
4 minute read
PATCH WORK
Rebuilding Supply Chain Efficiency
Late last summer, Master Printing & Mailing bought a new plant. While it was able to quickly execute the move and get its new press set up, the Master Printing team had to wait six months to get the press running. At the time, the supply chain issues spanning the globe hit the Berea, Ohio, high-quality printing and marketing solutions provider. It could not secure a new 800 amp electric panel to complete the upgrade of its building power from 240v to 480v.
Advertisement
Interestingly enough, Master Printing still does not have the panel it needs and is running the press on a 480v generator in what President & CEO Jeremy Dobos says is a very expensive proposition. To be fair, he admits the alternative—not having a running press—would be much worse. And while the arrival date of the new electric panel keeps getting pushed back, the Master team is confident it will happen.
“That was the biggest supply chain challenge for us,” Dobos says. “The current supply chain situation seems to be getting better, at least in terms of raw materials (paper and ink) for printing. Most paper types are now readily available again and we just made a decision recently to reduce our inventory back down to normal levels. We stocked up last year and hoarded a little bit because of scarcity and uncertainty.”
According to a KPMG supply chain study, 71% of global companies highlight raw material costs as their No. 1 supply chain threat for 2023. To help steady the reins and create a blueprint for success in dealing with supply chain trends, KPMG recommends three overarching things companies should have in place, including:
1. Capability — A mature supply chain planning capability to always be a step ahead and ready to tackle supply chain risks and opportunities.
2. Agility — Making sure your supply chain is responsive and agile to manage the unexpected, and to deal with threats and disruptions appropriately, efficiently and profitably.
3. End-to-end forward-looking visibility — Having “control tower” visibility on key real-time indicators; being able to maneuver beyond your own business borders; and building real-time collaboration with your supply chain partners likely will be critical.
Dobos admits that it is a hard game without proper inventory tracking and controls, emphasizing printers must have a process/system for entering inventory into a management system and then properly exiting the inventory as it turns into finished goods.
