SEPARATING FACT FROM FICTION IN FOOD SAFETY
Ensuring food safety along the cold food chain is a continuous ordeal, one that requires all parties, farm to fork, to participate in.
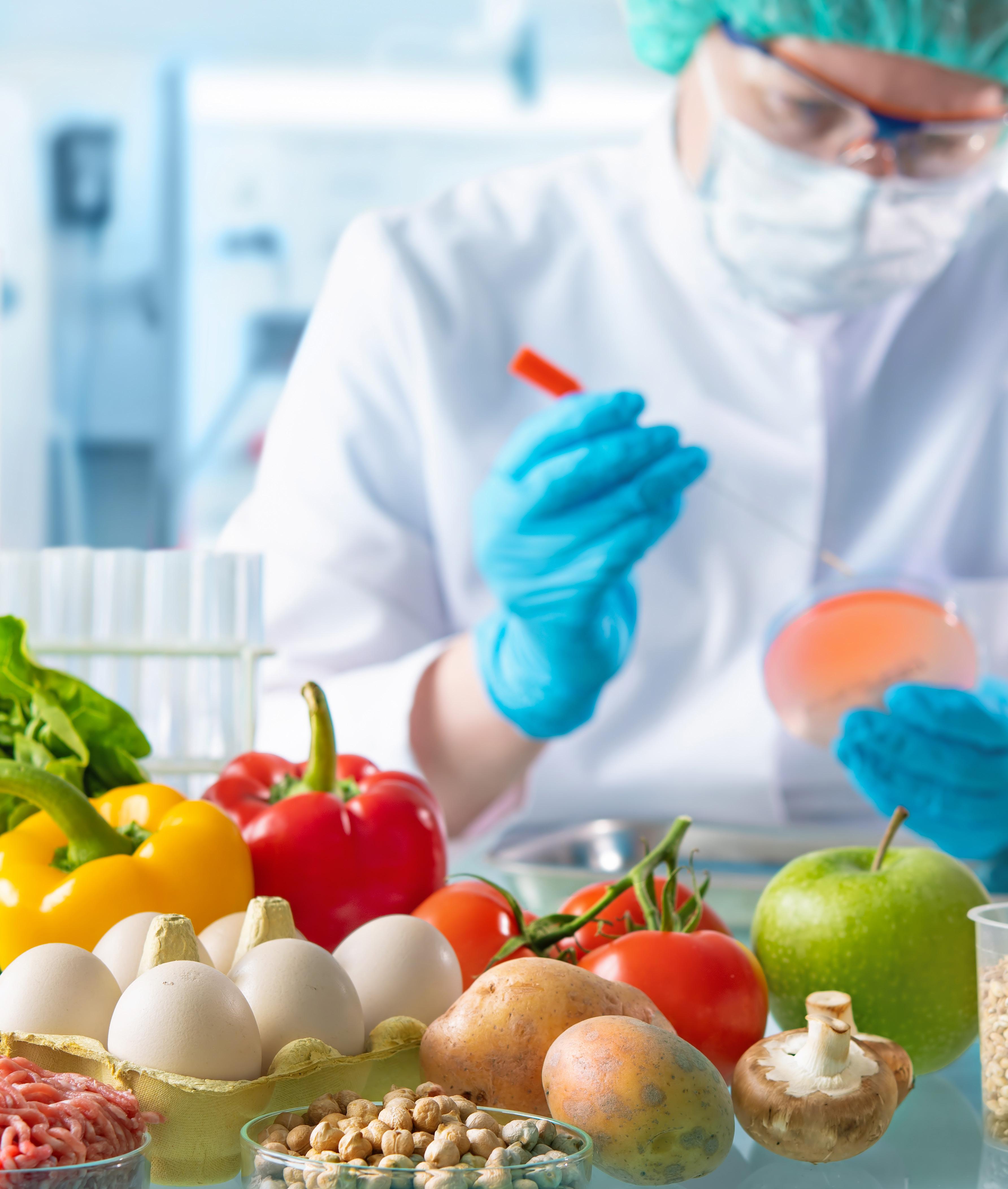
Ensuring food safety along the cold food chain is a continuous ordeal, one that requires all parties, farm to fork, to participate in.
In order to get perishable products to the market in the best condition, we use a foam mandrel process with foam-in-place insulation to wrap the 3000R® reefer with a 360-degree, 100% void free foam envelope. With no joints to foam later, our process delivers optimum thermal efficiency.
Contact your local Utility Dealer. Find out more at: www.UtilityTrailer.com
When I launched the Women in Supply Chain award three years ago on Food Logistics’ sister site, Supply & Demand Chain Executive, I was prepared for an uphill battle.
I envisioned a long road ahead in getting the supply chain industry educated enough as to why it was even important to recognize women in the supply chain. I was prepared for backlash and was ready for it come and go; an exper iment gone awry.
To my pleasant surprise, the opposite happened.
Fast-forward to present day, and that award, which today garners more than 300 nominations in its third year, has become the stepping stone to what is now the Women in Supply Chain Forum, an in-person event designed to bring together CEOs, Presidents, Partners, VPs and Director-level decision makers at shippers, DCs, warehouses and 3PLs to learn, grow, network and more.
Open to Food Logistics’ audience as well, this event, which will take place Nov. 8-10 at the Starling (soon to be The W
Midtown) in Atlanta, is the next step in further recognizing and celebrating women in the cold food chain.
We already have a host of leading females in the industry on board to talk supply chain risk, truck driver shortage, women in workforce and more.
Sarah Barnes-Humphrey, owner of Let’s Talk Supply Chain podcast, will kick off the event with a discussion on the overall landscape of women in supply chain and logistics.
Ellen Voie, founder of Women in Trucking; Rebecca Brewster, president and COO of American Transportation Research Institute (ATRI); and Lindsey Trent, president and Co-Founder of Next Generation Trucking will come together to discuss how to alleviate the truck driver shortage.
Kathy Fulton, executive director, American Logistics Aid Network (ALAN), and Stephany Lapierre, CEO of Tealbook, will detail how to overcome today’s supply chain disruptions.
And, Courtney Muller, president of Manifest and chief corporate development officer at Connectiv, will detail the ins and outs of women in workforce.
Go to www.
WomenInSupplyChainForum. com to register to attend and more.
And, together, let’s continue to share in the education and networking of women in the supply chain.
Editor-in-Chief Marina Mayer mmayer@ACBusinessMedia.com
Managing Editor Brielle Jaekel bjaekel@ACBusinessMedia.com
Associate Editor Alexis Mizell amizell@ACBusinessMedia.com
Audience Development Manager Angela Franks
PRODUCTION
Senior Production Manger Cindy Rusch crusch@ACBusinessMedia.com
Art Director Willard Kill
Brand Director Jason DeSarle jdesarle@ACBusinessMedia.com
Sales Associate Brian Hines bhines@ACBusinessMedia.com
Account Executive John Specht jspecht@ACBusinessMedia.com
Account Executive Paul Petterson ppetterson@ACBusinessMedia.com
Chief Executive Officer Ron Spink
Chief Financial Officer JoAnn Breuchel
Chief Revenue Officer Amy Schwandt
Chief Digital Officer Kris Heineman
VP, Audience Development Ronda Hughes
VP, Operations & IT Nick Raether
Content Director
Marina Mayer
GM, Online & Marketing Services ..............Bethany Chambers
Content Director, Marketing Services Jess Lombardo Director, Demand Generation & Education Jim Bagan Director, Enterprise Sales Kay Ross-Baker
P.O. Box 3605, Northbrook, IL 60065-3605 (877) 201-3915 | Fax: (847)-291-4816 circ.FoodLogistics@omeda.com
Sr. Account Manager Bart Piccirillo | Data Axle (518) 339 4511 | bart.piccirillo@infogroup.com
REPRINT SERVICES Brian Hines
(647) 296-5014 | bhines@ACBusinessMedia.com
Published and copyrighted 2022 by AC Business Media. All rights reserved. No part of this publication may be reproduced or transmitted in any form or by any means, electronic or mechanical, including photocopy, recording or any information storage or retrieval system, without written permission from the publisher.
