ALDI Program Guide
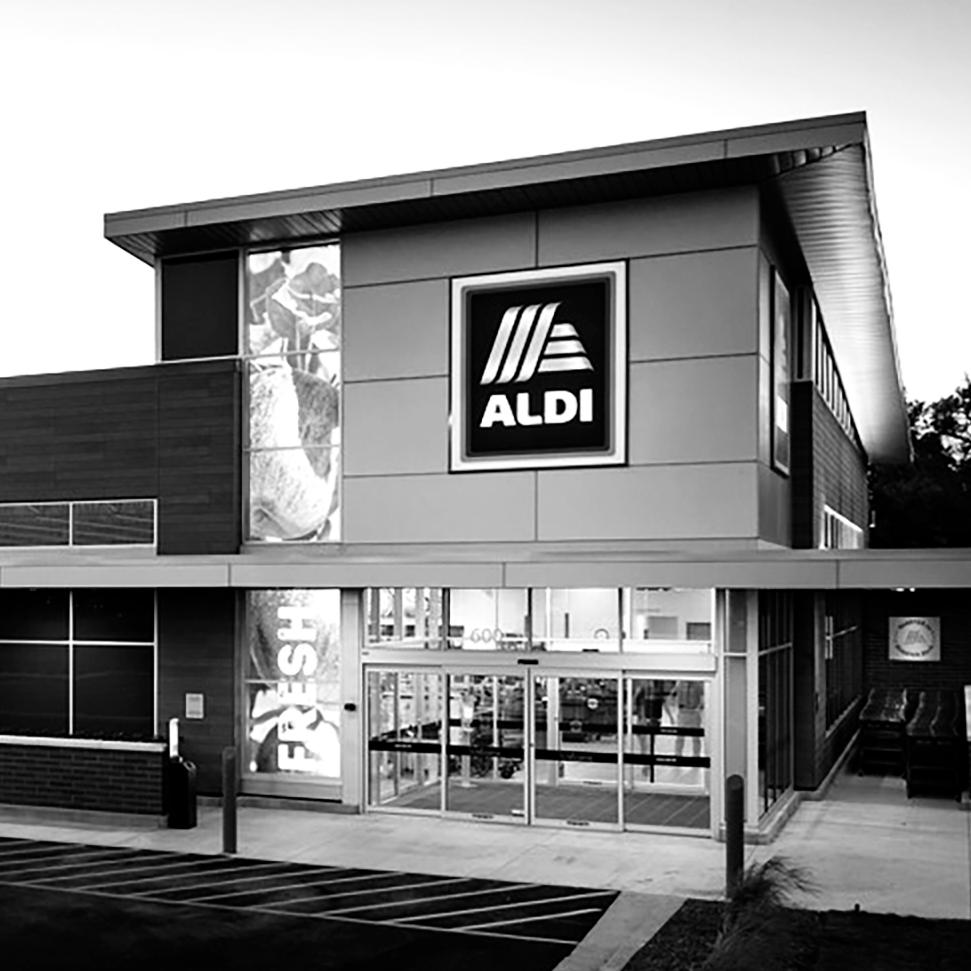
Crossland and ALDI have developed a strong working relationship that has lasted numerous years and hundreds of projects. We work hard to do what we say we will do in the timeline we say we will do it in. Keeping our word, no matter what, has established trust with ALDI, and it is up to all of us to value and protect that trust.
This guide was developed as a training resource for Crossland’s management team. The information Crossland created has been supplemented by members of ALDI’s construction team as a resource for our Crossland team to improve the way we do business with ALDI. While we summarize items in the ALDI program throughout this guide, it is essential to understand that project specifications, plans and details evolve and sometimes change. Please refer to your individual contract documents and use this program guide as an additional resource as you work through your preplanning and construction.
Crossland’s National Accounts vision is to “grow through new opportunities and longlasting relationships.” Our Mission is “Building up your communities nationally through trust, passion and integrity with our driven team motivated to consistently exceed client’s expectations.” Each project we build we must keep our Vision and Mission in the forefront as we strive for the best quality, overall value, and schedule with ALDI.
I hope that this guide provides insight into the fast-paced and fun ALDI construction projects. If you should ever need anything or have information to add, please reach out to me directly.
Mike Farrington Mike Farrington, Division Manager – National Accounts• No lump sums
• CCC has the responsibility to evaluate pricing, request backup, and justify pricing prior to submitting to ALDI.
• Provide credits where due and make the subs/suppliers do the same.
• Evaluate labor rates and provide clarity to pricing (don’t simply just pass it along).
Inform ALDI of ANY changes in scope that may impact pricing
• Don’t authorize work prior to discussion with ALDI. They shouldn’t find out about an issue at the same time a PCR is submitted, ever.
• Superintendents need to defer this responsibility to PM’s
Communicate issues that impact cost or schedule as soon as they are discovered to ALDI. Always keep them updated.
