Details of the winners on pages 4-6 of this issue
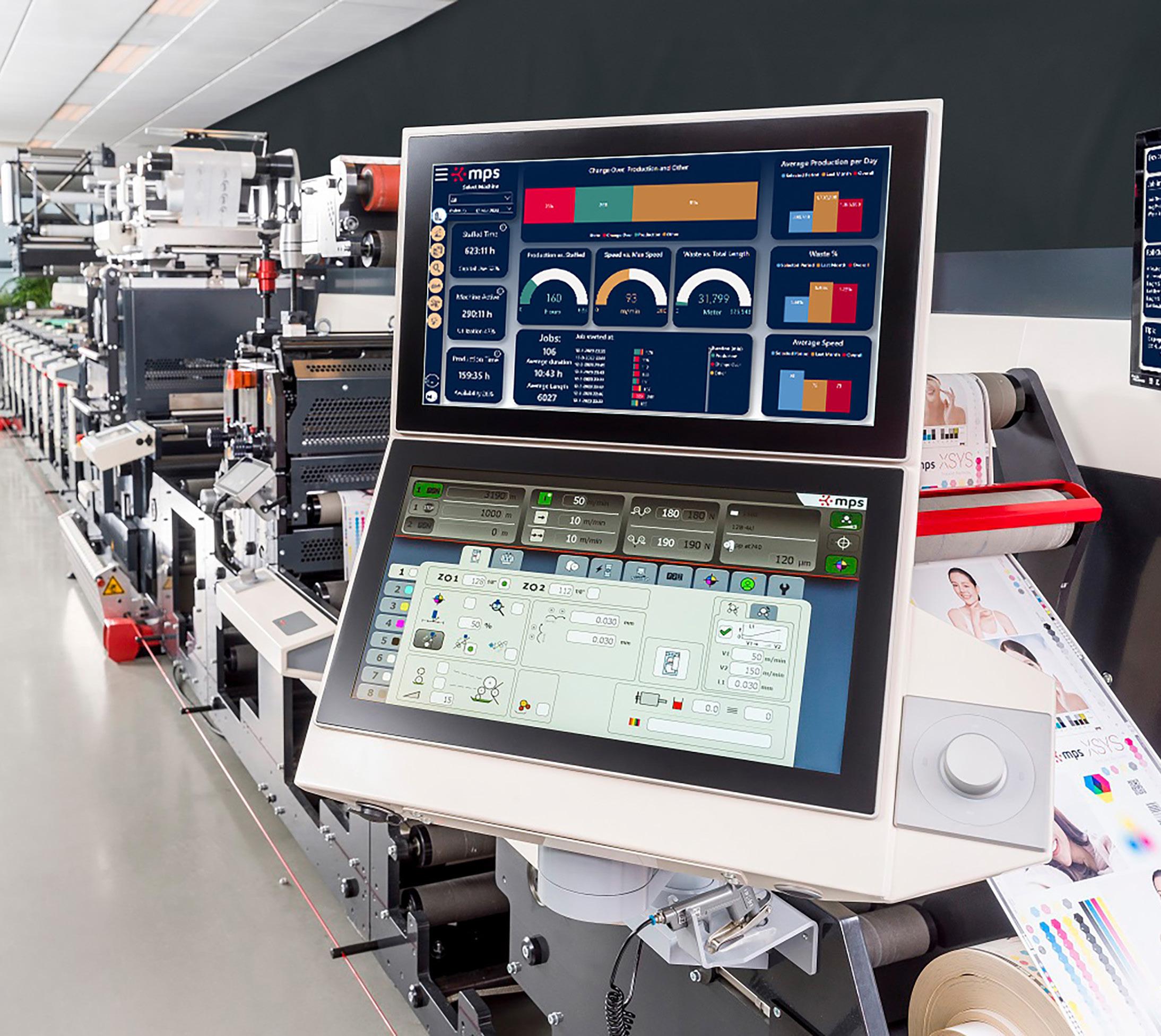
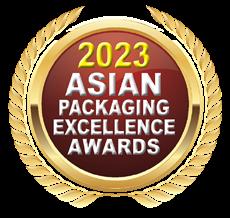
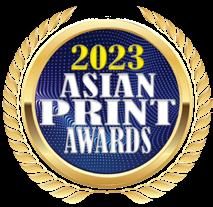
Details of the winners on pages 4-6 of this issue
ZERO-FAULT PACKAGING
Whatever the shape or size of your jobs, BOBST delivers the automated solutions and expertise you need for maximum productivity with zero defects and zero returns. Interested?
Find your local BOBST representative at www.bobst.com/contact
PACKAGING EXCELLENCE
AWARDS: 2023
Issue 3 - 23
Print - Packaging INNOVATION
Asia Magazine
Published by Asian Print Awards Management Pte Ltd 65 Chulia Street #46-23 OCBC Centre 049513 Singapore
Print Innovation Asia
Labels and Packaging Innovation Asia Asian Print Awards Packageing Excellence Awards
Label and Packaging Conferences
Publisher Paul Callaghan paul@printinnovationasia.com
Editorial Elizabeth Liew elizabeth@printinnovationasia.com
Packaging Sales Elizabeth Liew elizabeth@printinnovationasia.com
The Vietnam Printing and packaging industry has gone and is still going through some impressive growth over the last couple of years. It has also seen a big surge in foreign companies investing in these markets seeing lots of new equipment installations into print/packaging companies, and sees no sign of slowing down anytime soon. We talked with Lê Hữu Phú, G7 Expert from Mat Pho Consulting, who are leading the charge in the area of colour management, servicing the whole of Vietnam.
Q When did your company start, how many staff today and what products do you distribute/sell in Vietnam?
A Mat Pho Consulting was founded in the year 2019, and as of today we have 3 engineers, 2 sales people, supported by 3 people for administration/ marketing and accounting.
We are a distributor for CGS ORIS, Rutherford ClosedLoop system, IGT Testing system and Bodoni PressSign in Vietnam.
We deploy 3 solutions for Process Control and Color Management in the printing industry.
1. Proofing system – Print directly to Substrate (Mutoh628MP and CGS Flexpack)
2. Print quality management – Auto Scan and Rutherford system
3. Ink formulation system – Xrite IFS and IGT testing system.
We also provide the servicing for G7 and GMI for our customers who intend to acquire the G7Master and GMI Certification.
Q What markets are you dealing in, Printing, Packaging, Metal decorating etc?
A The main markets are Packaging and Labels
Q How is colour management accepted in Vietnam, do all companies know the importance etc?
A As you know, many people who work in the Printing/Packaging industry have been using or learning for a long time about “color management" They acknowledge that color management is beneficial, and their customers require color standards, not just for local print but for the big export markets that Vietnam now is involved in.
Every day, we still see some companies struggle with the colors that customers reject on the printed sheet, this should not be happening in the world of print in 2023.
But most of them have the same issue or barriers: the theory and practice are different because the technology/ software and hardware need to be
"reorganized" to help them understand the big picture, reduce make-ready time, increase quality, and increase productivity.
This process will most certainly go to a healthier bottom line for the company, and today it’s all about making profit to grow business.
Q How do you educate them, what do you do to help them understand this area of production
A We have built a demo center with many equipment measurements, software, and devices for training and giving our customers a demonstration and experiment with a hands-on training process.
. Especially the proofing system that can be printed directly to the actual substrate, which includes:
*Mutoh Valuejet628MP and an excellent color management solution from CSG.
During the Covid pandemic, I spent time experimenting and doing countless hours of testing on many kinds of different substrates.
So obviously, we found out and concluded that CGS Flexpack is the best solution that easily achieves any color standards like Forga/GraCoL.. and spot color as well. This proofing system gives our customers many benefits and helps them save time/
money; the color can be predictive before output.
