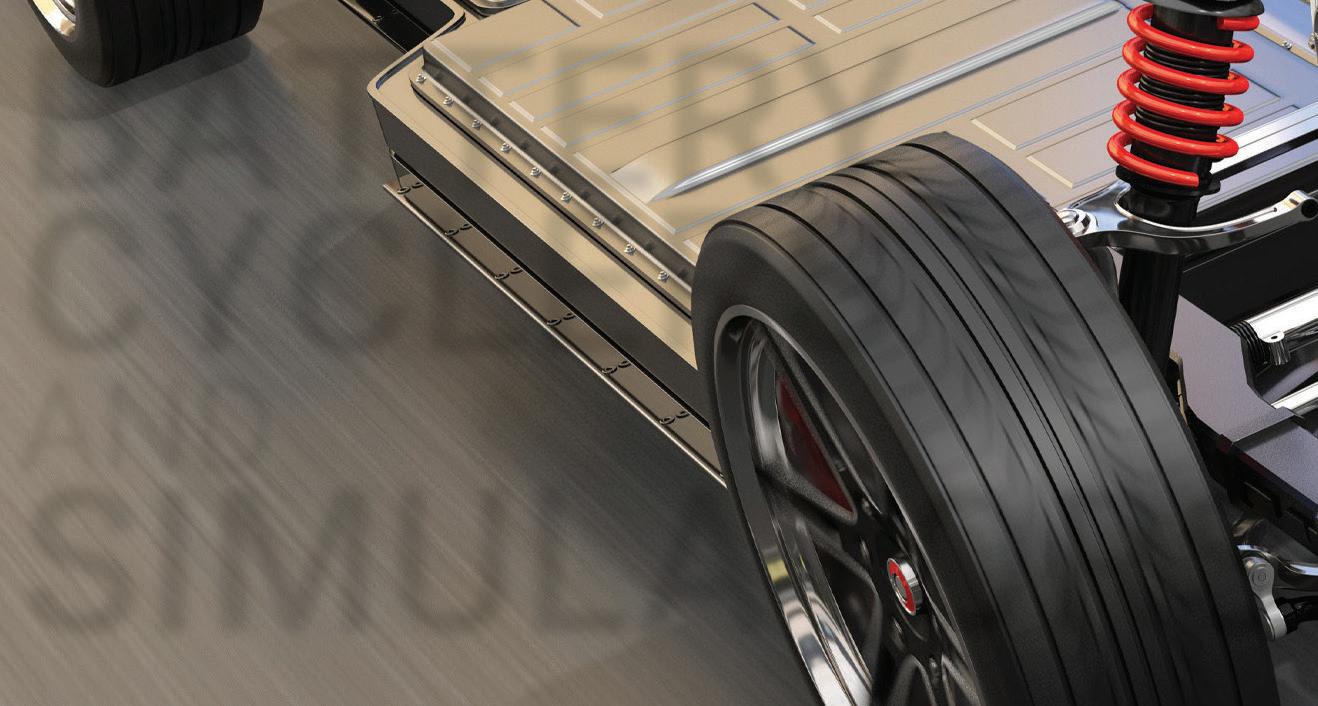
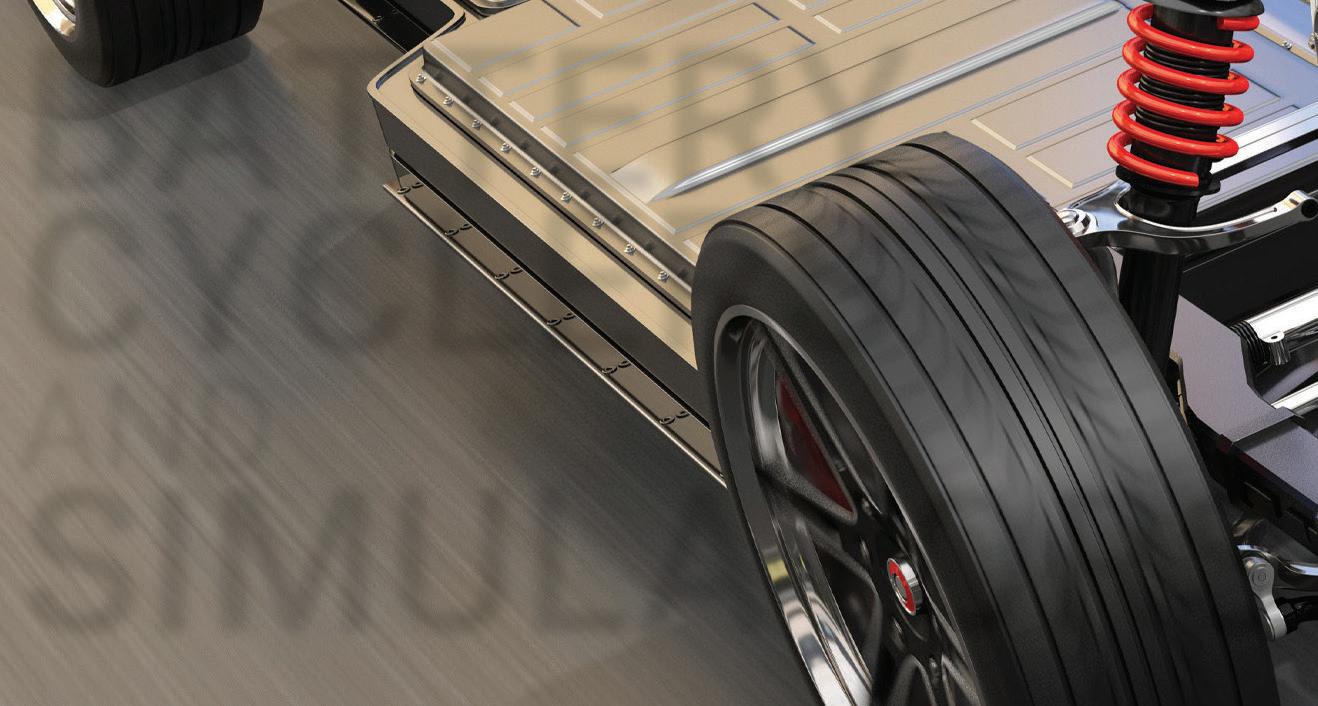
BATTERY CYCLERS AND SIMULATORS


CHARGE/DISCHARGE LIFE CYCLE TEST
Battery cell, module and pack level charge/discharge cycle testing solutions designed to provide high accuracy measurement with advanced features. Regenerative systems recycle energy sourced by the battery back to the channels in the system or to the grid.
BATTERY SIMULATION
Battery simulation for testing battery connected devices in all applications to confirm if the device under test in performing as intended. Battery state is simulated which eliminates waiting for the charge/discharge of an actual battery. Real time test results include voltage, current, power, SOC%, charge/discharge state and capacity.
To learn more about our Battery Test Solutions visit chromausa.com


THE TECH

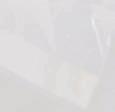


SK Siltron wins $544-million DOE loan to expand production of SiC wafers
INFICON’s ELT Vmax enables individual leak testing for mass-produced EV cells
ABS wins $166-million DOE loan to expand Ohio and Michigan EV battery plants
POSCO International’s drive motor core to power millions of Hyundai-Kia EVs
Optiphase and Opal-RT collaborate on real-time simulation for 5-phase EV motors
Sion Power raises $75 million to commercialize its Li-metal tech for EV batteries
Schaeffler/Vitesco merger will create the largest global EV powertrain supplier
Samsung SDI announces plan to mass-produce solid-state batteries
Farasis Energy researches plastic battery housing for increased EV safety

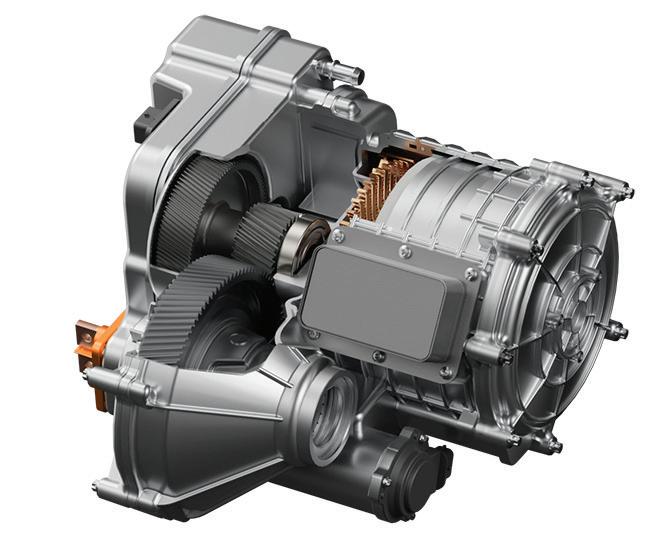
Layered oxide cathode could make sodium-ion batteries an attractive option
Microchip’s motor drivers include controllers, gate drivers and communications
Magna unveils its next-generation 800 V eDrive solution
Green Watt Power’s new 300 W DC-DC converters for EVs
QuantumScape begins shipping Alpha-2 prototype battery cells
ENNOVI introduces new production process for EV battery cell contacting systems
CATL warrants its new EV battery to last for a million miles or 15 years
Projected EV battery recycling capacity to outstrip supply
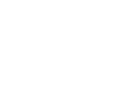

Thermo Fisher’s in-line metrology enables comprehensive inspection of electrodes
Avery Dennison’s new electrode fixing tapes for EV battery cells
THE VEHICLES
Xos receives order for 12 of its SV electric stepvans
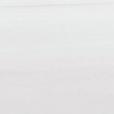

Skanska concludes North American pilot of Volvo EC230 Electric excavator
Volvo CE delivers electric excavator and refuse truck to Florida waste hauler
Thomas Built Buses delivers its 1,000th electric school bus
GILLIG to supply Seattle transit agency with up to 395 battery-electric buses
Daimler Truck North America delivers first electric Freightliner eM2 trucks
MAN rolls out battery repair centers across Europe
New fleet customer says Tesla Semi performs “well beyond expectations”
Fortescue’s electric excavator outperforms its diesel counterpart
Firstgreen reports growing US demand for its electric skid steer loaders
Electric trucks and buses show massive sales growth in Europe
Foxconn invests in light utility EV maker Indigo Technologies
Hyster to supply electric terminal tractors to APM Terminals in Alabama
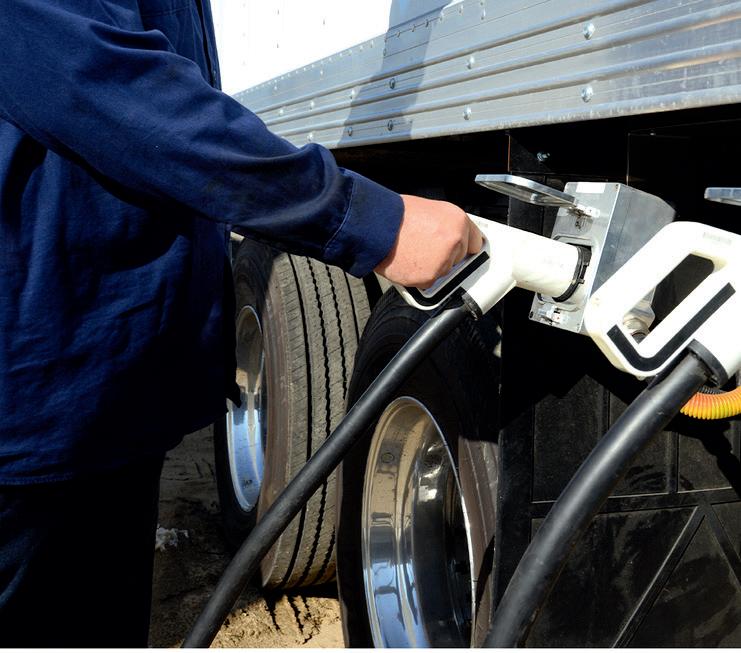
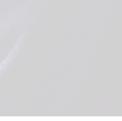
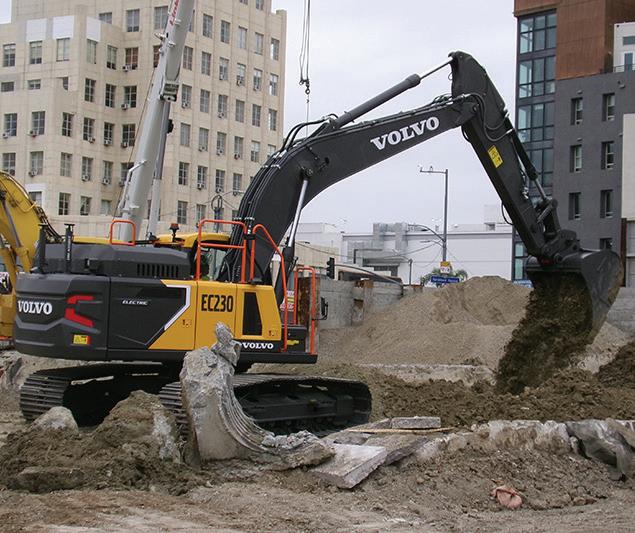
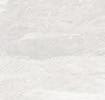
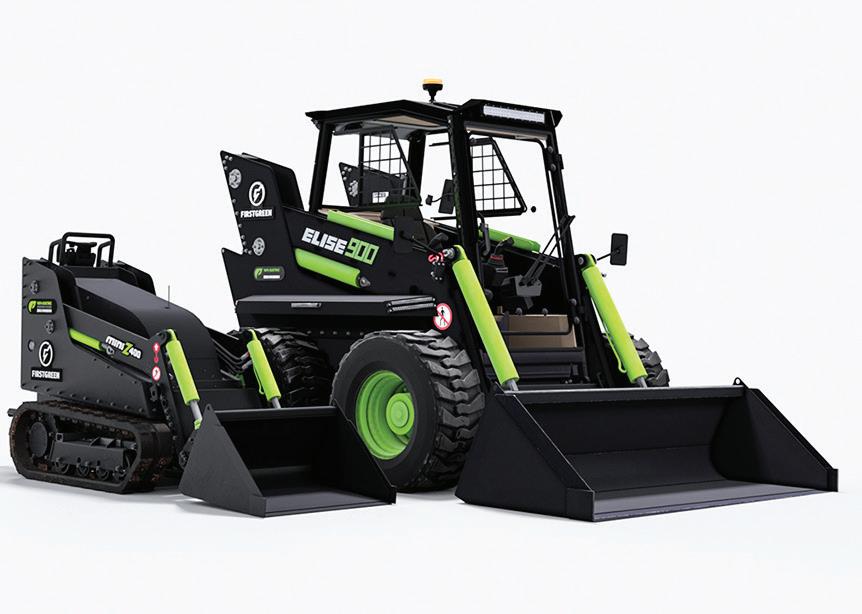
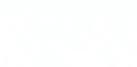
THE INFRASTRUCTURE
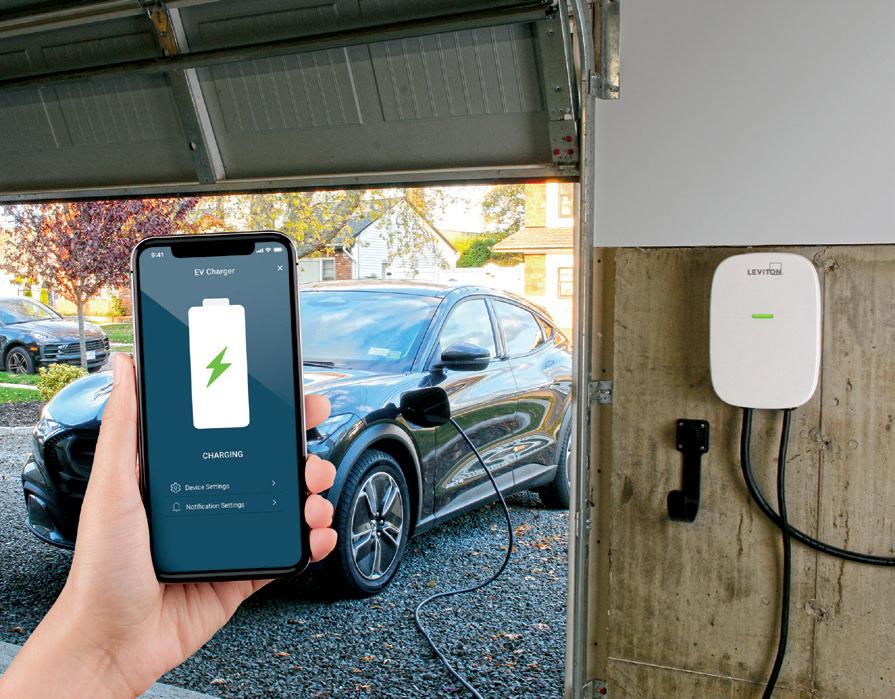
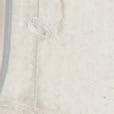
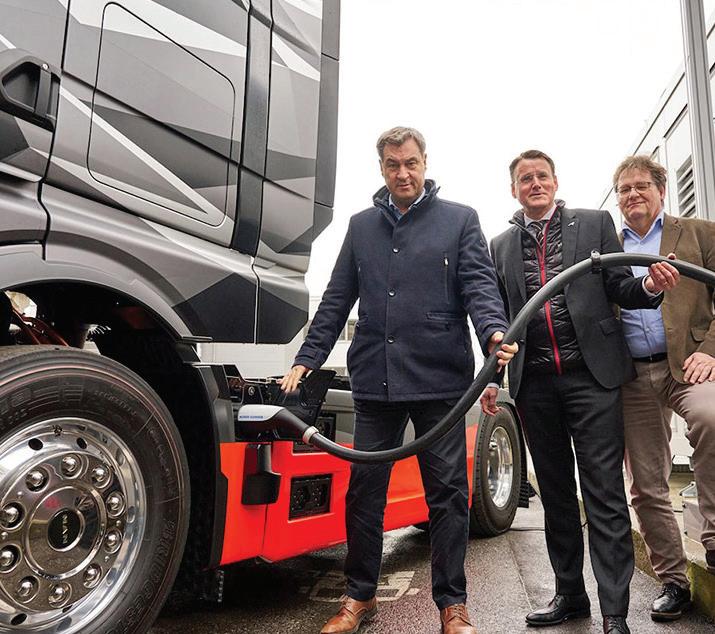
EV charging part of the smart home
Q&A with Leviton’s Andrew Taddoni
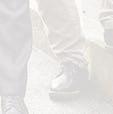
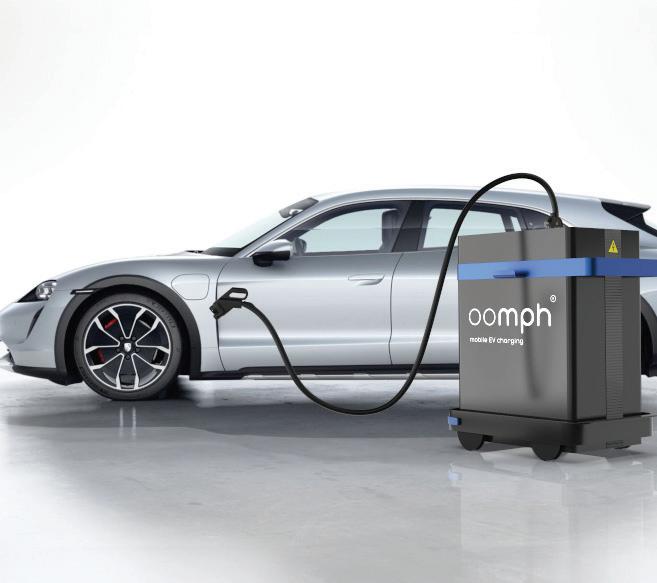
Study finds EVs are lowering electricity bills for all customers, not just EV owners
ABB E-mobility and MAN demonstrate megawatt charging on electric truck
Fermata Energy, BorgWarner, Lion Electric win $3-million grant for V2G project
Einride opens 65-plug heavy-duty EV charging site near California ports
Shell to divest 1,000 retail locations, and also expand EV charging. Coincidence?
Mack’s mobile off-grid charging system helps customers evaluate EVs
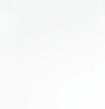
Oomph’s new Powerstream mobile rapid DC charger
EVBox supplies 300 EV charging stations to EVzen network in France
Project aims to accelerate construction of heavy-duty truck charging hubs
FreeWire program lets hosts custom-brand chargers with no upfront costs
Greenlane plans charging corridor between Los Angeles and Las Vegas
EnviroSpark to supply EV chargers to IHG Hotels in the US and Canada
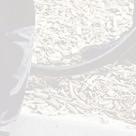
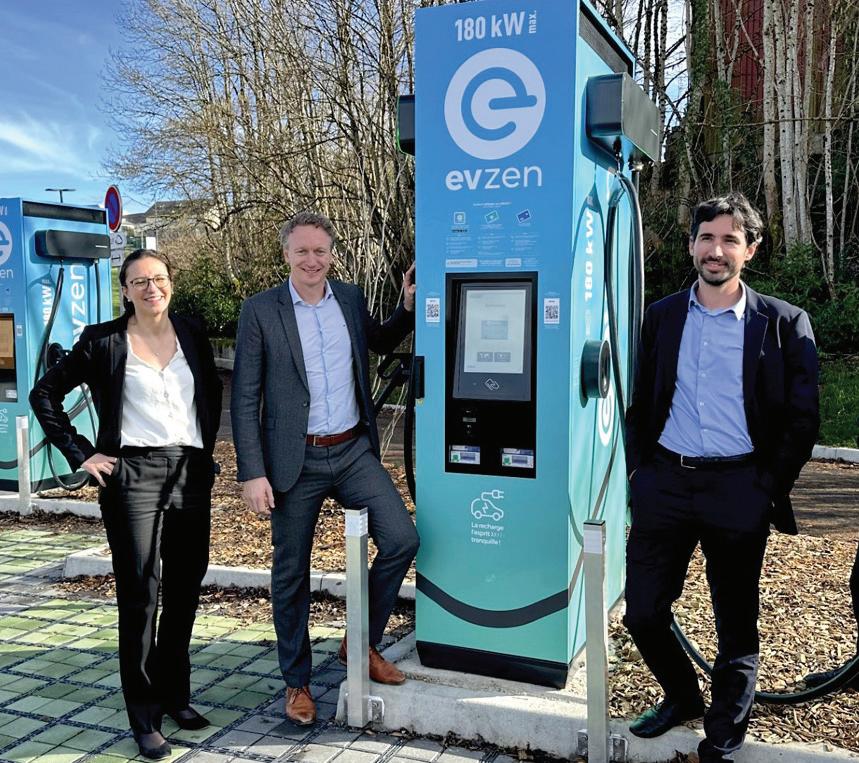
Dry electrode coating skips solvents for sustainable LiB solutions.
As lithium-ion battery (LiB) production ramps up to meet the growing demand for electric vehicles (EVs), manufacturers are choosing dry electrode coating as a more sustainable, cost-effective, high-performing alternative to the current wet slurry process:
NO EXPOSURE TO HAZARDOUS SOLVENTS
SMALLER FOOTPRINT
IMPROVED BATTERY PERFORMANCE
MORE COST EFFECTIVE

Publisher
Senior EditorTechnology Editor
Segment Leaders
Christian Ruoff
Charles Morris
Jeffrey Jenkins
Joel Franke
Mark Rogers
Greg Schulz
Graphic Designers
Tomislav Vrdoljak
Contributing Writers
Jeffrey Jenkins
Charles Morris
Christian Ruoff
John Voelcker
Cover Image Courtesy of
Stellantis North America
For Letters to the Editor, Article Submissions, & Advertising Inquiries Contact: Info@ChargedEVs.com
Special Thanks to
Kelly Ruoff
Sebastien Bourgeois
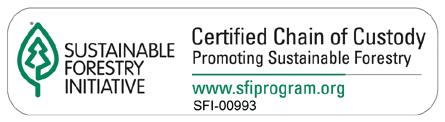
ETHICS STATEMENT AND COVERAGE POLICY AS THE LEADING EV INDUSTRY PUBLICATION, CHARGED ELECTRIC VEHICLES MAGAZINE OFTEN COVERS, AND ACCEPTS CONTRIBUTIONS FROM, COMPANIES THAT ADVERTISE IN OUR MEDIA PORTFOLIO. HOWEVER, THE CONTENT WE CHOOSE TO PUBLISH PASSES ONLY TWO TESTS: (1) TO THE BEST OF OUR KNOWLEDGE THE INFORMATION IS ACCURATE, AND (2) IT MEETS THE INTERESTS OF OUR READERSHIP. WE DO NOT ACCEPT PAYMENT FOR EDITORIAL CONTENT, AND THE OPINIONS EXPRESSED BY OUR EDITORS AND WRITERS ARE IN NO WAY AFFECTED BY A COMPANY’S PAST, CURRENT, OR POTENTIAL ADVERTISEMENTS. FURTHERMORE, WE OFTEN ACCEPT ARTICLES AUTHORED BY “INDUSTRY INSIDERS,” IN WHICH CASE THE AUTHOR’S CURRENT EMPLOYMENT, OR RELATIONSHIP TO THE EV INDUSTRY, IS CLEARLY CITED. IF YOU DISAGREE WITH ANY OPINION EXPRESSED IN THE CHARGED MEDIA PORTFOLIO AND/OR WISH TO WRITE ABOUT YOUR PARTICULAR VIEW OF THE INDUSTRY, PLEASE CONTACT US AT CONTENT@CHARGEDEVS.COM. REPRINTING IN WHOLE OR PART IS FORBIDDEN EXPECT BY PERMISSION OF CHARGED ELECTRIC VEHICLES MAGAZINE.
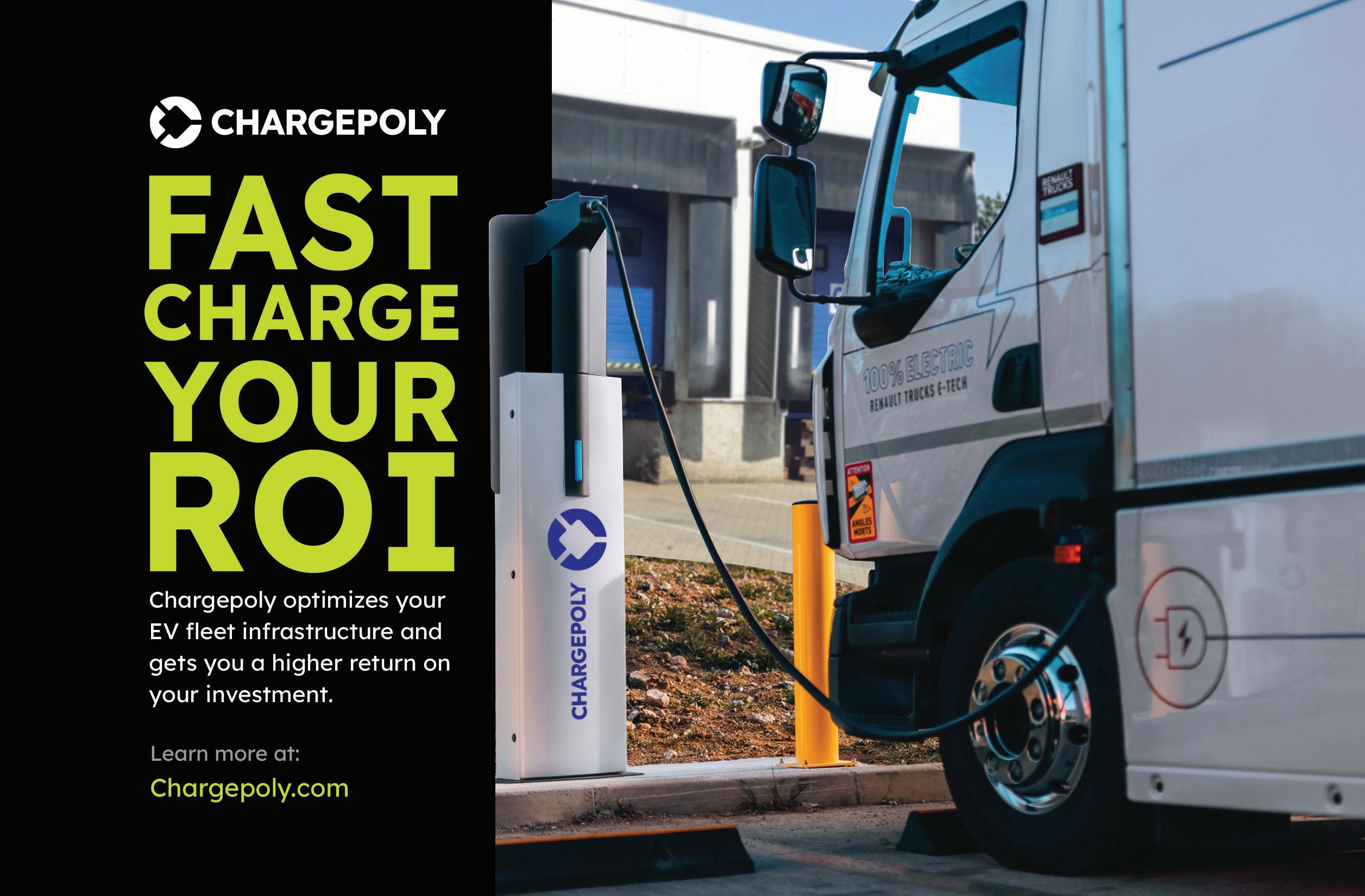


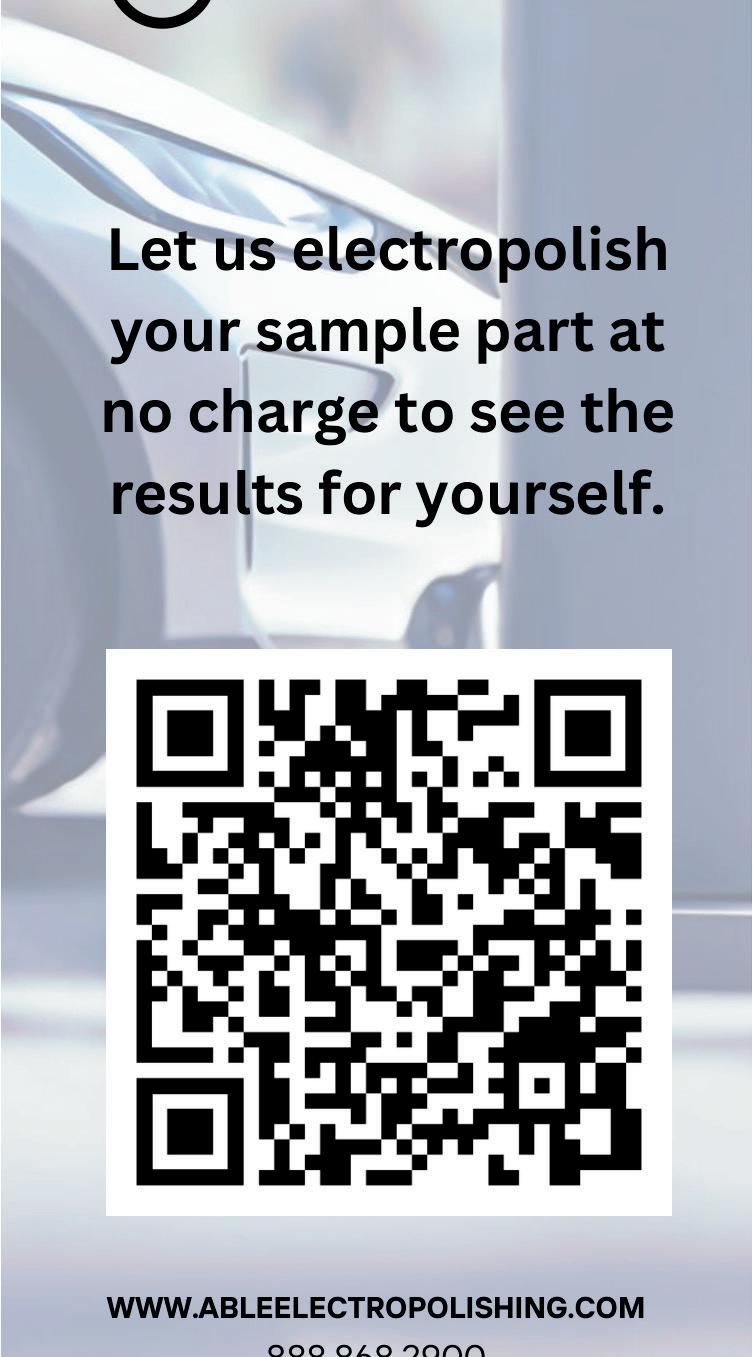

Publisher’s Note
What can we learn from China?
China and its auto industry are much in the news these days. e mainstream press seems to have suddenly discovered something that we’ve been writing about in Charged for years—Chinese automakers’ focus on electri cation poses a serious threat to the US (and other) auto industries.
ere are several aspects to this story. For years, China was considered a promising market for Western automakers, but now they’re running for home, tails between their corporate legs. Even Tesla let out a yelp recently when China sales fell below expectations. e reason for this setback is simple—the newest Chinese EVs deliver similar quality to that of US and European brands, at prices the latter can’t hope to match.
is is the same equation that the Chinese hope will help them conquer markets around the world. Chinese EVs are already on the streets of Europe, and they’re rolling o the country’s massive car-carrier ships (and, soon, o assembly lines at brand-new factories) in emerging markets in Asia, South America and elsewhere.
e world’s biggest EV maker, BYD, says it has no plans to sell passenger cars in the US for now (it’s been building e-buses in California for years), but Chinese suppliers and partly-Chinese-owned automakers (Volvo, Polestar) are already thriving in the US market.
Perhaps the most troubling of the China-related issues is the country’s dominance in raw material mining and processing. anks to the incentives in the 2021 Bipartisan Infrastructure Law and the 2022 In ation Reduction Act, companies are rushing to build supply chains in North America, but this will take time, and raw materials are likely to be a production bottleneck for years to come.
It’s hard to talk to any EV company these days without hearing about China. HummingbirdEV, pro led on page 56, recently provided 393 electric mining vehicles powered by its technologies to a China-based manufacturer.
ere is a silver lining here—the US and Europe badly need lower-priced EVs, and competition from China is one of the major factors spurring our automakers to cut costs and introduce new entry-level models, as Charles Morris discusses in this issue’s Charging Forward column, page 82. Localizing supply chains will also make them greener and more resilient.
Here at Charged, we’re happy to see China make the transition to EVs, but we’re well aware that the country is an economic competitor, and not a democracy. We support our home team, and we’d like to see Ford, GM, Stellantis, Tesla et al leading the EV transition. Unfortunately, the legacy brands are laps behind, and they’re not going to catch up using the compliance-based, quarterly-earningsobsessed mindset that’s prevailed in Detroit for decades.
I’m reminded of one of Stephen Covey’s 7 Habits of Highly E ective People: “ ink win/win.” Instead of trying to beat back the Chinese “threat,” the US should continue to take some pages from their book, bene ting from their EV expertise while still protecting US jobs and companies. China has been very strategic in experimenting with di erent pro-EV policies to establish its early lead in the market. We have a lot to learn about which policies work well and which get quickly ditched (at a speed only possible with China’s heavy hand).
For those who prefer a more combative aphorism, here’s one from Sun Tzu, recently cited by Michael Dunne, a top expert on the Chinese auto market: “Know the enemy and know yourself; in a hundred battles you will never be in peril.”
Christian Ruoff | Publisher EVs are here. Try to keep up.
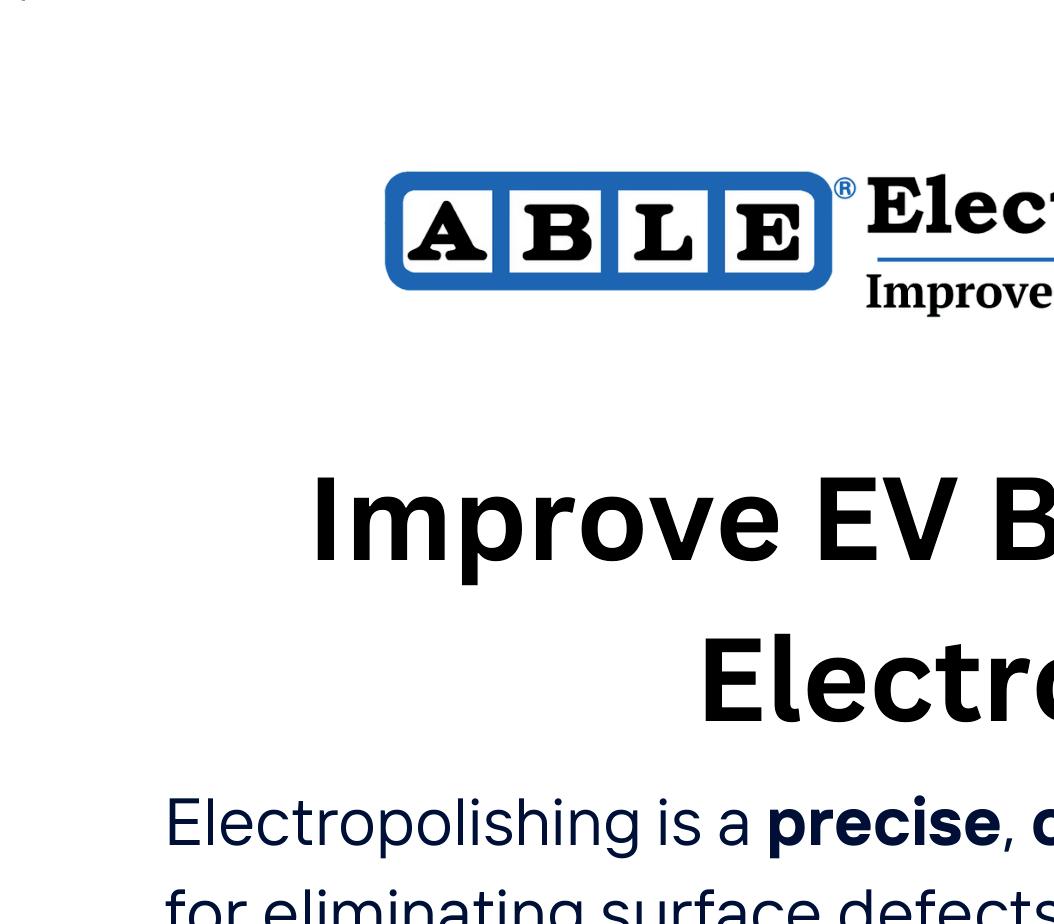
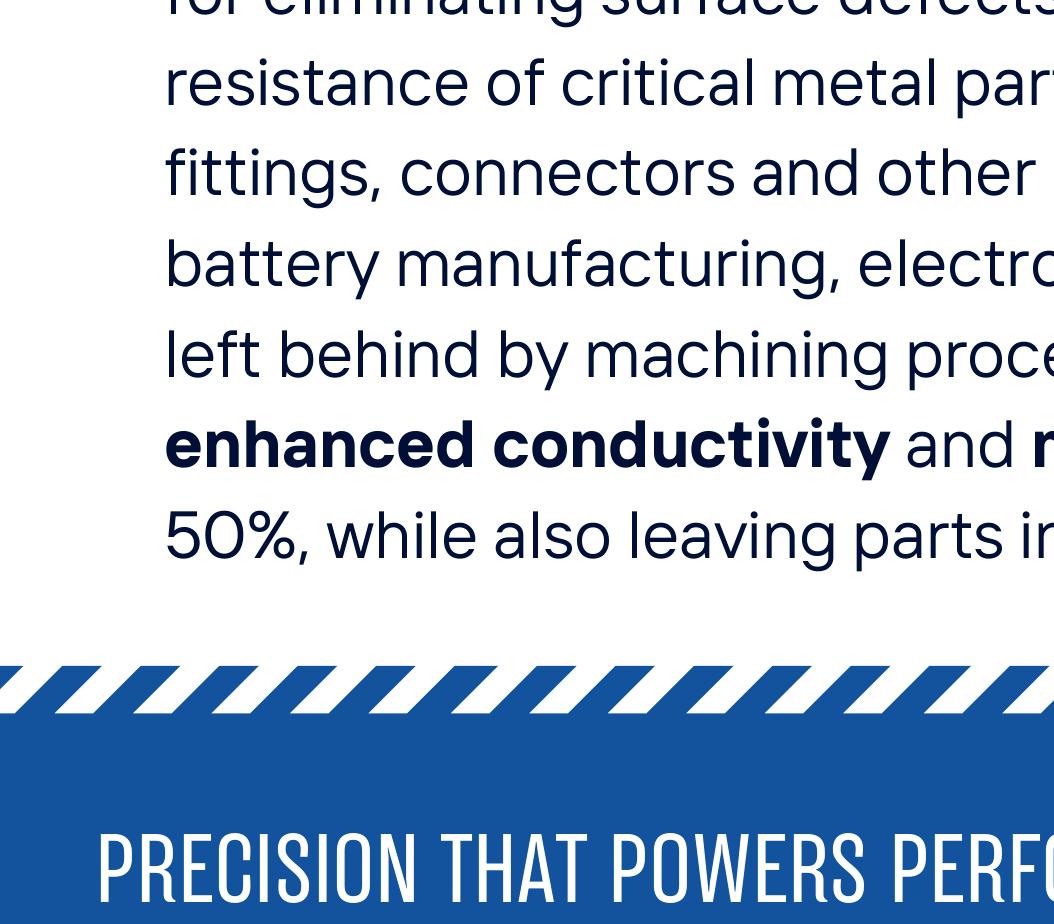

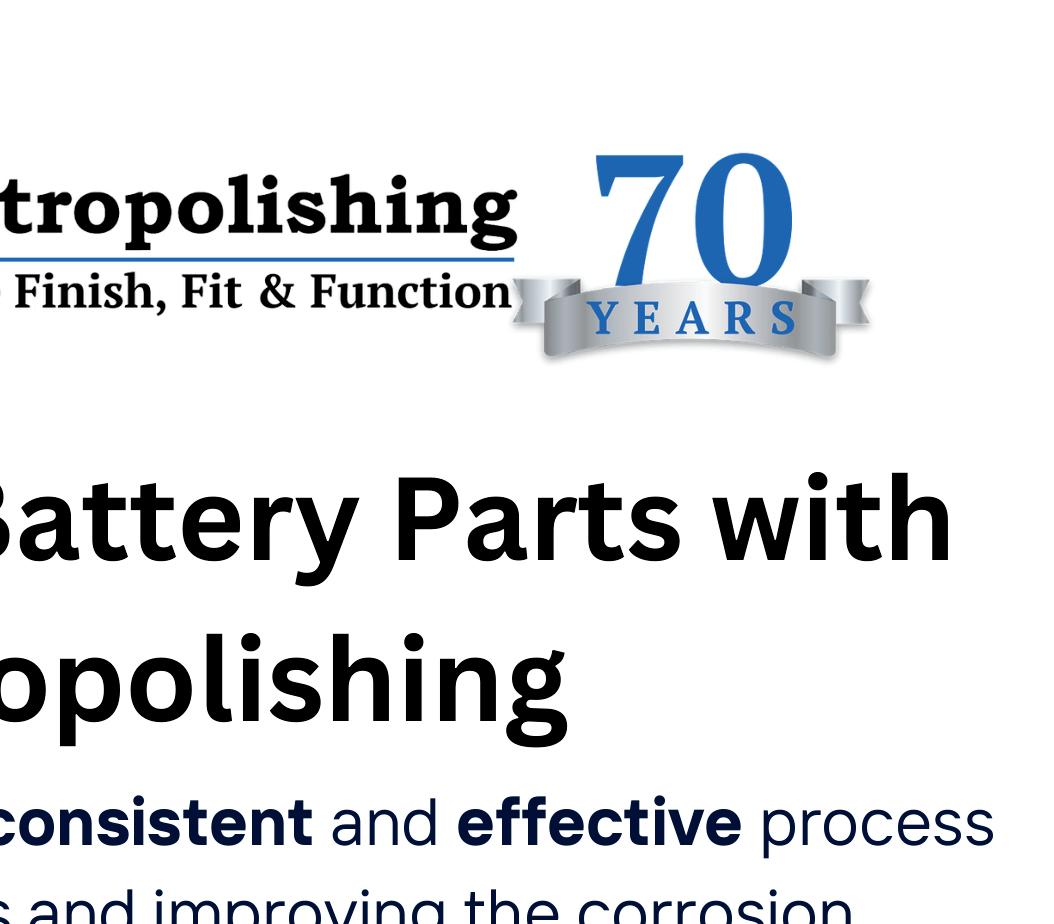
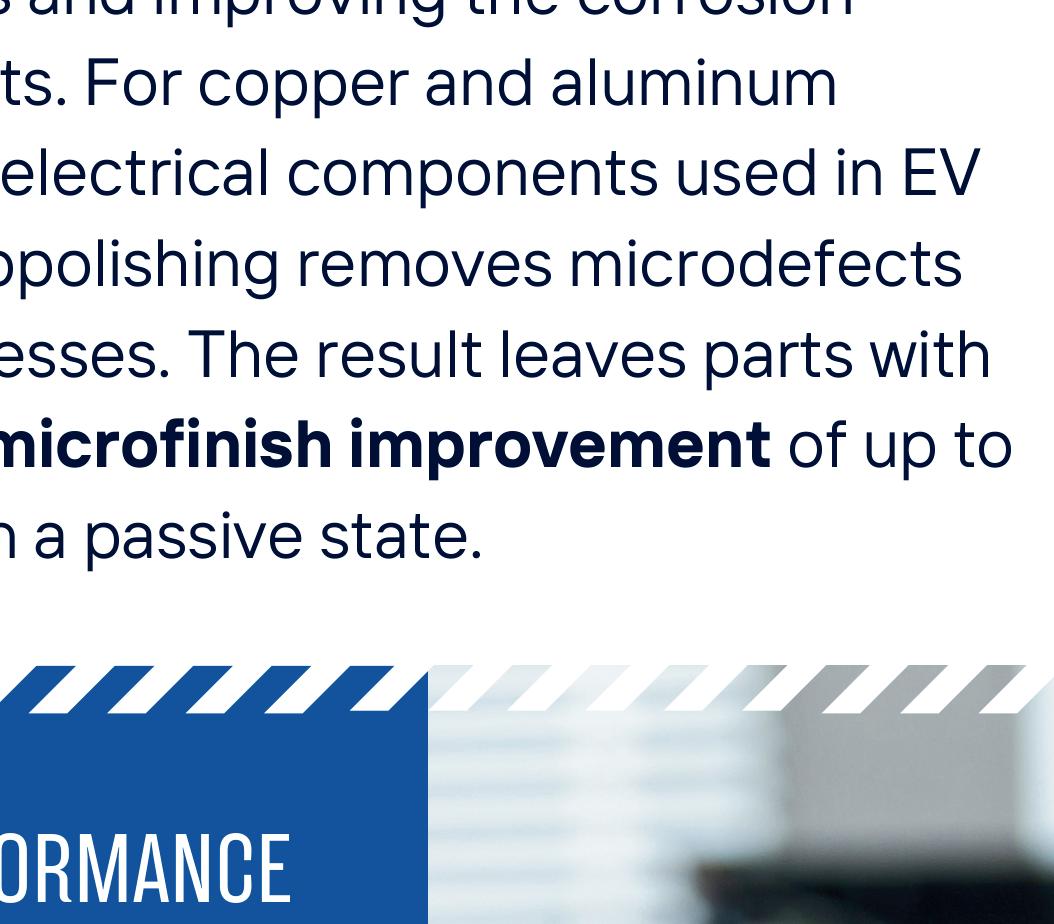
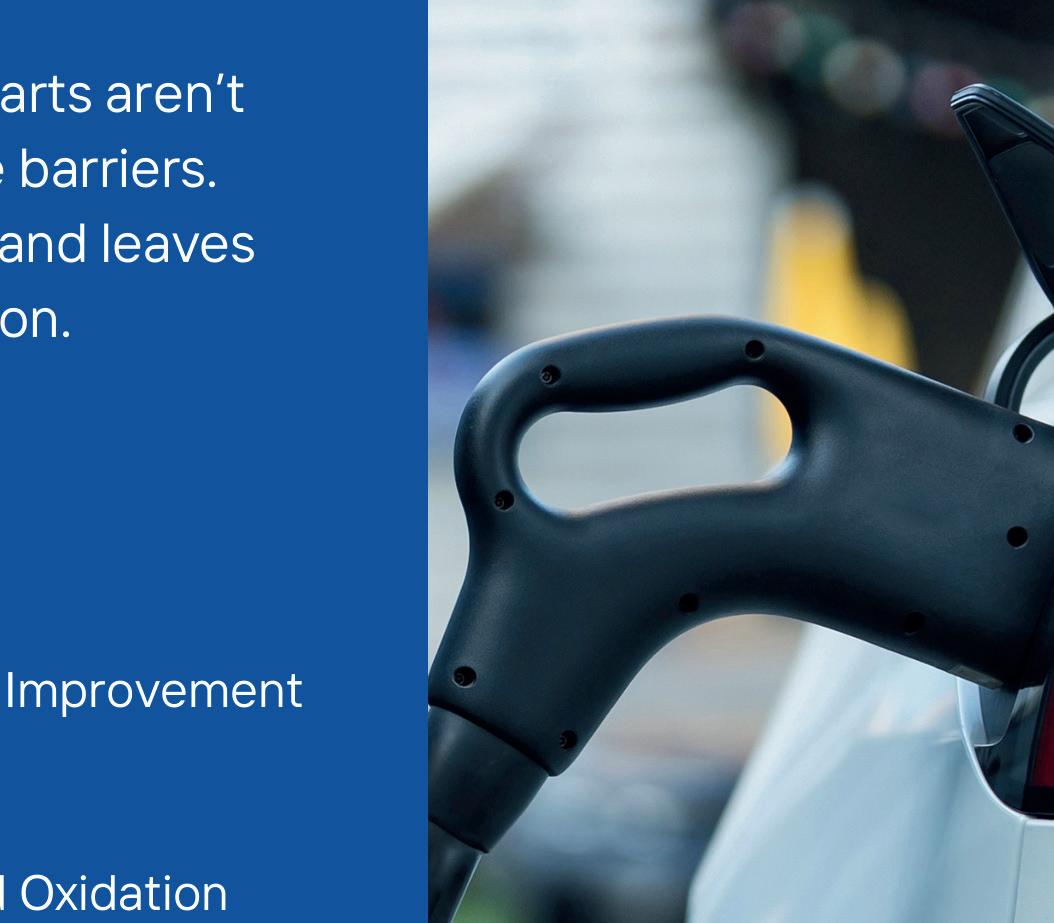

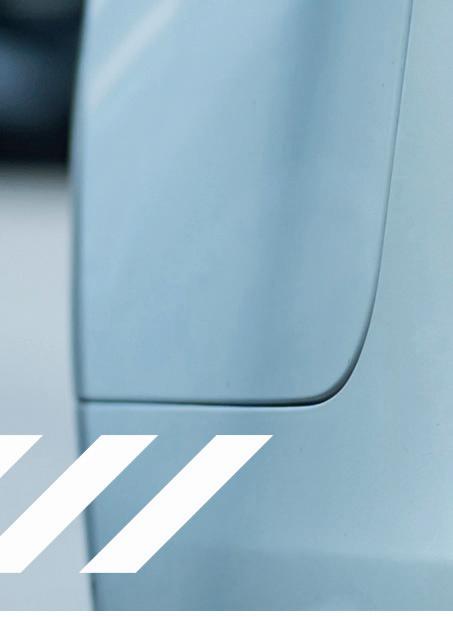

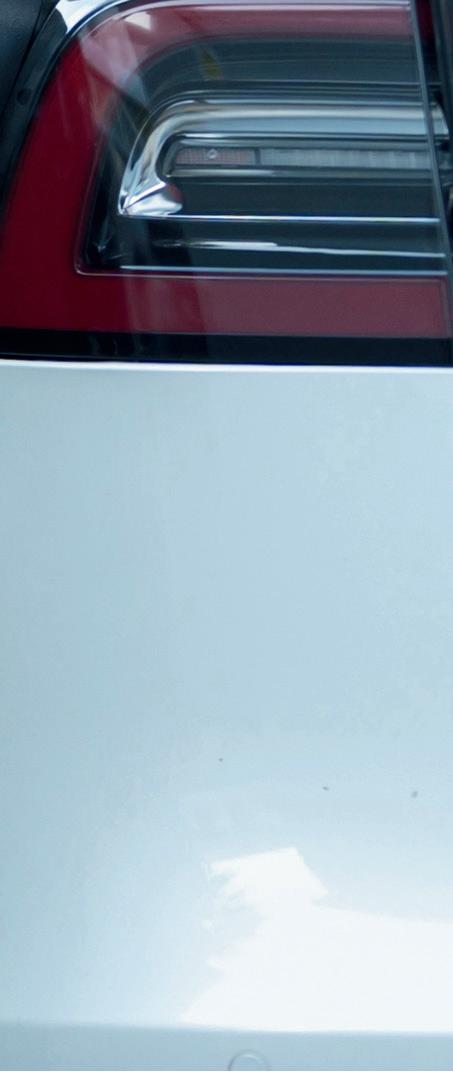
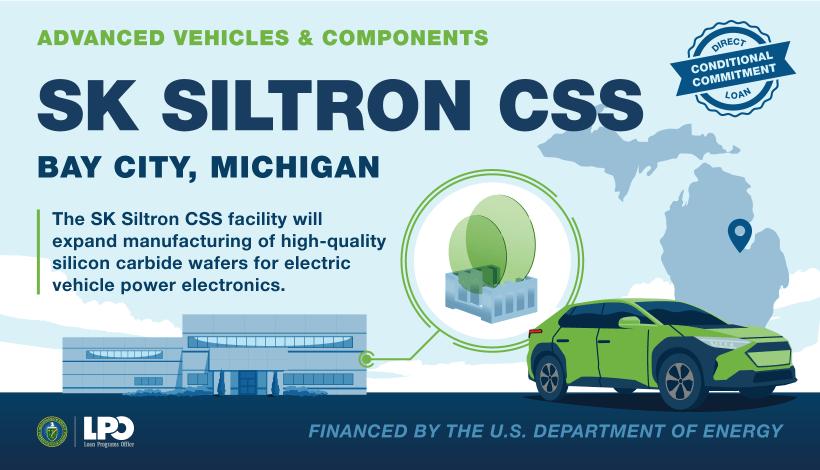
SK Siltron wins $544-million DOE loan to expand production of SiC wafers for EV power electronics
e DOE’s Advanced Technology Vehicles Manufacturing Loan Program, which supports domestic manufacturing of fuel-e cient vehicles, components and materials, has given a conditional commitment to SK Siltron CSS for a $544-million loan to expand manufacturing of silicon carbide (SiC) wafers for EV power electronics at the company’s two Michigan manufacturing plants. SiC semiconductors potentially enable higher e ciency and higher voltages compared with traditional silicon semiconductors, which can translate to faster charging times and longer range for EVs. Demand for SiC wafers is expected to rise with EV sales. e expansion of SK’s Bay City plant is expected to create up to 200 construction jobs and 200 permanent skilled positions. rough the Michigan New Jobs Training Program, the company will train local workers for SiC wafer fabrication in partnership with Delta College, located less than a mile from the project site.
INFICON’s ELT Vmax enables individual leak testing for mass-produced EV
battery cells
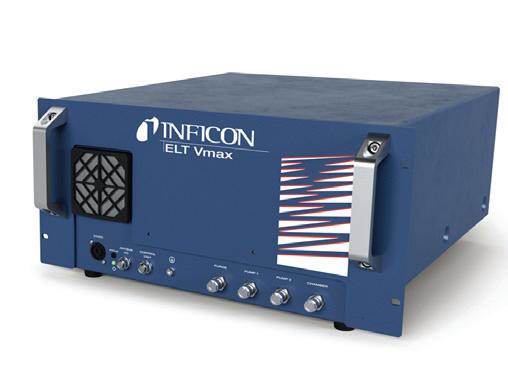
INFICON, a manufacturer of leak testing solutions, introduces the ELT Vmax—a leak detector speci cally designed for integration into leak testing systems for the industrial high-speed mass production of lithium-ion and sodium-ion battery cells.
e ELT Vmax tests the leak tightness of all battery cells lled with liquid electrolyte—lithium-ion or sodium-ion—in all formats, including prismatic, round and button cells with a rigid housing, or pouch cells with a so , bag-like housing. e device uses INFICON’s patented method of direct electrolyte leakage testing—it detects electrolyte leaking from lled cells in a vacuum chamber.
While INFICON’s ELT3000 PLUS can be used as a stand-alone device, INFICON created the new ELT Vmax speci cally for use in mass production, as a testing device for integrators’ individually designed, automatic leak testing stations. Designed to provide the same levels of accuracy and sensitivity as the ELT3000 PLUS, the ELT Vmax can identify the smallest leaks down to a helium equivalent leak rate of 5∙10-7 mbar∙l/s, equivalent to a diameter in the range of 1-5 micrometers for common battery designs.
e vacuum pumps are provided by the integrator to achieve industrial quality assurance. e ELT Vmax is designed for installation in 19-inch racks, making it easy to integrate into a mass battery cell assembly operation. With its multi-chamber mode in test stations, the ELT Vmax is designed to operate in near-constant measuring mode, eliminating the waiting time during evacuation and ventilation processes and optimizing the production line for maximum throughput.





