56 minute read
ENERGY STORAGE NEWS
Next Article
Recharge Industries and Accenture gets set to build 30GWh gigafactory in Australia
Recharge Industries announced on January 16 that Accenture, the Dublin-based information technology services firm, will be its engineering and design provider to build its gigafactory in Australia.
The large-scale lithium-ion battery cell production plant, to be located in Geelong, Victoria, at full capacity will generate up to 30GWh of energy storage per year. Recharge Industries says it will make it one of the world’s largest. Building will start in the second half of 2023, with the goal of producing batteries equal to 2GWh annually in the second half of 2024 and 6GWh by 2026.
At full capacity, the factory will employ up to 2,000 workers.
Recharge Industries has secured the production equipment for the first 2GWh production line, which is scheduled to arrive in Australia in May.
The two companies will also collaborate with Charge CCCV (C4V) a technology partner of Recharge Industries, to support the project’s timing. C4V will provide IP, supply chain blueprints and technology concepts for battery manufacturing, which will accelerate the project.
Rob Fitzpatrick, CEO of Recharge Industries, said: “Establishing a sovereign manufacturing capability to produce state-of-the-art lithium-ion battery cells is critical to Australia’s renewable energy economy — meeting national demand, generating export income and securing supply chains.”
Sacramento VPP aims to deliver 27MW/54MWh
Asahi Kasei wins China patents legal battle
Asahi Kasei revealed on January 10 that it had won a series of court challenges in China to protect its patent for lithium ion battery separators.
The Japanese tech firm said a final ruling by China’s supreme people’s court, handed down on November 2, has ended four years of legal wrangling concerning Li battery separator patents in Asia.
The final ruling brought to an end a protracted legal battle launched in August 2018, when Asahi filed a patent infringement lawsuit with the Shenzhen intermediate people’s court against Shenzhen Xu Ran Electronic Co Ltd and others.
The move sought to prohibit the companies from selling their ‘single-layer Wscope’ battery separators in China and to receive damages for patent infringement amounting to a total of Rmb1 million ($148,000).
Asahi said its claim was initially accepted in full by the supreme people’s court in December 2020.
However, Xu Ran then tried to have Asahi’s patent invalidated — a bid that was rejected by the China National Intellectual Property Administration and also by the Beijing Intellectual Property Court, which handed down its decision in September 2021.
Xu Ran made a final appeal to the supreme people’s court, whose November ruling ends the matter.
Asahi said it is paying close attention to protect its intellectual property rights, warning that it stands ready to deal with infringements. A new initiative using residential solar and battery storage systems to create a virtual power plant has been launched in California, the Sacramento Municipal Utility District (SMUD) and not-for-profit electricity supply firm Swell Energy announced on December 22.
The VPP aims to boost energy supply reliability and initially should give the district 10MW/20MWh of renewable capacity by recruiting, installing and aggregating capacity from customers’ battery storage systems in the utility’s service area.
However, the project could eventually be scaled up to 27MW/54MWh.
The initiative should start operating in April, with contract capability based on a two-hour deliverable capacity.
Around 600 SMUD customers already have domestic energy storage systems, with an additional 400 finalizing interconnections and “thousands more” projected over the next several years, according to the district.
SMUD chief zero carbon officer Lora Anguay said: “As more customers add solar panel systems paired with battery storage solutions, they’ll be better able to manage their carbon footprint.”
Italvolt enters strategic collaboration with StoreDot for XFC lithium-ion batteries
Italvolt, the Italian gigafactory developer, announced it had entered into ‘a strategic collaboration’ with Storedot, a lithium-ion battery developer, on January 16.
Italvolt will license StoreDot’s extreme fast charging technology (XFC) and IPR to manufacture XFC lithium-ion batteries at its plant, which is to start production in 2024 in Turin, Italy.
The agreement between the two companies will allow Italvolt to scale and upgrade its battery cell production.
It also enables StoreDot to buy Italvolt’s batteries for its own business, once production is complete.
StoreDot’s ‘100inX’ product roadmap has an ambition to develop advanced battery cells capable of 100 miles of drive range in five minutes’ charge by 2024, reducing to three minutes by 2028 and two minutes by 2032.
Lars Carlstrom, founder and CEO of Italvolt, said, “Our collaboration with StoreDot is an inflection point in our journey to deliver high-quality, lithiumion battery cells, at scale.”
Doron Myersdorf, CEO of StoreDot, said, “This agreement lets us obtain captive capacity so we can guarantee supply of cells to our future OEM customers. It is extremely important that StoreDot creates these strong relationships as we rapidly move towards mass production.”
Morrow signs deal for Norway battery plant shipments
Morrow Batteries has signed a logistics services agreement with Rhenus Norway for delivery of production equipment for its Norwegian battery cell factory, marking the starting point for Morrow’s operations through the deep water port of Eydehavn in Arendal, the company announced on January 11.
Lars Christian Bacher, who took over as CEO of Morrow on December 1, said the agreement includes the establishment of a new logistics hub.
“We are teaming up with an innovative and flexible agent. Rhenus Norway has developed a solution combining sea freight, integrated European locations handling and last-mile services in Arendal, tailored for this highly demanding logistics project,” Bacher said.
Norwegian prime minister Jonas Gahr Støre laid the cornerstone of Morrow Battery’s battery cells gigafactory on the country’s south coast in a ceremony last September.
Støre said Battery Factory 1, under construction in Arendal, was essential to his government efforts to make Norway an “attractive host country for sustainable and profitable activity along the entire battery value chain”.
Morrow has teamed up with Siva — the Industrial Development Corporation of Norway — in establishing a joint company to build the 30,000m2 plant in four phases with construction company Veidekke, at a cost of NOK400 million ($38 million).
Energy Vault in potential 700MWh ‘green hydrogen’ long duration BESS
Energy Vault Holdings is working with US utility Pacific Gas and Electric (PG&E) on plans to build a battery plus ‘green hydrogen’ long-duration energy storage system (BH-ESS) that will have a minimum capacity of 293MWh, the partners announced on January 5.
The system’s capacity could eventually be expanded to 700MWh.
The move comes after Energy Vault chairman and CEO Robert Piconi said in a third-quarter earnings update on November 14 that the introduction of green hydrogen into its technology portfolio “further validates our technical differentiation with our energy management software platform and the market for hybrid short and long duration integrated systems”.
Piconi said the company was positioning itself as the only energy storage company offering “a hardware agnostic portfolio of both short and long duration storage solutions, bringing innovative gravity, green hydrogen and hybrid solutions to the market for the first time”.
The system for PG&E, if given the go-ahead by the California Public Utilities Commission, would be owned, operated and maintained by Energy Vault on a one-acre site. It would be the first project of its kind and the largest utility-scale green hydrogen project in the US, the company said.
BH-ESS includes a hydrogen fuel cell powered by electrolytic hydrogen derived from renewable energy sources. Green hydrogen, also called renewable hydrogen, is produced through the electrolysis of water. The process is powered entirely by renewable energy.
The system will replace mobile diesel generators typically used by PG&E during broader grid outages to maintain its microgrid serving downtown and the surrounding area of the Northern California City of Calistoga.
Construction is to begin in the fourth quarter of 2023 with commercial operation by the end of second quarter of 2024.
Regional P&G VP Ron Richardson said: “This breakthrough collaboration provides a template for future, renewable community-scale microgrids that successfully integrate thirdparty distributed energy resources, which is expected to cost customers less than the benchmark set by state regulators based on the alternative use of mobile diesel generators.”
Last May, Energy Vault said it had broken ground on its first gravity-based energy storage system in China.
Saft wins Meridian Energy contract to build New Zealand’s first large-scale BESS
Saft, a subsidiary of oil giant TotalEnergies, said on January 10 it had won a contract from New Zealand power firm, Meridian Energy, to build that country’s first large-scale grid-connected BESS.
The 100MW/200MWh facility, to support grid stability as renewable power generation increases, should enter service in the second half of 2024.
The BESS is the first stage of a project that will include the building of a 130MW solar farm by Meridian, sharing the same location at Ruakaka in the country’s North Island.
The BESS will include 80 Intensium Shift battery containers, based on lithium iron phosphate technology with 40 inverters, 20 mediumvoltage power stations and a power management system provided by third-party suppliers. Saft will integrate this equipment with Meridian and Transpower 33kV switchgears, SCADA and power station.
This will open multiple new revenue streams for Meridian, with the ability to load shift between price periods and participate in the North Island reserve electricity market. Meridian anticipates that the BESS will deliver annual revenues of up to US$35 million.
Neal Barclay, CEO of Meridian, said, “The shared infrastructure provided by the BESS will significantly improve the economics of the future solar farm.”
Redwood to start work on US battery materials site in $3.5bn investment
Redwood Materials plans to break ground for a cathode components processing complex in the US state of South Carolina in the first quarter of this year as part of a $3.5 billion investment in the region, the company announced on December 14.
Redwood said its ‘battery materials campus’ (pictured) outside Charleston will recycle, refine and manufacture anode and cathode components on a site spanning more than 600 acres. Initial operations are expected to start by the end of this year.
The campus will eventually produce 100GWh of cathode and anode components a year, which Redwood said is enough to power more than one million EVs. Production capacity could be expanded to “potentially several hundred GWh annually”, the Nevada-based recycler said.
The site will form part of a new manufacturing corridor from Michigan to Georgia, becoming known as America’s ‘battery belt’, where hundreds of gigawatt-hours of battery cell production capacity annually are set to be built and start operating between now and 2030.
Redwood said the move is needed because anode and cathode components are not yet produced in North America and battery cell manufacturers have to source them from a global supply chain of more than 50,000 miles.
“As a result, US battery manufacturers will spend more than $150 billion overseas on these components by 2030,” the firm said.
Charleston will be similar to Redwood’s Nevada operations in that the site will be 100% electric and will not use fossil fuels, Redwood claimed.
The Charleston project follows Redwood’s November 15 announcement that it would supply recycled materials for use in Panasonic Energy’s EV lithium ion batteries.
Recycled copper foil will be used in batteries made at Panasonic Energy of North America’s plant in Nevada starting in 2024. Recycled cathode active materials will be used in batteries manufactured at Panasonic’s new facility in Kansas starting in 2025.
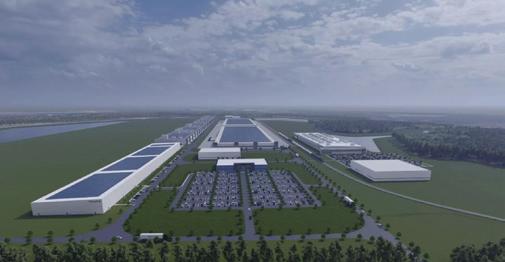
Russia gigafactory plan is ‘first step toward batteries independence’
Russia’s prime minister Mikhail Mishustin says work has started on the first of a potential series of gigafactories as it scrambles to ramp up domestic battery manufacturing capacity for energy storage systems and EVs, after foreign investors and partners quit the country over the war with Ukraine.