• Work as a partner with ALDI
• Volume Builder
• History of Success
• Understanding of schedules and Owner supplied items
• Self perform work capabilities
• Competative Pricing
• Providing consistency
• Learn from our issues and teach internally
² Avoid ALDI teaching our staff
• Complete every project by the contract completion date (i.e. possession/move in date NOT just by Opening)
• No lingering punchlist items
• Communicate issues and challenges – visibility to issues within the team
Understand that each individual project is important, BUT each job is part of a larger overall “program”
Decisions you make for “your job” to change something most likely will impact ALDI’s overall program. That’s why they have to be in the loop.
Our job is to know the details better than anyone.
Initial selection should follow Crossland protocol. Critical subs will be discussed prior to issuing subcontractors or purchase orders. Share resources when using the same subcontractor.
• Key Contractors & Suppliers in Remodel
– Demo Contractor
– Electrical Contractor
– Steel Supplier
² Don’t pick marginal contractors over proven contractors to make a dollar. These items need evaluated and discussed.
New subs allow for new opportunities and keep our “go-to” guys competitive. Again, they need evaluated and vetted extensively.
Refer to our ALDI do not use list for subs & suppliers.
We all have to communicate to avoid overloading subs on multiple projects at the same time. This is a good way to turn a good sub into a bad sub.
• Framing Contractor
• Electrical Contractor
• Concrete
• Glass (especially V8s)
• Steel Supplier
Use this guide to provide specific ALDI information to CCC management team.
ALDI #79 - Type City State
Types: LW, SW, New, New R, RM or REM
Example: ALDI #53 LW Lenexa, KS
1 Sketch proposed staging area and submit to the ALDI CM for review and approval, if a remodel.
• Finalize at the onsite preconstruction meeting for remodels.
• Entire staging and expansion construction area is to be surrounded by temporary fence and separated from the public.
• New stores will have entire site wrapped in temporary fence unless noted otherwise by CCC.
Determine LVC material and get sample to ALDI’s testing agent.
• Doesn’t matter whether it is a sub or CCC doing it.
Contact any utility companies that need to relocate their services for the expansions.
• Gas or gas meters
• Transformers or power poles
• Phone or Fiber pedestals
The same applies to all new utilities in new construction. Each company should be contacted during the pre-planning session.
Project schedules for new or remodels are too short to have delays from utility providers. Contact them early and often.
If not clearly spelled out on the plans, determine existing utility entry locations to the building for Remodels & Expansions.
• Determine if any will be in the way of the expansions
• Will temp services be needed?
• Call locates as soon as possible after the award to help identify the public items
Contact previous Crossland Superintendents who have completed similar projects to review lessons and remember...
• If you don’t know, ask
• If this is a PM or Superintendent’s first ALDI project, determine others like it and schedule a site visit to review completed or in-progress work.
Long Wall Expansions
• Steel supplier and shop drawings are critical
• 8 week Exterior Expansions
• 4 week Interior Remodel
• Entire wall of shoring - designed by engineer
• Concrete is more extensive
• Tile flooring scope grows
• Roofing is necessary prior to shutdown
Short Wall Expansions
• Steel supplier & shop drawings are critical
• 8 week Exterior Expansions
• 4 week Interior Remodel
• Minimal shoring generally
• Restrooms/offices added requiring further finishes over other expansions
All Expansions – **The first 5 days of award**
Steel Supplier & Shop Drawings
• Field Verification – done within the first week of award, don’t wait
• Joist bearing elevation
• Joist spacing
• Joist seat height
• Tie-in specific information as requested by the fabricator
Glass & Glazing – select and hire sub
• Guaranteed Openings – know what this means to CCC, framer, mason, glass sub
Brick & Precast samples – hire sub and release them for submittals finishes over other expansions
Electrical sub released
• Switchgear
• Lighting – cree and possibly others
Release dock equipment
• Request shop drawings immediately even though they aren’t a requirement
Utility relocations (talk to providers)
• If providers don’t respond or can’t find contact information call ALDI Construction Manager
**Award Email from ALDI OR receipt of prime contract, whichever comes first, is when we start.*
Week 1 - Expansion earthwork, partial & selective demo, temp fencing, temporary tunnel(s)
• Tunnels, temp openings
• Interior temp Walls
Week 3 – Slabs placed & cured
• Slab Placed and ready for steel
Week 2 – Foundations start and complete, underslab MEP
• Earthwork complete, foundations and stemwall complete
Week 4 – Steel delivery and erection complete, decking at least started.
• Steel Erection, joists and decking. Could be ready for metal stud framing depending on project.
Week 5 – Metal stud framing continues, exterior sheathing installed, MEP in wall rough in.
• Exterior stud framing well underway. Sheathing being installed.
• Masonry or exterior finishes started by the end of this week.
Week 6 – Tower framing complete, roof membrane if possible. Overhead MEP starting (Long wall should be starting masonry during this week)
• Brick progressing
• Exterior sheathing at new tower completed, ready for signage.
Week 7 – Exterior masonry/brick substantially complete, interior drywall if roof is on. Hold preconstruction meeting for shutdown remodel. A template agenda has already been developed and is available for your use.
• Brick or exterior finishes substantially completed other than what is left at entry tie-in.
