polymer VOL 20 NR 4 AUGUST / SEPTEMER 2022 www.sapt.co.za SOUTHERN AFRICAN TECHNOLOGY STARTUP ZARCAPLAS’S PLANT IS RUNNING FLAT-OUT solutionsWorkable to mitigate SA’s energy crisis We need time to ‘reinvent plastics’, says Reifenhäuser CSO ARMSADesignStudentevent 40 PlasticsAwardsRecyclingEurope2022 54 Eco Tanksacrobaticgoes 42OFFICIALPUBLICATIONOFTHEPLASTICSCONVERTERSASSOCIATION(PCA)&PLASTICSINSTITUTEOFSOUTHERNAFRICA(PISA) TECHNOLOGYPOLYMERAFRICANSOUTHERN 4NR20VOL www.sapt.co.za2022SEPTEMER/AUGUST Roediger accreditationbeginsAgenciesSANASprocesstotestpipes Int’l camper-trailerawarddesignforEdgeOutfrom4EVR
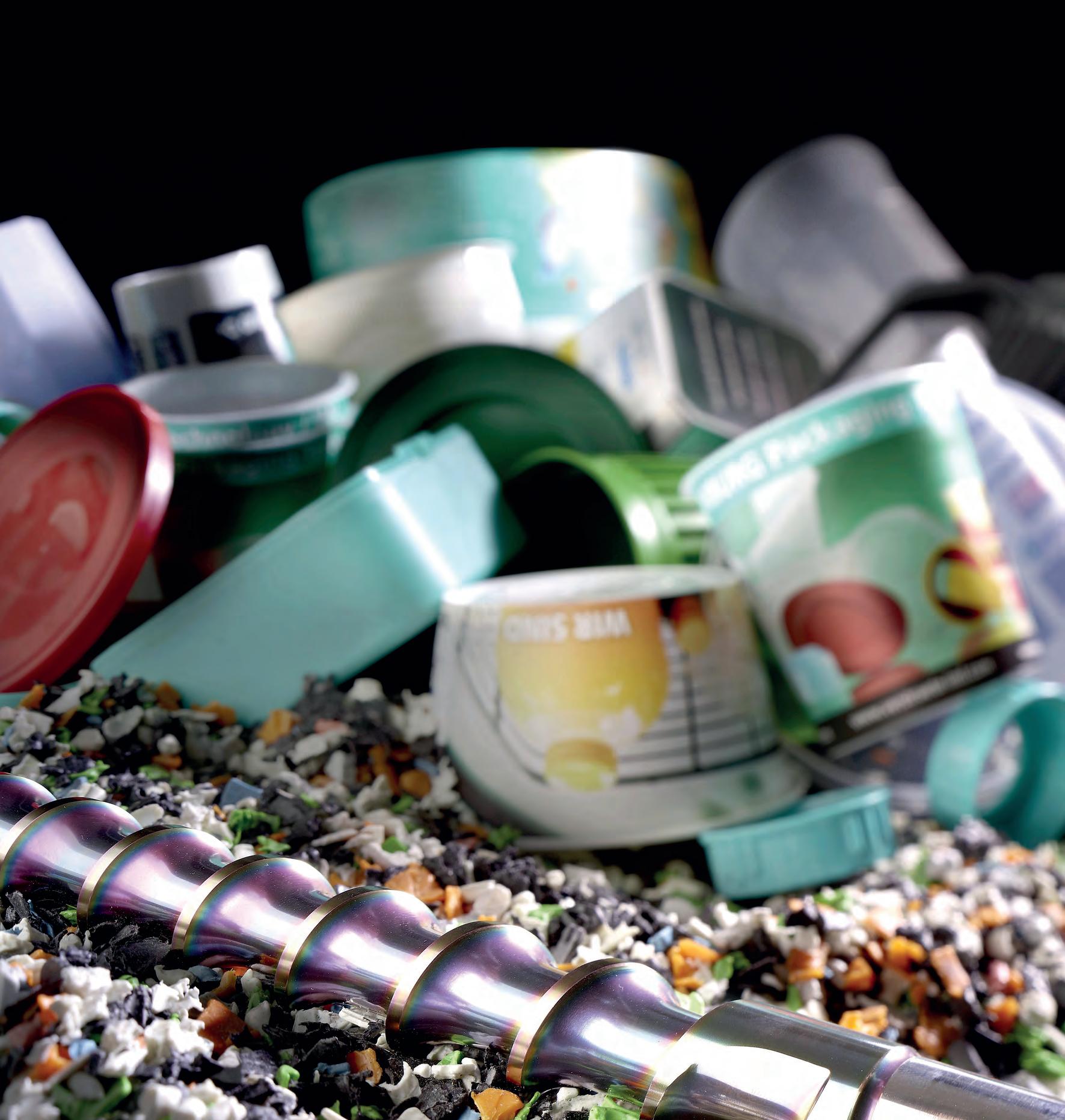

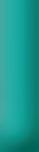


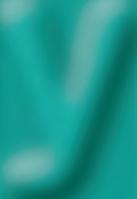
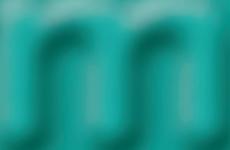
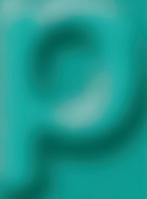

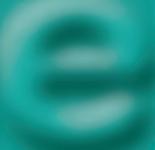
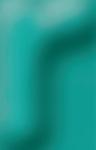



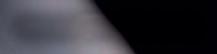

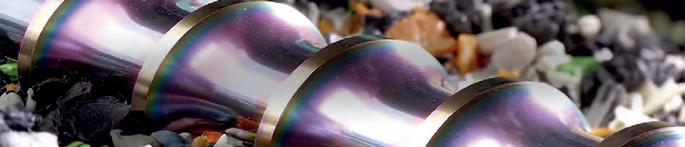

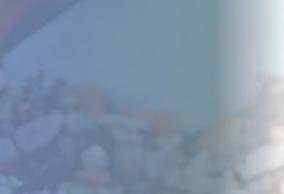
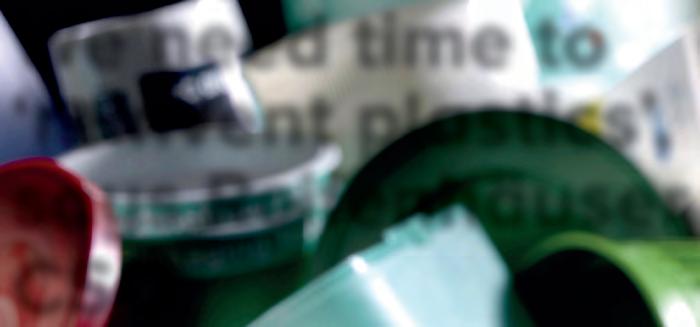
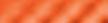
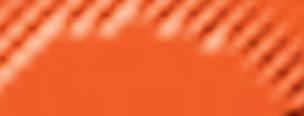
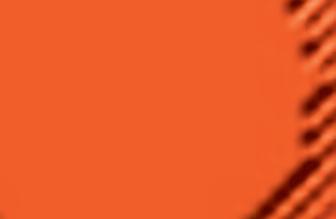




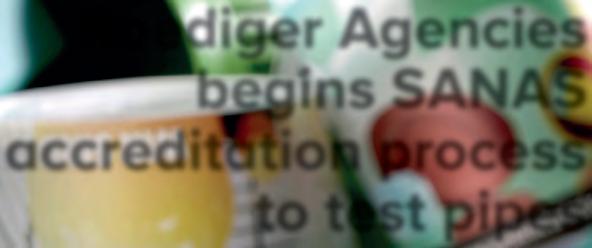



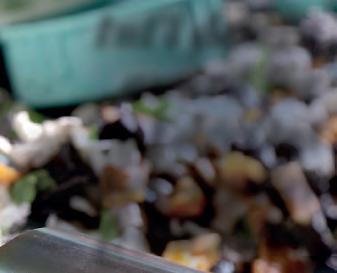
Synthetic rubber can be found everywhere in our everyday lives – whether in vehicle tires, shoes, or sports equipment, in hoses, seals, or machine conveyor belts. It dampens, seals, and drives. It holds fixed parts together and makes them movable. But rubber is by no means simply rubber: ARLANXEO has numerous different products in its range, tailored to countless applications in a wide variety of industries. And we are always developing new types of rubber – constantly searching for the even more perfect formula for our customers. FamiliesPolymer ■ BR ■ CR ■ EPDM ■ E-SBR ■ EVM ■ HNBR ■ NBR ■ S-SBR ■ (X)IIR Brenntag Rubber EMEA Please get in touch with us for any Rubber Material related enquiries Michael Dzivhani on +27 (0) 83 607 3720 Tel: +27 (0) 10 020 9100 michael.dzivhani@brenntag.co.za www.brenntag.com/en-za Our Brands ■ Baymod® L ■ Baymod® N ■ Baypren® ■ Buna® ■ Keltan® ■ Krynac® ■ Levamelt® ■ Levapren® ■ Perbunan® ■ Taktene® ■ Therban® ■ X_Butyl® Solutions ■ Adhesives ■ Automotive ■ Building and Construction ■ Consumer Goods ■ Industrial Goods ■ Plastics Modification ■ Wire & Cable ■ Tires
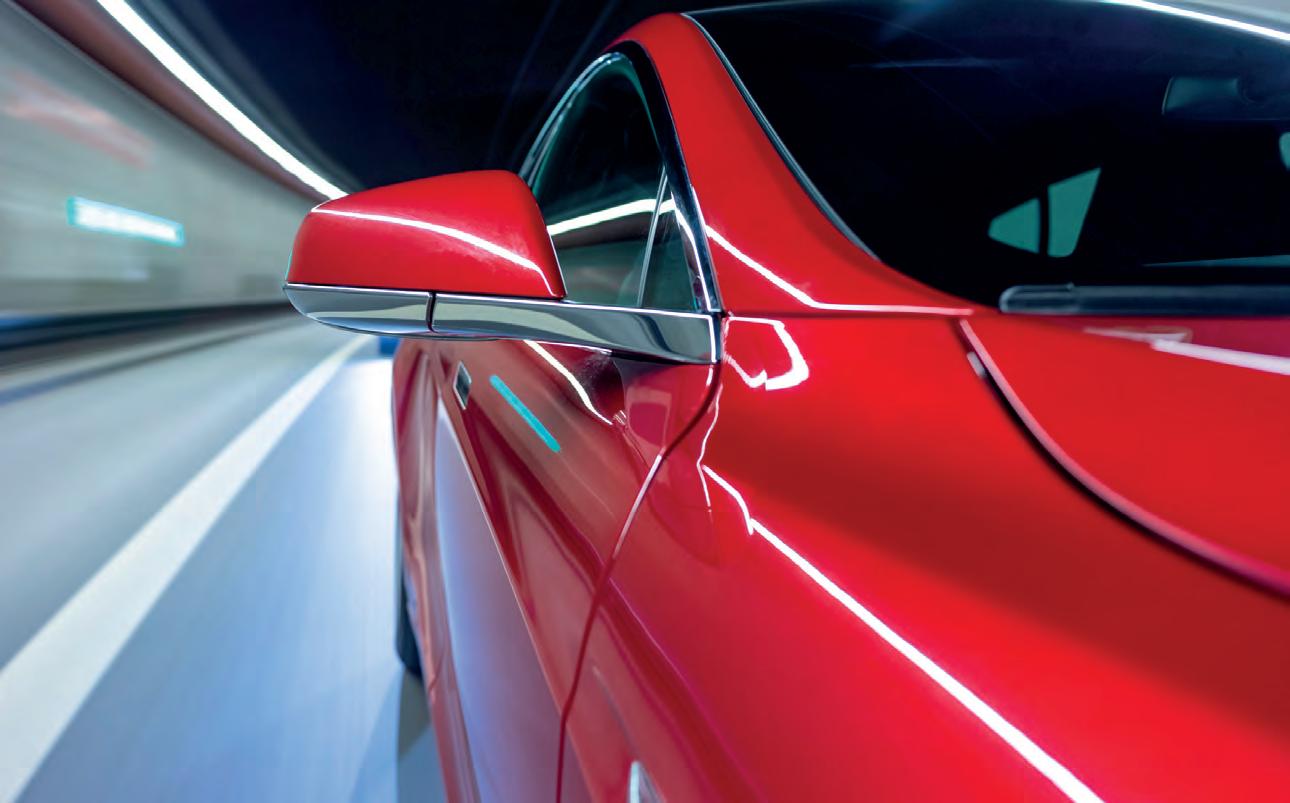
Proudlyassociatedwith 0315001755 www.innova�vepvc.co.zamarke�ng@innova�vepvc.co.za YourCompounderofChoice QUALITYPRODUCTS EXCELLENTSERVICEGUARANTEEDSUPPLY Innova�vePvcCompoundsisaleaderinPVCcompoundinginSouthAfricathat pridesitselfonqualitycompoundsandexcellentcustomerservice. IPCconsistantlysupplytheircompoundsintothelocalmarketsaswellasexpor�ngtheir compoundsintoAfrica,EuropeandtheAmericas IPCspecializesinflexibleandrigidcompoundsfortheinjec�onmouldingandextrusionindustries. EST.2010

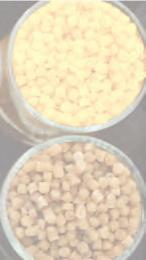
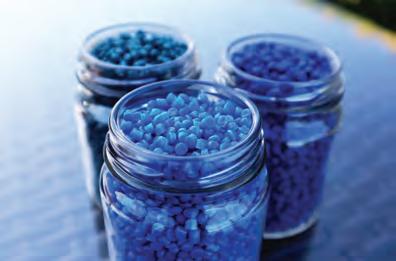



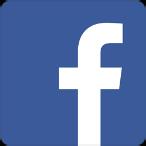
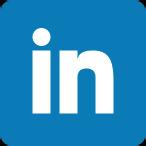
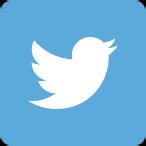
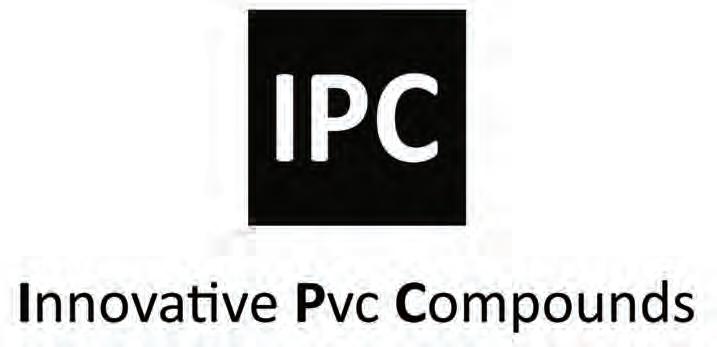
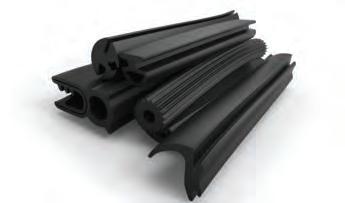
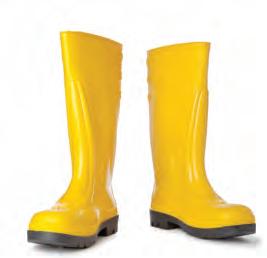

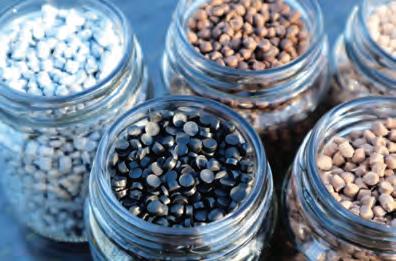
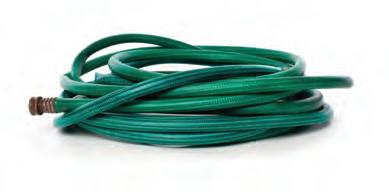

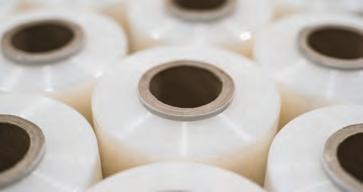
SPARE a thought for André de Ruyter, the former Nampak boss now CEO of Eskom, who has been trying to keep the lights on with accusations flying thick and fast. He was asked recently if he ever thinks he should have turned the job down? “Three times every day, before lunch,” he joked Douw Steyn of Plastics SA is here, there and everywhere, at clean-ups all over the country and continent and has been doing so for 25 years. We have an interview with him this issue (see page 44). Here Douw with Jonathan Welch of AfriEco of Durban, which is manufacturing some novel goods from collected plastic scrap, and we will have an article about this in our next issue! (21) 712
Summit Publishing cc t: +27
Alleged illegal workers harassed
1408 f: 086 519 6089 c: +27 (82) 822 8115 e: tessa@summitpub.co.za Postnet Suite 42, Private Bag X16, Constantia 7848, Cape Town, South Africa The Stoep, 3 Tiverton Road, Plumstead, 7800 www.sapt.co.zaGAUTENGLowrieSharpt: (011) 793 4691 f: (011) 791 0544 c: 082 344 7870 e: lowrieplasticsmedia@absamail.co.za KZN Lynne Askew c: 082 904 9433 e: lynne@summitpub.co.za Printed by: Novus Print, Paarl Southern African Polymer Technology is published six times a year and focuses on these industries in South and Southern Africa. We welcome news, articles, technical reports, information in general and photographs about events and developments related to the plastics industry. The views expressed in the magazine are not necessarily those of the publisher. Views expressed are not necessarily those of the Plastics Converters Association, Institute of Materials or Association of Rotational Moulders either. Copyright: All rights reserved. ISSN number: 1684-2855 (ISDS Centre, Paris) Summit Publishing: CK 9863581/23 VAT reg: 4600187902 Publisher & Managing Editor: Martin Wells (martin@summitpub.co.za)Editor: Tessa O’Hara (tessa@summitpub.co.za) Publishers Assistant: Heather Peplow Bookkeeper:(heather@summitpub.co.za) Gloria van Heerden (gloriavanheerden@gmail.com) Designers: Jeanette Erasmus Graphic (jeanette.erasmus@lateraldynamics.co.za)Design Bronwen Moys Blinc (bronwen.clarke@gmail.com)Design Plastics Institute of Southern Africa PET Plastic Recycling South Africa Association of Rotational Moulders of South Africa Plastics InstituteAssociationConvertersofMaterials BY THE WAY … if you somethinghavetosay Look at the bright side: if you have some gem of wisdom to impart, please write to us at tessa@summitpub.co.za
Bag levy, WTF, it could be worse
Eskom boss may be missing Nampak
we see
ELEVEN persons were arrested at a converting business after a very unexpected visit from Department of Labour officials who found they were illegal immigrants from Zimbabwe. Their papers were not in order, they were informed, whereas the owner of the business was of the view that they were. The papers in question were genuine documents which allowed entry at the border crossing, but which could have been obtained unofficially. We hear it is standard practice for people north of the border to gain entry to the country by paying bribes, and there are even set rates for this. For instance, Malawian workers here say the cost to obtain documents currently stands at R4 500 per traveller, which is a substantial amount for these people. The real question is who at this company advised the labour authorities? Most employees should not be familiar with whether any of their colleagues is legally present in the country or not.
JUST about every bagmaker in the country resents paying the bag levy, but not simply because they are opposed to paying a levy: it’s due to the fact that the levy has never been used for the purpose for which it was drawn up, way back in 2003. Had the government invested even a fraction of the total amount (at 28c a bag and applied to an estimated 3,5 billion bags per year, it’s about R98 million p/a) back into the industry in the form of recycling incentives or awareness programmes, feelings may have been a bit more positive. So there was some silent support for the KZN business which was caught out earlier this year for not paying the levy. The convertor paid a hefty fine and apparently, in exchange for leniency, struck a deal with SARS to the effect that he would inform the tax authority of other non-payers. Now, I ask you, how on earth is this person going to find out who else is not paying? The problem was bad and now it’s got worse. Let’s move on from that.

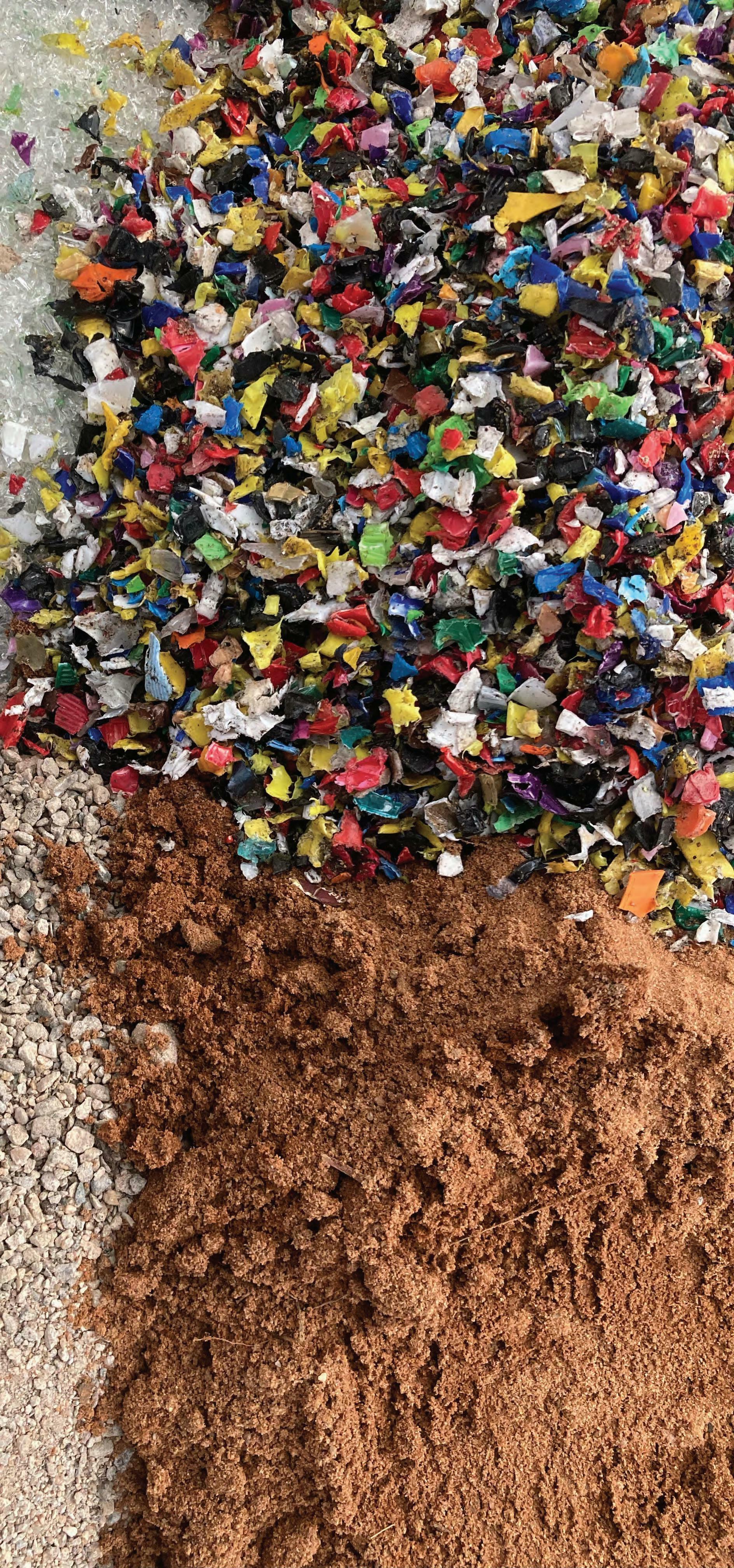






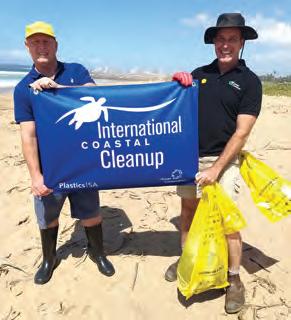
46 Contents 6 8 14 16 INDUSTRY NEWS We need to reinvent plastics, says Reifenhäuser Cso Roediger Agencies invests in equipment, sAnAs accreditation for pipes Startup Zarcaplas’s plant is running flat-out Continental Compounders expands at sites in KZn, Gauteng Clean-up and recycling sA week 2022 Chemicals, substances, mixtures, and wastes in the supply chain Delta engineering’s plasma treatment systems Blackstone tech’s new carbon trail bike for PYGA Workable solutions to mitigate sA’s energy crisis World-class quality printing technology from Greentech Plastics Machinery Hestico celebrates 60th anniversary ROTO NEWS Int’l design award for edgeout camper-trailer from 4EVR ARMSA student Design event revived after Covid interruption Eco Tanks goes acrobatic when its tanks starred too 18 20 22 24 26 28 32 36 40 42 Find out more at www.sapt.co.za AUGUST – SEPTEMBER 2022 Volume 20 No 4 3064 36 68 DouwSUSTAINABILITYSteyn : 25 years later Superworms with an appetite for polystyrene! PlasticsDESIGNRecycling Awards europe 2022 Design Innovation in Plastics 2022 44 54 46 56 66 ON THE COVER: Theprocessingofrecyclates is incorresponding“arburgGreenworld”consideredanimportantcomponentoftheprogrammeandhasmanyyears’experienceinthissectorwithsoftwareandhardwarefeaturesitsrange.Thesearenowcombinedinthenewrecyclatepackagesothatcustomerscanprocesstheever-increasingrangeofthesematerialsflexiblyandsafely. Readmoreatwww.arburg.com/en/
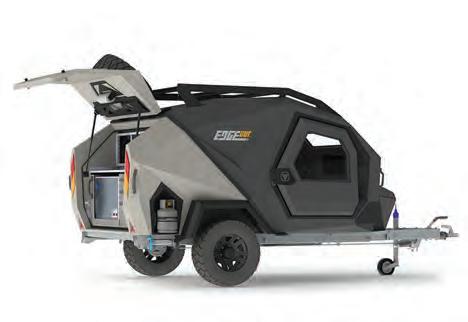


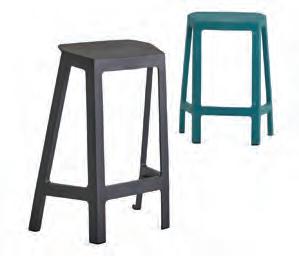
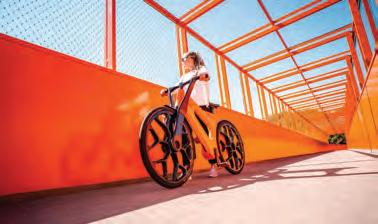
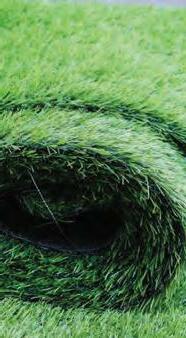
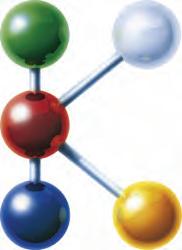
Consumption of plastics globally has increased over the past 20 years from an estimated 230 million tons to well over 400 million tons (it is difficult to get exact figures) and there is the risk the industry could smother itself in its own success. So it is welcome that the industry leaders are leading the charge to reassess the situation. In one of our lead articles this issue, Ulrich Reifenhäuser of the company of that name, one of the most successful German machinery manufacturers, talks of the need to ‘reinvent plastics’. ALL the other top manufacturers are focusing likewise, but how they get their customers – that is you, the convertors – to play ball may be challenging. It is a surprise to us that this topic is only being presented now, because for years many brand groups have been producing goods or using packaging which they knew could not be recycled or reused, and even if they could many of them had little intention of being involved in the recycling ‘value chain’ (i.e. did not want to use recycled material or be involved at all), but now they are increasingly being forced to.
Recycling costs, and there have even been cases where convertors have been cooperating by using recycled materials and taking precautions, adding to bottom-line costs, while their competitors have not and become non-competitive as a result. Now the situation is being reassessed and we even have the case where global material manufacturers are offering recycled materials as standard and where brand companies are demanding that packaging manufacturers supply containers using recycled materials, in some cases the goal is even for 100% ‘r’ materials (yes, that is the stated goal of Coca-Cola corporation, which is one of the leading global users of plastic packaging). But we also suspect that a large part of the problem lies elsewhere, in lacks or even non-existent municipal waste collection services, which we have no control over, and the absence of separation-atsource programmes. It could thus help us if the value of used plastic products increases to the point where consumers are encouraged to change the throwaway culture, and that is going to be a massive challenge.
Industry leaders say it’s time to reinvent ourselves
THIS ISSUE 4 2022SEPT/AUG In
Martin Wells, Publisher Risk exists that industry could smother itself in its own success Roto production line – What is effectively a production line has developed at 4EVR Plastics in Blackheath near Cape Town where it is manufacturing its EdgeOut camper/trailers. The main components are roto moulded on site by 4EVR with the other components, of which there are many, arriving there for JIT on-line assembly. The company also won a top design award for its work, see page 36 materialsforgoalcasessometheiseven100%‘r’
COMMENT
T HERE IS massive focus in the industry at present to improve the environmental impact of plastic products and this is especially evident among the machinery and material manufacturers who will be exhibiting at the K2022 show in Germany in October.
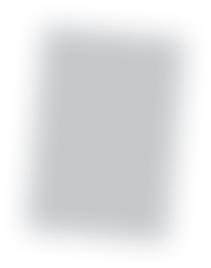
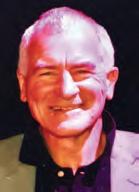


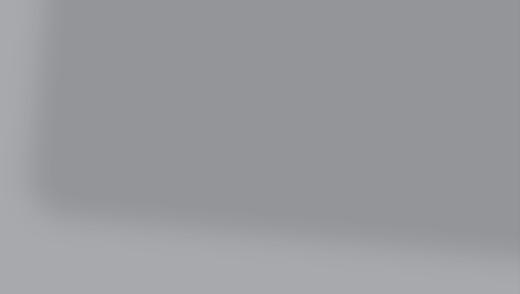
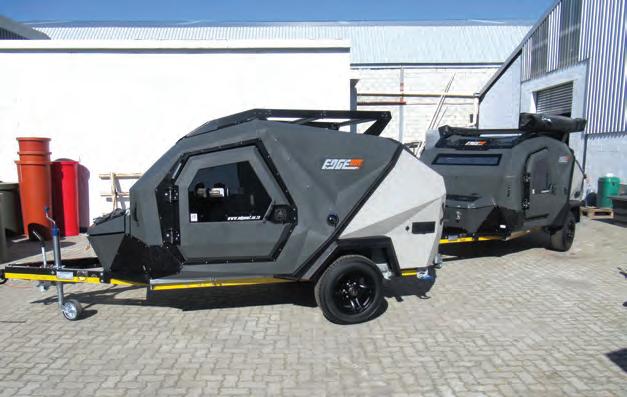
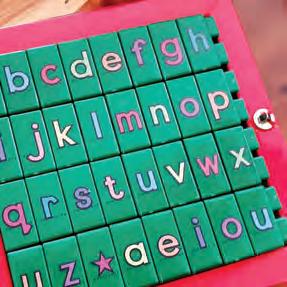

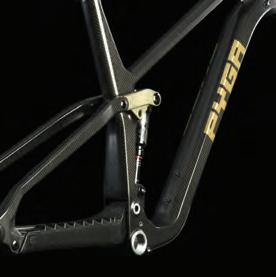
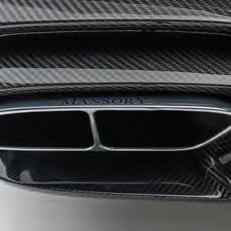
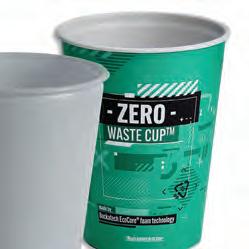
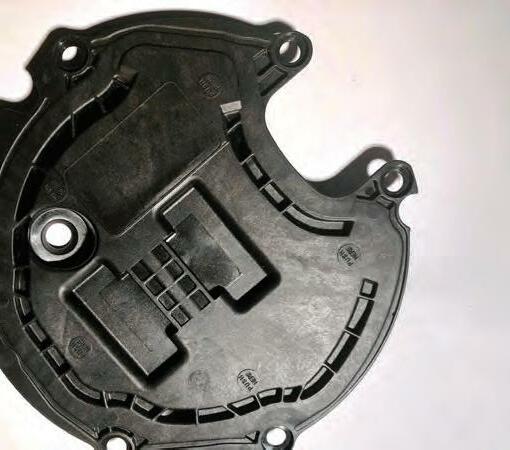
EST.2021 0315001756 www.arcompounds.co.zainfo@arcompounds.co.za Proudlyassociatedwith 0315001756 www.arcompounds.co.zainfo@arcompounds.co.za YourNewRotoCompounder Proudlyassociatedwith 0315001756 www.arcompounds.co.zainfo@arcompounds.co.za YourNewRotoCompounder EST.2021

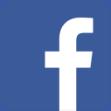

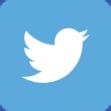
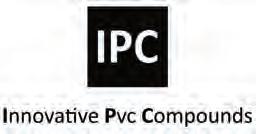
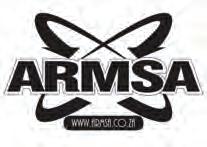
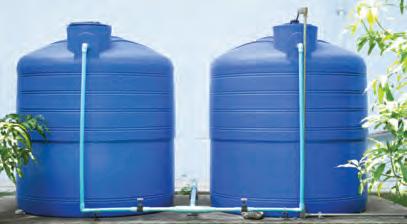
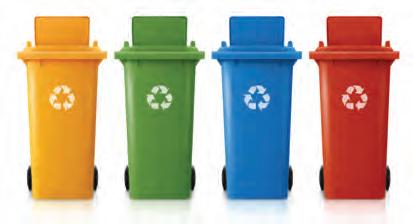
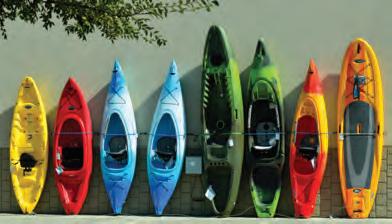

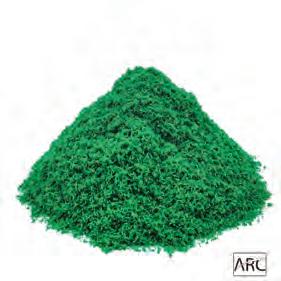
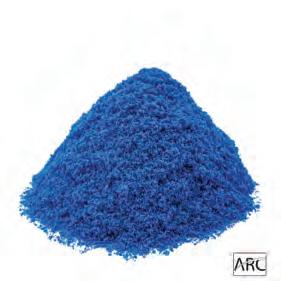

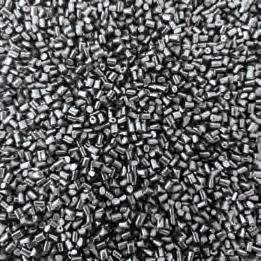
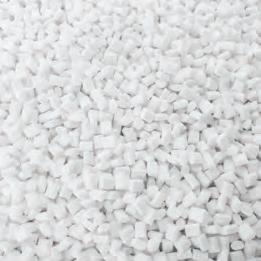


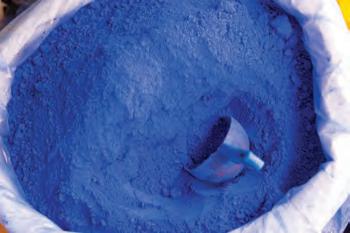
IN THIS latest Way2K interview conducted by the VDMA in the lead-up to K2022 in Düsseldorf in Germany in October, Ulrich Reifenhäuser, CSO of Reifenhäuser group, talks about the need for a plastics industry that is fit for the demands of the future.
What contribution does the Reifenhäuser company make? We are pursuing several approaches. One is to process low recyclate qualities easily and economically into high-performance products, and to be able to increase the recyclate content. For this purpose, we have developed a new extrusion technology we call EVO Fusion that can melt different polymers together in the extruder.
“We further supported transfer of all other products to nominated alternative suppliers with agreement with Froetek’s other customers,” he added. The effective date of transfer of business was 1 March. The ex-Froetek plant is thus now fully integrated into the Techniplas (Weidplas) world and operates as a multinational entity as part of the Techniplas group globally. Weidplas has in the interim further expanded its business with the development of a state-of-the art new manufacturing facility in Port Elizabeth and further intends to fill available production capacity and attract further business to the East London facility, added Krumbock.
reversedadvantagessuccessful.soButthesearewhere waste is concerned. Plastic floats, it does not decompose, it does not dissolve. If, in addition to function and cost, recyclability had been seen as an important criterion from the beginning, we would have fewer problems, and at least 80 per cent of plastics would already be recyclable. Today, they are not recyclable to this extent. The long pursuit of optimal function has even produced plastics that are difficult or impossible to recycle, such as multilayer films. I am convinced that we can and must change this. What is the appropriate course of action in your opinion? Ultimately, we have to reinvent plastics. I see the plastics industry at a crucial turning point. It has to show that it can turn things around, actually be sustainable and enable recyclability. In short: new plastic products must be created that meet the demands of the environment. The way to achieve this is through the circular economy. When plastics are recycled, waste is avoided by extending the lifespans of the products and allowing individual components to flow back into new production cycles. I consider establishing this cycle to be the main task of the plastics industry.
legislatorwouldfurther.willbrandthemustdevelopmentsthesecomefromusers,theowners.IgoonestepThebestthingbeforthetomake
specifications. I would like to see a recycling quota for every plastic product. Fortunately, this is already being discussed extensively at EU level. Once specifications of that nature are in place, it will be up to the mechanical engineering industry to develop process technology to meet those specifications.
“We decided to take over the facility and purchase the assets to minimize the risks in the supply chain to all customers,” said David Krumbock, MD of Weidplas in South Africa.
What role does plastics machinery engineering play in this? As a machine builder, we can go into the processes. We can develop technologies that produce recyclable plastic and save material. But the initiative for
What problems does the plastics industry face today? In recent years, plastic has fallen into disrepute, because of waste issues. We all have the pictures of marine litter in our minds. Used plastics are not really being handled well anywhere in the world. In many places they are simply thrown away. Plastic itself has many advantages: it is very durable, very flexible, very waterproof and very light, which is why it is
The world can’t do without plastics, but you can try to reduce the use of plastic whilefunctionality.maintaining
6 AUG / SEPT 202 JUST BRIEFLY NEWS
We need to reinvent New plastic products must be created that meet the demands of the environment
• Weidplas operates 14 production facilities around the world, with sites in Europe, Asia, South Africa, South, Central and North America and 16 sales and technical centres with more than 2,000 employees worldwide; its head office is in Switzerland. www.weidplas.com
Weidplas buys assets of Froetech, sets up in East London WEIDPLAS, an international injection moulding group focussed particularly on the automotive sector which operates out of Port Elizabeth in South Africa, has purchased the assets of Froetek in East London following the latter’s decision to withdraw from SA. Weidplas was in fact one of Froetek’s main customers, with it in turn supplying the components on to various automotive OEMs.
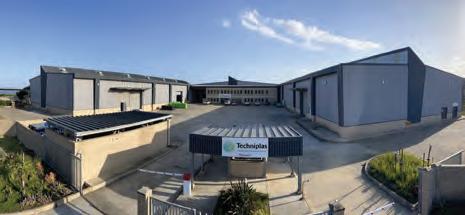
What has changed since the last K2019? Three years ago, there was a lot of talk about the circular economy at the K, and the first approaches showed what could be possible. In 2022, we are no longer talking and exchanging ideas. Today we already have new technologies, new products, and new processes that can meet the demands of the environment. And this is the path we need to pursue. We are facing a great challenge. There is uncertainty, a lack of direction, and unanswered questions on many issues, which cannot be put off. Now is the time to act and turn challenges into opportunities, which is why our chosen trade fair motto is: The Time is Now. , says Reifenhäuser CSO
“In short: new plastic products must be created that meet the demands of the environment. The way to achieve this is through the circular economy,” says Ulrich Reifenhäuser, CSO of Reifenhäuser Group
www.reifenhauser.com/en 202SEPT/AUG 7 plastics
Among polymers, there are products, such as PET and PE, for example, that previously could not be processed together because they have different melting temperatures. While one has not yet melted, the other is already burned. EVO Fusion, however, now allows them to be melted together. We use it to feed used plastic products into the extruder to make a new film. This is not a film for high-end applications, such as food packaging. But it can be used very well as construction film, as covers in agriculture, or to make rubbish bags. This film has high strength and density. So, with EVO Fusion, you can recycle and reuse products where that was not possible before. Are there any other methods available? We are also looking at the issue of saving materials. The world can’t do without plastics, but you can try to reduce the use of plastic while maintaining functionality. We call this downgauging.We’lldemonstrate this by taking the example of a spunbonded fabric, which is a fabric for nappies or medical products. We have reduced the amount of material used from 21 grams per square metre to 12 grams per square metre, plus we are about to reduce it to well under ten grams. In that case, we would have a product that fulfils the same function with half the material quantity. What role does digitalisation play in such improvements? Digitalisation has become enormously important in the plastics industry in recent years, and it has become increasingly better. Through digitalisation, processes are possible today that are no longer comparable with the automation capabilities of perhaps ten years ago. Processors are so much faster and more precise, that we can achieve much greater benefits with today’s digitalisation. For us in mechanical engineering, digitalisation means the possibility to optimally control processes. The extrusion process, for example, is perfectly monitored and also documented. We even go one step further: we focus on the empowerment and independence of operators – by deliberately turning away from usual manufacturercentric approaches and offering a digital solution to help producers of films or nonwovens to increase their production efficiency independently andAllsustainably.customers, regardless of company size, therefore benefit from a new dimension of process transparency, which for the first time includes all production equipment manufacturers and equipment types.

