Warehouse Solutions September 2022 Supplement insert for Material Handling Network
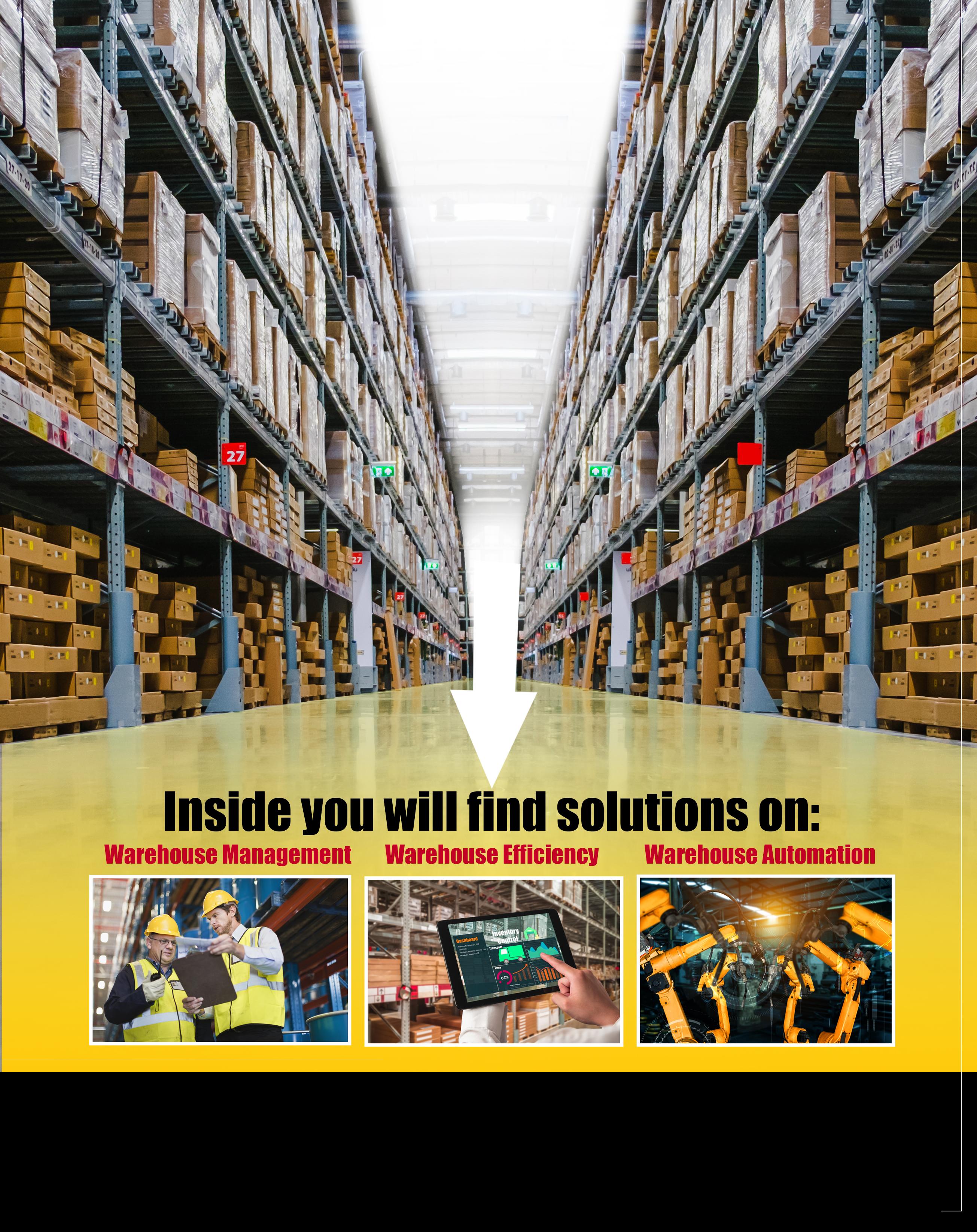
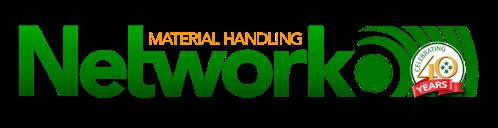
WS2 September 2022 Warehouse Solutions www.MHNetwork.com • Store product up and off the floor preventing product damage. • Racks store easily with little storage space required when not in use. • Standard rack designs/sizes can be changed to meet your specific needs. Portable Stacking Racks • For storing or transport, these long-wearing racks save space & time. • Utilize vertical storage space by safely stacking these racks up to 5-high. • Forklift portable for easy handling of loads up to 4000 lbs & more. • Rugged construction features stand up to heavy industrial requirements. • Save time by moving more material with fewer moves. “Ideal for materialcustomer’syourhandlingneeds.” STOCK AVAILABLEPROGRAM Call for 800-939-3962assistance.www.dyna-rack.comsales@dyna-rack.com Made in the USA Customized designs are considered!
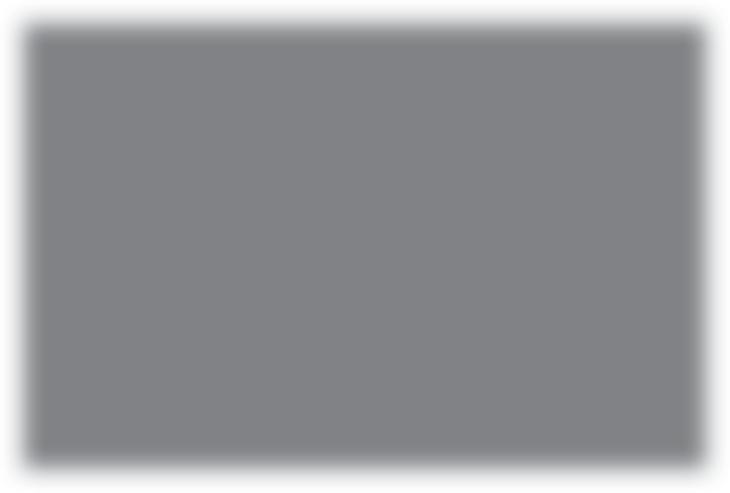
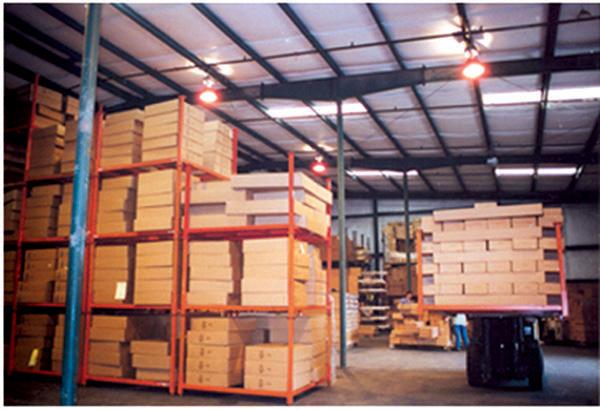
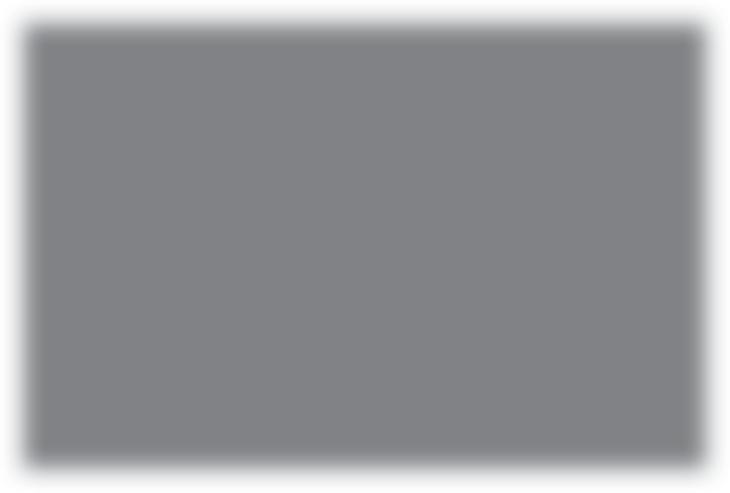

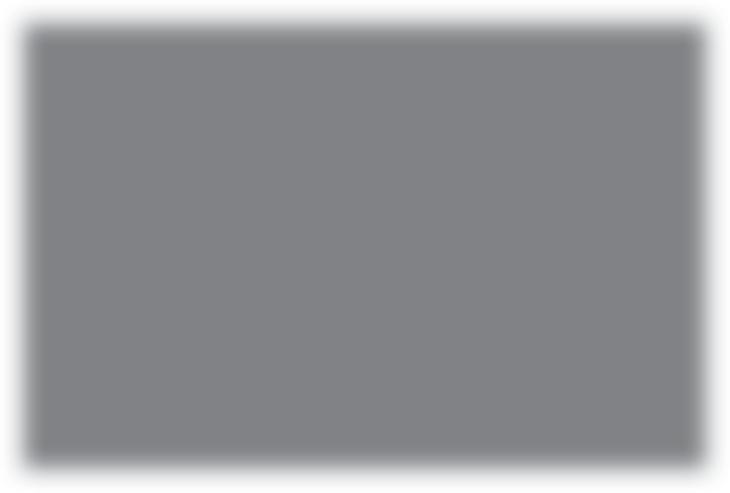
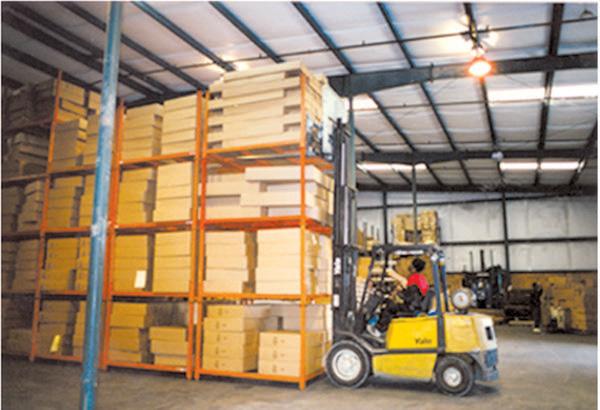
www.MHNetwork.com Material Handling Network September 2022 WS3 Contact Dyna Rack for your customer’s storage needs. 800.939.3962 | sales@dyna-rack.com | www.dyna-rack.com THE DEALERS' SOURCE FOR PORTABLE RACKSTM CUSTOMIZED DESIGNS ARE CONSIDERED STOCK AVAILABLE on some sizes & designs Stack racks utilize vertical storage by safely stacking racks up to 5 high. Add casters to your stack rack cart base to increase mobility and versatility. Dyna Pallet stacking frames turn your warehouse pallet into a stackable rack within Infiniteseconds.sizes available with custom made racks. application.engineeredCustomper PORTABLE STACK RACKS STACK RACK CARTS DYNA PALLET STACKING FRAMES CUSTOM RACKS Made in the USA
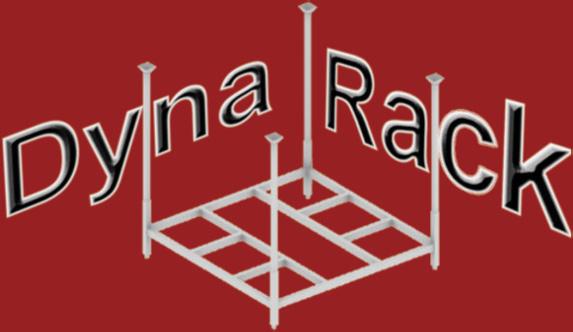

