7 minute read
Revolutionizing converter steelmaking
The continuous improvement and optimization of BOF process automation is essential to cope with operator demands such as high process accuracy, stability, flexibility, short ramp-up time, and low consumption figures. Primetals Technologies is constantly extending its principle equation-based process models and, in parallel, introducing data and rule-based functions, leading to hybrid simulation tools for process control and optimization.
THERE are various reasons why process optimization systems are applied for monitoring, control, and optimization of the converter process in steel plants: To meet the demand and maintain competitiveness, the highest flexibility, productivity, and metallic yield must be achieved. Optimization of consumption figures resulting in decreased consumption enables the reduction of costs. At the same time, the focus is on consistent quality. Different systems for monitoring and adjusting the process are applied, which support meeting these targets. Furthermore, the generation of know-how and the provision of it is essential. Tools for supervision of the process are developed, enabling data recording, evaluation, visualization, and reporting, increasing the transparency of the process.
Optimization systems must be continuously improved and adapted with new features to meet market demands. One approach is the expansion of the well-proven first principle process models with data-driven and rule-based functions, leading to hybrid process models.
The strengths of different models
By Anna Mayrhofer*
are used to improve the accuracy of the predictions and obtain a more comprehensive understanding of the process. Hybrid process models enable process control optimization by identifying the optimal process condition, resulting in improved product quality and reduced costs.
These hybrid process models are additionally used to form a Digital Twin –i.e., a virtual representation of a physical system, such as a machine, process, or entire manufacturing facility. They contribute to improving quality by detecting and removing quality-related problems and increase safety by allowing for a better understanding of the behaviour of the physical system. With a Digital Twin, it is possible to simulate and test different scenarios before implementing them in the real world.
Three types of Digital Twins are applied in Primetals Technologies’ automation and digitalization systems:
• Digital Twin Automation: Digital Twins are used as training simulators for operators and engineers. Simulations can help improve the workforce’s skills and reduce the risk of human errors during hot commissioning and actual production.
• Digital Twin Process: Digital Twins simulate the steelmaking process and test different configurations with defined parameters to find the optimal settings. In this way, it enables efficient offline development of steel grades.
