Contact Dyna Rack for your customer’s storage needs. 800/939-3962 • sales@dyna-rack.com • www.dyna-rack.com The Dealers’ Source For Portable RacksTM Customized designs are considered! Pallet Frames Stack Racks Nestable Racks Stock Available on some sizes & designs Made in the USA OCTOBER 2022 Call or email Kip Krady 563 kip.krady@MHNetwork.com557-4493tobeinournextissue!Deadline:October14th
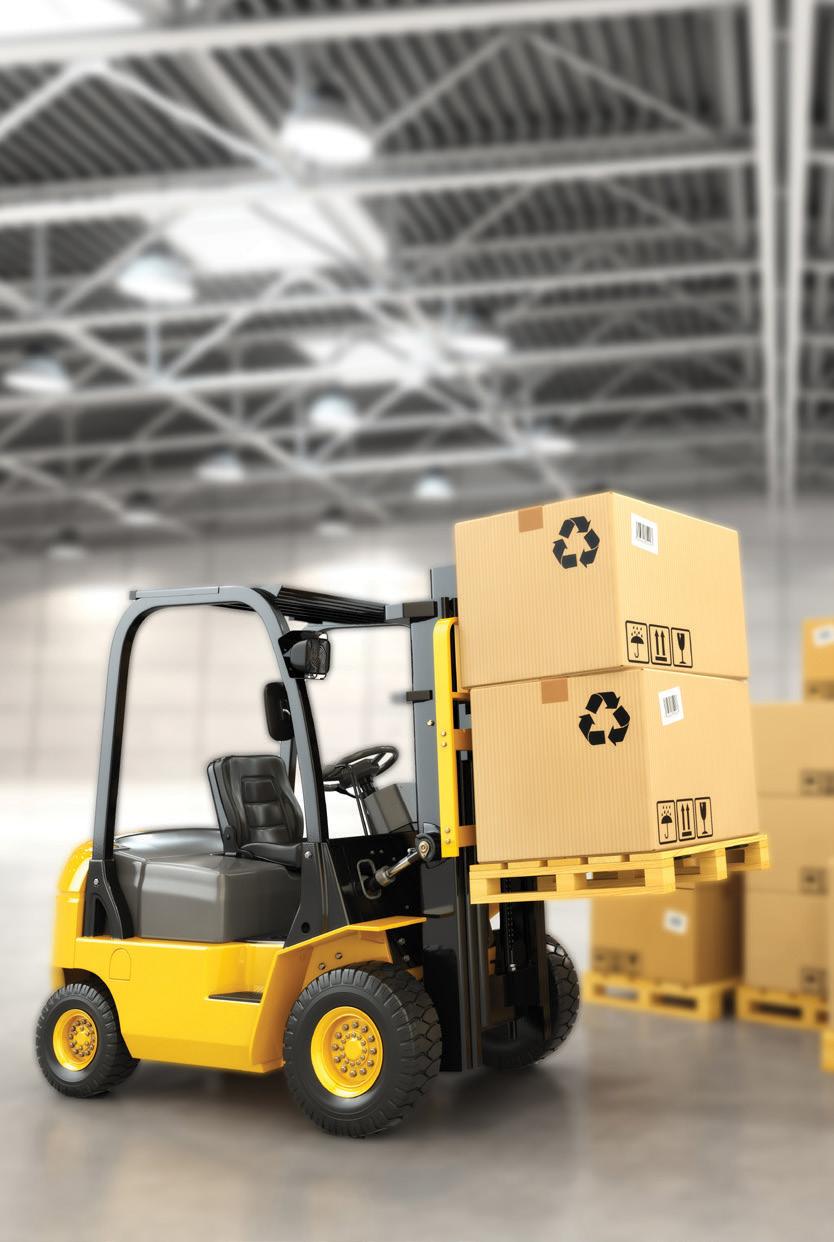


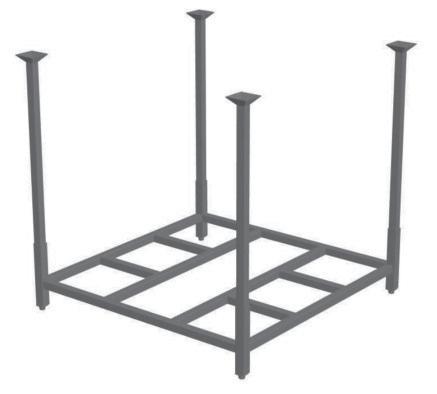
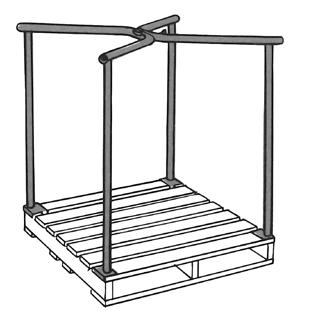
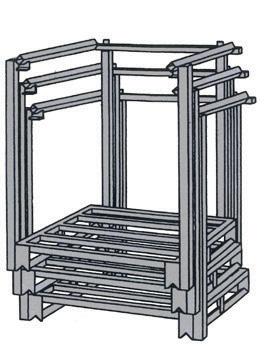
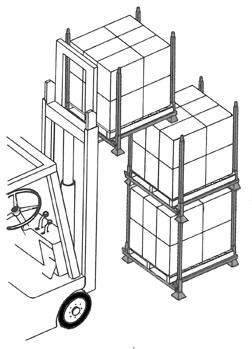
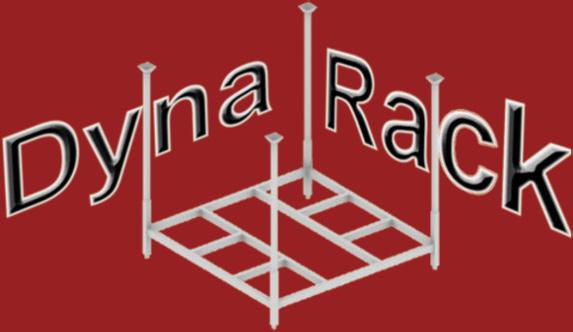
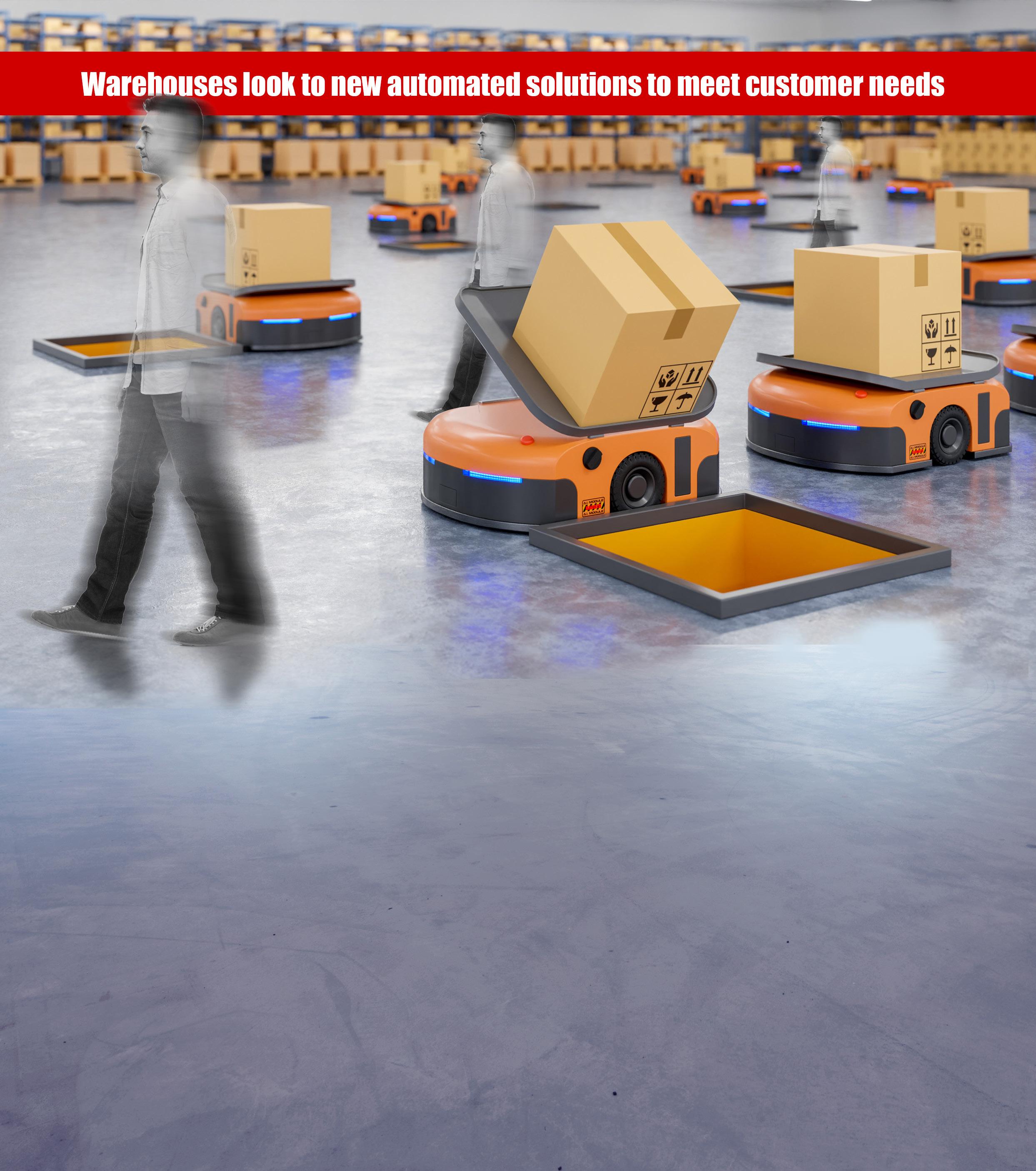
A2 2021Material Handling Network_Directory full page_7.25x 9.75.indd 3 6/28/21 1:00 PM
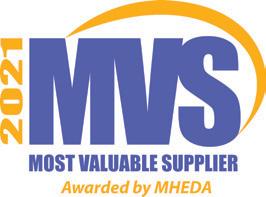
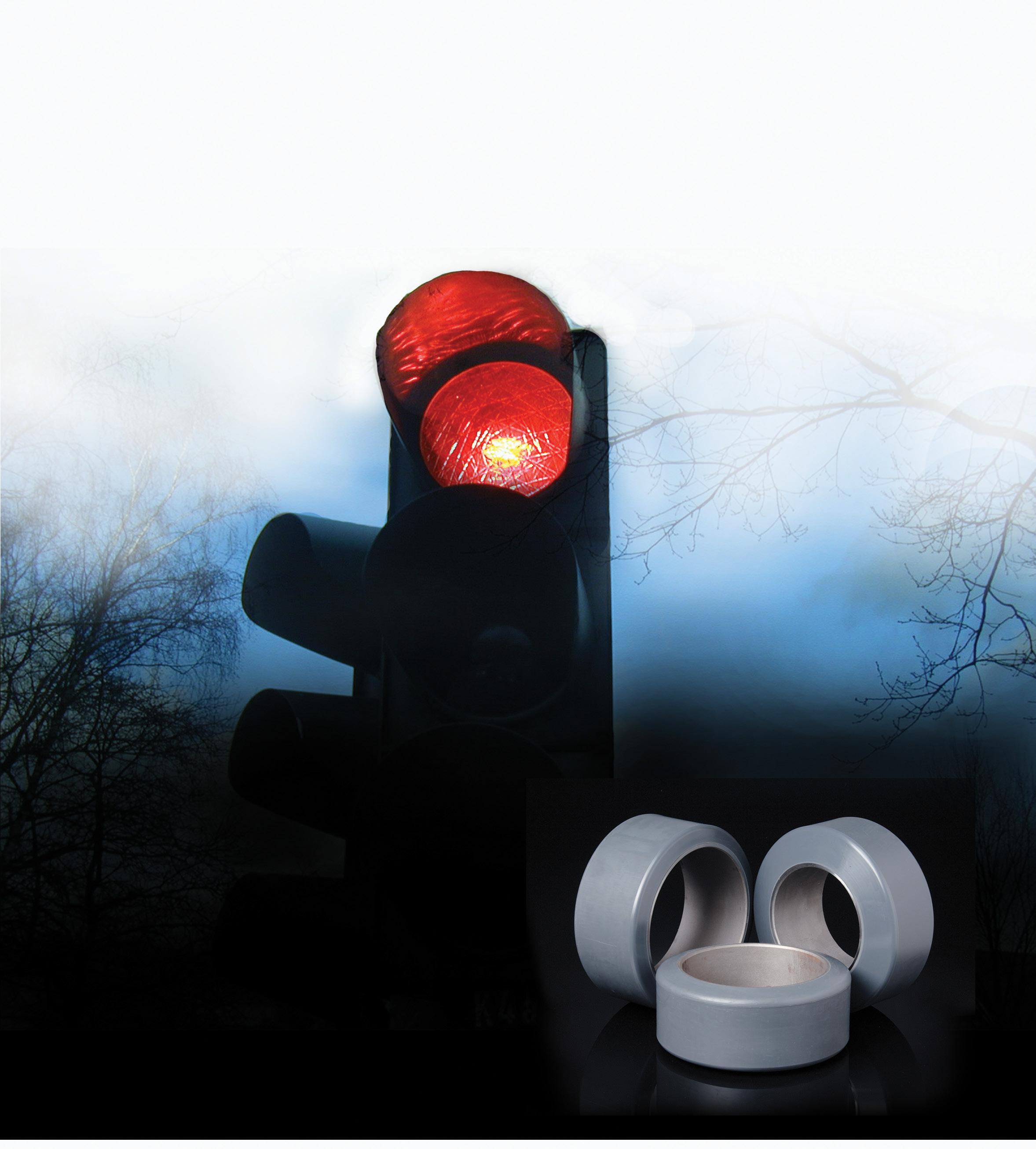
www.MHNetwork.com Material Handling Network October 2022 3 Give Them AIT’S QUALITY & YOUR SERVICE. American 20395TransmissionIndustrialInc.HannanPkwy.WaltonHills,OH Fx 440-232-8142 sales@aittransmission.com www.aittransmission.com 800-588-7515 Give ThanCustomersYOURMORETheyEXPECT. Reman Transmissions Reman Torque Converters Transmission Rebuild Kits Reman Drive Axles Reman Steer Axles Let us be an EXTENSION to your COMPANY!
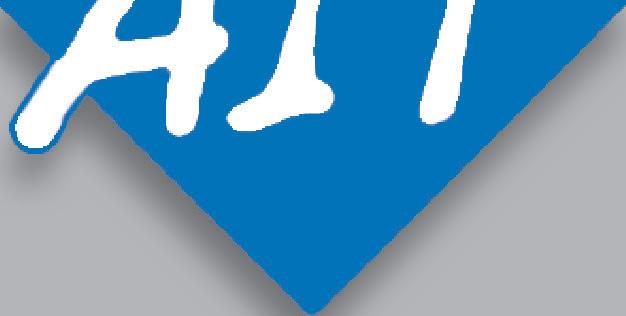
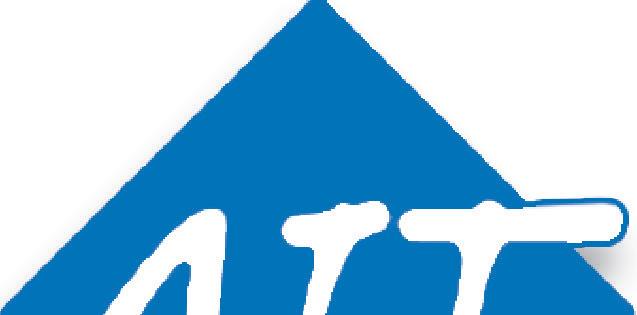
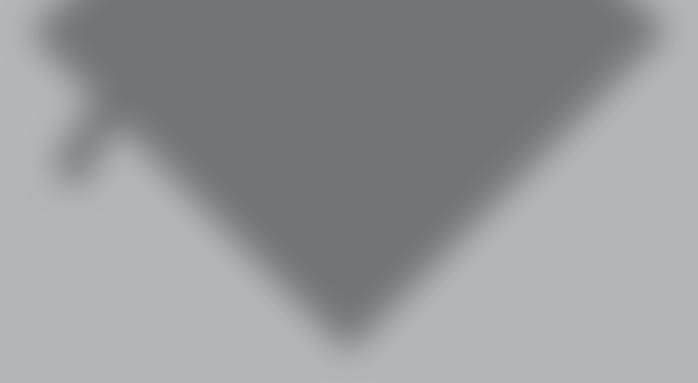
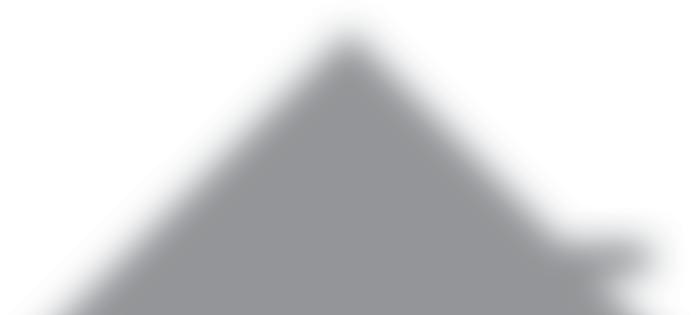
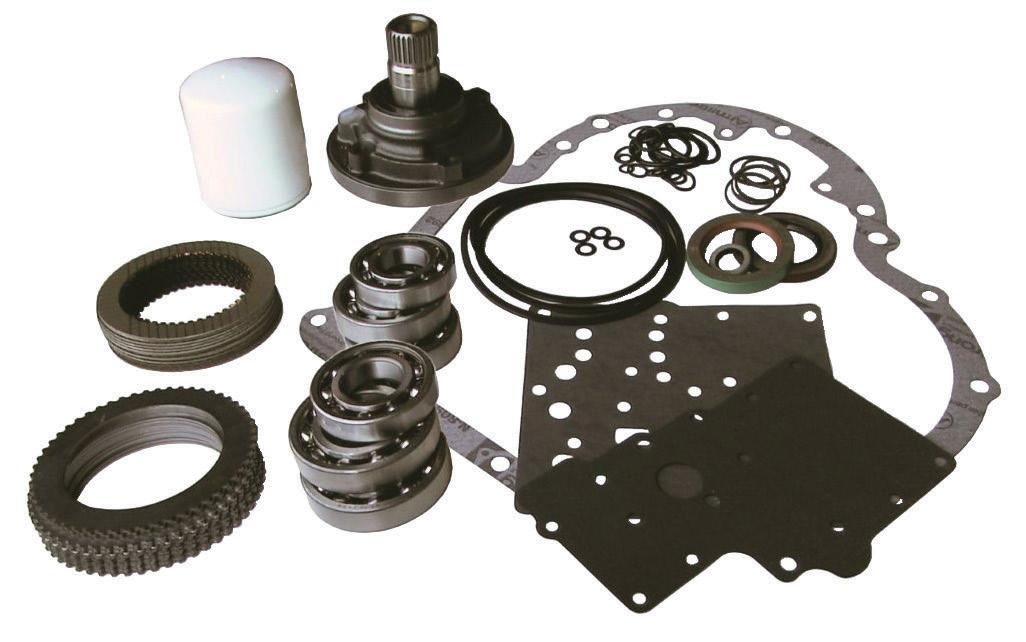
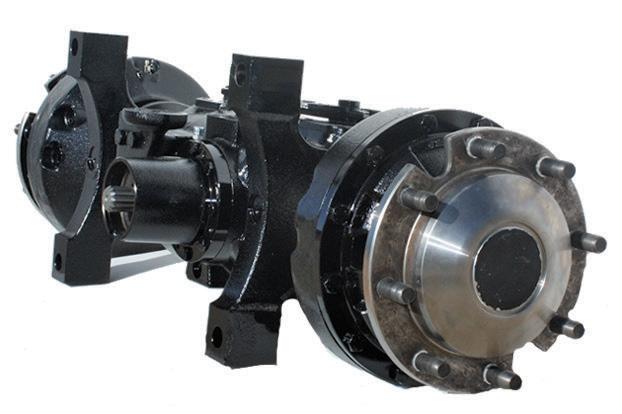
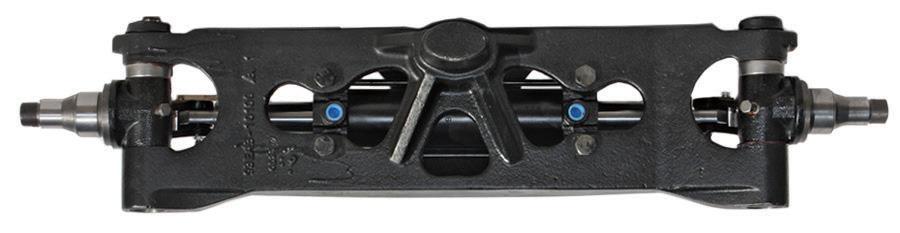
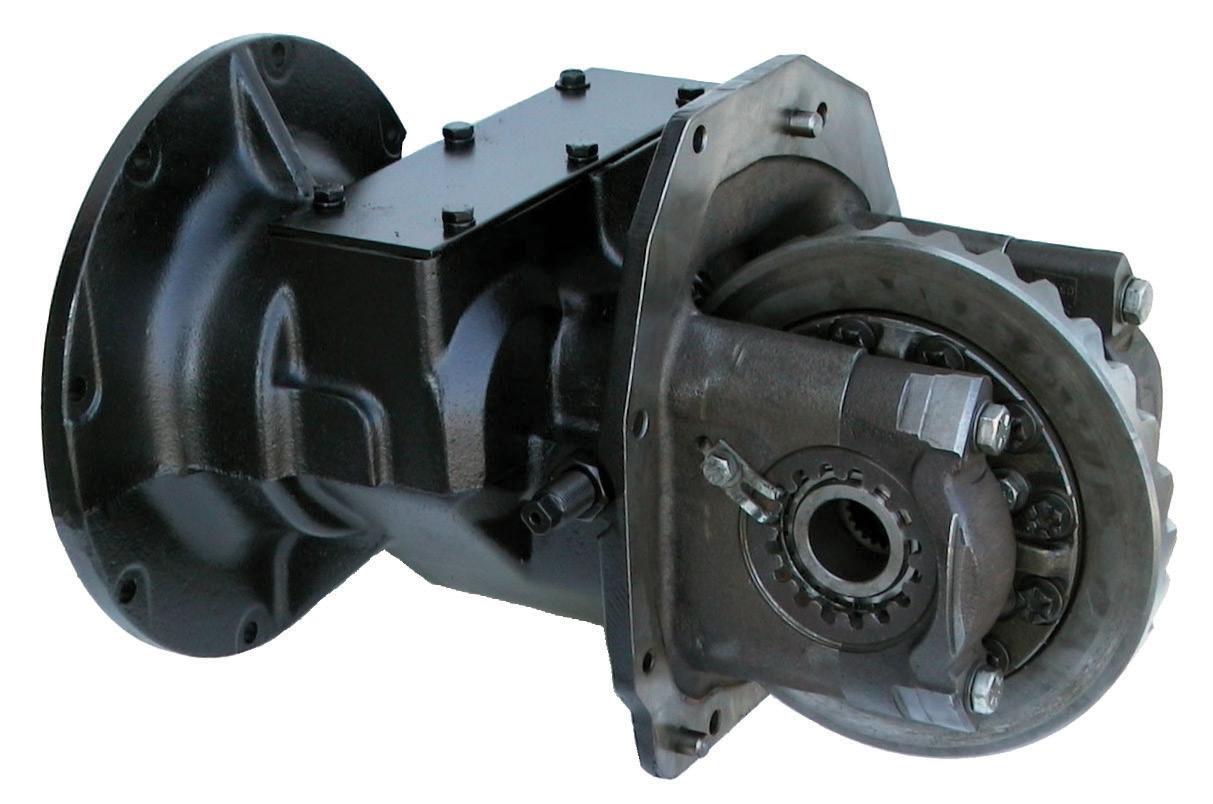
4 October 2022 Material Handling Network www.MHNetwork.com OCTOBER 2022 VOL. 41 NO. 9 6 Cover Story By: Eileen Mozinski Schmidt Automated Advances: Warehouses look to new automated solutions to meet customer needs 12 Safety First By: Patrick Hardy Transform employees to emergency responders in three easy steps 16 Chain Reaction By: Bill Denbigh The Future-Focused Playbook: What to do before automating your warehouse 20 Business Management By: Jeremy Eskenazi Why conscious curiosity is the Soft Skill separating good recruiting, from great recruiting 24 Industry News 28 People News 30 SalesLeads 36 Product Showcase 40 Marketplace 42 Advertiser Index Don't miss our next issue: Sales and Technology - This issue will examine ways to increase sales and time efficiencies by switching things up from your daily routines. Deadline: Friday, October 14th INFORMATIONCONTACT KipAccountKradyExecutive 563 557-4493 kip.krady@MHNetwork.com. Nikole Hoffman Production Lead, Graphic Design EricGraphicFaramusDesign Have some news to share with Network readers? Email a word doc and JPG photo when networkeditorial@MHNetwork.comavailableTOSUBSCRIBETOMATERIALHANDLINGNETWORKVISITUSATwww. MHNetwork.com Material Handling Network (ISSN #21551685) is published monthly serving the material handling industry. Editorial opinion expressed herein are the authors and do not necessarily reflect the opinion of Material Handling Network. Material Handling Network assumes no responsibility for inaccuracies, errors or advertising content and reserves the right to reject or cancel any advertising for any reason, at any time.
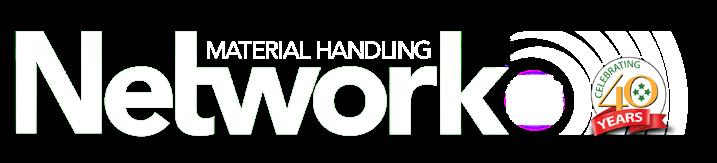
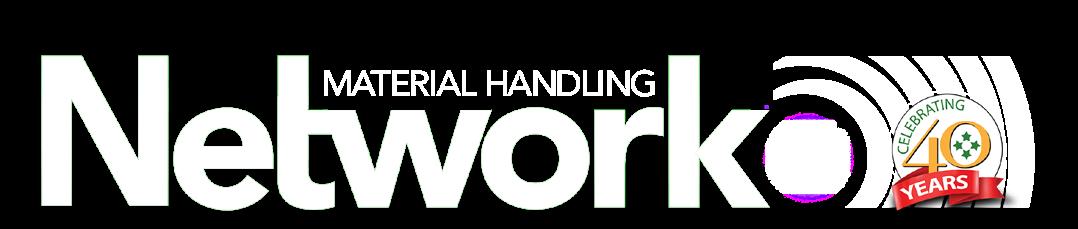
www.MHNetwork.com Material Handling Network October 2022 5Sans titre-2 1 2022-09-16 14:38:02
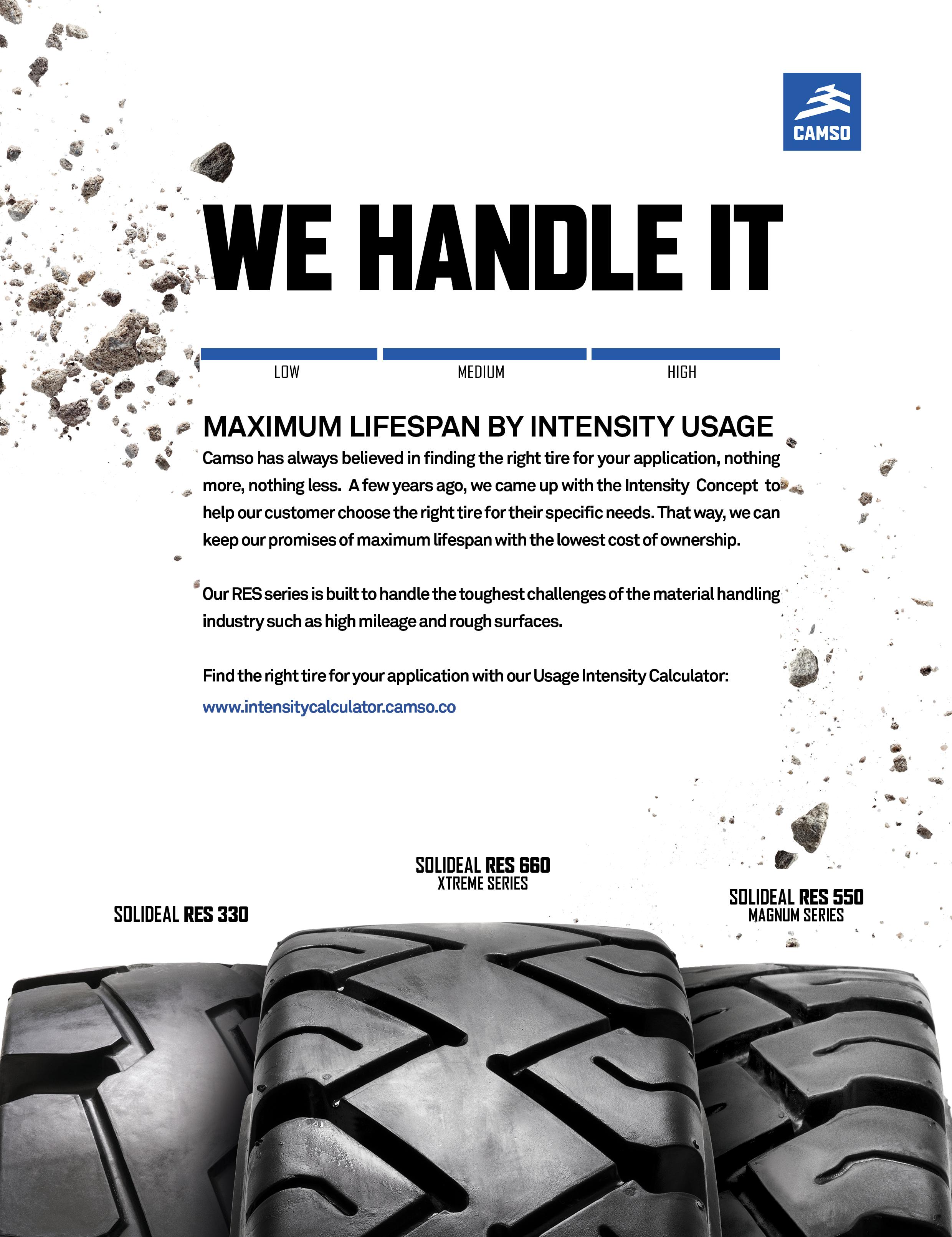
Pandemic conditions have improved, but the new era of labor shortages and increased demand continues for warehouses. In this environment, some say a steady increase of automation within warehouses is occurring. This month, Material Handling Network talks with industry leaders about how they see automated processes building new opportunities in warehouses across the industry.
At AutoScheduler, CEO Keith Moore said the company aims to be “the brain” inside distribution centers. The company launched two years ago inside Procter & Gamble, where Moore said the business founders “cut our teeth.” AutoScheduler.AI is a warehouse resource planning and optimization platform that “dynamically orchestrates all activities on top of your existing warehouse management system in real-time,” the business website said. The solution is designed to focus on and optimize all of a warehouse’s critical activities, including dock scheduling, loading, unloading, case picking, and creation of transfer orders, the site said.
A ‘time to shine’ for warehouses
“With more supply chain challenges than ever, AutoScheduler combines data from numerous systems into a single operational plan for warehouses and distribution centers. It takes disparate data, identifies bottlenecks, and prescriptively creates plans to orchestrate campus operations for optimized efficiency,” the website said. The aim of the company is to help planning to be more effective, according to Moore, who said today AutoScheduler workers with some of the largest consumer goods providers in the industry.
As a solution designed to work on top of a Warehouse Management System to orchestrate plans and processes, AutoScheduler is able to work many moves ahead of what is occurring, according to Moore. He said this is not unlike how technology is now able to orchestrate outcomes in a chess game. In chess, there are 64 squares and 16 pieces under a player’s control, and “since 1997, it has been impossible for a person to beat a computer,” said Moore, noting how many moves ahead a computer can see.
Similarly, AutoScheduler is designed to incorporate a bigger picture in coordinating items, people, and equipment. The more complexity, the more opportunity, according to Moore.
In the current environment, Moore said he believes inventory concerns for warehouses might “smooth out a bit” but labor will remain in demand. “That’s part of why automation has become so popular over the past few years,” he said, noting there are fewer employees working many years on a job, making it more difficult for companies to build the productivity and consistency desired.
Cover Story
6 October 2022 Material Handling Network www.MHNetwork.com

