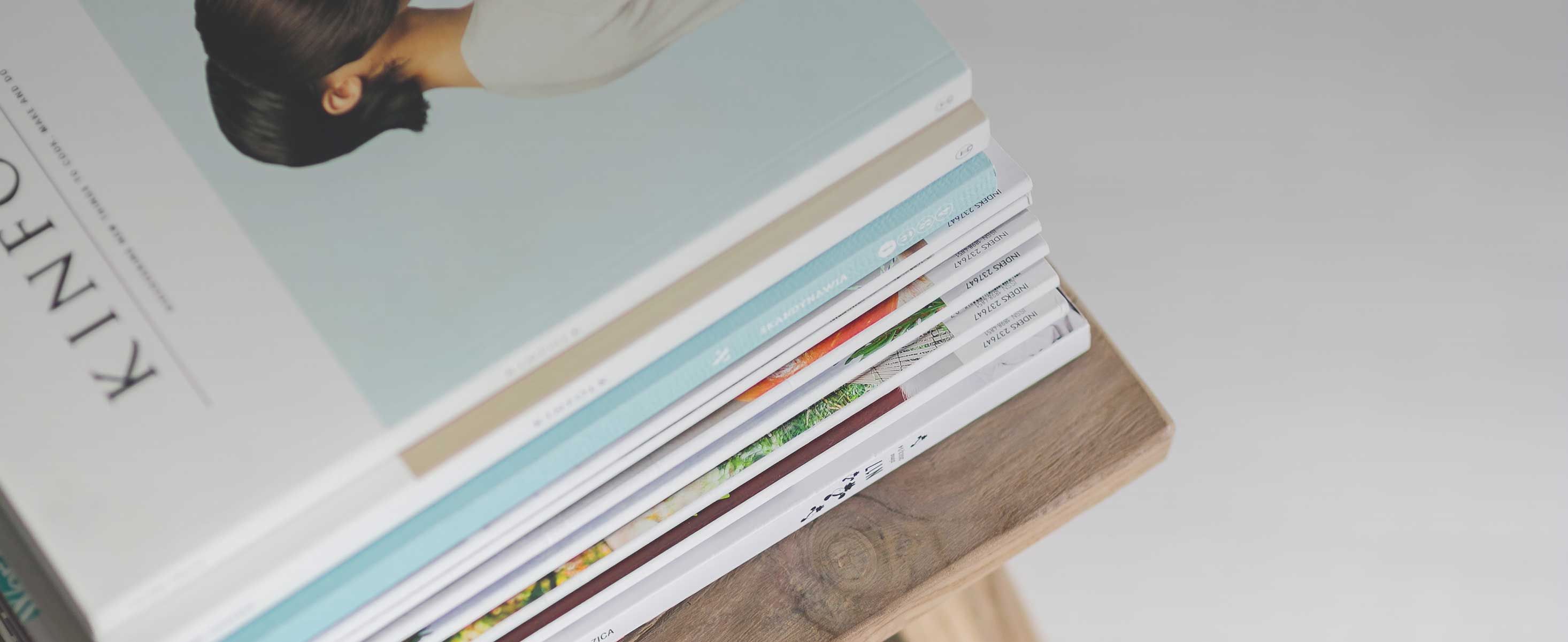
2 minute read
RESEARCH & DISCOVERY
by uiowaeye
“Keratoconus” continues from page 11 lenses were developed and manufactured. She also started collecting boxes of old lenses, which she keeps in her office.
“We think of the contact lens industry as being around forever, but we’re in generation 2.5 of the technology,” she says.
That also meant many contact lens pioneers were still alive, so she interviewed them about their process. Image
Sindt collected boxes of old lenses as she was learning to develop and manufacture customizable contacts. “They used to put plaster on people’s eyes to create 3D impressions,” she notes.
That outdated approach led Sindt to the UI College of Dentistry and Dental Clinics. Faculty and staff taught her about impression materials and compounds used for teeth, which prompted her to call companies that make impression compound materials.
She also got help from the dental college’s prosthodontics department and used their high-resolution scanner. She talked to chemists about what she wanted to do and what would work and be safe to put on an eye.
While working on a study project on immune cell complexes in the cornea, she got in contact with a company that did 3D analysis. After the study was over, she continued to work with them on making 3D images of the eye.
She then partnered with a Tippie College of Business master’s class on creating a business plan for what would become EyePrint Prosthetics, which she launched in 2015. Via 3D imaging and a Food and Drug Administrationapproved ocular compound and insertion tray, EyePrint can create lenses that “are whatever the shape of the person’s eye is,” Sindt says.
“Because of the unique shape of the lenses, it allows me to do things that other lenses might not be able to do. The optics don’t have to be in the center of the lens. I can move the optics to whatever the patient is looking through. I can be really narrow on what the prescription is.”
The company is based in a suburb of Denver but works with a network of optometrists around the country who create the impressions and send that information back to EyePrint to make and ship lenses.
Noyes recently worked with a 50-year-old patient who never knew he had keratoconus. With just a demo lens, his vision went to 20/20.
“He asked why no one told him about this before,” he says. “It’s just not commonly used, and the condition is still rare, but we’re getting the word out there.”
Von Roedern was fit for her first EyePrint lenses in 2016. “They sharpened up my vision and helped with light sensitivity,” she says. “I’m very functional and happy with my lenses.”
She has not undergone cross-linking because the lenses have corrected her vision to the point where she doesn’t need it.
The experience was so positive that she also became an EyePrint employee. After finishing her master’s degree, Von Roedern moved back to Colorado, where she’s from, right at the time EyePrint was setting up their headquarters.
“I’d probably been at EyePrint for six months when [Sindt] came to visit. She said she’d never seen my eyes so white. They were just red and angry all the time before,” Von Roedern says. “It’s really changed my life.”
By Jen A. Miller