6 minute read
On the surface
The COVID-19 pandemic heightened awareness around how diseases and viruses spread across surfaces. One company that was already at the forefront of antimicrobial surface technology is A3 Surfaces, based in Québec. Nadine Bloxsome* originally visited the company back in 2019 and now, after recently being granted a new round of financing of $4 million to support the commercialisation of its products in Europe, she spoke with Jean-Sebastien Lemieux** to find out how the technology has developed and why aluminium is the material of choice.
Q. GREAT NEWS ABOUT THE GOVERNMENT GRANT TO SUPPORT THE COMMERCIALISATION OF A3 SURFACES ALUMINIUM ANODISING TECHNOLOGY. WHAT DOES THIS MEAN FOR THE COMPANY’S PLANS GOING FORWARD? SHORT AND LONG TERM?
Q. ALUMINIUM INTERNATIONAL TODAY FIRST PROFILED A3 SURFACES BACK IN 2019.
HOW HAVE THINGS CHANGED SINCE THEN?
WHERE HAVE YOU SEEN THE MOST GROWTH?
A. What it means is that it allows us to keep moving forward with our project and the thing with A3 Surfaces and the innovation and technology is that it is so innovative, so new, and it has such a huge potential.
It is so different from all the competition that it is going to be a big deal, but a big deal requires a lot of fuel. Right now, we’ve put a lot of things in place, so we are ready to supply products to the world and at the same time, we need to increase our brand awareness and make partnership deals. We have short term, long term and very longterm ways to commercialise our products, so in order to do this, we need means and money. This money is going to support us to make sure we bring all the aspects of the project together.
A. It is simple, in a manufacturing business, you have selling and producing. In some companies, you can sell more than you can produce and sometimes you can produce more than you can sell! Different problems, but problems all the same.
You must have the selling and the production balanced, so you can bring them up together. What we did, since 2019, is that in 2019, we didn’t have a manufacturing plant and we started the project of installing production capacity.
