Circular plastics
CARBIOS Circularisation of plastics production and depolymerisation is the definitive goal of French biotech specialist Carbios SAS. In April, the company announced its biorecycling technology using enzymes is ready for global licencing. Europ E an Biot Echnology spoke with Emmanuel Ladent, CEO of Carbios, about the company’s plans for expansion and its impact.
EuroBiotech _Mr Ladent, what was the reason for you to engage with Carbios and how do you want to help solve the global plastic problem?
Ladent _The company was founded in 2011 by Jean-Claude Lumaret, and I became CEO of Carbios SAS two years ago. In the beginnings of our company, he had the idea “maybe we can find some enzymes that show activity on plastics.” So the first thought was on biodegradation rather than on enzymatic recycling. Soon after setting up Carbios, our founder met Alain Marty, who was then Head of Research at INSA Toulouse and is now Chief Science Officer at Carbios. So all fundamental research actually began in Toulouse, with collaborations with Toulouse White Biotech, INSA Toulouse, INRAE and CNRS working on enzymes for all sorts of applications. Some work started on plastics and, after a couple of years, we finally identified some esterases that had activity on polyethylene terephthalate or PET, the fourth most common plastics globally. Specifically, a cutinase depolymerised PET into its monomers, monoethlyene glycol or MEG and therephthalic acid or TA. The idea of biological PET recycling was born. After extensive enzyme engineering and optimisation, we built a demonstration plant in the centre of France, where Carbios is located, and operational since 2021. Our reference unit, a first-of-a-kind PET biorecycling plant, with an annual capacity of 50,000 tons of plastic waste, will start construction before the end of this year. To paint you a picture: that is about two billion plastic bottles! The enzymes needed will be provided by our exclusive partner Novozymes A/S. Novozymes will
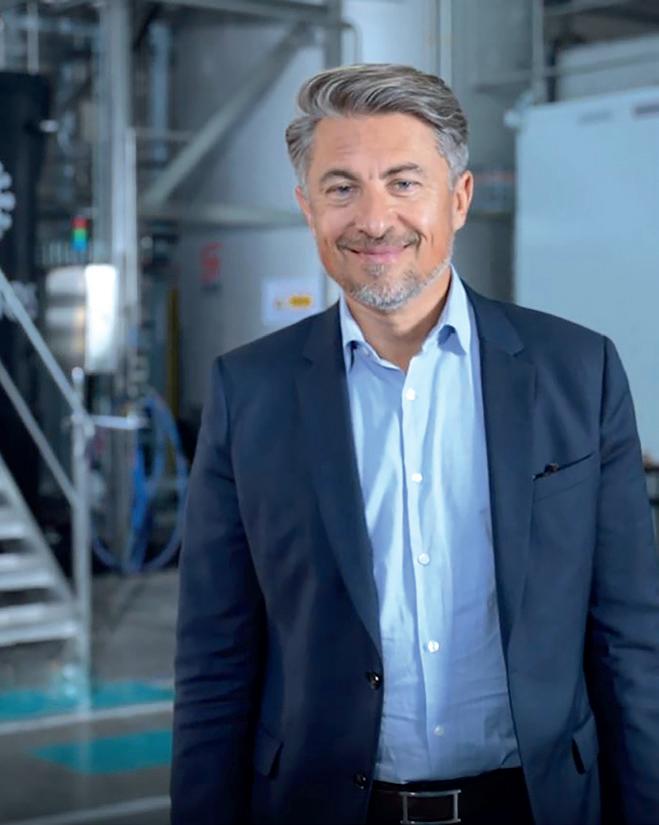
EMMANUEL LADENT, 52, CEO of Carbios SAS, has 30 years of experience in the automotive sector and more specifically in mobility. Most recently, he managed the MICHELIN Group’s largest business line, the Automotive Global Brands division. His management career is characterised by a strong international background, with more than 20 years spent working on several different continents. Through strong leadership, he has been able to unite interdisciplinary and intercultural teams around a common vision and ambitious goals.
also ensure the supply of enzymes for all the future plants under license.
EuroBiotech_What kind of waste will you use in that plant and what happens to residues?
Ladent _We can recover the monomers from any kind of waste that contains PET but we focus on items that are not yet reclyclable such as food trays, polyester textiles or cosmetics packaging. The beauty of the process is that we recover more than 90% of the monomers that are used in almost every plastic production plant globally, and can repolymerise them into virgin PET in the same quality as the original one. Our products are 100% identical to petrochemically-sourced monomers. At the moment, Carbios is focussed on the enzymatic depolymerisation of pure polyester waste such as sportswear, which contains more than 95% polyesters. However, we are currently extending our enzyme screening capacity, because, in the next step of our evolution we want to find enzymes that can do the same job as our cutinase is doing for PET, but for polyamides and polyolefins such as polypropylene or polyethylene. We are already working on this. We have to file the patents and optimise enzyme activity by protein design, but I am confident that we will have something to announce in the near future. This might also answer your question on what happens with residues in mixed-fibre textiles.
