6 minute read
THE CUTTING EDGE
from TCT Europe 30.6
by TCT Magazine
Next Article
THE CUTTING EDGESam Davies speaks to 3DEO about its role in the development of Blackland Razor’s TCT Award-winning Era razor.
It’s not very often that you have a consumer product that has a price point that can compete.” 3DEO President Matt Sand is reflecting on a TCT Award-winning project: The Blackland Razor Era double-edge safety razor, the company’s first mass-market offering. It was enabled by 3DEO’s metal additive manufacturing (AM) technology.
The razor, 3DEO and Blackland Razor believe, is the most advanced of its kind on the market. At a point-of-purchase cost of under 100 USD, it is up to three times less expensive than prior Blackland Razor products, but with no compromise on the quality.
“When we set out to create the Era, we didn’t choose metal 3D printing as a gimmick to get cheap attention,” Shane Swartzlander, founder and Chief Innovator at Blackland Razors, writes on his company’s website. “We chose it because this production method allows us the flexibility to design a razor with features that cannot be machined. Without a doubt, the Era is a razor unlike any other due to its 3D printed stainless steel structure.”
3DEO’s Intelligent Layer technology was leveraged to additively manufacture the top cap of the safety razor, as well as five varying open combs and five varying safety bar base plates. The technology works by spreading a thin layer of metal powder before a proprietary spray technology deposits a binder agent across the entire layer, indiscriminate of part location. Then, a bank of CNC micro endmills cut the predetermined internal geometry of each part across that layer, with these steps repeated until parts are fully formed.
The intelligence of the technology comes from the process’ capacity to work on many layers at the same and choose when to cut – for example, the CNC endmills could be programmed to cut every tenth layer for speed or surface finish purposes. Once parts have been built with Intelligent Layering, they are put through a sintering furnace with the help of robotic automation and then sent for post-processing. The Blackland Razor Era parts were finish-machined on Hass DM2 vertical mills with custom tooling and bead blasted, before inspection and shipping.
Through leveraging this workflow, Blackland is said to have enjoyed ‘much faster development and first article times’ than conventional methods. Per 3DEO, first article parts were delivered to Blackland Razors across 11 SKUs within four weeks of purchase orders. The 11 SKUs represent the 11 variations of printed parts across the top cap, open combs and base plates.
Initially, Blackland had come to 3DEO with the hope of launching a single 3D printed product.
“Instead of launching one product, with us, [they were] able to launch ten different variations [plus the top cap],” Sand told TCT. “There was a lot more development effort on our side, but the cost comparison – it didn’t cost Shane anything. We didn’t charge him anything to launch it [but] he would have been in for hundreds of thousands of dollars across all those products
SHOWN:
THE ERA RAZOR WITH 3D PRINTED COMB AND TOP CAP
“It's a highly functional design that's enabled specifically by 3D printing.”
[through conventional manufacture].” “If I were to launch this product with traditional manufacturing, I would have to pair it down to one to two options and it would cost three times as much to develop,” commented Swartzlander.
That conventional cost projection, which 3DEO calculates could have been up to 400,000 USD, is 50-70% more than Blackland Razors had to invest with Intelligent Layering. Not only that, but the companies were able to implement geometries that are not possible, or too expensive, to CNC machine.
One such example can be found on the Era’s base plate where the collaborators were able to create a deep overhang on the base plate that supports and clamps the blade as close to the cutting edge as possible. This is said to make the blade ‘extremely rigid’ while ensuring users can enjoy a ‘stable, repeatable shave’ similar to the performance of a single-edge razor. The same features also facilitate unobstructed lather flow, meaning there is little-to-no clogging even when cutting through multiple-day beards. 3DEO also points out that the teeth on each open comb baseplate would add 20-30% to the part cost via CNC, but the price of additively manufacturing the baseplates with Intelligent Layering doesn’t scale with geometric complexity.
“It’s a highly functional design that’s enabled specifically by 3D printing,” Sand says of the overhang/undercut feature. “That design means that you’d never clog your razor again as you’re shaving, you just keep shaving right on through.”
It isn’t the only design feature enabled by 3DEO’s Intelligent Layering technology.

“And then there’s the top cap,” Sand continues. “A razor blade sits on it and it’s pretty important that it be flat. If it’s not flat, you’re going to run into potential safety issues with the product. The dimensional accuracy and the tight tolerances we can hold with our technology are such that I think we were uniquely positioned with our patented technology to hit the specifications.”
After months of back and forth to land at the final design, hit the specifications 3DEO did. In the additive manufacture of the Era components, 3DEO leveraged precipitation-hardening stainless steel with a hardness value of 312HV (34 HRC), and is said to have achieved a tensile strength of 1000 MPa, elongation of 6%, and an assintered density of 99.5%. To get there, there was much design work and several iterations, where tolerances and surface finishes for the correct feel were surveyed before the Era went through user testing. At the end of all that, Blackland Razors took the Era to market at a price of 75 USD – nearly 250 USD less than its Blackbird Titanium razor – with units manufactured on-demand month by month.