• Digital Twin Product: Historical view of all heats produced with detailed analysis options for properties.
In the Process Pre-Calculation figure, the different models of the BOF Optimizer are explained based on the occurrence during the heat from scrap and hot metal preparation until the end of tapping.
Process Pre-Calculation (Fig a)
As an integral part of the Digital Twin Process, it simulates the whole process covering all production steps from charging to tapping.
• Calculation and distribution of gas volumes, heating and cooling agents, alloys, and fluxes to reach the target steel temperature, the target steel weight and analysis, and the target slag basicity
• Calculation of ongoing reactions to predict the weight and analysis of steel, slag, and off-gas, as well as the steel bath temperature after each process step
• Information and warnings for the operator if target values for a process phase are not reached.
The Process Pre-Calculation can be restarted anytime during the heat with the latest data or before production starts. Process Pre-Calculation enables an adaptation of the process treatment even if the heat is already ongoing. Additionally, it can be used for production planning, simulation, and the development of new steel grades. Fig 1
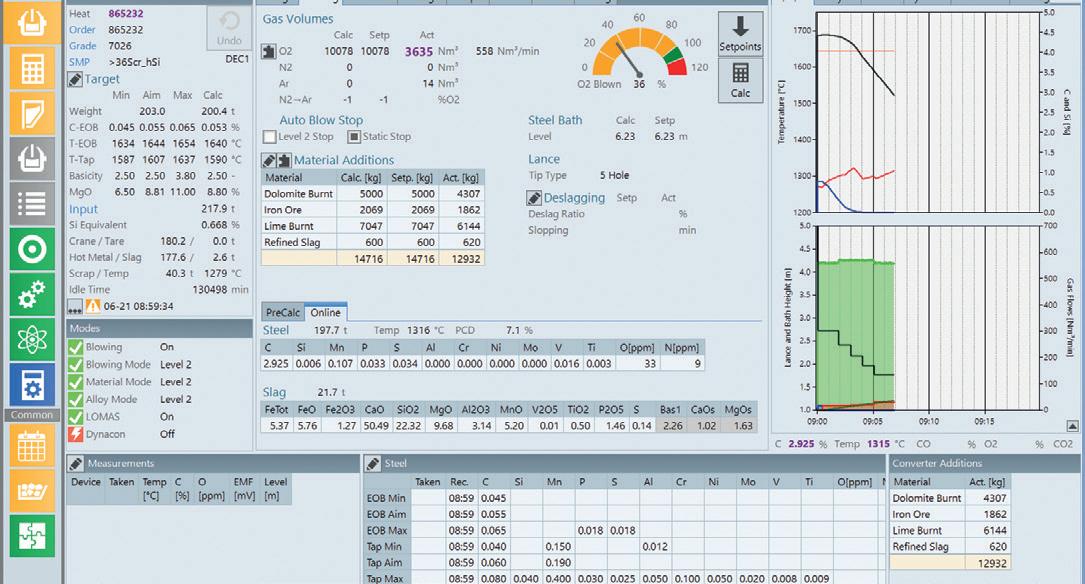
Hot Metal and Scrap Order Calculation
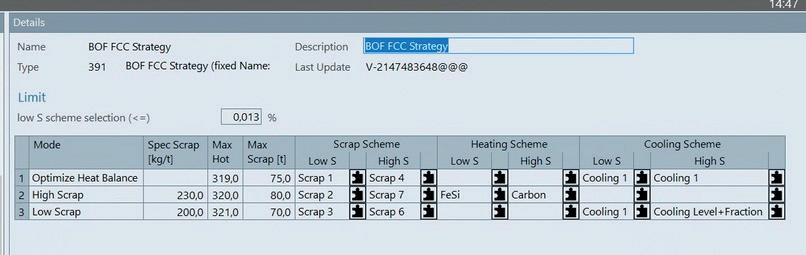
(First Charge Calculation FCC) (Fig b)
If the situation in the steel plant allows it, especially if a flexible provision of hot metal (HM) and scrap is possible, an optimization of the amount of HM or scrap, or both, can be done. In this way, the addition of heating and cooling agents is largely reduced, or in the best case, not even necessary. The Hot Metal and Scrap Order Calculation is part of the Process PreCalculation and determines the amount of HM and scrap before the treatment starts. A preparation of HM and scrap can be done accordingly.
The latest developments focus on the individual specification and selection of different HM-to-scrap strategies for controlling the input ratios of HM and different types of scrap. In this way, it is possible to optimize the mixing ratio depending on the current production philosophy and availability and the costs of HM and scrap. Fig 2
Standard Melting Practice and Automatic SMP Selection (Fig c)
Standard Melting Practices (SMP) define process setpoints covering various input settings to reach target figures.

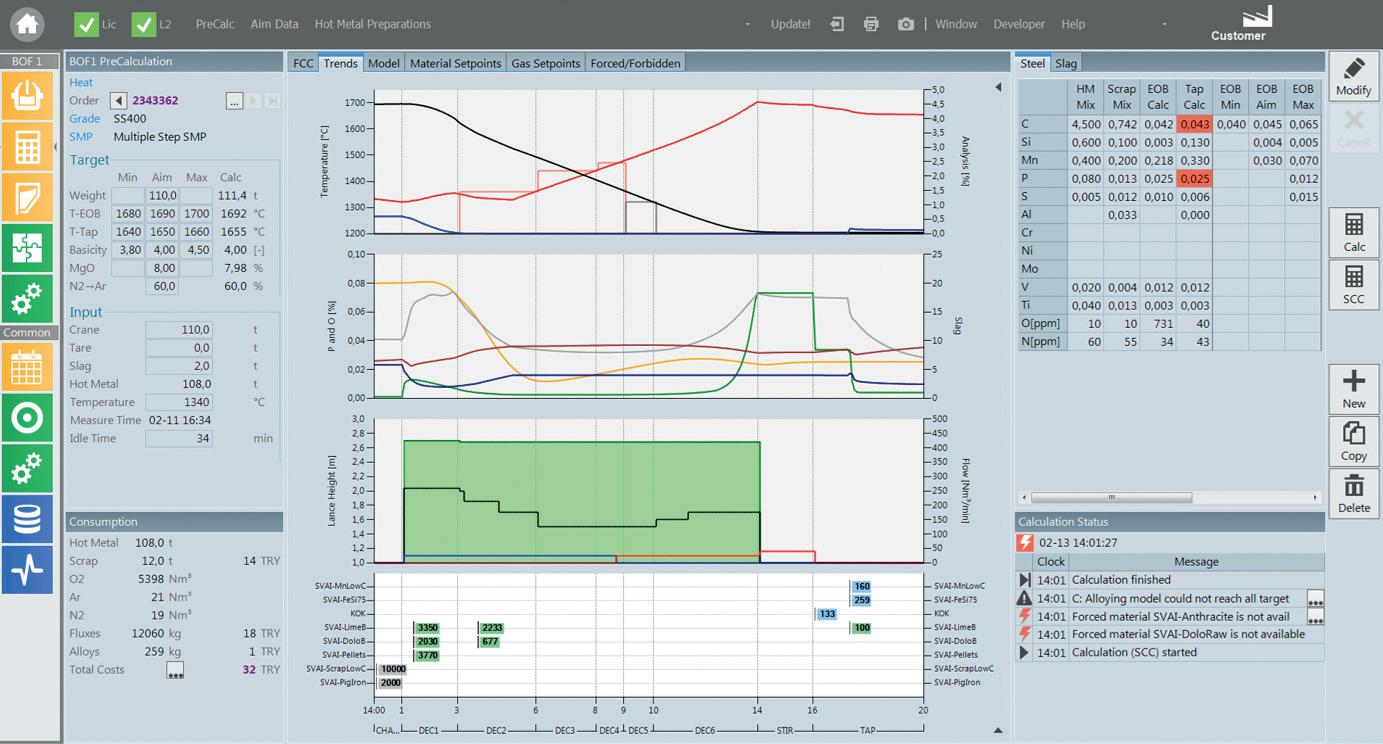
SMPs represent the technological and metallurgical know-how, forming a standardized basis for targeted control to changing initial situations. The main setpoints for the BOF are lance position and oxygen flow rate, bottom stirring, and material addition pattern. With customizable rules, the selection of SMPs is made automatically depending on HM and scrap properties, tapping target values and considering the used lance tip. Fig 3