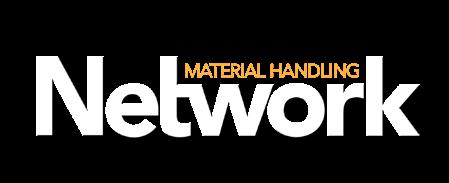
Automated Advances: Warehouses look to new automated solutions to meet customer needs
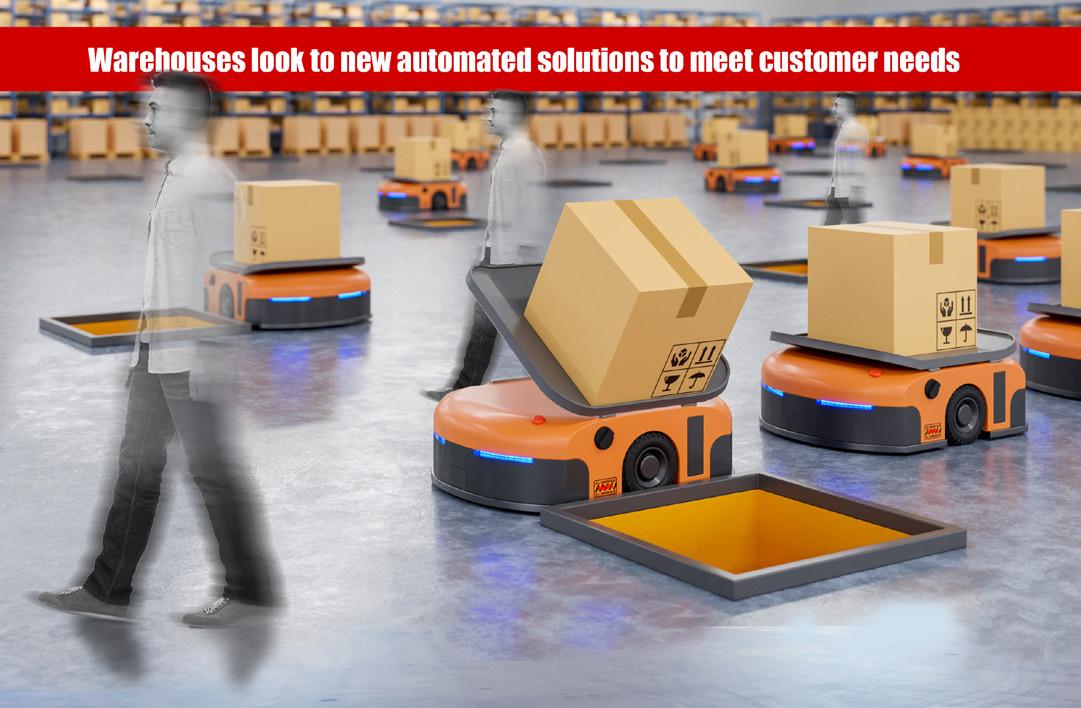
www.MHNetwork.com Material Handling Network October 2022 7 RedefinedSpaceautostoresystem.com When Productivity and Accuracy Matter AutomationMaking Easy AutoStoreTM is the fastest order fulfillment system per square foot on the market. It combines extreme storage density with high throughput technology making it a perfect fit from big warehouse to dark store to the backroom of small urban stores. AutoStore is custom configured and fully simulated, giving you assurance in your investment before the project begins. It delivers the automation you need for customerwinning order autostoresystem.comfulfillment. When Productivity and Accuracy Matter Enrich Your Customer Experience AutoStore reduces your storage footprint, providing space to expand services and products. Gain visibility of your operations and enhance your customer experience. 24/7 Operations Our unbeaten up-time (99.6%) and no single point of failure means you have access to your inventory supporting 24/7 operations. Making Automation Easy AutoStore is custom configured and fully simulated, giving you the assurance in your investment before the project begins. Grow While Running AutoStore is designed for easy system expansion. Grow your capacity without shutting down operations or experiencing downtime.
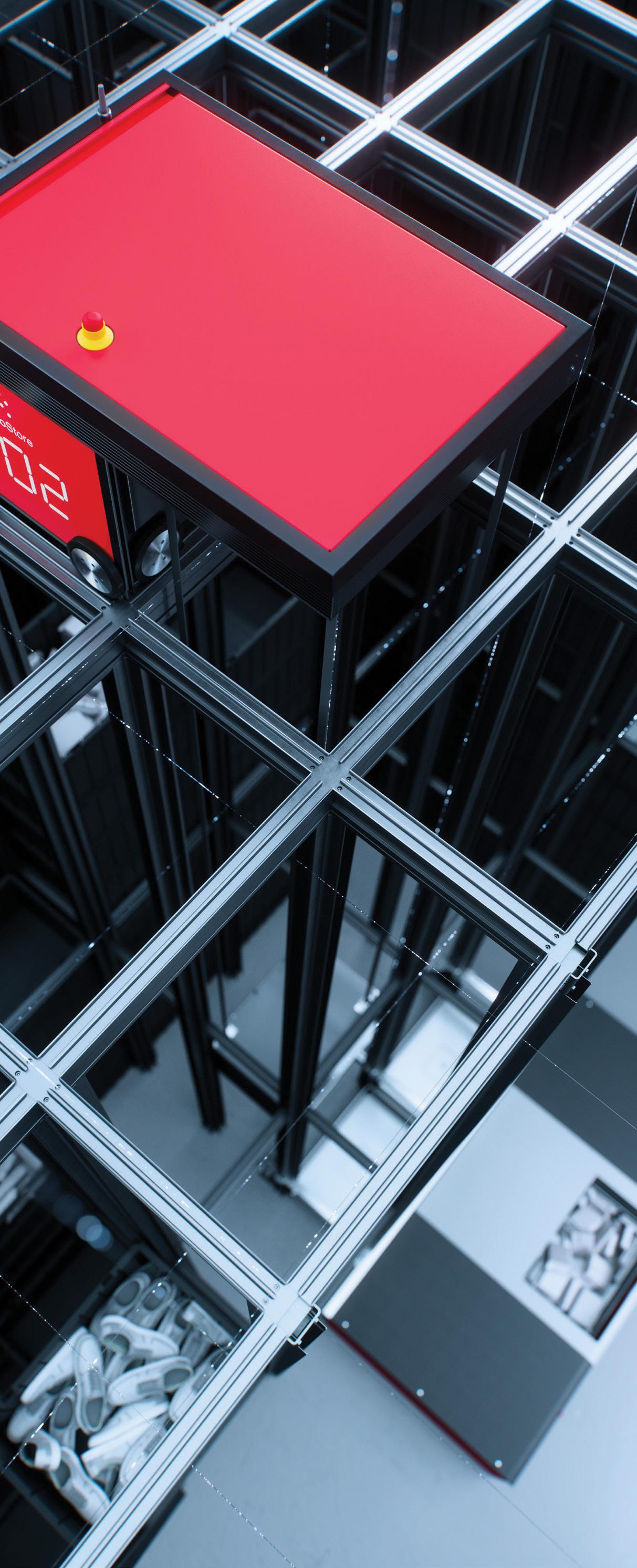
Automation advances
He said AutoScheduler solutions help to orchestrate planning systems, making sure all of the processes flow and work together. In general, Moore thinks productivity rates are a little lower today versus five years ago due in part to the impacts of labor shortage. “It’s hard to replace a really experienced forklift driver,” Moore said. That said, he also believes warehousing and operation teams are more innovative now.
8 October 2022 Material Handling Network www.MHNetwork.com
“Warehouses are probably getting the investment needed,” said Moore, who said there are more technologists and more investment in automation overall. And as focus outside the industry focuses on supply chain and material handling in general, Moore added that it is a “remarkable” industry to work in. “It’s warehousing’s time to shine,” he said. “We can take opportunities and take advantage of what we have to innovate and drive value.”
Automation offers ways to personalize, create unique packaging options, and more, according to Denbigh. He is seeing more engineering work in warehousing, describing one of Tecsys’ customers, a third-party logistics provider, that has many engineers on site. “They take an organization in and say, ‘We’re going to design a system for you. Specific racking, processes, we’re going to allow you to do these things,” Denbigh said.
He also described how one of Tecsys’ customers designed systems to create the special sustainable packaging their own customers wanted. “It’s not going to slow down. It’s going to be a force,” he said, of automated advances, describing how his wife’s shampoo company sends her the product she wants when she needs it and with her name on the label.All
“Think of the technologies that are required to supply that,” said Denbigh, noting how well this tailored approach works. “It’s locked in my wife as a consumer,” he said. A grocery retailer, however, would not require this type of system, according to Denbigh. So, he envisions a future of specialization withinTecsyswarehouses.offersdiverse solutions, from a simple warehouse management system that is implemented from the first touch to life in 28 days to an enterprise-grade system in which a project can be six to eight months, according to Polka. “Automation is not one thing,” he said, advising businesses to consider what a company needs and to make plans and adjustments from there.
Cover Story continued
there is a realization that adopting advanced supply chain solutions isn’t anymore just for the big boys,” Denbigh said. As automation solutions are explored in companies of all sizes, tighter circumstances are sometimes a driver, according to Denbigh. “I’ve got to get today’s orders out by 2 p.m. or I’ve got real estate issues I can’t outgrow anymore. Or I want to offer my customers a service that my competitors don’t offer or can’t,” he said.
Tecsys is also offering solutions for warehouses across the globe. The company’s supply chain solutions software is currently used in over 100 countries across the world, according to Adam Polka, Director of Public Relations. “Our solutions and services create clarity out of operational complexity with end-to-end supply chain visibility. Our customers reduce operating costs, improve customer service, and uncover optimization opportunities,” said the business website.
Bill Denbigh, Vice President of Marketing, described how many of the company’s Nordic partners have incorporated automation in operations of all sizes. “They look at automation as part of being a solution to the future. I think
“People are understanding they need to do something to get consistent productivity out of the warehouse, to be able to meet the demand in a consistent way,” Moore said. “The challenge is, people that run operations, they’ve been in supply chain and logistics for a while and they’re not technologists,” he said. This is where AutoScheduler can help, according to Moore.
of this requires a sophisticated process.
www.MHNetwork.com Material Handling Network October 2022 9 Before you invest in upgrading the infrastructure of your warehouse, find out how Combilift can increase your storage, improve productivity and enhance safety. With over 21 years’ experience in volume optimisation, our team of warehouse planning experts knows how to make your space work harder for Contactyou. us today to arrange a site survey! Our warehouse design consultancy service is FREE and without obligation. Save up to 50% more storage with CombiliftEfficiencyStorageSafetycombilift.com Combilift are leaders in providing innovative material handling solutions including sideloaders, 4-way forklifts and straddle carriers. They are designed to handle long and over-sized loads guaranteeing considerable improvements in space utilization and safety. With capacities ranging from 3,000 lbs to 220,000 lbs, it’s a safe choice to go with Combilift. Amanda 7.625 x 9.875.indd 1 03/03/2021 18:05:04
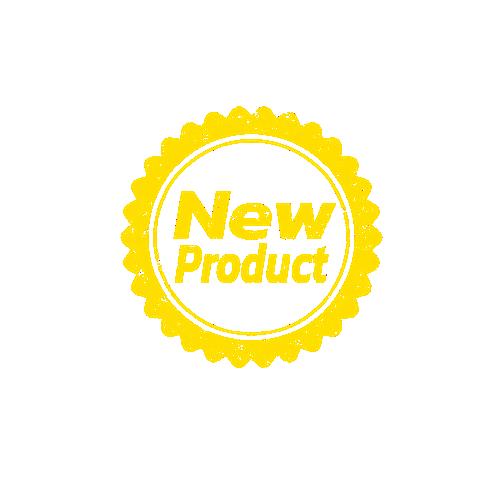
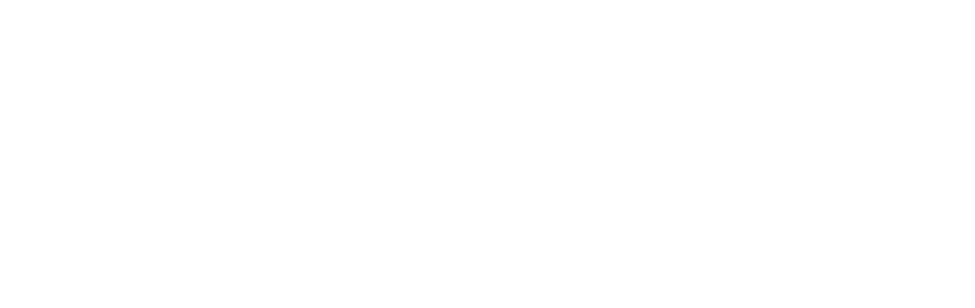
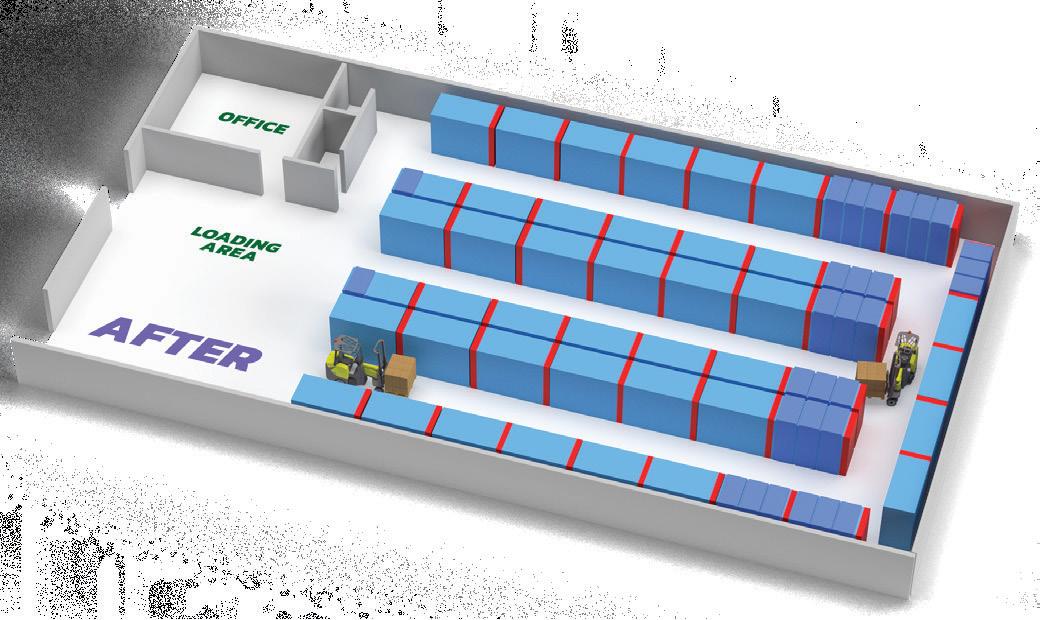
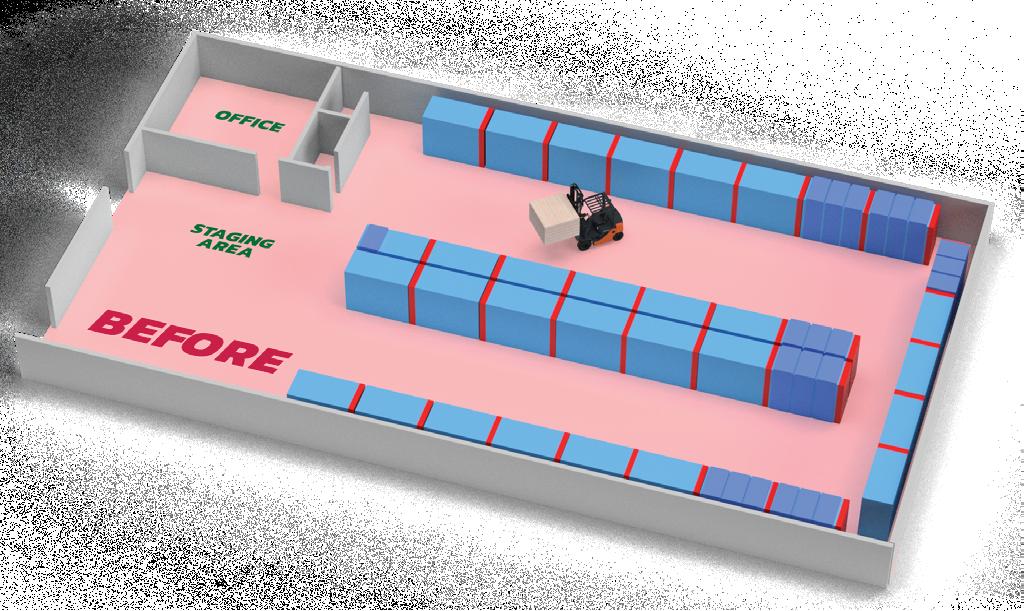
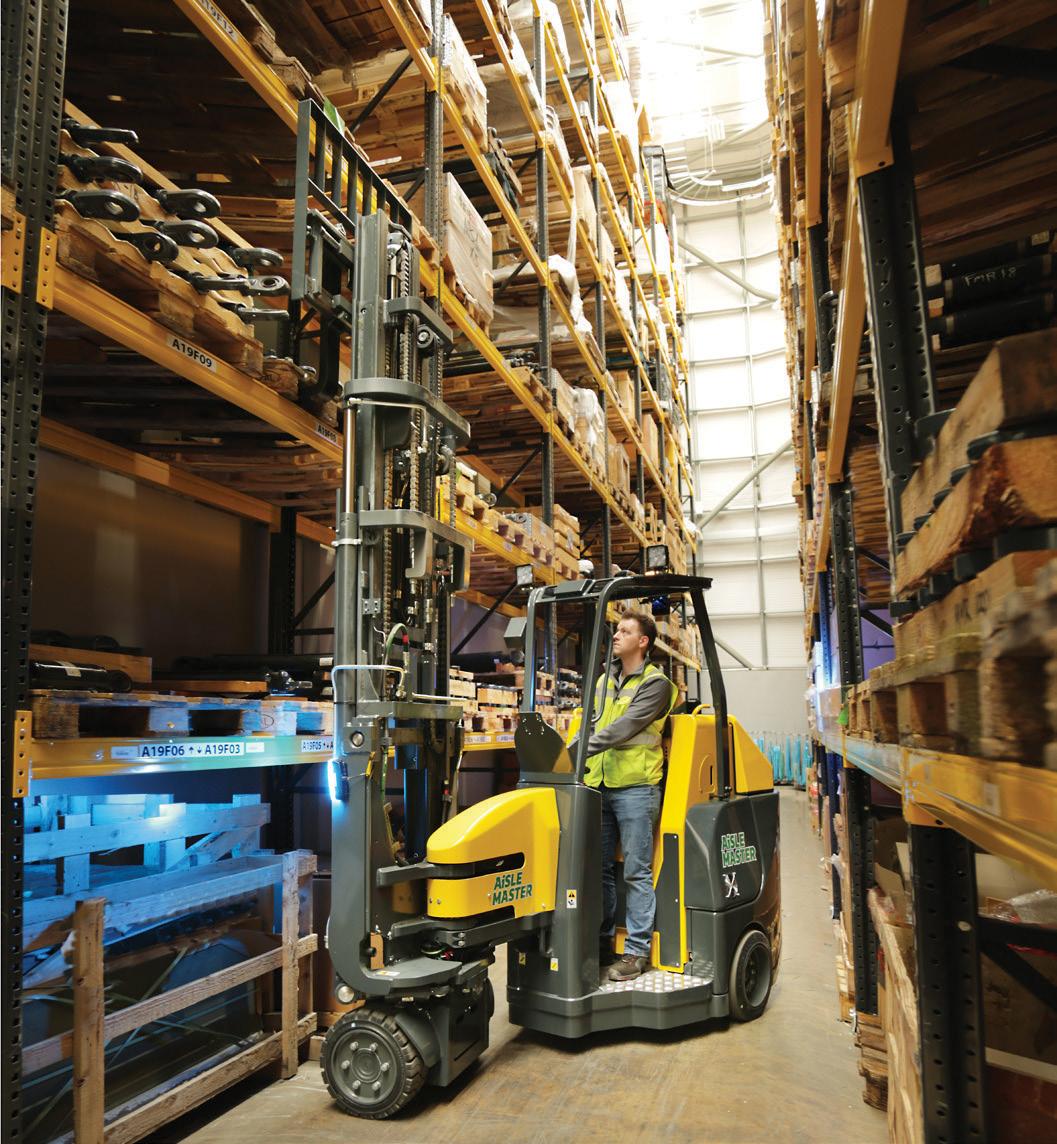
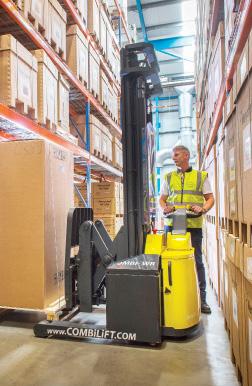
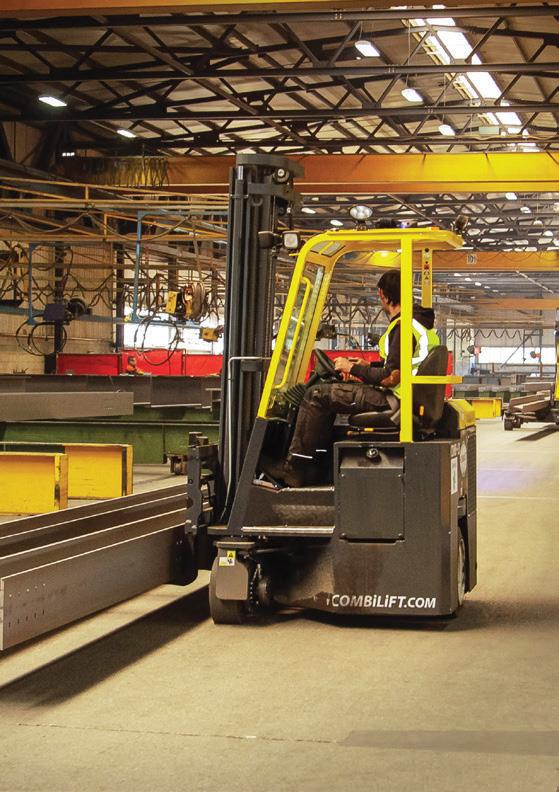
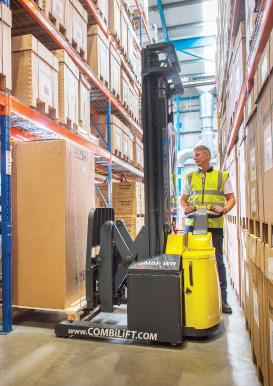
While automation used to be reserved for only large pallets or case warehouses, times have changed thanks to e-commerce, growing SKU catalogs, lean inventory policies, and increasing customer expectations, according to Jon Schechter, Business Development Manager at AutoStore. “In the past decade, new solutions, while important, have also contributed to the pile of brown cardboard boxes that accumulate outside our homes,” he said.
“For other brands, supply chain shortages have increased the need to expand storage depth onshore
“It’s a journey. You don’t take your first steps along a journey unless you know where you are going,” Polka said. “It’s all about understanding what you’re trying to solve, the specifics of where your business is going, and where you want it to be in a few years. The items you’re handling, the volume of orders, and the time frame. And then deciding what kind of automation is needed.”
In general, automation is becoming more accessible for warehouse operations, according to Denbigh. “It’s exciting times. There is a lot going on, there are a lot of people trying lots of things,” he said. While supply chain and labor issues continue, there is plenty of progress, too, according to Denbigh. “There’s a lot of success going on. Lots of projects happening,” he said.
Modern solutions tend to be modular, allowing warehouses to scale down to small and mediumsized facilities, according to Schechter. “What’s exciting is that this collaboration can increase the overall productivity of a workforce by 2 to 4 times,” he said, noting that modular solutions also allow for inventory to be condensed and therefore be located in distribution centers closer to consumers.
Automation is “an enticing draw” for employers in a tight labor market, allowing brands to restructure staff or to get more done with less workforce, said Schechter. In most cases, automation is a goods-to-person solution, which Schechter said can help increase order fulfillment ties exponentially and allow warehouses to better utilize existing resources. The time it takes to deploy automation in a warehouse hinges on several factors, according to Schecther.
Cover Story continued
Modular solutions
“At AutoStore, we’ve been able to deliver working systems in three months, but our standard lead time is 12 weeks from purchase order to delivery from our factory,” he said, noting that one of the most important things to keep in mind when moving to automation is the amount of time needed to implement the system in the distribution center. “So plan for six to 12 months for most automation projects. In this time period, detailed design, site readiness, software integration, and project planning need to be considered as well,” he said.Companies should also take into account business growth. “The storage capacity you have at the moment may not be best later down the road. Phasing can allow a seamless transition within a live operation, and more than half of the systems we deliver at AutoStore are expanded at some point to meet growing storage and/or throughput needs,” Schecther said.
10 October 2022 Material Handling Network www.MHNetwork.com
To help work around delays that sometimes occur, Schecther advised planning ahead. “The material handling industry has not been immune to the component and transportation delays of the past two years. Shortages put a major strain on distribution centers because e-commerce orders do not cease just because inventory is low,” he said. “At AutoStore, we’ve been able to predict and communicate lead times regularly to ensure we meet customer’s desired dates,” Schecther said.
Denbigh agreed. “Automation’ is such a multifaced thing. Just because you’ve got cobots running around doesn’t mean you’ve solved your problem,” he said. Denbigh noted some of the low-impact, easy-to-implement automated systems available today didn’t exist five to ten years ago. Mid-to-small size warehouses can adopt them with a level of skill and technology,” he said.
www.MHNetwork.com Material Handling Network October 2022 11
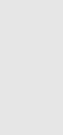
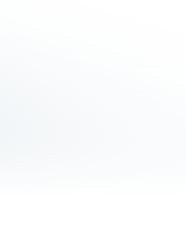
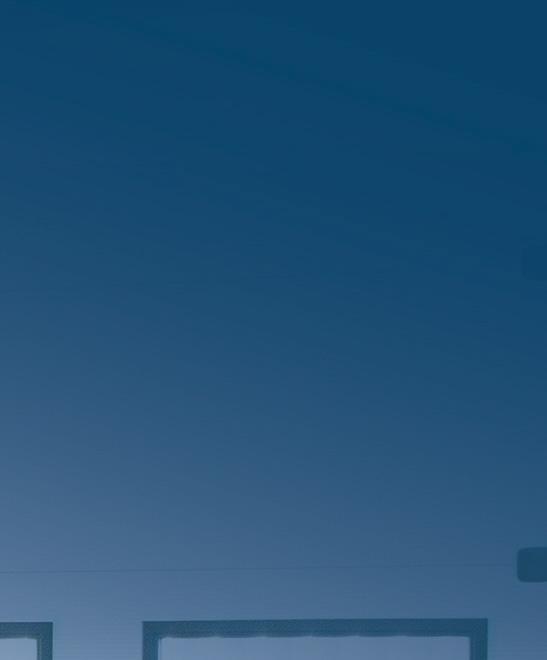

REMANUFACTUREDCONTROLLERS Keep Your Fleet Moving with FSIP's New and Remanufactured Controllers. Flight Systems Industrial Products 1-800-333-1194 · shop.fsip.biz Milwaukee, WI USA • docklite@phoenixlighting.com phoenixlighting.com/docklite The Original Always stocked. Always available. Industry-leading dock lights since 1960, available now with short lead timesFor more Cover Stories www.MHNetwork.comvisit
Cover Story continued to meet demand. This is where automation can play a major role. When the automation solution reduces storage footprint but increases the storage density, there is the potential to increase the SKU volume and breadth,” he said.
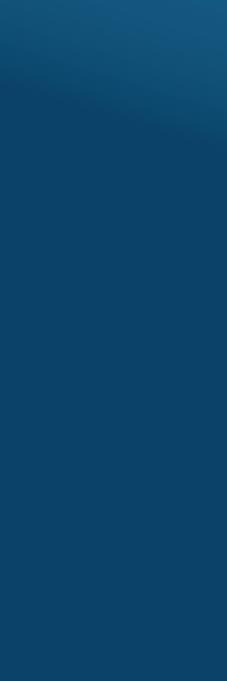
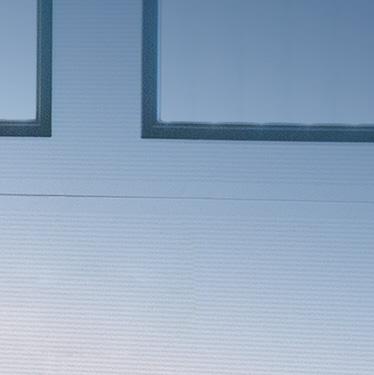
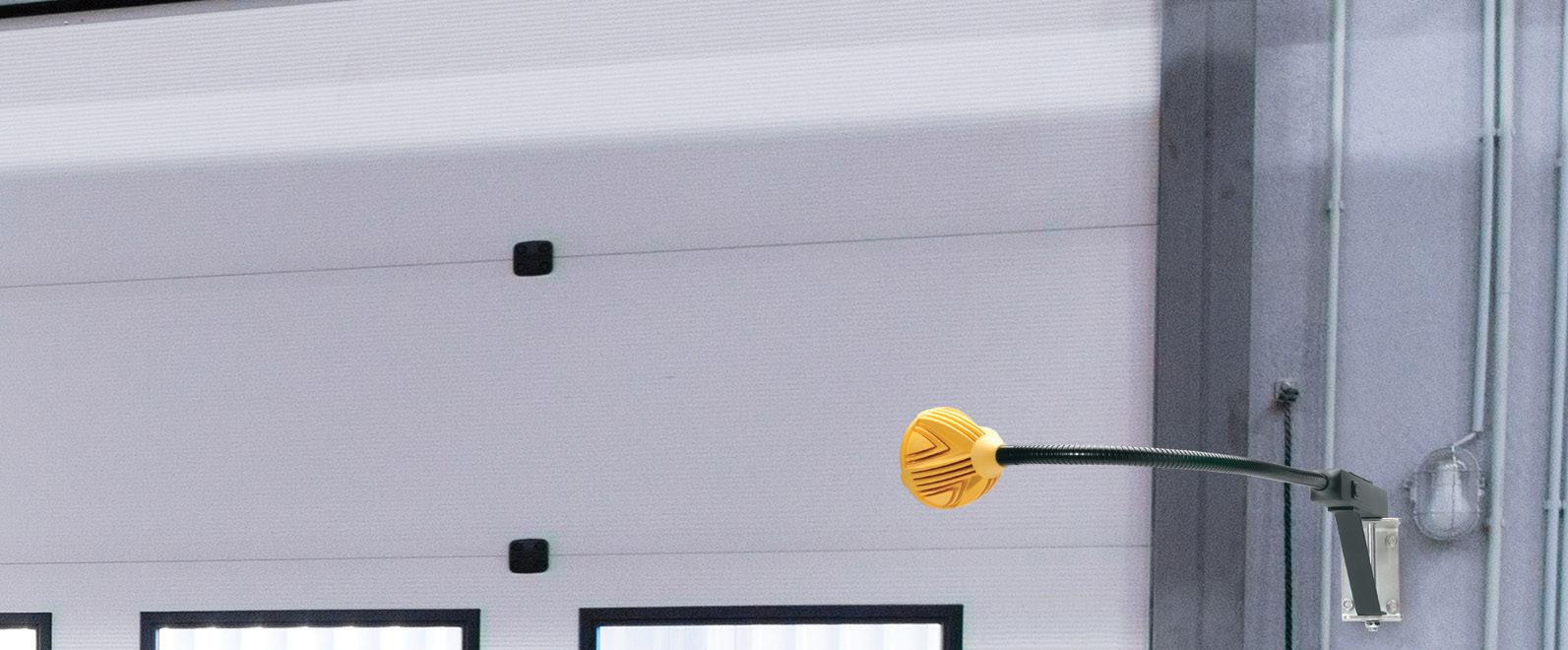