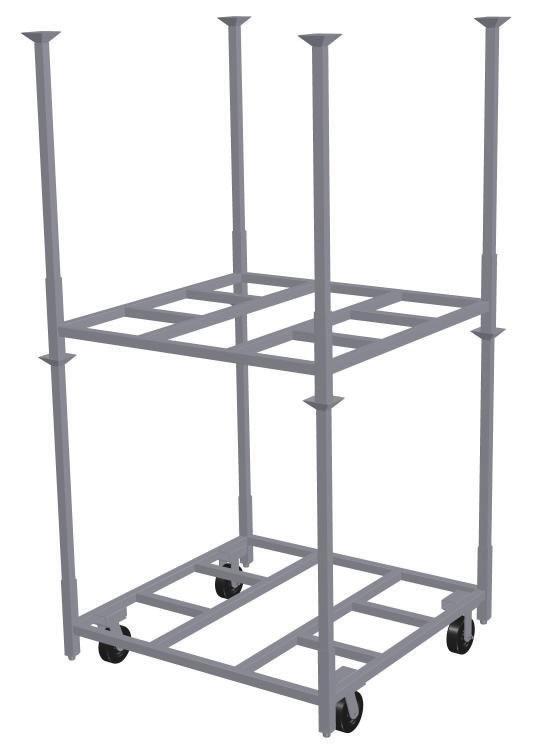
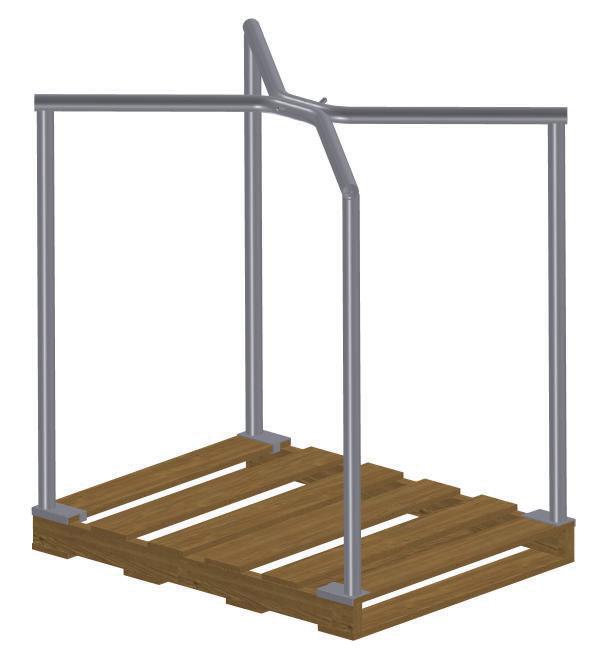
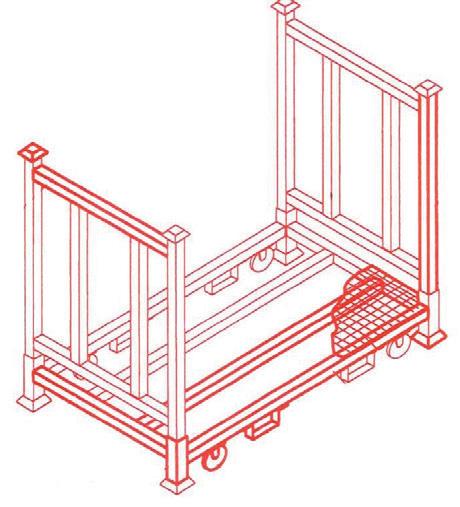
2:15 PM Now you don’t have the inventory needed to load an outbound shipment scheduled to depart at 3:00 PM. But, don’t panic as the warehouse accelerator dynamically changes inbound trailer management priorities and reprioritizes a trailer in the yard to cross-dock with the 3:00 PM outbound shipment to prevent a shortage of product. The system creates new plans directing the team on what trailer needs to be at a certain door at a specific time.
WS4 September 2022 Warehouse Solutions www.MHNetwork.com
2:15 PM – 2:30 PM This new schedule keeps inventory and activities steady while creating numerous additional cross docks. The result is that everything arrives on time, in full. Nobody has to double pick, reprioritize, or panic.
Warehouse process automation is booming like never This story compares a day in the life of a warehouse planner using a warehouse management system (WMS) accelerator versus a day without WMS planning optimization. Even if companies don’t like to admit it, there is a significant amount of wasted labor in warehouse operations due to poor coordination. For example, because receiving and shipping are operating on a different cadence, eliminating work by crossdocking inventory from inbounds to outbounds is totally missed. Or, if it happens, it happens by coincidence rather than by design. Also, due to there being many different responsibilities, all with slightly different objectives, existing warehouse management systems (WMS) often struggle to orchestrate ALL activities. In an ideal warehouse, everybody would work perfectly in concert to get inventory shipped on time and in full.
2:45 PM – 3:00 PM Now, another scheduled outbound, slated to leave by 3:15 PM, is short by twenty five pallets that are not in the warehouse. Should you take early retirement or what? A Day in the Life of a Warehouse Planning Using a Warehouse Accelerator Like AutoScheduler
2:30 PM – 3:00 PM In fact, the warehouse accelerator has already looked at the next 48 hours and optimized the schedule for you. Your staff is Warehouse Solutions
A Day in the Life of a Warehouse Planner Using a WMS 2:00 PM Your shift starts and you have 31 inbound loads and 35 outbound shipments scheduled in the next ten hours. The unloading team has been unloading boxes and pallets based on time, not need. The faster the team unloads, in their minds, the better. However, inventory for some shipments has just arrived.
To make a complex process even more confusing, the simple rules built into the Warehouse Management System that are used to orchestrate activities often cause problems. Inventory may not be available when a shipment is loaded. There may be too many shipments and not enough docks. Trailers may sit in the dock because there isn’t capacity to unload everything on the schedule. Or, a campus may have all of the right inventory and capacity, but it is in the wrong building, and transfer shipments are required. Traditional WMS implementations don’t have the analytics to orchestrate decisions that need to be juggled considering all constraints. These challenges equate to millions of dollars in lost money every year at most facilities.
2:30 PM – 2:45 PM Your staff will now have to double pick that order, causing a snowballing effect that results in a few additional late shipments. Those delays, coupled with a surge in demand, delay two more planned outbound loads.
2:10 PM – 2:30 PM You need to fill orders, but you don’t have the inbound needed to load an outbound shipment for a 3:00 PM pick-up time. You rush to the phone to expedite unloading more inventory with the inbound supervisor. You have a trailer waiting to load that is blocking dock space planned for another shipment.
2:00 PM – 2:15 PM Your shift starts, and you have 31 inbound loads and 35 outbound shipments scheduled in the next ten hours. The unloading team has been unloading based on arrival time, not on the schedule that the warehouse accelerator solutions chooses. Plus, inventory for some shipments has just arrived at the warehouse.
A Day in the Life of a Warehouse Planner
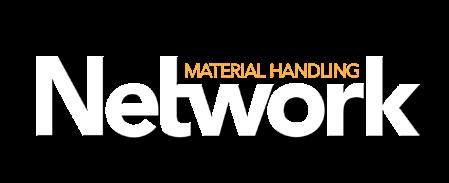
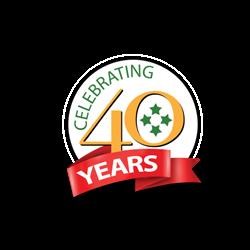
www.MHNetwork.com Material Handling Network September 2022 WS5 WMS Accelerator Optimizes Warehouse Activities improve OTIF • manage INVENTORY real-time SCHEDULING • optimize LABOR Contact Us for an initial assessment! info@autoscheduler.ai 615-428-2035 autoscheduler.ai
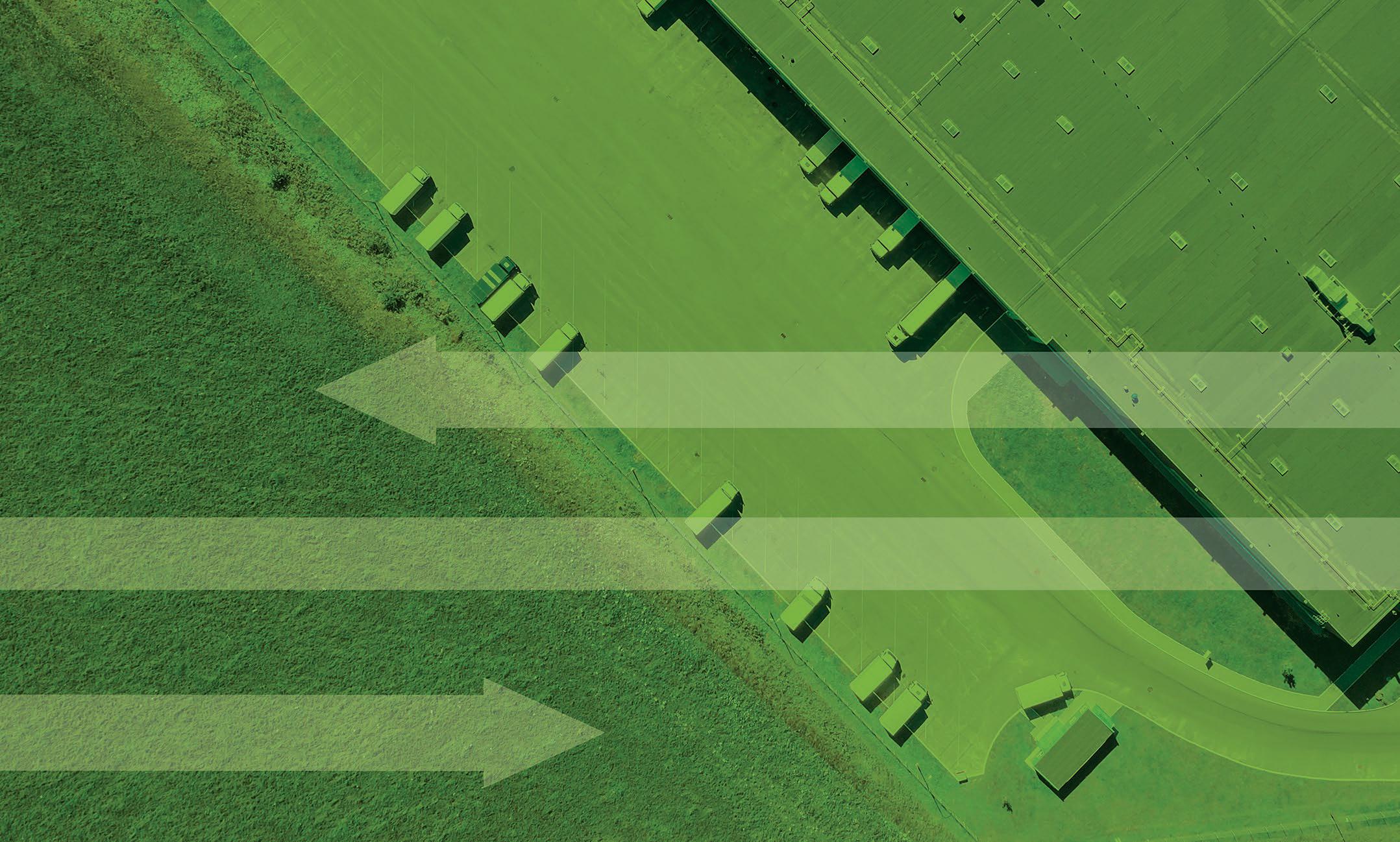
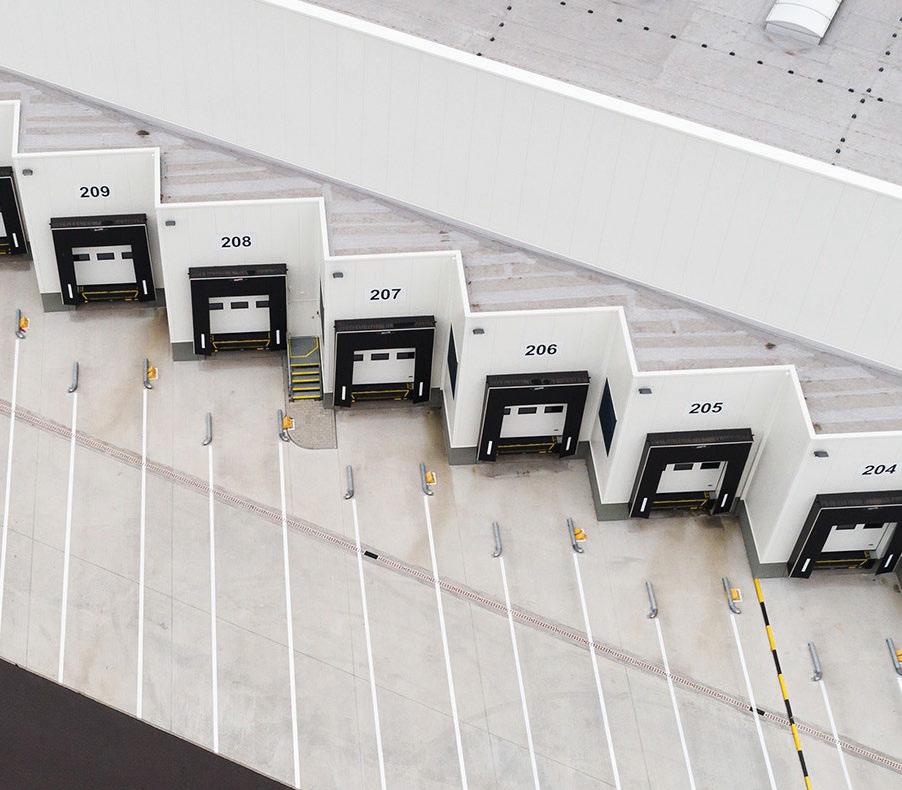


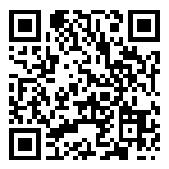
Warehouse Solutions continued Our species is special: Trelleborg experts have designed the new XP1000, the high performing tire that provides greater durability, more stability and comfort, while reducing the environmental impact even when handling heavy duty jobs.
AutoScheduler works by sitting on top of existing WMS, ERP, and even YMS systems to understand the delivery expectations for all warehouses over the next 6, 24, and even 72 hours. Because this solution sits on top of the WMS and other systems, the integration is much easier and quicker.
Versatile and
TrelleborgefficientbynatureXP1000trelleborg.com/wheelsTrelleborg.Aforceofnature.
AutoScheduler then algorithmically uses this information to identify inventory, capacity, and shipping constraints that will cause future challenges. These constraints can then be dynamically scheduled to ensure that when an inbound or outbound shipment arrives, the dock staff have the capacity to act on it. Because of this constraint-based orchestration across all schedules, AutoScheduler is able to not only quickly identify future issues, but also highlight the causes of those issues and potential resolution paths. This full scale orchestration also allows AutoScheduler to create opportunities, like shipping straight from the production line or scheduling more cross docks. At a single Procter & Gamble facility, these opportunities amounted to over $4 million in savings over a single year.
WS6 September 2022 Warehouse Solutions www.MHNetwork.com perfectly level loaded for all operations, all the time, saving on labor. Now you take another sip of coffee and debate if you want to go hunting or fishing this weekend.AutoScheduler is a WMS accelerator created to help orchestrate poorly coordinated facilities. It adds value by improving OTIF, managing inventory, and creating dynamic schedules that are feasible and change as conditions shift.
Keith Moore is CEO of AutoScheduler.AI, a warehouse optimization solution that improves on-time fulfillment, labor utilization, and costs for CPG companies. Keith is focused on bringing the future of technology into warehousing. He works with top 10 Consumer Goods, Beverage, and Distribution companies to drive efficiency in distribu tion centers. www.autoscheduler.ai. Prior to launching AutoScheduler. AI, Keith was voted by Hart Energy Magazine as an Energy Innova tor of the Year in 2020, was selected as a Pi Kappa Phi 30 under 30 member, and holds multiple patents in the fields of neural architecture search and supply chain planning. Keith has been published by jour nals and groups like SupplyChainBrain, Inbound Logistics, ISSA and OTC for his work in logistics, cyber security, and predictive mainte nance applications.

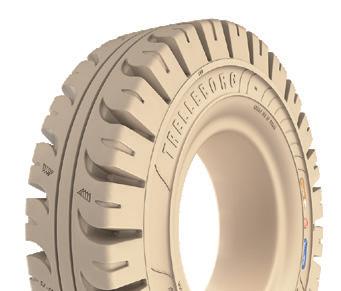
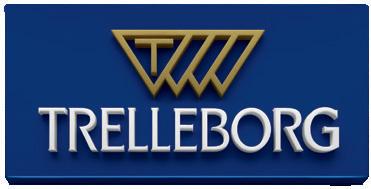
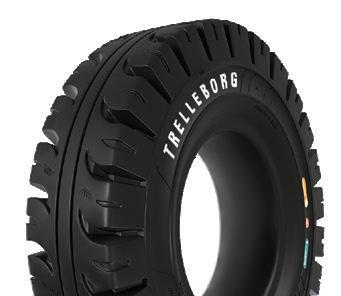
Full Service Engineered Rack R E pai R
Your One-Stop Shop for Engineered Rack Repair & Protection Products & Services We produce over 30 column designs which allows Mac Rak the flexibility to offer repairs for all types of racks to match your specific rack system. We also provide the nation’s best Turn-key solutions: Professional Pallet Rack Safety Assesments Comprehensive Rack system surveys are conducted by one of Mac Rak’s trained, professional inspectors.
Nationwide Expert Installation Professionally trained and certified installation teams guarantee the project is done on-time and on-budget with the least amount of interruption. Training Your team will be trained on how to identify and report emergency damaged rack conditions. Documents from baseline analysis will be used to facilitate this training and future reporting. Mac Rak is an associate member of the Rack Manufacturers Institute. (RMI) We are North America’s largest, most respected turn-key supplier of engineered approved pallet rack repair and protection solutions. Headquartered in the Midwest since 2001, our family owned and operated business achieves constant growth from focusing exclusively on one thing: the engineered pallet rack repair and protection business. Our performance commitment is backed by the “best in class” lifetime impact warranty. Since inception, Mac Rak’s products and processes have developed out of supervision and oversite from the country’s top structural pallet rack Professional Engineers; Seizmic Inc. is our engineer of record. All Mac Rak repair kits exceed ANSI/RMI 16.1 engineering requirements, and are guaranteed to result in a repaired frame as strong or stronger than the original. This strong engineering background has provided a baseline for continued innovative product and service offerings. Offerings range from rack engineering services, to damaged rack assessments, to turn key repair projects, to DIY training programs, to planning and documentation services.
For pallet rack repair assessments and a full line of engineered pallet rack repair and protection products 815-723-7400 or visit MacRak.com
www.MHNetwork.com Material Handling Network September 2022 WS7
Remediation and Protection Proposals Proposals include material, labor, estimated freight and estimated project duration.


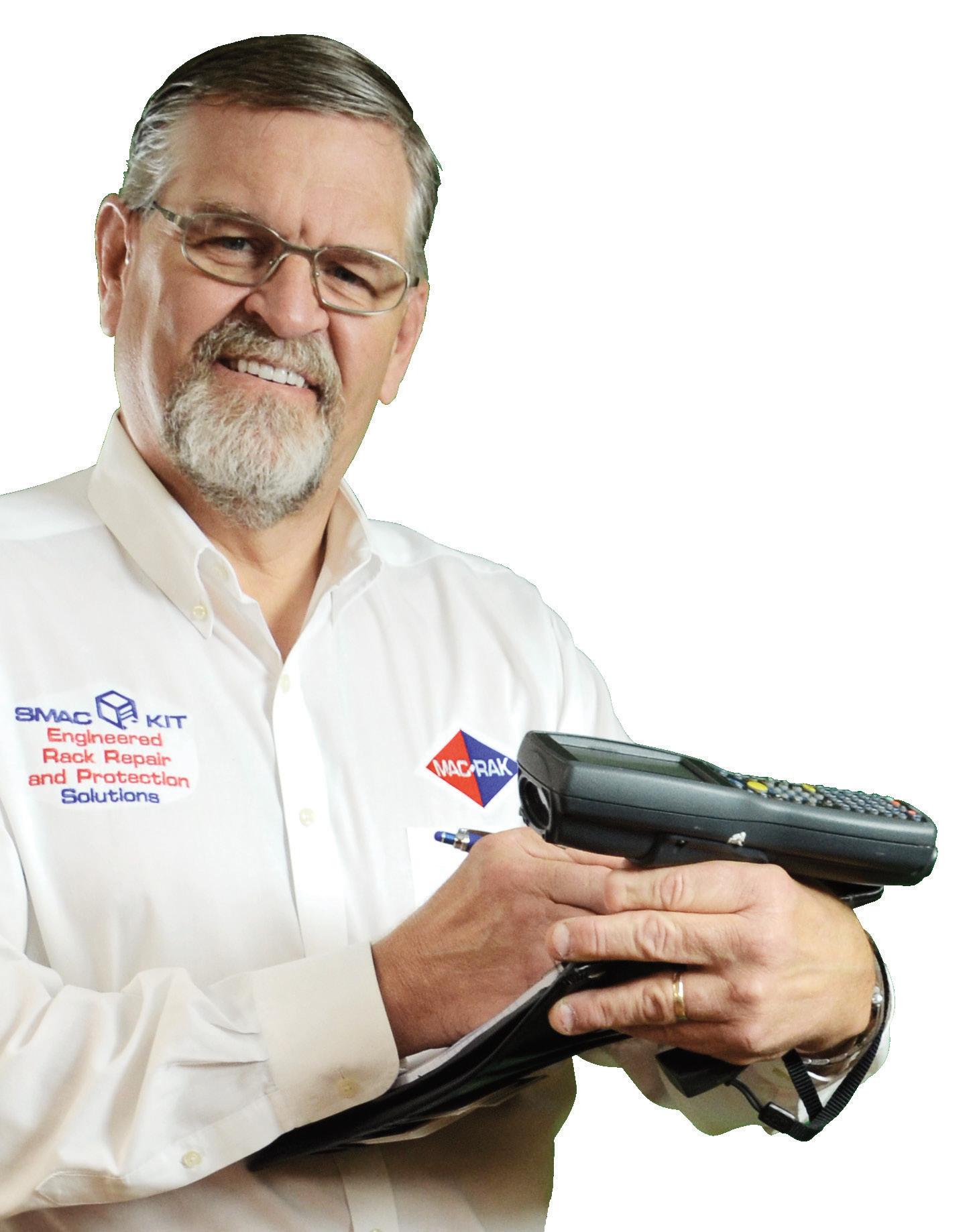
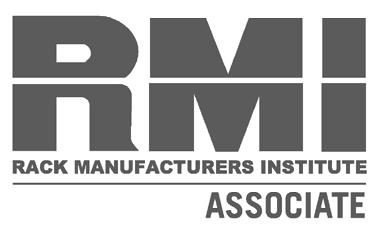