• Exterior sidewalk prep underway.
Week 8 – Aluminum storefront, where possible, exterior cleanup grading, sidewalk forming.
• Finish up exterior work
• Interior expansion walls all framed and ready
If the expansion portions aren’t substantially completed prior to shutdown, completing the entire project on schedule will be much more difficult.
Substantially completed expansions would include Brick veneer well underway, roof dried in, and partial windows installed. MEP overhead in the new structure should be roughed in.
• Work with the ALDI CM to find work that won’t disrupt the public that can be done before shutdown.
– Change out light pole heads
– Double check the type of heads. Cree heads are typical but some jurisdictions may require something special. Know what plans require and lead time.
• Add any new light pole bases
• New utilities (phase them)
• Parking lot expansions
• Landscaping
• Site sidewalks
• Exterior Painting and painting existing poles
• Prep work for electrical service upgrades (non-distruptive to operations)
• Use the early morning hours to our advantage where possible. Stores don’t generally open until 9AM.
All Remodels – 4 week shutdown
Week 1: Interior Demo and Concrete Pour back (Critical Path)
All interior demo, remove tunnel, all concrete demo inside complete. All concrete pour backs complete by the end of the week. Entry tie-in. End of week one, install new dock equipment (don’t remove old dock equipment until new is actually onsite).
Monday – Demo - Clear building contents Refrigeration Contractor – Remove cooler, freezer & MDU’s **Demo cooler/freezer curbs and framing above cooler and freezer ASAP. Fire Suppression demo heads in cooler and freezer first thing.
Tuesday – Demo, Demo existing freezer, Demo plumbing trenches
Wednesday – Demo Freezer pad Demo plumbing trenches Underground plumbing
Thursday – Prep Freezer pad Underground plumbing
Friday – Pour Freezer/Cooler and any other floor concrete.
Saturday & Sunday – Finish whatever you didn’t get done above.
Week 1 Keys: Don’t remove old dock equipment until new equipment is onsite. Finish all windows and exterior openings. The electrical sub needs 5-6 guys minimum during this time. If they don’t have at least this, you need to be concerned.
Week 2: Cooler Freezer Install, Metal stud framing & drywall
Cooler & freezer installation, metal stud and drywall complete at MDU walls, paint ceiling, all MEP overhead rough and in-wall rough in total, finishes begin (paint, tile etc… by the end of the week). Vestibule sliding doors by the end of the week. Building Signage installed.
Monday – Cooler Freezer Delivery and installation.
Tuesday – Complete Freezer Install and start Cooler install Start Framing Interior metal stud walls
Wednesday – Install Cooler Frame above Freezer CES unit delivery, CDRU delivery, Cooler Freezer Door, Nordeon Light Delivery
Thursday – Frame above cooler Spray deck off hours Tile delivery from ALDI Warehouse BOF Shelving delivery
Friday – All interior framing & drywall complete Start ceiling grid
Week 2 Keys: Install of Cooler/Freezer. Field measurement of cooler and freezer for bumper. All drywall hung by the end of the week and painting started behind MDU’s.
Week 3: MDU Set, Start of Finish package, Asphalt Milling & Paving, Sidewalks (if not already complete) MDU delivery and installation, finishes continue, ALDI floor tile begins, CCC finish package begins. Exterior sidewalks must be finished by the end of this week. Salesfloor lighting complete. Nichiha panels & ACM panels installed. Asphalt mill and overlay during Week 3.
Monday – Set MDU’s Tile installation starts (this will take them all week to complete. Reference spec book on all things floor tile). Finish Package Delivery (Finish package includes the check lanes (2 guys ½ day), wall paneling (2 guys 1 day), sacking counter (2 guys 1 day), valance (2 guys 1 day) (Rough estimates on durations), Graphics Package
Tuesday – install graphics & finishes
Wednesday – install graphics & finishes
Thursday – install graphics & finishes
Friday – Checklanes should be set, wall paneling up, sacking counter complete, all windows installed, store front, entry doors, good start on graphics.
Week 3 Keys: All refer equipment setting has priority. All tile must be finished including restroom tile. All electrical wire pulled by the end of Week 3.
Final finishes, shelving deliver, Refrigeration start up, finish package complete, final inspections with jurisdiction. Check lanes installed. Final clean over the weekend.
Tuesday – 3 Semi loads of sales floor shelving (Ideally you have 6 guys dedicated to this) Trucks are scheduled for 7am, 8 am & 9am
Wednesday – Bring Refrigeration system online Corporate IT Start ALDI Warehouse delivery Spot merchandisers and “Fresh” boxes
Friday – Start final clean FAP Complete & Tested out for Monday Inspections
Saturday – Final Clean
Week 4 Keys: Wrap up all finishes inside and out, final inspections and documentation. Final electrical devices installed by mid week of week 4.
Wrap up punchlists, TCO or C of O paperwork in had no later than Tuesday (generally consisting of Monday and Tuesday).
Monday – RE-Inspections if any. Punchlist.