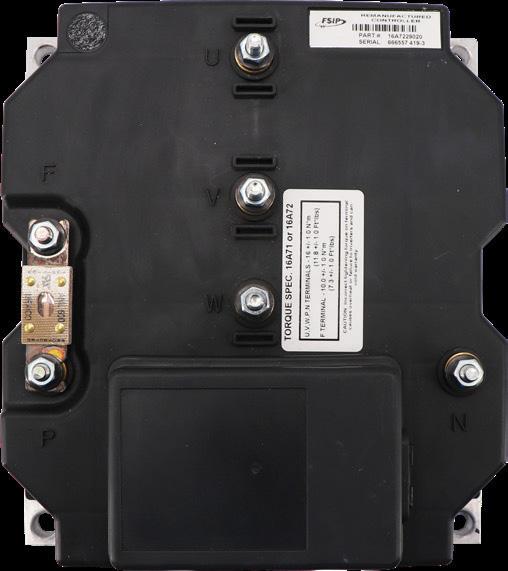
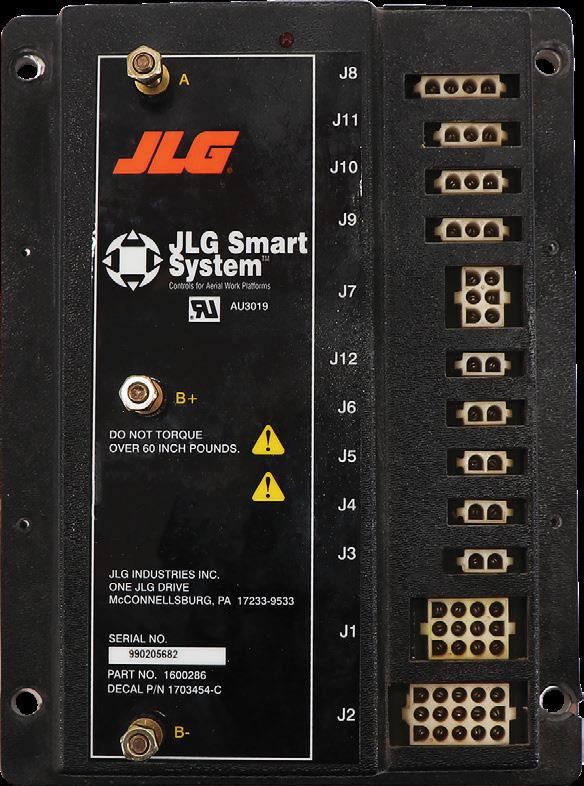
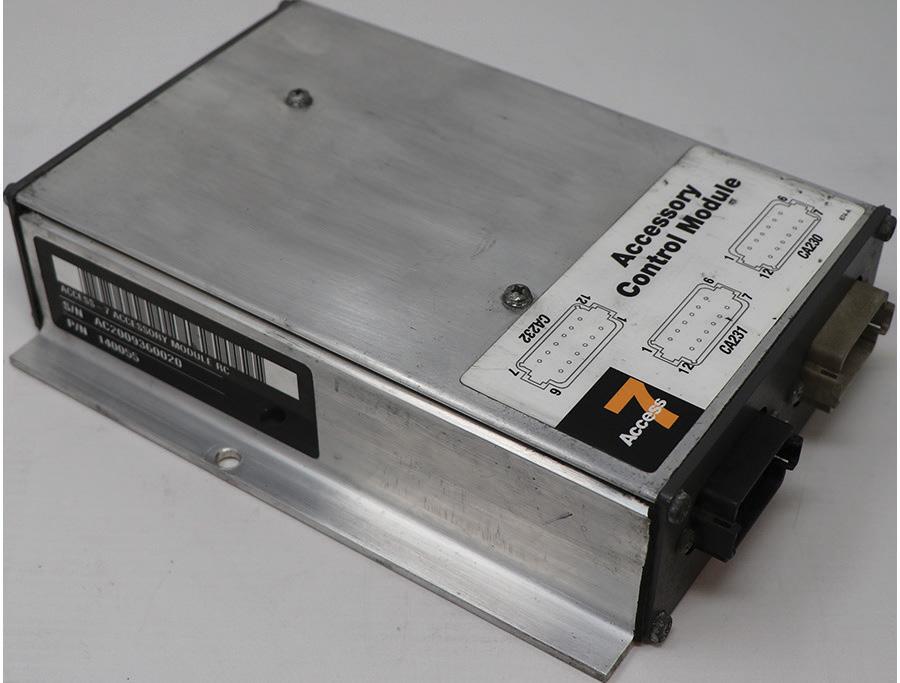
Eileen Mozinski Schmidt is a freelance writer and journalist based in the Greater Milwaukee area. She has written for print and online publications for the past 13 years. Email Networkeditorial@ MHNetwork.com or visit eileenmozinskischmidt.wordpress.com to contact Eileen. If your company would like to be featured, email Networkeditorial@MHNetwork.com
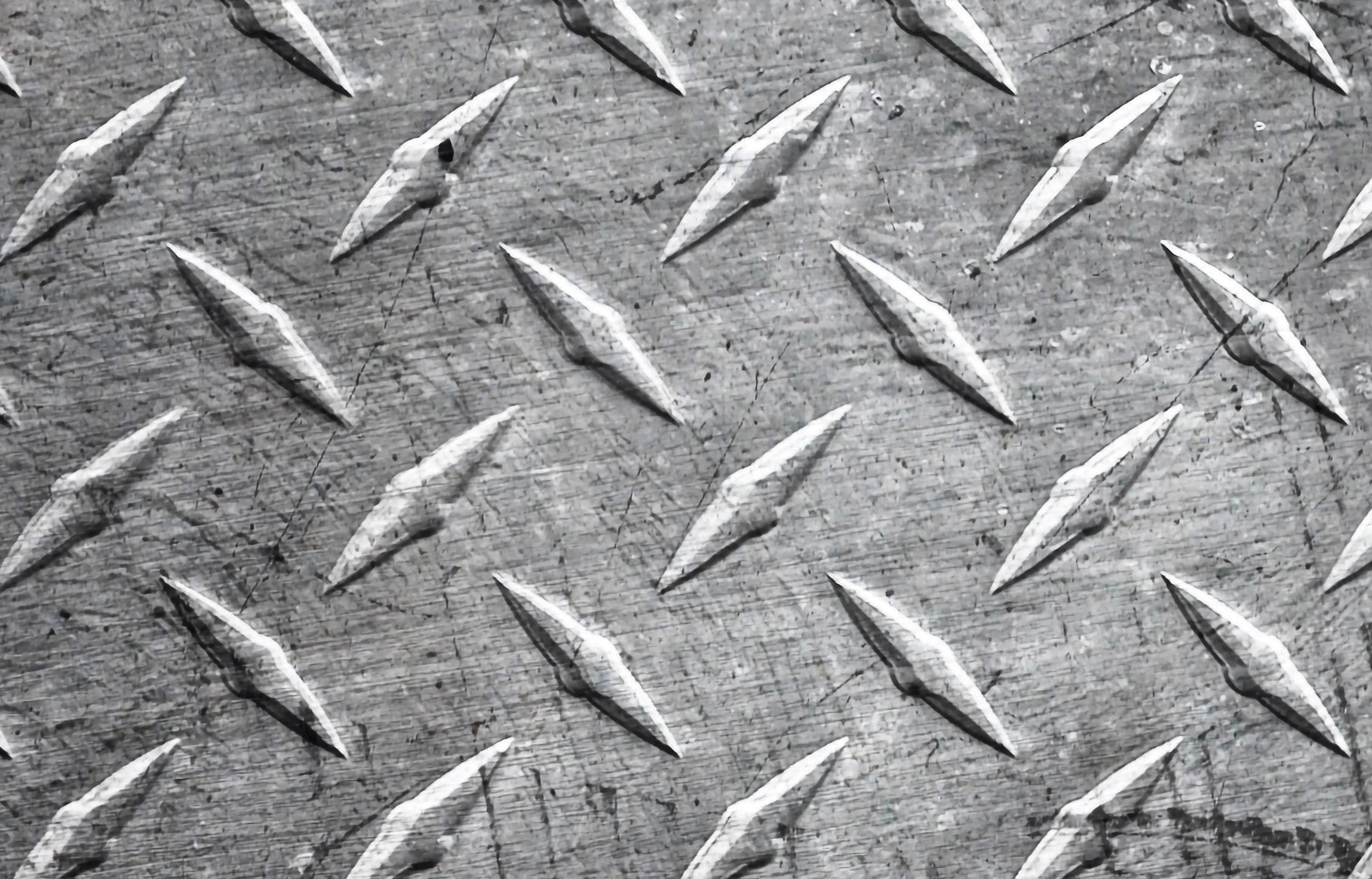
Safety First
Step 3 – Redesign Your Training and Drills
Disaster plans should be immediately rewritten so that employees are able to conduct any immediate response activity surrounding evacuation/shelterin-place/lockdown without the need for a manager. All manager titles and proper names should be removed from disaster protocols so that any employee can perform any action without any kind of permission required.
Responding to disasters is one of the most important activities that employees can be asked to grapple with. From natural disasters like hurricanes and earthquakes to technological situations such as power outages, chemical spills, and transportation accidents, as well as security emergencies like acts of terrorism and mass shootings, a property should be prepared for any of these. The metric for success in a disaster response is not the detail of the plans or the usefulness of the equipment. It’s the level of employee empowerment that makes all the difference. Employees must go beyond being just bystanders who are told what to do. They must be transformed into emergency responders capable of activating themselves and leading in the instant a disaster strikes.
Step 2 – Reevaluate Your Disaster Equipment and Supplies, and Technology (EST)
12 October 2022 Material Handling Network www.MHNetwork.com

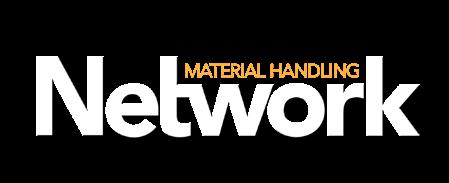
Currently, most property disaster plans expressly hand off leadership responsibility of a disaster response to management. This would seem the most logical way of handling it. However, in practice, this leaves a property underprepared. Disasters can be sudden events that either leave managers injured or unavailable through traditional communication devices. When disaster plans require a manager to approve a certain immediate disaster activity like initiating a basic evacuation or crisis communication method or explicitly stating that managers must perform it, they immediately convert employees into useless bystanders.
Transform employees to emergency responders in three easy steps
Disaster Equipment, Supplies, and Technology (EST) has long been considered a critical element in any property preparedness program. However, in most instances, EST has actually made properties less prepared. This is because either employees are not authorized to use them without permission of management, and/or they are inaccessible to employees. This goes way beyond the first aid kits or AED defibrillators. It also includes disaster equipment like search and rescue tools, emergency food and water, and critical use supplies like flashlights, rope, and PPE masks. Many properties also have specialized emergency communication mobile apps and expensive technology which they rely on. Ironically, this is what makes them not prepared because it shifts the dependency on equipment to do activities that, if they were not available, could not be performed by staff or management.Tobeeffective, disaster EST must be specifically tailored to your employees. It should sync up perfectly with your disaster plan. For instance, if your plan doesn’t include search and rescue, then don’t put those supplies in your bags. Technology should also be used sparingly in a disaster. But when it is utilized by a property, employees should have complete access to it, know the passwords, and how to effectively perform the process of sending messages or otherwise activating it.
Step 1 – Rewrite Your Disaster Plans
Training and drills are the most important elements of a disaster program. They are more important than disaster plans and EST combined. This is because the way a workforce is trained and drilled will not only reinforce the behaviors necessary in a disaster, but also exposes the strengths and weaknesses of your program overall. The problem is that most training is actually too detailed. Going through an earthquake or wildfire procedures point by point is boring and
www.MHNetwork.com Material Handling Network October 2022 13 Heavy Machinery Movers Cart 200 Ton Capacity • 20’L x 10’W x 2’H Dual Steering Direct lift, no chains Low profile 8’ - 10” high x 16’ - 7” long x 8’ - 0” wide Optional telescoping rigging boom solo matic tires REMANUFACTUREDRIGGERSPECIALS 80,000 lb. to 120,000 lb. at 24” L.C. Direct lift, no chainsFOLLOW THE REST, OWN THE BEST Bristol Manufacturing 4416 N. State Rd. (M-15) Davison, MI 48423 Phone: 810.658.9510 Fax: 810.653.5749 Contact Rachelle or www.bristolmanufacturing.comRay
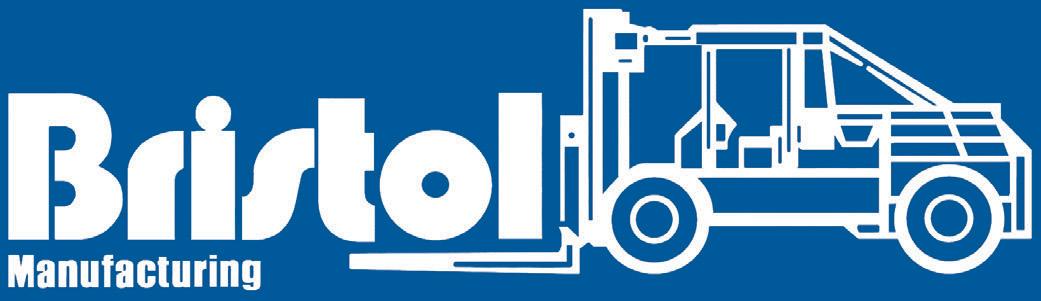
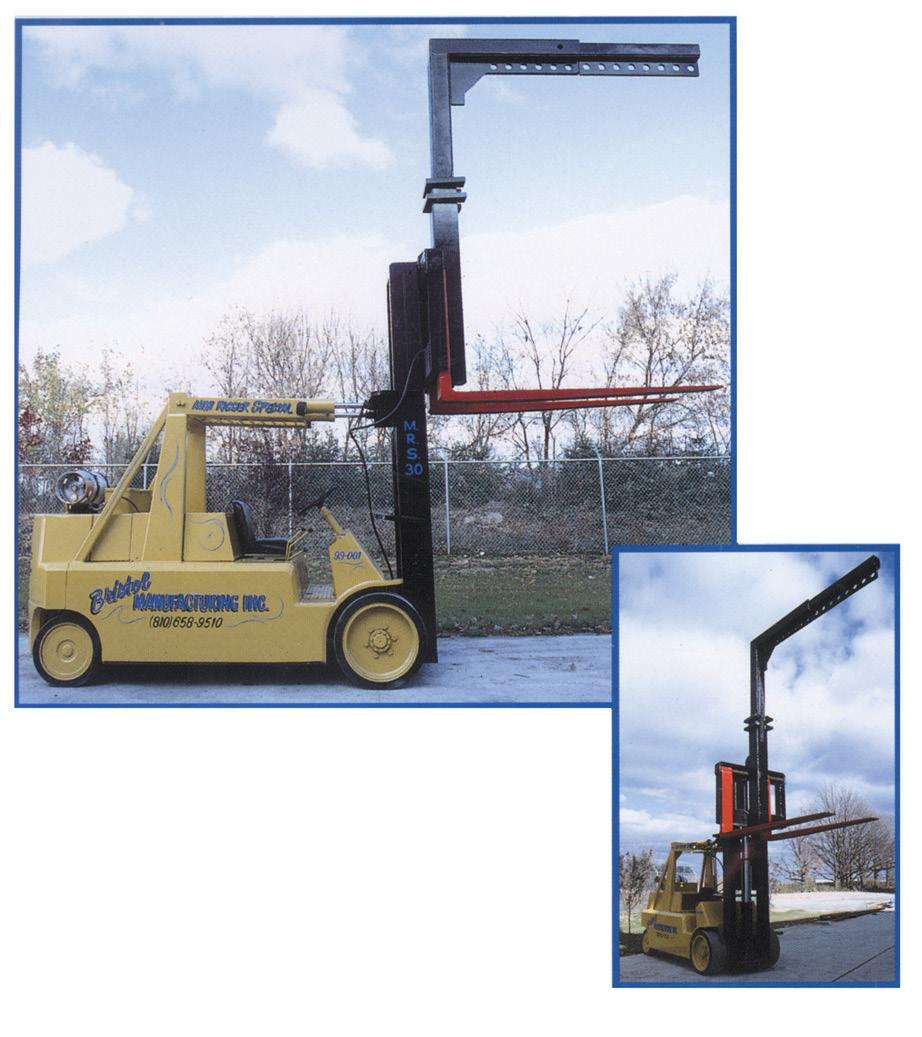
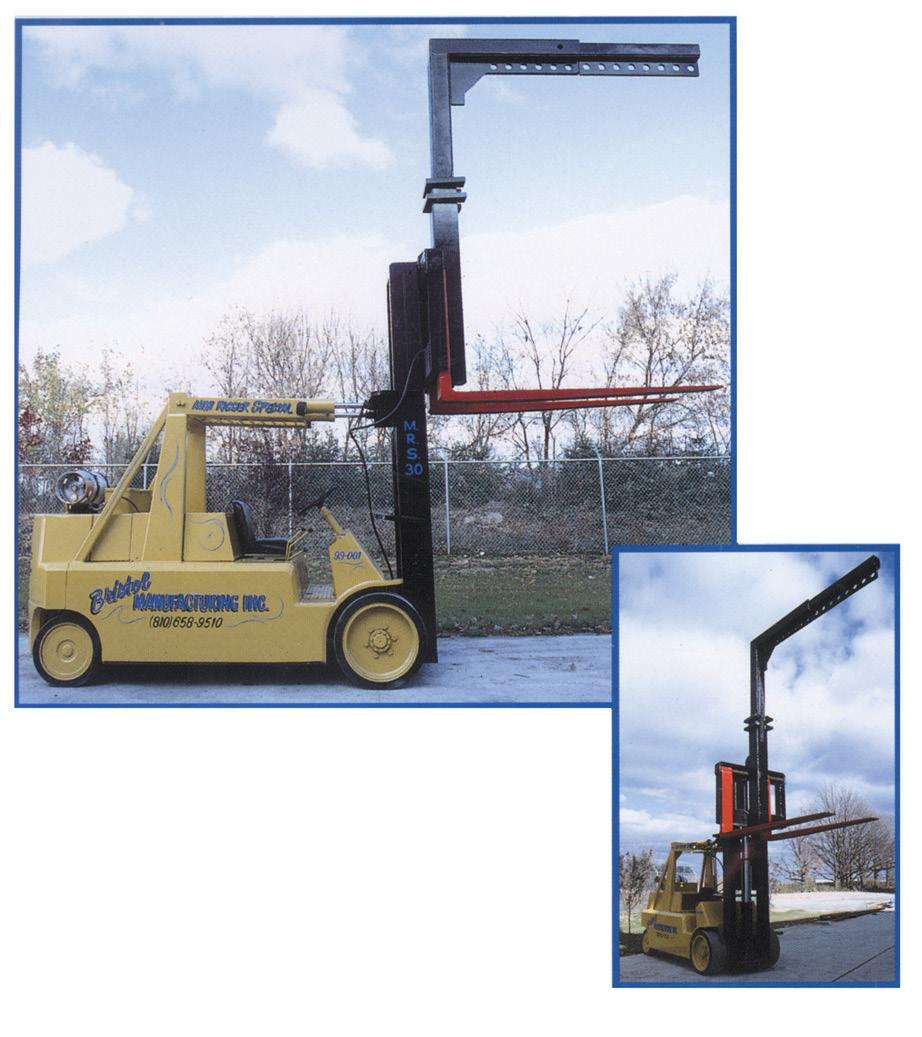
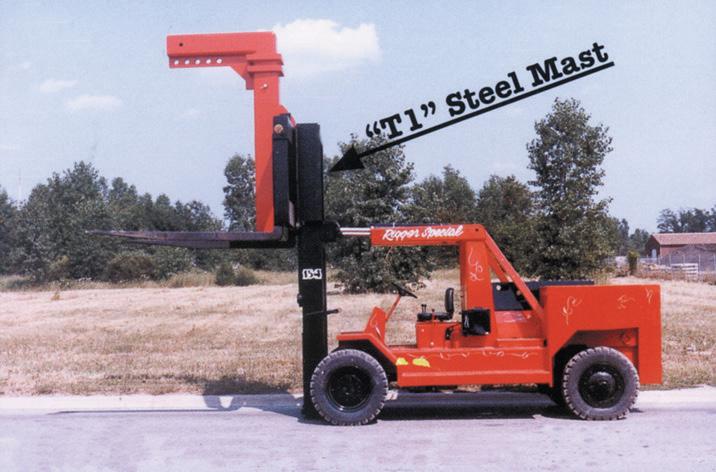
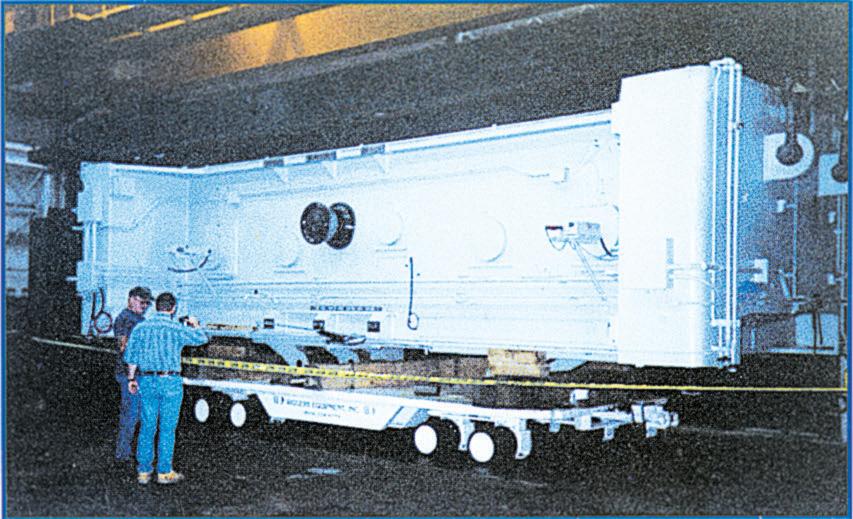
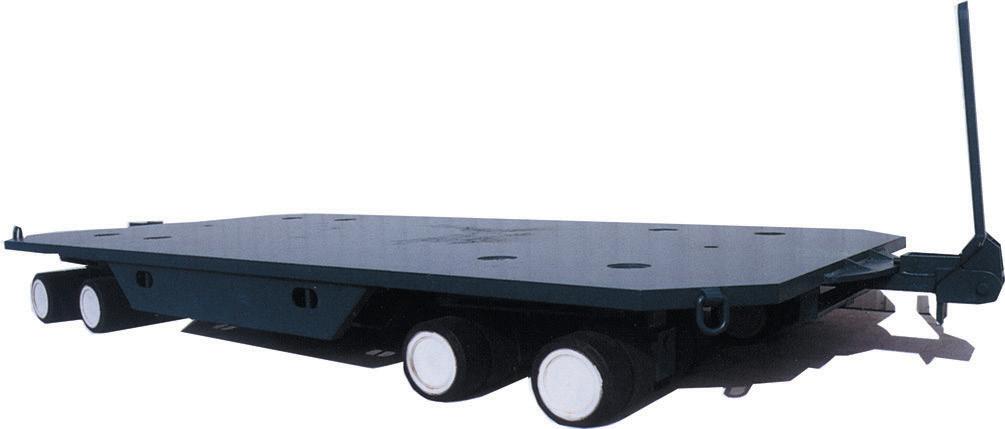
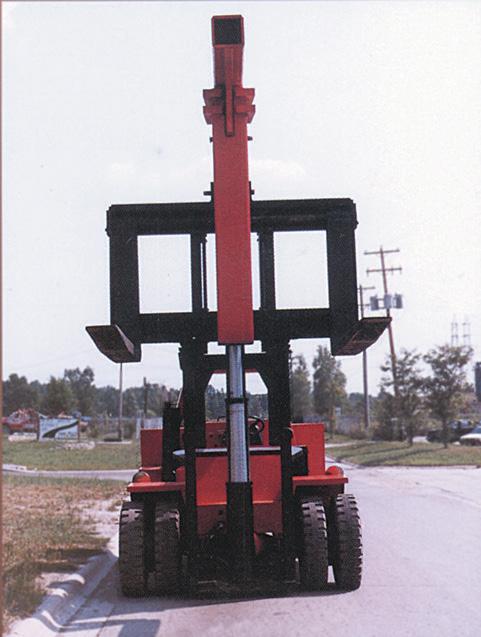
Whether you run a large or small property, with 5 or 500 employees, it is critical that each team member be prepared not to respond to a disaster, but to actually organize a disaster team. It is more than just red binders, written plans, fancy equipment, and an expensive communication mobile app. It’s about empowering employees to act with authority and lead during a disaster. If you don’t, you will turn them into bystanders who not only are excluded as part of the solution – they become part of the problem.
unnecessary. No one is going to remember it, and it detracts from information that really necessary for employees to act during a disaster. Drills are equally as useless because most times employees are converted into bystanders while managers do everything, and simply bark instructions at staff. This is not conducive to real situations where employees can be incredibly valuable members of a disaster
into emergency team members that can work for you in any disaster.
Safety First continued SAFE & EFFICIENT MATERIAL LIFTING SOLUTIONS Customized for your specific material handling application, PFlow material lifts optimize worker safety, workflow and throughput. MATERIAL HANDLING SOLUTIONS CONTACT US TODAY FOR A 414-352-9000CONSULTATION!|WWW.PFLOW.COM 100% EMPLOYEE-OWNED AND MADE IN MILWAUKEE, WI

Conclusion
Patrick Hardy is the founder and CEO of Hytropy Disaster Management™, the largest full-service small business disaster management company in the US. A Certified Emergency Manager® and a Master Business Continuity Professional®, in 2012 he was selected as the National Private Sector Representative to FEMA. His book, Design Any Disaster, will be published in March 2023 by Benbella Books. To talk about your next event, please go to: www. americasdisasterplanner.com
Redesignteam.your
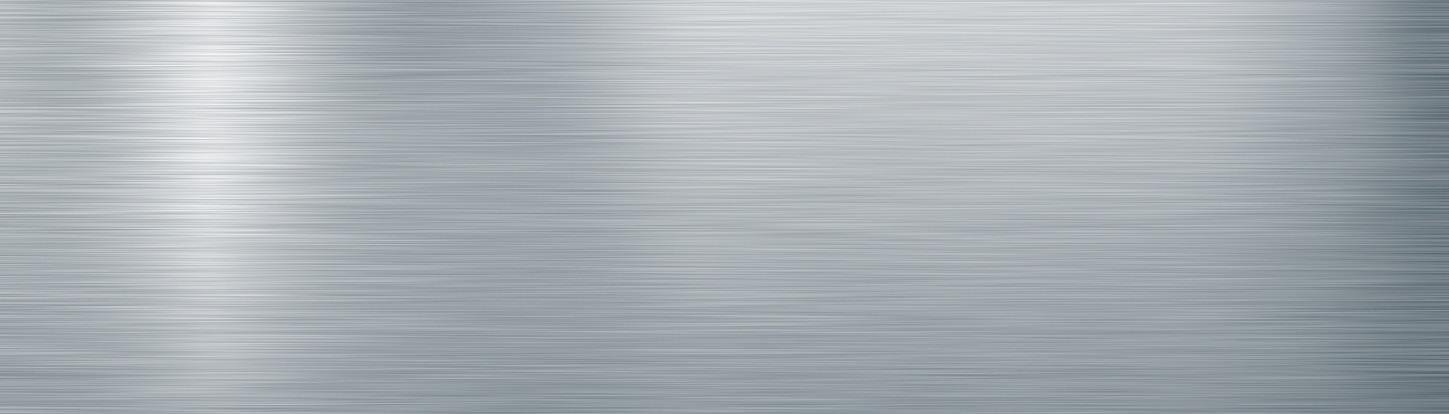
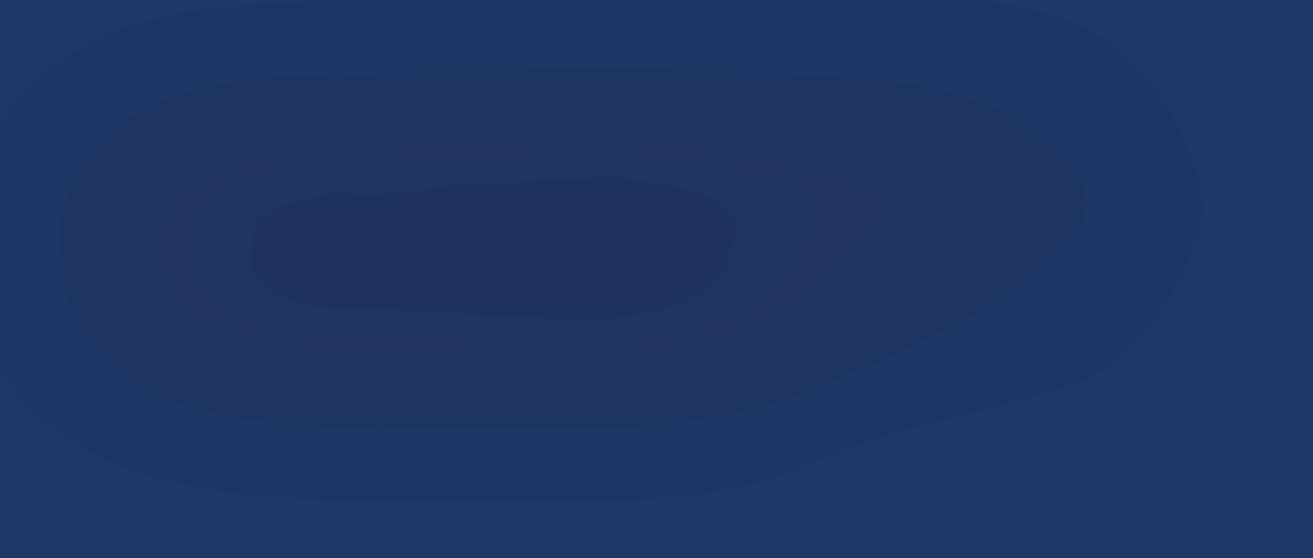
14 October 2022 Material Handling Network www.MHNetwork.com
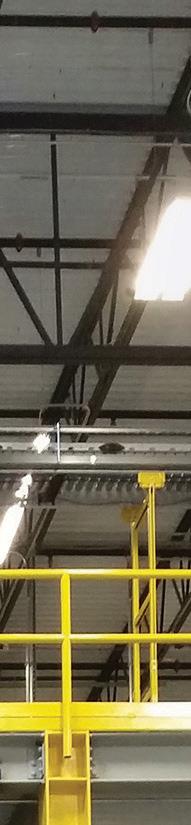
training and drills so that line employees are the stars. Training should focus on leadership ability and the basic steps in a disaster response and where to find the information they will need for more in-depth procedures. In fact, this should be reinforced with drills where managers are made to stand on the side, and employees are instructed to perform an entire disaster drill without management participation. This will give an accurate way to assess their readiness. It will also reinforce individual initiative and responsibility so anyone can put together an impromptu emergency team. That is how you turn bystander employees
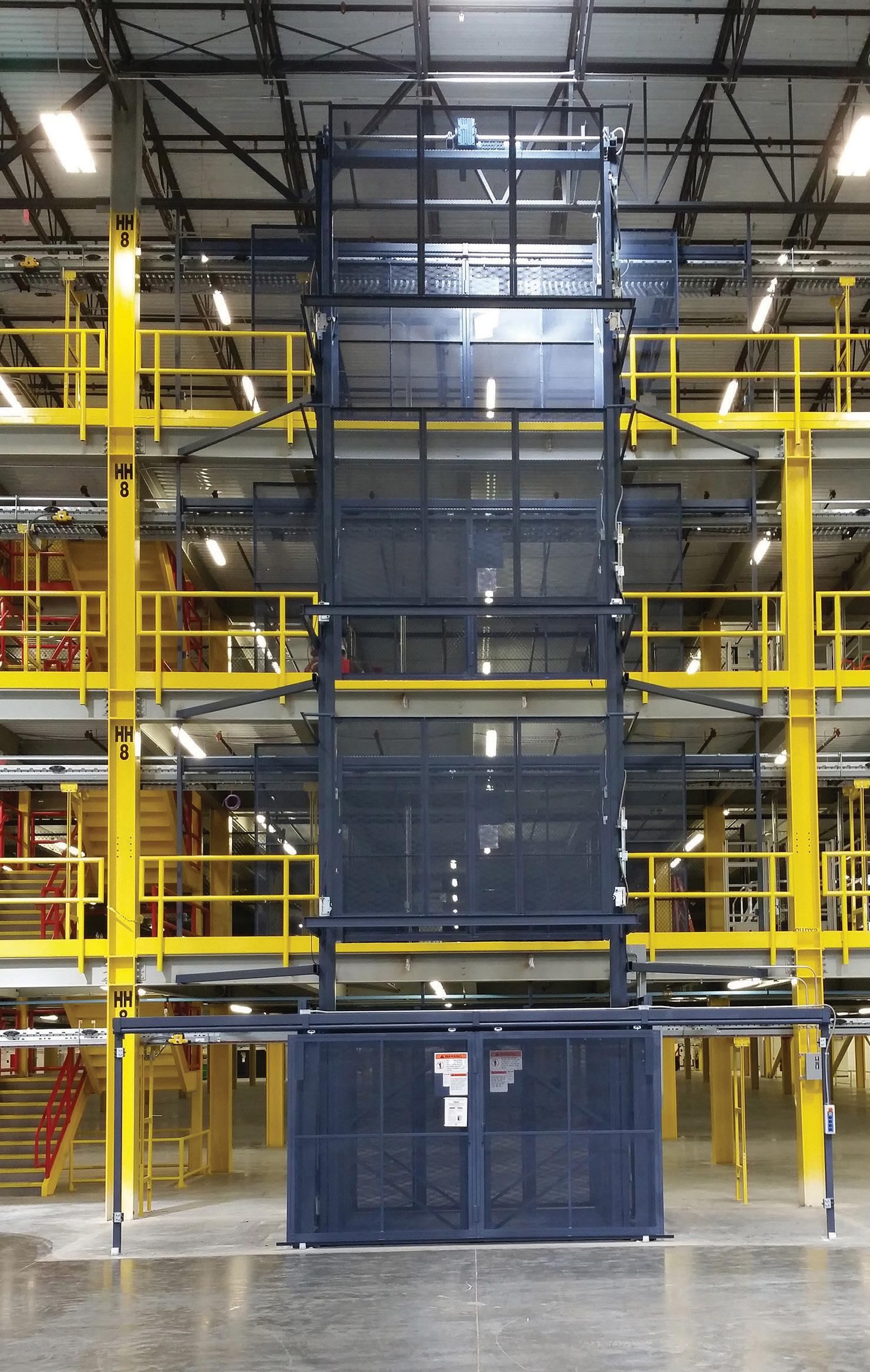
Designed for Women in Material Handling
www.MHNetwork.com Material Handling Network October 2022 15
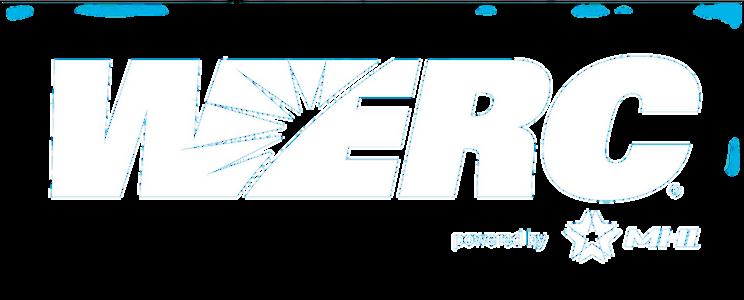

