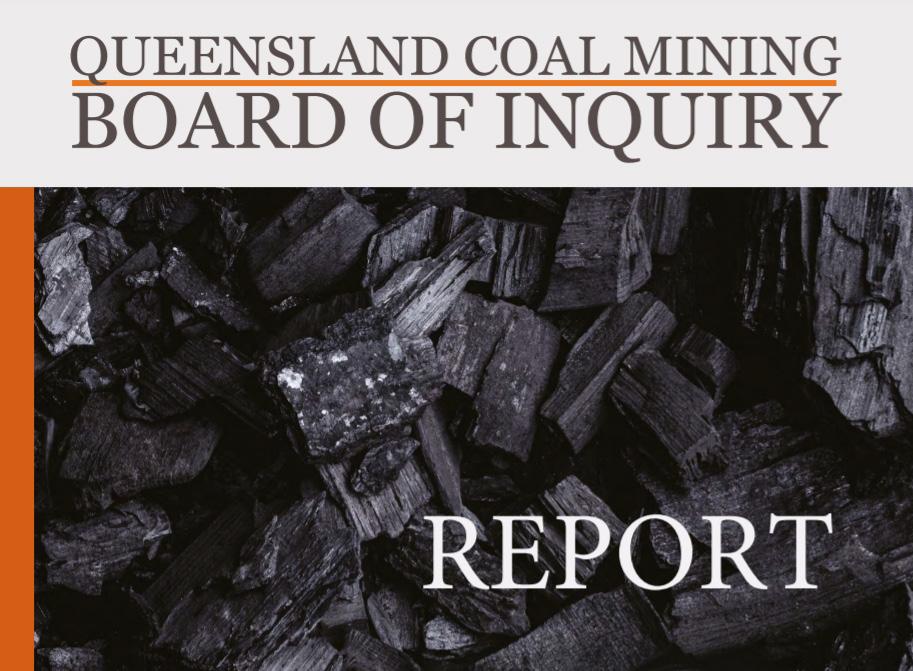
The report adds that the Queensland state regulator, Resources Safety & Health Queensland, should have been more proactive in imposing its regulations.
Another finding in the report is that there was a failure to complete a risk assessment of spontaneous combustions before work began on the section of the mine where the May incident occurred.
Among the report’s recommendations were a review of bonuses to ensure they do not discourage safety incident and injury reporting and location trackers on miners while underground.
CFMEU Mining and Energy Queensland President Stephen Smyth said the Union would review all the report’s findings and
recommendations in the days and weeks ahead. In a statement, Smyth said the most shocking thing to come out of the report was the detailed account of Anglo’s failure to manage dangerous gases at Grosvenor in the months leading up to the blast.
“I felt sick reading the detail about Anglo’s recklessness,” said Mr Smyth. “Management knew there were problems following a series of high potential incidents during March and April, but did not slow coal production to match its gas drainage capacity.
“The report clearly finds that ‘coal mine workers were repeatedly subject to an unacceptable level or risk’ (Finding 58).
Last year’s explosion was a shocking and traumatic event and it makes my blood run cold to think that the outcome could have been much worse. Coal mine workers put their lives in the hands of mine managers every time they go to work and they should be able to have confidence every possible measure is in place to protect them. They have been seriously let down in this case.”
Responding to the Board of Inquiry’s report, CEO of Anglo American’s Metallurgical Coal business, Tyler Mitchelson, said the company is already acting on the recommendations of the report, including $60 million of investment in safety initiatives over the last year.
“We are today committing a further $5 million to fund underground mining research, in partnership with our industry research and technology partners, to improve the industry’s knowledge in certain technical areas. We have been clear from the outset that the incident on 6 May 2020 in which five of our colleagues were badly injured was unacceptable. The safety of our workforce is always our first priority.
“Over the past 12 months, we have put in place a range of measures to address issues that have come to light through detailed investigations and evidence before the Board of Inquiry. Over this period, we have already committed more than $60 million in technology pilots, additional gas drainage infrastructure, expert reviews and further
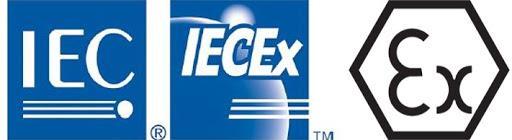
improvements to a range of processes and controls.

“The Board of Inquiry’s reports have made a number of recommendations, and we are confident we have already addressed, or will address, these ahead of the restart of longwall mining at Grosvenor Mine later this year.
“The use of automation and remote operation presents us with the single biggest opportunity to remove people from high risk areas and we are fast-tracking this work across our operations, including commissioning ground-breaking research into automation in development mining with CSIRO.”
Mitchelson said that following the implementation of the recommendations from the Board of Inquiry, the industry would be safer.
Read the Queensland Coal Mining Board of Inquiry’s report in full by visiting: https://bit. ly/3B4IqBB
UK Tank Storage Association publishes 2021 Annual Review of the

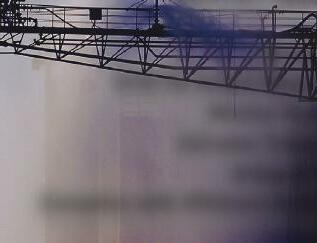














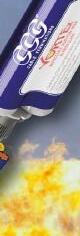


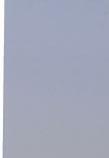
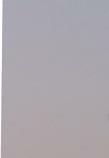
The Tank Storage Association (TSA) has published its 2021 Annual Review of the UK’s bulk liquid storage sector. The review contains key data and information on terminals, process safety, occupational health and safety as well as on the industry’s contribution to the UK economy.
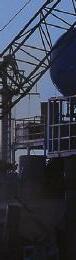
Peter Davidson, Executive Director of the Tank Storage Association, said: “I am pleased to launch the sixth edition of TSA’s Annual Review. The review continues to provide a comprehensive and timely insight into the bulk liquid storage sector in the UK. In addition to valuable industry data and information, this year’s report shines a light on the sector’s commitment to attract, develop and retain the next generation of talent. As we look ahead, it is clear to us that investing in the next generation today will ensure our sector continues to go from strength to strength.”
sector
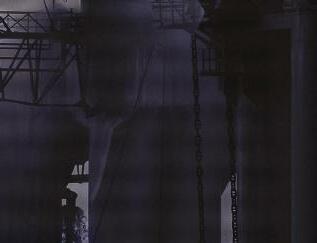
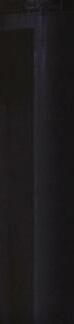
















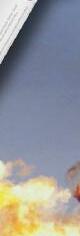

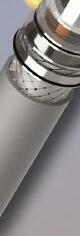
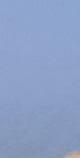
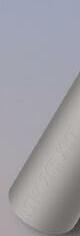
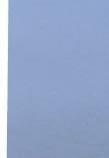

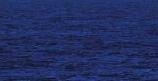
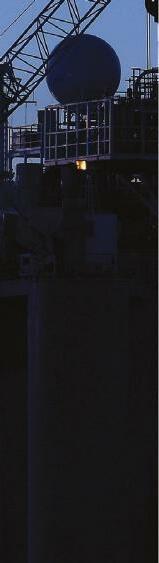
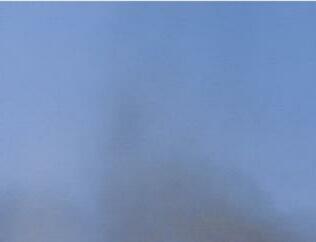

The Review details the sector’s process safety performance. In terms of Tier 1 events (significant losses of containment relevant to the hazard of the product stored), one was reported in 2020 with two Tier 2 events (smaller losses of containment relevant to the hazard of the product stored).
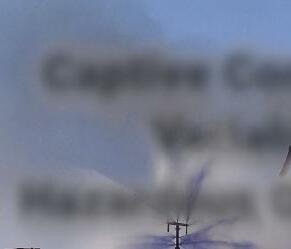

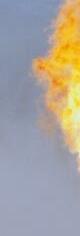
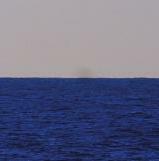

The Review says that even though there was only one Tier 1 and only two Tier 2 events reported in 2020, the TSA’s members are not complacent. In 2020, the TSA launched its Significant Indicators programme and, from January 2021, it has been collecting detailed data on individual barrier failures that cover receipt, storage, processing and export of bulk liquids, highlighting where it needs to focus its efforts in the future.

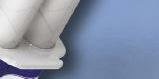
Tier 3 indicators (leading indicators) can be extremely useful in identifying areas of weakness before a more significant Tier 1 or Tier 2 event

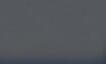


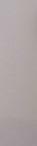

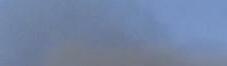







takes place, the Review adds. The TSA uses this information to determine if any further work is required in improving good practice or knowledge and skills. The indicators recorded in the Review include ‘fill above normal fill level’, ‘high level trip’, and ‘SIS failure under test’.





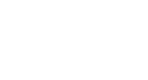
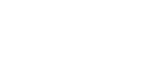


Throughout 2020, the TSA has been sharing safety messages regarding the Tier 3 leading indicators in its quarterly statistics report to members. The TSA is also leading and contributing to several technical working groups in the Chemical and Downstream Oil Industries Forum (CDOIF) and Energy Institute (EI) which are producing guidance to assist in the design, management and maintenance of process facilities.

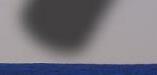
In all, the review says the tank storage sector continued to maintain very high standards of occupational safety during 2020. It remains one of the safest industries in the UK with proportionally fewer injuries than almost all other sectors.

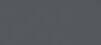


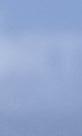






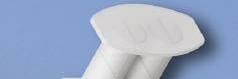

For an electronic copy of the 2021 Annual Review, visit: https://tankstorage.org.uk/assets/ Unorganized/TSA-Annual-Review-2021.pdf
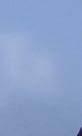
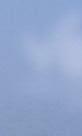

UK Health & Safety Executive releases annual workplace fatality figures for 2020/21
Provisional data released by the UK Health & Safety Executive (HSE) shows that a total of 142 workers were killed at work in Great Britain in 2020/21, an increase of 29 from the previous year, though the number of deaths in 2019/20 (113) was low compared to other recent years.
In statistical terms the number of fatalities has remained broadly level in recent years – the average annual number of workers killed at work over the five years 2016/172020/21 is 136.
Over the past 20 years there has been a long-term reduction in the number of workplace fatalities, demonstrating that
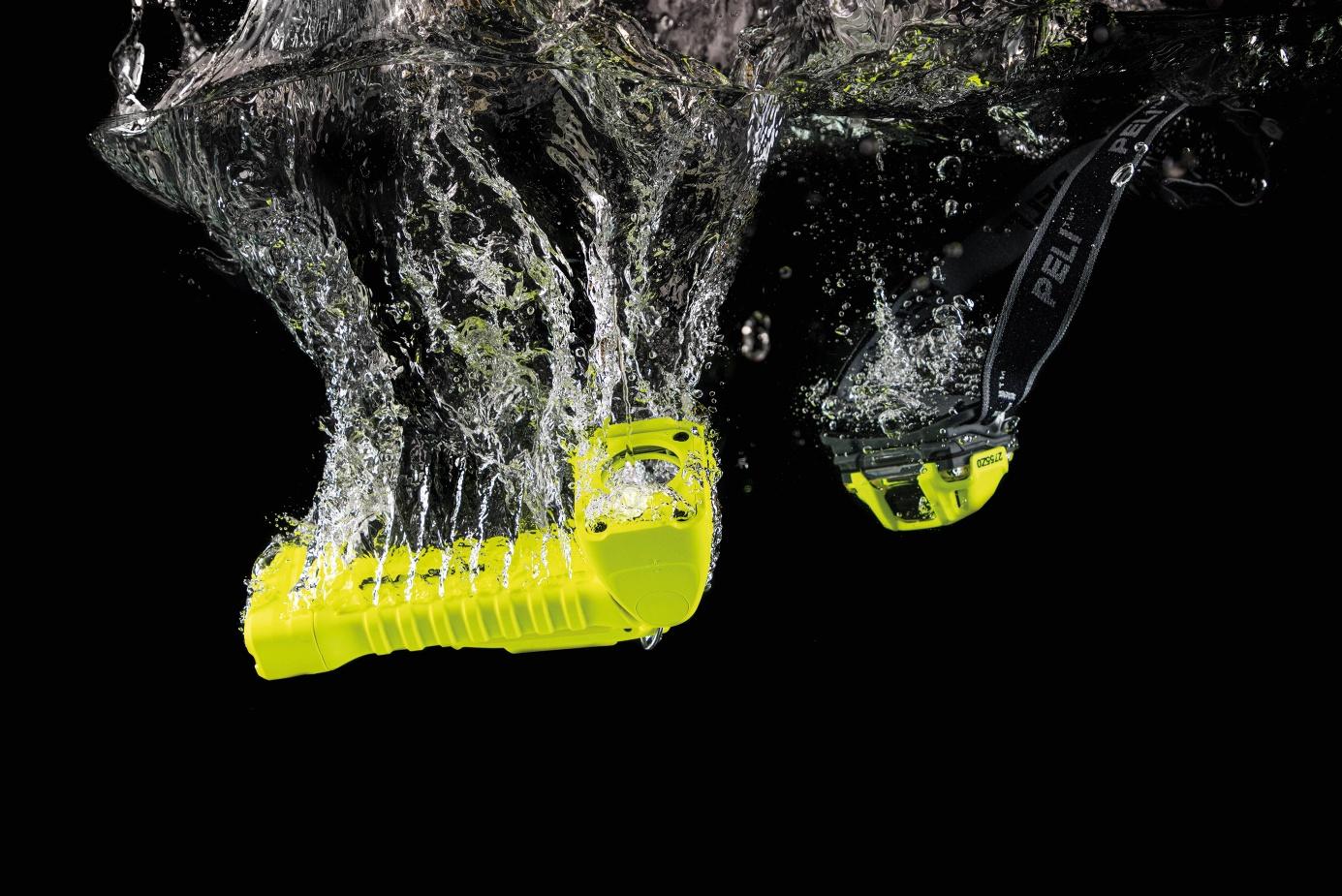
Great Britain is one of the safest places to work in the world.
The figures released by the HSE relate to workplace incidents. They do not include deaths arising from occupational exposure to disease, including Covid-19.
HSE’s Chief Executive, Sarah Albon, said: “Whilst the working world in which we now live has created new health challenges for workers and for those who have a duty towards them, safety must also remain a priority. Whilst the picture has improved considerably over the longer term and Great Britain is one of the safest places to work in the world, every loss of life is a tragedy, we are committed to ensuring that workplaces are as safe as they can
be and that employers are held to account and take their obligations seriously.”
The three most common causes of fatal injuries continue to be workers falling from height (35), being struck by a moving vehicle (25) and being struck by a moving object (17), accounting for more than half of fatalities in 2020/21.
These figures also continue to highlight the risks to older workers with around 30 per cent of fatal injuries in 2020/21 involving workers aged 60 or over, even though such workers only make up around 11 per cent of the workforce.
In addition, members of the public continue to be killed in connection with work-related incidents. In 2020/21, 60 members of the public were killed as a result of a work-related incident.
A fuller assessment of work-related illhealth and injuries, drawing on HSE’s full range of data sources, will be provided as part of the annual Health and Safety Statistics release on 16 December 2021.
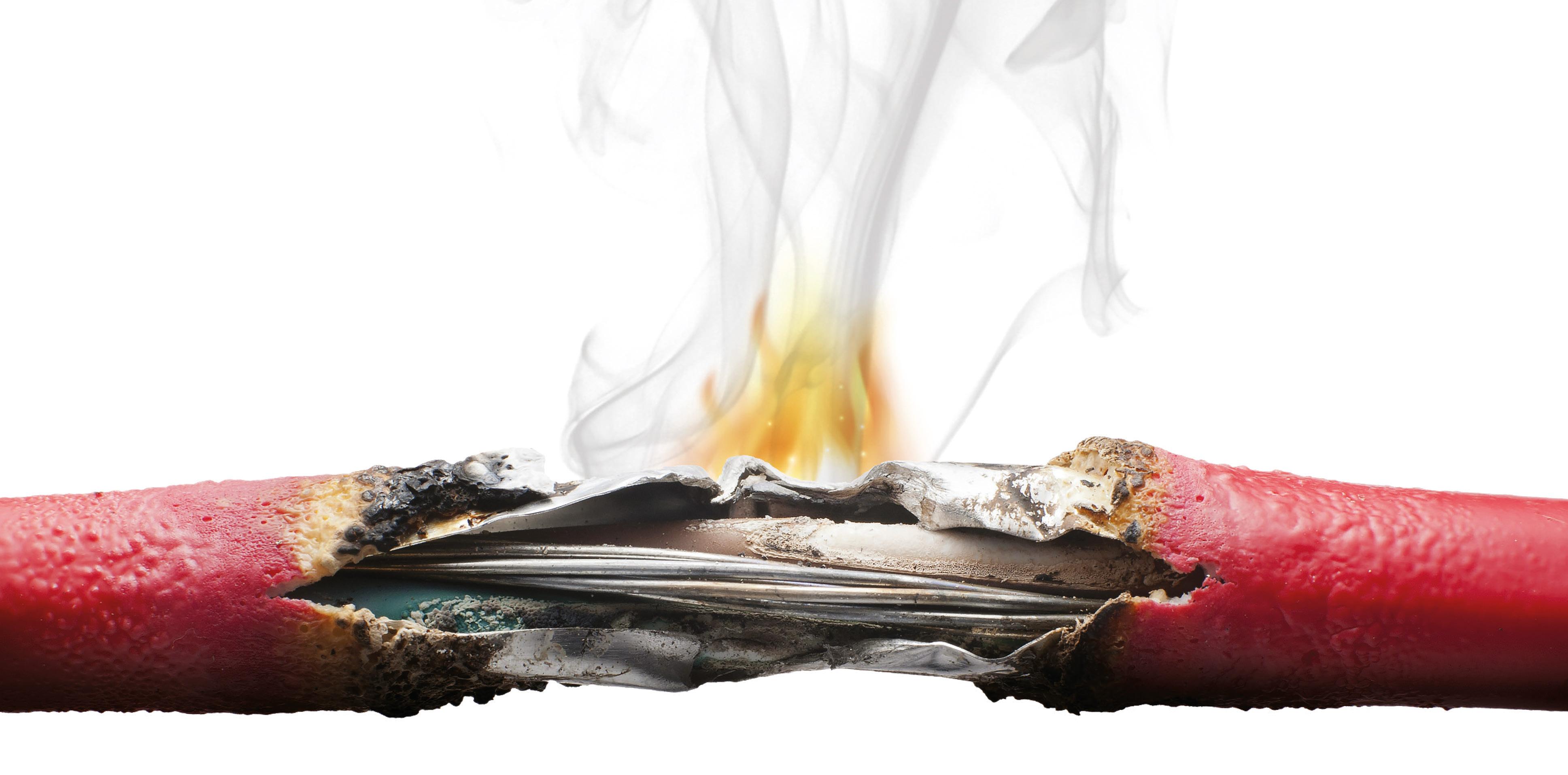
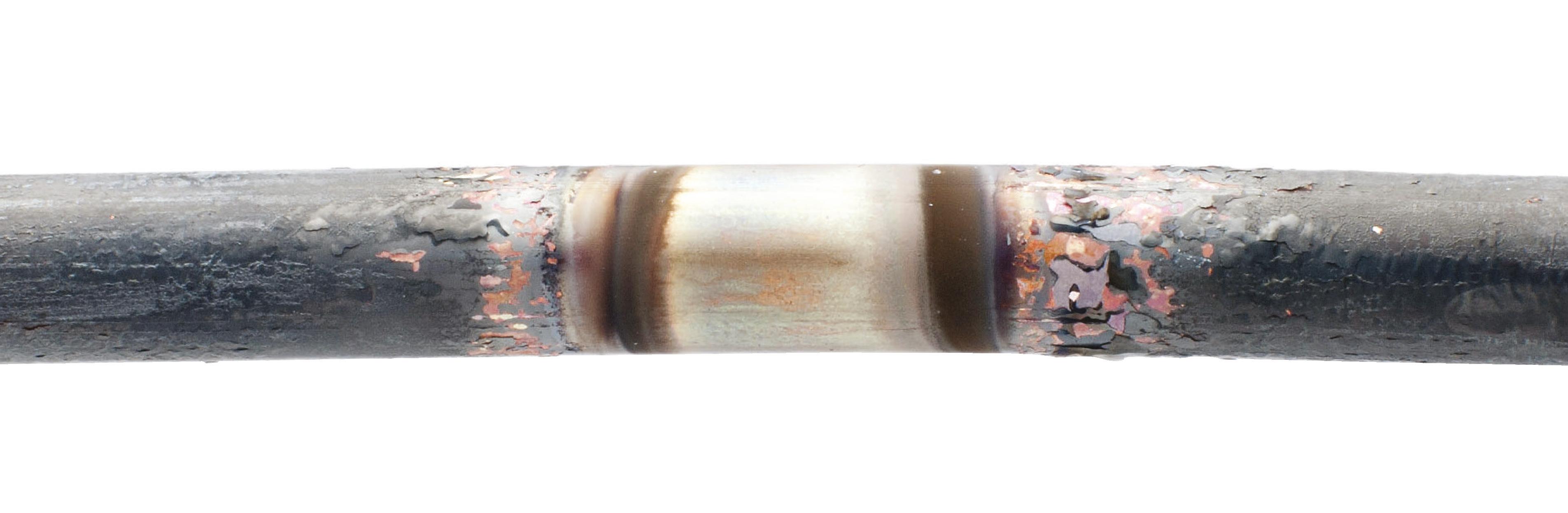