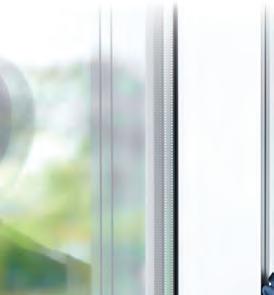

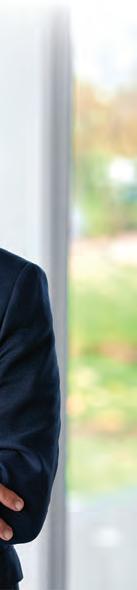

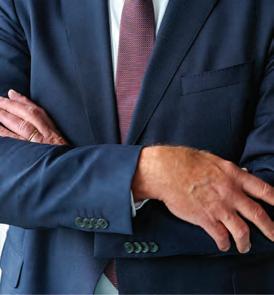
Roediger Agencies begins SANAS
The laboratory took delivery of the LC-MS in April and staff were trained on it during May.
The USAID TradeHub’s programming closely reflects the US government’s partnership with Southern African private enterprises, US government agencies, SADC member states, local and regional trade associations, and other development partners.
Roediger Agencies is a private analytical problem solving and technical research laboratory specialising in troubleshooting and research of polymers and related applications. The company is owned and managed by Dr Andy Roediger (Ph.D., Chem.); a polymer scientist experienced in various fields of polymeric applications. “We now have the capability to test all things physical and chemical to do with polymers,” says Roediger. Systems from Thermo-Fisher Scientific of the USA, Netzsch of Germany and Perkin Elmer, all top global test equipment marques, make up this comprehensive laboratory. With the new LC-MS, the laboratory will be able to fulfil the requirements of a new international customer, supplying packaging into Africa, for migration analysis testing on 10 different foodcontact plastic packaging. Roediger Agencies is working with the USAID Southern African Trade and Investment Hub, which will pay 60% of the cost of certification, while the customer pays 40% of the cost.
8 2022SEPT/AUG NEWS Can
SANAS accreditation At the same time, Roediger Agencies has implemented requirements of ISO17025:2017 with the aim of applying for SANAS accreditation, specifically for pipe testing.TheSouth African National Accreditation System (SANAS) is the only national body responsible for carrying out accreditations in respect of conformity assessment, as mandated through the Accreditation for Conformity Assessment, Calibration and Good Laboratory Practice Act (Act 19 of 2006) An audit was recently completed of the laboratory to ensure it can test HDPE and PVC pipes according to international and national standards, as stipulated in the individual product specification and to prepare the laboratory for a future SANAS technical assessment to ISO17025:2017. The stringency of the audit was based on the requirements of SATAS to ensure that the lab staff are competent in executing the test methods for HDPE and PVC-U, PVC-M, and PVC-O pipes and that the lab has the necessary equipment to do the testing. The lab test all things physical and chemical to do with polymers
ROEDIGER Agencies in Stellenbosch, a dedicated testing laboratory service for polymers, recently invested a six-figure sum in LC-MS (Liquid Chromatography Mass Spectrometry Analysis) testing equipment. For the layperson, the LC-MS* is able to separate and identify larger particles in the material, whereas the Gas Chromatography Analysis** (GCMS), of which Roediger Agency has two, separates and identifies smaller particles.
The USAID TradeHub engages with partners across the region to increase sustainable economic growth, global export competitiveness and trade in targeted Southern African countries.
Hugo-Ben van Renen is the pipe testing laboratory analyst at Roediger Agencies Dr Andy Roediger, flanked by Ilana Bergh (general manager and laboratory analyst) and Wernich Kühn (quality manager and laboratory analyst), with the new LC-MS equipment
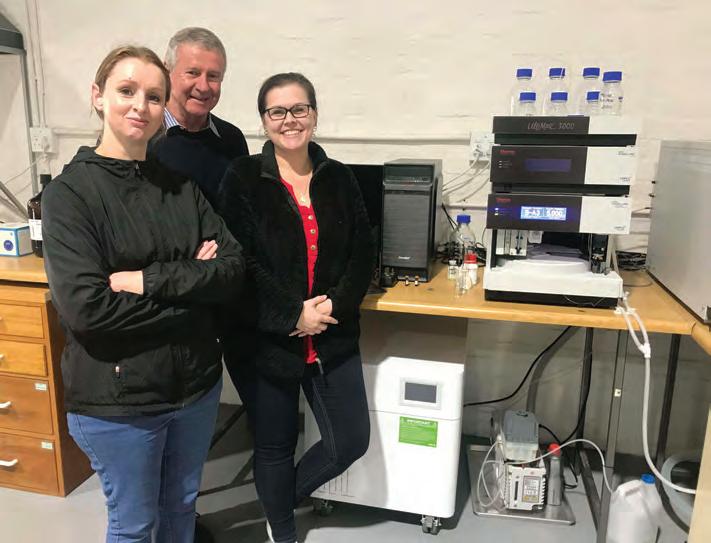
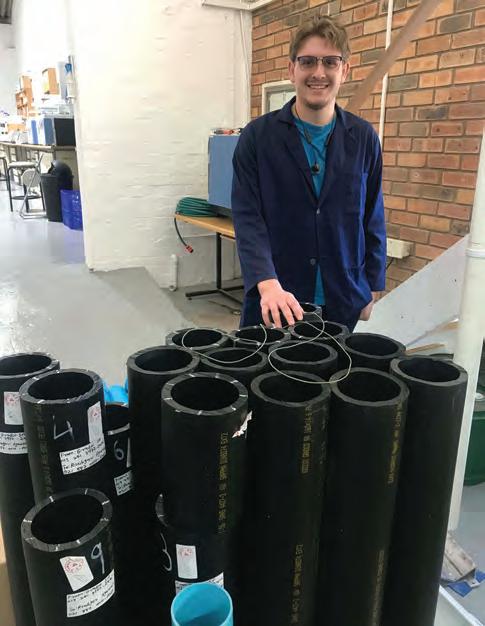
Analytical Problem Solving and Technical Research • We Test Plastics. • We Test HDPE & PVC Pipes. • We Certify Plastics In Contact With Food. With 40 years of experience, Roediger Agencies is a private industrial consulting company, specialising in analytical problem solving and technical research related to polymers and applications. Roediger Agencies cc Dr Andy Roediger (Ph.D., Chem.) +27 83 250 andy@roedigeragencies.co.za9281 Image by Michal Jarmoluk from Pixabay specialises in testing accredited by SANS 791, 966-1, 966-2, 967, 1283, 1601, 4427, and 9080. The South African Technical Auditing Services (SATAS) is a governing body, accredited by SANAS. It specialises in product certification and inspections to certify manufacturers in accordance with the relevant ISO and SANS standards. Their sole mission is to provide an internationally accepted South African Certification Scheme to allow their clients to compete in both the domestic and international market. 2022SEPT/AUG 9 LC-MS* – LC-MS is a variant of high-performance liquid chromatography (HPLC), and is a fundamental analytical technique used to separate complex mixtures of organic compounds. The incorporation of mass spectrometry allows for the structural analysis and trace quantitation (even in highly complex matrices) of a wide range of analytes, from small molecules to peptides and proteins, to polymers. The technique relies on separate mixtures with multiple components, while mass spectrometry provides molecular identity of individual components with high specificity and detection. GCMS** – Gas Chromatography is an analytical technique in which a complex mixture of compounds is injected onto a column and is separated based on their relative boiling point and affinity for a chromatographic column. Compounds analysed are generally volatile or semi-volatile in nature and have boiling points of less than 300 °C and molecular weights of less than 500 g/mol. Samples may be solid, liquid, or gaseous in nature. After separation, the compounds may be detected by a variety of detectors. www.roedigeragencies.co.za processaccreditationtotest pipes
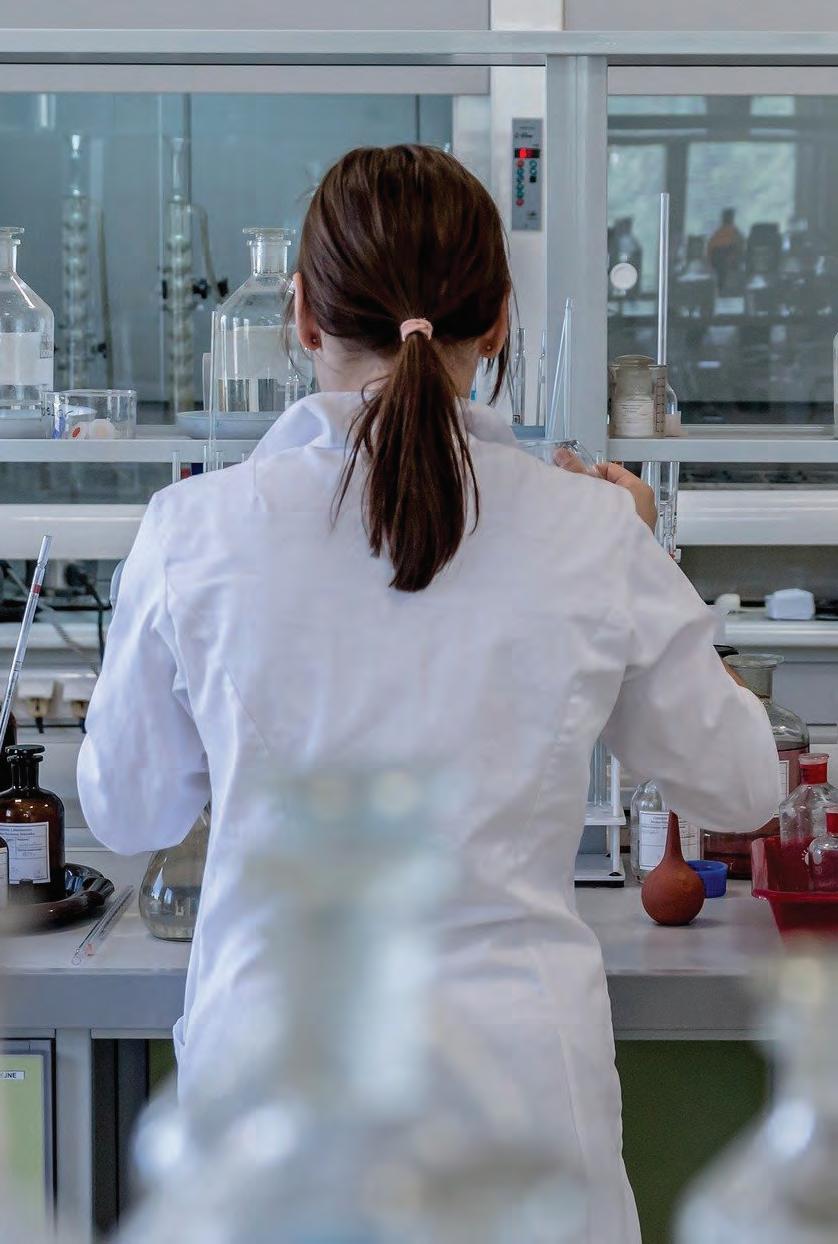
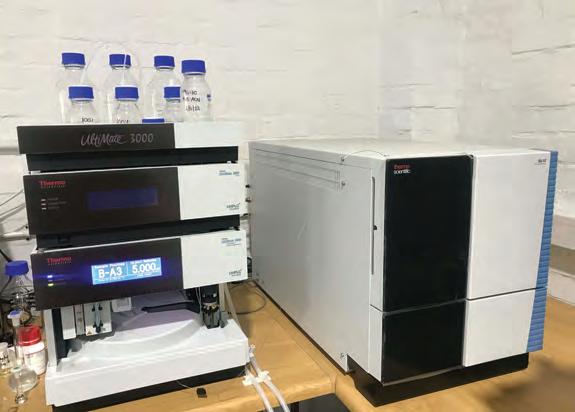
NEWS
“In 2021, we started to expand our reporting methodology in order to be able to track progress against all the identified products that our members place on the market for which we offer an EPR scheme. Using information provided by our members on exactly what they place on the market, in combination with assumptions provided by our recycling partners of the make-up of a typical bale that they purchase, we were able to measure collection of identified products such as beverage bottles, oil bottles, home and personal care bottles and non-PET elements such as labels and closures.
The PET recycling economy created real value, said Scholtz, generating a total of R1.2 billion for the South African economy through the placement of end-use products on local and international markets in the year under review. According to Scholtz, the food-grade and bottle-tobottle sector represented the most circular use of PET and accounted for one third of all collected tonnage in the PET recycling economy last year.
Despite a challenging year for the paper and packaging sector, PETCO, which represents producers of polyethylene terephthalate (PET) packaging, grew its collection of postconsumer PET bottles for recycling by 14% – from 79 078 tons in 2020 to 90 402 tons in 2021.
10 AUG / SEPT 2022
“In 2022, we will be doing full bale characterisation studies which will allow us to report with further granularity, not only meeting the requirements of the regulations but showing our diverse membership how we are tracking their particular products,” said Scholtz.
Over 2 billion plastic bottles recovered for recycling in SA www.petco.co.za
“In spite of the impact of prolonged Covid-19 lockdowns and curfews on collection rates, which restricted the movement of informal collectors, 63% of PET packaging that was placed on the market by PETCO members was collected for recycling in 2021,” Scholtz said. “Once lockdown regulations eased, PETCO made a concerted effort to stimulate collection by supporting informal waste pickers and formal collection businesses, buy-back centres, and recyclers, and encouraging them to grow capacity and capability.”
According to figures released at the PET Recycling Company’s (PETCO) annual general meeting in June, 2.1 billion PET bottles were diverted from landfill last year thanks to the various recycling efforts in which it was involved.
She said PETCO’s key objective was to keep members’ packaging out of the environment, where it does not belong, and increasingly get it recycled to be re-used in packaging.
CELEBRATING SUCCESS: Linah Ndala (left), of the Mpumalanga Department of Agriculture, Rural Development, Land and Environmental Affairs’ Zonda Insila Programme, and Swikoxeni Waste Management director Bethuel Mashele celebrate the positive environmental and community impacts of the collection and recycling of PET plastic bottles in South Africa PETCO grew its collection of post-consumer PET bottles for recycling by 14%
On the back of waste management experts warning that parts of South Africa could soon run out of landfill space, CEO Cheri Scholtz said PETCO’s efforts had saved an area equivalent to 560 495 cubic metres and prevented potential associated carbon emissions of 135 604 tons in 2021.
With mandatory Extended Producer Responsibility (EPR) regulations laying down Year 1 targets for PET of 60% for beverage bottles, 7% for oil bottles, 9% for thermoforms and 60% for single-use products, she said the current collection rate places PETCO in good stead to meet these targets.
STATISTICS from South Africa’s longest-standing plastics producer responsibility organisation indicate that the country’s PET plastic recycling rates are recovering after the lockdown regulations resulting from the Covid-19 pandemic.
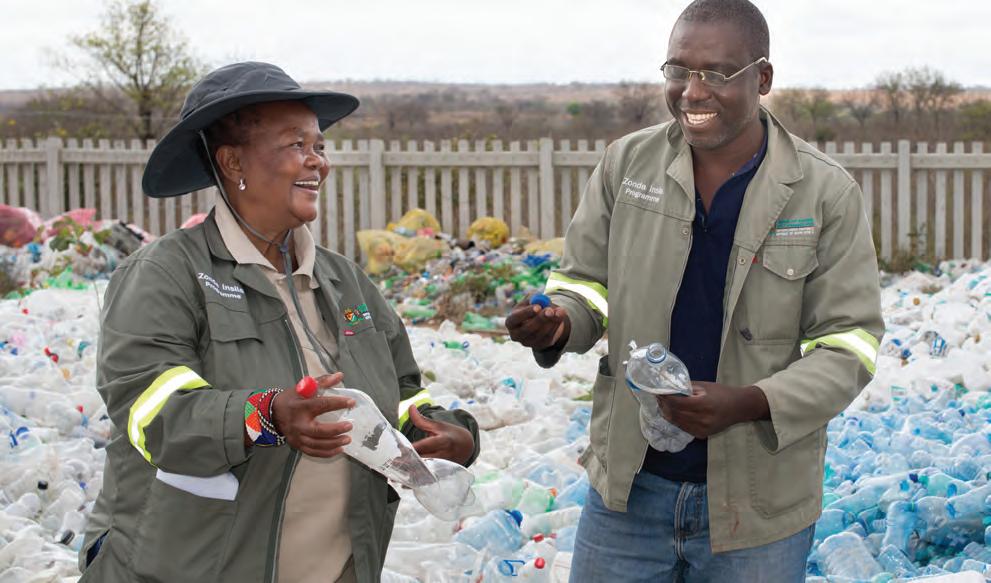

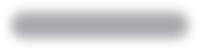
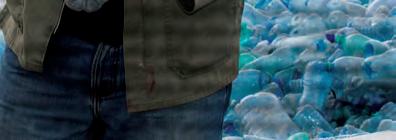
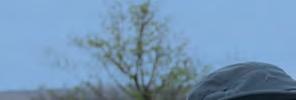
Manufacturing of new barrels and screws Bimetallic - Nitrided – Through harden Refurbishment of Barrels, Granulators,Screws,BlowFilmandT-Dies Suppliers of recycling/pipe/profile/ film & reduction industry MGMW Trading (Pty) Ltd Fine Fit Office: +27 66 250 1937 Wolf: +27 82 771 7271 Gunther: +27 83 441 3206 Unit 17 Log Roadwww.mgmwtrading.comadmin@mgmwtrading.co.zaRoodekop www.hitech-china.net
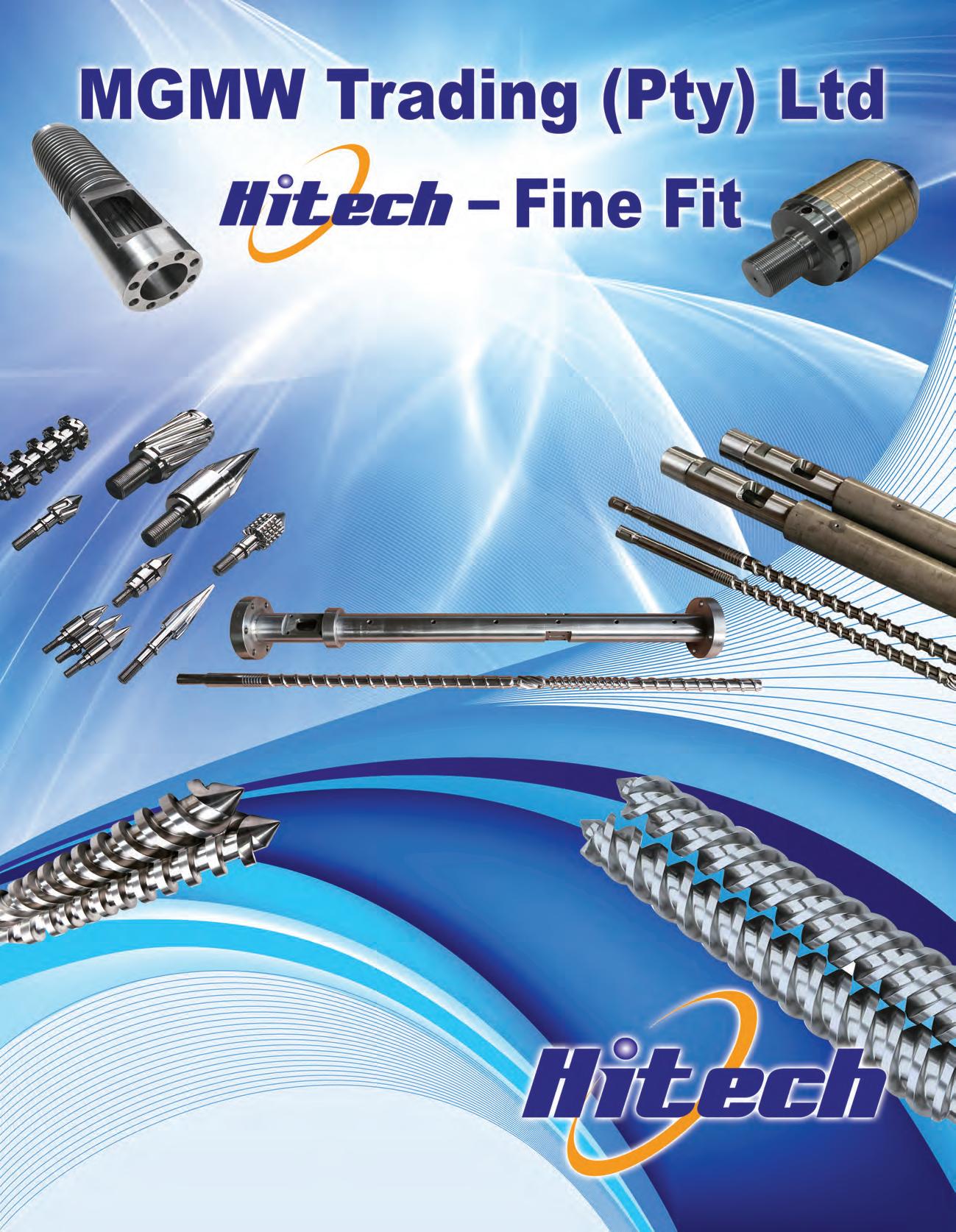

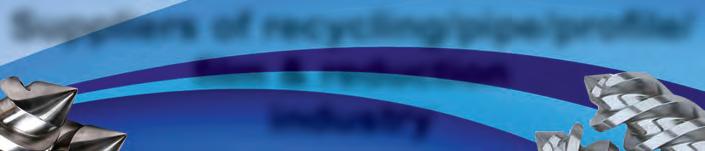
PET1 PE-HD2 PVC3 PE-LD4 6PS 5PP OTHER7 = Recycling Success Plastics Purpose Polyco PRO NPC is a registered Producer Responsibility Organisation (PRO) that invests in plastic recycling initiatives in order to grow the collection and recycling of all plastic packaging in South Africa.
SUCCESS To date, Polyco has invested over R72 million in to the South African plastics recycling sector, with a capacity growth commitment of over 140 000 tonnes through our 98 project partners. Polyco achieves this growth by collaborating with multiple stakeholders, funding collection and recycling businesses in South Africa, and by educating both the industry and the consumer about recycling.
Join Polyco today |
www.polyco.co.zaPOLYCO’S
MUNICIPALITY SUCCESS Polyco’s Municipal Project in Buffalo City Municipality in collaboration with the Border-Kei Chamber of Business, the Buffalo City Metropolitan Municipality and the Buffalo City Metropolitan Development Agency was completed with two static buy-back centres currently in operation.
To ensure the success of this initiative, Polyco funded private businesses in East London to facilitate the collection and recycling of plastic packaging materials to meet local market demand for recyclate. We urge municipalities across South Africa to get in touch in order to roll out similar initiatives in their areas. 021 276 2096
NEW PROJECT SUCCESS Polyco has recently approved funding for CRDC. CRDC’s aim is to create appreciating value from unrecyclable, mismanaged plastic waste by converting it into an eco-aggregate (RESIN8) which facilitates the creation of superior environmentally friendly construction products. No sorting by type of plastic is required, and RESIN8 can be made from any type of thermoform plastic, even if it has significant organic soiling or polymer degradation. This latest project is set to process over 630 tonnes of recyclable material per month.
Roger Kauerauf at the Zarcaplas plant in Blackheath near Somerset West with his bank of Yizumi machines, each fitted with Samfacc handling robots
Craft Trading and Projects currently manufactures fresh produce export crates from virgin PP with UV stabilizer, manufactured to BRCGS packaging standards, as well as JAB utility knives (non-snap-off blade, patent pending 2018). It also offers a turn key solution, including new business ideas and integrated design, including branding; 3D printed samples for new business; custom tooling design and manufacture; and mass production of plastic units with storage and delivery.
ZARCAPLAS, a new injection moulding business operating out of Blackheath in the Western Cape, went into operation in February 2020 in most
www.craftplastics.co.za
Startup Zarcaplas’s
Skills gained in earlier years
Certification process took 12 months of rigorous work
14 2022SEPT/AUG NEWS
Craft achieves BRCGS food safety certification
Craft uses a variety of machine brands and sizes, from 60 tons to 320 tonS. The newest are Borsche BS320-III servo Series plastic injection moulding machines. The facility runs 24 hours-aday production to ensure high volumes with short lead times.
Aftermanager,antestamenteventhere.mostwhichincircumstances,unexpectedandjusttimeforthelockdown–wouldhavekilledoffstart-upventuresrightThefactthatZarcaplasgotoffthegroundistoskillslearnedatearlyagebythegeneralRogerKauerauf.completingadiplomain FAMILY owned and run business, Craft Trading and Projects was recently awarded a Grade A food packaging certification fromBRCGS’sBRCGS.global standards set the benchmark for good manufacturing practice, and help provide assurance to customers that the products are safe, legal and of high quality. Established in February 2020, Craft Trading and Projects (Pty) Ltd was launched to facilitate the exponential growth of Craft Plastics which had been a sole proprietorship since its launch in 1994. Both companies operate from Alrode from separate premises. Son, Bevan Lambinon heads up Craft Trading and Projects, while his father Evan Lambinon runs Craft Plastics. Rachel Lambinon handles the finances, HR and compliance for both companies. “With our BRCGS certification, we can serve customers who require their product to be manufactured in a facility that has a food packaging certification, and is operated by staff who are committed to authentically producing high quality products made from strategically sourced materials,” Bevan comments. The certification process took 12 months of rigorous training, compiling info, procedure writing and hands-on facilitation from Wareham Associates based in KZN. The audit took two days and was carried out by external auditors, NSF.
Bevan and Rachel Lambinon
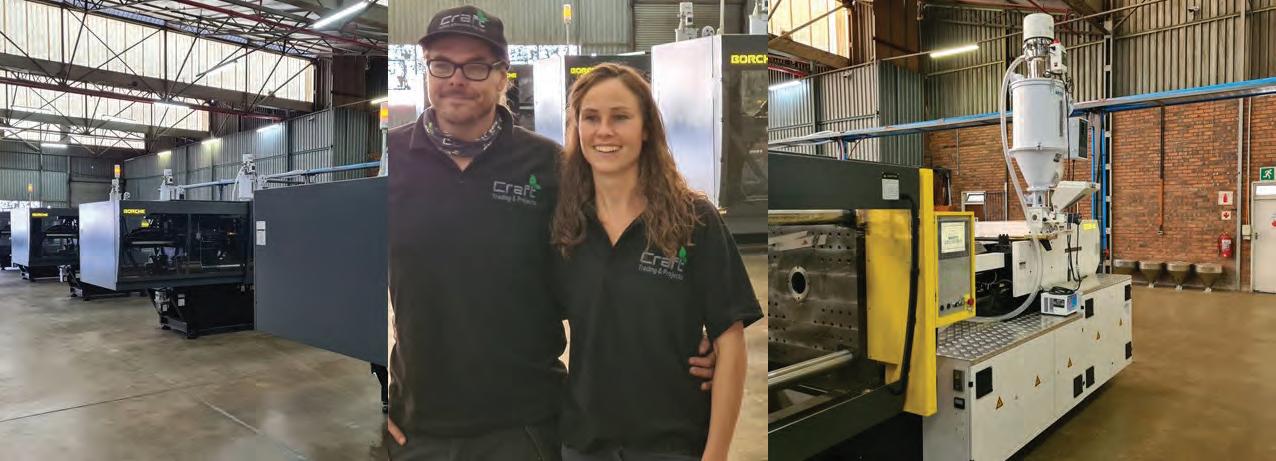
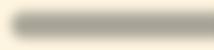

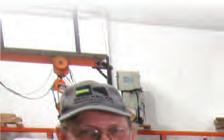
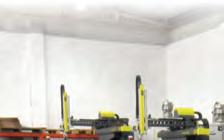
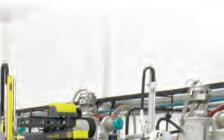
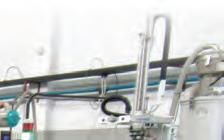
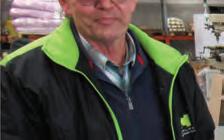
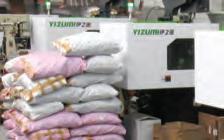
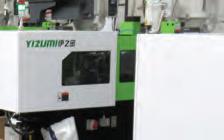
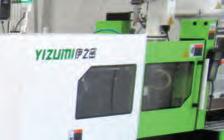
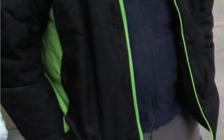
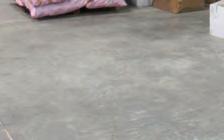
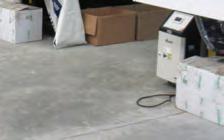
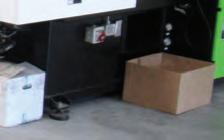

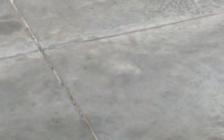
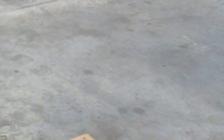
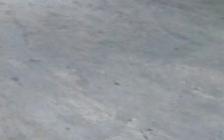
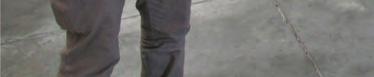
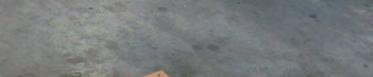
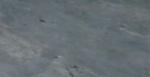

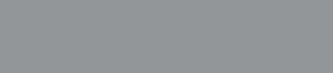
Plastics Technoloy in Austria, he joined his father at Calibre Plastics in Johannesburg. There Roger picked up many of the skills involved in managing an injection moulding and toolmaking business. He then left the plastics industry for some years and eventually moved to Somerset West, where he worked in the electrical industry, and stared doing some work for injection moulding companies in the region.
Roger began to realize that his skills in plastics manufacturing management were possibly more useful than he had estimated, at which point he took the plunge and started Zarcaplas together with his wife Zanele, who is responsible for HR and sales. It was originally intended for Zarcaplas to operate as a small toolroom producing moulds for their own products, but contract moulds and parts production soon became the main driver. With prior experience of the Yizumi injection moulding technology, Zarcaplas opted for five of the Chinese machines. Roger is happy with the Yizumi build quality and servo hydraulic system, which is energy efficient and quiet, and produces parts with consistent quality.TheZarcaplas toolroom under toolroom Manager Gavin Lewis, has worked extremely hard, building very complicated new moulds as well as repairing older and damaged moulds. Despite the many challenges, the two year-old business is doing well, not least due to the efforts of a young, dedicated and dynamic team who were keen to contribute to the growth of Zarcaplas. Roger and his team were blessed with the addition of a large new client in 2022, and are therefore optimistic about the future of this young company. help solve problems now
plant running
AUG / SEPT 2022 15 www.zarcaplas.co.za
flat-out
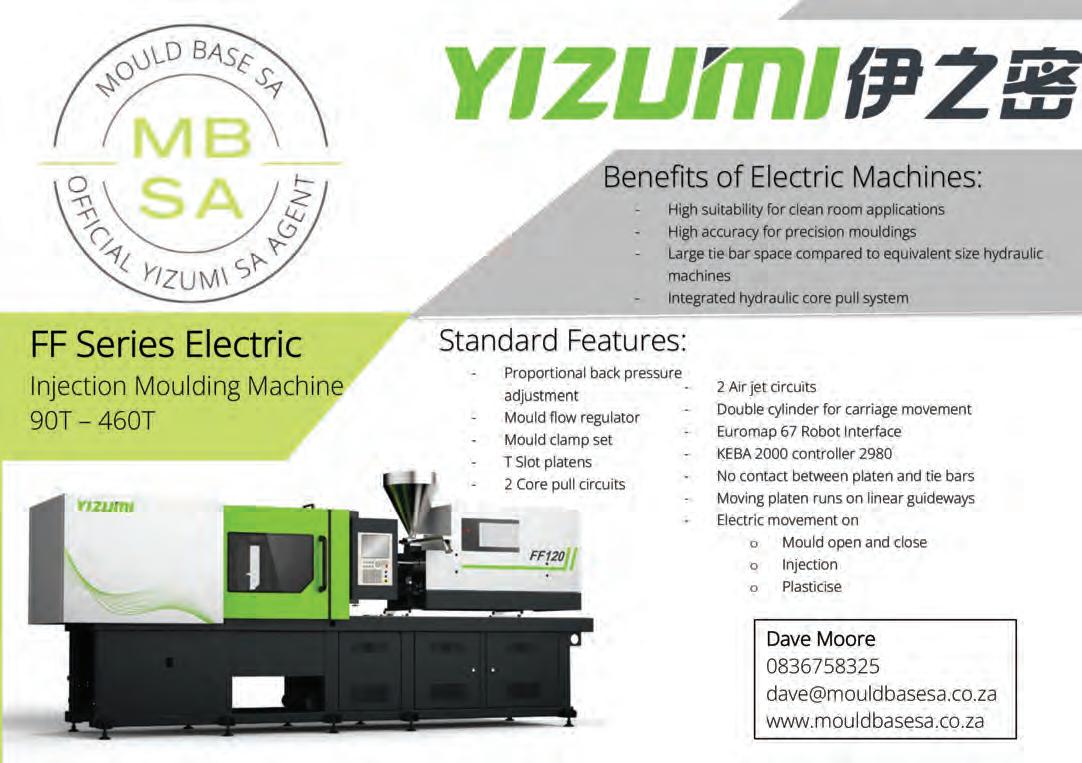
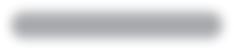

Continental Compounders expands at sites in KZN, Gauteng
Continental Engineering has also recently succeeded in qualifying for ISO 9001 accreditation and will be applying for IATF accreditation in the near future, which CEO George Dimond said was important to it, especially due to its increasing supply to the automotive Tier 1 and OEM businesses.
CONTINENTAL Compounders, one of South Africa’s leading polymer compounding companies, continues to expand and consolidate its operations at its two new sites in Westmead in KZN and Alrode in Johannesburg.
Mercedes-Maybach
GLS with carbon fibre body components
Continental has succeeded in qualifying for ISO 9001 accreditation, which CEO George Dimond said was important to it, especially due to its increasing supply to the automotive OEMs Capacity for 60,000 tpa, polyolefin and engineering volumes increasing
16 AUG / SEPT 2022
www.compounders.co.za
“Global shipping and supply chain complexities has made it crucial to localise key supply and develop longrange initiatives on lead times and working capital costs. The cyclical nature of commodity (polymer) prices and availability is not new, it has only become less predictable and more frequent. This is our challenge if we are to sustain a manufacturing sector in South Africa,” said Dimond.
Continental has been in operation since 2005 and was at first involved solely in PVC compounding, which remains its core business, but it has in recent years expanded into polyolefin and engineering plastics compounding business and more recently into polymer masterbatches and additive concentrate masterbatches. It has processing capacity for an estimated 60,000 tons per year, with the polyolefin and engineering volumes increasing.Inorderto streamline operations and supply for local, cross-border and deepsea exports, Continental has moved some of its compounding extruder locations in order to improve access to markets and transport. To this end it recently accessed an 8000m² site in Westmead, Durban, where it is now expanding production of ABS, polycarbonate, filled PE and PP materials as well as PA6 and PA66 compounds and a variety of masterbatches. Its PVC production and supply operations continue from the Mariann Industrial (Durban) and Alrode sites. Over time the PVC will also relocate to the Westmead site for efficiency and critical mass.
NEWS
WITH Mercedes’ (Stuttgart, Germany) market launch of the Mercedes-Maybach GLS, the off-road specialist is now providing another luxury SUV as the basis for further refinements. In the area of design, Mansory says almost all body components are either completely manufactured in carbon fibre or upgraded with carbon fibre applications. Customers reportedly have access to all carbon fibre variants that Mansory offers in its portfolio, which includes four different collections with a total of 10 different designs, all manufacturing via in-house autoclaves. More specifically, the apron with an integrated front lip, LED daytime running lights, side flaps and air outlets are comprised of carbon fibre. The complete front grille, including its vertical bars, is either left as standard, discreetly darkened on request or finished entirely in carbon fibre. Mirrors caps incorporate the composite material, as well as the rear apron diffuser. An engine cover in carbon fibre also visually complements the technical changes in the engine compartment.
Continental is exporting to more than 45 countries, including to Europe, UK, Ireland and Australia, with the appointment of two new agents in those regions. The company is also investing in high-efficiency equipment (which offers lower per ton energy requirement) and particularly lines that offer more flexible operation as much of demand for engineering materials in South Africa and the region is for shorter production runs. This is a requirement for all the non-PVC materials, where there is a need for a wider variety of fillers and additives, particularly in the automotive and electronics sector.
complexitiesshipping‘Globalandsupplychainhasmadeitcrucialtolocalisekeysupply’
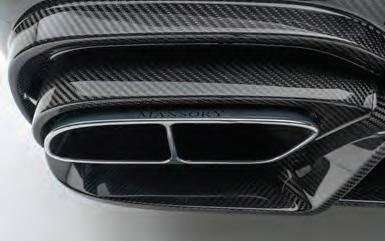
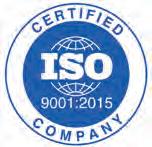
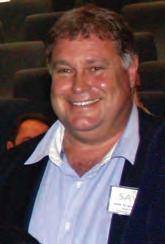

| CABLE COMPOUND | PACKAGING Low Halogen, Flame Retardant Bottle and Film applications such as and UV Resistance for low voltage applications Cling Film, Stretch Wrap, Labels, Wraps HFFR, XLPE & Sweet Twist | RIGID EXTRUSION & INJECTION MOULDING | FLEXIBLE EXTRUSION Ceilings, Fencing, Gabions, Gasketing, Pipes, Construction, Mining and multipurpose Hoses & Fittings industries +27 31 791 0600 +27 31 791 www.compounders.co.zainfo@compounders.co.za0081 3 Joule MariannCrescent,Industrial Estate DurbanPinetownSouthAfrica 3610 | MINERAL FILLED TALC & CALCIUM CARBONATE | FLAME RETARDANT 20% to 50% Halogen & Halogen-free systems | GLASS-FIBRE REINFORCED | MASTERBATCH & ADDITIVES 20% to 50% Black masterbatch, Antiblock/Slip, UV Stabilizers & Antioxidants | IMPACT MODIFIED | COMBINATION-FILLED GRADES Impact modified compound Mineral filler and glass-fibre, flame retardant and glass-fibre Continental Engineering Compounds offer locally manufactured compounds for Automotive and Industrial applications to meet your required specifications Continental Compounders specialise in the manufacture of Rigid and Flexible PVC and Thermoplastic Elastomer compounds for the cable, footwear, moulding and extrusion industries

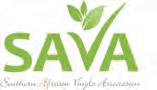
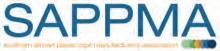
The week includes:
• ICC/World Clean-up Day (Saturday, 17 September) That unites 180 countries across the world for a cleaner planet. Apart from raising awareness to the general public and industry partners, Plastics|SA will also be actively supporting various clean-up initiatives taking place throughout the month of September. Plastics|SA will be distributing more than 500 000 refuse bags to support clean-up events.
SOUTH Africa is facing a waste crisis, but every citizen can make a difference to reduce the amount of waste that pollutes our environment or ends up in landfill. This is the opinion of Douw Steyn, sustainability director at Plastics|SA and coordinator of the annual Clean-Up & Recycle SA Week that will be taking place from 12-17 September. According to Steyn, approximately 54 million tons of waste is produced every year in South Africa – the majority of which ends up in landfill. “This is enough to cover an entire soccer field 10 metres deep every day. The amount of waste we generate puts our landfill sites under extreme pressure”, he says.
In partnership with volunteer organizations and individuals around the globe, the ICC engages people to remove trash from the world’s beaches and waterways. “Since its inception, more than 17 million volunteers have collected close to 1.6 million kilograms of litter globally – making our coasts cleaner and our oceans healthier. As a result of the success of this annual event, we decided to turn the entire week into a nationwide awareness campaign that encourages citizens of all walks of life, ages and backgrounds to make a conscious effort to pick up and remove litter from their streets, neighbourhoods, schools, inland water sources and streams or nearby beaches,” Steyn explains. Clean-Up & Recycle SA Week is actively supported by all the packaging streams, Producer Responsibly Organisations (PRO’s), various sponsors, business and industry, national and local government, community organisations and municipalities.
• River Clean-Up Day (Wednesday, 14 September)
This will be the 26th year that Plastics|SA coordinates South Africa’s involvement in the International Coastal Clean-up Day (ICC) that will be taking place at beaches around the country on Saturday, 17 September.
• National Recycling Day (Friday, 16 September)
17 million volunteers have collected close to 1.6 million kilograms of litter globally
www.cleanupandrecycle.co.za
18 AUG / SEPT 2022 NEWS

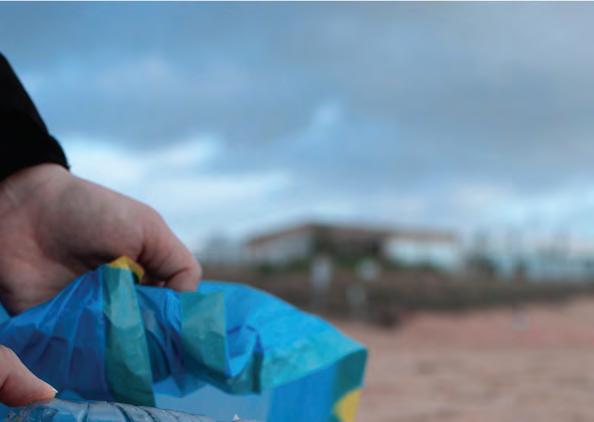
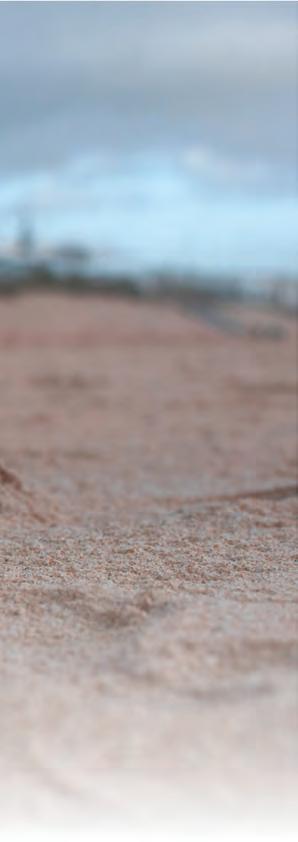
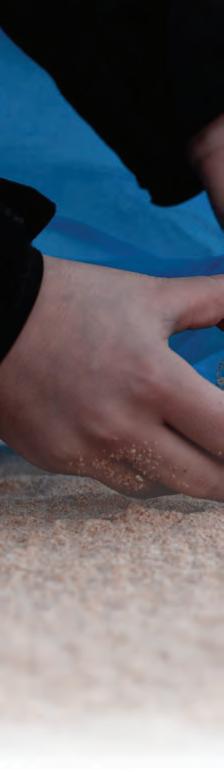
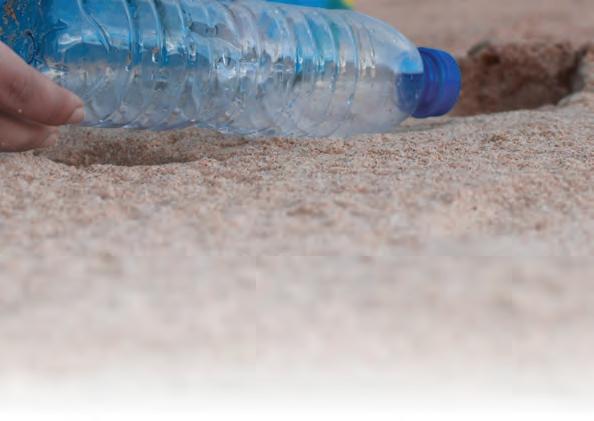
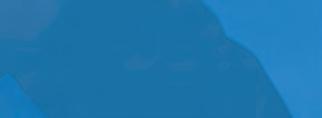


