5 minute read
KEEPING COOL
Next Article
WORDS: Sam Davies
KEEPING C L C L
What do the wings of a butterfl y, the feathers of a bird, the retinal cone cells of a tree shew, of a bird, the retinal cone cells of a tree shew, and this helicopter heat exchanger all have and this helicopter heat exchanger all have in common? It’s the use of gyroid structures to help fl ight, sight and, in It’s the use of gyroid structures to help fl ight, sight and, in the case of the aluminum component printed on an EOS M the case of the aluminum component printed on an EOS M 290 machine, the optimal cooling of a helicopter gearbox. 290 machine, the optimal cooling of a helicopter gearbox. At least, that’s the hope for Andreas Vlahinos, CTO of Advanced Engineering Solutions, who is currently seeing his TCT Award-nominated design go through a seeing his TCT Award-nominated design go through a qualifi cation process for use on commercial helicopters. qualifi cation process for use on commercial helicopters. Gyroids are a triply periodic morphology with no planes of symmetry, no embedded straight lines, and well suited to parts that need strength without too much weight. The heat exchanger developed by Vlahinos has an internal volume that is fi lled with gyroid structures which encourage uniform cross fl ow throughout the piece to cool the gearbox. Using lattice screens at the end of the internal gyroid domain lattice screens at the end of the internal gyroid domain has also helped to eliminate the need for support structures inside the component, while external lattice structures inside the component, while external lattice ribs minimize the shell thickness requirement. With the input of these design characteristics, the heat With the input of these design characteristics, the heat exchanger is said to exhibit 4x better performance than exchanger is said to exhibit 4x better performance than the original design, is around half the size and has an enhanced fatigue life since it is manufactured in a single enhanced fatigue life since it is manufactured in a single component as opposed to several brazed together pieces. component as opposed to several brazed together pieces. “The traditional design of these