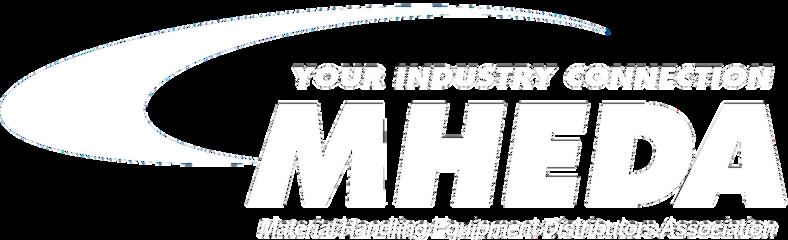
This is the value filled event you have been waiting for all year. Invest one day in yourself and rediscover your strengths, redefine your influence and release your stress. Let’s Recalibrate (together in person!) this November.
R E C A L I B R A T RE E C A L I B R A T E
MHEDA, MHI and WERC invite you to join us November 2nd in Rosemont, IL for the 2022 Women in Industry Conference. We’ve planned a powerful one day event designed to help move you through the ever changing Material Handling business climate. This is your opportunity to connect, learn and grow with other women who face similar daily challenges as you Discuss industry trends during the roundtable sessions, improve your business communication skills, improve the culture within your organization, gain strategies to overcome the imposter syndrome and so much more.
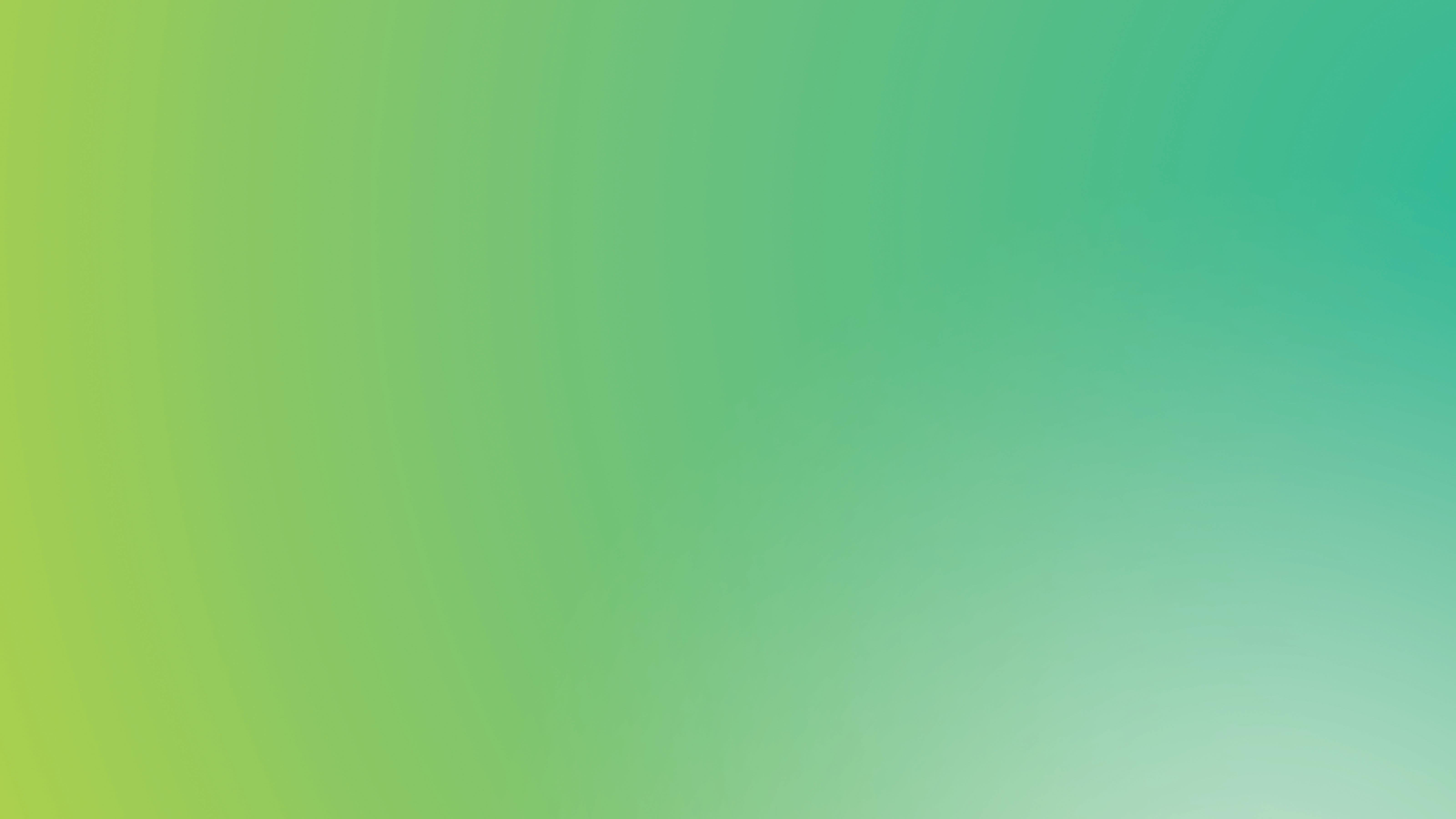
Women in Industry Conference
November 2, 2022 Loews Chicago O'Hare in Rosemont, IL
For more information, visit www.mheda.org/women
• Understanding where you want to be AFTER the automation is implemented requires some detailed soul searching and facing up to the reality that can often be an uncomfortable
You need to know every location in your warehouse, in terms of size and weight capacities, plus restrictions about what can or can’t be placed within them. This includes every place products might be kept, such as dock areas, staging areas, and overflow floor locations. Take into consideration processing stations where assembly, packaging or value-added activities take place. You’ll also need to know the locations for in-transit resources such as carts, forklifts, pickers, conveyors, and bots.
with highly reliable core master data about products; just a few “surprises” of non-standard or unexpected product types will hurt or sometimes cripple automation productivity.
16 October 2022 Material Handling Network www.MHNetwork.com

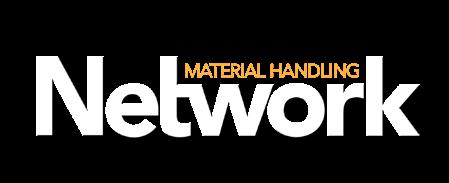
First and most critical is data, data, data; get your warehouse data right and clearly understood. The details will differ based on your specific situation, but here are some key categories to review: Products
Every physical change in product, location and resource status requires a data transaction that tells you what items did what, when, and where. An accurate recording of transactions is the lifeblood of successful warehouse automation. Modern data analytics and application of machine learning aren’t possible without accurate and timely transactional data to spot patterns, flag problems, and opportunities, plus provide situational awareness and options to well-trained industry professionals.
Assumingprocess.
Good automation preparation shines a light on what products are handled more often and which
Are you about to start the journey to warehouse automation but struggling with where and how to begin? There is so much interest and evaluation of automation projects in the warehouse right now, which is leading to confusion and concern around just how to start the journey since starting in the right direction will give you the highest chance of success. Warehouse automation can be treated just like any other large logistics project with a few caveats:•Automation
does not solve all warehouse problems and careful analysis must be performed before you sign the check for any type of automation;
Transactions
Understand Your Needs
• Getting the right kind of automation for the right problem is critical; and
you have considered these points, there is a good chance that you will succeed. If not, then it is likely that your automation project will be added to the long list of white elephant projects that were common in the early days of warehouse automation. So, what are the steps to prepare for warehouse automation?
Get accurate information about the sizes, weights, handling characteristics, environmental considerations, and time-based restrictions that influence how products need to be moved and stored. Successful warehouse automation starts
Chain Reaction
The Future-Focused Playbook: What to do before automating your warehouse
Every person and piece of equipment in your warehouse has a data profile which includes: Location, status, capabilities, limitations, and capacities that can be allocated and reallocated as needed to adjust to demands. Make sure you have a deep understanding of these resources to greatly reduce the time and effort of accurately and realistically responding to customer needs.
Locations
Figure Out Your Warehouse Data
Resources
www.MHNetwork.com Material Handling Network October 2022 17
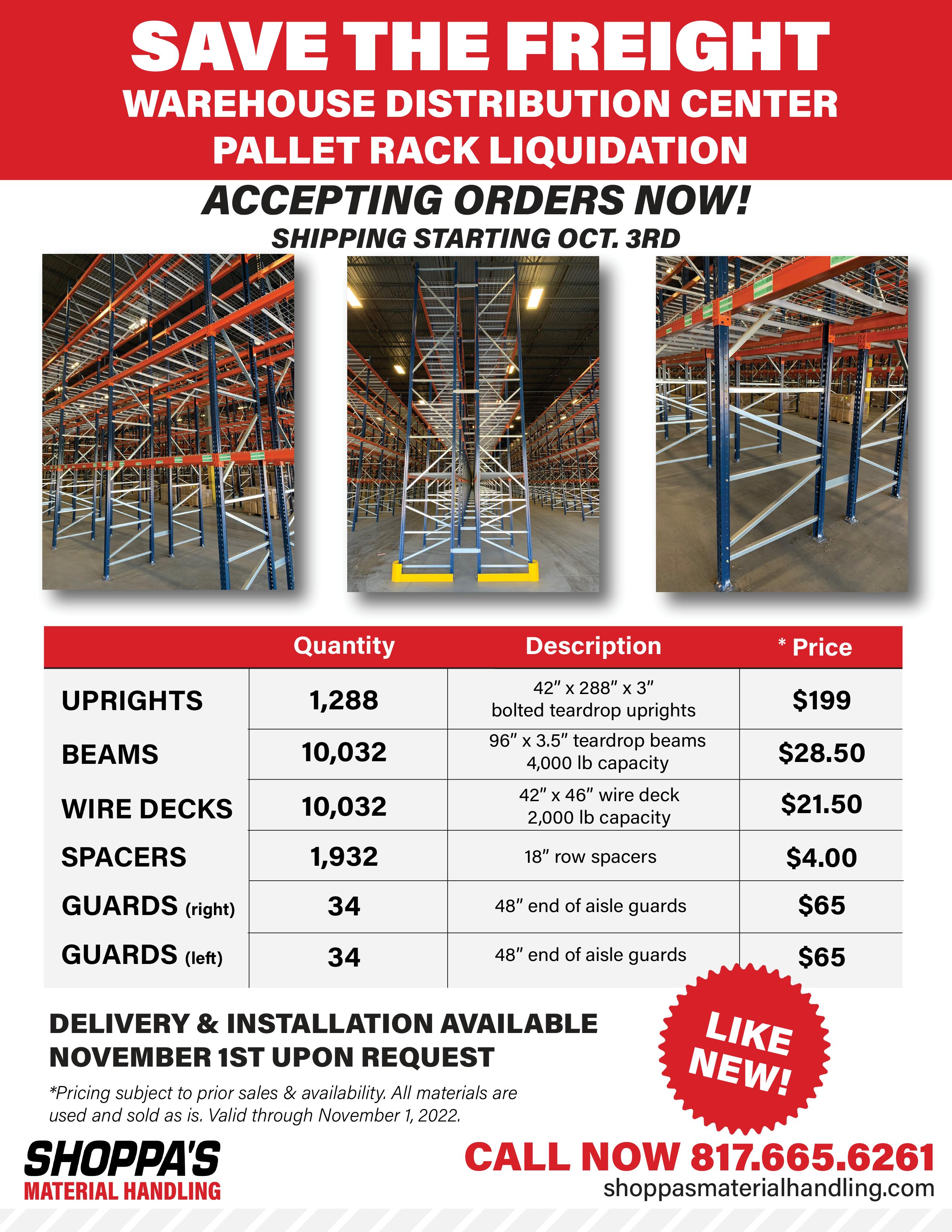
The preparation stage of warehouse automation is about obtaining your data and defining the fundamentals of what problem needs to be solved. While each stage is of equal importance and contributes to the overall success of your warehouse automation project, taking your time and putting extra focus on this preparation stage is going to help your business in the end. If you don’t, you’ll run the risk of wasting time and money by creating a solution that doesn’t do what you need it to do.
Bill Denbigh serves as the vice president of product marketing at Tecsys. Bill started working in supply chain software some 30 years ago; his entire career has been laser-focused on designing and building pragmatic supply chain solutions that address the real problems that customers are facing in their supply chain operations.
ones may be candidates to eliminate. Product variety and volume numbers as part of an ABC analysis are fundamental. You absolutely must develop detailed order and item profiles for your project. Average percentages over time can be misleading, so also look at how variable (growth/ decline rates, peaks and valleys, seasonality, etc.) each product can be.
Chain Reaction continued For WarehousemoreSolutions/ChainReactionsvisitwww.MHNetwork.com
What are your project motivations?
Prepare and succeed
How much more needs to flow through your facility? You must have performed steps one and two above to truly determine your current capabilities and customer needs before determining a realistic direction of where you want to be. A thorough self-assessment of future direction and needs is a must for warehouse automation projects. This information will be critical as you move into the evaluation stage for warehouse automation where you will review a wide variety of automation types and investigate possible consulting and integration partners.
Where do you want to be?
18 October 2022 Material Handling Network www.MHNetwork.com
During the preparation stage, make sure you are regularly evaluating forecast accuracy across the supply chain and within facilities to better understand how stable or unstable demand patterns really turn out to be. Segment the data and understand what inaccuracies in forecasts cause the greatest grief, then plan for them because you can’t be perfect, just less wrong.
After you have deep knowledge of your warehouse and customer data, you are ready to plan for growth. Along the way of collecting all this data, you’ve likely had many “are you kidding me?!” moments where you found process holes and wasted actions. This necessary step of discovery helps you right-size your products and your procedures.Herearethree questions you’ll want to discuss in the final step of your warehouse automation preparation stage:
What do your forecasts look like?
Know Where You Are vs. Where You Want to Be
Most warehouse automation projects focus on doing more with less. This means more orders, customers, product variety, channels, volume, and revenue growth — but in less time and with minimal investment in additional resources and space. Automation enables you to be more responsive, so you can scale up or scale down your operations. Targeting a part of the warehouse for automation within the larger warehouse facility might be the answer rather than sweeping automation of the whole facility. That’s why it’s critical for your business to have a firm consensus on what you’re trying to achieve, so you implement the right solution for your needs.
www.MHNetwork.com Material Handling Network October 2022 19 Quality Hydraulic Components SteeringPowerCylindersPumps Valves Quality & Value for Over 50 years New & ExchangeRemanufactured HADER Incorporated P.O. Box 510260 • New Berlin, WI 53151-0260 Shipping: 15600 W. Lincoln Ave. • New Berlin, WI 53151 Toll Free: 877.388.2102 • Phone: 262.641.8000 • www.haderind.com Toll Free Fax: 877.384.1654 • Fax: 262.641.8010 • Email: hadersales@haderind.com H a der INCORPORATED
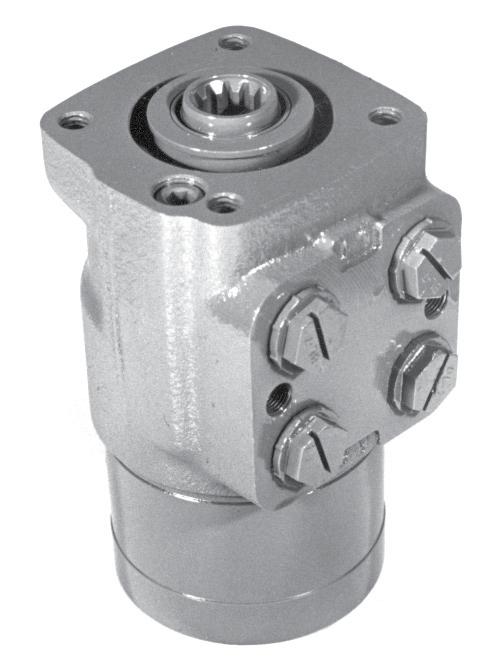
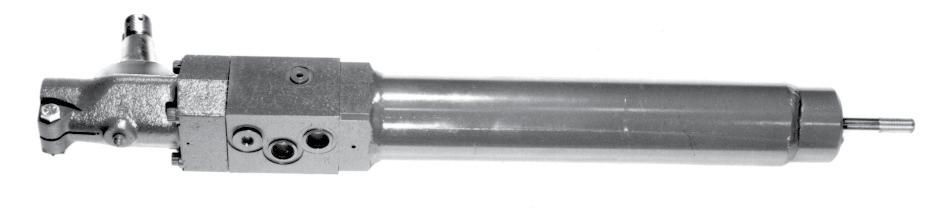


It's amazing how connecting dots makes the work of HR and recruiting teams so much easier. Knowing what the business does, how it makes money, and what’s happening in your industry is important. So is knowing what hiring managers are looking for – and how to interact with the right candidates. And yet, many are not doing these things.Thebest
• Gain credibility
Why conscious curiosity is the Soft Skill separating good recruiting, from great recruiting
2. Share your intention and take advantage of the discussion by asking questions. When you tell people you’re interested and want to learn, they’re often more willing to share with you. Build on answers they give and ask for their personal perspective on a matter. We will all invest more time when people show active listening, feel that their perspectives are valued, and the person is trying to understand what they are sharing.
training cannot fill a gap when employees are not curious – it may result in you retaining even less. If you’re not curious, it ultimately means you’re operating at a status quo. Forcing yourself through training that you find boring or ignoring the opportunity to gain more insight to improve your role as a consultative HR or talent acquisition professional is a lost opportunity. It doesn’t have to be so! Being curious on your own is important because it helps you:
3. Ask your questions in a way that demonstrates that you care about their answers and demonstrate some comprehension on your end. Repeat the response back to them in your own words and ask if you still have the information correct. Reply to them with your thoughts on why you find what they are saying interesting or ask clarifying questions about a particular aspect of the discussion. Most important – don’t forget to thank them for sharing with you.
• Improve your ability to assess candidates
Note that there is work in building this skill. These tips may give you some extra help developing this new cerebral muscle.
How a self-motivated desire to learn and ask questions drastically improves recruiting and hiring
The “process” of recruiting isn’t hard -- but it does take capabilities and competencies that are rarely taught. Setting and managing expectations tops the list, but what differentiates good from
• Become an expert in the commercial language of your organization and your industry
• Create a better candidate experience by better explaining the company’s strategy and how the role adds value
• Build and manage relationships with all key stakeholders: hiring managers, candidates, employees, and leaders.
20 October 2022 Material Handling Network www.MHNetwork.com

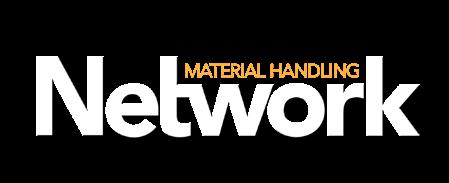
Five Key Tips to Practice Conscious Curiosity
great recruiters is the skill of conscious curiosity, and it requires focus. Corporate workplaces haven’t evolved to teach this yet – training rarely leaves us feeling more informed or energized. Conscious curiosity is also not a step you can build into best practice recruiting processes. Nobody will tell you to be more curious nor can it be measured, so how might you approach working your curiosity muscle?
1. Do your own research about the business or industry and actually use the answers to inform your next few steps. This can be through industry newsletters or podcasts, following influencers on social media, or even online courses. The point is to go beyond where you normally would in your quest for information, even if it’s hard and you feel that you have an answer – keep digging!
HR pros have learned that the only way to be successful is to be consciously curious-meaning they are self-motivated to learn more deeply about how their and other businesses work andCorporatethrive.
Business Management
www.MHNetwork.com Material Handling Network October 2022 21 The Superior Turret Advantage WhytheSuperior Turret ? • Save Money by Increased Storage Capacity • Not Difficult to Use like the Others • Work Both Sides of the Aisle • Versatility - Rack to Truck • Limit the Learning Curve • Simplicity in Design • Low Maintenance • Multiple Options • Electric or LP www.superioreng.com 800-359-3052 AmericanMade
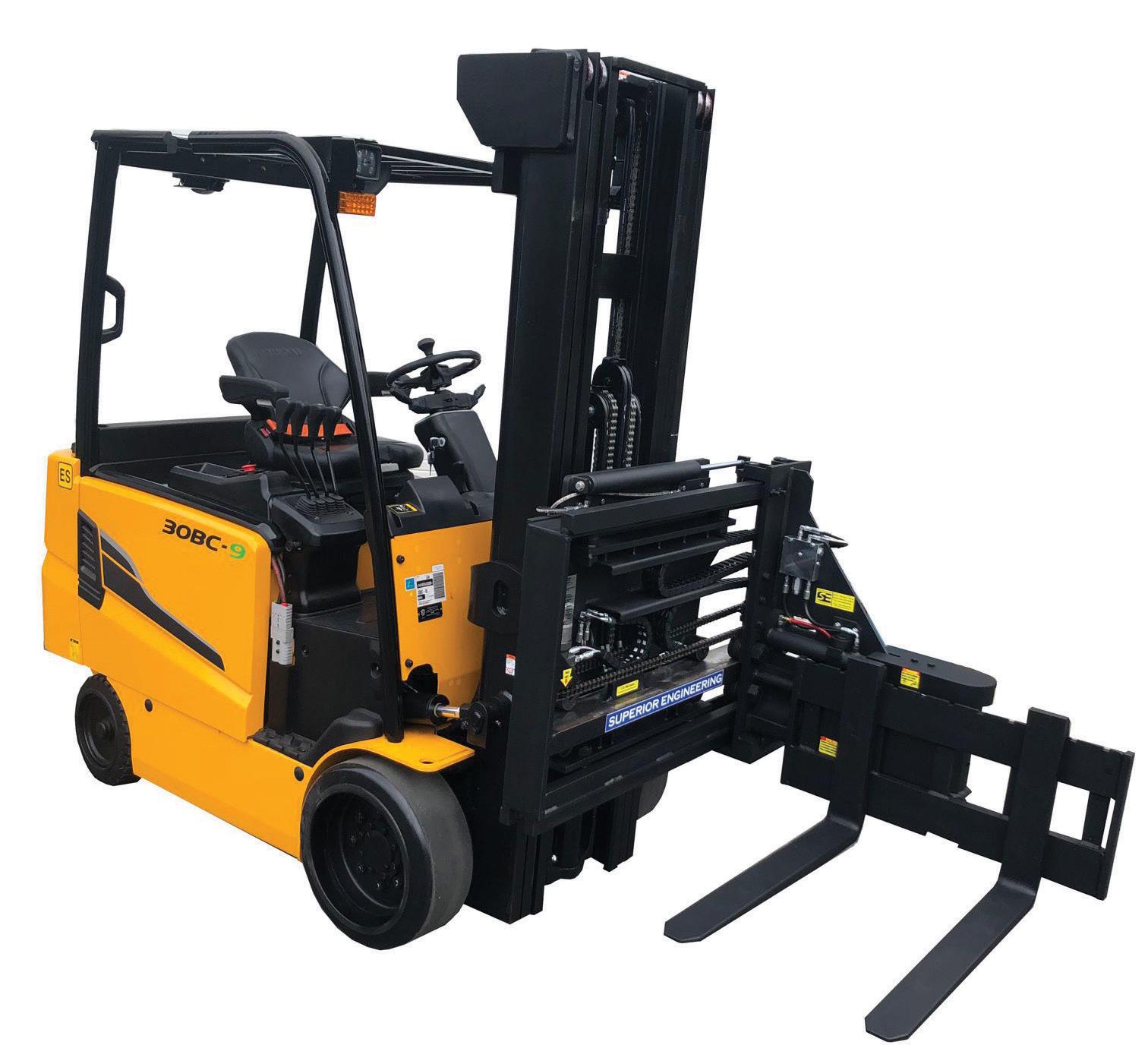
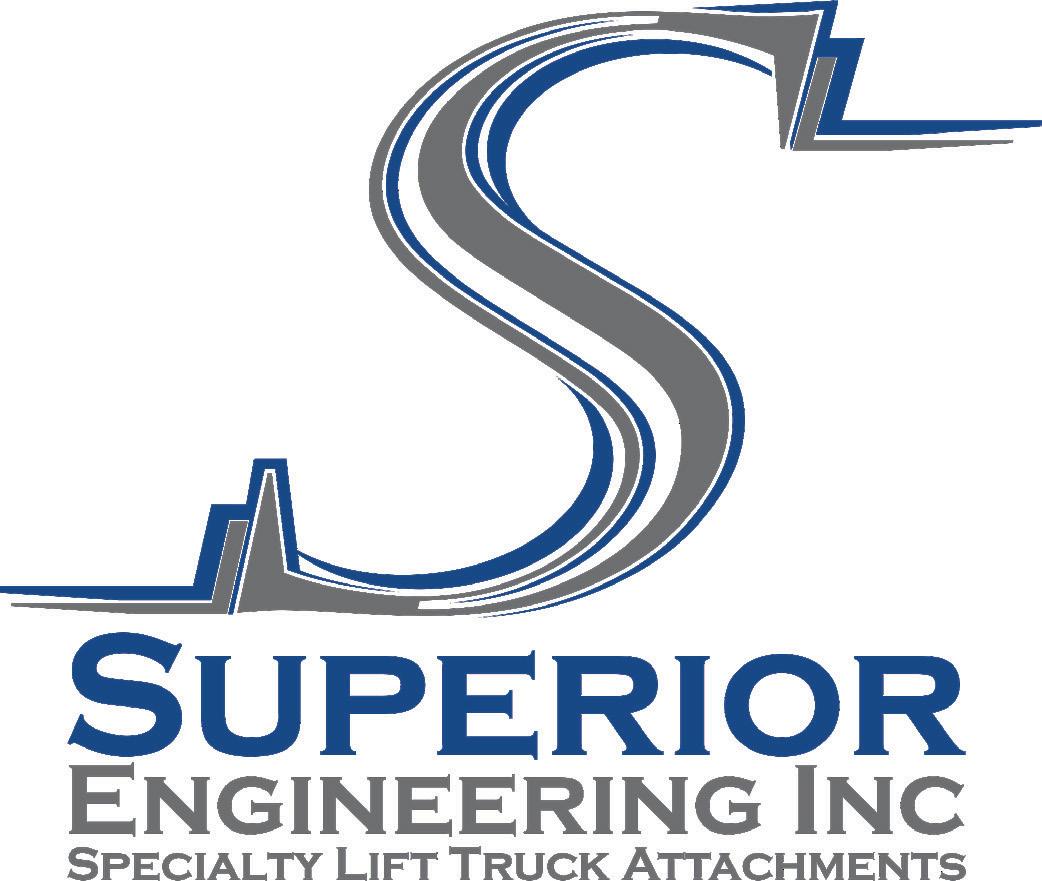
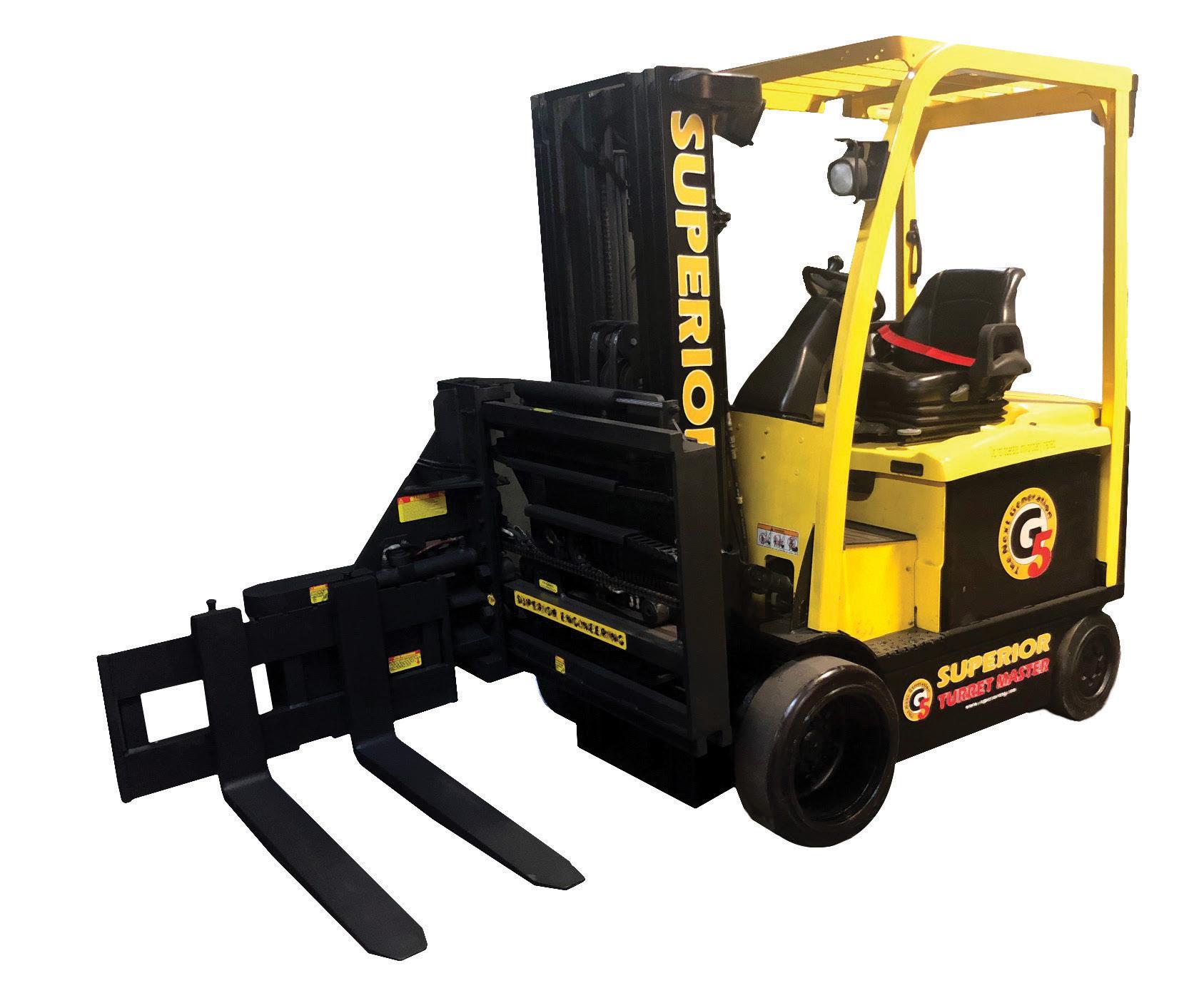
4. Admit you are not the expert and ask if there is anything else you should have asked to gain more knowledge of a particular area. Invite them to share info with you, even if you don’t ask. There is an opportunity to further connect with others when you admit you don’t know something and want their help to learn. Vulnerability is a strength when connecting with others and can often deepen the conversation to a more personal level which gives you new insights but is also a very human way to connect and build relationships.
Take the opportunity to be a cut above and turn on the conscious curiosity engine now. Understand how the company makes money, have chats with different departments, and probe deeper. Remember, being curious means listening twice as much as you speak. Recruiters are often chatty, to begin with, so this is your reminder to listen to show you’re interested in them! Asking insightful questions beyond where you do today will help shape your own brand as a top recruiter capable of bringing in top talent because you truly understand, and care!
Jeremy Eskenazi, SPHR, SHRM-SCP, CMC, is the founder of Riviera Advisors, a boutique talent acquisition optimization consulting firm. Riviera Advisors does not headhunt, it specializes in recruitment training and strategy consulting, helping global HR leaders transform how they attract top talent. For more information, visit www. RivieraAdvisors.com.
At its most tactical application, conscious curiosity can help you better understand roles in more business units faster which can make you more versatile. This can also lead to improving your ability to screen candidates and ask more probing questions to hire managers to hit the mark on what they are looking for the first time.
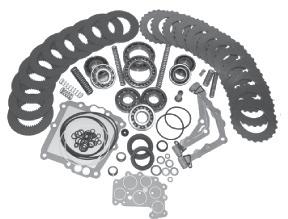
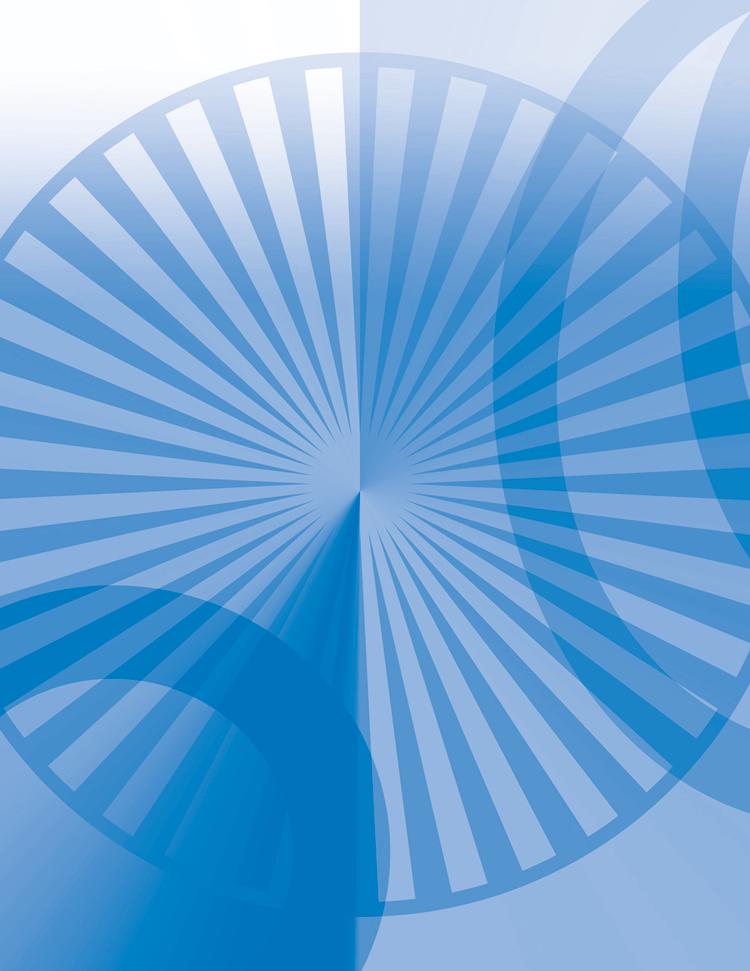
Business Management continued Remanufactured Transmissions, Engines, Torque Converters, Steer Axles, Overhaul Kits and Aftermarket Parts for: • Material Handling • Construction • Agricultural Equipment 800-321-9983 www.joseph.com sales@joseph.com Authorized Distributor Authorized Distributor Authorized DistributorAuthorized DistributorAuthorized Distributor For more Businesswww.MHNetwork.comvisitManagement
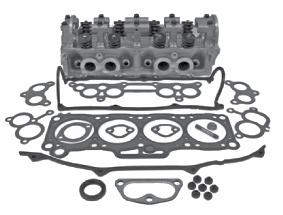
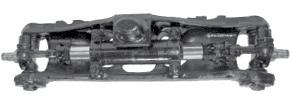
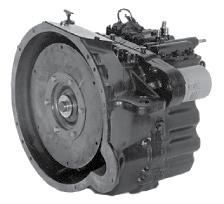

