July 2022 | supplychaindigital.com SupplySustainableChains DOKA CONSTRUCTION: Procurement lessons from a time of chaos ENTERPRISEALCATEL-LUCENT: Making PredictableUnpredictable,the BREWINGBUDWEISERGROUP: atsustainabilitySeekingscale PUTTINGCOMMUNITYINTOBROADBAND SUPPLYCHAIN: Why collaboration will shape supply chains of future LOGISTICS: How e-commerce is changing last mile logistics SUSTAINABILITY: Net zero role of consumergoodspackagedsector Community Fibre Head of Supply Chain Mike Brooman on how ESG is part of the company’s DNA
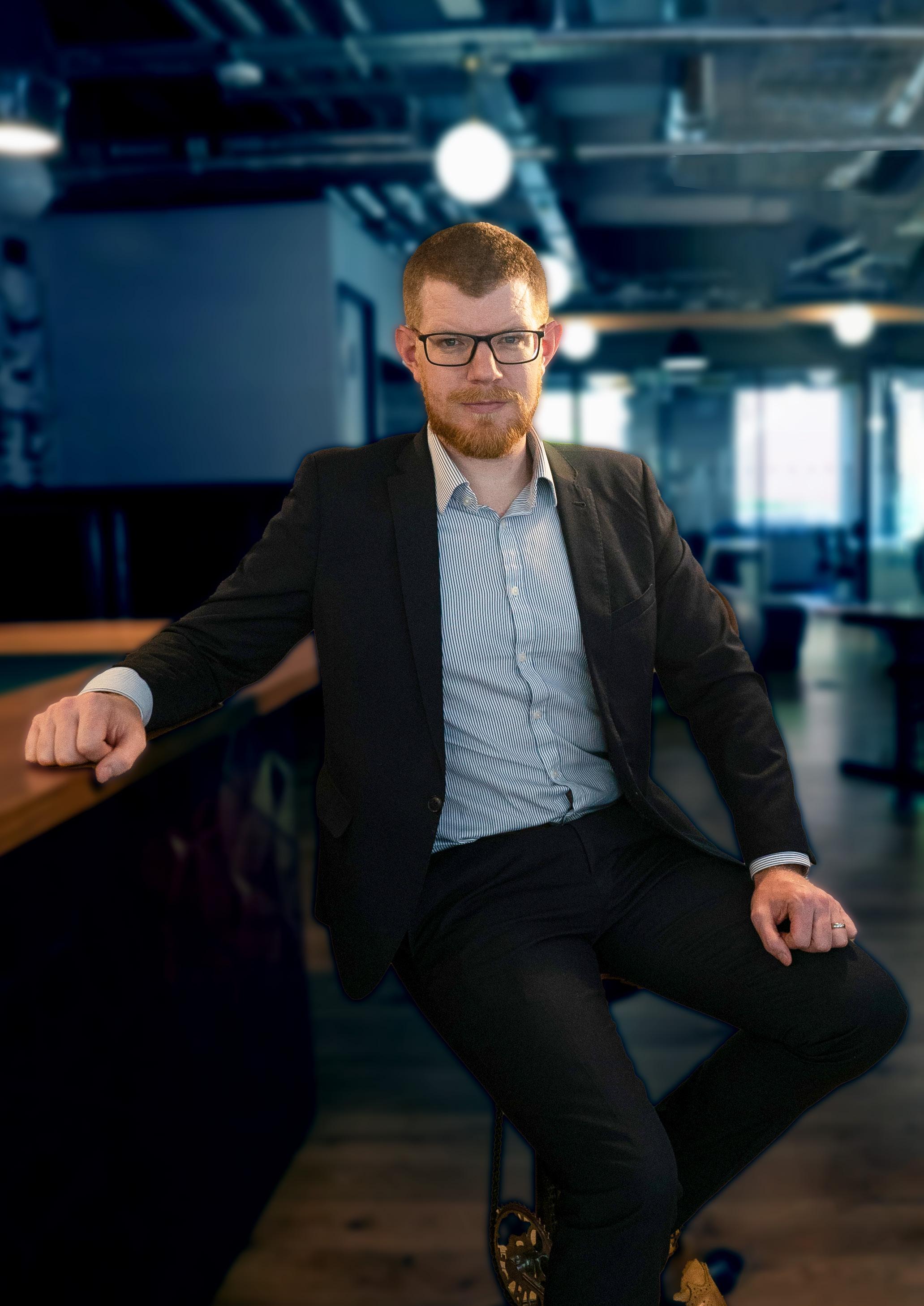
Get tickets Sponsor opportunities THE FUTURE OF PROCUREMENTDIGITAL A BizClik Media Group Event: 3,000+ Participants 2 Days 2 Zones 60+ Speakers 12 - 13 OCT 2022 STREAMED & IN PERSON QEII CENTRE, LONDON
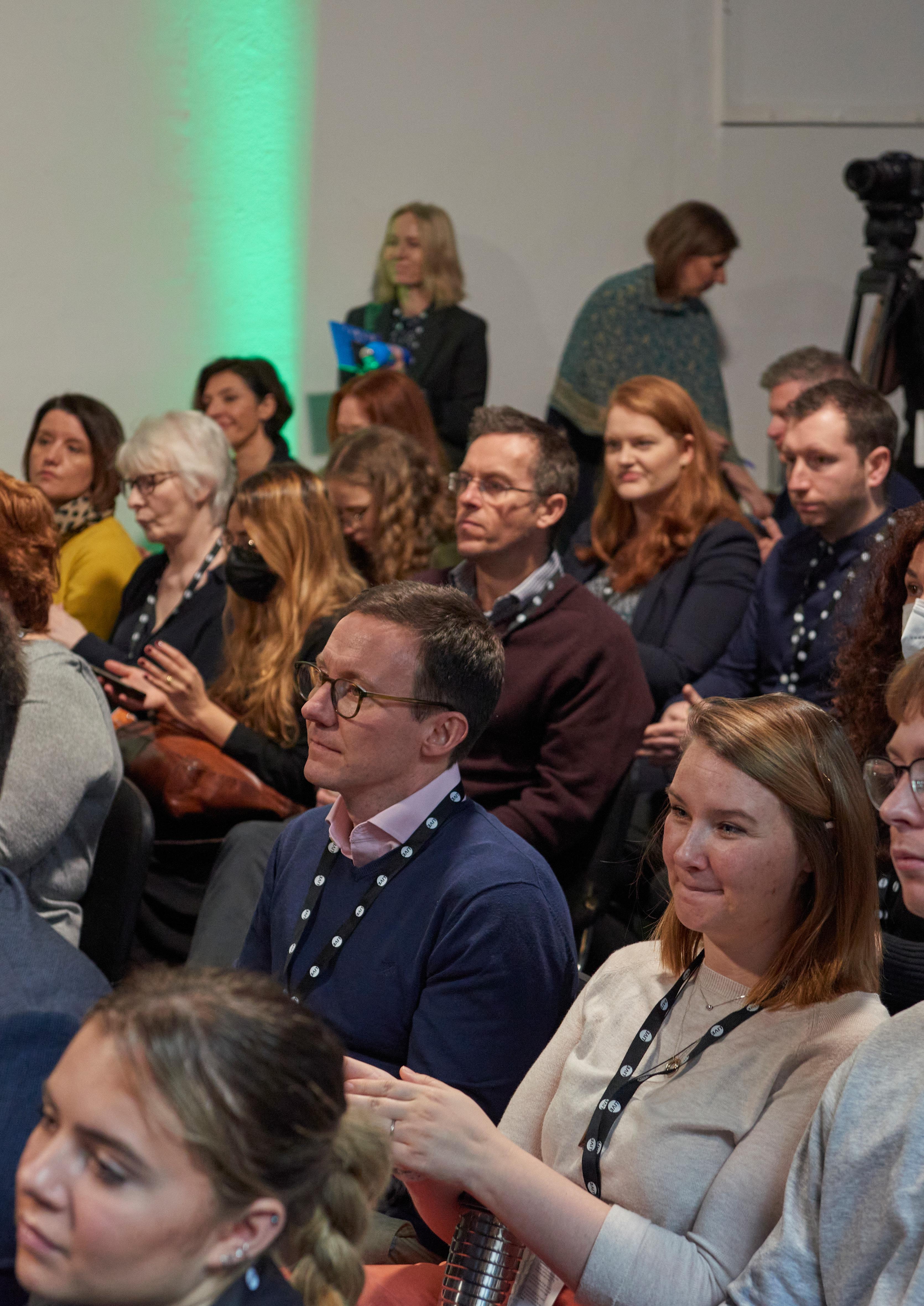
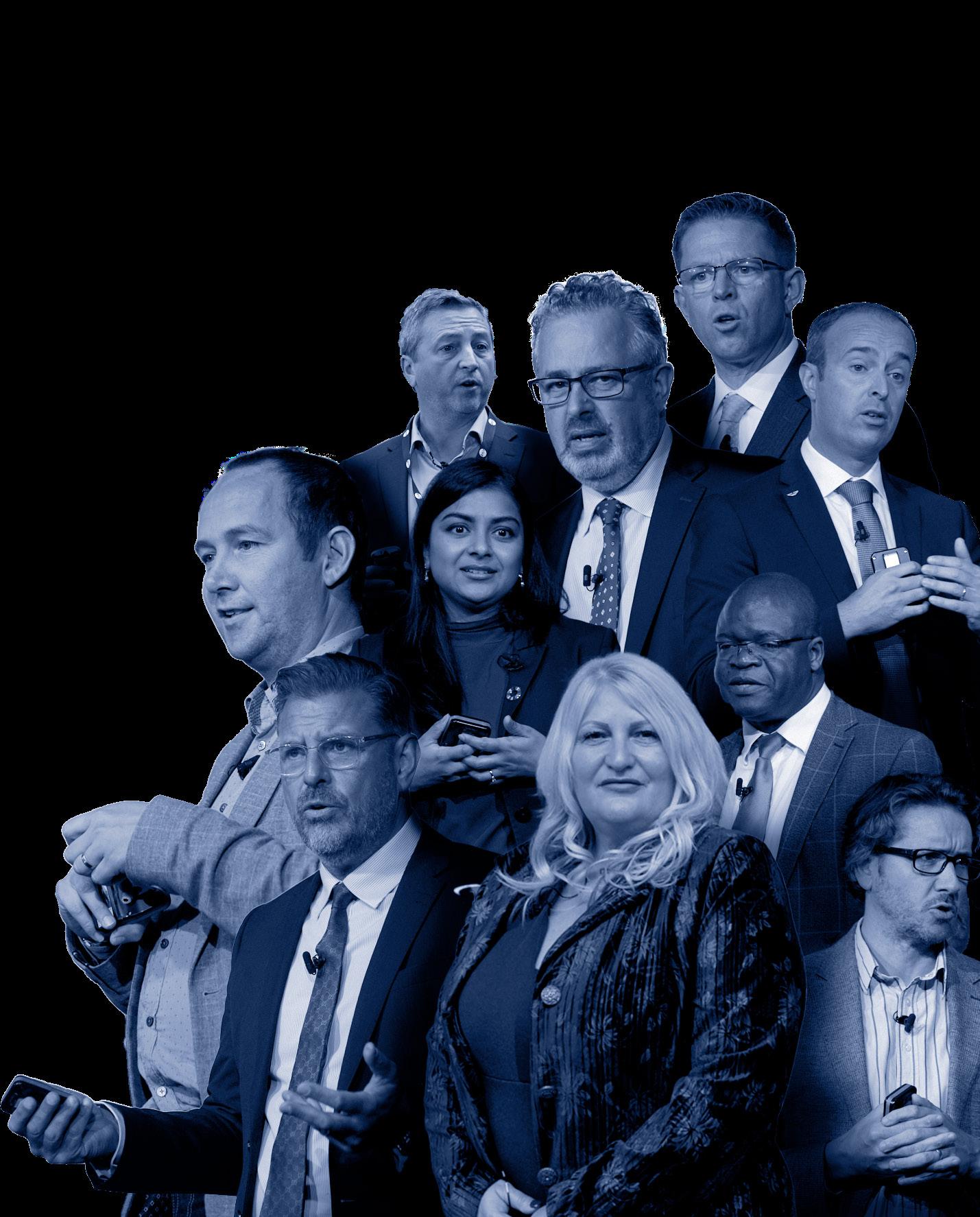
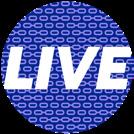

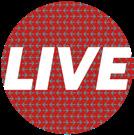
Join us at PROCUREMENT & SUPPLYCHAIN LIVE LONDON Get tickets Sponsor opportunities Showcase your values, products and services to your partners and customers at PROCUREMENT & SUPPLYCHAIN LIVE LONDON 2022. Brought to you by BizClik Media Group PROCUREMENT & SUPPLYCHAIN LIVE LONDON, the hybrid event held between 12th-13th October is broadcast live to the world and incorporates two zone areas of SupplyChain LIVE plus Procurement LIVE in to one event. With a comprehensive content programme featuring senior industry leaders and expert analysts, this is an opportunity to put yourself and your brand in front of key industry decision makers. From keynote addresses to lively roundtables, fireside discussions to topical presentations, Q&A sessions to 1-2-1 networking, the 2-day hybrid show is an essential deep dive into issues impacting the future of each industry today. Global giants and innovative startups will all find the perfect platform with direct access to an engaged and active audience. You can’t afford to miss this opportunity. See you on: 12 - 13 October 2022 Watch our 2021 Showreel
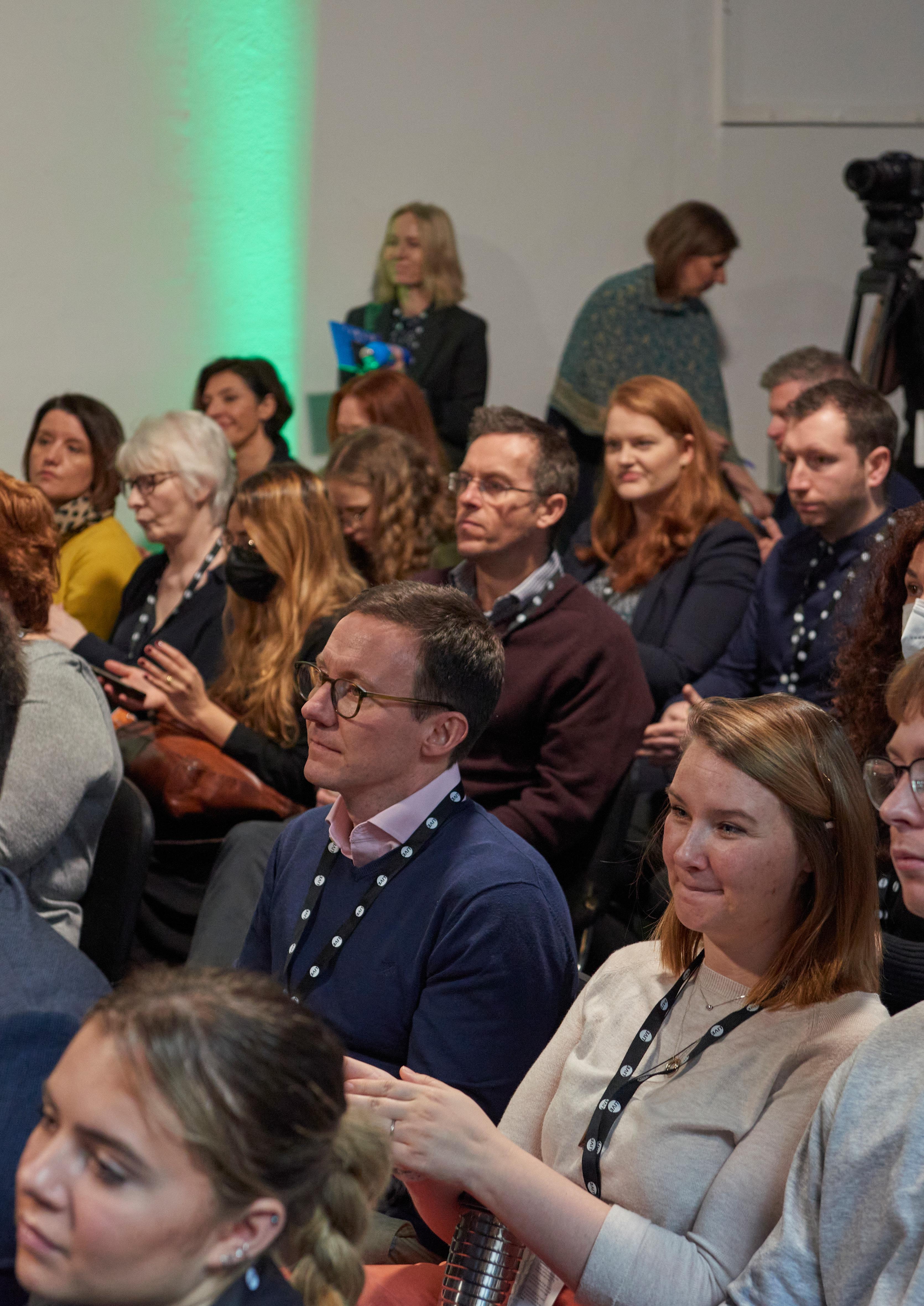
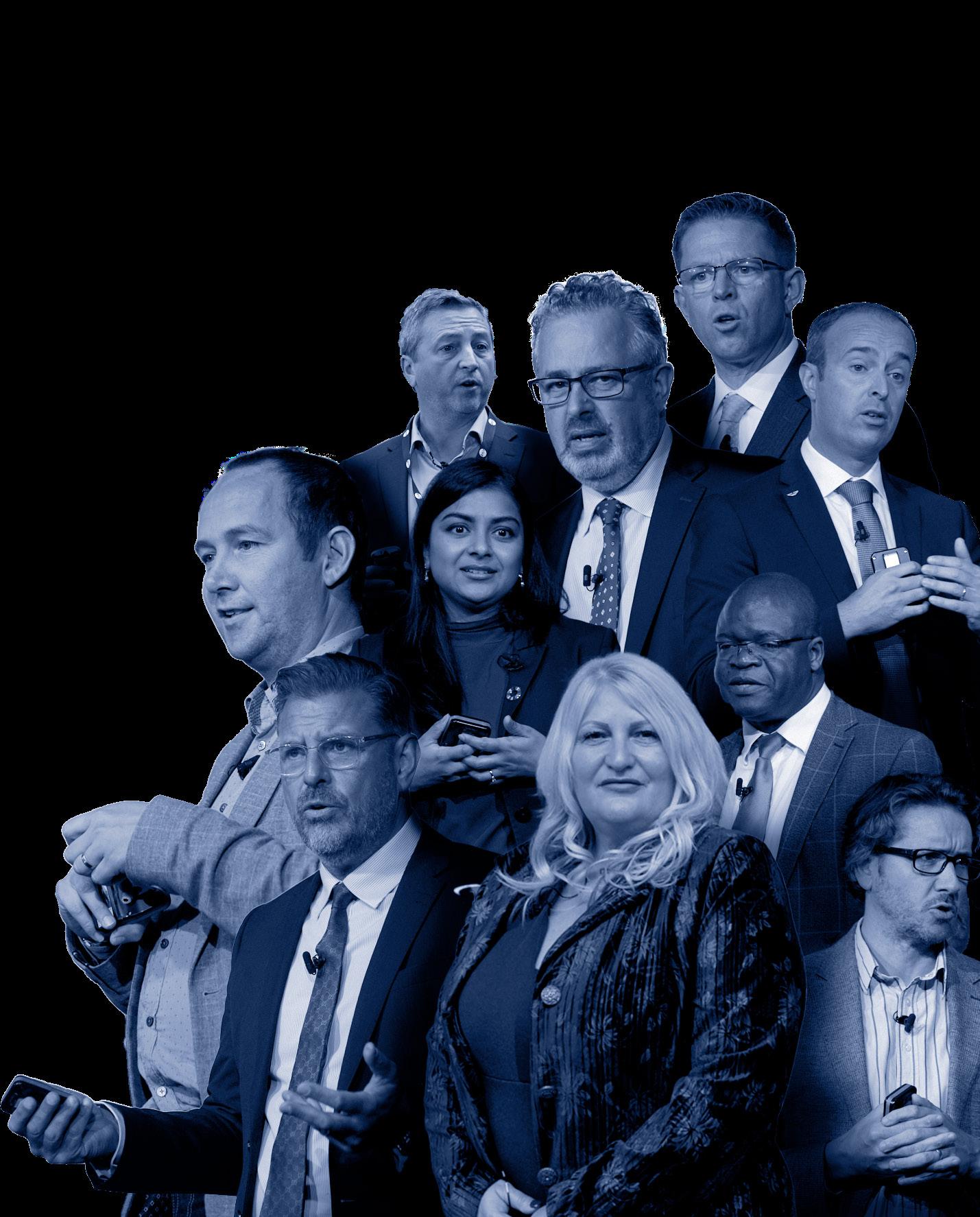

The SupplyChain Team JOIN THE COMMUNITY DANIELAPRODUCTIONEDITORIALSEANEDITOR-IN-CHIEFASHCROFTDIRECTORSCOTTBIRCHDIRECTORSGEORGIAALLENKIANICKOVÁPRODUCTIONMANAGERSPHILLINEVICENTEJANEARNETAELLACHADNEY CREATIVE TEAM OSCAR VIDEOSOPHIE-ANNHATHAWAYPINNELLHECTORPENROSESAMHUBBARDMIMIGUNNJUSTINSMITHREBEKAHBIRLESONJORDANWOODCALLUMHOODPRODUCTIONMANAGERKIERANWAITE DIGITAL VIDEO PRODUCERS MARTA THOMASERNESTEUGENIODENEVEEASTERFORDDREWHARDMANMARKETINGMANAGERKAYLEIGHSHOOTERPROJECTDIRECTORSMIKESADRCRAIGKILLINGBACK MEDIA SALES DIRECTOR JAMES WHITE SALES AND MARKETING DIRECTOR JASON CHIEFMANAGINGWESTGATEDIRECTORLEWISVAUGHANOPERATIONSOFFICERSTACYNORMANCEOGLENWHITE

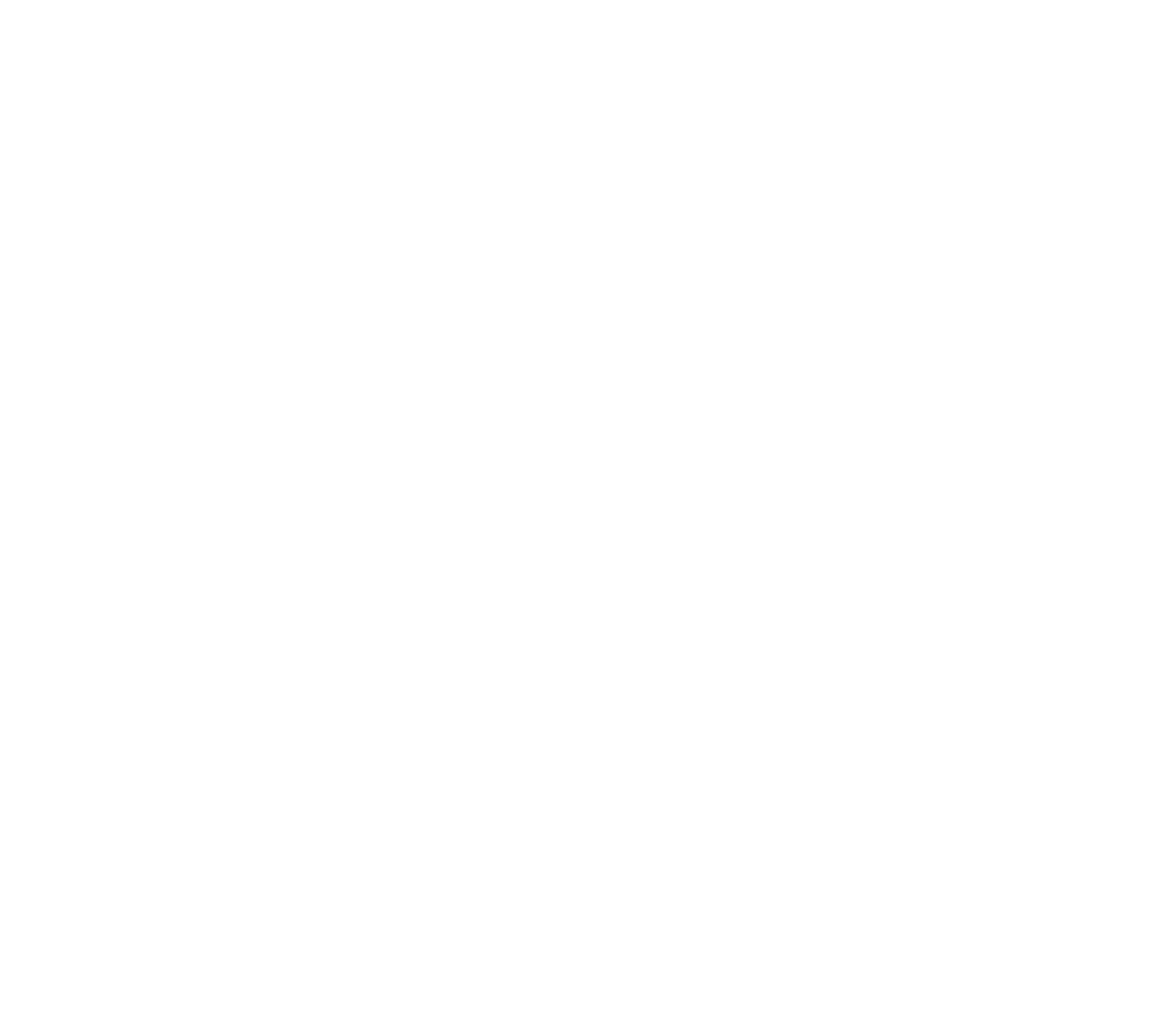
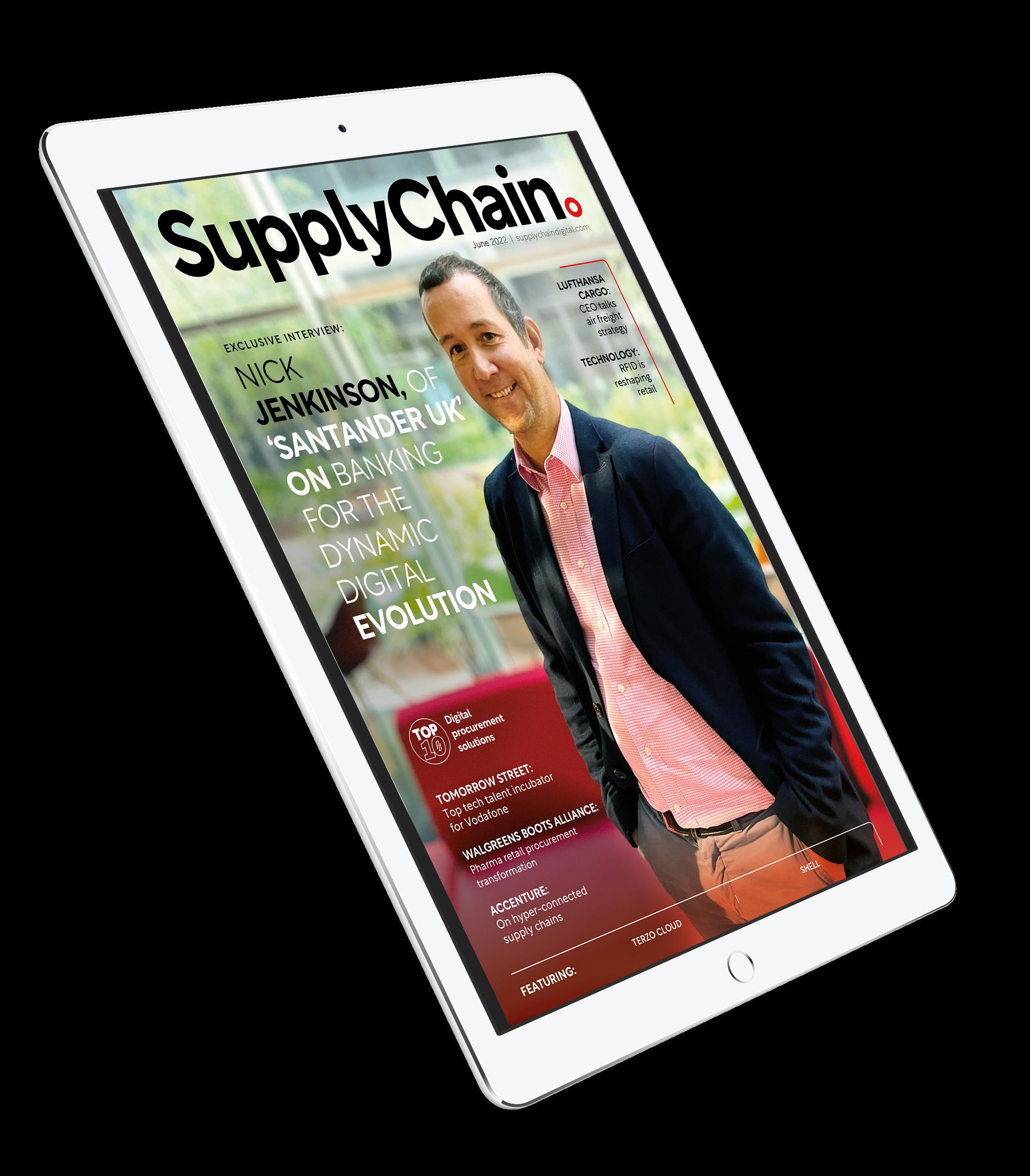
This is a clear and stark warning to any exec who thinks digital transformation is some kind of panacea to all manner of corporate ills.
Digital transformation is about people, not tech
SUPPLYCHAIN DIGITAL MAGAZINE IS PUBLISHED BY © 2022 | ALL RIGHTS RESERVED supplychaindigital.com 5 FOREWORD
More than one third of digital transformations fail because organisations focus on the technology rather than their people. Need an agile and resilient supply chain? Want to make headway on net-zero targets? Plan to rethink the procurement function? Simple. Digital transformation is the Exceptanswer.that it isn’t, because more than one third of such projects fail in terms of adoption, according to David Loseby, the noted procurement advisor who also boasts a doctorate in behavioural science. In this issue, Loseby goes on to say that he has met countless managers in manufacturing, logistics and procurement that have a first- or second-hand war story to tell of at least one tech project that went belly-up. The problem, he says, is “mindset failure” on the part of “Digitalorganisations.transformations are not technology-change projects,” he explains. “They are people-change projects. If you don't involve the people that are going to be impacted, and suddenly impose it upon them, guess what? You get lots of rejection.”
Theychangetransformations“Digitalarenottechnology-projects.arepeople-changeprojects”
SEAN ASHCROFT sean.ashcroft@bizclikmedia.com

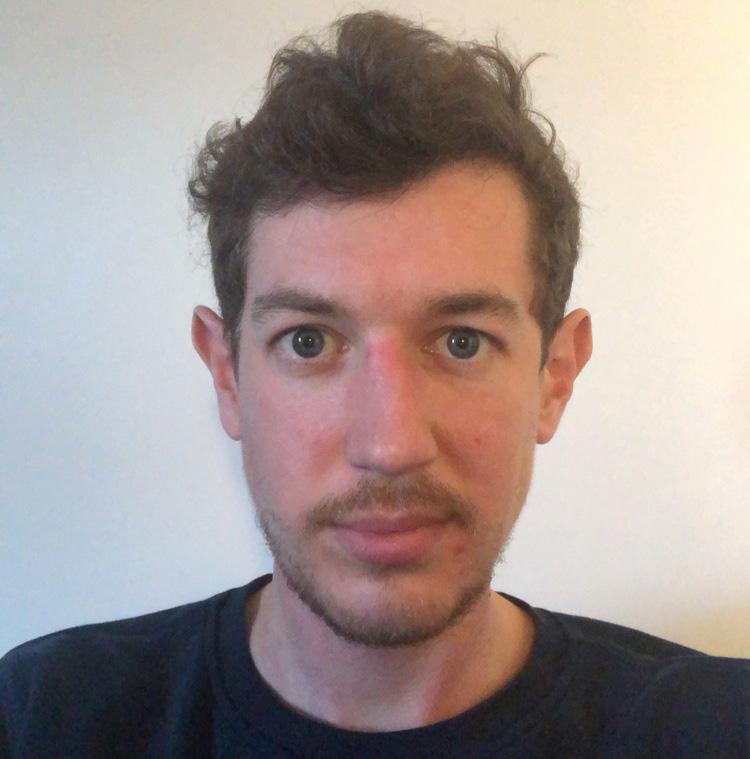


Community Fibre is more than living up to its name 24 Our UpfrontRegularSection: 10 Big Picture 12 The Brief 14 ofTimeline:AbriefhistoryDeloitte 16 Trailblazer:MitchHaynes 18 Five Minutes With: Ashley Naughton Supply Chain: Trust is key to future supply chain management 42 CONTENTS

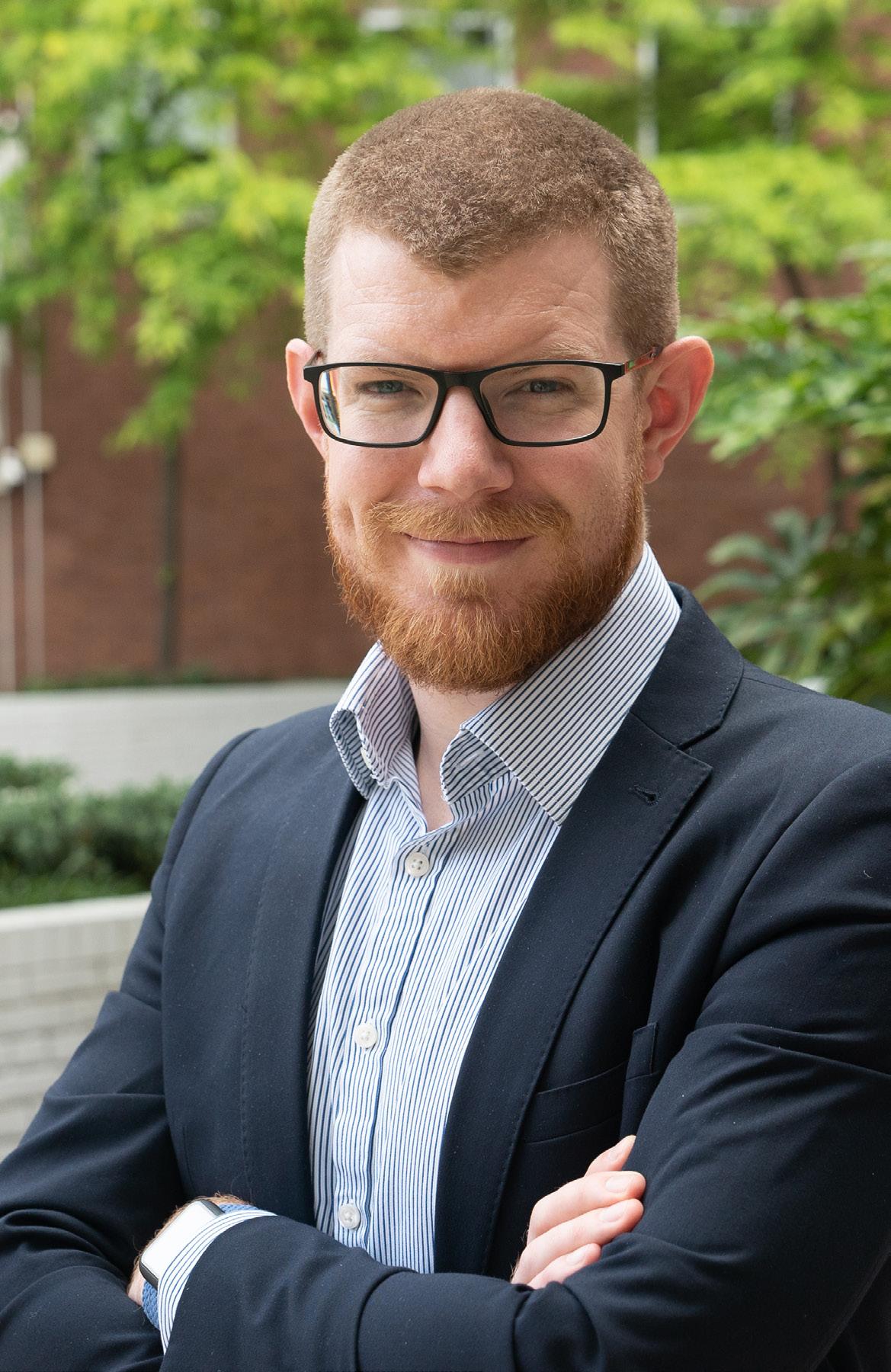
Budweiser Brewing Group: World’s largest brewer AB InBev, in sustainability vanguard 50 Alcatel-Lucent Enterprise Rasheed Mohamad of ALE: Making the Unpredictable, Predictable 74 Logistics: Last-mile logistics in grip of ecommerce boom 66 Sustainability: Big and small wins are driving energy efficiency 90 Doka Lessons learned from COVID-19 to prepare for the future 98 Tech and AI: Transformation is a ‘people project’, not a tech project 110 Top 10 Sustainable global supply chains 116
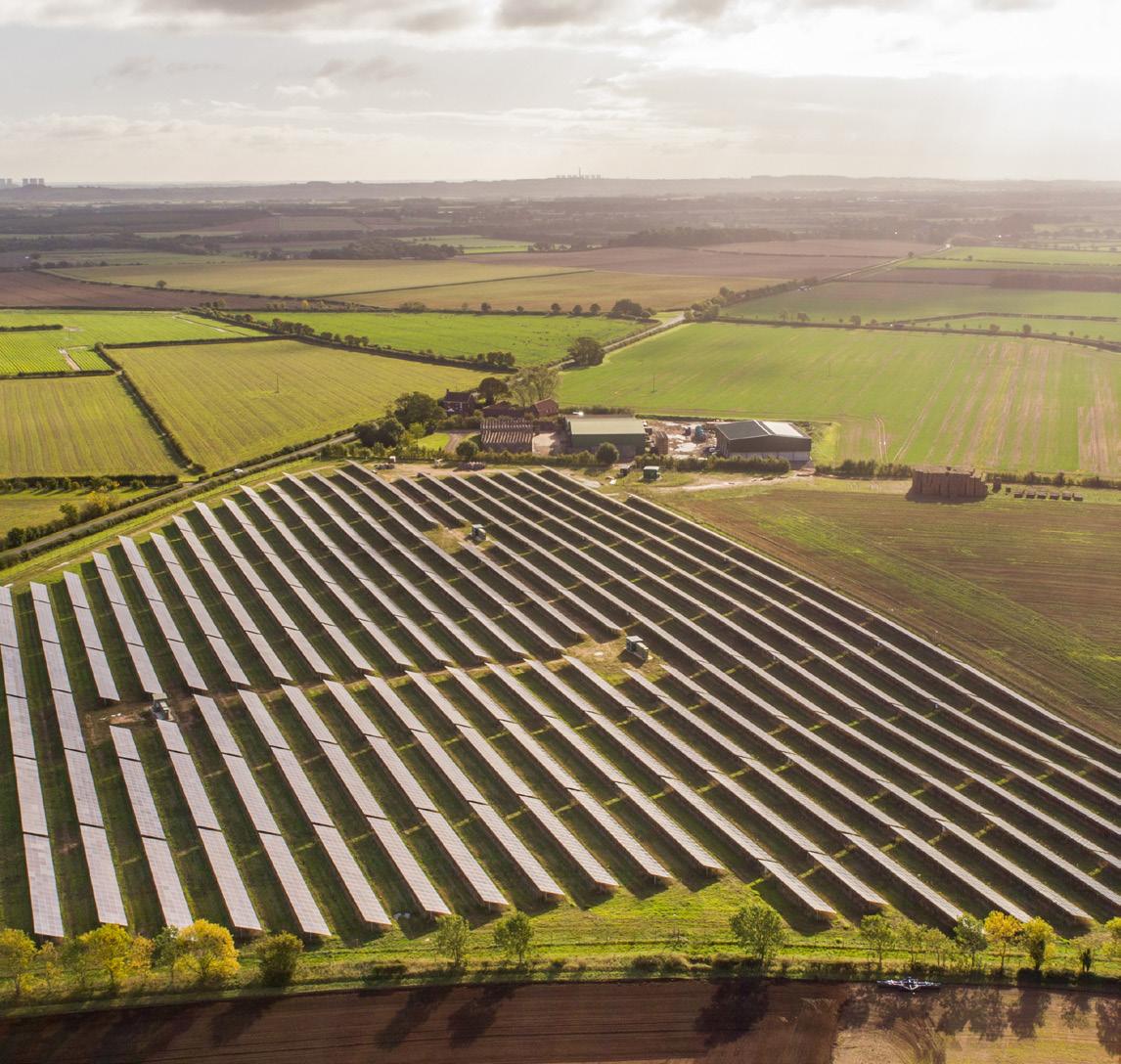
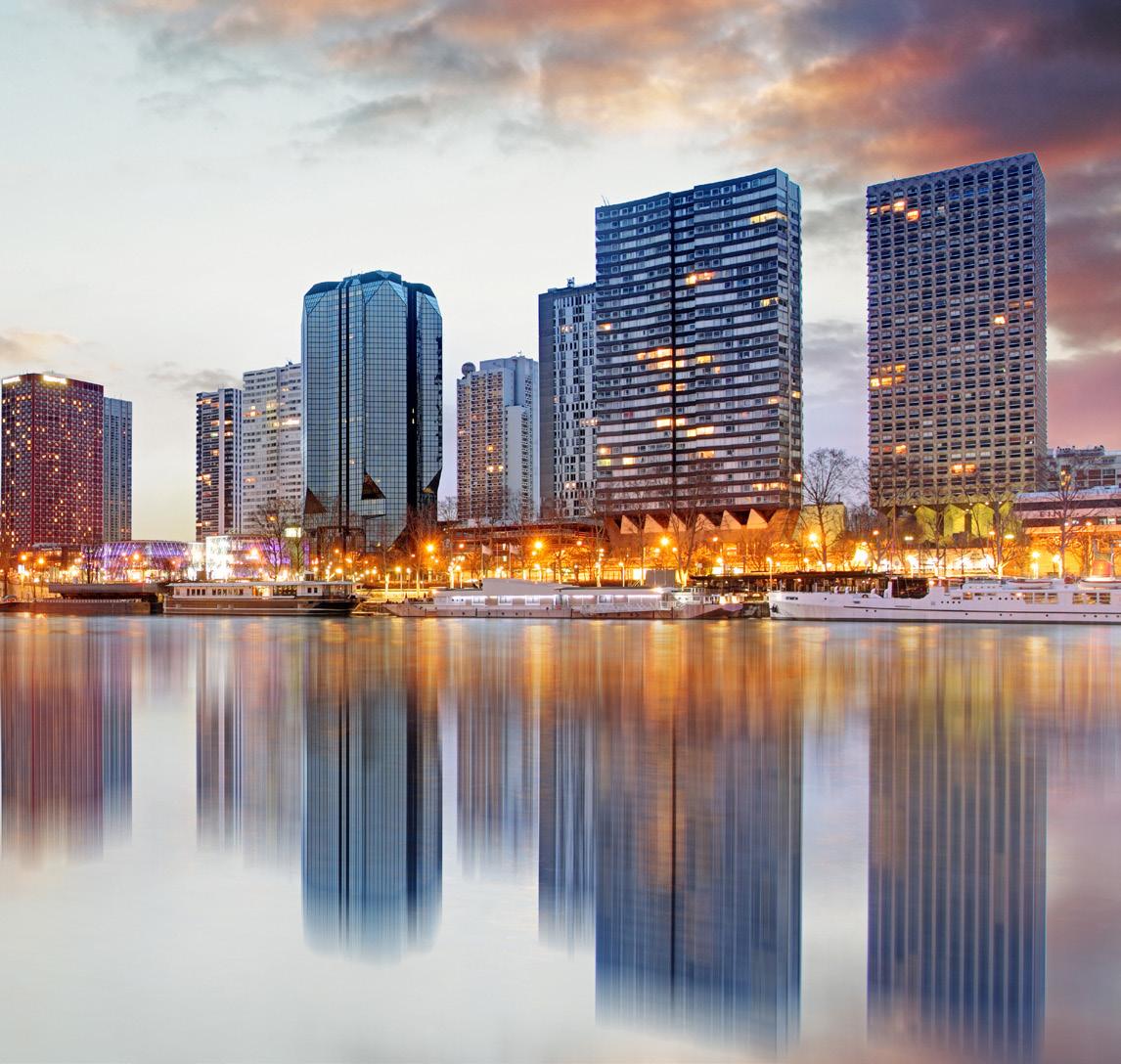
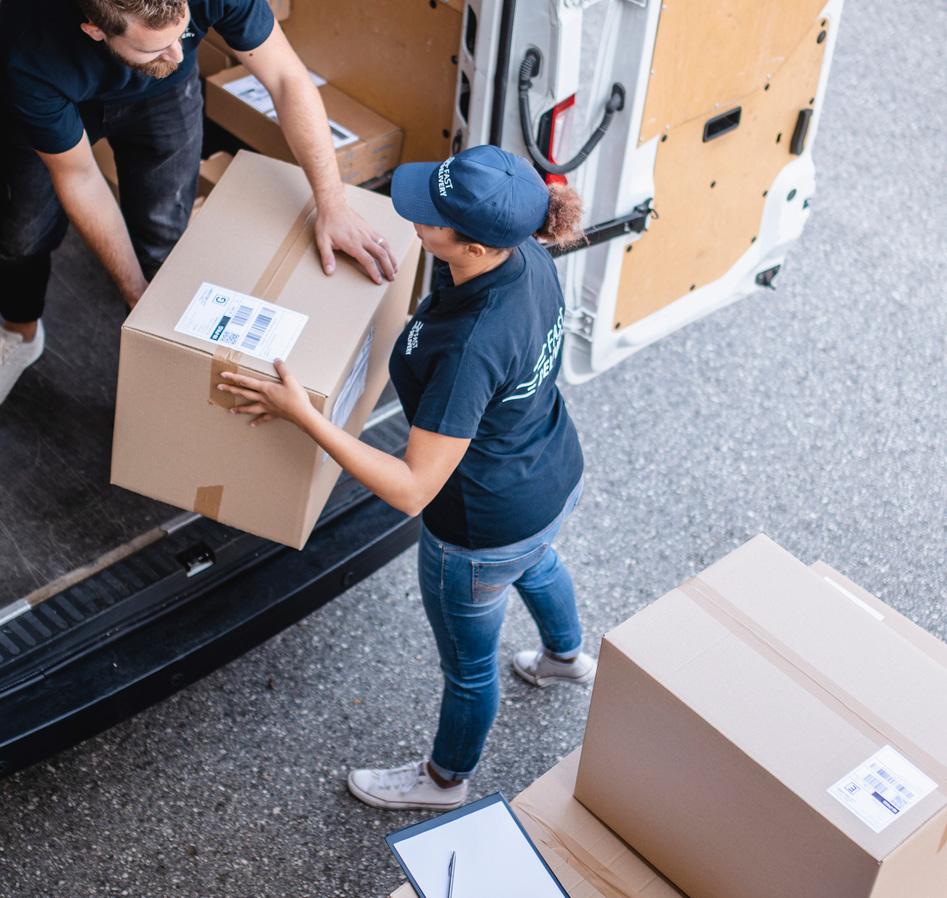
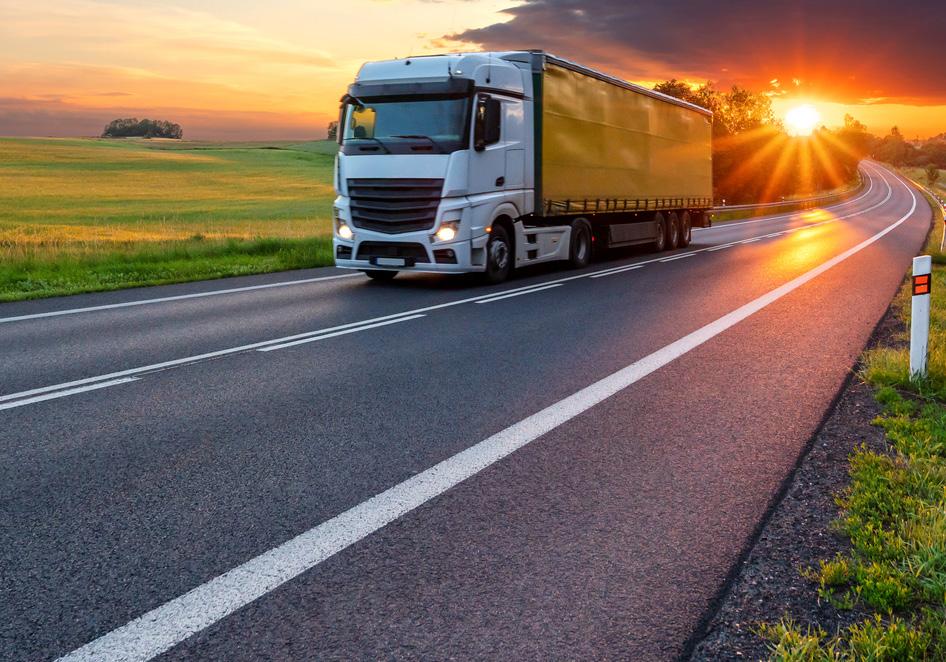


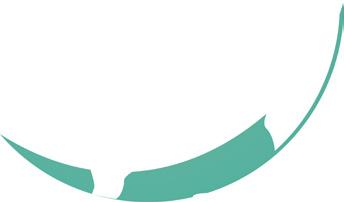
Meet who runs the world. A BizClik Media Group Brand
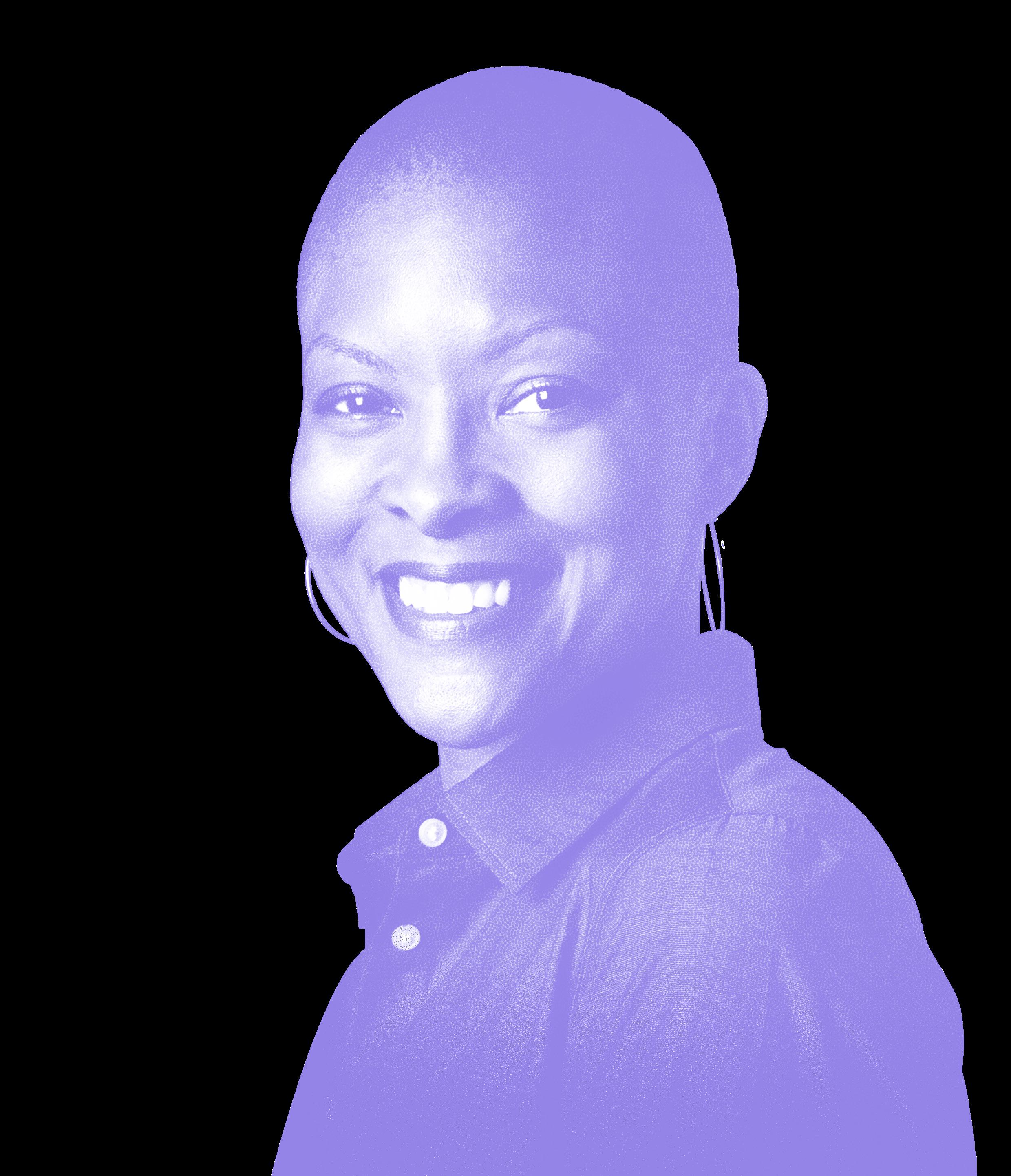
SUPPLYCHAIN in Read now TOP 100 Women NEW ISSUE OUT NOW In Association with: Creating Digital Communities
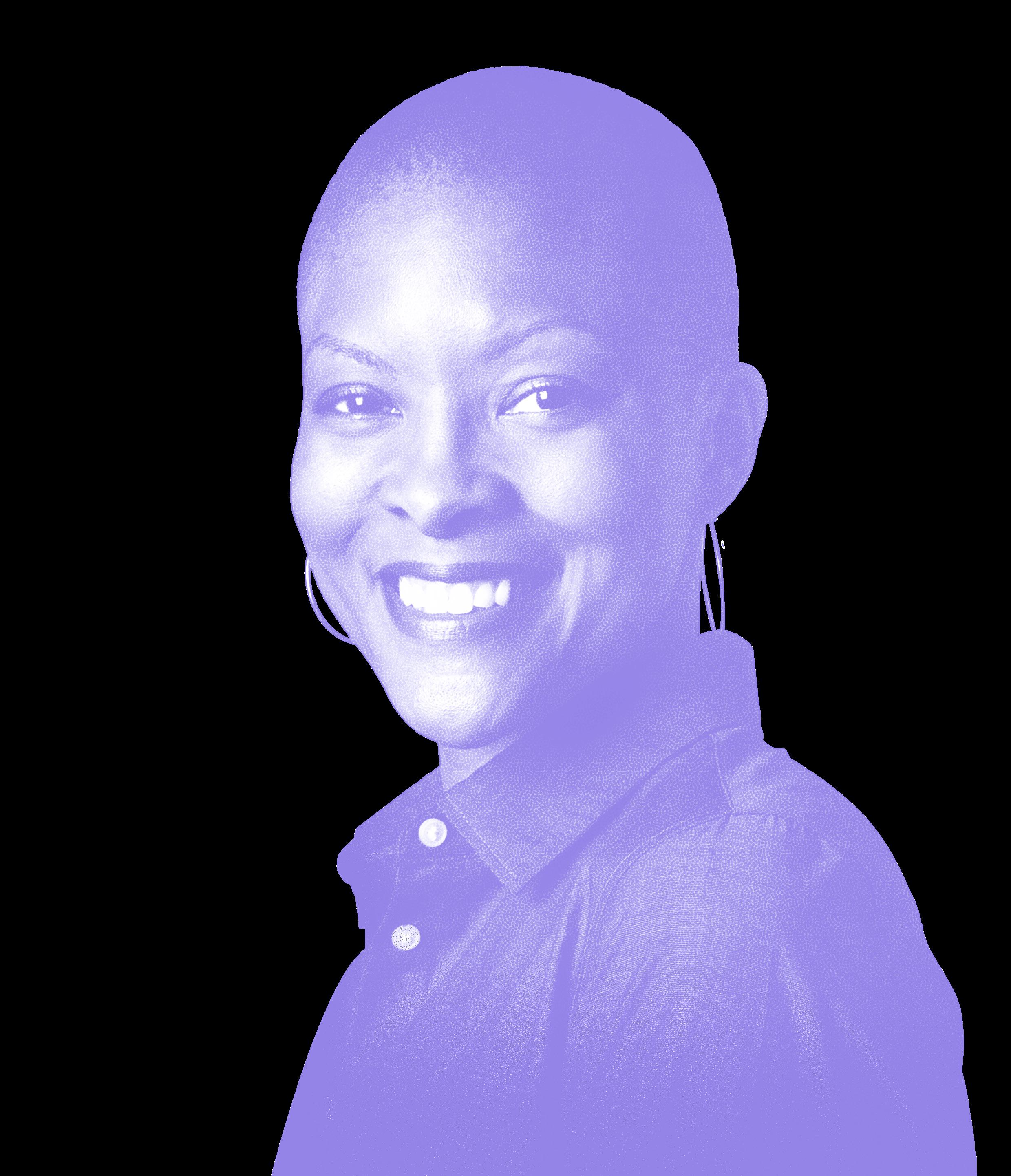
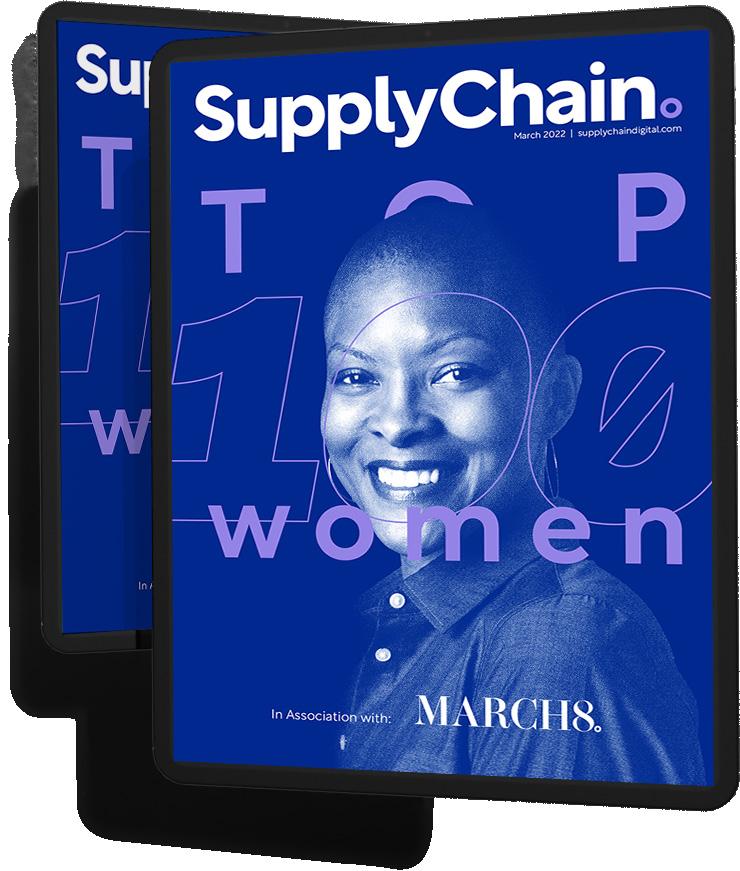
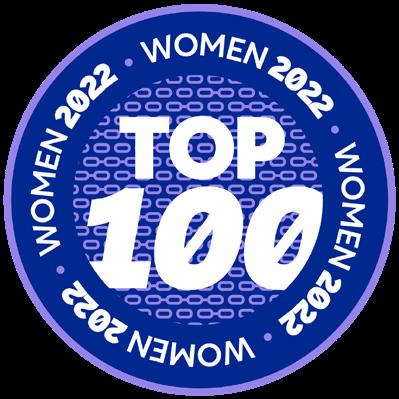
Supply chains in US brace for hurricane season Florida, United States
Every year, from around the beginning of July, states along the southern part of the Eastern Seaboard in the USA brace themselves for hurricane season, which can last until well into autumn. Florida, on the south-east coast, is the most hurricane-prone state of them all.
Companies whose supply chains are affected by this annual extreme weather phenomenon increasingly use Industry 4.0 tech for real-time data on rail, road and air routes, to keep supply disruption to a minimum.
10 July 2022
BIG PICTURE

supplychaindigital.com 11
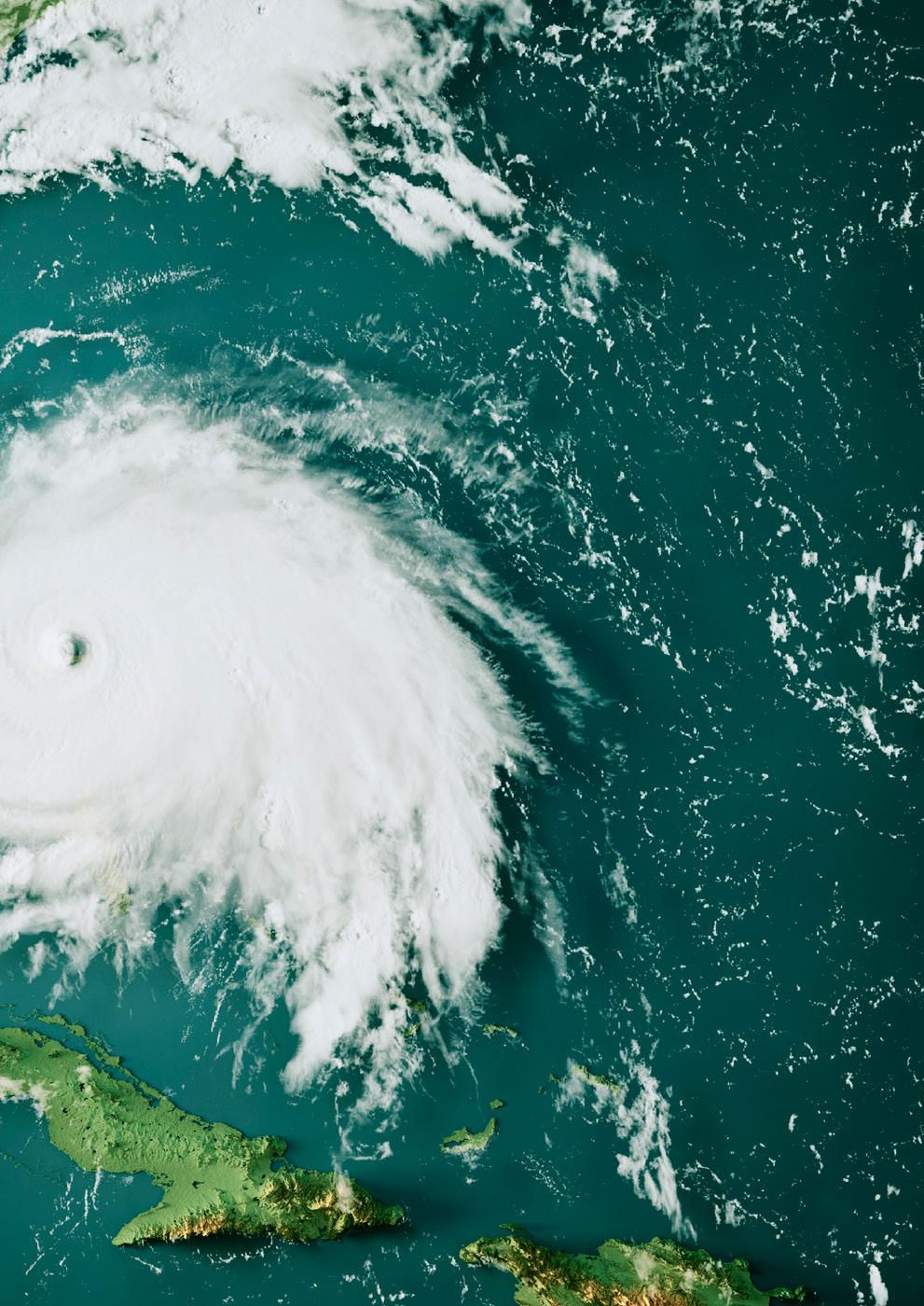
12 July 2022 THE BRIEF “Our Digital ProgrammeAmbassadorssetsusapartfromourcompetitors”MikeBrooman Head of Supply Chain Community Fibre “The only way to satisfy customer demand is by investing in your systems, people and processes”WayneSnyder VP Retail Industry Strategy EMEA Blue Yonder READ MORE “Our whichsustainabilitybiggestchallengeisaroundpackaging,accountsfor40%oftotalCO2emissions”MauricioCoindreau Head of Procurement and Sustainability Budweiser Brewing Group READ MORE READ MORE Container market trends (Container xChange) BY THE NUMBERS WALMART TO ROLL OUT DRONE DELIVERY TO 4MN US HOUSEHOLDS Walmart is set to have the largest drone-delivery system in the US, as it seeks a competitive advantage in last-mile delivery. TOP 10 INFLATION-BUSTING COST CONTROLS IN SUPPLY CHAIN Finding supply chain cost controls is a way to offset increasing production and logistics costs, with procurement being key to finding value chain savings. EDITOR'S CHOICE READ MORE READ MORE 26% Predict 2022’s peak container season will be less chaotic than in 2021 22% Expect the level of chaos to be the same 37.5% Say they’re ensuring clients receive enough inventory by shipping early 58% Report that lockdowns in China are making it hard to ship as much product as planned
SUSTAINABILITYCHAIN
supplychaindigital.com 13 JULWINNERSLOSERS22
Firms 'over-reached on sustainability targets' - Bain report
Nearly a third of organisations globally failed to meet their net-zero carbon emissions targets for 2020, research from Bain & Company suggests. Bain's study shows that 31% of businesses who set and published 2020 Scope 1 and 2 emission reduction targets did not meet them, with more than a quarter missing their sustainability goals by as much as 80% in someThecases.research was released at the World Economic Forum, held from May 22-26 in Davos, Switzerland. The report also reveals the wider picture of sustainability challenges that businesses face, as they struggle to meet the raft of net zero commitments made to investors, regulators and the public. Bain says many C-suite execs feel overwhelmed by the scale of the challenge.
US SECURITYPORTS
A Bain & Company report released during the recent Davos summit suggests 31% of businesses did not come close to hitting ambitious 2020 carbon emission targets
The US Department of Defense is using AI to manage security at its ports, for real-time supervision of people, vehicles and cargo.
WOMEN IN LARGE FIRMS
An annual Gartner report on women in the supply chain workforce shows that women are, largely, more likely to reach executive level.
The same Gartner report reveals 43% of SME supply chain leaders say the pandemic has hit the career progression of women. SUPPLY
WOMEN IN SMES
A Bain report (see left) suggests 31% of businesses did not come close to hitting ambitious 2020 carbon emission targets.
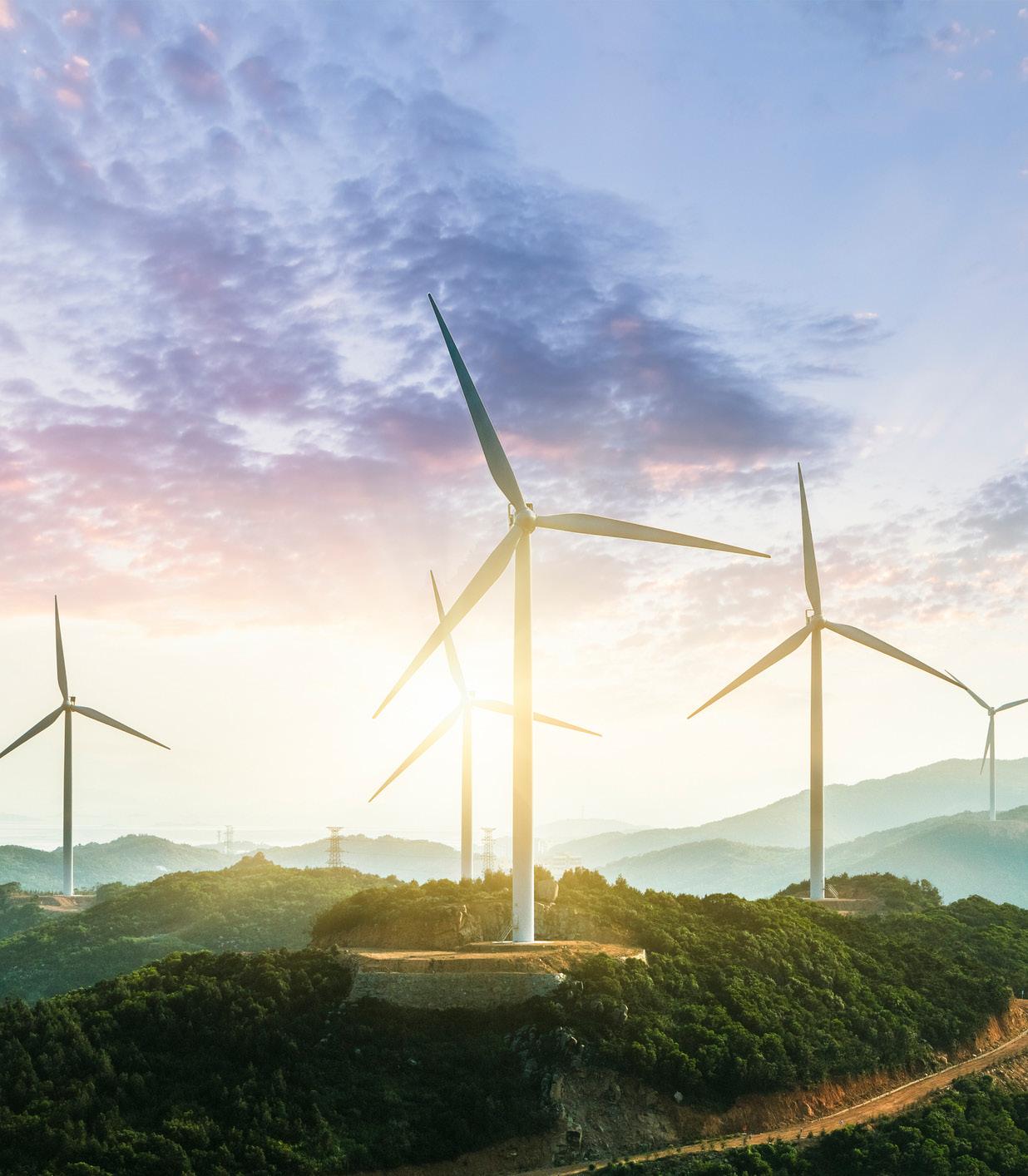