Tuesday – Inspections Hand Keys to Operations for Stock PM. Product will delivery Tuesday evening usually around 5PM. Must have Certificate of Occupancy in hand prior to owner move in.
Wednesday – Complete Punch list
Week 5 Keys: Wrap up all finishes inside and out, final inspections and documentation. Two days in week 5.
CCC Superintendents to layout with demo contractors before demo of existing asphalt. Sawcut at the new sidewalk line, don’t remove more than required or is necessary.
A best practice on a number of the remodels is to have the demo contractor work for their main crew at night during Week 1 and then leave a few guys to work during the day for coordination-type items. Crossland is to have supervision for the night crew.
Remove brick far enough down the existing wall to connect joists for the expansion. Brick needs to be removed during Week 1 of the expansion so the steel can be installed in Week 4 of the expansion.
Temporarily dry in the exposed area from the roof to past the remaining brick, as shown on the left side of the photo.
To assist ALDI’s Refrigeration Contractor with removal of the freezer and cooler on day 1 of the remodel, the following needs to occur:
• Soffit above cooler & freezer removed Day 1.
• Curbs inside cooler & freezer need removed Day 1
• Sprinkler heads in cooler & freezer need removed Day 1.
• It may be possible to do all of these items on Sunday night after the store shuts down. Review with the ALDI CM in pre-shutdown planning. Get a jump on anything we can!
Exterior Finishes – make them a priority
Loading Dock & Ramp – must be a focus from foundation start.
Site work – it will become the critical path if not pushed
Tile Flooring – when all drywall & T/F is completed on sales floor, ALDI sub will start.
Roofing & Dry in – Make sure we are ready and they can stay busy.
A large volume of work is on the front walls of the store.
Steel erection
CalWal translucent panels
Stud framing & sheathing
Front Wall
Exterior Paving is dependent on completing portions of this exterior front elevation. The schedule path is very LINEAR, meaning one sub has to follow another rather than being stacked on top and working concurrently.
Make the completion of the loading dock a priority during construction. The concrete ramp paving needs to follow as soon as the stemwalls are placed. The exterior dirt subgrade can be used to approach the concrete to make sure the ramp is usable. It must be done before the delivery of refrigeration equipment.
• Starting point for all work should be at the short wall adjacent to the entry (shown in RED)
• All trades are to start at this point and work in the same direction.
• This includes erection of structural steel, framing, finishes, etc.
• Next area of work would be the front wall (shown in Blue)
• For this particular project work will continue counter clockwise to the dock (shown in Green) and finish on the back wall of the building (in Yellow).
• This includes erection of structural steel, framing, finishes, etc.
• Some sites may require some modifications to this flow of work BUT it should be discussed in PrePlanning with the Crossland DM or Sr PM.
• Do NOT change the planned and agreed flow of work without discussion with the Crossland DM or Sr PM.
• Fire Alarm
– Get copy of the approved Fire Alarm plan to our electrician ASAP.
• Security
• Refrigeration
• Data/communication systems
– We should be talking to the public phone provider from day 1 o award to make sure they are onboard for installation.
• Commissioning
• Roofing
Be prepared for their arrival. It shouldn’t be a surprise. Superintendents will fill out the readiness checklist and return it to ALDI CM.
Once CCC signs off on the readiness checklists we are committed.
• Sign off so the so that the work can be scheduled (don’t hold the checklist until all work is done then send it in, it will be too late).
• Hold subs accountable
• Inform subs if they don’t complete and retesting or revisits are required that charges will be applied to them
• Crossland has committed to ALDI’s that any remobilization charges from their contractors and consultants will be paid by Crossland. Our job is to manage the project 100%
Remodels
Per ALDI - If the tower isn’t complete and ready for the membrane to run up you are not ready for the roof. It makes absolutely no sense to add a trip to Prime to get 80% of the expansion dry.
• ALDI’s fully supports roofing the expansion prior to shutdown. But it needs to make sense and the jobs need to be ready for Prime Roofing to get the full expansion in the dry. This is especially true for the projects that are outside of the Kansas City market. Also per ALDI - Superintendents need to be patient with Prime. If not being onsite on the exact day the Superintendent is requesting is somehow slowing the job…. Discuss with ALDI, do not come down hard on Prime Roofing.
Refrigeration Equipment
• Coolers and Freezers – shop drawings will be made available. Get them.
• MDU’s – shop drawings will be made available. Get them.
Auto Doors
• Overall shop drawings will be made available. Get them and share with aluminum storefront sub.
• Auto door glazing is by our sub – get the glass size list from ALDI.
RTUs
Nordeon Lighting
• Sub has 5 days to note any damage or missing items or the sub is responsible to pay for replacements. (reference Note 4 of lighting schedule)
Finish Package
Power Wall
Owner Supplied Equipment
Sit down with ALDI CM to review Owner provided items and delivery schedules at the Preconstruction meeting. PM’s and Supers should start on Sharenology for specifications, installation instructions etc… for ALDI provided equipment. Any site-specific items can be obtained from the ALDI CM.