Food Logistics (USPS 015-667; ISSN 1094-7450 print; ISSN 19307527 online) is published 6 times per year in January/February, March/ April, May/June, July/August, September/October, and November/ December by AC Business Media, 201 N. Main Street, Fort Atkinson, WI 53538. Periodicals postage paid at Fort Atkinson, WI 53538 and additional mailing offices.
POSTMASTER: Send address changes to Food Logistics, P.O. Box 3605, Northbrook, IL 60065-3605. Subscriptions: U.S., one year, $45; two years, $85; Canada & Mexico, one year, $65; two years, $120; international, one year, $95; two years, $180. All subscriptions must be paid in U.S. funds, drawn from a U.S. bank. Printed in the USA.
@FOODLOGISTICS
@
@FOOD-LOGISTICS-MAGAZINE
Published by AC BUSINESS MEDIA 201 N. Main Street, Fort Atkinson, WI 53538 (800) 538-5544 • www.ACBusinessMedia.com
WWW.
PepsiCo says supplier diversity offers more than just ethical improvements in the supply chain. Food Logistics’ managing editor Brielle Jaekel sat down with Melani Wilson Smith, chief procurement officer at PepsiCo, and Dr. Hazel Reed, executive director at the National Black Growers Council., to talk about the ways in which diversity offers a broad spectrum of thinking and collaboration. Both organization leaders agree that diversification within the supply chain brings forth new solutions and innovation.
Scan the QR code to hear more about this L.I.N.K. podcast episode.
https://foodl.me/fqm8jk
At only 7 months into the year, the Sedgwick’s brand protection division indicated over 1 billion product recalls in the United States, setting record-breaking numbers only matched by 2018 and 2021. FDA food and beverage recalls increased to 120, up 9.1%.
Chris Harvey, SVP of brand protection at Sedgwick says, “In the face of these obstacles, businesses should continuously evaluate and update their product recall, crisis and communications plans to ensure their brands and reputations will overcome whatever new challenges arise.”
Scan the OR code to learn more.
https://foodl.me/8xybev
The time to shift from COVID-19 survival mode is now, says Kari Hensien, president of RizePoint, in order to up the ante in environmen tal, social and governance (ESG) initiatives and improve supplier safety. Technology and brand management tools can produce transpar ency and bring about proper safety protocols, supporting ESG goals, to:
• Learn the depth of their food sourcing and safety.
• Identify inefficient, unreliable and unsafe sup pliers.
• Meet the increased demand for sustainability and commitment to ESG efforts, which include social justice issues within business practice.
Addressing environmental issues like soil degra dation, water and energy waste, the use of harmful pesticides and more impacts the 70% of global fresh-water withdrawal and nearly a quarter of global greenhouse gas emissions.
Scan the QR code to learn more.
https://foodl.me/mgkwwc
Post-pandemic has brought about many changes. In the food industry, the reality of an economy in inflation is being felt strongly in the checkout lines. According to NCSolutions, 93% of American’s agreed that inflationary times are upon us, with 85% being very concerned about its effects. Today, consumers are changing the way they shop to overcome these cost woes. About 58% of Americans now worry about the rise of simply the cost of living, believing it will be even more expensive in the coming year.
“For the second time in a little over two years, consumers are pivoting to new purchasing behaviors at the grocery store,” says Alan Miles, CEO, NCSolutions. “Since the start of the pandemic, they’ve been swapping their favorite brands for what’s available. Today, though, value is the centerpiece more often than availability, consumers are selecting brands and products to stretch their bud gets as far as possible. CPG brands that meet customers where they are both in this inflationary moment and as prices ease have the best shot at keeping them for the long-term.”
Although the July Producer Price Index (PPI) posted recent declines, the consumer packaged goods industry is coming in higher than overall wholesale prices, with an increase of 13.3% over last year, something the Consumer Brands Association (CBA) warns.
With high percentages for diesel fuel rates that effect freight transportation and a rise in commonly used ingredi ents and materials costs, Katie Denis, VP of communications and research at CBA, says “…we must remain cautious of looming threats that can quickly upset progress and not walk away from policies that help guard against disruption.”
Key commodities show notable increases over last year where diesel fuel is still 71% more than last year. Commonly used ingredients and materials showed spikes over last year. And, consumers are well aware of the link between supply chain pressures and inflation. While many respondents expressed no opinion (25%), nearly half (48%) said easing supply chain pressures would have a positive effect on inflation.
Scan the QR code to learn more.
For most food retail companies, food safety and loss prevention are not connected within their organizational hierarchy. Food safety typi cally reports to the risk or compliance department, while loss preven tion programs are run by operations, legal or HR teams. Guy Yehiav, president of SmartSense by Digi, explains how to shift the functions of food safety and loss prevention into collaboration through IoT’s com mon objectives and an understanding of these underlying synergies:
Total retail loss events and outcomes that negatively impact re tail profitability and make no positive, identifiable and intrinsic contribution to generating income.
Reducing waste through digital transformation of food safety.
Maximizing operational efficiency of facilities.
control and brand protection.
Artificial intelli gence (AI) is taking optimization by storm. In food
logistics, the potential for AI assistance is plentiful. Marcel Koks, industry and solution strategy director for food and beverage at Infor, says as long as business data is available, it’s possible to use AI to providing learning and insight within the business in many formats such as:
Precision farming. Where AI can analyze past harvests and weather forecasts to inform which fields need watering and when, or when to use fertilizer.
Sustainability. Insight generated by AI applications can minimize energy and water usage, ensuring energy efficient production alongside waste reduction in the manufacturing process. Pricing strategy. AI can quickly and effectively analyze all contributing variables, such as seasonality, competitor pricing, promotions, customer demand, etc.
Mitigating production. unpredictability through statistical prediction data to, for example, predict appropriate times for something like sea vessel arrival in manufacture delivery. Maximizing yield. IoT devices in combination with machine learning are optimizing machine setting to maximize yield.
The technology behind these processes can make the most of the huge amounts of data generated by the food and beverage sector and create solutions for better, faster and more profitable operations.
Scan the QR code to learn more.
https://foodl.me/4pfqr0
Food Logistics and Sup ply & Demand Chain
Executive present SCN
Summit: Future of Supply Chains, where
Editor-in-Chief Marina Mayer sits down with industry experts and thought leaders to talk future of supply chains, what’s in store for logistics companies, trends and technologies in the supply chain space and more. Topics revolve around warehouse automation, supply chain visibility, risk management, workforce development and more. Register now to learn more about what’s in store for the future of domestic and international supply chains.