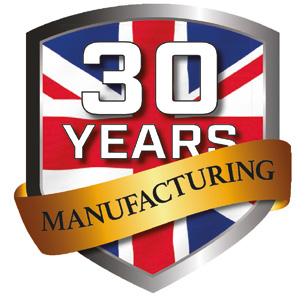
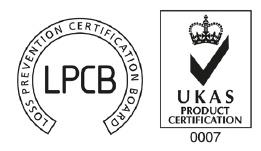
New call for ‘urgent action’ to ensure safety keeps pace in UK renewables sector
New independent research has found that 63% of managers in the oil, gas and renewables sectors have outlined concerns in their organisation about a major safety incident occurring in the next five years. Dräger Marine and Offshore, which commissioned the research, called for urgent action to be taken to ensure that safety in the UK’s fast-growing renewable energy and carbon capture sectors keeps pace in order to avert a major safety incident.
The warning comes as a significant majority of businesses involved in the study reported that safety has already been adversely impacted by Covid-19, with two thirds of managers (66%) reporting that safety training or investment within their organisation had been cancelled or delayed due to the pandemic.
Renewable energy and environmental
initiatives such as carbon capture are often perceived as being green, clean and therefore safe, but the risks are frequently overlooked, and often not dissimilar to those seen in the oil and gas industry.
For example, the future re-purposing of decommissioned offshore platforms for use within carbon capture and storage programmes will see the platforms’ operations change, but the hazards will remain with large volumes of hazardous gases still being involved. The gases might be different – hydrogen and carbon dioxide as opposed to methane – and they may be being pumped into the ground rather than being extracted, but the potential for a serious incident is much the same. For that reason, it is vital that sufficient funding and focus is given to safety in the sector.
Richard Ryan, Dräger Marine and Offshore spokesperson, comments: “The slow pace
of progress regarding safety standards in the UK’s renewable energy and carbon capture sector is becoming a major cause for concern, and it has been made worse by significant Covid-19 delays to safety training and safety-critical maintenance work.
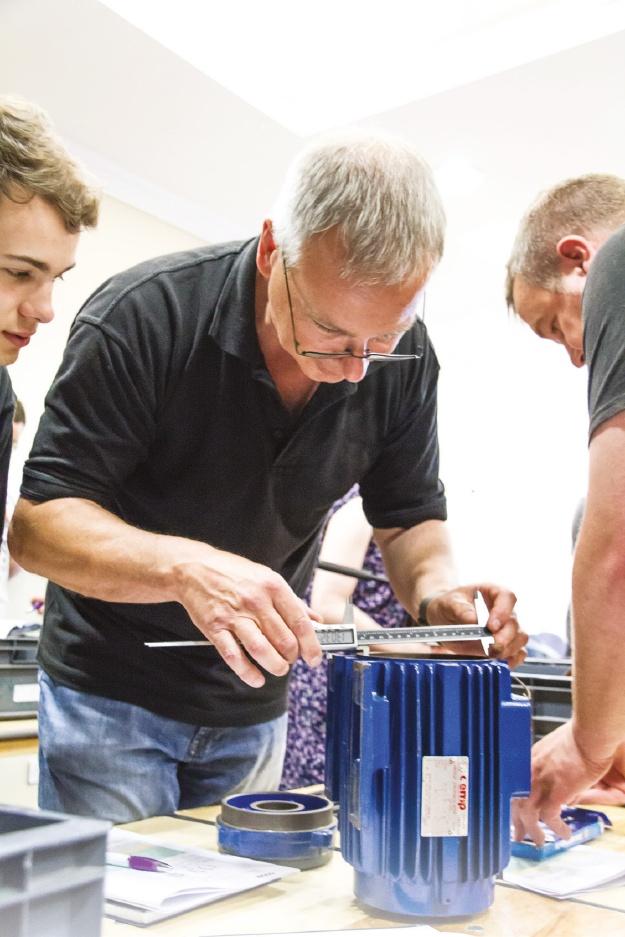
A key part of the problem is that there is a real lack of understanding or appreciation of the full extent of the hazards involved in renewable energy and carbon capture and storage. Whereas safety in the oil and gas sectors is now mature and ingrained in the whole operating culture, this is not translating across to renewable operations in all areas of the industry. It is vital amidst the current rapid growth of the UK’s renewable energy sector, that safety regulations keep up with the broader pace of developments within the sector.”
The full report is available to download from Dräger’s website.
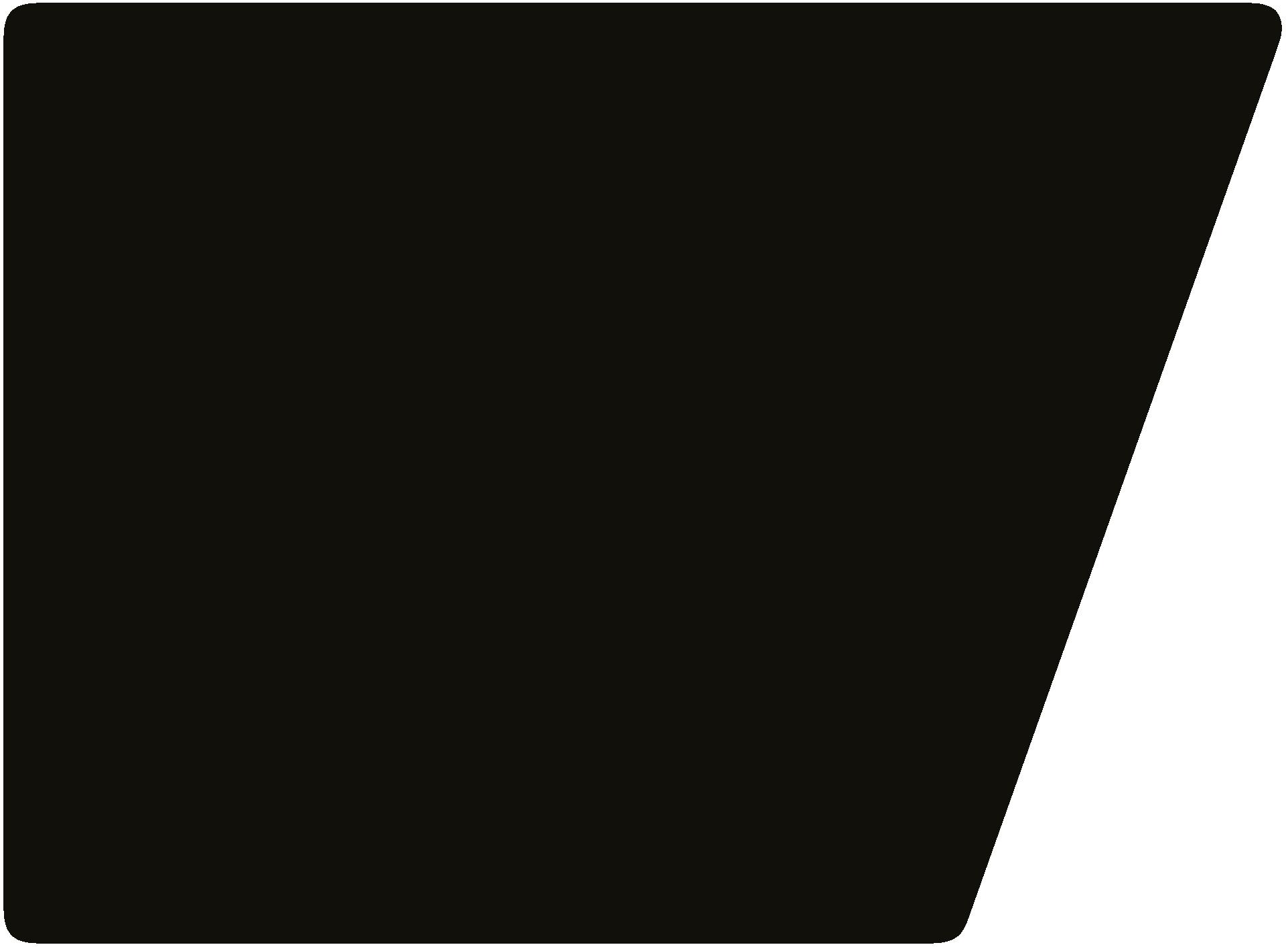
Jeff Bezos-backed fusion plant to be built in UK
The UK Atomic Energy Authority (UKAEA) and Canada-based General Fusion have announced an agreement under which General Fusion will build and operate its Fusion Demonstration Plant (FDP) at UKAEA’s Culham Campus in Oxfordshire.
General Fusion will enter into a long-term lease with UKAEA following construction of a new facility at Culham to host the FDP. The FDP will demonstrate General Fusion’s proprietary Magnetized Target Fusion (MTF) technology, paving the way for the company’s subsequent commercial pilot plant. General Fusion will benefit from the cluster of fusion supply chain activities in the UK, centred on UKAEA’s globally recognised expertise and presence in the field, a statement said.
Amanda Solloway, Science Minister for UK Government said: “This new plant by General Fusion is a huge boost for our plans to develop a fusion industry in the UK, and I’m thrilled that Culham will be home to such a cutting-edge and potentially transformative project. Fusion energy has great potential as a source of limitless, low-carbon energy, and today’s announcement is a clear vote of confidence in the region and the UK’s status as a global science superpower.”
The Fusion Demonstration Plant at Culham is the culmination of more than a decade of advances in General Fusion’s technology and represents a major milestone on the company’s path to commercialisation, General Fusion said. The Fusion Demonstration Plant will verify that General Fusion’s MTF technology can create fusion conditions in a practical and cost-effective manner at power plant relevant scales, as well as refine the economics of fusion energy production, leading to the subsequent design of a commercial fusion pilot plant. Construction is anticipated to begin in 2022, with operations beginning approximately three years later.
Commercial details of the project have not been released, however several news outlets have reported the development will cost around $400 million (£287m). In its last round of funding, General Fusion raised $100m. Jeff Bezos has invested in the company during several rounds of financing over the last 10 years.
General Fusion and UKAEA intend to collaborate on a range of fusion energy technologies for power plant design and operation.

US
The US government assessed China’s Taishan nuclear power plant in June after a French company that helped design the plant’s reactor approached the US Department of Energy (DOE) and warned of an “imminent radiological threat”. The company, which is also involved in the plant’s operations, also accused the Chinese safety authority of raising the acceptable limits for radiation in order to avoid having to shut it down.

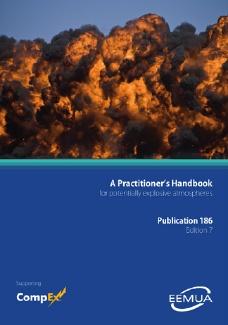
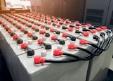
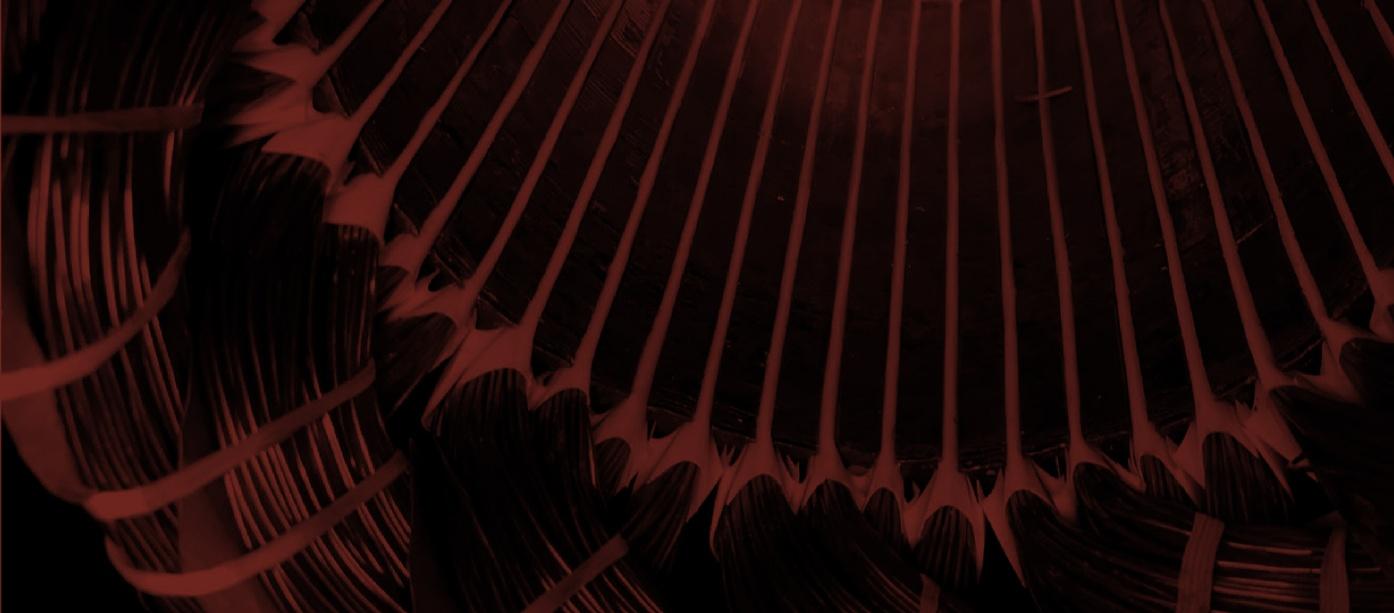
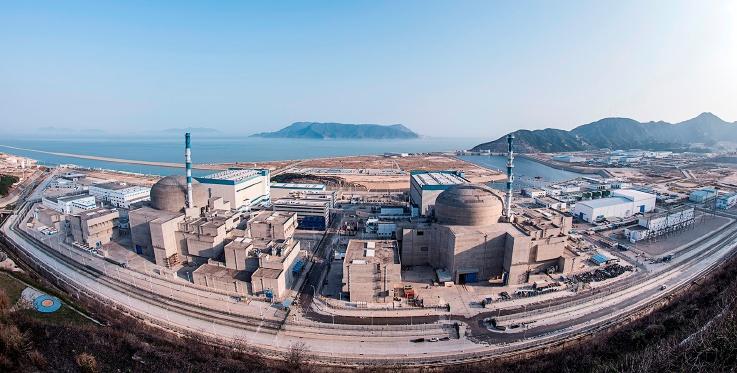
CNN reported on June 14 that it had obtained a letter sent from the French company Framatome, an EDF business which helped design the Taishan plant’s reactor and continues to be involved in operations, to the DOE which included the


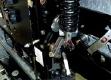
warning and accusation. The Taishan nuclear power plant in Guangdong province is a joint venture between EDF and China General Nuclear Power Group (CGN).
The letter was in relation to an operational safety assistance request previously sent to the DOE which had asked for a waiver that would allow Framatome to share American technical assistance to address an urgent safety matter at Taishan. CNN reports that despite the alarming letter from Framatome, the Biden administration decided the situation was not severe and that there was no immediate threat to workers at the plant or the wider Chinese public. However, the US held several National Security Council meetings and continued to monitor the situation.
In its memo asking for a response to the operational safety request, Framatome told the DOE that the Chinese safety authority could keep increasing radiation limits in order to keep the leaking reactor running despite safety concerns. The US discussed the situation with the French government and reached out to the Chinese government, although the extent of the contact is unknown. CNN says that the documents it obtained said that the US had given permission for Framatome to provide American assistance to help resolve issues at the plant, although it would ultimately be the Chinese government’s decision whether the plant needed to be shut down to conduct any repairs.
Following CNN’s reports, Chinese Foreign Ministry spokesperson Zhao Lijian said that radiation levels in the surrounding area of the Taishan plant were not abnormal.
On June 16, the International Atomic Energy Agency (IAEA) said that the China Atomic Energy Authority (CAEA) had said the Taishan plant was in normal condition and that operational safety is guaranteed. Unit 1 of the plant recently experienced a minor fuel rod cladding failure, which resulted in increased radioactivity in the unit’s primary reactor coolant, it said. CAEA said that this situation, as a common phenomenon in operations at the plant, is dealt with in accordance with accepted standards and procedures.
An explosion at a chemical plant in northern Illinois, US on June 14 caused a large fire and resulted in an evacuation order lasting for four days as firefighters fought the blaze. The incident happened at a plant belonging to Chemtool Inc., a lubricants and grease products manufacturer, in Rockton, northwest of Chicago.
The U.S. Chemical Safety and Hazard Investigation Board (CSB) said it had deployed two of its senior leadership to the scene and would engage with Federal, State and local emergency responders, the Environmental Protection Agency (EPA) and others to determine the conditions and circumstances that led to the incident and to identify the cause or causes so similar incidents might be prevented. The CSB said that early assessments appeared to indicate that the incident was a fire event and not a
chemical process safety event.
All 70 workers at the facility were evacuated without injury after emergency services were called to the scene at around 07:00 local time. One fire fighter suffered a minor injury and was transported to a local hospital for evaluation. According to local news outlets, the plumes of smoke caused by the fire were so large that they were picked up by weather radars.
The Rockton Police Department issued an alert at around 08:45 warning local residents of the mandatory evacuation of homes and businesses near the Chemtool plant. The evacuation zone was expanded from a one-mile radius to two miles later in the day as emergency services encouraged people to wear face masks to prevent inhalation of smoke and soot.
Firefighters had initially planned to allow
volatile substances to burn off due to the facility’s close proximity to the Rock River. There was significant concern surrounding release of firefighting water and suppression foam into the waterway. This initial approach was later reassessed, and emergency services began to berm and boom the access to the river and extinguish the remaining blaze.
The mandatory evacuation order was lifted after four days on June 18 with residents able to return home and businesses allowed to re-open. The fire was expected to continue smouldering for several more days.
Chemtool is a wholly owned subsidiary of the Lubrizol Corporate which acquired the company in 2013. In 2019, a French subsidiary of Lubrizol was charged with pollution and failing to meet safety standards after an explosion and fire at its plant in Rouen, northern France. The blaze at the lubricant plant in September and October 2019 produced a thick black cloud for several days that spread across the region and caused nausea, headaches, and vomiting amongst locals.
US OSHA proposes $215,000 fine for grain facility following dust explosion
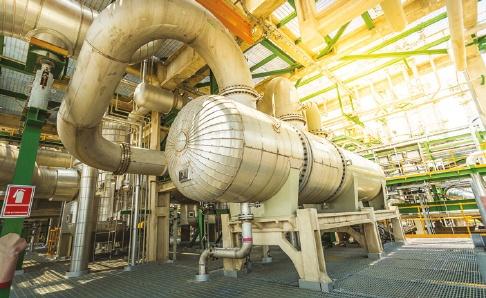
The US Department of Labor has cited a grain facility for workplace safety failures following a dust explosion that severely injured a worker in December 2020. In a statement, the safety regulator said that had MFA Enterprises – operating as West Central Agri Services –addressed potential dust ignition sources, an explosion that seriously injured the employee and caused the destruction of a main elevator might not have happened.
The US Department of Labor Occupational Safety and Health Administration cited the grain-handling facility for one wilful and six serious safety violations, and proposed penalties of $215,525. The West Central Agri Services is located in the town of Adrian, around 60 miles south of Kansas City in Missouri.
An OSHA investigation into the 31 December 2020 explosion determined that the company failed to equip bucket elevators with monitoring devices that
notify workers when a belt is slipping and potentially causing friction that could ignite grain dust. OSHA standards require these devices at grain handling facilities that have a storage capacity of over one million bushels. OSHA also found the company had not updated its dust collection system since its installation in 1974.
Additionally, OSHA found that the company exposed workers to falls by wilfully allowing them to walk atop railcars to open and close hatches without fall protection. The company also failed to repair an overhead trolley system
used for connecting fall protection devices. The agency determined the system was out of service at the time of its investigation, and noted violations involving lack of preventive maintenance and a failure to designate hazardous areas.
“West Central Agri Services failed to follow industry standards and create company policies for safe grain handling, and needlessly put their own workers in serious danger,” said OSHA Regional Administrator Kimberly Stille in Kansas City, Missouri. “Grain handling hazards can be avoided by using well-known safety measures that are proven to help prevent workers from being injured or killed.”
The company has 15 business days from receipt of its citations and penalties to comply, request an informal conference with OSHA’s area director, or contest the findings before the independent Occupational
and Health Review Commission.

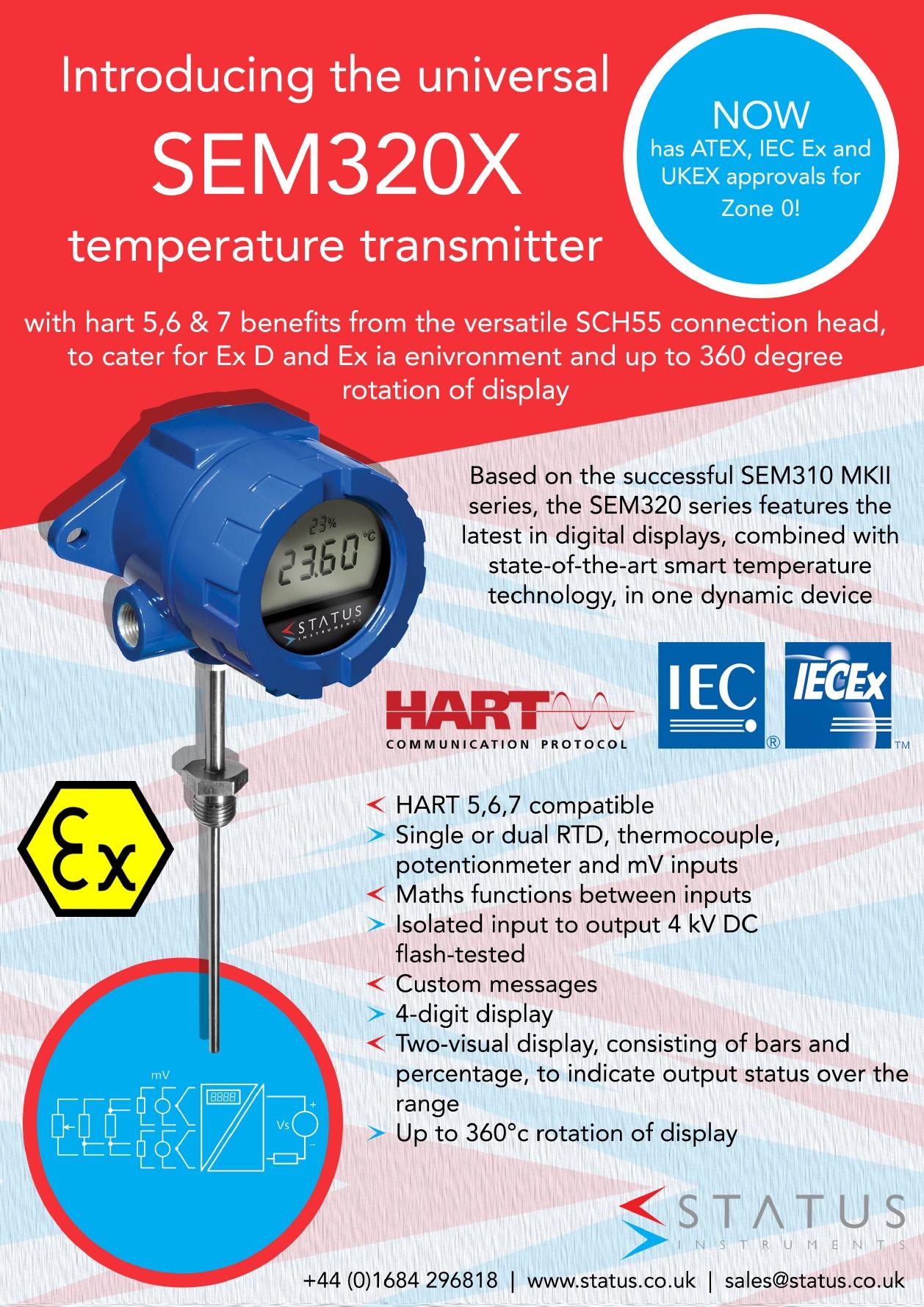
An explosion and fire at Romania’s largest crude oil refinery killed a worker and injured five others on July 2. The incident occurred at the Petromidia refinery on the Black Sea coast. The company which operates the refinery, Rompetrol Rafinare, said the explosion occurred inside the diesel hydrotreating unit.

