20 minute read
BATTERY FORMATION
In 2020 Inbatec and Kustan forged a partnership aimed at blending their special engineering skills in acid circulation and gel mixing in the battery formation process. John Shepherd reports on their progress to date.
Supply chains and the new world order
As the world emerged from the dark days of the pandemic lockdowns the lead batteries sector was not alone in being eager to return to business as usual.
However, ‘normal service’ has not resumed, particular in terms of supply chains, which is now a legacy issue of Covid.
“Everyone is struggling with supply chain issues,” says Inbatec MD Christian Papmahl. “Components needed to build equipment now need much longer lead times than before the pandemic hit.
“In the past, customers planned for projects with an equipment lead time of around six months, now they need to be planning ahead much earlier, a year or more.”
Global VP of sales and business development, Nick Hennen says the days of having warehouses filled with parts, ready to be shipped off the shelves at a moment’s notice, are long gone.
“Now people are manufacturing direct to order. To be honest — and we’ve been told this by firms such as the big players in electronics — they are now putting their end users first before supporting machine builders.
“So if the end user places an order to keep their operations up and running and we need the same part, we’re just so far down the list between the volumes that we buy and the fact that we are a machine builder, which puts us kind of toward the end of the pecking order.”
Both Hennen and Papmahl believe the situation is the new world order as far as supply chains go and if things do change, they doubt the situation will ever revert to pre-covid delivery levels.
Nevertheless, they rely on longstanding relations with customers to try and speed up supplies of parts they need.
Another challenge the partners have had to overcome is securing supplies of oil, which is the lifeblood of manufacturing a key product — plastic. In addition to getting hold of the raw material in a timely manner, there is the whole dynamic of price fluctuations to contend with against the backdrop of a global energy crisis.
Hennen says they been fortunate in that they have had a couple of “very good global partners”.
“They helped us put together a three-year plan under which we were able to buy some bulk supply at certain points, which helped us out when we did not know what our needs were going to be coming out of Covid. That also helped us to avoid some of the huge price increases.”
Hennen says Inbatec Kustan “lifetime customers” have been invaluable for the future planning of the business.
“These are people who know they are going to buy a certain amount of machines from us in one year or the next, which in turn helps our planning. Those kind of partnerships with our customers have given us some flexibility.”
Hennen says his first impression coming out of the pandemic was that it took about a year for investment to pick up again and to start painting a picture of where the battery formation market was heading.
He says the investment pipeline is opening up again, but the reasoning behind purchasing decisions have changed.
“One thing I’m hearing a lot more, not just in Europe and the US but other places too, is that people are
really looking closely at energy efficiency. Just how much energy is a plant consuming and — with formation being the highest user of electricity in a lead acid plant — are there better ways of doing things?”
The attention of industry leaders is also turning to the management of efficiency and costs across all lead battery plant operations, such as dealing with wastewater and looking far more closely at ways of reducing energy usage.
A key area of focus involves the age of the rectifiers.
“As rectifiers from the 1990s and early 2000s age, they just generate more heat and less actual energy to the battery.”
Another important consideration, where Hennen says Inbatec Kustan “really shines”, is with what would be considered charge acceptance — how much energy needs to go into the battery to create the final product.
“When you compare the charge factor to other methods, in any type of lead acid formation the acid circulation is always going to come out ahead and so that’s become a point for discussion.”
Supporting companies’ desire to increase the level of production while also improving the performance of batteries is in play to and for that, says Hennen, the lead sector could take a leaf out of the lithium production book.
One thing that the lead acid sector has not really taken advantage of in the past is a vertical formation process, Hennen says.
“Traditionally, everything is done on the ground, stretching from points A to B. We’ve been taking a very good look, working with customers around the world, on specific ideas to making battery formation go vertical.
“Anyone who has been into a formation room for lithium will have seen how they can form batteries 40 feet up in the air using trains that are moved around using robotics, which is something that’s not unusual but it is for the lead acid world.”
Hennen says taking advantage of the space that exists above existing formation floors for lead batteries could increase density of production while avoiding huge floorspace expansion costs.
“For lead, it’s just about thinking differently.”
