Empowering
Sustainment's
Unlocking
Revolutionizing
Design
Gearing
U.S.
Plasma
Exploring
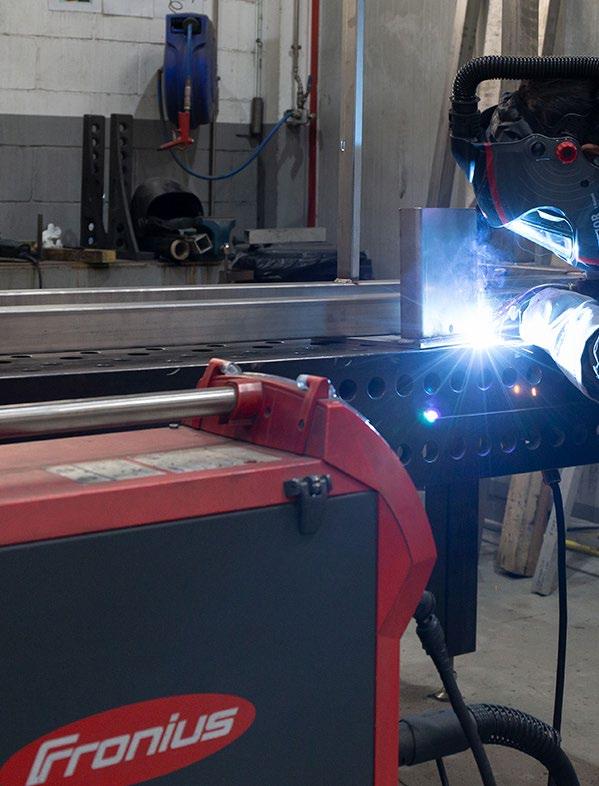
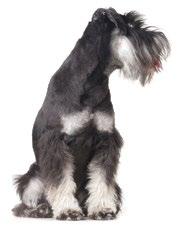
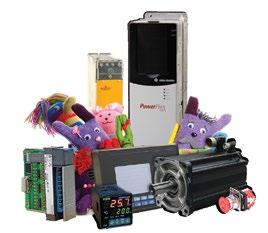
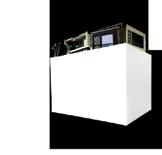
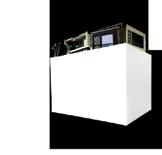

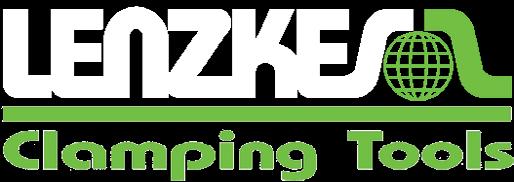
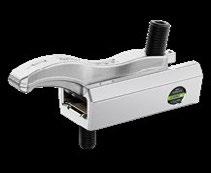
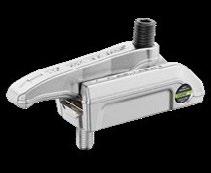
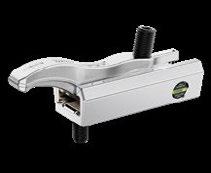
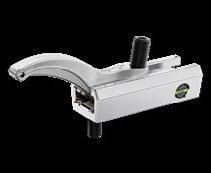
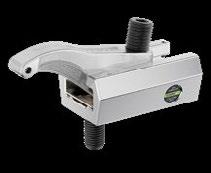

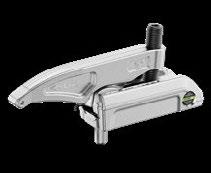
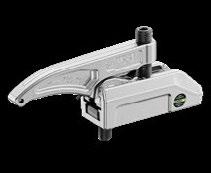
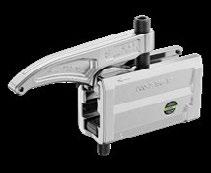





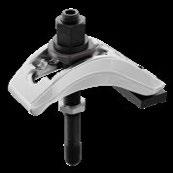
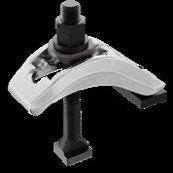
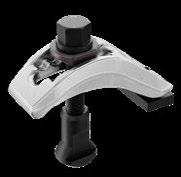






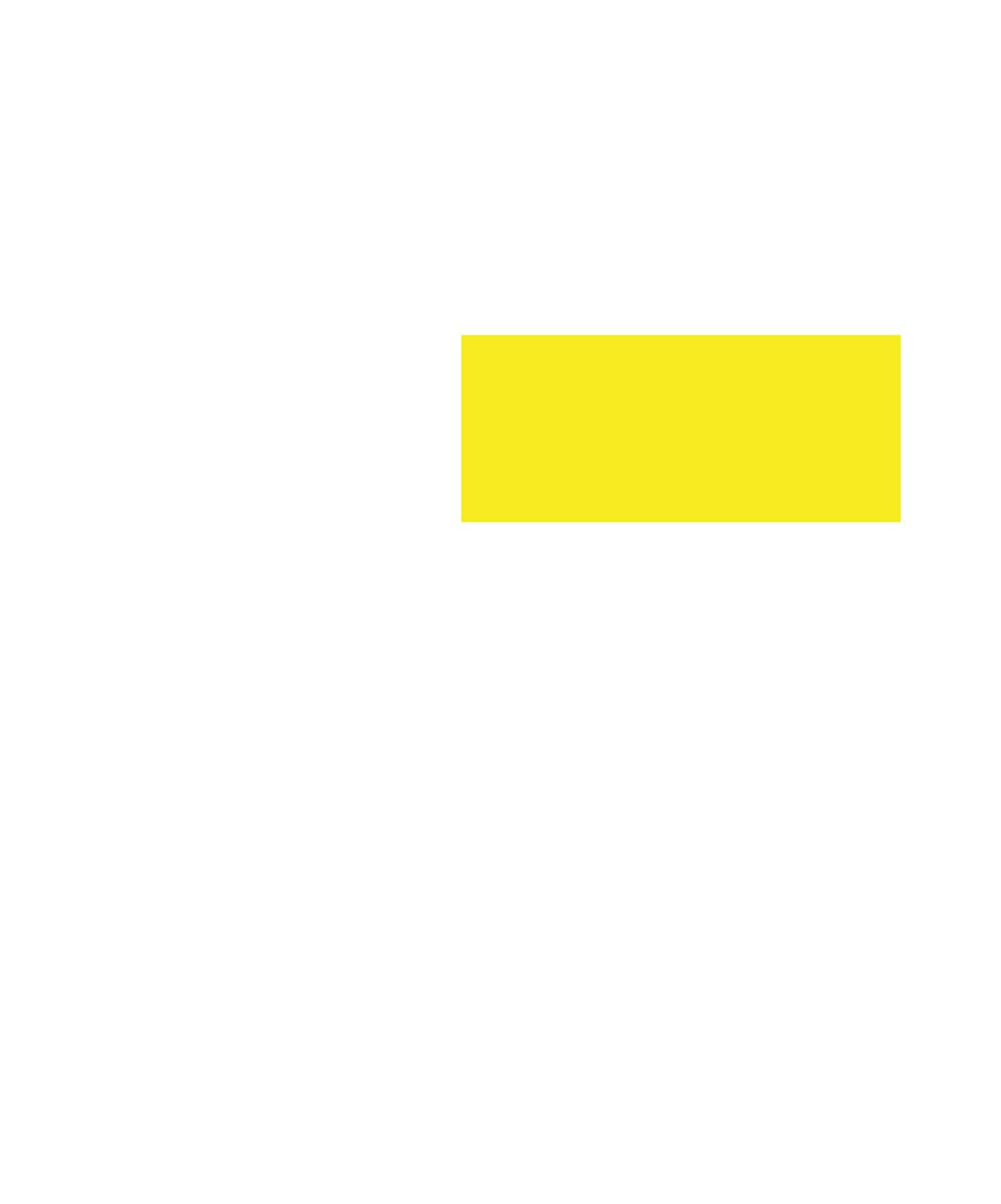
Empowering
Sustainment's
Unlocking
Revolutionizing
Design
Gearing
U.S.
Plasma
Exploring
Design
Powerful
WE LISTEN. WE OBSERVE. WE INNOVATE.
Dynabrade manufacturers air tools for use with automation systems. Random Orbital Sanders, Finishing Tools, Grinders, Disc Sanders, and Abrasive Belt Tools are just a sample of our new product offering for robotics.
In additional to air tools, we offer accessories and abrasives for complete process solutions with the know-how to get the job done right.
Ask about a no-obligation demonstration on any product in our line.
North America’s Manufacturing Resource for Industry Professionals Since 1986
William C. Strickland III, Publisher william.strickland@indmacdig.com 800-366-0676 ext. 103 | Fax: 866-826-5918
adrienne Gallender, associate Publisher/Media advisor agallender@indmacdig.com 847-612-1572 | Fax: 847-559-2909
Brian Self, associate Editor brian@indmacdig.com 800-366-0676 ext. 104 | Fax: 866-826-5918
Shane Bell, Creative Director sbell@indmacdig.com
SALES
Lisa Hanschu, Sr. account Executive lisa@indmacdig.com 785-965-9159 | Fax: 785-965-7199
William C. Strickland III, National Sales 205-903-9178 | fax 866-826-5918
Susan Strickland, accounting susan@indmacdig.com 205-542-1098 | Fax: 866-826-5918
CIRCULATION & SUBSCRIPTIONS
IMD, 3590-B Hwy 31 South, Suite 233, Pelham, aL 35124 circulation@indmacdig.com | Fax: 866-826-5918
REPRINTS
To purchase article reprints please call 800-366-0676 ext. 103 or email wstrickland@indmacdig.com
3590-B Hwy 31 South PMB #233 Pelham, aL 35124
INDUSTRIAL MACHINERY DIGEST (ISSN 1542-5223) is published 12x per year by Source 360 Media. POSTMASTER: Please send change of address to INDUSTRIAL MACHINERY DIGEST, 3590-B US Hwy 31 South, PMB 233, Pelham, AL 35124. Printed in the U.S.A. SUBSCRIPTION POLICY: Individual subscriptions are available without charge in the U.S. to qualified individuals. Publisher reserves the right to reject nonqualified subscribers. One-year subscription to nonqualified individuals in the United States: $96.00. Single copies available (prepaid only) $20.00 each.
a s we turn the pages of another eventful month, this edition of Industrial Machinery Digest encapsulates the transformative strides and technological advancements reshaping the landscape of the manufacturing industry. The narratives woven through this issue not only reflect the dynamism of our sector but also chart the course for its future.
This past month has been marked by significant expansions and collaborations that underscore the industry's relentless pursuit of innovation and efficiency. From aNCa's establishment of a new Technology Center in Korea to ESaB's unveiling of a revamped facility in Texas, companies are investing heavily in regions and resources that propel them closer to their customers and enhance their operational capabilities. These developments are not merely expansions but are strategic moves to harness local talent and technological advancements to serve regional and global markets better.