Footage posted on social media showed a large plume of black smoke rising into the sky. The Petromidia refinery is located around 13 miles (20 km) north of the country’s biggest port, Constanta.
On its Facebook page, Rompetrol Rafinare said the incident happened at around 16:45 local time and all processes were stopped safely. The company said that four of its employees and a contractor, who had all been in the vicinity of the diesel hydrotreating unit, were injured and taken to hospital.
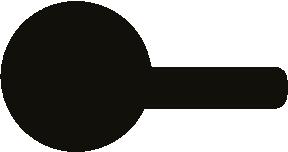
Another worker was confirmed as dead at the scene.
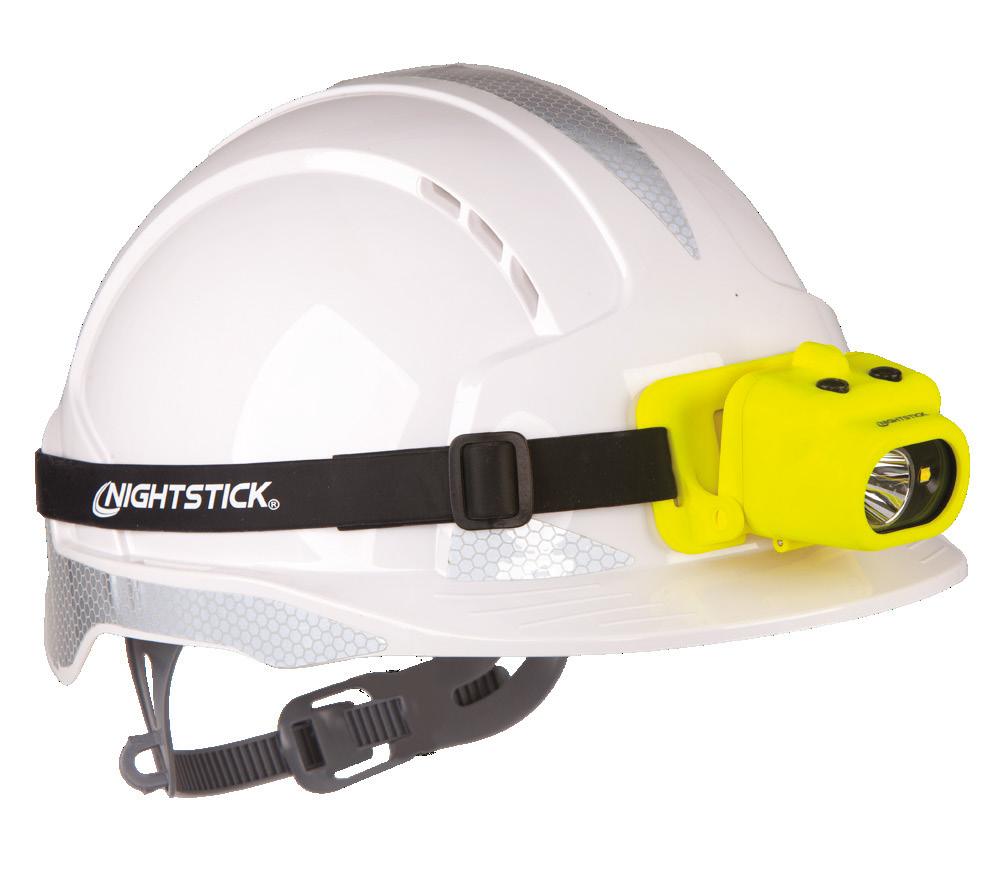
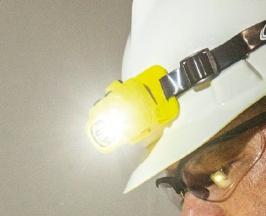

Two of the injured Rompetrol Rafinare employees were placed in medically induced comas and transferred to a specialist hospital in Germany to receive further treatment. The two men, aged 53 and 58, suffered burns to 30% of their bodies.
The other two injured Rompetrol Rafinare employees have been released having suffered minor injuries. The company said that all medical costs would be covered and that they are in direct contact with colleagues and family members.
In further updates posted on Facebook, Rompetrol Rafinare said the diesel hydrotreating unit was isolated and stabilised following the explosion while internal and external teams worked to extinguish a fire. The fire was extinguished after a couple of
hours after local firefighters were assisted by military firefighters.
The General Director of Rompetrol Rafinare, Felix Crudu Tesloveanu, thanked local authorities and the emergency services for their swift response. Tesloveanu said the company is doing everything it can to respond in a timely manner to the incident and to enquiries from workers and authorities.
Rompetrol Refinare said a team of specialists has been put together to work with the relevant authorities to determine the cause of the incident. At the same time, an analysis of incident’s impact on the refinery’s processes will also be done in order to gain a clearer picture regarding the restart of operations.
The company said that the refinery will continue to provide fuel for Rompetrol stations in Romania and the Black Sea region. It added that monitoring by environmental authorities had found that the limit values had not been exceeded and local areas, including tourist resorts along the coast, were not affected.
New plant near Hull could triple UK hydrogen production capacity
Plans for two first-of-a-kind, lowcarbon power stations in the UK’s Humber region have taken a significant step forward after SSE Thermal and Equinor submitted a planning (DCO) application. The plans, which could triple the UK’s hydrogen output, comprise one of the UK’s first power stations with carbon capture and storage (CCS) technology and the world’s first major 100% hydrogen-fuelled power station.
The proposed Keadby Carbon Capture Power Station, or ‘Keadby 3’, would be a new 900MW power station in North Lincolnshire, fuelled by natural gas and fitted with carbon capture technology to remove CO2 from its emissions. The new
power station would replace older, carbonintensive generation on the electricity grid, providing flexible and efficient power to support intermittent renewable generation and maintain security of supply through the net zero transition.
The power station would connect into the onshore CO2 pipeline infrastructure being developed by the Zero Carbon Humber (ZCH) partnership – which includes Equinor and SSE Thermal – and offshore CO2 infrastructure being developed by the Northern Endurance Partnership (NEP), which includes Equinor. This would see the captured CO2 transported from the Keadby site and securely stored under the Southern North Sea.
Keadby Carbon Capture Power Station would capture around 1.5 million tonnes (MT) of CO2 annually, meeting 15% of the 10MT target for 2030 set out in the Prime Minister’s ‘Ten-Point Plan for a Green Industrial Revolution’ last year. With the necessary policy mechanisms and shared infrastructure in place, Keadby Carbon Capture Power Station would have the potential to come online by 2027, in line with Government plans for ‘Track 1’ industrial cluster projects.
Given the readiness of carbon capture technology in power generation, projects like Keadby Carbon Capture Power Station can help stimulate the development of CO2 transport and storage infrastructure in the Humber, into which other energy and industrial emitters can then connect to capture and store their emissions, a statement from SSE Thermal said. This will accelerate the decarbonisation of the UK’s most carbon-intensive industrial region, while supporting a just transition to net zero for industrial workers and communities.
Europe’s largest PEM hydrogen electrolyser began operations on July 2, producing green hydrogen at Shell’s Energy and Chemicals Park Rheinland. As part of the Refhyne European consortium and with European Commission funding, the fully operational plant is the first to use this technology at such a large scale in a refinery.
Plans are under way to expand capacity of the electrolyser from 10 megawatts to 100 megawatts at the Rheinland site, near Cologne, where Shell also intends to produce sustainable aviation fuel (SAF) using renewable power and biomass in the future. A plant for liquefied renewable natural gas (bio-LNG) is also in development.
“This project demonstrates a new kind of energy future and a model of lower-carbon energy production that can be replicated worldwide,” Shell’s Downstream Director, Huibert Vigeveno, said at the official opening ceremony.
“Shell wants to become a leading supplier of green hydrogen for industrial and transport customers in Germany,” he added. “We will be involved in the whole process — from power generation, using offshore wind, to hydrogen production and distribution across sectors. We want to be the partner of choice for our customers as we help them decarbonise.”
Shell has a target to become a net-zeroemissions energy business by 2050, in step with society. As part of its Powering Progress strategy, Shell plans to transform its refinery footprint to five core energy and chemicals parks. This means Shell will reduce the production of traditional fuels by 55% by 2030.
The Rheinland electrolyser will use renewable electricity to produce up to 1,300 tonnes of green hydrogen a year. This will initially be used to produce fuels with lower carbon intensity. The green hydrogen will also be used to help decarbonise other industries.
The European consortium backing the project consists of Shell, ITM Power, research organisation SINTEF, consultants Sphera and Element Energy. The electrolyser was manufactured by ITM power in Sheffield, UK, and includes parts made in Italy, Sweden, Spain and Germany.
Armin Laschet, North Rhine-Westphalia’s Minister-President, said: “We are a hydrogen region. With the commissioning of the largest PEM electrolysis plant in Europe, we are further expanding our leading role in this field. We are therefore laying the foundation for a modern and green industry, with highly skilled jobs. Today, 30% of German demand for hydrogen already comes from North Rhine-Westphalia’s industry. Estimates predict that demand will double by 2030. This is why we need innovative solutions that will meet the demand for CO2-neutral hydrogen. Projects such as Refhyne demonstrate how innovation can benefit both the environment and the economy.”
Shell starts up Europe’s largest PEM green hydrogen electrolyser
Research
Anew development platform has been launched in Hamburg in order to test new hydrogen technology from as early as 2022. Funded by the Hanseatic City of Hamburg, Lufthansa Technik will work with the German Aerospace Center (DLR), the Center for Applied Aeronautical Research (ZAL) and Hamburg Airport over the next two years to design and test extensive maintenance and ground processes in handling hydrogen technology.
As part of the testing, an aircraft from the Airbus A320 family will be converted into a stationary laboratory at Lufthansa Technik’s base in Hamburg.
Liquid hydrogen (LH2) is increasingly being used in the development departments of large aircraft manufacturers as a sustainably producible fuel for future generations of commercial aircraft. In order to investigate the
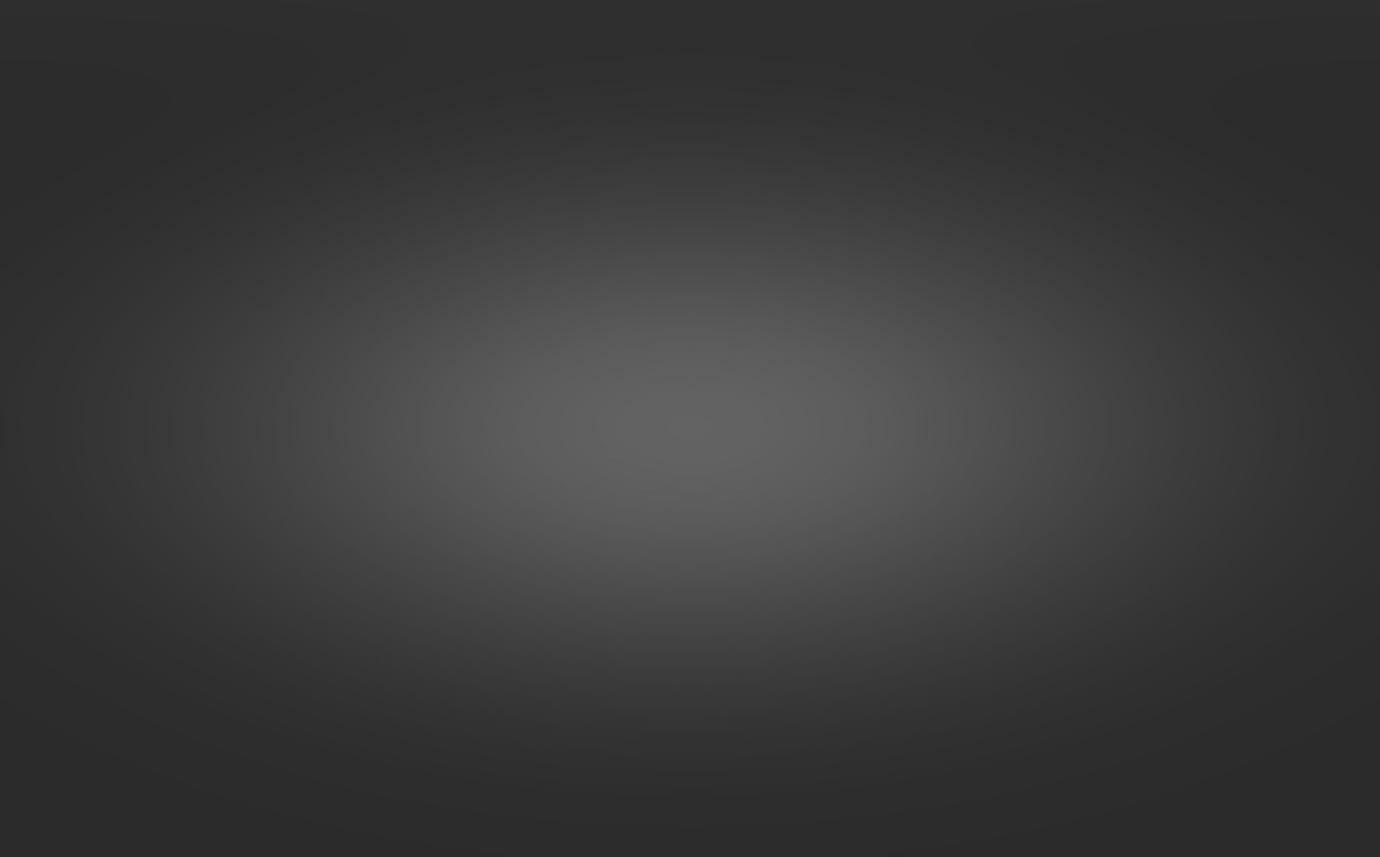

Hamburg
effects of the use of LH2 on maintenance and ground processes at an early stage, Lufthansa Technik, DLR, ZAL and Hamburg Airport are now pooling their extensive practical and scientific expertise. The aim is to jointly develop a pioneering demonstrator, and to operate it from 2022.
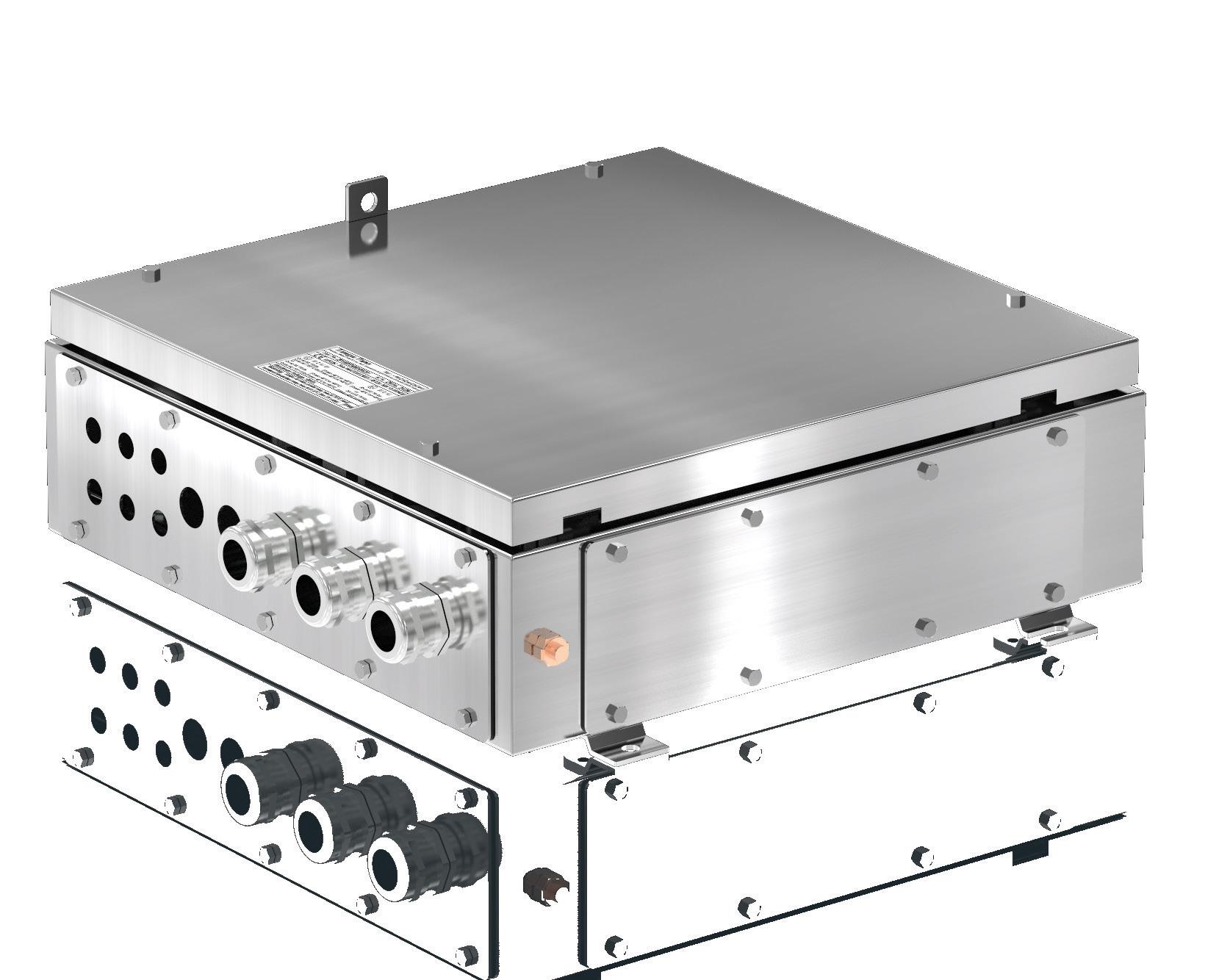

The City of Hamburg is funding the research project to help mitigate the economic impact of the coronavirus pandemic on the aviation industry.
“Hamburg is not just one of the three largest aviation clusters in the world, last year the city also developed the clear vision of becoming a major hydrogen metropolis,” explained Michael Westhagemann, Senator for Economics and Innovation of the Free and Hanseatic City of Hamburg. “I therefore see it as both a logical and gratifying step to combine these two core competences of Hamburg. The port, the energy sector, industry and the entire
mobility sector are involved and are preparing for this groundbreaking technology. With this project, we are now also making an essential contribution to the transformation of aviation into a climate-neutral mobility solution of the future. The clear goal is to build up a hydrogen economy in Hamburg that will occupy a leading position internationally.”
In the first phase of the project, the partners aim to identify the most urgent fields of development for closer scientific examination by the end of 2021 and, on this basis, to elaborate the concept for subsequent practical testing. The practical implementation of the concept will start at the beginning of 2022 and will involve the modification of a decommissioned Airbus A320 aircraft. It will be equipped with an LH2 infrastructure to be used as a fully functional field laboratory at Lufthansa Technik’s base in Hamburg. In parallel, a virtual environment is being created at DLR that will be used to achieve digital and highly accurate mapping of the defined development fields. The new development platform is to provide inspiration for the design process of the next generation of aircraft by means of parameterised and highly accurate virtual models.
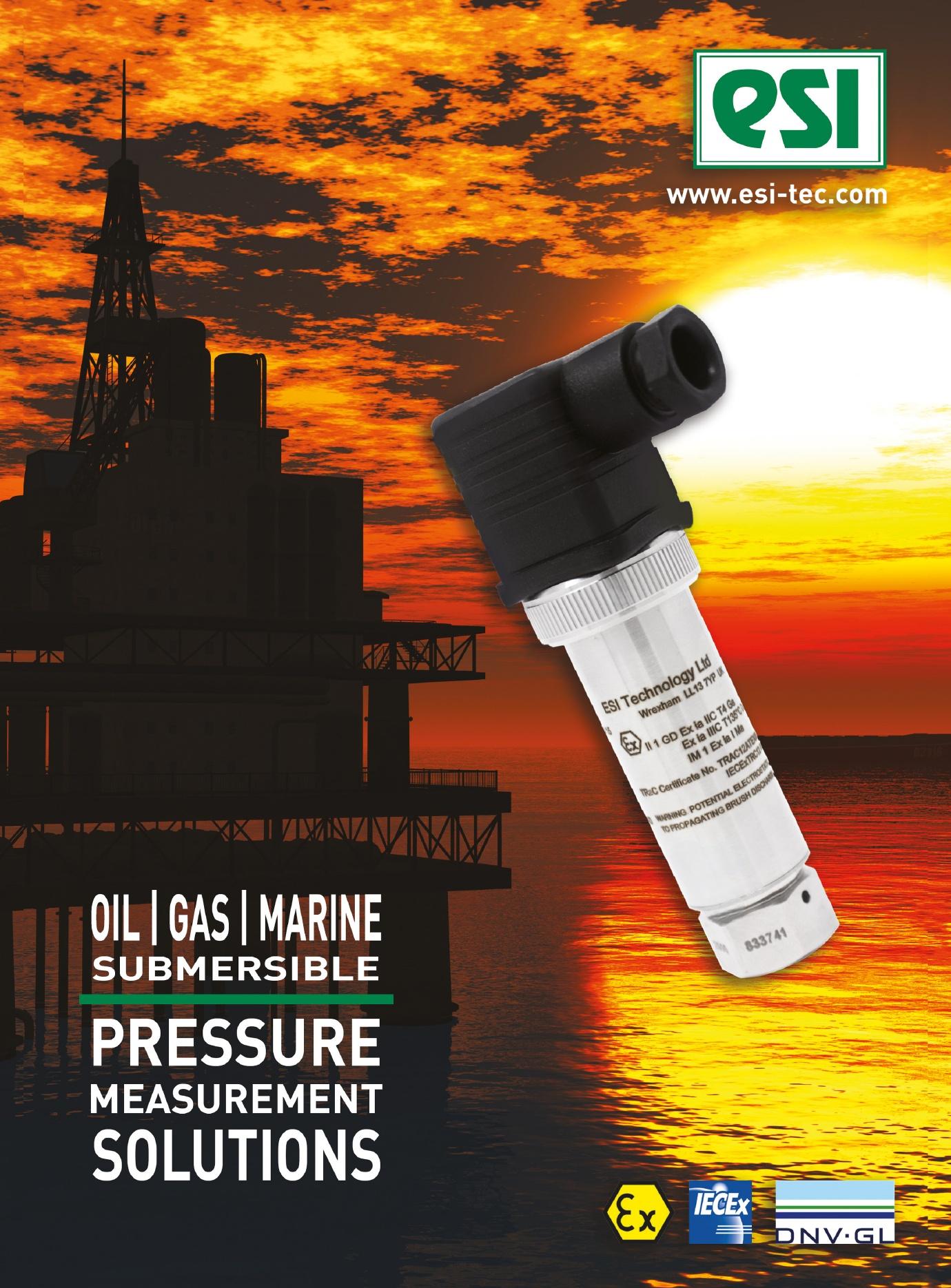
Afire and explosion at a plastics factory in Bangkok injured an initial 21 people on July 5. Despite firefighters’ efforts to extinguish the blaze, it reignited on July 6, causing a second blast which killed a firefighter and injured a further 18 people.
The incident happened at a factory belonging to Ming Dih Chemical, a plastic foam and pellets producer, in the Bang Phli district of Bangkok. The factory is located just a couple of miles from Bangkok’s Suvarnabhumi Airport.

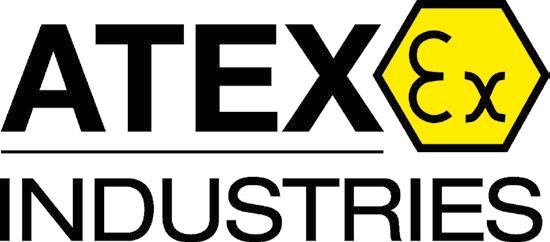

A five-kilometre evacuation order was issued shortly after the blast which happened in the early hours of the morning. The evacuation order was reported to have impacted around 80,000
local residents. Concerns were raised after the fire and explosion caused a large plume of dark, potentially hazardous smoke to rise into the sky. Emergency services were also concerned after the fire began to spread to other nearby factories which were also storing chemicals.
According to the Bangkok Post, the Ming Dih Chemical factory was housing around 50 tonnes of chemicals at the time of the incident. The fire, which was first reported at around 02:50 local time, engulfed the entire factory and even damaged other buildings located within a mile of the site. Black smoke from the site spread away from the factory and could be seen from Bangkok’s airport. Flights were unaffected, however.
Over 30 fire engines tackled the blaze with
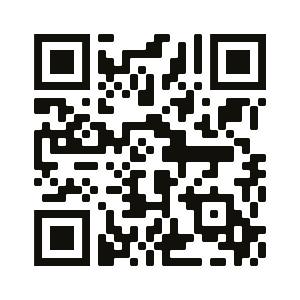
the help of military helicopters. It was said to be extinguished by dawn. However, a day later on July 6, the fire re-ignited and caused another explosion. A firefighter died at the scene while the blast injured a further 18 people.
Local officials monitored the air quality in the area surrounding the factory over the two days and said it was considered safe despite the reignition of the fire and second explosion. Officials also tested local canal waters which were also found to be safe. Locals were told to avoid drinking tap water as a precaution.
After the second fire was extinguished, officials tested the air quality at the site again and said that the level of Volatile Organic Compounds (VOCs) was high but at a harmless level.
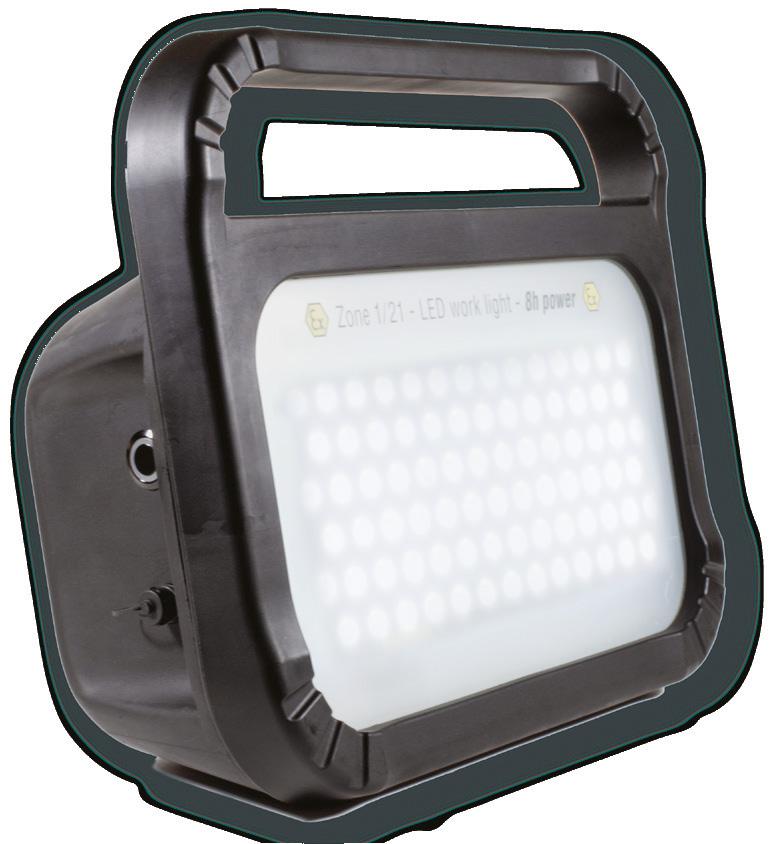
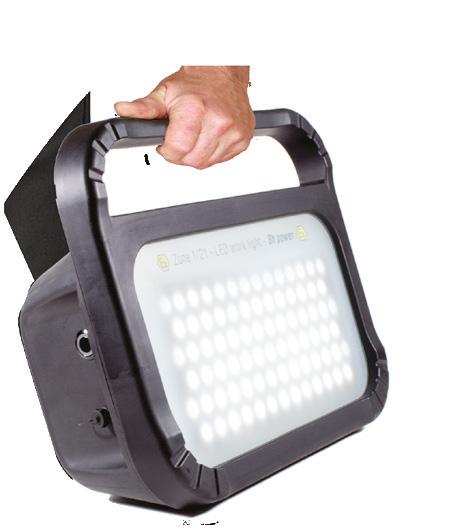
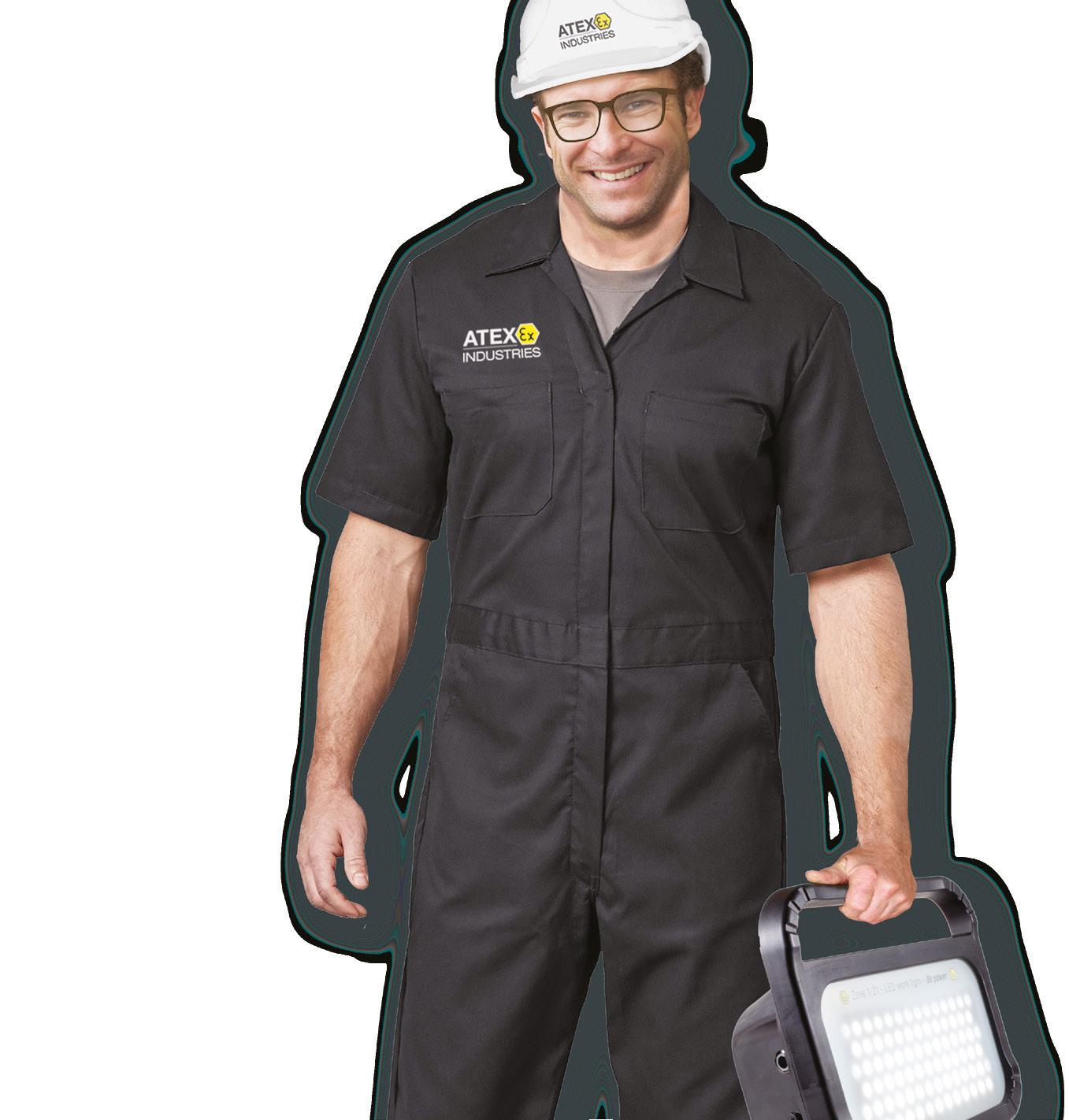


