6 minute read
EDUCATION WITH ULTIMAKER
from TCT Europe 30.6
by TCT Magazine
Next Article
Oliver Johnson speaks to UltiMaker CEO Nadav Goshen about the new MakerBot SKETCH Large
The merger between two leaders in desktop 3D printing, MakerBot and Ultimaker, was completed in September, promising to ‘fuel innovation and expansion into new markets’. Just a month later, the newly formed UltiMaker announced the launch of the MakerBot SKETCH Large, the first system to be released under the new brand.
The latest addition to the MakerBot SKETCH range of education-focused 3D printers is available as a single unit or two-unit classroom package. The machine includes a fully enclosed chamber, particulate filter, a heated and flexible build plate, touchscreen capabilities, onboard camera, materials sensors, and WIFI and USB capabilities. It also features a larger build plate compared to previous editions, hence the name, which can fit up to ten student projects in a single build, according to UltiMaker.
Nadav Goshen, CEO of MakerBot for close to six years, and now CEO of UltiMaker, recently spoke to TCT about the launch of the new printer, the importance of introducing additive manufacturing (AM) to those in education, and the future under the new brand.
Goshen said: “The build volume is significantly bigger, and with that comes the ability to service full classrooms with one printer, I think that’s the main advantage that we are going to bring to the market. That connects to our combined software workflow that we have, and all of our other materials. With the student submission forums, with our cloud offering, we can really build a package that is serving one classroom. The SKETCH Large is a continuation of our previous generation, the SKETCH, which we launched a few years ago, and since then we have seen a great adoption of this platform in schools.”
Goshen stated that after receiving feedback from educators about the previous models, it became clear that teachers would prefer to have one large printer that could service a whole classroom, rather than two separate machines.
The new system is compatible with MakerBot TOUGH materials, and arrives with three spools of MakerBot PLA. It also benefits from MakerBot’s 3D printing education ecosystem including its CloudPrint 3D printing software, which can be connected to Google Classroom, and allows users to slice and prepare prints from a browser.
A key aim of UltiMaker is to target STEM education. To make a real impact, Goshen believes the combination of the SKETCH printers, the curriculum and the cloud workflow is making it easier for teachers to integrate 3D printing.
When asked about the importance of introducing young people and students to 3D printing skills, Goshen said: “We are in a technical, digital world, and the sooner you get introduced to technology, the better prepared you become for the future. That goes for elementary school and beyond. When you talk about what 3D printing brings, it’s two things. One is dealing with futuristic technology, you have something that is very exciting, you have it in your mind, you work it out, and then you have the physical object in your hand. That experience for kids is transformational in the way that they think about what technology can do, it’s very inspiring to them to really experience technology and transformation first-hand. The second thing is the problem-solving element of it. The complexity of taking your idea and then materialising it is great, but when you combine some different challenges, and you think ‘How do I tackle that problem?’ then you iterate on it, and you print and try to solve it and it doesn’t work. The process of iteration and trial and error on the physical level is really important.”