Scan the QR code to learn more.
https://foodl.me/0jeasb
Felixstowe, a port town in Suffolk, England, saw a momentous strike begin Aug. 21 after 30 years of dedicated service. About 1,900 members of the Unite union at Felixstowe organized a walkout for eight days due to pay disputes, says the British Broadcasting Corporation (BBC). The port handles about one-third of Britain’s total container volume and a large share of direct trade with Asia. Simply put, just one day of this strike has the potential to disrupt more than $800 million in trade.
Further effects have yet to be seen, but the probability for higher costs of goods is looming, halting further the ever-difficult comeback put into play after COVID-19. Scott Wyatt, head of operations at DG International, says, “For the wider economy, it’s not good news either, as we are in peak season for businesses moving goods around the world ahead of Christmas. What’s happening in Felixstowe will create a significant backlog in the other UK and European ports.”
the QR code to learn more.
With five cranes to a berth, Wando Welch Terminal in Charleston, S.C., is now more capable of efficiently working three 14,000-TEU vessels simultaneously.
“It is truly remarkable to see the final crane of our new fleet moved into place on the Wando Welch Terminal wharf. This is the culmination of years of effort, planning and coordination by our team and project partners,” says SC Ports president and CEO Barbara Melvin. “Our modern equipment provides smarter operations and more fluidity for the supply chain.”
These efforts have modernized the ports operations and brought on new improvements in other areas, including new container handling equipment, new ship-to-shore cranes and extended gate hours for motor carriers through the peak season to improve rail dray dwell times. Additionally, the port has hired more than 150 people to handle the influx of cargo.
Scan the QR code to learn more.
https://foodl.me/h9mlao
The past 20 years have brought technological advancement to the consumer packaged goods (CPG) industry. While factories have long been implementing the use of high-speed conveyor belts and robotic arms, the creation of autonomous mobile robots (AMR) bring even more advancement to the segment. Vladimir Vovk, global accounts director at Mobile Industrial Robots (MiR), says there are three major considerations into the integration of AMR into your material transportation operations.
1. Knowledge, communication and support should drive preparation which start with choosing the application, reviewing the application, conducting a risk assessment and performing a pilot program.
2. Building out operations to after deployment to see the tangible efficiencies on the floor.
3. Educate employees on how to interact with the machines and capitalize on efficiencies themselves. AMRs are undoubtedly the future of automating material transport within CPG. Putting the time and resources into a thoughtful and strategic implementation—from preparation to deployment, to expansion—is critical to boosting your organization’s productivity and competitiveness in a marketplace where speed and efficiency win the day.
Scan the QR code to learn more.
https://foodl.me/wjdiou
The contract segment remains strong even as the market continues to level off.
“While the growth rate has moderated, our members continue to see volume gains, even as spot market volumes have settled,” says Transportation Intermediaries Association president and CEO Anne Reinke. “This clearly shows the vital role brokers play as ongoing partners for freight transportation shippers.”
According to the TIA. second-quarter growth in payroll employment among for-hire trucking was the strongest of any quarter on record. A decline in consumer spending could lead to an inventory correction in future quarters. The automotive sector will be a wild card as inventories remain severely depleted. And, potential changes to the market status quo and to the report’s forecast for volume and rates mostly favor weaker, not stronger, metrics except for diesel prices.
Scan the QR code to learn more.
https://foodl.me/m3khjh
The newly launched Top Tech Startup award from Food Logistics and Supply & Demand Chain Executive showcases the newest innovations offering new solutions to the field. This award is geared toward companies who’ve started operation within the last 5 years and have introduced a viable product. Marina Mayer, editor-in-chief of Food Logistics and Supply & Demand Chain Executive, says, “The future of the supply chain industry is directly impacted by the development of these new technologies, and I’m very excited to see what comes from these nominations.”
The award officially opens Oct. 10. Scan the QR code to learn more. https://foodl.me/6dv8x8
The increased price of gas is no mystery. From January to June, the price of regular motor gasoline rose 49%, while the price of diesel fuel rose slightly more at 55%, according to the Bureau of Transportation Statistics’ (BTS). After a lull in numbers following quarantine in 2020, prices began to rise steadily and some states have set a goal to provide relief. At least 29 states proposing legislation to change their state gas or diesel tax and ease the stress at the pump. These implications could see a positive uptick in the transportation prices within the food and beverage industry and beyond.
Scan the QR code to learn more, https://foodl.me/nkw86t
@iQoncept.stock.adobe.com
Control, clarity and actionable insight have unlimited use in last-mile transportation.
DispatchTrack’s new intelligent visibility platform is an AIpowered dashboard that, according to Satish Natarajan, DispatchTrack co-founder and CEO, “offers intelligence on a single pane of glass to make decisions at the speed of business. The right control means better routing, better driver management, and better inventory insights which results in a better delivery experience. Deliveries arrive as promised, instilling brand trust.”
For consumers, the platform also offers live order tracking, empowering end customers to check on order statuses and delivery ETAs in real-time.
Scan the QR code to learn more.
https://foodl.me/1piqpd
They say the future is female, as women fill spaces in historically male-dominated fields, working in many different capacities to further diversity. This year, Women in Trucking Association (WIT) finds a 40.5% increase in female safety professionals within for-hire and private fleets in the commercial freight transportation industry.
“More and more women are becoming safety directors and we are encouraged by these numbers and look forward to seeing the percentages increase in the coming years,” says Ellen Voie, WIT’s president and CEO. The index shows that approximately 20% of respondents report having 90% or more of women in safety roles.
Scan the QR code to learn more.
https://foodl.me/r8wydy
In the race to create the most efficient warehouse, the MULTIFLEX Pallet-Shuttle-System is in pole position. CARRIER, COMPACT SHUTTLE, and LIFT work perfectly together to achieve maximum storage density in the smallest warehouse space. With their amazing acceleration and operating speeds, these three modules achieve a phenomenal throughput. Join the fan club: www.dambach-lagersysteme.com
Capable: Up to 250 pallets per hour
Strong: Up to 1,500 kg Energy-efficient: Lightweight Design, Power Caps
While ensuring food safety along the cold food chain will always be a challenge, the fact is, separating out the fiction and focusing on the facts that matter will help companies pivot accordingly.
Fact—Almost one in 10 people in the world fall ill after eating contaminated food and 420,000 die every year, according to the World Health Organization (WHO).
Fact—$110 billion is lost each year in productivity and medical expenses resulting from unsafe food in low- and middle-income countries.
Also fact—More than 50% of foodstuffs in developed countries are sold under refrigerated conditions, according to Food and Agriculture Organization of the United Nations.
Fiction—Ensuring food safety along the cold food chain is under control.
It isn’t. And, never will be.
That’s because ensuring food safety along the cold food chain is a continuous ordeal, one that requires all parties, farm to fork, to participate in. And because rules and regulations continuously change, so too will the processes of growing, manufacturing, packaging and shipping be required to pivot accordingly.
“When it comes to food safety, the industry has a small margin for error and the pressure on businesses is constantly increasing. Companies are facing ongoing supply chain disruptions, which has renewed pressure on operators to bolster their capabilities for quick responses,” says TJ McReynolds, customer success manager, SafetyCulture.
Heightened financial volatility, sustainable development divestment, complex global supply chain reconfigurations and mounting trade costs stemming from the war in Ukraine continue to impact trade and development, according to a new study released by the United Nations Conference on Trade and Development (UNCTAD).
“The war in Ukraine has a huge cost in human suffering and is sending shocks through the world economy,” says UNCTAD Secretary-General Rebeca Grynspan. “All these shocks threaten the gains made toward recovery from the COVID-19 pandemic and block the path toward sustainable development.”
