6 minute read
Member Spotlight
from May 2021 O&P Almanac
by AOPA
Next Article
Creating Comfortable Sockets
Chicago company distributes system that recreates loading forces on the residual limb
CYPRESS ADAPTIVE’S flagship product is the Symphonie Aqua System, a method of casting amputees developed by the German firm Romedis GMBH. As the company’s exclusive North American partner, Cypress Adaptive markets and distributes the system, which recreates loading forces on the residual limb that match those under actual full weight-bearing conditions.
“Historically, prosthetists take an impression while the patient is in a seated position, which can’t mimic the anatomical needs or wants under full load,” explains Matt Doering, co-owner and head of sales, marketing, and education. “Most socket issues occur in a weightbearing position, so doing the hydrostatic full-weight capture allows the prosthetist to create more comfortable sockets, and that leads to great compliance.”
Another benefit, he notes, is the consistency the Aqua System brings to regional or national providers. “Even a skilled clinician who casts a patient multiple times won’t get identical results,” says Doering. “This system enables every office to create the same outcome, regardless of its location or the prosthetist’s experience.”
In addition to Doering, Adaptive is co-owned by Lynn Snyder, PT, who handles dayto-day operations and customer service, and Lazlo Dallos, head of product development. Snyder works from her home base in New Jersey, while Dallos is based in Boston. The company manufactures expulsion valves in Chicago, where Doering operates.
Some of the company’s recent developments include the introduction of a new transfemoral version of the Aqua System as well as a more portable unit for transtibial and through-knee amputations. The portable system is useful for facilities that want to share the system across several offices or satellites, because it doesn’t require a hookup to air and water sources. The standard system, which is designed to be fixed in place, is more modular, allowing users to add features as needed.
Several small research studies have focused on the Aqua System, and a three-year, multisite study by the U.S. Department of Defense is about midway through completion. A committee of practitioners and Cypress Adaptive representatives is investigating whether the system merits a specific L code for reimbursement.
In addition to the Aqua System, Cypress Adaptive works with independent inventors to develop other prosthetic products, including expulsion valves, suspension
Owners Laszlo Dallos, Lynn Snyder, PT, and Matt Doering
COMPANY:
Cypress Adaptive
OWNERS:
Matt Doering, Lynn Snyder, PT, and Laszlo Dallos
LOCATION:
Chicago
HISTORY:
Six years
The new Symphonie Aqua Compact System sleeves, elevated vacuum systems, and prosthetic knees.
The founder of Romedis, Andreas Radspieler, developed a new suspension sleeve that, unlike traditional sleeves, eliminates pressure across the patella and behind the knee. “It is a completely different concept, and you have to see it to understand it,” Doering says. “Radspieler, who has been the German equivalent of a CPO for 25 years, is the Elon Musk of prosthetics.” Doering expects the new sleeve to be available soon.
Like most companies, Cypress Adaptive faced an uncertain future during the pandemic, with a precipitous drop in sales during the first two quarters of 2020. “Fortunately, we were already a pretty lean company, so we just had to watch expenses and readjust our marketing dollars,” recalls Doering. The company began to recover in the third quarter and continues to rebound.
As travel halted last year, the company added instructional videos to its website and plans to expand virtual training even when on-site visits are possible again.
Doering says the company will continue to refine its products and seek innovations over the next several years. “Our goal is to create tools that make it easier for the practitioner and the user,” he says. “We feel fortunate to be part of this industry. It’s incredibly rewarding, even with changes in the past few years. We love the fact that we are a part of it.”
Deborah Conn is a contributing writer to O&P Almanac. Reach her at deborahconn@verizon.net.
Easy Access
Facility offers transportation for patients in need
FOURROUX PROSTHETICS goes the extra mile for its patients—often literally, according to Jenn Arnold, LPN, the company’s executive patientcare coordinator. Each of Fourroux’s Jenn Arnold, LPN eight clinics has an ADA-compliant van to offer no-cost transportation to patients within a 150-mile radius who need assistance getting to and from their Fourroux appointments.