heat exchangers, they “The traditional design of these heat exchangers, they call it shell and tube and there is a bunch of components call it shell and tube and there is a bunch of components brazed together,” Vlahinos told TCT. “Brazing thin components is not good for fatigue life because there’s components is not good for fatigue life because there’s a lot of vibration in the helicopter, so you need to keep a lot of vibration in the helicopter, so you need to keep monitoring the fatigue life of the heat exchanger and it’s monitoring the fatigue life of the heat exchanger and it’s dangerous because fuel goes through it, and you don’t dangerous because fuel goes through it, and you don’t want them to mix. This one is very robust because it doesn’t have any welded parts. In the testing, the design was 300 PSI and welded parts. In the testing, the design was 300 PSI and we went to 5,000 PSI to break it, so there’s a lot of margin.”
SHOWN:
HELICOPTER HEAT EXCHANGER DESIGNED WITH INTERNAL GYROID LATTICE STRUCTURES
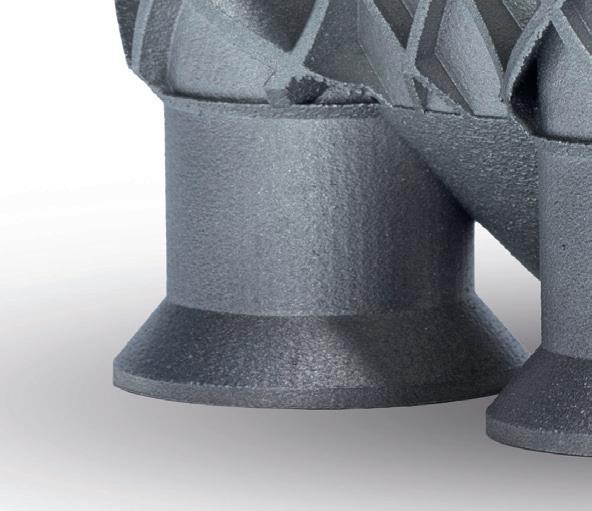
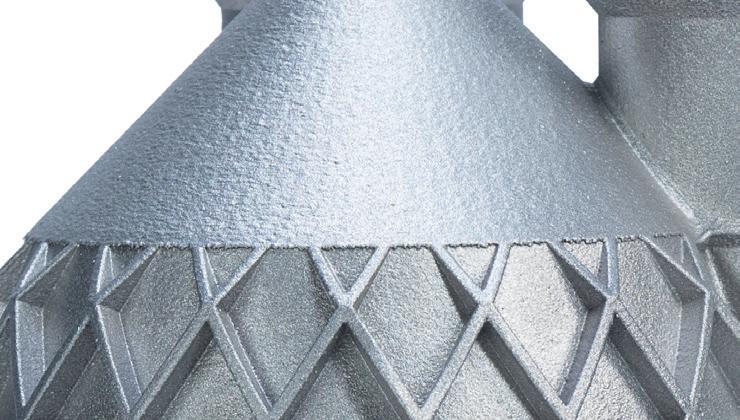
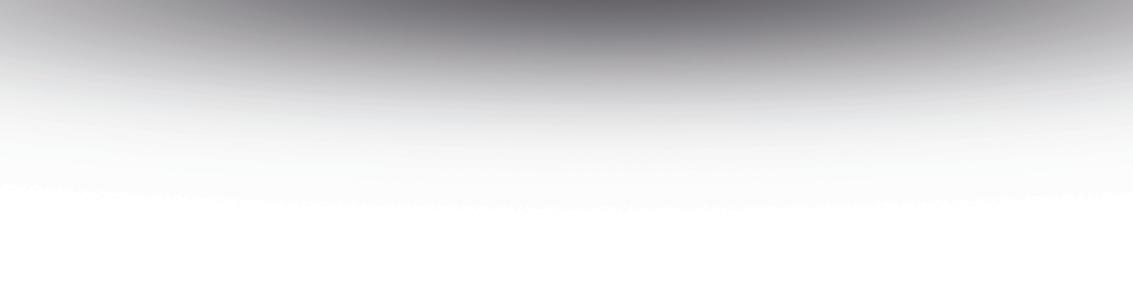
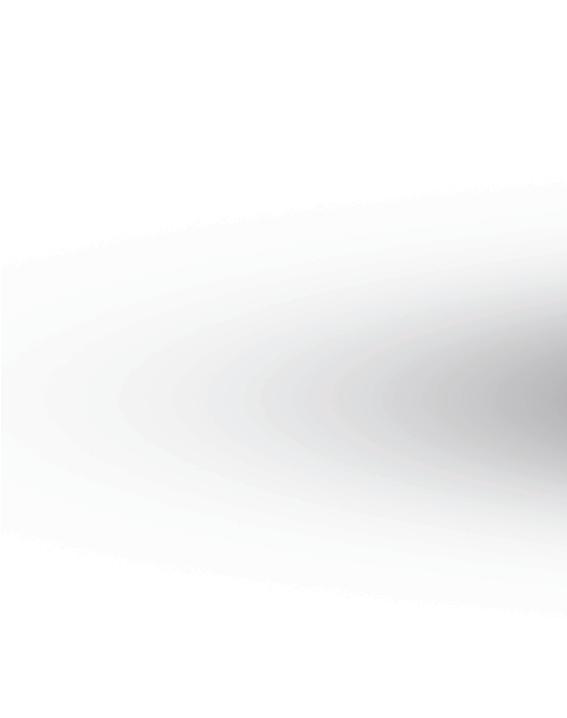
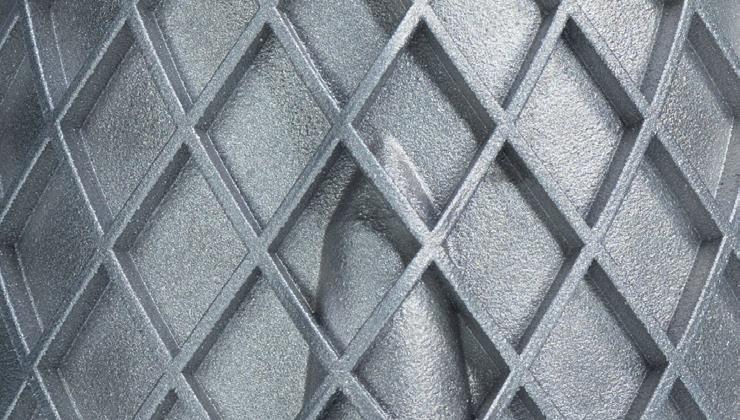
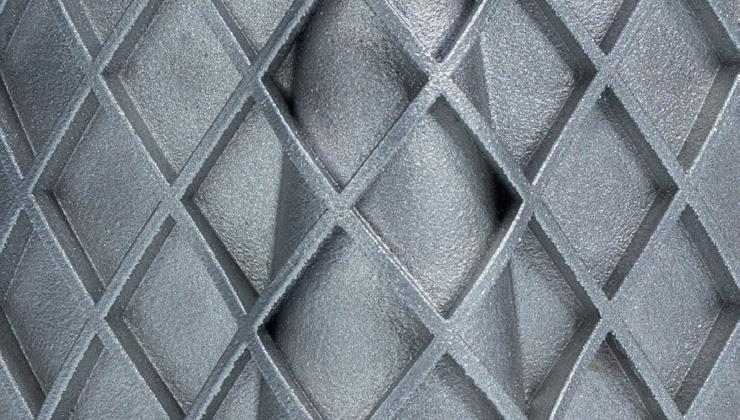
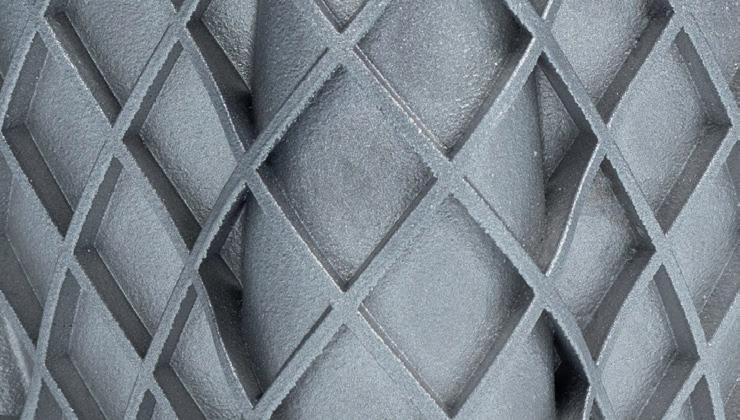
In the design and development of this heat exchanger, Vlahinos was responsible for much of the fi rst 80% of the work. For the fi nal 20%, he reached out to the Additive Minds consultancy arm of EOS, bringing Maryna Ienina, AM Academy - Product and Partnership Manager, and David Krzeminski, Additive Minds Consultant, into the fold. From early on, Vlahinos utilized the lattice generation tools of PTC CREO to create the gyroid structure on the inside and the lattice structure on the outside, with the gyroid thickness increased at the cold inlet and outlet to prevent hot fl uid from entering those channels. When Additive Minds was integrated, a digital twin of the process was set up to carry out simulations that would assess performance of the design and the manufacturing process, with EOS going slice by slice to identify potential trouble spots.