Second Charge Calculation (Fig d)
Once data from charged HM and scrap is available, the Hot Metal and Scrap Order Calculation is updated by the Second Charge Calculation (SCC). Slag formers, heating and cooling materials with timing and portioning, oxygen amount, blowing and stirring pattern, and the resulting steel bath level are determined. The basis for calculation is the target steel analysis and temperature, actual data of charged hot metal and scrap, the selected SMP, and the material availability.
Online Supervision (Fig e)
First-principle models like mass and heat balance are used for Online Supervision. Ongoing reactions, including melting and scrap dissolution, addition, oxidation, and reduction, are cyclically calculated. In this way, the current steel and slag analysis, weight, and temperature are provided. Supervision during the whole blowing period is also possible. Visualizing essential process parameters enables process diagnostics at a glance and gives the operator a good overview of the current status of the heat. Fig 4
Blow end control (Fig f)
The target window for steel temperature and analysis must be achieved at the end of blowing. The final correction of setpoints for remaining oxygen volume and automatic triggering of blow end based on actual parameters is done via pre-defined strategies. Additional measurements are required to get the current condition of the heat.
In the case of an inblow measurement system, the amount of cooling or heating agents, fluxes, and remaining oxygen to be blown is determined based on the latest results from this measurement (T, express C). Corrective measures due to influences from the blowing lance hot spot are considered. Alternatively, data from an off-gas analysis system – e.g., Primetals Technologies’ LOMAS (Low Maintenance Gas Analyzing System) – is used. The gas components – like CO, CO2, and O2 – are measured, and actual carbon content, decarburization rate, temperature, and slag FeO content are cyclically determined. These measurements are the basis for determining the remaining necessary amount of oxygen, triggering blow stop, and enabling dynamic process control. In the best case scenario, both systems are installed. Fig 5

Reblow Control (Fig g)
Suppose steel analysis or temperature are not within the specified target limits by the end of blowing. In that case, a pre-defined countermeasures strategy is selected depending on which values are not within the valid range. Actual steel analysis from sample and temperature measurements are used to determine the amounts of cooling or heating agents, fluxes, and oxygen to be blown. The analysis ensures targeted reaction, prompt execution, and standardized selection of correction measures.