First it was moving into a new building, ordering a production line and putting together a team who can make this production line work. It’s more complex than a dishwasher! It’s equipment, it’s a process, a chemical process. Making a few parts in the basement of a university is one thing, but making millions of parts is quite a big deal.
The progress that was made since 2019 to now, was to install that production capacity. That’s the main thing that happened. Today, we have a factory that can produce parts. We are producing at a certain rate, and we are producing inventory that we send to Europe. Right now, we have more production capacity than we are selling, so this grant will allow us to continue on the selling side, in order to sell our production capacity.
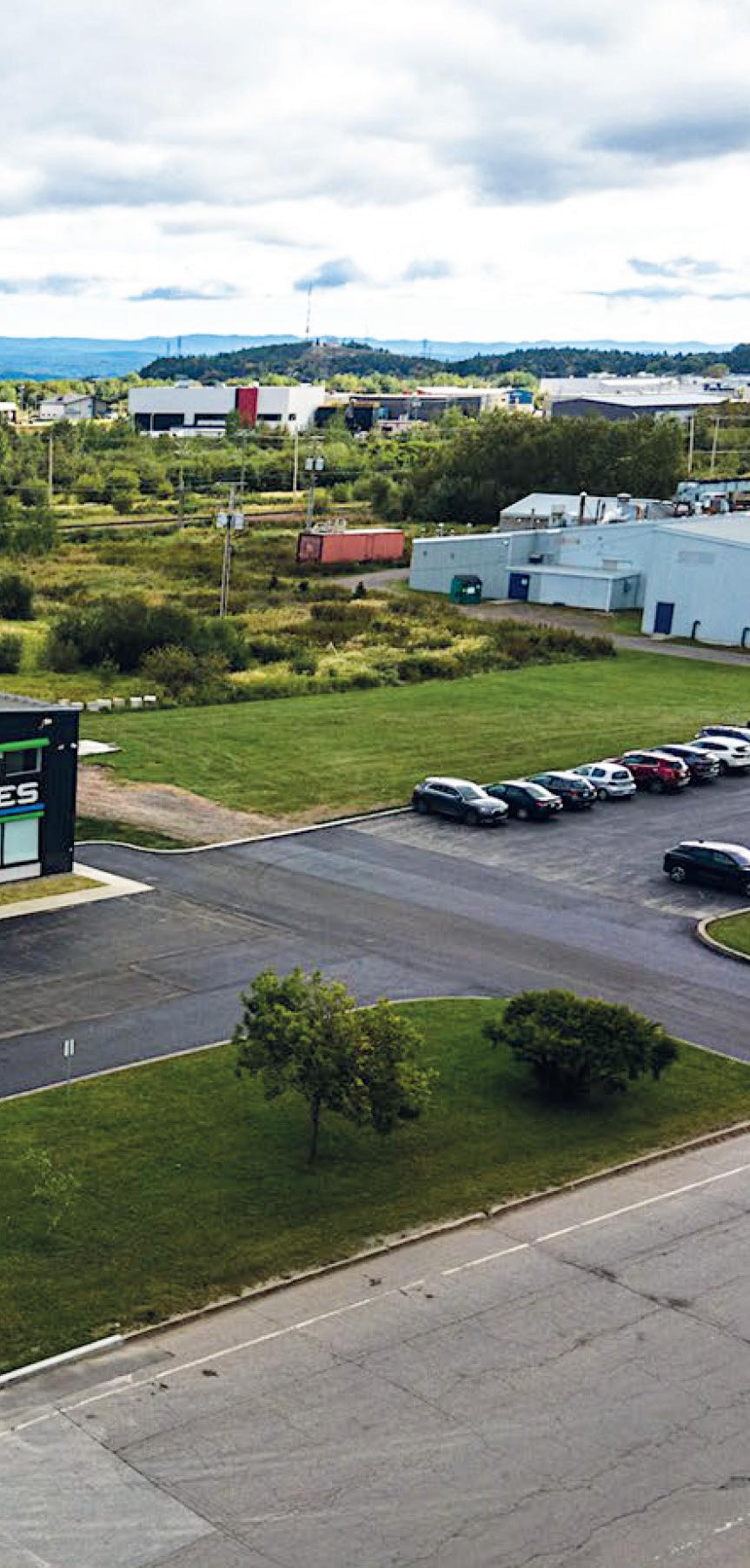
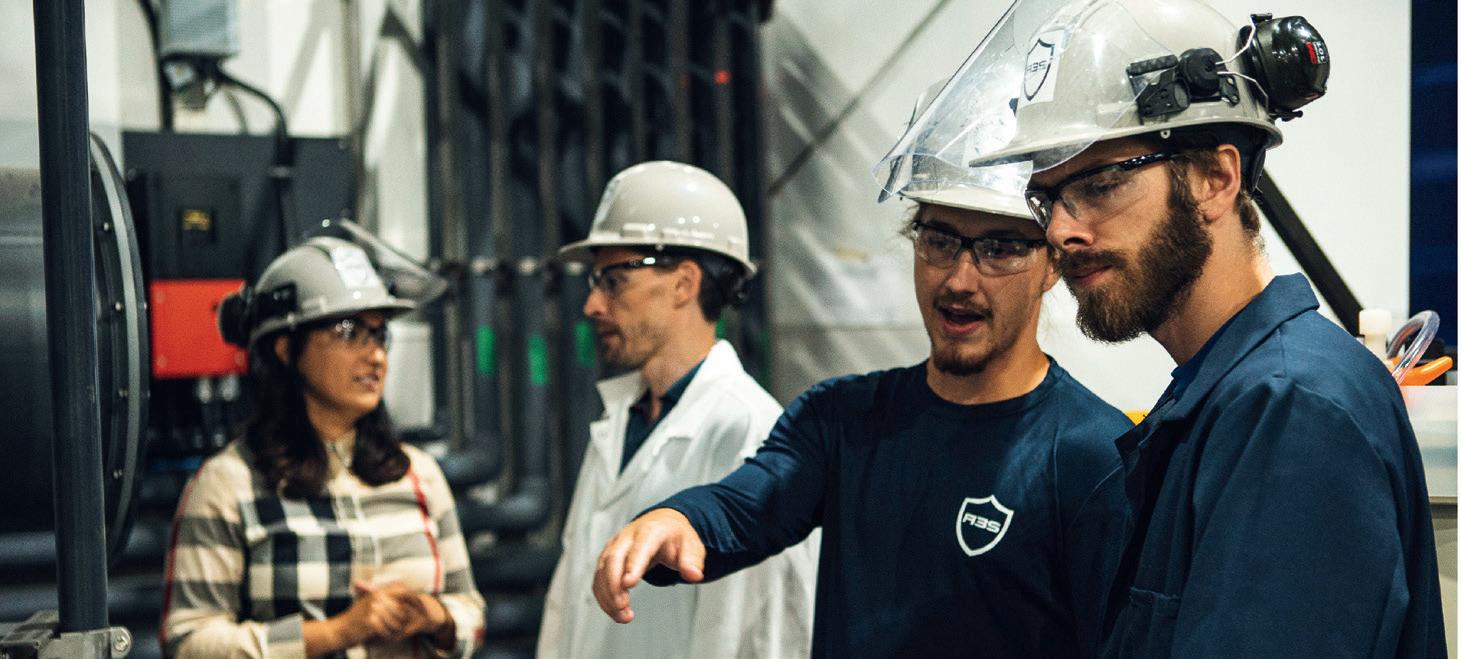
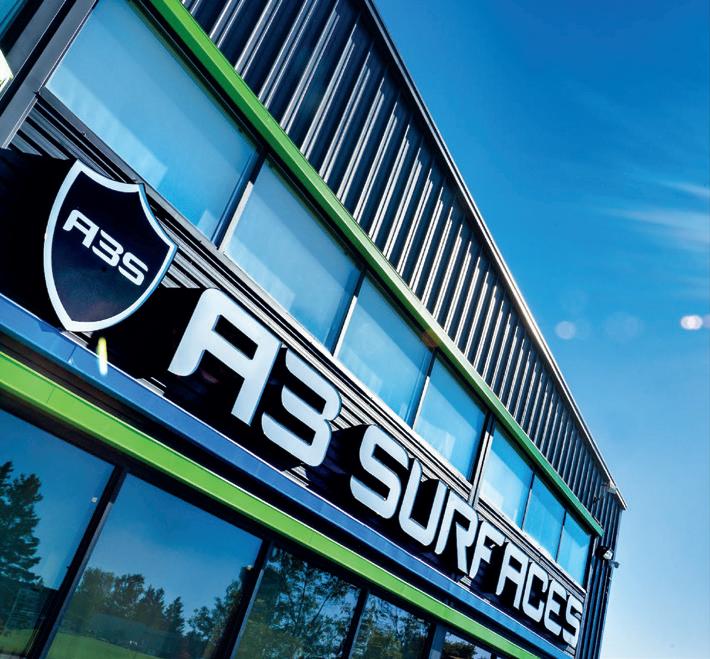
Q. CAN YOU EXPLAIN HOW THIS TECHNOLOGY WORKS AND WHY ALUMINIUM PLAYS A PIVOTAL ROLE?
WHY IS ALUMINIUM THE MATERIAL OF CHOICE FOR A3 SURFACES?