“By creating this digital factory, there is ways to understand whether the parts will be high quality, and there is also a place to monitor the machine health to do predictive health analytics for the machine and to understand whether the machine was up to the qualifi cation specifi cation,” Ienina said.
With the help of this digital twin, the part was printed successfully fi rst time. A demonstration part which had been scaled down was then exhibited at AMUG, and will be the focus of a presentation at the upcoming RAPID + TCT show in Detroit delivered by Vlahinos, who says the design wouldn’t be possible without the tools he had at his disposal.
“The bottom line is that type of geometric complexity cannot be manufactured with traditional manufacturing methods,” he said, before also adding: “It will be impossible to design something like this without the simulation tools, because tribal knowledge and intuition doesn’t cut it for these complex geometries. So, the simulation was necessary because we do the trial and error within the simulation instead of build and test. We went through at least a dozen iterations within the simulation.” When it came to the print, the decision was made to proceed with the EOS M290 machine, partly because two units of the component could be additively manufactured at once, but also because Additive Minds wanted to demonstrate the capacity to print a part with such complex structures on a not ‘overly sophisticated’ machine. Vlahinos thinks the printed part could be revolutionary, and with additive’s application for heat exchangers ever increasing, there’s also a belief at the EOS end that this could have a huge impact in aviation.
“To basically have almost every square centimeter or every feature be purposefully designed for its intention – you’ve heard of purposeful design? I think this demonstrates that,” off ered Krzeminski. “You can use every inch towards the end use, it’s not, ‘well, we have to have this feature here because of this manufacturing process, but it’s kind of a waste, or get more material here because it gets brazed or welded,’ you can squeeze every drop, if you will, out of this application in this space.”
“Every square centimeter is purposefully designed for its intention.”