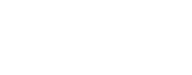

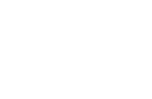

More advanced 3D vision systems are key to wider adoption of robots According to Universal Robots (UR), in 2019, around 38 per cent of the manufacturing labor force still moved parts manually between bins and manufacturing machines, rather than use industrial robots. Why the slow adoption? For designers and engineers of industrial robots, the random nature of automated bin picking presents some of the biggest challenges. Here, Claudia Jarrett, US country manager for industrial automation supplier EU Automation, explains why better 3D vision systems are the answer.
historically been repetitive, from the first industrial robot systems that appeared on General Motors’ US assembly lines in the 1960s, to modern tasks like screwing lids on bottles. In contrast, bin picking invites all kinds of random external factors. Automated bin-picking robots can reduce the time and costs manufacturers normally spend on these applications, while freeing up human workers to focus on more productive and valuable tasks. But, if that’s true, why were around 38 per cent of the manufacturing labor force still moving parts manually in 2019?
Overcoming the challenges of automated bin picking
Another issue for industrial robots are shiny, reflective objects - examples include products with shiny metal surfaces, or that are wrapped in plastic. Light reflected by these surfaces can cause point cloud artifacts, or irregularities, which interfere with the 3D vision systems robots rely upon. These systems determine the location where robots need to pick an object from, and communicate how they need to position the picking arm. However, reflection interferes with the necessary data quality and CAD matching processes, which can cause the robot to perform faulty calculated picking positions.Theseissues often arise from inadequate vision systems. Less-expensive 2D and 3D vision cameras are affordable for smaller manufacturers, but
WS8 September 2020 Warehouse Solutions www.MHNetwork.com
The act of picking-up and randomly sorting objects may come naturally for humans, who can perform the task countless times each day. However, it’s much harder for robots, which rely on 3D vision systems, data and programming rather than innate Productionintelligence.lineapplications
Let’s look at some of the major challenges of automated bin picking, and what manufacturers can do to overcome them.
Exceptional vision Bin picking robots are required to handle objects that may be tiny, thin, porous or deformable. The objects might be densely packed, or piled on top of each other. For instance, let’s imagine bottles are lying randomly in a bin, and must be picked and placed on a conveyer belt. A robot interacting with a production line will usually be placed in the same position, every time. So, if the chain suddenly accelerates or decelerates or a productlet’s say a bottle - falls over, the robot’s programmed movements will not adapt to this.
Feature Story
for robots have
A robot would need exceptional vision and sensors. First, to negotiate and grab the randomlypositioned bottles and, second, to perform its task without damaging any bottles. Because robots rely on wide baseline cameras, they can miss objectsif, for instance, they are obscured by shadows - or perform mispicks. In short, bin picking involves an array of tasks that are never the same, which many robots are ill-equipped to contend with.
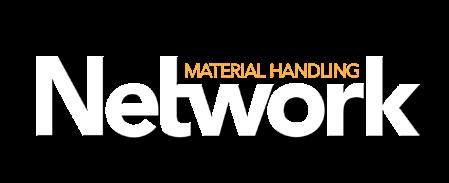
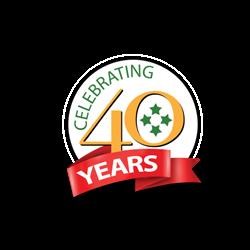
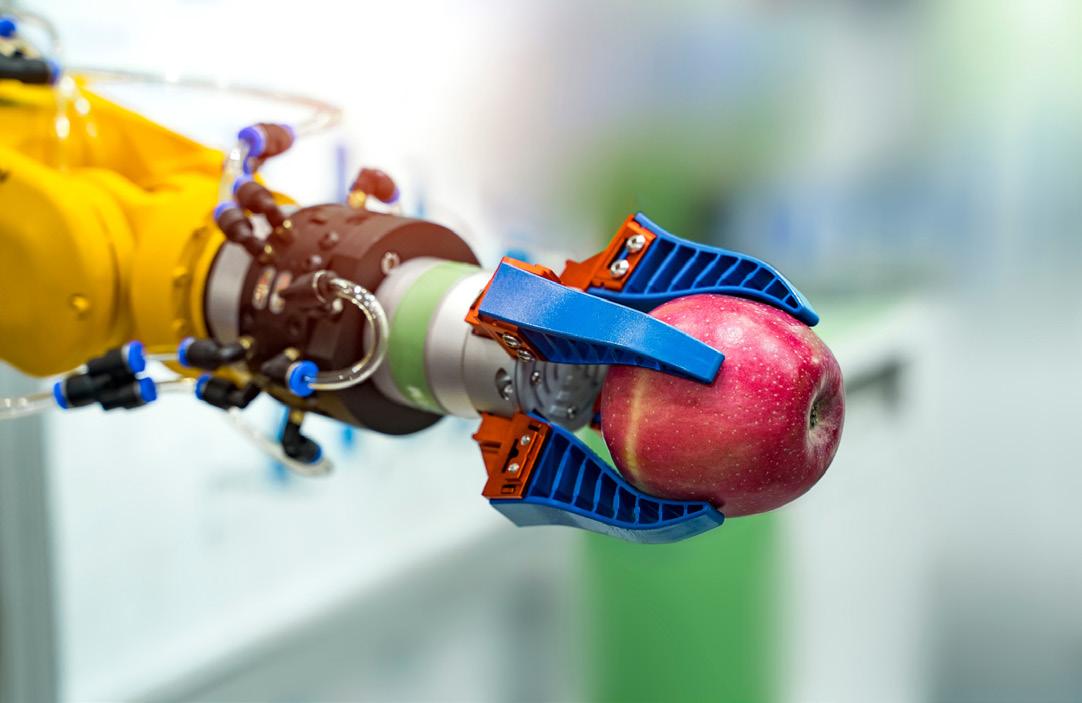
www.MHNetwork.com Material Handling Network September 2020 WS9

many of them are not optimized for piece picking applications. Robots might be able to detect objects with such a solution, but they cannot pick them every time due to scaling, rotation or translation errors.Instead, advanced 3D vision systems are needed that can quickly recognize objects of similar shapes, colors and material. After all, fast sorting is one of the major advantages of bin picking robots — in some cases, the process has been known to double time and costs when performed with humans.
A popular choice are solutions by Norway’s Zivid, which develops industrial 3D machine vision cameras and vision software. The company’s industrial Zivid 3D cameras, for instance, offer optimized resolution, precision and trueness to reliably capture both the fine details for large parts, as well as the tiny and thin objects. Other solutions are designed to overcome the effects of point cloud artifacts in automated bin picking. The new Zivid SDK 2.0, for instance, features a special artifacts correction filter that the developers describe as “groundbreaking”.
WS10 September 2022 Warehouse Solutions www.MHNetwork.com
Elsewhere, designers and engineers of industrial robots are attempting to apply Deep Learning techniques to automated bin picking applications. Although artificial intelligence (AI) is very effective for image classification, the results have so-far been disappointing, given the random nature of bin picking.Asrobots and smart sensors increasingly prove their worth, the support of an industrial parts supplier can be vital in helping manufacturers choose the right sensor for their packaging application. Parts suppliers, like EU Automation, can source sensors for packagers, ensuring the transition can be achieved without requiring a complete overhaul. Such advancements, along with ground-breaking technologies like sensor networks and the IoT, can help ensure that robots can handle the moving of parts between bins and manufacturing machines, freeing-up humans’ workers to focus on more demanding and valuable tasks.
Feature Story continued For more Features and more visit www.MHNetwork.com
Energid is among the companies helping to democratize automated bin picking. It offers a complete pre-integrated system with all the necessary complexity, including sensor configurations, imaging and path planning. The system is pre-figured within software previously used in mission-critical applications for NASA spacecraft, and in autonomous robots for oil drilling platforms and surgical applications. Users can simply plug-in and use the robot with no setup required. This reduces installation time to mere hours. The installation and training time are minimal, according to Energid. The robot then performs its tasks without the need for user-defined waypoints or tuning.
EU Automation stocks and sells new, used, refurbished and obsolete industrial automation spares. Its global network of preferred partner warehouses, and wholly owned distribution centers, enables it to offer a unique service within the automation industry, spanning the entire globe. It provides worldwide express delivery on all products meaning it can supply any part, to any destination, at very short notice.
The technology’s patented Artifact Reduction Technology (ART) also uses a Zivid Two 3D camera, specifically designed to handle reflections caused by shiny surfaces. Robots for all UR’s report also observed that most real-world bin picking deployments were found at large, sophisticated manufacturers like automotive original equipment manufacturers (OEMs). Yet, at the same time, most bins and manufacturing machines are found within small-mediumenterprises (SMEs), which have the least capital and expertise required to create a bin picking system. Therefore, SMEs need cost-effective bin picking solutions that can be easily used by non-experts and newly-trained staff.
www.MHNetwork.com Material Handling Network September 2022 WS11 THE BEST MATERIAL LIFT, AND WE CAN PROVE IT. INDUSTRIAL-GRADE U.S. SOLID STEEL FRAME THESE ARE JUST A FEW OF THE REASONS WHY OUR VRCs OUTPERFORM THE INDUSTRY. GO TO CUSTOMINDPROD.COM TO LEARN MORE. 100% DUTY-CYCLE MOTOR (MILLION+ CYCLES) RUGGED GEARBOXHELICALHEAVY-DUTYCOMPACTEDWIREROPE
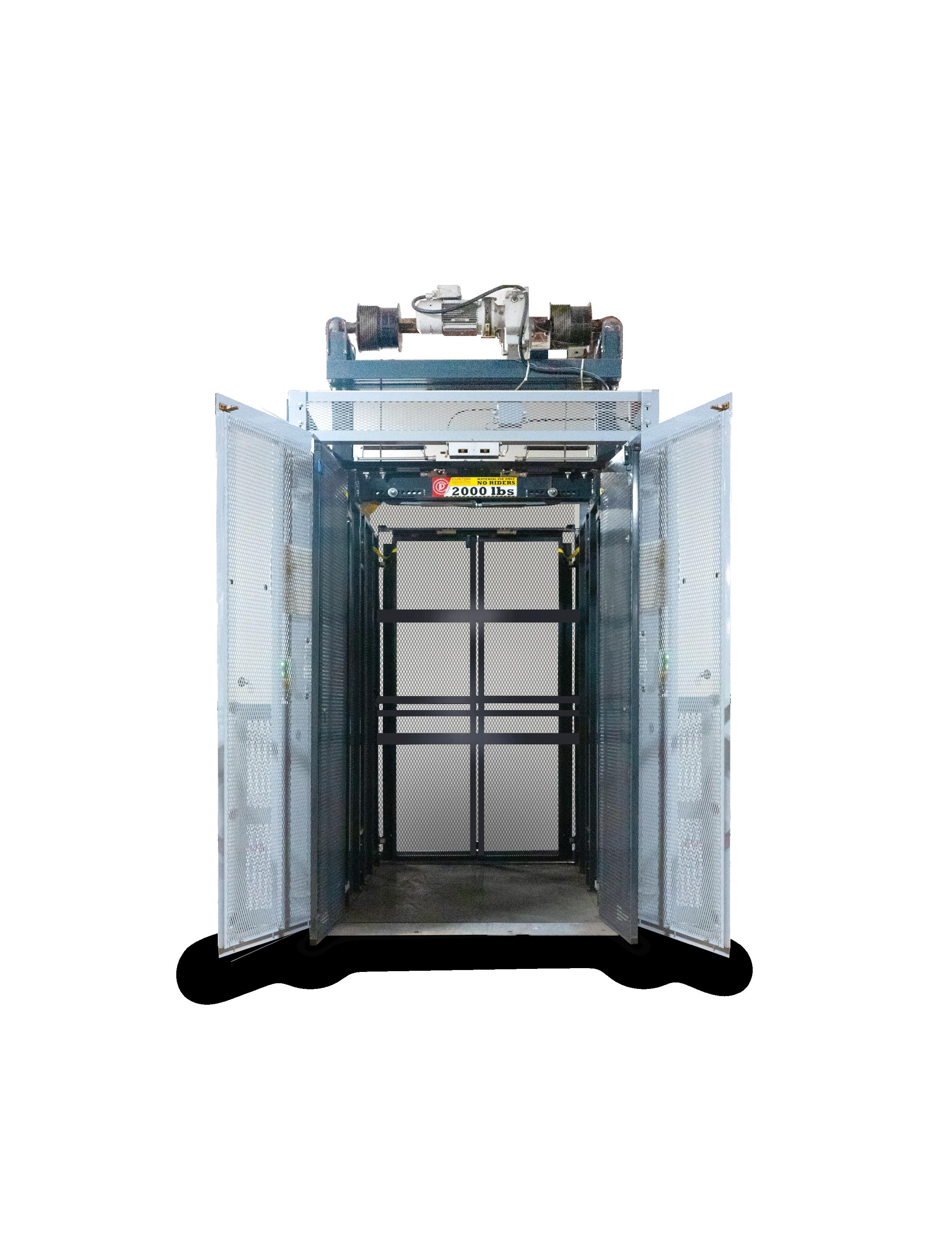
WS12 September 2022 Warehouse Solutions www.MHNetwork.com Nucor solutionsSystemsWarehouseisyourwarehousepartner. Nucor Warehouse Systems offers true end-to-end solutions from rack manufacturing and integration services to support from other Nucor businesses including insulated panels, overhead doors, metal buildings and mezzanines. Nucor Warehouse Systems is solving the most complex challenges for our customers every day with well over $1B in integration projects built across North America. By connecting our material handling expertise with broader resources, Nucor Warehouse Systems is ready to help you take on tomorrow’s challenges today. “ “
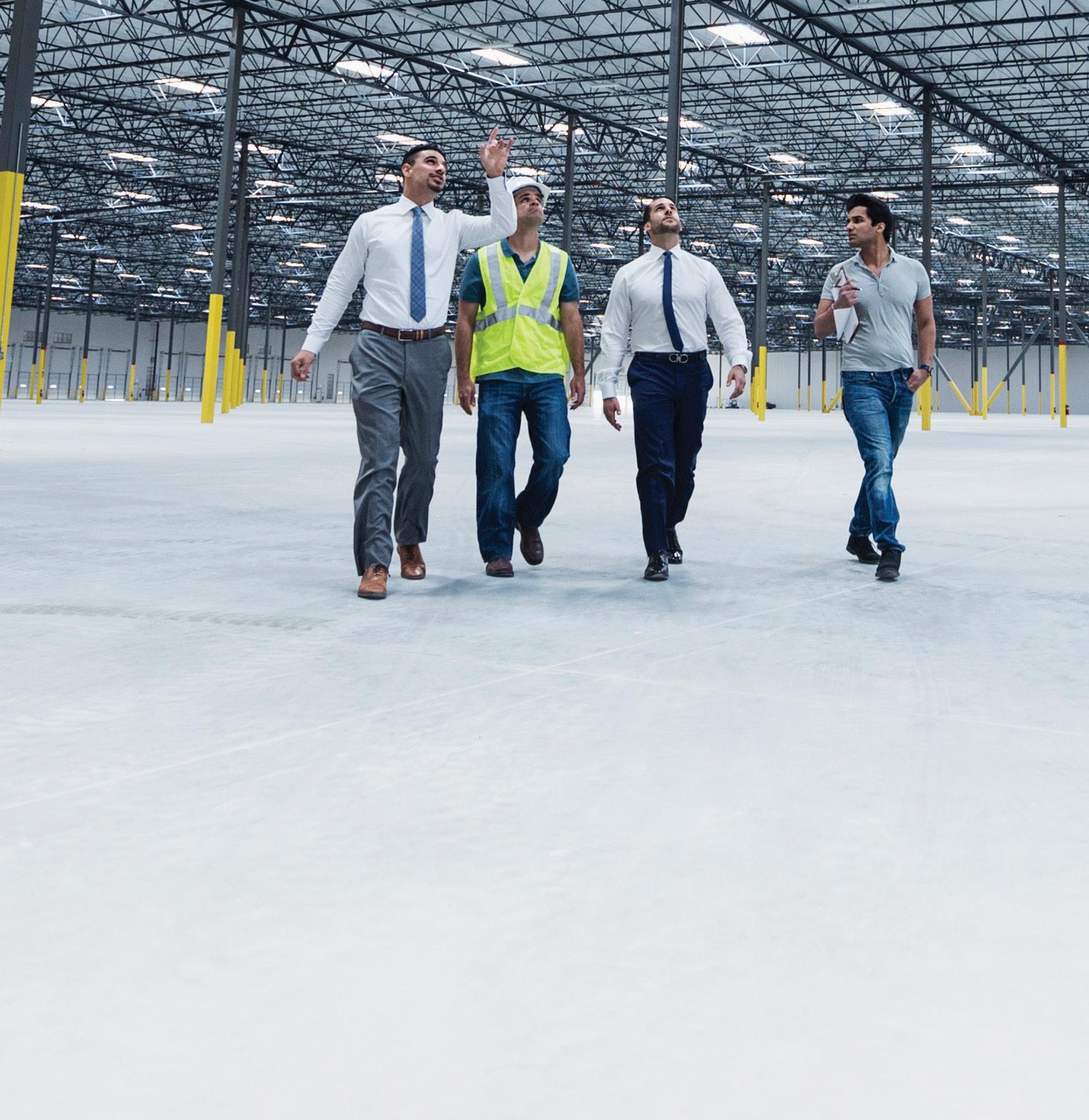
www.MHNetwork.com Material Handling Network September 2022 WS13 NUCORWAREHOUSESYSTEMS.COMWAREHOUSINGTHECONNECTINGWORLDOF
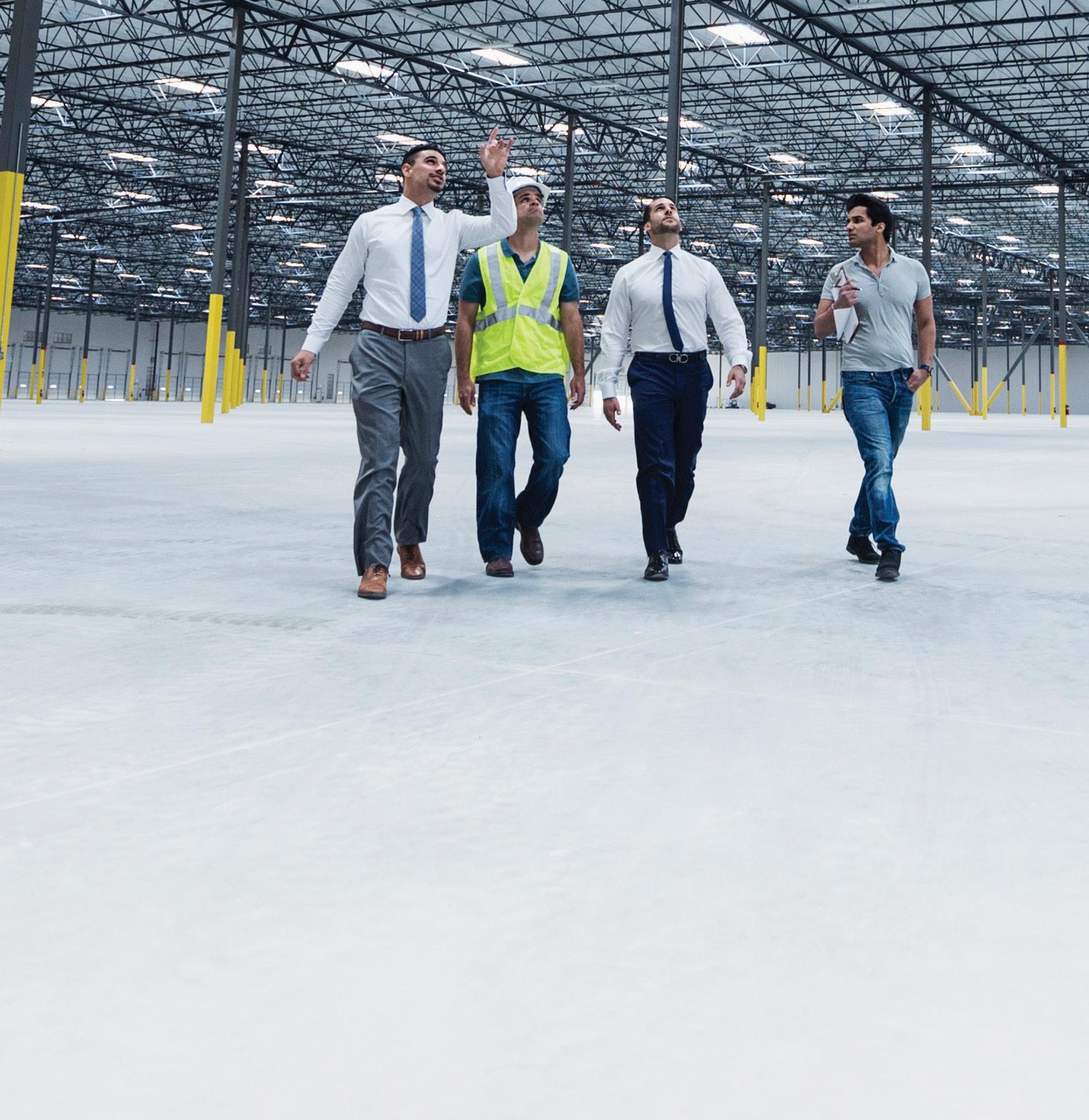
WS14 September 2022 Warehouse Solutions www.MHNetwork.com
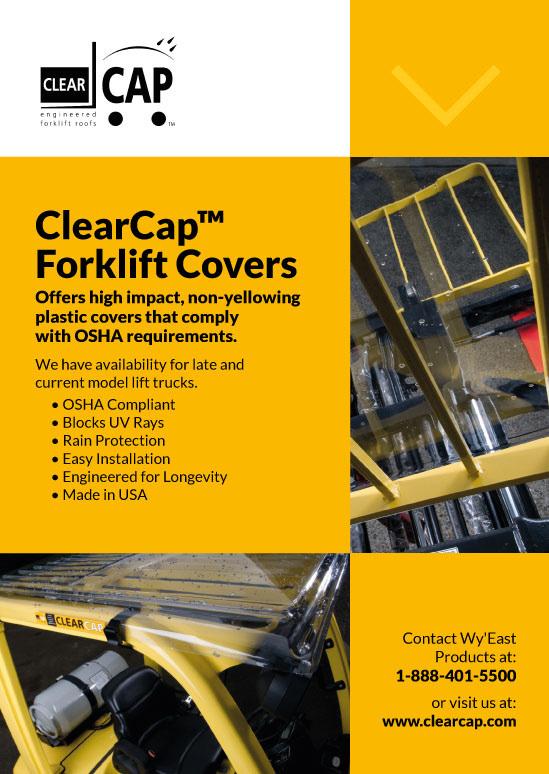
www.MHNetwork.com Material Handling Network September 2022 WS15 TM ClearCap Roof Covers! ClearCap & TuffCab! Easy Install Wy’East Products 1-888-401-5500 www.clearcap.com TuffCab Panel Cab Enclosures Vinyl Side Doors • ClearCap Roof Covers Keeps Operator Dry • Many Sizes to Fit Various Trucks • Easy to Install • Reasonably Priced • Clear or Tinted • UV Polycarbonate • Domed Roof Diverts Rain • Blocks UV Rays • O.S.H.A. Compliant • Full Enclosures or Individual Components • Durable Steel & Safety Glass Construction • Easy Clamp-on Installation • Affordable • Fast Lead Times • Windshield Includes 12v Wiper Engineered to Fit Hyster, Yale, Cat, Mitsubishi, Toyota & Unicarriers Clear Solutions to Common Problems
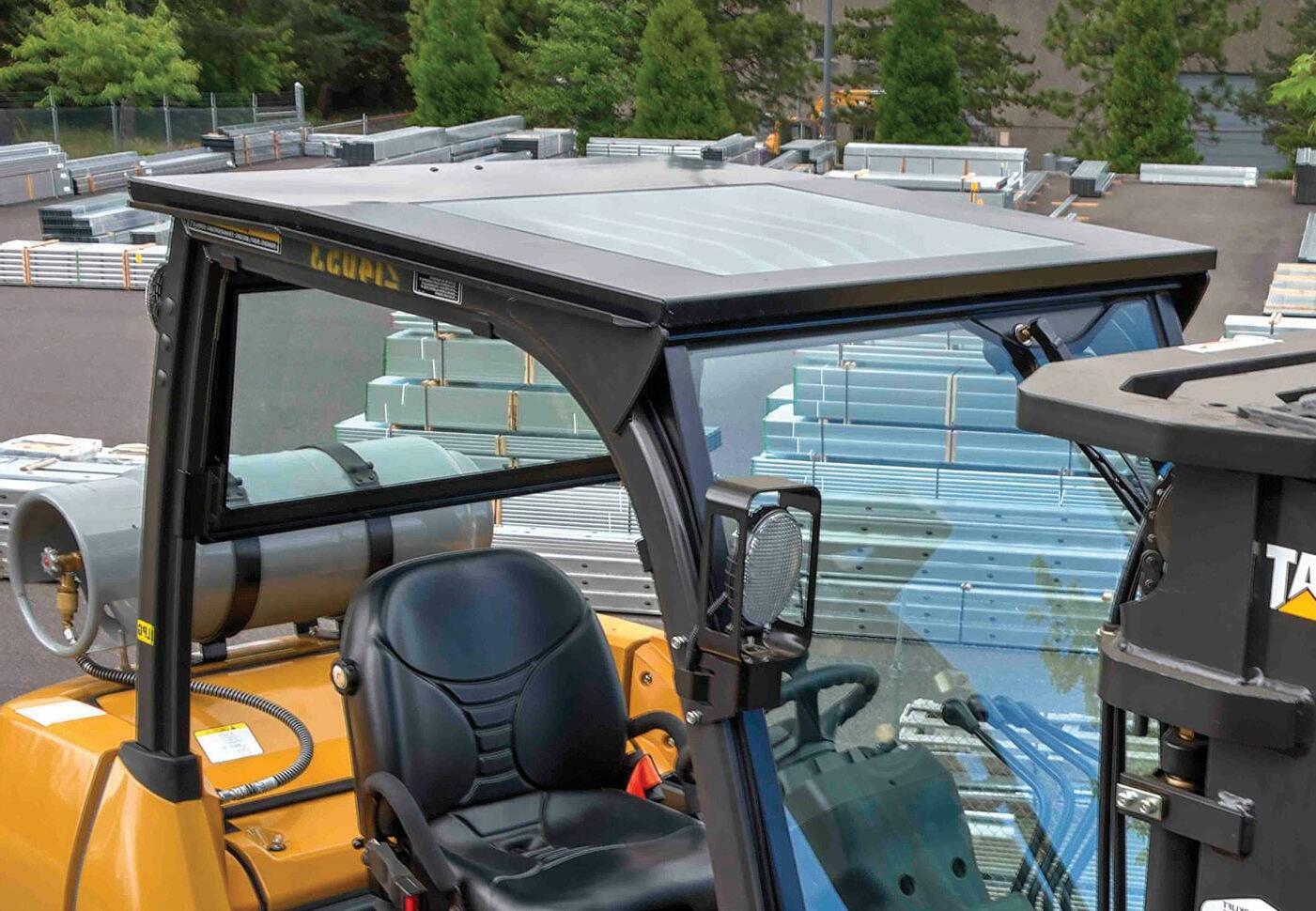
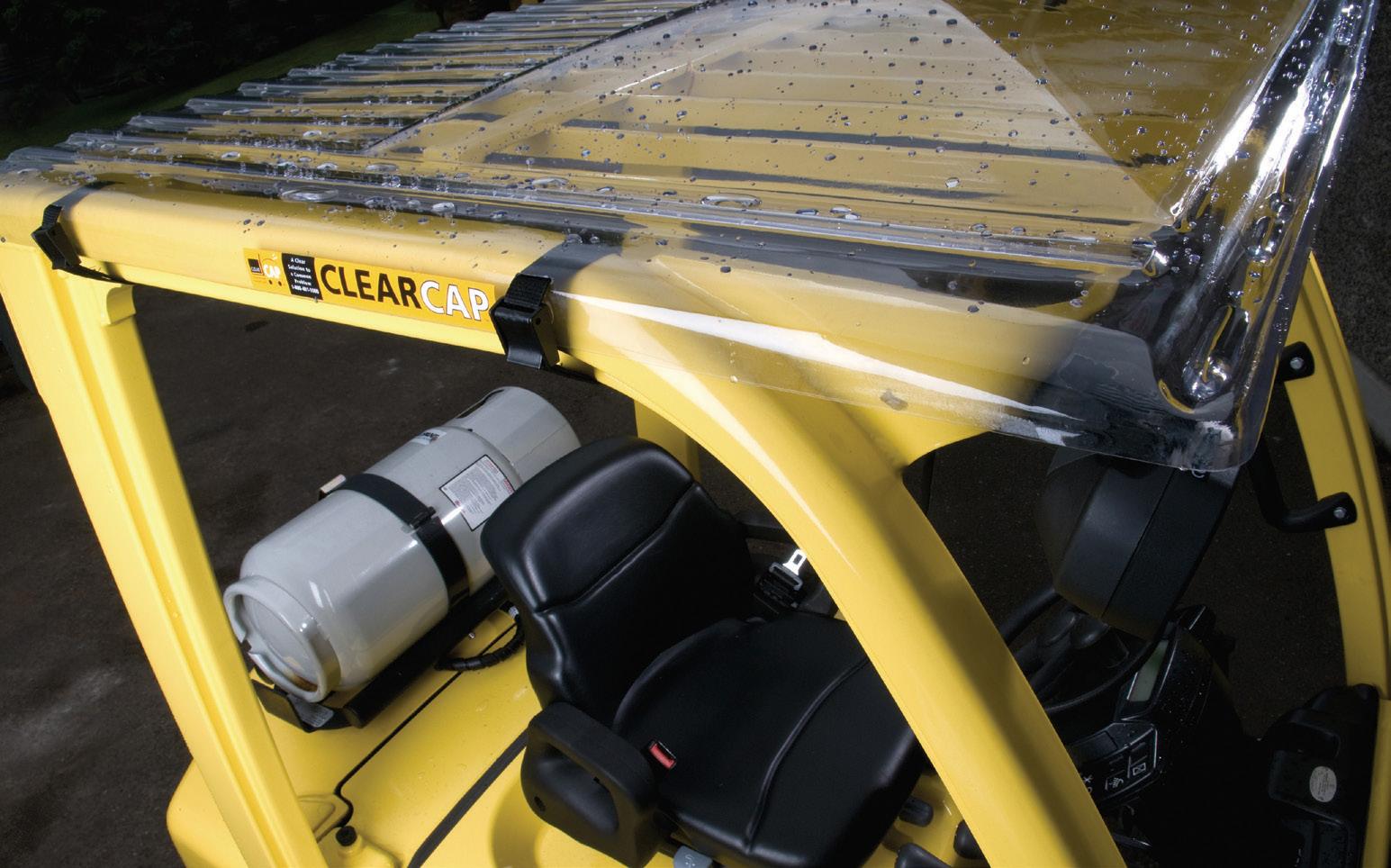