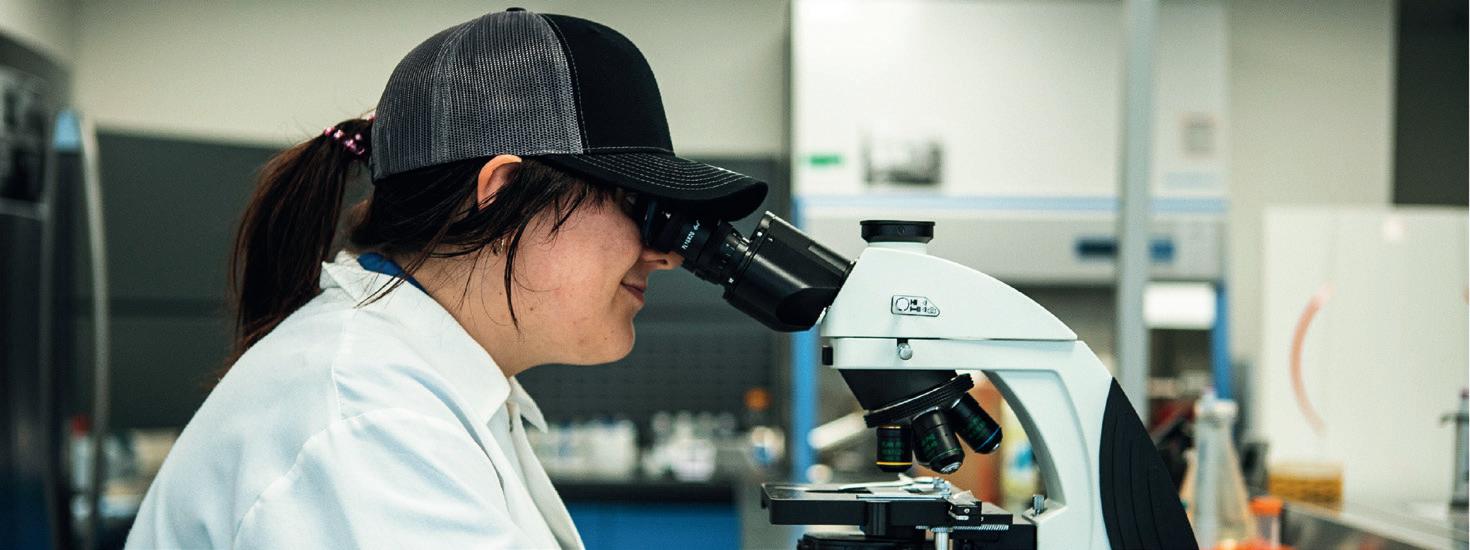
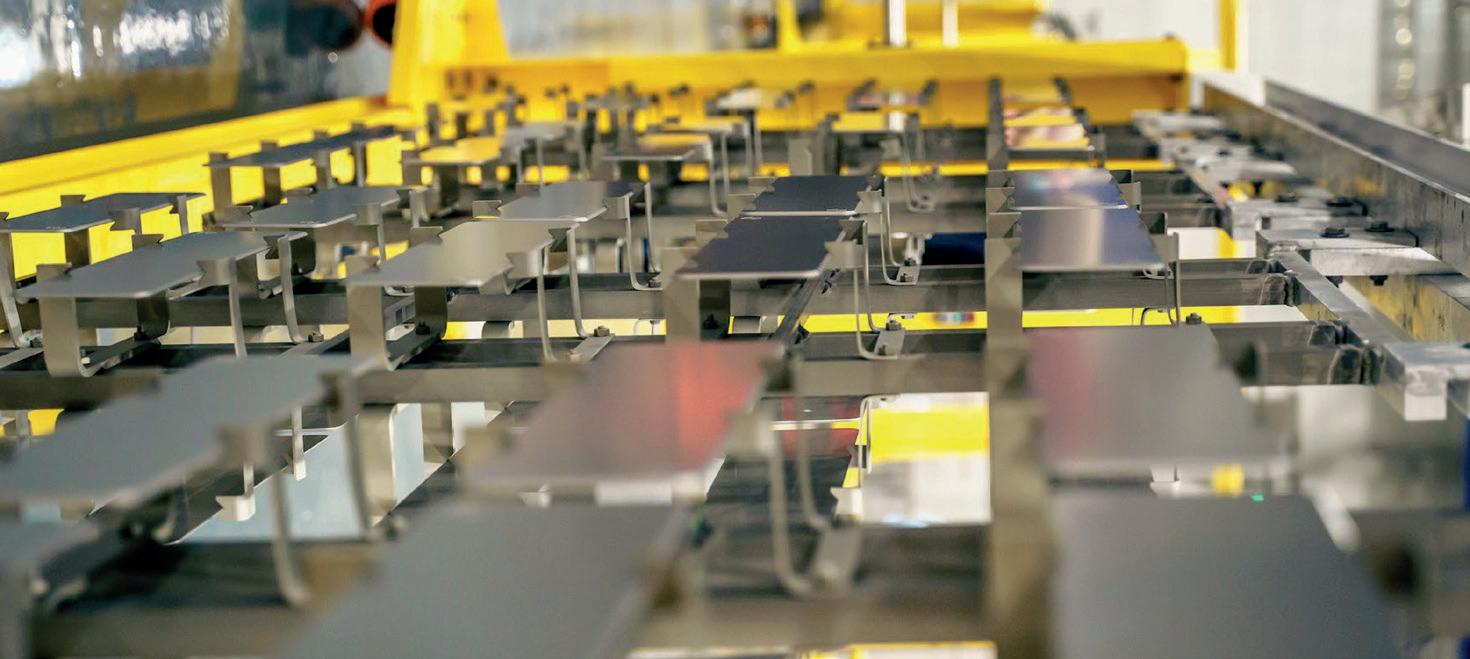
A. ‘Why aluminium’ is a good question and the best innovations are often the simple ones! I often refer to wheels on a suitcase…20 years ago no one had wheels and we all carried our suitcases around. But then, someone one day thought adding wheels would be a good idea and now, do you know anyone who doesn’t use a suitcase with wheels?!
The innovation is the same for us, we took an existing active ingredient and we embed it in the anodizing layer of aluminium. The anodization creates a surface with trillions of little holes, and we found a way to embed these molecules in the anodizing layer.
So, that’s why aluminium, because it creates a surface that is prone to receive the little molecules that will kill bacteria and viruses. The patent that we have filed and what we have invented is a way to make sure these molecules permanently stay there. As long as the anodization layer is there, then you will be able to efficiently kill bacteria and viruses.
So, ‘why aluminium’? Because of the surface finish anodizing creates.
The other thing that is special about our technology is that there is a lot of technology out there for antimicrobial right now, but there is no technology that can match our technology on both how permanent it is and the speed of action.
There’s a lot of solutions that make you think you are safe in using them, but most other ‘permanent’ technologies can take up to one or two hours before it will kill the bacteria on the surface. Now, if you have this surface on a door in your office for example, if there is a virus transmitted onto the surface, with competition products, if you touched this door five minutes after, then you would likely come into contact with the virus.