Thanks to CGS ORIS, especially Marcus Tang who have supported me and my company during that time.
We also have a program for selling called “Rent to own” or “Try and Buy” with a Closed Loop system for Offset presses combined with Auto Scanning (Seeing is believing)
Q Is G7 an important part of your business when it comes to colour and helping printers, If yes why?
A Yes, G7 is an entry point, and an excellent method combined with ICC managed to help them predict colors before output or easily tweet the color as they want. This is a real time and money saver and once our customers see this you see the reaction that they wish they had this much earlier.
Q Give us an understanding of the offset printing markets in Vietnam. Is it growing, staying the same size or decreasing with less volume of print etc
A Recently, many printing houses in Vietnam have invested the modern equipment to approach big customers or brand owners globally. And many print providers from China, Korea, Japan, USA, have jumped into the Vietnam market to seize the opportunity to export to the US/EU and other markets.
Give me an understanding of the Packaging industry in Vietnam. Flexo, Gravure, labels etc.
In Vietnam, we have almost 2000 Packaging printing houses. And since 2017, I have helped approximately 50 printing houses apply the G7 method with Offset, Flexo, Gravure, wide format, and Digital technologies. Most of them (approx 20 printing houses) obtain the G7Master, GMI certification done by me. So Yes, I think it's growing :-).
Q What are the challenges that face packaging printers today, what can they do to help their businesses grow
A The challenge is the increasingly high quality demanded by brands and customers. I think they must invest
in their people (knowledge) and technologies, especially Digital and Modernize their Offset press (CIP3/4 and ClosedLoop system)
Q A lot of attention has been placed on the Vietnam industry due to the big influx of foreign companies setting up manufacturing here. Will this continue and what impact with this have in terms of trying to get staff/operators etc for the Packaging/ Printing Industries. Will there be a shortage in the future.
A Yes, surely.
Q If yes, how can the industry overcome these challenges.
A Yes, I think sometimes they overlook the issue of color. But in my opinion, they have no choice but to understand and invest in this area. it’s hard for me to get this message across but what lies ahead is a great opportunity for me and the company.
Q Do you think digital will continue to grow in Vietnam, what areas do you see this having a major impact?
A Yes, digital is alive and well in Vietnam, especially in labels, short run commercial print and the advertising industry. I feel that we here in Vietnam are moving in the right direction and we will continue to get more share of the international print market.
Alongside of this our local print market due to the size of the population of Vietnam is also and a steep rise so we are lucky to have both factors in our favor.
Founded in 1978, NIPPAN PRINT. co.,ltd,. is a printing company located in Ikuno Ward, Osaka City that manufactures mainly packaging and promotional tools with cardboard throughout the printing production processes from prepress to postpress. In the compnay, the division who is focusing on web to print business is SPRIQ Division who has installed a Heidelberg digital sheet-fed press, the Versafire CV.
Launching short run production, on-demand printing business was an urgent task
"The volume of packages and promotional materials that we had been printing on offset presses was clearly declining. So our president decided to launch an on-demand printing business because he saw an urgent need to handle small runs in particular." said Takumi Goto, division manager who has led the SPRIQ division talks about the reasons for the introduction of the Heidelberg Versafire digital printing presses by Nippan print.
The keys to choosing a Heidelberg Versafire CV are quality, surface finishing, and the ease of postpress-processing. Since this was Nippan Print's first introduction of digital printing presses, the selection process was conducted carefully and meticulously. As Nippan Print has always emphasized top quality, therefore quality was also an important selection criterion when choosing a digital press.
When selecting a model, we prepared the same design and had each digital press manufacturer print it,
and compared the results. And the Heidelberg Versafire CV was the one that was completely consistent with offset printing. The finish of the printed materials from other companies had a strong contrast and was clearly different from that of offset printing.
I think Versafire was able to match the colors most consistantly because we were using the same color separations as offset and where able to match these color profiles easily with Prinect." Mr. Goto recalls. The next most important thing for us was the ease of surface processing and postpress-processing.
We actually tested and compared all of them.
The five surface finishes are OP varnish, matte varnish, clear PP, matte PP, and press coat. As a packaging printing company, the finishing process is very important to us. Versafire was able to meet the demands of all five of these surface finishes." He added, "We also checked the registration because registration is critical and cannot be ignored in the postpress process of die-cutting."
With other companies' digital presses, even when printing 310g paper at a reduced speed, there were about 20% of the 100 sheets that were out of registration by about 1mm. With the Versafire, however, the register was perfect. What's more, the ability to print through paper as thick as 360g is also very appealing for us." He also revealed that the Versafire CV cleared Nippan Print's digital press selection criteria one after another and was eventually installed at the end of 2017. In fact,
this was Nippan Print's first transaction with Heidelberg.
Launched SPRIQ (web to print shop) focusing on packaging
We wanted to launch an on-demand printing and digital printing business, but when we considered it, there were no jobs that could pay for themselves in small runs with our traditional customers. The idea that emerged was web to print business model with a focus on packaging.
However, unlike general commercial printing, packaging jobs have many variations of height and depth in addition to length and width. We had to re-calculate these dimensions on a flat surface and create a quote based on that calculation. Moreover, because we are a web to print shop, we must be able to display that estimate to the customer immediately.
Although SPRIQ left the online payment part to a third party, all other dimensional calculations and
programming were done in-house, and the software was developed in just over a year. When asked if it was possible to do a packaging business with A3 format, he replied, "Actually, we were not thinking of targeting all markets from the beginning. We initially focused on cosmetics and health food packaging.
We looked at the various box shapes used for cosmetics and health foods in advance, and confirmed that most of the packages could fit into the A3 format. Moreover, what we are aiming for here is a small lot runs. If we had to go to the Kikuzen format
More than 90% of SPRIQ's customers are end-users, and there is not much business from agencies or printing competitors. He says that almost 90.5% of his current approximately 1,000 clients are repeat customers.
He says, "The process used to take a week, but now we get the data, print it, die cut it, fold-glue it, and deliver the sample to the customer the next day. Customers are surprised at the speed of the process, but they are also impressed by the quality of the printing, which helps us maintain a high repeat rate. I truly believe that this would not have been possible without Versafire, and we are still 100% satisfied with our decision to invest with the Heidelberg Versafire.
As for the reasons for the short delivery time, "For one thing, the operation of the Prinect DFE is so easy that anyone can use it, and for another, the cluster system, where one operator can use multiple machines, is one of our strengths," he says. He continued, "Our customers are different from those of the past, and we are able to provide them with quick delivery.
He continued, "We are beginning to see customers differently from before. We want to make more different variations of box shapes and designs and see how the market reacts to them. We want to make a product, put it on the market,
which is Japanese typical format, 939mm×636mm, it wouldn't be very cost-effective." We had to make sure that our digital presses would be the best fit for the target market we had narrowed down.
New sales and a new image of the customer gained by Spriq with Versafire
In April 2018, SPRIQ finally launched its web to print site for packaging, which was created from scratch. "The first two years were really tough. We did everything we could. We put up online ads and did SEO measures. And even though it was a web to print site, we even went door-to-door sales to advertise. Four years later, SPRIQ, the package printing web to print site, has grown to account for just under 20% of the company's total sales.
and see how the market reacts to it. We realized that this was the true "smalllot, many kinds of product" approach. This is what customers are looking for! he reiterated his excitement at the time. There are cases where a customer who began business with 30 swing type POPs printed by the Versafire now has annual sales of several tens of millions Japanese yen. I am sure that many business owners have an image in their mind of whether or not they can make a profit from Versafire's operation rate and labor cost.
However, there are actually many cases in which the work done at Versafire has led to the acquisition of larger jobs. Without Versafire, we would not be able to do business with such clients. This is a huge benefit to the company as a whole." He also spoke of the indirect strengths of Versafire.