HII's recent $74 million contract to enhance U.S. Navy vertical launch systems and IperionX's partnership with United Stars to fortify the U.S. titanium supply chain reflect a broader industry trend towards enhancing national manufacturing capabilities and security. These efforts are critical as industries strive for greater resilience and sustainability, especially in critical sectors like defense and materials science.
Technological integration continues to be a significant theme, as seen in JR Machine's adoption of advanced CNC technology to broaden their manufacturing capabilities and Laser Photonics & Brokk's new partnership, which melds cutting-edge laser systems with robust robotic solutions for enhanced operational efficiency and safety.
The narrative of growth and innovation is further enriched by companies like Kurt Hydraulics and L&L Special Furnace Co., who are expanding their facilities and launching new products to meet the evolving demands of their industries. These developments not only highlight the companies' growth trajectories but also mirror the industry's overall advancement towards more sophisticated and customized solutions.
a s we look ahead, the stories featured in this issue of Industrial Machinery Digest reveal an industry that is not only recovering but thriving by embracing change and innovation. The strategic expansions, partnerships, and technological advancements highlighted this month are not just singular success stories; they are indicative of the broader trends that will continue to shape the manufacturing landscape.
Warm regards,
Hydraulic Shears:
1/8” (10GA), 3/16”, 1/4”, 3/8”, 1/2”, 5/8”, 3/4”, 1” and 1-1/4”
Press Brakes: 50-Ton to 550-Ton C-Frame Presses: 40-Ton to 200-Ton
Custom Designs: for Custom Applications
Retrofit Backgauges: for Shears and Press Brakes. Made to fit most machines with minimum modifications.
aNCa Expands in Korea with a New Technology Center
aNCa , renowned for its innovative grinding solutions, has unveiled a new Technology Center in Korea, marking a significant expansion in the a sian market. This facility represents a crucial step in aNCa’s long-term presence in Korea, spanning over three decades. Jake Farragher, General Manager of aNCa a sia, emphasized that the center embodies aNCa’s dedication to its Korean customers, offering them top-tier sales and service support locally. The facility, strategically located near Seoul, showcases aNCa's latest grinding technologies and automation solutions, including the advanced ULTR a technology with nanometer resolution control. It features aNCa’s MX and FX ULTR a machines and the aNCa Integrated Manufacturing System (aIMS), providing comprehensive demonstrations, support, and training services. The grand opening was celebrated with key stakeholders, customers, and local dignitaries, reaffirming aNCa’s commitment to maintaining its leadership in the grinding industry globally. This move aligns
with aNCa's 50-year legacy of pioneering in the precision grinding space, continuously pushing the boundaries of innovation with cutting-edge solutions like ULTR a and GCX technologies.
Michael Wilks, the Marketing Director of Bunting, is set to retire at the end of March 2024, marking the conclusion of a distinguished 23-year tenure with the company. Michael began his career in construction at age 15 before shifting to marketing, earning a business degree and later a master’s in business administration. His career spanned various roles, including working as an advertising account executive and later leading target marketing campaigns. Joining Bunting, he played a pivotal role in overseeing marketing and sales strategies that contributed significantly to the company's growth and adaptation through acquisitions and expansions. Under his guidance, Bunting navigated periods of substantial evolution, successfully expanding its product offerings and manufacturing capabilities. Michael's retirement plans include traveling and engaging in carpentry projects, reflecting on a legacy of leadership and innovation at Bunting.
ESaB celebrated the opening of its newly renovated facility in Denton, Texas, with a ribbon-cutting ceremony. This
facility, a longstanding manufacturing and distribution hub since 1965, now features a state-of-the-art Customer Experience Center, showcasing ESaB’s latest innovations. The renovation includes a top-notch training facility with new demonstration areas, highlighting ESaB’s commitment to providing cutting-edge solutions in welding and cutting. Powered entirely by renewable energy sources, this update aligns with ESaB’s sustainability goals during its 120th anniversary. The Denton facility is set to play a crucial role in ESaB’s mission, hosting distributors and partners and serving as a premier site for manufacturing, training, and engineering in North america.
HII’s Mission Technologies division secured a $74 million contract to enhance the Mk 41 and Mk 57 vertical launch systems used on U.S. Navy ships. This contract, managed by the Naval Surface Warfare Center Port Hueneme Division, will involve significant research and development to upgrade naval surface weapon systems, combat systems, and associated sensors. The contract tasks HII with outfitting the Zumwalt-class destroyer with cutting-edge universal canister electronics, supporting diverse missile capabilities. This initiative is part of ongoing efforts to integrate advanced technologies into naval defense, bolstering the U.S. Navy’s operational capabilities and ensuring its fleet remains robust against evolving threats.
IperionX Limited has partnered with United Stars Holdings, Inc. to strengthen the U.S. titanium supply chain with a framework agreement. This agreement forecasts the purchase of up to 80 metric tons annually of IperionX’s sustainable titanium products over a ten-year period. United Stars, a family-owned company founded in 1936, is a key supplier of industrial components for various sectors including aerospace, automotive, and defense. This partnership will focus on products for sectors requiring lightweight, strong, and corrosion-resistant materials. IperionX is building an end-to-end american titanium supply chain to enhance national manufacturing capabilities and support U.S. national security. The agreement is a strategic step towards reshoring titanium production capabilities in the U.S., aligning with efforts to secure and enhance america's manufacturing independence.
JR Machine has expanded its manufacturing capabilities by installing two DMG MORI NLX 4000 CNC turning centers, allowing the company to produce complex parts up to 18 inches in diameter. This marks a significant upgrade from their previous 10-inch diameter capacity. The new machines enhance JR Machine's capacity to serve industries like space exploration, green energy, and medical devices,
among others. The NLX 4000 machines are equipped with CELOS controls, enhancing production efficiency and quality, supporting JR Machine’s Industry 4.0 initiatives. They feature high rigidity, large through-spindle hole diameter, and improved milling power, which are crucial for machining nickel-based superalloys like Inconel and Monel. JR Machine continues to invest in advanced technologies to maintain its competitive edge and meet diverse industry demands.
Kurt Hydraulics has opened a new warehouse in Fridley, Minnesota, to enhance service delivery across the U.S. and Canada. This strategic expansion is aimed at optimizing logistics and enhancing customer service by leveraging the central location’s proximity to major transportation networks. The new facility boasts over 1,000 pallet locations and is expected to significantly improve delivery times. This move aligns with Kurt Hydraulics’ commitment to providing high-quality hydraulic hose and fitting solutions, and it reinforces the company's position as a leader in the hydraulic hose industry. The state-of-the-art facility will allow Kurt Hydraulics to maintain a larger inventory, thereby offering a more extensive selection of products to meet the growing needs of their diverse clientele.
L&L Special Furnace Co. has successfully shipped a QDD29 dual-chamber heat-treating and tempering oven to a Midwest equipment provider for use in a Snap On production facility. The QDD29, the smallest model in the QDD series, is designed for efficient space utilization and reliable operation, offering solutions directly on the production line without the
need for third-party involvement. The top chamber of the furnace can reach temperatures up to 2,200°F and is ideal for heat-treating tool steels, while the lower chamber, suitable for temperatures up to 1,250°F, is perfect for tempering and small aluminum works. This furnace features internal dimensions of 12x8x24 inches and includes digital controls with overtemperature protection to ensure precise and safe operations. L&L furnaces can be customized with various options and are compliant with the latest aSM2750 specifications, making them a versatile choice for manufacturing needs.
Laser Photonics Corporation and Brokk Inc. have entered into a technology partnership to integrate advanced laser systems into Brokk's robotic solutions for various industries including mining and construction. This collaboration combines Laser Photonics' expertise in laser cleaning and cutting with Brokk's experience in manufacturing remote-controlled robots, enhancing operational efficiency and worker safety. The partnership aims to address labor shortages and improve safety with technology that allows remote operation in hazardous environments. Brokk's robots will now be equipped with Laser Photonics' cutting-edge laser technology, providing a robust solution for demanding tasks in harsh working conditions. This strategic alliance is set to transform operations in multiple sectors by introducing more automated and safe technologies.
LexxPluss
advanced Mobile Robot Technology in the U.S. LexxPluss, a Japanese automation solutions company, has significantly expanded its presence in the U.S. by establishing a demo space in Fishers, Indiana, within the Indiana IoT Lab. This space showcases the capabilities of its autonomous mobile robots
(aMRs) and the LexxFleet management system, demonstrating their utility in manufacturing and logistics to enhance efficiency and worker safety. LexxPluss has further committed to the U.S. market by establishing a subsidiary and opening a sales office in Indiana. The company's aMRs are equipped with advanced sensors and a multi-sensor guidance system, designed for scalability and interoperability, allowing integration with existing automated systems and human workflows. The low upfront cost and capability to handle diverse and large payloads make LexxPluss's robots ideal for modern intralogistics challenges. With a recent Series a funding of $10.7 million, LexxPluss is poised for growth and plans to officially launch its products at automate 2024 in Chicago, highlighting their commitment to revolutionizing intralogistics with innovative automation solutions.
REGO-FIX, a leader in toolholding and metrology, will unveil two new tool clamping units and a spindle drawbar force testing tool at IMTS 2024, showcasing their commitment to Swiss precision and innovation. The new PG a 9500 unit is automation-ready, designed to facilitate unmanned tool
setups around the clock and integrates seamlessly with existing automation systems. Its compact design and safe operation make it ideal for various industrial environments. The powRgrip Single offers a quick, efficient tool clamping solution, accommodating one holder size series, optimizing operational efficiency and tool life. additionally, the ForceMaster tool provides a robust solution for measuring and documenting spindle drawbar forces, compatible with various spindle types and essential for maintaining machining accuracy and safety. These innovations by REGO-FIX enhance the productivity and technological capability of modern manufacturing environments, reflecting the company's ongoing commitment to high-quality, precision-engineered solutions.
Rootstock Software has refined its partner ecosystem with the introduction of a new Gold Partner tier, announced at the Rooted-In Manufacturing Conference. This enhancement is part of a strategic initiative to incentivize partners through a structured three-tier system, aiming to foster deeper engagement and success with Rootstock's ERP solutions across the manufacturing sector. Partners begin as Referral Partners, advancing through SI Consulting Partner, and ultimately to Gold Partner, each level offering increasing benefits, support, and opportunities for growth. This structured pathway ensures partners are well-equipped to implement Rootstock’s comprehensive ERP solutions effectively. The introduction of the Rootstock Implementation Certification highlights a commitment to excellence, ensuring partners meet high standards of product knowledge and implementation prowess. The Gold Partner tier signifies a pinnacle of achievement, providing customers with confidence in their partners' expertise and commitment to success.
aMa ZEMET has embraced Siemens Xcelerator to enhance its metal additive manufacturing capabilities, leveraging advanced software solutions to streamline
its production chain. This strategic adoption includes Siemens’ NX software for robust product engineering and Teamcenter X for comprehensive lifecycle management. By centralizing its data management and enhancing process efficiencies, aMa ZEMET addresses the critical needs of rapid prototyping and complex materials development. This integration underscores the increasing importance of digital transformation in manufacturing, enabling aMa ZEMET to maintain a competitive edge in metal additive manufacturing. Siemens Xcelerator supports aMa ZEMET's mission to innovate within the materials science sector, providing scalable solutions that enhance
Advantages & Benefits
• Cost savings (up to 90%)
• High load threads - stronger joints
• High process reliability
• Faster production cycles
• No special machinery required
• Small investment
• Increased material thickness
• Long tool life
• Chipless process
• Innovative technology suitable for steel, stainless steel, copper, brass, and aluminum
productivity and foster innovation in an industry ripe for technological advancement.
