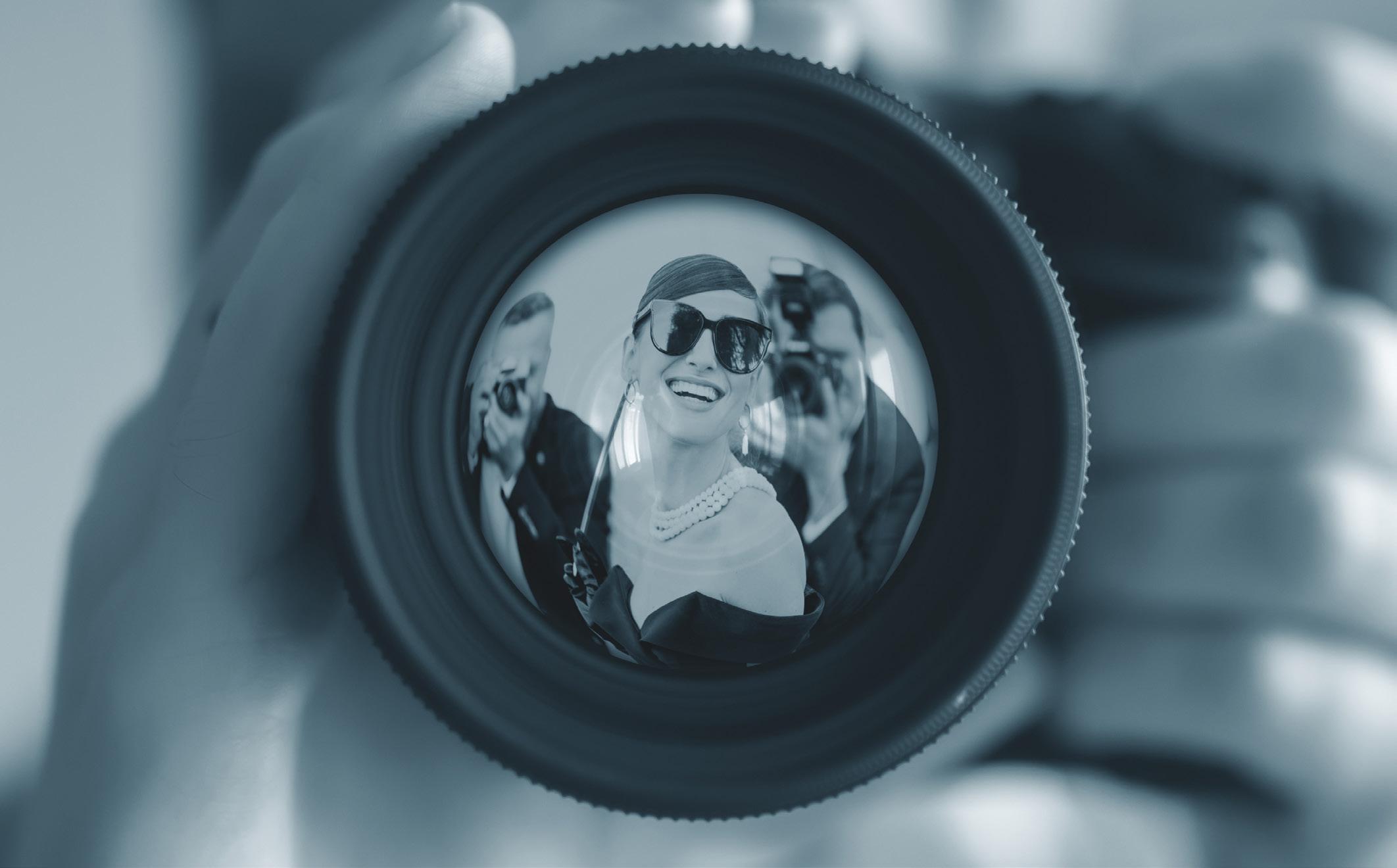
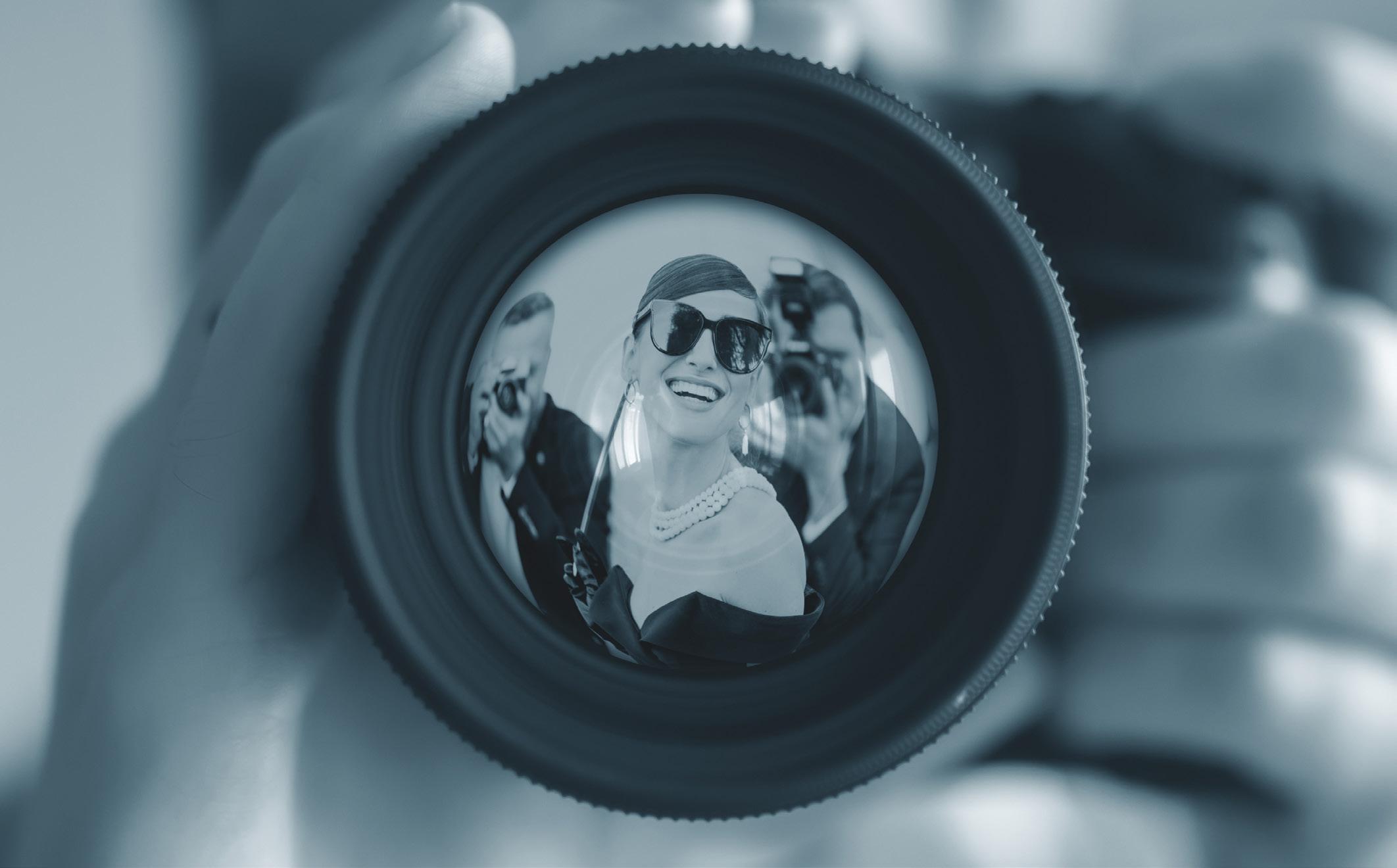
The lithium stars to watch
New luminaries find the limelight
Telling truth to power
Meaningful dialogue is being lost in a welter of confusing battery claims
Not too hot to handle
Lithium blazes may be devastating but they’re rare and in the end manageable
The darker side to unity
Battery recycling chaos imminent as new European waste rules advance





Advanced Battery Chemistry 90+ Years. 150+ Products. One Focus.

Hammond’s innovative signature products, SureCure® and Treated SureCure®, are two of more than 150 customized additives that are improving battery performance and lowering manufacturing costs for battery manufacturers around the world.
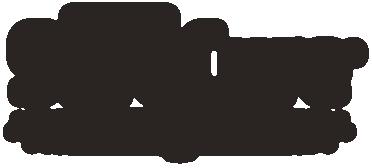
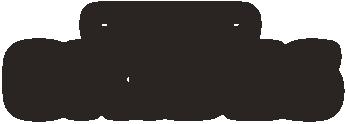
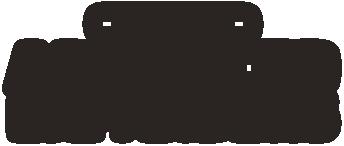
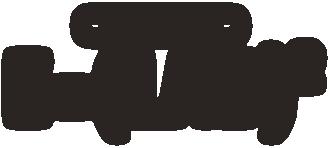
INDUSTRY NEWS
Hammond Group Announces CEO Transition as Long-Time Advisor Lucas is Named to Replace Murphy
Robert “Bobby” Lucas has been named the new President and CEO of Hammond Group, supporting the company’s continued global growth strategy and execution. Terry Murphy will continue to serve on Hammond’s Board of Directors.
Lucas, a trusted legal advisor to Hammond’s management team for over 15 years, most recently served as managing partner at Dinsmore &
Shohl’s Chicago office.“Bobby serves on our Board, knows our industry, and is a critical thinker whose wide range of professional expertise is unsurpassed,” said Murphy. In addition to more than 20 years as a corporate attorney, Lucas has served as Chair of Dinsmore & Shohl’s Corporate Department, Co-Chair of the Business, Acquisitions and Securities Practice
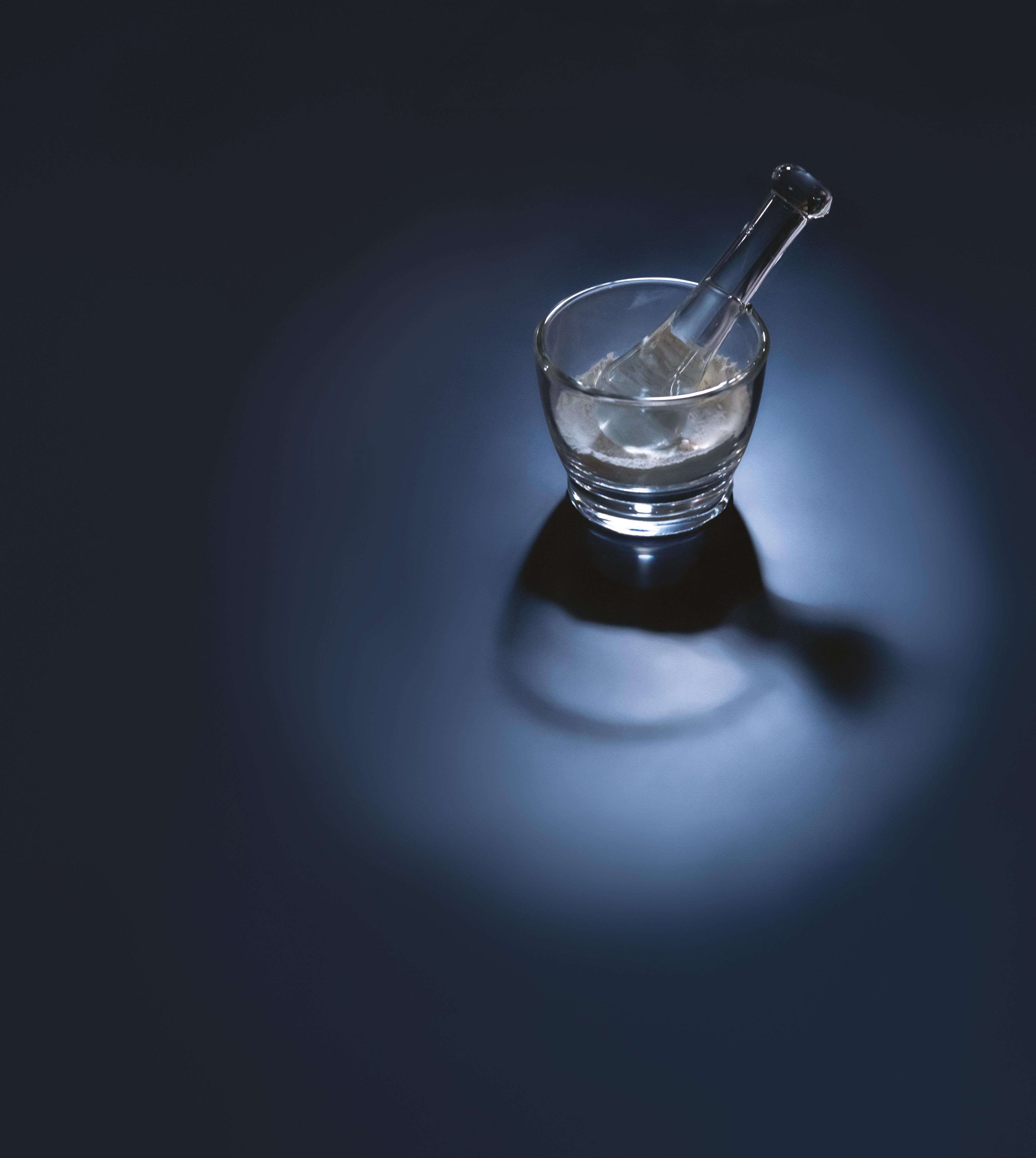
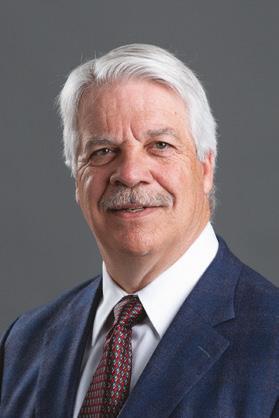
Murphy Lucas
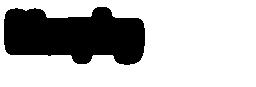
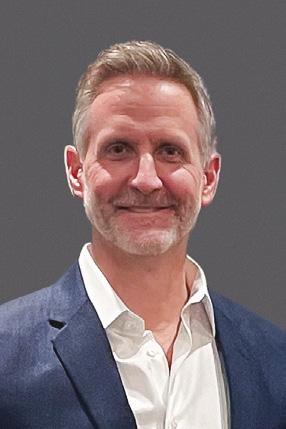
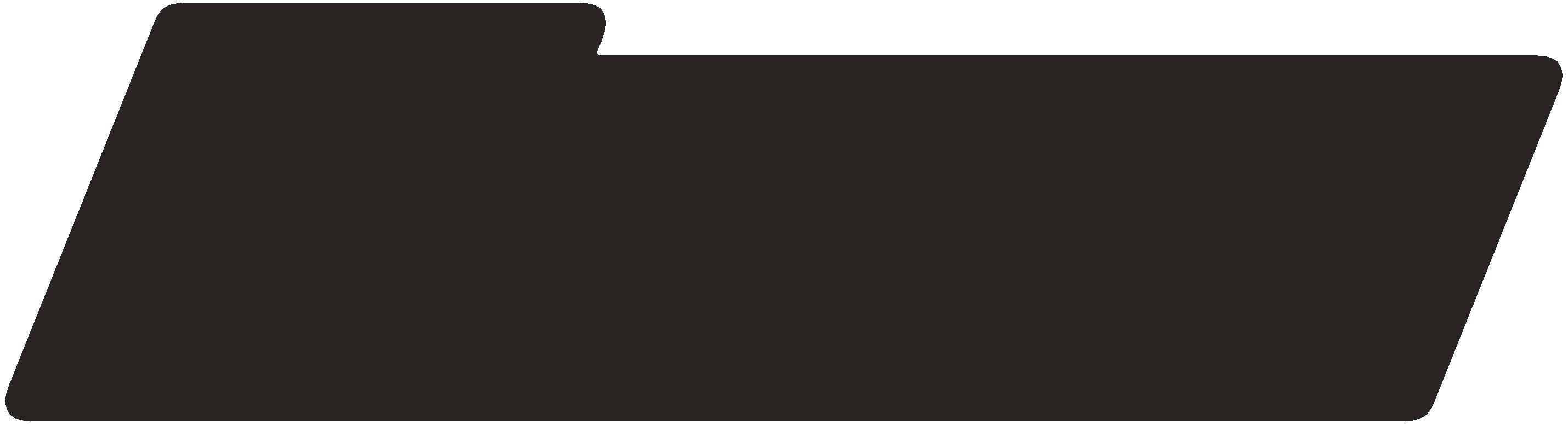

Group, a member of the firm’s Executive Committee, on their Board of Directors, and he was Vice Chair of the firm’s Finance Committee. He will officially join Hammond on June 3.
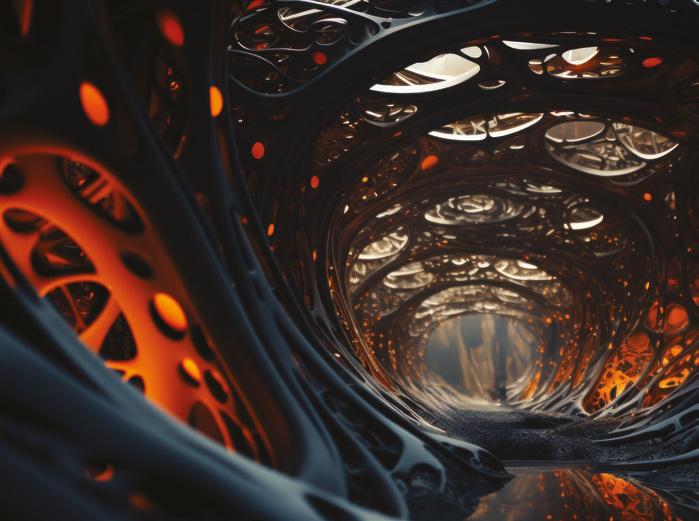
RECYCLING CHAOS ALERT
Political machinations are at the heart of unrealistic, and foolish, demands to be made on battery recycling across the European Union. Expert opinions are being ignored for longer term leverage over the sector.
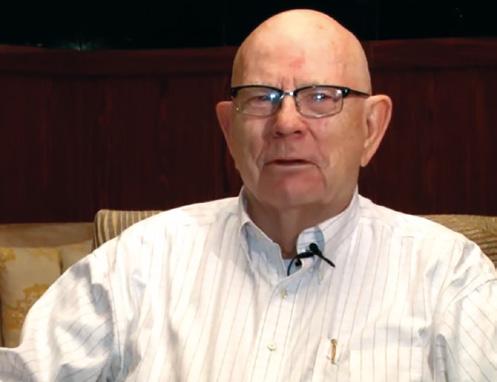
History made bold: Ralph Brodd, a key figure in the US lithium space is no longer with us.

THE NEW LITHIUM STARS
A new generation of EV battery businesses is moving into the limelight. With the teething problems of their initial start-up phases over they are counting on double-digit growth in the years ahead.
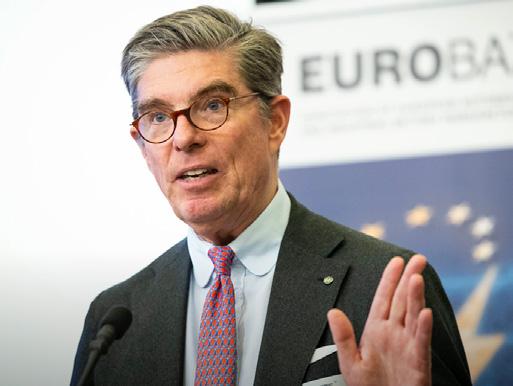
EUROBAT launches elections manifesto; batteries should be on the European ballot mind-set.
LITHIUM’S BURNING — FIRE, FIRE
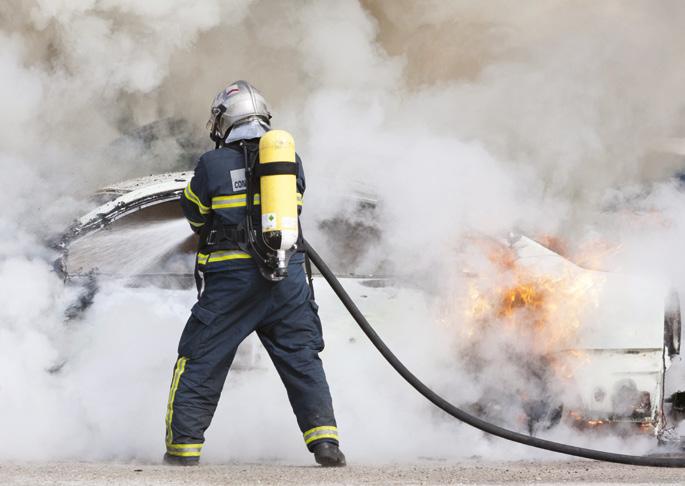
LITHIUM’S BURNING — FIRE, FIRE!
The dramatic growth in the use of lithium batteries from small-scale usage to large size BESS is being accompanied by a surge in electrical fires. But this isn’t something to lose sleep over. Or not much anyway.
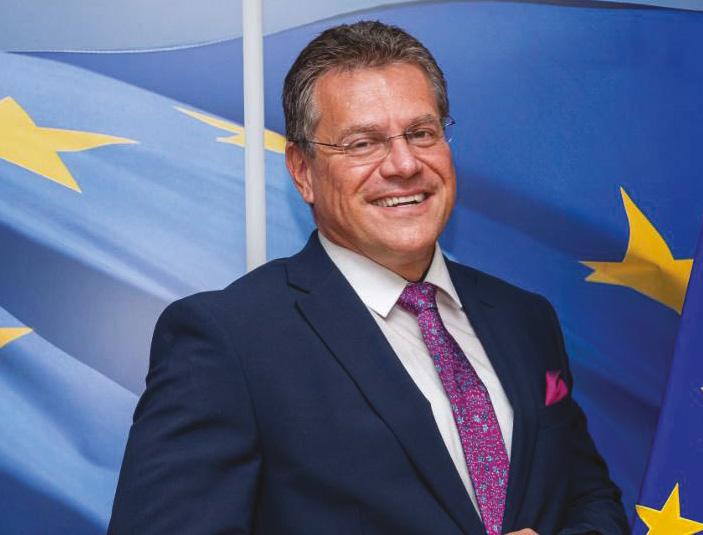
With EU elections imminent, It’s make-or-break time for Europe’s much trumpeted Green Deal.
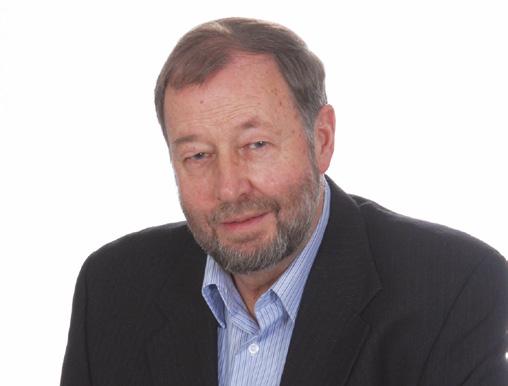
Time to find out more about Electrochemical impedance Spectroscopy. You won’t regret it.
2 EDITORIAL: In search of a truthful dialogue | 4 OBITUARY: Ralph Brodd: a giant in the US lithium industry has died 8 PEOPLE NEWS: Some of the key senior management changes in the past quarter | 11 NEWS FOCUS | 16 NEWS: A comprehensive round-up of the most significant news stories since our last issue | 30 COVER STORY | ONES TO WATCH: All to play for ... and everything up for grabs. Some of the new stars in the energy storage firmament | 36 MANAGING LITHIUM SAFETY RISK: Lithium safety may be a burning issue! But that’s not the complete story | 41 BATTERY TESTING: EIS: Electrochemical impedance spectroscopy | 45 UPCOMING EVENTS: ESJ details the conferences and shows ahead
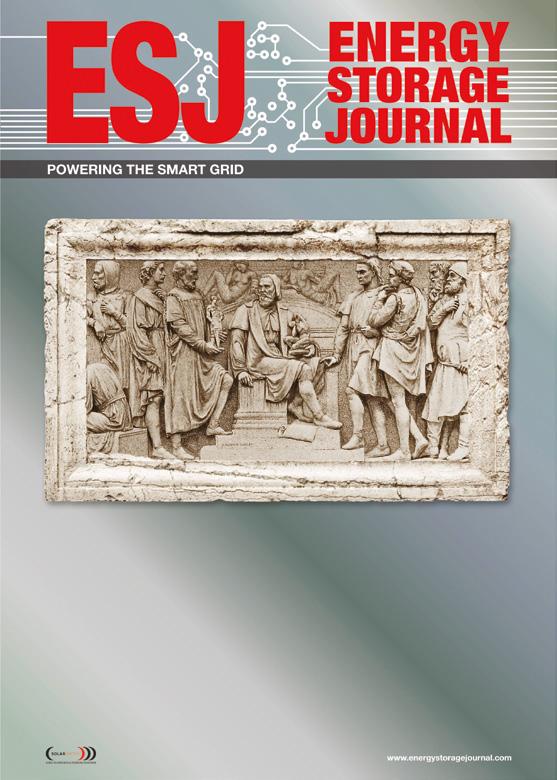
Editor-in-chief:
Deputy editor: Shona Sibery | email:shona@energystoragejournal.com |
Advertising manager: Jade Beevor | email: jade@energystoragejournal.com |
Finance: Juanita Anderson | email: juanita@batteriesinternational.com |
Subscriptions and admin: admin@energystoragejournal.com | tel:
Design: Antony Parselle | email: aparselledesign@me.com
Are we in the battery and energy storage business as full of doublespeak as the rest of the world? But do we want to do better?
In search of a truthful dialogue
“Europe is not known for its dynamism but it presently looks stagnant by any standard.”
That’s not a comment from this magazine but the March 30 top editorial in The Economist newspaper.
But in fact this is part of a broader question that needs to be flung to the architects of Europe’s current “situation”. (Or “deindustrialization”, as The Economist describes it.)
It’s about: the EU’s Green Deal that’s about to be torn to pieces; about its Batteries Directive that will be ineffectual for five years at least (if ever); and, the situation where any instinct for sensible business planning has been squashed by the European Commission’s crazed and unrealistic bureaucracy.
Underpinning this all, it’s also been about the use of language.
Europe’s big guns have talked their policies up hugely but — see our news focus article on European Commission second-in-command Frans Timmermans — have long never explained the situation properly. Instead they’ve used weasel words to discuss its thinking. (Or in the opinion of this magazine, its lack of it.)
Some of this neologistic use of language goes back to Victorian children’s writer Lewis Carroll, in Alice Through the Looking Glass who imagines this conversation.
“When I use a word,” Humpty Dumpty said in rather a scornful tone, “it means just what I choose it to mean — neither more nor less.”
“The question is,” said Alice, “whether you can make words mean so many different things.”
Yes, how can you make the same words mean so many things?
How, to paraphrase Mr Timmermans, EU regulators are open to every battery chemistry and technology. But, but, but! Not the one in use in every car battery, back-up power system, telecoms tower and the like.
As an aside one of the interesting features of listening to European Commission officials speaking at public meetings is that they — almost invariably — never stay for questions and at conferences, in particular, are known to scurry off the moment they have delivered their presentation.
But this debate about language and confusing words and truth, in the sense of what is actually going on, and mixing it up is part of a larger picture.
Making language mean less
Outside of the Americas most people are unaware of Frank Luntz, the US mastermind communicator, who has used language to change the political landscape.
Luntz helped coin phrases such as: “energy exploration” (sounds better than “oil drilling”), “citizens” became “hard-working tax payers” and “global warming” was sterilized to “climate change”.
Most masterful: to describe “punitive sanctions” as “economic diplomacy”.
It didn’t change what was happening but phrasing the ideas in a more acceptable — depending on your political standpoint — fashion to convey your message. Similarly, too, we’ve seen the way that the petrochemical giants have dealt with the way that they interpret our use of their products.
We now think more of our individual “carbon footprint” (courtesy advertising firm Ogilvy & Mather working for BP in 2004) than the petrochemical suppliers of kerosene to help us fly on holiday.
In my little village of Amberley in a very rural corner of southern England, a band of determined elderly people each week collect empty crisp packets, medical blister packs and milk bottle caps which can’t be recycled and then — perversely — once a fortnight drive to a collection point 10 miles down the road where it is picked up and processed.
Value of collected goods a hundredth of one US cent (if that). Landfill impact minimal. Gas to drop them off about $8.
This individual sense of culpability is not necessarily to be despised, though the logic of course is flawed, but their deeds need to be put into the media context. The fact is that since 1988, over 70% of global CO2 emissions have come from just 100 companies.
My villagers’ mistake is to accept any individual or collective responsibility for corporate brand posturing (and snide-talking profits).
The war of language continues unabated. BP hammered its message home later in 2004 with its
carbon footprint calculator — how much carbon did YOU use when you drove to work, when YOU bought that avocado in the supermarket, when YOU watched television?
Other
perspectives
The battery business is in a fundamentally different position. We’re part of the solution. We’re not the problem.
Yet, we as an industry tolerate the linguistic misinformation that comes from Brussels which continues to pretend that Europe is at the cutting edge of any kind of self-sufficiency in energy storage.
This is all the odder given that, outside of Europe’s top civil servants, everyone knows that the continent is some 15 years behind the Chinese in terms of creating a viable lithiumbattery supply chain and perhaps 10 behind North America.
It’s easy to tut-tut about other people’s misuse of language but it doesn’t take long for any outsider to spot the rank misuse the lead and lithium battery industry have achieved when mangling the communication language.
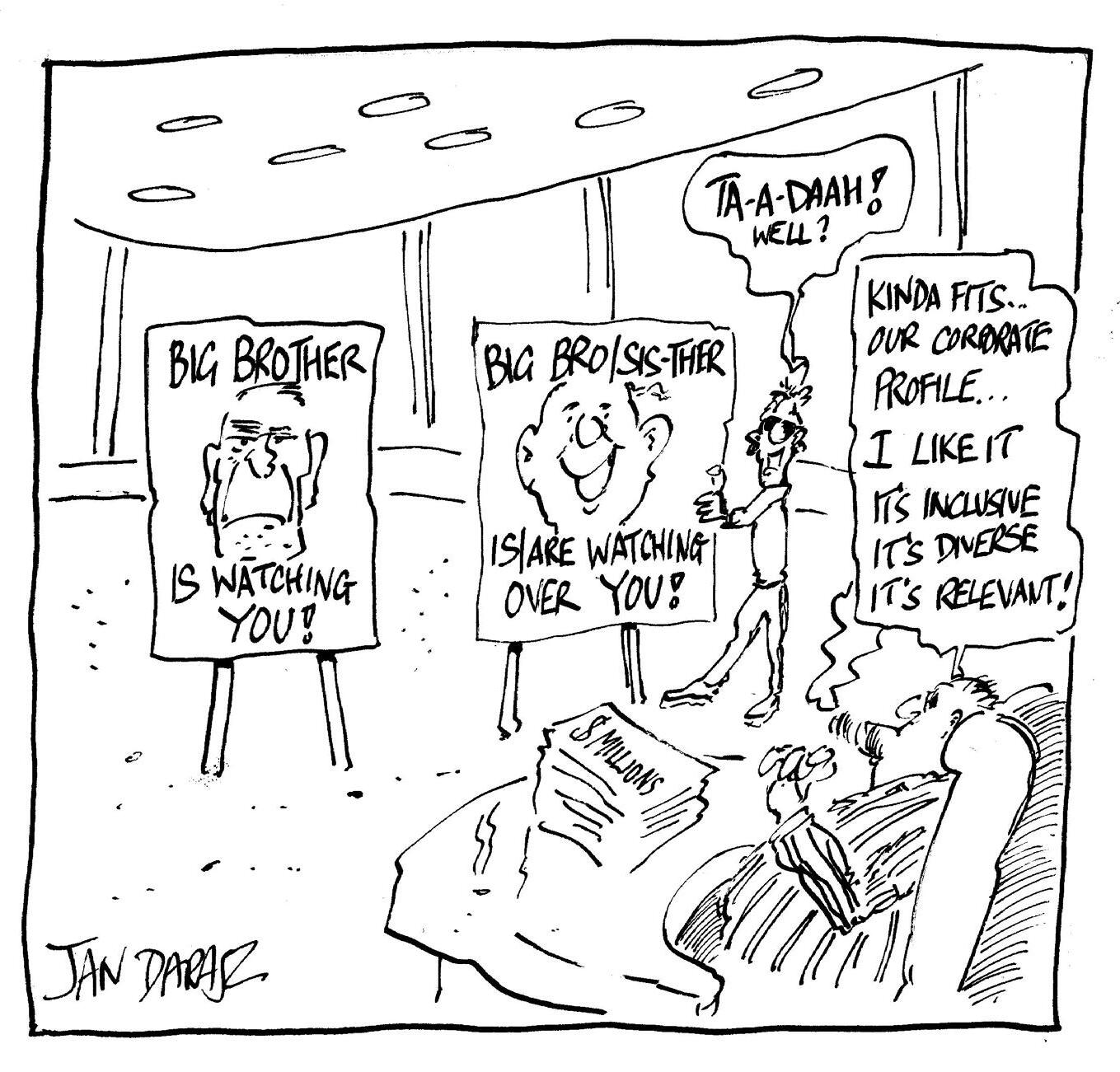
It’s worth focusing on three areas of this: misdirection; misleading jargon; and cliché, which renders words meaningless. Each is worth a complete essay on its own.
Perhaps the most striking example of misdirection — it’s one of the most obvious — is the concept of the Advanced Battery. (Note, capital ‘A’ and ‘B’!). It’s a particular favourite of the lead battery market.
For at least a generation, going back to the early 1990s, the idea has been bandied around that there were two types of battery.
There was the regular lead battery (most people used to think it was the car SLI battery, silly old them) and then there was the Advanced Battery.
But as soon as you dig deeper you find the Advanced Battery has been nothing more than a better version of the regular one. Yes, it may have a longer cycle life, be more robust, less gassing, water loss etc but has there been a huge step-change in the creation of this new Advanced Battery in the past 10 years?
Perhaps the biggest leap-forward in terms or what a regular lead battery can do, occurred well over a generation ago with the manufacture of VRLA/AGM batteries. (And, of course, the idea of ‘maintenance free’ batteries goes back to the 1930s and Otto Jache with gel batteries in the late 1950s.)
And jargon, why can it be misleading? From my earliest years as a financial journalist I realised that the primary use of jargon was not to work as a shorthand for those within a particular sector of business but one of exclusion, a blocking of an entry point for outsiders.
In the structured mortgage-backed markets of the early 2000s how many knew what the terms meant?
I remember seeing an investor offering that was an AAA-rated mortgage-backed security collateralized (wrapped) with other triple-A rated MBS that included triple-B and triple-C subordinated tranches. Pure misleading jargon. We knew what it meant and it was dodgy but investors didn’t and the banks wouldn’t tell.
The battery business pulls the wool over everyone’s eyes with clever little nonsenses such as storing “clean electricity”. So, in particular what is a “green electron”? Aren’t all electrons created equal? In scientists’ minds, electrons are electrons — they do whizzy things in extraordinary orbital shells around atoms — but green? When did they join any environmental movement?
Or storing clean electricity? One only has to think of the millions of petrochemical dollars spent to ship, build and install a large wind turbine and accompanying BESS to know that it’s probably on balance ‘green’ only in being better than a coal burning power station.
So green? Perhaps greener is a better term.
One can think of several battery firms, most recently that of Alsym Energy, which talk the green talk but won’t even reveal what their battery chemisty is, except it’s green. Very green. And non-flammable too. (Of course.)
And then there’s cliché. There’s masses here to say but probably the most overworked word in the battery storage business — as with other industry sectors too — is “innovation”.
This isn’t to criticise the fine work that many fine battery institutions — both lead and lithium. It’s simply to say that the battery business has now over-used the word to the point it’s close to redundancy. Innovative used to mean something, now we can’t be too sure.
Mike Halls, Editor-in-ChiefThe North American advanced battery landscape would be very different without the technical achievements and later advocacy of one lithium giant who realised its importance and campaigned for its future.
History made bold: a key figure in the US lithium space is gone
It is with sadness that Energy Storage Journal and sister magazine Batteries International, have to announce the death of lithium battery giant Ralph Brodd, who died in February aged 95.
Jim Greenberger, NAATBatt executive director and its joint co-founder with Ralph, described him as “one of the most consequential figures in the history of advanced battery technology in the US.”
Ralph’s most enduring impact on US industry grew out of his article Factors Affecting U.S. Production Decisions: Why Are There No Volume Lithium-Ion Battery Manufacturers in the United States? published in December 2004.
In that article, Ralph was the first to sound the alarm about the loss of lithium ion battery manufacturing capability in the US and the long-term consequences of that loss.
His influence has been extensive.
Greenberger first met Ralph in 2007. It was Ralph who convinced him to found NAATBatt, the US and international advocate and trade body for advanced battery research and development, to address the looming crisis of lithium battery technology in the US.
That effort in turn caught the attention of a first-term senator from Illinois named Barack Obama. The rest is history.

