New screw pumps increase wastewater treatment CAPACITY IN BALLARAT
Top five ways to reduce motor running costs
Electric pump system keeps threatened bats cool
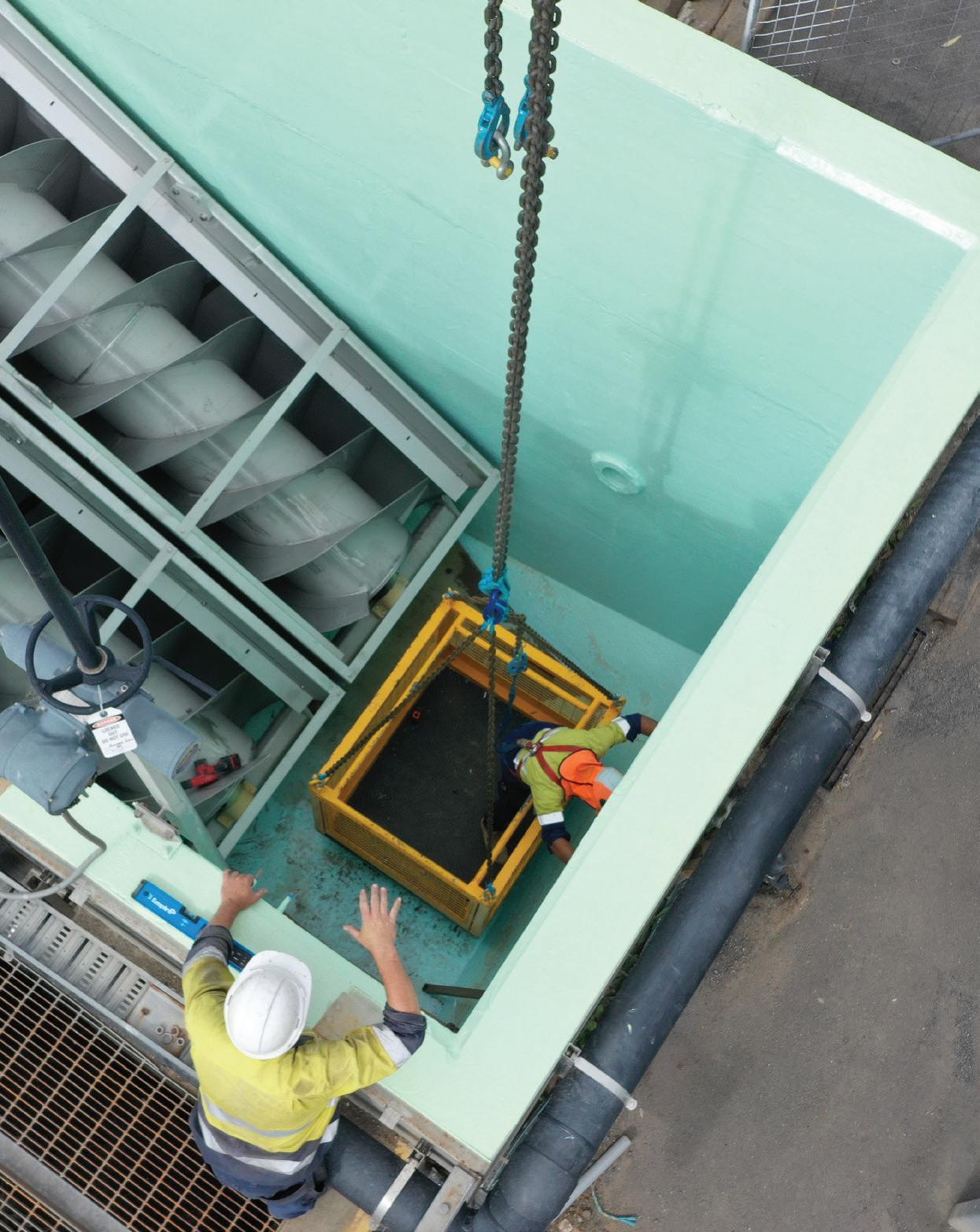
New screw pumps increase wastewater treatment CAPACITY IN BALLARAT
Top five ways to reduce motor running costs
Electric pump system keeps threatened bats cool
In everything we do, we never lose sight of what is more important to our customers: to work economically with a technology that is modern, innovative and reliable.
In everything we do, we never lose sight of what is more important to our customers: to work economically with a technology that is modern, innovative and reliable.
As the inventor of the elastomer-coated rotary lobe pump and innovation driver in the field of pumping, grinding and disintegration technology, Vogelsang has been one of the world’s leading mechanical engineering companies for decades. With progressive concepts and sophisticated technology, such as the RotaCut macerator or the wastewater twinshaft grinder XRipper, we work daily on efficient solutions for the individual applications of our customers.
As the inventor of the elastomer-coated rotary lobe pump and innovation driver in the field of pumping, grinding and disintegration technology, Vogelsang has been one of the world’s leading mechanical engineering companies for decades. With progressive concepts and sophisticated technology, such as the RotaCut macerator or the wastewater twinshaft grinder XRipper, we work daily on efficient solutions for the individual applications of our customers.
We use our extensive know-how, the continuous further development of our technical solutions and our many years of experience in the field of environmental technology to support our customers as a competent partner. Among other things, with powerful and service-friendly technology. You can rely on competent and personal advice and reliable service.
We use our extensive know-how, the continuous further development of our technical solutions and our many years of experience in the field of environmental technology to support our customers as a competent partner. Among other things, with powerful and service-friendly technology. You can rely on competent and personal advice and reliable service.
VOGELSANG – LEADING IN TECHNOLOGY
VOGELSANG – LEADING IN TECHNOLOGY
Unit 2/7 Dunn Road | Smeaton Grange NSW 2567 | Australia
Unit 2/7 Dunn Road | Smeaton Grange NSW 2567 | Australia
Phone: +61 2 4647 8511 | E-mail: sales.au@vogelsang.info
vogelsang.info
Phone: +61 2 4647 8511 | E-mail: sales.au@vogelsang.info vogelsang.info
Pump Industry Australia Incorporated
C/-340, Stuarts Point Road
Yarrahapinni NSW 2441 Australia
Ph/Fax: (02) 6569 0160
pumpsaustralia@bigpond.com www.pumps.org.au
PIA Executive Council 2023
John Inkster – President Brown Brothers Engineers
James Blannin – Vice President De.mem – Stevco
Kevin Wilson – Treasury/Secretary Executive Officer
Alan Rowan – Councillor Executive Officer – Publications and Training, Life Member
Ken Kugler Executive Officer – Standards, Life Member
Steve Bosnar – Councillor
Franklin Electric/Pioneer Pumps
Geoff Harvey – Councillor Irrigation Australia
Joel Neideck – Councillor
TDA Pumps
Jamie Oliver – Councillor Grundfos Pumps
Mat Arnett – Councillor
Ebara Pumps
Michael Wooley – Councillor
Tsurumi Pumps
Billie Tan – Councillor Regent Pumps
Hello all and welcome to the Autumn edition of Pump Industry Magazine and our second for 2023.
After enduring the very high summer temperatures across the nation I am sure you are all welcoming the cooler temperatures of Autumn.
As we head into April we may well wonder what the year ahead looks like with both global and domestic markets at play. Sadly, the war in Ukraine continues now into a second year with no end in sight, impacting on energy costs around the globe. I was in the Netherlands in December and was surprised to experience power cuts in the middle of the night which were considered normal.
The recent collapse and fall out of the three banks in the US will have a ripple effect around the globe but we are told should have minimal effect in Australia. Time will tell if there is any spill over into the Australian economy.
On the domestic front, we continue to see the RBA increase the cash rate in an endeavour to address inflation. At the time of writing, the RBA was signalling it might pause a further rate rise in April. Meanwhile the continued robustness of the Australian economy is reflected in the low unemployment rate of 3.5 per cent.
When I speak with industry colleagues I hear that there is still a strong demand for pumps and services with many indicating they have a full pipeline of work for the next six plus months; this pipeline of work ranges across the entire spectrum of our industry from mining to building services, agriculture, industrial, municipal and energy sectors.
This is good to hear and augurs well for the industry, because we all know there may well be a slow down in the economy in the coming months. It also demonstrates that our industry provides an essential service to Australian businesses whether in the private sector or in the municipal and public health arena.
For those involved in the $90 billion (predicted for 2023) agriculture market the BoM advises that the third consecutive La Nina weather pattern that brought wet conditions and devastating floods on the eastern seaboard is declared over, with a 50 per cent chance of El Nino occurring mid year bringing with it warmer, drier weather.
On 8 March, we had our first Breakfast Meeting, kindly sponsored by Cummins South Pacific in Scoresby who provided a warm welcome with breakfast, coffee and tea, and attended by about 24 Members.
The aim is having a Breakfast Meeting in each of the states so if you or your company would like to host a Meeting, please get in touch with our Secretary, Kevin Wilson, at pumpsaustralia@ bigpond.com.
An ongoing topic of the utmost importance to PIA Members and pump companies at large is the continuing dialogue with the Services Trade Council (STC) who govern the QBCC’s licensing of plumbing and drainage tradespeople.
On our behalf, the QBCC has petitioned the STC to consider recognising pump industry practitioners to lawfully perform work on pumps installed as part of a plumbing or drainage system as defined by the PD Act 2018
We understand to achieve this we may have to meet certain criteria as set out by the STC, and the outcome may well be some form of concession, regulatory change, new legislation, or the creation of a new Pump Service Licence.
Our last communication with QBCC was on 20 February where we were advised that our request for more information had been passed on to the Chair of the STC. We understand the STC is preparing a report to go to the Minister of Energy and Public Works; we are seeking clarification of the STC’s position.
Ken Kugler, our standards officer, has been busy in recent months engaged in the review of numerous ISO standards. These reviews relate to the question as to whether to confirm, review or withdraw a standard that is now aged. Of particular interest was ISO 9906:2012, the pump test standard that Australia accepted to be known as AS ISO 9906:2018. As the standard is now some ten plus years old, PIA has recommended its review.
Also under consideration is the most common pump standard ISO2858:1975 for 16 bar end suction pump designation, duty point and dimensions as pumps to this standard are still being manufactured in Australia today. There was a mixed response with the majority in favour of reconfirming.
And just another reminder to you all that the Pipe Friction Handbook has been updated and that the 6th Edition of the Pump Technical Handbook was released in September with 40 per cent more content – a must have on your desk or library.
Thank you for your continued support of Pump Industry Australia.
John Inkster – PresidentScan to subscribe to Pump Industry Magazine’s weekly newsletter – delivered to your inbox every Thursday afternoon.
ABN: 36 426 734 954
C/- The Commons, 36–38 Gipps St, Collingwood VIC 3066 P: (03) 9988 4950 monkeymedia.com.au info@monkeymedia.com.au pumpindustry.com.au magazine@pumpindustry.com.au
Managing Editor: Lauren Cella
Assistant Editors: Rebecca Todesco, Stephanie Nestor
Journalists: Tess Macallan, Tayla Oates
National Media and Events Executives: Rima Munafo, Brett Thompson
Design Manager: Alejandro Molano
Senior Designer: Luke Martin
Designers: Ozlem Munur, Danielle Harris
Marketing Manager: Radhika Sud
Marketing Associates: James Holgate, Jackson Barnes
Digital Marketing Assistants: Natalie Ta, Bella Predika, Rhys Dawes
Publisher: Chris Bland
GM Growth and Strategy: Laura Harvey
ISSN: 2201-0270
This magazine is published by Monkey Media in cooperation with the Pump Industry Australia Inc. (PIA). The views contained herein are not necessarily the views of either the publisher or the PIA. Neither the publisher nor the PIA takes responsibility for any claims made by advertisers. All communication should be directed to the publisher.
This document has been produced to international environmental management standard ISO14001 by a certified green printing company.
The publisher welcomes contributions to the magazine. All contributions must comply with the publisher’s editorial policy which follows. By providing content to the publisher, you authorise the publisher to reproduce that content either in its original form, or edited, or combined with other content in any of its publications and in any format at the publisher's discretion.
The first projects being funded under the Federal Government’s $150 million commitment to improve the disaster resilience of the Northern Rivers region have been announced, including over $18 million for new and upgraded pumps and pump stations.
As part of Phase 1 of the Northern Rivers Resilience Initiative, 16 projects were recommended by CSIRO following extensive community consultation, and agreed by the Federal and New South Wales Governments. They deliver on 41 individual project proposals put forward to CSIRO through their review process, with the scope of some proposals expanded to provide benefits across the entire Northern Rivers Region.
The announcement enables work to commence in the first tranche of projects while the New South Wales Government continues a due diligence review of the remaining recommended projects. All projects to be funded from the $150 million will be confirmed within the next six months.
The Tranche 1 projects, totalling $50 million, include $17.2 million for seven combined upgrades to pumps and pump stations in Lismore, $1.1 million for a new pump system to assist in draining East Murwillumbah, and $470,000 to install box culverts through a river bank levee to improve local drainage in Grafton.
Region-wide programs to increase flood risk awareness will benefit all seven regions, delivering floor level surveys, assessing evacuation routes and options for infrastructure upgrades and establishing community-led resilience teams.
Many of the projects align with recommendations from the NSW Flood Inquiry, and with local floodplain risk mitigation programs. All seven local government areas of the Northern Rivers region – Ballina, Byron, Clarence Valley, Kyogle, Lismore, Richmond Valley and Tweed – will benefit.
Federal Minister for Emergency Management, Murray Watt, said the recovery of the Northern Rivers region following
“The Albanese Government remains with the people of the Northern Rivers on this recovery and today’s announcement of projects funded under the Northern Rivers Resilience Initiative builds on the billions of dollars in assistance dedicated to the region.
“As previously announced, $150 million has been set aside for projects that local communities told us are a solid first step in improving the region’s resilience to future disasters.
“This money will be signed over to the NSW Government to manage the agreed projects and I’ve asked that this first tranche of projects commence implementation as soon as feasible.”
New South Wales Deputy Premier and Minister for Regional NSW, Paul Toole, said the State Government welcomes the Federal Government’s announcement of funding for these important projects.
“The successful projects align with the recommendations from the Independent NSW Flood Inquiry and play an important role in improving flood preparedness and flood resilience across Northern Rivers communities.
“With the funding secured, we look forward to work starting. The NSW Reconstruction Authority will manage the program administration and governance, and the Northern Rivers Reconstruction Corporation (NRRC) will be responsible for coordination and delivery of on-ground works.”
The NSW Reconstruction Authority and Northern Rivers Reconstruction Corporation (NRRC) will continue to undertake due diligence for the remaining $100 million of projects, including larger infrastructure projects requiring further engineering assessment to determine feasibility.
The CSIRO study that informed the allocation of the funding, and details of the first tranche of projects, are available at Northern Rivers Resilience Initiative | National Emergency Management Agency (nema.gov.au)
CSIRO is now preparing to undertake the second phase of
More than 100 million litres of water was pumped out of Blackwattle Bay to allow major structural works to begin on the new Sydney Fish Market site.
Pumping water out of the Bay created a dry working space within the cofferdam, which was constructed using more than 1,000 interconnected sheet and tubular piles and has been drained to about four metres below sea level.
New South Wales Minister for Infrastructure, Rob Stokes, said the draining of the cofferdam was a major engineering feat and created a dry working space so building can commence safely on the main structure.
“Infrastructure creates opportunity, and the relocation of the Sydney Fish Market to the head of Blackwattle Bay has been the catalyst to transform a patchwork of industrial uses to a stunning new precinct on the harbour foreshore,” Mr Stokes said.
“This is an engineering feat that has enabled the creation of a new public
boardwalk along the foreshore four football fields in length and 15 metres wide where people can walk, ride and linger after a long lunch at the Sydney Fish Market.
“This project will employ more than 700 people and their work to drain the cofferdam is a significant milestone in the construction of what will be one of Sydney’s great attractions for locals and visitors alike.”
Multiplex Regional Director, Daniel Murphy, said the draining of the cofferdam was an exciting milestone for the delivery team.
“For the first time, the dewatering of the cofferdam has given us dry ground on which to start building the main structure. It has been a unique and complex challenge, and we can’t wait to see the new Sydney Fish Market continue to take shape,” Mr Murphy said.
The new Sydney Fish Market is on track to be completed in 2024.
Dubbo Regional Council (DRC) quickly responded to the failure of the Fluoride Dosing System at Wellington’s Water Treatment Plant in January 2023, installing a new fluoride pump to allow fluoride dosing to recommence.
As a result, fluoride treated water could continue being supplied to all areas including Wellington township, Montefiores, Nanima Village, Wellington Caves, Wellington Correctional Centre and Macquarie Correctional Centre.
At the time of the system failure, there was an expected timeframe of mid-March 2023 for delivery of a new system, which remained on order.
However, Council staff were able to modify the fluoride pump not being used at Dubbo’s John Gilbert Water Treatment Plant.
Acting Director of Infrastructure, Chris Godfrey, said, “This is a fantastic outcome for the Wellington community and those who use Wellington’s potable water supply.
“Operational staff advised us earlier [in January] the pump could not be repaired and needed to be replaced, with a pump having to be sourced from Germany.
“Staff have worked hard to secure a new fluoride dosing pump within a much shorter than anticipated timeframe, allowing the fluoride system to be re-established.”
The fluoride treatment at the Dubbo facility requires a complete rebuild of fluoridation infrastructure with the tender process for a contractor undertaken.
The water produced at the Wellington Water Treatment Plant has always been maintained to the highest level and has met the required control points for provision of safe drinking water during the process.
Construction of Sydney Water’s $4.3 million state-of-theart Leura Water Pumping Station (WPS) in the Blue Mountains is almost complete, and will be crucial in mitigating the risk of water supply loss for up to 60,000 people during low rainfall events and drought conditions.
Operating at full capacity, the Leura WPS will transfer the equivalent of 16
olympic-sized swimming pools of water to the Blue Mountains region each week.
The Leura Water Pumping Station is due to be operational by July 2023, with the construction of the facility beginning in late 2021 and final preparations currently taking place.
Sydney Water Principal Project Manager, Trevor Mondon, said the plant is an important piece of infrastructure for the region and will leave a positive legacy for the Blue Mountains community.
“The Leura WPS upgrade works are part of an overall Strategic Drought Planning action. The network upgrades will increase and improve
reliability of supply within the Cascade Water Delivery System (WDS),” Mr Mondon said.
Sydney Water Senior Project Manager, Ben Samcou, said he believes the new facility will be a game changer for the people of the Blue Mountains when it comes to accessing reliable water supply, especially during drought conditions or bushfires.
“When in operation, the Leura WPS allows potable water to be transferred from lower parts of the Cascade water delivery system up to Katoomba Reservoir which is currently only fed from Cascades Water Treatment Plant,” Mr Samcou said.
