11 minute read
SETTING THE TONE
Next Article
WORDS: SAM DAVIES
SETTING THE TONE
The turn of the millennium brought about many changes. While our airplanes remained in the sky despite fears of the Y2K bug, advancements in technology would see the rise of the internet, and with it things like social media and mobile apps. Buying music would become a thing of the past, as would our tendency to read words like these in print publications. It also coincided with the launch of color 3D printing, meaning rapid prototypers would soon have an alternative to building parts layer-by-layer in monochrome.
Pioneering that particular movement was Z Corp. By the time the company had been acquired by 3D Systems 12 years later, its color 3D printing technology was enabling the likes of LAIKA to apply color during the build rather than painting parts postprint. But LAIKA’s Director of Rapid Prototyping Brian McLean would tell TCT in 2018 that, even by the time it was working on Paranorman (2012), they found color 3D printing to be inconsistent ‘from print to print.’ It wasn’t just the users who had reservations. RIZE CTO Eugene Giller worked as a Senior R&D Chemist at Z Corp between 2005-2010, and he too had been unsatisfied with the quality of the parts Z Corp’s color technology would output.
“I always thought it should be a technology that could provide a fully functional color part, not just form,” the RIZE founder told TCT. “For me, it was all about strength.”
Today, there are several suppliers of color 3D printers, including RIZE, Stratasys, HP and Mimaki. The latter launched the 3DUJ-553 platform with its capacity to print ‘more than 10 million colors’ in 2018. It boasts a build volume of 500 x 500 x 300 mm and uses a UV-curable inkjet process to print parts in full color. White and clear inks can also be mixed with colors to add transparency, while water-soluble materials enable post-processing in minutes.
Service provider Marketiger was among the first users of Mimaki’s color 3D printing technology. As of late 2019, the company was producing up to 20,000 custom figurines every year, though a second 3DUJ-553 was installed in early 2020. With the machine’s automatic cleaning sequence and queuing capabilities, Marketiger is able to print at up to 72 hours in a row without touching the printer, but generally sticks to overnight print jobs.
Because of the nature of its core business – custom figurines based on 3D scans of people – the company targets 100% yield. To ensure everyone who scans themselves gets a 3D printed full-color model, Marketiger only starts manufacturing models once it has confirmed the quality of the scans and models. But once the print button is hit, it barely stops.
“My company is built on this machine running 24/7,” Marketiger Director Maikel de Wit said at Formnext 2019. “It causes some issues because it’s a new technology, but we’re able to get above 80% utilization on a 24/7 basis.”
Evidently, much progress has been made in color 3D printing over the years. With the brittleness of early color 3D printed parts, building a business around the technology as Marketiger has with Mimaki’s tech was hardly possible. Yet, those bringing the tech to market know there is still more to be done.
Giller has always been of that mindset. He founded RIZE because, although he wasn’t happy with the quality of components coming off Z Corp machines, he has always had faith in color 3D printing's potential. With RIZE, Giller has aimed to deliver a printer that can operate in any environment to make functional parts in full color that require minimal post-processing. His answer is XRIZE, which uses the patented Augmented Material Deposition technology to build parts by jetting a formulated release agent between layers of extruded materials. While the extrusion process allows carbon composites to be printed, the jetting enables the voxel-level application of full-color graphics.
“Right now, color is nice to have, but we want to make it must-have.”
SHOWN:
PACKAGING APPLICATION ENABLED BY STRATASYS COLOUR 3D PRINTING. CREDIT: KINETIC VISION
INTELLIGENT MATERIALS
AMP ALUMINUM- POWDER EVOLVED
CNPC POWDER’s AMP Aluminium powder for Powder Bed Fusion (PBF) metal Additive Manufacturing signals an evolution in powder production. AMP Powder evolves the morphology and flowability of Aluminum providing you with critical advantages. AMP’s evolution in powder production is the result of our bottom-up redesign focusing on making the fittest powder. We have boosted efficiency, lowered production costs and increased output.