Dolfi1920, a specialist in airline luggage repair and claims, has chosen Rootstock Manufacturing Cloud ERP to advance its operations amid rapid global expansion. This ERP integration will streamline key functions such as inventory management, invoicing, and finance, creating a unified data environment that supports improved customer service and operational efficiency. Dolfi1920's collaboration with airlines worldwide necessitates a robust system to manage complex logistics and customer interactions effectively. Rootstock's platform, built on Salesforce, facilitates seamless integration and real-time data access, enhancing Dolfi1920's ability to respond to customer needs promptly and accurately. This strategic move is pivotal as Dolfi1920 scales its services to meet increasing demand, ensuring sustained growth and enhanced service delivery in the competitive airline industry.
Sintavia, LLC, the pioneer in digital aerospace component manufacturing, has announced a major $25 million expansion of its facilities and equipment, the largest since 2019. This strategic investment will significantly enhance
Sintavia's manufacturing capabilities, including new large format printers, post-processing equipment, and advanced testing apparatus. Positioned to support the U.S. Department of Defense's needs through this decade, the expansion underscores Sintavia’s commitment to maintaining its edge in digital aerospace manufacturing.
Brian Neff, Sintavia’s CEO, emphasized the necessity of investing in cutting-edge facilities and technology to meet future customer demands. The expansion will focus on the development of high-performance aerospace heat exchangers, which demonstrate superior heat rejection rates compared to traditional models, thanks to innovative design enabled by additive manufacturing. These components achieve near-perfect production yields, a stark contrast to the yields of traditional manufacturing processes.
The expansion includes a 25,000 square foot addition to its existing headquarters, intended for enhanced printing, post-processing, and materials testing. Sintavia will also add significant new machinery such as a second SLM NXG XII 600 printer, additional CNC machines, and advanced testing equipment. Notably, Sintavia continues to lead in technology adoption, being the North a merican launch customer for the a MCM M8K-K, the largest industrial laser powder bed fusion printer available.
Expected to complete by the end of 2024, this expansion will solidify Sintavia’s role as a leader in the
aerospace component industry, capable of meeting the most rigorous defense and aerospace requirements.
Slip Robotics Wins Innovation award at MODEX 2024 at MODEX 2024, Slip Robotics secured the MHI Innovation award for Best New Innovation with its groundbreaking SlipBot aLR, an automated loading robot. This accolade highlights Slip Robotics' significant contribution to enhancing efficiency at loading docks, a critical bottleneck in supply chain and material handling operations.
Chris Smith, CEO of Slip Robotics, expressed his enthusiasm about the recognition, emphasizing that SlipBots revolutionize dock operations, which have seen little improvement in speed and throughput over the past five decades. SlipBots enable rapid auto-loading and unloading of trucks in just five minutes without additional infrastructure, significantly boosting operational efficiency.
Prominent corporations, including John Deere and GE
a ppliances, have adopted SlipBots, achieving remarkable improvements: a 300% increase in dock throughput, a 91% reduction in truck idle times, an 85% decrease in labor downtime costs, a 40% drop in freight damage, and a 20% boost in facility output by reallocating space more productively.
The award was presented during North a merica's largest supply chain and material handling event, which hosted over 48,000 attendees and 1,200 exhibitors. Slip Robotics also offered live demonstrations at their booth, where attendees operated the SlipBots, successfully handling around 4,790 pallets throughout the event.
PUT A HYDRAULEX REMAN™ UNIT TO WORK FOR YOU.
Our on-the-shelf inventory of Hydraulex Reman™ pumps, motors and valves can get you back up and going in no time. Set to OEM spec, tested and backed by an industry-best 24-month warranty—purchase with peace of mind. Make Hydraulex your first call when you need replacement hydraulic components for your industrial equipment.
To learn more, give us a call, email us or visit us at HYDRAULEX.COM
In today's marketplace, where products and services proliferate and competition intensifies, businesses are realizing that they need to offer more than just a paradigm shift where companies are no longer just selling goods or services but crafting memorable experiences for their customers. This emerging ecosystem personalizes encounters that leave a lasting impression on consumers.
For consumers today, loyalty hangs by a fragile thread. With a single disappointing encounter, customers readily shift allegiance. This fickleness stems from facilitation by the digital age. Whether it's subpar service, a flawed product, or a lackluster interaction, consumers swiftly abandon brands, seeking refuge. We recognize that each interaction is a make-orbreak moment, where the slightest misstep risks losing not just a transaction but a customer's trust and allegiance.
at the heart of the Experience Economy lies the recognition that in an era inundated with choices, customers seek more than just functional benefits. They seek memorable moments. Businesses that prioritize delivering exceptional customer experiences gain a significant competitive edge. These experiences foster growth, brand differentiation, and sustainable success in the long term.
Exceptional experiences forge deep connections, creating loyalty, advocacy, and repeat business. Satisfied customers become brand ambassadors, spreading positivity. Investing in exemplary experiences is no longer a choice—it's an imperative for survival and success, but how do companies deliver great experiences to their customers?
While one traditional key principle in delivering great end-user experiences is getting the right product to the right customer at the right time, this doesn't end in a vacuum. Companies must also consider cost implications, accurate demand forecasting, trend analysis, process automation, and logistics considerations.
Cost implications play a pivotal role in delivering exceptional experiences for end-users. By optimizing expenses, businesses can allocate resources to enhance
customer satisfaction. accurate demand forecasting and trend analysis enable companies to anticipate customer needs, ensuring products are available when required. Process automation streamlines operations, reducing errors and inefficiencies, thus improving reliability and consistency in customer interactions. Logistic considerations ensure convenience for end-users. Together, these factors create a seamless and satisfying experience.
a nother way to ensure a great end-user experience is by improving customer interactions across multiple platforms—website, phone, chat, email, SMS, or social media. a user-friendly website offers intuitive navigation and personalized content, enhancing engagement and satisfaction. Responsive phone support operates efficiently and courteously. Live chat offers real-time assistance, resulting in instant rapport and problem resolution. Email and SMS communications deliver informed and engaged interactions. Social media platforms enable authentic engagement, allowing businesses to interact directly with customers, address concerns, and build trust. Through each touchpoint, companies cultivate meaningful connections, driving loyalty and advocacy among end-users.
While ensuring fantastic customer interactions is valid, it is important to note that roughly 85 percent of the issues
that customer service agents deal with are rooted in not receiving products in the right quantity with complete documentation. Not receiving a child's birthday present on time or not receiving paper instructions after purchasing a product can lead to frustrations. No matter how excellent customer service interactions are, issues like these deeply impact experience and ultimately brand loyalty.
Why do companies struggle to deliver great experiences?
First, siloed views within organizations can severely hinder the customer experience. When departments operate in isolation, critical information becomes fragmented, leading to inconsistent messaging, disjointed processes, and frustrated customers. Silos prevent a holistic understanding of customer needs and preferences, resulting in missed opportunities for solutions. also, disjointed systems often lead to inefficiencies, delays, and errors, further eroding trust and satisfaction. To deliver seamless experiences, businesses need departmental collaboration and data sharing. Only through a unified approach can organizations truly prioritize and enhance the end-to-end customer journey.
Secondly, identifying root cause inefficiencies presents a formidable challenge for businesses. Symptoms of operational flaws often manifest in various departments, making it challenging to pinpoint the underlying issues. additionally, interconnected systems and dependencies further complicate the analysis, obscuring the true source of inefficiency. Without accurate diagnosis, organizations risk implementing superficial solutions that fail to address the underlying problems. Overcoming this hurdle demands meticulous data analysis and a willingness to challenge conventional wisdom.
Lastly, specifically for manufacturers, shop floor productivity is lagging. Manufacturing shop floor productivity suffers as talent retention dwindles and fails to attract younger workers, and outdated perceptions render manufacturing less attractive to younger generations. The absence of modernization and technological integration exacerbates the issue. additionally, inadequate training and career development paths hinder employee engagement and satisfaction. To revitalize productivity, manufacturers must invest in upskilling initiatives and embrace technological innovations. Cultivating a dynamic work environment that values diversity, innovation, and professional growth will attract the next generation of skilled workers, revitalizing shop floor productivity for sustained success.
Why are great customer experiences important? a significant key performance indicator (KPI) around customer experience is the Net Promoter Score (NPS). NPS serves as a critical metric gauging customer loyalty by asking a simple question—"How likely are you to recommend our product/service to a friend or colleague?"—categorizing customers into promoters,
passives, or detractors. Studies have shown a strong correlation between high NPS scores and revenue growth. Promoters, enthusiastic advocates of a brand, not only drive customer acquisition through word-of-mouth but also have a higher purchase frequency and lifetime value. By focusing efforts on elevating NPS, businesses can cultivate a loyal customer base, stimulate organic growth, and ultimately drive profitability.
Supply chain management profoundly influences Net Promoter Score (NPS) by directly impacting key customer touchpoints. Delays in delivery, whether due to inventory shortages or logistical challenges, can lead to dissatisfaction and diminished trust. Product availability issues frustrate customers, potentially driving them to competitors. Inadequate quality control results in defective products and erodes brand loyalty. Moreover, cost increases passed onto consumers can provoke negative sentiment. By prioritizing efficiency, transparency, and reliability throughout the supply chain, companies can mitigate these risks, ensuring consistent and positive experiences.
It is crucial to find a partner that understands that digital transformation alone is not enough. Unlike point solution vendors who solve isolated problems, prioritizing transformation requires a holistic approach that integrates people, processes, and systems.
a good partner will begin its approach by understanding what is actually happening with missioncritical processes in the supply chain like inbound and outbound logistics, order management, help desk, and financial processes. Understanding these root causes helps identify opportunities for improvement and automation. a nalyzing data and feedback loops provides insight into performance within each process. Utilizing process mapping and performance metrics helps pinpoint areas ripe for enhancement. automation technologies, like aI and robotics, can eliminate errors and enhance efficiency. By continuously assessing and optimizing these processes, businesses can improve responsiveness, reduce costs, and enhance customer satisfaction, driving competitive advantage.
In short, the Experience Economy underscores the critical shift towards prioritizing immersive, memorable customer experiences as a key differentiator for businesses. Leveraging solutions that enhance operational efficiency, customer engagement, and overall competitiveness is essential. Partnering with a company that offers an Industrial Transformation platform can boost operational excellence and workforce productivity. Such platforms integrate advanced technologies, analytics, and automation to optimize processes and deliver exceptional experiences consistently. By leveraging these platforms, companies can adapt to evolving consumer demands, drive sustainable growth, and thrive in the Experience Economy, securing their position as industry leaders.
