7 minute read
Raising the game
Paying close attention to lubrication management can help steelmakers overcome key ongoing challenges says Luis Econom*
IF rotating equipment had a choice of where to work, it would surely never choose the steel industry. Here, the heat and the humidity alone are enough to give maintenance engineers nightmares – as they wonder just how long the bearings in their machines are going to last.
Water may be vital to life, and to many industrial processes, but it can play havoc with bearings. In steelmaking, where cooling water turns instantly to steam, moisture works its way into bearing housings to cause premature failure and potential line shutdowns. The lifespan of a bearing in steelmaking can be a short one.
There are ways to offset this, such as by using more robust bearings, housings and seals, though no single technique can overcome the challenges of such a harsh environment. However, when applied properly, lubrication – and lubrication management – can help to address the demands of such a harsh production environment. It can be a key tool to help steelmakers address many of their pain points around rotating equipment.
Lubrication management goes beyond simply choosing the most appropriate lubricant. It also includes factors such as storage, logistics, sustainability and delivery – typically through an automated lubrication system.
Vital factor
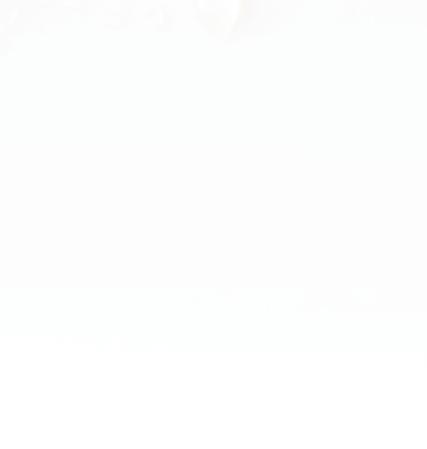
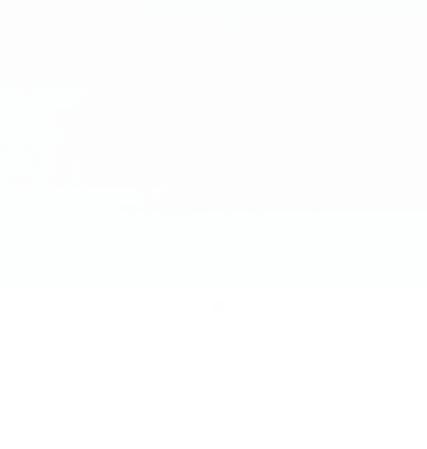
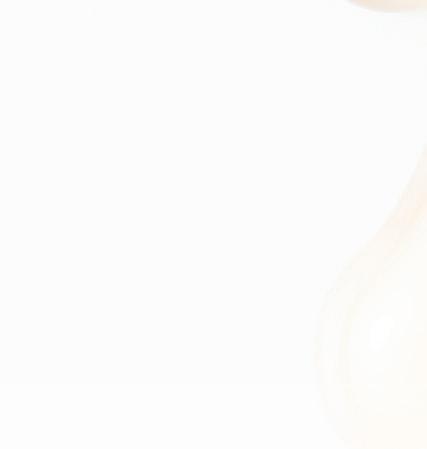
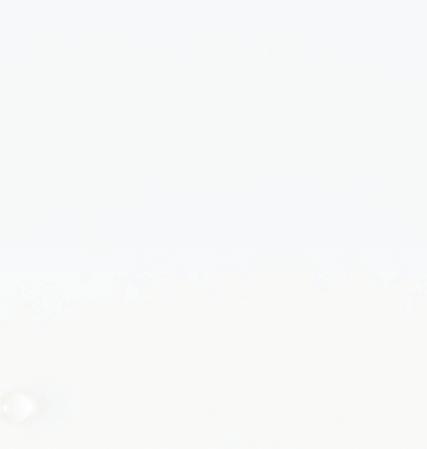
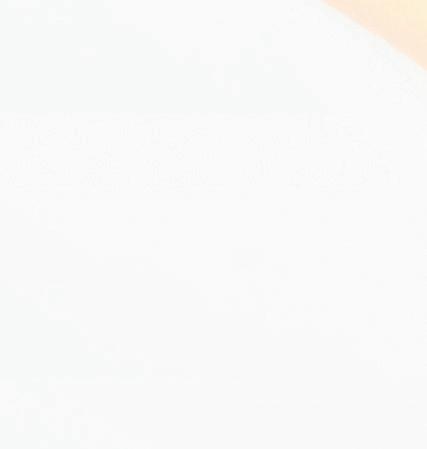
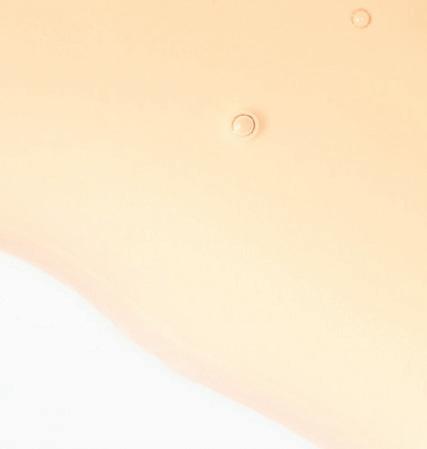
Lubrication is a vital, though often invisible, factor in engineering. Poor lubrication plays a huge role in machine downtime – and is the main cause of premature bearing failure. So, it stands to reason that better lubrication management can help to raise manufacturing efficiency.