“Ralph was one of the most consequential figures in the history of advanced battery technology in the US”
“Now Ralph belongs to that history he created. He had more impact on it than many realize,” says Greenberger.
Over the past few years, federal and state governments have made unprecedented investments in EVs and supply chain projects to try to help US manufacturers and workers regain the lead in lithium ion battery manufacturing, Greenberger said.
The revised Section 30D tax credit will inject about $7.5 billion of investment into US-made EVs. The Advanced Manufacturing Production Credit should generate tax credits of about $30.6 billion to US manufacturers through 2031. An additional $13.8 billion of subsidies has been awarded by states and localities to at least 51 EV and lithium ion battery plants.
“Every single one of those investments can trace its origin to Ralph Brodd and his forward-thinking article,” says Greenberger.
The early years
Ralph James Brodd was born in Moline, Illinois on September 8, 1928, his parents were of farming stock originally and his father had been a fighter pilot in the first world war. His mother was a teacher, a profession he spoke about with respect all his life and something that was deeply important as an academic. A chemistry set given to him, aged seven, for Christmas led to a love of science (“going boom was my favourite” he later described mixing zinc with acid and lighting the gases). “By the time I’d got to junior high school I’d decided to be a chemist,” he later recalled.
He obtained a BA in chemistry from Augustana College, a private Lutheran college in Rock Island, Illinois, in 1950, the year he married Dorothy who was to be his partner for the rest of his life. This was followed by an MA in physical chemistry from the University of Texas and his PhD there two years later.
His connections with the Electrochemical Society (ECS) run deep. He was invited to join in 1954 as a young researcher pursuing a PhD at the University of Texas. Little did he know on his first visit to an ECS meeting in Cincinnati that this was a start of a lifetime relationship with the society or that he would one day become its president
A lovely anecdote is told in a later interview for the ECS archives.
It was 1954 and Ralph and his wife, Dorothy, had been expecting their second child. As full-time students, the couple worried about finding the money to pay the hospital bills.
The morning Dorothy was set to come home from the hospital, after delivering the couple’s second child, Ralph was deeply worried about where they would find the money to cover the costs, especially as healthcare in the US was very expensive.
Ralph braced himself for the worst but before heading to the hospital, but to his surprise, he checked his mailbox and discovered a letter from ECS.
In this he learned he had won the 1954 Corrosion Division Essay Contest. The letter came complete with a prize cheque that would be the answer Ralph and Dorothy were looking for.
The essay paid the hospital bill. “That saved us!” Ralph said years later.
That moment also spurred what would become Ralph’s lifetime dedication to the ECS. He went on to be elected ECS vice president in 1978, later claiming the title of president in 1981. He was named an honorary member of the society in 1987 and served as an editor of the Journal of The Electrochemical Society
In terms of work, fresh from obtaining his PhD in 1955 the young Dr Brodd joined what was then called the National Bureau of Standards. Here he worked specifically on standard cells, kinetics of battery-related reactions, and the internal impedance of batteries.
He later used to say that his understanding of impedance had been both the discovery of “one of the most powerful tools [in battery analysis] but also offering all sorts of very interesting things.” He worked at the standards bureau for six years.
Meanwhile he was also pursuing an academic career. He taught physical chemistry in the US Department of Agriculture Graduate School from 1956 to 1961, and lectured in elec-
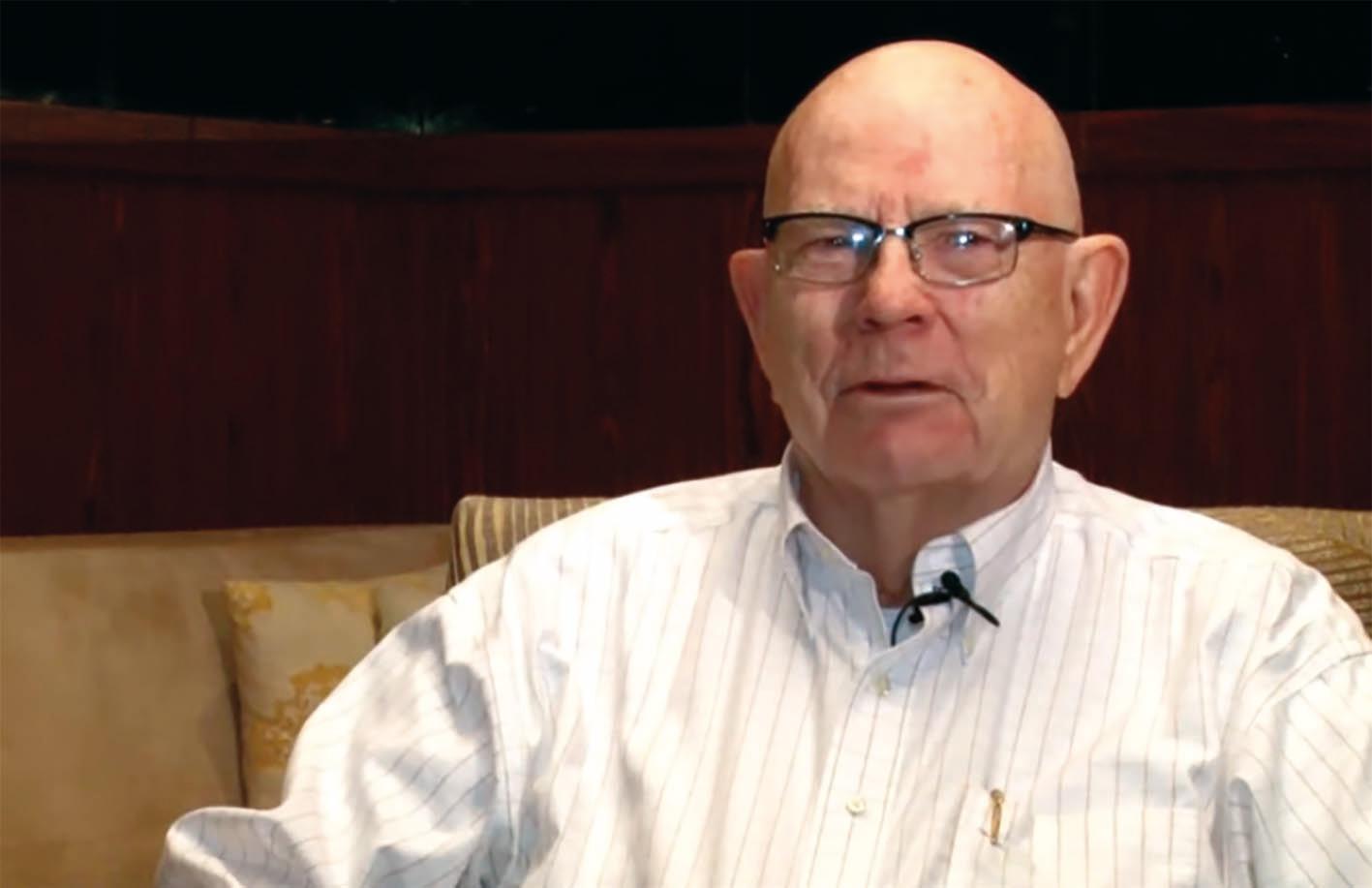
A young chemist discovers hydrogen: “…you’d drop a piece of zinc into a flask of hydrochloric or sulfuric and then put a match to it. I used to like it go BOOM! ... of course, mum wasn’t too happy with that.”
trochemistry at Georgetown University (1961) and American University (1958).
In 1961, Ralph joined LTV Research Center as a senior scientist and was appointed head of the energy sources section in 1962, which included fuel cell and plasma physics. During this time the fuel cells he had been helping develop were contenders for the first Apollo lunar landing series.
The Union Carbide years
His next move in 1963 was to the Battery Products Technology Center of Union Carbide Corporation in Parma, Ohio. He became group leader in 1965 and technical manager in 1966.
It was at Union Carbide he first encountered lithium batteries. He and a Japanese colleague were so excited about the possibilities of lithium manganese dioxide as a primary battery that they set up the International Battery Material Association and organized a conference where 200 people from Japan and elsewhere attended.
However, much to his disappointment Union Carbide wasn’t much interested saying that they reckoned it would take at least five to 10 years for lithium batteries to be commercially attractive.
Ralph recalls that indeed when some of the first lithium cells were
released, they first found a market for fishing floats in Japan. “Alkaline batteries were too heavy but a lithium battery was so light it could be used as a light for those wanting to fish at night. But we all could see it would soon outgrow the early limitations.
“There’s not much point in making a battery if you can’t sell it,” he said in an interview in 2015.
In 1978, he joined ESB which became INCO ElectroEnergy as director of technology.
He hit the ground running at INCO — in the next four years he established a Technology Surveillance group at the research center, this led him to having oversight and policy responsibility for the five INCO ElectroEnergy R&D laboratories. This was a huge remit as he had to cover many product areas ranging from primary and secondary batteries to uninterruptible power supplies and small electric motors.
It was after this he set up his own consultancy called Broddarp — a vehicle that he was to re-establish many years a later on his retirement when he reached the age of 70.
Consultancy clients led to other work, sometimes in new areas of energy storage.
He became project manager to the Amoco Research centre where he was responsible for rechargeable lithium sulfur dioxide battery project from 1984 to 1986.
It was here he developed a sophisticated business plan and commercialization strategy that included market research — something that was starting to become popular at that time.
He next moved to Gould Inc where he would spend the next six years helping establish and manage its lithium Powerdex battery venture based on flat lithium battery technology. He established production, sales and marketing, and the RD&E functions for the venture. He developed new primary Li-MnO2 production technology and expanded the product line in response to market opportunities.
Two new solid electrolyte batteries were developed: one an ultra-thin 0.5 mm thick cell for specialty and smart card applications as well as a small hermetic cell capable of withstanding SMT processing temperatures (+200°C).
Valence and byond
With retirement starting to loom he joined Valence Technology in 1992 as staff consultant/marketing director and later as vice president of marketing. Valence Technology, was a venture group developing a unique Li-Ion battery system for rechargeable batteries for portable consumer.
He also continued to pursue his academic and teaching work. In 1990 he became adjunct professor in chemistry at Michigan Technology University a position he would only step down from in 2014 (then aged 84).
Ralph worked in many areas of electrochemical power sources: primary and rechargeable batteries, including porous electrodes, exploratory new concepts, separator, lithium batteries, fuel cells, oxygen electrodes, and zinc air batteries, and fundamental electrode properties.
He held offices in Washington Capital and Cleveland sections of the ECS. In 1971, he received the Heise Award from the Cleveland section. He was general chairman of the MnO2 Symposium sponsored by the International Common Sample Office in 1975 and was chairman of the council of sections, the battery division, and honors and awards committee.
Ralph served on the education and contributing membership committees, and was chairman of the 75th year anniversary celebration ad hoc committee.
Ralph also served the society as representative to the Intersociety Energy Commerce and Engineering Conference and a battery division editor.
He was national secretary for the International Society of Electrochemistry (ISE) and chair of the 1979 Gordon Conference in Electrochemistry and secretary of the National Advisory ad hoc Battery Committee to EDRA. He was a member of ISE, ACS, AAAS, the Chemical Society (London), American Institute of Chemists, Sigma Xi, and the New York Academy of Science.
Ralph published more than 110 articles and was awarded five patents and his papers waswidely published. But that barely scratches the surface,” says Jim Greenberger. “Yet he was also one of the kindest, most decent and most humble men you could ever hope to meet.”
A work-leisure balance
A friend wrote about his time at the ECS and after that: “He loved to travel, enjoy fine dining and sipping good wine. He especially loved it when his wife would accompany him on his business and leisure travels, allowing them to see amazing sights in many countries.
“He had a true love for work, travel, and providing for his family. He was a gentle and humble man.”
Bob Galyen, who took over as CTO for NAATBatt, told Energy Storage Journal. ”He was a wonderful person to know professionally, and a very influential person to those who knew him. A humble giant of the industry from the era of time which many younger generations don’t know about.
“His gentle, yet intellectual approach, utilizing a great work ethic, was to be admired by all.”
Greenberger said: “Our sincere condolences to Dorothy and to the rest of the Brodd family. Ralph will be sorely missed.”
Kentucky governor Steve Beshear said, when appointing Ralph to head up the Kentucky-Argonne National Battery Manufacturing Research and Development Center: “Ralph Brodd literally has written the book on advanced battery technologies, and I am excited by his willingness to help us develop a renowned battery manufacturing research and development center here in the Commonwealth,” Looking back on his life it is strange that he is less well known than he deserves given his vital role in waking the US up to the challenges of the lithium battery revolution. Ralph will be missed by many, many more — knowingly or unknowingly — who have
benefited from his teaching, wisdom, humility and diligent intellectual integrity.
Ralph is survived by his wife of 73 years Dorothy (née Siegle). He was the father of Wayne, Lynn Faenza (Joe), and Bill; grandfather of Matthew Brodd, Stephanie Woodman, Stacy Rainwater (Chris), Angela Myford (Erik), David Faenza (Jocelyn), Alora Brodd, and Kendall Mareovich (Wes). He was also the great grandfather of 11.
SOUNDING THE ALARM
Ralph’s report Factors Affecting U.S. Production Decisions: Why are There No Volume LithiumIon Battery Manufacturers in the United States? — drew the following conclusions.
• Short termism. US battery companies opted out of volume manufacturing of Li-ion batteries, because of a low return on investment compared with their existing business. There was also significant time and investment required from conception to commercialization.
• US needed to think local Labor costs were not a major issue impeding large-volume production of the cells in the US. The Asian strategy of providing facilities and loans to establish manufacturing locally and create jobs was more important.
• Geographical link between manufacturing and technology Technological development tends to follow manufacturing to East Asia, as a natural consequence of developing manufacturing expertise. He said battery production will slowly shift to China, Korea, and Southeast Asia.
• Niche markets available Opportunities still exist for US companies to enter niche markets, such medical, military, or space applications. Mechanisms for cooperation between government, academia and industry need to be made so that advanced materials technologies have the resources and direction to succeed.
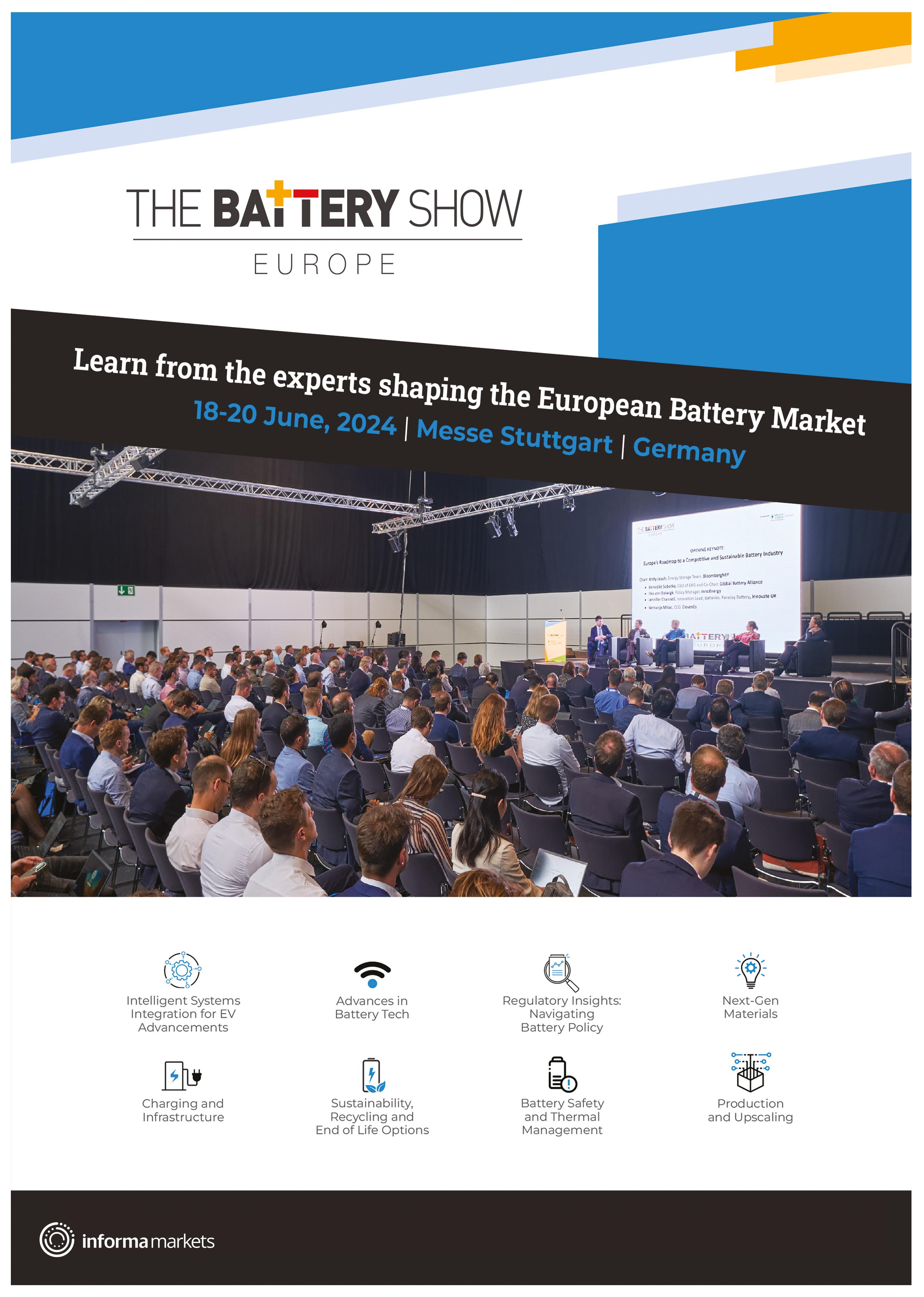
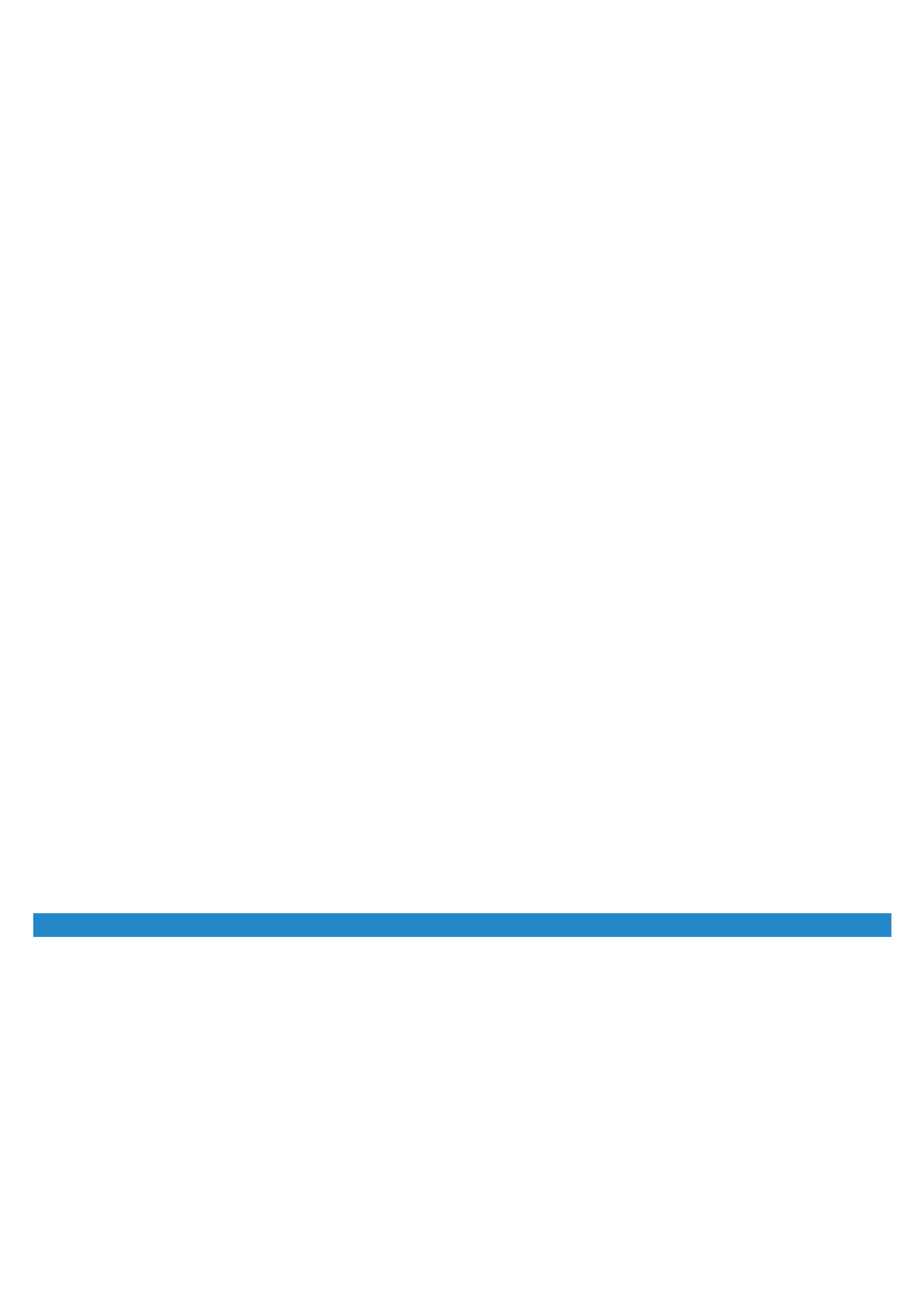
Arvers succeeds Narishkin as new Bitrode chief executive
Pierre-Jean Arvers has succeeded Cyril Narishkin as CEO of US-based energy storage and battery testing equipment company Bitrode — but no offiicial explanation surrounds the reason for the move.
The Schuler Group, which acquired Bitrode and the Sovema Group in 2022, confirmed Arvers’ appointment to Energy Storage Journal, but declined to say when he took up the post or comment on the reason for Narishkin’s departure.
Narishkin has yet to respond to questions but in a LinkedIn post said he was “looking for a new leadership role”.
He said he was proud of what Bitrode accomplished during his five years at the helm, “especially the launch of a new machine that has won contracts with major EV OEMs”.
Narishkin is the fourth CEO to stand down from their position at Bitrode in the past 12 years.
At the time of Bitrode’s acquisition by Schuler, Narishkin said the takeover would help the firm “accelerate new product offerings and help Bitrode reach its technological potential”.
Schuler, which is part of the international technology group Andritz, said Arvers has more than 20
years of international experience including chemistry and chemical engineering.
“The plan is to propel Bitrode to new operational heights through Arvers’ astute customer-centric approach to executive leadership in the EV, energy storage, and battery testing industries,” it said.
According to Arvers’ LinkedIn profile, he was most recently general manager of speciality wires, cables and braided sleevings group Omerin USA.
He is also a former president of NAATBatt International and president of Digatron Power Electronics USA.
Slabe takes over as Ecobat CEO, president
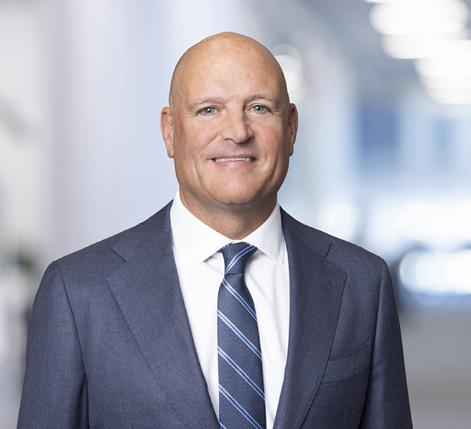
Ecobat said on January 29 Thomas Slabe had been appointed as the company’s third CEO and president in five years with immediate effect.
Slabe, who will also sit on the board, succeeds Marcus Randolph.
Randolph became president and CEO in March 2022 — following Jimmy Herring’s sudden departure — and he will continue to sit on the board of the lead and lithium recycler as chairman.
Slabe is a former CEO of castings company Neenah Enterprises and a corporate president of Contech Engineered Solutions’ building
materials division — both in the US.
Energy Storage Journal reported on January 25 that Ecobat had commissioned its first lithium recycling plant in the US.
Ecobat’s lithium sales VP Elliott Ethridge said despite the company’s long history in lead recycling, it made sense to go into lithium: “We see lithium coming on to augment a lot of spaces that lead doesn’t serve.”
GM appoints Kelty as VP of batteries
Kurt Kelty has been appointed VP of batteries for General Motors, the auto giant announced on February 8.
In the newly created post, Kelty, a former Tesla executive, will take charge of GM’s battery cell strategy — including overseeing the use of raw materials, research, developing and investing in new technology, commercialization of cells and packs and end of life opportunities.
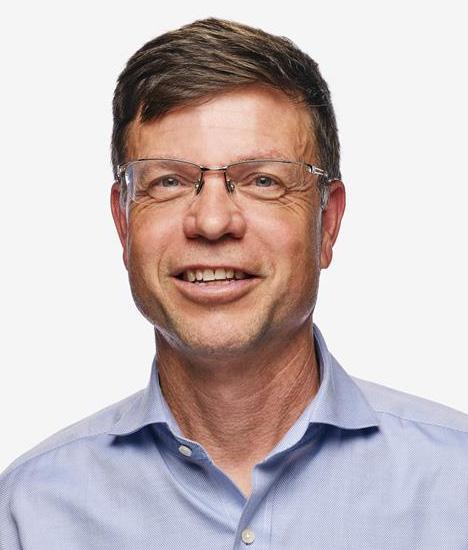
KMost recently, Kelty was a VP at silicon anode material company Sila with responsibility for
Janssen steps up as global CEO of Nyrstar
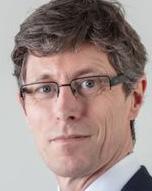
Guido Janssen has been appointed global CEO of the Nyrstar Group effective February 2.
Janssen was previously co-CEO of the group, with operational responsibility for European and US activities, including operating the German lead production plant Stolberg — acquired from Ecobat in 2022.
Dale Webb, who had been co-CEO alongside Janssen since December 2022, has resigned for personal reasons.
However, Nyrstar said Webb would continue to support Janssen and colleagues until the end of March.
sales, business development, battery cell manufacturing partnerships and battery engineering.
Before Sila, Kelty led the Tesla battery development team for 11 years, where he was responsible for technical exchanges and commercial negotiations with battery cell suppliers and early-stage battery cell developers.
He began his work in lithium ion batteries in 1993, working for Panasonic.
Australian operational and functional leaders will report to Janssen while a review of reporting structures is completed, Nyrstar said.
Nyrstar, which is a subsidiary of Trafigura, the mining giant, is a multi-metals mining and smelting company that is a market leader in the production of zinc and lead metal.
Last September, Nyrstar Australia said it was considering options to expand its battery recycling operations backed by South Australia’s state government.
Morrow appoints Boudgoust as CCO, Jon Fold von Bülow becomes chief science officer
Morrow Batteries said on January 23 it had appointed Christin-Marie Boudgoust as CCO, while co-founder Jon Fold von Bülow has been promoted to chief science officer.
Boudgoust’s first day at the company was January 15 while Fold von Bülow’s promotion was effective on January 1.
Boudgoust’s responsibilities will include securing off-take agreements, building partnerships and driving technical sales, Morrow said.
Fold von Bülow is now leading Morrow’s R&D department with responsibilities including further developing the company’s LFP cell technology and transferring product designs and specifications to the manufacturing team.
He will work alongside co-founder Rahul Fotedar who continues as CTO.
The appointments follow that of CFO Steffen Føreid who joined Morrow last October, after the company said it was raising up to €70 million ($74