1845 1845-50 1890 14 July 2022 A BRIEF HISTORY OF Deloitte
TIMELINE William Deloitte opens an accountancy firm The firm is founded in 1845 London by William Welch Deloitte, a British accountant with a grandfather who fled France during the French Revolution, Count de Loitte. Deloitte is the first person to be appointed an independent auditor of a public company – the Great Western Railway.
Deloitte expands his British presence Deloitte uses his appointment as auditor of the Great Western to win business in other growing industries, including docks, collieries, ironworks, hotels, banks, insurance companies, newspapers, and other railways, such as the Great Northern. has 300,000 employees in 150 countries and is often hailed as the leading
Deloitte opens first overseas branch Deloitte opens a branch office on Wall Street in the US, with Edward Adams and PD Griffiths as branch managers. It is Deloitte's first overseas venture. Other branches soon follow in Chicago and Buenos Aires.
servicesprofessionalmultinationalcompany

Co-founder paves way for League of Nations Elijah Sells, a co-founder of Deloitte legacy firm Haskins & Sells, produces a detailed peace plan during World War I that forms the basis for the League of Nations, which was established in 1920.
Deloitte tilts East Deloitte demonstrates its commitment to the Asia Pacific region, with an estimated US$500mn of investment in China and Japan. In 2018, Deloitte Asia Pacific is established, giving it the ability to serve the largest global clients. 1950s supplychaindigital.com
15 present1990s-
The Third RevolutionIndustrial In the mid 1950s, Deloitte and its predecessor firms embrace technology, leading the way in using statistical sampling in auditing. Its ‘Auditape’ programme required minimal training, handled computer records in most formats, and put client information at employees’ fingertips.
1917
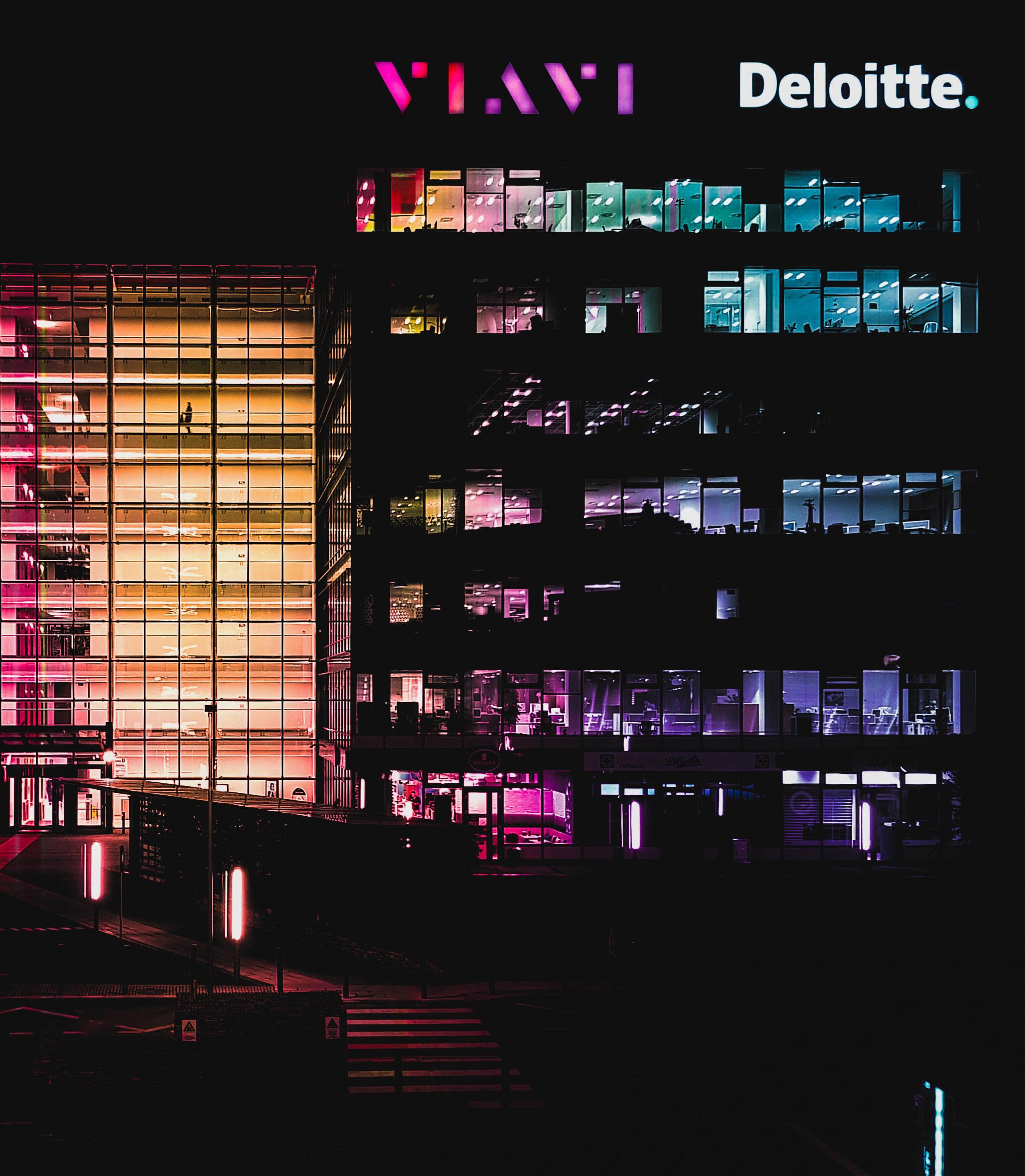
J uniper might just be one of the biggest companies you’ve never heard of. A US multinational corporation, it manufactures networking products including routers, switches, network management software and security products. In fact, every link you have clicked on Google in the past 15 years – and every video Keeping tech giants supplied when the chips are down
JOB TITLE: VICE PRESIDENT, SUPPLY CHAIN PLANNING & FULFILMENT COMPANY:
HaynesMitch
16 July 2022 TRAILBLAZER
JUNIPER NETWORKS or advert Google has served you – would not have been possible without Juniper, or Mitch Haynes, for that matter. That’s how long Juniper has been working with the search-engine giant, whose service is underpinned by its network solutions. Among its roster of cloud providers, clients include Amazon, Facebook and Microsoft. Haynes has been at Juniper for six-anda-half years, having worked his way up from Director of Supply Planning Operations. Prior to this, he was Senior Manager of Cisco’s Customer Excellence Program. He says the key to Juniper’s supply chain is partnerships.“It’sallabout gaining visibility,” he says. “Knowing where and how the customer is deploying is vital for meaningful planning with our manufacturing partners.” He adds: “Just think what it takes to deliver a global network from raw silicon – the number of steps, partners, and man-years of effort that go into that is pretty significant.” This is why Haynes says “tight partnerships” are vital for Juniper, if it is to have “the right product for our customers at the right time and the right place”.
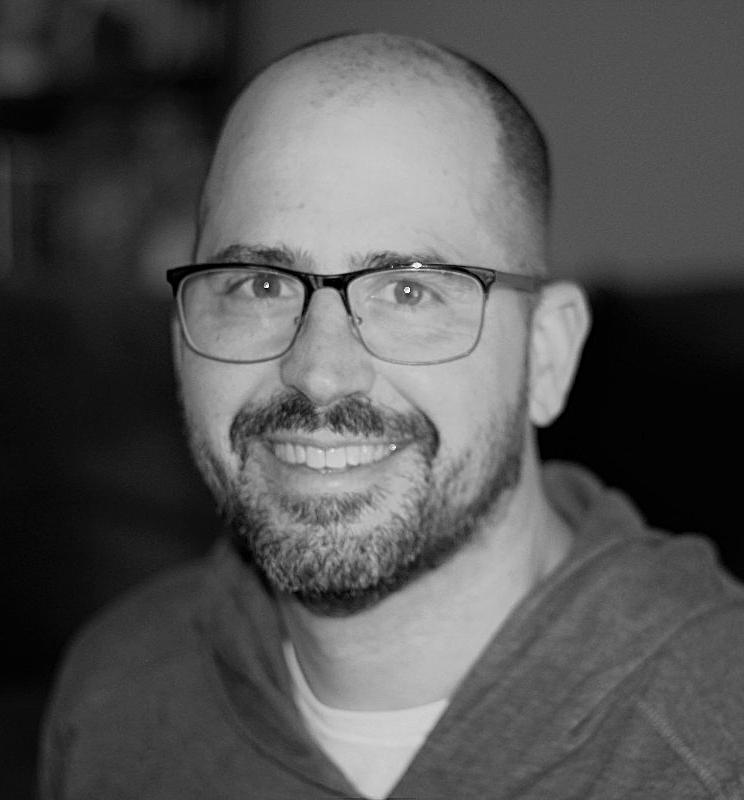
But for any business these days, ensuring products end up in the required quantities in a timely fashion is not a-given. Disruption and uncertainty have been constants over the past two years – so how has Haynes kept Juniper’s colossal supply chain ticking over, especially between the teeth of ongoing microprocessor shortages? He says: “This is probably the most unique time we've seen in the supply chain industry. The simple fact is there is more demand for semiconductor wafer manufacturing than they have the capability to build and ship.
17
Juniper employs 8,700 employees worldwide 53 offices in 53 countries 30,000 around 30,000 customers and partners
supplychaindigital.com
He adds: “In a world where you can’t give customers everything, you need to stay truthful about what you are capable of providing, and this allows us to come up with the best choices we can make.”
“In a world where you can’t towhattruthfulyoueverything,customersgivemuststayaboutyou’reableprovide”
A number of businesses that are reliant on chips have decided to reshore chip production, with Samsung US and Tesla amongHaynesthem.says that reshoring “is certainly a conversation that we're having with our partner base”. He adds: “At the moment, when we design an ASIC (application-specific integrated circuit), we partner with a manufacturing company – like Broadcom or GlobalFoundries – who will produce it. It’s a partnership we have with our supply base. In terms of having our own manufacturing footprint, that’s something we are constantly looking at. With so much geopolitical risk today, we need to make sure we have good geographic diversity in terms of where our products are built.” 8,700
“The ability to make such decisions goes back to the idea of close partnerships with customers, which allow you to get ahead of the wave of demand.” Haynes adds that it is also a matter of prioritisation.“Sometimes, it simply comes down to knowing what is a realistic number of things you can build and ship with the components that you have? What's the best way to use them? Where's the best place to deploy them? These are some of the tactical decisions that are most helpful.”
“The ability of vendors like Juniper to get material to market a little bit faster means making decisions earlier than we typically would've wanted to.
18 July 2022 FIVE MINUTES WITH...
Capgemini is a French multinational information technology services and consulting company. As director of supply chain transformation, I work with many different clients in numerous sectors to help them drive resilience and sustainability into their operations, largely through target operating model changes, process changes and technology enablement. That's really my focus of the organisation.
NAUGHTONASHLEYQ.TELLUSALITTLEOFYOURROLEANDCAPGEMINI»
» I think third and fourth party logistics (3/4PL) providers have a critical role to play, because they are often able to see disruptions early, particularly with regards to logistics routes.
Speaking to Supply Chain Digital Editor-in-Chief Sean Ashcroft at Procurement & Supply Chain LIVE, Capgemini Supply Director Ashley Naughton discusses the pivotal role logistics has to play in the future of supply chain.
Q. HOW CAN 3PLS AND 4PLS HELP WITH SUPPLY DISRUPTION?
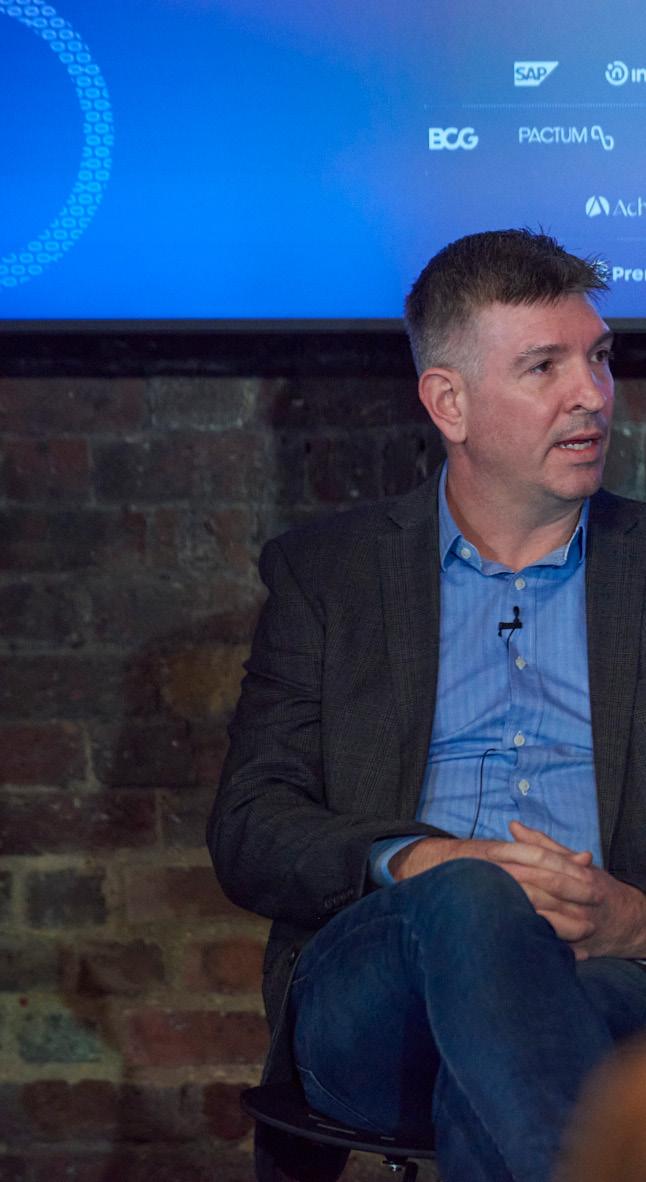
A lot of disruption that we've seen over the past couple of years has come through logistics issues. The Suez Canal issue, for example, is a classic example of where transportation was severely affected. 3PLs and 4PLs are often best placed to analyse how such disruptive events might impact a company’s ability to deliver products and goods on time. In turn, this enables an organisation to assess how that impacts their ownSocustomers.availability and access to logisticsroutes data is really an area where I see they can add a lot of value.
Many of the logistics companies are an important resource, because they are undergoing their own digital transformations themselves. Businesses need to work with them to understand how their digital transformations can add value to their own organisation. Only through
» Logistics organisations are of course a key part of the value chain, and, as such, I think organisations need to work more carefully on collaboration.
Q. WHERE DO GLOBAL LOGISTICS STAND WITH DIGITAL TRANSFORMATION?

Q. WHAT IS THE BIGGEST BARRIER TO THE DIGITAL TRANSFORMATION OF SUPPLY CHAINS? » Developing the business case for change is still a huge challenge for many organisations. Lots of businesses still tend to focus on the top- and bottom-line, which is understandable because that's how we're all Imeasured.thinkthatmigrating towards more of a value-driven assessment is required if an organisation is to start moving things forward in the right direction. And businesses – particularly those with limited investment capabilities – need to focus on the important aspects of their supply chains. Seeing past the immediate first tier can be a tricky one for a lot of organisations.
20 July 2022 collaboration will we see such benefits coming through. But not only do organisations need to collaborate with logistics companies, the logistics companies also need to collaborate with one another. This is an emerging area. It isn’t happening enough at the moment but it will become more prominent going forward, particularly as regards sharing capacity. A good example is the delivery of goods and services. Traditionally, logistics will measure delivery ‘fill’. It doesn't necessarily always measure and monitor its return fill. Sometimes return vehicles don’t contain any products –so-called empty running. So there is definitely an opportunity for logistics companies to consider sharing capacity, in order to make the entire network more efficient. With the drive towards sustainability becoming more and more important, reducing the amount of inefficient transport moving around is definitely something logistics providers will seek to tackle, in my opinion.
“3PLs and 4PLs have a critical role to play in supply as they’re often able to see disruptions early”
FIVE MINUTES WITH...
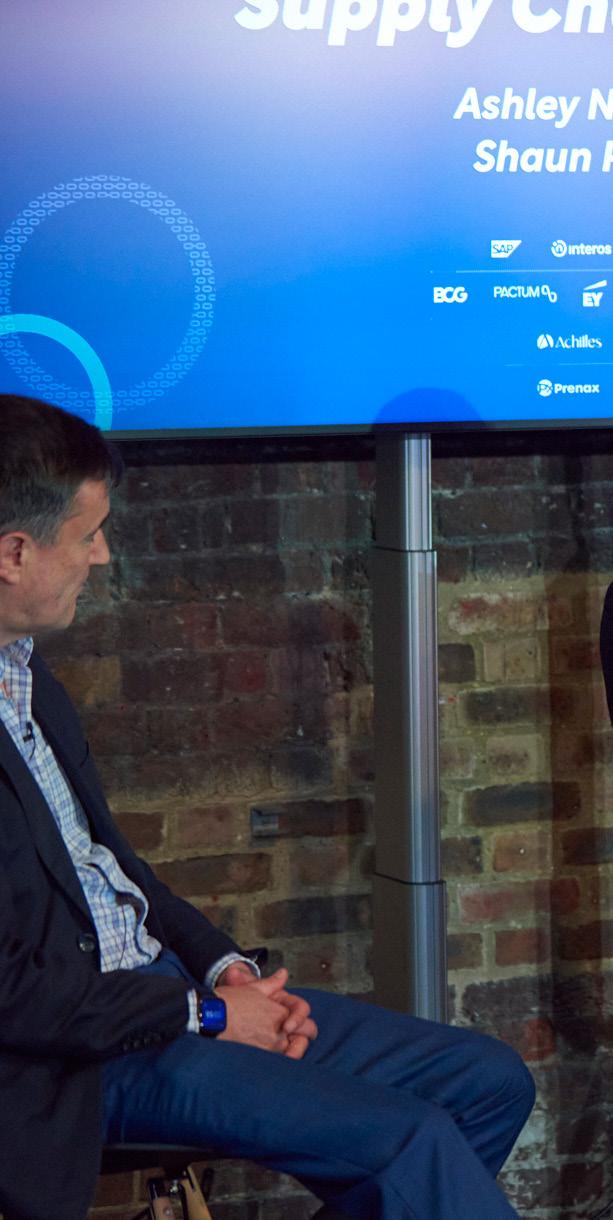
supplychaindigital.com
Different sectors also face slightly different challenges but that insight is quite limited right now, and I think there is an investment from both the financial perspective and a resource perspective that will be needed to decide what you actually want to focus on within your supply chain. I also think that skills and expertise – and the need to reskill the workforce – can also be a barrier; that's something that firms also need to be focused on. This is especially true right now because of labour constraints in the supply chain network due to the Great Resignation.
21
• This October, we return to London for an all-new event - Procurement & Supply Chain LIVE, London 2022. Held at the QEII Centre between from 12-13 October 2022, this hybrid event incorporates two zones - SupplyChain LIVE and Procurement LIVE - to create a single EXPO-style event.
To find out more about the event, click here
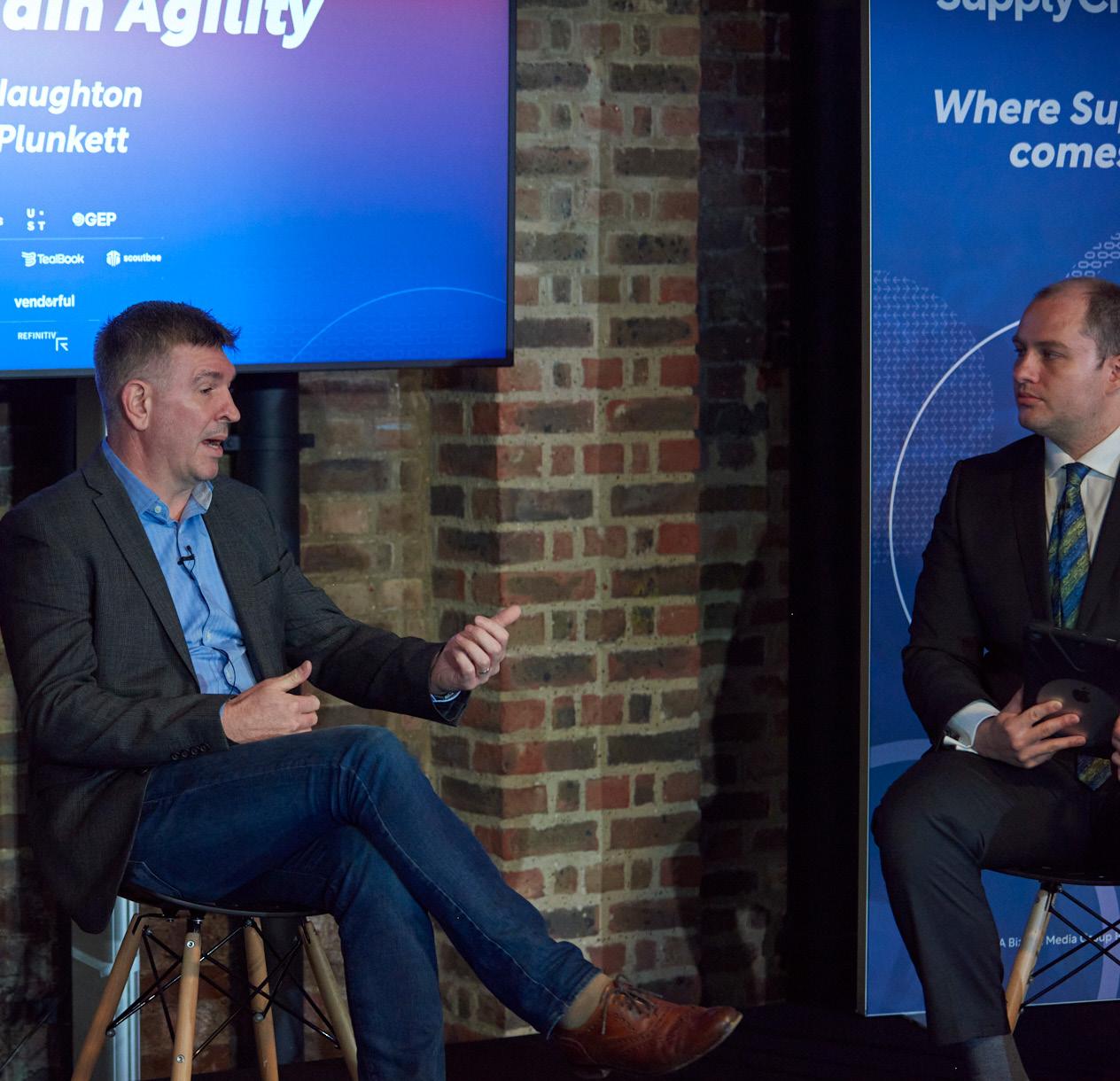
A BizClik Media Group Brand DISCOVER WHO MADE THE CUT. Top 100 Companies in Supply Chain Read Now

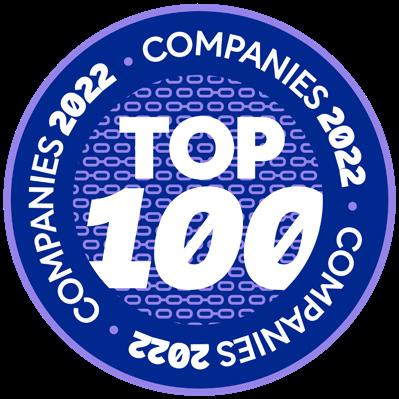
Creating Digital Communities

24 July 2022 PRODUCED BY: CRAIG KILLINGBACK WRITTEN BY: SEAN ASHCROFT COMMUNITY FIBRE IS MORE THAN LIVING UP TO ITS NAME
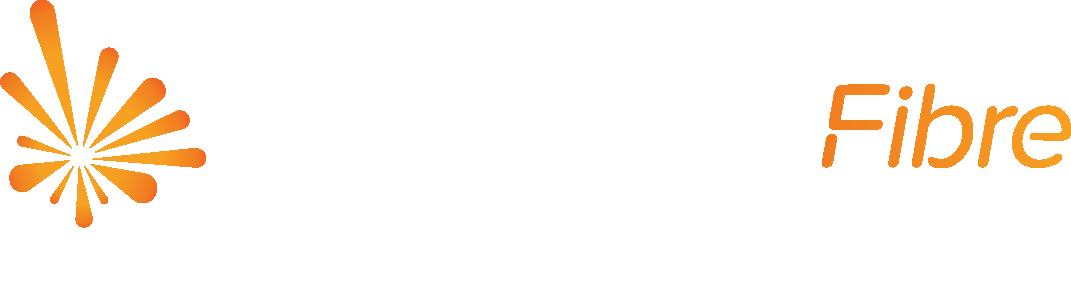
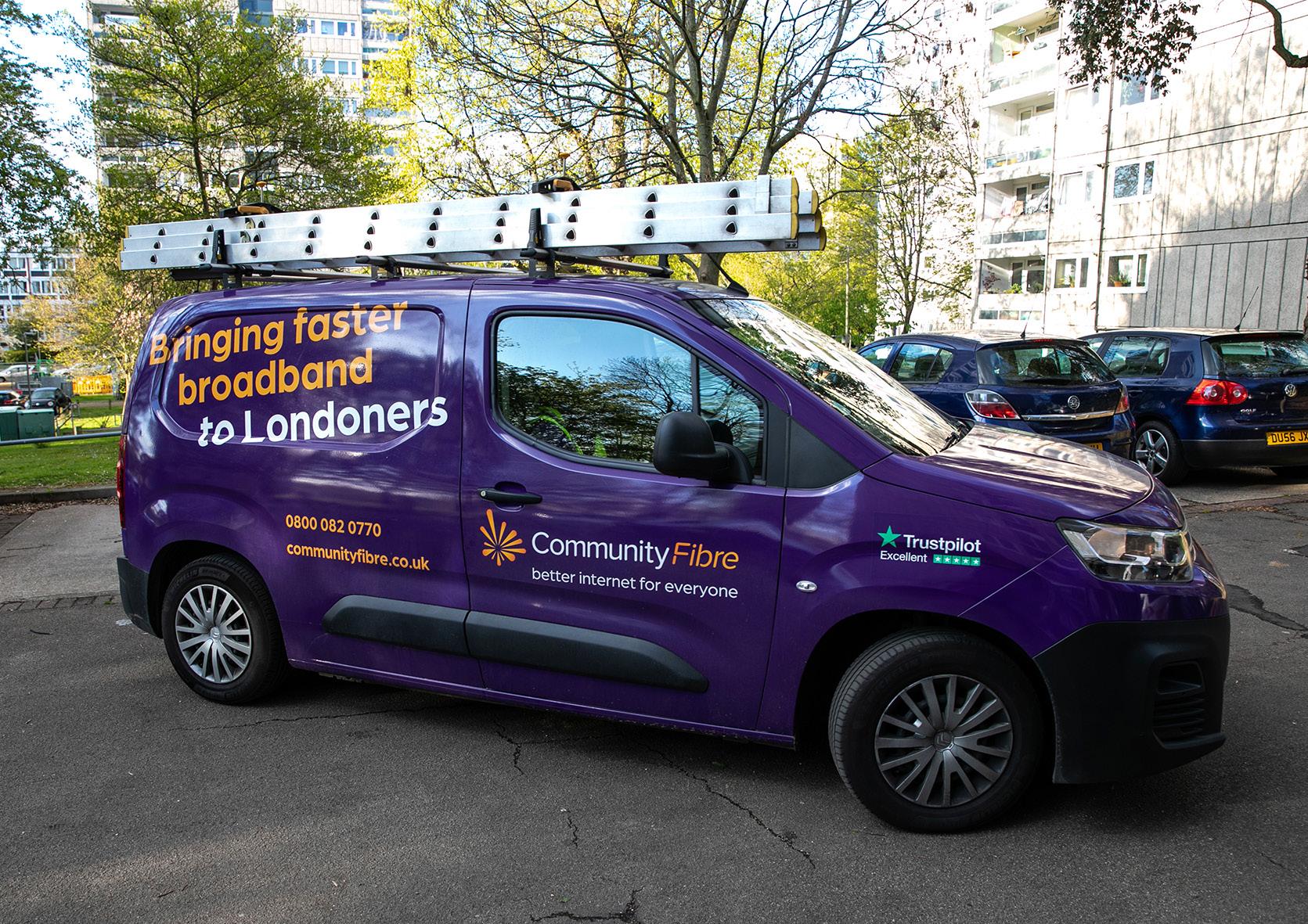
COMMUNITY FIBRE supplychaindigital.com 25
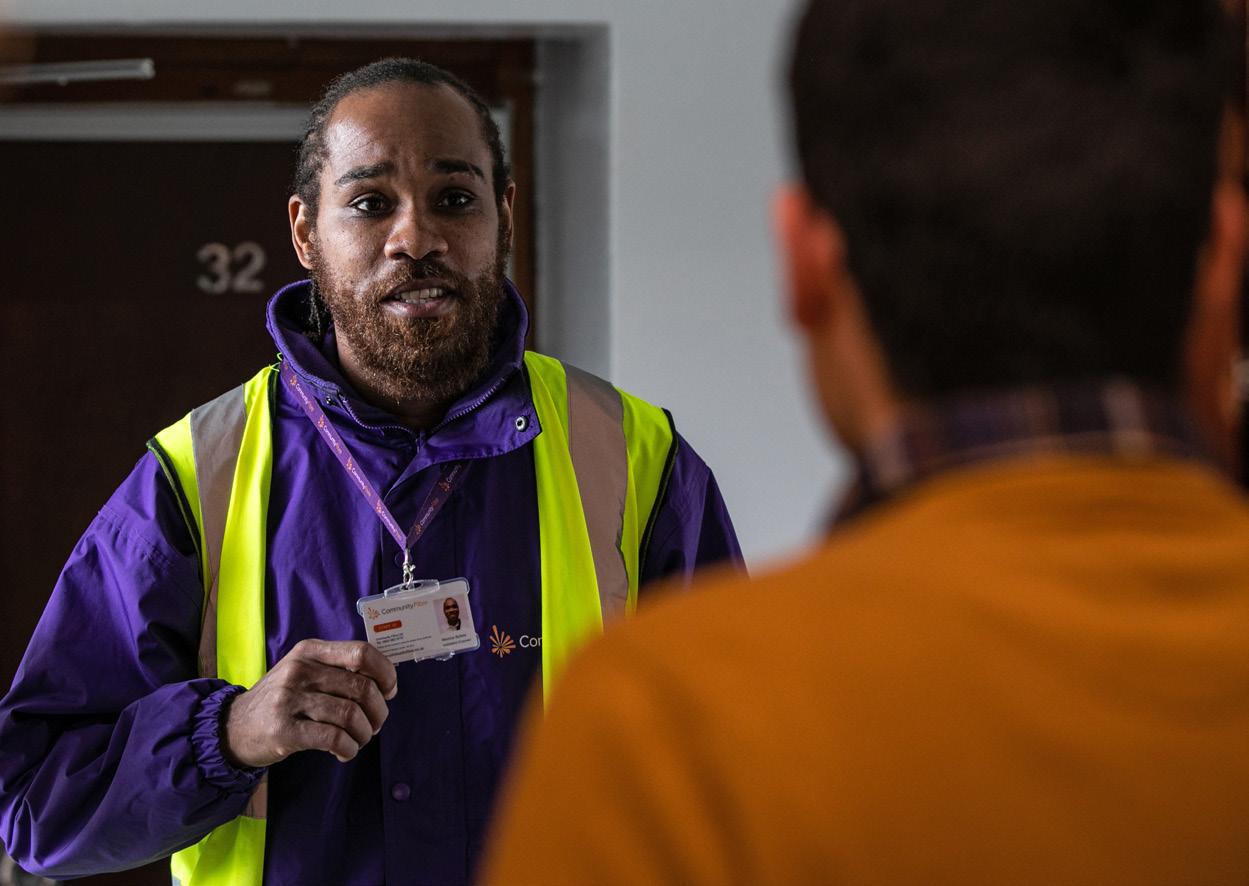
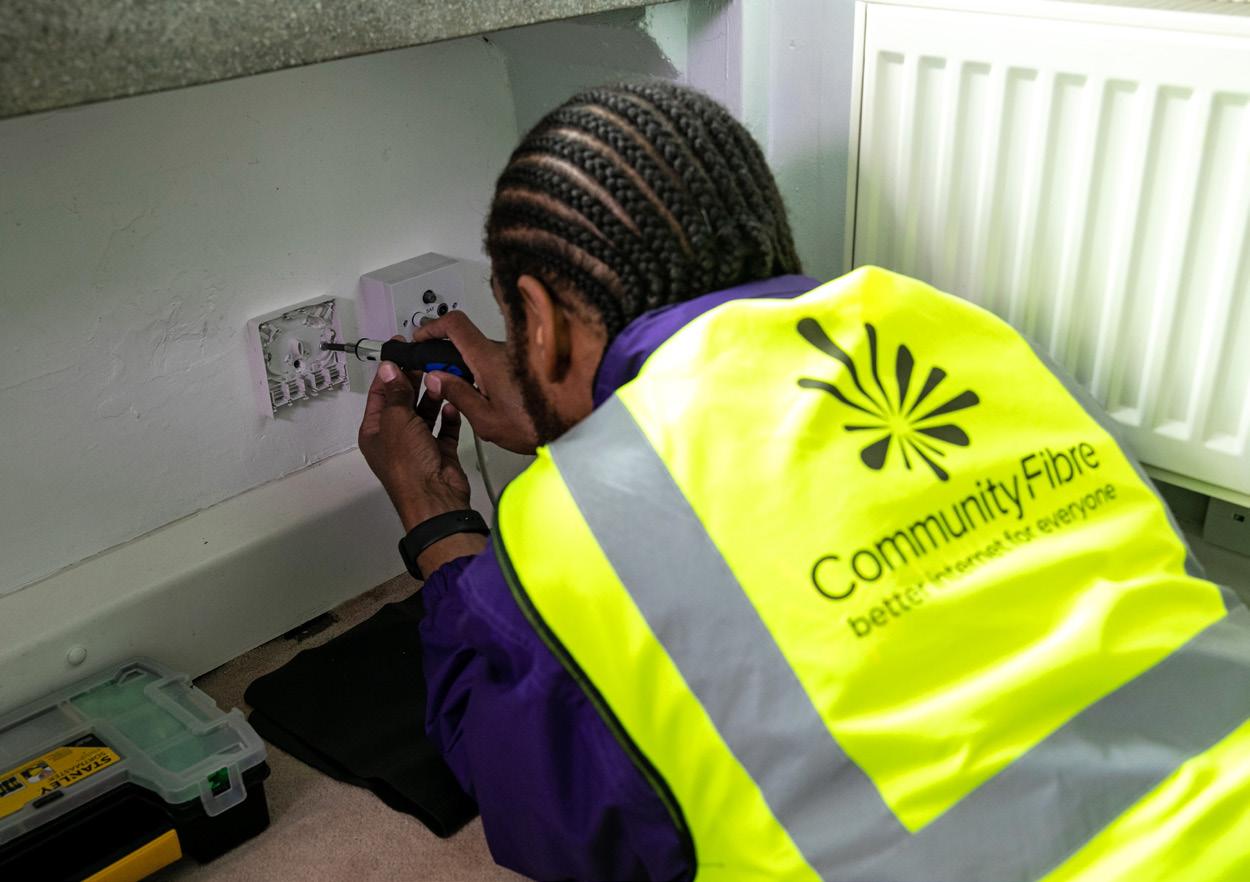
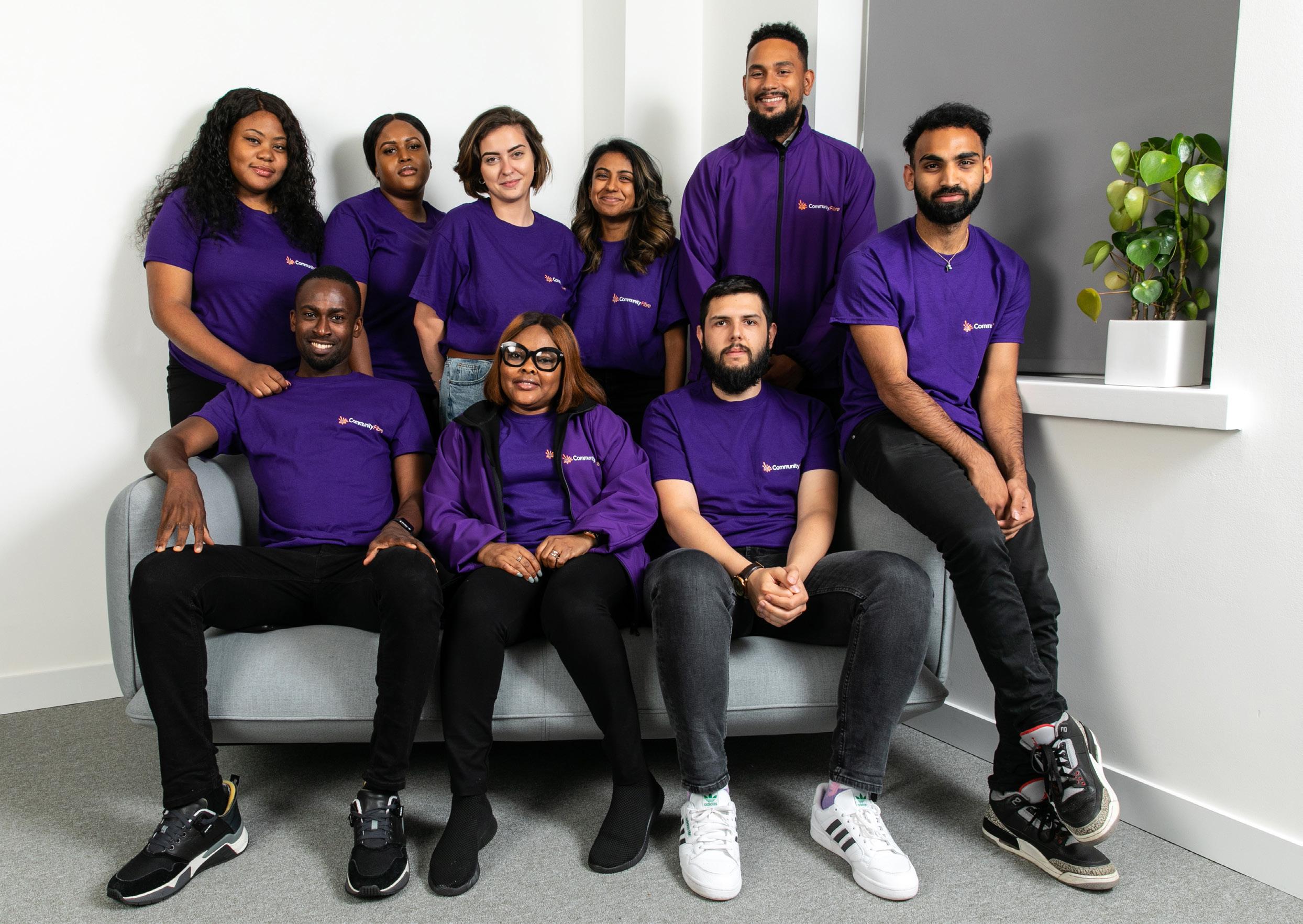
M any companies will claim ESG “is in our DNA”, but how many can point to their company’s name as evidence it behaves in a responsible and nurturing fashion? Community Fibre can, and its community mindedness runs all the way down from its branding to the communities across London that it serves, by installing fibre-based broadband connections. Unlike most providers, Community Fibre builds, owns and operates its own dedicated fibre-optic network. This means it does not have to rely on anyone else's cables, be it Openreach or any of the other major broadband players. And where most broadband providers use a combination of fibre-optic cable Community Fibre strives for excellence both in the service it provides and the good it does through ESG initiatives
26 July 2022 COMMUNITY FIBRE
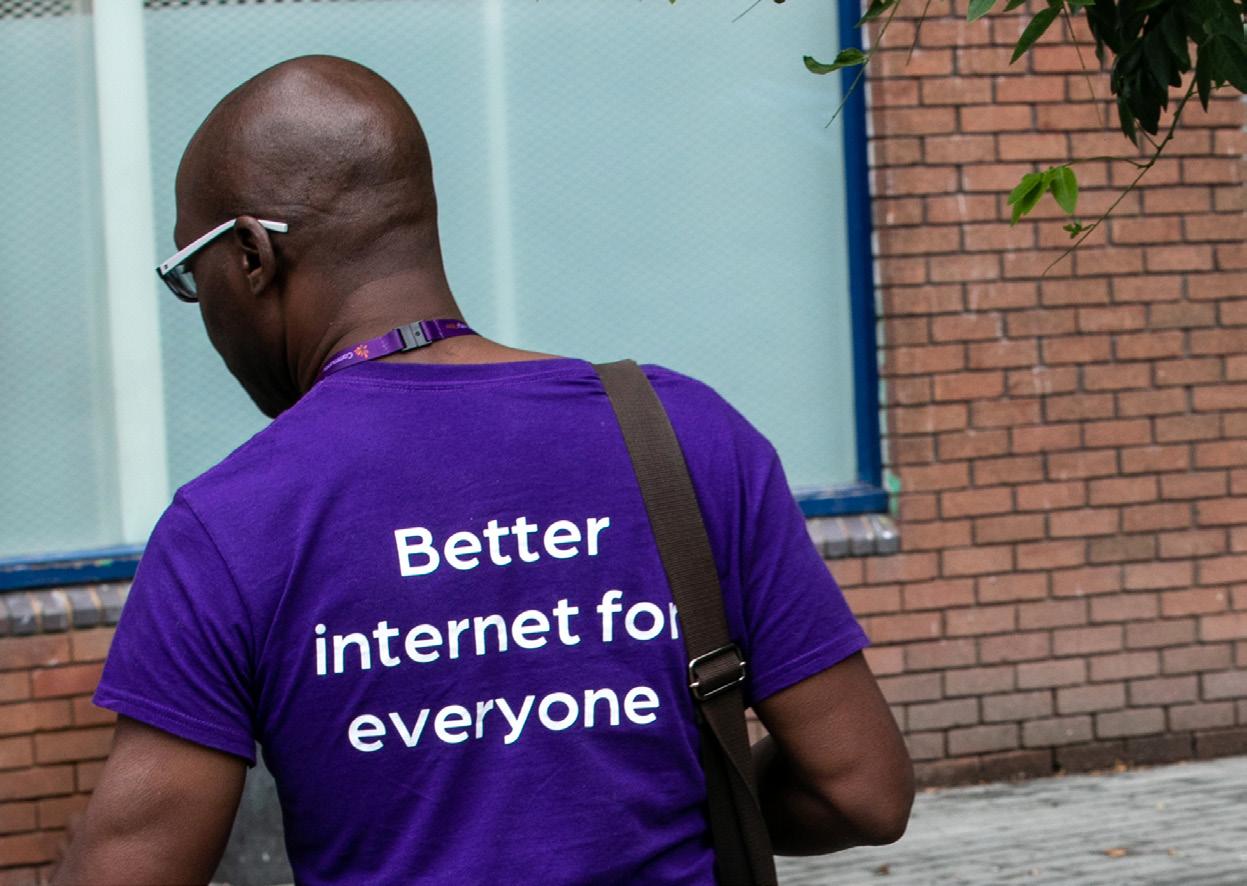
2013 foundedFibreCommunitywas supplychaindigital.com 27
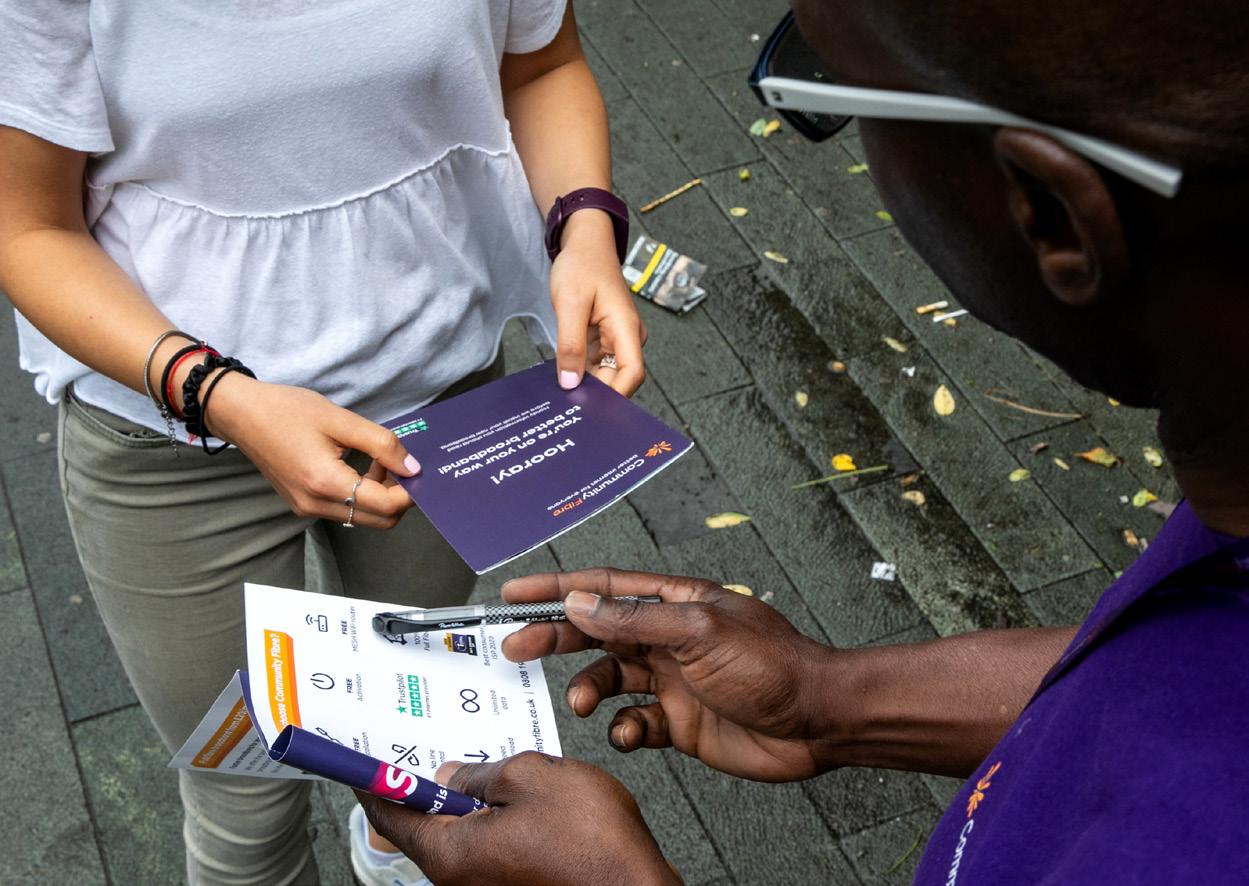
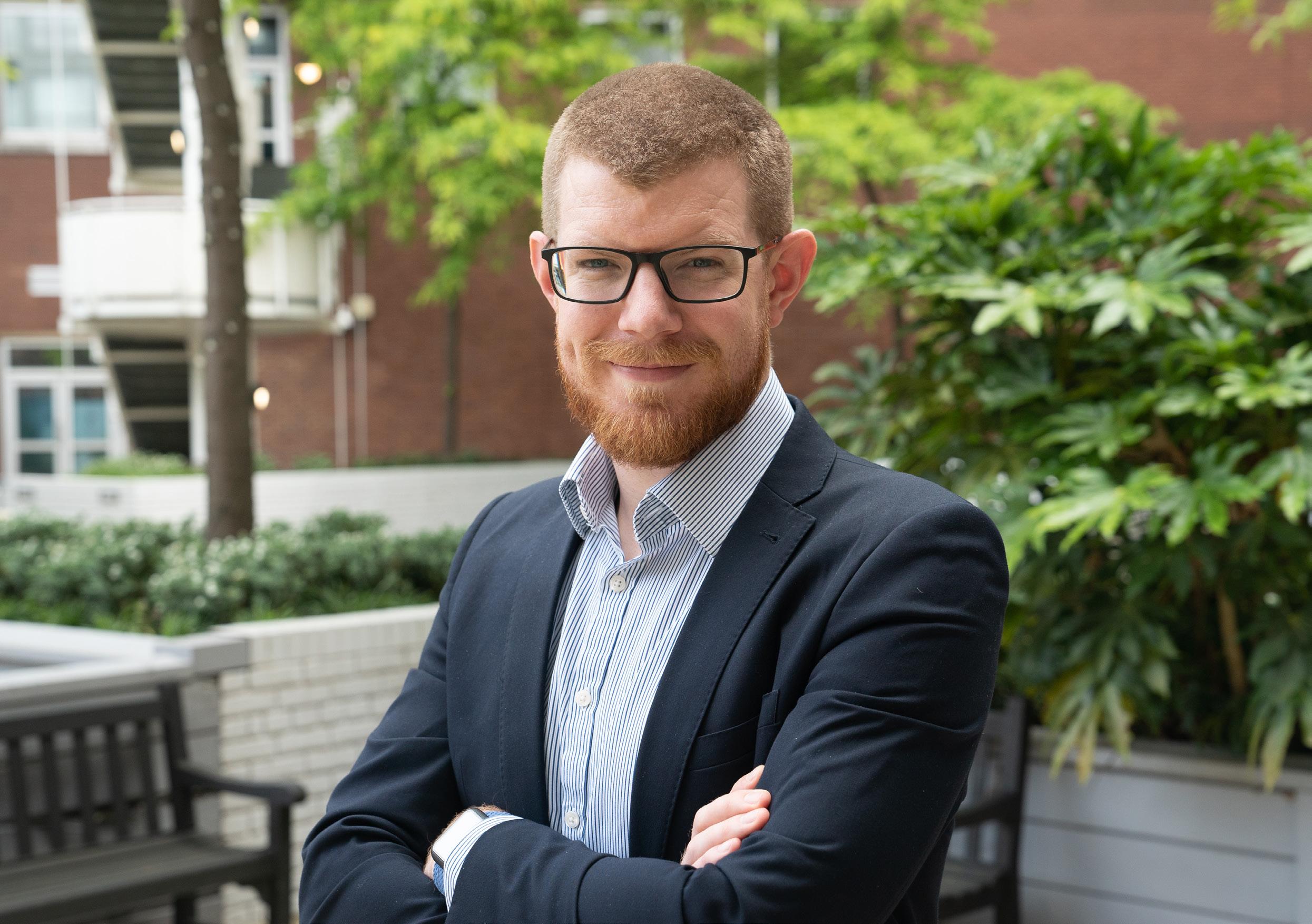
“As Head of Supply Chain, it’s my responsibility to make sure our supply chain matches and supports those ESG goals and purposes.” To this end, he is part of the company’s Green Team, which is led by CEO Graeme Oxby. The Green Team helps the business focus both on short- and long-term projects designed to reduce its impact on the“Myenvironment.involvement in the Green Team is in supporting those who deliver these benefits, by ensuring they've got access to the products and services they need to deliver to the communities that we serve.”
MIKE BROOMAN HEAD OF SUPPLY CHAIN, COMMUNITY FIBRE
COMMUNITY FIBRE 28 July 2022
“We've got a very strong ESG focus at Community Fibre,” he says. “It’s one of our company goals and one of the main reasons I wanted to work here.
The company also has a Digital Ambassador Programme (DAP) as part of its strong line-up of ESG programmes. Under DAP, Community Fibre trains members of the community to become qualified ‘digital ambassadors’, who then go on to connected to old copper phonewires, running its open network means Community Fibre’s network is fibre-only.
“Our AmbassadorsDigitalProgrammesetsusapartfromourcompetitors”
Fibre by name, fibre by nature – and the same goes for the ‘community’ portion of the company’s proposition – all of which is great news for its customers across 29 London boroughs. ESG element of Community Fibre is very strong The ESG element of Community Fibre’s business is strong, and, as Head of Supply Chain for the business, Mike Brooman is as heavily involved in helping the company deliver in this area as he is helping ensure its customers receive a great service.
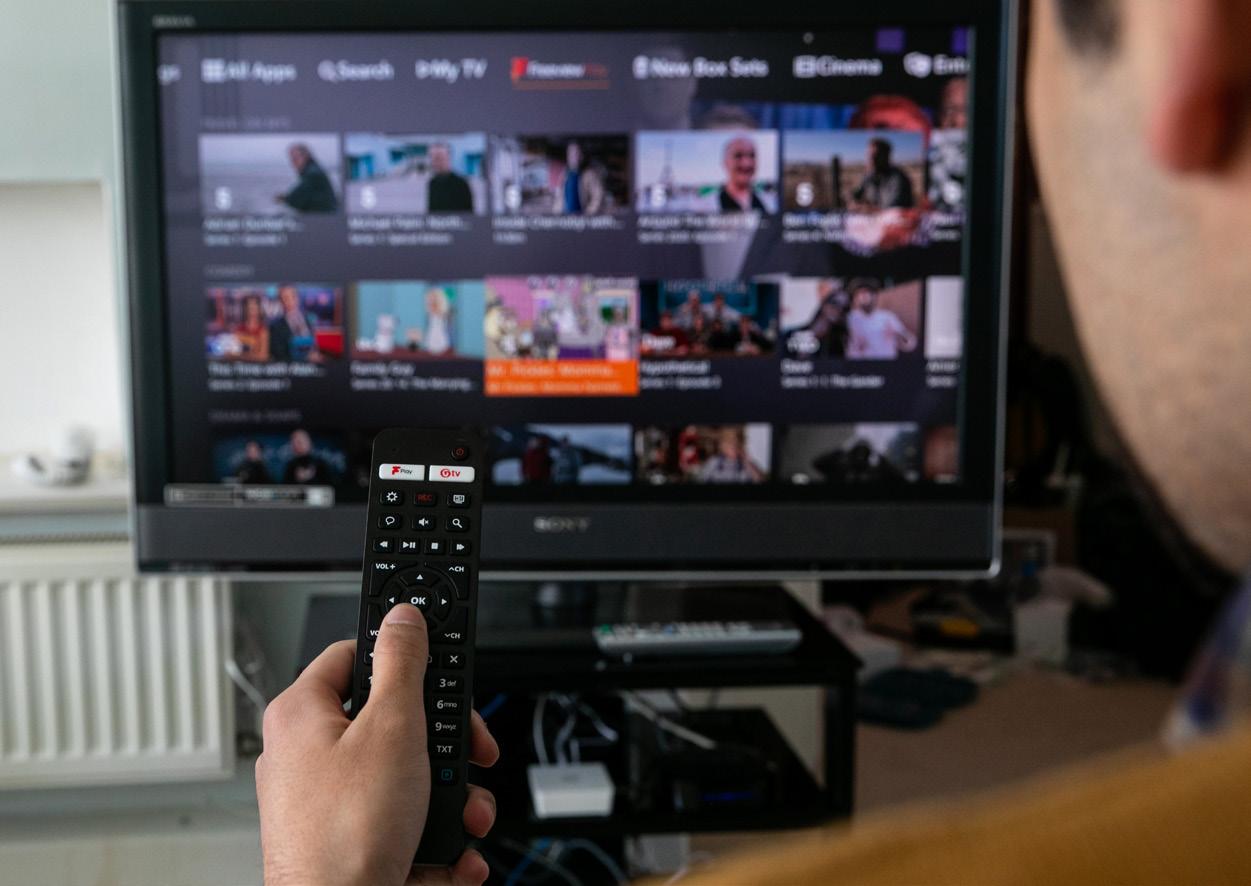
The company’s people-minded corporate ethos is also evident in its Community Connect Programme,
help residents in their community be more digitally empowered. “Our ambassadors teach everything from online banking to basic internet security,” says Brooman. “It helps prevent members of London’s communities falling victim to the digital divide.” Digital Ambassador Programme is USP for Community Fibre He adds: “DAP sets us apart from our competitors. It’s definitely a USP. It not only supports our commitment to build a better broadband service for London but puts something back into the communities we're working in, and selling to.”
BIOEXECUTIVE MIKE BROOMAN TITLE: HEAD OF SUPPLY CHAIN INDUSTRY: TELECOMMUNICATIONS LOCATION: UNITED KINGDOM supplychaindigital.com 29
Michael Brooman has a track record of delivering improvements in performance, wherever he has worked. He is a strategic head of supply chain with more than 11 years’ experience in senior positions across operations, supply chain and procurement. He says: “I’m an expert in strategic vision and development, and accomplished in transforming supply chains, leading teams, managing people and BusinessstudyingofengineeringB2Be-commerce,andsub-contracting,logistics,experienceBroomanchange.”hasbroad-basedacrosstransportandconstructionmaterials,IT,utilities,labourSG&A,andhasalsoworkedine-procurementandoncontracts.HeholdsaMaster'sinmechanicalfromtheUniversitySouthampton,andiscurrentlyforanMBAatWarwickSchool.
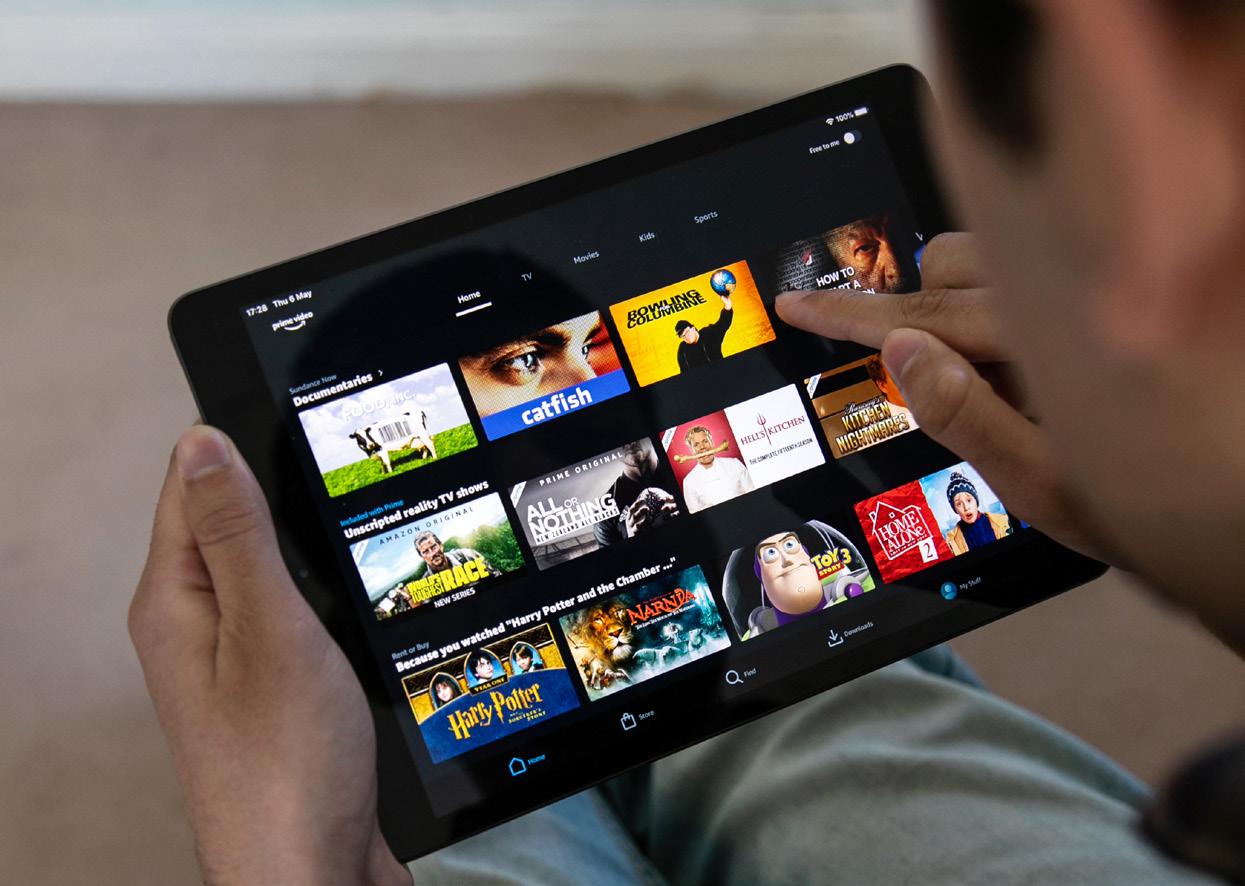
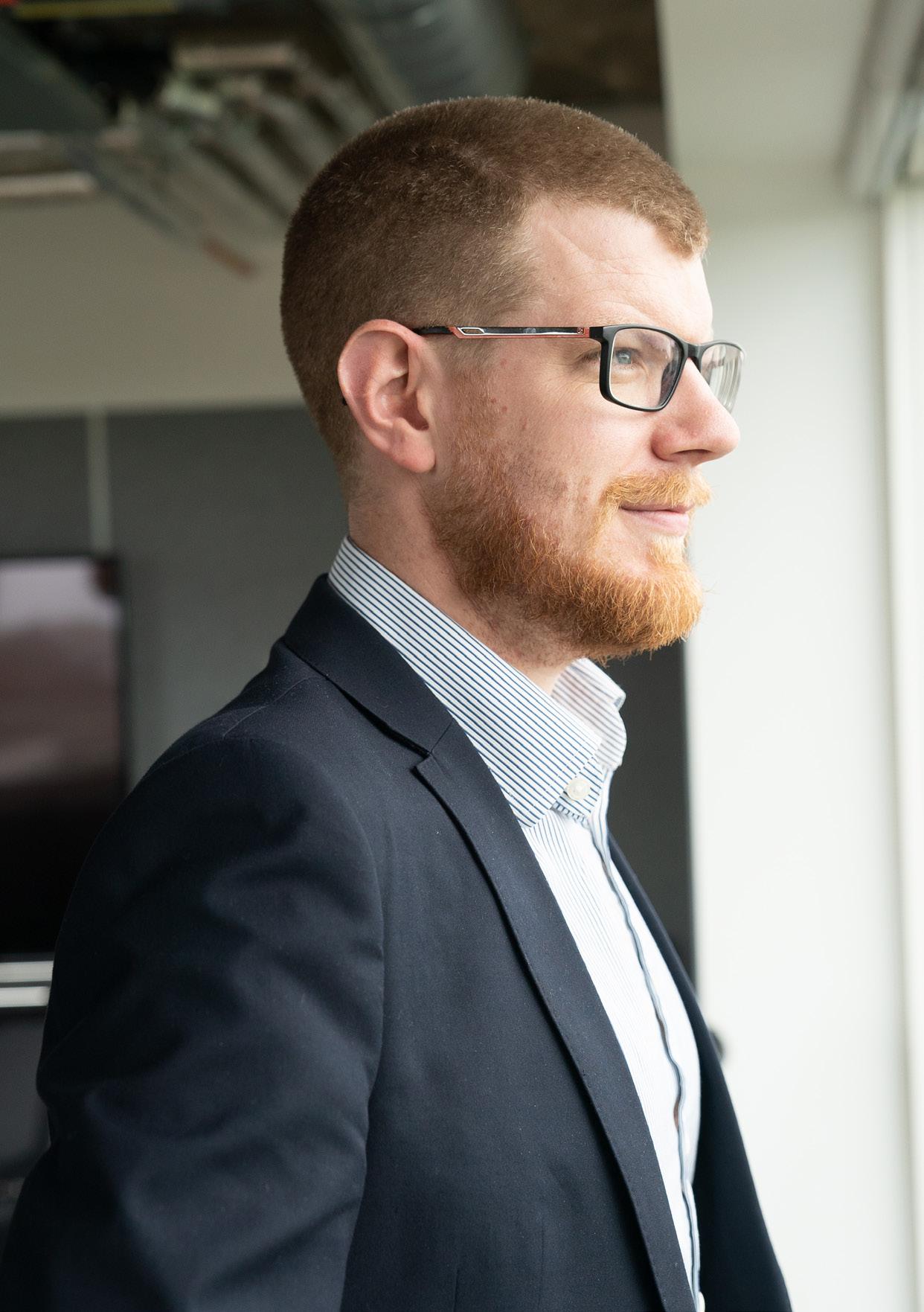
COMMUNITY FIBRE 650+ 30ofNumberemployees July 2022
community centre and everywhere in the area. Then we'll add you to the list, and we'll come and connect you.”
Making huge strides on sustainability Sustainability is also hugely important to Community Fibre. Evidence of this can be seen in the big strides the company has been making, with Brooman revealing that it has a batch of 20 fully electric vehicles arriving “very soon.” “We’re well on our way towards moving to an electric fleet. They'll be replacing traditional diesel vans,” Brooman says. He admits that a barrier to a wider adoption of EVs is lack of infrastructure around charging, but this too is something Community Fibre is seeking to address.
Brooman says: “Community Fibre co-founder Tim Stranack is working with local authorities and landlords on a daily basis, seeking to install charging points around our network, for use by our engineers. For us, it's vital that the infrastructure is in place to enable the charging of our vans during the working day.” Brooman says Community Fibre would like to make its entire fleet electric but that, currently, the limited range of such vehicles is a sticking point. “Many of our engineers work and live in London, where you can't necessarily charge a van, because you might not have a driveway to charge it on. Infrastructure for EVs is going to take more than people having a private charging point on their driveway,” heBroomanexplains. adds that, although currently unable to provide a fully electric fleet because of a lack of infrastructure, he believes the company will have made “a significant move” to making the majority of its fleet electric “within the next four years”. through which it connects community centres to gigabit broadband for free. To date, 300 such centres have benefitted from“We'vethis. got many more planned in the coming months,” reveals Brooman. “That's 1GB internet access available to everybody who uses those centres. It helps bring communities together in all sorts of ways – for training, entertainment, and social interaction. It’s all about digital inclusion. It's a really good part of our mission to bring better broadband to all of London. “The scheme is advertised heavily by housing associations and local authorities, as well as by landlords and also on our website. You can go to the Community Connect part of the website and apply to have broadband provided to your
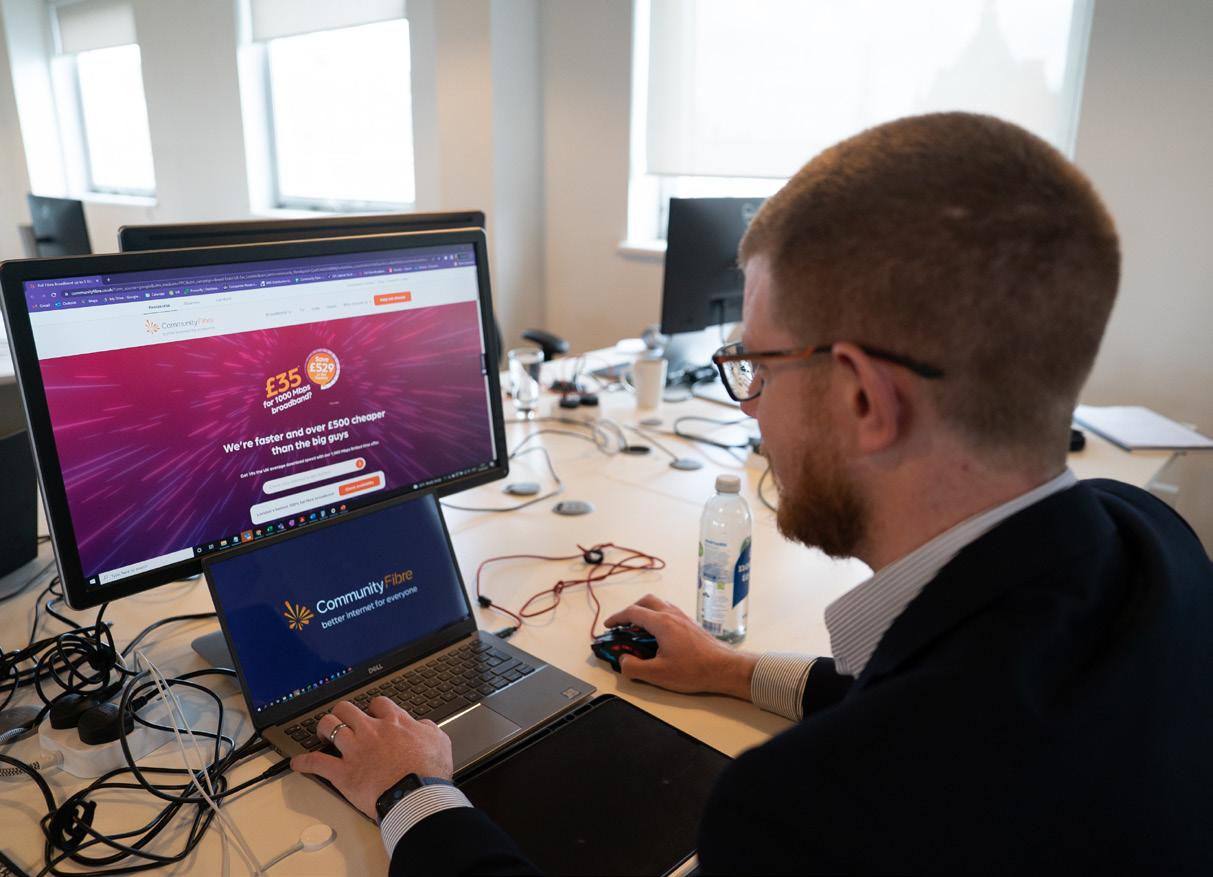
“We’re well on our anmovingtowardswaytoelectricfleet” MIKE BROOMAN HEAD OF SUPPLY CHAIN, COMMUNITY FIBRE Community by name and nature supplychaindigital.com 31
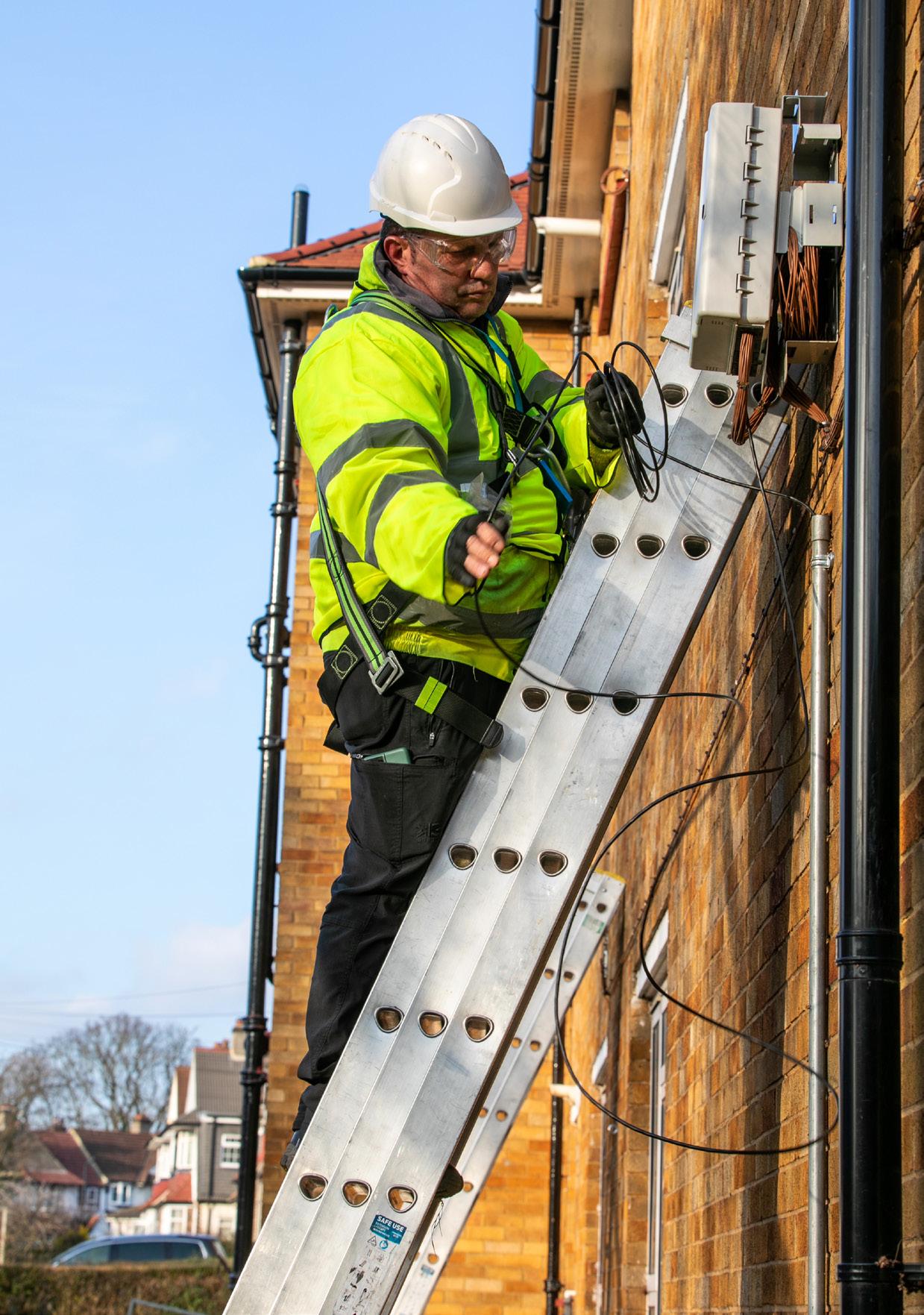
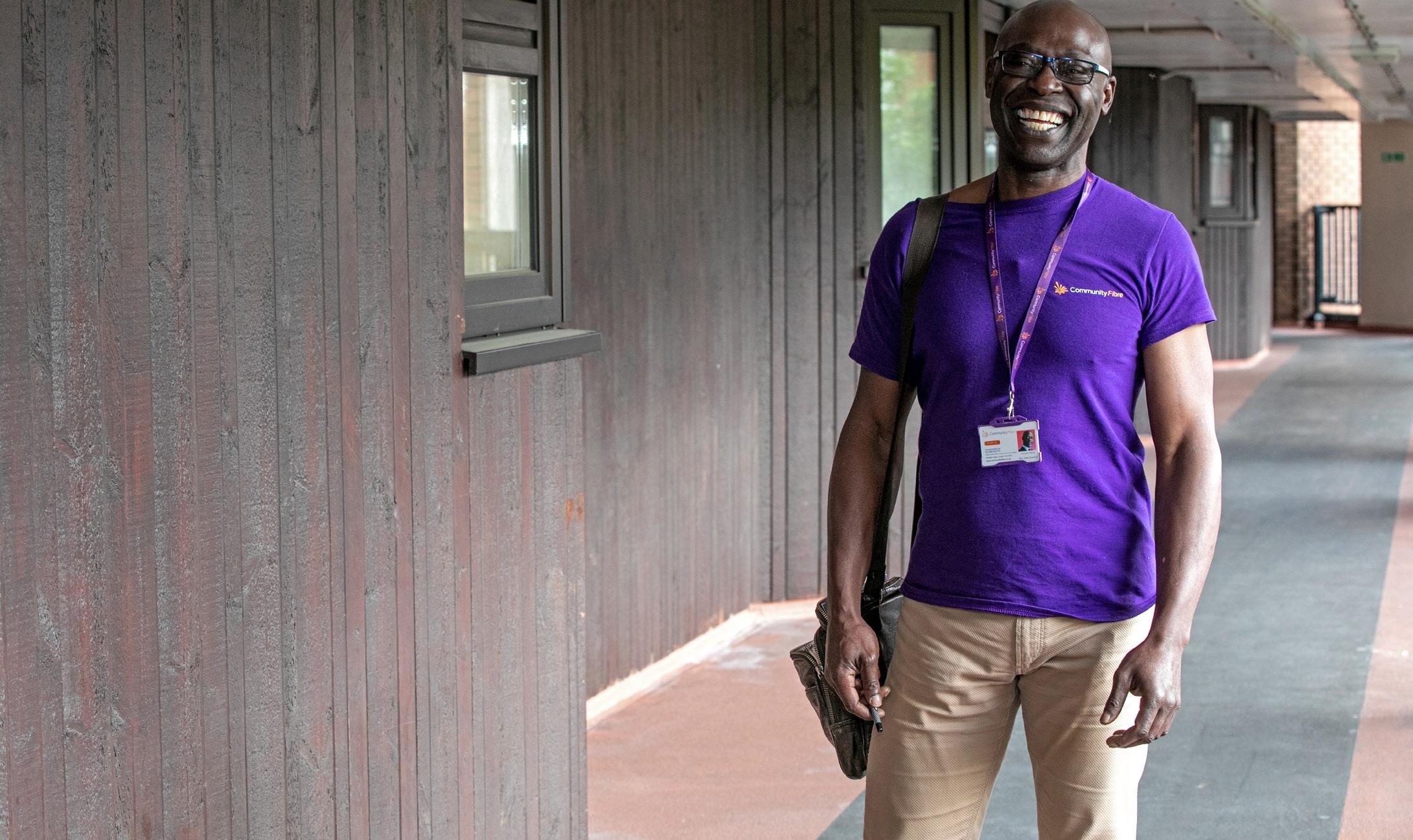
The comprehensive solution for all your telecom and FTTx needs We offer fibre cables and connectivity for every requirement Webro cables and connectivity products support many Altnets and Integrators in delivering FTTx throughout the UK and globally y Cables up to 3456 Fibre y Singlemode G652.D G657.A1 G657.A2 y Overhead, Ribbon, Duct, Microduct, Direct Burial, Armoured, and Last Drop Cables y PIA Approved y Connectivity solutions including Pre-terms, Panels, Closures, Cabinets and Cable Management y Products available up to B2ca for high CPR-compliance areas y Most Products Available from Stock CONTACT US