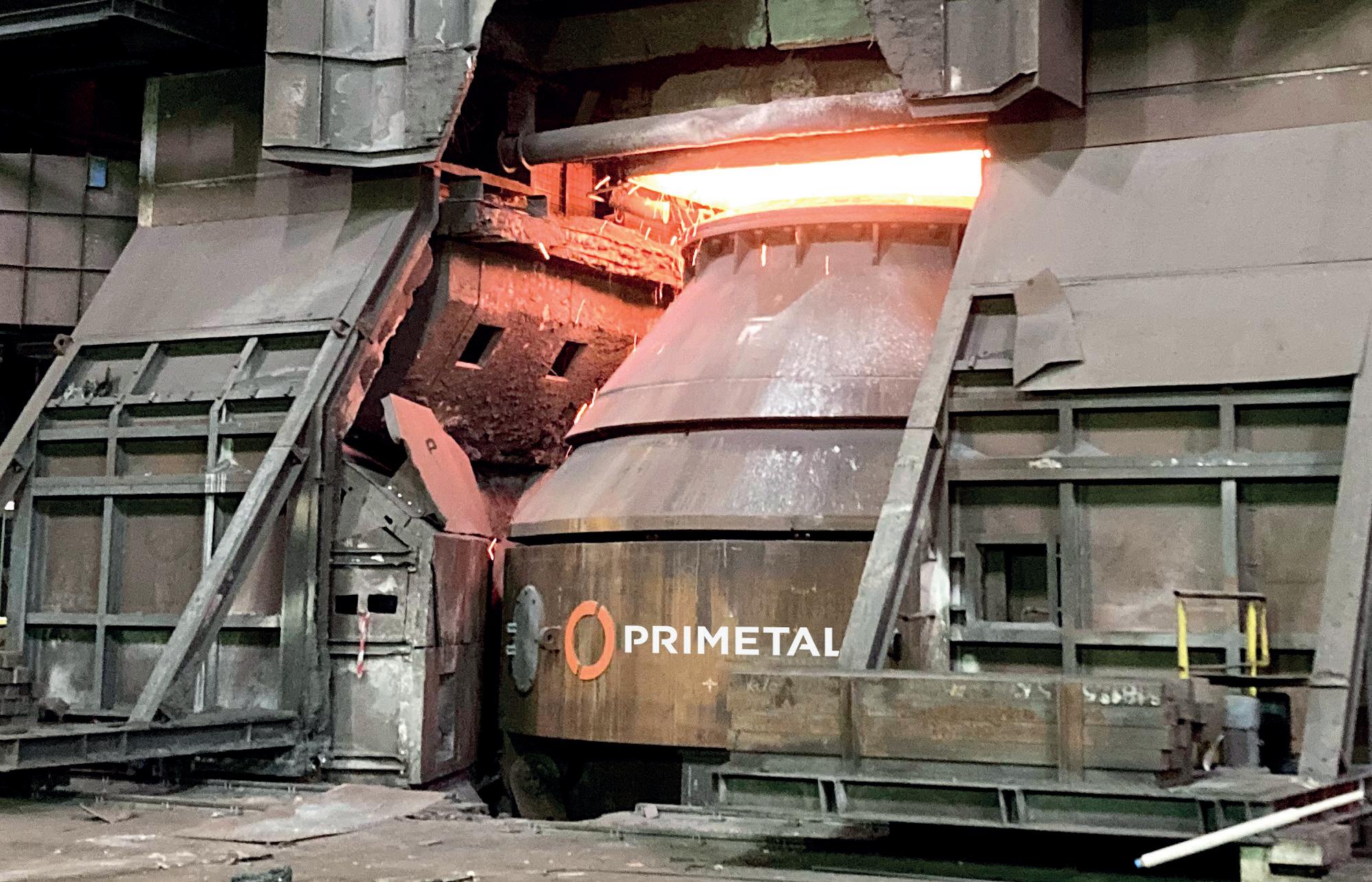
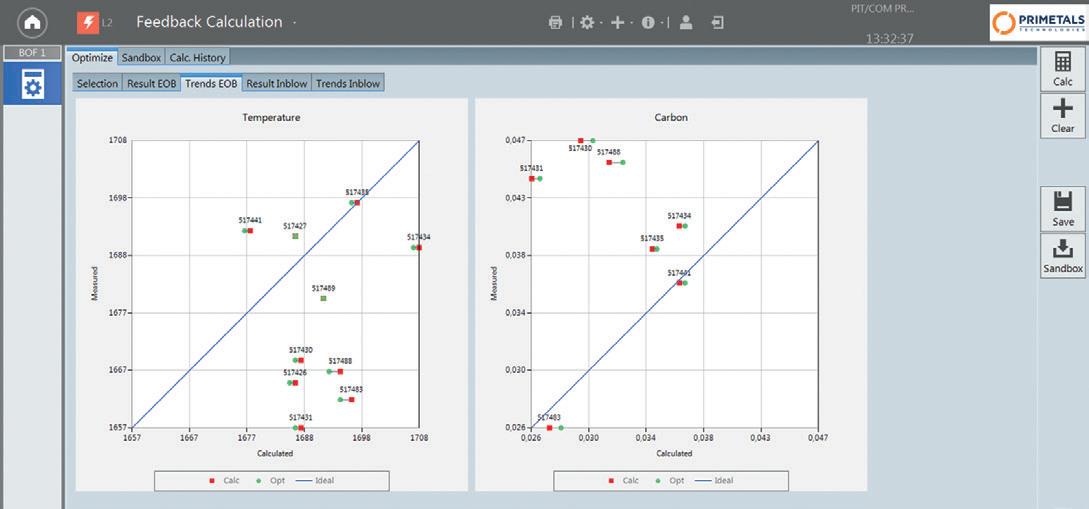
Alloy control (Fig h)
The necessary types, weights, and timing of deoxidants and alloying materials during tapping are determined to reach the target steel analysis. At the same time, the costs of the used materials are considered. Steel and slag analysis in the converter before tapping, target steel analysis after tapping, material properties and constraints, and, if available, the thermal condition of the teeming ladle are also considered.
Feedback Calculation
The tuning of process models is essential to achieve the required accuracy. Current developments focus on Feedback Calculation, a tool that uses the measured and calculated data from the heats produced to improve the tuning parameters used for calculation. Completed heats can be recalculated with modified tuning parameters. There are two different methods to select new tuning parameters:
• Sandbox Mode: manual selection and adaption of tuning parameters
• Optimize Mode: an optimal set of tuning parameters is calculated
The results for a set of completed heats are calculated by the optimization system with the selected tuning parameters and compared to the temperature and steel analysis measurements of the heats. In this way, it is possible to gradually improve calculation accuracy by selecting more suitable tuning parameters, resulting in reduced deviations between calculated and measured values. Fig 6
Automatically selected tuning parameters from Optimize Mode show an overall better match between measured data (y axis) and calculated values (x axis) for both temperature and carbon. One can see that the calculated values with the optimized parameters (green) are overall closer to the ideal line (blue, measured = calculated) compared to the calculated values with the previous tuning parameters (red).