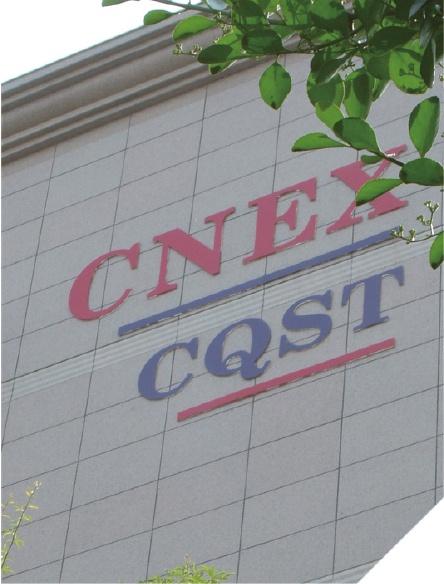



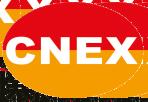


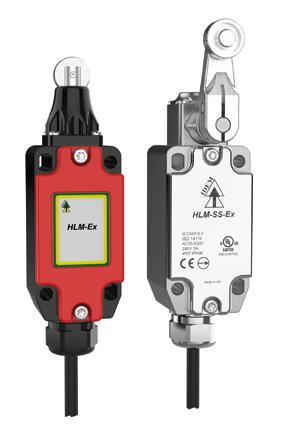
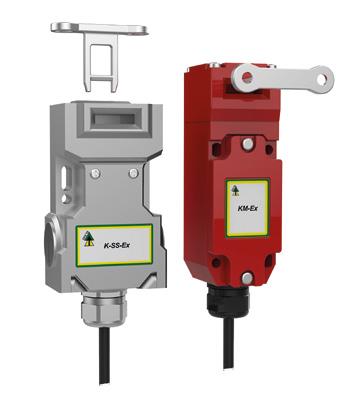
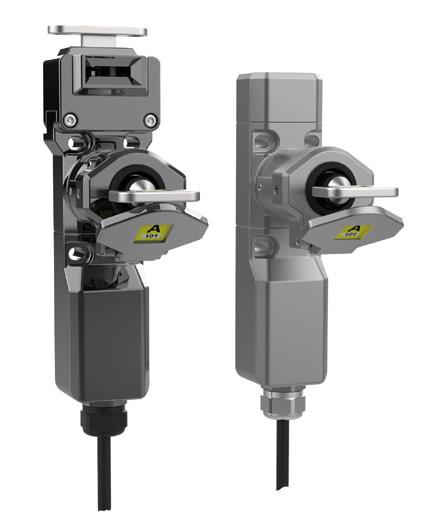
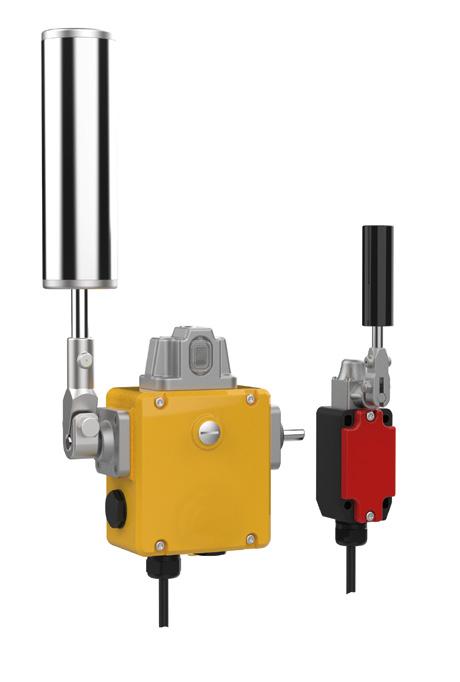
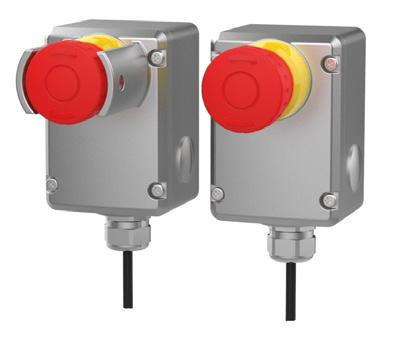
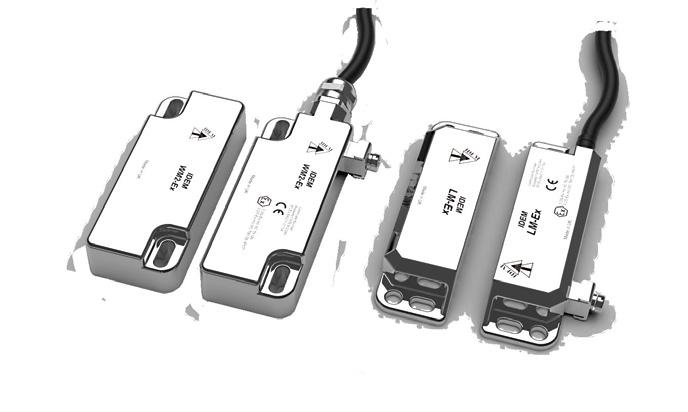
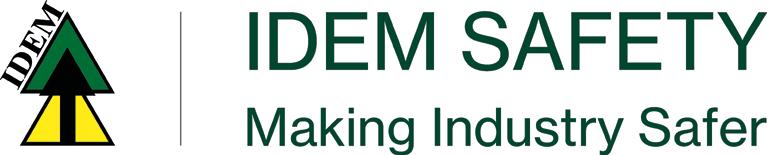
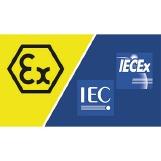

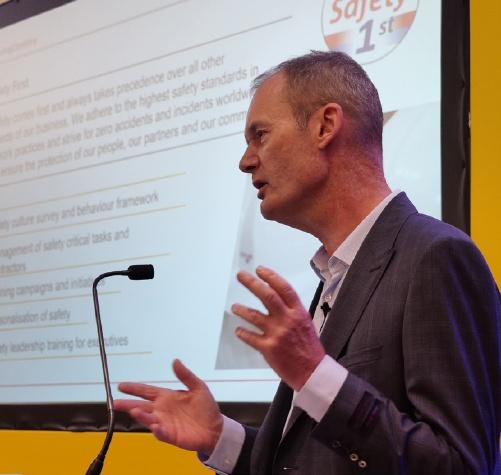
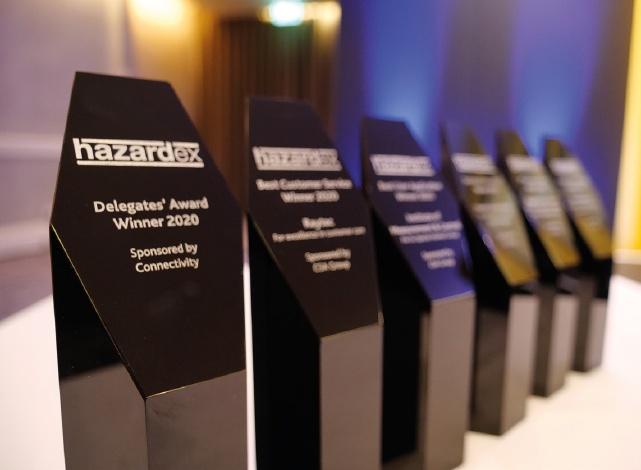

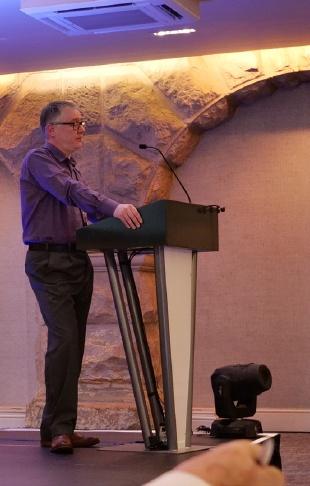
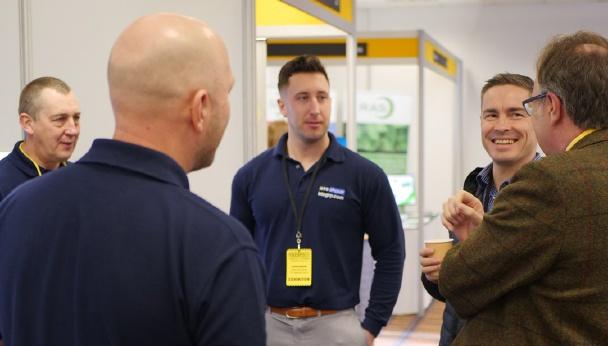
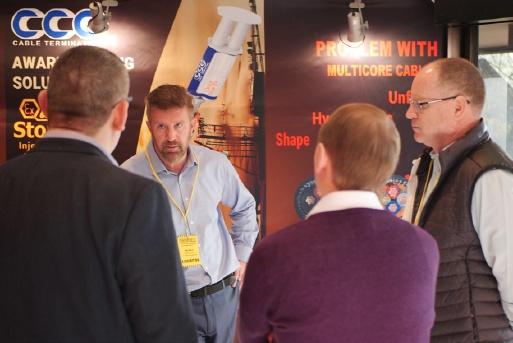
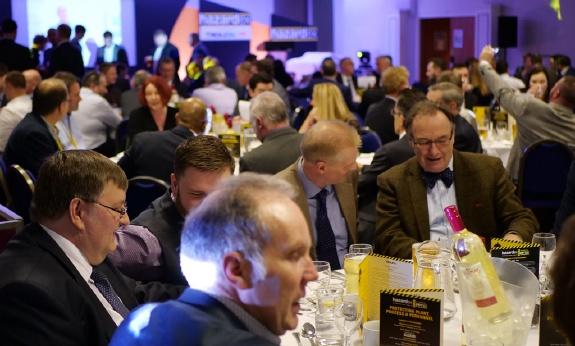
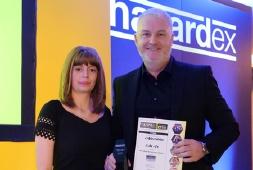
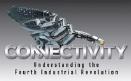


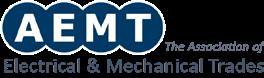
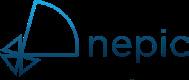
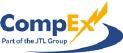

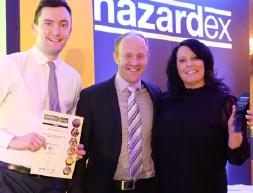
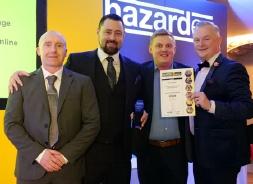
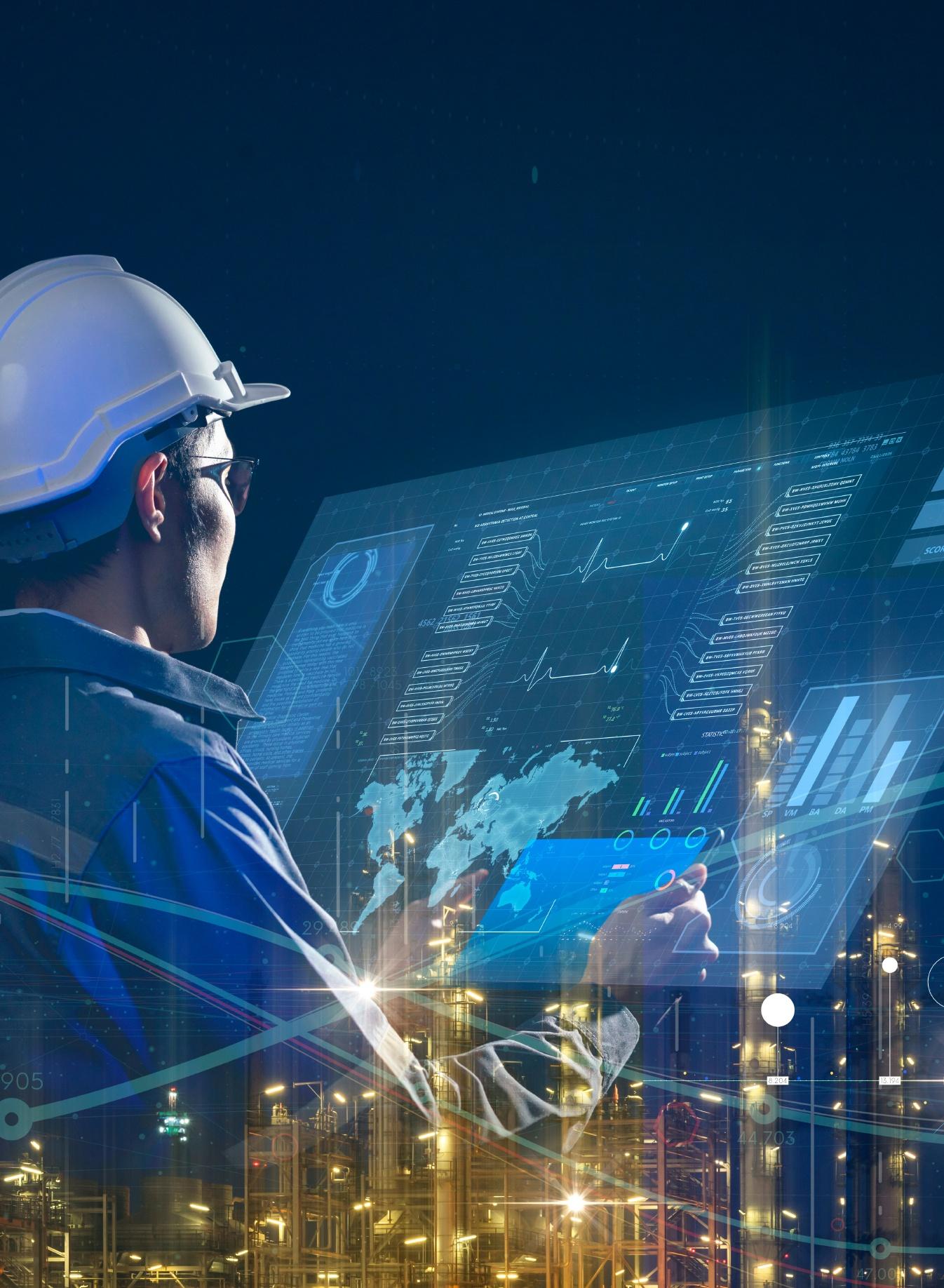
New robot set to save lives, cut CO2 and support construction
A robot made famous by dancing on YouTube is set to help save lives and cut carbon dioxide emissions by supporting hazardous environment research at the National Robotarium, based at Heriot-Watt University in Edinburgh. The robot is part of the ‘Spot’ range created by Boston Dynamics.
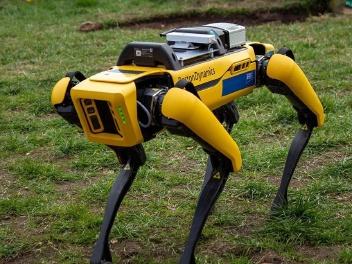
Experts at the National Robotarium, a worldleading research facility for robotics and artificial intelligence, will use the new hardware to carry out research into how robots can support humans in hazardous environments like offshore energy inspection and disaster recovery.
The £60,000 robot will be fitted with “telexistence” technology, which lets humans experience an environment without being there, using devices like microphones and cameras to relay sounds and videos.
Professor Yvan Petillot, professor of robotics and autonomous systems at Heriot-Watt University and co-academic lead of the National
Robotarium, said: “Fitting this robot with our telexistence technology means we can carry out a range of experiments. We can test how the robot can help and support people working in hazardous environments, including oil and gas platforms and oil refineries. In search and rescue operations or following accidents, Spot robots fitted with our sensors could monitor a casualty’s vital signs and transmit images and sounds back to a hospital, allowing doctors to offer advice on treatment or decide when it’s safe to move a patient.
Dr Sen Wang, an associate professor at Heriot-Watt University and robotics and autonomous systems lead at the National Robotarium, added: “Through a project with the ORCA Hub, the first application for our research with this new robot will be supporting the construction industry. We are going to fit lidar to our robot, which is similar to radar but uses light instead of radio waves. That will allow the robot to build up a picture of its surroundings while spotting obstacles like rubble on construction sites.
“Our Spot, however, is unique. We have set it up to be a moving data collector and data centre, equipped with advanced telepresence solutions. When we deploy it on construction sites, it will collect and measure in real time, relaying the data to multiple experts at once, all around the world. This means construction companies, regardless of their location, can benefit from worldwide expertise. Using Spot in this way has the potential to speed up the construction process, reduce costs of rework, detect hazards, increase efficiency and improve quality control.”
Improved safety of people and machinery in the industrial workplace
People working in and around machinery in industrial, engineering and maintenance sectors can be protected and better managed using an innovative real-time location system from Salunda Limited. The patent protected Crew Hawk delivers the latest in advanced location capability, integrating multiple technologies into a reliable, robust zone management system that improves the location of both people and mobile and autonomous machinery, providing position performance to avert incidents and cut the risk of workplace injuries and accidents.
Crew Hawk is suitable for industrial health and safety applications where people could be at risk from contamination, intense heat, high pressure, high voltage, heavy plant, blind lifts, high noise levels and crush injuries.
Crew Hawk connects wearable locators attached to PPE and compact magmounted equipment sensors to a reliable
and secure network, to automatically trigger personalised warnings and pause equipment to prevent a collision if someone is too close.
The individual is alerted to the risk of danger by an alarm on the wearable device, with the system also preventing the equipment from moving until the individual has left the area and returned to a secure location.
An intuitive user interface allows swift setup to create a portable safety system that can be rapidly deployed across different industrial zones and will warn people before they enter a restricted or red zone, reducing the occurrence of costly lost time incidents or production downtime. ‘Flight recorder’ playback features permit incident investigation, while analytical tools pinpoint accident blackspots.
Crew Hawk can be deployed in an explosive atmosphere due to being ATEX and IECEx certified. This ‘Ex’ certification
grants access to multiple industrial applications previously gated before the development of Crew Hawk.
Being modular, the system is upgradeable and the incorporation of digital ranging cameras (i.e. time of flight or Lidar) provides additional levels of work area access, safety and security. It can also be integrated with machine vision to discriminate between ‘authorised’ and ‘unauthorised’ personnel and detects those workers that do not have wearable sensors, providing a uniquely failsafe solution.
System versatility allows configuration for extended levels of access control to critical areas, assigning a serial number to an individual, or their role, to allow only authorised personnel to enter restricted or hazardous areas. Access control is also configurable more dynamically to manage different stages of an operation.
www.salunda.com
Guardhat received IECEx and ATEX Zone 1 certifications for its IS-HC1.1 communicator hardhat earlier this year. These certifications allow industrial operators across Europe, Australia and parts of the Middle East to deploy Guardhat smart hardhats as part of the company’s connected safety and productivity solutions. The Guardhat ISHC1.1 Communicator hardhat, as well as the company’s ultra-wideband gateways for precise location tracking, are currently under review for similar certifications across North and South America.
“These certifications validate years of design and engineering effort to create the most ruggedized and technologically advanced system for worker safety in existence,” said Saikat Dey, founder and CEO of Guardhat. “To
design an electronic, battery-powered, audio/ visual, multi-network and cellular connectivitycapable device to be incapable of generating heat or spark was extremely challenging. Not to mention that it has to sit comfortably atop a worker’s head, protecting them in all the ways a traditional hard hat would. I’m extremely proud of our team, and hopeful about the impact this offering can have. Every worker should be able to go home at the end of a shift.”
Guardhat partnered with i.safe MOBILE GmbH in the certification process. The intrinsically safe hardhat retains all the features and capabilities of the original HC1 Communicator, including sensor-based, contextual awareness; multimodal, high-precision real-time positioning (RTLS) and proximity detection; comprehensive

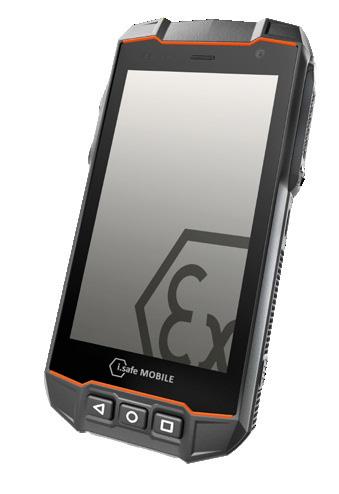
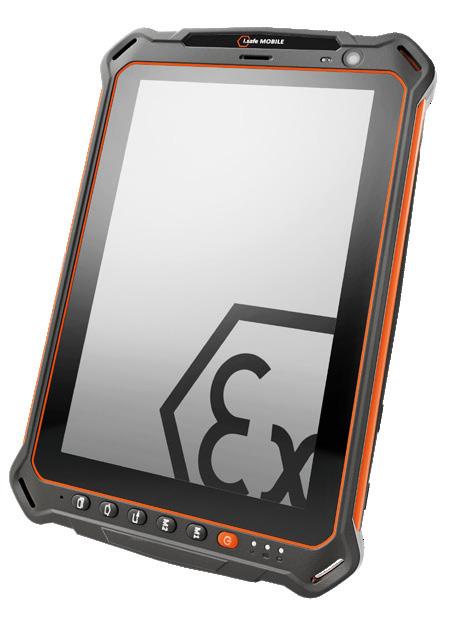
audio-visual telecommunications; peripheral connectivity; and multiple wireless backhaul options; with an ergonomic and userfriendly interface; and safety certifications including ANSI/ISEA Z89.1. The IS HC1.1 Communicator hardhat is available now.

www.guardhat.com
ABB has launched a Virtual Assistance support service which uses a virtual platform to provide fast access to expert support to help solve technical queries and issues face to face, reducing downtime and increasing productivity.