In a significant development for the industrial automation sector, Kawasaki Robotics Inc. has partnered with Olis Robotics to integrate state-of-the-art remote monitoring and error recovery technology into their robotic systems. This collaboration marks a pivotal shift in how industrial robots are managed and maintained, promising to drastically reduce downtime and enhance efficiency across various industries.
Kawasaki Robotics, known for its robust and versatile industrial robots, has joined forces with Olis Robotics, a leader in remote error recovery technology. This partnership is set to transform the operational dynamics of robotic systems by enabling faster production restarts, slashing troubleshooting and downtime costs by up to 90%, and facilitating swift access to expert support.
Olis Robotics’ innovative technology allows users to connect directly to their Kawasaki robots via an on-premises device, ensuring a secure and reliable connection. This system is designed to prioritize physical safety by adhering strictly to the robot controller’s safety restrictions, thus maintaining a secure environment for both the machinery and the operators.
The practical applications and benefits of this partnership were vividly displayed at MODEX 2024 in atlanta, where Kawasaki and Olis Robotics showcased their integrated technologies. attendees witnessed a cutting-edge robotic corner board system, which included a mixed palletizing and depalletizing cell equipped with a Kawasaki RS007L robot. This setup demonstrated the robot’s capability to stabilize pallets efficiently, a critical function in logistics and warehousing operations.
The system featured Olis Robotics’ software, which alerted users to any operational disruptions, such as unexpected stops or failures in picking or placing items. In the event of a system failure, attendees had the opportunity to engage directly with the technology, using Olis to perform remote error recovery. This hands-on demonstration highlighted how quickly and effectively the system could return to full operational status, minimizing downtime.
Paul Marcovecchio, Director of the GI Business Unit at Kawasaki Robotics, emphasized the transformative impact of adding Olis’s remote monitoring capabilities to their robots. “This is a game-changer for the market,” Marcovecchio noted, explaining that the technology caters to a broad spectrum of industrial applications, from small end-users to complex, aI-driven operations in large plants. The partnership addresses critical user concerns such as cybersecurity
and the ease of retrofitting existing machines, making advanced robotics more accessible and manageable.
Fredrik Ryden, CEO of Olis Robotics, pointed out that the durability of Kawasaki robots, combined with the advanced capabilities of Olis's remote support, offers significant value to end-users and integrators alike. The technology not only enhances operational efficiency but also enables integrators to expand their service offerings more rapidly, potentially increasing their business growth by up to 25%.
a critical component of this partnership is the enhanced cybersecurity measures integrated into the remote monitoring systems. a s industries increasingly rely on digital technologies, protecting sensitive data and operational integrity becomes paramount. Olis Robotics has developed advanced encryption and secure communication protocols to ensure that all interactions with the robotic systems are protected from unauthorized access, thereby safeguarding industrial operations against cyber threats.
Looking ahead, Olis and Kawasaki plan to extend their technological advancements to a broader range of robotic applications. The versatility of Kawasaki’s robotics combined with Olis’s remote capabilities is expected to open new opportunities in sectors such as manufacturing, logistics, and even healthcare. These developments are poised to further automate complex processes, reduce human error, and increase production efficiencies.
The Olis remote monitoring and error recovery solution will be available across all Kawasaki robot models starting in the second quarter of 2024. This rollout will likely set a new standard in robotics automation, with both companies poised to lead the way in innovation and efficiency.
Olis Robotics has been a frontrunner in automation technology since its inception as a spinout from the University of Washington’s applied Physics Lab in 2013. Building on decades of telerobotics research in collaboration with the U.S. Navy and Na Sa , Olis has established a robust platform for the remote operation of industrial robots, enhancing the capabilities and reach of automation technology across industries.
Kawasaki Robotics brings over half a century of expertise in automation and robotics solutions. With a commitment to quality and customer support, Kawasaki offers a diverse array of robot models designed for high performance and flexibility across different applications.
This partnership between Kawasaki Robotics and Olis Robotics not only reflects the evolving landscape of industrial automation but also underscores a shared commitment to innovation, safety, and operational excellence. a s industries continue to embrace automation, the collaboration between these two leaders is set to redefine the standards of robotic operations, making them more efficient, secure, and adaptable to the needs of modern manufacturing and logistics.
The efficient filtration of cooling lubricants and grinding oils is a significant prerequisite for the cost-effectiveness and quality of the tool grinding process. By selecting the right filter system, considerable cost savings can be achieved and product quality improved. Vomat GmbH, based in Treuen, Germany, offers the metalworking industry innovative solutions in the field of filter technology - for example the range of compact ultra-fine filtration systems in the Fa series 120 to 420.
In the low to medium flow rate range, these compact class systems guarantee an extremely economical 100% separation of clean and dirty oil in a full-flow process. Steffen Strobel, Sales Manager at Vomat: "In an automatic cycle - depending on the amount of dirt - this technology not only guarantees 100% separation of the dirty and clean oil via a frequency-controlled system pump, but also ensures that oil with a filter fineness of 3-5 µm is always available for the production process over a long period of time during cleaning using special high-performance precoat filters."
Vomat relies on the use of highly efficient pumps to make the operation of the ultra-fine filtration systems energy-efficient. In conjunction with optimized process control, unnecessary energy losses are avoided. Vomat systems automatically control the filter flow and backwash cycles according to demand. This extends the service life of the filter elements and leads to significant energy and cost savings.
In contrast to conventional systems, which often work continuously at maximum filter performance, Vomat systems adapt to the current production process. For example, if grinding machines are running at a lower speed, only the required amount of cooling lubricant is filtered. In Vomat central systems that filter several grinding machines, some of which are not in operation, the filter capacity is automatically adapted to the cutting volume. This simultaneously reduces the heat supply to the medium, which means that less cooling capacity is required and energy consumption is further reduced.
During the full-flow backwashing process, on-demand backwashing brings further benefits: With Vomat filters, the backwash cycles are controlled depending on the
degree of contamination of the filter elements. a s soon as relevant contamination levels are reached, the time-delayed backwash starts for each individual filter. The other filters continue to ensure a continuous supply of clean oil. This fully automatic control and adjustment of the filter capacity enables efficient control of energy and operating costs.
The grinding sludge is disposed of using a special sedimentator with fully automatic treatment of recyclable materials with a residual moisture content of between 5 and 10 percent. Overall, the treatment process is extremely user-friendly. The sludge is fed directly into the recycling companies' transport containers.
Steffen Strobel: "If cooling lubricants remain clean for longer in the machining process, they can also be used for longer periods of time. Vomat Technologie achieves this, for example, thanks to the needs-based backwashing of the Vomat ultrafine filtration systems in conjunction with special cooling concepts. This leads to significantly reduced machine downtimes for users and increases production efficiency while minimizing losses due to contamination and heat input into the medium. a s a result, this also leads to considerable savings in energy costs."
Sustainment is a groundbreaking technology company on a mission to revolutionize the american manufacturing industry. By developing innovative software solutions, Sustainment aims to empower U.S. manufacturers, particularly small and medium-sized manufacturers (SMMs), to become more competitive, efficient, and profitable.
In a world where global supply chains are increasingly vulnerable to disruptions, supporting domestic manufacturing has never been more crucial. Sustainment recognizes the vital role that U.S. manufacturing plays in the economy, national security, and job creation and is dedicated to ensuring its success through cutting-edge technology.
The global manufacturing landscape is undergoing a profound transformation, with a growing emphasis on localized production and supply chain resilience. Several factors, including heightened geopolitical risks and the rapid advancement of manufacturing technologies, are driving this shift. a s companies navigate this new reality, Sustainment is positioning itself as a catalyst for change, empowering american manufacturers to adapt and thrive in an increasingly complex and uncertain world.
Geopolitical risks have emerged as a significant driver of supply chain restructuring in recent years. From trade disputes and tariffs to regional conflicts, the global manufacturing ecosystem has been buffeted by a series of shocks that have exposed the vulnerabilities of heavily outsourced supply chains.
To compound these issues, an increase in energy prices has driven up freight shipping rates. Residual supply chain issues brought on by the COVID-19 pandemic still exist, which have led to longer shipping times. There is also an additional risk of infrastructure issues, such as the collapse of the Francis Scott Key Bridge in Baltimore, MD. Quality control is also vulnerable as communication can break down over cultural or process differences.
These disruptions have prompted manufacturers to
reevaluate their reliance on international suppliers and explore ways to build more resilient, localized networks. at the same time, rapid advancements in manufacturing technology are making domestic production increasingly viable and competitive. The rise of automation, robotics, and artificial intelligence is transforming the factory floor, enabling manufacturers to produce goods more efficiently, flexibly, and cost-effectively than ever before.
a s these technologies evolve, the traditional advantages of low-cost labor in overseas markets are diminishing, making localized manufacturing an increasingly attractive option. Even as this trend is taking place, U.S. manufacturers are facing a number of unique issues.
The american manufacturing industry, a vital pillar of the nation's economy, faces significant challenges that have hindered its growth and competitiveness in recent years.
The fragmentation and friction within manufacturing supply chains are some of the most pressing issues. The industry is comprised of at least 243,687 manufacturers, with the vast majority categorized as small businesses. This landscape, while vibrant and diverse, has led to a siloed and disconnected ecosystem where manufacturers often struggle to communicate and collaborate effectively with one another.
Compounding this problem is the lack of modern digital tools designed specifically to help manufacturers efficiently engage with domestic suppliers. The manufacturing sector has lagged, relying on outdated methods such as rolodexes, local networks, and email to manage their supplier relationships. This analog approach has created significant inefficiencies, making it difficult for manufacturers to access new opportunities, scale their operations, and adapt to changing market demands.
These issues led to the founding of Sustainment.
With an unwavering commitment to supporting american manufacturing, Sustainment has embarked on a journey to bridge the gaps in the industry. By developing cutting-edge
software solutions, the company aims to eliminate the friction and fragmentation that often hinder the growth and success of domestic manufacturers.
With so many SMMs (small to medium manufacturers) in the United States, the industry struggles to act efficiently "as one" to compete globally. Sustainment's Supplier Relationship Management (SRM) software is designed to streamline the project collaboration between manufacturers. The technology allows buyers to organize their suppliers, communicate and collaborate with them in real-time, and view their supplier networks more strategically.
This platform accelerates the onboarding of new suppliers, facilitates rapid quoting of jobs, and tracks purchase orders from acknowledgment through to delivery. When each manufacturer moves faster, the entire industry moves faster together.
as manufacturers in the U.S. mature in how they manage their relationships, they also have the opportunity to address weaknesses in their supplier network at a high level. Often, overseas suppliers have hidden costs and may be underperforming in areas such as quality and on-time delivery.
Sustainment gives manufacturers visibility and the tools to improve.
Sustainment is committed to creating a positive impact on the manufacturing community, its employees, and the organizations that support and rely on them. The company actively seeks partnerships with state governments and other organizations to further its mission and contribute to the strengthening of the U.S. manufacturing ecosystem.