Our job as the General Contractor is to control the schedule, so coordinating Owner deliveries is part of that responsibility. Shelving delivery and Crossland installation will be a topic of discussion.
Owner Supplied Equipment (cont.)
Schedule New Store Deliveries
A schedule can be adjusted based on the amount of site work or project specifics. As a general rule, ALDI does NOT like to move delivery dates once they are established at the beginning of the project. IF dates have to be moved, we have to give as much notice as possible and not less than 2 full weeks’ notice. If it is less than that we need to receive and protect deliveries.
Owner Subcontractor - Tile
Sales Floor Tile (ALDI Sub)
Read specification 093000
• Section of specific focus include 093000-4 & 093000-5
• Sections related to International Ceramic Construction LLC (ICC) and our responsibilities as the General Contractor
• 093000-4 shown here
Owner Contractor - Tile
Sales Floor Tile (ALDI Sub)
Read specification 093000
• 093000-5 shown here
Items to note
• Take away excuses for ICC not to be able to work. No different than any other sub.
• Clean the floor
• Remove all stored material (all of it)
• Don’t paint ceiling while they are laying floor.
• Provide a water source for ICC
ICC will follow Crossland’s safety policy. Non-compliance is an issue on almost every project. This has been handled in the past to notify ICC, the ALDI CM, and document non-compliance in our Daily reports and emails to appropriate parties.
Concrete is better to be low than high. For a proper installation, a 2” mud bed is a minimum. Supers should be aware of this in all areas but particularly at transition points (Milk doors, Impact doors, Vestibule, ancillary spaces)
Often ICC is running behind schedule, and this has a tendency to slip in the 3rd quarter as all divisions are trying to bring everything in by November 1. When they are late Supers should know they are not dead in the water. They need to take a proactive approach and move new work into the area. Tile is nice to have, but it’s generally only a problem when you need to set shelving.
ICC will work towards a door. Generally speaking, this is the 1st aisle exit door on new and remodeled construction. Super should work with the installer to find the best execution plan. Work to find the method that will open up all the finish work at the front, access the backroom quicker, and allow work to be performed on the 1st aisle. Every installer is different, so it’s essential to establish the day they arrive.
The installers are generally from Germany. Working with them is different than what most people are used too.
Before their arrival, Superintendents should be planning where materials will be staged. The tile should be stored in the building. Sand/mortar piles are stored outside but will take up room and can present a challenge on remodels for doing parking lots or sidewalks. Plan ahead of the work impacted by ICC’s stored materials.
Refrigeration – Climate Pros or Design Mechanical
• ALDI handles all things refrigeration
• Crossland is to strictly coordinate the refrigeration
• Crossland is not responsible for unloading deliveries
• If a delivery shows up early call ALDI CM immediately to inform them Crossland is rejecting the order. (Once we take receive it – WE OWN IT)
If CM wants Crossland to receive order, CCC must have permission in writing so that we
Super unloaded Protocol
Protocal secured by 4 screws and 4 nails
Faulty packaging caused pallet to break and fall off fork lift.
Manufacturer will not warrant damaged equipment
CCC paid 41k to replace
Moral of the story - any Refrigeration
• Completion date defined in Prime Contract – we will meet this
• Any work or punchlist item that is incomplete after that date is unacceptable
– This includes cleaning
• Understand the city & jurisdiction you are working in
• TCO requirements
• C of O requirements
• Stocking requirements (stocking permit)
• Owner move in
• Call the city during preplanning to review their requirements
PM’s will submit weekly update and next week forecast to ALDI CM’s each week. Issues to be communicated to ALDI as they are discovered
Subs that slip must be dealt with, get the team involved.
Share CCC finish carpenter labor.
• Often times we have multiple ALDI projects completing in the same weeks. Crossland needs to coordinate schedules internally to ensure that finish carpenters are being properly allocated.
Concrete - Pay attention to the details and to the shop drawings.
• Block-outs in slab must be big enough to accommodate column base plates.
• Get the loading dock done early as possible including paving the ramp.
• There are limited submittals on these project, if you need shop drawings ask the appropriate sub or supplier.
• ALDI will provide shops for all of the items they supply
• Brace Bays & Concrete Stemwalls
– At perimeter walls be sure to stop the concrete stemwall pour a minimum of 4’ back from the gridline to allow the steel brace to be installed.
– After the brace is installed the wall and concrete can be completed
Submittals (uploaded in Sharenology)
• ALDI only requires the following
– Structural
– Structural steel
– Joists
– Decking
• Mix Designs (all different types of concrete & asphalt)
• Life Safety – fire sprinkler submitted design team
• Certain jurisdictions require additional submittal to their fire department. Be sure our subs have contacted the city’s/states and supply these to them.
• Samples/Mockups as required for color selections
• Multiple other items might be necessary for our construction, ask before you assume. Plans are a guide but actual shop drawings matter.
Schedules
• Overall schedule sent with subcontracts. NO exceptions.
– Schedules MUST be project specific
• Update overall schedule monthly and share with project team including ALDI.
• Store on Box.