Speaking more broadly about his ambitions for the future under the new brand, Goshen added: “Engineers’ time is very expensive and valuable, and they want access to technology that has to perform to a certain degree. Both companies are introducing products that are really aiming to get to the point where the technology is accessible in many ways, price points, workflow, even physical accessibility to the engineers, but they’re performing to the level of an industrial machine.”
Start your Innovation Journey with us!
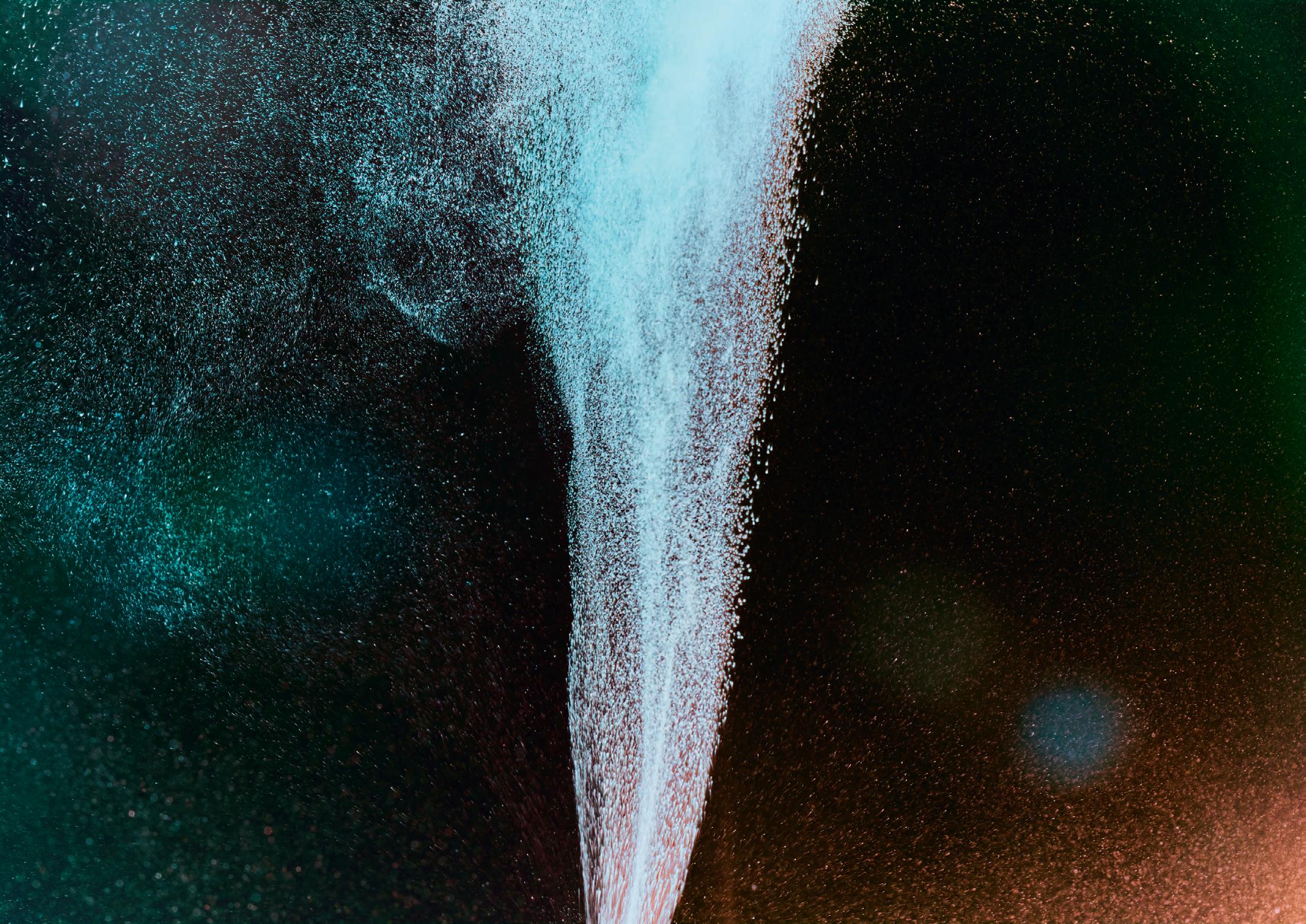
Meet our DG Meet our DG plastic powder experts plastic powder experts at Formnext 2022 from at Formnext 2022 from November, 15- 18. November, 15 - 18. Hall 12 Booth C121 Hall 12 Booth C121
Dressler Group as the missing link for your 3D printing powder.
The family-owned Dressler Group (DG) has become known among its customers worldwide as “The Grinding
Authority”. The individual powder solutions are primarily used in 3D printing, pharmaceutical/medical technology and speciality applications. Bioplastics are also playing an increasingly important role. At the DG Innovation Campus, complete with R&D facilities, DG works closely with its customers to create powders that deliver genuine added value.
Research and development have been part of the Dressler Group DNA
since 1978. As a result, DG effectively becomes the external R&D department for many of its customers. They recognise that DG’s decades of know-how in processing and optimising plastic powders is an asset in its own right. And this expertise is backed up by seamless, audit-proof documentation. Existing customers can have their individual powder produced in the desired quantity and specification at any time.
The three pillars of the DG Innovation Campus
Starting in spring 2023, the new campus will provide a new structure for DG’s theoretical and practical knowledge. It rests on three pillars: DG Knowledge, DG Services and DG Dialogue. The previous R&D facilities – the Innovation Lab and Technical Centre – will also be brought together under the roof of the new campus. What’s more, the campus will enhance partnerships with customers and suppliers as well as cooperation with universities, it will expand the DG network and support the development and recruitment of young talent. The bottom line is that customers get a competitive edge in relevant and applicable knowledge.
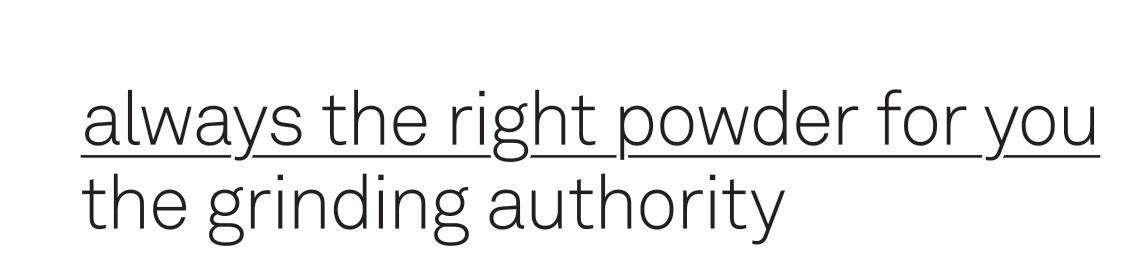
“With the Innovation Campus, we are expanding our competence as a problem solver and systems partner into the digital space. Together with our customers and partners from practice, research and education, we create customised solutions with relevant added value along the entire value chain. Discreetly yet impactfully, we present use cases, practical tips and conversation starters – whenever it’s a matter of getting just the right powder.” Jan Dressler, CEO
Added value powder by Dressler Group
The question always remains in focus: How can DG best support its customers and partners in order to strengthen their existing market position or develop new markets? As a driver of novel ideas and solutions, the Innovation Campus therefore benefits customers receiving standard services as well as those who want to substantially develop their portfolio. What all customers get, thanks to the individual powder design, is powders with genuine added value. That may come in the form of improved sustainability or cost-effectiveness thanks to greater material and energy efficiency, less scrap and waste. In 3D printing, DG powders can optimise component quality and ensure troublefree production – including simplified post-processing. This is the realisation of the DG vision: “Always the right powder for you!”
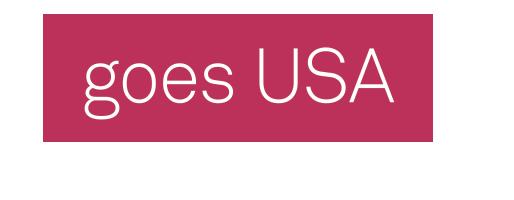
Not only are we the game changer who will develop just the right powder for you, we are now applying our know-how to achieve significant advances in sustainability.