At that price point, 3DEO believes it has taken a significant step: a metal 3D printed consumer product at a fairly affordable price. It is cause for optimism.
“I don’t see it competing in true mass quantities yet, but with that, 3DEO and a lot of other companies like 3DEO in the ecosystem are all working in concert to lower the cost structure, so they can one day compete,” Sand finishes. “I think it’s inevitable, especially when it comes to lower and medium volume products, especially when it comes to products with high degrees of variation like mass customisation on one extreme, but also products like Blackland where there are ten different SKUs. And based on demand, they want to vary what’s produced across those ten different SKUs. Those will all play into 3D printing’s wheelhouse.
“I think it’s only a matter of time before the cost curve comes down to the point where it's going to be a question of, ‘can I justify traditional manufacturing when I get all these benefits with additive for maybe a slight premium in the price point?’”
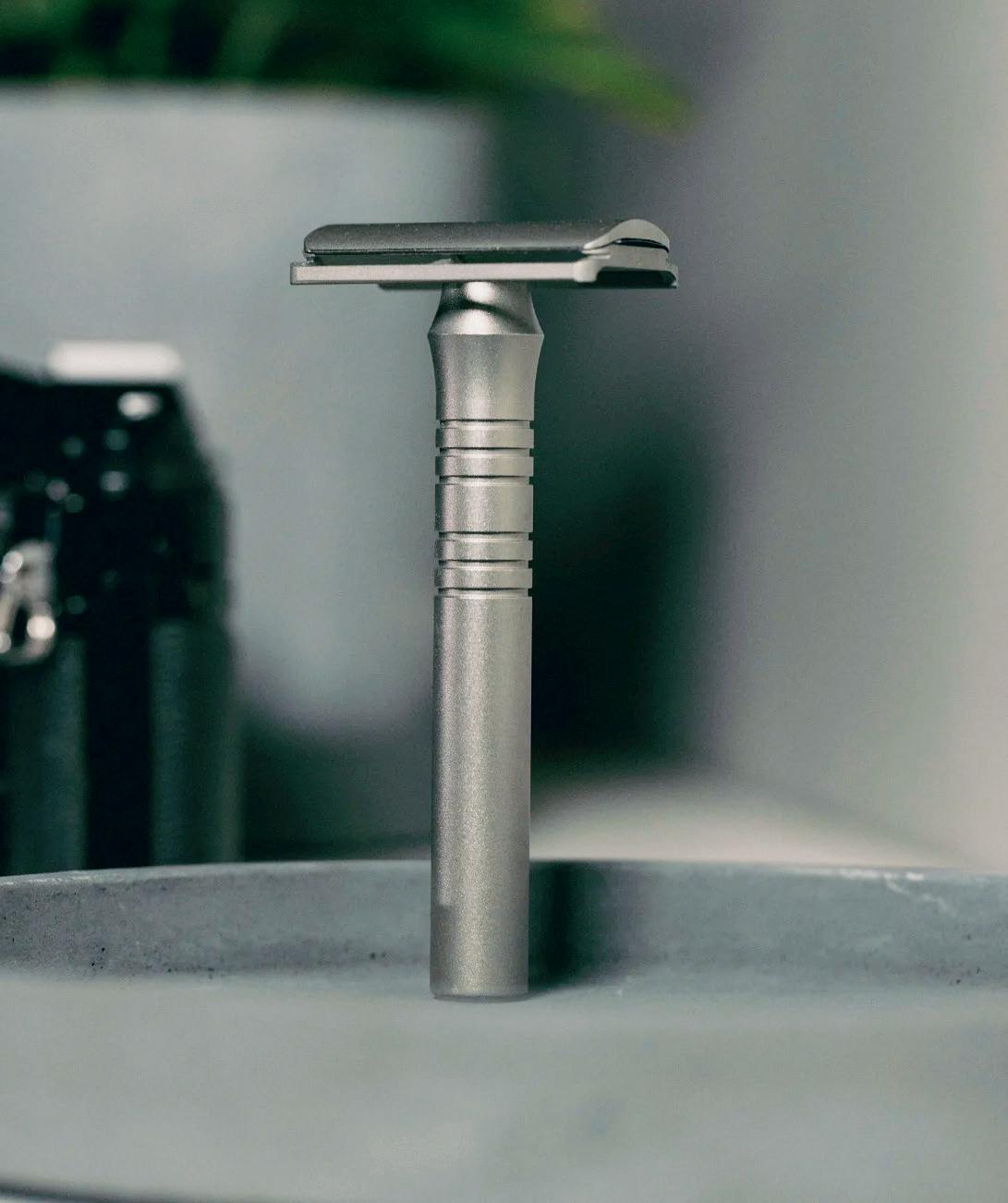
SHOWN:
3D PRINTED WITH INTELLIGENT LAYERING TECHNOLOGY
SHOWN:
THE ERA IS AVAILABLE WITH VARIOUS BASE PLATES & COMBS
WATCH THIS SPACE:
Submissions for TCT Awards 2023 are now open at tctawards.com