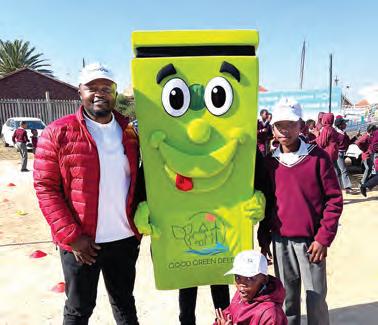
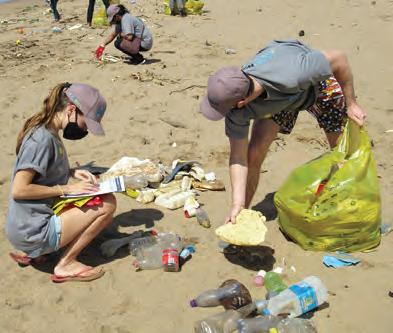
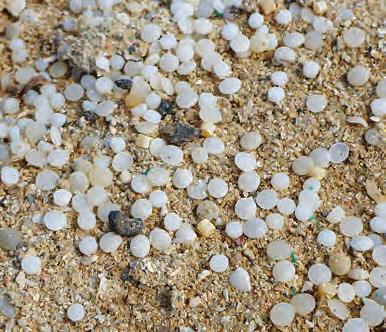
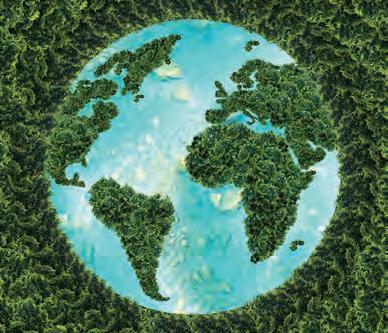
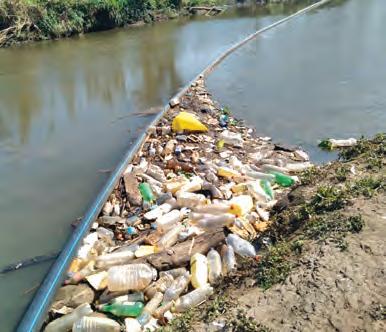
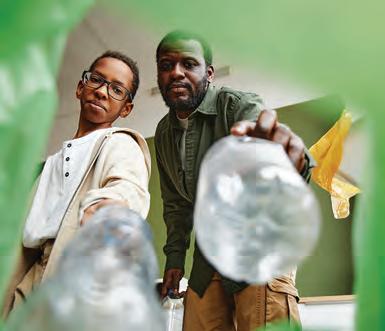
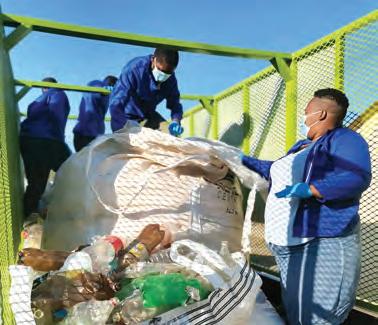
20 2022SEPT/AUG JUST BRIEFLY NEWS
The centre is now also ISO 9001 accredited, such has been the initiative of the team led by De Beer.
Chemicals, substances, BY CLAUS MAURER
billionofannum,200totradedquantity2020).(Chemistrychemicaldistinctidentity.WorldThetotalofwasteamountsapproximatelymilliontonsperwithavaluearoundUS$100(OECD2018), and an estimated of 330 million tons of chemicals traded, valued at around US$3.4 trillion (CEFIC 2020), with increasing trends being reported especially for certain groups of chemicals such as pharmaceuticals. Of course, some chemical and waste trade has been controlled or even banned internationally, as enforced by the Montreal Protocol (Ozone depleting substances) Basel Convention (Waste trade), Stockholm Convention (Persistent Organic Pollutants - POPs), Rotterdam Convention (Prior Informed Consent Materials – PICs), Minamata Convention (Mercury) However, with such an enormous number of chemicals and wastes distributed in the supply chain, it is often difficult to keep track of the hazards such chemicals and wastes pose on the supply chain intermediaries. Hazards are defined as the capacities to inflict harm. To provide an updated and globally aligned methodology of assessing hazards, their classes and categories, South Africa updated the requirements for the Globally Harmonised System for the Classification and Labelling of Chemicals (GHS), which led to the issue of SANS10234:2019, used for the preparation of Safety Data Sheets (SDSs). In addition, the waste regulations, in accordance with the National SANS10234themorearticlesrealsimpleregulationsManagementEnvironmentalWasteAct(NEM:WA)wereupdatedin2013,andmoreprovisionsenactedbytheseregulationsarecomingintoforce.Although,theassessmentofchemicals,substances,andmixtures,aswellaswastestothesestandardsandmayappearforindividualchemicals,thecharacteristicsofmixtures,andwastesmaybemuchcomplicated.Asaresult,provisionsoftheGHSormustbefollowed.
THE Product Development Technology Station at the Central University of Technology in Bloemfontein is leading the way in South Africa in terms of additive manufacturing, an area which it has pioneered over the past two decades-plus. The centre has evolved its plastic component design and development process from Stereolithography in the 90s to comprehensive additive manufacturing and 3D abilities, in which area it possesses of one of the most powerful FreeFormer printing machines, from Arburg of Germany, in the country. It creates prototypes for a wide range of industry sectors which can then be honed into full production and commercialisable items. It has focussed particularly on the medical area, where its MedAdd subsidiary programme develops medical devices as well as prostheses for patients who have suffered disfiguring injuries. In some of the cases, it has ‘grown’ structures for individuals who have suffered facial injuries, where it able to 3D print structures based precisely on the facial shape of each injured person. The CUT is the leading South African university in the application of medical 3D printing using additive manufacturing processes. 3D printing is the consecutive layer-by-layer process where powder or liquid material is bonded together to form three-dimensional parts. For South Afica to compete internationally, the local medical device manufacturing sector needs to be supplemented with latest technology, expertise and skills, according to Professor Deon de Beer, head of the faculty. Originally the goal was to stimulate industry in the Free State, but the CUT’s success and motivation over the past few years has seen it become a leader in the region. The CUT team has been a regular exhibitor at trade shows around the country, where it’s interaction with the plastic and composites sector as well as visitors from the public has enabled it to become involved in a wide range of development projects, including novel and unexpected applications. The aim of the centre is to work on up to 100 projects a year, and in some of the cases the results have been life-changing for the injured individuals. It has also been involved in the developments of children’s toys that enable and encourage learning.
However, further difficulties in assessment may be encountered due to the following facts, which should not be consider as an exhaustive list: a) Ingredients in mixtures may have a compounding effect in terms of their hazards, whilst some do not act in this manner, b) Ingredients change structure when being combined,
Additive manufacturing centre at CUT leads way in SA
SINCE the early 1800s, 194 million organic and inorganic substances, including alloys, coordination compounds, minerals, mixtures, polymers, and salts have been disclosed in publications, according to CAS FurtherRegistry.reports indicate that more than 350 000 chemicals have been registered world-wide (Environ. Sci. Technol., 2020), of which 174 000 have been registered in Europe through the European Chemical Association (ECHA). Of those, it is estimated that more than 50 000 industrial chemicals remain publicly unknown because they are considered ‘confidential’, while a further 70 000 materials could not be clearly described because they are polymers, complex mixtures, or biological substances with no
With an enormous number of chemicals and wastes distributed in the supply chain, it is difficult to keep track of the hazards such chemicals and wastes pose on the supply intermediaries.chain
Claus Maurer, who holds a degree in Chemical Engineering and a PhD in Business/Supply Chain Management, is a Fellow Member of PISA and a well-known material specialist who has spent 35 years in the cable industry. www.iscat.com
• For further information on assessments of chemicals, substances, mixtures, and wastes contact ISC Consulting and Trading, Claus Maurer, on +27 (0)83 260 3305 or clausm@isccat.com, and visit us at
202SEPT/AUG 21
mixtures, and wastes in the supply chain
c) The shape and size may limit or exacerbate the interaction with human organs or with the environment, i.e. large objects and homogenous liquids versus dusts and aerosols. This fact does not relate to exposure, however to the inherent capability of a substance to cause Furthermore,harm.it is important to observe, that in the case of wastes (but not limited to wastes), the ingredient substances should be traceably identified. However, substance hazards are only traceable to CAS, EN and EINECS registry items and chemicals correctly identified to the IUPAC naming convention of chemicals. Consequently, complex mixtures and wastes should be identified by their exact ingredients, and an overall hazard assessment be conducted based on the ingredient hazards, taking into consideration the above and additional factors as may be required. The original UN GHS Document, Revision 8, 2019, which is referenced by RSA legislation, also makes provision for additional hazard communication, which have not been standardised in the GHS system. This includes the production and distribution of material that has been determined hazardous or may become hazardous by downstream processing, and appropriate information about these hazards, in form of an SDS, should be provided to the downstream users. In SA, the concept of an “article” as defined by the EU and US regulations is not available. In SA, all wastes must be assessed to SANS10234, with the exception of some defined wastes, whose hazard status has already been established, or such wastes are covered by other relevant regulations. SDSs serve a wide variety of audiences across the supply chain. In order to protect workers and employees of companies working with possibly hazardous materials, the provisions of the GHS have also been adapted in the “Hazardous Chemical Agent (HCA) Regulation” in 2021. Of course, SANS 10234 is based on the same principles and hence the latest version of GHS is in force in RSA. However, as many chemicals, substances, and mixtures as well as wastes are traded across the world, care must be taken, to observe compliance to SA legislation, when importing materials into SA. As indicated above, not all definitions may be translated from other national legislations and verifying or SDS compiling agents need to be aware that full SDSs are required, even if such materials are covered by the article-concept elsewhere or thought to be non-hazardous. This provision must also be considered when compiling SDSs for wastes to SANS10234 in order to establish any physical, health or environmental hazards, and to NEM:WA, in the case of classification for the suitability of disposal of waste to landfill. In addition to the above it must be noted that Extended Producer Regulations for waste electric and electronic equipment (WEEE), paper and packaging materials and lighting equipment have been enacted and registration in terms of these regulations is required.
and the original ingredients are not contained in the final mixture anymore, i.e. by some polymerization processes of monomers into polymers.
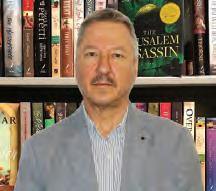
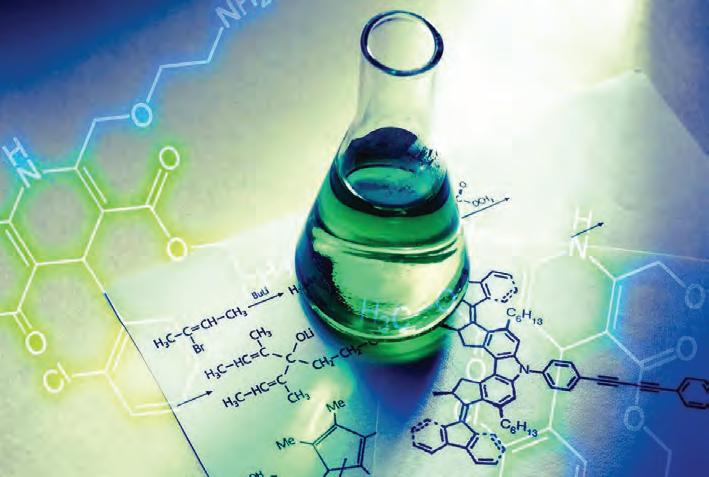
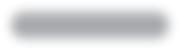
NEWS
Rapid treatmentplasma–
Delta Engineering’s plasma treatment systems offer efficiency, cost advantages
The Delta machines use only environmentally friendly gasses, including Argon, which is an inert noble# gas. The toxicity of acetylene is negligible and widely used in the welding industry. It also uses the new environmentally friendly HFC gasses, with a low GWP (global warming potential) value and well-known in the world of refrigeration. Furthermore, the gasses are largely consumed during the process, reducing the exhaust quantity to a minimum. The remainder could be captured with an active carbon filter, should local legislation require this. Other advantages Plasma coaters primarily replace fluorination of HDPE containers. According to Henk de Klerk of Wrapetfill, batch fluorination is dangerous and expensive with significant costs associated with the transporting to and storing of empty containers at fluorination sites. machine is still in production today. After several years of joint development, Delta launched a range of fully automated plasma coaters during an open house event at its plant in Romania in 2019. Customers from across the globe attended, including several from South Africa. What is plasma treatment?
22 2022SEPT/AUG
Plasma coating replaces multi-layer technology
CMYCYMYCMYMCK
Interior of DPC403 plasma system from Delta Engineering, a fourreactor unit typically used for containers from as small as 10ml up to 2 litres
Plasma enhanced chemical vapour deposition (PECVD) uses electrical discharge in low vacuum pressure conditions to decompose a gas and create a thin coating layer on the inside wall of the product in the reactor. It is an environmentally friendly way to create fully recyclable coated products where different physical and/or chemical properties are achieved as desired, depending on the material and the plasma gas used. Different properties can be obtained, including modification of the surface tension for better sliding, adhesion or wettability; an improvement of the barrier in different applications, to prevent migration or permeation. Multilayer technology is used in some containers to achieve the latter features, namely good barrier properties, but these containers cannot be recycled because of the different layers, which can’t be separated.
The Delta Engineering plasma coaters
WRAPETFILL, the consultancy/machinery/materialintegrated supply business, has noticed some new opportunities for the plasma treatment systems from Delta Engineering of Belgium, which it represents. Delta’s plasma systems offer improved efficiency with reduced costs compared to technology used in South Africa to date. Delta Engineering is primarily a downstream automation company for container producers, offering standard automation equipment such as conveyors, leak testers, palletisers, baggers, lost head trimmers and checkweighers. It has, more recently, begun to supply plasma coating machines, in which area it partners with Isytech of France, a global plasma coating specialist.Isytech has recorded some noteworthy achievements in plasma treatment, including amorphous carbon plasma coating for PET bottles, where it developed the Actis system for Sidel in 1998 to produce gas barriers for PET bottles. Applications were however limited to high-output projects. Then in 2005 it developed and patented amorphous fluorinated carbon barrier coating technology for HDPE agrochemical packaging. In 2007, the first plasma coater was installed in an extrusion blow moulding factory in France, which have the ability to apply an amorphous carbon coating to PET bottles and also an amorphous fluorinated carbon coating to HDPE bottles. This process is often used on PET bottles and increases the oxygen barrier by about 30 times. Water vapour and CO2 barrier are improved as well. Environmentally friendly gasses
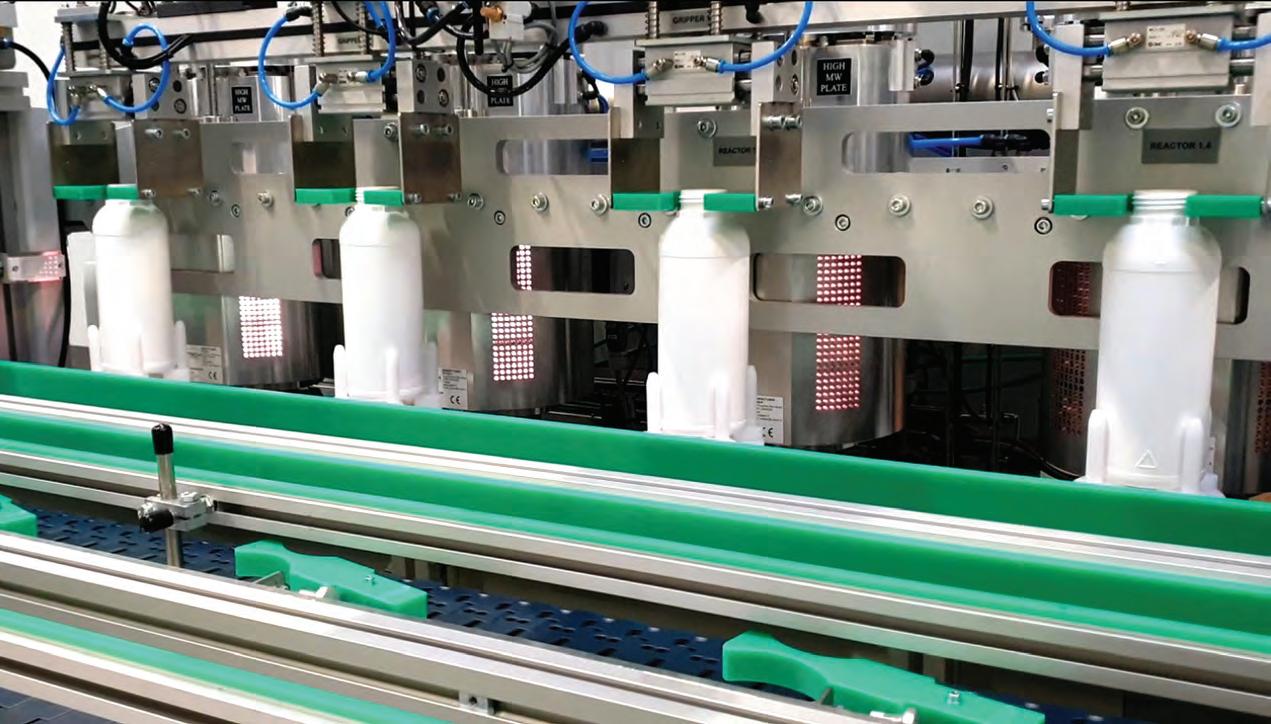
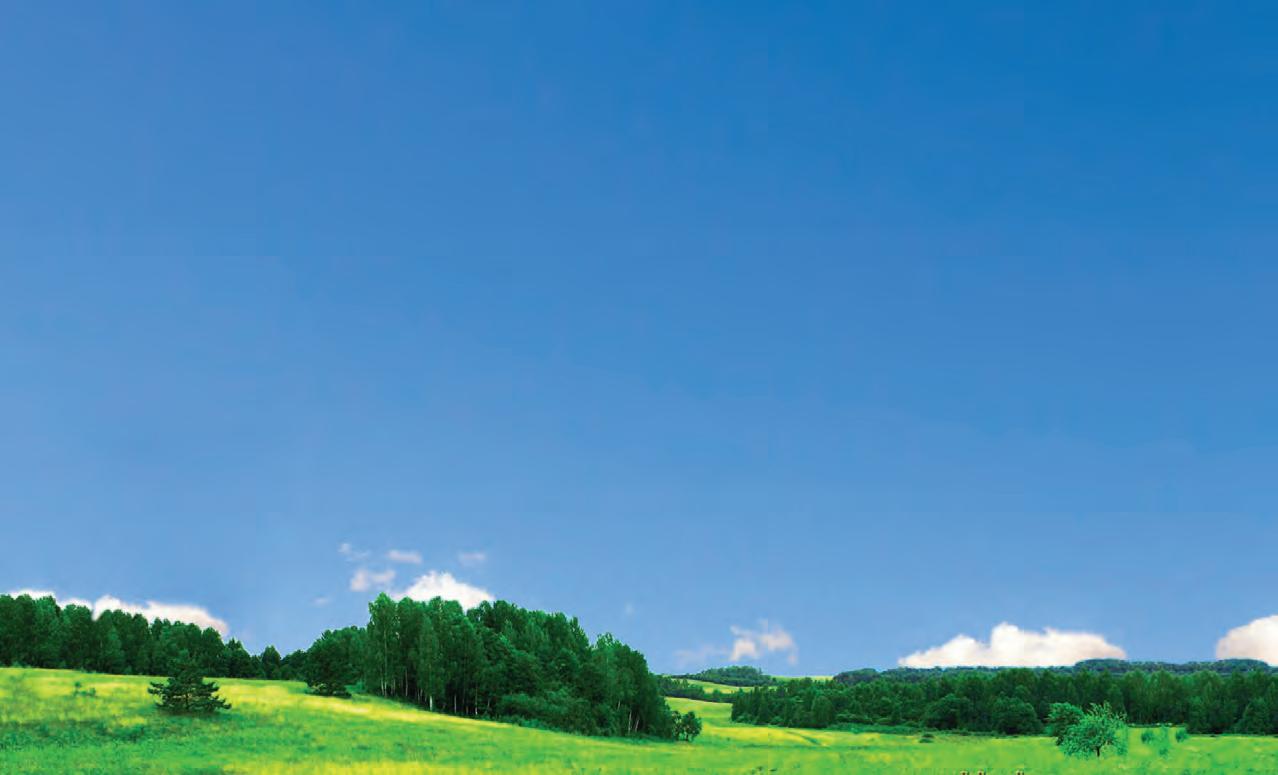
www.wrapetfill.com www.delta-engineering.be C008.pdf 1 2022/07/27 09:39
Bigger containers –The DPC133 plasma coater is designed for 50 up to L-ring250-litredrums
2022SEPT/AUG
The DPC223 unit is a two-reactor system developed for containers from five to 30 litres “Plasma coaters allow converters to coat their HDPE bottles or drums in-line with extrusion blow moulders or offline, thereby eliminating transport and warehousing costs as well as the high cost of fluorination. Plasma coating costs a fraction of fluorination and the gasses required for plasma coating are widely used and available in South Africa,” heDeltaadded.Engineering has already integrated its range of plasma coating machines into several industrial applications to achieve different outcomes, including treating bottles (inside) without adding gasses in order to obtain different physical properties/ surface structures such as crosslinking, sterilisation, surface treatment for medical applications, bonding and plasma carbon deposition. Leadership in plasma technology Delta’s focus on the plasma technology over the past few years has already achieved significant results. It has shown that its systems can allow a plasma coated mono-layer container to perform as well or better than a multi-layer or fluorinatedApplicationsequivalent.areprimarily in food, non-food and agrochemical containers, or wherever there is a need for a solvent barrier. The difference in cost reduction is high, added De Klerk. 23
NOTE: The Noble or inert Gases are the Group 8A elements of the periodic table that include helium, neon, argon, krypton, xenon and radon. The name comes from the fact that these elements are virtually unreactive towards other elements or compounds.
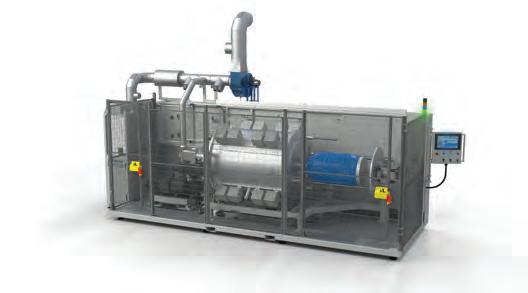
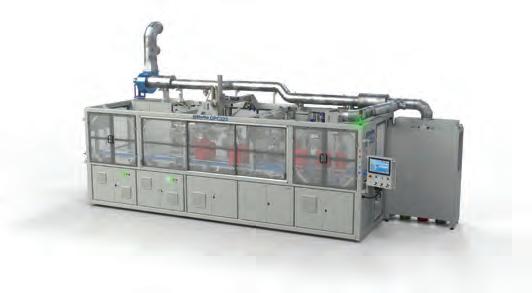
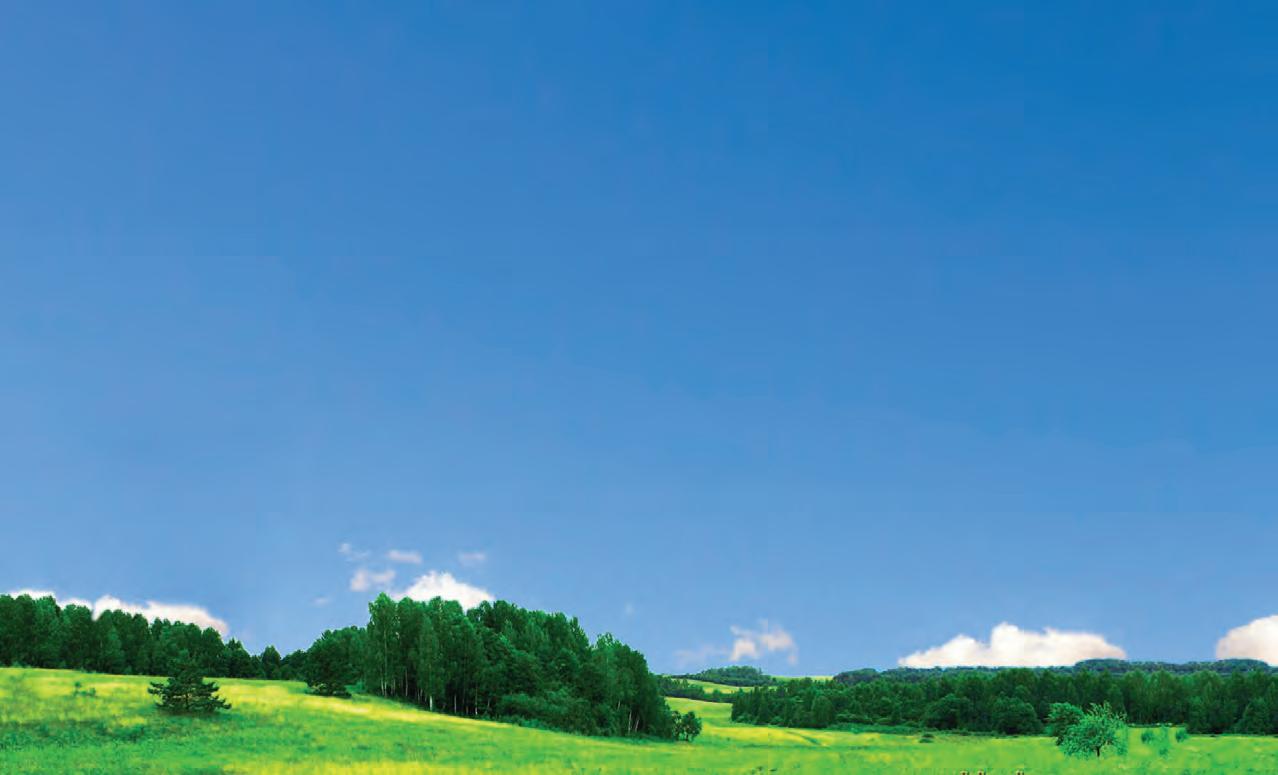
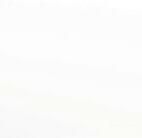
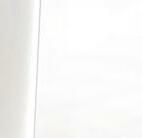
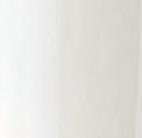


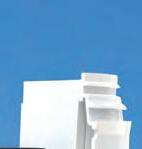
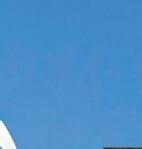
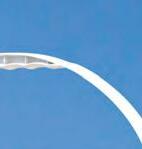

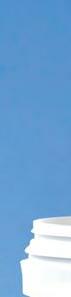
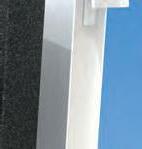
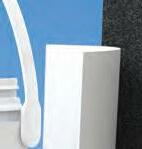
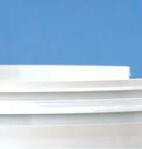
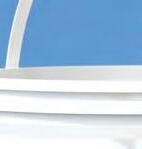
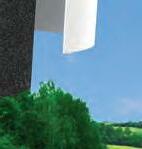
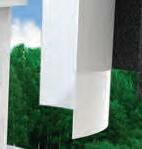
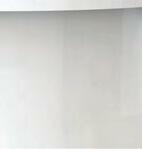
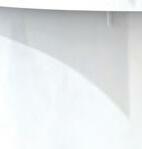
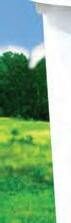
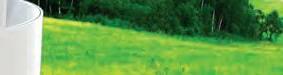
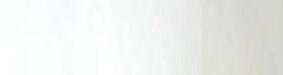
www.blackstonetek.com www.pygamountainbikes.com24 AUG / SEPT 2022
JUST BRIEFLY NEWS
Realisation of a dream to build the best carbon fibre mountain bikes in the world
To fulfil Morewood’s dream, PYGA needed to find a manufacturing partner who shared its passion for innovation and belief that things can always be done better. PYGA found such a partner right here in South Africa, BlackstoneThroughoutTek.the MoBu project PYGA had access to Blackstone Tek’s unique and proprietary manufacturing techniques that have resulted in a frame that has unparalleled quality, strength and rideability. Morewood said that PYGA are so confident in Blackstone Tek’s method and precision of manufacturing that PYGA offer a lifetime warranty on frame and bearings.
Teknor Apex replaces standard PA66 glass-filled with PP option
Everyone who cycles is familiar with the PYGA mountain bike brand that makes full-suspension mountain bikes and the only South African company to design, manufacture and build its bikes in South Africa – from scratch.
The MoBu was designed with input from PYGA Euro Steel pro-riders and Heinrich Wichmann of Blackstone Tek, who are world leaders in the production of highperformance carbon fibre wheels and components for brands including Ducati, MV Agusta, Arch, Norton, Vuhl and Ariel Atom.
PYGA are so confident in Blackstone Tek’s method and precision of manufacturing that they offer a lifetime warranty on frame and bearings.
TEKNOR Apex, a global market leader in the area of compound manufacturing, has developed a family of glass-filled engineering PP grades with E-modules that reach 11 000 MPa and a HDT that reaches 160°C.
The MoBu has uniquely engineered flex that translates into better cornering traction, forgiveness and overall ride quality. The frame holds two full size water bottles, has a lower shock mount flip-chip and will run a 185mm x 55mm length trunnion Rock Shox Ultimate on the Trail/Down country version and a 185mm x 47.5mm length SIDLux on the XC/Marathon setup.
The first 50 frames were pre-sold in 2020 and once in full production, the MoBu will remain an extremely high quality, small batch model with the anticipation that the frames will continue to be sold on a pre-order basis. Manufacturing a carbon frame without waste
The name MoBu is derived from the Sesotho word meaning “soil” or “of the earth”.
A major incentive for PYGA was to find ways to manufacture a carbon frame without the waste that traditional techniques incur. Blackstone Tek has a proprietary process that uses no air bags, polystyrene cores or polyurethane formers that need to be disposed of. Instead, they used re-usable internal formers that are the precise shape of the inside form, enabling near perfect compaction throughout the frame time after time, something that is not easily possible with current production methods. Blackstone Tek also developed a resin-system specific to their wheel production with incredible impact resistance.
Blackstone Tek’s new carbon trail bike for PYGA
In addition to a 148mm boost rear end, the drive-side is offset by 2.5mm to improve the chain-line and rear wheel stiffness while allowing the use of a standard wheel in emergencies. There’s a two bolt ISCG 05 chain guide mount and all pivots use additionally sealed double-row full complement bearings.
BLACKSTONE Tek, the largest carbon wheel manufacturer in the world, known for manufacturing the world’s first and only 100% carbon wheel, achieved something quite different when it helped PYGA to design and manufacture the MoBu mountain bike, using techniques never seen in bicycle manufacturing.
The purpose of this development was to replace glass-filled PA66 and PA6 with modified glass-filled PP in an effort to offer customers alternative solutions that have similar properties to but are more economical than glass filled PA. Advantages of the Teknor Apex engineering glass filled PP include easy to process material even through existing moulds; similar shrinkage to polyamide; a more environmentally conscious process as there is no need to pre-dry the material and the melting temperature, processing temperature, and mould temperature are all lower than those of PA; very good dimensional stability (no water or moisture absorption); good temperature resistance (130°C/3000h) and UV stabilized; superior surface aesthetics; and good laser marking ability. To date, the Teknor Apex modified PP has replaced several glass-filled PA66 and PA6 applications on existing moulds.Inone of the replacement jobs, a Teknor Apex PP GF45 grade was used to mould the cover for an AdBlue tank for a Mercedes Benz diese vehicle, substituting a PA66 GF30. AdBlue, or diesel exhaust fluid, is a liquid used to reduce the nitrous oxide emissions of diesel engines and is made up of a mixture of urea and deionized water that is sprayed into the exhaust system. Without AdBlue, it would be much more difficult to lower the emissions of diesel cars and get them to comply with the latest •standards.Advanced Polymers in the agent in South Africa www.advancedpolymers.co.zawww.teknorapex.com
PYGA Mountain bikes’ latest concept bike, the MoBu, was a project led by coowner and PYGA founder, Patrick Morewood, who wanted to build the best quality mountain bike in the world.


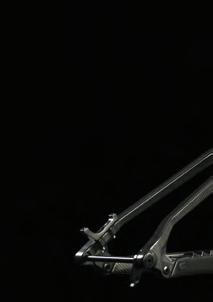
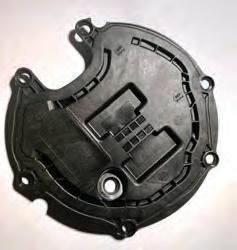
BRIEFLYJUST AUG / SEPT 2022 25 Trail setup with 130mm fork and 132mm rear and the Marathon race mode with 120mm
and 118mm rear PYGA’s
UltraPolymers is new distributor for Borealis Ultrapolymers South Africa has been appointed as the official distributor for the range of polyolefins from Borealis, this includes products from their joint venture with Abu Dhabi National Oil Company (ADNOC), Borouge. In 2021, ADNOC and Borealis announced the final investment decision for the Borouge 4 plant expansion, construction of which is underway. Borouge 4 will have a specific focus on sustainability, the partners said in a press statement. Borealis is also a leading manufacturer of materials for the wire and cable sector.
Caxton in market for Mpact too IN APRIL we reported that Caxton group had put in an offer to buy two of the Amcor Flexibles business units, in Cape Town and Port Elizabeth, only to find that the matter had been referred to the Competition Commission. The commission is due to make a decision by August. Sometimes we find these developments difficult to comprehend, as – as you probably know – it’s difficult enough finding a buyer for a business, and possibly even more difficult if the seller wants to exit the market. Now we hear that Caxton has even bigger plans in the plastics industry in South Africa, and welcome they are as the industry needs investment. Already with a 34% stakeholding in Mpact group, Caxton now wants to increase its holding to a 51% majority share. It is actually a smaller business than Mpact, with a market capitalisation of R3,6 billion compared to that of Caxton’sAccordingR4,9bn.tothe Financial Mail, Mpact listed on the JSE at R13.60 in May 2011 and went up to R49 in March 2016, its highest point, but things did not go well subsequent to that and it hit its nadir of R8 in March 2020. But the share price is now trading at about R33, against a net asset value of R26.38 a share. fork Patrick Morewood with the new MoBu
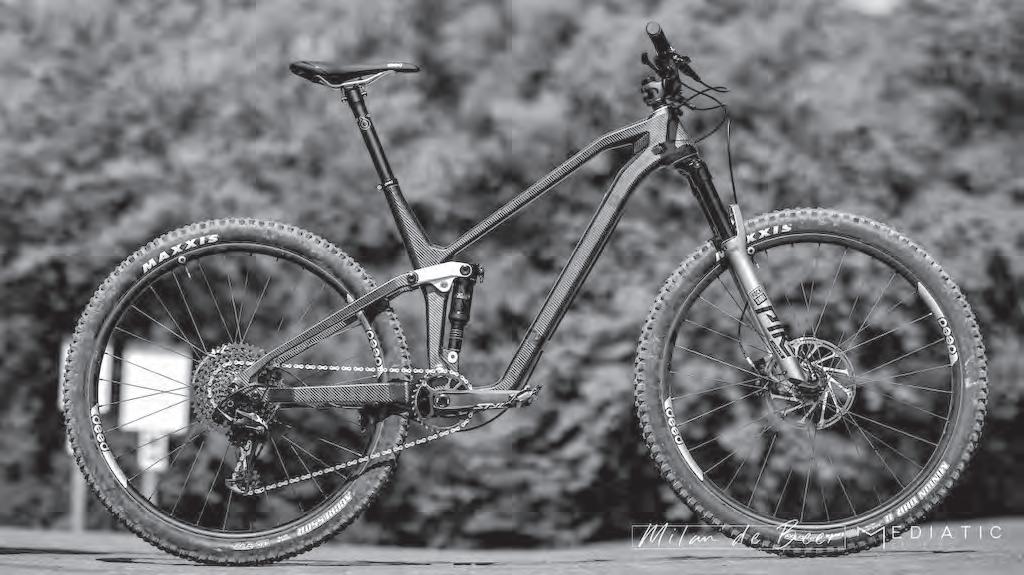
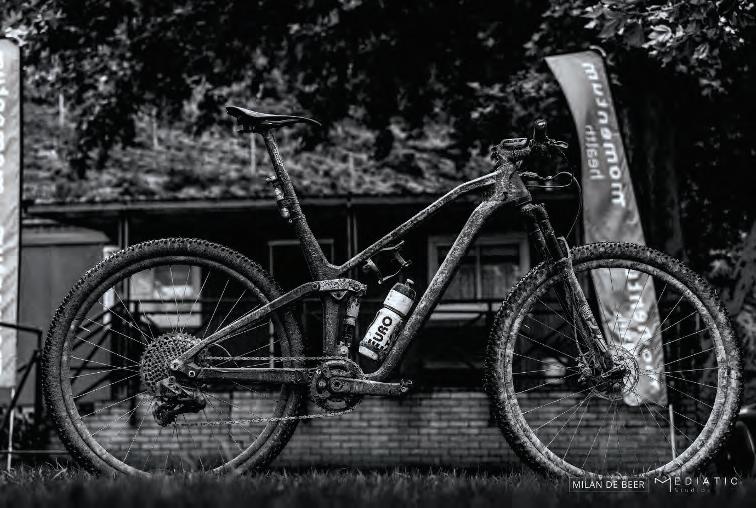
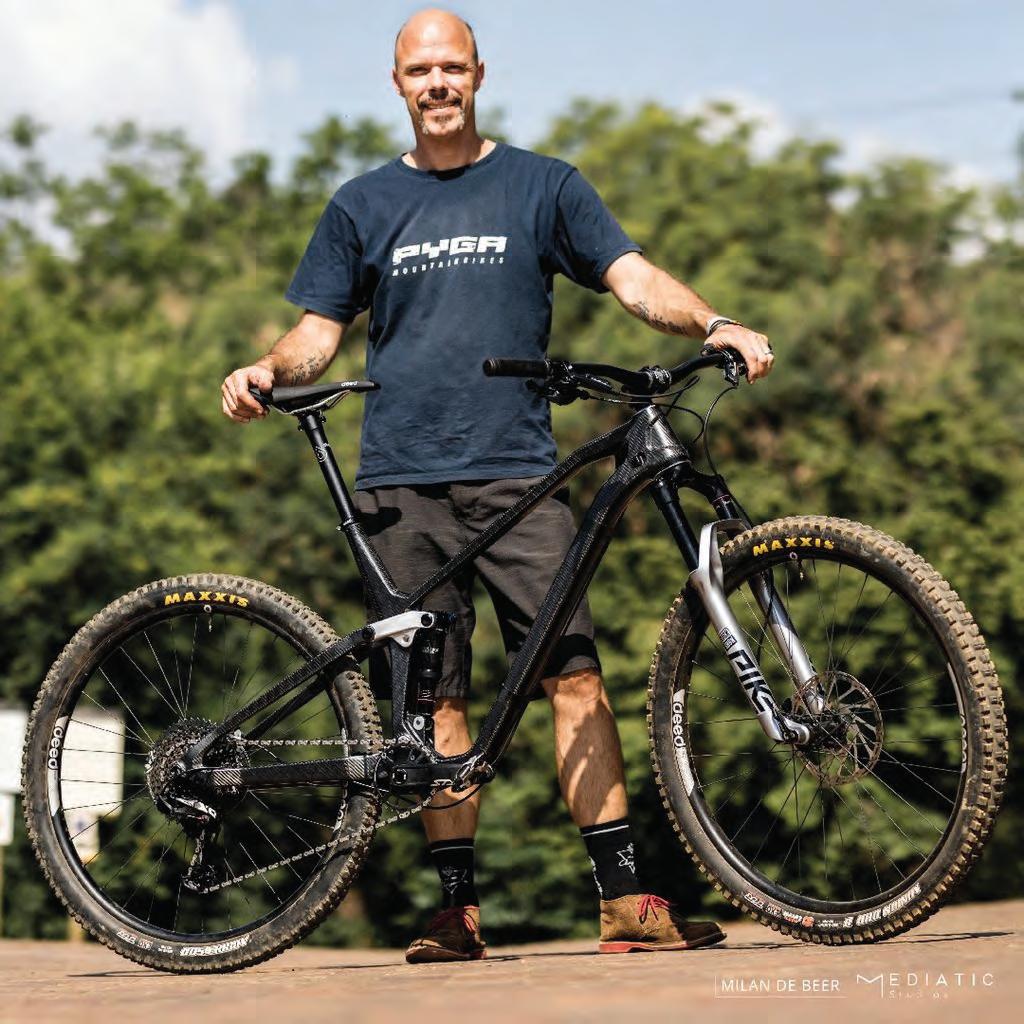
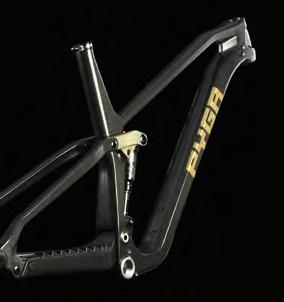
Workable solutions to mitigate SA’s energy crisis Loadshedding and interrupted power supplies will continue to be with us for a long time to come
www.fm-solutions.co.za/utility-efficiency-services/
The question arises whether home and business owners who have invested in solar panels might be able to feed their excess electricity back into the grid in order to reduce the impact of loadshedding on the rest of the country or the municipality.Petrieexplains that technically it is possible for commercial and residential property owners to feed renewable energy back into the power grid. “Small-scale embedded generators (SSEG) can get around 72 cents for every kilowatt hour pumped back into the grid via a bi-directional electrical meter. Whilst this sounds like a workable solution and an easy way to recoup the money you have spent on installing the system, unfortunately the high monthly admin fee and cost of changing over from a pre-paid electricity meter to the required bi-directional electricity meter makes it unattainable for most households or businesses,” he says. Although there still are a few outstanding details that need to be gazetted by municipalities before the purchasing of privately produced power becomes a workable reality, it could become a feasible solution in the near future. Measuring your success Government gazetted on 8 December 2020 that nonresidential buildings and organs of state must declare their energy consumption by displaying an energy performance certificate at the entrance to their buildings. This will necessitate detailed and ongoing reporting of a company’s energy usage as part of the National Energy Efficiency strategy under the National Energy Act 2008 (Act no 34 of 2008) aimed at improving the country’s energy consumption.
For more information on the energy solutions and special offers being offered by FM Solutions Technical, visit purchasingThe of privately produced power could become a feasible solution in the future.near
SOUTH Africans have become accustomed to working and living with loadshedding over the past few years.
Scheduled and unscheduled power outages have become a reality, with 1 130 hours of planned power cuts experienced in 2021 alone. Recently, the country was warned that the future of its electricity supply does not look bright and to prepare for approximately 61 days of load shedding between 1 April 2022 and 31 August 2022, depending on unplanned unavailability. Energy experts at FM Solutions recommend that companies who have been considering investing in solar power, avoid delaying this decision any longer.
“While we are not able to predict the future, we can say with a fair amount of certainty that loadshedding and interrupted power supplies will continue to be with us for a long time to come. Organisations are being impacted in productivity and ultimately profitability due to this problem. If they wish to remain competitive, they should aim to become as self-sufficient as possible,” suggests David Petrie, technical manager of utilities at FM Solutions. Prepare for higher costs, longer delays Renewable energy has become more affordable in recent years, with the cost of solar PV reduced by approximately 90% since 2000 . Unfortunately, recent global events had a negative impact on the solar industry’s value chain and negated these savings. According to Petrie, the negative impact of the Covid-pandemic, growing global demand for solar PV equipment and international shipping delays have caused a sharp increase in the cost of solar PV systems in South“CurrentAfrica.world events such as wars, pandemics and unstable economies are impacting fuel prices. This has a knock-on effect on transportation and shipping costs. South Africans have the added burden of being reliant on fuel to keep their generators running during load shedding. On the other hand, our country’s power utility also relies on diesel to supplement the electricity demand during peak times and when coal supplies are insufficient – necessitating the 300% increase in electricity tariffs we have seen over the past ten years ,” he explains. Unfortunately, it appears as if there is currently no quick and easy way to escape this conundrum. South African businesses and homeowners wishing to install solar-powered systems should prepare themselves for long delays before they will finally be able to unshackle themselves from erratic supply and surging electricity tariffs. Feeding solar energy back into the grid
26 AUG / SEPT 2022 NEWS

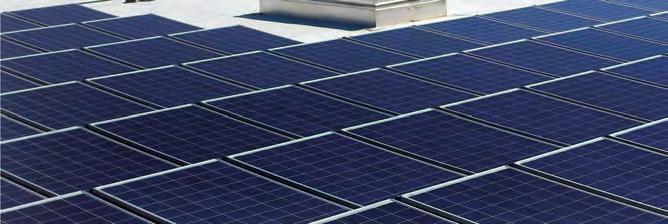

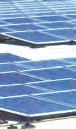
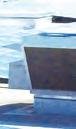
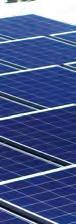
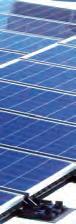
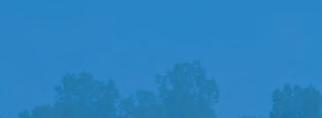
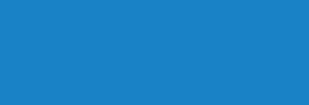
www.carst.co.za POLYMERS DIVISION Our Winning Formula Sets Us Apart ELASTOMERS SBRPVC/NBRNRNBRIRHTVHNBRFKMEpichlorohydrinEPDMCRACMSiliconeBlends&BR PLASTICS & COMPOSITES TPUTPEPVCPCNylonHIPSEVACSMCPECompositesAdditivesAcetalABS&GPPS&TPV FILLERS & ADDITIVES AntimonyAluminas Products Blowings Agents Carbon Blacks Flame ZincSulfurSilicaSilanesRubberProcessPeroxidesMineralMCMasterbatchesMagnesiumHydrocarbonRetardentsResinsOxide&PEWaxesFillersAidsChemicalsOxide AUXILIARIES & SERVICES SparesReleaseReleaseOtherMachineryServicesAgentsliners ANCHOR CHEMICALS Batch TollProcessMasterbatchingFacticeCoatedBondingOffSystemsPowdersAidsMixing Johannesburg (T)011 489 3600 Durban (T)031 313 8500 Cape Town (T)021 506 4598
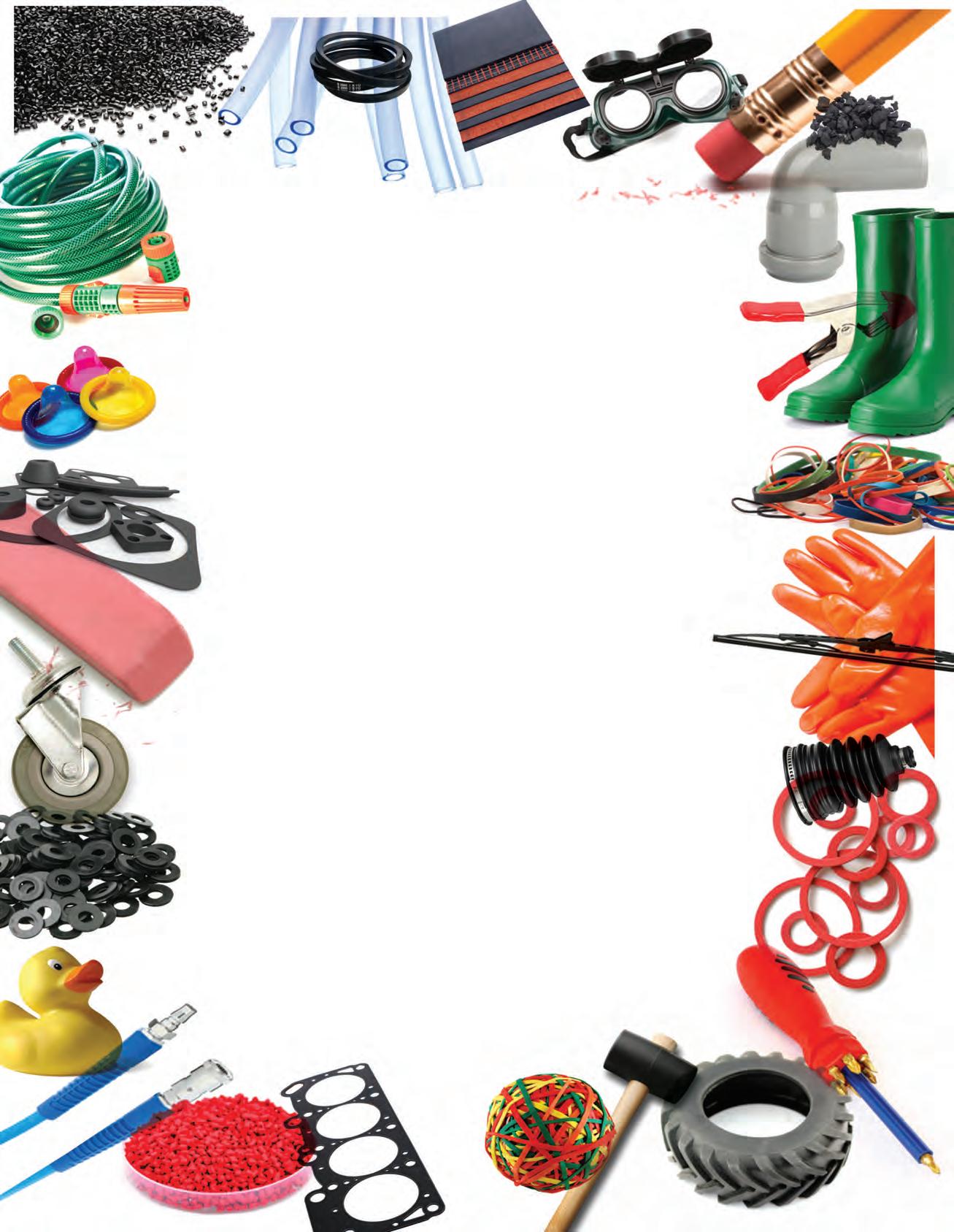

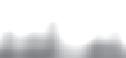
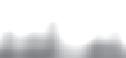

Pact has also recently commissioned one of the biggest PET recycling plants in Australia, at Albury-Wodonga in Melbourne. The $45 million venture is helping to build a domestic circular economy along with increasing the amount of locally sourced and recycled PET in Australia by two thirds, from around 30 000 tons to over 50 000 tons perBesidesannum.recycling, which is a big thing in Australia at the moment, our correspondent Down Under says the business environment there remains tough.“Our proximity to Southeast Asia means barriers are low and cheap imports an issue. As a result of Covid many businesses and brand owners opted to ‘re-onshore’ some activities/purchases (to be less dependent on SEA). And this year has seen significant attempts by convertors to try and pass on massively increased costs and of course this is never a fun exercise.”
DEVELOPMENT finance institution, the International Finance Corporation (IFC), is providing a $30 million loan to emerging markets integrated waste management company Averda, to support waste management, and part of the loan is being used to fund the construction of a new plastics recycling plant in Rosslyn, Gauteng.
SAVA is now Proudly South African
JUST BRIEFLY COMPOSITES
Laser technology ideally
Tampoprint’s in-depth process knowledge in industrial product printing and marking, allows focuses on the interaction of all procedures and system components in
Pact group in Australia buys competitor, opens big rPET plant PACT Group of Australia, one of that country’s biggest manufacturers of rigid packaging, has recently purchased Synergy Packaging, a manufacturer of PET and rPET containers, from Berry Group, the international operation which is involved in South Africa too.
The loan is expected to help deliver climate change benefits through private sector-led integrated waste management services.
28 AUG / SEPT 2022 World-classGreenTechquality
GreenTech offers printing technology, which includes laser systems, manual workplace and automated platform solutions as well as accessories, from the globally renowned Tampoprint brand
Part of this loan is already being used and supporting several of Averda’s existing sustainable waste management projects in South Africa, Oman and Morocco. “Locally, most of the investment has been used in the construction of a new plastics factory in Rosslyn, creating 50 new jobs,” says director of Averda South Africa, Chris O’Neill.Theloan will help Averda dramatically accelerate other sustainability projects, enabling Averda to reduce waste sent to landfills, while increasing the volumes of waste composted, recycled and converted into energy, and advancing South Africa. South towards a more circular
Construction of a new plastics factory in Rosslyn will create 50 new jobs GREENTECH Plastics Machinery is an end-toend product and service solutions provider to South Africa’s plastic injection moulding and packaging industries. “Thanks to our partnerships with leading global companies, we are able to offer customers a wide range of premium brand plastics machinery, ancillary products and accessories from Europe,” says GreenTech business development manager, MartinGreenTechHollinger.offers printing technology, which includes laser systems, manual workplace and automated platform solutions as well as accessories, from the globally renowned Tampoprint brand. Based in Germany, Tampoprint is a leading manufacturer and supplier of standardised and customised pad printing and laser automation system solutions for many different and complex fields of application in beverage, medical technology, toy, tool, automotive, sports and electrical industries.
THE Southern African Vinyls Association (SAVA) has taken up membership with the country’s official “Buy Local” campaign, Proudly South African. Explaining the reason for the move, Monique Holtzhausen, CEO of SAVA says South Africa has a dynamic and burgeoning vinyls manufacturing sector that stands to benefit from displaying the Proudly South Africa logo as a recognised endorsement of local content and quality. It makes business sense for us as a company to be affiliated with the country’s “Buy Local” movement. orwww.proudlysa.co.zawww.savinyls.co.za
Averda to build plastic
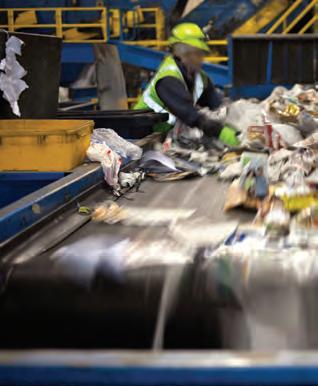
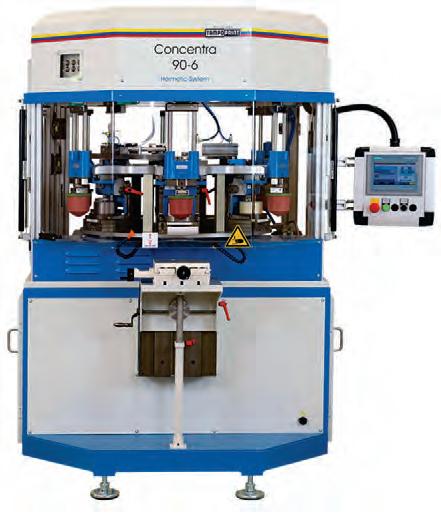
29
www.greentechmachinery.co.za
GreenTech supports the complete Tampoprint portfolio of machines, components, consumables and printing technology accessories with professional advice and services provided by the company’s highly trained and skilled team of technicians.
Permanently laser-individualising of products with graphics, texts, and various data codes can be done efficiently, quickly and easily.
Tampoprint laser technology is ideally suited for creating variable markings on the inside and outside of closure caps. Owing to the use of ‘iTAMPOPRINT’ software, the workflow from the creation of the motifs to the marking is purely digital. A further benefit of the software is that the user is only required to make a few technical settings during implementation, saving valuable time on the production floor.
BRIEFLYJUST suited for variable markings on inside and outside of closure caps 2022 the printing process. In addition to high-precision individual components such as pad printing and laser machines, software, process-critical accessories and consumables, which are manufactured in Tampoprint’s own production facilities, the company also provides complete process solutions.
printing technology from PlasticsrecyclingMachineryplantinRosslyn
www.averda.com/rsa AUG / SEPT
Tyre tariffrequestmanufacturers’foranti-dumpingiscomplex
Hollinger wraps up, “Our strategic network in Gauteng (HO), Kwa-Zulu Natal, the Eastern and Western Cape as well as in Sub Sahara, puts us at our customers‘ doorstep, ensuring seamless product and service delivery.” economy, he adds. “With the new plant, which will be operational by the end of the year, we aim to process up to 12 000 tons per year of high-density polyethylene (HDPE) and low-density polyethylene (LDPE) by converting them into reusable polyethylene, Grade A plastic pellets, with volume production beginning in the first quarter of 2023,” O’Neill notes. These pellets will be used by Averda customers to re-mould or extrude new products. Averda will also operate a materials recovery facility where source-separated recyclables will be further separated and where some of the incoming plastics will come from, which will be used for the plastics plant, O’Neill adds. Averda started operating in South Africa in 2015. Through a combination of acquiring and integrating existing businesses, including a healthcare waste company and an existing collections company, and targeted investments to develop its own facilities and services, Averda has built a country-wide business able to provide end-to-end waste management and recycling solutions for most types of waste.
The SATMC has approached ITAC to request that duties of between 8% and 70% be applied to manufacturers in China. But it’s going to be a difficult matter to resolve. For instance, Continental and Goodyear in SA import the bus and truck tyres they supply, so they would effectively be asking for duties against themselves, and Goodyear China is effectively opposed to Goodyear SA’s application.
“The advantage for us in partnering with such an industry specialist is that we are able to meet our customers’ individual and highly diverse demands,” notes Hollinger.
Data from the SATMC shows that there has been a steady decline in local production of tyres in South Africa, from about 10 million tyres produced in 2016 to about 6.5 million in 2020, which is a massive deterioration. Tyre exports from SA are down too, from just more than 1.5-million in 2019 to 1.3-million in 2020, revealing a steady decline in total local production by the local manufacturers, Bridgestone, Continental, Goodyear and Sumitomo. All of these manufacturers are part of global tyre making groups and it is logical to conclude that their selling pricing would be based on international pricing strategy.
THE application by the Tyre Manufacturers Conference in South Africa for anti-dumping duties to be placed on tyres imported from China has been met, not surprisingly, with stiff resistance from the Tyre Importers Association, with the latter trundling out all sorts of data and stats to show that this would hugely inflate costs, for both drivers and the road transport industry as a Butwhole.aretyres from China being dumped in this country? The definition applied by ITAC (International Trade Administration Commission) for dumping is focussed on whether a manufacturer is selling in foreign markets at lower prices than it can achieve in its domestic market, but these figures are also subject to viarables and price sways, so dumping has come to be defined as selling in foreign markets at prices that are considerably lower than manufacturers would obtain in their local markets and substantially undercut manufacturers in the destination market.
Turning to the quality of the Tampoprint range, Hollinger says that this premium brand delivers unrivaled reliability and subsequent product longevity. “The valueadds for our customers are reduced maintenance requirements leading to low operational costs, high uptime, increased production levels, low total cost of ownership and ultimately, sustainable operations.”