Sustainment is also proud of its partnerships with the Defense Logistics agency and the United States air Force. The intrinsic benefits of building software in partnership with the Department of Defense have meant that security and privacy have always been nonnegotiable at Sustainment. Sustainment passes those benefits through to commercial manufacturers to operationalize their processes and communication securely and resiliently. This commitment includes NDa management and secure file sharing.
In today's world, many of the improvements manufacturing buyers desire to make are related to enhancing the presence of local manufacturers in their supplier networks. By regionalizing supply chains, companies aim to mitigate disruption risks, prioritize product quality and delivery speed, reduce logistics expenses, and shrink their carbon footprints.
alongside its SRM platform, Sustainment supports an extensive and vibrant market network of U.S. manufacturers, enabling buyers to start new relationships with one click to achieve their local strategic sourcing goals.
Sustainment's economic approach also makes it easy to achieve Sustainment's higher-order goals as a Public Benefit Corporation (PBC). Participation in the market network is free for all, and Supplier Relationship Management is free for very small businesses and pricing scales up based on usage. This model ensures that Sustainment's tools are accessible and beneficial to all stakeholders. This approach fosters a collaborative environment where manufacturers can work together more efficiently and effectively.
Sustainment's dedication to supporting U.S. manufacturing is exemplified by its incorporation as a PBC. This legal structure allows the company to prioritize its mission of promoting the growth and success of small and medium manufacturers in the U.S. alongside its financial objectives. as a PBC,
Perhaps most importantly, Sustainment's ecosystem is built on a foundation of direct customer relationships. Unlike traditional marketplace platforms that can sometimes create barriers between buyers and suppliers, Sustainment's approach is designed to foster genuine, long-term partnerships. The company's platform enables manufacturers to connect and collaborate directly with their customers, building trust, transparency, and mutual success. This direct engagement not only helps manufacturers better understand and meet the needs of their customers but also allows them to develop the kind of deep, lasting relationships that are essential for long-term growth and success.
Sustainment is at the forefront of driving the future of american manufacturing. By developing innovative technologies that empower U.S. manufacturers to be more competitive, efficient, and resilient, Sustainment is playing a crucial role in the industry's transformation. The company's commitment to its mission, as evidenced by its incorporation as a Public Benefit Corporation and partnerships with key stakeholders, sets it apart as a leader in the field. a s the manufacturing landscape continues to evolve, with a growing emphasis on localized supply chains and advanced technologies,
Sustainment is well-positioned to support and guide the industry through these changes. The success of Sustainment and other innovative technology providers will be essential to ensuring the long-term prosperity of U.S. manufacturing and the millions of americans who depend on it for their livelihoods. By supporting companies like Sustainment, we can help to create a stronger, more resilient, and more competitive manufacturing sector that will drive economic growth and job creation for years to come.
Viñolas Metall is a family business specializing in the construction of metal components, sheet metal processing, and boiler making. as part of their latest innovation measures, a CMT robotic welding cell was introduced in combination with a TPS 400i power source for the series production of identical parts. at the same time, the iWave Pro series—the new generation of Fronius multiprocess welding machines—is being used for certain applications.
Josep Viñolas founded Viñolas Metall in 1968 in Cornellà del Terri, Spain, and the company has been producing metal constructions for companies and private consumers ever since. years later, his son David Viñolas joined the company and invested in new machinery and technologies for the export business and to optimize project workflows through computerization. a 4,000
m2 production site in Banyoles was recently opened to complement the existing 800 m2 assembly workshop in Cornellà del Terri. In addition, Viñolas Metall has been certified to ISO 3834-2 by the Fronius Welding academy. The company has a diverse range of customers from different industries, including winemaking, water treatment, swimming pool accessories, mechanical engineering, plant construction, toolmaking, power plant construction, and railway construction. Viñolas Metall is known for its innovative solutions, high quality of service, and efficient, customer-oriented project management.
Current situation and new challenges
Welding currently accounts for 70 to 80% of production times. Carbon steel, stainless steel (304, 316, duplex, and
super duplex), aluminum, and COR-TEN® are the most common materials processed.
It is mainly smaller components that are joined, but also large and heavy components too. Sheet thicknesses range from 2 to 40 mm. Welding is carried out in the Pa (flat position), PB (horizontal vertical position), and PC (horizontal position) positions. Out-of-position welding on vertical beams and pipes is performed in the PF (vertical up position) and PG (vertical down position) positions. The most frequently used processes are TIG and MIG/MaG for manual tasks, as well as the arcTig keyhole welding process for automated applications. Orbital welding systems are also used, whereby the welding torch rotates around the component during joining.
a s they specialize in technically demanding, complex metal structures, Viñolas Metall faced two new challenges.
The solution: Robotic welding cell with TPS 400i CMT
a s a result of the good experiences Viñolas Metall has had with Fronius welding machines and processes, the company trusts in the professionalism and reliability of Fronius both from a technical and efficiency perspective.
“When we need to weld identical parts with the highest weld quality, we turn to Fronius, as they always have the solution we’re looking for,” says David Viñolas, managing director of Viñolas Metall.
One specific challenge for Viñolas is welding beams for swimming pool roofs from austenitic chrome-nickel steels 304 and 316. The welding solution consists of a robotic welding cell equipped with a TPS 400i CMT welding machine, a hollow arm welding robot, and a H reverser, which has two vertical turntables on a horizontal axis on
be carried out by trained operators who do not have to be experienced welding specialists—a particular advantage in times of skills shortages.
“We want our best welders to work on large projects with high added value, while smaller series parts can
• Heavy Gauge Steel Design
• Press Bed bolted on, not welded, to prevent distortion.
• Large press bed to accommodate a variety of tooling other than just punching.
• Pump, motor, valve and reservoir are all easily accessible for maintenance.
• Large rectangular tubes used at base of machine to give safe, instant portability.
be welded with the robotic welding cell,” explains mechatronics engineer Matheus Borborema.
The Cold Metal Transfer (CMT) process used in the welding cell is characterized by its minimal heat input, which reduces the heat-affected zone and thus the deformation of the base material. at the same time, it impresses with its extremely high arc stability. CMT enables higher welding speeds with low spattering, minimizing uneconomical rework and costs for consumables.
Viñolas Metall has been placing its faith in Fronius since 2016, when the first TPS/i welding system for intelligent MIG/MaG welding was introduced. Recently the company has been facing a new challenge: the welding robot must weld various components using both the TIG and MIG/MaG process—with rapid process changes and programmed configurations. Welding quality and system stability must be kept constant throughout. The welding solution to meet this challenge is the iWave Pro aC/DC multiprocess welding machine from Fronius.
“The reliability of the equipment and service quality of technology partners are key factors for us,” emphasizes David Viñolas. “The Fronius support team fully supported us during the test phase of the new iWave Pro. We have now purchased four more devices.”
Viñolas plans to gradually replace all the old equipment, so that by 2025 all 15 welding cells will be equipped with the iWave Pro, and all the company’s welding machines will be Fronius devices. The main reason for purchasing the multiprocess welding machines is the fast process change. Overall, the iWave increases productivity, saves consumables, and requires less space. What’s more, production efficiency is increased because welding
specialists can use the welding process immediately required—without wasting time switching between TIG and MIG/MaG.
On Viñolas Metall’s journey towards Industry 5.0, the iWave Pro stands out for its compatibility with WeldCube, the advanced Fronius welding data management and documentation software. Further advantages include the CycleTig and PMC (Pulse Multi Control) functions, which significantly contribute to the reduction in uneconomical rework. The optional DynamicWire Welding Package, enabling dynamic wirefeed during manual TIG welding, is another plus. The devices are robust and feature a long service life with low maintenance, significantly improving the ecological footprint. Their large digital color display is easy to use even with welding gloves.
From now on, Viñolas Metall’s demanding projects involving tanks and other components made of carbon steel, stainless steel, and aluminum for the aerospace, pharmaceutical, and food industries will be joined by hand with the iWave Pro aC/DC.
David Viñolas explains: “Fronius products are far more powerful and reliable than the devices we’ve used before. They’re robust and have been developed with the needs of welding professionals in mind. Since owning Fronius
equipment, we have never had to stop production due to failures. The devices are very intuitive and easy to use, and the training offered allows us to make the most of what they can do.”
In addition, Viñolas points out: “We have been working with Fronius for many years because we trust the renowned technology company. Their sales team is very empathetic and professional. The fast, reliable, and solution-oriented service has shown us that we can rely on Fronius. We were looking for a company that would not only demonstrate to us the latest technology in welding, but also support us as we embarked on the process of technological transformation.”
Viñolas and Fronius: Past, present, and future
Since the application engineers at Viñolas Metall first tested a Fronius device and the decision was made to purchase, the business relationship has gradually grown. In the meantime, further systems have been acquired, including an arcView camera system for visual weld pool control during robotic welding, an arcTig keyhole welding system, and ten iWave and TPS/i welding machines.
Where the shared success story began with the introduction of a robotic welding cell, it has now moved forward thanks to the purchase of four iWave Pros.
Today, Viñolas Metall is convinced by Fronius at every level.
Article based on analysis from Deloitte Insights, "Supporting US Manufacturing Growth Amid Workforce Challenges."
The resurgence of the U.S. manufacturing sector has become a cornerstone of economic growth and technological advancement. Recent reports indicate a robust expansion, with the sector not only regaining its pre-pandemic strength but also setting new benchmarks in terms of employment and investment. This article delves into the current state of U.S. manufacturing, the impact of legislative measures, the persistent workforce challenges, and the innovative strategies being employed to navigate these hurdles.
The U.S. manufacturing industry has shown remarkable growth, achieving employment levels near 13 million as of January 2024, a stark contrast to the downturns seen in other sectors. The increase in the number of manufacturing establishments by more than 11% from the first quarter of 2019 to the second quarter of 2023, reaching nearly 393,000, underscores a sector in rapid expansion.
Moreover, construction spending in manufacturing has nearly tripled since June 2020, culminating in a record $225 billion by January 2024. This surge is fueled in part by strategic initiatives to mitigate supply chain risks and localize manufacturing bases closer to U.S. consumers.
Significant legislative actions have further propelled this growth. The Infrastructure Investment and Jobs act (IIJa), the Inflation Reduction act (IR a), and the CHIPS act have collectively spurred the development of nearly 300 new technology and semiconductor manufacturing facilities, poised for completion by 2031. These projects represent an unprecedented injection of over $430 billion into the sector, coupled with the creation of more than 234,000 manufacturing jobs.
Despite these promising developments, the manufacturing sector faces a looming challenge: a significant skills gap coupled with a shortfall in applicant numbers. The 2024
Deloitte and The Manufacturing Institute Talent Study
illuminates this issue, with findings indicating that not only are technical and digital skills in high demand, but there is also a notable deficiency in applicants for these roles. The study identifies a pressing need for workers across all levels, from entry-level positions to skilled engineers, exacerbated by evolving skill requirements as the industry moves towards more sophisticated manufacturing technologies like smart factories and Industry 4.0.