The steel industry has similar performance goals as other manufacturing sectors: reducing the cost of production; maintaining or raising safety; improving sustainability; and raising product quality. Correct lubrication management can contribute to all these goals.
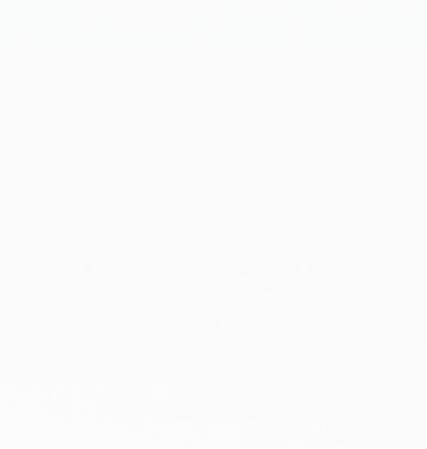
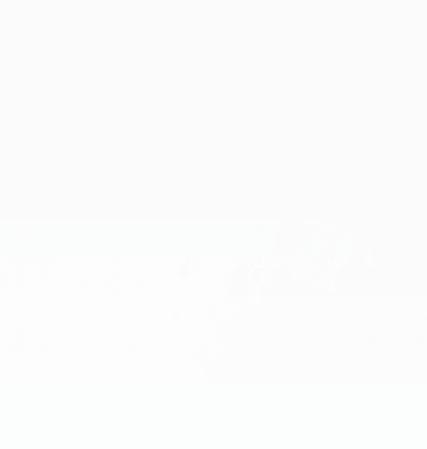
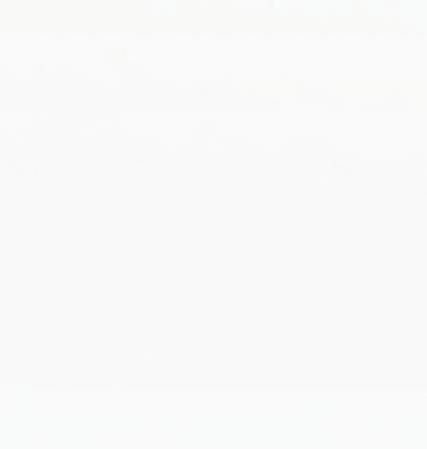
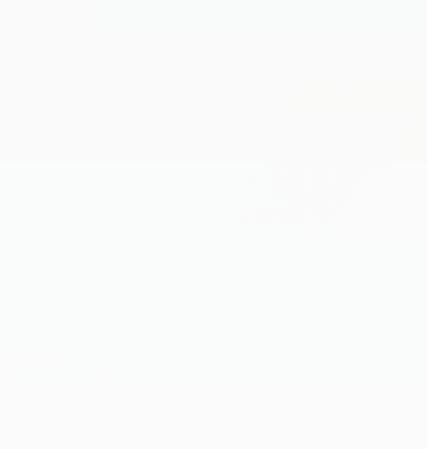

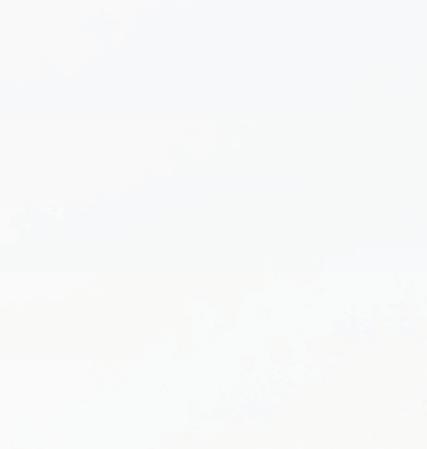
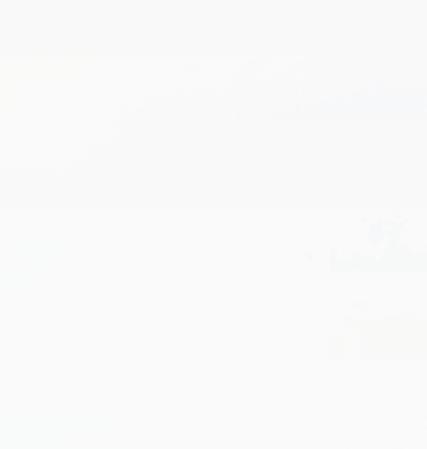
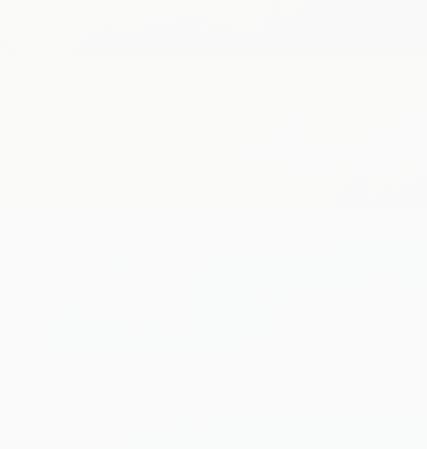
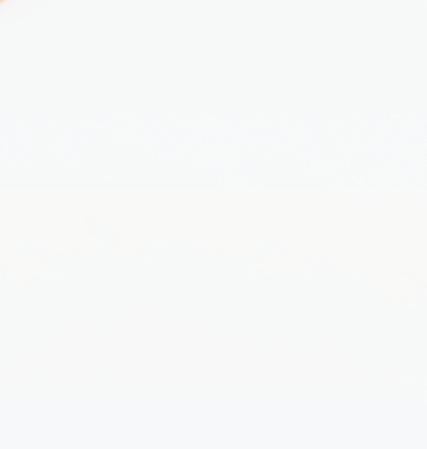
A good place to start is with water. It is vital to steelmaking – but can also cause problems. The most pernicious of these is lubricant emulsification. Here, water that makes its way into bearings, via an oil circulation system, mixes with the lubricant and degrades it. Once lubricant loses viscosity, it needs to be replaced. The challenge is to keep the oil circulating and maintain its quality – so that it still acts as a lubricant.

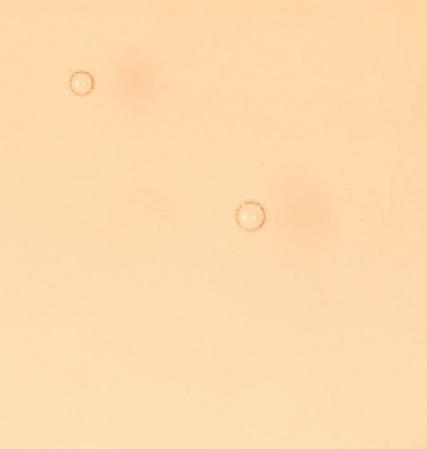
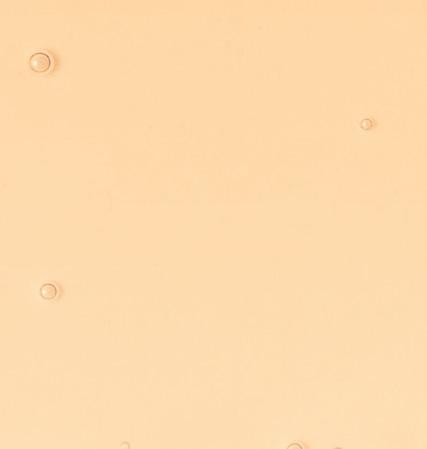
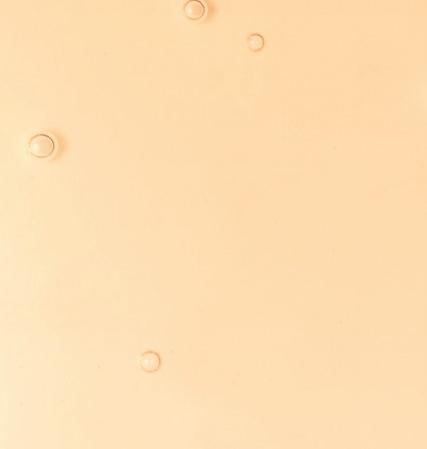

– on the principle that oil and water do not mix. The trick is to do this quickly enough and recirculate only ‘clean’ lubricant.
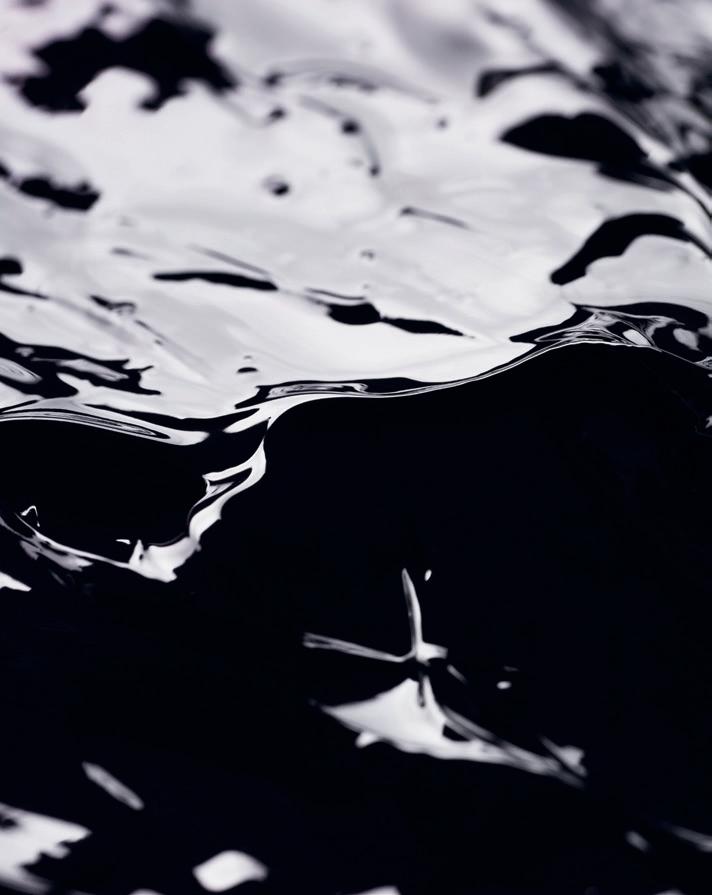
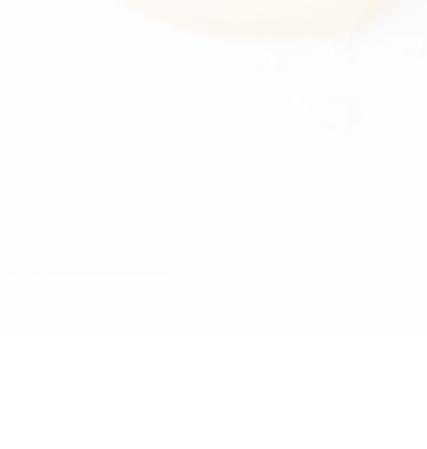
In a modern automated lubrication system – such as SKF Flowline – this is done by storing circulating lubricant in a tank, where the two components (lubricant and water) quickly separate out. The water is drained off from the bottom of the tank – and the lubricant recirculates. The latest tank designs are around one-third the size of older versions, so offer separation in a much smaller footprint.
Swapping out
Different applications within the steel industry – from continuous casting to sheet-making – may require different types of lubricant, or different ways of applying it. Sometimes, circulating oil is more appropriate; in others, grease is the way to go.