million) in new capital as it moves toward commercial production.
Morrow’s first giga-
watt-hour LNMO battery cells factory in Arendal in the south of Norway is set to start up this year.
Sunlight appoints Mantzoufas as chief funding officer for giga project
The Sunlight Group has appointed Nikos Mantzoufas as chief funding and institutional affairs officer for construction of a lithium ion cells gigafactory project in Greece.
The lead and lithium battery manufacturer said on January 17 Mantzoufas would also be responsible for the integration and monitoring of the group’s projects funded through development initiatives and investment schemes in Europe and America.
Mantzoufas was most recently governor of Greece’s EU-backed Recovery and Resilience Facility. He is also a former board member of the European Investment Bank.
Sunlight said in September 2021 it would invest
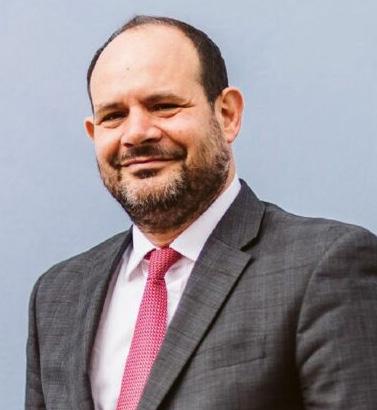
€50 million ($54 million) to expand its lead and lithium manufacturing unit in Xanthi, north-eastern Greece.
Of that amount, €20 million would be spent toward an annual production capacity of 1.7GWh
of lithium batteries, on top of €105 million already invested at Xanthi on R&D and a prototype lithium ion cell production line.
Last August, Sunlight announced the completion of an R&D program into developing ‘smarter
and healthier’ lithium ion batteries.
In November, Sunlight confirmed it was spinning off its lead recycling operations into a new subsidiary to guarantee raw material supplies for lead battery production.
Webster joins board of About:Energy
Tech investment expert
Laura Webster has joined the board of London-based battery software developer About:Energy, the company announced earlier this year.
Webster, a partner at investment firm Coltrane Asset Management, has a successful track record in navigating technology market volatility, About:Energy said.
She also specializes in angel investing and made what About:Energy said was a notable investment in its June 2023 seed round, valued at £1.5 million.
“This investment underscores her forward-thinking approach and her ability to identify and support promising ventures in the energy sector,” the firm said.
Founded in 2021, About:Energy is a spinout from Imperial College London and the University of Birmingham.
The company’s software platform, ‘The Voltt’, can be
used by customers developing their own battery programmes to cut development costs and use the modelling software to reduce time to market for their own products.
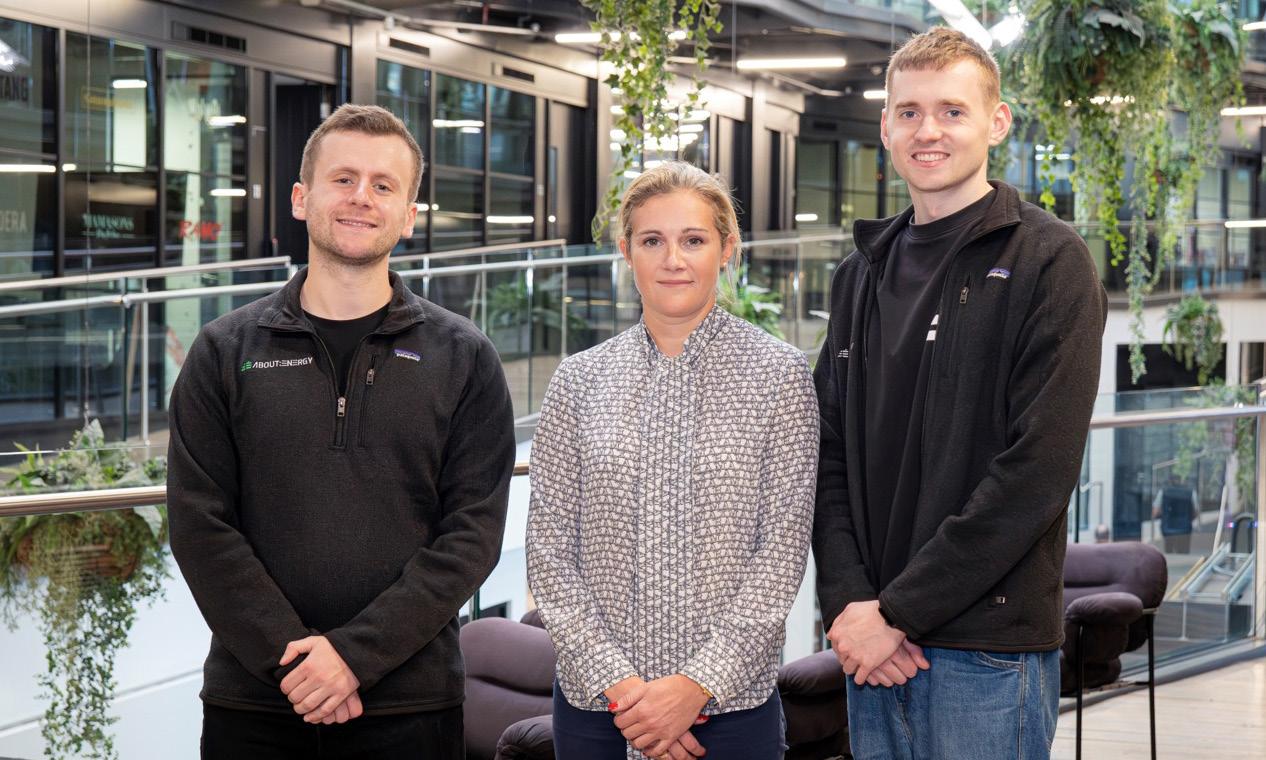
Cockerill quits Cornish Lithium to go for gold
Ian Cockerill has stepped down as independent non-executive chairman of UK exploration firm Cornish Lithium, following his appointment as CEO and executive director of gold mines multinational Endeavour Mining.
Cornish Lithium said on March 6 founder and CEO Jeremy Wrathall will also take on the role of chairman on an interim basis.
The process of finding a replacement independent non-executive chair will start soon.
Wrathall thanked Cockerill for his work with the company over the past two years saying the firm had made significant progress including securing an undisclosed landmark financing package.
Meanwhile former direc-
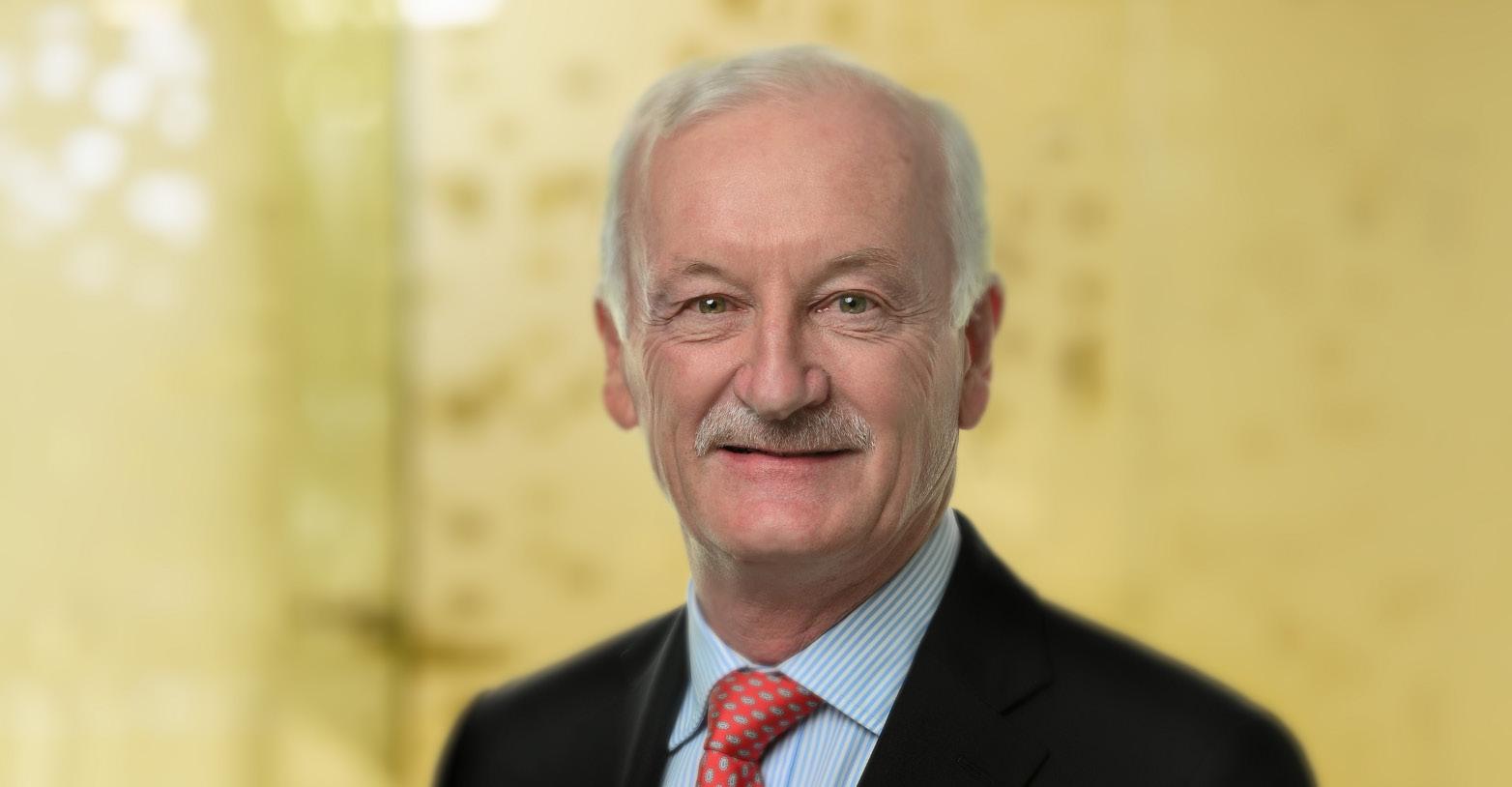
tor Keith Liddell has rejoined the board as a non-executive director.
Alongside his long association with Cornish Lithium, the company said Liddell brings a wealth of knowledge of mineral extraction techniques
and management of such projects worldwide.
In 2021, the company was granted permission to also go offshore in its search for lithium to supply the UK’s future EV battery market.
Last month, Cornish
Valente joins Nano One as CFO
Carlo Valente has joined Canada’s Nano One as CFO effective January 15, the company has announced. He succeeds Dan Martino, who will remain with the company as VP of finance.
Valente was most recently CFO of a private, international renewables company and has more than 26 years of experience supporting companies as they scale-up with capital raising, M&A transactions and strategic planning, Nano One said.
Nano One founder and CEO Dan Blondal said Martino had worked as CFO since January 2020 on a fractional basis through Donaldson Brohman Martin CPA — where he holds other CFO positions for publicly traded companies.
By staying on as VP of finance, Martino would ensure continuity and support in financial reporting and finance-related projects, Blondal said.
In September 2023, Sumitomo Metal Mining announced a C$16.9 million ($12.5 million) investment in Nano One as part of a new battery materials development partnership.
The firms said the equity investment boost was part of a collaboration that
would have a particular focus on LFP and NMC production.
On October 23, Nano One said a pre-feasibility study indicated the firm could realize an estimated 10-fold increase in production capacity at its lithium iron phosphate cells facility in Quebec.
Lithium announced details of a community engagement programme in Redruth, Cornwall (southwest England) about its plans for a geothermal project to extract lithium from mineral-rich groundwaters.
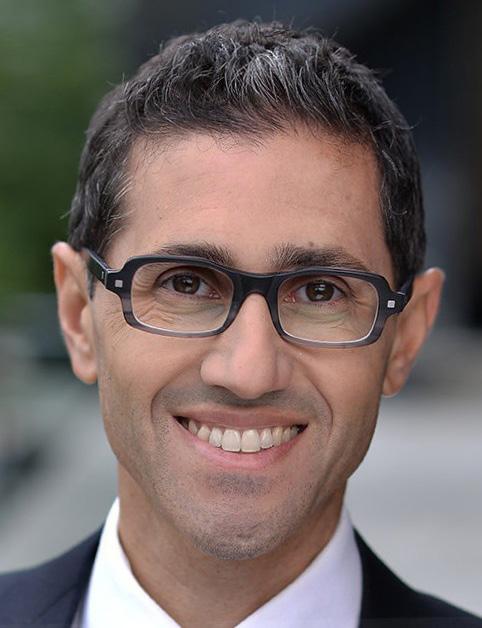
Hoppecke wins platinum medal from business sustainability ratings firm
European lead battery manufacturer Hoppecke said on January 10 it had received its first platinum medal from business sustainability ratings firm EcoVadis.
The accolade puts the company into the top 1% of all firms assessed by EcoVadis based on the organization’s reviews of business practices relating to the environment,
ethics, labor and human rights and sustainable procurement.
EcoVadis assesses more than 100,000 companies across 175 countries annually.
Medals are awarded based on a company’s performance compared with all rated companies in the EcoVadis database over the preceding 12 months.
Hoppecke sustainability officer Ludwig Merz said the battery maker had received several gold medals from EcoVadis in recent years.
Last year, Hoppecke’s new batteries production plant in Poland secured ISO 9001:2015 and ISO 14001:2015 certification for quality and environmental management.
EUROBAT has hit the campaign trail ahead of European elections in June that could supercharge the fortunes of the battery industry, or see political support wane if voters turn away from green energy.
EUROBAT EU elections manifesto launch — batteries on the ballot
Elections to the European Parliament will take place in June and could be pivotal in shaping the future of battery technologies.
EUROBAT, the European association of automotive and industrial battery manufacturers, hit the campaign trail in Brussels on February 20 with the launch of its own manifesto — a five-year plan featuring policy proposals to help shape the post-election agenda in support of the industry.
The event was both imaginative and necessary, as could be testified by the 150 or so who attended.
Champagne and canapés were served up to welcome guests even before the event had begun inside the art deco Résidence Palace — originally the city’s first luxury apartment block that was designed in the 1920s for the city’s bourgeoisie and aristocracy.
One mischievous member of the throng mused on the parallels of an industry raising its glass to a sparkling future amid rising energy and manufacturing costs, just as legend says Nero fiddled away in opulent surroundings while a great fire engulfed Rome.
Today, Résidence Palace is home to the International Press Centre,
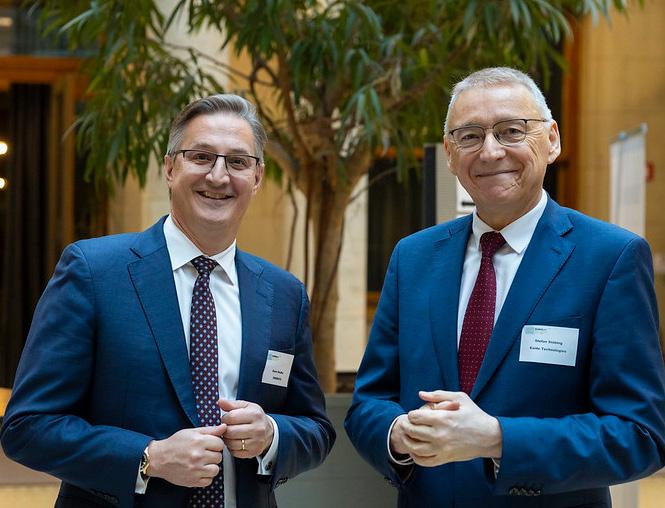
suitably located in close proximity to the headquarters of the European Commission.
The location was ideal for ensuring a blaze of publicity that could only serve to impress on the press and politicos the importance of the battery industry to Europe’s future.
Suitably fizzing with anticipation, delegates were ushered in to hear EUROBAT’s opening election pitch from association president Marc Zoellner who, as CEO of Hoppecke Batteries, knows the business inside and out.
He said all mainstream battery technologies, namely lead, lithium, nickel and sodium, were vital to underpin-

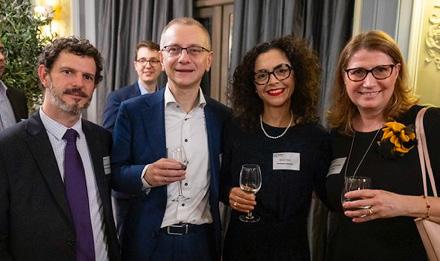

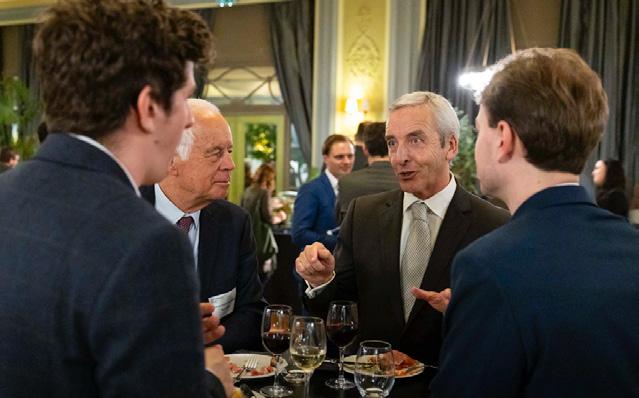
ning the EU’s Green Deal decarbonization and circularity goals.
The entire battery industry should be front and center of proposals to combat CO2 emissions and the clean energy transition.
Zoellner’s words were reassuring to those in the audience who recalled a time not so long ago when lead was viewed by some as the Cinderella of batteries. The technology that was required to do the heavy lifting in the shadows but not be allowed to share the spotlight with newcomers such as lithium.
There are those in the corridors of power in Brussels that still not dare give lead the credit it is due, but times are changing.
Keynote speaker, German Christian Democrat European Parliament member Peter Liese, issued an impassioned cry for all battery tech to be deployed as best suits requirements.
Liese also made clear he and other politicians welcomed the departure last year of former Green Deal supremo Frans Timmermans, who was widely regarded as a thorn in the side of the lead battery sector.Liese diplomatically described Timmermans’ time as former European Commission executive vice president as “problematic”. (See panel on following page.)
And in the spirit of transparency, Liese explained why he also had a personal interest in ensuring the success of batteries: he has a son working for Hoppecke.
The EUROBAT manifesto was billed as “key asks” or recommendations for those who will decide the direction of travel for the EU over the five years from June 2024 based on three pillars: innovation, a “global level playing field” and circularity.
One of the manifesto’s key recommendations is the appointment of an EU commissioner with specific responsibility for safeguarding the bloc’s battery materials supply chain.
Peter Javorčík, the Commission’s
NEWS FOCUS: EUROBAT THINKING
current director general for transport, energy, environment and education, rejected the idea of a dedicated commissioner for strategic autonomy, saying the task should be uppermost in the minds of all commissioners.
He was followed on to the stage by a panel including Inga Petersen from the Global Battery Alliance, William Roberts from Rho Motion, Céline Domecq from Platform for Electromobility and Christian Rosenkranz — VP for sustainability and corporate affairs EMEA at Clarios and chairman of the Consortium for Battery Innovation.
It was a pity Javorčík slipped out of the event and did not take part in the subsequent hour-long panel discussion, although such luminaries frequently depart quickly before they have to mingle with delegates’ questioning — more than could be said for the time it takes to get legislation on to the EU statute books.
In the event there was no time for any members of the audience to put a question to the panel, which was far from ideal. Nevertheless, the mini conference catalyzed many of the substantial issues that will arise on the election trail and that can impact the battery industry.
According to the European Council on Foreign Relations, the European Parliament elections will result in a major shift to the right, with populist radical right parties gaining votes and seats across the EU, and centre-left and green parties losing votes and seats.
In a policy brief published in January, the ECFR said a populist right coalition of Christian democrats, conservatives, and radical right MEPs could emerge with a majority for the first time.
This sharp right turn is likely to have significant consequences for European-level policies and the biggest post-election policy implications are likely to concern environmental policy.
In the current parliament, a left/ center-left coalition has tended to get its way on environmental policy issues, but many of these votes have been won by small margins. A significant shift to the right in the new parliament would mean that an anti-climate policy action coalition could dominate.
This would deeply undermine the EU’s Green Deal framework and the adoption and enforcement of common policies to meet the EU’s net zero targets.
Protests across Europe before and after the manifesto launch highlight the political volatility across the region.
Some of Europe’s major cities have been engulfed by protests from angry farmers and food producers who say climate policies, increasing costs and tiny margins are threatening their livelihoods.
At one point towards the end of February, acrid black smoke engulfed parts of Brussels as farmers burned tyres and used fossil-fuel guzzling trac-
tors to block the boulevards. So have the farmers planted the seeds of political change that indicate a move away from the EU’s cherished Green Deal policies? Europe is at a political crossroads and the fortunes of the battery manufacturing sector and associated supply chains, like it or not, are inextricably linked to the EU’s political fate.
THE ‘PROBLEMATIC’ TIMMERMANS YEARS
The lead battery industry can breathe a sigh of relief and help energize Europe’s clean energy transition now one of the industry’s bogeymen — former EU Green Deal supremo Frans Timmermans — is out of office, a senior MEP has said.
German Christian Democrat European Parliament member Peter Liese, speaking at the launch of EUROBAT’s manifesto in Brussels on February 20, said: “We should not go back to the Timmermans years.”
Liese diplomatically described Timmermans’ time as former European Commission executive vice president in charge of the Green Deal as “problematic”.
“Since Timmermans has left we’ve had a different focus,” he said.
In June 2020, when in charge of the Green Deal, Timmermans issued an implicit warning during a EUROBAT webinar that the future of the lead battery industry was limited.
“We have to assess which technologies have reached a maturity that will not allow more innovation, we shouldn’t be throwing money at those,” he said. “We look at things that have a future rather than things that have had a great past” — implying that the Commission was eager only to advance lithium batteries over lead ones.
“We are more reluctant [to invest] when a technology doesn’t seem to have much potential for development and has a huge negative impact on the environment … we’re technology agnostic but we’re not stupid.”
One industry commentator at the time said: “I was dumbstruck when he said this … phrases like a ‘technology’ ie a battery chemistry with no potential for development but a great past and having a huge negative impact on the environment and the like. There was no doubt