To combat these challenges, manufacturers are adopting multifaceted strategies aimed at both attracting and retaining talent. Over 65% of respondents in a recent survey indicated that workforce challenges are their primary business concern. Companies are increasingly turning to innovative solutions such as offering flexible work arrangements, enhancing benefits packages, and integrating cutting-edge technologies to make manufacturing jobs more appealing to a younger, tech-savvy demographic.
Educational trends also play a crucial role in addressing the skills gap. While there has been a rise in the number of degrees conferred in fields relevant to advanced manufacturing, the growth in associate degrees, which are vital for training skilled tradespeople, has not kept pace. This disparity highlights a critical area of focus for educational institutions and industry leaders: developing curricula and training programs that are aligned with the changing needs of the industry.
One of the most promising approaches in tackling the workforce dilemma is the adoption of an ecosystem approach. This strategy involves creating synergies between manufacturers, educational institutions, local governments, and other stakeholders to develop a sustainable talent pipeline. By fostering collaboration and leveraging the strengths of various partners, manufacturers can enhance their recruitment efforts, improve training programs, and ultimately close the skills gap more effectively.
a s manufacturers push towards the frontiers of Industry 4.0 and smart factories, the integration of technology into manufacturing processes has become paramount. This not only involves the adoption of advanced robotics, aI, and data analytics but also the cultivation of a workforce proficient in these technologies. To this end, manufacturers are increasingly focusing on digital skills alongside traditional manufacturing skills, preparing employees to handle more complex tasks and machinery.
The digital transformation in manufacturing not only enhances production capabilities but also serves as a key strategy for attracting digital natives to the industry. younger workers who are comfortable with technology find the high-tech aspects of modern manufacturing
appealing, which can help in bridging the generational skill gap and ensuring a continuous influx of talent into the industry.
Recognizing the shifts in workforce expectations, particularly among millennials and Gen Z, manufacturers are also rethinking their approach to employee engagement and retention. Flexible working conditions, improved work-life balance, and opportunities for growth and development are becoming standard offerings aimed at attracting and retaining valuable employees.
Some manufacturers have set up internal training academies that provide ongoing education and skill development, ensuring that their workforce remains at the cutting edge of manufacturing technology. These programs often include partnerships with technology providers and educational institutions to offer both theoretical and hands-on training that is directly applicable to the workers’ daily responsibilities.
a key part of expanding the talent pool involves reaching out to underrepresented groups and communities that may not have traditionally participated in manufacturing. Initiatives to include veterans, women, and minorities are not just about filling jobs but enriching the workplace with diverse perspectives that can drive innovation.
Manufacturers are also exploring programs aimed at second-chance hires and individuals from non-traditional backgrounds, such as those with disabilities or those who have been incarcerated. These efforts not only help in mitigating the skills shortage but also contribute to social responsibility goals by providing opportunities for meaningful and gainful employment to more members of the community.
a s the U.S. manufacturing sector continues to grow and evolve, the challenges of building and maintaining a skilled workforce remain formidable. However, through a combination of legislative support, technological adoption, innovative workforce strategies, and a commitment to inclusive hiring practices, the industry is well-positioned to capitalize on its current growth trajectory.
The continued collaboration between industry, government, and educational institutions will be crucial in cultivating a robust manufacturing workforce that can support the ongoing renaissance of a merican manufacturing. a s this sector becomes increasingly vital to the national economy, the strategies implemented today will determine its sustainability and success in the decades to come.
This holistic approach not only addresses immediate workforce needs but also sets the stage for long-term prosperity in the manufacturing sector, ensuring it remains a key pillar of economic strength in the United States.
Plasma cutting produces rapid, clean cuts and has highly versatile applications. It’s the most efficient method for precise metal cutting.
By: Rob GoldiezPlasma cutting stands as one of the most versatile and efficient methods for slicing through metals with precision and speed. This process, utilizing a constricted electric arc and ionized gas, offers fabricators unparalleled flexibility in various industries, from manufacturing to construction. In this article, we delve into the intricacies of plasma cutting, exploring its mechanics, applications, and why it's a preferred choice for many fabricators.
at its core, plasma cutting involves the utilization of a high-velocity jet of ionized gas, known as plasma, to cut through electrically conductive materials. This process, often likened to welding but with distinct differences, relies on the transformation of gas into a conductive state through intense heating by an electric arc. The resulting plasma, akin to a fourth state of matter, facilitates the cutting process by generating extreme heat, enabling precise and efficient material removal.
Plasma cutting operates on a relatively straightforward principle: initiating and guiding an electric arc along the desired cutting path. Unlike traditional methods, plasma cutting offers remarkable ease of use, making it accessible to both seasoned professionals and novices alike.
The process typically involves several key steps:
» Ground Clamp attachment: The ground clamp is affixed to the workpiece to complete the electrical circuit, ensuring proper conductivity during the cutting operation.
» Setting adjustment: adequate settings for material type and thickness are selected, optimizing the cutting parameters for the task at hand.
» Plasma Torch Engagement: The plasma torch, equipped with consumables such as electrodes and nozzles, is brought into contact with the workpiece, initiating the plasma arc.
» Trigger activation: With the trigger engaged, the plasma arc is initiated, generating intense heat capable of slicing through the metal in any desired direction.
Proper safety precautions, including avoiding grounding the clamp to the portion of the workpiece to be cut off and adhering to manufacturer guidelines, are essential to ensure a safe and efficient cutting process.
Fine-tuning plasma cutter settings is crucial to achieving optimal cutting results. Key parameters, including amperage, voltage, and torch-to-work distance, play pivotal roles in determining cut quality and efficiency.
» amperage: Dictating the arc's heat and cutting capability, amperage directly influences cutting speed
and quality. Selecting the appropriate amperage for the material thickness is essential to avoid distortion and edge irregularities.
» Voltage: Voltage, akin to electrical pressure, affects the arc's stability and penetration depth. adhering to manufacturer specifications for voltage settings ensures consistent and precise cutting outcomes.
» Torch-to-Work Distance: Maintaining the ideal standoff distance between the torch and workpiece is critical for achieving desired bevel angles and minimizing cut defects. adjusting voltage and standoff distance in tandem allows for precise control over the cutting process.
Plasma cutting systems employ various arc starting methods, each offering distinct advantages and suitability for different applications:
» High-Frequency (HF) Non-Pilot arc Start: Common in entry-level systems, HF non-pilot arc starting utilizes high-frequency current to initiate the plasma arc. While effective for manual cutting, it may pose compatibility issues with CNC equipment.
» HF Pilot arc: Similar to HF non-pilot arc start, HF pilot arc introduces a pilot arc, enabling smoother arc transfer and enhanced performance, particularly in removing surface impurities.
» Mechanical Blowback arc: Utilized in advanced plasma cutting setups, mechanical blowback arc initiation relies on gas pressure to separate the electrode from the nozzle, creating a pilot arc without high-frequency current. This method offers superior compatibility with CNC systems and precise arc control.
Central to the plasma cutting process is the plasma torch, comprising a body and consumable components essential for maintaining optimal performance. Consumables, including swirl rings, electrodes, nozzles, and shields, ensure consistent arc stability and cutting precision. Torch configurations may vary, with options for air or watercooled systems depending on the application's demands and amperage requirements.
Plasma cutting necessitates a reliable source of compressed air or gas to sustain the plasma arc. While compressed air is a cost-effective option for general cutting tasks, specialized gases such as oxygen, nitrogen, and argon offer superior cut quality and consumable longevity. Proper filtration and gas selection are imperative to mitigate contamination risks and ensure optimal cutting performance.
Plasma cutting finds extensive applications across various industries, owing to its versatility and efficiency. Some notable applications include:
» Gouging and material removal
» Demolition and decommissioning projects
» Cutting wire mesh and extruded metals
» Fabricating electrically conductive components
» Flush cutting and fastener removal
» Manual, mechanized, and automated cutting operations
» Plate, sheet metal, and pipe cutting and beveling
» Marking and engraving for identification and alignment purposes
Industries benefiting from plasma cutting technology span HVaC, mining, energy, shipbuilding, construction, transportation, petrochemical, auto-body repairs, and general fabrication. The ability to accommodate diverse materials and thicknesses makes plasma cutting a preferred choice for fabricators seeking efficiency and precision across various applications.
Fabricators favor plasma cutting for its myriad advantages, including:
» Excellent Cut Quality and Versatility: Plasma cutters excel in slicing through a wide range of materials with exceptional precision and speed. Whether cutting thin sheets or thick plates, plasma technology delivers consistent and high-quality results.
» Low Cost and High Production Speed: Compared to alternative methods such as oxy-fuel, plasma cutting systems offer superior cost-effectiveness and productivity. Lower equipment and operational costs, coupled with faster cutting speeds, translate to significant savings and enhanced throughput.
» Safe Cutting Process: Plasma cutting is inherently safer than some alternative methods, with fewer inherent hazards and simpler operational requirements. While safety precautions remain essential, plasma cutting poses minimal risks compared to oxy-fuel and other techniques.
Plasma cutting stands as a cornerstone of modern fabrication, offering unparalleled versatility, efficiency, and precision. From its fundamental principles to advanced applications, plasma technology continues to revolutionize the manufacturing landscape, empowering fabricators to achieve unparalleled results with speed and accuracy. a s industries evolve and demand for high-quality, cost-effective cutting solutions grows, plasma cutting remains at the forefront, driving innovation and enabling progress across diverse sectors.
Innovative solutions, such as Hirebotics' Cobot Cutter, further enhance plasma cutting capabilities, streamlining operations and maximizing productivity. With cutting-edge technology and a commitment to excellence, fabricators can harness the power of plasma cutting to conquer challenges and unlock new possibilities in the ever-evolving world of manufacturing.
Every aspect of manufacturing operations continues to grow in complexity, presenting challenges at every turn—and learning to manage this complexity is essential to success. a s we witness the evolution of industrial machinery from automated production lines to adaptive, flexible, connected production facilities, it becomes evident that the integration of autonomous, self-optimizing machinery throughout manufacturing is reshaping the way machines are designed, built and operated.
This new approach to manufacturing can be summarized by the term “smart factories” – which in turn drives the need for smart machines. Machine builders must invest in new technologies to meet these evolving customer demands – but this paradigm shift also creates a high demand for workforce skills that are in short supply. a midst this uncertainty, there emerges the pressing need for a strategic approach to simplify technical challenges and allow the assimilation of technological and process change.
In this article, we will examine the three fundamental pillars—electrification, automation and digitalization— that not only enable but also provide new approaches to simplifying technical issues for machine builders. To meet the smart manufacturing requirements of customers, machine builders must transform their approach to design, engineering, manufacturing and field support. This transformation is an opportunity to grow business, improve sustainability, and deliver financial predictability. By embracing repeatable processes enabled by these pillars, manufacturers can meet future demands with confidence and agility, ensuring continued success in an ever-changing landscape.
Manufacturing is challenged with rising energy costs, along with a drive to meet increasingly demanding sustainability regulations. The integration of sensors into machines resulting from initiatives such as Industry 4.0 and the Industrial Internet of Things (IIoT)
helps companies to effectively manage energy use, improve operational efficiency and reduce waste. The ability to measure and quantify improvements supports sustainability goals.