CNPC POWDER’s suite of Aluminium alloy powders provides its end users with a value proposition that is hard to refute. It has been designed to meet the stringent needs of large-volume additive manufacturing applications in industries like automotive and aerospace.
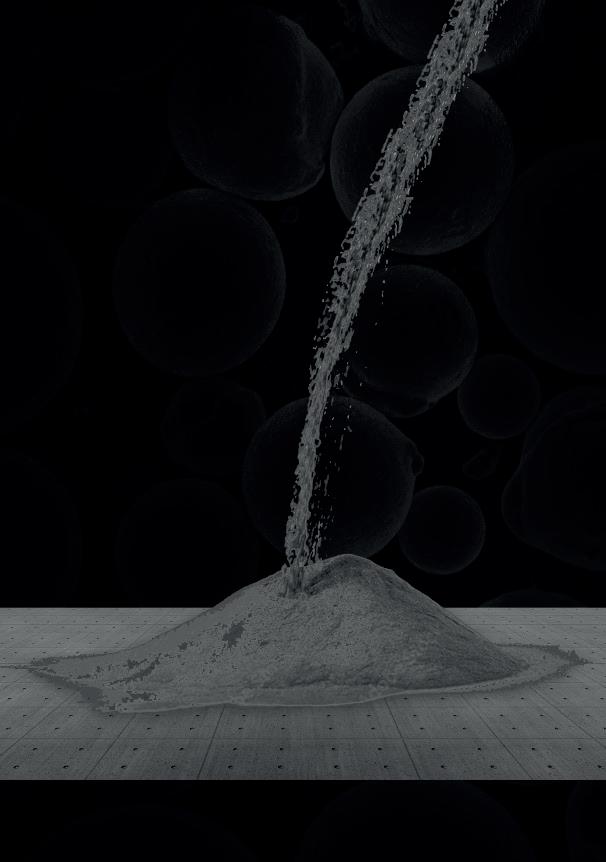
Low Oxygen and Low Nitrogen Levels High Sphericity and Fluidity
High Efficiency for Targeted Particle Sizing Higher Production Output with a much Shorter Production Cycle
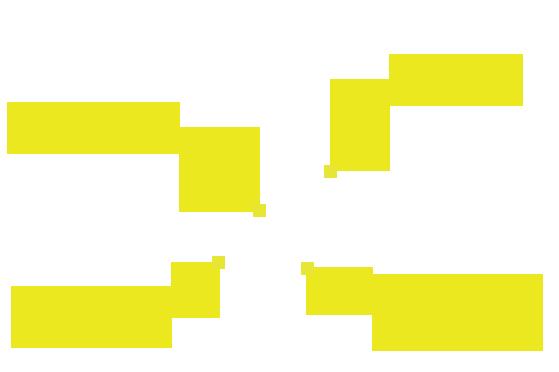
WWW.CNPCPOWDER.COM
©2021 CNPC POWDER GROUP CO., LTD.