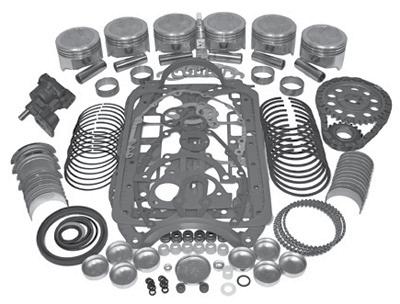

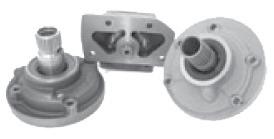
5. Show you care! Don’t forget human interaction and how it feels when people are interested in you as a person, what you care about, how you are doing, and what’s new in your world. As you practice curiosity, you will seem like a more caring person as well. Caring for people attracts positive energy and makes it easier to ask more questions or have people trust you with more information. Recruiting is all about relationships and they are extremely hard to build when people

www.MHNetwork.com Material Handling Network October 2022 23 TM ClearCap Roof Covers! ClearCap & TuffCab! Easy Install Wy’East Products 1-888-401-5500 www.clearcap.com TuffCab Panel Cab Enclosures Vinyl Side Doors • ClearCap Roof Covers Keeps Operator Dry • Many Sizes to Fit Various Trucks • Easy to Install • Reasonably Priced • Clear or Tinted • UV Polycarbonate • Domed Roof Diverts Rain • Blocks UV Rays • O.S.H.A. Compliant • Full Enclosures or Individual Components • Durable Steel & Safety Glass Construction • Easy Clamp-on Installation • Affordable • Fast Lead Times • Windshield Includes 12v Wiper Engineered to Fit Hyster, Yale, Cat, Mitsubishi, Toyota & Unicarriers Clear Solutions to Common Problems
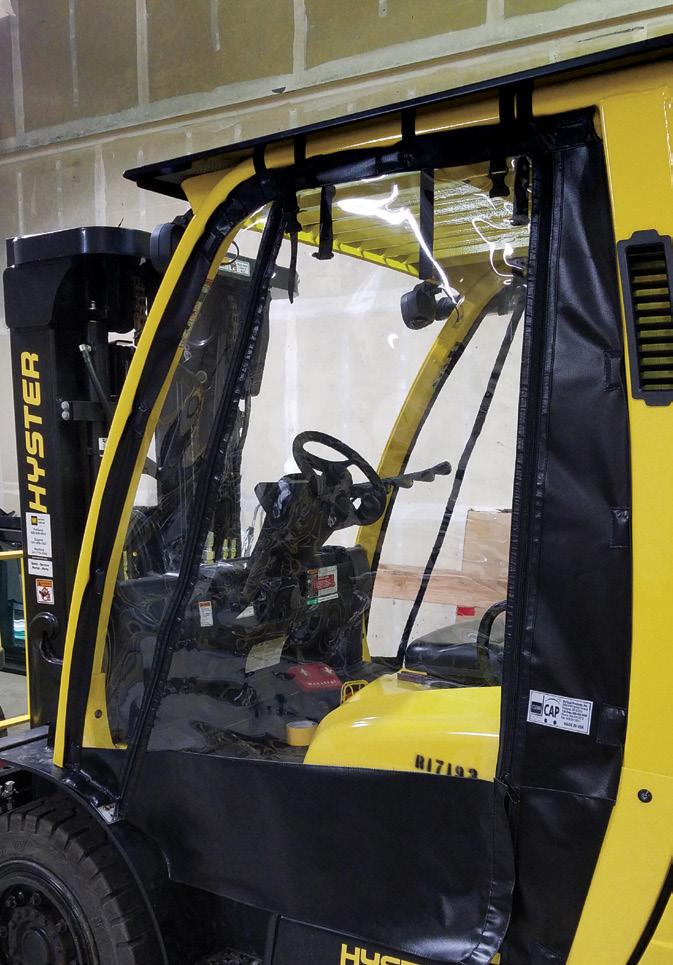



CLARK appoints Leavitt Machinery USA as authorized dealer
24 October 2022 Material Handling Network www.MHNetwork.com
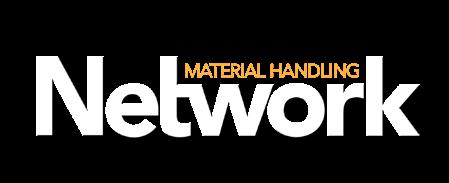
demand, its US-based subsidiary has opened a new Client Experience Center and expanded its fulfillment operations. The new 30,000 sq ft facility in Flowery Branch, GA allows AGILOX to welcome existing and future clients to experience the full width of capabilities of all AGILOX AMR solutions available to date: The allrounder AGILOX ONE, the powerhouse AGILOX OCF, the box carrier AGILOX BCO, and soon the brand-new dolly mover AGILOX ODM. www.agilox.net
Flux Power Holdings, Inc has announced combined purchase orders from new and existing customers in excess of $64 million in the fiscal year June 30, 2022, which was more than 82% over the order volume for fiscal year June 30, 2021. While not an exact measure, Flux Power estimates that purchase orders indicate future revenue potential from new customers in the fiscal year 2022 was 26% of revenue, with the remaining 74% from repeat customers.
www.amtonline.org
www.clarkmhc.com www.leavittmachinery.com
2022, according to the latest U.S. Manufacturing Technology Orders report published by AMT –The Association For Manufacturing Technology. July orders decreased 6.1% from June 2022 and were off 14.3% from July 2021. Manufacturing technology orders in 2022 have reached a total of $3.22 billion, an 8.7% increase over the first seven months of 2021.
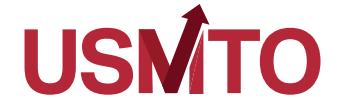
Flux Power announces record new Purchase Orders of $64 Million in fiscal year 2022

WERC’s 46th Annual Conference in June 2023 will be held in Orlando

www.fluxpower.com
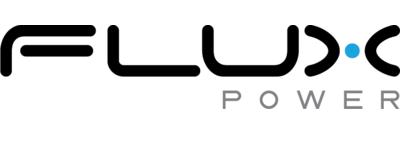
Pullback in July 2022 Manufacturing Technology Orders may signal return to typical patterns
CLARK Material Handling Company announces the appointment of Leavitt Machinery USA, Inc. as an authorized distributor of CLARK products for the Washington, Idaho, and Montana markets. Leavitt Machinery USA will support CLARK’s new equipment, aftermarket parts, and service efforts in these areas.
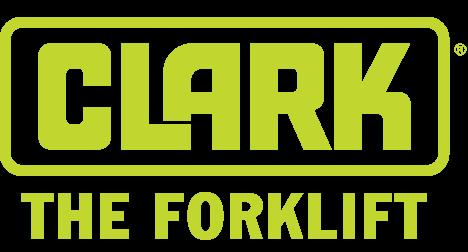
theAGILOX,provider withorderatsolutions,RobotAutonomousofMobileforkliftisgrowingarapidpace.Intokeepuptheincreased
Industry NewsFor more Industry News www.MHNetwork.comvisit
The WERC Advisory Council has selected Orlando, Florida as the destination for WERC’s 46th Annual Conference. Please mark June 4-7, 2023, on your calendar now to share and hear others’ best practices for “Growth Through Disruption” — our theme for this event.WERC members will gather in person at the Hilton Orlando. There’s no better place to meet and reconnect with friends, colleagues, and peers — old and new — from across North America www.werc.org/2023
AGILOX North America opens new Client Experience and Fulfillment Center
New orders totaledmanufacturingoftechnology$291.9millioninJuly
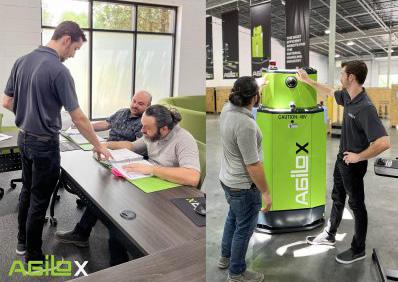
www.MHNetwork.com Material Handling Network October 2022 25 Largest online market for used forklifts, attachments and work platforms. DEALERS DID YOU KNOW YOU CAN GET YOUR EQUIPMENT ONLINE FOR JUST $99 A MONTH? PLUS, WE HAVE AN EQUIPMENT QUOTING TOOL INCLUDED AT NO ADDITIONAL CHARGE. CALL KIP 309.699.4431 | KIP.KRADY@MHNETWORK.COM OR MONTY 563.588.3855 | MONTY@FORKLIFT-INT.COM TO BE PART OF THE FORKLIFT FAMILY OF DEALERS. WWW.FORKLIFT-INTERNATIONAL.COM 2017 Doosan G25P-5 Russell TwinsburgEquipment|(330)405-8300 7 Toyota 8FG45U Toyota Material Handling Northern Livermore,CaliforniaCA|800 527-3746 1 2019 Hyster H100FT MH Equipment Company Des Moines, IA | 515 288-0123 5 2012 HOIST P360 Chicago Industrial Equipment Rockdale | 815 569 6499 12 2013 Hyster H70FT Lift CharlotteOne | 704 587-1040 4 2022 BYD ECB40 1 Source Material Handling Irwindale, CA | 818 838-1688 10 2001 Elwell-Parker ESI160 H & K Coraopolis,EquipmentPA| 412 490-5311 7 2018 Toyota 8FBCU25 Toyota Material Handling Northern Livermore,CaliforniaCA|800 527-3746 1 2021 Doosan B18T-7 Cromer Material Handling Oakland, CA | 510 534-6566 1 2010 Hyster S155FT Chicago Industrial Equipment Rockdale | 815 569 6499 14 2017 Hyundai 18LC-7M Russell TwinsburgEquipment|(330)405-8300 7 2016 Toyota 7FBCU55 Toyota Material Handling Northern Livermore,CaliforniaCA|800 527-3746 1 2019 Doosan D70S-7 Russell TwinsburgEquipment|(330)405-8300 7 2019 CAT Lift Trucks 2C5000 Cromer Material Handling Oakland, CA | 510 534-6566 1 2016 Toyota 8FBE18U Toyota Material Handling Northern Livermore,CaliforniaCA|800 527-3746 1 2010 HOIST F180-36 Box Car **On Rent** H & K Coraopolis,EquipmentPA| 412 490-5311 1
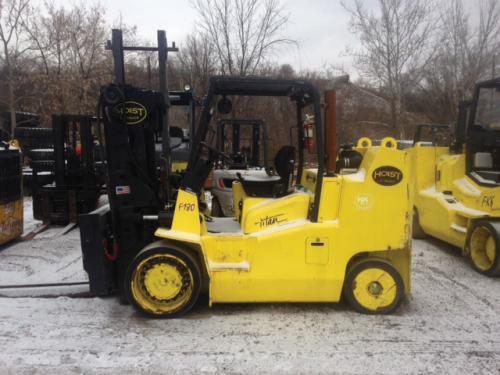
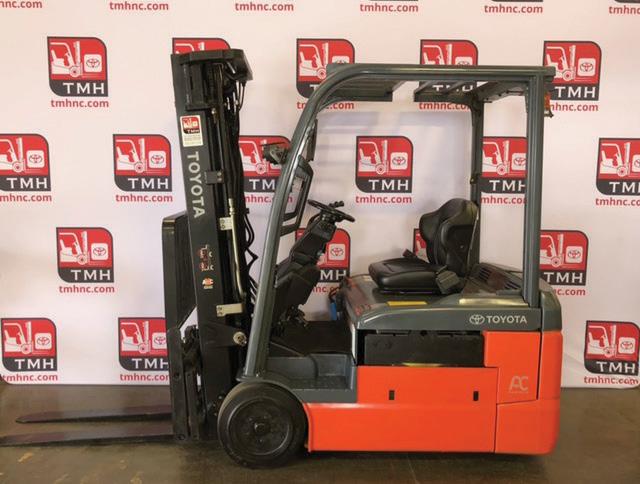

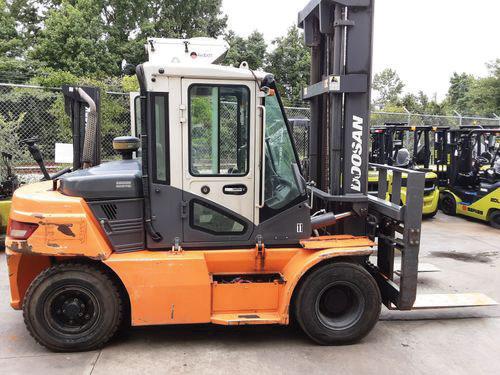
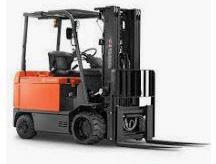
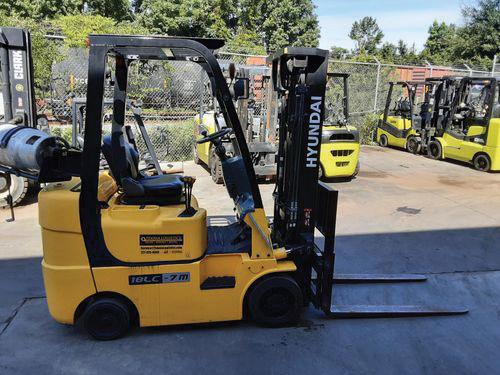
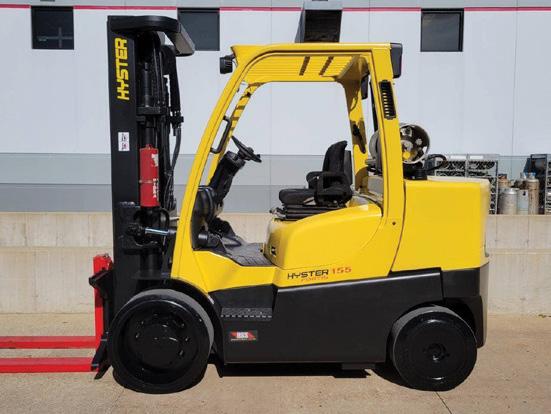
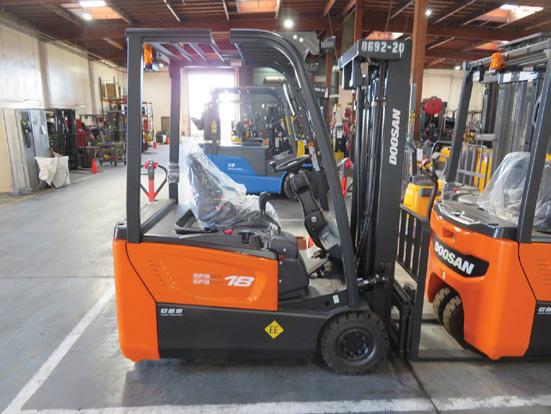
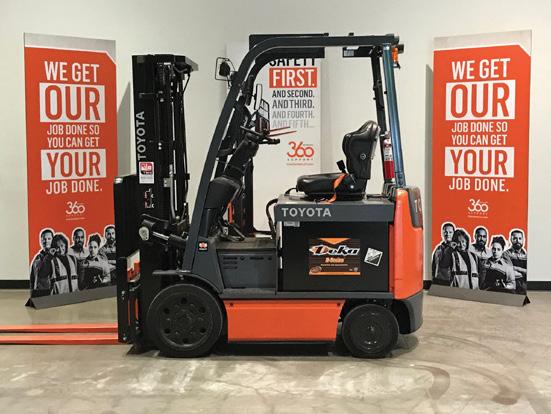
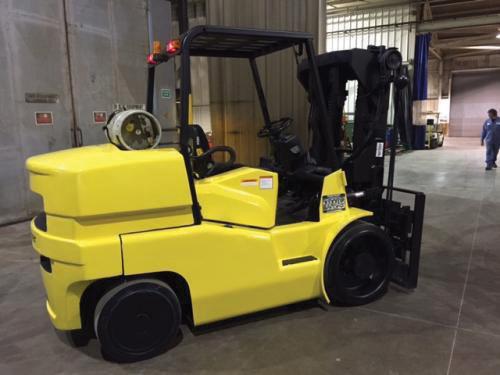
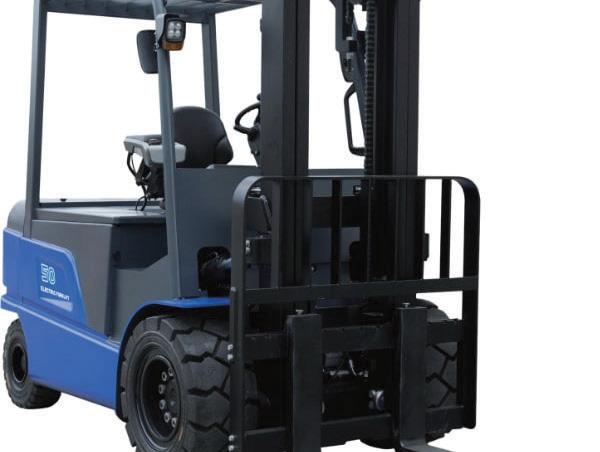

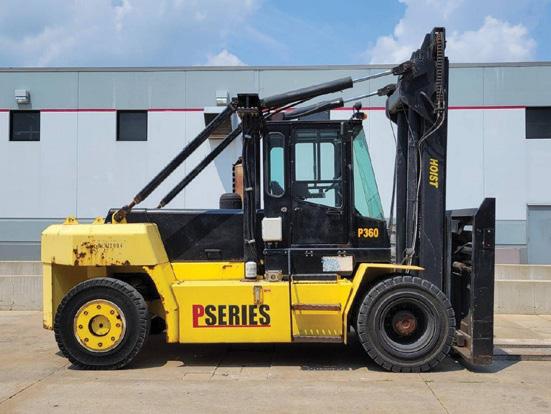

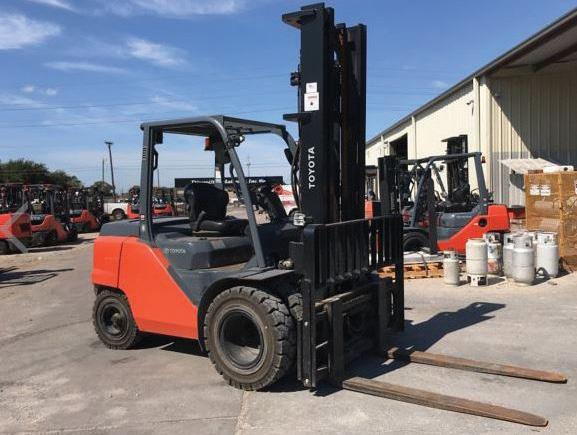
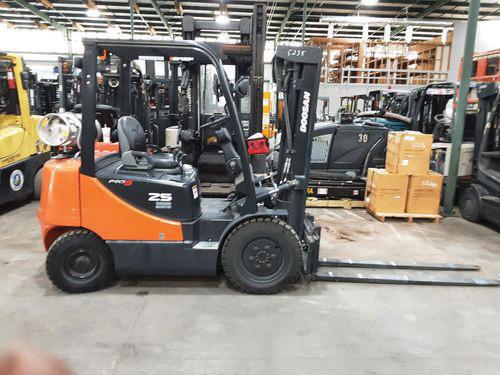
www.linnworks.com
Supreme Systems, a courier and trucking solutions provider in North America, marked its 35th anniversary on September 14th. Supreme Systems was founded by Eric Bennett in 1987 and has since grown into a premier on-demand courier and trucking provider with more than five million deliveries made to date, reaching an estimated 30 million customers coast to coast.
LiuGong North America has added Bristol, Pennsylvaniabased Modern Group Ltd. to its growing dealer lineup. Founded in 1946, the company has become a premium industrial equipment distributor and service provider in the Mid-Atlantic region, with eight locations across New Jersey, Pennsylvania, and Maryland. Modern Group is an employeeowned company that strives to provide world-class sales and service assistance for forklift, recycling, construction, arborist, generator, dock and door applications.
www.moderngroup.com
Raymond kicks off its eighth annual Manufacturing Day event, Celebrating a Century of Innovation The CorporationRaymondwill kick off its eighth ManufacturingannualDay event, Celebrating a Century
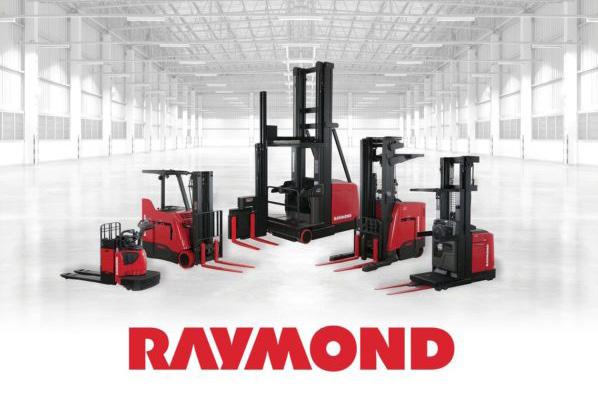
Linnworks, an e-commerce enablement software and order management systems (“OMS”) provider, has announced its formal agreement to acquire SkuVault, a U.S.-based provider of inventory management software (“IMS”) and warehouse management systems (“WMS”) solutions. The deal brings together two companies with a shared vision of accelerating growth for omnichannel sellers. Marlin Equity Partners (“Marlin”), a global investment firm with over $8.1 billion of capital commitments under management, will be the majority shareholder of the combined company.
As Raymond continues to build on its 100year history of innovation and continuous improvement, the intralogistics leader is committed to helping ensure the next generation of manufacturing leaders continues to have the tools and resources needed to positively impact the supply chain.

LiuGong North America adds Modern Group to dealer network
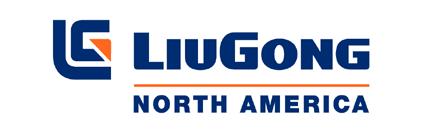
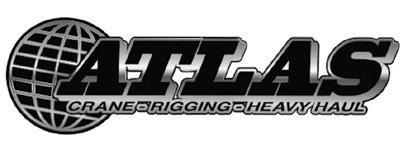
www.atlascraneserviceinc.com
Industry News
of Innovation, on Friday, Oct. 7, 2022. National Manufacturing Day is an annual celebration of the manufacturing industry and is organized by the National Association of Manufacturers (NAM).
Atlas Crane Service, a fullservice crane rental company that primarily serves the wind industry, announced recently that a fund managed by the Infrastructure Opportunities strategy of Ares Management had acquired a controlling interest in the company. Founded in 2009 and headquartered in Aurora, Ill., Atlas is a full-service crane rental provider offering turnkey maintenance, repair, and overhaul solutions to over 250 customers.
Supreme Systems celebrates 35 Years of success
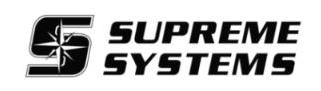
www.skuvault.com
www.supremesystems.com
26 October 2022 Material Handling Network www.MHNetwork.com
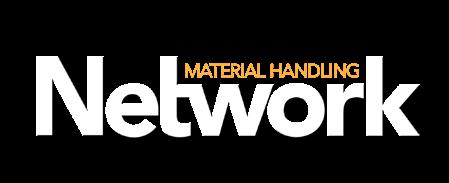
www.raymondcorp.com
www.liugongna.com
IMS/OMS Linnworks completes acquisition of Louisville-based WMS Provider SkuVault
Atlas Crane Service acquired by Ares Management
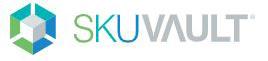
www.MHNetwork.com Material Handling Network October 2022 27 Kip Krady | Account Executive 563 Kip.Krady@557-4493MHNetwork.com Reliable bi-annual desktop reference guide published in print and digital format for our January 2023 issue! Don’t miss out! Directory of Material Handling www.MHNetwork.com AD DEADLINE December202212 Why invest in Network’s Directory? ➥ Longer life in print, MHN website and MHN newsletters ➥ Easy to access when finding new vendors and services ➥ Proven tool to Network readers for sourcing www.MHNetwork.com
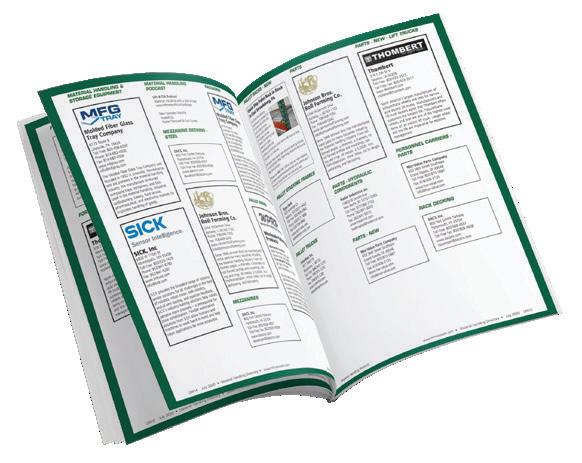



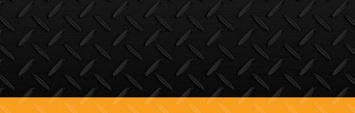
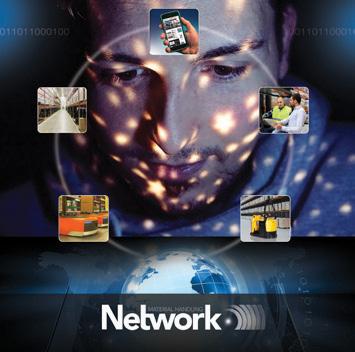
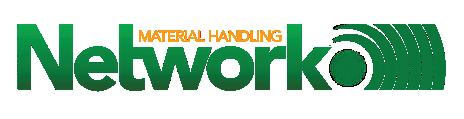
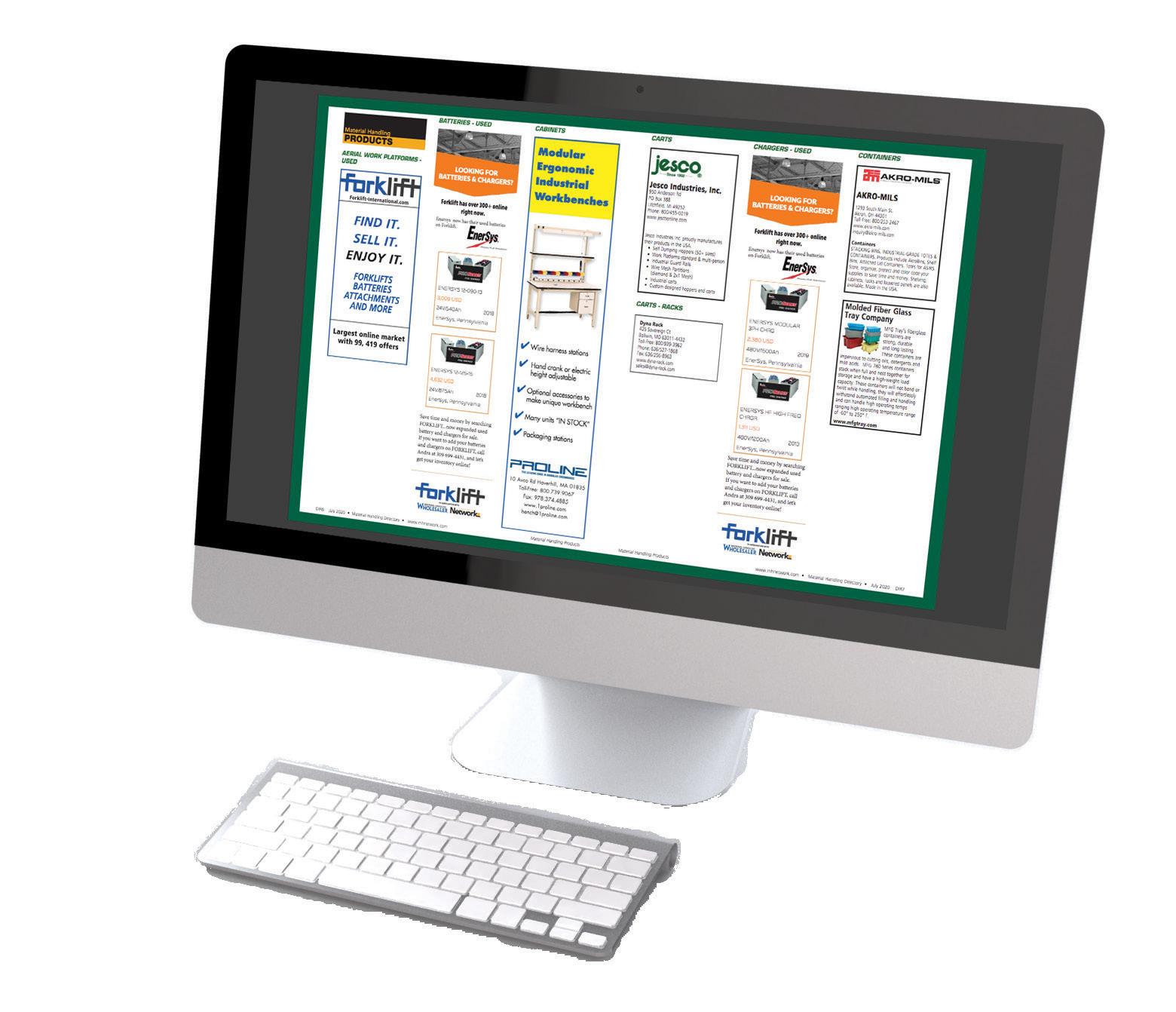
28 October 2022 Material Handling Network www.MHNetwork.com

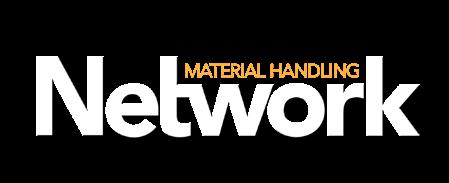
PLA has announced the opening of its newest pallet services facility in Houston, Texas. The addition of this facility brings PLA’s total number of facilities to 76. Conveniently located just off I-45 and the Sam Houston Tollway, this location will serve PLA’s supply chain customers across a 150-mile radius, overlapping service areas with the company’s San Antonio and Dallas facilities. The nearly 23,000 square foot facility on over eight acres will feature 10 dock doors and process over 3 million pallets annually.
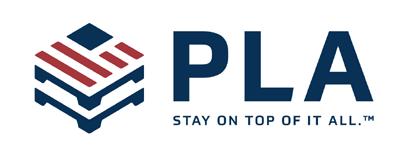
www.plasolutions.com
Orbis Corporation’s Alison Zitzke named 2022 PMMI On the Rise winner
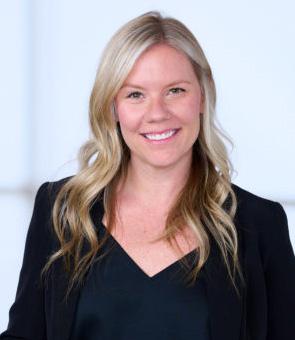
www.orbiscorporation.com
Following nearly three years of bargaining, the Brotherhood of Locomotive
For more People News www.MHNetwork.comvisit
Trew announces new President and COO
Engineers and Trainmen (BLET), a Division of the Rail Conference of the International Brotherhood of Teamsters, and the Transportation Division of the International Association of Sheet Metal, Air, Rail, and Transportation Workers (SMARTTD) reached a Tentative National Agreement with the nation’s largest freight rail carriers that include wage increases, bonuses, with no increases to insurance copays and deductibles. For the first time, our unions were able to obtain negotiated contract language exempting time off for certain medical events from carrier attendance policies. Our unions will now begin the process of submitting the tentative agreement to a vote by the memberships of both unions.
Trew,has announced the appointment of Alfred (Al) Rebello as the president and Chief Operating Officer. Al is a 30year industry veteran providing customer-focused organizational leadership and proven success delivering highly integrated Automation Systems. Before joining Trew, Al was the Business Operations Leader for Honeywell Intelligrated responsible for the delivery of the solutions from presales to installation. Previously he was the Senior Vice President of Operations with Intelligrated when acquired by Honeywell. Al is a graduate of the Harvard Business School General Management Program.
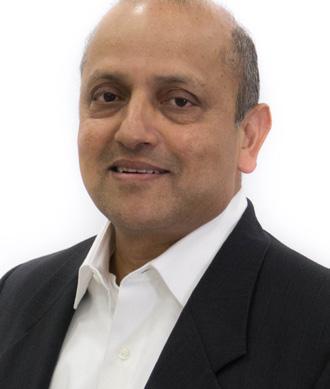
PLA announces opening of Houston pallet management facility
Alison Zitzke, senior product manager for ORBIS® Corporation, has been named a 2022 On the Rise Award winner by PMMI, the Association for Packaging and Processing Technologies. This award recognizes 10 young professionals who have demonstrated extraordinary leadership qualities in the packaging and processing industry. One of Alison’s most recent achievements has been spearheading the development and launch of ORBIS’ flagship 40-by-48-inch pallet, the Odyssey®, bringing the pallet portfolio into new manufacturing technologies, applications, and markets within the reusable packaging space. Alison is also passionate about promoting the circular economy and experimenting with incorporating post-consumer and post-industrial recycled materials back into the manufacturing of new products.
People News
www.trewautomation.com
Tentative agreement reached between Unions Representing Conductors and Engineers and the Nation’s Class I Railroads
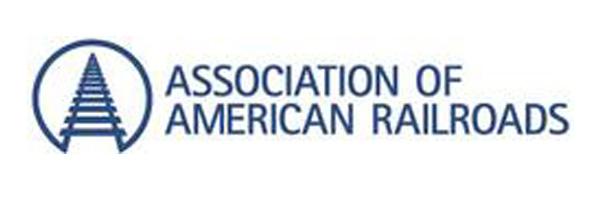
Nucor announces Leon J. Topalian as Chair of the Board of Directors
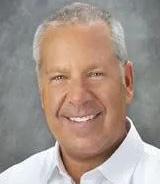
People News


CSX Corp. has announced that, as part of a planned succession process, its Board of Directors has appointed seasoned executive Joseph R. Hinrichs as the Company’s new president and Chief Executive Officer, effective September 26, 2022. Hinrichs succeeds James M. Foote, who plans to retire as president and Chief Executive Officer, as well as from the Board, on September 26, 2022. Foote will continue to work with the Company through March 31, 2023, as an advisor to facilitate a seamless leadership transition.
www.MHNetwork.com Material Handling Network October 2022 29