Warehouse Logistics
What exactly is a mid-size motorized material handling vehicle?
The concept behind today’s industrial midsize motorized material handling vehicles can be traced to similar vehicles originally designed to provide a dependable mobility solution for disabled individuals. For example, motorized shopping carts are commonly seen every day across the U.S. providing ease of mobility for the disabled in grocery stores, department stores, and a variety of other retail environments. Also, not to be confused with the rising trend in automated guided vehicles (AGVs) and autonomous mobile robots (AMRs), motorized material handling vehicles are still very much human-operated. However, due to their extremely simple design, relatively low-tech operation, durability, and reliability, they’re much less costly and easier to service than their high-tech counterparts.Mid-sizemotorized material handling vehicles also utilize a variety of detachable cart and/or trailer designs to accommodate loads of different weight capacities. Typical loads range from parcels delivered for distribution throughout a manufacturing floor to tools and heavy spare parts for machinery repairs.
When an industrial manufacturer or warehouse operation needs to move large and heavy items, they typically rely on the traditional forklift. For smaller, lighter loads, a pallet jack or even a pushcart might be just the perfect solution. But somewhere in between lurks an often-ignored middle-of-the-road gap that neither forklifts, pushcarts — and dare we say electric golf carts — are the best approach. One proven answer that’s quickly gaining traction in a variety of industrial environments — filling the void between forklifts and manual pushcarts — is mid-size motorized material handling vehicles.
Many manufacturing operations, warehouses, and distribution centers are finding themselves in the market for such a beneficial solution to their material handling needs.
Must-Have #1: High Durability As with any material handling equipment investment, the capability to withstand a high level of wear and tear is very important. Mid-
WS16 September 2022 Warehouse Solutions www.MHNetwork.com
Top five must haves to look for in Mid-Size Motorized material handling vehicles
This white paper covers five “must-haves” to carefully consider when evaluating investing in mid-size motorized material handling vehicles. Something always needs to be moved One of the major drawbacks of traditional forklifts is that they’re not always able to maneuver in tight spaces or down extremely narrow aisles. And for expansive operations — involving long distances due to their huge footprints — relying on manual pallet jacks or pushcarts for an entire eight-hour shift will gradually fatigue the fittest of employees over time. And as with any industrial manufacturer or warehouse operation, there’s always something that needs to be moved. From scrap cardboard in shipping and receiving, spare parts to fix a broken piece of machinery, to transporting janitorial supplies that help keep work stations as well as lavatories clean and sanitary, the need to keep things moving is seemingly endless.
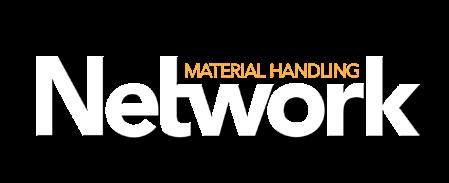
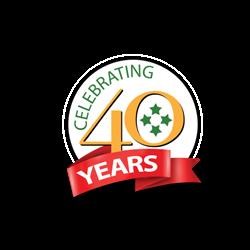
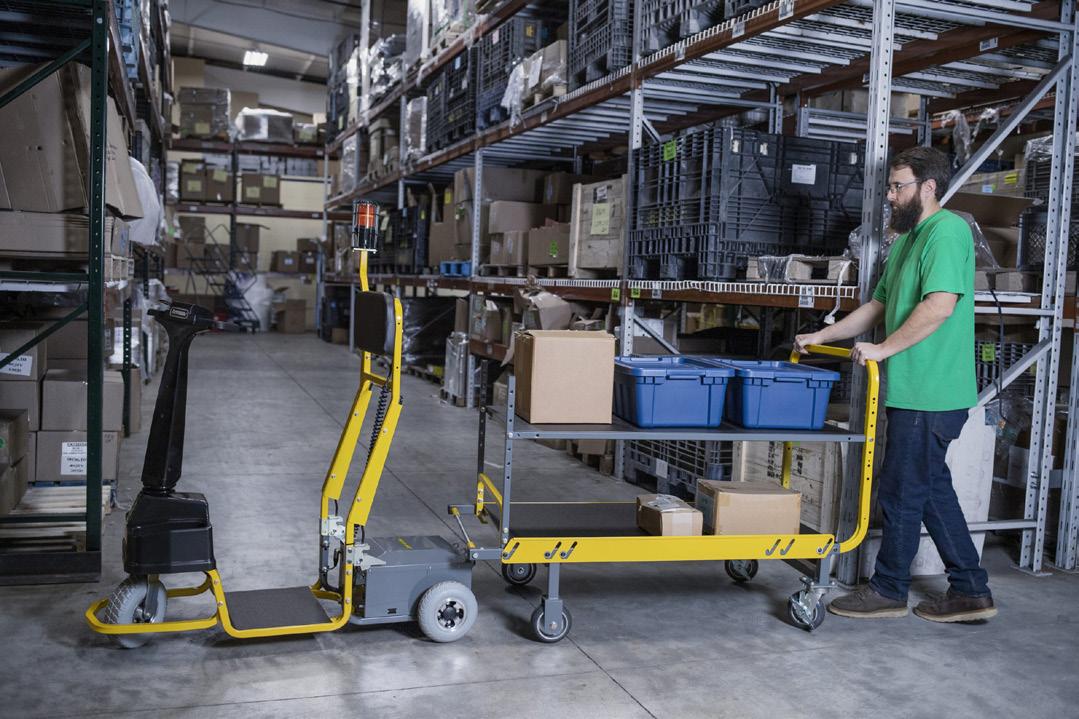
www.MHNetwork.com Material Handling Network September 2022 WS17 “The Amigo material handling cart is invaluable from a safety and ergonomic standpoint. Pulling and tugging on carts with 1,000 lbs. was an extreme risk from an ergonomic standpoint. The Amigo has eliminated that threat from our facility. I would suggest safety professionals from all industries take a close look at this product.” Ernie Fryer, Safety Manager, Boride Abrasives Learn more about Amigo Mobility’s midsize motorized material handling line at myamigo.com/industrial Dex Pro+ Burden carrier Comfort grip rectangle steering wheel Durable foam filled tires Padded backrest Optional strobe light Customizable, detachable24-volttrailerbattery system ThrottleAdjustablelevers speed Speed / Fault codes Battery gauge Horn button
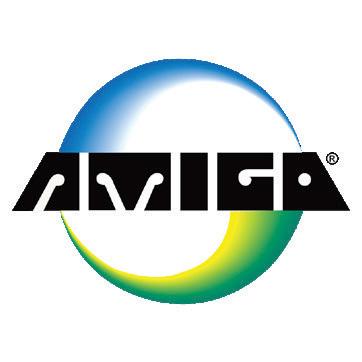
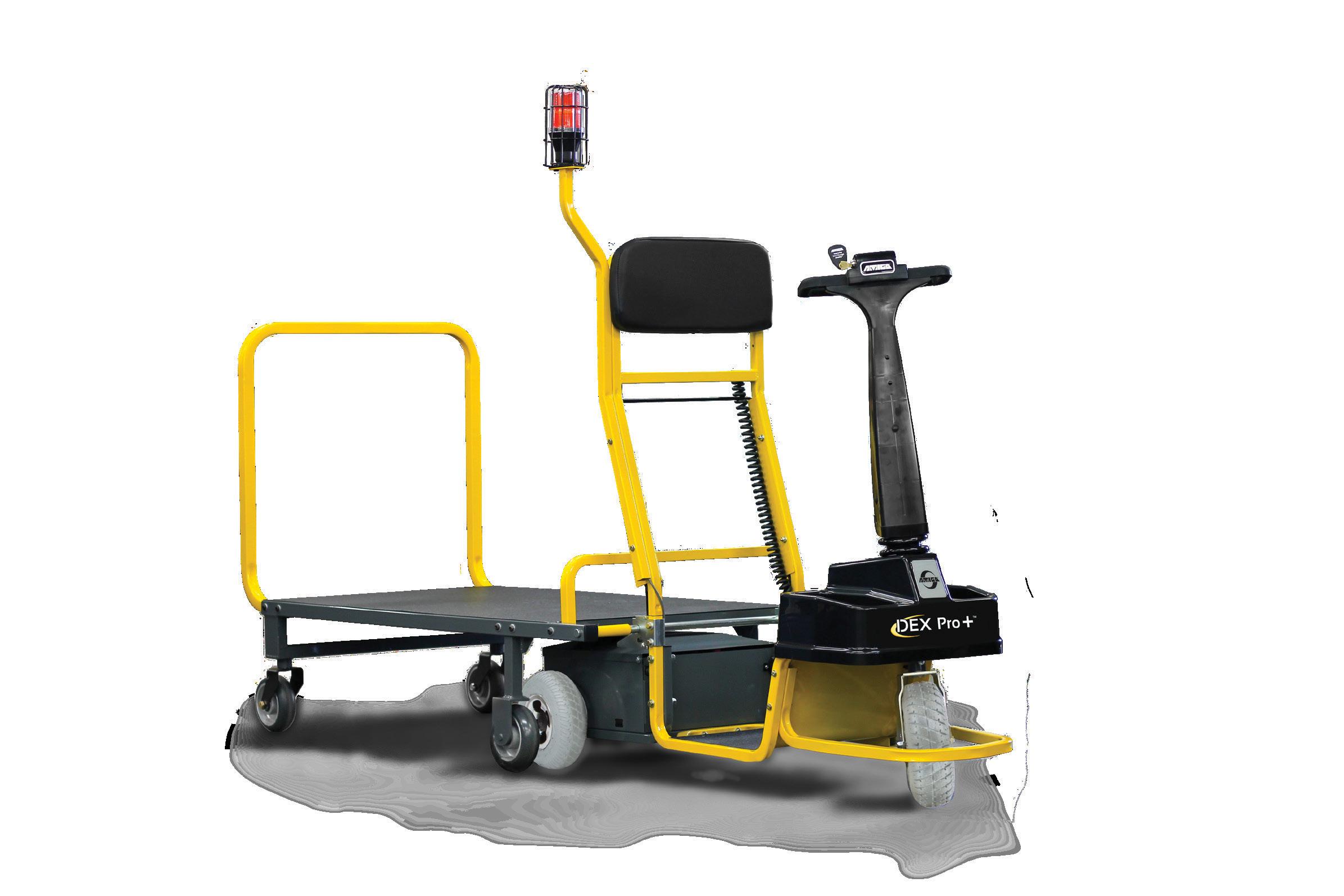