Mishustin told a meeting of deputy prime ministers on December 26 that Russia had to achieve “technological sovereignty” for the automotive industry in particular — and state-owned corporation Rosatom had started building a 4GWh lithium ion batteries plant in the Baltic Sea enclave of Kaliningrad.
The plant should start operations in 2025.
“We will need to create conditions for saturating the domestic market with cars, while many foreign corporations have left Russia under pressure from their authorities, and to create our own components base with the widest possible range, from the simplest parts to complex elements,” Mishustin said.
Russia must also “create an infrastructure for charging stations” for EVs, he said.
Rosatom announced on November 23 that it had established a new subsidiary — Renera — dedicated to the manufacture of energy storage systems.
Lithium ion batteries are already being produced by Rosatom, but the group said Renera’s task would be to coordinate and expand manufacturing capacity and “consider” building additional gigafactories.
Kaliningrad, which lies between Poland and Lithuania, does not border mainland Russia but is home to Russia’s Baltic fleet. Rosatom says the Kaliningrad gigafactory will produce 50,000 EV batteries annually.
US-based battery producer EnerSys announced last March that it was suspending its operations in Russia following the country’s “illegal military action against a sovereign Ukraine”.
Last April, Batteries International reported that tougher new EU proposals to restrict trade with Russia were likely to include exports of lead batteries and related battery tech products and services. Lithium battery systems manufacturer BMZ Group said on September 15 it intended to acquire a stake in German plastics supplier Schütz Kunststofftechnik, in part to shore up its materials supply chain.
BMZ said it would act as a strategic investor in supporting its supplier of battery cell holders.
The planned deal would give Schütz access to BMZ’s network of clients, including those in the energy storage and e-mobility sectors.
Schütz is a longstanding supplier of cell holders and spacers installed in BMZ battery systems.
BMZ founder and CEO Sven Bauer said: “Procurement bottlenecks, price developments and a shortage of skilled workers means we are in very challenging economic times. At the same time, our market is a future-proof growth industry.”
Strategic partnerships that enable BMZ to secure and expand its market presence “are only logical”, he said.
Schütz managing partner Michael Schütz said the investment deal was “a door opener for new sales markets, across industries and worldwide”
Nala’s Belgium BESS set for commercial start
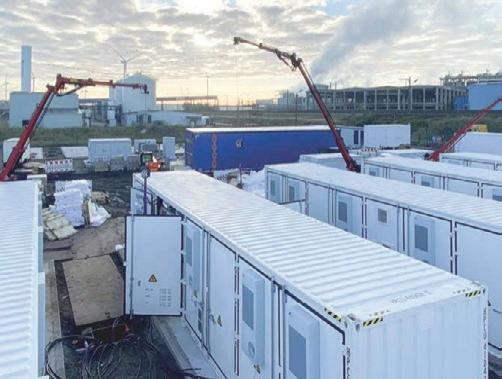
BASF in materials supply first for Toyota-Panasonic joint venture firm
BASF has delivered the first batch of customized nickelcobalt manganese cathode active materials (CAM) for high performance EV battery cells being produced by the Toyota-Panasonic joint venture Prime Planet Energy & Solutions (PPES). BASF said on December 19 that its majorityowned BASF Toda Battery Materials company produced the CAM at its Onoda calcination plant in Japan. Work to expand cell production capacity at Onoda to up to 45GWh is underway and the increased capacity will come online in the second half of 2024.
Toyota holds a majority 51% stake in PPES, which started operations in April 2020 to produce automotive prismatic batteries.
Construction launch for Neoen’s 200MW Blyth Battery in South Australia
Neoen said on January 5 had launched construction of its 200MW/400MWh Blyth Battery in South Australia.
Blythe is one of seven new grid-scale battery projects across the country that will be supported in part by financial backing from the Australian Renewable Energy Agency.
NHOA Energy will be the battery storage specialist for the project. Details of the battery tech were not disclosed, but NHOA produces a range of lithium ion-based energy storage systems.
Blyth will mainly be deployed in combination with Neoen’s Goyder South Stage 1 wind farm to deliver 70MW of renewable baseload energy to mining group BHP. Neoen said the energy will power BHP’s Olympic Dam operations in South Australia.
The construction period will last between 12 and 16 months and the battery will be Neoen’s fifth biggest in the country, taking the company’s overall Australian asset portfolio close to 3GW in operation or under construction. UK-headquartered Nala Renewables is on course to start commercial operations at one of Belgium’s largest battery energy storage systems to date in the first quarter of this year, joint owner Trafigura said on December 8.
The 100MWh Balen lithium ion battery project (pictured) involves investment of up to €30 million ($32 million) said Trafigura, which is the 50-50 partner with IFM Investors.
Balen is being built at a zinc smelting facility owned by Trafigura subsidiary Nyrstar.
Trafigura said the BESS will be able to store 25MW for more than four hours and provide stability and balancing services for the Belgian grid, as well as help shift renewable energy production into high-energy demand periods.
Nala is developing renewable energy generation and storage assets in Belgium, Chile, France, Greece, Netherlands, Poland and the US.
The company has grown its renewable energy asset portfolio to 2.8GW and is on track to meet its 4GW target by the end of 2025, Trafigura said.
Nala announced last March that it would also be developing four new BESS projects in New York State.
The company is working with New York-based power and infrastructure firm, Rhynland Energy, to start building the facilities by mid-2024. The units will have a combined storage capacity of 280MW.
US ‘set for 1,000GWh surge in EV battery capacity by 2030’
EV battery manufacturing capacity in North America is set to accelerate from 55GWh annually in 2021 to nearly 1,000GWh by 2030 as a wave of new manufacturing facilities come online, according to a US government forecast published on January 2.
The figures underline separate analysis, which indicated that the US is outpacing Europe in the battery gigafactories investment race, following tax incentives unveiled by the federal government in the Inflation Reduction Act last August.
According to the latest forecast by the federal Vehicle Technologies Office, most of the announced battery plant projects are to begin production between 2025 and 2030.
By 2030, this production capacity will be capable of supporting the manufacture of roughly 10 to 13 million allelectric vehicles per year, the report said.
Many of the battery plants will be co-located with automotive plants to optimize supply chains, according to the report.
Most of the planned projects in the US are concentrated along a north-south band from Michigan to Alabama. Based on current plans, Kentucky, Tennessee, Georgia, and Michigan are projected to see the highest growth in battery manufacturing capacity.
$58bn pledged for long duration storage projects since 2019
Commitments have been made to invest more than $58 billion in long duration energy storage (LDES) projects around the world since 2019, according to analysis released on December 7 by Wood Mackenzie.
If all of the pledges made by governments and companies went forward, it would lead to the installation of 57GW of LDES projects — equivalent to three times the global energy-storage capacity deployed in 2022, says Wood Mac’s Longduration energy storage report 2022.
The report said projects representing $30 billion are already either under construction or in operation.
However, most LDES technologies are still nascent and developers will “struggle” to scale costeffectively before 2030.
The report also showed what are described as clear geographical disparities in the development of the LDES market. For the Asia Pacific region, the deployment of vanadium redox flow batteries and compressed air energy storage has accelerated rapidly in China, which has been largely driven by strong policy support.
Kevin Shang, senior research analyst at Wood Mac and report lead author said: “In the western hemisphere, the US continues to invest in and build its LDES industry, with companies actively pushing for innovation, and promoting pilot and demonstration projects.”
By contrast, most European countries have been less enthusiastic, said Shang, although the UK government has been an exemption, as it explores the role LDES technologies have to offer, while actively seeking to support industry players.
“Long-duration energy storage technology, with longer durations of eight to approximately 100 hours, holds great promise as a low-cost solution to enable a grid with more renewable sources.”
Wood Mac said support from governments is needed to help lower upfront capital costs, provide revenue certainty, and “generate market signals for investment” and the broader deployment of projects.
However, companies need to create new business models to attract private investors with a view to making profits without subsidies in the long term.
Amara Raja building lithium cells plant in Telangana
Amara Raja Batteries has agreed to a build a 16GWh lithium battery cells factory together with research facilities in the southern Indian state of Telangana, the company confirmed on December 2.
The lead batteries major said the new plant would include a 5GWh battery pack assembly unit, under the terms of a memorandum of understanding signed with the state government.
Amara Raja chairman and MD Jayadev Galla said Telangana would become the company’s ‘giga corridor’, featuring advanced laboratories and testing infrastructure for material research, prototyping, product life cycle analysis and proof of concept demonstration.
He said the partnership with Telangana was “a giant leap for Amara Raja and will bring in the impetus for innovations in sustainable technologies for the whole region, in addition to generating employment opportunities”.
The partnership follows Amara Raja’s launch of a new subsidiary, announced on November 3, to spearhead the addition of lithium ion tech to the group’s lead battery manufacturing operations.
The company said then that a site for the subsidiary’s “multigigawatt” battery cells facility would be confirmed soon.
RPC partners BESS firm Eelpower to target UK market
Renewable Power Capital has announced its entry into the battery storage market in Great Britain in a partnership with BESS constructor-owneroperator Eelpower.
RPC said on November 23 that the joint venture will acquire, build and operate utility-scale projects and is targeting up to 1GW of storage capacity with a near-term 240MW projects pipeline.
The partners will take part in wholesale electricity markets and provide ancillary services to the UK’s National Grid.
RPC’s focus on the UK market follows its recent acquisition of a 528MW ready-to-build onshore wind portfolio in Sweden.
London-headquartered RPC was established in 2020 and is backed by the Canada Pension Plan Investment Board — operating as CPP Investments.
Since its formation, RPC has committed nearly €1.5 billion ($1.6bn) in acquisitions including wind and solar PV in Spain and the Nordics.
According to RPC, Great Britain represents the largest utility scale battery storage market in Europe with 1.7GW installed by the end of 2021 and with growth forecast to be up to 10GW by 2030 on the back of increases in renewable power generating projects.
Eelpower announced in July that it had bought a 20MW lithium ion storage system from British firm Anesco for an undisclosed sum.
The Rock Farm battery storage system, which consists of 16 1.25MW BYD-made storage units, was developed, constructed and commissioned by Anesco in June.
‘Europe’s largest BESS’ goes online in England
Investment firm Harmony Energy Income Trust, an investment firm announced on November 21 that its Pillswood project, in Yorkshire, UK had gone live some four months’ earlier than previously planned.