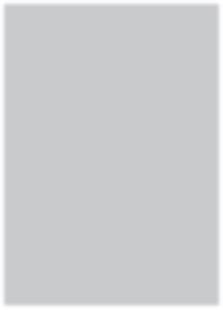
An optimal database must be available for the Optimize Mode of Feedback Calculation to function properly. An evaluation of data of the heats produced ensures this. With Heat Data Evaluation an index is calculated, which gives feedback on the quality of process operation, data, and calculation accuracy. The following information is considered:
• Quality of input data, e.g., hot metal weight, chemical analysis
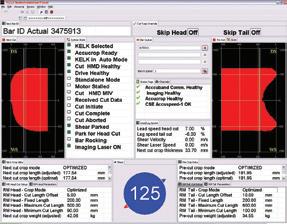
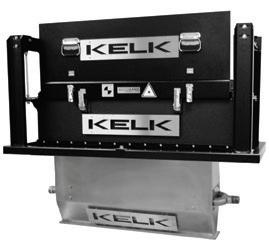
• Deviation from a standard operation, e.g., material additions shortly before measurements
• Availability of measurements and sample results for metal and slag, e.g., complete inblow and endblow measurement
• Matching of model results and measurements
• Occurrence of abnormal events, e.g., blowing interruptions, slopping
Furthermore, the Heat Data Evaluation supports process metallurgists and engineers in evaluating the heats by providing a fast overview of the right KPIs.
Conclusion
Dynamic and accurate process control is enabled by combining first principle models applied over decades with the latest developments containing data-driven and rule-based functions. This results in hybrid process models with the highest hitting rates for carbon and temperature and leads to low reblow rates, ensuring efficient and flexible high-quality carbon steel production. A targeted selection of hot metal, scrap, and materials that are added during the process reduces production costs.
Tools are developed focusing on improving the calculation accuracy by selecting more suitable tuning parameters and enabling an even better prediction of the whole process. These tools significantly impact the Digital Twin, perfectly reflecting reality. �