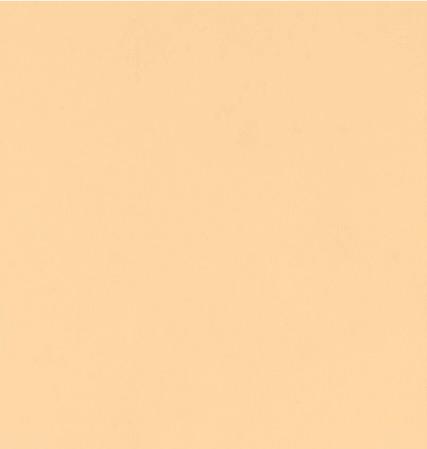
In each case, the recommendation comes from the original equipment manufacturer (OEM), though often the original advice may now be out of date. Machinery is typically driven harder and faster than it was in the past – and this cannot be done using an outdated lubrication management regime.
A modern lubrication circulation system can help. It is designed to carry out two vital tasks: cooling and cleaning. Firstly, heat exchangers help to cool the oil – and ensure that bearings do not run ‘hot’. This all happens against a background of having to circulate the oil quickly, in order to run machinery faster. Newer systems are better able to achieve this.
In addition, it removes contaminants in a number of different ways. Solid particles are removed by filtration, for instance. Water can be more complicated. As long as an emulsion has not been created, any water in the lubricant will naturally separate out
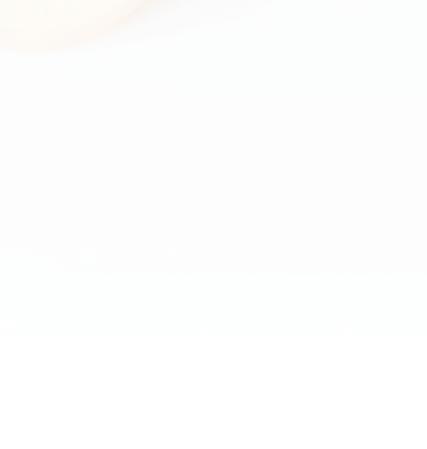
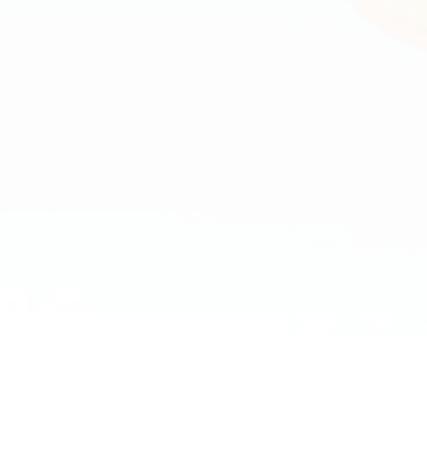
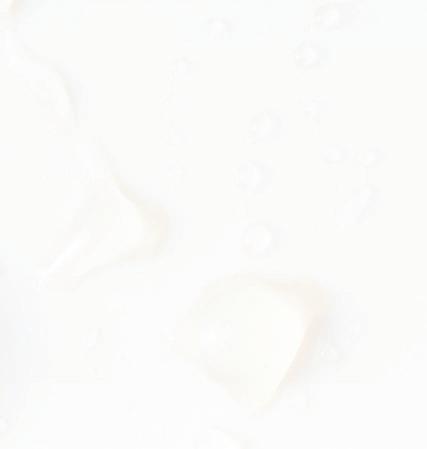
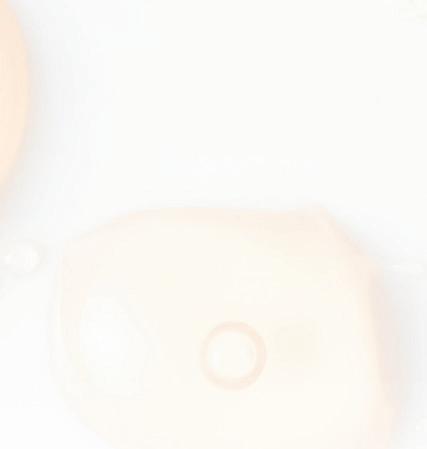
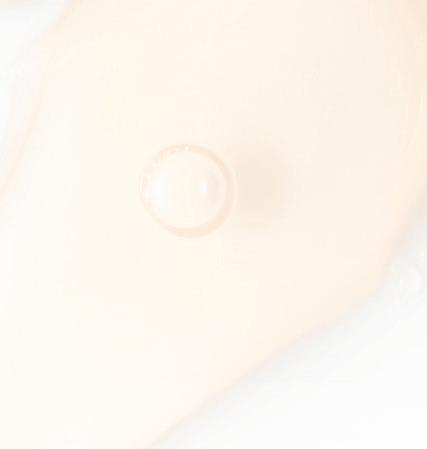
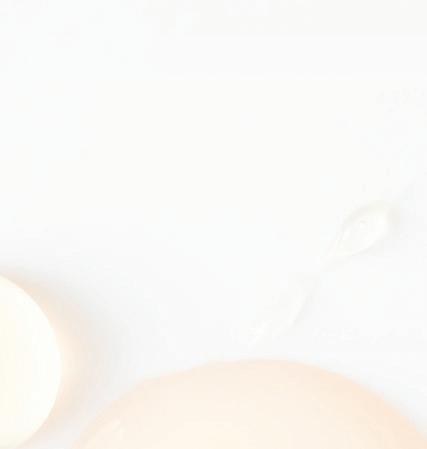
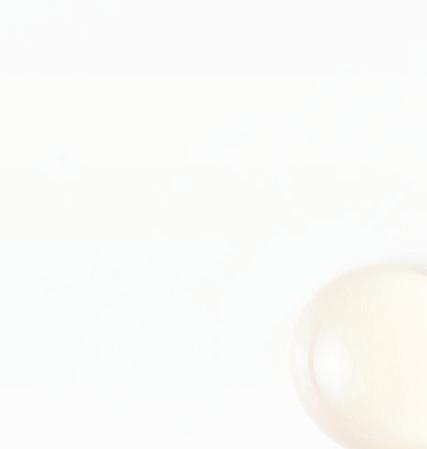
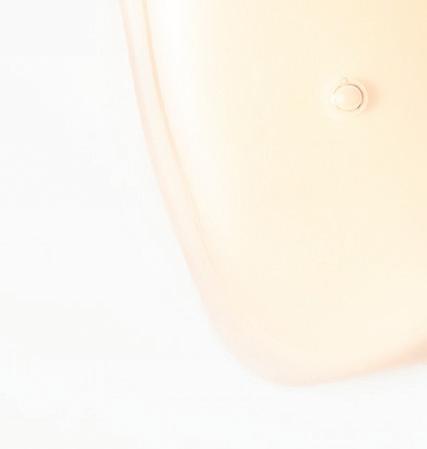