he was mentioning lead batteries — what else could he possibly have been talking about?”
Timmermans resigned his post last August to stand as a candidate in the Netherlands’ general election. He was replaced by Maroš Šefčovič. His apparent animosity to the lead battery sector was a major area of concern for lead battery manufacturers and an issue frequently highlighted by Energy Storage Journal
Timmermans also issued a preposterous soundbite just months after the Russian attack of Ukraine, saying Europe was on the cusp of achieving energy self-sufficiency, if it had not already done so.
However, industry observers point out that even today the EU has a long way to go — as evidenced by EUROBAT’s call for the appointment of an EU commissioner with specific responsibility for safeguarding the bloc’s battery materials supply chain.
Meanwhile, Liese used EUROBAT’s manifesto launch to also confirm a Energy Storage Journal article, published last November, that a decision on controversial proposals for lead metal to be added to an expanded European chemicals authorization register has been shelved until late this year at the earliest.
EV lithium battery recycling activities in Europe risk grinding to a halt within months, shaking investor confidence in the sector, if new waste classification rules come into force, Energy Storage Journal can reveal.
EV battery recycling chaos alert as EU waste rules loom
Proposed EU regulations designating lithium black mass as hazardous waste — which could limit its storage before processing to just six months — could be in force by the summer.
However, industry insiders warn the move, coupled with existing bottlenecks disrupting shipments of used lithium batteries for processing between EU member states, could be a hammer blow for Europe’s fledgling recycling sector — depriving battery manufacturers of domestic supplies of raw materials.
The warning comes just weeks after trade associations urged EU leaders to scrap “cumbersome, lengthy and costly” processes holding back lithium battery recycling services and hampering competition.
Julia Poliscanova, senior director of vehicles and e-mobility for clean transport campaign group Transport & Environment, confirmed to Energy Storage Journal early this year that the European Commission is planning to designate black mass as hazardous.
Regulations
Poliscanova said experts in the sector met to discuss the proposals last November and the Commission’s Joint Research Centre (JRC) is now compiling final recommendations.
“We expect the JRC’s report to come out in the first quarter of this year and to recommend designating black mass as hazardous,” Poliscanova said.
If the Commission accepts the recommendation, it has the power to immediately amend existing waste regulations.
Transport & Environment’s raw materials policy officer Franziska Grüning told Energy Storage Journal that the smooth functioning of inter-EU waste transportation is key to enhancing the recycling industry and ultimately advancing the EU’s circular economy plans.
He warned that the hazardous waste classification could hinder the efficient collection of batteries as companies
would be required to follow stricter requirements on declaration and notification.
Digital systems
However, he said the Commission could consider exemptions that would allow initial transports of lithium battery waste to be delivered to designated processing facilities.
Grüning said the Commission has already reviewed regulations on waste shipments and proposals on the table include using digital systems to keep track of such cargoes within the EU.
The European Battery Recycling Association (EBRA) says disruption in the materials supply chain is inevitable, “given the low number of existing battery recycling facilities across the EU, and the fact that there is often only one facility or sometimes no facility in a country”.
EBRA has called for battery manufacturing waste to be classified according to the battery’s chemistry.
As pressures on the sector starts to increase, German chemicals giant BASF and Stena Recycling have had to announce a new EV battery recycling partnership.
Prototype
Stena said it will collect, assess, and pre-treat end-of-life batteries and battery production scrap to produce black mass at its facility in Halmstad, Sweden.
BASF will further process and refine the black mass at its battery recycling prototype metal refinery in Schwarzheide.
Asked about potential disruptions to lithium recycling in Europe, Stena’s product area manager for batteries, Marcus Martinsson, told Energy Storage Journal: “From an industrial point of view, we do not wish to store black mass any longer than necessary, due to the general risk and raw material exposure.
“We therefore hope that a restriction in storage of black mass would be balanced with swift permit approval
processes to allow for efficient transport of material across borders in Europe.”
The president of BASF’s catalysts division, Daniel Schönfelder, who is also responsible for the company’s battery materials and battery recycling business, said: “We believe that black mass exports to non-OECD countries should be banned.”
‘Shut downs’
“However, this is not yet the case across all Europe and we support the EU’s action to establish a Europe-wide binding regulation.”
On black mass, Schönfelder said storage was needed “to a certain extent” to support reliable material flows for production and refining.
“If regulation is too strict this can pose challenges to the production and in a worst case can lead to production shut downs if allowed storage limits are reached.”
Ecobat’s VP of global sales Elliott Ethridge said in an article posted on the group’s website in January : “If you’re in the recycling market, you’re playing the long game. You can’t be short-term.”
Bottleneck
On challenges facing the sector in Europe, Ethridge warned: “If you can’t export the material, but you also don’t have the capacity to properly refine it, you create a bottleneck that you’ll have to deal with, and that might actually incentivize companies to reclassify the material and not report it correctly.”
According to a study published last month by Germany’s University of Münster, China will become self-sufficient in meeting its needs for key EV battery materials lithium, cobalt and nickel around 10 years before Europe and the US.
The study said China is expected to have the capacity to cater for its domestic demand for lithium from 2059 onwards — but this will not be the case in Europe and the US until after 2070.
Seven years after the launch of the European Battery Alliance, the EU battery industry is still short of cash and raw materials, while BESS and renewable power projects struggle to get on to the grid.
‘It’s make-or-break
time for Europe’s Green Deal’
In a dire assessment of Europe’s vulnerability in the highly competitive global battery manufacturing sector batteries supremo Maroš Šefčovič, the European Commission’s executive VP for the EU Green Deal, has said the bloc currently supplies only 1% of its own needs for key battery raw materials.
Šefčovič told a European Investment Bank (EIB) forum attended by policymakers, business leaders and academics in Luxembourg on February 8 the EU also needed to find at least €700 billion ($767 billion) in additional investment each year up to 2030 — a staggering €4.2 trillion — to achieve the objectives of the Green Deal and REPowerEU, which is the Commission initiative aimed at ending reliance on Russian fossil fuels before 2030 in response to the invasion of Ukraine.
Securing easy access to new, climate-related financing, is now among the “make-or-break” conditions for the Green Deal, according to Šefčovič.
He revealed that Europe’s “stagnated” power sector infrastructure is in urgent need of an overhaul, with thousands of connection requests including those for renewable energy generation and energy storage facilities being rejected because of insufficient grid capacity and other issues.
However, he said despite concerns about the region’s power infrastructure, he regarded the EU’s combined electricity grids as being the best worldwide — at least for now.
Šefčovič called for the EIB to establish a dedicated ‘sustainable critical raw materials task force’ focusing exclusively on financing projects securing reliable European supplies of key battery materials including lithium, cobalt and nickel.
The task force should be able to take higher risks than a normal bank, innovating new financing solutions to address market failures and acting as venture capital when necessary, he said.
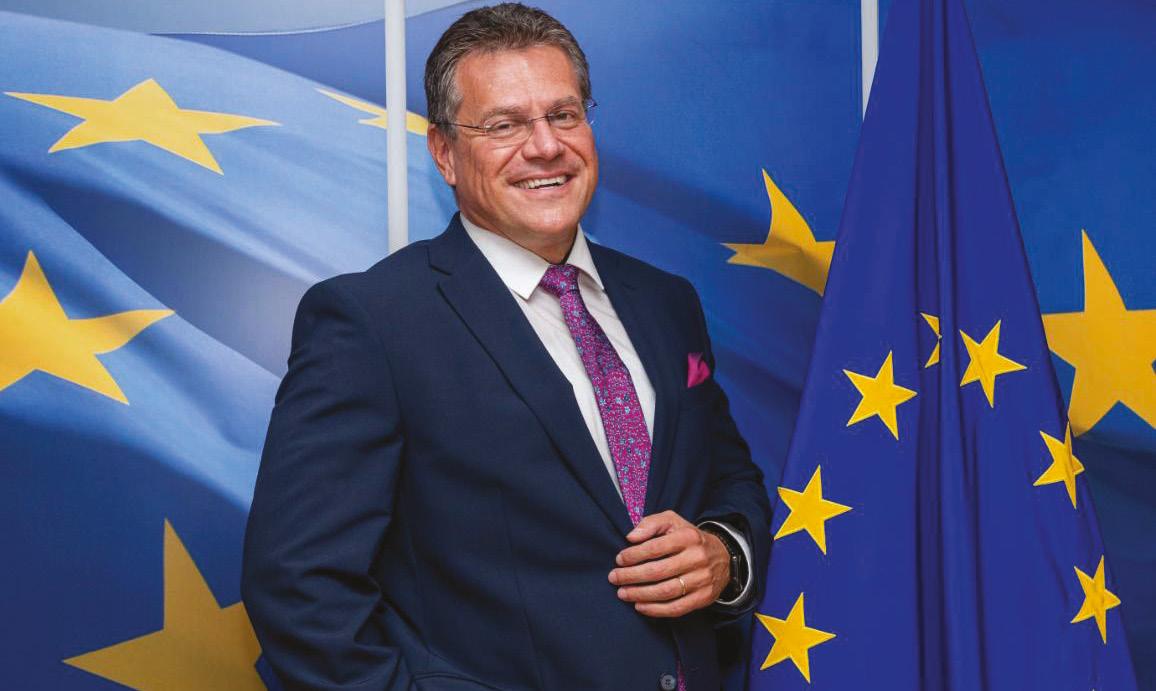
The task force could also lead the efforts of national funds dedicated to raw minerals, such as those in Germany (worth €1 billion) and France (€2 billion), and a newlylaunched €500 million fund launched by EU sustainable energy investor EIT InnoEnergy and Demeter, an actor in venture capital and private equity.
Taking more direction action to secure critical raw materials would be in line with a call by EUROBAT, the association of European automotive and industrial battery manufacturers, for the appointment of an EU ‘commissioner for strategic autonomy’ with specific responsibility for safeguarding the bloc’s battery materials supply chain. (See our report elsewhere in this issue.)
The Commissioner’s remarks are his starkest to date on the challenges facing Europe’s energy sector but he has, so far, declined an invitation from Energy Storage Journal sent via his team to comment in depth.
The grid, the grid
However, this magazine has unearthed a briefing document prepared by the European Commission that analyzes
these problems in greater detail.
The briefing, appropriately titled Grids, the missing link — an EU Action Plan for Grids, was released a few weeks before last Christmas.
According to the briefing, the electricity network that zigzags the 27 member states of the EU internal market spans more than 11 million kilometres.
The briefing acknowledges that, in many EU countries, renewable generation projects face long waiting times to get connection rights.
Waiting time for permits for grid reinforcements are between four to 10 years, and eight to 10 years for high voltages.
Connection backlogs in the distribution grid are escalating rapidly, with several thousand new requests per month for a single medium-size distribution system operator, according to the briefing.
And in the face of uncertainty over connection timelines, permitting procedures and costs, projects are being stalled and even scrapped.
Comparing Europe’s challenges with other countries, the briefing said the US estimates the need to expand that nation’s electricity transmission
NEWS FOCUS: EUROPES MISSING 99%
systems by 60% by 2030.
Meanwhile, China’s State Grid Corporation has announced investment of just over Rmb 1 billion ($142 million) in power grids in 2022-23.
The briefing references International Energy Agency data, released in October 2023, that says more than 80 million km of grids are needed worldwide by 2040 — the equivalent of the entire existing global grid.
The agency estimated around 1,500GW of advanced renewable projects are waiting in grid connection queues globally.
However, while accepting the need for more investment in grids, the European Commission’s briefing points out that grid operators cannot do this in isolation.
Grid operators, both at the transmission and distribution levels, are faced with an unprecedented increase in the volume of capital expenditure, the briefing said.
For example, the size and rapid extension of a company’s investment programme may affect its credit rating, with negative consequences in trying to secure finance.
That is why a new range of tailormade financing products and instruments to support grid investments is needed.
Fears over cybersecurity are another factor in the need to nurture ‘homegrown’ European solutions to expand and modernize grid infrastructure.
Relying on third country suppliers to meet critical energy infrastructure needs, in particular nations “not aligned with EU values and positions”, can create risks in terms of cybersecurity and the potential weaponization of such supply chain dependencies, the briefing warned.
And it is not only battery makers who have concerns about securing raw material supplies. The briefing said EU grid operators also face challenges in getting sufficient access to raw materials such as copper or steel.
Given the ambitious deployment objectives, boosting domestic production capacities and diversification of supplies of raw materials and key components will have to be pursued domestically and via EU agreements or partnerships with reliable third countries.
“As insufficient investment in distribution grids and storage is already hampering citizens and businesses, a new approach to identify and support local grid projects appears necessary to prevent gaps in the future.”
PUTTING IT ALL TOGETHER
According to Eurelectric’s Power Barometer 2023 study, Europe has suffered a stagnating rate of electrification of around 20% for the past 15 years.
The association, which represents the common interests of the electricity industry at a European level, said decarbonizing Europe, extricating the bloc from dependency on Russian fossil-fuel supplies and ensuring long-term fossil-fuel-free energy sovereignty, requires a tripling in electrification by 2050.
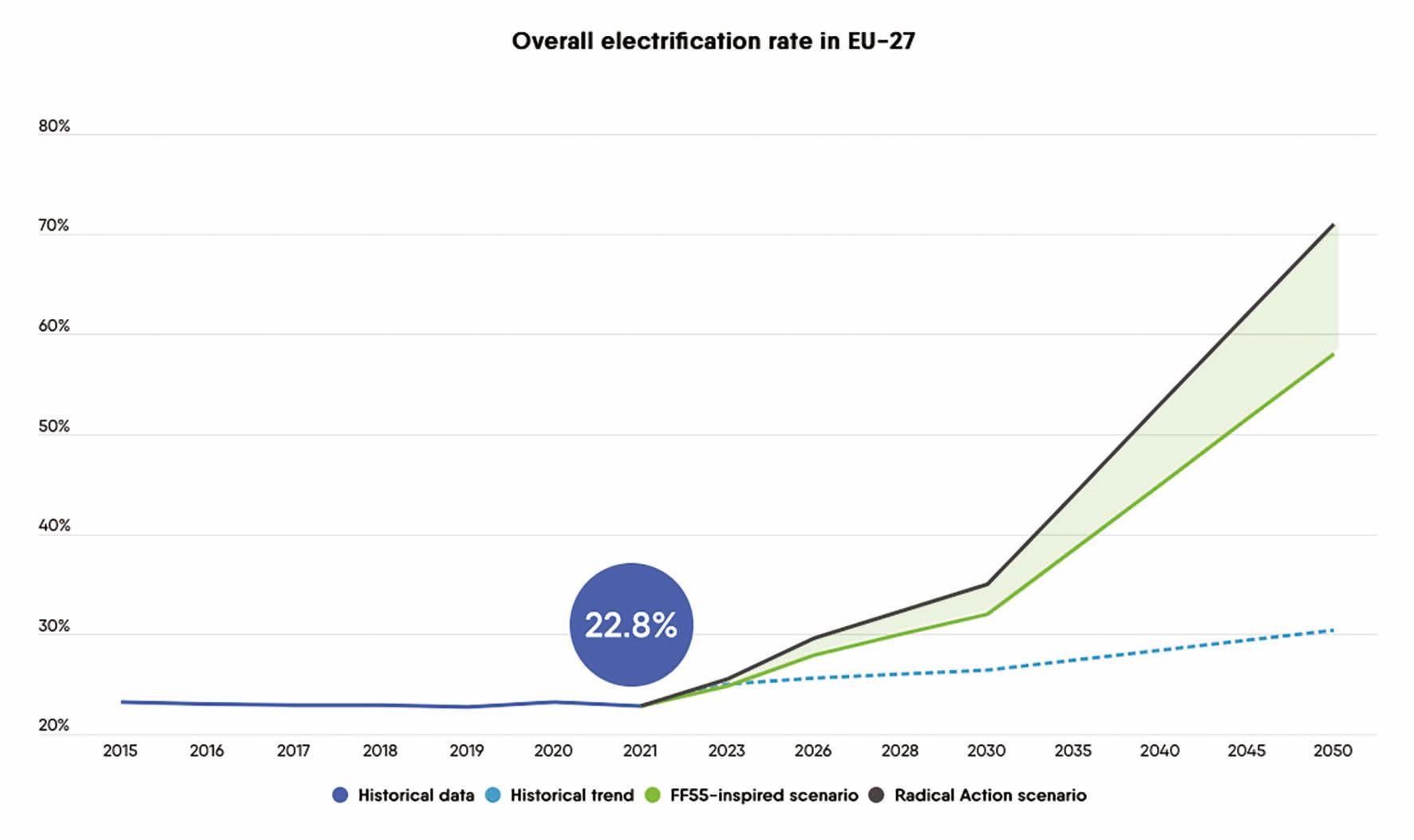
(In the graphic, FF55 refers to the EU’s target of reducing net greenhouse gas emissions by at least 55% by 2030.) Graphic: Eurelectric
BANKING ON BATTERIES, BUT RUNNING ON EMPTY
The European Investment Bank, which is owned by EU member states, has yet to respond officially to Šefčovič’s proposals and would not comment on his specific remarks.
Sources told Energy Storage Journal on March 5 that bank chiefs had a “positive” opinion on the critical raw materials task force proposal.
However, in an on-the-record comment, an EIB official said coordination efforts at the EU level are important to avoid fragmentation in the support of the development of infrastructure needed for the green transition.
“We are working closely with the European Commission and industry to bridge gaps by providing financing at advantageous rates,” the official said.
Research by Energy Storage Journal shows that, over the past three years, the EIB financed electricity networks in the EU at an average rate of nearly €4 billion annually.
Last summer alone, the EIB announced €45 billion in additional financing, on top of the bank’s
regular lending sums, to support the REPowerEU plan and European manufacturing in state-of-the-art ‘strategic net-zero technologies’. Eligible projects also include investments in the extraction, processing and recycling of EU-designated strategic critical raw materials.
A battery industry insider who has a particular focus on the EU market told Energy Storage Journal on condition of anonymity: “The eye-watering sums that the EIB has already poured in to try and shore up Europe’s entire energy sector show that investment alone is clearly not the answer to the challenges faced.
“Seven years after the European Battery Alliance was launched, the EU has precious little to show for the billions of euros invested to date.
“It also cannot be right that the few gigafactories Europe has to date cannot rely on secure supplies of raw materials. Meanwhile, BESS and renewable energy projects risk being scrapped because of delays in securing connections to grids.”
Ford’s EV investment slow-down, $5bn loss, unsettles battery investors
Ford looks set to continue a freeze on selected investments in its EV business after revealing the unit’s $4.7 billion loss outstripped overall net income of $4.3 billion in 2023, which one industry commentator said equates to nearly $65,000 for each EV it sold.
CFO John Lawler said on February 6 that mainstream customer take-up of EVs was happening at a slower rate than the industry expected — and he reiterated last year’s shock announcement that the auto giant had “deferred
certain capital investments” in EVs until they’re justified by demand.
However, Lawler insisted EVs are here to stay and said it is developing next-generation EVs that will “surprise customers” and be profitable within a year once launched.
Industry observers have told Energy Storage Journal the move will unsettle investors in the lithium battery supply chain — and the slowdown in sales of EVs will likely lead analysts to revise forecasts for the fortunes of the lead battery sector.
Meanwhile industry
commentator Robert Bryce — who said last November that Ford was facing up to the “truth bomb” that motorists don’t want to pay a premium for EVs — said on February 7 the firm’s losses are only part of a train wreck in the EV market.
“Perhaps the most remarkable thing about the staggering losses at Ford and the other automakers is that the carmakers didn’t understand the limited appeal of EVs,” Bryce said.
According to Bryce, who hosts the Power Hungry Podcast, EVs are a niche
market, primarily defined by class and ideology, with some 57% of EV owners in the US earning more than $100,000 annually, 75% are male and 87% are white.
Last October, Tesla CEO Elon Musk said he was concerned about the impact of high interest rates on car buyers and said the firm was hesitating on its plans for a factory in Mexico as it assesses the economic outlook.
“You know the EV business is in trouble when Musk makes such comments,” Bryce said.
GCube study charts BESS ‘failures’, warns insurers need confidence
More than half of BESS failures happen within the first two years of operation, according to analysis published by renewable energy projects insurance underwriter GCube yesterday.
GCube said its report — Batteries Not Excluded: Getting the Insurance Market on board with BESS — is based on analysis of 12 years of public BESS
failure data. However, the company said underwriters are increasingly supporting the battery storage sector, but need confidence about the management of thermal runaway risks, public safety liabilities and transportation “challenges”.
GCube itself expects BESS assets to represent 30% of its underwritten renewables portfolio by the end of this year.
Key findings include that, overall, the market now has around 10 failures reported on average each year — a 10=fold increase compared to 2016.
While this escalation suggests an expanding battery market, it also highlights the absence of well-established safety and reliability procedures.
GCube says while the statistics broadly align with
industry growth, there is concern that failure trends may persist as the market deploys larger 100MW+ utility-scale assets, leading to increased financial losses for owners, developers, and insurers.
“This concern arises from a recurring pattern in rapidly expanding market segments, where new technologies often face challenges related to quality control — a dynamic recently observed in the offshore wind market,” the report said.
US-based speciality chemicals producer Albemarle said on February 20 it had agreed a battery-grade lithium hydroxide supply deal with BMW.
Under the multi-year agreement, which starts next year, the companies will also partner on technology to develop next-generation lithium ion batteries for EVs.
Albemarle said its agreement is the second with BMW, but the first to include a shared interest in research opportunities to accelerate lithium
battery innovations. But the agreement comes against a backdrop of a fall in global interest in EVs, with motorists reluctant to switch amid concerns over the vehicles’ high price tag and availability of charging stations.
The sudden and sustained drop in the price of lithium to what one analyst called “totally unsustainable levels” is set to reverse, however. The issue is when.
Last October, Tesla CEO Elon Musk said he was concerned about the impact of high interest rates on car buyers and said
the firm was hesitating on its plans for a factory in Mexico as it assesses the economic outlook.
Meanwhile industry commentator Robert Bryce — who said last November that Ford was facing up to the “truth bomb” that motorists don’t want to pay a premium for EVs — has said the firm’s losses are only part of a train wreck in the EV market.
“Perhaps the most remarkable thing is that the carmakers didn’t understand the limited appeal of EVs,” said Bryce.
GCube urges developers and owners to take measures including ensuring sufficient spacing between battery modules and careful selection of the most appropriate battery tech for projects.
Fraser McLachlan, GCube founder and CEO, said: “We don’t want to repeat the mistakes of the past of allowing growth in deployment and technological scale to take priority over quality control, and the large-scale losses and market destabilization that are possible to result from that.”
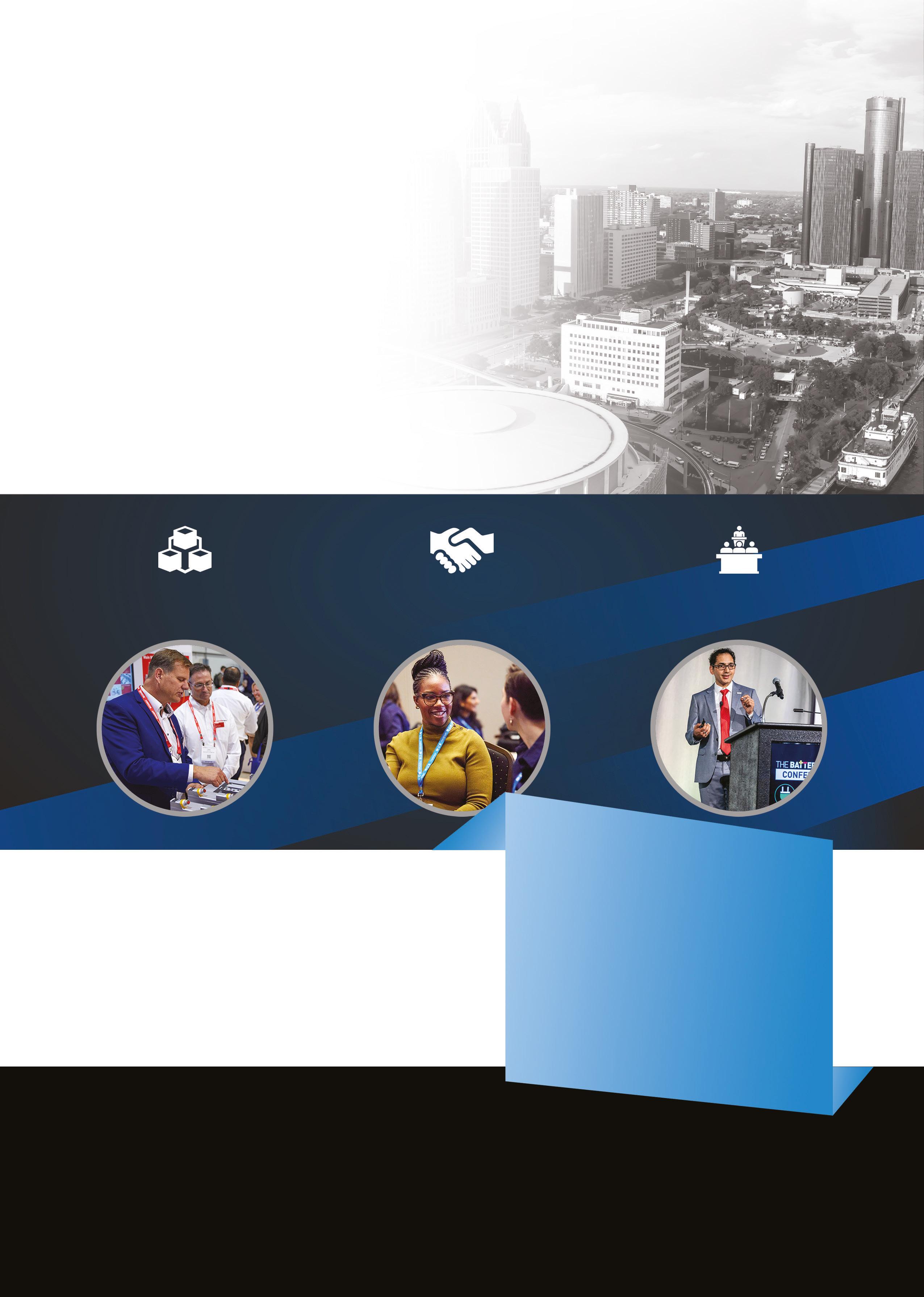
Duke Energy to ‘phase out CATL from supply chain’ after security row
Duke Energy is scrapping a BESS supplied with batteries from Contemporary Amperex Technology (CATL) amid a national security row — and has pledged to “phasing out” the Chinese battery giant’s tech from its entire supply chain, according to US lawmakers.
The move comes after Duke shut down the BESS at US military base Camp Lejeune last December, amid allegations the CATL battery tech posed a poten-
tial threat to national security.
Senior members of the US House Select Committee on the Chinese Communist Party, led by chairman Mike Gallagher, said in a statement published on February 9 Duke had since committed to decommission the CATL battery storage system at Camp Lejeune and will instead install an American alternative.
“Additionally, in our most recent meeting with company leadership, Duke
committed to entirely phasing out CATL products from its supply chain.
“We are grateful to Duke for taking this first step to protect US grid security from Chinese Communist Party-controlled companies operating in Americans’ backyard.”
And in what might be regarded as an ominous warning to other companies, the statement added: “Others that continue to work with CATL, and other companies under the
control of the CCP, should take note.”
Duke and CATL has not responded to a request for comment.
In a statement issued through Reuters last December, CATL said accusations about its batteries posing a potential security threat were false and misleading and that its products had passed rigorous safety and security reviews including those by US authorities and businesses.
NatPower plans to create new generation of UK BESS ‘gigaparks’ with £10bn renewables
NatPower is to develop 60GWh of battery storage in the UK as part of a £10 billion ($13 billion) package of investment in renewables, the group announced on March 7.
The UK arm of the European energy group said it will apply for planning permission for the first of three battery gigaparks this year and 10 more in 2025.
NatPower has earmarked £600 million to develop new substations — strengthening the UK’s ability to feed more renew-
able power into the grid.
The group will also announce new solar and wind projects for the UK this year.
Stefano Sommadossi, CEO of NatPower UK, said investing in the grid and working with grid operators was key to solving bottlenecks slowing the shift to clean energy.
“By investing in substations and focusing on energy storage first, we will enable the next phase of the energy transition and bring down the cost of
energy for consumers.”
Meanwhile, the founder director of UK clean energy developer Kona Energy, Andy Willis, warned on March 12 the UK must do more to tackle grid connection delays.
Commenting on UK government plans to build new gas-fired power stations, Willis said: “Arguments for/against gas plants aside, on current grid connection processes any new gas stations would be at the back of the queue and therefore would not
Exide Technologies acquires Li battery tech firm BE-Power
European lead acid battery manufacturer Exide Technologies said on March 11 it had acquired German lithium battery tech firm BE-Power for an undisclosed sum.
BE-Power, which develops and assembles battery and power modules, was founded in 2004 by Volker Klein.
Klein has more than 30 years of experience in lithium ion technology.
BE-Power and its proprietary battery management system and software is now part of Exide’s energy solutions division.
Exide president and CEO Stefan Stübing said the acquisition would propel the company to new heights in providing sustainable and cuttingedge energy storage solutions.
Energy Storage Journal reported recently on
Exide’s plans to achieve a binding target of a 30% reduction in emissions by 2030.
The company, which already operates three solar power generating facilities across Spain and Portugal and has three battery recycling plants, said it eventually hoped to go beyond 20% by embracing other “environmentally focused initiatives”.
be connecting until at least 2037.”
Willis said any projects that can get online fast to increase energy security should be given priority.
Wuxi Lead, Tiamat plan
€500m French sodium ion gigafactory
Proposals for a
5GWh sodium ion battery manufacturing plant in France have been unveiled by Wuxi Lead Intelligent Equipment and Tiamat.
The companies said on February 1 they had formed an alliance for the project in Amiens, backed by investment in excess of €500 million ($538 million), with construction starting for an initial 0.7GWh line in the first quarter of this year.
Batteries will initially start rolling out of the plant in the fourth quarter of 2025, with completion of the entire 5GWh facility scheduled for 2030.
BESS investments in Europe set to surge, says Aurora Energy
Europe is on the brink of a significant surge in gridscale battery energy storage with a sevenfold increase in capacity projected by 2030, according to analysis published on February 13 by Aurora Energy Research.
Great Britain, Italy and the wholesale electricity market for Ireland and Northern Ireland have emerged as the top three sectors for BESS investments in the region.
But Aurora, an energy
markets analytics company founded by University of Oxford professors and economists, says Spain and Greece are showing promising signs of “compelling investment opportunities”.
The third edition of Aurora’s European Battery Markets Attractiveness Report, which examined 24 European countries, says installed grid-scale BESS capacity across the region was 7.1GW in the third
quarter of 2023. That is projected to rise to 51GW by 2030 and 98GW by 2050.
These new capacity additions represent a cumulative investment opportunity of €78 billion ($85 billion) up to 2050, Aurora says.
To date, dedicated auctions for standalone or co-located battery storage in Europe have subsidized at least 1.8GW of batteries in Germany, Greece, and
Telangana boost for Amara Raja giga corridor investment project
Leaders of India’s Telangana state government pledged further backing for national battery giant Amara Raja’s ‘giga corridor’ investment plans, in talks held on January 3.
Amara Raja broke ground in May 2023 for its 16GWh lithium battery cells factory and research complex in Telangana.
The lead and lithium battery manufacturer — renamed Amara Raja Energy & Mobility last September — said the project would feature advanced laboratories and testing infrastructure for material research, prototyp-
ing, product life cycle analysis and proof of concept demonstration.
Amara Raja chairman and MD Jayadev Galla said in the January 3 talks with Telangana leaders that the state has the potential to become “a major force in the growing EV and new energy sector”.
Galla thanked ministers for the government’s support for the giga corridor project as part of an expansion of Amara Raja’s operations in India.
Telangana chief minister Revanth Reddy indicated the state was ready to step up support for attract-
ing increased investment for the project. He said promoting clean energy and battery storage technologies was a priority for the state.
Telangana has already agreed a memorandum of understanding with Amara Raja Advanced Cell Technologies (ARACT), a wholly owned subsidiary of the battery group, which has been working on Li ion cell chemistries specifically suited for Indian subcontinent conditions.
ARACT already supplies lithium battery packs and chargers to some two and three-wheel vehicle OEMs.
Spain.
Upcoming auctions could procure over 15GW across Europe by 2030, notably 9GW of procurement from Italy’s new storage capacity procurement mechanism, MACSE, which aims to cover both capital and operational costs.
AAC secures €4.4 billion debt for new gigafactories
The Automotive Cells Company has secured €4.4 billion ($4.8 billion) debt to support construction of three European gigafactories, in addition to the lithium ion facility it opened in France last year.
ACC said on February 12 the finance boost would accelerate its expansion of battery cells and modules production for EVs.
The new plants will be in France, Germany and Italy and ACC, which is backed by Stellantis, MercedesBenz and TotalEnergies-owned Saft, said it would also step up R&D investment.
The debt is underwritten by a consortium of commercial banks including BNP Paribas, Deutsche Bank and ING.
Albania’s Vega Solar Energy has unveiled plans to build a lithium ion battery manufacturing plant in the country in partnership with India’s Sainik Industries. The companies confirmed on February 27 they had signed a memorandum of understanding for a joint venture project — including developing energy storage systems and inverters.
The agreement was signed in New Delhi on February 23, although details of the proposed partnership, including investment cost and construction timetable for the manufacturing plant, were not disclosed.
Sainik, established in 2005, produces a range of batteries and modules in India under its Getsun Power brand for the BESS, telecoms and solar markets.
Albania’s government said in March 2023 it was ushering in changes to laws to make it easier for renewable energy projects to be sited on agricultural land and other sites.
Prime minister Edi Rama said the government was receiving increasing requests from domestic and foreign investors to support development of renewable energy projects including wind, solar and hydro.
ACC chief executive Yann Vincent said the firm’s customers must be able to rely on robust and reliable European players capable of delivering high volumes of competitive batteries with a low CO2 footprint.
He said more production sites could happen in the future. “We will determine our needs as and when we conclude additional contracts. We are resolutely looking to the future, with a view to achieving our objective of growing our production capacities.”.
EnerSys picks South Carolina for $500m lithium cells giga-project
EnerSys said on February 14 it had chosen South Carolina as the site to build its planned $500 million lithium ion battery cell gigafactory.
The lead and lithium battery major said it is seeking an incentives package worth around $200 million to support the project — plus potential federal funding including tax benefits under the Inflation Reduction Act.
EnerSys said construction is to start early in 2025 and operations to be online in late 2027.
The 500,000ft2 facility,
with a production capacity of 4GWh annually, will be built on a business park in Greenville. It will produce various form factors of lithium ion cells for commercial, industrial and defence applications.
EnerSys president and CEO David Shaffer said the new plant would benefit a range of customers, including those with specific manufacturing requirements for US-sourced batteries.
The announcement of the project, which is subject to regulatory and other approvals, follows the sign-
ing of a non-binding memorandum of understanding last June with French lithium battery cells developer, Verkor, to consider developing the US gigafactory.
Last October, the European Commission cleared a €659 million ($703 million) French state aid grant for Verkor to support R&D in France into battery cells and modules for the large-scale deployment of EVs.
Verkor laid the foundation stone for its 16GWh per annum lithium gigafactory in Dunkirk in the north of France last November.
Agratas names site for UK gigafactory
Agratas, the Tata Group’s international battery business, confirmed in March the UK location where it will invest more than £4 billion ($5 billion) to build an initial 40GWh battery cell factory.
The Gravity Smart Campus near Bridgwater, Somerset, will host the plant that will eventually create up to 4,000 jobs with thousands more in the supply chain, Agratas said.
Tata chairman Natara-
jan Chandrasekaran said last July the gigafactory would start producing cells in 2026 following a “rapid ramp-up phase” — supplying batteries for EVs and battery storage systems in the UK and mainland Europe.
The UK government, which is reportedly providing hundreds of millions of pounds to support the project, has previously said details will be disclosed at a later date.
According to the UK government, the plant’s initial output will provide nearly half of the battery production that the Faraday Institution estimates the UK will need by 2030.
Tata has said the new plant will deploy innovative technologies and resource efficient processes such as battery recycling to recover and reuse all the original raw materials “to deliver a truly circular economy ecosystem”.
Batteries part of $135bn clean energy investment in 2023, says report
Clean energy tech investment including equipment factories and battery metals production hit a new record of $135 billion in 2023 — up from just $46 billion in 2020, according to new analysis released on January 30.
Clean energy supply chains are split into clean-tech factories making equipment, and battery metal mines and refineries in Bloomberg NEF’s Energy Transition Investment Trends 2024 report.
Combined spending across those areas rose to $135 billion in 2023 and is set to surge, according to the report, with investment plans showing a 66% increase from 2023 to 2024, driven by a bulging pipeline of battery gigafactories.
Meanwhile, overall global investment in the low-carbon energy transition increased 17% in 2023, reaching a record $1.8 trillion.
The report said there was strong growth in emerging areas such as hydrogen (with investment tripling year on year), carbon capture and storage (near-doubling) and energy storage — which increased by 76% to $36 billion.
Celgard said on January 29 it has secured a deal to supply separators required by nickel-zinc batteries developer AEsir.
Under the terms of the agreement, Celgard will supply all battery separators for AEsir’s existing requirements and for its planned US Gigafactory.
The companies will also collaborate on research projects to further develop next-generation nickel-zinc, zinc-air, lithium zinc and sodium-zinc batteries used primarily in aviation, data-
centers, telecoms, energy infrastructure and EV charging applications.
Celgard — a subsidiary of Polypore International, an Asahi Kasei company — says the agreement also paves the way for it to offer separator products to future Ni-Zn and Li-Zn AEsir licensees or joint ventures.
Additionally, Asahi Kasei could support the Ni-Zn supply chain and AEsir will evaluate component supply opportunities for items such as plastic battery packs
and thermal retardant materials.
Celgard’s dry-process coated and uncoated microporous membranes are used as separators in various lithium ion batteries used primarily in electric drive vehicles, energy storage systems and other applications. In February 2023, Celgard said it would step up its partnership with lithium ion tech company C4V as part of a new strategic alliance to develop high-voltage batteries for gigafactories.
BNEF’s head of trade and supply chains Antoine Vagneur-Jones said abundant supply chain investment should continue to reduce equipment prices across most sectors, which is good for the energy transition.
But the “ensuing oversupply heralds an era of squeezed margins for solar and battery manufacturers”.
BNEF deputy CEO Albert Cheung said despite the 17% growth in energy transition investment, the amount needs to grow more than 170% if the world is to get on track for net zero in the coming years.
EnerSys unveils TPPL tech boost for batteries
EnerSys has unveiled details of advances in its thin plate pure lead tech that the company said now offers a major performance boost for batteries.
The optional ‘accelerated throughput package’ (ATP) for select batteries in its NexSys TPPL line was announced on March 5.
EnerSys said the ATP upgrade, available in the EMEA, South America and Asia-Pacific regions, can provide a significant increase in daily energy throughput compared to standard NexSys TPPL batteries — making them ideal for harder-running, higher-reaching class 1 and 2 equipment applications previously
requiring battery changing.
According to the battery maker, the extra energy capability from ATP is achieved through improved thermal management that enables faster, more efficient energy uptake during brief charging periods such as operator breaks, shift changes or any period of non-use.
Senior director of marketing for motive power global, Harold Vanasse, said: “Switching from battery changing to opportunity charging significantly alters battery selection.”
With changing, the battery is removed from equipment and recharged separately, over an extended period of time. This means the crit-
ical factor is overall energy storage capacity — determining how long equipment can work before needing a battery change.
Opportunity charging equipment during breaks and other brief intervals adds energy intake efficiency as a consideration to maintain charge levels, Vanasse said.
EnerSys will be showcasing NexSys TPPL with the new ATP upgrade at upcoming international trade shows.
Energy Storage Journal reported last September that EnerSys had secured a new $91.8 million multi-year contract to supply its TPPL batteries to the US Navy as main storage batteries on all four classes of nuclear
ESS starts up long-duration battery
ESS said on January 15 it is using its iron-based flow battery technology to demonstrate how long-duration energy storage could help the US military reduce its consumption of diesel for generators.
An ESS Energy Warehouse system has been coupled with a tactical microgrid at the US Army Corps of Engineers’ Engineer Research and Development Center in Missouri. The unit replaces a prototype ESS system, installed at the center in 2016.
ESS said the new system aims to specifically demonstrate the role iron flow battery tech can play in reducing diesel consumption — by as much as 40% — to power generators at remote contingency bases, where the military is needed to respond to conflict and emergency situations.
According to ESS, most contingency bases are powered by diesel generators, but variations in output hampers efficiency.
Maintaining generator fuel supplies also increase risks
to personnel and ramps up emissions.
The tactical microgrid is additionally being used to test the potential of utilizing solar power and battery storage.
Tom Decker, the center’s operational energy program manager, said: “Flexible, long-duration energy storage, like the ESS system, reduces total runtime on generators while increasing efficiency and allowing generators to last longer at forward operating bases.”
Gravitricity plans Finnish mine gravity storage prototype
Scotland-based gravity storage system start-up
Gravitricity said on February 6 it plans to deploy its technology in a prototype project at a disused mine shaft in Finland.
The company has signed an agreement with Callio Pyhajarvi to turn the 530 metre deep shaft at the Pyhäsalmi Mine into a 2MW demonstration project that will connect to the grid and provide balancing services.
Gravitricity says its GraviStore system is a gravity-harnessing method of generating electricity by dropping weights in underground areas such as abandoned mines. The company is also working on below-surface green hydrogen storage.
Executive chairman Martin Wright said: “This project will demonstrate at full scale how our technology can offer reliable long-life energy storage
submarines. The company recently said it had chosen South Carolina to build its $500 million lithium ion battery cell gigafactory.
Construction is to start early in 2025 and operations to be online in late 2027.
BMZ adds sodium ion to battery tech range
Germany-based lithium battery systems group
BMZ announced on March 11 it is expanding into the sodium ion tech sector.
The company said series production of its new ‘NaTE’ battery cell product range, which will include cylindrical and prismatic cell formats, is to start in mid-2025.
The first prototypes are already being tested with cell formats 21700 and 46130 and additional cell formats will follow.
BMZ subsidiary TerraE will develop and distribute the NaTE series cells.
BMZ group CEO and founder Sven Bauer said sodium ion technology offered the company and its customers rapidly growing market potential, but said BMZ would not abandon lithium.
that can capture and store energy during periods of low demand and release it rapidly when required.”
The project announcement comes after Gravitricity secured nearly £829,000 ($1 million) from a crowdfunding raise last May.
A company spokesperson told Energy Storage Journal then that it had exceeded its initial goal of £550,000, with 1,085 investors participating.
“Sodium ion technology is the perfect solution for applications where energy density is not paramount. This includes industrial and home storage systems or industrial trucks, such as forklifts,” he said.
In January BMZ entered the energy storage sector with the launch of its first ESS system — lithium-chemistry based Power Bloxx — for the commercial market.
In February, Shanghai-based Wuxi Lead Intelligent Equipment and France’s Tiamat unveiled proposals for a 5GWh sodium ion battery manufacturing plant in France.
Stryten ‘Quick Ship’ programs keep supply chain moving
Stryten Energy has launched two ‘Quick Ship’ programs designed to underpin a rapid supply chain for forklift lead batteries and accessories.
Stryten executive VP Dan Autey told Energy Storage Journal on January 30 the move allows its customers to reduce downtime and keep motive power fleets moving.
The standard Quick Ship lets customers order forklift batteries and accessories to be shipped within three business days.
Now a new ‘Quick Ship 24’ scheme offers shipping within 24 hours on select batteries and accessories.
Stryten says orders placed before midnight Eastern Time (ET) on one day will be processed the following day and scheduled by 10am ET.
A range of Stryten’s M-Series flat-plate batteries and tubular batteries are available through Quick Ship. Both programs are dependent on motive power batteries and accessories being available to be shipped. Select M-Series chargers are available for the standard Quick Ship, but are not included in Quick Ship 24.
Accessories featured in the programs include kits to ensure watering levels are properly maintained and electrolyte level sensors.
Dalton Electric announces quality improvements for customers
Dalton Electric Heating, the international split sheath cartridge heater supplier, announced mid-March a series of advances to products and strategies aimed
at helping battery manufacturers.
Key to the changes was the hire of George Lantz, vice president of operations & strategy, to oversee Dalton’s transformation, says Chris Stevens, president of Dalton Electric Heating.
“We know unplanned downtime eats into our customers’ throughput,” said Lantz. “So we focused on ways to further minimize their disruptions.” To that end, Lantz has so far led the completion and implementation of improvements in the company’s organization structure, product quality and manufacturing processes. Operational efficiency is what WattFlex long life, even heat and superior heat transfer heaters do.
Lantz also led the redesign of Dalton’s organizational structure to improve oversight and quality at each stage of production. “We’ve integrated greater accountability into our process by creating a leadership team to oversee critical areas in our process,” said Lantz. “
New investments to improve coil construction and assembly are two examples of Dalton’s move to “engineer-in quality”. “These measures ensure coil consistency and verify reliability before they are used in our customers’ equipment,” said Lantz.
Plus Power starts up 185MW Hawaiian BESS
Plus Power said on January 11 it had started operating the 185MW/565MWh Kapolei BESS on the Hawaiian island of Oahu.
The facility comprises 158 Tesla Megapack 2XL lithium iron phosphate batteries.
Plus Power executive
chairman Brandon Keefe said the BESS’s grid balancing capabilities would enable the increased use of renewable power generation on Oahu’s isolated grid and spur a move away from relying on coal and oil.
Keefe said the facility’s virtual inertia systems replicate the powersmoothing function of a spinning turbine, while black start capabilities will support grid recovery in the event of a blackout
The BESS will also act as an electrical ‘shock absorber’ — often provided by combustionpowered peaker plants — “responding in 250 milliseconds rather than the several minutes it takes combustion plants to come online”.
Keefe claimed the company is the first to use batteries “to provide such a diverse range of gridforming services at this scale”.
Hawaiian Electric senior VP and COO, Jim Alberts, said to date the utility had to regularly curtail or turn off large volumes of existing utility-scale solar and wind to keep the electric system in balance — because solar power fed into the system from homes and businesses has become so abundant, Alberts said.
Epsilon finalizes takeover of German LFP cathode tech center
Epsilon Advanced Materials said on February 2 it had finalized the acquisition of a lithium ion phosphate cathode active material technology center from Johnson Matthey in Germany.
Mumbai-based Epsilon said the center in Moosburg gives it the potential to help reduce the battery market’s reliance on China.
The center is equipped to produce LFP and
lithium manganese iron phosphate cathodes in small laboratory-scale batches.
Additionally, the center has a pilot customer qualification plant (CQP) designed to validate new materials that uses what Epsilon says is a hydrothermal process to provide a cleaner metal processing solution.
The acquisition follows Epsilon’s announcement of a $1.1 billion investment to set up an anode battery materials manufacturing facility in India — where it is scheduled to break ground this year for a large-scale CQP to be built in 2025.
The plant will scale up to 100,000 tonnes by 2030.
Epsilon said it also plans to build a $650 million graphite anode material manufacturing facility in the US, as well as investing €600 million to develop a graphite processing plant in Finland.
Johnson Matthey said in November 2021 it wanted to sell all, or parts of, its battery materials business.
Solid Power in Korea battery tech cooperation talks
Korea is in talks about cooperation in nextgeneration battery tech with US-based solid-state developer Solid Power, the country’s deputy minister for trade, industry and energy has announced.
Yang Byeong-nae said he met Solid Power COO Derek Johnson in Seoul on January 18 — after the battery company signed R&D collaboration agreements with Koreabased SK On and organizations including the Korea Electronics Technology Institute and the Korea Evaluation Institute of Industrial Technology.
Deals signed by Solid Power with SK On
included a battery cell line installation arrangement and an electrolyte supply agreement.
Yang said the government plans to invest KRW117.2 billion ($88 million) by 2028 into a ‘green mobility high-performance nextgeneration secondary battery technology development project’ and solid-state was a promising contender for support.
He also outlined Korean incentives to encourage foreign investment in the country’s battery sector.
Separately, Solid Power said on January 23 its board had authorized the repurchase of up to $50 million of the company’s shares up to the end of 2025.
Lyten gets $4m grant to boost Li-S battery tech
Graphene materials developer Lyten said on January 30 it had been awarded a $4 million US Department of Energy grant to boost manufacturing of its advanced lithium-sulfur battery technology.
The grant specifically targets Li-S technologies that can alleviate offshore supply chain risk for EV batteries and increase the driving range of EVs.
Lyten says Li-S batteries have the potential to have a greater energy density of their lithium ion counterparts and the firm’s development of 3D graphene material to develop a sulfur-graphene composite cathode has accelerated its progress toward commercialization of the technology.
In June 2023, Lyten opened a semi-automated, Li-S pilot line producing pouch and cylindrical cells at its 145,000ft2campus in Silicon Valley and said it would begin to deliver non-EV battery cells commercially in 2024.
Also last year, Lyten announced it had raised $200 million through a series ‘B’ round, bringing total investment up to $410 million to scale 3D graphene applications and Li-S battery manufacturing.
Lyten investors include auto manufacturer Stellantis.
The battery developer is working with Stanford University, the University of Texas-Austin and industrial partner
Arcadium Lithium
Arcadium was formed by the merger of Allkem and Livent — a deal that was finalized earlier in January.
Hammond says global supply chain helping battery firms navigate trade turmoil
The Hammond Group has urged battery manufacturers to check the reliability of their supply chains as two key global trade arteries are hit by major disruptions.
Escalating attacks on vessels in the Red Sea and persistent Panama Canal shipping delays as a result of drought are causing turmoil for industries and ramping up costs.
In an exclusive article in the latest edition of Energy Storage Journal magazine — online now — Hammond says international trade needs to learn a lot from the strong global supply chain it has established to support the lead battery industry.
While delivery prices are rising and firms are being forced to rethink production schedules, Hammond says its facilities across North America, Europe and Asia make it an invaluable and reliable link in the supply chain.
Data analyst firm Sea-Intelligence said on January 18 that shipping
disruption in the Red Sea was already more damaging to the supply chain than the early stages of the Covid-19 pandemic.
Oil giants Shell and BP have already introduced temporary suspensions of shipments through the Red Sea, along with major shipping companies Maersk, Hapag-Lloyd and COSCO.
Meanwhile, Tesla announced it would largely suspend production of EVs at its new Berlin-Brandenburg plant in Germany up to February 11 because of a lack of components as a result of supply chain disruptions.
The auto giant cited problems caused by ships under attack in the Red Sea while en route to the Suez Canal and associated shifts in transport routes between Europe and Asia via the Cape of Good Hope.
Meanwhile, the Panama Canal Authority has restricted the number of shipments through the vital trade waterway to 24 daily as of January 16, compared to 36 vessels a day before restrictions introduced in 2023 — the driest year in the region’s history.
Earlier this month, some ships queuing to pass through the canal had to wait 11 days.
Hammond says it want to highlight how its strategically-located plant in Malaysia is helping mitigate supply chain risks for Asian battery manufacturers, while other US producers of material for the lead battery sector remain reliant on the canal.
Hammond’s Kuala Lumpur plant manufactures expanders and its SureCure TTBLS products, serving an extensive Asia Pacific customer base. Asian firms
sourcing the Malaysia operation also avoid intercountry regional tariffs, Hammond says.
The company’s UK facility offers an additional link for the battery supply chains into Europe and the Middle East.
Morrow agrees battery cell scrap recycling deal with Stena Morrow Batteries said on February 27 it had agreed a deal to send production scrap from its Norwegian battery cell factory to be handled by Sweden-based Stena Recycling.
Stena will collect and store production scrap and its new Halmstad battery recycling facility in the south of Sweden for the next 1-1/2 years.
The companies will also consider the potential for establishing a bigger facility in the south of Norway to handle Morrow’s waste.
Stena said its advanced recycling process enables enable battery material to be recovered and used to manufacture new batteries with high recycling rates. Stena’s product area manager for batteries, Marcus Martinsson, told Energy Storage Journal: “Black mass is not one homogenic product, but a great variety of qualities depending on the type of cathode and sometimes also anode properties in the different lithium ion cells being recycled.”
Martinsson said Stena produces “several black mass qualities” which are sent on to various processing partners depending on type.
One of the company’s processing partners is Germany’s BASF, which in common with others uses a hydro-metallurgical refining processes aimed at achieving the smallest possible energy footprint, Martinsson said.
International partners back LFP Project America plan
An agreement to produce LFP cathode active material and battery cells in North America has been signed by Canada’s First Phosphate, the American Battery Factory (ABF) of Utah and Integrals Power of the UK.
The firms said on January 24 that the LFP Project America agreement is to support ABF’s eventual production plan of up to 40,000 tonnes annually by 2028.
Under the agreement, the partners will launch a pilot production facility as a first step to creating a domestic production supply chain serving the BESS sector in North America.
First Phosphate said it has access to clean igneous anorthosite phosphatebearing rock in Quebec that it intends to purify into a large quantity of battery-grade purified phosphoric acid to support LFP Project America.
ABF is building its first LFP battery manufacturing plant in Tuscon and plans several other LFP battery manufacturing facilities across North America, each of which should require a similar amount of LFP cathode active material.
The company broke ground on the 2 million ft2 Tuscon site in October 2023. The first phase of construction is to be completed by 2025.
Powin, HiTHIUM confirm 5GWh
ESS battery cells deal BESS developer Powin said on January 16 it had finalized plans for the supply of 5GWh of LFP cells from stationary battery firm HiTHIUM over the next three years.
The deal builds on an agreement unveiled in June 2023 for an initial 1.5GWh of 300Ah LFP cells.
HiTHIUM claims the 300Ah cells have an energy efficiency of 95% and an energy density of 170 Wh/kg.
The China-based manufacturer, which has sites in Germany, the United Arab Emirates and California, claims the cells can operate for more than 12,000 cycles.
HiTHIUM VP Monee Pang said the agreement with US-based Powin represents its largest order to date outside its home market.
Powin says it has more than 6GWh of energy storage systems deployed or under construction worldwide to date.
Last May, Powin announced the selection of Florida-based Jabil to produce its Stack750E utility-scale energy storage system product in the US.
Jabil was contracted to produce an initial annual capacity of 2GWh, with plans to ramp up to 4GWh per year.
BMZ enters commercial ESS market with Power Bloxx
Germany-based lithium battery systems group BMZ has entered the energy storage sector with the launch of its first ESS system for the commercial market.
A BMZ spokesperson told Energy Storage Journal on January 8 its Power Bloxx system uses the company’s proprietary lithium ion battery tech and can support a range of applications including peak shaving and emergency back-up.
The plug-and-play system comes in modular, air-conditioned standard
steel containers of about 10ft in length.
Depending on the modules deployed, the ESS can store and use 68-204kWh of electricity with power requirements of 50-300 kW.
The ESS can be used to store power from solar power generating units that are increasingly popular with businesses such as farms, small shops, retail outlets and filling stations, BMZ said. Campsites and remote facilities such as ski huts are also target markets.
BMZ said the first made-in-Germany iteration of the ESS has been designed for use with systems operating in European summer and winter weather conditions.
However, the spokesperson said Power Bloxx could easily be adapted for use in other global markets, supported by equipment and technical back-up from BMZ’s production sites beyond Germany — in Poland, North Macedonia, China, the US and Brazil.
Nano One launches
new LFP feasibility study
Nano One said on February 27 it had launched a new feasibility study into proposals to build its first commercial lithium iron phosphate cells facility.
The company announced last October that a front-end loading pre-feasibility study (FEL 2) indicated it could add 25,000 tonnes per annum of LFP production at an expanded Candiac plant in Quebec — boosting the value of its proprietary One-Pot process.
The results of that study will be factored into the new study —
FEL 3 — for which the tender has been awarded to Canadian engineering company BBA.
FEL 3 will look into the design of the 25,000 tpa plant and “further refine” capital and operating costs and the construction period required.
However, Nano One said talks with provincial and local governments had identified options for the plant to be built in Quebec and Ontario.
Key requirements before taking a final investment decision to build the plant would include customer offtake and feedstock supply agreements.
Chief operating officer Alex Holmes said the study would also inform proposals to potentially design and build similar facilities under licence or as joint ventures with partners around the world.
Meanwhile, Nano One will file a preliminary shelf prospectus potentially allowing it to make offerings of various financial securities, up to an aggregate total of C$175 million ($130 million), for an effective period of 25 months.
The company said this would help provide the most flexible and efficient access to capital markets, if and when it is needed — but said it had no immediate plans to issue securities.
In February last year, Nano One said it had completed a key milestone in its cathode materials and technoeconomic modelling process with an unnamed global auto manufacturer. Last September, Sumitomo Metal Mining announced a C$17 million investment in Nano One as part of a new battery materials development partnership.
Monbat mulls sales of three subsidiaries
European lead battery major Monbat is considering plans to sell off three subsidiaries including EAS Batteries — for which a planned deal fell through last year.
Energy Storage Journal has learned CEO Viktor Spiriev told an investors meeting on January 22 there was “still a chance” of selling EAS to potential investors that had expressed an interest in the Germany-based lithium-ion subsidiary in recent months.
Spiriev also said Monbat
is considering the possible sale of its Piombifera Italiana lead recycling facility in Italy, which it acquired in 2017, plus its Monbat Batterien lead battery production subsidiary based in Austria.
There were no plans to sell Monbat’s Nour lead battery subsidiary in Tunisia, in which the group acquired a 60% stake in 2022, Spiriev said prospects for that business continued to be very good as the group seeks to expand its market share
across North Africa and the Middle East.
Energy Storage Journal asked Monbat to elaborate on its business plans and why it was considering the potential sales, but the company had not responded at the time of going to press.
In January 2023 Monbat’s plans to sell EAS to UK gigafactory developer Britishvolt in a cash and shares deal fell through after Britishvolt collapsed into administration.
Queensland unveils A$570m battery jobs plan
Queensland published plans on February 22 to invest A$570 million ($375 million) to create clean economy jobs in the Australian state based on battery technologies and manufacturing.
Queensland’s battery industry could contribute up to A$1.3 billion to the economy and generate more than 9,000 jobs by 2030, the state government said.
Ministers say the five-year program focuses on developing advanced manufacturing of battery materials,
cells, pack assembly, installation, and recycling.
The program includes establishing an Australian Battery Industrialization Centre in partnership with the federal government.
Queensland premier Steven Miles said: “We have already made great progress in building out our battery industry supply chain, with substantial investment in battery projects right across the state.”
Miles said the state can draw on its ability to mine minerals critical to the
battery industry to underpin its manufacturing program.
In March 2022 Australian renewables and energy storage developer Genex Power announced the financial close of its first agreement in a planned series of major battery projects in the state of Queensland.
In February 2023, flow battery maker Redflow said it would step up its collaboration with partners toward developing new commercial projects in the state of Queensland.
Precursor materials investment boost for Korean battery enterprise zone
Chemicals company Paik
Kwang Industrial is to start building a KRW300 billion ($224 million) precursor materials plant at a new battery enterprise zone in South Korea, the country’s Saemangeum Development and Investment Agency (SIDA) announced on January 12. Energy Storage Journal reported last August that South Korea’s government had designated the Saemangeum Industrial Complex, in the west of the country, as a “future growth engine” for batteries.
SDIA said Paikkwang’s 100,000m2 facility will produce materials including phosphorus trichloride (PCI3) and phosphorus pentachloride (PCI5) — precursors for an electrolyte material used in lithium ion batteries.
Paikkwang’s production of PCI3 and PCI5 will eventually replace most of that imported from China, SDIA said.
SDIA administrator Kim Kyung-ahn said Paikkwang’s project takes total pledged investment at Saemangeum to date
EIB mulls €500m finance for Vulcan’s zerocarbon lithium project
The European Investment Bank is considering a financing boost of up to €500 million ($542 million) for Vulcan Energy Resources’ Zero Carbon Lithium project in Germany.
Australia-listed Vulcan said on February 23 the proposed financing for the first phase of the project, in Germany’s southwest Upper Rhine Valley, is formally under appraisal by the bank following preliminary due diligence.
Support from the bank, which is the EU’s lending arm, would be a cornerstone to securing other debt funding for which talks are underway with credit agencies and international banks, Vulcan said.
Phase one of Vulcan’s project is targeting the production of 24,000 tonnes per annum of lithium hydroxide, which the company said would equate to supplying batteries for 500,000 EVs.
Vulcan aims to supply key auto and battery makers in the European supply chain, including its second-largest shareholder, Stellantis.
to KRW10 trillion ($7.6 billion).
Saemangeum, built on reclaimed land, is already home to divisions of hightech national and international companies including separators firm Toray and battery tech group Solvay.
Korea pledged in April 2023 to launch a multibillion dollar program to defend and expand its battery industry amid fears that many of the lucrative US tax breaks and incentives are tipping the global battery trade balance stateside.
Cris Moreno, MD and CEO of Vulcan, said the bank’s consideration of financing represented “a strong and tangible signal of confidence at the European level” for the Germany project.
Vulcan announced the completion of a pre-feasibility study for its Germany project in 2021.
The company said its production process is more environmentally friendly because hot salar brine feedstock produces heat for renewable power production in addition to providing lithium.
Trent Capital takes full control of Microporous
Private equity firm Trent Capital Partners said on February 12 it had acquired full control of separator company Microporous.
Trent has been a minority owner of Microporous for the past 10 years and Trent’s founder and MD, Ray Desrocher, has been on the Microporous board since that time.
Microporous CEO John Reeves said Trent’s purchase of full control, for an undisclosed, sum would spur the firm’s growth in lead acid and lithium ion separator markets.
Energy Storage Journal reported in January that Microporous had started talks aimed at securing a $100 million US federal grant for the production of
lithium ion battery separators.
Corporate development and innovation VP Brad Reed said the company was told last December it had been selected to negotiate the Department of Energy grant.
That triggered the start of a detailed negotiating period that will take several months after which, “barring any unanticipated eligibility problems”, the grant will be formally awarded and payments can start, Reed said.
The grant talks position Microporous as a key player in strengthening domestic clean energy supply chains, Reed said.
Microporous will make an announcement about where
to build a new separators production plant once the grant application process has been completed.
The company said locations under consideration include Virginia and North Carolina — and the Southern Virginia ‘megasite’ is a top contender.
However, the final decision will be based on the findings of an environmental assessment by the US Department of Energy, which will be required before the grant agreement is signed.
More than 280 jobs will be created as a result of the grant, of which at least 85% of full-time employees will be from local communities, Microporous said.
The lithium battery
Frontier, Mitsubishi agree Ontario lithium joint venture
Frontier Lithium and Mitsubishi Corporation have agreed a joint venture deal to launch a lithium mining and processing operation in Ontario.
Under a definitive agreement signed on March 2, the partners will secure funding to develop the PAK Lithium Project mine and lithium chemicals conversion facility to supply the North American EV battery supply chain.
Mitsubishi will acquire an initial 7.5% stake in the project for C$25 million ($18.4 million) with Fron-
tier holding the remaining shares.
The Japanese firm has an option to increase its stake to 25% following completion of a definitive feasibility study.
The partners said the joint venture has been structured to cover the equity funding for the planned mine and mill while maintaining at least 75% of future off-take.
The joint venture is already providing immediate and near-term financing to “aggressively advance the first fully integrated lithium mining and processing
operation in Ontario”, the companies said.
A pre-feasibility study released in May 2023 confirmed the PAK project could be the continent’s highest quality, largest and lowest-cost producer of lithium hydroxide able to supply the rapidly growing EV industry in North America.
Canada and Japan signed a memorandum of cooperation last October committing the countries to working more closely to establish sustainable and reliable global battery supply chains.
Investor Sosteneo buys into Enel BESS unit for €1.1bn
Enel said on March 1 it had agreed to sell a 49% stake in a subsidiary set up to develop mainly BESS projects in Italy to investor Sosteneo for €1.1 billion ($1.2 billion).
Under the terms of the deal, Sosteneo Fund 1 HoldCo will buy into Enel Libra Flexsys, of which
Enel will continue to have majority control.
The agreement values ELF at around €2.5 billion including debt.
ELF was established to build and operate 23 BESS projects with a combined capacity of 1.7GW and three renovation projects for open cycle gas turbine plants.
Enel Group CFO Stefano De Angelis said the agreement with Sosteneo will support the speeding up of the group’s BESS development projects.
The sale should close in the first half of this year subject to regulatory approvals.
separator commercialization project is based on using wet process polyethylene separator film technology similar to the PE lead battery separators produced in the firm’s plants in the US state of Tennessee and Austria.
Addionics invests $400 million to boost EV battery tech plans
Battery tech developer
Addionics is investing $400 million in the first stage of a multi-factory development plan in the US.
The firm said on February 26 it is in the final stages of site selection for the first in a series of plants that will produce its proprietary ‘smart 3D current collector’ copper foil products for high-performance EV batteries.
Addionics claims its 3D structured foil improves the performance of any battery, regardless of its chemistry.
The product design increases the surface area of the coating, mechanically strengthens the bond between the active material and the foil, and creates a highly porous structure for improved performance, according to the company.
AI software is used to determine the best structure of the foil for application requirements.
Once completed, the new factories will generate 3D copper foils to support 90GWh of battery capacity a year.
Addionics was founded in 2017 and has production facilities in the US and Israel plus sites in the UK and Germany.
However, the first of the new plants to be built in the US will be the company’s biggest manufacturing facility to date, CEO and co-founder Moshiel Biton said.
NEWS — FINANCE
Vanevo cash raise boost for flow battery
Redox flow battery components firm Vanevo is to use a fresh funding boost to set up a new cell stacks production line in Germany.
Vanevo CFO and MD Uwe Boegershausen told Energy Storage Journal on February 8 the undisclosed capital boost will allow the firm — spun off from the German Aerospace Center in 2018 — to set up the 10MW automated serial production line at a new site in Lower Saxony.
Boegershausen said production capacity will be ramped up to 50MW annually as the firm moves toward full commercialization of its patented stack technology, which it says
avoids fluorinated sealings and uses a single adhesive sealing instead.
As only one seal is required instead of 160, the battery cells are cheaper to produce, more energy-efficient and easier to handle, he said.
Vanevo had already raised €4.7 million ($5 million) in equity, as well as grants from the European Innovation Council, before the latest boost.
The firm said it already has supply agreements with a number of unnamed customers and completed its initial deliveries last month.
Renewables investors Smit Asset Management and Bookjans Asset Manage-
ment took part in the latest capital increase along with Boegershausen, Vanevo founder and CEO Jan grosse Austing and others.
Vanevo says it intends to target the global energy storage market with its standardized stacks and modules for final battery assemblies.
“From our perspective, standardization is the only way to achieve significant cost savings that are crucial for the commercialization of the technology,” Boegershausen said.
A key backer of the company to date is NBank
Capital Beteiligungsgesellschaft, a subsidiary of the Investment and
SQM increases Altilium investment to $12m
SQM Lithium Ventures said on February 21 it had made a further investment of $9.5 million in UK-based Altilium.
The cash injection takes the investment by the corporate venture arm of the lithium business of Sociedad Química y Minera de Chile in Altilium to $12 million — the lithium producer’s largest such investment to date.
The financial boost also completes Altilium’s series ‘A’ funding round.
Altilium said the addi-
tional funding will accelerate the scale-up of its UK and European activities to eventually encompass EV battery collection, black mass recycling and chemical refining direct to cathode active material.
Key developments for 2024 include the construction of a small commercial plant in southwest England to process what Altilium said will be significant volumes of battery precursors and cathode active materials for qualification with automakers
and cell manufacturers.
The company also wants to build an EV battery recycling facility in northeast England and launch hydrometallurgical refining by retrofitting an existing industrial plant in eastern Europe, with plans to process 8,000 tonnes of black mass later this year.
Last December, SQM said it had reached a framework deal to give a majority stake in its Chilean brine assets to the country’s state-owned copper corporation Codelco.
TotalEnergies acquires German BESS developer Kyon
TotalEnergies, the French oil giant, said on January 23 it had agreed to take over German BESS developer Kyon Energy. TotalEnergies has signed an agreement to acquire Kyon’s entire share capital from its three founders for an upfront payment of €90 million ($98 million) plus some payments linked to the achievement of development targets. Kyon has led development of 770MW of
energy storage projects since its launch in 2021, of which 120MW are in operation, 350MW are under construction and 300MW are ready to build.
In addition, Kyon’s portfolio includes a 2GW pipeline of advanced-stage projects.
TotalEnergies, which also owns French battery firm Saft, said it will develop, build, and operate those projects, mainly
Development Bank of the German state of Lower Saxony.
NBank investment manager Marc Löffler said the institution would continue to support Vanevo’s growth after backing the company’s development stage as a seed investor.
“We are impressed by the team’s technical expertise and the technological lead that the company has gained.”
LGES leads $75m
Sion Power capital boost
Lithium metal developer
Sion Power said on January 24 it had raised $75 million backed by LG Energy Solution to expand R&D production capacity for EV batteries.
LGES led the series ‘A’ funding round through its venture capital arm LG Technology Ventures with Bricks Capital Management, supported by Euclidean Capital and including new investment from former Google CEO Eric Schmidt’s Hillspire.
New directors joining Sion’s board as a result of the investment boost include Robert McIntyre, the MD of LG Technology Ventures and the managing partner of Bricks Capital Management, Hansol Kim.
located in the north of Germany.
The Kyon deal, which is subject to regulatory approvals, comes after TotalEnergies was: awarded a maritime concession by German authorities to develop a 3GW offshore wind farm; acquired renewable energy aggregator Quadra Energy; and was awarded a contract to install and operate 1,100 high-power charge points for EVs.
Sion said it will use the new capital to achieve technical and market validation of its Licerion technology, while pushing ahead with plans to build a fully automated manufacturing line for high quality, large format lithium metal cells for testing and market development by automotive OEMs and cell manufacturers.
Sion is expanding its existing 100,000ft2 plant site in Arizona by 11,400ft2 by 2026.
Ecobat, VW finalize UK lithium recycling deal ...
Lead and lithium recycling giant Ecobat said on February 28 it had finalized a new contract to recycle EV batteries for Volkswagen Group UK.
Texas-headquartered Ecobat said VW will be the first to use the firm’s newlyopened UK lithium ion recycling facility.
Financial terms of the deal were not disclosed, but Ecobat said it covers the collection and recycling of VW’s EV batteries and collection of high-voltage batteries from dealers, distributors, and end-oflife recycling centers using Ecobat’s ADR -compliant vehicles.
ADR is a set of guidelines and processes that businesses must follow when transporting dangerous goods by road.
Ecobat has a longstanding relationship with VW UK dating back to 2014 when it started collecting lead acid batteries for TPS — VW’s parts provider to the independent motor trade.
The contract was expanded in 2019, when
Ecobat started working with high-voltage batteries. Since the company opened its Diagnostics and Disassembly Centre in Darlaston, in the West Midlands, it has processed and upgraded thousands of batteries.
Elliott Ethridge, Ecobat’s VP of global sales, said the
firm’s lithium recycling operations can handle scrap, by-products, end-of-life and damaged products.
The UK is home to Ecobat’s third lithium ion recycling facility after those in Germany and Arizona — the commissioning of which was announced last month.
Ethridge said then Ecobat had a long history in lead recycling worldwide, but added:
“It makes sense to go into lithium now, but we don’t see lead diminishing. We see lithium coming on to augment a lot of spaces that lead doesn’t serve.”
... and new US lithium plant commissioned
Separately Ecobat confirmed on January 18 that it had commissioned its first lithium recycling plant in the US.
The new Casa Grande facility in Arizona, announced in February 2023, has a capacity of around 10,000 tonnes of recycled material a year with the ability to expand capacity.
Lithium sales VP Elliott Ethridge said the new plant will sort, shred and separate battery materials to produce black mass.
Ecobat already has a lithium battery recycling plant online in Germany and another is being prepared for start-up in the UK, Ethridge said.
Technology in use at Ecobat’s facilities can process everything from portable small format batteries to EV batteries, he said.
The company has a long history in lead recycling worldwide. It said: “It makes sense to go into lithium now but we don’t see lead diminishing. We see lithium coming on to augment a lot of spaces that lead doesn’t serve.”
Former Ecobat CEO Jimmy Herring told Energy Storage Journal in December 2021 that the company aspired to bring all kinds of chemistries under its wing to become the biggest all-round recycler in the world.
Last November, Ecobat announced it had sold its Zimco Group businesses in South Africa including lead manufacturing, recycling and chemicals firms to AutoX.
Ecobat CEO Marcus Randolph said that sale would allow the group to focus on its “core business” of battery recycling in North America and Europe.
The move followed the sale, announced in 2022, of Ecobat Resources Stolberg to commodities firm Trafigura. The sale included the Stolberg multi-metals processing plant in Germany.
Taiwan’s ACME Metals installs ACE Green’s systems module after testing
Taiwanese lead refiner
ACME Metal Enterprise has installed its first modular lead battery recycling equipment supplied by ACE Green Recycling.
ACE’s VP for global strategy and business development Farid Ahmed told Energy Storage Journal on January 15 the first of three equipment delivery phases was completed last month.
The move follows initial testing of ACE’s technology in 2023 for the treatment of lead oxide drosses from ACME’s refinery in Keelung City.
Under the first delivery phase, ACE handed over
equipment with a 2,400tonne per annum recycling capacity. Completion of the third phase will expand this capacity to 20,000-tonne per annum, giving ACME the ability to produce around 12,000 tonnes of what it calls ‘GreenLead’ annually, which is worth over $25 million a year to the refiner, Ahmed said.
Over the 10-year duration of the contract, ACME will acquire the capacity to recycle more than 14 million scrap batteries, which ACE says will prevent the emission of nearly 120 million kilograms of carbon dioxide equivalent, stop 18 million
kg of solid waste from going into landfill and enable recycling of more than 14 million kg of plastics.
The lead recycled by ACME will be sold into markets in Taiwan and Japan including battery OEMs across Asia, ACE said.
ACE claims its technology replaces the smelting furnace, operates at room temperature, runs on electricity and has zero Scope 1 greenhouse gas emissions (direct GHG emissions such as those made while running boilers and vehicles) and reduces solid waste by more than 85%.
ACE’s CEO Nishchay
Chadha said: “It is our goal as a battery recycling technology platform to provide all players in the ecosystem a way to meet not just their commercial goals but their environmental ones as well.”
ACE Green unveiled plans in 2022 to build and operate what it claimed would be an “emission-free” lead and lithium batteries recycling facility in Texas.
The firm has since signed several deals — including an equipment supply and licensing agreement last June with Hakurnas Lead Works, to set up battery recycling facilities in Israel and Romania.
Sunlight to acquire full control of Ubatt
The Sunlight Group said on February 7 it had signed a binding agreement to acquire the remaining 50% stake in its German lead battery recycling subsidiary Ubatt.
The deal, for an undisclosed sum, will be finalized by the group’s Sunlight Recycling subsidiary and is subject to the approval of
competition authorities.
Sunlight Group CEO Lampros Bisalas said Ubatt, which also started collecting lithium batteries for recycling a few years ago, handles a combined total of 58,000 tonnes of batteries annually.
Bisalas said the acquisition will strengthen the group’s position in the battery recy-
cling market for lead and lithium chemistries.
Sunlight Recycling was set up after being given the go-ahead at an extraordinary meeting of the Greece-based group’s shareholders last October.
In November, Sunlight said it was spinning off its lead recycling operations into the new subsidiary to guarantee
raw material supplies for lead battery production.
Bisalas said then that the move would create one of the largest secondary lead producers in the world, help to expand the group’s collection of used batteries in Europe and America and make its lead battery production operations more competitive.
Li-Cycle gets liquidity boost from Glencore, Germany grants approval for new plant
Li-Cycle said on March 12 it had received an extra $75 million investment from mining group Glencore would boost its liquidity.
The month before it won approval for a €6.4 million ($7 million) grant for its new lithium ion recycling plant in Germany.
Pressure has been mounting on Li-Cycle after it suspended construction of its Rochester lithium battery recycling hub in New York last October over escalating costs.
The suspension came after Li-Cycle said the estimated cost could double to up to $1 billion.
Li-Cycle has since formed a special committee “composed solely of
independent and disinterested members” of its board to work with investment bank, Moelis & Company, on a review of the Rochester project and “to evaluate potential financial and strategic alternatives”, co-founder and CEO Ajay Kochhar revealed on March 12.
Glencore originally invested $200 million in Li-Cycle in 2022.
Kochhar said the latest Glencore investment represented an interim step in Li-Cycle’s funding strategy. “We also continue to work closely with the US Department of Energy (DOE) on the conditional commitment for a loan of up to $375 million.”
Key Republican members of the House of Representatives have called on the DOE’s Loan Programs Office to give details of the proposed loan — saying they were concerned about the government making possible “reckless investments”.
Separately, at least two law firms have announced the filing of class action lawsuits against Li-Cycle, relating to statements made by the firm about Rochester’s costs.
German grant
The firm said the grant approval for its Magdeburg ‘spoke’ facility in Saxony-Anhalt was given by the state’s government.
Regenerate Technology to launch lead ‘upcycling’ plant by the summer in Bologna, Italy, says CTO Athan Fox
Regenerate Technology
Global, an Anglo-American lead battery recycling firm said on February 13 it had secured a longterm lease of a former lead battery manufacturing plant in Italy where it will launch a lead recycling operation.
Regenerate co-founder and CTO Athan Fox said the company, which also has an option to buy the plant, is renovating the
125,000 ft2 facility in Bologna and plans to start “upcycling” of lead acid batteries by this summer.
Fox claimed operations at the site will mark a “significant leap in commercial-scale, upcycled leady oxides production”.
Regenerate’s CEO is David Batstone, founder of US-based social impact investments company Just Business. Batstone was an early investor and former
board member of the American Battery Technology Company.
Batstone is also a former CEO of Blackstone Technology — the German 3D printed batteries tech development subsidiary of Swiss holding company Blackstone Resources.
The general manager of Regenerate’s EU and UK operations is Miles Freeman who has worked with Fox for years,
Spoke facilities are where all types of lithium ion batteries are transformed from a charged state to what Li-Cycle describes as an inert product.
The resulting black mass is then transferred to a hub, where cathode and anode materials are processed into battery grade end-products for reuse in battery production or other applications.
Li-Cycle said last year that black mass produced at Magdeburg would be processed at a hub operated under a proposed European joint venture with Glencore.
However, the future of that joint venture project is unclear and the partners have yet to respond to repeated questions from Energy Storage Journal about the status of the project.
Magdeburg spans more than 20,000m2 with 10,000m2 warehouse capacity.
Li-Cycle said the facility can process full EV and energy storage battery packs without the need for disassembly, discharging, or thermal processes.
Magdeburg has an annual lithium ion battery processing capacity of up to 10,000 tonnes, with potential to expand up to 30,000 tonnes annually.
A new generation of EV battery businesses is moving centre stage. With the teething problems of their initial start-up phases almost over, they are counting on double-digit growth in the years ahead. By Sara Verbruggen.
All to play for ... and everything up for grabs
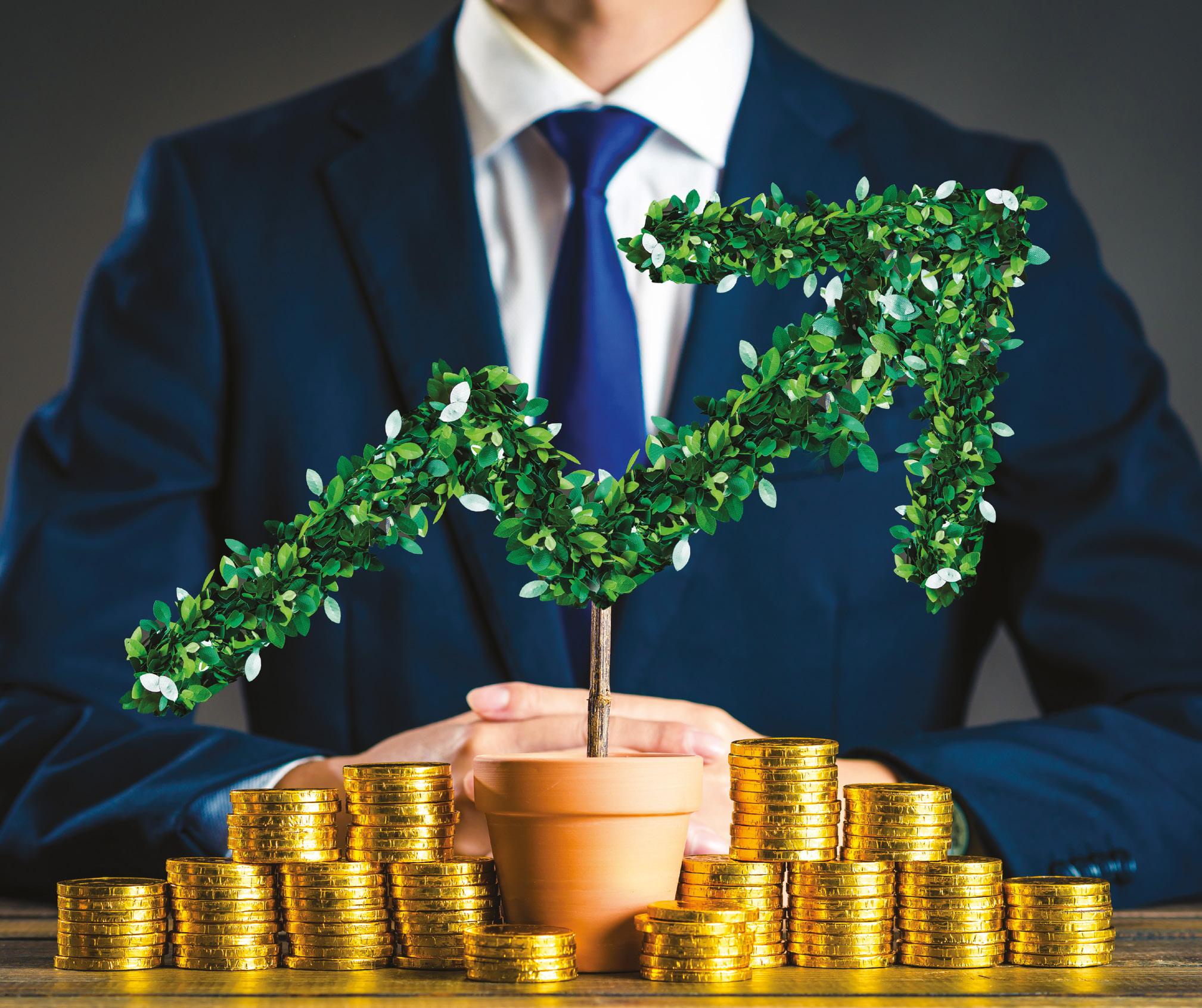
With the US and Europe seeding localized lithium ion battery value chains and ecosystems, everything is up for grabs when it comes to what goes into making the cell.
In less than four decades the lithium ion battery industry has gone from enabling a revolution in portable and mobile electronics, to powering energy transition ambitions.
The global demand for batteries across electric vehicles and stationary storage applications today is a fraction of the calculations for future need. Cost, safety, resource scarcity, supply chain security are major concerns that cannot simply be resolved with new gigafactories pumping out cells based on tried and tested chemistries.
With the US and Europe seeding localized lithium ion battery value chains and ecosystems, everything is up for grabs when it comes to what goes into making the cell.
The single ingredient that is common across all variants EV batteries — ie lithium! — has become a whipping boy for concerns about the unsustainability of the industry, long term.
It’s a perverse thought. But mining lithium for EV batteries upsets environment focused-politicians in a way
that mining oil for producing petroleum does not. (And irrespective of the huge difference in terms of emissions and ecological impact.)
Silicon switch
US-based Group14 Technologies’ SCC55 is a silicon-carbon composite anode material that affords up to 50% more energy density than conventional graphite for lithium battery anodes, resulting in batteries that recharge more quickly.
Its hard carbon-based scaffold-
VULCAN ENERGIE: GREEN LITHIUM AND THE JOYS OF GEOTHERMAL BRINE
Germany — one of the biggest car markets in the EU — could also meet much of the bloc’s lithium needs, according to Cris Moreno, CEO of Vulcan Energie.
“Europe has set clear targets for an emissions-free transition by 2035. Securing a domestic source and production capability for lithium now is critical to ensure that targets can be met and the European automotive industry remains globally competitive,” says Moreno.
“Vulcan is working towards producing enough green lithium for 500,000 EVs by 2026 and scaling up from there, enabling a secure domestic supply chain in Europe, well into the future”.
Vulcan has secured 16 exploration licences in the Upper Rhine Valley Brine Field where it intends to extract lithium contained within hot geothermal brine using a technique called adsorption-type direct lithium extraction (A-DLE).
The hot brine containing lithium is channelled through a proprietary sorbent, where the lithium ions remain suspended. This process is heat-driven, so the natural waste heat in the brine can power the lithium extraction process. The brine is then returned to the natural reservoir in a closed cycle.
The first phase of Vulcan’s commercial production aims to produce 24,000 tonnes of lithium
hydroxide — enough for half a million EVs a year. The second phase aims for the same amount.
The individual steps in the Vulcan extraction process are not new in themselves.
Geothermal renewable energy has been used to produce energy for many years and A-DLE has been used commercially since the 1990s and accounts for 10% of global lithium supply.
What is new is Vulcan Energie is putting the different steps together. Where lithium and heat are present in sufficient quantities in the brine, A-DLE can work commercially, but also with net zero carbon emissions, by harnessing the geothermal energy.
The company recently completed pilot facilities, where it is optimizing its process. Its first tonne of lithium will be produced in the first quarter this year in Landau, which will then be converted into lithium hydroxide monohydrate at Frankfurt-Hoechst.
The metal will be tested by Vulcan’s lithium offtake partners, Stellantis, Volkswagen, Renault, Umicore and LG. Both optimization plants will serve to train the production team, contributing to shorter ramp-up times.
Vulcan is planning to build an integrated geothermal and lithium extraction plant in Landau, and has