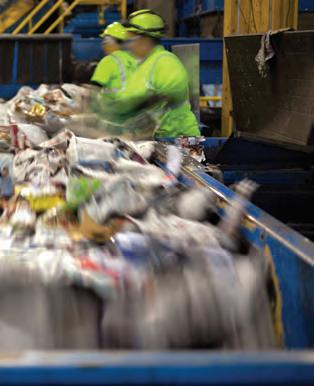

runnerslocalPC&TpreferredMold-MastersbusinessesthisCockramproducts,”Mold-Mastersheadds.Induecourse,believesmayencouragetochooseastheirsupplierofhot-runners.alsohavetheskillstosupporttoolmakersinsourcingtherighthot-fortheirtools.
“This would mean that we keep common spares here in South Africa, or efficiently manage the sourcing of critical spares from Canada. It would mean we have technicians who can service and troubleshoot hot-runners,thethecontrollers,and the E-Multi units or any other
Able to supply the type of tailored support to keep them running
PC&T now keeps common Mold-Masters hot-runner spares in South Africa, and also efficiently manages the sourcing of critical spares from Canada It meanwouldwehave technicians who can service and troubleshoot the hot-runners, the controllers, and the E-Multi units or any other productsMold-Masters
NEWS PC&T
PLASTIC and Chemical Trading (PC&T) now offers an active and tailored service to all users of Mold-Masters hot-runners in South Africa. PC&T was recently appointed as the agent for machines.injectioncontrollersspecificallyandequipmentplasticmanufacturesMold-Masters,Canadian-basedwhichprocessingsystems,hot-runners,temperatureandauxiliaryandco-injection“Wewanttoofferanactive and tailored service to all users of MoldMasters hot-runners. SA businesses may buy moulds from local toolmakers or elsewhere in the world, but if they arrive here with Mold-Masters hot-runners in them, we aim to able to supply the type of tailored support to keep them running,” says Ben Cockram, PC&T owner. “We have the skills ready to be developed to offer this sort of service and we are available if anyone needs support,” Cockram adds. PC&T already supply the Mold-Masters E-Multi Units to businesses who need to upgrade a machine to be able to make 2-K parts. This is an important part of the business for PC&T and is also important in its quest to be relevant to its customers as a solutions Mold-Mastersprovider.patented the first commercially viable hot runner system in 1963. Today, the Mold-Masters hot runner product line has expanded and represents the broadest selection of hot runner products from any manufacturer. to offer tailored service for all Mold-Masters hot-runners in SA
30 2022SEPT/AUG
www.plastrading.com www.moldmasters.com
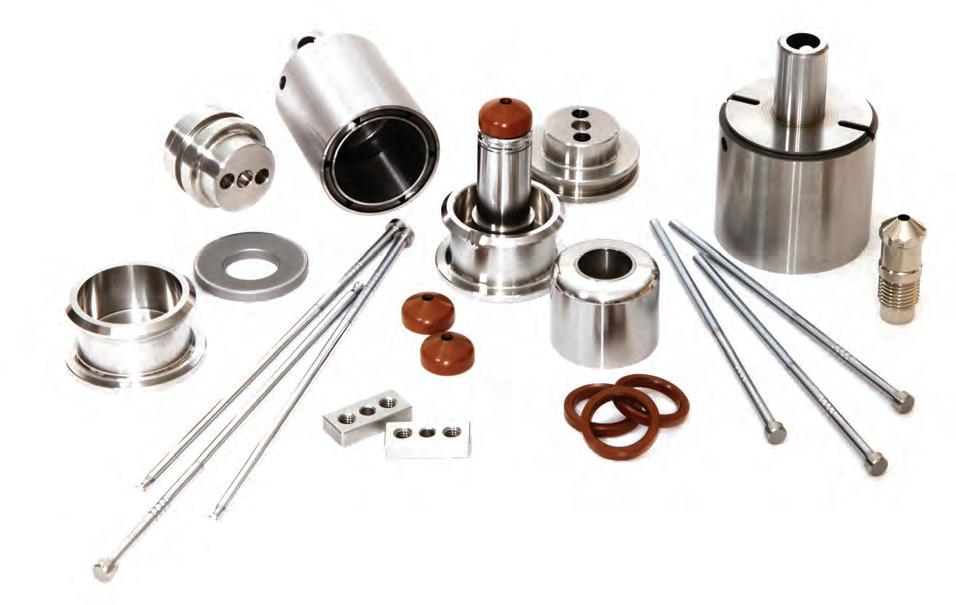
2022SEPT/AUG 31
USA
IN WHAT must rate, internationally, as a unusual precedent, the USA’s Plastics Industry Association has filed a lawsuit in a federal court against its former CEO, Tony Radoszewski, alleging he violated his employment contract.Thegroup filed the suit in the US District Court in Washington, DC, alleging that Radoszewski, who was its CEO from September 2019 until he was fired on 25 March 2022, collected a relocation bonus in his contract but did not move from his home in Texas to the PIA head office in Washington as was requested in his employment contract and also owes at least $163,000 in improperly paid expenses. Radoszewski had previously filed a lawsuit in May in state court in Texas seeking more than $609,000 in severance payments as well as a similar lawsuit on 11 July in in Dallas. He argued that his employment agreement did not require him moving to the Washington DC area and, since his contract was being terminated without cause, he was owed his $546,000 annual salary, a $30,000 bonus for 2021 and other monies. The end of Radoszewski’s tenure had been rocky, reports the USA publication PLASTICS NEWS, with several key staff leaving and some association member companies saying they had become concerned about staff upheaval and the direction of the association. COCA-Cola is eliminating the use of green PET in North America, a move designed to help boost bottle-to-bottle recycling. The use of green PET for beverage containers has long been a topic of discussion within the plastics recycling sector. Recyclers collect and reprocess green PET, but the resin has to be separated from clear PET containers to avoid colour contamination. The segregated PET is often used for non-bottle applications such as strapping and carpeting.
witinassociationtradedisputehCEO
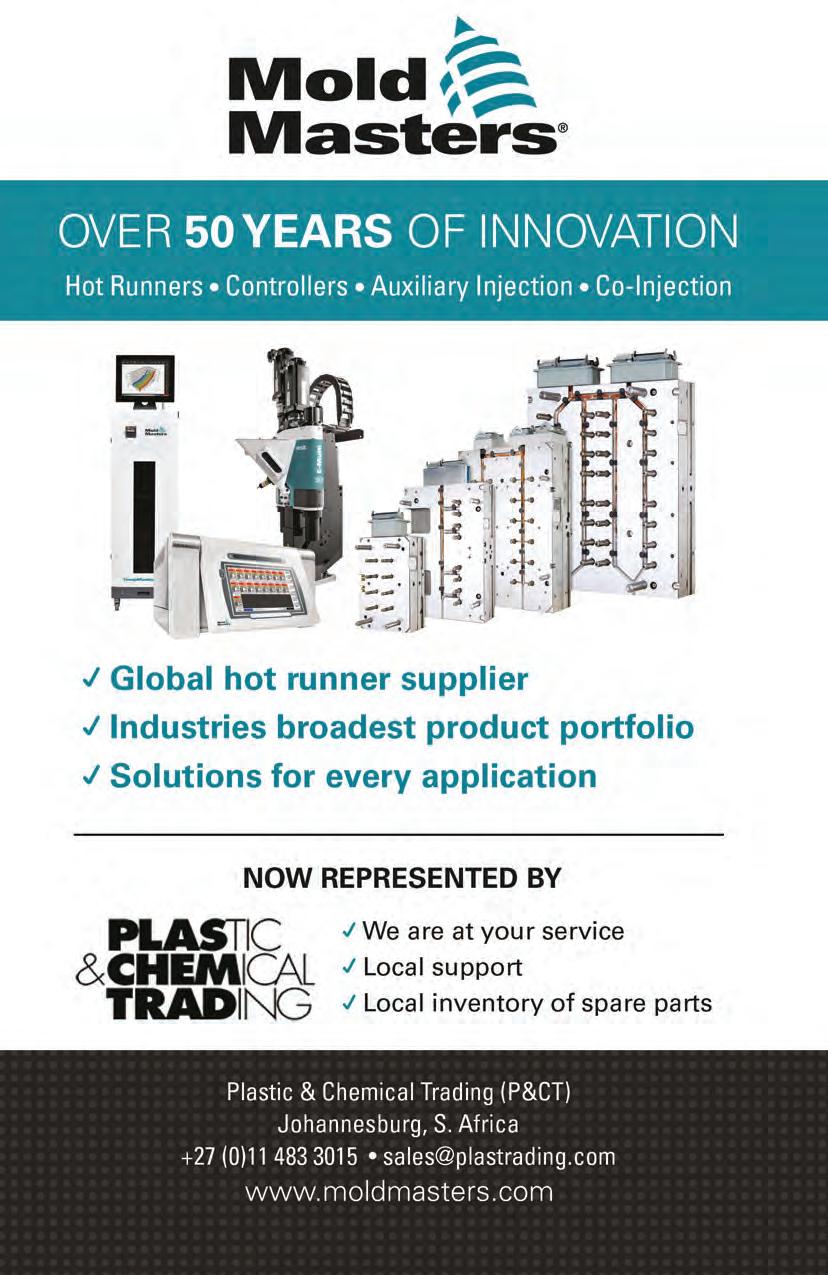
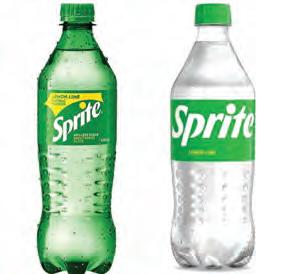
Hestico is celebrating 60 years of active operation this year, almost certainly making it the oldest equipment supply business in the industry in South Africa. At the time of its founding in May 1962, the purchase of production machinery was a difficult undertaking for convertors since most of the equipment was imported from Europe.
32 2022SEPT/AUG NEWS
Many of
Played important role in development of plastics manufacturing industry in SA Hestico celebrates 60yrs
Forget about email and the internet, those days were even pre-fax! The efficiency and reliability with which the company’s founders handled this responsibility helped get many of the convertors of that era – many of whom were completely new to plastics – off to a good start. Providing quality machinery at fair prices with reliable back-up still forms the core of the service that Hestico provides. Hestico was founded in Johannesburg by Herman Ernst Stiegler, who had immigrated to SA from Germany, and Conrad Niehaus. At first the company operated as CF Niehaus & Co, but that changed in 1970 when Niehaus left and Herbert Seitz joined, creating Hestico, being an abbreviation of these gentleman’s names. From inception the company’s sole activity was the supply of machinery to the plastics and rubber industries, and the partners managed to gain the agencies for some top-flight European machine manufacturers, the first of which included Werner & Pfleiderer, Berstorff and Mann + Hummel. Stiegler was integral to the early success of Hestico. Besides the fact that he was a popular and gregarious man, he also oversaw the implementation of the systems that enabled the company to operate effectively. Most important of these was the system to provide technical back-up to users of machines it supplied and doing so in a professional and convincing manner. As the company grew, more agencies were added, including that of tooling component/hot runner maker D-M-E of Belgium.
The Johannesburg team includes (back row) Lourens Erasmus, Ernest Green, Daniel Strydom, Rita Venter, Shanitha Wade, Tasneem Syed, Vicky Ackermann, Monique van Eeden, Liesl Lottering, Ivan Forrest, Tshidi Mokaba, Andries Bosman, Michael Mahlati and Juanita Stiehler-Brits; with (in front) Raymond Sinclair, Christiam Manamela and Erot Shivuri
PLASTIC and rubber machinery supply business
Extensive inventory Besides its comprehensive customer services and well trained team of technicians, from the start Hestico maintained an extensive inventory of spare parts at its customised premises in Kew, Johannesburg. This enabled the company to offer efficient technical support.Hestico has exclusive agreements with a number of top international OEMs, and its technicians are Siemens OEM qualified. With this high level of service, the environment at Hestico was in some cases a ‘training ground’ where a number of technicians
Hesticoindividualstheatlaterswitchedtotheconvertingsector,helpingbuildtheindustrytowhatitistoday,ahealthyworld-classoperation
Kelvin currentBritsJuanitaFrancisMills,YuandStiehler-(Hestico’sMD)in Korea finalizing the 2011arrangementYudoAbiman/shareholderin One of the strengthscompany’shasbeenthefactthatithas maintained offices in both Durban and Cape Town. The KZN team includes Victor Stiehler, Craig Knight, Estie de Beer and Siyabonga Goge

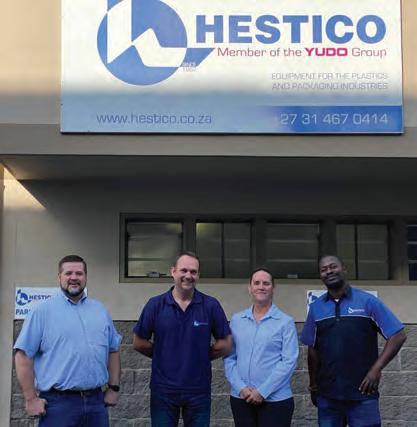
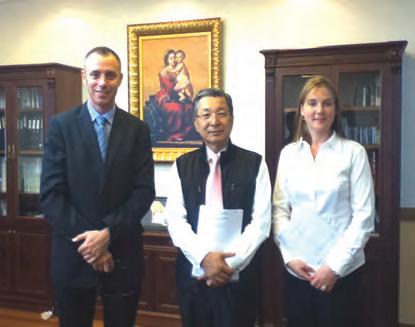
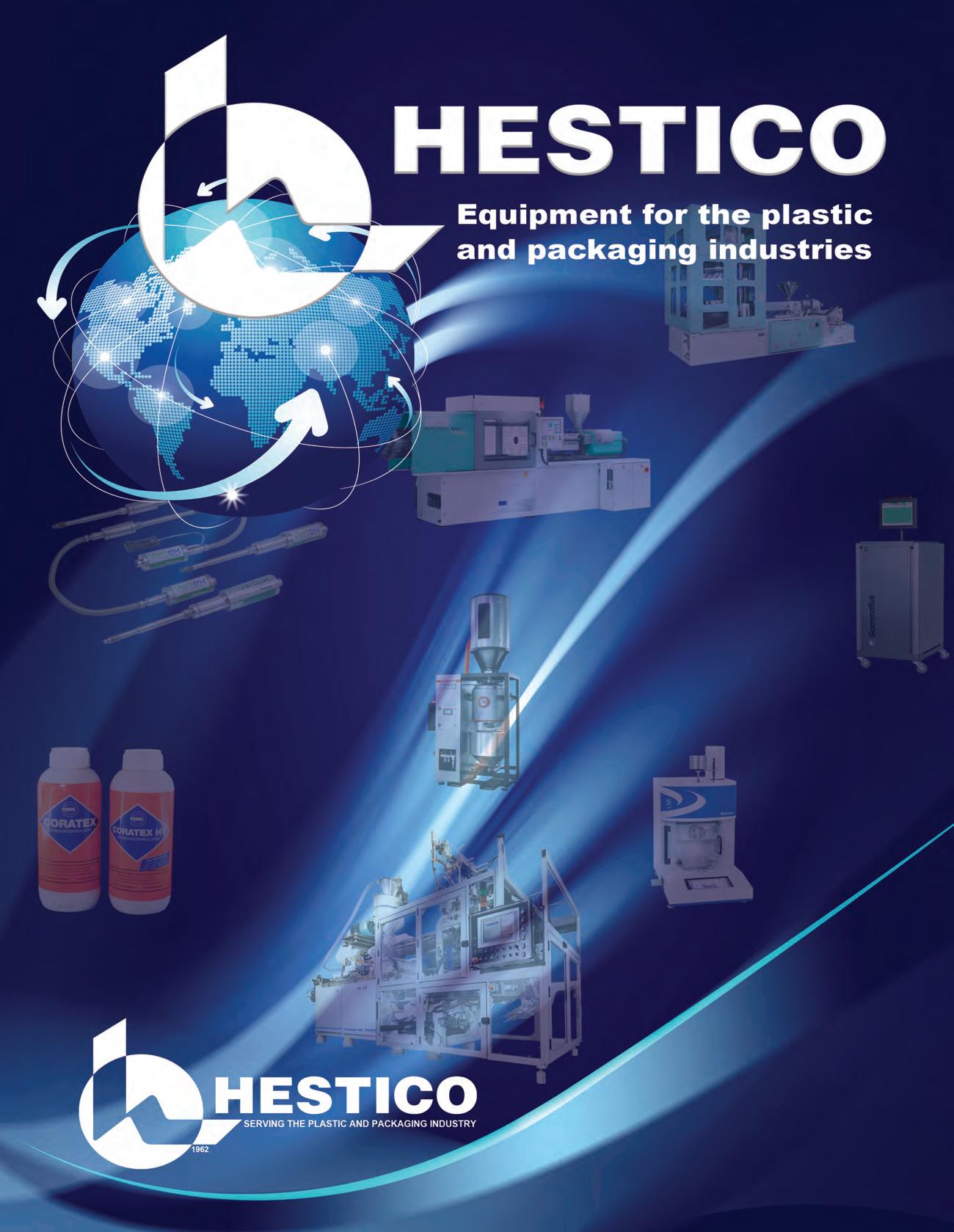
SINCE Durban Telephone:Office+27 31 467 0414 Email: dbn@hestico.co.za Cape Town Office Telephone: +27 21 510 8322 Email: cpt@hestico.co.za Johannesburg Head Office Telephone: +27 11 786 5228 Email: nickie.s@hestico.co.za www.hestico.co.za Injection moulding machines Purging agent Injection stretch blow moulding machines Cooling water flow Blending,regulatorsdryingand central feeding equipment Blow UltrasonicGlobalmachinerymouldinghotrunnercontrolsolutionsweldingRecycling and grinding Loaders and dryers Melt pressure and instrumentationtemperatureMould components Plastic auxiliary equipment Robotics and equipment.ancillary Mould components Extrusion blow headsmoulding Extrusion and equipmentrecycling Vacuum forming machinery Polishing and filing machines
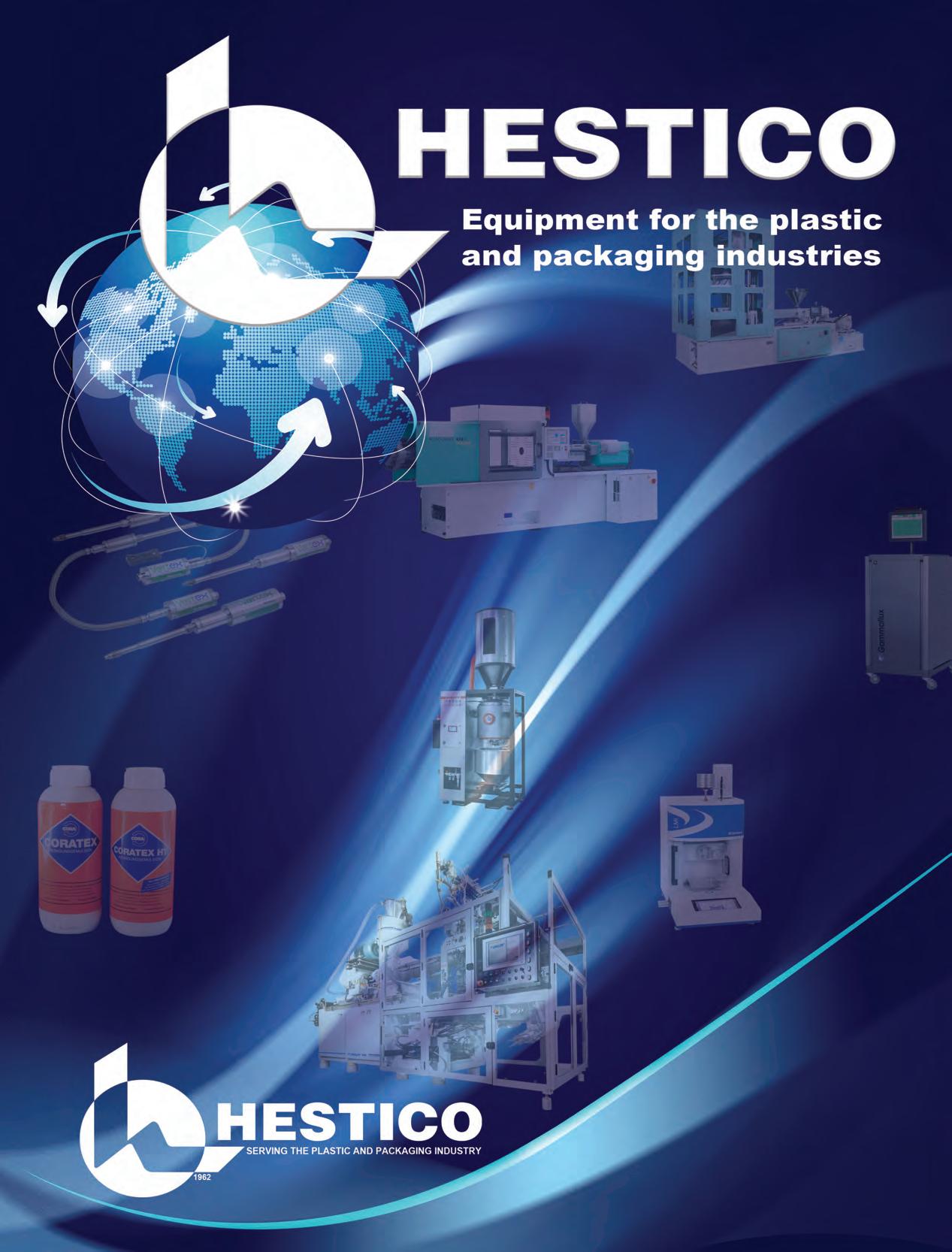
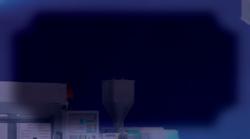
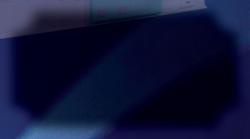
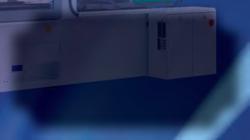
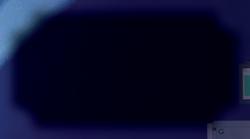

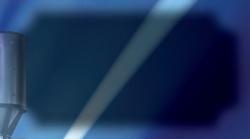

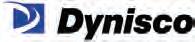
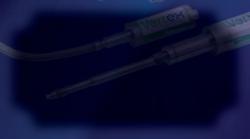
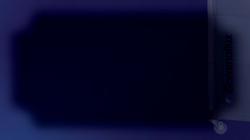
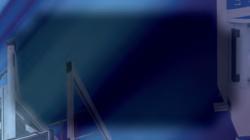
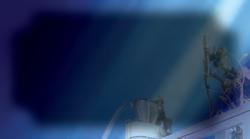
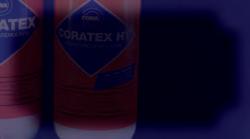
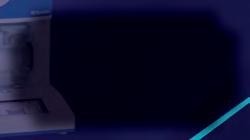
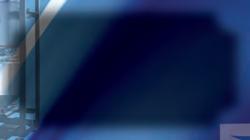
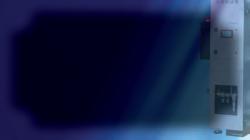
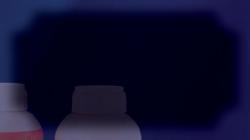
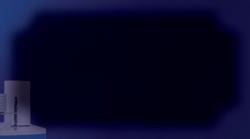
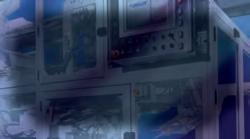

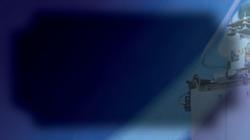
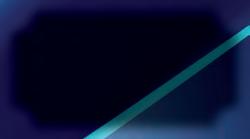

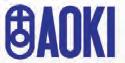
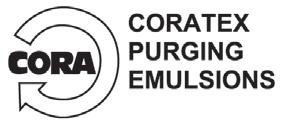
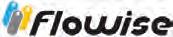

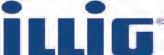
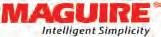
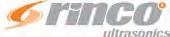
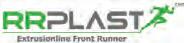

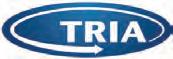
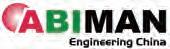

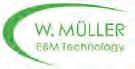


1974operation.wastobecome
enjoyed the opportunity to work on high-standard converting equipment. Over the years, the Hestico team has included individuals who – with the acquisition of such skills – went on to become respected field service technicians in their own right. And quite a number of these individuals later switched to the converting sector, in the process helping build the industry to what it is today, a healthy worldclass one of Hestico’s standout years: Heiner Wolber joined as sales engineer, also tasked with sales of D-M-E and related products. Heiner actually spent the rest of his career at theBycompany.thistime the company had grown and was employing nine people, operating from premises in Richard Street, Selby. Durban, Cape Town Up till that time Hestico had operated solely out of Johannesburg, but in 1978 it started cooperating with Internatio, a Dutch group involved in machinery and material sales which operated outlets around the country. Internatio from then acted as a sub-agent in Durban and Cape Town, selling and distributing Hestico’s range of products. In 1981 Fritz Kettner and Heiner Wolber became directors and shareholders, paving the way for one of the company’s heyday periods. Kettner specialised in the supply of Illig thermoforming machines, which are stillUnfortunately,popular.
Setters, technicians, production managers and others have benefited from the injection moulding workshops presented by Eduard Stückle of Arburg of Germany, sponsored by Hestico
The Cape Town team includes WilliamJunaidJohnstone,Jacobs, Zaytoom Simons and Lukas Prinsloo
34 AUG / SEPT 2022 NEWS ...continued from page 32
Hermann Stiegler died after a heart bypass operation in October 1985. So ended the career of one of the best known individuals in the industry in South Africa, a man whose accomplishments also included involvement in the setting up of the Plastics Federation of South Africa. Herbert Seitz took over as MD from Herman. Later that year, Herbert’s son Wolf Seitz joined Hestico as a sales engineer. In 1988 the company purchased a 3000m² property in Kew and built its own premises. It moved there in 1989 and has remained there since.The tie-up with Internatio had an unexpected spinoff in that, after the Dutch group closed its plastics machinery division in South Africa in 1990, the Internatio managers in Durban, June Smith, and Cape Town, Gerhard Greiner, continued working with Hestico. Greiner, along with some Internatio staff, joined Hestico in Cape Town. The Cape branch became a separate company, Hestico Cape, with Greiner as MD. June Smith took over responsibility for management of Hestico in KZN. Smith and Greiner, who both remained with Hestico for the rest of their careers, helped establish Hestico’s presence in the two coastal cities. Arburg Hestico also inherited the agency for Arburg injection moulding machines from Internatio, a machine line which was to become one of its most popular. Various other agencies, namely Rinco ultrasonic welding equipment and Madag printing equipment, also came to Hestico as a result of Internatio’s departure.Bythistime Hestico had become the biggest plastics machinery supplier in South Africa, with a staff of around 40. Herbert Seitz retired in 1992 and Heiner took over as MD. Then, in 1997, Hestico merged with Affirm Machinery Sales. This was essentially the renamed entity which Peter Hengst had started when he had left Hestico and formed Bekum SA in 1976. Hengst had, during his absence, achieved considerable
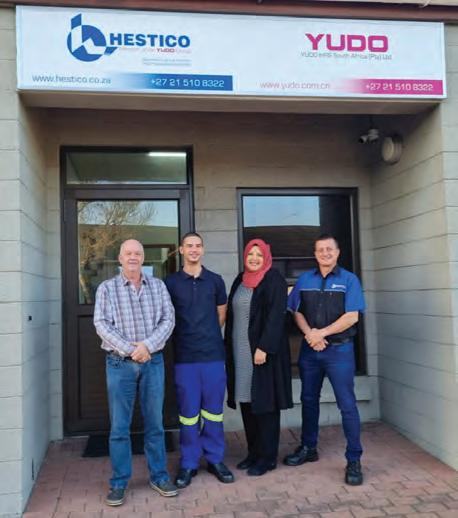
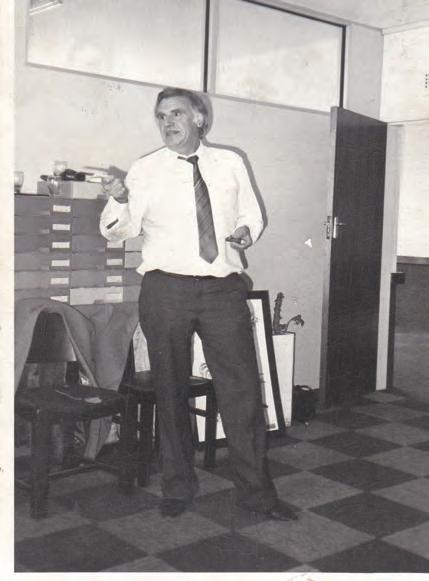

Gerhart Greiner ran Hestico’s Cape Town office for a number of years, very successfully
Hestico’s founding strategy included agreement that directors and staff had to depart on reaching the age of 60, and this clause resulted, obviously, in several individuals moving on. One notable departure was that of the popular Fritz Kettner, who left at the end of 2002 and moved with his family to Austria. That in turn resulted in Juanita becoming a director and shareholder. The wheel, as always, kept on turning and the next to arrive was Kelvin Mills, who signed on in 2004, with the intention of taking over from Peter Hengst. Kelvin had worked in the blow moulding area and was well suited to sales of this equipment. Following Hengst’s retirement at the end of 2004, Kelvin took over responsibility for blow moulding. He became a director in Further2006. evolution was in store too, however. At the K show in Düsseldorf in 2010, discussions with one of Hestico’s top principals, hot runner manufacturer Yudo of Korea, resulted in the Yudo buying a stake in the SA company. This resulted in Yudo CEO Francis Yu becoming chairman of Hestico following the retirement of Heiner Wolber in March 2011. Juanita was then appointed managing director and Kelvin to director. Kelvin subsequently opted to return to the converting sector, in 2014, leaving Juanita at the helm, and it’s got to be said that she has managed serenely since, with Hestico sticking to its business model and principles and continuing to support its customers around the region.
Congratulations to the Hestico team! AUG / 2022 35 www.hestico.co.za
The outcome of this international participation opened opportunities for Hestico, not least as far as trade with the Far East was concerned. Although it has over the half-century supplied mainly European brands, Hestico has over the past decade been supplying far more equipment from China and Taiwan, falling in line with the many competitors selling machines from the Far East.
SEPT
Affirm’s entry to the group signified the acquisition of several important new agencies for blow moulding equipment, including Aoki of Japan (ISBM) and Uniloy (blow moulding and structural foam machines). In 1998 Juanita Stiehler-Brits joined Hestico as a sales engineer, responsible for sales of Arburg machinery as well as certain downstream equipment.
It can safely be said that Juanita and the Hestico team have set a high standard and backed up the equipment they supply in an efficient and convincing way throughout.
Other highlights Besides this chronology, Hestico has created opportunities for many people in the industry in a number of other ways, including its donations of machines to PlasticsSA (formerly the Federation); the hosting of technical workshops (specifically by Arburg); and hosted visits by representatives of the global companies which it represents, who on many occasions gave presentations to industry gatherings and also imparted their knowledge to guests at the Hestico stand at trade shows over the years, including the Propak Africa, Propak Cape and other events.
success with the sale of Bekum blow moulding machines, which in the 1970s and 80s were the standard for container production in SA. Affirm had a strong presence in the blow moulding market, one of the only areas where Hestico was not involved. Hengst became a shareholder of what had, with the formation of Coprah Investment Holdings, effectively become a business group. Hestico, Satcor and Affirm Machinery Sales fell under the holding company.
There was also time to relax, here Crystal Hengst, Horst Seute, Herbert Seitz and Heiner Wolber enjoy a social function at the German Club
Hermann Stiegler, founder of Hestico in 1962, was an entertaining and foresightful man who was also involved in the establishment of the Plastics Federation of SA, what is now PlasticsSA
The Hestico offices in Kew, Johannesburg, which the company built in 1981, don’t look very different today, seen here with a state-ofthe-art sedan of the era. The premises have been expanded and now feature an extensive workshop and parts storage area

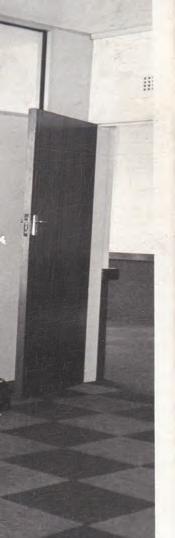
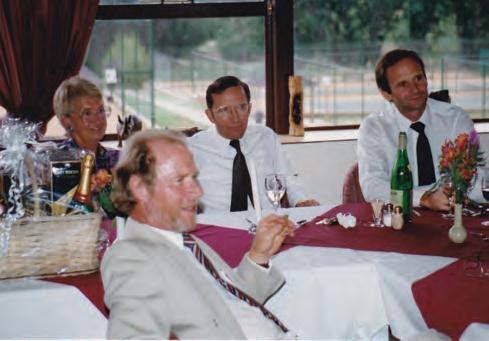

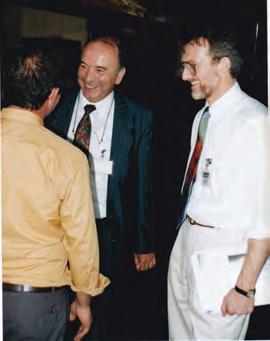
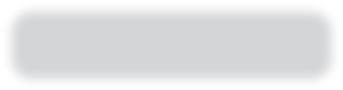

CAPE roto moulder 4EVR took centre stage at the prestigious Red Dot Design Awards in Germany in June when it won a top award for its new EdgeOut camper-trailerDesignedand manufactured in South Africa, the EdgeOut camper-trailer is a world-first roto moulded solution suitable for use on tar and gravel roads, with just one of its standout features being that it is relatively lightweight – coming in at less than 750kgs – which allows it to be drawn by standard saloon cars. The Red Dot Design Award programme – organised by the Design Zentrum Nordrhein Westfalen in Essen, Germany – is an international design competition for product design,
tanks, agricultural containers, marine/ aquaculture and jetty parts, Jacuzzis and related large mouldings. EdgeOut came about virtually by surprise when, on a camping trip to the Cederberg, a friend asked Vonnie, ‘Why don’t you roto mould a caravan?’ He hadn’t thought of that, but a seed was sown, and a dream was born. Heyns researched the basic design, with the basic concept being two seamless pods in a teardrop shaped trailer. Having worked with Retief Krige on projects before, the Stellenboschbased designer was the logical choice to cooperate with the design development. The design consists of two separately moulded units, being a sleeping cabin and a compact, well-equipped cooking and entertainment area (kitchen) at the back. The individual units – or ‘pods’ –are seamless (which means no leaks) and aesthetically secured together and mounted onto a galvanised steel chassis. The robust unit sleeps two, but a rooftop tent offers the option to sleep two more.
Cape roto moulder recognised by Red Dot Design award
Organic bushveld colours have been selected for the EdgeOut caravan, which appear to be proving popular as the units are selling well. So well in fact that 4EVR has what is virtually a production line running at its plant in Blackheath in the Western Cape
4EVR Plastic Products, one of the oldest Cape roto moulding businesses having been started in 1975, has been owned and run by Vonnie Heyns and Simon Botha since 2008, following which, if anything, product development abilities and efficiencies have been firmly embedded at the Blackheath-based company. The comparatively short threeyear development of the EdgeOut trailer and the accolades it has drawn have thus come as no surprise. Before this latest project, 4EVR specialised in the production of
NEWSInt’l design award for
36 AUG / SEPT 2022
fromcamper-trailerEdgeOut4EVR
EdgeOut’s insulated sleeping cabin features an array of cleverly located overhead cabinets and various shelves and cubbyholes that provide an communication design and design concepts which has garnered global recognition, largely due to the success of many of the winning designs it has recognised. 4EVR received the award in the category Product Design category, which attracted 7,900 entries from 60 countries from across the world. With this award, EdgeOut finds itself in the company of global groups such as Ferrari, Philips, SiemensLenovo,Google,HPandandnow has the approval to use the coveted Red Dot seal as an acknowledged and revered international seal of outstanding design quality.
Why don’t you roto mould a caravan?’ He hadn’t thought of that, but a seed was sown, and a dream was born.
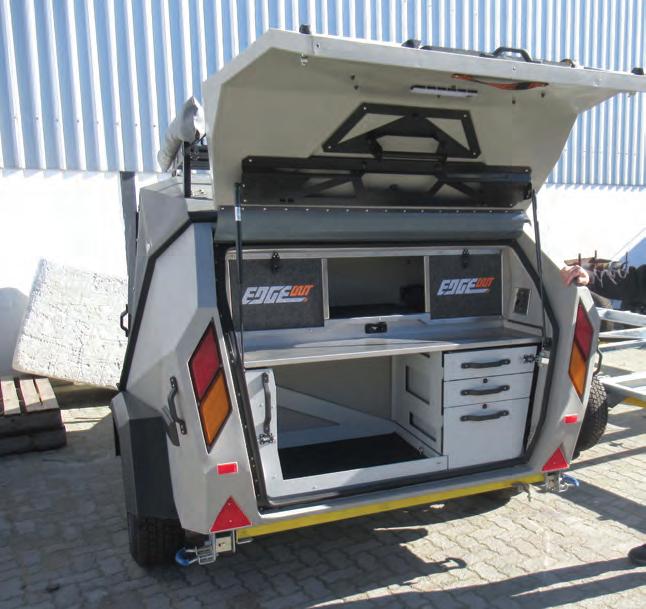

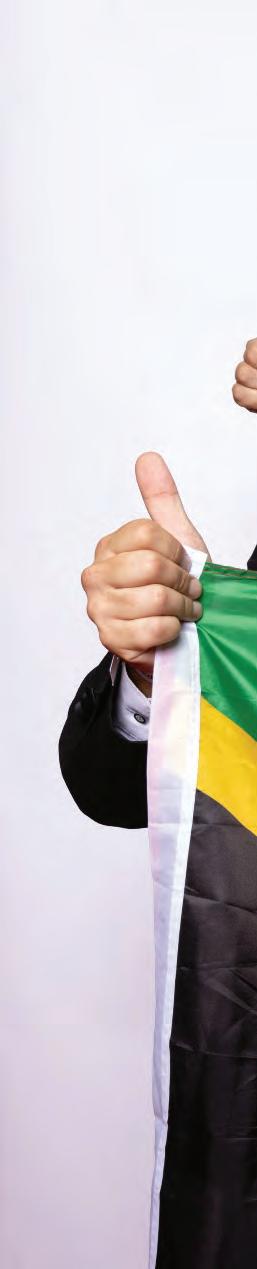
The trailer also features a microwave oven – rather atypical for a rugged teardrop trailer – and water is stored in a 110-litre tank and distributed via a built-in 12V pump. This, together with the trailer’s built-in LED lighting, is powered by a deep-cycle battery. Included is a charging system which can be hooked up to the vehicle or wired to optional solar panels.
4EVR operations director manager George Lotz, already quite busy, was at first hoping that Heyn’s caravan project was a joke, but after the shock, he’s enjoying it a lot more now
Clever maximumentertainmentthefeaturesdesigninkitchen/areaallowforuseofspace
www.4evr.co.za
Vonnie Heyns of 4EVR and designer Retief Krige were happy to accept the Red Dot Design Award at the function in Germany in June.
No stone has been left unturned as the 4EVR team and designer Krige have thought of virtually every aspect that is important to the camper and caravanning enthusiast, and there are many, such as fold-away taps, positioning of lights and sliding drawers and storage compartments. And it has opted for top range fittings, which should result in enhanced customer ratings.
Foaming of the inner layer of the main structures has improved insulation. The roto moulded ‘pods’ have a wall thickness of ±15mm, which is relatively dense
2022SEPT/AUG 37 abundance of storage space. The tailgate galley provides for a full-width countertop with two slide-out draws underneath. One drawer accommodates a built-in glass-top dual-burner gas stove, sink faucet and bucket, as well as storage drawers. The other holds a built-in refrigerator or cooler.