Comet Ridge has partnered with Denison Gas to transport gas from Mahalo North via the nearby Denison compression and dehydration plant and pipeline infrastructure, with the contract for the Front-End Engineering Design (FEED) study – including equipment selection –now awarded.
Verbrec Infrastructure Services has been nominated to undertake the FEED study which is being jointly funded by Comet Ridge and Denison.
The intent of the FEED study is to undertake process design, equipment selection, develop plant layout, project scope, schedule and budget for the Denison Infrastructure upgrade to accommodate the supply of 10TJ/d of gas production from the Mahalo North Early Production Scheme (EPS) within ATP 2048.
Once the results of the FEED study are finalised, Comet Ridge and Denison will finalise the commercial arrangements under which Denison
will compress, dehydrate and transport Mahalo North gas production, enabling Comet Ridge to move the project very quickly from recent appraisal and reserves certification activities, through development, and onto gas sales.
Comet Ridge Managing Director, Tor McCaul, said, “We are very pleased with the considerable progress we have made with the team at Denison, our near neighbours in the Denison/Mahalo gas province.
“Whilst Comet Ridge will have a path to market for Mahalo North gas, there are other potential opportunities for this partnership to benefit both parties, such as the sharing of technical resources and data, operating efficiencies, and reducing drilling and other field related costs by rig sharing and gas blending arrangements.
“The investment in engineering studies for this project comes at a modest cost, which is appropriate at a time of uncertainty for the gas production industry.
“We remain hopeful that the Australian Government will listen to industry concerns about the negative impact its current domestic gas policy will have on future gas supplies and make necessary changes that will allow companies like Comet Ridge to invest with confidence in the development of the new sources of gas that are urgently needed for Australian consumers and manufacturers.”
Denison Chief Executive Officer, Benson Wong, said, “Denison is pleased to be working with Comet Ridge and assisting them in getting their gas to market more quickly. This is an excellent example of two companies working together to help satisfy the needs of the East Coast energy market.
“In addition to expanding our processing and transportation capacity in our established, integrated processing facilities, Denison is also focused on expanding our supply of gas to market from our conventional gas reserves and CSG resources.”
The Queensland Government has approved the $983 million Fitzroy to Gladstone pipeline project, which is expected to provide water security to the Gladstone region.
The 117km pipeline will run from the Lower Fitzroy River in Rockhampton and connect to Gladstone Area Water Board’s existing water network at Yarwun.
The project is crucial for supporting the existing industries that generate $6 billion in gross regional product every year and these activities depend on significant quantities of water now and into the future.
400 local jobs will be supported during the project’s construction and it is due to be completed in 2026.
Queensland Premier, Annastacia Palaszczuk, said the Government is committed to building the infrastructure Queensland needs to support good jobs in new industries during the clean energy industrial revolution.
“Nearly $1 billion has been committed to this important project, which guarantees water security and sends a powerful signal to the hydrogen sector that Queensland is the place to be for clean energy,” Ms Palaszczuk said.
“Gladstone will be the engine room when it comes to delivering our landmark Queensland Energy and Jobs Plan – that means good secure jobs now, and into the future.”
The infrastructure approval also aligns with recommendations made in the Bradfield Report, commissioned by the State Government and prepared by the expert Bradfield Regional Assessment and Development Panel.
Hydrogen proponents under development with future water requirements include:
• Fortescue Future Industries hydrogen electrolyser manufacturing facility
• Mitsubishi Gas’s proposal for a hydrogen to green methanol plant
• Stanwell/Iwatani Central Queensland Hydrogen Project
• Orica and H2U’s proposed green ammonia plant
• Rio Tinto and Sumitomo’s proposed hydrogen plant
Queensland Treasurer and Minister for Trade and Investment, Cameron Dick, said, “The Government’s contribution towards this vital infrastructure for Central Queensland is the first investment from our new progressive coal royalty tiers.
“This revenue was generated in Central Queensland and as we promised, it will be invested in regional Queensland.”
Queensland Water Minister and Member for Gladstone, Glenn Butcher, said the Gladstone pipeline project will support the emerging hydrogen and renewables sector that is set to expand in Gladstone, with several companies expressing interest in coming to the region.
“The Bradfield panel recommended investing in the use of water closer to where it falls as well as developing Regional Water Grids, and this is exactly what we are doing,” Mr Butcher said.
“The Fitzroy to Gladstone Pipeline is clear evidence the Palaszczuk Government is serious about listening to experts and taking action to ensure water security in Queensland.
“This pipeline will also allow Gladstone to access their water allocation from Rookwood Weir, which we know means security in good jobs and the delivery of safe and reliable water services to enhance the liveability of our region.”
Gladstone Area Water Board was appointed by the State Government in August 2021 to deliver pre-construction activities for the pipeline, which included undertaking procurement activities, addressing land access arrangements and determining long lead time items to ensure construction readiness for the pipeline.
Gladstone Area Water Board CEO, Darren Barlow, said the project is pivotal in securing water for Gladstone’s industry and will support the hydrogen and renewables industry, as well as help sustain the Queensland economy and provide jobs.
“As the Delivery Authority for the project, we look forward to partnering with local suppliers to deliver tangible benefits to the Gladstone region such as jobs, supply contracts and local capability raising,” Mr Barlow said.
On 8 March, the PIA held its first Breakfast Meeting of 2023, with Cummins South Pacific hosting the event at its head office in Scoresby, Melbourne. Over 20 people attended, hearing presentations from Cummins about its Australian branch and support network, as well as its main product groups in Australia and their applications and ratings.
James Blannin, PIA Vice President and Director De.mem – Stevco, opened the meeting, talking about the PIA Council members for 2023 and providing attendees with an overview of the PIA AGM held in November 2022. He also provided an update on ongoing discussions with the Queensland Building and Construction Commission (QBCC)
about who can complete works being undertaken that are covered by the Plumbing and Drainage Act 2018. Attendees were also reminded about the current version of the Pipe Friction Handbook and the newly updated Pump Technical Handbook, which are available with custom covers and can be ordered online at https://pumps.org.au/publications.
Running an optimised and sustainable mining and mineral processing operation has never been so important with pressures on water availability, rising costs and environmental regulations becoming stricter.
Water conservation is vital in countries such as Australia, the driest inhabited continent in the world, and good water management reduces disruption to mining operations as well as damage to the environment.
Using reliable and efficient peristaltic pump technology from Watson-Marlow Fluid Technology Solutions (WMFTS) for mining procedures can produce water savings of 71% in comparison with typical centrifugal pumps.
Bredel hose pumps from WMFTS can be considered water-saving devices in their capabilities, such as being able to handle undiluted tailings and thickener underflow with up to 80% solids. Since Bredel hose
pumps do not have seals, it eliminates the requirement of water for flushing, to treat process wastewater and provide pump service water.
A reduction in water usage also delivers associated benefits through lower chemical usage and energy required for the treatment of process wastewater. Pumps must be capable of high operating pressures and flow rates to ensure a smooth liquid passage and deny the opportunity for the product to settle. Bredel hose pumps are self-priming to 9 metres, can run dry safely and can meter accurately to ±1%.Reducing water usage is better for the environment too, as less storage is needed for tailings and the number of basins can be minimised.
The wear-free performance of clog-free peristaltic pumps also means the need for routine maintenance and spare parts is reduced greatly.
For more information on how peristaltic pump technology can deliver significant water savings for mining and water treatment companies, go here: wmfts.com/en/mining/
Following the opening presentation, attendees heard from Michael Hicking, Manager - Construction and Agriculture Business for Cummins Asia Pacific.
Mr Hicking spoke about Cummins’ global manufacturing and distribution footprint as well as its five operating segments: engines, power systems, components, distribution and new power.
The key takeaway for attendees was that Cummins is looking ahead to keep up with changes happening in its industries and regions so that it can bring customers the right technology at the right time. In particular, there is a focus on innovating and investing in helping customers, and the world, on the path to net zero emissions.
Then Vince Sessano - Victorian Sales Rep for Cummins, spoke about the three main product groups in Australia – the CustomPak, ComPak and FirePak – and outlined their applications and ratings.
Following the presentations, attendees were given a tour of part of the Cummins South Pacific facility by Dwayne Brito - Project Manager Off Highway, and had the opportunity to further mingle with others to discuss all things pump related.
Ranging from 100ml (4”x 4”) to 300ml (12”x 12”). (larger sizes to come).
Mixed-flow pumps feature:
• Table D flanges
• Oil bath / Mechanical seals
• Stainless steel shaft
Ebara Pumps' new GSD close-coupled EN733 motor pump has been selected as one of the primary water pumps for the new billion-dollar Festival Plaza upgrade in the heart of the Adelaide Arts and Culture precinct. The Ebara GSD range of ED coated pumps will be used on chlorinated water for the Festival Plaza's new water feature.
The Ebara GS/GSD range of EN733 pumps are a true 16 bar working pressure with a high grade SiC/Carbon/EPDM Burgmann mechanical seal fitted as standard. Galvanised steel baseplates that have been fully engineered by Ebara Japan engineers are also available as an optional extra for the GSD motor pumps.
The Festival Plaza Water Feature is one of the many new highlights and attractions that have been incorporated in this new development of public realm that connects Adelaide CBD and the riverbank.
The specialist contractor who supplied the pumps and water treatment equipment for the new water feature – Total Water Resources chose the Ebara GSD pump due to its quality, proven hydraulic design and competitive pricing.
The GS/GSD pumps come as standard with a high-quality electro deposition corrosion resistant coating to the ferrous static components, both internal and external making them ideally suited to treated fresh water environments.
The GS/GSD range is the Ebara Corporation (Japan) new global range of EN733 water pumps and utilising the most advanced hydraulic computer software available, Ebara Engineers in Japan have been able to improve and increase the pump efficiencies of the new GS/GSD range above most other available pumps of similar design and standard on the global market. The majority of the GS/GSD pump range are MEI>0.7 efficiency index with the balance MEI>0.6, an indication of the high-quality design and manufacture by Ebara.
The Ebara GSD range of close-coupled motor pumps and the GS range of bare shaft EN733 end suction pumps are both manufactured in component form at Ebara Corporation (Japan) owned and managed factories in South East Asia.
After being assembled from these components by skilled tradesmen at the Ebara Pumps Australia facility in Melbourne, the pumps are then hydrostatically tested and inspected to our Japanese parent’s strict QA policies and procedures.
In addition to the GS/GSD range of pumps Ebara Pumps has also recently introduced the GSO range of semi-open impeller ISO 2858/5199 process pumps, which are also available in 304,316L and Duplex stainless steel. The GSO range of pumps have been designed by Ebara Japan with a unique reverse open impeller reducing axial thrust and creating a low seal/stuffing box pressure. The pumps can be fitted with a vast range of single/double mechanical seal options and piping plans. They are also available with the option of oil lubricated bearings and ANSI drilled flanges.
Ebara Corporation was founded in Japan in 1912 as a manufacturer of industrial pumps. Today, as a group it consists of more than 70 companies in six continents with a workforce of more than 12,000 and with company-owned and Japanese-managed factories covering nine countries and four continents.
The huge scale of production and distribution is matched by a constant commitment to research, development and design of new products and the modern technologies for the manufacturing of them. Ebara products have gained a worldwide reputation for their technology and quality.
Combining over 100 years of experience with the latest computer aided design, EBARA has developed the new GS series of pumps that offer world leading performance and efficiencies.
Pumps to EN733 dimensions
16 Bar rated. PN16 flanges (24 Bar hydrostatic test pressure)
High efficiencies. MEI ³0.6 (Minimum Efficiency Index)
Mechanical seals to EN12756
Protectors to ISO13852
O’ Ring seal for casing
Cast iron components ED painted (Electro deposition painting)
GS range - 41 pump sizes from 32-125 to 200-500
GSD motor pump versions available from 1.1 kW up to 75 kW (4 pole) and 110 kW (2 pole)
Water hammer is a destructive phenomenon, best described as hydraulic shock. Its cause is from a sudden change in fluid motion as the liquid travelling through a pipe system has momentum. Changing that momentum, by closing a valve suddenly, results in the build up of kinetic energy and, if left untreated, causes a shockwave to propagate through the pipe system. The result can be as low key as an audible bang or pipe shudder, however there is potential for more catastrophic results such as pipeline blowouts.
One cost-effective solution to water hammer is to avoid sudden changes in fluid motion. This can be achieved by reducing the flow of fluid prior to closing a valve and is where WEG’s SSW900 soft starter comes into its element. The modern soft starter controls motor torque to gently start a motor, however it’s capable of much more than a controlled start. The technology used to gently start a pump can also be used to decelerate the pump. The SSW900 includes an algorithm, called Pump Control, which was purposefully designed to maintain a level of torque output during deceleration. This maintained torque output prolongs the deceleration and provides time for valves to be slowly activated and thus avoiding water hammer.
Combining convenience and innovation, WEG’s SSW900 is a highperformance device with integrated PLC functionality, providing fully programmable algorithms for regulating induction motors as well as fully flexible torque control. It offers a complete solution for motor start/stop control and protection. Developed for industrial
or professional use, the new line of soft starters adds unfounded ease of use and application flexibility.
and events. Being a full text display, the alarm code is followed by a fault description and critical diagnostics data captured at the time of fault, aiding in troubleshooting and reducing production downtime.
Featuring a full text and graphical interface, user interaction has never been more intuitive allowing simple access to configuration settings and data. Oriented Start-up provides guided step-by-step parameter configuration. On the occasion that help is required, simply pressing the ‘Help’ button will bring up a complete description of the parameter function removing the dependence of referring to a manual.
The inclusion of a Real Time Clock allows time and date stamping of alarms
Extending the benefit of the Real Time Clock is the SoftPLC. Custom code can be written to control inputs and outputs, control process requirements, and extend the protection capabilities by creating industry specific protection features. Whether you want a pump to start at a particular time of the day, run for a specified time, control a jacking pump or even create a dry run protection algorithm all is within the SoftPLC’s capability providing the user the ultimate in application flexibility while reducing component count and circuit complexity.
The SSW900 design includes a builtin bypass which optimises space and reduces heat dissipation in electrical panels. This leads to better efficiency of both cabinet space and electrical efficiency leading to longer term energy savings and a longer lasting product.
The SSW900 from WEG offers the ultimate solution in pump control.
Micropump has announced a new distribution partnership with Kelair Pumps Australia, a leading source of pumping systems and fluids handling expert in Australia.
Micropump, established in 1960, is the originator of magnetic drive gear pump technology. Today, Micropump is a part of IDEX Corporation and the market leader in low-flow gear pumps offering standard models, configure-to-order options, and custom solutions.
Founded in 1975, Kelair Pumps is one of Australia’s largest pump distributors with an established sales footprint in all Australian states. Kelair Pumps, a member of The AxFlow Group, has been working with IDEX Corporation for the last 23 years of which it has been the sole importer of several IDEX brands in Australia (including Sandpiper, Viking and Pulsafeeder).
After 12 years absence of a dedicated distributor in the Australian market, Micropump will work with Kelair Pumps to solve challenging fluid handling applications as well as provide local availability of Micropump products and services that are critical to keeping plant operations running.
Fabian Stiegler, European Sales Manager for Micropump, said, “Micropump could not be happier to have Kelair Pumps join the distribution family. Kelair Pumps strong reputation
with end users and leadership position in Australia make them the ideal partner to drive long-term growth for Micropump in this region.”
Myro Bratkovic, General Manager of Kelair Pumps, stated that he was extremely enthusiastic about the new relationship while noting that Micropump has such a high standard of performance in their positive displacement and dynamic pump products, and their lead in design and innovation, and technology is second to none.
“The entire Micropump range has a high reputation for reliable performance and long product life, which is essential for precise, low flow applications,” Mr Bratkovic said.
“The addition of Micropump to our wide range of pumps, drives and controllers, along with our extensive knowledge and expertise means we can package their products with other IDEX family products for complete fluid assemblies.
“Micropump complement our current product offering and ensure we are continuously meeting the needs of our customers.”
For more information about Micropump, visit https://micropump.com/ or for more information about Kelair Pumps Australia, phone 1300 789 466 or visit https://kelairpumps.com.au/.
Kelair Pumps Building & Fire Division is one of the most technically-competent suppliers in Australia. We can provide a complete range of fire pumpsets for all applications, fully compliant to technical specifications.
- Purpose built to individual requirements
- Compact, pre-fabricated, complete packaged solutions
- Fully tested to AS2941-2013 and AS/ISO9906-2018 Grade 1U
- Turnkey installation saves time and labour costs
- Simple to mobilise and transport
- Routine maintenance packages also available
We know the importance of choosing the right equipment to match your process. With our extensive range of pumps, first class customer service and ongoing comprehensive support, Kelair Pumps are second to none when it comes to your pumping requirements.
Pump Industry’s Managing Editor, Lauren Cella, is leaving the publication after seven years in the role. Lauren has been the magazine’s longest serving editor, shaping the conversation and being instrumental in making Pump Industry the number one trusted source for pump news in Australia.
An experienced journalist and editor with a wide variety of news and B2B publishing experience across print, online and radio, Lauren quickly became interested in pumps and their different applications when she joined the team as a journalist in 2016, which led her to taking on the role of Editor.
It’s an understatement to say that Lauren has been the heart and soul of the magazine and she has provided high-quality technical content issue after issue, allowing readers to learn about the latest developments and sparking new ideas they can implement in their jobs. Lauren spearheaded some of Pump Industry’s most beneficial features including the Industry Capability Guide and annual State of the Industry survey.
Managing director of Pump Industry and its publisher, Monkey Media, Chris Bland, said Lauren will be greatly missed as she has been the backbone of Monkey Media for seven out of the company's ten years.
“Monkey Media wouldn't be the same company without Lauren – she will always be a vital and much loved part of the Monkey Media and Pump Industry story,” Chris said.
“She was the person we relied on to create client content when we knew it had to be the best, and her work on Pump Industry and relationships she had with the PIA and pump users around Australia has made the magazine the important resource it is today.
“However, we’re extremely happy for Lauren to be pursuing her dream job with the Department of Defence and wish her all the best for the future.”
While this edition of the magazine is Lauren’s last, we’re excited to welcome the new Pump Industry Editor, Katie Livingston, and look forward to seeing the direction Katie takes the magazine.
MAIRS Technology uses traditional technologies and innovative engineered solutions to service a range of industries and customers to help manage their environmental needs and systems, whilst meeting environmental and health safe regulations, and health of nearby communities.