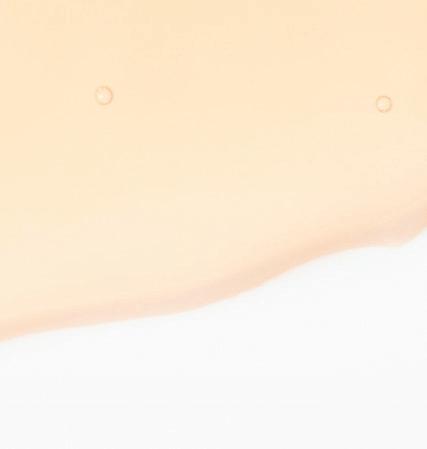
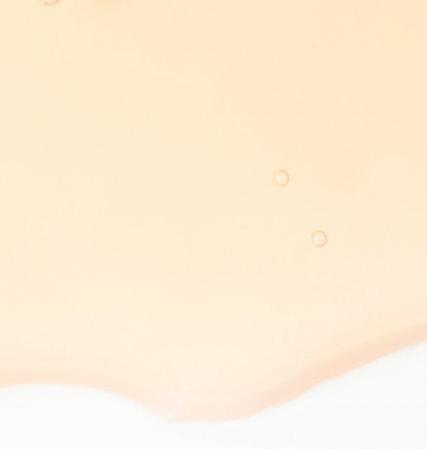

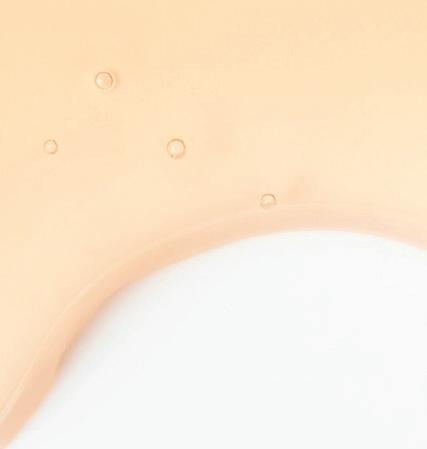
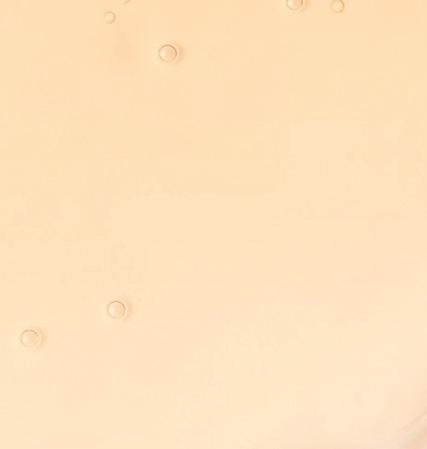
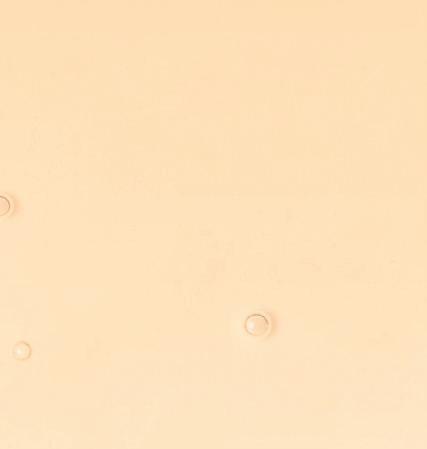
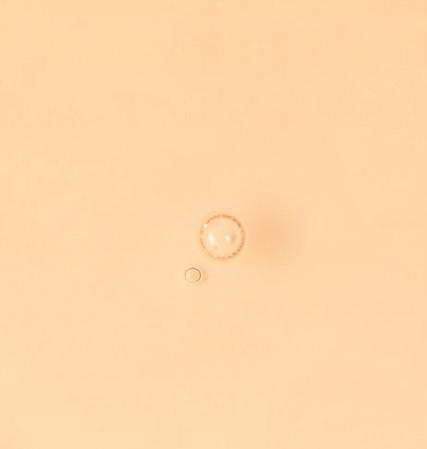
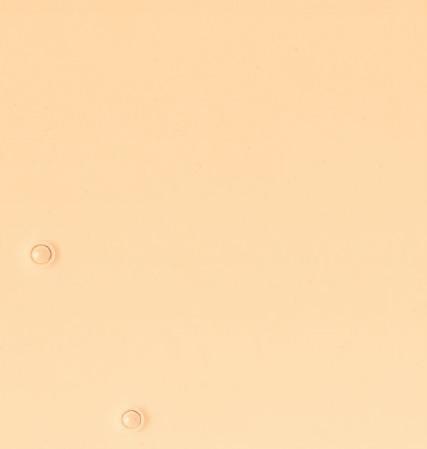
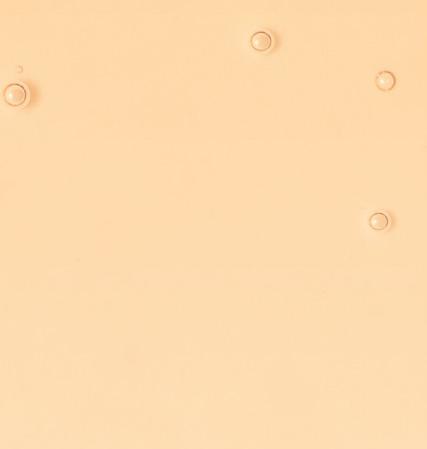
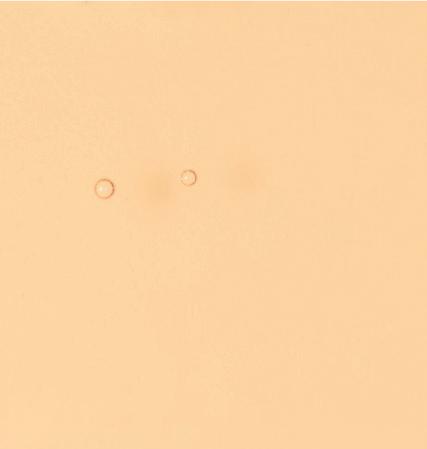

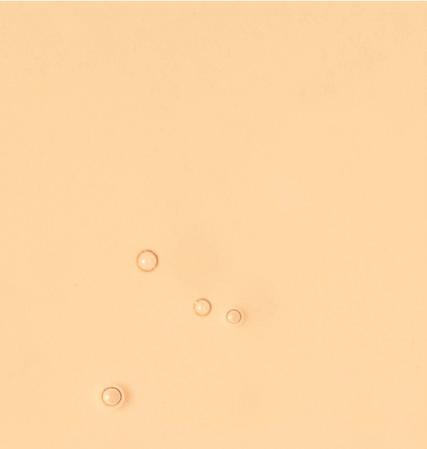
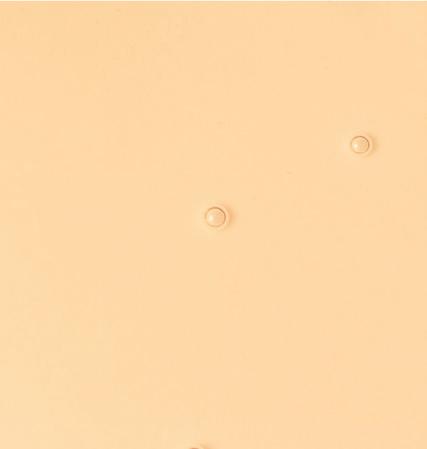
It’s a delicate task to balance performance with longevity. For instance, lubricant can be pumped into bearings using an ‘oil/air’ system. Here, compressed air both cools the oil and improves its circulation. However, it is vital that the system has a good filter, otherwise there is a danger of introducing contaminants –including both air and water.
Another avenue is to use solid grease, rather than liquid lubricant. This has two main benefits: it excludes water from the bearing (by filling the space); and, it can withstand higher temperatures. However, it can cause an environmental issue – as at some point the grease will be ejected as waste. It’s true to say that there is no single

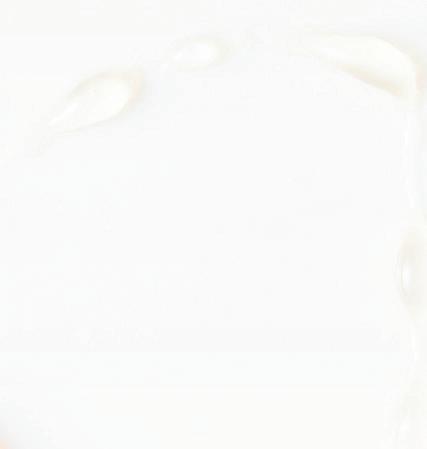
‘right’ answer. This is where the advice of a lubrication expert is critical.