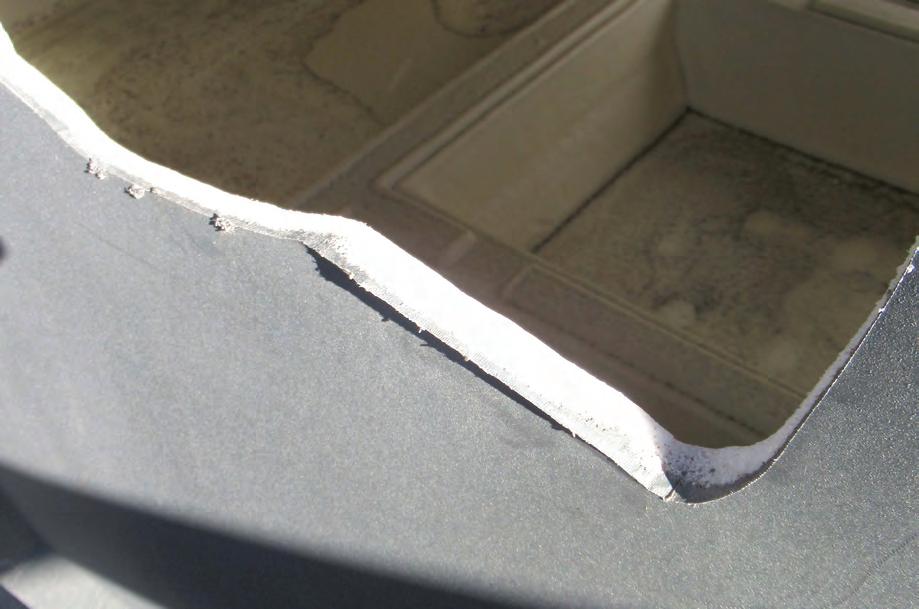
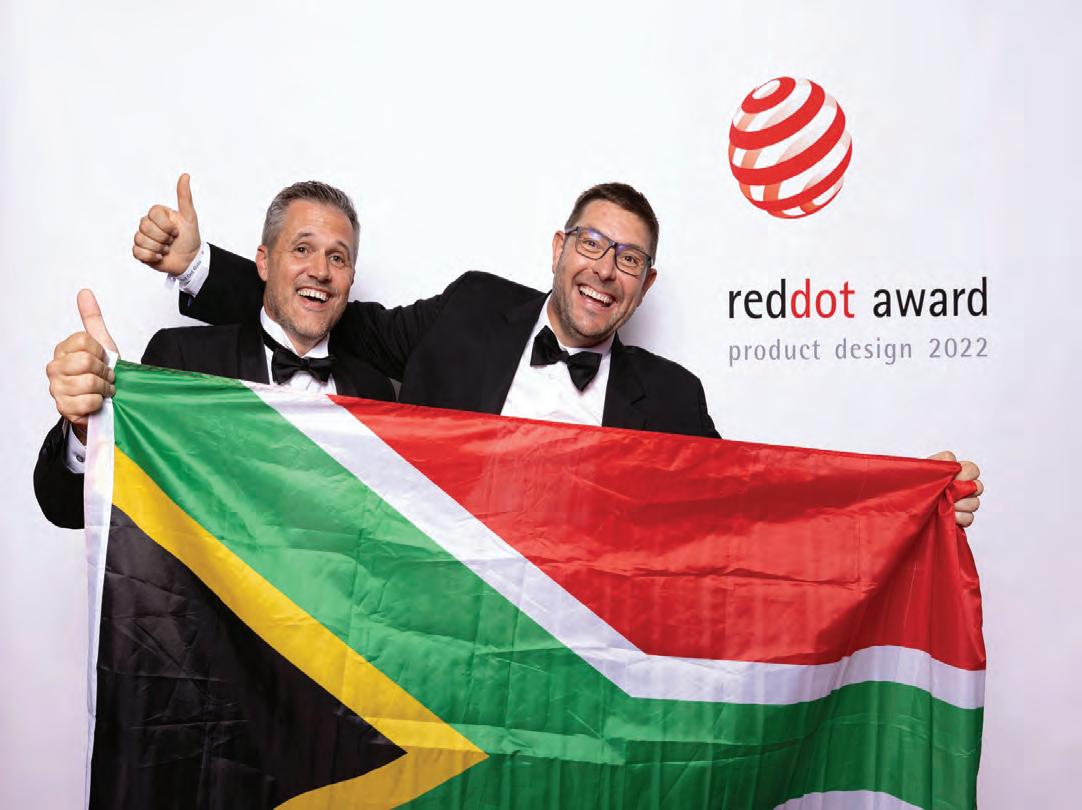
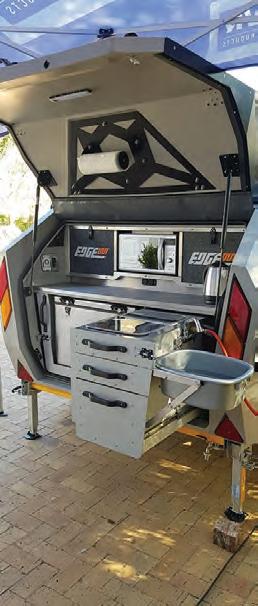
(+27) 012 997 2148 (+27) 071 642 7188 315 Boschkop rd, Boschkop,info@btcap.co.zaLynnwoodwww.btcap.co.za Rotational mould maker shows off hybrid design
GERMAN rotational mould maker Maus GmbH made a mould using steel and machined aluminium sections to rotomould a portable toilet. Regardless of the mould technology, Maus designs every rotational mould with computer-aided design, that includes every part of the mould, down to bolts, so customers can be sure they get the exact mould they want. Maus has invested $1.4 million for a five-axis CNC milling machine, which is very robust for turning out the milled moulds quickly.Inarecent project for a portable toilet, the customer had used older steel moulds, and the top and bottom of the toilet had several through holes and other components. When it came out of the cooling stage, the operators had to use a lot of force to slam out the pins for the through holes. Maus made a steel mould for the side sections but decided to make CNC machined aluminium moulds for the large roof and the bottom floor, complete with pneumatic cylinders for easy opening and closing of the clamps. In traditional rotomoulding, operators unbolt the mould on every shot to remove parts and load resin.
The new company will have annual sales of about EURO134 million (R2,24 billion).
NEWSUSARotoviarotoIcelandicmoulderbuysbusiness
www.maus-gmbh.de/en
ROTOVIA, an Icelandic roto moulding business with plants in Europe and Canada, has purchased Berry Global Group’s rotational moulding business in the USA, creating one of the largest global roto moulding groups. Rotovia has 14 operations in 10 countries and employs about 800. The company is owned by Icelandic private equity funds Freyja and SÍA IV and key management of its rotomolding operations. Once known as Promens Group AS, the company was purchased in 2014 by England-based RPC Group, which subsequently bought the Astrapak group in South Africa. RPC was in turn bought by Berry Global in March 2019, as a result of which the Astra businesses in SA are now part of the Berry business. “Under the new ownership, Rotovia plans to continue to build important long-term relationships with customers, invest further in automation and proprietary products, with increased emphasis on sustainable products,” said Rotovia CEO Daði “RotoviaValdimarsson.willhaveastrong global footprint through a wide sales office network and serve a diversified customer base across several end industries, with specific focus on the food segment,” the statement added.
38 2022SEPT/AUG www.saeplast.com
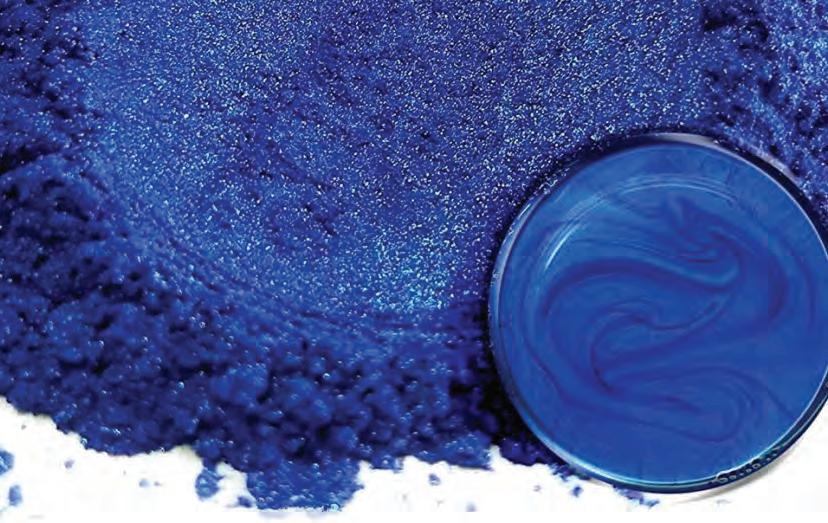
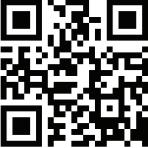
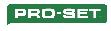
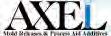
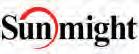
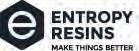
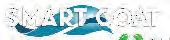


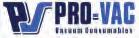
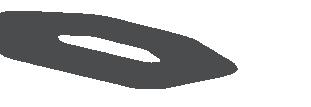
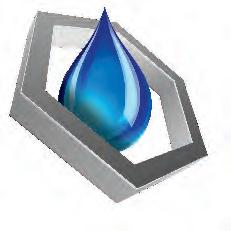
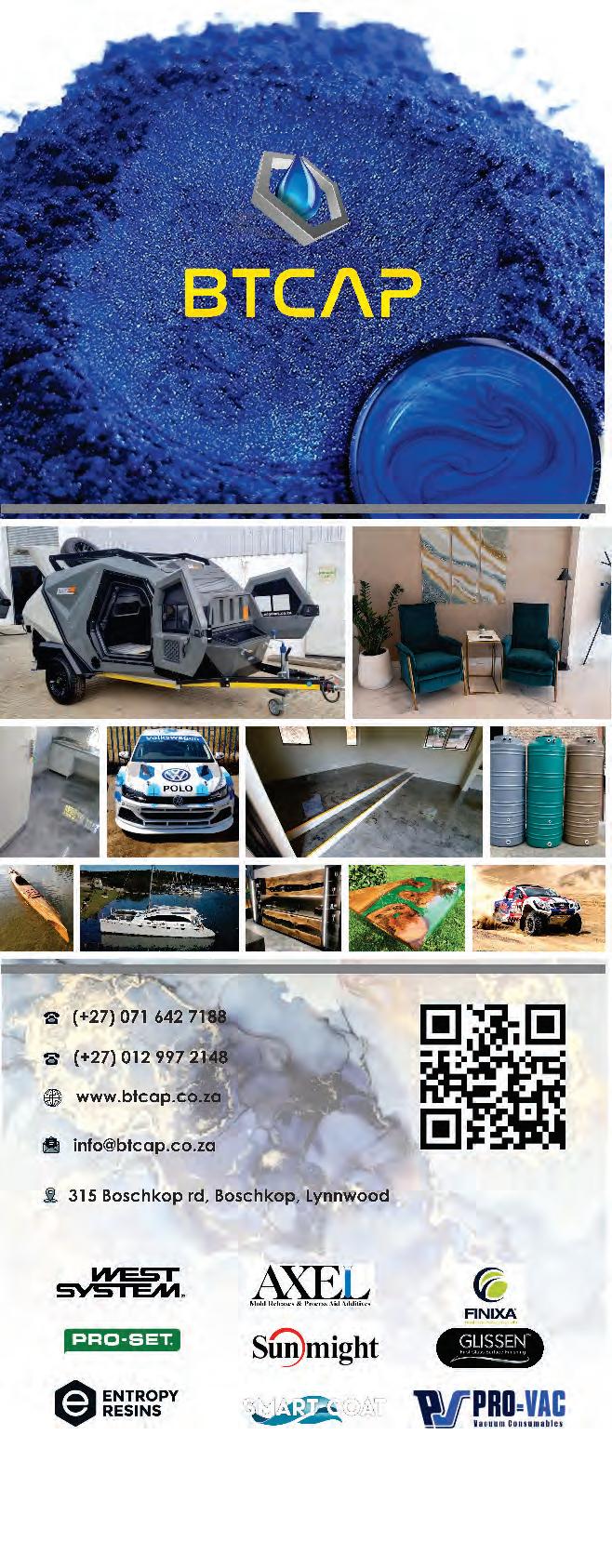
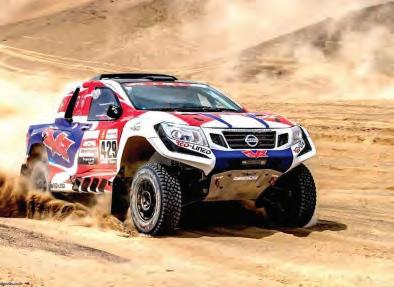
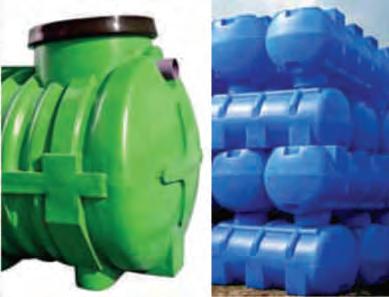
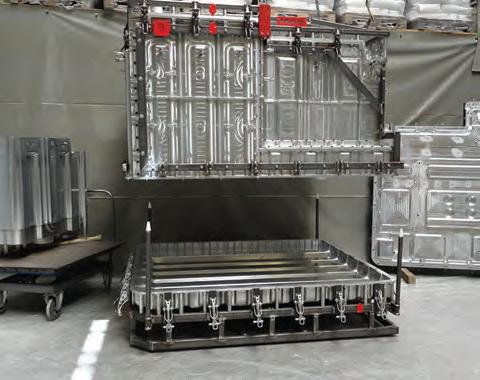
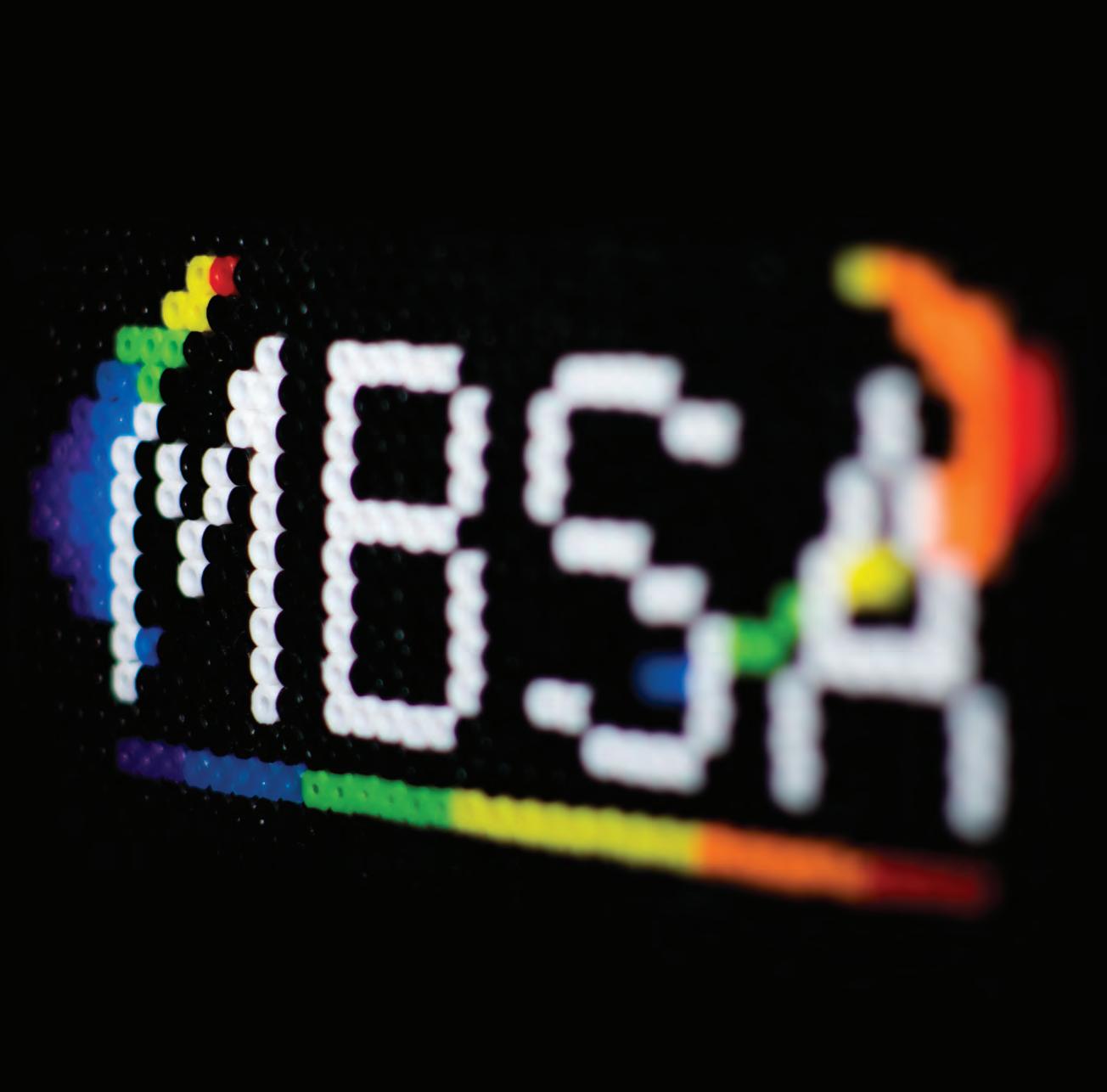
40 2022SEPT/AUG
ZolaniMaqabanqaofTUTwasthewinnerwith his ‘Roundabout’ design. Part of the challenge for the students this year was to come up with solutions which factored in Covid lockdown precautions, in this case that parks, and public places were often closed, and children had to play at home. Zolani’s design of four cubes on a revolving axis would entertain kids and could readily be roto moulded
ARMSA Student Design event
NEWS
THE ARMSA Student Design Competition, an initiative by the Southern African roto moulders’ association, recently celebrated its 20th year of student design promotion for the roto moulding industry. The competition has proved to be one of the most enduring design events for students in the industry, if not the country. And it even survived Covid, with the prize-giving for the 2022 competition taking place at the ARMSA Rotation 2022 conference at Kloofzicht in interest, arguably more so than in the roto industry itself. The topic for the 2022 competition was ‘Outdoor Sports & Recreation’ and there was no shortage of ideas. Zolani Maqabanqa of Tshwane as adjudged first and Monic Moleko, also TUT, second. Both are second-year students studying industrial design at the Tshwane University of Technology. Started in 2002 The competition, originally known as Gauteng in May, almost three years after the previous conference. Students from the Tshwane University of Technology (TUT) and the University of Johannesburg (UJ) participated this year. The competition has over the last few years focused on these two universities as the lecturers at their design faculties are now familiar with roto moulding and the programme, which does specifically offer design possibilities for young people and has if anything attracted an unusually high level of
Students have lots of bright ideas – and designs


“We saw that it was done at the ARMA (Australasian Roto Moulding Association) conference, and it was thought that it would be a good way of promoting the roto moulding industry among designers and possibly help to grow the market, as well as fitting in with one of the aims of ARMSA – which is education,” said Nick. “The aim of the competition is to promote roto moulding among designers, and one way to do this is to make industrial design students aware of the process and the possibilities of what it can do. To this end, we initially approached lecturers at one of the local institutions in 2001 to get their buy-in and the project was launched, with the first competition being held the following year. “Sasol Polymers sponsored the first competition and has done ever since. ARMSA supplies input in the form of introductory lectures so that the students understand the process, design aspects etc. There have been the odd problems along the way, but generally we have found that the universities offering industrial design have been supportive, such that Tshwane University of Technology have started a design course and are keen for their students to be involved. By having roto moulding as part of the course work the students do not necessarily have to do something extra which makes it easier to get the entries,” added Nick.
2022SEPT/AUG 41
Monica Moleko, also of TUT, was runner-up in 2022 with ‘2-in-1 See-saw Bridge’ design. Most seesaw in use are made of wood, which can be heavy and sharp edge, said Monica, whereas the roto-moulded design, being hollow, is far lighter and has smooth edges
revived after Covid interruption
the ‘Sasol Polymers Students Design Competition,’ was started in 2002 following a visit to Australia by Nick Aggett and Leon Joubert of Sasol.
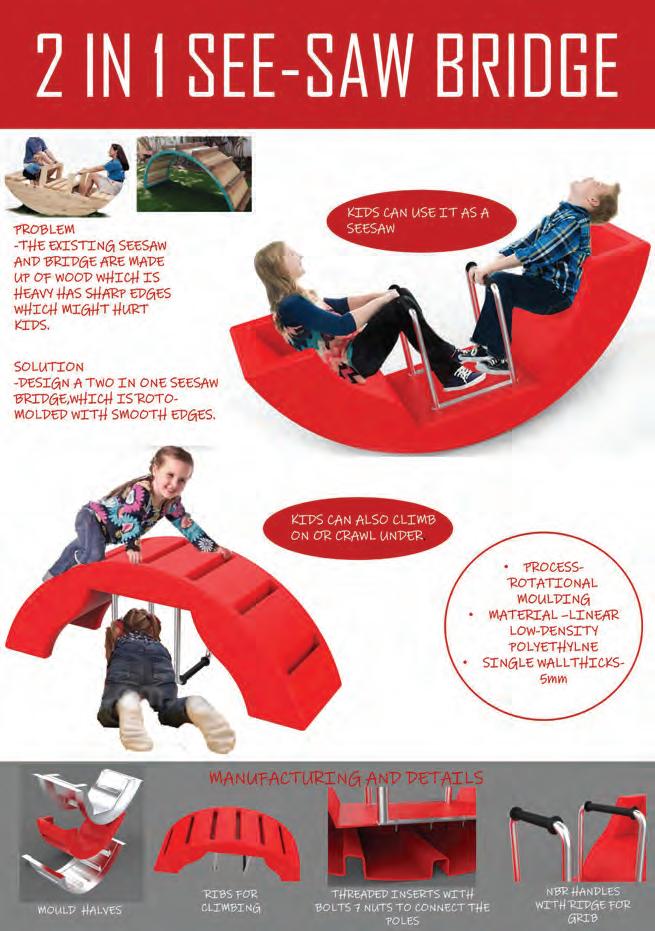
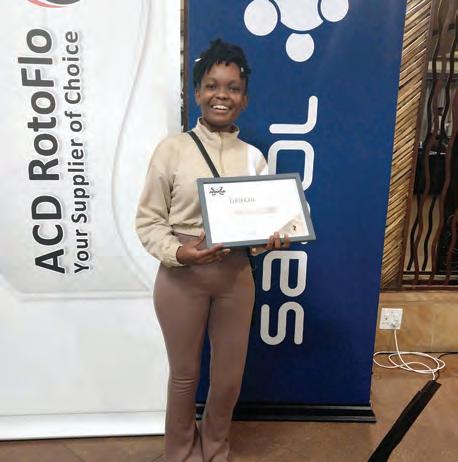

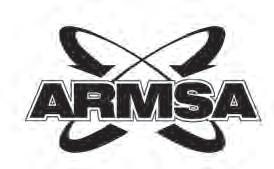
The event played out at Wings Park in East London with Eco Tanks director Darren Hanner being one of the contestants in his YAK 52 plane (named ‘Valentine’) and, believe it or not, he won the sportsman section of the competition Loopy de loop – With the G forces beginning to kick in, the passenger may have been experiencing thebeforecalm the …
Eco Tanks goes acrobatic when its tanks starred too on a fine day in the Eastern Cape. Eco took the opportunity to present some of its latest innovations at the event, including its Big Red sanitation system. The event THE British Plastics Federation (BPF) has produced the world’s first rotational moulding health and safety guidance.
It provides a list of what to look for when a rotational moulder is carrying out a risk assessment, how to safeguard machines and ensure that all necessary control measures are in place, as well as information about fulfilling legal duties.
2022SEPT/AUG
Darren Hanner with his plane Valentine at the Acrobatic Champs in East London in June. There is a similarity between Eco’s Big Red tanks and the plane, but the latter is NOT roto moulded
The document has been approved by the Health and Safety Executive (HSE) and is now available free of charge on the BPFThewebsite.guidance gives advice on the safeguarding requirements for foreseeable hazards associated with rotational moulding machines, including whole body entrapment.
World’s first rotational moulding health and safety guidance launched
Will help workers recognise and successfully avoid hazards, promote safe working practices
www.bpf.co.uk/rotational_moulding/Default.aspxwww.ecotanks.co.za
NEWS
BPF senior industrial executive, Dr Sara Cammarano said: “We are very excited to release this health and safety guidance. We hope that rotational moulders across the UK ensure they are implementing these best practice measures, and that this document will help workers clearly recognise and successfully avoid hazards, and promote safe working practices.”TheBPF Rotational Moulding Group was consulted during the document’s development, which represents all those involved in the rotational moulding process: moulders, material suppliers, service providers, and machinery and ancillary equipment manufacturers. As well as being fully endorsed by the HSE, the industry-led initiative, Safety in Manufacturing Plastics (SIMPL) was also involved in the document’s development.
ECO Tanks, the national roto moulded tank manufacturer, was the joint sponsor of the recent SA National Acrobatic Championships … along with who else but Red Bull. You need horns … I mean wings … to do this sort of thing, although maybe not a helluva lot more than you do to be a tank manufacturer.
• To obtain a copy, visit 42
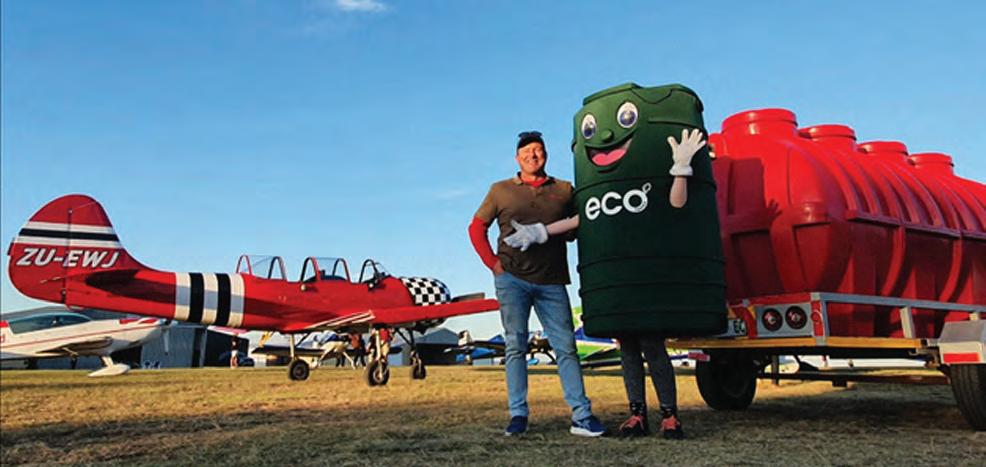
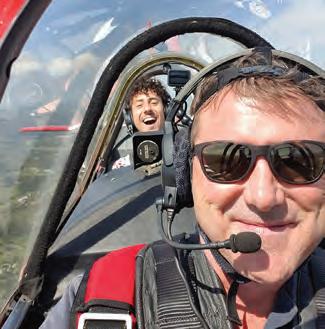
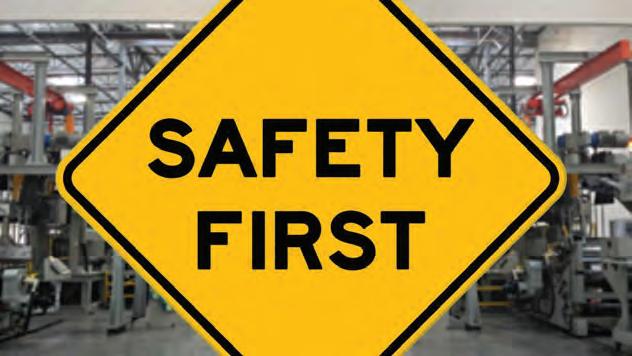
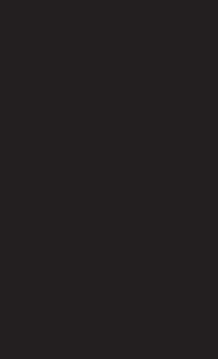
InsIghts on the For more information about
2022SEPT/AUG 43
THE “Global Rotomoulding Powder Market to 2027” report has been added to ResearchAndMarkets.com’s offering. RotomouldingThegrowing demand for lightweight vehicles in the automotive industry is a key driving factor which expected to boost the global rotomoulding powder market growth over the forecast period. Furthermore, the increase in demand for rotomoulding powder from furniture and home interior industry due to the rise in use of rotomoulding powder in the manufacture of furniture components include, wWhat are the Key Opportunities in Global Rotomoulding Powder Market; What will be the growth rate from 2019 to 2027?; Which segment/region will have highest growth?; What are the factors that will impact/drive the Market?; What is the competitive Landscape in the Industry?; What is the role of key players in the value chain?; and What are the strategies adopted by key players? and interiors will positively influence the market growth. Also, the rise in travel and tourism owing to improved consumer spending in water adventure events and the growing use of recreational boats is projected to drive the demand for rotomoulding powder market in near future. Moreover, the growing demand for hollow plastic products including playground equipment, storage tanks, and containers is expected to support the market growth. Key questions addressed by the report market to 2027 this report
rotomoulding powder global
www.researchandmarkets.com/r/nskznxvisit Largest Supplier of Colour Compounded LLDPE in Sub Saharan Africa Compounding of Rotomoulding Speciality Polymers and Speciality Powders PSD Rotoworx PP, LaPlastecnica Vents and MIGS® +27 82 880 4976 +27 84 540 2896 +27 76 101 7805 +27 11 708 3361 (Tel) +27 11 708 1919 (Fax) Contact: Clive Robertson clive@rotoflo.co.za +27 82 880 4976 Michael Böltau tech@rotoflo.co.za +27 84 540 2896 Andrew Robertson andrew@rotoflo.co.za +27 76 101 7805 Beverley Cooper sales@rotoflo.co.za +27 11 708 3361 (Tel) +27 87 721 1701 (Alt) Website: www.rotoflo.co.za Address: 28 Hilston Road Kya Randburg,Sands Johannesburg South Africa Largest Supplier of Colour Compounded LLDPE in Sub Saharan Africa Colour Compounding of Rotomoulding Speciality Polymers Pulverising of Rotomoulding and Speciality Powders Agents for PSD Rotoworx PP, LaPlastecnica Vents and MIGS® RotoFlo Holdings Your Supplier of Choice Members of: LaPlastecnica Agents for: Largest Supplier of Colour Compounded LLDPE in Sub Sahara n Africa Colour Compounding of Rotomoulding Speciality Polymers Pulverising of Rotomoulding and Speciality Powders Agents for PSD Rotoworx PP, LaPlastecnica Vents and MIGS® Contact: Clive Robertson clive@rotoflo.co.za +27 82 880 4976 Michael Böltau tech@rotoflo.co.za +27 84 540 2896 Andrew Robertson andrew@rotoflo.co.za +27 76 101 7805 Chanda Mukuka sales@rotoflo.co.za +27 11 708 3361 (Tel) +27 11 708 1919 (Fax) Website: www.rotoflo.co.za Address: 28 Hilston Road Kya RandburgSands, Johannesburg South Africa Mold In Graphic www.moldingraphics.comSystems®
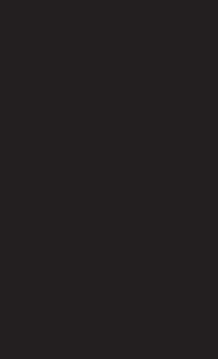
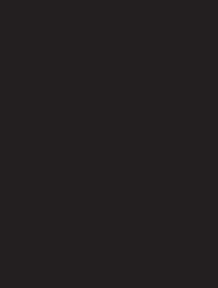
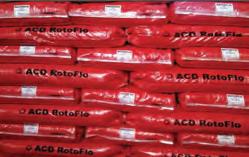
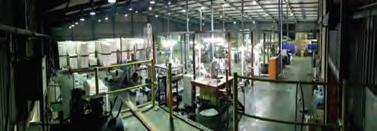


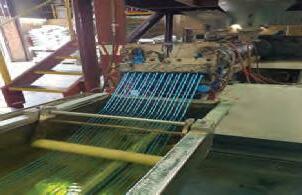
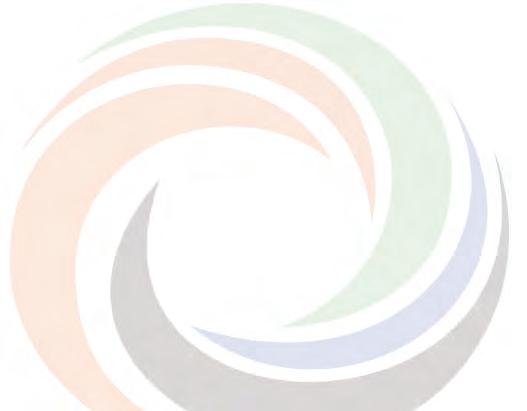
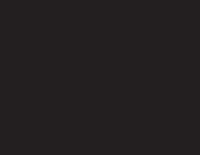
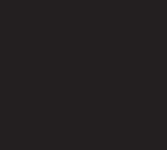
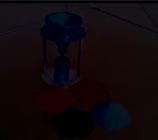
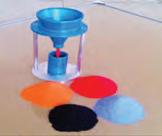
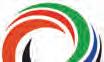
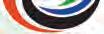


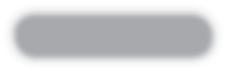
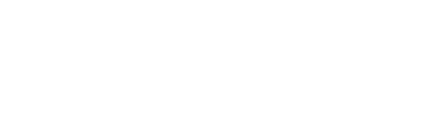
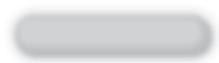






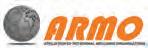
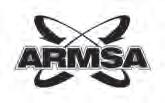
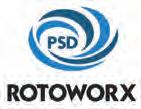
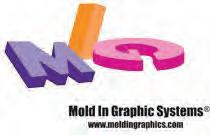
25 years later, ‘Still a big problem that requires
DS: For many years I thought so, but if we don’t educate our society not to litter, to recycle their products and to ensure people have access to waste management, we will not win the war against litter – sadly so. Have personnel in the industry been well represented at clean-ups? Or has it been Plastics|SA and other environmentally aware people who’ve coordinated the projects?
DS: Well, I studied Physical Education, ended up later working for the Population Development Programme in Durban, KwaZulu-Natal, where I was responsible for population education and business sector projects. I had a chance meeting with the then director of the Plastics Federation of SA (now Plastics|SA) and he had a position for an environmental officer – a new position that was established to develop and drive what was then the Enviromark, the plastics industry’s environmental initiative … and I got the job! I did not know much about plastics but I learned from the industry and by developing educational resource materials –of course I knew Tupperware, pipes and bags! It appears that the rate of plastic litter entering water systems and leading to the ocean has increased rapidly over this period. Would you say the problem was underestimated at first?
DS: When I was appointed, we did not know much about the volumes of plastics entering our environment, from roadsides to rivers to beaches to the ocean. The more we got involved with projects such as Ocean Conservancy with the International Coastal Clean-up, KZN Wildlife, other ‘keep clean’ organisations, and people such as Prof Peter Ryan of UCT doing research on plastics litter along our coastline, we realised that we had huge problem. I now know more waste is entering our ocean due to human behaviour to litter, lack of waste management infrastructure and the demand for products due to population growth. With regards beach and river clean-ups, have you noticed any trends over the period?
DS: Plastics|SA encourages all to support clean-ups in the area where they live or work – that is people from industry, business, brand owners, retailers, NGO, civil society, schools and the list continues. Since the launch of the Enviromark in 1997 and the support of the polymer groups such as Petco (PET Recycling Company), Polyco (Polyolefin Recycling Company), SA Vinyls Association and Polystyrene Association (now PROs), I’ve had the support in terms of clean-up finances and participation. The fact is we should not be doing clean-ups – the country should be clean!
Coastal clean-ups tend to be hard work, but many volunteers commit to the projects annually
SUSTAINABILITY
www.sabic.com 44 2022SEPT/AUG
DS: It depends which areas we look at. Plastic bags used to be a big problem, but now that we have a plastics bag regulation in place and people pay for the bags, we see less bags in the clean ups. However, we now see more of other products such as bottles, bottles tops, and other packaging products. As many people live next to our rivers in the catchment areas, especially in metropolitan areas, we find more litter ends up on our beaches. Rivers are used as dumping grounds and when it floods all the material gets washed downstream. This is a huge problem that needs urgent attention. Do clean-ups help?
Bottom line is, we all need to work together to ensure a clean environment
DOUW Steyn, sustainability manager at Plastics|SA, recently completed his 25th year in the position, which milestone he celebrated quietly. We asked him what changes he’s observed with regards plastics in the environment over this period. How did you get involved at Plastics|SA in the first place? Did you know anything about plastics at that stage?
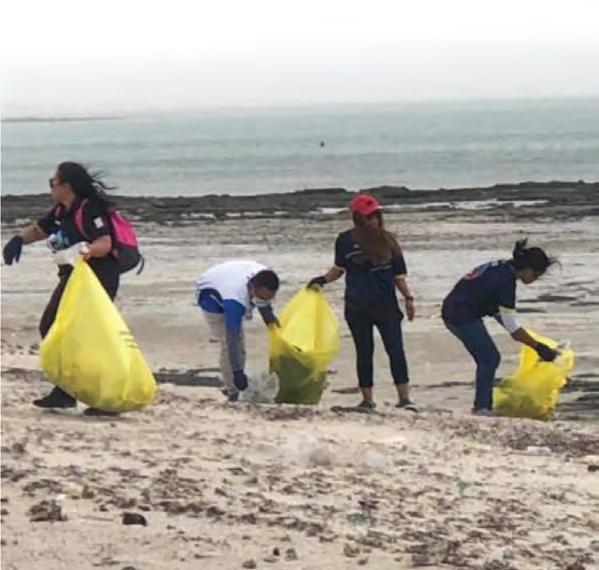
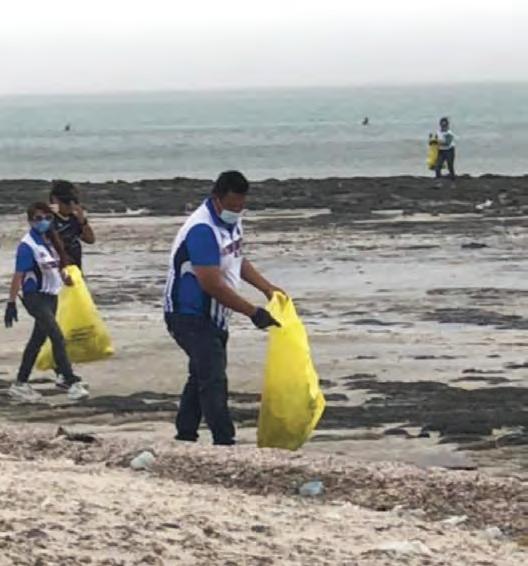


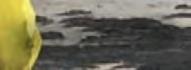

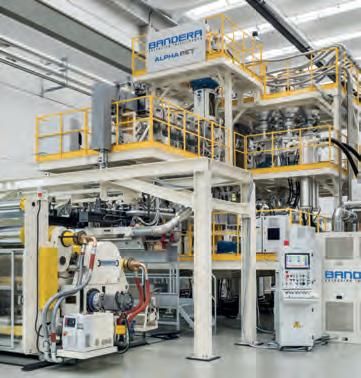




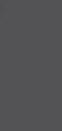

Recyclables should be sorted and sold to recycling companies. Plastics waste has value and is a resource that should not be going to landfills. And of course, change human behaviour about littering.
• This year’s Clean-up & Recycling campaign is from 12-17 September and includes the River Clean-up Day on Wednesday 14 September, Recycling Day on Friday 16 September, International Coastal Clean-up Day and World Clean-up Day on Saturday 17 September.
Douw Steyn has been involved in clean-ups around the country for 25 years; here we see him at a clean-up on the KZN coast with Jonathan Welch of AfriEco
2022SEPT/AUG 45
DS: We need to address waste management in the country, encourage separation at source (e.g., two bag/bin system –one for wet waste and one for dry waste) for all recyclables.
DS: Many projects and activities have been conducted over the years by Plastics|SA and other organisations to address littering and many are still active, including schools’ recycling projects, waste education campaigns, clean-up campaigns such as the Clean-up & Recycle SA Campaign (initiated by Plastics|SA in 1997) and more. One of the collaborations involving Plastics|SA and partners is a focus on river catchment projects – especially in the Durban, Queberha (Port Elizabeth), Cape Town and Gauteng areas.
The bottom line is, we all need to work together to ensure a clean environment!
MachineryMACTECcc
In terms of reducing plastics litter and improving the industry’s image, what would you say are the biggest problems in South Africa?
The projects we support and promote in these catchment areas include waste management and recycling, technology innovation for plastics waste, education and training, litter booms and clean-up activities.
Given your experience over the past 25 years, what would you say could be done to reduce the rate of plastics litter, and hence help the industry improve its public image?
plastics litter is urgent attention’










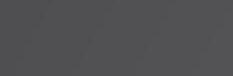







































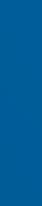
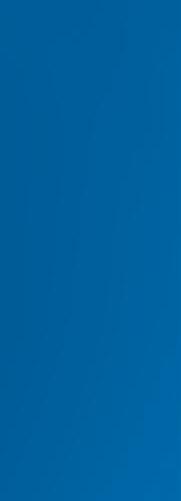

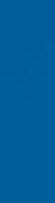

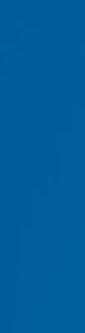
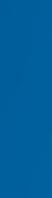
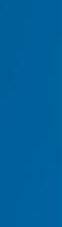
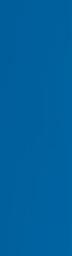
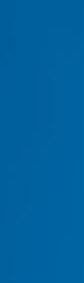
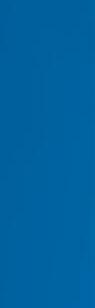
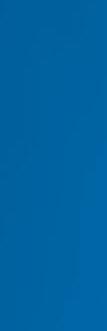
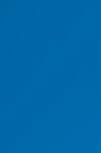
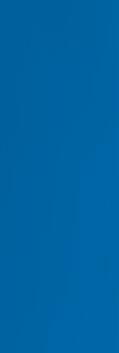
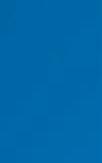
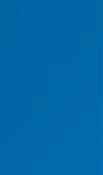
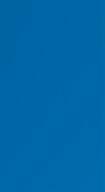

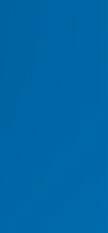
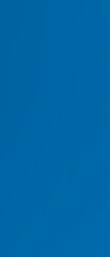
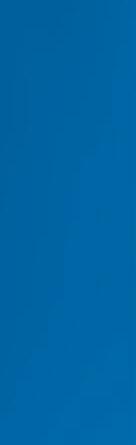


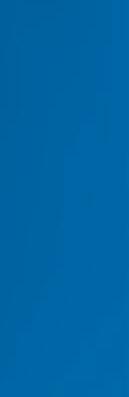
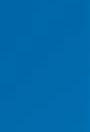
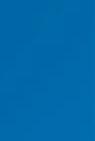
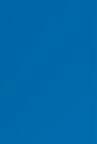
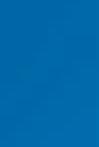


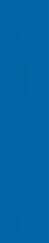
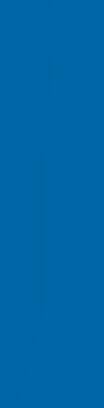
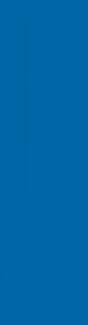
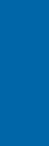
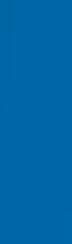
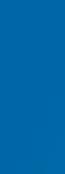
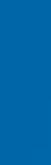
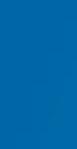
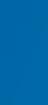
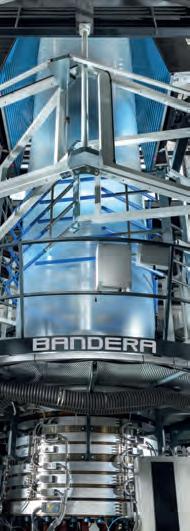
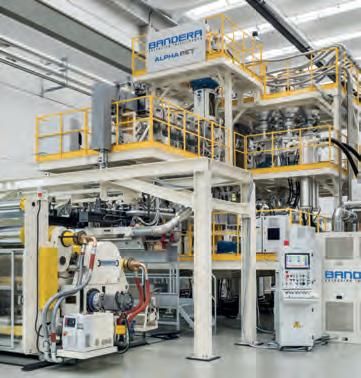

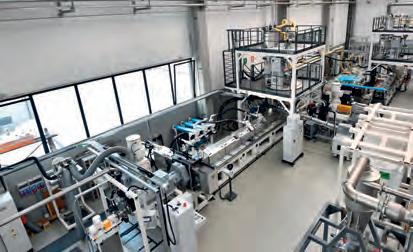
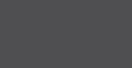



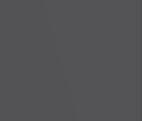
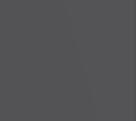

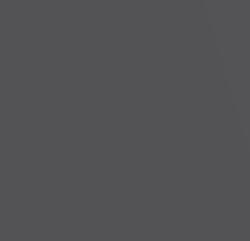
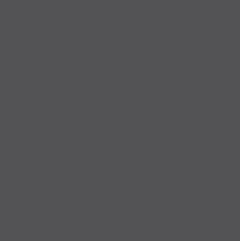
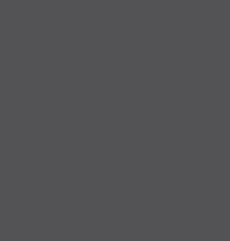
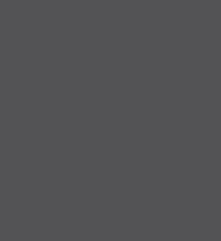
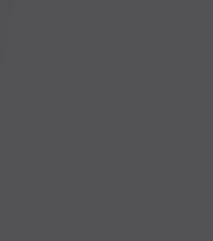
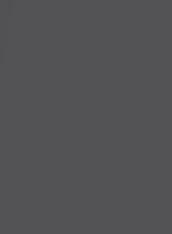
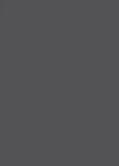

www.igus.bike
RESEARCHERS found a species of worm with an appetite for polystyrene. Thanks to a special enzyme in their gut, they could be the key to plastic recycling on a mass Enzymesscale.have emerged as particularly promising candidates in the search for a remedy in the fight against the flood of plastics. Back in 2016, Japanese scientists discovered a bacterium that can completely degrade PET within weeks with the help of two enzymes. Last year, researchers at the University of Leipzig isolated an enzyme from compost that breaks PET down into its basic components in such a way that new PET can be produced from it. Now, researchers at the University of Queensland, Australia (UQ) have discovered a species of worm with an appetite for polystyrene. The larvae of the common large black beetle (Zophobas morio), also known as superworms due to their length of around 6cm, can eat through polystyrene, thanks to a bacterial enzyme in their gut.
Deep insights deep impact Meraxis South Africa (Pty) Johannesburg +27 11 4552889 Cape Town +27 21 556 7787 Durban +27 31 8169381 NEWS Deep insights deep impact Trade. Create. Elevate. Meraxis South Africa (Pty) Johannesburg +27 11 4552889 Cape Town +27 21 556 Durban +27 31 8169381 NEWS Trade. Create. Elevate. > www.meraxis-group.com NEWS Deep insights, deep impact Trade. Create. Elevate. > www.meraxis-group.com NEWS
SUSTAINABILITY 46 AUG / SEPT 2022 Ocean
In their research, Dr Chris Rinke and his team from UQ’s School of Chemistry and Molecular Biosciences, fed superworms different diets over a three-week period, with some given polystyrene foam, some bran and others put on a fasting diet.
In the original paper, the USbased organization claimed that the Philippines, China, Indonesia, Thailand, and Vietnam are the top five plastic polluters in the world. The report stated that “over half of land-based plastic-waste leakage” could be attributed to these five countries. Another significant claim that the paper made was its endorsement of incineration and waste-to-energy solutions as part of possible routes to minimize the presence of plastics in the oceans. In its accountability statement, the organization has admitted that it was wrong on both counts. “We failed to confront the root causes of plastic waste or incorporate the effects on the communities and NGOs working on the ground in the places most impacted by plastic pollution,” it said. “Further, by focusing so narrowly on one region of the world (East and Southeast Asia), we created a narrative about who is responsible for the ocean plastic pollution crisis – one that failed to acknowledge the outsized role that developed countries, especially the United States, have played and continue to play in generating and exporting plastic waste to this very region. This too was wrong,” the statement read. In rescinding its endorsement of incineration as a type of solution to the global plastic problem, it has shifted its stance to support the circular economy model. The statement cited that incineration may increase plastic demand and serve as a barrier to a carbon-free future. IGUS (Cologne, Germany) is making the engineering concept and key components for bicycles made completely of recycled plastic available to all bicycle manufacturers via the company’s Igus bike platform. This includes the unveiling of a new durable urban bike made entirely of plastic, from frame to bearings to toothed belt. The first model should be available by the end of the year. One special feature of this new bike is that the recycled version will be primarily made of single-use reused plastics.
Researchers used a technique called metagenomics
“We found the superworms that were fed a diet of just polystyrene not only survived, but even had marginal weight gains,” Dr Rinke said. However, the weight gain of the styrofoam larvae was only a quarter of the mass gained by the superworms fed bran. Nevertheless, the observation indicates that “the worms can derive energy from the polystyrene, most likely with the help of their gut microbes”, said Rinke. apologisesConservancyforreport
Superworms with an appetite
Lightweight, lubrication-free highperformance plastics are used in all parts of the bicycle, from two-component ball bearings in the wheel bearings to plain bearings in the seat post, brake levers and pedals. All of these components have integrated solid lubricants and ensure low-friction dry operation — without a single drop of lubricating oil. This ensures that sand, dust and dirt cannotProductionaccumulate.andsale of a children’s model and an adult bicycle for cities will begin by the end of 2022. Other versions, such as an e-bike, have also been planned. In the future, the allplastic bicycle is to be available both in a variant made of new plastic and in one made entirely of recycled material — first prototypes, successfully produced and tested, were made of material from old fishing nets, for example. Lightweight plastics from landfills used in all parts of the bicycle
Urban bike made from recycled material
Ocean Conservancy has released a statement apologizing for its groundbreaking 2015 paper that stated that the Philippines was among the top three plastic waste producers in the world. Ocean Conservancy issued an apology in July regarding the paper, “Stemming the Tide: Land-based strategies for a plastic-free ocean” for “the framing of [the] report.”