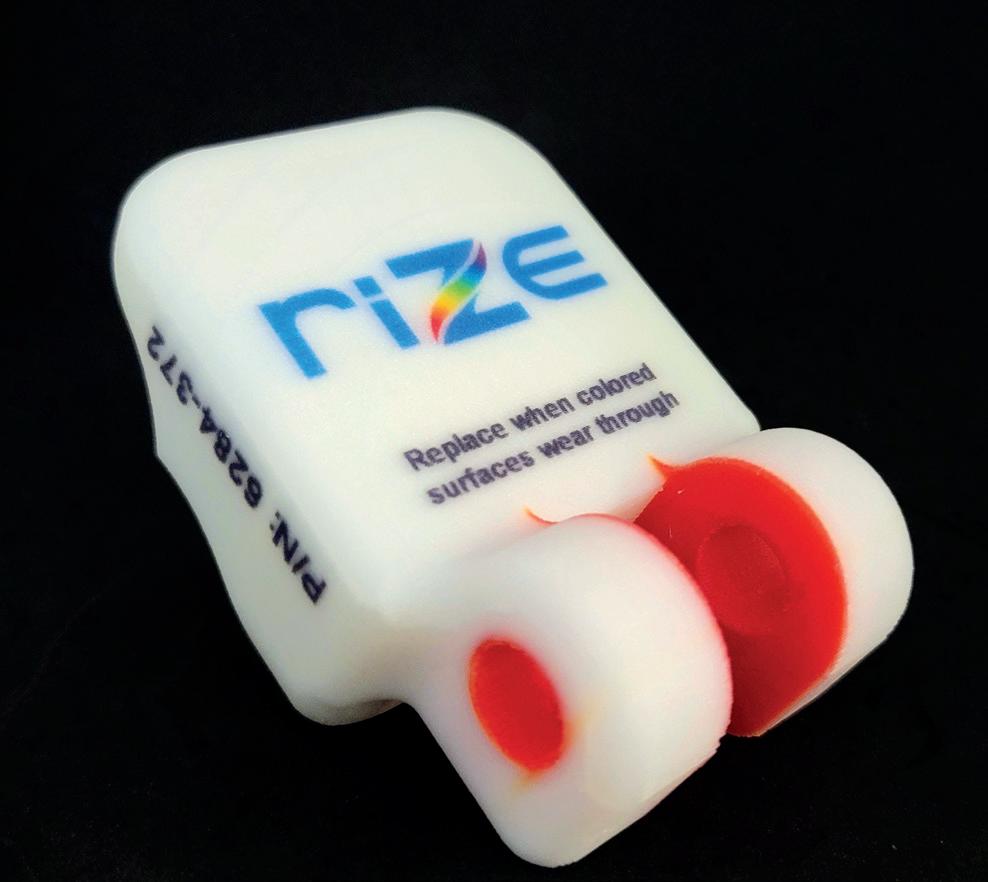
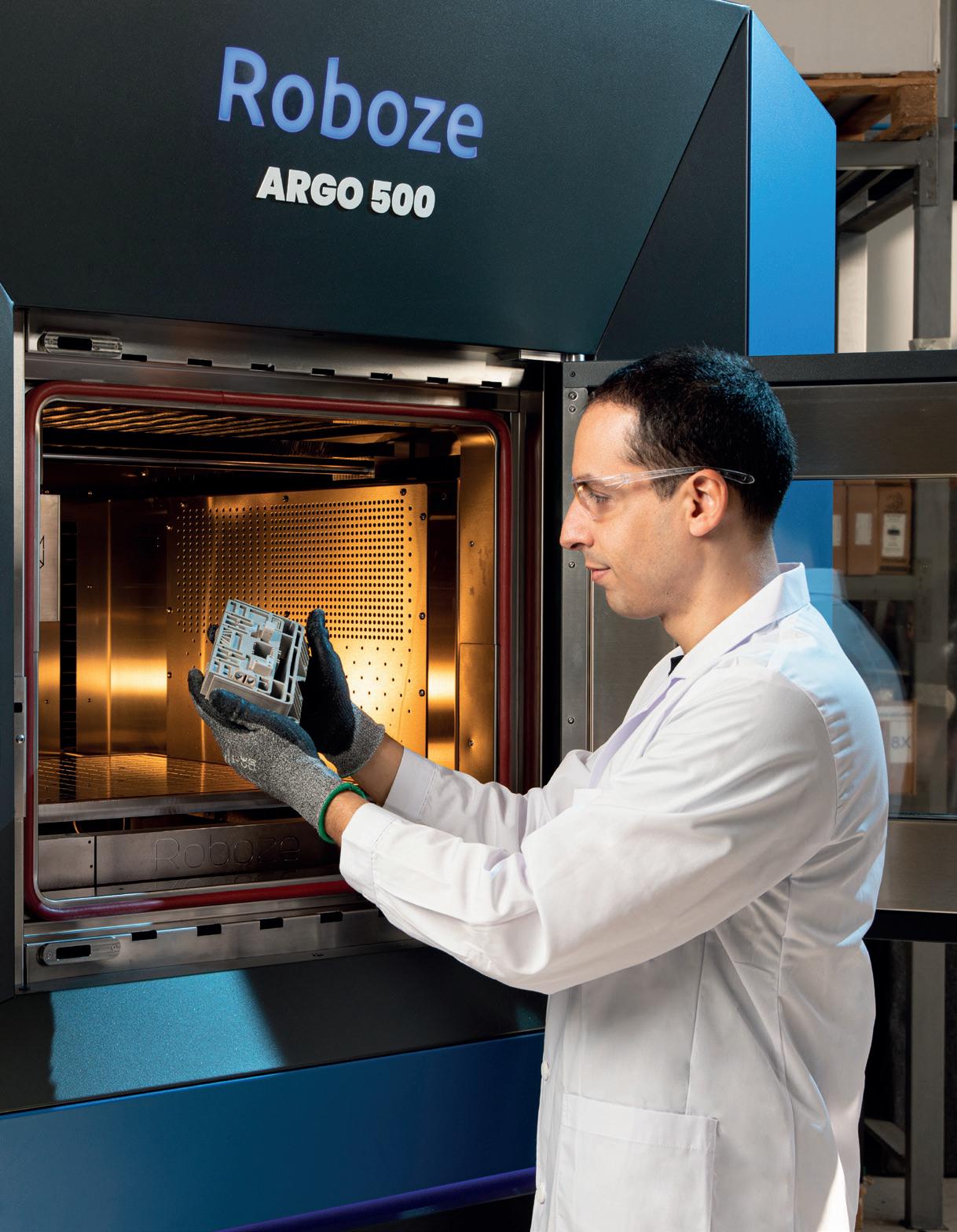
SHOWN:
MANUFACTURING FIXTURE PRINTED WITH XRIZE
For RIZE, the potential applications go beyond prototyping and figurines. Multi-colored medical models is a key play for this technology, as are jigs and fixtures. With the latter, the use of high-performance polymers and composites ensure parts can withstand the factory floor, while color can be used to indicate when a part needs replacing, as with the part pictured above. These are just some of the ways RIZE’s customers are using its full-color technology, and they’re not shy of telling the Boston-based firm how they can still improve.
“They want new materials,” Giller says. “That’s why we are working hard to introduce a new set of materials. They’re really happy with [the current materials], but there are a subset of customers that want parts to go inside of vehicles where they are exposed to oil. They also ask for elastomeric materials.”
As a result, RIZE is working to add such products to the Rizium One, Rizium GF (Glass Filled), and Rizium Carbon materials it already offers. Unsurprisingly, the company is not alone in building out its color 3D printing portfolio to meet rising customer demand.
Stratasys now offers more than half a dozen full-color 3D printing systems in its J Series portfolio, with some designed specifically for the healthcare markets. In June, it introduced the J55 Prime, an office-friendly fullcolor system that operates as quietly as a refrigerator, alongside a range of new functional materials. The expansion of material products is seen as the primary way to nurture the company’s color printing offering.
In line with the J55 Prime, Stratasys rolled out the Elastico Clear and Black rubber-like materials, the Vero ContactClear translucent Biocompatible material for prolonged skin or bodily contact, Digital ABS Ivory for high-impact designs, and ultra-opaque colors enabled by the VeroUltra family. Other colour material options include the flexible VeroFlex and the versatile VeroVivid.
With advancements being made with the 3MF file format, the company is confident in its capacity to deliver the details and aesthetics that any designer could want, but like RIZE is continuing to push on the performance side through ongoing materials development.
“When it comes to mechanical properties, this is still in the works,” says Zehavit Reisin, Stratasys Vice President, Head of Materials Business and Design Segment, ROW. “When we discuss PolyJet materials, it’s about acrylicbased photopolymers and they behave differently versus, let’s say, thermoplastics. Their heat conditions or their dimensional stability is subject to change if you put the part under stress, under heat, under aggressive environmental conditions and that’s where durability is questionable. That’s where [there is a question mark around] manufacturing end use parts with PolyJet. But we are continuing to work very hard on improving the material properties of what you see today on the J Series, meaning the colors, the transparency, the mechanical and thermal properties are better to withstand the required environmental conditions.”