In the future, we would like to increase the variety of designs, and at the same time, we would like to create an easyto-order flow within the site according to the type of business our customers are in.
We started from scratch, but we have managed to come this far with the vision of becoming the No. 1 packagefocused web to print site in Japan in terms of quality, speed, and price, together with Versafire CV. And that vision has remained unchanged. We all want to continue with persistence."
Mr. Goto,Division Manager of Spric Division, concluded the interview by expressing his strong will for further growth.
THE
BEST MACHINE FOR SHORT RUNS, EVER
Onyx Go continues the long-lasting success story of Uteco’s Onyx flexo presses.
The new evolution of the machine, one of the most popular in the BOBST line-up, is designed to help packaging printers and converters accomplish more in today’s rapid and resourceintensive converting market.
The new generation EXPERTFOLD comes equipped with a host of new features to this highly modular and extremely versatile folder-gluer, which delivers an impressive number of box styles at speeds of up to 450m per minute. Indeed, from ACCUBRAILLE to ACCUCHECK, SPEEDWAVE and GYROBOX: this machine can be adapted to the most complex needs. It also offers the possibility to add the matching peripherals allowing converters to create a complete, highperformance folding-gluing line.
In the quest to continually improve its equipment, BOBST only recently introduced the A3 version of the EXPERTFOLD, enabling a reduction in changeover times from crash-lock bottom to 4&6-corner boxes by up to 80%. The objective for the new version was to enhance this all-rounder, increase productivity and move closer towards the BOBST vision of a fully digitalized and connected converting process with maximum automation and sustainability.
With new designs and adaptations, the ergonomics of the EXPERTFOLD has been improved and the machine footprint cut down. Cleverly designed security doors allow easy access to the 4&6-corner module. The leaner design
provides maximum safety and frees up space at the back of the machine. The handles on the upper conveyors have been redesigned, adding further precision and stability to the positioning of the equipment. Plus, the machine now features pneumatic feeder ramps, reducing the workload for operators and cutting down machine setup time by 20%. These and many other changes make this EXPERTFOLD the most modern and accomplished version yet.
“The evolution of our EXPERTFOLD is another example of how we want to offer converters the most performant and ergonomic machines” says Pierre Binggeli, Head of Product Line Foldergluers at BOBST. Apart from the obvious advantages for the operators,
The pneumatic feeder ramps allow a much faster and convenient setup
clever ergonomics can help to reduce setup times and increase the precision of the machine settings.
“With the most recent changes, we managed to cut down setup time and improve both productivity and box quality even further - because converters need to be agile and deliver zero-fault products. At the same time, user-friendliness and practicality plays an important part in creating a sustainable work environment” adds Binggeli.
The integration of the BOBST machine control SPHERE followed the same reasoning. Like the current platform, it offers the possibility to retrieve repeat jobs, control the machine functions and provides access to the BOBST Connect
Essential package, which was launched last year. This end-to-end digital solution already enables companies to drive productivity by accessing accurate performance data, progress indicators and reporting.
It also ensures high-priority remote assistance. However, SPHERE has been designed to include a whole range of other functions which will be part of the BOBST Connect platform, enabling efficient data flow between physical equipment and digital solutions for rapid, transparent communication throughout the supply chain, optimizing the entire production workflow.
Pierre Binggeli comments: “Our EXPERTFOLD line has an extremely
strong reputation as one of the most trusted and high-performance in-line folder-gluers on the market. Naturally, as we continue to evolve our product line in response to developing market needs, we are continually adding new functionality and our new iteration is a perfect example.
Each individual change is implemented because of real benefits to our converting customers, whether it’s faster setup and changeover or the possibility of accelerating the transition to Industry 4.0. This is what innovation is about: continually thinking about how to improve even the best of products.”
The VirtualCoach is a pioneering new product of the MPS connectivity & performance service offering to enhance the quality and efficiency of printing press performance. It is a real-time innovative operating tool that works within MPSConnect and is available on all new MPS presses.
• Offers real-time training and guidance based on detected operator skills.
• Allows new and experienced operators to develop skills based with AI guidance.
• Updated every 5 seconds for maximum assistance with continuous personalized feedback.
“VirtualCoach is an innovative module that brings printing press functionality and efficiency into the world of AI for today’s operators,” said Kelvin van den Bunt, MPS Product Manager Connectivity. “Its connectivity and performance services unleash the full potential of IoT MPS machines throughout the world and is a powerful tool for owners and operators to maximize press efficiency.
As a personalized, data-driven AI instructional and guidance application, VirtualCoach is based on intelligent algorithms that gives the operator awareness on the quality and efficiency of all the activities they are performing on the press.
More than a training and instructional coach for new and experienced printing press operators, the Virtual Coach uses AI to constantly monitor and respond to processes in real time. This could be related to register settings, machine speed, pressure settings, job preparation, job memory, web tension, service feedback and many more.
Its AI-driven intelligent algorithms uses the input from printing press functions and combines it with actual operator behavior. Using the combined data, which is updated every 5 seconds, the
AI VirtualCoach analyzes and offers real-time solutions and warnings.
Key Benefits of VirtualCoach include:
• Algorithms in tune with operator behavior that syncs with printing press processes.
“In 2022, MPS customers that participated in our connectivity and performance program achieved 35% less waste, 30% lower changeover times, 35% lower setup times, and 15% higher speeds. We are confident that the data-driven AI VirtualCoach will improve that performance year over year.”
Connect to Grow. That is your key to stay ahead in a demanding market. By connecting with MPSConnect, you ensure the best in reliability and productivity from your printing press. You will increase competitive advantages and maximize profits.
To improve productivity and profi tability, it’s critical to increase the understanding of your overall label print operation. With MPSConnect, you get real-time insights in the operator activities. You dive into the printing press and see exactly what’s happening.
With MPSConnect we see recurring annual cost savings of €50,000 - €100,000 and even more thanks to a more efficient workflow, time management and waste reduction.
mps-printing.com/connect-to-grow
Recent study reflects adding an EFI Nozomi LED digital printer to the shop floor generates extra analog capacity, improves profitability and speeds time to market
An Electronics For Imaging, Inc. business case study examining data from a corrugated packaging plant demonstrates the overall productivity and opportunity advantages the EFI™ Nozomi 14000 LED digital singlepass printer can deliver in a real-life production environment. The study conducted at a North American EFI Nozomi printer user that also operates analog equipment for corrugated printing details how the addition of an EFI Nozomi 14000 LED single-pass inkjet industrial press increased analog capacity by 42%.
The study demonstrates that investing in digital technology adds capabilities and extra flexibility by:
Allocating jobs to the equipment that produces high quality graphics most efficiently – based on the characteristics of each order Leveraging existing analog capacity without the need to invest in new flexo presses
Maximizing overall equipment effectiveness (OEE) and overall plant profitability
Delivering a rapid return on investment (ROI).
EFI conducted the study by analyzing data collected from two of the corrugator plant’s flexographic printers that, combined, produce 5.6 billion square feet of printed board per year. By identifying jobs that were more appropriate for digital and moving them to the Nozomi single-pass digital inkjet production system, the company increased its analog capacity 42%, added 3.77 billion square feet of total capacity, and will realize a payback on their Nozomi digital press investment in less than 2 years.
In addition, adding the Nozomi singlepass digital press for corrugated enabled the company to take on work that would have been unprofitable to produce with analog technologies, including doublesided printed e-commerce boxes, versioned packaging for promotions, and fully customized boxes.
The EFI Nozomi 14000 LED press is a 55-inch-wide UV LED single-pass inkjet system that prints at speeds up to 328 linear feet per minute and offers outstanding high-graphic packaging production with superior color registration. Designed to deliver
high uptime and reliability in heavy industrial production environments, it gives corrugated packaging converters the ability to print high-quality graphics direct to board, on all flute types.