The risk of civil unrest, food shortages and inflation-induced recessions cannot be discounted, the report says. And, restrictive measures on airspace, contractor uncertainty and security concerns are complicating all trade routes going through Russia and Ukraine.
To add to the challenge, there simply aren’t enough people in place to help curtail any food safety misgivings that may arise in the plant, on the line and along the chain, McReynolds adds.
“There is a need to maintain consistent quality and reduce costs, all while meeting evolving regulations. The scale of technology is increasing, and so is the need for operations leaders to find cost-effective compliance solutions for businesses,” McReynolds says. “That’s why it’s important to invest in innovation to both help with delivering on the basics, but also deliver value-added opportunities. Tackling many of the competing challenges for this industry can start with a simple step—going paperless. Data captured within temperature logbooks, manual processes and paper documentation is far more powerful in digital form. In digitizing operations, organizations can raise visibility in real-time and gain powerful preventative analytics, which are crucial to building continuity strategies and operating in this volatile market.”
What’s more is, one of the biggest challenges is getting—and keeping—all the employees and partners on the same page, says Shaun Trejo, chief revenue officer, CMX.
“Fortunately, modern-day digital risk management platforms help tremendously in managing the cold chain and keeping food safe and of high quality until it arrives at the local grocer, restaurant or fast food
outlet. However, it’s very important to view the entire cold chain as consisting of multiple links. It consists of many different employees and participants—from farm, to warehouse, to store. All these supply chain partners must each do their part. The cold chain can fail even if there is only one weak link,” Trejo adds.
To strengthen the U.S. food supply chain, U.S. Department of Agriculture (USDA) Secretary Tom Vilsack announced more support, resources and new rules to promote fair and competitive agricultural markets, prevent abuse of farmers by poultry processors and make prices fairer for farmers and American consumers. These actions build on President Biden’s Executive Order to promote competition in the American economy and fulfill key pillars of the Meat and Poultry Supply Chain Action Plan.
“Under the leadership of President Biden and Vice President Harris, USDA is committed to making investments that
promote competition—helping support economic systems where the wealth created in rural areas stays in rural areas— and strengthening rules and enforcement against anticompetitive practices. The funding and new rule we’re announcing today ultimately will help us give farmers and ranchers a fair shake, strengthen supply chains and make food prices fairer,” says Vilsack.
But, what does all of this mean for the future of food safety? Here’s how the cold food chain can stay in front of the facts.
Food recalls. The worker shortage has created gaps in the system where standards, policies and sometimes even audits have slipped through the cracks.
Fact—the United States experienced more than 1 billion recalls this year already, according to the U.S. product recall index released by Sedgwick’s brand protection division, with 120 of those recalls being food and beverage events in Q2 2022, up 9.1% from Q1.
“This is the second consecutive year in which we have seen more than 1 billion units impacted by U.S. product recalls. If the first half of the year is any indication, we should expect 2022 to eclipse all previous years on record for recalled products,” says Amanda Combs, recall advisor in Sedgwick’s brand protection division. “While regulatory agencies may not be back to pre-pandemic work levels, companies can’t relax their focus on product safety. Inspections and enforcement actions are still occurring.”
Cargo theft. Widespread congestion at ports and inland facilities has led to increased opportunity for thieves, according to a recent TT Labs report.
A reduced workforce, growing
e-commerce demands, backlogs at ports, COVID-19 lockdowns and union strikes continue to hammer the supply chain industry. But, in doing so, it’s created opportunity for thieves to hone in on the weak links of a supply chain. Sometimes it’s a truck sitting idle; sometimes it’s a truck at the dock; sometimes it’s the drivers themselves.
Fact—a major part of the problem lies at the storage facilities, Trejo says.
“Apart from standard things such as CCTV monitoring and alarms, measures can be incorporated into cargo to track products and make them tamper proof, such as smart labels (e.g., radio-frequency identification tags) and tamper-evident seals. Since food and beverage items are a big target, using discreet packaging could also help mislead thieves,” Trejo adds.
Technology. Fact—technology is revolutionizing the way companies track, manage and achieve food safety.
Technology can exist in the form of Internet of Things (IoT), asset tracking, lot code traceability and more. In fact, top software supply chain organizations are currently investing or planning to invest in advanced analytics, big data, artificial intelligence (AI)/machine learning and blockchain, in that order, according to Gartner. Following close behind is RFID/ electronic tagging, robotics, robotic process automation (RPA), conversational systems (chatbots), wearables and digital twins.
Either way, the right technology will act as an early warning system to help freight forwarders transport their loads safely
and securely, according to McReynolds.
“Look to digital operations platforms that allow for custom workflows and inspections that track alongside the transportation journey—from load checking or freight security (TAPA) checks to warehouse stock audits. Automated information capture makes it easy to record information across a number of vehicles and locations. If instances of non-conformance arise when auditing against best practice, create SMART actions within the platform to deliver a compliant end result,” adds McReynolds. “Data equals visibility, but it’s not just about responding to incidents. Analytics are the bread and butter of good operations—it’s essential to be able to visualize and monitor data about anything from equipment and compliance to safety and environmental performance.”
Traceability is also pertinent in ensuring food safety along the cold chain, helping
to eliminate food recalls, maintain temperature control and better detail the journey certain food products took to get from Point A to Point B.
“The quicker products can be traced and removed from shelves, the better. Being able to prove that you crossed every T and dotted every I will be the best defense against a lawsuit, should a recall happen. You will essentially have a much better defense if you can prove you exercised ‘reasonable care.’ A digital platform that enables regular automated checks and audits is the only way to do this,” Trejo adds. “Increased supply chain digitization also creates more opportunities for cybercriminals to hack these systems and processes (as with most other technologies). To combat this, companies should invest in a digital platform that already accommodates appropriate cyber protection against such attacks.”
Packaging. For many brands, packaging is the gateway to the consumers’ cart. But, if and when a label misprints or misleads a consumer, then it automatically compromises the safety of the food item.
Fact is, “smart” packaging may help solve all food safety challenges.
“Having a robust product lifecycle management (PLM) strategy is a key method of improving food safety,” says Trejo. “It’s therefore imperative to have total visibility of all product ingredients and their origins so that such info can be declared. The only way to achieve this is to be able to incorporate all of this into a single digital platform.”
For its part, GS1 US is facilitating industry’s capability for creation and use of two dimensional (2D) barcodes on product packaging.
“In collaboration with GS1 US, the industry is enabling the use of 2D barcodes by 2027 (under the initiative dubbed Sunrise 2027) for point-of-sale scanning, which allows data for consumer engagement and business use cases to be encoded in a single barcode,” says Angela Fernandez, VP of community engagement, GS1 US. “2D barcodes allow for a single, standardized way to meet both evolving
consumer requirements and supply chain needs. The 2D barcode also provides a machine-readable format to look up batch/lot number, sell-by date and more— expediting the recall process and/or the removal of expired food off the shelf.”
Visibility matters. Risk can only be identified if you have proper visibility, according to Trejo.
“Whenever you lack visibility anywhere in your supply chain, as well as your locations, then you’re in the dark,” Trejo adds.
The fact is, while supply chain innovations have created opportunity, with opportunity comes risk.
“Take a multi-sectoral approach to your data and integrate with different parties along the food supply chain. This will allow monitoring to occur in transit, bridging the gap between food processors and logistics, and encouraging collaboration from farm to fork,” says McReynolds.
Food safety culture. Just like with any initiative, rules are meant to be followed and processes are meant to maintain order.