EuroBiotech _What markets does Carbios target, and why?
Ladent _We recently announced that we are ready to licence our technology. Our dream would be to have plants everywhere, but in the beginning we will focus on Europe, North America, and certain Asian countries. We are going to start with our commercial plant in France in 2025. By 2050, we hope to also have some plants in Africa because from the
perspective of feedstock availability, this is a highly interesting market that we have not yet analysed in depth: Most plastic waste that is produced in Europe ends up in Africa because 90% is not recycled, today. Our technology is interesting for different industries, but particularly for PET producers as their market is shifting because it is currently 95% petrochemically sourced. Due to environmental and political pressures, the demand for recycled plastics is increasing. Our process needs significantly less energy and has a much better CO2 footprint than the petrochemical way to produce MEG and TA. Producers – there are around 50 large groups globally producing PET – can save 50% GhG emissions. The same is true for the chemical industry, and finally waste management companies, which currently make most of their revenues through incineration rather than collection– are interested in licencing our technology. They know that incineration may be profitable for the moment but not in the long-term. So, they are looking for new business opportunities, and we already had discussions with some of them. We also have contact with a large German automotive company, which uses recycled PET in its car doors. All in all, we have an abundance of potential licencees across diverse markets.
EuroBiotech_To what extent do new laws that set targets for emissions and energy consumption play a role in Carbios’ licensing business?
Ladent_Regulation is important because it is going to put obligations on producers. The percentage of recycled products is going to improve. For instance, the packaging industry will have to include 30% r-PET in its products by 2025. This percentage will likely increase to 65% by 2040. From one ton of PET, we get at least 900 kg recycled material. Our vision is to increase this number to more than 950 kg. Carbios’ biorecycling technology allows for a much greater number of cycles as opposed to two or three cycles with today’s recycling technologies. Thus, the more regulations pushing for recycling, the better for Carbios. That was a big motivation for all the companies that are partnering with Carbios such as L’Oréal, Pepsi Cola, Nestlé. Companies such as PUMA, Patagonia, or Solomon have made commitments to become circular in the near future. This trend is positive for the promotion of technologies like that of Carbios.
EuroBiotech _Products made from enzymatically recycled PET are more expensive than those made from petrochemically produced PET. Can new, sustainable recycling technologies ever be scaled up to compete in terms of profitability with petrochemical production, which has been optimised for over 50 years and has long since been written off in terms of plant technology?
Ladent_You are right, traditional recycling technologies are still not ready to deliver. Scaling petrochemically sourced plants –
in Germany we see 500.000 t plants, in the US there are 1.2 millon t plants – is only possible in the chemical industry, not the recycling industry. For a recycling plant with an annual capacity of 1.2 million t PET you would need huge amounts of waste from far away. What we can do is build plants of up to 200.000 t capacity. Regarding costs: yes, we have a premium price compared to fossil sourced PET, because it has a high value both in terms of circularity and quality. But this only represents a few cents for the consumer on a Tshirt or a bottle. However, as our recycling process runs at lower temperatures during depolymerisation and saves 50% of CO2 emissions it may pay back. After all, our monomers can be repolymerised using the existing production infrastructure.

EuroBiotech_Carbios has another product that is staying out of the spotlight so far: a PLA additive...
Ladent_PLA is a biosourced plastic mostly used in the US and Asia – around 300,000 t of PLA is produced annually, much less than PET (90 million t/a). PLA is not easily biodegradable, it needs 65°–70° C to degrade. By incorporating 5% of Carbios’ patented enzymatic formulation during the production of PLA, flexible and rigid packaging becomes 100% compostable at room temperature. The biodegradability is accelerated and it takes less than eight weeks for the PLA to be completely disintegrated without residue or toxicity allowing a safe return to the soil. We are going through the process of Food Contact certification in North America, so it’s an interesting market.
EuroBiotech _What is Carbios’ ambition for the next years?
Ladent_In the short term our focus is on ramping up the global commercialisation of our PET technology, but we will also never stop to improve our enzymes – and add new ones such as those who can crack PE, PP or polyamides. While it took us ten years from the discovery of out PETesterase to our reference unit plant, I am very optimistic that we will go much faster with the polyamide- and polyolefin-degrading enzymes.
t.gabrielczyk@biocom.eu