7 minute read
A new refractory solution to increase productivity
Calderys is an expert in specialty bricks, refractory monolithics and casting, with a comprehensive portfolio to support customers in many sectors. For aluminium customers – and secondary remelters particularly – a new product is tackling a long-term problem of operating in harsh environments.
We spoke to Sebastien Duguet, Aluminium Market Manager for Calderys, who explains how ALKON® SOL CAST HT is helping customers save time after relining and repair work.
WHO ARE YOUR TARGET CUSTOMERS FOR ALKON® SOL CAST HT?
ALKON® SOL CAST HT is ideal for harsh environments where the refractory operates in extremely hot temperatures – greater than 1200°C. Generally, the customer that ticks the box will be a secondary aluminium producer – those who re-melt aluminium scraps to make new products. Customers that are mainly melting very corrosive alloys with a high level of magnesium, with high melting rates, heavy charge and heavy skimming tools.
Once the liquid aluminium has melted, the contact areas inside – the hearth, the ramps, the sill, the bath walls – face combination of flame impact & thermal shocks, mechanical wear, and corundum growth, that is when aluminium alloys react with the refractories and destroy them. So, customers rely on a special product for protection, and ALKON® SOL CAST HT is pushing the limits the process operation can achieve.
CAN YOU DESCRIBE THE MAINTENANCE PROCESS? SO THIS MAY ENCOURAGE MORE PRODUCERS TO SWITCH FROM BRICKS TO MONOLITHICS?
Typically, the maintenance work involves replacing some parts of the refractory lining. The most common repairs are to the sill – the bottom part of the opening, where you are charging the material - and the ramp next to it. Sometimes, repairs are needed to the hearth or on the walls or spout.
There are four phases. First, the customer needs two or three days to cool down the furnace to a temperature where they can safely enter the area, then to remove the faulty or damaged part. Third, they cast or install new products. Finally, they have to dry it all by heating the furnace back up.
It’s a long process and Calderys’ product goes some way to resolving frustrating and costly restart delays. Customers want to get their production back up and running as quickly as possible. They can’t reduce the time it takes to cool the furnace, they can’t save time on demolition and they can’t change the time it takes for installation. The only stage where you can save time is the dry out – and that’s the tricky part for refractory monolithics.
A normal solution would take six days to dry, because most monolithics are cast with water that takes time to evacuate without risking an internal failure of the material. But ALKON® SOL CAST HT uses a sol binder, which means the cast can heat up quicker from 200 degrees to 700 degrees, and it’s dry between 24 to 48 hours later.
A standard cement-bond monolithic repair solution - needing 5-tonne or 10-tonne monolithic - might take ten days, but ALKON® SOL CAST HT can save five days while delivering a high quality performance.
And that’s key for secondary aluminium producers with only half of production loss. For medium or large repairs, or emergency repairs, time is of the essence. Some customers might be able to divert production to another line, but for those who can’t, they are not producing at all. Depending on the size of the furnace, the loss per day could be as much as €20,000.
Customers can make substantial savings to their bottom line not only by reducing the time it takes to make repairs, but by choosing a product that will extend the lifetime of the critical area of their equipment.
Also, less gas is wasted for the simple reason that the heating-up and dry out period with such a product is only two days, rather than six days for the standard.
Yes, producers can take advantage of the characteristics of monolithics. In secondary melting furnaces, the usage of phosphate bonded bricks is still largely used. The main reason is that up to now monolithic products were losing their corrosion performance after being exposed to the high temperatures of a melting furnace, up to 1600°C with the impact of burner flames. The “P-bond” bricks were therefore keeping a technical advantage over monolithic solutions, even the best ones, in harshest melters. This is no more the case with ALKON® SOL CAST HT, and thus you can combine the best of bricks and monolithics.
So it is seen as an advantage that monolithics can propose large panels – of 1.5 meters squared, for example – and thereby reduce the number of joints in contact with the liquid aluminium, providing more stability, as there are fewer joints, which means less infiltration and less exposed edges and less risk of early degradation. Other known advantages of monolithics are the shorter lead time, superior hot mechanical strength, easier installation as well as higher freedom in lining design. Last but not least, ALKON® SOL CAST HT is borrowing other usual benefits of bricks: longer shelf life and of course the higher speed to heatingup.