The press also drives greater sustainability in corrugated converting, printing exact quantities needed in contrast to the overproduction and make-ready waste of analog processes. Plus, EFI Nozomi technology leads the corrugated market in digital print energy efficiency, based on data from print research organization Fogra, and its printed output is certified for
repulpability and recyclability by the Western Michigan University Recycling, Paper and Coating Pilot Plant.
The business study and analysis mirror the consulting EFI performs with prospective EFI Nozomi press users and can be applied to any corrugated packaging operation. During the analysis process, EFI consultants identify the type of work a packaging company has and advise on how to can gain the greatest impact using EFI Nozomi technology.
“The data we have collected from corrugated packaging EFI Nozomi users across the globe indicate that EFI Nozomi C18000 Plus and EFI Nozomi 14000 LED presses have the greatest positive impact on converting operations that produce a significant amount of high-quality work requiring complex processes, such as flatbed diecutting, folder-gluer work, and other, more-complex manufacturing steps,” said Evandro Matteucci, vice president and general manager, Packaging and Building Materials, EFI.
“EFI Nozomi digital printing technology can mitigate existing market stresses converters face,” Matteucci added, “by generating new total production capacity, while increasing productivity and adding extra flexibility.”
For complete details of this groundbreaking study and to begin thinking about how adding an EFI Nozomi can benefit your operation, download the free white paper here http://tinyurl.com/mtwrvtk2 which includes a deeper level of detail and documented results.
Sungwon Adpia is one of the largest web-to-print businesses in South Korea, with multiple locations across Seoul. Established 18 years ago, the company produces a range of commercial print products including books, direct mail, marketing and promotional collateral, flyers, and catalogues. Short turnaround times, productivity and quality are key for Sungwon Apia to meet customer demand and with this in mind, Sungwon Adpia turned to Scodix to find the right solution.
YounHee Lee, Deputy General Manager at Sungwon Adpia, comments: “The Scodix Ultra 6000 is perfect for
our evolving needs as a business, our customers require a lot of versioning and consequently short runs. As one of largest printers in South Korea, the Scodix Ultra 6000 gives us that, and the high volume production capacity we need. This investment allows us to deliver whilst also allowing customers to produce creative, impactful designs that enhance the customer’s experience with their brand.”
Applications such as Scodix Foil™ and Scodix Sense™ allow Sungwon Adpia customers to elevate their designs without compromising on turnaround times thanks to the large B1 format of
the Scodix Ultra 6000. The flexibility of the digital enhancement press is another key advantage to Sungwon Adpia; it’s ability to support both offset and digital production, and a range of ten embellishments on one platform, further aid productivity and the rationalising of workflows.
“We are delighted to see Sungwon Adpia become the first business in Asia to install our Scodix Ultra 6000,” says Slawomir Iwanowski, Scodix Global Channel Director, “South Korea tends to be a very price-sensitive market, so we’re pleased to see the market understands the economic benefits Scodix brings as well as the addition to productivity for turning around jobs.”
“Whilst the larger format and the automation benefits of the Ultra 6000 are usually a match for packaging applications, it also meets the large capacity requirements of Sungwon Adpia for its commercial online printing needs. We are excited to support them and their reputation for delivering outstanding value and nextday promise.”
Scodix, the leading provider
for the graphic arts industry, today announces the first installation of the Scodix Ultra 6000 in Asia will be at Sungwon Adpia.
Fujifilm will exhibit its extensive portfolio of analogue and digital packaging solutions at interpack (stand F65, Hall 8a, 4-10 May 2023) under the theme of ‘Analogue. Digital. Sustainable’.
Fujifilm recognises how print can add value to packaging, and is combining expertise in the latest digital print technologies with an analogue heritage to create a unique portfolio that supports the production of both analogue and digitally printed packaging, all while demonstrating a commitment to sustainability.
Showcased on the stand will be Fujifilm’s range of narrow web inks, which Fujifilm has been manufacturing for many years, and which have earned a market reputation for both quality and versatility.
In addition, Fujifilm’s retrofittable LED UV curing system will be on the stand. The system uniquely combines both LED UV curing hardware and a brand new range of LED UV inks, radically reducing energy consumption, eliminating harmful VOCs, requiring lower maintenance and producing less waste. This results in lower costs, along with higher, more consistent quality.
The Jet Press 750S High Speed Model, which has set a new standard for print quality whatever the technology, will be running live on the stand, producing folding carton packaging in conjunction with a Kama finishing unit. Well-known and highly respected in the commercial print sector, it is also designed to print short-run, foldingcarton packaging at exceptionally high
levels of quality, with many customers using it exclusively for this purpose.
Fujifilm also offers a wide range of scalable imprinting systems that bring the benefits of digital printing to analogue processes by combining Fujifilm’s proprietary technologies across printheads, inks and transport systems with the company’s in depth integration expertise. Based on
Fujifilm’s world-leading Samba piezoelectric printbars, the company’s imprinting solutions allow digital inkjet printing to be integrated directly into existing analogue production lines for a broad range of industrial applications.
The Jet Press FP790 digital flexible packaging press will also feature on the stand. Built on decades of Fujifilm inkjet expertise, the Jet Press FP790 is designed to offer a digital alternative to flexo production for mainstream applications and print runs, and meets the strategic needs of businesses faced with the challenge of dealing with the proliferation of SKUs, a widening variety of products and shorter delivery times.
Fujifilm’s LED UV curing system slashes energy use, and the company’s narrow web inks are solvent-free and manufactured in the UK at Fujifilm’s award-winning Broadstairs factory, where extreme care is taken to ensure all manufacturing and operational processes are as environmentally responsible as possible.
Similarly, Fujifilm’s imprinting solutions can breathe new life into an analogue production line, bringing additional functionality without the investment in a new line. Where a new investment is necessary to meet market needs, the Jet Press 750S and Jet Press FP790 digital presses eliminate many of the processes and consumables associated
with traditional analogue production. Much has also been written about how the Jet Press 750S can contribute to a more circular economy.
FUJIFILM are delighted to be exhibiting at interpack 2023, the flagship show for the global packaging industry. It’s great to see the show finally back up and running, after a long 6 years. We are looking forward to connecting with our existing and potential customers.
We work with packaging producers at all stages of their journey, whether
it’s helping them to optimise analogue production lines to maximise efficiency or to introduce a digital capability. We don’t do one-size-fits-all – we do the right solution, for the right producer, at the right time. And all our solutions, whether analogue, digital, or somewhere in-between, are designed to reduce waste and the use of environmentally harmful chemicals, minimise energy consumption, and to be as sustainable as possible.
To learn more visit Fujifilm at interpack 2023, stand F65, Hall 8a
Jet Press FP790HP has unveiled its new HP Indigo 200K Digital Press, designed to give digital flexible converters the competitive edge with better productivity, on-demand delivery, no minimum orders, unique designs, reduced energy consumption, and minimal waste.
- Increases productivity – pushing the break-even point by 50 percent and allowing customers to triple their volume. Opens door to more flexible packaging converters who want to enter the digital market.
- Delivers gravure-matching color quality – using HP Indigo Liquid Electro Photography (LEP) and OneShot Color technologies. With patented Indigo Spot Master technology, converters can easily reachthe right color fast, keep it consistent, and share the color results online with the brand.
- Improves sustainability – carbon-neutral manufactured, minimizes waste during set-up and production, reduces energy consumption and is food packaging compliant.