Must-Have #3: Ease of Service / Virtually Maintenance-Free
size motorized material handling vehicles that have evolved directly from personal mobility cart design — which has stood the test of time for decades in a variety of heavy-use environments like supermarkets and grocery stores — is a major plus.
Must-Have #2: Engineered for Simplicity & Ease of Use
In addition, a mid-size motorized material handling vehicle that features a simple design with the fewest number of operating parts means a high degree of dependability and a product that’s easy to service if ever needed.
Must-Have #4: Proper Load Capacity
The power of right-sizing your fleet Today, “forklift-free” is a growing buzzword in manufacturing facilities and warehouses around the U.S. But implementing forklift-free plans can be extremely challenging. There aren’t many existing plants that can halt operations to design a completely new layout that eliminates the use of forklifts.Instead of complicated logistics and a new layout, first, consider looking at gradually implementing small changes. Right-sizing material handling equipment based on the need of the job can be a more manageable plan than going completely forklift-free.Theresult is using a smaller, more agile option, such as mid-size motorized material handling vehicles. They not only increase employee job
And just because mid-size motorized material handling vehicles are relatively compact in size, simple in design, and have a limited number of operating parts compared to other types of material handling equipment, don’t let their appearance fool you.Compared to more cheaply designed products on the market that are considered “throw-away” equipment, well-built mid-size motorized material handling vehicles are much more durable and powerful than they might appear on the surface. Robust tubular steel frames and specially-designed tires that can withstand the sharpest of metal shards are just two features to look for in a high-quality product.
Virtually no maintenance requirements or no mandatory service plan will quickly translate to less total cost of ownership (TCO).
Based on their size and design, a high degree of maneuverability is one of the stand-out strengths of mid-size motorized material handling vehicles. With a tight 52-inch turning radius (and even down to a zero turning radius on certain models), this type of optimal maneuverability is useful for a variety of applications where a limited amount of space is a factor.
In contrast with traditional forklifts, mid-size motorized material handling vehicles require virtually no user training for safe operation. And unlike forklifts or other battery-powered material handling vehicles that require dedicated charging stations, being able to plug a vehicle into any convenient 110V outlet for overnight charging is a significant convenience. In addition, an ergonomically-designed low-deck standing platform that’s three inches off the floor dramatically reduces the amount of energy required for operators who need to repeatedly step on/step off their material handling vehicle (such as for parcel deliveries) during their shift.
Warehouse Logistics continued
Must-Have #5: Maneuverability
A mid-size motorized material handling vehicle is ideal for load capacities of anywhere from 1,000 to 2,500 lbs. (including the operator), especially when you don’t need to handle significantly higher weight capacities of 5,000, 7,500, or even 10,000 lbs. Many companies just don’t have that kind of need.For example, a 1,000 to 2,500 lbs. load capacity is perfect for a facility that needs to empty scrap cardboard from an exceptionally high number of 55-gallon garbage containers per day. Keep in mind though that while grades of 4% to 6% still fall within the guidelines for safe operation, even a 1% grade will start to limit weight and towing capacity.
WS18 September 2022 Warehouse Solutions www.MHNetwork.com
Consider too an employee who’s responsible for preventive maintenance, such as for a company’s numerous fire extinguishers in a large facility. The employee could easily make their entire round of inspections without ever needing to step off of the material handling vehicle.
www.MHNetwork.com Material Handling Network September 2022 WS19
2. Ask your employees for feedback to gauge their interest level.
4. Find out how the vendor’s customers are using their mid-size motorized material handling vehicles. This will provide you with vivid examples of what such equipment can do for your own company and your valued employees.
When
satisfaction but help employees perform their jobs more efficiently while safely moving materials throughout their facilities. By right-sizing your fleet of material handling equipment, you’ll further improve safety by containing forklifts where they’re most needed (and appropriate) while using mid-size motorized material handling vehicles for other dedicated purposes, such as for intra-facility transport. considering investing in such highly useful and versatile material handling equipment, here are a few closing thoughts and recommendations:
3. Most importantly, once you decide to talk to a mid-sized motorized material handling vehicle vendor, ask for a demo of their various products. Due to their compact size, an entire product lineup will easily fit in a van for an on-site visit vs. a full-size semi-trailer full of large forklifts.
1. Identify your most pressing material handling needs and applications.
Warehouse Logistics continued Material Handling TM Hammerhead Material Handling designs and installs state-of-the-art storage and material handling solutions nationwide. This includes both static and dynamic racking systems, from popular selective and drive in racks, to pick modules, pallet-flow racks, automated shuttle systems, push back racks and mobile racking systems. WHY HAMMERHEAD • Faster Return on your Investment! • Systems designed for your application. • Large variety of storage and MH solutions. • Better space utilization in your facility. • More organized, clean and orderly. • Quick, accurate order picking. • Safer workspace for employees. • We - Design it, Maintain it, Expand it. OUR SERVICES • Site Survey & Rack System Designs. • Turn-Key Proposals. • Structural Engineering & Permi. • Warehouse Fire & Safety Consulting. • Project & Site Management. • Pallet Rack Installation. • Repair & Maintenance & Inspections. • Sprinklers, Lighting & Alarm Systems. • Removal, Relocation & Trade-In. Talk to a storage expert today! West: (323) 543-5013 Central: (346) 699-RACK(7225) East: (973) 801-0309
Amigo is a manufacturer of motorized shopping carts, material han dling carts, burden carriers, tuggers, and personal mobility vehicles.

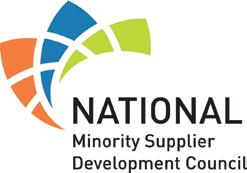
WS20 September 2022 Warehouse Solutions www.MHNetwork.com combilift.comESSafetytoragefficiency • S a f e r p r o d u c t h a n d l i n g • O p t i m i z e d p r o d u c t i o n s p a c e • I m p r o v e d s t o r a g e c a p a c i t y • I n c r e a s e d p r o d u c t i v i t y & o u t p u t • E n h a n c e d p r o f i t s double page ad Amanda General Warehouse opt rev 2.0.indd 1 877-266-2456
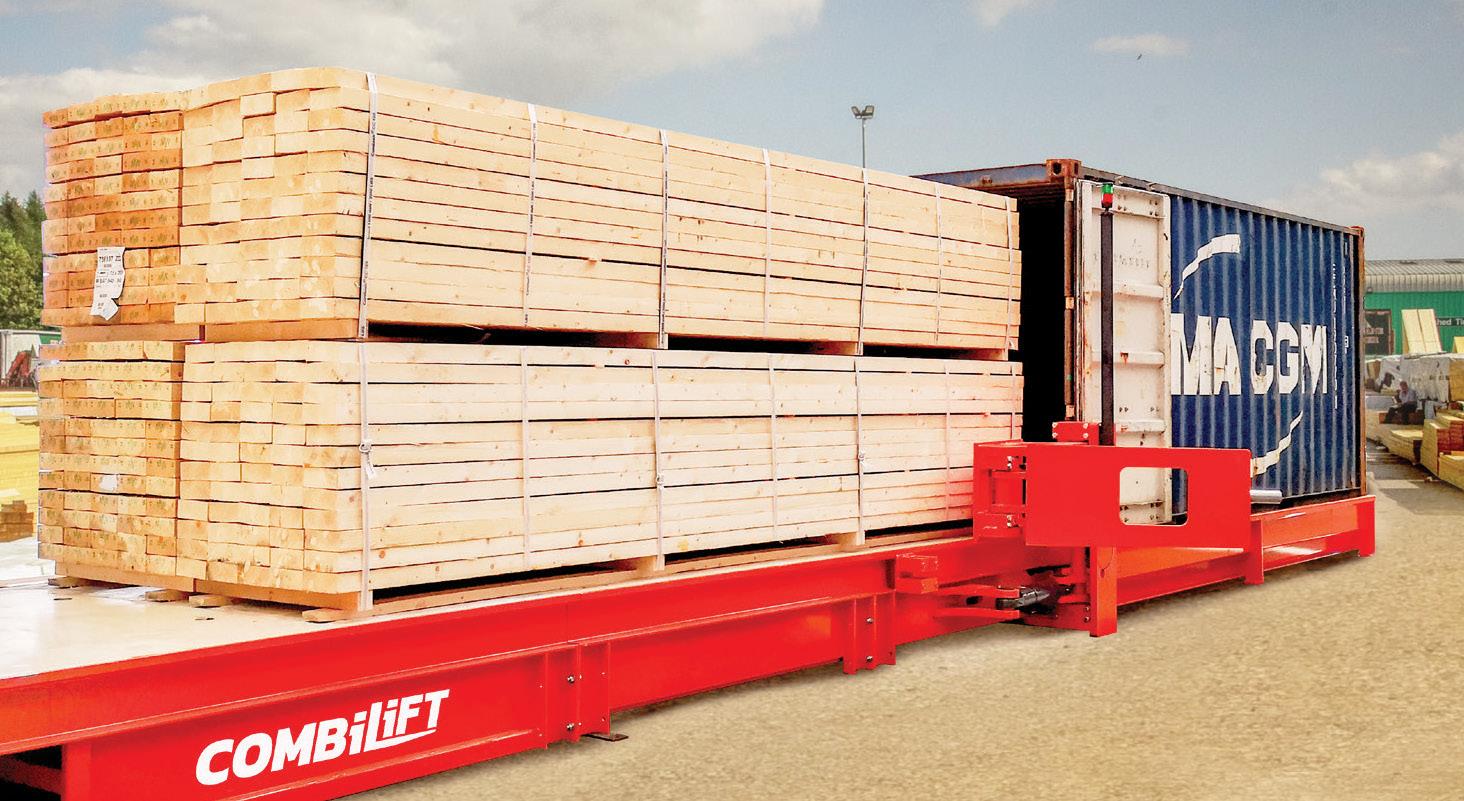
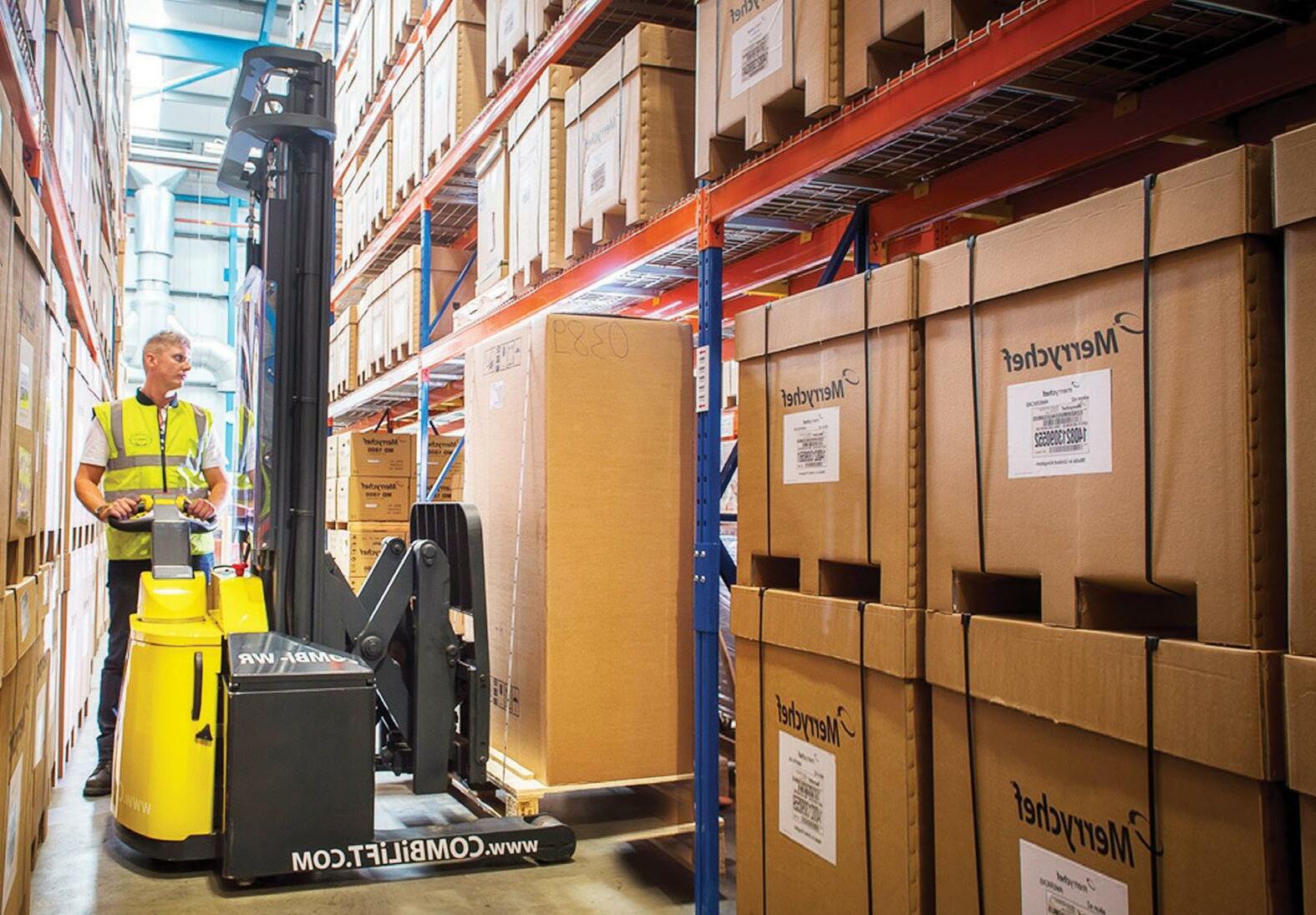