The 98MW/196MWh facility is the largest BESS project in Europe by MWh, Harmony said. This is equivalent to power around 300,000 UK homes for two hours.
The project, using a Tesla two-hour Megapack, will provide balancing services to the UK electricity grid network, underpinning energy security and enabling the replacement of coal and gas power stations to renewable power sources.
Pillswood sits next to the National Grid’s Creyke Beck substation. This is planned to be the connection point for Phase ‘A’ and ‘B’ of Dogger Bank, the world’s largest offshore wind farm. Its first phase should go live in summer 2023.
The project was developed by Harmony Energy with construction managed by Tesla. Pillswood will be operated through Autobidder, Tesla’s algorithmic trading platform which has a strong track record. Two of its projects have been the top performers in terms of revenue
generation in the UK this past year.
Harmony Energy Advisors director Peter Kavanagh said: “All stakeholders have recognized the importance of achieving energization for this project ahead of winter to ensure the BESS services can be provided during the initial winter months.”
Harmony Energy Income Trust has five battery energy storage systems under construction, set to go live next October and three new pipeline projects which will increase its portfolio to nine projects with a total capacity of 500MW/1GWh.
Canada clamping down on China investments
Canada has ordered Chinese companies to divest their holdings in three Canadian-listed junior mining companies planning to develop lithium deposits, in a bid to safeguard critical battery material supplies for the domestic market.
Industry innovation and science minister FrançoisPhilippe Champagne said on November 2: “While Canada continues to welcome foreign direct investment, we will act decisively when investments threaten our national security and our critical minerals supply chains, both at home and abroad.”
Champagne said the decision had been taken under the Investment Canada Act following a review, supported by the nation’s intelligence services, into Canadian firms engaged in the critical minerals sector, including lithium.
As a result of that process, the government ordered Sinomine (Hong Kong) Rare Metals Resources to divest itself of its investment in Power Metals Corp, which is exploring and developing caesium, lithium and tantalum assets in Canada.
Chengze Lithium International was told to divest itself of its investment in Lithium Chile, which is developing projects in Argentina and Chile.
Zangge Mining Investment (Chengdu) was also required to divest itself of investment in Ultra Lithium — a publiclytraded Canadian mineral exploration company focused on advanced lithium and gold projects in Argentina, Canada and the US.
Champagne said the decision coincided with the finalization of the government’s critical minerals strategy.
“Canada’s critical minerals are key to the future prosperity of our country,” he said.
“Increasing demand for these all-important minerals are presenting Canada with a generational economic opportunity. The federal government is determined to work with Canadian businesses to attract foreign direct investments from partners that share our interests and values.
Power Metals chairman and CEO Johnathan More said on November 3: “While we are surprised by Canada’s stance towards Chinese investment into Canada’s critical minerals industry, it clearly shows that they see the opportunity and assets of Power Metals as too valuable for such foreign investment.”
More said then that Sinomine was looking into the appeal process.
Ultra Lithium said the announcement had been detrimental to its many Canadian shareholders and the company was “assessing its legal and other options to preserve value” for shareholders.
ESS lands Schiphol airport storage deal
Iron-based flow battery storage company ESS said on January 19 it had landed a deal to supply its long-duration storage system for a pilot scheme at Amsterdam’s Schiphol airport.
The company’s Energy Warehouse BESS will be deployed in the first quarter of this year.
For the pilot project, the BESS will be used to recharge electric ground power units (E-GPU) — which will replace the diesel ground power units currently used to supply electrical power to aircraft when parked, ESS said.
Oscar Maan, Royal Schiphol Group manager of innovation, said: “If this pilot is successful, this is a double win as it both reduces our carbon footprint and reduces air pollution.”
The project is part of the Royal Schiphol-led ‘Tulips’ consortium, funded by the EU, to speed up the rollout of sustainable technologies in aviation.
ESS announced last March that it was expanding its European operations — to meet expected demand for long-duration storage as the continent attempts to scale back its dependency on Russian gas.
ESS said the RussiaUkraine conflict was accelerating Europe’s ramping up of renewable power and gave new impetus for investments in long-duration energy storage as countries sought ways to reduce use of gas-powered generation of electricity.
According to ESS, the European region is to require up to 20TWh of long-duration energy storage capacity if it is to meet UN climate change goals of ‘grid net zero’ by 2040.
Tesla to use SolarEdge tech in Romanian solar project
A Tesla group company is to design and build rooftop solar installations in Romania on buildings for industrial properties developer Element Industrial using inverter technology from SolarEdge, the companies announced on January 19.
Tesla 50Hz said the first stage of the project, which will run for the next three to five years, will cover 250,000m2 of industrial parks, with a total installation of 40MW of industrial-scale photovoltaics.
With each PV installation providing independent onsite energy generation for Element industrial parks, the company will benefit from increased grid independence and power quality — and reduce electricity costs for Element’s tenants, the partners said.
The installations will be supported by T50Hz’s sister company, Tesla Blue Planet.
“This partnership reflects our strategy to develop a sustainable portfolio that will allow our tenants to cover at least 30% of their consumption from green energy,” said Element MD Andrei Jerca.
Jerca said all installations will be equipped with SolarEdge’s DC-optimized technology that connect to each power of the solar modules.
Last May, Israelibased SolarEdge announced the opening of a 2GWh battery cells manufacturing plant in South Korea to meet growing demand for battery storage.
SolarEdge said it would be producing cells at the Sella 2 facility with its lithium ion batteries subsidiary Kokam.
Europe’s ambition to become an EV batteries powerhouse could stall as lucrative US tax breaks lure gigafactory investors away and China extends subsidies. John Shepherd reports on EU crisis moves to salvage its electric dreams as industry leaders accuse policymakers of being asleep at the wheel
Time to fix Europe’s competitiveness problem
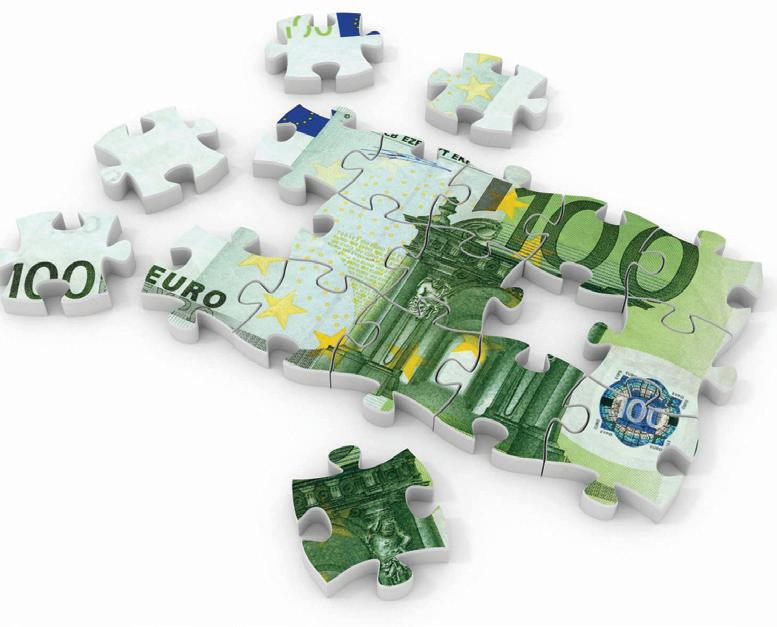
A make-or-break summit deciding Europe’s battery future looks set to be held by early spring Batteries International has learned. At issue is whether the continent can compete globally — and quickly enough — with its rivals.
This follows a warning that at least €100 billion ($106 billion) is needed to avert a potential investments meltdown for gigafactory plans, as the US and Asia is luring developers away with more lucrative deals and incentives.
Industry leaders and trade bodies issued a damning report in December effectively accusing EU leaders of not doing enough to successfully steer policies aimed at creating a home-grown battery manufacturing industry.
The European Battery Alliance report cited a litany of failings, including how permit procedures for battery and raw materials projects in the EU and individual member states lacked “speed and clarity, compared with that of other global economies… contributing to additional risks and delays in investment and project execution”.
The Alliance, whose 800-strong membership includes companies involved in the battery supply chain, revealed talks had been held earlier in December, with EU Commission vicepresident and batteries czar Maroš Šefcovic.
He was told of the damage being done to Europe’s fledgling battery plans by billions of dollars in tax credits for plants being awarded under the US Inflation Reduction Act (IRA) — unveiled in August 2022 and which took effect on January 1 — plus similar support schemes in Canada, Japan and South Korea and Europe’s continued “unbroken dependencies” on Asia.
In a December 15 statement the Alliance, which was launched by Šefcovic in October 2017 to create an innovative, sustainable and globally competitive battery value chain in the EU, warned: “The upcoming weeks will be decisive for decision makers to act and prevent the outflow of investment from Europe.”
Batteries International understands a follow-up summit will be held in March, although the European Commission declined to comment as this issue went to press.
Meanwhile Commission executive vice-president Margrethe Verstager, who has responsibility for competition issues, wrote to all EU member states on January 16 to get their views on whether state-aid rules should be loosened further to allow governments to support companies that may be affected by the IRA.
Any relaxation of the rules would be in addition to the ‘temporary crisis framework’ adopted by the Commission last March, which was drawn up to support national economies in the wake of energy price hikes caused by Russia’s invasion of Ukraine.
A spokesperson for Verstager told
The EU lacks speed and clarity in handling permit procedures needed to launch battery and raw materials projects and still suffers from “unbroken dependencies” on Asia
Batteries International that member states had already used that “flexibility” to generate a total of more than €672 billion of funding so far, adding: “In the current context, however, more may be needed.”
Market fragmentation risk
The spokesperson did not refer explicitly to the IRA, but she said Verstager’s consultation would consider further simplification of EU state aid rules, possible new measures to accelerate the green transition and the need to “balance support for production in certain types of sectors strategic for the green transition with the possible risk of fragmentation of the single market”.
Industry insiders say Europe’s political leaders know they have to act fast. Independent analysis says the US is already outpacing the EU in the batteries investment race.
Meanwhile gigafactories being built in emerging markets such as India and Malaysia will have a combined battery production capacity of 104GWh by 2030.
Verstager’s letter to member states is, in part, a response to proposals discussed in the Alliance’s December round of talks with Šefcovic, which included calls for emergency measures to unlock more than €100 billon ($108 billion) of investments and speed up projects through 20232024.
The Commission was also urged to make the entire battery manufacturing chain, including raw materials through to recycling, a priority for cash awards under a planned new EU sovereignty fund.
If state-aid rules are loosened further, battery industry leaders say this could get cash quickly pumped into battery-related projects, together with the fast-tracking of planning applications and permits for batteryrelated projects.