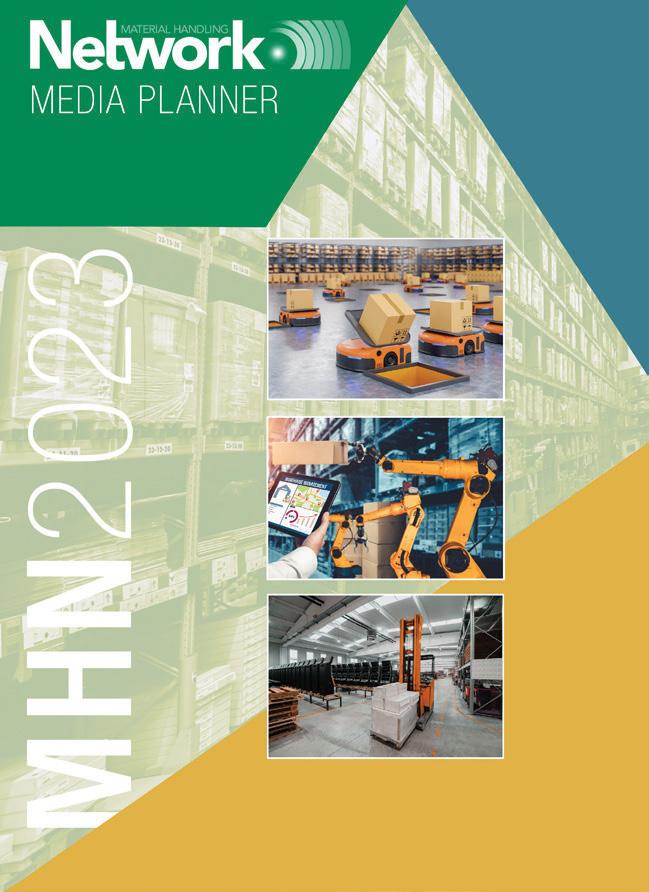

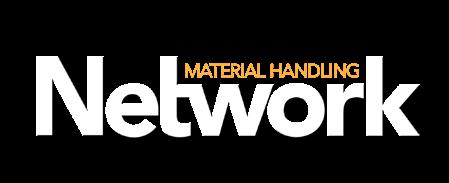
www.nucor.com

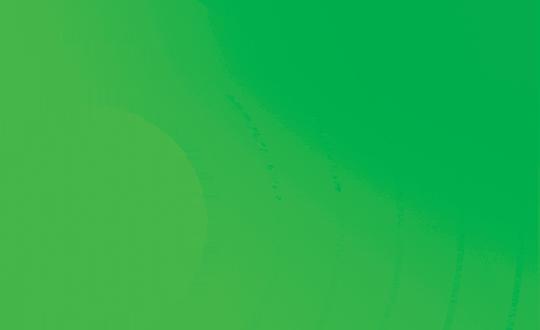
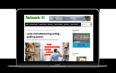
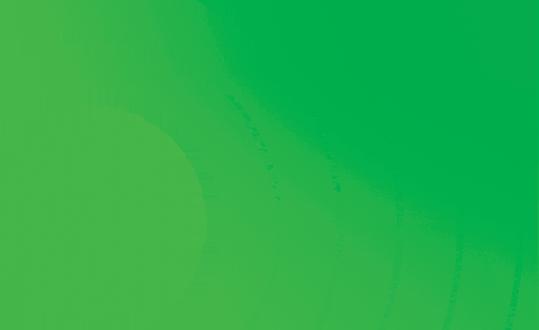
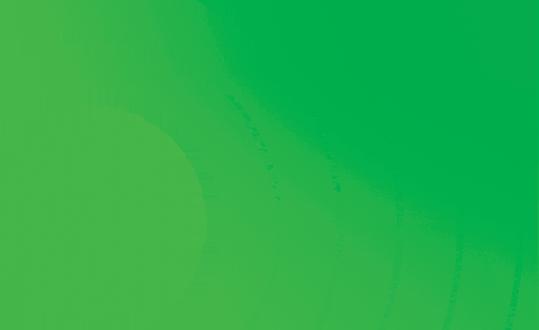
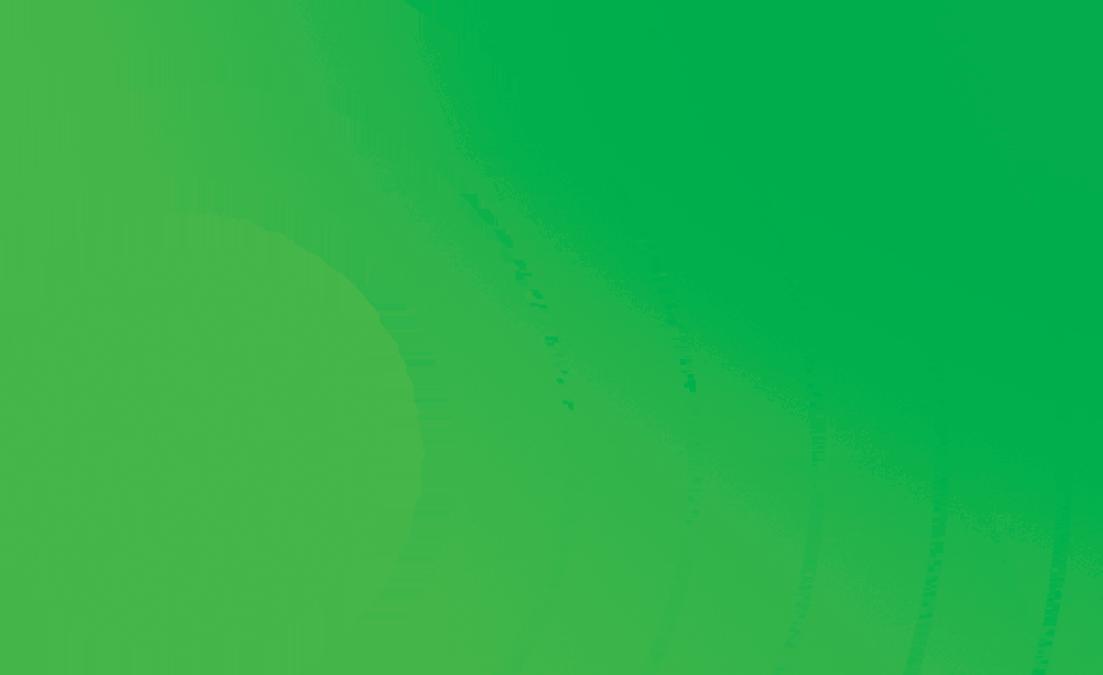
Joseph R. Hinrichs appointed president and CEO of CSX
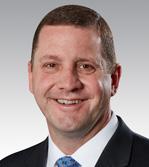
Nucor Corporation announced that its President and Chief Executive Officer, Leon J. Topalian, has assumed the additional role of Chair of the Board of Directors and that Board member, Christopher J. Kearney, has been appointed Lead Director of the Board. John H. Walker, a member of the Board since 2008 and most recently its Non-Executive Chairman, will continue to serve as a Board member.
DIGITAL & PRINT | NEWSLETTERS | LEAD GENERATION Are you ready for 2023? New for 2023! • Lead Generating Opportunities • Automate 2023 Supplement • More Guest Columns • Newsletters become weekly and so much more... Call Kip today to plan your 2023 advertising! 563 557-4493 Calendar January Material Handling Network showing off what your product in this issue! February Deadline: January 16 Supplement: Deadline: January 12 March April 29 May 2023 in Nashville, TN attending. Deadline: February April May 22 25, 2023 Detroit, MI A3 Association for Advancing Automation May Automation/Robots/Driverless Material Handling Equipment Issue the answer for many employers. In this issue warehouse operation managers on successes June Annual Safety Issue will also look at ITA’s National Forklift Safety Day on June 13, 2023 and OSHA’s Safe+Sound week August 7-11, 2023. Deadline May 12 July Battery and Charger Issue the charge and what you need to do to profit August Choosing the right Warehouse Management Systems integrations and which one right for your September technology trends in making the warehouse efficient and profitable. Supplement: Deadline: August 11 October Staffing Your Warehouse take look at some warehouse operations and how they balance warehouse personnel with automation technology. Digital Advertising & Rates Website Units available: rotating Spots: Prices per month sent every Tuesday Digital eNewsletter 4th Friday Digital Ad + Leaderboard 8.375” 10.875” pdf Network’s Guest Column The Network editorial staff will edit your article and provide stock art necessary. (Stock art may include fee.) Note: will be maximum two Network Guest columns per month, and each will have industry exclusivity. Why Sponsor Content? You become the trusted expert when they’re ready buy. Space reservations: Two months prior to publication editorial date which Final approval your page must be made www.MHNetwork.com WE ARE!

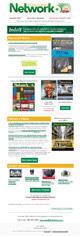
www.csx.com
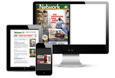
• Expansion - 54 New Projects
• Michigan - 10 • New York - 8
• Pennsylvania - 6 • Alabama - 5
• California - 5 • Minnesota- 5
Industrial Manufacturing planned Project Report
Industrial Manufacturing - By Project Scope/Activity
30 October 2022 Material Handling Network www.MHNetwork.com
• New Construction - 55 New Projects
Industrial Manufacturing - By Project Type
• Renovations/Equipment Upgrades - 35 New Projects
Industrial Manufacturing Shows Weak Growth in August 2022 with 140 New Planned Projects
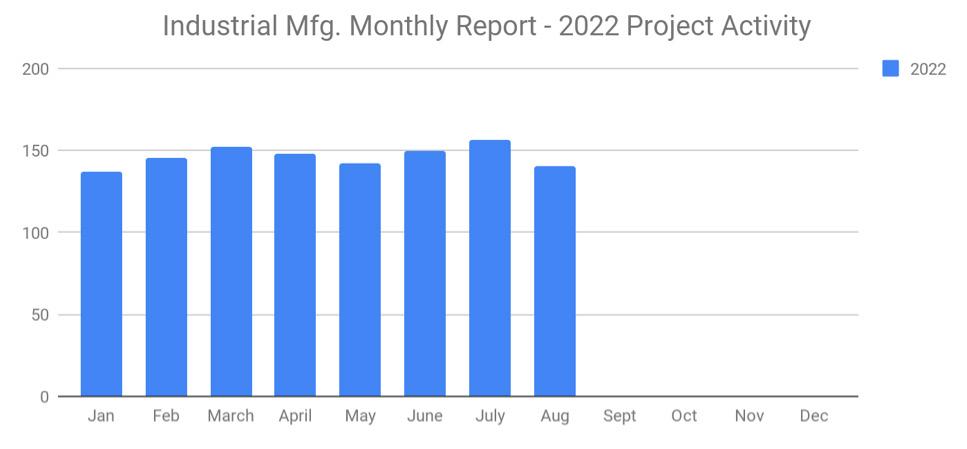
Industrial Manufacturing - By Project Location (Top 10 States)
TEXAS: Solar panel mfr. is considering investing $2 billion for the construction of a manufacturing facility and currently seeking a site in the FORT WORTH or DALLAS, TX area.
The following are selected highlights on new Industrial Manufacturing industry construction news
OHIO: Woodworking tools mfr. is planning for the construction of a 425,000 sf warehouse and manufacturing facility at 1564 W. 130th St. in BRUNSWICK, OH. They have recently received approval for the project. Construction will occur in two phases. They will relocate their operations upon completion.
• Manufacturing/Production Facilities - 125 New Projects
• Texas - 13 • North Carolina - 11
Data provided by SalesLeads
Top 10 Tracked Industrial Manufacturing Projects
ALBERTA: Specialty building materials mfr. is planning to invest $210 million for the construction of a manufacturing facility in CARSELAND, AB. They have recently received approval for the project. Construction is expected to start in 2023.
Since 1959, SalesLeads, based in Jacksonville, FL is a leader in delivering industrial capital project intelligence and prospecting services for sales and marketing teams to ensure a predictable and scalable pipeline. Our Industrial Market Intelligence, IMI identifies timely insights on companies planning significant capital investments such as new construction, expansion, relocation, equipment modernization and plant closings in industrial facilities. The Outsourced Prospecting Services, an extension to your sales team, is designed to drive growth with qualified meetings and appointments for your internal sales team.
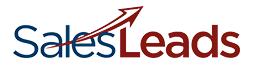
TENNESSEE: Tire mfr. is planning to invest $550 million for an 850,000 sf expansion, renovation, and equipment upgrades on their manufacturing facility in MORRISON, TN. They are currently seeking approval for the project. Renovations are
During the month of August, our research team identified 19 new Industrial Manufacturing facility construction projects with an estimated value of $100 million or more.
• Plant Closings - 11 New Projects
Largest Planned Project
NORTH CAROLINA: Pharmaceutical packaging product mfr. is planning to invest $94 million for the expansion and equipment upgrades on their manufacturing, warehouse, and office facility in MORGANTON, NC. They have recently received approval for the project.
KENTUCKY: EV Battery component mfr. is planning to invest $310 million for the construction of a 450,000 sf manufacturing facility in HOPKINSVILLE, KY. Construction is expected to start in late 2022, with completion slated for late 2023.
• Distribution and Industrial Warehouse - 41 New Projects
TEXAS: Aerospace company is planning to invest $50 million for the construction of a manufacturing facility in AMARILLO, TX. They are currently seeking approval for the project.
The largest project is owned by Honda Motor Company, who is planning to invest $4 billion for the construction of an EV battery manufacturing facility and is currently seeking a site in the MARYSVILLE, OH area.
expected to start in late 2022, with completion slated for Spring 2024.
• Ohio - 8 • Wisconsin - 7
ALABAMA: Wood product mfr. is planning to invest $210 million for the construction of a sawmill and manufacturing complex in MOBILE, AL. They will relocate their operations upon completion in Fall 2024.
INDIANA: Battery mfr. is planning for the construction of a manufacturing facility on Fillmore Rd. in NEW CARLISLE, IN. They are currently seeking approval for the project.
SalesLeads announced today the August 2022 results for new planned capital project spending report for the Industrial Manufacturing industry. The Firm tracks North American planned industrial capital project activity; including facility expansions, new plant construction and significant equipment modernization projects. Research confirms 140 new projects in the Industrial Manufacturing sector down from 156 in July.
MICHIGAN: Building materials mfr. is planning to invest $194 million for a 134,000 sf expansion and equipment upgrades on their manufacturing facility in SAGOLA, MI. They have recently received approval for the project.
www.MHNetwork.com Material Handling Network October 2022 31
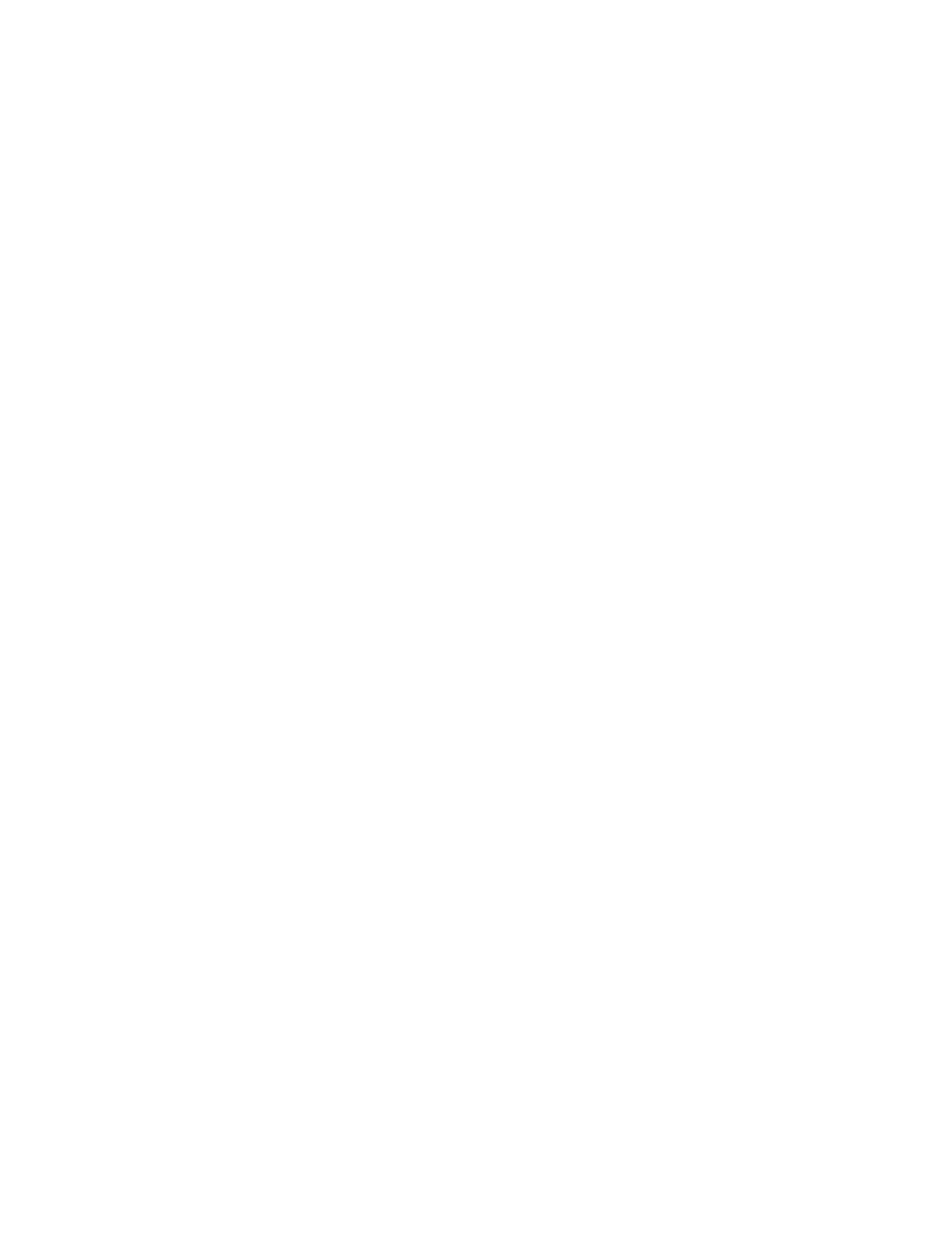
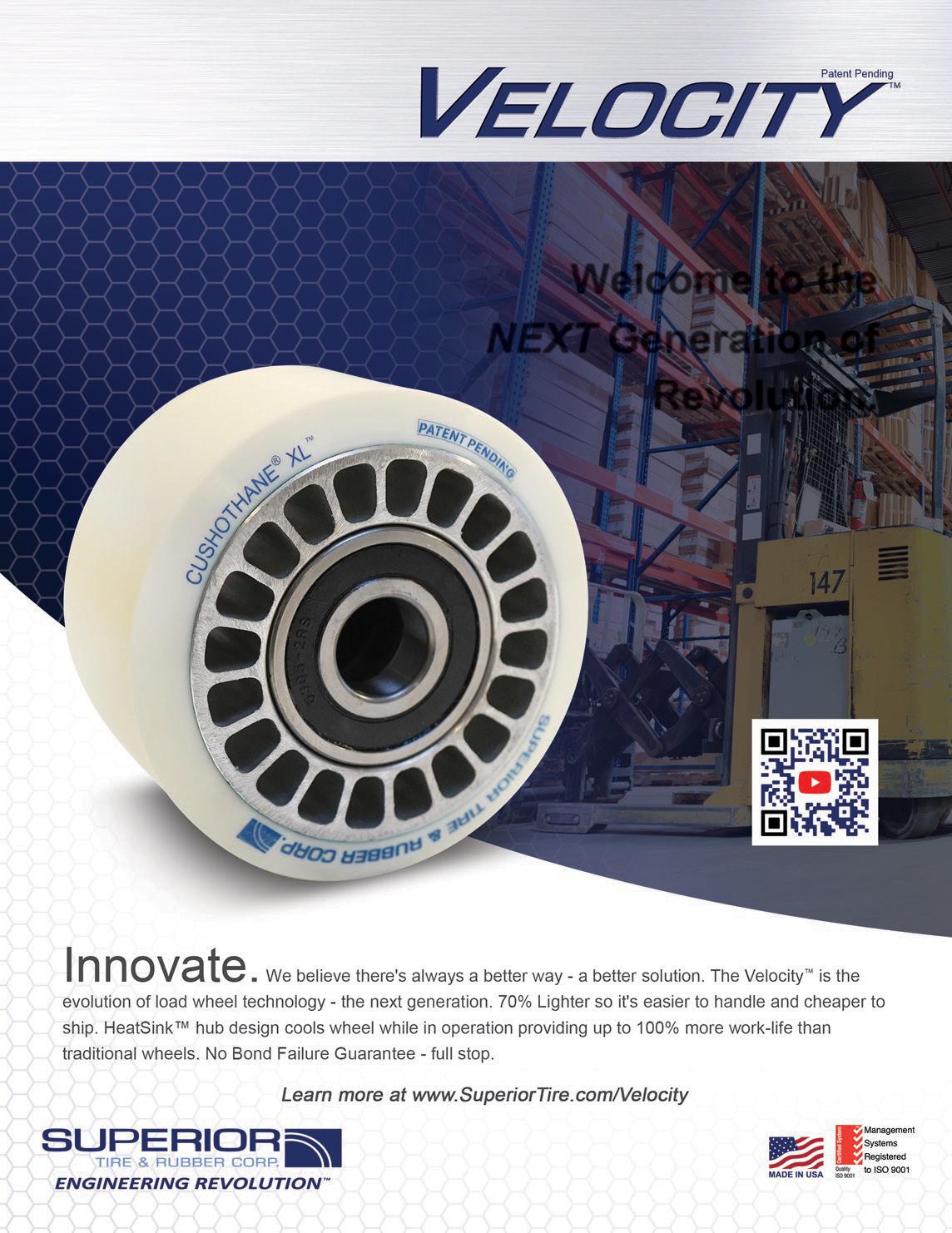
FLORIDA: Logistics service provider is planning to invest $116 million for the construction of a 272,000 sf warehouse and distribution facility at 8730 Somers Rd. in JACKSONVILLE, FL. They are currently seeking approval for the project.
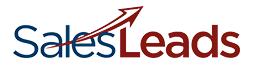
• Indiana - 12 • Texas - 12
Data provided by SalesLeads
32 October 2022 Material Handling Network www.MHNetwork.com
Distribution and Supply Chain - By Project Scope/Activity
Distribution and Supply Chain - By Project Location (Top 5 States)
Top 10 Tracked Distribution and Supply Chain Project Opportunities
NORTH DAKOTA: Bitcoin mining company is planning to invest $500 million for the construction of a data center, manufacturing, warehouse, and office complex in NEKOMA, ND. They are currently seeking approval for the project.
GEORGIA: Foodservice equipment supplier is planning to invest $87 million for the construction of a distribution center at 54 Logistics Dr. in ELLABELL, GA. They are currently seeking approval for the project.
FLORIDA: Beverage bottling company is investing $112 million for the construction of an 800,000 sf distribution and office facility at 2261 S US Hwy. 301 in TAMPA, FL. Construction has recently started and they will relocate their operations upon completion in Spring 2025.
The following are selected highlights on new Distribution Center and Warehouse construction news.
• Washington - 10
SalesLeads announced today the August 2022 results for the new planned capital project spending report for the Distribution and Supply Chain industry. The Firm tracks North American planned industrial capital project activity; including facility expansions, new plant construction and significant equipment modernization projects. Research confirms 172 new projects in the Distribution and Supply Chain sector down from 156 in July.
Largest Planned Project
The largest project is owned by Amazon, who is investing $550 million for the construction of a distribution center in BUFFALO, NY. They have recently received approval for the project.
• California - 16 • Florida - 13
NEW MEXICO: Production company is investing $75 million for the construction of a 300,000 sf studio complex on West Amador Avenue in LAS CRUCES, NM. They will relocate their headquarter operations upon completion. MINNESOTA: University is planning to invest $55 million for the construction of a warehouse and storage facility in MINNEAPOLIS, MN. They have recently received approval for the project.
Distribution and Supply Chain Project Report
• Distribution/Fulfillment Centers - 26 New Projects
Distribution and Supply Chain Shows Weak Growth in August 2022 with 172 New Planned Project
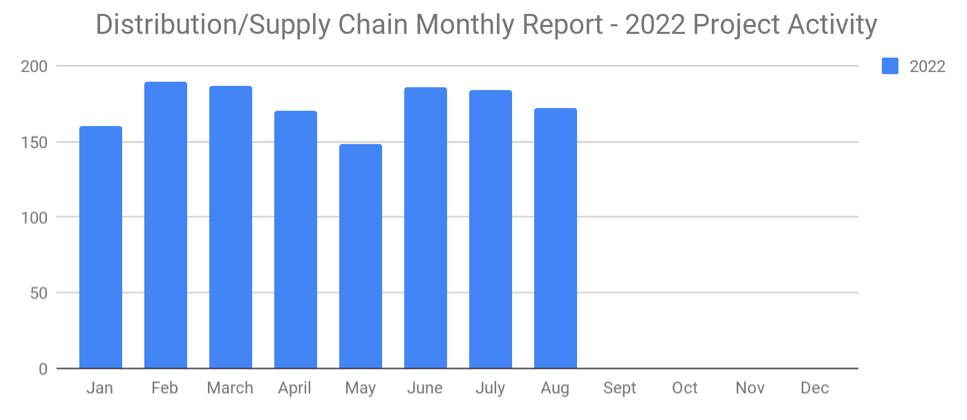
• Closings - 6 New Projects
Distribution and Supply Chain - By Project Type
TEXAS: Meat processing company is planning to invest $200 million for a 143,000 sf expansion, renovations, and equipment upgrades on their processing and warehouse facility in AMARILLO, TX. Construction is expected to begin in Fall 2022, with completion slated for 2024.
INDIANA: Motorsport company is planning to invest $200 million for the construction of a 575,000 sf warehouse, office, and maintenance facility in FISHERS, IN. Construction is expected to start in Fall 2022, with completion slated for 2025.
During the month of August, our research team identified 7 new Distribution and Supply Chain facility construction projects with an estimated value of $100 million or more.
SOUTH CAROLINA: Pet products retailer is planning to invest $53 million for the renovation and equipment upgrades on a recently leased 535,000 sf distribution center in ORANGEBURG, SC. Completion is slated for early 2023.
Since 1959, SalesLeads, based in Jacksonville, FL is a leader in delivering industrial capital project intelligence and prospecting services for sales and marketing teams to ensure a predictable and scalable pipeline. Our Industrial Market Intelligence, IMI identifies timely insights on companies planning significant capital investments such as new construction, expansion, relocation, equipment modernization and plant closings in industrial facilities. The Outsourced Prospecting Services, an extension to your sales team, is designed to drive growth with qualified meetings and appointments for your internal sales team.
• New Construction - 102 New Projects
ILLINOIS: Beverage company is investing $90 million and has recently started the construction of a 250,000 sf distribution center in WEST DUNDEE, IL. They will relocate their regional operations upon completion in 2024.
• Expansion - 28 New Projects
• Industrial Warehouse - 155 New Projects
• Renovations/Equipment Upgrades - 36 New Projects
www.MHNetwork.com Material Handling Network October 2022 33 WMS Accelerator Optimizes Warehouse Activities improve OTIF • manage INVENTORY real-time SCHEDULING • optimize LABOR Contact Us for an initial assessment! info@autoscheduler.ai 615-428-2035 autoscheduler.ai
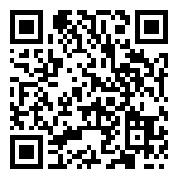