The platform enables video and images of technical problems to be transmitted live from the field where they can be seen by a remote ABB technician who can provide expert assistance.
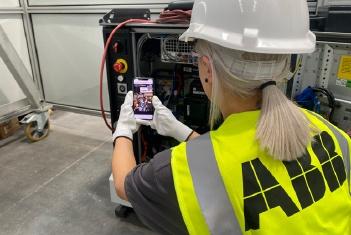
Using a smartphone camera, users can establish a video link with the technician to allow them to see the robot or controller. The technician can then make recommendations to the user on the appropriate steps to take,
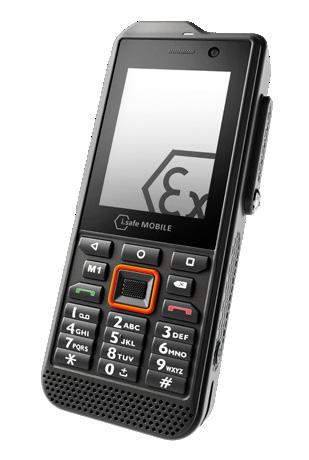
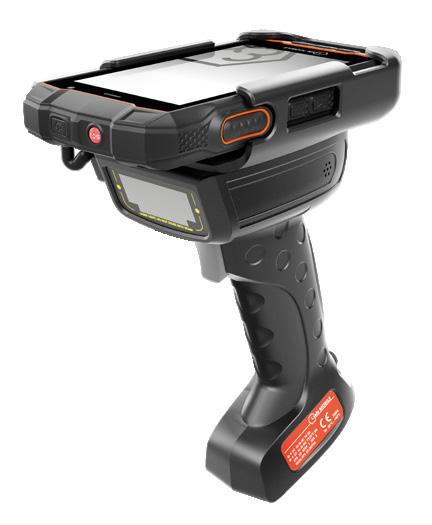
talking them through the steps needed to resolve a query or issue or obtain a further diagnosis for onsite assistance.
As a means of providing customers with remote access to 24/7/365 technical support, the Virtual Assistance support service is ideal for helping to address the current restrictions on travel and site access surrounding the COVID-19 pandemic. By enabling around 25 per cent of enquiries to be resolved virtually, it can also help to reduce the environmental impact of engineers travelling to site.
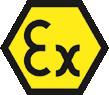
As well as a standalone service, the Virtual Assistance app is also being offered as part of an expanded offering called Technical Support
Plus. Including Virtual Assistance, a conditionbased monitoring report and one ABB certified training course, Technical Support Plus is aimed at providing companies with a development path for training their own dedicated on-site engineers with basic robot programming, operation, and maintenance skills.
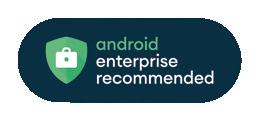
Safeguarding lone workers with
Communication amongst teams is an essential part of conducting an efficient, effective and safe business.
But when it comes to selecting a communications device to appropriately safeguard the lone workforce, with a growing number of options, choosing the right solution that addresses the needs of employees and the business as a whole, can be challenging.
Businesses need a way to combine different functions, such as communication and lone worker protection into one streamlined device. A smartphone is often the first choice for procurement managers in this instance. We’re all familiar with them in our personal lives, but is this necessarily the best option for every job role?
There are a number of considerations to take into account. For example, do staff need to be contactable all of the time? What
if employees work in remote parts of a plant alone, in the evenings or at weekends? For those workers to feel safe and the employer to fulfil its duty of care, there must be a way for them to raise an alarm to get the immediate support they require in the event of an emergency.
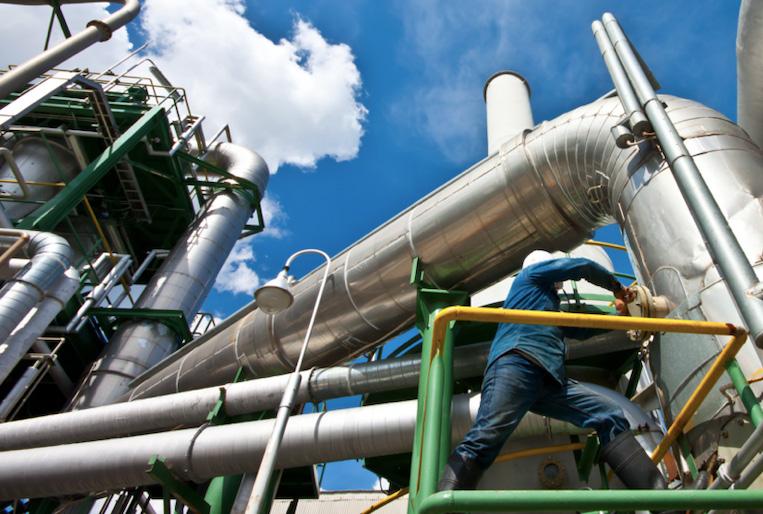
Providing lone workers with a communication device to contact staff in an emergency would mitigate some of the risk. But bear in mind that in 2019-2020 there were 20 fatal incidents and 66,000 non-fatal injuries within the UK manufacturing sector alone.
Having a communication device would certainly be better than nothing at all but if a worker falls from height, gets struck by a moving object or comes into contact with machinery – does a communication device offer enough protection? If workers can’t call a number or communicate easily and inform colleagues where they are, then this
form of protection will leave them and the business horribly exposed.
However, providing staff with a device that is easy to raise an alert such as a panic button and can trigger alerts automatically if they’re rendered unconscious, can ensure that staff are better protected against the ongoing incidents that occur within the sector every year.
Better still by combining different functions into one streamlined device means that workers don’t need to carry around multiple different handsets, which can be a common occurrence when businesses address lone worker challenges in isolation. While this isn’t necessarily an issue, it can mean unnecessary expense as hardware is duplicated. Most importantly, organisations should work with experts to ensure they have the right device for their requirements and infrastructure setup, for example buying
technology
lone worker devices that work in areas with limited mobile connection will be avoided. Additionally, panic buttons, tilt and nomotion sensors and other comprehensive lone worker protection functions can all be integrated into one device. Based on smartphone technology, devices can be compact and robust, capable of reliably transmitting communications and alerts over 2G, 3G, 4G and Wi-Fi networks.
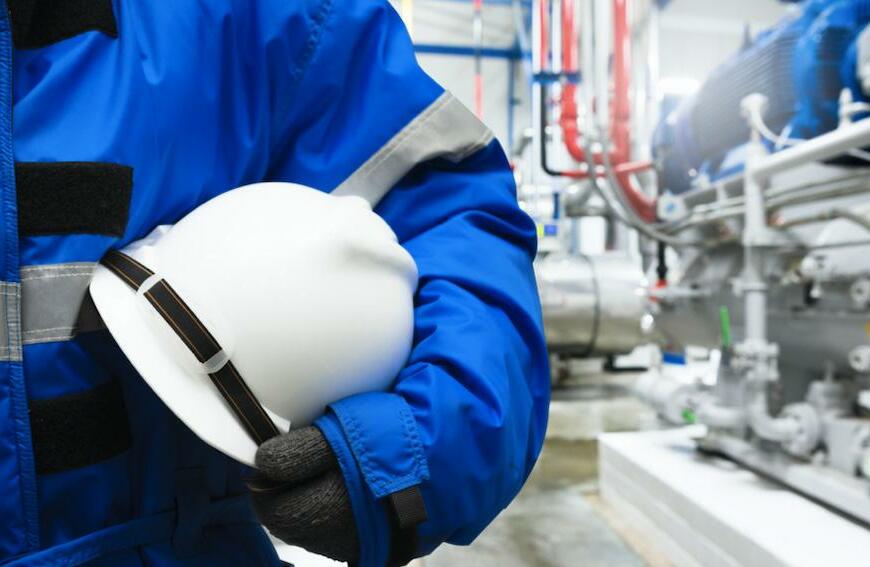
While technology is important in detecting an emergency situation, the process that follows to ensure a timely and appropriate resolution to an incident is just as critical. If an incident were to happen, how quickly and easily could the emergency services locate and treat the individual? Consideration of how responders can locate the member of staff in an emergency must therefore be a priority. Any lone worker solution should have the ability to provide location information, such as GPS, or for indoor location, WiFi access points or beacons, as staff could be spread over a huge distance on a manufacturing site, for example.
In any emergency response scenario, response teams will need to work together to locate the critical employee and to coordinate the first aid team and emergency services. When seconds count instant communication is critical to ensure a timely resolution – especially if a worker’s life may be at risk. But rapid communication is also important for a critical machinery incident – if experts or support can be reached with simply the press of a button, then any parts, tools, actions or advice needed can be delivered immediately. Companies that deploy technology solutions such as integrated Lone Worker and communication devices – for example, Push to Talk over Cellular (PoC) or Digital Radio – can ensure that all employees are connected, optimising communication, collaboration and employee welfare.
There are communication devices available, for example, Smartphones, Digital Radio and IP DECT with integrated lone worker functions to safeguard staff and can be fine-tuned to suit a business’ requirements – which is essential to ensure that the end
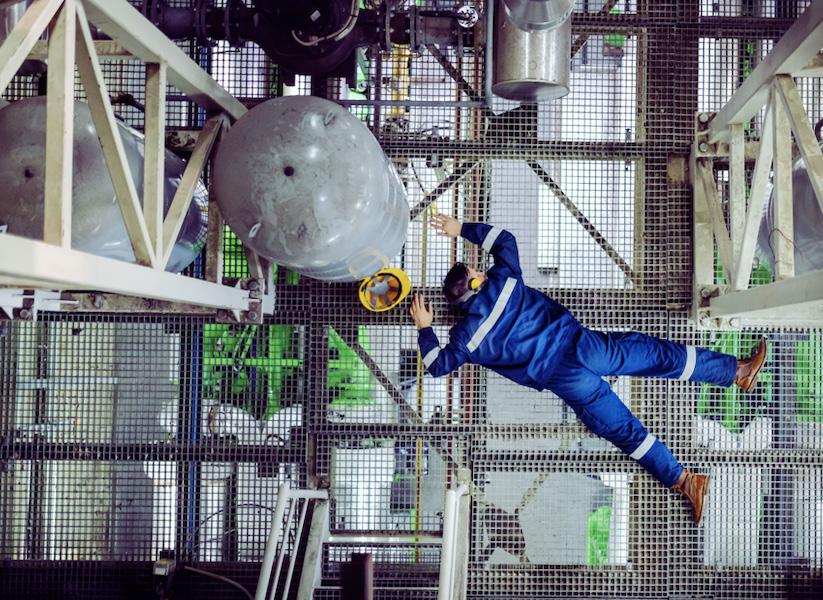
About the author
Chris Potts is marketing director at ANT Telecom, a bespoke telecommunications provider based in High Wycombe. Chris has over 15 years’ experience working for telecommunications companies and his current role includes promoting ANT’s comprehensive range of telecoms products and services, from telephone systems to wireless technology, such DECT and Radio. Chris is also responsible for developing, planning and executing all marketing activities as well as managing an internal sales team to maximise sales lead opportunities for ANT Telecom.
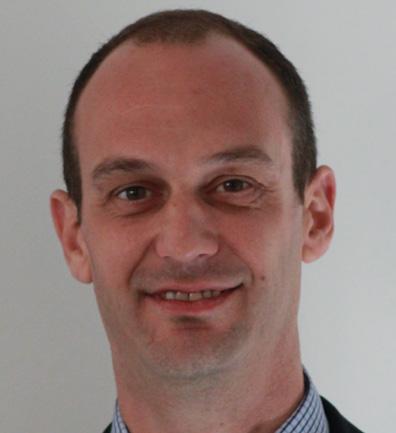
solution fully addresses the needs and nuances of a company and its employees. By working with an unbiased supplier that adopts a consultative approach, businesses can work collaboratively to analyse these components and ensure they get it right for employees, to maximise productivity and safety at the same time, and to achieve the optimum level of tailored functionality at ease.

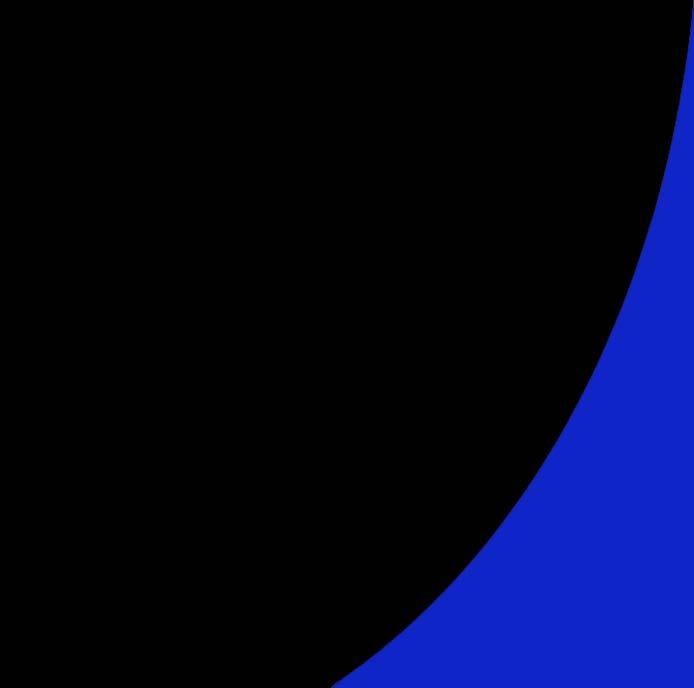


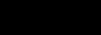
















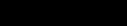



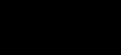






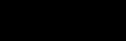


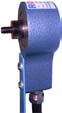
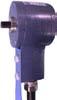
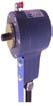
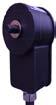
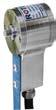
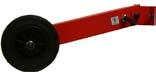
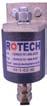





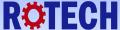

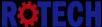

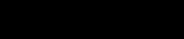


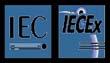



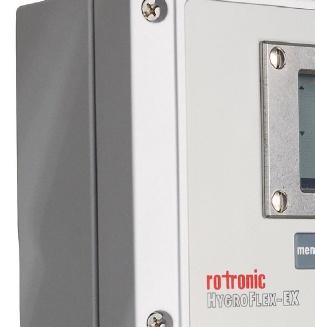
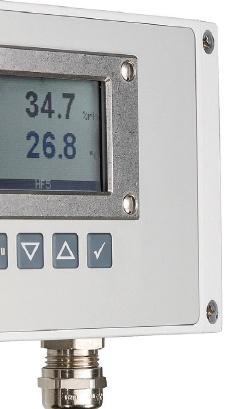

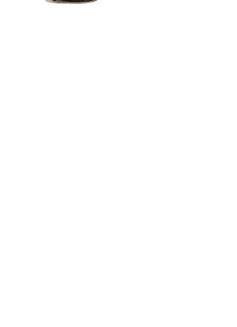
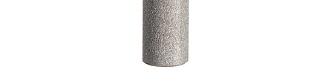
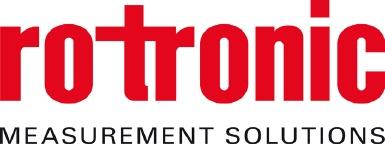
Using assisted reality to maximise safety and worker productivity
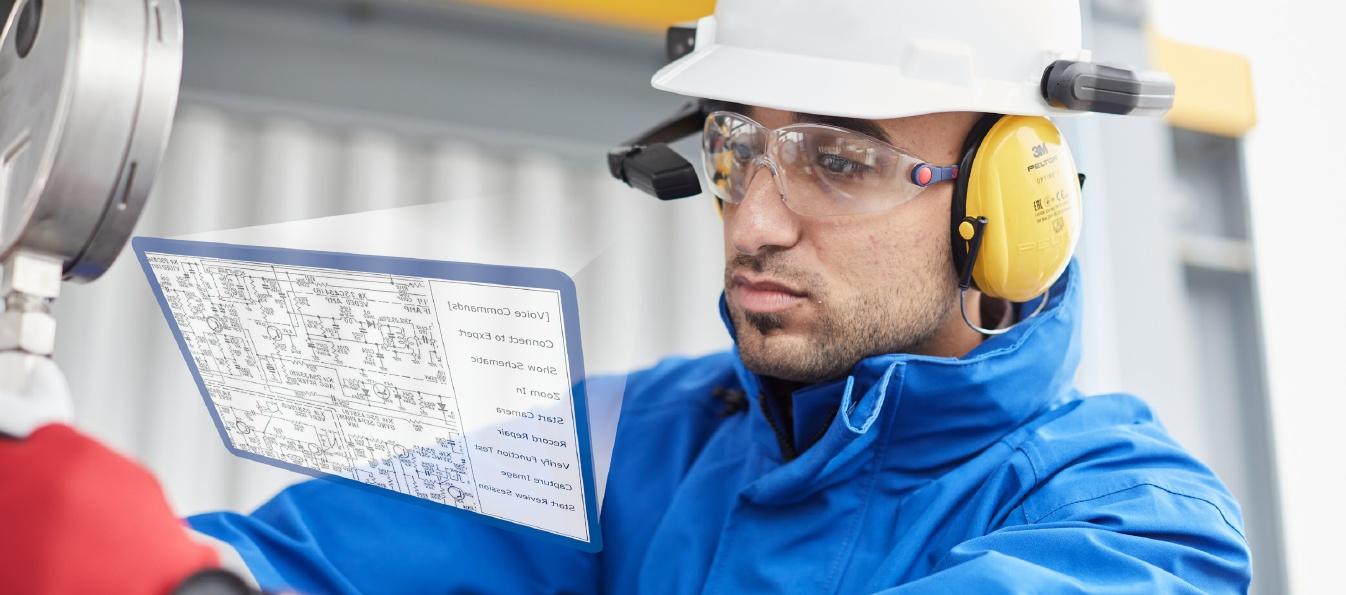
According to the HSE, 142 workers were killed in work accidents in the UK in 2020/2021. Such a sobering statistic is another reminder for organisations across all industries to continue to focus on health and safety measures in the workplace. Increasingly, organisations are looking for ‘fit for purpose’ technology to enhance worker safety and productivity. In this article, Jon Arnold, VP of Sales, EMEA, RealWear, Inc. explains how to get the most out of your assisted reality wearable deployment.
One trend is the deployment of assisted reality wearable solutions. The best of these solutions are designed as “reality-first, digital-second” in nature. Unlike immersive VR or AR headsets, the notion is that Assisted Reality is not digitally immersive for the user, to allow full awareness for the frontline worker, whilst still providing proper guidance. Assisted reality was developed for workers to be more efficient and productive whilst maintaining situational awareness. The technology enables workers to view content on a microdisplay. Digital information is displayed in the worker’s peripheral line of sight without compromising their vision.
It’s no surprise then that wearable technology can be fundamental to job safety, and that’s just as well given that field and on-premise engineers around the world face challenges every day. They must stay alert to the performance of countless systems while navigating complex and often dangerous environments, while also processing information and procedures for repairing, maintaining or assessing equipment. Therefore, technological solutions, like wearables, need to be designed to complement and support workers at hazardous worksites. Hands-free, voice-controlled wearable technology enables real-time collaboration, inspection, extended learning, rapid response and potential for step-change improvements in personal and process safety. Additionally, they need to hold up to the rigors of frontline work if they are to empower workers, and – most importantly –help workers stay safe.
Assisted Reality wearables extend safety and risk management to the edges of the organisation where hazardous work is performed. However, it’s important to ensure that the technology is being used properly for it to be fully effective. It’s vital that those who use the technology are well-trained in best practice by the suppliers and experts. In the following, we outline some key points for frontline workers within hazardous areas that
are currently using wearable technology or considering using it in the future.
Mitigate risk
First, mitigating risk from dropped objects is particularly key. Ensuring that your device is securely attached to your PPE is basic step number one. Often an assisted reality wearable device will come shipped with clips that work directly with the PPE that workers are using on site. Secondly, securely fasten your device to your head using a chin strap. You can also get a drops lanyard that will fasten onto your wearable device and directly onto your helmet, ensuring that if all other risk mitigation measures fail, you have a third and final method of ensuring that your workers are wearing the device safely. It’s imperative that wearables are properly fitted to the protective equipment that you would wear in your everyday job.
Noisy environments
Significant advancements in noise cancellation technology mean that assisted reality can be highly effective and perform well in loud or noisy work environments, which many highhazard industries are. It is of course important though to wear hearing protection so that your hearing doesn’t degrade overtime. It’s likely that your device won’t be compatible with traditional hearing protection that clips onto
Mounting a device above the brim frees up space for behind-the-neck hearing protection. Using this type of ear protection with a wearable device enables workers to work in louder noise environments with the confidence that their hearing is protected.
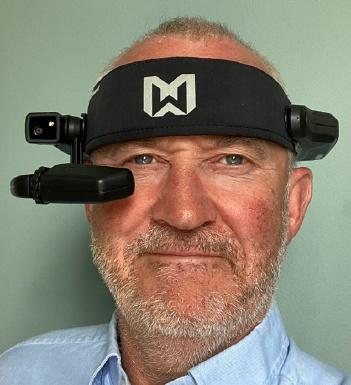
Using the viewfinder on your wearable device
When you have your wearable device on and you don’t necessarily need to be looking into the display – or you’re in motion or movement and need to make sure that the viewfinder is out of the way – it’s important to note that there is a right way to do it. In RealWear’s case, for example, this would be to take the boom arm and flip it underneath the device. By doing it this way you don’t have any way for it to get hooked on to anything. The wrong way to do it would be to push the boom arm out to the side – which could yank the device off your head.
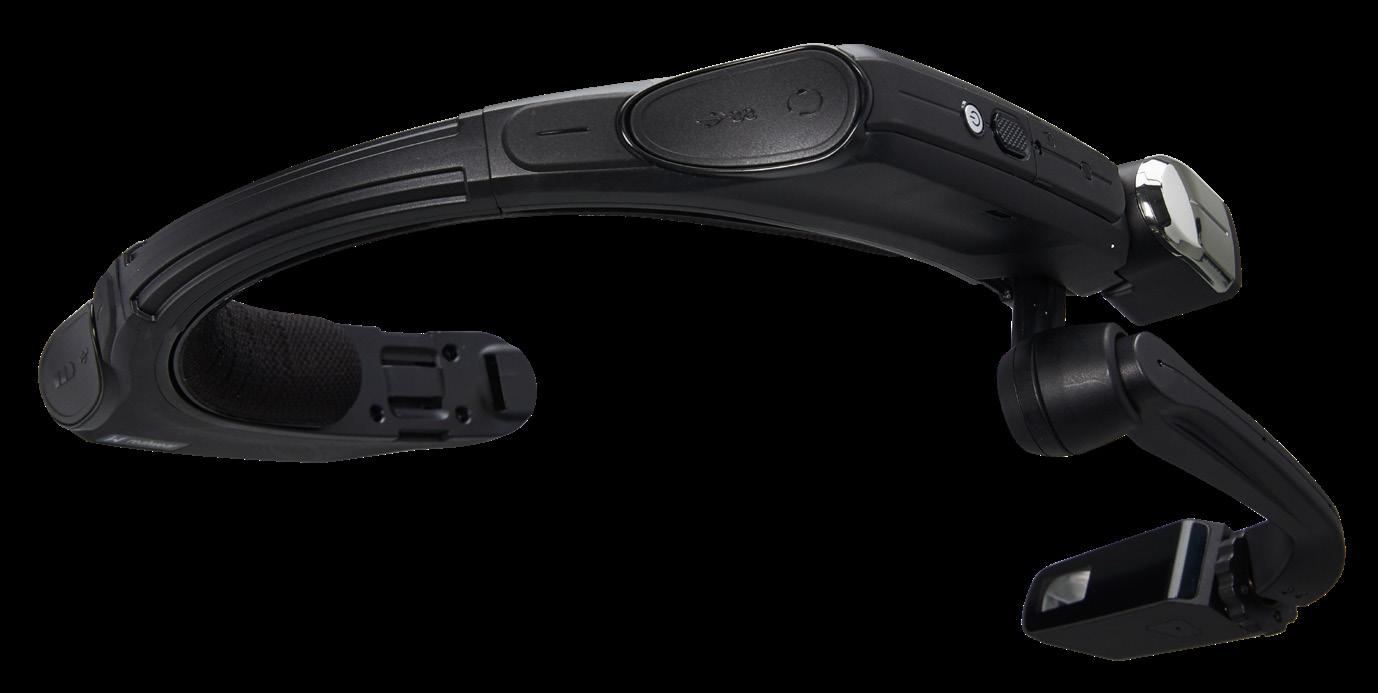
Using Assisted Reality to train employees
Proper training is the top priority in hazardous work environments. Poor training can increase the risk of severe injury or death, and the best safety practices are useless unless the worker can properly identify or understand the risks. Assisted reality gives enterprise companies an easy way to complement classroom learning with ongoing reinforcement in the field. This highlights one of the key benefits of wearable devices: they can reduce training time and improve overall profitability.
For training purposes, assisted reality enables workers in the field to get assistance from experienced technicians via an enhanced twoway video call experience, where the expert can remotely see and hear from the worker’s point of view. One of the biggest advantages is its flexibility. The pandemic response of travel
restrictions and social distancing has allowed organisations to continue to onboard or train their employees.
However, it’s important to note that when training employees remotely this will differ from the physical experience - which has been the de facto up until now for heavily regulated work environments.
Getting the most out of an assisted reality technology deployment is imperative for organisations looking to protect personnel in hazardous environments. By ensuring that best practices are followed, frontline workers can ensure that they’re as safe as possible whilst performing their jobs.
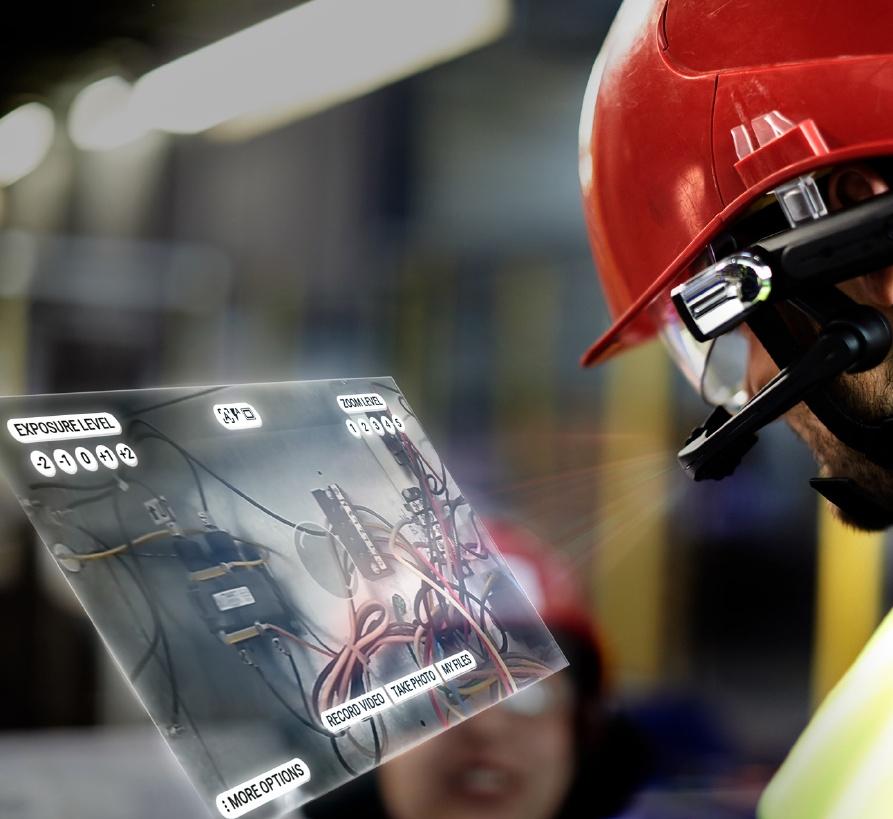
About the author
Jon Arnold VP of Sales, EMEA at RealWear, is an accomplished IT professional, having worked in the industry for the majority of his career. He is a veteran of six previous start-ups including Riverbed that successfully became public in 2007. Simplivity, that was acquired by HPE, Viptela, acquired by Cisco and VeloCloud, acquired by VMware. Jon has demonstrated proven success in leading and growing RealWear’s European presence by formulating a channel strategy that has seen RealWear attract new distributor and reseller partners globally.
HAZARDOUS
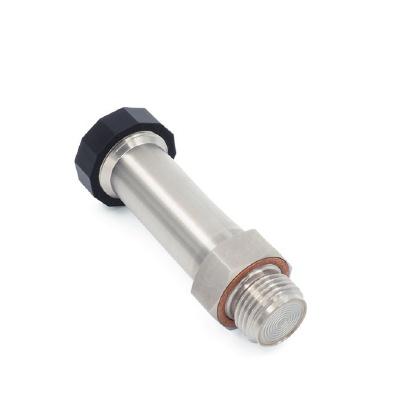
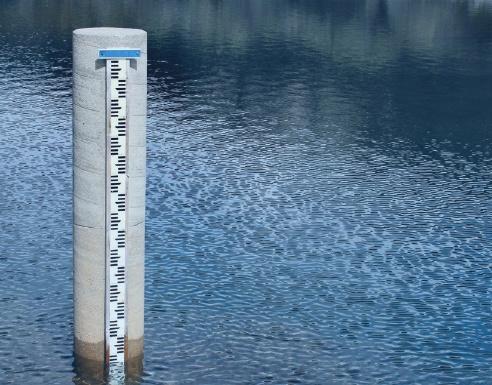