Electrification offers huge opportunities to drive efficiency improvements into manufacturing operations. The ability to measure actual energy consumption, combined with simulation tools to illustrate the benefit of process change and equipment upgrades, can help to justify investments.
Modern electric-powered machinery operates with great precision and reliability, leading to smoother production processes, reduced energy consumption and lower maintenance costs.
a digital twin can be created at the factory or machine level, raising understanding of production processes and identifying prime areas for improvement. Machine performance can benefit from the selection of high efficiency electric
advanced control algorithms. Simulation can help to improve robot efficiency through path planning and gripper optimization.
Machine sensors support a transformation in the way machines are maintained. These sensors can
parameters that provide visibility of a machine’s condition. We will discuss this in more detail in the third pillar, digitalization.
In addition to a workforce shortage and sustainability concerns fueled by the global climate crisis, the industrial machinery industry is experiencing new levels of competition. Customers expect better products at an expedited rate, leaving machine builders to search for solutions that allow them to produce products faster while maintaining quality—and increasing factory automation is one way manufacturers can remain ahead of the competition.
automation eliminates repetitive manual tasks, reducing the risk of errors and ensuring consistent quality. From assembly lines to packaging, robots and smart machines work tirelessly, boosting overall efficiency. Employees can focus on higher-value tasks, reducing physical strain. automation enhances workplace ergonomics and overall well-being.
Machine builders are transitioning from traditional mechanical reliant designs to integrated mechatronic-based approaches, where mechanical, electrical and automation design activities seamlessly converge. This multi-domain approach benefits greatly from the creation of a digital twin encompassing entire machines and workflows. The digital twin allows a machine builder to improve overall performance in the virtual world before building a physical machine.
Moreover, advancements in technology are redefining internal operations, enhancing agility and responsiveness. Real-time monitoring capabilities enable adaptive modifications, optimizing equipment functionality in real-world scenarios. This proactive
approach not only minimizes downtime but also fosters continuous improvement.
While initial investment in automation might seem high, long-term savings are substantial. Reduced labor costs, fewer employee-related expenses, and minimized downtime contribute to a healthier bottom line.
Electrification and automation pave the way for companies to embrace and implement digitalization. By harnessing the power of digital technologies such as aI, machine learning (ML) and IT, manufacturers can gather, analyze and leverage data to drive informed decision making from top floor to shop floor.
In the electrification pillar, we introduced machine sensor data. The integration of aI tools to analyze this data can deliver new opportunities to machine builders through the adoption of new service strategies such as condition and predictive maintenance. Notifications of changing parameters can be generated, prompting the machine builder to investigate and diagnose using secure remote monitoring tools. Problems can sometimes be affected through software updates, but should a service activity be required, the field technician can be dispatched with the correct tools, parts and repair instructions before a problem impacts production.
It is vital to continually evaluate the electrical and behavior model of machines within the context of the factory to discover the impact of any proposed changes across the more extensive operation. The simulation capabilities for industrial systems encompass the component, machine, and plant levels, providing many tools to the customer to evaluate the entire performance of a production plant, from production planning to actual operations.
Initially, simulation enables the creation of a digital twin of the machine during the design process, which is used to explore a broader range of design possibilities and virtually prototype them. Then, this digital experience generated in the design process is maintained over the machine operation’s lifecycle, merging the physical and digital versions of the machine and process. During machine operation, real-world data is fed back into the machine’s digital twin to optimize the twin’s fidelity. It is possible to explore “what if” scenarios for improving machine quality or line modifications before committing to actual changes. Equally important, it provides a way to optimize continuously for sustainability over the lifecycle of the machinery.
Navigating complexity with confidence and agility a s manufacturers face the ever-growing challenges of sustainability, changing workforce skills, and increasing competition, the pillars of electrification, automation and digitalization help them gain the tools they need to navigate hurdles with confidence and agility. By embracing repeatable processes and implementing new technology into factories and processes, they can streamline operations, drive sustainability and above all, simplify the technical challenges of the smart factory.
Rahul Garg is the Vice President for Industrial Machinery and SMB Program at Siemens Digital Industries Software, responsible for defining and delivering key strategic initiatives and solutions, and global business development. He and his team are responsible for identifying key initiatives and developing solutions for the industry while working closely with industry-leading customers and providing thought leadership on new and emerging issues faced by the machinery industry. Rahul’s experience and insight are derived
from a 25-year career delivering software-based solutions for product engineering and manufacturing innovation for the global manufacturing industry, spanning a career in R&D to program management, sales and P&L management and having focused exclusively on the industrial machinery and heavy equipment industry since 2007.
AXIAL PISTON PUMPS… Oilgear open loop
axial piston pumps are offered in a variety of models and displacement sizes to match required performance. Models include both medium and high horsepower, medium and heavy duty, low viscosity pumps, plus a series of multiple fixed delivery pumps. Of the many industries Oilgear serves, a primary one is mobile and off-highway applications. Oilgear pumps are recognized for high performance in the toughest environments. Their heavy duty designs resist contamination as well as operating on low viscosity specialty fluids.
VARIABLE PUMPS…
Whatever the application, Oilgear has the ideal pump to fulfill the requirements.
MULTIPLE FIXED DELIVERY CHECK VALVE PUMPS…
• High pressure to 15,000 psi
• Heavy duty construction
• High contamination tolerance
• Operation on low viscosity fluids
• Multiple deliveries up to three displacements from a single pump
Paradigm-shifting design-build solutions require finding a company that thrives on providing solutions to impossible industrial design and manufacturing challenges.
Industrial manufacturers understand the importance of efficient and streamlined processes to stay competitive in the market. Industrial design-build encompasses just that – a project delivery method where a design-build company takes on the responsibility of both the designing and manufacturing or assembly phases of a project.
Tebots, Inc., for example, is an industrial design-build firm with diverse experience designing devices, products, automation, and
manufacturing to find solutions to seemingly impossible challenges through creative solutions. The company specializes in industrial prototyping and production. They have extensive and diverse experience that allows them to be bold and propose uncommon results, often in the form of an invention.
The founder of the company, Robert Tegel, considers himself a “disruptive innovator” and thrives on coming up with solutions to challenges that are thought to be
unachievable. The solutions he creates are specifically designed to speed-up cycle times, reduce costs, and eliminate unnecessary complexity.
Tebots prides itself on offering tailored solutions rather than cookiecutter approaches. With a focus on innovative methods and original ideas, they are the go-to company for those seeking transformative solutions. The only thing required of the customer is “a positive perspective to give me the go ahead to do something different,” says Tegel.
The strength of Tegel’s designbuild experience lies in the diverse range of his specific background, resembling a “Swiss-army knife.” With a career marked by maintaining, engineering, and inventing various types of equipment, he views it as an “agglomeration of success.”
During his early years, he initially pursued a career as an auto mechanic but ultimately transitioned into diverse roles in the field. These included installing grain elevators, operating in foundries, improving high-speed sewing equipment, designing pumps for home coffee systems, manufacturing valve seals and inkjet cartridges, applying industrial testing and automation, and contributing to auto part assembly.
The common thread throughout his career is in the wide range of equipment he has handled.
“One piece of equipment was the length of a city block running very low RPMs and moving garbage and separating all kinds of different things and material processing different temperatures and heat and then going into stuff that was running 400 cycles per minute. and then the next job I took was microprocessor-controlled high speed sewing equipment that was running 10,000 cycles per minute,” says Tegel.
Throughout his career, Tegel left a string of inventions in his wake. His first patent was issued in 1988. Within the textiles industry, he devised an innovative patented solution for efficiently and repeatedly sewing t-shirt sleeves. His more than 30 issued patents include a pallet positioning system, a variety of dunnage systems and apparatus, and a discharge control valve.
Then, in 2005, he decided to go into business himself. The company began as Tegel Design. However, one customer was so thrilled with the engineering that he asked the
company to manufacture the product. Industrial design-build firm, Tebots, was born in 2007 of this request.
The company’s name, Tebots, in many ways is a precursor of the now popular term “cobots”. a cobot, or collaborative robot, is a robot intended for direct human-robot interaction within a shared space, or where humans and robots are in proximity. an early Tebots logo depicted a robot engaging in a handshake with an individual, symbolizing the harmonious relationship between humans and machines – a philosophy infused in many of Tegel’s designs.
From those beginnings, they began to accumulate internal production resources such as machine centers, test and measurement equipment, and other production capabilities.
When parts are outsourced, the company works with supply chain vendors to receive high quality finished parts. Before delivering assembled sub-assemblies or complete machines, an exhaustive quality control procedure is carried out utilizing cutting-edge test and measurement systems.
Tegel now regards Tebots as a skunkworks-style operation – an innovative endeavor led by a select group of individuals operating outside the conventional research and development channels of the organization.
Engineer ed Tough for Year After Year Reliability
In every design, Tebots consistently aims to optimize material usage and streamline assembly processes while upholding high-quality standards. Meeting strict delivery schedules is an ongoing priority, with a dedicated focus on enhancing part efficiency, expediting production, and reducing costs. a s such, Tebots' designs are rooted in principles encompassing Design for Manufacturing (DFM) and Design for a ssembly (DFa).
Design for Manufacturing (DFM) refers to the process of designing parts, components, or products with the objective of improving product quality while reducing costs through simplified, optimized, and refined product designs. Similarly, Design for a ssembly (DFa) focuses on designing products that are easily assembled, aiming to minimize assembly time and associated costs by reducing the number of components involved.
To remain competitive against the a sian market, for example, Tegel has developed innovative strategies to streamline manufacturing processes and remove any unnecessary steps, ensuring efficiency and cost-effectiveness.
“There was constant competition with my customer to meet delivery costs in the a sian market, so I had to come up with extremely lean, net zero bill of materials,” says Tegel.
In one example, his customer was purchasing a machined structure to hold the machine up like a stand. They were buying them from China for $420, shipping them to the United States all welded together. Tebots produced the same part using patent pending tubular connections that provide a similar strength and rigidity to a welded connection for a third of the cost. The Omni Stand can be used to support just about anything that can be attached to it and disassembled easily if needed. The patented methodology, now called the OmniStand, is now being offered by Grundlage Solutions (https:// grundlage.solutions/).
an Eye on Future Paradigm Shifts
according to Tegel, the primary objective in design-build is to devise a solution that is efficient, cost-effective, and
feasible to meet the immediate requirement. However, he also consistently keeps an eye on future potential iterations or models.
“When designing, it is crucial to consider the potential development of the product over time, with an eye on how we can move to a new paradigm or segue into new way of doing things,” says Tegel.
So, when the pandemic occurred, Tegel identified an opportunity that he felt would hold significant value in the future beyond the crisis. Despite lacking dedicated customer funding for the project, he decided to invest his own efforts and expertise.
The result was a unique and patented UV disinfection system called the POZ. The device utilizes shortwavelength ultraviolet C (UV-C) light to inactivate pathogens including viruses (such as S a RS-CoV-2), bacteria, mold spores, and yeast.
Never one to shy away from collaboration when required, Tegel reached out to Turan Erdogan, a former research professor at the University of Rochester’s Institute of Optics.