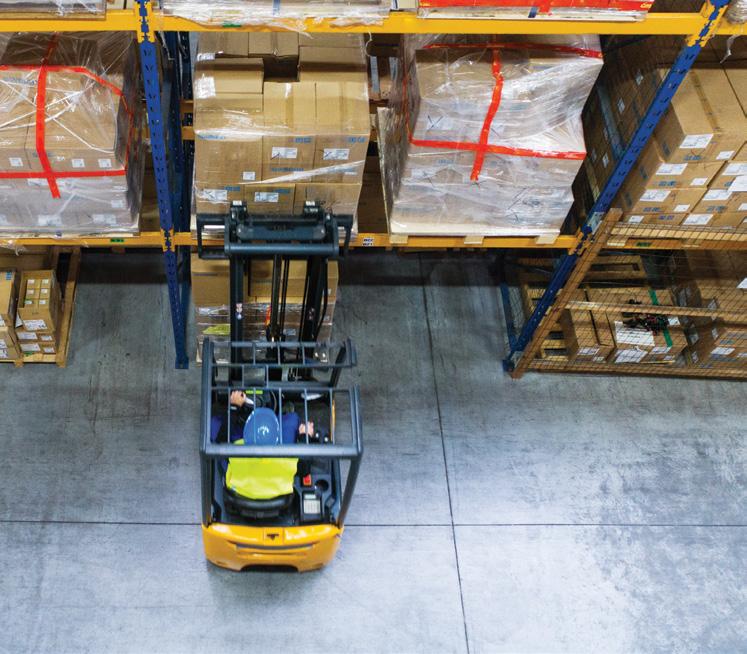


Data provided by SalesLeads
• New Construction - 211 New Projects
• Florida - 17 • Illinois - 17
• Mine - 0 New Projects
34 October 2022 Material Handling Network www.MHNetwork.com
Planned Industrial Construction - By Scope/Activity
• Pipeline - 0 New Projects
TEXAS: Oil and gas company is planning to invest $5 billion for the construction of a processing facility in VICTORIA, TX. They
are currently seeking approval for the project. Construction is expected to start in 2023, with completion slated for early 2025.
The following are selected highlights on new industrial construction news and project opportunities throughout North America.
OHIO: Automotive mfr. is considering investing $4 billion for the construction of an EV battery manufacturing facility and currently seeking a site in the MARYSVILLE, OH area.
• Power/Energy/Oil and Gas - 7 New Projects
During the month of August, our research team identified 39 new General Industrial facility construction projects with an estimated value of $100 million or more.
Planned Industrial Construction - By Project Type:
Top 10 Tracked Industrial Construction Projects
OKLAHOMA: Electronic products mfr. is considering investing $4 billion for the construction of an EV battery manufacturing facility and currently seeking a site in OKLAHOMA.
TENNESSEE: Tire mfr. is planning to invest $550 million for an 850,000 sf expansion, renovation, and equipment upgrades on their manufacturing facility in MORRISON, TN. They are currently seeking approval for the project. Renovations are expected to start in late 2022, with completion slated for Spring 2024.
GEORGIA: Aerospace company is planning to invest $1.6 billion for an expansion of their manufacturing facility in MARIETTA, GA. They are currently seeking approval for the project.
BRITISH COLUMBIA: Oil and gas company is planning to invest $4 billion for the construction of a liquified natural gas processing plant in SQUAMISH, BC. They are currently seeking approval for the project. Completion is slated for 2027.
Planned Industrial Construction - By Location (Top 10 States)
Largest Planned Industrial Construction Project
ILLINOIS: Energy company is planning to invest $500 million for the construction of a 280 MW power plant in DECATUR, IL. They are currently seeking approval for the project. Completion is slated for late 2024.
• Plant Closing - 24 New Projects
Planned industrial project activity increased 1% from the previous month.
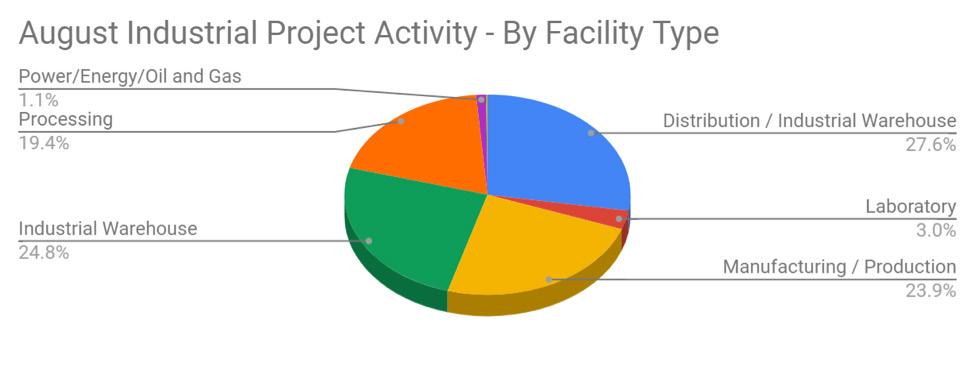
• Terminal - 1 New Project
The largest project is owned by Penn LNG, who is planning to invest $7 billion for the construction of a natural gas export terminal and is currently seeking a site in the PHILADELPHIA, PA area.
• Renovations/Equipment Upgrades - 120 New Projects
TEXAS: Biofuel producer is planning to invest $2 billion to repurpose their biodiesel processing facility into a sustainable aviation fuel (SAF) processing facility in GALENA PARK, TX. They are currently seeking approval for the project.
NEW YORK: Global online retailer is planning to invest $550 million for the construction of a distribution center in BUFFALO, NY. They have recently received approval for the project.
• Michigan - 18 • Ohio - 18
• Indiana - 17 • Pennsylvania - 17
• Laboratory Facilities - 19 New Projects
• Expansion - 103 New Projects
MISSISSIPPI: Specialty aviation fuel mfr. is planning to invest $1.5 billion for the construction of a processing facility in NATCHEZ, MS. They are currently seeking approval for the project. Construction is expected to start in early 2023.
Since 1959, SalesLeads, based in Jacksonville, FL is a leader in delivering industrial capital project intelligence and prospecting services for sales and marketing teams to ensure a predictable and scalable pipeline. Our Industrial Market Intelligence, IMI identifies timely insights on companies planning significant capital investments such as new construction, expansion, relocation, equipment modernization and plant closings in industrial facilities. The Outsourced Prospecting Services, an extension to your sales team, is designed to drive growth with qualified meetings and appointments for your internal sales team.
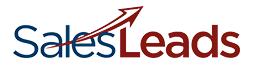
Industrial Construction Project Report
• Distribution and Industrial Warehouse - 172 New Projects
Research by SalesLeads’ experienced industrial market research team, shows 435 new planned industrial projects tracked during the month of August up from 429 in July.
• Manufacturing Facilities - 149 New Projects
• Texas - 32 • California - 24
• New York - 24 • North Carolina - 20
• Processing Facilities - 121 New Projects
www.MHNetwork.com Material Handling Network October 2022 35
Quality Ergonomic Lifting Equipment Since 1940
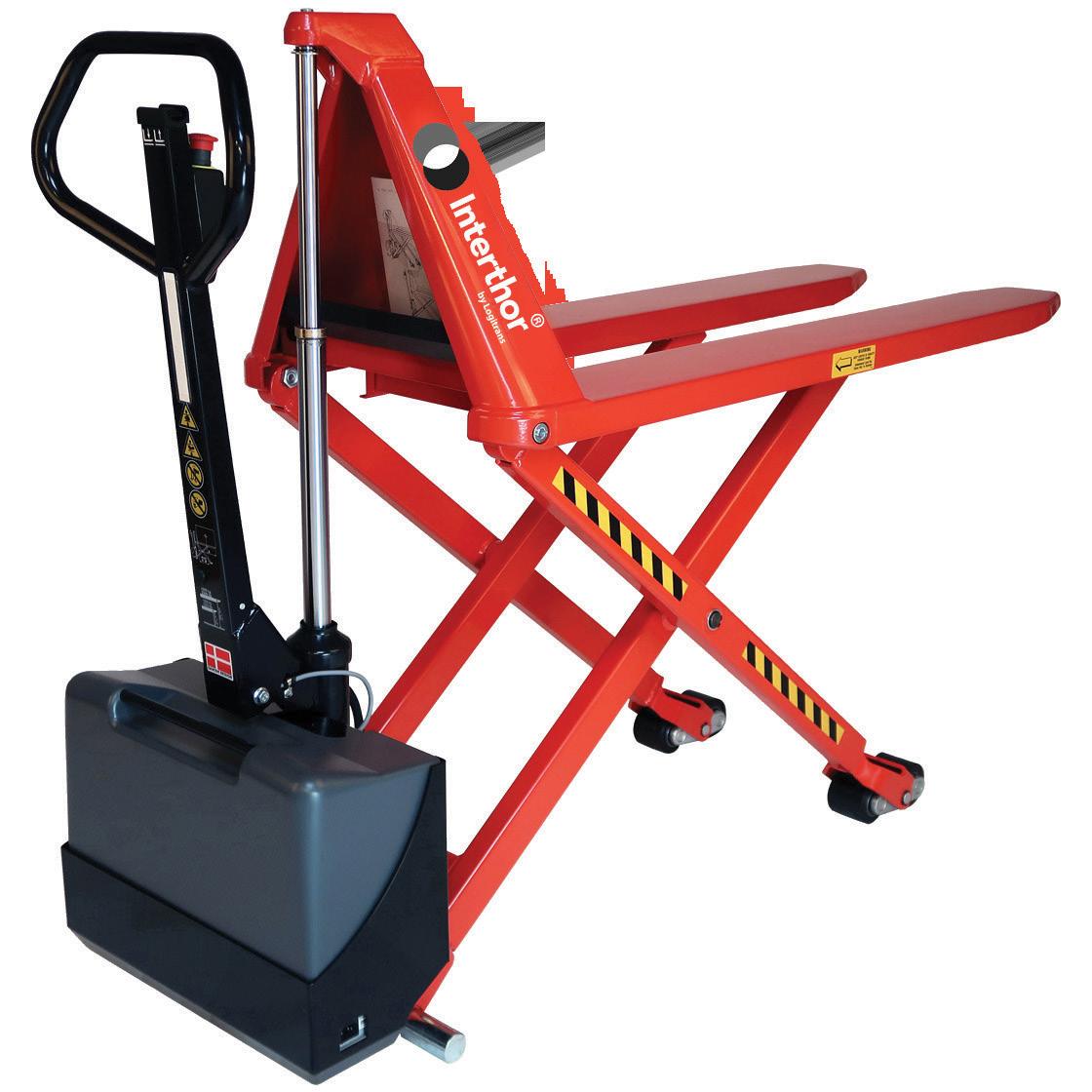
Explore the widest range in the market Tel. (888) 345 1270 Email: sales@interthor.com www.interthor.com ®
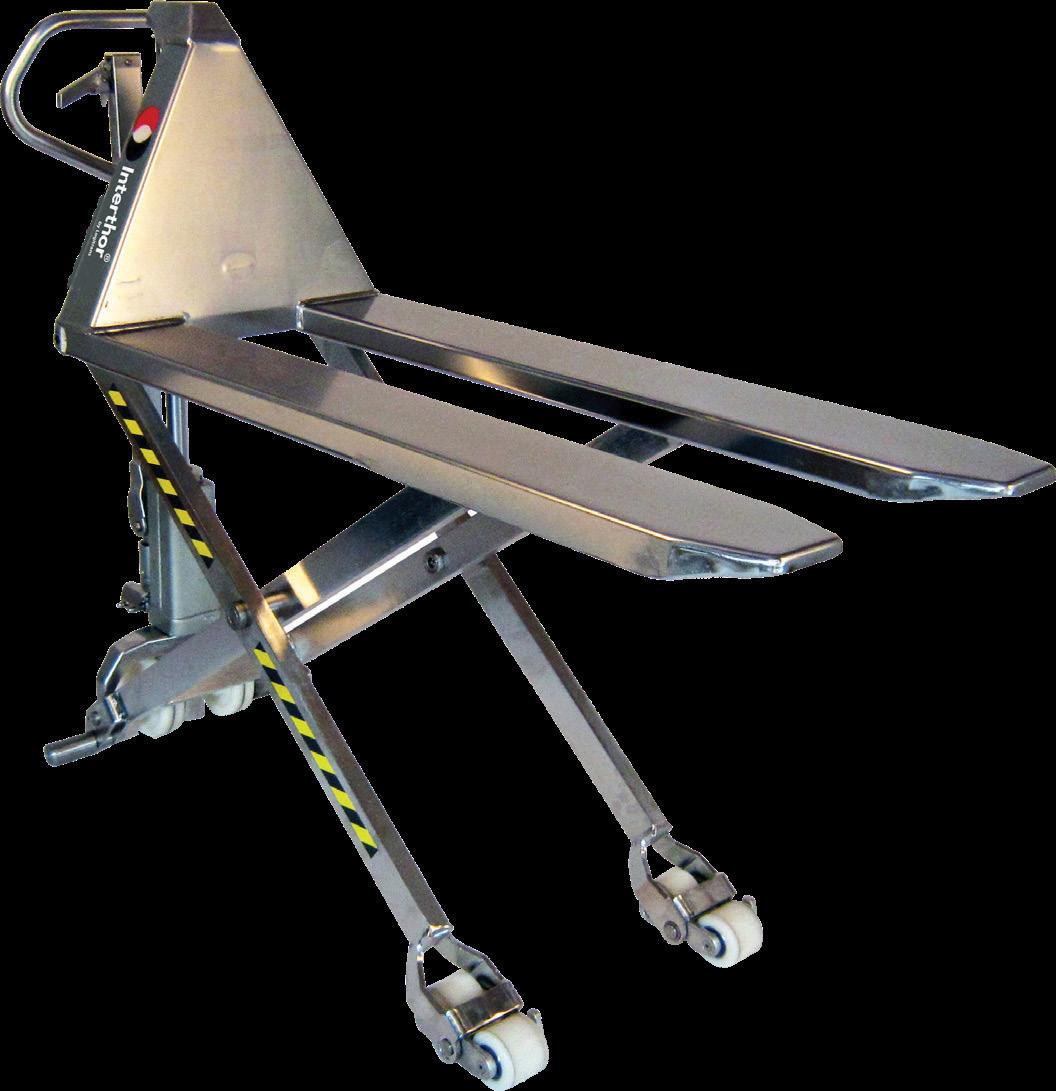
The new M3000 Case Packer from Brenton Reach speeds up to 50 cases per minute
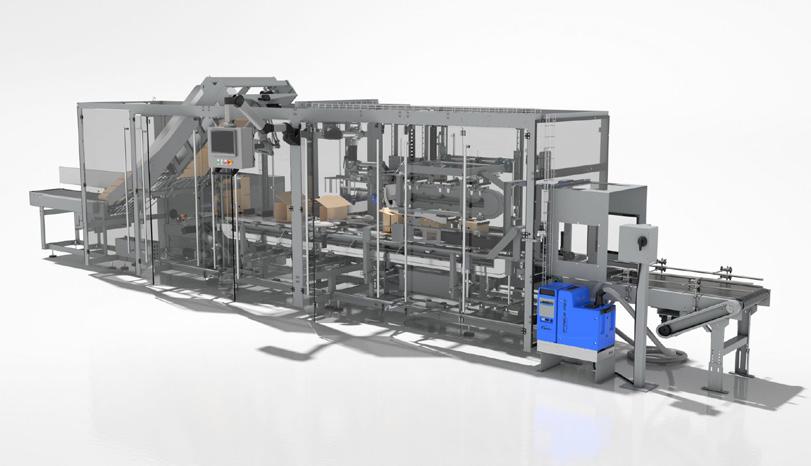
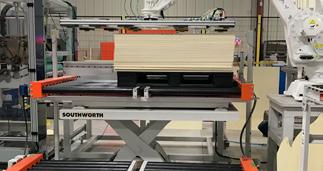
SupplyOne Packaging Management Program promises savings guaranteed in writing
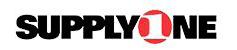
Product Showcase
www.brentonengineering.com
Noblelift introduces Four Wheel Lithium-Iron Phosphate forklifts
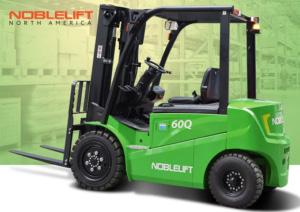
The Noblelift FE4P50Q (5,000lb capacity), FE4P60Q (6,000lb capacity), and FE4P70Q (7,000lb capacity) Four Wheel Lithium-Iron Phosphate (LiFe4OP) Forklifts are highly efficient, durable Lithium-iron forklifts. They are designed for indoor and outdoor applications. The mast system, front/rear axles and chassis are engineered to be tough like an Internal Combustion Engine (ICE) forklift, but with all the advantages of Lithiumiron. AC drive technology is used to achieve high performance with low operating and maintenance costs. www.nobleliftna.com
For applications that require frequent cycling (lifting and lowering) of lift tables, Southworth offers high-duty cycle packages that increase recommended maintenance intervals from 50,000 cycles to 200,000 cycles. The dramatic increase in cycles is attributed to upgraded components including more rugged and durable wear parts. In addition to better accommodating higher cycles, these components also deliver longer life and better performance in applications that involve oversized or non-uniform loads which can cause uneven wear in standard lifts. www.southworthproducts.com
Bally Ribbon Mills (BRM), has announced the availability of a wide range of lightweight twoand three-dimensional woven materials that serve as the structure or substrate for critical rigging and tie down applications that require strength, interlaminar shear, enduring resistance, or conductivity. BRM custom designs specialty applications with high strength-to-weight ratios, flame/heat resistance, flexibility, low elongation, and abrasion resistance. www.ballyribbon.com
36 October 2022 Material Handling Network www.MHNetwork.com

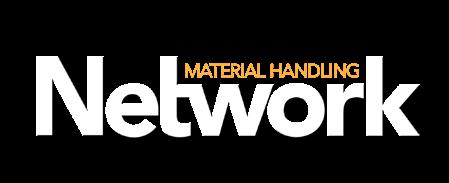
Brenton is launching a new continuous motion side-load case packer aimed at CPQ customers looking to pack between 30 and 50 cases per minute. Plan to see the M3000 demonstrating its capabilities in booth N-5546 at PACK EXPO 2022, Oct. 2326 at McCormick Place in Chicago. The M3000 Case Packer is designed to fill a need for mid-range manufacturers of packaged personal care and food products to pack up to 50 wrap-around or tray-style cases per minute.
High-Duty Cycle Lift Tables offer extended time between maintenance
SupplyOne, Inc., an independent supplier of custom corrugated and other value-added packaging products, equipment, and services in the U.S., highlights its Packaging Management Program. The Packaging Management Program, or PMP, simplifies the complexities associated with packaging ownership to reduce the total cost of packaging and contribute to more sustainable operations. The PMP has the unique distinction of guaranteeing the customer’s savings in writing. www.supplyone.com
Bally Ribbon Mills offers custom-designed woven materials for critical rigging and tie down applications
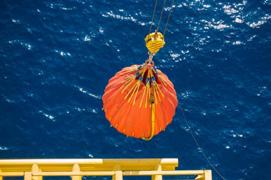
www.MHNetwork.com Material Handling Network October 2022 37 Largest online market for used forklifts, attachments and work platforms. DEALERS DID YOU KNOW YOU CAN GET YOUR EQUIPMENT ONLINE FOR JUST $99 A MONTH? PLUS, WE HAVE AN EQUIPMENT QUOTING TOOL INCLUDED AT NO ADDITIONAL CHARGE. CALL KIP 309.699.4431 | KIP.KRADY@MHNETWORK.COM OR MONTY 563.588.3855 | MONTY@FORKLIFT-INT.COM TO BE PART OF THE FORKLIFT FAMILY OF DEALERS. WWW.FORKLIFT-INTERNATIONAL.COM 2000 CAT Lift Trucks FGC55K MillerSTC Equipment Co Garland | 469-366-4227 14 2015 Hyster S60FT Lift CharlotteOne | 704 587-1040 4 CAT Lift Trucks 2P6000 Kensar Equipment Company Indianapolis | +1 (317) 787-3400 4 2021 CAT Lift Trucks DP40 Cromer Material Handling Oakland, CA | 510 534-6566 2 2012 Hyster S50FT Alta Equipment Company Livonia, MI | 248 449-6700 ext. 1898 1 2013 Hyster S80FTBCS Lift CharlotteOne | 704 587-1040 5 2022 BYD ECB18S 1 Source Material Handling Irwindale, CA | 818 838-1688 10 2009 Hyster S50FT Alta Equipment Company Livonia, MI | 248 449-6700 ext. 1898 1 2021 BYD ECB18S-B Cromer Material Handling Oakland, CA | 510 534-6566 1 2015 CAT Lift Trucks EP3500 Cromer Material Handling Oakland, CA | 510 534-6566 1 2008 Yale GLP030VXNUSE084 Miller Equipment Co Garland | 469-366-4227 10 0 Toyota 7-8FBCU35 Toyota Material Handling Northern Livermore,CaliforniaCA|800 527-3746 1 2009 Toyota 7FBEU15 Miller Equipment Co Garland | 469-366-4227 5 0 CAT Lift Trucks 2EP8000 Kensar Equipment Company Indianapolis | +1 (317) 787-3400 4 2017 Hyster H300HD2 MH Equipment Company Des Moines, IA | 515 288-0123 4 2022 BYD ECB50 1 Source Material Handling Irwindale, CA | 818 838-1688 10
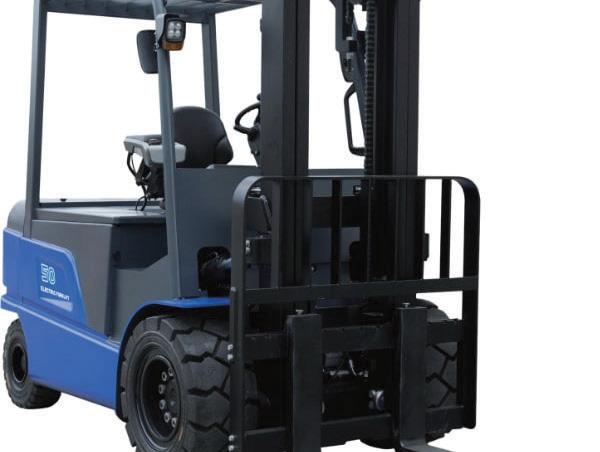


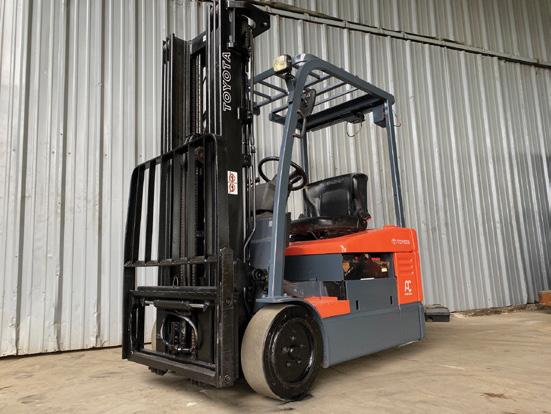

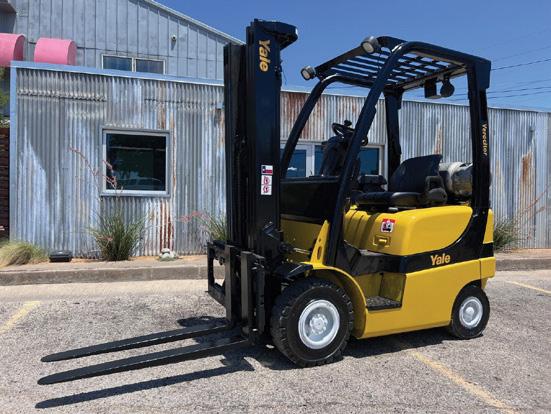
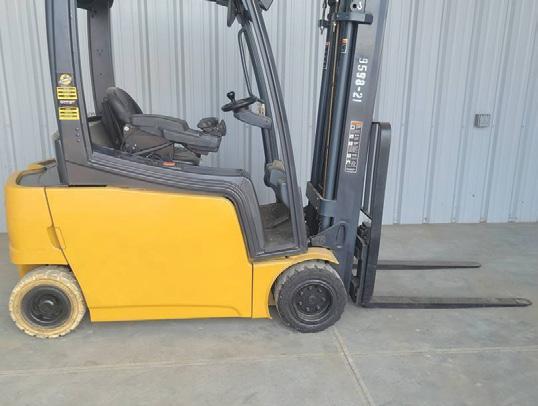

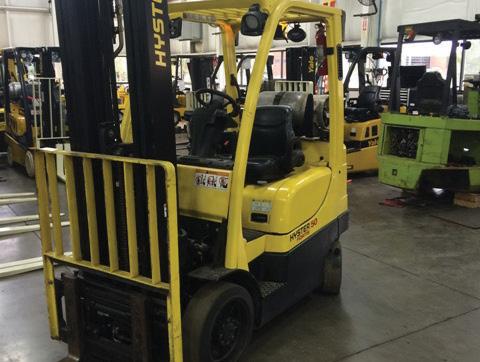
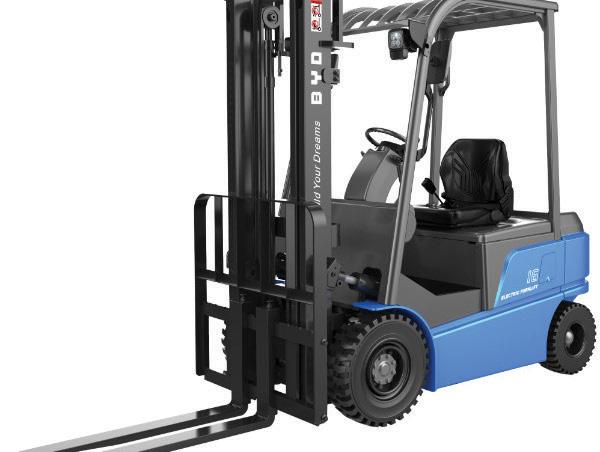
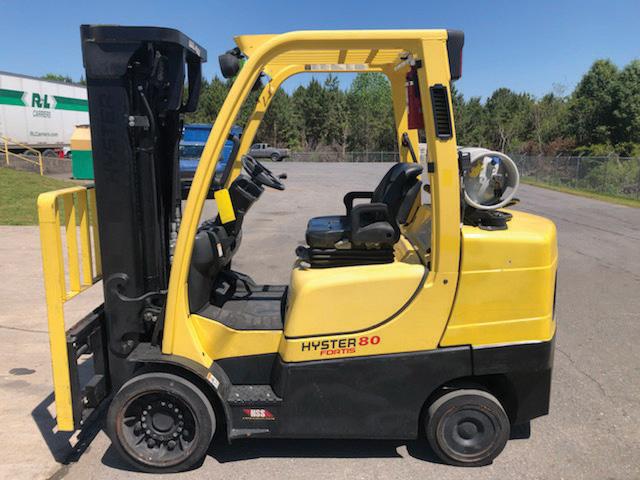
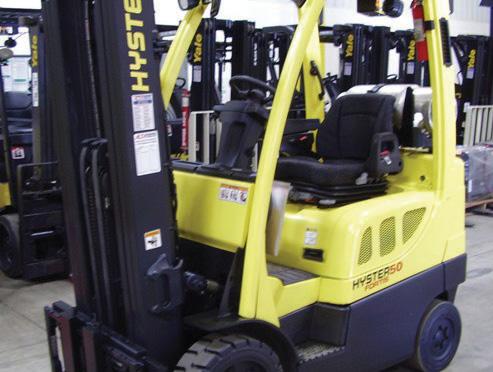

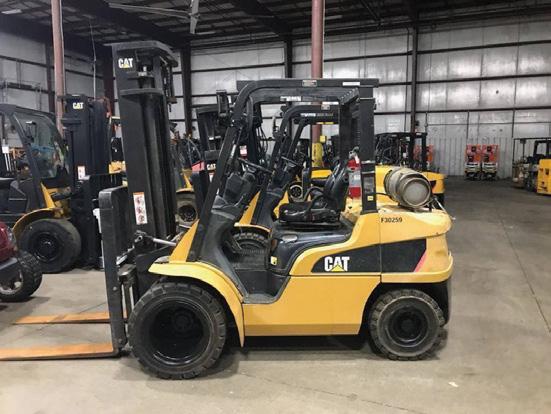
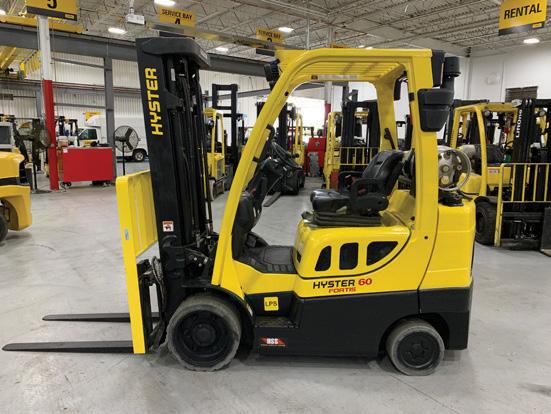
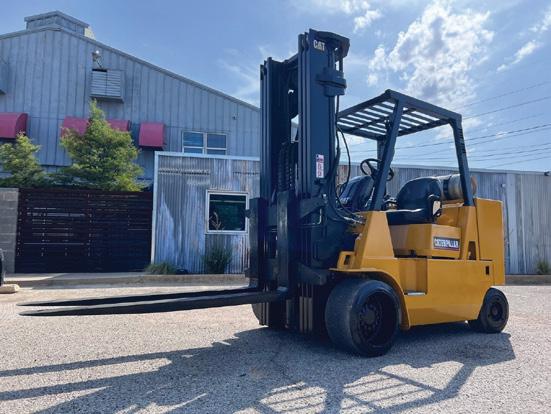
GEODIS launches fast integration API Self-Service Portal to enable quick, seamless integration
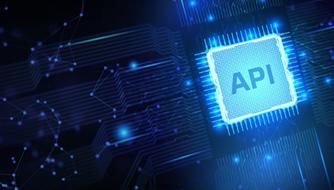
Cementex, highlights the Cementex Feature Series of Arc Flash Protective Clothing PPELEDtronics® Inc. has announced its newest series of UL-listed LED Post Top Lamps that put out an impressive amount of uniform, omnidirectional and brighter light for their compact size, with much more energy efficiency and longer life compared to the old technology and larger post-top bulbs. Because they are thermally managed, these LED bulbs are UL approved for enclosed applications (-40°F to 113°F) and are perfect for easy, direct drop-in installation into existing E26 Edison medium and E39 mogul screw-based lighting fixtures.
Smart Vision Lights (SVL) announces the release of its JWL150, the first in the new Camera-to-Light (CTL) series. Unlike other external illumination products designed for machine vision cameras and smart cameras with built-in illumination that falls short, the JWL150 delivers an intense, compact light source with an integrated camera mount. Compatible with most major machine vision cameras.
www.interroll.com
www.SmartVisionLights.com
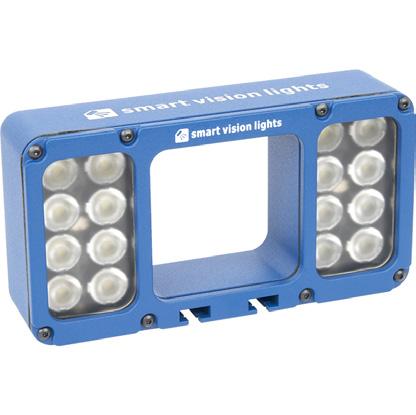
38 October 2022 Material Handling Network www.MHNetwork.com

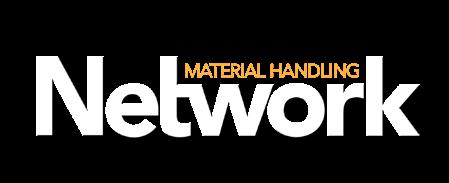
HexcelPack introduces Sustainable, Cushioning Void Filler Solution
Global transport and logistics provider GEODIS has announced the launch of its Fast Integration technology, a new application programming interface (API) self-service portal to enable quick, seamless integration for contract logistics customers in the Americas region. With Fast Integration, the company is now providing its clients with an easyto-use portal and one-stop solution
With the new Helical Modular Chute (HMC), Interroll provides a simple and easy solution for vertical transport in confined spaces. With durable and robust steel construction, this product serves a wide range of material handling applications for the retail & E-commerce, warehousing & distribution as well as courier, express & parcel sectors.
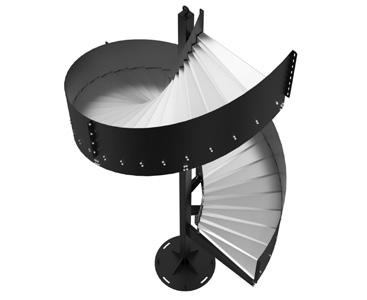
New Interroll Helical Modular Chute provides optimum use of space
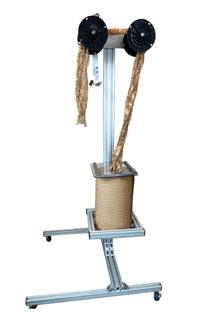
www.geodis.com
UL-Listed Omnidirectional LED Post Top Lamps provide up to 85% energy savings over Halogen & HID
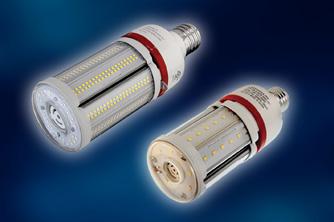
Smart Vision Lights introduces JWL150 External Light
www.cementexusa.com
Product Showcase
HexcelPack has introduced HexaFil™, an innovative, 100% paper-based void fill solution that provides superior block and bracing and additional cushioning in the box vs. traditional paper and plastic-based void fill options. Available with either automatic or manual dispensing units to accommodate various shipping speeds, HexaFil™ delivers ultimate void fill combined with sustainability benefits, including being curbside recyclable and fully biodegradable.
www.hexcelpack.com
www.prestolifts.comcarousels.
www.bisongear.com
TomTom (TOM2), the mapmaker and geolocation specialist, has introduced GO Navigation’s truck plan – an offer designed to meet the needs of professional truck drivers. In addition to GO Navigation’s premium navigation capabilities, enables drivers to plan routes that account for their vehicle’s dimensions, fuel requirements, desired maximum speeds, and cargo (such as dangerous goods).
www.tomtom.com
www.MHNetwork.com Material Handling Network October 2022 39

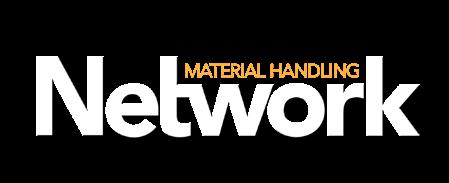
The world’s thinnest glove with maximum cut protection
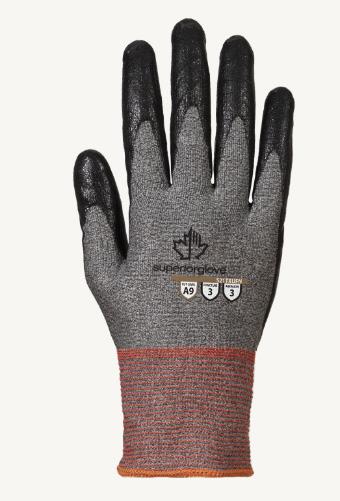
www.superiorglove.com
TomTom’s GO Navigation app introduces truck navigation
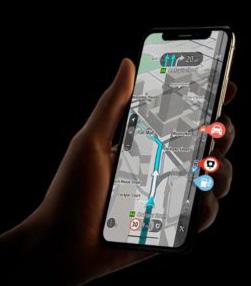
Bison Gear & Engineering Corp. has added an Automated Gear Tooth Grinder to their gear hobbing department. This new equipment offers a range of benefits that improve product quality and increase production capacity. This unique machine frees up capacity on four other machines, improves the quality of gear geometry, improves the cycle time, and effectively grinds spur and helical gears.
Bison Gear and Engineering adds Automated Gear Tooth Grinder

Elevating worker platforms vertically position employees
Elevating Worker Platform Lifts from Presto ECOA are the perfect solution for assembly, repair, or maintenance of large or tall workpieces, awkward shaped items that must be accessed at elevated or varying heights. Not only do they position workers at a comfortable, convenient height, but they also provide a stable platform with room for multiple workers, tools, workstations, etc. Because platform height can be quickly and easily adjusted at the touch of a button, Presto ECOA Elevating Worker Platforms are commonly used for stock picking at high shelves, racks, and horizontal storage
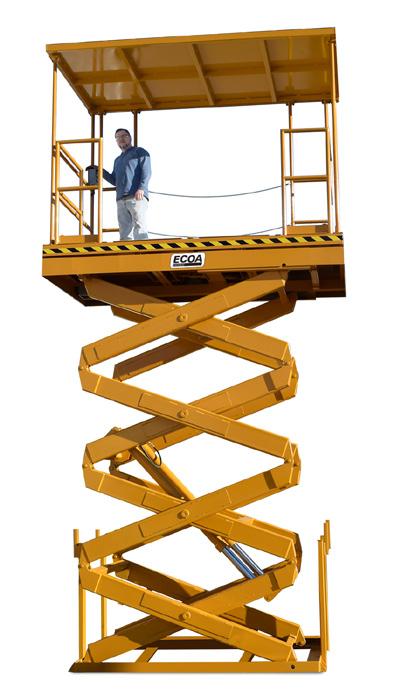
Product Showcase
www.ek-tech.com
Electro Kinetic Technologies adds swappable lithium iron phosphate batteries
Electro Kinetic Technologies, Inc. has introduced the all-new Pony Express 1061 LITHIUM and 1061-HD LITHIUM electric tuggers, the electric tugger line is more powerful than ever, with each tugger able to pull or push a load of up to 1500 lbs. and 2000 lbs., respectively. These new products feature a wide range of capabilities, including lithium iron phosphate swappable battery packs, and the tuggers’ namesake. This innovative tech allows for 24/7 operation, leading to more efficient project timelines and major cost savings.
The Tenactiv™ S21TXUFN is the world’s first 21-gauge glove to deliver the highest-level of cut protection. With a barehand feel, it also provides both durability and puncture protection without sacrificing flexibility. The ultra-thin nitrile palm coating offers a strong grip that won’t slip, all while being touchscreen compatible.