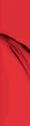

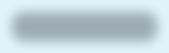
VinylPlus exceeds 810 000 tons of PVC recycling in 2021 AT the 10th VinylPlus Sustainability Forum participants could look back at a successful first year of the new VinylPlus 2030 Commitment, the voluntary 10year commitment adopted last year by the European PVC industry aimed at minimising the environmental impact of PVC production and manufacturing. Despite the fraught conditions of the past year, 810 775 tons of PVC waste were recycled and used in new products by European PVC industry through the voluntary commitment, which represents around 26.9% of the total PVC waste generated in 2021 in the EU-27, Norway, Switzerland and the UK.
for
www.microbiologyresearch.org/content/journal/mgen/10.1099/mgen.0.000842 2022SEPT/AUG 47
VinylPlus’ recycling rate is above the 23.1% recycling rate estimated by AMI Consulting for the overall plastics recycling in Europe in 2021. In total, some 7.3 million tons of PVC having been recycled into new products since 2000, preventing the release of more than 14.5 million tons of CO2 into the atmosphere. polystyrene!
The researchers used a technique called metagenomics to find several encoded enzymes with the ability to degrade polystyrene and styrene. “Superworms are like mini recycling plants, shredding the polystyrene with their mouths and then feeding it to the bacteria in their gut,” Dr Rinke said. “The breakdown products from this reaction can then be used by other microbes to create high-value compounds such as bioplastics.”
However, since a Styrofoam diet alone is not healthy for the larvae, he suggests adding food waste materials or agricultural biowaste to the polystyrene to be degraded. “This could be a way to improve the health of the worms and at the same time use the mass food waste in western countries.” Co-author of the research, PhD candidate Jiarui Sun, said they aim to grow the gut bacteria in the lab and further test its ability to degrade polystyrene. “We can then look into how we can upscale this process to a level required for an entire recycling plant,” Sun said. The long-term goal is to engineer enzymes to degrade plastic waste in recycling plants, that is to develop a superworm-free recycling system that mimics the mechanical shredding of plastic by the larvae and then decomposes it through enzymatic •processes.Thisresearch has been published in Microbial Genomics, The larvae of the large black beetle (Zophobas morio) can eat through polystyrene
23 Trade. Create. Elevate. > www.meraxis-group.com NEWS 23 Deep insights, deep impact. Trade. Create. Elevate. > www.meraxis-group.com Meraxis South Africa (Pty) 4552889Ltd55677878169381 NEWS 23 Trade. Create. Elevate. > www.meraxis-group.com 23 Deep insights, deep impact Trade. Create. Elevate. > www.meraxis-group.com 23 Deep insights, deep impact. Trade. Create. Elevate. > www.meraxis-group.com Meraxis South Africa (Pty) Ltd Johannesburg +27 11 4552889 Cape Town +27 21 7787 Durban +27 31 8169381 NEWS 23 Deep insights, deep impact. Trade. Create. Elevate. > www.meraxis-group.com Meraxis South Africa (Pty) 4552889Ltd55677878169381 NEWS Thank You! Classifieds Feb/Mar'2021.indd 80 2021/02/01 11:06 23 Deep insights, deep impact. > www.meraxis-group.com 4552889Ltd77878169381 23 Deep insights, deep impact. > www.meraxis-group.com (Pty) 4552889Ltd55677878169381 Thank You! SouthMeraxisAfrica Importers, Stockists and Distributors of polymers into Africa Paul Gripper - Commercial Manager & Cape Sales paul.gripper@meraxis-group.co.za0824566659 Steven Coates - Gauteng, Botswana, Swaziland, Lesotho & Zimbabwe Sales steven.coates@meraxis-group.co.za0636995105 Tiago dos Ramos – KZN, Free State & Mozambique Sales Tiago.dosramos@meraxis-group.co.za0827755344 Carlotta Stafford – Zambia & Malawi Sales Carlotta.stafford@meraxis-group.co.za0826007403 23 23 LLDPE LDPE HDPE PET PVC PP PS
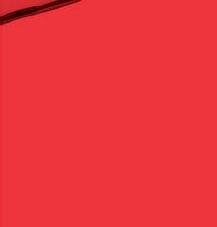
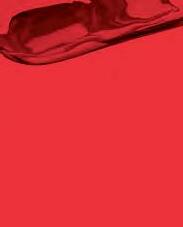
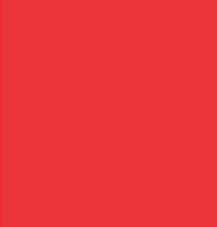
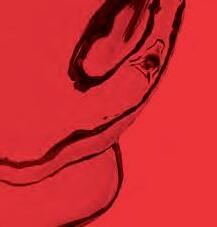
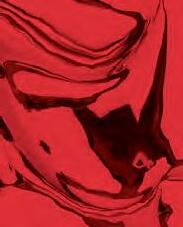
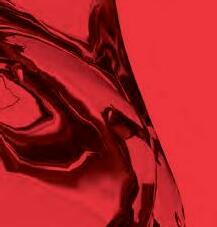
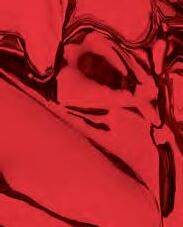
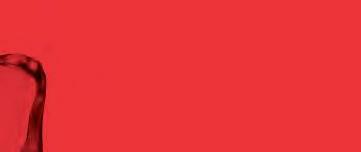
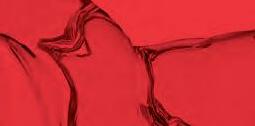
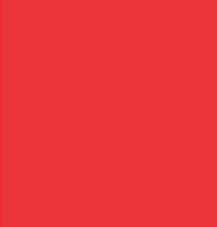
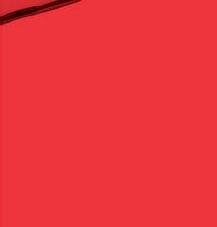
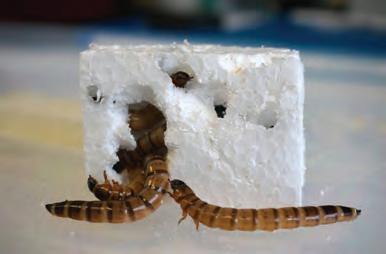
A six-year project in France to develop a recycling solution for monolayer and multilayer food packaging PET trays has led to a new technology that makes it possible to process the monolayer trays into a recycled product that is suitable for new tray production. With the support of the French notfor-profit organisation Citeo, Indoramaowned Wellman France Recycling and Valorplast, a company specialised in the collection and management of household plastic packaging, collaborated for six years on the project. Post-consumer PET trays were collected, and a number of industrial runs conducted. The flakes produced in the process have been tested to explore the quality and potentially possible applications for this material. The outcome of these tests has now enabled a commercially feasible, circular recycling solution for monolayer PET trays to be developed by the project’s participants who are now working on its further implementation.Thenewtechnology is expected to result in over 50 million postconsumer PET trays being diverted away from landfill or incineration in the future. The project is still working on solutions for multilayer PET trays. Coperion InnovationRecyclingCentre
The 200-page report is available at Mapping advanced recycling technologies for plastics waste
Overall, the report presents 103 advanced recycling technologies that currently are available on the market or will soon be. A majority of the identified technologies are located in Europe, including first and foremost the Netherlands and Germany, followed by North America, Asia and Australia.
A new trend and technology report by the nova-Institute aims to provide a structured, overview and in-depth insight of advanced recycling technologies for plastics waste – providers, technologies, and partnerships. It focusses on profiling more than 100 available advanced recycling technologies and related providers. Target audiences are the chemical and plastic industry, brands, technology scouts, investors and policy decision-makers.Thereport“Mapping of advanced recycling technologies for plastics waste” provides a structured, overview and in-depth insight. It focusses exclusively on profiling available technologies and providers of advanced and especially chemical recycling solutions including new technologies and updated company profiles.
The report also features the first identified post-processing and upgrading technology providers which will also play a key role in the conversion of secondary valuable materials into chemicals, materials, and fuels. The study covers different technologies in various scales including gasification, pyrolysis, solvolysis, dissolution, and enzymolysis. It further describes technical details and the suitability of available technologies for specific polymers and waste fractions.
48 AUG / SEPT 2022
Collaboration delivers recycling solution for monolayer PET trays
COPERION GmbH has started the construction of a state-of-the-art recycling test lab at its Niederbiegen/ Weingarten, Germany, production facility. Here customers will be able to develop and test new, sustainable products and recycling processes. All essential recycling process stages will be covered within the facility, including materials conveying, feeding, extrusion, pelletizing, and materials postprocessing. In addition, Coperion will conduct its own research activities on plastics recycling in this new centre. With this new addition, the company will expand its test lab capacities, throughout Germany alone, up to 5 000m. For packaging and single-use applications
compostableBioplasticsresins
GREEN Dot Bioplastics of Kansas, USA, a leading developer and supplier of bioplastic materials for innovative, sustainable end-uses, has expanded its Terratek® BD line with nine new compostable grades that are targeted for single-use and packaging applications.
www.renewable-carbon.eu/publications
The expanded offering for film extrusion, thermoforming and injection moulding is in line with Green Dot Bioplastics’ goal to achieve faster rates of biodegradability in ambient conditions. These new compostable materials are an integral part of the company’s extensive bioplastics portfolio which includes biocomposites, elastomers and natural fibre-reinforced resins all produced at the company’s newly expanded manufacturing facility in Onaga, Kansas. The five new film grades are compostable starch blends that require no tooling or process modifications when run on traditional blown or cast film equipment. Among them are Terratek® BD3003 which exhibits high puncture resistance and tear strength and is heat sealable like LDPE film. Meanwhile, Terratek® BD3300 is a stiff, high-modulus material with high heat resistance and overall properties similar to HDPE film. The film grades deliver faster rates of biodegradability for home composting, industrial composting, and soil biodegradability. They are targeted for a range of applications including produce bags, bubble wrap, agricultural films, and other lawn and garden packaging. Green Dot’s new compostable offering also includes three new thermoforming grades which provide a range of properties including clarity. Other grades provide higher heat performance and greater flexibility for applications such as food service packaging, takeout containers, deli packages, and straws. Two injection moulding grades round out the new compostable offering. They deliver higher heat performance and
SUSTAINABILITY
Green Dot
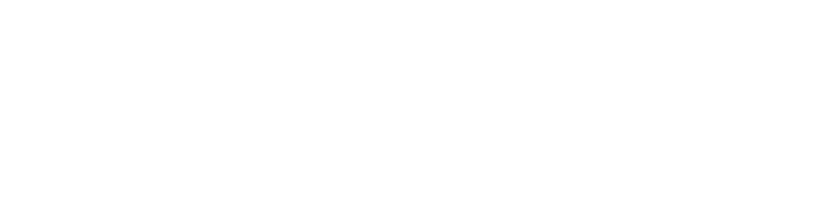

www.greendotbioplastics.com
1 Boon Leat Terrace, #08-03, Harbourside Building 1, Singapore 119843 TEL : 65-6778-4633 FAX : 65-6778-9440 E-Mail : sales@nisseiasb.com.sg Unit 2 The Shields, 33 Victoria Link, Route 21 Corporate Park, Nelmapius Drive, Irene Ext.30, 0062, 0157, South Africa TEL : 27(12) 345 4924 E-Mail : sales@nisseiasb.co.za California passes strictest plastics law in US CALIFORNIA lawmakers passed the country’s toughest plastics pollution and recycling plan at the end of June, setting a 65% recycling rate target and putting in place an extended producer responsibility (EPR) system forThepackaging.plancalls for a 25% reduction in single-use plastics and requires companies to pay $500 million a year for a decade into an environmental clean-up fund. The law creates an EPR programme for packaging, making California the fourth state in the US, and the largest so far, to adopt such a regulatory approach. The EPR programme requires the industries set up a producer responsibility organization (PRO) by 2024 to develop plans to meet the law’s recycling and source reduction goals. The law requires that materials be compostable or recyclable within 10 years.
expandsrange
AUG / SEPT 2022 49 enhanced processability (lower cycle times) for caps/closures, food service ware, and takeout containers. In a breakthrough application development effort, Green Dot worked with a customer to commercialize a living hinge design for an injection moulded package. Physical and mechanical properties of typical bioplastic resins have not previously allowed the moulding of a living hinge capable of hundreds of flexural openings and closures while delivering mechanical properties necessary for a polypropylene-type enclosure.
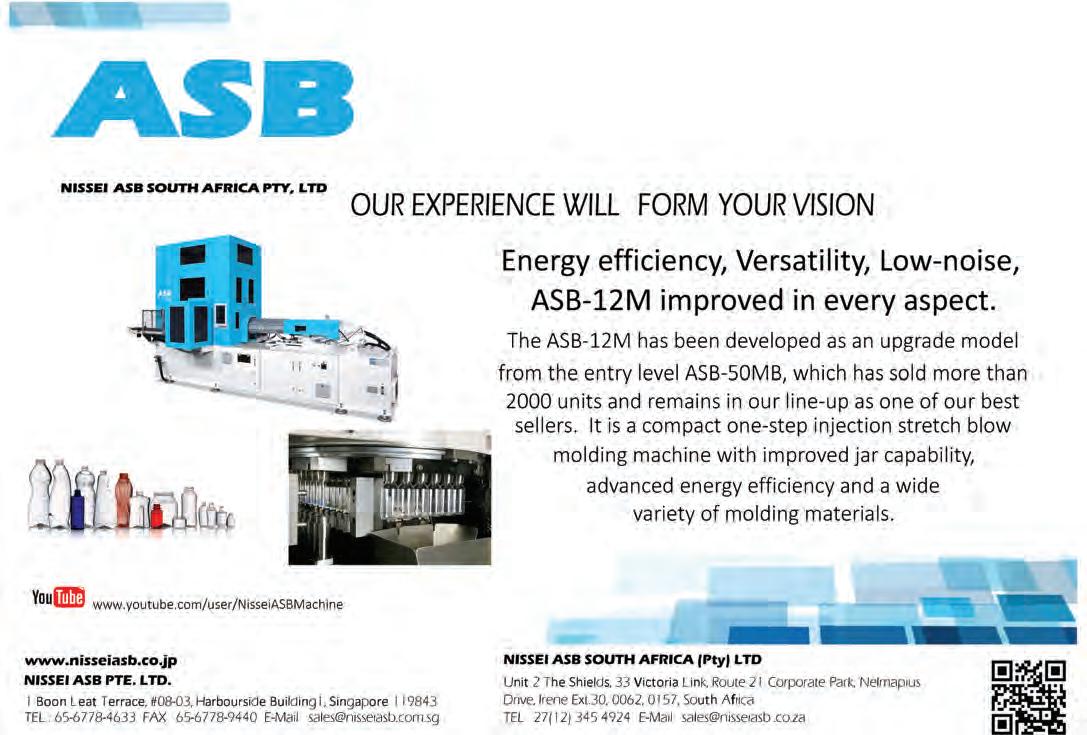
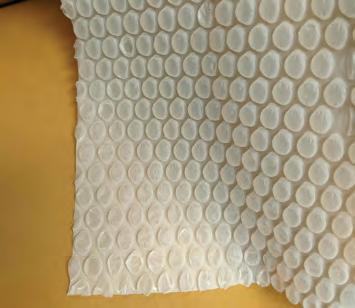
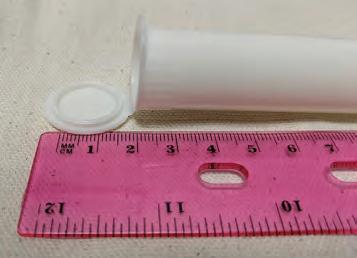



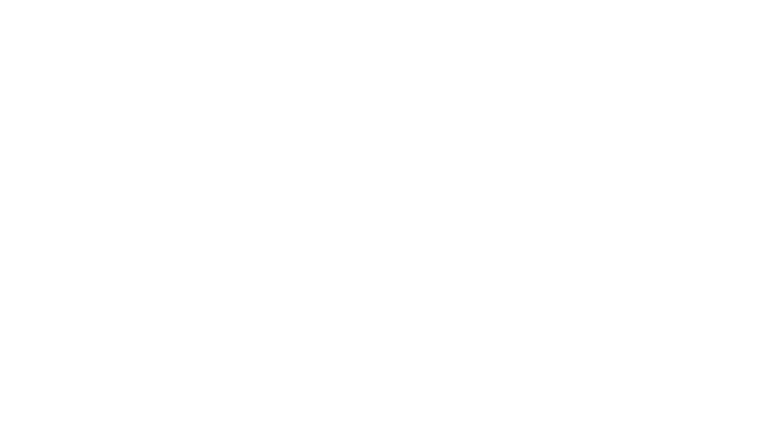
THE Associatione-wasteof South Africa (eWASA) has appointed Adri Spangenberg as packaging executive, with effect from 1 July 2022. “For us to be compliant with the National Environmental Management: Waste Act and the Industry Waste Management Plan (IWMP) in which manufacturers, wholesalers, retailers, and distributors of electrical and electronic equipment are obligated to take back and recycle all types of end of life products, eWASA has registered as a PRO in all three sectors, i.e. electrical and electronic equipment, lighting as well as paper and packaging,” explains Keith Anderson, chief executive officer of eWASA. “All three these sectors have their own types of packaging which need to form part of our strategy as we aim to create a one stop shop for our members. Having the calibre of person like Adri onboard who has ample experience in dealing with packaging, recycling, developing end-markets and understanding the challenges in the industry, is of great benefit to us”, heAdriadds.is seasoned marketer, communicator and strategic thinker. Over the past 12 years she was instrumental in growing South Africa’s polystyrene recycling industry to become one of the world leaders in her position as chief executive officer of the Polystyrene Association of SA (PolySA). She was also the CEO of the SA Vinyls Association (SAVA). Commenting on her new position, Adri expresses that she is very excited about the opportunities and experiences that await her as part of the eWASA team.
fellow directors was unwavering, which commanded much respect from all who knew him. Eddie was a keen golfer, enjoyed all sports and the outdoors with an acute awareness for the environment. He proudly supported many national clean-up campaigns and sport events with the ‘Garbie Clean-Up’ initiative.
– JAN DREYER APPLE Inc of the USA, which has used plastic moulding as one of the chief attractions of its products for close to three decades, has parted ways the designer credited for the development of many of its most popular items, Jony Ive. Products such as the translucent plastic iMac in the 1990s to the rounded corners of the iPhone in the early 2000s and the iWatch in the 2010s have been among the most valuable plastic items everThreeproduced.yearsafter Ive stepped down to run his own design agency while retaining Apple as its major client, Apple and Ive have terminated the arrangement, The New York Times reported. Some Apple executives had questioned how much the company was paying Mr Ive as well as that several of its designers left to join Ive’s, LoveFrom. Ive had also wanted the freedom to take on clients without needing Apple’s clearance.
Apple Inc parts ways with designer people eWASA forpackagingappointsexecutiveSection18EPR
He leaves behind his wife Carol, five children and many grandchildren. His untimely passing is a huge loss to all who had the honour and pleasure of working with and knowing him.
50 2022SEPT/AUG
Farewell to ERP’s Eddie Wallace
EDDIE Wallace, a doyen of the flexible passedinpackagingplasticindustryJohannesburg,awayon11June.Hewas66.Amanofthehighestintegritywith
an endearing sense of humour, Eddie was an outstanding businessman with a passion for East Rand Plastics, Transpaco and the industry. His career spanned 34 years with East Rand Plastics, commencing as a financial manager and culminating with his appointment as managing director in 2016 after the business was acquired byEddieTranspaco.wasinvolved in all aspects of flexible plastic manufacturing. He will be remembered for the roll he played in growing the Garbie brand of refuse bags and his participation in establishing the South African National Standards for garbage bin liners. His devotion to his customers, suppliers, colleagues, employees and
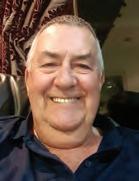


Plastics|SA welcomes Meraxis South Africa as member
AUG / SEPT 2022 51
Farewell
Ivan Horowitz of Meraxis SA with Dick Coates.
MIKE Herald of Castec Johannesburg,of one of the sector,foraluminumproducingtoolmakersforemostcastmouldstherotomouldingpassedaway
recently at the age of 78. Originally from East London, Mike qualified as an industrial engineer at Wits Technikon and initially worked at a number of foundry businesses, among them being the now defunct Ferrovorm, where he gained experience in working withHealuminum.startedCastec at the age of 32 in 1976, operating at first from the garage at his home in Dunvegan, Edenvale. Castec produced tooling for the plastics industry from the start. He grew the business and later employed, trained and upskilled many people to assist with the business and mould production. Castec later moved to premises in Spartan in Kempton Park. Mike was one of the experts in roto moulding in terms of the design, manufacture and production of moulds, if not THE expert in this sector in South Africa. Since, in the roto sector, this was usually for large-dimension prodcuts, his skills were very specific and specialised. Mike was able to guide customers through the whole process and was often needed to advise whether a desired product could be made at all or was better suited to a different technology or process all together. He would be able to suggest changes in design in order to make product manufacture possible and was an expert in terms of wall thickness, shape and details of product dimensions in order to preserve the integrity and quality of the final product.
According to one of his former colleagues, John Davies, Mike showed exceptional skill at all casting activities from an early stage in his working career: “At FerroVorm, Mike was tasked with developing the newly acquired technology of using ‘lost urea’ to produce investment castings for the newly developing defence industry. Using a range of different ferrous and nonferrous alloys, he contributed immensely to the development of accurately cast components for the defence as well as mining industry by mass producing ‘cast-to-size’ boring tools used in the mechanisation of the coal mining industry.“Inthe decade in which I had worked closely with Mike, he consistently demonstrated his leadership skills, tenacity and absolute integrity in all his business dealings. His success during his career is testimony to his ‘in-depth’ knowledge and dedication to achieving the highest standards in all his ventures,” addedSailingDavies.wasamong Mike’s interests, in which area he was one of the founding members of the erstwhile Transavaal Catamaran Club, helped build the club’s clubhouse and served as its commodore for a number of years. He held positions on the South African Sailing Association and Hobie Class Association and won many sailing regattas over the years. to Mike Herald of Castec
PLASTICS|SA is proud to welcome Meraxis South Africa (formally MBT South Africa) as a new Switzerland.thein1996wasMBTmember.SouthAfricaestablishedinbyDickCoates,partnershipwithEndresfamilyofIn2019, MBT merged with Rehau’s procurement Division to create the Meraxis Group. Meraxis South Africa is an important part of an international organisation with an reputationexcellentasan importer, stockist and distributor of plastic raw materials (including PE, PP, PET, PVC and PS). With offices and warehouses in Johannesburg, Cape Town and Durban, as well as a warehouse in Beira Mozambique, Meraxis South Africa supplies a wide variety of Southern African customers, across the various sectors of the polymerCommentingindustry.on why it was important for Meraxis SA to become member of Plastics|SA, Ivan Horowitz, Managing Director Meraxis South Africa says: “At a time when plastics are under considerable scrutiny, Meraxis South Africa felt that it was important for us to be a member of a strong organisation that represents the interests of a broad variety of role players in the plastics industry. We look forward to working closely with Plastics|SA to promote their vision of a sustainable plastics industry, with a focus on education and recycling”.
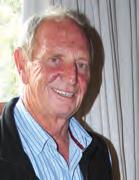
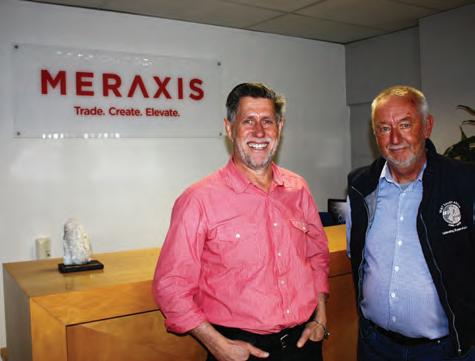
Murray takes over from Isabelle Brettenny, and Reddy takes over from Suzanne Stevens. As training specialists, Isabelle and Suzanne have launched their own business, Aspire Intervention Services, who have a combined 50+ years’ experience in industry spanning multifaceted roles in water quality, FMCG manufacturing, R&D, packaging, strategy, business and people development. They have also started a recruitment company focusing on the manufacturing sector and assist with mentoring youths.
SimonOBITUARYMbata, founder member of the SA Waste Pickers Association, passed away on 19 Feb. Mbata did a lot to lift the image of waste pickers in SA as well as elsewhere in Africa, as he attended a number of conferences on plastics issues in Kenya and elsewhere.
Sean Kleingeld has started on his own, having established Masshiro Plastics in Gauteng. After over 10 years with Ipex Machinery in Johannesburg, Sean began operations with Masshiro (which means ‘immaculate’ in Japanese) in April.After training as a turner-machinist at General Motors in PE, Sean first worked in the mould manufacturing sector, at Caledonian Pneumatics and then Lehle Engineering in Gauteng, making tools for electrical components. Besides standard engineering service work, Masshiro’s main focus is on the printing sector, for both narrow and wide web applications. It supplies a full range of machinery, including blown film lines (from India), recycling equipment, blow and injection moulding machines (Taiwan) as well as extrusion equipment. It also offers automation equipment (including labelling machinery) and a range of auxiliaries ex-China.
Jared Khoury has been appointed commercial manager at Chemipol. Jared started his career as a Process Technician at Engen refinery, basically a plant operator. He worked on their Kerosene Hydro-treating, White Oils, Naphtha and Alkylation units before resigning to join Performance Colour Systems as a junior sales representative in Durban. Not long thereafter he was transferred to Cape Town as a Sales Representative before becoming Branch Manager of the production facility in Cape Town, about two years later. From Cape Town Jared was promoted to Commercial Manager and relocated to Johannesburg a position he held for about 6 years before resigning and joining Chemipol Solutions as Commercial Manager.
Andrew Murray
Douw Steyn of Plastics|SA, who participated at some of these events with Mbata, said the man always made time to discuss and debate issues surrounding plastics in the environment with industry stakeholders. “He had great passion for waste management and recycling,” said Steyn. He was just 51, and was laid to rest in Kroonstad.
Plastics|SA has welcomed Kabelo Phakoe as its new sustainability project coordinator based at the company’s head office in Midrand, Gauteng. Kabelo’s appointment forms part of the plans to expand Plastics|SA’s technical skills and knowledge base to provide evidence-based, up-to-date industry information by attracting experienced minds who would be able to help grow, expand and support the industry. As sustainability project coordinator, he will be responsible for supporting environmentally responsible actions that benefit the industry by focusing on four main key deliverables: waste management and recycling; influencing human behaviour towards good waste management practices; product stewardship and extended producer responsibility; and resource efficiency.
52 2022SEPT/AUG KhouryJared SuzanneStevens SeanKleingeldKabeloPhakoe Isabelle Brettenny
people o n the move
Plastics|SA has also appointed longtime employees Andrew Murray and Prean Reddy as acting regional managers for the Western Cape and Port Elizabeth areas, and KZN and East London areas, respectively.
Eugene Barnes has retired from Alpla in Cape Town … but not quite, he’s been retained as a consultant, working on recycling, sustainability and training projects. Eugene was one of the first people to be employed by the-then Boxmore International group when it opened in South Africa in 1995, when it set up a plant in Harrismith, KZN. The Irish group was one of the first multinational plastic container manufacturers to open in the industry in South Africa. Eugene continued with the group for the next close to 30 years, and retired recently as GM of the group’s Cape Town plant.
News from Down Under – Gary Wolman, formerly of Cinqplast-Plastop in SA, who moved to Australia in 2000, has opened a new chapter in sports management as the CEO of Manly Sea Eagles, a rugby league or Aussie Rules rugby team (five tackles and then you have to kick) in Sydney. CinqplastPlastop Australia was purchased by Pact group, one of Australia’s biggest plastic converting businesses.
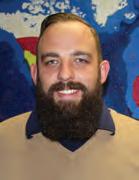
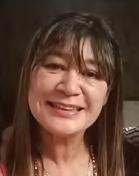

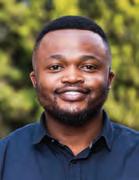
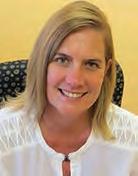
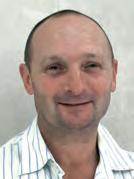
chemistrystudyinsteadcompoundsformulationinterestwithMostGroupWestbusinesssupplypolymerinspentFrederica19yearthewithAfricanyoungerpeopleacademicintheofrubberhavepursuedinthepolymerarea
Freddie Smith says farewell
AFTER 19 years in the polymer supply business with West African Group, Frederica Smith is moving to England later this year, but she’s filled with gratitude for the unexpected career path that opened for her in polymer sales with WAG and is leaving in a more accomplished position than when she started in 2003.
AUG / SEPT 2022 53
occasions. He was involved in the organisation of six national rubber conferences held in Johannesburg.Hewasalso involved with PISA in the writing and registration of national rubber training courses to SAQA standard but this ultimately did not have a successful outcome with training in the rubber sector tapering off in the 21st century to the point where it was no longer practical to offer the courses. He believes that most younger people with academic interest in the formulation of rubber compounds have instead pursued study in the polymer chemistry area, whereas his tuition was aimed at developing practical knowledge, and in turn effective abilities for the production of rubber moulded goods for highperformance applications.
“With time and gained knowledge of the products, I got more and more involved in internal sales with the local customer market,” said Freddie, who has since become an account executive and accomplished at polymer sales and customer support.
“West African Group has been a phenomenal company to work for and it has been an absolute honour to be a part of such a caring, honest and strong team for all these years. West African Group have given me so many great opportunities, I have learnt so much and met so many wonderful people in the industry, many of which I speak with almost daily. It will be very hard to say goodbye,” she added.
After leaving school, Freddie completed an administrative diploma and started at WAG, her first job, as a PA to Brent Hean (who is now CEO of the company) and assigned to assist with export opportunities into Mozambique, based on her knowledge of the Portuguese language.
RUBBER chemist Dr Dave Duncan, who has had an interesting career in the rubber industry in South Africa over the past 45 years, during which time he was involved in some of the most exciting developments seen in the sector, has returned to England. Dave came out to Africa in 1975 when he accepted an appointment at General Tyre, which was then operational in Boksburg where it was manufacturing rubber technical goods. Interesting times lay ahead for the then young Dave: he was appointed as a director of Pigott Maskew (general rubber moulding, hose and rubber lining) in Boksburg, then MD of Paragon Rubber (reclaimed rubber) in Alrode; and Tensile Rubber (injection moulding of technical rubber goods) in Wynberg (Jhb). General consolidated its technical rubber plants into Mining & Industrial Rubber of which he was a director (its tyre manufacturing business was later acquired by Continental of Germany, operating out of Geberqha). He and partners founded Beruc Equipment in 1984 where they moulded items up to 200kgs, which it doesn’t need to be said is a formidable item. In 2008 Beruc was purchased by Tega Industrial of India, with Dave continuing to work for Tega on a contractual basis. The period during the 1980s was synonymous with ‘sanctions busting’ and Dave was involved in the development of several military and other rubber product solutions, including the moulding of rubber items for South Africa’s satellite programme, in which there was a lot of development but no actual nationalBranchofrolesseveralperiod(laterinvolvedDavelaunch.wasactivelyinthePRIIOM)duringthisandservedtermsintheofchairman,treasurerorsecretarytheNorthernaswellaschairmanonseveral
Now 77, Dave and his wife are moving to Lincolnshire, north of London, where he hails from way back.
Rubber chemist Dave Duncan returns to England


2. Building & Construction Product: SOLAR HEAT panels from recycled plastic by Montello spa & WET/Ecopixel srl
3. Household & Leisure Product: StepUp Pedal Bin by Brabantia
1. Automotive, Electrical or Electronic Product: Sustainable modular headliner for vehicle interiors and downstream recycling solutions by Grupo Antolin
Inspirational rise in circular use of plastics in 2022
6. Product Technology Innovation: Recyclable Mono PE Pouch by Procter & Gamble
Building & Construction Product
4. Plastic Packaging Product: Recyclable collation shrink film with outstanding PCR content by Freiberger Lebensmittel GmbH, alesco Folien GmbH & Co.KG, Ecoplast Kunststoffrecycling GmbH, Borealis AG
5. Plastics Recycling Ambassador: Mik Van Gaever, Fost Plus
The winners each received a trophy, with a 3D printed base made from 100% recycled ABS plastic car dashboards and the multi-colour top which is laser cut from compressed HDPE beach clean-up bottle caps.
WINNERS of the Plastics Recycling Awards Europe 2022 witnessed a dramatic and inspirational rise in the circular use of plastics through increased recycling and recyclability over the last the five years.
Household & Leisure Product
The judges really liked Brabantia’s StepUp Pedal Bin, the company’s first waste bin that is also made from waste. A clear winner of its category, this one had it all. Made of 91% recycled post-consumer PP waste, the bin is sturdy yet attractive enough to fit into household and office interiors. A great design that delivers.
Automotive, Electrical or Electronic Product
The solar heat panels from recycled plastic by Montello spa & WET/Ecopixel srl impressed the judges by the originality and aesthetics of the concept combined with the fact that the panels are made from minimally 95% post-consumer recycled plastics. In addition, the design allows for recyclability at the end of life, creating a circular product that has the potential to provide a sustainable source of heating in areas where the sun shines.
The seven Plastics Recycling Awards Europe winners are:
The winning submission stood out for a number of reasons. As a leading supplier of overhead systems, Grupo Antolin has developed a modular headliner that not only incorporates high percentages of recycled content but that also requires less energy to produce and generates less waste during production. The headliner answers market demand for more sustainable car interiors and, because of its modular design, has the potential to really make an impact in the industry.
7. Recycling Machinery Innovation: Mistral+CONNECT by Pellenc ST
DESIGN 54 AUG / SEPT
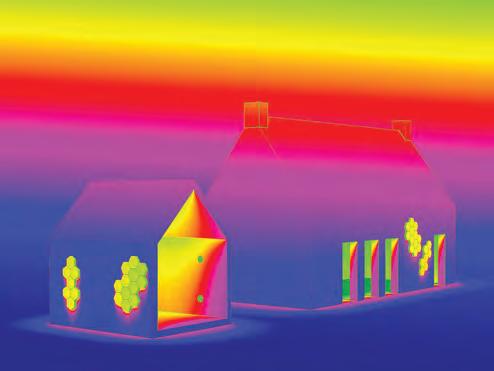
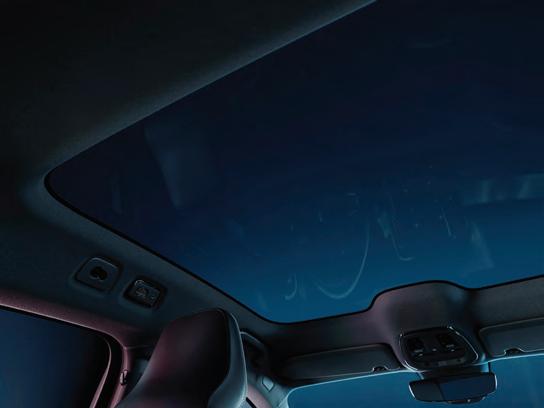
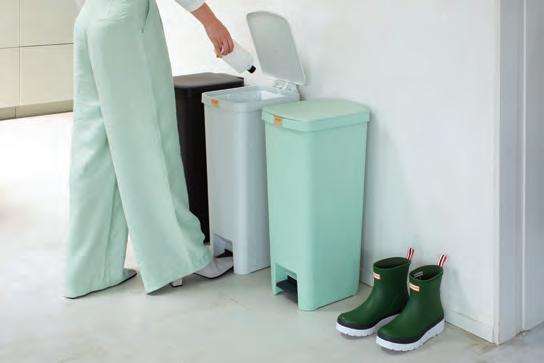
Plastics Recycling Awards Europe 2022
Plastic Packaging Product
AUG / SEPT 2022 55
The judges selected the recyclable collation shrink film developed by Freiberger Lebensmittel GmbH, alesco Folien GmbH & Co.KG, Ecoplast Kunststoffrecycling GmbH, Borealis AG as the winner in this category, citing this as an excellent application for the use of recycled material. Staggering volumes of collation shrink film are used and the market continues to grow. Thin, strong, and lightweight, collation films can help to reduce packaging wastage and considerably reduce the weight of freight thus also contributing to a reduction in carbon emissions. Using recycled resin derived from commercial postconsumer and municipal waste further serves to enhance the ecobenefits of this product.
The recyclable Mono PE Pouch by Procter & Gamble, impressed the judges because of its underlying concept: as part of a refill system, consumers purchase the product in the recyclable PE packaging, pour it into a durable, recyclable aluminium container that will not rust in bathroom use. The pouch currently has a lid made from PP, but this will be replaced by one made from PE in the future, making it possible to recycle the pouch in a single stream. The judges called it a forward-thinking and creative alternative packaging solution, with built-in convenience for consumers seeking more sustainably packaged products.
Product Technology Innovation
Recycling Machinery Innovation Improvements in the sorting of waste are essential for ensuring high-quality plastic recycling and the judges were pleased to see several new sorting technologies in this category. The Mistral+CONNECT by Pellenc ST drew unanimous praise from the panel for its impressive sorting performance, in terms of material types, speed and accuracy which is achieved through the implementation of an array of sophisticated technology. This submission was the clear winner in its category.

