5 minute read
welding
from Issue 5 2019-20
by Trojan Times
Next Article
06 TROJAN LIFE
WRITER Daisy Ann Hipolito
PHOTOGRAPHER Reese Yamamoto
DESIGNER Jenna Lee Bundalian
Though welding may not be a common hobby amongst MHS students, it is not overlooked by a select few, who follow the practice of state and national welders alike. Welding is defined as the process of uniting or mending together multiple pieces of material (metal, thermoplastic, wood, etc.) through the application of heat and pressure. This process results in a wide variety of creations, such as: tables, stands, chairs and other usable pieces of furniture or equipment. At MHS, students taking automotive technology (auto tech) are presented the opportunity to begin welding and advance their skills if interested. Senior Matthew Leonard was one of the few students to take up this opportunity and now considers welding as a unique and intriguing hobby. “If you’re not consistent with working then you’re never going to get anywhere. It’s just about consistent practice, getting out there, grinding your stuff and then practicing other things,” said Leonard. Similar to other high school welders, Leonard’s interest was sparked in auto tech. Auto tech is a class that allows students to learn the basics of automotive repair and maintenance while being able to work interactively with automotive equipment and electronics. “They have this little section that you can weld in. It has this little welding table and we’re currently trying to build a stand where we can hang sheets off of so that people can look in and see (the) welding so that we don’t have to worry as much,” said Leonard. Welding is known to be a very tedious and time consuming process. Students interested in welding learn about the steps and techniques that go into a quality weld. Later on, the students are able to execute their own knowledge into projects of their own. “The first thing is you want to make sure the metal is nice and clean and then, from there, it’s just making sure everything lines up and then from there you just want to have good technique,” said Leonard. Welding can be used in a variety of situations. While hobby welders usually More than 50 percent of all human-made products require welding, including planes, cars, furniture, pipes, etc. work on smaller projects such as furniture and sculptures, more seasoned and professional welders work on grander-scale projects, such as pipelines, bridges, power-plants, refineries, cars or ships. “The first major project I did was — well we’ve done things on an axel, for like a trailer, and we've also done a grill where I kind of just welded some stuff to hold it together,” said Leonard. “I definitely have something that’s going to be there for a while. The stand I just made, that’s probably going to be there for who knows how long. So you get to contribute actively to the shop.” Welding results in more than just a self-made product; welders have gained many valuable and applicable life lessons through the process and practice. These lessons and skills can be used both in and outside of a welding environment or situation. “I think with anything it’s more like work ethic and you gotta stick with the project. If you aren’t consistent then that’s something you can transfer into life, anywhere. If you’re not consistent with working then you’re never going to get anywhere,” said Leonard. Aside from Leonard, only a few other students at MHS are known to weld as a hobby, and those that do understand that welding is not for everyone. However, that does not stop them from encouraging those who are intrigued by the activity to give it a try. “I think it’s because they think it’s (welding) tedious. We’ve given people the chance to weld and they’ll kinda just go and they kinda just play with it for a little bit, but to actually get good at it is a tedious process,” said Leonard. There are many benefits to taking welding up as a serious profession or side hobby. According to TopWelders.com, welding is currently one of the highest-paid labor jobs in the United States, with a yearly salary of around $50,000 to $185,000, or $160,000 to $2 million for military support welders in the United Arab Emirates. “I know in college I’m potentially thinking about getting a welder, so depending on when I can use it, I can just go to different job sites and as I get better people can just pay me and I can go do small projects. It’s just another source of income,” said Leonard. If you are interested in welding, you can look into MHS’ auto tech class or research local welding teaching companies.
Every year before NASCAR , at least are spent welding and working on each individual car. 950 hours
at its current demand, the u.s. will need
372,664 welding professionals by the year 2026.
Welders do not need college degrees to practice their trade, making welding one of the highest paying jobs without a higher education.
They do, however, need to be certified and licensed.
07 TROJAN LIFE
Leonard uses two welding techniques: a C pattern and a figure eight pattern.