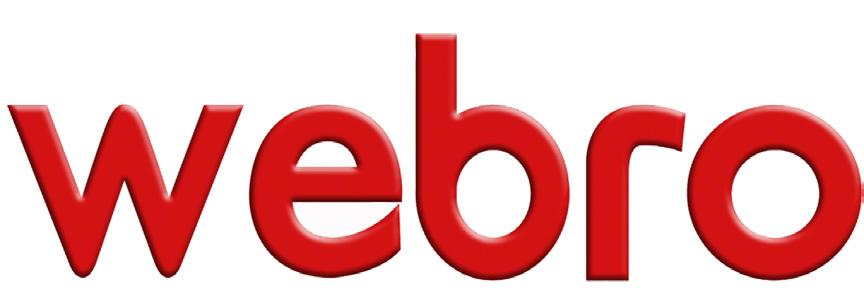

Webro’s future business strategy includes the pursuit of new market areas.
Webro was created in 1980 and is the foremost cable and connectivity provider based in the UK, supplying critical solutions to the wider European market
Chris Bacon is Sales Director of Webro, and has been in the Cable and Connectivity Industry for over 27 years. “I was quite a young man when I started as a Planning Assistant at a local manufacturing company, Raydex, who made cables for communication and RF markets. “Over time, I’ve performed many roles, which have included Technical, Design, Process Engineering, Sales and Business Management.” Webro was created in 1980 as UK agents for Pope. With over 42 years of trading history, Webro has developed business in many different product areas outside of the original wiring, TV and satellite portfolio’s. This includes Industrial, Data, Telecoms, Broadcast, Control and Instrumentation. Webro’s facility, as it stands today, has 4,600SQM of internal warehouse floor space. “Our narrow aisle racking allows us to stack up to four pallets high, resulting in over 18,000SQM of racking storage,” says Chris. “In addition we have over 2,500SMQ of yard space, enabling storage of external product types. With such a large amount of space, our stock value is typically high, helping us to service our customers with ease on a next-day-delivery basis.”
Webro are ISO 14001 certificate holders, so have obligations in terms of Sustainability and Environmental commitments. Chris says, “over the past few years, we’ve adopted the policy of reduction in nonrecyclable plastics.” “In addition, product miniaturisation within select markets will reduce plastic use within both packaging and product manufacture. We’ve also reduced our internal combustion vehicle fleet. Our current profile includes 50% electric vehicles and 25% hybrid, with the long term commitment to completely move away from internal combustion.”
LEARN MORE Webro’s Director Chris Bacon talks Cables and Connectivity



“The company is year-on-year”doublingalmostinsize MIKE BROOMAN HEAD OF SUPPLY CHAIN, COMMUNITY FIBRE 34 July 2022

Plus, the company is almost doubling in size year-on-year, which is compounding these supply problems. Brooman says: “We are enjoying exceptionally fast growth, so forecasting far in advance is obviously prone to errors, which means we have to be flexible and quick to react.”
As such, strong relationships with Community Fibre’s supply chain is vital. “Furnishing suppliers with robust and accurate forecasts as early as we can is important. We try to get products onto a purchase order as soon as we can, to help offset some of the challenges that we're seeing. Purchase orders always trump forecasts,” states Brooman. 29 Community Fibre serves Londoners across 29 boroughs in the capital supplychaindigital.com
35 COMMUNITY FIBRE
Moving from the ‘community’ element of his job to the ‘fibre’ part, Brooman emphasises that the company is facing serious supply challenges, just like everyone else. Strong supplier network vital for Community Fibre Asked what the main challenges are, Brooman says: “We've got the chip-set shortage, which is creating quite an issue for us. Because the big players are taking so much of the supply, we've had to be quite clever about the way that we're ordering. We've seen some lead times in excess of 60 weeks from some of our suppliers, where they were traditionally 12 to 26 weeks.”
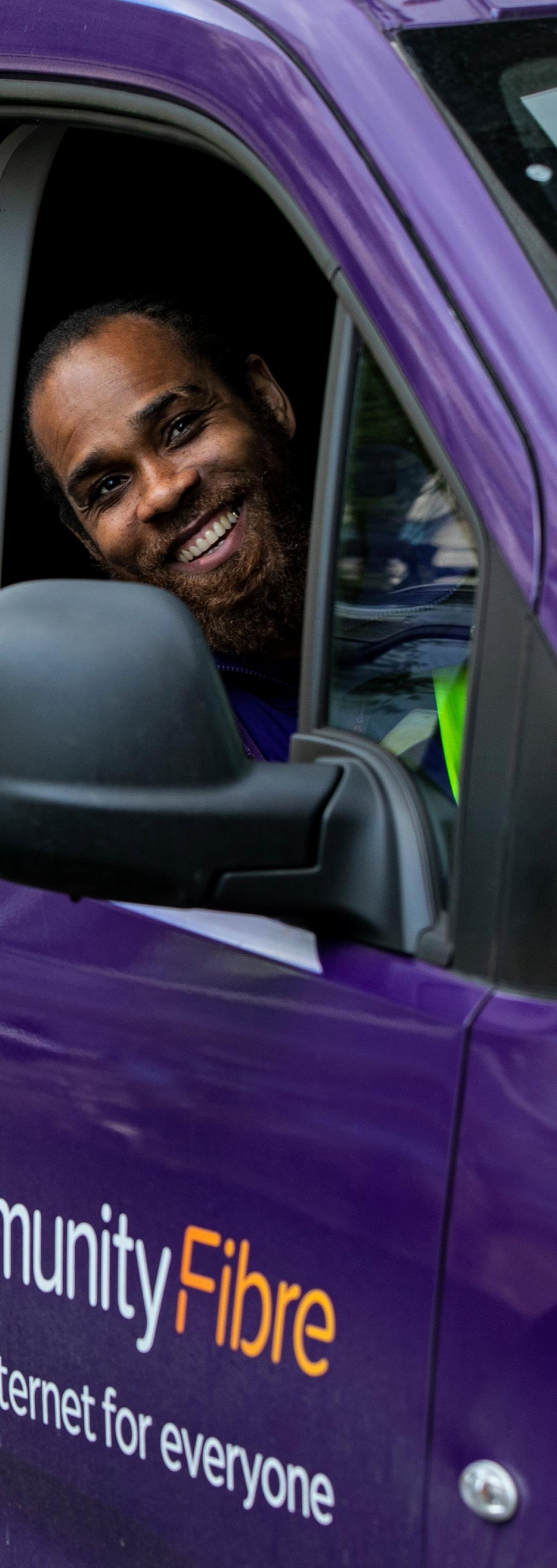




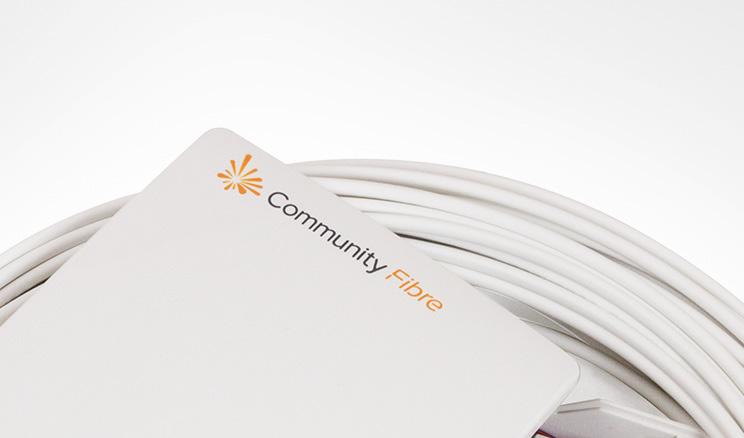

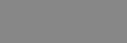

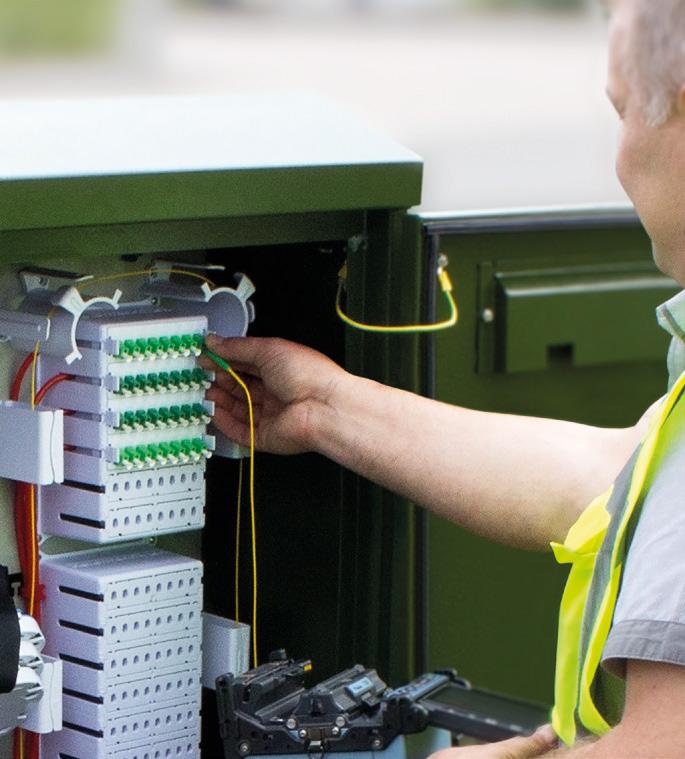
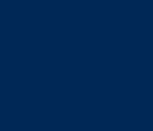

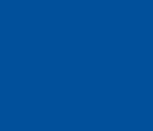
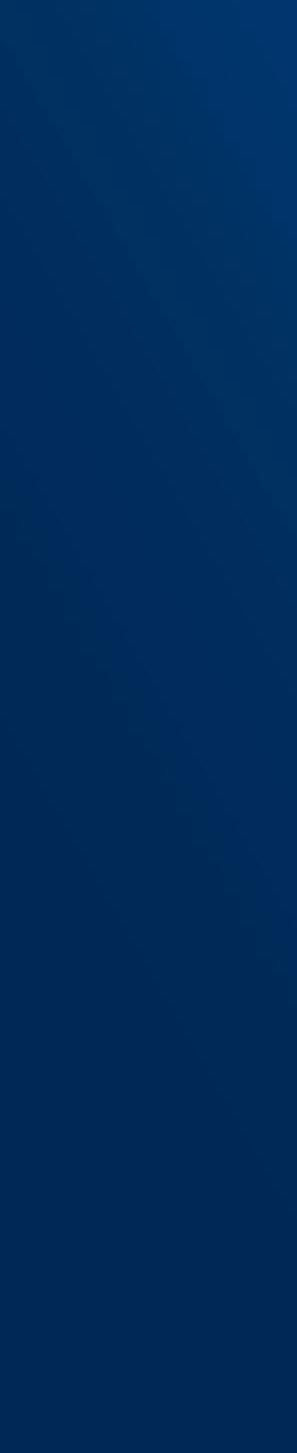
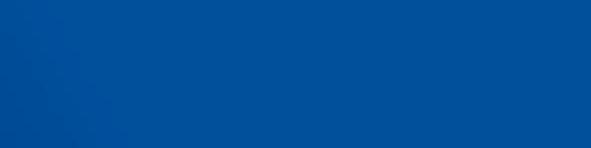
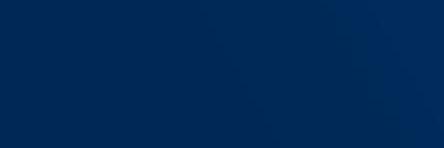
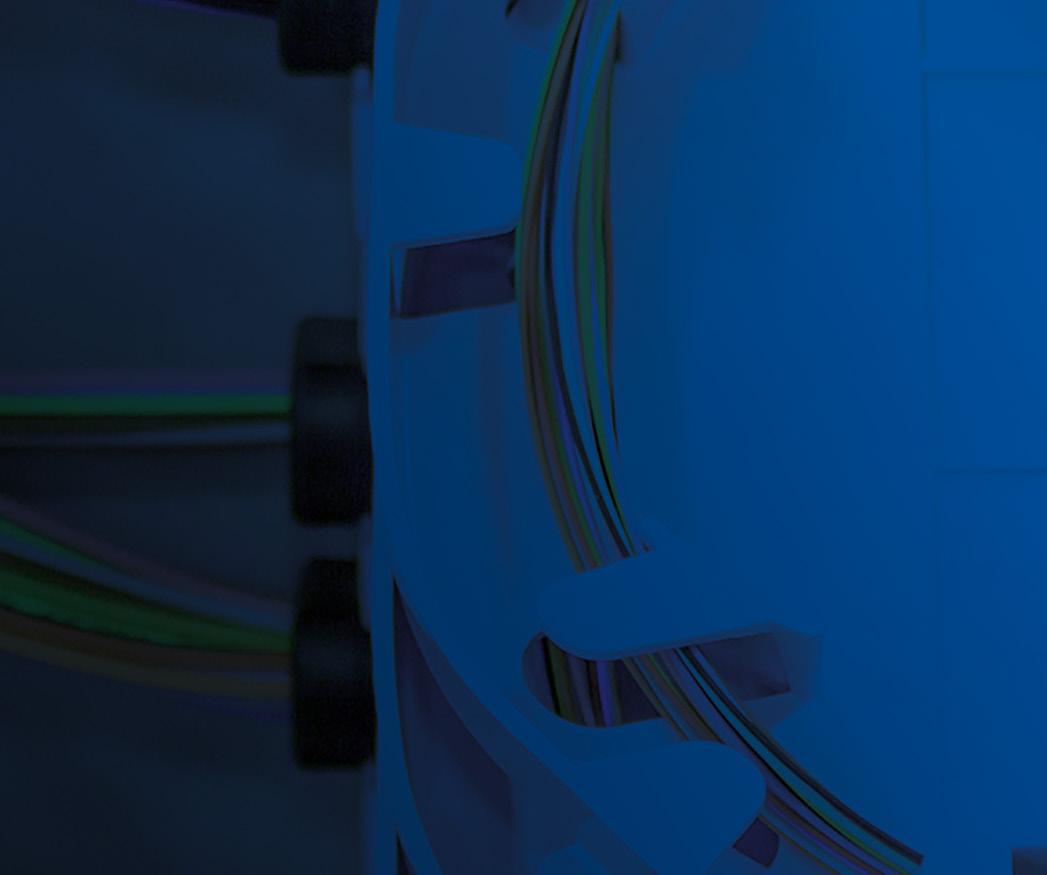

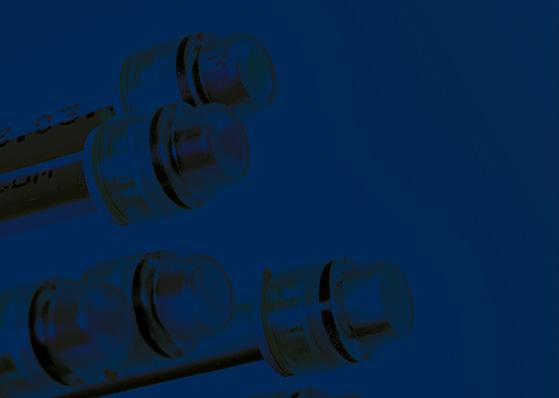



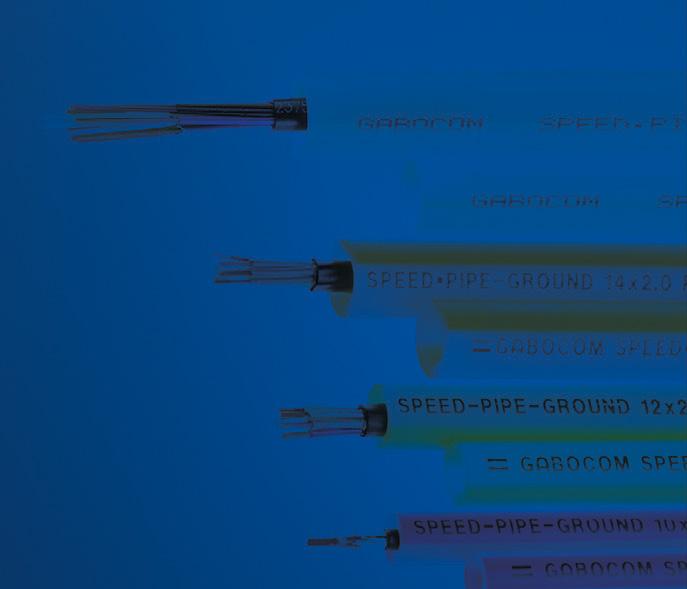
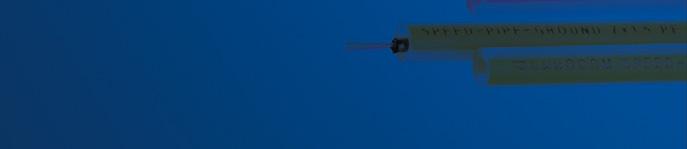

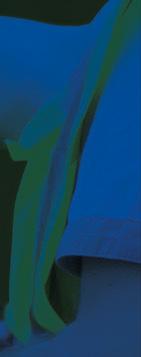
“We've been fortunate enough to be able to get products into the UK and into our warehouses as early as possible,” says Brooman. “So, rather than running as lean as we'd like, we're having to get products in early and stack things high, just to make sure our customers are not let down.”
“Communityisatthecoreofeverythingwedo” MIKE BROOMAN HEAD OF SUPPLY CHAIN, COMMUNITY FIBRE supplychaindigital.com 37 COMMUNITY FIBRE
Securing supply has meant Community Fibre, like so many other companies, has had to move from just-in-time inventory to a just-in-case model.
Community Fibre is growing fast, yet so too is fibre broadband adoption, which brings further pressures to supply. In 2019 London alone, just 6% of homes had a broadband connection; today, Brooman believes around 65% of homes have access to a gigabit connection.
“This means the competition for products is very high,” he says. “So we make sure to secure raw materials
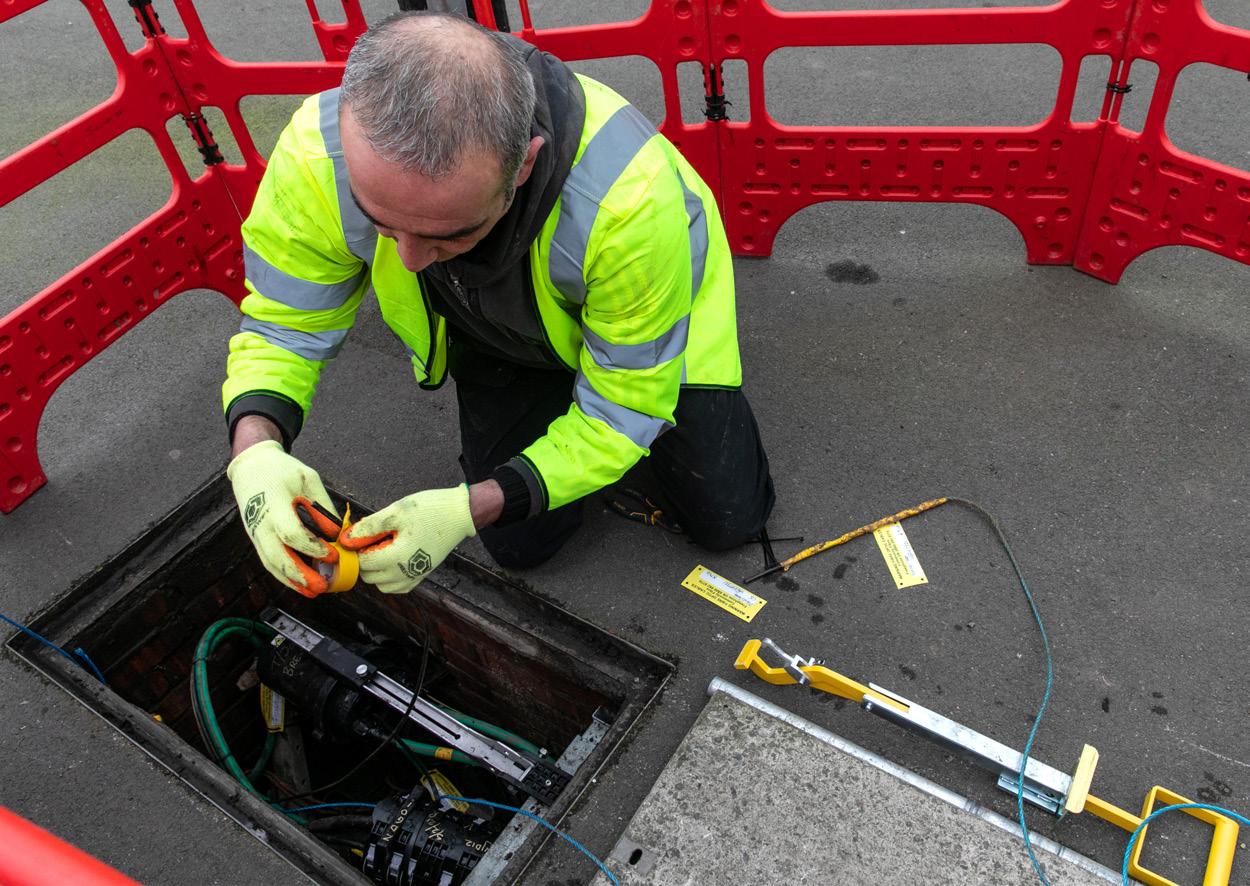
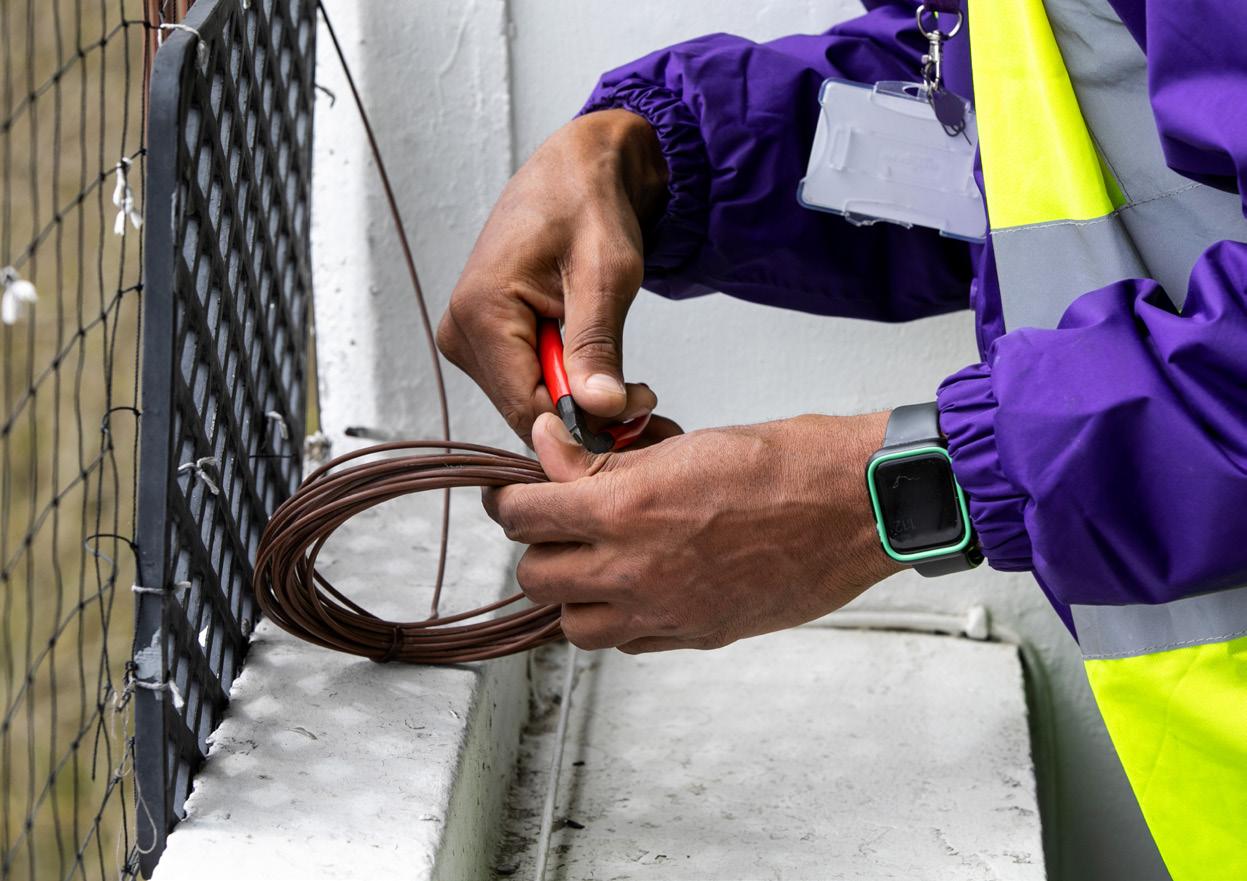
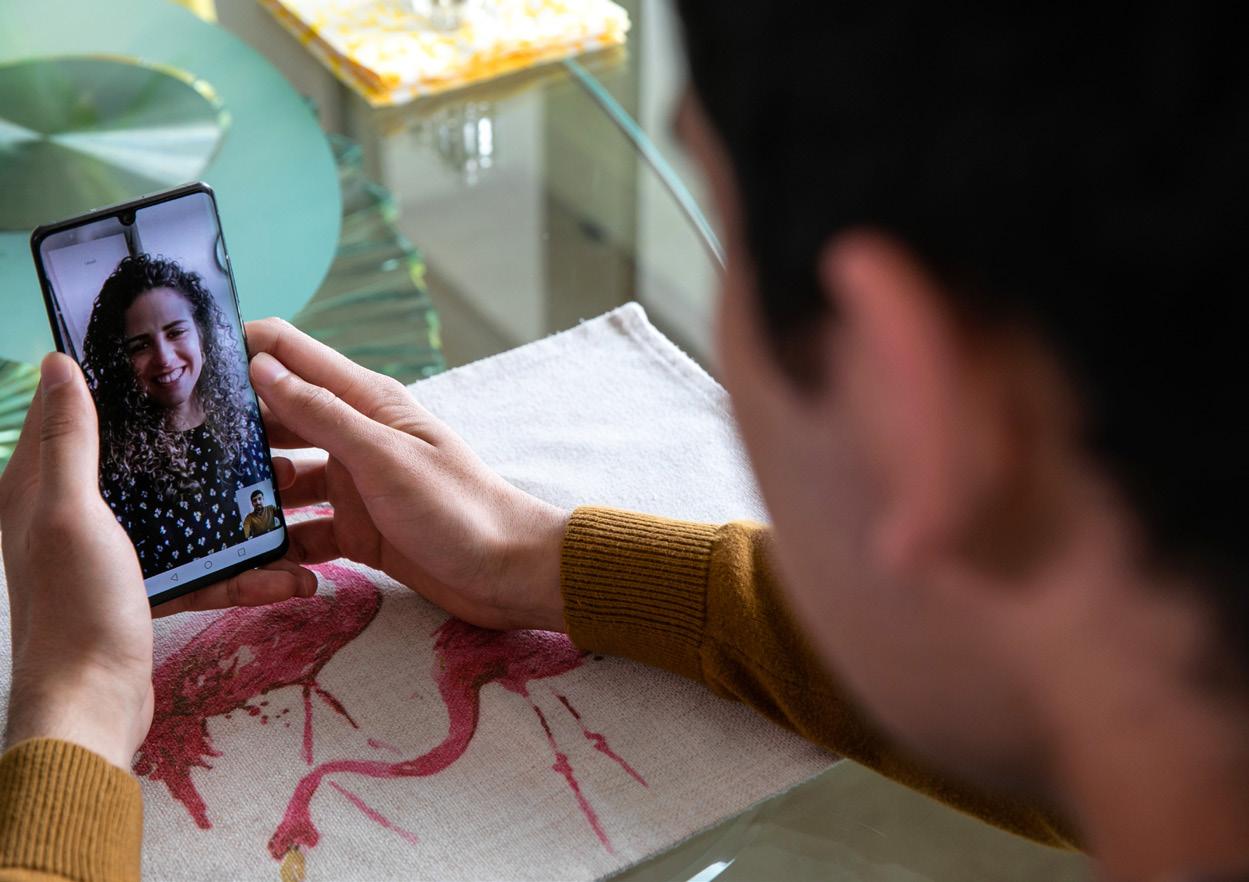
“To this end, Community Fibre is putting training programmes in place to encourage more people into the industry.”
MIKE BROOMAN HEAD OF SUPPLY CHAIN, COMMUNITY FIBRE 38 July 2022 COMMUNITY FIBRE
Community Fibre looks to engage with suppliers who share their values, both in terms of ESG but also, crucially, excellence. But how does it identify such suppliers, exactly?
“It's a tricky one,” admits Brooman. “Our purpose is to provide Londoners with fast broadband at an affordable price, so it's really important our supply chain helps us achieve this.” As it expands its supply chain, the company communicates its story, culture, and purpose to suppliers.
“Everyone is fishing from the same pond, so we work hard with our subcontractor partners to make sure we're a preferred customer. They're not only critical to us being able to deliver our fibre to the homes of Londoners, but also in helping us grow and keep pace with demand.
early, giving our manufacturers order forecasts as early as possible, in order to get products in.” Company training schemes ease struggle for labour Another challenge is the huge demand in London for labour and subcontractors.
“During any request-for-information process, we assess how closely they match our culture,” says Brooman. “It's tricky assessing the culture of a company from a desk-based assessment, but we do all we can to qualify their claims during this process. Plus, we attend trade shows and engage with trade associations in order to widen our supply chain. This allows us to look at a much wider variety of suppliers and hopefully find those that match our values.”
“Every supplier in our value chain is importantancoginthewheel”

Brooman says its supply chain is focused on delivering customer excellence, stating that “they understand the importance of their role in this”. He adds: “They help us deliver excellence in a number of ways, such as subcontractors delivering high-quality assets that give our customers a fast connection.”
Brooman reveals that the company’s materials’ suppliers “are always pushing the boundary of innovation” and that their goal is to “bring the best products to market for our customers”. Every supplier ‘is an important cog in our wheel’ “Every supplier in our value chain is an important cog in the wheel, both in terms of the physical assets customers experience and also in supplychaindigital.com
39
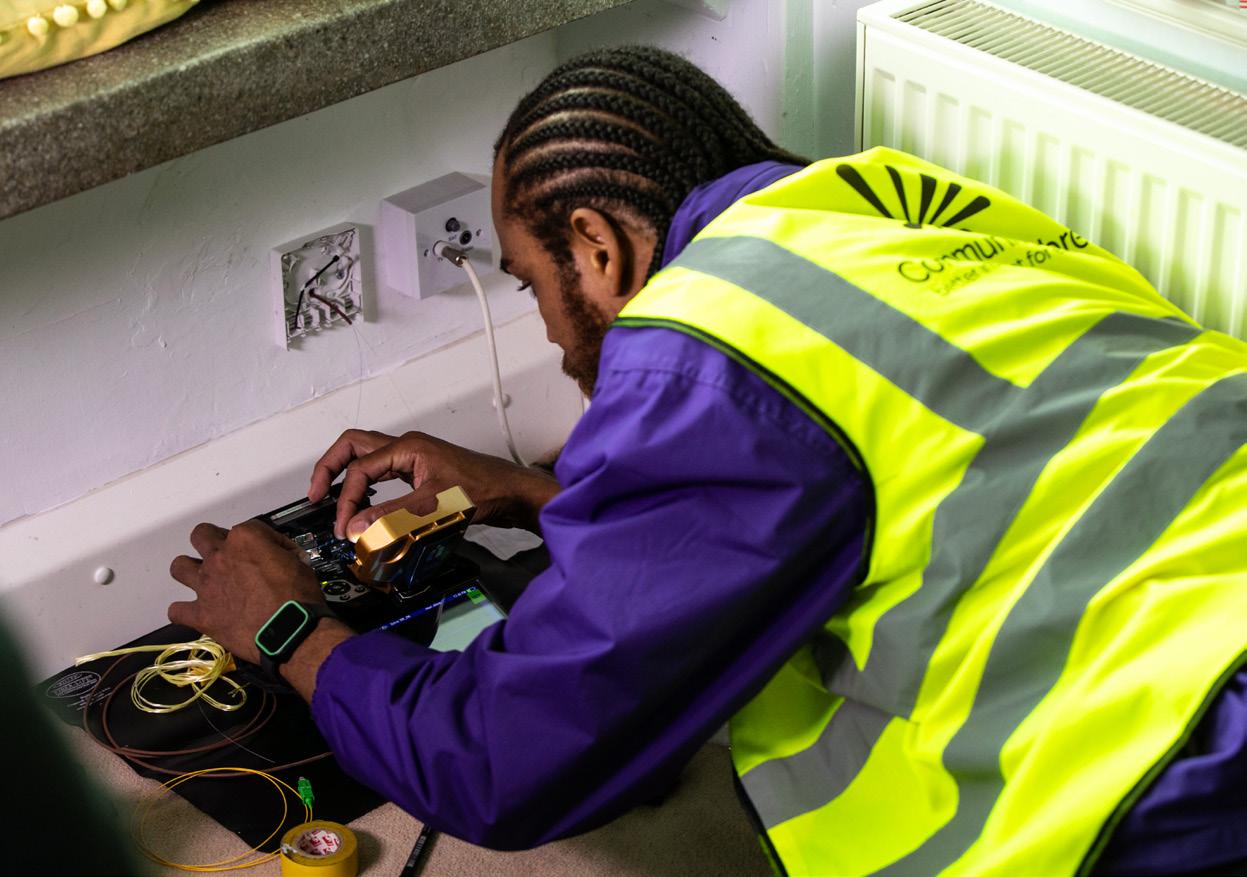

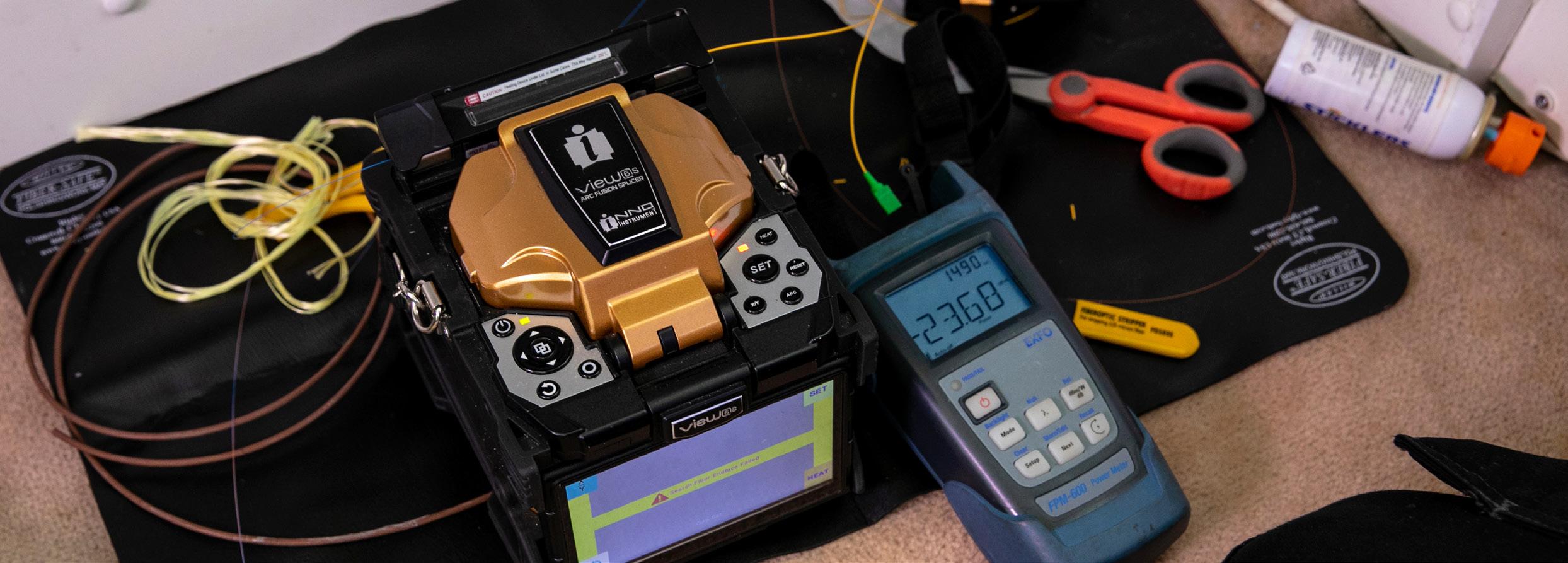
helping us deliver post-installation support,” Brooman asserts. “Because of this, we've got the ability to quickly help customers who are struggling with connection issues by using state-ofthe-art tech products. They're a brilliant addition to our supply chain. They all have a huge role to Collaborationplay.”with suppliers is also absolutely key, according to Brooman, who reveals the company “has a strong collaborative relationship with the majority of our supply chain”. He adds: “We work very closely with our fibre-cable supplier, for example, to ensure they have got visibility on our forecasts, changing demand profiles and bill-of-materials changes. Their factories in Europe are aligned
40 July 2022 COMMUNITY FIBRE
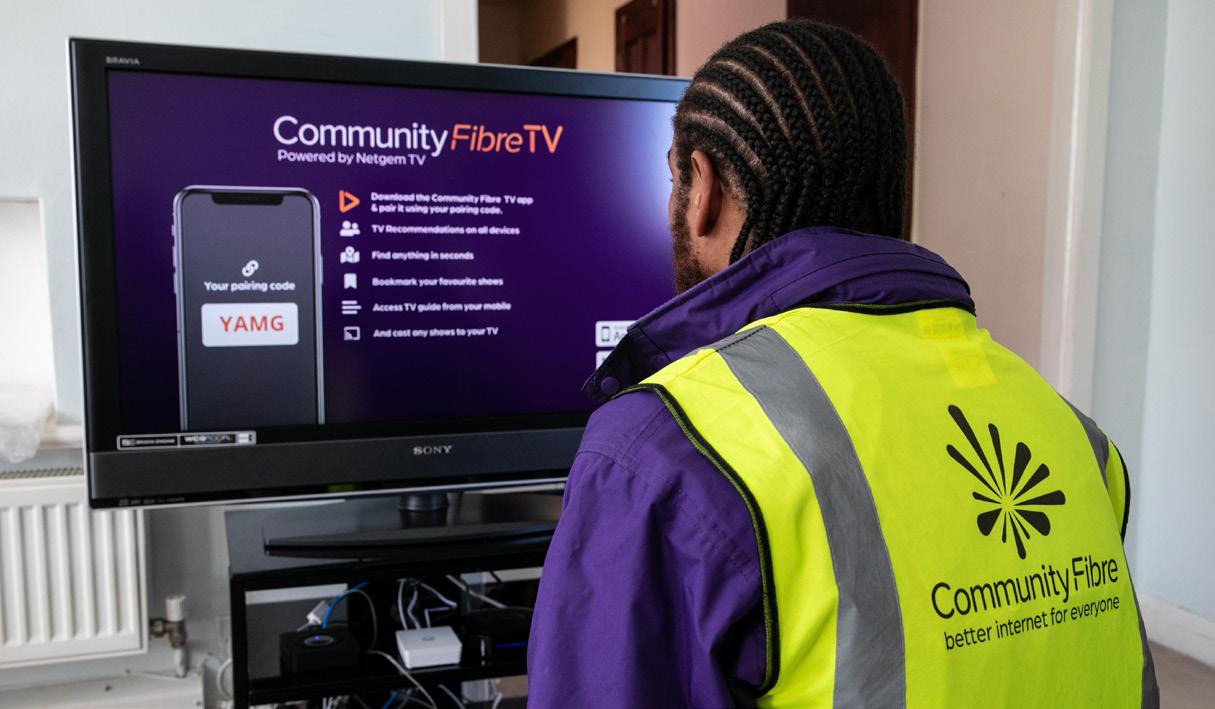
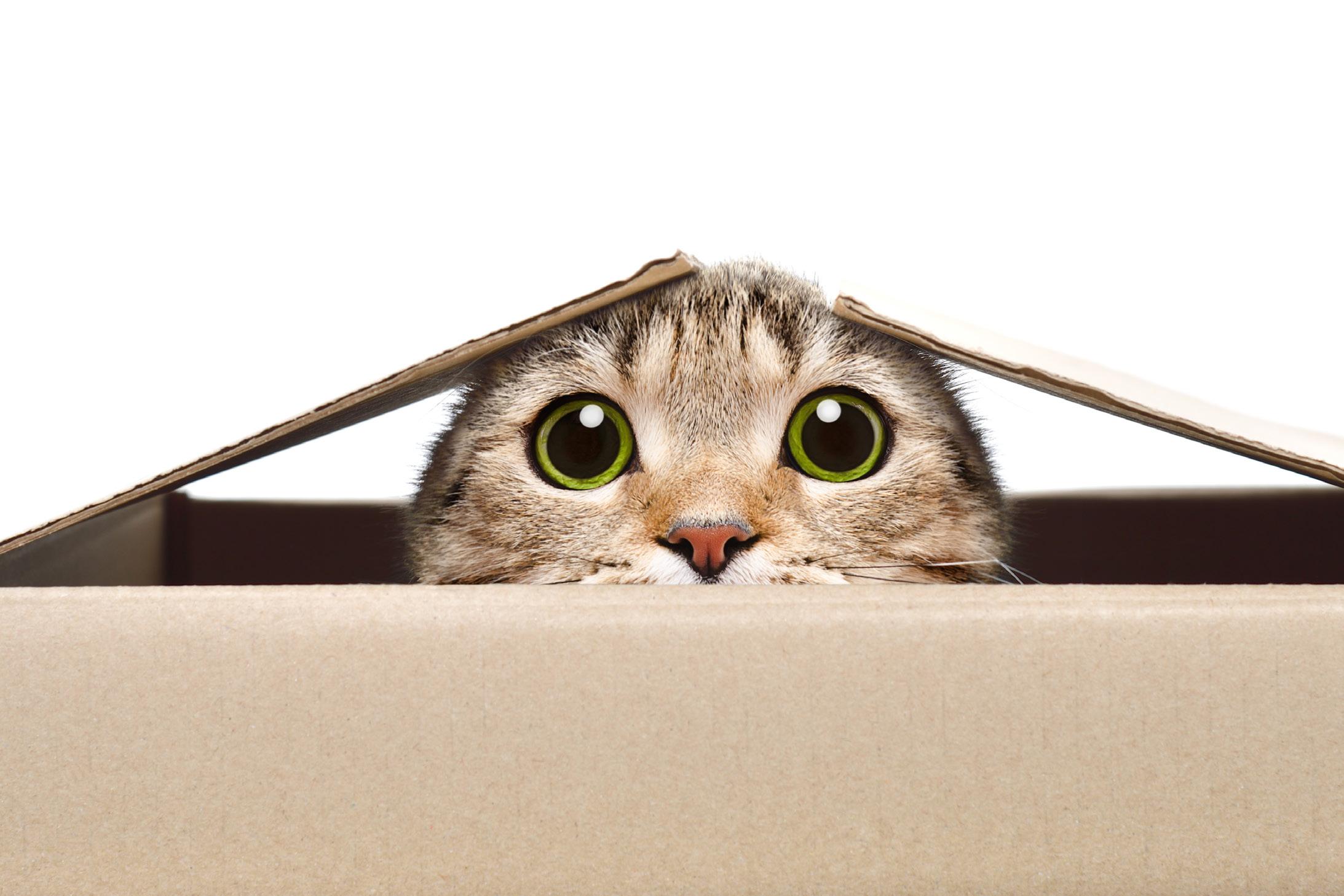
This allows Community Fibre “to roll with the punches”, so to speak. He adds: “We also collaborate with our technical team and other departments internally to bring new, improved solutions to market.”
From its cables under Londoners’ feet and training programmes to the community hubs across the capital that enjoy free broadband, Community Fibre is living up to its name in every conceivable way.
with our demand. They hold our stock and product in expectation of any kind of microvariations of expected build forecasts.”
supplychaindigital.com 41 COMMUNITY FIBRE
By way of example, Brooman says the company recently made a decision to upgrade its fibre cable to the ‘armoured’ variety, which reduces the damage from customers accidentally vacuuming the cables or causing damage in other ways.
“We collaborate with our technical team and other departments internally to bring new, improved solutions to market”
MIKE BROOMAN HEAD OF SUPPLY CHAIN, COMMUNITY FIBRE