ABS wins $166-million DOE loan to expand Ohio and Michigan EV battery plants
e DOE has o ered American Battery Solutions (ABS) a $169-million loan under the Advanced Technology Vehicles Manufacturing (ATVM) Loan Program.
e company plans to use the funds to expand its battery pack assembly facilities in Springboro, Ohio and Lake Orion, Michigan.
e project will support the company’s goal of delivering standardized and customized battery packs for various battery market segments. Applications in high-voltage market segments include electri ed eet and commercial vehicles and other EVs. Low-voltage market segments include low-speed EVs and industrial equipment, as well as auxiliary batteries for EVs. ABS has customers and o ake agreements in both market segments.

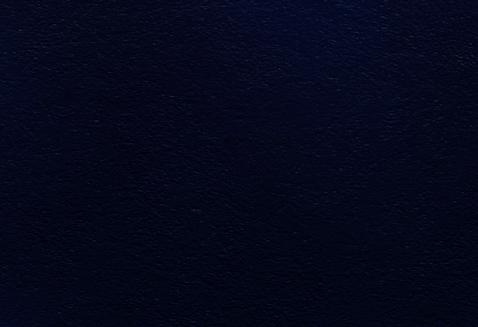
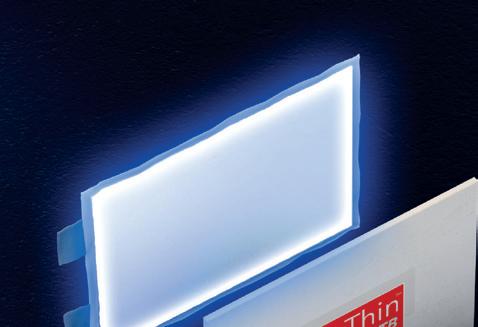
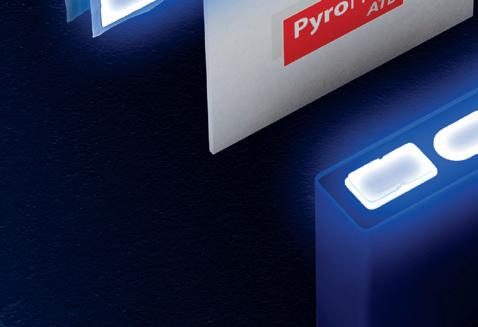

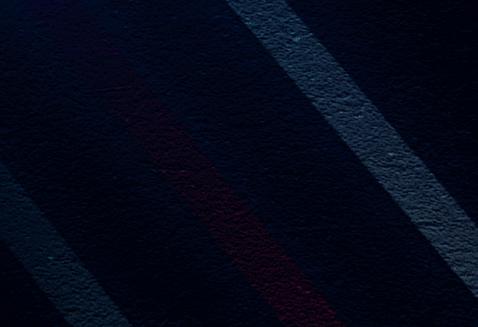

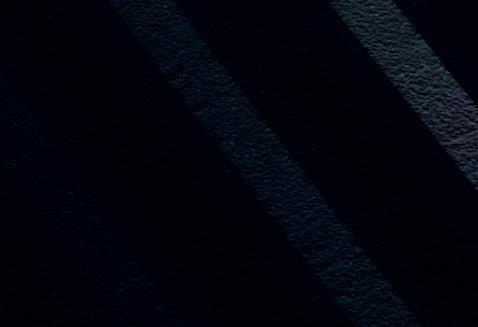



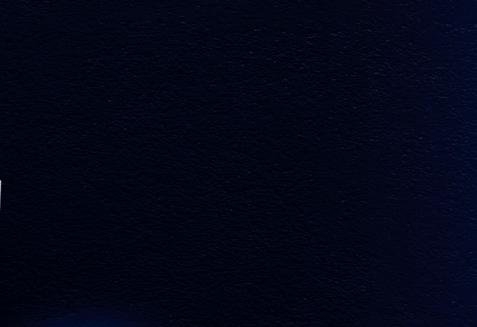
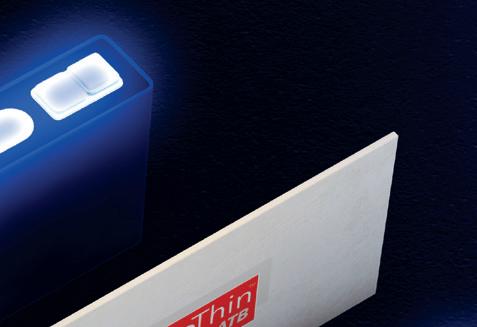
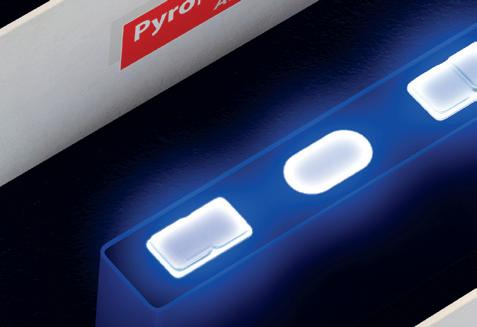
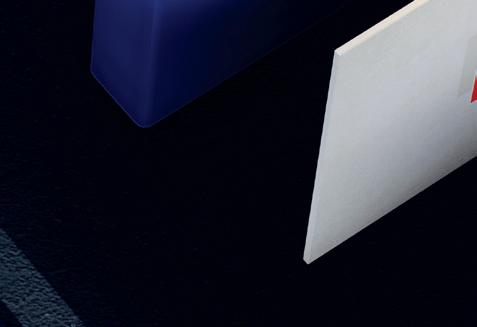
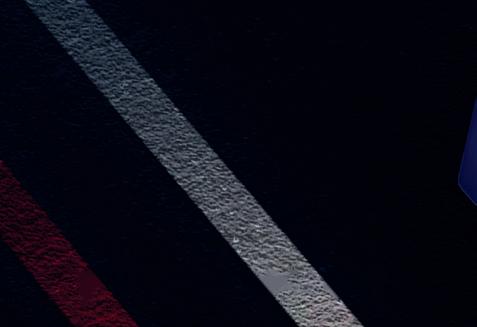
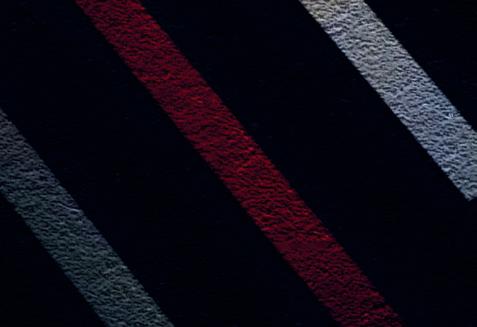
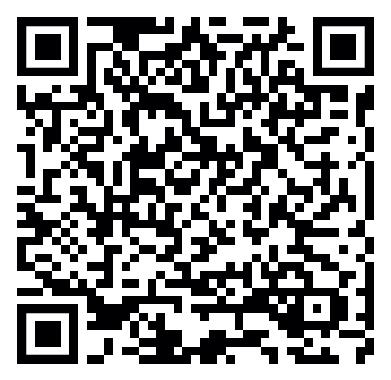
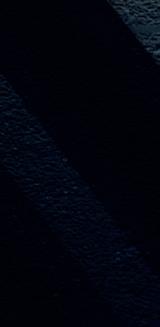

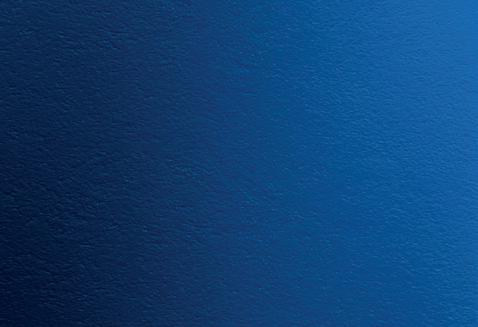
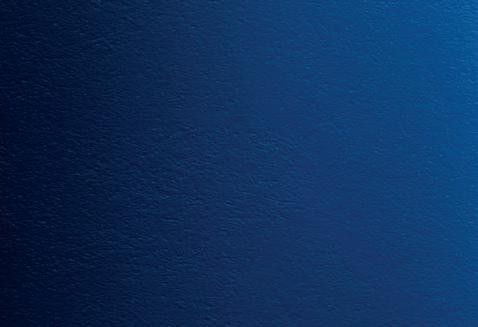
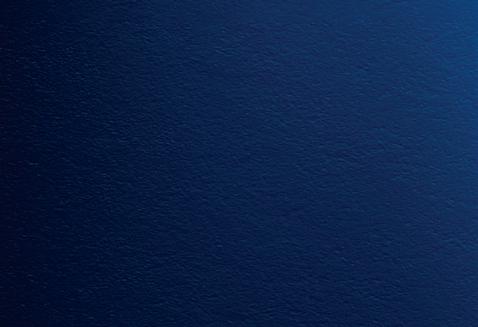
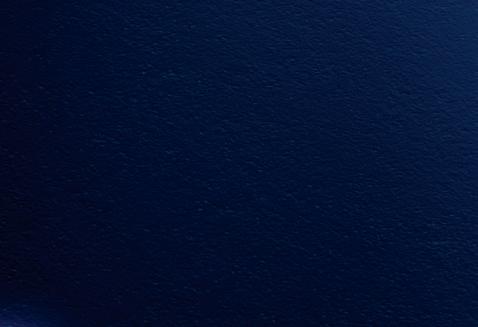



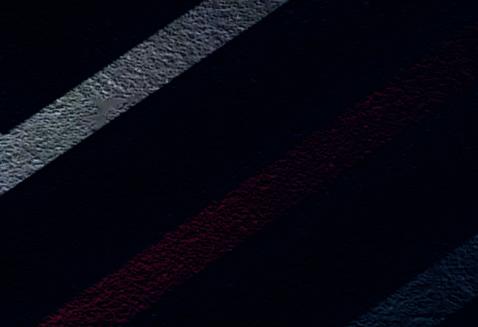
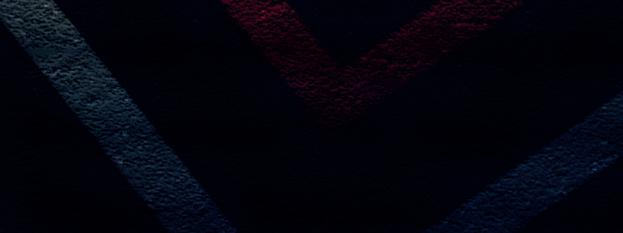



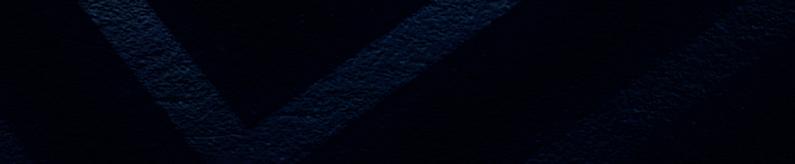
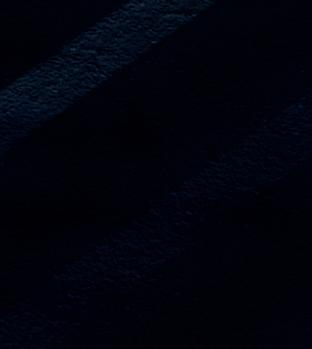


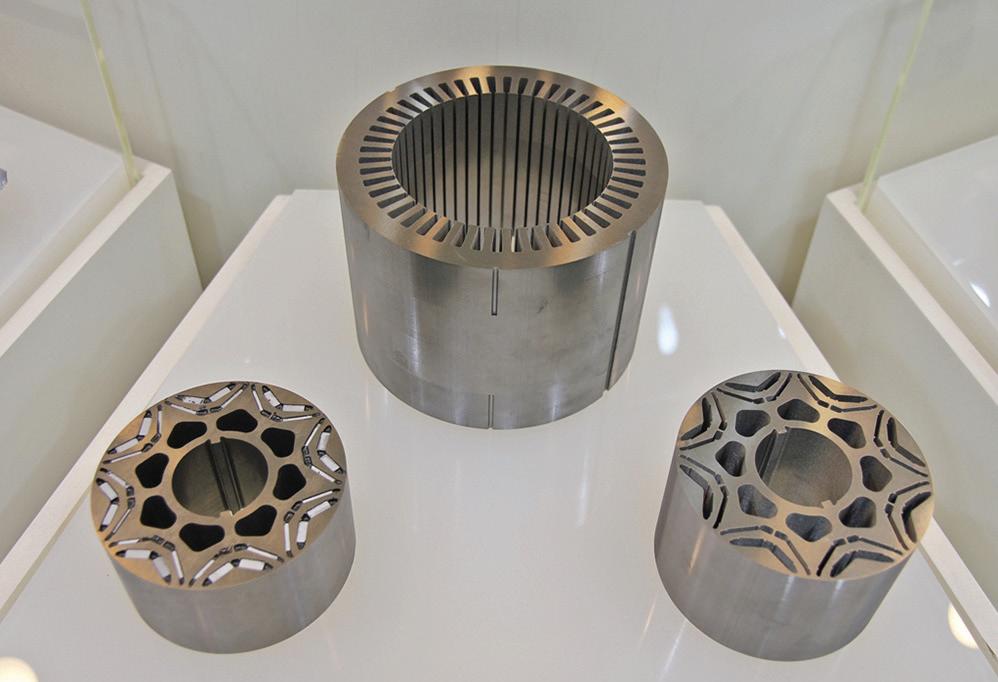
POSCO International’s drive motor core to power millions of Hyundai-Kia EVs
South Korean manufacturer POSCO International has secured an order for several million drive motor cores to be tted on Hyundai-Kia’s Seltos class EVs and produced locally in Europe from 2025 to 2034.
e order supports POSCO’s plans to build a production plant in Brzeg, Poland, which will become the center of its European drive motor core business. Construction of the new 100,000-square-meter facility is expected to start in the rst half of this year and nish in the rst half of 2025.
POSCO aims to produce 1.2 million drive motor cores per year in Europe by 2030. By 2030, the company also hopes to produce and sell over 7 million drive motor cores per year in South Korea (Pohang, Cheonan), Mexico, Poland, China and India.
“ is order is meaningful because Hyundai Motor Group, an eco-friendly automobile company, will continue to collaborate with us in Europe following the US,” said an o cial from POSCO International.
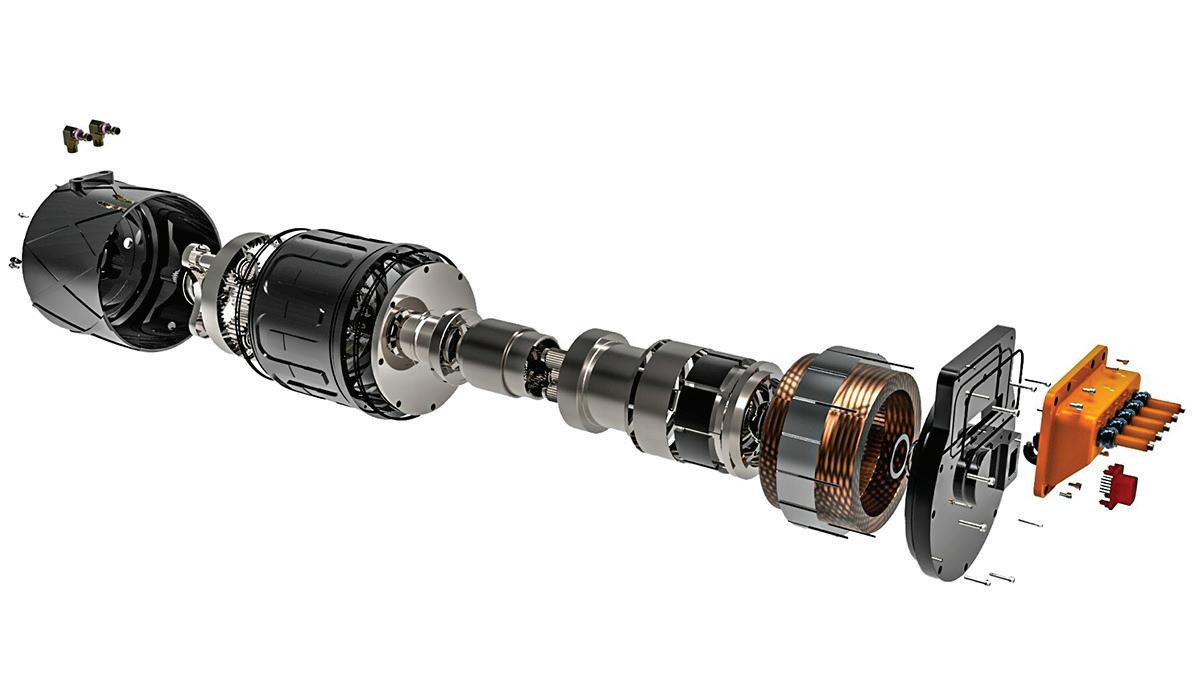
Optiphase and Opal-RT collaborate on real-time simulation for 5-phase EV motors
Optiphase Drive Systems and OPAL-RT, a specialist in simulation and hardware-in-the-loop testing, have formed a strategic alliance to o er real-time simulation capabilities for vehicle designers that integrate Optiphase’s 5-phase electric motor and drive system.
Optiphase says it developed its 5-phase electric power and control technologies to overcome the limitations and workarounds inherent to 3-phase systems.
“When you look at the research and testing data, 5 phases provide the optimal balance of power and reliability with minimized cost and complexity,” said Siavash Sadeghi, CTO for Optiphase. “Even the most innovative 3-phase systems in the market today still use technology from the last century and require redundancy, stacking, or other workarounds to meet the demanding requirements of advanced vehicles.”
Optiphase designs o er outputs from <5 kW to over 1 MW, speci c power in excess of 8 kW/kg, and sha speeds from 1,000 RPM to over 100,000 RPM.
“ is collaboration unlocks greater access for advanced vehicle designers to the groundbreaking advantages of 5-phase electric motor technology,” said Daniel Vicario, CEO of Optiphase.





Sion Power raises $75 million to commercialize its Licerion tech for lithium metal EV batteries
As the EV market expands, there’s a pressing need for more standardization of DC power distribution, especially for buses and heavy-duty vehicles. SAE International’s new standard, SAE J-3105: Electric Vehicle Power Transfer System Using Conductive Automated Connection Devices Recommended Practice, promotes the safe testing and performance of mechanized conductive power transfer systems, primarily for vehicles using a conductive automated-charging device .
SAE J-3105 addresses three interfaces required to ensure power delivery is consistent. It de nes a conductive power transfer method, including the curbside electrical contact interface, the vehicle connection interface, the electrical characteristics of the DC supply, and the communication system. It also covers the functional and dimensional requirements for the vehicle-connection interface and supply-equipment interface.
In addition to the main document, there are three supplements, which address connection-interface requirements for power transfer systems based on cross-rail designs, conventional rail vehicle pantograph designs and enclosed pin-and-socket designs.
“SAE J-3105 will help industry ensure that each connection type is safe and interoperable among manufacturers,” said Task Force Committee Chair Mark Kosowski. “ e industry has been waiting for this Recommended Practice.”
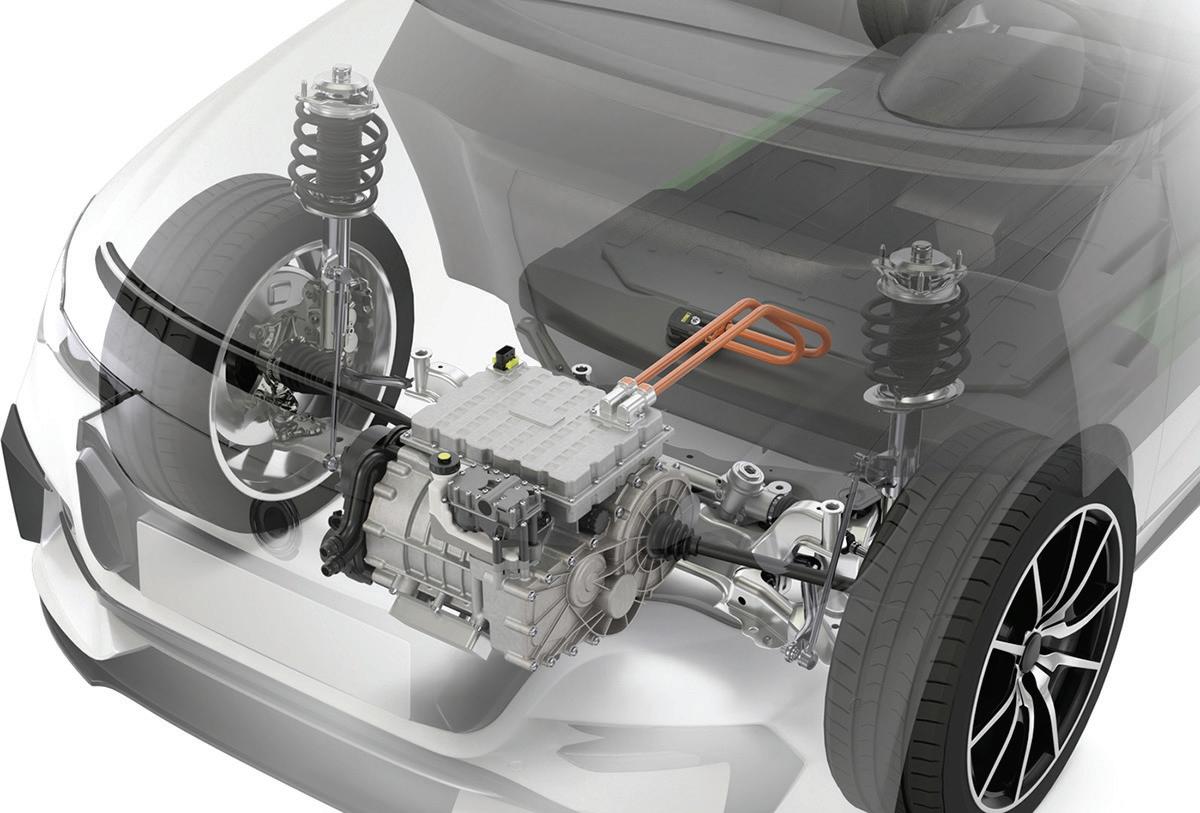
Schaeffler/Vitesco merger will create the largest global EV powertrain
supplier
EV component suppliers Schae er and Vitesco Technologies Group have entered into a merger agreement. e transaction is expected to be completed in the fourth quarter of 2024.
e two companies make components such as e-drives, power modules, BMS, control units, motors, steering systems and much more. Schae er recently built an electric version of the Ford F-250 pickup to showcase the EV technology that the company o ers to vehicle OEMs.
According to HSBC Global Research, the combination of Schae er and Vitesco will create the largest EV powertrain supplier in the world, with 25 billion euros in current sales and a cumulative order intake of 36 billion euros over 2021-23.
“Vitesco enhances Schae er’s EV o er with battery management systems (BMS), in our view the most pro table product thanks to its high technological content and more limited competition,” wrote HSBC’s analysts. “Otherwise, the EV portfolios of the two companies overlap completely. In our view, this allows for unprecedented cost saving potential.”
“Preparations for the integration of Vitesco into Schae er are making good progress,” said Klaus Rosenfeld, CEO of Schae er. “We are con dent that we will complete the transaction as planned in the fourth quarter and successfully realize our plan to establish a leading motion technology company in the best interest of our customers, shareholders and employees.”

Samsung SDI announces plan to mass-produce solid-state batteries
EV battery manufacturer Samsung SDI has announced a suite of battery technologies, including fast charging and ultra-long-life batteries, as well as its roadmap for mass production of all-solid-state batteries (ASBs).
Samsung SDI plans to mass-produce 900 Wh/L solid-state batteries using its solid electrolyte and anodeless technologies, the latter of which enables higher cathode capacity. e design’s energy density is 40% higher than that of P5, Samsung SDI’s prismatic battery in production.
Samsung SDI has also unveiled its ultra-fast charging technology, which delivers high charging speeds by optimizing lithium-ion transfer path and enabling low resistance. e company aims to develop the technology to mass production by 2026.
Samsung SDI also plans to create and mass-produce a battery that has a 20-year lifespan by 2029; cell-to-pack (CTP) technology for prismatic cells, which reduces the number of components by more than 35% and the weight by 20%; and its “no thermal propagation” technology, a safety feature that prevents propagation of thermal runaway in the event of a re or impact.
“Our preparations for mass-producing next-generation products of various form factors such as an all-solid-state battery are well underway,” said Yoon-ho Choi, President of Samsung SDI.
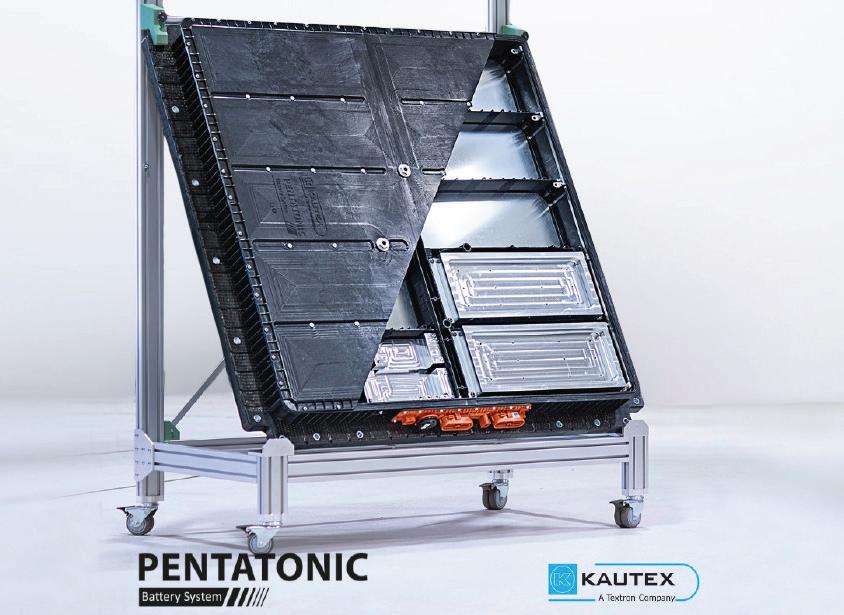
Farasis Energy researches plastic battery housing for increased EV safety
Farasis Energy, a battery manufacturing company, Kautex Textron, a supplier of energy storage systems, and the Fraunhofer Institute for High-Speed Dynamics are working together to make plastic-based EV battery housings safer by means of virtual design.
Farasis, which develops and produces lithium-ion battery technology and pouch cells for electromobility, is developing a simulation model for mapping the thermal runaway of individual cells and module propagation.
e company also supports all battery topics within the three-year SiKuBa project, which has received €2.6 million from the German Federal Ministry for Economic A airs and Climate Action.
e project aims to analyze the formation and propagation of hot gas and particle ows and their interaction with structural elements, transferring the data to simulation models. It will also assess battery safety using various load case scenarios, materials and component designs.
Farasis Energy and its partners will develop a detailed model for simulating thermal runaway, or enhance the existing models within the company. ese simulation models will enable the company to achieve a quicker and safer integration of plastic-based module and pack enclosures.
“Plastic enclosures have many advantages over metal enclosures,” the company notes. “ ey are lighter, more sustainable, and cheaper to produce, and have better electrical insulation. In the event of a damaged cell, the battery housing can be exposed to enormous thermal loads if thermal runaway of individual cells occurs.”




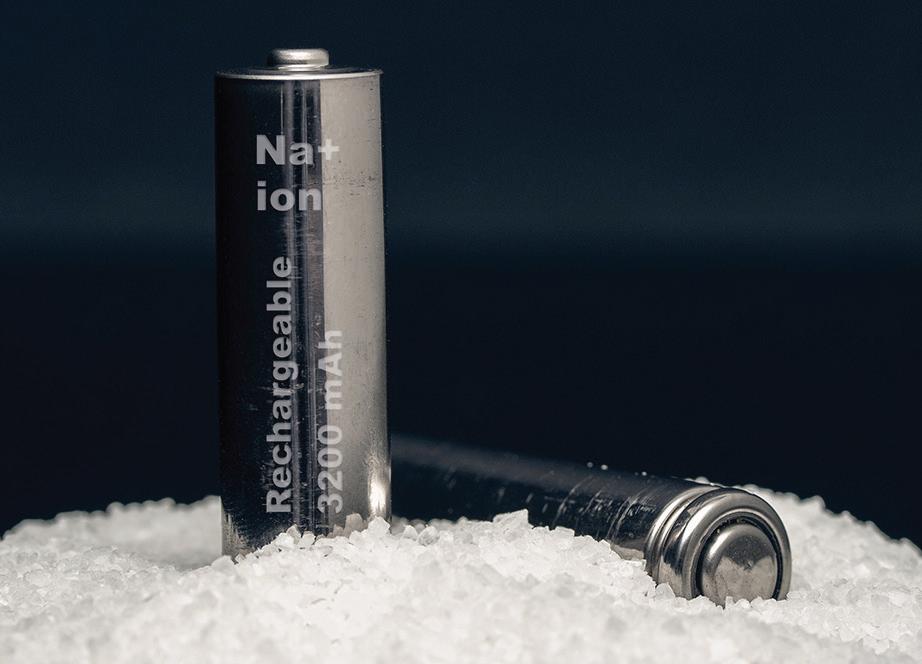
Layered oxide cathode could make sodium-ion batteries an attractive
option for EVs
Researchers at the DOE’s Argonne National Laboratory have invented and patented a new battery cathode material that replaces lithium ions with sodium and could be signi cantly cheaper.
e research team has developed a layered oxide cathode for sodium-ion batteries. A layered sodium nickel-manganese-iron (NMF) oxide cathode e ciently inserts and extracts sodium, which is available abundantly and is more easily mined than lithium. e absence of cobalt in the cathode reduces cost, scarcity and toxicity.
e team says its cathode has a higher energy density than other sodium-ion technologies, and that its cathode material allows battery cells to be charged and discharged as many times as lithium-ion batteries. e sodium-ion batteries can also retain their charging capability at below-freezing temperatures.
e research has transitioned from the laboratory phase, and the cathode will now be tested within battery cells similar to those in a real EV battery. e team is also working to develop di erent electrolyte and anode materials to further increase energy density.
“Our estimates suggest that a sodium-ion battery would cost one third less than a lithium-ion one,” said Christopher Johnson, Senior Chemist and Argonne Distinguished Fellow. “ ere is one catch to this wonder battery. Sodium metal is about three times heavier than lithium, and that adds considerably to the battery weight.”

Microchip’s new integrated motor drivers include controllers, gate drivers and communications
Microchip Technology has launched a new family of dsPIC digital signal controller-based integrated motor drivers. ese devices incorporate a dsPIC33 digital signal controller (DSC), a three-phase MOSFET gate driver, and optional LIN or CAN FD transceiver into one package.
is integration is designed to reduce the component count of a motor control system design, and allow smaller printed circuit board (PCB) dimensions. e devices are supported by development boards, reference designs and application notes, and will be included in Microchip’s eld-oriented control (FOC) so ware development suite, the motorBench Development Suite.
e integrated motor driver devices can be powered by a single power supply up to 29 V (operation) and 40 V (transient). An internal 3.3 V low dropout (LDO) voltage regulator powers the dsPIC DSC, which eliminates the need for an external LDO to power the device. Operating between 70 and 100 MHz, the dsPIC DSC-based integrated motor drivers provide high CPU performance, and can support e cient deployment of FOC and other motor control algorithms.
“Automotive, consumer and industrial designs are evolving, and require higher performance and reduced footprints,” said Joe omsen, VP of Microchip’s digital signal controllers business unit. “ ese expectations o en come at a higher expense and increase in dimensional size. By integrating multiple device functions into one chip, the dsPIC DSC-based integrated motor drivers can reduce system-level costs and board space.”

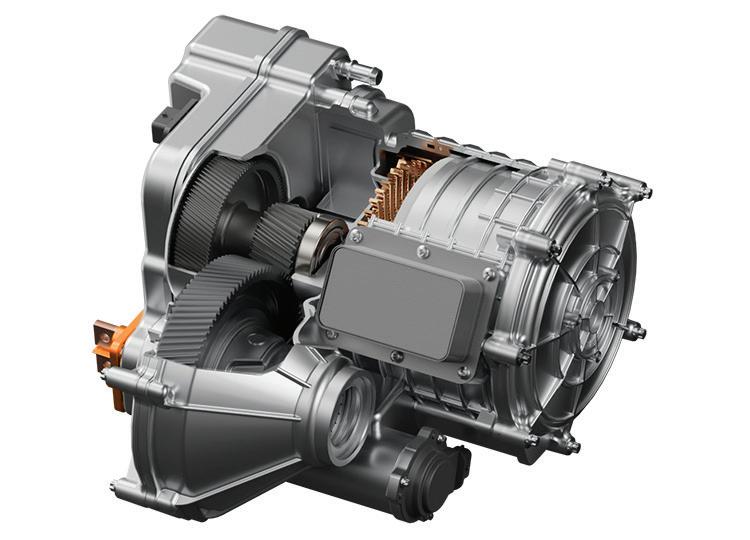
Magna unveils its nextgeneration 800 V eDrive solution
Magna has unveiled its next generation 800 V eDrive solution, which it says o ers improved e ciency, powerto-weight ratio and torque density.
Magna claims that its 75 kg next-generation eDrive is lighter, 20% shorter in height and faster than its prior generation eDrive, providing a longer driving range. Rotating the eDrive 90° around the drive axis improves system integration in the front and rear vehicle area. e system delivers up to 93% e ciency in real-world driving, based on Worldwide harmonized Light duty Test Cycle (WLTC) and highway testing.
Magna’s next-generation eDrive can be applied as a primary or complementary secondary drive solution with an optional eDecoupling unit for vehicles in the C, D, and E segments. It delivers a peak power of 250 kW and a peak axle torque of 5,000 Nm.
“We have successfully reduced our reliance on aluminum and heavy rare earth materials, resulting in a signi cant reduction of CO2 emissions during production by approximately 20% compared to previous generation eDrives,” said Diba Ilunga, President of Powertrain at Magna.

Green Watt Power’s new 300 W DC-DC converters for EVs
Green Watt Power, a division of Powerland Technology, has launched a new addition to its Marble Series line of DC-DC converters. e new EVD300 is a fully encapsulated, IP67-class ruggedized DC-DC converter designed for EV applications. It has two DC input ranges (30-65 V and 50-130 V), and two output voltages (13.2 V and 24 V) for powering vehicle accessories.
Output power is 300 W, and up to 10 units can be connected in parallel for total power of up to 3,000 W. E ciency is up to 93%. e operating temperature range is -40° to 85° C. e converters are designed to meet IEC, UL and CSA safety standards.
e Marble Series has a constant current function, so it can connect directly to a battery load—a feature that most DC-DC converters in the EV market lack, according to the company. Additional features include Enable/ Remote on/o , a quiescent current draw of less than 30 uA, and IP67 ingress protection.
e EVD300 Marble Series is fully input-to-output isolated. Protection features include Input Under Voltage Lockout, Reverse Polarity, Over Voltage, Short Circuit and Over Temperature. e converter can be connected either via ying leads or via a standard Molex connector. Parts are available direct for high-volume OEMs, or through DigiKey. Higher-power Marble Series variants, additional output voltages, and other isolated and non-isolated single and dual output DC-DC converters are also available.
Join us for the second annual
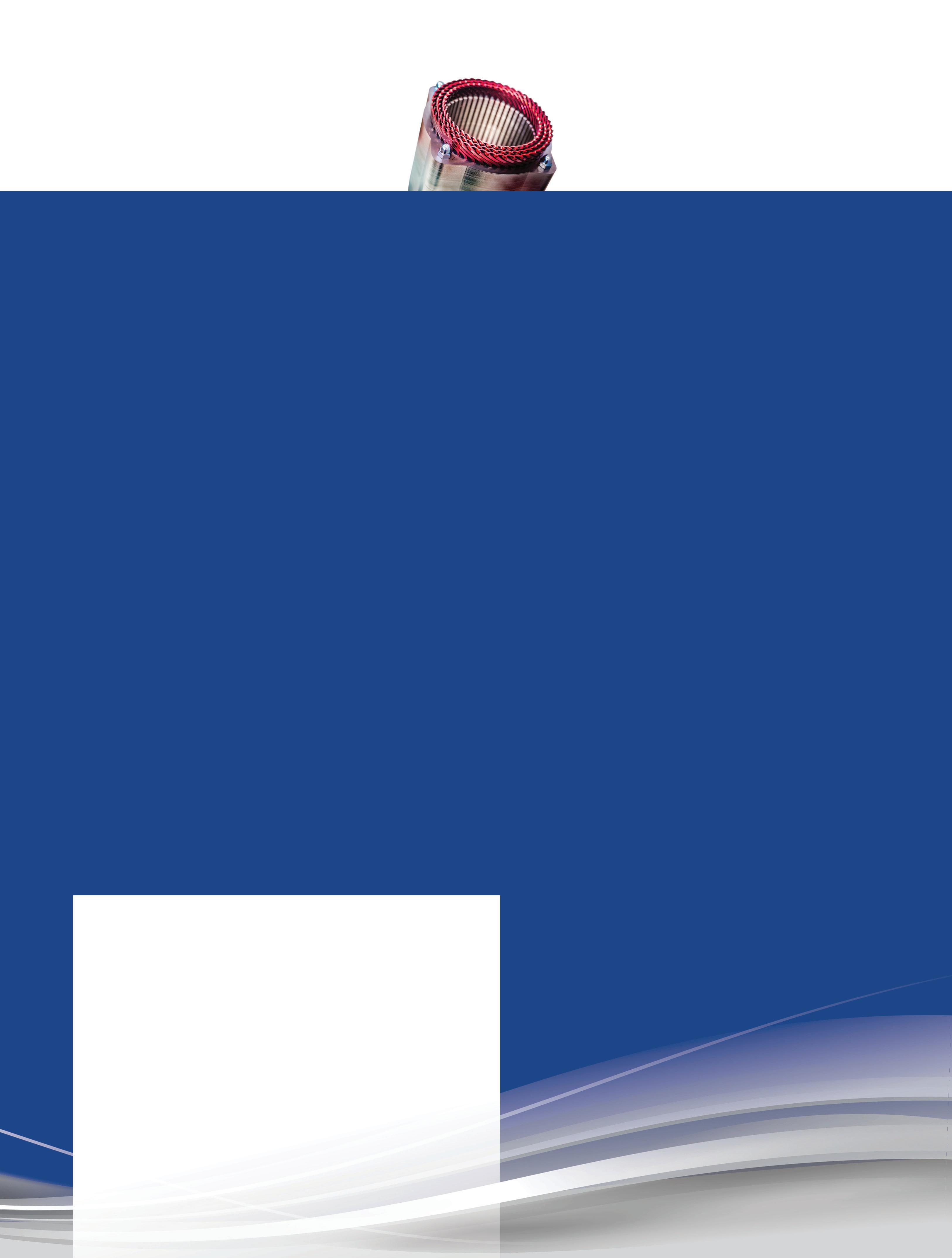
EDUCATIONAL OPPORTUNITIES
Turnkey production solutions for hairpins, axial flux coils and busbars
Bending machinery for hairpin and busbar production
Keynote speakers
Technical presentations and exhibits from our event part n ers
NETWORKING OPPORTUNITIES
Meet key suppliers
• Magnet wire and wire processing
• Equipment for electric motor production
• Electronic a viation / e VTOL
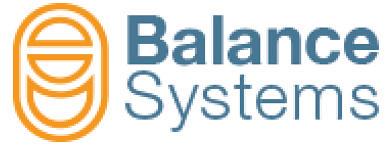
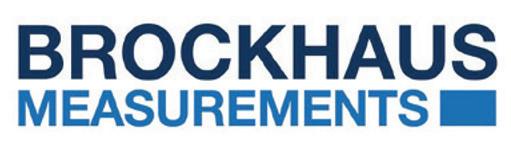
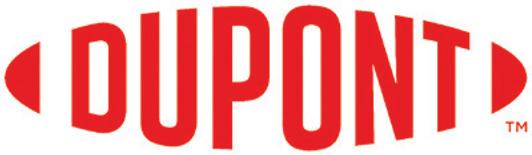


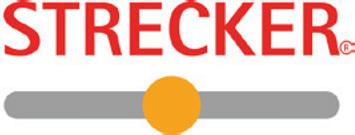
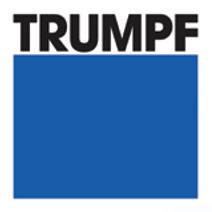


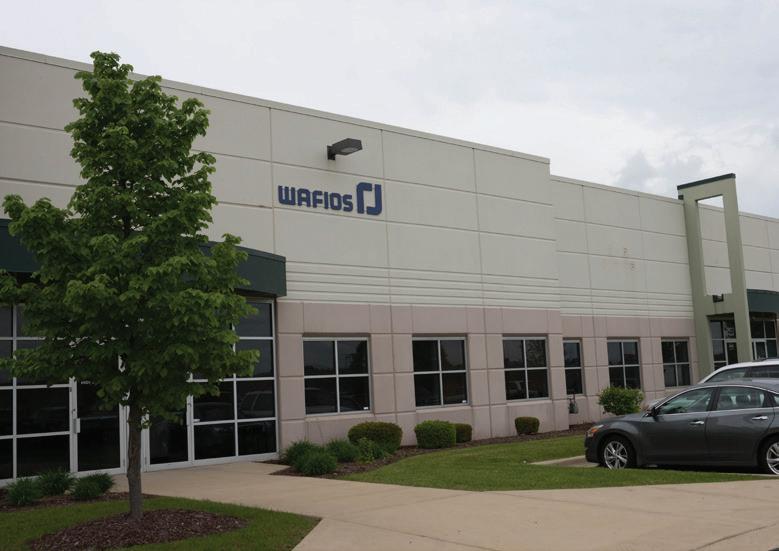
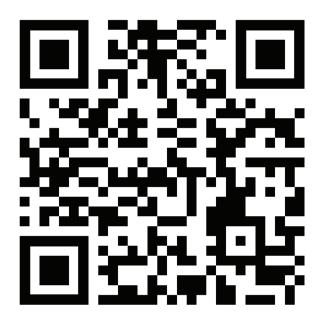
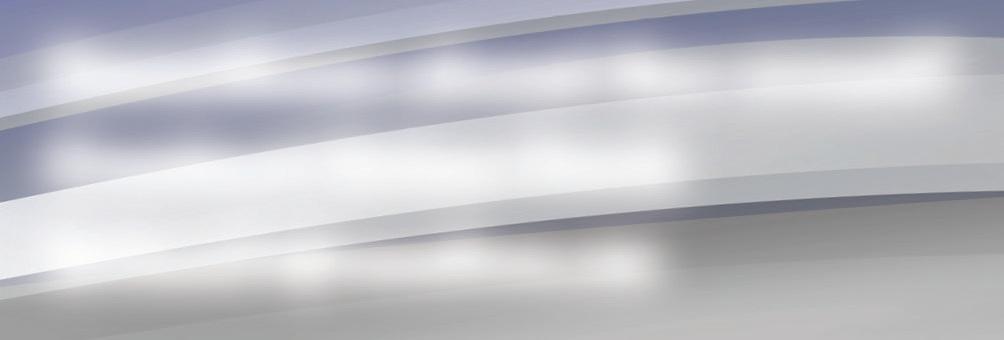
THE TECH
QuantumScape begins shipping Alpha-2 prototype battery cells
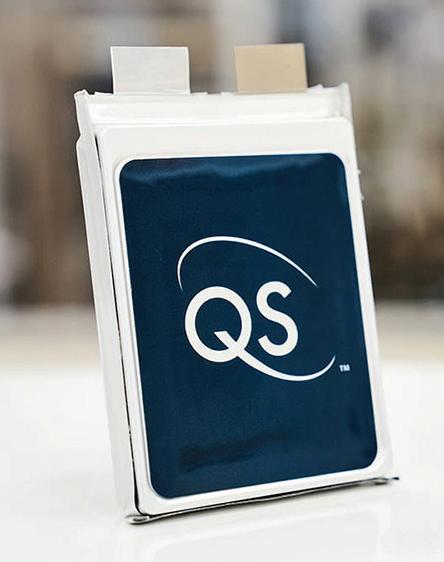
QuantumScape is developing solid-state lithium-metal battery technology that promises signi cant performance improvements compared to current lithium-ion cells. Now the company has started customer shipments of Alpha-2 prototype battery cells, a significant milestone on the road to delivery of its rst planned commercial product, called QSE-5.
QuantumScape’s Alpha-2 prototypes integrate many signi cant component improvements made over the last year. e 6-layer Alpha-2 prototype is more energy-dense than the earlier 24-layer A0 prototype. is is primarily due to higher-loading cathodes (packed with more active material) and more e cient packaging within the cell. Packaging improvements include tighter internal margins, thinner current collectors and a slimmer design.
As an intermediate step between the A0 and the B0 prototypes planned for later this year, Alpha-2 cells feature the main functionality of the QSE-5, and represent an opportunity for customers to test key performance parameters and prototype-level reliability.
“Customer feedback is the most critical input in the product development cycle, as it provides insight into areas that need improvement, and strengthens collaboration,” said QuantumScape CEO Dr. Siva Sivaram. “ e faster we can get new product iterations into customers’ hands, the faster we get to production. We are encouraged by the initial Alpha-2 performance results and excited about the rst QSE-5 cells we expect to manufacture later this year.”
“ e improvements in energy and power densities demonstrated by the Alpha-2 prototypes indicate that QSE-5 can push the boundaries of solid-state battery performance,” said co-founder and CTO Tim Holme. “We continue to advance our anode-free, solid-state battery in performance and maturity with methodical execution on our milestones.”

ENNOVI introduces new production process for low-voltage EV battery cell contacting systems
ENNOVI, a provider of mobility electri cation solutions, has introduced a new process for producing exible circuits for low-voltage signals in EV battery cell contacting systems. “While exible printed circuits (FPC) are o en employed in these systems, they are the most expensive component in the current collector assembly,” says the company. “ENNOVI’s exible die-cut circuit (FDC) technology o ers a more cost-e ective and sustainable solution, with fewer manufacturing procedures and faster continuous reel-to-reel production.”
ENNOVI explains that FPCs are typically manufactured using a multi-stage, batch photolithography process to etch copper traces for the exible circuit, using corrosive chemicals to dissolve the unwanted copper. Extracting the waste copper from the chemicals is a complex process, making it challenging to e ectively recycle. e die-cutting process allows for instant recycling of the waste copper.
Compared with FPCs, which have a size limitation of 600×600 mm, FDCs have no length restrictions, as they are manufactured reel-to-reel.
“Adapting the FDC capability for exible circuits enables ENNOVI to o er battery manufacturers a CCA design solution that balances their imperatives in terms of cost, time and performance, allowing them to design to cost,” said Gustavo Cibrian, Product Manager, Energy Systems at ENNOVI.




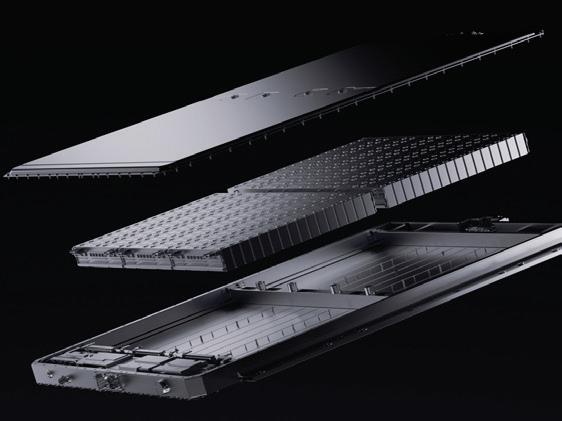
CATL warrants its new EV battery to last for almost a million miles or 15 years
e million-mile EV battery is in sight. Chinese battery supplier CATL and bus maker Yutong have partnered to launch an EV battery that’s warranted to last 1.5 million km (932,000 miles) or 15 years.
e new battery pack is designed to power commercial EVs such as buses and trucks. Yutong says the new pack, which it plans to use in upcoming EVs, exhibits zero degradation through the rst 1,000 cycles.
Yutong’s buses are sold in over 40 countries, including Italy, France, the UK, Spain and Qatar. CATL’s batteries are used by Tesla, Ford, BMW, Toyota, Mercedes, Kia, Toyota and other automakers. According to SNE Research, the company almost doubled its sales in the US and Europe last year.
ere’s more: in January, CATL said it would reduce the cost of LFP battery cells by 50% by the middle of this year.
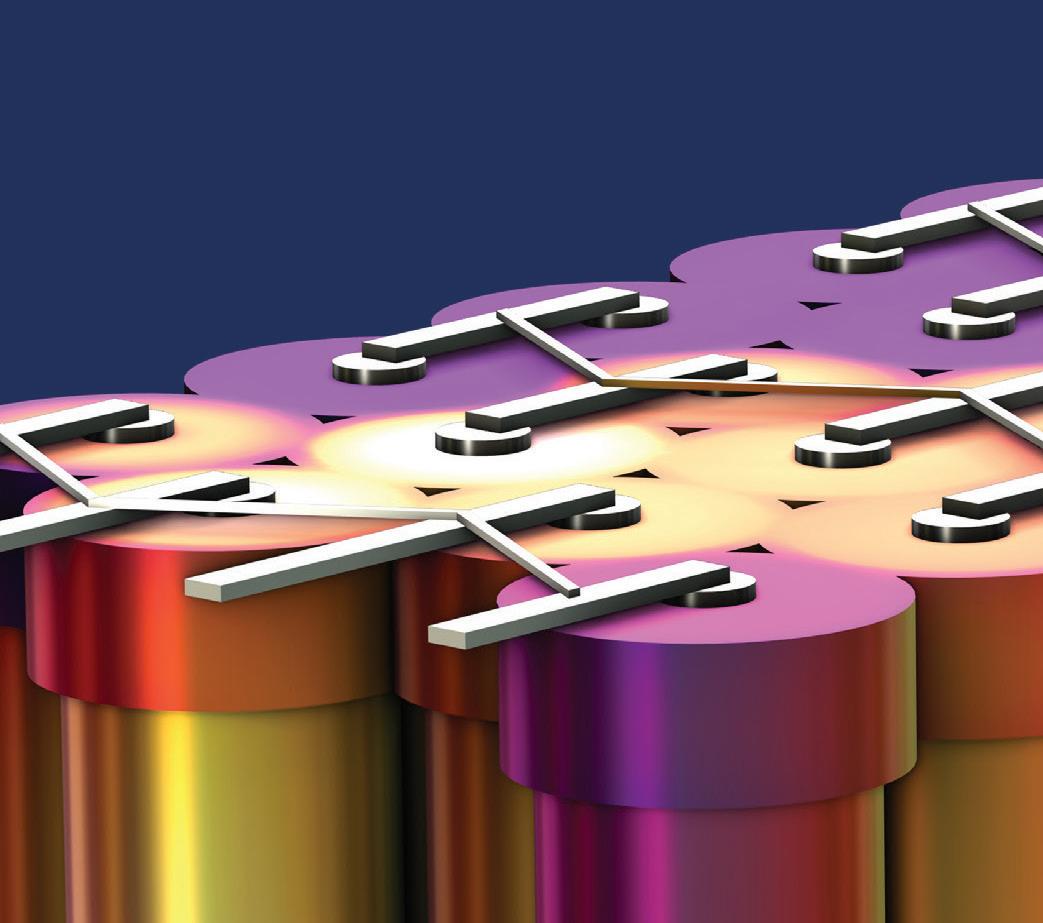
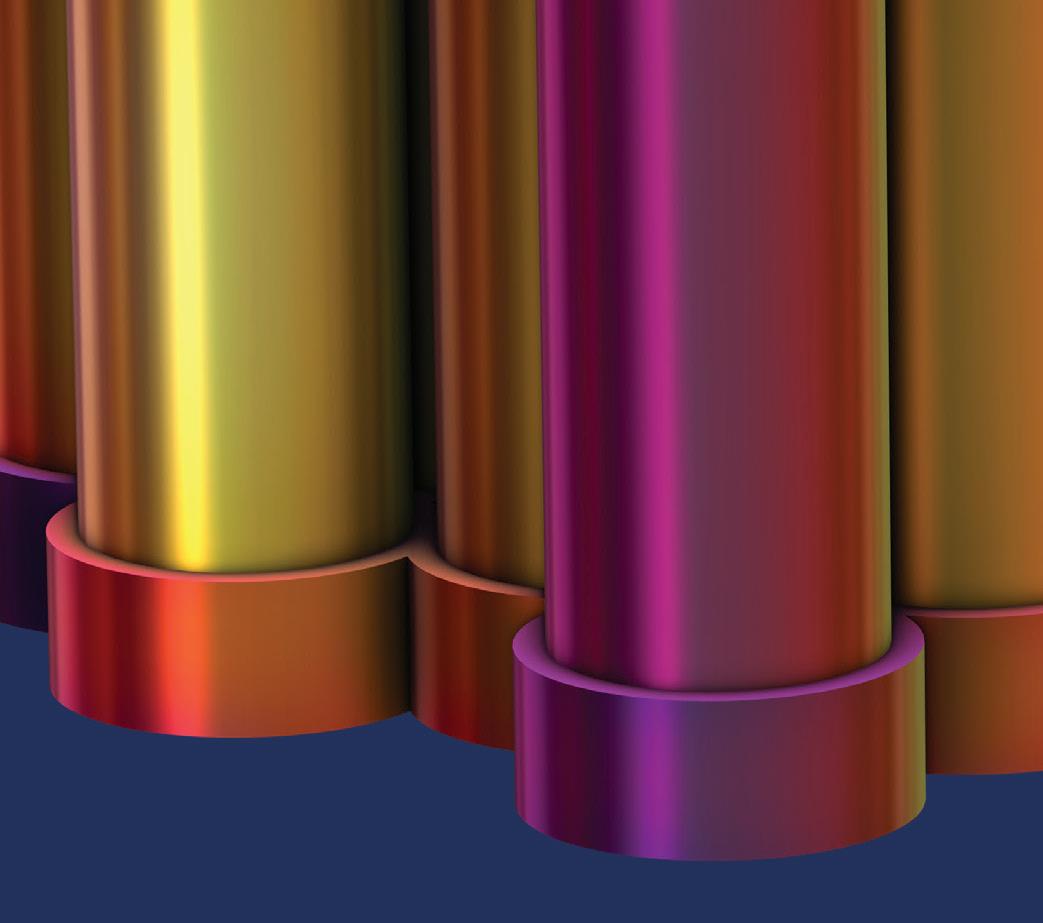
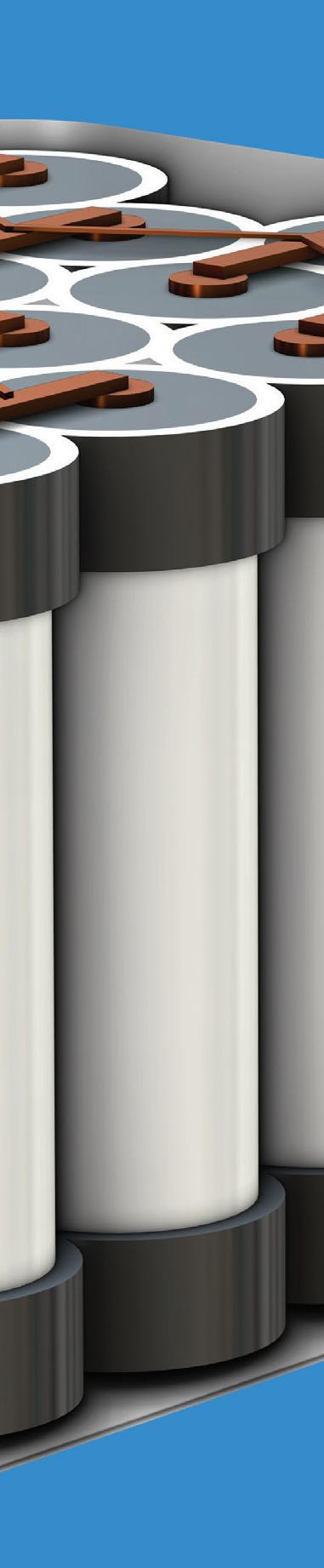
Charge Ahead in Battery Design
with COMSOL Multiphysics®
Multiphysics simulation helps in the development of innovative battery technology by providing insight into mechanisms that impact battery operation, safety, and durability. The ability to run virtual experiments based on multiphysics models, from the detailed cell structure to battery pack scale, helps you make accurate predictions of real-world battery performance.
» comsol.com/feature/battery-design-innovation
THE TECH
Projected EV battery recycling capacity to outstrip supply
According to new research from technology intelligence rm ABI Research, companies are planning to build enough EV battery recycling capacity by 2030 to recycle 1.3 million EV battery packs per year, but only some 341,000 per year are expected to be available at that time.
“ ere are concerns about a lack of capacity for EV battery recycling, but the opposite is true,” says Dylan Khoo, Electric Vehicles Industry Analyst at ABI Research. “Current plans for recycling plants see capacity greatly outstripping the supplies of waste batteries. is will lead to uneconomic utilization rates or, more likely, a delay or scaling down in recycling projects.”
ABI Research details its ndings in a new report, “Securing the EV Supply Chain: Battery Recycling in the United States.”
ABI believes that in 2030, around one third of waste EV batteries will be end-of-life batteries from vehicles. e rest will come from factory scrap—batteries that fail quality control on production lines and go directly to recycling.
“Given the expected shortage of waste EV batteries, battery recyclers must be highly competitive to win,” says ABI. Several companies, including Ascend Elements and Aqua Metals, are developing innovative recycling processes that they say are more cost-e ective and greener. If a shortage of recyclable batteries develops, such companies could have the advantage. “Recyclers that are building up a supply chain of non-recycled materials to ensure a consistent output of processed materials, such as Redwood Materials, will also be better poised to make it through the supply shortage,” says ABI.
Of course, battery recycling is still an emerging technology, and predictions about what the market will look like in six years must be taken with a dose of lithium salt. Some of the plants on the drawing board may not get built, and EV sales could grow faster than predicted (they always have). On the other hand, improvements in battery tech could lead to longer-lived batteries, and thus less feedstock for recyclers.
In any case, recycling rms will surely make their own predictions about the market, and plan their build-outs accordingly.
Thermo Fisher’s new inline metrology enables comprehensive inspection of electrodes during battery manufacturing
Uniform, defect-free electrode coatings are essential for battery performance. at’s why battery manufacturers inspect electrodes during production to ensure the uniform quality of the coatings. However, as ermo Fisher Scienti c explains, traditional in-line coating weight measurement gauges use a single spot sensor traversing the electrode sheet to assess coating quality, but several meters of electrode are produced in the time it takes to complete a single pro le scan, so much of the electrode goes unmeasured.
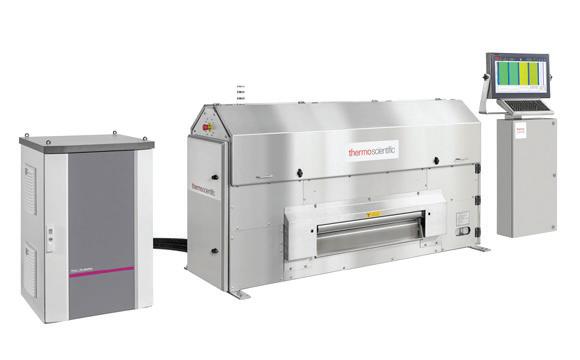
ermo Fisher says its new ermo Scienti c LInspector Edge In-line Mass Pro lometer measures the entire electrode in real time, at full production speed, providing battery manufacturers with the data needed to make better, safer batteries. e LInspector Edge analyzer uses a new analytical technique, in-line mass pro lometry, to measure complete edge-to-edge coating pro les in milliseconds with high resolution and precision.
“ anks to a greater insight into mass loading of active material on the coating edges and a complete mapping of mass loading on the entire electrode, battery manufacturers can now bene t from previously unobtainable richness of data for production control and full traceability for each electrode patch, stripe, or roll, allowing them to meet increasingly stringent quality requirements for energy storage devices,” says the company.
“ e LInspector Edge In-line Mass Pro lometer sets a new benchmark for electrode coating analysis and provides a foundation for higher-performance batteries, reduced risk to quality, better process control, and more pro table operation,” said Miguel Faustino, President of Chemical Analysis at ermo Fisher Scienti c.