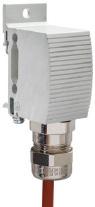
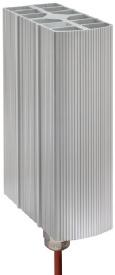
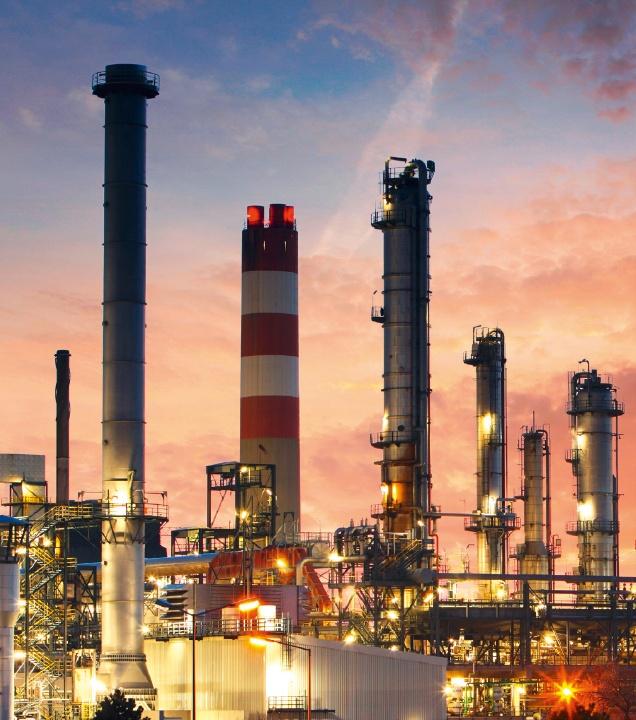
Augmented Reality drives real change in remote training
safety
Augmented reality technology is allowing field engineers to connect directly to off-site experts for more efficient maintenance, data collection, training and safety, as Kim Fenrich, global AR/VR and digital services product manager, ABB Process Automation, explains.
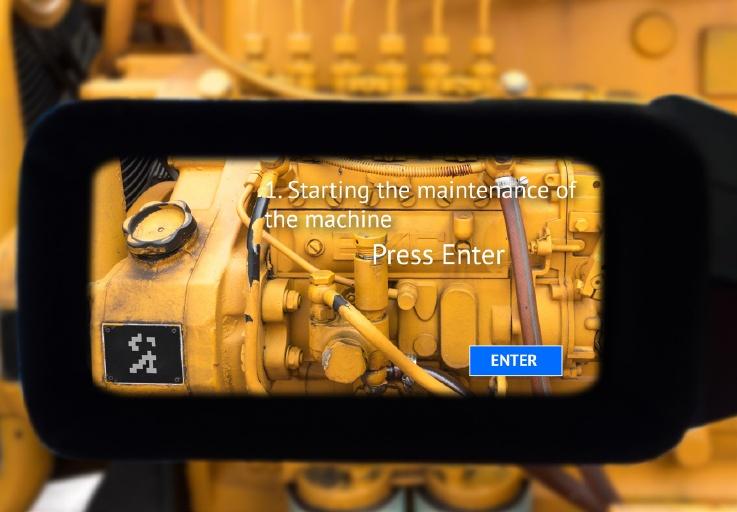
Once the domain of gamers, augmented reality (AR) now has multiple uses in the industrial space as companies recognise that putting this visual enhancement technology into the hands of field workers can improve safety, reduce human error and increase operational efficiency.
An advantage of AR is that it can provide data to users in a specific context of an operational asset, with three-dimensional imagery and instructional text laid over specific components; expediting both the understanding of instructions and follow up action. This capability makes data more meaningful,
improves situational awareness, and enables fast, real-time collaboration with experts.
AR is being employed in all phases of industrial plant lifecycles to provide visual, interactive guidance. A recent study by Aberdeen Research found that 23% of customers’ issues were not resolved on the first visit. Using AR effectively can improve quality and consistency of field work, and significantly reduce costs by eliminating rework and travel expense.
Augmented and mixed reality explained
What exactly is AR? Simply, AR is the overlay of digital images or data onto real-world objects. It is one of several technologies that enhances a user’s visual perception of their environment or replaces it completely.
Unlike virtual reality (VR), where the user is completely immersed in a digitally created artificial environment, AR adds to a real-world visual perspective by projecting digital data or
objects on top of actual objects. In an industrial environment, this allows the user to stay aware of their physical surroundings, freeing both hands and eyes from paper documentation, and benefitting more directly from instructional information.
Another version of this technology is mixed reality (MR). MR extends AR functionality by allowing the user to interact with the digital object by manipulating it rather than only viewing a static image. Another iteration of this technology is extended reality (XR), which is a combination of AR and MR.
While AR technologies continue to mature, they are gaining acceptance in industry due to their ability to help users learn, visualise, interact and expedite issue resolution. For example, object recognition technology is currently being used in industry to ensure an asset being worked on in the field is the correct one.
This technology works by overlaying a digital 3D image on the physical equipment using the camera of a phone or tablet. Once the AR system detects it is the correct asset, the guided step-by-step procedure is automatically started. This ensures that when an engineer or maintenance technician is sent into the field to perform a task such as recalibrating a transmitter or replacing a part, operations management knows that it will be performed on the correct asset.
AR industrial use cases
AR or MR technology, deployed on tablets, smartphones, glasses or headsets, are an excellent training tool. Interactive 3D models of a real industrial facility, along with procedure and process models, is now being used to train and certify operations and maintenance teams.
Imagine a scenario in which a critical asset in a remote location, such as offshore, an oil & gas pipeline or a mine, needed to be addressed. Previously, a certified engineer with specific domain expertise may have had to take a lengthy international flight or be flown by helicopter. This could be very costly in terms of maintenance expenditure, missed production opportunity and even safety risk. Such a scenario was made even more difficult in 2020 due to pandemic-related travel restrictions.
By using AR, companies can conduct the work safely from a remote location and at a fraction of the cost, while at the same time upskilling personnel. With this technology, an engineer or maintenance technician who arrives on site and finds the job is different from what they expected can connect with an expert via a video call, who can see the same thing the local person sees, and together they can address the situation expeditiously and cost-effectively.
Visual Remote Support
ABB has applied its version of this technology for an energy company which required maintenance on an oil and gas platform off the coast of Africa. Rather than proceed through a list of verbal instructions, a remote expert contacted an engineer on the platform through an AR headset. This arrangement allowed the onshore expert to see exactly what the field worker saw, and draw step-by-step instructions that could be viewed on the field worker’s tablet, alongside their headset. This is where AR comes into its own; taking the eyes and ears of the expert and placing them virtually alongside a local resource to jointly address a field situation.
Conclusion
AR and MR are still in their infancy in terms of technology and its adoption in the industrial world. There are hurdles: in order to see the benefits of AR, those who deploy the
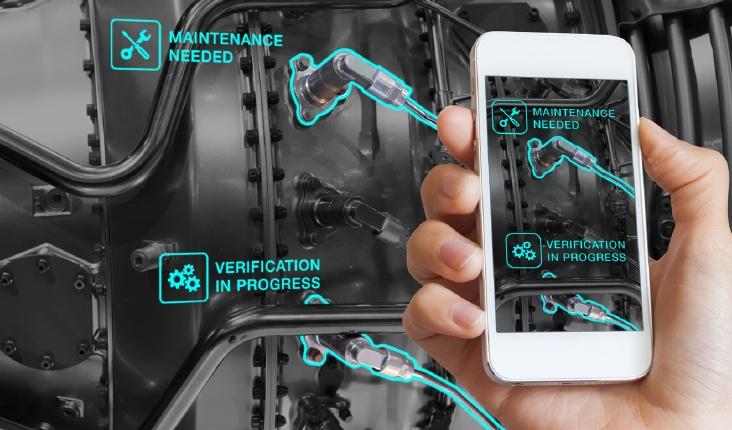
technology must first build 3-dimensional models of the assets being addressed, embed the necessary guidance into the system, and arrange a network of competent experts to interact with the local AR users.
As is often the case, early adopters of this new technology are the ones gaining the fastest rewards. Before the Covid-19 pandemic, AR was viewed as a futuristic technology. Now, having experienced situations in which companies were unable to deploy employees with the requisite skill sets where they were needed, the adoption of such services is accelerating.
By putting virtual expertise into the hands of

Case study: motors and drives training
field workers, AR has the potential to mitigate human error, improve safety and operational efficiency, reduce the time spent using and interpreting data, and truly transform the future of work.
ABB
recently launched a training programme remotely where its domain experts were able to train and recertify new and existing business partners to be able to work with new products. Rather than trainees gathering in a single office, ABB sent a drive device to each business partner along with an AR headset. The drives experts then used traditional classroom training via Microsoft Teams, with both audio and visual instructions via the AR headsets. With this program, one instructor was able to teach and monitor four trainees simultaneously. Other key benefits: were that the training was able to go ahead when it
would have otherwise been impossible due to pandemic restrictions. Other benefits were that engineers became more productive during times of low utilisation and partners were able to remain certified so that they could continue servicing customers.
ABB could also use fewer experts to train a larger number of people (i.e. experts could conduct multiple classes per week instead of just one) and people from multiple locations could participate in the same training course. Attendees were trained without incurring travel costs, and the trainees gained hands-on experience with drives equipment from global experts.
Kim Fenrich is currently Digital Services Product Manager for ABB Process Automation, Energy Industries. In this role he leads the global development of innovative digital products and services that bridge technology and practicality to help customers optimise performance. He has over 30 years of automation industry experience, across a wide variety of disciplines and industries including power generation, process and manufacturing. His roles have included field service, product management and marketing, business development, and IoT enterprise solution architect. Kim holds a Bachelor of Science in Electrical Engineering from the University of Akron, and currently lives near Wilmington, North Carolina.
How mobile tech is reducing risk in hazardous environments
Keeping employees healthy and safe is a challenge for many employers –perhaps none more so than those whose staff work in hazardous environments.
Fortunately for these organisations –many of which are now responsible for a higher number of lone workers – safety technology is evolving rapidly, with mobile solutions now providing a high level of protection for workers in even the most hazardous of workplaces.
The COVID-19 pandemic forced a great number of businesses to change their ways of working, which has left many workers facing new health and safety risks. The number of lone workers has risen significantly in businesses across the world, as more workers now operate in isolation or out of earshot of their colleagues due to social distancing measures. While working alone, these workers are at a greater risk of health and safety incidents because they might not have anyone to call on if something goes wrong. This could mean it takes longer for lone workers to receive assistance when they need it, which could result in more serious injuries or even fatalities.
At the same time, the pandemic has also accelerated technology adoption across all sectors. A recent McKinsey study concluded
that ‘companies have accelerated the digitisation of their...internal operations by three to four years’. And it appears that many businesses are turning to technology and smarter solutions to help protect lone working employees. When Peoplesafe surveyed over 120 health and safety professionals from public and private UK businesses in March 2021, almost half (47%) were already using lone worker technology, and 71% said that they expect their use of lone worker technology to increase.
Clearly, tech solutions are becoming a critical element in many lone workers’ health and safety toolkits – but for workers operating in hazardous environments, finding tech that’s designed for dangerous environments hasn’t always been easy. However, innovation in this area means that today, even those operating in the most hazardous environments can access the technology they need to stay connected and safe at all times.
Designed for dangerous environments
A wide range of workplaces are deemed hazardous by DSEAR (Dangerous Substances and Explosive Atmospheres Regulations) from nuclear power plants to petrol stations, although the level of hazard to employees
will vary. Employers that require their employees to work in hazardous areas must therefore carry out a hazardous area study in addition to their standard risk assessment to determine how the environment may increase the health and safety risk to their employees and the measures they must put in place to protect them.
Employees working in a hazardous environment classed as Zone 0 can only carry equipment that is ATEX approved category 1, for example. Category 1 equipment is designed to be intrinsically safe, as its electrical and thermal energy is limited to a level below that required to ignite a specific hazardous substance. Until recently, this meant that smartphones – and the lone worker mobile apps that keep so many workers safe – were off-limits in hazardous areas.
The many benefits of mobile tech
Today, however, technology has advanced and there are now a number of smartphones that are approved by ATEX for hazardous environments. This is good news for workers who are required to work alone in these areas, as it means that they can use a lone worker app to stay in communication with their colleagues and call for help if needed.
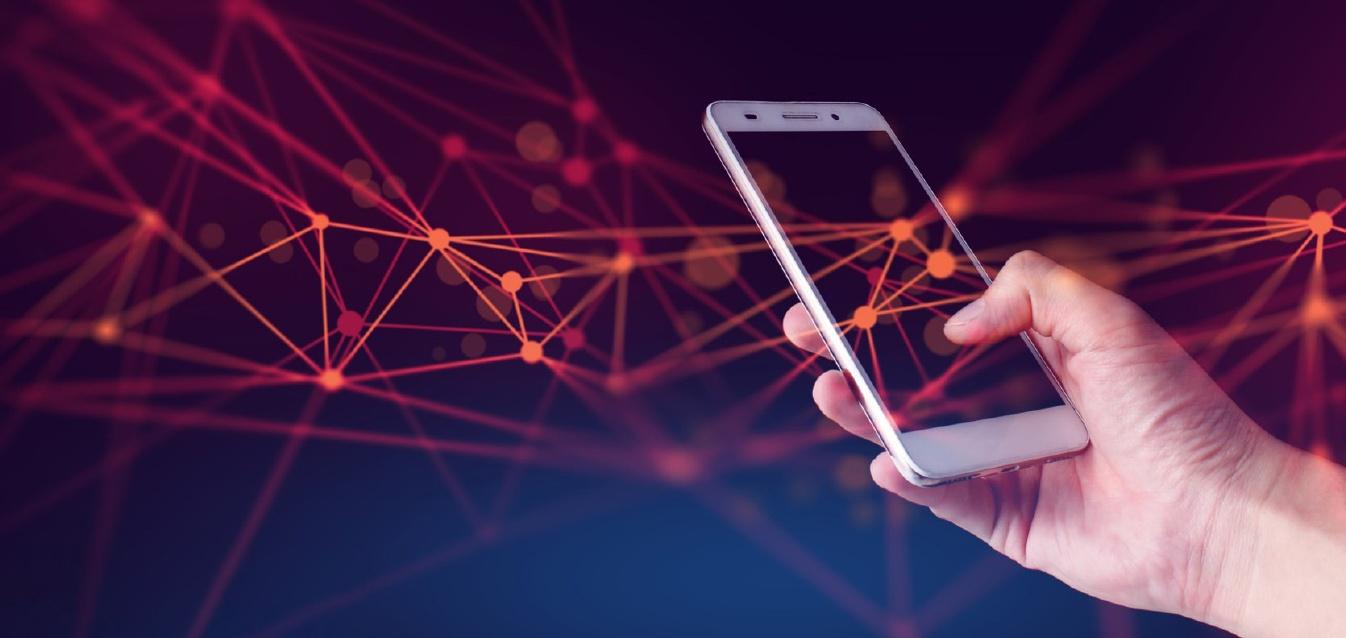
While ATEX-rated lone worker devices are available, many employers prefer to provide their workers with lone worker mobile apps wherever appropriate, because it’s easier for them to combine multiple solutions into one app. This gives them the ability to create a truly bespoke solution that provides full protection for their employees. Lots of employees also prefer to use a mobile app, because it means they can stay safe without adding to the equipment they’re required to carry. And with rugged smartphones proving a more practical solution, remaining connected via a mobile device is an increasingly feasible option for remote workers.
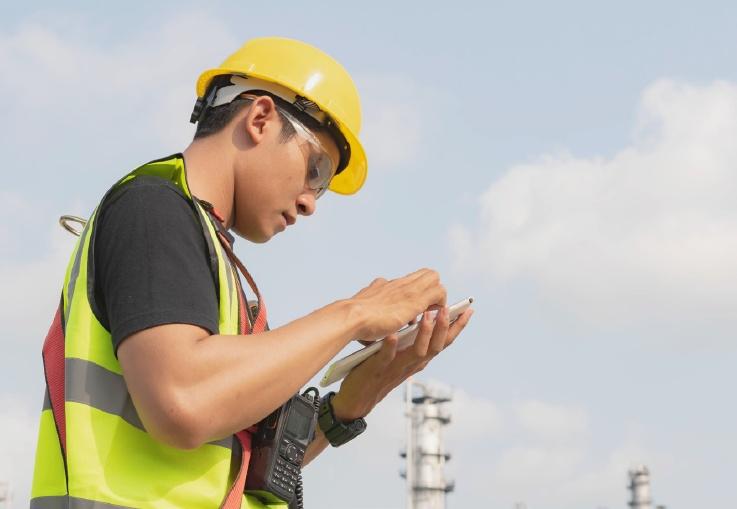
Health and safety risks to employees don’t disappear the minute they leave a hazardous environment – many still face risks when travelling home at unsociable hours, or in inclement weather conditions, for example. Employers are also aware of the mental health impact that the pandemic has had on many of their employees. They therefore want to provide a lone worker solution that staff can use to access support 24/7, and a mobile app is one of the easiest ways that they can do that. Workers are much more likely to take a smartphone home with them, which means employers can continue to provide them with protection beyond the normal working day.
Investing in innovative solutions
When it comes to lone worker apps, however, they’re not all created equal. It’s important for employers to look out for apps that are not only compatible with ATEX approved
smartphones, but also provide them with tools and features that will enable them to provide their employees with a superior level of protection.
Any lone worker app should provide 24/7 emergency support, for example, to ensure that workers can call for assistance whenever they need it. Employers should explore how this support is provided, as this could affect response times in the event of an emergency –an app that’s supported by a dedicated Alarm Receiving Centre (ARC) is likely to provide better protection for employees than one that doesn’t have its own call response team.
Those working in hazardous environments could also benefit from lone worker apps that feature geofencing alerts. Geofencing uses GPS technology to create a virtual ‘fence’ around a particular area, and some apps enable employers to set up their own geofences that will trigger a response when the smartphone enters or leaves a geofenced area. Employers that are striving to protect workers in hazardous areas could use this feature to remind employees to check or put on specific PPE when they’re entering a dangerous area, for example.
Connectivity is a core feature of the evolving safety technology market. By integrating technologies, for instance video tech or body worn devices with emergency support tech, employers are able to improve access to the right kind of help in the event of an incident, including alerting the emergency services.
About the author
Naz Dossa is CEO at Peoplesafe and Chair of the BSIA Lone Working Group. Naz joined Peoplesafe in February 2020 as Chief Commercial Officer, becoming CEO in June that year. Having spent much of his career in the IT and telecoms sector, Naz is particularly interested in the role of technology in keeping workers safer.
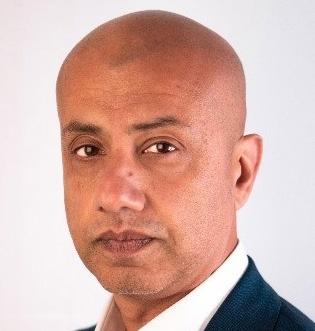
Smarter solutions, safer employees
Lone worker solutions now come with so many useful features, from video links to geofencing, that many businesses are opting for a smarter approach to health and safety by investing in specific personal safety technology for their workers. In fact, over three quarters (78%) of the health and safety professionals Peoplesafe surveyed said that they believed lone worker technology should be re-classified as Personal Protective Equipment (PPE), with many firms stating they already classify lone worker tech as PPE because they believe it is so vital to keeping workers safe.
Now that workers can safely take ATEXrated and rugged smartphones into hazardous areas, lone workers in these dangerous environments can be given the same level of health and safety protection as their co-workers in less volatile locations. The easier it is for workers to use safety technology, and the less there is for them to carry, the more likely they are to access support when they need it –and that’s something that every employer should actively encourage.
Improving process safety culture – what’s required?
Much of the emphasis on the subject of ‘process safety culture’
originates from the Buncefield and Texas City incidents that occurred in 2005. Both incidents resulted in significant fires and explosions that had repercussions industry wide. In the decades since those events occurred, there’s been an increased emphasis on the subject of process safety and safety culture.