TRUST TO FUTURE SUPPLY 42 July 2022
He says: “In my opinion, traditional supply chains will become more like private trading networks. In traditional supply chains, suppliers typically have visibility one layer up and one layer down.”
To be optimally effective, SCM software requires that data is shared between vendors in a value chain – sensitive data, concerning inventory levels, demand forecasts, customer orders and delivery information –and data scandals in recent years have made firms wary.
igitalisation of the supply chain was already well underway before COVID-19 struck, but the pandemic – and its attendant disruptions – has rapidly accelerated the process. It did so because crisis-hit organisations realised that building resilience and agility into their supply chain was a matter of urgency; indeed, war in Ukraine has only served to stoke the coals of this fact. Supply Chain Management (SCM) solutions are all about data-driven visibility, which allows businesses to predict disruption, and to plan around it.
Trust ‘will be issue’ on data sharing – UST’s Colehower Jonathan Colehower, global supply chain strategy practice lead at digital transformation specialist UST, says modern supply chains are more network-based than in pre-pandemic times, and that it’s this change that goes to the heart of the trust issue.
WRITTEN BY: SEAN ASHCROFT
Yet there’s a thorny issue at the heart of the digital transformation of supply: trust.
supplychaindigital.com 43 SUPPLY CHAIN
At UST, Colehower says they are fashioning “many-to-many trading networks that are permission-based”. Digital transformation and increasingly complex value chains will see the supply chain management solutions of the future being built on trust IS KEY
SUPPLY CHAIN MANAGEMENT
D
Making forAskdrivenAskintoresilience,excellence,tocustomer-suppliershiftSuppecoMeasurableValuedeliversaparadigminB2Battitude-leveragingrelationshipsdrivecollaborativeperformancerelationshipdrivenandsustainabilitydeeptheecosystem&supplychain.usaboutcollaborativerelationshipco-resilience.usaboutoperationalcompliancesustainablesupplychain. BOOK A DEMO


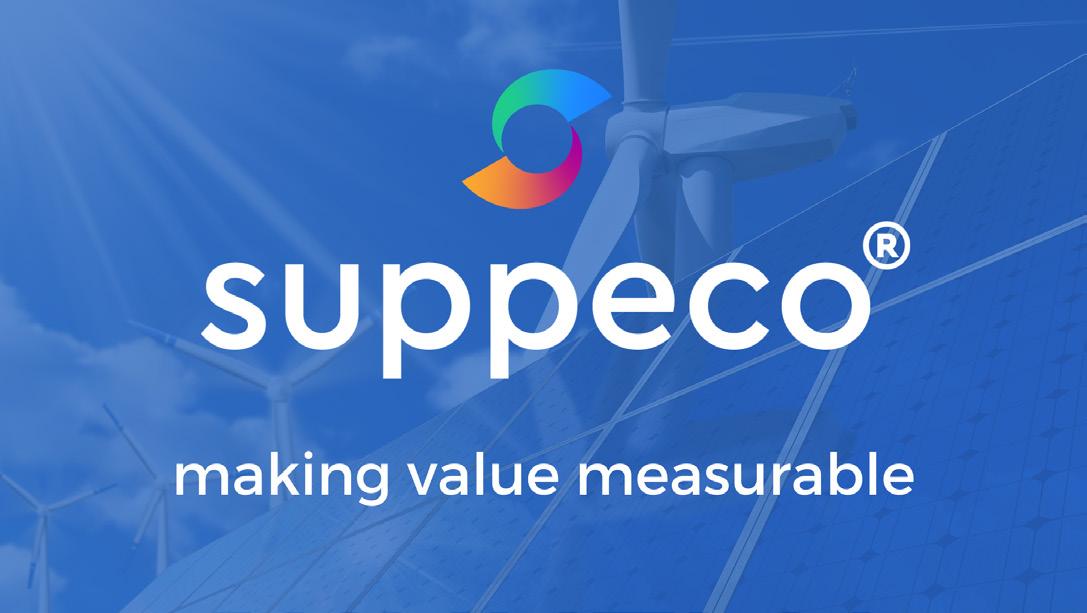
JONATHAN COLEHOWER, GLOBAL SUPPLY CHAIN STRATEGY PRACTICE LEAD,
Synder believes that data sharing will deliver value, while still respecting data privacy, and says that as artificial intelligence and real-time technologies are adopted
Data sharing will feature in SCM solutions of the future
“Traditional supply chains will become more like private trading networks”
Wayne Snyder – VP of retail industry strategy
“This means you can turn visibility on and off, depending on who the actors are, because you don't want every supply chain actor to see what everybody else is doing.
supplychaindigital.com 45 SUPPLY CHAIN
EMEA at Blue Yonder, one of the world’s leading supply chain management companies – agrees that data sharing will become a more common feature of SCM solutions.
“We harvest data from many internal and external sources but currently do not share data across our customers. However, we foresee that in the future more retailers will look to share data to help deliver better insights.”
“One of the biggest challenges for such networks will be trust. Will trading partners trust one another enough to shareColehowerinformation?saysit will take a “pioneer” to help establish such trust-based networks: “It's going to take somebody who's comfortable and confident in that supply chain, who are willing to share, and who can actually demonstrate what the results are.” UST

“It’s imperative that businesses do not choose to stick with legacy SCM software, rather than upgrade,” he says, adding: “Companies must adopt the latest technology to support operations, resolve disruption and minimise risk, because supply chain challenges look set to continue.”
He adds that recent Blue Yonder research found that just 3% of organisations have escaped supply chain disruption in the past 12 months. Crucial to leverage AI and ML, says Blue Yonder Synder believes that, to stay ahead of today’s supply chain complexities and effectively manage their priorities, organisations must be able to plan intelligently, while having the visibility and flexibility to respond at pace.
He points out that the Suez Canal blockage in March 2021 showed precisely how companies can overcome disruption by utilising such tools.
optimise actions, and it needs to be built into both short and long-term strategies.”
“This can only be achieved by having a real-time, end-to-end view of the supply chain,”he says. “This will leverage technologies such as AI to recommend and
WAYNE SNYDER VP RETAIL INDUSTRY STRATEGY EMEA, BLUE YONDER
“there will be opportunities to glean intelligent analysis and insights to improve business operations and efficiency”.
“The adoption of AI and ML remains too low, due to unfounded concerns around control”
46 July 2022 SUPPLY CHAIN
Snyder says the use of AI and machine learning (ML) to predict demand, optimise inventory and resolve issues at pace have proven critical over the past two years. “Improved decision-making – alongside better predictability, real-time insights, and tracking through IoT – are transforming the supply chain minute by minute,” he says.
On SCM solutions, trust is an issue for the future, according to Snyder, whereas an issue at present is that businesses cannot afford to drag their feet on digitalisation.
The positive news, believes Snyder, is that organisations clearly understand the impact of disruption and, as such, are proactively managing concerns by investing time and resources in the supply chain.
The report says: “By using machine learning, AI, and IoT to enhance delivery chain transparency, supply chain leaders can improve time-tomarket and widen their product ranges andTheservices.”reportalso said that companies adopting cloud-based SCM solutions are concerned about privacy and cybersecurity issues, with one concern being that corporate data can be leaked on the internet and viewed by unauthorised users.
supplychaindigital.com 47
A report from market insights company Verified Market Research shows that the supply chain management (SCM) market is projected to reach US$19.3bn by 2028.
The report says that the demand for enhanced supply chain visibility is the main driver of growth in this market.
The report said: “Businesses with confidential data need to be protected to avoid data breaches and theft, as this can affect a business's reputation “Unauthorised user-data access can threaten a company's competitive position. Such security issues are one factor that is hampering the market growth of the SCM Market.”
“Those that had adopted controltower technologies were able to quickly understand which ships, containers and products were impacted, and then evaluate required mitigations. This was not possible for those that managed their supply chains through legacy systems and disparate spreadsheets.”
As well as Industry 4.0 tech, the report noted that other growth factors were cloud computing, 5G, blockchain, and 3D printing.
SCM market ‘will be worth $19bn by 2028’
“The only way to satisfy customer demand is by investing in your systems, people and processes”
48 July 2022
WAYNE SNYDER VP RETAIL INDUSTRY STRATEGY EMEA, BLUE YONDER
49 SUPPLY CHAIN
He adds: “Yet those companies that are not choosing to adopt this technology into their operations are allowing their competitors who are to move ahead, because such technology is providing them with the answers and optimum responses to today’s supply chain challenges.”
“For many, this is due to unfounded concerns around control,” explains Snyder.
“The only way to overcome this and satisfy customer demand is through investment in your systems, people and processes,” he advises.
Snyder recognises that investment decisions “are never easy”, and that a focus for many business leaders today is short-term cost reduction, in the face of inflationary pressures. “But the supply chain must remain a priority,” he warns. “Not only to help deliver some of those cost reductions through better efficiency and availability, but also because it is becoming a strategic differentiator.”
“Research shows that 83% of organisations have increased investment in the supply chain over the past 12 months. Technology is the common factor when it comes to such investment, with companies realising throughout the pandemic that the supply chain must be at the heart of their operations; it’s become crystal clear that the required technological investment must follow suit.” Too many firms dragging feet on Industry 4.0 techs Snyder feels that, although investment in tech is riding high, too many SCM solution upgrades fail, because the adoption of AI and ML technologies remains too low.
supplychaindigital.com
Snyder says that intense competition, the need for fast delivery, and the increasingly complex omni-commerce world continue to create obstacles for retailers.
WORLD’SSUSTAINABILITY BREWER, 50 July 2022 PRODUCEDBY: BENWIGGER WRITTENBY: SEANASHCROFT BUDWEISER BREWING GROUP

ABINBEV, IN SUSTAINABILITY VANGUARD WORLD’S LARGEST BREWER, supplychaindigital.com 51
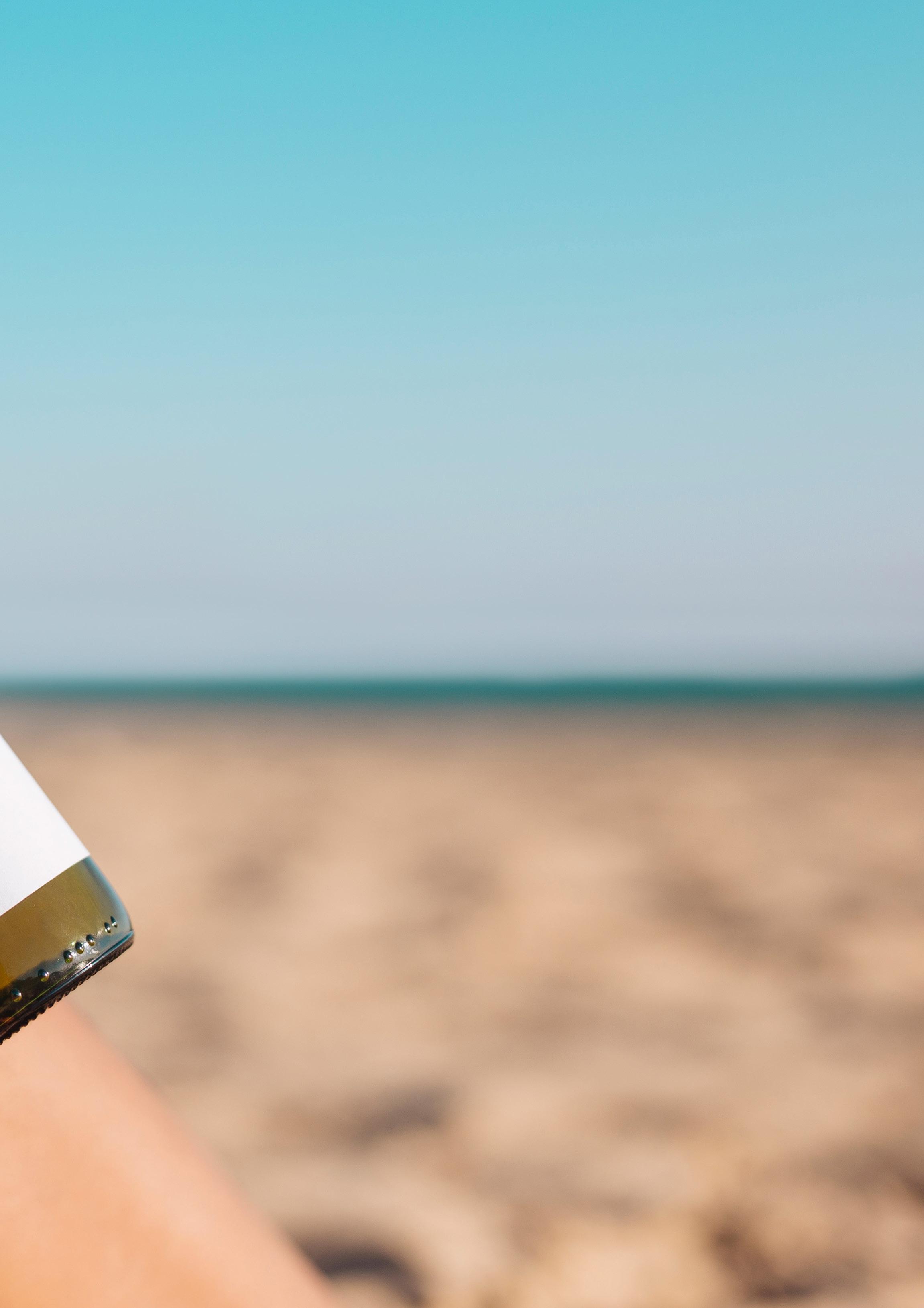
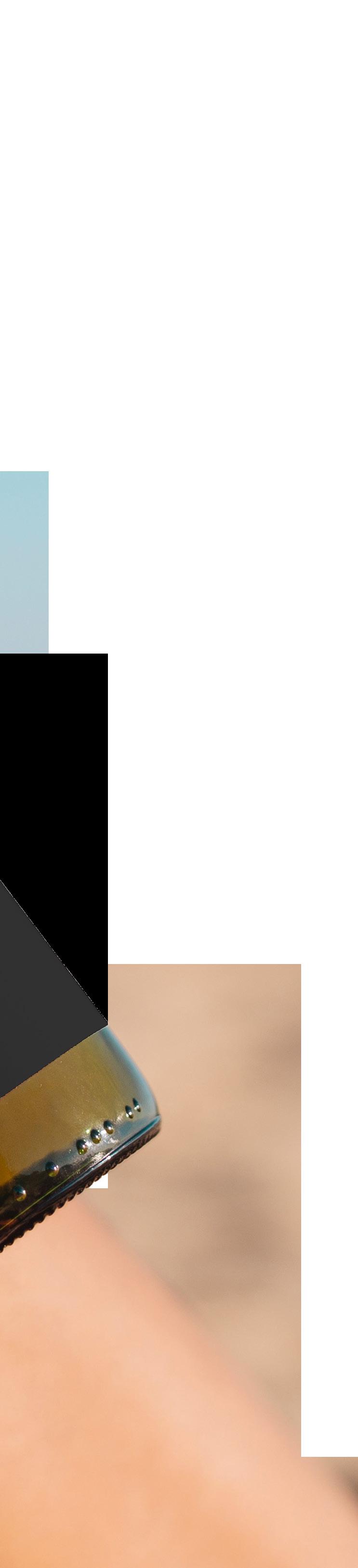
52 July 2022 BUDWEISER BREWING GROUP
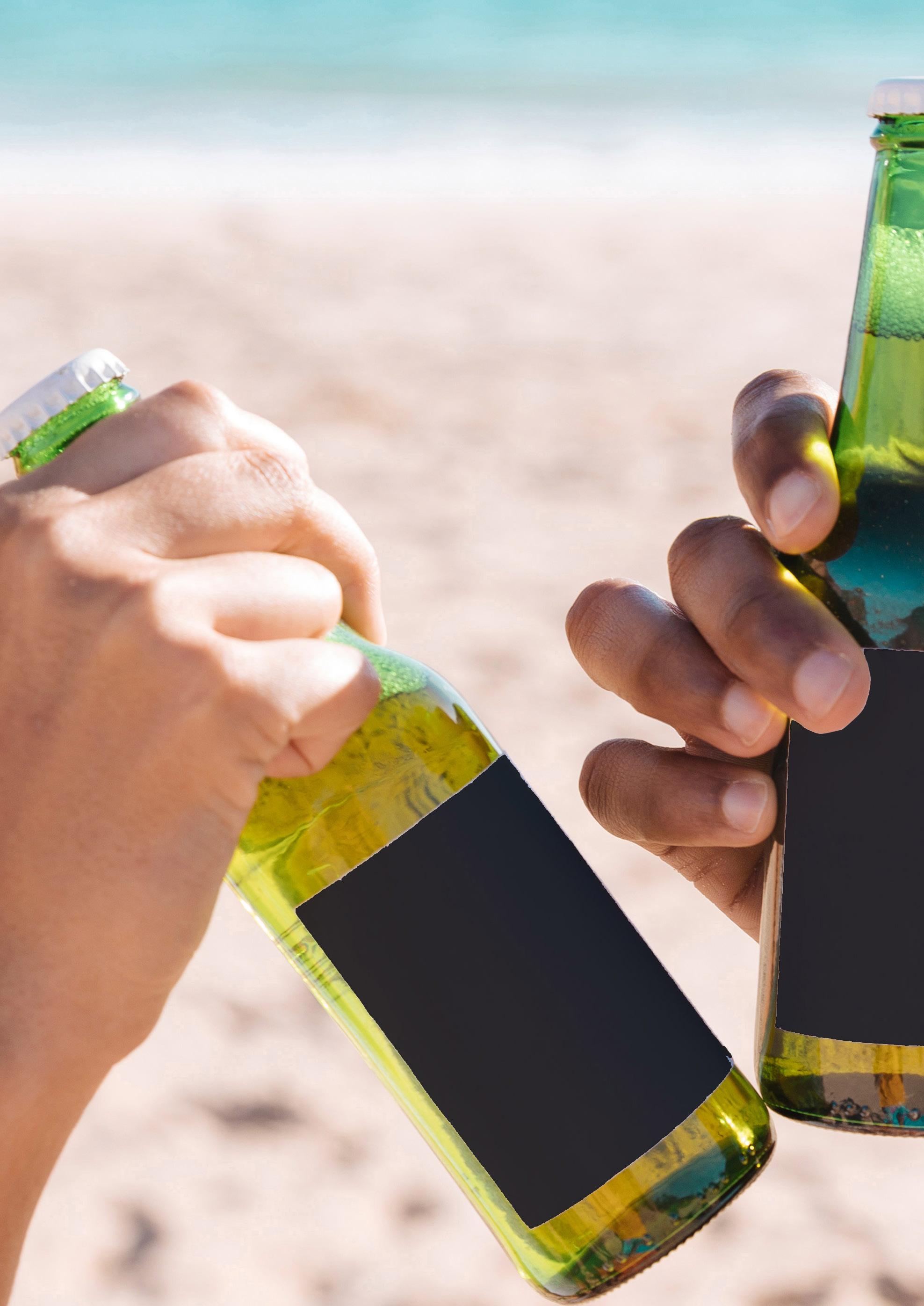
Budweiser Brewing Group is meeting goals on sustainability, with ambitious measures on water use, agriculture and renewable energy A nheuser-Busch InBev (AB InBev) is the world’s largest brewer, both by volume and revenue. A truly global company with local brewing operations across 150 countries and 170,000 staff worldwide. Businesses don’t get much bigger, and neither do sustainability undertakings. AB InBev was formed in 2008, when Budweiser brewer Anheuser-Busch joined with Stella Artois-maker Interbrew and Brazil’sBudweiserAmBev.Brewing Group (BBG) UK&I remains a proud part of AB InBev globally. In the UK, BBG Budweiser Brewing Group employs 1,400 people in its three breweries in Magor, South Wales, Samlesbury, Lancashire and Enfield, North London and in its local headquarters in central London. The organisation continues to grow, following acquisition of a number of US and international craft brewers, including Goose Island, Blue Point, and Camden Town Brewery and is innovating and growing the Beyond Beer category.
supplychaindigital.com 53
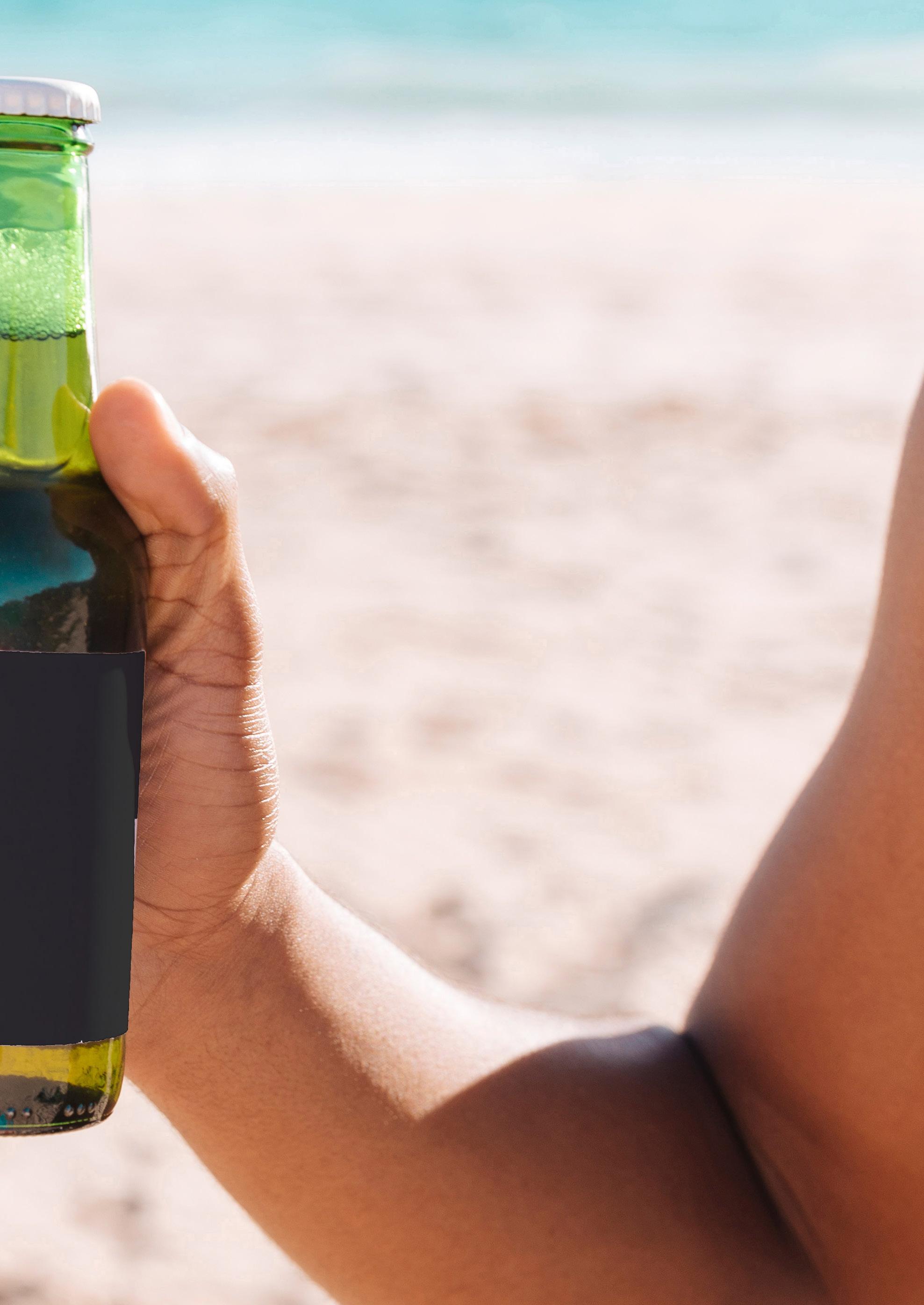
As a member of the Science Based Target Initiative and a signatory to the UN Global Compact and its sustainable development goals, EV Cargo has powered the introduction of sustainable initiatives for many of its key customers to help reduce carbon emissions associated with their distribution operations.
Helping to
decarbonise customer supply chains @EVCargowww.evcargo.com
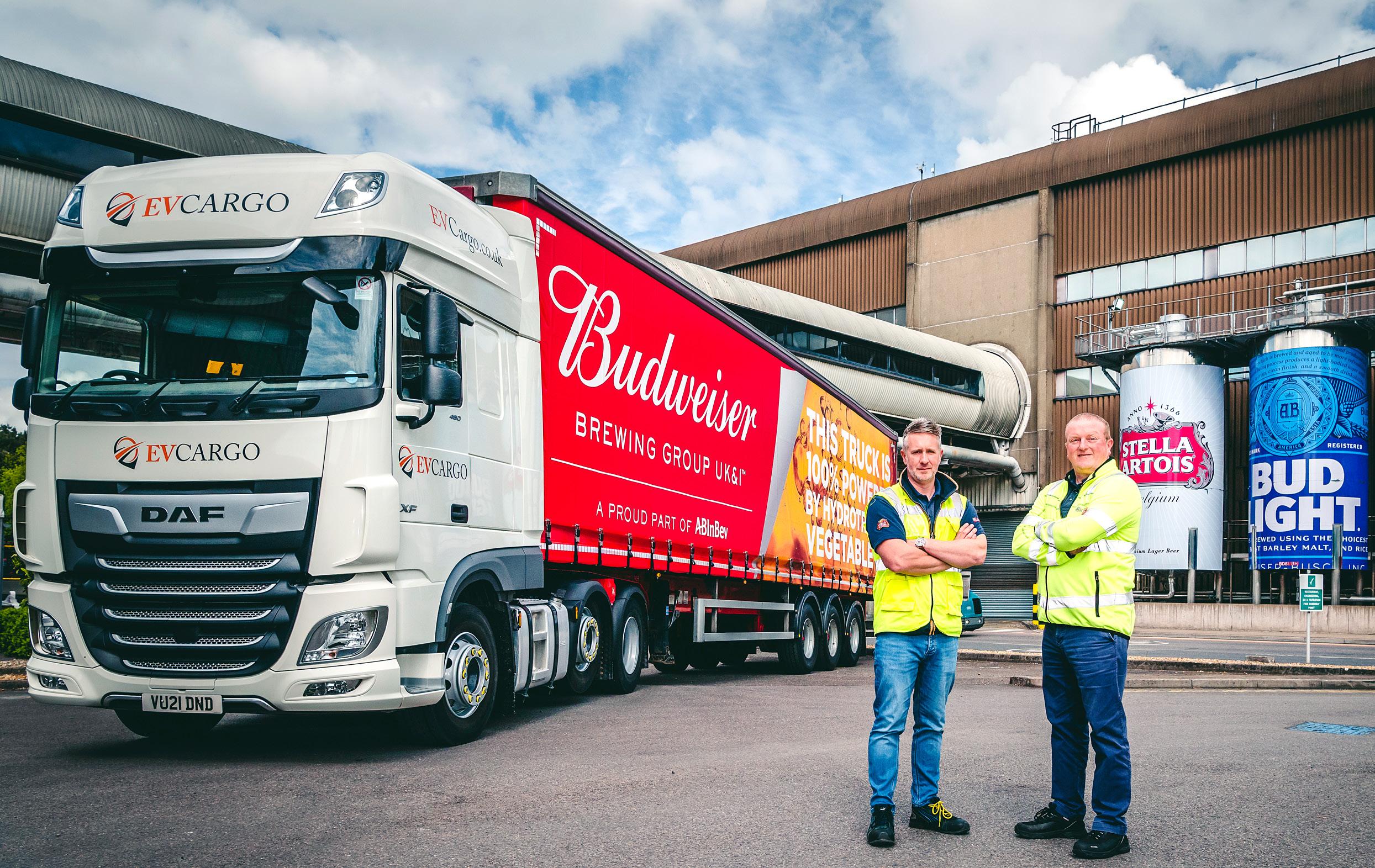
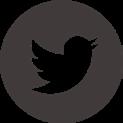
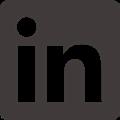

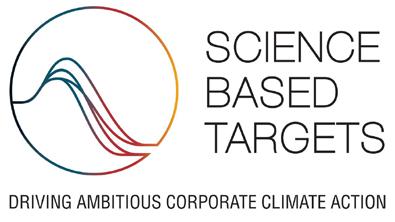

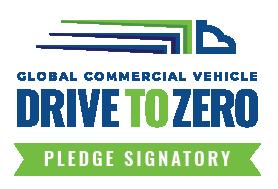
Debbie Oram, Account Director at EV Cargo, discusses its partnership with AB InBev, which is driving sustainable transport of the brewer’s products
Debbie Oram, Account Director at EV Cargo, explains the company’s focus on sustainability, the support for its partnership with AB InBev and how it has helped reduce carbon emissions associated with the brewer’s distribution operations. Oram oversees the account for AB InBev at EV Cargo, which covers logistics and warehousing solutions in the UK, global supply chain management and related technology solutions for the world’s leading brands. EV Cargo promotes a sustainable future Sustainability has become embedded in the organisation’s overall operation and is driving its work with partners. “Our sustainability strategy is driven from the top, with CEO Heath Zarin and the sustainability committee responsible for all sustainability practices,” says Oram.
EV Cargo is a signatory to the UN Global Compact and supports the UN’s Sustainable Development Goals. It endorsed a global memo of understanding at COP26 to achieve 30% zero-emission new truck sales by 2030, increasing to 100% by 2040. It is participating in the UN’s Science Based Targets initiative for reducing emissions and committing to targets that will help limit global warming. EV Cargo is aiming to achieve carbon neutrality across Scope 1 and 2 emissions by 2030, by implementing an ambitious decarbonisation roadmap. As a critical logistics partner of AB InBev, EV Cargo carries more than 65% of its current capacity across the UK. “EV Cargo led the introduction of hydrotreated vegetable oil (HVO) fuel, a direct replacement for traditional diesel, at Budweiser Brewing Group UK&I, part of AB InBev. Distribution trucks at Budweiser’s Magor brewery in Wales switching to the replacement fuel delivered an immediate 92% reduction in CO2 emissions,” says Oram. Learn more
The consumer goods industry is increasingly reliant on logistics and, with almost a third of global greenhouse gas emissions coming from transportation, this is a major area to be decarbonised to meet climate change targets.
EV Cargo initiatives drive decarbonisation of AB InBev distribution
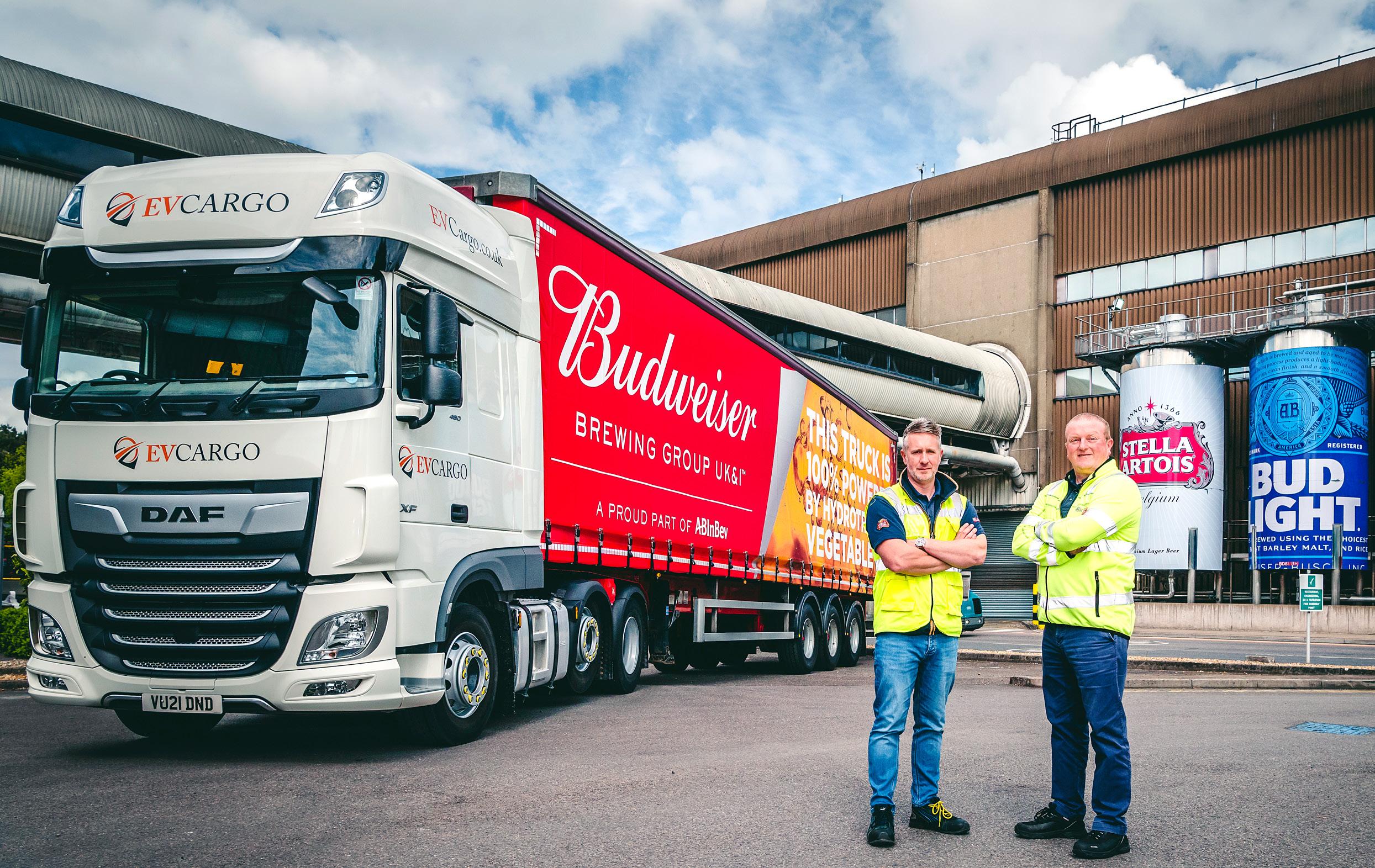
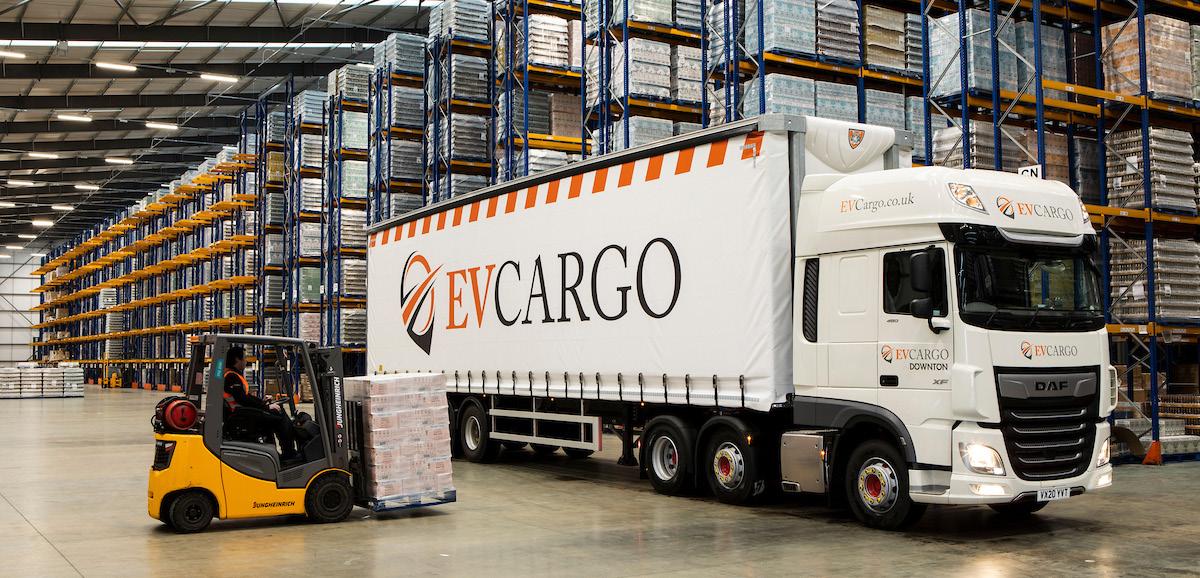
Packaging biggest sustainability challenge for Budweiser Brewing Group Coindreau says the biggest sustainability challenge faced by BBG is its packaging, which accounts for almost 40% of its total CO2 emissions. In 2021 it went 100% plastic ring free and there are ongoing projects to minimise plastic in tertiary.
AB InBev’s global headline targets on sustainability were set as far back as 2017, and it aims to achieve these by 2025. Its goals in this area comprise four pillars: Packaging, CO2 Emissions, Water, andInAgriculture2021,following the COP26 United Nations Climate Change Conference, it set out a new goal: to become net-zero by“We2040.want to lead by example,” says Mauricio Coindreau, Head of Procurement and Sustainability for Budweiser Brewing Group (BBG), the UK arm of the business.
“We're looking to become the first major brewer to have carbon neutral operations in all of our breweries in the UK in 2026. We're looking at many different ways to achieve that commitment.” One of those ways is through renewable electricity. In 2019 BBG signed the largest private solar power deal to build solar farms which now, in combination with the wind 56 July 2022
BBG is also investing in new technologies, such as green hydrogen with plans to build a first of its kind green hydrogen plant to power brewing and logistics. Already there is a comprehensive program of projects to reduce brewing emissions, including the world’s largest wort cooler at its brewery in Wales.
turbine constructed near their Magor site, meaning all beers are brewed with 100% renewable electricity. Its investments in renewables mean BBG produces more electricity than it needs, which has enabled it to donate to good causes.
BUDWEISER BREWING GROUP
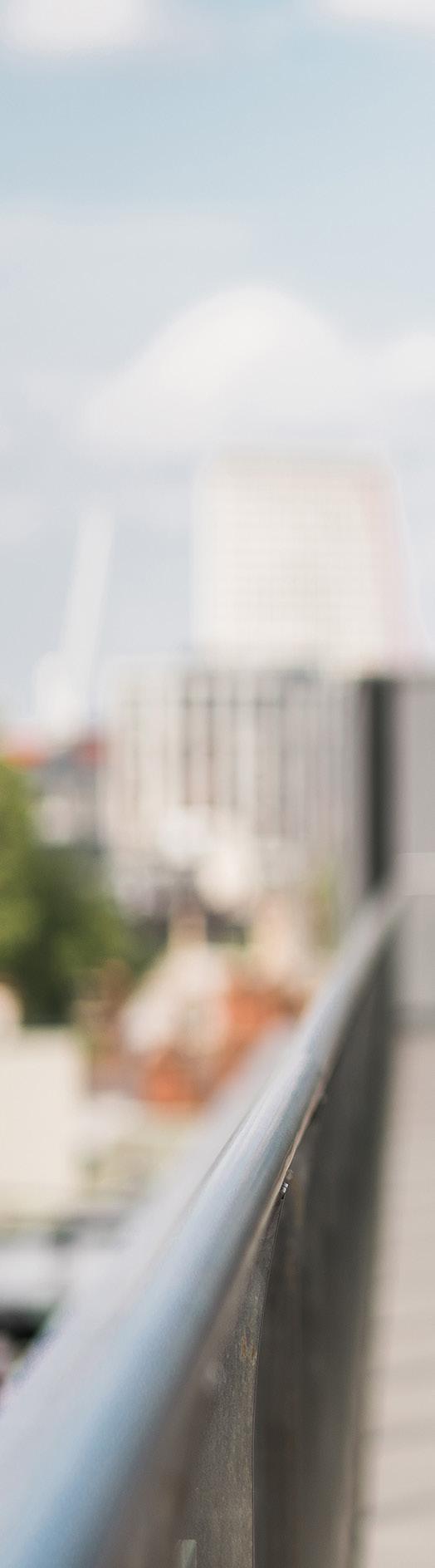
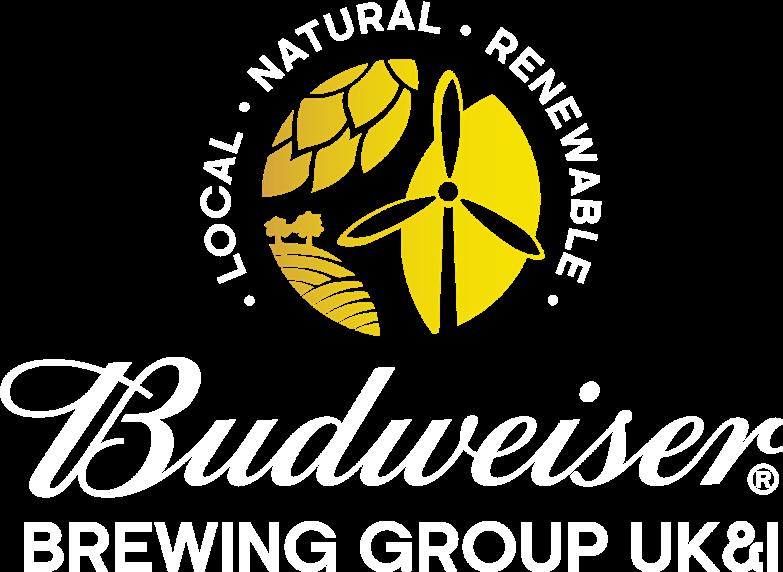
Mauricio has 10 years of international experience in sustainability, entrepreneurship, consulting, e-commerce/retail, blockchain and procurement. He also has a successful track record in team leadership towards developing new products and services. Mauricio joined ABInBev in July 2019 and in January 2021 was appointed the Head of Procurement & Sustainability for Budweiser Brewing Group. He holds an MBA in Business Administration and Management from London Business School and University of Hong Kong. Within Budweiser Brewing Group, he is responsible for all procurement operations across the Business Unit, which covers functions such as: packaging, raw materials, WaterSmartPackaging,bySustainabilityincludingsustainabilityBrewingacrossalsovalueelectricity,renewabletransportandcreation.MauricioleadsateamworkingBudweiserGroup’smultipleinitiatives,the2025GlobalGoalssetABInBevaroundCircularClimateAction,AgricultureandStewardship.
MAURICIO COINDREAU TITLE: HEAD OF SUSTAINABILITY & PROCUREMENT INDUSTRY: MANUFACTURING LOCATION: UNITED KINGDOM supplychaindigital.com 57
BIOEXECUTIVE
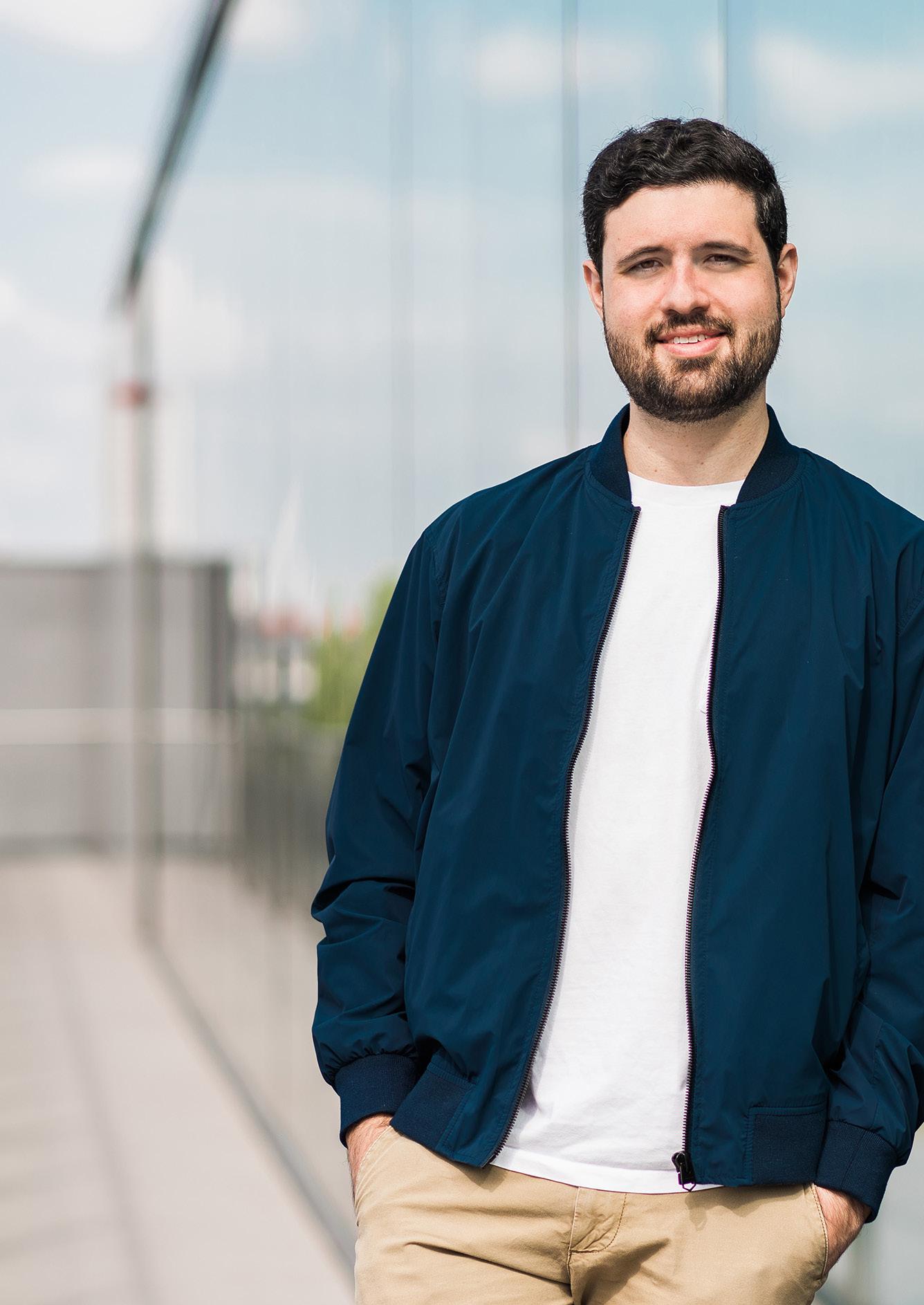
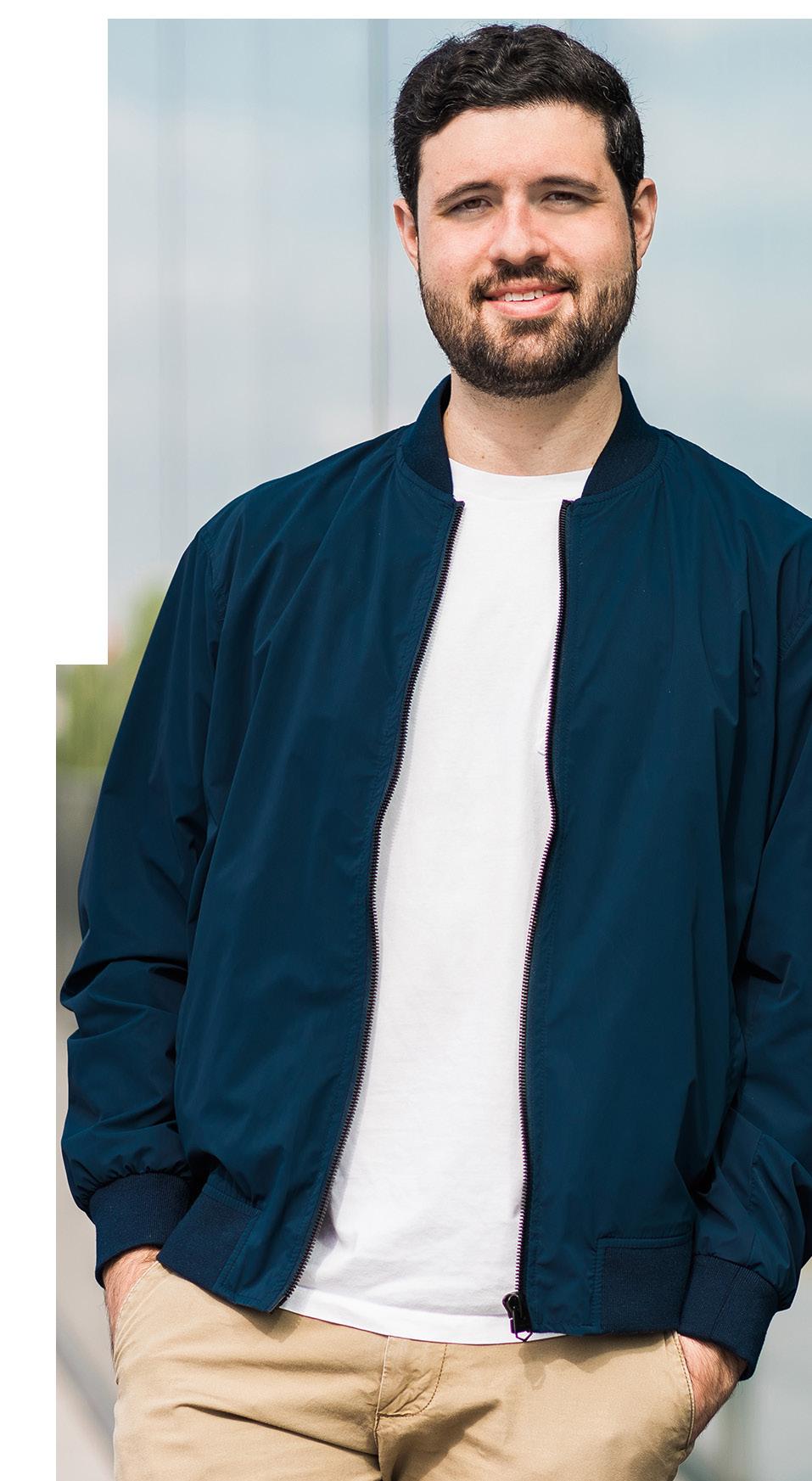
Learn more Leading the way in sustainable logistics Howard Tenens delivers exceptional service whilst embracing carbon reduction initiatives with investments in: y Solar photovoltaic panels and battery technology y Introduction of Hydrotreated Vegetable Oil in place of diesel y Compressed Natural Gas rigid trucks y BioLPG y Green energy supply y Recycling waste materials
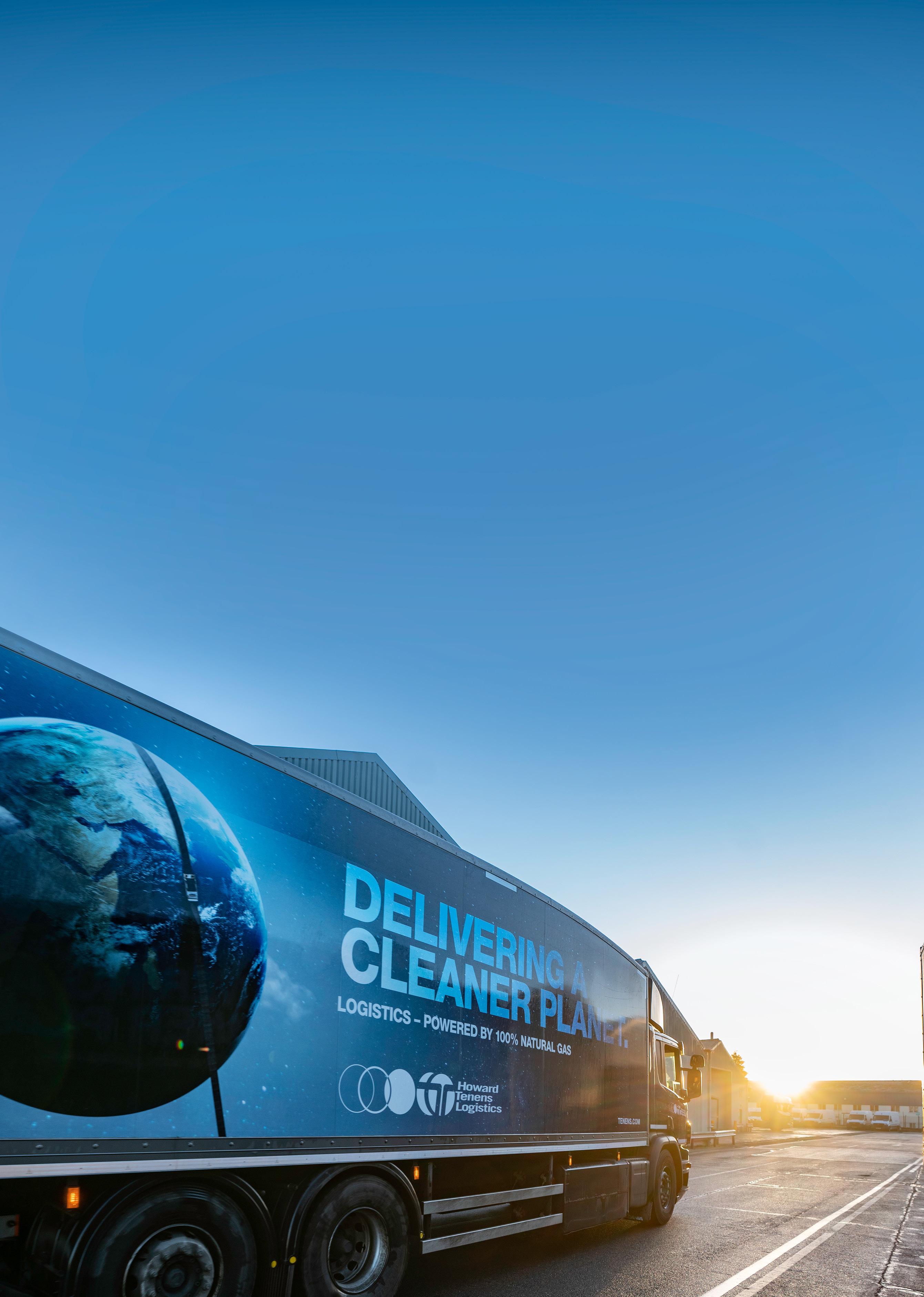

MAURICIO COINDREAU HEAD OF SUSTAINABILITY & BUDWEISERPROCUREMENT,BREWINGGROUP “OUR SUSTAINABILITYBIGGESTCHALLENGEISAROUNDPACKAGING”
says that this is why sustainable drink packaging is a challenge for the entire drinks
“Beyond this, we are also exploring lots of innovations around packaging,” says Coindreau. “Last year for example, we introduced the world's lightest beer bottle, and also a low carbon can.”
Every year it is taking hundreds of tonnes of plastic out of circulation. One of its targets is to have 100% of its packaging come from recyclable and reusable materials. But this is easier to achieve in some countries than it is in others, according to Coindreau.
BUDWEISER BREWING GROUP
For a brewer of such scale, the main raw ingredients that make up beer – grain and water – also present significant sustainability challenges, which is why the global business, AB InBev, has ‘smart’ sustainability programmes both for agriculture and water.
‘Smart’ programmes around water and barley
supplychaindigital.com 59
“For example, in the UK, every time someone consumes a drink from a glass bottle, they chuck it in the bin and it goes into recycling,” he says. “But imagine if we could make this a returnable system, so that every bottle gets used maybe up to 30 times. That’s the most sustainable way to package beer, other than a keg. Another way is through renewable electricity so it is also investing in new technologies, such as greenSuchhydrogen.”asystem requires a high level of collaboration, because the majority of consumers need to be on board. Coindreau
“Weindustry.needto convince retailers and other players in the drink industry to create a single approach, because consumers will respond best if it is easier for them to also participate, which it would be if there was just a single approach.”
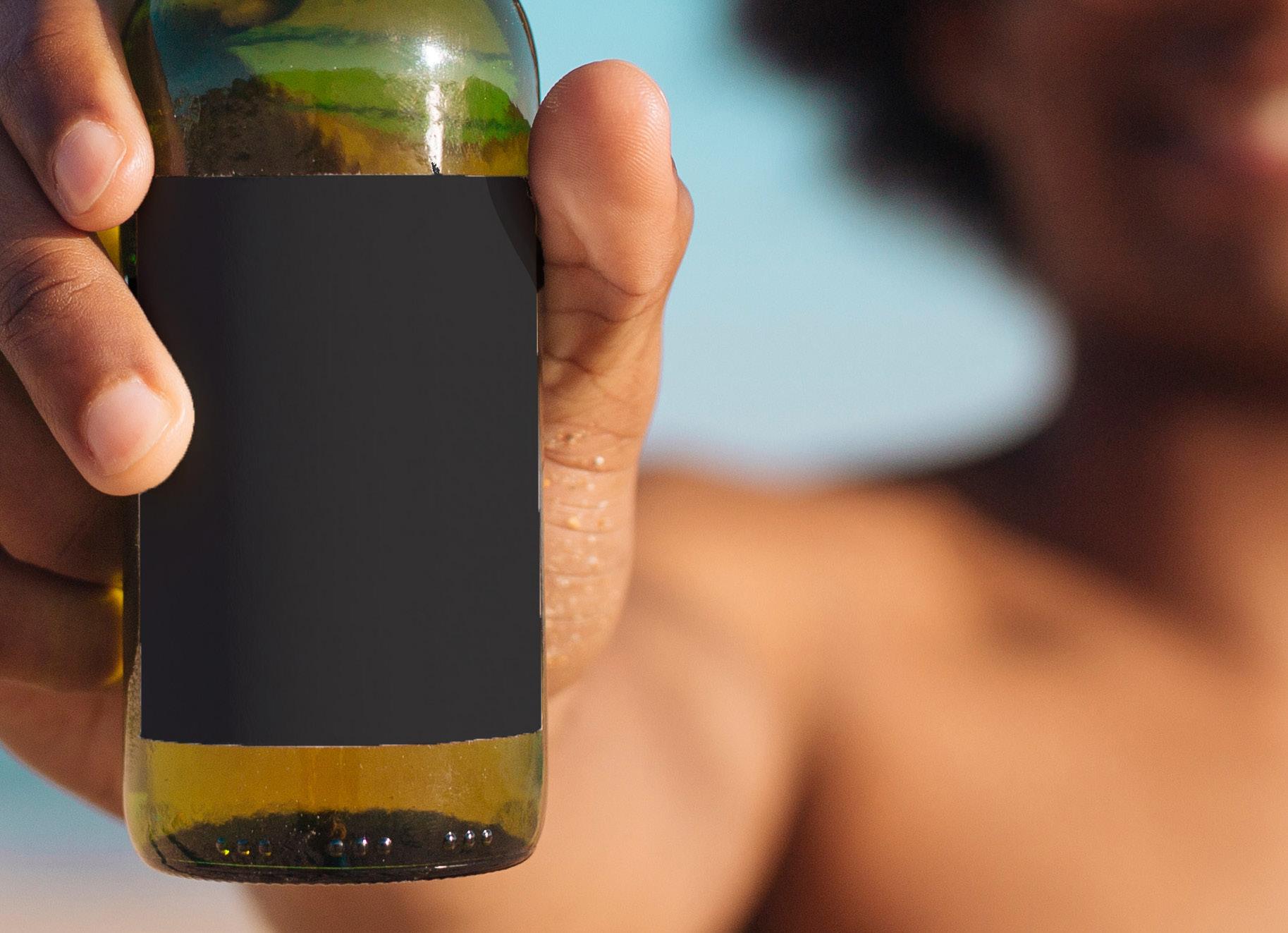