08 TROJAN LIFE
Welding Process Welding Process the
Hidden near the tunnel in MHS’ lower campus, select students like Senior Matthew Leonard weld in J building. There, they join materials like metal to create anything from furniture to equipment. Here is the process: WRITER Emma Lee
PHOTOGRAPHER Reese Yamamoto
DESIGNER Jenna Lee Bundalian
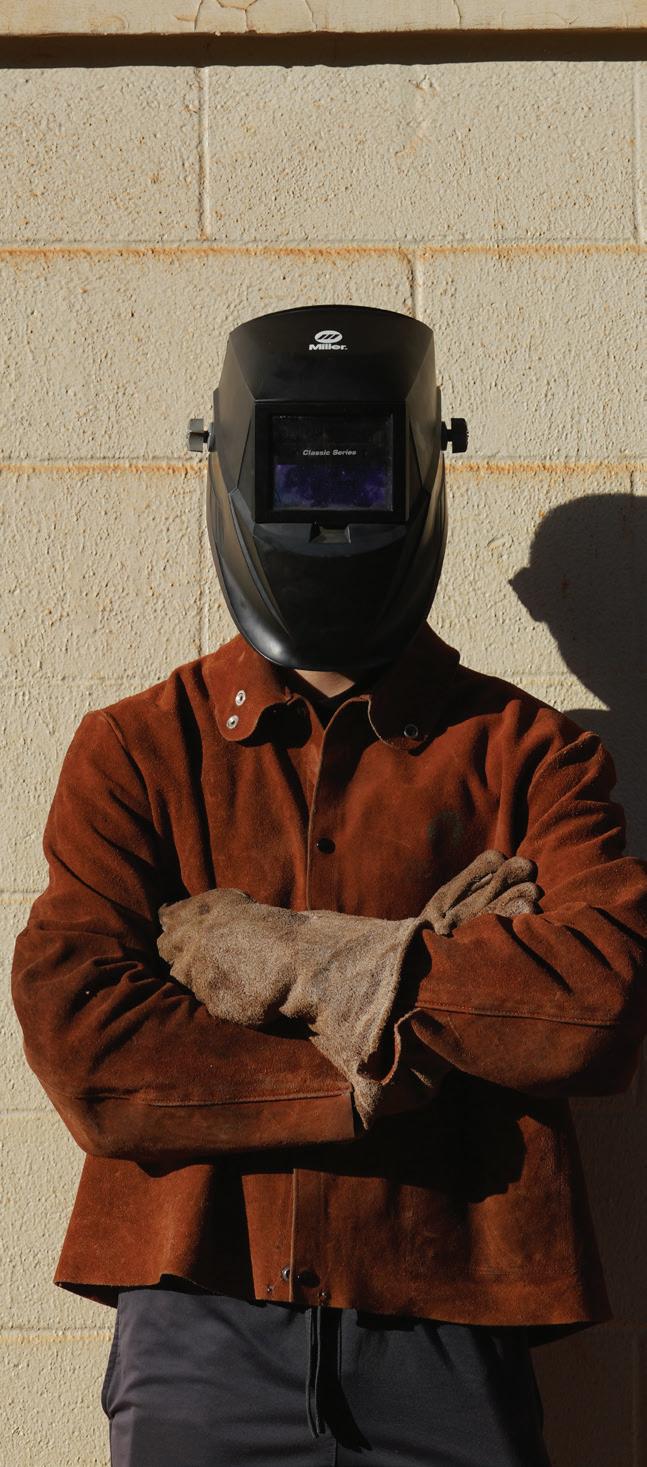
Safety first. In an appropriate working area, welders put on gloves, masks and jackets for protection against sparks. No shorts are allowed.
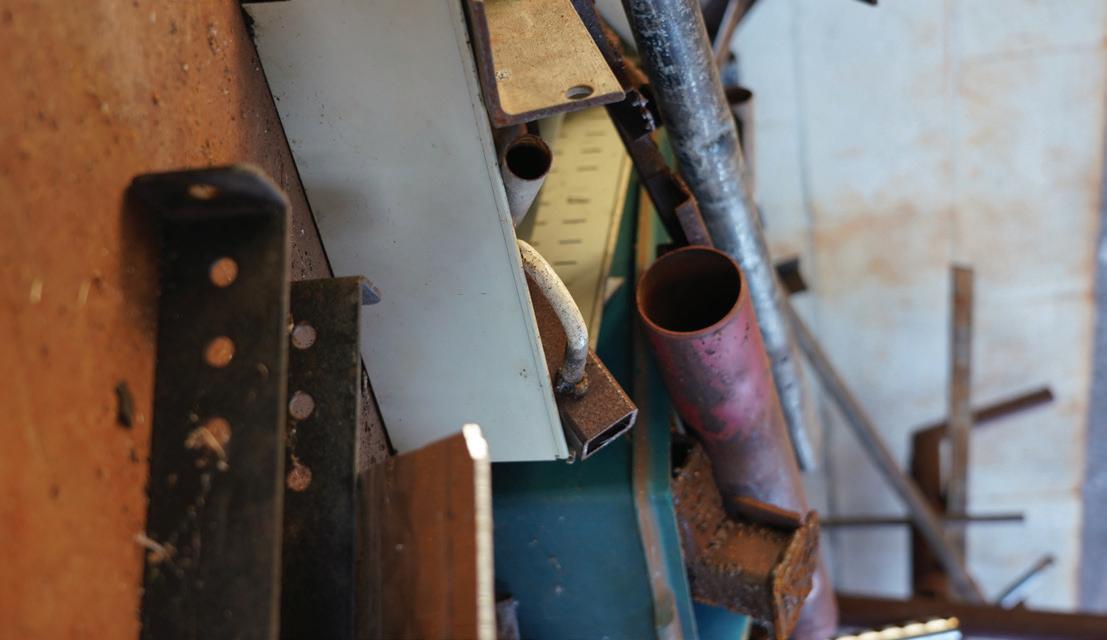
Various scrap metals can be found throughout the building. Every project is different, and selecting the right metal ensures a quality weld. Leonard advises against aluminum — a specific welding machine is needed for that.