“Vulcan
is working towards producing enough green lithium for 500,000 EVs by 2026 and scaling up from there, enabling a secure domestic supply chain in Europe, well into the future”
— Cris Moreno, Vulcan Energie
an agreement with the city for it to construct the first phase G-LEP. Vulcan submitted the building permit for the lithium extraction plant last November.
In the lithium extraction plant, Vulcan will produce the precursor lithium chloride, which will be converted into 24,000 tonnes of lithium hydroxide monohydrate at a central lithium plant in FrankfurtHoechst. This is enough to produce batteries for around 500,000 EVs. Vulcan is planning on starting operations of its lithium extraction plant in H2 2026.
There are only a few locations where the process can be realised at all; one of the others is the Salton Sea in California, US, which has hot geothermal brine.
The Upper Rhine Valley is home to one of the largest lithium resources in the world and the largest in Europe. It has also been explored for oil and gas for many years, so there are already many wells with data showing that the lithium concentration increases at depth.
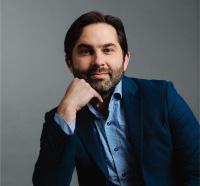
“Over the next 12 months we’ll continue to progress preparations for our German factory to enter production sometime in 2026, to supply the European EV battery market. There is huge scope for growth in future”
—
Christ Timmons, Group 14
ing keeps silicon in the most ideal form — amorphous, nano-sized, and carbon-encased. In February 2023 Group14 announced that consumer electronics batteries produced by Amperex Technology Limited (ATL) began incorporating SCC55.
Group14 vice president of engineering Chris Timmons estimates 80 lithium ion battery manufacturers, which collectively supply 90% of the world’s lithium ion battery demand — in the consumer electronics and EV markets — have been supplied with Group14’s material and are at various stages of implementing it into anode production.
By 2030 demand for graphite, driven by growth in lithium-ion batteries for EVs, is expected to outstrip supplies.
Timmons says: “There’s a significant advantage in terms of a carbon footprint given the lower energy density. The overall carbon footprint per amp hour of the battery is significantly improved over graphite, which is generally where the industry is going. This is an enabling technology for that.”