The Centre for Chemical Process Safety defines process safety as a ‘blend of engineering and management skills focussed on preventing major catastrophic accidents such as fires, explosions and toxic releases’ – all of which have the potential to cause significant harm to humans, the environment and businesses.
Safety culture, as defined by the UK’s Health and Safety Executive, is the “product of the individual and group values, attitudes, competencies and patterns of behaviour that determine the commitment to, and the style and proficiency of, an organisation’s health
and safety programmes.” This definition can often be simplified with the answer relating to one question: ‘What happens in our business when no one is watching?’
The keywording in the HSE’s definition is that culture is a product of both individual and organisational attitudes and behaviours.
So, if an organisation wishes to develop a good process safety culture, then it needs to ensure that the organisation and its employees behave in an appropriate manner.
An important factor, that is often overlooked, is that the individuals of an organisation must be fully aware of the process safety standards. Where process safety is concerned (preventing fires and explosions etc.), certain tasks must be completed correctly every time that it is undertaken.
Humans generally tend to comply with requirements if they understand and agree with their necessity. The problem for organisations, however, is that attitudes and behaviours are outputs.
Instead, there should be a focus on inputs to help achieve any necessary organisational attitude and behaviours. The inputs required are threefold:
1. Targets & Objectives
2. Policies & Procedures
3. Coaching & Mentoring
Targets & Objectives
The first of the inputs revolves around targets and objectives. Organisations should therefore ask themselves if they have clear, achievable targets and objectives for improving process safety and safety culture. These targets and objectives need to be both believable and attainable.
If people believe in both the purpose and the ultimate goal of a target, then their behaviour will change.
As an example, just consider a health improvement app based on completing a specific number of steps per day. The app states that if we do a certain number of steps each day we will eventually be
fitter and healthier. You then monitor your progress each day and you will consciously change your behaviour to achieve the set target. Small behaviours change. Rather than settling down after dinner to relax, you check the number of steps or get a reminder that your steps are yet to be reached, and if your target is not met, then you take the dog for a walk.
Policies & Procedures
Policies and procedures set the standard requirements for an organisation. Good policies focus on the 5W’s – What, When, Where, Who and Why. Procedures, on the other hand, tend to focus on the How. The HAZOP procedure, for example, will instruct us on how to do a HAZOP. Alternatively, a risk assessment policy will consider, through the 5W’s, the wider picture. This will include all the available risk assessment tools to be used, when they should be used, by whom, and importantly why. Again, we as humans function better if we understand the reasons why something is being done.
Having policies and procedures is, in a sense, easy. Having policies and procedures that people understand, use, follow and implement is difficult.
When undertaking process safety management audits for organisations, finding a procedure can be a long drawnout process, but once found, employees can be surprised at some of the steps outlined in a particular procedure. This, therefore, indicates that people spend little time getting to know the content of an organisations policies and procedures. When a near miss or incident is investigated, how many times do we find that procedures have not been followed? Often, the results are incorrect procedures that were not followed, could not have been followed and, more generally, because an interpretation of procedure was required.

Other aspects of an organisation may prevent employees from correctly following policies and procedures. Many organisations pride themselves on being responsive to a client and the elements of a process safety management system (the policies and procedures) are essentially designed to make sure that an organisation
maintains a safe working environment. Examples of this will include hazard identification exercises (e.g. HAZOP, LOPA etc) and the Management of Change. Practitioners across the sector will understand that quick answers from these elements do not happen.
As an example, a business may have told a client that they can have a new product manufactured within 3 months. But, is the reality of ensuring that all the hurdles that have been created and implemented for a new process, set by organisational policies and procedures, achievable within that set time frame? Are the sales and business development departments aware of these particular issues? With a well structured
within the set time frame, but many of the necessary steps required by the policies and procedures are missed.
One real-life example, from my career, occurred as a company undertook a 3-week maintenance shutdown which had taken one year to plan. The plant was planned to restart operations on a Monday. On the preceding Friday afternoon, the plant was instructed that the maintenance had finished early, and the plant could be started up on Saturday. Normally, in this situation, everyone is congratulated and bonuses are paid out. But, with this particular case, an investigation was instigated over the weekend to find out why the project was completed early – after all, this took one year
The investigation found that the maintenance had been done correctly. When required equipment was needed to complete a specific job, it was discovered that they were already present and just waiting to be used. It was these efficiencies that became apparent and resulted in the tasks being completed ahead of schedule.
What would happen in your organisation in similar circumstances?
Coaching & Mentoring
The third, and arguably most important input, is coaching and mentoring. At this stage, the awareness and understanding of an organisations standards should be set and enforced. This requires both time and effort to be completed successfully, but ultimately, everyone in the business has to be able to coach and mentor.
As in life, some people will naturally be better coaches and mentors than others, but the knowledge and attitude it takes to coach and mentor should be present across the organisation. As seen across the sector, the above can be achieved by undertaking ‘safety observations’. Individuals are tasked with making observations and probing awareness of others. A target or objective set by an organisation could be a set amount of safety observations undertaken each month.
An issue that arises with such exercises, however, is in the understanding of what is trying to be achieved. Process safety requires organisations to be in continual improvement mode – always looking for improvements to be made.
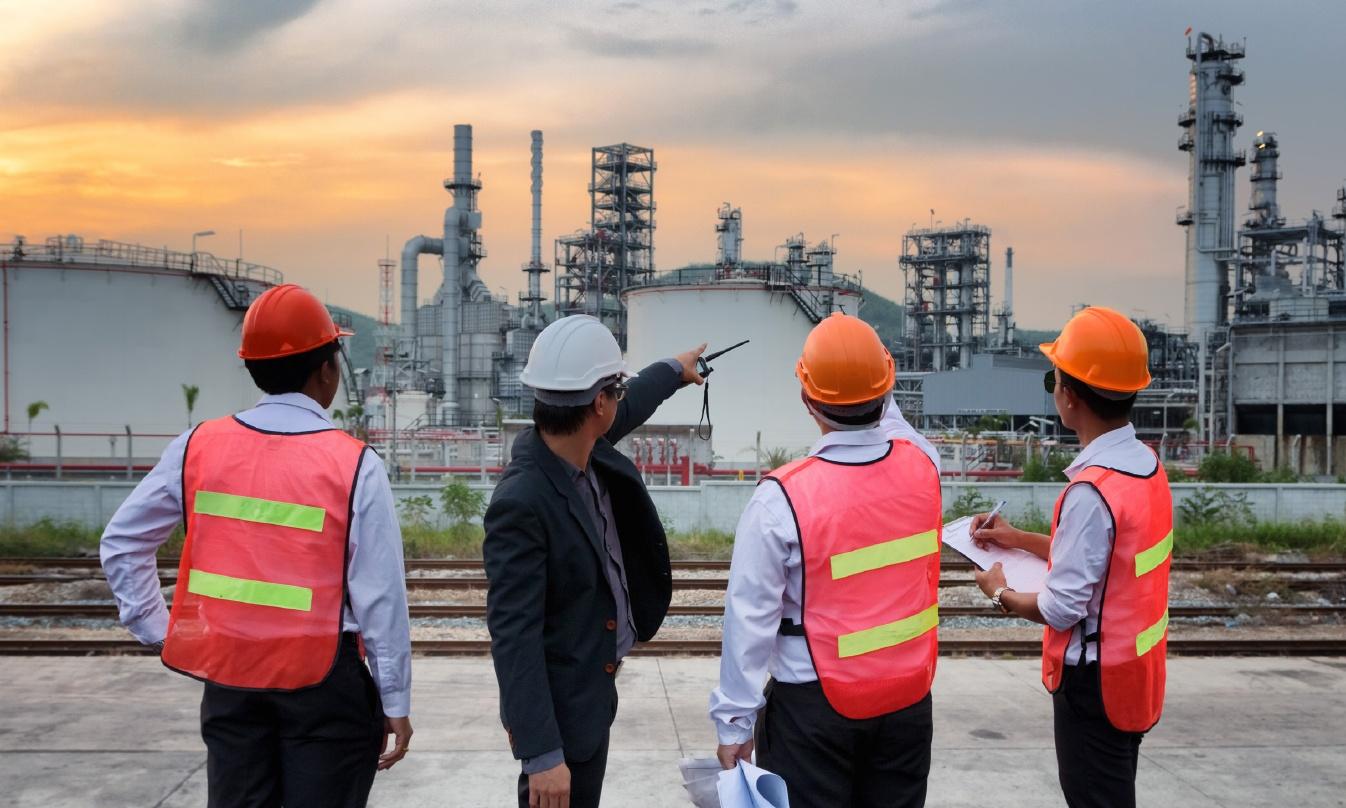
When undertaking safety observations in practice, we tend to search for somebody doing something incorrectly, and the resulting discussion then becomes a one-way exercise. If we are doing safety observations with the objective of improving organisational culture, we should probe the individuals’ awareness and understanding even when correct practices are being done. This generates a two-way conversation that involves listening and thinking, and ultimately, both parties learn.
If this approach is used, organisations will quickly generate a structured culture. Following these discussions, everyone should benefit, and improvements can then be made to create a safer working environment.
The key behaviour required for a good process safety culture is the continual improvement mode mindset. From the very top-down, everyone in an organisation should always try to seek out problems, because problems can be solved, and improvements can be made. Ultimately, the problems you cannot see cannot be improved.
About the author
Dr. Andrew Fowler is currently Technical & Operations Director at Sigma-HSE based in Winchester – a recognised process safety consultancy and hazardous materials testing facility. Prior to joining Sigma-HSE, he spent 10 years in the chemical manufacturing industry, 17 years as a Process Safety Specialist Inspector with the UK HSE, and 12 years as the Technical Director at a process safety consultancy.
In conclusion, does everyone coming to work on your site every day chant the mantra ‘I must find a problem today? I will not be happy unless a find a problem – something that needs to be fixed.’ Is this what your employees do? Is this what your managers do and require of others? Is this what those at the top of your organisation do? Is this your organisation?
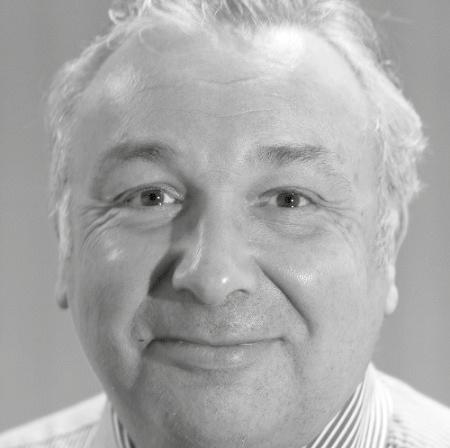
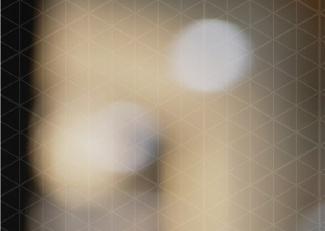
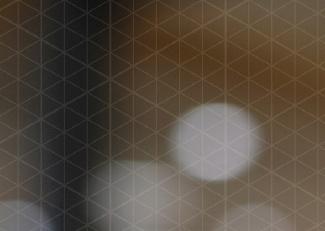
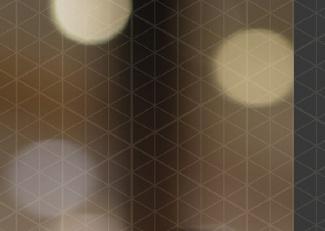
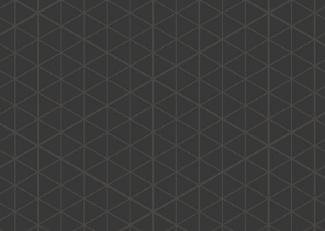

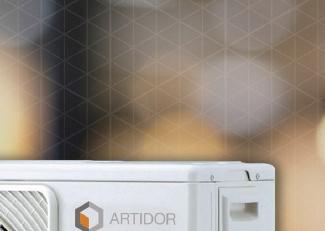
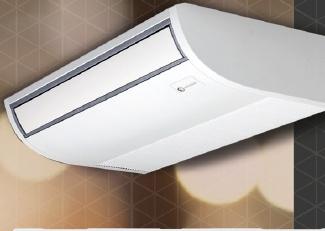
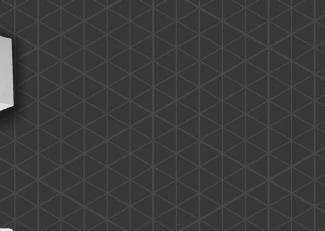
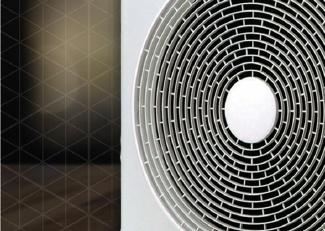
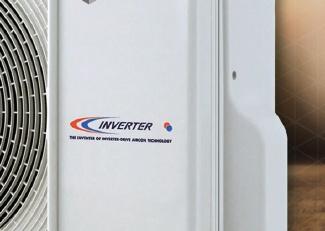
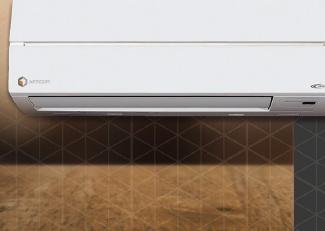


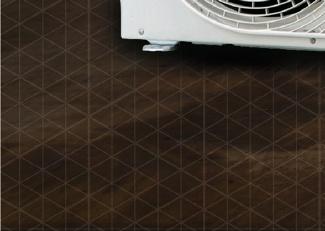
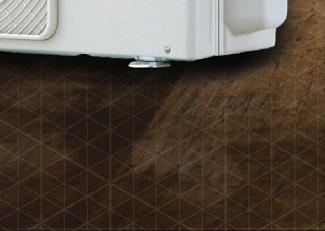
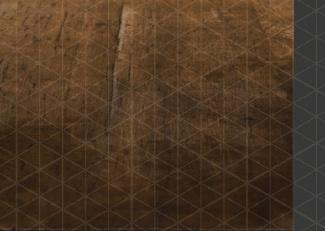
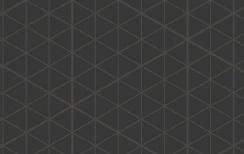

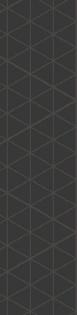
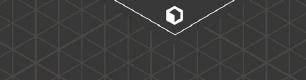



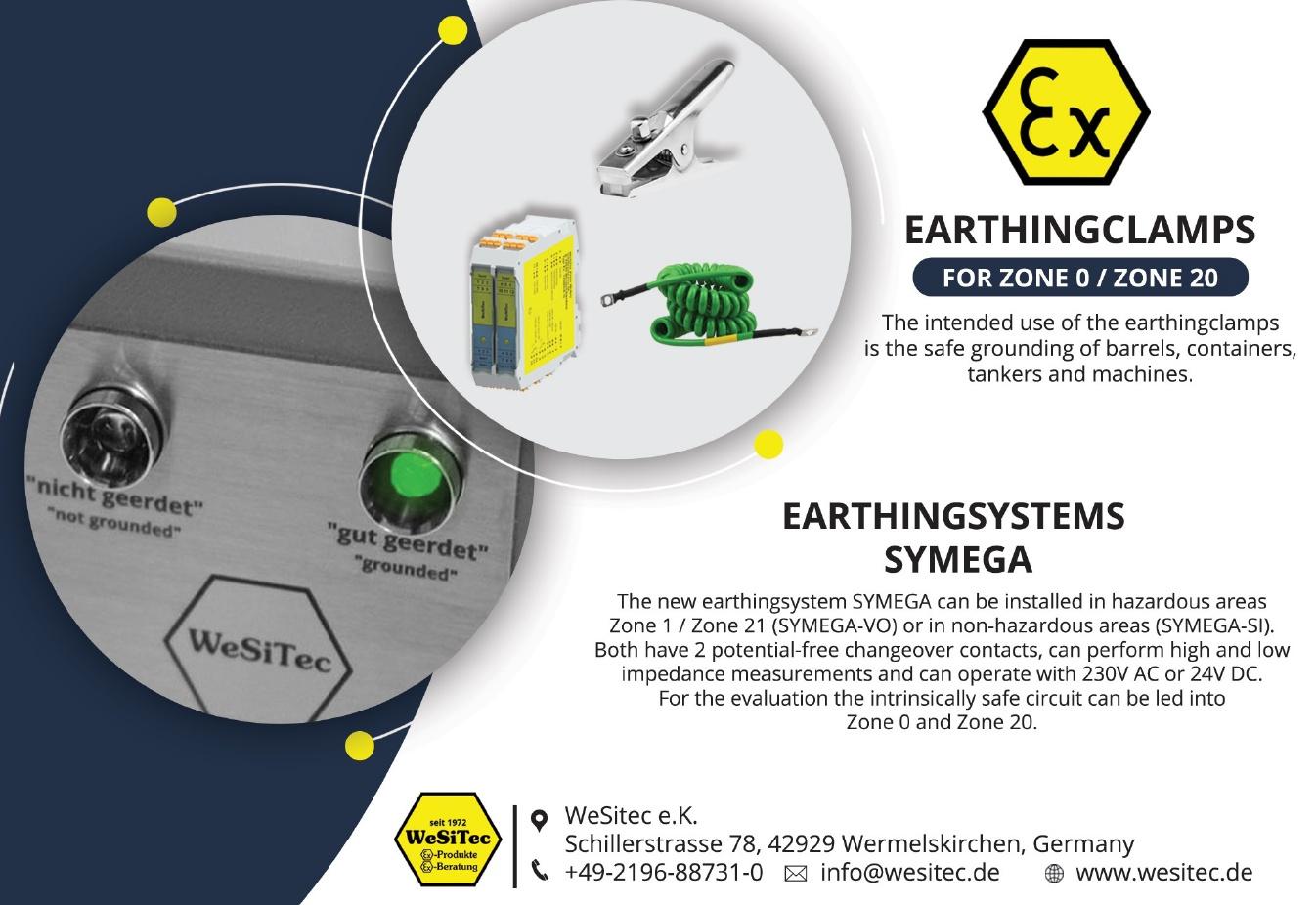
Large volume liquid hydrogen releases: results and outcome of modelling
Decarbonising shipping and transportation remains a significant challenge as storing electrical energy from renewables in significant capacity makes it of little use against the requirements of running a ship at sea where space and load requirements inhibit battery options. Liquid hydrogen (LH2), commonly used as fuel in the space industry, forms one potential solution where the required energy density/ volume can feasibly be met for ships of all sizes.
However, its use in the maritime sector poses significant technical and safety challenges around the scale of operations, number of usage points, and its proximity to personnel. Potentially critical scenarios for LH2 on ships can be described through a variety of phenomena including outflow, dispersion, accumulation, cryogenic
exposure, ignition potential, explosion, and fire.
In 2018, the NPRA gave the go ahead for a hydrogen-electric ferry to serve one of the routes along the coast of Norway. One concept for zero-emission ferry transportation involves LH2 as a concentrated form of hydrogen storage (Figure 1).

To identify and quantify safety related issues which may need to be resolved, DNV was commissioned by Norway’s Defence Research Establishment and the Public Roads Administration to conduct a series of experiments investigating the behaviour of large releases of LH2 into the atmosphere and in a closed but ventilated area.
The build and operation of the experimental facilities at DNV’s Research and Development Centre in Cumbria,
UK, delivered a programme of research pertaining to the outdoor and confined leakage phenomena.
Experimental arrangement
A total of 15 large releases (up to 50 kg.min-1) from a liquid hydrogen storage tanker were performed with variations in source tanker pressure, flow rate, orientation, ignition, and atmospheric conditions – both directly to atmosphere or within a 27 m3 steel confined space simulating a Tank Connection Space (TCS) complete with ventilation mast.
The outdoor releases were initially illustrated using predictions from DNV’s GasVLE, FROST and Phast software packages to analyse the expected behaviour for:
• Outflow – assessments of the mass flow versus pipeline and outlet conditions are made including assessments of the level of flashing
releases: key modelling exercises
(liquid mass fraction) within the pipe.
• Pooling – measurements of ground surface and subsurface temperature around the releases were made and interpreted for the presence of liquid hydrogen or condensed products of air.
• Dispersion – determination of the extents of the flammable limits near to ground level from each release.
• Thermal properties - thermal radiation measurements recorded around each ignited release are interpreted against simple models and existing correlations and guidance for hydrocarbons.
Bulk LH2 delivery was from a bulk tanker located in a protective mound at the test site, which included a tall camera tower equipped with wind instrumentation. A 30x30m concrete pad was constructed to contain the release arrangement.
This incorporated a 40m long vacuum insulated pipe with instruments to analyse temperature and pressure conditions, the release point was located in the centre of the 900m2 concrete pad. Some obstacles in the form of ISO containers and smaller infrastructure were located on the test pad, as shown in Figure 2. The release of LH2 was directed both downwards and horizontally.
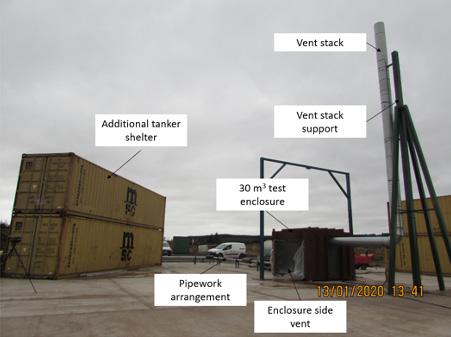
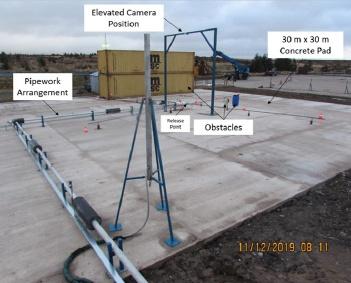
Measurements in the outdoor releases focused on the temperature of the surface and subsurface of the concrete close to the release while dispersion measurements using oxygen sensors were taken further afield. The oxygen sensors measured the hydrogen gas concentration by examining the depletion of oxygen in the atmosphere. Two of the experiments were ignited after a delay to gather information on thermal radiation and overpressure.
Where releases were conducted into confined spaces, the TCS was located at the release point with the releases directed onto the floor of the chamber as illustrated in Figure 3. The chamber was equipped with ventilation openings, ventilation mast and an explosion relief vent to avoid significant damage to the chamber in each experiment. The chamber itself was instrumented to acquire measurements of temperature, gas accumulation and explosion overpressure in addition to the field measurements of gas dispersion and temperature laid out for the outdoor releases.
All experiments were conducted within a 250m exclusion zone and controlled remotely. This followed the method for purging and cooling the pipe that went from gaseous nitrogen (N2) to liquid nitrogen (LN2) to gaseous helium (He2) to cold gaseous hydrogen (H2) to LH2.
The images on the next page show the varying views of the outdoor, downward and horizontal releases and an ignited confined release.

A full video showing the various views can be viewed with this article on www.hazardexonthenet.net
Results
Using the legacy British Gas model FROST and the DNV PHAST models, prediction of the vapour quality by mass and outflow were considered, with knowledge of the geometry of the release point orifice and the saturations conditions near to it.
The liquid/vapour fractions along the pipe during releases were calculated based on the pressure decay and assuming isenthalpic expansion. Releases in all experiments produced high liquid mass fractions (i.e. the proportion of the mass flowing in the pipe being in the liquid phase) with experiments being driven above saturation pressure in the tanker producing higher liquid mass fractions (i.e. little or no flashing in the pipe).
One of the key considerations when assessing the risk of releases is how much of the twophase flow ends up on the floor, forming a pool, perhaps, or raining out from the jet.
Taking the measurements of the surface and subsurface temperature of the concrete and in the experiments allowed DNV to conclude there was no evidence for any LH2 beyond 0.5m from the releases in the downward releases conducted onto concrete in the programme and there was zero evidence of any rainout in the horizontal releases.