The new press is based on the only field-proven digital technology for digital flexible packaging and on a successful install base of over 300 HP Indigo 25K digital presses, series 4, worldwide2. The new, series 5, HP Indigo 200K digital press, prints up to 56 m/min (183 ft/min) and dramatically increases the productivity
of high-margin, sustainable short runs of digital flexible packaging, to be delivered in days, not weeks.
“The HP Indigo 200K is a mid-web digital press especially designed for converters addressing the needs of brands in flexible packaging, but it also serves the growing requirements of the
label and shrink sleeve industries for higher productivity and wider format,” said Noam Zilbershtain, VP & General manager of HP Indigo & Scitex.
“Flexible Packaging is a growing market, and as HP Indigo customers are growing much faster than the market3, I have no doubt that the HP
Indigo 200K digital press will open the door for more flexo converters who want to join the success, and reign in industry 4.0.”
The HP Indigo 200K digital press showcases a 30 percent increase in speed and 45 percent boost in productivity compared to the HP Indigo 25K4. Featuring gravure-matching color quality based on the HP Indigo Liquid Electro Photography (LEP) and OneShot Color technologies, the new press offers the widest available range of ElectroInks and is designed to print
high coverage packages with white on the majority of industrial substrates, both surface and reverse. Additional business opportunities include unique brand protection elements.
Following the announcement of UK-based Sirane Group as one of the press' first beta customers, Peter Ralten, Commercial and Business Development Director said: “At Sirane, we have been looking into digital print for a while now, realizing it is where the future lies. The HP Indigo 200K digital press, with its incredible increase in productivity, opens new business opportunities for us. With
the unmatched HP Indigo quality and versatility, we can’t wait to see the results of adding it to our portfolio.”
The HP Indigo 200K digital press achieves efficient production with HP Indigo’s PrintOS software automation capabilities for batching, ganging, and variable data, as well as faster, accurate color match and workflow. Automation tools for operator efficiency5, coupled with sustainable production, circular packaging and food packaging safety6, all amount to an outstanding digital solution.
Many processes in the printing industry are becoming increasingly digitalized – it is no coincidence that these developments will be the main topics at drupa 2024. But how far has digitalization come in label production in this respect?
The future is digital, not least in the printing industry. That’s why digitalization is one of our megatrends at drupa 2024. To keep a constant eye on the extent of digital progress in the printing industry, we regularly obtain an overview of this from our exhibitors.
Matt Bennett, label zone business director of packaging machinery and equipment manufacturer at Bobst, spoke about digital progress in the company and label production and expectations for 2023 in an interview with L&NW.
Bobst’s overall aim is to provide converters of label production with industrial-powered solutions that optimize the production flow without increasing costs and – at the same time – are more sustainable and profitable. They see digital printing technology and greater automation as the future of label production.
Hybrid systems are particularly suitable for this, as they are flexible and fast and thus offer sustainable technology with low costs and a shorter time-to-market.
At Bobst, these are primarily all-inone machines that seamlessly combine digital and flexo, which enables simultaneous printing, converting, and embellishments. These machines integrate highly automated flexo presses and digital presses.
The Digital Maser series 340 and 510 are this kind of all-in-one machine. They combine the strengths of Bobst flexo and inkjet technology to ensure
that processes such as prime, print, embellish, inspect and cut can be performed in a single workflow. The 510 series enables new opportunities for printers. Digital automation on each module of the presses enables on-thefly changeovers. This automation also reinforces a higher press uptime and repeatability, guaranteeing a faster timeto-market. Even though this machine series can produce higher volumes, it requires only one operator.
With the machines being wholly owned, developed, manufactured, installed, and maintained by Bobst, the introduction or upgrade to the new models is as easy as it is seamless, and – in case of any questions – the customer does not have to contact different companies, but simply can contact Bobst. The machines are also particularly customer-friendly because their highly modular nature makes it possible for customers to adapt them
Given that the full integration of digital printing and flexo technology brings some clear benefits, this was also the most impactful trend from label production for Bobst in 2022. The all-in-one solutions not only provide more variety in label products but are also very beneficial in terms of sustainability, as waste can be reduced by incorporating quality control.
For 2023, the company hopes for further developments and wishes for the expansion of digital inkjet printing systems. Digitalization cannot be stopped. That’s why Bobst sees a development toward a 100% digital future in label production.
- Company launches energy efficiency campaign for print shops
- Using state-of-the-art HEIDELBERG equipment clearly exceeds 1997 Kyoto Protocol targets
- Energy consumption of latest Speedmaster XL 106 generation around 40 percent lower than that of a press from 1990
Back in 1997, the Kyoto Protocol stipulated that, by 2020, industrial processes should be at least 20 percent more efficient than they were in 1990. Today, due to the general trend for more sustainability across the whole of society, ambitious climate protection targets, and the present energy crisis, there is growing pressure on the print media industry to make the entire production process even more energyefficient – and to do so quickly.
Heidelberg has therefore launched a campaign for print shops featuring information, advice, and tips from experts on how to considerably increase energy efficiency in printing companies while simultaneously driving down costs. The company will
be focusing on several headline issues in its communications over the next few months.
“The subject of sustainability and energy efficiency has become a crucial competitive and cost factor for suppliers in the print media industry – and that applies equally to our customers and to Heidelberg itself,” says Dr. Ludwin Monz, CEO of Heidelberg. “Alongside its customers, Heidelberg aims to extend its leading role in the industry to include energy efficiency as well.
Due to our technological and data expertise, we are able to offer our customers attractive options for achieving energy-efficient production and can provide comprehensive advice and consulting. We all need to work
on these issues if we are to hit climate protection targets.”
Speedmaster XL 106 – energy efficiency as standard
To launch the campaign, Heidelberg is showcasing the energy efficiency of the Speedmaster XL 106. For example, a comparison between the Speedmaster CD 102-6+L from 1990 and the current Speedmaster XL 1066+L reveals that energy consumption per 1,000 sheets has been reduced from 13.8 kWh to 8 kWh – a reduction of 40 percent. A whole range of innovations and improvements throughoutthe entire system is responsible for this achievement.
Besides investing in cutting-edge equipment, print shops can also
further boost their energy efficiency by optimizing the way they use their equipment. This is where one principle in particular comes into play – one that highlights a key difference between printing presses and automobiles, for instance, which consume more energy the faster they travel.
By contrast, a printing press has a basic level of energy consumption that covers the fundamental operating functions. Beyond this, energy consumption increases in line with rising printing speed, but since the basic level of energy consumption is spread over more printed sheets, overall energy efficiency improves. This means a press is at its most efficient when a job is being printed at full speed – ideally on a fully automated basis – and when, after that job, the system either moves on immediately to the next job or switches to standby mode if there is nothing else to be printed.
“When it comes to energy efficiency in print shops, although the equipment being used is an important basis, operating that equipment in the best way possible is at least equally as important. This is often where companies can really make a big difference. It is at precisely this point that the Heidelberg campaign for greater energy efficiency comes in and creates a basis for fully utilizing preexisting potential,” says Dr. Eva Boll, head of ESG at Heidelberg.
Starting April 2023, the Speedmaster XL 106 will be supplied with an energy measuring device as standard, albeit only in Germany initially. This will enable users to permanently monitor the energy consumption of their press – measured in kilowatt-hours per 1,000 sheets – from the control station. This read-out encourages operators to run
the press in an energy-efficient way – in other words, at maximum speed. All in all, various energy-efficiency measures also help print shops reduce the CO2 emissions associated with their industrial processes.
The second theme of the campaign highlights the potential in terms of savings offered by peripheral units for the Speedmaster, which makes energyefficient production possible. Next, the campaign addresses the issue of “maintenance”, revealing the extent to which regularly maintained machine systems can conserve resources and improve the energy balance. To complement the campaign, Heidelberg offers relevant consulting services so it can work with customers to identify potential for energy savings in the print shop and draw up plans for leveraging that potential.