CAN YOU SUMMARISE CALDERYS’ DEVELOPMENT AND TESTING OF ALKON® SOL CAST HT? WHAT MAKES ALKON® SOL CAST HT UNIQUE AND INNOVATIVE?
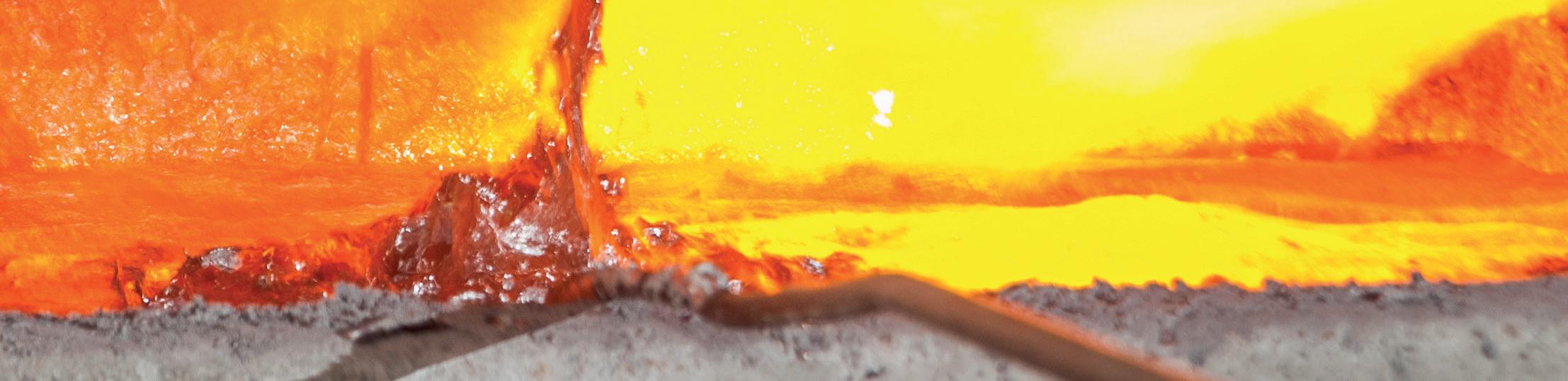
Calderys is a leader in monolithics in the aluminium industry, with a range of 50 products dedicated to the aluminium alloys KONtact, under the umbrella name ALKON. We have a deep understanding of the corrosion of aluminium alloys on refractories that was built over the past four decades. We had already mastered the use of non-wetting systems and we wanted to develop a product that would solve the issue of working in high temperatures while keeped protected from the destructive corrundum growth. ALKON SOL CAST HT can work up to 1600°C
It was a long process – almost four years. We fi nally selected a product and then carried out more than 15 trials, starting in March 2021, with recognised players in this market. They all had interests in different benefi ts. One needed something strong and resilient, another needed something that could be installed and dried out quickly, one was sensitive to the high temperature and corrosion resistance, another valued the speed it offered, but was less concerned about the corrosion resistance.
Over 15 months, we did more than 140 tonnes of industrial testing. The feedback from customers was all positive. In fact, we didn’t need to make any changes to the product after the pilot. And those customers we piloted it with have come back to us to use it for their other furnaces. We are really pleased to have added this to our ALKON® range. It’s not intended to be one product to replace others, but it should be used in conjunction.
A patent was fi led in December 2021 and ALKON® SOL CAST HT launched commercially in April 2022. There are refractory products that work at a high temperature with aluminium – but on bricks or ramming mix. This is the fi rst product for monolithics that brings with him all the best of monolithics: superior mechanical strength, ease of installation etc.
There are refractory monolithics that work with aluminium with fast dry out - but on chemical bonds with low service temperature, 1250°C maximum.
There is nothing like ALKON® SOL CAST HT – it combines the best of monolithic and brick in one product.