Avery Dennison’s new electrode
fixing tapes for EV battery cells
Adhesives giant Avery Dennison has introduced new electrode xing tapes for use in the assembly of EV batteries.
Electrode xing tapes represent a highly specialized category of adhesive tapes. ey are used to bind multilayer electrode constructions consisting of current collector foils, anode and cathode material and separator lms in EV battery cells.
Avery’s new electrode xing tapes are available with polyethylene terephthalate (PET) and polypropylene (PP) plastic facestocks. e PP facestock is chemically inert to prevent self-discharge due to DMT redox shuttle.
e new electrode xing tapes feature electrolyte-compatible acrylic adhesives, and sport a highly visible green color. Various widths are available on plastic cores. ey are manufactured in the United States, and are fully compliant with the In ation Reduction Act.

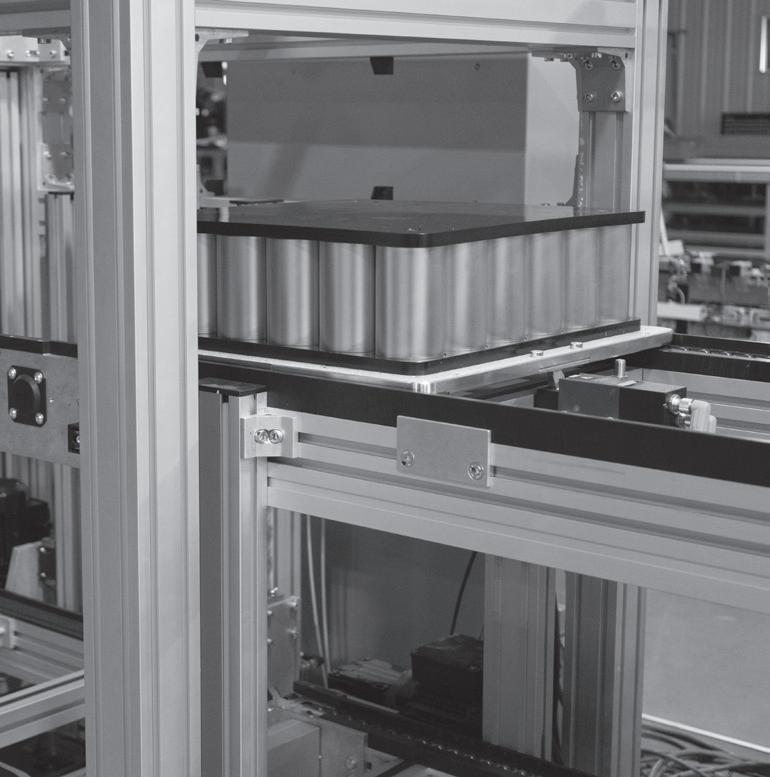
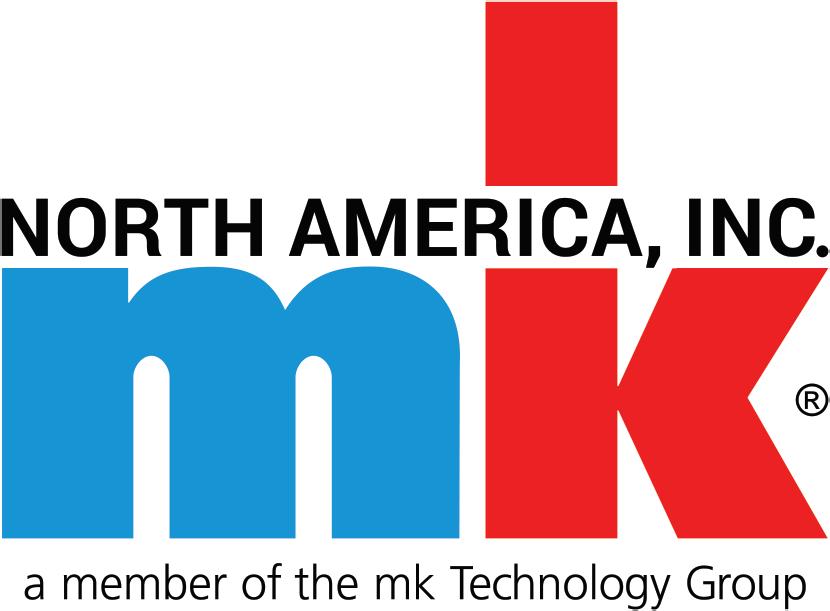




PRACTICAL ASPECTS OF OFF-GRID EV CHARGING
By Jeffrey Jenkins
The holy grail for many EV owners is to obtain all of the energy needed for recharging from renewable energy sources, and while that’s difficult to justify on a purely economic basis if grid power is available, for those living off-grid it will be all but necessary to rely on renewable energy sources, as in this case running a fossil-fuel powered generator is the economically non-viable option (except on an occasional basis, as is its intended purpose).
An off-grid energy system basically consists of just four key components: 1) a battery to store energy; 2) one or more renewable energy sources (e.g. solar panels, wind turbines, hydroelectric turbines); 3) an appropriate DC-input charger for said source; and 4) a DC-to-AC inverter to power the house, EV charger, well pump, etc. from the battery. Since no renewable energy resource is available 100% of the time, you will probably need to incorporate a backup generator to supply an AC-input charger, but the good news is that this generator can be a lot smaller than if it were sized to power the house directly, because the inverter and storage battery will handle the peak power demands.
To properly size an off-grid energy system you need to know two key parameters: the peak power demanded by all of the loads that are likely to run concurrently; and the average daily energy consumption. The peak power demand sets the minimum size of the inverter, obviously, but it also influences the size of the battery (bigger batteries can supply more current, all else being equal), the size of the
For estimating the average daily energy consumption, a typical value for us spoiled Americans is going to be in the range of 10-25 kWh per day for the fi rst person in the house, and around another 2-5 kWh per day for each additional person.
To properly size an off-grid energy system you need to know two key parameters: the peak power demanded by all of the loads that are likely to run concurrently; and the average daily energy consumption.
wiring, fuses/breakers, etc. The average energy consumption dictates pretty much everything else, from the number of solar panels or the swept area of the wind turbine to the storage battery capacity, and the power rating vs runtime of the backup generator, its attendant AC charger, etc. A good way to get accurate values for these two parameters is with a whole-house energy monitor that uses current clamps on each incoming phase leg in the main breaker panel. If that isn’t an option (perhaps because the off-grid location isn’t yet up and running) then you can estimate the power demand with rules of thumb (e.g. assume that major appliances draw 80% of their breakers’ amperage ratings), appliance data labels, and even anecdotal evidence (e.g. the neighbor’s well draws 9 A at 240 VAC). As for estimating the average daily energy consumption, a typical value for us spoiled Americans is going to be in the range of 10-25 kWh per day for the first person in the house, and around another 2-5 kWh per day for each additional person. Given that the size of the storage battery scales directly with this figure, it pays to determine it as precisely as possible rather than just relying on a thumb rule in an article you read in a magazine…ahem. Lastly, factor in the power rating of the EV charger, and if said EV will be charged when the renewable energy source isn’t producing—say, at night with a photovoltaic system—then you’ll also have to add the typical daily consumption of its battery capacity to that of the storage battery rating (in kWh, not Ah, since the two batteries will not be the same voltage unless the EV is a golf cart).
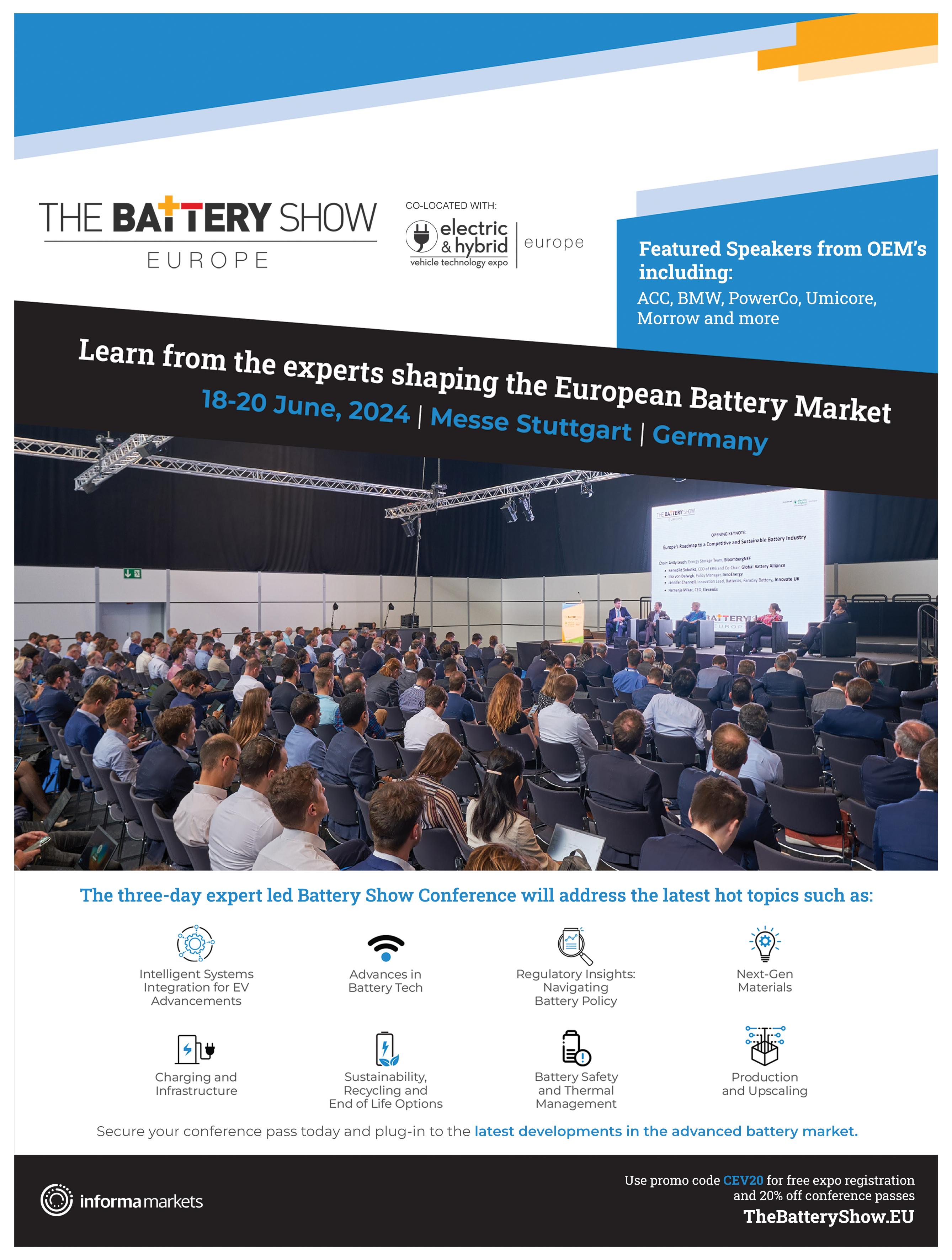
Lithium iron phosphate is arguably the best all-around battery type for off-grid systems, as it has a very high cycle life, and it can tolerate high peak and continuous current draws of up to 4 C and 1 C, respectively.
e storage battery is what makes an o -grid energy system possible, so it is arguably the most important component, but it is also one with a fair amount of exibility. e three key parameters to consider here— assuming a nominal 48 V rating—are the energy capacity in kWh, the current rating vs time (that is, how much current is allowed over timescales of seconds, minutes and hours and/or continuously, o en given in C rather than amps) and the cycle life vs Depth of Discharge. When it comes to the size of the storage battery, bigger is better, budget (and space) permitting, but a practical minimum is enough energy capacity to run everything as per usual for at least a full 24 hours, so that if the renewable source isn’t producing you don’t have to immediately re up the generator (or, worse, go rushing o to get fuel for said generator…at night…in the rain). For those wanting more concrete numbers, I feel that 200 Ah (again, at 48 V nominal) is the bare minimum for a single person (speaking from experience here), while 400 Ah would allow for an almost carefree lifestyle (assuming there is su cient renewable energy available to feed said battery).
The most common choices of battery type are lithium iron phosphate (aka LFP or LiFePO 4), all of the other lithium-ion chemistries (including recycled batteries from junked EVs), and, finally, lead-acid. To reach the de facto standard of 48 V nominal (the actual voltage can go up to near 58 V, depending on battery chemistry) you can either wire four 12 V batteries in series, or the appropriate number of bare
cells (typically 16 for LFP). There are also ready-made “whole-house” batteries available, such as Tesla’s Powerwall, but these are often aimed at grid-tied solar systems to be installed by licensed contractors, rather than DIYers, and they carry a correspondingly hefty price tag.
LFP is arguably the best all-around choice for offgrid systems, as it has a very high cycle life (in the range of 2,000 cycles at 100% DoD to 10,000 cycles or more if operated over the range of 80% State of Charge down to 20%), and it can tolerate high peak and continuous current draws of up to 4 C and 1 C, respectively, with negligible impact on longevity or energy capacity. There are two main choices of LFP batteries: those intended as drop-in replacements for lead-acid batteries; and bespoke 48 V batteries—often in convenient 10-inch rackmount cabinets—that are specifically designed for off-grid use. The former come in a wide range of Ah ratings (from 7-10 Ah for a computer UPS to 200+ Ah for off-grid systems) and have an internal BMS that protects against overcharge, overdischarge and overcurrent.
These typically lack the ability to communicate with other batteries in a series string (or other devices), nor do they come with any means of monitoring total charge in and out of the battery. The former shortcoming can be addressed with an external active balancer (aka charge equalizer) that automatically shuttles charge from the highest-voltage battery in the series string to the lowest until all are at the same voltage. The latter shortcoming is easily handled by an external battery monitor/coulomb counter (ideally with the ability to report such data to a remote display or smartphone via Ethernet, Bluetooth or WiFi). Note, however, that charge equalizers typically have modest current ratings in the range of 1 A to 10 A, so they can’t correct a grossly out-of-balance pack, nor one with a battery that has significantly less Ah than the rest. The higher price of the rackmount 48 V batteries will be offset somewhat by not needing an external balancer, of course, as well as being easier to wire up. They will also likely be able to communicate with other batteries (wired in parallel) and/or devices (e.g. to notify the inverter to shut down at the minimum DoD, rather than a minimum voltage) and include some form of monitoring and/or coulomb




counting, along with a local display of such information. That said, an external battery monitor will still be more versatile and convenient, especially if the batteries are located in a different building.
The more adventurous (and technically capable) can drop the $/kWh metric even lower by repurposing old EV traction batteries for off-grid storage use, but this is not for the faint of heart (or short of time). Unless the EV was a golf cart, you’ll have to reconfigure the cells to deliver 48 V nominal, so don’t count on using the original BMS (which probably won’t work, anyway, without a lot of code-hacking) and you’ll still be taking the risk that the battery was abused so much that it has no real usable capacity left.
The last option is venerable old lead-acid, though perhaps it’s best to relegate it to the proverbial dustbin of history. Sure, the prohibitive weight of lead-acid batteries is less of an issue in off-grid systems than it is in EVs (until you need to build the racking to hold 10 kWh or more of capacity with them, anyway) and they are notorious for not liking to be discharged below 50% of their rated capacity, though even then you shouldn’t count on more than a few hundred cycles of life. Furthermore, continuous current draw needs to be limited to a fraction of a C (typically C/4) to avoid loss of capacity from the infamous Peukert effect. This basically means that a lead-acid storage battery will have to be 2x to 5x larger in energy capacity relative to LFP, which effectively eliminates all the cost differential between these two chemistries.
The next key component in an off-grid system is an inverter, which converts the nominal 48 VDC from the storage battery into the 120/240 VAC required by the house, EV charger, etc. Eliminate the cheaper “modified sine wave” type from consideration, as its output is really just a 50/60 Hz square wave of less than 50% duty cycle that a lot of devices won’t like (standard dimmers and induction motors being two notable examples). The other type creates a pure sine wave by sinusoidally modulating the duty cycle of a much higher-frequency square wave, then filtering out the high-frequency components with an LC network. If this sine wave is available directly, it’s called a “high-frequency” type, and if it feeds an internal 50/60 Hz transformer it’s called—somewhat misleadingly—a “low-frequency” type. The LF type
Eliminate the cheaper “modifi ed sine wave” type of inverter from consideration, as its output is really just a 50/60 Hz square wave of less than 50% duty cycle that a lot of devices won’t like.
is supposed to be better at starting heavy loads like AC compressors by virtue of the energy stored in its transformer’s inductance, but better HF inverters will cope with such loads by going into current limiting mode, rather than outright faulting off (this should be explained in the user manual [you did Read The Fine Manual, didn’t you?]), so this might be a distinction without a difference. Furthermore, the LF type draws more no-load power (1-2% of rated power is typical) to maintain the magnetizing flux in that LF transformer, and this can add up to a lot of energy over the course of a 24-hour period. The last major choice to consider is whether to go with a standalone inverter with separate DC- and AC-input chargers, or a unit that combines one or both charging functions (the latter is often called a “hybrid solar inverter” or AIO, for All In One). Note, however, that you do not want a “grid-tie” inverter in an off-grid system, as such will not function without the presence of AC from the mains. The AIO type can be a little less expensive, because it combines all three devices into one box, but its main advantage is the ability to prioritize whether energy for the AC loads comes from the solar panels (or, very rarely, a wind turbine), the AC mains or generator, or the battery. This is an excellent solution for partial off-grid operation—e.g. running off solar during the day and the grid at night—but if you’re going purely off-grid, there is more flexibility in using separate devices, as the intelligent prioritizing won’t be nearly as useful. And speaking of solar and wind (and hydro, for those lucky enough to have it), we’ll cover that—and the appropriate DC-input chargers for each—next time in Part Two.
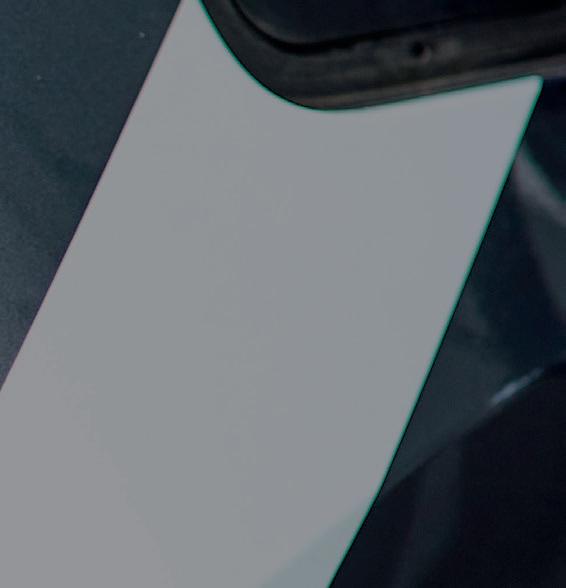
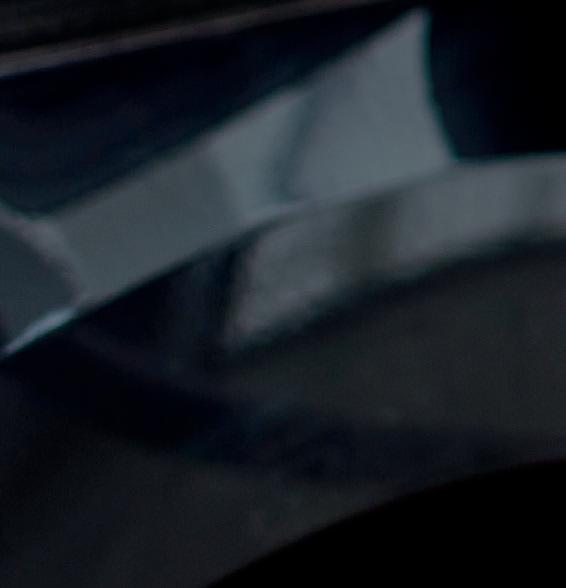

ENABLING THE NEXT PHASE
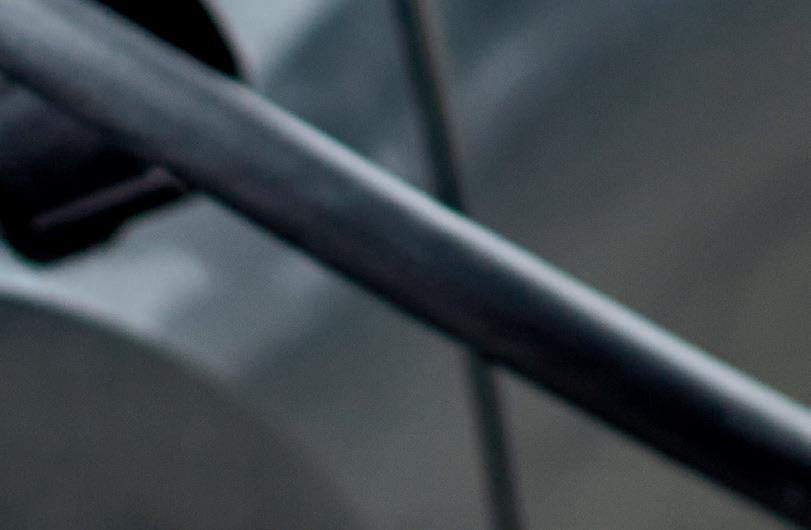

OF EV CHARGING STATION MANUFACTURING





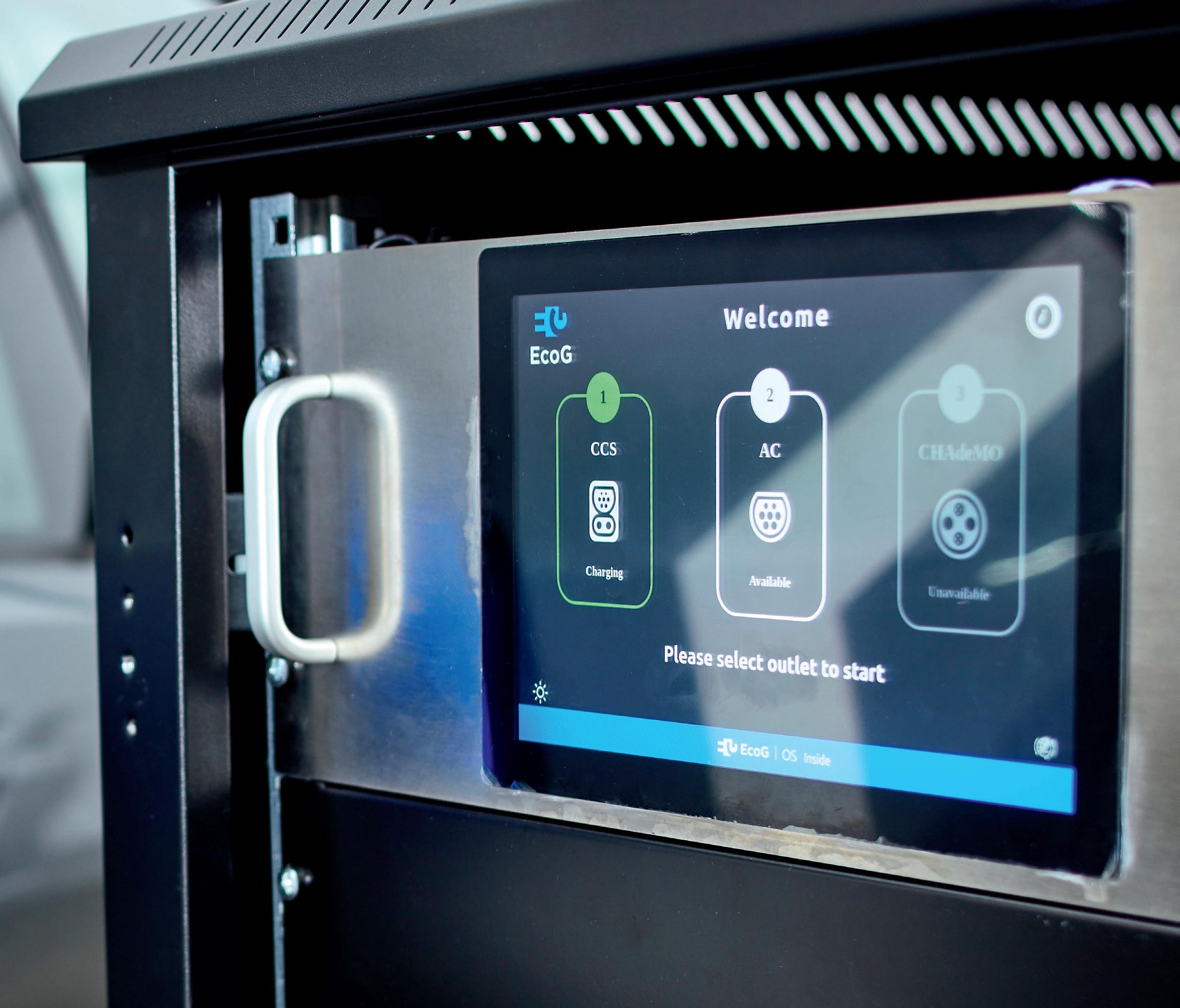

EcoG helps EVSE manufacturers streamline the process of bringing new products to market.
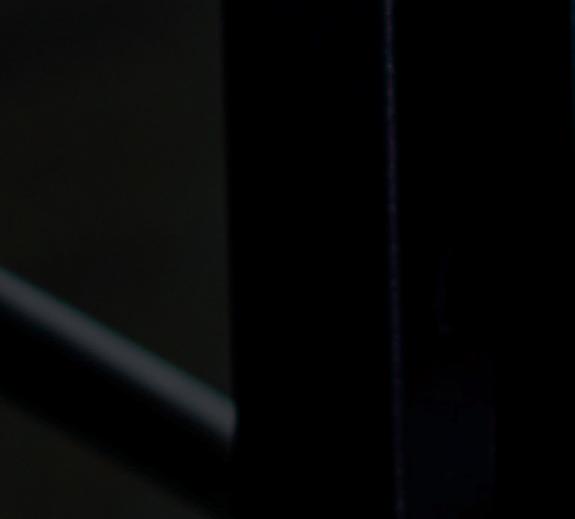
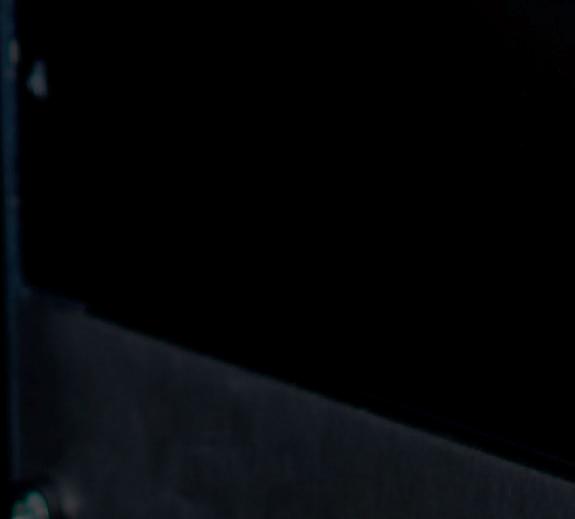
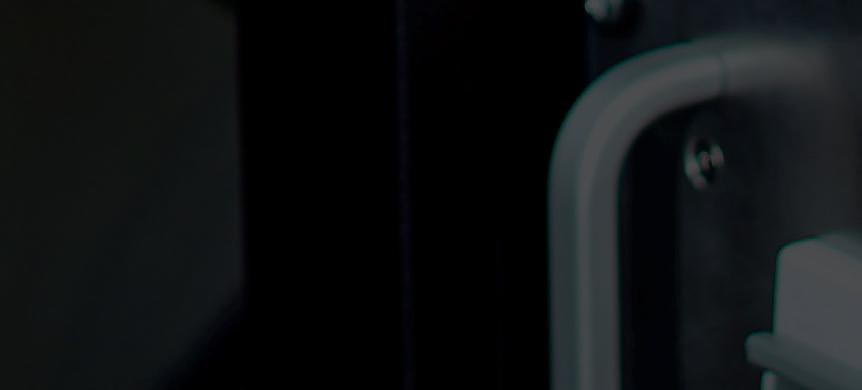
We tech writers o en refer to “ecosystems,” and biologists may shake their heads at our appropriation of the term, but the analogy is an apt one in many ways. A biological ecosystem has its charismatic megafauna (elephants, lions, whales), but it couldn’t function without its lessglamorous denizens (ants, fungi, bacteria). Likewise, a technological ecosystem has its headline rms (Apple, Microso , Tesla), but these rely on interrelated networks of companies that are little-known to the general public (FoxConn, Panasonic, ABB), but that provide indispensable services (and sometimes substantial pro ts).
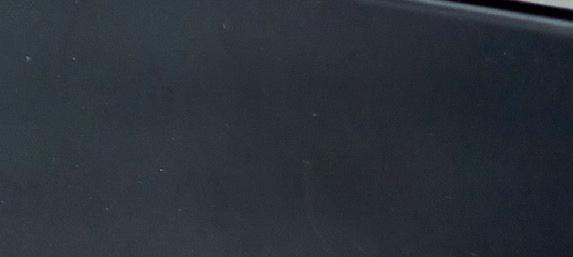

you’re unlikely to see its name in a headline outside of the trade press. In fact, most of the journalists working for newspapers and consumer mags, who so o en write about the Teslas and ChargePoints of the world, might be hard-pressed to gure out what EcoG actually does (we’ll do our best to explain it).
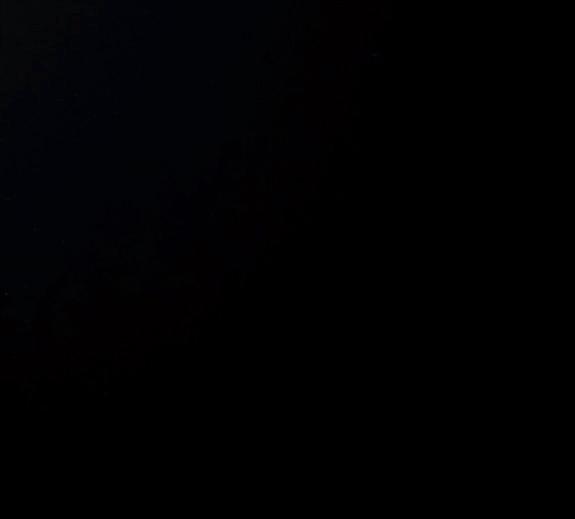
EcoG is an example of the latter kind of company—its logo doesn’t appear on a lot of EV charging stations, and
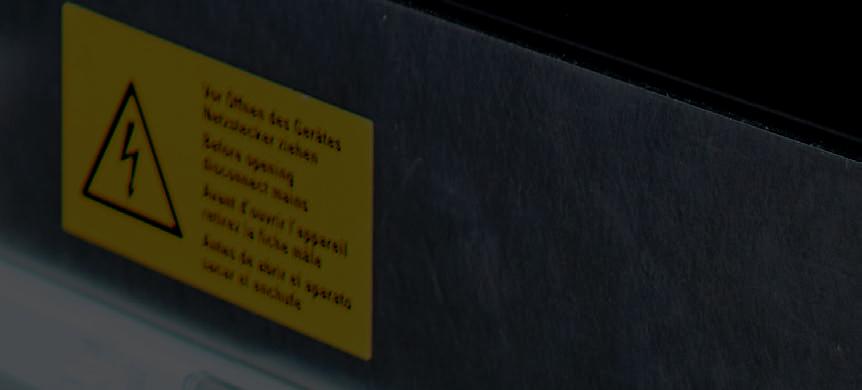
Like the ant, which makes up some 20% of the world’s biomass, Munich-based EcoG has a surprisingly large footprint in the EV charging infrastructure market. e company was founded by three former Siemens professionals in 2017. By 2022, its so ware was being used in 15% of the DC EV chargers sold within the EU. At the 2022 CharIN Testival, 30% of the new DC chargers being tested were running EcoG’s OS.
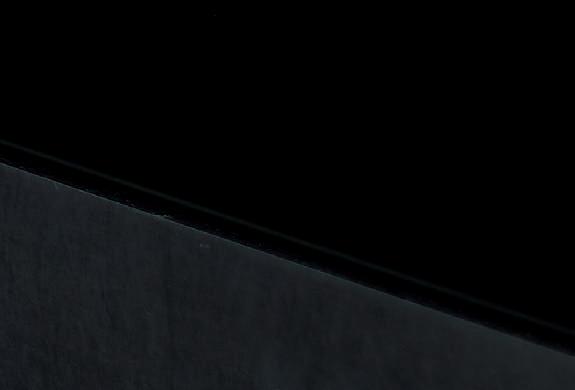

THE TECH
The tech behind the chargers
Like every other digital device, from a mainframe to a hearing aid, an EV charging station runs on so ware. EcoG’s Universal Core is a universal operating system designed to give charger manufacturers maximum exibility. According to the company, the OS supports six architectures that are used by more than 40 types of chargers, and it integrates over 15 di erent power converters, and all chipsets on the market. It can be delivered integrated in a charge controller device or as a rmware release for a customer’s own control hardware. e so ware features Open APIs and a customizable web platform to help customers build their own application layers.
EcoG also o ers a suite of hardware and so ware tools to help companies develop and manufacture charging stations as quickly and e ciently as possible. e EcoG Starter Kit prototyping environment is a fully-functional DC and AC charger that allows customers to modify components, develop their own applications, and verify charging functionality.
ree hardware tools provide additional functionality. e EcoG Charge Controller handles circuit control and charging status, and ensures vehicle interoperability. It works with multiple I/Os and interfaces. e CPPP Monitor provides a redundant monitor of the charging status between the vehicle and the charger, and can shut down the charging process if an irregular state is detected. e Application Board provides an application layer that interfaces with the user and with systems running in the cloud, allowing the EV charger to be upgraded with new features, and to use third-party services to run custom applications.
Of smart phones, mainframes and EV chargers
EcoG CEO Joerg Heuer has helped to shepherd several developing technologies from birth to maturity, and he sees parallels between the progression of the EV industry and the development of mobile telephony. As he sees it, 15 years or so into the EV industry’s development, it’s at a stage where companies need to “professionalize”—that is, to be able to quickly ramp up manufacturing of standards-based, interoperable vehicles and infrastructure. EcoG o ers an architecture that’s designed to enable manufacturers to build EV chargers at scale. Returning to the mobile phone analogy, Heuer says, “We are not targeting the Nokias, but the Foxconns. ose who
“
We are not targeting the Nokias, but the Foxconns. Those who really professionalize how to build chargers and make that a reliable, robust thing in the market, that’s where we focus.
really professionalize how to build chargers and make that a reliable, robust thing in the market, that’s where we focus.”
Heuer expects that there will be a few di erent operating systems in the EVSE market, and his company provides the reference architecture that allows manufacturers to build an ecosystem that can incorporate a wide variety of hardware. “We have 50 ecosystem partners on the component level—converters, isolation monitors and so on.”
Some of EcoG’s customers are charging network operators (aka charge point operators or CPOs) and some are site hosts or integrators, but most are manufacturers—two prominent customers are Siemens and icharging. “We are very much focused at this stage of the market on the manufacturing side,” Heuer tells us. “In Europe, we now have a 15% market share, so more than every tenth charger is produced with our architecture and operating system.” EcoG is also well-established in India, and is quickly moving into North America.
Heuer sees EcoG’s OS and its design tools not as separate products, but as integrated parts of a whole. “We are an IP tech company, something like a Qualcomm in the mobile phone industry,” he told Charged. “If you contract with Qualcomm, you not only get their chip, you get the whole ecosystem around it, so it makes you fast at building smart phones. at’s what we want to do in the EVSE market. We want to enable those who have manufacturing capability to be fast to build professional products. is wave of electric mobility is running, and the question is, are you fast enough to catch the wave? We address those who are really thinking not about how to design the product, but about how to scale the manufacturing.”


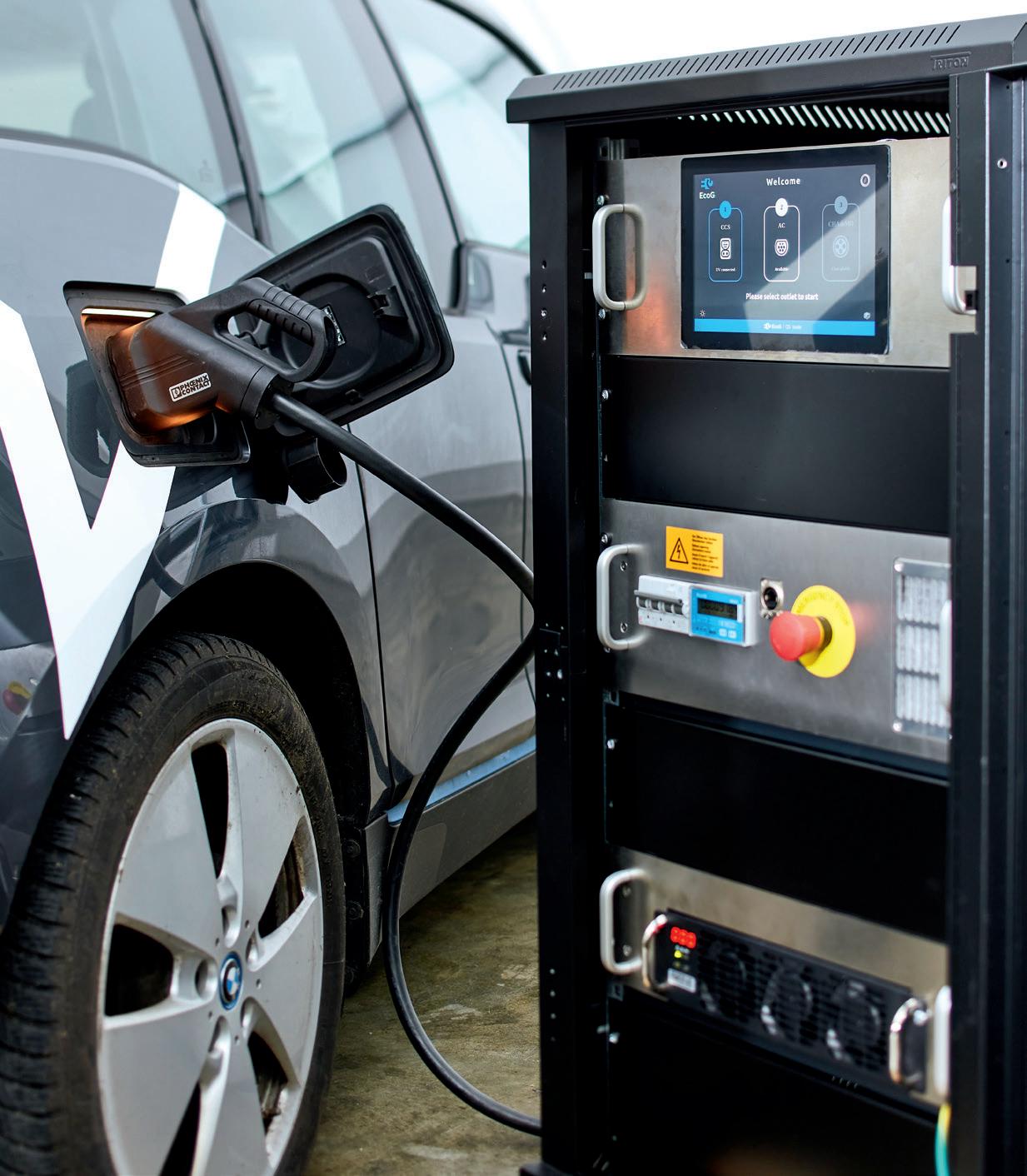

Walled garden or open ecosystem?
EcoG has called “infrastructure segmentation” one of the biggest obstacles to EV adoption at this stage of market development. But what is meant by segmentation in this case?
When Heuer started working in the EVSE market back in 2008, he was struck by the irony that one of the most global industries—automotive—is having to learn to work with one of the most regional industries—electric utilities, which operate di erently in di erent countries, and indeed in di erent US states. “What we saw then was that, especially in North America, the market started with very vertical o erings like ChargePoint and others. And this is good for a kickstart, but in the medium term, it o en results in user fragmentation. It’s good to get started fast, but to scale up the market it’s good to think of how you collaborate and integrate stu together.”
“ ink of roaming and the mobile phone networks— it increases reliability if you make it the right way. And that’s what we believe is going to happen. I think getting away from these vertical networks is important because electric mobility is really a cool opportunity to get more renewables into the electric grid. But this needs di erent business process integrations, and a monolithic company will not have the expertise in how to integrate into the energy system. We are an enabler of that.”
Enabling V2X
EcoG’s system supports bidirectional charging, which is widely expected to be a key technology enabling a variety of useful applications (V2X). Obviously, ensuring interoperability among V2X-capable chargers and EVs will be critical—and interoperability testing is one of EcoG’s specialties.
Last July, EcoG presented an ISO-compliant bidirectional charging solution that follows charging standards association CharIN’s guidelines. EcoG’s so ware is designed to support all V2G-capable vehicles—including those still under development. e company has tested its bidirectional solution with multiple vehicle manufacturers in accordance with the new ISO 15118-20 bidirectional power transfer (BPT) standard, as well as the BPT Application Guide from CharIN.
e company has partnered with power semiconductor manufacturer In neon to develop a starter kit with an integrated 22 kW bidirectional converter and controller.
“ e fact that bidirectional charging actually works according to ISO 15118-20 BPT is a major step forward,” said Xi Zhang, EcoG’s Director of E-mobility. “ is allows the technology to be applied to the mass market, as customers can now be sure that their wallbox can communicate with any V2G-enabled vehicle in the eld.”
“V2G as a standardized feature is essential for broad adoption of this technology,” said Heuer. “EcoG provides the V2G technology in the form of a starter kit to charger manufacturers to enable products with short lead times to market, and to OEMs for interoperability testing.”
Heuer told Charged that the key to enabling wider V2X tech is to make it available on a low-cost product. “When we look at chargers today, they’re built like photovoltaic inverters 20 years ago—they include something like 100 components. Today, if you look at PV inverters, they have maybe 10 components—and in the last 20 years, the price has declined by something like a factor of 10 to 20.”
Where does vehicle-to-grid tech stand today from a commercialization standpoint? Like most of the EVSE industry folks we talk to, Heuer concedes that V2G is still mostly a pilot-level technology, but he expects more commercial applications to start appearing soon. “We have several pilots, but Volkswagen recently announced that every Volkswagen is supporting V2G— it’s already in the menus of the vehicles.”
Ford, Hyundai and Tesla are also now selling EVs with power export capabilities, and the market for
THE TECH
bidirectional-capable charging hardware could expand quickly. “With partners like In neon, we are targeting this market, because then you are talking about 10,000 units per year [as a conservative estimate].”
Reliability, reliability, reliability
e poor reliability of public chargers is an industry-wide scandal. Some casual observers seem to assume that adopting Tesla’s NACS charging system will solve all the problems. However, like many industry players we’ve spoken to, Heuer believes that one of the main reasons Tesla’s Superchargers are so reliable is that the system is controlled by a single company—which will no longer be the case once large numbers of EVs from other brands start using the Superchargers.
“We have been working a long, long time in standardization, and I remember the days when we had the discussion of Microso versus Apple,” says Heuer. “Here we see basically the same. We see probably 20 or 30 implementations out there on the vehicle side and on the infrastructure side. With Tesla, you have both in one, and with their automation they can do testing to ensure that things are working with each other.”
“Right now, we’re looking at a landscape with about 100 charging station manufacturers and a growing number of EV manufacturers. Tesla might test its EVs with ve to ten charger types, but the broader challenge is much more complex. To achieve a truly seamless charging experience for any EV driver, we’re tasked with ensuring that every electric car can use any charging station. Achieving this interoperability means testing over 500 di erent combinations of cars and chargers.”
One thing that will hopefully facilitate interoperability over the coming years is the fact that Tesla’s NACS is not radically di erent from CCS. “ e plug is quite di erent, but all the processing behind it is quite similar,” Heuer explains. “ at’s also the reason why in Europe they can easily use a CCS plug, and in US they have these adapters. Of course, in the foreground, it looks very di erent because the plug looks di erent. But in the background, the automation, the really complex stu , that’s quite similar.”
“About two weeks a er the announcement that Ford would adopt NACS, a customer of ours just added a Tesla cable to their CCS station, and the thing worked with a Tesla vehicle. at’s the nice thing. It’s no longer this competition between CHAdeMO and CCS, which
“We’re tasked with ensuring that every electric car can use any charging station. Achieving this interoperability means testing over 500 different combinations of cars and chargers.
were really totally di erent systems. Compared to CHAdeMO, I would say 90% or 95% is really the same between CCS and NACS.”
Some nd it ironic that in Europe, Tesla adopted the CCS plug, whereas in the US, vehicle OEMs and EVSE manufacturers are adopting the Tesla plug. Heuer explains that there are several reasons for that. “One reason is that in Europe we have a three-phase AC system, so this would be a shortcoming of the Tesla plug because then they would be only be able to charge one phase. In Europe, we would then be limited to three kilowatts in most countries, maybe maximum seven. at’s one physical aspect.”
A second di erence between the North American and European markets is that the latter has developed in a less vertically-integrated way. “ e networks started quite early with roaming and so on—it was not so dependent on what network or mobility service provider you contracted with, so the advantage Tesla had compared to the rest of the networks was not as signi cant.”
e North American market could bene t by learning from some mistakes that were made in Europe. “ ere’s obviously a di erent development in markets and there are learnings out of that, which I think are bene cial for all. I think what’s interesting to see in North America is how to integrate vertically like a ChargePoint, for example how to integrate direct payment via app or credit card, conveniently including all the processing behind it with logistics and so on.”
“On the other hand, I think Europe is doing quite well to think about this more collaborative role, how you create ecosystems. What we see right now in the market in the US is really more the speed and integration, whereas we see more of an ecosystem approach in Europe. And now that things become more integrated with Tesla as a crystallization point, we have the opportunity to combine networks and to really move forward.”