SHOWN:
THE EOS M290
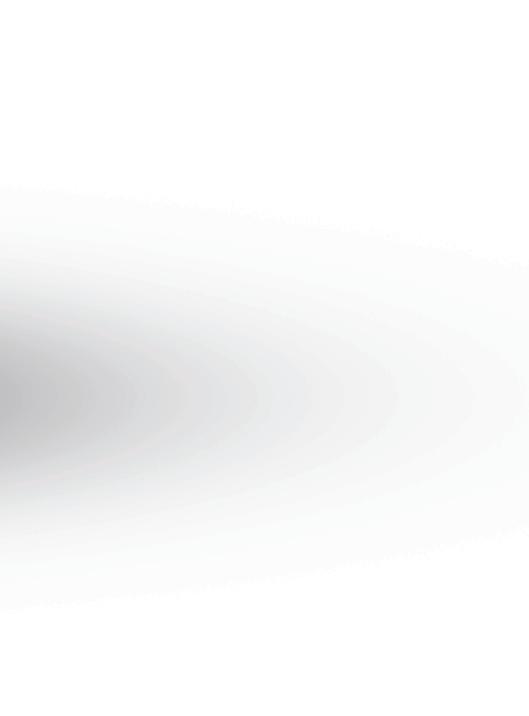
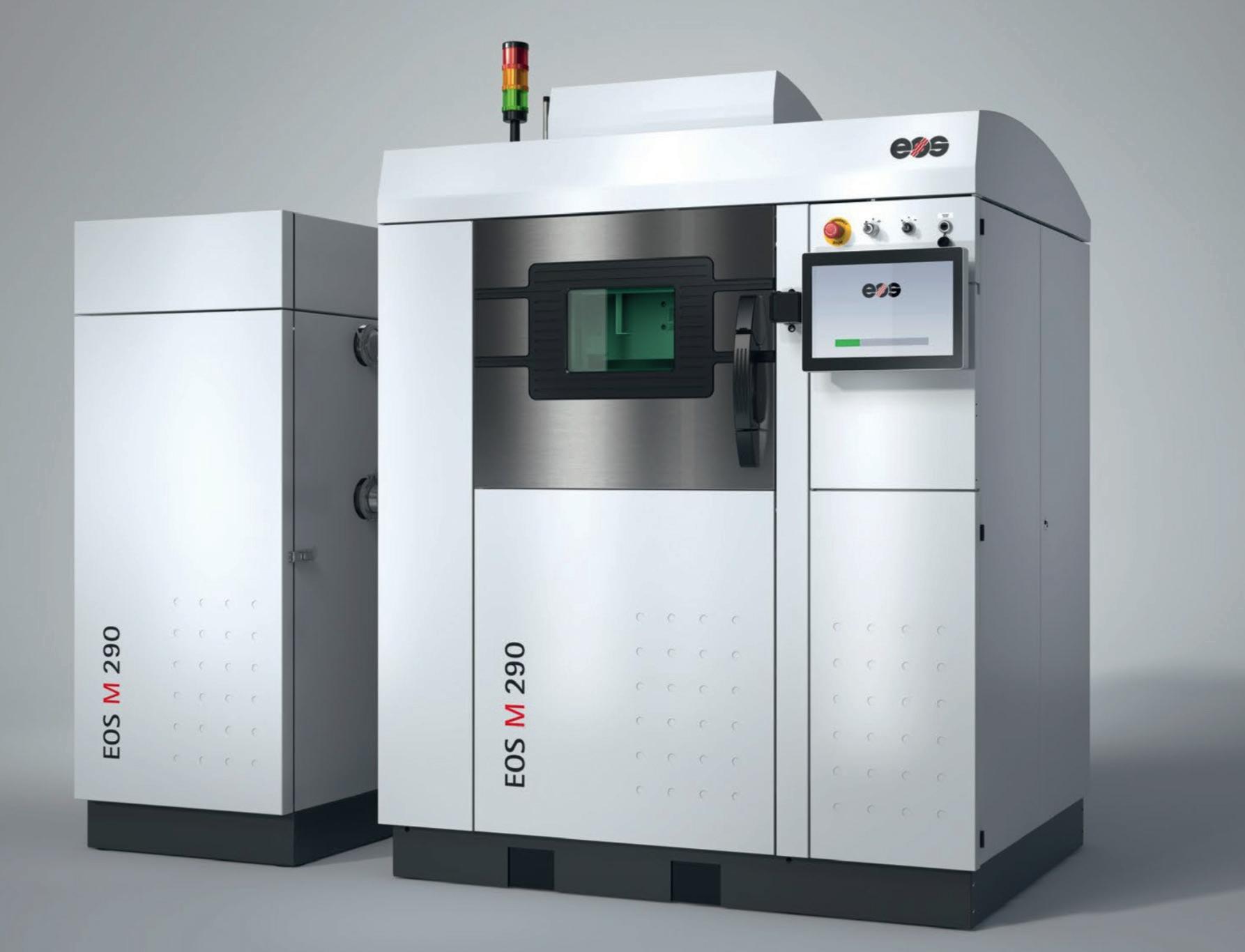