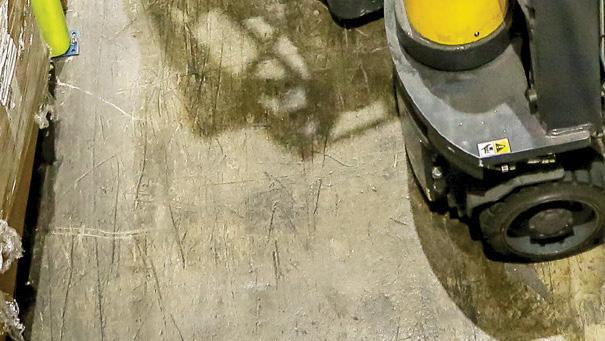
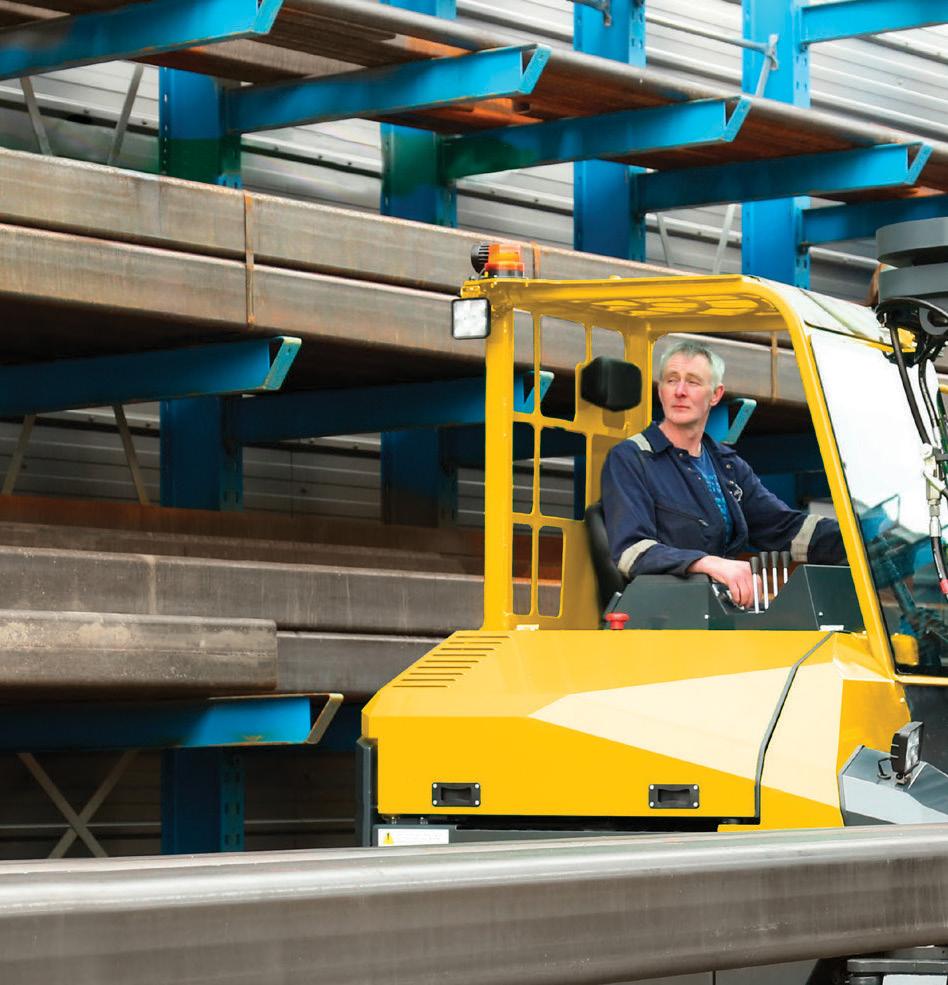
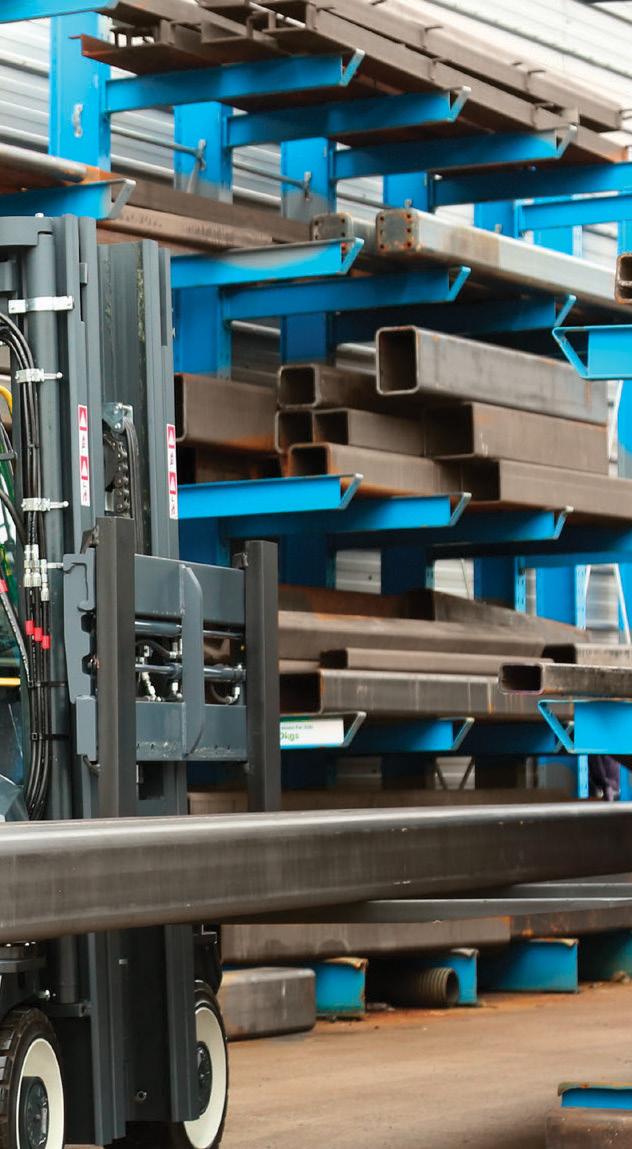


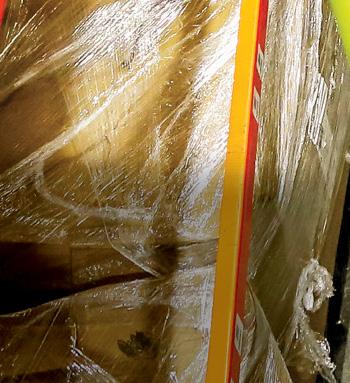


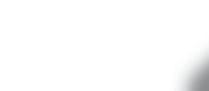


20/05/2021 10:02:11
B e f o r e y o u i n v e s t i n u p g r a d i n g t h e i n f r a s t r u c t u r e o f y o u r w a r e h o u s e , f i n d o u t h o w C o m b i l i f t c a n i n c r e a s e y o u r s t o r a g e b y u p t o 5 0 % W i t h o v e r 2 1 y e a r s ’ e x p e r i e n c e i n v o l u m e o p t i m i z a t i o n , o u r t e a m o f w a r e h o u s e p l a n n i n g e x p e r t s k n o w h o w t o m a k e y o u r s p a c e w o r k h a r d e r f o r y o u . C o n t a c t u s t o d a y t o a r r a n g e a s i t e s u r v e y ! O u r w a r e h o u s e d e s i g n c o n s u l t a n c y s e r v i c e i s F R E E a n d w i t h o u t o b l i g a t i o n . up to 50% more storage with Combilift
Save
www.MHNetwork.com Material Handling Network September 2022 WS21
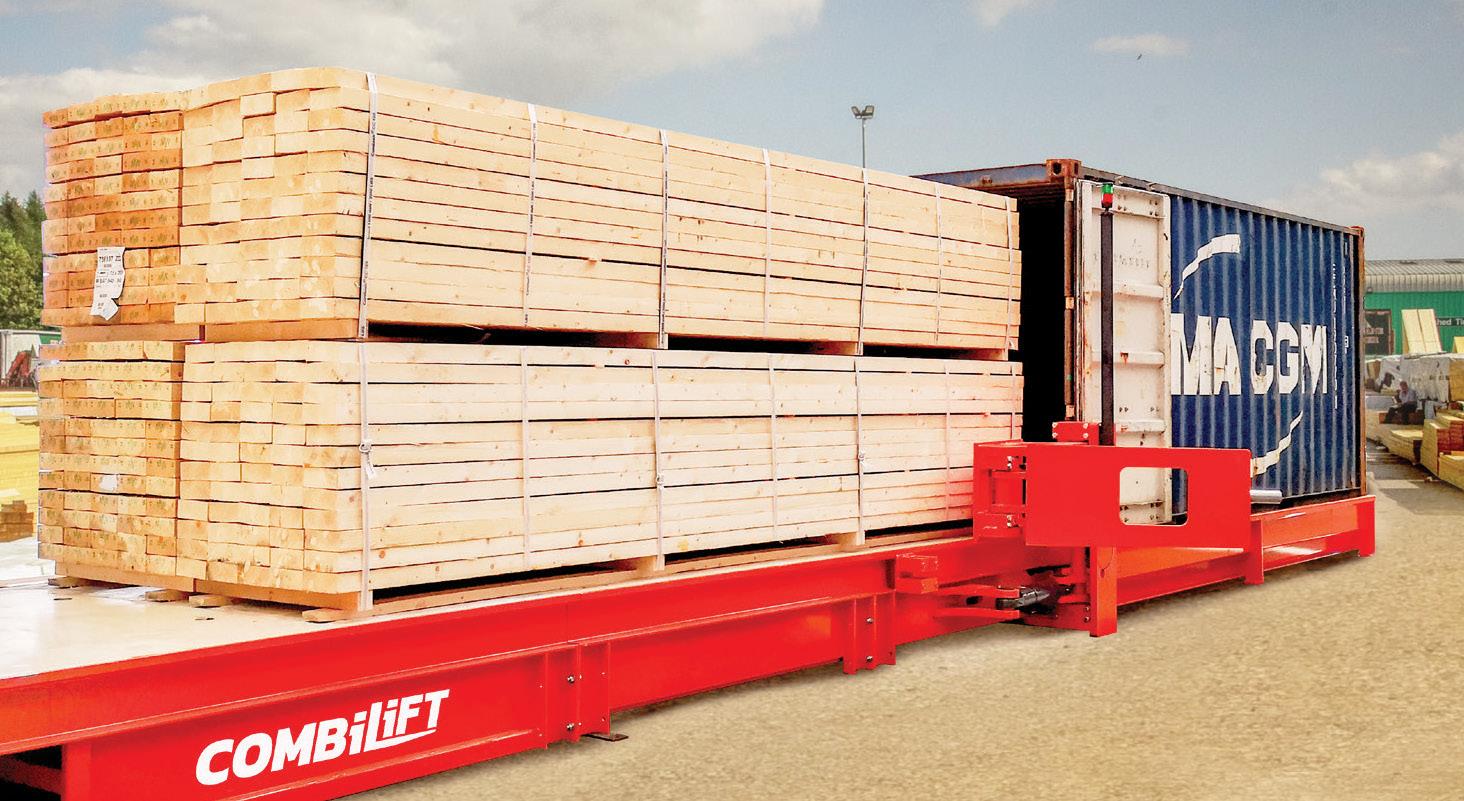
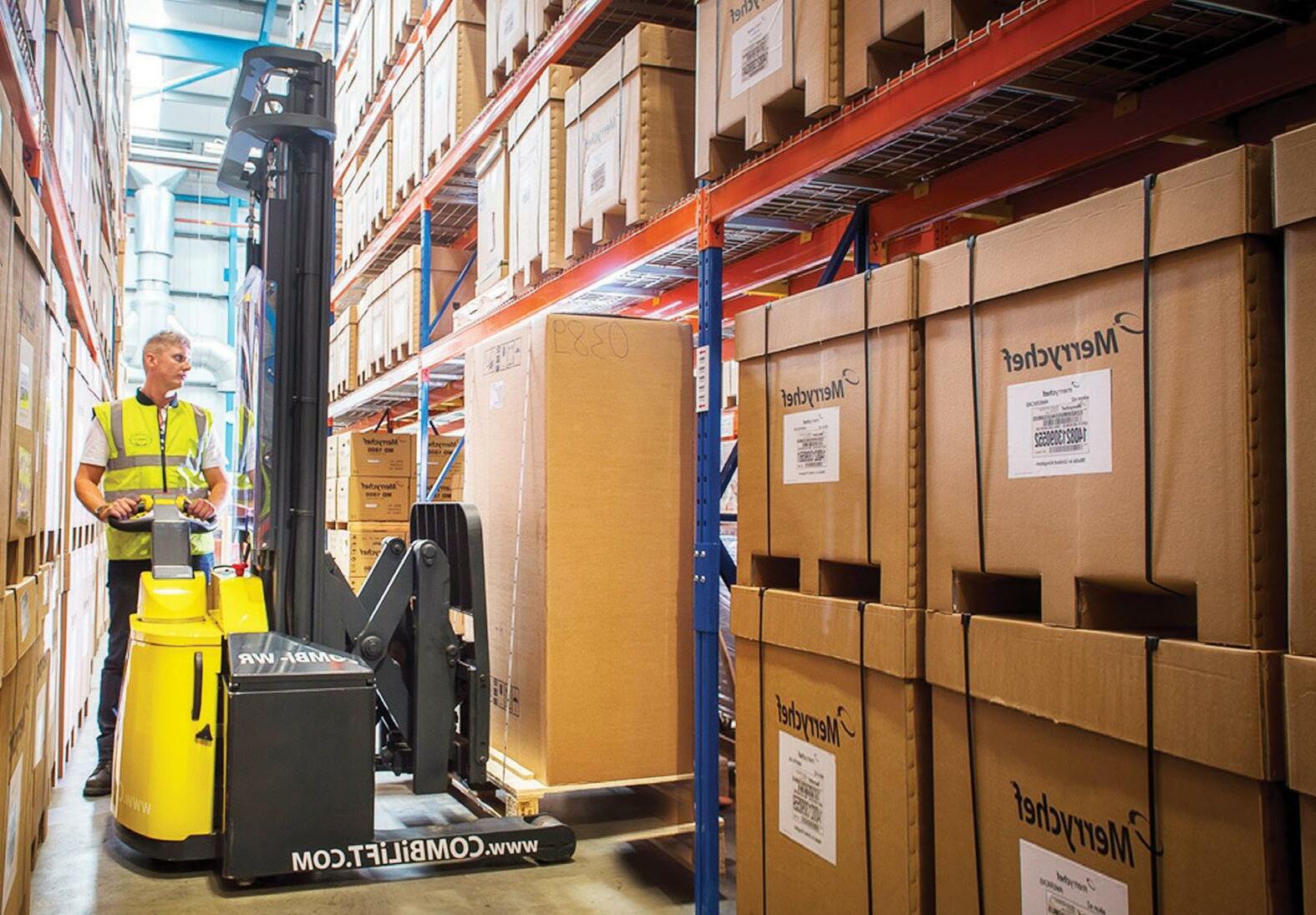