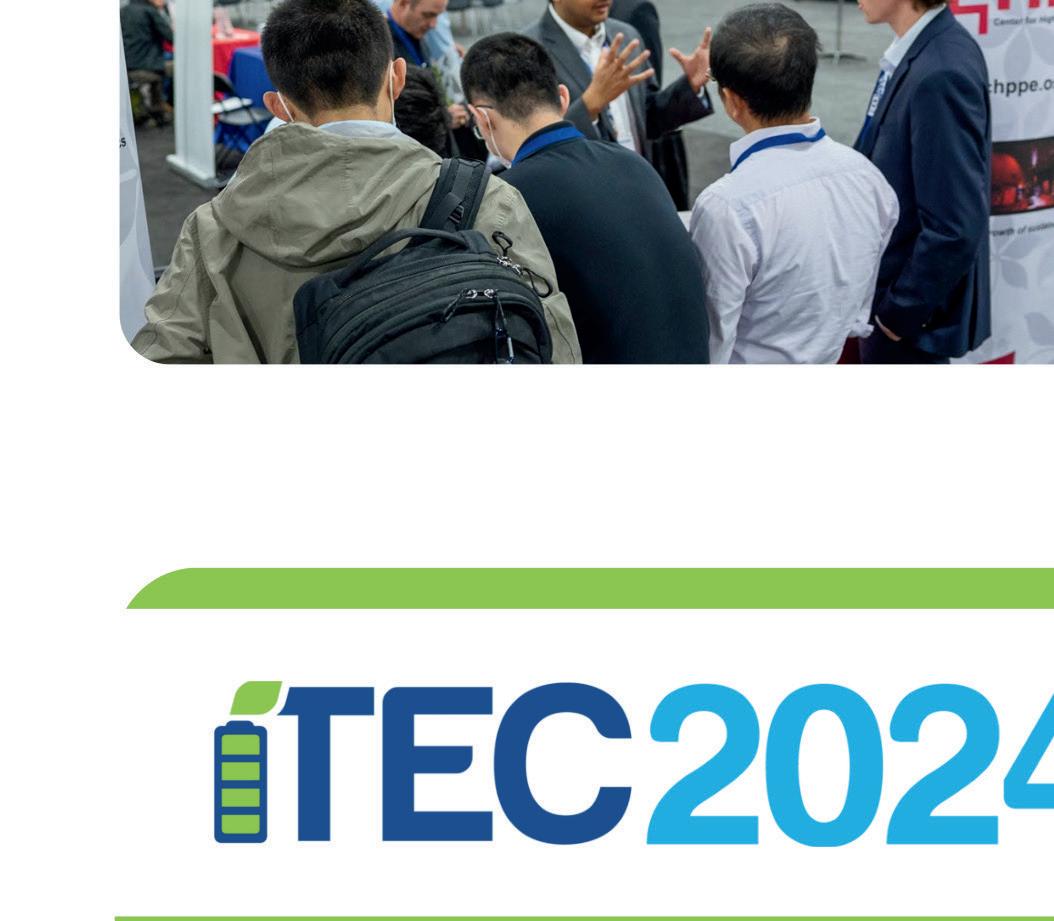
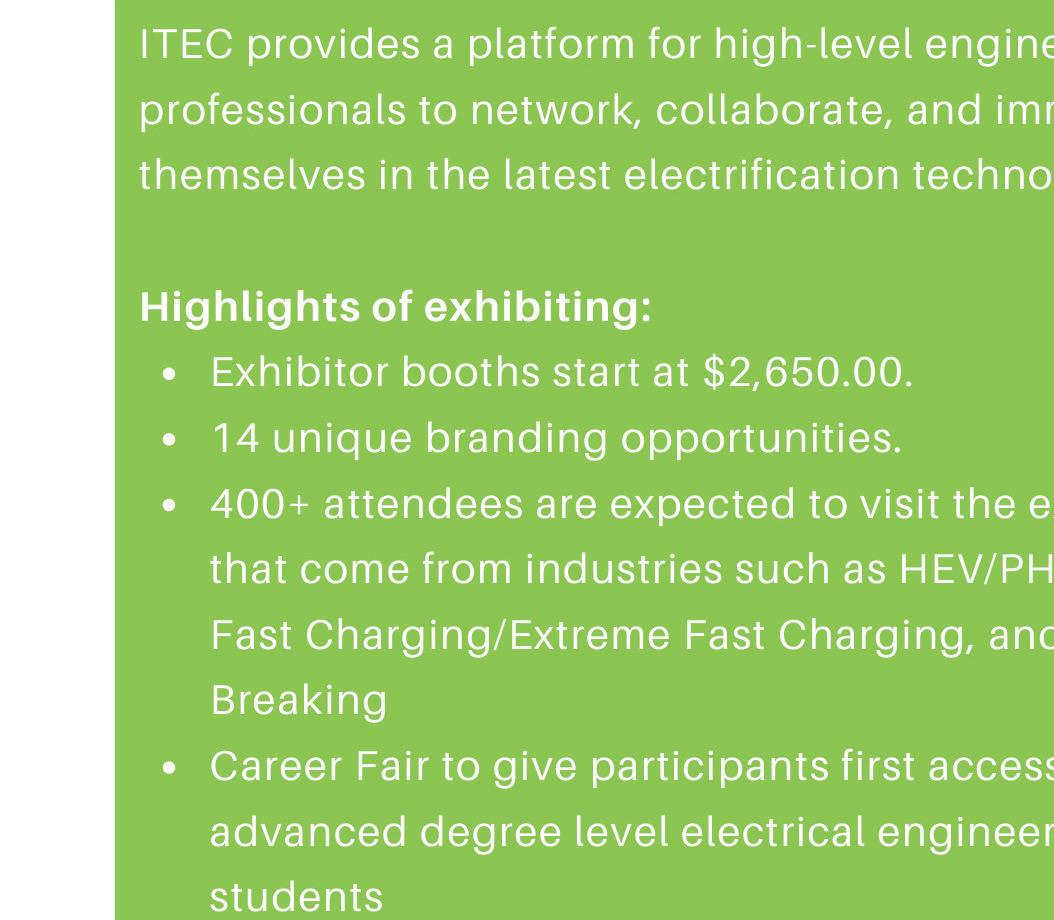
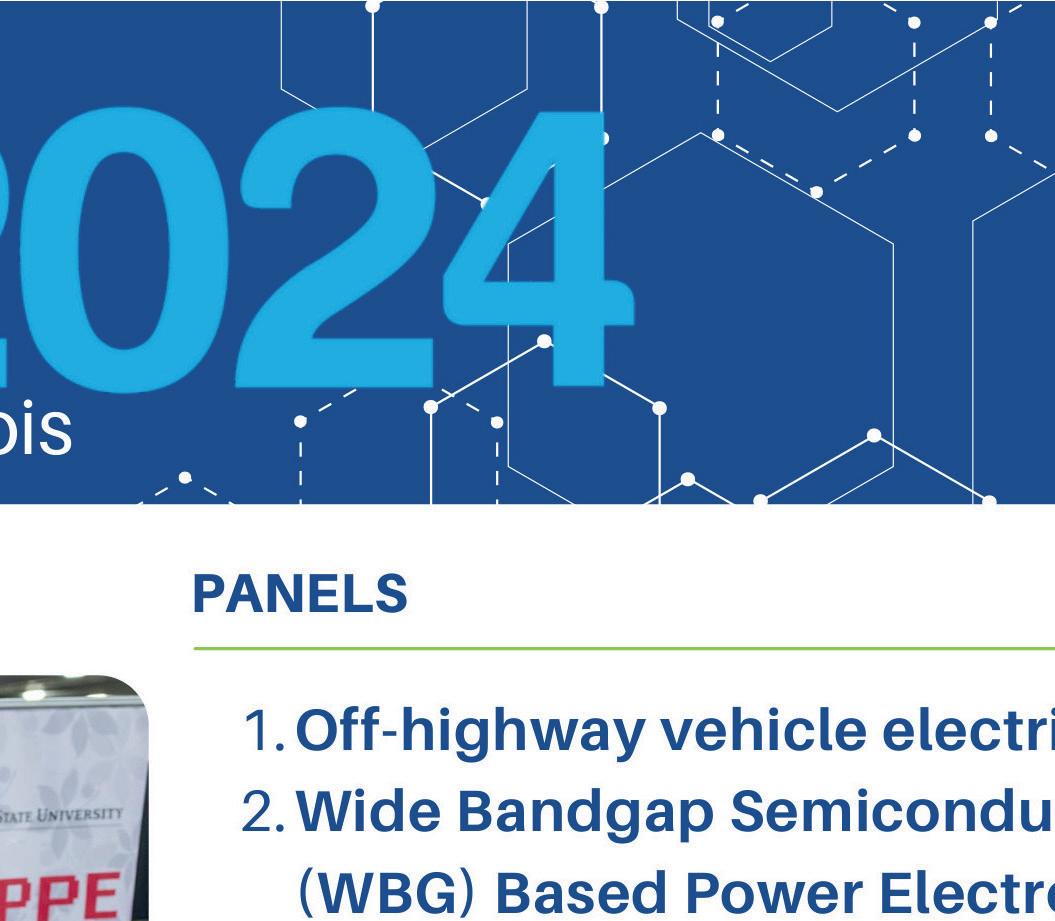
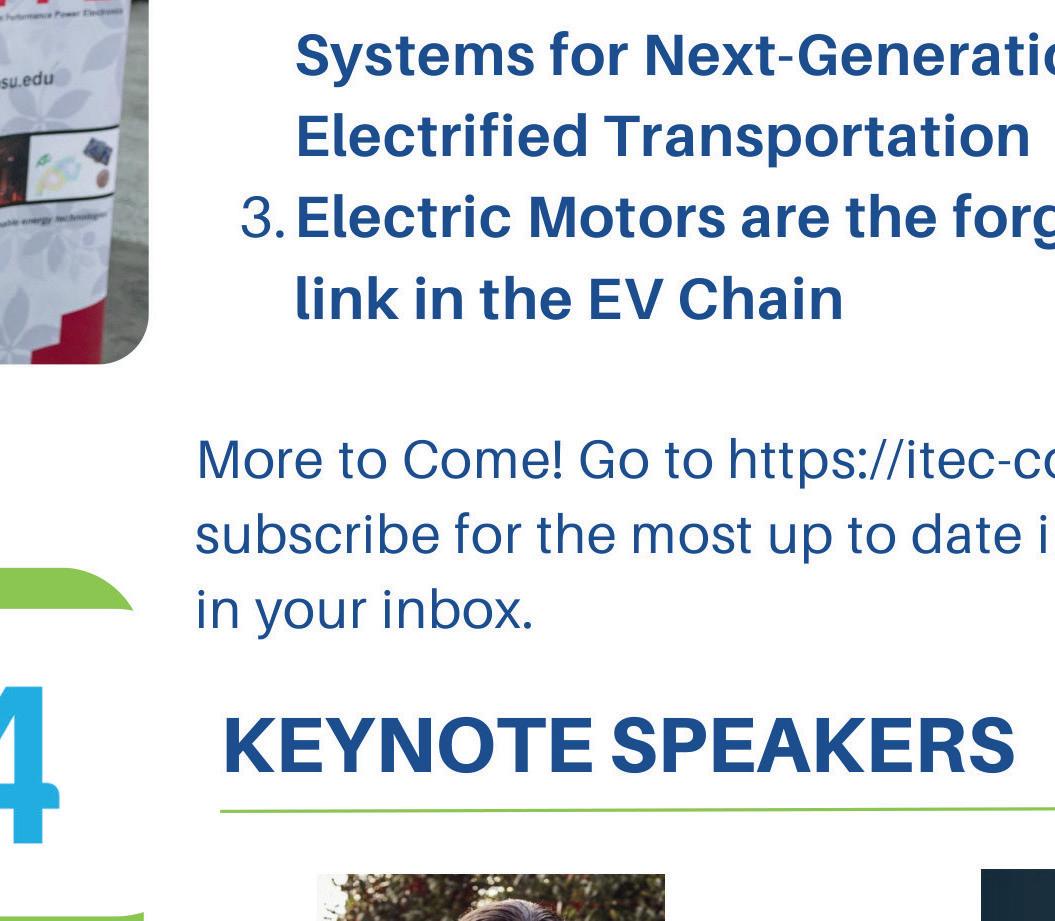
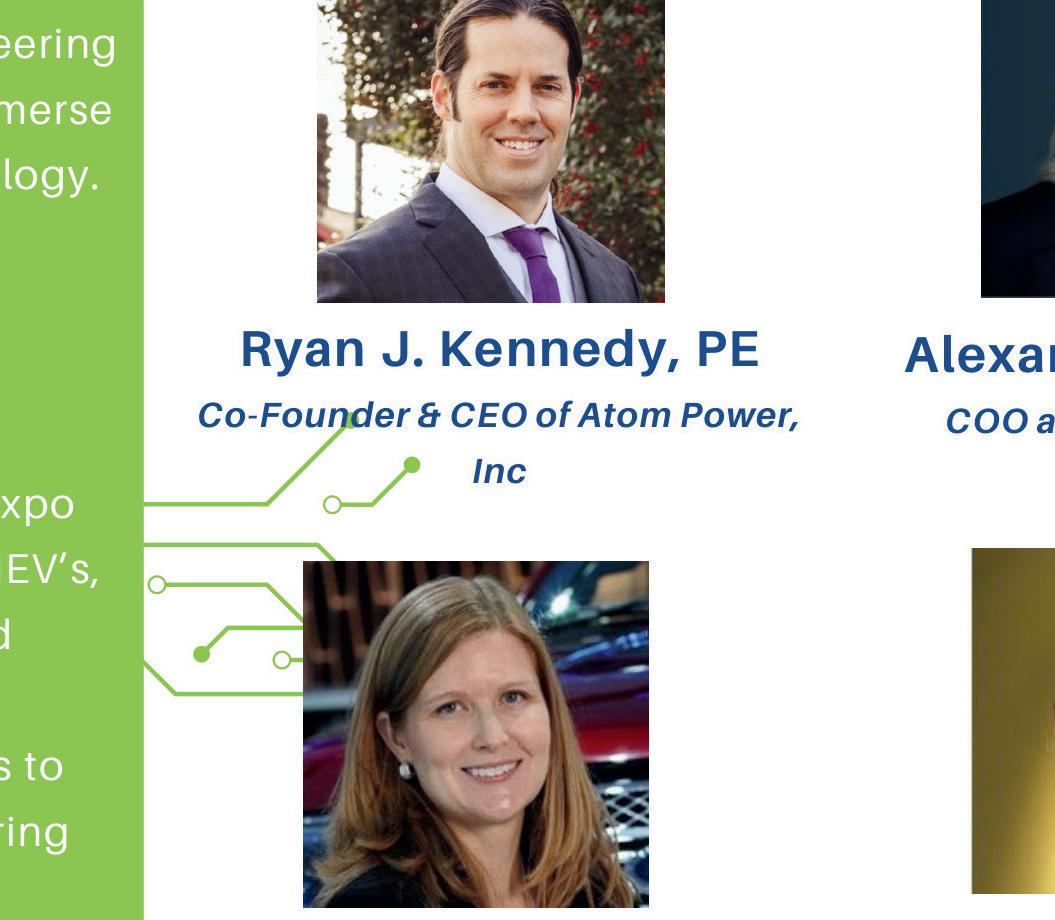
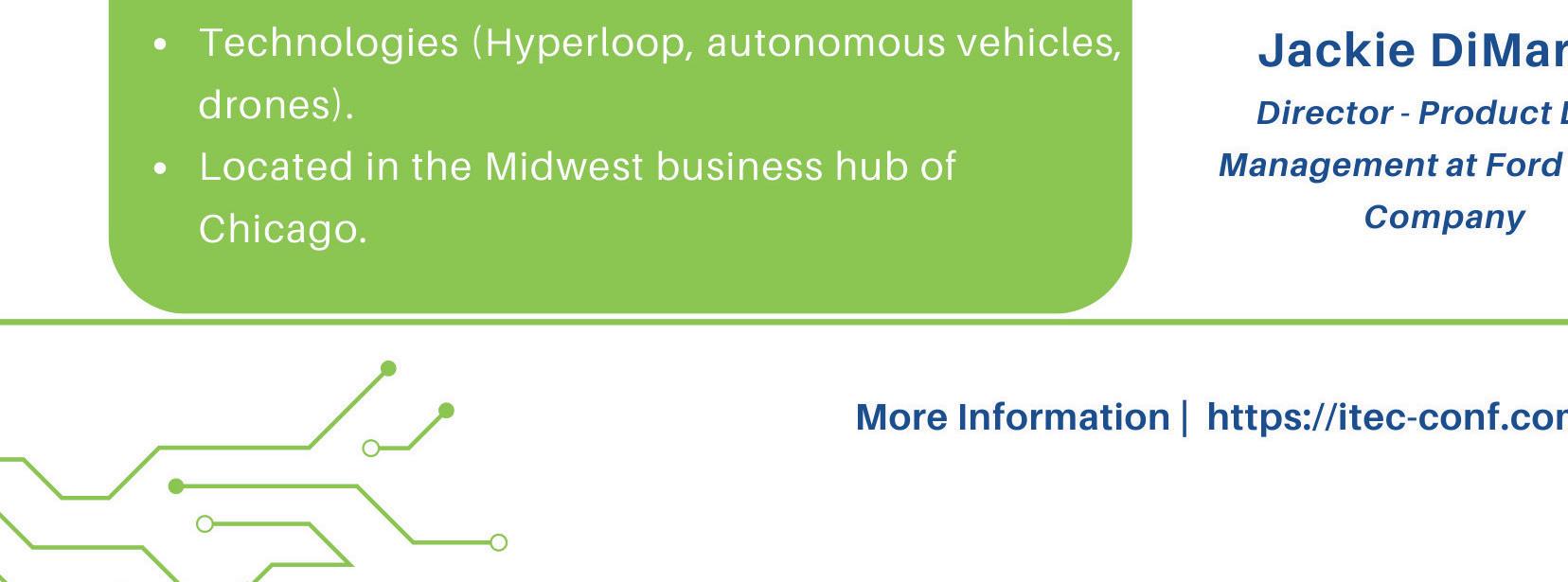
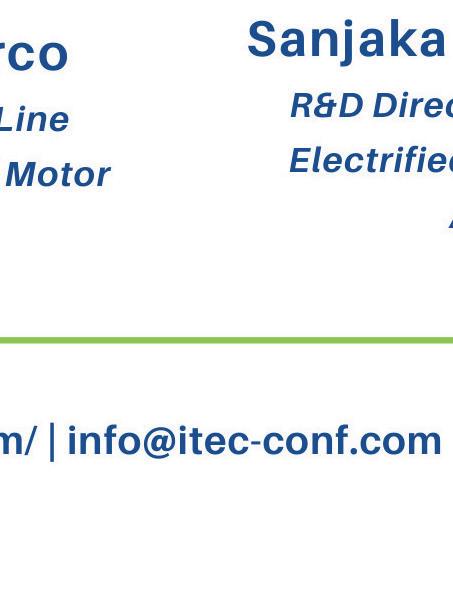


THE VEHICLES
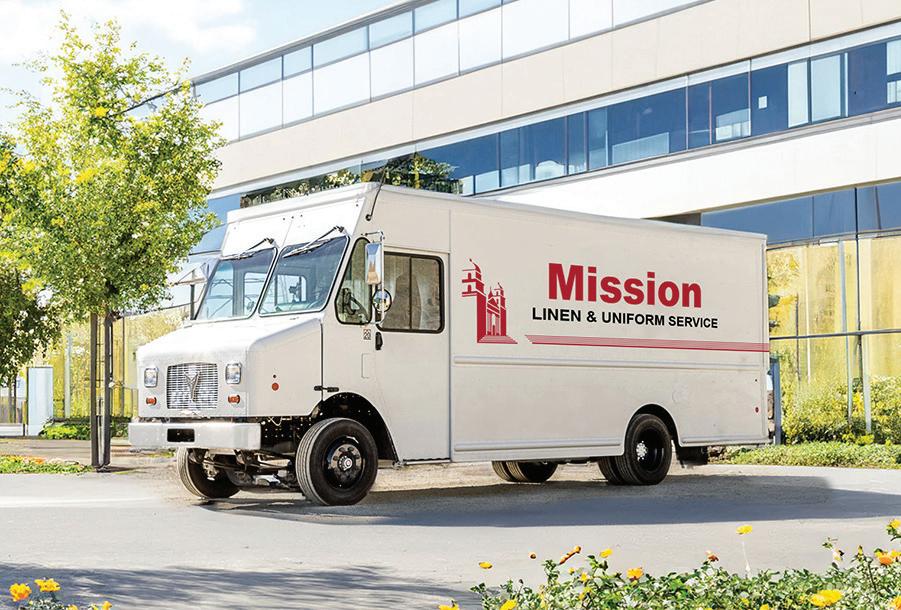
Xos receives order for 12 of its SV electric stepvans
US electric truck manufacturer and eet services provider Xos has received an order for 12 of its 22-foot SV stepvans from California-headquartered commercial laundry company Mission Linen Supply.
e vehicles will be among the rst of the longer 22-foot models to be delivered by Xos. ey are suited to a variety of applications, including linen services, parcel delivery, utility and repair services, and armored transport. e SV line has modular chassis and battery systems, and is o ered in a variety of con gurations to meet customers’ speci c needs.
“We are thrilled to partner with Mission Linen Supply on this signi cant step toward electric eet adoption,” said Dakota Semler, CEO of Xos. “Our electric stepvans are setting new standards for the textile and linen industries, and we are con dent that they will bring immense value to Mission Linen Supply’s operations.”

Skanska concludes North American pilot of Volvo EC230 Electric excavator
Construction giant Skanska has completed a 90-day pilot program using the Volvo EC230 Electric excavator on the Purple (D Line) Extension Transit Project in Los Angeles. e goal of the trial was to test the capability of a battery-powered excavator to match the performance of a legacy diesel-powered machine.
e excavator was used to load trucks with construction material. Results from the trial indicate that the Volvo EC230 Electric performed the necessary activities as intended while keeping the pace of work on schedule. Compared to a diesel-burner, the electric machine emitted 66% less carbon, and saved an estimated 74% in costs per hour of operation.
Operators also noted health and safety bene ts. ey found the electric excavator easier to use, and found that it generated much less vibration and noise than the old fossil-burners.
“ e successful completion of this pilot program represents a signi cant stride forward for the entire industry,” said Mason Ford, Director of Sustainability and Equipment Services for Skanska USA Civil. “Change doesn’t happen overnight, but this type of investigation into the possibilities furthers the conversation around electri cation and sustainable innovation within civil construction.”




Volvo CE and Mack Trucks deliver electric excavator and refuse truck to Florida waste hauler
Volvo Construction Equipment and Mack Trucks, both Volvo Group companies, recently delivered an electric excavator and an electric refuse truck to Boca Raton, Florida-based Coastal Waste & Recycling, which has 25 locations in Florida, Georgia and South Carolina, and operates more than 700 vehicles.
Coastal is piloting a 23-ton Volvo EC230 Electric excavator at a materials recovery facility, where the company receives and sorts recyclable materials. e EC230 Electric is performing the same work as its equivalent diesel model, the EC220EL, feeding material into a sorting line.
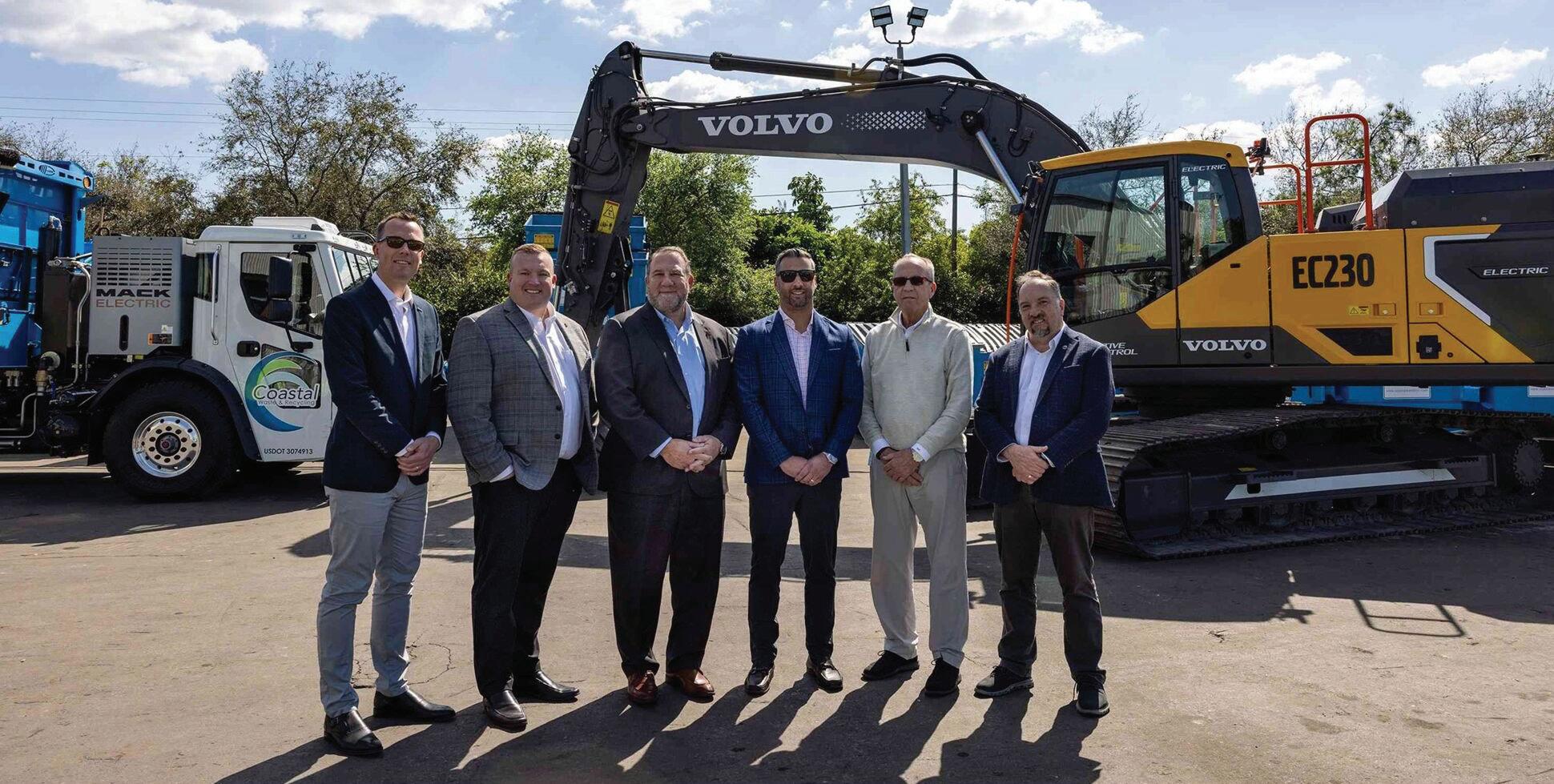
e electric excavator not only produces zero emissions, but also o ers signi cantly lower noise and vibration levels, as well as instant torque. e company estimates that the EC230 Electric will deliver a 60-70% reduction in running costs compared with the legacy machine, as well as greatly simpli ed maintenance.
e EC230 Electric has been in testing with other companies in North America over the past year, and is expected to be commercially available later in 2024.
Coastal Waste & Recycling also took delivery of a Mack LR Electric Class 8 refuse vehicle, which will operate in residential and commercial areas in southern Florida. e company worked with Mack to develop favorable routing for the electric truck.
e next-generation Mack LR Electric features 4 NMC battery packs with total capacity of 376 kWh. Twin electric motors produce 448 continuous horsepower and 4,051 lb- of peak torque. Onboard accessories, including an automated side loader, are powered through 12 V, 24 V and 600 V circuits. A two-stage regenerative braking system helps recapture energy from the hundreds of stops the vehicle makes each day with an increasing load.
e EC230 Electric and the Mack LR Electric will both be fast-charged with a mobile Heliox 50 kW charger provided by Volvo CE. Volvo CE and Mack experts consulted with Coastal Waste on charging to help identify the ideal solution.
Nextran Truck Centers in Fort Lauderdale will provide service and support for the vehicles.
“We are excited to add both pieces of equipment to our eet,” said Brendon Pantano, CEO of Coastal Waste & Recycling. “As the rst private hauler in Florida to invest in electric, we look forward to harnessing the strength of this strategic move.”
“ e shi to o -road electri cation, especially in heavy construction machines, can’t be accomplished by one single team or company,” said Scott Young, head of the North American region for Volvo CE. “We’re grateful for the chance to partner with customers and other Volvo Group companies to advance sustainability in a variety of industries.”
“Coastal Waste & Recycling has been a great partner and has always been interested in any new technology they can incorporate to drive e ciency and excellence throughout their operations,” said Martin Mattsson, director of Key Account Sales, Waste and Recycling, Volvo CE. “Testing this electric excavator directly against its conventional equivalent will teach us a lot.”
THE VEHICLES
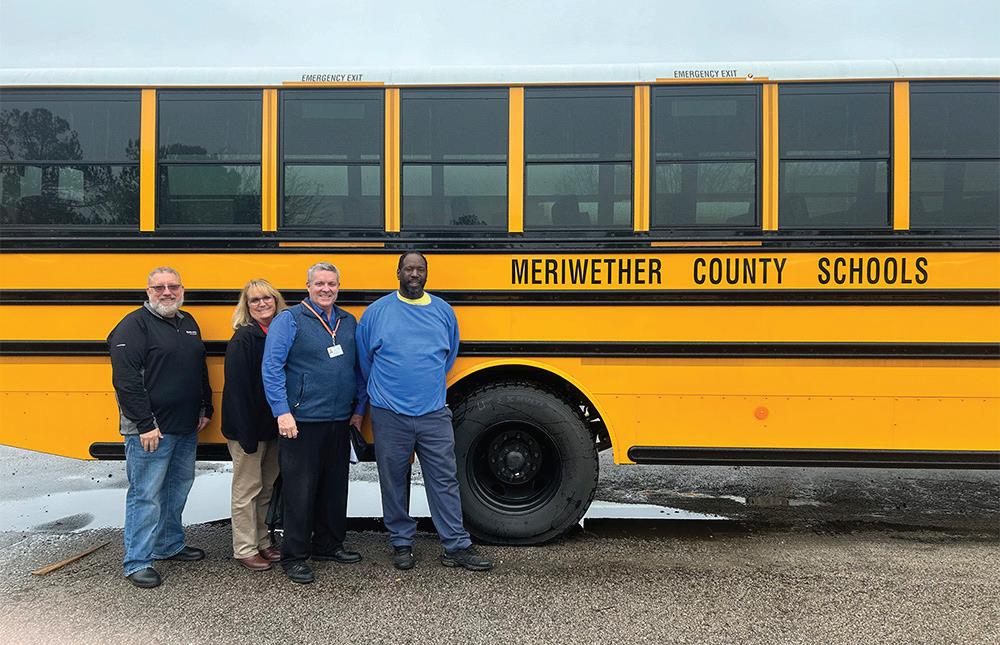
Thomas Built Buses
delivers its 1,000th electric school bus
US school bus manufacturer omas Built Buses, a brand of the Daimler Group, has delivered its 1,000th Saf-TLiner C2 Jouley battery-electric school bus as part of an order for eight of the buses placed by Meriwether County School System (MCSS) in Georgia.
e new buses are fully funded through the EPA’s Clean School Bus grant program. ey are MCSS’s rst electric models and will replace some of its current diesel eet of 46 buses.
e Saf-T-Liner C2 Jouley has a maximum passenger capacity of 81. It delivers 295 peak horsepower, has a standard battery capacity of 244 kWh, and has a range of up to 150 miles.
“Jouley was a natural choice because of the available long-term battery energy, access to fast DC charging and safety- rst construction,” said MCSS Superintendent Robert Gri n.

GILLIG to supply Seattle transit agency with up to 395 batteryelectric buses
Transit bus giant GILLIG has announced a new veyear contract with King County Metro, which serves the greater Seattle area. GILLIG will deliver an initial order of 89 Low Floor Battery Electric buses, with the option to purchase up to 306 more units.
Built on GILLIG’s Low-Floor platform, the GILLIG Battery Electric Bus features 686 kWh of onboard energy storage. GILLIG says King County’s buses are “equipped with opportunity charging capabilities in addition to plug-in charging.” We were unable to verify what the company means by this, but we do know that, in the past, GILLIG has sold buses equipped with wireless charging systems from WAVE Charging.
e initial deployment of these buses will equip King County Metro’s rst fully electri ed bus base in Tukwila, Washington, currently under construction. “ e buses operating out of this base will serve surrounding south King County communities, where air pollution levels are higher than in other parts of the region.”
“Acquiring these next-generation battery-electric buses from GILLIG moves us closer to our goal of being the rst large transit agency in North America that is 100% zero-emission,” said Dow Constantine, King County Executive. “With these new additions to our eet, our community members, customers, and operators will bene t from cleaner air as we continue to combat climate change.”




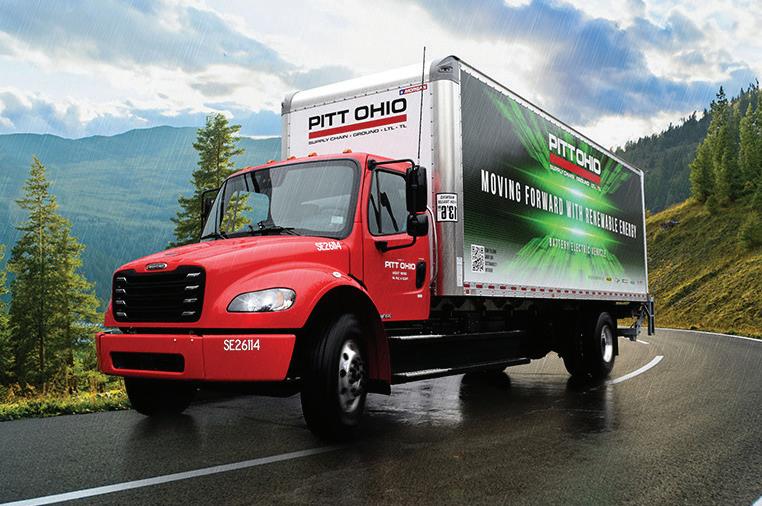
Daimler Truck North America delivers first electric Freightliner eM2 box trucks
Daimler Truck North America (DTNA) has announced that its electric Freightliner eM2, which went into series production at its Portland, Oregon, facility at the end of last year, is now being distributed to US customers.
PITT OHIO, a transportation and supply chain management company based in Pittsburgh, is the rst to deploy the medium-duty EVs. e company’s two eM2s, with 26-foot-long box bodies, will operate out of its Cleveland terminal as part of its less-than-truckload freight business.
e Freightliner eM2 has typical ranges of 180 miles for Class 6 and 250 miles for Class 7. It is designed for pickup and delivery applications. DTNA’s electric lineup also includes the Jouley electric bus from omas Built Bus, available since 2020; the FCCC MT50e walk-in van chassis for nal-mile delivery, available since 2021; and the Class 8 Freightliner eCascadia, available since 2022.
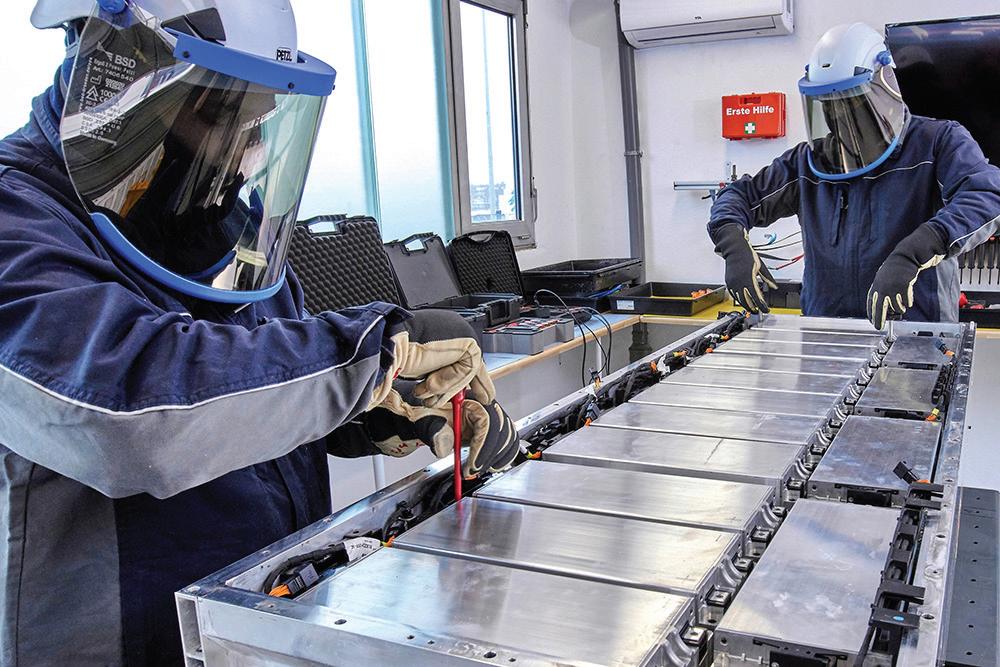
MAN rolls out battery repair centers across Europe
Over the next two years, MAN Truck & Bus, headquartered in Munich, Germany, plans to establish battery repair centers in Italy, Denmark, Norway, Austria, Belgium, the Netherlands, France, Poland and the UK. Two of the facilities, in Hanover-Laatzen, Germany, and Barcelona, Spain, are already in operation.
MAN is ramping up electric truck production as it plans to begin deliveries of its next-generation eTruck this year. More than 1,000 MAN electric buses and more than 2,400 MAN electric vans are already on European roads.
e knowledge gained at MAN’s rst repair center in Hanover-Laatzen, which launched in 2020, is being transferred to its other European markets, in each of which certain criteria must be met, based on practical experience and speci c legal standards.
Since 2023, MAN has been leading the three-year REVAMP project, a consortium of nine partners from industry and science. e aim is to automate assessment of used vehicle batteries in order to economically remanufacture them for use in vehicles or for other purposes.
“Battery repair is a necessity for MAN in order to ensure the economic e ciency and operational readiness of our customers’ electric vehicles at a high level,” said Christopher Kunstmann, Senior VP of Customer Service Management. “We also make a major contribution to the closed-loop approach of traction batteries, as this extends the battery life in the vehicle, which conserves important resources.”

THE VEHICLES
New fleet customer says Tesla Semi performs “well beyond expectations”
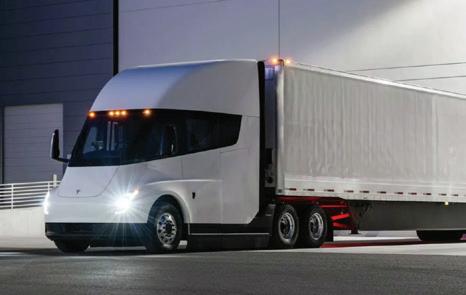
e rollout of the Tesla Semi has been slower than EVangelists would have liked. e electric semi tractor was rst unveiled in 2017, and o cially entered production in late 2022. Since then, it has been deployed in limited numbers.
Last October, it was reported that Tesla had built about 70 Semis, which were being used internally and by one con rmed customer, PepsiCo. Tesla recently broke ground on a new facility at its Nevada Gigafactory site, where Semis are slated to be produced.
Now Electrek reports that Tesla has delivered Semis to at least one more customer: Martin Brower (MB), a logistics company that serves the restaurant industry and operates a eet of hundreds of trucks.
MB has con rmed that it used two Tesla Semis in a pilot program earlier this year, and the company’s drivers certainly seem to like them. “A group of ve MB drivers…were trained to operate the Tesla Semi, which uniquely positions the steering wheel and driver’s seat in the center of the cockpit and has other design features to increase driver visibility and safety,” MB told Electrek. “Overall, our drivers had positive feedback on how the vehicle performs.”
“ e Tesla Semi rises above any other tractor with mobility, center seat con guration, and precise movement that allows the driver to navigate safely,” said MB driver Casey Kamp.
“ e Tesla Semi experience has been impressive since day one,” said Megan Yamaguchi, Assistant Transportation Manager at MB. “Our drivers had no problem learning the systems and maximizing the features that set these tractors apart. We’ve been able to push these tractors well beyond expectations and look forward to our electric future.”

Fortescue’s electric excavator outperforms its diesel counterpart
Australian mining giant Fortescue has been testing an electric excavator at its Chichester operation site. Over the past three months, the excavator has been running at partial capacity while the site team familiarized themselves with the new piece of equipment. Now the e-excavator is operating at full speed, and has reached the milestone of one million tonnes of rock moved since it became operational.
Fortescue says the excavator’s performance continues to steadily improve, and at times it performs better than its diesel equivalent.
Fortescue worked with Liebherr to convert several diesel excavators to run on electric powertrains. “ e modular design of Liebherr equipment makes it possible to repower existing diesel excavators to new zero-emission con gurations, such as electric powertrains,” said Liebherr Mining Executive VP Oliver Weiss. “ is means that the diesel equipment customers buy today is also future-proofed for many years to come.”
Fortescue is testing a couple of di erent ways to get power to the work sites. e machine in use at Chichester is partially powered by a solar installation. Fortescue installed a 6.6 kV substation and more than two kilometers of high-voltage trailing cable. At another site, the company is testing a hydrogen fuel cell-powered e-excavator.
Fortescue says it plans to deploy more than one gigawatt of solar, another gigawatt of wind energy, and around four gigawatt-hours of battery storage in its quest to reach zero emissions for its iron ore mining operations. e company’s eet of mining equipment that will eventually be electri ed includes 80 excavators, 350 haul trucks and 70 drills.
“We will have two additional electric excavators commissioned by the end of April,” said Fortescue Metals CEO Dino Otranto.
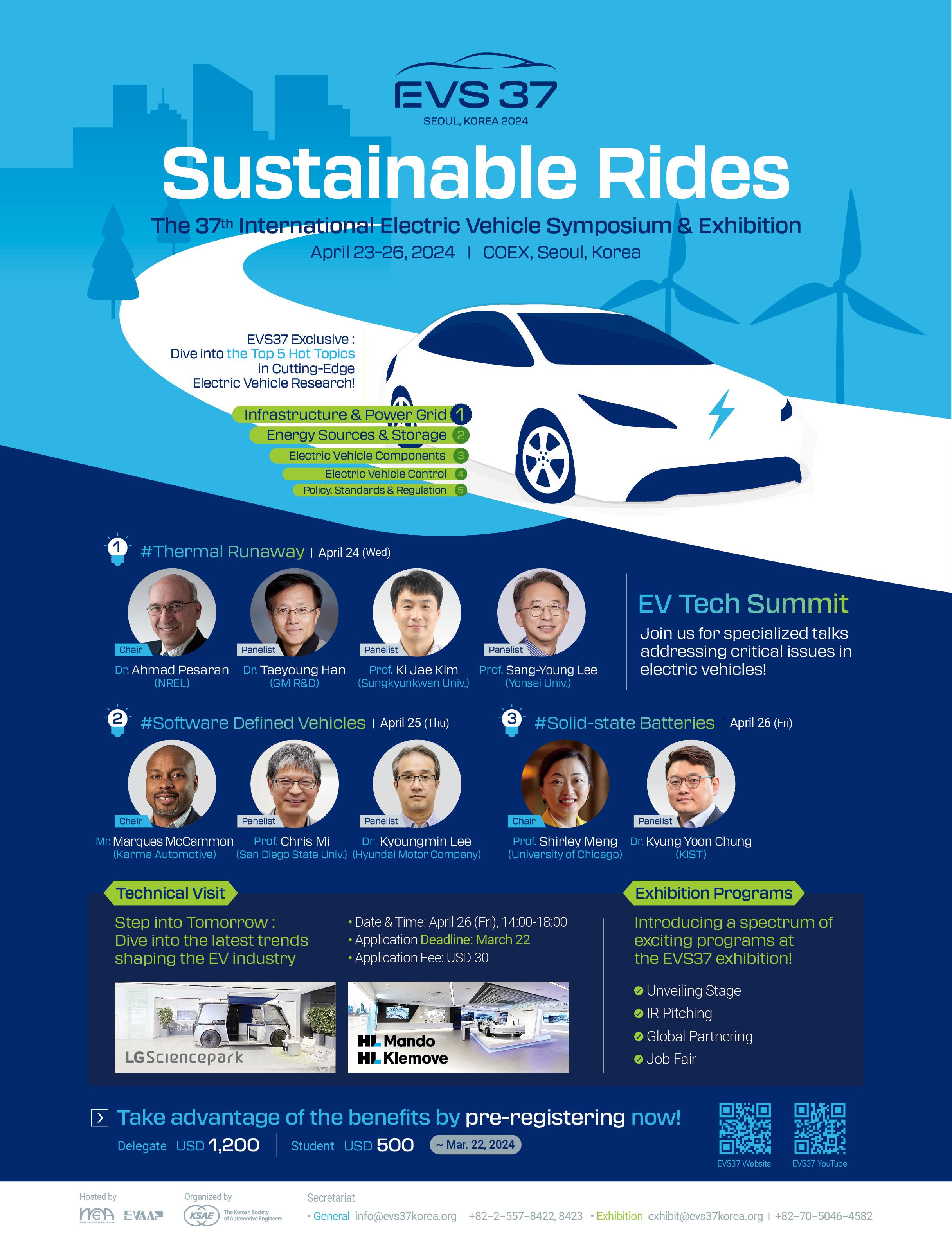

THE VEHICLES
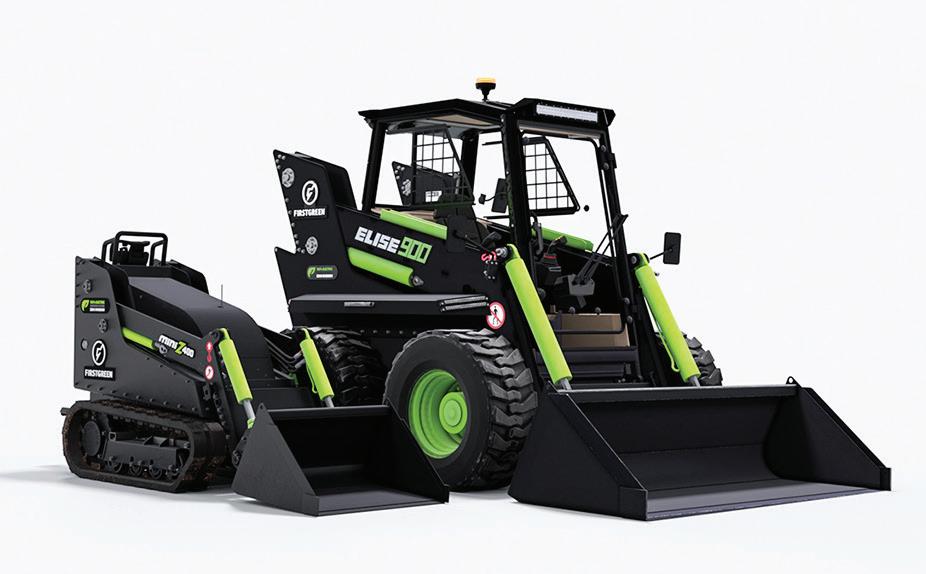
Firstgreen reports growing US demand for its electric skid steer loaders
Electric skid steer loader manufacturer Firstgreen Industries, headquartered in the Czech Republic, reports North American sales growth: More than 120 of its loaders are operating in the US and Canada, and it sells through nearly 20 dealerships in New York, Washington, Missouri, Illinois, Iowa, Ohio and Maryland.
Firstgreen entered the American market in 2021 with US headquarters in Asheville, North Carolina. Sales are geared toward the agriculture, construction and demolition sectors. e company o ers four models in its Elise line as well as the MiniZ, designed to t through a standard doorway. It plans to unveil a cabinless teleoperated loader in 2024 and to begin production in 2025.
“In the US we’ve seen a signi cant spike in interest for our skid steer loaders over the last year, with expanding use cases in waste management, landscaping, power plants, mining and more,” said Marcus Suess, COO of Firstgreen Industries in the US.
Electric trucks and buses show massive sales growth in Europe
e market share of fully electric trucks and buses is growing at an impressive pace in Europe, according to a new report from the International Council on Clean Transportation (ICCT). e ICCT reports that 11,000 zero-emission heavy-duty vehicles were sold in Europe in 2023, more than double the number sold in 2022, and that 18% of all buses and coaches sold in the EU in 2023 were electric. It says 5% of light- and medium-duty trucks and 1% of heavy-duty trucks sold were electric.
e real stars of the show are city transit buses, which currently represent one of the best use cases for EVs. According to the ICCT, in Q4 of 2023, 43% of all new city buses sold in Europe were fully electric. In the overall bus market, including long-haul interurban coaches, electric bus market share was “only” 22%—but that represents a ve-fold increase in market share since 2019.
EU member states are by no means on the same track when it comes to electrifying their bus eets. In 2023, battery-electric transit buses made up 100% of purchases in Luxembourg, Ireland and Denmark, and 98% in the Netherlands. In Germany, Austria and Belgium, by contrast, diesel buses still made up 75% of new bus sales. e market share of electric trucks is far smaller than that of buses, but it’s growing fast. e ICCT tells us that light- and medium-duty electric truck sales in Europe increased by 200% year-on-year in 2023. e Ford E-Transit is the leading zero-emission model.
Sales of heavy-duty trucks (over 12 tonnes GVW) are also seeing rapid growth—some 2,600 were sold in 2023, up from 820 sold in 2022.
According to the ICCT, Volvo Group (Volvo Trucks and Renault Trucks) produced 70% of all the electric heavy-duty trucks sold in Europe in 2023. e group’s sales of electric heavy-duty trucks for the EU market are now double those of legacy diesel trucks.
Another recent study found that, in addition to already having far lower running costs, electric trucks will hit purchase price parity with comparable diesel models much sooner than predicted, thanks to plummeting battery costs.
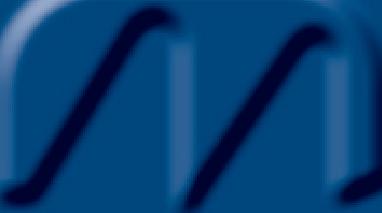
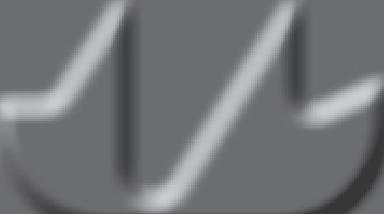
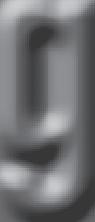
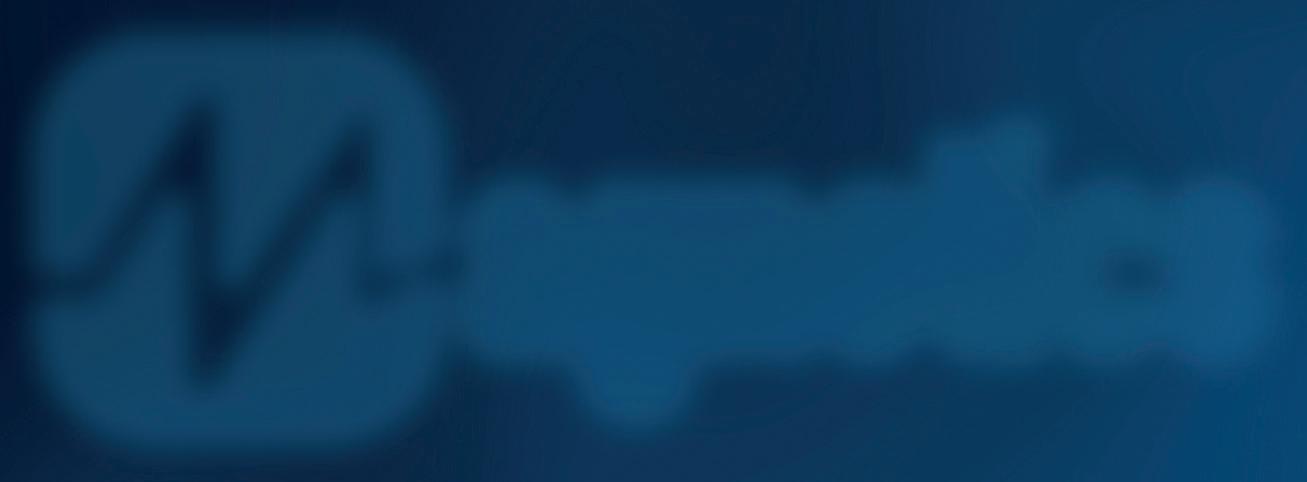
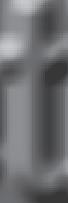

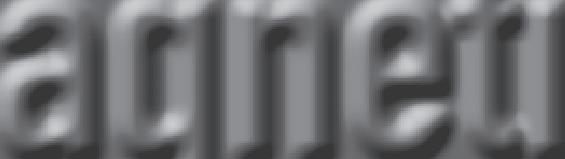

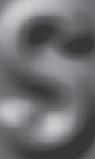

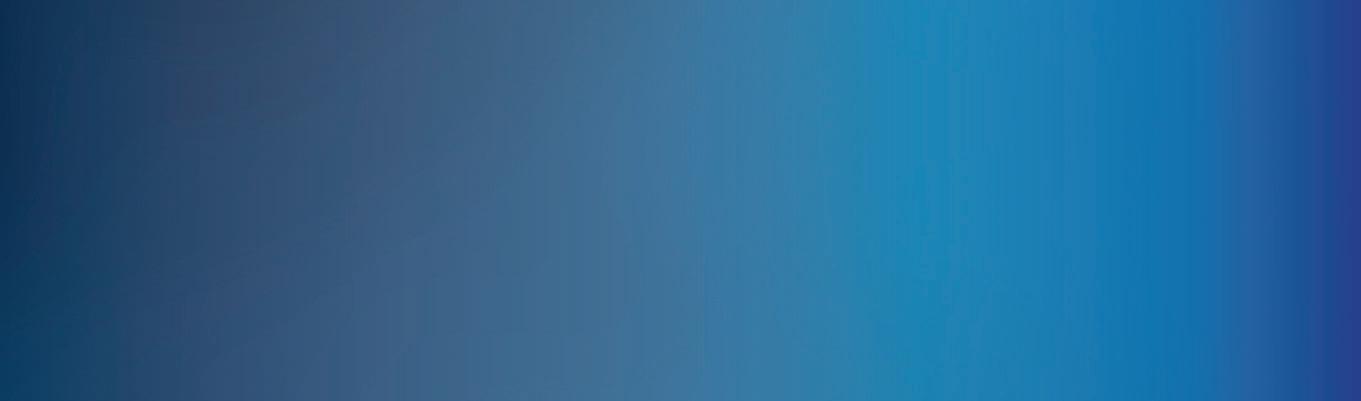


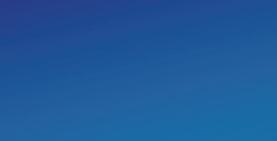





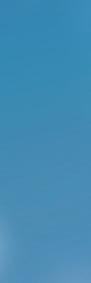

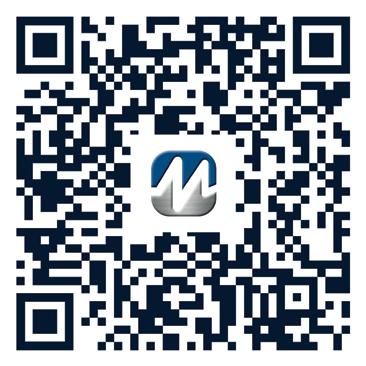



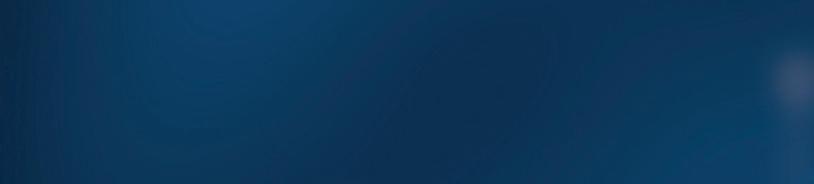

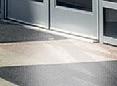



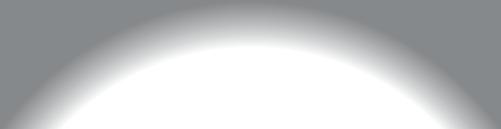





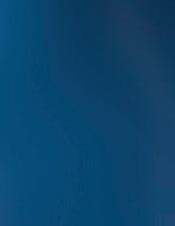
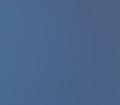
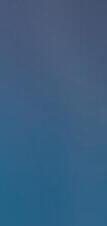
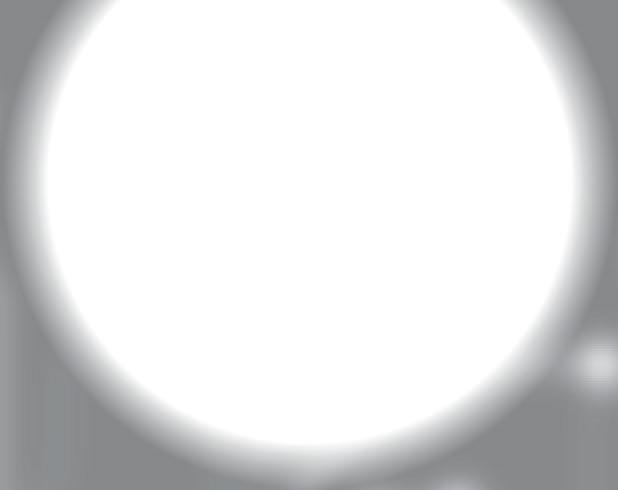




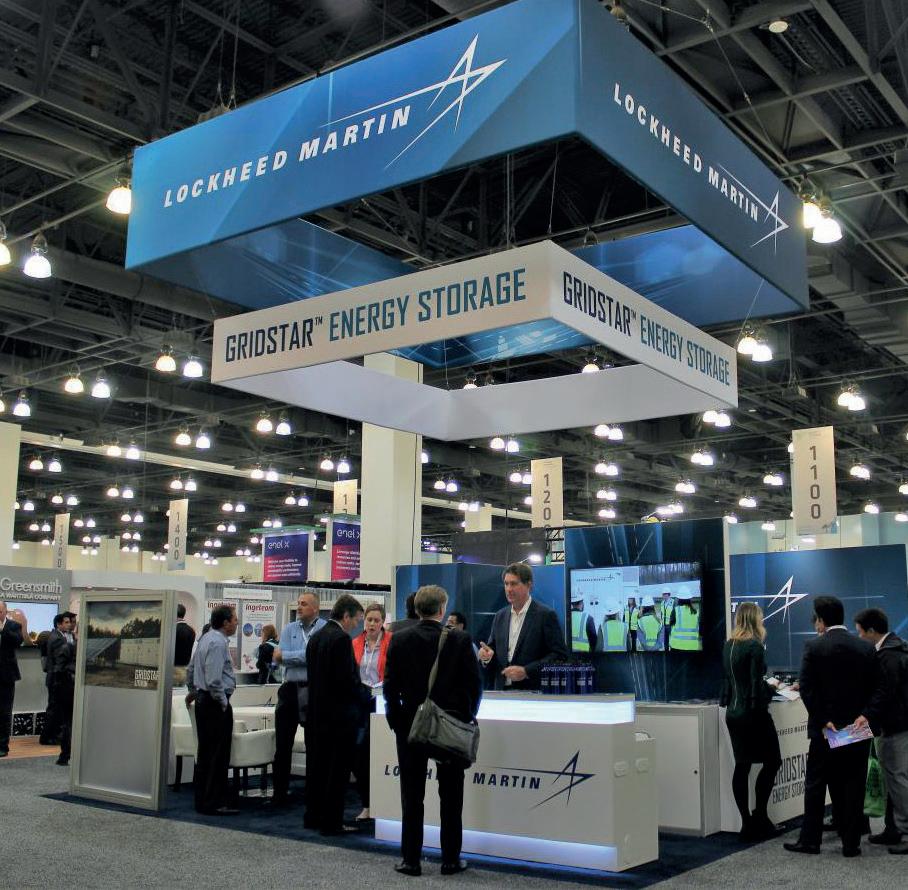
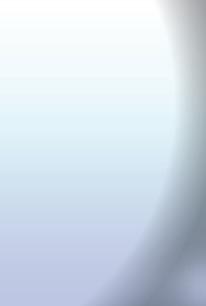