So does Inbatec Kustan have a prototype in play and who else might they be up against in thinking ‘vertically’?
Papmahl says the partners are not yet in a position to talk about their plans in detail. “It’s not something that’s secret, but the secret will be in doing this effectively, with technology that we can provide to our customers. That is what we want to achieve.”
Talk of ‘secrets’ and tantalizing hints about the commercial and technological wizardry at play behind the scenes is always a tantalizing prospect for any reporter…
Pressed further, Hennen says: “We are at a point now where we are getting close to wanting to prototype something we’ve been working on for around 18 months.
“One of the dynamic changes I wanted to bring to the Inbatec Kustan teams when I joined the company two years ago was to ensure we had greater customer involvement when it came to business and product development.”
Instead of Inbatec Kustan teams huddling in a room to develop, conclave-like, a product that they might emerge with in the hope that customers like it, Hennen says the approach has been to spend time listening to customers about their needs.
“Using that approach, we have come up with prototype 3D models of different ideas which we then share with our customers who know the practicalities of the production world in a lead acid environment.”
The goal is simple — increasing the production of batteries per square metre.
However, the Inbatec Kustan group as an organization (both sister firms within the Red Dot holding company), has been working to expand the range of services they are known for.
Today, only about 50% of the group’s business has anything to do with formation, Hennen says. Wastewater management projects are now a key element of the business portfolio.
“We have worked hard over the past couple of years in identifying ourselves as experts in the management of any of the caustic or corrosive liquids in a plant,” says Hennen.
Papmahl says the group has been particularly active in supporting companies in Europe, helping them to conform to sulphate requirements for wastewater streams.
“Most of the authorities dealing with wastewater streams are increasingly limiting sulphate content and we have developed a process that enables our customers to meet the given limits.
“This is an area where we expect to see a lot of projects in the future, especially with an increasing focus on issues of sustainability.”
In terms of the future direction of the lead battery industry, St Louisbased Hennen says there are around six large producers remaining in North America and all are taking fast-charging seriously.
He cites work by the Consortium for Battery Innovation that is pushing fast-charging as a growth market specifically for the stationary storage industry.
“With my background being somewhat in grid development for EVs, I can tell you that it’s a terrific market for the lead acid industry. From the US side and with CBI’s involvement, people are really gearing up for going after that market space over the next few years.”
Hennen says his company is also a player in India’s lead acid market. “There appears to be a significant amount of investment and a big growth curve going on in India right now.”
Papmahl agrees that there are still opportunities for lead acid to shine, not least in the European market because of a need to combat energy and economic crises.
“There is a recognised need for all battery technologies to expand energy storage systems and lead acid has a role to play alongside other chemistries,” he said. “I am very optimistic about the further development of the lead battery industry. Lead is still a serious challenger in the mix of technologies.”
“I am very optimistic about the further development of the lead battery industry. Lead is still a serious challenger in the mix of technologies”
Christian Papmahl, MD, Inbatec
Battery formation is the last electrochemical stage in preparing a battery for market. Sara Verbruggen reports on the firms and machinery servicing this essential developmental process
The bright sparks at batteries’ journey end
BATTERY FORMATION – OVERVIEW
Lead acid battery manufacturing is made up of multiple steps, spanning the oxide and grid production process through to final assembly and inspection.
The formation process is a distinct, critical step, which typically used to be a manual process. However, demand by the lead acid battery industry for competitive products, higher volumes and better performing batteries has led companies to design and produce equipment for automating the formation process.
Today, formation equipment manufacturers supply to a global market, for making different types of lead acid batteries for various industrial and automotive applications. Most specialize in formation equipment that uses water bath processes, while some also specialize in acid recirculation.
Battery formation During the battery formation process, the first chemical reaction occurs which prepares the battery to receive an electrical charge. After the battery’s positive and negative plates have been produced, the forming step occurs, which is when the battery is prepared to receive an electrical charge.
Formation can be performed with the plates installed in the battery case or before their installation.
The plates are immersed, either singly or in positive/negative pairs, into a solution of sulphuric acid for several hours. The reaction between the lead and sulphuric acid causes layers of lead sulphate to form on the plate surfaces, which is critical to the electrochemical reaction that allows a battery to do its job.
