7 minute read
3D PRINTING HITS THE SPOT
Next Article
WORDS: Sam Davies
3D PRINTING HITS THE SP T
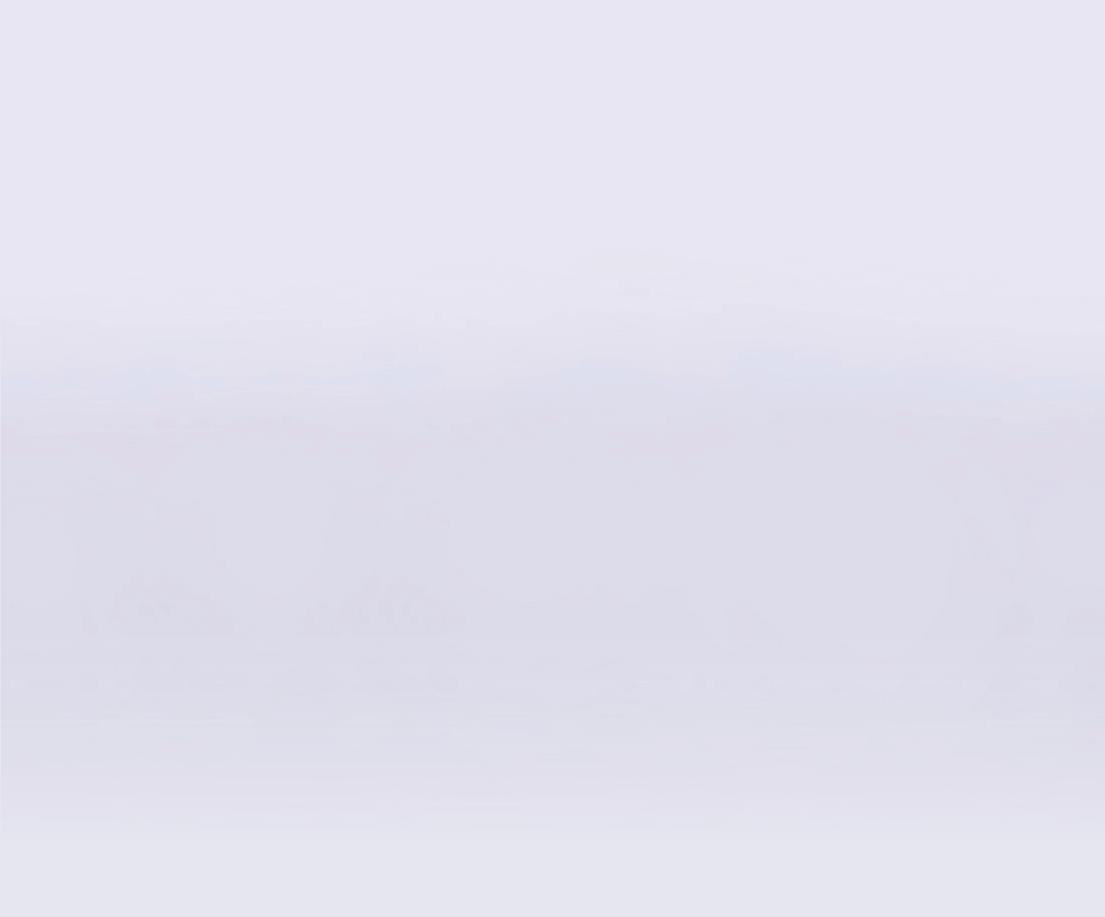
In one of PepsiCo’s more renowned dalliances with 3D printing, a series of complex masks that fi tted onto themed soda cans helped to generate more than 10 million social media impressions to promote the movie premiere of Marvel’s Black Panther.
While the company’s latest application of the technology has so far had less reach and revere, it is having no less impact.
Max Rodriguez, Sr. Manager of Global Packaging R&D, and Thangthip Tekanil, R&D Packaging Engineer, are part of a team that covers performance simulation, advanced rapid prototyping and advanced system capabilities at PepsiCo. In these endeavors, they serve a team of 120 R&D engineers with the ‘right tools and right capabilities,’ so they can deliver projects ‘with excellence.’