40 October 2022 Material Handling Network www.MHNetwork.com ERGONOMIC HOLSTERSENGINESToll Free 877-303-LIFT • 440-943-9546 • FAX 440-943-9547 www.all-industrial.com ✓ Remanufactured engines ✓ Engines in-stock for same day shipment ✓ Quality assured workmanship from people who know the business! ASSOCIATIONS Your direct connection to the Material Handling Industry’s hottest trends, newest products, best management training workshops & represents a wealth of resources for all material handling businesses. www.mheda.org — 847.680.3500 DECKING PROVEN SOLUTIONS ONE SOURCE DACS inc. 800-909-4937 dswanson@dacsinc.com Punch Deck ® & Punch Deck Plus® Open Area Rack Deck FlueKeeper ® Keeps Flue Spaces Open Fire and Heat Barriers Racking / SolidMezzanineShelvingDeckingRackDeck BATTERIES FIND IT. SELL IT. ENJOY IT. forklift-international.com Marketplace For more articles, news, products and more www.MHNetwork.comvisit

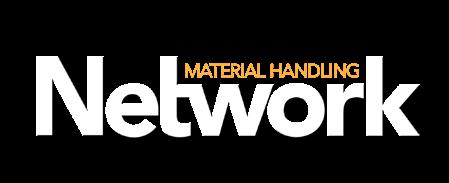
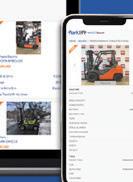
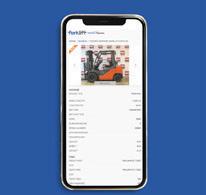
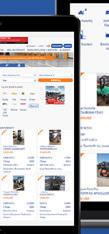
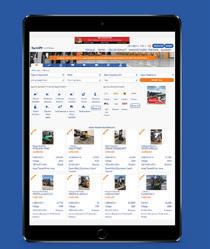
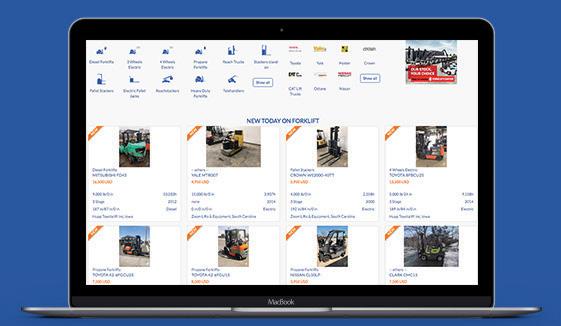
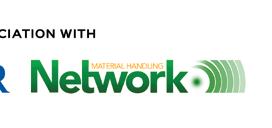



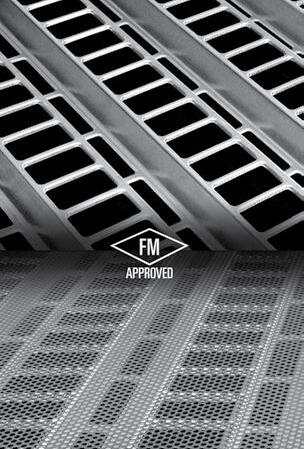
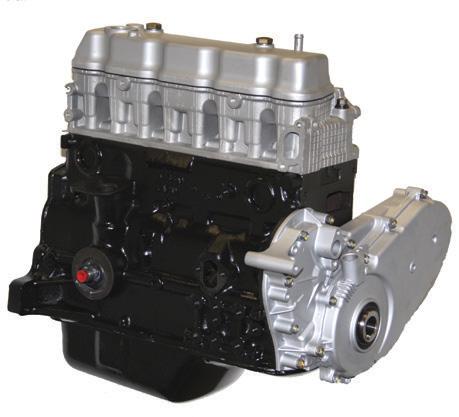

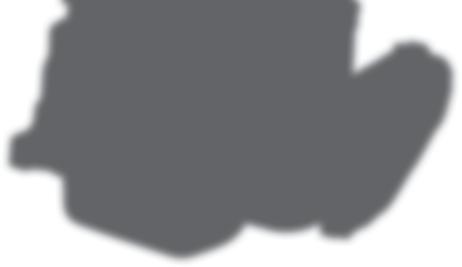
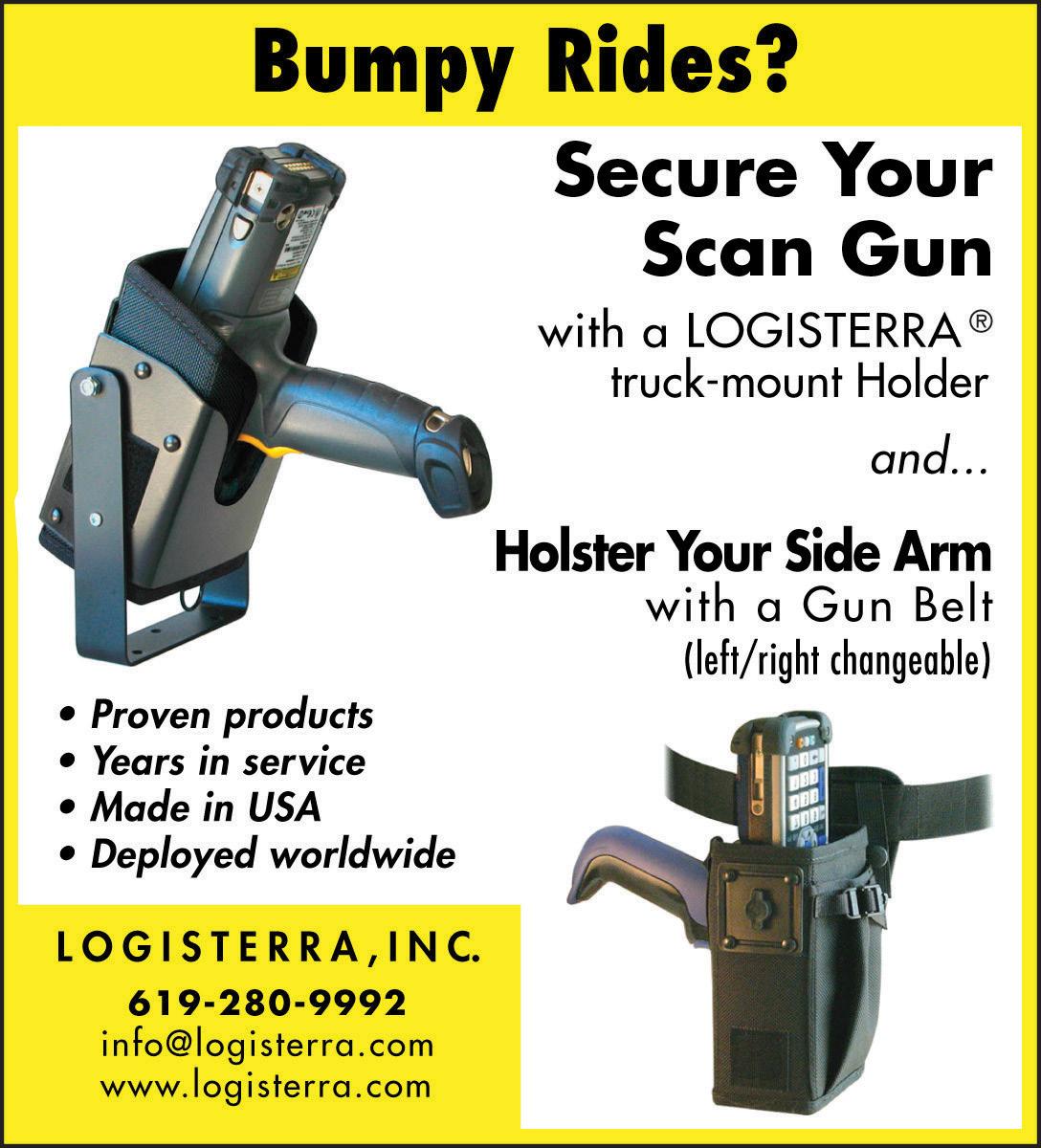
www.MHNetwork.com Material Handling Network October 2022 41 Interested in this space? Next Deadline: October 14 www.MHNetwork.com TRANSMISSION REBUILD NEED A REBUILDTRANSMISSIONKIT? ◆ OUR KITS ARE DESIGNED FOR TECHS, BY TECHS! ◆ AIT CARRIES KITS FOR MOST TRANSMISSION www.aittransmission.com800.588.7515STYLES. AMERICAN INDUSTRIAL TRANSMISSION, INC. TIRES At Tires International Corp., we offer a variety of solid tires for forklifts, telehandlers, skid steer loaders as well as larger loaders and other construction equipment. If you don’t see the tire you need on our website or need help in making your selection, call us. We’re always ready to help! “We ship our solid tires nationwide!” (800) WWW.TIRESINTERNATIONAL.NET818-1139 FORKLIFTS PA Industrial Equipment, Inc. Delivering Quality Since 1977PA CONTACT: ROY BRAMM www.PAIndustrial.com610/369-9778 215 S. Washington St. Boyertown, PA 19512 USED FORKLIFTS & INDUSTRIALFORKLIFTEQUIPMENTPARTSRENTALS FIND IT. SELL IT. ENJOY IT. forklift-international.com FORKLIFTS Marketplace

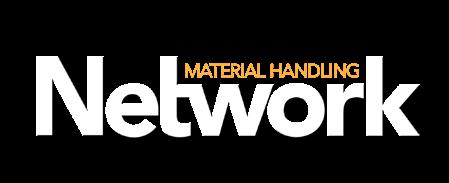
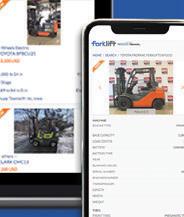
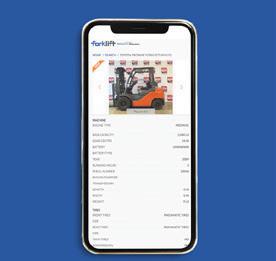
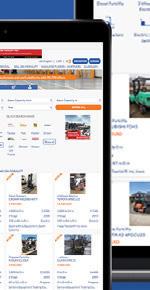

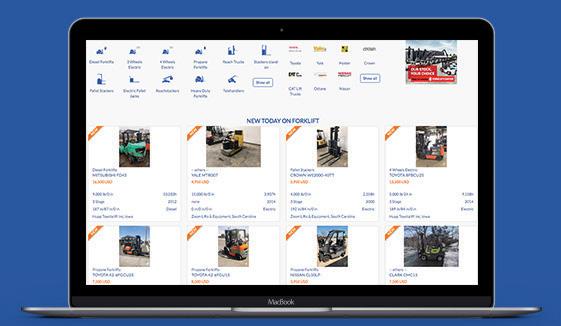
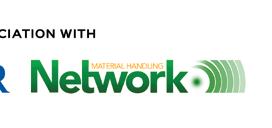



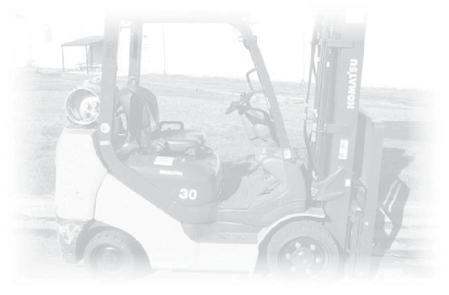
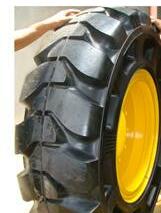

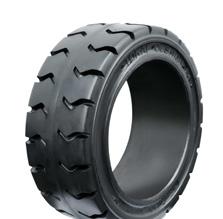
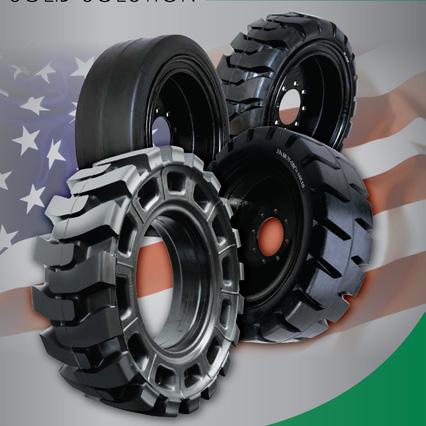
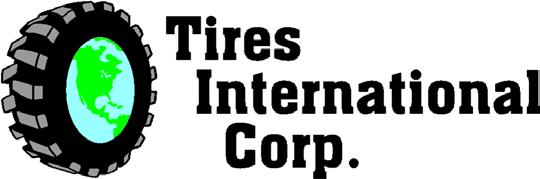
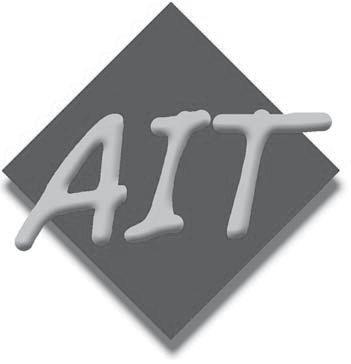
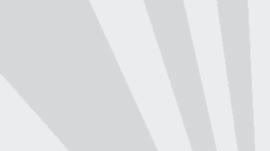
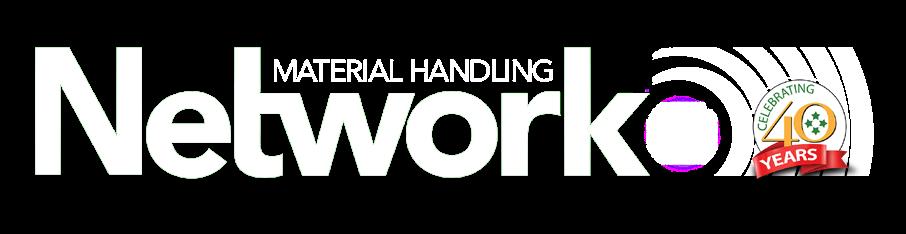
............................................
ADVERTISER INDEX • TRANSMISSIONS • REBUILD KITS • DIFFERENTIALS • DRIVE AXLES • STEER AXLES • TORQUE CONVERTERS TRANSMISSIONS WE KNOW American sales@aittransmission.comTransmissionIndustrialInc.800-588-7515www.aittransmission.com
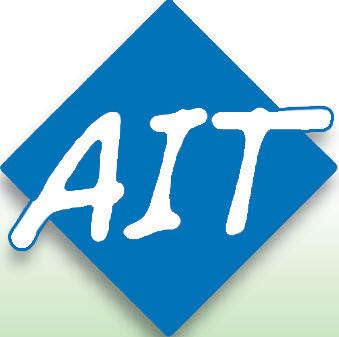
FMH Material Handling Solutions A3 www.fmhsolutions.com
Thombert, Inc. ................................................ A2 www.thombert.com
42 October 2022 Material Handling Network www.MHNetwork.com
AutoScheduler 33 www.autoscheduler.ai AutoStore 7 www.autostoresystem.com
Camso Inc. 5 www.camso.co/en Collision Awareness Insert www.save-ty.com
Interthor, Inc. .................................................. 35 www.interthor.com
PFlow Industries, Inc. 14 www.pflow.com
Phoenix Lighting 11 www.phoenixlighting.com
The advertisers’ index is an extra service to the advertisers. The publisher does not assume liability for errors.
Superior Tire & Rubber Corp. 31 www.superiortire.com
Hader Industries Inc ........................................ 19 www.haderind.com
Flight Systems Industrial Products (FSIP) 11, A4 www.fsip.biz
Bristol Manufacturing 13 www.bristolsteel.com
Wy'East Products 23 www.clearcap.com
Joseph Industries, Inc. .................................... 22 www.joseph.com
Dyna Rack A1 www.dyna-rack.com
Shoppa's Material Handling 17 www.shoppasmaterialhandling.com
MHEDA 15 www.mheda.org
American Industrial Transmission, Inc. 3, 42 www.aittransmission.com
Forklift-international.com ......................... 25, 37 www.forklift-international.com
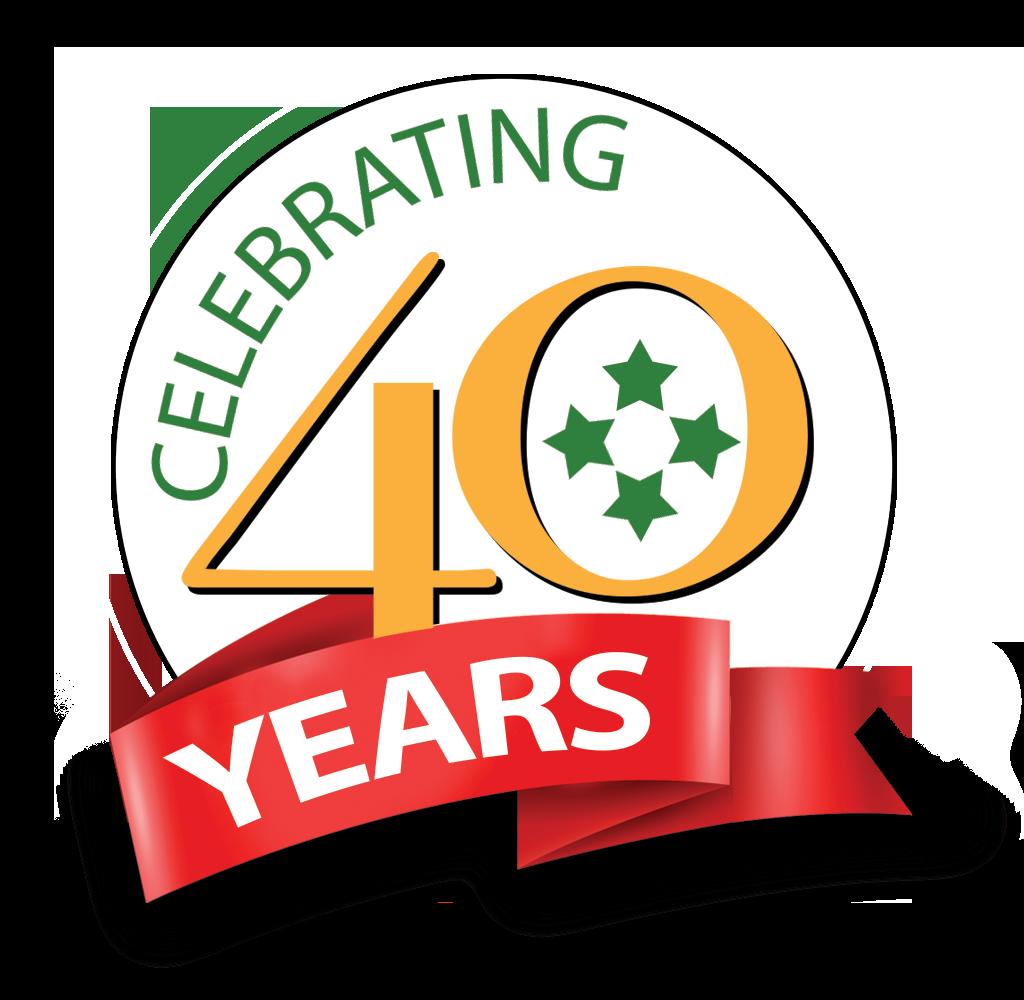
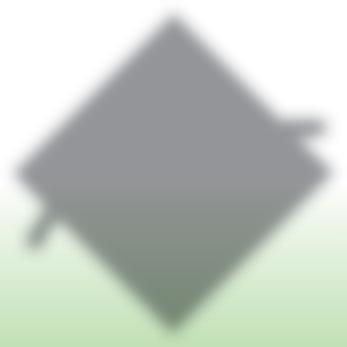
CombiLift USA 9 www.combilift.com
Superior Engineering 21 www.superioreng.com
A3 ROUGH TERRAIN FORKLIFTS off road like never before! FEATURES • 5,000 - 7,000 lb Base Capacity • Kubota Diesel Engine • Wide Off-Road Tires • Wide View Mast • Anti-Skid Front and Rear Axles • Low Center of Gravity for Stability • Available in 4-wheel drive and 2-wheel drive UNITS FactoryOrder18-20WeeksDelivery!INSTOCK Call Today! 5165 Vasquez Blvd. • Denver, CO 80216 888-639-HELI • www.HeliForkliftUSA.com303-453-8973
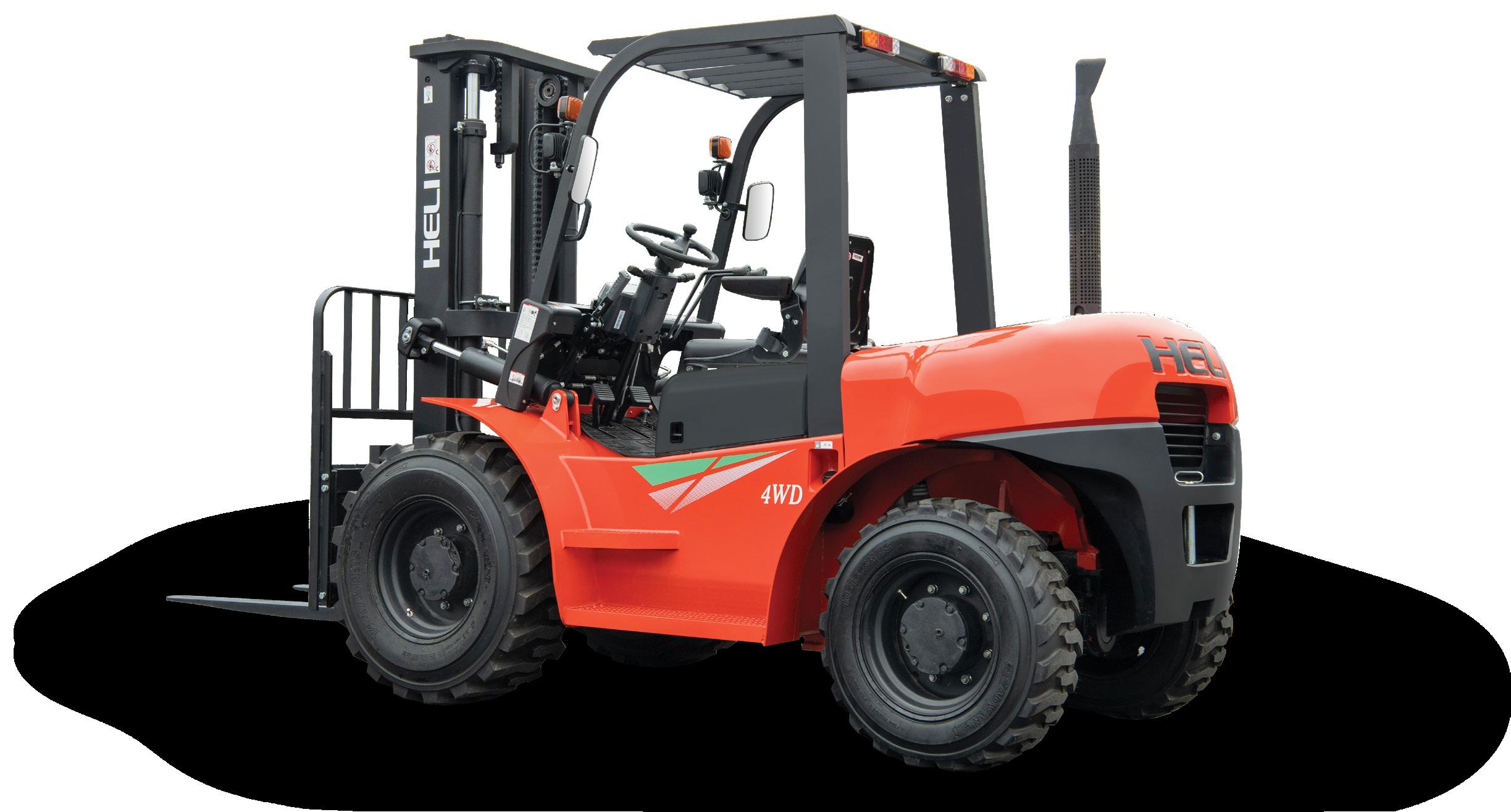
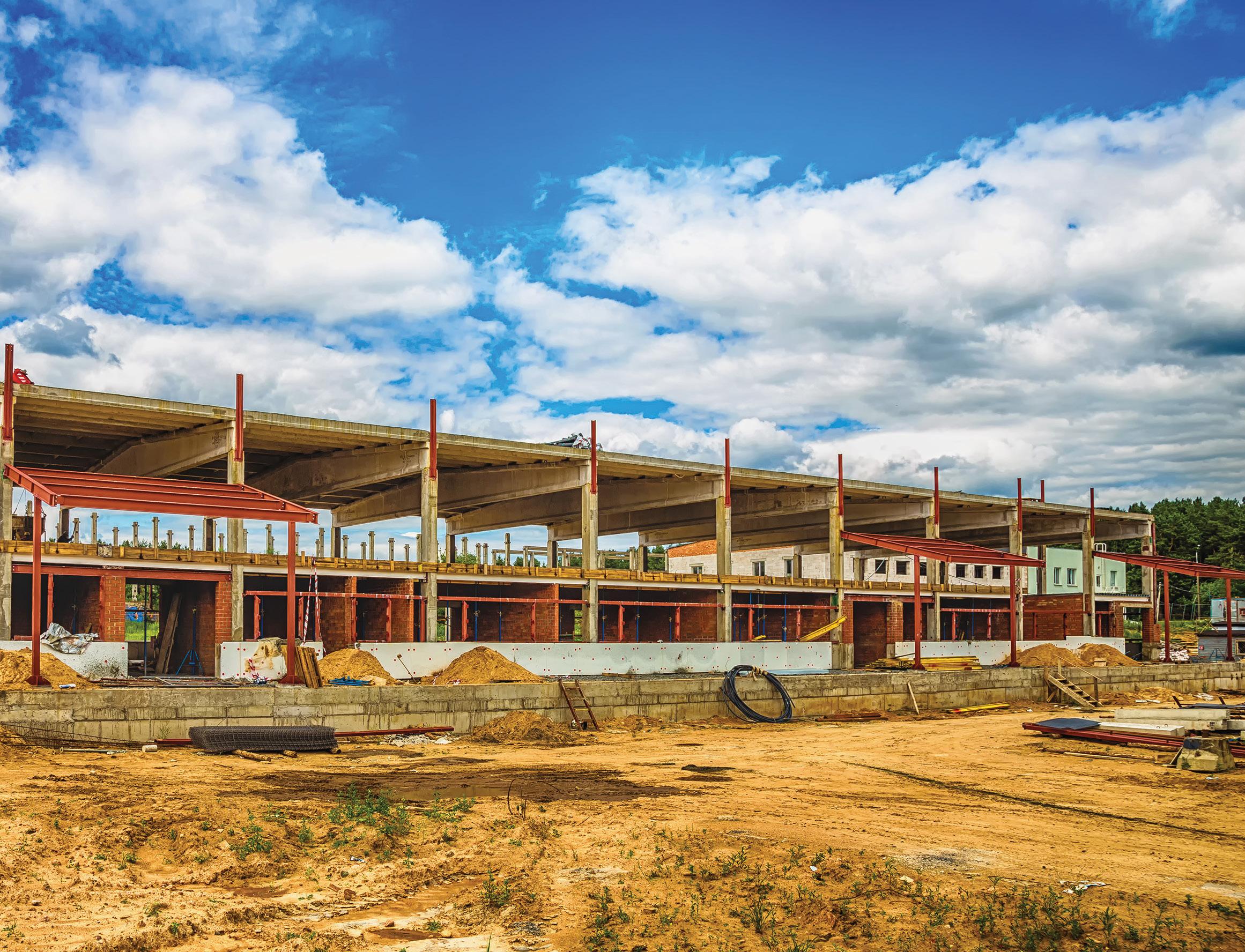
A4 Available: • 12- to 96-Volt options • Standard or Modular Designs • Pre-programmed Charging Curves • Customized DC Connectors • Floor or Wall-mountable Designs From Basic to Specific Battery Charging Needs, and Everything In Between, We Have You Covered. Charging Solutions for: • Lead-Acid or Lithium Batteries • Single or Three-Phase Power Distribution • Opportunity Charging • Low Voltage Charge Cycles (2-Volts) • Personnel Carriers to Forklifts Flight Systems Industrial Products Your Battery Care Experts. 800-333-1194 · shop.fsip.biz YOUR INDUSTRIAL BATTERY HEADQUARTERSCHARGER Reliable. Configurable. Versatile.
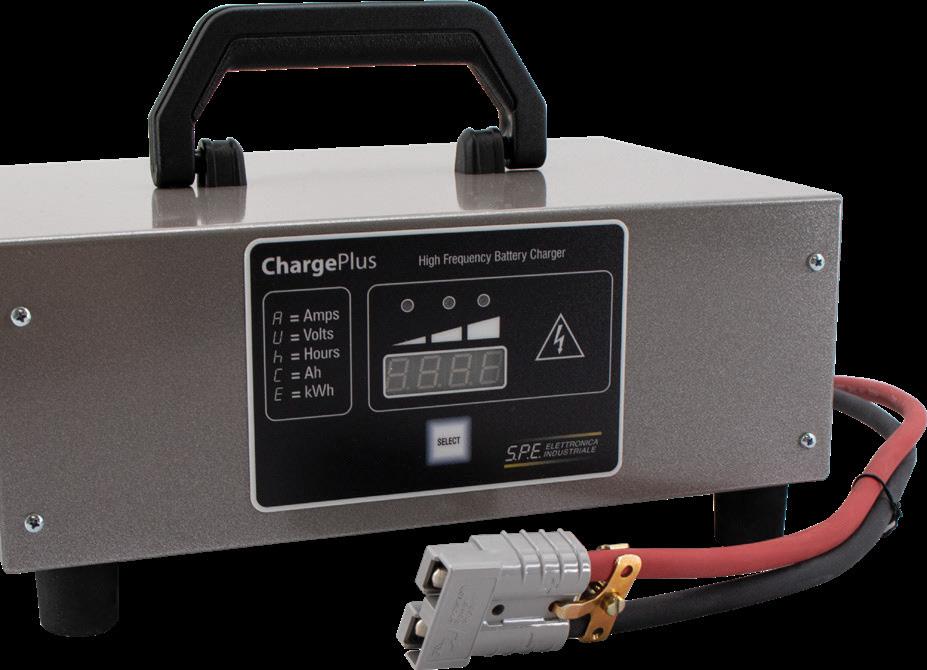


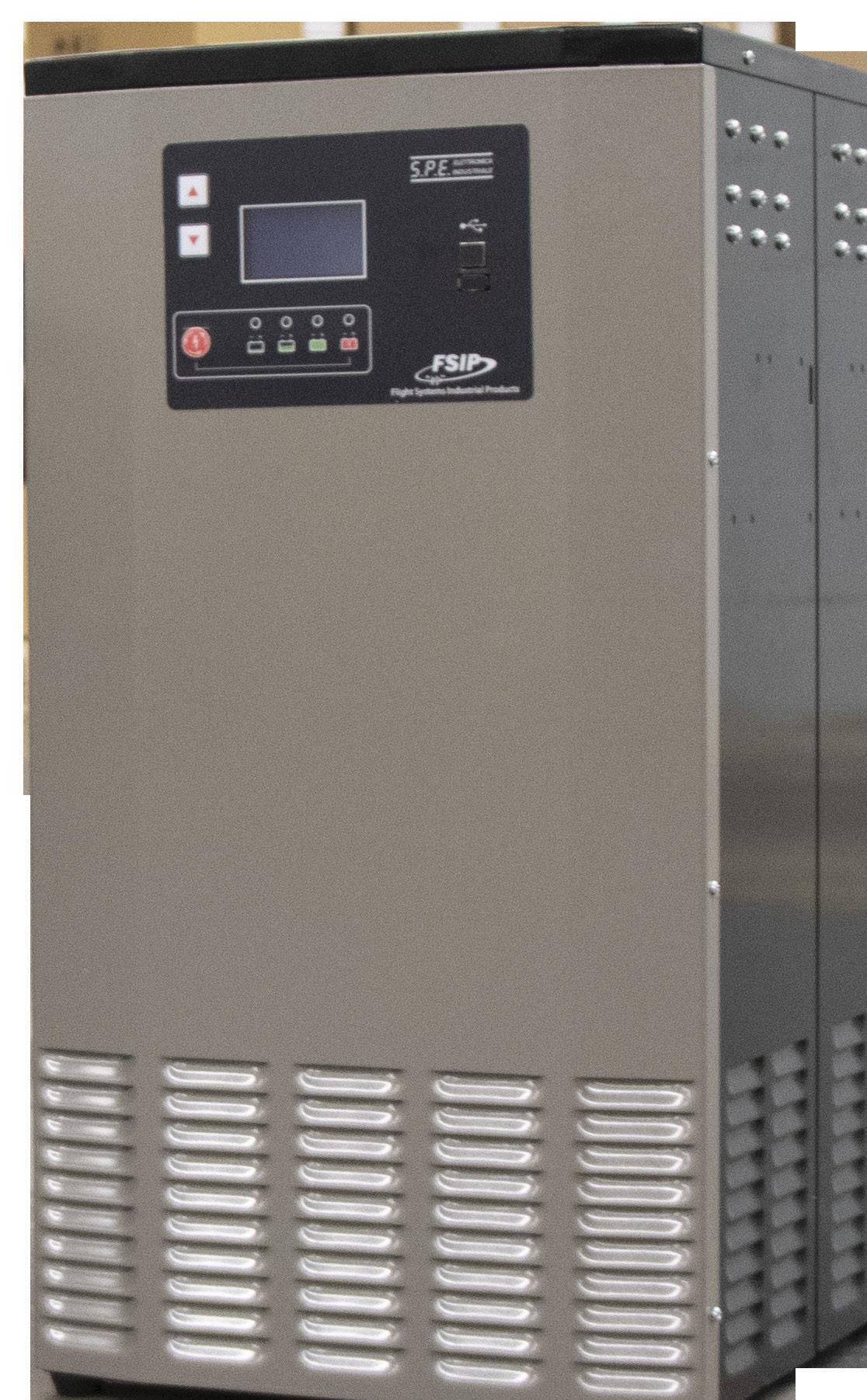
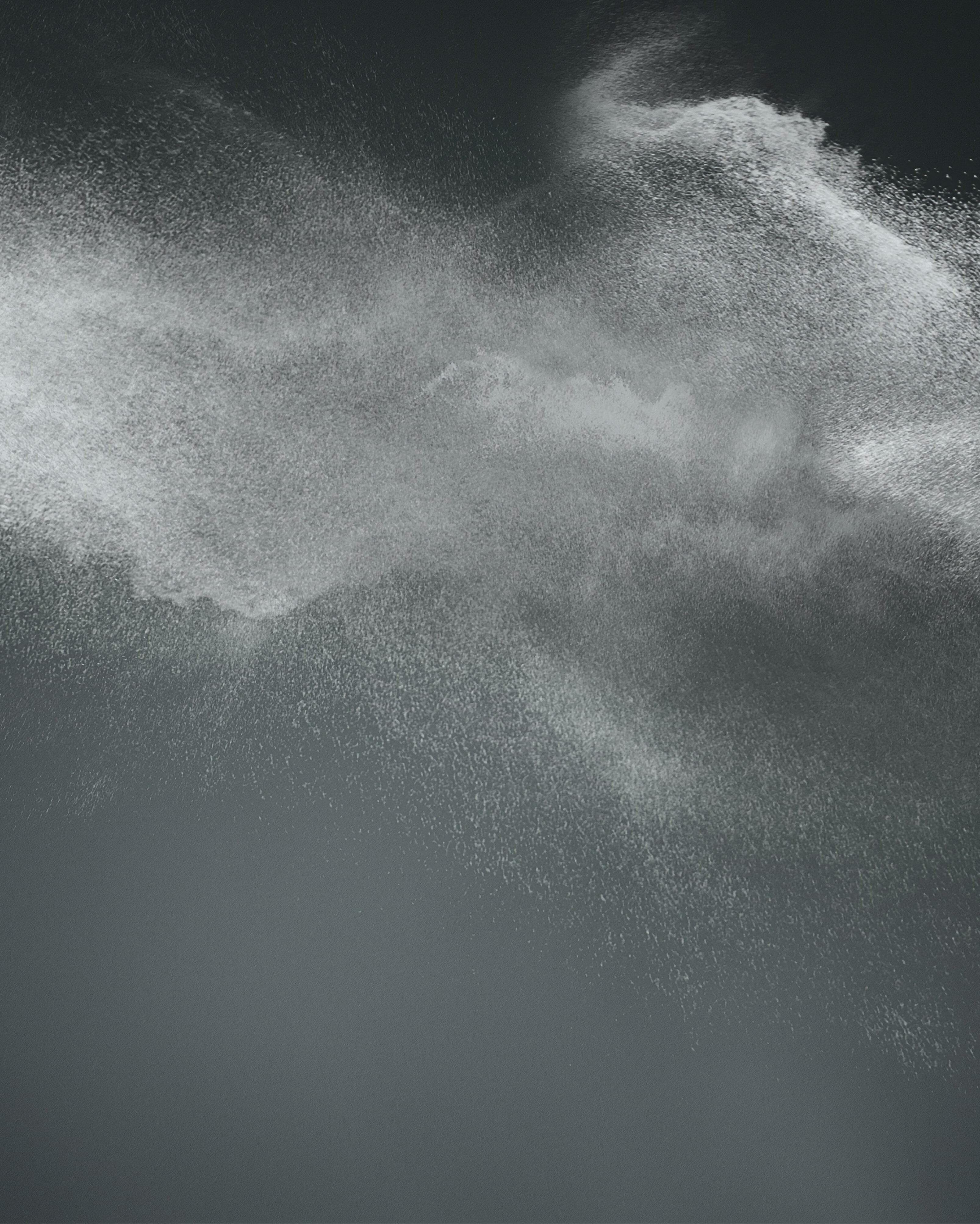