“Smaller printing companies (under $1 million in sales) don’t usually do inventory well and don’t usually have good systems in place to track it,” he says. “The lack of systems and of information about what you have on your floor impacts your bottom line. Smaller printers understand it intuitively, but don’t have formalized systems in place most of the time to capture the necessary information. As you grow, putting a good inventory system in place is an absolute must.” and by the time it was running full steam, the new mill was not able to deliver any stock to us. We were able to ensure we met the client’s needs because we had honest conversations with our trusted partners. Supplier relationships are critical because without the raw materials we don’t have a business.”
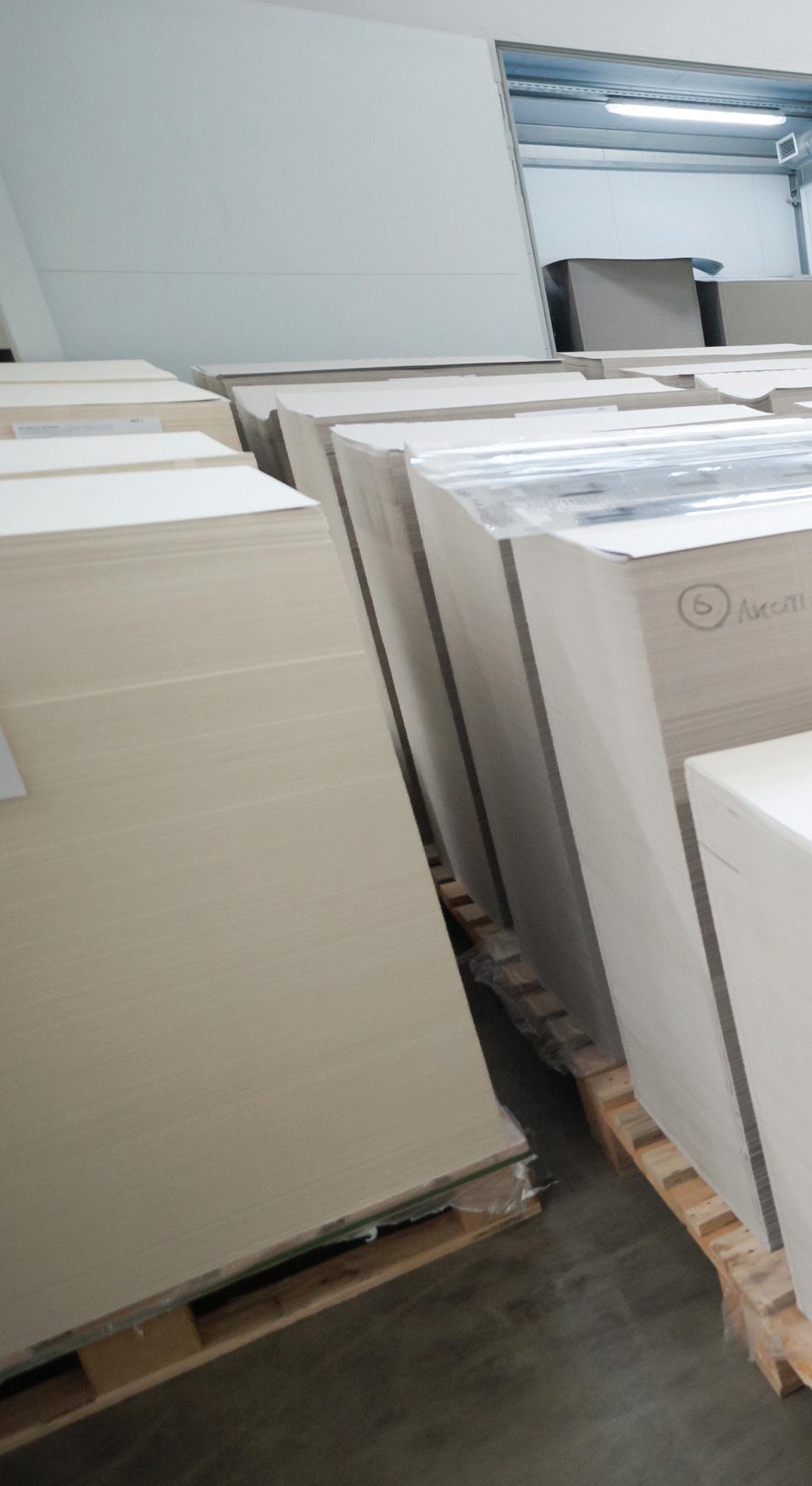
Strategize. Revisit. Repeat. More than anything else, building stable supply relationships is critical, especially when you create relationships with vendors that are willing to go the extra mile for you. Still, it is important to not let “relationship creep” take over. That means continually checking on the status of your relationships and keeping your vendors honest by checking pricing from time to time to make sure it is in line with other vendors.
In late 2019, NextPage was looking at sourcing some critical stock with a new mill for an ongoing project. At the time, the Kansas City multi-channel marketing solutions and custom print provider service was going to save 5% on the stock. Owner and CEO Gina Danner says it was enough money to make a difference.
“The plan was to ease into the new mill over time,” Danner recalls.
“We started off with an allocation agreement of 90% from our existing relationships and 10% from the new relationship. The project was delayed,
While the process of supply chain management can appear to be a cookie-cutter approach from the outside, there are a multitude of steps printers can and should take to ensure their strategies—from the process, vendors and customers— are streamlined.
For starters, respect is a critical element with vendors, clients and the process. “The one good thing from the last couple years is that we have started having conversations with clients to ensure they understand that we aren’t making widgets,” Danner says. “We try to help them understand the ‘why’ behind the ‘what’ of the challenges we face every day in our business so that we can provide them with their critical communication items.”
Another factor is to stay vigilant. Conduct monthly inventories no matter what the situation looks like. “One person is the recorder and one is the checker,” Dobos says. “Two-person integrity ensures that nothing is amiss. Ensure inventory is adjusted in the accounting system regularly, preferably monthly, or in real time if you can afford it.”
NextPage has implemented a strategy on maintenance items in which it ensures it has a solid “parts cabinet” for each functional area of the company, as parts continue to be a challenge for printers everywhere.