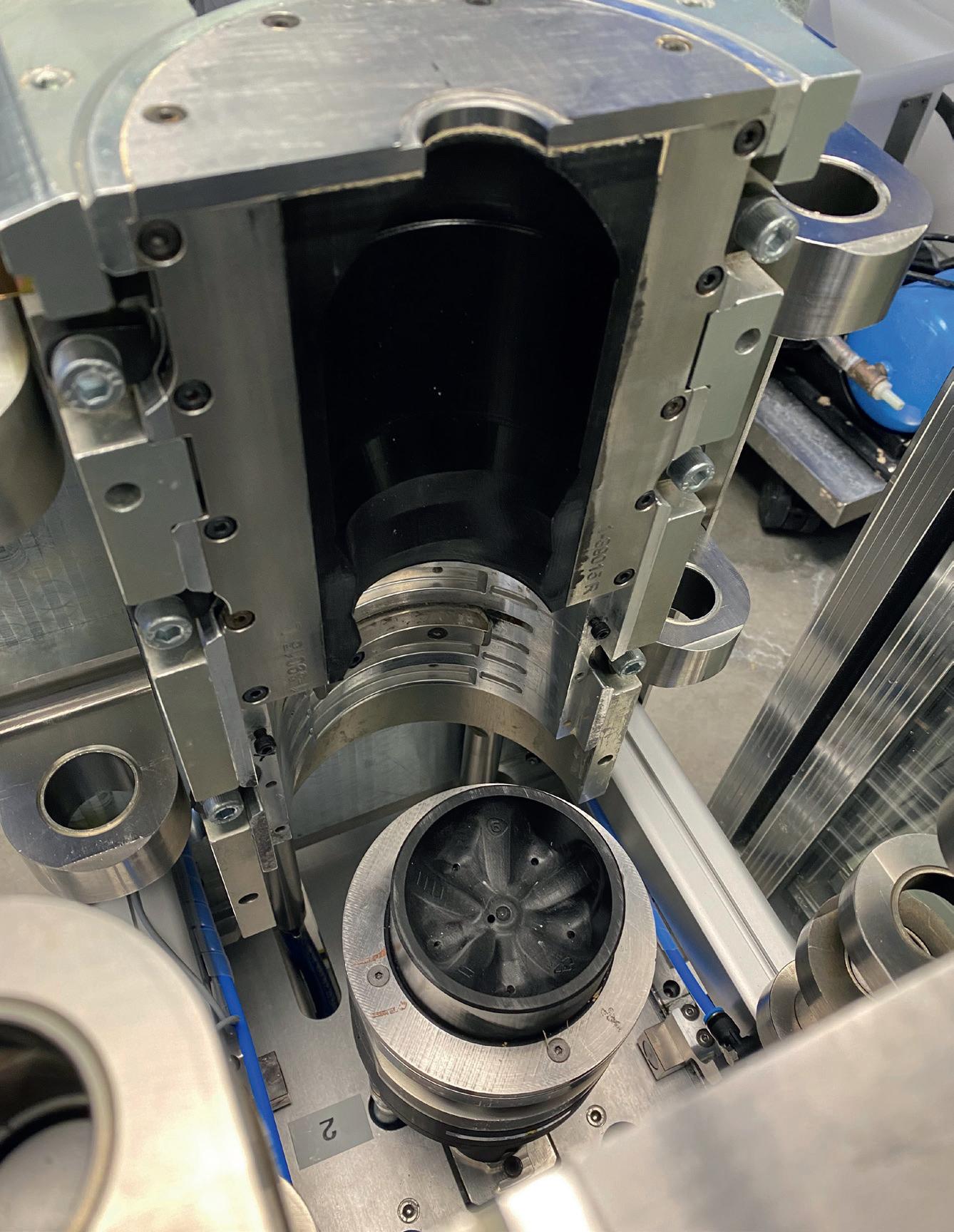
Among those tools and capabilities is PepsiCo’s patented Modular Mold Set, which is compatible with most standard blow molders and comprises an aluminum shell, dental stone, and 3D printed inserts for various bottle designs from 100ml to 3L. “The Modular Mold Set is a means for us to be able to very rapidly and quickly generate a customized mold that we can then utilize in our lab-scale or Pilot Plant scale stretch blow molding equipment,” Rodriguez told TCT.