“Water is not only a critical ingredient to beer, but it's also a critical ingredient to economies,” Coindreau says. “For humankind, water is one of the basics of wellbeing. Because of this, our challenge is to look beyond our operations and to increase water availability for all the communities with whom we operate.”
60 July 2022 BUDWEISER BREWING GROUP
Another strand to its Smart Agriculture Programme is to use locally grown crops – as BBG currently does in the UK, where in 2020, all its barley was locally came from British farms.
He continues: “Sometimes, this is about helping communities dig wells, or it can be about bringing piped water in from cities. But it is also about reducing the amount of water we use, per beer.”
The goal of its Smart Agriculture Programme is to ensure 100% of its grain farmers are skilled, connected, and financially empowered by 2025.
Water stewardship vital to AB InBev Beer’s primary ingredient is of course, water, and on this front, AB InBev’s Water Stewardship Programme is vital to its sustainability efforts, because a number of its operations are based in high-water-stress areas, where water availability and quality are issues.
“Climate change is affecting many of the regions that we work in; we want to minimise those risks and build resistance through crop management,” explains Coindreau. “We know that, from high-quality crops comes high-quality beer, and so we want to continue working with the same growers. We are taking a farmer-centric approach and supporting sustainable agriculture to help our farmers increase productivity and profitability, and also to efficiently use natural resources, such as soil and water, along the way. It's about giving them access to data, to technology, and supporting them throughout the process.”
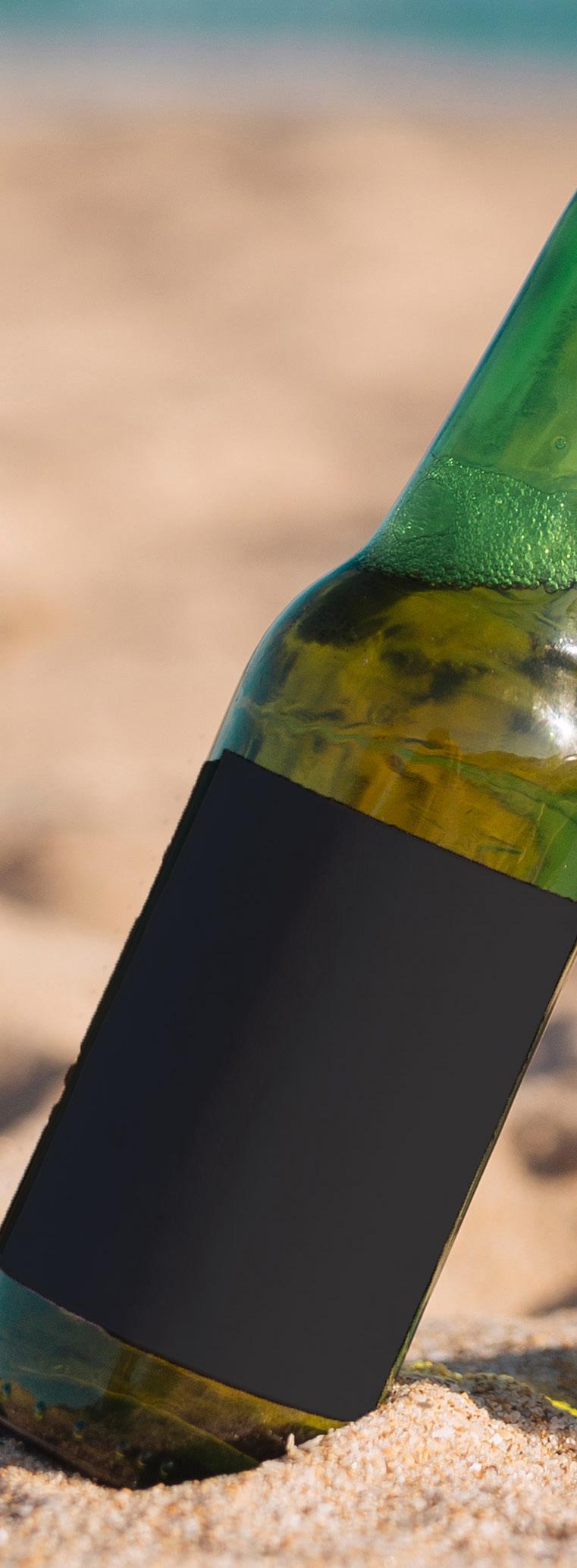
“It's all about finding efficiencies,” saysEnergyCoindreau.efficiency measures are a focus in another area of its business: logistics. The company has a mammoth fleet of delivery and service vehicles worldwide, and its use of electric vehicles – and vehicles using renewable fuel – is a key plank of its drive towards net zero carbon emissions. Partnering with EV Cargo on sustainable transport For example, the Budweiser Brewing Group building on previous route optimisation projects to reduce traffic and emissions, recently announced the launch of a sustainable transport initiative with a number of its industry partners, including EV Cargo, which offers solutions around international freight delivery, warehousing and distribution.
On that note, in some countries, AB InBev uses roughly two litres of water for every litre of beer it produces. On average, just five years ago, this was as high as four litres.
“WATER IS NOT ONLY A ALSOTOINGREDIENTCRITICALBEER,IT'SACRITICALINGREDIENTTOECONOMIES” MAURICIO COINDREAU HEAD OF SUSTAINABILITY & BUDWEISERPROCUREMENT,BREWINGGROUP supplychaindigital.com 61
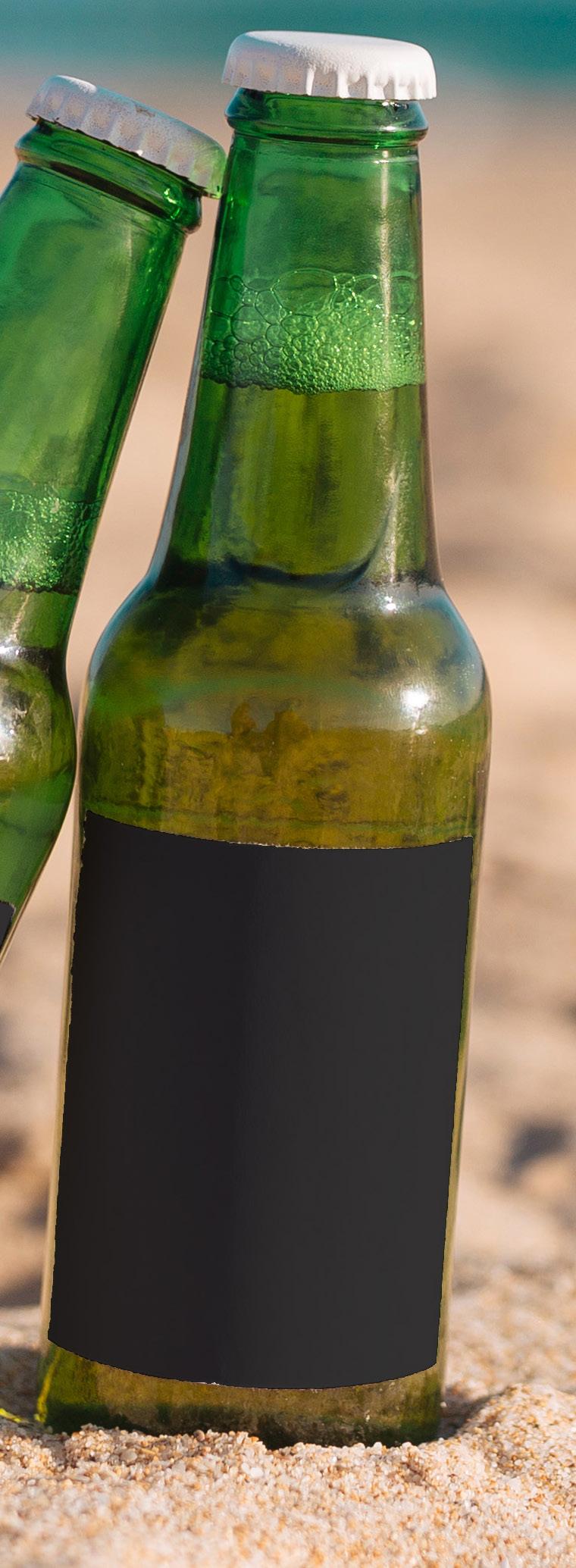
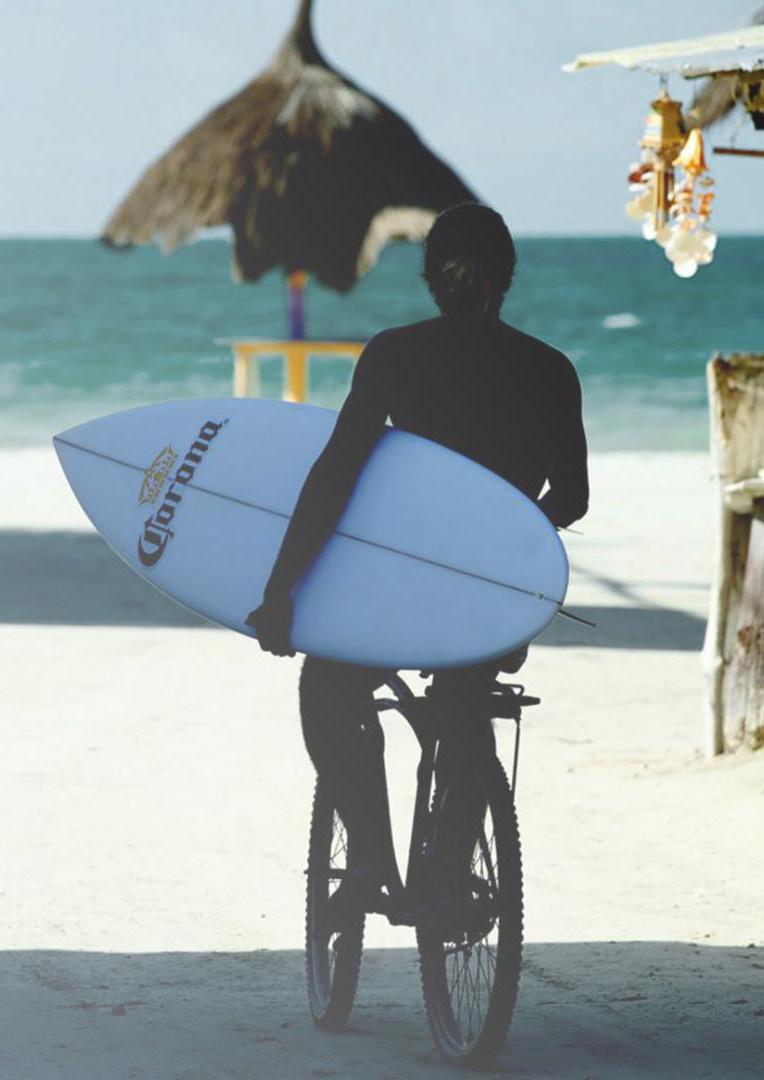

In the climate crisis that we are facing, citizens, businesses, and governments, all have a critical role to play to mitigate climate change before it’s too late. Product manufacturers can be part of the solution by reducing the impact of their product lines and packaging on the environment.
As a B Corp certified business, our purpose is to accelerate change towards an environmentally sustainable world, where we waste less resources and we recycle more.
Through and beyond environmental producer responsibilities existing across the world, manufacturers have the opportunity and the power to make a genuine impact by using business as a force for good, towards a circular economy.
See complianceenvironmental differently
We enable UK businesses to make sustainable packagingSupportdecisionsachieving ESG goals
•
At Ecosurety we support UK manufacturers to make sustainable packaging decisions and therefore contribute to achieving their sustainability goals.
If you share the same values and would like to discuss how your organisation can reduce the environmental impact of your products and packaging, please get in touch at: www.ecosurety.com
62 July 2022
Preparing for Extended Producer Responsibility Packaging data collection and insights Modelling environmental costs Learn more
•
We help businesses with their packaging data collection, creating dashboards for them to reveal insights triggering decision making, modelling environmental costs and facilitating supply chain engagement.
• By thinking reuse, repair, before recyclability By thinking recycled content By thinking packaging material switch and minimisation.

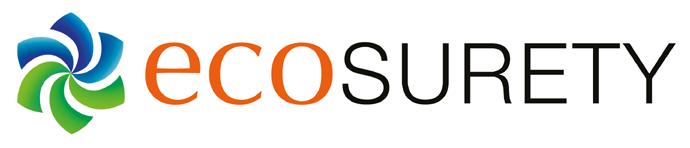


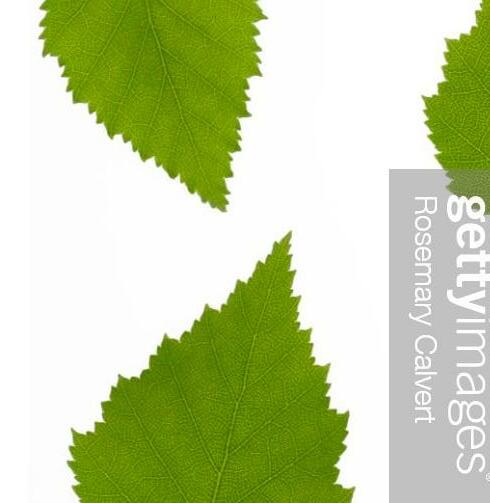
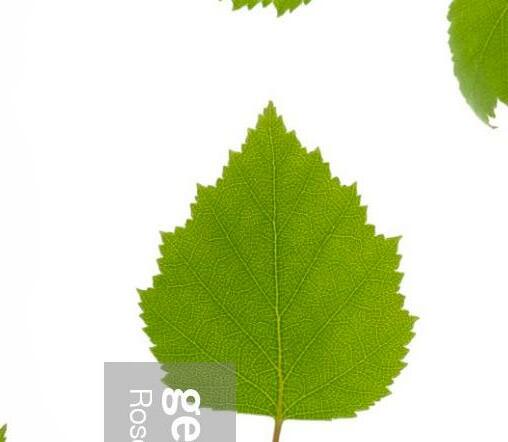
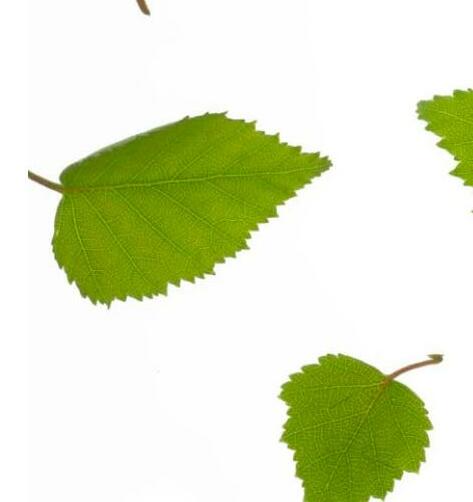
“After working together for so many years we've come to see them as an expert in so
Coindreau also says that AB InBev makes the choices that achieve the most sustainable outcomes taking into account all the features of the local environments.
Key collaborations with Ecosurety & Howard Tenens
“Electric vehicles will make sense in some countries but in others it might be that rail is the way to go, or green hydrogen.”
For shorter routes, he says, BBG will depend “heavily” on electric vehicles, where the need for infrastructure is greatest. If the infrastructure is slow in materialising then BBG will fall back more heavily on HVO as a diesel replacement fuel, because this produces 92% fewer emissions than diesel.
Across all its sustainability initiatives, Budweiser Brewing Group places great stock by collaboration with its partners, along similar lines to its work with EV Cargo on fleetSuchsustainability.akeypartner is Ecosurety, a company that partners with food and drink brands to ensure sustainability compliance. “We've been working with Ecosurety for over seven years,” says Coindreau. “They have become an extended part of our procurement and sustainability team.”
The initiative is designed to create modes of transport that can be powered by fuel made from hydrotreated vegetable oil (HVO), a biofuel that can be produced from a range of different vegetable and non-vegetable feedstocks, including used vegetable cooking oil, animal fat residue and ‘tall oil’, a by-product of wood-pulp manufacture “We have a longstanding partnership with EV Cargo,” says Coindreau. “As a company, this helps you move past operational work and allows you to collaborate on strategic goals, such as finding efficiencies throughout the supply chain, such as with HVO. The next step is green hydrogen. If we're able to power our fleet with green hydrogen, which has no emissions, our supply chain in the UK will truly be sustainable, end-to-end.”
But Coindreau admits that a lack of charging infrastructure is “is a problem” with EVs and that “we’re not in complete control of this”.Headds: “For example, with our solution for green hydrogen we will have filling stations inside our breweries, where trucks pick up the beer. But we also need to convince one of our retailers to add a strategic filling point en route, because this is the only way you can get the range needed.”
supplychaindigital.com 63 BUDWEISER BREWING GROUP
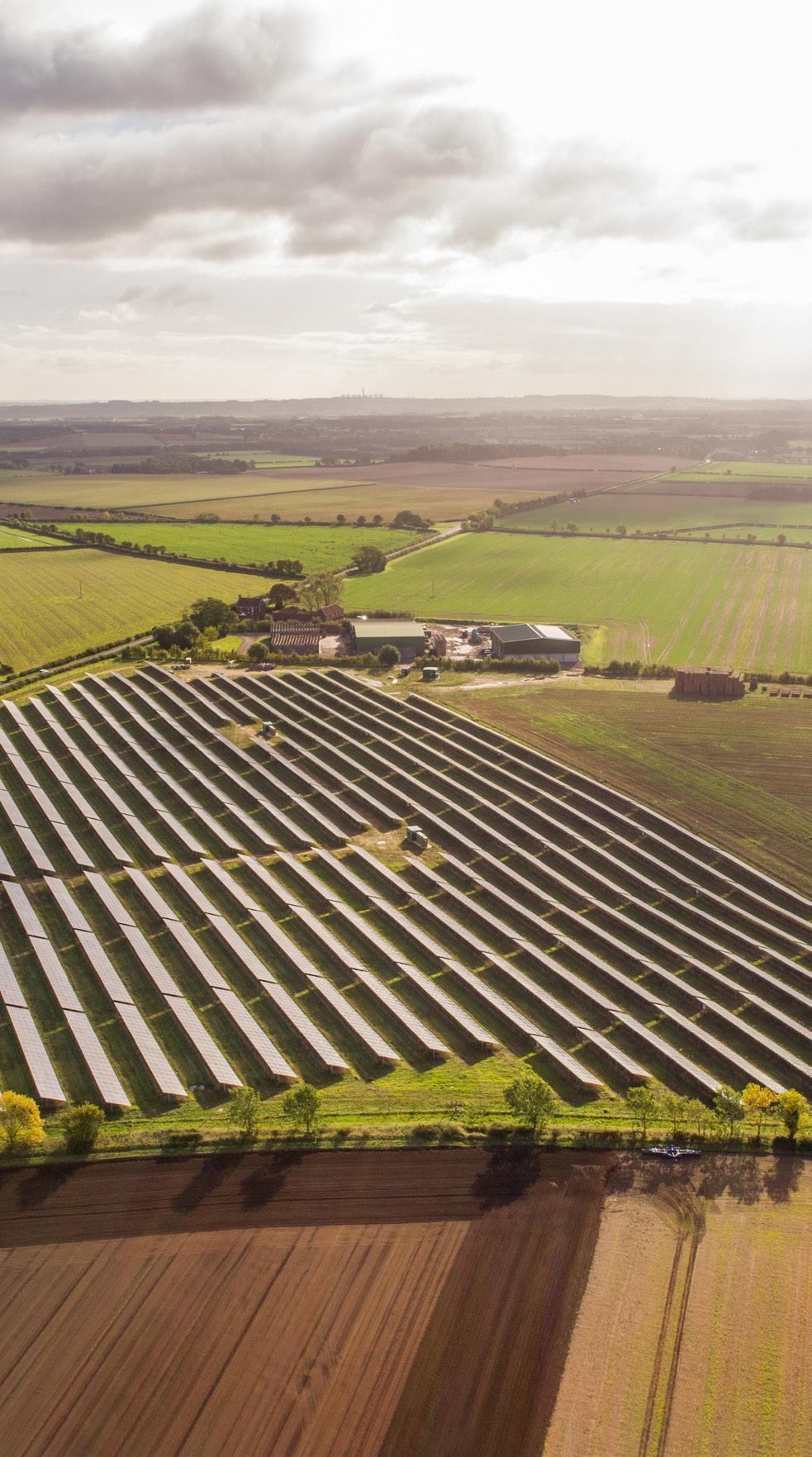
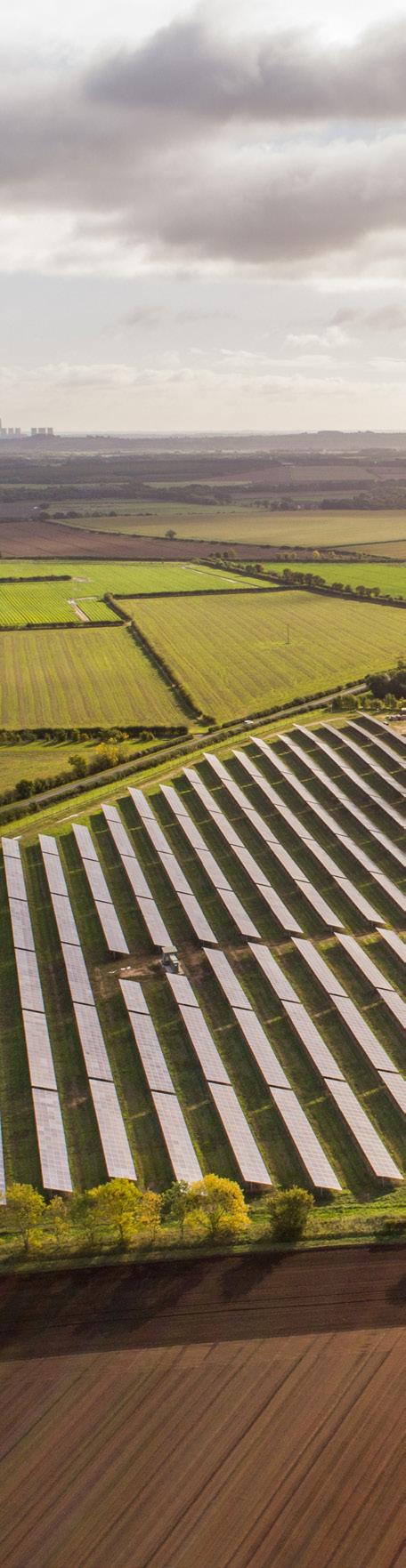
64 July 2022
The present is challenging enough around sustainability, but does Coindreau see happening on this front in the upcoming 18 “Imonths?thinkwe will see some really interesting solutions come into play,” he says. “Because when we set our 2025 goals in 2017, even though it was early in the game, we had a good sense of what was to come.”
“For example, when supply chains were being bottlenecked at ports, they were able to support us massively by bringing their warehouse throughflow to more than 250% of their initial capacity.”
Another of BBG’s ABInBev’s key collaborative relationships is with logistics company Howard Tenens, with whom it has been working for three years. Coindreau says: “They help us with some of our warehousing, both for materials and finished goods. We've always had a strong working relationship, whereby they're able to provide solutions for the ever-changing flow we're seeing in UK logistics.
many areas, such as eco taxes and packaging measures. They are a strategy partner that helps us get a better sense of the everchanging future. “It also helps that they are certified by B Corp, which is a global non-profit network helping transform the global economy to benefit all people. So this gives us the assurance they are looking for a better future.
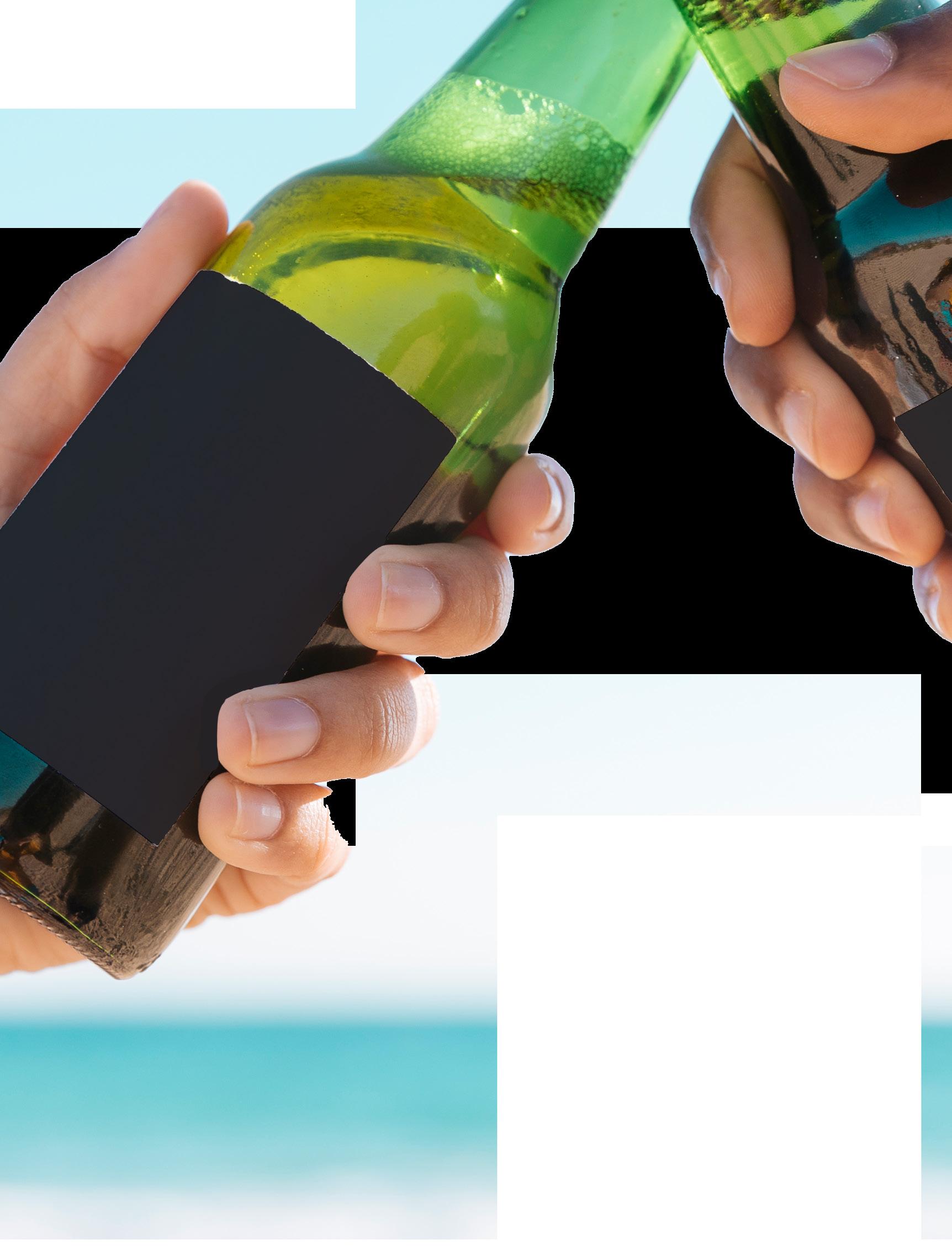
MAURICIOCOINDREAUHEADOFSUSTAINABILITY&PROCUREMENT,BUDWEISERBREWINGGROUP supplychaindigital.com 65 BUDWEISER BREWING GROUP
“We're thrilled with the progress we've made on our sustainability goals for 2025, and we’re very excited to continue our work towards a net zero target. Looking forward to a more sustainable future with more cheers” He adds: “Today, we need to be thinking about net zero at 2040, and it will be all about where we are going to find innovation and collaboration across the supply chain to solve global sustainability issues. Every year it funds and mentors entrepreneurs innovating in sustainability via its Accelerator competition. This year one of the winners was a small business working on washing and reusing packaging.
“I think this is a massive challenge for the industry and for the world as a whole. This is the biggest single issue that we will face in the near future. But we are all facing it together, and so we need to come together to find theHesolutions.”concludes:
“WEWANTTOMINIMISECLIMATECHANGERISKSBYBUILDINGRESISTANCETHROUGHCROPMANAGEMENT”

BOOMECOMMERCEINLOGISTICSLAST-MILEGRIPOF 66 July 2022
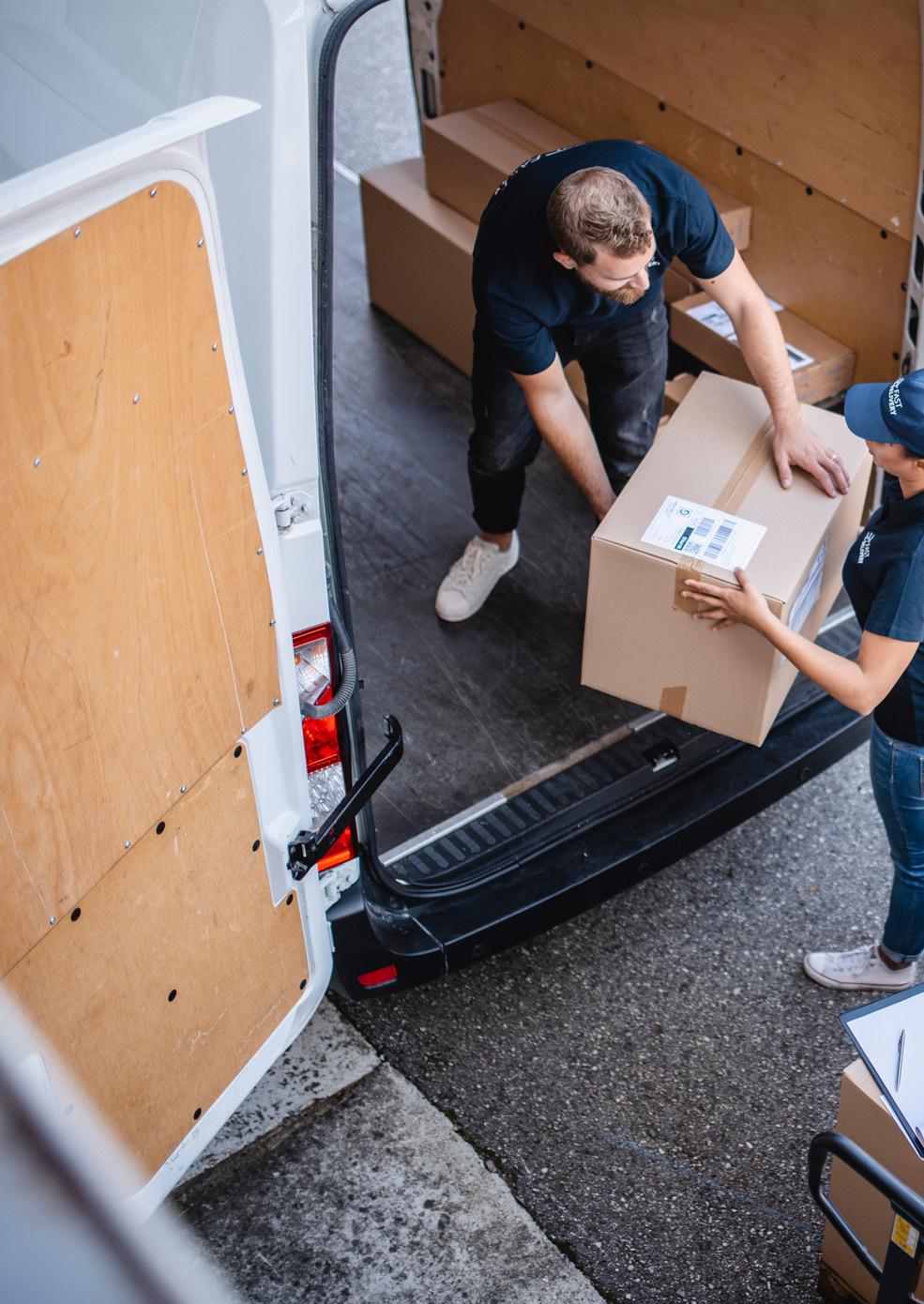
W ith so many moving parts, last-mile logistics has always been the most expensive and problematic part of the supply chain, but, following the meteoric rise of ecommerce during repeated lockdowns, the pressure on last mile has never beenThegreater.global move towards net-zero carbon emissions is also leaving freight companies trying to achieve the seemingly impossible: increasing delivery levels in a sustainable way. To throw light on some of the challenges that last mile operators are facing, we spoke to two people who know the industry insideSarahout:Banks (SB) is global freight and logistics lead at Accenture and has spent 25 years in the logistics industry.
The ongoing rise of ecommerce and omnichannel retail is placing last-mile freight operators under enormous pressure to handle greater loads, sustainably
67 LOGISTICS
How has the move to ecommerce changed last-mile logistics? SB: The biggest impact on last-mile has been the volume. The entire last-mile ecosystem – including post and parcel organisations, retailers, delivery companies, governments
WRITTEN BY: SEAN ASHCROFT Sarah Banks (SB) Global freight and logistics Accenturelead, FletcherVincent(VF) CartonCloudCEO, supplychaindigital.com
Vincent Fletcher (VF), meanwhile, is CEO of CartonCloud, whose software allows logistics SMEs to compete against major players in the industry.

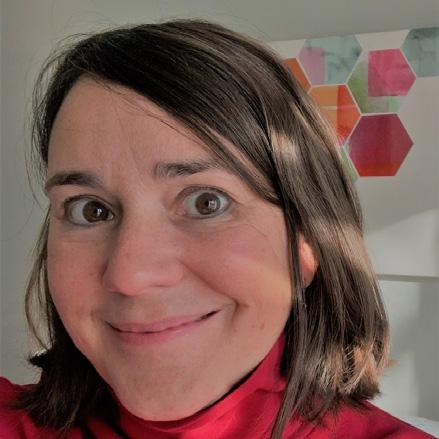
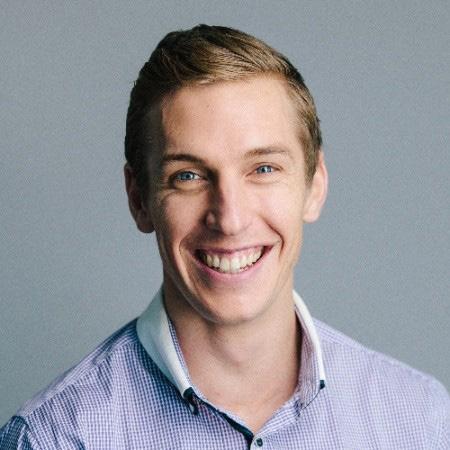
Simplifying the way everyone buys, pays & saves. Invoice Automation | Online Buying | Purchase to Pay | Advanced Analytics Advanced#TheFutureIsNowSpend Analytics. It’s that Empoweringsimple.businesses to achieve the extraordinary. To achieve the extraordinary go to www.compleatsoftware.com Make savings whilst also reducing your carbon Integratefootprint.intothe world’s most popular retail marketplaces... See what you’re spending in each procurement spend category Review spend over time for future savings Build a constant reflection of your spend Save money on items you already buy Track spend in multiple locations

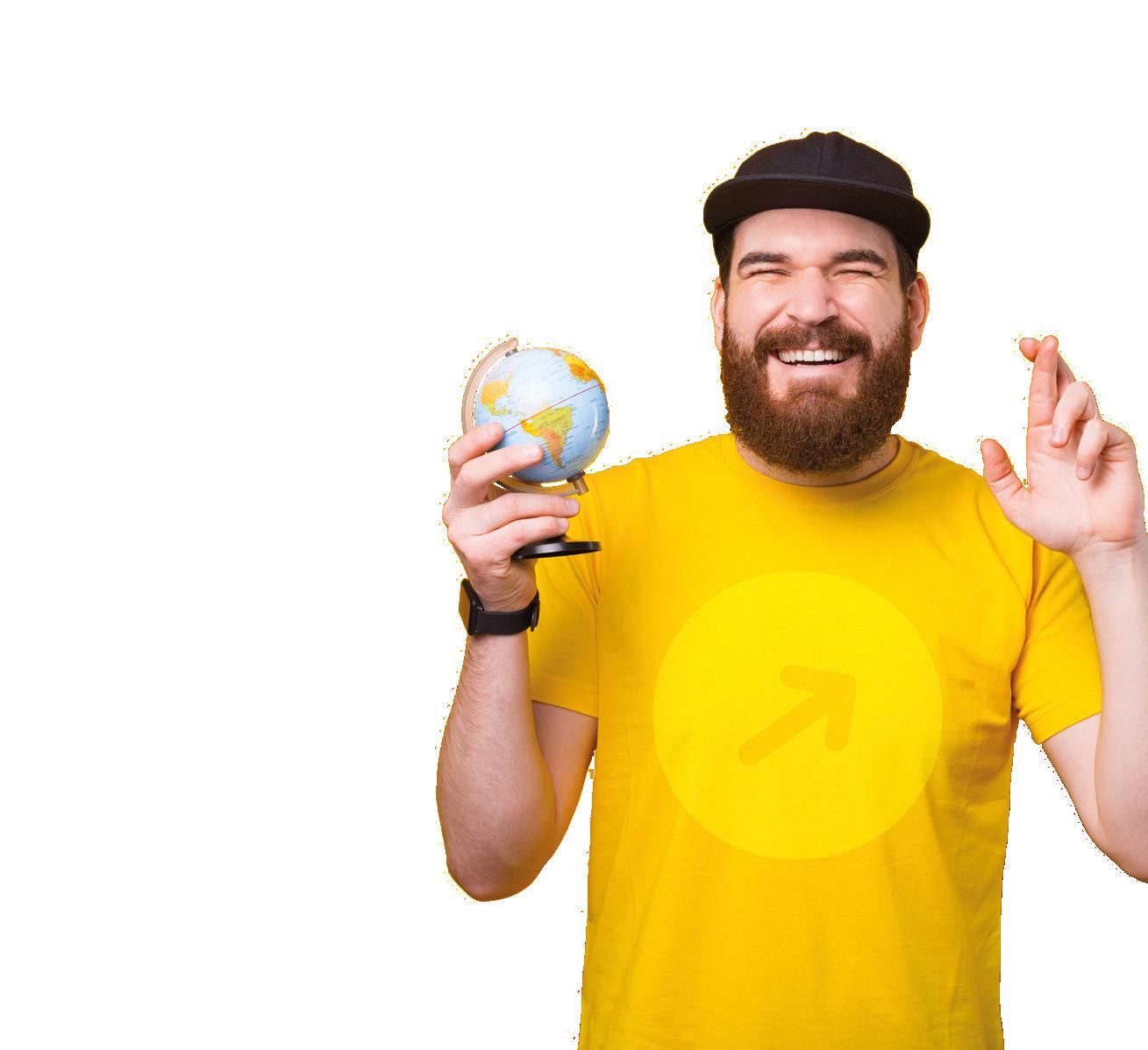
tracking and reporting, as well as flexible options in ordering and delivery. For last-mile providers, providing tracking data to customers is now paramount. Having instant access to orders, transit tracking and incoming goods means companies can plan ahead and move goods between transport, warehouse, or cross-docking services with speed and accuracy. How is last-mile meeting ecommerce challenges? SB: Companies are looking to expand the use of different delivery models. For example, retailers and omnichannel fulfilment, where they use their stores to place inventory closer to customers than ever before. As more items come from market-based inventory, there will be opportunities for and consumers – needs to respond to the permanent shift in the overall volume increase. Companies are looking for ways to create sustainable last mile delivery options that are more efficient, less expensive and more eco-friendly.
LOGISTICS
“One of the best ways to thecloseissustainableachievedeliverytoputinventoryasaspossibletocustomer”
GLOBAL
SARAH
supplychaindigital.com
VF: Pre-pandemic, anything faster than four-day delivery was seen as exceptional but today, consumers have come to expect delivery overnight. Not only do customers want items faster, but they expect real-time BANKS FREIGHT AND LEAD, ACCENTURE
69 LOGISTICS


shippers to create new experiences around local fulfilment for consumers.
Ford E Transits have a range of 140 miles and a payload of approximately 1000kg, similar to the diesel vans being replaced.DHLisalso infrastructuredevelopingtosupport the electric vehicle (EV) roll-out. In addition to stand-alone charging points across the company’s network, it now operates 10 fully integrated EV-ready sites, with 13 more planned later thisTheyear.integrated charging infrastructure is scalable to allow for extra EVs as its fleet grows. Deutsche Post DHL Group, meanwhile, plans to have 80,000 EVs on the road and 60% of last-mile delivery electrified by 2030.
VF: Logistics companies have to meet higher order quantities, while coping with rising operation costs and workforce shortages. For many, this means optimising operations. Cloud-based management software gives businesses eyes across their processes. Accuracy is so important. It means no lost stock, better use of resources, and fewer returns. Logistics companies are also increasing operating times and putting 70 July 2022
DHL making strides on sustainable last-mile delivery DHL Express has announced the roll-out of 270 new electric vans in the UK, which will take to roads across the country as part of its lastmile fleet. By 2030, the business is committed to a 100% electric UK-wide courier fleet. The 270 vans will enter operation between May and September, servicing 30 locations, including: London, Manchester, Leeds, Birmingham, Bristol, Southampton, Liverpool, Sheffield, Edinburgh, andTheGlasgow.zero-emissions
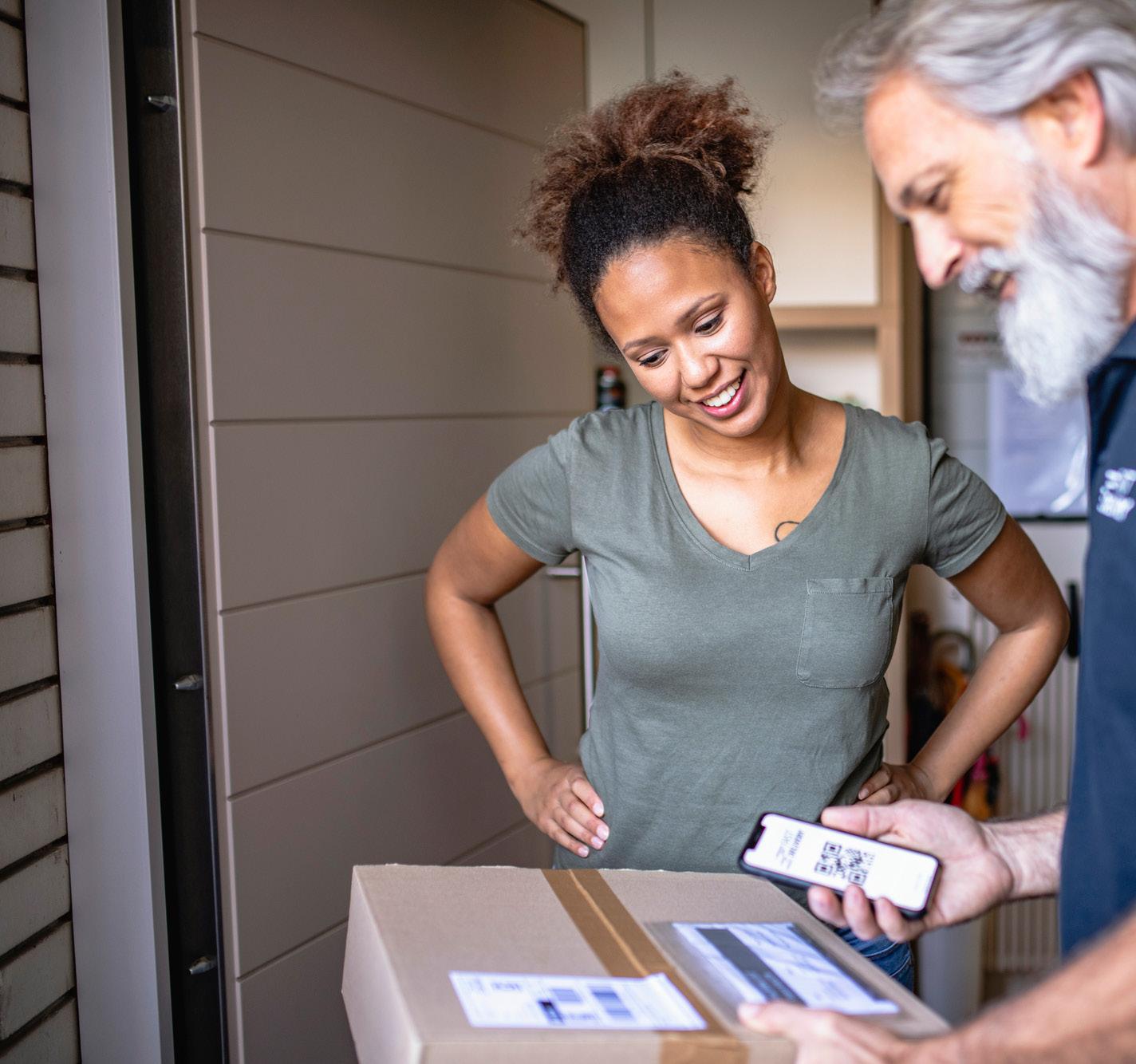
SB: The extent of their usage will be dependent on other enabling mechanisms, such as regulatory approvals, customer “Today, instead of doing one delivery to a single store freight companies might be doing 10 deliveries to individuals” FLETCHER CARTONCLOUDCEO,
against climate change. Looking specifically at last mile, an economic model created by Accenture and Frontier Economics, it shows that, by 2025, local fulfilment centres could reduce last-mile emissions by up to 26% in Chicago, London and Sydney. That’s because the closer inventory gets to the consumer, the more opportunity for alternative lastmile delivery modes – such as electric vehicle, bicycle, or even pedestrian.
SB: Overall, supply chains generate around 60% of all carbon emissions globally –making them a key element in the fight
supplychaindigital.com 71 LOGISTICS
VF: We surveyed our customer base in Q4 2021 and many of them recognised the need to do something about emissions, but said the next step was taking action. It’s not just about net zero, either. The soaring price of petrol has driven many operators to explore ways to reduce fuel consumption. When fuel goes up by as much as 50%, companies can’t pass all that extra cost on to customers, so they’re more willing to make hard decisions to create efficiencies in their operations.
What role will drones and robots end up playing in last-mile?
VINCENT
more effort into what to do when a parcel can’t be delivered – such as pick-up points. Not all companies are coping, though. Some are trying to operate the same way they always have. We’re seeing a push from partnering businesses for more companies to bring operations online. What impact is net zero having on last-mile operations?

• Route optimisation technology to reduce CO2
• Expansion of delivery modes (cargo bikes, lockers, localised inventory)
VF: I believe drones will have a place for certain deliveries – particularly for lightweight, high-value goods. They could play a viable role in quickly delivering small tools or parts that are critical for businesses, for example. However, the idea that drones will be delivering coffees is just a publicity stunt.
Driverless vehicles could also be used for heavy items or routine deliveries, something already being trialled in the industry. They have the potential to have a big impact by allowing operators to become a lot more efficient.
preferences and last-mile infrastructure availability, including localised inventory availability and sortation centres. Companies need to understand how such delivery models can address demand. With demand projections remaining high for last-mile delivery, drones and robots will likely play only a small part, but can work well alongside the more-traditional delivery modes.
A single person will be able to focus on making the right drop, ensuring stock is sorted correctly, and taking care of customer communication and relations, while the driverless vehicle is there to support their operations. Are there more sustainable alternatives to last mile?
• Capturing customer delivery preferences, leading to more sustainable deliveries.
SB: Companies are considering options to drive sustainable value and impact, including:
72 July 2022 LOGISTICS
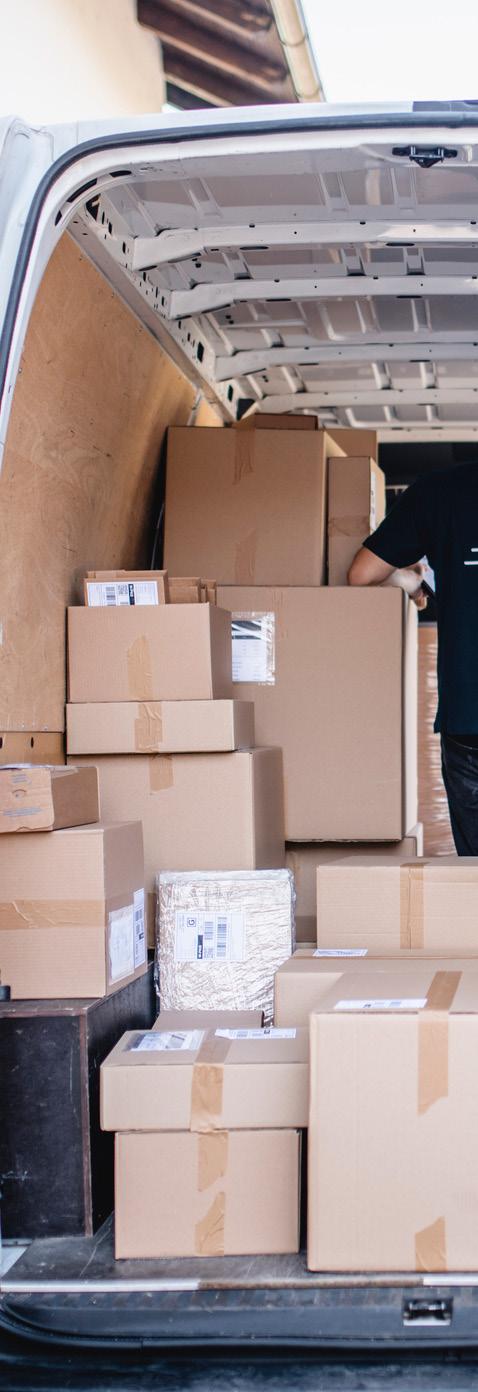
73 LOGISTICS
VF: Today, instead of doing one delivery to a single store, freight companies might be doing 10 deliveries to individuals; this means more fuel usage. More than ever, last-mile operators need to find efficiencies to allow them to take on more business with the resources they have on hand. Our warehouse and transport management software gives last-mile operators the tools they need to optimise their operations, be more efficient, and, ultimately, create a more sustainable business. How can companies make lastmile more sustainable?
SB: Our research on last-mile shows many ways a company can become more sustainable. These include: Local fulfilment. One of the best ways to achieve fast, low-cost and sustainable delivery is to put inventory as close as possible to the customer. Collaboration. A more sustainable last-mile will require thoughtful collaboration across the ecosystem. Cross-ecosystem data sharing via the cloud is also critical. Incentivise greener choices. Last-mile must make consumers more aware of the environmental impact of delivery options, and be more transparent by offering greener delivery choices at checkout. Rethink asset use. For example, delivery companies could provide access to one another’s networks, including fulfilment, open locker, and pick-up and drop-off locations. Harness data and analytics. With realtime data and insights into consumer preferences and purchasing patterns, companies can innovate and optimise inventory and route management for a lower last-mile carbon footprint. supplychaindigital.com
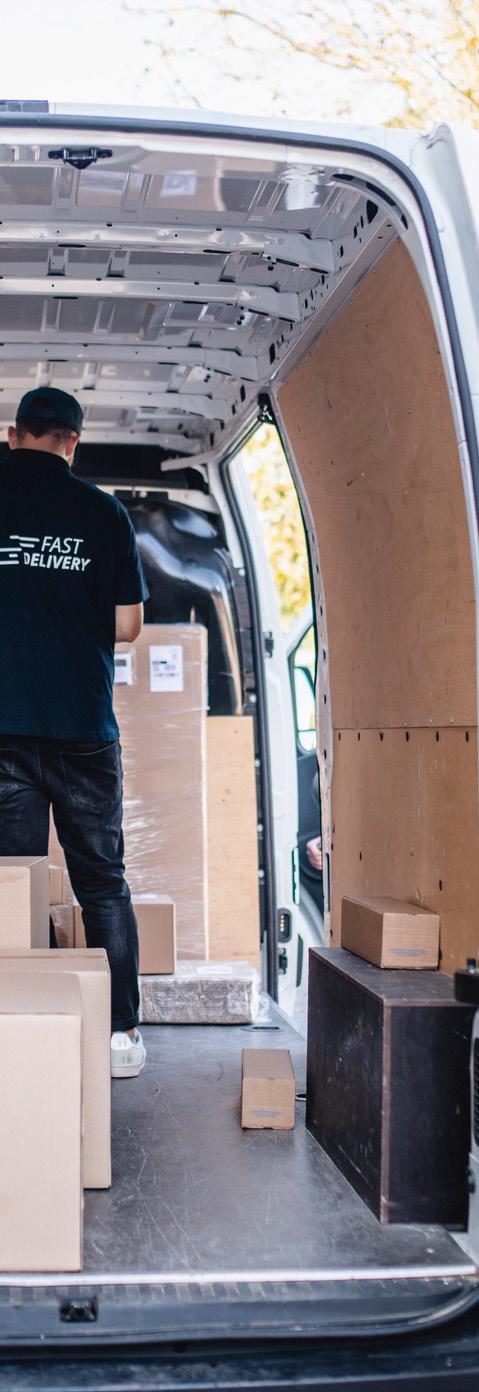
Making the
74 July 2022
Rasheed Mohamad of ALE: Unpredictable,
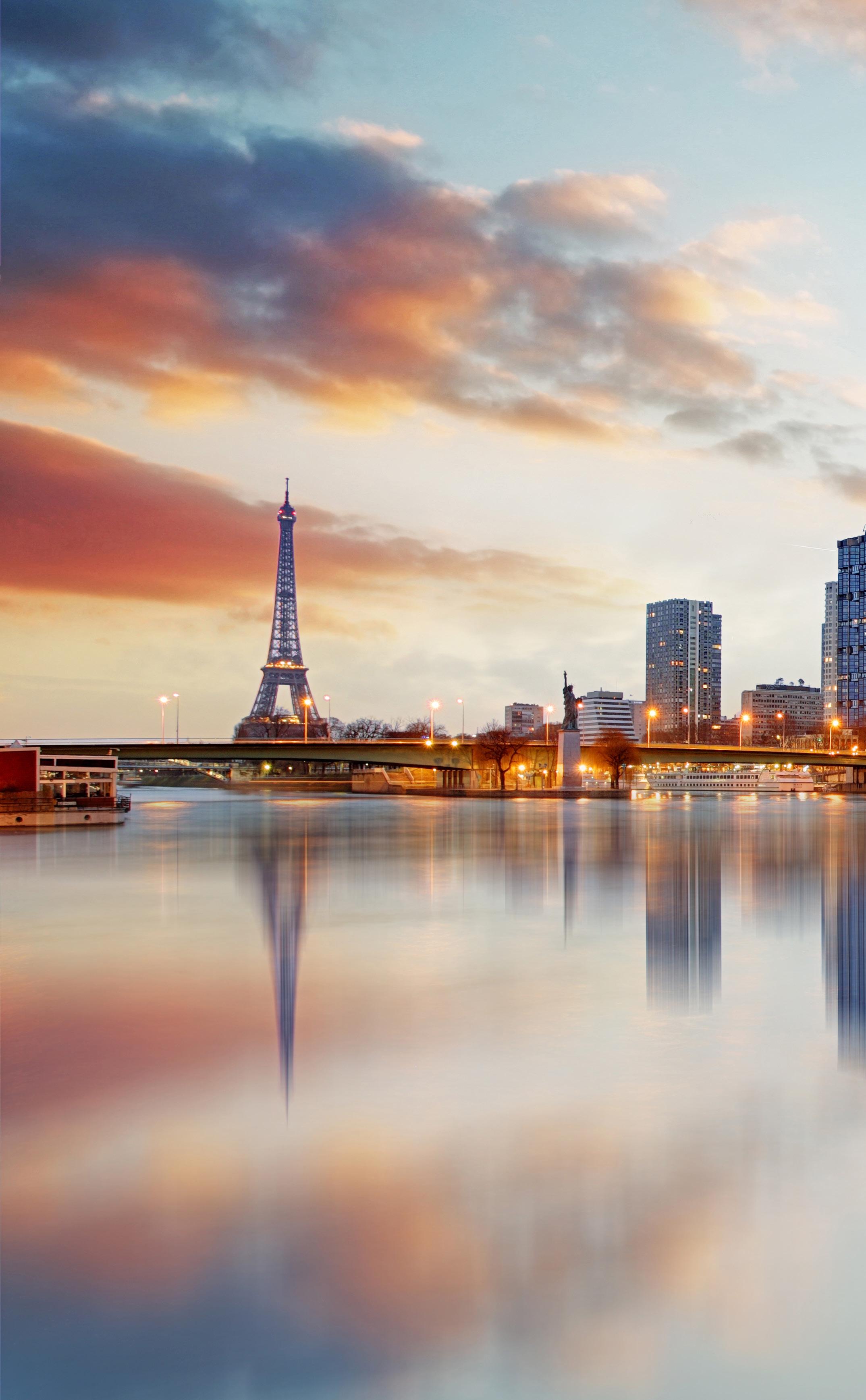