Sparks fly as Leonard grinds half an inch of his chosen metal. Grinding gets the metal clean and removes any paint that can make more sparks during welding. Leonard wears safety glasses for protection, but these sparks are minor compared to those created while welding.
The metal is clamped down. It must be grounded to create a closed circuit, and the two metals are aligned to be mended together.
09 TROJAN LIFE
Leonard sets the gas pressure between 30 to 40 psi (pounds per square inch). This range is ideal for quality welding. Now everything is ready. Leonard puts on his welding mask.
There are three main patterns for welding, the first of which Leonard uses here: the ‘C’ pattern, circles and a figure eight. The ‘C’ pattern is the easiest to control and is used by beginners. Circular movements are good for uneven surfaces, and figure eights (for the more experienced) create a really nice weld.
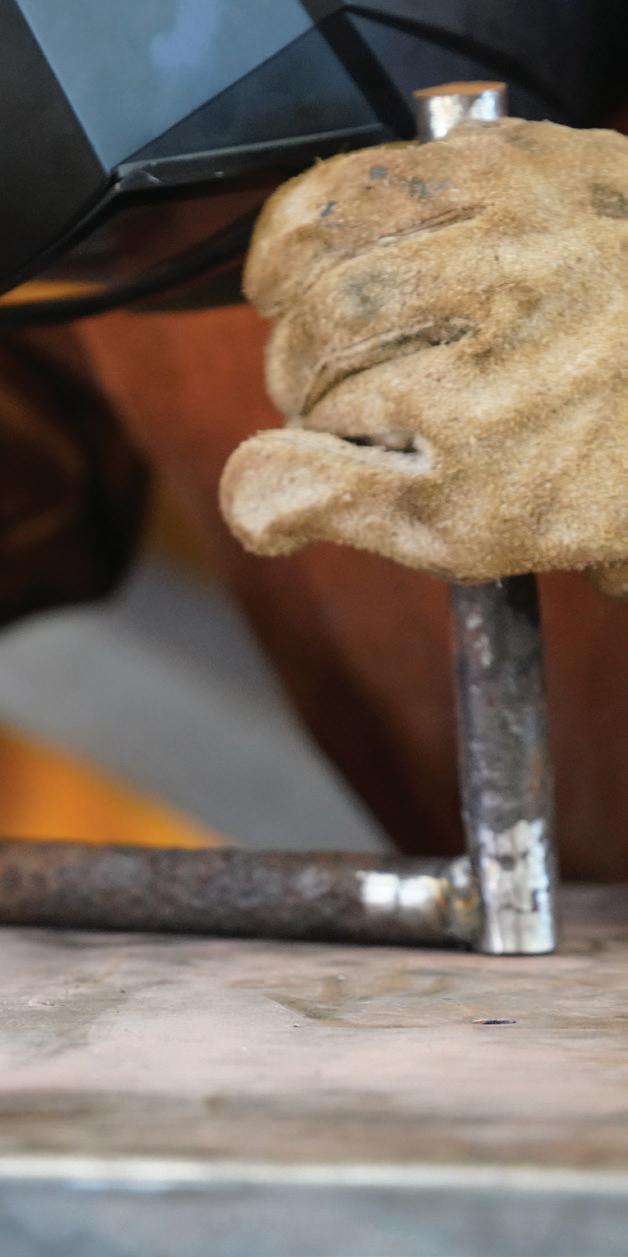
The final product might be used for a table or reinforcement in a building. The popped bubbles are a result from high heat and the deep crevice, but the metals are welded securely.