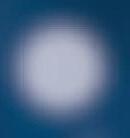



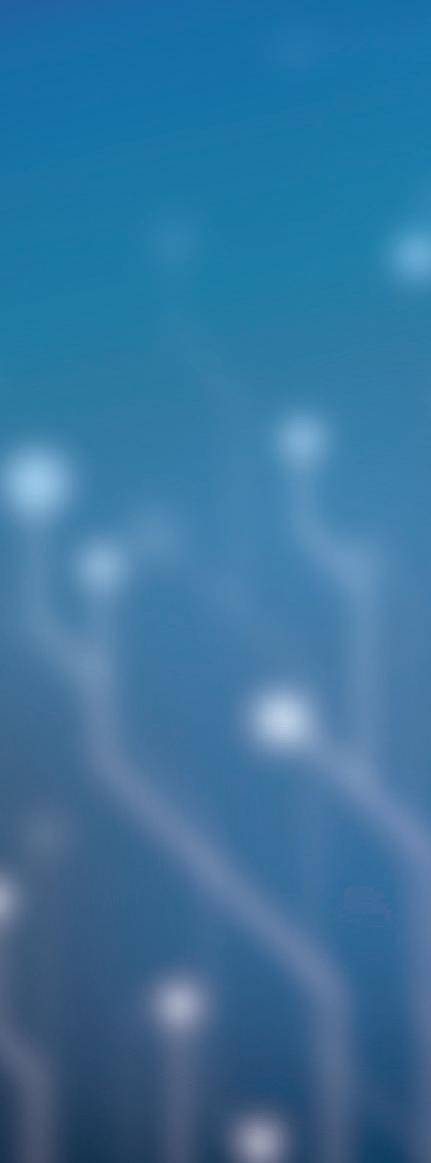




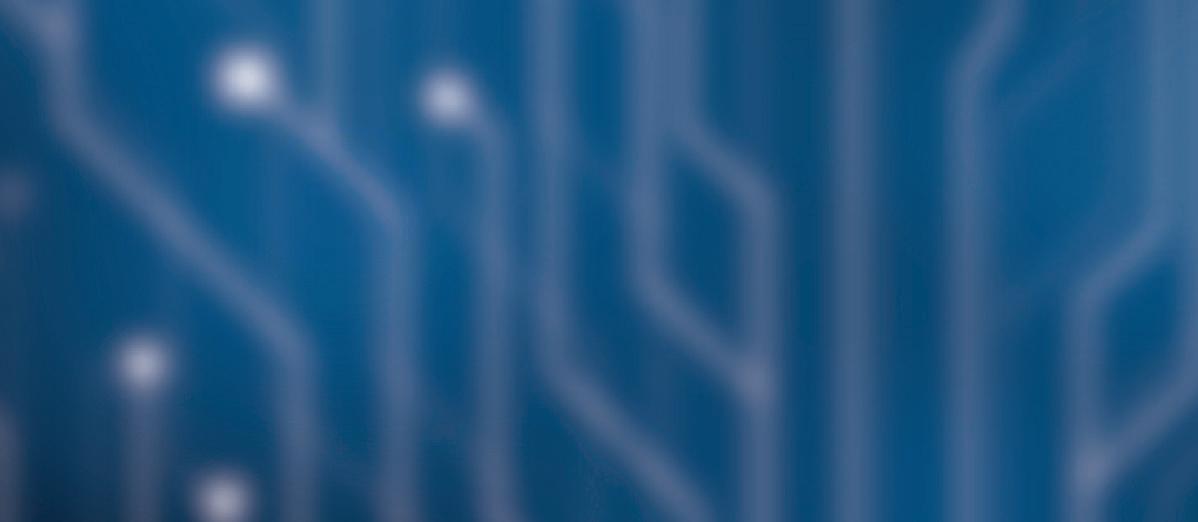
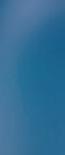


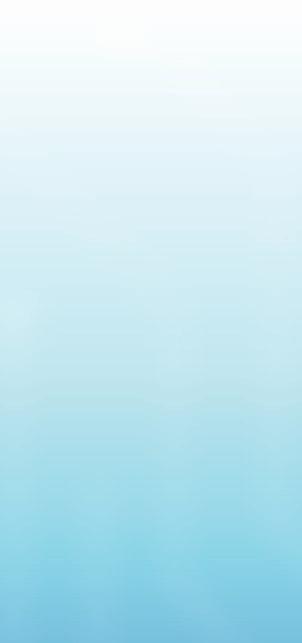






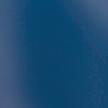

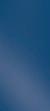


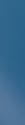
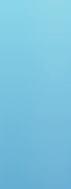
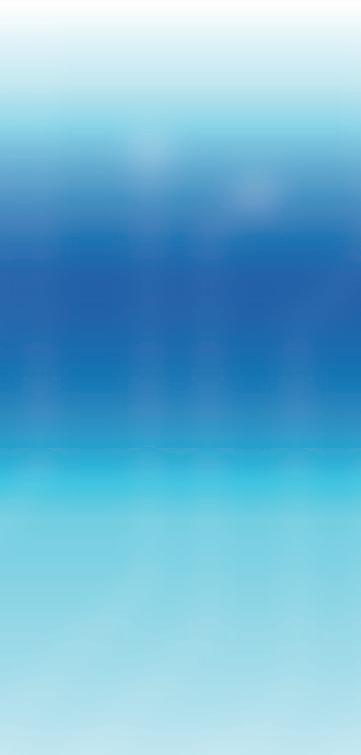



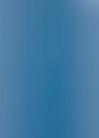

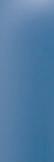
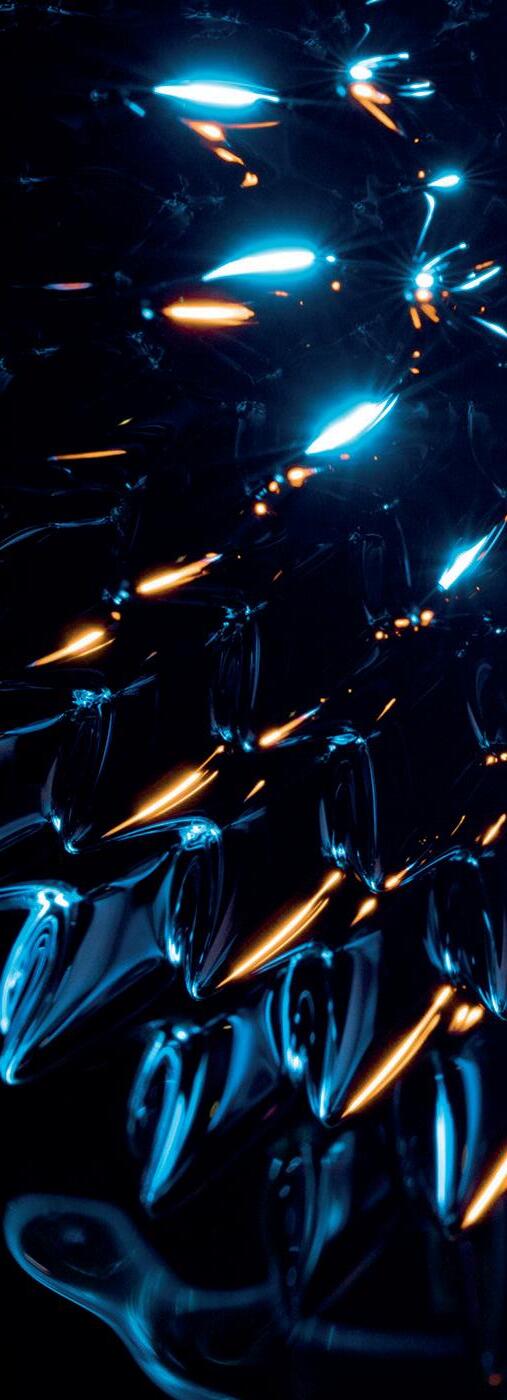

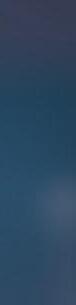

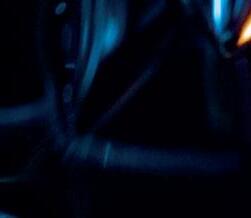

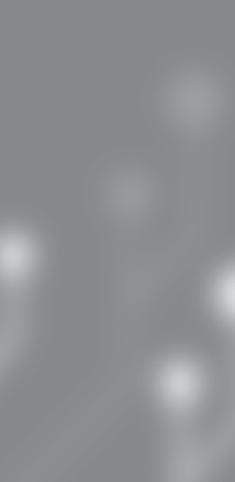



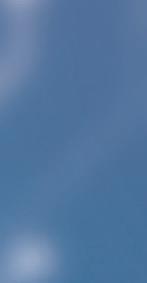
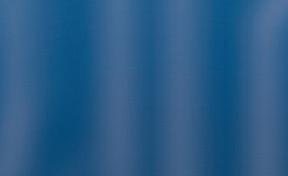


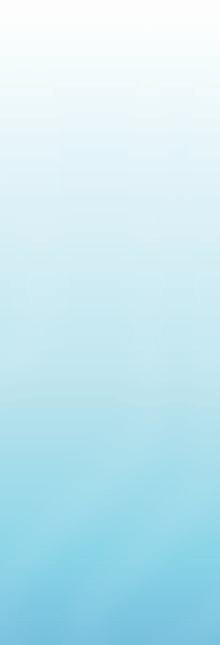


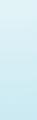

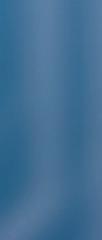




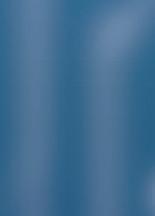
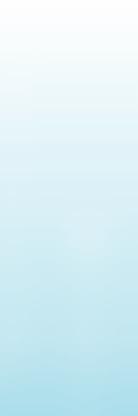


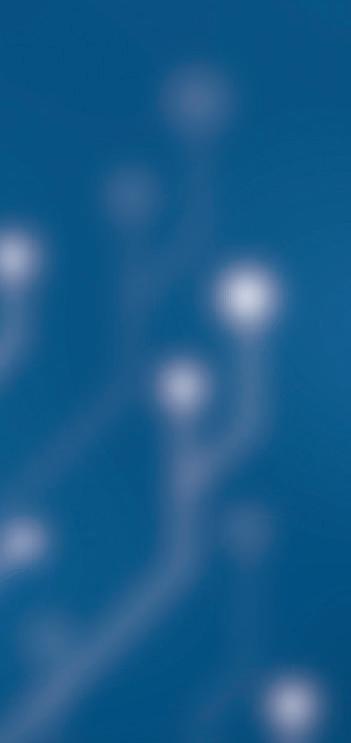
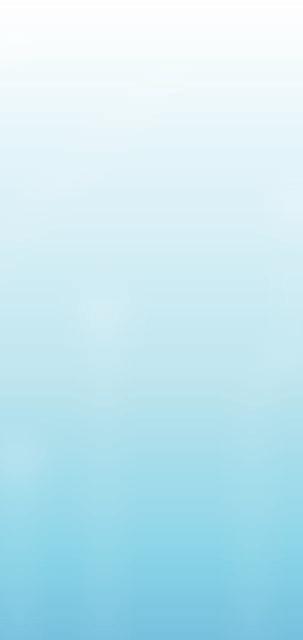
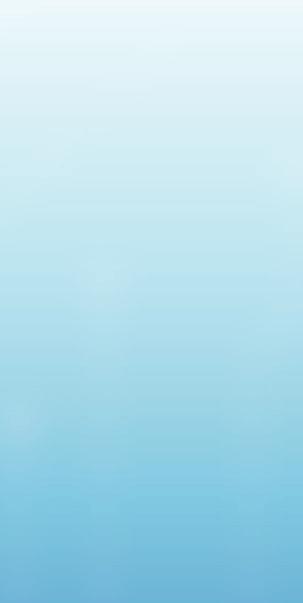
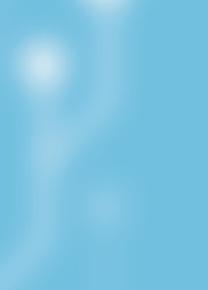
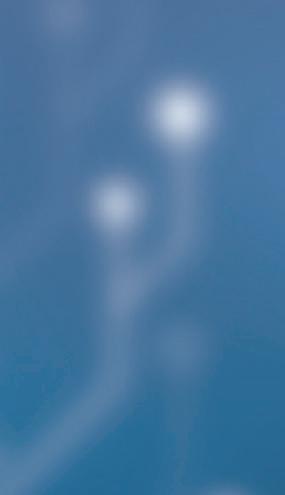
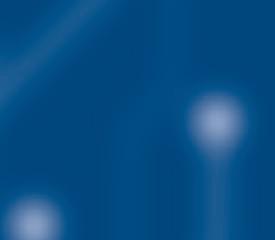

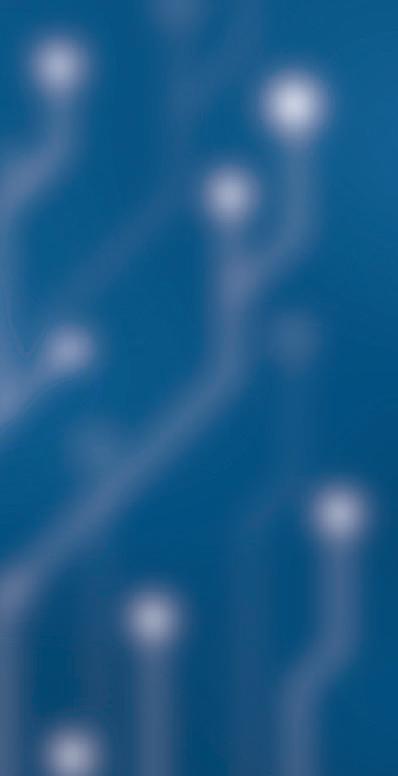

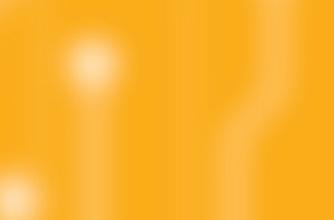
THE VEHICLES
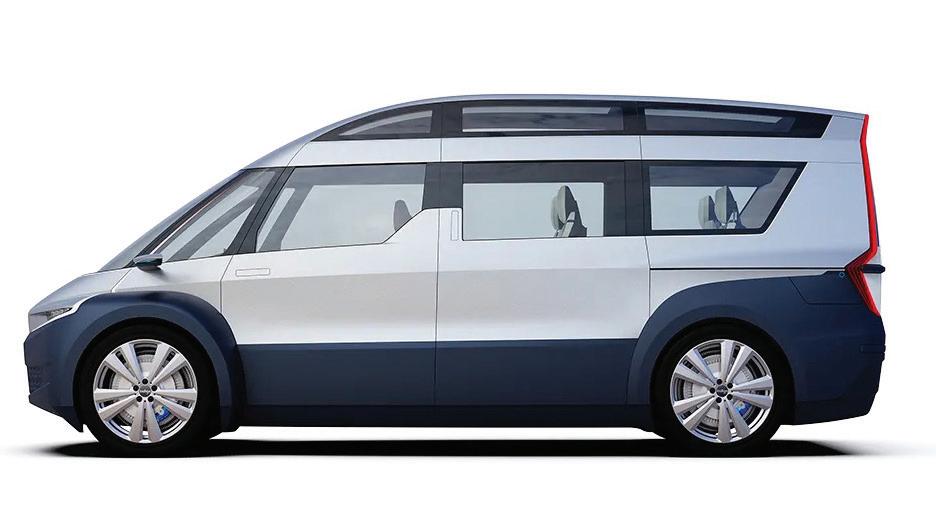
Foxconn invests in light utility EV maker Indigo Technologies
US light utility EV maker Indigo Technologies has secured an investment from Taiwanese multinational electronics manufacturer Hon Hai Technology Group, also known as Foxconn.
e investment will help the company to accelerate the development of its smart EV technologies for light utility EVs, which are designed for ride hailing, delivery and autonomous transportation applications.
Building on its proprietary road-sensing SmartWheels technology, invented by a team out of MIT, Indigo is using robotics hardware and so ware that integrates drivetrain and suspension as a technology package to enable a new vehicle architecture.
e company’s rst SmartWheels-powered EV, the FLOW, will have 180 cubic feet of space and a range of approximately 200 miles. Priced at around $37,000, it is expected to be available in late 2026. Indigo’s smaller model, the DASH, will have 90 cubic feet of space and a range of 140 miles. It will be priced at around $27,000 and be available for delivery in 2025.
“Our cities, citizens and businesses need a ordable and desirable EVs that improve safety, utility and comfort,” said Indigo CEO Will Graylin.

Hyster to supply electric terminal tractors to APM Terminals in Alabama
Hyster, a US manufacturer of forkli s and materials-handling equipment, has agreed to provide 10 battery-powered terminal tractors to shipping company APM Terminals at its facility in Port of Mobile, Alabama.
e tractors are part of APM’s $60-million investment in port equipment electri cation pilots, and are scheduled to be delivered this year. Each has a 182,000-pound gross combined weight rating and features a 260 kWh battery pack that provides approximately 9.5 hours of continuous run time. e tractors were developed in collaboration with Capacity Trucks and will be manufactured at its Texas facilities.
Operating as a gang, the tractors will be used to move laden and unladen containers between the ship-to-shore crane and the yard at APM Terminals Mobile, which is a hub connecting sea, road and rail transport on the Gulf Coast.
“We are seeing a clear demand for zero-emission port equipment, including terminal tractor options. Our history of electrifying forkli s and our work to electrify container handling equipment positions us to bring expertise and learnings to terminal tractors,” said Niek Willems, Manager, Big Truck Global Accounts at Hyster.


Co-located with:
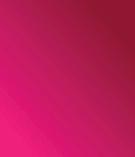


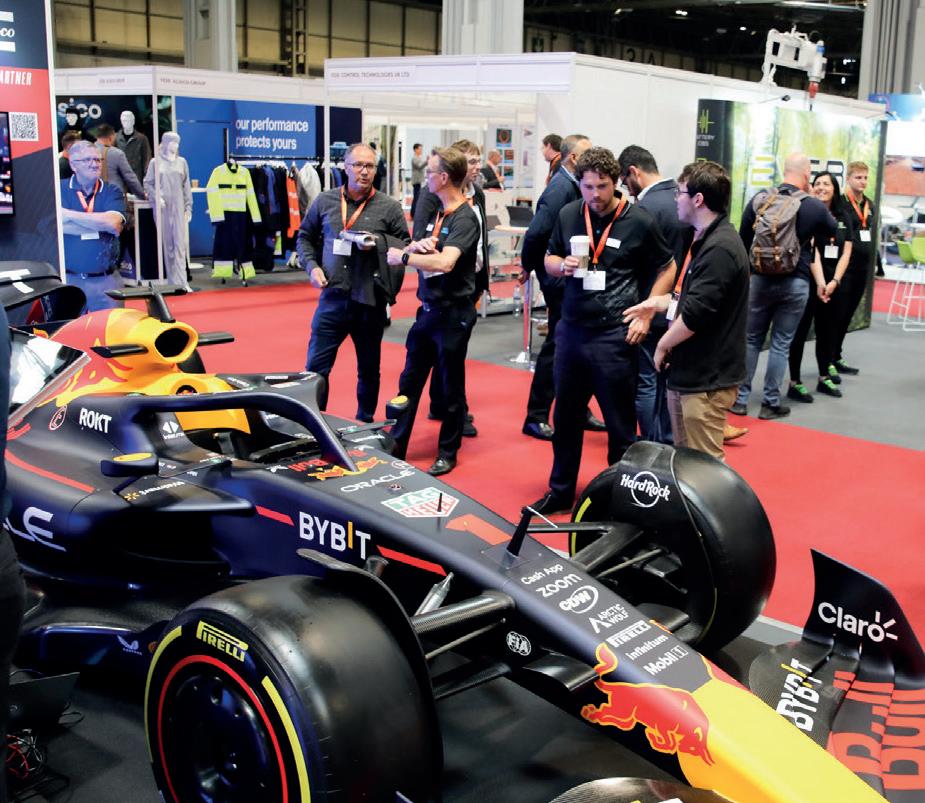
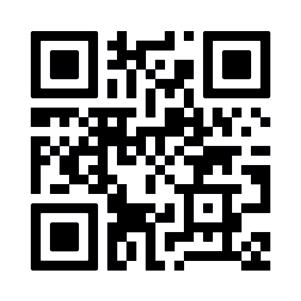


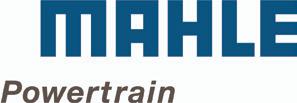
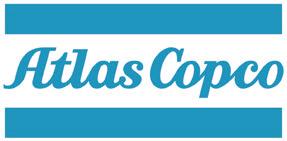

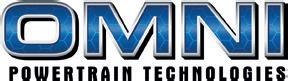
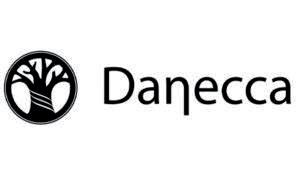
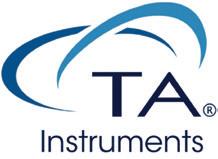

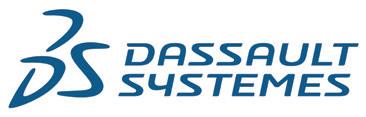

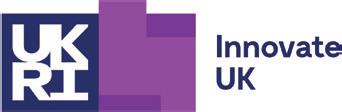
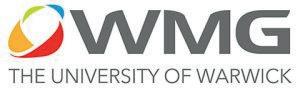

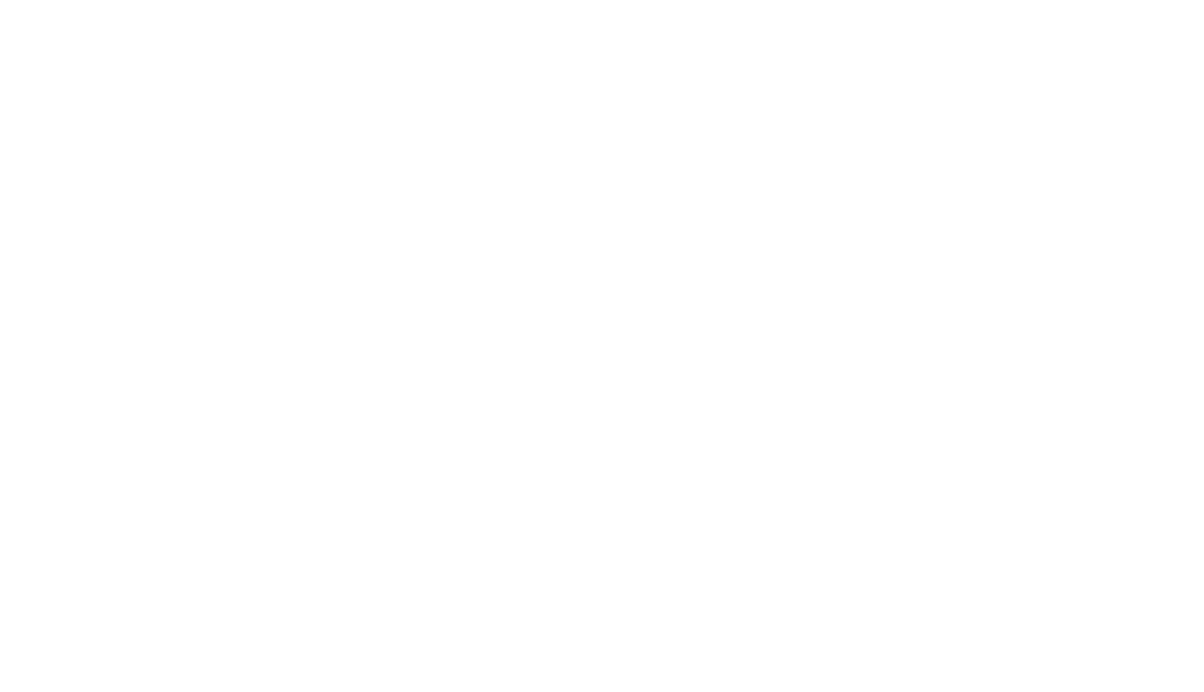
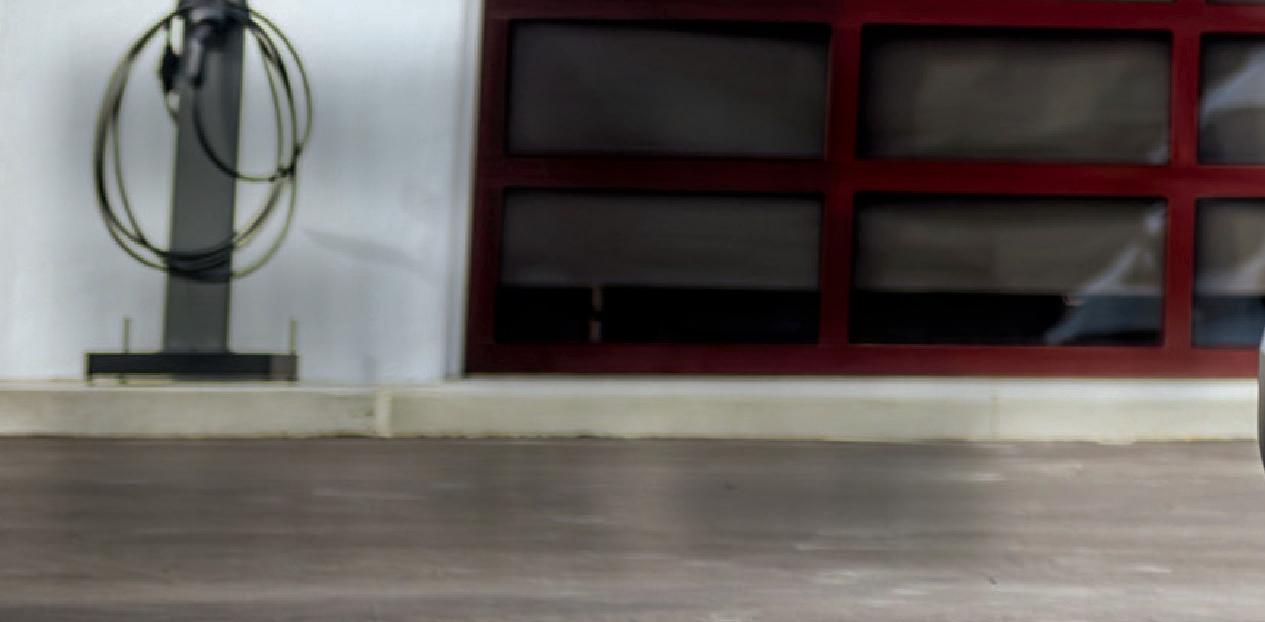
RAM PROMASTER EV BRINGS DETROIT’S
THIRD MAKER INTO ELECTRIC VANS
By John Voelcker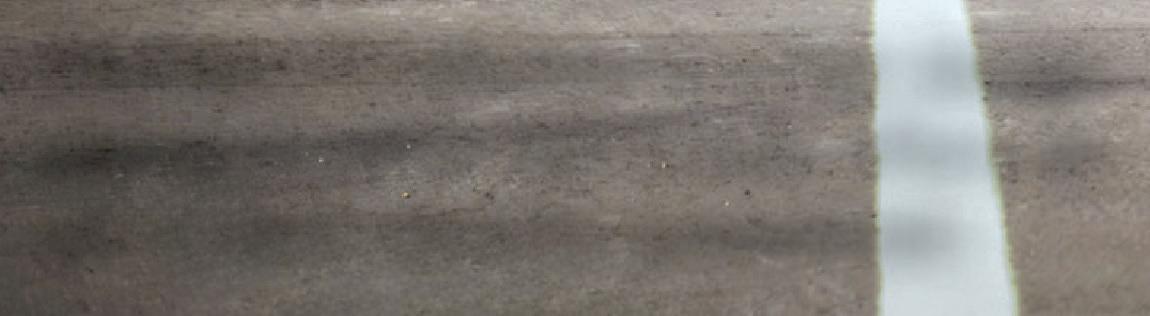
The Ram ProMaster is a Fiat design dating to 2014, but it now offers an up-to-date electric powertrain







THE VEHICLES
In January, Stellantis said its Ram truck brand would start selling the ProMaster EV, a battery-electric model of the ProMaster van that it restyled and updated for 2023. at van, launched in 2014 as the Fiat Ducato, is sold under multiple brands in Europe and elsewhere—but in North America, the company’s truck brand is Ram (no, not Dodge). So we’ve had Ram ProMasters since the 2015 model year, replacing the Dodge Sprinter van based on a design from previous owner Mercedes-Benz. Got all that?
It’s long been known that urban and suburban deliveries are one of the best duty cycles for battery-electric vehicles. is reporter recalls a presentation from the long-vanished British rm Modec, a startup making light delivery vans, which said even back in 2009 that eet managers would see a lifetime payback on what were then very expensive BEV cargo vans.
e Ram ProMaster EV’s per-mile operating costs are undoubtedly just a fraction of those for its siblings powered by the company’s 3.6-liter V6 gasoline engine, but the new EV is still quite pricey. It starts just under $90,000, including the mandatory destination fee, while the cheapest gasoline Cargo Van version costs half that. e gas version wins on payload, too, holding 700 to 1,500 pounds more cargo than the EV’s maximum of up to 3,020 pounds.
Taking their time
It’s taken a while to get electric vans into the US market at all. Ford announced its E-Transit only in November 2020, and deliveries started in February 2022. GM started an entirely new brand—BrightDrop—in 2021 to sell not just EV commercial vans but electric cargo containers that work with them, all based on its new Ultium EV platform. Production of those vans was halted in September 2023 as GM struggled to get its higher-volume Ultiumbased passenger vehicles into production, but resumed in April.
at makes Ram’s announcement signi cant, because Stellantis is the last of the 2.5 Detroit automakers to o er a battery-electric van for the delivery eets found throughout the US.
None of the “import” brands currently o er light commercial EVs in the US. Nissan never o ered its e-NV200 compact electric van here (and the gasoline NV200 itself is now gone too). A er an abortive e ort to o er a third-party electric conversion of the rst-
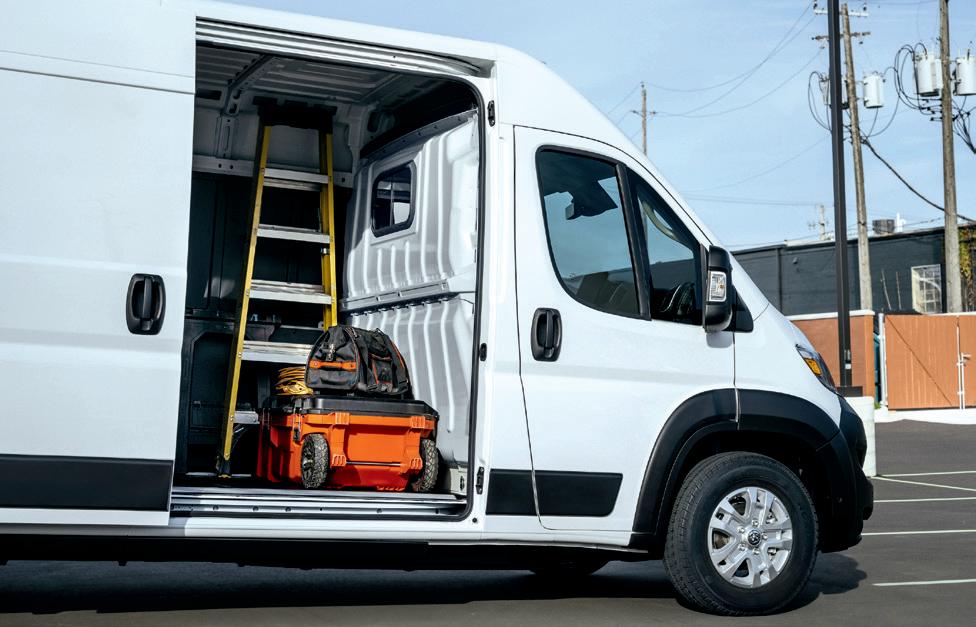
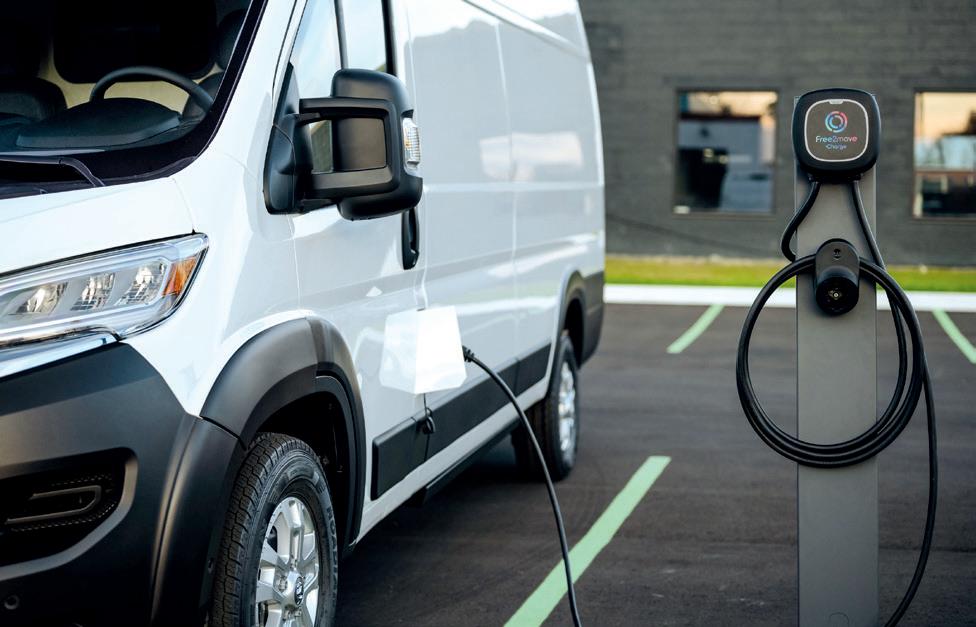



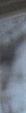

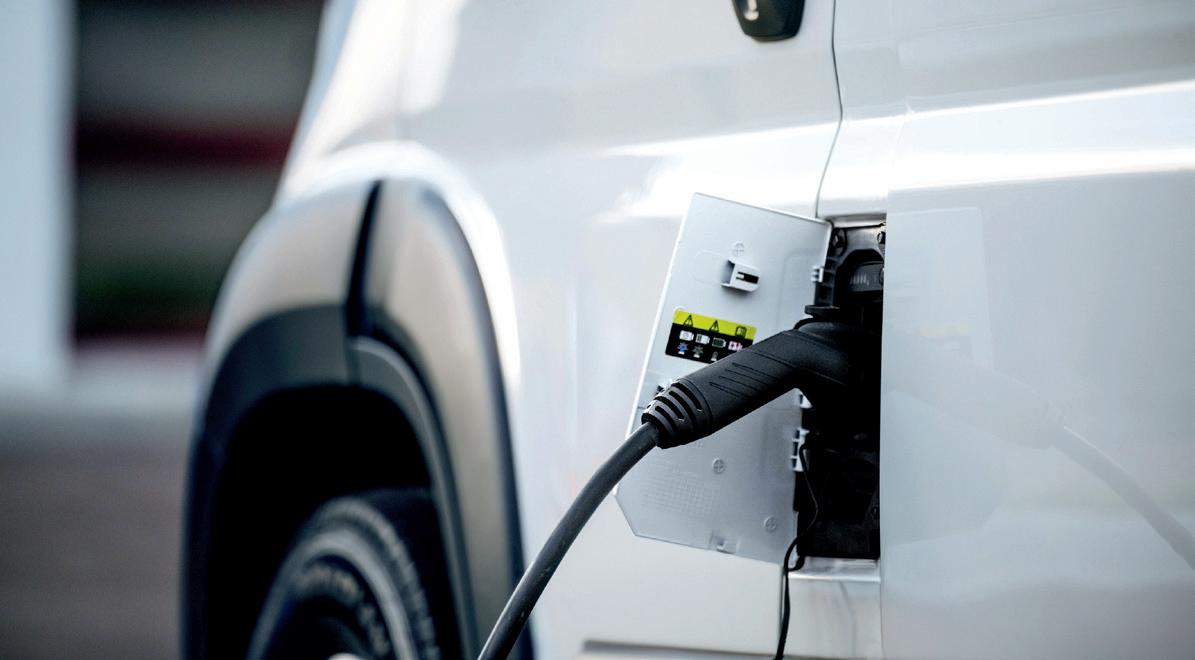

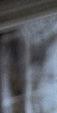
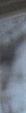

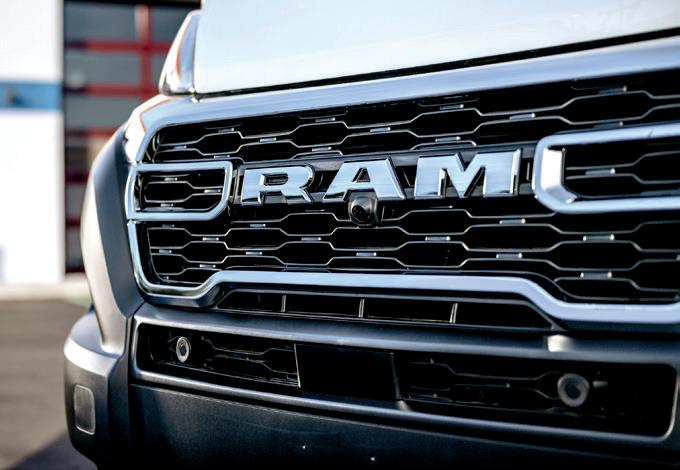
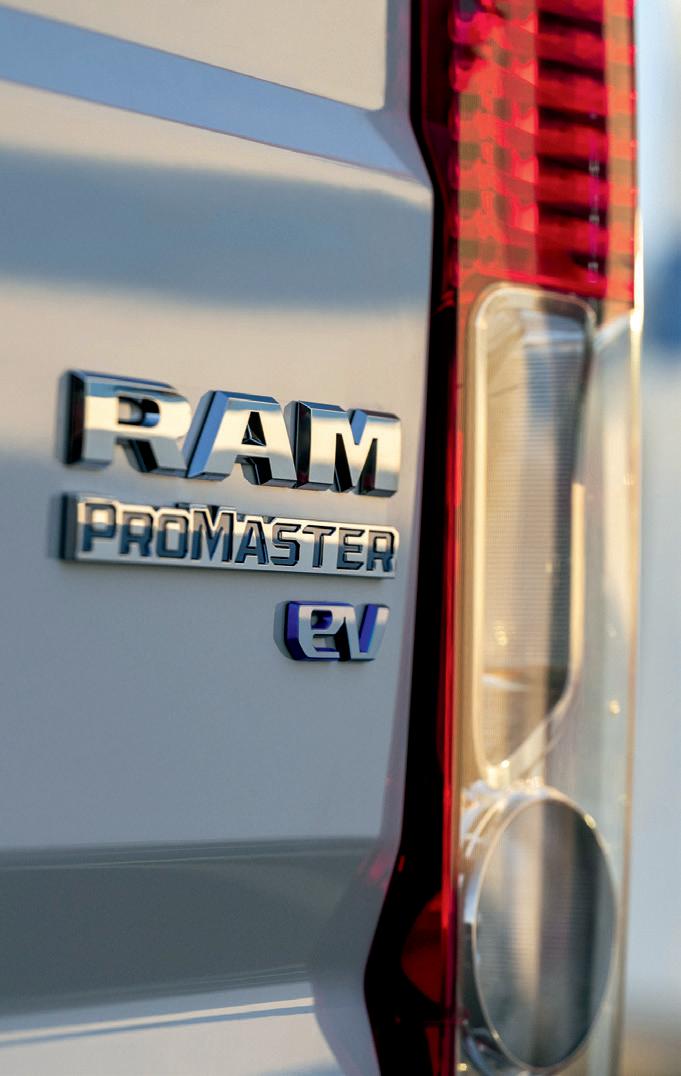
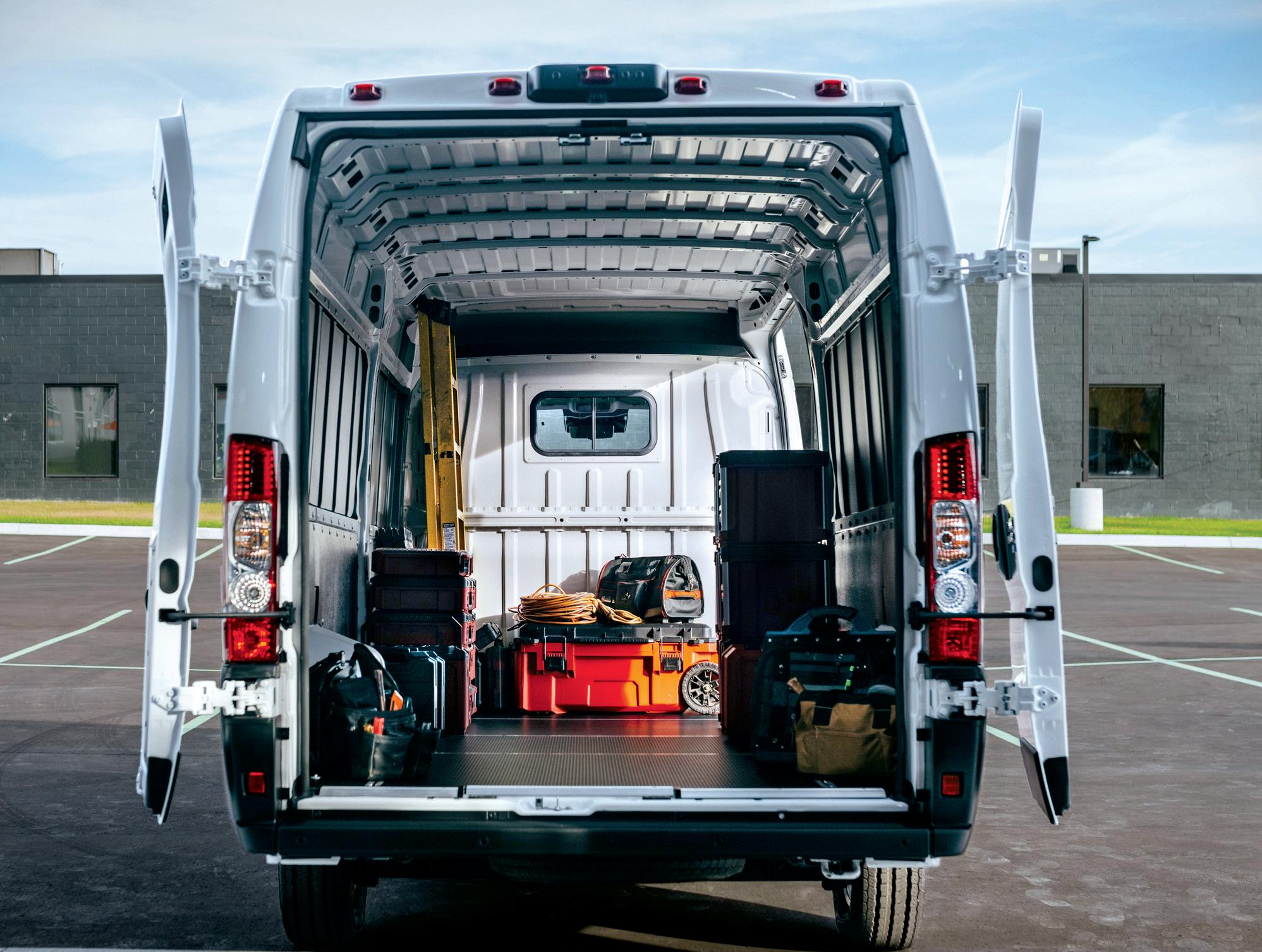

THE VEHICLES
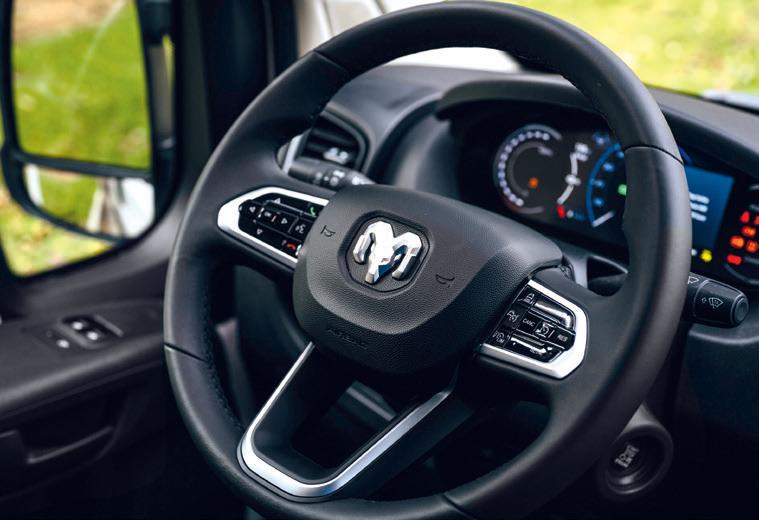
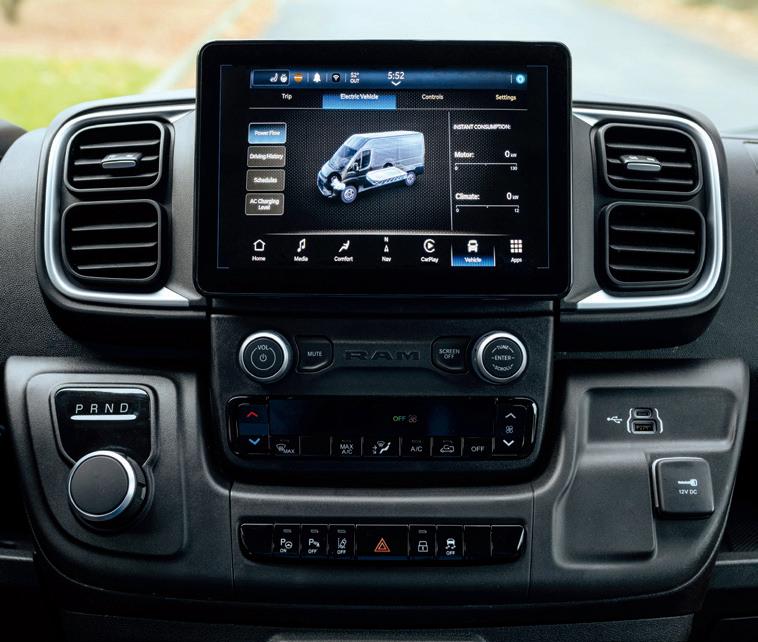

generation Transit Connect, Ford hasn’t done another compact EV delivery van. (Now it’s even withdrawn that compact van from the US market, shortly a er Ram itself killed o its ProMaster City counterpart in 2023.)
Ram is importing its ProMaster EVs from Saltillo, Mexico, while Ford builds E-Transit vans at its Kansas City Assembly plant in Missouri. GM’s BrightDrop vans are assembled in Ingersoll, Canada.
Target: Ford E-Transit
e specs on the ProMaster EV seem designed to go head-to-head with the E-Transit, which Ford just updated for 2024. e ProMaster EV’s 110-kilowatthour battery pack is larger than the E-Transit’s newly enlarged 89 kWh, and Ram quotes a “targeted range” of up to 162 miles “in city driving” against the Ford’s estimated 159 miles (for low-roof cargo vans).
e Ram’s battery powers a 200 kW (268 hp) motor driving the front wheels, rated at 302 lb- of torque. All-wheel drive is not o ered. e Ford, while almost identical on power, has a rear-mounted motor that’s rated at 198 kW (266 hp) and produces 317 lb- of torque.
Unusually, Ram o ers a choice of no less than four
The ProMaster EV’s 110 kWh battery pack is larger than the Ford E-Transit’s newly enlarged 89 kWh, and Ram quotes a “targeted range” of up to 162 miles “in city driving” against the Ford’s estimated 159 miles (for low-roof cargo vans).
DC fast charging speeds: 50 kW, 85 kW, 125 kW and 150 kW. (In comparison, the Ford E-Transit added a second onboard charger for 2024, boosting its peak charging power to 176 kW from the previous 115 kW peak.) We’re not aware of any other maker with the variety of charging speeds o ered by Ram. Ram also o ers a Level 2 wall charging station capable of delivering up to 11 kW.
Specs for commercial users
e ProMaster EV comes in two versions: the Delivery model, with a “super-high” roof and an aluminum rollup rear door, and two Cargo models with conventional rear “church doors,” one with a 12-foot cargo length and one with 13 feet. e Delivery model also eliminates the side cargo doors and even the passenger seat,