Because SCC55 delivers higher energy density, less of the material is required than graphite for the same performance.
Porsche is the first EV maker in the public domain that is using SCC55, which will enter the car maker’s battery production this year. Porsche will initially be supplied with the material produced at Group14’s factory, with SK Materials in South Korea, which will go online in H1 2024 and will supply enough material for 100,000 EV batteries annually.
By the end of 2024, Group14 expects to be producing SCC55 from its new US factory. Combined the US and South Korean factories will have enough capacity to supply 300,000 EV batteries annually.
Timmons says: “Over the next 12 months we’ll continue to progress preparations for our German factory to enter production sometime in 2026, to supply the European EV battery market. There is huge scope for growth in future. For now, Group14 will supply its materials to customers and is focused on supplying the EV lithium ion battery market.”
One of the main advantages of the material that appeals to customers is that it can be almost readily blended or dropped into anode production with very little adjustment to processes. Customers can adjust quantity or ratio to their anode as required. Or, in some cases, automakers may displace graphite entirely in the anode.
As well as being compatible with all kinds of lithium-ion batteries based on different cathode chemistries, including NMC and LFP, SCC55 is also applicable for solid-state cells.
Nano One
LFP cell research originated at the University of Texas, before being developed, piloted and first commercialized in Québec in the early 2000s and Canada’s Nano One has ambitions to establish a supply chain for these batteries on its home turf.
The company’s One-Pot process involves mixing lithium, other metal feedstocks and coatings in a single reaction to produce metalsrich cathode active materials. It is less emissions-intensive, energy and water-intensive than current processes and eliminates waste byproducts in the form of sodium-sulphate.
In 2023 Nano One completed its first full year of ownership of its Candiac LFP pilot plant, in Québec,
during which time trial production of LFP cathode materials production using the One-Pot process has got underway.
The Candiac facility is the “bridge between bench and industrial production, taking the risk out of the equation while leaving the reward to play for,” says Alex Holmes, chief operating officer. Over one tonne of the LFP powders made at the Candiac plant are being shipped to a global automotive manufacturer and other collaborators.
With policies in the US and Europe encouraging the reshoring of battery supply chains, new cell gigafactories will decouple supplies of critical materials from sources in Asia, Nano One aims to influence emerging ecosystems.
In addition to the automotive/electric vehicle market Nano One is also working with players within stationary storage that will create the pull within supply chains to source its cathode materials. Defence applications are also in Nano One’s sights.
The company has a strong pedigree in terms of partnerships across the value chain, including Rio Tinto, Sumitomo and Umicore.
It has also signed a joint development agreement with Our Next Energy (ONE), a Michigan-based energy storage technology company to collaborate on the validation, qual-
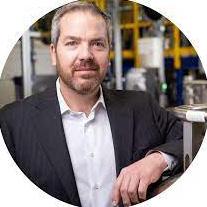
“The Candiac LFP pilot plant, in Québec is the bridge between bench and industrial production, taking the risk out of the equation while leaving the reward to play for”
— Alex Holmes, Nano One
ification and production of a North American supply of LFP cathode active materials.
The cathode active materials will be produced at Nano One’s Candiac pilot and future commercial facilities for potential use in ONE’s production of LFP cells used in its Aries and Gemini batteries.
Partnerships are key, says Holmes and he says Nano One is focused on working with those companies willing to provide collaborative feedback and facilitate information exchange. This year, pending offtake agreements within the energy storage sector, Nano One will secure financing to build an industrial scale facility planned to come online in 2027.
Québec has the right mix of raw materials, strategic location, secure green power, plus a skilled and experienced workforce, says Holmes. There is a provincial strategy for Developing a Battery Industry and for Critical Minerals, along with a federal strategy to support the battery supply chain.
Solid Power: a $60bn electrolyte opportunity
Solid Power, based in the US state of Colorado, aims to commercialize liquid and gel-free battery technology (100% solid state) for improved performance, safety and cost advantages over lithium ion cells used today.
The company is differentiating itself by investing in sulphide-based solid state electrolyte manufacturing. This requires a fraction of the Capex required to invest in a cell gigafactory, while also allowing it to partner with, as opposed to compete with, cell makers.
“We can do business with virtually any battery chemistry that is out there with the proper work,” said CEO John Van Scoter in an investor-focused presentation this January. The company’s estimates point to a $60 billion addressable market assuming the electrolyte is 10% of future total battery cost.
The fact that most major EV brands have announced sulphide-based solid state cell technology in their roadmaps is reason to feel bullish, Van Scoter believes.
The company is targeting three major EV markets through three publicized partnerships: in the US with Ford, Europe with BMW and South Korea with SK On. SK On has overtaken Samsung to become the fifth largest supplier of EV batteries, with ambitions to become the
“We can do business with virtually any battery chemistry that is out there with the proper work”
— John Van Scoter, Solid Power
number one by 2030. Its portfolio includes different lithium ion cell technologies, spanning nickel-rich to LFP.
This January Solid Power and SK On announced an expanded partnership, comprising three agreements.
The first concerns R&D, where SK On will license Solid Power’s solidstate cell designs and manufacturing processes for R&D purposes only, in exchange for payments totalling $20 million from 2024 to 2027.
The second concerns line installation, where Solid Power will design, procure, and install a cell manufacturing line at one of SK On’s South Korean facilities in exchange for $22 million. The line will be based on Solid Power’s Colorado-based line and will produce cells using Solid Power’s electrolyte technology. Construction is to be completed in 2025.
The third, which is the first of such an agreement Solid Power has negotiated, concerns electrolyte supply, where SK On will purchase Solid Power’s electrolyte for use on the South Korean line, initially for validation purposes, after which it will be required to purchase at least eight tonnes of electrolyte from through 2030, for use in collaboration with Solid Power to advance its cell technologies, which will net Solid Power at least $10 million in sales.
Van Scoter said the partnership will create opportunities to work with South Korean supplies of equipment, raw materials, existing lithium ion flow as well as collaborations with national laboratories there.
Different automotive OEMs all have different approaches. BMW is duplicating Solid Power’s pilot production lines at its own facility in Germany, which includes staff exchange between the companies. The carmaker plans to put Solid State’s cells into modules to power a demonstration EV before the end of this year.
Other brands are sampling the elec-
trolyte as they have cell capability in-house but are looking for an electrolyte supplier.
Solid state EV batteries offer a large scope for improvement, especially in terms of safety by removing the liquid electrolyte. “We think we’ll match lithium ion to begin with but range, lifetime, safety and cost of solid state will all be improved. Raw material input will be lower cost as well due to less required on the battery management side,” according to Van Scoter.
Ascend Elements: maximizing battery metals recycling
Reusing metals from spent batteries is critical to new value chains for cell manufacturing. But there is cost involved, in sorting different battery product or application waste streams, in the multiple steps to produce black mass or metal salts, not to mention the further steps to make production-ready cathode materials.
Ascend Elements’ process extracts the impurities and leaves cathode minerals intact in an aqueous solution, rather than extracting individual metals in series — first lithium, then nickel, then cobalt, for instance.
Microstructure engineering techniques adjust the elemental crystal structure needed to produce cathode precursor (pCAM).
Marketing director Thomas Frey says: “In other words, we can recycle a 10-year-old battery from a first-generation EV, break it down to an aqueous solution containing lithium, nickel, and cobalt atoms, and then rearrange those atoms into the newest type of cathode active materials such as a NMC 811 or a high nickel NMCA.”
The incoming feedstock can be a mixture of different lithium ion battery types and elemental compositions, such as used batteries from old EVs, laptops, cell phones, scooters, and power tools. Even gigafactory scrap and waste can be mixed in. Because there is no need to sort batteries into different categories before recycling, this should facilitate increased recycling rates.
In a recent study Ascend Elements battery cells made with the company’s upcycled cathode material, using its own Hydro-to-Cathode direct precursor synthesis process, exhibited over 50% longer cycle life than tradi-
tionally made cells, and power capacity was increased by 88%.
“The microstructure of the Hydroto-Cathode particles have increased porosity and larger voids, which improve properties such as lithium diffusivity — the ease with which lith-
“We can recycle a 10-year-old battery from a first-generation EV, break it down to an aqueous solution containing lithium, nickel, and cobalt atoms, and then rearrange those atoms into the newest type of cathode active materials such as a NMC 811 or a high nickel NMCA”
— Thomas Frey, Ascend Elements

ium ions travel through the material as the battery is charged and discharged — and result in higher power capability,” says Frey. The porosity of the cathode particles can be engineered to customer requirements.
For end-of-life batteries, Ascend Elements is working with Honda and other automotive OEMs as well as with automotive dismantlers and automotive recyclers to process lithium ion batteries. There is an agreement with Honda to return recycled battery materials back to the OEM in North America for use in new EV batteries. This is a step toward creating a closed-loop supply chain for recycled battery metals, including cobalt.
Ascend Elements has also signed a contract to supply $1 billion of sustainable pCAM for use in a US company’s battery manufacturing process, beginning in Q4 2024, with the potential to increase up to a value of $5 billion.
A wave of end-of-life EV batteries is expected to hit in the 2030s.
Until then, Ascend Elements says its recycling facilities won’t be sitting idle. In 2023, EV battery gigafactories produced approximately 790,000 tonnes of manufacturing scrap, which includes various metals, including lithium, nickel and cobalt, according to FastMarkets.
Ascend Elements is also working with battery makers, including SK Battery America to process battery production scrap, such as cells and modules that don’t pass quality. The primary focus is on building a 140-acre cathode manufacturing campus in Hopkinsville in the US state of Kentucky.
Once operational in the first half of 2025, the facility will produce enough cathode precursor for 750,000 EVs a year.
A commercial-scale EV battery recycling facility in Covington in nearby Georgia, which has been open for just over a year has a capacity to recycle 30,000 tonnes of used lithium-ion batteries using Ascend Elements Hydro-to-Cathode process.
More recently the company has begun commercializing its Hydro-toAnode process, where it is in talks to supply IRA-compliant, battery-grade graphite to several EV OEMs and battery makers. Joint commercialization is being explored with Koura Group though location or timeline for construction of a new facility has not been publicised.
OTHER PLAYERS IN CELL MANUFACTURING
The impetus of the IRA has made the US the main draw for cell gigafactory investments this decade, much of these focused on capturing demand from the EV market.
Several also have their eye on stationary storage and the opportunity to invest in significant capacity for making LFP cells, suggesting the industry may coalesce around this technology, for stationary storage initially, then EVs.
LG Energy Solutions (LGES), Our Next Energy (ONE) and Freyr are some of the companies backing LFP. Their different approaches span proven chemistry but also riskier technology that could pay off by driving down cost.
ONE’s first gigafactory (29GWh) is a $1.6 billion investment, supported by a $215 million state grant, located in Michigan which slated to be operational in late 2024 but reaching full capacity by the end of 2027.
ONE will begin delivering cells from pilot production to customers in commercial truck, automotive and utility grid markets, to validate performance and durability in the first half of 2024.
ONE’s roadmap includes dualchemistry architecture, Gemini, which combines LFP and anodefree chemistries into one battery pack, eliminating the need for graphite and anode manufacturing equipment, reducing production costs to $50/kWh cell cost at scale.
In 2023 LG Energy Solution (LGES) announced one of its biggest LFP investments outside of Asia, a $2.3 billion LFP pouch facility with a capacity of 16GWh. It is part of a $5.5 billion battery manufacturing complex in Queen Creek, Arizona, which will also include a facility for making cylindrical batteries for EVs.
In 2023 investors voted in favour of redomiciling Norwegian LFP cell start-up Freyr to Delaware from Luxembourg in part to benefit from US incentives.
The company has been banking on licensing partner 24M Technology’s semi-state technology because it could yield LFP cells that are 25% cheaper to make, due to simpler production. However, it is not
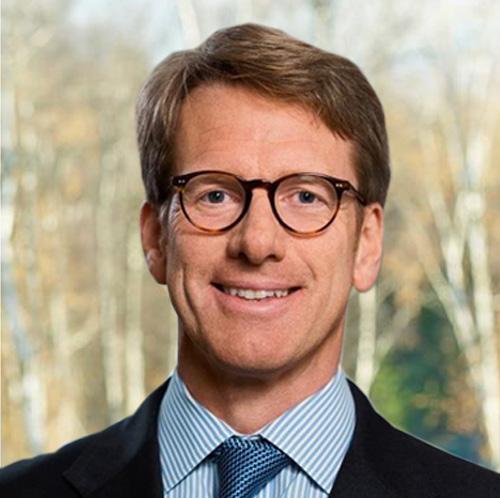
“We’re getting into the harder stuff, discovering aspects which don’t have technology readiness level and which were difficult to foresee in front.
— Birger Steen, CEO, Freyr
mature. The company has built a customer qualification plant, in Mo i Rana, northern Norway, a critical step in going to fully automated production that will be replicated in a $2.5 billion 34GWh battery plant in Georgia, US.
In its most recent quarterly investors call, in late 2023, the company communicated the delays it has run into.
Reiterating his confidence Freyr will achieve scalable and automated cell production, CEO Birger Steen said: “We’re getting into the harder stuff, discovering aspects which don’t have technology readiness level and which were difficult to foresee in front.
“We see a path through to that and we are making changes to debottleneck and unblock that path.” He said delivering cells in an automated way at the customer qualification plant is the company’s first priority involving all of its battery engineers and close cooperation with partners, including Nidec.
As an insurance policy the company has begun negotiations with other potential partners to license commercial LFP technology.
Lithium’s burning, fire, fire!
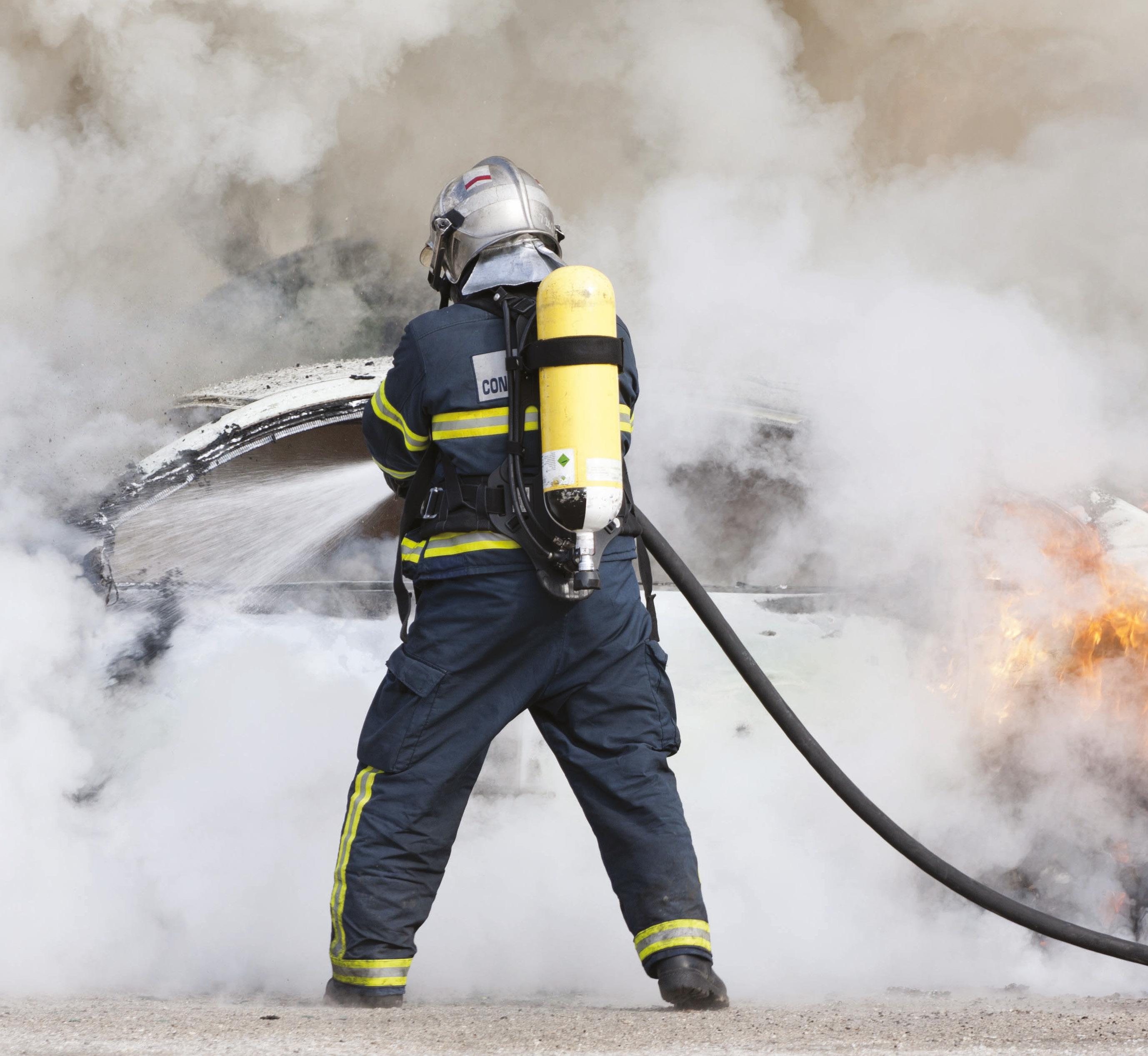
(But that’s not the complete story.)
The dramatic growth in the use of lithium batteries from small-scale usage to electric vehicles — and now even large size BESS — is being accompanied by a surge in electrical fires. That’s the bad news headline, reports Sara Verbruggen, but let’s not forget that greater safety protocols and technologies are being developed and eagle-eyed insurance companies scrutinizing their progress.
Ten years ago, almost to the month, Sony had to recall some 26,000 laptops around the world warning that its Vaio Fit 11A containing Panasonic batteries was in danger of catching alight — although, to be fair, in fact only three models had overheated.
The trouble then was that this wasn’t the first time it had happened. Go back almost another decade and you’ll find that in 2006, the company initiated a $360 million global recall
of its own battery packs, affecting Toshiba, Dell, Fujitsu, Lenovo, and Hewlett-Packard users. There had been high-profile fires at conferences and even onboard a plane at LA International. Just two years later some 100,000 Sony computer battery packs were also recalled.
This wasn’t just a Sony or Panasonic problem. Fast forward from 2006, 2008 and 2014 to 2024 and similar fears still plague the laptop industry. In the UK, London Fire
Brigade recently urged people not to use their laptops in bed! (to avoid risk of their batteries overheating and catching the bedding alight. The issue isn’t with Sony or Sony’s battery suppliers. Nor is it confined to laptops. It’s generic to lithium batteries and their applications.
Across the world fire chiefs and safety experts have warned, or are warning, of the very real dangers of lithium battery fires. As this magazine was going to press the
MANAGING LITHIUM SAFETY RISK
Australian Competition & Consumer Commission had issued a proposed recall notice for some 5000 LG solar batteries after 13 household fires, including one serious enough to burn it to the ground.
In New York the fire authorities are clamping down further on the way that e-bikes can be charged in apartment blocks — lithium battery energy storage systems have been banned in basements of residential and commercial buildings for at least a decade.
Over the past five years in the US alone the cost of lithium battery recalls for EVs can be calculated in the high single figure billions of dollars. And back in Australia to add insult to injury the use of disposable vapes (e-cigarette batteries) has caused a series of rubbish trucks to catch fire — one has even been named Phoenix having caught fire on several occasions!
And in January 2022 Norwegian shipping company, Havila Kystruten announced it was banning electric cars, hybrids and hydrogen vehicles on its ferries because of a potential fire hazard. This follows a risk analysis conducted by Proactima, a Norwegian risk management advisory consultancy, according to chief executive Bent Martini.
The review followed the fire and subsequent sinking of the container ship the Felicity Ace, carrying $400 million of top range electric vehicles.
Exceptions not headlines
But is it fair to paint such a grim picture when accidents are just part of life?
Not really has to be the answer.
As a proportion of the sheer number of lithium ion batteries in circulation, fires are unusual. On a per-motor vehicle basis, ICE fires are far more likely to catch fire that EVs.
That said, EV fires are more difficult to put out. They require a considerably larger amount of water to extinguish. While a burning petrol or diesel vehicle may need 1,600 to 2,000 litres of water to be put out, a fire in an EV often requires as much as 11,000 litres, mainly to cool down the burning battery.
Moreover, the safety protocols put in place means that the regulations are tight as evidenced by some of the huge recalls have demonstrated.
But here lies two problems.
The first is the fact that though lithium fires are relatively rare, the
LiFePO₄, THE INSURERS’ FAVOURITE
GCube advises developers to take into account that insurers prefer to underwrite LFP batteries over NMC batteries or consider other non-lithium options, due to their lower fire risk and higher safety.
“LFP has a wider operation
devastation that they create is usually a couple of orders of magnitude greater than regular conflagrations.
Lithium ion cells are prone to thermal runaway, a sometimes explosive chemical reaction caused by a number of factors, such as an internal short circuit, overheating through overcharging or due to external damage, from the cell being pierced or torn.
The second problem is how to ensure safety concerns are addressed as the battery chemistry becomes ever more ubiquitous. It is here that the balance between assessing the risks and insurance possible comes into play.
The ability of lithium ion cells to deliver high power quickly while storing lot of energy, along with their rapid commodification, has underpinned the growth in wireless mobile gadgets, appliances and tools and, more recently, personal mobility devices. Fire suppressant goods supplier Battery Fire Safety says, “Lithium-ion batteries are small and lightweight but are capable of storing a large amount of energy. They are volatile under stress. If damaged or incorrectly charged they can be a fire risk.”
International insurance firm Allianz has issued advice following what it describes as a significant increase in property fire claims caused by lithium ion batteries. It states that the highest risk of a fire occurring is when a battery:
• is being charged.
• is being transported, therefore at increased risk of damage has been damaged previously, as thermal
range than NMC, making it less thermally volatile. It’s also easier to remove pollutants and contaminants from the soil if a fire involved LFP batteries, compared with NMC,” says GCube’s Zeeshan Junedi.
runaway can occur hours, days or weeks later.
• has been abused from over-charging or continual charging and discharging.
EV FireSafe, which is funded by the Australian Department of Defence to research EV battery fires and emergency response, has produced a matrix to show what types of lithium ion battery fire risks can be found in daily use.
• Road registered electric vehicles (EVs, electric motorbikes): very low risk
• Battery energy storage systems, including home and commercial: very low risk
• Smaller devices (laptops, smartphones): moderate risk
• Utility task electric vehicles (vans, carts): moderate risk
• Personal mobility devices (electric scooters, bikes, skateboards): high risk
It also details how long, roughly fires for each category last: five to 30 minutes for a personal mobility device versus hours up to a few days for BESS fires.
Despite these differences in duration of fires, in terms of risk to life or property personal mobility devices and utility task electric vehicles are high risk, while smaller devices and road registered EVs have a moderate risk and battery energy storage systems have very low risk, according to EV FireSafe’s matrix.
EVFireSafe states that BESS installations carry the lowest fire risk
In New York the fire authorities are clamping down further on the way that e-bikes can be charged in apartment blocks — lithium battery energy storage systems have been banned in basements of residential and commercial buildings for at least a decade.
MANAGING LITHIUM SAFETY RISK
compared with other applications, thanks in part to their use of high quality (so-called tier one) batteries and other components. But when fires have occurred some have had serious consequences.
One event in Arizona, US, in 2019 hospitalized eight firefighters, some with chemical burns, while in 2021 two died trying to put out an energy storage fire in Beijing, China. Other notable blazes of BESS included
the Neoen-VBB fire in Australia in August 2021 when the fire at a Tesla Megapack installation set alarms about the speed of scaleups.
But it is also worth remembering most of these can be regarded as teething problems.
The container fire at a 20MW BESS blaze in Liverpool in November 2019 was Danish power company Ørsted’s first standalone grid-connected battery project, built using
storage system equipment supplied by the now-defunct Energy Solutions division of NEC Corporation, housed in three containers.
Similarly too, the ENGIE fire in November 2017 took place at an experimental site in Drogenbos (near Brussels) of a 20MW facility that took half a day to extinguish.
Perhaps the biggest headline came from a series of ESS fires in South Korea between 2017 and 2019
ONE IN THREE ELECTRICAL VEHICLE FIRES OCCUR IN PARKED VEHICLES ... WITH ‘NO OBVIOUS CAUSE’
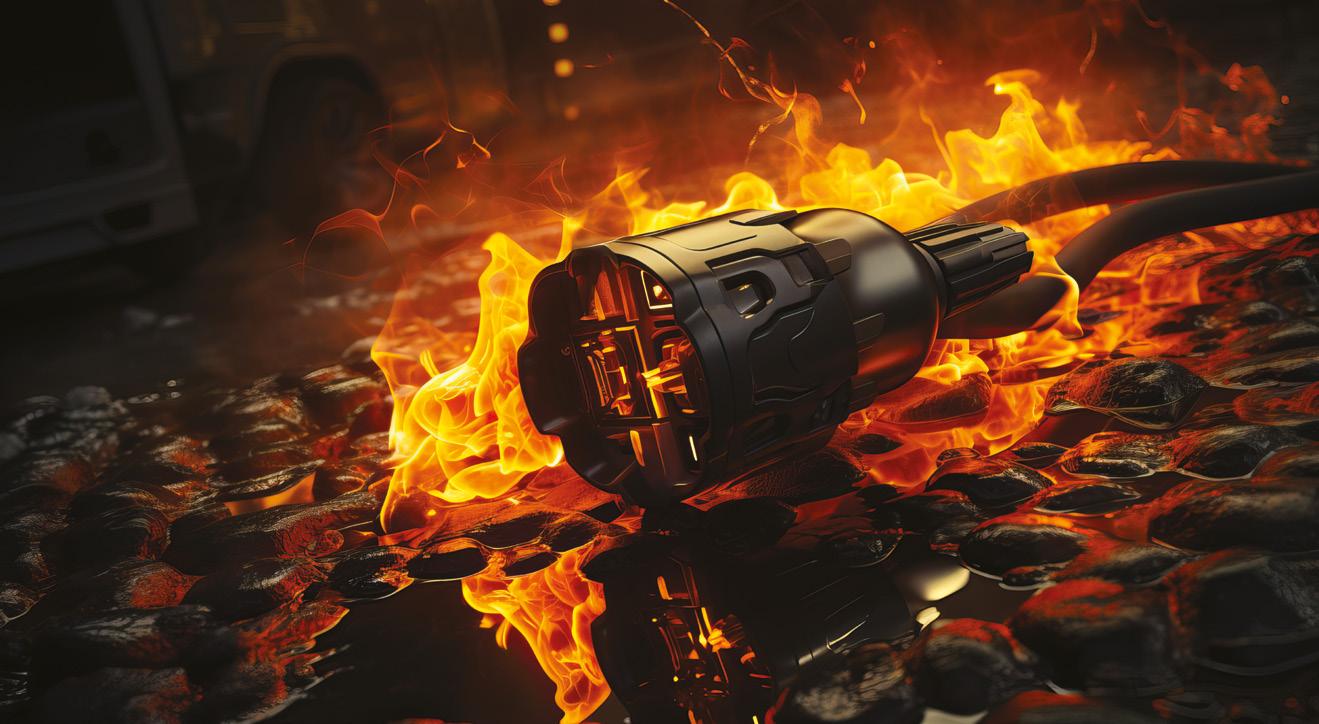
One in three electric vehicles fires has occurred with ‘no obvious cause’ while the car was parked, according to a 2021 report by research consultancy IdTechEx.
The startling figures show that 17% of EV fires occur in regular driving and a quarter occur when charging.
More predictably, 20% of fires occur in a crash situation or 4% when immersed in water when the reactive lithium is exposed to the air or water.
IdTechEx’s report —Thermal Management for Electric Vehicles 2021-2031 — also points out that the cost of recalls to solve problems continues to be hugely expensive and sometimes intractable to solve.
GM’s first recall of the Bolt in 2020, for example, entailed a call back of 69,000 cars produced between 2017-2019 for potential battery fires.
“The ‘solution’ was a software update limiting the battery capacity to 90% and an inspection of the battery,” says the report. “In 2021, two more Bolts have caught fire,
both of which had the recall.
“Continued investigation between GM and LG Chem has determined the cause is the ‘presence of two rare manufacturing defects in the same cell’. This has prompted another recall by GM to replace the battery modules.
“This recall is said to have cost GM around $11,000 per vehicle, totalling nearly $800 million.”
Other carmakers have faced similar bills. Hyundai, for example, recalled 82,000 EVs due to battery fire risk at an estimated $900 million. Much of this was paid for by LG Chem, the report says.
“Ford’s Kuga plug-in hybrid also faced issues with cells supplied by Samsung, resulting in a recall of 33,000 cars costing Ford approximately $400 million,” it says.
The effects of EV fires are typically far more severe than fires in conventional ICE vehicles.
A Tesla Model S fire required nearly 30,000 gallons of water to extinguish it because “it kept reigniting, burning continuously
for over four hours,” says one media report. By comparison, a typical car fire involving a ICE can be extinguished with about 300 gallons.
One effect of these high-profile fires and their severity is their press coverage, which runs contrary to the desire of governments and OEMs that have recently been setting out bold decarbonization targets based on energy storage for fossil-free renewables.
The reports concludes: “We expect EVs to continually improve in safety, there will always be the risk of a battery fire due to many potential causes. This presents an opportunity for those material suppliers making thermal interface materials, flame-retardant materials, or fire protection materials. These materials can help with the thermal management of EV batteries making it less likely they will overheat.
“Fire-retardant construction materials and fire protection materials are beneficial to enclose a fire or prolong the time between a thermal runaway event and the fire exiting the battery pack.”
Regulations are also evolving in the UK. China implemented new EV fire safety regulations at the start of the year, which include a five-minute warning between a thermal event and fire or smoke exiting the battery pack.
The EU also has various draft regulations with a similar focus. IDTechEx expects regulations in this field to become more stringent, presenting greater opportunities for material suppliers.
MANAGING LITHIUM SAFETY RISK
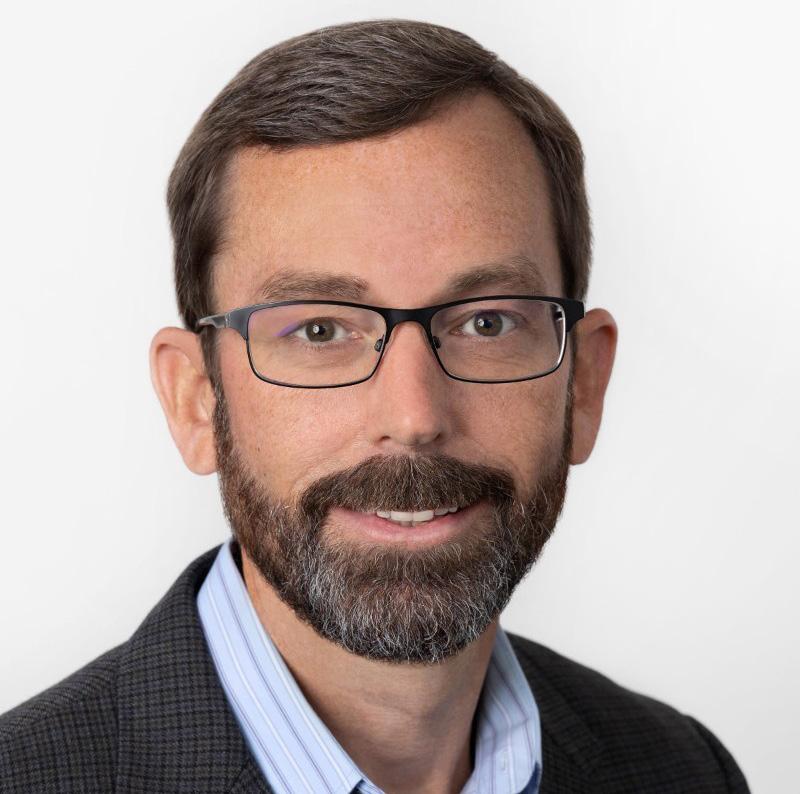
“A
holistic solution includes not just fire suppression for lithium ion batteries but this other equipment as well”
—
Brian Cashion, Firetrace International
where some 21 separate events resulted in the temporary shutdown of 584 facilities.
Compared with other renewable energy sectors, such as wind power and solar photovoltaics, the BESS industry is less mature. The last few years have been focussed on getting these assets built and connected to the grid.
Now data is emerging underscoring that more can be done to reduce failures and fire risks.
A study published by Clean Energy Associates (CEA) this February found that 26% of inspected energy storage systems had quality issues related to the fire detection and suppression system while 18% of inspected systems had quality issues related to the thermal management system.
Brian Cashion, an engineer at fire suppression systems provider Firetrace International, says: “As well as addressing lithium ion fires there is other equipment in the BESS that poses a fire risk, such as some of the power conversion equipment, chiller equipment and so on. A holistic solution includes not just fire suppression for lithium ion batteries but this other equipment as well.”
Firetrace is targeting US based and international players selling battery storage systems in the US. Maintaining proper exposures is crucial to
prevent any BESS fire from spreading to other containers or other nearby buildings or structures, Cashion says.
“It is also important to look at how batteries and ancillary components within the container are arranged and connected, such as spacing between modules, to prevent fire from happening or spreading.”
He says OEMs and systems integrators should be performing risk analyses looking at the design of the battery and the battery module, the unit as a whole and also the installation as a whole and doing hazard analysis to determine where risks are.
“We are seeing variations in requirements and standards, based on where BESS will be installed, not only within North America but internationally. It reflects the infancy of this market and lessons are being learned from events that have happened. As a result, codes and standards are being updated as the industry learns more so it is important to keep up with these as they change and in terms of what local authorities require,” says Cashion.
Thermal runaway and other failures are also more frequent in their early years of operation. More than half of BESS failures happen within the first two years of operation, according to fresh analysis published by renewable energy projects insurance underwriter GCube.
BESS projects are vulnerable to mechanical breakdown and serial defects. Adding a new dimension to risk management for the BESS industry is the threat of thermal runaway fire and off-gassing, says its report, Batteries not excluded — Getting the insurance market on board with BESS.
REASONS TO BE CAREFUL (PART 1)
The failure of lithium-ion batteries and the consequent risk of overheating and thermal runaway can be caused, among other things, by:
• Internal design or manufacturing defects, such as, for example, material defects (electrode, separator, electrolyte), contamination, assembly, or construction faults
• Physical damage during construction, assembly into finished products, shipping, handling, waste disposal or during use; whether accidental or malicious
• Physical damage with mechanical effects, such as crushing, excessive vibration, impact
• Rapid degradation of batteries over time
• Undetected ageing and subsequent internal short circuit
• Effect of use:
— Rapid charging
— Discharging the device faster than necessary
• Use or storage in wet environments
• Thermal effect:
• Exposure to high temperatures
• Exposure to flames
• Heat from adjacent or nearby cells
• Low temperatures, mainly during charging
• Electrical effect:
— Excessive overcharging or over-discharging
— Short circuits
“From extensive discussions with the industry, involving companies that specialize in condition monitoring of BESS, the likelihood of thermal runaway is highest at first power/commissioning phase and then during the initial operation of the system, within that first two years. This is likely due to the changes in battery cells being picked up via the BMS and monitoring software,” says Mohammed Zeeshan, an underwriter at GCube.
GCube’s analysis draws upon
Compared with other renewable energy sectors, such as wind power and solar photovoltaics, the BESS industry is less mature. The last few years have been focussed on getting these assets built and connected to the grid. Now data is emerging underscoring that more can be done to reduce failures and fire risks.
MANAGING LITHIUM SAFETY RISK
a decade of public data sourced from the US-based Electric Power Research Institute’s BESS Failure Event Database, which reveals that the market now sees around 10 failures reported on average each year — a 10-fold increase compared with 2016.
Failures, including those resulting in fires, are likely to continue to increase but this will be due to more BESS installations in operation than at any other time.
Critical design considerations
When designing the BESS layout, ample spacing between battery modules, racks, containers, or buildings can mitigate fire and explosion risks. Anything less 2.5 metres between containers or clusters significantly affects insurers’ exposure.
Measures that mitigate fire risks in BESS design mean insurers look on them more favourably and that can also be relevant to battery safety management plans, which developers should submit as part of their planning applications.
These might be elevation of the BESS in case of flood risk, vegetation management, especially during the summer to reduce fire hazards, and ensuring that the local fire department has good access so that a truck can come in so that the fire can be managed if not put out. Seismic considerations are now also being taken into account.
Maintaining proper exposures is crucial to prevent any BESS fire from spreading to other containers or other nearby buildings or structures, Cashion says, “It is also important to look at how batteries and ancillary components within the container are arranged and connected, such as spacing between modules, to prevent fire from happening or spreading.”
OEMs and systems integrators should be performing risk analyses looking at the design of the battery and the battery module, the unit as a whole and also the installation as a whole and doing hazard analysis to determine where risks are.
In the event of project failures, the least likely cause is cell failure, while a higher probability is linked to BMS failure and the non-cell related infrastructure such as cabling or where connections are terminated, says Zeeshan. “As the containerized BESS space and projects are quite new, it will be over a year to 18 months or more till we have sufficient data to establish accurate trends on why failures, including fires, occur,” he says.
Looking to the future, he believes one area with lots of potential to improve the safety of BESS assets is the use of software. “The BMS has attracted a keen focus and is where we believe investment should be made. But it is also promising to see companies that have developed condition monitoring software.”
This can process data from multiple individual BMS in each container across various projects and sites, to generate comparative analysis. “This means that you are not only flagging an event, such as cells in a rack in a container crossing a temperature threshold, but also the action that needs to be taken,” Zeeshan says.
One of the worst things you can do to a lithium ion battery cell is crush it, pierce it or tear it. In a lithium ion cell, the cathode and anode electrodes are physically separated by the separator. Any defects or damage, from an external force that compromises the separator’s integrity can cause an internal short circuit leading to thermal runaway.
While batteries are manufactured with controls for protecting against this happening, in certain environments where these controls are not incorporated or are damaged such as during processing of waste for example, chances of thermal runaway are increased.
Waste fires too
Worldwide evidence is mounting that lithium waste fires are on the rise. Exact up-to-date data, that is standardized is hard to find but in 2021 the UK-based Environmental Services
We are seeing variations in requirements and standards, based on where BESS will be installed, not only within North America but internationally. It reflects the infancy of this market and lessons are being learned from events that have happened