Our capabilities:
• Project Management Services
• Engineering Service Support
• Equipment Spares Supply
• Construction services and supervision
• Sub-contract management
• Commissioning and training
• Asset inspections and reports
• Asset maintenance and management planning
• Optimisation and system improvements
03 9028 8080
sales@mairstech.com
www.mairstech.com
While traditional trade publications have quality audiences and high levels of trust, they can lack the full range of services to guarantee a return on your investment. And while traditional marketing agencies offer the latest marketing techniques, they don’t have the audience or the industry understanding the B2B sector needs.
Monkey Media is the missing link that brings together a trusted brand and powerful audience, with a complete agency offering.
Hydropower energy recovery is an effective response to rising energy prices. SAER has an extensive product range that can be used as pump as turbine (PAT): small and medium-scale modular hydropower generating sets suitable for sites up to 500+ kilowatts of nominal power.
Pumps used as turbines can transform the surplus hydraulic energy of water into electricity and the newly generated electricity can be selfconsumed or exported to the grid. With low investment and maintenance costs, pumps as turbines (PAT) allow the recovery of the energy from existing pipe networks and achieve considerable energy savings.
Instead of a specifically designed conventional turbine, SAER proposes a standard water pump designed for reverse operations, which is easy to maintain and offers a low lifecycle cost. This technology allows water-intensive organisations (e.g. water, irrigation, mining companies) to conveniently exploit an untapped energy source in a costeffective way. Due to the use of existing infrastructure, all of this can be done with negligible environmental impact. How?
PATs are suitable for applications in existing pipe systems where water pressure needs to be reduced or where water flows by gravity into a reservoir.
• Short investment return time, especially in the presence of high energy prices
• The turbine is optimised to operate in a reliable and fail-safe way
• Easy maintenance, with spare parts readily available
• Real-time information: a complete telemetry system can be supplied for real time monitoring
• SAER’s PATs are made in Italy with a quick lead time with a wide choice of performances and design configurations to fit your system
Due to the different materials available in the SAER range, from cast iron to super duplex, several kinds of liquids may be handled.
Case study: pilot energy recovery installation at a mine site
Pictured is a successful installation recently designed by SAER partner Easy Hydro.
Head: 210m
Flow: 22L/s
Maximum output: 30kW
Annual generation: 200MWh
The PAT has been installed in parallel to an existing pressure reducing station
PATs can be installed on either manmade water networks (e.g. drinking water or irrigation networks) and natural ones (rivers, lakes); next to the water supply of underground mines; or at the outfall of wastewater treatment plants or in pressurised irrigation pipelines, etc.
on a DN 150 pipeline carrying cooling water from the surface into the depths of the mine. The turbine location is 300m underground. Instead of just dissipating the water pressure as heat and noise via the pressure reducing valves, the E-TMZ multistage turbine is generating power, which helps the mine operator to reduce the electricity import from the grid.
For more information about the project, visit https://easyhydrosolutions.com/en/energy-recovery-from-the-water-supply-of-tara-mines/.
Pumps can be used as turbines to generate low-cost electricity from existing pipe systems with no associated environmental impact.
change, population
and water scarcity
creating new challenges, and desalination is becoming an important alternative to traditional freshwater
With climate change causing an increase in extreme weather events – including floods, fires and drought – organisations and councils around Australia are repairing and upgrading pre-existing infrastructure to futureproof their communities. To help Southern Downs Regional Council (SDRC) improve drought resilience, the Queensland Government has invested $19.34 million to extend local water supplies, providing much-needed water security to more than 24,000 residents in the region. The latest works completed under this funding are upgrades to the SDRC owned Leslie Dam Pump Station, including the replacement of three 55-year-old pumps.
In January 2020, Warwick was projected to run out of water by the end of the year with Leslie Dam down to less than 4.6 per cent capacity, creating a difficult and challenging time for the region. However, feasible solutions that could be delivered quickly were limited as water carting to a town the size of Warwick – which has a population of about 15,000 – is not viable.
While recent rain has bolstered short-term water supplies by filling both Leslie and Storm King Dams, historical data shows rain cannot always be relied on at the time of need, with this funding vital to providing drought resilience for Southern Downs’ drinking water supply.
The funding for the Queensland Government’s drought resilience package includes the following activities:
• Connection of a new bore at Warwick to the Warwick water supply system
• Recommission of the Allora bores, and in the longer term to the Toowoomba to Warwick Pipeline for treatment at the Warwick Water Treatment Plant
• Investigation into the potential use of Connolly Dam as a supplementary supply for Warwick without impacting Stanthorpe’s water security
• Upgrades to the Warwick Water Treatment Plant to treat blended water from various sources of supply
• Infrastructure to access remaining Leslie Dam dead storage by Sunwater
• Investigation into potential new local groundwater sources around Warwick, Stanthorpe and Yangan
• Investigation into the potential availability of water allocations in Leslie Dam for urban use has been completed by Sunwater
One of the activities being undertaken as part of the drought resilience package is installing the infrastructure needed to access a portion of the water from Leslie Dam that was previously below the level of the pumps, and couldn’t be reached (dead storage).
Leslie Dam holds around 1,700 megalitres in its dead storage. By funding new capital works to access that water, the drought resilience package makes the best use of the Southern Downs’ locally available supplies and ensures as little water as possible is inaccessible, but allowing for some water to be left in the dam as per the Upper Condamine Water Supply Scheme Resource Operations Licence.
Works to access the dead storage – including upgrades to the Leslie Dam Pump Station – are being carried out by SDRC who is responsible for reticulated supply to its service areas, and Sunwater who owns Leslie Dam. The $4.54 million upgrade to the Leslie Dam Pump Station was completed in December 2022 and in conjunction with a low level pumping station currently under investigation and in planning by Sunwater, it will enable SDRC to utilise the dead storage.
The upgrade consisted of the replacement of three 55-year-old pumps, pipework and the electrical switchboard, with Vosloo Consulting Engineers (VCE) undertaking the design work.
The Leslie Dam Pump Station was originally constructed in 1966 and employed three single stage horizontal split case centrifugal pumps (Pump Class EC) by Thompsons (Castlemaine). The 125HP pumps were installed in a parallel arrangement and operated in a duty/assist/standby mode.
The existing raw water transfer scheme involves pumping approximately 1,946m through a DN525 rising main from the Leslie Dam wall to a 118.39kL balance tank, before water flows under gravity head for approximately 7,427m to the water treatment plant in Warwick.
The original system resistance curves indicated nominal duty points of 67.82L/s at 80.77m head for a single pump operating, or 126.18L/s at 83.82m head for two pumps operating simultaneously. The pumps are controlled by the water level in the balance tank via level sensors, control and SCADA systems.
One of the original pumps failed in June 2018, which impacted on the ability of the remaining pumps to supply the water treatment plant. The failed pump was removed and a temporary diesel backup pump installed in its place. The remaining two pumps delivered approximately 66L/s when a single pump was operating and 119L/s when both pumps were operating simultaneously.
SDRC indicated that winter demand in 2020 was approximately 120L/s, and summer demand approximately 160L/s. To keep up with current water demands the two remaining original pumps were both running as duty pumps, with the temporary diesel pump serving as a standby pump and to assist the existing pumps when demand was high.
Due to the age of the pumps and considering future demand, SDRC decided to upgrade the existing pumps and switchboard to ensure that the raw water supply to the water treatment plant is uninterrupted. SDRC appointed VCE to undertake the design required to upgrade the existing Leslie Dam Pumping Station.
VCE’s scope of services included the following:
• Undertaking hydraulic analysis and review of the existing pumping system to assess its hydraulic capacity to cater for current and future demands
• Estimating future demand flow rates to be used in the sizing and pump selection for the replacement pumps
• Do a pump selection for the replacement pumps
• Undertake hydraulic modelling and make recommendations regarding the suitability of the existing rising main and balance tank with regards to future demands
• Assess the existing power supply’s suitability for the proposed pump upgrade
• Prepare detailed design for the replacement of the existing pumps, control system and replacement of the existing Dall Tube (Venturi) type flow meter with an electromagnetic flow meter, including upgrade of the power supply
VCE appointed ECG Engineering (ECG) to undertake the electrical design, SafeGroup Automation (SGA) for the control and telemetry designs, and Minstaff Survey for the detail survey and 3D laser scan of the internal of the pump house.
Preliminary pump selections were undertaken with the aim of designing a pumping system that can deliver a nominal pump rate of 243L/s, which is the 50-year (2070) Mean Day Maximum Month (MDMM) flow rate over 20 hours. Two pumping options were considered, option one being a duty/ standby arrangement and option two being a duty/assist/ standby arrangement.
System resistance curves were developed for each of the two options, which included increased pipework sizes inside the pumping station, suitable to ensure flow velocities and friction head losses are acceptable and in accordance with
adopted standards. The pipe upgrades included increasing 5.83m of DN200 DICL suction pipework to DN450 DICL and DN375 DICL for options one and two respectively. The 1.56m length of DN200 DICL discharge pipework required upgrading to DN375 DICL and DN300 DICL for options one and two respectively.
VCE undertook a Net Present Value (NPV) analysis to quantify the most economical pump selection of the two options considered. The NPV analysis was undertaken for a 50-year period. The duty/assist/standby arrangement (option two) with 160kW pumps proved to be the most economical pump selection according to the NPV analysis results and energy cost estimates. It was anticipated that the construction cost for option two would be higher than for option one, but the pumps will operate closer to the best efficiency point (BEP), resulting in lower operating cost over the life of the asset.
Option two can also supply a wider flow range than option one, starting from approximately 70L/s at 80.36m head (at 47Hz) with one pump being operational, to approximately 247L/s at 88.36m head (at 50Hz) with two pumps being operational simultaneously, for the dam mean water level (MWL) scenario. The duty/standby 315kW pump selection (option one) can deliver a flow range in the order of 165L/s at 83.20m head (at approximate frequency 47.9Hz) to 243L/s at 86.87m head (50Hz) for one pump being operational and dam MWL. SDRC approved VCE’s proposal to proceed with the detailed design of the duty/assist/standby arrangement and the horizontal split case centrifugal pumps with 160kW motors.
The electrical mains cables between the existing 500kVA transformer and the main switchboards needed to be upgraded to prevent overloading during pumping above the nominal pump duty point. The 500kVA transformer and mains cable, as well as the main switchboards were replaced as part of the pump station upgrade.
The pump selection was undertaken with the intent of delivering the nominal pump rate of 243L/s at dam MWL and two pumps operating simultaneously, not for the worst case – dam bottom water level (BWL) scenario. This was done to reduce the power loading on the existing 500kVA transformer and avoid the need for upgrading the same. The disadvantage of this approach is that for the dam BWL scenario, the proposed pumping system will be limited to deliver a maximum flow rate of approximately 106L/s for dual pump operation at full speed (50Hz).
SDRC is currently working with Sunwater and the Queensland Government to design a low level pumping station that will enable it to utilise water below the pumps’ BWL, the remainder of the ‘dead storage’. The low level pump station will be additional to the existing Leslie Dam Pump Station, and will enable the new 160kW pumps to deliver the full 50-year planning horizon flow rate of 243L/s at dam BWL and lower water levels. This investigation and planning work into a ‘dead storage pumping station’ are currently being undertaken by Sunwater as part of the Queensland Government’s drought resilience package.
VCE’s analysis of the pumping system confirmed that the balance tank storage volume is sufficient for the existing and proposed pumping systems if it is setup and operated in accordance with its original design intent, which is not to provide raw water storage, but only as a small holding facility to utilise the available gravity head between the balance tank and the water treatment plant.
The purpose of the balance tank is to limit pumping to it, and thereby minimise pumping costs.
Adjustment to the pump stop and start level within the balance tank was proposed to reduce the number of pump starts and minimise pumping time (and power costs).
SDRC appointed Repump for the replacement pumps, VSDs and switchboard, including pipework, valves and fittings inside the pump house, and installation of a DN500 flowmeter and isolation valves in the existing DN525 MS pressure main outside the pump house.
Three Grundfos type LS horizontal split case centrifugal pumps (Model LS200-150-508B) with 485.2mm diameter impellers and 160kW motors were selected for a duty/assist/ standby arrangement, to operate at a nominal duty point of 153L/s at 83.23m head with 82.6 per cent pump efficiency, for the dam MWL scenario and single pump operation at full speed (50Hz). Two pumps operating simultaneously in a parallel arrangement were estimated to have a nominal duty point of 247L/s at 88.36m head with 81.9 per cent pump efficiency, for the dam MWL scenario and full pump speed. The pumps will be controlled with Schneider Electric’s model floor-standing model Altivar Process ATV650C20N4F Variable Speed Drives (VSD).
Repump was also responsible for design and installation of a bypass pumping system that would maintain pumping operations while replacing the civil, electrical and control equipment. Ergon Energy was responsible for installation of a new 500kVA pole-mounted transformer adjacent to the pump house. Repump also installed a new hoist and hoist beam inside the pump house as part of their contract with SDRC.
Works are continuing on other projects to secure the region’s water supply funded by the Queensland Government, including the construction of a pipeline to connect a new bore near Warwick to augment its water supply network, and recommissioning its Allora bores for supply to Council’s construction purposes in the short term and connection to the Toowoomba to Warwick Pipeline in the long term.
The Queensland Government has invested more than $380 million for the construction of the Toowoomba to Warwick
Pipeline project, which forms part of its wider commitment to providing longterm water security for the region.
With an expected completion date of early 2027, the Toowoomba to Warwick Pipeline pipeline will transfer water from Wivenhoe Dam when needed, to ensure a drought contingency water supply to 24,000 Southern Downs residents (which includes contingency supply for water carting to Stanthorpe when required), and a permanent water supply to 3,400 residents in the Toowoomba Regional Council towns of Cambooya, Greenmount, Nobby and Clifton along the Pipeline route.
The drought resilience package funding also allows SDRC to upgrade the Warwick Water Treatment Plant so that it can effectively blend, treat and distribute all of the new (and existing) water sources available to Council.
Getting the best use from its locally available water sources not only gives the Council more water – it also contributes to reducing Council’s demand on the Toowoomba to Warwick Pipeline, and hence the costs for operating the pipeline.
The Queensland Government will continue working closely with Seqwater and the Southern Downs and Toowoomba Regional Councils to optimise the operation of
the Toowoomba to Warwick Pipeline, keeping costs low for the Southern Downs without impacting Toowoomba’s water security.
The Southern Downs drought resilience package and the Toowoomba to Warwick Pipeline will create 460 local jobs, and deliver on the Queensland Premier’s November 2019 commitment that Queensland families will not run out of drinking water.
Since the construction of the Ballarat South Wastewater Treatment Plant (BSWWTP) in 1925, the population of Ballarat has grown, compliance requirements have changed, and technologies have advanced. To keep up with these changes and to mitigate challenges associated with storm events, Central Highlands Water undertook a major upgrade of the plant, which involved the installation of new Archimedes screw pumps, and new coarse and fine screens.
BSWWTP is the primary wastewater treatment plant for the City of Ballarat, treating approximately 70 per cent of the Ballarat catchment – currently the equivalent population of 85,000 – with the other 30 per cent treated at Ballarat North Wastewater Treatment Plant. Ballarat has been experiencing significant development and growth – primarily in the western corridor which is treated at BSWWTP – and the population is expected to continue to grow, with the BSWWTP expected to be servicing an equivalent population of 110,000 by 2035.
Furthermore, wet weather inflows to the plant have been historically challenging to manage.
With storm events predicted to increase, combined with population growth, Central Highlands Water decided to upgrade BSWWTP to increase its capacity to allow it to better deal with wet weather events, and to ensure the plant’s ongoing sustainability.
The key aims of the upgrades were:
• Contribute to the sustainable treatment of wastewater, for the benefit of the environment and local community, and treat wet weather inflows to meet Environmental Protection Agency (EPA) licence conditions and General Environmental Duty (GED) obligations
• Increase the capacity of the inlet pumping station and inlet works to manage wet weather inflows
• Reduce potable water usage by constructing a new plant service water system for the inlet works and a new pipeline for the distribution of Class A equivalent recycled water
• Improve automation and decrease reliance on manual intervention when transitioning from normal dry weather to wet weather control modes
The wastewater treatment plant’s new screw pumps
The upgrade focused on inlet works, which was estimated to cost $9.2 million and came in under budget, at $7.5 million. This allowed for other complementary site improvement works to be funded, to further improve the efficiency and safety of the operations. By maximising the capacity of the existing inlet works structure, Central Highlands Water was able to avoid building a replacement inlet works, as originally planned.
The inlet works design, done by Jacobs Group, was able to increase the hydraulic capacity of the inlet works to provide a coarse screening capacity
of 2,000L/s (up from 700L/s) and a minimum fine screening capacity of 1,200L/s. It improved solids capture performance of the coarse and fine screens to approximately 70 per cent (up from approximately 30 per cent).
The project involved the installation of new Archimedes screw pumps and new coarse and fine screens to help filter out unwanted material from the wastewater, as it arrives at the treatment plant first before it makes its way through several additional treatment process steps.
“The screw pump is a technology more than 2,000 years old and is probably the most efficient technology for low head pumping,” a spokesperson for Central Highlands Water said.
“The last upgrade of the inlet works was in the early 1990s, which included the installation of two smaller capacity epoxy coated mild steel Archimedes screws. Over the last 30 years the screws had been periodically removed, one at a time, for maintenance and recoating and were at the end of asset life.
“The two new STM1400 316 stainless steel Archimedes screw pumps were manufactured in the Netherlands by Spaans Babcock. They are a selfsupporting unit supported on top and bottom bearings, inclined at 33 degrees, 1,400mm diameter, approximately 8m in length, and rotate at 42 rpm.
“These pumps lift the influent 3.52m to provide hydraulic grade through the treatment process so that pumping in the downstream processes is minimised.
“The drive motors are 37kW, and the fabricated self-supporting trough ensures a perfect fit of the screw with a small tolerance between the screw and trough, which maximises the efficiency.”
The screw pumps also have VSD inverter drives, with the speed varying to maintain a level setpoint in the inlet pump station.
“Central Highlands Water engaged Bureau Veritas to perform an inspection of the equipment once it was fabricated and tested before shipping from the Netherlands. This included all facets of the manufacture from compliance with drawings and tolerances, material composition, electrical certification, and welding,” a Central Highlands Water spokesperson said.
“Once the units arrived on-site they were inspected and treated for minor rust defects prior to installation, and full wet-commissioning was undertaken with recycled water prior to putting in service.”
The ongoing maintenance of the screw pumps involves inspection and maintenance of the screw pump body, the drive unit, and the upper and lower bearings.
“The gap between the spiral blade and the trough is key to maintaining the pumping efficiency, so this is inspected quarterly. The drive unit inspection and maintenance regime is typical for a motor and gearbox (noise, oil level, leakage, grease lines, etc.). The bearings are inspected for wear and tear, and alignment,” a Central Highlands Water spokesperson said.