However, with A3 Surfaces technology, within 30 seconds, 99.4% of the virus and bacteria will be killed. Between 0 – 30 seconds, it’s going so fast that we can’t even measure it!
The technology allows us to reduce cross-contamination, which is why it is so unique. The challenge that we have is to tell the world and convince the world that this really does exist and really does work. This is the challenge we have ahead of us.
Coming back to why this money will be helpful, it is a big project with a lot of things to do in order to share the technology and encourage people to partner with us in order to accomplish our mission!
Q. WERE THERE A LOT OF ADVANCEMENTS MADE DURING THE COVID-19 PANDEMIC?
DID THIS SITUATION HIGHLIGHT THE IMPORTANCE FOR SUCH ANTIMICROBIAL SURFACES?
***NB guessed three miles, which was a good guess! A. The market for antimicrobial used to be a market, which we could call niche, but it’s a big niche in medical areas, because it’s an area that has always been more aware of the impact. Now, COVID put a big spotlight on this, and I would say the market that it opened is in public transportation and retirement homes.
It also opened the market to public areas, such as planes and cruise ships. Do you know how many kilometres of handrails there are on a big cruise ship?*** It can be four kilometres, so about three miles, but that is for an average boat.
On a cruise ship, you tend to have older people who are more sensitive to catching viruses and when you go on a cruise, you don’t want to spend your trip in your cabin because you’re sick! So, it has opened cruise ships up to providing safer areas for guests and guests will have more satisfaction and get more out of their trip. It can also limit the time for cleaning, if the surface is permanently antimicrobial, so there are plenty of benefits.