As color 3D printing establishes itself in the medical and prototyping sectors, there is now a glance towards other opportunities. For a surgeon or a designer, the benefits of color 3D printing are obvious, but in other markets the uptake is slower. That may not be a problem since there will always be medical procedures to carry out and parts to design and redesign, but in this industry, there is always an appetite to push the boundaries. And Giller remains optimistic about the impact full-color 3D printing can have.
“The way I think about it, we all have color TVs, and nobody wants to go back to black and white,” says Giller. “But I’m old enough, I did have a black and white TV and I remember some people saying, ‘I don’t need color, TV is an art’, and now, no one thinks this way. If we can get it to a [lower] price point, I think people would get used to printing in color. Right now, color is nice to have, but we want to make it must-have.”
PEEK | CARBON PEEK | CARBON PA | ULTEM™ AM9085F
3D Printed Wide Body Kit by STREETHUNTER DESIGNS & BCT Entertainment
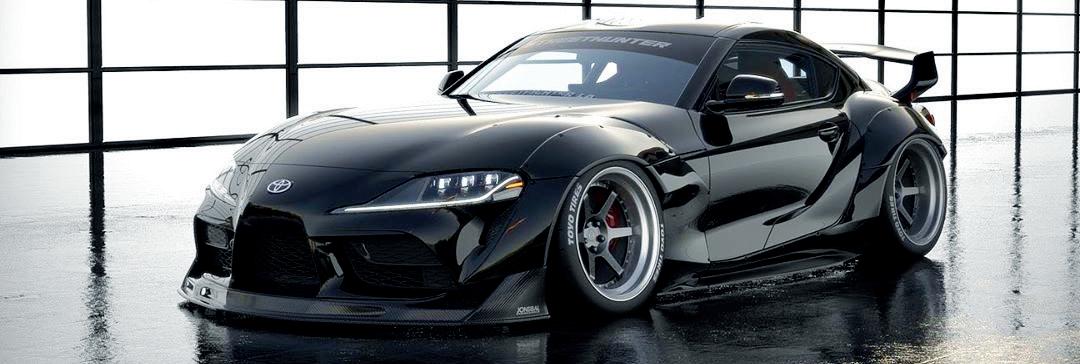
Large-Scale Additive Manufacturing to Touch Down at RAPID+TCT 2021
It’s hard to express the collective adrenalin building up towards Rapid + TCT 2021. Over the course of three days this September, the muchanticipated event brings together the shining stars of the additive manufacturing industry. Undoubtedly one of the major players to keep your eye on this year is Massivit 3D, an emerging powerhouse in the world of additive manufacturing. Bigger and faster are the hallmarks of the Massivit 3D product lines and by developing and integrating innovative technologies and materials, they have launched their most impressive largescale 3D printer yet - the Massivit 5000.
The new machine marks a fresh era in the scope of design and development applications available to engineers as well as large custom end-use parts. In a field where time is of the essence, this next-generation wunderkind enables lightningfast production of full-scale parts, prototypes, molds, and models for a constantly expanding range of industries.
Photo Polymer Innovation for Speed and Scale Massivit 3D’s cutting-edge Gel Dispensing Printing technology (GDP) leverages proprietary, instantly curing photo polymer gel that cures on-the-fly with the help of UV light, enabling production of mega-scale, hollow models at unprecedented speed. These unique and innovative printing materials provide a major advantage in speed and overall efficiency, allowing designers and engineers to push the boundaries of what they thought possible, especially when compared with the use of other technologies, such as FDM and SLS.