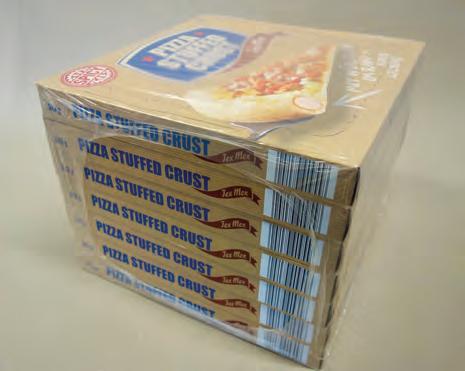
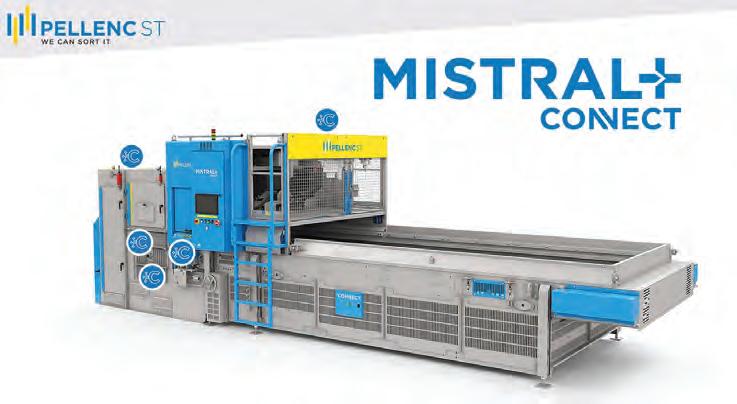
Crutch
Design Innovation
DESIGN
Kenneth Thornton, (Edinburgh Napier University), with his product Catheter Bag Carry, a reusable portable catheter bag holder
Zara King designed EasyMode, a re-usable bedpan for a pulp liner to fit inside, providing a safe and comfortable base for people to use in any healthcare setting
University student creates new bedpan solution for patiens in healthcare settings
56 AUG / SEPT 2022
Catheter Bag Carry
A STUDENT from the UK’s Teesside University has claimed top prize in the 2022 Design Innovation in Plastics (DIP) competition, with a re-usable bedpan. DIP, supported by the Institute of Materials, Minerals and Mining (IOM3) and headline sponsored by Covestro, is the longest running plastics design competition of its kind for university undergraduates in the UK and Ireland. Students were asked to design a product made primarily of plastics, for the healthcare sector, which can be used in demanding applications, but which also exploits the longevity of plastics. Product design undergraduate, Zara King, designed EasyMode, a re-usable bedpan for a pulp liner to fit inside, providing a safe and comfortable base for people to use in any healthcare setting. The bedpan is moulded with a wide base so that it sits comfortably into the bed and presses down into the mattress, and when the patient is rolled off, it doesn’t tip. Zara designed the product after hearing first hand from a nurse about the awkwardness of using existing bedpans, and the distress it often causes. She used reaction injection moulding to create her product, which is made from polyurethane. She designed it after hearing first-hand from a nurse about the awkwardness
EasyMode
Charlie Gould-Hocking (Bangor University), with his Crutch, a shower stand for amputees with a lower limb loss that allows them to stand whilst showering
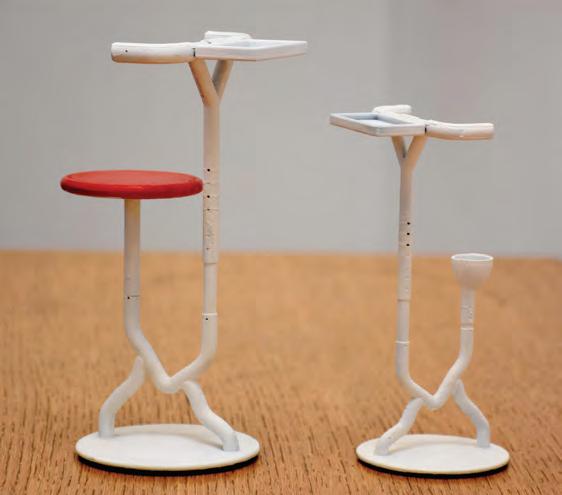
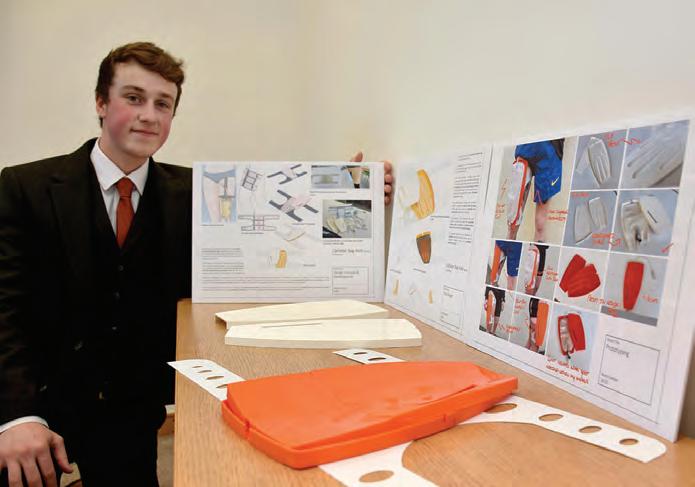
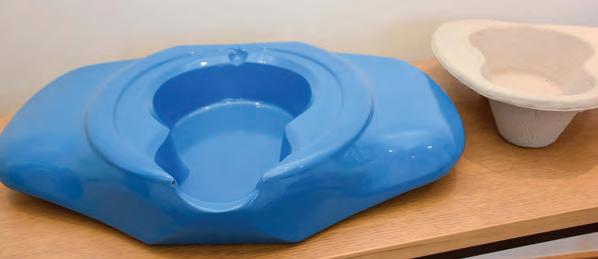
Burns Kit Daniel Warren, with Cura, a first aid kit for first treatingassessingaincorporatingresponders,newwayofandburns
“She impressed the judges with her methodical approach to solving a major problem in the NHS,” said chairman of judges, Richard Brown. “Her holistic approach incorporated both user and patient issues, to come up with a solution which met both needs. She gave due consideration to sustainability, manufacturing and the materials used and has registered this product as her intellectual property, so that it is market ready, should she want to take it forward.”
ANAP Dimitri McGrath Karvelis, London South Bank University, with ANAP, a double capacity inhaler that combines the preventer and reliever medication in one compact twist-and-carry device
in Plastics 2022 AUG / SEPT 2022 57 of using existing bedpans, and the distress it often causes.
Cirrus Highly Commended was awarded to Daniele Di Paolo, London South Bank University, with CIRRUS, a device to help with breathing exercises to promote relaxation
The judges awarded second place to Kenneth Thornton, (Edinburgh Napier University), with his product Catheter Bag Carry, a reusable portable catheter bag holder which conceals and protects the catheter bag. Kenneth used silicone (NinjaFlex) for the bag holder and polypropylene for the belt. In third place came Charlie Gould-Hocking (Bangor University), with Crutch, a shower stand for amputees with a lower limb loss that allows them to stand whilst showering. He used a combination of reinforced PET with a 30% blend of SEBS and silicone rubber, to create his product.
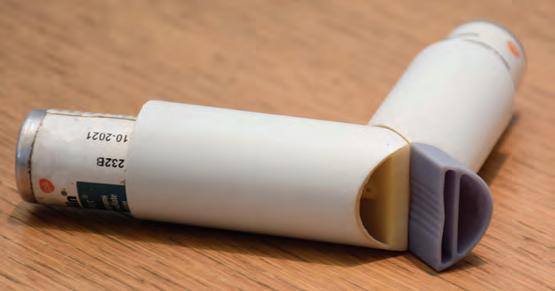
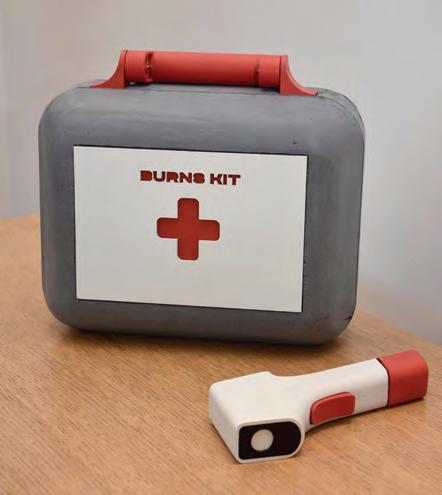
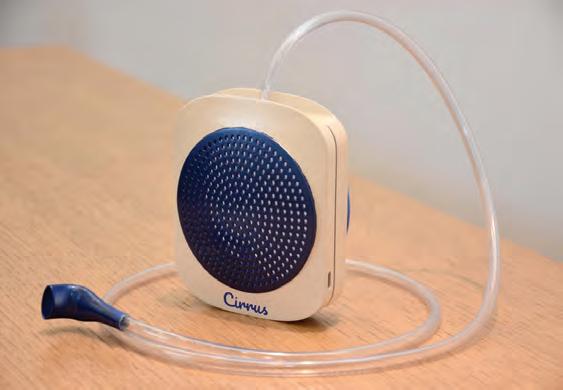
While the ‘energy’ side of petrochemicals are produced in refineries, the ‘raw materials’ side of petrochemicals are mostly produced from crackers. Steam-crackers heat up the feedstock, which can be a liquid (either naphtha or crude oil) or a gas to temperatures up to 900°C to ‘crack’ or break the hydrocarbon chains into small molecules such as methane, ethylene, propylene and butene. These are the chemical building blocks that are used to produce hundreds of socalled intermediate chemicals such as acetic acid, ammonia, ethylene glycol, methanol, phenol, acrylonitrile, purified terephthalic acid, styrene which are the raw materials from producing nylon, polyester, PET, polycarbonate as well as tens of thousands of other products.
MIDDLE EAST
The petrochemical industry in the Middle East started with exporting crude oil. It then invested in refineries and ethane crackers to add value to the crude oil and associated natural gas, and then moved further downstream, producing basic polymers (polyethylene and polypropylene), fertilizers and basic commodity chemicals. The next generation of investment moved the industry further downstream from oil and included a larger portfolio of chemicals and polymers which required the monomers be synthesized using the chemical feedstock produced by the refineries and crackers.
focus is usually on only one sector of the petrochemicals industry – polymers – but it is also interesting to look at how polymers fit into the broader petrochemicals industry, and how these developments will impact the polymer industry in future.The petrochemicals industry is essentially about two things: energy and raw materials. From the earliest of times the progress of mankind from watching shadows on the walls of caves to watching Netflix streamed into a modern skyscraper has been made possible by having cheaper and more convenient access to energy and raw materials. From burning wood to burning coal to burning oil to burning gas; the need for abundant, cheap energy is now moving away from energy dense carbon-fuels to nuclear-, geothermal-, solar- and wind-generated electricity. The ‘energy’ side of petrochemicals are refineries where crude oil is separated into its different components which are then used to generate energy. This is done by heating the crude oil and separating the different fractions based on their boiling points – as you heat the crude oil the first fractions to evaporate are the petroleum gases (ethane, propane, butane). Next off is gasoline, followed by kerosene and jet fuel and then diesel. Heavier fractions include lubricants and greases, waxes, marine fuel oil and bitumen. Most refineries are optimised to produce the most important (by volume) gasoline and so there are processes to ‘crack’ the heavier fractions (higher boiling point products) to the more useful lighter fractions. What is important to note is that all of these products are present in the crude oil (there will be some variation in the relative amounts of each fraction depending on the source of the crude oil) and refiners do their best to balance the production of each fraction by demand. Typically, about 80% of the output of an oil refinery will be primarily used for energy, either directly (for example LPG for heating) or in the case of gasoline, kerosene, diesel and marine oil, indirectly in electrical power stations or in internal combustion engines. The remaining 20% which includes aromatics and sulphur as well as petroleum gases are either used directly (waxes in candles or fruit or cheese coating, bitumen in asphalt) or as chemical feedstock in the ‘raw materials’ part of the petrochemical industry.
As the industry evolves and continues investing it will lead to a growth in the volumes of polymers produced in the Middle East, but it will also allow the polymer industry to further diversify into producing polymers not yet made in the region. Even as the world moves away from using oil for energy, the importance of petrochemicals for raw materials will not so easily be substituted. As the world moves away from oil for energy, importance of petrochemicals for raw materials will not be easily substituted
Petrochemicals are more than plastics
58 2022SEPT/AUG
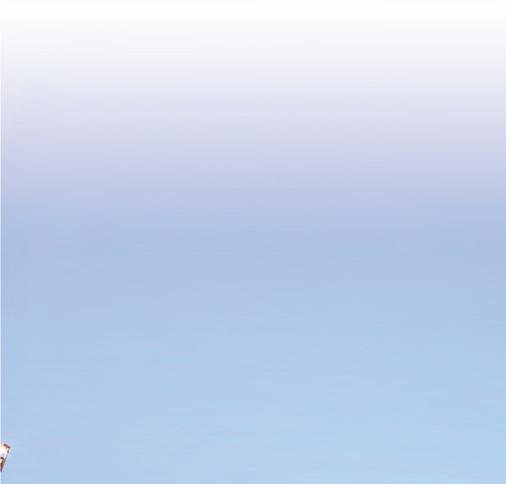
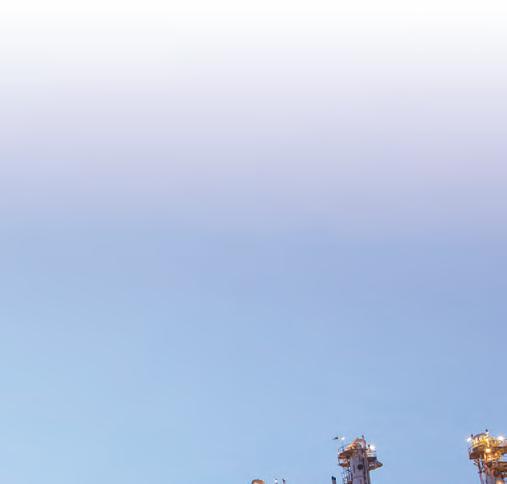

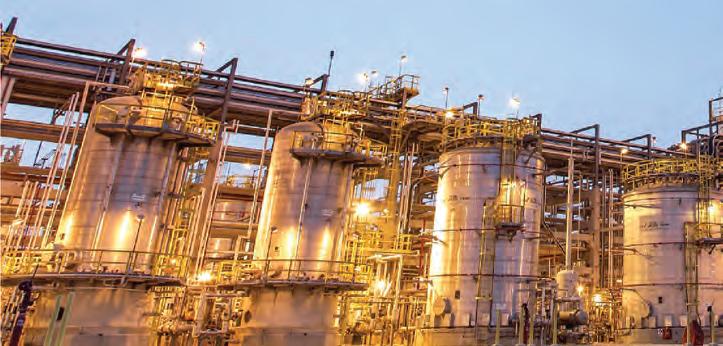
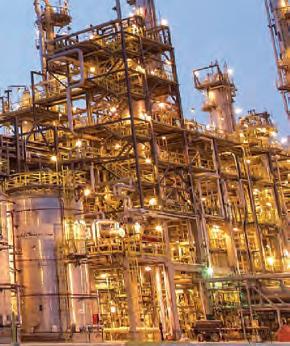


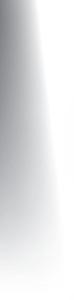


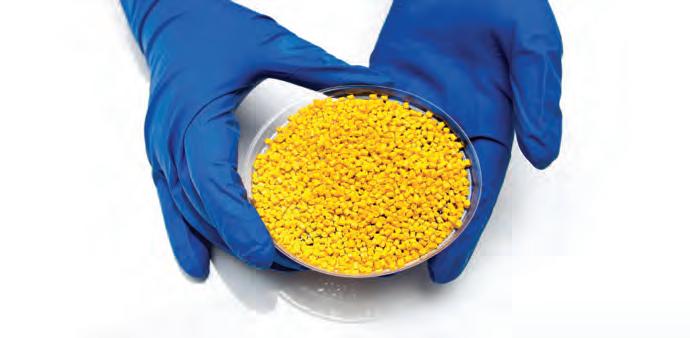


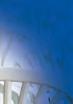
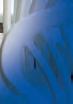
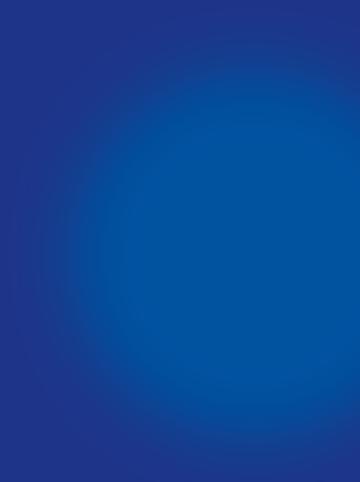
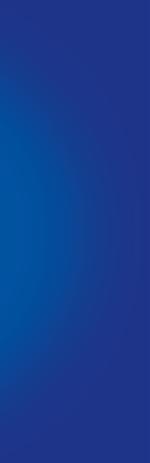
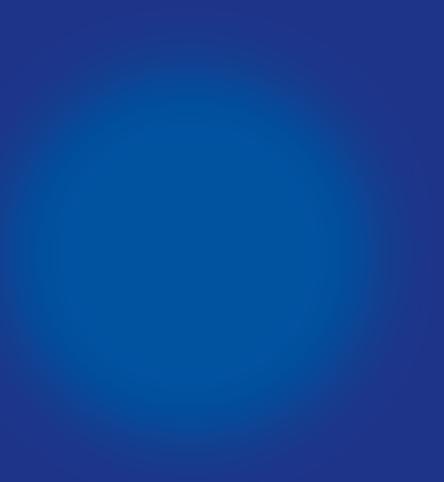


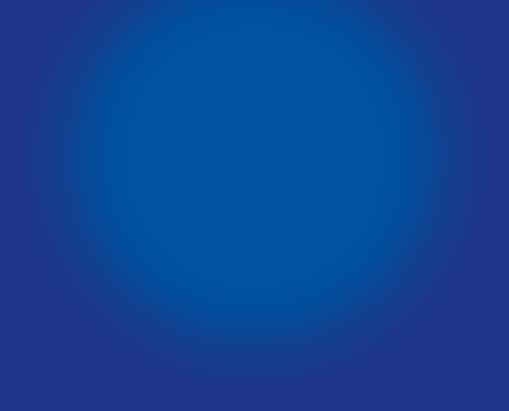
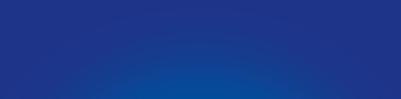
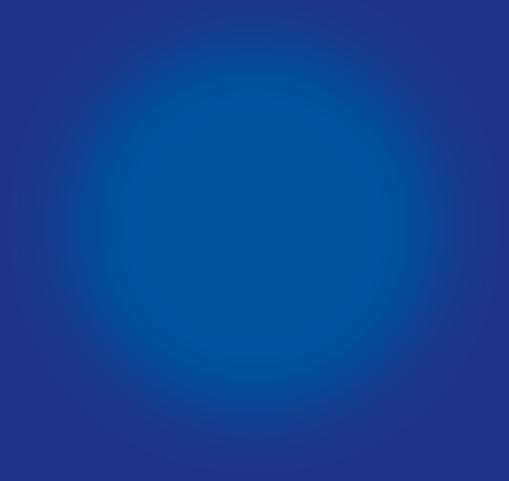
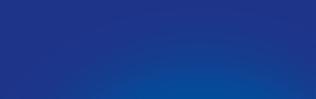


1. Group Index Method of US Highway Engineers is an empirical quantity calculated from the soil’s grading and Atterberg limits. 2. Shear Strength Method links it to theoretical stress imposed on pavement and subgrade that ignores repeated loading effects. 3. Californian Bearing Ratio (CBR) Method subgrade empirical property measured by empirical penetration test. 4. Modulus of Elasticity Method considers this to be the critical soil property. The foregoing four methods are for the design of roads and runways not for the bedding, embedment and backfill of pipelines (see Table2). necessarily“Moreisnotbetter.”
BY MIKE SMART, PR. ENG., B.SC. (HONS) CIV. ENG., MSAICE
A road or runway consists of two parts: 1. Pavement to distribute the wheel loads over sufficient area. 2. Subgrade the material, natural or constructed, underlying the pavement. There are four methods of designing the total thickness of a road or one of its layers:
Arthur Casagrande’s (1902-1981) soil classification is shown in Table 1.
1 Coarse-Grained Soils Well graded gravel/gravel/sand; little fines GWLarge, visible Gravel and gravelly soilsWell graded gravel/sand-clay; good binder GCparticles mostly Poorly graded gravel/gravel-sand; little fine GP> 2.411 mm Gravel excess fines; clayey gravel; bad grade GF Sands and sandy soils Well graded sands; little/no fines SWMostly visible Well graded sand/clay; excellent binder SCparticles. Soil Poorly graded sands; little/no fines SPfeels gritty to Sand excess fines; silty/clayey sands, bad gr SF
60 2022SEPT/AUG PIPE MATTERS
EVERYTHING a civil engineer designs and constructs rests on, or in the earth. Therefore, soil mechanics is fundamental to this profession, like air is to aeronautical engineers, it supports the structures they design and construct. Reinforced concrete pipes dominate the non-pressure gravity pipeline market because the design engineer knows when a concrete pipe is delivered, the conduit and the structure is delivered; when a thermoplastic SWP (Structured Wall Pipe) is delivered, only the conduit is delivered and the structure must be constructed on-site. Thermoplastic SWP relies on the “soil-pipe” structure that is constructed in-situ with the pipe and its embedment.
Major Divisions and Soil Groups Common Descriptions SymbolGroup V Characteristicsisual/Physical
Under certain circumstances, reinforced concrete pipes may be more appropriate for stormwater, for example where the water table is above the pipeline’s invert. However, in aggressive sewage applications where gases attack concrete pipes, thermoplastic SWP is undoubtedly better. All engineering soils are the product of disintegration of part of earth’s rocky crust. These residual soils have changed in character but there are no minerals present that were not in the parent rock, although erosion may have moved material considerable distances from its source, changed particle shape from angular to rounded, and sorted and graded it.
Table 1: Casagrande’s Classification
fingers 2 Fine-Grained Soils Inorganic silts, fine sand, mo, rock flour, silty MLNot gritty, can’t Fine-grained/low plasticityClayey silts (inorganic) CLroll into threads Organic silts with low plasticity OLmoist LL<35% Fine-grained/medium PISilty clays (inorganic), sandy clays MIRoll thread moist Clays (inorganic), medium plasticity CIcracks on drying Organic clays, medium plasticity OILL 35-50% Fine-grained/high PI Micaceous/diatomaceous fine sand/silt; elastic MHGreasy, thread Clays (inorganic), high plasticity; fat clays CHmoist >40% clay Organic clays, high plasticity OHLL>50% 3 Fibrous Organic Soils Peat, organic swamp soils; very compressivePt Dark/fibrous “Mo” Scandinavian word particle sizes between fine sand and silt – schluff in German. necessarilybetter.”Plastic pipeline construction To be continued... If you would like to read the full article, email tessa@summitpub.co.za
Limestone rock is attacked by acids, producing sedimentary rocks like sandstone consisting of inert particles of silica, impervious to weathering, cemented by eroded or dissolved material. In tropical regions with heavy rainfall, the continuous and cumulative leaching of soluble material may weather the bedrock to great depths. Water is the most productive of all soil-forming agencies. In geologically young rivers, or near the source of old ones, gravels and coarse sands are found, but in older ones and downstream reaches, where velocities are lower, silts and clays are found.
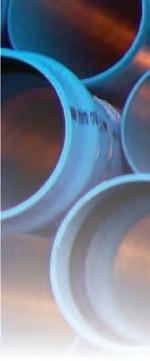
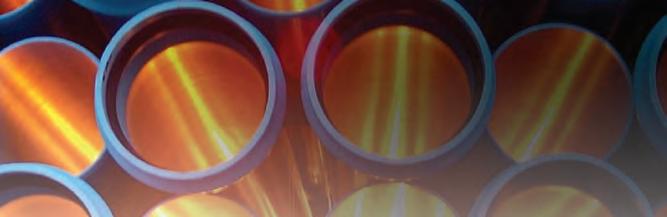
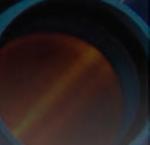
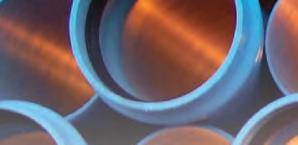
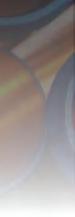
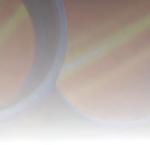
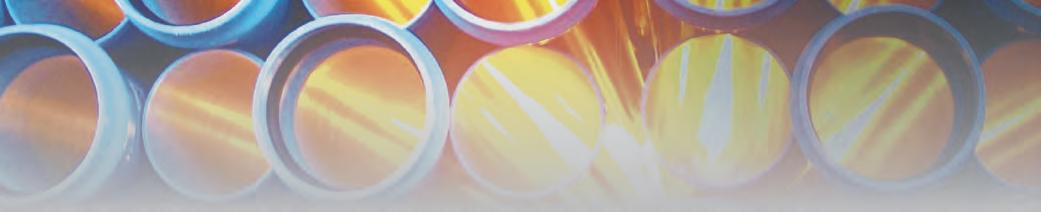
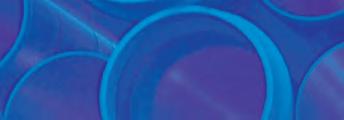



50 •Wessel Safl Suppliers
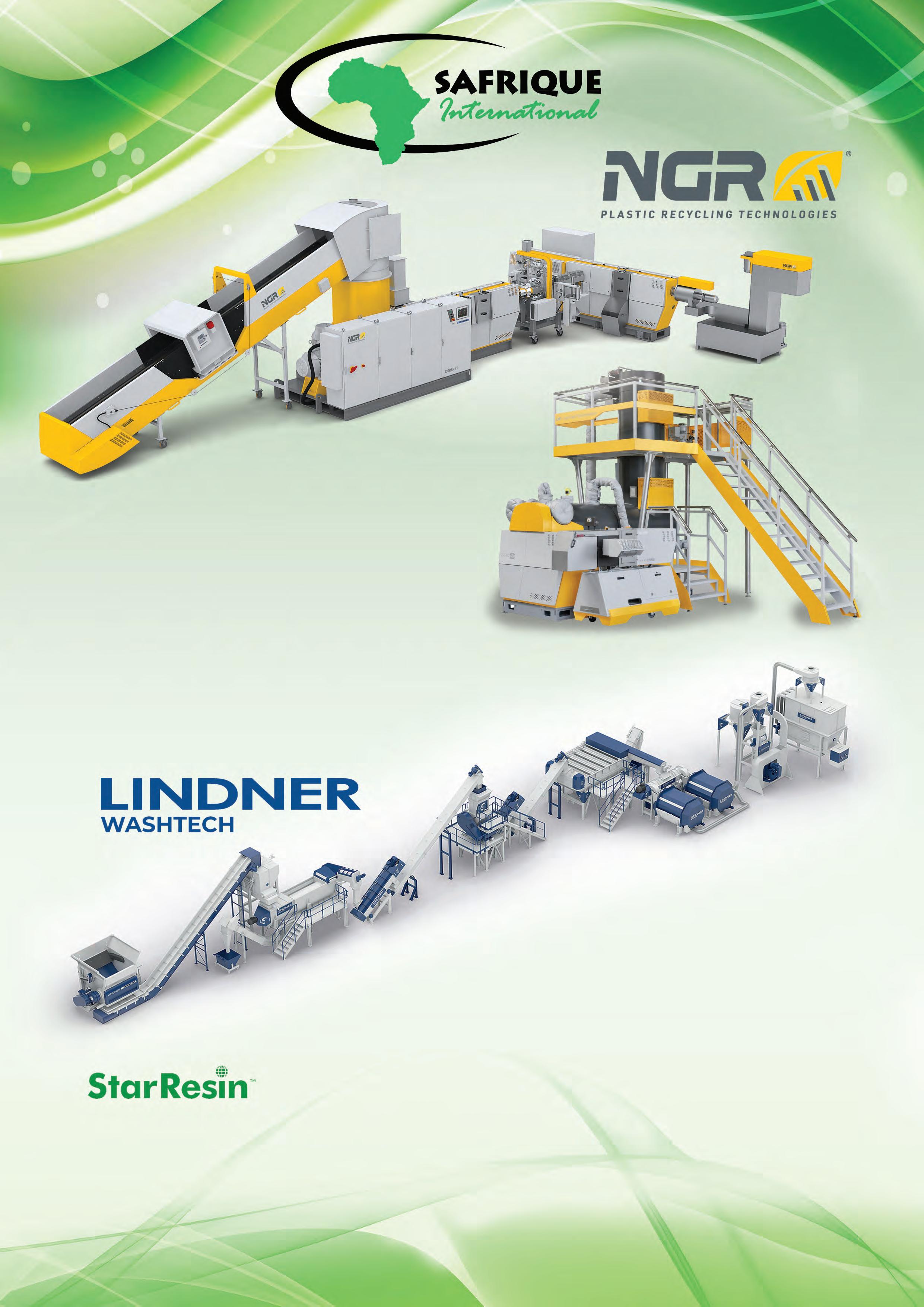
www.rawmacplastics.co.za Johannesburg Durban Port Elizabeth Jeremy Goosen Sagree Muthu Charl Foreman (T) 011 626 1030 (T) 031 577 0505 jeremy@rawmac.co.za Cape Town sagree@rawmac.co.za (T) 041 484 3390 charl@alben.co.za With 40 years’ experience in supplying engineering polymers to the industry, our logistics & technical backup provide the highest level of service and support. ABS – Polylac MABS – Polylac ASA – Kibilac SAN – Kibisan GPPS – Taitarex / Kaofu / Supreme Q’ RESIN – Kibiton / Denka HIPS – GPPC / Supreme EPS – Taitacell / King Pearl PMMA – Acryrex SMMA – Acrystex PC –PC/ABS Wonderlite ALLOY – Wonderloy PA 6 – Zissloy PA 66 – Gramid / Zissloy POM – Kocetal PBT – Spesin EVA –SBR/SBS APC – Kibiton TPV – Globalene TPE – Kprene PP GLASS FILL – Woori PE – HDPE / LLDPE UREA COMPOUND – Sprea Bronwyn October Zita Rodrigues (T) 021 933 ct@rawmac.co.zabronwyn@rawmac.co.za3331/2
AS part of its continuous education process, Southern African Plastic Pipe Manufacturers Association (SAPPMA) continues to enlighten design engineers, contractors and all users of plastic pipe of the critical importance of getting the highest quality of polymers in the products they specify or “Theprocure.controlling product standards, national and international, of HDPE and PVC pipes are clear about the importance of the quality of polymers,” says Sappma CEO Jan Venter. He stresses that apart from the stringent material specifications, most standards prohibit the use of recycled materials, other than the small percent created in the same factory.
“Because the cost of polymer can constitute more than 75% of the cost of the finished pipe, it is clearly a target for unscrupulous operators, trying to reduce cost and increase profit,” he stresses. SAPPMA also insists its members must ensure its tender documents and contracts are perfectly clear on the fact that recycled material is not allowed at all. “It is of utmost importance that you ensure you have a knowledgeable individual undertaking regular inspections of factories or manufacturers,” adds Venter. He attributes the lack of continuous standards upkeep to the fact that pipelines are mostly hidden from view and therefore there is a tendency to forget about it. No country and civilisation can exist without the conveyance of fluids under controlled conditions, including instances such as potable water, wastewater, fuel, chemicals, slurries, gas, and many more. quality control is imperative www.sappma.co.za
SAPPMANEWS stresses

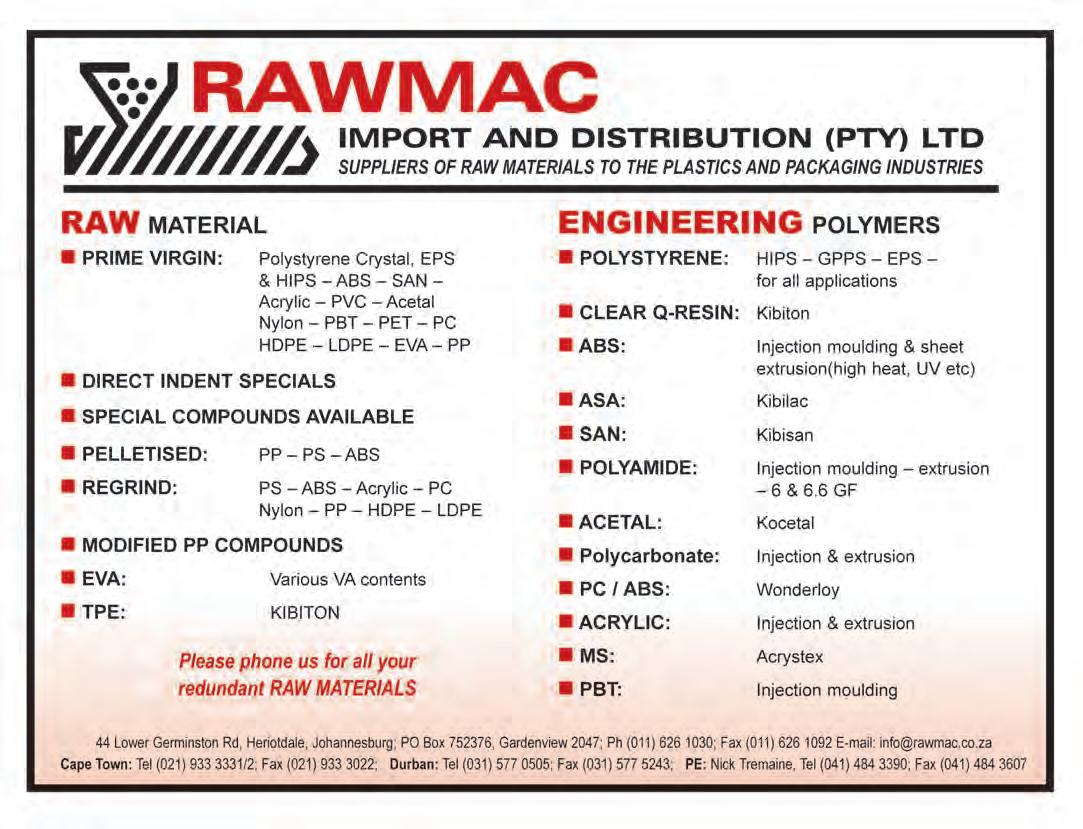
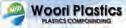




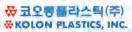




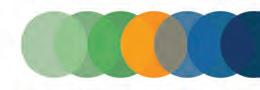
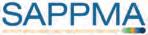
PIPES CONFERENCEXIII
year, our PIPES conference attracts people from a wide range of different ages, backgrounds and industries who benefit from this valuable learning opportunity. The event is a must for students and academics, engineers, industry representatives, local government, parastatals, pipe fittings and extrusion equipment manufacturers, raw material suppliers and consultants who need to remain at the top of their game. For two days, they will not only have the privilege of being exposed to the latest industry research and best practice, but there will also be ample networking opportunities with fellow professionals,” Jan concluded.
For more information or to register for PIPES XIII, visit the Events Page on www.sappma.co.za or contact Enrike Albasini via email at admin@sappma.co.za.
SPEAKER LINE-UP
SPONSORS We would not be able to host this event without the financial support of our sponsors. In particular, we wish to thank Molecor, who has come onboard as a Gold sponsor and Plastic & Chemical Trading, our silver sponsor.
The versatility of Plastic Pipe SPONSOR SILVER SPONSOR
The Southern African Plastic Pipe Manufacturers Association (SAPPMA) has released an exciting line-up of local and international speakers who will be presenting at the PIPES XIII Conference that will be taking place on 6 &7 September 2022 at Emperors Palace in Gauteng, in collaboration with the Plastic Pipes Conference Association.
PRESENTERS INCLUDE: Dr Mike Troughton (TWI LTD), George Diliyannis (Safripol), Dolores Herran (Molecor), Dominique Gueugnaut (GRTgaz), Kirtida Bhana (Plastics SA), Beverley Manikum (Sasol), Antonio Rodolfo Jr (Braskem S/A, Vinyls), Sylvie Famelart (European Council of Vinyl Manufacturers), Albert Vaartjes (Rollepaal), Christian Schalich (SIKORA AG, Corporate Communications), Joerg Wermelinger (Georg Fischer Piping Systems Inc., TEC), Ilija Radeljic (Pipelife Norway), Gunter Dreiling (Borouge Pte. Ltd., Innovation Centre), Peter Sejersen (TEPPFA), Mario Messiha (Polymer Competence Center Leoben GmbH), Prashant D.Nikhade (Borouge Pte Ltd), Sjoerd Jansma (Kiwa Technology), Gregory Vigellis (Union Pipes Industry LLC), Norbert Jansen (PE100+), Lennert Bakker (Suloforce), Simon Thomas (Simon Thomas Consulting), Moshodo Motebele (Department of Water & Sanitation), Jacques van Eck (Avesco), Mike Smart (Genesis Consulting), Alaster Goyns (Pipes CC), Victor Pinedo (Georg Fischer Piping Systems Inc., TEC), Ian Venter (SAPPMA), Bruce Hollands (Uni-Bell PVC Pipe Association), Ricardo Pascual Galan (Aenor) and Kate Kleingeld (Plastic & Chemical Trading).
GOLD
6 – 7 SEPTEMBER 2022 EMPERORS PALACE, GAUTENG
Jan Venter, Chief Executive Officer of SAPPMA says they are looking forward to the hybrid conference after a two-year absence owing to the COVID-19 pandemic. Whilst SAPPMA encourages as many people as possible to attend in person, there will also be the opportunity for delegates to log-in virtually.
The opening keynote speaker for the event will be popular economist Roelof Botha, followed by various local and international speakers who will be covering all elements relating to pipeline design and installation, standards, testing and certification, extrusion technology, addressing water problems in Southern Africa, infrastructure, raw materials and the rehabilitation of old pipelines.
REGISTRATION FEE: •R4 300 or 300 Euro (excluding VAT) •R3 400 SAPPMA members (excluding VAT) •R3 000 for 5 or more in group (excluding VAT) •R2 200 virtual attendance (excluding VAT)
EXHIBITORS In addition to listening to this line-up of world-renowned speakers, delegates will also be able to visit exhibitions by leading plastic pipe manufacturers, suppliers and industry partners such as Aenor, Alprene, BSI Group, MacNeil, Molecor, Pipeflo, Plastiweld, Pipestar Africa, SAVA, Zerma etc.
“We are very fortunate that our event will take place in collaboration with the Plastic Pipe Conference Association (PPCA) - hosts of the biggest international pipe conference that takes place every second year either in Europe or the USA. A spin-off conference is organised every alternate year and this year it is coming to South Africa!” Jan “Eachsays.
The theme of PIPES XIII is “The Versatility of Plastic Pipe”. Local industry experts will share the stage with some of the best international papers that were presented at the PPCA’s PIPES XX conference in Amsterdam last year.

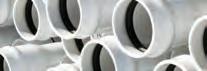
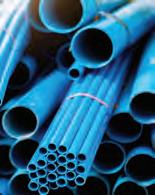

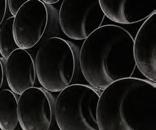


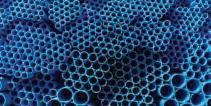


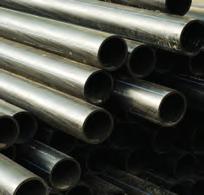
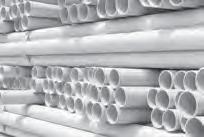

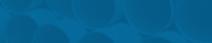

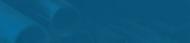
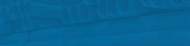
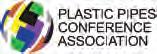
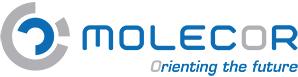



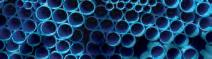
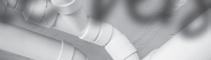
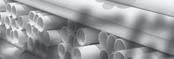
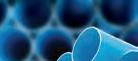
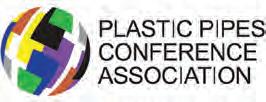
The approximately 3 000 exhibitors from 61 countries will occupy Düsseldorf Exhibition Centre in its entirety. K2022 is already providing pooled expert know-how with its K-Talk. Once a month this digital live talk (in English) features exciting panel discussions with a line-up of international participants dealing with different focal themes but always with a focus on the three guiding themes of LaunchedK2022.inApril 2021, the online magazine K-MAG targets all industries related to K and delivers facts, news, stories and trends from the international plastics and rubber industry in German and English all year round.64 2022SEPT/AUG
The approximately 3 000 exhibitors from 61 countries will occupy Düsseldorf Exhibition Centre in its entirety
K2022 PREVIEW
active for climate protection, circular economy and digitalisation a constant high for several years now. We can expect impressive appearances, especially from China, Taiwan, India, South Korea and Japan.
m
THE plastics and rubber experts all agree: K2022 in Düsseldorf from 19-26 October, will be the most relevant meeting point for the entire industry worldwide. Exhibitors from throughout the world will come to Düsseldorf to demonstrate the operational excellence of the industry and actively chart the course for the future – a course that leads to climate protection, circular economy and digitalisation – also the three guiding themes of K 2022. Suppliers from Europe, especially from Germany, Italy, Austria, Turkey, the Netherlands, Switzerland and France will be particularly well represented again this year, but also from the USA. At the same time, K clearly reflects the changes affecting the global market: the number and presentation areas of companies from Asia have remained at
Global plastics & rubber industry 3 000 exhibitors from 61 countries Tickets for K2022 can bought online at www.k-online.com/2410Thewww.k-online.com.K2022exhibitorsisaccessibleat
FO and sampling shop in ct management team and over 20 2D & 3D CAD, weeklyprogress rep Mould Validation procedure. America, Oceania, Africa, Asia a eneralpurpose, home appliance a reen T: +27 (0)79 371 5508 E: www.yongshenmould.com
h
K-monthly is the name of the new Newsletter of K in Düsseldorf. Subscribers not only receive the most interesting news and stories from the K-MAG via e-mail on a monthly basis but also current information revolving around K in Düsseldorf and the international trade fairs of the K-Global Gate family of products. Subscription is possible on the K website or the K-MAG.
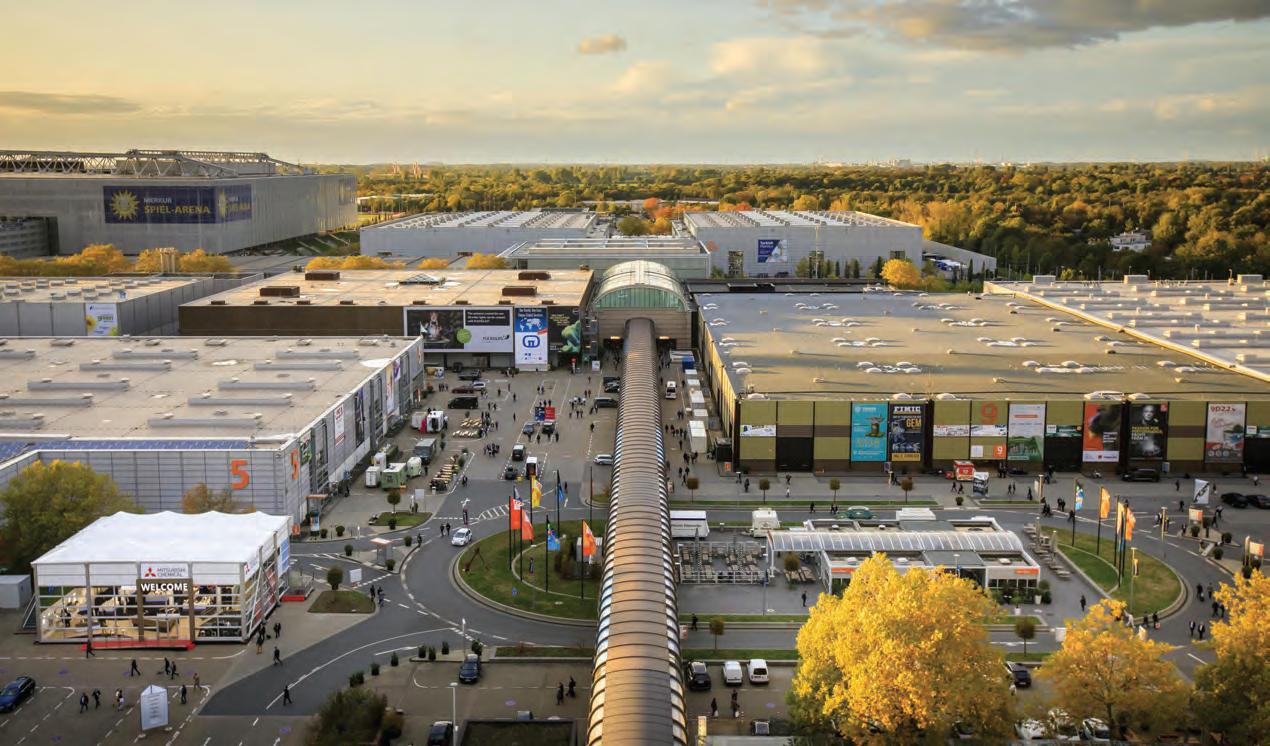
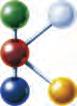
The thin-walled containers are produced directly from rPET in a single step. An Engel e-speed 280/50 injection moulding machine was specifically developed by Engel, with its electrical clamping unit and hydraulic injection unit, for the high performance requirements of thin-wall injection moulding.
FOConventional two-plate moulds, Three-plate injection moulds Twin Shot Hot runner moulds Rubber moulds CoreFamilypulling and Unscrewing Fully equipped Tool Room and sampling shop in ShenZhen China With our team of highly trainedproject management team and over 20years experience we offer Moldflow analysis, DFM, fully 2D & 3D CAD, weekly progress reports and a stringent Mould Validation procedure. YongShen exports to Europe, North America,
Processing rPET in thin wall injection moulding
Engel will produce containers are being produced directly from rPET in thin-wall injection moulding at the K show combines the new injection unit with a plasticising unit from in-house development and production specifically designed for processing recycled material. During plasticising and injection, the viscosity of the PET is configured for thin-wall injection moulding. Oceania, Africa, Asia and South America for the Au-tomotive, Medical, Industrial, Generalpurpose, home appliance and agricultural industries For more information, contact Bert Green T: +27 (0)79 371 5508 E: bert@yongshenmould.com www.yongshenmould.com in ShenZhen China 0years experience –we offer eports and a stringent and South America for the and agriculturalindustries bert@yongshenmould.com
Rubber moulds
Conventional two-plate moulds, Three plate injection moulds
High-performance injection unit achieves injection speeds up 1400 mm per second
Engel at hall 15, stand C58
ENGEL is presenting a quantum leap for the packaging industry at K2022. For the first time, thin-walled containers made of PET can be produced in a single injection moulding process step. Engel will be processing recycled material (rPET) at its stand on an e-speed injection moulding machine with a newlydeveloped and extremely powerful injection unit. Featuring a wall thickness of 0.32, the transparent, round 125ml containers and thanks to integrated in-mould labelling (ILM), the containers are ready-for-filling as soon as they leave the production cell.
Twin Shot Hot runner moulds
CoreFamilypulling and Unscrewing Fully equipped To With our team of highly tra Moldflowanalysis, YongShen exports to Eu Au-tomotive, Medical, In For more information, cont AUG / SEPT 2022 65
The new unit achieves injection speeds up 1400mm per second at a maximum injection pressure of up to 2600 bar when processing small shot weights with an extreme wall-thickness to flow path ratio. To process rPET, Engel