• Use National Accounts template schedule
– Short Wall
– Long Wall
– New Store V8
– New Store other
• Customize for your specific project
3 Week schedules
Will be done every week until completion.
Distribute to subs via email following weekly meeting.
• A four week schedule has been developed that is proven to work. It communicates the work that will occur in the remodels. Use it for the final four weeks. No need to recreate the wheel. Customize it for your specific project.
• End date on these projects don’t change.
• The completion date is the completion date.
– Weather extensions are not granted.
– Delays for other reasons are not granted.
• Guaranteeing the openings is the only way we can ensure the windows will be installed at the right time in the schedule.
• Push to get shop drawings early
• CCC PM will review them and compare to most recent project plans as well as steel shop drawing. CCC Superintendent will review as a backup prior to release of the order.
• CCC PM will release the order to the glass sub and ensure that the CCC Superintendent has a copy as well as the project framing contractor.
• CCC Superintendent will review with framing contractor in preplanning meeting prior to the start of framing.
• CCC Superintendent will personally verify opening sizes with at tape measure as they are being framed to ensure accuracy with approved SHOP DRAWINGS. Check height, width and squareness.
Be aware that this is a possibility and be on the look out for this condition to make sure it is addressed.
New Stores
Breathable plastic without ink markings or logos on it (ink can bleed onto floor)
Rolled Cardboard (typically available at Grainger.com)
Remodels (skidloader traffic)
Usually Masonite or other inexpensive board type product needs used to protect existing tile floors from skidloader tire marks and heavy traffic during demo.
Rolled cardboard is effective after week 1 of remodel
Survey the site with the CM at the preconstruction meeting. Document any failing areas at that time. Take plenty of photos of the existing building, site and parking lot prior to start of construction.
Civil plans are typically limited in spot elevations
• Survey existing parking lots and ensure proper drainage.
• Pay attention following rain events and identify any areas of holding water so they can be corrected during mill/overlay construction
• New parking lots need to be investigated and CCC must be involved in elevation control between inlets and between curb islands to ensure proper fall is achieved
Superintendents will need to spend time with subs to ensure proper fall is obtained.
Sitework is as important or more important than the building. Depending on time of year the site could be the critical path!
Civil plans are minimal are best (lack of detail, lack of information). Build the project in your head before it is built on the ground.
Ensure construction is completed so that water will drain properly away from buildings.
• Plans may or may not provide good grading contours or spot elevations.
• Photo shows an existing slope in the background and new slope in the foreground.
• The store experienced water intrusion due to the steep slope in the foreground.
Minimal inspections are required by other parties. It is up to Crossland to ensure work is completed correctly. Crossland needs to witness utility trench backfill and compaction. Include ALDI’s testing agent to test densities.
• This includes light pole conduits
Parking lot failures become Crossland’s issue years down the road.
It is Crossland’s responsibility to ensure construction is completed correctly.
• Photo shows construction of a NEW storm sewer line on an ALDI project.
• Notice the “dogleg” just before the structure
• Pipe was separated and gasket was not engaged at joint.
• Minimal side clearance between pipe and excavation to allow for proper compaction of backfill.
• No bedding material present
• Almost everything about this was wrong and had to be removed and replaced.
Must look new at turnover (no dirt stains, topsoil, grime etc….)
• Keep heavy and dirty traffic off of new paving.
All existing electrical exposed to public view must be removed or relocated to bottom of the decking.
• Here are the references regarding electrical demo and raceway relocation.
• Sheet D102 – General Note 1
• Electrical Demo note Sheet D-102 – E01, E02, E04
• Electrical Demo General Notes Sheet ED-101 note 5, note 6 (plenum space referring to the area between top of existing acoustical ceiling and the roof deck), note 7, note 10, note 11, note 12.
• Electrical Demo Key Notes D1 and D2 on sheet ED-101
• Sheet E-001 note 12
• All of these notes refer to complete removal and compliance with other electrical notes which go to E-001 note 12 which states that all conduit is to be as high as possible just below the roof deck. There is enough information on the electrical drawings and demo sheets noting removal of existing conduits (even for devices that are to be reused) that indicate that if it is going to be exposed that it has to comply with note 12 on E-001.
• Ideally the joist supplier designs to allow passage of this duct. Diagonal webbing conflicts with size of duct.
• HVAC sub must be aware that duct must be as high as possible and above the lighting.
• This is obviously an after thought and the entire line had to be raised at the subs expense.
• Sub should be strongly encouraged to use cable hangers. Specs do allow other hangers though.
• In addition the perimeter all penetration needs coordinated for elevation to avoid rework.
• Elevation needs to allow for graphics to be installed.
Tile sub should know that the Stainless strip specified at the intersection of wall and floor doesn’t work for the floor tile’s thickness, but they still miss it. Inform the sub at contract buyout, so they order the right material.
One solution for the narrow flange trim is to put the long leg on the wall in lieu of the floor. The portion on the bottom still has to be held off the floor to flush itself with the tile as shown in the illustration.
Another solution would be the alternate product shown here with the approval of the ALDI CM.