“Collaboration is key when it comes to areas where you may not have expertise,” says Tegel.
a lthough there are already many UV light devices on the market, Tegel and his team had to overcome several inherent limitations in design. Many require direct contact and manipulation to operate the appliance, and there can be questions about the intensity and contact time of the applied UV light. If the item is treated in a static manner, for example placed in an enclosure without being rotated or moved, it is like tanning on the beach on only one side. The UV-C light may not reach all the relevant surfaces.
“Simply adding a UV lamp to a product and expecting it to destroy pathogens does not mean it will be effective,” says Tegel. “UV light sources can vary in intensity and output, and there can be line-of-sight issues as well. you have to make sure the UV light is directed at the items from many angles with uniform intensity, and all this requires a high level of engineering.”
The patent-pending UV disinfection appliance resembles a small, portable charcoal grill. Tablet sized, or smaller items are placed on a rotating platform and then move in a 360-degree arc through the chamber where they are bombarded from all angles by UV-C light for approximately 10 seconds.
“Because the item is moving through the chamber, we can direct the UV-C in a way that ensures it will hit the targeted surface. By controlling the internal environment and the time within the chamber very precisely, we can kill more than 99.9% of the pathogens on the surfaces of the item,” says Tegel.
baseball caps, sunglasses, keys, wallets, jewelry, credit cards, bills, and coins.
The company hopes to engage in discussions with several entities to license the technology. The initial design and several full prototypes have already been created.
a lthough at the time the primary driver to develop this technology was COVID-19, Tegel says the intention was to create a device that addresses both existing and future health challenges as well.
“This isn’t just a COVID-related product,” says Tegel. “It is a product and an approach that could have a lasting impact on hygiene now and in the future using a technology [UV-C] that has been around long before the pandemic.”
To remain competitive in their respective industries, many companies consider industrial design-build to be essential. Collaborating with an experienced and versatile industrial design-build firm can decrease cycle times, lower costs, and simplify operations by finding innovative solutions.
For those seeking creative and efficient problemsolving, partnering with a firm that can provide paradigmshifting solutions can be an ideal choice.
For more information, visit https://tebots.com/ or contact Robert Tegel at 847-669-6876.
• Provide reliable, low cost, ink code marking.
• May be mounted in any orientation.
• The sealed ink system allows discontinuous operations with immediate start-up of comparable previous impressions.
• Can be modified or made to order for your particular marking application.
Tegel envisions the self-service disinfection stations being installed in front of entries/exits or bathrooms at public venues, retail stores, healthcare facilities, academic institutions, airport terminals, and nursing homes – to name a few. The units could be used to disinfect personal items such as cellphones, tablets, face masks, ID badges,
Industrial Machinery Digest's Monthly Product Showcase features the latest from some of the manufacturing industry's top suppliers.
aeSolutions Introduces FM-approved FGS 5000 on Rockwell automation Platform aeSolutions partners with Rockwell automation to launch the FM-approved FGS 5000, built on the ControlLogix platform. Combining aeSolutions' extensive experience in PLC/DCS-based systems with Rockwell's technology, the FGS 5000 promises regulatory compliance and scalability for various industries. Scheduled for a summer 2024 release pending FM approval, the FGS 5000 is poised to enhance safety standards in industrial environments. With features catering to hydrogen production, oil & gas, semiconductor, pharmaceutical, chemical, and manufacturing sectors, it aims to meet regulatory and compliance needs efficiently.
arnold Magnetic Technologies Showcases Molypermalloy
Precision Thin Metals
a rnold Magnetic Technologies highlights its Thin Molypermalloy products, tailored for effective RFI and EMI shielding in industrial applications. With high magnetic permeability and customizable options, these products ensure efficient energy storage and transfer. Ideal for industries requiring precision and reliability, a rnold's Molypermalloys offer advanced shielding capabilities across diverse frequencies. Through adapted testing and unique material customization, a rnold ensures optimal performance, making its Molypermalloy an ideal fit for various industrial applications seeking superior electromagnetic shielding solutions.
Cortec® Innovates with Vapor Phase Corrosion
Inhibiting Edge Sprays
Cortec® introduces Vapor Phase Corrosion Inhibiting edge sprays, designed to combat steel coil corrosion effectively. These sprays, ideal for steel coil processors, promise improved productivity and reduced maintenance costs by preventing rust formation during storage and shipping. With their ability to form a molecular protective layer, the sprays ensure long-term corrosion protection, especially in challenging environments. By offering solutions that simplify corrosion prevention and maintenance processes, Cortec® addresses critical industry needs and enhances the durability and longevity of steel coils in various applications.
Coxreels® presents a new line of industrial duty LED lights for PC10 reels, featuring robust design and enhanced functionality. Backed by Coxreels®' legacy of quality and innovation, these lights ensure optimal performance in demanding industrial environments. With a focus on durability and practicality, Coxreels® continues to deliver solutions that meet the evolving needs of industrial users, providing reliable illumination for various applications. The introduction of industrial-grade LED lights underscores Coxreels®' commitment to delivering high-quality products that enhance safety and efficiency in industrial settings.
Introduces EcoGun a S MaN DC/EC
Dürr introduces the EcoGun a S M aN DC/EC, an electrostatic air spray gun designed for efficient painting processes. Backed by Dürr's commitment to sustainability and innovation, it sets a new standard for painting efficiency. With features such as reduced overspray and ergonomic design, the EcoGun a S M aN DC/EC offers improved performance and user comfort, making it suitable for various manual painting applications. By optimizing paint consumption and application efficiency, Dürr enhances productivity and reduces environmental impact, contributing to more sustainable painting processes in industrial settings.
Enhances aluminum MIG Welding Wire for Increased
alcoTec® upgrades its 4000 series aluminum MIG welding wires, promising smoother feeding and improved performance. Designed for high-volume welding applications, these wires offer increased uptime and reliability. With enhanced surface treatment technology, alcoTec® ensures optimal wire feed performance, minimizing downtime and improving welding efficiency. The upgraded wires are ideal for automotive, bicycle, and general fabrication applications, providing consistent and reliable performance in demanding industrial environments. alcoTec®'s commitment to innovation and quality underscores its leadership in the aluminum welding wire market.
Fairlane Products introduces Covered Bearings Rollers, ensuring quiet, non-marring operation for materials handling applications. With various durometers and sizes available, these rollers promise optimal performance and versatility. Designed for smooth and quiet operation, Fairlane's Covered Bearings Rollers provide reliable and efficient handling solutions for a wide range of industrial applications. The rollers' durable construction and precision engineering ensure long-term performance, making them ideal for demanding materials handling environments where reliability and performance are paramount.
Fixtureworks® launches quick release quarter turn "retractable" fasteners/clamps, enhancing productivity in quick change applications. With positive locking and consistent fastening force, these fasteners ensure reliability and ease of use. Designed for frequent disassembly and reassembly, Fixtureworks®' retractable fasteners provide efficient solutions for various industrial applications,
including packaging, food processing, and assembly fixtures. By simplifying and streamlining changeover processes, Fixtureworks® helps industrial users improve productivity and reduce downtime, contributing to overall operational efficiency and cost savings.
HEMCO presents Island Canopy Hoods, engineered for superior corrosion and chemical resistance in industrial environments. Ideal for collecting and exhausting corrosive vapors, these hoods ensure safety and performance. With their lightweight and durable construction, HEMCO's Island Canopy Hoods provide reliable and efficient ventilation solutions for various industrial applications. The hoods' chemical-resistant materials and seamless design offer long-term durability and easy maintenance, making them an ideal choice for industrial facilities where corrosion resistance and safety are paramount.
Miller Introduces Bobcat™ 265 air Pak™ and Trailblazer® 330 air Pak™ Engine-Driven Welders
Miller Electric Mfg. LLC launches the Bobcat 265 a ir Pak and Trailblazer 330 a ir Pak, equipped with integrated air compressors for enhanced job site efficiency. These all-in-one machines, featuring rotary-screw air compressors, eliminate the need for separate compressors, saving operators time, money, and space. Both models offer multiprocess weld quality, auxiliary
power, and battery charge/crank assist, along with the new air compressor feature. Designed for maintenance, repair operations, and field fabrication, these machines cater to professionals across industries, providing versatile solutions for diverse welding needs.
Miller Electric Mfg. LLC introduces the Copilot collaborative robotic welding system, now featuring the new auto Deltaweld® power source. This innovative system simplifies welding automation with advanced features and a user-friendly interface, enhancing weld quality, consistency, and productivity. Designed for welders of all skill levels, the Copilot empowers users to amplify their capabilities and increase outputs rapidly. With features like accuGuide™ positioning control and IntelliSet™ weld settings assistant, operators can achieve repeatable, high-quality welds effortlessly, accelerating training and enhancing efficiency in welding automation processes.
ModuleWorks Releases 2024.04 Update with Enhanced Software Components for Digital Manufacturing
OPEN MIND Introduces hyperMILL® 2024 CAD/CAM Software Suite with Enhanced Functionality
Rootstock Unveils aIRS™: advanced aI Solution for Manufacturers
Rootstock Software launches aIRS™ ( a rtificial Intelligence from Rootstock), a cutting-edge aI solution designed to revolutionize manufacturing decision-making. Leveraging Rootstock's ERP dataset and industry expertise, aIRS™ delivers predictive and generative aI capabilities for optimizing manufacturing operations. By analyzing data across the Signal Chain, aIRS™ enables smart, autonomous decisions, empowering manufacturers to enhance efficiency, reduce costs, and mitigate risks. With applications in inventory planning, demand forecasting, supplier collaboration, and financial management, aIRS™ represents a significant step towards building agile manufacturing and driving supply chain resilience.
SprutC aM Tech Releases SprutC aM X and SprutC aM X Robot 17.0.13 Update
SprutC a M Tech announces the release of SprutC a M X and SprutC a M X Robot 17.0.13 update, featuring over 100 enhancements for improved workflow and usability. Key updates include enhanced job assignment for 6D contour operations, spline handling improvements, and updates to machining reports. The update also introduces usability enhancements, machine-specific updates for Fanuc and Dobot robots, and improvements to the user interface. With these enhancements, SprutC a M X continues to provide manufacturers with advanced C a M solutions for optimizing machining processes and increasing productivity.
Walter unveils the Tiger·tec® Gold WMP45G button insert, designed for turbine blade machining with the F2334R copy milling cutter. Featuring a sintered insert for cost-effectiveness, the WMP45G provides high process reliability and wear resistance in challenging machining environments. The F2334R milling cutter offers stable pocket design and radial positive geometry for soft cutting action, making it ideal for blade machining. With multiple insert geometries available, including light cutting and high stability options, Walter's solution delivers exceptional performance and durability in turbine blade manufacturing.
Quickly grind and remove welds, deburr rough edges, and polish hard-to-reach areas. American-made quality tools are precision designed and manufactured, allowing for fast and efficient production with less rework.
Experience the ease of working with Dynabrade with free on-site demonstrations, excellent customer service, and products that are in-stock and ready for immediate shipment.