“In the event of project failures, the least likely cause is cell failure, while a higher
probability is linked to BMS failure and the non-cell related
infrastructure”
— Mohammed Zeeshan, G Cube
Association (ESA) and Eunomia published a report suggesting that lithium ion batteries cause 201 waste fires, equating to 48% of all waste fires occurring in the UK each year, at a cost of around £158 million annually, up from 25% in 2016.
The ESA told this magazine that although an update to this figure was being updated, the clear trend was that this was on the increase. In many ways this is to be expected given the greater number of lithium batteries in circulation.
Battery Council International has been campaigning for almost a decade about better labelling and standardization of lithium batteries given that greater numbers are entering lead recycling battery streams across North America over the past years.
It says there are genuine concerns that explosions and runaway fires in lead battery processing facilities will maim or kill employees.
According to ESA executive director Jacob Hayler, carelessly discarded batteries are responsible for at least one significant fire at a recycling and waste management facility in the UK every day.
Electrochemical impedance spectroscopy continues to offer further insights into the heart and performance of batteries, writes Isidor Buchmann, CEO and founder of Cadex Electronics.
EIS and Nyquist plotting analysis opens up inner battery dynamics
New technologies often lead to innovative blind spots, and this is happening with electrification in batteries.
Lithium-ion batteries, for example, are a winning chemistry to store electrical energy in many ways but there is fear of failure that often starts in a faulty cell that propagates and engulfs the battery in fire. Such incidents are becoming well known with e-bike batteries and other devices.
Cadex is developing a technology that reads the electrochemical evidence of a battery with a frequency scan and displays the results in a Nyquist plot.
Figure 1 demonstrates Nyquist plots taken from 100 high-quality 8650 Li-ion cells with Spectro Explorer.
The Spectro Explorer services Li-ion and lead acid batteries from 3V to 48V with capacities of up to 300Ah. The test is minimally-invasive with a frequency scan from 2,000Hz down to 0.1Hz that takes about 30 seconds; longer for large batteries.
Applications for the Explorer are quality control in manufacturing, examining uniformity of incoming batteries, and battery validation before shipment. Best results are achieved with preparations such as a prior full charge, followed by a short rest.
Dormant lead acid batteries develop sulfation, a deficiency that can be removed with battery exercise if the sulfation is soft. Hard sulfation that occurs during long dormancy at low charge can be permanent.
Primary lithium batteries also develop passivation while in storage. The passivation layer is removable with a brief discharge. These are added services that a Nyquist scan can discover.
What
is
a Nyquist plot?
A Nyquist plot consists of a resistive reading (Real Z) that is positioned on the horizontal axis, and a reactive analysis placed on the vertical axis. The resulting signature reflecting battery characteristics is divided into migration at high frequency on the left of the scale; charge transfer in mid-range; and diffusion at low frequencies on the right.
Figure 2 illustrates a Nyquist plot serving as “golden sample” with adjustable pass/fail envelopes to set
Dormant lead acid batteries develop sulfation, a deficiency that can be removed with battery exercise if the sulfation is soft. Hard sulfation that occurs during long dormancy at low charge can be permanent
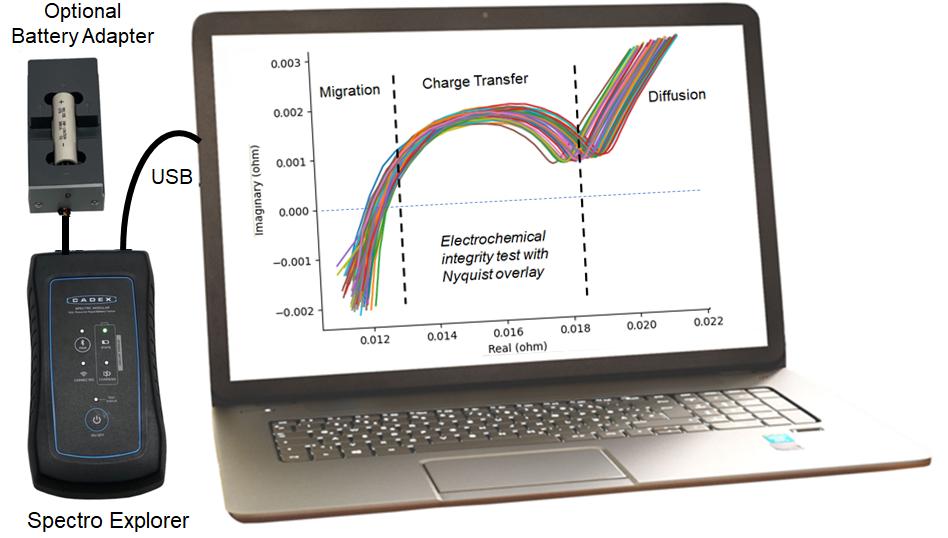
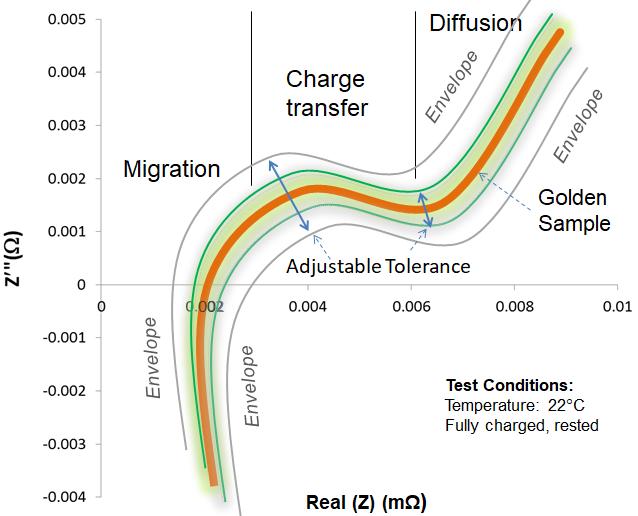
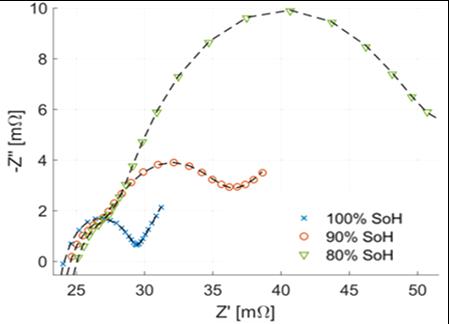
BATTERY TESTING: EIS
PUTTING IT ALL TOGETHER
Testing batteries by EIS is not new, but scientists predict that future battery diagnostics rests in EIS analysis. Evaluation by Nyquist using the Spectro Explorer has the potential of becoming a household name, led by versatility, ease of use and low cost. Using these technologies will reduce innovative blind spots to maintain safety as the world electrifies with batteries.
Typical EIS applications include:
• Research labs: checks cathode and anode materials with additives.
• Manufacturing: evaluates consistency between battery batches.
• Quality control: verifies incoming batteries and warranty claims.
• Environmental: Tests battery aging under extreme temperatures.
• Stress test: observes capacity-loss under abusive load conditions.
• Safety: detects dendrites and lithium plating in an integrity check
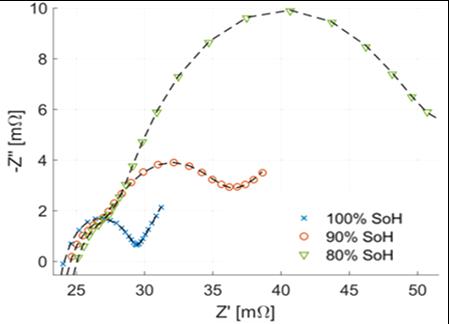
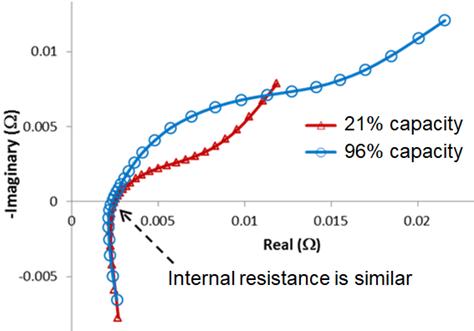
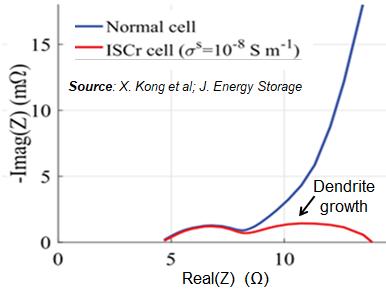
Lead acid batteries stored for six months or longer develop sulfation; a dormancy effect that reduces performance but is reversible by exercise if done in time
acceptance levels for quality control in manufacturing and performance check before deployment.
Figures 3 compares Nyquist plots with different battery performances, Figure 4 overlays a Nyquist plot of a good battery with one of low capacity and Figure 5 illustrates a battery with dendrite growth. Figure 6 compares a Nyquist signature of aged lead acid batteries with sulfated packs. Unless otherwise noted all readings were taken at the Cadex labs in Canada and Germany.
Lead acid batteries stored for six months or longer develop sulfation; a dormancy effect that reduces performance but is reversible by exercise if done in time.
Figure 7 shows the Nyquist plots of a lead acid battery that had a low charge transfer with a capacity reading of 75% when first serviced. After exercise with a charge/discharge cycle, charge acceptance improved and the capacity increased to 92%. Other lead acid
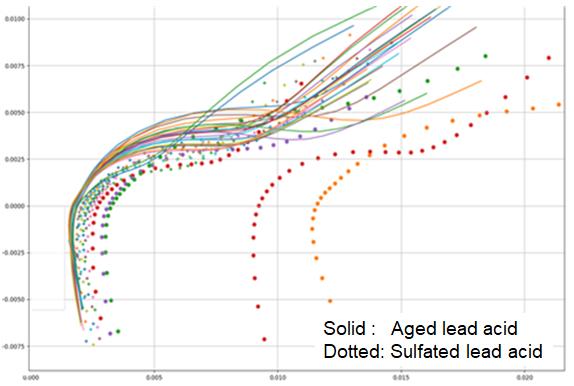
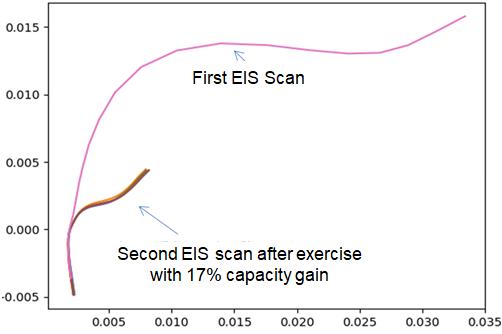
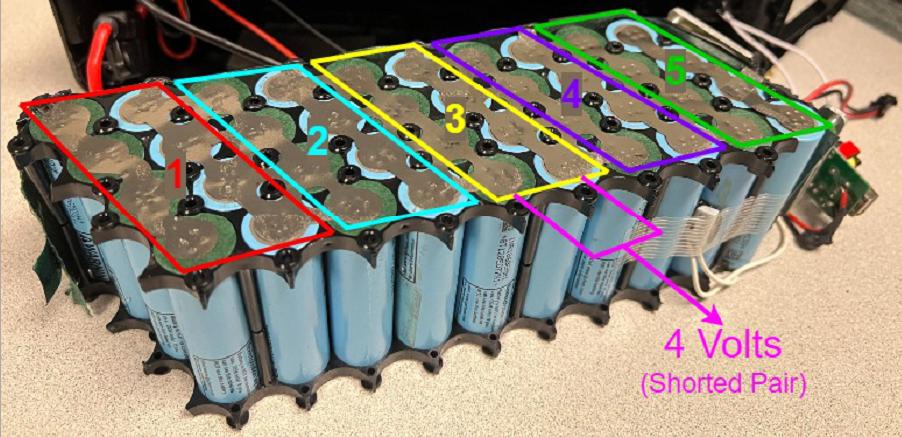
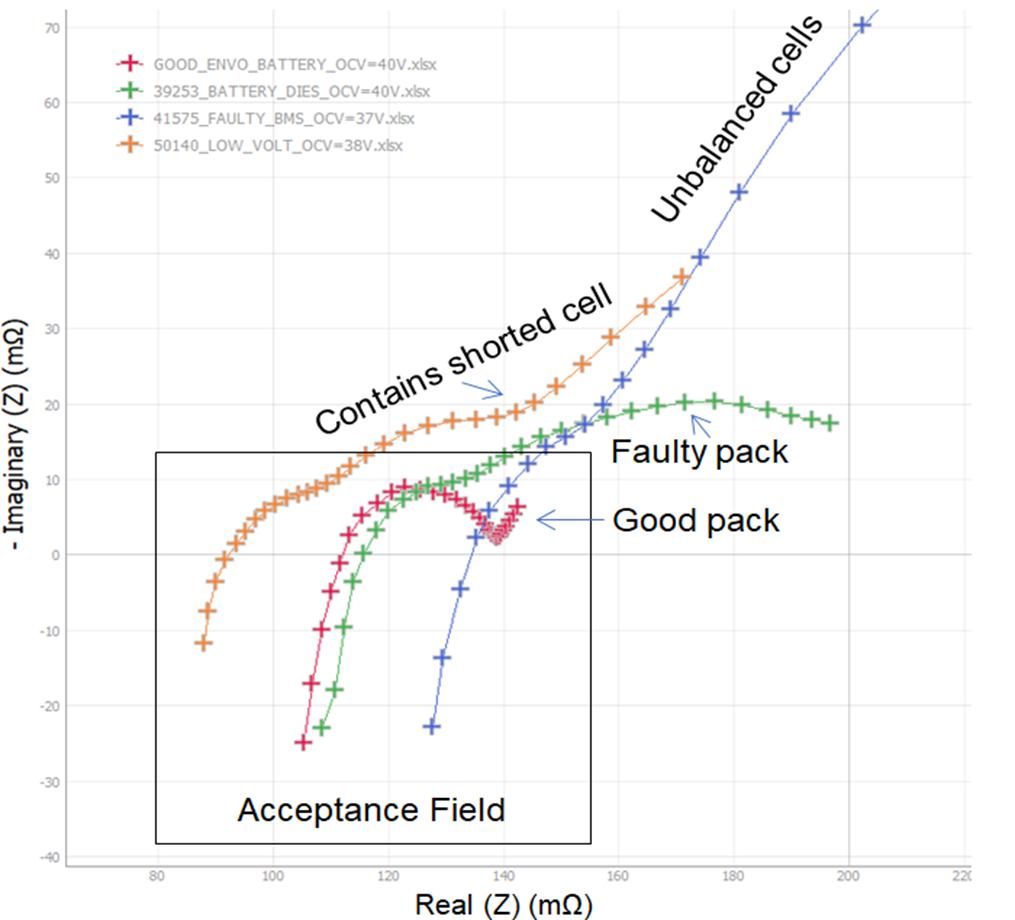
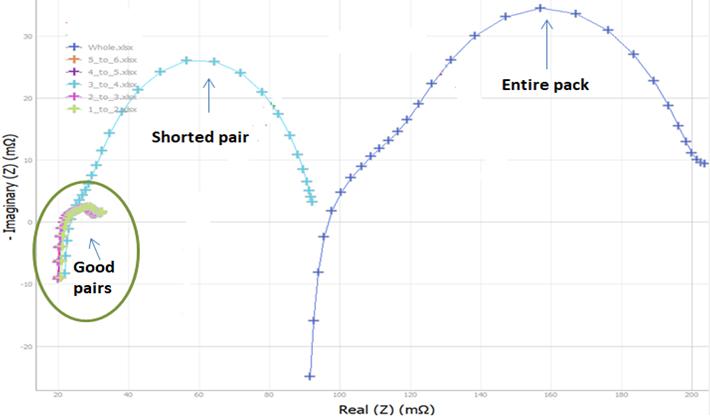
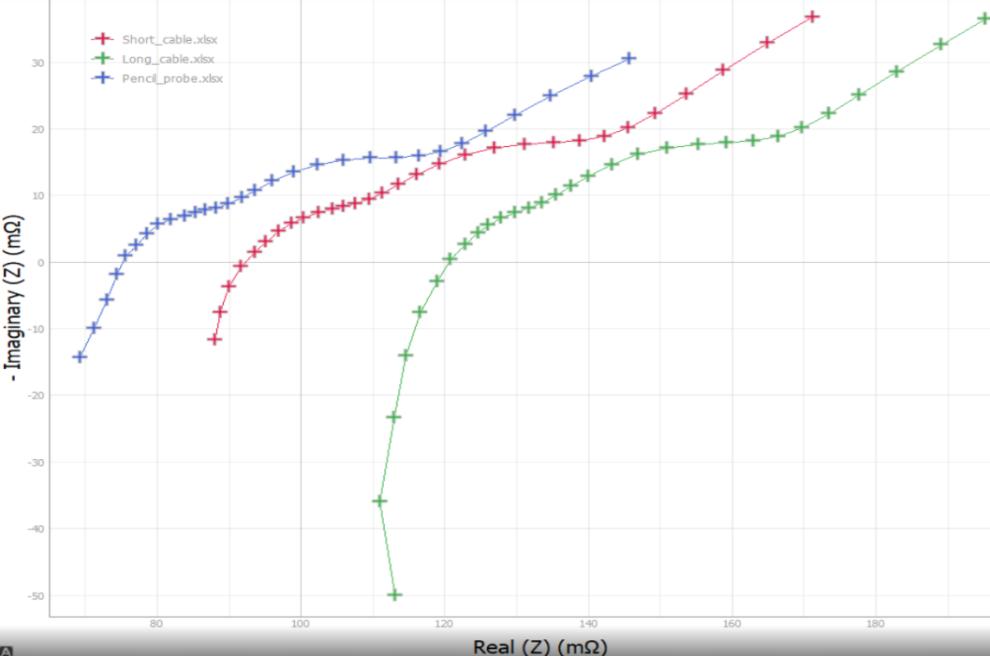
batteries tested with various dormancy effects had similar improvements. More studies are needed in how the Nyquist can identify sulfation that lead to restoration
Testing E-bike batteries
E-bike batteries are failing and in some cases catching fire. However, handled correctly, Li-ion is safe but the chemistry is less forgiving than lead acid and nickel-based chemistries.
We now scan batteries with the Explorer in an entire pack, as well as in parallel pairs. Figure 8 shows an open e-bike battery; Figures 9, 10 and 11 show the test results.
With acquired knowledge, a Nyquist plot can easily be deciphered by technical staff. The task is simplified by comparing a faulty pack with a good one, knows as golden sample.
As Figure 9 illustrates, a normal pack has a small footprint that is contained in the user-adjustable Acceptance Field, while a faulty battery steps outside set limits. The shapes of the “cat tails” may one day lead to identifying the nature of defect
Figure 10 shows an entire pack with one cell shorted. The graph also does a comparison with a parallel pair in which all cells are good as shown in the small oval. Adding one bad apple changes the order.
Protection circuit and series connections add non-reactive resistance that shift the Nyquist plot of the pack to the right.
Mixing non-reactive resistance with the reactive component of a battery is further exemplified in Figure 11. Here the protection circuit and long cables move the Nyquist plot to the right while retaining the signature of the Nyquist plot. The shift reflects the pure resistive part of the battery that will also assist in troubleshooting.

Buchmann is the founder and CEO of Cadex Electronics. For three decades, Buchmann has studied the behavior of rechargeable batteries in practical, everyday applications, has written award-winning articles including the best-selling book Batteries in a Portable World, now in its fourth edition.
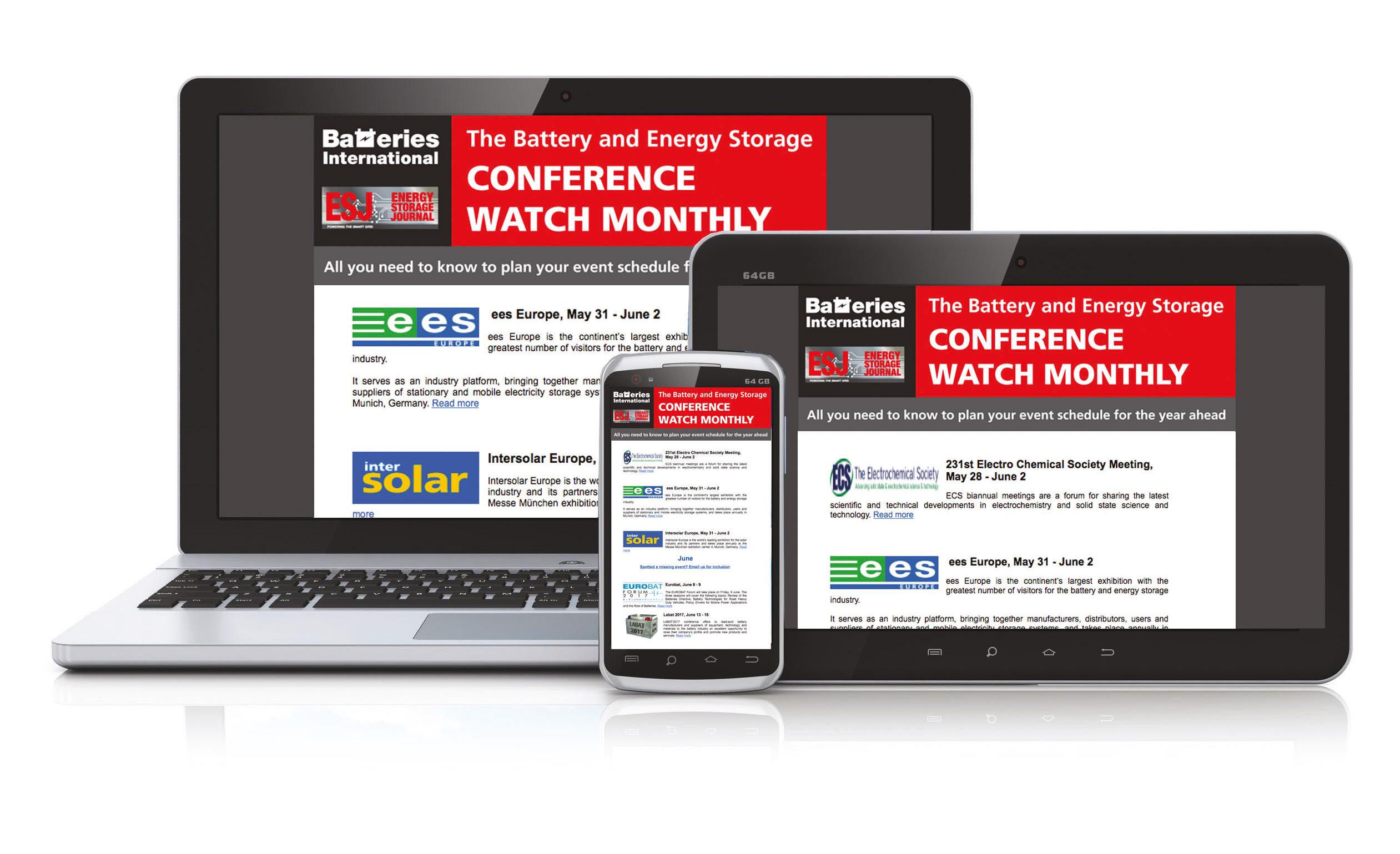
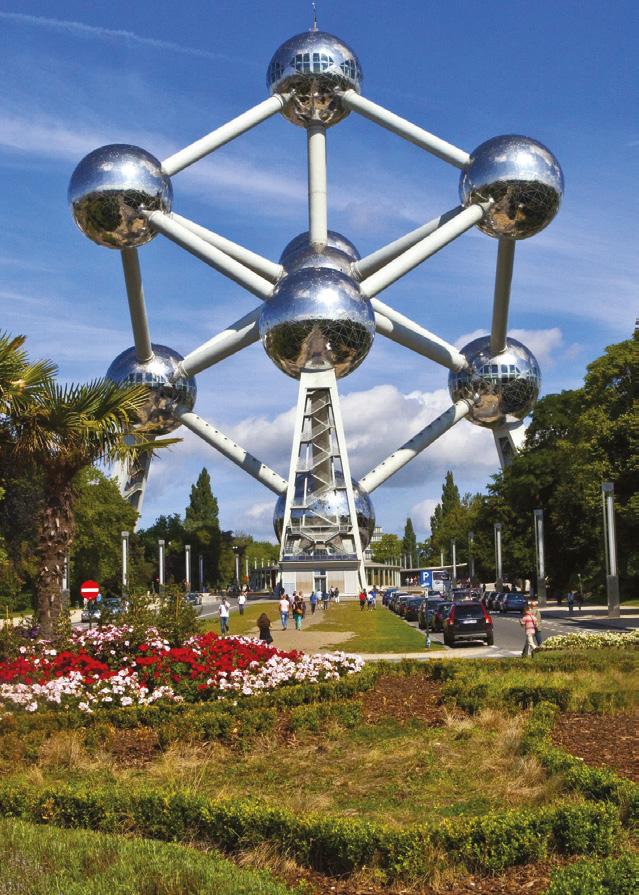
International Renewable Energy Meet
May 17 – 19 Lahore, Pakistan
The International Renewable Energy Meet is a gathering of leaders and international stakeholders driving the renewable energy transformation. This must-attend event will bring together the entire renewable value chain to discuss the latest technologies and solutions, low-carbon energy production, logistics, efficient storage, transportation, hybrid infrastructure, advanced design, research and development, manufacturing and overall development in the field of renewable energy.
Contact White Paper Summits www.iremexpo.com
Automotive Europe 2024
May 22 – 23 München, Germany
Automotive Europe 2024 will address the biggest disruptions in the industry across two stages: Automotive Tech and Electrification. Where there is disruption, there is opportunity. Through panel discussions, interactive workshops, and roundtable discussions, this event will lay out the automotive agenda in Europe for the years to come through sharing of knowledge and collaboration.
Contact Reuters Events www.events.reutersevents.com/ automotive/automotive-europe
EUROBAT Forum
June 4 – 5
Brussels, Belgium
The EUROBAT Forum is the annual event of the association of European automotive and industrial battery producers, bringing together more than 100 key European automotive and industry stakeholders, including senior company executives, policy-makers, association and NGO representatives and more.
In 2024, the two-day event will take place on June 4 and 5 in Madrid at the Hotel Melia Princesa.
Contact Gert Meylemans, General Manager E: gmeylemans@eurobat.org www.eurobat.org
Battery and Critical Metals Recycling Conference
June 17 – 18
Atlanta, Georgia, USA
Immerse yourself in the battery and critical metals conference agenda, which is brimming with sessions designed to provide you with valuable insights, innovative concepts, and actionable strategies that can be directly applied to your operations.
Contact
GIE Media & Recycling Today Events E: conference@gie.net www.batteryrecyclingconference.com
The Battery Show Europe
June 18 – 20
Stuttgart, Germany
The Battery Show Europe provides attendees the chance to explore the latest products and solutions at the largest trade fair in Europe. The only place to find all your supply chain contacts in one place — from raw materials to battery recycling.
Join Peers at the Leading Meeting Place for the Advanced Battery and H/EV Technology Community and meet manufacturers, suppliers, engineers, thought leaders and decision-makers for a conference and trade fair focused on the latest developments in the advanced battery and automotive industries.
Contact Informa Markets
E: thebatteryshowcs@informa.com www.thebatteryshow.eu
International Automotive Recycling Congress — IARC
June 19 – 21
Antwerp, Belgium
Calling all automotive recycling industry specialists! IARC 2024 gives you the unique opportunity to hear and exchange with industry leaders and pioneers in a privileged business environment.
IARC is the international platform for discussing the latest developments and challenges in circular economy and automotive recycling.
We bring together up to 300 decision-makers from the automotive and recycling sectors –car manufacturers, metal suppliers, traders, recyclers, shredder operators, and policy-makers.
Contact ICM AG
E: info@icm.ch www.events.icm.ch/event
SAVE THE DATE ees Europe
June 19 – 21 Munich, Germany
Discover future-ready solutions for renewable energy storage and advanced battery technology at ees Europe! Europe’s largest, most international and most visited exhibition for batteries and energy storage systems is the industry hotspot for suppliers, manufacturers, distributors, and users of stationary electrical energy storage solutions as well as battery systems.
In 2024, more than 450 suppliers of products for energy storage technology and systems will be present at ees Europe and the parallel exhibitions of The smarter E Europe taking place in Munich. The exhibition will be accompanied by a two-day energy storage conference where leading experts delve into current questions of this industry.
Contact
Solar Promotion GmbH
E: thesmartere@fwtm.de www.ees-europe.com/home
UPCOMING EVENTS