INNOVATIVE FURNACES FOR ALUMINIUM
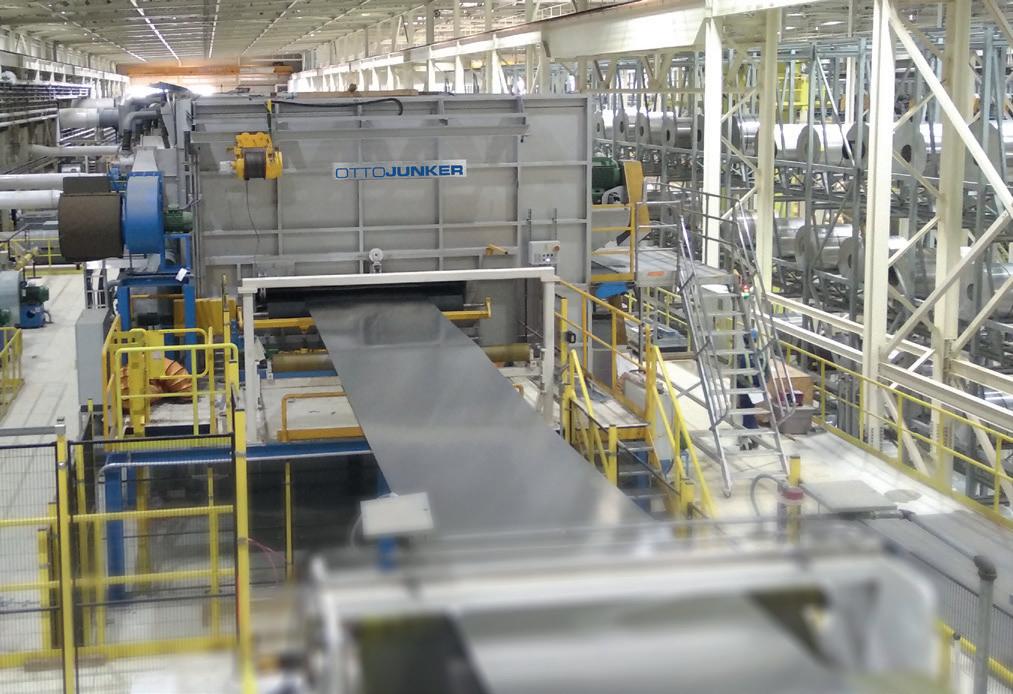
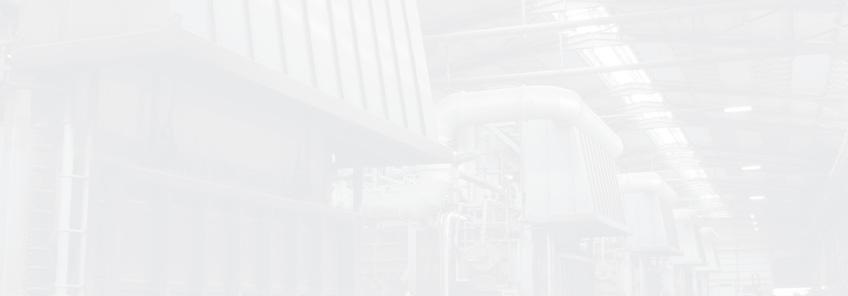
Rolling Mills Extrusion Plants
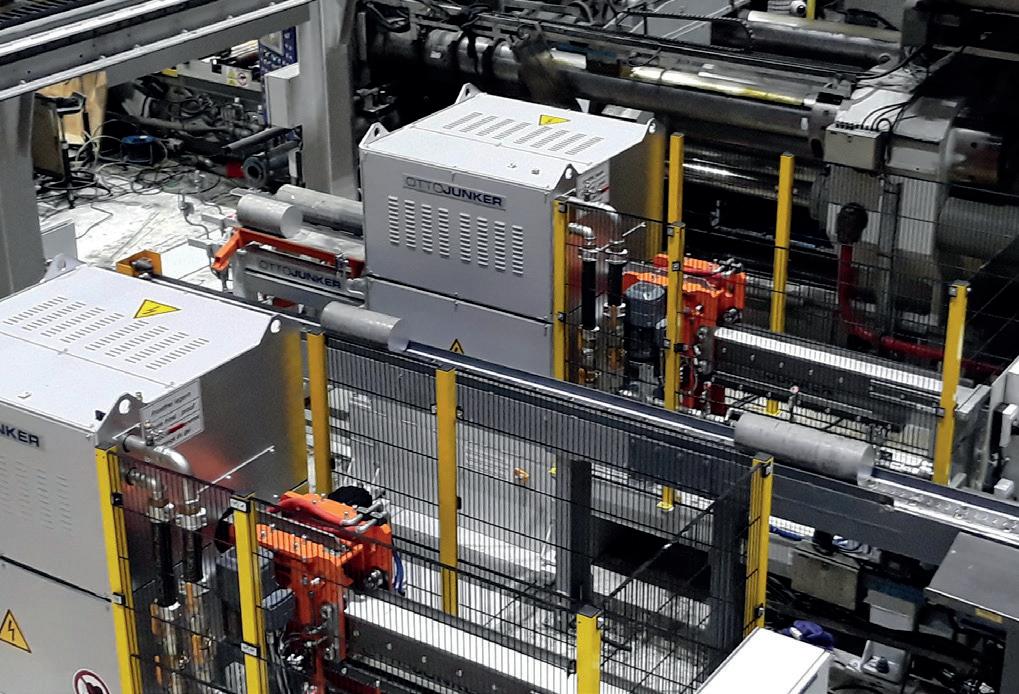
OTTO JUNKER GMBH - GERMANY | ) +49 2473 601 0 | * SALES@OTTO-JUNKER.COM JUNKER INC - NORTH AMERICA | ) +1 630 231 377-0 | * SALES@JUNKERINC.COM