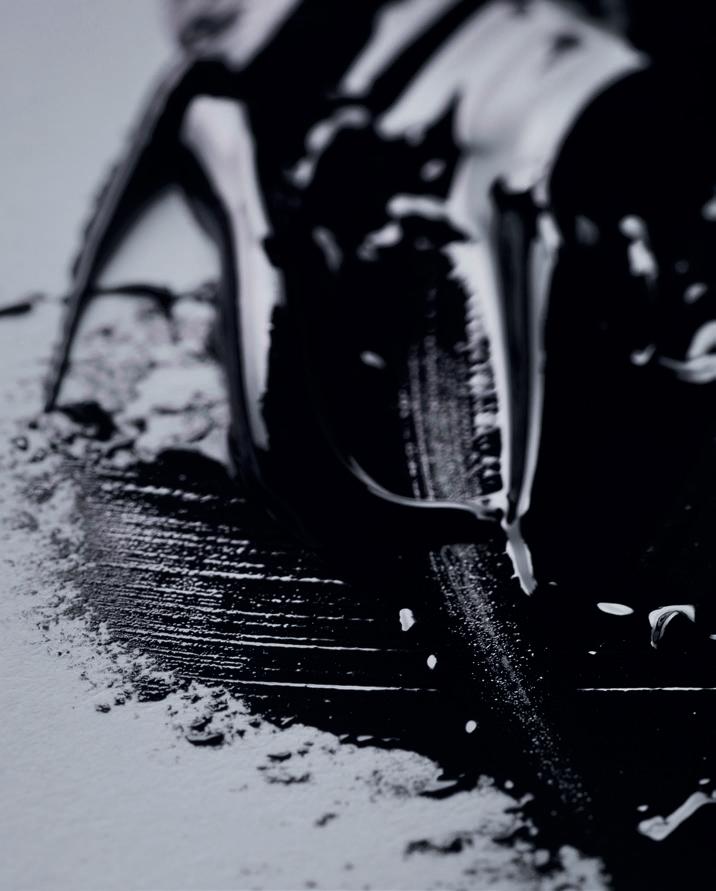
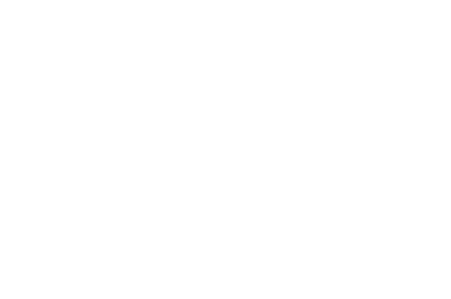
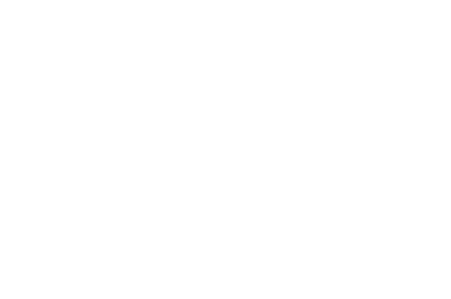
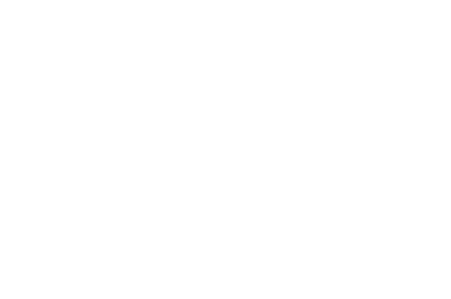
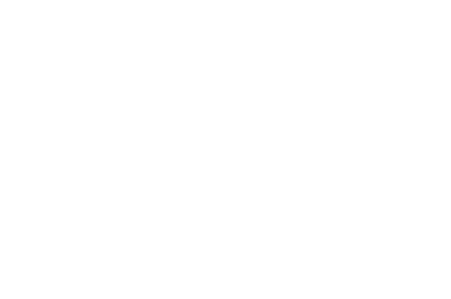
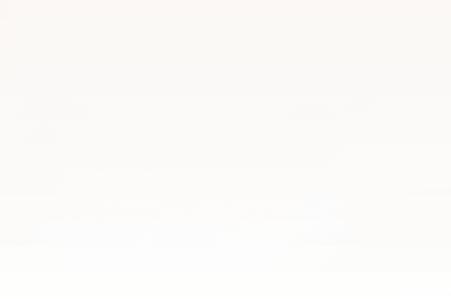
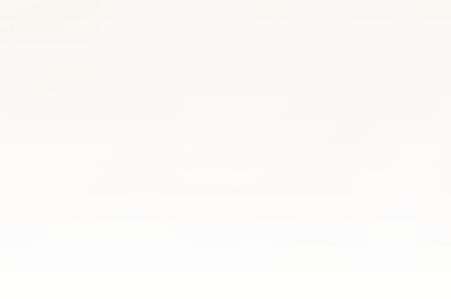
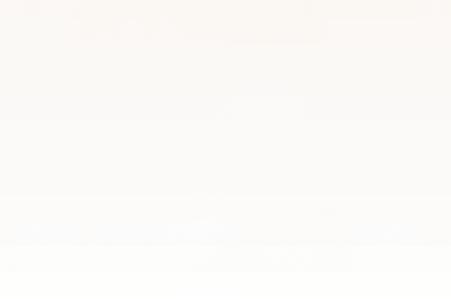
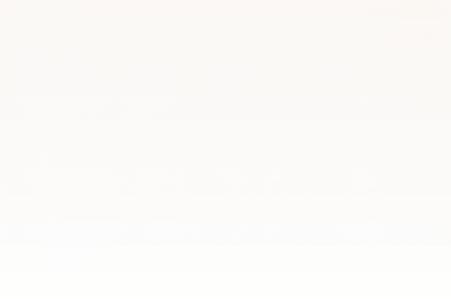


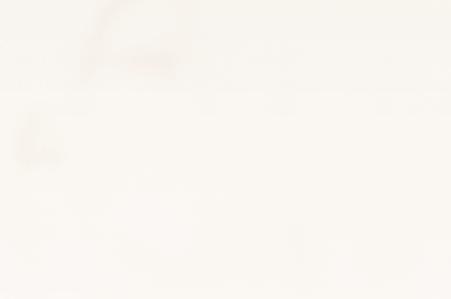
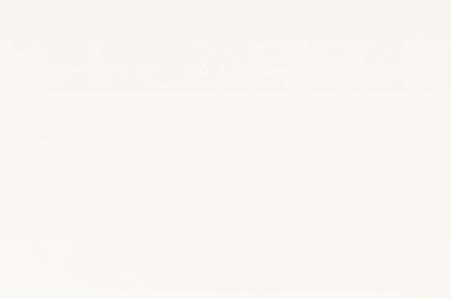
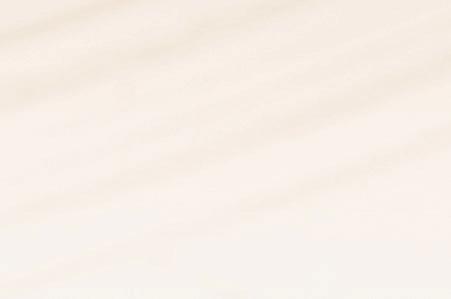
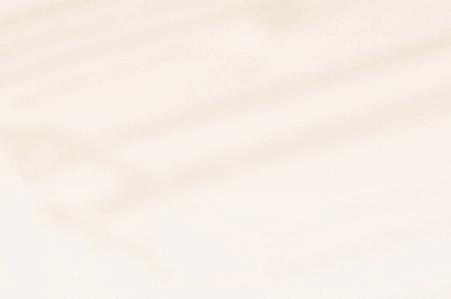
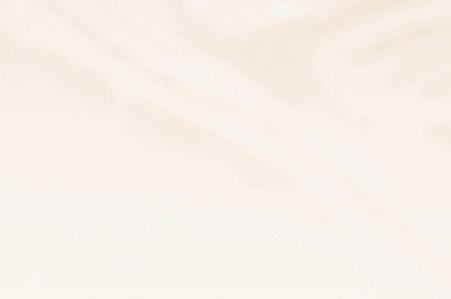
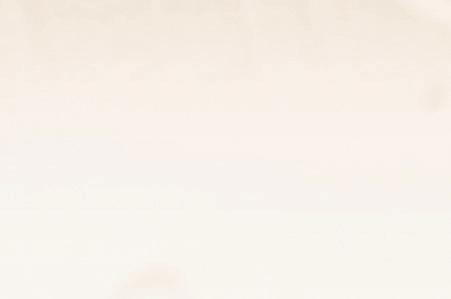
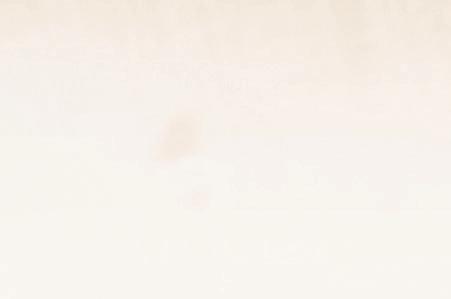
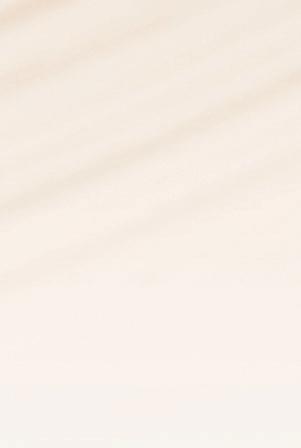
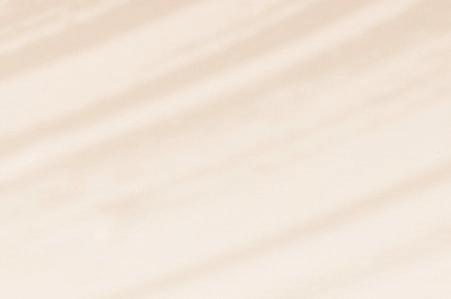
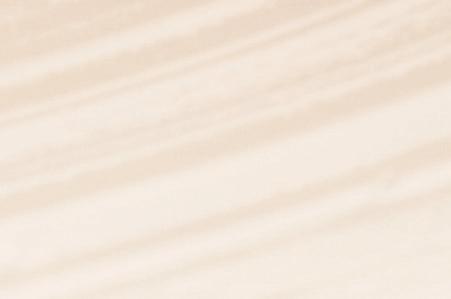
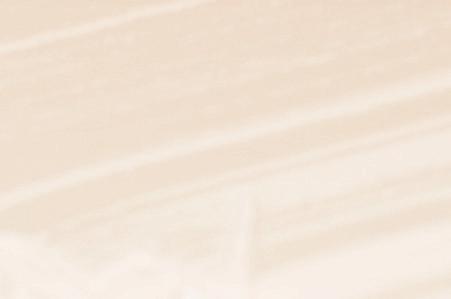
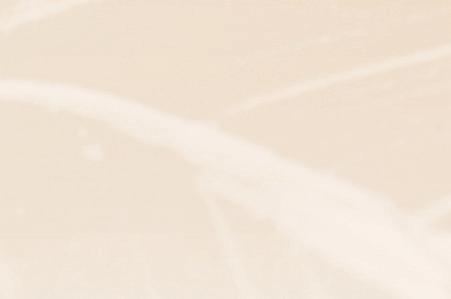
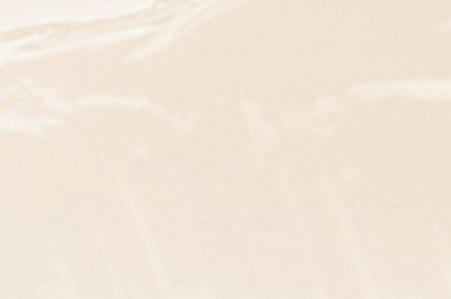
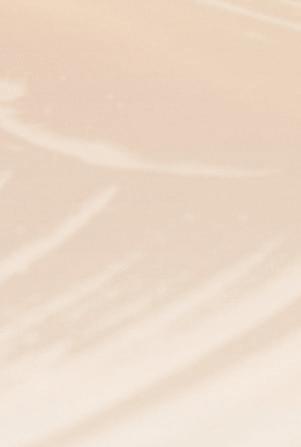