- Chroma 2S technology for all models of Chroma High Tech series and Chroma Smart series by Koenig & Bauer Celmacch - Unique HBL solution for inside-outside printing - The first machine was successfully tested at Koenig & Bauer Celmacch’s facilities - Technology available for flexo printers and rotary die cutters - Modular design to easily add future printing units - The technology of the new Chroma 2S allows to open up new business fields - Further technical innovations planned for next year
Koenig & Bauer Celmacch offers the new technology of inside and outside printing in a single pass to all companies of the corrugated industry. The twosides printing in one single working process allows not only a significant increase of efficiency, but also a considerable reduction of production costs.
Luca Celotti, CEO of Koenig & Bauer Celmacch, says that “This tendency
Bottom-Printing for the Chroma High Tech and Chroma Smart, we can really satisfy almost all Customer’s needs.” After successful tests of the Chroma Smart 2S in our workshop in Desenzano, the first machine is currently ready to be installed at one of our Customer’s premises.
Chroma 2S, technologically stateof-the-art, modularly retrofittable
The new High Board Line Chroma 2S
Thanks to the user-friendly construction, the bottom printing units momentarily not in production can be prepared for follow-up process without stopping the machine.
In this way, the new Chroma 2S technology opens new market potentials for our Customers, featuring also an optimal price/performance ratio.
Koenig & Bauer strengthens its presence into the growth market for machines processing corrugated cardboard
The focusing on the growth market, and on both the conventional and digital packaging printing, is a keyfactor of the strategy of Koenig & Bauer. After reentering the market for machineries in the field of corrugated cardboard processing, the company continued this route. Thanks to the new partnership with the Italian Company Celmacch, the Group Koenig & Bauer widened last September 2022 its large product-portfolio.
has completely transformed the cardboard industry, with a particular focus on corrugated packaging. For box factories, it has become essential to be able to print quickly and at low cost, even inside the box, to get the socalled "wow-effect" during unboxing or to simply print instructions and howto-use.“
Hannah Potrawa, Director Corrugated at Koenig & Bauer, underlines: “We offer all price and performance levels. With the presettable die cutting unit for the Chroma X Pro, and the Top-
technology produces at a max. speed of 10.000 sheets per hour. Furthermore, the printing units for inside printing are equipped with the well-known automatizations of the Chroma High Tech or Chroma Smart series.
Thanks to an innovative solution, foundation pits or changes are not necessary. Nevertheless, the machine operator has easy and ergonomic access to change the cliché in all printing units. The number of the colors is freely configurable, and it is thus possible to fulfill almost all Customer’s needs.
Both companies joined more than 40 years’ experience in the field of processing corrugated cardboard and more than 200 years of printing technology on different levels. With the Chroma X Pro Series, Koenig & Bauer successfully developed and placed in the market highly-automated machinery. With ChromaCUT Smart and ChromaCUT HighTech, through the partnership with Celmacch, Koenig & Bauer offers nowadays a wideranging product portfolio for all prices and performances stages.
• Suitable for flexographic printing on film substrates with solvent inks
• Offers exceptional and consistent print quality with finest highlight dots
• Optimized for both bank and LED exposure for reduced complexity
• New formulation is less prone to plate swelling
XSYS has announced the introduction of nyloflex® FTV Digital, a hard durometer photopolymer plate for flexographic printing of flexible packaging with solvent inks. Developed with inherent flat-top dot technology and a smooth plate surface, the new plate formulation will appeal to customers serving brand owners who require the highest-quality printing of film-based substrates, while also offering maximum flexibility and higher productivity.
“Our customers are under constant pressure to deliver consistent print results quicker and more efficiently,” said Simon Top, Product Manager at XSYS. “With the nyloflex® FTV Digital, XSYS has introduced the latest plate innovation for the printing of high-end flexible packaging. Moreover, the new plate does not require any changes to existing solvent digital
washout processing equipment or any additional costs from auxiliaries or consumables.”
In combination with standard bank exposure, the nyloflex® FTV Digital can hold the finest highlight dots resulting in a wider tonal range and achieve excellent solid ink densities in combination with surface screenings. In the print room, higher OEE can be achieved thanks to its AIF (antiink filling) technology for longer and cleaner print runs with solvent based inks.
As the new formulation is less prone to plate swelling, benefits also include reduced plate waste and longer durability on press. High consistency and excellent repeatability is achieved due to the 1:1 image transfer on the plate, making it suitable for optional surface screenings. The new plate works
exceptionally well with ThermoFlexX Woodpecker surface screening patterns, including Woodpecker Sharp and Nano, as well as being ideal for extended gamut printing.
Unlike similar plates in the market, nyloflex® FTV Digital has been developed to achieve brilliant quality regardless of whether it is exposed using conventional UV-A tube lights or LED UV-A light technology, before being processed in a solvent washout system. The LED-optimized plate formulation makes the nyloflex® FTV Digital plate perfectly suited for exposure on the ThermoFlexX Catena-E unit, resulting in superior Overall Equipment Effeciency (OEE) in plate production.
“The nyloflex® FTV Digital offers customers the best of both worlds because it is equally efficient in both conventional bank exposure and newer LED systems. Since it also reduces complexity in the plate room, it perfectly complements our portfolio for the high end flexible packaging market. Next to well-established nyloflex® NEF Digital, which was the first LED-optimized plate for the highend flexible packaging segment, we can now offer a second LED-optimized plate that also brings excellent print results with bank exposure.” commented Simon Top.
“The new plate will give those customers who plan to move to LED exposure, such as our Catena-E technology, an easy and straightforward path to the future with a market-leading quality.”
Hard photopolymer flexo plate with inherent flat top dots LED optimized plate formulation
Developed for the high end flexible packaging market Smooth plate surface is able to hold all customized surface screening patterns (e.g. Pixel+ and Woodpecker
+ Highest ink transfer and excellent highlights out of the box
+ Robust and consistent on press, simple to process, already includes flat top dots and a surface screening pattern
+ Optimal for short (quick to color) and long clean print runs (anti ink-filling)
+ Known in the market as THE digital plate for high quality Flexible Packaging Print
+ Excellent print results even under challenging printing conditions
+ Very good for long clean print jobs (anti-ink filling)
To help realise its dream of becoming the world's 3D packaging center, long term Manroland partner Push Group 3D Co Ltd of Yibin City, Sichuan Province, has installed a brand new ROLAND 700 eight color Evolution press with coating and inline foiler.
Founded in November 2002, the Push Group is a large-scale modern packaging printer, named as one of Sichuan's Top 100 Enterprises in 2021 and part of the Wuliangye Group.
Sited in Yibin City, the 'first city along the Yangtze River', the company applies world-leading innovative packaging printing technologies such as those from Manroland. It specializes in functional materials and deep processing, 3D display, composite packaging boxes, gold and silver cardboard and holographic positioning special paper.
Push Group 3D provides customers with a range of plastic lenticular sheets and plates for such purposes such as blister, printing, and optics, 3D anti-counterfeiting packaging, 3D stationery, 3D light box advertisements, naked-eye 3D display terminals, as well as a full range of high quality customer services.
Discussing the introduction of the new press, Mr. Yang, Director of the company's 3D Business Department said: "Since we started, we have been committed to the revitalization and development of the Chinese industry's 3D packaging and 3D vision, promoting the application of 3D technologies around the world and striving to become the world’s 3D packaging center. The newly introduced ROLAND 700 Evolution with its coating module, broad range of substrate thickness, productivity, print quality and finishing effects is helping us realize our dream."
Equipped with various innovative automation technologies, the ROLAND 700 Evolution promises unprecedented efficiency, productivity and quality, offering printing speeds of up to 18,200 sheets per hour along with premium print quality and highly stable consistent colors to match all the requirements of 3D packaging printing. In addition, ROLAND 700 Evolution has a wide range of substrate thickness (0.04-1.0 mm), ideal for 3D printing on lenticular films.