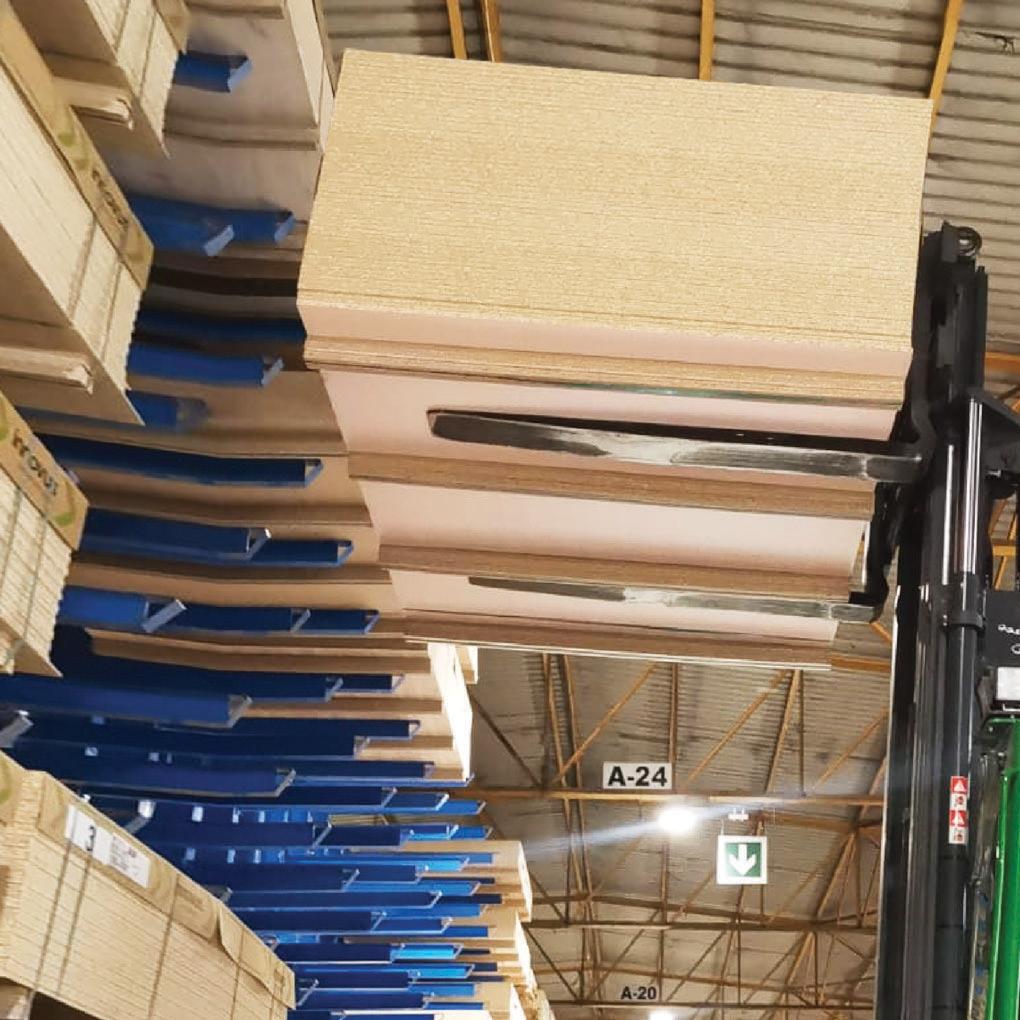
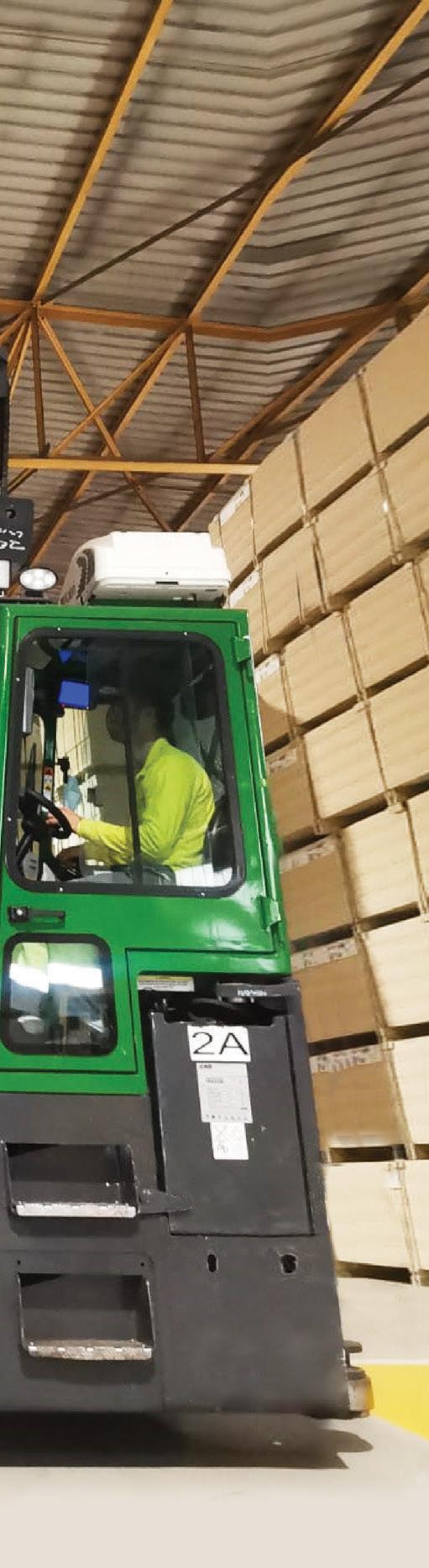
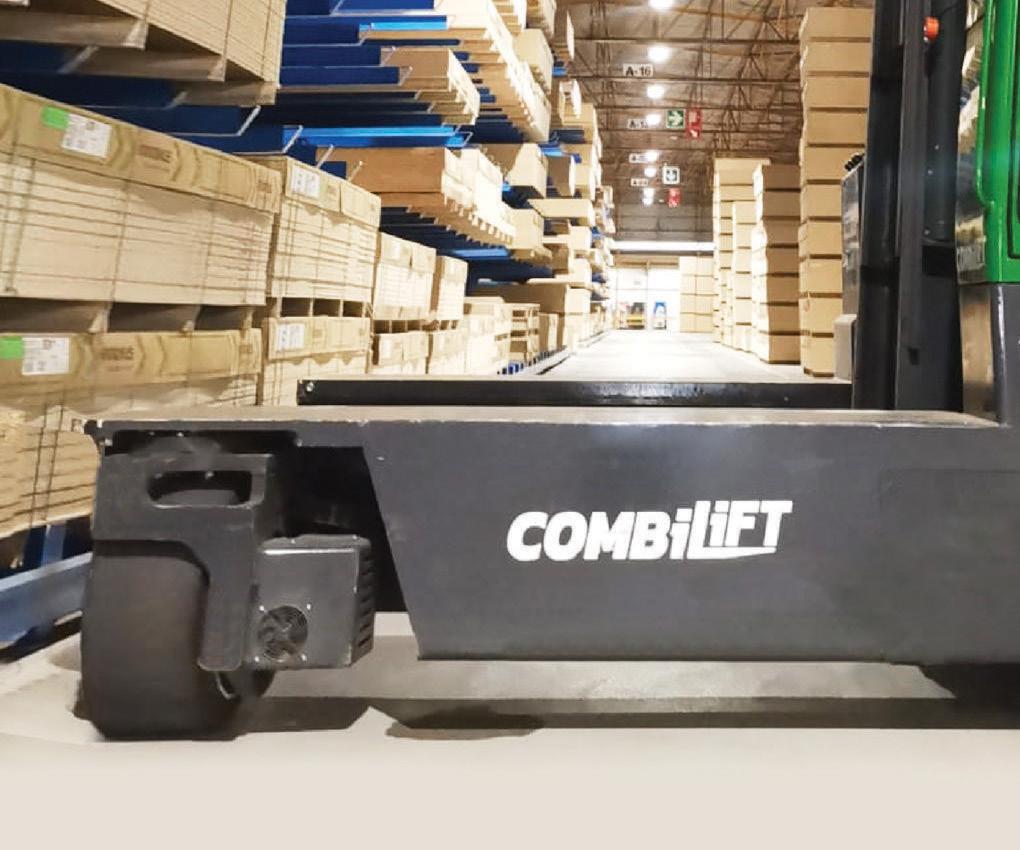
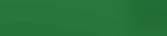


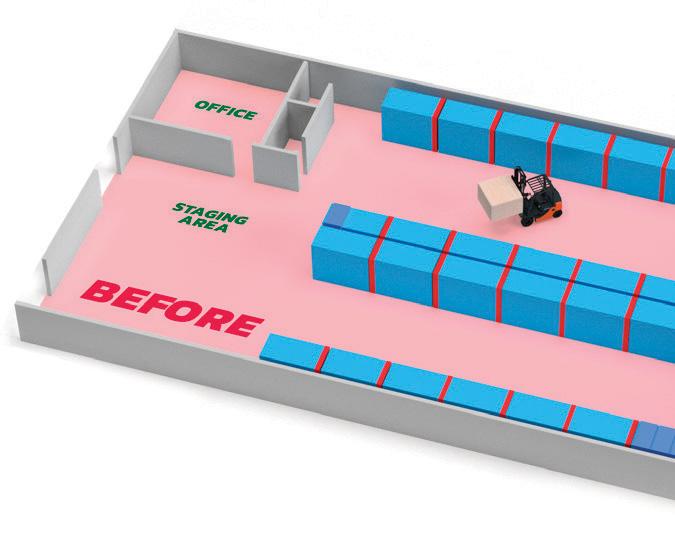
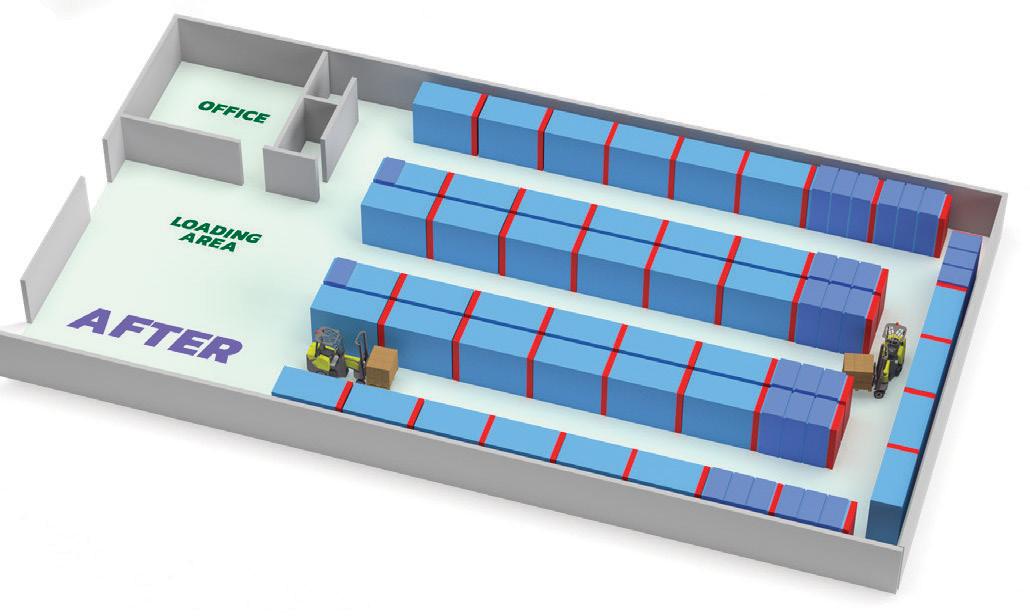
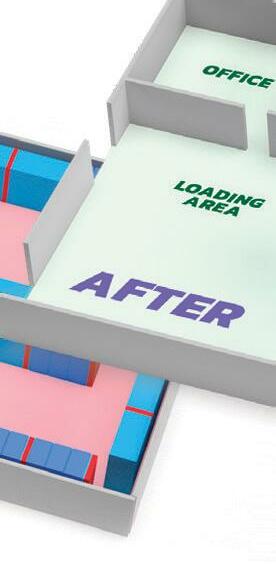
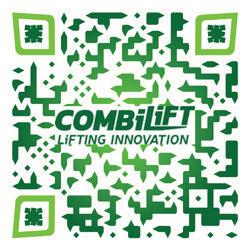
• Long loads…everywhere: You’ll discover how Combilift can maneuver even long loads down narrow aisles, through standard doorways, and around obstacles with ease, enabling racking to be placed closer together, reducing the amount of operational space required.
• Workplace training- Training your employees on the proper use of equipment will prevent injuries.
A complimentary service using CAD design to find and show your facility's capacity and ideal layout, a Combilift warehouse analysis will provide layout proposals, site inspection, and diagrams to evidence where and how improvements can be made.The free review includes racking layout proposals and storage density calculations to create the best possible performance from any warehouse and will show how to achieve results like the below and more in safer, more innovative ways:
Combilift offering safety review for warehouse planning Any serious warehouse safety review should also consider a warehouse planning analysis for some simple reasons: there are improvements in visibility, materials handling processes and most of all driver fatigue to be found in looking at a warehouse as a ‘big picture’.
Here are some of the most important things you can do:
www.combilift.com/warehouse-planning
• The direction of travel: Find out more about the clever Combilift approach that enables the operator to change the direction of travel by 90 degrees at the flick of a switch.
Safeguarding your workplace
Warehouse Safety
There are thousands of different kinds of businesses and manufacturers creating all types of products all across the country. While they all create different products, one thing ties them all together: workplace safety. Safety in the workplace is a top priority for all of these companies. There are myriad ways that employees can be injured (or worse) in the workplace by industrial hazards like heat, dust, flak, sparks, flash, molten metal, and even noise.
WS22 September 2022 Warehouse Solutions www.MHNetwork.com
• Workplace safety meetings- Regular meetings to discuss workplace safety is important and helpful for everyone.However, there are also many items you can utilize in your workplace to safeguard your employees. This would include noise control systems, industrial curtains, vinyl strip doors, welding and safety screens and fire safety equipment.
There are several ways you can utilize products in order to safeguard your workplace and create a safer work environment for your company, your employees, and yourself: Noise Control Systems, Industrial Curtains, Vinyl Strip Doors, Welding & Safety Screens, and Fire Safety Equipment
There are several things you can do to keep your workplace safe and your employees away from danger.
www.singersafety.com
• A workplace designed for older operators: Ask how the better layout and easier vehicle access can reduce tiredness and injuries as well as make a workplace easier for more senior colleagues.
• Signs and labels- Using signs and labels can warn employees of potential hazards.
• Maintaining a clean work area- A messy workspace can lead to unintentional accidents and falls. Keeping your workplace clean and organized can help to prevent this.•Encourage breaks- Even though breaks mean less productivity, your employees will be able to focus on their tasks better and work more efficiently
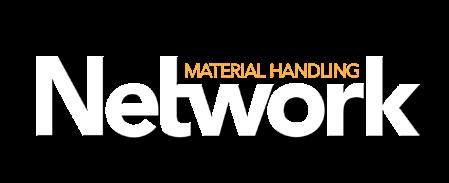
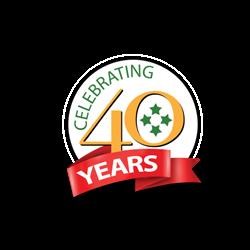
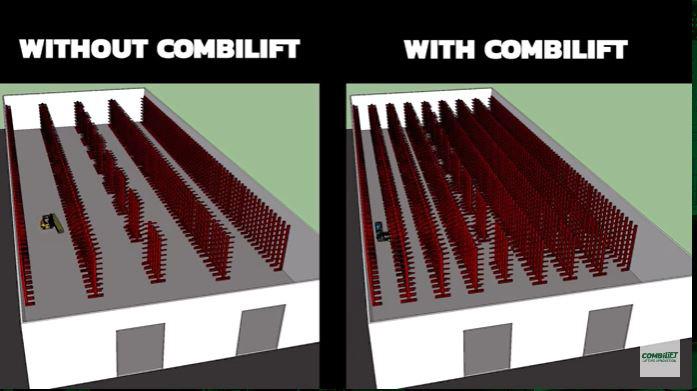
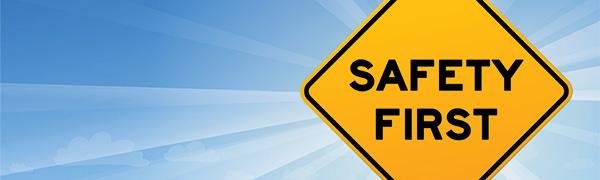
www.MHNetwork.com Material Handling Network September 2022 WS23 For pallet rack repair assessments and a full line of engineered pallet rack repair and protection products 815-723-7400 or visit MacRak.com “I stand by everything we build” Shawn MacDonald Owner of Mac Rak, Inc. We offer a CompIete Line of Engineered Rack Repair and Protection Products We produce over 30 column designs which allows Mac Rak the flexibility to offer repairs for all types of racks matching your specific rack system. On Time, On Budget with Minimal Disruption Over 53% of quotes become orders! One of the highest conversion percentages in the industry is a testament to the value our products and services are to customers. We’re Cold Storage Experts! Faster cold storage turn rates mean greater opportunity for forklift abuse and rack damage! Engin EE r E d r ack rE pair
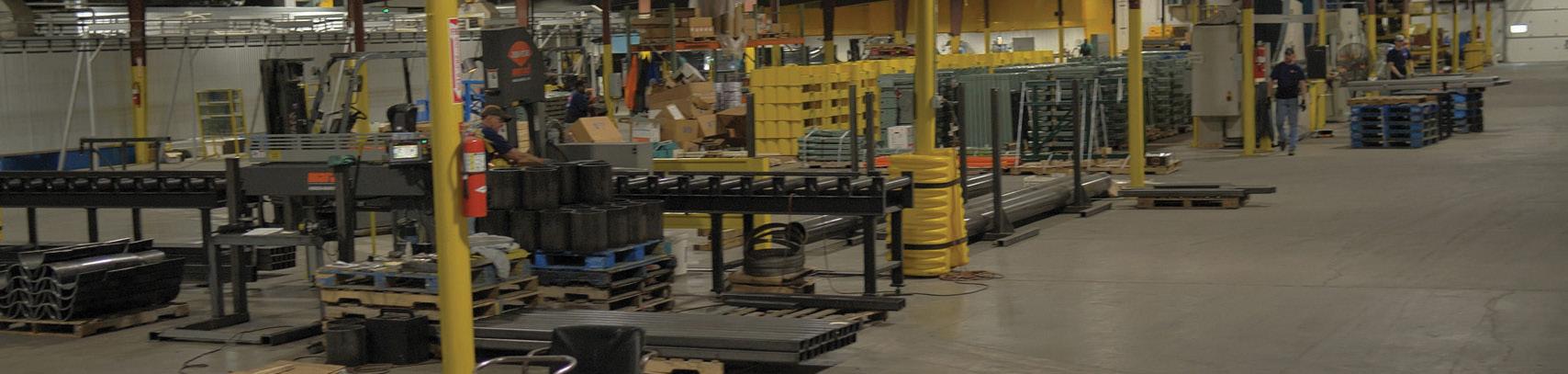
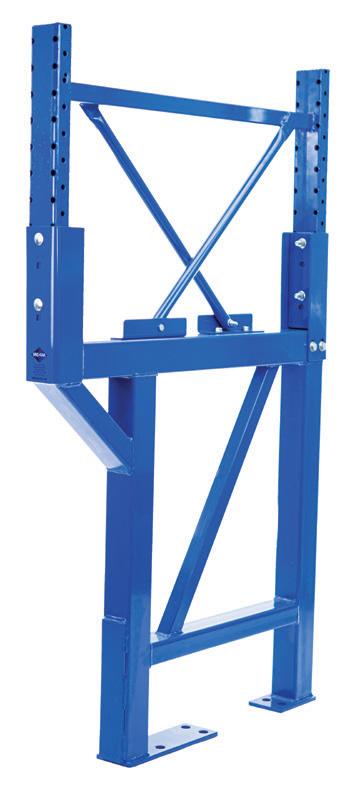
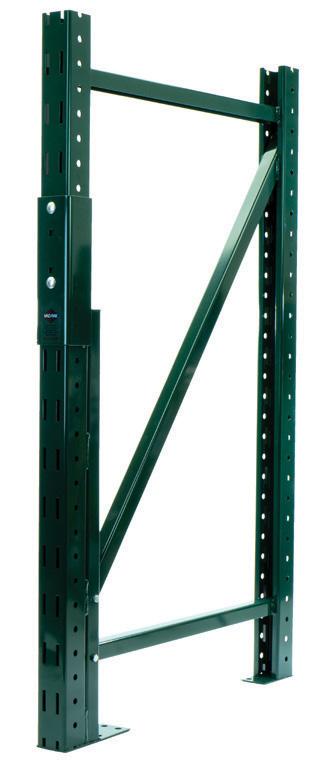
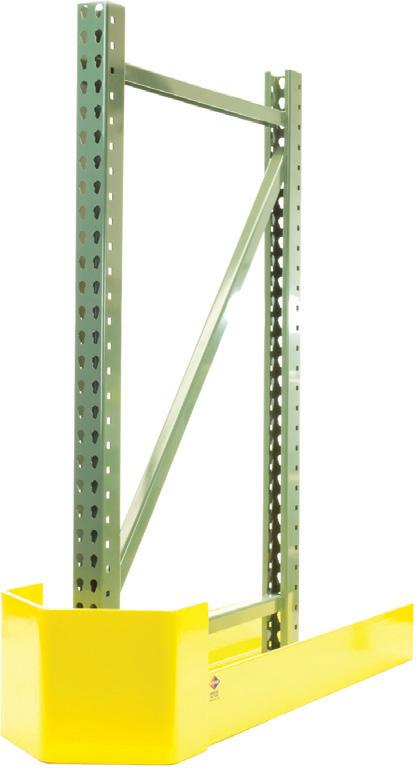