An energy task force is also expected to be set up to ensure spiralling energy costs for industry in the wake of the Russia-Ukraine war are brought to a “competitive level” across the EU in the next two years.
The Alliance also urged EU chiefs to find ways to combine European measures with US incentives laws and create a “level playing field, where battery manufacturers producing in Europe compete on equal terms, independent of higher subsidies or lower sustainability standards in Asia and the US”.
WTO challenge
It is not clear if, when or how quickly the proposals might be adopted and the US is not expected to drastically dilute its renewed domestic support for battery manufacturing to help Europe overcome its own difficulties — Chinese and other Asian battery makers less so.
However, the nuclear option understood to be under consideration is to challenge US financial support for its battery production and related supply chain industries at the World Trade Organization (WTO).
This could be coupled with a review of existing EU trade rules, including duties for EV components and EVs from third countries with different regulatory requirements and incentive schemes.
Thierry Breton, the Commission’s internal market chief, discussed technological sovereignty and European industrial policy with French prime minister Elisabeth Borne on December 19, when he said there was no time to lose in formulating a response to the IRA.
The spectre of taking the US to the WTO, risking a full-blown trade war, does appear to be a real prospect. France’s economy and finance minister Bruno Le Maire and Germany’s vice-chancellor and economic affairs minister, Robert Habeck, said in a joint statement after talks on November 22 that they would “closely coordinate a European approach to challenges such as the IRA… to prevent downside effects of protectionist measures by third countries and ensure that WTO rules are respected by all”.
However, it remains to be seen just how EU leaders will agree on a coordinated response to pressures from Asia and the US. Swedish EU affairs minister Jessika Roswall, whose country took over the presidency of the EU for six months as of January 1, has been widely quoted as telling a conference in Stockholm just days later that “a subsidy race is not the answer” in tackling US competition.
US policy ‘game-changer’
Tensions between the EU and US are a far cry from the harmonious tones of less than two years ago, when in June 2021 Commission president Ursula von der Leyen and US president Joe Biden established the US-EU Trade and Technology Council with a commitment to renew and reinvigorate the transatlantic partnership and deepen cooperation.
Biden said during a visit to the White House last December by his French counterpart, Emmanuel Macron, he was confident “we can work
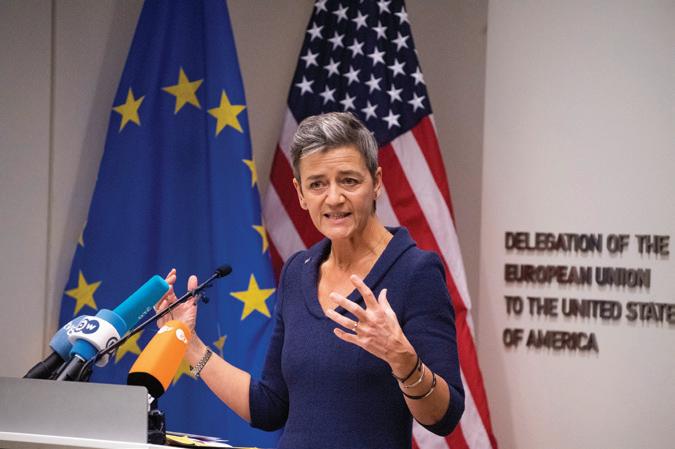
Margrethe Verstagen consulting EU member states amid calls to challenge US tax credits for batteries sector. Photo: Roberto Schmidt / EC-audiovisual service
The Inflation Reduction Act has been a game-changer in its potential to draw investments for battery manufacturing projects away from Europe to the US
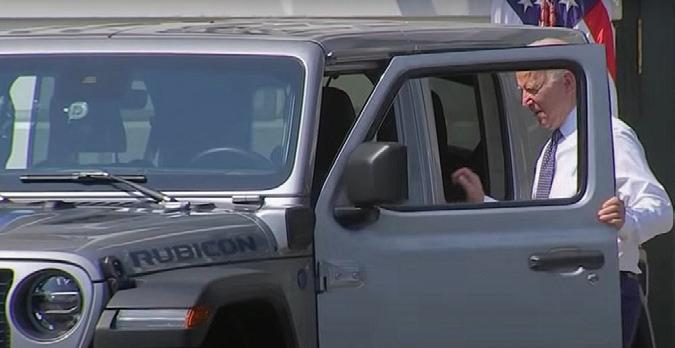
Joe Biden gets into an electric Jeep Wrangler at the White House in 2021. Photo: C-SPAN
out some of the differences that exist” over the IRA.
At the end of that month, in an attempt to reduce tensions, the US Treasury Department indicated in a white paper that some imported cars would qualify for EV tax credits under the IRA. However, the move has not cooled EU tempers.
A senior official in one of the European industry bodies that is closely involved in Brussels talks aimed at coordinating Europe’s response, said on condition of anonymity that it was “beyond doubt” that the IRA had been a “game-changer” in terms of its potential to draw more investments and battery manufacturing projects away from Europe to the US.
The problem for Europe is that there is still no clear plan of action by way of response, he said.
The official warned that there was a real risk, however small, that if part of Brussels’ response is to refer the issue of US incentives and subsidies to the WTO, this could trigger a trade war that could further undermine recent EU-US efforts to forge closer economic ties.
Such a move would also undoubtedly see the US question its pledge to cooperate with the EU in shoring up energy supplies disrupted by Russia’s invasion of Ukraine.
“Some may argue that IRA-like tax incentives run the risk of creating boom and bust cycles for technology adoption, much as we have seen in the renewable industry in Europe over the last decade,” the official said.
‘No silver bullet’
However, he warned that if Europe were to launch a copycat economic strike to expand incentives and subsidies, especially for the energy storage sector, that in itself would not be a “silver bullet that is going to make the European Union the leader in this field”.
“If incentives are deployed, they must be coupled with other ambitious initiatives,” he said. Indeed, incentives can only work if energy storage “already has a market-based path toward technology adoption” — but Europe still appears to be floundering.
He cited the example of US states such as California, where clear investment strategies have been put in place to actively encourage development of battery energy storage projects.
Industry initiatives in the state include the development of pilot programmes announced last May by utility Pacific Gas and Electric, working with auto giants such as General Motors and Ford, to test how bidirectional EVs and chargers can provide power to the grid.
Europe needs a “better energy market design, so that battery energy storage potential can be deployed in multiple sectors, such as microgrids for residential areas and supporting utilities at grid level”, the official said.
A spokesperson for the European Association for Storage of Energy (EASE) told Batteries International much still needed to be done beyond EV applications.
“While the Batteries Regulation focused extensively on EV batteries, which is to be expected as the market is huge, it is important to avoid focusing on that type of application alone.
“Energy storage uptake is extremely relevant and it’s a market where the EU can lead — we are talking about 200GW of storage needs in 2030 in Europe alone.”
In its review of energy policy developments for 2022, EASE said the Batteries Regulation draft approved by the European Parliament failed to reflect “the diversity of the battery ecosystem and could add regulatory complexity in an already extremely regulated segment, such as battery safety, recycling and reuse”.
The stark warnings of failings in EU policies to date have overshadowed the unveiling of what was supposed to be one of the jewels in its green energy policy crown, when it was announced on December 9 that a provisional deal had been agreed that would pave the way to introducing the long-awaited battery laws.
Now even that seems to be a hollow achievement. It immediately became clear that the new regulations still require secondary legislation to be passed between 2024 and 2028 before they can become fully operational — further highlighting, if it were needed, the glacial pace of decision-making in the EU at a time when the battery industry is crying out for urgent attention.

Northern lights over Freyr Battery’s Mo i Rana customer qualification plant in Norway. Freyr intends to install 200GWh of annual battery cells production capacity by 2030. Photo: Freyr
Global giga investments tip scale in favour of US
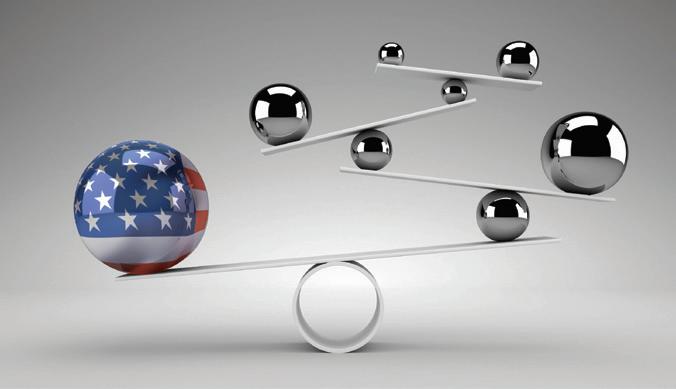
Since the US Inflation Reduction Act was unveiled on August 16, 2022, billions of battery investment dollars in the country have been announced.
On August 29, LG Energy Solution and Honda Motor said they had agreed to establish a joint venture company to produce lithium ion batteries in the US exclusively for Honda plants in North America to power battery electric vehicles (BEVs) sold in North America.
Fast forward to January 13 and the partners revealed their 40GWh plant would be in Ohio, with their overall investment related to the joint venture projected to reach $4.4 billion.
LG has a majority 51% stake in the tentatively-named L-H Battery Company joint venture. Construction of the plant is to start this year with completion scheduled by the end of 2024 and the start of mass production by the end of 2025.
Meanwhile, Toyota is pushing ahead with an expansion of its Toyota Battery Manufacturing North Carolina site following the announcement last August 29 of $2.5 billion in additional investment for the project.
Toyota said battery production is to start in 2025 for hybrid electric vehicles and BEVs.
Jane Nakano, a senior fellow in the energy security and climate change program at the Center for Strategic and International Studies in Washington, said that under the Inflation Reduction Act, tax credits that came into effect in January are available at different levels to both new and used EVs, and also for non-passenger vehicles.
Specifically, half of the EV tax credit is available if EV battery components are manufactured or assembled in North America. The other half of the credit is available if battery minerals are extracted, processed, or recycled in the US or come from a country that has a free trade agreement with the US.
“The number of eligible models will likely decrease as the mineral content threshold rises to 80% by 2027, and the battery component manufacturing and assembly threshold will rise to 100% by 2029,” Nakono said.
“If companies wish to access the credits, they will need to change their production plans and build new supply chains, potentially slowing EV deployment.”
However, she said the share of EVs in the total light-duty vehicle sales was still expected to hit 57% by the end of the decade as a result of the Inflation Reduction Act.
Nakono said the US vision for secure EV supply chains has “an undeniable dose of geopolitical assertiveness”, because the law prohibits the application of EV tax credits where any components or critical minerals are sourced from a foreign entity of concern, such as China, Russia, Iran, or North Korea.