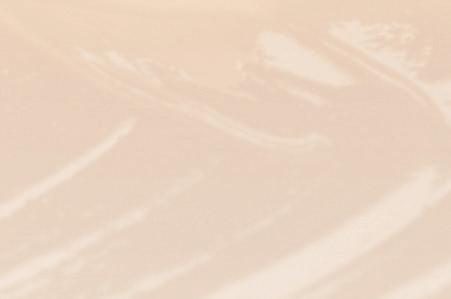
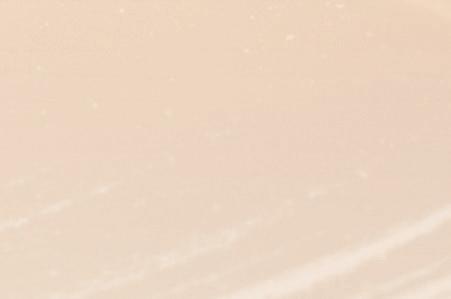
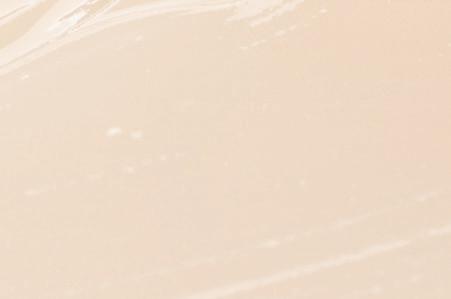
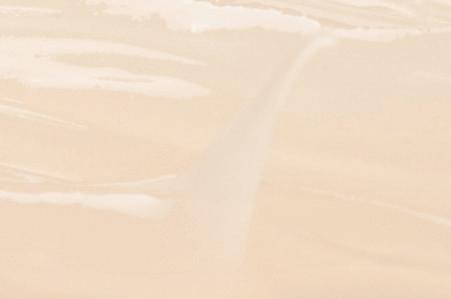
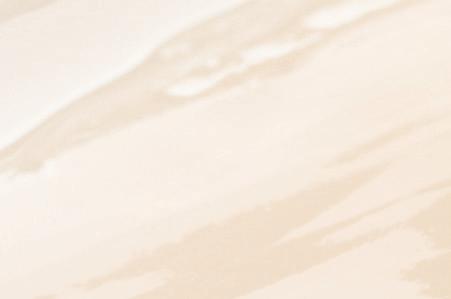

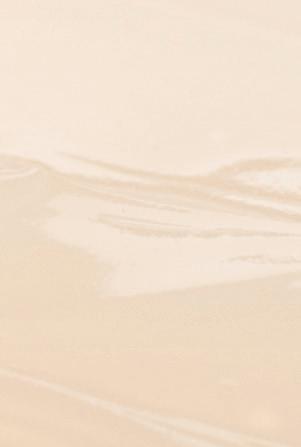
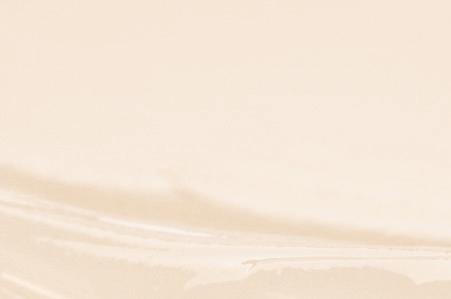
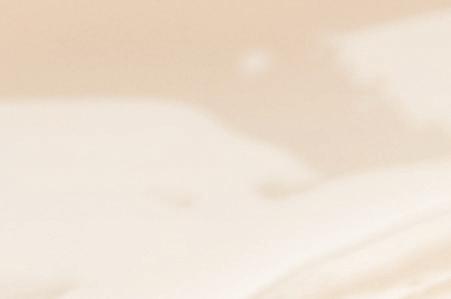
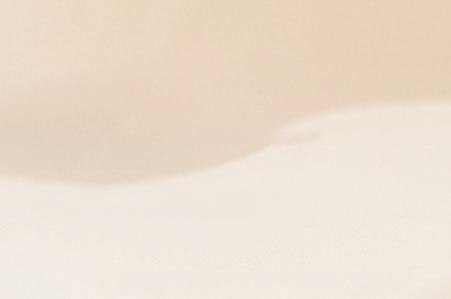
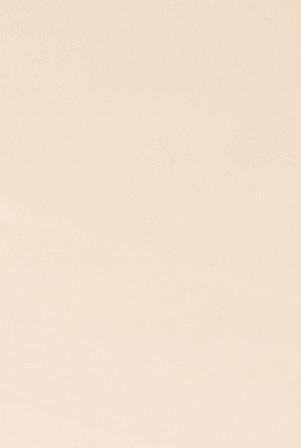

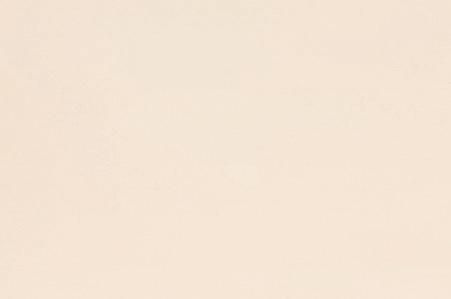
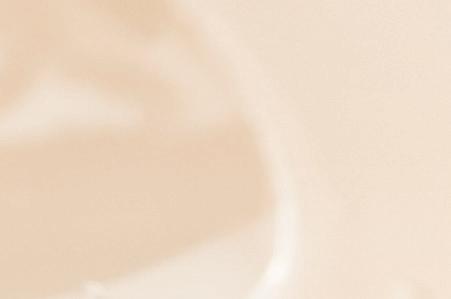
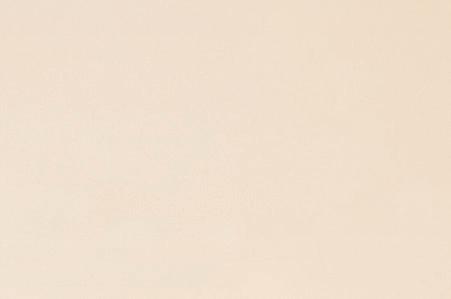
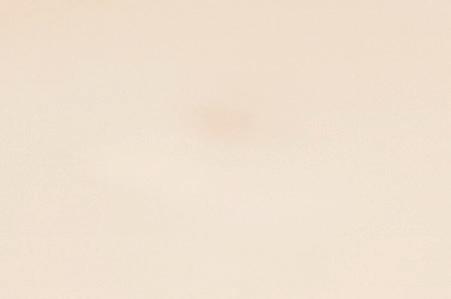
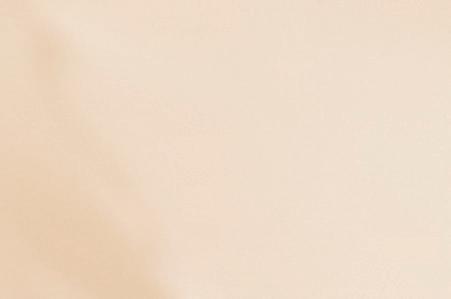
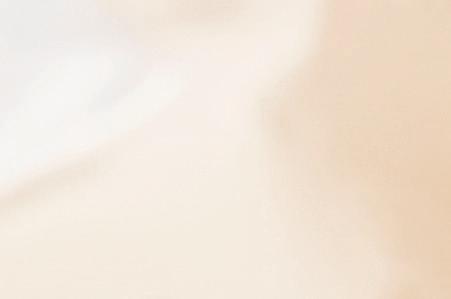
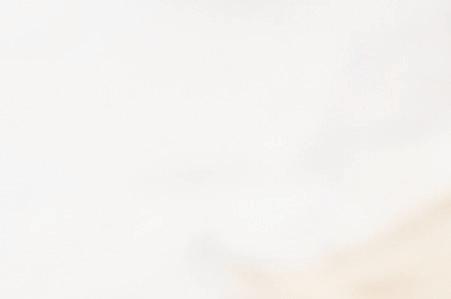
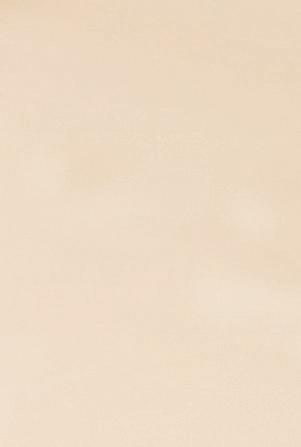
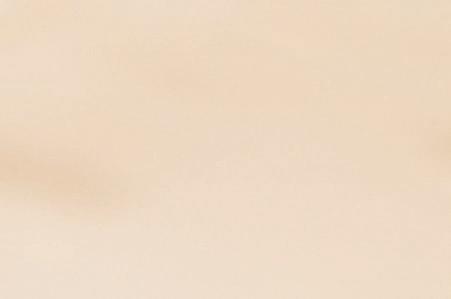

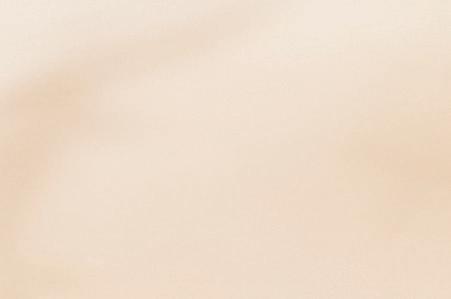
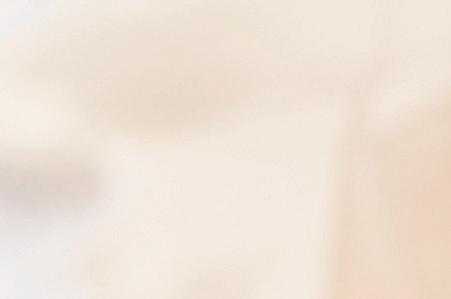
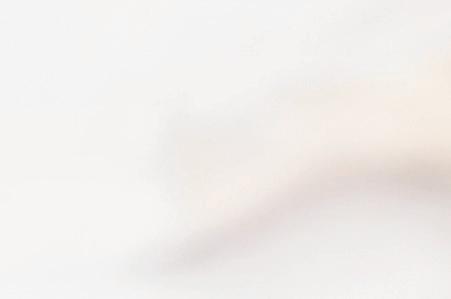