Fact—No facility can afford not to develop a healthy food safety culture.
“Cultivating a food safety culture is a never-ending process of continuous improvement, but commitment to this area yields benefits for the bottom line, for employee satisfaction and for the families who eat your product. You can’t afford
to neglect it,” according to the Safe Food Alliance.
That’s because it takes just one employee to compromise the entire chain, Trejo says.
“Implementing at least some type of food safety training for everyone should certainly be a top priority. This means that everyone in your company must be aware of the risks involved, and what can happen when unsafe food is consumed. This should be accomplished by regular training,” Trejo adds.
Furthermore, dramatic improvement in food safety doesn’t happen without influencing and changing human behavior, McReynolds adds.
“This happens when you work on creating a safety culture from the ground up, and driving cultural change looks different in today’s distributed workforce. Remove the red tape from safety operations and enable them with intuitive, easy-to-use technology like self-serve sensors and digitized checklists,” adds McReynolds.
While ensuring food safety along the cold food chain will always be a challenge, the fact is, separating out the fiction and focusing on the facts that matter will help companies pivot accordingly.
As the nation’s largest technology-driven fleet management company dedicated exclusively to the cold supply chain, PLM recognizes 50 successful years. Since it was founded in 1972, PLM has managed customized leasing partnerships, each crafted to address the customer’s unique business needs.
With their comprehensive fleet management approach, PLM Fleet LLC creates flexible and customerspecific solutions to reduce costs and drive productivity for businesses nationwide. Located in the state-of-the-art fleet solutions center in Newark, NJ, PLM is
recognized as the only nationwide company that is dedicated exclusively to the leasing, renting, and ColdLink® telematics of over 13,000 refrigerated trailers. With 32 locations nationwide, PLM conveniently offers flexible and unique equipment in all the key markets.
For the third consecutive year, PLM Fleet has won the NJ Top Workplace Award. Another 2022 company achievement is earning Food Chain Digest’s Top Food Chain Technology Provider, in addition to Food Logistics 2021 awards of Top Green Providers and Rockstars of the Supply Chain.
“I can think of no better way to honor PLM’s 50th Anniversary than to again win the NJ Top Workplace award,’’ said Keith Shipp, President and CEO. “This year our team has innovated and launched several new digital tools to support our customers and streamline their operations. We have really focused on how to drive engagement and simplify interactions for our customers, and it is so gratifying to see our employees champion this direction forward.’’
PLM continues to examine and implement new ways to improve efficiency and customer service. Recently the company has moved to computerized inspections of leased vehicles to streamline and integrate operations. MyPLM, a secure, online customer portal, has released new enhancements to manage invoices, rental reservations, damage notifications, and ColdLink® telematics for trailer location, temperature monitoring, mileage, and more.
Among recent product launches, PLM has introduced Zero Emissions trailers, the only California state approved refrigerated units for multi and single temperature applications. Also recently launched is PLM TrustLink™, a comprehensive, cloud IoT management platform that provides real-time, track and trace capabilities for the sensitive cold supply chain.
Resiliency seems to be a keyword in today’s supply chains, especially for the third-party logistics (3PL) sector. While Allied Market Research recorded the global fleet management market as valued at $19.47 billion in 2020 and expects it to climb to $52.5 billion by 2030, this does not mean the industry is free from problems.
It is true; there is significant growth and potential in the industry, but continued ups and downs and uncertainty since COVID-19 warns to proceed with caution. Freight rates see continued instability, and as of late, are falling. Additionally, the significant increase in fuel prices, especially diesel, which most of the industry runs on, adds stress to fleets. Many smaller fleets also maintain older vehicles and the older a vehicle is, the less fuel efficiency.
Unfortunately, investing in newer fleets and equipment to combat these issues is not as easy as it sounds as well due to the rising manufacturing costs of these products. It now costs companies considerable budget to invest in newer machinery and trucks.
“Just a few years ago, a truck cost $120,000—today, that same truck costs $160,000,” says Chris Orban, VP and business area manager, supply chain insights at Trimble. “Resources are expensive, and so are people. Not to mention fuel costs, trailer costs, warehouse space and more. It’s true that you could potentially do more with more resources, but it’s going to be more expensive as well.”
Additionally, the steady and extremely high freight demand of last year is not likely to repeat this time around, simply because cultural and supply chain events caused an
unusual spike in demand. Unlike traditional slow increases, this was an unprecedented example.
While some may think investing in electric vehicles could solve the problem of higher fuel prices, many small or legacy fleets still use traditional diesel machinery and trucks because of cost and installation problems involved with switching over. It is much easier for big name logistics companies to integrate electric and emerging strategies and technologies into their operations.
“There’s no question that resiliency needs to be a strategic pillar for any 3PL
fleet, but that resiliency doesn’t need to come at the cost of a company’s financial wellbeing,” says Steve Whaley, director of autogas business development at the Propane Education & Research Council.
“As fleets consider the resiliency of their energy source, they need to be aware of the upfront and long-term expenses they may face to avoid a costly setback.”
Another concern for fleets is the idea of safety. According to GPS Insight, fleets see an average of 4.5 accidents per driver per year, with over one-third of those attributing fault to the driver. The top motivation behind the need to address safety concerns was to reduce fleet maintenance costs.
With all these concerns on managers’ minds, how do 3PLs stay on top of fleet resiliency today? Here are the Top 5 suggestions from industry experts:
There are serious fluctuations in the cost of every aspect of fleet operation today. To stay resilient during this pivotal evolutionary period of the supply chain through cost monitoring is imperative. Costs to consider include driver pay, insurance, debt service,
fuel, maintenance, working capital financing and more. Fleet managers must pay attention to next year projections, whether costs are likely to fluctuate up or down and determine what costs are controllable. According to George Thorson, president and CCO at Triumph Business Capital, managers should input information into a cost-per-mile calculation to see what rates can run and still cover other fixed expenses. Then, if possible, negotiate
today’s logistics environment to stay resilient. There are constant changes in prices, regulations, best practices and more. For 2023, 3PLs must have flexibility in setting contract rates. In the eyes of the shipper, 3PLs benefit unreasonably. While this might not be accurate due to the large spread between contract rates and spot rates, shippers still want a payback and want to be sure they are not being price gouged during a tough time.
It can be tempting to post all loads and on a load board for the lowest bid. However, this leaves open opportunities for carriers with lower standards, safety practices and other risks that create potential backlash. Double-brokering is also apparent today. 3PLs that know their carriers well have less of a chance of getting re-brokered, according to Thorson.
some lanes with a shipper or broker, sign contracts and have a portion of your revenue not subject to the variance of the spot rate market.
“This is the real importance of a resiliency plan—know your costs: cost of driver pay, cost of insurance, cost of debt service, cost of fuel, maintenance and cost of working capital financing,” he says. “Which are going up or down in the next year? What can you control, what can you hold down?”
It is vitally important to be flexible in
“Competition will be fierce,” says Thorson.
One of the keenest best practices to come out of the worst parts of the lockdowns from COVID-19 and further Black Swan events was the need to build a network of trusted partners. For shippers, carriers and 3PLs, when times were constrained, companies went to the partner company they trusted most. 3PLs can learn from this today and create a strong partnership network to last long term.
Data and analytics are extremely effective for 3PLs today. For resiliency efforts, companies should have a clear plan and tap data to find inefficiencies that may cause greater overhead, open operations up for numerous issues and slow down output without even being aware. This is even more important in the food industry as products can easily spoil with added hidden obstacles.