But how the US addresses trade concerns from close partners such as the EU, South Korea or Japan is an issue. Some of them are also “important investors in the emerging US EV battery supply chains and this warrants close attention,” said Nakono.
European fears of battery investments draining away to other parts of the world were heightened by
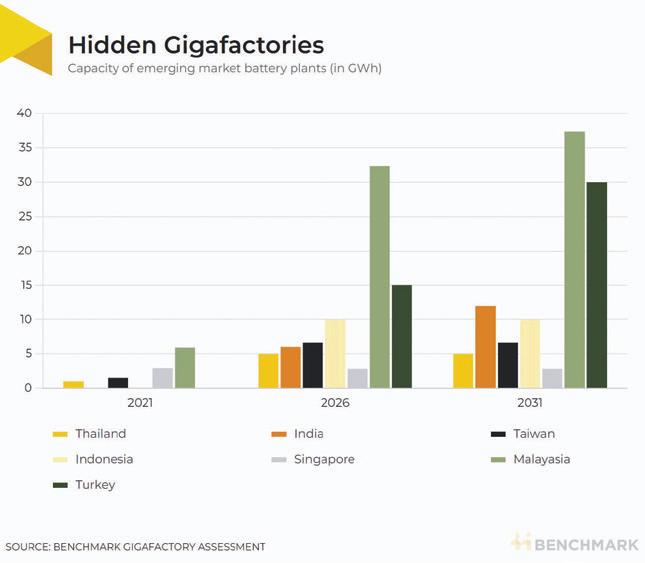
the publication of analysis indicating that 13 gigafactories being built in seven emerging markets are set to lead a surge in batteries capacity to around 104GWh by the end of the decade.
Benchmark Source’s ‘Gigafactory Assessment’, released on December 13, said the new plants being built across seven countries including Malaysia, Indonesia and India would be enough for nearly two million EVs.
Further analysis by Benchmark indicates that the US is outpacing Europe in the battery gigafactories investment race, following tax incentives unveiled by the federal government in the Inflation Reduction Act.
A total of 242GWh of battery capacity was added to the US pipeline in the second half of 2022, an increase of 34.3% since July, according to Benchmark’s separate ‘Lithium ion Battery Gigafactory Assessment’, released on November 23.
In comparison, Europe’s battery capacity pipeline increased by 16.7% or 170 GWh over the same period, with Chinese companies responsible for all new gigafactories.
Benchmark analyst Evan Hartley said: “The effect of the Inflation Reduction Act can be clearly seen within the announced North American pipeline, and while the European pipeline has increased, that growth is more stable, continuing the trend seen throughout the year.”
In its December 13 Gigafactory Assessment, Benchmark said the list of developing economies where 13 gigafactories are being built includes Turkey, where South Korea’s SK Innovation plans to build a battery plant with Ford and local player Koç Holding.
The plant in Ankara is to start production of high-nickel NCM batteries in 2025.
Benchmark says the developing economies’ gigafactories should come online by as early as 2026 and add about 78GWh capacity initially, which would be scaled to 104GWh by the end of 2030, led by Malaysia.
According to the analysis, the gigafactories would contribute about 37.6% of Asian (excluding China) capacity of 205GWh by the end of 2026 and about 40.5% by the end of 2030.
Benchmark says the investment in gigafactories in emerging markets comes as EV sales start to accelerate in Southeast Asia and India, highlighting the growth potential beyond the major developed markets.
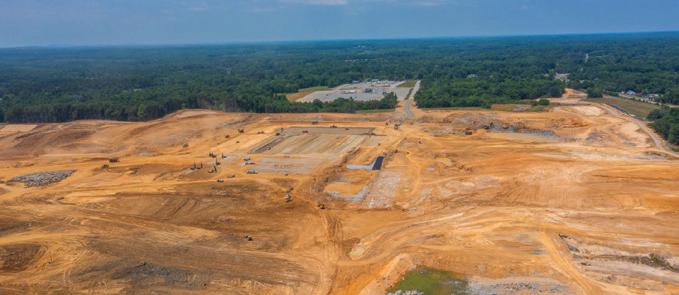
Toyota is pushing ahead with an expansion of its Toyota Battery Manufacturing North Carolina site
CHINA WARNS US OVER TAX CREDITS AS BEIJING EXTENDS EV SUBSIDIES
China has kicked off 2023 by extending government subsidies for purchases of EVs for the rest of the year — with a warning that it suspects that US tax credits could be in breach of WTO trade rules.
Tax exemptions on EV purchases had been set to expire at the end of 2022, but new energy vehicles bought up to December 31 of 2023 are now also exempt from vehicle purchase tax, the finance ministry and other government bodies confirmed.
Despite Beijing’s own attempt to boost EV sales, the government said it was reviewing US polices aimed at favouring domestic EV battery investment.
Chinese commerce ministry spokesperson Shu Jueting claimed on September 22 that granting tax credits for EVs in the US on the condition of final assembly in North America discriminated against other similar imported products and could violate WTO rules. Meanwhile, data from the China Automotive Battery Innovation Alliance, published by state news agency Xinhua on January 14, said the country’s battery manufacturing capacity for new energy vehicle batteries totalled 294.6GWh in 2022, which the organization claimed was a year-on-year increase of 91%.
The installed capacity of batteries in December 2022 alone increased 38% year-on-year to hit 36.1GWh.
The China Association of Automobile Manufacturers said China sold nearly seven million new energy vehicles in 2022 — a year-on-year increase of 93%.
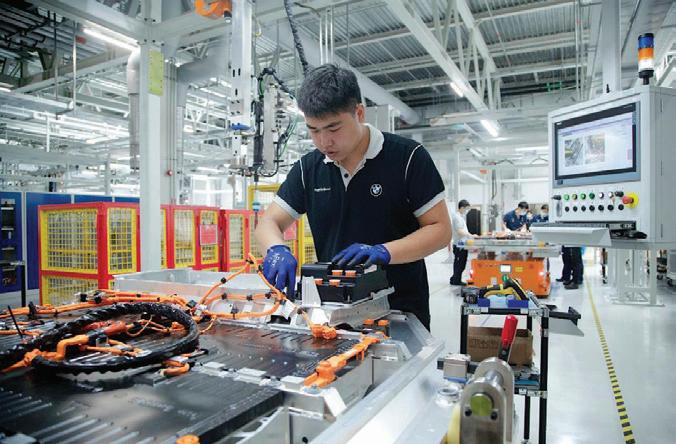
Production of the fifth generation of high-voltage batteries at the BMW Brilliance Automotive joint venture factory in China
Investment needed to secure critical materials to power EU’s electric future
As EU leaders are under pressure to do more to support investments in gigafactories, European institutions are also calling for urgent action to plan for a reliable and sustainable battery materials supply chain — including new mining and recycling projects.
The European Commission says it will publish legislative proposals for raw materials critical to the battery industry in the first quarter of 2023.
On issues of materials supply the Commission is under pressure from industry representatives too including Europe’s metals association, Eurometaux, which is warning that the US Inflation Reduction Act also risks draining much-needed investment in the supply chain away from Europe.
Eurometaux sustainability director Kamila Slupek said on December 12 new rules set to be introduced as part of the EU’s Batteries Regulation must be accompanied by “an even stronger industrial plan to grow Europe’s battery materials supply chain in the face of US subsidies and China state support.
“In the next two years we need much more European investment into mining, refining, and recycling operations for battery materials,” Slupek said.
Recycling will be Europe’s best longterm opportunity to establish strategic autonomy for battery metals, she said, but the batteries market will expand rapidly this decade and no one knows now how much battery scrap will be available by 2030.
Eurometaux said in a study published last spring that Europe needs to combine long-term recycling growth with new primary metals supply and make “strategic choices on how it will supply its accelerating metals demand”.
According to the study, the EU will require significant new supplies of nickel, lithium, and cobalt for its domestic battery cathode manufacturing plans. Of these metals, Europe only has a significant existing market for nickel, which is mainly used in stainless steel.
By 2050, batteries will be Europe’s major use for lithium, nickel, and cobalt under all the study’s scenarios, with new demand reaching up to 3500% of Europe’s lithium consumption today, 350% of cobalt, and 110% of nickel.
The battery market will need to be the subject of regular attention because uncertain technology developments after 2030 will likely impact these long-term projections, and so regular attention will be required to the battery market.
For the next 14 years, Europe’s energy transition will predominantly require new primary metals supply from mining and refining, Eurometaux said.
However, plans for most new mines expected to be started up in Europe face an uncertain future due to lack of local acceptance, technical uncertainties or permitting challenges.
Secondary supply from recycled sources will take a more prominent role as current clean energy technologies begin reaching their end of life.
After 2040, recycling could be Europe’s major supply source for most transition metals, alongside the continued need for primary metal, but Eurometaux said this would need major efforts to build new recycling capacity and overcome bottlenecks.
Research by Batteries International shows little has changed since the European Commission’s lofty ambitions for lithium ion battery recycling were unveiled several years ago.
A report by Germany’s independent non-profit environmental research body the Oko-Institut, published in March 2018, told the Commission that the best thing it could do was to follow the example of the lead acid industry in recycling batteries to create a “sustainable” process for conserving raw materials and repurposing EV batteries for energy storage.
That report — ‘Ensuring a Sustainable Supply of Raw Materials for Electric Vehicles’— showed that China was already “well ahead” in having a transparent structure that efficiently regulated the use of materials in the electro-mobility sector.
Fast forward to the present day and the needle on the Commission’s sustainability dial has barely moved into more positive territory.
In its most recent study, ‘Mobility sector: roadmap for responsible sourcing of raw materials until 2050’, published in August, the institute notes that lithium is still not being recycled in the EU.
And the study warns that while there is a transition in cell chemistries away from “expensive resources like cobalt- and nickel-containing lithium nickel manganese cobalt oxide towards cheaper materials like lithium iron phosphate… there is as yet no recycling concept specified for LFP, as the focus of material recovery has been on cobalt, nickel and copper”.
The study also highlights a growing trend where used batteries are, in the institute’s words, donated to countries outside the EU for use in projects such as solar power systems in Africa.
The institute says it is hard to justify the shipping of old batteries to low- and middle-income countries while using new batteries to cover the need for electricity storage in the EU.
“In many countries around the world, recycling structures for LIBs are still lacking. Exporting the batteries back to Europe for recycling, as often announced, is also nearly impossible, as shipping companies are reluctant to take on board LIBs at their end of life due to the risk of fire and the resulting insurance costs.”
Now the institute is calling for restrictions on exports of cars and used batteries from the EU and a program of “mandatory recycling”.