In the forming step an electrical current is introduced to the battery.
In dry formation, the plates are charged outside of the battery case in a large tank of electrolyte solution, while wet-formed batteries are charged inside the battery case.
During wet formation, the battery cases are often submerged in a water bath to dissipate heat generated by the charging process as too high temperatures can decrease battery lifespan and impact performance.
The charging process comprises several charges, with breaks between, and so can take many hours to complete. The battery is then discharged and recharged. After forming, the battery acid is then dumped, the battery is refilled and the charge is topped off.
Dry formed plates are removed from the electrolyte tank, dried, and assembled into the battery case. Dry formed batteries are shipped dry, without electrolyte solution in the battery.
After formation, the battery is given a high-rate discharge test using a high rate of current for a short period of time and after receiving the finishing charge, the battery is sent for final assembly and shipment.
After forming, the battery discharges a high rate of current for a short period of time. The high-rate discharge test is a quality assurance electrical load test conducted to verify the battery’s performance.
Zesar
Zesar is an Istanbul-headquartered supplier of battery equipment and processing lines. Since 2008 the company has been using its own patented designs for its equipment. The company’s factory for making its lead acid battery production tools is based in Manisa, in Turkey.
In 2014, Zesar developed its first formation line, delivered as a turnkey project for an automotive battery factory that year. Customers for Zesar’s end-to-end formation processing equipment include INCI GS Yuasa Turkey.
The company’s formation equipment consists of a water bath and associated equipment. The baths are operated to maintain a consistent temperature throughout the entire volume of water.
Zesar can provide a complete equipment package for the formation process, starting from planning the layout, ending with supply scrubber and cooling system, as well as charging jumpers.
Customers can be supplied with formation equipment all in one package, from a single provider, including water bath, loading and unloading equipment, as well as equipment for cooling, scrubbing and filtering processes.
The company says it also offers a quick turnaround for its turnkey battery formation equipment.
Additionally, Zesar manufactures acid and gel filling machines.
The main markets for Zesar’s formation equipment are in Europe, Africa and Australia.
Zesar’s newest innovation is an AGM lead battery water bath with capacity for 80 batteries, designed to speed up the loading and unloading process, since the AGM battery chemical reaction starts almost as soon as acid filling is completed.
DITEC Engineering
Established around 20 years ago, in Vicenza, DITEC Engineering is an Italian manufacturer of equipment for the production of lead acid batteries. The company has, over the years, designed solutions and built machines for the formation of lead acid accumulators and offers complete equipment from assembly to finishing, including formation.
In more recent years the company has focused on formation and acid preparation equipment.
DITEC’s machines are mainly used in production lines for motive as well as industrial batteries.
The company has installed its equipment in countries mainly in the EMEA region, including Turkey, Egypt, Greece, Italy, Hungary, Belarus, Slovenia, Russia, Algeria and Qatar.
DITEC provides equipment that can be customized for different customers’ requirements. Its machines can be supplied with different levels of automation for OEMs. Recent installations include supplying a complete formation plant to a customer in Hungary.
The formation water baths can be operated to maintain a homogeneous temperature of the water in all the areas of the bath, to achieve a better quality battery.
DITEC provides complete turnkey delivery of battery formation equipment, including design of the line, based on customers’ requirement, manufacturing the equipment, transport, installation and commissioning.
Innovations include an automatic formation system with a smaller footprint, aimed at battery manufacturers that want to increase production capacity within same available space.
The company cites the growth of the lithium ion battery market as a longterm challenge but also is confident about the future of for lead acid batteries. It is seeing new sources of demand in the Americas, with its first equipment installation in Argentina occurring in the coming months.
DITEC’s formation equipment range: • Formation water baths • Automatic loading and unloading systems • Motorized conveyor belts • Handling units (rotation, translation, cadencer) • Buffering system • Air suction and treatment plant • Water treatment plant • Cooling plant • SCADA supervision
OMI
OMI, based in Milan, Italy, is a family-owned company founded by Osvaldo Maggioni, who has worked in the battery industry for more than 40 years.