“This data is absolutely critical in the cold chain to ensure food safety, and in a
connected supply chain, we can ensure that a perfectly good load of produce is meeting all temperature requirements during transit and doesn’t end up sitting in a trailer or at a dock for a moment longer than it needs to,” says Orban.
“3PLs should be planning now to find ways to capture this data and work toward a willingness to share information and connect data between their partners,” he adds. “As an industry, we are inefficient, and I think most of us are willing to admit that. So instead of being competitively inefficient, let’s find ways to be cooperatively inefficient and find ways to work together to be more efficient. There’s plenty of margin on all sides to go around.”
New communication tools and data analytics make true visibility in operations more real than ever, which is vital for resiliency. It is important to tap data and communication tools to better bridge gaps in the transportation area. For instance, working through these tools to ensure the warehouse is ready to receive at the
trailers, trucks, generators and other equipment. However, it is imperative to make informed decisions today, especially with so many resources at managers’ fingertips that give insight to important questions.
“Perhaps you do need more trucks, or to build larger warehouses, but it’s worth taking a step back to ask if that actually solves your problem,” says Orban. “If you buy more trucks, do you have enough drivers to take them where they need to go?
“In our current environment where ‘stuff’ and labor are harder to come by, there is a trend in thinking toward increasing efficiency and a focus on removing friction points versus simply adding more ‘things’ to the equation,” he adds. “Supporting better connectivity, transparency and data-sharing with your partners—and even competitors—can help bolster fleet resilience in meaningful ways.
“For example, instead of relying on a particular warehouse as your sole distribution point, perhaps a 3PL should build
very same time the delivery driver arrives. GPS, sensors and even messaging can work to bridge these gaps.
Last year, profits were at a record high due to unprecedented demand. For many shippers, 3PLs and transportation companies, it was difficult to keep up with that demand. For those struggling with how to maintain quality and output at the same time, it seemed that the answer was to buy more equipment, add to fleets, etc. However, buying more equipment for the sake of it will not automatically solve the labor problem and other operational issues. Also, the record high of profits from last year was likely due to Black Swan events due to current events. While the cold chain space is expected to remain high in demand, that unique spike in demand from the past year is just that; unique. Transportation operations quick to invest in adding to a fleet may see extra overhead soon when demand slows.
In years past, this was the traditional method of planning, simply by adding more physical resources such as more refrigerated
partnerships with other organizations or think about setting up a more regional supply chain.”
For true longevity and resiliency in the supply chain, 3PLs need to focus on the future while keeping an eye on today. The more you know, the more you can prepare. This makes a modern strategy vital in today’s modern world.
It will always be incredibly important to budget correctly and have a clear view of costs and projections as well as contingency for fluctuations in those costs. Because these costs as well as processes are often in such flux, agility is also key, combined with a network of reliable partners to make that flexibility possible.
Through the use of data, it is now possible to truly find inefficiencies in operations to better prepare for the future and hold up against the unexpected. And, honing that information to budget for truly useful business additions instead of simply adding more physical resources in the hopes to keep up with demand will be vital.
Today’s supply chains are met with the challenge of increased consumer demand amid labor shortages and inflation, while also finding ways to produce and transport products as sustainably as possible. And as a leading contributor of global emissions, the food sector feels an even greater responsibility to reduce its carbon footprint and implement sustainable practices at every point in the supply chain.
As these companies work to reduce CO2 emissions, landfill waste, water usage and more, here are the trends driving the importance of green warehousing and sustainable supply chain management practices:
The explosive growth of e-commerce is presenting challenges for distribution and order fulfillment. To keep up with demand, companies are needing to scale up and out as quickly and sustainably as possible. And to do so, companies are adopting more automation and robotics in their warehouses. Reusable plastic packaging can provide dimensional consistency and repeatable performance for all types of automated systems. In adopting reusable packaging within these systems, companies increase their uptime and reduce their waste and subsequent environmental impact.
According to a Blue Yonder survey, nearly 65% of consumers are willing to spend more on a product just to ensure it is being produced and packaged sustainably.
One way companies can refine their practices to drive sustainability is by reducing expendable packaging. A switch
to reusables effectively stops waste at the packaging source to prevent the entry of single-use packaging into the solid waste stream.
Adopting reusable packaging can drive efficiencies, while reducing costs and improving their ecological footprint. For example, the durability of reusable plastic packaging solutions allows them to last for many cycles through the supply chain, leading to a compelling ROI. In fact, making the switch to reusable plastic pallets reduces solid waste by 72% and energy usage by 71%, based on typical application of 3,000 reusable pallets, 6 trips per year for 8 years. What’s more, companies don’t need to constantly order new wood pallets or corrugated boxes to keep up their operations due to the long useful life of reusables.
4.. New forms of fulfillment Companies are adopting new methods of fulfillment, like micro-fulfillment centers, to meet consumer demands. This allows retailers to consolidate their e-commerce activity, provide greater picking efficiencies and lessen their environmental impact
by reducing last-mile emissions and expendable packaging. These centers can use reusable totes or bins, removing the need for intermediary packaging between manufacturers and regional distribution centers.
5. Rise in energy-efficient systems
Energy savings can be found through different forms of lighting, including skylights, solar panels and LED. Energy management systems also can be implemented to make effective use of power.
Everything from production to storage, processing, packaging and shipping contribute to a sustainable supply chain.
This looks like a simple plastic pallet. But it’s so much more than that — it’s a critical component of a more sustainable and optimized supply chain.
The 100% recyclable iGPS plastic pallet is lighter, cleaner, and more durable than wood. It’s rackable, trackable, and compatible with all standard materialhandling equipment.
There are no nails or splinters, making the pallet safer for workers and products while helping it flow through automated systems with ease.
Every pallet is equipped with RFID tags, to give you data-driven intelligence for better decision-making.
Combined with our nationwide pallet pooling rental program, the iGPS pallet is an extraordinary asset that reduces greenhouse gas emissions, minimizes fuel consumption, and can save you up to $4 per pallet load while streamlining every aspect of your operation.
This is more than a pallet. It’s the competitive advantage you need to meet the business challenges of today and tomorrow.
Call 855-918-3991 or visit iGPS.com today.
As more organizations commit to timebound sustainability goals, pressure continues to mount for the transportation industry to reduce greenhouse gas (GHG) emissions. After all, the transportation sector accounted for about 27% of total U.S. GHG emissions in 2020.
Federal guidance that defines how companies should measure their environmental impact suggests that regulatory and market pressure for efficient fleet services will continue.
As a result, shippers and carriers are turning to alternative fuels to help reduce their emissions. Instead of relying solely on one alternative fuel and transitioning a fleet all at once, organizations can identify what fuels will provide optimal performance for their fleets now and through the fleet’s transition. Using a combination of alternative fuels, such as renewable natural gas, electric, hydrogen and renewable diesel, fleets can gain a competitive edge.
1. Establish corporate commitments. Organizations should establish companywide decarbonization commitments to streamline their transportation emission reductions. By identifying measurable objectives for all departments and documenting progress made, organizations will have a succinct, compelling sustainability story to share with external stakeholders.
2. Create a fleet baseline. Once an organization establishes a goal, fleet managers should create a fleet inventory and prepare for implementation, factoring in all of the variables.