And that’s just on one boat! There are hundreds of cruise ships all over the world and handrails can easily be made of extruded aluminium, so this is one of the products we are trying to commercialise.
So, to answer your question, transportation and public areas are markets we are seeing the most demand.
Cities are even starting to specify ‘antimicrobial’ in their applications for new transport!
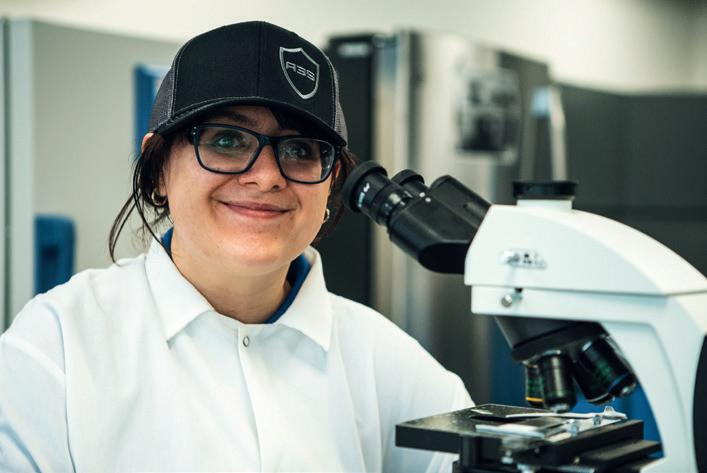
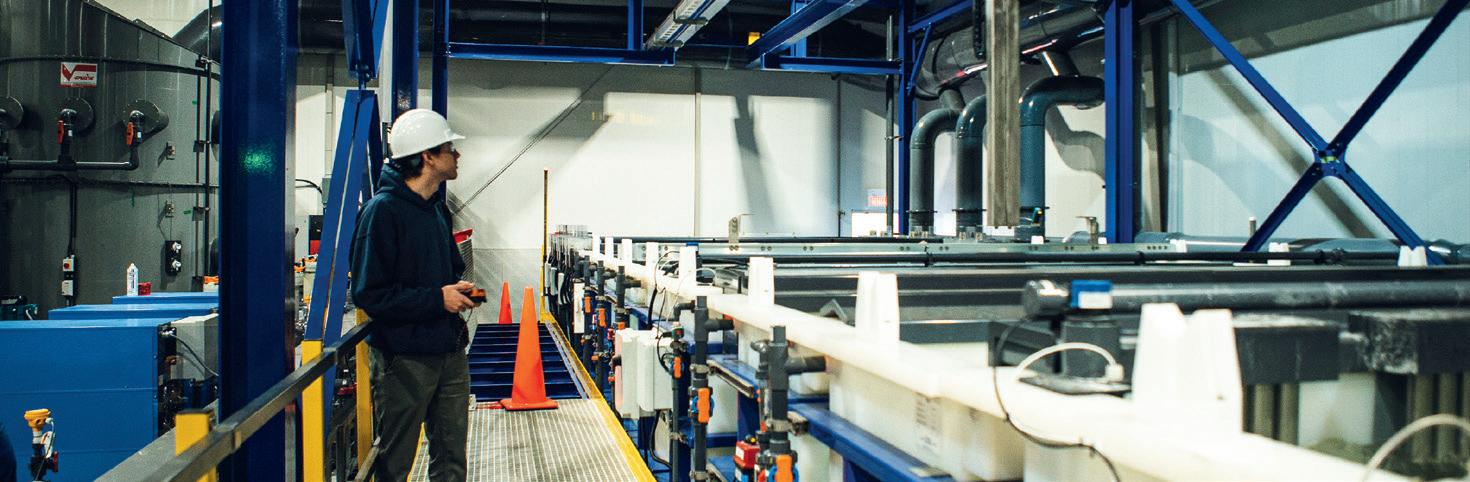