Expansions Temp Roofing - Once the decking is tied into the existing structure, this is your most significant risk for lots of water coming in leave the membrane roof several feet past the insulation demo so that a screw can be put in every high rib and the (flutes) low ribs be filled with spray insulation this will minimize the water traveling into the store in the low rib. Multiple options are available; the point is that the system must work and be checked on regularly until the permanent roof is dried in.
to fill the gap between new and old roof on this short wall remodel. Then covered with plastic and taped the seams.
This is an extremely venerable time for the roof. Great caution and planning needs to go into the temp dry in. Water can pool/pond in the low ribs and work into the existing building and cause damage to the operating store. Take this very serious.
The control conduit for the irrigation system has been missed on several project drawings and/or several project installations.
• Verify what your project has for irrigation
• Determine what is necessary to power the system and work with the electrical contractor to maintain the existing system.
• This applies to both new stores and remodels.
In most cases, the Short Wall expansions won’t be required to remove drywall along this aisle, BUT drywall will need to be removed so the refrigeration contractor can install new refer lines and evac system inside the existing wall. This can be addressed early if not on the project plans.
• First – obtain shop drawings for the MDU’s from the Owner.
• Second – verify with refrigeration contractor AND the framing contractor the required finished elevation of the header based on the shop drawings and plans.
• Third – verify with the refrigeration contractor the room they need to be able to install the MDU’s if the header is already constructed.
• It may be necessary to wait until the MDU’s are installed prior to building the header depending on the specific set up.
• Some remodeling projects will require the removal and replacement of existing joints.
• If the job does NOT require removal and replacement, review the existing joints on CCC’s first visit to the job to verify the joints are adequate. Review our findings with ALDI’s representative. The goal here is to make sure the building is watertight.
• Notice the missing existing sealants in photo.
Interior Curbing
• Protection MUST be placed on cooler/freezers and plywood prior to placing concrete.
• Concrete splatter is not acceptable
• Poor job of rubbing
• Not broomed but a random pattern.
• No saw cuts for relief
• Top edge not consistent (use a tooled edge so it is consistent)
• Rub finish while still wet.
• Don’t attempt to place more than the crew can handle.
• Good job of rubbing
• Broomed parallel with broom of sidewalk
• Top edge is consistent (used a tooled edge so it is consistent)
• Expansion joint between curb & brick
• Would still need sawcut at changes of direction
• Preplan with all trades, especially electrical sub.
• These items must be avoided. Conduits should be in the wall. J-boxes should be in the wall
• All these conduits have to be moved
• Read the installation guide.
• Enforce the requirements on the subcontractor and review the requirements in a pre installation meeting.
• Make sure the mason uses the correct ties and fasteners.
• This is NOT an acceptable installation
Plywood
• Read the installation guide from APA for standard on spacing
• Enforce the requirements on the subcontractor and review the requirements in a pre installation meeting
• Don’t slam the joints tight, leave room for expansion
• This is NOT an acceptable installation
• Review the details with the concrete contractors, refrigeration contractor & Electrical Sub.
• Check for required conduits for heat trace at the door openings that prevent freezing/frost of the concrete floor
• Review the details with the concrete contractors.
• Exposed wood forms should not be left in the door openings.
• Plans may require a pour back after freezer is installed
Cooler/Freezer Floor Finish
• Review the details with the concrete contractors.
• The Freezer always gets a medium broom finish
• The Cooler always gets a smooth finish.
• Check your individual Structural and Architectural Plans
• If the plans differ the ALDI CM should be notified immediately.
Mock UPs (blue)
• Require Mock ups not only to verify color of brick on remodels and new stores but also to verify:
• Ties
• Flashing
• Sealants
• Quality
Top of Wall Protection (red)
• Notice the brick already is showing signs of efflorescence on the face.
• One possible cause of this is the open cells of the brick being left exposed at the end of each day.
• Masons should be covering the cavity and the open cells at the end of each days work.
Masonry Ties & Insulation Board (yellow)
• During the submittal process ensure the mason has the right ties ordered.
• During PreInstallation meeting verify again
• Once construction starts verify they are using the correct ties again.
• During the submittal process ensure the mason has the right ties ordered.
• Review specifications and discuss in detail at the Pre-Install meeting
Edge Sealant, made by manufacturer of flashing and part of the flashing “system”.
Notice the termination bar and edge sealant
Notice the pre-manufactured corner flashing
Require subs or CCC steel erectors to stringline joist bridging
Once the existing exterior walls are removed the overhang creates potential for uplift of the existing roof from winds. Standard practice would be to attach steel cable from existing steel and anchor to slab to hold overhang down. The larger the overhang, the higher the risk of uplift
• Ensure subs have sealed all new items installed to exterior finishes.
• Notice here light is not sealed to masonry.
• Water will be able to run down the wall and enter the conduit penetration
Visit the site as soon as possible after award to Field Verify all existing building dimensions and elevations before starting. Develop a plan with the ALDI Rep to deal with any discrepancies before starting foundations. Calculate the overall width of expansions, including structural steel, framing, Exterior Insulation board, brick, and spacing (or other exterior finishes), to determine any issues. We need to match the existing, but not all existing buildings have the same wall section, so it can vary. This needs to happen before structural steel is released for fabrication!