OMI specializes in manufacturing formation equipment, ranging from individual formation equipment to turnkey projects for new battery manufacturing lines.
The company’s equipment spans production of lead acid batteries for different markets, including automotive and industrial, as well as different lead acid technologies, including flooded, AGM and VRLA.
All OMI equipment is produced in its factory in Italy and exported all over the world to lead acid producers, from Ecuador to the Philippines.
OMI says its acid recirculation system has specific characteristics, a result of many years of experience of working with this technology investment in R&D.
Key differentiators include: • Recirculation is not continuous but based on the batteries’ internal temperature during the formation process • Acid filling and recirculation are by gravity force only • Acid preparation and acid fumes treatment included onboard • All circuits are independent to enable maximum flexibility in production schedules
Equipment is designed to obtain better quality batteries, with the usual PbO2 transformation between 85%92%, while charging a total lower amount of ampere (up to 20% less) compared to any other formation process.
OMI supplies two main equipment models. The ARS modules, with external battery positioning, are mainly used for industrial 2V cells formation. The BFRT acid recirculation formation bench has integrated conveyors for battery loading/unloading and is mainly used in production of monobloc batteries, from truck dimensions to industrial.
OMI’s water cooling formation systems consist of patented water baths designed to manage water flow with a cooling system that maintains the internal battery temperature during formation. This intelligent management of all the parameters of the process reduces formation time while increasing battery quality.
All OMI equipment is managed by a software-based supervisory system, developed by OMI, which fully controls production parameters. All relevant process data can be stored in a database and analysed by the customer quality team. OMI Rectifier Management Protocol also allows the full integration of chargers.
OMI also manufactures stations for acid filling. These consist of a direct filling solution for flooded batteries, used for first filling or the levelling process after formation and a volumetric Filling system for flooded batteries first filling and for AGM batteries.
The company offers integrated solutions for a complete control of filling parameters and batteries weights for AGM battery production lines.
OMI also provides acid preparation, storage and recovery systems that can be connected to formation plant.
For a total turnkey formation processing line, customers can also order machines for the battery finishing process, ready for dispatching to the final customer.
Additional services provided by OMI include design of all equipment in-house and customized specifically to meet customer requirements. After complete assembly at its premises, OMI tests equipment before shipping to customer factories. It can supply detailed instructions for equipment installation onsite or provide onsite support, as well as for commissioning and start-up operation.
OMI also provides remote support for equipment functioning and optimization as well as services equipment and maintains stocks of parts and raw materials to meet delivery times and control cost increases, which materials such as steel are experiencing.
The company says it is continuously upgrading its machines, to better fit with customer needs and to increase equipment performance.
Materials and components costs
OMI says it is continuously upgrading its machines, to better fit with customer needs and to increase equipment performance
increasing and lack of availability is an important criticality nowadays, as well as transportation costs.
OMI formation product range: • Acid recirculation formation — fast formation for flooded batteries • Advanced water bath formation — batteries are handled on free rollers, motorised conveyor belts, or with OMI’s exclusive tray system, from fully automatic to manual • Filling process for flooded and
AGM batteries — filling, levelling or recirculation stations, for car and truck batteries, for industrial cells, and for AGM and VRLA batteries • Finishing and dispatching equipment — dumping stations, washing and drying tunnel, poles brushing, HRD and dielectric test stations and other equipment • Acid preparation, storage and recovery — automatic and flexible systems, with continuous or batch preparation, based on customers’ preferences.
Inbatec
Inbatec, based in Hagen, Germany specializes in lead acid battery formation based upon acid recirculation equipment.
The company has developed customized systems that differ in their special type of process technology from conventional formation systems. Active circulation during the entire formation period reduces the formation time. with a high degree of reproducibility.