After 2040, recycling could be Europe’s major supply source for most transition metals, alongside the continued need for primary metal
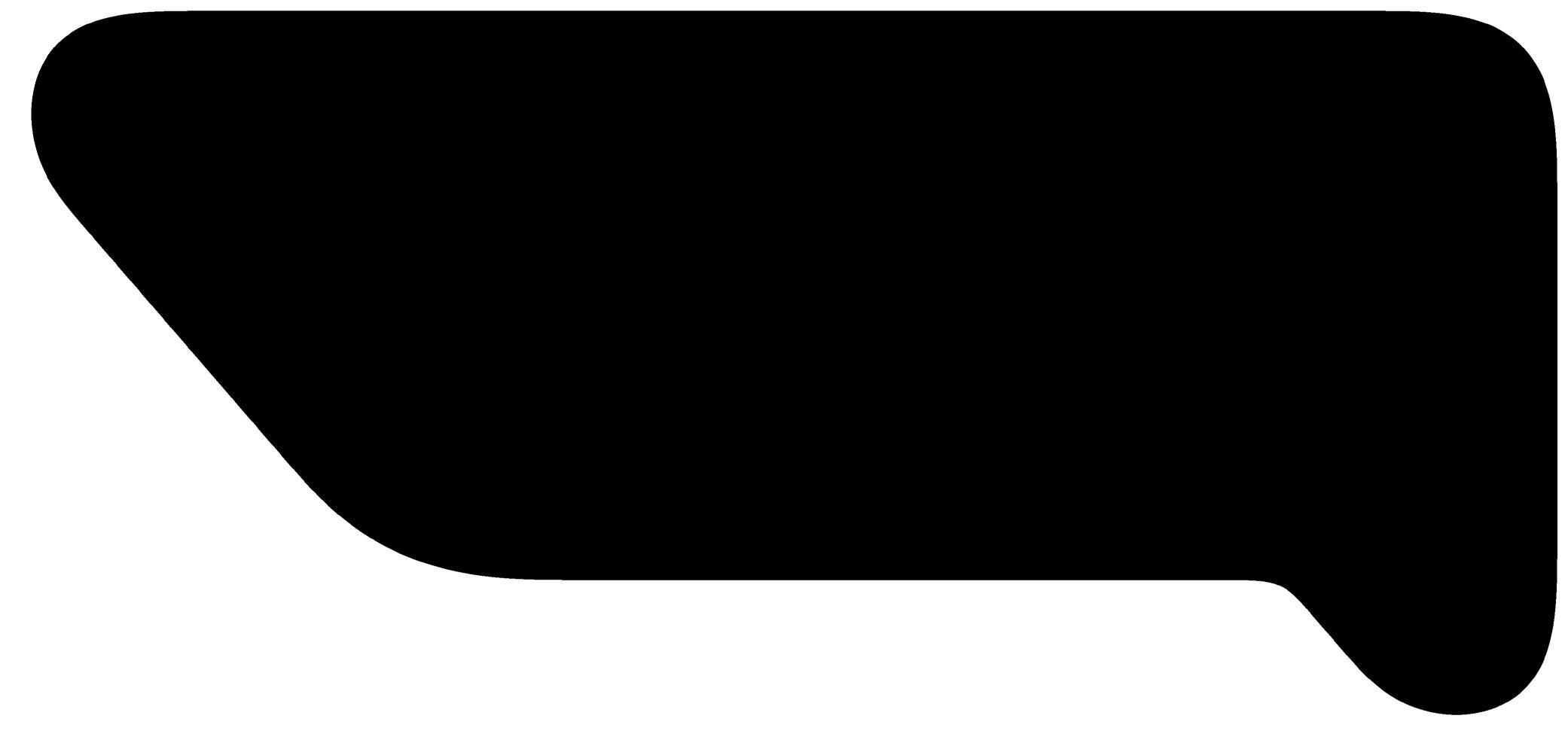

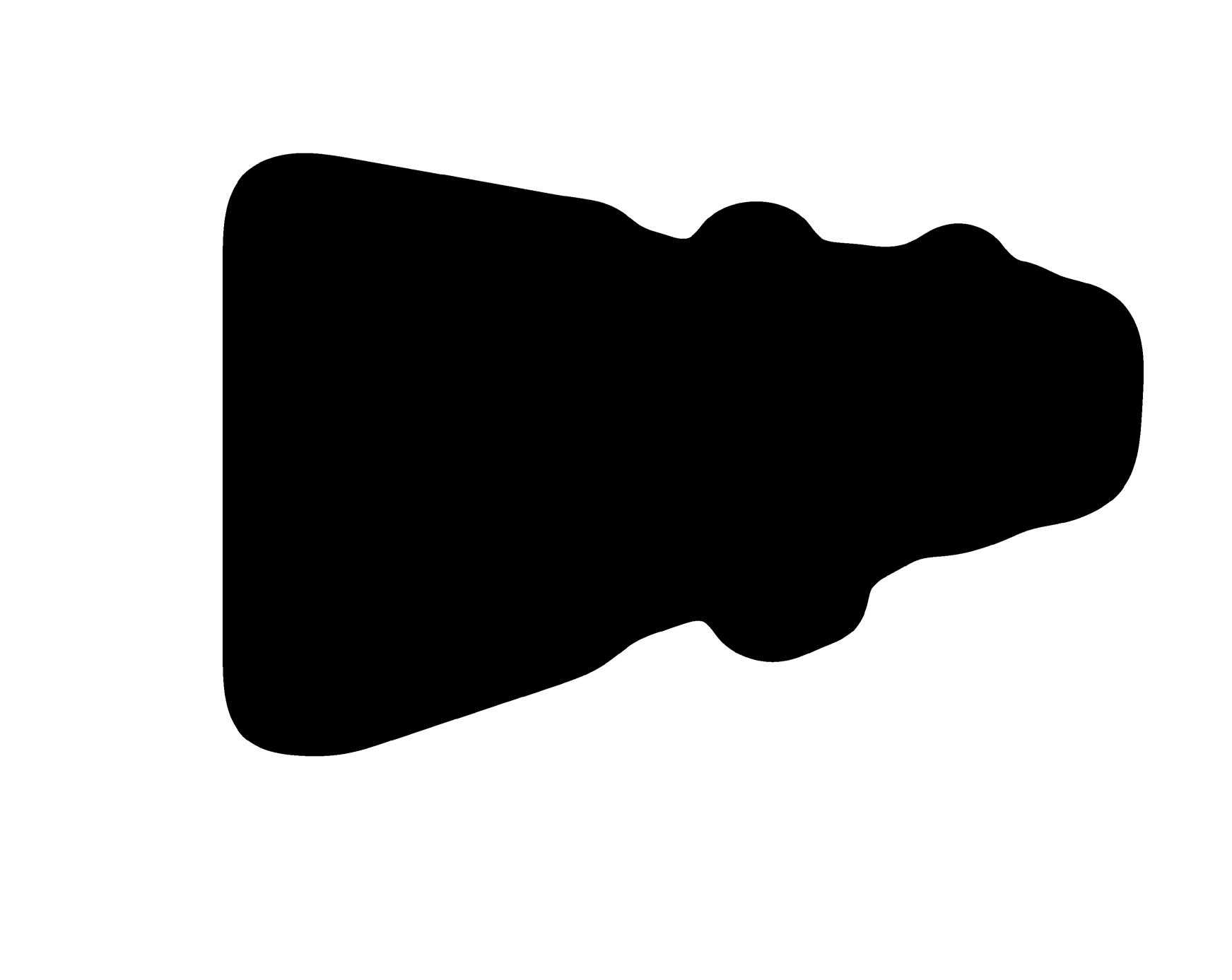
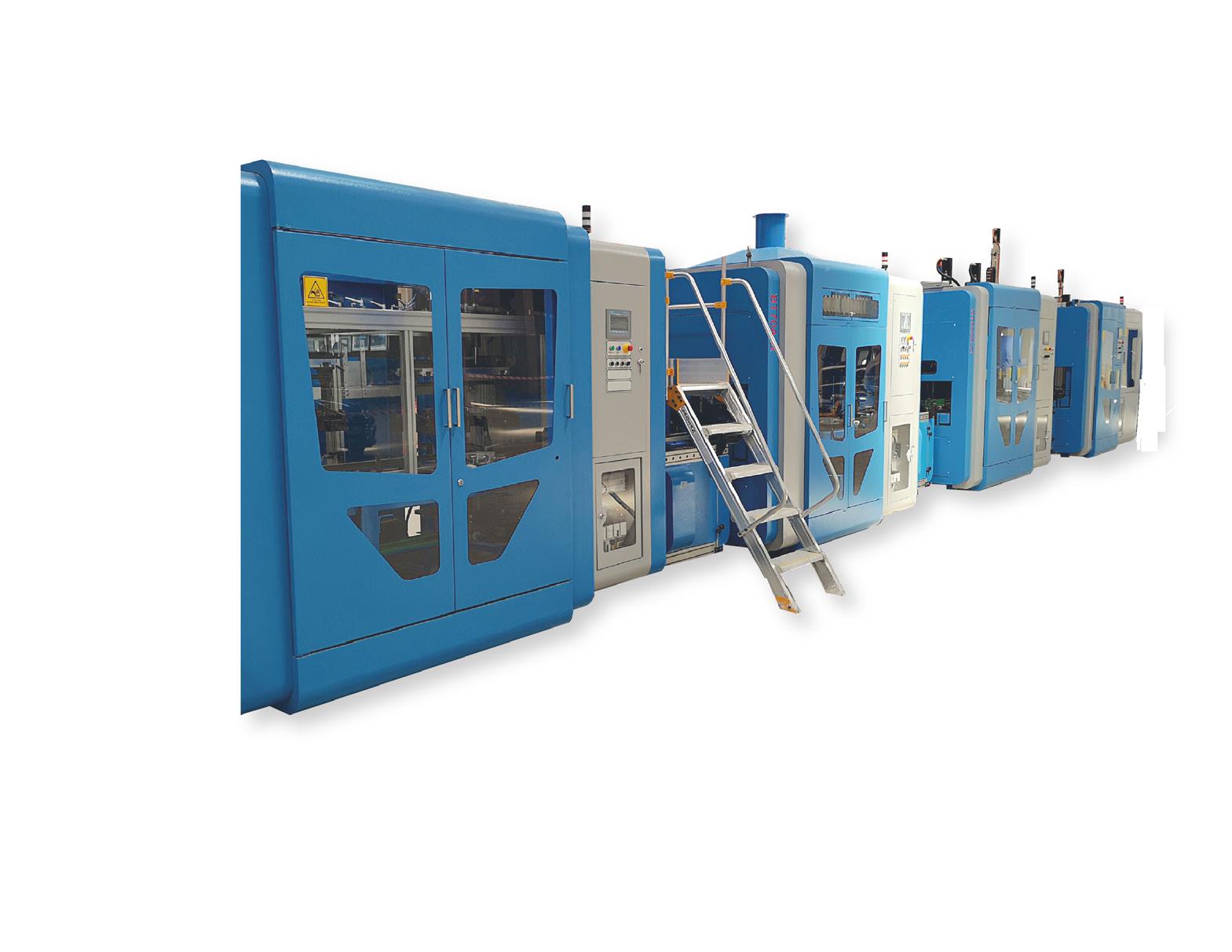
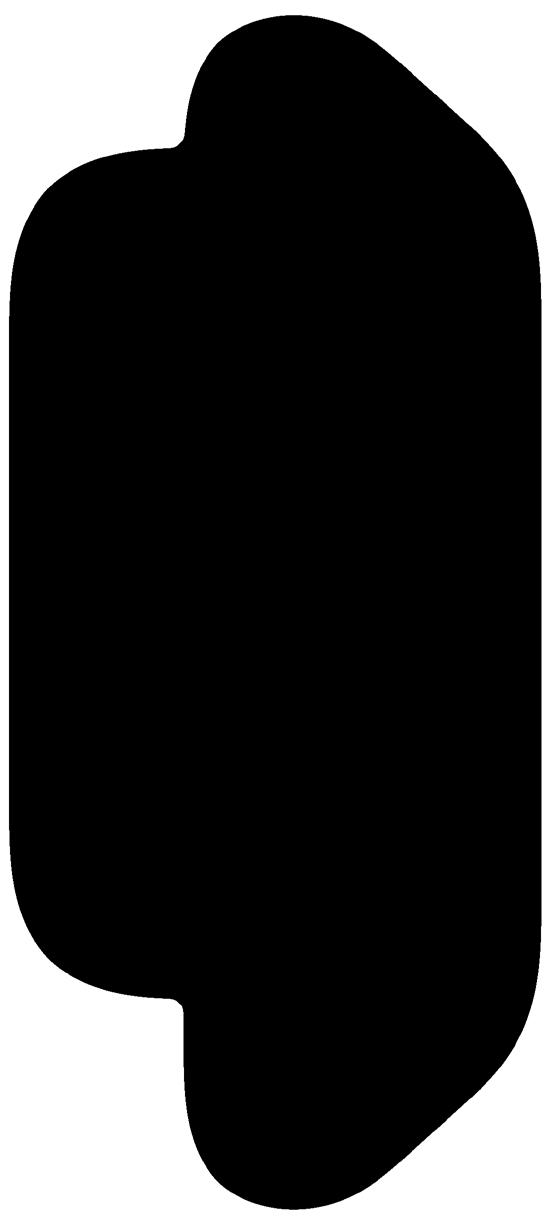
A net zero world will require a global network of battery gigafactories, but these have to be properly resourced, function independently and within a local energy and industrial landscape.