WWW.OTTO-JUNKER.COM

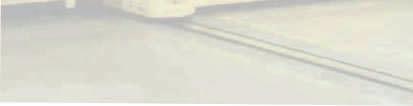

AUTONOMOUS CHARGING & SKIMMING MACHINES
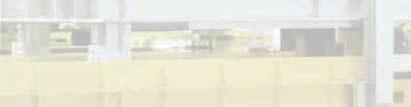
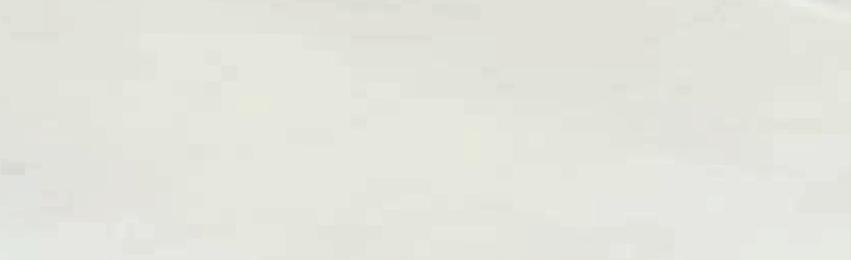





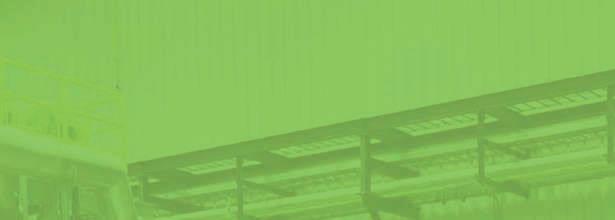
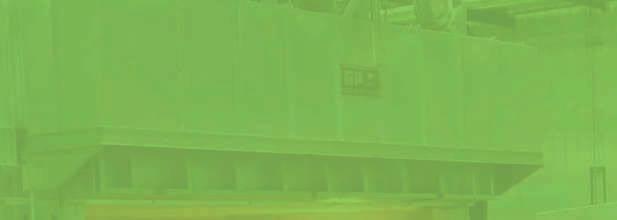