Previously, to get functional mold samples, PepsiCo would contract an external service provider who would leverage a subtractive manufacturing technique – CNC or EDM, depending on the complexity – and return the tool within two-to-four weeks at a typical cost of up to 10,000 USD.
“What we wanted to do was fi nd a way that we can very quickly and rapidly do it internally at a fraction of the cost,” Rodriguez continued. “We developed the Modular Mold concept by looking at what is it that we really need? What we need is the capability of being able to print the features of the tool that are unique. If we try to print the entire mold, it will take forever, and we will use a signifi cant amount of material. We decided to take the external dimensions of a conventional mold and utilize that as a shell, and then only print the parts that are unique and customized for the application, which is essentially the cavity of the bottle, which we call the inserts and the base.”
The Modular Mold Set application is 3D printer agnostic, but PepsiCo generally opts for Digital Light Processing technologies ahead of FDM and PolyJet, for example, for their faster print speeds. PepsiCo started its development on this project with Carbon’s Digital Light Synthesis technology, utilizing the Cyanate Ester (CE) material – which boasts a heat defl ection temperature of 230°C according to the Carbon datasheet – on the M2 platform. But it has since moved forward with the NXE400 system and xPEEK 147 material from Nexa3D, citing a larger build volume, preferences over the Nexa business model, and a slight edge in terms of heat defl ection temperature – 238°C and tested against ASTM D648 according to Nexa’s datasheet.
SHOWN:
MOLD INSERT 3D PRINTED ON NEXA3D’S NXE400 MACHINE WITH XPEEK 147.
“We’re able to print two mold halves and a base within eight hours and then curing would take an additional four hours, so technically in 12 hours, we can get a complete mold from start to fi nish,” Tekanil explained. “We wanted something that was faster and more durable during printing. I’d say the CE was [also] a little more prone to warpage during the curing process because the curing cycle was 12 hours in a thermal oven. The PEEK material only requires three hours in the oven, so we experience minimal warpage, but we do have to account for shrinkage and make sure that the tolerancing is correct for when we’re assembling the mold.”
For PepsiCo’s 3D printed Modular Mold Set applications, the engineers have to account for deviations within plus or minus 0.5mm in the dimensions versus 0.1mm with subtractive manufacturing. While Rodriguez suggests this is reasonable for the kind of parts PepsiCo is producing with 3D printing, he and Tekanil still yearn for the warpage issues during curing to be addressed, while they also noted the brittleness of DLP materials can also be a pain point.
There are more pros than cons to its Modular Mold Set, however, as PepsiCo has projected cost savings up to 90%, a lead time reduction from several weeks to just a few days, and worked out it can produce thousands of bottles with one printed mold insert.
“We’re able to blow 10,000 bottles with this tool, which are the quantities that we need for us to be able to validate a new design because when we bring it into our manufacturing environment, we’re running 600 bottles a minute, 800 bottles a minute,” Rodriguez said. “A couple of hundred bottles are not going to do us any good. We need thousands of bottles to be able to do what we need to do. With this technology, we’re able to demonstrate that we can get comparable performance as we would with a metal mold, and we can produce thousands of bottles for us to evaluate downstream.”