The inlet works were offline for approximately nine months, which required the project team to consider flow management and impact of providing no screening or grit removal on downstream processes.
“The northern and western sewers both discharge to the inlet works but fortunately a bypass channel around the inlet works already existed for the northern sewer. A new diversion structure was built over the western sewer to divert flows around the inlet works directly to the primary sediment tanks
(PSTs). Bypass pumping was entirely avoided during construction, by building the pit over the sewer and cutting out a pipe section using a wire saw,” a Central Highlands Water spokesperson said.
“An automatic 30mm coarse screen was installed in the common channel to the PSTs. This reduced handling and safety associated with manually raking the two existing trash screens during the upgrade works. Despite the reduced screening capacity, no significant downstream equipment issues were experienced while the inlet works were offline.”
3D point cloud and models were also prepared for all new works by designers, who were based interstate. The use of the 3D models significantly improved operator engagement and the elimination of OH&S risks through visual representation.
Great consideration was also needed to reduce the risk of delays.
“The tender for the project was released in December 2019, prior to the outbreak of COVID-19 later that month. With the progression of transmission, and subsequent travel restrictions imposed, there was a great deal of
consideration put into managing the risks for delays and likely impositions before awarding the contract to head contractor Guidera O’Connor in June 2020,” a Central Highlands Water spokesperson said.
“As there was a long lead time involved with procurement of the screw pumps and screening equipment, the design inputs for these were essential to obtain quickly. The use of 3D surveying and video conferencing enabled the contractor’s design team to engage with the operators and quickly and efficiently resolve the design and place orders. This then reduced the time risk for the period between the equipment landing on-site and the mobilisation of the work team to site.
A new pumping station and pipeline were also constructed as part of the upgrade to transfer recycled water to the inlet works. This is used as service water to clean screens within the wastewater treatment plant, and enhances water recycling efficiency to the operations by reducing the demand on potable water use at the plant.
These works involved replacing existing recycled water pumps
and installing a new pipeline to transfer recycled water to the solids dewatering process.
“Potable water usage at the site has been reduced with service water demand being met by Class B recycled water and filtered tertiary lagoon water which is supplied to the inlet works, saving approximately 400kL of potable water use per day,” a Central Highlands Water spokesperson said.
“A new pipeline was constructed from the Class B booster pumps to the dewatering, digester and primary sedimentation with a new pump skid installed with three CRNE 20-6 Grundfos pumps running in parallel. The pumps are configured to operate in a duty/duty/assist configuration, depending on the water demand required, and the overall capacity of the system is 25L/s.
“A new service water pipeline has also been constructed, taking secondary clarified effluent from the lagoon system and pumping it to the inlet works. Effluent is filtered to remove particulates using a 100μm AMIAD filter to comply with the inlet works screening equipment manufacturer’s water quality requirements in order to prevent the spray nozzles on the band screens and washer/compactors from blocking.”
Upcoming projects at BSWWTP include upgrading and refurbishment of critical process units such as the primary sedimentation tanks and mechanisms, the dewatering process facility, and augmenting aeration capacity.
The inlet works are part of Central Highlands Water’s top ten priority projects for the 2018 to 2023 period. Additional ongoing and/or planned capital works project being undertaken, include:
• Ballarat Sewer Growth Project –Ballarat West
• Ballarat Sewer Build – Ballarat East Trunk Sewer (Stage 2)
• White Swan Dam Safety Improvement
• Digital Water Metering
• Ballarat North Growth Project –Northern Growth Area
• Ballarat Sewer Build – Ballarat South Outfall Project
• Regional Recycled Water Scheme Upgrades
• Daylesford Water Treatment Upgrade
• Daylesford Raw Water Pipeline
• Ballarat Sewer Growth Project –Northern Growth Area
Access to clean water is a fundamental right of humans as well as animals. Today, we are deploying multiple pumping technologies to get drinkable water including building wastewater treatment plants and saline water desalination plants; drawing water from rivers, wells and creeks; filtering water; etc. Apart from this, multiple industries deploy effluent treatment plants at their manufacturing facilities to process their end effluent and reuse clean water in their processes.
With our 22 years of experience, we have supplied numerous pumps for these applications and solved various critical pumping challenges. Today, we have developed a comprehensive range of helical rotor positive displacement pumps for water, wastewater, agriculture and many other industrial applications. Also, we are hugely trusted for designing customised fluid engineering solutions for our customers.
Wastewater pump range Industrial pumps
Built on a heavy-duty and proven platform, the Tirrana range of helical rotor pumps offers peace of mind and the best solutions to all types of surface water transfer duties.
Capacity: up to 360LPM
Head: up to 120m
Applications:
• Ideal for tank filling or stock watering from dams, creeks, wells, and rivers
• Can handle clean water, brown water, dirty water with sand, silt, or algae
• High suction lift applications
• Viscous, abrasive and solid laden media
• High/varying discharge pressure applications
• Dirty/salty water
Capacity: up to 500m3/hr
Pressure: up to 48 bar
Roto’s industrial pumps are designed for continuous or intermittent transfer duties in innumerable applications for varying viscosities, abrasiveness and even fluids with high solid content across every industry. These pumps are also used to handle all the wastewater application from the preliminary treatment process to final sludge dewatering.
Applications:
• Primary/secondary/tertiary sludge
• Thickened and stabilised sludge
• Digested/undigested sludge
• Bio sludge
• Secondary activated sludge
• Floating/settled sludge
• Secondary excess sludge
• Dewatered sludge and sludge cake
Capacity: up to 500LPM
Pressure: up to 24 bar
Roto dosing pumps are developed for low flow applications that demand high accuracies and repeatability (+/- one per cent) with the unique advantage of smooth and non-pulsating flow. These dosing pumps can handle clean and clear liquids. The pump is ideal for either intermittent or continuous dosing duties. These pumps ensure proportionate dosing of media via the use of a frequency controller.
Applications:
• Milk of lime
• Polyelectrolyte
• Concentrated flocculant
• Poly-aluminium chloride solution
• Polymer solution
• Polyacrylamide flocculant
• Metallic salts
• Alum flocculant
For more information, visit rotopumps.com.
Climate change, bushfires and extreme heat have forced many bat colonies to relocate to avoid exposure to fatally high temperatures. One innovative way to alleviate heat stress among these threatened animals is by implementing large sprinkler systems, which effectively operate as a large evaporative cooler, to mitigate the effects of heat during summer. Parks Victoria has utilised this method, installing an electric pump and generator in an internationally applauded sprinkler system designed to protect Yarra Bend Park’s grey-headed flying-fox colony.
During summer heatwaves and bushfires, these native bats have been devastated with both habitat loss and loss of life. Thousands of grey-headed flying-foxes – which are a protected species – die of heat exhaustion each summer, with climate change exacerbating the length and intensity of the season.
Yarra Bend Park, home to Victoria’s largest permanent colony of greyheaded flying-foxes, was especially impacted – over a three-day period in 2020, temperatures reached 43ºC and caused the death of more than 5,000 bats at the park.
But a new permanent sprinkler system, powered by an electric pump and generator, will protect the colony of approximately 30,000 bats at Yarra Bend Park, functioning as a giant evaporative cooler for the area.
Parks Victoria Area Chief Ranger, Brendan Sullivan, said the aim of the project is to protect and enhance grey-headed flying-fox habitat and conservation.
“The grey-headed flying-fox is a threatened species listed under the Commonwealth Environment Protection and Biodiversity Conservation Act 1999 and Victoria’s Flora and Fauna Guarantee Act 1988. Their numbers have declined due to loss of prime feeding habitat and disruptions to their campsites. They are also threatened by climate change, with increased heat-stress mortality in hotter-than-average summers,” Mr Sullivan said.
Grey-headed flying-foxes are subject to heat stress mortality when temperatures exceed 40ºC, and Yarra Bend Park experiences heat stress events most summers.
“During these events, volunteers are traditionally mobilised to prevent greyheaded flying-fox deaths by spraying them with water from a 20L backpack sprayer and taking them into care for rehydration.
“These events require substantial planning and present significant safety risks to volunteers and staff,” Mr Sullivan said.
The custom-built, $180,000 sprinkler system was funded by the Department of Energy, Environment and Climate Action (DEECA), and delivered by Parks Victoria in partnership with Zoos Victoria, who led the design of the system. Additional partners included Melbourne Water, Yarra Bend Golf, Wildlife Victoria and passionate volunteers. This internationally recognised initiative forms part of a $5.3 million boost for wildlife from the Victorian Budget 2022/23.
Following a series of similar sprinkler system trials at the Warrnambool, Bendigo and Colac botanical gardens, the Yarra Bend Park sprinkler system is the first to be installed as a permanent fixture.
Mr Sullivan said the sprinkler system has been fully installed and commissioned as of January 2023, with the completion date extended from the expected November 2022 as a result of October 2022 storms that led to flooding of the Yarra River, making access to complete the pump installation impossible.
The system is made up of aerial sprinklers that are placed in the trees and are turned on for a few minutes each hour to rain down on the bats. Thirtytwo sprinkler heads have been installed across two sites identified as important refuges for the flying foxes.
“The main objective of the new, Victorian Government-funded sprinkler system is to prevent bats going into heat stress/heat stroke by cooling the ambient temperature using water. The system acts like a massive evaporative cooler,” Mr Sullivan said.
The sprinklers are activated on days when the colony is likely to experience heat-induced illness. This is determined by both behavioural monitoring and when temperatures rise above 38ºC. The system works to rapidly cool the environment by five to six degrees on days of extreme heat.
Since the installation of the system, the colony of approximately 30,000 have enjoyed these major temperature drops throughout February, especially on days where the mercury reached 41ºC.
“We also wanted to use off-the-shelf materials and not create a completely bespoke system that requires special orders for parts. This allows any repair to be undertaken quickly and keeps production costs down,” Mr Sullivan said. “The sprinkler mainline runs for more than 750m and reduces in diameter towards the end of the line to sustain appropriate pressure. It starts off at 125mm and reduces incrementally down to 90mm.
“Given terrain type, the mainline was winched through in sections and welded together on site.”
Mr Sullivan said that after testing numerous sprinkler heads, the Rain Bird 8005 was selected based on coverage and customisation of the spray pattern.
“Thirty-two sprinkler heads on galvanised poles extended beyond the tree canopy make up the sprinkler component of the system and when all are operating provide coverage across 3ha.”
The system at Yarra Bend Park was bolstered by successful trials of similar systems at Warrnambool, Bendigo and Colac botanical gardens.
At the Bendigo Botanic Gardens, where 200 bats died from heat stress in the summer of 2020, a temporary sprinkler system was able to lower the atmospheric temperature and reduce fatalities in 2021.
Data from the trial showed that temperatures in the test zone dropped by up to 2ºC, and no flying fox deaths were recorded. The trial ended in the summer of 2022.
Mr Sullivan said that the Yarra Bend system had unique specifications.
“The system will challenge even the most experienced engineer; water must be drawn from the Yarra into the colony and the system needs to reach the eucalypt canopy eleven metres up, covering three hectares.”
Bats are extremely sensitive to noise, and excessive noise can potentially disturb bats and discourage them from roosting in the area. The sprinkler system’s electric pump and generator allow for minimum noise and disturbance to the animals, compared to a diesel motor, a quality Mr Sullivan said was a key factor when it came to selecting which pump to use.
“Previous trial pumps were petrol and produced noise at about 89db which caused disturbance to the bats. Given there were up to five of these pumps spread out across the colony the impact was deemed to be significant.
“The electric pump is silent and the 75kW diesel generator that powers the pump runs at about 55db and is away from the main colony.”
Additionally, Mr Sullivan said it was important that operators were given the ability to close off sprinklers if bats were not in the area, as well as having the option to operate a reduced number where appropriate.
“The only way we could achieve this was by installing a variable drive pump that maintains a constant pressure of 600Kpa even if all sprinkler heads are off.
“The use of a non-variable drive pump would see maximum pressure not being maintained at 600Kpa likely resulting in blown joins and valves.”
The design and installation of the system was not without its complications.
“There were two main challenges in designing the system. Soil disturbance – which wasn’t permitted due to cultural sensitivity – and no power on site,” Mr Sullivan said.
“Given the length of the mainline we also had to decide whether multiple pumps made up the system, or just one large pump. In the end we made the decision to go with a large pump floated in the river, powered by a diesel generator.
“The mainline and valve infrastructure was all left above ground to assist with leak detection and maintenance.”
Mr Sullivan said that automating the system is the plan for the next 18 months.
“We’ll be gathering data on temperature reduction when the sprinkler system is used and develop optimum on and off times to maintain a suitable temperature differential.”
With no end to climate change in sight, Mr Sulliavan hopes that the Yarra Bend Park system will serve as an example of positive human intervention for these threatened animals, and something other locations can utilise.
“There has been a lot of good work and collaboration between everyone working with the same goal: to look after the grey-headed flying-foxes. We’ve caused so much damage to these bats, it’s great to be able to do something that’s going to be of benefit for them.
“This is going to be a game changer for this colony and for our management,” Mr Sullivan said.
Maxijet Polyethylene Pump Wells are typically used for stormwater and sewage transfer, rainwater retention and harvesting for domestic, commercial and industrial applications.
Maxijet Polyethylene Pump Wells are designed and constructed to meet Australian Standards AS/NZ 1546, AS/NZ: 4766 tank standards for water and chemical storage, also comply with AS4020 standards for contact with potable water.
Rotomoulded polyethylene tank with heavy-duty ribbing adds strength assists in anti-flotation.
Dual heavy-duty submersible sewage or stormwater pumps. Wide range of options available.
• Liquid Level Alarm
• Options to suit Single, Dual and Triplex systems
• Single phase or 3 phase power options
• Available with an inner door or an outer door
Optional guide rails with auto-couplings for quick removal and reinstallation of pumps.
During a Maxijet commissioning, we thoroughly check all aspects of your pump station installation.
We check that your system and pumps are fully compatible, that pumps and controller are correctly installed and aligned, and that the system has been tested and is ready to go.
For tank sizes above our stocked range, including our fibreglass options, please contact our sales and estimating team.
Access CoverThe green energy transition is forcing companies and organisations to investigate ways that they can transition to greener options. With public-use buildings some of the biggest offenders in greenhouse emissions, local councils across the country are leading the way into the green energy transition, revamping emissions-heavy public buildings to be more environmentally friendly. As part of this transition, there is a strong push in the local government sector towards all-electric buildings powered by renewable energy. Pump Industry Magazine spoke to Brimbank City Council about its recent leisure centre revamp and heat pump installation that is setting the precedent for other councils to follow suit in the journey to all-electric.
In June 2020, Brimbank City Council endorsed the Brimbank Climate Emergency Plan 2020-2025 (Plan), which included a goal to reach net zero emissions by 2030 for Council operations, and by 2040 for the Brimbank municipality as a whole. Included was a commitment to assess the feasibility of electric alternatives to building new – or upgrading old – gas infrastructure in Council buildings.
Alongside the Plan, the Brimbank Environmentally Sustainable Design Framework (ESD Framework) establishes design and performance standards to reduce the water, waste and energy generated by Council’s buildings, including a requirement for Green Star certification.
The ESD Framework is designed to help reach environmental targets and demonstrate leadership and innovation in building performance.
With the above regulations and guidelines in mind, Brimbank City Council planned to replace the old St Albans Leisure Centre with a contemporary facility to better meet the needs of the growing community.
The St Albans Leisure Centre was built in the 1960s, with additional facilities added in 1985, including the indoor pool hall and gym.
Brimbank City Council Mayor, Bruce Lancashire, said Council had completed two feasibility studies on the replacement of the Centre before a decision was made.
“The feasibility studies identified that the centre was outdated, which was supported by the aging assets and a poor standard of amenities and service areas when compared to contemporary standards.”
These issues were found to have negatively affected the Centre’s usage, particularly by casual users whose preference was to use more modern facilities. The reduction in usage and the increasing annual costs of labour, services and maintenance were significantly impacting on the annual operating cost of the Centre.
Around the same time that Council had plans to replace the Centre, an Advancing Renewables Program grant from the Australian Renewable Energy Agency (ARENA) became available.
“A shift from your standard gas-powered aquatic centre to one that was all-electric was endorsed and a decision was made to pursue funding in order to cover the extra costs of making the centre fully electric and renewable, which would help meet our net zero goals and to save on future gas use costs,” Mayor Lancashire said.
In considering the Centre redesign, a range of sustainable design features were included, including a 500kW rooftop solar system, rainwater harvesting, double glazing throughout, promotion of natural lighting, recycled content materials, reuse of demolition waste, water sensitive urban design and electric vehicle charging points.
A key ESD design feature was the all-electric, renewablespowered energy system which had been developed in parallel with a business as usual (BAU) gas boiler-based design option.
“This all-electric option is a nationally-significant project and is an important step towards Council’s ambition for zero net emissions by 2030,” Mayor Lancashire said.
“Compared to the BAU gas design, it will avoid 1,192 tonnes of greenhouse gas emissions per annum, which is represented as approximately 17 per cent of Council’s overall annual greenhouse emissions.”
The road to updating the Centre has been a long one, with Council initially settling on the existing site as the preferred location for the development of a new leisure centre at the Council Meeting on 28 October 2014.
Council received an update about the replacement of the Centre at the Council Meeting on 12 December 2017.
The report described the approaches to planning for the Centre, including infrastructure planning and a partnership approach that aimed to:
• Ensure the redevelopment also delivers significant measurable social and health benefits to the community, and leverages the benefits of co-located services
• Build strong community collaboration built on collective impact principles and commitment to delivering measurable social and health outcomes over time
• Develop at least one targeted intervention with measured outcomes suited to securing social finance, and leverage the collaboration with multiple service providers
• Become an example of how to combine social health outcomes with infrastructure redevelopment
The initial concept design of the upgrade project recommended a four-pipe low charge ammonia (LCA) heat pump system, but this was changed to a four-pipe Hydrofluro-Olefins (HFO) heat pump system during the procurement process.
Brimbank Acting Director Infrastructure and City Services, Tom Razmovski, said, “Both options were assessed as being capable of providing the facility’s year-round heating and cooling requirements without resorting to backup gas boilers.
“The decision to proceed with the HFO heat pump option was based on the lower capital cost associated with this type of heat pump. The decision also took into account the HFO option’s energy efficiency and performance capabilities.”
Although the HFO efficiency and performance is lower than the LCA option, its parameters were sufficient to meet the project’s overarching objective of an all-electric, net zero greenhouse emissions leisure, aquatic and wellness centre.
The chosen heat pump equipment provides the energy for domestic hot water and direct pool heating, and is required to meet the heating load of the HVAC equipment within the facility.