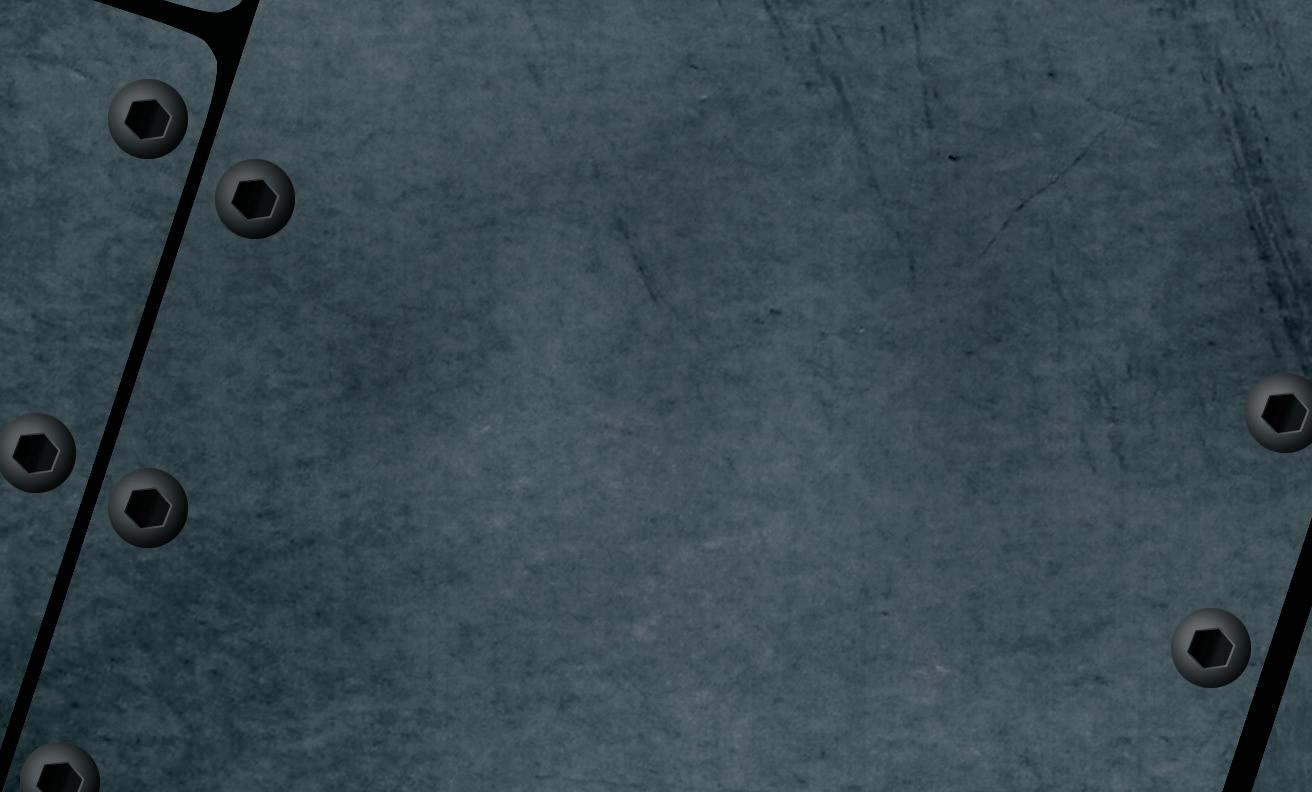
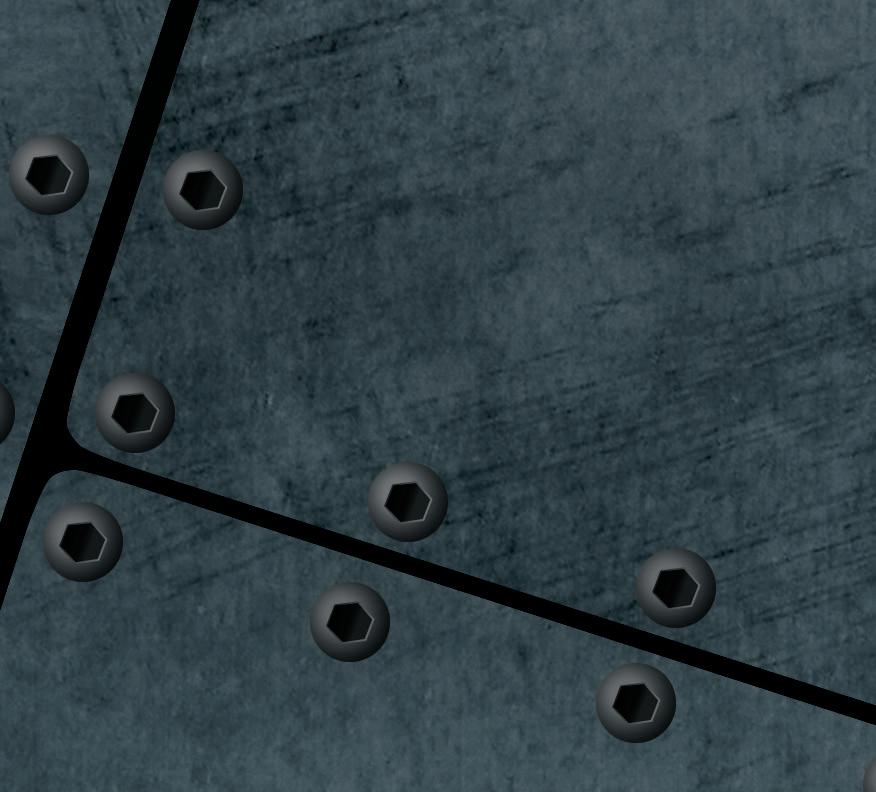
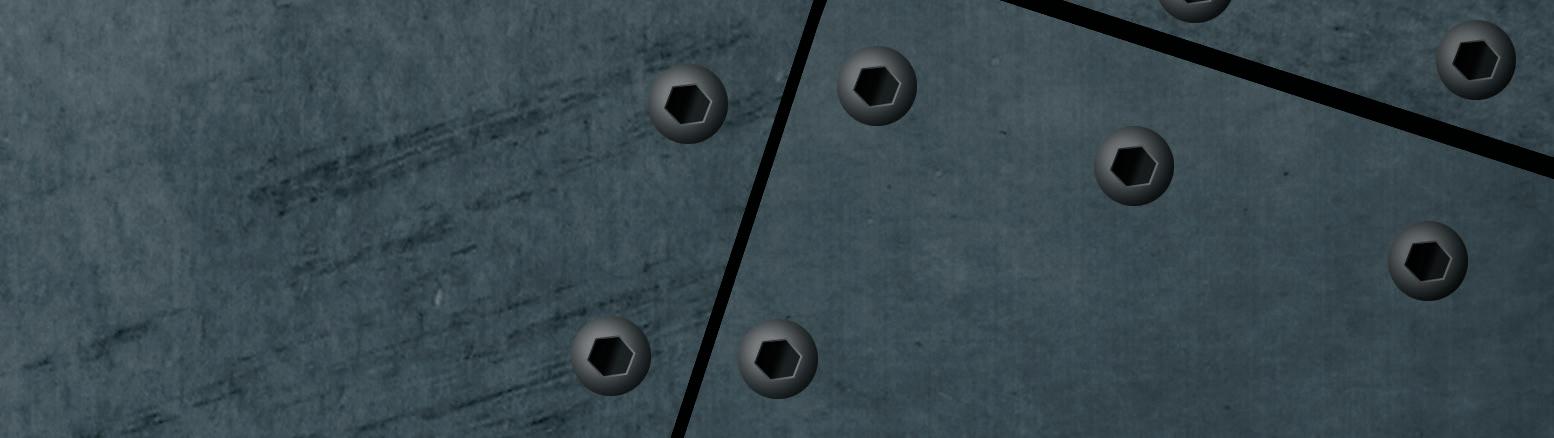
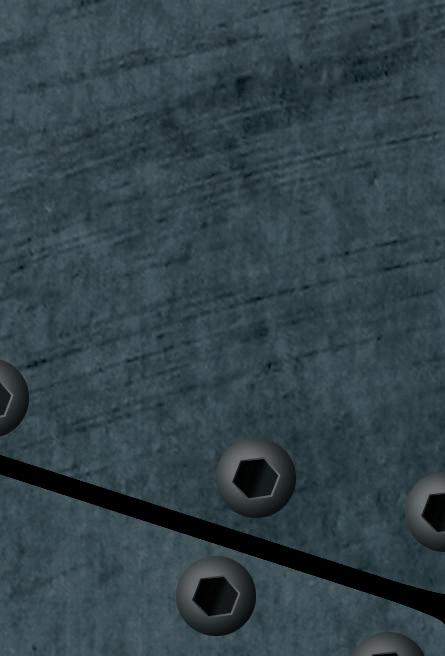
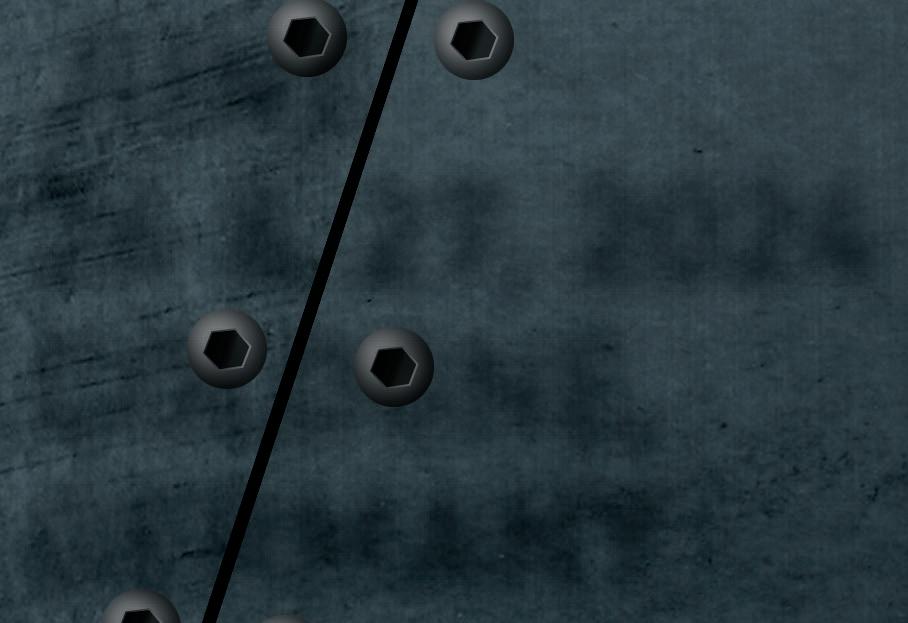
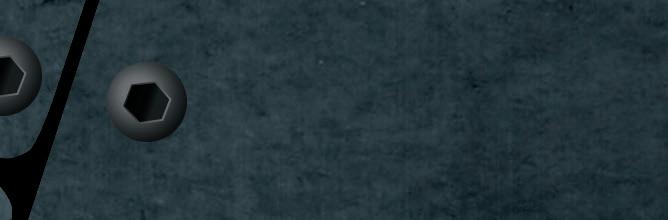
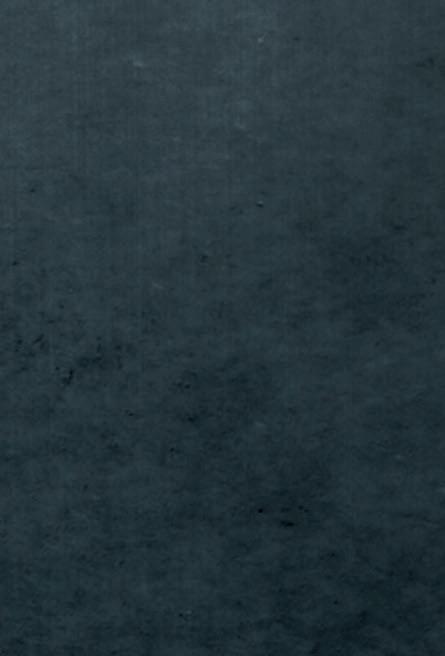
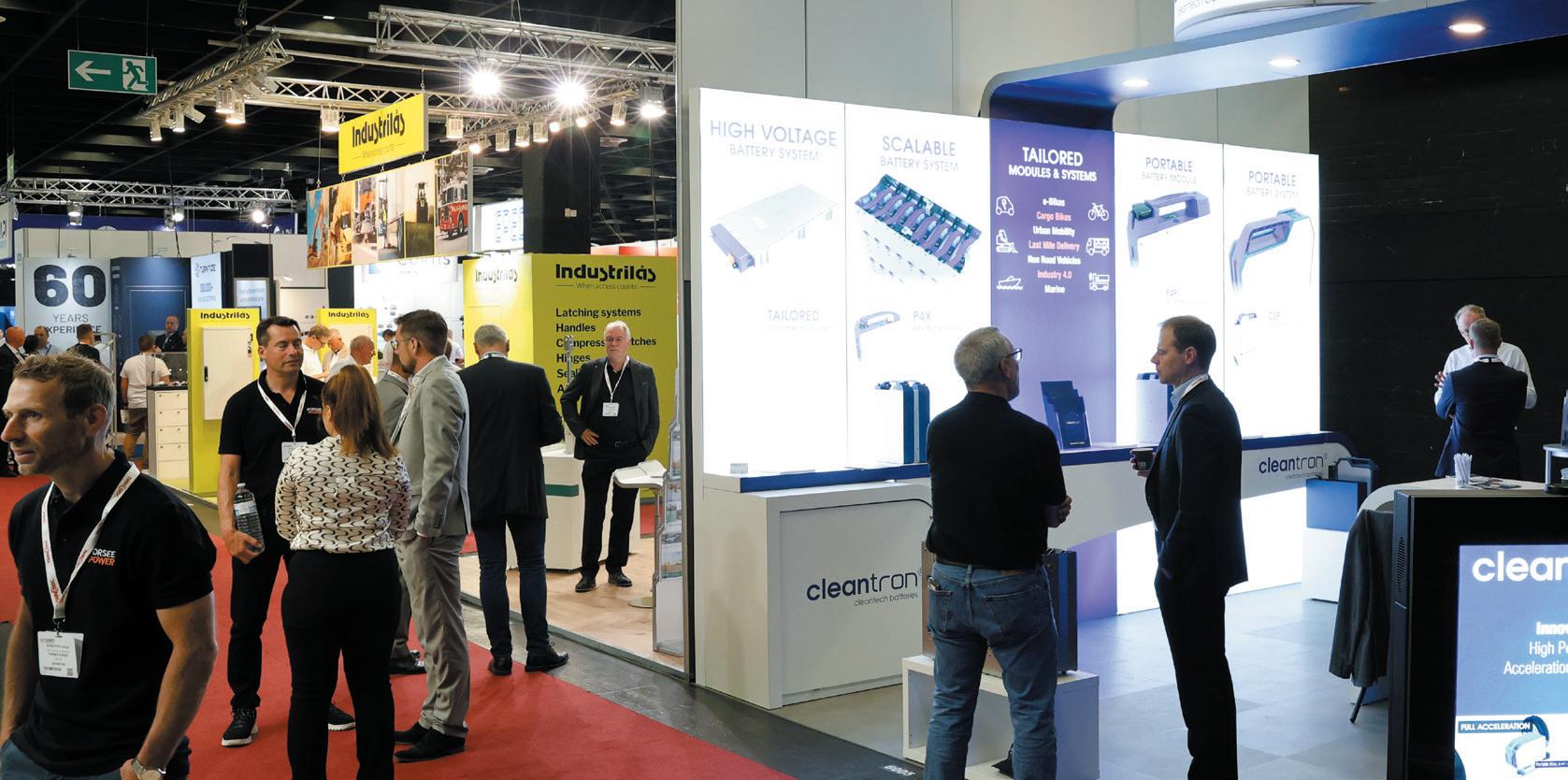
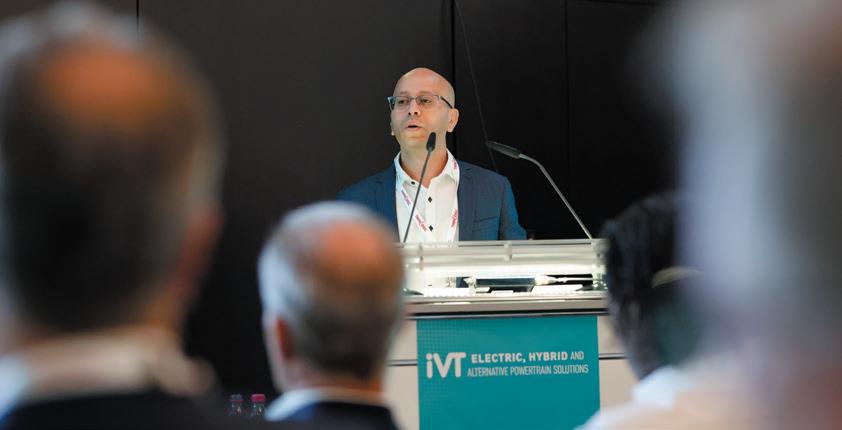

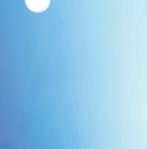

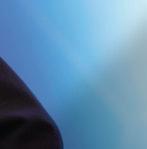
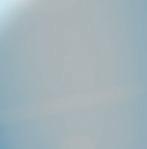
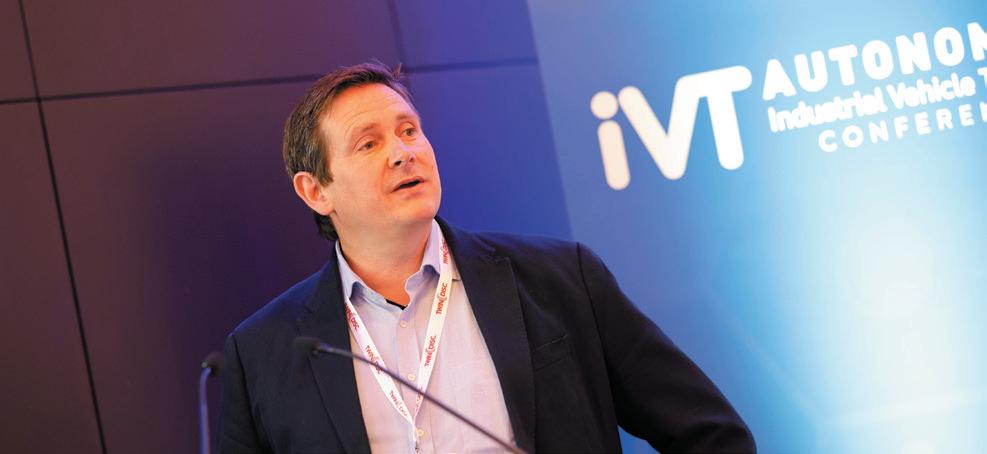
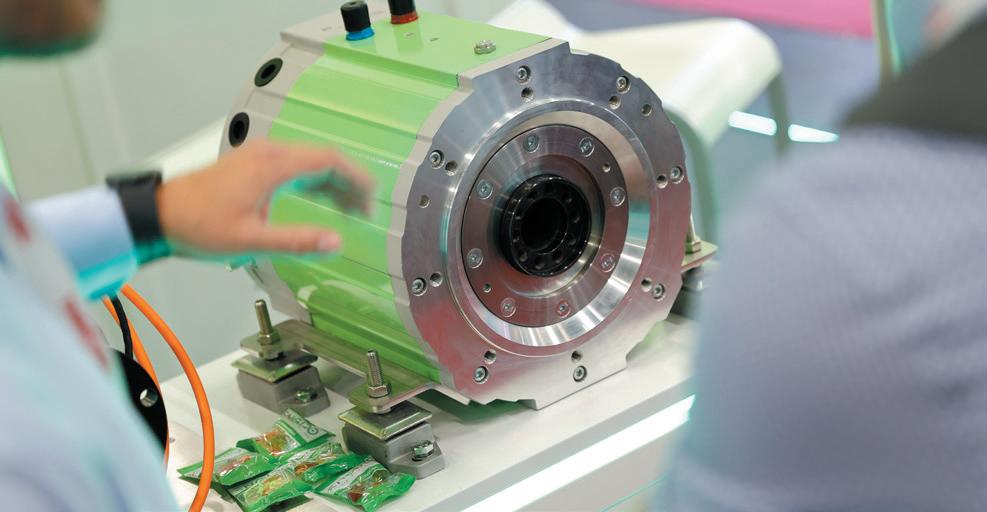
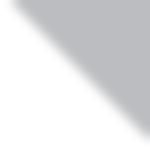
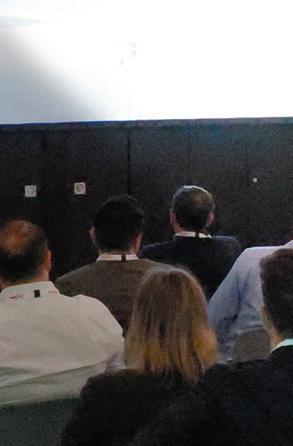

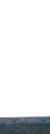
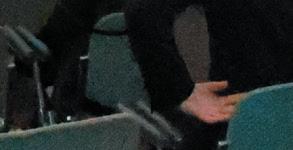
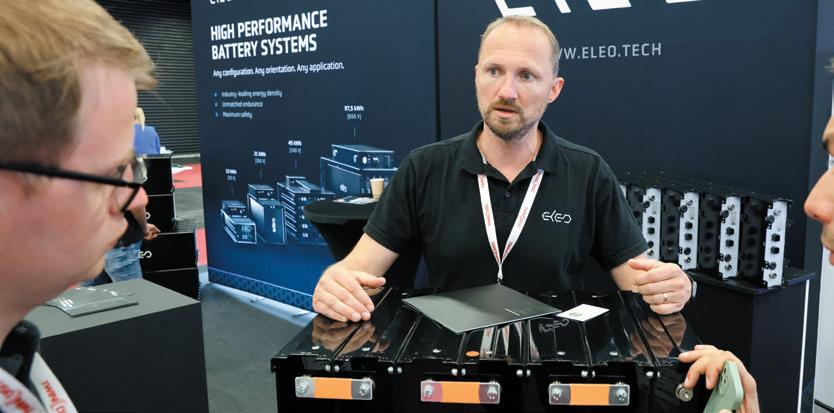
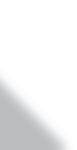
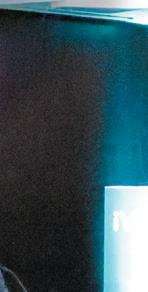
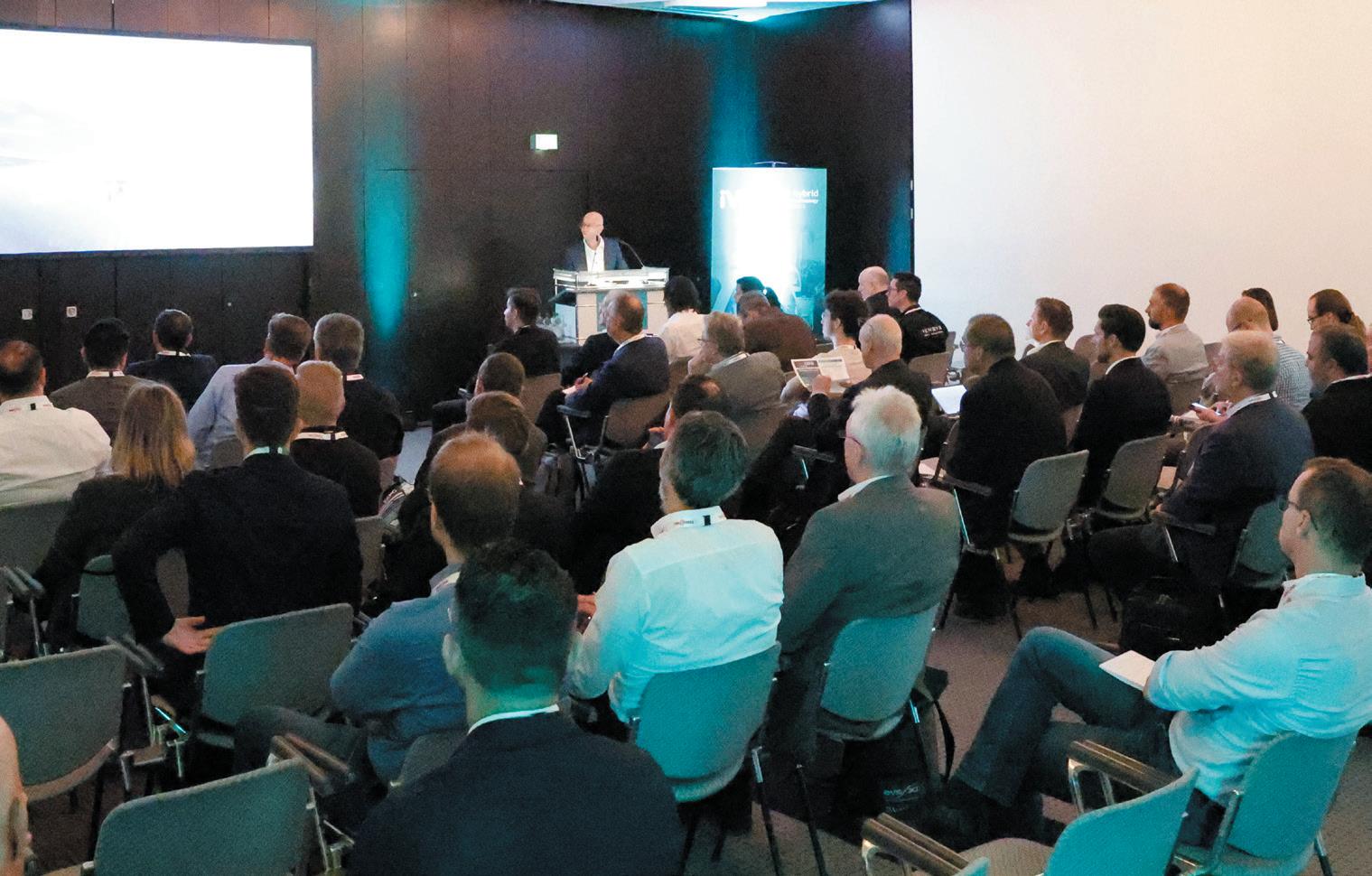

THE VEHICLES


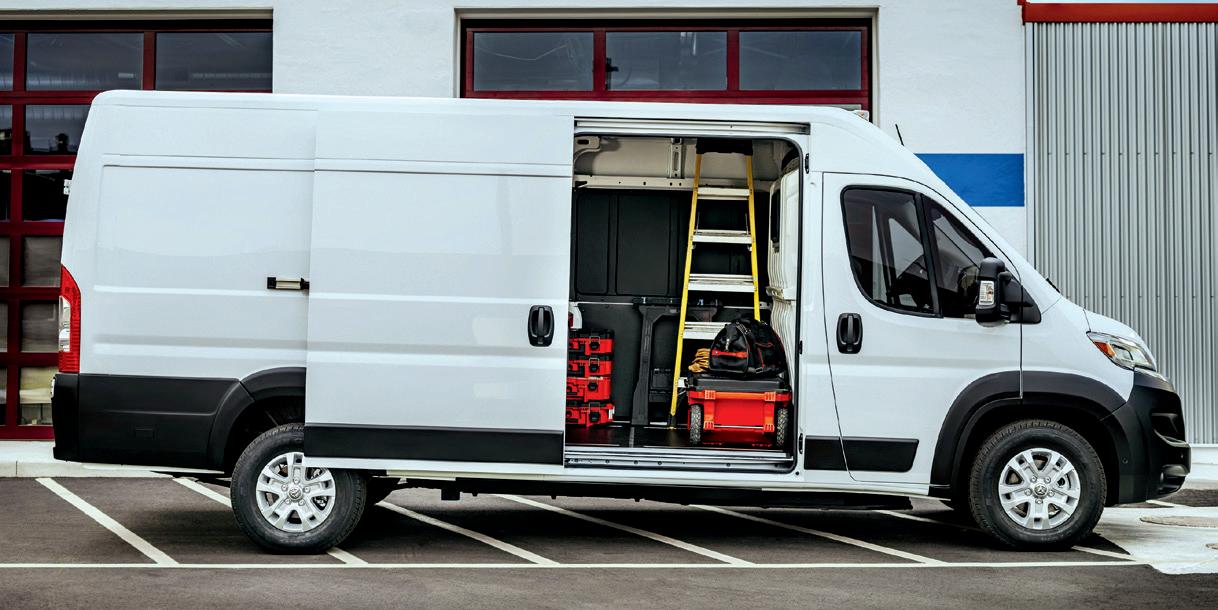
but has a right front “pocket door” for easier access. All three versions ride on the same 159-inch wheelbase.
e Delivery model can be ordered now, while the two Cargo versions will be available for order later this year, though Stellantis did not specify when. Ultimately, Ram says, ve models will be available, spanning two roof heights, two cargo lengths (12 feet and 13.5 feet), and two body styles.
e Delivery con guration, the rst to go on sale, has a higher roof and o ers up to 2,030 pounds of payload—perhaps suited to Amazon cartons, though maybe not to an entire load of industrial components or heavier goods. e two Cargo models’ payload is higher, rated at 3,020 pounds.
Ram says the ProMaster EV has the most vertical side walls of any available cargo van, and that its cargo height and width are best-in-class 86 inches and 75.6
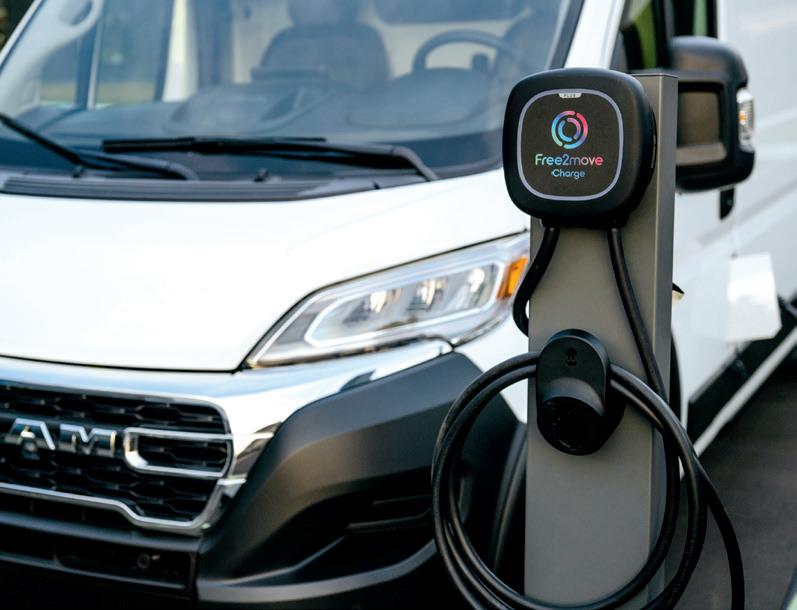
Ultimately, Ram says, fi ve models will be available, spanning two roof heights, two cargo lengths (12 feet and 13.5 feet), and two body styles.
inches respectively. Total cargo volume is 524 cubic feet, identical to that of the gasoline ProMaster.
Telematics key for fleets
Crosstown competitor Ford has split out its commercial vehicles and data services into the Ford Pro unit, which it expects to be a major pro t center for the
11 – 13.6.2024
NUREMBERG, GERMANY

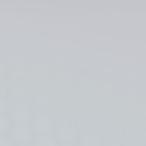
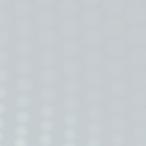

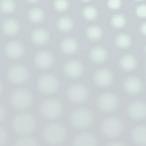
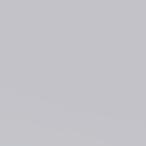
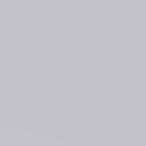
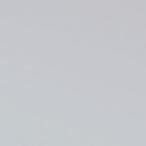

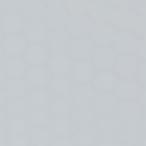
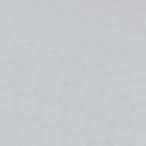
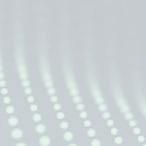



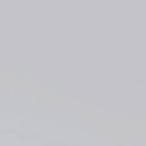
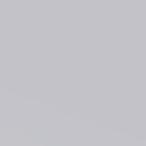
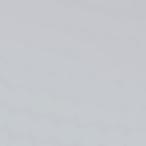
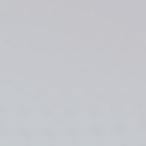

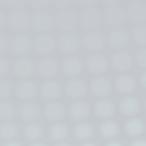
Be part of the industry’s leading exhibition and discover cutting-edge trends along the entire value chain at firsthand.

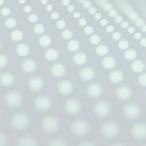

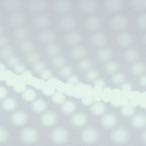
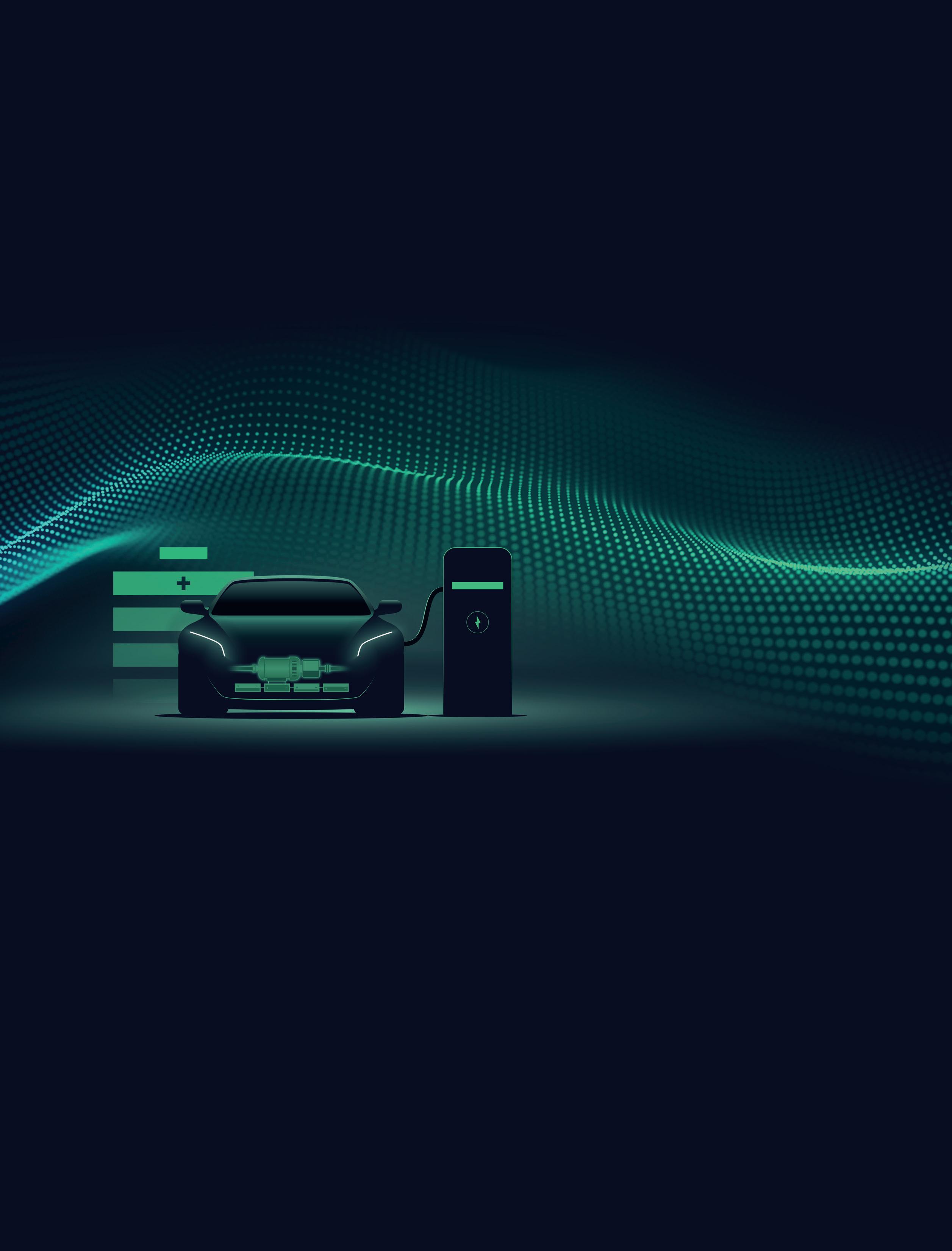
Discover the future of power electronics for E-Mobility and Energy Storage at the PCIM Europe 2024.
With over 600 exhibitors and a top-class presentation program on four stages, the leading industry event offers you an ideal opportunity to discover new trends and product innovations along the entire value chain, expand your specialist knowledge and exchange ideas with international experts.
Specialist presentations at the E-Mobility & Energy Storage Stage illustrate what power electronics is capable of achieving for these exciting areas of application now and in the future. In addition, you can look forward to daily Live Product Demos at the exhibition stands of specialized companies.
Find out more: pcim-europe.com/emobility

THE VEHICLES
company as it transitions to EVs over the next 15 years. Ram, too, o ers a suite of telematics services to let eet managers monitor their vehicles, oversee driver behavior, and maximize the e ciency of routing, usage and in the case of EVs, charging.
Fleet-friendly features include Ram Telematics, which tracks vehicle locations, provides real-time diagnostics and performance data, and o ers driving insights to optimize route e ciency, promote safer driving and cut energy usage. Last-mile navigation features o er drivers instructions to get from the van’s parking spot to their nal delivery destination, via the company’s UConnect infotainment interface and its companion smartphone app.
Another crucial feature for eets will be the Charging Station Locator, for drivers whose routes exceed the van’s rated range. EV Dynamic Trip Prediction keeps an eye on remaining range, modeling it against predicted energy use. Operating information appears inside the vehicle on a recon gurable 10.1-inch Uconnect touchscreen in the center of the dash. Android Auto and Apple CarPlay are standard.
Automated driver assistance for safety
While delivery vans were once spartan, basic vehicles, they now come equipped with standard and optional features that rival any passenger car on the market. e Ram ProMaster EV comes with forward-collision alert, crosswind assist, post-crash braking, driver-drowsiness detection, tra c-sign information and automatic high beams—all as standard equipment.
Because the most requested feature for large-van buyers is better visibility around the entire vehicle, the ProMaster EV includes a high-resolution backup camera with dynamic grid lines that show the vehicle’s trajectory as it backs up. A video rear-view mirror that shows an unobstructed view from a rear-facing camera is optional, as is Surround View 360-degree camera display.
Active Driving Assist comprises adaptive cruise control with lane centering, which Stellantis terms an SAE Level 2 automated driving system. It requires not only that the driver keep eyes on the road, but also hands on the wheel—unlike GM’s Super Cruise, Ford’s BlueCruise, or the Mercedes-Benz Drive Pilot, all of which allow hands-o operation as long as the driver watches the road. at said, neither the Ford E-Transit nor GM’s BrightDrop electric vans o er hands-o adaptive cruise control either.

A crucial feature for fl eets will be the Charging Station Locator, for drivers whose routes exceed the van’s rated range. EV Dynamic Trip Prediction keeps an eye on remaining range, modeling it against the predicted energy use.
Images courtesy of Ram
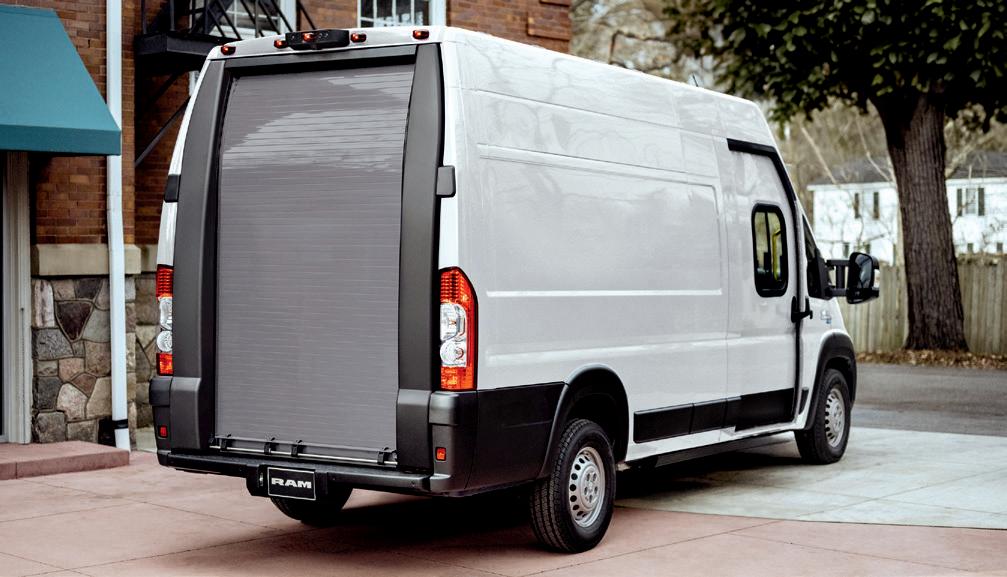
USING MODULAR PLATFORMS AND MICRO-FACTORIES TO
LOWER THE COST OF COMMERCIAL EVS
HummingbirdEV is laser-focused on keeping costs down for its broad range of EVs and drivetrain components.
The commercial EV market is hot—a bit too hot for some. Over the past decade, we’ve seen dozens of startups come and go. Many of these built promising vehicles, but starved out while waiting for customers to place volume orders.
California-based HummingbirdEV, which was founded in 2015, is taking a di erent approach. e company has focused on developing its own technology, and now o ers not only complete vehicles, but also a broad range of components, including electric drivetrain systems, control so ware, bidirectional charging systems, modular batteries, battery management systems and more.
To date, the company’s technology has been successfully deployed in more than 500 commercial vehicles, including trucks, buses, and agricultural and mining equipment. Customers include vehicle OEMs, up tters and startups.
Hummingbird is addressing several global markets—it has customers in the US, Europe and China, and is now making a major push into India and the




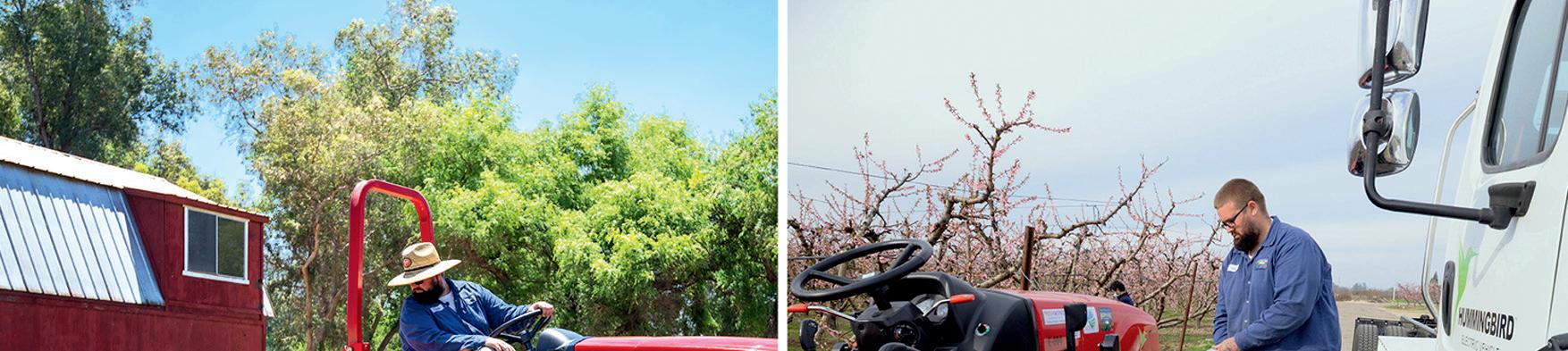
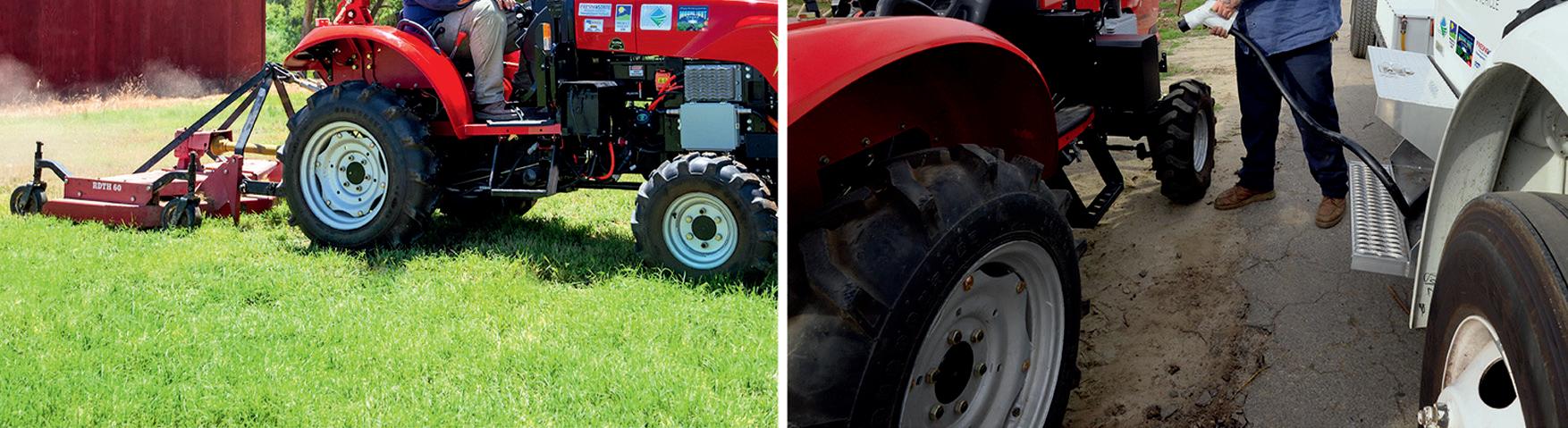

Q&A with HummingbirdEV CEO Rakesh Koneru
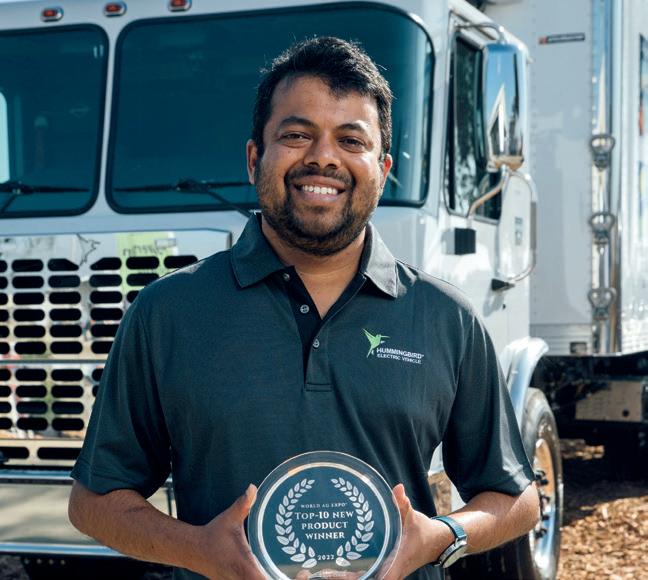

THE VEHICLES
GCC (Persian Gulf) region. e company is laser-focused on keeping costs down, and a key part of that strategy involves setting up micro-factories to serve speci c customers, and building local supply chains.
Charged spoke with HummingbirdEV CEO Rakesh Koneru about his company’s plans for rapid expansion, and how it has avoided the pitfalls that have trapped other commercial EV players.
Q Charged: What stage of business development would you say you’re in at this point?
A Rakesh Koneru: From a customer traction perspective, we’ve deliberately kept a low pro le while we developed our technology. It’s important to know that we’re coming at this with upwards of 14 years of experience in the commercial vehicle electri cation
The new-age companies, they’ve gone through SPACs in the rush to raise money, and companies went public too early, burning cash too fast, misinterpreting the demand and not having the right technology.
space. We’ve retro tted European chassis, Indian gliders, and US-made OEM trucks. We have seen all the pitfalls, and we’ve tried to address these technological challenges in terms of commercialization. at takes time and focus. How do you build a vertically integrated modular vehicle platform that can not only t the North American market, but can also scale up to growing markets like India? How do you take a $200,000 truck and make it a $40,000 truck? at’s been the biggest challenge. We believed in the technology, and we’ve focused on building that tech, and that’s what the last seven years were all about. We’re also growing, and want to build up the team to get to mass production in the next three to ve years.
Q Charged: We’ve seen so many commercial EV makers come and go. It sounds like you’re taking a di erent approach than most of the companies that have addressed this space.
A Rakesh Koneru: at’s true. We believe technology and mass adoption have to be done in a di erent way right now. Everyone’s doing electric, and whether it’s a traditional OEM or a new company, everyone has their own set of problems. e traditional guys come in from a compliance standpoint, not from a standpoint of acquiring the market, so there is a high initial cost to building and selling the product, which, to a regular user and a consumer, is well out of reach. On the ip side, the new-age companies, they’ve gone through SPACs in the rush to raise money, and companies went public too early, burning cash too fast, misinterpreting the demand and not having the right technology. ey’re getting into the market with the wrong technology and high capital investment costs.
I think everyone misinterpreted the demand to be a curve similar to the car segment, but it’s not. e commercial market is a bit unique and niche, and they’re very traditional too. How do you convince someone who’s been driving diesel all their life to go electric if you


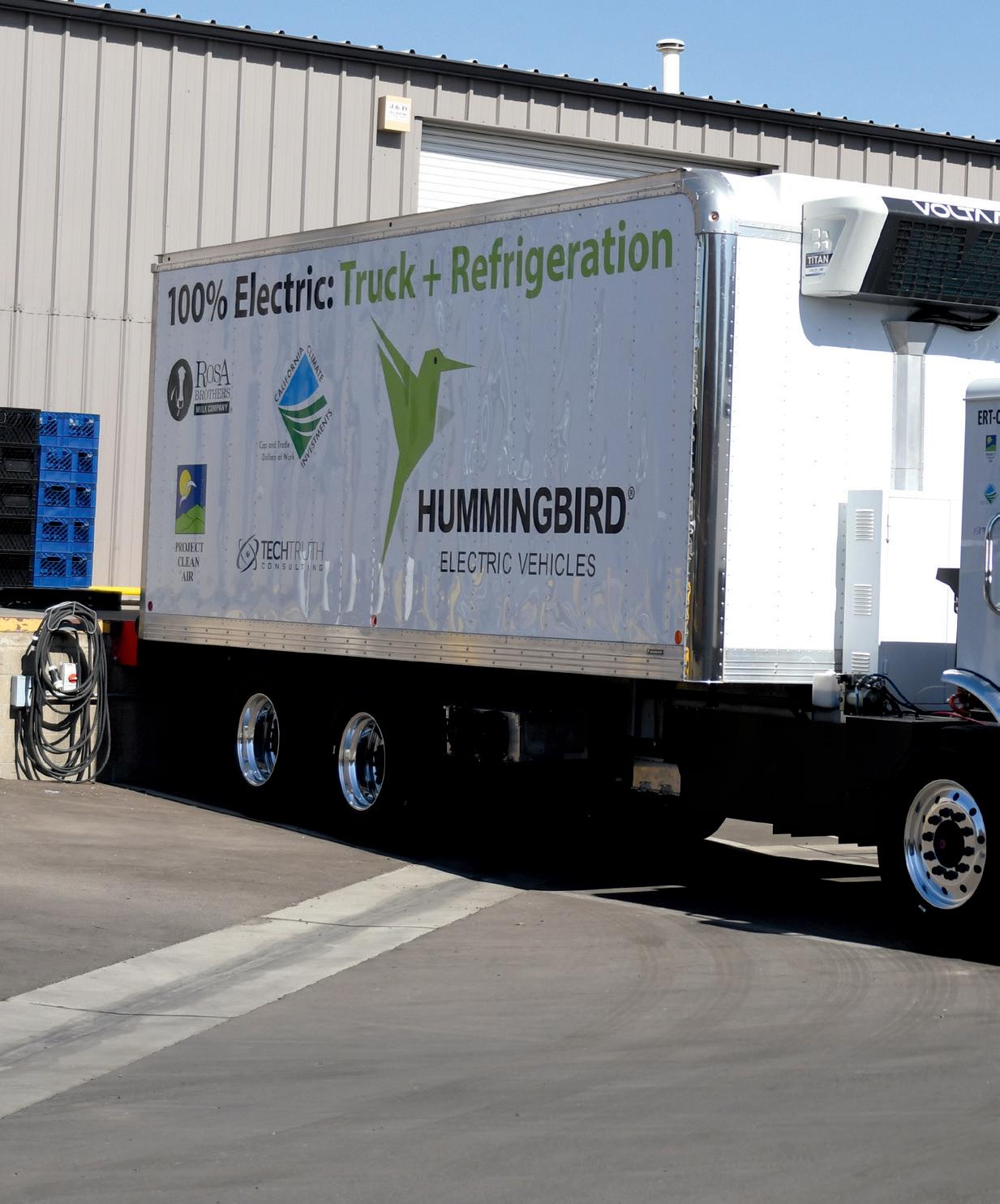



Electric power upgrades typically take about 18 to 24 months. And that’s with a handful of vehicles.
have a xed range and a weight compromise, and by the way, you have to pay double the cost?
ere are infrastructure limitations as well. When it comes to commercial EVs, electric power upgrades typically take about 18 to 24 months. And that’s with a handful of vehicles. Now, how do you want to do your whole eet electri cation, and how do you reduce the infrastructure deployment time? How do you increase grid reliability, and how do you manage the peak hours?
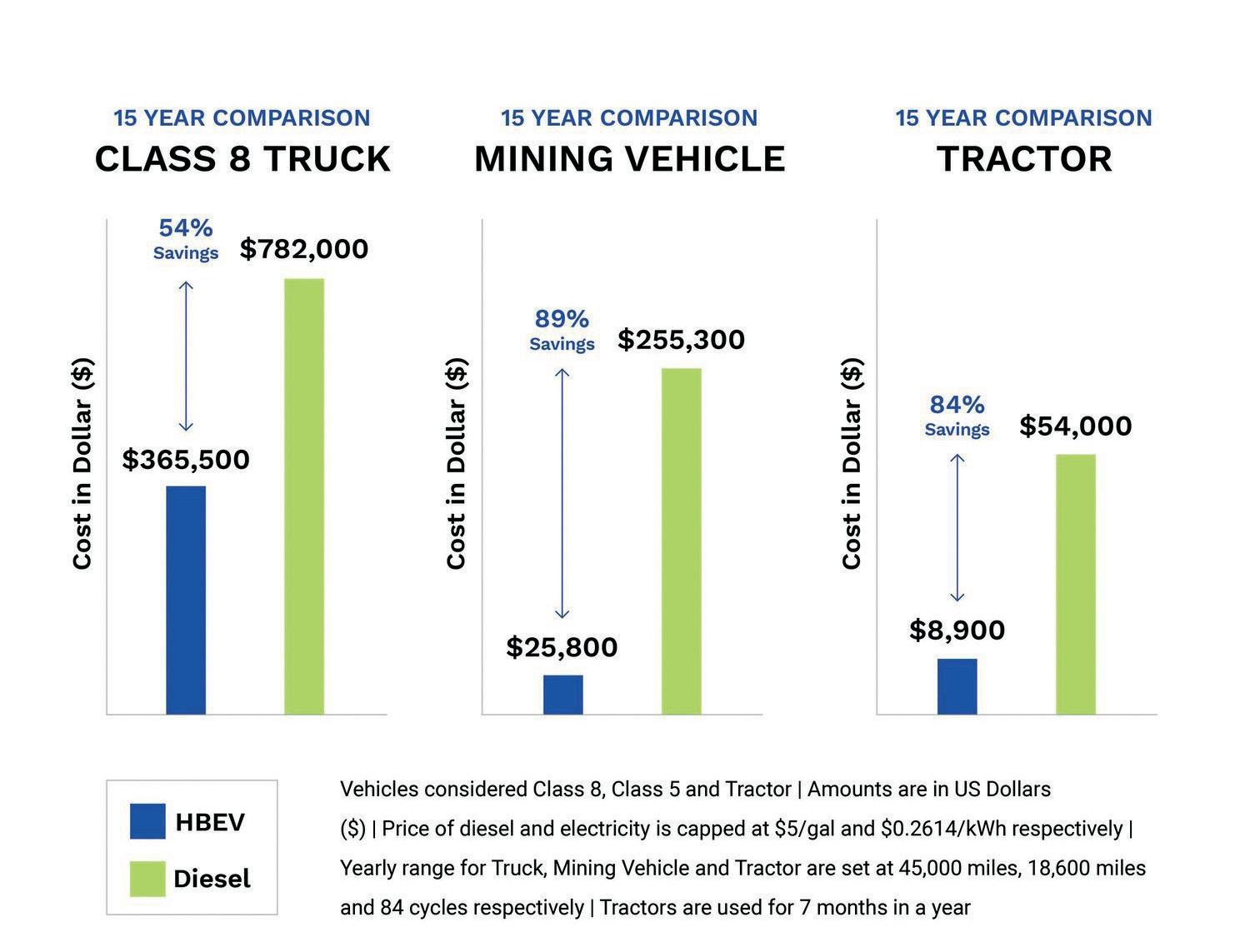
THE VEHICLES
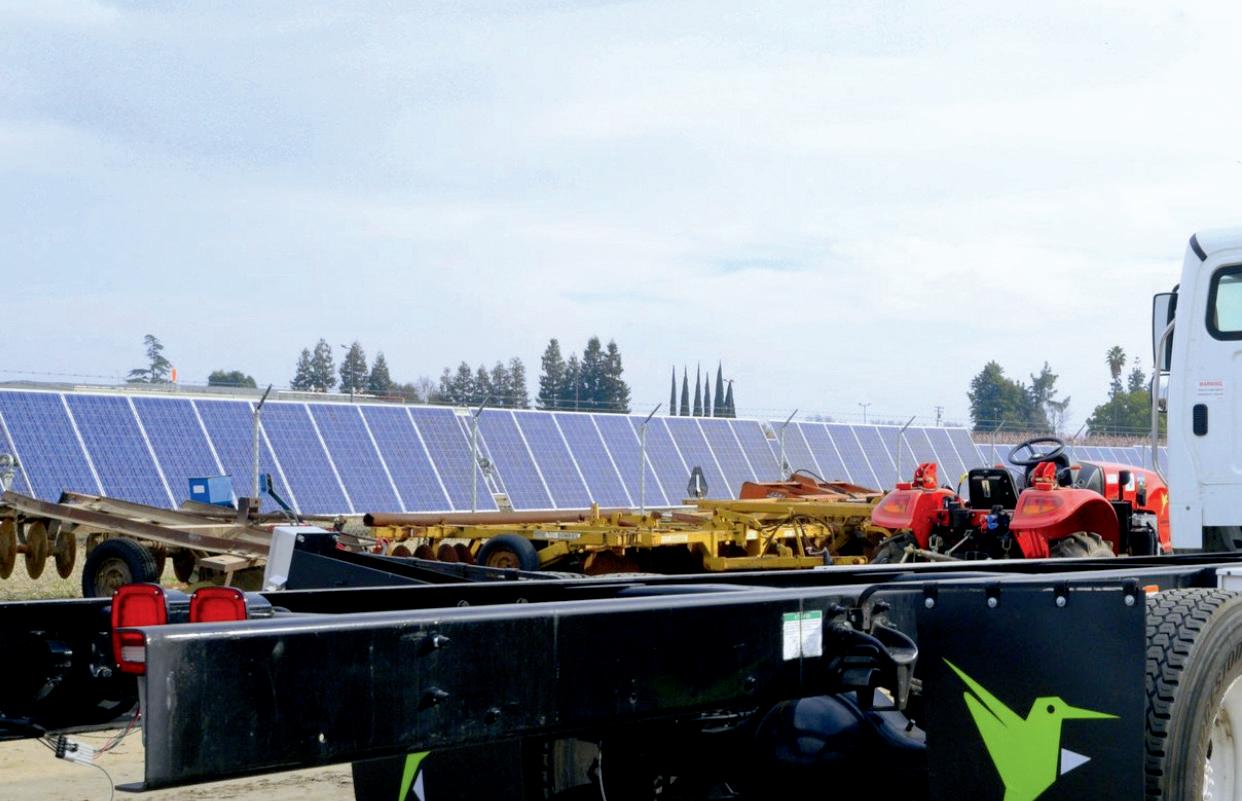

Q Charged: All issues that we’ve heard about from a lot of companies. Can you give me some speci c examples of how you got around those challenges?
A Rakesh Koneru: For us, technology comes rst right now. Cars, to a certain extent, in the next ve years, everything’s going to be pretty standardized. Whether it’s a Tesla or a Volkswagen, you’ll get to a point where everyone uses more or less a certain battery pack to drive a certain range. In the commercial vehicle segment, that’s not going to work.
If you look at the new-age companies and the traditional OEMs, they’re still stuck with the diesel thought process: I’ll give you one or two xed battery pack combinations and it’s up to you to gure it out. But trucks are used in a gazillion di erent applications. If you take a Class 6, from a walk-in to a box truck to a refrigerated truck to a port vehicle, a tractor, every application is unique, and going in with a traditional mindset of a standard-size battery pack, it’s not going to work. So, what Hummingbird is trying to accomplish is to bring modularity into a vehicle platform, where on the same production line, we can have combinations of vehicles. Whether it’s a bigger or smaller battery pack size, the
If you take a Class 6, from a walk-in to a box truck to a refrigerated truck to a port vehicle, a tractor, every application is unique, and going in with a traditional mindset of a standard-size battery pack, it’s not going to work.