When PepsiCo fi rst began to explore utilizing 3D printing for this type of application, the company could only achieve 100 samples per mold set with Stratasys’ PolyJet technology and Digital ABS material, which exhibits a heat defl ection temperature of 58-68°C. The company still runs this technology in-house – with FDM solutions in other facilities – and is prepared to harness PolyJet when pairing up with a lab-scale blow molder for small volumes of samples, but when volumes between 5-10,000 are required, they will likely opt for a DLP system. It has been a Carbon M2 previously, is currently a Nexa3D NXE400, but with tabs kept on cost, machine performance and material capabilities, could easily be a solution from another provider in the future.
“We’ve been able to streamline the workfl ow between the diff erent printers, found the appropriate scaling factors for each printer, and because the mold is pretty much standard, the modular mold is printer agnostic,” Tekanil said. “Once we get a scaling factor in place, outside of that everything else is the same because we have the plugin from SolidWorks that automated the mold generation for the fi les. In that plugin, we also have an option to modify the shrinkage, the scaling, so we can just plug in the numbers that we need for the printer, and then it’ll generate a fi le that’s appropriate for this type of printer. We’ll use that fi le, and we print it. We can go from CAD to 3D print fi les within fi ve minutes utilizing our mold generator plug-in.”
This process is said to return accurate parts 95% of the time, with tooling fabricated within 48 hours and functional product samples returned within a week. A proof-of-concept exercise saw the Modular Mold Set produce up to 10,000 cold-fi lled, single-serve bottle products, while PepsiCo is now also exploring the application of metal 3D printing to integrate conformal cooling channels for heatset applications, as well as injection mold tooling with its polymer technology.
PepsiCo has previous when it comes to beverage packaging innovation, becoming the fi rst soft drinks company to introduce the two-liter bottle in 1976 and regularly redesigning its soda cans throughout its 123year history. With 3D printing, it believes it will have a future too. “It's having a huge impact,” Rodriguez assessed. “And it's going to continue to have a huge impact as we make it more prevalent, because [of] the ability for us to be able to go from a 3D CAD fi le to a physical prototype that is comparable to what you will get out of the production environment. It facilitates decision making with our marketing folks and our business folks. It facilitates the evaluation of impact on our manufacturing operations with our supply chain and operations folks. It facilitates the same concept in consumer acceptance with our consumer insights folks. So, across the board, it facilitates us being able to evaluate how it is going to perform on our lines, how's it going to perform in our bending machines and so on. It accelerates our development cycle by weeks and possibly even months.”
“We're also looking into using polymer printing systems for injection molding tooling as well,” added Tekanil. “So, we're in the process of acquiring a lab-scale injection molder and similar to what we're doing with the stretch blow molding technology and the Modular Mold Set, it's something that we're also looking to shift over for injection molded applications such as caps, closures [for example]. Those are things that we would be looking at rapid tooling for.”
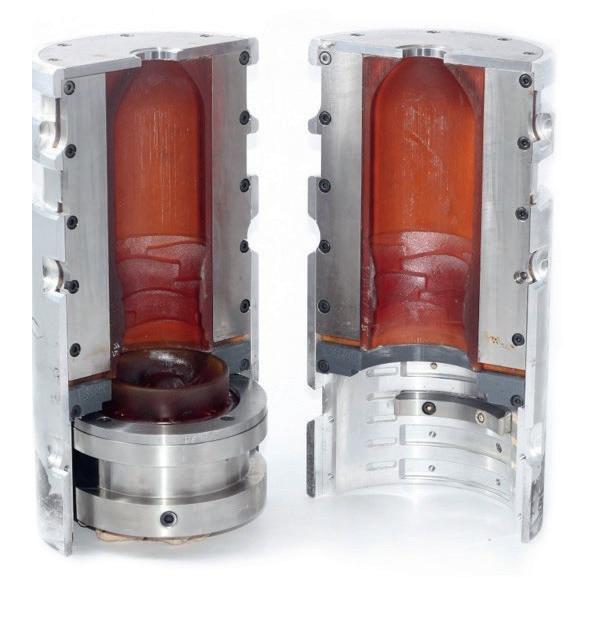
SHOWN:
MOLD INSERT 3D PRINTED ON CARBON’S M2 MACHINE WITH CE MATERIAL.