Unpredictable,ALE: Predictable supplychaindigital.com 75 PRODUCED BY: JAMES BERRY WRITTEN BY: İLKHAN ÖZSEVIM ALCATEL - LUCENT ENTERPRISE
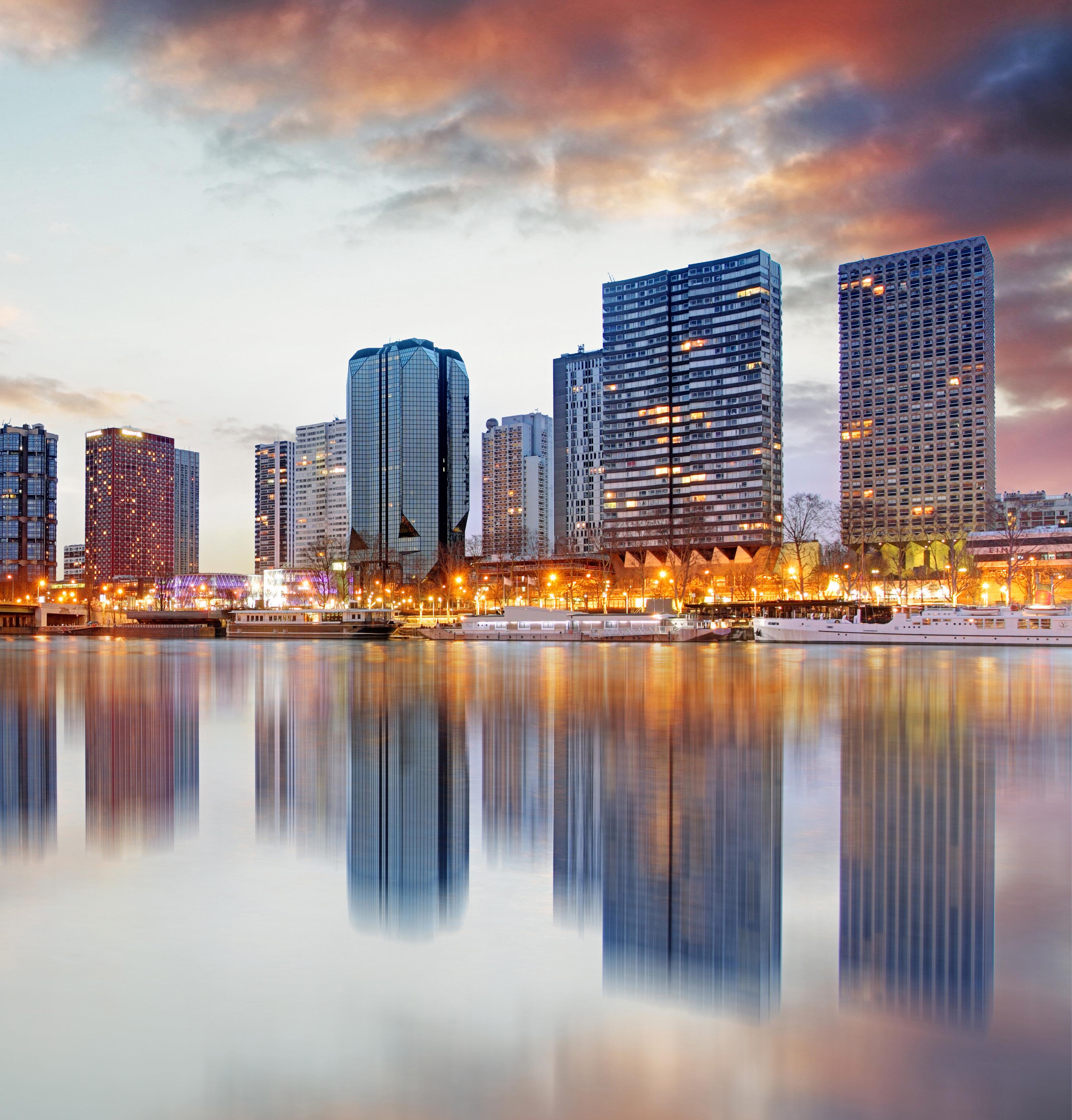
76 July 2022 ALCATEL - LUCENT ENTERPRISE
Mohamad began his career as an engineer with SFO technologies in India, moving on to network design roles with the Indian government, before finally joining Alcatel-Lucent Enterprise (‘Alcatel’ at the
F or any modern business to be successful in procurement, supply chain and logistics, ‘systemisation’ is the name of the game. Rasheed Mohamad, Executive Vice President of Global Operations, Business Technology and Quality of Alcatel-Lucent Enterprise, knows that for a business’ transformation journey to be successful, this systemisation must be applied to its entire infrastructureincluding its internal processes.
Rasheed Mohamad, Executive Vice President at Alcatel Lucent Enterprise, gives insights into transformation, automation and the importance of predicting outcomes
“It is important that innovation is approached holistically, rather than being confined to one department or an isolated aspect of your business,” he says.
Mohamad manages the end-to-end (e2e) delivery of the whole quote-to-cash (q2c) ecosystem at ALE. After a customer places an order, the procurement, planning, supply chain and logistics all work together as an e2e delivery process. He is also responsible for business technology, which is a CIO function, ensuring that all of the tools, infrastructure, and, he says, “perhaps most importantly, the mindset of the people” are kept in accordance with ALE’s transformation and “coined with quality”, to make sure that they deliver the best results for their customers.
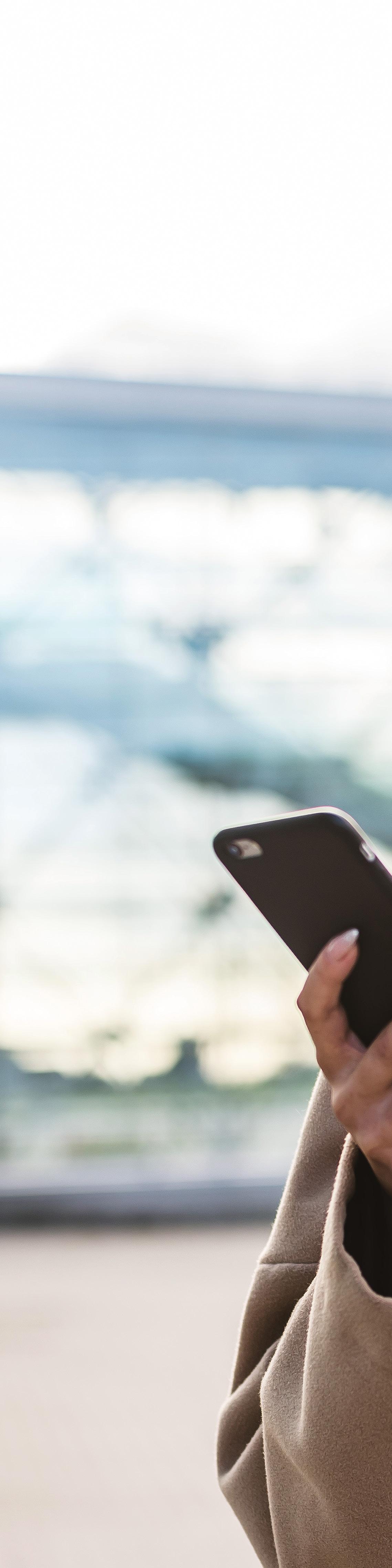
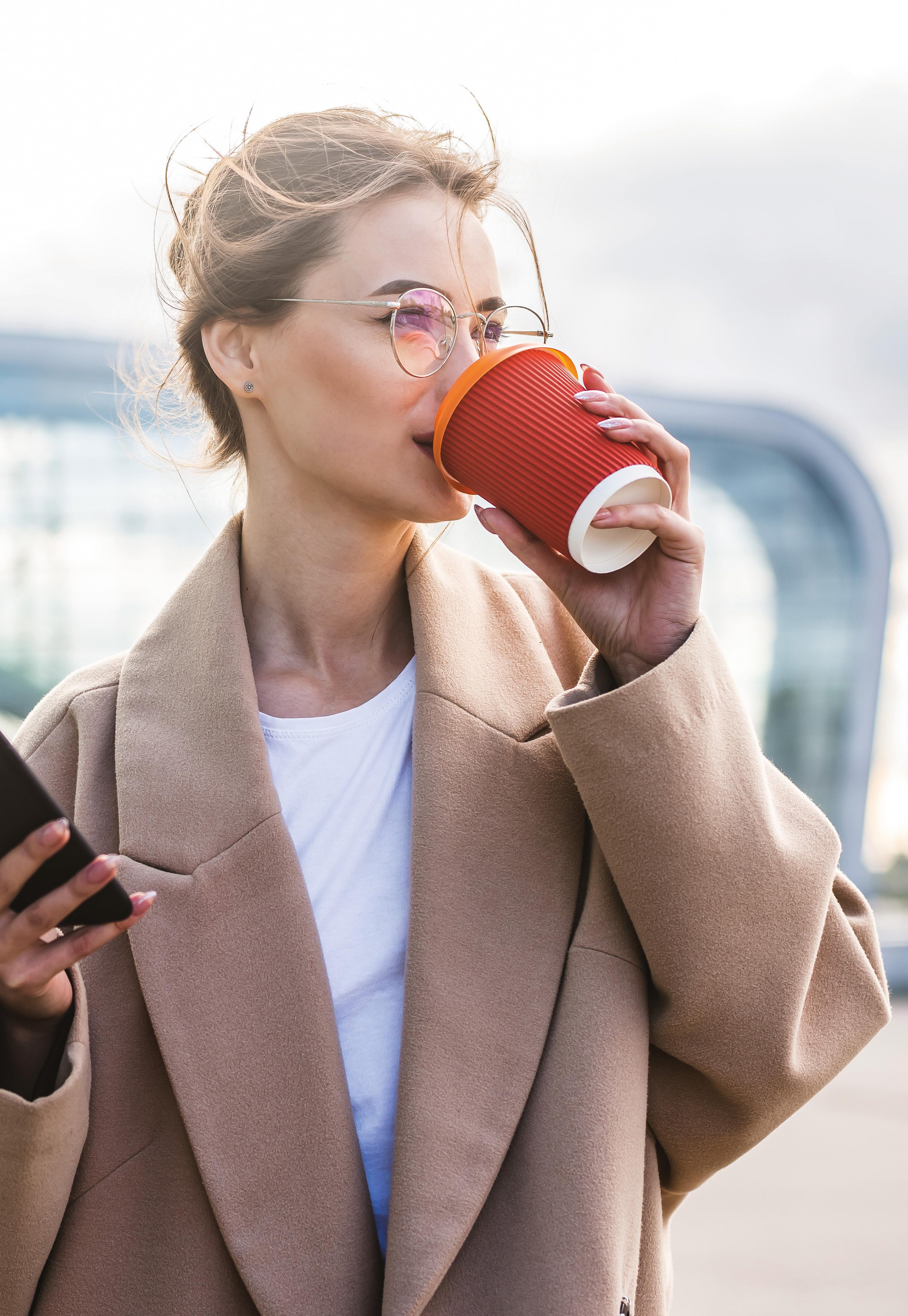
2017.
ALE (then Alcatel), is a 100-year-old telecoms company, and though now global, it started out from humble beginnings in the Alsace region of France. In the second half of the 20th Century the company became decidedly more disruptive. Following acquisitions, Alcatel merged with Lucent Technologies to create Alcatel-Lucent – a global communications powerhouse. “Alcatel-Lucent Enterprise separated from the Alcatel-Lucent Group in 2014,” explains Mohamad, “and we moved away to
customerorganisationsagilityreliability,onofourglobe.”toapplicationsandcommunicationsdigitalindustry-specificdeliveragenetworking,cloudsolutions,andservicesenterprisesacrosstheHesays,“Now,valueslieattheheartwhatwedo.Focusingcustomercentricity,speedandenablesustoofferatotalexperience.”
time) in 2000. Here, he journeyed through different aspects of ALE’s divisions such as Operations, Finance, R&D and ManagementjoiningManagementProgrammeuntiltheExecutiveteamin
ALE’s uniqueness derives from several elements working in unison. They provide an extensive e2e portfolio of network, communications and cloud solutions for enterprise customers with flexible business models in the cloud, on-premises and hybrid. This means that ALE customers can choose solutions that are tailored to “Our challenge is to turn unpredictabletheintothepredictable”
Rasheed Mohamad of ALE: Making the Unpredictable, Predictable
78 July 2022
RASHEED MOHAMAD EXECUTIVE VICE PRESIDENT, ALCATEL-LUCENT ENTERPRISE

COVID-19 lockdowns pushed ALE into remote operations, accelerating its transitional process. This helped ALE generate a platform where they could do e2e tracking from order to delivery.
ALCATEL - LUCENT ENTERPRISE
Asked about ALE’s digital transformation process, Mohamad says: “when we started this journey in 2019, just prior to COVID19, we had a five-year plan. The key to a strong delivery was creating clear processes, procedures and business enablers. To implement these successfully, we first had to gather accurate information on ALE’s infrastructure. Only then, could we develop efficiencies such as automating regular processes, and using AI (Artificial Intelligence) and NLP (Natural language Processing). Anticipating outcomes was our goal, and in the supply chain world, what is most important for a customer is on-time delivery at the most optimised cost possible.”
Rasheed is an expert executive with global leadership experience in business transformation at both strategic and operational levels. He currently leads the Global Operations, Business Technology and Quality teams at Alcatel-Lucent Enterprise. Rasheed’s success in transforming operations by delivering the highest level of efficiency and excellent customer satisfaction has been recognised by international awards. As sponsor of the ALE #GoGreen programme, Rasheed is committed to finding new technologies that contribute to protecting our natural capital, building sustainable cities, and limiting global climate change. Rasheed has over 20 years
ALE is focused on four verticals: Healthcare, Education, Transportation and Government. “Transformations used to be confined to a single department or area within an organisation,” says Mohamad, “but to deliver the highest level of efficiency and customer satisfaction, we believe innovation has to take place in every single department, in synergy with the whole business. In this regard, we also make sure we are using our own products for transformations. In recognition of this, we have been consecutively awarded the prestigious CIO 100 award for the past two years, and also for our work in several other domains.”
BIOEXECUTIVE RASHEED MOHAMAD
TITLE: EXECUTIVE VICE PRESIDENT, GLOBAL OPERATIONS, BUSINESS TECHNOLOGY AND QUALITY INDUSTRY: TELECOMMUNICATIONS
LOCATION: CALIFORNIA, US their unique needs and business goals. Mohamad says: “ALE’s uniqueness stems from our distinctive go-to-market offers. Our solutions are tailored to each industry and we have a commitment to our 3400 business partners to ensure continuous customer proximity.”
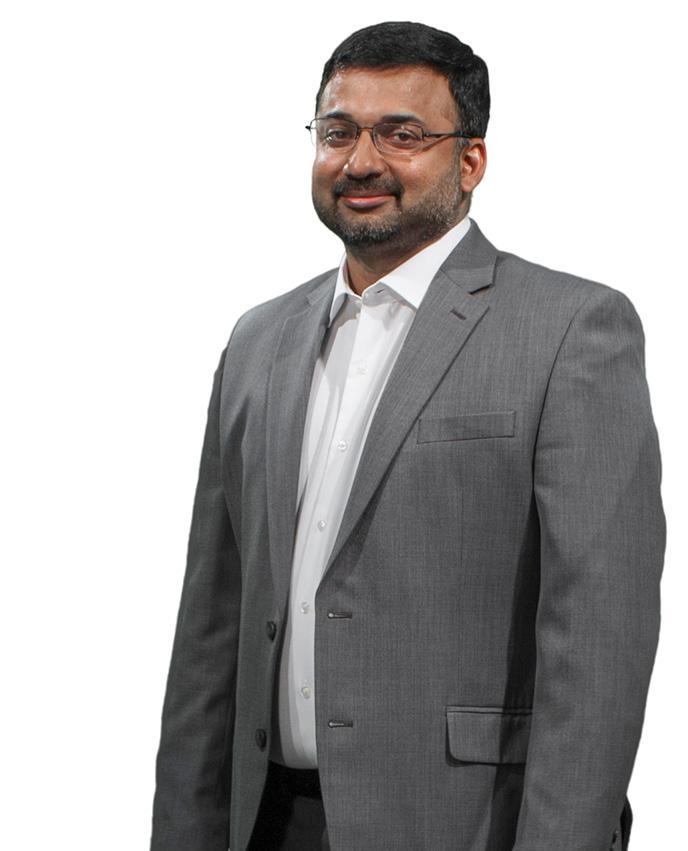
Find out more We shape the world of logistics. Every day, we go above and beyond to meet the needs of our customers. By anticipating challenges and applying our visionary mindset, we advance global trade and bring communities together.
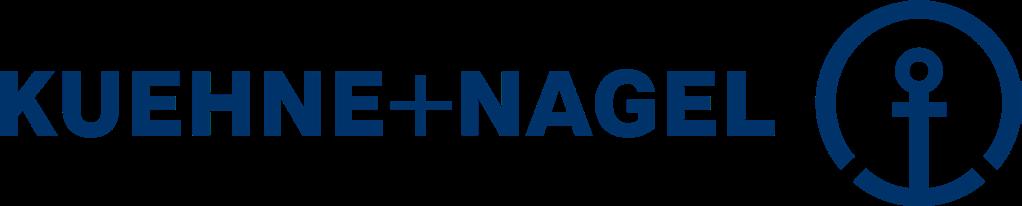
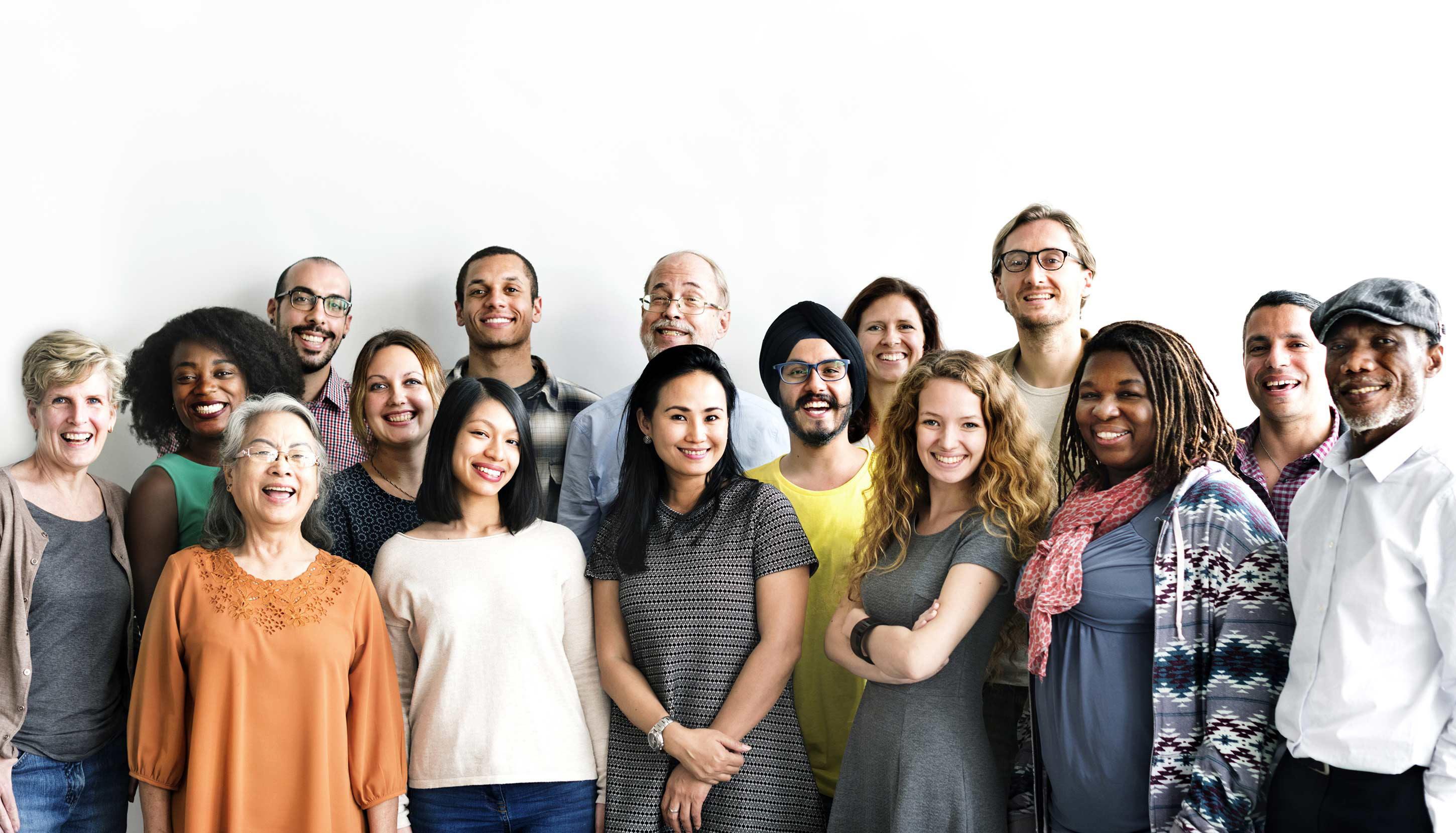
“ALE has full visibility on all events in our visibility portal’. We use advanced tools such as a Transport Management System (TMS) with strong dynamic planning and optimisation capabilities to automate processes, and our own in-house collaboration platform for customer service, which provides a single point of contact for all requests and deviations relating to order life-cycle execution. The ability to execute request trend-analysis and determine rootcauses really drives improvement!”
The Art of Supply Chain Orchestration
“CI is the next step in the evolution of our partnership with ALE,” says Edenburg. “It’s key, especially in these times, to concentrate on supply chain optimisation and – together –find effective answers and solutions.”Findout more
Kuehne+Nagel’s flexibility of service makes its customer’s supply chain more resilient. For example ALE’s volumes fluctuate, with peaks at year- and quarter-end. ”We have a transactional model in place. The shared multi-customer environment in our Luxembourg control tower is a key enabler when handling these spikes in volumes”. Kuehne+Nagel takes the burden from ALE in a multitude of ways, such as managing its relationships with carriers, KPIs, the lifecycle of complex tariff arrangements and, very importantly, continuous improvement (CI).
As Alcatel-Lucent Enterprise’s 4PL provider, Kuehne+Nagel leverages its data-centric IT architecture and its global control tower footprint to support ALE’s competitive positioning.
In December 2019, Alcatel-Lucent Enterprise, one of the world’s leading networking, communications and cloud solutions, chose Kuehne+Nagel as its 4PL partner for Europe. Kuehne+Nagel maintains a network of partnerships with other supply chain operators, innovators and disruptors throughout the world – customers can achieve a distinct competitive advantage by leveraging its Software AND a Service delivering three key advantages, visibility, resilience and sustainability With ALE, seamless integration is ensured using a full EDI set up (based on EDIFACT messages) between the two partners, the European Distribution Centre, and carriers, explains Mark Edenburg, Global Business Manager High Tech at Kuehne+Nagel.
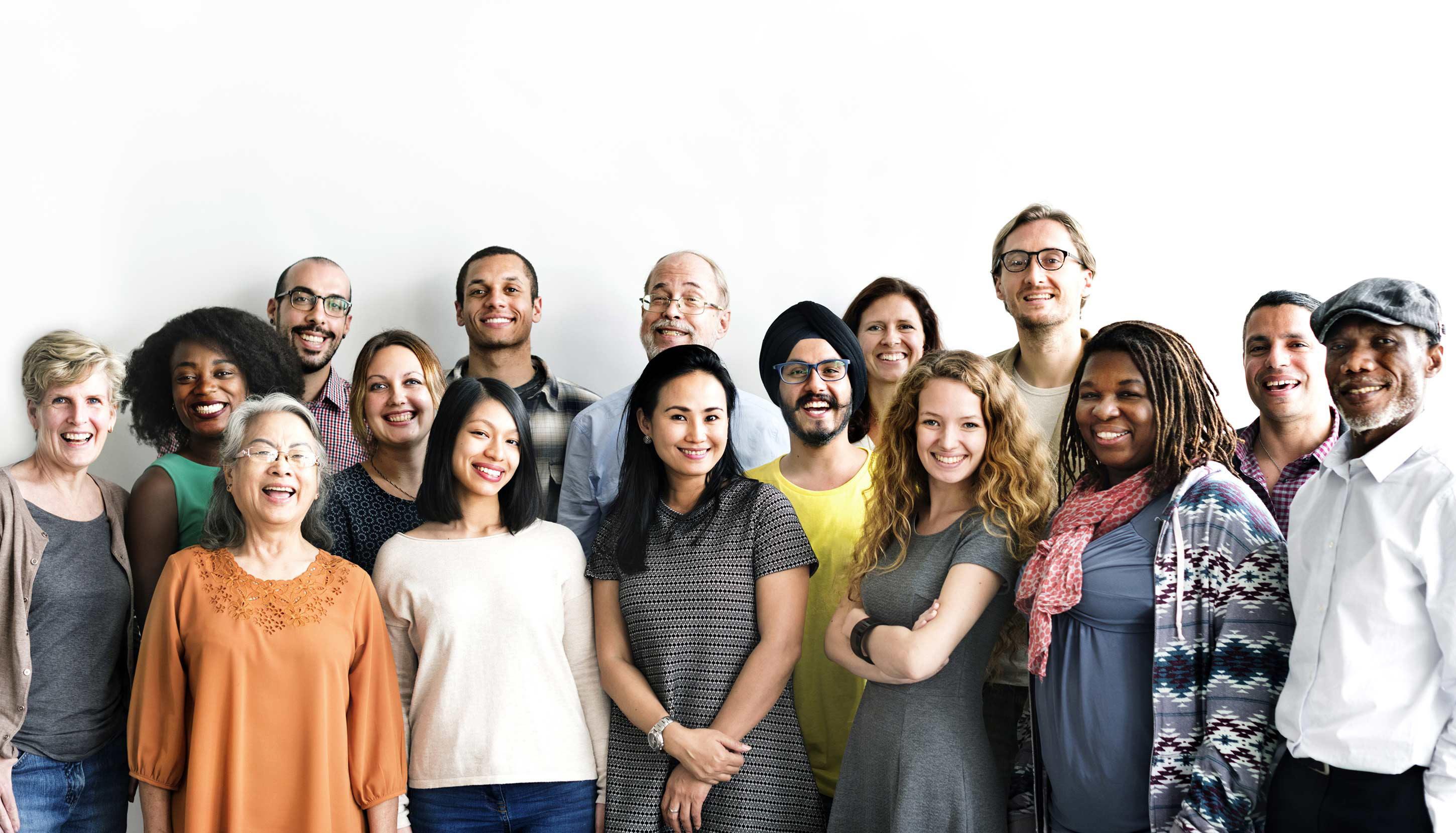
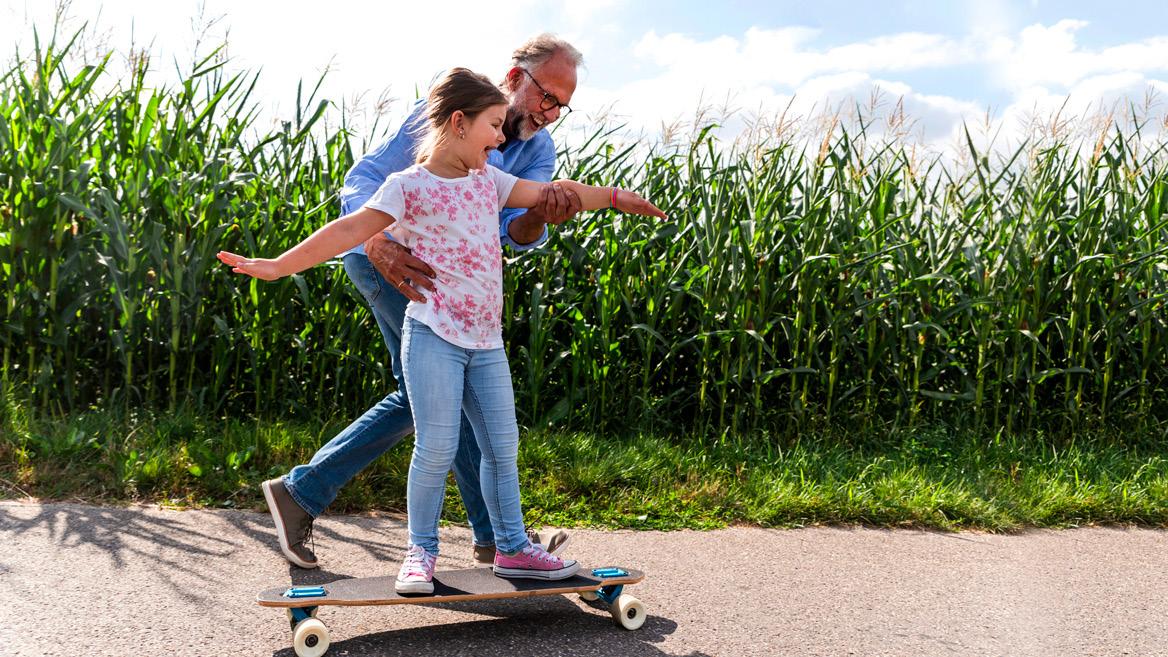
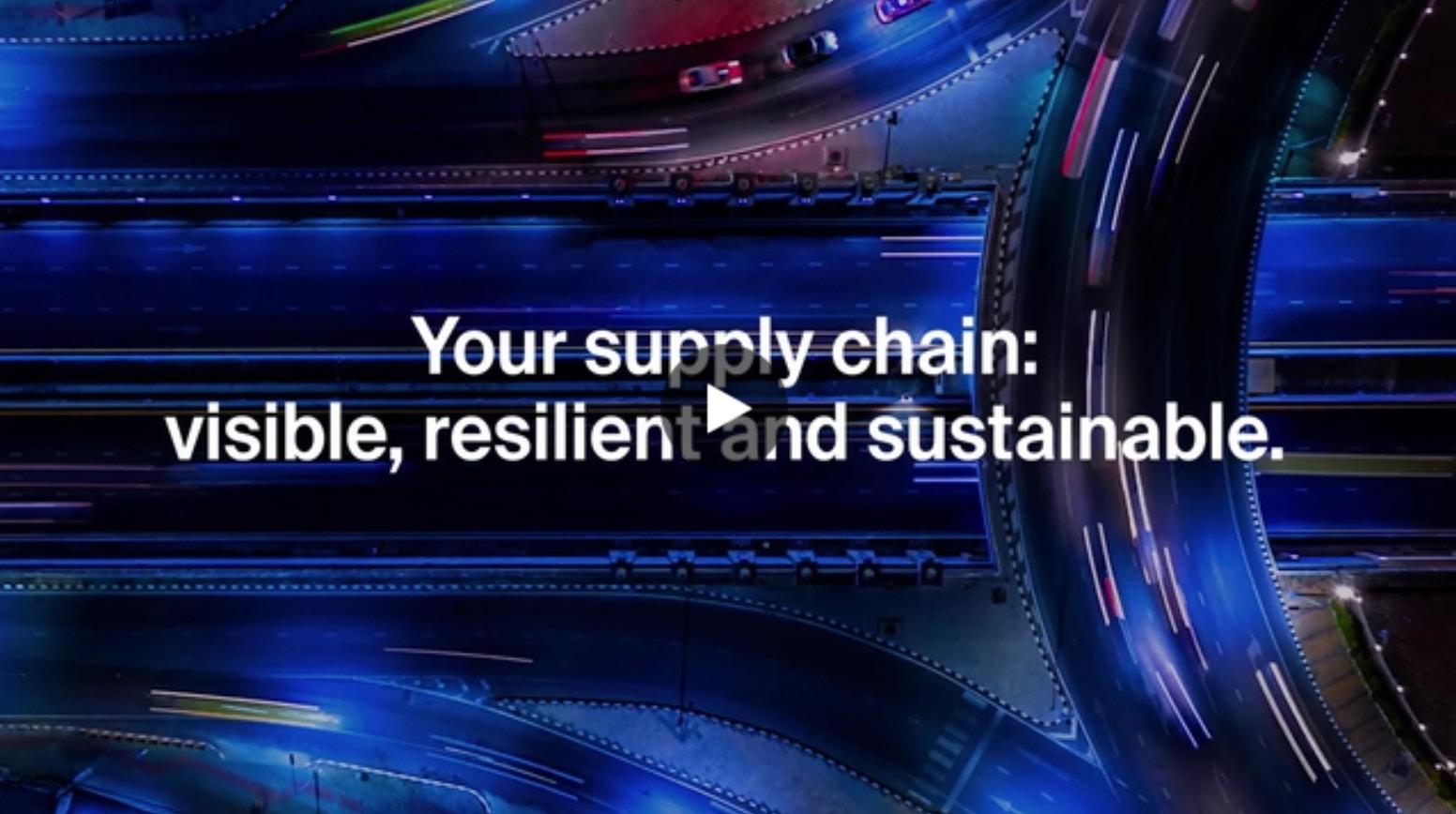
“It's a great tool,” says Mohamad, “which provides us with some features similar
“The transformation helped to provide that fundamental baseline of forecasting, like optimising our supply chain, flow and delivery,” he says. “The good news in terms of the structures we’ve implemented alongside the reactive and proactive teams, which we have called ‘daily escalation’ and ‘the shortage target teams’, is that we were able to effectively manage the entire process and haven’t had to cancel a single order, which is a great thing”.
ALCATEL - LUCENT ENTERPRISE 82 July 2022
Rainbow (ALE’s cloud-based communications platform), provides connectivity across voice, video and messaging, enabling remote connectivity for all employees globally.
“Historically, the accuracy of our data has allowed us to provide trends for that, so we can plan and project outcomes,” says Mohamad. “When COVID-19 hit, we had to identify the challenges which arose, but because we already had the infrastructure in place, we had the capability enabled on our internal platform ‘RainbowTM by Alcatel-Lucent Enterprise’, which allowed us to fully transform. Of course, the supply chain also transformed along with that, and we were able to identify clear goals in terms of our expectations and resilience towards customer needs.” In 2020, COVID-19’s knock-on effects worldwide, began leading to material shortages – shortages that only began to increase at the start of 2021.
KNOW...YOUDID
“Typically, the lead time of the components was 16 weeks,” says Mohamad, “but it went up to almost 70 weeks, which meant that we had to anticipate for 18 months in advance when securing components. This unusually long lead-time made forecasting really challenging.”
With lead times now at 70 weeks - which we see continuing into 2023 - and with price increases across the globe, we need to be vigilant and dynamic in terms of anticipating those outcomes that yield to calculation and therefore prediction.
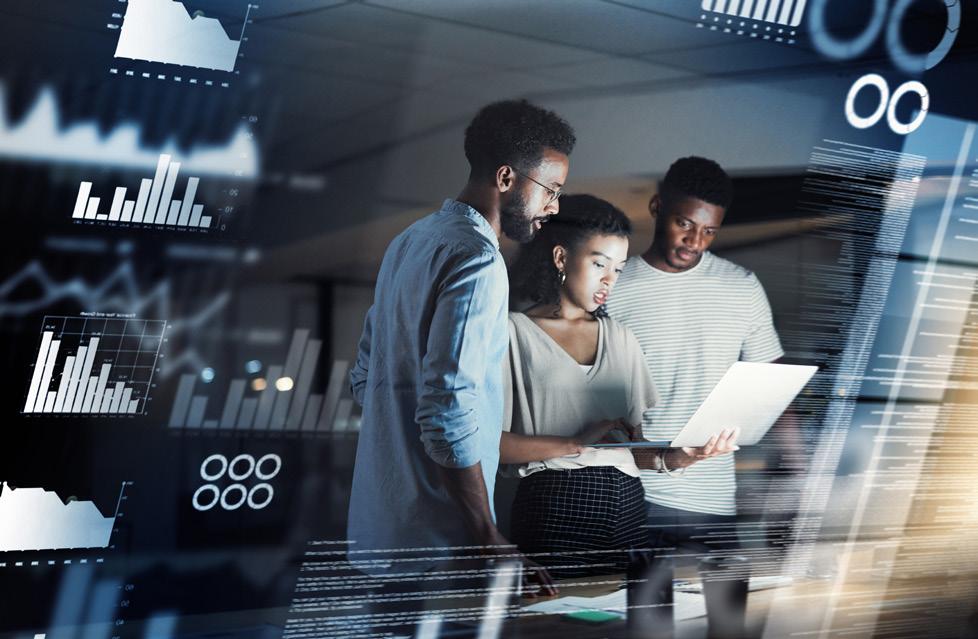

RASHEED MOHAMAD EXECUTIVE VICE PRESIDENT, ALCATEL-LUCENT ENTERPRISE
“Innovation must take place in every single department in synergy with the organisation”whole to those offered by other vendors in the industry, but it’s far more unique and tailored to the business’ needs, and because it also integrates the backend, this makes it an incredibly powerful tool. The Rainbow platform provides much more than just simple communications, it also provides tracking of all of our orders. We have also developed chatbots, called ‘ALE delivery chatbots’, and these enable access for ALE colleagues and business partners to realtime stock estimation, the ability to order directly and highly accurate order tracking capabilities. It’s our cloud-based go-to marketOperationally,tool.” all of ALE’s systems are driven to streamline processes as much as possible, ensuring maximum efficiency. Mohamad says: “The Digital Age Communications’ (DAC) three pillars – Digital Workplace, Enterprise Agility and Flexible cloud models – support enterprises in their digital transformation journey”. Because many office-based businesses have now adopted remote working, it is important to facilitate digital workspaces. “This is where we stand out,” says Mohamad.
supplychaindigital.com 83
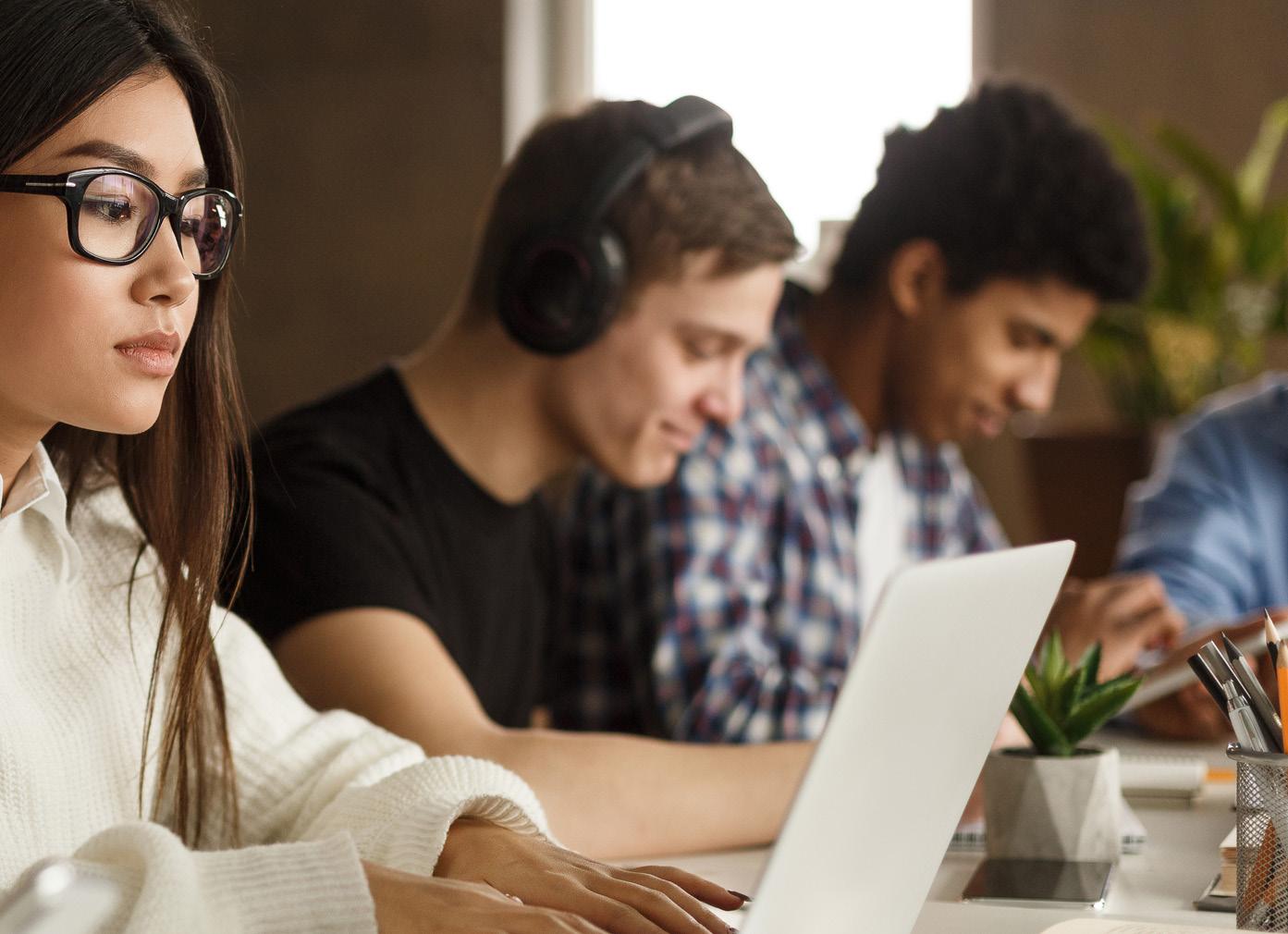
RASHEED MOHAMAD EXECUTIVE VICE PRESIDENT, ALCATEL-LUCENT ENTERPRISE
“Then there’s enterprise agility, where connectivity has to be both seamless and flexible, and our Digital Age Networking (DAN) solutions help to achieve this. Lastly, we have flexible cloud platforms that connect all of these things together, so that everybody can work collaboratively within one integrated system.”
“At
84 July 2022 ALCATEL - LUCENT ENTERPRISE
“We have our cloud platforms including Rainbow Office powered by RingCentral which enables the connection of devices, people and processes, and we’ve recently signed a strategic partnership agreement with Avaya that extends the availability of Avaya’s OneCloud CCaaS (Contact Center as a Service) composable solutions to ALE’s global base of customers, while also making ALE, people are our strength and we work like a family”
“Another great change that came out of this situation was that we had to push the subscription model with more total cloud-enabled solutions,” says Mohamad.
ALE’s unanticipated remote operations meant that they had to identify how best to adapt their q2c chain under such challenging circumstances and to understand how predictability could be improved as a system. But this obstacle delivered unexpected results for their processes as well as their outlook.


“So how do we integrate such variables into our system to enhance reactivity when they arise?”, asks Mohamad. “When I look at challenges, I classify these into three areas: the first are internal challenges, which are ever present; the second are external-predictable challenges; 86 July 2022
ALE’s digital networking solutions available on a global basis to Avaya customers. So we have all the geared solutions available, and this structure has been focused to provide the growth that we actually need for our five-year plan.”
Automation assumes regular and uninterrupted processes. But irregular events like material shortages, pandemics and regional conflicts are of a different ilk and have an unavoidable impact on entire ecosystems.
To understand ALE’s present processes, you need to consider them in context of the transformation journey they had a few years“There’sback.no shortage of processes in our company,” says Mohamad. “As well as being ISO certified, our operating model identifies and defines key areas to optimise the company's quality system. Giving our processes a definition allows us to run the business in a systematic and structured way. Most importantly, we automate any processes that are routine.”
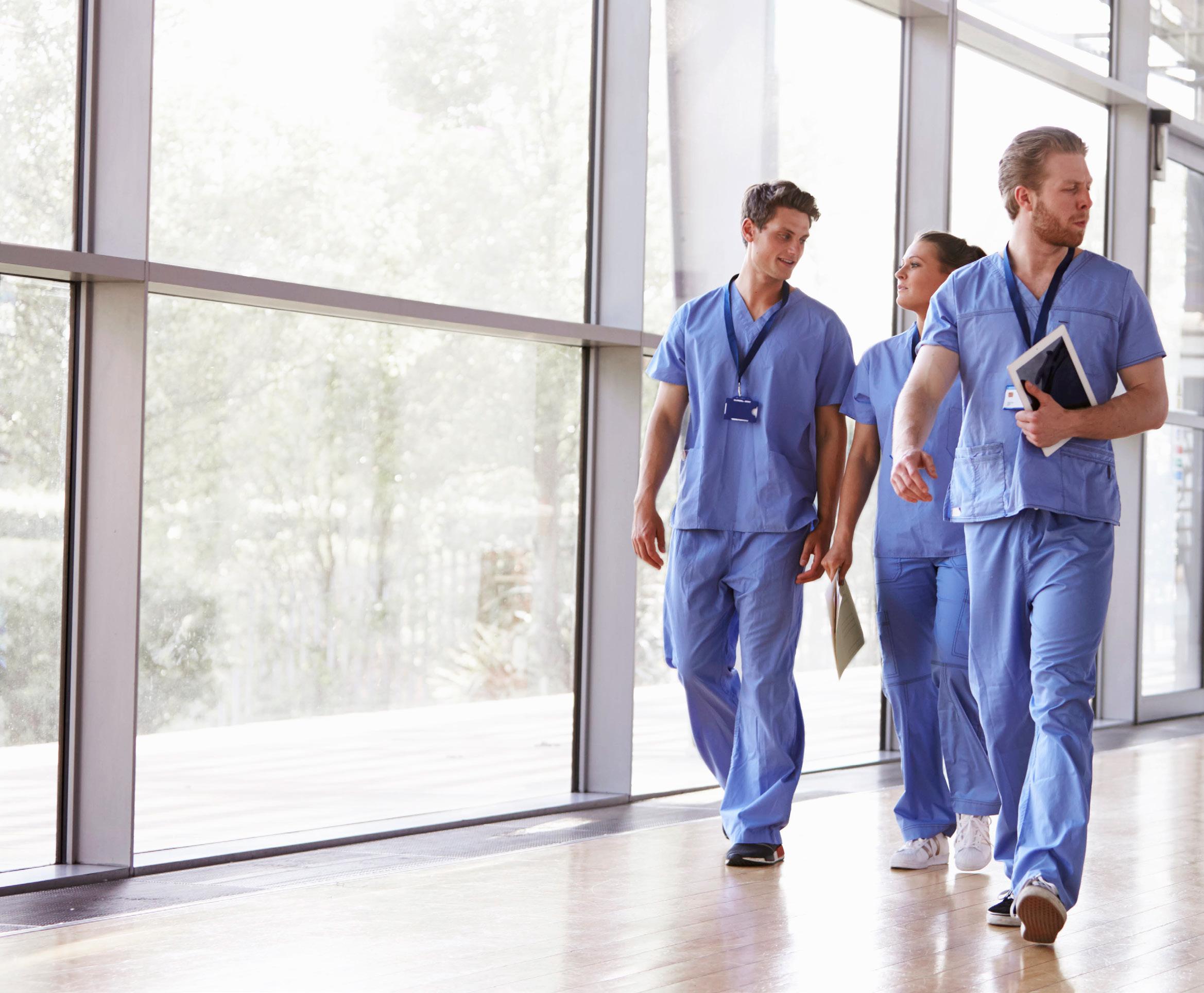
The optimisation of systems, digitalisation and automation are critical to the business
K&N Engineering is a fundamental element of ALE’s partner community, ensuring that the supply chain is resilient, and the third are external-unpredictable challenges, which are essentially the unknowns. Our focus at ALE is to make sure that all predictable challenges, whether they be internal or external, are handled by automation processes supported by AI to ensure that we work as flawlessly as possible. If the predictable systems are optimal, then we are able to focus on the unpredictable and react effectively, thanks to data analysis.”
as a whole, but behind the scenes, it’s the people at ALE - their minds and creativity - who are the heart of the organisation. “At ALE, people are our strength and we work like a family,” says Mohamad. “We help each other to make things happen, and it is the foundation of our teamwork, and it is very important to us. This is also very personal to me as I've been with the company for 20+ years now. The satisfaction you get when you are working on something with a purpose is fundamental to ALE, and I attribute that mainly to the people that I’m working alongside, and their mindsets to make things happen. Culture plays a key role at ALE, and we place a lot of importance on it.”
“It is important that innovation is isolateddepartmentratherholistically,approachedthanbeingconfinedtooneoranaspectofyourbusiness”
RASHEED MOHAMAD EXECUTIVE VICE PRESIDENT, ALCATEL-LUCENT ENTERPRISE
supplychaindigital.com 87 ALCATEL - LUCENT ENTERPRISE
This is where ALE’s adaptability and agility comes in. “We optimise according to requirements on a regular basis, tweaking the systems as needed to reach KPIs,” he says.
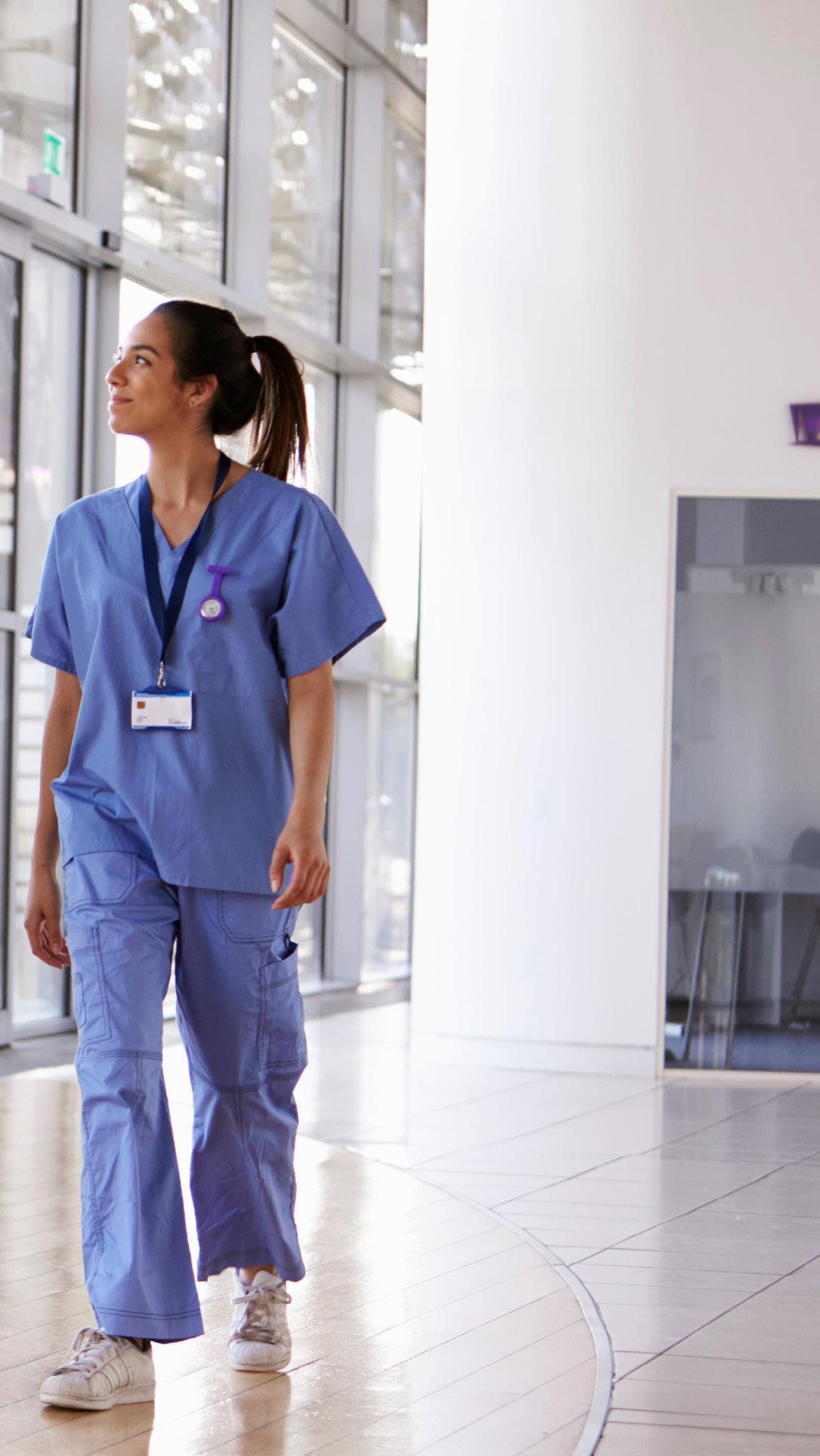
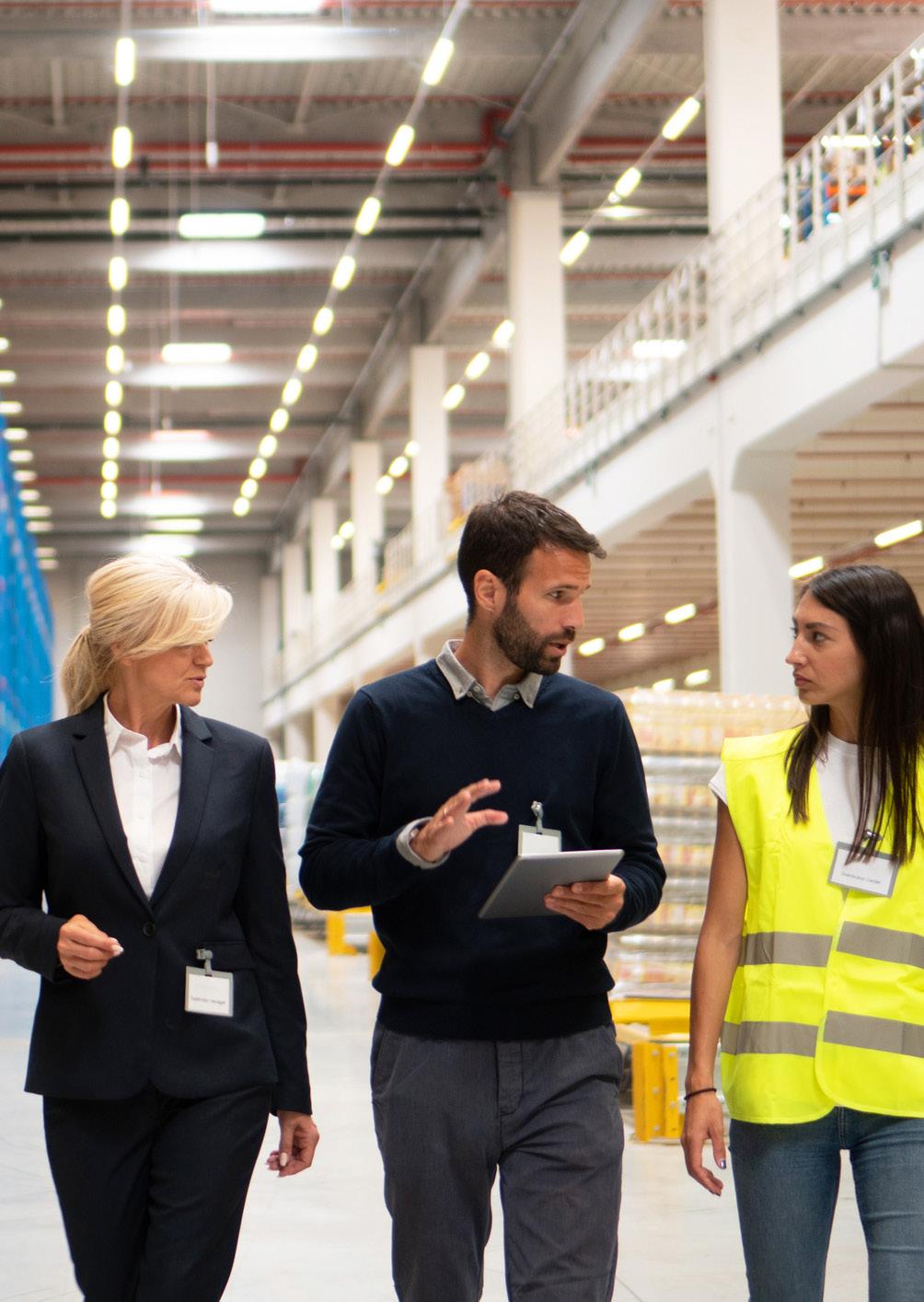
supplychaindigital.com 89 ALCATEL - LUCENT ENTERPRISE
Orienting himself with an eye to the future, Rasheed Mohamad concludes: “With all of these changes, we predict a huge increase in uptake for our subscription model. Significantly, with lead times now at 70 weeks – which we see continuing into 2023 – and with price increases continuing across the globe, we need to be vigilant and dynamic in terms of anticipating those outcomes that yield to calculation, and therefore prediction. Integrating intelligence throughout the supply chain will result in precise forecasts, tracking and automated pick and pack with added valueUltimately,activities.”atALE, Mohamad and the wider team always strive, he says, “to turn the unpredictable into the predictable.” and as a 4PL partner (Fourth Party Logistics), provides ALE with the ecosystem to make sure they have a clear e2e delivery mechanism for their system.
“It's almost the fifth year of our partnership,” explains Mohamad. “K&N’s innovation and technology continues to hugely benefit us as well as aligning with our willingness and vision to undergo such a technological evolution. Working together as a team to make this happen has been great. And as a bonus it’s also one of the reasons for our improvement in on-time deliveries over the last few years, which has made our customers very happy, of course.”
There are other notable developments too. Mohamad is a sponsor of ALE’s #GoGreen program. This initiative aims to find new technologies that will contribute to protecting natural capital, building sustainable cities and limiting global climate change.
“With price increases continuing across the globe, we need to be vigilant and dynamic when anticipating outcomes which yield to calculation and therefore prediction”
“The ALE #GoGreen programme aims to decrease the organisation's overall carbon footprint. By reducing paper files and the use of excessive emails, as well as sharing files in a more ecofriendly, agile and efficient manner, we can reduce our overall CO2 emissions,”
explains Mohamad. “At ALE, we continue to encourage remote work, and an important part of this initiative is enabling effective hybrid-working which contributes to cutting travel emissions. As part of the effort, we are also utilising our facilities to host key events remotely, such as our annual Connex conference.”
RASHEED MOHAMAD EXECUTIVE VICE PRESIDENT, ALCATEL-LUCENT ENTERPRISE
AND SMALL WINS AREENERGYDRIVINGEFFICIENCY 90 July 2022 SUSTAINABILITY
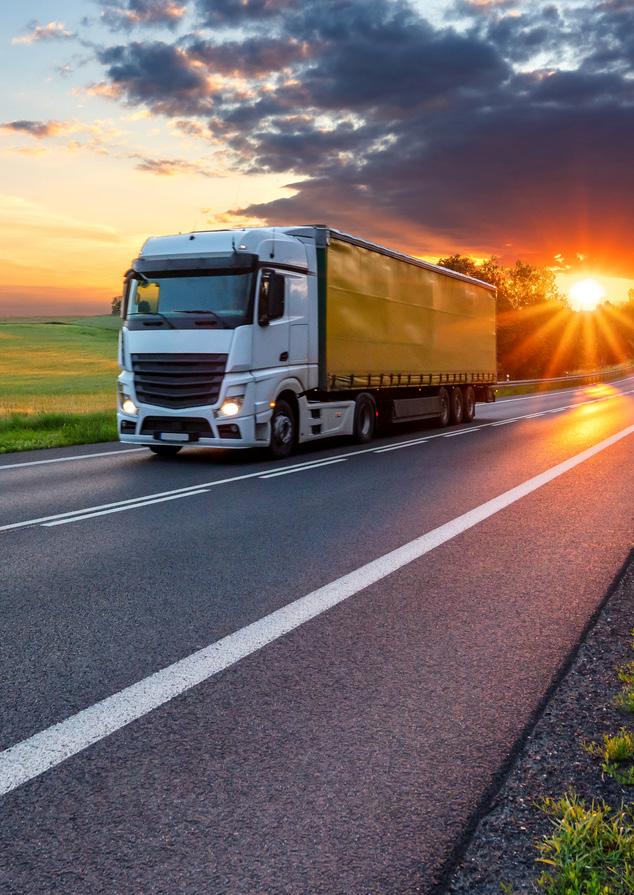
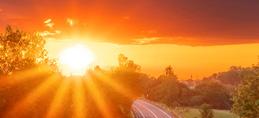
WRITTEN BY: SEAN ASHCROFT I t is a generally accepted truth that supply chains contribute up to 80% of an organisation’s total carbon emissions – or so-called Scope 3 emissions. As such, a huge responsibility rests with the logistics industry to help the globe hit its net zero targets by Innovation2050.and collaboration are already key drivers of success in supply’s bid to clean itself up. As we shall see, such sustainability successes and goals come in all forms – from low-resistant truck tyres to technology that can provide at-a-glance snapshots of global supply chains with 10,000 moving parts. But big or small, local or international, every move to save energy in the logistics industry moves us closer to carbon neutral nirvana. Let’s start with the macro moves –sustainability on a grand scale.
Craig Roseman is APAC consumer packaged goods (CPG) leader at Schneider Electric, the multinational electronics company with a payroll of 75,000.
CPG has major role to play in global sustainability Roseman – who oversees the alignment between Schneider’s products and services with market needs and trends – says CPG has a “significant” role to play in achieving world sustainability goals.
DRIVINGSMALLEFFICIENCY
Whether macro or micro, local or international, steps to reduce energy consumption in logistics are contributing to global net zero goals supplychaindigital.com 91
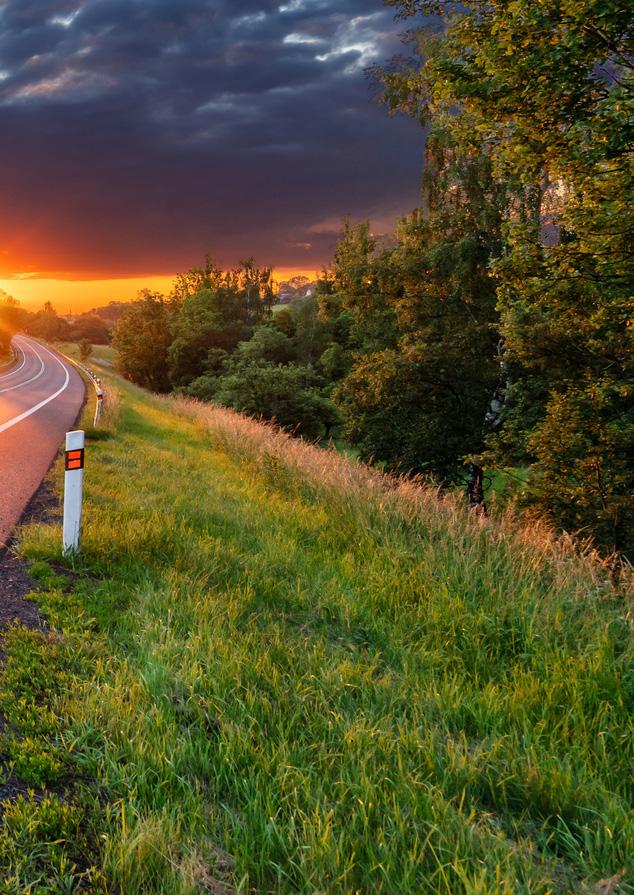
Supplier performance. Supplier risk. Supplier diversity and ESG. You've got big plans; Vendorful has the tools to help you execute. www.vendorful.com
He says: “Supply chains are major contributors to environmental impact, from high energy consumption to mass waste disposal.” He believes digital tracing in supply chains – and monitoring in cold chains –are vital steps to cutting industrial carbon emissions, saying: “While becoming more resource-efficient can reduce greenhouse gas emissions, decarbonising indirect emissions from industry remains a significant challenge.”
Measuring logistics emissions is crucial first step
Roseman says product emissions increase throughout their lifecycle and that measuring this “gives a visual on how production, manufacturing and distribution affect overall carbon emissions”. He adds: “Lifecycle traceability is particularly important, because guidelines are forever changing to ensure companies are ethically and sustainably accountable for their climate targets.”
“ FOR DIGITALISATIONSHIPPERS, BRINGS DOWN COSTS DUE TO NETWORK EFFICIENCIES”
supplychaindigital.com 93 SUSTAINABILITY
He adds: “In the food industry, indirect emissions result from the transportation of raw materials and the distribution of final products. Traceability can help identify and remedy inefficiencies throughout the supply chain.”
WENJIA TANG HEAD OF DIGIHAULDATA,
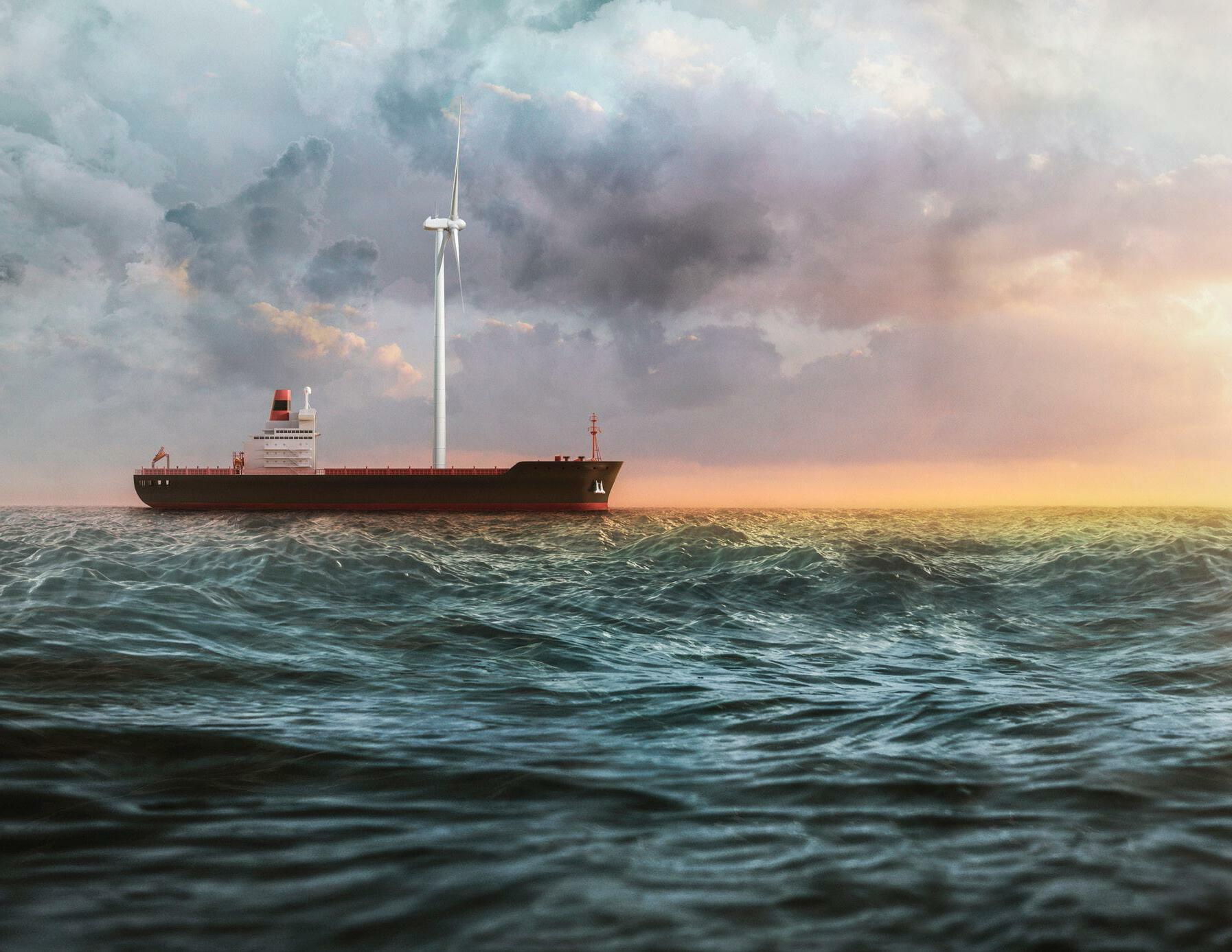
THEIR
Roseman also urges action on the monitoring of so-called ‘cold chains’, which are environmentally-controlled domains that protect temperature-sensitive goods – such as food and biopharmaceuticals –during transport and storage.
“Green Premium delivers strong value propositions through its portfolio of products, services and solutions. By collaborating with third-party organisations, we can support our customers to meet their sustainability goals.”
GIVES A TAKE ON OVERALL CARBON EMISSIONS” CRAIG ROSEMAN APAC CONSUMER PACKAGED GOODS LEADER, SCHNEIDER ELECTRIC 94 July 2022 SUSTAINABILITY
On a more strategic level, Roseman says ‘regionalisation’ – the process of sourcing INCREASE THROUGH LIFECYCLE, SO THIS
“Cold chain monitoring is essential to ensure journeys along the cold chain are as efficient as possible. Monitoring also helps reduce wait times at ports, where further energy is required to maintain storage temperatures and control systems.”
“ PRODUCT EMISSIONS
Another action he feels can contribute hugely to lower CPG emissions is the embedding of sustainability into manufacturing design.
MEASURING
Roseman also says Schneider’s Green Premium programme is making a difference.
“Not only does this result in a reduced carbon footprint, but it also provides transparency – both on environmental impact and circularity attributes, through third-party labels and product certifications.” Regionalisation is way to reduce mass transport
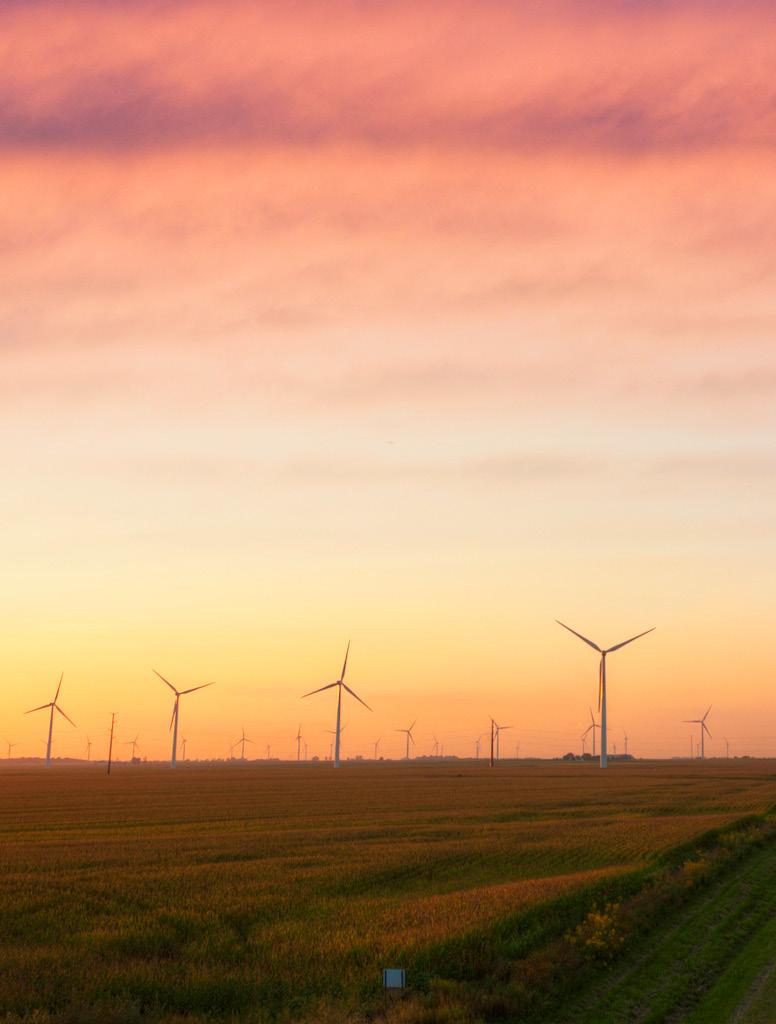
Roseman concedes that such a move will impact costs but says these are offset by reduced costs through decreased inventory, greater working capital from shorter supply chains, and also higher levels of Sosustainability.thisisenergy conservation on a global scale. But what about the small wins, which, when added together, are just as Wenjiasignificant?Tangishead
Schneider and Henkel team on decarbonisation
• Implement activities. “We are fully committed to the Schneider Electric programme,” said Ulla Hüppe, director of sustainability for Henkel´s Adhesive Technologies business unit. “Together, we can advance our positive environmental impact.”supplychaindigital.com 95
Henkel outlined detailed actions that can be implemented as part of its four pillar approach:
SUSTAINABILITY
Customer-supplier partners Henkel and Schneider Electric have come together to cut CO2 emissions in the supply chain. In 2021, Schneider launched its Zero Carbon Project, in which it is partnering with its top 1,000 suppliers to halve their collective emissions by 2025. As a key member of Schneider’s supplier community, Henkel is also part of this drive and has made great strides on cutting emissions. As of 2021, Henkel’s CO2 emissions per tonne of product were down by 50%; Schneider therefore invited the company to share its best practices with other Zero Carbon Project participants at a recent training event.
of data at digitalfreight business DigiHaul. In this role, she is responsible for the company’s UK datadriven insights on shipment information,
• Set targets within scopes of control.
• Determine the baseline from which progress is assessed.
• Understand sustainability focus areas and their objectives.
goods locally instead of internationally –will be a major factor in reducing mass transportation. He says: “A purely local footprint is not feasible, because one disruption can bring down the whole chain. So organisations need to empower at the regional level and maintain tight coordination of local sites.
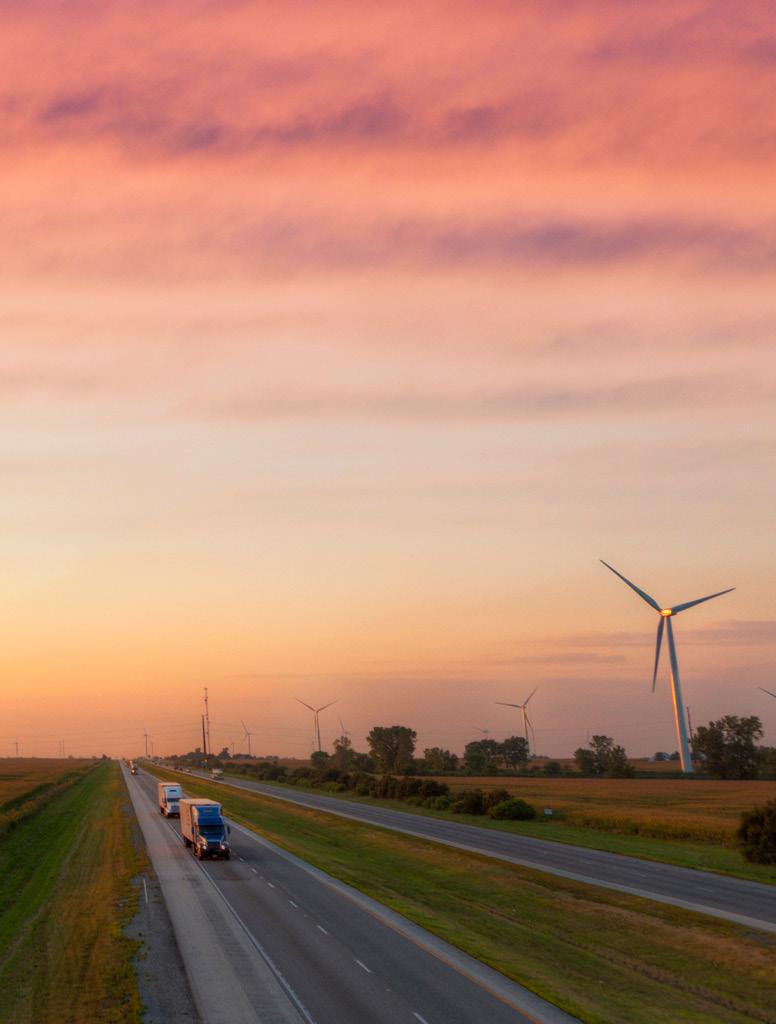
Tang says addressing this issue has the potential to solve two of the biggest issues in commercial transport: cutting carbon emissions and unlocking extra capacity to alleviate some of the pressure on supplyTangchains.saysa degree of empty running is “inescapable”, but insists that, with better planning and the right technology, “we can reduce it to what is considered a more efficient and sustainable level”. She adds: “This can be achieved with quality data analysis. A good model can produce a better quality of match compared to the traditional labour-intensive brokerage method.” Tang says that the biggest barrier to tackling empty running is visibility across the commercial road transport network. “The more visibility we have, the more we can optimise things through data analysis and connecting the various parties,” she explains. “For shippers, digitalisation makes logistics much more transparent and gives them 96
July 2022 SUSTAINABILITY
better visibility of where their shipments are,” says Tang. “They will also see their costs coming down due to the network efficiency.”
She adds: “For carriers, it allows them to better plan their journeys, including accessing new revenue by taking on jobs they might not otherwise have access to. “A major part of the solution is onboarding carriers and showing them the benefit of being involved in a wider network. Transport is a really fragmented industry, so we can only achieve proper gains if we have a drawn from geospatial data, and IoT (Internet of Things) devices, such as vehicle trackers. One of the areas Tang is focused on is improving efficiency by reducing the empty running of road freight. Empty running often happens on one leg of a journey, when freight is offloaded and not reloaded with anything for its return journey. It’s believed that, in the road haulage sector, empty running is as high as 20%, and this doesn’t take into account partial loads. ‘Empty running’ in haulage is huge waste of energy “This is a problem not only for carriers who are looking to optimise their fleet, but also shippers who may be struggling to find capacity,” says Tang. “Not to mention the carbon footprint for both.”
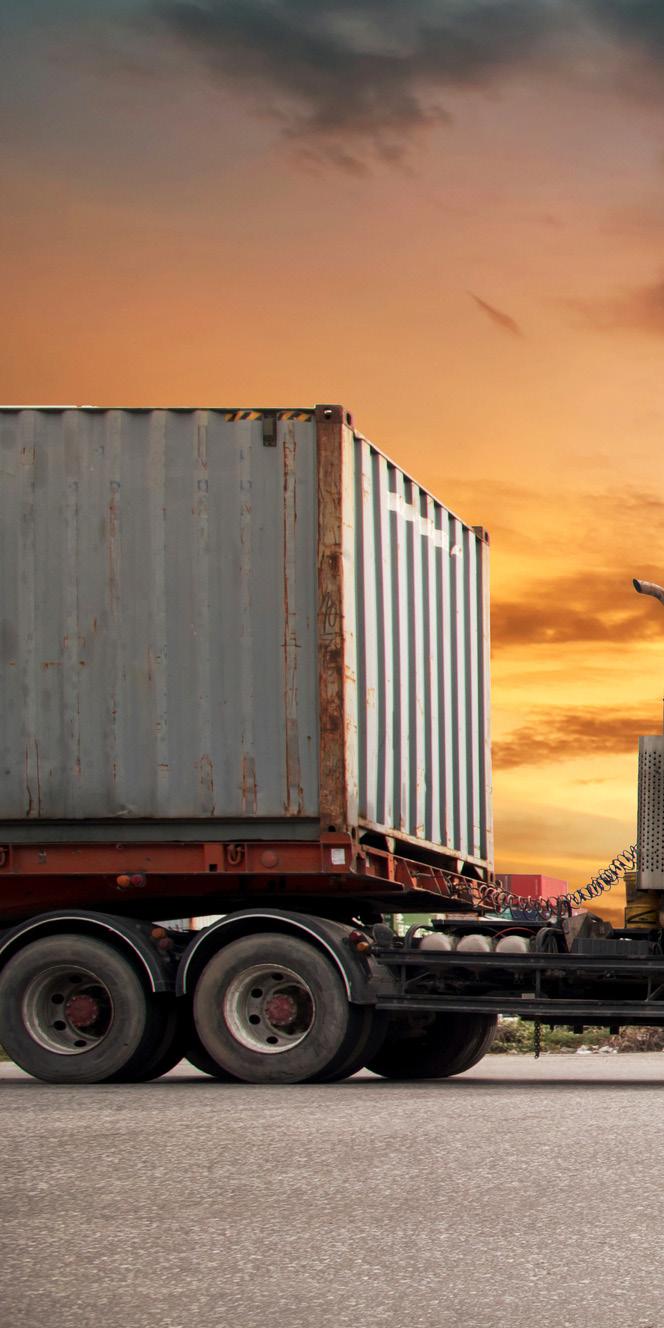
The programme also looks at basic fleet features, such as low-resistance tyres, aerodynamic enhancements and idle cutoff, as well as advanced green tech, such as sustainable fuels and alternative drivetrains.
Big and small energy wins across logistics are inching us closer to our green goals.
“A MAJOR PART OF SUSTAINABILITY IS SHOWING CARRIERS THE BENEFIT OF BEING INVOLVED IN A WIDER NETWORK ” WENJIA TANG HEAD OF DIGIHAULDATA,
supplychaindigital.com 97
critical mass of hauliers. On the whole, when carriers see the opportunity to maximise their own fleet, bring down their carbon footprint and make drivers lives a bit easier, they’re very keen to be a part of it.”
She says: “This identifies subcontractors that are contributing to sustainable logistics. Carriers are assessed on the sustainability measures they have in place, as well as their ability to measure their carbon footprint and share data.”
Overhaul teams with DHL on sustainability Decarbonising commercial road transport isn’t just about cutting empty-running levels. In partnership with DHL, it has launched the Green Certification programme, reveals Tang.