The company’s formation machines
are used for the manufacturing of automotive starter as well as industrial batteries. The standard module has a capacity of 320 cells per cycle, while the equipment can be customized for specific capacities based on customer requirements. The company’s automotive modules have production capacities of up to 180 truck batteries or 600 car batteries as standard, while higher capacities are also possible based on customer needs. Inbatec’s range includes: • Acid mixer — for concentrated acid and demineralised water, to fully automate production of any desired process acid with a defined concentration and temperature • Acid cooling unit — these draw off the heat produced in the mixing process and cool finished process acids down to a defined temperature and can be used as an integrated part of an acid mixing unit or as a standalone application • Acid recycling — this is a closed circuit process reduces the cost for disposal and wastewater treatment, delivering fresh water and fresh acid that can be reused • Process tanks — these are made to measure based upon required storage volumes, relevant space available and maximum permissible media temperature • Automation systems — measuring, instrumentation or control technology applicable optimally matched to production systems, Excellence in Engineered including the planning and construction of control cabinets and PLC programming.Formation Solutions.
Inbatec’s formation machines are used for the manufacturing of automotive starter as well as industrial batteries
V-Efficharge
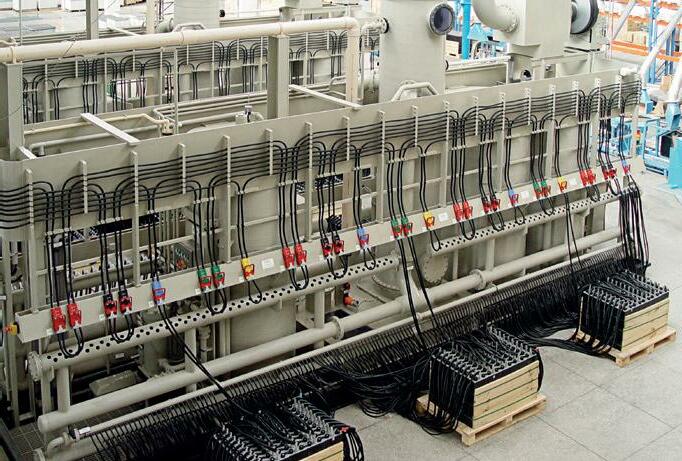
V-Efficharge Power Systems, in India, is an exclusively global licensed manufacturer of battery formation rectifier and test equipment, for Sweden-headquartered KraftPowercon.
Since 2021, V-Efficharge and KraftPowercon have been jointly offering solutions to the battery industry. V-Efficharge manages operations and KraftPowercon provides technological support.
The battery formation rectifier and testing equipment is used with lead acid batteries as well as with nickelcadmium and magnesium-sodium battery chemistries.
Key markets for the equipment include the Indian subcontinent, Russia, Turkey, South America, Middle East and south-east Asia.
Main features and advantages of V-Efficharge’s battery formation rectifier and test equipment: • Highly efficient and reliable SCR controlled rectifiers • True IGBT rectifiers with active front-end technology • Web-based formation software • In-house R&D facility to cater to the dynamic needs of battery industry • In addition to manufacturing battery formation rectifiers and test equipment, V-Efficharge services this equipment, through annual maintenance contracts, and provides online technical support.
It also upgrades older rectifiers through the addition of its control mechanism.
Innovations include a 64 bit highspeed controller, composite material magnetics for higher efficiency and less power consumption.
Globally, V-Efficharge is expanding into North America, Brazil, eastern Europe and also Africa. The company has been diversifying its offering, beyond lead acid. New markets include formation rectifiers for lithium ion cells, DC fast chargers for electric vehicle charging and rectifiers for electric railway locomotives. www.inbatec.de | www.kustan.de
Globally, V-Efficharge is expanding into North One Team. America, Brazil, eastern Europe and also Africa
Stronger Together. Early in 2020, INBATEC and KUSTAN combined our talents and manufacturing expertise to create a new company focused on engineering excellence. As one team, we are industry leaders in the lead-acid formation process. Going forward, we focus beyond just acid recirculation to be your consultant for formation solutions. Our Threefold Mission Is Simple. • Quality Engineered Solutions by working with our customers to provide all aspects of a formation system that leads to you meeting your specific formation goals while focusing on operator safety. • Process Innovation that pushes the lead-acid industry forward with products and services that help you build and form batteries safer, less expensively and with the highest quality possible. • Satisfied Customers over the life of our equipment. We listen and consult when offering a system and then partner with you through the years to responsively maintain safety and the highest production standards.