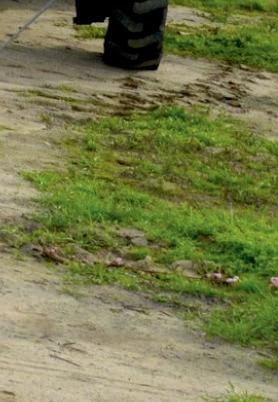
type of batteries, the type of motors, you need to have sort of a Lego block design where you can add a thing or delete a thing on the same production line.
at’s from the technology side. From the manufacturing side, we’re trying to localize it. We’re going with a micro-factory approach because our systems are very unconventionally built—we do not need a typical thought process of how factories look. We will not be requiring huge real estate. We will not be getting into foundries and welding and heat treatments. A lot of stu is minimalized in our case, and also cleaner in how we produce the vehicles. We’re approaching it from both the tech and the manufacturing standpoint to be modular, to enable and deploy for any vehicle application.


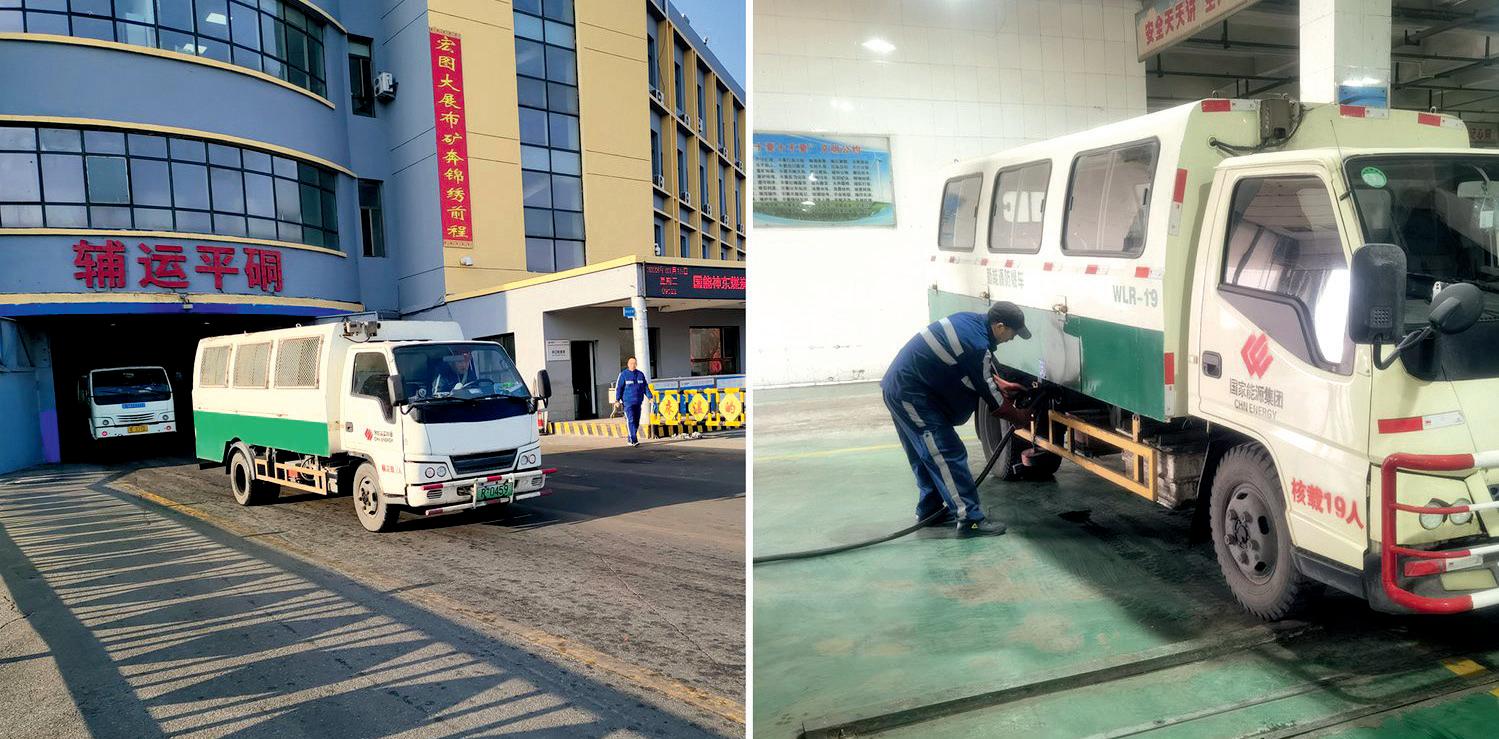
We are trying to be in that end-to-end mobility space. What I mean by that is we look at an application. For example, in India we’re working with one of the biggest e-commerce companies. We worked with the customer to de ne their duty cycle, and we’ve built a vehicle around that.
We have a lot of perks from our tech—we have onboard bidirectional charging systems, which enables the customer to do fast onboard charging, which is the rst of its kind in the commercial vehicle space. And we also have a fast vehicle-to-vehicle DC charging protocol that is unique to us. We’re looking at an end-to-end, plugand-play modular vehicle platform that can be built on a low CapEx.
Q Charged: So, you would set up a micro-production facility for a particular customer?
A Rakesh Koneru: Be where the customer is, and that helps us in multiple di erent ways, from a geopolitical standpoint to knowing the customer better in the local market. And from an investment standpoint too, to diversify and get local investment rather than raising from one big investor.
Q Charged: Are most of your customers or potential customers vehicle OEMs, or are they mostly end users like eet operators?
We’re going with a micro-factory approach because our systems are very unconventionally built— we do not need a typical thought process of how factories look.
A Rakesh Koneru: ey’re mostly end users at this point. We are doing a few things to get into a strategic partnership with OEMs, but I think we’re a bit too early for that. We just have to go with the traction that we have with the end users and we’ll see what comes out of it.
Q Charged: Tell me more about this vehicle-to-vehicle charging system. We hear a lot about vehicle-to-grid and vehicle-to-building, but what’s the application for vehicle-to-vehicle charging?
A Rakesh Koneru: Vehicle-to-vehicle is nothing new when you look at it from a naming convention standpoint, but how we do it is unique. In the market today, you have two di erent types of vehicle-to-vehicle technologies. One is like a Rivian or a Ford F-150 Lightning that has an onboard charger that charges another vehicle using Level 2 AC charging.
e second application is that you have a diesel truck that has all the EV components in the back of the truck,

THE VEHICLES
and that does vehicle-to-vehicle charging using a DC power source. So, you necessarily have two technologies right now—what we’re trying to do is bring in the third. We are building a truck, which is electric and can do V2V at DC power levels. We’re trying to move away from slow charging AC V2V into fast CCS V2V charging. And at the same time, we’re not loading batteries and power electronics in the back, but rather the vehicle itself moves the energy from its battery to the other side.
As an example of the type of end customer that would bene t from V2V tech, say today you run out of gas and you’re a AAA member. You call AAA, they’ll come and bring you a gallon of gas. Now, how do we give you a gallon worth of electricity for that rst 25 to 30 miles so you can get home or go to a charging station? How do we do it fast? at is a unique technology that we’re trying to bring into the market. We demonstrated this about four years back on a farm where we were charging electric tractors. You can nd a few videos on our company web site.
Q Charged: You sell a lot of di erent components: drivetrains, batteries, chargers. Do you manufacture most of that stu in-house or do you get some of it from suppliers?
Rakesh Koneru: It’s designed from our side, and a lot of it we work with contract manufacturing—a combination of our strategic suppliers and our Tier 1 OEM suppliers where we buy some outside components with our design tweaks in.
Q Charged: Is that going to be more localized also? For example, you have a customer in India—are you going to build a network of component suppliers there in India, so you don’t have to ship things around the world?
Rakesh Koneru: at’s right. For us it’s just the cost. At the end of the day, we want to be as close to a diesel cost as possible in the next ve years without incentives. Now, how do we go there? With all that said, suppliers in India are also there. For example, Dana is in the US, Dana is in India, Dana is there globally. We have local players who know the local markets. How do I take my base technology and work with the local partners in the
There’s going to be a certain level of raw material that still has to be sourced internationally among all our entities, but our focus is to get at least 75 to 80% of the cost in the local market.
various regions to get to the price point?
However, there are certain technologies—batteries for example—which cannot be done in India. To a certain extent, the batteries that we use on our trucks in North America today also do not have a local supplier because we’re not using cylindrical cells, we’re using a prismatic cell. ere’s going to be a certain level of raw material that still has to be sourced internationally among all our entities, but our focus is to get at least 75 to 80% of the cost in the local market. at’s from chassis, axle, suspension, battery assemblies, building local components. How do we create that local cluster around our micro-factories?
Q Charged: Is it mostly just batteries that come from China?
Rakesh Koneru: At this point the only thing we depend on China for is battery cells. Not the complete pack but just cells. With the exception of that, I would say 90% of what we do is all sourced in the US and probably about 3 to 4% is from the UK and Europe.
Q Charged: I guess everyone would like to get their batteries from somewhere other than China, but that’s not going to happen overnight. What kind of timeline do you think we’re looking at?
Rakesh Koneru: I don’t know about the consumer side, but for a commercial vehicle application, optimistically I would say the rst batteries are probably four to ve years out. Mass production is probably seven to ten years out.
Q Charged: Any new things in the pipeline you’d like to tell us about?
Rakesh Koneru: We have some cool products that we’re
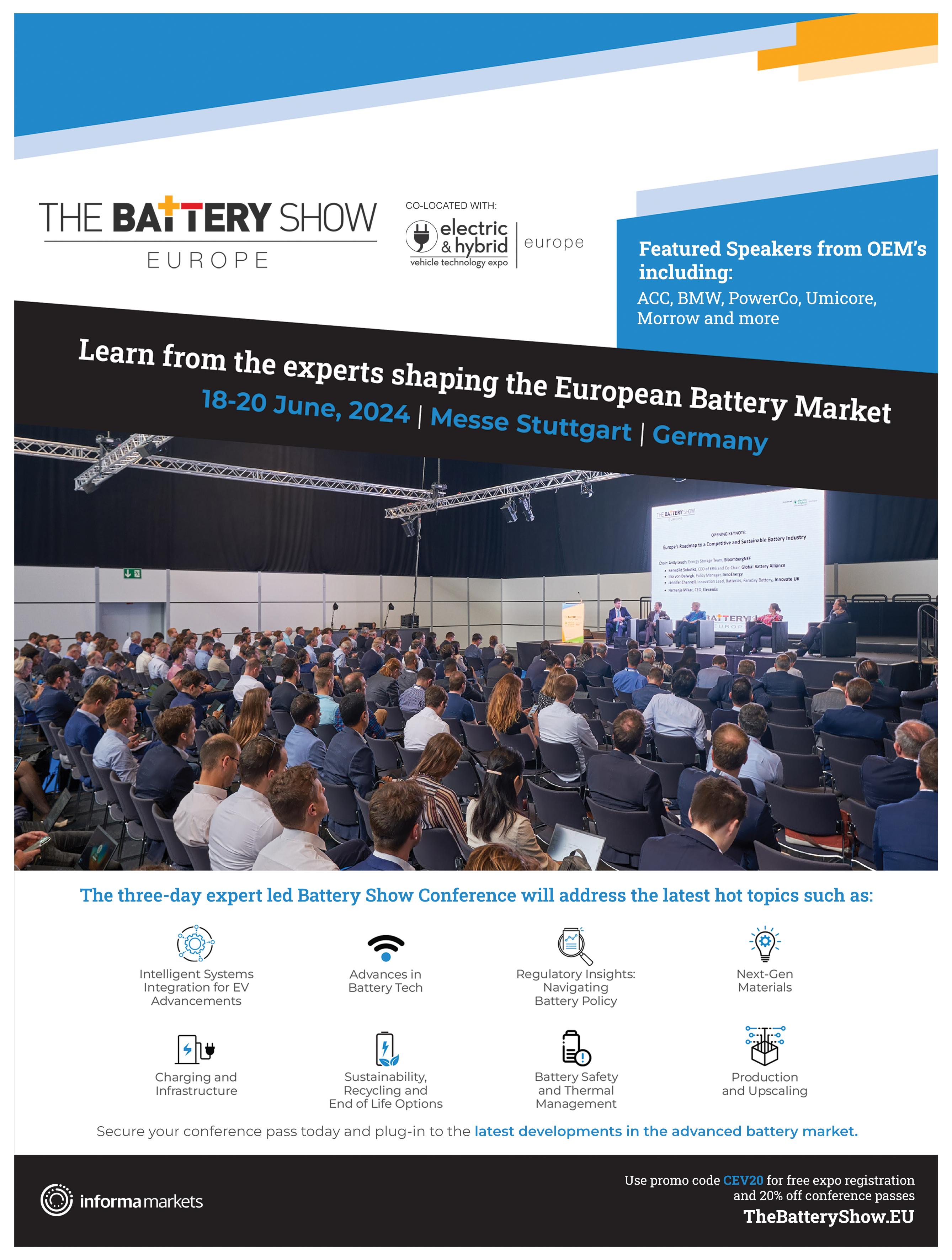

THE VEHICLES
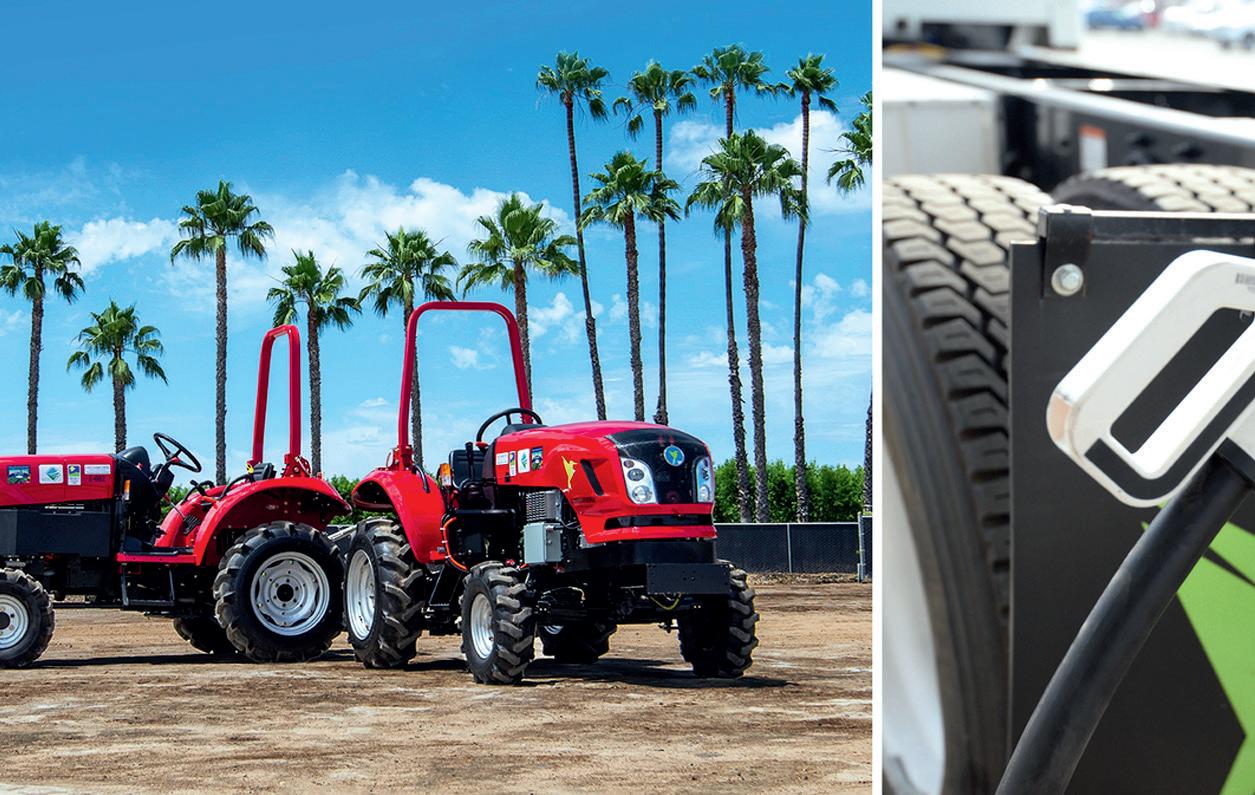



trying to unveil with our own skateboard chassis platform in the next couple of months. at’s our rst mass go-to-market product. Our current facility today can produce about one truck a month. By the end of this year, we’re trying to get to one truck a day in California. We’re trying to scale it up into both the two other places [India and the UAE].
But unlike the traditional OEMs, we’re not going to get stuck with just selling a truck. We’re trying to open up a lot of revenue-based models. We will sell a complete truck to an end user, but we will also be selling
our skateboard architecture to the users, to white-label for say, their own cab application. And we will also sell di erent layers of our systems—our powertrains, our onboard chargers, whatever it is. We will get into selling components as well. at’s how we see we can get to high volumes quickly. And because we control the whole nine yards, from hardware to so ware, it enables us to do things in a exible manner with a reduced time to market. It’s going to be a completely di erent approach in how we engage with the market when we start this full-scale in the next couple of months.

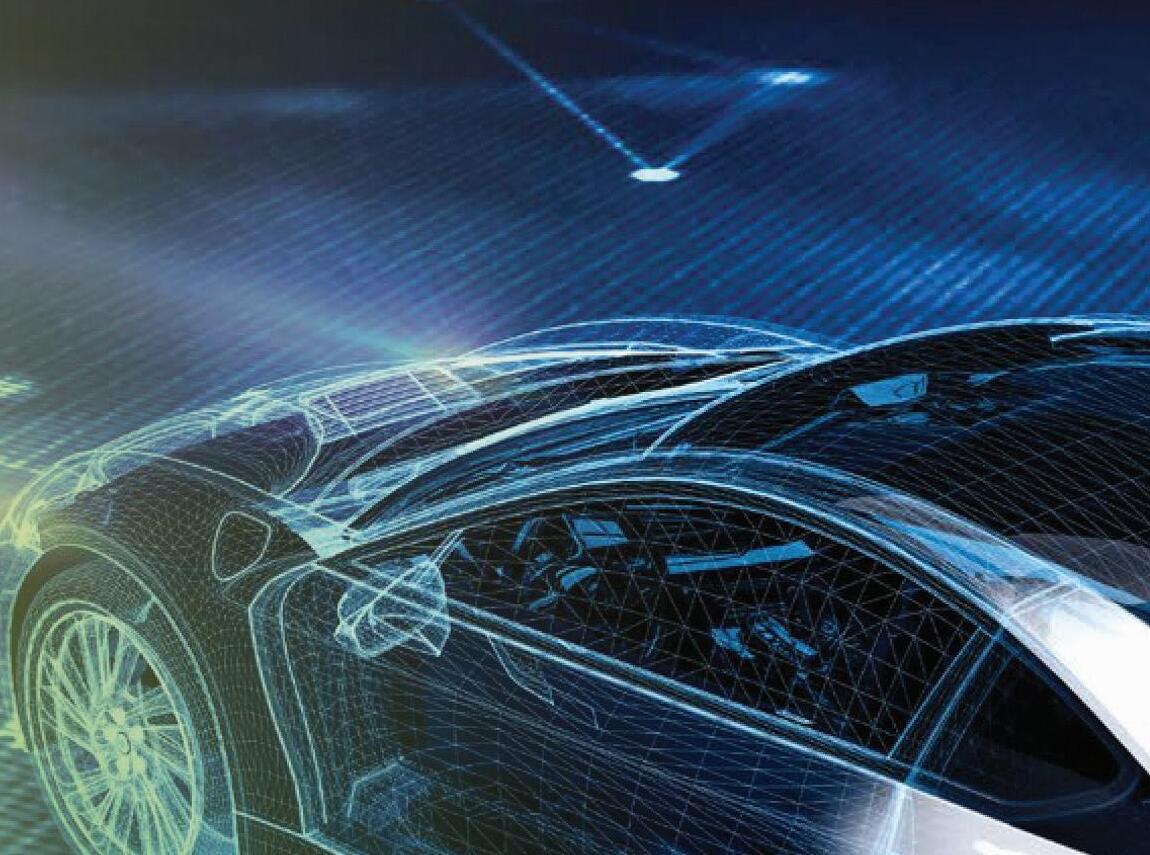
May 15-16, 2024 in Bamberg

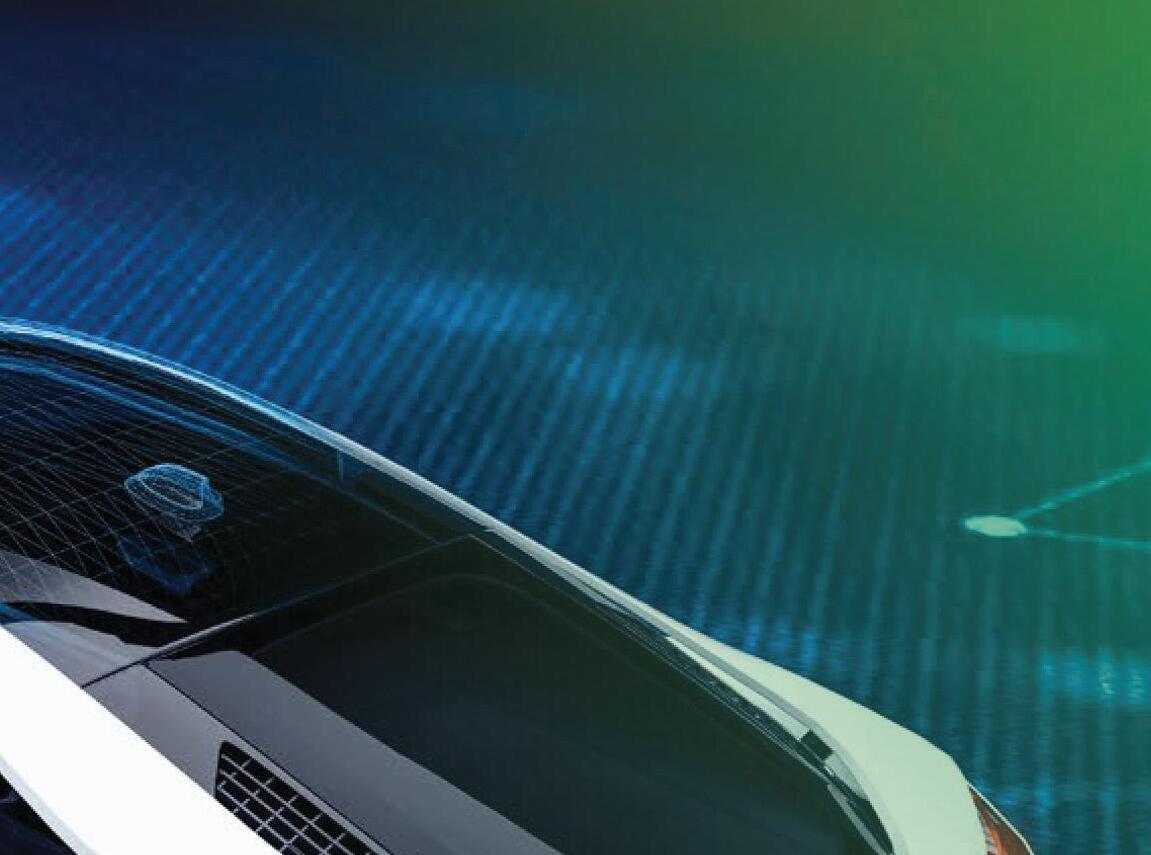
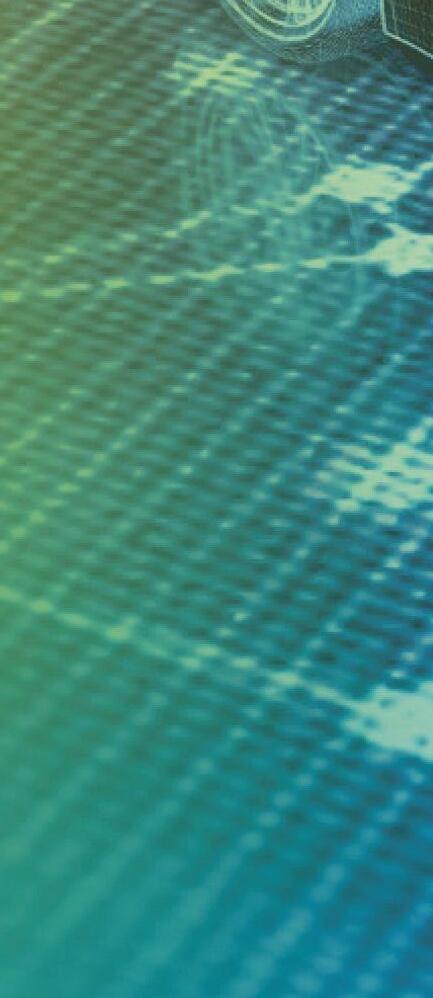
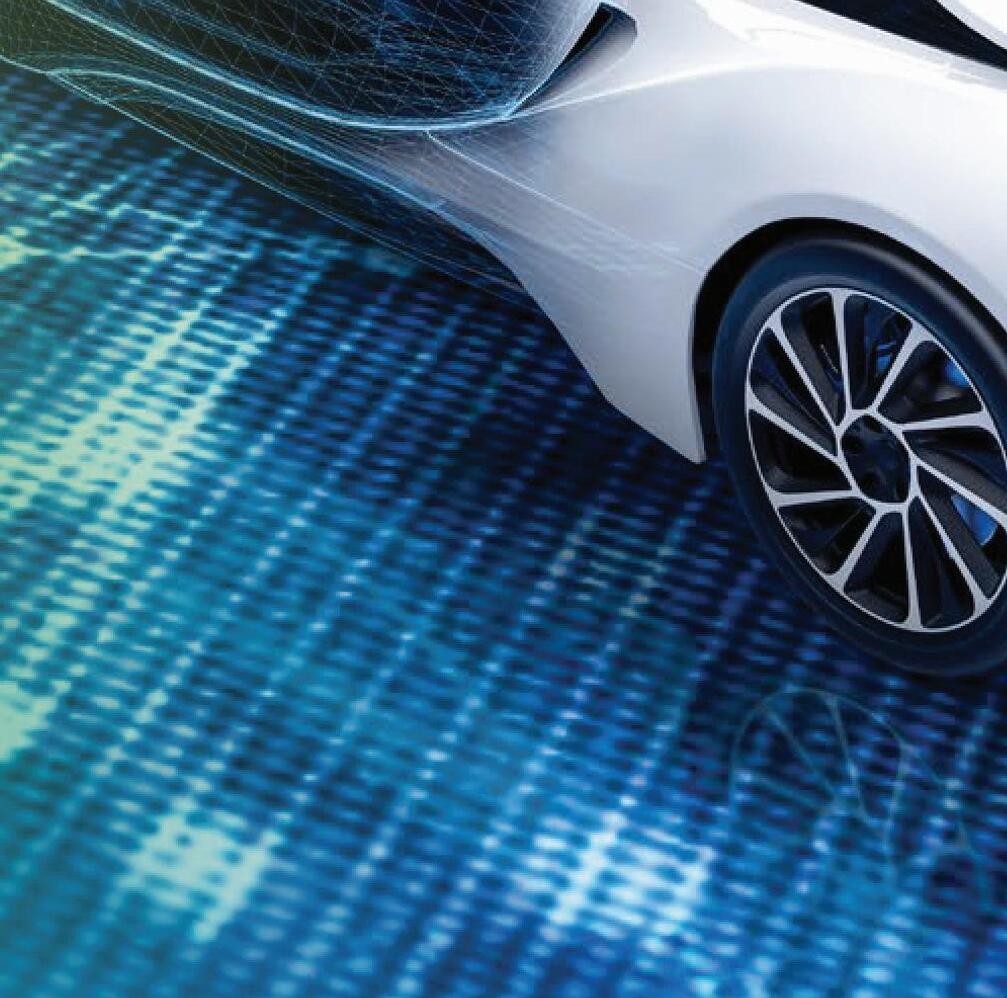

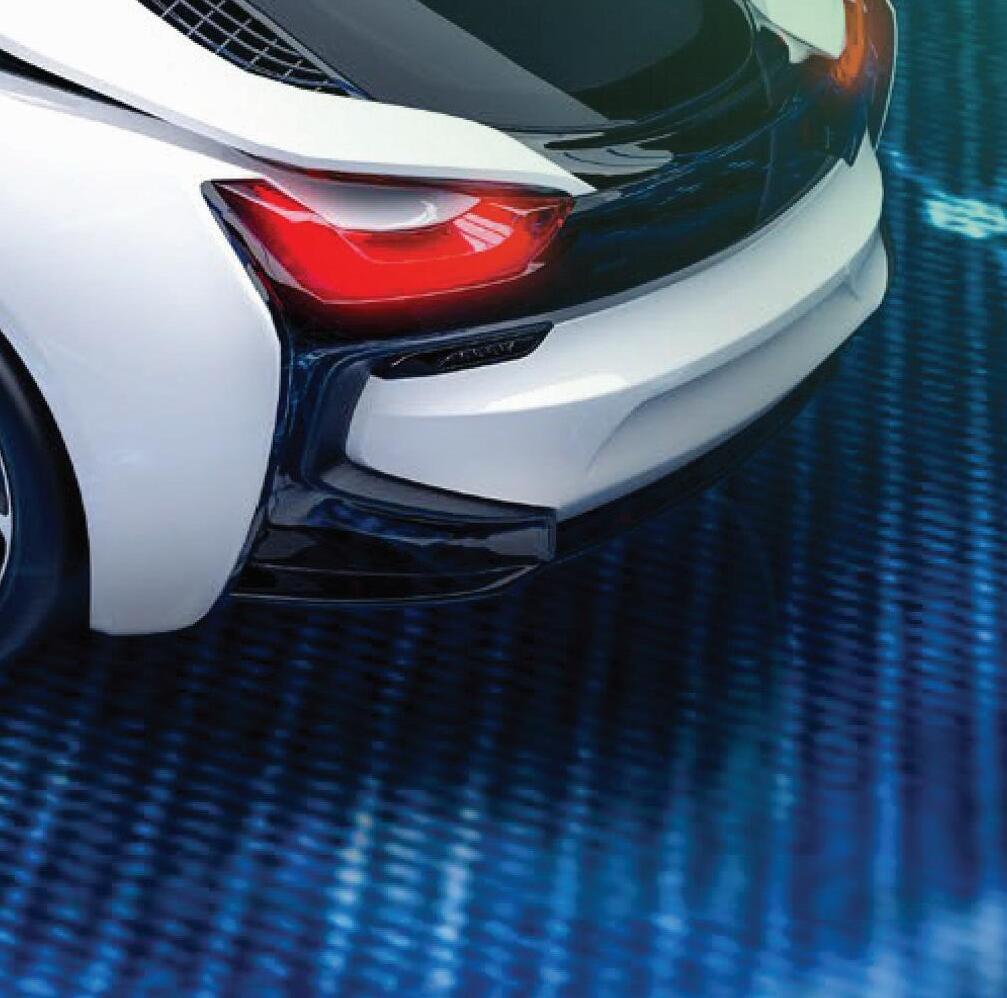

THE INFRASTRUCTURE
Study finds EVs are lowering electricity bills for all customers, not just EV owners
A recent study has found that, so far, EVs are having a salutary e ect on the grid, saving ratepayers billions of dollars on their electricity bills. e analysis, which was commissioned by the National Resources Defense Council, and performed by Synapse Energy Economics, compared the prices EV owners paid for electricity with the costs for utilities to build power plants and to generate and distribute the energy. e study found that, in the aggregate, EVs delivered billions of dollars in net revenue to the grid between 2011 and 2021.
e main reason that EV charging is lowering the cost of electricity for all consumers is that EV drivers tend to charge at home overnight, when demand for electricity is far below the electric grid’s capacity. Customer savings are projected to increase in the coming years as more EVs and more renewable energy sources are hooked up to the grid.
“Many future-looking studies have predicted that vehicle electri cation would have this downward pressure e ect on rates,” writes Jordan Brinn, a Clean Vehicles and Infrastructure Advocate at NRDC. “ is study uses real-world data to show that this e ect isn’t just a future theory—it’s been happening for over a decade across the US.”
According to NRDC’s data, utility savings due to EV adoption has outpaced the additional costs (for charging station deployment and other programs designed to encourage EV adoption) by $2.44 billion. is savings doesn’t always go to utility shareholders—many states require revenue decoupling, which mandates that additional revenue be returned to utility customers in the form of lower rates and bills. Even in states that haven’t adopted revenue decoupling, utilities have to report revenue through rate case proceedings, and rates and bills are adjusted accordingly, so EV charging should still put downward pressure on rates to the bene t of all customers, not just EV owners.
Furthermore, the study found a correlation between the net rate impact and the number of EVs on the road in a given state. e more EVs there are on the road, the higher the net revenue is for utilities, and the lower utility bills are for all customers.
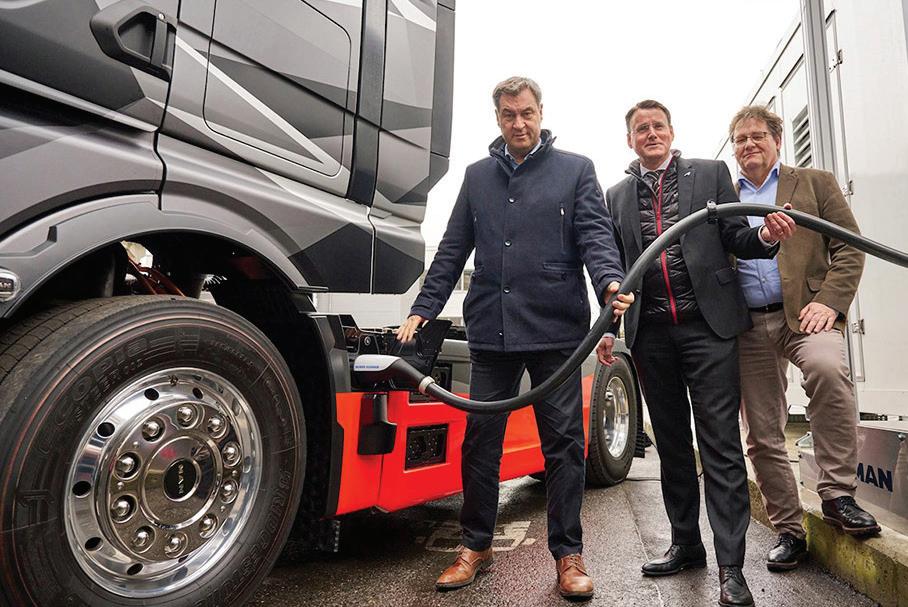
ABB E-mobility and MAN demonstrate Megawatt Charging System
e Megawatt Charging System (MCS) is a new charging standard that enables super-fast charging for heavy-duty electric vehicles (up to 3.75 MW, compared to a maximum of 400 kW with CCS). e international standardization process is expected to be completed this year, and companies are already close to commercial implementation.
MAN Truck & Bus, one of the truck OEMs that has implemented MCS, recently demonstrated MCS charging with a MAN eTruck at the company’s development center in Munich. e heavy-duty truck was charged at a level of over 700 kW and 1,000 A using a charging station from ABB E-mobility, one of the rst megawatt charging points in Germany.
MCS chargers are intended to provide a fast charge for an electric truck or coach during the driver’s legally prescribed driving break. e new technology complements existing depot charging solutions, which provide a slower overnight charge.
“With MCS, sustainable long-distance transport with trucks and buses will be possible in the near future. We have proven that today, even if we are still showing a prototype here,” said Michael Halbherr, CEO of ABB E-mobility. “With the new MCS standard, we have not only doubled the amperage but also the charging capacity within just a few years.”
“ e goal is 30,000 MCS charging points in Europe by 2030, around 4,000 of them in Germany,” said Alexander Vlaskamp, CEO of MAN Truck & Bus. “We put one of the rst charging points into operation today. e electric trucks are available, megawatt charging is working. We now need clear signals from politicians, not least to build trust among our customers in favor of electri cation.”




Fermata Energy, BorgWarner, Lion Electric win $3-million California Energy Commission grant for electric school bus V2G project
e California Energy Commission (CEC) has awarded a $3-million grant to BorgWarner, Fermata Energy and Lion Electric to bring grid-supporting and cost-saving vehicle-to-grid (V2G) solutions to electric school buses. e companies will deploy V2G technology for the Conejo Valley Uni ed School District and the Los Angeles County O ce of Education, in cooperation with school bus eet operator American Transportation.
e project is intended to serve as a large-scale demonstration of how electric school buses can provide value to the grid while parked. e buses will charge their batteries with excess power from renewable sources during the day, and V2G tech will enable them to generate revenue through participation in demand response programs, sending energy back to the grid during high-demand evening hours, or during emergency events.
e grant will fund the installation of 21 BorgWarner 125 kW UL-listed bidirectionally-enabled CCS chargers, paired with at least 20 LionD electric school buses.
Fermata Energy’s Vehicle-to-Everything (V2X) so ware platform will optimize and manage the charging and discharging of the buses to maximize grid bene ts and V2X revenue for the school districts.
Fermata’s V2X so ware platform continuously analyzes thousands of data points to manage and optimize EV charging and discharging, and sends signals to the vehicles and bidirectional charging stations.
“ is CEC grant and project underscores the power of partnerships and our collective dedication to sustainability as we deploy this cutting-edge V2G bidirectional hardware and so ware solution,” said Tony Posawatz, CEO of Fermata Energy. “Together, we are advancing electric vehicle integration and grid support in California schools while enabling a viable path toward renewable energy.”
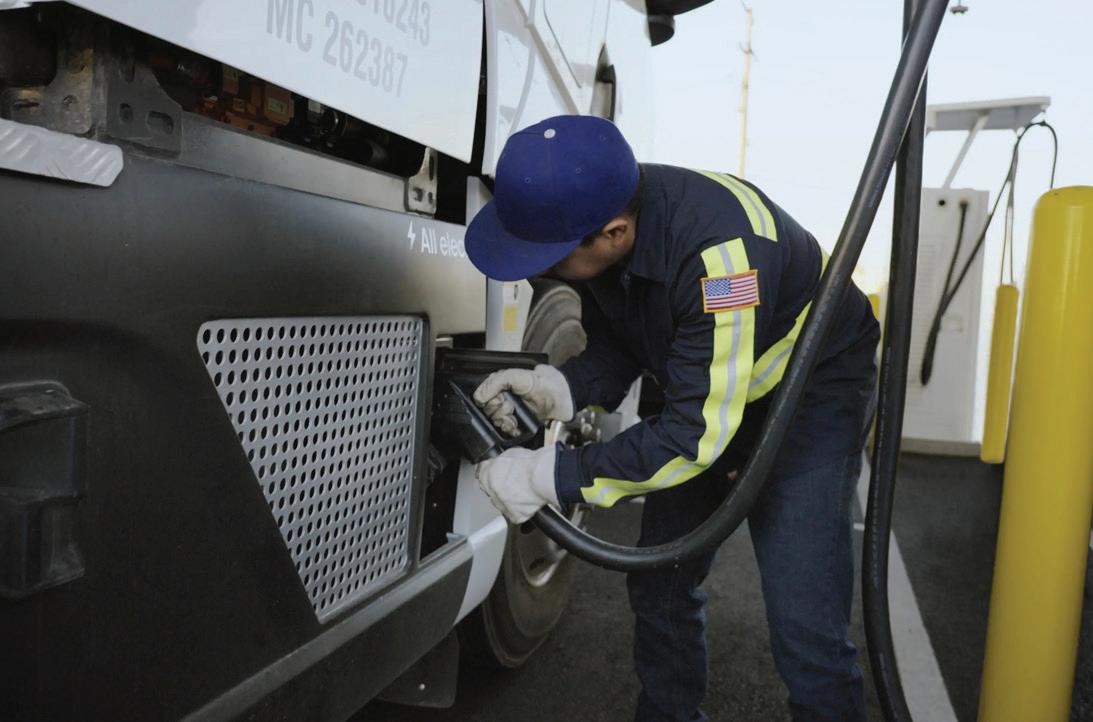
Einride opens 65-plug heavyduty EV charging site near California ports
Freight mobility company Einride has opened a charging hub for heavy-duty EVs in Lynwood, California. Einride’s Smartcharger Station has 65 chargers, and can charge up to 200 vehicles a day. e site was built in collaboration with charging infrastructure developer Voltera. e charging station, which is strategically located near the Ports of Los Angeles and Long Beach along I-710, currently serves Einride’s connected electric eets, including routes for global shipping giant A.P. MollerMaersk. Einride will make the station available for more customers in the future.
Einride’s Smartcharger Station o ers truck drivers a lounge with key amenities, and is integrated with Einride’s Saga intelligent freight operating system, which provides customers with real-time updates on demand, location, timing and utilization of charging infrastructure.
is location is the rst of many the company plans to build throughout the US. Future stations are planned for the West and East coasts, and construction is to begin on new sites later this year. Einride also recently opened a charging hub for heavy-duty EVs in Sweden.
“ e launch of Einride’s rst Smartcharger Station in the US marks a momentous stride in establishing digital, electric freight as an important enabler to a more resilient US freight system,” says Robert Falck, CEO and founder of Einride. “ is facility will enable a key region to fast-track to electric, given its proximity to the Port of LA, one of the world’s busiest container ports and a driver of the US economy.”
“Our team was able to get Einride’s Lynwood site permitted, built, energized and operational in under 18 months—in the world of charging infrastructure, that’s pretty remarkable,” said Matt Horton, CEO of Voltera.

THE INFRASTRUCTURE
Shell to divest 1,000 retail locations, and also expand EV charging. Coincidence?
Oil giant Shell has announced plans to divest 1,000 retail sites over the next two years, and also says it plans to expand its public EV charging business.
Is Shell shutting down gas stations in order to replace them with EV charging hubs? Well, that’s what several media reports implied, but that’s not what the company said.
Shell’s “Energy Transition Strategy 2024” mentions electric vehicles at least 30 times (accompanied in almost every case by a mention of biofuels), and concedes that growing EV adoption may cut into the demand for petroleum (at least a little). But we didn’t nd anything in the report that speci cally linked the company’s decision to trim its retail network to its plans to expand EV charging.
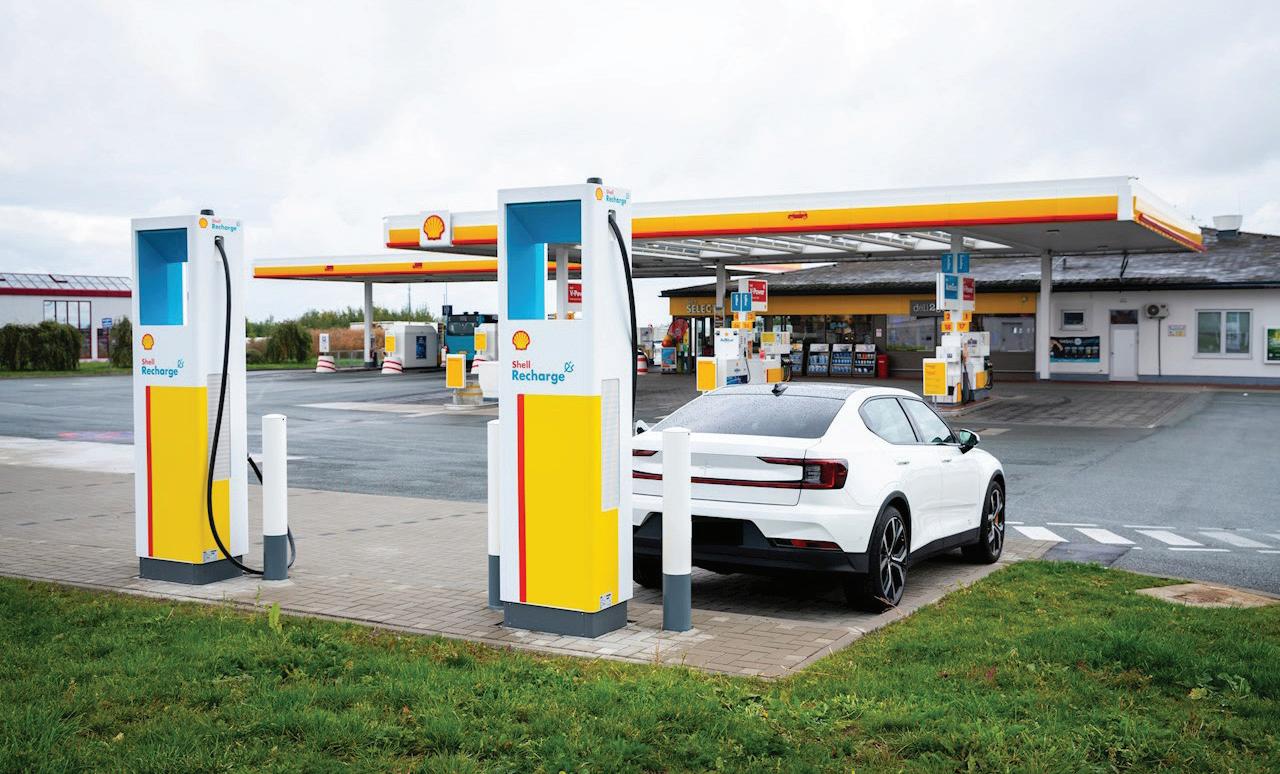
2025 and around 200,000 by 2030. Shell Recharge, our public charging network, currently operates in around 33 countries.”
As for the retail site “divestments,” Shell hasn’t said whether the sites in question will be closed or simply sold to other operators.
So, is it out with gas, in with electrons? It’s too early to say. We know that correlation does not equal causation, but we’re also mindful of the relationship between smoke and re, and the handwriting that sometimes appears on walls.
One thing is certain: Shell is moving into EV charging in a big way. e company sees “attractive growth opportunities in charging for electric vehicles and in biofuels,” and plans a major expansion of its public EV charging network.
“At the end of 2023, we had around 54,000 public charge points for electric vehicles at Shell forecourts, on streets and at locations such as supermarkets. We expect to have around 70,000 public charge points by
What’s more, Shell expects EV charging to be profitable: “As we grow our business o ering charging for electric vehicles, we expect an internal rate of return of 12% or higher.”
Are existing gas stations good sites for charging hubs? Shell obviously thinks so: “We have a major competitive advantage in terms of locations, as our global network of service stations is one of the largest in the world. We have other competitive advantages, such as our convenience retail o ering which allows us to o er our customers co ee, food and other convenience items as they charge their cars.”
Many industry observers agree. “If you have the right street corners with the right amount of tra c and the right footprint, if you can turn over some of those existing stations that already have a convenience store, that already have a car wash, that’s a really good cocktail for business success,” Nathan Niese, an Associate Director at Boston Consulting Group, told Automotive News.
THE INFRASTRUCTURE
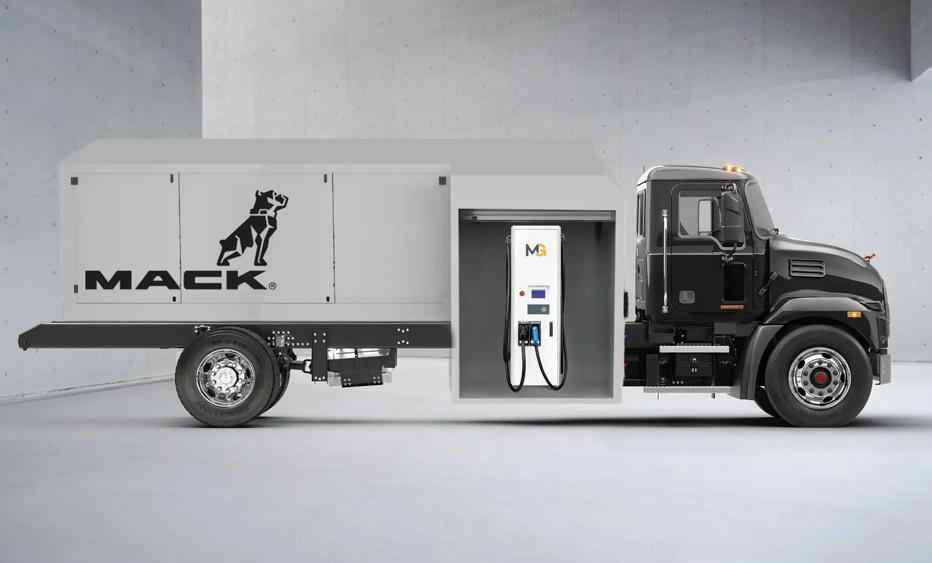
Mack’s mobile off-grid charging system helps customers evaluate EVs
Mack Trucks, part of the Volvo Group, has built a mobile o -grid charging system that’s integrated into the body of a Mack MD Electric truck. e system’s raison d’être is to help Mack customers test Class 6-8 electric vehicles, and evaluate their feasibility for their eets.
e mobile Mack MD Electric charging unit can be used for a limited time by customers who want to test the technology, and by dealers to facilitate EV demos.
e o -grid charging system consists of a generator powered by renewable propane, along with a 120 kW DC fast charger. e system will be mounted on the back of an MD Electric truck.
Mack currently does not have plans to make the truck-charger con guration commercially available, but can support customers interested in purchasing the combo through their supplier relationships.
“ is system will allow the customer or dealer to charge trucks—whether it’s a demo unit or a multi-unit ride-and-drive event at the dealer—without having charging infrastructure readily available at their site,” said Ryan Saba, Energy Solutions Manager for Mack Trucks. “ is option will help customers more easily experience the bene ts of e-mobility.”
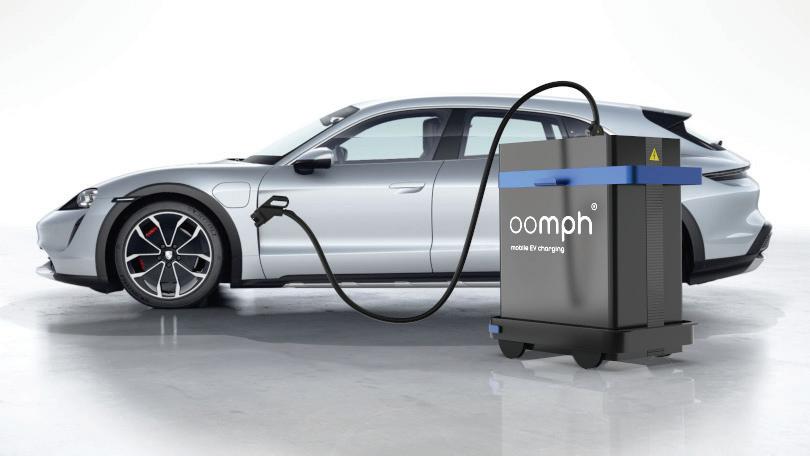
Oomph’s new Powerstream mobile rapid DC charger
British EV charging technology company Oomph has introduced the new Powerstream mobile 30 kW DC charger.
e Powerstream is portable, and requires no installation. It’s aimed at applications in which xed chargers are not an appropriate solution and at locations where deploying xed charging infrastructure would require long installation times, high utility and groundwork costs, and/or signi cant site disruption.
e Powerstream is suited to either temporary or permanent deployment. It operates as a DC in/DC out mobile energy storage device, and can be mounted in the back of a light commercial vehicle (LCV) or manually wheeled around.
According to Oomph, the unit recharges as fast as it discharges energy. Real-time GPS tracking and remote monitoring allow users to locate units and monitor performance parameters.
e company says it is “setting up a UK-based manufacturing route.”
“We see mobile rapid chargers and xed chargers as complementary parts of the EV infrastructure,” said Oomph CEO Marc Ottolini. “In a sector that is experiencing rapid growth and change, we believe it is vital that solutions exist that can be implemented quickly, with low risk and without breaking the bank.”





EVBox supplies 300 EV charging stations to EVzen network in France
Amsterdam-based EVSE provider EVBox will supply 300 EVBox Troniq Modular DC fast charging stations for the second stage of the rollout of charging network EVzen.
e 120-180 kW chargers will be installed at more than 100 commercial sites across France. e EVzen network currently comprises 150 fast charging ports.
EVzen is an initiative of Monaco-headquartered SMEG, a gas and electric utility company that has diversi ed to include renewable energy and vehicle recharging.
e collaboration between EVBox and SMEG began in 2019 with the provision of EVBox BusinessLine commercial charging stations in Monaco. Since 2021, SMEG has been deploying the rst stages of its EVzen fast-charging network in southern France, based mainly on EVBox hardware.
“Our strong collaboration with SMEG over the years has met the various needs of EV drivers, from rst installing commercial EV charging, to now public fast charging infrastructure. We are committed to supplying EV charging solutions tailored to each business’s needs to make EV charging accessible,” said Amélie Trégouet, EVBox’s Regional Director for France.
National Zero-Emission Freight Corridor Strategy aims to accelerate deployment of charging infrastructure for heavy-duty electric trucks
e Biden Administration has released the National Zero-Emission Freight Corridor Strategy, which will guide the deployment of zero-emission medium- and heavy-duty vehicle charging and hydrogen fueling infrastructure from 2024 to 2040. e Strategy is designed to target public investment to amplify private sector momentum, focus utility and regulatory energy planning, align industry activity, and improve air quality in local communities impacted by diesel emissions.
e goal of the Strategy is to align public policy and investments by prioritizing, sequencing, and accelerating infrastructure along the National Highway Freight Network (NHFN) in four phases. A core objective of the Strategy is to meet freight truck and technology markets where they are today, determine where they are likely to develop next, and set an ambitious pathway that mobilizes actions to achieve decarbonization.
As part of the Strategy, the Federal Highway Administration is designating National EV Freight Corridors along the National Highway Freight Network and other key roadways, as required by the Bipartisan Infrastructure Law.
e National Zero-Emission Freight Corridor Strategy will prioritize the deployment of EV charging infrastructure along key freight corridors and hubs in four phases:
1. Establish priority hubs based on freight volumes (2024-2027)
2. Connect hubs along critical freight corridors (20272030)
3. Expand corridor connections initiating network development (2030-2035)
4. Achieve national network by linking regional corridors for ubiquitous access (2035-2040)
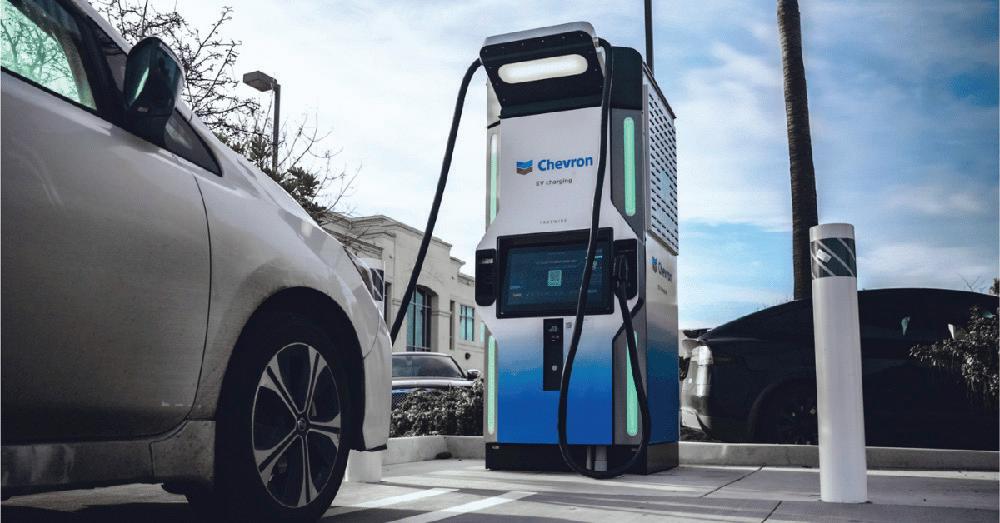
FreeWire’s Accelerate program lets businesses host custombranded EV chargers with no upfront costs
FreeWire Technologies, a provider of battery-integrated EV charging stations and energy management solutions, has announced a new program that allows businesses to o er and collect payments from EV charging, while FreeWire owns and operates the equipment.
e Accelerate program will o er a zero-risk option for charging hosts. FreeWire manages upfront installation, site design and permitting, along with ongoing maintenance and electricity costs. Participating businesses receive a revenue share from charging sessions, subject to a guaranteed minimum payment, and have the option buy the charging stations a er ve years.
e Accelerate program gives the host business control over the chargers’ branding. FreeWire’s Boost Charger features a 24-inch screen that enables promotions and direct customer engagement at the point of charge. e Accelerate Program allows hosts to tap into data on charger usage and customer behavior.
Chevron will be one of the rst customers to participate in the Accelerate program.
“ e Accelerate program demonstrates our conviction in the improving economics of EV charging. We are investing our capital to promote our customers’ businesses, enabling them to market an EV o ering under their brand with zero upfront costs,” said Arcady Sosinov, FreeWire founder and CCO.
Greenlane plans commercial EV charging corridor between Los Angeles and Las Vegas
Greenlane, a joint venture between Daimler Truck North America, NextEra Energy Resources and BlackRock Climate Infrastructure, has announced plans for a 280-mile corridor of charging stations linking Los Angeles and Las Vegas. e stations will provide more than 100 chargers.
e initial sites will be along Interstate 15 in California at Colton, Barstow and Baker. Additional sites will be added later, extending the network to Southern Nevada and San Pedro, California.
e agship station in Colton is targeted for a spring groundbreaking and an opening in late 2024. It will o er 60 charging points, including 400 kW DC fast chargers, as well as 200 kW charging options and multiple passenger car charging stalls.
EnviroSpark to supply EV chargers to IHG Hotels in the US and Canada
British hotel multinational IHG has an agreement with US EV charging infrastructure company EnviroSpark to make its EV chargers available to the more than 4,100 IHG-branded hotels in the US and Canada, each of which can partner with EnviroSpark to meet its individual needs.
e agreement will expand on the number of IHG locations worldwide that o er EV charging, which currently stands at 1,100. e EnviroSpark units, which are suited for overnight charging, will be searchable on the IHG One Rewards mobile app.
“ rough our agreement with EnviroSpark, we’re providing even more options for IHG owners to install EVCs at hotels while making travel easier for a growing segment of sustainability-minded travelers,” said Brian McGuinness, SVP of Global Guest Experience, IHG Hotels & Resorts.