LESSONS LEARNED FROM COVID - 19 TO PREPARE FOR THE FUTURE PRODUCED BY: CRAIG KILLINGBACK WRITTEN BY: GEORGIA WILSON
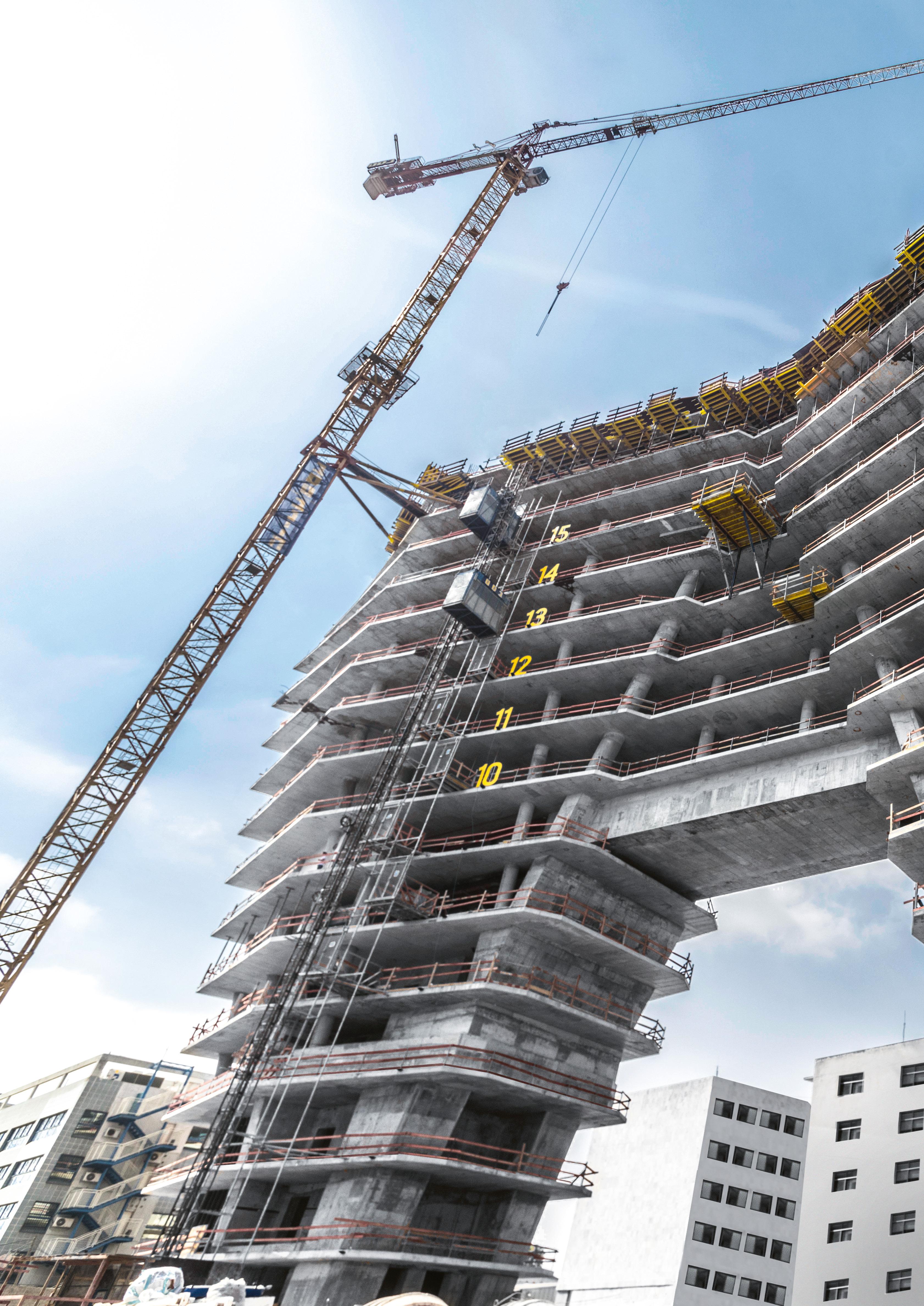
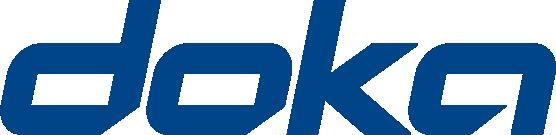
supplychaindigital.com 99
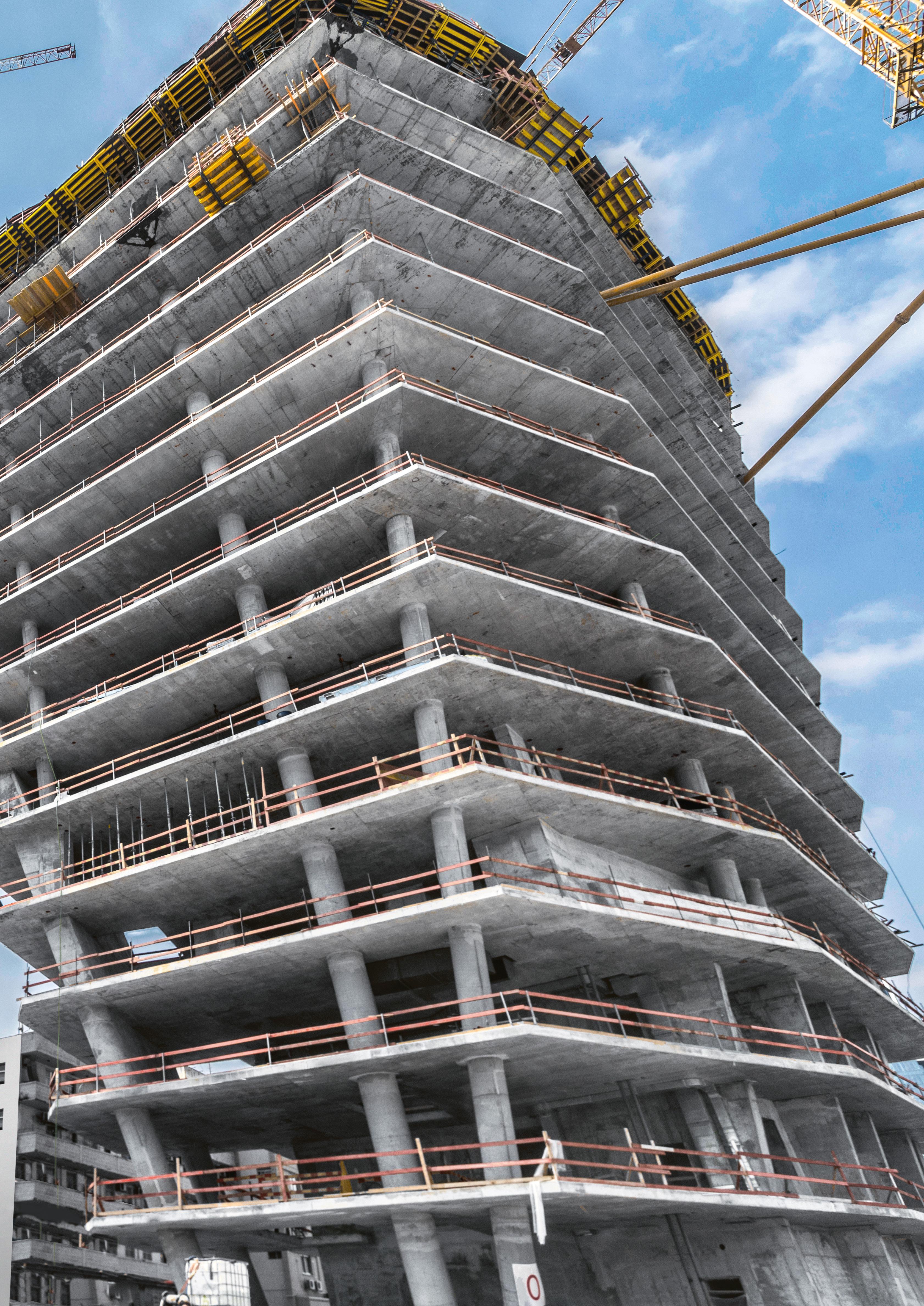
100 July 2022
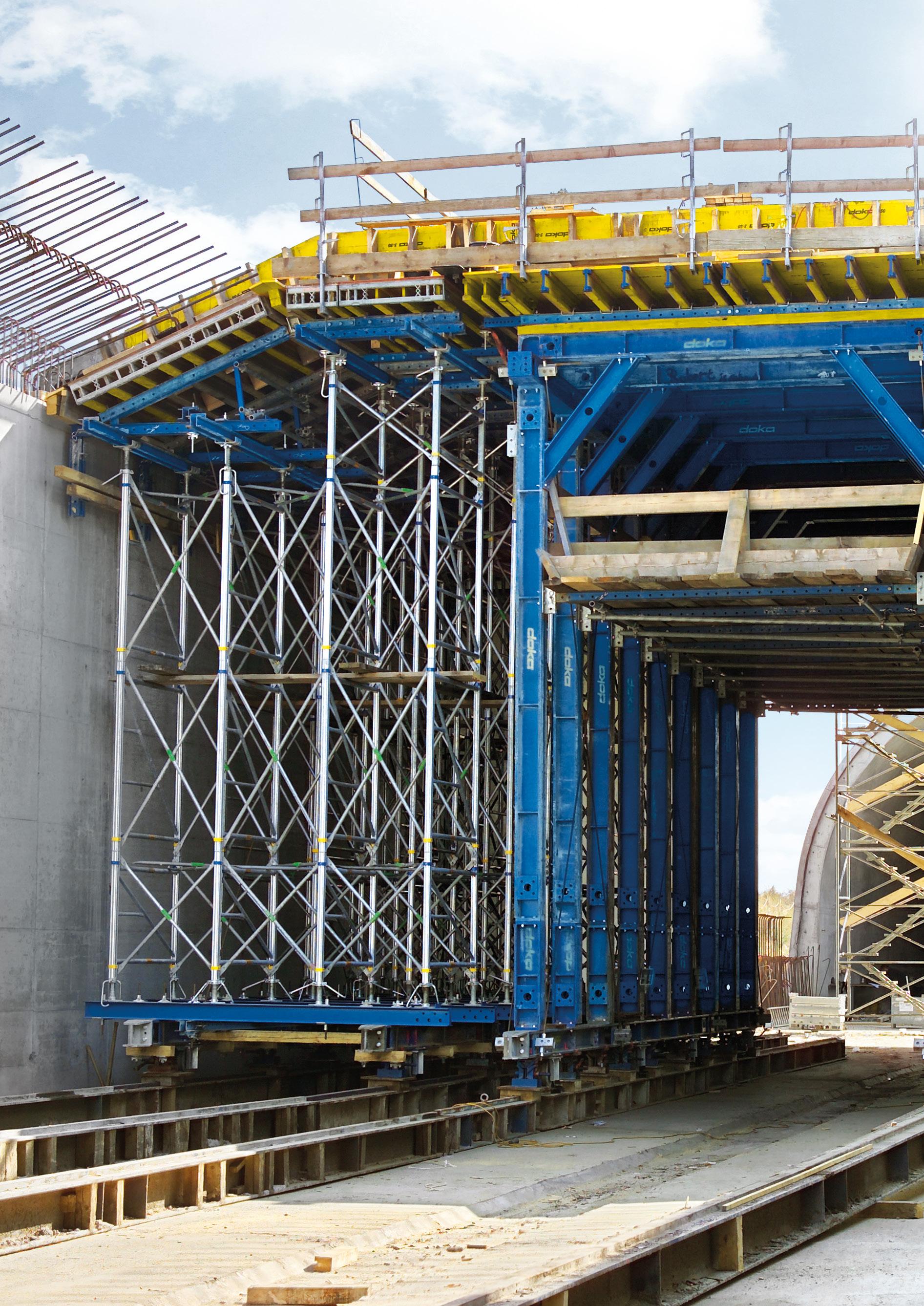
W ith a more than 115-year heritage in the construction industry, Doka has perfected the provision of reliable, trustworthy services to customers.
“Our values provide a solid foundation for developing and selling high-quality solutions, from initial planning through to reliable implementation on site. We help our customers to build better, safer and moreDokaefficiently.”isadynamic company in the construction industry. “Alongside our quality formwork – scaffolding solutions – Doka offers digital solutions and helpful gadgets to support those on the construction site to become more efficient,” says Mirko Loos, Head of Material Group Management at Doka. He continues: “We are constantly developing a range of new digital solutions, tools, ideas and concepts for our customers.” The impact of two highly disruptive years Since the outbreak of COVID-19 back in 2020, Doka Global Procurement has had to embark on a steep learning curve – and it has learned a lot from the experiences of the last couple of years. “The question for us has been what now needs to change? What has affected us the most during these highly disruptive years? And what do we take with us into the years ahead?” says Loos.
Doka’s Thomas Zsulits & Mirko Loos discuss lessons learned over the last two years to better prepare procurement for the future and their upcoming plans supplychaindigital.com
DOKA101
“We are listening intently to understand the world through the eyes of our customers,” says Thomas Zsulits, Director of Global Supply at Doka.

EXECUTIVE BIO MIRKO LOOS TITLE: HEAD OF MATERIAL GROUP MANAGEMENT LOCATION: GERMANY 102 July 2022 DOKA
20 years of straight procurement expertise. Started his career 2002 in the Strategic Supplier Management department at Mercedes-Benz near Stuttgart. In 2007 he moved on to join the anglo-dutch provider of online-paid content Reed Elsevier (later RELX Group), where he held different local, regional and later global roles in Procurement. In 2018, Mirko joined Doka as Head of Category Indirect and has recently taken on the role as Head of Material Group Management. He holds a degree in Business Administration from PFH Private University of Applied Sciences in Goettingen, and he lives with his family near Dusseldorf in Germany.


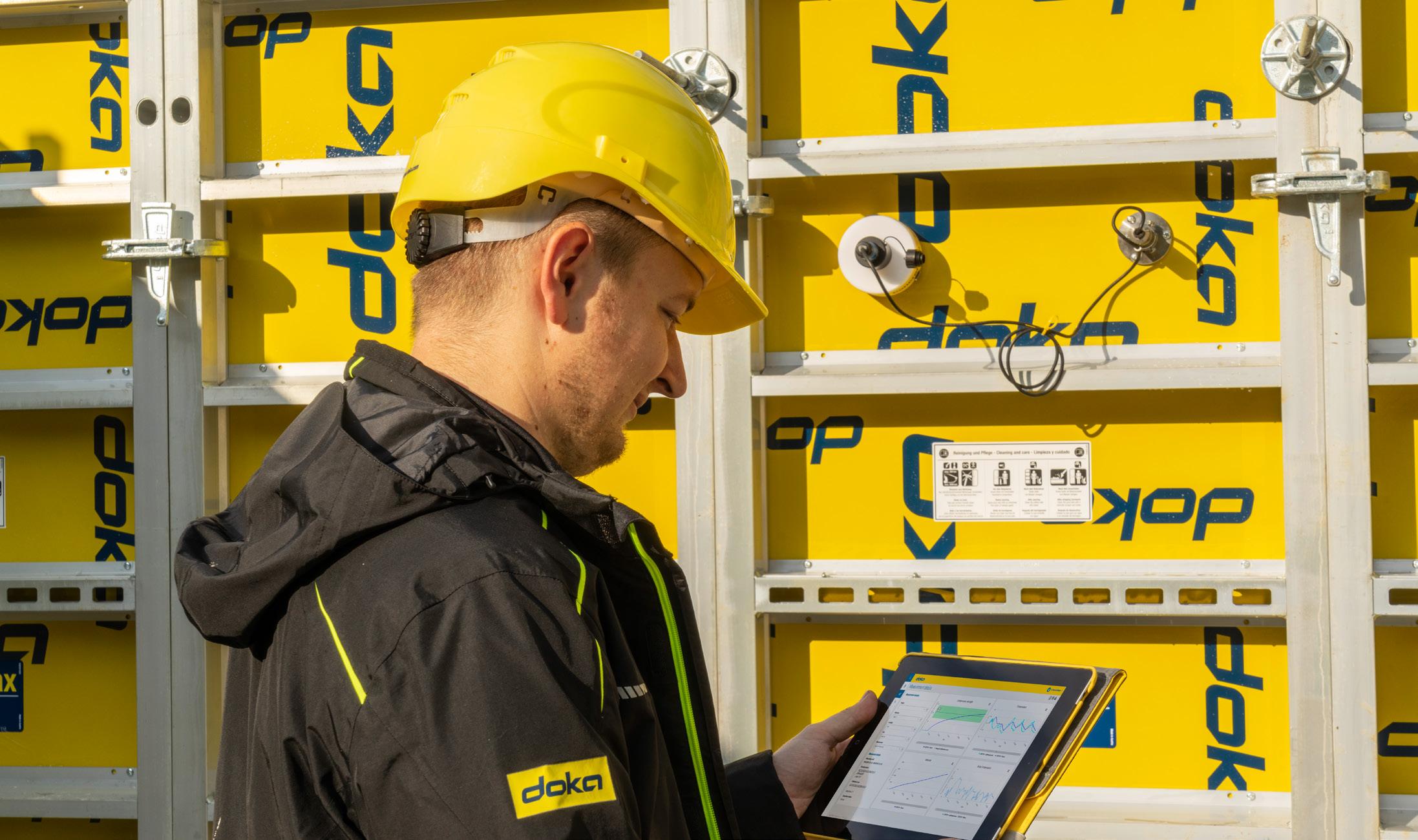
EXECUTIVE BIO THOMAS ZSULITS TITLE: DIRECTOR GLOBAL SUPPLY LOCATION: AUSTRIA supplychaindigital.comDOKA103
More than 20 years of experience in different functions along the supply chain process. Gained broad experience in global leading companies like Bosch and Mondi, as well as in mid-range organizations across the globe. Degrees in electronics and later on a Bachelor in BA supported his strong implementation and process skills. With his charismatic leadership skills he is used to being successful also in turbulent times and has proven his leadership skills in turnarounds, M&A’s, restructuring programs and more.
He lives close to Vienna in Austria with his family. Beside his passion for the job and family, he runs a diving school where he loves to give people an insight into his passion for diving.
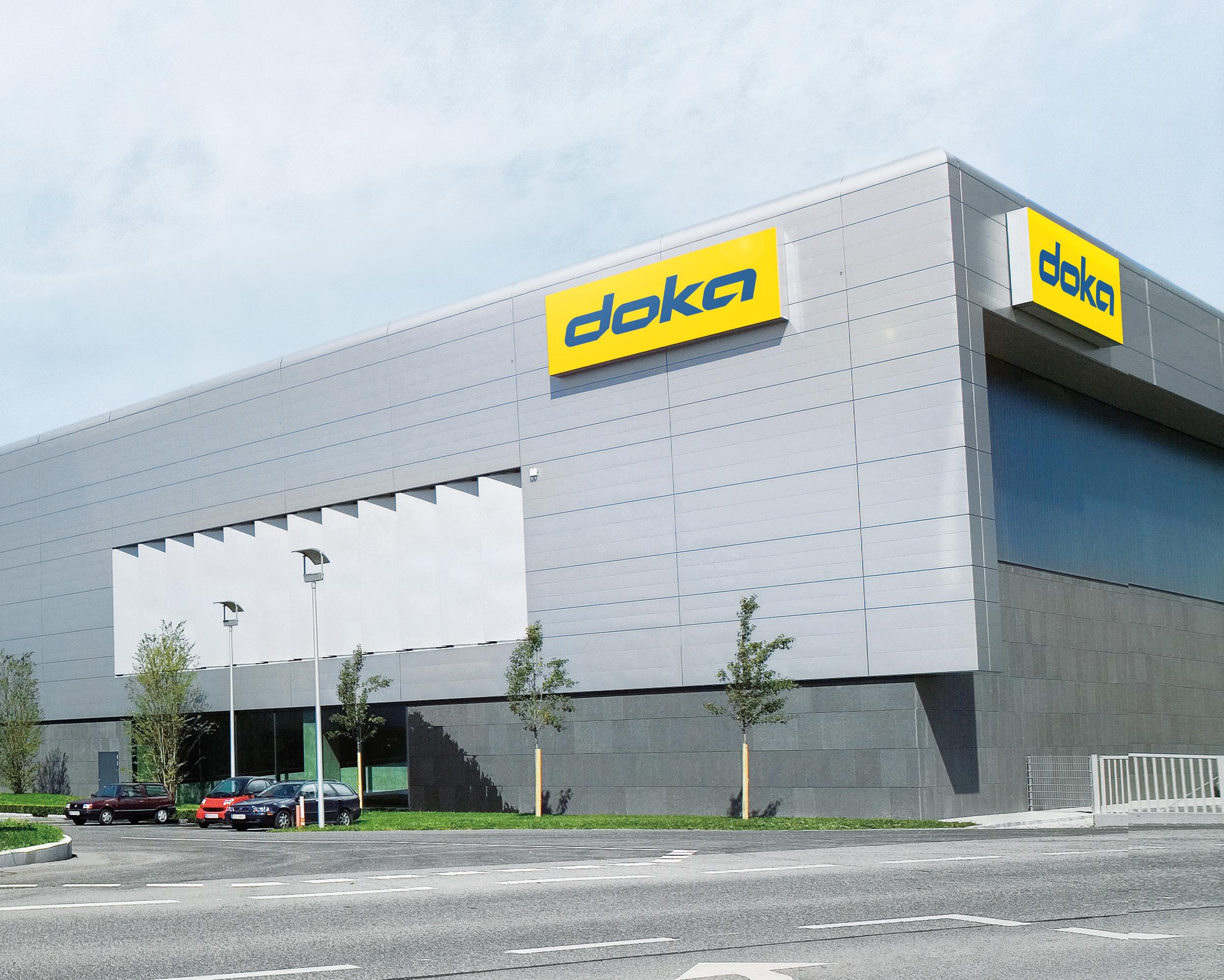

WE ARE BUILDING THE FUTURE The Market Unit Composites is your strategical partner for the development of innovative multilayer panels for formworks. Our materials have excellent mechanical resistance, which multiplies the reuse of your panel and further more it is 100% recyclable. If you want to know more about our products for formworks applications check our website: www.renolit.com/formworks. RENOLIT: for a long life of your panels #longlifetoyourpanelsOrcontact us directly: Axel Kulke, E-Mail: axel.kulke@renolit.com
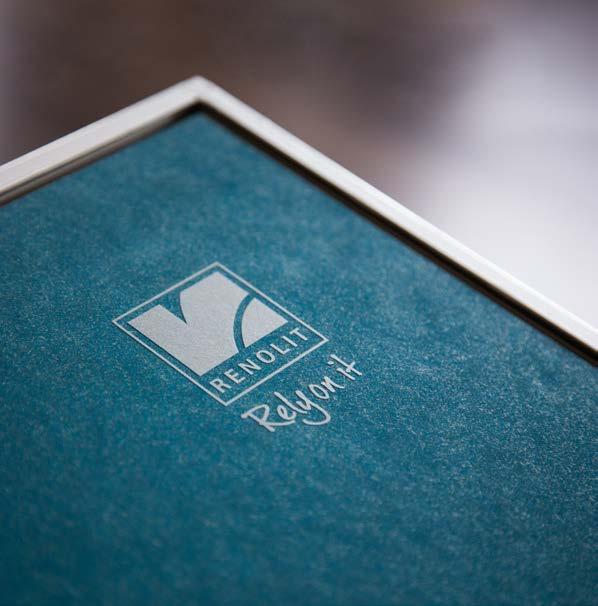

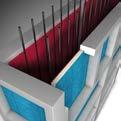
“At Doka, we offer a lot of digital solutions and helpful gadgets to support those on the construction site”
With this, Doka hopes to be more flexible in some ways, while remaining stable enough to face these challenges and bringing together its partnerships as one supply stream.
“Today, the deeper we look into our supply chain, the less we know. This transparency is a major risk to our security of supply and a learning from the past years is that we must not leave this entirely to our Tier-1 to manage. So we are approaching our partners across the tiers to discuss potential risks together.”
Agreeing with Zsulits, Loos also speaks from an internal viewpoint: “We now collaborate a lot more than we did supplychaindigital.com
DOKA105
MIRKO LOOS HEAD OF MATERIAL GROUP MANAGEMENT, DOKA
Countries around the world have been affected and are reacting differently to the shortages, as well as the fluctuation of demand driven by COVID-19. “But one particularly common experience is the inability to foresee or plan any scenarios,” addsHeZsulits.adds:“Many of the scenarios we thought would happen, didn’t come true. And with that, we realised that it is not enough to primarily talk to our direct partners in Tier 1. We also need to ask ourselves where risks might lie in the tier-n supply chain and monitor them regularly.”
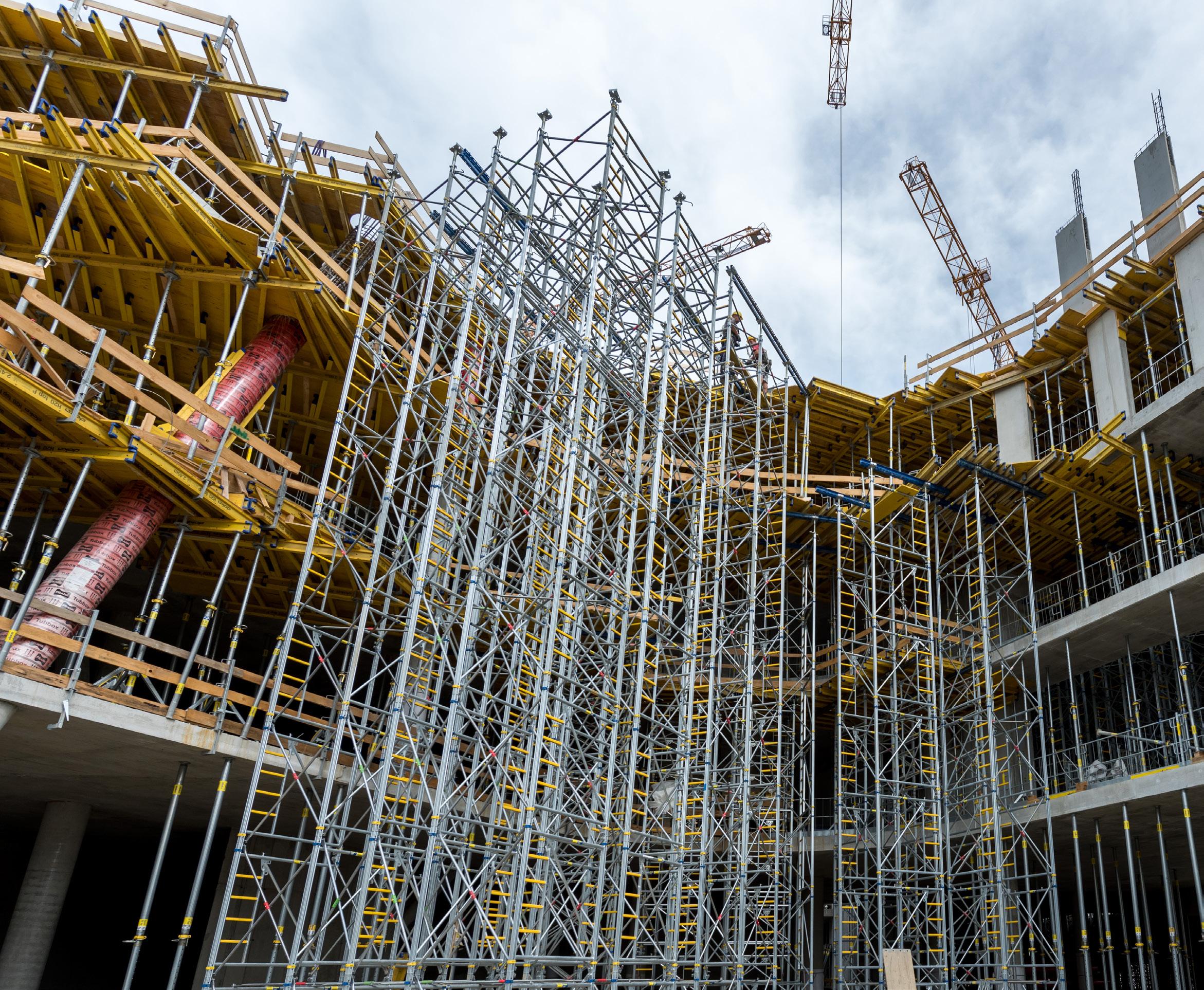
Future trends While nobody knows what is in store for the supply market, Zsulits and Loos expect the volatility of the past few years to continue. “This makes it quite hard to predict,” says Zsulits. He adds: “We will remain in close contact with our suppliers and increase our collaboration. Doka will also focus on more than just its Tier 1 suppliers to improve our risk monitoring capabilities, transform our procurement strategies, and enable quick decision“Thesemaking.willbekey to successful operations in the future. So key trends in procurement’s future will continue to be flexibility and the ability to respond with speed.”
Doka is also working on its predictive capabilities when it comes to material prices. “From a materials group management perspective, we are trying to predict fluctuating prices in a volatile market,” says Loos. “The market is being impacted by the likes of material shortages and price inflations, and so we are working to better predict these disruptions.”
106 July 2022 DOKA

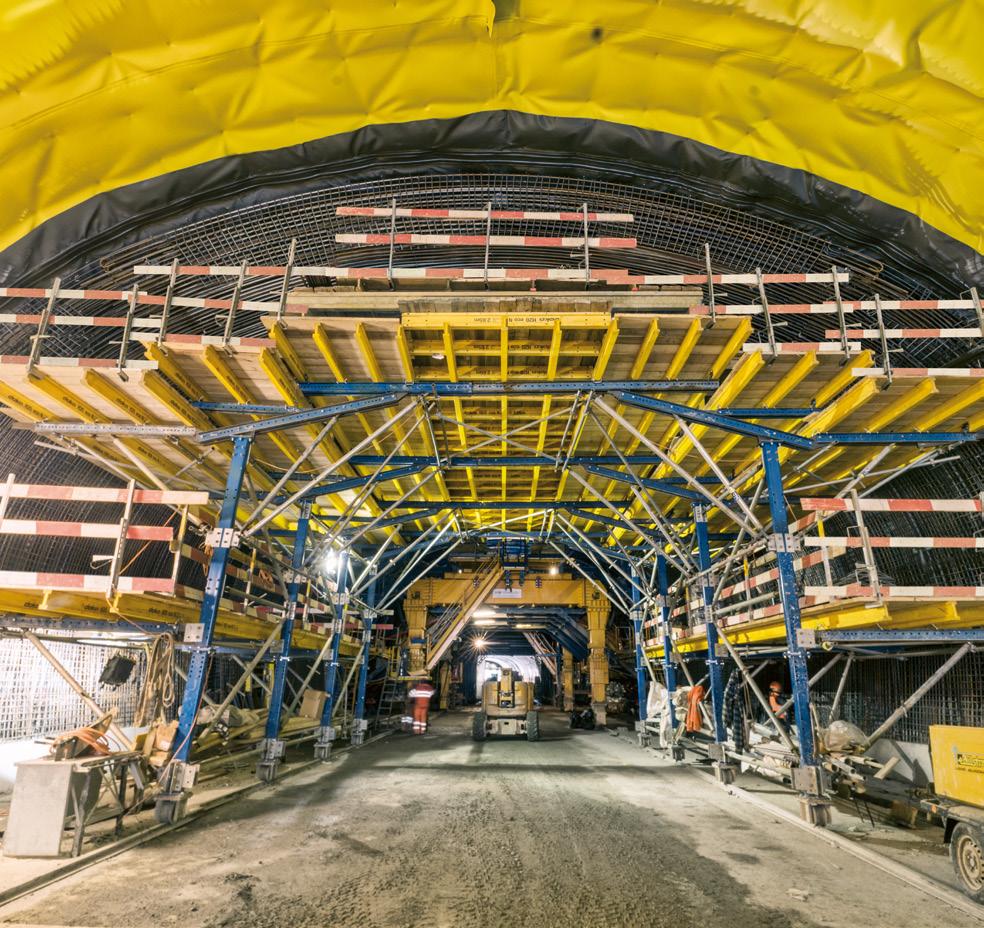
THOMAS ZSULITS DIRECTOR GLOBAL SUPPLY,DOKA supplychaindigital.comDOKA107
So what exactly makes the future so different from now? “More diversity,” says“It’sZsulits.more development of our colleagues and employees, and it’s more internationalisation. The last couple of years have shown us that being on one side of the strategy – whether its globalisation or localisation – wouldn’t have helped; in fact, it would have hit us much more. So we have to diversify our supply market to balance the global influences.
pre-COVID-19. Over the past two years, whenever our security of supply was at risk, we collaboratively worked together within procurement. The industry has shown great contribution and dedication to solving the industry challenges. This, in turn, has helped us to grow as a team.” Doka’s future plans
“Don’t try to think in a common way, continuing with processes that you have done for the last 10, 20 or 30 years; think about new processes, new opportunities. You have to be brave, commit to decisions and make them fast. We discovered that fast decisions lead to success and motivates people.”
Agreeing with Zsulits, Loos adds: “We have learned that you can set up a strategy now and then have to redo it again some weeks later, but it’s important for us to think “We are listening intently to understand the world through the eyes of our customers”
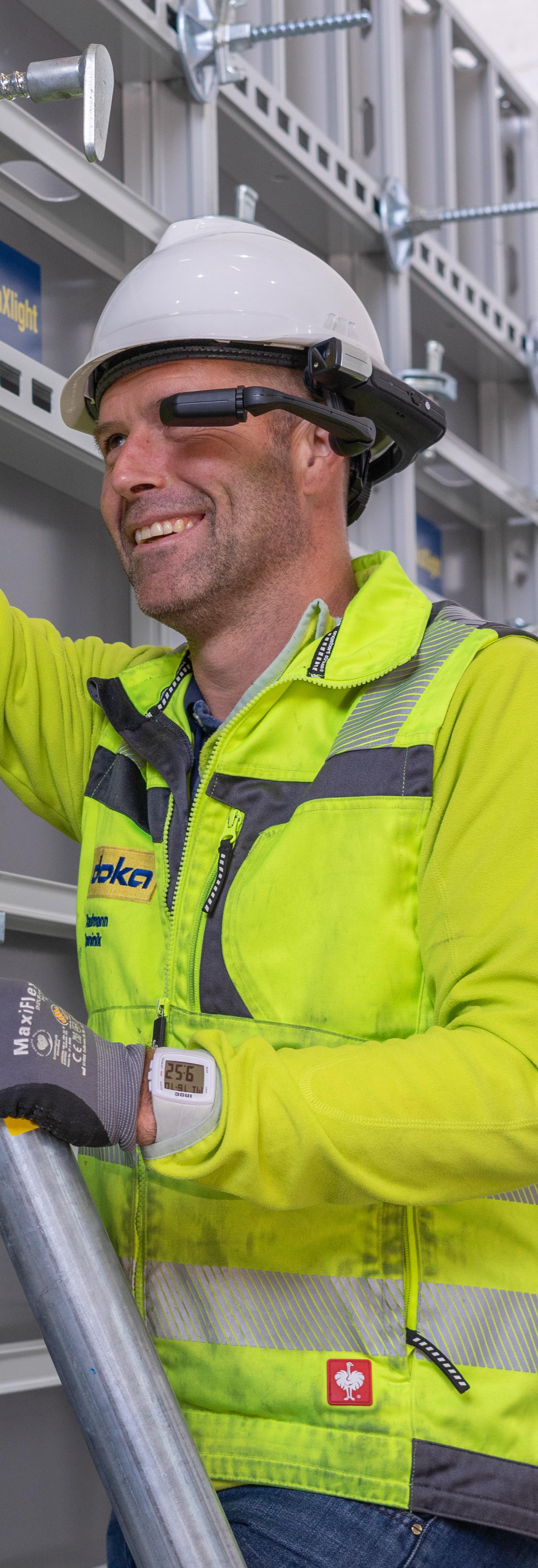
108 July 2022 DOKA
The importance of partnerships More and more, partnerships for Doka are becoming crucial to its operations. “In today’s fluctuating and uncertain markets, we rely on our partners' insights into the industry to stand by us and support our operations. In the next few years, we will be focusing much more closely on our partnerships and be working in closer collaboration with our most important partners,” says Zsulits.
ahead and work on a long-term strategy, nonetheless. In procurement, there are outside influences that we need to consider such as ESG, so we need to set those longterm strategies alongside both short and medium-term goals that will get us there, and will help us to measure whether we are still on the right path. We need to start looking forward and predict what will happen in the future, where possible, and determine how these market changes could impact our business, and how we can flexibly adapt to different scenarios.”
A key partner for Doka is RENOLIT GOR S.p.A.. “We have a unique and long-term partnership with RENOLIT,” adds Zsulits.
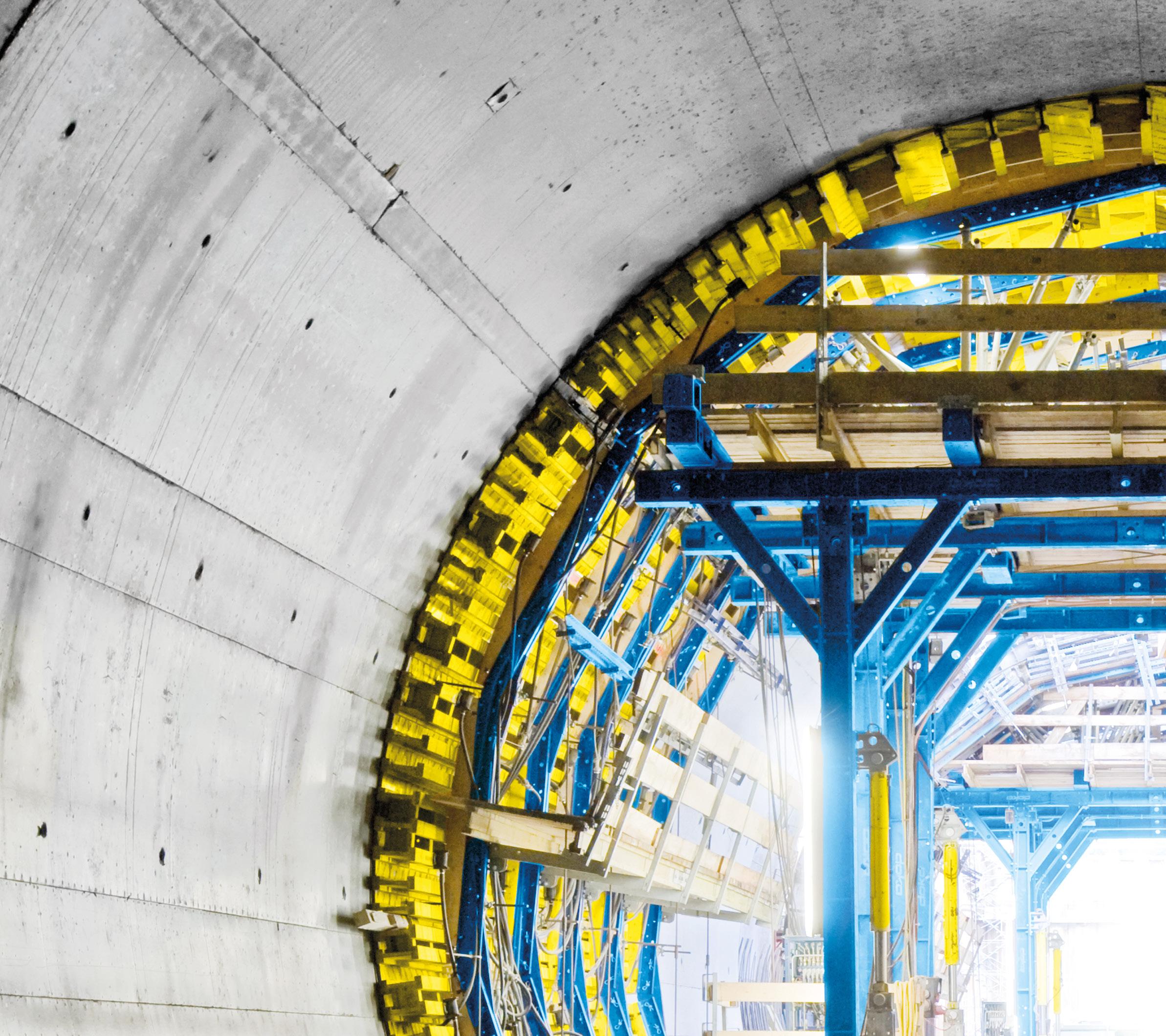
supplychaindigital.com
DOKA109
We also share common views on the market, as well as common values.” It is this value alignment that Zsulits states is key to “Beyondsuccess. the regular supplier/customer relationship, if the culture of two organisations are the same – as well as the way they approach industry challenges and their long-term targets – then chances are it becomes a valuable partnership for both sides,” explains Zsulits. He adds: “For example, ESG is gaining significant interest in our company, not only due to customer demands, but we are seeing the value in successfully managing our environmental impact and supporting the people around us. Not having partners that are like-minded and adopting the same approach would keep us from being successful.“WithRenolit we have that like-minded partnership we are looking for, which is great.”
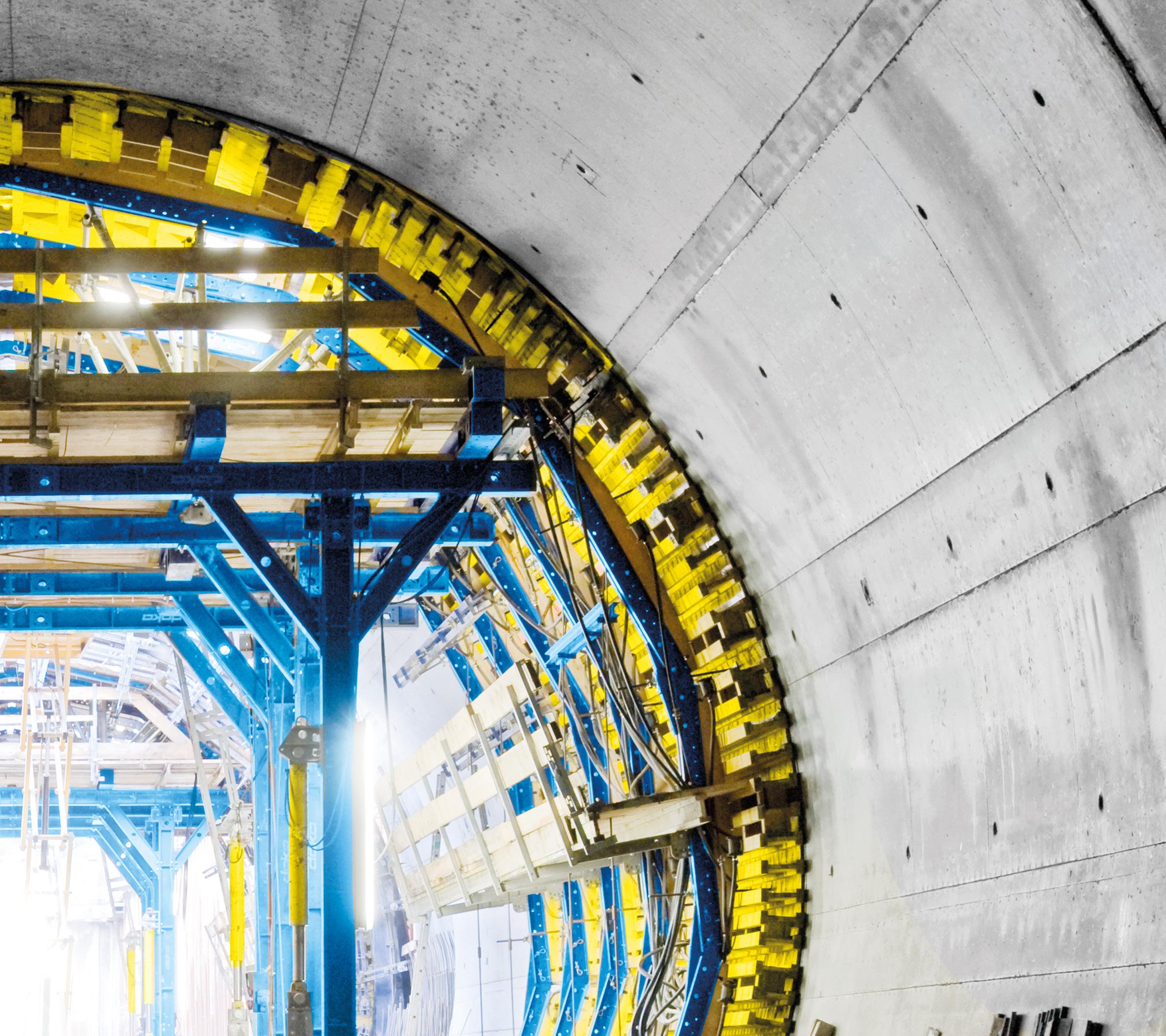
110 July 2022 TECH & AI
digital transformation? WRITTEN
ML tech,
Supply chains are facing a pressing need to adopt and but are too many businesses neglecting the human side of BY: JOE FITZPATRICK
TRANSFORMATION IS A ‘PEOPLE PROJECT’ , NOT A TECH PROJECT
AI
“Most digital implementations have a success rate of about 30-40%, in terms of adoption,” says David Loseby, the noted procurement advisor who also boasts a doctorate in behavioural science.
Loseby says the failure rate is so eyewateringly high because of a “mindset failure” on the part of organisations. “Digital transformations are not technology-change projects,” he says. “They are people-change projects. If you don't involve the people that are going to be impacted, and suddenly impose it upon them, guess what? You get lots of rejection.”
T
For Loseby, re-skilling employees and clearly demarcating their changing roles supplychaindigital.com
111
he digital transformation of business – being driven by Industry 4.0 technologies such as artificial intelligence (AI) and machine learning – is, by its very nature, a complex affair.
Technically complex, yes, but also complex in terms of what such vast programmes of change demand of people, particularly regarding old skills they no longer need and new skills they mustDigitalacquire.transformation is sometimes seen as a panacea to every contemporary corporate challenge, which, of course, it is not. Many managers across the supply chain – in manufacturing, logistics and procurement – have a first- or second-hand war story to tell of at least one tech project that has failed.
Because Insight Beats Hindsight Ensuring the agility and resilience of your business and supply chain starts with identifying the risks. Download our report to start your resilience planning today. Inform your supply chain reporttime-measuredplanningresiliencewithourseries Download ASCRI Report
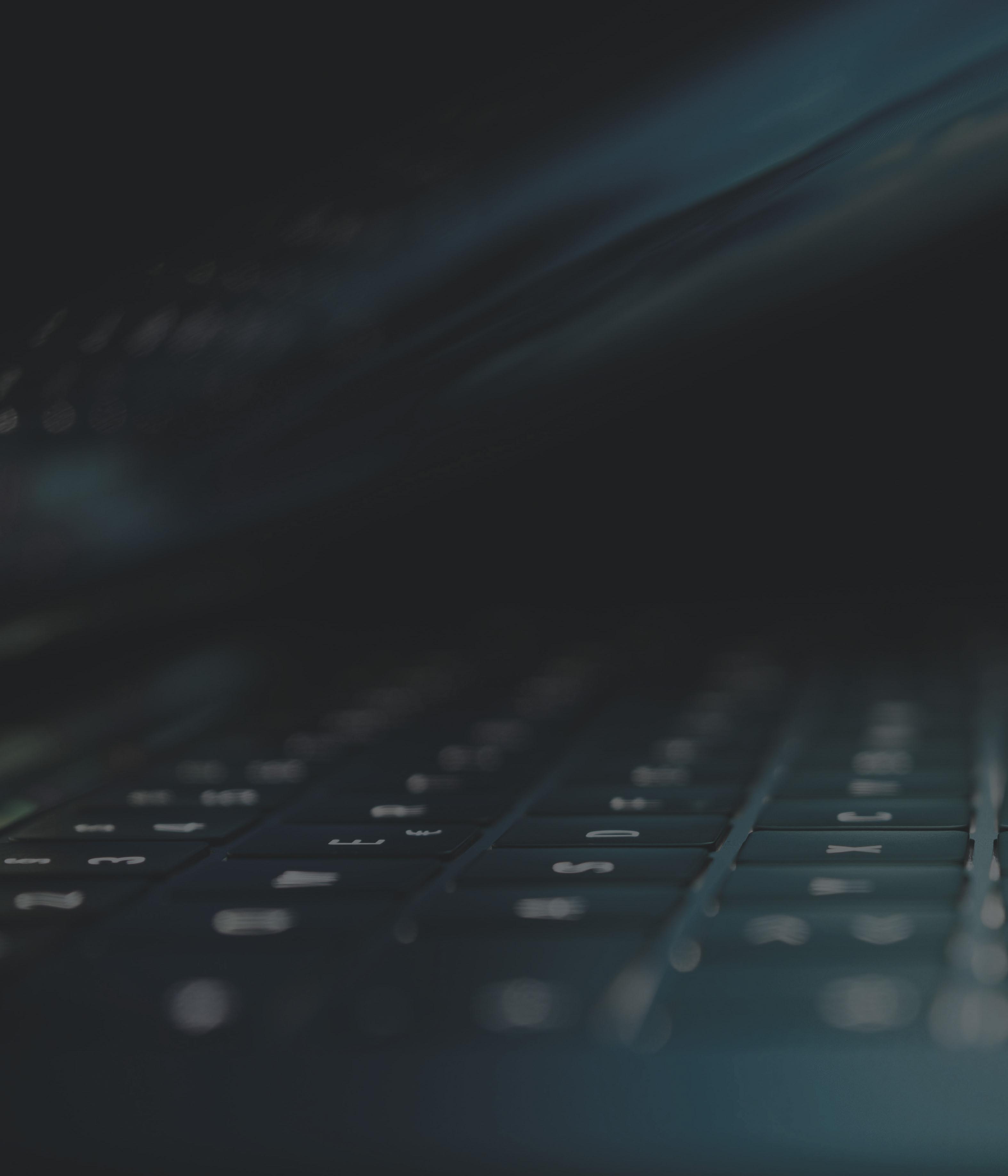
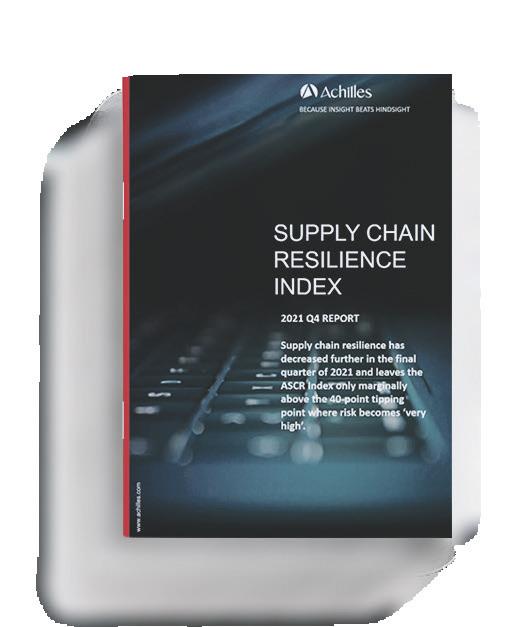
being tool-centred. To work, he says that AI and ML programmes must be mindful of all stakeholders – staff, suppliers and alsoFewcustomers.intheworld of supply chains have a stronger sense of what people want, and expect, from their jobs in today’s uncertain, ever-changing world than managers working in recruitment.Onesuchperson is Jeremiah Kaltz, VP of operations at Talascend, an industrial recruitment agency. Kaltz says that, at the lower end of the supply skills spectrum –warehouse material handlers, for example – many see such roles as a short-term means to an end, but by no means all. “Some view such opportunities as the start-point to their career and their long-term development,” he says, adding that developing specialised skills “is motivating to most”. Kaltz echoes Loseby’s view that, when it comes to automation, companies must take employees of all levels along with them. “It’s a candidate-driven market,” he says. “But once a material handler trusts and respects their employer, you’ll see a very high level of Losebycommitment.”believes that every digital transformation has a “sweet spot”, where tech and humans work in harmony.
Slater offers examples of where Crane has achieved a synergy between people and tech – Loseby’s elusive ‘sweet spot’. is an inviolable step in any technology change project. He warns: “You’re pulling them into the fear of the unknown. You’ve got to balance the equation by making sure there’s something in the change process for them. If I’m an employee and you want me to give you my heart and soul, my knowledge and IP, then don’t leave me fearing I might be shunted somewhere else at the end of it all.”
“SUPPLY WILL ALWAYS BE AN INDUSTRY BUILT AND RUN BY REPLACETECHNOLOGYPEOPLE.DOESNOTLEADERSHIP”
Loseby stresses that the common thread running through successful digital transformations is the people-centred nature of such processes, as opposed to SAM SENIORSLATERVP,GLOBAL OPERATIONS, CRANE WORLDWIDE LOGISTICS
Sam Slater, senior VP of global operations at Crane Worldwide Logistics, agrees, saying that many supply chain workers see technology as a means for their employer to compete in a tough market, and that this gives them a sense of security.
“People want to be assured their organisation is positioned to compete,” he says. “They see technology as a key component of that competitiveness.”
supplychaindigital.com 113 TECH & AI
Supply Chain software specialist Kinaxis recently released an advanced AI solution for supply chain planning. Part of the Kinaxis RapidResponse platform, Planning.AI automatically fuses the best combination of heuristics, optimisation and machine learning(ML).Planning.AI
Slater continues: “In fleet management, automation has reduced wait-times and the matching of loads. The more the wheel turns, the more money people make – and this contributes significantly to their Whenretention.itcomes to automation, Slater believes the key to success is always leadership: “The worst thing is to make the process more complex than necessary. This will always be an industry built and run by people. Technology does not replaceSuccessfullyleadership.”rolling out automation in white-collar supply environments, such as procurement, is arguably more nuanced and layered than in blue collar settings, such as warehouses. Yet, says Loseby, this doesn’t stop many companies from trying to run before they can walk. “Typically, organisations don't assess their digital maturity,” he says. “If you want to go straight from a paper-based procurement system to an all-singing, all-dancing automated system, the best advice I can give you is: don't, because you'll kill your organisation.
DAVID AUTHORGLOBALLOSEBYCPO,&SPEAKER
He says the company has an automated online learning management system that can be used for personal development plans, as well as a global reporting system that can be accessed by any Crane employee, at any time, from their smartphone.
114 July 2022 TECH & AI
“OFTEN THE PROBLEM WITH AI AND ML PROGRAMMES IS THAT SENIOR MANAGERS START FROM THE WRONG PLACE”
leverages ML to gain insights from vast amounts of internal and external data, then uses analytics to improve forecasting across short and long-term horizons. When combined with Kinaxis' planning solutions, this eliminates data silos, and balances demand and supply in real-time. It also allows for scenario management in the event of market"Supplydisruptions.chainplanners often have to choose between making an accurate decision and making a fast one," says John Sicard, CEO of Kinaxis. "Planning.AI eliminates that struggle by empowering people to make fast, accurate decisions through the use of multiple advanced analytical approaches.”
Kinaxix planningadvancedlaunchesAIsupplysolution
“So rather than cutting headcount, automation increases value, by allowing people to focus on tasks involving ESG, and partner and customer relations,” says Loseby. He adds: “The key is to acknowledge your workers’ stake in the change process, and to give them opportunities to acquire new skills and to progress alongside the technical sophistication of the firm.
supplychaindigital.com 115 TECH & AI
“With AI and ML, the skill sets you'll need on that journey will change, so involve the people that are going to be impacted early in the process, because they will need to take ownership of whatever the end-solution might look like.”
He says that, although AI and ML do take over what were once labour intensive tasks – such as contract renewals – this frees up those who once performed such tasks to be more strategic in their roles.
“They need to plan their journey through several stages of development to reach digital maturity, and it’s a journey that has to take into account customers and suppliers, but most importantly, the workforce. Firms have to start by understanding their level of readiness for cutting-edge technology, in terms of management, organisational structures and skills.”
In Loseby’s experience, the problem is often that senior managers “start from the wrong“Moreplace”.often than not, the original business case for digital transformation will be that there will be a loss of headcount,” he says. “But, usually, this is not true.”
TOP 10 116 July 2022
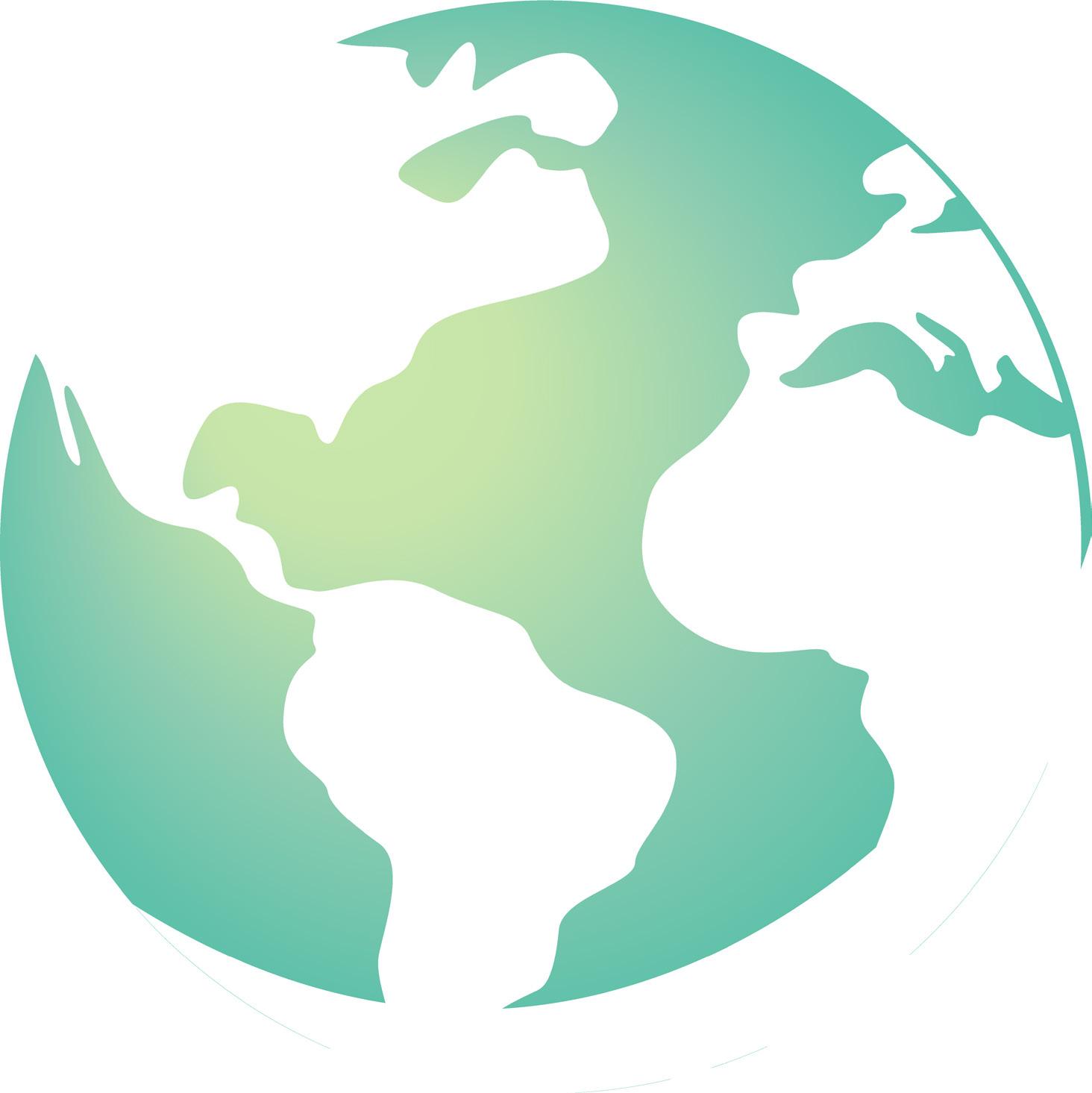
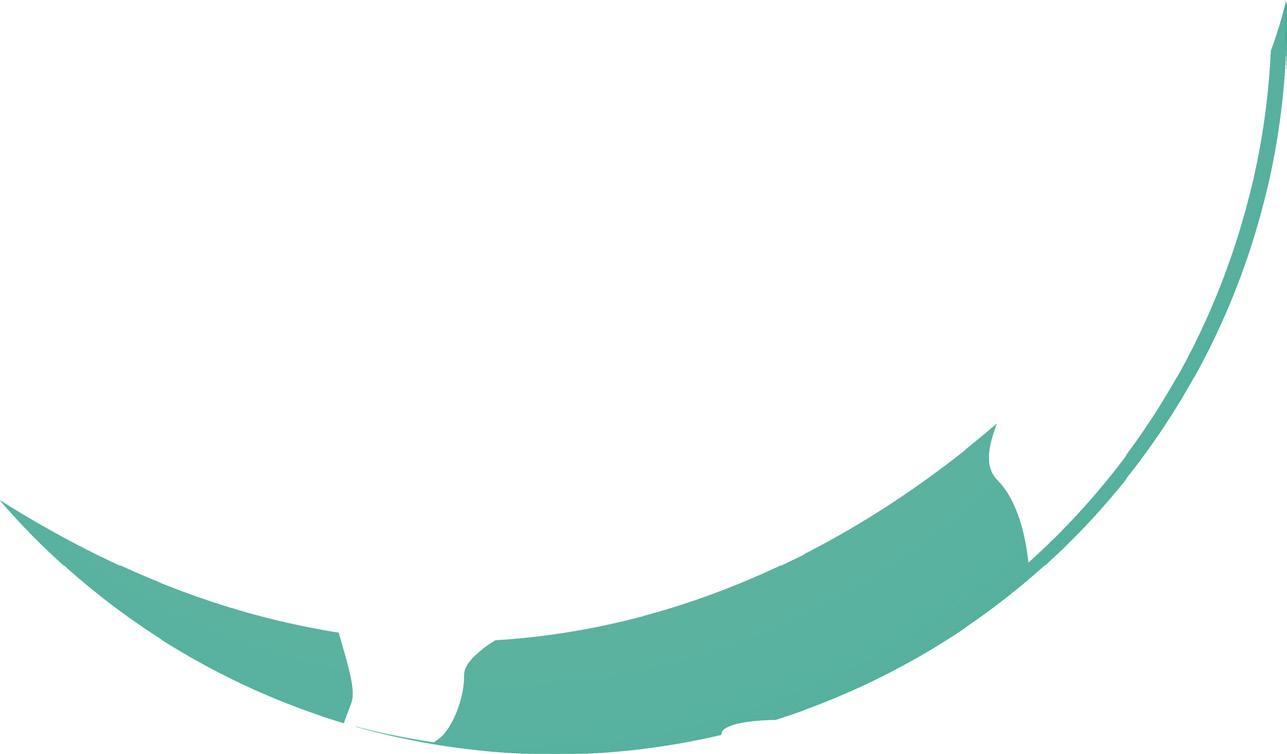
GLOBALSUSTAINABLESUPPLYCHAINS
Here at Supply Chain Digital, with much of the business world focused on supply chains and sustainability at the minute, we cast our eyes over 10 of the world’s leading ESG-friendly global supply chains, as well as the unique tech innovations and programmes that contribute towards making each organisation a sustainability leader.
WRITTEN BY: SEAN ASHCROFT
117
TOP 10
Supply Chain Digital looks at 10 of the world’s leading ESG-friendly global supply chains, and the tech innovations and programmes that make each organisation a leader in sustainabilitysupplychaindigital.com
According to USP the global logistics giant’s sustainability initiatives have been shaped by “the international focus on social and environmental betterment, led by the United Nations’ 2030 Sustainable Development Goals”, in addition to the company’s ability to “enact meaningful change during a time of technological advancement in Onebusiness”.ofUSP’s key initiatives is its alternative fuel and advanced technology fleet – or “rolling laboratory”, as the company calls it. This consists of more than 10,000 vehicles across the globe, including electric vehicles and electrically-assisted cycles.
Mitch Jackson CSO FedEx 09
As one of the world’s leading logistics providers, FedEx’s environmental responsibilities are a key aspect of the company’s global supply chains. Responsible environmental practices have been embedded across its operations, designed to boost efficiency while simultaneously cutting both waste and emissions – plus, it’s working towards a series of ambitious climate-oriented targets. Having worked to cut its aircraft emissions by 30% and increased its Express fleet’s efficiency 30% by 2020, FedEx’s sights are now set on its 2030 goals – when it’s thought that 30% of the company’s jet fuel will consist of alternative fuel sources.
Kate Gutmann Executive VP & President, International, Healthcare & Supply Chain Solutions UPS 10
“Regarding our urban operations, these are two techs that will be of paramount importance for us in the medium-term,” the company says.
118 July 2022
TOP 10
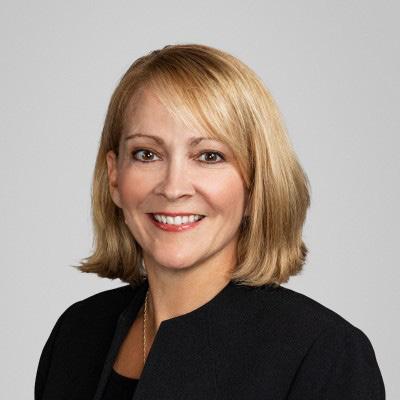
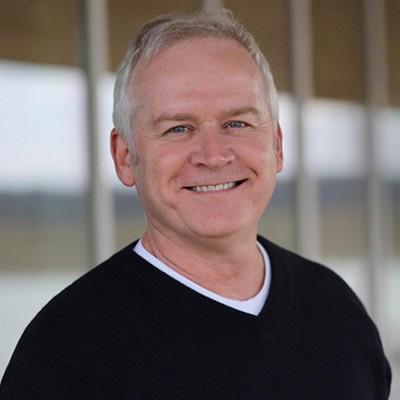
TOP 10
The company’s 13,500-strong fleet of vehicles, equipped with their alternative drive mechanisms, is just one example of progress among many. Across its sites and suppliers, DHL also provides socio-economic support and development initiatives, community action programmes, and delivers training to individuals along the entirety of its supply chain to drive employability and plug skills gaps.
Johnson & Johnson’s ethos is centred on one purpose: to improve the health of humanity. This aim comprises its customers, staff, communities and the environment. As such, its annual Health for Humanity report sheds light on the ways in which the organisation’s operations are geared towards CSR and committedNotably,sustainability.thecompanyUS$50mnto help support all-important frontline health workers during the COVID19 pandemic. It also introduced its Race to Health Equity initiative – a US$100mn commitment to invest in, and promote, health equity solutions for communities of colour in the United States.
119
Deutsche Post DHL Group has taken considerable steps to optimise its supply chain to high ethical and environmental standards. It has centralised sustainability and CSR in its wider business strategy, and claims a 35% efficiency gain across all operations since 2007.
08 07
Johnson & Johnson Monika Schaller Executive VP, Responsibility Deutsche Post DHL Group
Philip Dahlin Global Director of Sustainability
supplychaindigital.com