Breathtaking speed
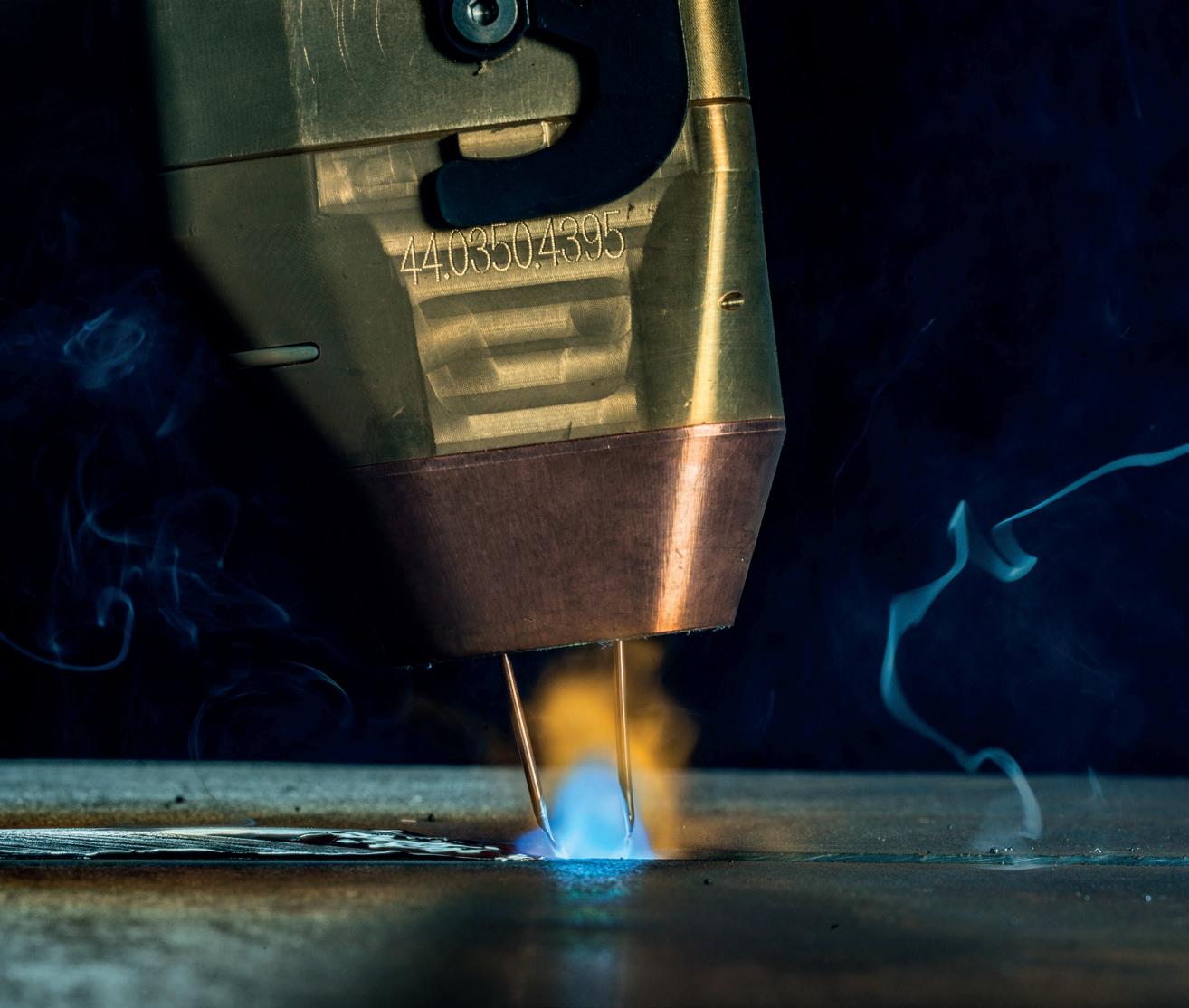
to unleash your welding potential.
TPS/i TWIN systems –Breathtaking speed
Thanks to the high deposition rate, our TPS/i TWIN systems enable speeds of up to 330 cm/min. This makes welding 2.5 times faster than with just one arc without and you get a weld you get a weld with reliable penetration and without notches. For further information, visit: www.fronius.com/tpsi-twin-systems