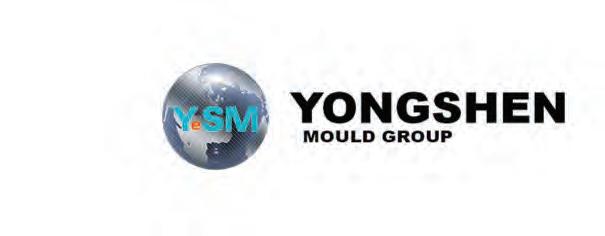
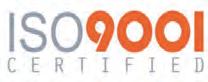
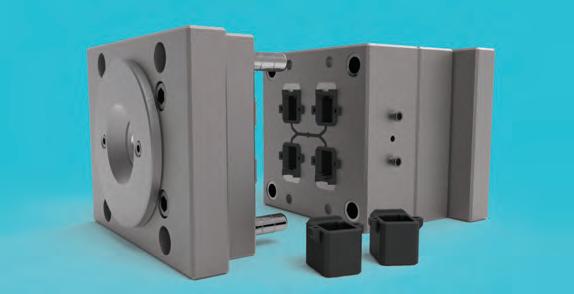
At K2022, Dutch company MEAF Machines will demonstrate its best in class extrusion solutions at booth A22 in Hall 17. Thanks to its highly efficient design, MEAF’s extrusion have a 30 to 65% smaller carbon footprint than many of its competitors, while allowing for a further reduction in raw material use. In addition its in-build flexibility allow MEAF’s extruders to work with almost any thermoplastic material, including biopolymers and recycled materials like bottle flakes and post-consumer regrind, thus helping plastics processors to go ‘green’.
ISWA World Congress: 21-23 September Sands Expo & Con Centre, Singapore www.iswa2022.org
Drinktec: 12-16 September Munich, Germany: www.drinktec.com
MEAF
São Paulo, Brazil: www.feiplar.com
2023 Africa Energy Indaba: 7-9 March CTICC, Cape Town: www.energyindaba.co.za events Arburg at innovativeDrinktec:reusable cups ARBURG will attend Drinktec in Munich from 12-16 September to showcase a pioneering application: at the Arburg stand 224 in Hall C5, visitors will discover an outstanding innovation in the field of reusable cups. Arburg will demonstrate how an electric Allrounder 520 A injection moulding machine can produce foammoulded IML cups from Bockatech, which are not only very light and very well insulated but also recyclable after multiple uses. This reusable cup by Bockatech is more stable than a paper or thermoformed cup of the same weight. In addition, the manufacturing process uses significantly less material. By combining EcoCore technology from Bockatech and Arburg’s high-performance machine with the “aXw Control ScrewPilot” for stable mould filling and the “aXw Control PressurePilot” for bionically optimised pressure control, the cups can be manufactured quickly and with low energy consumption. The cycle time for a 430mm container is only around 5.5 www.arburg.comseconds.
Artifical grass is another product for which MEAF can provide an extrusion line to produce recyclable backing shows best in class ‘green’ extrusion solutions
66 2022SEPT/AUG
SAPPMA Pipe XIII Conference: 6-7 September Emperors Palace, Kempton Park: www.sappma.co.za
Fachpack 2022: 27-29 September Nuremberg, Germany: www.fachpack.de K 2022: 19-26 October Düsseldorf, Germany: www.messe-duesseldorf.de Recovered Carbon Black: 16-17 November Berlin, Germany: www.carbonblackworld.com
Propak West Africa: 22-24 November Landmark Centre, Lagos, www.propakwestafrica.comNigeria Valve World Expo 2022: 29 Nov – 1 Dec Düsseldorf, Germany: www.valveworldexpo.com
Manufacturers in the food packaging sector are under huge pressure from regulators, supermarkets and consumers to reduce the amount of plastics used, while still maintaining food safety, attractiveness and recyclability. By partnering with Swiss manufacturer Promix Solutions, MEAF has added physical foaming capabilities to its extrusion lines. This allows for a further reduction in material use and lower weight, without compromising on features such as stackability and strength. Thanks to the use of nitrogen rather than the often used butane and propane, the process has almost no environmental impact. An industry sector which only recently has started to move towards a ‘greener’ future is the carpet and artificial turf sector. Where previously they would use non-recyclable materials like bitumen and latex, they are now looking at switching to thermoplastic elastomers (TPE) and TPU for their carpet backing to allow for their products to become fully recyclable rather than being incinerated or ending up in a landfill . This however requires a considerable switch in the production process and a new way of thinking for many carpet manufacturers, a reason for MEAF to adjust its in-house extrusion test line for various carpet backing solutions. www.meaf.com
2022 Feiplar Composites & Feipur: 16-18 August
K2022 PREVIEW
Wire China 2022: 26-29 September Shanghai, China: www.wirechina.net
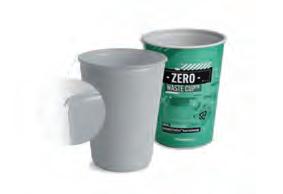
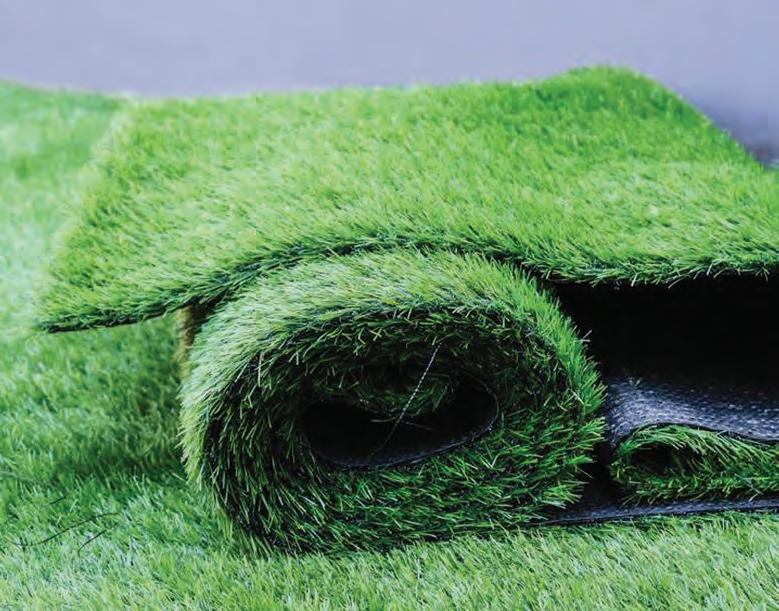
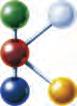
ARBURG has adopted a clear message for its trade fair appearance in Dusseldorf: “There is only a Plan A”. ‘Plan A’ conveys that the machine manufacturer is committed to making its contribution and presenting solutions for the important global issues of sustainability, the circular economy and carbon reduction. With its trade fair stand A13 in hall 13 and with the arburgGREENworld pavilion in the VDMA Circular Economy Forum, Arburg will showcase its pioneer role in resource conservation. Arburg will illustrate how highly networked, digitalised manufacturing helps to conserve resources and increase production efficiency. It is all about the synergy between the circular economy and high-tech with the help of targeted digitalisation. In the arburgGREENworld pavilion, ‘Greenline’ plugs from Fischer will be produced on an electric Allrounder 370 A with recyclate package and Multilift robotic system. The sprue is deposited directly in a mill. It is then returned straight back into the process as regrind and reused. A total of eight hydraulic, hybrid and electric Allrounders with a clamping force of between 350 and 6 500kN and two Freeformers for industrial additive manufacturing will be on show. All injection moulding machines will be automated with robotic systems, in some cases integrated into complex turnkey systems and connected to the arburgXworld customer portal. No less than three exhibits are equipped with the Arburg recyclate package: an electric Allrounder 470 A produces PP handles from post-consumer recyclate (PCR), while a hydraulic Allrounder 270 S compact uses glass-fibre-reinforced PPS recyclate to make tweezers. A definite highlight in terms of mould technology will be the Allrounder Cube 1800 with a 8+8+8-cavity cube mould with new CITI technology of Arburg’s partner Foboha. The three-component cube mould produces a functional component from PP, TPE and POM. A six-axis robot simultaneously fills the mould, cools it and removes the parts. AUG / SEPT 2022 67
Arburg at K2022:
• Official Distributor in Southern Africa for BASF on TPU Elastollan® Thermoplastic Polyurethane • Official Distributor in Southern Africa for Elastron on TPE, TPV Elastron® SEBS and EPDM/PP • Official Distributor in Southern Africa for CGFSE on FSE® Fluoroelastomers and Perfluoroelastomers • Distributor for Weifang on Weipren® CPE • Suppliers of EPS, Various Grades • Engineering Polymers • Polyolefins • Reworked and Repaletised Materials • Official distributor for Politem on PA6, PA66 unfilled and filled compounds • Official Distributor in Southern Africa for BASF on TPU Elastollan® Thermoplastic Polyurethane • Official Distributor in Southern Africa for Elastron on TPE, TPV Elastron® SEBS and EPDM/PP • Official Distributor in Southern Africa for CGFSE on FSE® Fluoroelastomers and Perfluoroelastomers • Engineering Polymers • Polyolefins • Reworked and Repaletised Materials • Official distributor for Politem on PA6, PA66 unfilled and filled compounds Contact Carlo Cell: 084 506 7660 Tel: 011 760 orders@dhpolymers.co.za1089
THE plant footprint and energy consumption are increasingly important key efficiency indicators, and Engel is establishing new records in both disciplines at K2022 in hall 15, stand C58
“There is only a Plan A” Digitalisation is the future of plastics processing Engel show maximum output on the smallest footprint
Arburg is represented in SA by Hestico (Pty) Ltd www.arburg.com www.hestico.co.za
. On a minimal footprint, an all-electric high-performance machine will produce sample vessels for medical diagnostics in two-component injection moulding under cleanroom conditions. At the heart of the production cell, is an all-electric Engel e-motion 160 combi M injection moulding machine, and again this is a first. Where Engel previously exclusively offered the combi M design with larger injection moulding machines, it is now presenting an injection moulding machine with just 160 tons of clamping force and a horizontal indexing table. In the combi M design, the indexing table divides the injection moulding machine’s mould closing area in the centre to operate two moulds in parallel. This makes combi M technology useful both for integrating two-component injection moulding and for efficiently doubling the output, if two identical moulds are mounted. The combi M machines are equipped with two injection units as a standard feature. One injection unit is fitted on the stationary platen, the second on the moving platen.
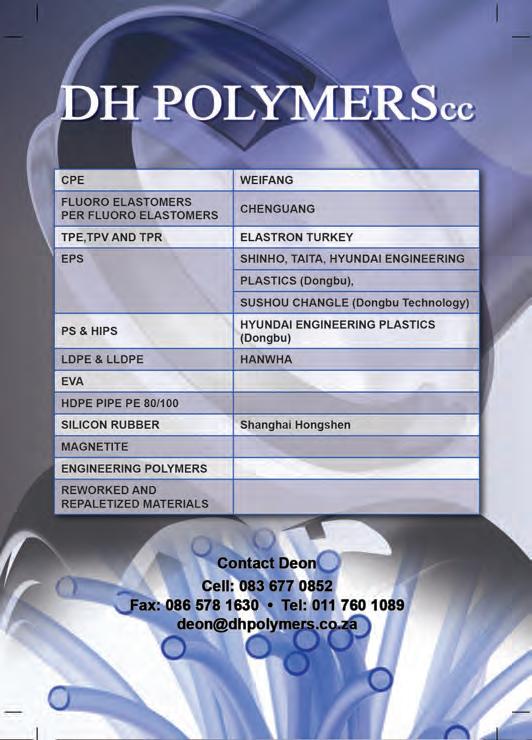
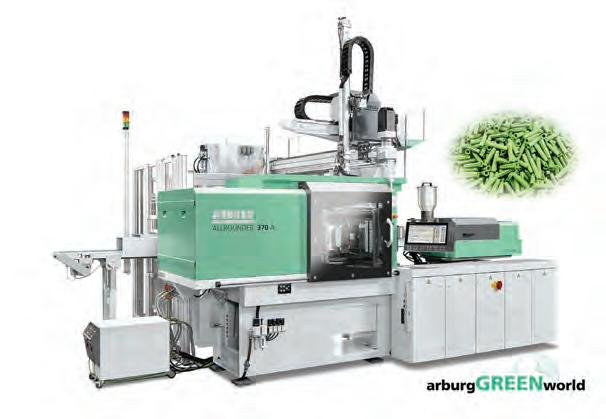
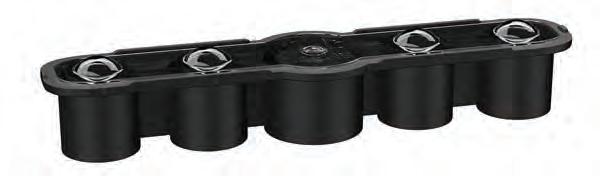
BASF will present its journey to advance towards the goal of a circular economy at K2022 in hall 5, booths C21/D21. BASF has been exhibiting at K ever since the trade fair debuted back in 1952, continuously showing its commitment to the plastics industry and ability to create breakthroughs together with its BASFcustomers.willdemonstrate its capabilities, exhibiting numerous co-creation projects with partners and customers from industries like automotive, construction, e&e, packaging, and consumer. These projects range from products that have net-zero or low product carbon footprints, to new products made from recycled raw materials to conserve fossil raw materials. Another strong focus will be on digital and data-driven value chain models that help BASF’s customers transform towards a CO2 neutral future. In this area, BASF has introduced an industry-leading digital application to calculate the CO2 emissions of around 45 000 BASF salesBASFproducts.willalso showcase a number of solutions to reduce the product carbon footprint using renewable or recycled feedstock like in the case of the Styrenics portfolio in packaging and construction. BASF’s biomass balance certified materials are also used by customers from the furniture industry or by a safety shoe brand offering a carbon neutral safety shoe containing BASF’s biomass balance polyurethane certified according to REDcert. Another example how plastics and thereby consumer products can be manufactured more sustainably are outdoor pants made of raw materials obtained via the chemical recycling of end-of-life tyres using BASF’s Ultramid® Ccycled™. At K 2022, BASF will show several examples of plastics as true performance materials for sustainability. An example of this are safe and durable polyamides for high-voltage components within the e-mobility charging infrastructure to enabling a green miniature circuit breaker (MCB) for the E&E business that uses a 100% recycled PA6 based compound using pyrolysis oil from end-of-life tyres – without any compromise on the MCB’s robustness.
www.plastics.basf.com/K2022
Sustainable closure solutions At this year’s Drinktec in Munich from 12-16 September, the Swiss group, Corvaglia, will be presenting its latest generation of tethered caps. Corvaglia has been able to develop a wide range of tethered caps solutions based on 30 years of experience in the development and production of one-piece caps with various types of tamper-evident bands and production technologies. Many of these solutions have now been implemented on an industrial scale, including the world’s first commercial production of an aseptic 38mm tethered cap. Corvaglia sales representatives from all regions of the world will be on hand in Hall C5/ Stand 275. www.corvaglia.com
BASF and Steelcase have collaborated on Steelcase’s Flex Perch Stool, which has sustainability and circularity at the forefront of its design. The stool is made with an injection mouldable polyamide 6 that uses material from a waste stream generated during electronics production. The stool itself at 100% recyclable
68 AUG / SEPT 2022 K2022 PREVIEW
BASF accelerating the journey towards a sustainable future
Plastics recycling show Europe attendance tops 5 000 THE Plastics Recycling Show Europe (PRSE) 2022 exhibition and conference held recently in Amsterdam in The Netherlands attracted a record number of visitors and exhibitors from across Europe and 80 different countries internationally. The annual event had a total attendance of more than 5 000 over two days and attracted over 200 exhibiting companies. Over 4 700 attended the in-person event and over 500 more attended the hybrid event virtually. The two-day PRSE conference showcased the latest innovation in plastics recycling technology and applications, as well as exploring the legislative landscape within the EU and outlining future challenges and objectives for the industry. “PRSE 2022 has proved by far our most successful show to date, attracting more visitors and exhibiting companies than ever before,” commented Matt Barber, PRSE event director at Crain Communications. “Even after expanding the floorplan we sold every stand that would fit into Hall 12, so we are adding Hall 11 as a second hall to the floorplan for 2023 with a chemical recycling feature and an additional conference theatre.” To revisit on-demand PRSE 2022 conference sessions: demand.com/prse2022/en/page/livestream-2022-on-https://prseventeurope.www.prseventeurope.com

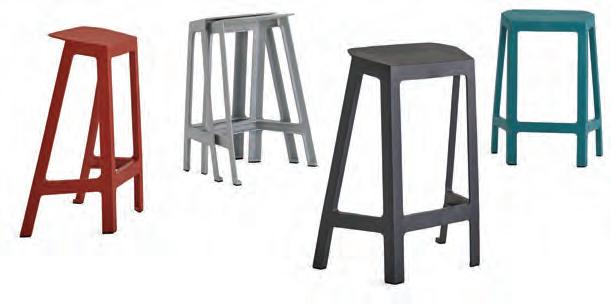
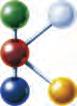
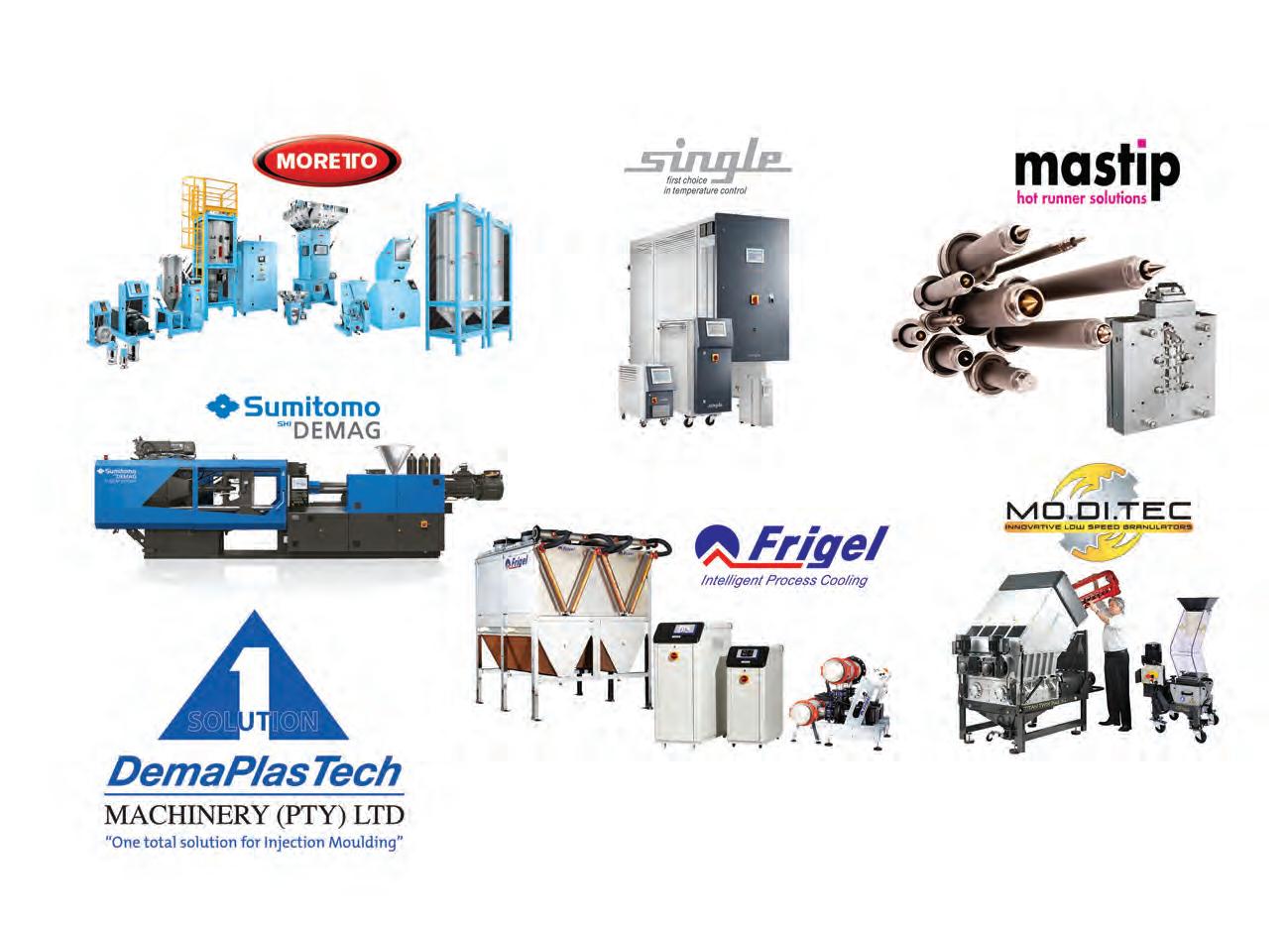
2022SEPT/AUG 69 AT the K2022 trade show, booth A75 in Hall 6, Covestro will present a number of developments for the unmixed recycling of used plastics. The company’s focus to date has been on proven mechanical recycling, in which the plastic is chemically preserved, and more recent chemical recycling processes, in which the polymer molecules are broken down chemically. Under the guidance of Covestro, a consortium of industrial partners in the Circular Foam project is researching processes for the chemical recycling of rigid polyurethane foam, which provides excellent insulation for buildings and refrigeration equipment Used PU rigid foams, which provided efficient thermal insulation for buildings and refrigeration equipment, should also be able to be broken down into their constituent parts again by means of chemolysis or even pyrolysis. This is the goal of the Circular Foam research project with 22 industrial partners from nine countries, coordinated by Covestro. Over the next four years, experts from science, industry, and society want to develop a comprehensive solution model for the waste management and recycling of suchHere,foams.too, the aim is to recover both raw materials originally used – polyols and an amine used as a precursor for the isocyanate MDI. If the material cycle is successfully closed, up to one million metric tons of waste, 2.9 million metric tons of CO² emissions and 150 million euros in incineration costs could be saved in Europe every year from 2040. Covestro develops innovative recycling technologies PRODUCTS FOR EVERYONE... SOLUTIONS JUST FOR YOU we know Injection Moulding TEL: 011 462 2990 info@demaplastech.co.za www.demaplastech.co.za we know Cooling we know Granulators we knowControlTemperature we know Hot Runners we know Material Handling
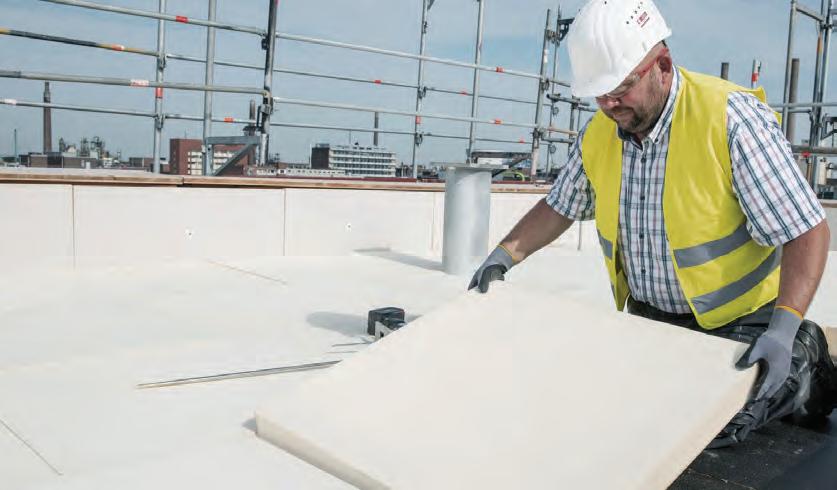
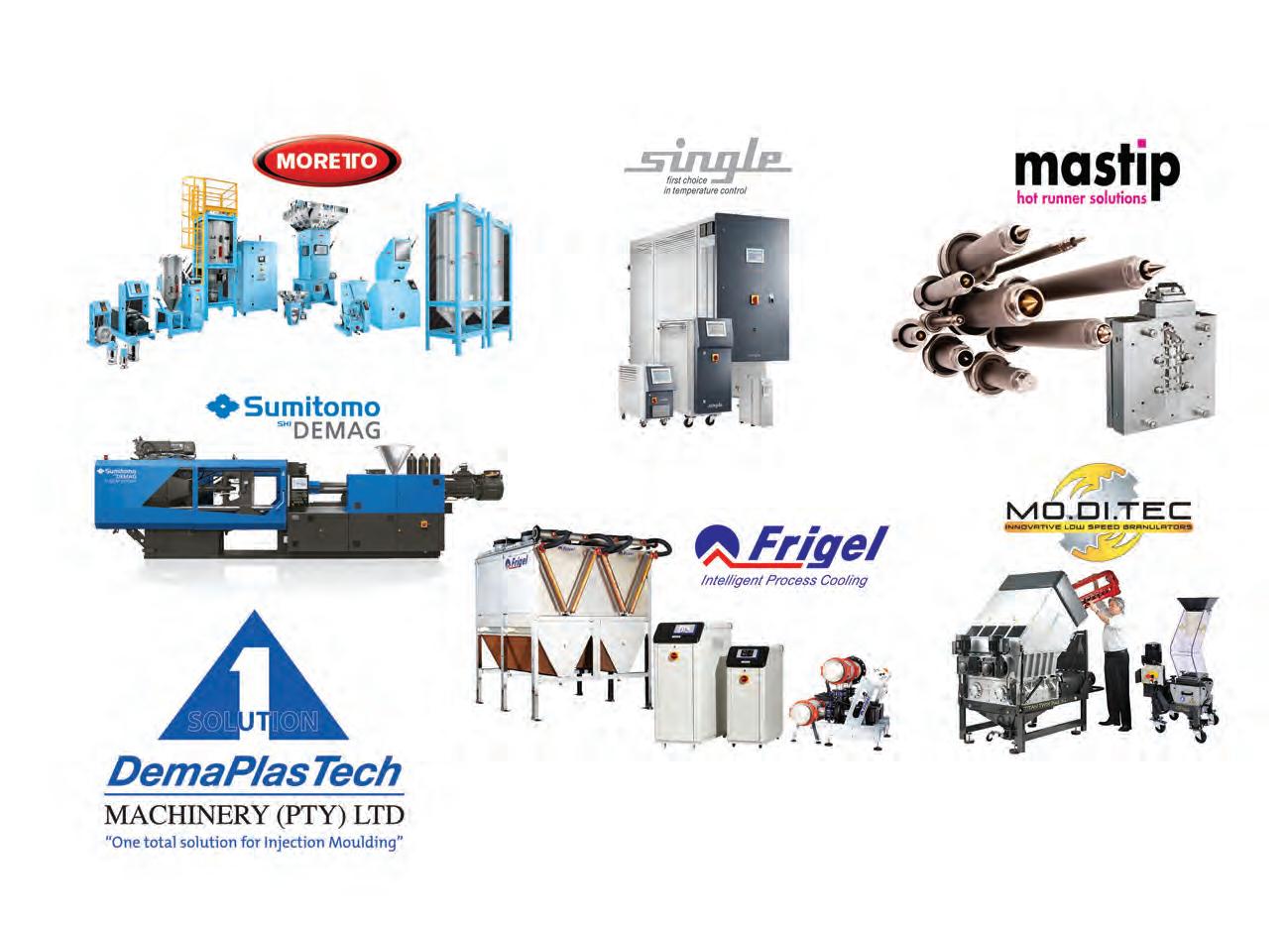
Lanxess,PREVIEW
www.lanxess.comwww.reifenhauser.com
Reifenhäuser Blown Film provides solution biggest challenge in the processing of recyclate Energy savings in processing novel hot cast and cold cure systems for high performance elastomers 70 2022SEPT/AUG With EVO Fusion, even fluff (film snippets) and all kinds of production waste and PCR material can be directly processed into functional films for applications such as trash bags or mailing bags
Lanxess has also developed “hot cast and cold cure” systems for high performance PU cast elastomers. With this new technology, Vibrathane MDI ether prepolymers can be cured with novel Vibracure curatives at ambient temperature. As the systems do not need to be heated during casting process and can be cured at ambient temperature, the specific energy consumption is dramatically reduced down to about 40% compared to “hot cure/hot table” technology.
Adiprene Green LF provides a range of bio-based low free monomer prepolymers for polyurethane CASE applications
K2022
THE line manufacturer Reifenhäuser Blown Film has developed a technology that makes blown film producers independent of highly fluctuating recyclate qualities and ensures a stable production process – even when processing low-quality input material: EVO Fusion upgrades recyclate qualities, which will be demonstrated at the Reifenhäuser mainC22,boothhall17 With Fusion,EVOblown film producers also process previously unusable, lowest-quality recyclates into high-performance blown films for simple applications, such as trash bags or mailing bags. Until now, such low-grade recyclates could only be used for simple and thick-walled injection-moulded products. In addition, producers can make higher-quality film from recyclates that could also be processed in the past. With EVO Fusion, Reifenhauser offer a unique process that enables customers to process even low recyclate grades easily and economically into high-performance products and increase the recyclate content.TheEVO Fusion process relies on direct extrusion, which eliminates the need for energy- and cost-intensive regranulation of the raw material. This means that fluff (film shreds) and all types of production waste and PCR material can also be processed directly. This is made possible by the twin-screw technology, which homogenizes the melt better and thus ensures a stable process. In addition, processors can degas the system very easily and effectively, removing unwanted components in the recyclate.
LANXESS will be showcasing its extensive product range designed to improve sustainability in the polyurethane industry. Visitors will get an insight into a wide range of sustainable products ranging from low free monomer technology (Adiprene LF), innovative Adiprene Green prepolymers with high bio-based content, novel hot cast and cold cure systems for processing with reduced energy consumption, and water based lacquers to meet high requirements of modern and innovative automotive interior. With Adiprene LF, Lanxess offers a wide range of prepolymers with less than 0.1 wt.% free MDI (methylene diphenyl diisocyanate) and other free isocyanates. The range has been successfully extended for use in hot melt adhesives, e.g. in the automotive, construction, electronics and bookbinding industries.
sustainablenewproductsforthepolyurethaneindustry
Lanxess’ toolbox of low monomer prepolymers is able to tailor the reactivity, viscosity and polyol backbone of the prepolymer to adjust it to the need of the formulators. By controlling the chemical structure, the prepolymers have a highly structured morphology to offer more consistent processing. On curing with chain extenders, their special chemical structure leads to highly structured elastomers with excellent performance. With Adiprene Green LF, Lanxess provides a range of bio-based, low free monomer prepolymers for polyurethane CASE (coatings, adhesives, sealants, elastomers) applications. Bio-based LF prepolymers focus on renewable chemical building blocks that are designed to the specific needs of many different applications by exploring additional chemistries and optimization of molecular weight and structure.
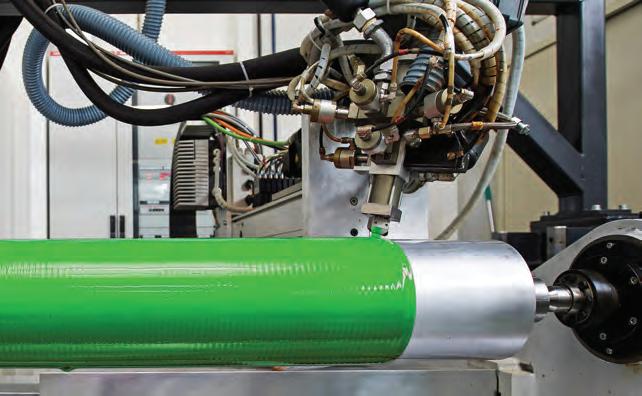
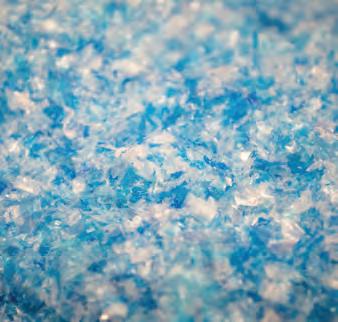
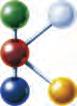
Bioplastics specialist presents broad product portfolio WHEN FachPack opens its doors from 27-29 September, FKuR will present (Hall 7, booth 7-523) its material alternatives based on renewable raw materials, as well as recyclates and bio-recyclate hybrids for functional and simultaneously recyclable packaging solutions.
Bioplastics such as Green PE or Terralene® are an excellent alternative for the production of packaging because they are based on renewable raw materials, but are chemically identical and therefore have the same properties as their conventional counterparts. They can be easily integrated into existing recycling systems and, as a recyclate, represent a valuable resource for the manufacture of other products. In this way, they create a contribution to a well-functioning circular economy. FKuR has certified compostable types (according to EN 13432) for applications such as organic waste bags, agricultural, household and hygiene films in its portfolio. However, FKuR’s Bio-Flex® PLA blends with varying degrees of flexibility can not only be blown into films, but also injection moulded, extruded or extrusion blow moulded. Bio-Flex consists mainly of natural raw www.fkur.com/en/materials.
South Africa to host high-profile tooling & machining event
ACD RotoFlo 43 Africa Roto Compounds 05 Aries Plastics (YongShen) 65 Bandera Extrusion 45 Brenntag SA IFC BTCAP 38 Carst & Walker 27 Continental Compounders 17 DemaPlasTech 69 DH Polymers 67 HESTICO 33 Innovative PVC Compounds 01 Masterbatch SA 37 MBSA 39 Advertisers: August / September 2022 To place a classified advert please Tel: 021 712 1408 or Email: heather@summitpub.co.za CLASSIFIEDS Meraxis SA 47 MGMW Trading 11 MouldBase 15 Nissei ASB 49 Performance Colour Systems IBC Plastic & Chemical Trading 31 PlasticsSA 19 Plastomark 59 POLYCO 12, 13 Polyoak Packaging 23 Rawmac 62 Roediger Agencies 09 Safrique International 61 SAPPMA 63 Zerma Africa OBC 2022SEPT/AUG Contact: Tim Forshaw (083 381 5253) or Phil Hopkinson (083 408 5253) or 021 671 5253 or mail to tim@bre.co.za EXTRUSION TECHNOLOGY FROM AGRIPAK OF ITALY Mono & multi-layer extrusion lines for the production of: • ‘Cartonplast’ (twinwall/hollow profile sheet) • Multilayer sheet for packaging • Semi-foamed sheet for thermoforming MATERIALS FOR THERMOFORMED PACKAGING • Sealing films for trays and top web for FFS machines • OPS, PP, PET sheet for general packaging • PP/EVOH/PP for high barrier containers BRE EXTRUSION,THERMOFORMING,INNOVATIONSSHEETANDMATERIALSTHERMOFORMING TECHNOLOGY SAVE 90% of your electricity use with GN! • GN (Canada): machines for reduced waste and reduced energy • Thermoforming Moulds for GN and other thermoformers • ToolVu technology for productivity and quality improvement on thermoforming machines • Complete lines for EPS foam trays and EPS cup moulding Heat seal lidding films for trays and top web for FFS machines THERMOFORMING, SHEET EXTRUSION, AND MATERIALS BRE INNOVATIONS Contact: Tim Forshaw (083 381 5253) or Phil Hopkinson (083 408 5253) or 021 671 5253 or mail to tim@bre.co.za THERMOFORMING TECHNOLOGY BROWN MACHINE GROUP NOW OWNS GN SAVE 90% of your electricity use with GN! • Full range of equipment from Brown Machine group • GN (Canada): machines for reduced waste and reduced energy • Thermoforming Moulds for GN and other thermoformers • Complete lines for EPS foam trays and EPS cup moulding EXTRUSION TECHNOLOGY FROM AGRIPAK OF ITALY Mono & multi-layer extrusion lines for the production of: • ‘Cartonplast’ (twinwall/hollow profile sheet) • Multilayer sheet for packaging • Semi-foamed sheet for thermoforming MATERIALS FOR THERMOFORMED PACKAGING • Sealing films for trays and top web for FFS machines • OPS, PP, PET sheet for general packaging • PP/EVOH/PP for high barrier containers Plastique Classified Cycliq ClassifiedBagman High-quality recycled HDPE, LDPE, PP phone Danie tel: (021) 931 danie@maltarecycling.com9658MALTARECYCLING Multi Plastic Bags, classified FOR SALE Injection householdmachines,mouldingandmoulds For details info@thengaplastics.co.zacontact 70 NOV/OCT2019 EQUIPMENTFORSALE • 11kw motor with new Vickers pump for 80ton injection moulder – will take offers • 2kw double side corona treater hardly used 1000mm wide R70 000 • 2 x new 60mm barrels and screws 32:1 LD ratio with mixing zones ideal for LD & LLDPE materials R50 000 each • 2 x new 90mm barrels 32:1 LD ratio R50 000 each • 1 x new 65mm PVC screw with 28:1 LD ratio R25 000 • 1 x used 65mm screw in good condition R15 000 If you have any redundant equipment you would like to sell please email a list with photos and I will try and sell on behalf of you. Contact: Sean Varrie 083 407 3600 or savarrie@gmail.comemail: All end-of-life moulds are re-purposed for our own products and not used to produce the original intended items. Contact Cycliq (Pty)Ltd at: Graham 082 551 graham@cycliq.co.za2086 WE BUY YOUR OLD INJECTION MOULDS • PE Safety fence production line 1.5m wide. • PLC Controlled. • Dual 30:1 – 65mm Barrel & Screws. • ABB Inverters. • Moog hydraulic controllers. • Omron temperature controllers. • Siemens Motors 22Kw. • Complete with stretch unit. • Capable of making as well as square • For netting.construction • Dual windup. Training available. Price Jacquesnegotiable.R490,000.00Contact:on084 FOR SALE • PE Safety fence production line 1.5m wide • PLC Controlled. • Dual 30:1 – 65mm Barrel & Screws. • ABB Inverters. • Moog hydraulic controllers. • Omron controllers.temperature • Siemens Motors 22Kw. • Complete with stretch unit.• Capable of making as well as square • For construction and netting. • Dual windup. Training available. Price Jacquesnegotiable.R490,000.00Contact:on084581 FOR SALE: We’re looking for injection grade white PVC regrind CycliqCONTACT(Pty) Ltd at: Graham 082 551 2086 –graham@cycliq.co.za LOOKING FOR Bagman Classified • Polymers for sale, 1st generation, pre-consumer • PC/ABS 10 ton/month • Black Automotive UV stable pp 20-40 ton/mnth • Injection grade LDPE (red) 4 ton • White pp 20 ton/mnth • We also do HIPS, PC, PA, PMMA, PBT, ABS, LDPE, ASA We are looking for clean, pre-consumer polymers, Pp lumps, HDPE lumps, woven pp Contact: Wouter de wouterbagman@gmail.comLangecell0727058597 POLYMERS FOR SALE Waste Licence AM/A/3/L3/2018no. 083Re-PelletizedABSWANTED!!!orHIPSWHITEorRegrindContactAndrew:6773369
The Group Chief Executive Officer of PtSA, Tapiwa Samanga, says the event will offer significant benefits to manufacturing in Africa as the local tooling manufacturing industries will be exposed to the latest global manufacturing technology, the world’s leading tooling houses and the most influential people in the industry. He emphasises that All Africa Expo ISTMA 2023 can serve as an important catalyst to ignite the growth of the African tooling manufacturing sector. “African countries have policy frameworks to promote manufacturing but sometimes lack the knowledge, resources and networks. Governments and industry should focus on the key role of tooling in the establishment of a sustainable manufacturing economy. This was the blueprint for the successful turnaround of the SA tooling industry and can offer valuable lessons to other African countries”, says Samanga.
THE focus of the global manufacturing industry will be on South Africa next year as representatives of 22 countries meet in Cape Town for the 16th World Conference of the International Special Tooling and Machining Association (ISTMA).The16th ISTMA World Conference will take place in Cape Town from 18-22 September 2023. This follows a unanimous decision by ISTMA World to move the Association’s 16th World Conference, originally scheduled to take place in Shanghai, China in 2023, to Cape Town due to Covid-19 restrictions in TheChina.International Association’s triennial World Conference, General Assembly and constituent meetings of regional groupings ISTMA Europe, Americas, Africa and Asia will coincide with the All Africa Expo and the event will collectively be known as All Africa Expo ISTMA 2023. The Production Technologies Association of South Africa (PtSA), the industry representative body for the tooling manufacturing industry in SA and the only African member association of ISTMA World, will host All Africa Expo ISTMAISTMA2023.World is a non-commercial international association serving as a global platform for cooperation and knowledge sharing between 23 member associations in 22 countries in the tooling and machining industry. Collectively, ISTMA member associations represent more than 8 000 companies with a collective annual turnover in excess of US$120 billion.
• For more information, contact: ISTMA World: Manuel Oliveira, secretariat@istma.org

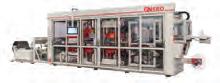
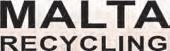
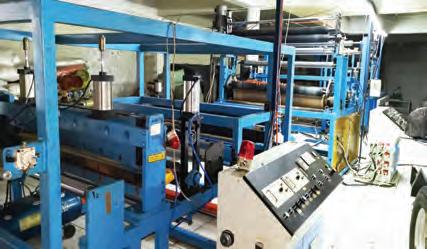
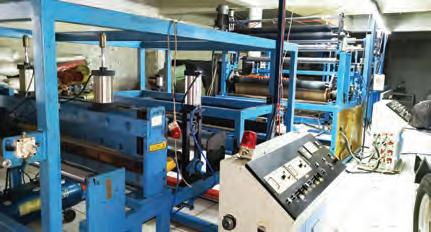


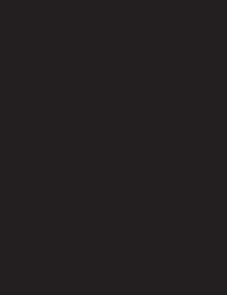
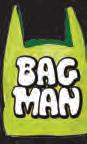
BELGIAN multinational chemical company Solvay Group has partnered with three international medal winners and record holding athletes for the Paris 2024 Paralympic Brussels-basedGames.Solvay will work with South Africa’s Kgothatso Montjane, Italian Ambra Sabatini, and American Trenten Merrill to promote values embodied by the athletes such as performance, dedication, perseverance and winning drive, through its Solvay 4 Sport initiative. The games are set for 28 August to 8 September 2024. Montjane is Africa’s most successful tennis player. She was born with a congenital disorder, and at the age of 12, her left leg was amputated below the knee. On the tennis court, Montjane currently holds 29 singles titles, and is the first Black South African woman to ever play at the Wimbledon championships.“Noworthwhile journey is without its challenges,” she said. “It’s the rough road that ends in greatness.” Sabatini of Italy is the fastest paralympic sprinter in the world. In 2019, she survived a car accident that resulted in the amputation of her left leg. Sabatini now holds the Paralympic record for completing the 100m sprint in 14.11 seconds, set at the Tokyo 2020 Paralympics. Her goal for the Paris 2024 Paralympics is to complete that event in under 14 seconds. Merrill is an American and holds the 2021 US long jump record. At age 14, he was hit by a car, resulting in his right foot being amputated. Merrill held onto his childhood dream to become a professional athlete and shortly after the accident, was competing in volleyball, mixed martial arts and motocross. He made his first Paralympic team in 2016 and broke the American record for long jump that same year. He has set the record twice more in 2018 and 2021. The three athletes “are role models on and off the field and court, an inspiration for everyone and the demonstration that nothing is impossible,” said Nathalie van Ypersele, chief diversity, equity and inclusion officer at Solvay. “We believe opportunity, possibility and greatness are achievable when we collectively recognize, respect and celebrate that which makes each of us unique, yet intrinsically human,” sheSolvay’added.s partnership with the athletes helps to reinforce the Group’s diversity, equity and inclusion programme, which aims to create equal opportunities regardless of backgrounds, ages, genders, races, nationalities, ethnicities, religions, sexual orientations and identities and abilities.
72 2022SEPT/AUG
Kgothatso Montjane is the first Black South African tennis player to play in a championshipWimbledon www.solvay.com/en
sport
Solvay employs more than 23 000 worldwide and posted sales of $11 billion in 2021. In March, the firm announced plans to split itself into two public companies, including one making specialty materials that would include plastics and composites.
susolvaypportforsA
paralympic tennis player
Helps to reinforce the Group’s diversity, equity and inclusion programme
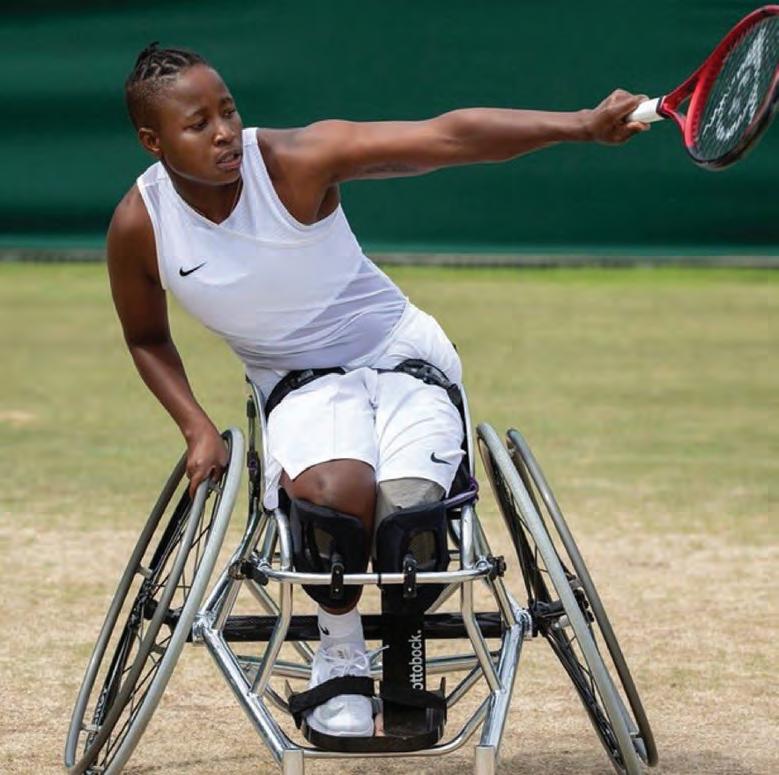
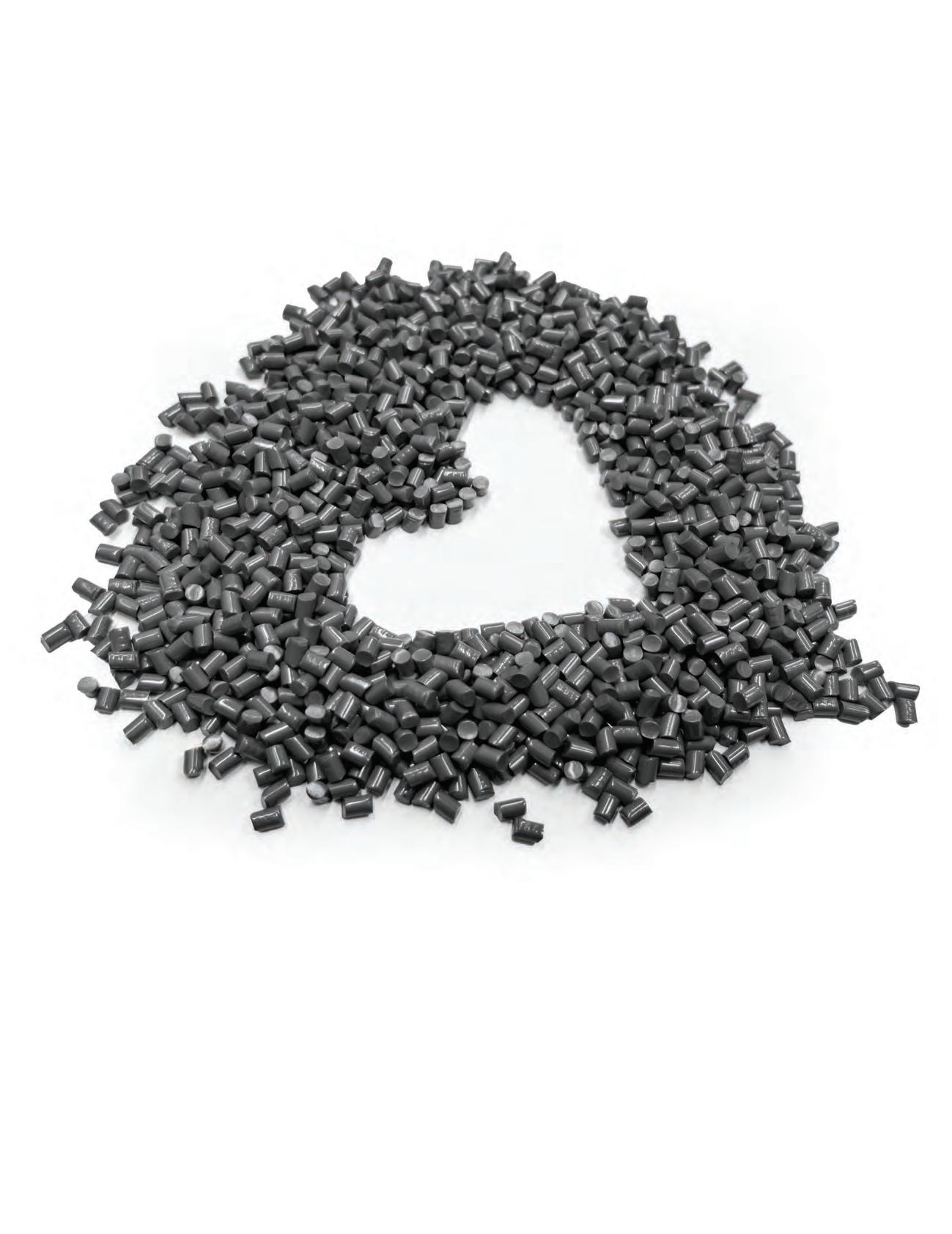
















Closed-loop recycling for injection & blowmoulding production lines Inline recycling systems for sheet & thermoformed skeletal rolls Shredding & granulating systems Shredding, granulating & pulverising systems for 6000mm pipe Jeff Cawcutt Tel: +27 82 781 0082 Email: jeff@zerma.co.za Web: www.zerma.co.za
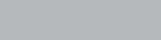