When it comes to aquatic centres, the requirement for HVAC is critical to the function and operation of the facility, specifically:
• Heating of water for pools
• Heating of air in pool spaces – with pool spaces heated to similar temperatures as the pool
• Heating and cooling of ancillary spaces
• Domestic hot water
Since the upgrade to the Centre, heating and cooling water has been provided by three heat pump machines:
• A Climaveneta four-pipe Hydrofluro-Olefins heat pump unit to provide simultaneous heating and cooling (424kW cooling capacity, 419kW heating capacity)
• A Mitsubishi two-pipe reverse cycle unit capable of producing heating or cooling depending on building demand
• A Mitsubishi two-pipe heating only unit sized to complete heating capacity demands of the building
The four-pipe chiller/heat pump is supplied by Mitsubishi Electric (Climaveneta) and is manufactured in Italy, while the two pipe chillers/heat pumps are supplied by Mitsubishi Electric and manufactured in Japan.
The heat pumps are complemented by thermal storage with a capacity of 88,000L, a heat recovery system and other environmentally sustainable design features, including 500kW rooftop solar system, which enable efficient electric functionality.
This new equipment creates an all-electric plant which can be powered by solar and renewable electricity as opposed to a traditional gas boiler system used for heating water.
One of the key advantages of this equipment – which is an especially important feature for an aquatic centre – is the pump’s capability of outputting simultaneous heating water and cooling water.
“In an aquatic centre we take advantage of this as we generally always have a heating load,” Mr Razmovski said.
“This means if this chiller is heating, the cooling circuit is almost free cooling, as making the cooling water cold is a byproduct of making the heating water hot.”
Key details of the four-pipe chiller/heat pump include:
• Manufactured by Climaveneta
• Model ERACS2-Q-G05
• CHW flow/return temperature 0°C 7/13
• 425kW cooling capacity
• CHW flow rate 16.95L/s
• Cooling – total input power of 150kW
• HHW flow/return temperature 0°C 48/40
• 419kW heating capacity
• HHW flow rate 12.94L/s
• Heating – total input power 143kW
• Heat rejection method air-cooled
• Compressor type screw
• Number of stages – six
• Refrigerant R513
• Sound power level of 99dBA
The two-pipe reverse cycle unit is capable of producing heating or cooling depending on building demand.
Key details of the two-pipe reverse cycle unit are as follows:
• Manufactured by Mitsubishi
• Model EACV-M1500YCL
• Number of modules: two
• CHW flow/return temperature of 0°C 7/13
• 296kW cooling capacity
• CHW flow rate of 8.89L/s
• Cooling – total input power 88kW
• HHW flow/return temperature 0°C 48/40
• 328kW heating capacity
• HHW flow rate of 11.95L/s
• Heating – total input power of 91kW
• Heat rejection method air-cooled
• Compressor type inverter scroll
• Number of stages – N/A (turn down to ten per cent)
• Refrigerant R32
• Sound power level of 83dBA
The two-pipe chillers/heat pumps are full inverter compressors, which is generally not normal for large chillers, and are very efficient module types.
Mr Razmovski said, “Being inverter compressors means that they can operate from around five per cent of capacity up to 100 per cent of capacity with a lot of capacity steps in between. On a conventional chiller with fixed speed compressors this is not an option.
“We generally operate at two steps (i.e. 50 per cent and 100 per cent only) or four steps (25 per cent, 50 per cent, 75 per cent, 100 per cent).”
Key details of the two-pipe heating unit are as follows:
• Manufactured by Mitsubishi
• Model EACV-M1800YCL
• Number of modules: three
• HHW flow/return temperature 0°C 48/40
• 533kW heating capacity
• HHW flow rate 15.92L/s
• Heating – total input power 162kW
• Heat rejection method air-cooled
• Compressor type inverter scroll
• Number of stages – N/A (turn down to ten per cent)
• Refrigerant R32
• Sound power level 85dBA
Mr Razmovski said installation of the pumps and other equipment was not dissimilar to other large-scale projects.
“Once the design, engineering and drafting is carried out our installation crew follow schematics and drawings as normal,” Mr Razmovski said.
“The large chillers, tanks, pumps and boiler were all craned into place on concrete plinths; we erected hurdles and then the pipework installation started.”
The installation of the heat pumps was designed to meet the maximum heating and cooling requirements, and were installed throughout the facility (ground outside, roof and plant room). Additionally, the sizing of the heat pumps was selected to accommodate the max building operating load and provide year-round electric operations.
Mr Razmovski said that certain measures were undertaken to reduce redundancy in the new centre.
“To assist with redundancy, a thermal storage system was included. While this provides some redundancy by adding additional capacity to the system, it also allows our control strategy to take advantage of times where heat pump efficiency is higher, which allows the storage of heat to be used in less favourable times.
“A gas boiler was also installed as a backup device to supplement any operational issues with regards to the heat pump units.”
The installation of the new pumps was not without its challenges, and necessary allowances needed to be made for the new equipment.
“The original design with boilers meant we would have a heating water temperature (boiler output) of 70°C to work with. Moving to electric heating using heat pumps, we needed to design to around 48-50°C as this is the maximum they can currently output,” Mr Razmovski said.
This kind of change often results in design challenges as water flow rates need to increase significantly to deliver the
same capacity. Additionally, pipework and pumps need to be increased to deliver the additional flow rates required with a lower supply water temperature.
Coefficient of Performance (COP) analysis for heat pump systems can be quite complex, the operations crew found out as challenges arose in determining the most efficient way to deliver the buildings heating and cooling load.
“Ambient temperature and the operation of units at different capacities were crucial factors in attempting to understand and ensure the systems were at optimum performance capacity range,” Mr Razmovski said.
“During installation, this resulted in us having to use conservative measures when determining sizing and heat pump capacity, given the unknown elements and unprecedented nature of the project.
“An example of how this applied to installation is the change from a gas boiler to heat pump hot water generation, the aquatic heat exchanger used to heat the pools needed to be upsized to accommodate the lower primary water supply and return temperatures.
“It was determined that each coil had to generate the equivalent heat capacity with a primary water temperature of 4555 degrees. This resulted in an expansion of the capacity of heat pumps and in turn an increase to the project costs.”
Despite these challenges the Centre upgrade has already reaped the benefits of the change, with Mr Razmovski saying the site illustrates Council’s commitment to its net zero emissions targets.
“The increase in gas prices and the possibility of future gas supply issues have resulted in operational cost savings for this all-electric facility,” Mr Razmovski said.
“Storage and solar capability have allowed for the production of energy to offset the energy use of the site.”
Council reported that there have been no complications with the system since its installation. Henceforth, the ongoing services for the new equipment and pumps include quarterly services carried out by a mechanical contractor and Mitsubishi Electric maintain pumps/chillers quarterly, alongside a mechanical contractor.
Brimbank Council Director City Development, Kelvin Walsh, said that a key measure in achieving its goal to net zero emissions for Council operations by 2030 will be to disconnect all Council facilities from the gas network.
“As gas is a fossil fuel it cannot be made renewable. Alternatively, our electricity supply is 100 per cent renewable. Council generates renewable electricity through rooftop solar systems on our facilities. Our remaining electricity needs are powered from wind farms in regional Victoria via a long-term contract with Red Energy as part of VECO – the Victorian Energy Collaboration.
“Council owns and operates two aquatic centres,and the heating and cooling requirements for water and air conditioning mean these are the most energy intensive of our facilities.
“Being able to showcase the most modern energy efficient technology to make our new Brimbank Aquatic and Wellness Centre fully electric and renewable was an essential and huge step on our 100 per cent Renewable Brimbank journey.”
As the first all-electric aquatic centre in Australia powered by 100 per cent renewable energy, the Brimbank Aquatic and Wellness Centre is a shining example of how other councils around the country can work towards their own emissions reduction targets.
“As part of our funding agreement with ARENA, we are committed to a number of knowledge sharing outreach projects and reporting. As part of this we have developed the All-Electric Councils Foundation paper – a guide for councils to electrify everything,” Mr Walsh said.
“We have already had a lot of interest in the model and have been able to provide support and advice to other councils in Victoria and New South Wales in developing their new centres.
“So far two tours and seminars for industry professionals have also been held at the Centre.”
With the new Centre completed and already proving its worth, Council is turning its sights onto the future and the next course of action for an all-electric future.
“We’re working on our actions as outlined in our Climate Emergency Plan 2020-2025 to decarbonise our facilities and provide support to the wider municipality. Our goal is to reach net zero emissions for council operations by 2030 and for the Brimbank municipality by 2040,” Mayor Lancashire said.
“We’re continuing to support our community to transition to all-electric and renewable energy through our 100 per cent Renewable Brimbank Program and our Climate Emergency Community Grants Program.”
The Brimbank Aquatic and Wellness Centre is supported by a $2 million grant from the Victorian Government. The Australian Government committed $1.53 million towards an integrated renewable energy system, through the Australian Renewable Energy Agency's (ARENA) Advancing Renewables Program.
Against a backdrop of increasing energy costs, significant savings can be made by upgrading old motors to more efficient modern alternatives. However, simply swapping a motor for a modern equivalent is not always practical or even possible. With this in mind, Thomas Marks, General Manager and Secretary at the Association for Electrical and Mechanical Trades, looks at how a motor's efficiency can be improved as part of a repair or refurbishment and highlights some things you should consider.
Astudy carried out jointly by the Association of Electrical and Mechanical Trades (AEMT) and the American Association, the Electrical Apparatus Service Association (EASA), has shown that motor efficiency can be widely maintained when a repair is carried out to a defined set of standards. The findings of the 2019 study, which have been published in a paper entitled The Effect of Repair/Rewinding on Motor Efficiency, established that efficiency was maintained on repairs to current machines up to IE3 efficiency. This guide has been incorporated into the latest international repair standard IEC 60034:23:2019 and the latest American ANSI/ EASA standard, AR100.
There are, however, some circumstances under which the efficiency of a motor can actually be improved by refurbishment and rewinding. This generally applies to older, less efficient motors and the decision to repair rather than replace typically involves a broader range of factors than simply to improve efficiency.
Generally, the most effective way to improve a motor's efficiency is to add more copper to its coils. It is often possible to add more copper to a set of coils, or, more specifically, increase the copper cross-sectional area. This is achieved through the very tight tolerances modern coils can be manufactured to and the ability of state-of-the-art CAD systems to optimise coil design.
This has several benefits, such as reducing the coil's resistance, increasing the potential output, and reducing the operating temperature of the machine, which can increase an asset's life.
It is, however, important to understand that adding more copper will affect other characteristics in a motor that may require the wider system to be adapted. Adding more copper into a machine will affect not only efficiency but also other parameters. For example, an increased inrush-current – which might be in conflict with existing protective measures – should be expected.
The ability to increase the amount of copper in a motor has been supported by advancements in insulation materials' which means that less insulation is required, and therefore space in the motors' slots becomes available. The thickness of insulation needed for various voltage systems has significantly decreased over the years, and modern insulation systems can offer 15 per cent reductions in thickness. As this is on the outside of the coil, the effect on the copper cross-sectional area can be greater still. Furthermore, these thinner insulations assist with heat dissipation and can again offer both an increased asset life and improved efficiency of the coils.
It is worth noting, however, that care is needed when comparing pre- and post-repair efficiency levels in a motor. Efficiency should not be compared simply by looking at a motor's datasheets. Before a 2007 update of the IEC / EN 60034-2-1 standard, which defines methods of determining a rotating machine's efficiency, efficiency figures were more generous due to how certain effects could be calculated out. Efficiency levels could previously be calculated with smaller additional losses than today – a standard 0.5 per cent of absorbed power, regardless of the motor output.
Since the 2007 update, the methods have become much stricter. Now stray load losses have to be determined by a factor that reflects the motor's output, ranging from 0.5 per cent (≤1MW) to 2.5 per cent (≥10MW). So, to avoid potentially misleading comparisons calculated from individual losses, efficiency should be measured directly at nominal load.
The decision on whether to repair or replace a motor typically involves several factors. These can include cost, the availability of a suitable replacement, system compatibility and, of course, efficiency. So, while increased efficiency is possible in certain circumstances, it is not often the only reason to carry out a motor repair. If efficiency is one advantage you are looking for from your motor refurbishment, it may well be available, but you need to take care when calculating the actual benefits you are set to gain.
The farm, near Laidley, is a large producer of vegetables with a large packing shed. The farm is irrigated yearround depending on rainfall. Water is supplied from on-site irrigation dams that are replenished from bores and rainfall. The irrigation systems are gradually being changed from high pressure systems to drip tape to be more water efficient and as a result there is a variety of pressures required.
Due to the current drought conditions, the level of the aquifer is low and the amount of water in the bore is lower than usual. For this reason, all the submersible pumps are oversized and to reduce the flow rate and to avoid pumping air the discharge valves are heavily throttled.
It is a large site consuming approximately 234,000kWh per year at a cost of $53,000. The farm offsets its current consumption using an installed 100kW solar system. Irrigating over 70ha and harvesting roughly 4,200t of vegetables sets a current energy benchmark of approximately 119kWh/tonne of produce.
The infrastructure contributing to the energy consumption on site consists of:
• A 30kW centrifugal pump
• A 11kW submersible pump
• A 22kW centrifugal pump
• Two large cold rooms totalling 53kW of cooling capacity
The energy audit recommended the following changes to improve efficiency and reduce costs:
• Installation of a VSD on the 22kW pump
• Installation of a VSD on the 11kW submersible pump,
• Replacing the 30kW pump with new efficient pump with a Variable Speed Drive
• Installing a 12kW solar system
Of the energy saving opportunities evaluated, four initiatives were identified with potential energy savings of 18 per cent of the site total, approximately 42,000kWh per year, a combined payback period of approximately 5.09 years and emission savings of 34tCO2-e per year.
The audit recommended installing a new pump on one of the dams. The existing 30kW pump was inefficient and was throttled with a valve to compensate for the different pressured systems. The replacement pump suggested is the same size and includes a VSD will allow for accurate adjustments of irrigation pressure and reduce electricity consumption. The new pump with the VSD has an estimated payback period of 6.3 years. It was also recommended to install VSDs on the 11kW and 22kW pumps because of varying pressures in the irrigation system. These resulted in an estimated payback period of 2.7 and eight years respectively.
Other recommendations included installing a 12kW groundmounted solar system at the site of the 11kW submersible pump, which resulted in an estimated payback period of 3.4 years.
In this Queensland Farmers' Federation case study, an Energy Savers audit for a mixed vegetable farm located near Laidley in the Lockyer Valley found it could benefit from recommendations in a recent energy audit. The audit recommended replacing an irrigation pump, installing Variable Speed Drives on existing irrigation pumps and installing a solar PV system to offset the energy consumption.
The energy audit recommendations and potential benefits are summarised below:
Following the audit report recommendations, the grower proceeded with installation of the new pump and three VSDs, with actual energy savings of 12 per cent over total farm consumption and emission reductions around 23tCO2-e per year.
An energy audit is a great way for a business to identify the most effective way to cut costs, reduce emissions and boost productivity. By implementing the suggested recommendations, the farm could expect a new benchmark of 94kWh/tonne, a 21 per cent reduction.
This case study was originally published by Queensland Farmers' Federation. To view more irrigation and energy saving case studies, visit www.qff.org.au/energysavers
Electric motors are often used to drive pumps, fans, compressors and other equipment. In Australia, it is estimated that they account for nearly 30 per cent of total electricity consumption across all industries. Globally electric motors and electric motor-driven systems are estimated to account for almost 50 per cent of global electricity consumption and 70 per cent of electricity consumption in industry. With electrical energy comprising around 97 per cent of the total cost of ownership (TCO) of an electric motor – compared to one per cent of TCO for the purchase of a new motor and about two per cent for maintenance – optimising electric motor performance is key to improving energy efficiency to reduce energy costs, as well as reduce maintenance and improve reliability. Here, we look at five ways to reduce the running costs of electric motors.
As well as directly or indirectly drive devices such as pumps, fans or compressors, motors typically form part of a larger system comprising many elements like pipes, valves, ductwork, controls and dampers. This means the interactions between all the components that comprise the system will affect overall performance. Therefore, it is crucial to comprehend motors in the context of their operational systems. Focusing solely on the motor may lead to overlooking substantial and frequently inexpensive opportunities for savings.
Measuring the performance of equipment is crucial to detect where wastage is occurring and what energy saving actions will produce worthwhile savings. By monitoring the system, end users can track and understand the energy performance of the equipment and system to:
• Inform immediate no-cost or low-cost energy saving solutions that can be made
• Identify savings opportunities that are not obvious
• Highlight potential issues by analysis of trends
For small systems, low cost and temporary monitoring can be used where the potential for energy savings is unlikely to be significant. Larger, more complex systems might benefit from more permanent automatic monitoring solutions that can identify variations and problems in real time for ongoing system optimisation.
No matter if monitoring activities are temporary or ongoing, measurements should be taken after energy saving activities have been implemented to confirm the savings actually made to justify future spend if needed.
There is a variety of equipment and options to undertake monitoring and measurement activities, with the cost of these varying.
Equipment that can be used for measurements include:
• Hours-run meters: these measure the time the equipment has been running which can be used to identify if a motor is running longer than necessary
• Energy meters or portable energy loggers: these can be installed or temporarily connected to the motor’s energy supply to show energy consumption and motor loading instantaneously and over time. This information can be used to assess a motor’s performance and determine the motor load required for a task; for example the load can be checked against motor nameplate and if they don’t closely match it is an indication that the motor is not suited to the application
• Permanent kWh meters: these are installed as submeters and are useful in larger motors to provide ongoing information on energy consumption so that trends can be identified
Condition monitoring is another tool that can be used to not only identify energy consumption trends but also to predict the risk of failure of mechanical components. It is usually implemented on sites with large equipment or where a breakdown is a critical issue. Tools that can be implemented include:
• Vibration analysis: used to analyse noise and vibration, with a frequency logger able to record levels which can be used to identify potential issues such as bearing failure, shaft alignment discrepancies and lubrication problems
• Oil analysis: used to identify wear or contamination issues through gearbox oil samples
• Thermographic surveys: used to identify overheating issues and electrical faults
As motors are often ‘hidden’ within machinery, there is a tendency for them to be ignored and left to run even when they do not need to be in operation. The first step is to identify if there are periods of time that the motor and/or other equipment can be turned off, such as circulating water in a heating or cooling system when there is no demand, or ventilating spaces that are unoccupied. When it has been identified that a motor and/or equipment can be switched off, the next step is to consider how it can be safely turned off, what is required to switch it off, and the ease of implementing the solution. These considerations should take into account risks of manual switch-off procedures such as health and safety risks, a motor being switched off at the wrong time, or the wrong motor being switched off.