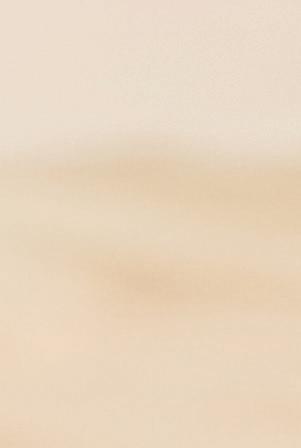
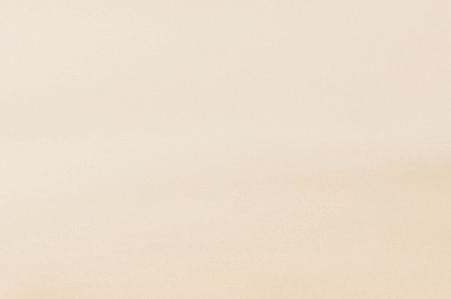
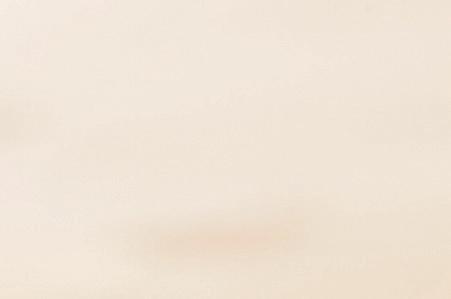
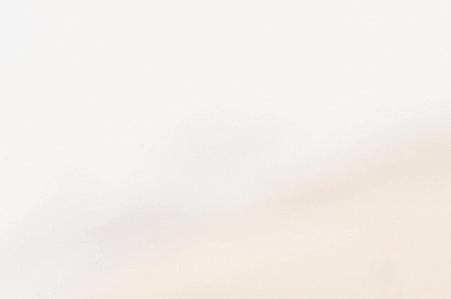
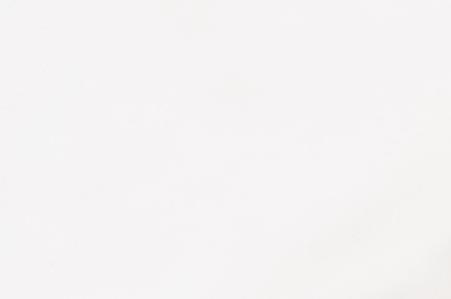
Automatic benefit
In a busy manufacturing environment, automated systems – which deliver lubricant to a set of lubrication points via a tubing system – offer many advantages. Firstly, they dispense the correct amount of lubricant to the right places when it is needed. This is vital for the smooth running of rotating equipment.
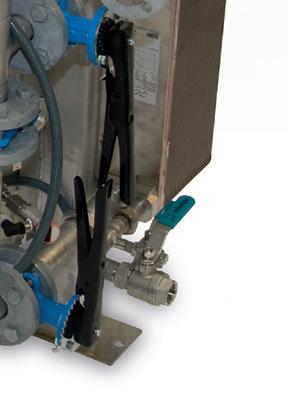
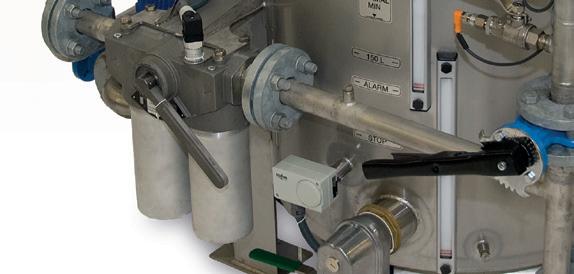
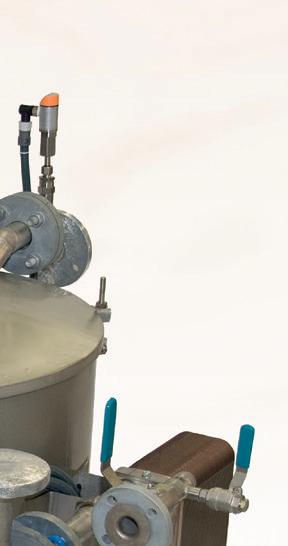
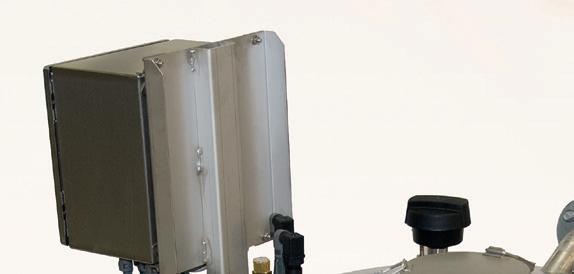
In a harsh environment like steelmaking, it also has a huge safety advantage. Some areas are so hazardous that manual lubrication is either dangerous or impossible. Here, an automated system helps to ensure worker safety and efficient relubrication.