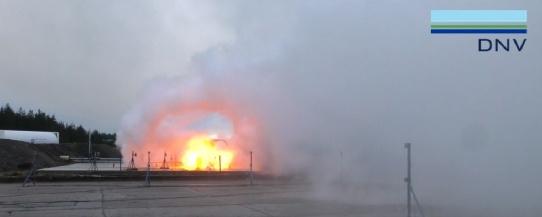
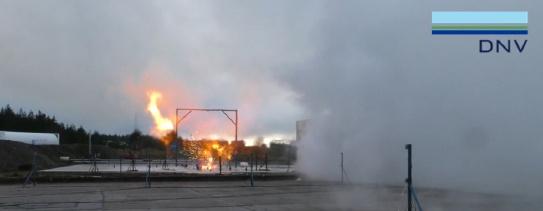
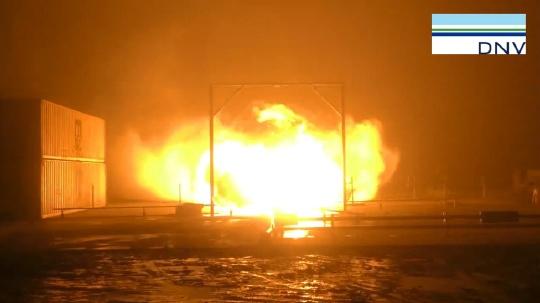
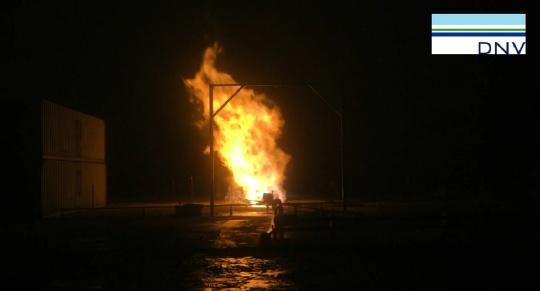

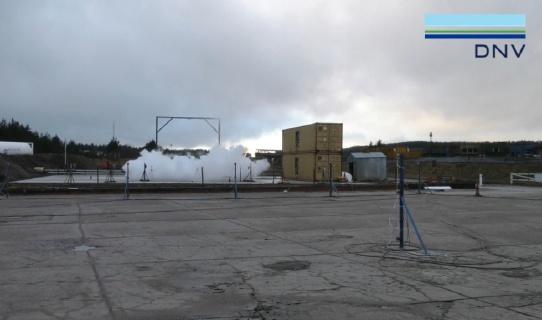
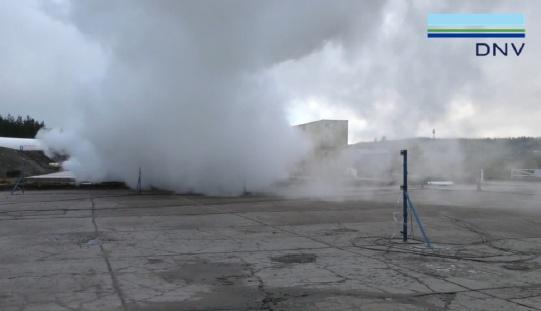
Having set or determined the source conditions by looking at the outflow, the dispersion and ultimately, the lower flammable limits (LFL) of the dispersing cloud was analysed. The trends in the experimental results were also represented in the model results:
• Reducing concentration with distance
• Reducing concentration with radial departure from the downwind direction of about 90º
• Peak gas concentration versus the peak dip in temperature, giving a nominally linear relationship, worsening as the concentration gets higher
• Higher concentrations at higher positions above ground level
• LFL was not exceeded in downward releases beyond 30m from the release point and 50m in the horizontal releases.
The relationship between the peak concentration and the peak temperature drop across several experiments was further compared to the predictions from GasVLE, a fluid properties calculation tool from DNV, the predictions are slightly below that of the actual observations. This may be because the GasVLE model does not include heat transfer from the ground, possibly evident in the measurements.
At the point of ignition there is an explosion effect creating an initial expanding fireball which can give rise to local dynamic overpressures with the potential to cause harm.

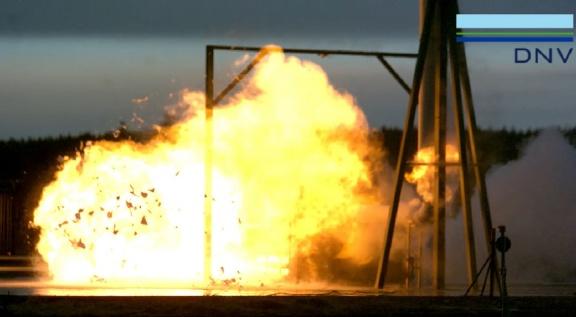
At all measurement locations, in all ignited experiments, the peak pressure did not exceed 30mBar in the horizontal jet and around about 15mBar in the downwards jet.
Results of the confined, ventilated releases and explosion experiments are still being analysed.
In most cases, the releases were so large that the atmosphere within the chamber quickly became very cold and non-flammable (i.e. air was either condensed to liquid or displaced by the high-volume release). It was noticeable that no evidence of any flammable concentrations of hydrogen were found at any of the ground level measurement points down-wind of the ventilation mast.
Two of the confined experiments were ignited at the top of the ventilation stack after isolation of the release resulting in two very different severities of explosion; high overpressure was observed when the ventilation in the chamber was higher, with low overpressure observed when the ventilation levels were low. Considering the large array of variables influencing the severity of explosions in

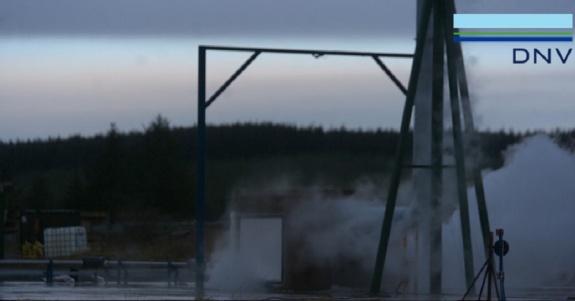
these geometries, particularly with cryogenic atmospheres, more experimentation is required to obtain greater understanding of large scale, cryogenic hydrogen explosions.
The releases conducted as part of this programme provide a valuable, extensive and unique dataset in relation to the phenomena contributing to the severity of events following a loss of containment of liquid hydrogen. The outdoor release data has been compared to predictions from existing software models and found to be of a high quality and suitable for further model development / validation.
Hydrogen is one of the most suitable solutions to contribute to the replacement hydrocarbons in the future and its consumption is expected to grow significantly over the next three decades. Despite being a clean fuel, concern surrounds its chemical and physical properties and the gaps in engineering techniques, tools and implementation experience and the potential impact on safety. Further investigation and model analysis is recommended.
Offshore Europe 2021 Preview
The organisers of SPE Offshore Europe 2021 announced in June that the show’s face-to-face event would be moving to 1-4 February 2022 at P&J Live, Aberdeen while the conference will run virtually from 7-10 September 2021.

Jonathan Heastie, Portfolio Director – Energy & Marine at RX (Reed Exhibitions), co-organiser with the Society of Petroleum Engineers (SPE) said: “With September rapidly approaching, many health and safety uncertainties still exist around holding major indoor events of the scale of SPE Offshore Europe. The Offshore Europe (OE) Partnership has consulted widely across the industry including operating and service companies, SMEs and industry organisations on options for the 2021 event. The overwhelming support is to proceed with the conference programme in a virtual format in September 2021, which will facilitate timely discussion pre-COP26, and to hold the faceto-face event in February 2022.”
The virtual conference taking place between 7-10 September will include opening ceremony, plenary panel, and keynote and technical sessions. Energy transition topics will take centre stage with conference chair and executive vice president oilfield equipment at Baker Hughes, Neil Saunders and SPE President 2022 Kamel Ben-Naceur welcoming delegates to the 4 day, SPE-curated programme. The programme comprises an opening plenary, 10 keynote, and 14 technical sessions incorporating more than 50 technical papers. 7 of the 10 keynote sessions and 50% of the technical programme will be related to energy transition subjects.
Keynote sessions with a net zero focus include: Delivering carbon capture, utilisation and storage; CCUS and hydrogen at scale; energy islands; roadmaps to net zero; scaling up digital to enable a low-carbon industry; facilities of the future and breaking the silo paralysis.
During the opening plenary, Chris Stark, CEO of the Committee on Climate Change will join Gordon Birrell, Executive Vice President, Production & Operations at bp; Al Cook, Executive Vice President, Development & Production International at Equinor and Phil Kirk, CEO of Harbour Energy for a panel session on the event theme ‘Oil & Gas: Working Together for a Net Zero Future’.
For the first time in the history of the biennial event, due to the coronavirus pandemic, the conference and exhibition have been split. The virtual conference will be followed by the in-person exhibition across 1-4 February 2022, which will include new keynote conference content that will be developed after the UN Climate Change Conference (COP26) taking place in Glasgow 1-12 November 2021.
With the two SPE Offshore Europe events ‘bookending’ COP26, oil and gas industry leaders, innovators and decision-makers will reconvene in person at the P&J Live in Aberdeen to advance the energy transition outcomes and realign strategies.
Neil Saunders, SPE Offshore Europe 2021 conference chair and executive vice president oilfield equipment at Baker Hughes said: “The conference programme at SPE Offshore
Europe has always been a ‘must-attend’ event for those wanting to keep in touch with industry-leading thinking strategically and at a technical level. The industry’s path to decarbonisation and role in supporting net zero is top of the agenda this year, and with COP26 just seven weeks later, the programme promises to be a real curtain-opener. The future of oil and gas in the energy mix is in our hands and SPE Offshore Europe gives us the chance to work together, before and after COP26, to secure our place in a net zero future.”
Kevin Gallagher, SPE Offshore Europe
2021 technical committee chair and digital transformation lead, CNOOC International commented: “The offshore industry has an important role to play in the transition to the low carbon economy. The timing of the conference, prior to COP26, and content of the technical programme are both opportune and highly relevant as we experience an acceleration of the energy transition and the industry response. Audience members will have the opportunity to join high quality sessions ranging from decarbonisation, floating wind and hydrogen to drilling and decommissioning. We look forward to informative and inspiring technical sessions which prompt numerous important discussions at this pivotal time for our industry.”
The virtual conference programme will begin each day at 12 noon (BST) / 7.00am (EDT) to accommodate international participants. Full programme details and registration can be found on the website: www.offshore-europe. co.uk
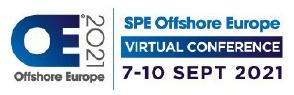
Process Safety Congres
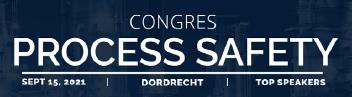
Date: 15 September 2021
Location: Dordrecht, Netherlands
The aim of Process Safety Congres is to strengthen process safety culture by networking and sharing knowledge. The process safety conference is aimed at the technical safety specialists, managers and inspectors that are related to companies that are dealing with hazardous chemical processes. The expectation is that with vaccination and testing, this event can
CHEMUK 2021
Date: 15-16 September 2021
Location: NEC, Birmingham – UK
CHEMUK 2021 will be hosted at the NEC in Birmingham on 15 & 16 September having previously been held in Harrogate in 2019. With 350+ exhibitors, the event will see attendees from across the UK’s chemicals, chemical products, & chemical-using industries converging to see the latest plant, equipment, supply chain materials, & services driving operational performance, plant & process efficiency, future-proofing, safety, compliance, supply chain fulfilment, and much more.
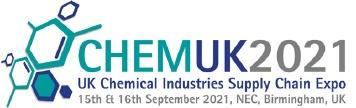
take place safely on September 15.
Individual companies can be strongly internally focused but learning together speeds-up the process. To help facilitate this, this event brings together world class speakers to present on interesting topics and share their experiences and learnings. Furthermore, a network forum supports the knowledge exchange on an individual level.
The event will see speakers from DNV GL, HIMA,
Tronox, Shell, Bilfinger, Fluor, Antea, VNCI, DSM, Esso, Dekra, INBISCO, and more come together to share their experiences and knowledge at the Van der Valk Hotel in Dordrecht.
https://pscongres.nl/
Date: 21-23 September 2021
Location: Dubai, UAE
Taking place from 21-23 September 2021 at the Dubai World Trade Centre, United Arab Emirates, the global gas, LNG, hydrogen, and energy industry will meet once again to do business live and in-person. The event is to be held under the patronage of His Highness Sheikh Mohammed Bin Rashid Al Maktoum, Vice President and Prime Minister of the United Arab Emirates and Ruler of Dubai.
As we look towards the future, navigating the
CHEMUK is dedicated to bringing together the multi-layer Chemicals/Chemical Product development, specification & processing/ manufacturing communities, with crucial supply chain supplier groups. With some 2,500+ specialist businesses contributing to the UK’s chemical industry – embracing raw materials, chemicals, intermediates & consumables, equipment & apparatus, high tech innovation streams, sub-contracting & business services and much more, CHEMUK is the event where the UK’s chemical industries meet.
The “free-to-attend” 2-day event also has a
speaker programme with over 150 experts sharing their knowledge and experiences. The programme also includes a feature session and panels discussing big trends, challenges, opportunities & innovations affecting the UK’s chemical industries.
https://www.chemicalukexpo.com/
new energy landscape with our shared global mandate to lower carbon emissions and provide affordable energy for all, Gastech 2021 will bring together the full energy value chain, with over 3 days of networking in a safe and secure environment.
Gastech is an enabler of conversations, collaborations and connections that drive the energy transition agenda. Now, more than ever before, we need to connect in-person to continue to adapt and respond to the collective challenges and opportunities the industry faces.
Co-located with Gastech will be Gastech Hydrogen – a global platform that convenes industry leaders annually in their mandate towards lower and zero carbon fuels that will play a central role in the delivery of the new energy landscape.
www.gastechevent.com
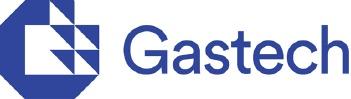
Bitumen is an important material used in a wide range of industrial processes such as refining, pipe coating and in road, pavement, and roof construction. Also referred to as asphalt, it is insoluble in water and has glue like properties that allow it to bind with aggregate particles to create strength.
Bitumen needs to be handled at high temperatures in its liquid form, most commonly around 140 to 170°C, this state allows it to be sprayed, transferred, or unloaded to be used in processes such as mixing with aggregate and laying roads. Even when hot it is viscous, these properties combined with its sticky nature require very careful consideration during the pump selection process. An engineering consultancy group specialising in the energy and industrial sectors secured a €2.1 million project
An innovative non-contact radar sensing technology from SICK is opening up the prospect of robust and reliable real-time monitoring of the levels of liquids and bulk solids in challenging industrial applications. The SICK SicWave uses higher-frequency 80 gigahertz free-space radar to overcome the limitations of lower-frequency radar sensors or mechanical devices to achieve precision continuous level measurement in demanding environments.
Where previously operators have settled for switch point level indication or have been defeated by the challenges of using noncontact sensors in harsh environments, the narrowly focused, highly effective microwave
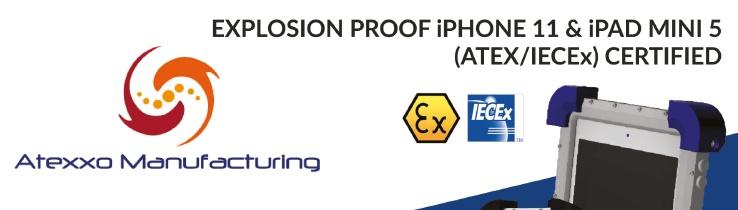
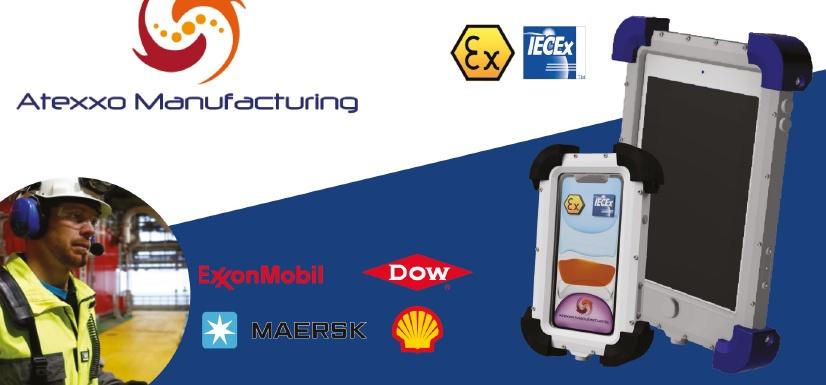

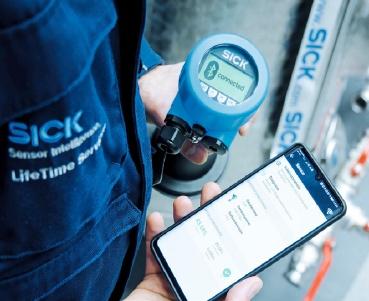
for upgrading a fuel and bitumen processing plant. This project required 6 units in 3 different sizes, with differing internal design (External and Internal Gear) to produce the varying flow rates and pressure demanded on site. We delivered two 2” Internal Gear Pumps, two 4” External Gear Pumps and two 10” External Gear pumps, the largest unit delivering 250m³/hr at 9 bar, all fitted with ABB Atex motors suitable for installation in non-safe areas.The site now has reliable and robust bitumen pumps which will enable increased plant output and productivity, ensure larger bulk carriers can be accommodated, decrease tanker loading time, and reduce the likelihood of vessel demurrage.
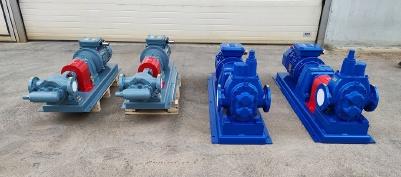
If you have an application you are unsure of the correct solution, visit www.northridgepumps.com to see how we can help.
The SICK LBR SicWave is a bulk solids level sensor with an exceptional range up to 120m and the SICK LFR SicWave a fluid level sensor with a maximum range of 30m. Both represent a breakthrough in technology for continuous level measurement to optimise material storage in silos, tanks and other vessels in industries as diverse as mining and cement manufacture, to chemical processing and food and drink processing.
Andrea Hornby on 01727 831121 or email andrea. hornby@sick.co.uk. www.sick.co.uk
pulses of the SICK SicWave sensors penetrate through dust, vapour and material build-up to output highly accurate results.AUTOMATION CONTROL & TECHNOLOGY
Data files
Data files
AUTOMATION CONTROL & TECHNOLOGY
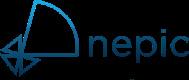



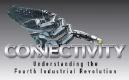
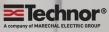




Heaters
Heaters
Heaters

Training
Training
Control Panels
Control Panels
Panels
website: www.hazarex-event.co.uk Entry is free, and this is the ideal opportunity to reward those companies and individuals you think most deserve recognition for the most innovative products, systems and services. The deadline for nominations is August 6 after which Hazardex readers and website users will be asked to vote for the winners in each category.
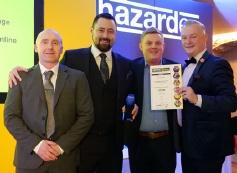
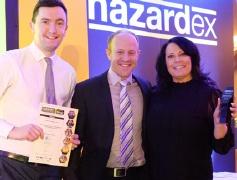
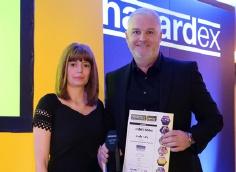

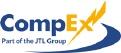
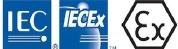
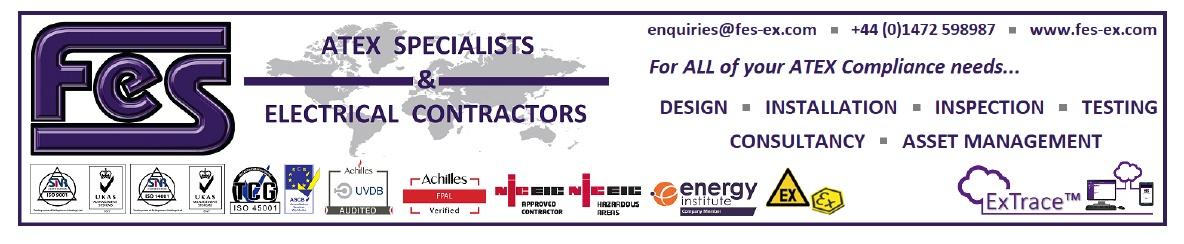
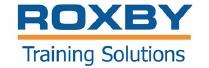


All COVID-19 regulation and UK government guidelines will be observed to ensure the safety of all participants.
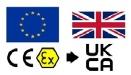




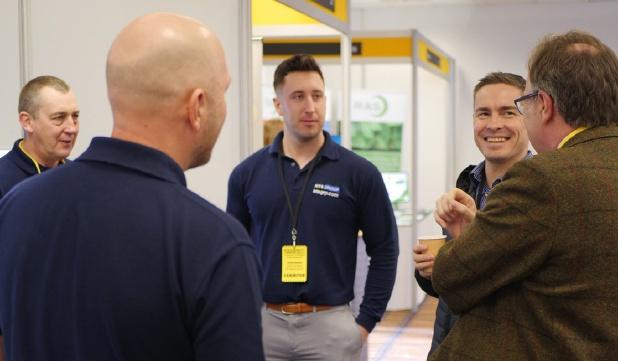


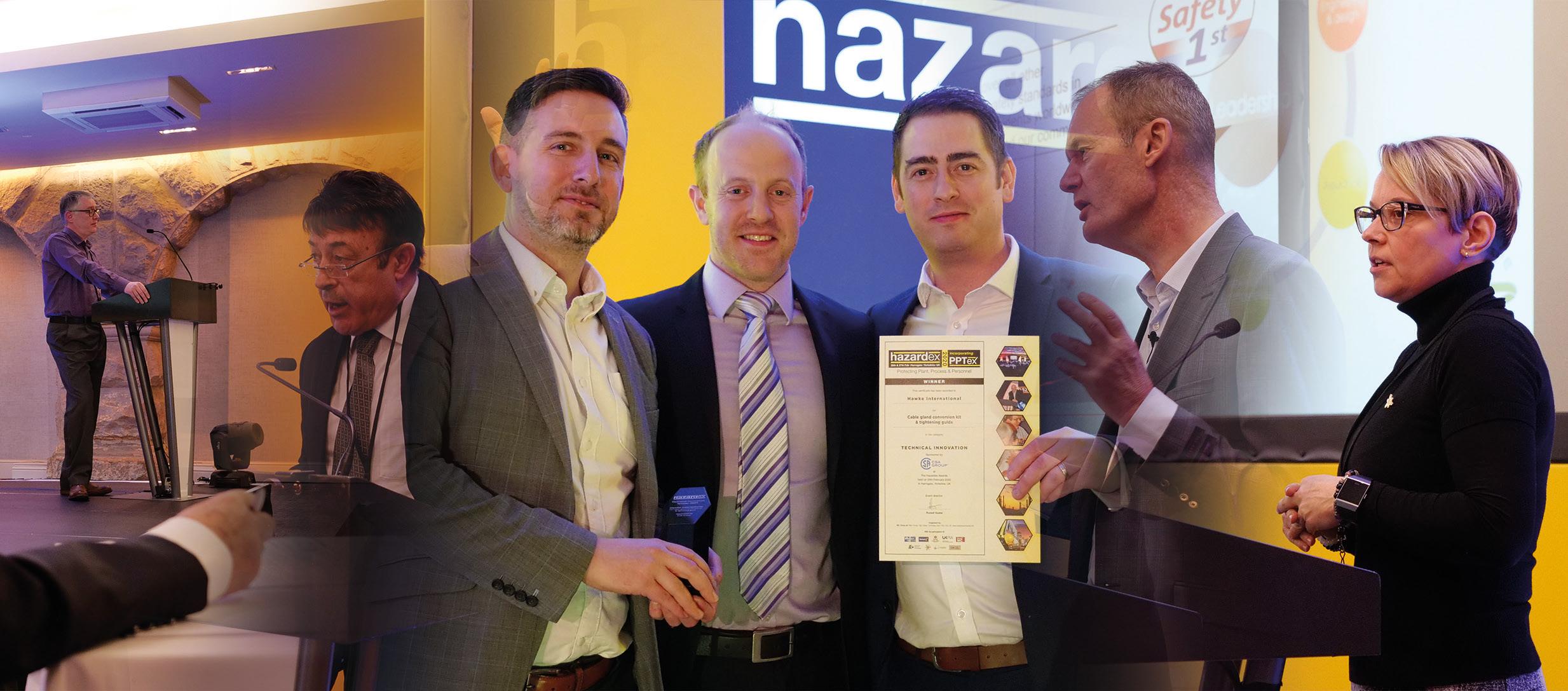
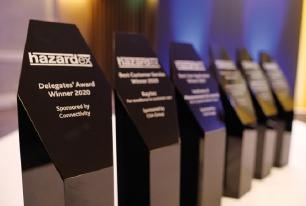
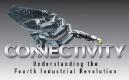



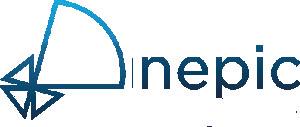
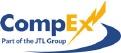