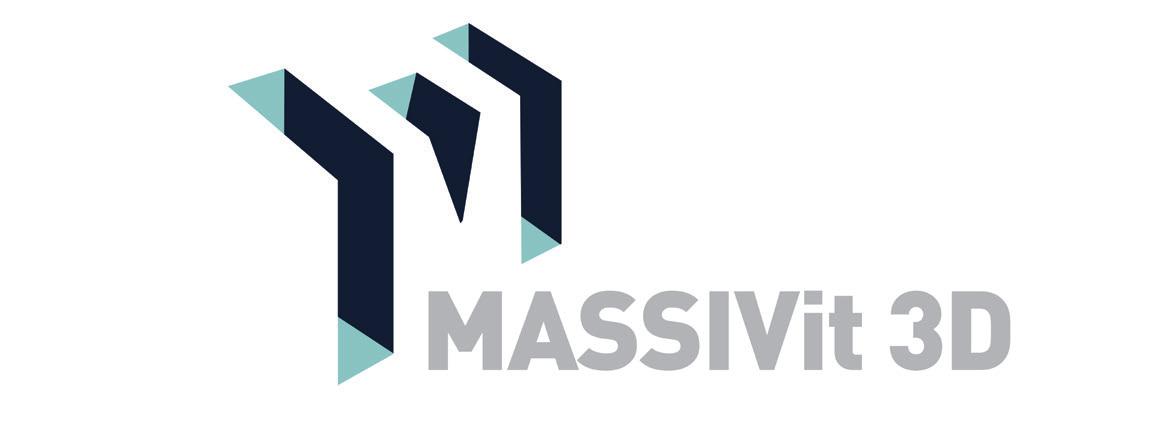
A Ton of Features for Workflow Efficiency Furthermore, the Massivit 5000 employs a dual material system which allows it to print with a different material on each head, according to the specific application requirements. This enables cost-effective production of industrial-grade, large parts for a multitude of industries including automotive, marine, rail, and more. Massivit 3D’s proprietary GDP technology has been adopted across 40 countries to date.
Wide Body Kits at Unprecedented Speed One example of its scale and efficiency benefits is the wide body kit collaboration between TJ Hunt, STREETHUNTER DESIGNS, and BCT Entertainment for the SEMA convention in Las Vegas, 2019. For this launch of the Toyota Supra MK5 tuning kit, 16 unique parts were 3D printed in just 64 hours using the Massivit 1800 Pro. This printing capability – 14 in/hr (35cm/ hr) – is up to 30x faster than other existing technologies. And with great benefits for producing full-scale parts in a single printing session, Massivit 3D facilitates production of large prototypes, such as a 5.9foot car bumper, in a mere 22 hours, instead of weeks.
The benefits, in terms of almost-instant design iterations, are obvious. Massivit 3D printers have a build volume of 57” x 44” x 70” (145cm x 111cm x 180cm), meaning that they are capable of creating individual parts nearly six feet long/tall.
A Range of Layer Thicknesses & Materials The Massivit 5000 is not merely bigger and faster than existing additive manufacturing systems – it is also far more versatile, offering an increased range of available materials and layer thicknesses, as well as other new features intended to optimize workflow, resulting in a vast spectrum of potential applications. The uniquely resilient characteristics obtained through AM provide a major advantage over traditional manufacturing and prototyping methods and materials, benefits that are not overlooked by the marine and rail industries. In yet another example, a European nautical engineering firm, Velum Nautica, uses Massivit 3D’s new generation of 3D printers to produce uniquely tailored end-use parts all in less than one day, such as a yacht stern extension and a bowsprit that doubles as a boarding ramp for a 30-passenger yacht
Full-Scale AM for Accuracy The reduction in the total number of components required for final assembly allows engineers to achieve much higher levels of precision by designing a single, integral unit that allows less opportunity for deviation. Additionally, Massivit 3D’s integrated, proprietary slicing software, remote monitoring capabilities, and new flat panel display show that the company has not forgotten the importance of a pragmatic and comfortable user interface.
See MASSIVIT 3D printers in action at Rapid + TCT 2021 or contact us at +1 7706766116