The faltering march of the gigafactories
Rising energy costs, disruptions in the supply of equipment components, hikes in the cost of raw materials and potential shortages have delayed giga-projects across Europe in 2022.
Some major projects seem to have stalled almost completely.
In December, for example, Volkswagen postponed a decision on where to build a battery gigafactory in eastern Europe. And in January Britishvolt’s gigafactory at Blyth in England went into administration after a long tangle with raising enough finance.
Rescue packages from the UK government were being discussed as Batteries International went to press.
In Europe — see other parts of the cover story — two defining situations have hampered the continent’s giga dreams: the introduction of the Inflation Reduction Act in the US with its tax breaks and China’s extension of subsidies to its battery manufacturers.
But other factors are also in play.
One commentator points to the overall lack of expertise in creating, managing and operating these giga plants. “There is only a finite amount of talent to go round,” he says. “So in one sense it will make sense to consolidate this expertise in partnerships.”
There’s also the post-Covid recovery where the shortage of materials has hit price expectations. “In 2020, it was thought EVs would hit price parity with ICE vehicles around this year or next,” says one industry commentator. “But increasing battery prices have put paid to that.
“It could happen by 2026, or even 2025 though,” he says. “As massive battery gigafactories start to come online and supply ramps up dramatically.”
Simon Michaux, associate professor of geometallurgy at the Geological Survey of Finland believes that gigafactories need to be part of larger thinking.
The supply of lithium, cobalt, nickel and graphite will not be enough to manufacture enough renewable units to replace the existing fossil fuel based system, of which batteries make up a large proportion.
“The simple solution is to make batteries out of another material set such as fluoride, sodium, zinc or even silica,” he says. “These don’t have the same supply shortage problems.”
A UK perspective
Stephen Gifford, chief economist at the Faraday Institution in the UK, regards the energy and supply chain crises as short to medium-term issues: “Geopolitical risks and disruption to global supply chains after the pandemic have resulted in rising commodity prices,” he says.
“Average battery costs had fallen by around 80% since 2013 but increased for the first time in 2022, with a 7% increase in real terms”
Meanwhile, in the UK alone, there is a demand forecasted of 22,000 tonnes of cobalt, 135,000t lithium carbonate equivalent and 170,000t nickel under a projection of 196 GWh of UK EV battery production.
Gifford does not believe current market issues and supply bottlenecks will affect the gigafactory industry in the longer term given, for example, the transition to net zero by 2050 in the UK and ending of new ICE vehicle sales by 2030.
“With global commodity prices increasing, the market for EV batteries has begun to move to lower cost chemistries to remain competitive, particularly lithium iron phosphate,” says Gifford.
Shortening the battery raw materials supply chain, or finding ways to minimize the use of certain minerals because of availability or expense, has become a priority
The current production of raw materials is far from sufficient.
Globally, in 2040 there is projected to be demand for around 520kt cobalt, 3,000kt lithium carbonate equivalent and 4,000kt nickel under a projection of 5.9TWh of global EV battery production.
One analyst predicts that: “there should be demand for 100GWh and five large gigafactories in the UK by 2030, with each producing 20GWh per year of batteries. By 2040, demand rises to nearly 200GWh and the equivalent of 10 gigafactories.”
However, says Gifford, “There are more than enough resources to supply the manufacture of EV batteries to 2050, giving time for the EV battery recycling industry to become widely established.”
When assessing planned cell capacity figures, not all that capacity will come online, with many gigafactories projects unable to produce the quantity and quality of cells right for the market, says Benchmark Minerals analyst, Evan Hartley.
Lithium is the key raw material causing significant supply disruption and driving up cathode and cell prices.
Some cathode manufacturers in China are reporting recent failures to receive deliveries of material from long term supply contracts, having to resort to the tight spot market.
Demand is outpacing supply, with new lithium mines taking longer
“There are more than enough resources to supply the manufacture of EV batteries to 2050, giving time for the EV battery recycling industry to become widely established”
to achieve viable production than downstream projects.
Gifford says that global production of lithium and cobalt will need to increase by six times and three times respectively up to 2040. However, nickel supply does not need to increase to the same degree.
Hartley says some companies are shifting their battery materials business towards localization, and vertical integration. “Cities such as Debrecen in Hungary provide an example of these strategies; now host to a number of projects planning to produce pCAM, cathode material, cells, and EVs, increasing supply chain integrity,” he says.
“However, as energy-intensive operations, we are beginning to see gigafactory plans hit by energy price crises, with multiple cell producers in Europe for example, either delaying plans, or reconsidering the location of planned gigafactories, with countries offering subsidies to counter rising energy costs now more likely to be favoured.”
Geopolitics is also key to gigafactory success with preferential treatment such as the US tax breaks from the Inflation Reduction Act moving markets. “Since the act was announced, North American pipeline capacity has grown significantly, with many of the companies scaling up their plans from Japan, and South Korea,” says Hartley, “while the large tier 1 Chinese producers have been excluded from the market.”
Recycling
Reducing reliance on battery raw materials is part of gigafactory strategy. Consequently, there are moves to overcome the difficulties in recycling EV batteries.
Unfortunately, says Gifford, current end-of-life battery processing techniques do not optimize or maximize the recovery of all of the materials contained in EV batteries.
Making better use of resources and minimizing the amount of raw materials being sourced to manufacture is an imperative for battery production. That includes an increase in recycling. Key steps suggested by Gifford include: ensuring that EV batteries are designed in a way that enhances recycling; ensuring that EV batteries are designed with second-life applications in mind; use policy and regulation to help to manage environmental impacts; encourage investment in the infrastructure for recycling lithium-ion batteries from EVs; and to consider government support.
“What a gigafactory looks like in 20 years will depend on the type of batteries being manufactured, particularly whether there has been the successful development of alternatives such as solid-state and lithium-sulphur batteries,” says Gifford.
Multiple cathode and cell producers have versatile production lines capable of switching focus in line with demand — between different NCM cells, or between NCM and NCA, says Hartley:
“As battery technology evolves, we will continue to see versatile production lines brought online, or further investments into existing facilities to redesign the manufacturing process, as the development of existing infrastructure will be cheaper and more efficient than new gigafactories for new technology.”
Gifford says that global production of lithium and cobalt will need to increase by six times and three times respectively between to 2040. However, nickel supply not need to increase to the same degree
LIFE AFTER LITHIUM — ALTERNATIVE TECHNOLOGIES
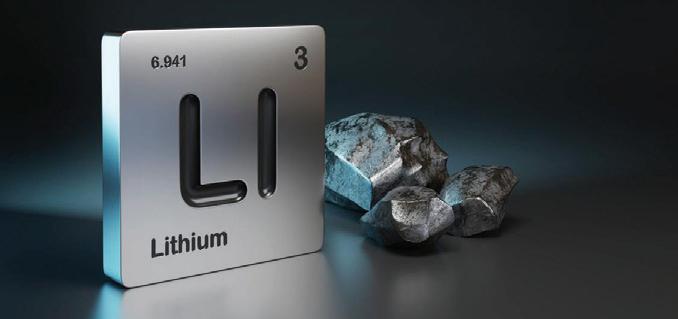
There are limits to the performance improvements that can be expected from Li-ion technology.
“Next generation battery technologies such as solid-state, sodium-ion and lithium-sulfur offer exciting opportunities for EVs but also for applications in marine, rail, aviation and heavy goods transportation,” says Stephen Gifford, chief economist at the Faraday Institution. “Solid-state batteries are expected to be the next successor to lithium-ion batteries, offering a step-change in energy density, range and safety advantages.
“Sodium-ion batteries have a much lower cost than lithium and solid-state batteries, making them an attractive next generation technology. Simpler manufacturing techniques are needed, with inexpensive and naturally abundant materials used.
“Sodium-ion batteries are well suited for future large-scale stationary storage applications, particularly where large amounts of storage are required to help balance electricity grids with a high supply of renewables.