There is also a balancing act in play here. For instance, the system cannot be located too close to a continuous casting line, due to the excessive heat. However, it must be close enough to deliver lubricant quickly. The line that delivers the lubricant must work at elevated temperatures – which typically means using stainless steel.
Trouble in store
Storage is an often-overlooked factor in lubrication management. Where should lubricant be kept until it is needed?

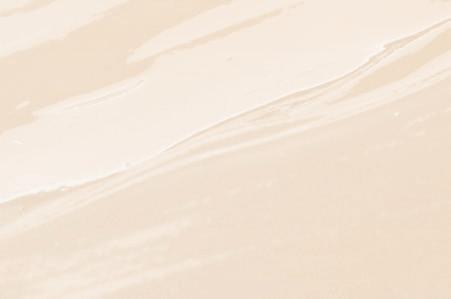
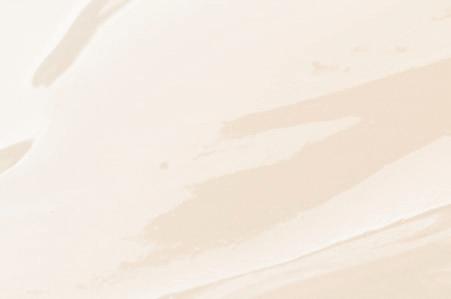

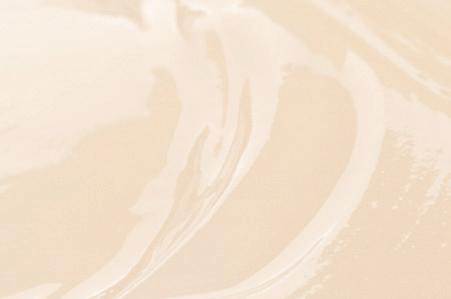
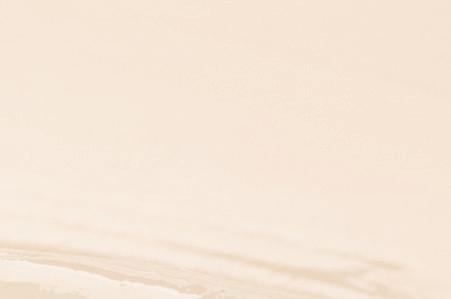
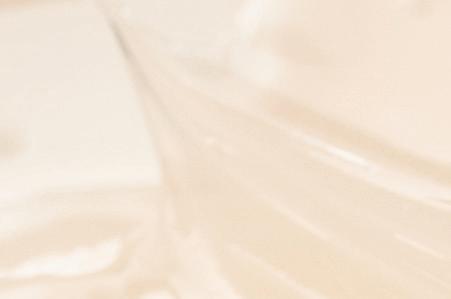
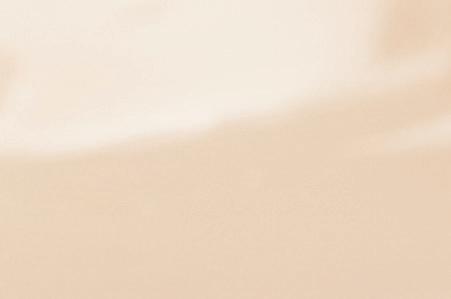
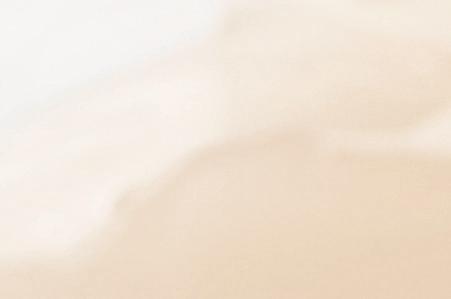

SKF routinely carries out lubrication management audits, and we see it stored in the most inappropriate ways. Outdoors, in the sun and rain, is a favourite; we’ve also seen barrels of lubricant in rooms that have water dripping from the ceiling. These customers might have the bestquality bearings and systems in place but their lubricant is highly likely to introduce contaminants into their sophisticated machinery.
management. It consists of 40 questions in four sections, including one on ‘strategy’. One question asks customers what their strategy is on lubrication management –but many leave this blank. We also find that many have no storage room. When we go through the answers with them, they see that lubrication management is much more than delivering barrels and putting them in a corner until they are needed.
The ‘40 questions’ usually leads to a full audit of their lubrication management programme. This will take two or three days, as our engineers delve into factors such as lubrication systems, lubrication points and training needs.
The first move was to install an oil circulation system. One key issue that we solved was under-lubrication in a set of gearbox bearings. A root cause analysis showed contaminant ingress, and little – if any – lubrication. Part of the reason for this was that lubricant was not leaving the gearbox sump quickly enough.
Changing the flow rate of the lubricant – and opening up a larger outlet at the bottom of the sump – helped to solve the oil return issue. At the end of the year, there had been no line shutdowns.
SKF has also initiated a pilot project to help a steel mill in the UK improve one of its automated grease lubrication systems – by pairing it with condition monitoring (CM). Here, if the CM system detects an issue with a bearing, it triggers a dose of grease in the problem area. SKF calls this condition-assisted lubrication, or CAL. It is not the same as ‘lubrication on demand’ –which automatically ‘tops up’ lubrication points. The pilot system lubricates in direct response to a ‘trigger’. It also offers targeted lubrication – to a single bearing. This is in contrast to existing automated systems – including those from SKF – which will lubricate all bearings at the same time.
Customer benefits
One steel industry customer was having constant bearing issues on a casting line. Here, SKF signed a performance contract, where we took responsibility for the line – promising no more than one bearingrelated shutdown in one year.
This has involved redesigning our dosers and valves, allowing them to dispense at an individual level. Another challenge was to introduce ‘logic’ to the process – something automated lubrication systems do not possess. We did this by using an industrial PLC to control the pump. The PLC effectively acted as the ‘connection’ with the CM system.
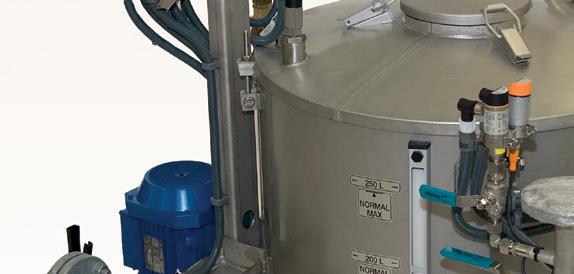
Condition-assisted lubrication cannot be deployed across an entire continuous casting operation in a steelmaking mill. Instead, it targets critical equipment that uses up to eight bearings. This limitation is based on the CM system – which can only have eight vibration channels linked to eight lubrication points – though this may change in future.
proper storage facility is not just a place to
Manufacturers, including steelmakers, work under constant challenge – including thinly stretched resources. One issue is the deceptively simple one of running a store room – or not, as is more likely the case. A proper storage facility is not just a place to keep things until it is needed. It should be properly managed and controlled – with dedicated, qualified members of staff. When resources are tight, it is common to assign staff to the production line –contributing to profits – rather than sit them in a storage room, eating up cost.
This is where an audit can help – and these come in several forms. One is called a client-need analysis of lubricant
The customer has been so impressed with the system that it now wants to order 10 more – and make it a company-wide standard.
Steelmaking is undoubtedly one of the more punishing industrial environments – where early bearing failure seems inevitable. However, paying close attention to lubrication management – from selection and storage, to the intelligent use of automated systems – can help to extend bearing life and avoid costly shutdowns. �