3. Partner with trusted providers. Making sense of data and translating it into an actionable plan shouldn’t fall solely on fleet managers. Instead, organizations should partner with a transportation consulting firm that can help evaluate their data and engage with energy experts to help determine what alternative fuels are practical (and effective) for their fleet
4. Pilot alternative fuel technology. To ensure supply chain disruptions don’t occur and technology performs as expected, organizations can create a pilot project to test the impact (and effectiveness) of
new technologies and provide actionable feedback for any improvements required after their pilot testing concludes.
5. Scale up decarbonization commitments.
At the fleet level, if all employees participate in troubleshooting and measuring fleet performance accurately, new processes will be optimized and quality service will remain constant
Lowering emissions now helps companies take a proactive approach to get ahead of future decarbonization regulations. Further, alternative fuel vehicles can experience a longer road life and require less maintenance than diesel trucks.
A McKinsey & Company article highlights that shippers are willing to pay a premium for sustainable transport offerings if key expectations are met; however, all parties need to work together for a long-term commitment that may include reshaping customer behavior, collaboration and supply chain emission transparency.
Implementing a multi-step approach that includes a polyfuel strategy, fleets can identify the right blend of alternative fuels to help transition their fleets to the fuel solutions that are right for them.
5 steps to implement a polyfuel strategyLYNN
Freight transport is becoming more efficient, as well as both environmentally and socially responsible. And looking past today’s supply chain disruptions, its future is bright. Why? Because SmartWay is sharing with its Partners — nearly 4,000 companies and organizations — information about market-based incentives and technology solutions to help cut fuel costs and reduce emissions. If your company ships goods, SmartWay has laid out a road map to help you achieve greater sustainability.
Share a bright future. Become a SmartWay Partner at epa.gov/smartway.
SmartWay. Driving sustainable freight.
Warehouse management systems (WMS) and transportation management systems (TMS) are fixtures in supply chain technology, starting decades ago. The legacy technologies are how warehouses and transportation companies control their operations in an all-encompassing software.
But in today’s extremely different retail landscape than years past, where e-commerce is king and demand for shipping times is remarkably tight, newer evolutions of WMS and TMS are needed. Real-time monitoring is now an essential part of the process. This is a very fast evolution that is much different compared to the warehousing industry of yesteryear.
Today’s systems are—and need to be—more adaptable to fit a company’s operations as personalization in technology becomes a trend in both consumer day-to-day lives and business strategies. A system tailored to an operation’s specific needs is more likely to be more efficient.
“E-commerce growth and supply chain disruptions over the past couple of years have heightened the need to manage warehousing and transportation in as close to real-time as possible,” says Lucas Buchholz, senior director of enterprise strategy at Transportation Insight and Nolan Transportation Group. “Today’s cloud-based technology solutions have given rise to WMS and TMS that can be easily and quickly adapted to fit shippers’ requirements. Plus, the costs of these systems are more affordable to smaller shippers than in years past. Legacy technologies are adapting as well by offering similar solutions.”
Additionally, employees today are more capable with technology, which makes outdated legacy systems even more of hinderance. Those with older WMS and TMS that lack modern functionality may find themselves
struggling. But most warehouse operations now look to automation and technological advancement, as digitization and process automation are the highest supply chain priority for 84% of all businesses, according to a report from Supply Chain Benchmarking.
As these systems become more modern, with greater capabilities, their physical footprints are lighter as technology of today gets smaller and smaller. The price of these systems continues to decrease as well, making it more accessible for smaller businesses and also allow for multi-channel support now that e-commerce spans all sectors.
“Retail and wholesale operators are typically buying supply chain technology solutions that satisfy a multi-channel environment,” says Korber. “Since many manufacturers are buying warehouse management systems in a second- or third-generation mode, selection and installation of these systems require meticulous attention to detail. Many tech stacks are still managing their solution portfolio in a static mode when the reality of today’s market calls for a fast-paced experience. The supply chain portfolio needs to address the evolving needs of the customer, including the need to drive a low cost of ownership with key value points built along the way.”
As for the technology itself, artificial intelligence (AI) and numerous forms of automation are integrated into WMS and TMS for both prediction and analysis functions. These systems can now predict possible outcomes based on past trends and current data, while also analyzing current data to create a clear picture of current operations in real time.
“One of the big trends in WMS and TMS is the use of artificial intelligence. AIpowered solutions provide a higher degree in predicting outcomes such as fulfillment and delivery times,” says Buchholz. “Statistical analysis also benefits from AI technology such as forecasting the amount of inventory needed, what warehouse to place inventory in, appointment setting and also labor planning. For TMS, evaluating carriers, rate management and performance down to the zip code are among the benefits.”
One vital component of a modern WMS or TMS is the ability to integrate with other technology throughout the entire supply chain, to better serve customers and the industry. This ties into the concept of personalization, as every operation is different, has different needs and uses different platforms. Cloud capability is also extremely important, keeping the physical footprint light as well as providing convenient access from anywhere, giving access to total data and creating a streamlined view of that data.
“In today’s world, the best-in-class providers are making available cloudbased solutions that can drive a low cost of ownership and provide a level of governance and efficiency for the business operator to change as needed,” says Korber. “Operators today are more educated and mature than ever before and need tools that drive relevance in today’s
ever-changing environment rather than relying on concepts that are 10-plus years old.”
Because employees today are so well versed in technology in their personal and professional lives, WMS and TMS makers now leverage new hardware that is user friendly, optimizes operations and drives safety. Today’s systems are often equipped with modern handheld devices, voice activation, Google glasses capabilities and more.
For those looking to implement new WMS and TMS, it is important to keep a few things in mind. For one, ease of use is vital as numerous employees throughout the hierarchy must be able to use these systems. While most technology is modeled after common platforms, some technology might be cumbersome to use and not fit well into an organization. It’s imperative to explore the user experience before introducing it into operations to ensure it is the right technology platform for that particular business.
Additionally, some platforms see frequent updates that can be beneficial but also can cause problems. Warehouses and transportation companies should get a clear understanding of how many updates, large or small, the platform is likely to see and what the costs associated with that are. Often an update could be a much bigger project than expected.
Sustainability has become synonymous with the packaging industry these days. What started as a rare practice by only a handful of niche and forwardthinking companies has now became a global phenomenon.
2021 was the year of sustainability, as global markets witnessed surge in eco-friendly and smart packaging options from startups and brand owners. And, as we usher in 2023, expect sustainable packaging and circular economy to make deeper inroads across industries as a means to optimize resources, limit food waste and address packaging waste generation.
Leveraging sustainability to mitigate packaging waste will be the key area of focus among global packaging leaders. Expect to witness introduction of novel business models and practices developed around new packaging legislations.
Here’s a deep dive into the prominent sustainable packaging trends and ecofriendly packaging best practices likely to play a critical role in shaping the future of the global packaging industry.
Sustainable packaging is needed more than ever
Plastic is still an integral part of daily life. In fact, most retail store purchases and food items come in plastic packets, bags and boxes. So it’s no wonder that around 9.2 billion tons of plastic is produced, of which only 9% is recycled properly every year.
Excessive packaging and extensive use of plastic packaging in e-commerce is further adding to plastic pollution. In 2021, containers and packaging from e-commerce made up a major portion of municipal solid waste, amounting to 82.2 million tons of generation (28.1% of total generation).
Developing nations are suffering the
most from plastic pollution as their garbage collection and recycling system is almost non-existent. Developed economies have low recycling rates and are facing problems of collecting discarded plastic packaging.