International Flow Battery Forum — IFBF
June 25 – 27
Glasgow, Scotland
In June 2024 the IFBF will hold its thirteenth in-person conference in Scotland, supported by Invinity Energy Systems and Flow Batteries Europe.
Over three days the conference will feature talks, panel sessions, open discussions, networking breaks, a poster session, conference dinner and a local site visit. We will discuss the latest innovations, policy updates and market challenges for the development of the flow battery sector.
Business leaders, policy makers, developers and researchers will share information and forecasts around the thriving world of energy storage and the important role of flow batteries.
Contact Swanbarton
E: info@flowbatteryforum.com www.flowbatteryforum.com
Battery Recycling Conference and Expo
June 26 – 27
Messe Frankfurt, Germany
Battery Recycling Conference & Expo 2024 is the must-attend event for battery producers, recycling companies, critical raw material suppliers, and the entire battery supply chain to come together on a single platform.
Discover the latest innovations and solutions to create a circular economy for used batteries and help create sustainable supply chains for the future.
Contact Transglobal Events
E: info@trans-worldevents.com www.batteryrecycling-expo.com
India Energy Storage Week — IESW
July 1 – 5
New Delhi, India
India Energy Storage Week (IESW) is a flagship international conference & exhibition organised by India Energy Storage Alliance (IESA)
It is India’s premier B2B networking & business event focused on renewable energy, advanced batteries, alternate energy storage solutions, electric vehicles, charging infrastructure, Green Hydrogen, Battery Manufacturing & Supply Chain and micro grids ecosystem.
The forthcoming edition of IESW is expected to attract global participation with an intent to facilitate bi-lateral trade, which will invite 30+ countries, 100+ regulators & policy makers, 1000+ industry leaders, 150+ partners & exhibitors.
Contact
India Energy Storage Alliance — IESA www.energystorageweek.in
Energy Storage Asia
July 9 – 10
Singapore
The Asia-Pacific region plays a pivotal role in the global battle against climate change. Every country in the region has the power to spur on the transition and deploying more energy storage will play a huge part in this.
The Energy Storage Summit Asia promises a diverse and exciting event filled with investors, developers, policy makers, solutions providers and networks who will help guide you in the right direction.
Contact Solar Media www.storageasia.solarenergyevents.com
5th EV Charging Infrastructure
Summit North America
July 15 – 17
Chicago, USA
Organized by the Smart Grid Observer, the Summit convenes top industry experts and utility professionals to examine how EV adoption rates will impact the network, and what investments are needed to ensure grid stability and benefit.
Case studies of current utility programs and deployment will be discusses with an eye toward refin-
ing strategies, identifying technologies, and implementing business models that will ensure widespread EV adoption is optimised for all parties involved.
Contact
Smart Grid Observer
Daniel Coran, Editor
E: dcoran@smartgridobserver.com www.smartgridobserver.com/EV-SummitChicago/
Plugvolt Battery Seminar
July 16 – 18
San Jose, California, USA
Conference fostering joint development efforts to advance energy storage solutions
Key Event Highlights:
• Entire day of in-depth technical tutorials on solid-state batteries, next-gen anodes and cathodes, battery diagnostics, failure modes and best design practices for cell engineering, securing North American supply chain for gigafactories, etc.
• Latest industry updates on use of energy storage systems in automotive applications by subject matter experts from major OEMs, Tier 1 system developers and battery makers
• Latest industry updates on use of energy storage systems in largescale stationary grid/utility storage applications by subject matter experts from major Utility companies, Tier 1 system developers and providers
• Poster presentations
• Complimentary meals and refreshments
• Plenty of industry networking opportunities
• An evening cocktails reception hosted by Exponent
In an era of radically-accelerating change, Exponent is the only premium engineering and scientific consulting firm with the depth and breadth of expertise to solve your most profoundly unique, unprecedented, and urgent challenges. Event attendees will get an exclusive opportunity to ask questions to their resident battery experts, and enjoy some light appetizers and beverages while networking with industry peers.
Contact Plugvolt www.batteryseminars.com
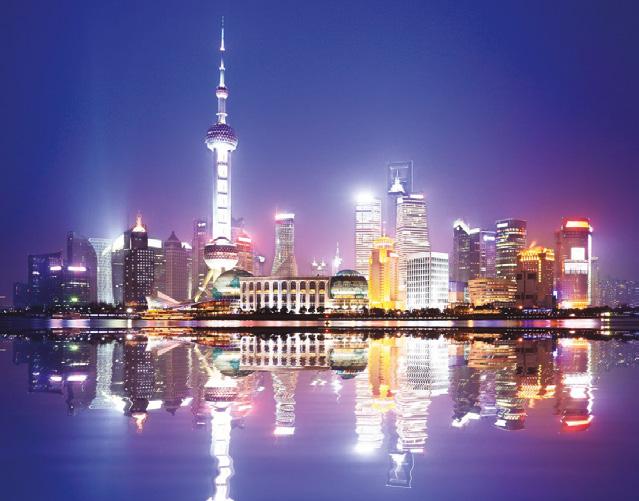
Shanghai, China
CNIBF Battery Exhibition
August 2 – 4
Shanghai, China
In order to promote the innovative development of the power battery industry and the exchange and cooperation between the power battery industry chain, the 16th Shanghai International Battery Industry Exhibition in 2024 will be held in Shanghai New International Expo Center on August 2 – 4, 2024 to build a platform for the cooperation and exchange of the whole industrial chain of north-south power batteries.
The show area is expected to reach 30,000 square meters, while more than 600 exhibitors from the whole industry chain will show their latest products and technology at the scene.
Furthermore, over 100 visitor groups and 35,000 people are going to visit the site with a purpose to purchase or communicate, making sense to promoting industrial innovation and development.
Contact Zhenwei Exhibition Group www.cnibf.net
Oslo Battery Days Conference
August 19 – 21
Oslo, Norway
The 6th OBD Battery Conference will meet to discuss and provide a platform for technological innovations and business opportunities with the latest updates in that field from Norway and abroad.
For the 2024 event we will offer a spectacular Monday-evening on at the beautiful Akershus Fortress and for the second evening we plan for a Fjordcruise on the fully electric vessel “Legacy of the Fjords”.
Contact Schive AS and Shmuel De-Leon Energy Ltd www.oslobatterydays.com/
SAVE THE DATE
ees
South America
August 27 – 29
São Paulo, Brazil
With three parallel energy exhibitions, The smarter E South America is LATAM’s innovation hub for the new energy world. It takes a comprehensive approach to the topics of the energy system transformation by presenting cross-sector energy solutions and technologies.
The smarter E South America creates opportunities to address all key areas along the value chain. Focusing on the generation, storage, distribution and use of energy and the ways in which these aspects interact and can be intelligently combined, The smarter E South America brings together international stakeholders of the energy future from across the world’s most influential markets.
Contact Solar Promotion www.ees-southamerica.com/home
SAVE THE DATE
ees Mexico
September 3-5
Mexico City, Mexico
ees goes Mexico — this year with a special exhibition and a dedicated ees Pavilion at Centro Citibanamex during Intersolar Mexico 2024, taking place from September 3-5 in Mexico City!
The ees Mexico special exhibition offers various exhibit opportunities tailored for every budget. Design your own stand or book a fully equipped stand and pavilion pod which allows your company an easy participation without any organizational efforts. Build your network in Mexio and concentrate on your business, while we facilitate the rest.
Contact Solar Promotion https://www.intersolar.mx/home
International Congress for Battery Recycling — ICBR September 10 – 12 Basel, Switzerland
ICBR 2024 is the international platform for reviewing the challenges faced by the Battery Recycling Industry on a global basis.
For 29 consecutive years, ICBR has brought together the international community of experts and decision makers of the entire Battery Recycling value chain, including battery recyclers and manufacturers, collection organizations, OEM’s, policymakers, materials and services providers and many more.
Contact ICM AG www.events.icm.ch/event
ELBC — The Global Lead Battery Innovation Conference and Expo
September 16 – 19
Milan, Italy
ELBC is the major lead battery innovation conference, bringing together global lead battery experts, researchers, companies and suppliers. The conference’s technical program showcases the latest updates on technical improvements and electrochemical research on topical areas from energy storage to automotive lead batteries.
Now in its 38th year, ELBC is expected to attract over 1000 attendees interested in lead battery innovation.
Contact
International Lead Association and the Consortium for Battery Innovation E: elbcexpo@ila-lead.org www.elbcexpo.org
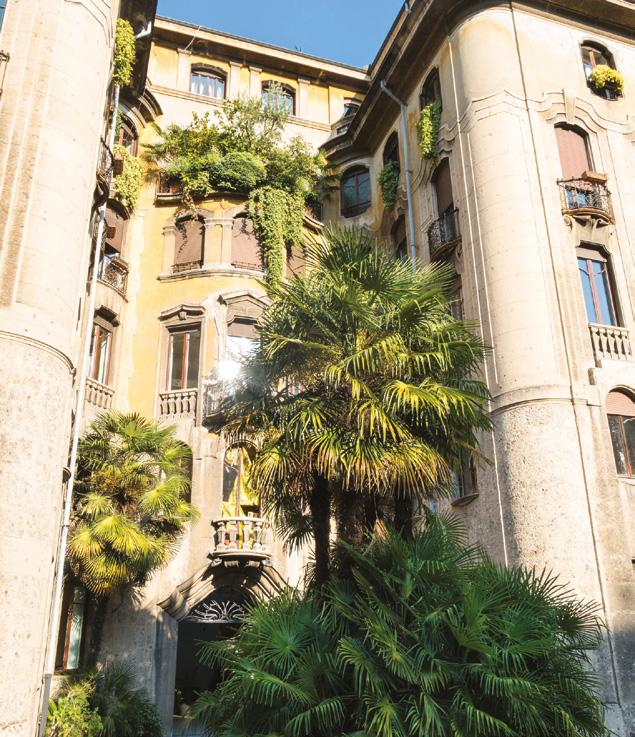
Milan, Italy
UPCOMING EVENTS
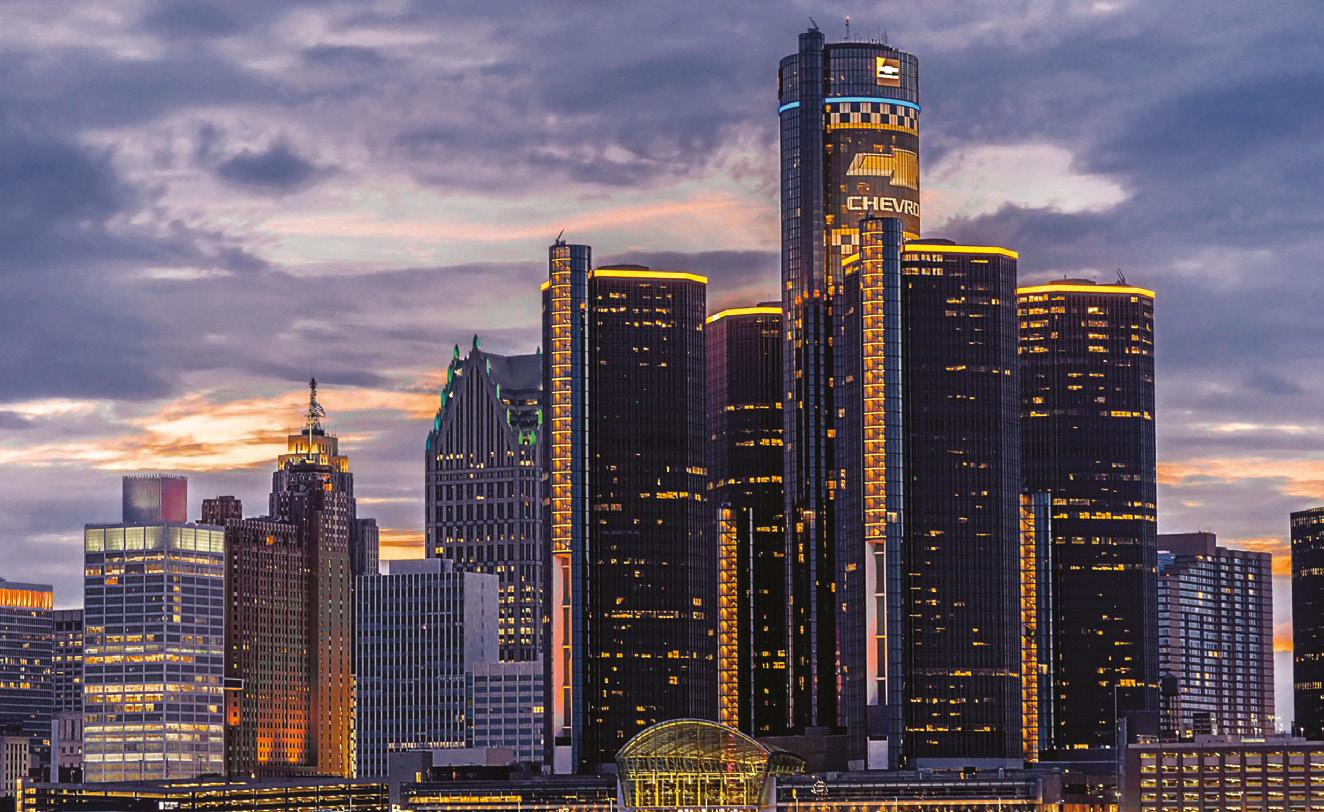
Battery Show North America
October 7 – 10
Detroit, Michigan, USA
Discover the Latest Tools, Trends, and Technologies at The Battery Show and EV Tech Expo.
Connecting expert industry leaders, top battery manufacturers and inquiring buyers all under one roof! Get ready to learn about and explore the latest advancements in battery and electric vehicle technology in 2024.
Contact Informa Markets www.thebatteryshow.com/en/home.html
Batteries Event
October 15 – 17
Lyon, France
The Batteries Event will cover all aspects of the circular economy value chain, starting from the production of the battery through raw materials, cell manufacturing, use and safety, management and applications, going through market trends, research and development, new technologies and finally closing the loop with a focus on recycling, second life and regulations.
International battery industry key players such as OEM, cell and pack manufacturers, end users, experts, researchers and recyclers will come together to discuss and exchange on new chemistries, manufacturing process, battery components, battery second life, recycling, regulation, future expectations and innovations.
Contact AVICENNE Energy www.batteriesevent.com
October 21 – 23
Detroit, USA
Join Reuters Events for Automotive USA 2024 for 2 days of in-depth conference discussions across two stages with the industries most advanced and disruptive leaders. From new market entrants and spinoff business units to legacy OEMs, this is the place to be for the latest technological advancement.
Contact
Reuters Events www.events.reutersevents.com/automotive/automotive-usa
The Energy Management Exhibition — EMEX
November 20 – 21 London, UK.
EMEX is the UK’s must-attend energy event for everyone wanting to increase their organisation’s energy efficiency and reduce carbon emissions.
EMEX connects all commercial energy consumers with leading experts, policy makers and suppliers. EMEX is more than just an event. It’s a platform where practitioners and experts from various backgrounds and sectors are coming together to share their knowledge and experiences from successful implementations of energy efficiency strategies. Whatever the size of your business there is an opportunity to find more efficiency in your energy use.
Contact MA Exhibitions www.emexlondon.com
Global Automotive Components and Suppliers Expo
December 3 – 5
Stuttgart, Germany
Global Automotive Components and Suppliers Expo is the only show in Europe dedicated to showcasing automotive components and component suppliers, making it the must attend event for all automotive OEM and Tier 1 procurement managers, component specifiers and engineers.
Contact
UKi Media and Events
www.globalautomotivecomponentsandsuppliersexpo.com/en/
Battery Bharat
December 6 – 8
Bengaluru, India
Battery Bharat will bring together from world over leading battery manufacturers interested in technology and business cooperation, battery equipment and component manufacturers, experts in waste management and in environmentally sound technologies for the recycling of batteries, recycling equipment manufacturers and recyclers.
Contact
Battery and Recycling Foundation International www.bfi.org.in/index.htm
Advanced Automotive Battery Conference USA — AABC USA
December 9 – 12
San Diego, California, USA
AABC was founded more than 20 years ago to review the status of automotive battery technology and provide informed glimpses into the future. The program will uncover the underlying technical and business issues that will impact the pace and path of vehicle electrification worldwide.
Join us to network with chief battery technologists from some of the world’s leading automotive OEMs, who will share their development trends and projected battery needs, as well as their key suppliers who will present their latest offerings and roadmaps for the future.
Contact Cambridge Enertech — CET www.advancedautobat.com/us
www.ees-events.com
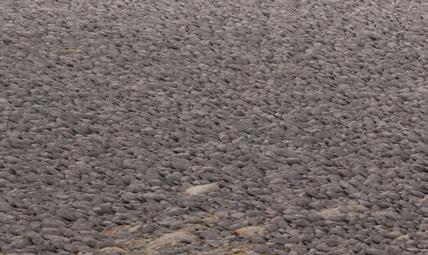
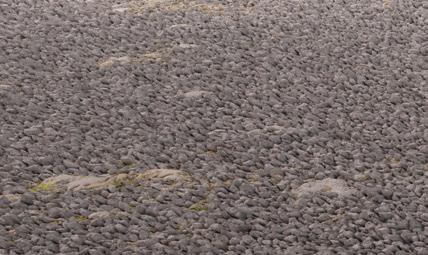
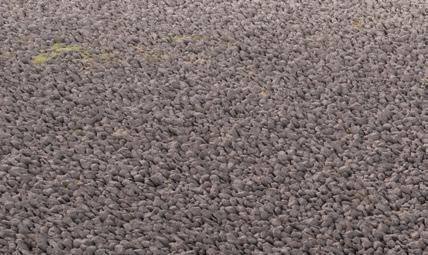
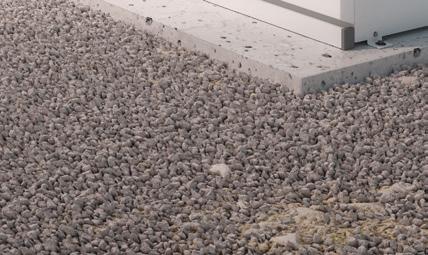
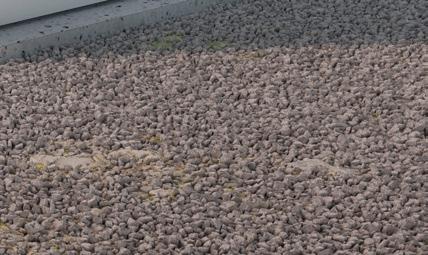
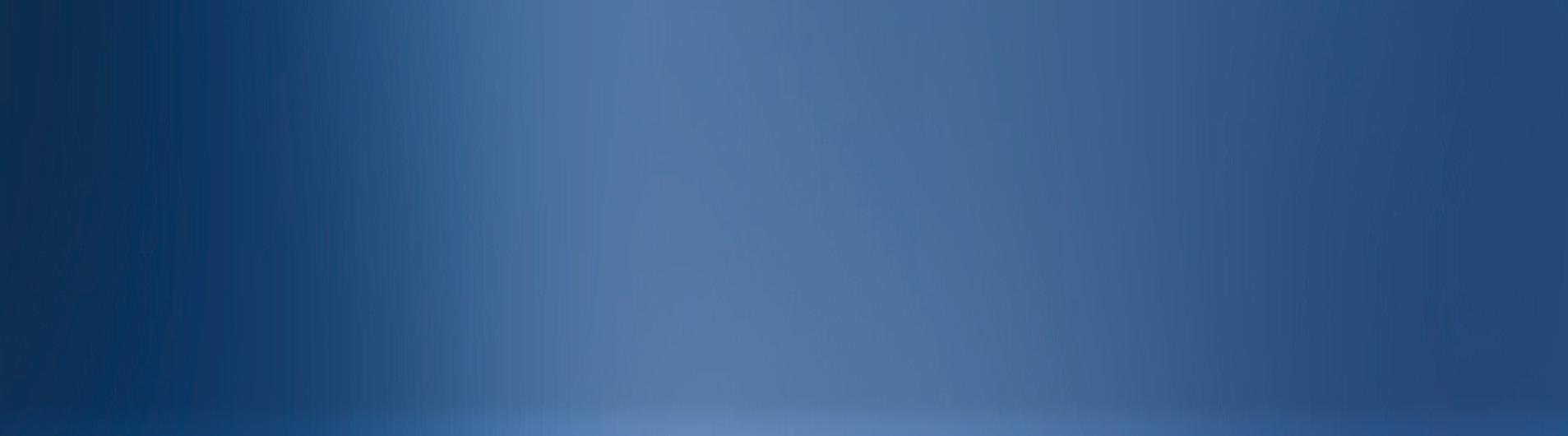
■ JUNE 19–21, 2024, MUNICH, GERMANY www.ees-europe.com
■ AUGUST 27–29, 2024, SÃO PAULO, BRAZIL www.ees-southamerica.com
■ SEPTEMBER 3–5, 2024, MEXICO CITY, MEXICO www.intersolar.mx
■ FEBRUARY 2025, GANDHINAGAR, INDIA www.ees-india.in
■ APRIL 7–9, 2025, DUBAI, UAE www.intersolar.ae
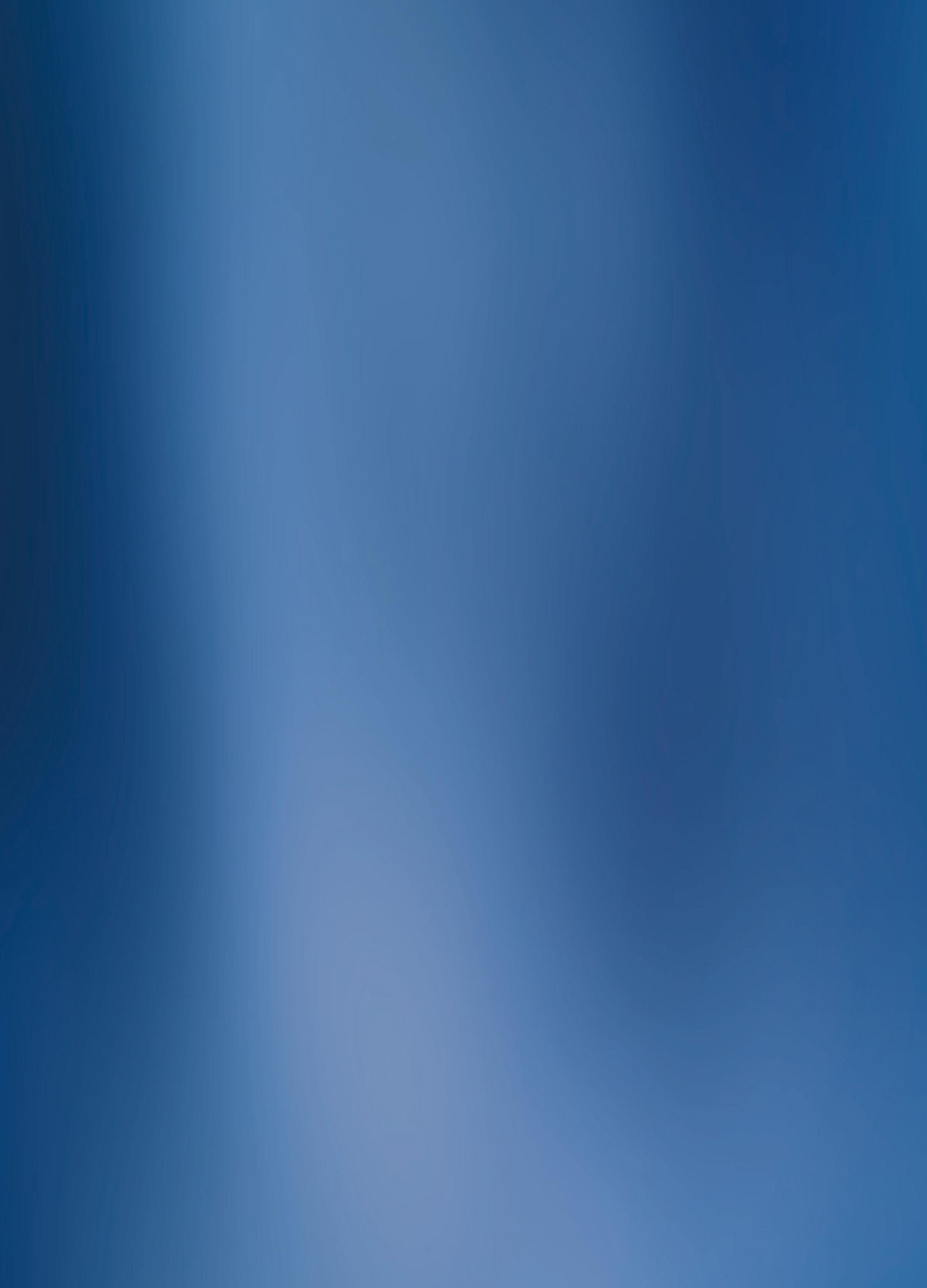
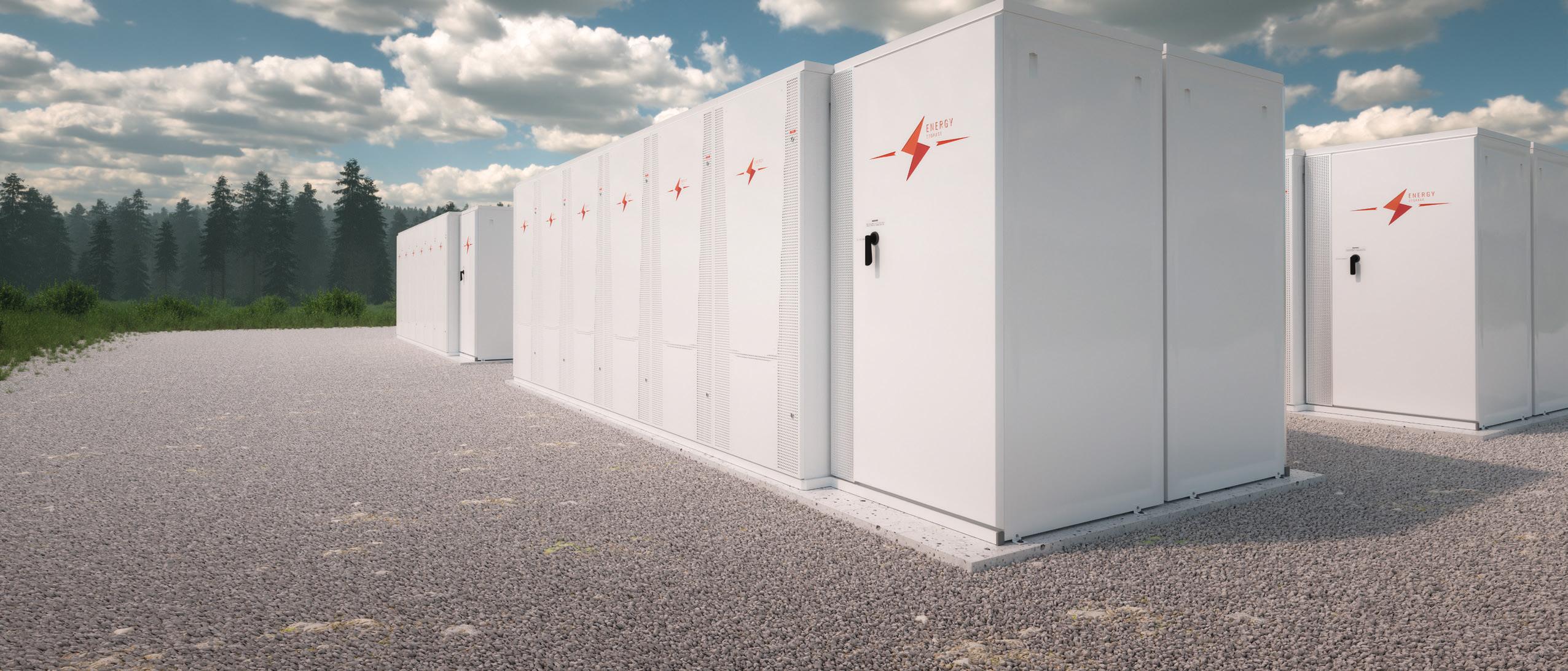
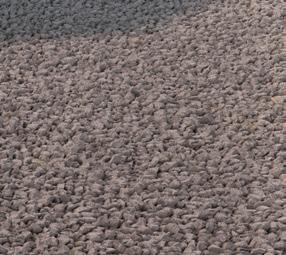
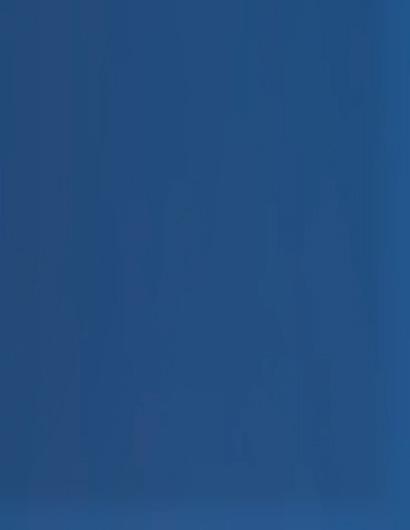





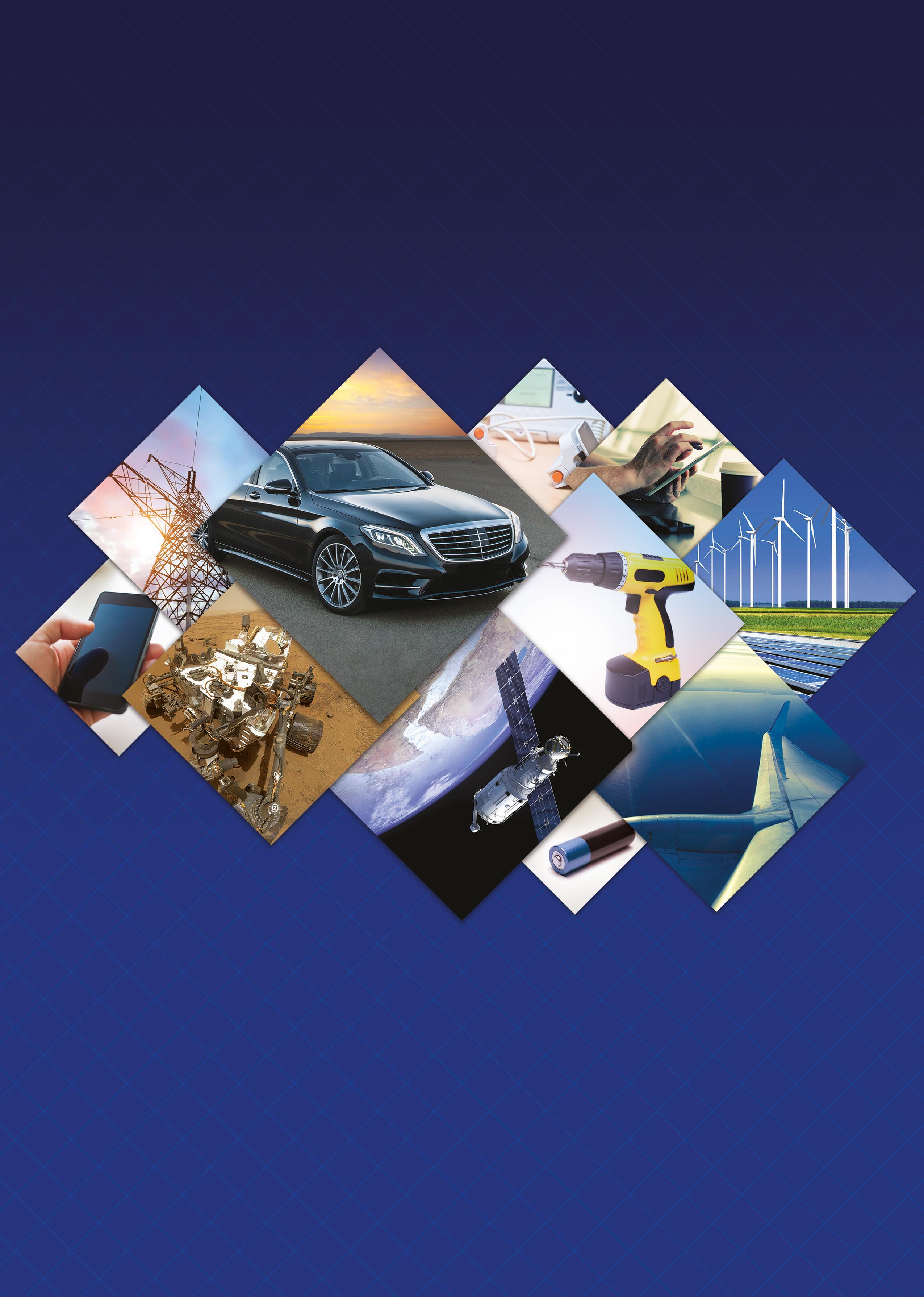