In some situations, a manual switch off will be appropriate with proper procedures put in place to ensure the correct processes are followed, including the maximum number of starts allowed for a motor is not exceeded, and any warm up or initialisation time is taken into account.
Where manual switch off isn’t appropriate, automatic switch off should be considered. A timer and operational control can be installed to automatically turn the motor on and off at specific times. Interlocks are also useful to switch the motor on only if another piece of equipment or device is running, and it will automatically shut off the motor when the other equipment or device is turned off. Load-sensing devices are also useful as they can sense when there is no load, signalling for the motor to be switched off after a set period of time. Another device that can be used is a sequencer. Sequencers can switch parallel equipment on and off depending on the process needs.
When correctly used, motor timers and controls can save significant amounts of energy, reduce wear on the mechanical system, and improve performance.
Sustainability Victoria’s Boosting Business Productivity program worked with more than 300 businesses to explore their energy use and minimise their energy cost, and based on the data gathered, it found that on average, installing timers and operational controls cost less than $7,100 to implement, had a $5,000 annual saving and payback period of 1.5 years, and saved more than 13 tonnes of greenhouse gas emissions annually.
3. Install variable speed drives (VSDs)
Installing VSDs can be beneficial where a motor is required to serve a range of load conditions or has a variable demand, as they adjust the motor’s speed to match the load requirement for the task. By adjusting the speed, VSDs can reduce energy consumption, with up to 50 per cent savings on operating costs possible by reducing the motor speed by 20 per cent. Further to energy savings, VSDs can offer other benefits such as improved process control (and therefore output quality), and the ability to control more than one motor.
While VSDs are usually more expensive to install than simple motor controls, their payback can be less than two years in some applications if they have been applied correctly. Furthermore, according to the Sustainability Victoria results, on average VSDs cost around $18,600 to implement, with an annual saving of more than $10,000 and an annual reduction of greenhouse gas emissions by 45 tonnes.
Integrated motor drives (IMDs) or smart motors can also be considered. These are a combined package where the VSD comes attached piggy-back style to the motor. Some advantages these have over separate units, including lower total cost, reduced wiring time, no electromagnetic interference, and optimum matching of the motor and VSD.
If a motor is old, it could be worth replacing it with a high efficiency motor. While high efficiency motors are more expensive to purchase – typically ten to 20 per cent more than standard motors – they can reduce energy consumption by around three to four per cent. Further savings can be achieved if the old motor was incorrectly sized for the task and the new motor is the correct size.
Replacing a motor can require time to correctly specify, and the efficiency of the entire system is worth considering at the time. Thought should be placed on if there is an opportunity to minimise demand, as well as sizing the equipment correctly. This second point is especially important as it is not uncommon for equipment to be oversized for an application. This is because equipment designers sometimes add a ten per cent safety margin, and then an additional ten per cent is often added by specifying engineers for safety. For example if a 200 hp motor is required, a specifying engineer may suggest a 250 hp motor to provide a safety factor and so that it runs cooler. However, this requires a more expensive initial motor purchase, as well as a larger motor starter. Together, these added safety margins result in lower efficiency and wasted energy, so specifying components that suit the current inefficiencies will only limit the potential energy savings of the system.
According to Sustainability Victoria, on average, upgrading to a more efficient motor will cost less than $15,000, with a payback period of 1.5 years and annual saving of $10,000, as well as reduce greenhouse gas emissions by 39 tonnes annually.
Regular preventative maintenance maximises the reliability and efficiency of a motor, and can reduce energy consumption by up to ten per cent.
Maintenance activities should be carried out in accordance to the manufacturer’s instructions, and servicing should include:
• Performing periodic checks to identify potential problems. Inspections should include daily or weekly noise, vibration and temperature checks, and approximately twice a year, test winding and winding-to-ground resistance should be performed to identify insulation problems. Bearing lubrication, shaft alignment and belts should also be checked
• Checking temperatures to ensure there is adequate cooling for the motor as high temperatures reduce insulation life and motor reliability. Make sure motors are shaded from the sun, located in well ventilated areas, and kept clean from dirt and debris as these act as an insulator
• Lubricating motors – including greasing, oil top-up and oil replacement – according to the manufacturer’s specifications. High-quality greases or oils should be applied carefully to prevent contamination by dirt or water, and it is important to not under or over grease
• Maintaining a record for each motor which include technical specifications, repair, testing and maintenance data. Having this information on hand will make identifying motors that are likely to develop mechanical or electrical problems easier
Optimising electric motor performance is crucial to improve energy efficiency and reliability, and reduce energy costs. Although there is no one-size-fits-all solution to improving the efficiency of a motor, monitoring the system and measuring performance to inform reconfiguration, installing timers and operational controls, and implementing energy-efficient technologies are some of the actions end users can consider implementing to achieve this.
Pumps are essential components in a wide range of industries, including mining, water supply and treatment, power generation, food and beverage etc. The sealing mechanism of a pump is crucial in maintaining its efficiency and reliability. There are two primary options for sealing a pump: mechanical seals and gland packing. Each of these options has its unique advantages and disadvantages, and the choice depends on several factors.
Mechanical seals are a great choice for many industrial applications due to their superior sealing capabilities. Unlike gland packing, which relies on compression to create a seal, mechanical seals use a rotating and stationary element to create a barrier that can withstand higher pressures and temperatures. The reduced friction on the shaft leads to lower energy consumption and reduced maintenance costs.
Additionally, mechanical seals can handle a wide range of fluids, including corrosive and abrasive substances, making them more versatile than gland packing. The downside of mechanical seals is that their initial setup costs can be more than gland packing and require more specialized knowledge and equipment for installation and maintenance. This is why finding a reliable mechanical seal company is important.
Gland packing is an older sealing technology that is still in use in many applications. Gland packing consists of a
braided rope or cord that is compressed into a stuffing box to create a seal. The advantage of gland packing is that it is cheaper and easier to install than mechanical seals. Gland packing is also more forgiving of misalignment and vibration, making it a better option for older or less efficient pumps.
However, gland packing is less efficient than mechanical seals and requires more frequent replacements due to wear and tear. Additionally, gland packing is not suitable for handling corrosive or abrasive substances, making it less versatile than mechanical seals.
How to choose between them
When choosing between mechanical seals and gland packing, several factors should be considered. The first is the type of fluid being pumped. If the fluid is corrosive or abrasive, mechanical seals are a better choice as they can handle a wider range of substances. Additionally, if energy efficiency is a priority, mechanical seals should be used as they provide less resistance on
the shaft. However, if the pump is older or less efficient, gland packing may be a better option as it is more forgiving of misalignment and vibration.
Another factor to consider is the cost. Mechanical seals are more expensive initially than gland packing, but they also last longer and require less frequent replacements, leading to cost savings over time. Additionally, if the pump is being used in an application where downtime is critical, mechanical seals are a better option as they require less maintenance and can be replaced more quickly.
Finally, the expertise and knowledge of the maintenance team should be considered. Mechanical seals require more specialized knowledge and equipment for installation and maintenance than gland packing. If the maintenance team is not experienced in working with mechanical seals, gland packing may be a better option. A good mechanical seal supplier will provide support for installation and troubleshooting.
In conclusion, the choice between mechanical seals and gland packing for pump sealing depends on several factors, including the type of fluid being pumped, energy efficiency, cost, and the expertise of the maintenance team. Mechanical seals offer superior sealing capabilities and are more versatile, making them a preferred option in many industrial applications. However, gland packing is cheaper and easier to install and maintain, making it a better option for older or less efficient pumps. Ultimately, the choice should be based on a careful assessment of the specific needs and priorities of the application.
For more information, please visit mechsealengineering.com.au.
The environment a seal will be exposed to is crucial when selecting the design and material.
There are a number of key properties that seal materials need for all environments, including creating a stable seal face, able to conduct heat, chemically resistant, and good wear resistance. In some environments, these properties will need to be stronger than in others. Other material properties that should be taken into account when considering the environment includes hardness, stiffness, thermal expansion, wear and chemical resistance. Keeping these in mind will help you to find the ideal material for your seal.
The environment can also determine whether cost or quality of the seal can be prioritised. For abrasive and harsh environments, seals may be more expensive due to the materials needing to be strong enough to withstand these conditions. For such environments, spending the money for a highquality seal will pay itself back over time as it will help prevent the costly shutdowns, repairs, and refurbishment or replacement of the seal that a lower quality seal will result in. However, in pumping applications with very clean fluid that has lubricating properties, a cheaper seal could be purchased in favour of higher quality bearings.
Carbon used in seal faces is a mixture of amorphous carbon and graphite, with the percentages of each determining the physical properties on the final grade of carbon. It is an inert, stable material that can be self-lubricating. It is widely used as one of the pair of end faces in mechanical seals, and it is also a popular material for segmented circumferential seals and piston rings under dry or small amounts of lubrication.
This carbon/graphite mixture can also be impregnated with other materials to give it different characteristics such as reduced porosity, improved wear performance or improved strength.
A thermoset resin impregnated carbon seal is the most common for mechanical seals, with most resin impregnated carbons capable of operating in a wide range of chemicals from strong bases to strong acids. They also have good frictional properties and an adequate modulus to help control pressure distortions. This material is suited to general duty to 260°C (500°F) in water, coolants, fuels, oils, light chemical solutions, and food and drug applications.
Antimony impregnated carbon seals have also proven to be successful due to the strength and modulus of
antimony, making it good for high pressure applications when a stronger and stiffer material is needed. These seals are also more resistant to blistering in applications with high viscosity fluids or light hydrocarbons, making it the standard grade for many refinery applications.
Carbon can also be impregnated with film formers such as fluorides for dry running, cryogenics and vacuum applications, or oxidation inhibitors like phosphates for high temperature, high speed, and turbine applications to 800ft/ sec and around 537°C (1,000°F).
Ceramic
Ceramics are inorganic non-metallic materials made from natural or synthetic compounds, most commonly alumina oxide or alumina. It has a high melting point, high hardness, high wear resistance and oxidisation resistance, so it is widely used in industries such as machinery, chemicals, petroleum, pharmaceutical and automobile. It also has excellent dielectric properties and is commonly used for electrical insulators, wear resistant components, grinding media, and high temperature components.
In high purities, alumina has excellent chemical resistance to most process fluids other than some strong acids, leading it to be used in many mechanical
seal applications. However, alumina can fracture easily under thermal shock, which has restricted its use in some applications where this could be an issue.
Silicon carbide is made by fusing silica and coke. It is chemically similar to ceramic, but has better lubrication qualities and is harder, making it a good hard-wearing solution for harsh environments. It can also be re-lapped and polished so a seal can be refurbished multiple times over its lifetime.
It is generally used more mechanically, such as in mechanical seals for its good chemical corrosion resistance, high strength, high hardness, good wear resistance, small friction coefficient and high temperature resistance. When used for mechanical seal faces, silicon carbide results in improved performance, increased seal life, lower maintenance costs, and lower running costs for rotating equipment such as turbines, compressors, and centrifugal pumps.
Silicon carbide can have different properties depending on how it has been manufactured. Reaction bonded silicon carbide is formed by bonding silicon carbide particles to each other in a reaction process. This process does not significantly affect most of the physical and thermal properties of the material, however it does limit the chemical resistance of the material. The most common chemicals that are a problem are caustics (and other high pH chemicals) and strong acids, and therefore reaction-bonded silicon carbide should not be used with these applications.
Self-sintered silicon carbide is made by sintering silicon carbide particles directly together using non-oxide sintering aids in an inert environment at temperatures over 2,000°C. Due to the lack of a secondary material (such as silicon), the direct sintered material is chemically resistant to almost any fluid and process condition likely to be seen in a centrifugal pump.
Tungsten carbide is a highly versatile material like silicon carbide, but it is more suited to high pressure applications as it has higher elasticity which allows it to flex very slightly and prevent face distortion. Like silicon carbide, it can be re-lapped and polished.
Tungsten carbides are most often manufactured as cemented carbides so there is no attempt to bond tungsten carbide to itself. A secondary metal is added to bind or cement the tungsten carbide particles together, resulting in a material that has the combined properties of both tungsten carbide and the metal binder. This has been used to an advantage by providing greater toughness and impact strength than possible with tungsten carbide alone. One of the weaknesses of cemented tungsten carbide is its high density.
In the past, cobalt-bound tungsten carbide was used, however it has gradually been replaced by nickel-bound tungsten carbide due to it lacking the range of chemical compatibility required for industry. Nickel-bound tungsten carbide is widely used for seal faces where high strength and high toughness properties are desired, and it has good chemical compatibility generally limited by the free nickel.
As Buna is a synthetic rubber copolymer, it performs well in applications requiring metal adhesion and abrasion-resistant material, and this chemical background also makes it ideal for sealant applications. Furthermore, it can withstand low temperatures as it is designed with poor acid and mild alkali resistance.
Buna is limited in applications with extreme factors such as high temperatures, weather, sunlight and steam resistance applications, and is not suitable with clean-in-place (CIP) sanitising agents containing acids and peroxides.
EPDM
EPDM is a synthetic rubber commonly used in automotive, construction and mechanical applications for seals and O-rings, tubing and washers. It is more expensive than Buna, but can withstand a variety of thermal, weather and mechanical properties due to its long-lasting high tensile strength. It is versatile and ideal for applications involving water, chlorine, bleach and other alkaline materials. Due to its elastic and adhesive properties, once stretched, EPDM returns to its original shape regardless of the temperature.
EPDM is not recommended for petroleum oil, fluids, chlorinated hydrocarbon or hydrocarbon solvent applications.
GFPTFE has good chemical resistance, and the added glass reduces the friction of the sealing faces. It is ideal for relatively clean applications and is cheaper than other materials. There are sub-variants available to better match the seal to the requirements and environment, improving its overall performance.
Buna
Buna (also known as nitrile rubber) is a cost-effective elastomer for O-rings, sealants and moulded products. It is well known for its mechanical performance and performs well in oil-based, petrochemical and chemical applications. It is also widely used for crude oil, water, various alcohol, silicone grease and hydraulic fluid applications due to its inflexibility.
Viton is a long-lasting, highperformance, fluorinated, hydrocarbon rubber product most commonly used in O-Rings and seals. It is more expensive than other rubber materials but it is the preferred option for the most challenging and demanding sealing needs.
Resistant to ozone, oxidation and extreme weather conditions, including materials such as aliphatic and aromatic hydrocarbons, halogenated fluids and strong acid materials, it is one of the more robust fluoroelastomers.
Choosing the correct material for sealing is important for the success of an application. While many seal materials are similar, each serves a variety of purposes to meet any specific need.
A geothermal installation at Fairwater – a major residential community in Sydney by Frasers Property Australia – is one of the largest of its kind in the southern hemisphere, using heat pumps and ground loops to provide heating and cooling to 750 homes. The innovative solution was part of a $1.71 million, three-year study known as the Fairwater Living Laboratory that examined the effects of ground source heat pumps (GSHPs) on energy costs for residents and investigated its viability for industry-wide adoption of the technology as part of local, renewable and efficient energy infrastructure.
Fairwater is a 38-hectare residential development located 1km from Blacktown in Western Sydney, with over 2,000 residents. Developed by Frasers Property Australia, it has been designed for sustainability. With more than 800 homes in Fairwater incorporating geothermal – GSHPs – for HVAC, it is the first large-scale residential development to use it in
Australia and is one of the largest installations in this application in the southern hemisphere.
The use of this technology also helps to make it one of the most environmentally friendly residential developments in the country and the first project in the state to achieve the highest recognition from the Green Building Council of Australia – a 6 Star
Green Star - Communities rating. It is one of only a handful of projects nationally to receive this rating.
The geothermal installation was used for the Fairwater Living Laboratory – a study funded by the Australian Renewable Energy Agency (ARENA), Frasers Property Australia, and the New South Wales Office of Energy and Climate Change. The three-year study
was undertaken at the development between September 2019 to August 2021 by Climate-KIC Australia and carried out by researchers from University of Technology Sydney and Curtin University, with the findings now being used to inform government policy and encourage broader industry adoption of the efficient energy geothermal infrastructure.
A sustainable solution
Geothermal has been used in applications for many decades in North America and Europe as a highly efficient and reliable source of heating and cooling, helping to reduce dependence on fossil fuels. Until the Fairwater project, most geothermal applications in Australia were single dwelling, small commercial applications and pool heating.
Nicholle Sparkes, General Manager, Delivery and Operations, Frasers Property Australia, said the company is always looking at opportunities to invest in smart sustainable technology that benefits its customers and the environment. This led to the choice to install geothermal.
“The decision was made as part of our initiative to develop and lead by example to ensure we looked at emerging technologies and to drive sustainable outcomes in our communities,” Ms Sparkes said.
“Geothermal was selected due to its ESG advantages, with a proportion of energy sourced from the ground, ensuring it’s a renewable energy outcome and helping us reduce our carbon footprint.
“Another advantage is the ability to roll it out in a scalable area to provide an affordable heating and cooling outcome for customers.”
The geothermal systems in Fairwater are able to deliver over 14,000kW of heating and cooling, with a Coefficient of Performance (COP) approximately double that of conventional air conditioners.
The key difference between geothermal and conventional HVAC systems is that geothermal uses the ground as a heat source in winter and as a heat sink in summer. On the other hand, normal air conditioning systems have a condenser sitting outside the home, which has a coil that refrigerant runs through and a fan sitting behind the coil to disperse air across it. This means in summer it’s using the outside air to reject heat from the condenser coil, and in winter it’s using outside air to collect heat.
This difference is important as air temperatures vary not only on a seasonal basis, but also on a daily basis, whereas ground temperature is constant. So regardless of what the outside air temperature’s doing, it will always be 22-23˚C below the ground.
Another benefit of geothermal over conventional HVAC is the design and amenity of the equipment. The GSMI heat pumps provided by Alinta Energy for the project are smaller and quieter than normal air conditioning condensers, so they don’t have the same noise and airflow issues associated with conventional systems.
This becomes more beneficial as housing lots get smaller or, like many houses at Fairwater, when there is no backyard. This is important for design and amenity outcomes as having an air conditioning condenser sitting in an al fresco area makes that area unusable when the system’s running. With the geothermal system, it operates much quieter, and doesn’t disperse air into that space.
before it is circulated through the fan coil unit in the home to absorb the heat in the air and cool the house.
In heating mode, a cool refrigerant is circulated through the geothermal loops to absorb the heat from the ground. It is then compressed and circulated through the fan coil unit to provide heating.