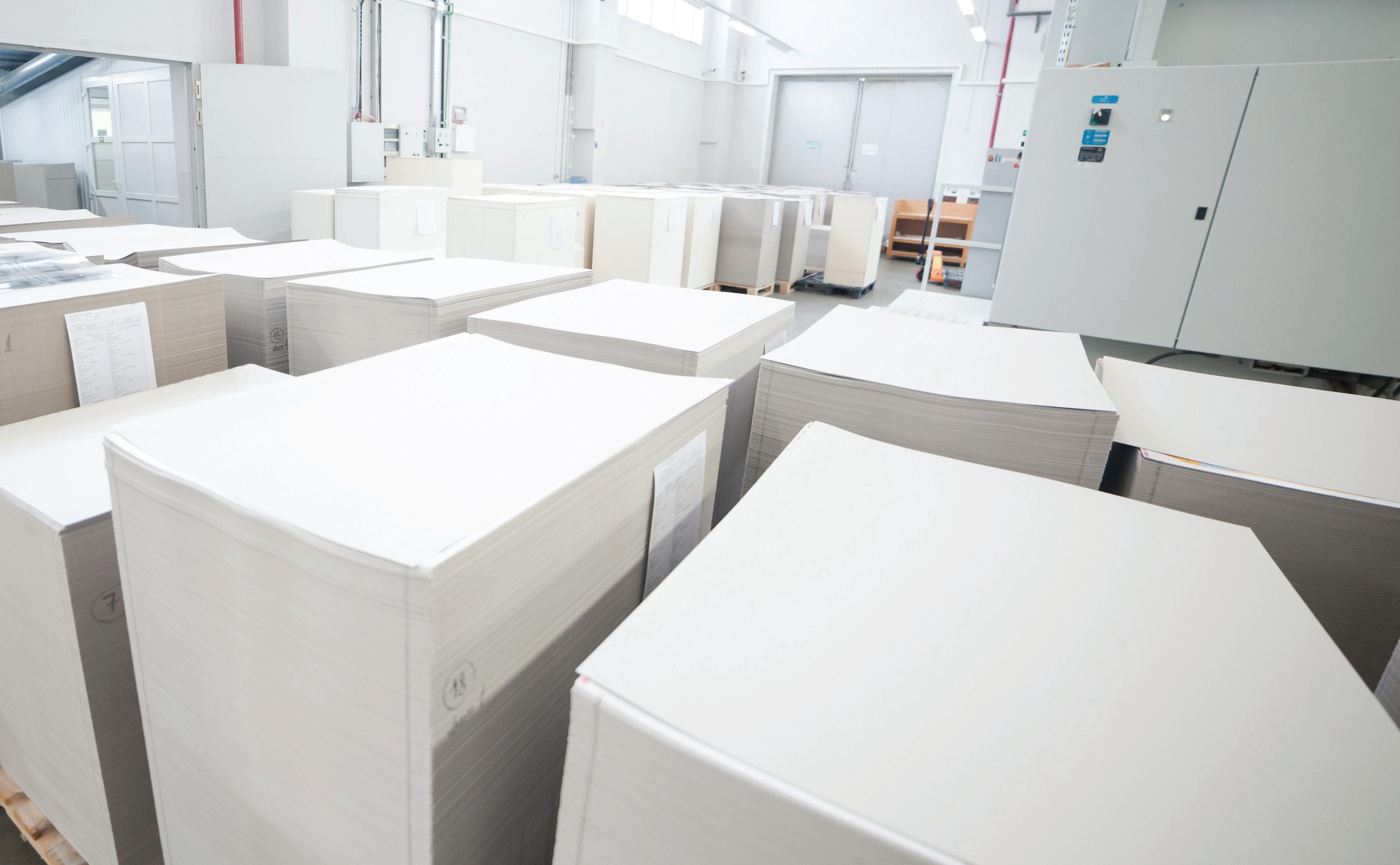
In addition, being flexible is paramount. Dedicate a staff representative to be your supply chain supervisor. “Pin the responsibility on one person if you aren’t big enough to have a full-time person doing it,” Dobos says. “Consistently and systematically check on pricing and availability. A proactive approach means there won’t be any surprises, even in a downturn.” supply chain processes, data synthesis and analysis capabilities.
One of the biggest and most vital areas for supply chain efficiency is technology. Over the past year, KPMG reports that cloud-based digital transformation will be a key trend to watch in 2023, as organizations seize technology as a strategy to streamline their processes. KPMG data shows that six in 10 companies plan to invest in digital technology to bolster their
“Ideally, organizations should have a seamless ordering entry to inventory system in place that basically runs the company,” Danner says. “That is the promise of the ERP systems. But you also are required to have strict adherence to material management. That means people who specifically receive and distribute raw materials. And an environment where staff cannot just go pull an extra 100/1000 sheets off the shelf because it was a hard makeready or they missed something. That is a level of overhead that most PSPs can’t justify. The key is to get as close to ideal as possible and then ensure frequent cycle counts.”
With supply chain disruption a seemingly permanent fixture, honing in on your strategy can be the difference between what you can and cannot do.