“They have potential usages in low-cost and low-performance vehicles, particularly micromobility vehicles such as e-bikes, e-scooters, two-wheelers and three-wheelers.
“Lithium-sulfur batteries offer greater gravimetric energy density than lithium-ion, and are cheaper to make. These should open up new markets and have a transformative effect on aerospace applications, such as drones, high altitude satellites and unmanned aerial vehicles.
“For the moment, lithium-sulphur cells suffer from short cycle lives and research to solve these challenges is underway.” The Faraday Institution’s LISTAR project led by University College London is looking at how to fix this.
As the EU scrambles to keep its gigafactory ambitions on course, the demise of Britishvolt underlines the high stakes involved in securing investment to power an electric future
UK giga-project runs out of road
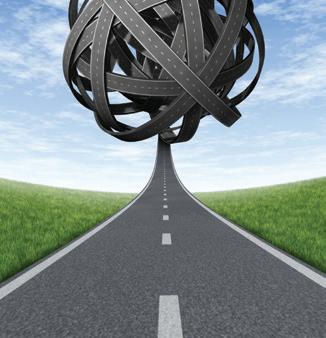
As Batteries International went to press Britishvolt, the company behind one of the UK’s flagship gigafactory projects collapsed into administration.
On January 17, Dan Hurd, Jo Robinson and Alan Hudson of EY-Parthenon’s Turnaround and Restructuring Strategy team were appointed joint administrators of Power by Britishvolt Limited — incorporated in 2019 as the main UK company in the wider Britishvolt Group set up to build and operate the plant.
The move was due to insufficient equity investment for the research the company was undertaking and the development of its sites in the Midlands and the north east of England, according to the administrators.
Hurd said the priorities were to protect the interests of creditors, explore options for a sale of the business and assets and to support the impacted employees.
However, most of Power by Britishvolt Limited employees have been made redundant. No other entities in the Britishvolt Group, including a number of UK entities, are in administration.
The omens had not been good for some time and came to head on November 2, when Britishvolt confirmed it had received an undisclosed cash injection, after reports that the lithium batteries start-up was on the brink of collapse.
Company CEO and president of global operations, Graham Hoare, also revealed that top executives would be working “without pay for the next month or so, while an overwhelming number of employees had volunteered to take substantial pay cuts”.
The identity of the investor that had provided short-term bridging aid remains confidential.
Speculation about the firm’s future had mounted after the UK government reportedly refused a request for an advance on promised state funding, said to be worth £100 million ($115 million).
The Department for Business, Energy and Industrial Strategy declined to comment when contacted by Batteries International.
CEO Hoare said the funding would be available to draw down in 2023.
The financial crisis came just months after Britishvolt lost its second CEO in the three years that the project had been underway. The departure of Orral Nadjari, a co-founder of the company, was announced on August 20 but no reason was given for his leaving.
Nadjari founded the company with former CEO Lars Carlstrom, who had stepped down in December 2020.
Carlstrom went on to launch a namesake but entirely separate gigafactory project in Italy, Italvolt, of which he is now CEO.
Ironically, the collapse of Britishvolt came after the UK government announced a new post-Brexit subsidy control system, which came into force on January 4 and which scrapped the “restrictive aid scheme the UK was subject to as part of the EU”.
Previously, the EU would regularly block local authorities and others from delivering funds to businesses “that most needed it in their communities”, the government said.
Work began on building Britishvolt’s facility in northeast England in September 2021. The total investment cost was put at an estimated £3.8 billion ($4.3 billion).
Curiously, former Conservative opposition leader and now member of the House of Lords, William Hague, blamed Britishvolt’s failure on Brexit at this January’s World Economic Forum in Davos
Hague said that such projects “need scale and access to a big market”. However, one industry commentator told Batteries International at the time: “If that were the case, why is the EU saying its giga projects could also be at risk?”
‘Insufficient equity investment for both ongoing research the company was undertaking and development of sites in England’
INTERNATIONAL IMPACT OF BRITISHVOLT’S FAILURE
Britishvolt had agreed a number of deals and partnerships over the past year and the demise of the company will have an impact on other international firms.
Last February, Britishvolt said it had secured the further backing of an existing investor, mining giant Glencore, to launch a £200 million ($270 million) funding round.
The gigafactory developer announced on May 24 it had signed a sales purchase agreement to acquire German battery cells producer EAS Batteries from the Monbat group, in a cash and shares deal worth €36 million.
And on June 7, Britishvolt said its plant would use large scale production lines from Swiss manufacturer Bühler for the production of electrode slurries for the first go-to-market phase of 4.8GWh, which would be expanded to 38GWh towards the end of the decade.
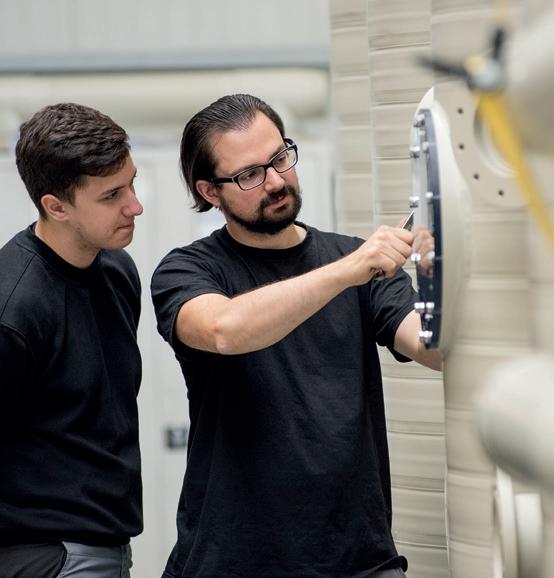
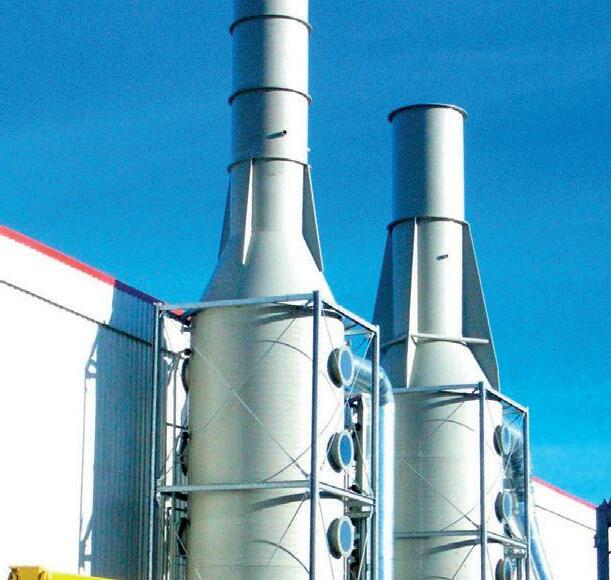
Excellence in Engineered
Formation Solutions.
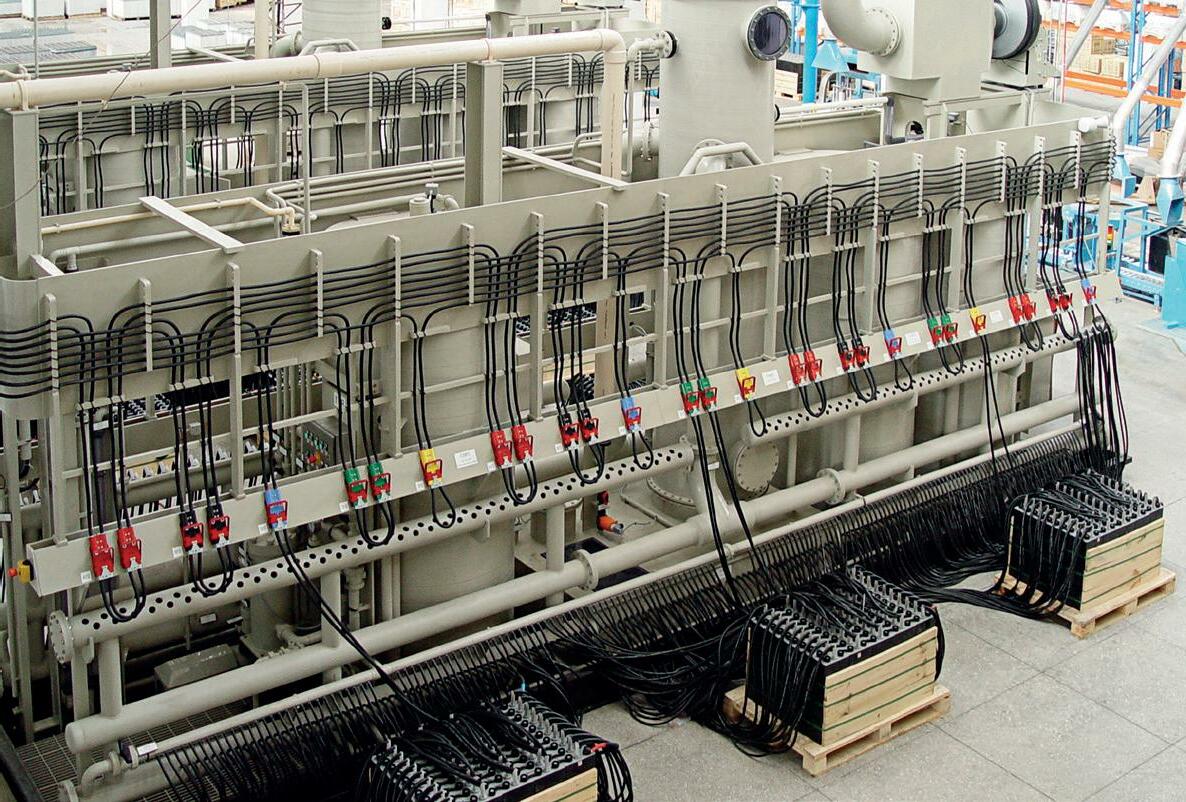
One Team.
Stronger Together.
Early in 2020, INBATEC and KUSTAN combined our talents and manufacturing expertise to create a new company focused on engineering excellence. As one team, we are industry leaders in the lead-acid formation process.
Going forward, we focus beyond just acid recirculation to be your consultant for formation solutions.
Our Threefold Mission Is Simple.
• Quality Engineered Solutions by working with our customers to provide all aspects of a formation system that leads to you meeting your specific formation goals while focusing on operator safety.
• Process Innovation that pushes the lead-acid industry forward with products and services that help you build and form batteries safer, less expensively and with the highest quality possible.
• Satisfied Customers over the life of our equipment. We listen and consult when offering a system and then partner with you through the years to responsively maintain safety and the highest production standards.