The ROLAND 700 Evolution's automation technologies include: Triple Flow. With three separate ink distributions at the push of a
button, TripleFlow delivers high color consistency during the whole print run resulting in drastic savings in waste and reduced production costs.
InlineFoiler 2.0. A groundbreaking enhancement solution to meet market demands for more creative, more eyecatching and more vibrant print. With InlineFoiler, printers can cold foil and overprint a full spectrum of colors inline on a broad range of substrates in a single pass. Combining this with delicate embossing and effect or spot coatings or varnishes enables excellent printing effects, along with increased productivity.
CEO Alejandra Acosta Salati puts this down to what she describes as the company’s “restless DNA, which is always motivating us to improve. As a result, we have become something of a laboratory of innovation that has driven change in other trade shops.”
Cromograf’s embrace of sustainable production is a good example of the company’s pioneering spirit. While the thoughtful, planned use of resources may now be a mantra for all stakeholders in the packaging supply chain, Cromograf already embarked on the path in 2008. And Alejandra can almost pinpoint the precise date: “In a way, it started the day my father, Miguel Angel Acosta, saw the FLEXCEL NX System. He immediately recognized the potential of a technology that eliminated variables and brought new levels of consistency to the flexo process.
“We believe in streamlining and standardizing processes as much as possible, and the FLEXCEL NX System provided the best platform for standardized, repeatable production. That’s the way it was then, and it’s the same now.”
A technology leader in ECG
Cromograf installed the first FLEXCEL NX Mid system in Latin America in 2008, and a few months later began experimenting with Extended Color Gamut (ECG) printing; a process in which - 14 years later – Cromograf is recognized as the technology leader in Latin America and beyond.
ECG is the foundation of Cromograf’s sustainability policy, explains Alejandra, because of the savings and efficiencies that are inherent in the basic idea of printing
as much as possible using a fixed CMYK ink set. “ECG uses fewer plates, fewer special inks, and cuts substrate wastage during job set-up. In addition — and this is very important for brand owners — the standard ink set means we can print multiple jobs simultaneously. This makes it easier to meet converters’ minimum order quantities despite ordering smaller volumes, which helps with test-marketing of new packaging ideas.”
None of this, Alejandra continues, would be possible without FLEXCEL NX Technology. “The whole concept of ECG is to remove variables that can impact on productivity and reduce sustainability. FLEXCEL NX Technology allows for standardized production to achieve predictable, consistent results. It’s an exceptional plate technology that offers high productivity and process stability. The dot reproduction remains stable print after print, giving us consistency, longer plate life and fewer unscheduled press stops for cleaning.”
The company’s achievements have now been rewarded with a Gold Award in the Miraclon-sponsored Global Flexo Innovation Awards (GFIA), awarded for excellence in Print Production Workflow, Commitment to Sustainable Print, and Creative Use of Graphic Design.
For Alejandra, the Global Flexo Innovation Award is a welcome recognition of the strategy started by her father and continued under her management. “We have been printing with CMYK and ECG since 2008, and take pride in the quality of what we produce. The difference today is that people are taking notice.”
Over the last decade and a half, Uruguayan flexo packaging prepress trade shop Cromograf has reached beyond its Montevideo base to become a model for similar businesses in Latin America.
Jointly with long-standing converter customer of more than 30 years, Strong SA, Cromograf submitted a series of packaging jobs, accompanied by a level of detail that impressed the judging panel by clearly demonstrating the savings and benefits delivered by ECG. For example, the winning entry — flexible packaging for a range of flavored rice — achieved remarkable savings by using ECG instead of the previous production process:
0 special inks (compared to 15 using CMYK + Special Inks)
28 plates (compared to 49)
28 mounting tapes (compared to 49)
28 washouts (compared to 49)
Similar levels of savings were achieved on every one of Cromograf’s entries, including one job for which Cromograf saved 10.8 kg of red ink. Add in the reduced usage of mounting tapes and cleaning solvents, less time spent setting up jobs, and a reduced storage space for inks and plates and the savings quickly add up.
The GFIA judges were also impressed by how Cromograf approach each new packaging project in order to decide how best to apply ECG. Dr Chip Tonkin, from the Sonoco Institute of Packaging Design and Graphics, observed: “They do a lot of analysis on an incoming job to determine if it needs anything beyond CMYK, and they take extreme measures to do it within CMYK for the vast majority of jobs. For most colors, you can achieve it with CMYK, particularly when you optimize your CMYK.”
Says Alejandra: “The packaging value chain begins with an idea and ends when the packaging is in the hands of the consumer. Along the way, we consider the use of every resource input, controlling the process at every stage with the goal of producing a stable product with a minimal carbon footprint.”
Analysis begins with an initial discussion with the design team, and Cromograf’s extensive experience immediately comes into play. Explains Alejandra: “The way we manage color, media and inks means we know immediately which colors work best with ECG and can advise how slight design modifications can reap major efficiency and sustainability benefits.” (As an example of this attention to detail, for one of the jobs entered for the GFIA Cromograf positioned cut marks and process control targets inside the job, leading to a 1% saving in media, which, as the judges noted, added up to significant figures over the total production run.)
As we wrap up our discussion, she also acknowledges the contribution made by the teams at Miraclon. “It helps to be dealing with an excellent team of individuals over many years. We regard both Miraclon and our local dealer, Lumila, as a vital part of our business.”
This technology has now overcome the technical hurdles of tube laminates. With newly developed UV inkjet inks and a digital printing system that offers the shortest web paths, including the option of inline coating, it’s also ideal for achieving reasonable margins with short runs.
Digital printing has become a hot topic in tube printing. This has been made possible by new developments from Heidelberger Druckmaschinen AG and Gallus Ferd. Rüesch AG with their coordinated solutions for this application. Tubes, which are bent and crushed during squeezing, require a flexible ink film. In addition to good adhesion to the laminate, above all, it must not crack.
For this purpose, Heidelberg developed the UVF01 inkjet ink, which has proven itself not only in tube laminates
but also primarily in the printing of folding carton. The new ink system required a different drying system, which Gallus integrated into the Labelfire "Tube-Edition" in the form of UV-LED lamps. The advantage of using UV-LED technology instead of the mercury vapour lamps that were previously used, is that the energy penetrates the ink layers better thanks
to the high intensity of the UV-A beams and leads to more uniform curing.
The high intensity of the UV LEDs eliminates the need for boosters to intensify drying. This allows the temperature-sensitive tube laminate to be processed without being affected by heat. Inert gas is also used to cure the ink film quickly and completely.
The resulting increase in curing performance and the reactivity of the photoinitiators ensures complete curing of the ink film. In addition, the ink system adheres very well to the substrate without the need for priming.
How is digital printing developing for tube laminates?
At Interpack from the 4th to the 10th of May 2023 in Düsseldorf, Gallus will be demonstrating the prospects this opens up for tube printing together with well-known partners. These include AISA Automation Industrielle S.A. for tube production machines and IWK Verpackungstechnik GmbH for tube filling machines, as well as Stora Enso Oyj for printing stock. Patrizio Vaninetti, who is responsible for sales in Central Europe at Gallus, has summarised some of the key points of future developments in tube printing for those interested in printing who will not be attending Interpack.
“For Gallus, the technical development in tube printing is associated with a further decline in print runs, which is changing the printing technology used. It makes perfect sense to produce the shorter runs by printing digitally now," he says, describing the development in tube printing.