In both modes, after the refrigerant has re-heated (cooling mode) or cooled (heating mode), the cycle repeats itself. Ground source heat pumps for the Australian market
The heat pump for the Fairwater development was provided by Alinta Energy – the GeoAir system. Measuring just 600mm by 600mm and standing 890mm high, it has no external fan or condenser coil, and the units operate at 51dB.
It was developed and designed specifically for Australian conditions and to be similar to a conventional system so that the developer’s existing air conditioning contractors could be retained to provide installation.
As it’s compact and quiet, it is also easily integrated into any design, meaning there are no visible or perceptible differences to occupants compared to conventional systems, and it is well received and deployed by occupants.
Ms Sparkes said the geothermal system installed at Fairwater consists of three main components: the loop, the heat pump, and the fan coil unit.
The geothermal loops are installed by a drilling rig vertically adjacent to each home to a depth of around 80m. The system then connects to a typical ducted air conditioning system that can be installed by air conditioning trade contractors.
Once in operation, the system works much like the standard reversecycle air conditioners, but with much greater efficiency and fewer moving parts, meaning it also requires less maintenance.
The heat pumps used at Fairwater work similar to a conventional air conditioning system, with one major difference – the condenser coil is in the ground in the geothermal loop rather than sitting beside it.
In cooling mode, the heat pump circulates a hot refrigerant gas through the geothermal loops in the ground so that it can absorb the cooler temperatures found below the earth before becoming a liquid. It then gets sent to the heat pump where the pressure is lowered so it cools further
“The above ground air conditioning system is serviced in the same way a standard unit is serviced, which is generally on a yearly basis to ensure everything is running correctly and any filters are cleaned and or changed to ensure the best air quality is circulated around the home to maintain comfort levels,” Ms Sparkes said.
Installing geothermal systems at a larger scale, such as for Fairwater, needs close coordination and planning before building even commences.
In a normal build process, air conditioning installation is one of the last things that is done, but for geothermal systems it needs to be one of the first things completed on site.
The process requires the development application drawings to have the location where the geothermal loop has to go. The developer can then do the bulk of earthworks and survey the location as per the drawings where the geothermal loop is to be installed.
A specialised installation process was developed in partnership with Frasers to integrate within the company’s existing processes. This included:
• Locating the position of the heat pump on the DA drawings
• Ensuring the surveyor on site would mark the location of the heat pump immediately following bulk earthworks
• Approval for works received from NSW Water
• Geothermal loop installed at the nominated location before any other works began
• The geothermal loops are capped and protected with building works following to program
The geothermal loop was the first part of the system to be installed at Fairwater using specialist drilling equipment.
The loops were installed at 200mm off slab and the heat pumps were placed adjacent for connection.
To install the loops, a 125mm diameter hole is drilled into the ground at a depth that is dictated by the system size, with larger systems requiring the hole to be deeper to ensure there is enough surface in the ground for heat rejection.
Once the hole is completed, the geothermal loop is installed in the ground using gravity feed and a thermal conductive grout is injected around it.
The grout has two purposes:
1. Thermal conductivity –air is an insulator, so if the loop is suspended in a hole, heat will not be transferred between the geothermal loop and the subsurface material
2. Environmental – cementless grout is used to plug the hole and prevent any cross-aquifer interference. It also prevents surface water contamination of groundwater
Once the loops have been installed, the house can be built and the normal air conditioning installation process follows including installation of the fan coil unit and ductwork. The geothermal heat pump is then installed once the house is finished and landscaping is done.
Findings from the study have been positive. The study found that when installed at scale, and at the beginning of the building process, geothermal can be both a profitable and environmentally beneficial addition to a home despite the additional upfront cost to construction. The GSHPs added value to houses, and reduced power consumption by 21 per cent on average, as compared to nearby homes without the technology.
Cameron Jackson, General Manager Development NSW, Frasers Property Australia, said the company has an ambitious target of being net zero in development and operation by 2028, and that means investigating new technology and spending the time to analyse and evaluate it.
“This has been such an interesting project to support, and watch unfold,” Mr Jackson said.
“We were confident the installation of geothermal heating and cooling technology in our Fairwater homes would help our customers reduce their
energy consumption, and their bills, and now we have confirmation of that.
“We will use the findings of this ground-breaking study to guide us on our pathway to net zero.”
The project also encompassed the Sydney COVID-19 lockdowns, finding that the demand reduction aspects of the geothermal technology had the potential to ‘smooth out’ electricity grid usage, which could help avoid spikes that can lead to blackouts and power cuts in extreme weather. Fairwater homes recorded an average of 3kW of avoided power demand per household during critical peak events.
Professor Leena Thomas, Research Project Lead, University of Technology Sydney, said, “A major benefit of geothermal air conditioning beyond energy savings for individual home owners is its benefits to electricity grid networks to reduce the peak demand.
“Our statistical modelling of smart meter data indicates that for every degree that outdoor air temperature moves away from the comfortable range, demand from conventional air conditioning (heating and cooling) increases by between six and eleven per cent in hot weather and between 3.5 per cent and nine per cent in cold weather.
“On the other hand, geothermal air conditioning reduces this rate to between 4.5 per cent and nine per cent for hot weather and between two per cent and six per cent for cold weather. Due to the compounding nature of these rates, savings rapidly increase in terms of electrical kilowatts when temperatures are extreme, but also differ depending on time of day.
“When used at scale, depending on location within the network, this could play a role in deferral of network augmentation.
“These benefits are all the more relevant in current scenarios of warming temperatures, increasing housing demand and urbanisation in Western Sydney and other locations around Australia.”
As well as offering a number of insights in relation to environmental performance, the results also provided insight into occupant behaviour and experience.
“It is pleasing to see that the research demonstrated clear energy benefits from geothermal technology and high ratings for comfort in the Fairwater homes,” Prof Thomas said.
“An overwhelming majority of residents at Fairwater also reported that living in the precinct has had a positive effect on their health and wellbeing.
“Our findings highlight that an integrated precinct-based approach for incorporating sustainability and energy efficient technologies when combined with an understanding of occupant practices offers the best pathway for decarbonisation and getting beyond net zero.”
User behaviour and occupant preference is important as it plays a key role in the actual performance and savings that can be realised when installing new technology such as GSHP. The results found:
• Residents would benefit from a targeted program of user engagement and education
• Engaging with residents and consumers is a critical way for industry and regulatory bodies to gain feedback and insights in relation to interventions (such as GSHP) that are implemented
“It is commendable that the developers were actually interested to gain feedback of the performance in practice and engage in knowledge sharing – this is not always how the building industry operates,” Prof Thomas said.
The results from the study provide tangible evidence on the performance in practice of geothermal air conditioning and actionable insights for various stakeholders. They have been widely disseminated through ARENA knowledge sharing deliverables.
Belinda Whelan, Director of Strategic Projects, Climate-KIC Australia, said the study provides governments and the property industry with solid information on which to base their geothermal decision-making.
“The built environment sector in Australia has a really important role to
play in helping Australia meet its net zero ambitions. Studies like Fairwater provide policymakers and the property sector with deep insight and data to guide informed decision-making to make rapid change at scale,” Ms Whelan said.
In addition to communicating the results to ARENA, Frasers Property's design and development team, and Fairwater residents, special briefings have also been conducted for policymakers at New South Wales Government Department of Planning and Environment, Office of the Government Architect NSW, as well as through forums for property and design professionals (Green Building Council of Australia’s Transform, Parlour Lab, etc.) and for the electricity network.
While there are no immediate plans to undertake another study of this kind, Prof Thomas said that a full cost-benefit investigation, including the capital costs of systems,
installation and maintenance, embodied energy or direct emissions (including global warming potential from possible refrigerant leakage) which was outside the scope of the present study should be considered as a next step when commissioning additional research.
“We also believe it would be useful to conduct more detailed comparisons between various system configurations such as geothermal refrigerant loops like the one included in this heat pump study, geothermal systems with water loops and standard heat pumps.
“More rigorous studies to investigate the wider application of geothermal should be considered beyond residential settings. Additionally, we are engaging with various stakeholders as to how the living laboratory approach can be replicated in other contexts.”
Pumps are an essential component, and one of the most used pieces of equipment, in the oil, gas and petrochemical industries. They can be found at all stages of these applications – upstream, midstream and downstream – from delivering oil from the ground to a ship, oil refinery, or storage to speeding up the fluid flow from one point to another. Due to the varied tasks pumps are required to perform, the types of pumps used are also extremely diverse, varying in type, size and materials. Here, we take a look at some of the key considerations during pump selection in these industries.
Ensuring you select the right pump for the application is important to ensure maximum efficiency, and minimal operating and maintenance costs. Poor pump selection is also likely to result in downtime and heavy costs to repair or replace a damaged pump.
Pumps in the oil, gas and petrochemical industries are usually divided into two categories: centrifugal and positive displacement pumps.
Centrifugal pumps are the most commonly used type as they can be utilised in a wide range of applications. They are usually found in applications such as handling low viscosity fluids that don’t contain air, fumes or large amounts of particles like lighter hydrocarbons and water, as well as filthy fluids and where there are higher flow rates. For example, single stage centrifugal pumps are primarily used for transferring low viscosity fluids that require high flow rates. They are usually used as part of a larger pump network comprising other centrifugal pumps such as horizontal multistage pump units for crude oil shipping or water injection pumps for secondary oil and gas recovery.
Positive displacement pumps are used in services with viscous and gas entrained liquids at a lower flow rate but at higher pressures and often under difficult suction conditions. There are special types of positive displacement pumps available such as high pressure piston pumps for drilling and hydraulic fraccing operations. Progressive cavity pumps have also become a popular option due to their highly versatile design enabling them to handle sand particles, gas and oily water for a range of applications including transportation and injection.
There have been many pump codes and standards that apply to different pumping applications. Due to the critical nature of the oil, gas and
petroleum industries, it is important to ensure the selected pump meets the relevant standards.
The main relevant standards for these industries are American National Standards Institute (ANSI), American Petroleum Institute (API), International Standards Organization (ISO), and American Society of Mechanical Engineers (ASME). In the past, some standards have had more impact in certain regions of the world than others, however, there has been a degree of convergence as they have borrowed from each other and the rise of globalisation.
API sets the standard for pumps in the oil, gas and petroleum industries. They are used to define systems, tests, equipment design and ability to handle high temperature and pressures. Pumps that meet these standards are some of the highest quality available.
There are various applicable API standards depending on the type of pumps, but some of the most important are API 610 for mechanically sealed pumps, API 685 for sealless pumps, API 676 for positive displacement pumps - rotary, and API 764 for positive displacement pumps - reciprocating.
API pumps have some advanced features over ANSI pumps, manufacturer’s standard pumps and other types in these harsh applications, such as having the capability to withstand relatively high allowable nozzle loads, provisions for larger and better mechanical seals, better bearings and components. These result in higher performance and reliability. It is also generally easier to align, commission, operate and maintain API pumps as well.
ANSI pumps are horizontal, end suction, single stage centrifugal pumps with an overhung impeller and back pull out. Their defining feature is that they are interchangeable across manufacturers and brands as they must
meet dimensional standards set by ANSI, making them identical in interface and envelope dimensions regardless of the manufacturer.
ANSI B73.1 is the main standard of interest for the oil, gas and petrochemical industries as it sets the key dimensions for 27 pump sizes –including overall height and length of the bare pump, nozzle and shaft diameters, the size, location and spacing of mounting bolts, etc. – giving end users a range of options.
It also specifies some performance characteristics and a number of design features intended to ensure reliable service and simplified maintenance. It is comparable with ASME B73.1 standard.
The ISO is an independent organisation that oversees, creates, and promotes internationally accepted standards for numerous industries, and ISO safety symbols are recognised across language barriers to increase hazard awareness and safety compliance.
These standards have historically had more impact in Europe and Asia, and are comparable to ANSI standards.
ISO 5199 and ISO 2858 cover the same type of industrial pumps as ANSI B73.1. The main difference between these two ISO standards is that the older ISO 2858 is focused on external dimensions and mounting details, while ISO 5199 also specifies a variety of performance requirements (e.g. minimum bearing life) and construction features (e.g. general layout, seal configurations).
In general, ISO 5199 compliant pumps will meet or exceed ANSI B73.1 requirements in terms of performance, reliability, serviceability and longevity. However, they can’t be used as direct substitutes for ANSI B73.1 pumps without some adaptations to the mounting plates and motor couplings.
ISO 15783 specifies the requirements for sealless rotodynamic pumps that are mainly used in chemical processes,
water treatment and petrochemical industries. It includes design features focused on the selection, installation, maintenance and operational safety of the pumps. However, it doesn’t cover dimensional and hydraulic performance requirements and further technical requirements which are detailed in ISO 5199.
ISO 2858 relates to end suction centrifugal pumps and specifies the main parameters and designation. It specifies the principle dimensions, mounting details and nominal duty point of a maximum operating rating of 16 bar.
There are a couple of relevant ASME standards for pumps in the oil, gas and petroleum industries.
ASME B73.1 and ASME B73.3 are relevant for horizontal end suction centrifugal pumps used in chemical processes. The difference is ASME B73.1 is applied to sealed horizontal, end suction, overhung, radially split, singlestage, mechanically sealed pumps, and ASME B73.3 is applied to sealless versions of these. They are comparable to ANSI standards.
These standards specify a number of key dimensions for pumps including overall height and length of the bare pump, nozzle and shaft diameters, and the size, location and spacing of mounting bolts. They also specify some performance characteristics and a number of design features that are intended to ensure reliable service and simplified maintenance.
ASME B16.5 relates to pipe flanges and flanged fittings, including defining and standardising pressure and temperature ranges for: flange ratings within various material groups, flange dimensions for various ratings and fitting designs and flange bolts.
Pumps in the oil, gas and petroleum industries are frequently required to operate under extreme environmental conditions, such as extremely high temperatures and pressures, or extremely low pressures and cryogenic temperatures, depending on the specific application.
Pumps must be manufactured from materials capable of withstanding their operating conditions and be nonreactive with any chemicals they will be exposed to.
Material choice is often governed by the prevention of corrosion, erosion, wear resistance, oxidisation and build-
up on pump components. Some pumps must also be able to handle abrasive or volatile materials.
Selecting metallic and non-metallic pump components that are compatible with the liquid can help decrease the onset of premature and costly downtime or failure.
The most common materials in the oil, gas and petroleum industries are carbon steel and stainless steel due to their strength, corrosion resistance and ability to handle high heat.
Pumps are often oversized for an application and therefore operate in an unstable region of the performance curve. There are a number of reasons a pump could be oversized.
A certain degree of error can occur at the specification stage due to the need to estimate the equipment requirements, as well as the possibility of the published literature having different reference values for flow resistance coefficient or fittings losses.
Another reason a pump may be oversized is to account for the system design to be expanded in a few years if needed, as a correctly sized pump for the current conditions would be unable to meet possible future additional demand. Sometimes a safety margin will be added and a larger pump procured and installed to cater for future expansion of the system.
Other reasons oversizing may occur include a pump was oversized to account for expected build up of corrosion products on the pipe interior, which would increase the pump total head requirement, or a safety factor was added to increase pump capacity and head to counter the effects of wear. Oversizing can also be the result of factors such as a pump was urgently needed and the right size was out of stock, a pump was selected from the spares inventory due to budget constraints, or a new pump was bought to replace an existing pump that was already oversized.
However, oversizing – along with misalignment – is one of the biggest problems contributing to excessive pump maintenance. This can cause a number of problems, including shortening the mean time between repair on seals and bearings, as well as turned and cast components. It also has the knock on effect of resulting in higher energy costs due to a higher performance in terms of flow and
pressure requiring more power from the motor, which can lead to unnecessary energy consumption.
Undersizing is also an issue. If a pump is undersized in regards to power it will lead to a lower flow rate than required in the system and the need to either install additional pumps or make adjustments to the system like adding recirculation lines or opening discharge valves. Some pumps such as progressive cavity pumps can have additional problems if undersized. As the flow of a progressive cavity pump is a function of cavity size, if the pump is undersized and the cavity size is too small for the application, it will need to pump faster. This can result in reduced suction, increased wear, and pump failure.
These problems can be avoided by properly sizing the pump and configuring the system with a variable frequency drive (VFD).
Selecting the right seal is also important. If an improper mechanical seal is selected it can result in premature seal failure. Misapplication of a seal design is one of the most common reasons for centrifugal pump failure, and once the seal fails it can have costly consequences like loss of product, environmental contamination and other maintenance issues.
These are just some of the considerations to take into account when selecting a new pump for operation in the oil, gas and petroleum industries. Ensuring the right pump is selected is key to optimum performance and minimal maintenance costs.
Valentina Tripp did not start her professional career expecting to make her way into the pump industry, but after almost two years as CEO of Davey, she feels like she’s found her bearings. Here, Valentina talks about the path that led her to the pump industry, the changes she’d like to see unfold during her career, and the challenges facing the industry in the future.
The journey to pumps
When Valentina started her professional career, it was not in the pump industry.
“I started a career predominantly in food and beverage, taking Australian brands into international markets back in the '90s.
“I did my MBA and then shortly after commenced with KPMG in their advisory practice in management consulting, which essentially gave me the opportunity to work across many different industries, solving lots of different problems and I ended up leading the strategy practice there for a number of years.”
Following her time at KPMG, Valentina joined global agribusiness giant JR Simplot, where she led the meat business
throughout Asia Pacific and Corporate Development for Simplot Australia. In Australia, Simplot has a diverse portfolio of growing, manufacturing and processing assets across the country, and is home to a large number of leading food brands. The broad exposure across the supply chain saw a strong interest develop in agriculture and sustainable food systems.
“I was curious to understand the agricultural part of our business, keen to learn more about where our food was coming from and how we were managing our agricultural assets here in this country – right through the value chain from growing, processing to exporting, to building brands that have a global presence.”
It was during her time leading a large-scale agricultural business, Murray River Organics, that Valentina first came
across Davey and its range of products. With 13 organic vertically integrated farms in the Sunraysia region, they were growing wine grapes, dried fruit, table grapes, and citrus, as well as processing a range of organic health products from their facility in Dandenong.
“Coming across Davey in that environment was probably the first time I really understood the role of [pumps], particularly in irrigation…and why water and water management was so important as we traded through the prolonged drought with limited water allocations.”
When the phone call came through from Davey asking her to consider entering the pump manufacturing industry, she was honoured and excited by the possibility.
“I thought, ‘What an amazing opportunity with the most well-known brand of pumps in Australia and the last remaining large-scale pump manufacturing left here in Australia. We could make a real difference in people’s lives, especially in our critical food and fibre growing regions. We could tackle some of the big water access and management challenges. We could find the innovative solutions to water security that our growing community really needs.”
As with any new role, one of the first things Valentina did was try “broadening [her] horizon” by finding out as much as she could about the almost AU$2 billion industry she was entering.