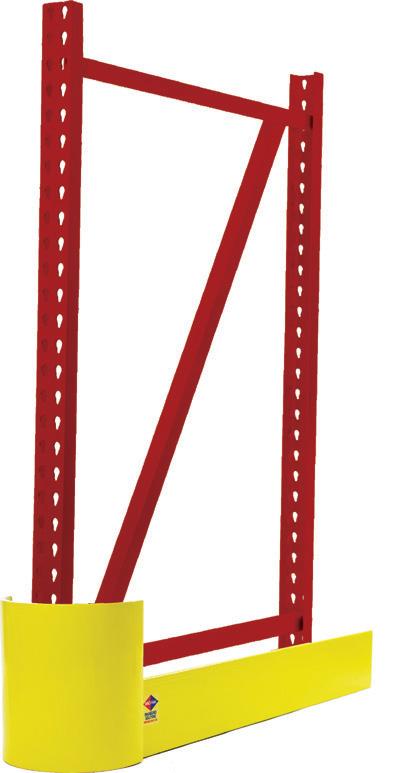
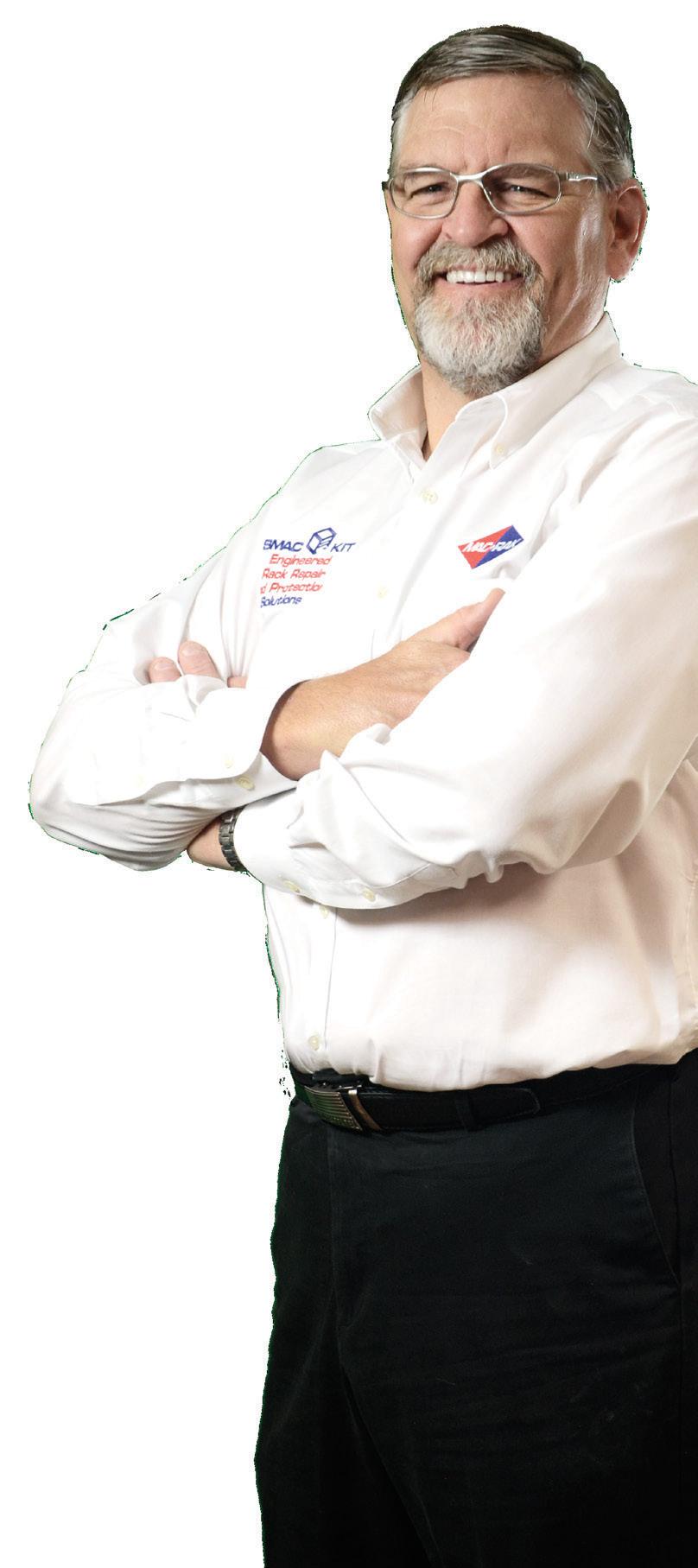
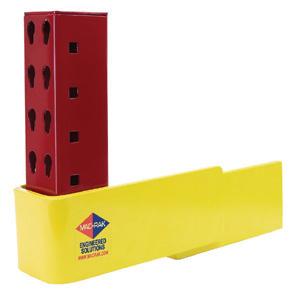
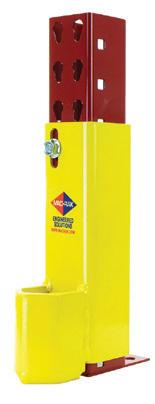
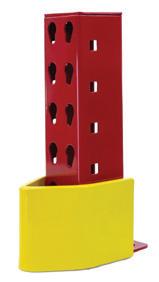

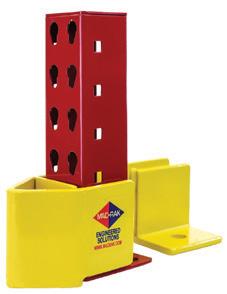
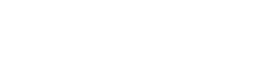
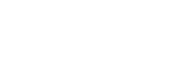
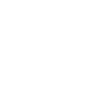


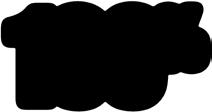
WS24 September 2022 Warehouse Solutions www.MHNetwork.com West Point Rack “We don’t just promise…we deliver!” 13591 Chandler St. • Omaha, NE 68138 866-245-3630 • Fax 866-245-3631 reva@westpointrack.com www.westpointrack.com For Excellent Ser vice Contact Reva Bily • Quotes in 2 hours on most requests • Delivery in 2-3 weeks on most orders • Qualit y • Dependabilit y • Satis fac tion Cantilever Structural PalletPortable Stacking West Point Rack is one of the fastest growing companies in the industr y. Our customers recognize quality products, de pendability of service and competitive pricing. Our Primar y Goal is to suppor t our dealers, satisf y their customers, earn trust and be the “ Vendor of Choice” for rack products and racking systems We of fer a full line of light duty, intermediate duty, heav y and extra heav y duty cantilever racks. We provide multiple configu rations of a wide variety of stacking racks. Our structural pal let racks can be configured for a wide range of applications West Point Rack h as the products that generates solutions for your storage needs We also of fer specialty products such as bar cradle trucks, drum racks, hand car ts and other specialty transpor t and storage products. Give us a call at 866. 245. 3630. We may have what you need Look forward to hearing from you Cantilever Racks • Structural Pallet Racks Portable Stacking Racks Specialty Transport & Storage Products

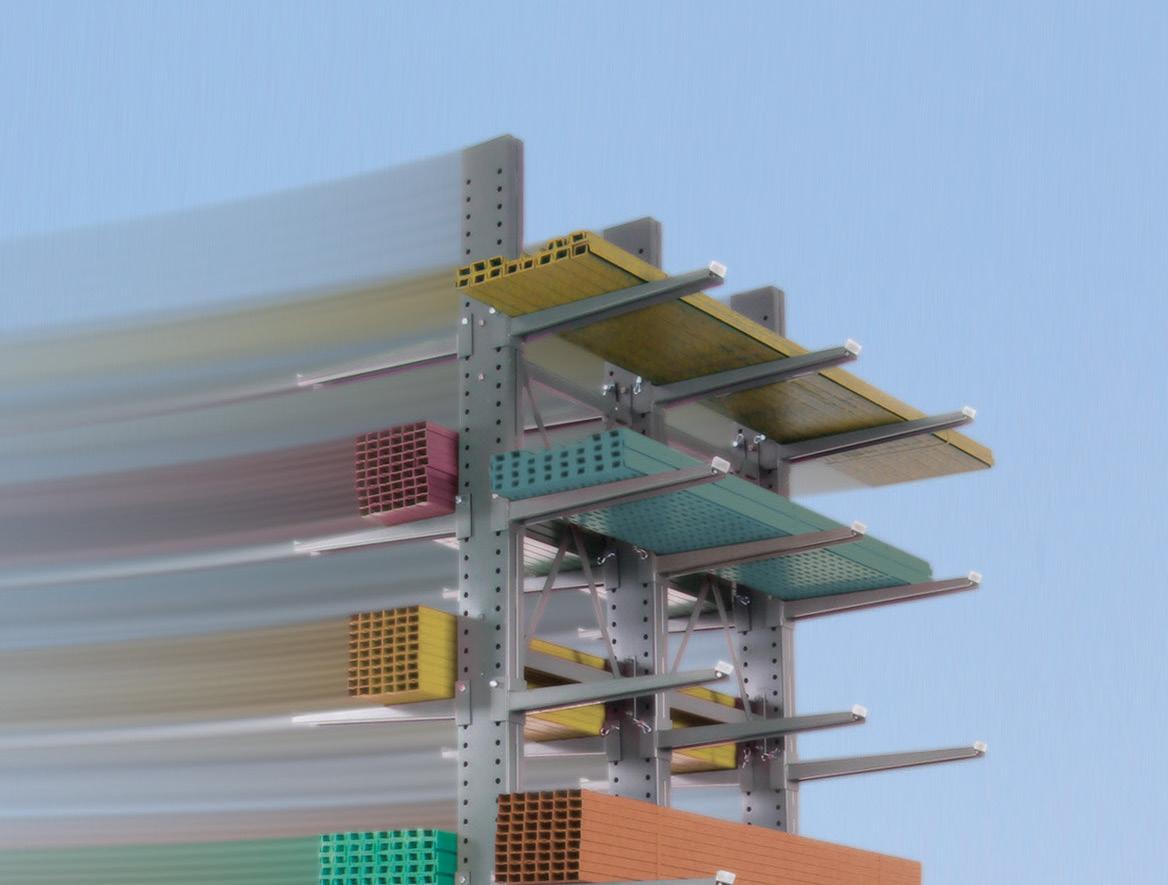
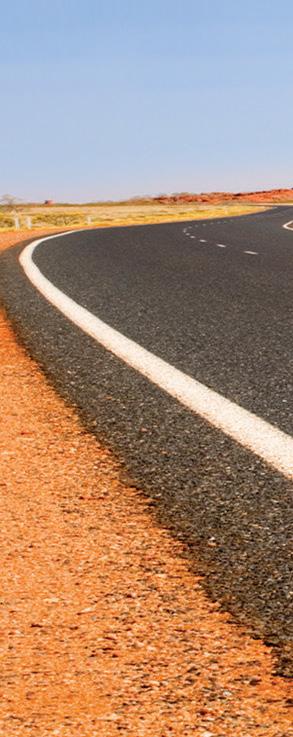

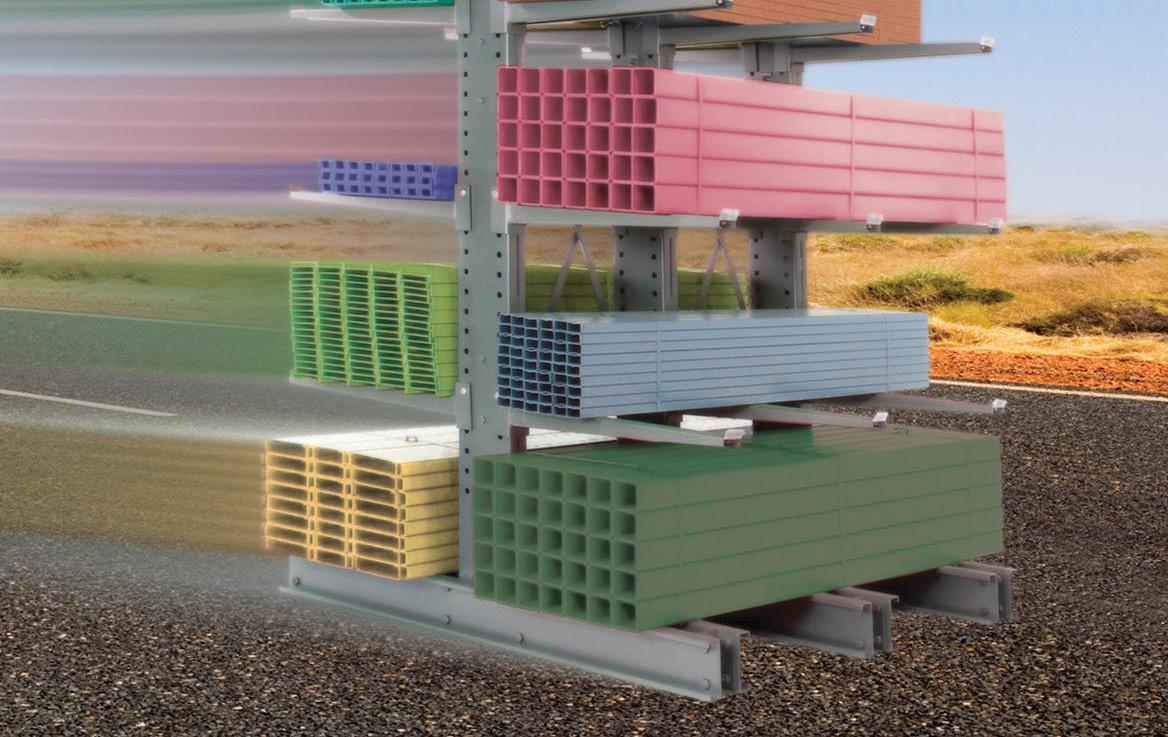
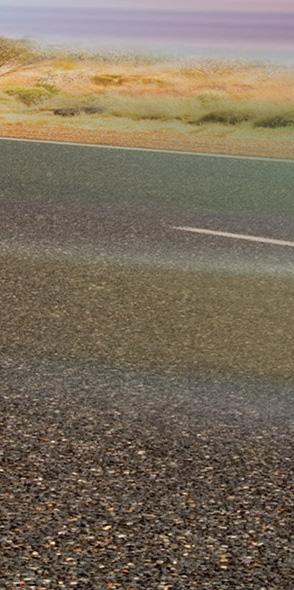
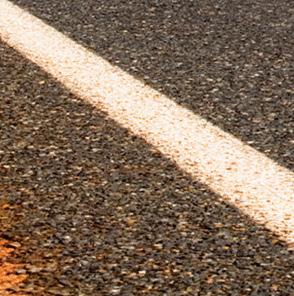

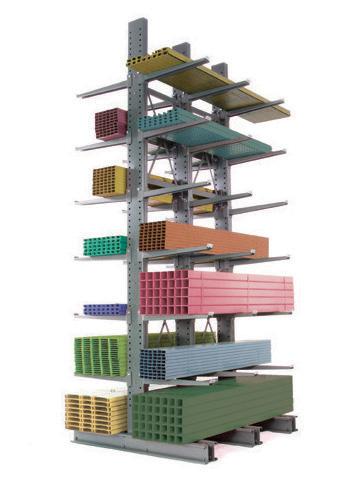
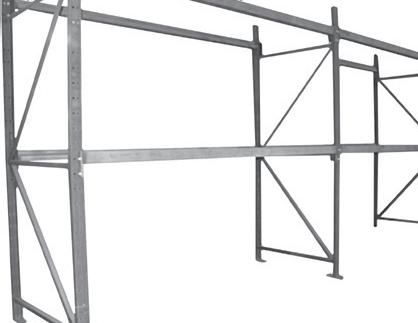

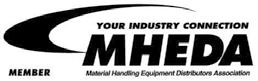
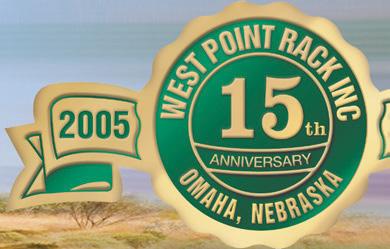
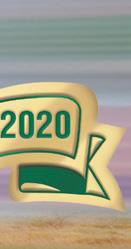