"And it also makes sense to produce them on hybrid digital printing systems," states Thomas Schweizer, Head of Business and Product Management at Gallus, adding: "With a stand-alone digital press, a second production step would be needed on a coating unit, which increases complexity and reduces costeffectiveness. From today's perspective, the existing production method will remain in place for current longer runs. The conventional hybrid machines are automated to such an extent that they are already very efficient”
„It makes perfect sense to produce the shorter runs by printing digitally now,” says Patrizio Vaninetti, who is responsible for sales in Central Europe at Gallus, describing the development in tube printing.
The importance of the material costs and thus the web path in a machine is revealed by considering profitability, especially with decreasing order sizes. The material costs make up a significant part of the total cost and thus the profitability of a job. To do justice to this aspect, the web path in
the Labelfire "Tube-Edition" has been kept as short as possible. Instead of a double rewinder, a single rewinder is used and the printing units have an ultra-short web path of only 1.1 metres from printing nip to printing nip. Between unwinding and rewinding, the web path of the "Tube-Edition" is only approx. 25 m in total. With comparable machines in tube laminate printing, it is about 80 m. The short web path reduces waste during makeready and production and thus lays the foundation for the economical production of small orders.
With the Labelfire "Tube Edition", Gallus is expanding another area of application in special packaging, after the company has already been present with industrial solutions in the folding carton market for tobacco applications for several years. The Labelfire «TubeEdition», makes a digital printing system for tube available, which represents an investment for further decreasing order sizes in the market. For a transitional period, the system would offer the possibility of producing tube laminate and label jobs on one machine, to make full use of its capacity right from the start.
launch of its new LED UV cured thermoforming inks
Fujifilm announces the launch of its new LED UV cured thermoforming inks, designed especially for use with its Acuity Prime flatbed printers.
The inks, which are quickly cured with conventional LED UV lamps, are the ideal solution for decorating a wide range of materials commonly used in thermoforming applications.
The inks offer superb dot reproduction, light-fast colours with outstanding adhesion and elongation, and deliver excellent quality for applications involving deep-draw thermoforming, line bending and dome blowing. Other benefits of the inks include high quality finishing, bending, creasing, routing, guillotining.
Inks in the range are suitable for internal and external applications, and form perfectly between 150-200*C (302-392*F).
They are also free from volatile solvents and hydrocarbons, meaning that they have less impact on the environment when compared with solvent-based products.
Matthew Whiting, Product Manager at Fujifilm Wide Format Inkjet Systems, comments: “With our extensive knowledge of the sector, as well as the award-winning manufacturing facilities at our Broadstairs site, Fujifilm proudly creates inks to maximise the capability of its printers, such as the Acuity Prime.”
He continues: “When thermoforming, you don’t want the ink to crack, become brittle or flake. Our Uvijet HZ inks are very flexible and maintain their high quality throughout the thermoforming process, resulting in an excellent finish.”
“This is just the start of our drive into the packaging industry. We will add more products to this area as we move forward. However, our first priority is to make sure that existing XSYS customers are looked after, and we will make sure that the changeover is seamless and that our clients will only benefit, our FERAG team will be second to none when it comes to sales, service and technical support,” commented Batty.
Roy Schoettle, Regional VP APAC XSYS, stated, “We are pleased to have FERAG join us and representing XSYS in this part of the world. We know they have been around for many years in the graphics industry and have a reputation that is second to none. Now that they have moved into the packaging area, we feel confident that our customers will truly benefit from a company that will focus on their needs day to day. It’s an exciting time as packaging around the world is growing and Australia and New Zealand is very much a part of this growth.”
FERAG appointed as agents for XSYS world leading flexographic plates in Australia and New Zealand
Flexographic printers in Australia and New Zealand will now benefit from FERAG’s long history and experience in the graphic arts industry, having looked after both countries over many years with their existing portfolio of graphics products. Now FERAG has moved into the growing Packaging industry and will bring this wealth of knowledge to flexo printers, looking after their needs with the leading range of plate products.
FERAG Australia/NZ managing director Philip Batty stated that it has long been the dream to move the company into the Packaging industry but would only do this if the right portfolio of products were to become available. “Now that XSYS (formerly part of the Flint Group) has decided to move agencies, both the ‘time and product line’ were the perfect fit to start our push for FERAG into the growing Australian/NZ packaging industry.”
FERAG will stock and supply nyloflex® flexographic plates, nyloprint® letterpress plates as well as nylosolv® washout solvent. The agreement came into effect in Australia and New Zealand on the February 24th 2023.
NDigitec Prepress is known as an innovation trailblazer, always seeking out the latest plate-making technologies to stay ahead of developments and to deliver leading solutions to its global brand owner customers. Some 55% of the annual
50,000 sqm plate output is supplied to the flexible packaging industry, another 25% goes to the corrugated segment, while the remaining 20% is divided between folding cartons and labels.
We were the first prepress company in the region to bring in LED exposure technology for making flexo plates with the Flint Group nyloflex® NExT system back in 2016,” said Shahe Kavlakian, Executive Manager for Prepress at NDigitec and brother of the company’s CEO Vatche Kavlakian, who as a pioneer of integrated prepress and printing services, laid the roots for the business in the early 1990s.
“Now we are once again taking the lead as the first to install the XSYS ThermoFlexX Catena-E system; an investment we have made because we believe that this solution will best support us in responding to the many varied customer demands we are currently facing and to allow us to continue our global expansion.”
Mimaki expands their textile portfolio with the TxF150-75, a printer designed for high quality, customisable textile applications.
Mimaki, a leading manufacturer of inkjet printers and cutting systems, announces its first ‘direct to film’ (DTF) inkjet printer, the TxF150-75, at its Global Innovation Days event. Utilising a heat-based transfer method, the printer is ideal for creating premium, customised merchandising, sportswear and various other promotional textile applications. This is the latest entry from Mimaki for the decorated apparel segment and will be making its EMEA at-show debut at Printwear & Promotion Live! in the UK (26th-28th February 2023).
DTF printing provides an easy and
affordable process for decorating apparel, most commonly T-shirts. The design is initially printed directly onto a special transfer film, which is then sprinkled with hot-melt powder. Once heated and dried, the transfer sheet is ready to be applied to the fabric using a heat press.
Based on Mimaki’s existing 150 Series, one of its best-selling models, the new TxF150-75 responds to the market need for a reliable, stable DTF technology. Built-in ink circulation system and degassed ink pack design prevent common DTF issues, such as poor ink ejection and white ink clogging. These core technologies, which also include the nozzle check unit and nozzle recovery system, all ensure that processes are carried out efficiently with minimal intervention needed.
Mark Sollman, Sr. Product Manager EMEA, Mimaki Europe comments, “Apparel decoration is a hugely popular and dynamic sector, one which we are already operating in with our other textile technologies. However, we could see the impact DTF technology has had on the industry in recent years, with its significant advantages over existing technologies. Namely, DTF avoids the time intensive process of plate creation in screen printing and the required weeding in traditional vinyl
heat transfer. The technology can also create vibrant designs with its full colour printing capabilities. We’re excited to bring a solution to the market that is designed for those already active in the decorated apparel sector and those looking to enter it, which excels in usability, reliability and quality.”
As the company’s first entry into a new segment, Mimaki has created its own range of water-based pigment inks (PHT50) especially for this solution. As of March 2023, these inks are OEKO-TEX® ECO PASSPORT certified[1], guaranteeing safety and environmental standards are met in line with Mimaki’s sustainability pledges. Unlike sublimation heat transfer printing, DTF is much more versatile when it comes to materials, able to work with more than just polyester and TC blended (polyester blended) materials, and on light or dark coloured fabrics.
The printer also comes with Mimaki’s RasterLink7 RIP software, allowing users to have full oversight and the ability to streamline the process from the design to the final product. Like with all Mimaki technologies, buyers can expect extensive in-house support from Mimaki throughout the initial set-up and use.