As the world recovers from the pandemic, now is the time for countries to reevaluate the recovery plans, reverse current trends and change consumption and production patterns toward sustainability.
Sustainability stands on the principles of doing more with less. It promotes economic growth without environmental degradation. New sustainability trends and practices in packaging will improve resource efficiency and aid in smooth transition toward a carbon negative tomorrow.
As we enter 2023, let’s investigate the top trends in sustainability packaging anticipated to become big.
Minimalism is the way forward. Minimalist packaging was set to take off in 2022, and continues into 2023. As customers are becoming more conscious and concerned about their packaging waste, companies are offering novel sustainable packaging options. Minimalist packaging simply means stripping down packaging to its bare essentials without compromising in its functionality. Minimalist packaging reduces raw material consumption and eliminates waste without compromising the durability or function of the package.
Companies are already planning to employ minimalist packaging and printing on their products to deliver a clear and understandable brand message.
Bio-plastic material making headway in food and beverage packaging. Experts believe that the global consumption of disposable plastics will decline significantly in the next five years.
Companies are pouring investments in next generation of packaging materials development to cope with the changing public attitude toward plastic consumption and waste.
Bio-plastics mimic the beneficial qualities of conventional plastic such as barrier properties, durability, shelf stability, etc. with one key difference, i.e. these materials are fully compostable.
Anti-microbial packaging to address the global food waste issue. Antimicrobial packaging is anticipated to make waves. Antimicrobial packaging aids in minimizing product waste by preventing the growth of microorganism, killing harmful pathogens and extending shelf life of perishable food items. According to Future Market Insight’s report, anti-microbial packaging solution is expected to reach a market value of $3.31 billion by 2031.
As the world suffers from depleting agriculture and other natural resources required to feed growing global population, antimicrobial packaging will become a stepping stone in reducing food loss and achieving overall sustainability.
Refillable packaging to strengthen zero waste initiative. Refillable packaging will gain mainstream appeal, as brands begin to introduce modern packaging options. Companies will offer their products in refillable lifetime containers and direct customers to their brick-and-mortar stores for refilling. Refill packs consume less plastic and allow consumers and the company to save money and help environment without compromising on the design.
Gusseted bags: a sustainable solution for retail packaging. Gusseted bags are an innovative sustainable packaging option as it allows customers to become a part of a larger environmental initiative.
While the main benefit for manufacturers is low manufacturing cost, these eco-friendly gusset bags result in lighter and smaller packaging, reduced material and manufacturing costs and easier product transportation.
Adopt these trends at the earliest to gain competitive advantage and reap big profits. This will aid in gaining better perspective about sustainability and generate new ideas related to green packaging.
market researcher and content writer
Future Market Insights
Home delivery refrigeration solutions. The livelihood of your home delivery business depends on getting food there at the perfect temperature. You need to know—not just hope that your refrigeration equipment is up to the task. Frozen, fresh or anywhere in between, Thermo King has you covered with a complete line-up of temperature control solutions for small vans and trucks. Units feature quiet, multi-temperature operation, with electric standby options available. We continually test and innovate our products so your business can STAY ON THE MOVE
Learn More at:
They must juggle constantly changing global regulations and keep the multi-step, manufacturing process up and running like a welloiled machine. Therefore, even the tiniest labeling error can halt the entire process and cost companies millions of dollars.
In Q1 2022, the FDA recalled 84 products and 35% of them were likely a result of labeling issues, ranging from not meeting labeling requirements to not declaring an ingredient on the label. This equates to almost $2 million in damages, based on Loftware survey data.
With specific regulations across the United States, UK, and European Union, food and beverage manufacturers can’t afford to fall behind the regulatory curve. Rules such as the U.S. Food & Drug Administration’s Food Safety Modernization Act (FSMA), the U.K.’s Natasha’s Law and EU Regulation 1169/2011 all have different labeling requirements for everything from content to font size and language. Furthermore, the governing bodies across the
globe are constantly looking to improve their regulations. If a company utilizes an outdated labeling system, keeping in line with these various guidelines becomes increasingly difficult. Statistics such as these cause many businesses to ask, what’s causing errors in the first place, and what can be done to
Many companies currently employ a disjointed labeling system, which adds to the logjam from mislabeling issues. These systems vary across all facilities and are often not updated to align with the latest industry innovations. As a result, the antiquated system in place makes correcting errors a very costly process. Despite this, many of these businesses do not have a solution in place that allows for real-time collaboration and editing.
Typically, when a company encounters a labeling error, the solution is to reprint and replace each label manually. This process is incredibly inefficient as it requires reverting manpower away from production and costs more as workers spend time tediously replacing individual labels.
In a business that spans many regions across many time zones, increasing collaboration and efficiency in the editing process helps stifle this cost of correcting and replacing labels.
With the public becoming more conscious of the quality of food they consume, governing bodies need to update their regulatory guidelines more frequently than other industries. As a result, the food and beverage industry must become more agile to respond to an ever-changing regulatory environment, especially as it relates to their packaging and labeling processes.
For example, when FSMA requirements were signed into law in 2011, they brought along sweeping changes to the food supply chain, including the traceability of all ingredients. Companies must be fully transparent regarding how their product is made and adhere to multiple regulations aimed at providing consumers with the necessary information to make safer and more informed consumption decisions.
New guidelines, such as FSMA, will continue to adapt over time, making accuracy and completeness of the content on labels and packaging imperative. This requires companies to be agile, accurate and efficient in their labeling to prevent recalls and serious health and safety risks.
Before the Coronavirus disease (COVID-19) pandemic, many companies sourced all materials from one producer. When the pandemic hit, many of these producers were forced to shut down, which stalled the entire production process. This compelled many companies to rethink their supply chains. Rather than utilize just one supplier, they diversified and began employing multiple suppliers across many regions. However, if suppliers are using different labeling systems, there is a higher risk of encountering a labeling error that results in product recalls, similar to the FDA recalls from Q1 of this year. Therefore, these new supply chains require technology that enables suppliers to integrate with a company’s business applications to ensure that labeling is a seamless part of the data ecosystem.
To get ahead of competitors and future-proof their business, companies should look to change their labeling process to a modern cloud-based solution. By doing so, businesses of all sizes can reduce the cost of correcting errors and even prevent many from occurring in the first place.
When companies employ enterprise labeling systems that can seamlessly share information between supply chain partners, they gain an important combination of efficiency and accuracy. These solutions reduce the possibility of
human error
and increase the potential speed of food production and shipment. In the event of a recall, having such an updated custody chain can reduce the money and time spent on removing affected goods from the market.
Cloud-based labeling software can integrate directly with critical applications, like warehouse management systems (WMS), enterprise resource planning (ERP) or product lifecycle management (PLM). With this integration, along with utilizing business logic, organizations can leverage data from their systems of record and configure rules that dynamically change label content based on that data. This streamlines label formatting and printing, which allows companies to meet regional, language, regulatory and customer specific requirements in a matter of hours or days rather than months.
Organizations can also extend controlled access to labeling across various suppliers, thereby eliminating potential errors, reducing time-consuming and costly relabeling and alleviating the issue of a fragmented supply chain.
This innovative technology will not only bring so many businesses into the 21st Century, but also alleviate pain points, such as FDA recalls.
Xtreme Performance. Xtreme Value.
Our new Arctic Xtreme™ labels feature a freezer-grade, hybrid adhesive specially formulated for cold storage environments. They’re rated to perform at temperatures as low as -65F. And they can be applied at -20F to avoid any interruptions to operations.