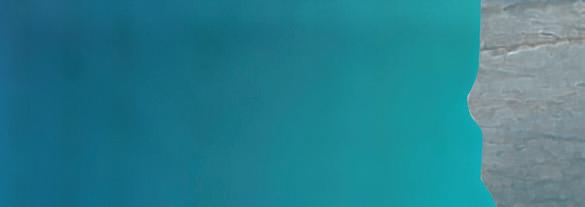
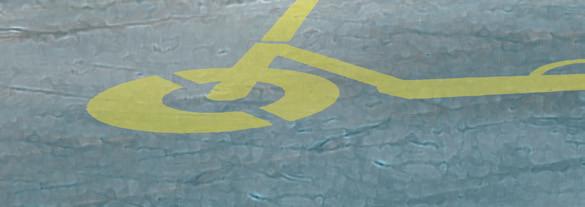
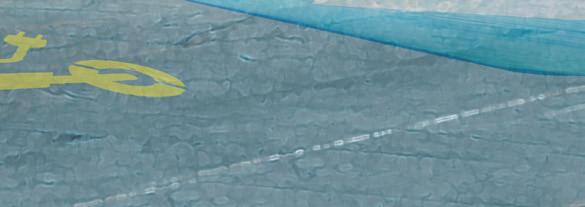

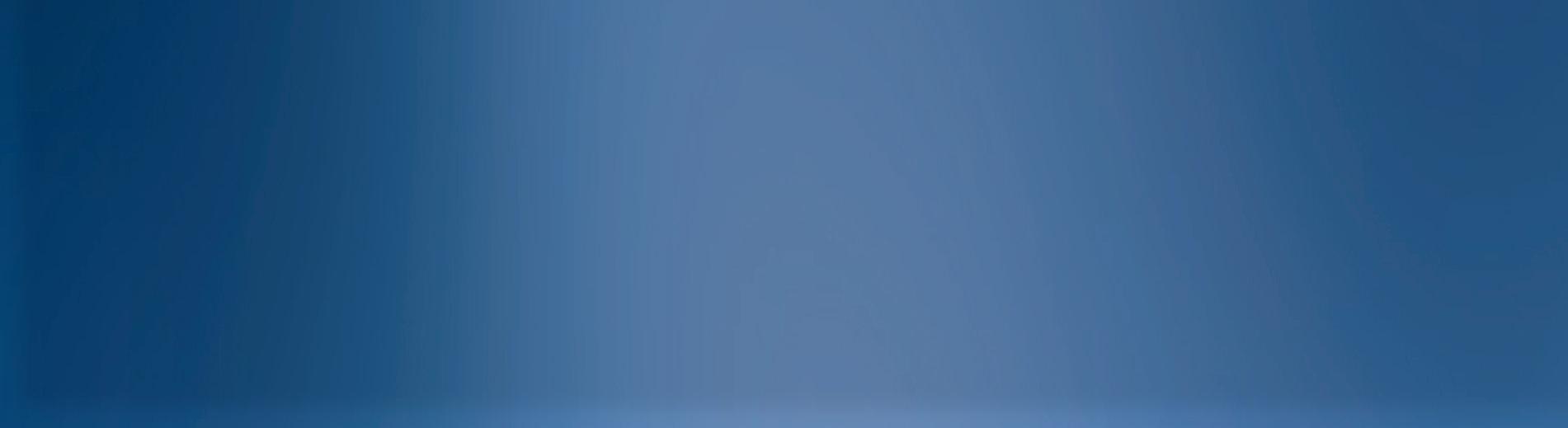
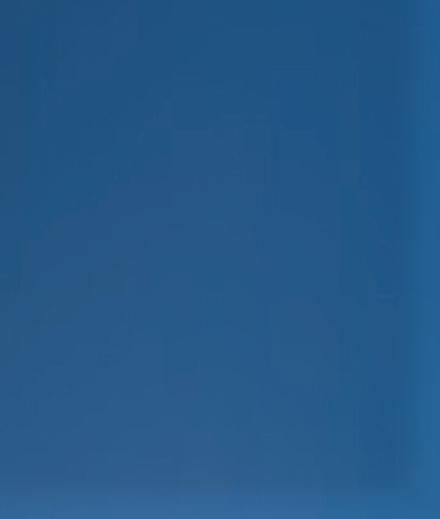
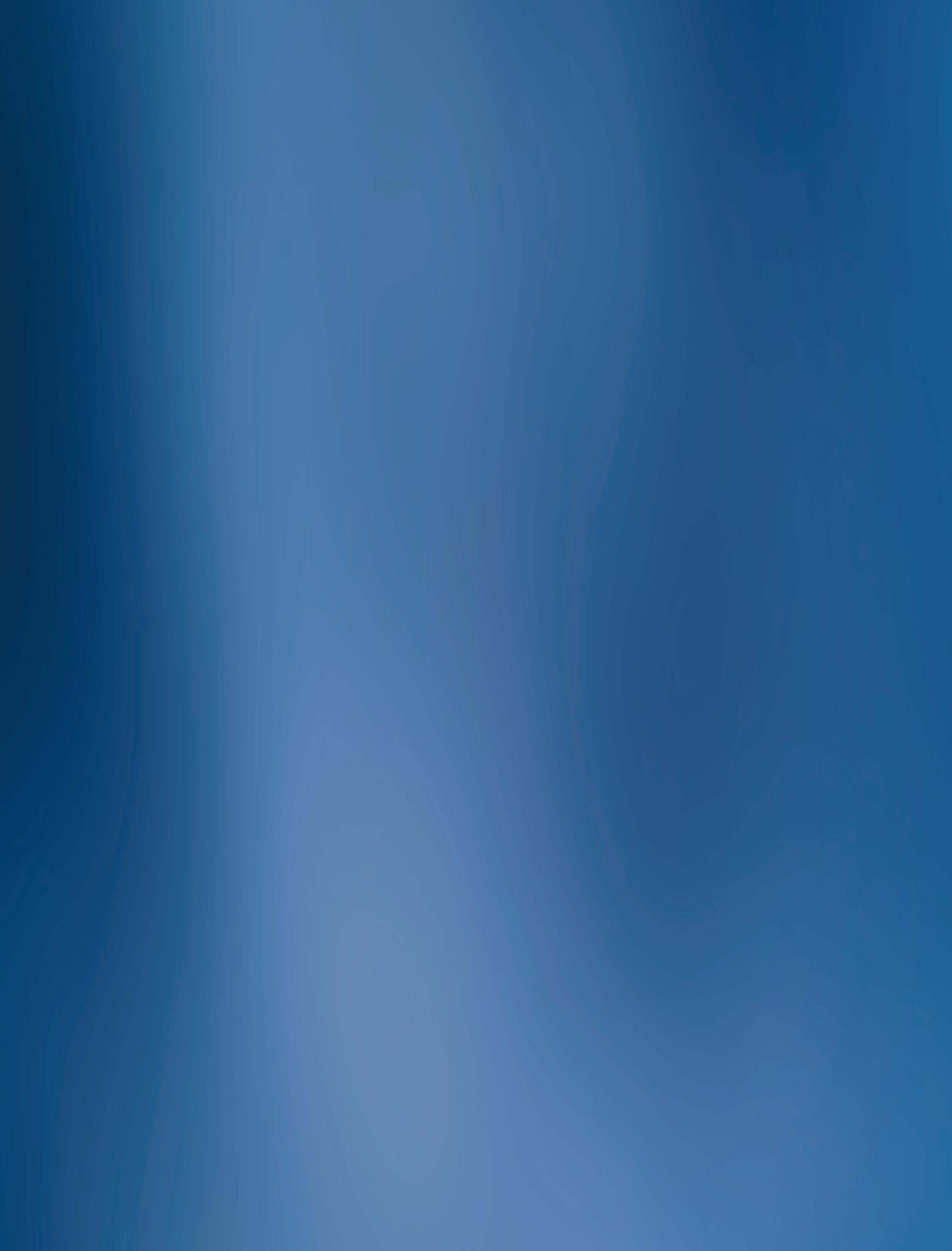
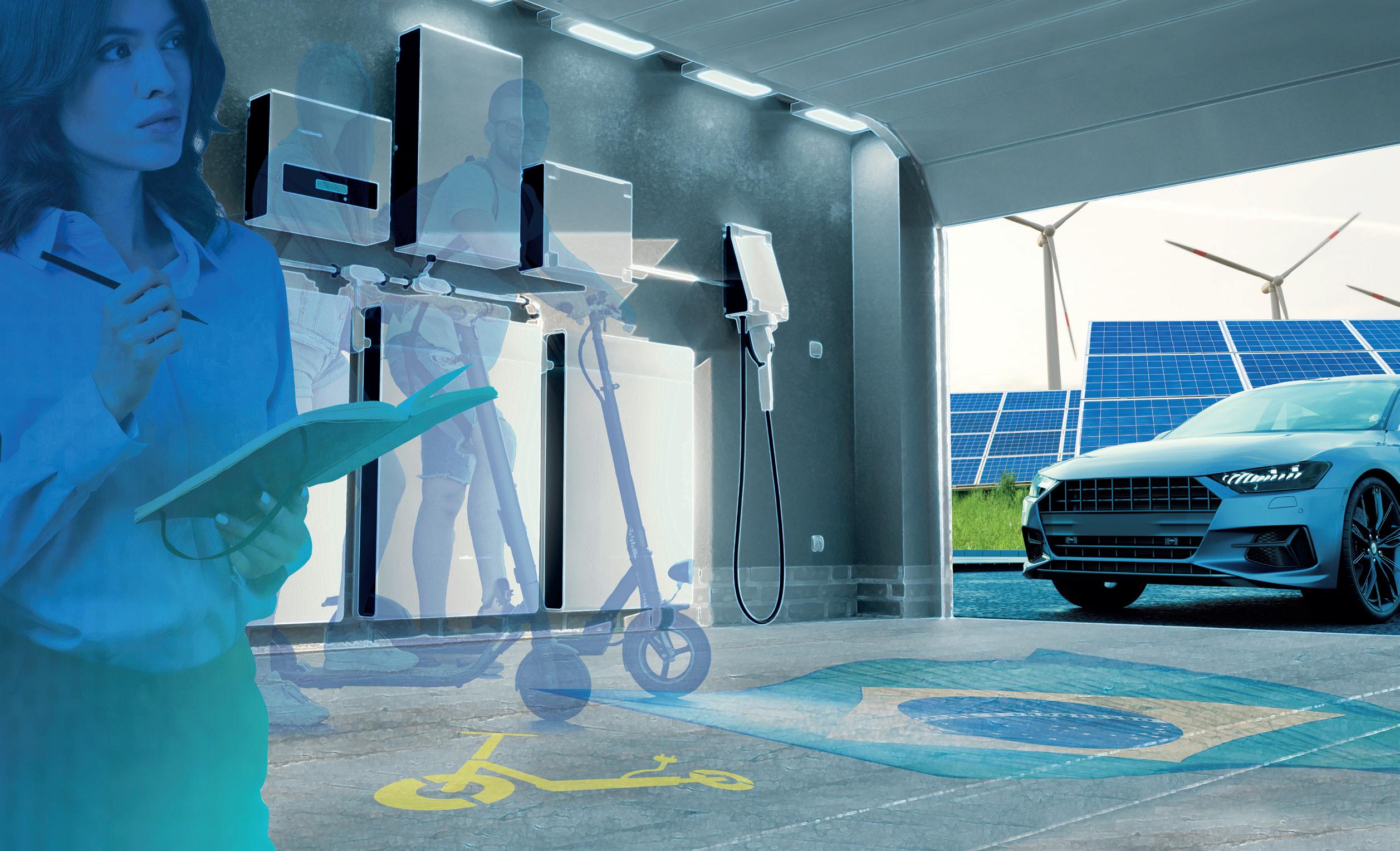
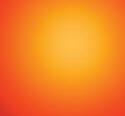
THE INFRASTRUCTURE





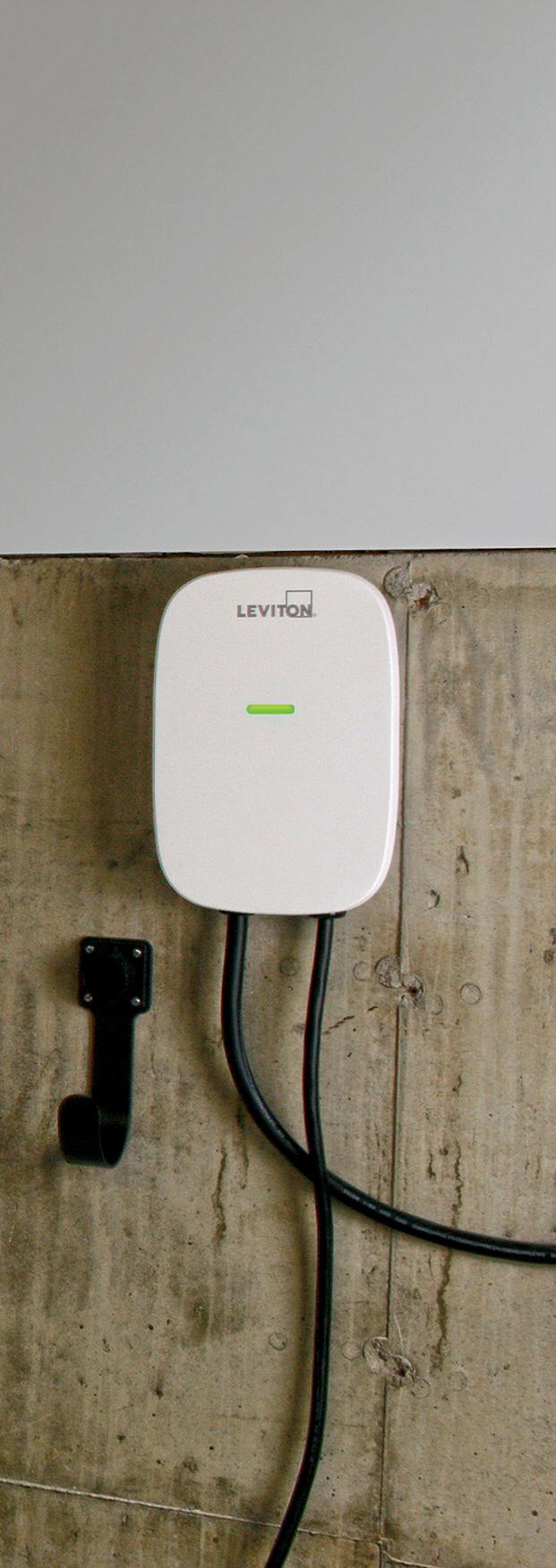
MAKING EV CHARGING PART OF THE
Q&A with Leviton’s Andrew Taddoni SMART HOME
By Charles MorrisThe “house of the future” is a perennial American theme—from the Homes of Tomorrow Exhibition at the 1933 World's Fair to e Jetsons, futurists have predicted a proliferation of laborsaving devices and home entertainment options. Nowadays, the focus is increasingly on the energy that these ni y gadgets require. e home of the future that we envision today is an intelligent home, and much of the intelligence has to do with optimizing energy consumption—shi ing demand to times when energy is cheaper and/or cleaner.
A smart home can manage energy consumption across one or more EV chargers, possibly solar panels and/or battery storage, and thirsty appliances such as climate control systems and refrigerators.
Leviton is perhaps best known to consumers for its stylish light switches and dimmers, but the 118-year-old company makes a vast array of electrical equipment, and it has long been interested in integrated “whole-home” solutions. Leviton has also been in the EVSE space for a little over 12 years, and has produced chargers for a couple of major auto manufacturers, so it’s no surprise that the company is a leading proponent of the EV-enabled smart home.
Charged spoke with Andrew Taddoni, Leviton’s Director of Business Development and Product Management for EVSE.
THE INFRASTRUCTURE
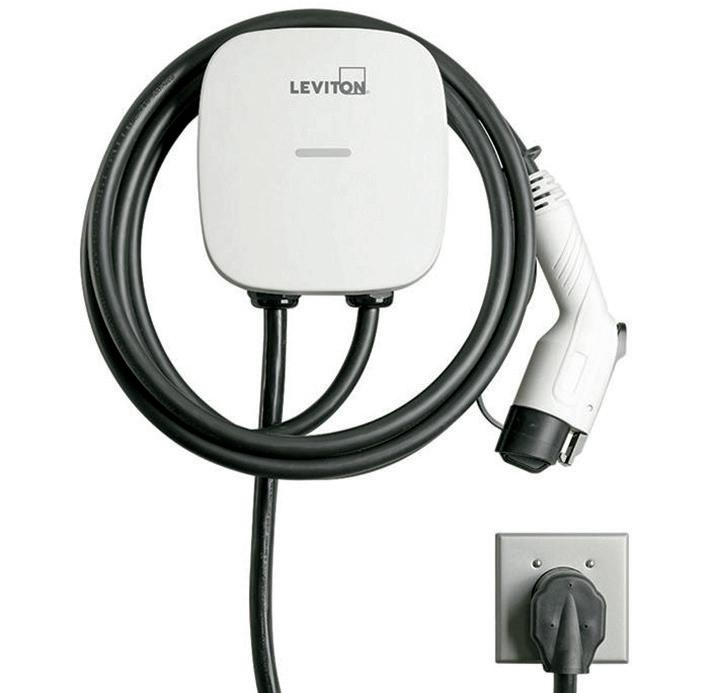
Q Charged: It looks like Leviton is concentrating on Level 2 chargers at the moment.
A Andrew Taddoni: We are heavily focused on Level 2, and the reason is that it’s really within Leviton’s sweet spot of the contractors and customers that we deal with globally, and Level 2 is the most common charging level in the North American market. Leviton is well known and respected in the home market—everyone knows our switches. In the US alone, it’s estimated that over 75% of homes have at least one Leviton device. People know the Leviton name—they see us in the Home Depots and the Amazons of the world.
And then we have relationships with a lot of electrical contractors that serve both residential and commercial public use settings—they’re doing installs in commercial buildings, garages, parking lots, hospitality and healthcare.
Q Charged: Are you equally focused on the residential, commercial and public charging markets?
A Andrew Taddoni: On the residential side, we have a full o ering that services the single-family home as well as multiple dwelling units and communities. Our EV Series Smart Home Charger is compatible with the My Leviton app, allowing for a whole-home smart ecosystem solution.

In the US alone, it’s estimated that over 75% of homes have at least one Leviton device. “
A big goal for us is to be the number-one player in the residential charging world. is goes hand-in-hand with what we do in residential settings already. A lot of people know us, a lot of contractors know us, and this idea of building on smart technology and systems that are inside your home is becoming more and more popular. Our customers don’t just want switches anymore. ey want these switches to have schedules and they want to control them. ey don’t just want an EV charger—they want a charger that they can control and that can send data to their smartphones in real time.
We are also very focused on the commercial market. We service a lot of hospitals—they have a lot of people coming to them that need chargers. In the hospitality world, the Level 2 play is more about convenience: “We have charging at our establishment. Come in, eat, shop, charge for a couple hours on us.” Again, because we’re already in there, we’re already talking to these contractors and customers.




In the hospitality world, the Level 2 play is more about convenience: “We have charging at our establishment. Come in, eat, shop, charge for a couple hours on us.”
A Andrew Taddoni: I would say it’s a mix, based on the application. On the residential side, Amazon and Home Depot are big avenues for us. ere are a lot of homeowners that are buying these chargers themselves from these retailers.
e automakers, a lot of them only o er Level 1 chargers, and leave the homeowner to do their research, buy a Level 2 unit themselves, and then hire an electrician to come and install it. So that’s a big focus for us, not just through retail stores and online, but also, we have a lot of electrical contractors that are getting calls to do installations. at’s a big, big piece of the market.
at speci c solution is our new EV Series Pro, which is a public charging solution that allows the site host to collect analytics and collect revenue if desired. For that we have a partnership with AmpUp, an EV charging management company, which takes care of the so ware side of things.
e focus is on two situations: somebody says, “I want the ability to collect analytics, have data at my ngertips and understand who’s charging, when they’re charging, and the energy usage.” at’s one piece of the pie. e other big piece is revenue collecting: “I want to be able to bill at the charger, and make a certain amount of money every time people charge.” Our EV Series Pro enables any commercial public use property to know what’s going on at the site, and allows the site host to control all of those settings.
e other big market that the EV Series Pro plays a role in, and that’s really starting to take o , is the eet market. Big distributors are starting to get EVs, and they need the ability to charge on-site. Amazon is the best example—they have a partnership with Rivian where they’re using electric trucks for deliveries. You have a ton of distributors that want to do the same thing, so that’s another big focus for us.
Q Charged: As far as sales channels, automakers are partnering with equipment manufacturers like yourself. ey want to sell a charger with the car. ere are also installers that are buying hardware from various manufacturers. en I guess there’s a certain amount of selling directly to eets and end users. rough which of those sales channels are you selling most of your hardware?
I went through the process of buying a plug-in hybrid myself, and aside from startups like Lucid and Rivian, and Tesla of course, I don’t feel that they are focused on actually selling the charger. I think they’re more focused on selling the cars. Some are doing a better job than others, but a lot of customers need education, not just on the product side, but on the installation side in their homes, which we’re trying to give at Leviton.
We’re also spending a lot of time with third-party companies that are selling turnkey solutions. I think we need to strategically work with everyone right now, because the opportunities are coming from all di erent areas and directions.
Q Charged: At the other end of the spectrum from the EV newbie who just wants to know how to plug it in, what do you have for the nerds who want to keep track of how much energy they’re using and how much it costs?
A Andrew Taddoni: With our whole-home smart solution connected via the My Leviton app, we o er the Leviton Load Center, which includes a smart panel; the core of smart devices and switches controlled by WiFi; and now our EV Series Smart Home. With the Leviton Load Center, there are smart breakers that will tie right to our charger, and every time you plug in, it will tell you your kilowatt-per-hour usage. is is going to continue to evolve over time, but I have the My Leviton ecosystem, and I can see in real time every day what my energy usage is per charge.
I have a plug-in hybrid, so I only have 45 miles of true electric driving, but I plugged in every single day at home for a month, to understand what my electrical bill would increase by, and it was 32 bucks. I knew the exact number down to the penny.
THE INFRASTRUCTURE
Q Charged: Your smart panel, does that require replacing the whole panel, or can it be retro tted to the existing panel?
A Andrew Taddoni: Right now, it involves replacing the whole panel. It’s a whole new system, but easier to install. Once the Leviton Load Center is installed, homeowners can snap smart breakers in and out, rather than wiring each breaker. It is a very, very cool system, but it’s an investment.
What we’re seeing more o en than not is two scenarios. e customer installs a charger in a residential setting, realizes there’s not enough room in the panel, and the contractor says, you can either upgrade your current panel or put in a sub-panel, but you’re spending a lot more money. Some of the contractors do know about devices that allow you to do some sort of load management or load shedding in the home, which is becoming more and more popular. Leviton is looking into adding these types of products to our o ering.
Q Charged: How much does the smart panel cost?
A Andrew Taddoni: It depends. If you go with the panel itself, regular non-networked, it’s comparable to all the big names that are out there. If you put a level of smartness in it, it depends how many breakers you want to make smart.
Smart switches can be expensive compared to standard lighting controls, but as I always tell people, every single switch in their homes does not need to be smart. You probably have 10% of the switches or less in your home that actually need to be connected. It’s the same situation with the panel. You really want certain loads to be monitored—your EV charger, your refrigerator, your heating system, stu like that. Maybe four or ve of the breakers, so it’s not a huge expense. e bigger piece is the electrical contractor’s charge to install a new panel—that can get pricey.
Q Charged: So, if someone’s going to have to install a new panel anyway, they might not be spending much more to go with a smart panel.
A Andrew Taddoni: Correct. As long as you do it right. A couple of those breakers, you make smart. For the rest
of them, we have non-networked breakers that are in line with everyone else’s, which can be switched as needed.
Q Charged: You make a 50-amp heavy-duty receptacle that appears to be speci cally designed for an EV charger—it’s even got a little picture of an EV on it. Now, the average homeowner probably doesn’t see any di erence from one receptacle to another, but I’ve been told by EVSE installers that the cheap receptacles at the big-box stores aren’t suitable for the sustained high power levels and the frequent plugging and unplugging of a portable EV charger.
A Andrew Taddoni: e residential team at Leviton spent a lot of time redesigning the new 14-50 NEMA receptacle for the reasons that you just said.
Say somebody has had a receptacle in their garage for a long time and they come home with a plug-in charger, and say, “Let me just plug it in and I’m good to go.” But they don’t know who installed that receptacle, they don’t know what it’s rated for. And very few of them, other than our new receptacle, are rated to pull power for four to six hours or more. If I start my dryer, in 50 minutes it’s done and I’m not going to do it again for another few days. But charging an EV might mean pulling current for four to six hours every day. Wouldn’t you want a product that has been tested? e torque requirements are way more robust. Everything on the inside of that product is built to survive regular charging four to six hours at a time or more to ensure that there are no issues from a safety standpoint.
Leviton recently launched a 40-amp plug-in version of our EV Series Smart Home charger as well, so this and the receptacle bundle nicely together. If you prefer a hard-wired unit, we have 32-amp, 48-amp, and even 80amp models for the home. e homeowner can choose what’s most convenient for them.
Q Charged: It seems like every day I read about a new company getting into the game, some of them startups that make nothing but EV chargers. You’re at the other end of the spectrum—you make loads of di erent electronic devices. Does that give you a competitive advantage over these other companies?




Very few of them, other than our new receptacle, are rated to pull power for four to six hours or more. If I start my dryer, in 50 minutes it’s done and I’m not going to do it again for another few days. But charging an EV might mean pulling current for four to six hours every day. “
A Andrew Taddoni: Yeah, I think it gives us a huge advantage. If there’s a slowdown in the overall market, some of these startups, are they going to face challenges? Customers need the right service and support. Leviton has been doing it for 118 years, and we don’t only rely on our EV charger sales. We have a whole infrastructure of products that supports the overall company.
Here’s what we’re hearing from site hosts and electrical contractors: “I want to come to Leviton because I’ve dealt with you in the past and I know the name.” It’s been a really strong message for us to say: “Yes, we will be here to support you. We’re not going anywhere in the EV charging world—we’re continuing to invest in it.”
Also, we’ve been in the manufacturing world for quite some time, so we understand the dos and don’ts, the pressure points, etc. We have an army of people, not just on the product side, but design manufacturers, a full marketing team, a very large customer service team, and a tech team that will take care of the products that are installed.
Q Charged: Do you have some other new products coming out that you’d like to tell us about?
A Andrew Taddoni: Now that Tesla’s NACS connector is becoming more common, we’re going to be in this world of adapters for a little bit, so we have an NACS
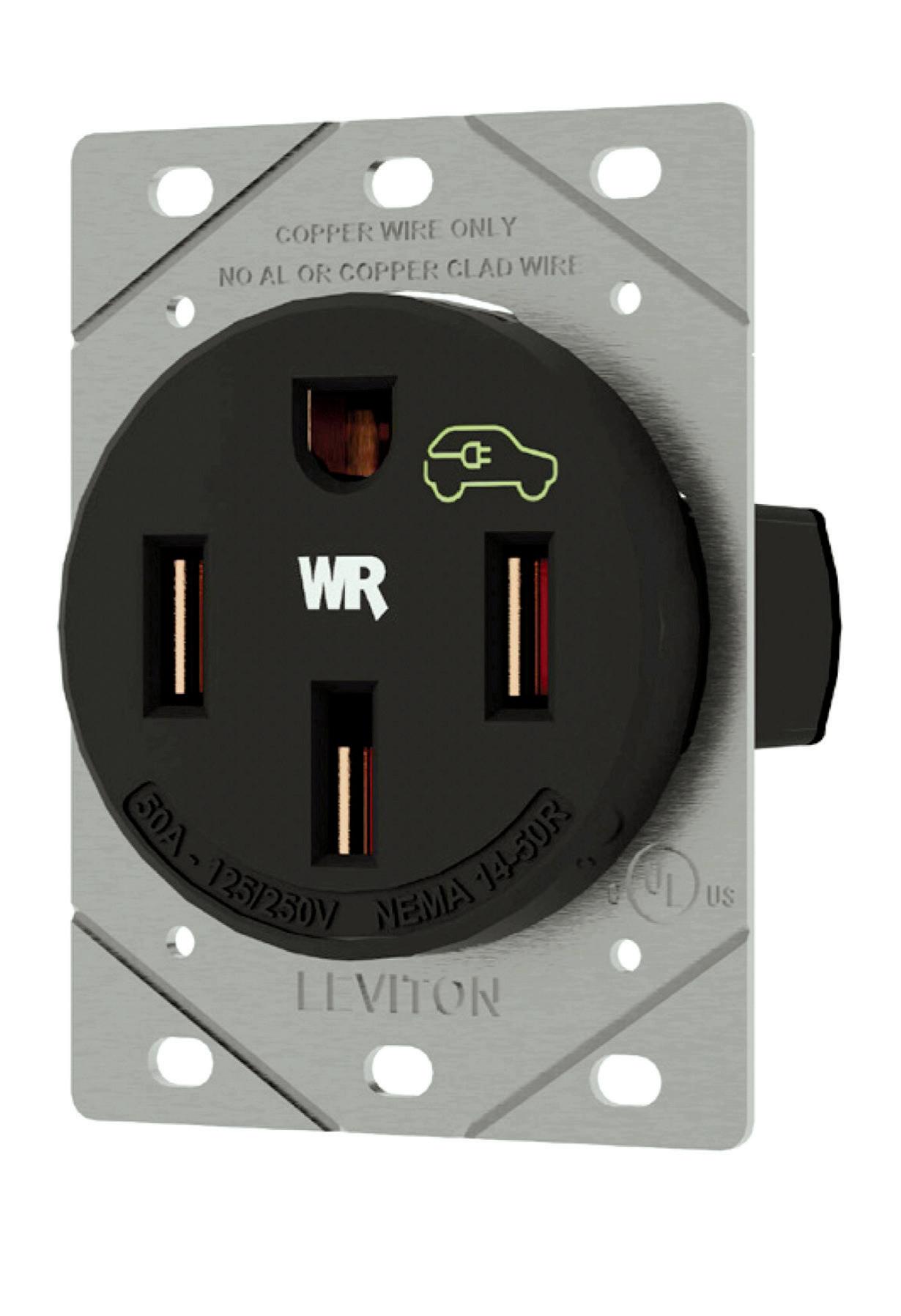
adapter that will easily pop right onto the front of our J1772 connectors, and it will make sure that our chargers can charge any of the Tesla models, or any future cars that are going to require a NACS port. It’s going to take some time for automotive manufacturers to ush through their inventory and put this new NACS port on there, but it is something that’s going to happen, and we have an easy, convenient solution.
And then we’re coming out with a dual-port unit for the commercial, public use customer. We have a single-port charger today—that’s our EV Series Pro with AmpUp so ware. Our dual-port 48-amp model allows multiple cars to charge at the same time if you don’t want to install two on the same pedestal. We’re giving options to people. “What is your situation? What would you like to do? We’ll have a solution for you.”
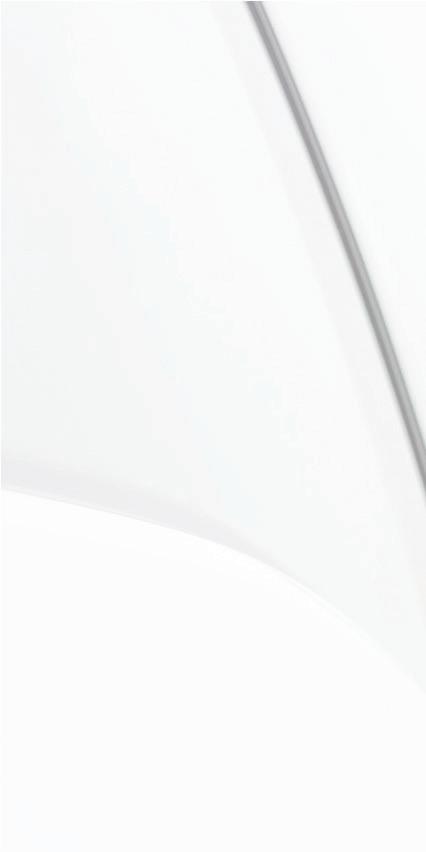
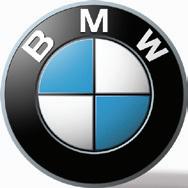
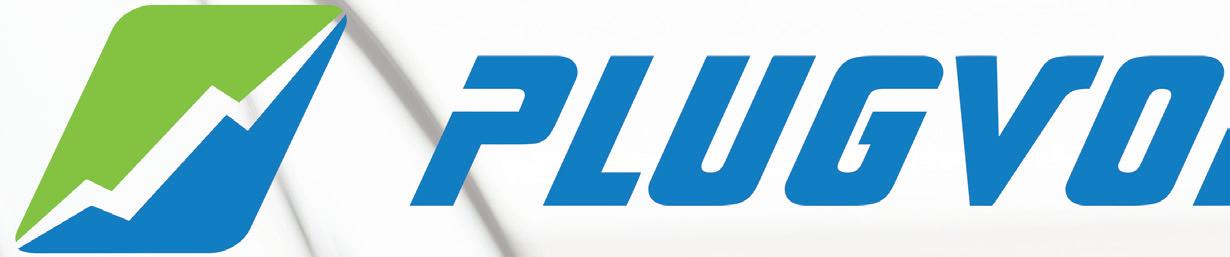
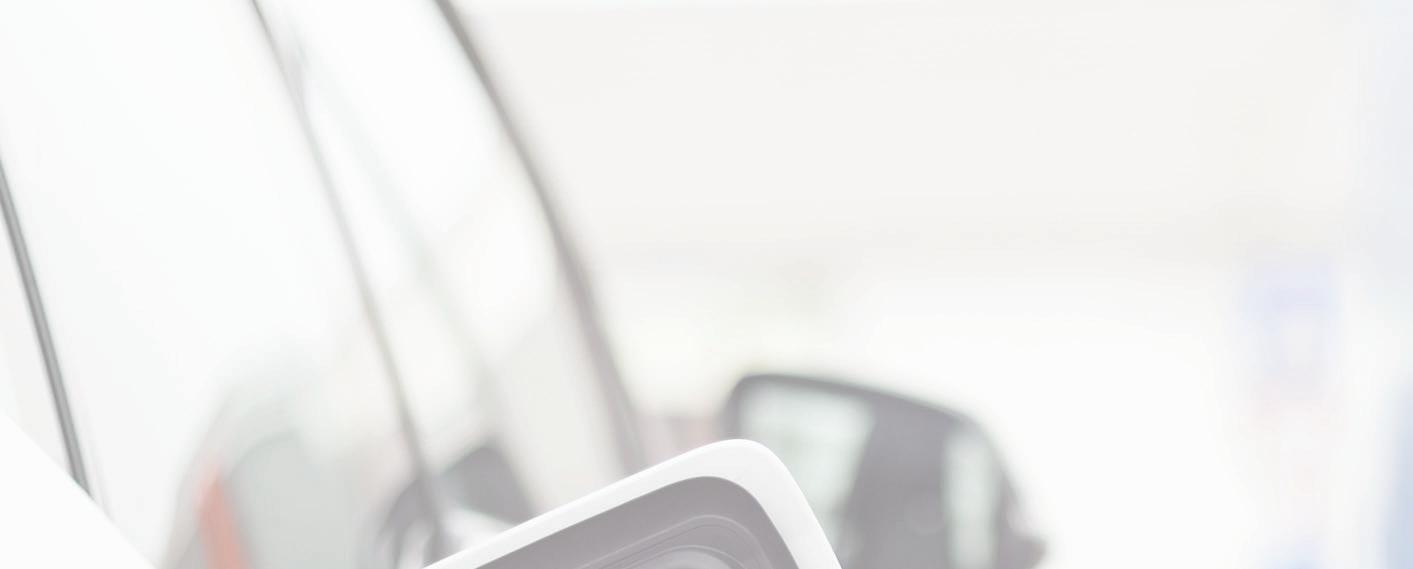

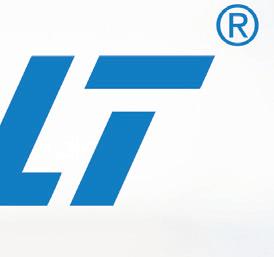
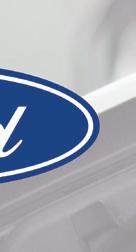

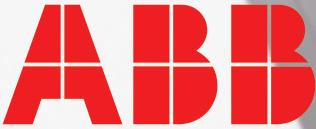
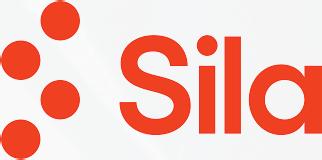
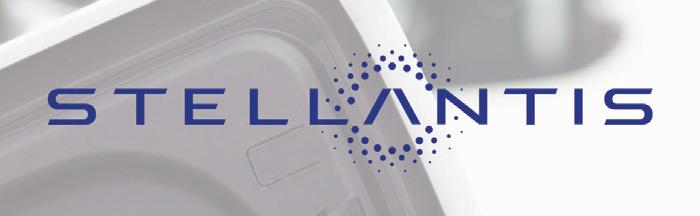
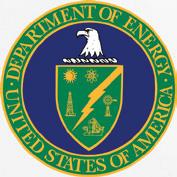

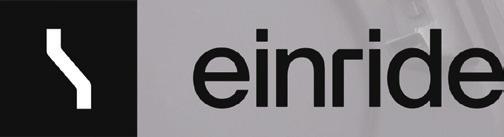

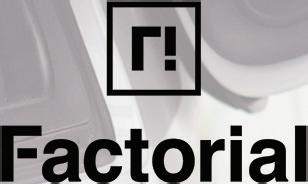
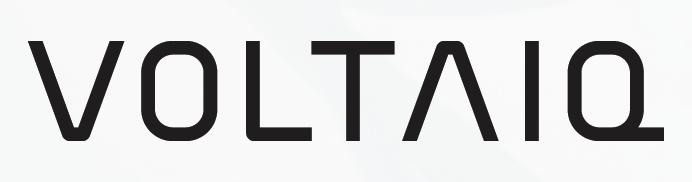




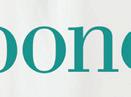
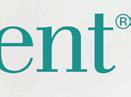







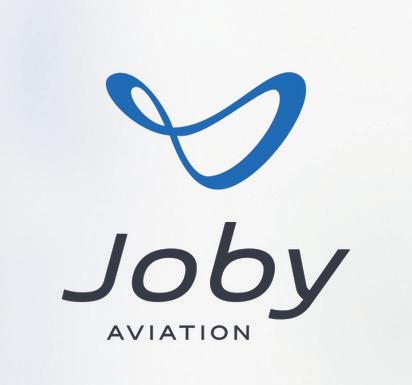

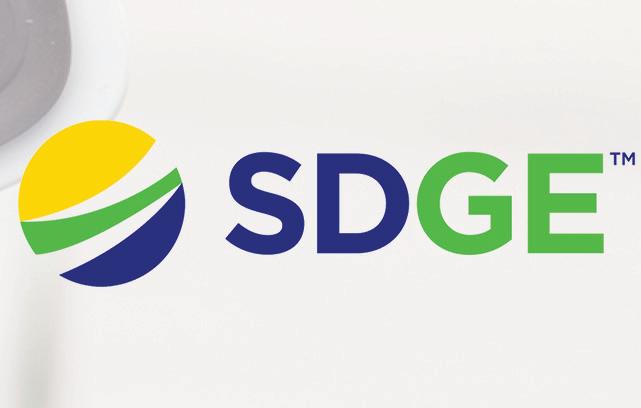
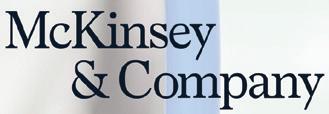


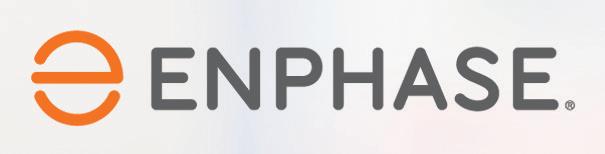
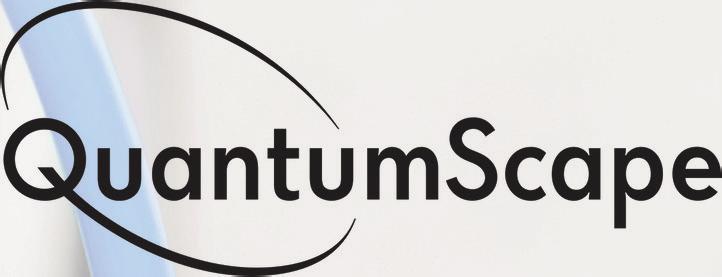

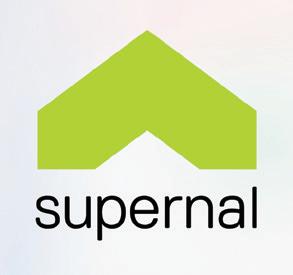



Will 2024 be the year EVs achieve price parity?
Twenty years into the EV transition, many roadblocks to EV adoption have been dealt with, but one remains: stubbornly high purchase prices compared to legacy vehicles. Only once EVs reach price parity will the end of the Oil Age truly be in sight.
Is that tipping point at hand? A new BloombergNEF study commissioned by Transport & Environment found that light-duty EVs will be cheaper to make than fossil vehicles in Europe by 2027 at the latest, thanks to falling battery costs and growing production capacity.
Before you give away your Hummer, however, let’s consider a couple of caveats. First, T&E’s ndings apply to Europe, which is further along the path to electri cation than the US. To cite one example, BMW, the world’s fourth-biggest seller of plug-in vehicles, claims that its EVs are pro table, whereas GM and Ford are by all accounts not even breaking even. (Tesla has long enjoyed comfortable margins, though these have been somewhat eroded by recent price cuts.)
Second, lower costs don’t always translate to lower prices Consumers expect to pay more for products that save them money (see hybrids) and automakers will charge what the market will bear. Furthermore, if lower prices juice demand, production could soon become supply-constrained—it’s going to take years to build supply chains and retool factories. For better or for worse, my pet scenario in which consumers abandon ICE vehicles the way they did CRT televisions is unlikely to come true any time soon—product cycles for cars are much longer than those of TVs, and the introduction of at-screens met no opposition from manufacturers, much less politicians. But when EVs reach price parity, assuming that dealers can keep them on the lots, demand for ICEs could drop quickly. Price parity will unleash complex economic forces, and we won’t presume to predict the results. Let’s content ourselves with considering several current trends that are pointing in the direction of lower EV prices.
BloombergNEF expects battery pack costs to drop below the “Holy Grail” level of $100/kWh in 2024 (Tesla is widely believed to have already surpassed this), and to reach $58/ kWh in 2030. Chinese battery supplier CATL recently said it would reduce the cost of LFP battery cells by 50% by the middle of this year.
But wait, there’s more! An obscure provision of the IRA could cut the e ective cost of US-produced packs to near zero over time. Section 45X promises a subsidy of $35/kWh for battery cells, and an additional $10/kWh for packs. is currently amounts to a third of total cost, or more, and because it’s a xed dollar amount, as battery costs come down that fraction will increase. Battery experts predict that this will cause battery-makers to relocate to North America en masse, and push carmakers to build their own US battery factories. Market research rm Gartner expects production costs to drop faster than battery costs, and predicts that EVs will be cheaper to produce than ICEs by 2027. Plain old economies of
By Charles Morrisscale will help too—a recent study by the Environmental Defense Fund found that the US has seen $167 billion in private EV manufacturing investments in the last three years (more than any other region of the world).
And then there’s China, where automakers are building EVs at costs far, far below anything Western brands can achieve—and they’re just getting started. As China expert Michael Dunne recently noted, China’s EV and battery production is 10 times greater than that of the US.
BYD’s cheapest Seagull EV sells for $10,000 in China, and Western automakers can no longer compete there. Jeep has already le the market, and Ford and GM appear to be eyeing the exits too. But it’s exports that are keeping auto execs awake. e Chinese are already selling cars in Europe, and they’re moving into markets like Mexico and Brazil. For now, the US market is protected by a 27.5% tari , but if the Big ree can’t solve the EV price conundrum, they may cease to be global companies.
eir leaders are well aware of this. Ford CEO Jim Farley recently said that 20% to 30% of his company’s revenue is at risk if it can’t catch up with Chinese automakers. “As the CEO of a company that had trouble competing with the Japanese and the South Koreans, we have to x this problem,” he added.
In the commercial EV market, buyers don’t care about style—they care about cost per mile. Electric truck expert Rustam Kocher told me in 2023 that he expected TCO for battery-electric trucks to reach price parity with diesel by 2030, at which point truckers will have to electrify quickly or perish. Now he says, thanks to the dramatic drop in prices for LFP packs, parity “might be just around the corner, at least for some applications.”
By all accounts, some segments of the EV industry are ripe for a wave of consolidation. Gartner thinks 15% of the EV companies founded in the last decade will be acquired or bankrupt by 2027. A little creative destruction should allow surviving companies to cut costs, and allow capital to be redirected to more e cient operators. To give one example, the pending Schae er/Vitesco merger will create the largest global EV powertrain supplier, and analyst HSBC foresees “unprecedented cost-saving potential.”
Also worth mentioning: the cost of building gas engines is expected to rise, thanks to emissions standards in all the major markets.
None of this is news to the legacy automakers. Ford, GM, VW, Tesla et al have recently announced plans for low-priced entry-level EVs. Competition among these global players is another megatrend that should lead to lower prices soon.
Naturally, all these predictions come with caveats: charging infrastructure and supply chains are bottlenecks; an economic slowdown in China could delay the game; and political upheaval in the US and/or Europe could send the chessboard ying.
Ever y thing You Wanted To Know About DC/DC ’s, But Were Afraid To Ask….
• 300W & 500W
• 12Vdc Outputs/Batteries
• 30~130Vdc Inputs
• Can Parallel up to 10
• Enable/Remote, On/Off
• Low Quiescent Current
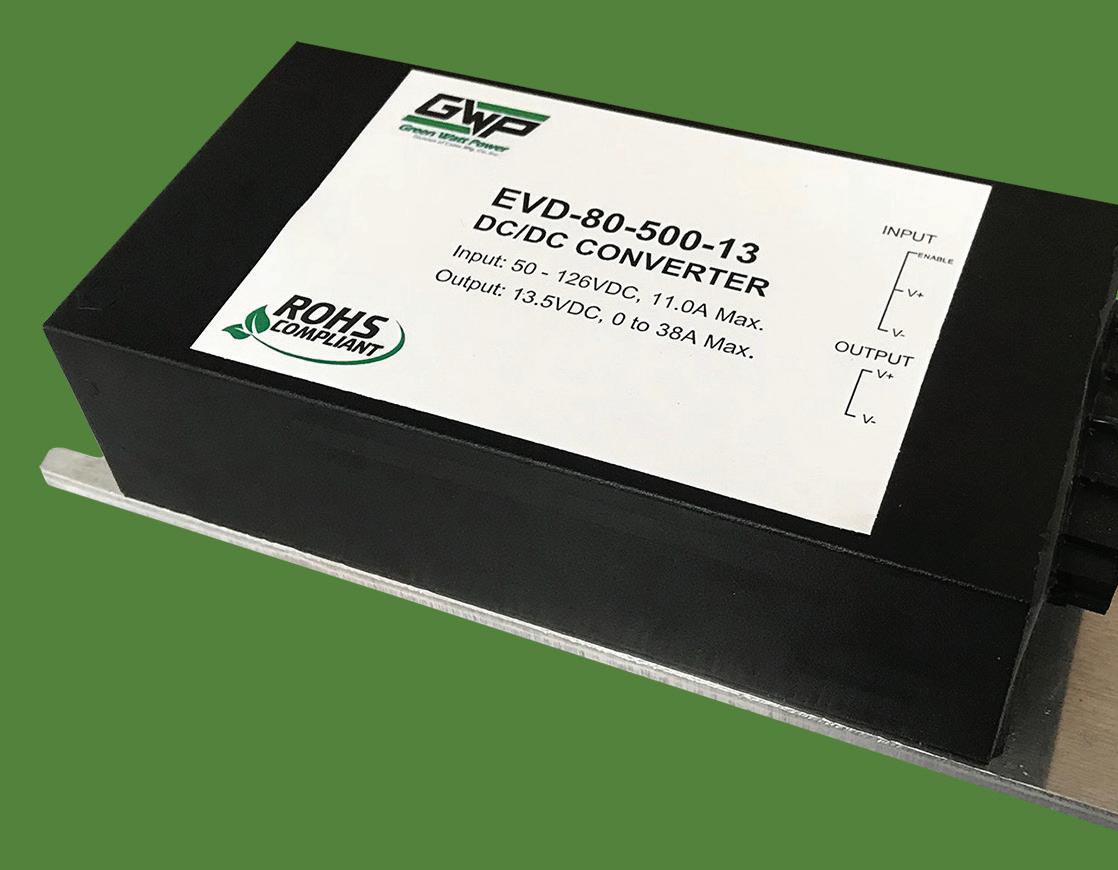
Is it Uni-directional or Bi-directional? Can I get parts when I need them? You bet –we’ve got the best delivery – through Digi-Key or direct. What about pricing? Price and quality through our low-cost factories and advanced automation. Plus others…Isolated, non-isolated, single & dual outputs and bi/uni-directional – from 40W to 66kW!
How about 2nd sourcing and customs/proprietary? We do both – with industry standard DC/DCs like Sevcon/Borg-Warner or Delta footprints: Chargers Too… Including the World’s Smallest 6.6kW!
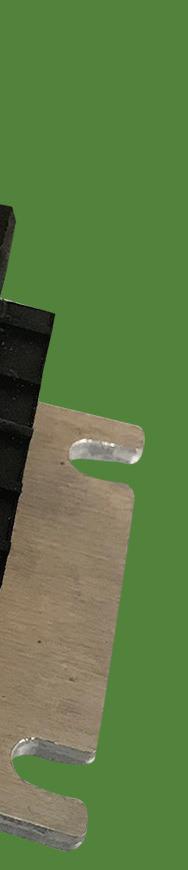
Ph.+1-310-881-3890 greenwattpower.com
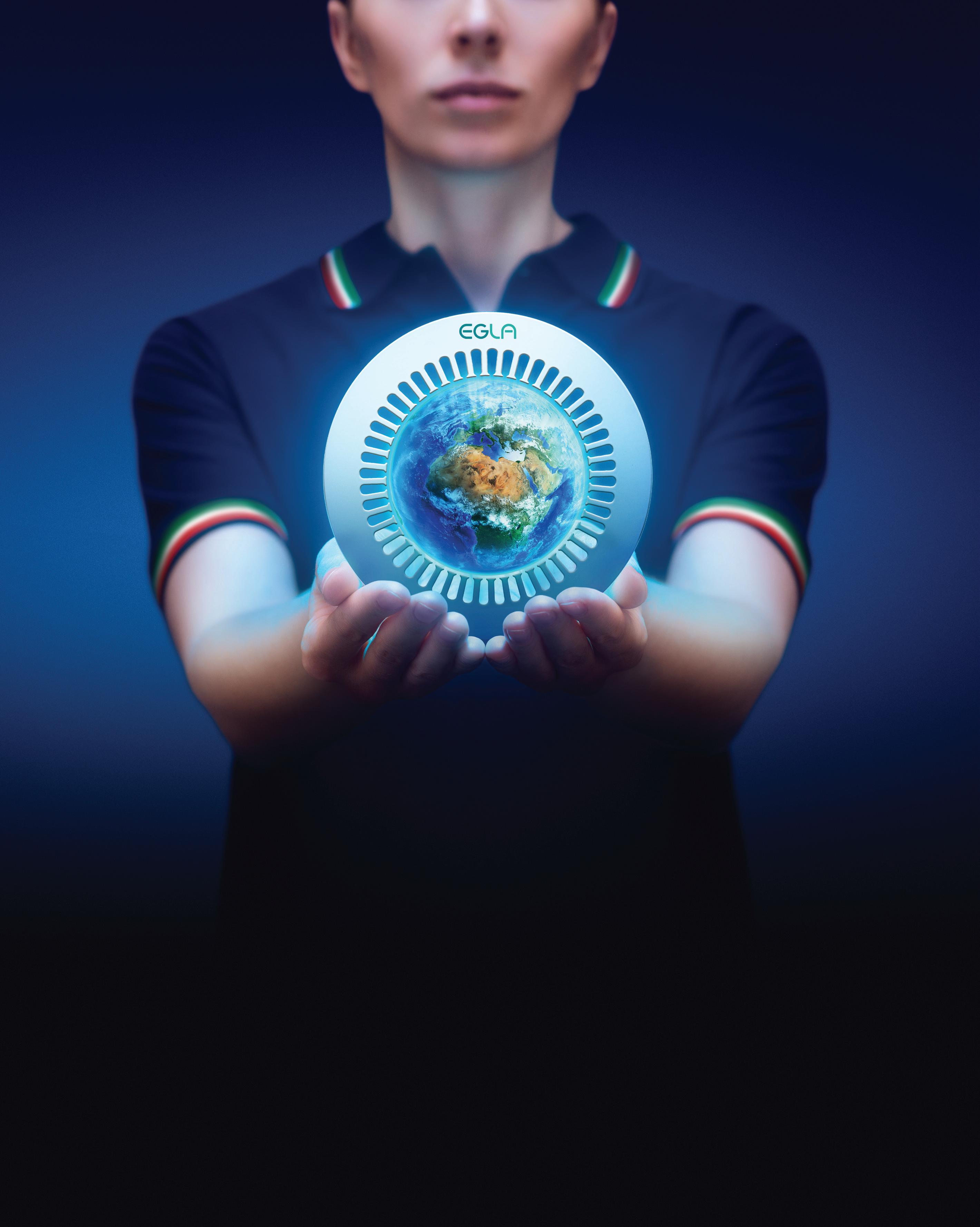