The following items will be required on all expansions and remodels. The steel supplier may need other items as well.
• Measure Existing joist bearing elevation
• Measure Existing joist seat at the wall you are adding on
• Verify existing decking profile
• Verify spacing of existing joists
• Verify quantity of joists that we may tie into
Try to trace existing light pole conduits and conductors if possible. Locate companies won’t do this on their own because it is private, but you might be able to catch them onsite and talk them into giving you some locates for these items. Utilize existing store as-builts whenever possible.
Foundations should be built and elevation of the foundation established using two key factors:
• Length of new columns based on steel shop drawings
• Bearing elevation of existing joists.
– Field adjustments can be made to foundation elevations provided that the structural steel will work and tie-in correctly to the existing building.
• Don’t paint the structure too early in new stores. Allow enough time for subs to get their overhead work installed.
• While not ideal, painting can occur after new flooring is installed.
• Drywall should be installed and taped/floated around the perimeter of the sales before painting the structure.
• Prepaint j-boxes some extra conduit etc…, for the items that get installed later (drops, small missed items etc…)
• In a remodel, the structure needs to be painted after shutdown typically at the middle or end of week 2
• This is typically done as a late afternoon/evening shift
• Paint the expansion and remodel ceiling at the same time.
• Be sure you have enough painted to be able to set MDU’s in week 3 and for the finish package to start in week 3
These projects typically don’t require a SWPPP permit but
• Contain spoil piles
• Protect inlets (photo here is what NOT to do)
• Clean dirt/debris from existing parking lots
• Don’t pile spoil piles near entrances as shown here
• Install & Maintain silt fence
New Store Erosion Control & SWPPP
These projects typically do require a SWPPP permit
Maintain silt fence or perimeter BMPs. If the earthwork contractor installs the BMP they also need to maintain it.
Protect all inlets
• Protect existing
• Protect new as they are constructed
Complete SWPPP reporting per state and federal laws.
Temporary Interior Walls
Make them look clean and professional. This photo is a fairly good example.
• Good tight plastic at the top of the plywood.
• Sealed plywood at the bottom
Owner maintained website for
• Plans
• Specifications
• Construction Plans
• Submittals
• CCD’s
• Vendor information
• RFI
Both Project Managers and Superintendents are to have access.
Finish carpentry package is 2 weeks for 4-5 carpenters. This includes the shelving.
• If this takes anymore time we aren’t profitable
The following are photos of the typical finish package items. Crossland typically provides and/or installs these items. The purpose is to allow someone who has not seen these items before to get familiar with them. All items supplied by ALDI must be unloaded, inventoried, and protected by the contractor who installs them. Most items have shown that Crossland supplies take 2-3 weeks to get. Plan ahead and order early.
Keynote A16 SSBR (Stainless Steel Bumper Rail at Cooler and Freezer).
• This has to be field measured for length.
• Provided and installed by Crossland
Keynote A17 Door Protectors (18” tall)
• Provided and installed by Crossland
Keynote A42 Floor Mounted Corner Guard
• Provided and installed by Crossland
Keynote A35 Floor Mounted Bumper Rail
• Provided and installed by Crossland
• Use 12’ rail for 12’ MDU
• Use 8’ rail for 8’ MDU
Graphics Frame
• Provided by ALDI
• Installed by Crossland
• These must be installed prior to the soffit so they need released for delivery prior to other portions of the finish package.
• Provided by Crossland
• Installed by Crossland
WP1 Eco Panel
• Often times this particular scope of work is sold to the framing contractor.
• It takes 2-3 weeks to get materials
• Know who has it up front.
Sacking Counter
• Keynote A07 stainless bumper guard with pre-manufactured corner.
– Notice the countertop protection installed on this particular project Good best practice to avoid scratches and damage.
• Counter supplied by ALDI installed by Crossland
• Stainless bumper supplied and installed by Crossland
Wall Laminate
Window Sill
Aluminum trim
• All items supplied by ALDI and installed bay Crossland
Well maintained and professional looking temp fencing
Well maintained signage
“Danger keep out” or similar Crossland signage (as approved and allowed by ALDI)
CCC project Management team will draft a fence and signage plan and it will be approved in PrePlanning by the Crossland DM or Sr PM.
Post shutdown, you will get shoppers who don’t understand the store is closed for business
• Ensure entrance/exit is clearly marked that the store is closed. ALDI will typically provide a banner, as shown here
• When possible close all entrances except one.
Ensure that temporary fencing goes all the way to the temporary entry tunnel
• Avoid having items protrude into walkway.
• This photo shows sand bag and fence stand in the way.
• This needs moved and reworked to avoid these trip hazards for the public
Remember if any of the following items change or need to change, they must be discussed with the Division Manager or Sr. Project Manager immediately.
Schedule
Critical Path
Completion Date concerns
Cost
Relationship
Includes subs or Owner
www.crossland.com