“With the services we provide, it’s super important that [patients] come into the office,” Arnold Fourroux Prosthetics was explains. “We do see patients established in 1955 in Huntsville, in their homes and in rehab Alabama. Over the past 66 centers, but treating them in the years, the practice has added office, where the lab is located, is facilities in Atlanta; Birmingham, essential.” Because most patients Alabama; Memphis and Nashville, need to be seen every three Tennessee; St. Louis; and Tampa months for follow-ups, “we want and Pensacola, Florida. Each to make it as easy as possible.” facility is a standalone, with its Fourroux also own fabrication capabilities where offers same-day nearly all devices are built. fabrication, says “We have a talented fabricaCaitlin Ratliff, CP, tion team,” says Ratliff. She cites LP, co-clinic lead. an example from two years ago, Caitlin Ratliff, CP, LP “For lower-extremity amputees, we can when the Atlanta facility “built a hybrid body-powered and often go from a test fitting at myoelectric upper-extremity 9 a.m. to a laminated, delivered prosthesis that was simpler and socket by 5 p.m. For a lot of lighter for the patient than a patients, that can be crucial— completely myoelectric device.” particularly those in rural areas.” The company has made several Ratliff says this service is benefi- adjustments during the pandemic, cial to her as a clinician “because such as limiting transportation I am not hurried in my assess- services to one patient at a time ment,” she explains. “I see how and isolating patients at the office, the socket looks at 9 [a.m.] and as well as acquiring new cleaning how the volume of the residual equipment for vans and offices. “A limb fluctuates throughout the lot of facilities had to lay off staff or day. The patient also has many close offices, but Fourroux never hours to walk and test the fit, had to do any of that,” says Eli giving us good feedback.” Walls, a board-eligible prosthetist,
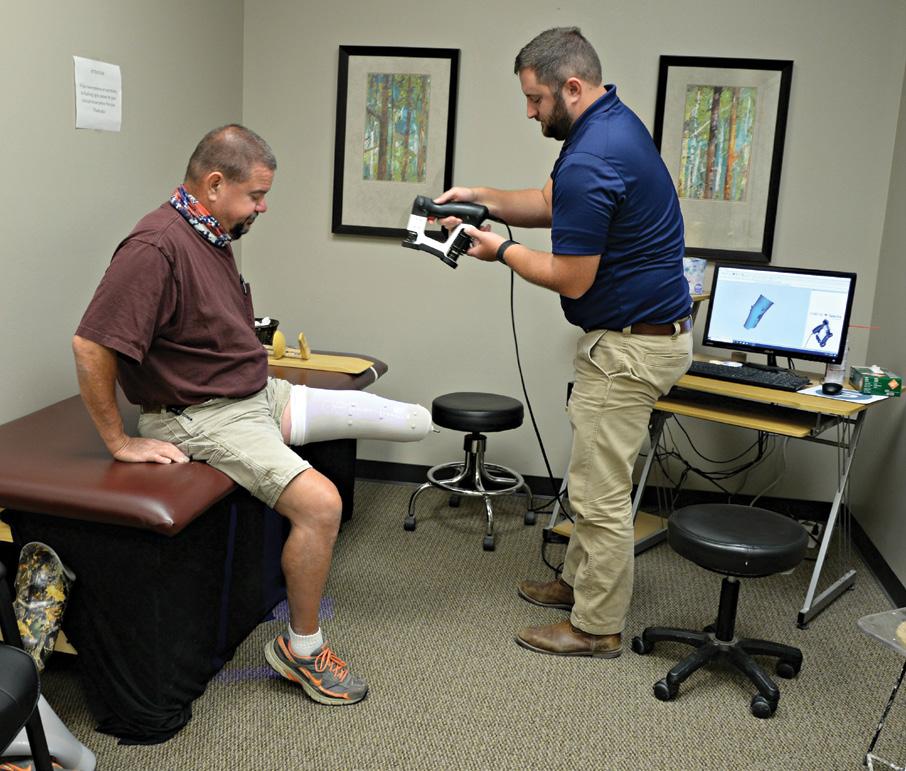
Justin Hanes, CPO, LPO, co-clinic lead, digitally scans a patient.
FACILITY: Fourroux Prosthetics
OWNER:
Keith Watson, CPO
LOCATION:
Headquartered in Huntsville, Alabama, with locations in five states
HISTORY:
66 years
who served his NCOPE residency at Fourroux. “In fact, we opened three new facilEli Walls ities last year.”
Fourroux has temporarily put its amputee support groups, which normally meet quarterly, on hiatus, but hopes to reconvene with appropriate guidelines, says Ratliff. Other community-based activities include offering educational sessions to students at local colleges, universities, and technical schools to raise awareness of prosthetics as a career. Both Arnold and Ratliff participated as event staff at the U.S. Paralympic Cycling Open in Huntsville in April.
The facility leverages advanced technology, such as computer-aided design and manufacturing, although technicians also use hand casting when appropriate, depending on the level of amputation and the patient’s needs. “We are also primed and ready to convert to 3D printing when it becomes more available and accessible,” says Ratliff. “We can already save files to that format. It’s an exciting time to be a clinician with technology advancing as it is.”
Fourroux had to forgo a big bash for its 65th anniversary in 2020, but it may have even more to celebrate the next time a milestone comes along. “We’re not interested in growth for growth’s sake,” says Walls, “but we will do so if the right people come along.”
The right people, according to the company philosophy, exhibit four attributes: honesty, integrity, an innate ability to care for people, and self-motivation. As a result, Arnold notes, staff turnover is rare; everyone unites in putting patients first.
Deborah Conn is a contributing writer to O&P Almanac. Reach her at deborahconn@verizon.net.