“My first goal was really trying to understand and talk to as many people as possible to learn about industry, what were the key issues, how was the industry performing and what were key success factors to prosper and grow. I wanted to understand the industry’s relative strengths and needs, and how Davey could play a significant role. Learning about the big issues from longtime industry stalwarts who were very generous with their time and insights helped a lot in the early days. It was fascinating.”
Something that struck a chord with Valentina was the pump industry’s continued resilience in times of hardship and ups and downs in the economy, something she said is “really important in times of global uncertainty like climate change and the supply shocks that we've had because we're looking at moving from droughts to floods, to fires”.
“In all those instances, the infrastructure and the support that we give to the community is critical.
“The sovereign capability element became more evident and how important it is to maintain a level of capability in our country from a policy perspective. We need to ensure we can support our country through tough challenges such as flood, fire, droughts, and some of the most extreme conditions in the world. As well as ensuring we can support our community during times of global uncertainty.”
This, she said, also provides a real competitive advantage overseas when people see and come to value the work Australia can provide.
“If it can work in Australia, in some of the toughest conditions in the world, it's just seen as a really reliable, highquality offering.”
Talking to and learning from the people who know the industry best has not only provided valuable insight but has also helped Valentina recognise and identify the global trends that are going to drive change in the industry.
“Climate change, growing global demand for water, water security, societal changes, technology and digitisation, are all critical issues and trends driving our think tanks and R&D teams to develop innovative products and solutions. We are working on how to make our products more efficient, user friendly, connected, and anticipate the issues for the future to solve these problems for our customers.”
A major component of this is working to mitigate the effects of the water scarcity issues that are predicted to arise in coming years.
“They are upon us, and they will continue to be upon us over the coming decades, even though we are in flood situations in big parts of the country, and now in our New Zealand market as well.
“Whilst the immediate climate impacts are quite different and we're responding to those, we know that droughts are around the corner. We know that fire events are likely in the near term given the level of fuel from significant vegetation growth. We know we need to be ready to respond as a company and as a whole industry.”
Shifting her focus inward, Valentina believes another key obstacle ahead for the industry is the challenge of drawing in new people and talent.
“We're doing a lot to change, shift and refresh ourselves so that we can attract the best people to come into our industry.
“There may have been some perceptions; it's not the most attractive place to choose when you're deciding on your career
path out of graduate school or considering a move from other industries. We are really working hard to change that.”
Davey offers internships and graduate recruitment programs to attract new talent and diversify the workforce.
“We're focusing on diversity and attracting talent from other industries.
“I think as a whole industry, I'd love for us to be able to do that on a much bigger scale. And give people careers, longterm careers, and transferable skills as well. We are a global industry; these skills are important, and you can take them into lots of countries.”
overwhelming support for the transformation journey we have embarked on over the next five years.
“We're excited about what that means for us, not just here in Australia, but also from a global perspective and how we turn that energy into innovative new products and services that we're working on. All designed, engineered and manufactured right here in Australia and exported around the world to our 47 countries we service with our 97 global distribution partners.”
Renewable energy’s potential in future innovations is being explored in industries throughout the world, and Australia’s pump industry is no exception, with a lot of research and development and trials concerning renewable applications in pump operations in the works.
Of particular importance to Valentina is shifting mindsets away from the disposable economy that has developed over the last decade to more of a repair and maintain, whole-of-life cycle and sustainable economy.
This was kicked off at the Davey Master Dealer Conference in 2022, where pump dealers gathered for a few days and Davey was able to launch its strategy which includes a focus on renewables and innovation.
Valentina identified this conference as the highlight at Davey, saying it was humbling and unforgettable to see the level of support and engagement behind the company from its dealer partners.
“They were so engaged and welcoming of some of the changes that we had made and want to continue to put in place over the coming years. It was thrilling to receive such
Pumps is often considered to be a male-dominated industry, something Valentina is no stranger to, having worked for most of her career in sectors with similar demographics. But more than it being a gender issue, it should have a broader focus.
“I encourage people to focus on broad diversity. It's not just about gender, we also consider ethnicity, diversity of thought and different non-traditional backgrounds and life experiences.
“When we bring people together from different industries, different experiences, we create a better environment to foster innovation, collaboration, problem-solving and it enables us to test and challenge ourselves, to stretch our thinking and create better, more sustainable solutions.”
When it comes to an industry mentor, there’s no one person Valentina can nominate, rather a large network of colleagues, clients, and professionals that have helped her over the many years and throughout her career journey.
“I feel that whilst it's not one mentor, there's many.
“I've just been really fortunate here at Davey because we have some amazing people in our team, people who have been with us for 30, 40 years. I love talking to them because they
have an incredible amount of knowledge and insights. And they'll answer all my questions, my endless curiosity. They have been very helpful to fast track my learning.
“I think we've got some amazing talent right through the industry that we're tapping into. And, for me, it's trying to get the best people and the best minds together around solving some of these issues.”
If there’s one thing Valentina hopes people can take from her time as CEO, it’s the idea of just having a go.
“Just get in there and have a go because your voice is really valuable. And us as leaders, we need to encourage that and create the forums and the environment that encourages the interaction and engagement.
“Surround yourself with talented, passionate, curious and engaging people. Ask for help. It's okay.
“Put your hand up and call on others when you are not sure. And then make sure you give back in that process as well, because people want to help other people. They do. It's just a natural thing that we do. There is great joy as a leader as you get further in your career, in being able to mentor, inspire and help others coming through. To help mentees stretch, learn, and achieve great things is very rewarding personally.”
It’s the same advice she would give to those who are just entering or considering a career in the pump industry.
“It's a place where there is a broad breadth of opportunities, and transitioning from other industries is possible, and you can have a big impact with new ideas, a new perspective or new skills… if you can listen, learn fast and seek to engage well, there are many ways to contribute and build a rewarding career.
“There's no shortage of opportunities across all areas, whether it’s in R&D, innovation, engineering, manufacturing, supply chain, and the commercial, marketing and category management functions. We are on the lookout for talent across all these areas. We even have our very own dedicated in-house talent specialist who engages with new talent every day. It’s critical, our people capability is our most valuable asset.
“We have a bright future as a company and our whole industry.”
The PIA’s Australian Pump Technical Handbook is a cornerstone text for the Australian pump industry and, in our opinion, a must have for anyone who deals with pumps on a regular basis. In this ongoing series, we feature abridged chapters from the classic book to showcase the various areas covered and to reacquaint readers with the technical aspects of pumps. In this issue we take a close look at pipe systems.
Poor pipeline design or improper application of a pump bring about many of the problems experienced by pump users. Taking care when designing the layout of the total system and adhering to good pumping practice will result in a comparative improvement of performance. Pumping systems, irrespective of the type of pump used, can be split into two fundamentally different sections: the suction and the discharge.
The suction is the part of the system between the source of the liquid to be pumped and the pump itself. When the pump is located above the liquid source, it is said to operate with a suction lift. When the pump is located below the liquid level, it operates with a suction head.
The rest of the system constitutes the discharge.
There are a number of key points to keep in mind when designing the system:
• It is good practice to keep the suction pipe as short and straight has possible
• The pump should operate with a suction head where possible
• Eliminate all possibility of air pockets being trapped in the suction pipework
• When bends in the suction pipe are unavoidable, priming valves, and nonreturn or foot valves must be fitted to the line in the correct position, otherwise the pump may not prime
• The suction pipe should be accessible
• When selecting foot vales, strainers, bends, etc., select ones that will provide minimal restriction to flow
• Some care must be taken in the design of the solution inlet
Furthermore, the diameter of the section pipe should be sized according to the flow and allowable head loss; in any case, it should be equal in diameter to the pump inlet connection.
If the pipe is larger than the pump inlet, it is good practice to fit an eccentric reducer to avoid the possibility of air pockets.
Discharge pipework
Discharge pipeline should be designed to minimise losses. All bends, valves, strainers, reducers and other fittings in the line contribute to friction losses.
Accurate calculation of friction losses is essential, and it follows that the characteristics of the liquid to be pumped must also be considered.
The PIA’s Pipe Friction Handbook, available to purchase from pumps.org.au/publications, presents a comprehensive tabulation of head losses that can be expected for given flow rates in commonly used pipes and fittings.
Several factors need to be considered when selecting the pipe:
• Fluid: viscosity, temperature, chemical properties, flow rate, pressure
• Pipe: length, roughness, strength, cost
Of these factors, temperature and chemical properties of the fluid will probably determine the material the pipe is made of, or at least exclude the use of certain materials. For example, plastic pipes would not be suitable for applications pumping oil at 300°C. The pumping of high viscosity fluids increases the friction head, and may require a larger diameter pipeline and long radius bends to be used.
While high friction loss can be tolerated in short lengths of pipe – such as can be found in processing plants –on longer pipelines, like those for water supply, friction is a major part of the total head and should be kept to an economic minimum. An average velocity in the pipe of 2m/s is usually acceptable when pumping over long distances.
It is recommended that a centrifugal pump is fitted with a non-return valve at discharge. When the pump is shut
down, the valve prevents reverse rotation of the pumpset and possible damage to the pump and/or driver depending on the mechanical arrangement.
Valves should be installed in a way that the pump can be isolated for maintenance and inspection.
Pipelines that have crests and troughs should be fitted with an air vent valve at the highest points to allow accumulated air or other gases to escape from the pipe. These valves should be fully automatic and close when liquid enters the valve.
If it is necessary to pipe liquid to more than one discharge point, a ‘Y’ type connection should be used to reduce losses at the branch.
If a number of branches are taken off the main pipeline, it may be possible to reduce the diameter of the main pipe as it can be sized to suit the reduced flow.
However, sudden changes in diameter need to be avoided as these produce friction losses. Therefore the change in diameter should be effected gradually by a taper piece. In order to get the best results, the included angle of the taper piece should be 10-13°.
Regardless of whether the pipes are laid above or below ground, adequate support and anchorage for the pipes must be provided. Detailed requirements should be sought from the pipe manufacturer to ensure that no mechanical or hydraulic loads are imposed on the pump.
Particular attention should be given to pipework design where anti-vibration devices are incorporated.
If flexible piping is used, particularly on the discharge of a pump, it must be adequately supported and restrained. For example, the coupling alignment may be correct when the pump is shut down, but becomes badly misaligned when flexible hoses are allowed to impose forces on the pump during operation.
There are certain aspects of pump and pipeline design that require special consideration, and these are usually related to the liquid being pumped. In these instances, the pump manufacturer should be consulted.
Any system in which a fluid is in motion or capable of being set in motion is susceptible to pressure surge or waterhammer. Surges occur whenever the velocity in a conduit changes from one steady state to another. The most severe conditions will most likely correspond to the pump starting or stopping or the ‘instantaneous’ opening or closure of a valve in the pipeline.
The effects of pressure surges in a system can be compared with the forces on a moving vehicle during periods of acceleration or retardation. For example, when a vehicle is brought to rest by the brakes being applied suddenly and violently, severe stresses are imposed on parts of the vehicle. In the context of a pumping system, the system may be subject to quite dangerous pressures during acceleration and retardation of liquid in pipes.
Accordingly, if a valve is slammed shut at the end of a delivery line, a transient surge or wave resulting from the sudden gate closure moves towards the pump. If the pipe walls are rigid and inextensible, the speed of the pressure wave would
approach the velocity of sound in the liquid – about 1,400m/s for water – and since the magnitude of the pressure rise in the pipe due to instantaneous gate closure is proportional to the speed of the wave and change in water velocity, then extremely high pressures can be propagated. Consequently, if those pressures are not properly controlled they may cause noise and vibration in the system, piping to burst, or pump casing to crack.
Waterhammer calculations are complex so it is recommended that specialised engineering services are employed in cases where it may be a problem.
It should be noted that waterhammer effects are always possible and may determine the design loads for a system. The pipeline longitudinal profile is also important and route selection could be influenced by the waterhammer implications.
Syphon lines are often used in groundwater pumping stations to feed the discharge from industrial wells or boreholes into a collecting well from which the water is then pumped into a reservoir.
Equations are available to find the maximum static suction lift allowable for satisfactory operation without damage to the pump. These equations and examples can be accessed in the Pump Technical Handbook.
Further information and detailed diagrams, equations and schematics can be found in the Australian Pump Technical Handbook, available at pumps.org.au/publications/. The Handbook has recently undergone an update, with the new sixth edition available now. In the next edition of Pump Industry, we take a deep dive into intake design.
The pump industry relies on expertise from a large and varied range of specialists, from experts in particular pump types to those with an intimate understanding of pump reliability; and from researchers who delve into the particulars of pump curves to experts in pump efficiency. To draw upon the wealth of expert knowledge the Australian pump industry has to offer, Pump Industry has established a panel of experts to answer all your pumping questions.
In this edition of Ask an Expert, we will look at custom-built progressive cavity (PC) pumps for oil and gas applications. The oil and gas industry uses PC pumps to convey sludge or oily water and in specific circumstances such as when light hydrocarbons raise the vapour pressure to a level where other pump types would cavitate.
Q: What credentials, product experience and services should a customer look for in a pump manufacturer?
A: Since oil and gas applications are complex with a high level of documentation, I recommend finding a reliable partner with many years of experience and high-quality products that excel in harsh conditions. A manufacturer with a dedicated sales and project management team, or better still, a dedicated engineering and document handling team can provide first-class order processing capabilities for complex projects along with specification compliance and quality requirements typical of the industry. Local offices and partnerships in your region for quicker response times and more personalised service are key additions.
Q: What are the main reasons for using PC pumps in the petrochemical industry?
A: Manufacturers offer PC pumps, skids and systems for upstream, midstream and downstream applications. PC pumps are used in the oil and gas industry for the following main reasons:
• They provide stable performance regardless of viscosity or solids content (sand, slops, sludge, coke, catalyst, fibre) and are ideal for drain applications with polluted oily fluids of unpredictable composition and for crude oil transfer over a wide temperature range
• As they have the lowest shear rate of all pump types, they are often used to feed separators, since they do not cause emulsification of oil and water, which enables efficient separation
• They can handle the lowest NPSH and avoid/resist cavitation better than other pumps, which is useful with high vapour pressure hydrocarbon fluids
• They are the only positive displacement pumps that can be easily installed in a vertical, semi-submersed position in sumps or vessels
• They can handle very high and variable gas contents (up to 99.5 per cent gas) in multi-phase boosting systems, where they can even be used as a wet gas compressor
• They have a linear performance curve with capacity proportional to speed, which is excellent for dosing systems, in particular for the dosing of catalyst slurry
Q: Oil production presents many challenges to the producer. How are PC manufacturers helping them?
A: The focus must be on the best product quality. Premium manufacturers have pumps in their portfolio known for their reliability and good lifecycle costs, which customers appreciate. Long-term experience with the key applications allows them not only to meet the pumping challenges of the producers, but also to guide them towards the best overall solution. Some manufacturers, such as SEEPEX with its BNA pump range –tailored to the oil and gas industry – offer as standard the best API compliance. They are also able and willing to customise their designs to the customer's specifications.
Peter Vila, Managing Director of SEEPEX Australia, is a progressive cavity pump expert. He has been involved with pumps for over 40 years. Peter spent the first five years repairing pumps and the following 35 years in technical sales, 20 of which have been with SEEPEX progressive cavity pumps. For more information on progressive cavity pumps, please contact SEEPEX Australia on (02) 4355 4500 or at info.au@seepex.com
y First-class API compliance along with heavy-duty design
y Pressure rating 300# and duplex stainless steel as standard
y Non-welded, cast casing reduces documentation and inspections
y High allowable nozzle loads and design pressure improve operational safety
When the pressure of flowing liquids drops to, or below, the liquid’s vapour pressure, the liquid boils and vapour cavities (bubbles) form locally inside the liquid. If the pressure within the flow path subsequently increases above the vapour pressure, the vapour cavities implode, releasing energy. The formation and sudden collapse of these bubbles is called cavitation.
When the pressure of flowing liquids drops to, or below, the liquid’s vapour pressure, the liquid boils and vapour cavities (bubbles) form locally inside the liquid. If the pressure within the flow path subsequently increases above the vapour pressure, the vapour cavities implode, releasing energy. The formation and sudden collapse of these bubbles is called cavitation.
The presence of cavitation due to inadequate NPSH can be diagnosed during pump operation by a steady crackling noise in and around the pump suction. This should not be confused with a random crackling noise with high intensity knocks which indicates another condition termed suction recirculation (not covered below).
If the problem was one of noise alone, it is likely that most situations would call for no remedial action. However, continual cavitation causes mechanical and operational problems as follows:
1. Erosion of impeller, particularly at the leading edges of the impeller vanes. In some cases, the casing itself will show signs of erosion. The extent of damage experienced is significantly affected by product-related factors such as corrosion and abrasion. Apart from the damage to the parts, the erosion can cause loss of pump efficiency and out-of-balance problems with the impeller
2. The vibrations caused by cavitation and unbalanced loads significantly accelerate the rate of bearing and mechanical seal failures
3. The vapour cavities will impede the flow of liquid through the impeller. In some cases, the flow may be completely blocked. This will result in reduced capacity plus reduced and/or unstable developed head
With a vast array of pumping designs and solutions available, ensuring you have the right pump for the right application involves a thorough set of considerations. Moreover, proper pump selection at the initial stage is essential in preventing cavitation. Consider consulting your pump supplier to discuss your pumping requirements.
Polymaster’s unique Enclosed IBC Bund solves many of the problems associated with IBC storage and chemical/fluid decanting in a weather resistant, purpose-built enclosure.
Æ Full weather protection – stops rain entering the enclosure
Æ Easy forklift loading with wide forklift access from both side and back
Æ 250ltr day tank
Æ Lockable cabinet to keep system secure Æ Venting by two sides
Æ Viewing windows incorporated into the doors
Æ 110% bund capacity complies with AS3780
Æ Sight tube and low-level alarm available
Æ Chemical resistant – high grade polyethylene construction
WINTER 2023
Deadline: 9 June 2023
MAIN FEATURE Also featuring
SPRING 2023
Deadline: 1 September 2023
MAIN
Also featuring
Plus the 2024 Industry Capability Guide
SUMMER 2024
Deadline: 24 November 2023
MAIN FEATURE Also featuring
State of the Industry
AUTUMN 2024
Deadline: 22 March 2024
MAIN FEATURE Also featuring
Volvo Penta. Robust, fuel efficient industrial diesel engines that keep running even in the toughest conditions. Easy to install, operate and maintain. A powerful partnership you can trust all the way from the drawing board throughout the operational life of your engine. Competitively priced complete power-pack units ready for delivery Australia wide with a local support team on hand 24/7. To find your nearest dealer visit www.volvopenta.com