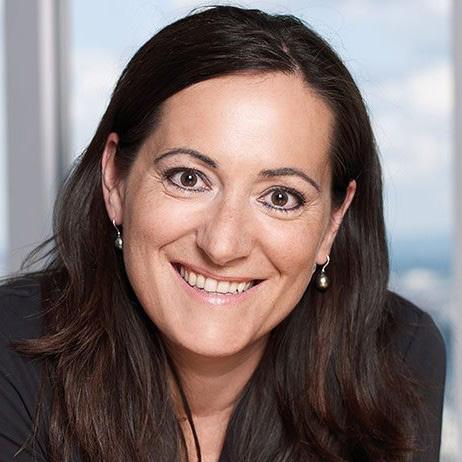
THE FUTURE OF PROCUREMENTDIGITAL A BizClik Media Group Event: 12 - 13 OCT 2022 STREAMED & IN PERSON QEII CENTRE, LONDON Get tickets Sponsor opportunities ShowreelourWatch2021
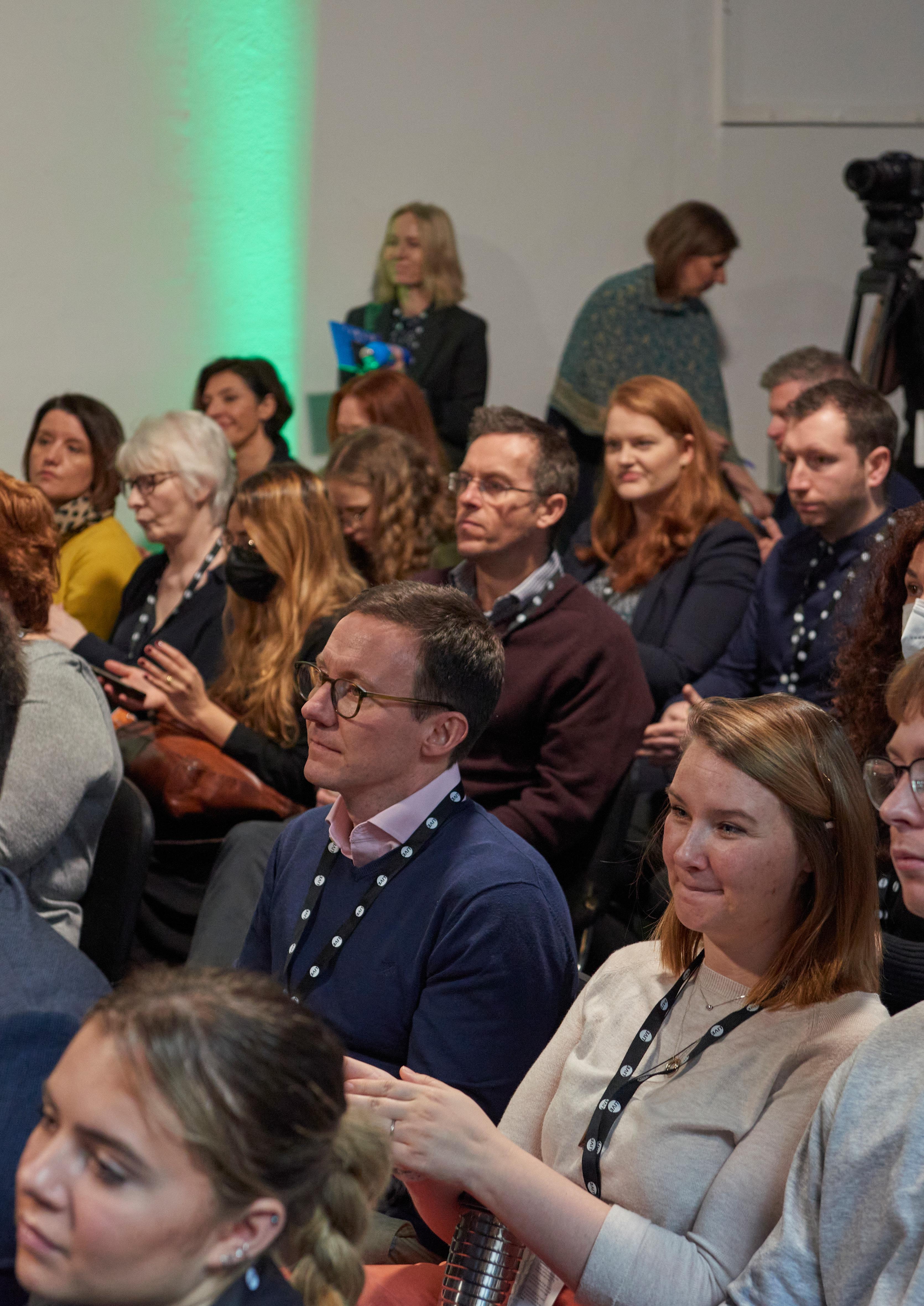

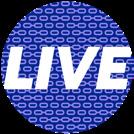

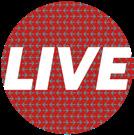
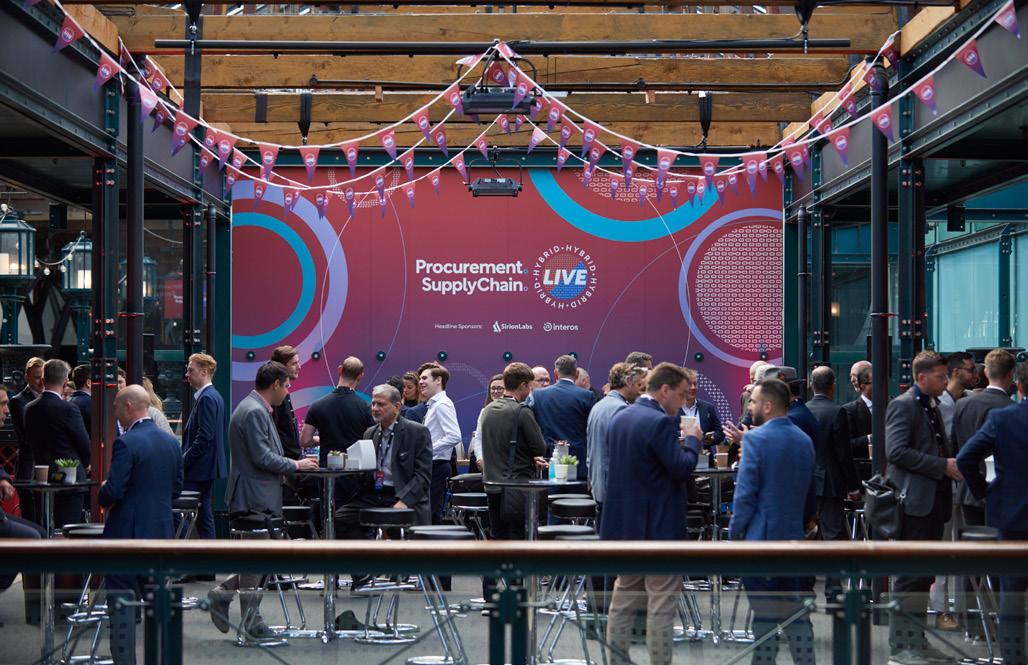
The world’s largest beverage producer, Coca-Cola relies on a decentralised supply chain that encourages flexibility, agility andForinnovation.instance,its primary European bottler – the Hellenic Bottling Company (HBC) – leverages IoTenabled tech such as intelligent coolers, which track and moderate temperature while measuring vending statistics. HBC has also maximised efficiencies across its value chain, while minimising waste and energy usage. In 2017, Bea Perez became the company’s first chief sustainability officer. This was followed in 2021 by a win at the Sustainability Leadership Awards, where EcoVadis – the leading platform for environmental, social and ethical performance ratings for global supply chains – awarded Coca-Cola European Partners with Best Supplier Engagement. Since 1992, Japanese automotive manufacturer Toyota has been publicly integrating environmental and ethical standards into its business practices, with a focus on driving sustainable development across the world through CSR. This is reflected in its commitment to the UN’s Sustainable Development Goals, including cutting pollution and waste, improving water quality, and promoting sustainable lifestyles, educationmanagementenvironmentalprojects,andinitiatives.
Yumi Otsuka
06 05
supplychaindigital.com
CSO Toyota
121
Bea Perez Senior VP & CSO Coca-Cola
TOP 10
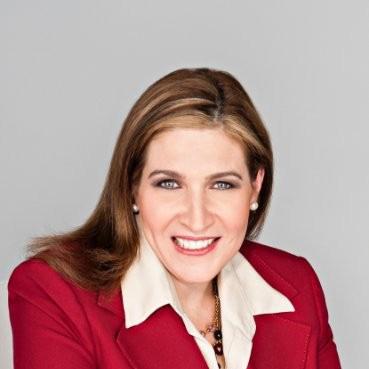
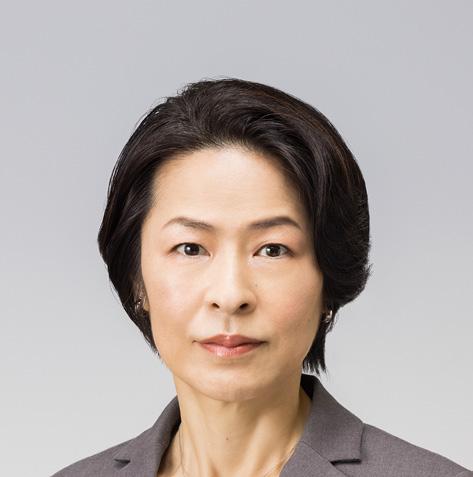
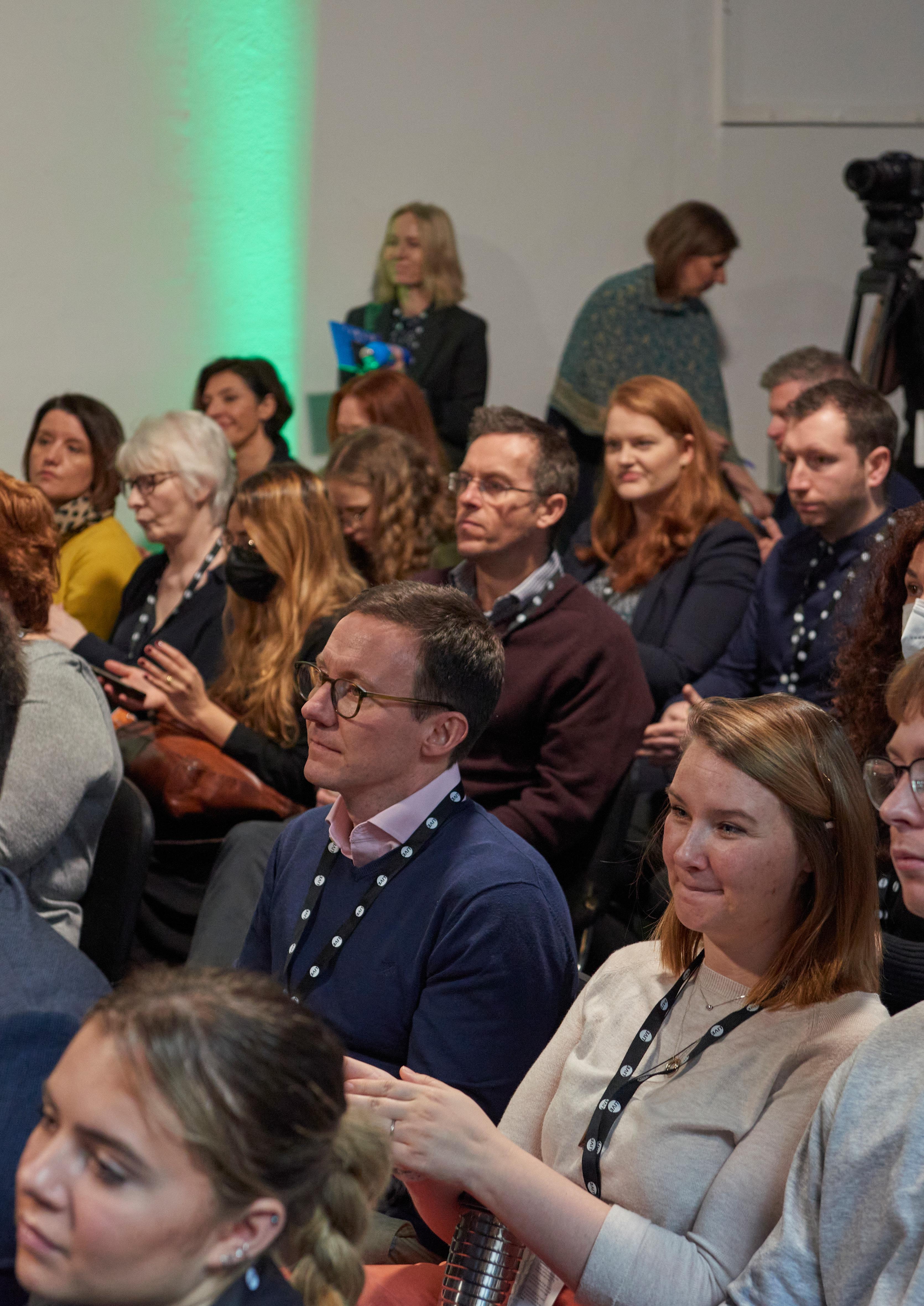

The Swiss food and beverage multinational’s Creating Shared Value strategy drives sustainability through partnerships with suppliers and environmental organisations, as well as with other corporations.
Examples of Nestlé's work include its Caring for Water initiative, which promotes water conservation throughout its supply chain, and is also a founding member of the Sustainable Agriculture Initiative.
Stefan Palzer CTO Nestle 03
122 July 2022
Kristen Sieman CSO General Motors 04
As chief technology officer, Stefan Palzer leads Nestlé's R&D activities to deliver nutritious, healthy, sustainable and affordable food and beverage innovation, globally.
TOP 10 GM’s supply chain boasts transparency and focused initiatives on workplace safety and environmentally-friendly innovation. It has a company-wide ethos of “zero crashes, zero emissions, and zero congestion”, and is viewed as a leader in automotive sustainability. The firm’s directors regularly review the company’s ESG performance and progress, ensuring it remains a central focus for global operations – in line with shifting global expectations and regulations. In April 2022, GM announced an innovative new pledge, inviting global suppliers to join the company in a commitment to carbon neutrality, the development of social responsibility programmes, and the implementation of sustainable procurement practices in its supply chain operations.
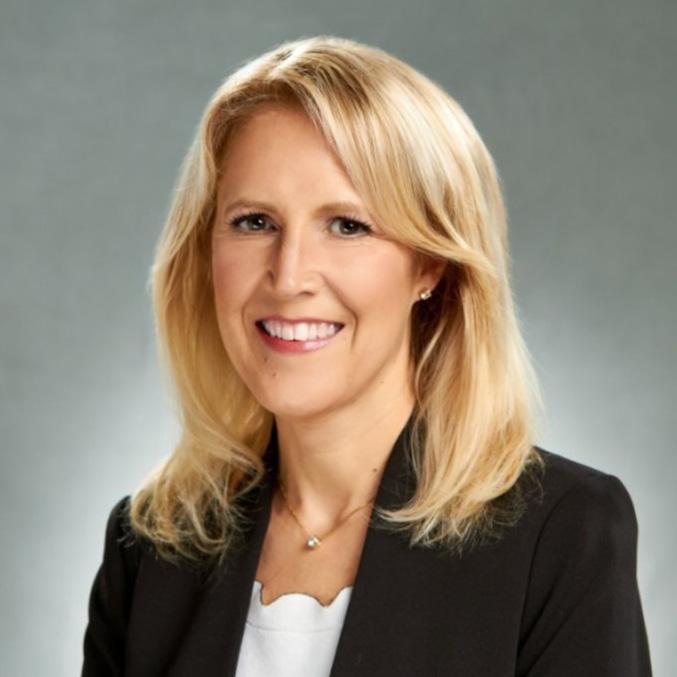
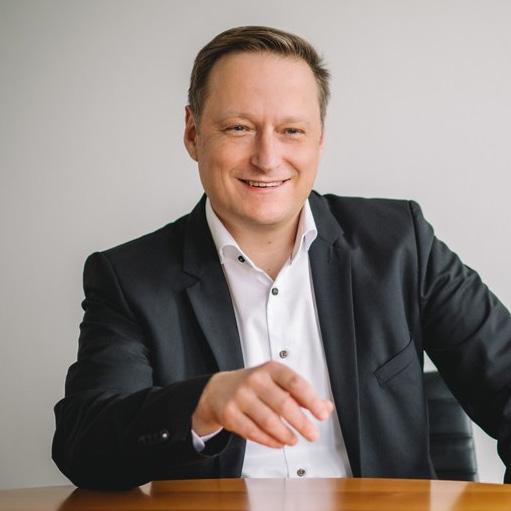
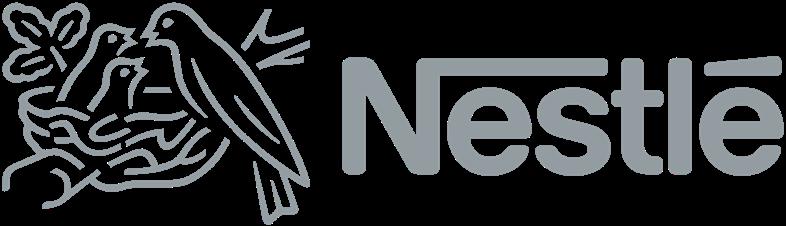
World-renowned professional services firm Accenture makes quite the statement of intent with its responsible supply chain ambitions: “We have the purchasing power and multi-billion-dollar supply chain to cultivate a culture of responsible buying on a global scale.” To bolster its claims, the organisation focuses on five core pillars – corporate citizenship, social impact, environment, inclusive workplace, and core values – that tackle the breadth of the world’s most pressing CSR drivers.
TOP 10
Peter Lacy Sustainability Services Lead Accenture
02 supplychaindigital.com 123
Accenture’s environmental policy is to play a key role in the shift to a low-carbon economy. To this end, it has a clear focus on: decarbonisation, emissions reduction, cultures of responsibility, adherence to and surpassing of compliance standards, and fostering sustainable supplier relationships that capitalise on opportunities to excel.
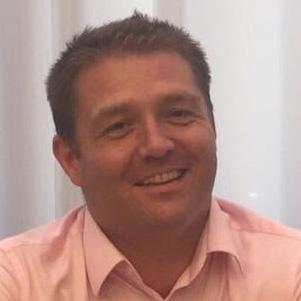
Get tickets Sponsor opportunities SHAPING SUSTAINABILITYBUSINESSTHEOF A BizClik Media Group Event: 3,000+ Participants 2 Days 3 Zones 60+ Speakers 7 - 8 SEPT 2022 STREAMED & IN PERSON BUSINESS DESIGN CENTRE, LONDON
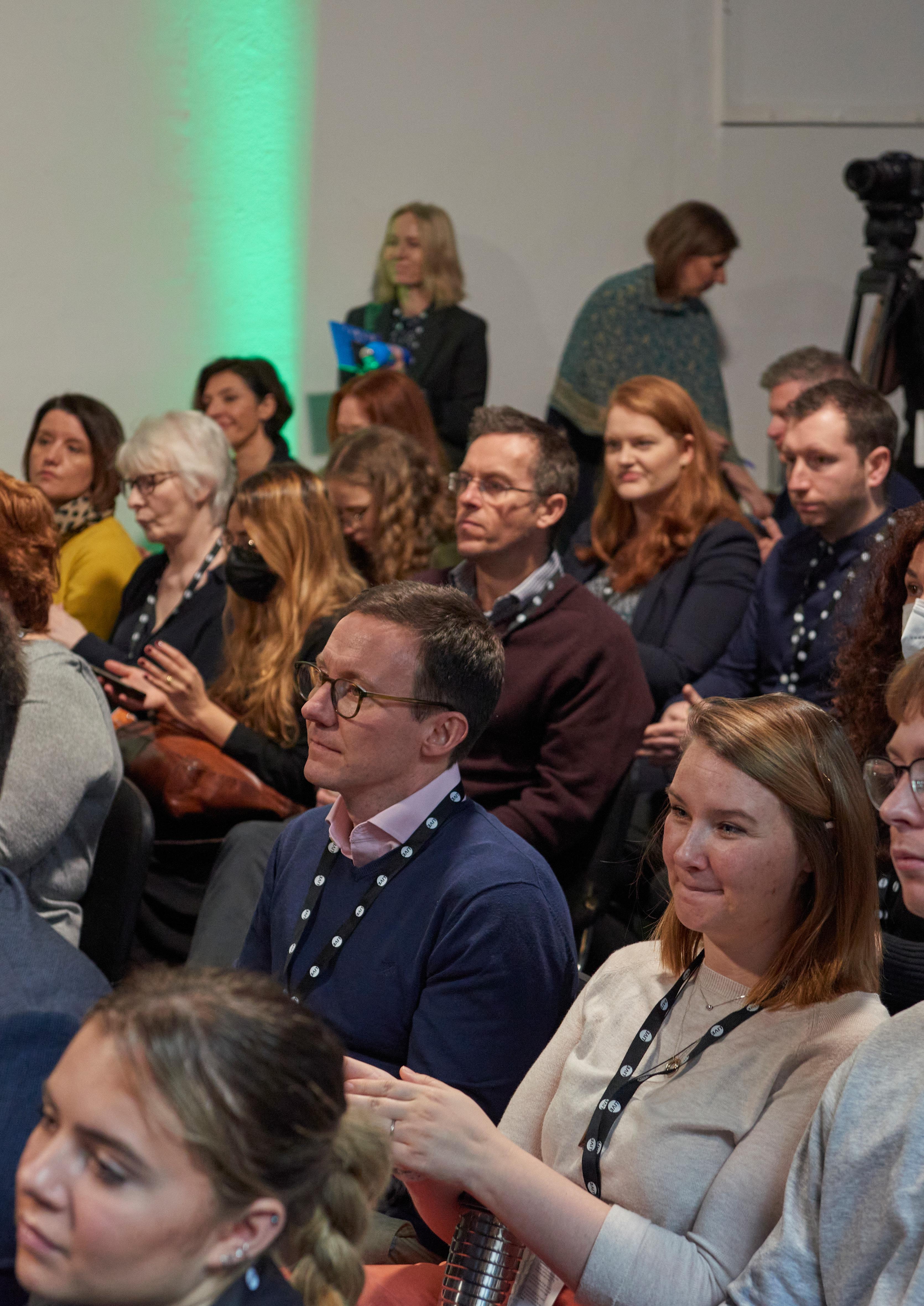
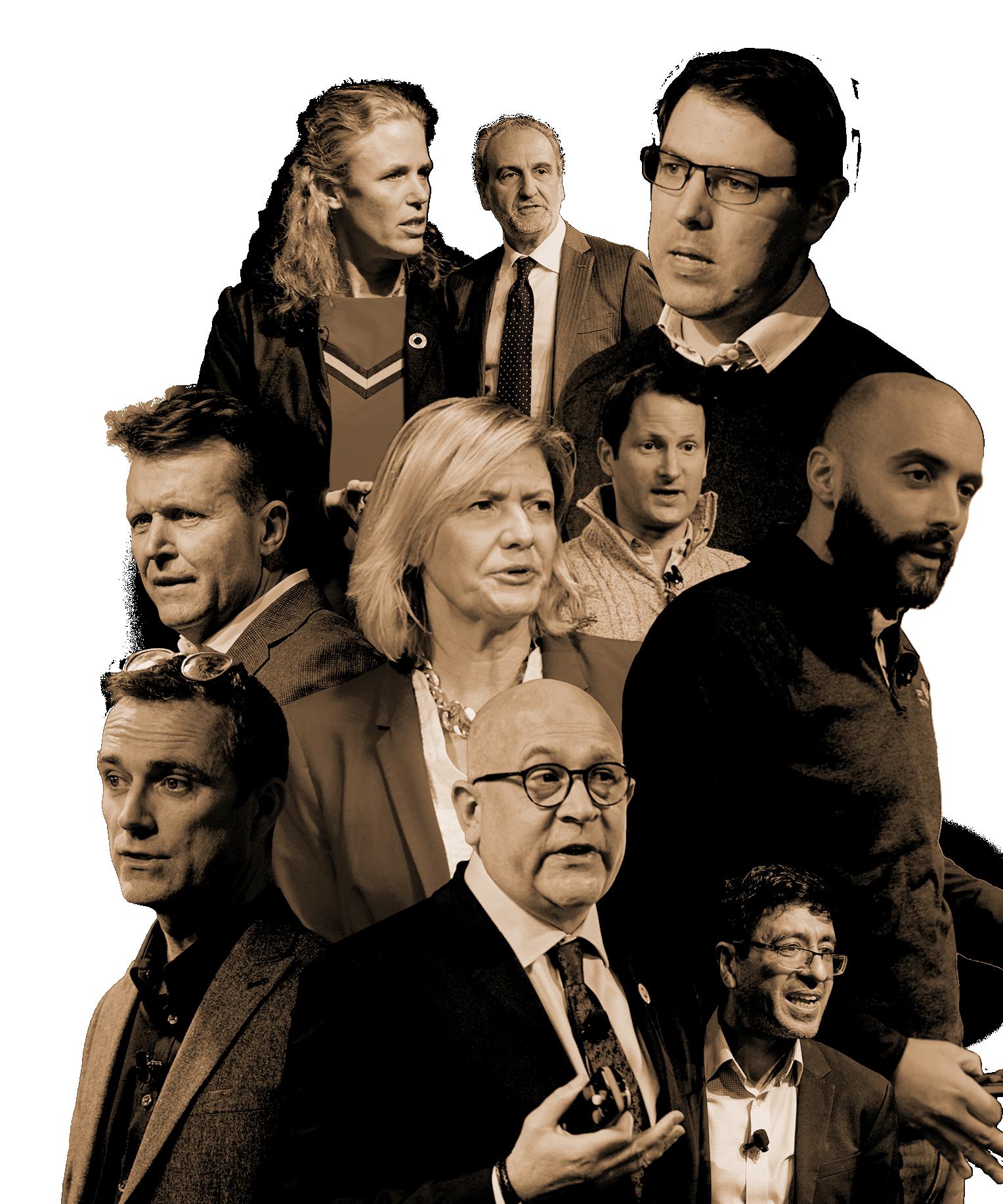


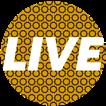
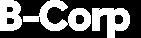
Brought to you by BizClik Media Group
SUSTAINABILITY LIVE LONDON, the hybrid event held between 7th-8th September is broadcast live to the world and incorporates three zone areas of Sustainability LIVE, B-Corp LIVE plus March8 LIVE in to one event. With a comprehensive content programme featuring senior industry leaders and expert analysts, this is an opportunity to put yourself and your brand in front of key industry decision makers. From keynote addresses to lively roundtables, fireside discussions to topical presentations, Q&A sessions to 1-2-1 networking, the 2-day hybrid show is an essential deep dive into issues impacting the future of each industry today. Global giants and innovative startups will all find the perfect platform with direct access to an engaged and active audience. You can’t afford to miss this opportunity. See you on: 7 - 8 September 2022 Watch our 2022 Showreel
Join us at SUSTAINABILITY LIVE LONDON Get tickets Sponsor opportunities Showcase your values, products and services to your partners and customers at SUSTAINABILITY LIVE LONDON 2022.
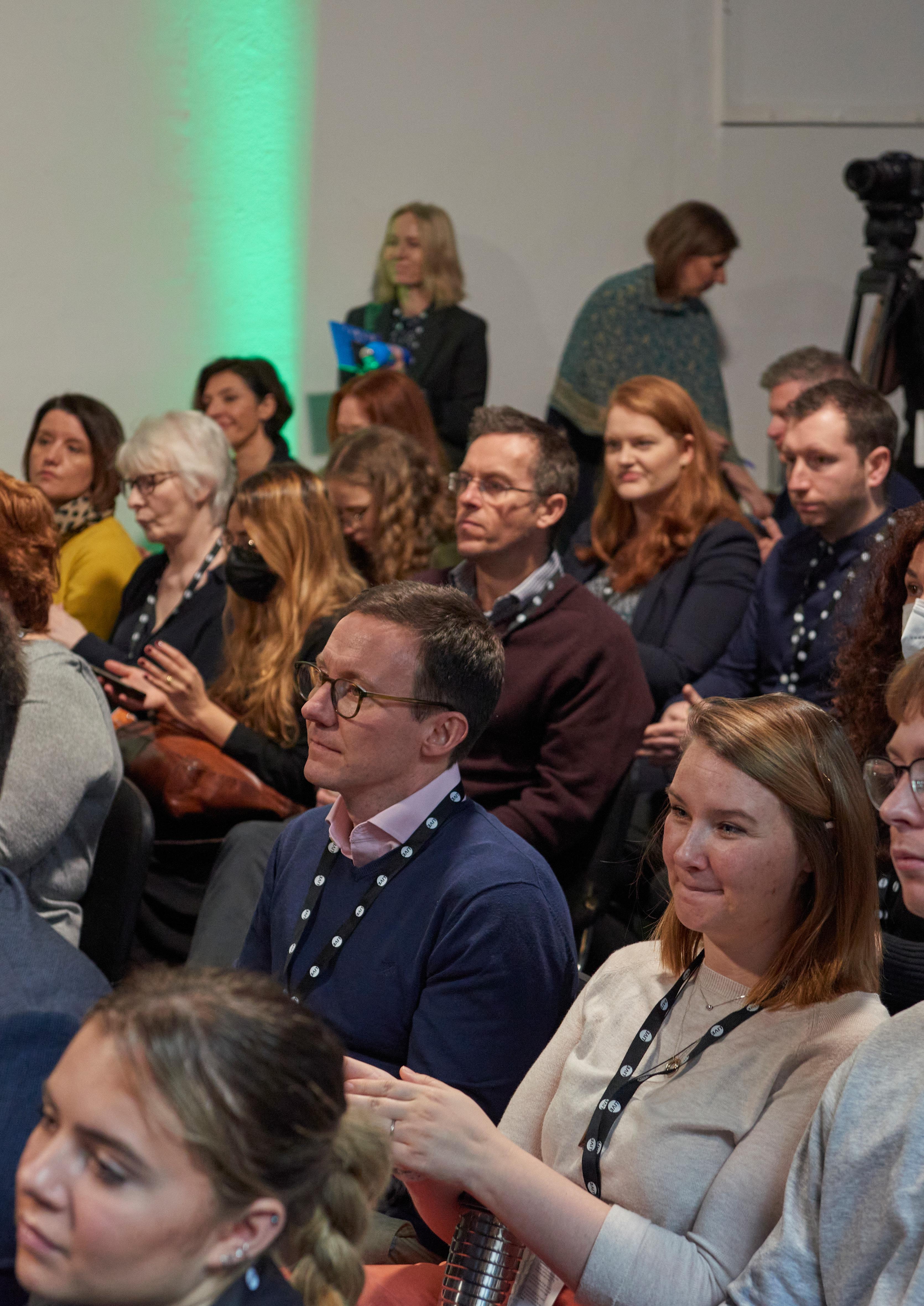
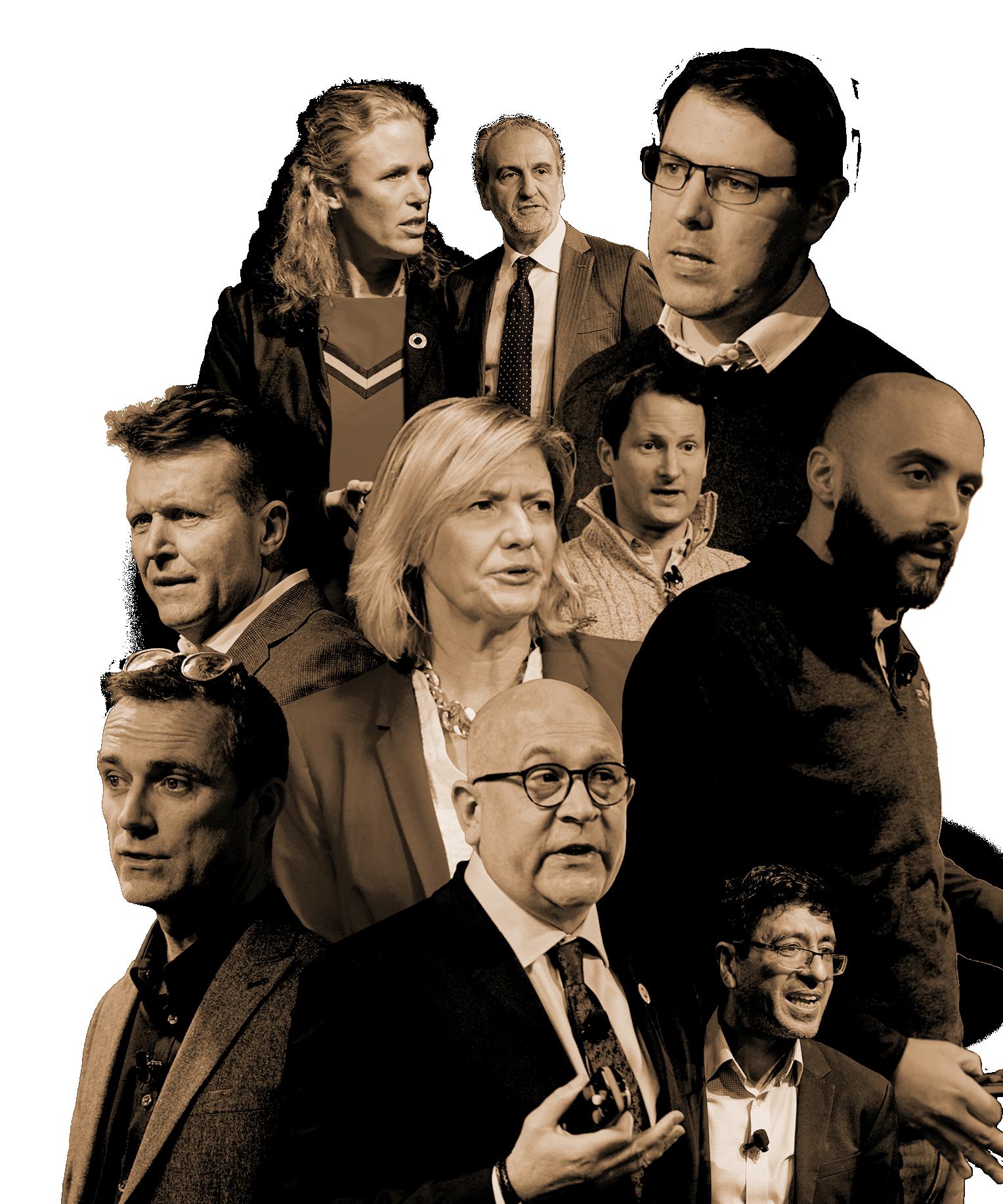
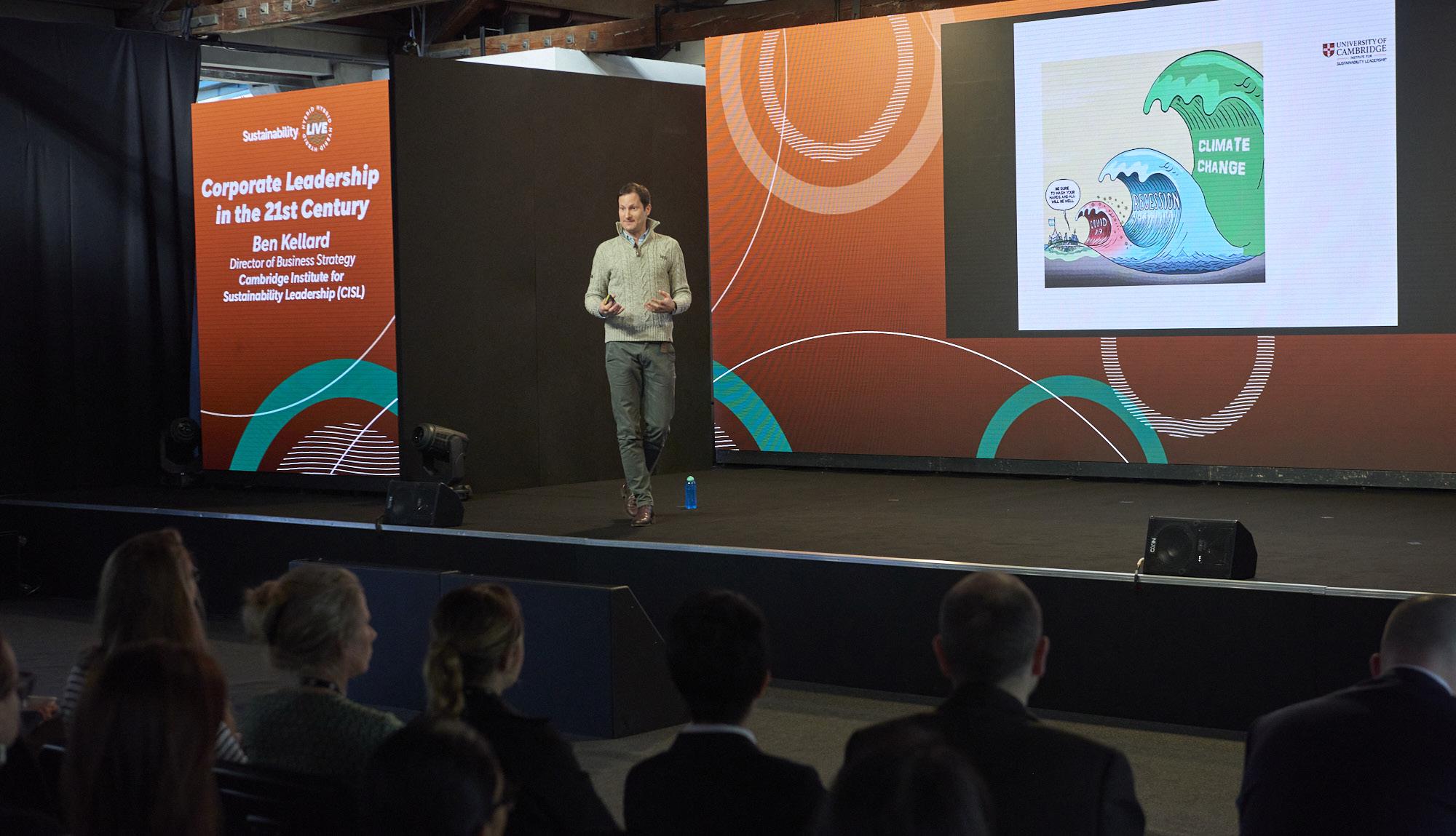
TOP 10 126 July 2022

TOP 10
“My job is to manage the social valueimpactenvironmentalandofourglobalchains”
127
Ezgi Barcena CSO AB InBev As the world’s biggest brewer, AB InBev is contributing to the UN Sustainable Development Goals “while building resilient supply chains, productive communities and a healthier environment”. Its global sustainability team reports twice a year to the Finance Committee of the Board of Directors, reviewing topics relating to supply chain security and sustainability. To strengthen its collaborative approach to sustainable development, the brewer engages in industry associations and organisations such as: the World Business Council for Sustainable Development; the World Economic Forum; the Beverage Industry Environmental Roundtable; the Climate Group; the Water Resources Group; and Sustainable Food Lab. Its supply chain sustainability programmes include Smart Agriculture, Water Stewardship, Circular Packaging and Climate Action.
supplychaindigital.com
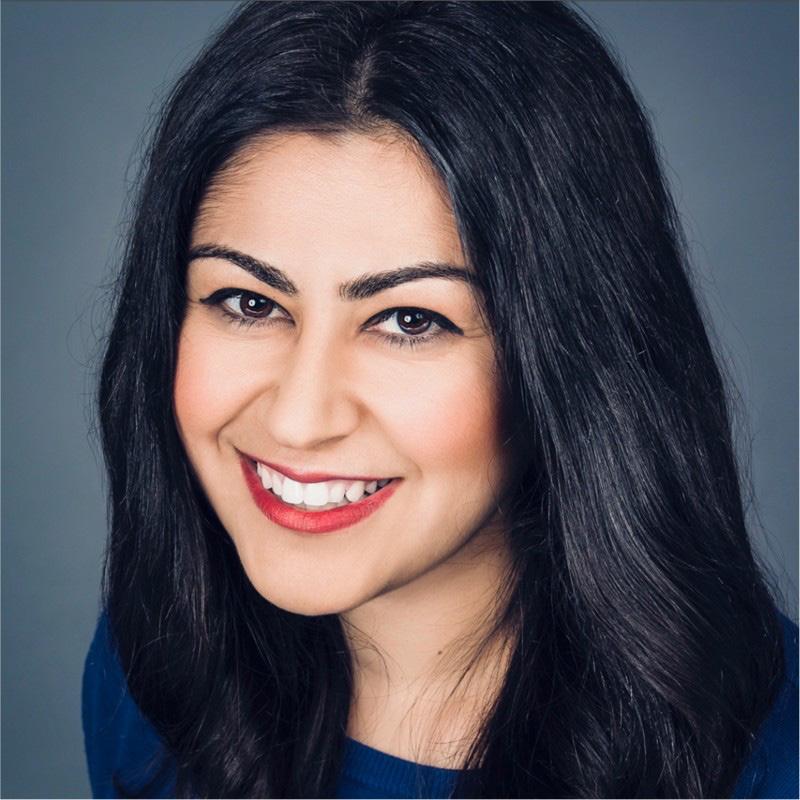
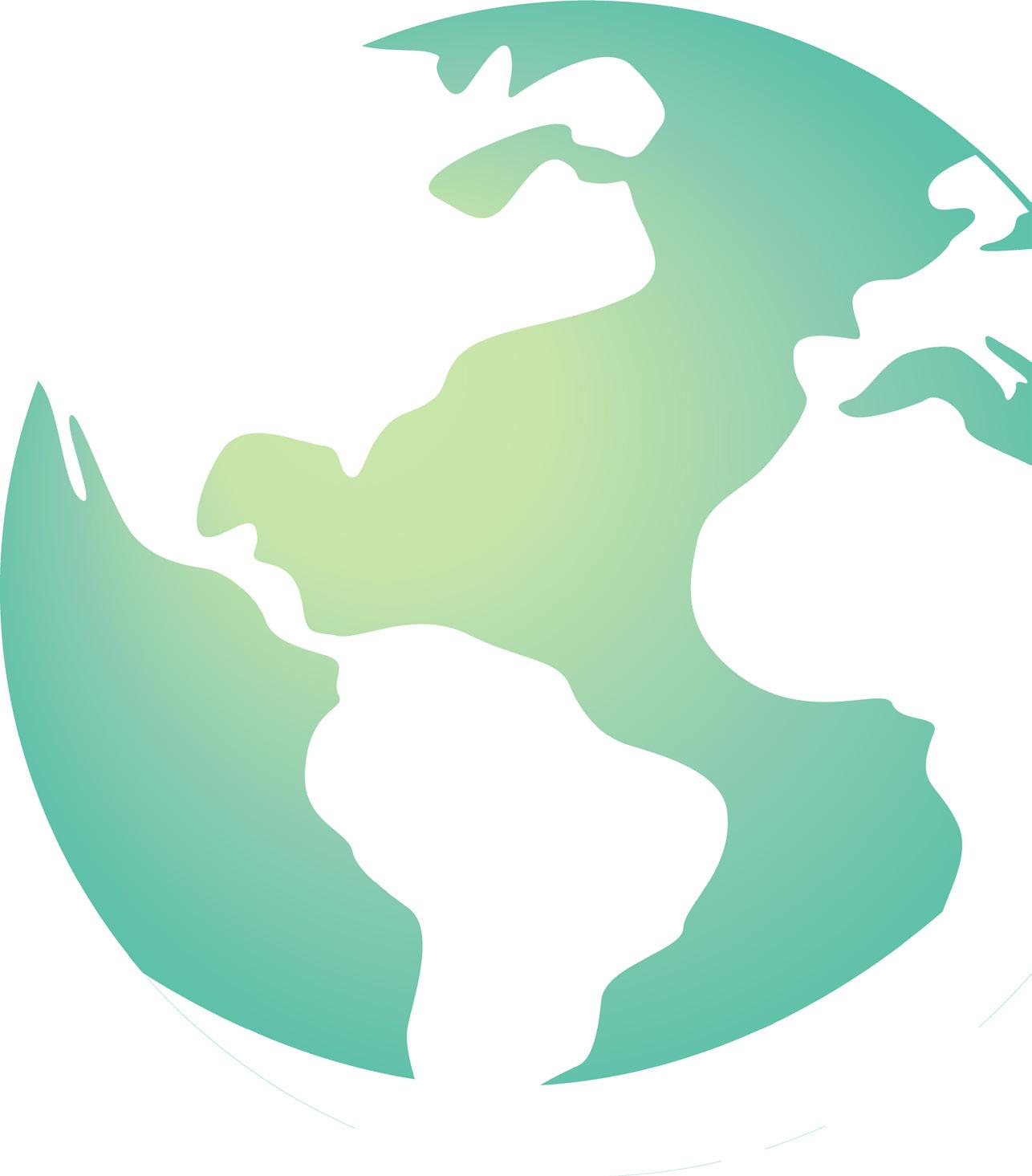

evmagazine.com A BizClik Brand
